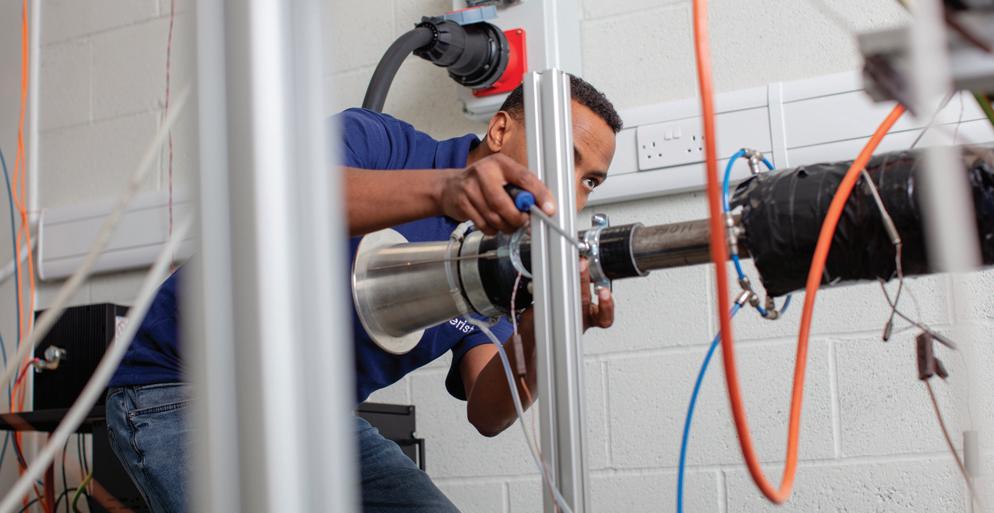


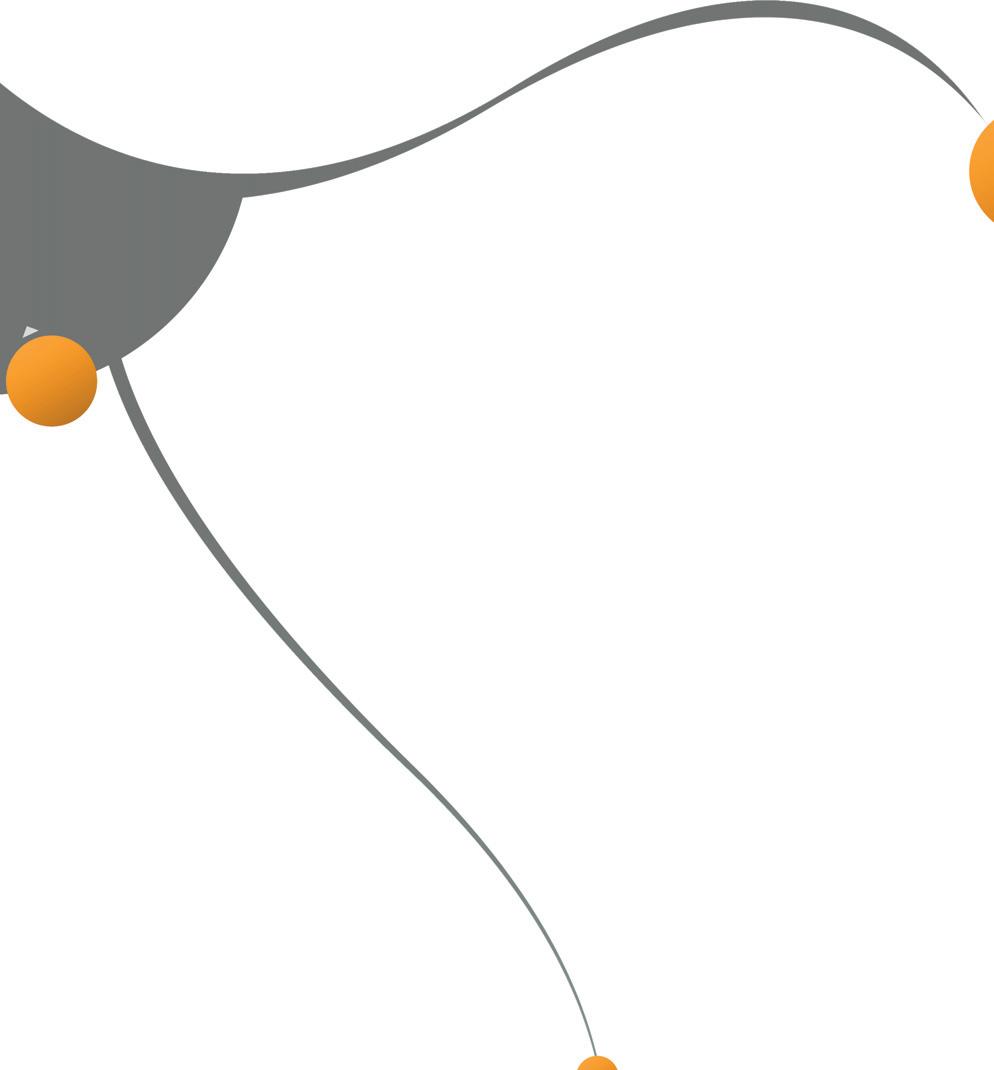

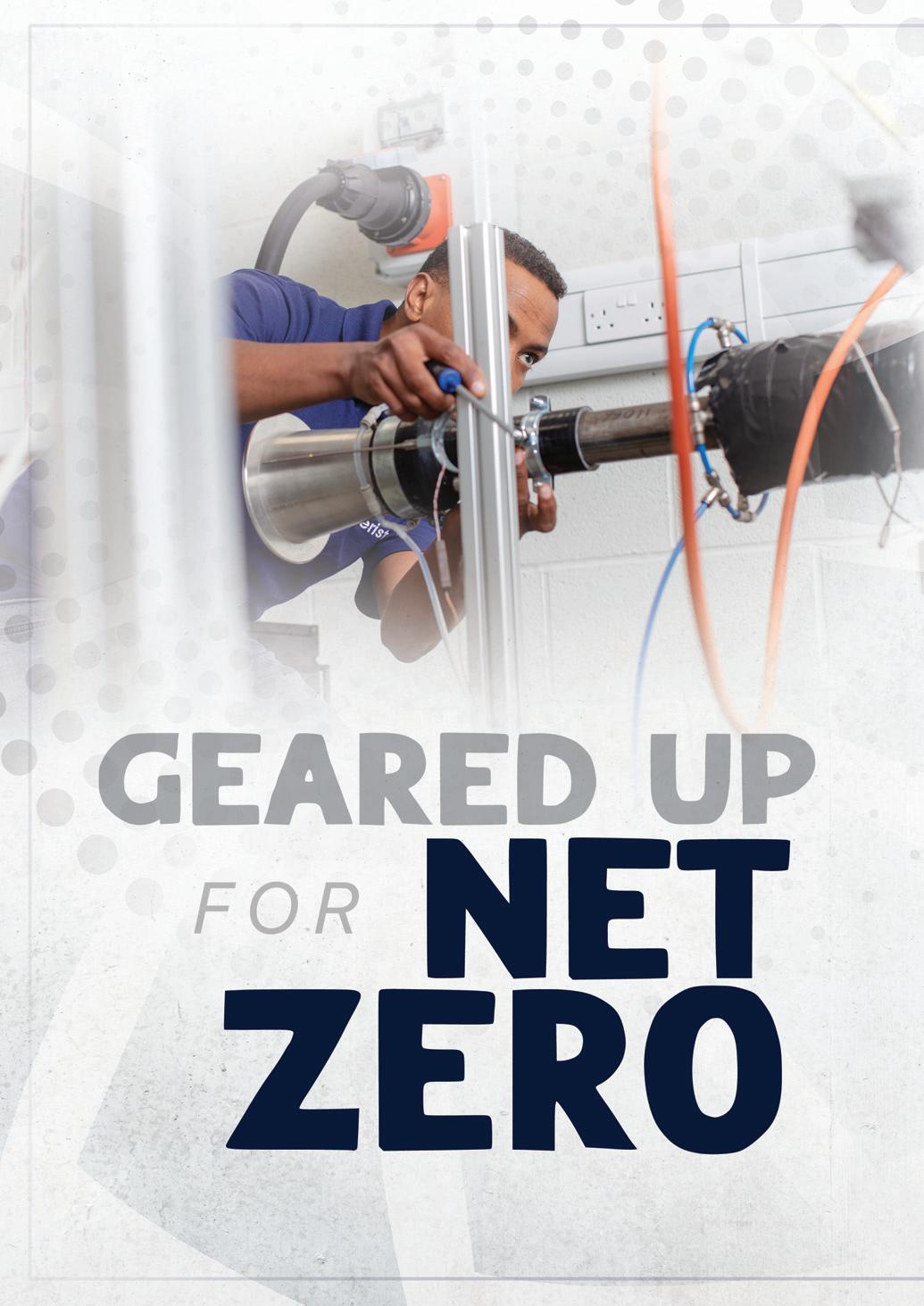
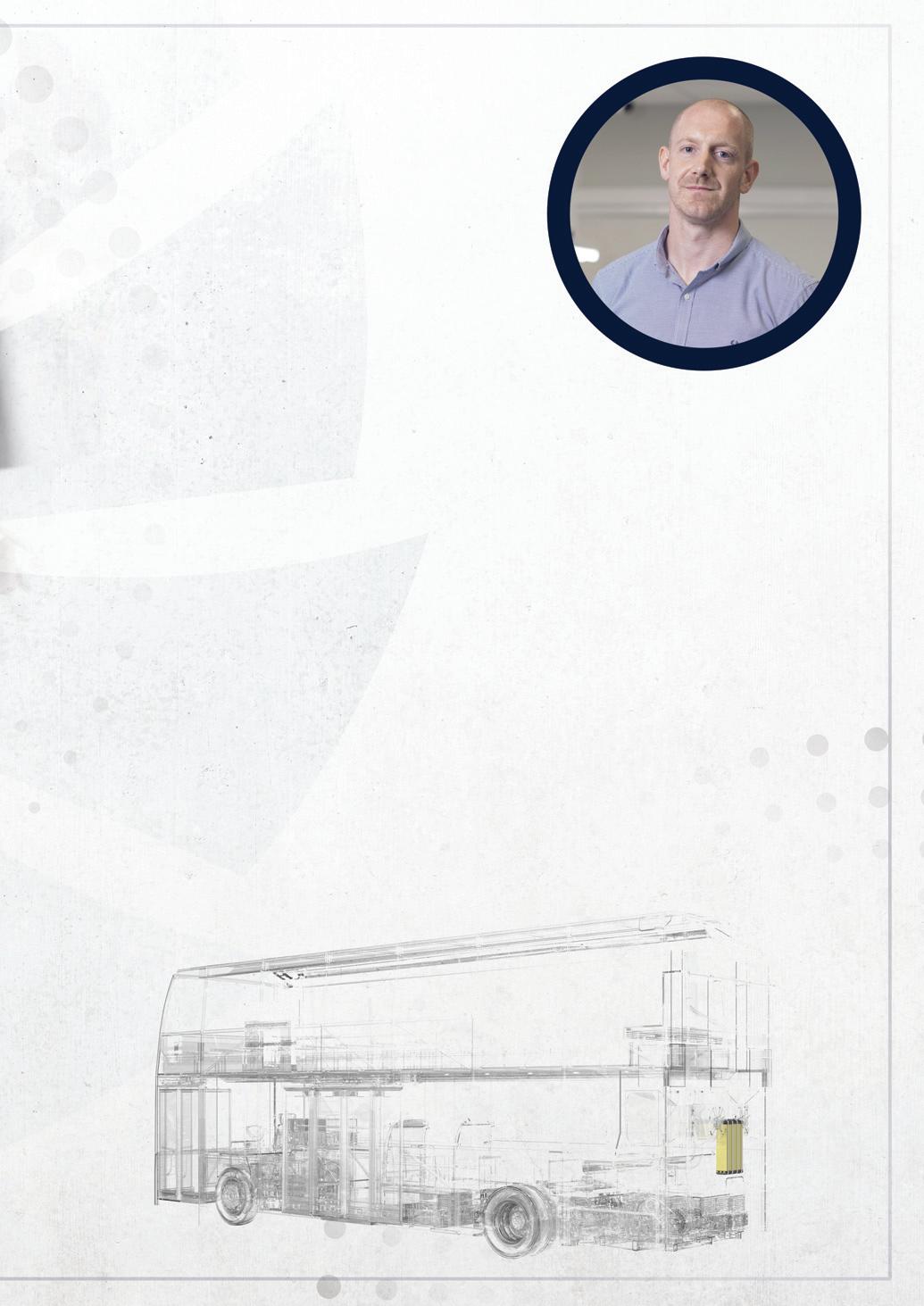
Aeristech is renowned for its market-leading development of hydrogen fuel cell technology, and the company’s latest project is no different: as it helps to change the public transport scene, COO Luke Read explained more, in an exclusive interview with Inside Sustainability. Report by Imogen Ward.
With a knack for innovation, manufacturing and engineering firm, Aeristech is a prominent player in