IN

REFIT, REPAIR & MANUFACTURING

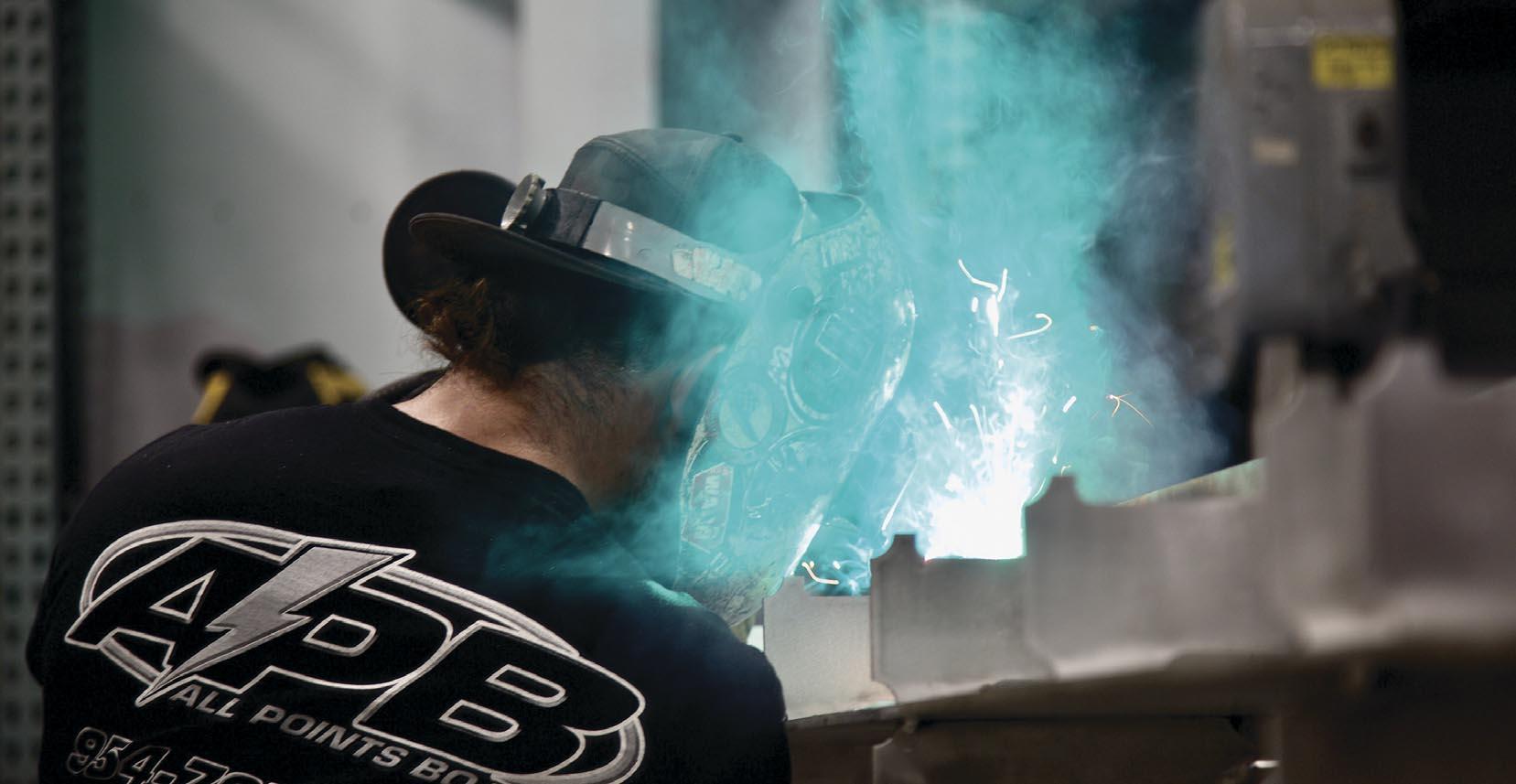

E XPERTS IN refit, repair & MANUFAC TURING
All Points Boats (APB) has more than 25 years of experience providing metal fabrication and manufacturing services to the thriving yachting community in South Florida. President and Founder Nate Goodwin spoke to Andy Probert about the company’s commitment to innovation and diversity.
