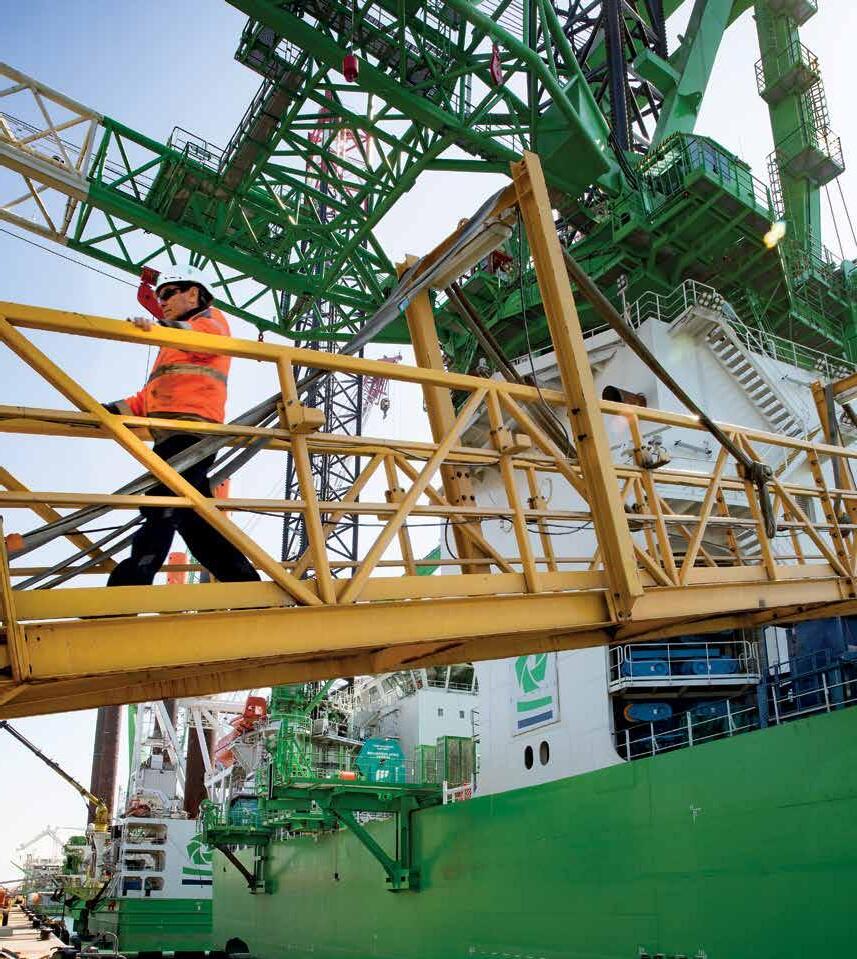
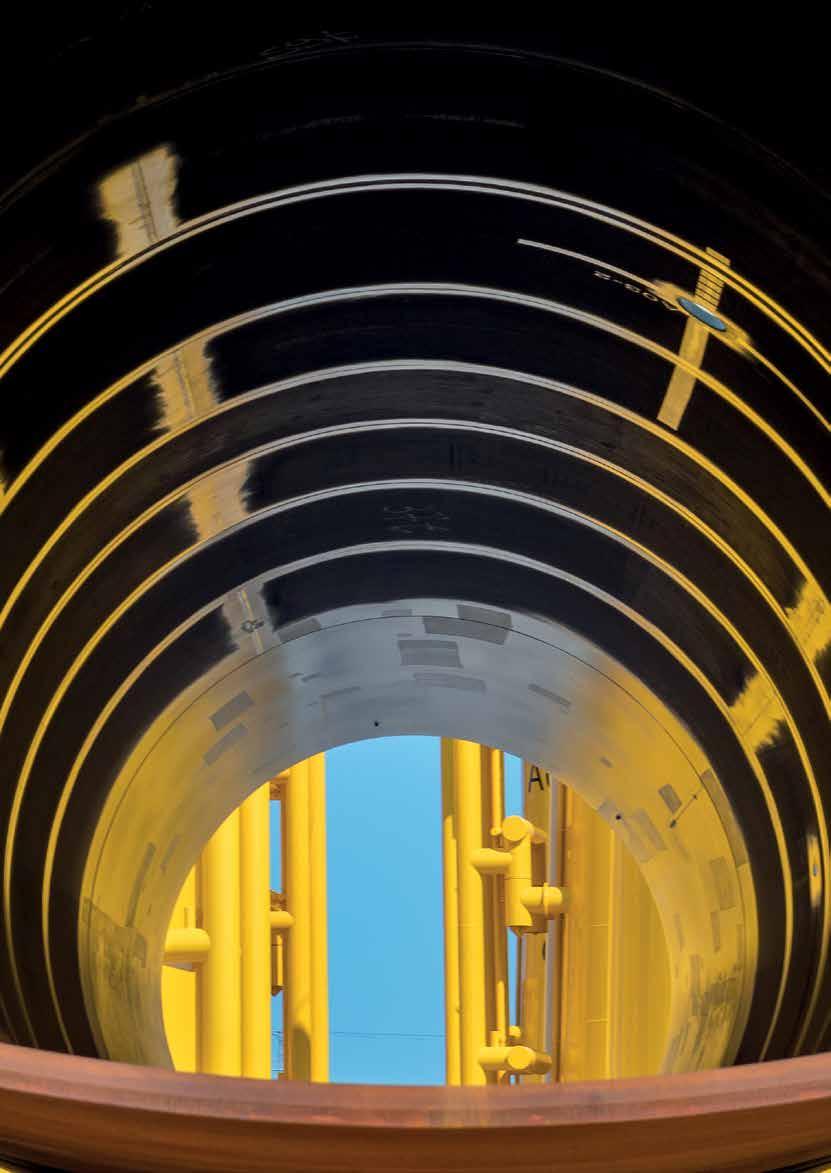
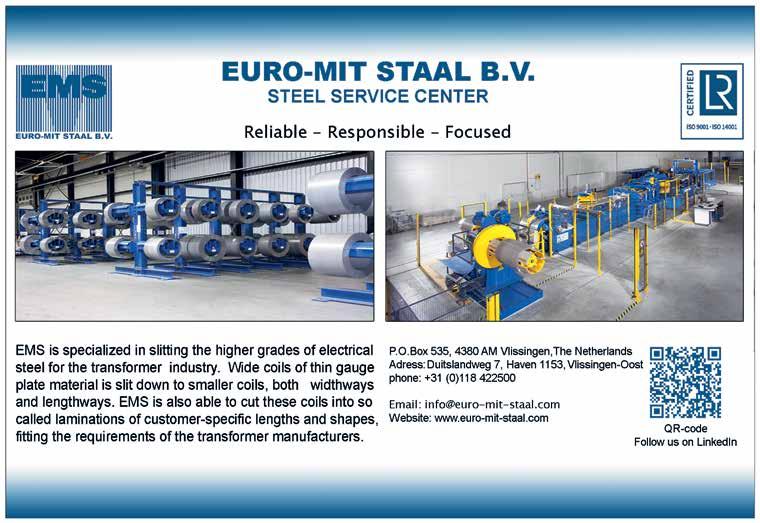
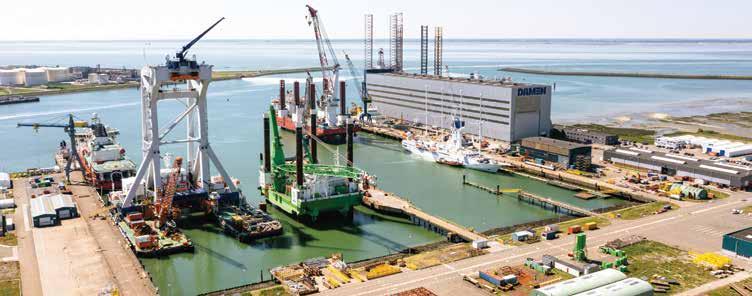

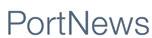
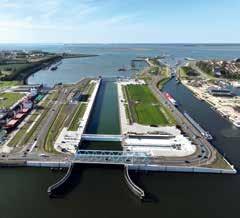
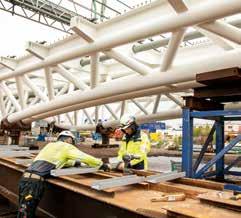
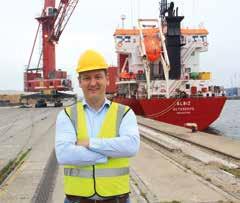
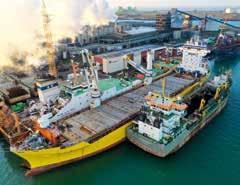
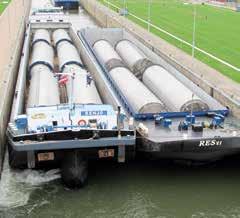
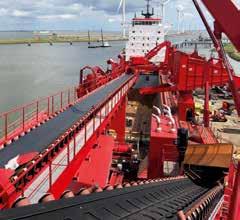
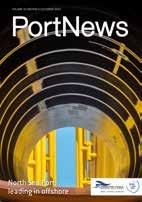
North Sea Port and Promotion Council North Sea Port will be in attendance at various events and trade shows. Below you’ll fnd a snapshot of the upcoming events that might be of interest to you.
