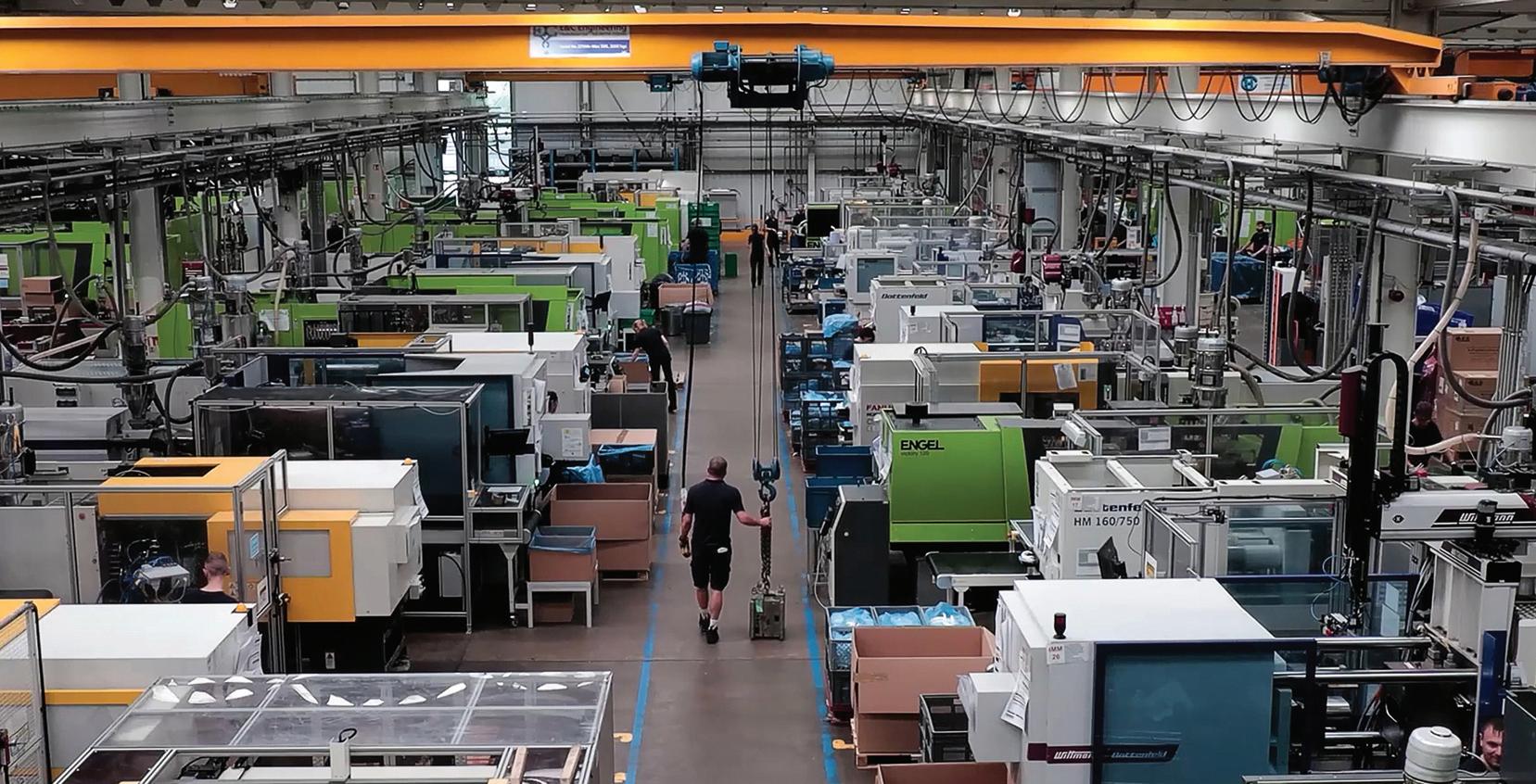

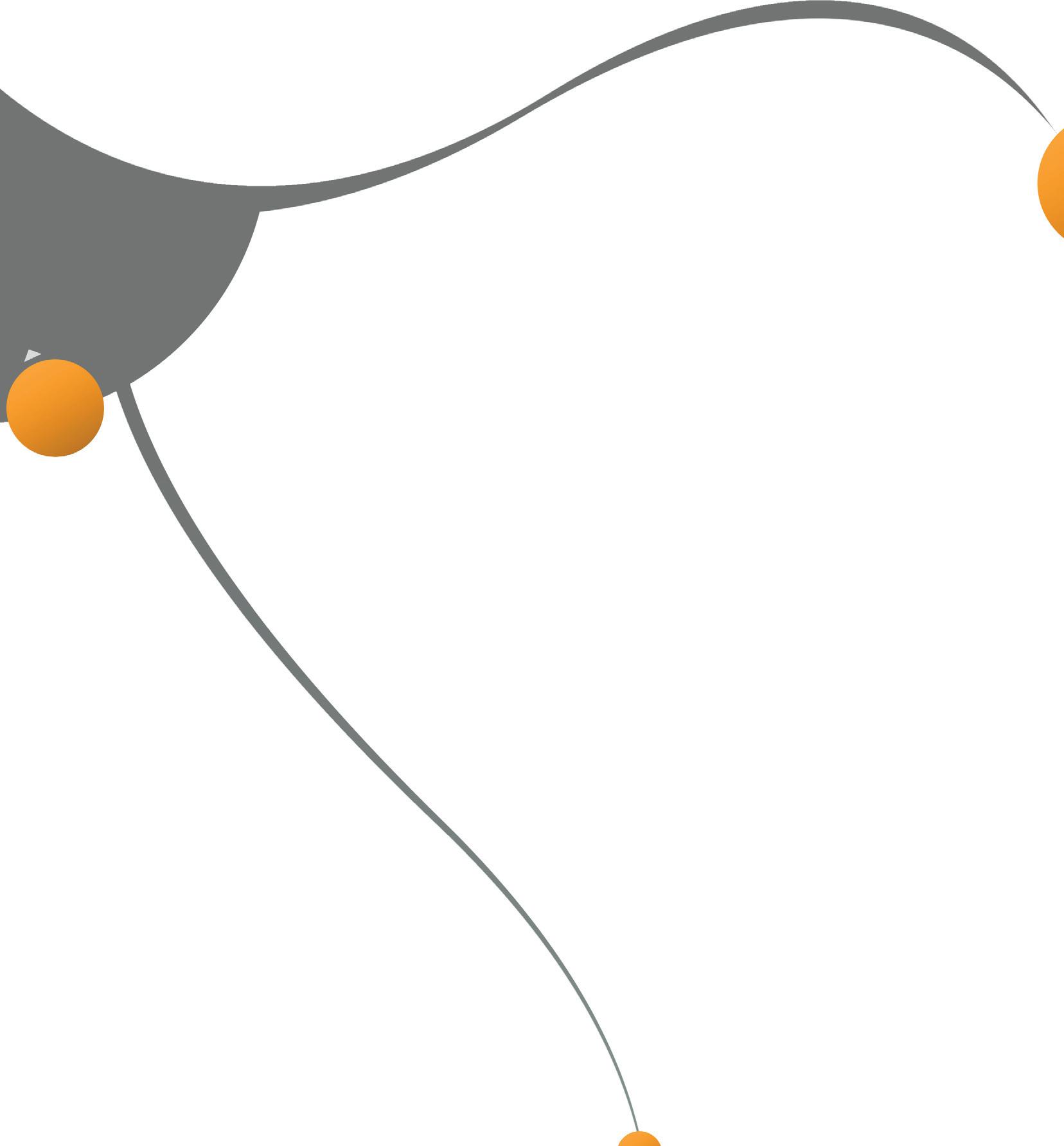
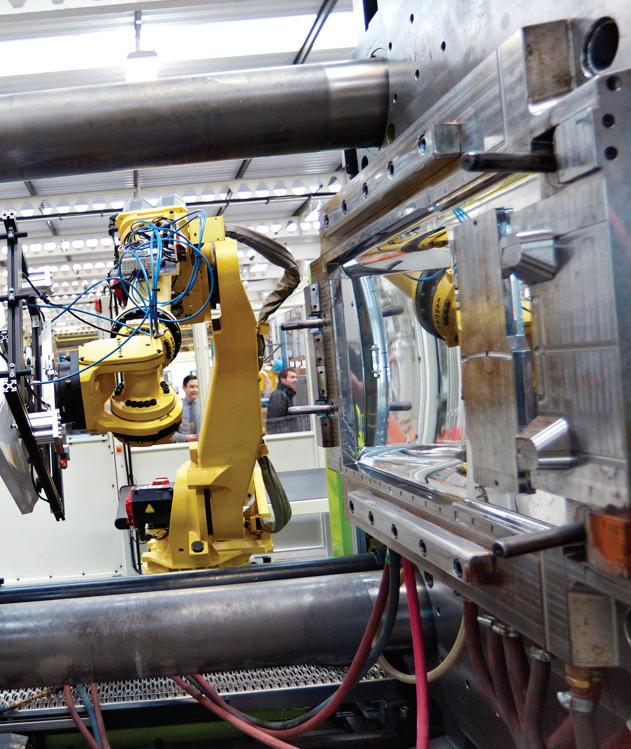
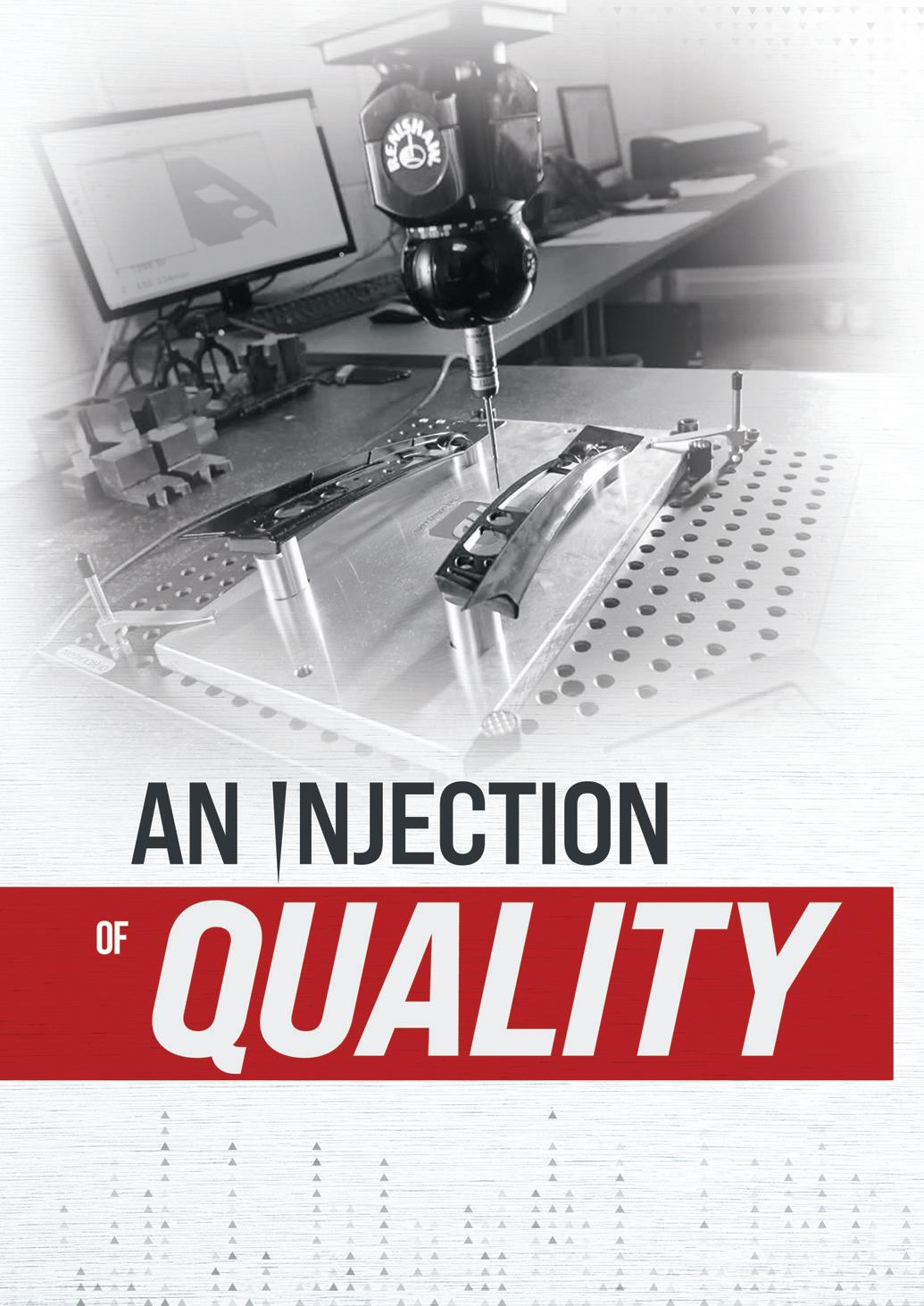
Founded in 1992 by three engineering partners with the goal of exploiting materials technologies and pushing the boundaries of what was possible with polymers, Advanced Plastics has since grown to become the largest privately-owned injection moulding