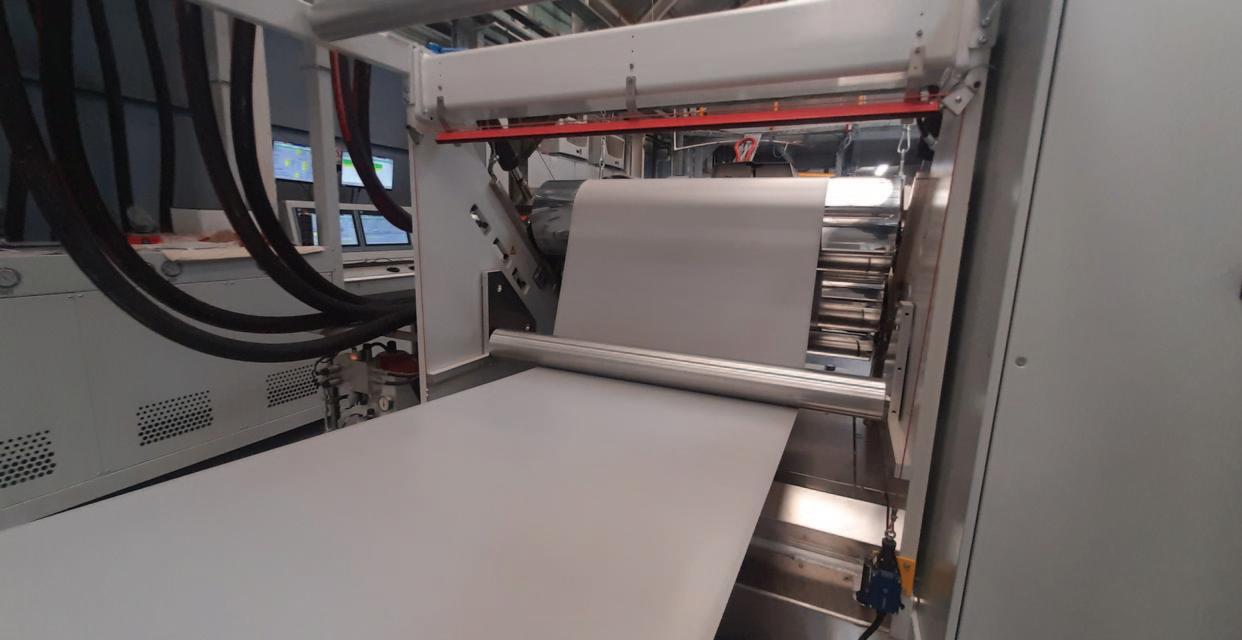
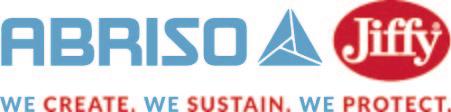

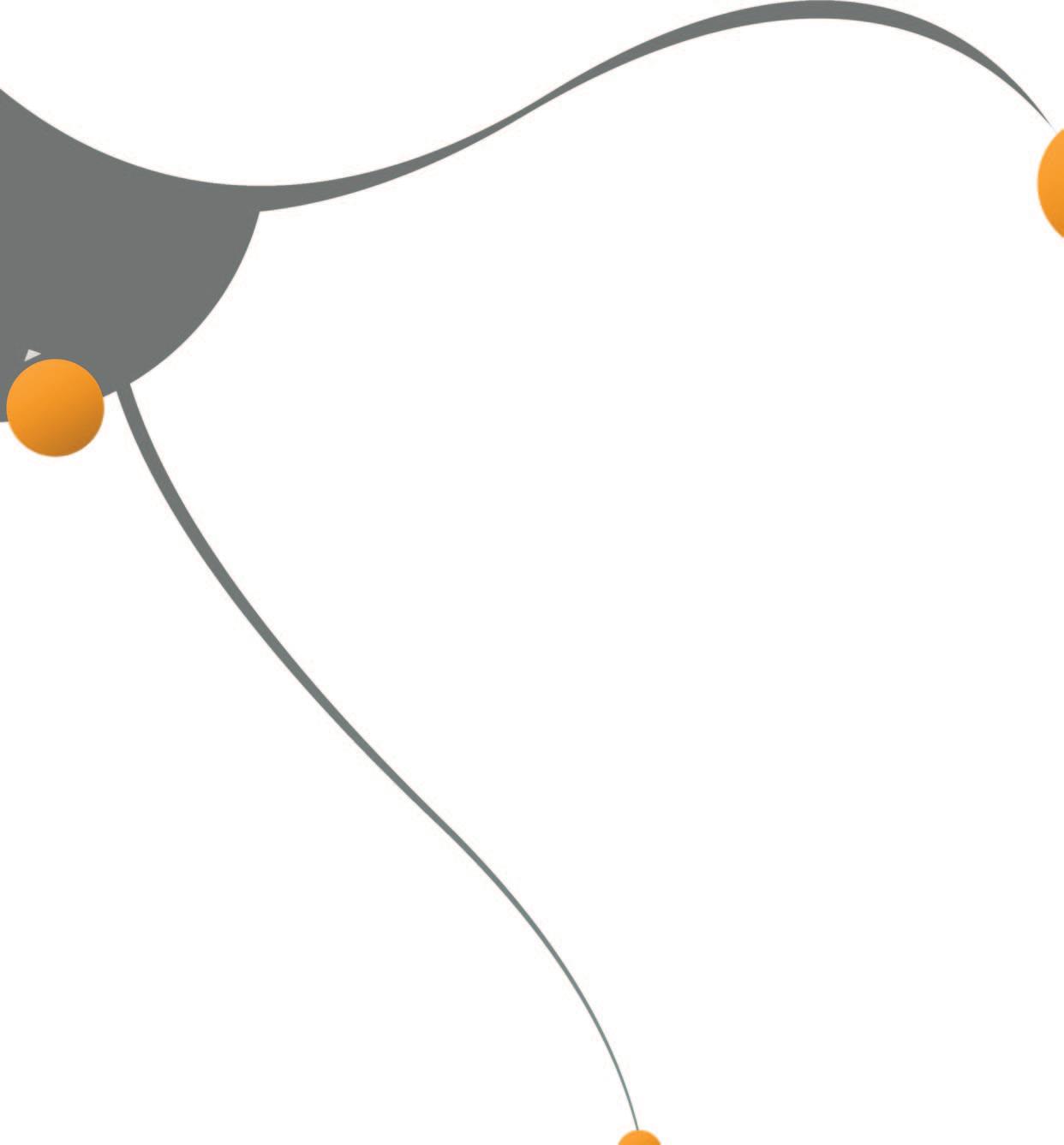

As a leading manufacturer of protective packaging and insulation, Abriso Jiffy specialises in the extrusion of plastic polymers into technical foam solutions and air bubble products. Now, at one of its facilities, the company is fortifying a commitment to sustainability via the circular economy. Hannah Barnett spoke to Nicolas De Koker, Marketing Manager, and Dan Gavriliu, General Manager at the Piatra Neamț facility, to find out more.
The last few years have been a time of flux and growth at Abriso Jiffy. In 2019, Belgian film producer Abriso took over the Italian packaging company Jiffy, becoming a much larger group in the process and heralding an entire change of structure. This consolidation meant the

group significantly increased its annual turnover from roughly €100 million for each company to €350 million as a collective entity.
According to Marketing Manager Nicolas De Koker, the financial benefits of becoming a large group have not been the