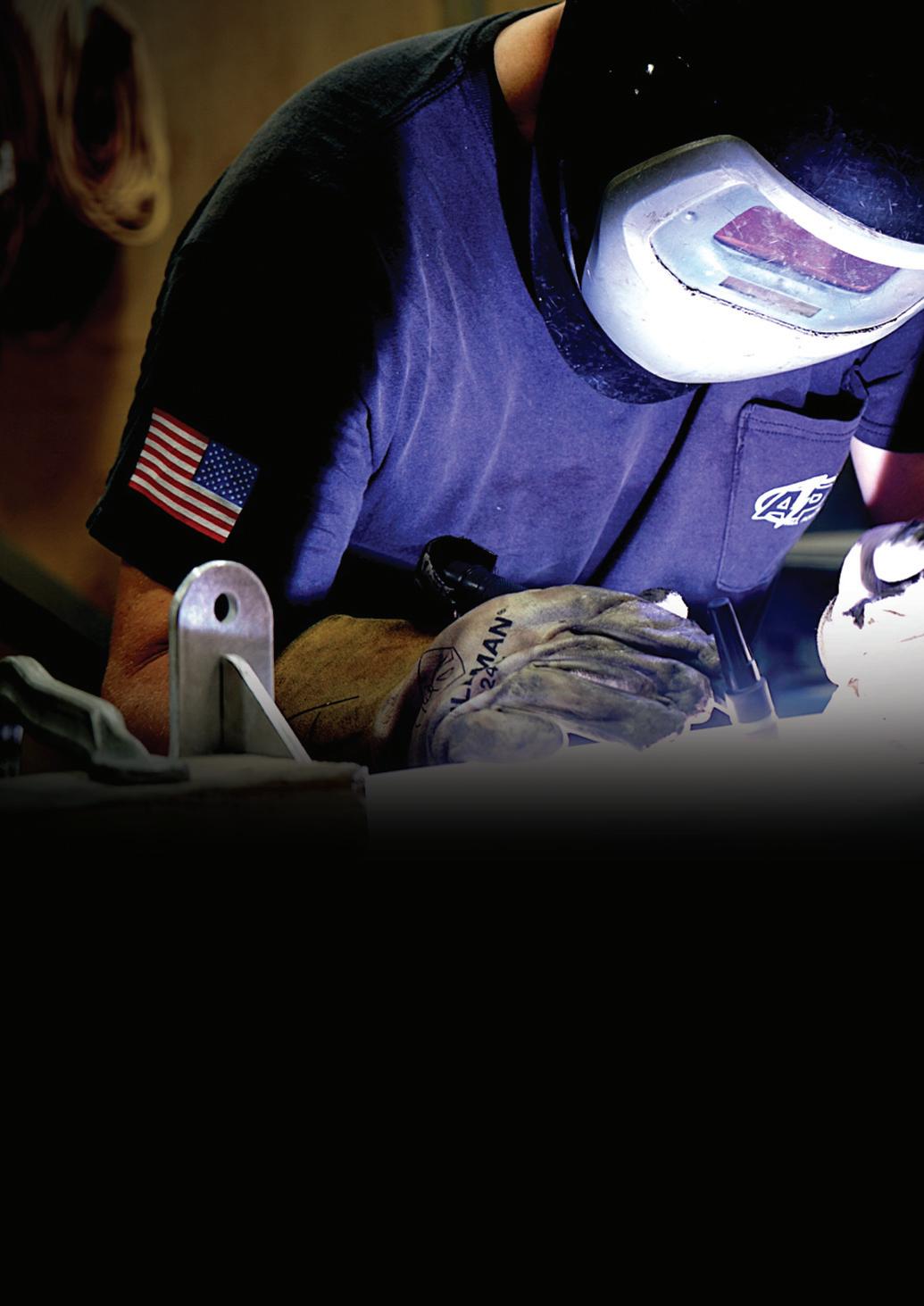
For Nate Goodwin, sailing is in his blood. Having raced sailing boats from a young age, he found himself in South Florida setting up a small business in 1997 to repair and outfit 60ft70ft motor yachts. Through a process of acquisitions, investments in cutting-edge equipment and employees, APB is now a leading comprehensive manufacturer and metal fabricator in the superyacht sector.