business in the UK. Aided by its high-tech, high-efficiency sites across the UK, the company has steadily grown not only its production capabilities, but also its market share and its turnover. Group Sales Director Michael Hadfield spoke with Richard Hagan.
Following the company’s establishment by engineers Peter Thompson, Glyn Barrick and Rob Anderson, Advanced Plastics quickly found a niche with its ability to rapidly convert concepts into production jobs.
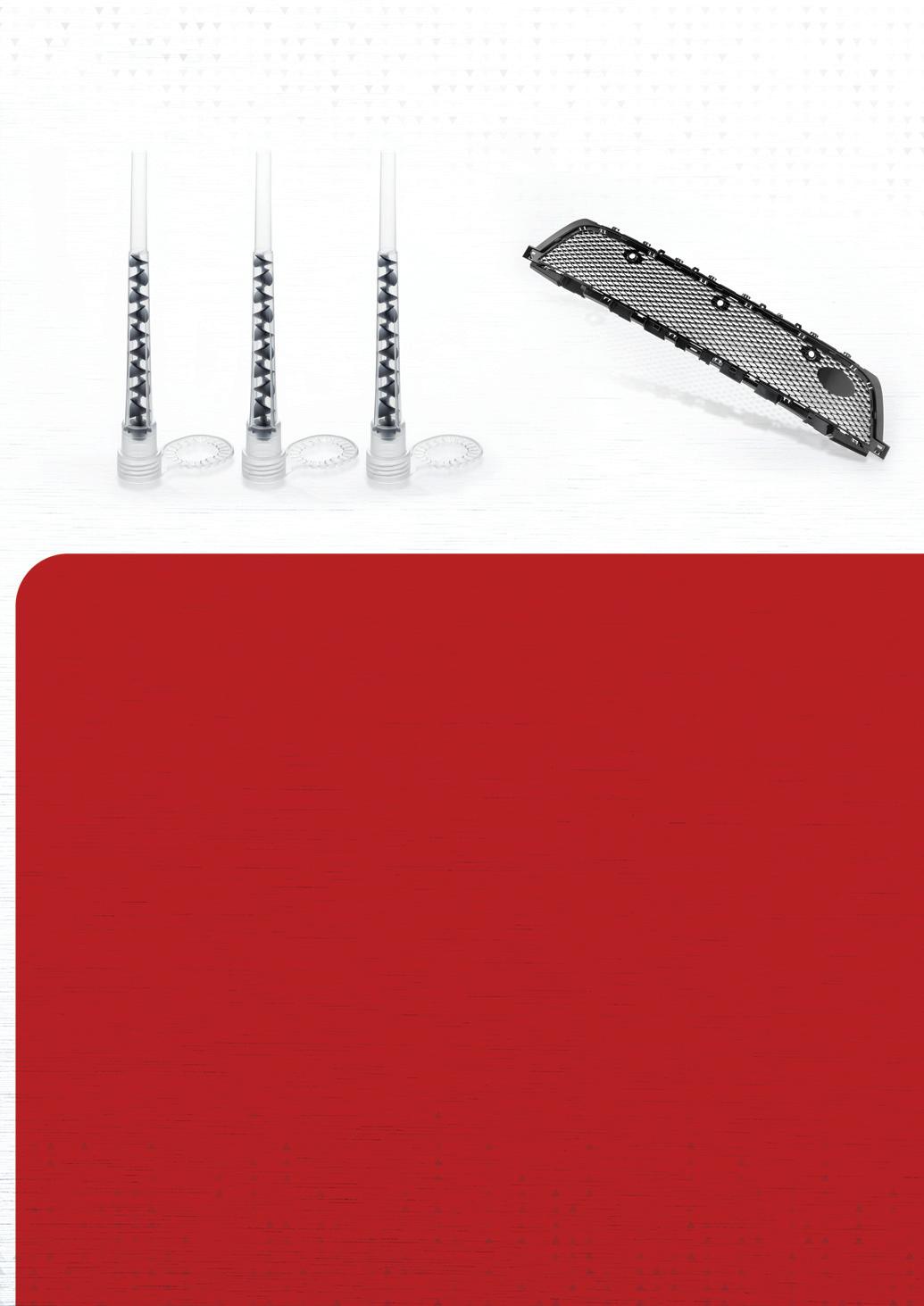
That would lead to the company’s successful penetration of the automotive sector only a year later, in 1993. This major milestone would go on to define a substantial part of the company’s journey, with projects over the years being completed for the likes of Ford (parts for the Fiesta and Mondeo models) and flagship Jaguar vehicles.