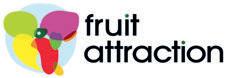
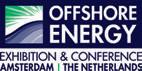
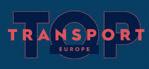
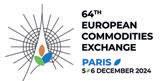
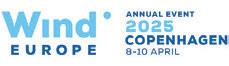


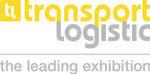

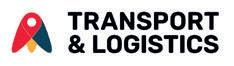
North Sea Port and Promotion Council North Sea Port will be in attendance at various events and trade shows. Below you’ll fnd a snapshot of the upcoming events that might be of interest to you.
We had known for quite some time that on Friday, 11 October, the New Lock in Terneuzen would offcially be opened. This moment is a milestone for the development of our crossborder port where 550 companies provide 106,000 direct and indirect jobs. Both the Zeeland and Ghent regions will beneft, as will the Netherlands, Flanders, and Belgium as a whole.
The presence of Dutch King Willem-Alexander and Belgian King Philippe at the opening underscores the importance of this joint investment. And that importance is multifaceted. With the new lock, larger seagoing vessels can pass through the lock complex into the Ghent-Terneuzen Canal. The New Lock adds a second, larger sea lock. Additionally, more ships can pass through the three North Sea locks simultaneously. This improves the connection of our port area with the Netherlands, Germany, Belgium, Northern France, and other parts of Europe. As a result, goods and raw materials can be transported faster and more sustainably, meanwhile reducing costs. The New Lock offers many opportunities for the development of the port area. This benefts existing companies, new investors, and employment.
While construction is complete, the work is not yet fnished. After the opening of the New Lock, it will be put into full operation. In the frst phase, test sailings with ships up to 37m wide will allow the partners of the nautical chain to get accustomed to the New Lock. These experiences can then be used in 2025 for trial sailings with ships up to 38.5m wide. In the second phase, the trial sailings can be expanded to ships between 43 and 45m wide.
As port authority, we are looking forward to the deepening of the frst kilometres of the canal, making it suitable
for vessels with a maximum draught of 14.5m. This will eliminate the need for seagoing vessels to lighten their loads in the Western Scheldt River, which increases safety in the river and reduces the number of inland vessels and barges passing through the North Sea locks. Also, it leads to greater effciency and reduces CO2 emissions.
I hope that after the trial sailings, we will soon be able to allow ships up to 43m wide to sail through to Ghent. In the meantime, we can look into where the canal can be further optimised. This will give a strong boost to North Sea Port’s development as an energy and circular economy port.
Peter Van Parys COO of North Sea Port
On 11 October the Nieuwe Sluis Terneuzen (New Lock Terneuzen), as part of the Noordzeesluizen (North Sea locks), will be offcially opened. For North Sea Port the new lock is more than just an improved entrance to the Ghent-Terneuzen Canal.
In this article we put this infrastructural achievement in perspective with Daan Schalck (CEO) and Peter Van Parys (COO) of North Sea Port. “11 October, between 9.00 and 11.00 AM the Nieuwe Sluis Terneuzen will be offcially opened,” Daan Schalck explains. “The opening will be witnessed by the Belgian and Dutch Kings, the Belgian and Dutch ministers of infrastructure, the King’s commissioner of the province of Zeeland, the provincial governor of East-Flanders, and the mayors of Terneuzen and Ghent as well as by 75 Belgian and 75 Dutch invitees from various stakeholders. In the afternoon our annual Port Conference will take place in the Scheldetheater in Terneuzen, close to the Noordzeesluizen.”
According to Daan Schalck, the reason for organising the congress as part of the opening festivities is evident. “For North Sea Port,” he states, “the Nieuwe Sluis means that the entrance to our port area behind the locks will be much better compared to the current situation. It will enable bigger sea vessels to enter, and will also improve the entrance of barges, as they will be able to pass the Noordzeesluizen much faster than they used to. But this is only part of the story, which is why during the congress, we will pay attention to all related effects of the new lock. The congress theme will be ‘The opening of the New Lock Terneuzen’. The congress will start with looking back. Why was it decided to build the new lock? Also, as part of the congress, a discussion is planned with representatives of companies in the Terneuzen and Ghent port area to fnd out what the new lock will entail for them in the future.”
The new lock is not only relevant for the port and its nearby region, but according to Peter Van Parys the improved entrance is of national and even international relevance.
“North Sea Port is part of two European logistic corridors,” he explains. “The North Sea-Rhine-Mediterranean Sea corridor, and the North Sea-Baltic Sea corridor. This way, we act as a European hub in all directions and the new lock is of great importance to these corridors as it helps to improve the circulation on both of them. Of course, this will highly strengthen the position of North Sea Port as important hub for Northwestern Europe, and the companies in our port area will proft. However, the new lock will be benefcial to other ports alongside the corridors as well. It is not for nothing that, for the construction of the new lock, the European Union granted considerable fnancial support. Apart from this, the new lock is the entrance, or depending
on how you look at it, the exit, to the Seine-Nord barge connection. This connection between Paris and the Western Scheldt River is under construction and will not be completed before the 2030s, but with the new lock the entrance is already future proof for the barges that will make use of the SeineNord connection.” Peter Van Parys continues, “Also, outside of Europe the new lock will have its effect. As it equals the size of the new Panama locks, even larger seagoing vessels will be able to enter the port area and using bigger vessels means that the cost of transport per cargo unit will be reduced.”
At the end of the congress, the Dutch and Flemish government will be thanked for their support to make the new lock possible. However, they will also receive a message for the future, stating that work is far from over. “Our situation today can be compared with the sixties of the past century,” Daan Schalck elaborates. “In that period, the Westsluis (Western Lock) was opened as part of the Terneuzen lock complex to act as the lock for seagoing vessels. New companies, such as ArcelorMittal, Volvo Cars, and DFDS settled down and, throughout the years, many existing companies profted from the improved entrance such as EuroSilo, Verbrugge Terminals and Ovet. Now, the Nieuwe Sluis will give new opportunities. However, to fully proft from the benefts, we should also look further behind the locks as the level of competitiveness and the willingness of new companies to settle down in the Ghent and Terneuzen area not only depends on the new lock, but also on the further development of the Ghent-Terneuzen Canal. Longer, wider and deeper seagoing vessels need more space to manoeuvre and to moor. This might lead to undesired situations on the canal that could hinder the entrance of seagoing vessels to our port, but it could also hinder our efforts to promote inland shipping as a sustainable modality. Therefore, we have to investigate the options for keeping the canal on track with the maximum size of the vessels that can enter the Nieuwe Sluis.”
Daan Schalck continues, “Our strategic plan 2020-2025 entails seven focal points that are all based on the existing business activities in our port. We offer a diverse range of activities in the logistics and manufacturing industry and the Nieuwe Sluis perfectly fts in our strategy to remain a diversifed port as it will help all kind of seagoing vessels and barges to make use of our port. This is why we have put a lot of effort, not least fnancially, to realise this project and now, as part of our strategy to grow into a leading European port, we are going to aim for the development of the entire canal. We do not do this on our
own, but together with the same parties we were working with to get the plan to construct the new lock implemented. This collaboration is important as many stakeholders play a role in the use of the canal.”
“With the Flemish ‘Departement Mobiliteit en Openbare Werken afdeling Maritieme Toegang’ (Flemish Department of Mobility and Public Works – Maritime Access) and its Dutch equivalent ‘Rijkswaterstaat’, we will work on this new project in different steps. Also, the Dutch and Belgian pilots are involved,” Peter Van Parys voices. “First, we are going to investigate the current situation. What is possible at the canal once the new lock will be operational? For this we will run digital simulations to investigate various scenarios. Also in this phase, real trial runs on the canal will take place with bigger vessels. This real trial run is not as easy as it looks. Take only the fact that a company should be willing to send a vessel of the desired dimensions to the canal in the period we would like to do the tests. In this trial, numerous variables will be taken into account, such as the waves and the wind, the water level, other vessels on the canal, etc.. All these variables are important as they may affect the way a vessel reacts and what this will mean for other sailing and moored vessels, quays and so
on. We will also investigate the various possible solutions and their effects, such as deepening the canal, adjusting corners, and creating passing lanes. Will it also be necessary to improve quays and embankments? Many solutions and questions will be taken into account. Later in our research we will look at the existing tunnels (Zelzate tunnel) and bridges. Are they still ft for the bigger types of vessels or do they need replacement or adaptations? After all, port infrastructure is built for 100 years.”
But, frst things frst. On 11 October, the ‘frst’ vessel will pass the Nieuwe Sluis, marking the end of a unique infrastructural project and the start of a new opportunities for North Sea Port and the industry. “Today, at the moment of our interview, it is still not known what vessel will be invited for the opening ceremony. Of course, for everyone involved it would be great to have one of the biggest vessels possible, but only time will tell and after this frst vessel, no matter the size of it, many vessels, big, long, and small will make use of the lock for a safe and fexible passage to the Ghent-Terneuzen Canal and we will be happy to receive them in our port,” Daan Schalck concludes.
I. NORTHSEAPORT.COM
As Area President for the Western European region, Tabita Verburg is navigating Dow on its path towards growth and decarbonisation.
In April this year, Dow announced its new area president for the Benelux, France, Spain, Portugal, UK, and the Nordics. Tabita Verburg was no stranger to the company. She began her career at the Terneuzen-based materials science company back in 2001, on a nine-month internship in the HR department.