Project HEIDI, a consortium focused on the electrification of London’s public transport sector.
“Larger vehicles such as commercial, on and off highway and buses, are where hydrogen technology really shines,” said COO Luke Read. “Project HEIDI is an excellent test to show peopl e just how capable our technology is.”
Making history
Entering the automotive scene more than a decade ago, Aeristech was quick to build a reputation with those in the industry.
“The company evolved in 2010 from the idea of being able to spin up an electric motor very quickly, with speeds in excess of 100,000 rpm,” Mr Read explained. “This was accomplished using a patented method of controlling the motor. Initially, this technology was used to investigate fully electrifying a mechanical turbocharger, to

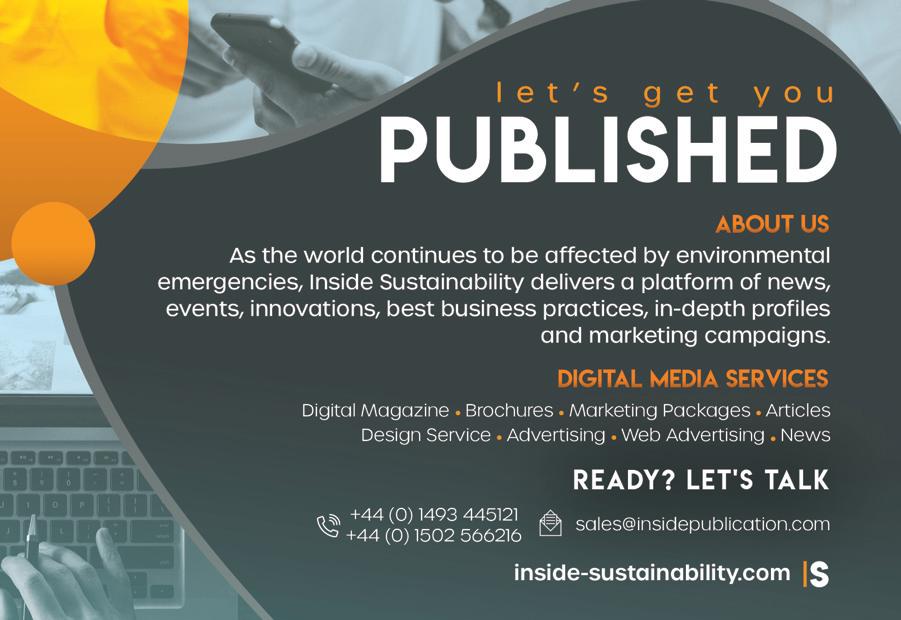
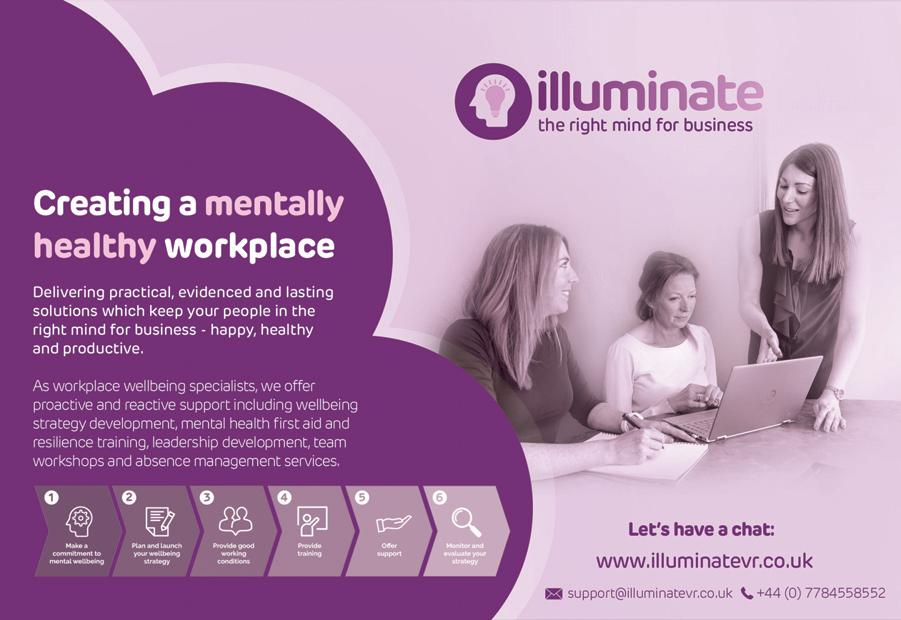
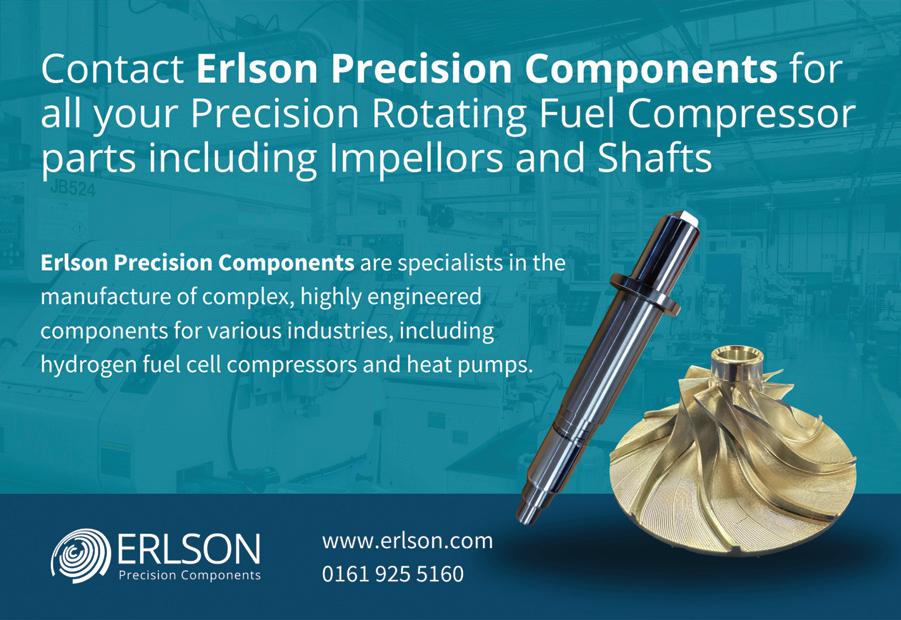
allow for easier downsizing of internal combustion engines, which would result in an emissions reduction.”
From there, the company went on to explore the electrification of superchargers, whilst continuing its development of downsized internal combustion engines. In 2015, following Dieselgate, development of internal combustion engines became less desirable, and Aeristech made the decision to reduce its R&D in this area.
“At that time, we noticed the emergence of hydrogen fuel cells, which, just like diesel engines, require a supply of compressed air,” said Mr Read. “Similarly, because they are also used in mobile applications, the fuel cell compressors also needed to be compact and power dense. Then in 2019, battery electric for passenger vehicles really came into its own.