Diversification and growth
A further milestone was reached in 2006 when Advanced Plastics was sold to its original founder Rob Anderson and partner Chris Pearson (formerly Ford Business Unit Manager of Nifco). The company rapidly diversified into the HVAC and filtration sectors, all whilst continuing to prove its ability to develop technically challenging applications for its core automotive clients. Turnover, meanwhile, increased from £2.75m in 2006 to £38m in 2023, and its workforce grew to 317 staff.
Today, Advanced Plastics boasts highly automated, world-class manufacturing
facilities located in Hull, Fareham and Manchester. Across the three sites, the company owns 70 injection moulding machines ranging from 22 tonnes to 1,600 tonnes. The Hull facility boasts several fast-cycling high efficiency, low energy all-electric machines that specialise in high cavity, high volume mass production. The company continuously invests in the latest and most efficient machinery, delivering premium products from its three stateof-the-art facilities.
Specialised manufacturing
Across its machinery assets, Advanced Plastics is able to offer several speciality manufacturing services including Foam in Place (FIP) technology, within which it produces over 500,000 sealed mouldings per year, and over moulding and 2k
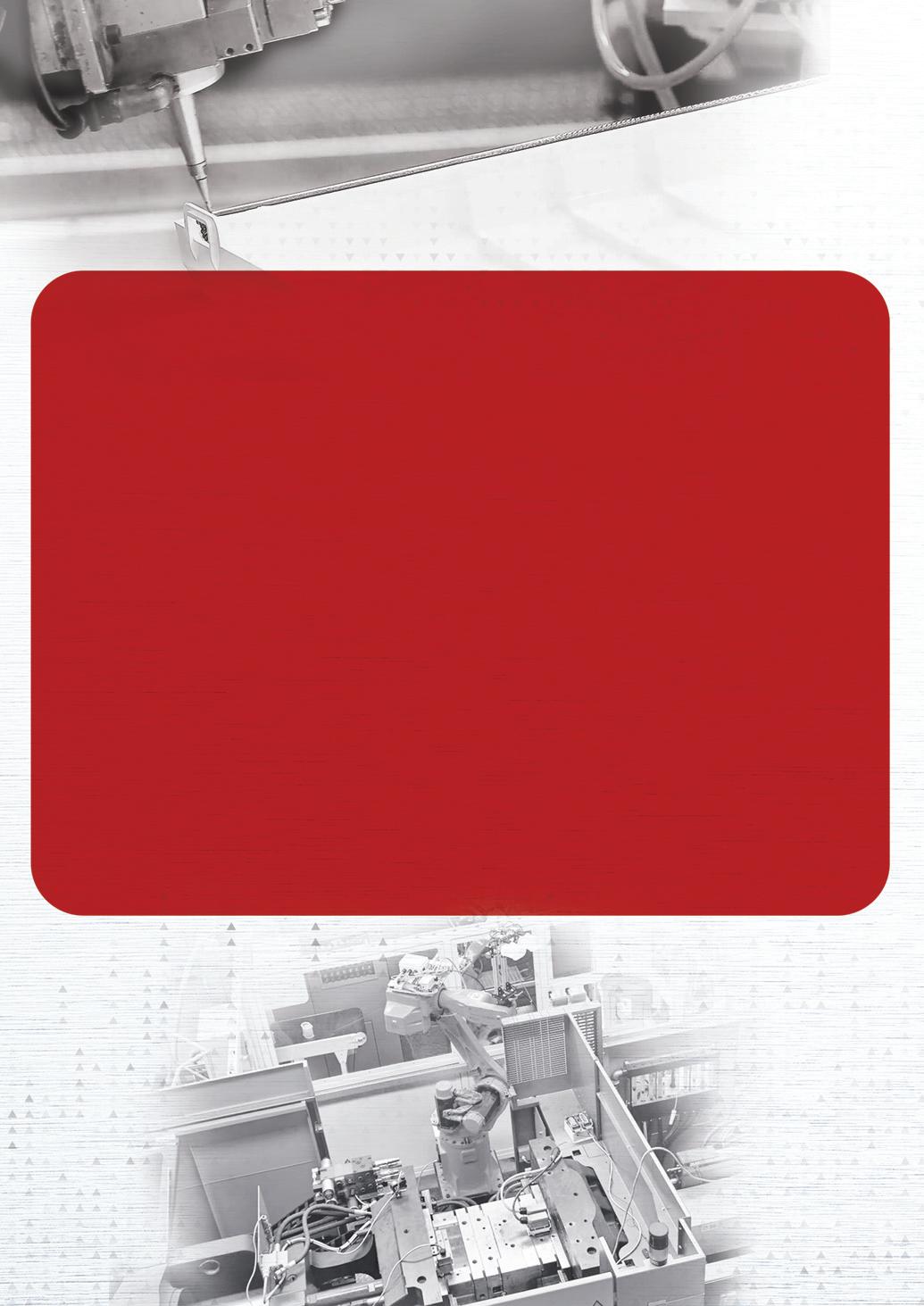
moulding, in terms of which it produces several million parts per year.
The company’s Hull facility is a particular highlight for its advanced Industry 4.0 technology. It features a fully integrated Enterprise Resource Planning system, real-time monitoring of production machines and six axis robotics on each machine, while offering significant assembly automation.
However; according to Group Sales Director Michael Hadfield, Advanced Plastics’ high-tech manufacturing capabilities are only half of the company’s secret to its success: “We recognise that people are the key to our ability to continue achieving the quality and performance demanded by our clients. Attracting talented individuals and developing them within the Advanced Plastics way, immersing them within our core values of Partnership, Respect, Integrity and Commitment is critical to our success.”