only rewards: “It was our goal to project a European outlook. We have shown the benefits of small operations coming together to make one bigger, uniform company.
“We now have 17 factories across Europe. I think we are the only company in our industry with this European-wide coverage. We can serve more than 5,400 customers and have a big range of clients who all receive the same excellent quality and service.”
Pioneering Piatra Neamț
One of the 17 factories, Piatra Neamț in Romania, is an excellent case study, demonstrating how Abriso Jiffy is embracing change to become as sustainable as possible.

The company is focused on both postconsumer and post-industrial recycling at the facility. The former means collecting plastic waste from clients to be reused: the latter involves optimising every product process in the factory to recycle waste internally and reuse it.
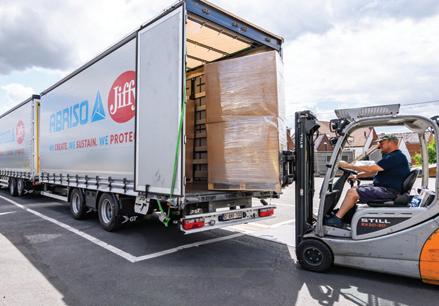
At Piatra Neamț, the company is closing the circle on the circular economy in three ways: cutting down on waste, reducing the plastic content in products through decreasing their density and reusing the packaging it collects from consumers as raw material resin.