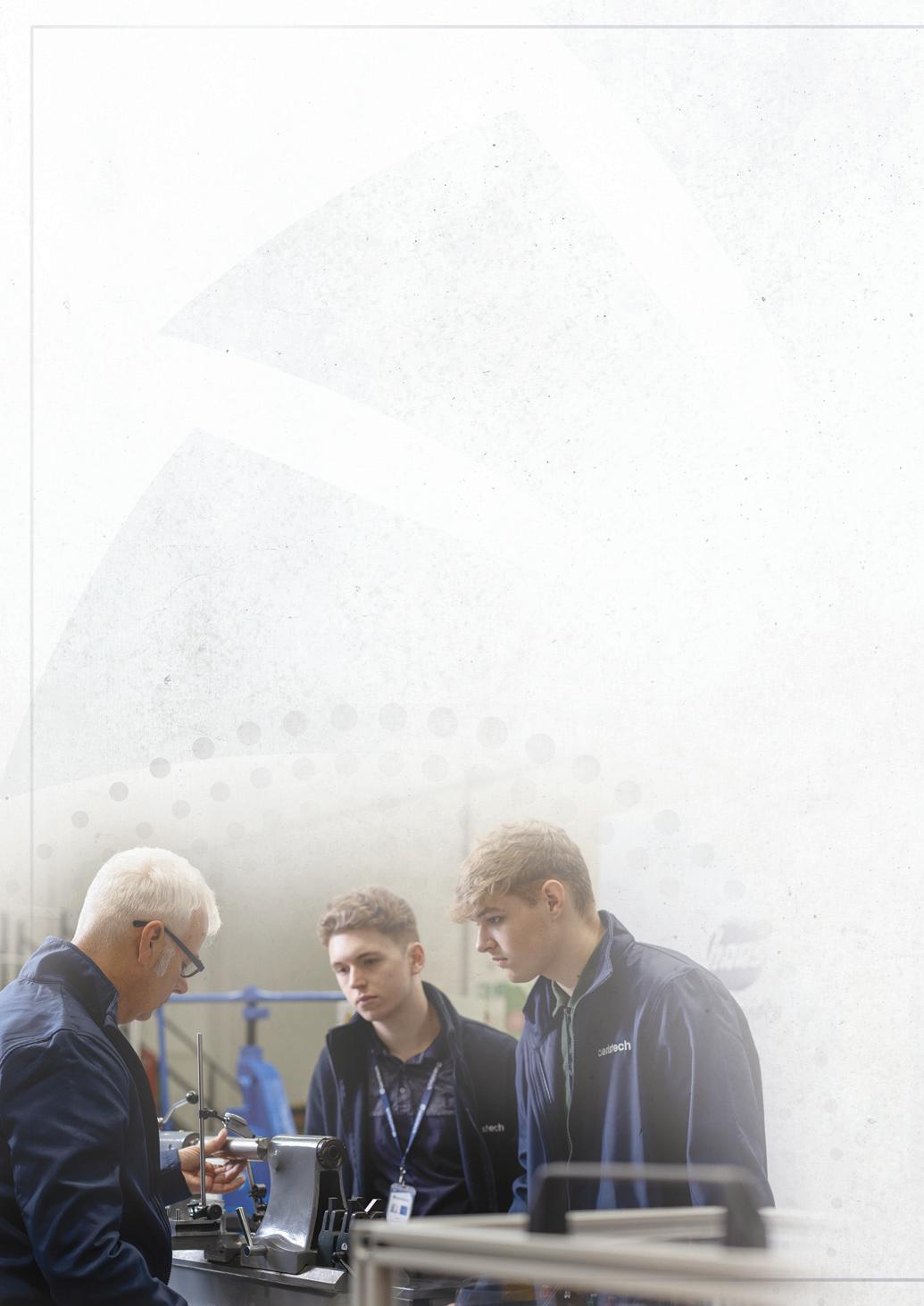
“Now, we produce high-speed electric compressors for on and off highway commercial applications using our patented technology.”
Project HEIDI
When it comes to London, the city is known for a number of things, including Big Ben, the Tower of London and its iconic red buses. The latter are about to become even more iconic for a reason relating more to the colour green than red.
One of the UK’s most prominent ongoing projects relating to green hydrogen is Project HEIDI. An abbreviation of Hydrogen Electric Integrated Drivetrain Initiative, HEIDI is set to electrify London’s red doubledecker buses, and Aeristech is one of the companies making it happen.
Joined by Aeristech are the University of Bath, Equipmake and Bramble Energy, the
“As we look to the future, we would like to capitalise further on the platforms we are generating for the APC projects and start getting them out to a much wider audience”
likes of which will combine their knowledge and expertise to develop the hydrogenpowered buses ready for the 2026 deadline.
“Bramble Energy is producing the fuel cells, and we are developing the compressor to supply the air to the cathode side of the fuel cells,” Mr Read clarified. “With that, the main challenge for us is to produce a compact compressor that will meet the requirements of Bramble’s fuel cells, whilst allowing them to generate the power necessary to run the bus.”
This process is particularly challenging due to the requirement for oil-free compressors, meaning the systems are required to run at high speeds without the aid of lubrication. Thankfully, Aeristech has vast experience in developing oil-free compressors.
“When it comes to oil-free compressors, the bearing technology is key,” said Mr Read. “We use a foil-air bearing which allows the compressor shaft to sit on a cushion of air that acts in place of the lubrication.