“Our business has evolved as the industry has grown over the past 25 years,” said Mr Goodwin, “and APB has built a well-earned reputation as a quality one-stop shop. Our core business is around vessel operating systems.”
Full-service profile
Employing 65 skilled craftsmen at its 30,000 sqft workshop in Fort Lauderdale APB’s primary services include reverse engineering and refurbing damaged, corroded or deteriorated components through replicated construction back to original condition.
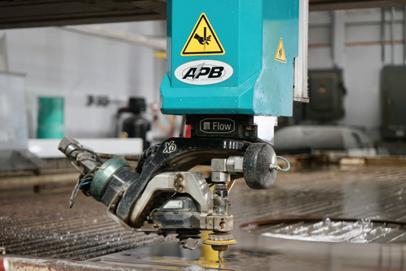
Services include class certified welding, plumbing, valve and pipe fitting, hydro static pressure testing, FRP repairs, and carpentry outfitting. The company is class-approved to perform repairs and modifications in stainless steel, aluminium, bi-metallic and coppernickel. Class-approved repairs are backed by ABS, Lloyds, Rina, MCA, and USCG.
APB also provides one-, five- and 15-year class surveys of vessels, along with valve inspections and testing for all class societies. As well as being an authorised dealer and service provider for Seakeeper, and SeaVision, it has a thriving composite business.
APB recently completed a $3 million infrastructure upgrade of its workshop, investing in a state-of-the-art CNC 5-axis FLOW waterjet, CNC 3-axis router, CNC plate rolling machine, high capacity metal shear, 3-axis CNC press brake, and two climate control spray booths.
The company’s CNC 4-roller plate rolling machine, which can be deployed to produce complex shapes, ovals, cones, ellipses, and any style tank or piping assembly, was recently used to fabricate a 6ft section of an ABS marine-grade pipe for a new ship’s sea chest.
Mr Goodwin said: “As overseas supply chains choke on material availability, APB is actively solving these problems by manufacturing quality components in-house. In the current market that has proved exceptionally beneficial.”
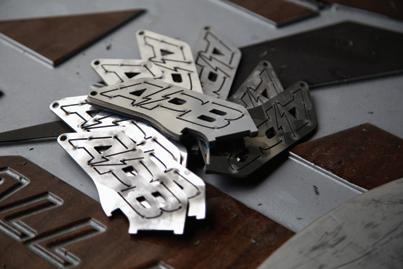
Diversity and innovation
APB services facilities and clients on the U.S. East Coast, including BAE Systems Shipyards in Jacksonville. “While most of our clients are in the Fort Lauderdale area,” continued Mr Goodwin, “we also travel to assist them wherever they are, as we are fully mobile and set up to work in any facility.”
