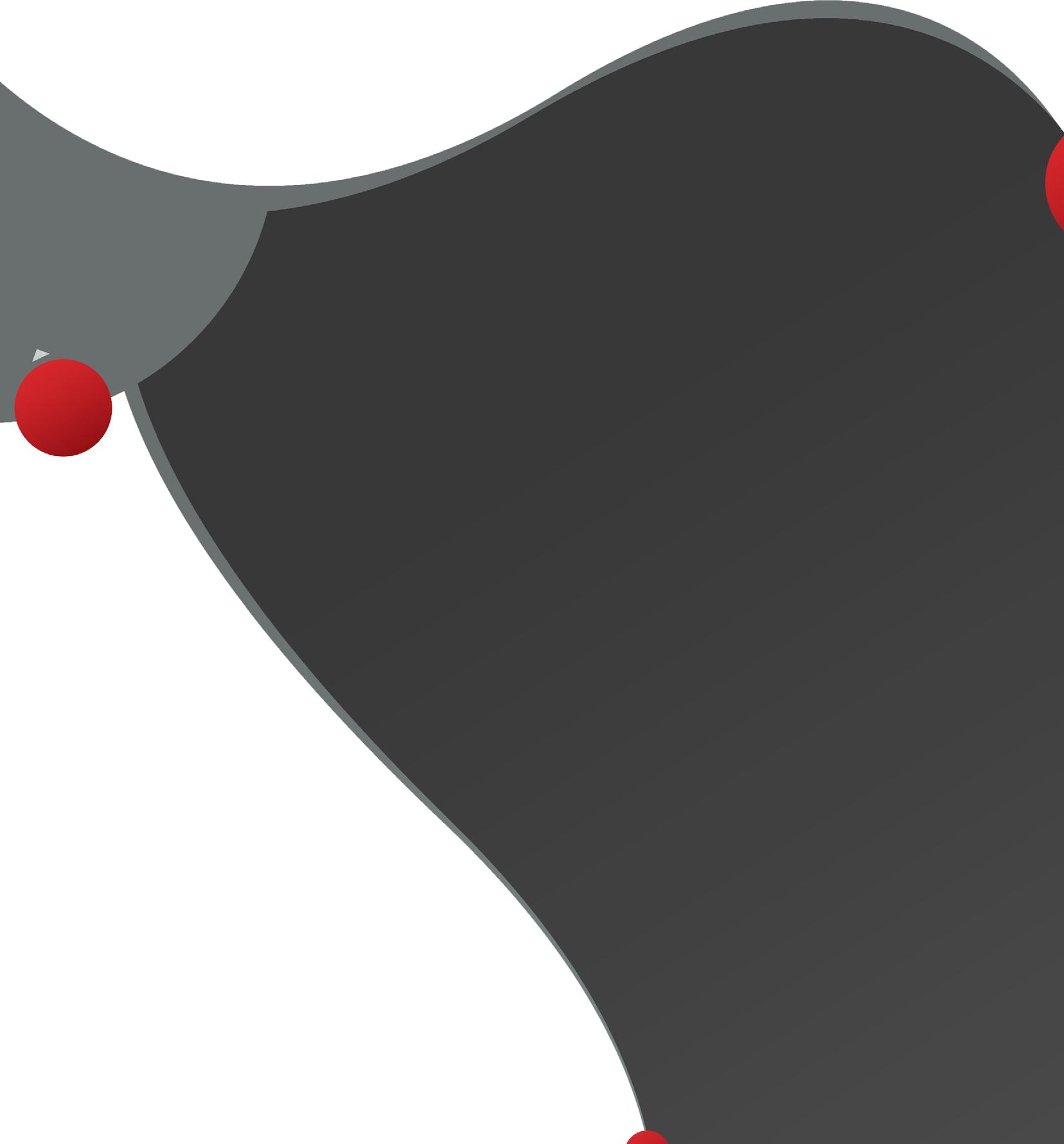
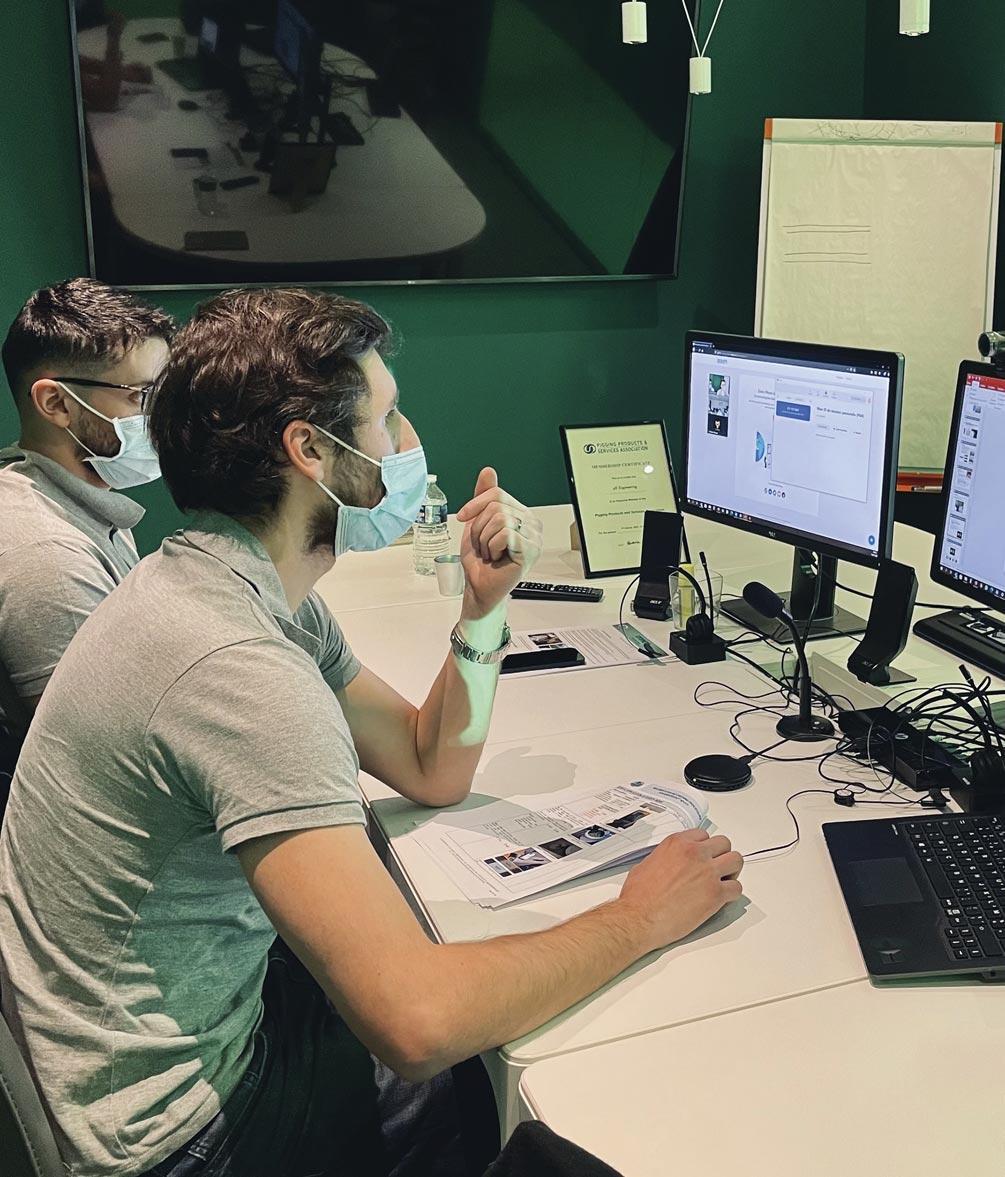
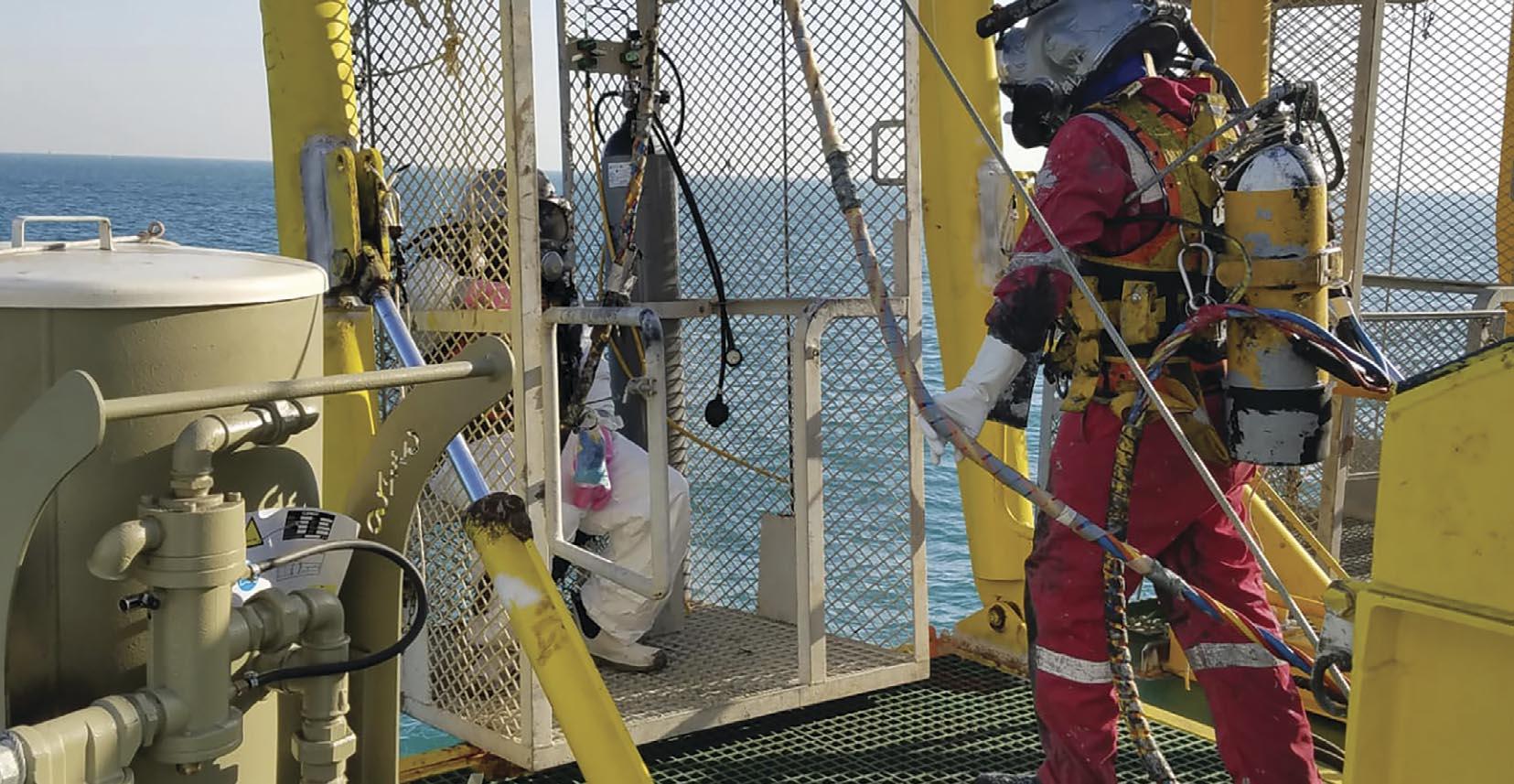


Monaco-based 3X ENGINEERING is one of the world’s leading companies specialising in pipeline maintenance using patented composite technology, primarily serving the oil and gas sector. Andy Probert spoke to Sales Manager (Europe) Jean-François Ribet about the company’s scope of work and its ambitions to become a prime mover with North Sea operators.
Asubsea leak of any kind in the oil and gas sector can run to millions of dollars and cause long-lasting environmental damage if it isn’t dealt with promptly and efficiently. For most oil majors, contractors and partners, 3X ENGINEERING’s patented solutions are often the first lines of defence.
Since 1990, 3X has become a globally acknowledged leader in pipeline maintenance using composite technology.
Founded by Stanislas Boulet d’Auria, the company is a proven developer, manufacturer, supplier and installer of a portfolio of quality products that are not just a quick fix – but a long-term solution.
“Our holistic philosophy means a comprehensive approach to leaks in any environment,” explained
Jean-François Ribet, Sales Manager (Europe). Its patented solutions, such as StopKit, ReinforceKit, RollerKit and
TanKit, are highly sought-after worldwide through its qualified distribution network of over 60 partners.