This all takes place at a state-of-the-art recycling workshop that opened in March
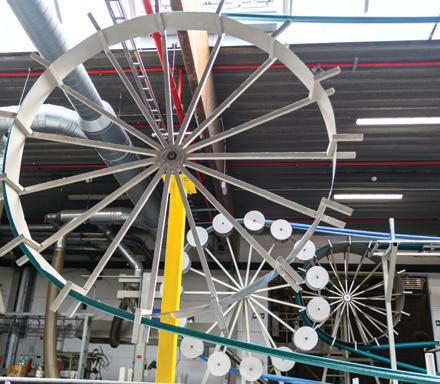
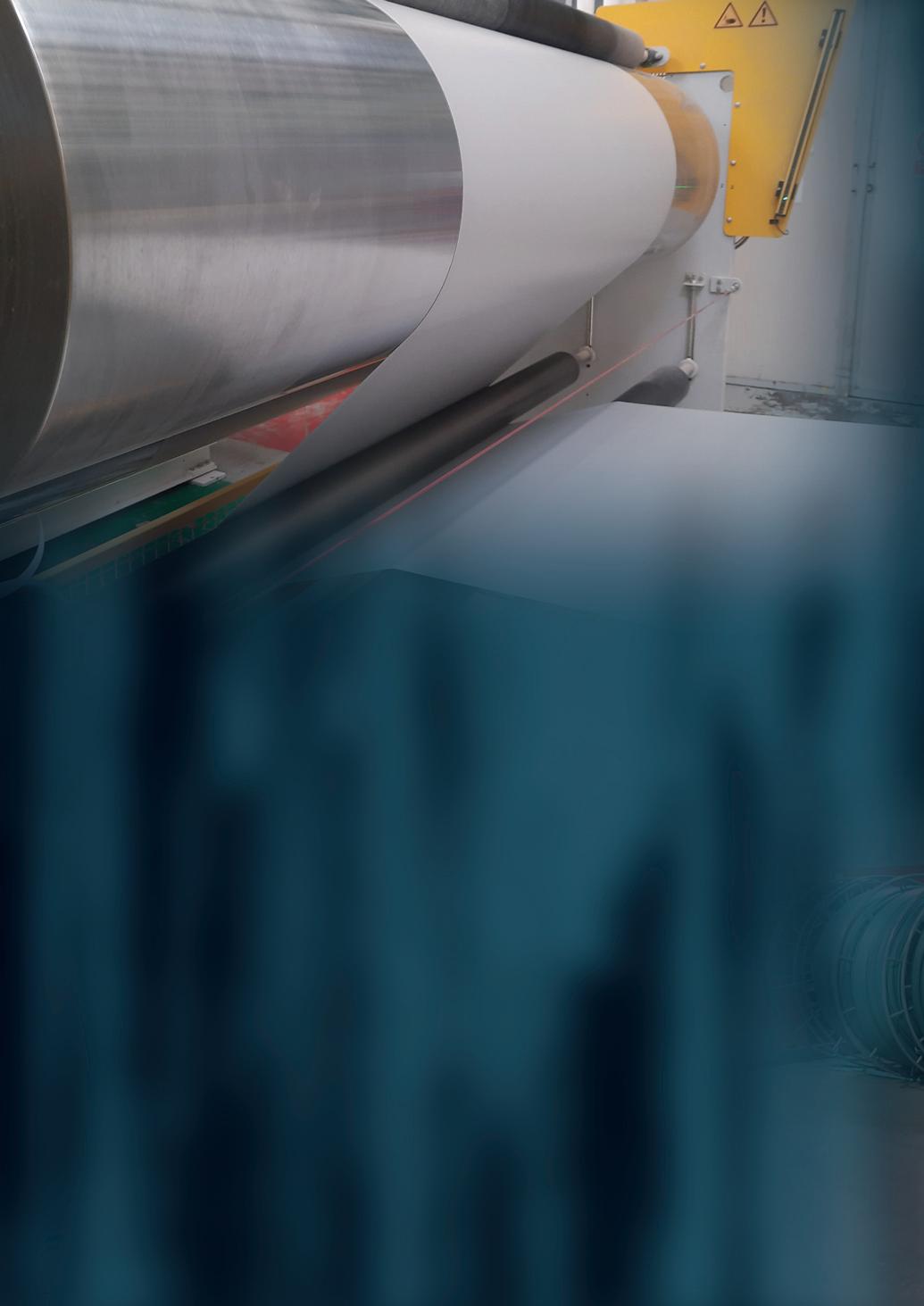
2023; a €1.5 million investment. The new site can produce the iconic Ocean Green® bubble film from between 50% to 90% recycled plastic resin. By putting the product back into the manufacturing process, its lifespan is significantly increased.
“Bubble wrap has sustainable properties when used and disposed of properly,” Dan Gavriliu, General Manager at the Piatra Neamț facility, explained. “Our Ocean Green® bubble film packaging is a special product that can be easily made from 100 per cent recycled low density polyethylene without compromising the quality or the features for which it was created.”
The company is also transforming waste from its manufacturing process into 100% recycled resin, without having to use any fossil fuel-based raw materials. This not only significantly minimises Abriso Jiffy’s carbon footprint, but it also prevents plastic getting into the ocean and other associated littering.