Even then, she says, it was evident there was a click; Tabita was quickly invited to continue her work with Dow after the internship ended.
“I worked for five years in the HR team,” she says.
“It was a special time. The 90s had been a low point economically and Dow had limited recruitment activities during that time. All of a sudden in the early 2000s things were looking up and there was a lot of work to be done. We had to build relationships with local universities, create new hiring strategies and generally re-establish the Dow brand.”
After those initial years in HR, Tabita Verburg decided it was time to do something new – something that the company was willing to facilitate. The following years saw her undertake roles in procurement, international trade, logistics and operations, before arriving at her current position. Quite the remarkable journey, though, not an unusual one for Dow, she says.
“This is quite normal for Dow. It’s one of the things that makes us unique. If you’re curious, interested and willing to learn, there’s a lot of opportunity here.”
Her diverse background places Tabita Verburg in a good position as she helps Dow work towards its ambition of becoming the most innovative, customer-centric, inclusive, , and sustainable materials science company in the world.
It sounds like a tall order, but she is clear; while there are certainly challenges to overcome, there are also opportunities to be had.
“One of my aims is to create more awareness about the
essence of our industry – the products we make and the technology we have – so that we can make a positive contribution to the society we operate in.”
To this end, Dow, like many companies today, is focusing much of its energy on the energy transition. The company is working on numerous initiatives to accelerate decarbonisation and promote responsible business practice.
One example of this is Dow Terneuzen’s Path to Zero plan. With this, the company has laid out clear steps and a timeframe for its journey to carbon neutrality by 2050.
Two of its sites in the Netherlands, Terneuzen and Dordrecht have recently received Operation Clean Sweep (OCS) certification, demonstrating best practice in handling plastic pellets. If handled improperly, these small raw materials can easily end up as pollutants on land or in the water and can be ingested by wildlife.
Dow has committed more of its sites to achieving OCS certification in the near future.
Dow also actively promotes sustainability in its supply chain, for example awarding its logistics partners for their safety, sustainability, client-centric and socially responsible practices.
However, the challenge posed by sustainability is such that Dow cannot achieve all its aims alone, Tabita Verburg states.
“Dow has always been good at reaching out to partners, whether they are universities or other companies.
It’s one of the benefits about being located here in North Sea Port. In addition to our proximity to the Westerschelde and excellent port infrastructure, there are so many companies, with such diverse knowledge, to collaborate with. We’ve always been very active in the port community. With sustainability, this has become increasingly important. It’s helping to create a new level of collaboration across different industries.”
As we always say at Dow, ‘if something is difficult, give us a day. If it’s impossible, give us a week.’ That’s the power of the team we have here.
An example of Dow’s involvement in such a cooperation is the Smart Delta Resources Partnership (SDR). This cross-border initiative has seen energy and resource intensive companies in the Scheldt Delta region – including numerous businesses in North Sea Port – team up to address the topics of CO2 reduction, circularity, sustainable raw materials and green energy.
Dow has also recently extended its partnership with the Jaguar TCS Racing team. The partnership began in 2020 with Dow becoming the team’s official materials science partner. The partners are continuing their work to integrate next generation materials that will advance the performance and efficiency of the Jaguar I-Type 6 electric race car. Dow is working with the team on several primary areas including Thermal Management, Adhesion, and EMI (electromagnetic interference).
Recently, Dow has re-committed itself to another local partnership, extending its collaboration with the local HZ University of Applied Science by a further five years to 2029. This mutually beneficial cooperation sees the HZ working together with the company on diverse research projects, frequently on themes related to the energy transition. Since 2019, the two parties have collaborated on over 20 projects covering topics such as water management, increasing sustainability in chemistry, and the potential of hydrogen as a green energy source.
Going forwards, Dow and the HZ are planning to increase their
collaboration on research into digital solutions, with a particular focus on AI.
Digitalisation, intrinsically linked to increased sustainability, is very high on Dow’s agenda right now. The company has an enviable track record as a pioneer of digital technology. Dow was, for instance, one of the first companies in the material science sector to establish its own e-commerce platform, several years ago.
Now, as it works towards goals of sustainability and ensuring its ability to compete, the company is increasingly applying digital solutions to boost productivity and efficiency.
“It’s important we stay abreast of digital developments,” says Tabita Verburg. “Things are moving quickly, much quicker than in sustainability, even. The big theme at present is AI. We are actively educating our teams, teaching them how to use it efficiently in a safe and controlled internal environment.”
The close connections it has built with universities will also play an important role in helping Dow build its teams for the future. Despite moves towards increasing digitalisation, Tabita Verburg states very clearly that the human element remains of crucial importance at Dow.
“We have an amazing team here, made up of lots of
We try to listen to the needs of all the different groups in the company. We cannot face all the challenges and opportunities with a one size fits all approach. You want people to bring their uniqueness, their creativity. We need everything if we are to find the solution.
professional talent in diverse fields and they will continue to play an important role as we move forwards.”
Alongside Dow’s reputation as an employer, its location, she says, helps to attract top talent.
“We are in a very exciting part of Europe. We are close to a lot of the larger cities in the Benelux and Germany. Paris is just a few hours away. We’re well connected to the rest of Europe and the world and there’s a lot happening here. This, combined with our flexible work culture, really helps us to attract people.
Within the fields of recruitment and retention, diversity has long played an important role at Dow.
“When I first started in HR in 2001, we were already starting to implement diversity and inclusion policies. We were quite advanced in this area and I was pleased to be able to contribute to that.”
Many of the colleagues working in Dow’s Diamond Center location in Terneuzen hail from the local area – the provinces of North Brabant and Zeeland, and also from across the border in Belgian Flanders.
With the company’s international scope, however, colleagues are just as likely to hail from other countries. Depending on the nature of the role, Tabita Verburg says, the world is Dow’s recruitment pool.
“We are very proud of the fact that we have people from 55 different nationalities (speaking more than 30 different languages) working here. Dow is a melting pot of cultures.” Nationality is just one example of how the company approaches the subject of diversity. Dow has set up a range of employee resource groups for colleagues of different (9) social groupings – women, LGBTQ+, Asian, those longer working in Dow, those just starting out on the career ladder, amongst others.
“We try to listen to the needs of all the different groups in the company. It’s really important that everybody can bring their whole self to work every day. We cannot face all the challenges and opportunities, not least in the sustainability space, with a one size fits all approach. You want people to bring their uniqueness, their creativity. We need everything if we are to find the solution.”
And does Tabita feel confident that Dow will be able to find that solution?
“Without a doubt,” she says. “The future will be green and digital. It’s everyone’s ‘North Star’, everyone is working towards the same goal – industry, society, governments. It will be an intense journey and there will be challenges along the way but, in the end, that star will lead us where we want to go.”
It’s a very optimistic assessment, but that, it seems, is part of the Dow culture.
“As we always say at Dow, ‘if something is difficult, give us a day. If it’s impossible, give us a week.’ That’s the power of the team we have here to contribute to finding solutions to the challenges we face – in our company, but also in our society.”
I. DOW.COM
In 2018, Sagro started its frst decommissioning activities. Since then, the multidisciplinary company successfully executed various decom projects for the offshore industry.
“Our frst decommissioning contracts were signed in 2018,” Abco Liek, manager at Sagro says. “These contracts entailed the decommissioning of various structures of the TotalEnergies Tyra Redevelopment phase 2 project. Tyra is Danmark’s largest gas feld and for further processing of gas, the feld needed new assets. Before these could be installed, the old ones needed to be removed.”
Abco Liek explains, “The frst contract for this project was granted by Allseas for the dismantling of four jackets. The work consisted of the cleaning, dismantling, recycling, and
disposal of the structures with a weight of more than 10,000t. A second contract for the project was granted by Heerema Marine Contractors (HMC) and was executed in 2020 before the Allseas campaign, which took place in 2021. In this HMC project we cleaned, decommissioned recycled, and disposed of multiple topsides, bridges, fare towers, and a jacket, with a combined weight of more than 16,000t. As this was quite a large project, we decided to frst extend and strengthen our quayside to have enough space for the safe reception of the steel structure. The existing quay was enlarged from 100m to 185m and part of the existing 100m was dismantled and renewed by a heavy load quay (15t/m2).
In 2020, we had to deal, like almost every company, with the effects of COVID-19 as we were only able to execute jobs with a limited employment of workforce. After that, things went quite well again and with the expected volume of offshore structures to be removed, we see a lot of opportunities for our offshore decommissioning department.”
According to Abco Liek, Sagro’s idea to start with decommissioning already arose ten years ago however, it lasted until 2018 when the company seriously entered this market. “Around ten years ago we investigated the decom market,” he
says. “However, in that period our existing business activities did not really gave us room and time to start. Despite this, we already applied for a permit for low level radio-active material, necessary to be able to take care of offshore constructions at our yard, and this also took some time.” Abco Liek continues, “Entering the decom market was quite exciting for us. First of all, there were already quite a few decom yards around the North Sea in the Netherlands, Denmark, Norway, and the UK. Also, we had to take many steps in the feld of the offshore safety rules and regulations that are much more stringent compared to our traditional onshore related decom projects. With our frst successfully executed assignments we have been able to show what we are capable of, and now we have our order book for decommissioning flled and received many requests in 2023, 2024 and for next year. We are even involved in tender processes for projects up to 2030.”