Boiling up success
This combination of highly skilled and motivated staff and high-tech machinery was put on full display during a significant project involving the manufacture of parts for a consumer product, as Mr Hadfield explained: “Our team worked closely with the customer’s design team to establish cost-effective solutions to meet the client’s design and performance criteria for a new high efficiency gas boiler that the client wished to produce.
“The project scope included aesthetic and end user interface elements of the boiler, fluid and flue gas carrying systems with chemical resistance, heat and sealing performance requirements accounted for, as well as the integration of electronic components.
“In addition to injection moulding, complementary manufacturing processes had to be adopted including automated assembly, linear vibration welding, spin welding, Ceracon FIP sealing, digital and hot foil printing.”
The gas boiler project ultimately saw Advanced Plastics design and manufacture 36 injection mould tools ranging in size from 250kg to 7,000kg, (with the largest running in a 1,500t injection
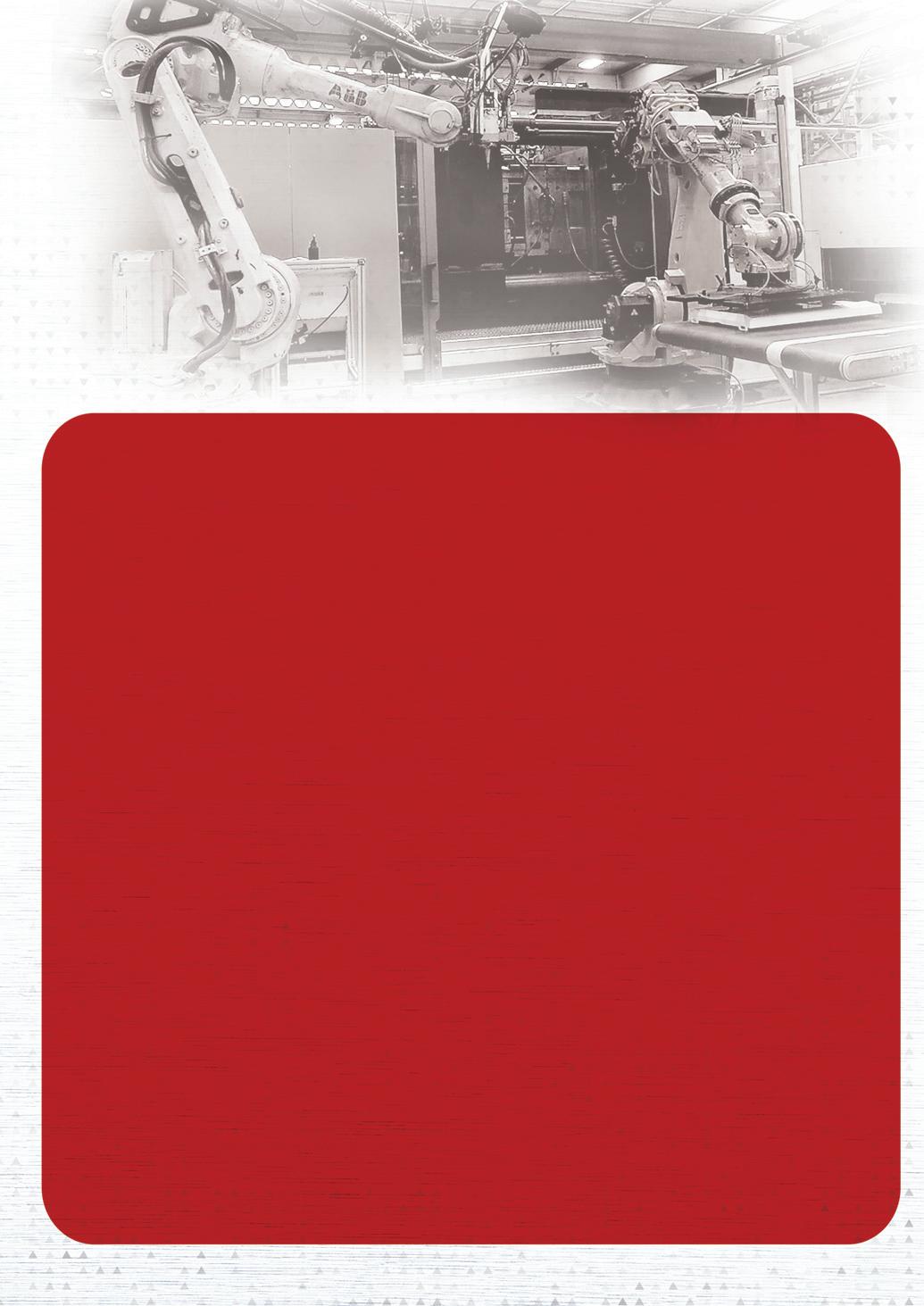
moulding machine), and the integration of all downstream manufacturing processes.
“This significant project was delivered on time and within budget, clearly demonstrating our overall design, development and manufacturing capability,” said Mr Hadfield.
The recycling revolution
Amidst global concerns about plastic pollution and a general increased emphasis on sustainable industry, Advanced Plastics has embraced a number of sustainability programmes. One of these is a major focus on the use of recycled materials, especially at its Fareham and Manchester factories. “Wherever possible, we choose to use recycled resins and invariably that creates opportunities for reduced cost and improved environmental impact,” Mr Hadfield explained.