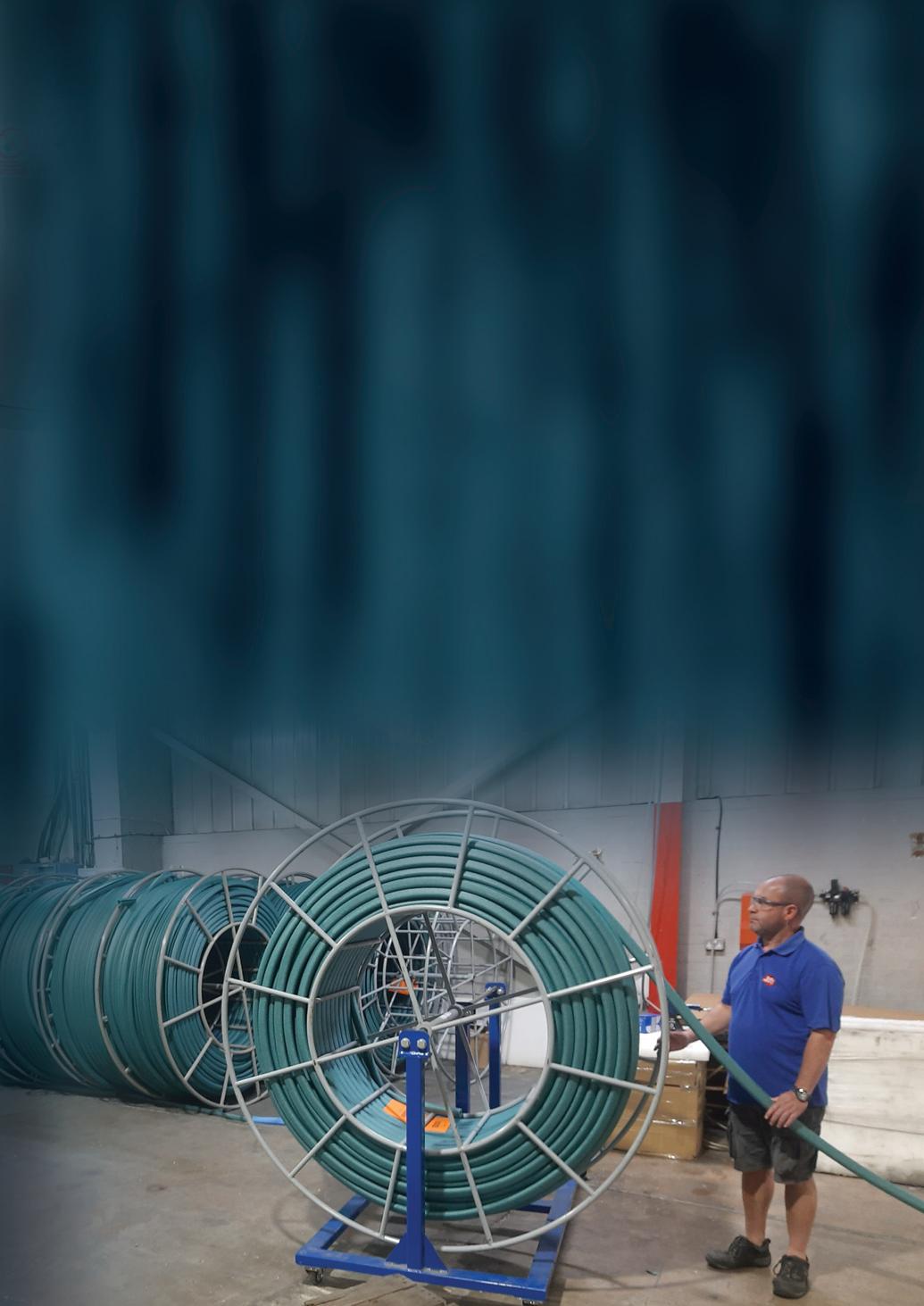
A mindset of innovation
Abriso Jiffy maintains strong partnerships with successful companies like Lidl, as well as a significant automotive spare parts manufacturer, to collect plastic waste and reuse it as part of its postconsumer recycling programme. And the company is continuing to push the boundaries of innovation.
“We need significant investment in advanced technology to incorporate more recycled material in our products,” Mr Gavriliu explained “In 2023, we succeeded in using multicoloured recycled resin in a special product that we call break bubbles.
“This is mainly used in the building sector as reflective insulation; the product is called RoFlex ®. It’s a reflective insulation bubble field with an aluminium barrier that
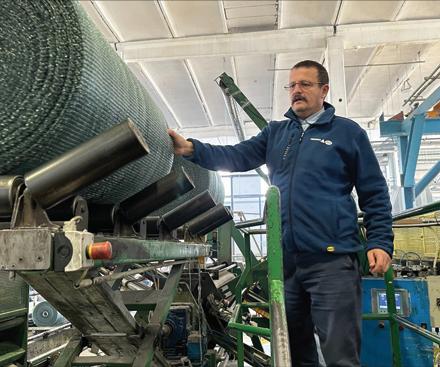
is laminated on both sides to reduce heat transfer. It can be utilised in transportation of refrigerated products and to insulate the interior of vehicles.”