“When looking at our decom activities, I think that our strength lies in the fact that we are focusing on the mid-size constructions that are located in the southern part of the North Sea,” Abco Liek states. “We learned a lot from every new project and managed to create suitable procedures and processes for the receipt, cleaning, dismantling, recycling, and disposal of this smaller to mid-size offshore oil & gas structures. Now, with the offshore wind having reached its stage of maturity in the North Sea, this market too, is also becoming of interest when looking at decommissioning. With our expertise in smaller constructions, we see ample opportunities in this market, too.”
Sagro has ample experience in the dismantling of civil and infrastructural constructions. However, according to Abco Liek, this does not mean that this experience could be copy-pasted to the offshore market. “Apart from the stricter rules,” he states, “there are more differences between the decommissioning of onshore and offshore constructions. “First of all, offshore means a lot of preparatory engineering,” Abco Liek elaborates.
“It takes a lot of calculations, cutting plans, etc. in the project preparation, for which we lacked expertise. This is why, for example, we recently hired a project engineer that is working only for our offshore decom projects. Also, as decommissioning of offshore structures takes place on our yard, we also need people that have a lot of experience in the safe moving around of large objects. Of course, our goal is to receive structures as clean as possible from the sea. However, it is always a surprise what exactly is the state of things. When we want to bid for the dismantling of, for example a building, we can simply drive to it and see by ourselves, what the state of this building is. Offshore this is hardly possible. Although we sometimes get the chance to look at an offshore structure at sea ourselves, for most offshore decommissioning projects we have to rely on pictures, movies and drawings.”
Altogether, the share of offshore decommissioning is growing in Sagro’s activities. Looking at the current situation and future prospects, he expects business to continue in a positive way
for Sagro. “Both in oil & gas and in the offshore wind,” he says, “there will be many opportunities for decommissioning in the upcoming years and this is why we expect to be able to handle around 20,000t of structures per year.” Space at Sagro’s yard is becoming an issue because of the growing number of projects.
“It always is a challenge to deal with our space,” Abco Liek says.
“Of course, in the ideal situation, a project is fnished before the next one arrives, but this is not always the case. Luckily, we have been able to obtain a plot of terrain at the Westhofhaven close to our yard, which we can now use for the storage of dismantled material. Also, in the context of sustainability and reuse, more and more of our customers make use of this location in case they want to keep some parts of the dismantled structures that are still fne to use. Currently, we are preparing this new terrain. For this we are moving halls from their current location to the new terrain. This way, we create additional space on our yard and quay for the handling of structures. To be able to make use of the new terrain we also have made good arrangements with our neighbour so, when necessary, we can make use of their quay to move things from our yard to our new facility.”
When looking at decommissioning we have had a very steep learning curve which is something we all can be very proud of.
Abco Liek continues, “Because of safety reasons, we try to keep a team working on a decom project as small as possible with a total of eighteen people of which no more than three are torch burner operators. With the growing amount of projects, skilled people, especially cutting torch operators, are scarce. This means that we put a lot of effort in keeping these specialists and it is good to see that we have a relatively loyal team.” Abco Liek started his career at Sagro in 1991 and this way a has had many roles in the company. Also, he saw the company grow into what it is today. “Throughout the years I have been involved in many things at Sagro,” Abco Liek says. “I started in soil remediation and after that I
had many roles and responsibilities at the company. What I like most are the challenging projects, and therefore I was very pleased when Sagro gave me the chance to become part of decommissioning. Compared to the other sectors I have been involved in, the offshore decommissioning world is a totally different, international world, which was quite new to me.”
Abco Liek is very pleased with how things developed for Sagro in its decommissioning activities. “When looking at decommissioning we have had a very steep learning curve which is something we all can be very proud of. We have been able to execute various serious decom projects successfully with high safety standards which is recognised by our customers and results in excellent relationships with them. With a relatively small and dedicated team we have achieved a lot, and I look forward to continuing business with them and our clients in the same positive and successful way.”
I. SAGRO.NL
Earlier this year, a milestone was reached in the Vlissingen port area, when Smulders Projects Netherlands fnished its frst offshore jacket made in North Sea Port.
Smulders Projects Netherlands (SPN) is as part of Smulders, a subsidiary of the French stock exchange listed Eiffage. Eiffage’s 78,200 employees work in construction, property development, urban development, civil engineering, metallic
construction, roads, energy systems and concessions. Smulders is part of the Eiffage Metal business line that focusses on infrastructural metal constructions on land and offshore.
Smulders bought the assets of Hillebrand/ASK Romein in Vlissingen early 2023 where it started to construct among other structures, jackets, and structural parts of topsides for the offshore wind industry. Apart from Vlissingen, Smulders also has other fabrication facilities in Belgium, Poland, and the UK and is furthermore operating an engineering department in London (UK) and in India.
To make the new colleagues used to Smulders’ working methods, the company frst started with smaller construction projects such as for the sea fastening of wind turbines on vessels and barges, but soon could take on bigger projects as well.
“At Smulders, we have everything in our own hands to execute a broad range of EPC projects,” Pascal Van Gucht, Director SPN, says. “We are a multidisciplinary and international construction company with an established reputation in the engineering, production, supply, and assembly of heavy, technically complex and architectural steel structures. With the acquisition of the real estate of Hillebrand ASK Romein in Vlissingen we have obtained a location that is ideal for the assembly and outftting of large constructions for the offshore market. It is close to the lock free port entrance to the North Sea. Furthermore, one can guarantee a safe load out of the
large structures, which we are planning to build, as the new quay has suffcient draught and bearing capacity.”
“In Vlissingen,” Jan Krielaart, technical director of SPN, adds, “we will focus on the larger size one offs, such as jackets and topsides for offshore substations, which will be additional to our location in Hoboken (Belgium) where we usually construct in series, items such as TPs and jacket foundations for offshore wind turbines. For TenneT we have constructed the jacket of the Hollandse Kust (west Beta) project, starting in May 2023
at SPN’s yard facility. Its timely load out end of April of this year marked the successful start of our construction activities in Vlissingen. Next to this jacket, we also constructed the frst of six new IJburg bridges that are under construction in Amsterdam. So, for civil constructions, too we have found an excellent facility over here.”
“The offshore structures we are building today,” Pascal Van Gucht explains, “include AC (alternating current), substations which have a weight of 5,000 up to 6,000t. For the future, we are also looking at the DC (direct current) market for which we have the facility to fabricate and construct jacket structures up to 20,000t in Vlissingen. The construction and load out of these kinds of large structures require a lot of space, so it is a real opportunity that this site came our way. In Vlissingen we are therefore ‘upgrading’ the yard to be able to execute the fnal assembly, electrical outftting and complete commissioning of the AC substations.”
“Vlissingen is not an unknown location for Smulders as we have been making use of terminals in the port area for the construction of offshore projects for many years,” Pascal Van Gucht elaborates. “The opportunity however occurred early last year to buy the real estate of Hillebrand, here at the port area of Vlissingen, and this way Smulders could start to
It really is unbelievable how fast we were able to get everyone and everything operating at the current high level.
establish its own assembly yard, directly located on the North Sea. What is good to mention is that North Sea Port, together with the municipalities of both Vlissingen and Borsele, is very collaborative, which really helped us to realise our plans for ‘upgrading’ the yard ft for our purpose. When we were looking for additional storage and assembly area, North Sea Port could offer us soon 13,50ha alongside the Frankrijkweg opposite our yard. All parties have been supportive in achieving the required permits to build and operate the new plant. A good example of this is the construction of a new L-shaped quay alongside our yard (with lengths of 137m and 134m). The constructive working together with all key players – North Sea Port and local authorities – has led to a successful project. Despite the limited building period, SPN has been able to fnalise the construction of the frst part of the quay in April 24, allowing the timely frst load out of the Hollandse Kust (west Beta) jacket. Furthermore, the second part of the quay will be fully completed in September 24 as initially planned.
impressive 160t lifting capacity. With these dimensions it is one of the largest covered construction halls in the Netherlands. Unhindered by any bad weather conditions we are now capable to construct even the largest structures.”
Pascal Van Gucht explains about the time of acquisition, “Soon after the acquisition we’ve introduced new fabrication work at the SPN facility to guarantee the continuity of the production capacity. Fabrication and assembly of heavy grillages and structural components for AC stations have been introduced. As unfortunately Hillebrand faced a bankruptcy early April 23, it has been crucial to implement new works on the yard and to secure the continuity by taking Hillebrand’s’ employee’s on SPN payroll.” “To get the new colleagues used to Smulders’ working methods,” Jan Krielaart explains, “we frst started indeed with smaller construction projects such as for the sea fastening of wind turbines on vessels and barges, but soon we could take on bigger projects as well. It really is unbelievable how fast we were able to get everyone and everything operating at the current high level. This really says something about the fexibility and enthusiasm of everyone involved. Usually, starting up a production site will take several years, and now, with everyone very fexible and collaborative, we managed to be up and running within a few months, which can be considered a performance, not in the least because during the production of high quality structures we were also busy fnalising our yard facilities. I really have never seen such an achievement in my entire career.”