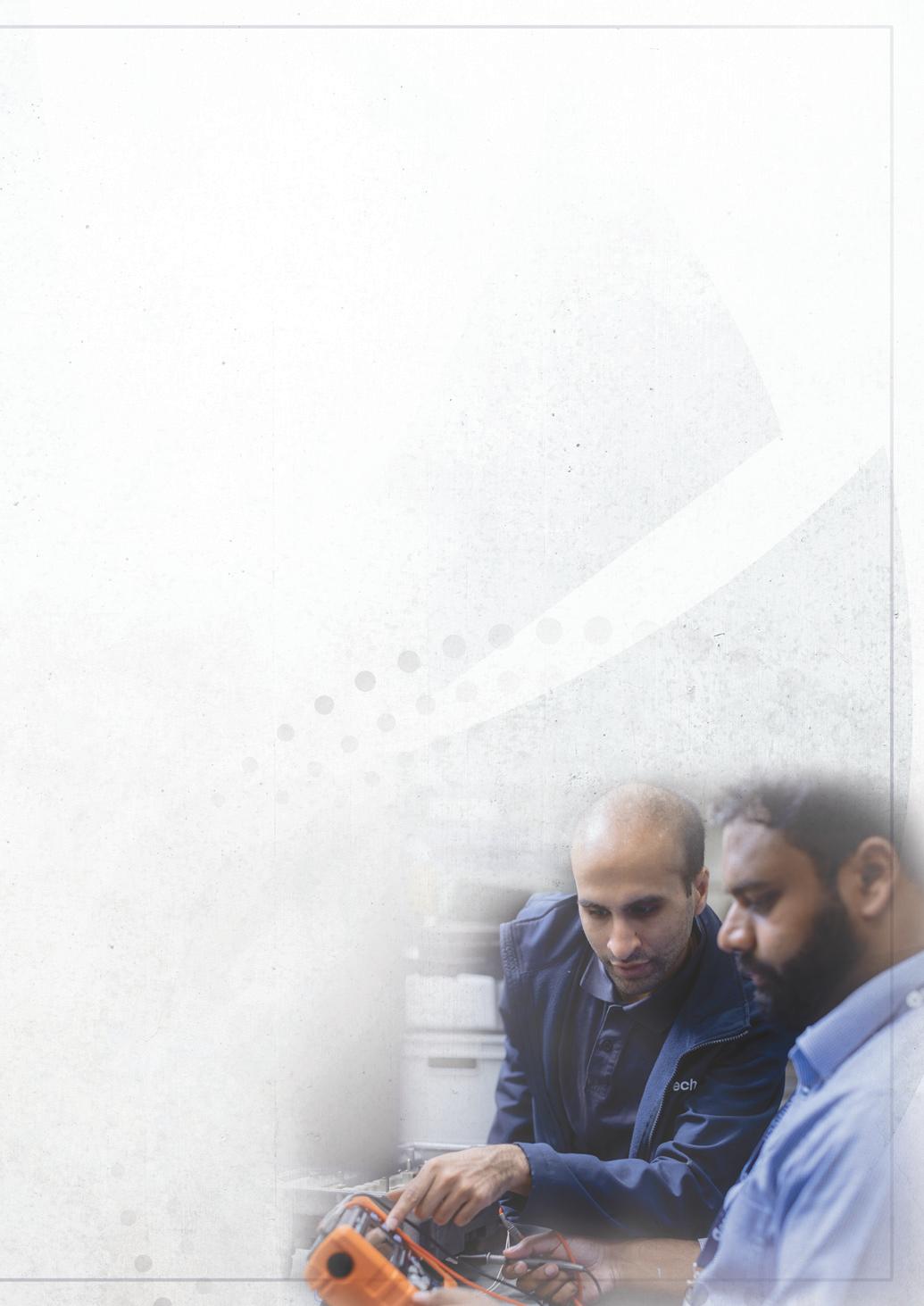
“Of course, foil-air bearings bring their own set of challenges because they do not have the load capacity of more traditional bearing types. This becomes a real issue when looking at the axial force applied on the compressor, so further steps are required to make the system work. To overcome this, we have dedicated a lot of time to developing elements of thrust reduction into our designs.”
Aeristech is developing 40kW high-speed oil-free turbo compressors for Project HEIDI and expects the first prototype to be ready for delivery in April 2024. At this stage, the compressor is expected to hold a technology readiness level (TRL) of 3 – offering experimental proof of concept. Following the success of this prototype, the company plans to progress to TRL 5 in July 2025, with the validation of the technology in the relevant environment.
“Our 40kW turbo compressor prototype generates a significant amount of axial force,” Mr Read explained. “That’s on the higher end of what our competitors can achieve at the moment. So we have an exceptional handle on the force on our machines.”