The company has a significant commercial undertaking in certified welding and emergency repairs for vessels entering ports. “Our teams also manufacture components for cruise lines and suppliers
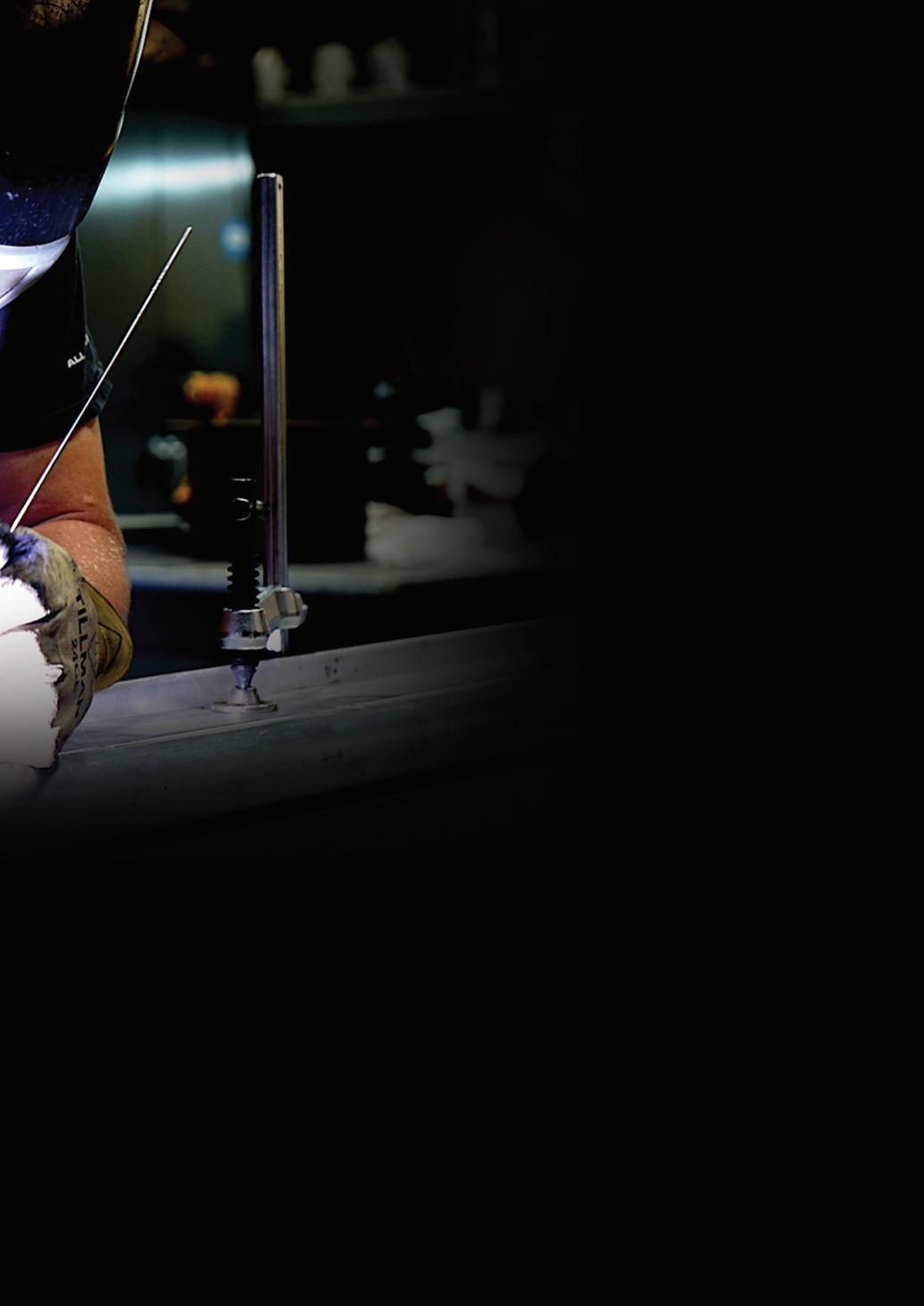
to the cruise industry, and can make modular components ready to ship into a vessel,” Mr Goodwin added.

APB’s performance has been stable, including through the pandemic, as it remained open as an essential business. He said: “We never stopped, kept a majority of staff, and found opportunities where we could in our manufacturing specialisms. During the pandemic, we made strategic decisions to reduce overheads and our teams took on extra responsibilities. APB came through stronger knowing it can do more with less.”