Jan Krielaart adds, “In the meantime we also made the main fabrication hall at our premises fully operational. We’ve taking out the existing slipway by levelling the complete foor construction and increasing the bearing capacity of its fooring. Now, we have a huge 170m long and 39m wide covered production hall, with a 25m height below the hook and an
The Vlissingen location will also be involved in the unique Princess Elisabeth Energy Island project. Whereas only a few kilometres for Smulders’ yard the concrete parts of the energy island are constructed, will Smulders construct two AC substations and two facility stations for this project. “Of course we are proud of this new project,” Pascal Van Gucht states, “as it shows the trust of our customers in our new facility. A guarantee for a successful and prosperous future.”
De Baerdemaecker, the agency and forwarding branch of Stukwerkers Group, has renewed its capabilities over the past years and stands ready for further growth of its in-house and third-party business. “We have transformed the way we work to ensure we continuously improve the way we serve our customers,” says general manager Yelle Deketelaere.
Only a handful of companies in the Belgian shipping business can boast of the longevity that De Baerdemaecker has demonstrated, reinventing itself more than once in the course of a history that stretches back to the 19th century and that left its architectural mark in streets around the older docks in Ghent. The most recent turning point came in 2001, when De Baerdemaecker became part of Stukwerkers, strengthening the group’s stevedoring, storage and logistics activities with its own agency, freight forwarding, customs clearance and transport services.
It provided De Baerdemaecker with a solid foundation to build on, both as the group’s in-house agency and freight forwarder and when servicing third party clients, says Yelle Deketelaere,
Even if forwarding and transport services are growing, agency remains the dominant pillar of De Baerdemaecker’s activity. From its headquarters in Ghent, the company handles about 500 calls a year in the Belgian sea ports. The main emphasis lies on Ghent and Zeebrugge, with a fairly equal number of calls but a very different clientele. In Ghent the focus is on a mix of bulkers and multipurpose vessels, fruit juice ships and container vessels, with liner business and tramping balancing each other. In Zeebrugge car carriers represent the principal line of business. The company’s reach has been extended to Ostend and Antwerp, often at the demand of existing clients.
the general manager of the company. “Being part of Stukwerkers offers us the ability to respond to specifc customer demands at a very competitive rate. High-capacity mobile harbour cranes stand ready to handle large breakbulk cargo, for instance. Storage space is readily available. Multimodality is a common feature on the group’s terminals, with far more cargo by water and rail than by truck. These are trump cards that not every agency or forwarder can play out in the same way. Furthermore, this is a family business, with short lines of communication, fast decision-making and a characteristic ‘can-do’ mentality to complement the technical know-how and the logistic and commercial expertise any shipping line expects from its agents.”
A fne example of possibilities available through the interaction with the group is I-Motion Shipping, Stukwerkers’ own shipping
line offering regular sailings between Ghent and Hull. “This provides us with a high level of expertise in the trade with the UK. We know our way in and out of the British market. We handle customs to and from the UK on a daily basis and can rely on our UK-based contacts to solve any custom-related problem that could arise.”
“When it comes to customs services, we have a full AEO (Authorised Economic Operator) certifcation with simplifed procedures and fewer physical and document-based controls. And we actively participate in various customs forums, ensure continued training and provide feedback through local customs on the development of new customs platforms.”
Zooming out, Yelle Deketelaere also draws the bigger picture. “Clearing goods through customs isn’t the end of the logistics process. As a licensed commission forwarder and thanks to the fve congestion free terminals of Stukwerkers, we can offer an effcient solution by sea, river, rail or road towards the end destination. It all enables us to offer hassle-free one-stop-shop solutions to Stukwerkers’ customers as well as third party clients, for instance picking up deep-sea containers from China in Antwerp or Rotterdam through our own barge service and delivering them to Ghent for local delivery, stripping, storing of the goods in our warehouses, or shipping them onwards. We take care of several transports a day to various destinations, including specialised transportation and out-of-gauge carriage.”
“We have focused on transforming the way we work, to continuously improve the way we serve our customers. To do so, we keep upgrading our custom-made agency system, that complies to all our requirements.”
The interaction with Stukwerkers has gained further traction in recent years, Yelle Deketelaere explains. “Through an interface with the Stukwerkers terminal operating system, we have full information integrated into the agency system, to follow up on
Ship agency remains a people’s business and being a ship agent comes with a commitment. We take that literally.
our in-house agency activity. Through this feature we monitor cargo operations live and are notifed on any events that can have an infuence on sailing times, allowing us to adapt vessels’ port stays and brief our customers from these live data. It represents a signifcant improvement that helps us to gain valuable time for our customers. On top of that, we provide a single point of contact, keeping follow up and communication towards our customers simple and direct.”
Finding the right staff is crucial, the general manager stresses. “Our team is a good mix of experienced colleagues and young talents, some of whom have been trained cross-functionally to ensure suffcient working capacity in all activities. Ship agency remains a people’s business and being a ship agent comes with a commitment. We take that literally. We are available 24/7 and we pride ourselves on being able to handle any request for our customers, from crew changes to fnding repair technicians for class-certifed installations during summer holidays to delivering a Christmas tree for the crew in December. Ensuring we frequently have direct contact with the crew, is something that is much appreciated, believe me.”
Along the way, De Baerdemaecker is acquiring a higher profle of its own, with its own website, a new house style, more active communication... The aim clearly is to enhance the company’s visibility in the market and grow its portfolio.
I. DBMSHIPPING.COM
On November 26 and 27, Offshore Energy Exhibition & Conference (OEEC) 2024 will bring together some of the most prominent names in the offshore wind, hydrogen, oil & gas, and marine energy industries at RAI Amsterdam.
Across two days flled with conference sessions, stage time, networking, and showcasing, OEEC 2024 aims to help fulfl in the offshore energy sector what it chose as its 2024 event theme, Harmony.
North Sea Port is one of Europe’s leading ports in offshore and has been an Offshore Energy exhibitor from the very beginning. This year North Sea Port again will be host to a broad range of international companies and organisations.
Present at the booth of North Sea Port
(as known on 10 September)
• Actemium
• BOW Terminal
• Dixstone
• Draftec
• Overlasko Konstruktie
• Promotion Council North Sea Port
• Shipyard Reimerswaal
• Supermaritime Nederland
Visit them at booth 1.704
Also present at Offshore Energy Exhibition & Conference (as known on 10 September)
Members of Promotion Council North Sea Port who will be represented at the exhibition with their own stands:
• Date: 26 and 27 November 2024
• Opening hours: 09:00 – 18:00h
• Venue: RAI Amsterdam Convention Centre, Europaplein 24, 1078 GZ Amsterdam, the Netherlands
• Exhibition: Hall 1 and 2
• Conference sessions: Conference Area
• You can enter the exhibition and conference via entrance K.
Shipyard Reimerswaal constructing new offces as latest stage in development
Shipyard Reimerswaal was originally founded in 1985. At the time, the yard was located along the banks of the Western Scheldt river in Hansweert.
Back then, the main customers were operators of fshing vessels and inland waterway barges. A wide range of repairs, conversions and maintenance works were carried out on the yard’s two slipways.
Just fve years later, in 1990, Shipyard Reimerswaal was on the move with the opening of a second location nearby, on the Canal through Zuid Beveland. Here, the yard was able to begin operating frst one, then two foating docks. With this, it was able to cater to larger vessels and its work catering to the general cargo sector began.
It was at this time that Rudi Pieters came onboard as project manager. Later, in 2002, with the retirement of the original owners, Rudi Pieters undertook a management buyout and the stage was set for the company to grow into the yard it is today. First, however, it was time to relocate. In 2017, Shipyard
Reimerswaal left Hansweert behind and relocated to the Quarleshaven in North Sea Ports’ Vlissingen East location.
“Moving to North Sea Ports offered us a lot of advantages,” says Rudi Pieters. “For one thing, we’re in the heart of the industry close to the action and away from residential areas.
For another, the new site offered us signifcantly increased berth and draft capacity.”
Altogether, the site covers some 2.6ha on land and enjoys exclusive access to 450 by 109m of water. The move was not without its challenges, however, as Rudi Pieters explains.
“We started the discussions about the move back in 2013 and the new yard didn’t open until 2017. There was a lot to do as the site was completely undeveloped. We had to start from scratch. For example, we had to construct all the infrastructure including for the internet, gas, electricity and water.”
The move though, provided the opportunity to build a modern yard optimised to Shipyard Reimerswaal’s requirements. This includes the yard’s 120m long by 22m wide (inner width) foating drydock with a 6,000t lifting capacity.
The company also constructed new offces and a new workshop of 75 x 20m. The workshop is ideally suited for jobs such as section building, hatch cover repairs, pipe-ftting, repairs of dredging equipment, and a range of construction work. It also features a dedicated electrical workshop.
When the yard was opened, it offered 350m of deep water quayside. However, in 2023, North Sea Port extended this by 60m to 410m. With its increased capacity, Shipyard Reimerswaal today caters to a wide range of large vessels.
“We offer maintenance, repair, reft and conversion to all types of vessels,” states Rudi Pieters. “If it foats, we do it. The only thing we don’t do is newbuild.” Business, at the present time, he says, is good. Even during the quieter periods of the year, the yard is busy. Given its location in North Sea Port, it’s no surprise to learn that the majority of vessels the yard caters to today are either large dredgers, or the ships supporting the construction and maintenance of offshore wind farms in the North Sea.