Keen to remain on the cutting-edge of the industry, Aeristech exposes all its products to rigorous testing, ensuring it maintains some of the top speed units in the industry. To achieve this, the company relies on bi-directional power supplies which enable it to recover energy used during testing. This is then used to
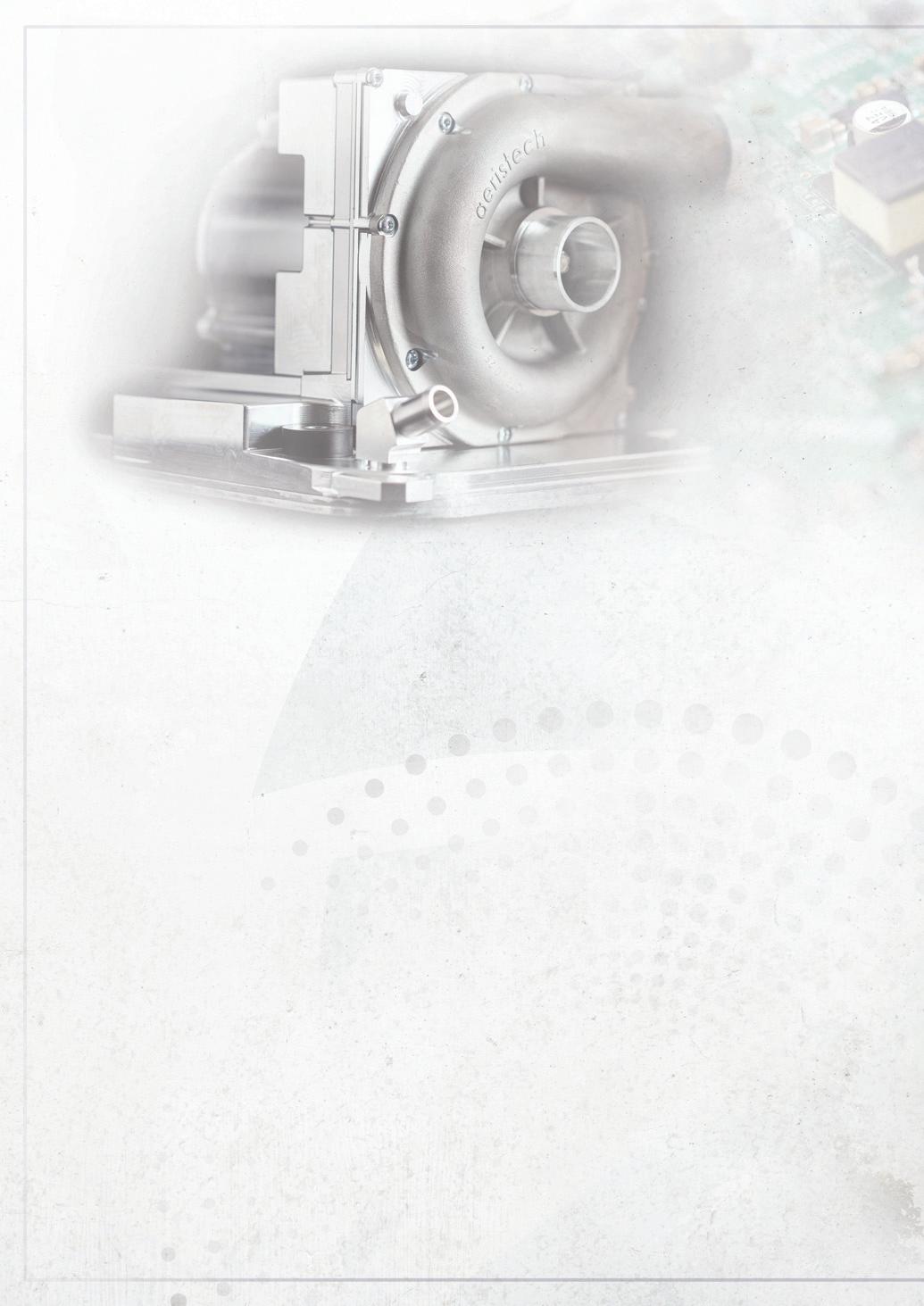
supplement the company’s energy demand, and any excess is put back into the national grid.
Key collaboration
According to Mr Read, the success of Aeristech can be attributed to the strong partnerships it has developed over the years. The company is proud to be part of the Advanced Propulsion Centre’s (APC) programme for accelerating the transition to a net zero automotive industry. Through APC, the company met Cummins Turbo Technologies, an important partner that has supported Aeristech’s exploration of prototype development.