While the marine industry accounts for 80% of its business, APB diversified into commercial, industrial, architectural and residential work five years ago. “We do all engineering in-house,” Mr Goodwin said, “so we have programmed our CNC machines and do 3D modelling for prospective clients on new projects.”
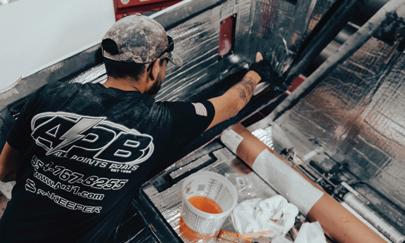

On innovation, APB now rebuilds vessel sea chests using ABS-certified Wencon Epoxy. During a recent 10-year ABS annual inspection, APB’s certified applicators utilised Wencon’s state-of-the-art coatings to rebuild a sea chest and recondition a hull’s penetrating systems.
Mr Goodwin explained: “Wencon Epoxy is a revolutionary, environmentally friendly, non-hazardous, low CO2 emission epoxy coating system. It extends the lifespan of the substrates where erosion and corrosion are most prevalent. Using this superior technology, we can offer customers a quick and cost-effective way to repair deteriorated surfaces.
“APB partnered with Dantech Offshore and Marine Group to bring this product to Florida. We completed 12 months of testing
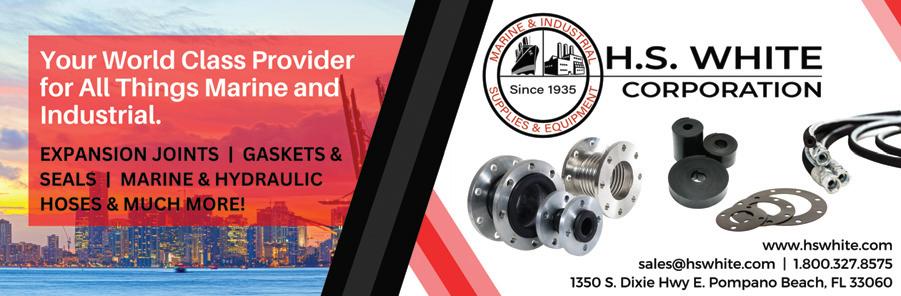
and are excited with the results.” The intention is to showcase Wencon Epoxy’s capabilities at boat shows, introduce the product to the U.S. market, and expand it to Canada and Mexico.
Leading the way
The company continues expanding and investing in cutting-edge equipment, leading the way for other companies and facilities to attempt to copy what APB does.
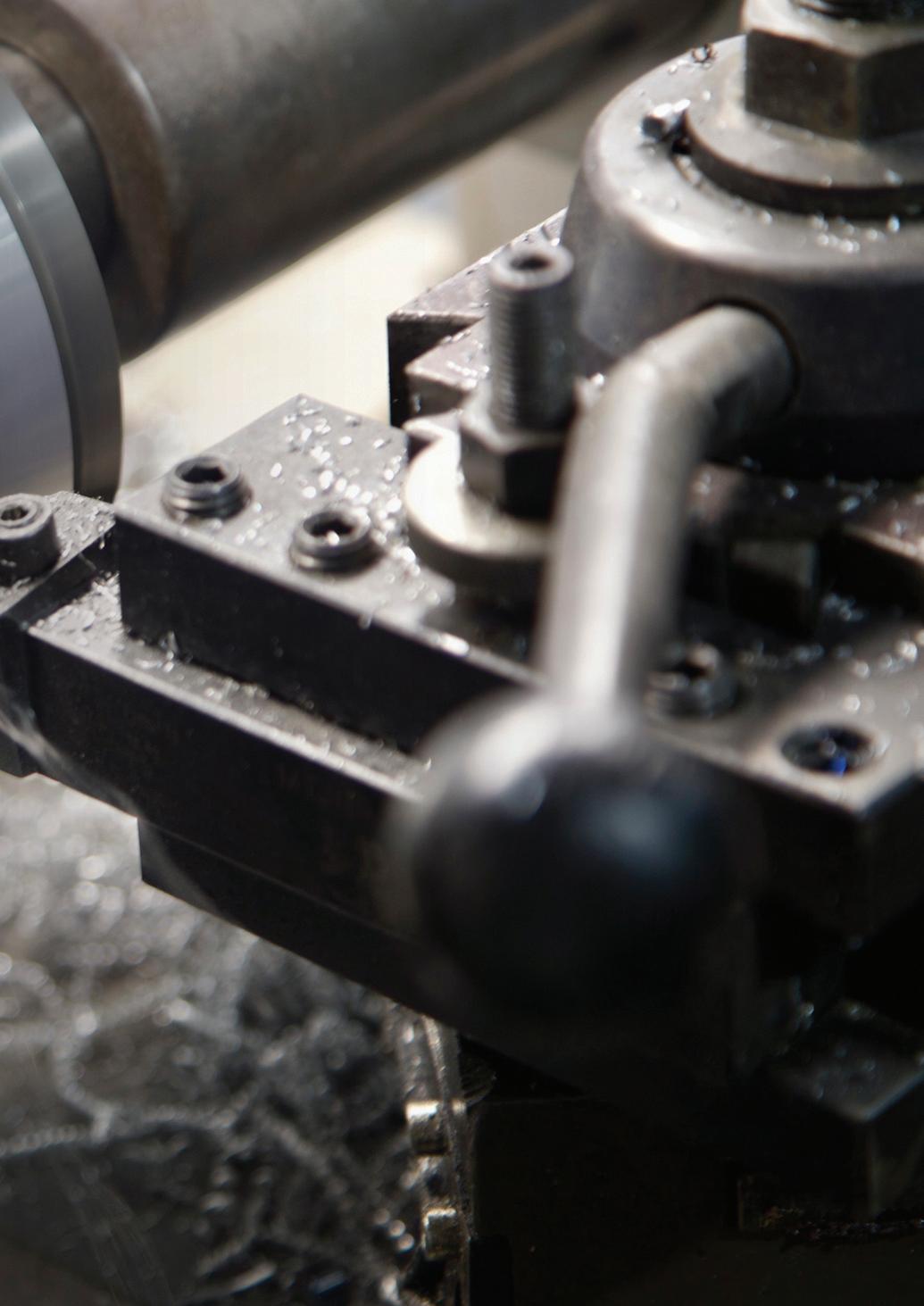
“It is standard in the industry for APB to pioneer techniques and repair services that others have picked up,” Mr Goodwin reflected. “The industry is evolving and adapting, and we must find ways to fix boats and achieve the unobtainable. The demand from clients is to be faster, cleaner and neater than ever.

“Our industry is heading in the way of aviation. More regulation will be applied and enforced as boats become bigger, and insurance liability will become more extensive. It means more complex navigation through the processes before we even do the work.”
APB’s aim over the next few years is to provide its manufacturing to a broader base of customers and industries, according to Mr Goodwin: “Where we see shortfalls is in supply from other countries. Lead times are quite extensive and challenging, so we are narrowing our focus on filling those voids by providing highquality parts with fast turnaround times.”
He emphasised that APB is keen to increase staff numbers, with continual training to ensure the quality of its end product remains high. “A key differentiator for us is that we do the right thing safely. Our hands-on experience, critical solutions and in-house expertise ensures we keep tight control on production quality.”
Mr Goodwin concluded: “We have built lifelong relations with suppliers and clients. In doing so, APB intends to continue to grow and expand its influence through creative thinking, highly motivated staff and value-added US-based services that fill the void that the global supply can’t.”