In addition to the above mentioned vessels, the yard also accommodates the larger heck trawlers, general cargo vessels, and tankers of all kinds, amongst others. Furthermore, Shipyard Reimerswaal is in possession of a permit to receive and repair vessels under gas conditions.
Growing awareness of environmental concerns is at present also a stimulating a lot of business for Shipyard Reimerswaal Rudi Pieters says.
“We get a lot of call to install ballast water treatment systems, scrubbers or exhaust gas after treatment systems at the moment. I expect we will see increasing amounts of this type of work in the coming years with all the new regulations that are coming.”
With a favourable looking market for the foreseeable future, Shipyard Reimerswaal continues to invest in growth and development.
“We’re currently building a new offce complex for our clients’ project teams. With increasingly complex projects taking place, the teams are getting larger. The portacabins we have traditionally used are becoming too small. Besides, they’re not very maintenance friendly. These new offces will provide our clients’ teams with a modern, clean, comfortable location that is completely outftted with Wi-Fi, printers, copiers, catering facilities, air conditioning, screens, etc. from which to carry out their work.”
What makes us special as a company is that we are a relatively small, family business. We’re a fat organisation with short lines of communication between our clients and us.
The new offces are set to be completed towards the end of the year. They will be located in a two storey building, featuring six individual offces.
Today, Rudi Pieters continues to oversee the running of the company together with this two sons operations manager Robbert Pieters, and project coordinator Rick Pieters, as well as technical director Werner Verras.
“In addition to our managers, we are fortunate to have an excellent, highly skilled team in place. Without them, there would be no yard.”
With an eye on the next generation, Rudi Pieters has plans to continue to grow the business.
“We would like to add an extra, larger foating dock in the region of 160 - 170m in length. With that we would have increased fexibility. W ith this in mind, during the move of our yard to the Quarleshaven, a second dock was already accounted for in the application of the permit. Now it just a matter of fnding the right dock, but that is certainly something we will be looking to do in the near future.”
There are limits on how far he feels the company should grow, however.
“What makes us special as a company is that we are a relatively small, family business. We’re a fat organisation with short lines of communication between our clients and us. I think that’s why people choose to dock their vessels with us,” he explains. “If we were to become too big then we would run the risk of becoming overly bureaucratic. We aim to strike a balance so that we can grow in line with our customers’ requirements while maintaining our ability to respond quickly and fexibly when they need us.”
I. SHIPYARDREIMERSWAAL.COM
As experts in industrial insulation, EIB Group offers its customers complete concept solutions. With in-house workshops, a scaffolding division and certifed teams of experts on fre-proofng, asbestos removal and industrial painting, EIB is the company to turn to for an energy-effcient production process.
“Many of our customers are port-based,” Filip De Wilde, CEO of EIB Group says, “as our customer base includes some major players in the petrochemical industry and tank storage sector. We have several customers in North Sea Port, mainly in the Ghent area, but we have a major project planned in Vlissingen as well. However, due to our technical expertise in thermal, cryogenic and even acoustic insulation, we are active in multiple process industries throughout the entire Benelux, from food storage to tank storage, from breweries to pharmaceutical companies, and many more.”
“We have a very broad customer base,” Alex Vanlerberghe, EIB Business Development, adds. “Combined with many years
of experience in the feld, this results in great technical expertise, which is one of the strengths of our company. Along with a great emphasis on customer service, our technical knowledge ensures the quality and effciency of our work, which results in strong and long-lasting partnerships with our customers. We handle both new projects as well as day-to-day maintenance for our customers.”
“An important part of our company’s philosophy is a strong focus on the quality and reliability of the materials we use. We only use superior quality, durable products that ensure durable solutions,” Filip De Wilde states.
“We even have our own in-house workshops for aluminium and stainless steel sheeting and insulation jackets,” he adds. “These insulation jackets – or “mattresses” – are tailor-made for each installation. This has several advantages. First of all, the jackets ft perfectly, regardless of the shape or size of the installation, ensuring the best possible enclosure and insulation. Second, the insulation jackets can easily be removed and reinstalled, which is an absolute must for parts that require regular maintenance or inspection such as pumps and valves. The jackets we install are laser cut and handstitched in our workplace. Furthermore, the materials used are custom-ft for the customers’ requirements, to withstand high temperatures,
An important part of our company’s philosophy is a strong focus on the quality and reliability of the materials we use. We only use superior quality, durable products that ensure durable solutions.
chemicals or other factors. With our integrated manufacturing of sheeting and sleeves we are quite unique in the feld, which gives us a competitive advantage and fexibility for our customers.”
“This fexibility is precisely the reason why our thriving scaffolding division was created. The industrial installations we work on almost always require the use of scaffolding. The work is nearly always at height, for some part. Aligning our philosophy and approach with the scaffolding subcontractors has always been very important to us, so integrating our own scaffolding division into our core business was a very logical step. Established in 2021 mainly to support our insulation work, the scaffolding division has grown quickly into its own business unit with its own customer base.”
However, there’s even more to insulating work than placing the material and building scaffolds to do it. That is why EIB also has team of experts on fre-proofng, asbestos removal and industrial painting: EIB Specialty Services. Filip De Wilde explains: “A lot of installations, for instance in the Port of Antwerp, were built in the 20th century, at a time when asbestos was still used regularly. Naturally, this has to be removed before we can do any work on the installation. Creating our own certifed teams to handle this is part of the complete concept service we offer our customers.
Safety is the number one priority for every employee working for EIB Group. We are convinced that every activity we undertake can be done without accident or injury.
The same goes for fre-proofng and industrial painting. Where pipes go through walls, the edges need to be sealed with freproof material. Only trained and certifed experts are allowed to do this. Some installations also require a fre-proof coating as immense heat can be developed in the pipes. In our experience, our customers value the multiplicity of our services. It is not only easier and more effcient to work with just one partner for your installations, it also increases safety on the plant having just one contractor on site which knows the installation and your safety regulations thoroughly.”
“Safety is indeed an important factor in the work we do,” Filip De Wilde says. “In fact, safety is the number one priority for every employee working for EIB Group. We are convinced that every activity we undertake can be done without accident or injury. We pride ourselves in having accomplished over 2,500,000 accident-free work hours. Additionally, we also focus on the well-being of our employees. Providing a safe and tolerant workplace is very important to us.”
Alex Vanlerberghe adds: “As insulation is key in energy
conservation, sustainability is one of our core values. We put great effort into improving the sustainability of our activities. We are always investigating ways to improve and reduce our waste fows and are currently in the process of ‘greening’ our feet. We also closely follow the market for developments in the storage of new fuels, hydrogen, and ammonia, as this also creates new opportunities for our business. Installations using new technologies or processing new materials require us to keep learning and stay ahead of our customers’ needs. In fact, in the last three years, we have done some very interesting projects in this feld.”
Since 2019, EIB Group has a new branch in the port of Rotterdam, which has seen steady growth over the last few years. But the EIB Belgium branch is much older, Filip De Wilde explains: “EIB Group was founded over 30 years ago as a family-owned business. Since then it has been taken over two times but was always kept in private ownership. The current owner came aboard fve years ago and has expanded the company from handling mainly cryogenic installations and smaller processing industries to the thriving multidisciplinary service provider we are today. Still, we managed to keep a family-like atmosphere, which also serves our customers well since we have a short chain of command that results in swift, effcient decision processes and a personal approach and solution for every customer.”
I. EIB-GROUP.EU/NL
Kole Transport, part of Sagro Company, took delivery of two fully electric Volvo FH trucks. This milestone marks an important step in making the company’s transport operations more environmentally friendly and is in line with its ambitious sustainability goals.
Making the fleet more sustainable
With the purchase of two Volvo FH Electric trucks, Kole Transport is investing in a cleaner future for the logistics sector. The fully electric trucks are an important addition to the company’s fleet. With its advanced battery technology and emission-free driving performance, the Volvo FH Electric offers the opportunity to contribute in a sustainable way to the transport of goods within the region and beyond.
“These electric trucks are just the beginning of a broader shift towards emission-free transport, something that we, as a company, find very important.”
Part of wider sustainability strategy
The electrification of the fleet is in line with Sagro Company’s broader sustainability strategy. Sagro focuses on minimising its carbon footprint in all its activities, from transport and logistics to demolition, infrastructure works and recycling. The deployment of the new electric trucks contributes directly to this objective and is an important step in the transition to a circular economy.
With the introduction of the Volvo FH Electric, we reinforce our commitment to a future-oriented and sustainable transport sector.
Raoul de Jonge of Kole Transport.
“Our investment in the Volvo FH Electric is a logical continuation of our previous steps towards a more sustainable business,” Raoul de Jonge continued. “We aim to further electrify our fleet in the coming years and actively contribute to a cleaner living environment.”
Future-oriented transport
The arrival of the Volvo FH Electric marks the beginning of a new chapter for Kole Transport. With the commissioning of these trucks, the company is taking a clear step towards the future of transport. This step is not only in line with the growing demand for sustainable logistics, but also helps Kole Transport comply with increasingly stringent environmental and emission standards.
By deploying the electric trucks, Kole Transport positions itself as a forerunner in the transport sector and shows that economic growth and sustainability can go hand in hand.