He highlighted an example of how the company’s sustainability programme substantially benefits one of its larger customers: “A major worldwide telecommunications customer traditionally used virgin polymer, reaching a peak of 800 tonnes in 2015. As of 2023, its use of virgin polymer has been switched for 90% post-industrial and post-consumer recycled materials,
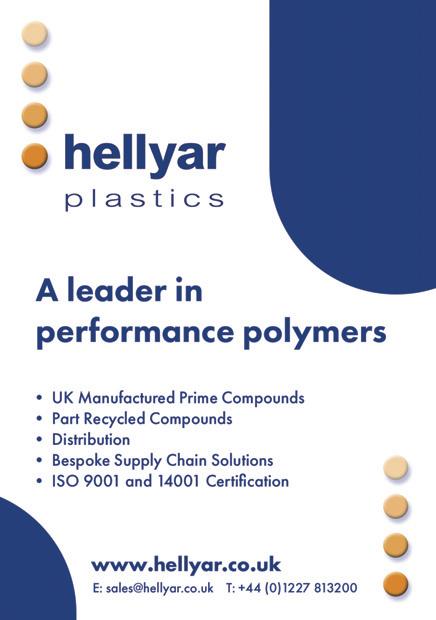
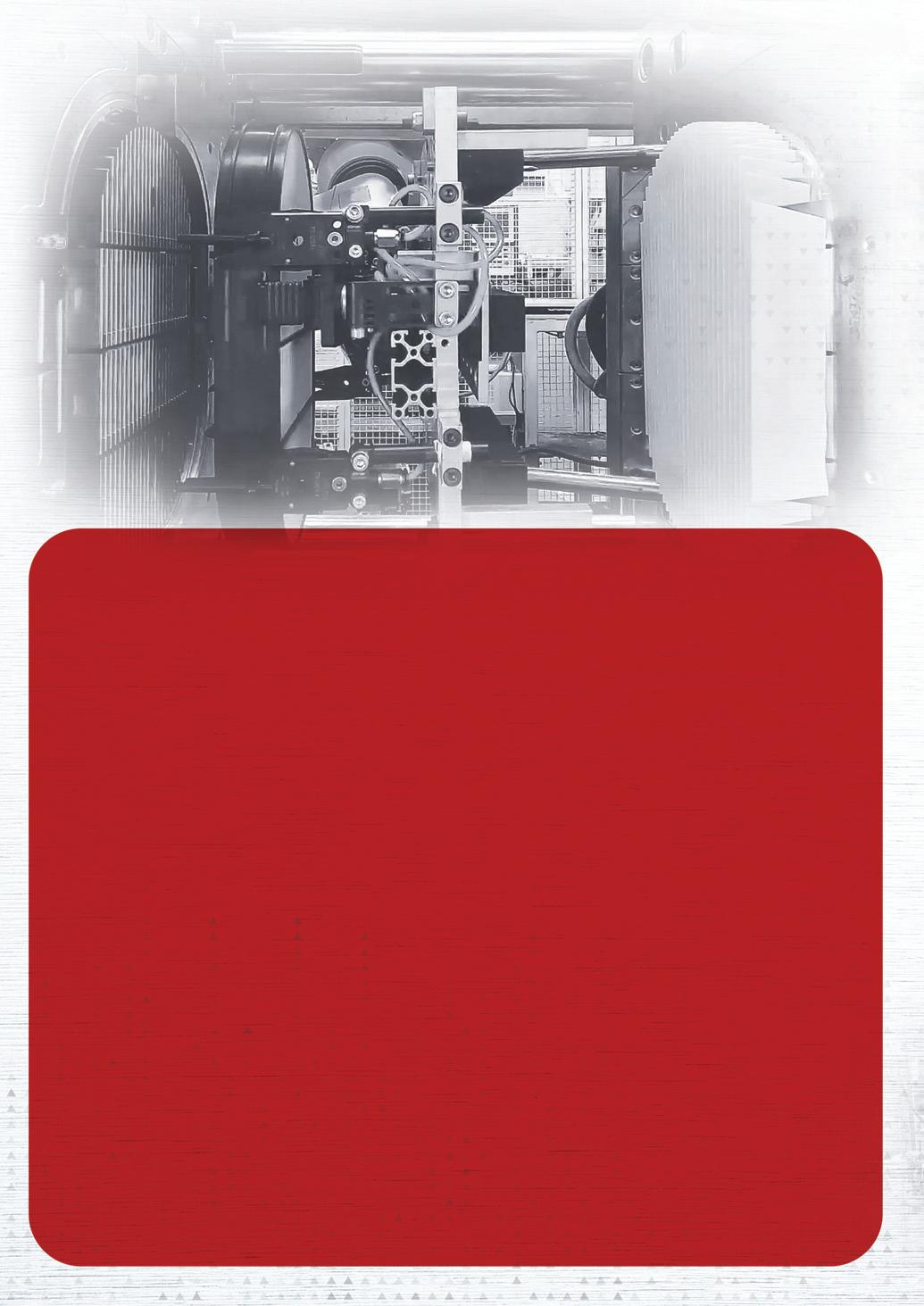
all with the full knowledge and collaboration of the customer’s technical and commercial teams.”
Meanwhile, Advanced Plastics has become an industry leader in its ability to supply to customers the energy usage data and carbon footprint information for its polymers, for use with Environmental Product Declarations (EPDs). The EPD document transparently communicates the environmental performance or impact of any product or material over its lifetime.
“Many of our customers readily embrace this programme and supply the required data, increasing their market share and overall turnover,” Mr Hadfield said.
New board and future plans
In September 2023, Advanced Plastics announced the appointment of a new Board of Directors, with majority shareholders Chris Pearson and Rob Anderso n becoming joint CEOs of the business. The new board, with collectively over 150
years’ worth of plastics industry experience, is developing a five-year business plan with the stated goal of driving Advanced Plastics to £50m turnover, which is set to be achieved organically and through site growth and strategic acquisitions.