“As we look to the future, we would like to capitalise further on the platforms we are generating for the APC projects and start getting them out to a much wider audience,” said Mr Read. “In the next 12 months, we want to be able to start supplying these on a more regular basis, especially to markets in North America and Asia. We also want to simplify the core of the product to make it more modular, allowing
us to address more markets and develop a simpler supply chain.”
The supply chain is, and will continue to be, an important element of Aeristech’s journey towards the mainstreaming of hydrogen fuel.
“There’s still some way to go – mainly when it comes to the supply chain and ensuring the technology remains reliable,” Mr Read concluded. “We are used

to technology being incredibly reliable, especially when it comes to internal combustion engines, so we must ensure that continues on to the next platform of technology. With that in mind, we are probably still around five to ten years away from becoming mainstream. Despite that, now is absolutely the time to begin integrating this technology, and it is an incredibly exciting time for everyone involved.” n
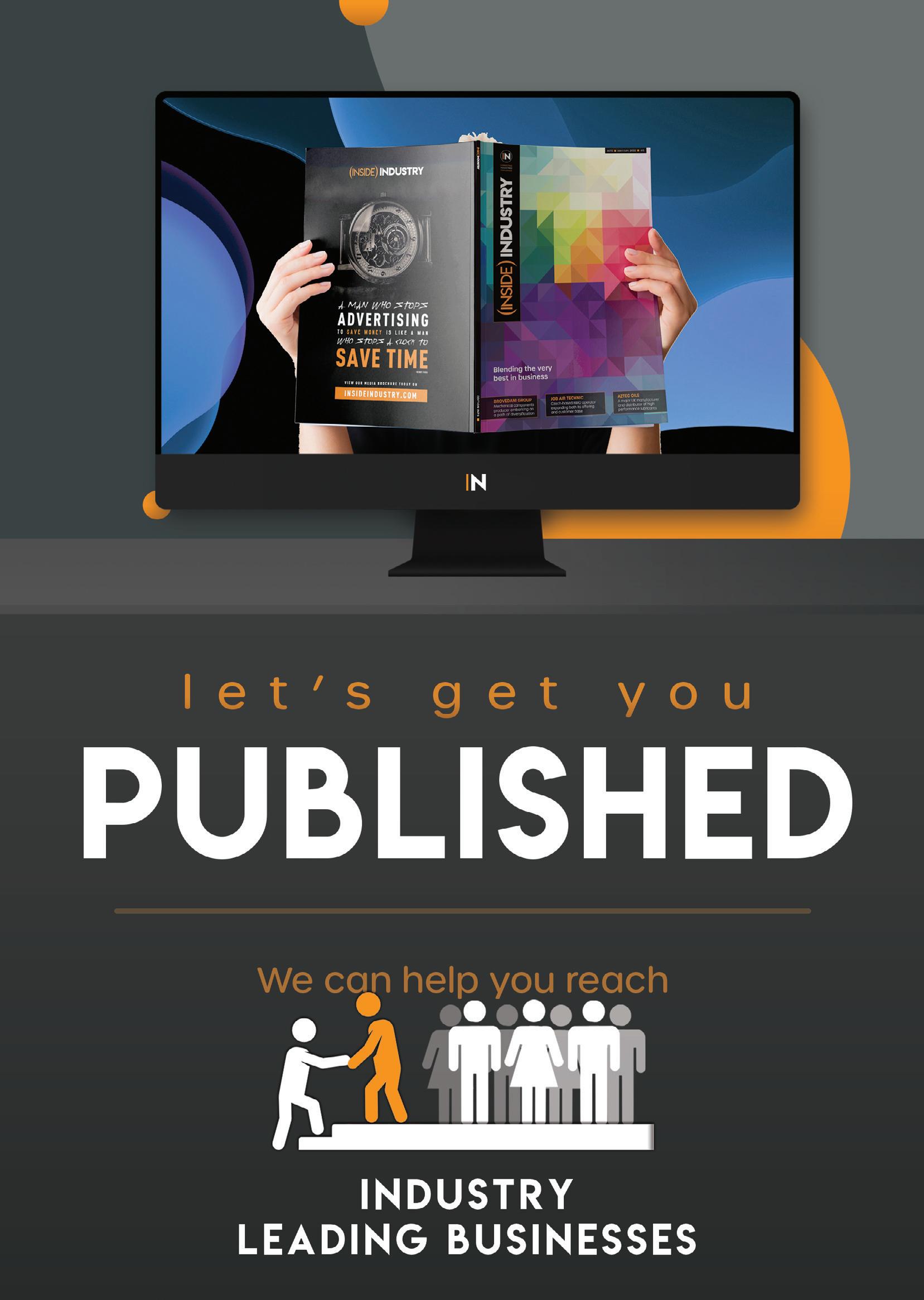
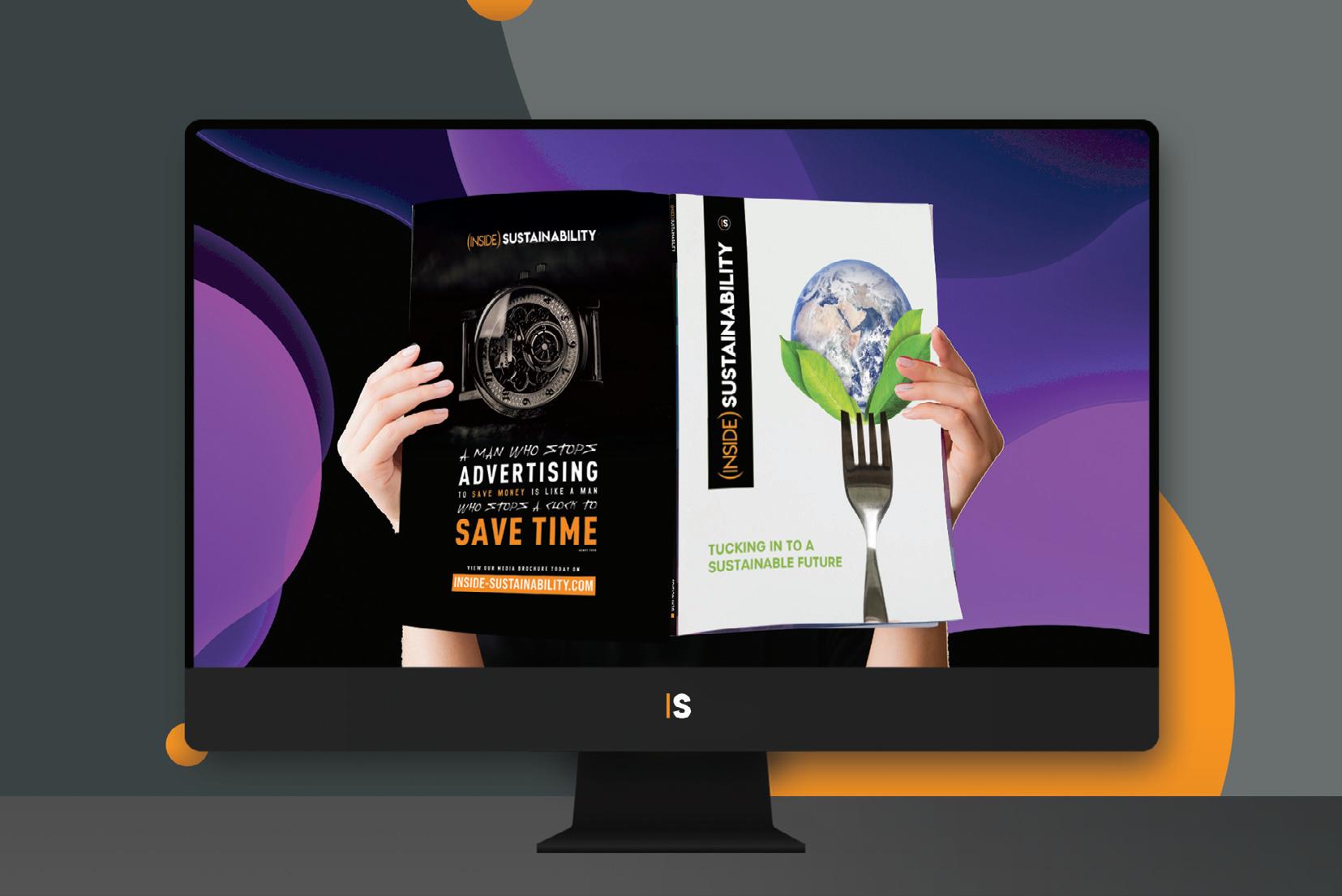