Ben Maelissa returns as Danser
Inland container shipping company, Danser Group has experienced its fair share of changes over the last two years. In 2022, long-serving CEO and shareholder Ben Maelissa passed the company into new ownership.
At the same time, the economy entered a turbulent period, with the company experiencing some challenging times as a result. Now, however, things seem to be settling down again thanks to an improving economic situation and a new joint venture at the helm.
In February this year, logistics specialist Euro-Rijn acquired Danser. Once in position, Euro-Rijn invited Ben Maelissa to take up the CEO position again and become, together with Danser’s management team, shareholder to help the company prepare for the future.
Having worked at Danser for 35 years, the last 24 of which he was a shareholder, Ben Maelissa certainly knows the company – and the market – inside out.
“Coming back was a logical step for me. I’d been here for a very long time. That never goes away. The company stayed in my heart.”
Ben Maelissa hopes that the return of the company’s old management team will help to bring some stability to a company that has been through a dynamic time – in particular to the employees who have experienced a lot of turbulence.
“This year, our work is all about providing the company with a good basis to move forward and gaining the confdence of the employees.”
The improved economic picture, he says, is certainly helping to put the company on course.
“Things have defnitely improved. Already at the end of February this year we could see that volumes were picking up again. There is a lot happening in the world at the moment. Events in Ukraine and Gaza are causing a lot of uncertainty. I think there is a sense among traders that they should have their warehouses stocked. That way they can continue to trade no matter what happens next. As a result, there is more traffc on the water. Things are better for shippers than last year, and certainly better than anticipated.”
For Danser, the growth in activity, he says, is particularly pronounced in the North Sea Port and surrounding area.
“This is very promising for us. We are very grateful to our local partners, companies such as Stukwerkers, Katoen Natie, 3MCT and Verbrugge. The increase in volumes we are transporting for them not only helps us to grow, it also enables us to provide a better service. For example, as a result of these increased volumes we are able to offer more sailings. We are now sailing three-four times a week to and from North Sea Port and moving towards our goal of offering a daily sailing.”
Another trend that Danser is observing at the present time, is an increase in demand, not only for container transportation, but also breakbulk and project cargo.
“This is another positive development. We work with a wide range of vessels, both large and small. All of them are open with no hatches and, therefore, well suited to the transportation of, for example, cranes or large silos.”
Clients in North Sea Port, for example, Mammoet, are already taking advantage of the availability of this capacity.
This promising picture, combined with the new Joint venture with Euro-Rijn, puts Danser in a good position to face the challenge that lies ahead of it – the challenge that is facing all maritime operators at the present time; sustainability.
It’s a word that is on everyone’s lips at the moment. Increasingly stringent regulations are continually being drafted. As a result, vessel operators are required to improve the environmental performance of their assets, and to demonstrate it. Danser Group is able to approach the situation with some experience.
“Ten years ago, we were the frst inland container shipping
A
green vessel costs somewhere between three and four times the price of a conventional one. That’s just not in reach for many vessel operators...
company to retroft one of our vessels with hybrid diesel-LNG propulsion. This experience gave us a good insight into how challenging this can be. Frequently operators encounter a market that has not yet reached maturity. The legislation is not yet in place to ensure a level playing feld, or the infrastructure is lacking. And, not least of the challenges is that greening a vessel is very expensive.
“A green vessel costs somewhere between three and four times the price of a conventional one. That’s just not in reach for many vessel operators, especially when they are forced to compete with lower costing, non-sustainable vessels. It’s diffcult to make a return on investment at this stage.”
Danser, however, is not resting on its laurels. A signifcant part of his task at present, Ben Maelissa says, is to ensure that the company is fully prepared for a green future. Danser is already operating two hybrid diesel-electric vessels between North Sea Port and the Ports of Antwerp-Bruges and Rotterdam.
“With Euro-Rijn on board we have a green light to invest in sustainable solutions. We are already working towards using bio-fuels on our vessels. Preparations for this are in full swing and I expect we will sail with bio-fuel before the end of this year. This won’t take us to zero emissions of course, but it’s a step in the right direction.”
“Part of my job right now is to watch the market closely to see what is happening and make sure that we make the right choice at the right time.
The big challenge, however, is that no one can say with certainty at the moment, which way things will go. Ultimately, there will be a mix of alternative propulsion solutions, depending on the operational profle and the route in question.
“In our operations, we cover both short and long distance routes. Therefore, I fully expect we will apply a variety of solutions in the future. In the North Sea Port corridor, given the short distances involved, battery technology may well be the best option. However, we also sail to Basel and that’s a completely different operation. You cannot think of doing that with batteries.”
Greening its own vessels, however, is only a part of the puzzle for Danser. While the company operates four of its own barges, its service is also dependent on the approximately 70 privately owned vessels it charters.
“The owner-captains of these vessels are also having to think about greening their vessels. Typically, however, these are mostly smaller operators with just one vessel, or three to four at most. We have a role to play here to achieve ourjoint sustainability goals.
“We’re in a fortunate position that we transport in the region of 1.6 million TEU per year. This provides us with a stable enough foundation to be able to offer captains for instance an extended contract. With that longer-term view they are able to invest in retroftting their existing tonnage or newbuilding more effcient vessels.”
The importance of ensuring the greening of the inland waterway feet becomes clear, Ben Maelissa says, with a simple glance at a map of Europe.
“You can see very clearly the importance of the mix of modalities – road, rail and water – to transport goods to and from the major ports. These are essential to the commerce and livelihood of people all over the continent. As such, we will need to fnd solutions to ensure their continuity.
“That’s what we will be focusing on in the short term. We cannot do it alone, however. We will need to communicate together with other industry players and with local and national governments and the European Union to forge a way forward. I hope this will give us clearer direction and, in the course of the coming year, that we will be able to take some crucial decisions about our future.”
I. DANSER.NL
Since offcially taking over in 2021, Robbert Pfauth has navigated a signifcant transition at Pfauth Logistics, following in the footsteps of his father, Hans Pfauth. Having spent years ingrained in the company’s operations, Robbert gradually assumed greater responsibilities, culminating in a smooth leadership transition that has resulted in positioning Pfauth Logistics for continued growth and innovation. Now efforts have been made to expand storage facilities and build new offce space.
We speak with Robbert Pfauth while these construction activities are in full swing. The conversation takes place at the Business Centre Seaports of the S.T.T. Group of Companies, where Pfauth is temporarily using offce space until the new offces are completed.
“We are very grateful for S.T.T.’s hospitality,” says Robbert Pfauth, “but I will be glad when we can return to our own location because I do miss the logistics action. Although we’re practically just around the corner, working remotely from our
Preparative activities for the expansion of the storage facilities and the new offces.
company is still challenging. Being at a distance from the dayto-day operations has made me realise how often we quickly walked from the offce into the warehouse with questions and how easily the warehouse operators could step into our offces with theirs. Now, that’s more diffcult. Our strength doesn’t lie in wanting to be the biggest, but in the dedication of our entire team to respond to our customers’ needs. Although being distanced from the action, our customers and partners do not notice the fact we’re not located in our own offces. This is a huge team effort! Still, we look forward, if all goes well, to moving into our newly built offces somewhere in October.”
A few years ago, the offcial transfer of the company from Hans Pfauth to his son Robbert took place. Since then, Robbert has been solely at the helm. He explains, “I joined the company already in 2010, and of course I was destined to take over my father’s job. However, we didn’t speed things up. Sometime in 2018, I started to gradually take over things from him. In 2021, my father offcially stepped back (see also PortNews 16.3, page 28, New at the helm). For me it is a reassuring thought that I can still go to him for advice and to discuss things whenever I feel the need to do so. Today, the world is changing rapidly, also when looking at logistics. And for us it is important to look for the best way to respond to these changes. In the past, my father and I took those decisions together. Now, I try to have the whole team involved in the process. Also, as we have a good relationship with our customers and our business partners, we talk a lot with them about how to adapt to changes.”
Although many changes have occurred, the dedication of our team and our collaborative spirit remains unchanged, and I intend to keep it that way.
Not only is the world changing, so is Pfauth Logistics. Robbert Pfauth continues, “Throughout the years, we have been expanding our team, and now we have a good mixture of young and old people. The input of young people together with the experience of the older ones, really reinforces our organisation. We specialise in the storage and transport of hazardous chemical products. Increasingly, our clients in this sector began asking if we could also store more and more other non-hazardous, though often chemical, products for them. We noticed it was becoming more challenging to store these goods at our current location due to capacity issues. Our strong reputation with current clients, who often refer their contacts to us, has certainly played a role in this. As a result, we recently decided to expand our storage capacity by approximately 2,500m2.” The plans don’t stop at the storage expansion; Robbert highlights Pfauth Logistics’ forwardthinking approach. “Our new offce space, which will be doubled, prepares us for future growth in a modern and nice environment. Additionally, we can now offer rented space to our customers, further capitalising on market demands.”
In a landscape that requires quick adaptation, Pfauth Logistics stands ready. “Like a chameleon, we evolve to meet the logistical challenges of today’s world,” Robbert Pfauth affrms. He acknowledges the importance of fexibility and responsiveness, especially as international transport
routes evolve. “We focus more on growth in knowledge and experience than sheer size. Our approach has allowed us to foster relationships with even the largest international players. We listen keenly to our customers and ensure we fulfll our promises.” Moreover, Robbert Pfauth emphasises the value of clear communication and the signifcance of maintaining high standards, particularly in handling chemical products –hazardous or otherwise. “Despite ongoing automation, our business remains fundamentally a people-centric endeavor, reliant on strong human interactions.”