“It is all about confidence: at 3X, we provide confidence to our clients with our engineering knowledge in composite expertise, as well as the field knowledge, flexibility, responsiveness and product quality. Failure can never be an option.”
One of the key focus points for Monacobased 3X in 2023 is to increase its presence in the North Sea area with clients and operators, ensuring that its products are on offer through its network.
“As a global operator, we want to maximise our coverage across different seas and continents,” said Mr Ribet, “and
the North Sea’s oil and gas sector is a prime area we want to leverage our products into.
“3X has extensive composite knowledge, unique know-how and experience in critical fields of industry. Subsea applications take into account more constraints, and there is no place for uncertainty.
“Thanks to our R&D team, we have developed specific solutions to ensure successful and long-term repairs for up to 20 years. Technically, our resins have been certified by well-established third parties, such as DNV GL in Norway. We have proven results with, for example, an adhesion result of 10Mpa compared to the standard 5Mpa.
“We can repair all kinds of defects, such as external and internal corrosion, holes
and leaks, crack and dents. We have developed a range of products to respond to every eventuality, with a design lifetime approach. We reinforce assets to give them back their integrity.”
Through its large distributor network, it has certified applicators situated close to facilities worldwide to apply 3X products: and if they are needed, 3X’s dedicated technical team can be deployed on-site to perform the repair.
3X’s products, which comply with ISO 24817 and ASME PCC2 standards, have also been tested with Bureau Veritas, TUV, ABS, Lloyd’s Register and private labs of well-known petroleum companies.
Mr Ribet emphasised their patented products are proving popular and reliable for operators in Africa, the Middle East and Europe. Its Stopkit is an online leak-sealing solution which can stop a live leak up to 150 bars and up to 150°C. “We have developed specific and unique know-how regarding subsea repairs and have successfully concluded many projects,” he said.
In 2018 and again in 2020, 3X was called on to repair several subsea caissons for a Norwegian oil and gas company. “Thanks to our solutions, the client could still operate their offshore platforms without shutdowns and in complete safety,” Mr Ribet explained.
One of the many technological advances made by 3X has been its REINFORCEKiT®4D SUBSEA (R4D-S). This is a wet lay-up system wrapped helicoidally around a pipe to bring mechanical resistance to
the damaged pipe section. The number of layers, determined by calculation, is linked to the pipe pressure, temperature, diameter and thickness, as well as the pit depth and length, the steel grade and the pipe location.
R4D-S can repair and reinforce pipelines operating at temperatures between +5°C (+41°F) up to +65°C (+149°F) subject to external/internal corrosion, leaks, dents and mechanical damages for the underwater environment.
Mr Ribet reflected that the 3X teams had installed R4D-S across many projects, including repair to reinforce a 48” subsea pipe damaged by an external corrosion defect and leak at 5m depth.
This project was the longest one performed by 3X in a subsea environment. It was successfully repaired using R4D-S despite various complicated parameters: a 48” large diameter pipe, leaking defect,
and 27m length of repair requiring a composite wrapping in many sections. As part of another project in Vietnam, R4D-S was utilised by 3X’s local distributor Petroenertech to reinforce a 16” subsea pipe with a dent at a depth of 49.4m.
“Despite Covid, the project was conducted by our distributor under the supervision of 3X by videoconference throughout the repair,” said Mr Ribet. “This demonstrated the adaptability of 3X and its distributors to work remotely during the pandemic.”
3X had enjoyed considerable growth in recent years despite the pandemic, according to Mr Ribet: “Our company has continued growing every year, increased its activities and still managed to successfully meet the demands of each and every project. 3X would like to thank its clients
and partners who have trusted our know-how and solutions.
“However, even as the company grows, it is important to stay focused on our core v alues of responsiveness and quality. Clients depend on us and our products, and we will never lose sight of that.”
Mr Ribet outlined how the company’s growth had also taken its proven solutions from the energy industry into the power plant and nuclear sectors with its Reflangekit product, an online SF6 leaksealing solution. “3X has also developed solutions for structural repairs to reinforce beams in the railway sector,” he said.
“Because our core values are innovation and quality, the research and development team keep exploring new technologies to improve the standard of our products and technical services and to develop
new repair solutions,” Mr Ribet concluded. “ 3X is also continuing to expand its network of distributors globally, so that even more end-clients can benefit from our experience and expertise.” n