“Our advantage is that we have a wide range of product portfolios, designed for different industries,” Mr De Koker added.
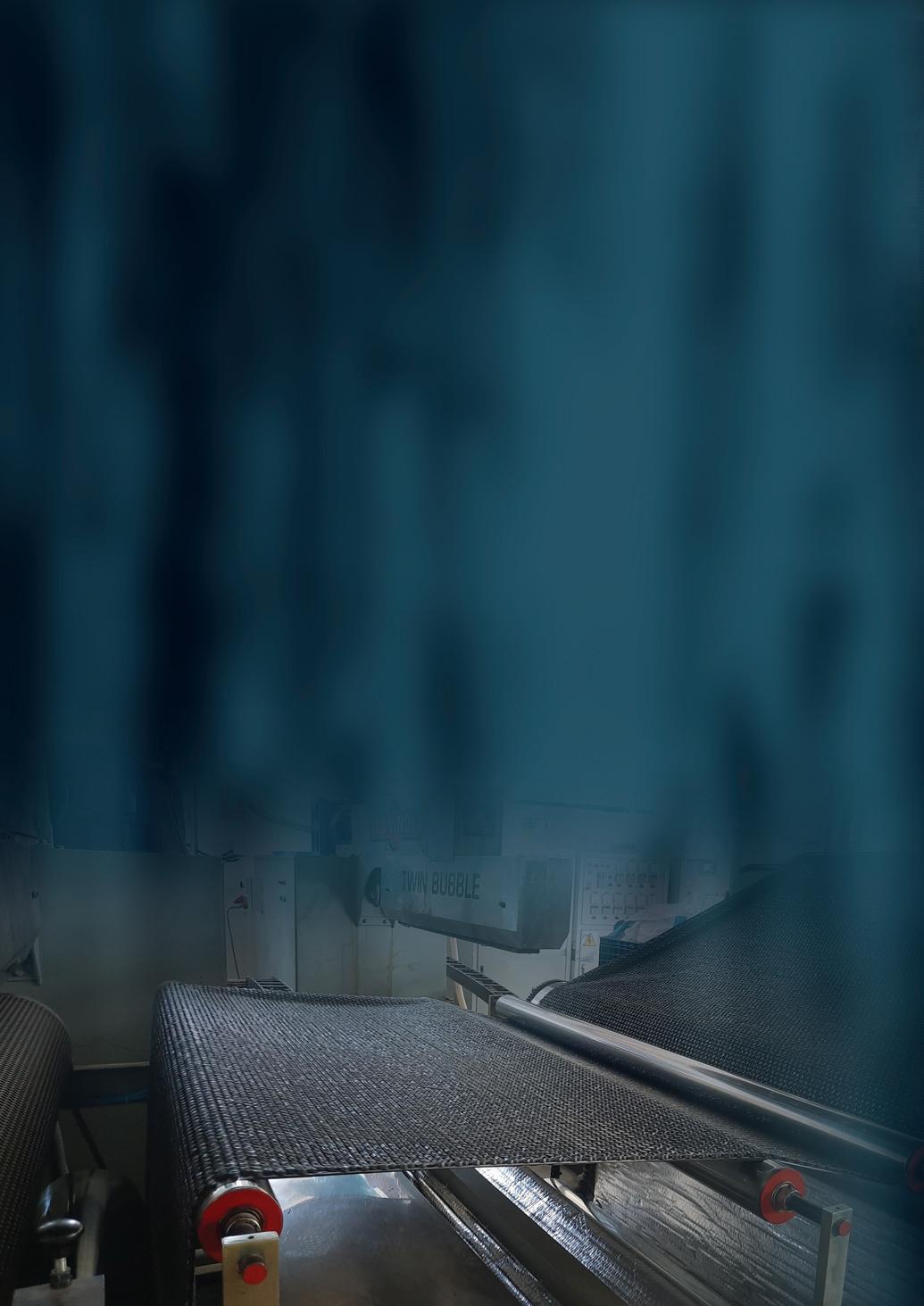
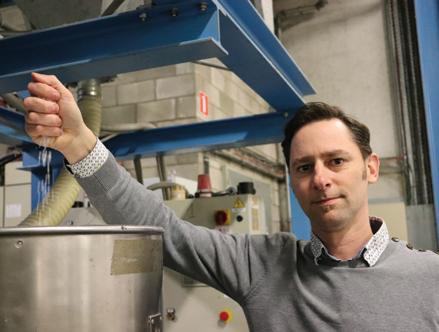
“We have products for packaging, but also for building. So we can offer innovative and unique solutions that meet the specific needs of our clients.”