The company expects organic growth to be partially driven by further diversification as well as continued investment in the latest manufacturing technology and automation, allowing the company to continue to offer its
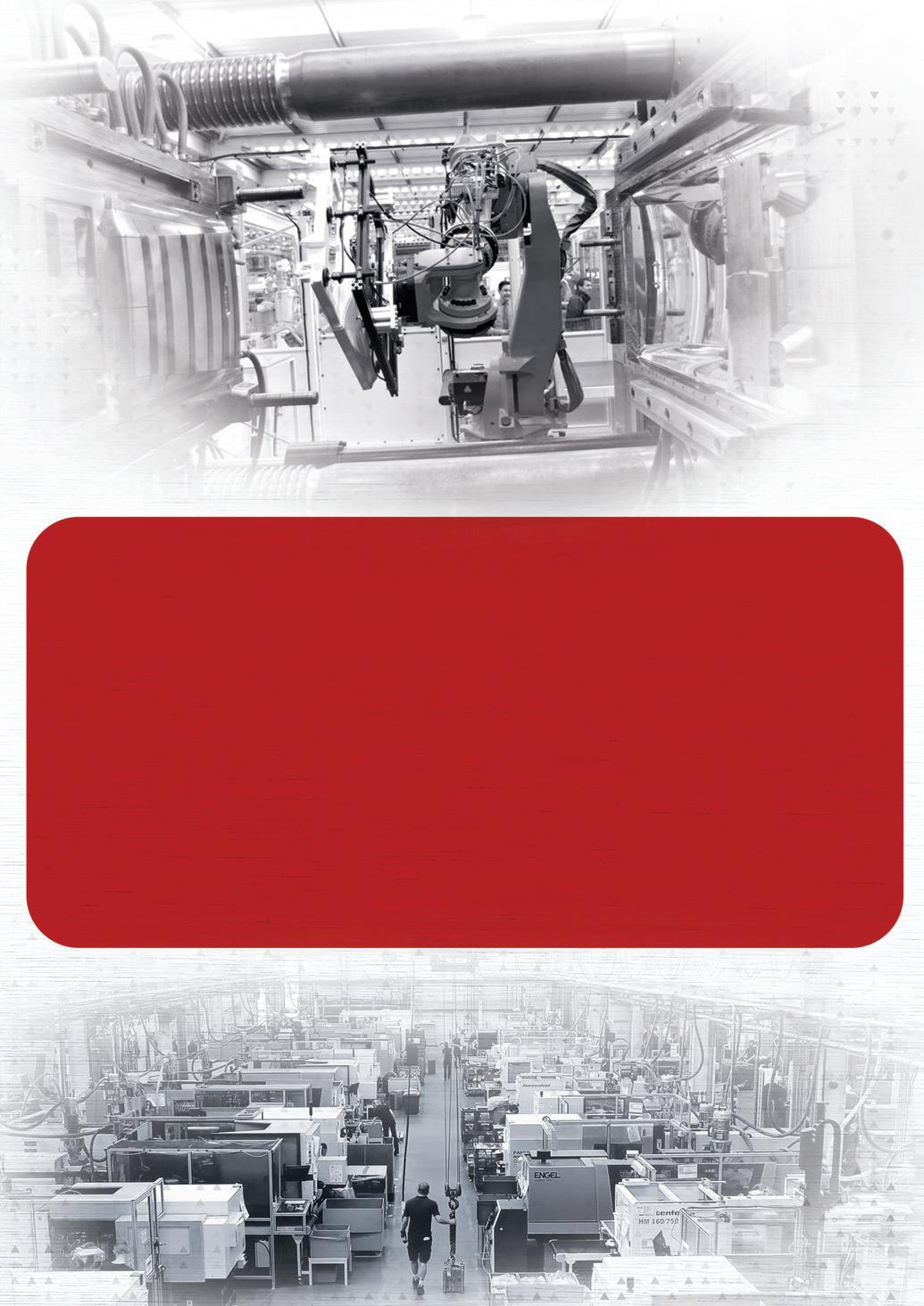
customers the best and most competitive technical solutions.
In conclusion, Mr Hadfield reflected on the company’s prospects: “Our team is very