Building and maintaining long-term relationships with its supply chain is crucial for a company with the wide reach of Abriso Jiffy. “We have very open and transparent communication with suppliers, maintaining regular contact to discuss expectations and share feedback,” said Mr Gavriliu. “This gives us the opportunity to develop new technology and also implement better solutions for the circular economy in our organisation.”
Future challenges
Abriso Jiffy currently has the capability to use 100% recycled material to make bubble film, but is not yet capable of the same with foam packaging. This is therefore the company’s next challenge, and it is breaking ground already. Abriso Jiffy has been working with two big chemical factories to develop resin that can contain up to 40% post-consumer recycled content for foam packaging.
“This is a significant step forwards to achieving our main objective and reducing the fossil fuel-based raw material for plastic,” said Mr Gavriliu. “We want to get up to 70 per cent post-consumer recycled material in our foam, which will depend on regulation and the technological development of the coming years.”
The company is also working out how to recycle multi-layer plastic more efficiently, though this remains a challenge. The circular economy surrounding plastic extrusion is clearly a field with plenty of activity, but also one in need of more R&D.
“Transitioning to sustainable products requires a lot of investment in ecofriendly technology, new materials and processes,” Mr Gavriliu reflected. “The demand from the customer is uncertain and regulations vary from country-tocountry. When we have the same legislation everywhere, I believe we will have better opportunities to embrace more sustainable alternatives.”
Abriso Jiffy’s aim is to maintain a sustainable operation and achieve net zero by reducing its carbon footprint and offsetting any remaining emissions. In Piatra Neamț, the company utilises geothermal ground cooling systems instead of an electrical chiller, reducing water usage and electricity consumption by 15% across the whole factory.
“My personal objective is to create a healthy working environment here in Piatra Neamț to facilitate the teamwork that can improve people lives,” said Mr Gavriliu. “I want our employees to be happy because a happy employee leads to a happy customer: and happy customers create happy share holders. So I strongly
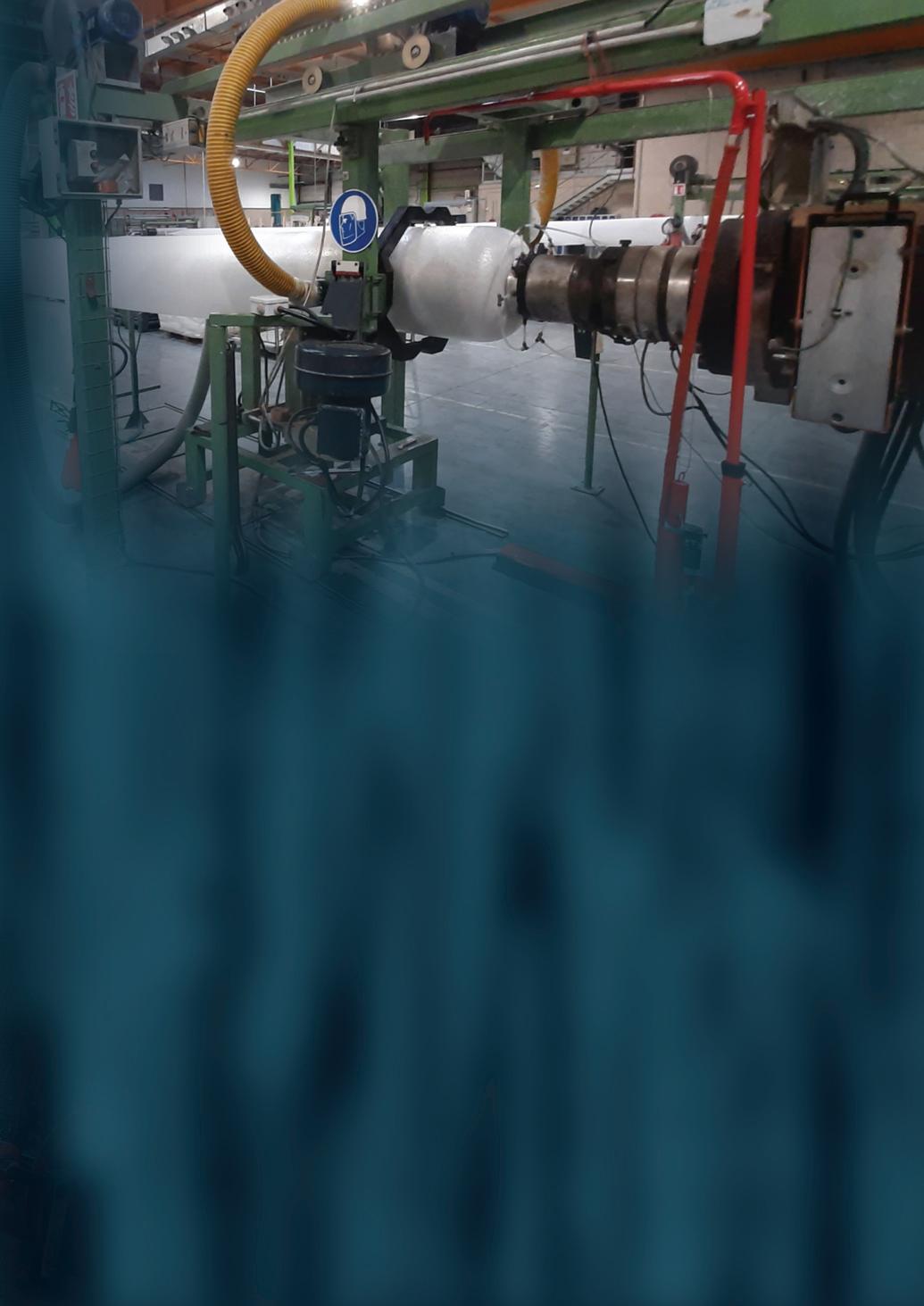
believe that my job is to take care of our team and create more value for the company.”