confident about our future; we believe that our business covers so many market sectors that we’re well protected from major turbulence in individual ones. Our financial stability remains a major strength and we look forward to continuing to deliver excellent projects on-time to customers all over the UK and Europe.” n
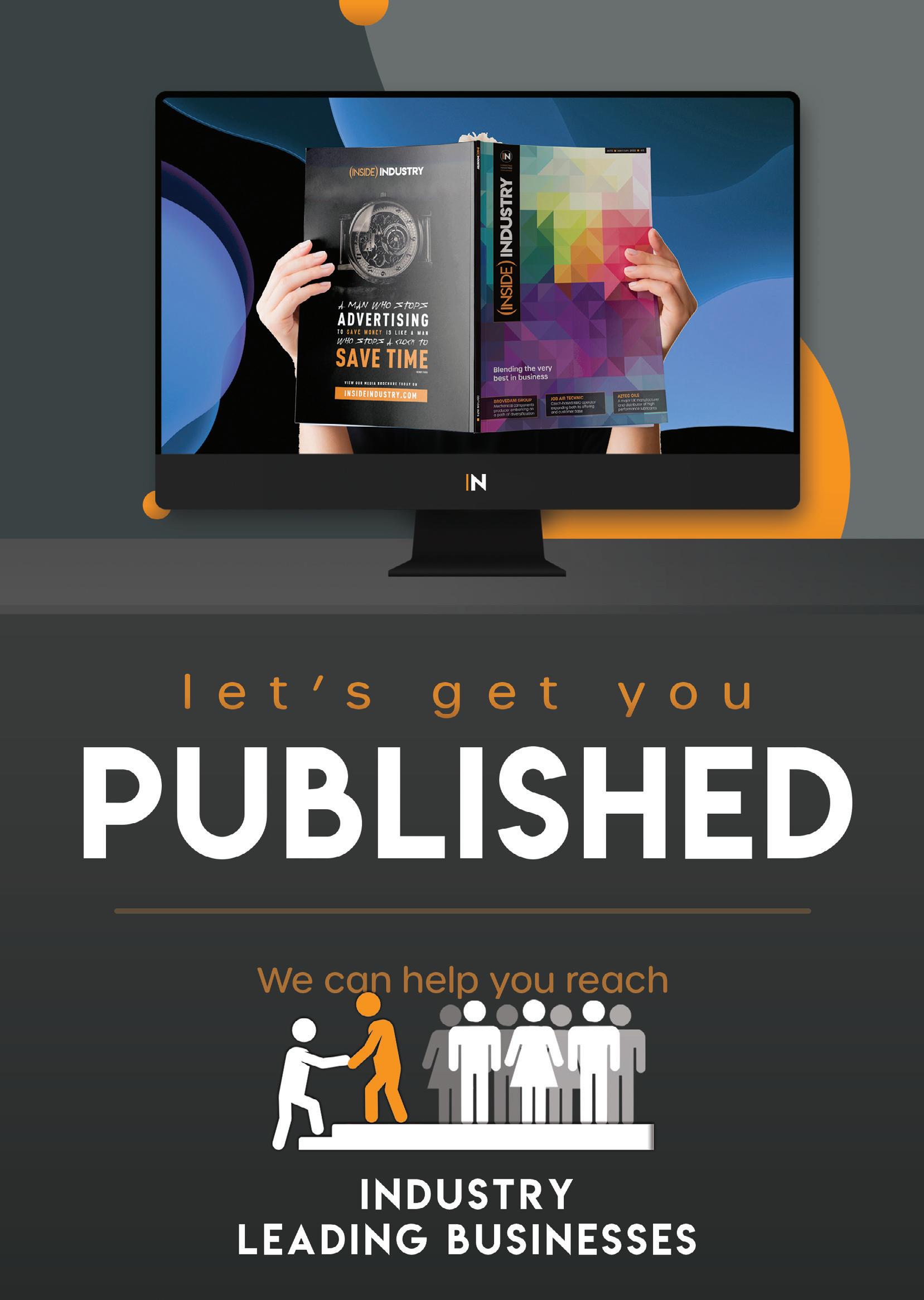
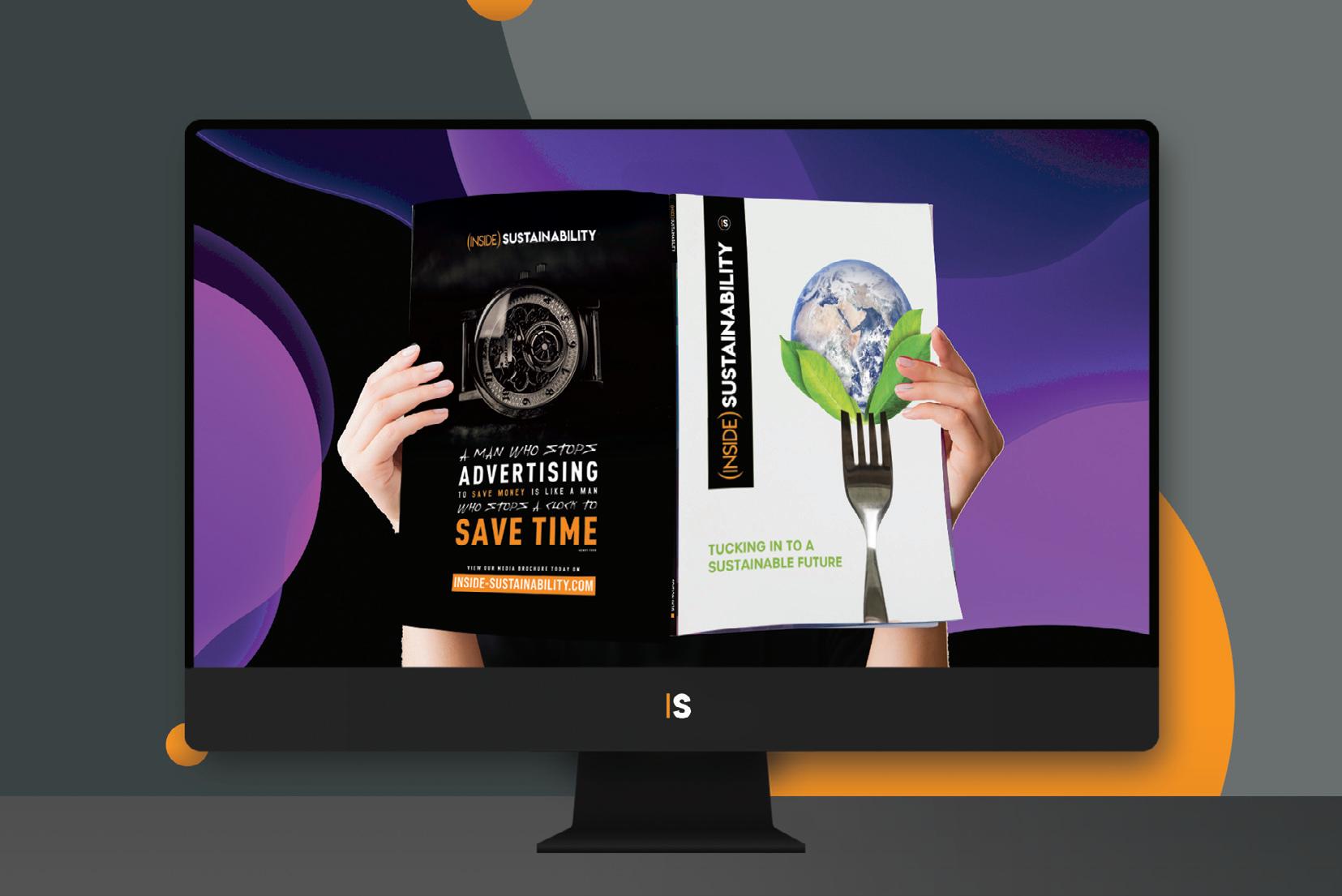