For Mr De Koker, investment is needed into changing mindsets more generally about the sustainable benefits of plastic. “We do a lot of investment in R&D,” he concluded. “But people can be sceptical and think plastic is always bad for the environment. If it is used in the correct way, it’s better for nature than alternatives like paper, which can only be reused seven times and for which the production process requires far more electricity and water than ours.
“Plastic is a valuable resource when it is used – and reused – properly.” n

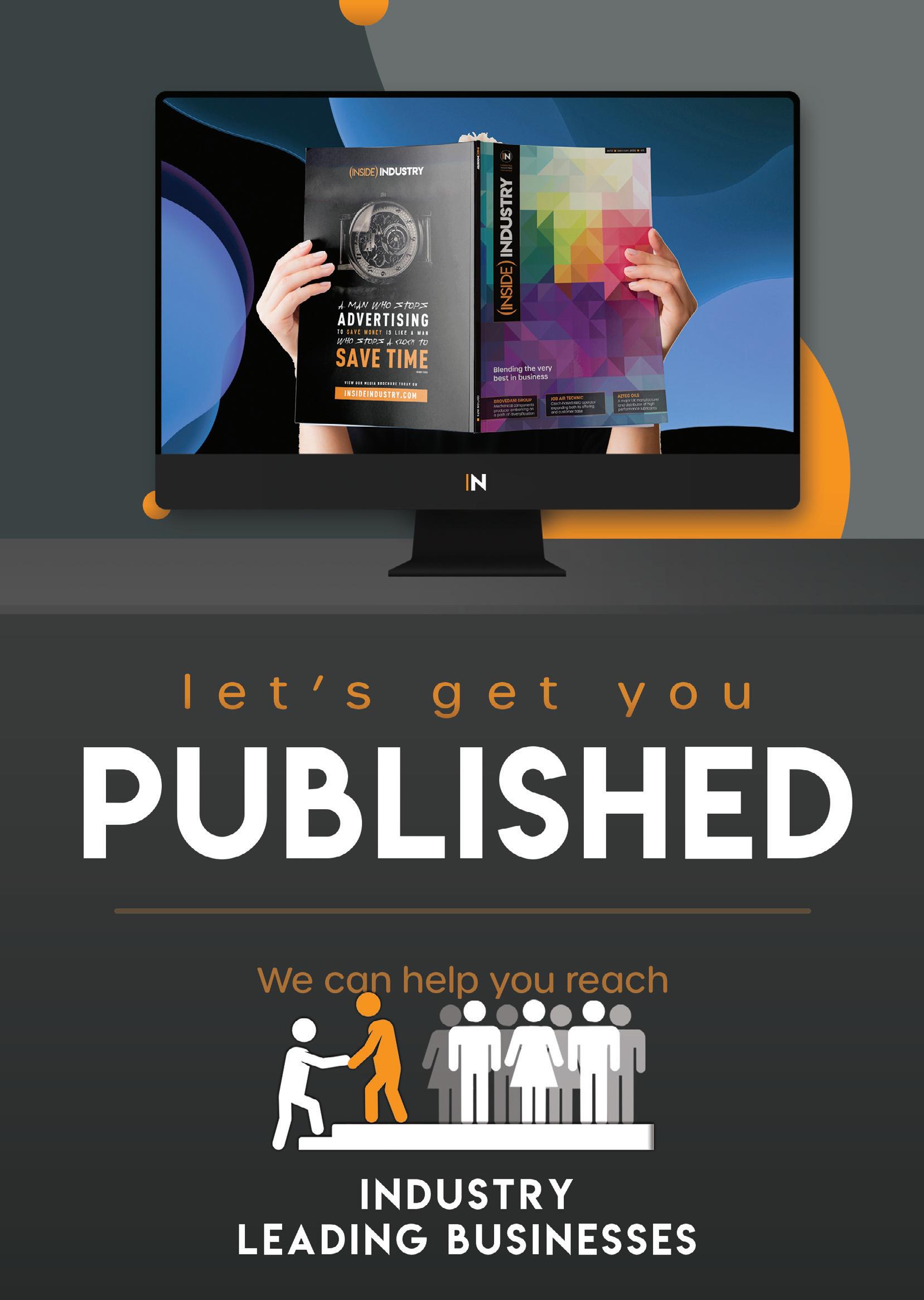
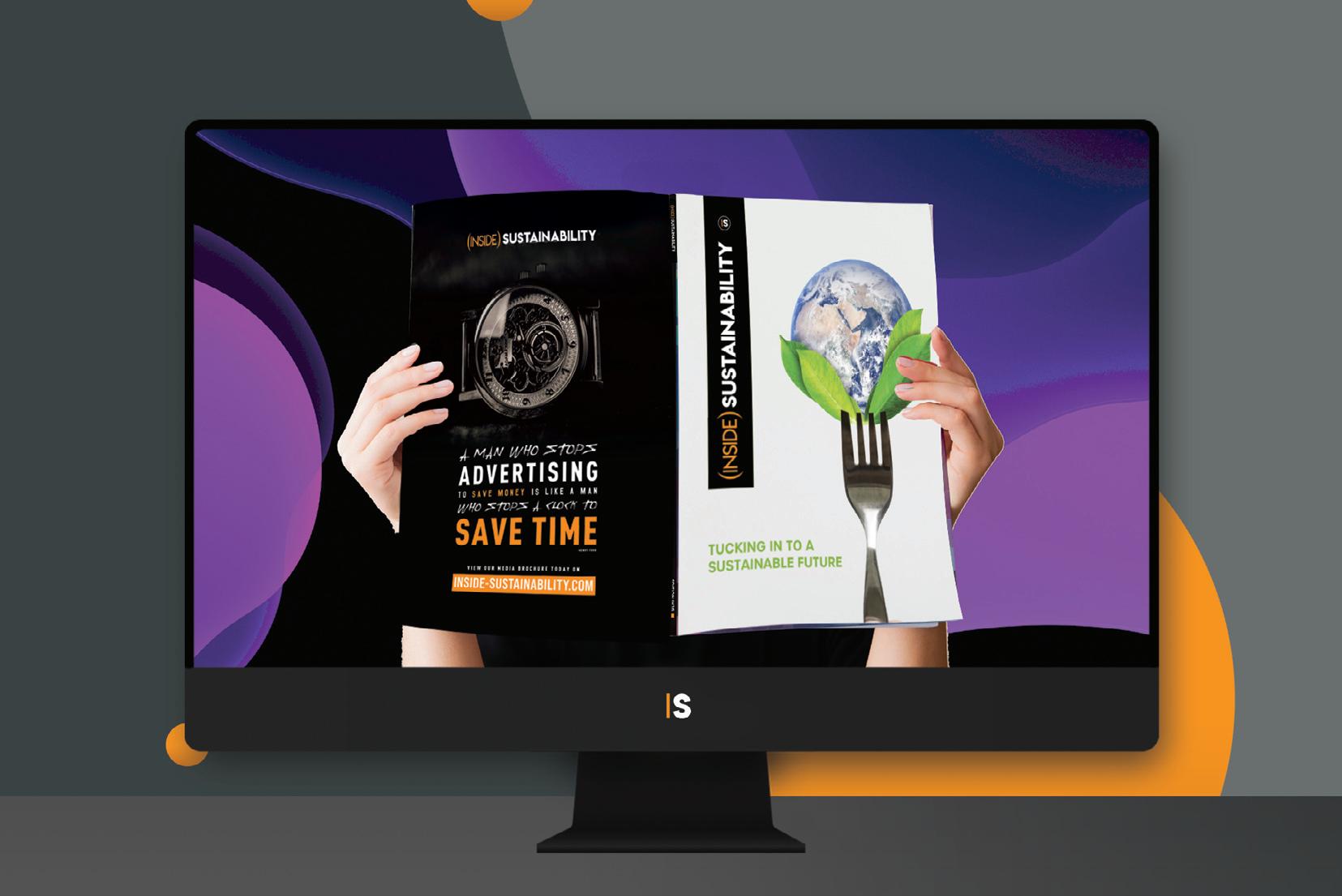