As Pfauth Logistics enhances its facilities and embraces future possibilities, Robbert Pfauth remains committed to the principles that have long defned the company. “In the upcoming years, we hope to carry on our successful practices,” he says. “At Pfauth, we are truly a family-owned company. Some of our employees have connections dating back to my grandfather, the founder. Although many changes have occurred, the dedication of our team and our collaborative spirit remains unchanged, and I intend to keep it that way.” Robbert Pfauth’s leadership exemplifes how a company can change, maintaining core values while evolving to meet new challenges in the dynamic logistics industry. With a focus on collaboration, growth in knowledge, and a familial approach, Pfauth Logistics is poised for a promising future.
I. PFAUTH.NL
TPT has sets its sights on the long-term and is forging ahead with entrepreneurial spirit
TPT was founded in 1998 following a management buyout of the Engelhard factory. The Terneuzen-based company specialises in the processing and transshipment of chemical products for diverse sectors. TPT, for example, produces everything from de-icing products for airport runways, to GMP+ certifed additives and mould prevention products for the animal feed industry.
For the food sector, TPT produces the caustic soda that is used, for instance, by beer breweries as a pipe cleaning agent. For the oil industry, the company stores base materials in silos, subsequently blending them to client specifcations.
TPT has a storage capacity of 14,000m3. This is divided over approximately 30 silos for chemicals and powders with tank capacity ranging from 180m3 to 640m3, and 24, stainless steel and carbon steel tanks, complete with heating and cooling facilities, for liquid storage with capacity ranging from 80m3 to 1,300m3.
Facilities include a screening plant, drying plant, centrifuge, mixing plant and ammonia plant. The plants are connected and can be combined or used separately.
Located on the Ghent-Terneuzen Canal, TPT has its own quay where inland waterway vessels and coasters with a draught of up to 7.5 metres can dock. The site is also easily accessible from the road for trucks.
In the quarter of a century since it began operations, TPT has grown from a six-person enterprise into a family of 45, looking towards the dot on the horizon.
Husband and wife duo, Rahul Krishnan and Renate KrishnanHuijbregts, joined the company in 2020 following a share transfer, taking the lead as Co-CEOs. Since then, they’ve presided over a period of positive change at TPT, including a signifcant – and ongoing – increase in tank storage capacity. All enabled by a growing, passionate workforce.
Never before, they say, has their industry experienced such a dynamic period as it faces today. This is the result of multiple factors including geopolitical challenges, technological advancement, regulatory and climate change to name but three examples. Throughout this period, the husband and wife team are taking a positive approach, moving forwards and positioning their company for the future.
“When we started out on this journey, Renate and I expected that we would be on a 3-4 year change curve,” states Rahul Krishnan. “We made a plan to focus on strengthening the infrastructure of the company, how we operate and how we serve our customers. At our foundation is our focus on our people; culture, growth and development opportunities.
“During the last three years, we have been ambitious and have learned a lot along the way. We have had to adjust our plans, provide support and request help, recognising we are all in this together. We’ve had to make choices with key investments
and hold optimism through a wave of dramatic change in our industry and supply chains.
“This period has included the expansion of our tank farm, a new e-learning platform, maintenance models and a complete renewal of the factory automation software and hardware. There are numerous benefts to this. In the short term, it helps us to send a message to our colleagues, partners and customers that, even in these diffcult times, we are investing in the future. The future is dependent on many factors, we do keep our eyes set on the dot on the horizon. These choices prepare us to be ready for when the tide changes.”
Given the nature of the company’s operations, safety plays a prominent role in all developments at TPT. The Co-CEOs are acutely aware of the importance of safety in their industry and have responded accordingly. The revitalisation of infrastructure at the company has involved a full renewal of all company procedures and work instructions. In-depth, in-house developed training also goes a long way to ensuring everyone is fully aware of their tasks and tools in a further boost for safety and education.
Other straightforward measures include introduction of a registration system, providing a clear oversight of who is on site at any moment so that, in the event of a crisis, action can swiftly follow.
“Our motto is safety frst, quality second and quantity third,” explain the Co-CEOs. “From a purely commercial perspective, quantity is what drives the top line, only when safety and quality is in place.”
We made a plan to focus on strengthening the infrastructure of the company, how we operate and how we serve our customers.
TPT’s strategy of renewal has a decidedly local favour to it, with suppliers and contractors sourced regionally whenever possible.
“It’s a delight, when so often today things take place in the virtual world, to see everyone here, at our location, face-to-face.
“We believe frmly in developing strong, long-term relationships with business locally – including our neighbours in North Sea Port,” Renate Krishnan-Huijbregts explains. “We always look for local partners, right down to the suppliers of the Christmas hampers we give to our employees. It’s not always cheaper, but it does mean that we can help create a strong local eco-system, and help each other grow. Zeeland is a region which has tremendous potential, with the right support and businesses working together the region. We share a passion for promoting entrepreneurial spirit in the province and bringing more investment in to the region.”
This local focus feeds into an area particularly close to TPT’s heart – sustainability. It’s a topic that everyone is focusing on right now, and TPT and its clients are no exception.
“Our clients are, in comparison to TPT, large establishments with a rigorous focus on sustainability and they expect certain standards,” says Rahul Krishnan. “It’s our aim to both meet –and exceed – those expectations.”
Last year, TPT obtained ISO 14001 accreditation – the internationally recognised standard for environmental management systems.
Renate Krishnan-Huijbregts goes on to explain, “This helps position us well for the future. We now have a clear view on the ecological footprint of the company. With this, we can take steps, in the coming years to improve even further in this direction.”
These steps include TPT’s recent switch to running a 100% electric plant. The company also recently introduced plans to encourage biodiversity onsite with the introduction of a bee garden.
For TPT, the topic of sustainability extends beyond the environment alone. The company recently secured EcoVadis rating, demonstrating the quality of its operations in terms of
Once it fnds the right people, TPT does its utmost to hold on to them, by providing a positive working experience.
We’re really focused on creating a good work-life balance. This is important to us, personally, and we want to make sure it applies to our team, too.
environmental impact, labour and human rights standards, ethics and procurement.
The employment element of this, the Co-CEOs explain, is particularly relevant to TPT. The company has a specifc type of person in mind, when looking for new recruits.
“We embrace diversity – anyone is welcome at TPT so long as they have the right growth mindset and values. We believe frmly in the idea of ‘being the change you want to see; it doesn’t matter if you’ve not got the right piece of paper from school, or you don’t have a certain type of background. If you’re entrepreneurial and willing to learn – let’s go!” Supporting training and development, they intend te develop future leaders who grow with the company.
TPT invests a lot of energy into its recruitment process, conducting a range of interviews and taking the time to make sure someone is the right ft.
“Being a relatively fat organisation, we are able to give people hybrid opportunities. At larger companies, they would be working in parallel to their colleagues. Here, everyone is exposed to multiple functions, working in diverse sectors on a variety of projects” Rahul Krishnan states.
“We’re really focused on creating a good work-life balance. This is important to us, personally, and we want to make sure it applies to our team, too. We aim to give everyone the care they need, help them to learn and grow towards their full potential. Giving real responsibility, ownership and driving accountability in an environment where learning comes also from the mistakes we will all make. The question is what did we learn and how do we solve it?”
Whether it’s the local suppliers the company looks to work with, or the entrepreneurs it seeks to recruit, as it looks towards tomorrow, TPT is placing great emphasis on shared values.
“We think of TPT as building a family. That’s the root of our slogan ‘Samen staan we sterk’, which is Dutch for ‘Together we are strong’,” says Renate Krishnan-Huijbregts. “Rahul and I worked together before we embarked upon this journey so we knew from the start that we shared a vision and passion for how the company would be run.”
I. TPT.NL
Many people know SEC Catering for catering parties, events, dinners, and receptions, both at home and at work. However, the company offers much more, as it also arranges delicious meals for many organisations in the workplace.
“When we started in 2009,” René Willems, co-founder and co-owner of SEC Catering explains, “our initial focus was on providing catering for parties, receptions, and events. Various corporate clients increasingly asked us if we could also take care of meals. For instance, for staff working overtime or temporary personnel working on a project. Gradually, we began providing regular meals for many of these companies’ cafeterias, in addition to what we call project-based meals.”
His business partner and co-owner Martijn van de Woestijne, adds, “We have now grown into one of the largest B2B caterers in the southwest region of the Netherlands. In the port area of North Sea Port, we similarly relieve several companies of this responsibility. You see that
construction companies, such as shipyards, often work on projects where many permanent and fexible workers are employed in irregular shifts. It’s a relief for these workers not to have to rely on pizza when they work late, but instead, to have a varied, healthy, fresh, and of course, delicious meal. These projects often
involve large-scale assignments. For instance, we provided all the meals for the US and Dutch soldiers that took care of the logistic operations for military equipment on one of the terminals in the Vlissingen port area. That is something we are very proud of, of course. From these projects, companies increasingly ask whether we can also handle all meals for their company cafeteria. Naturally, we are happy to accommodate, and by now, we have several satisfed clients for these services as well.”
Since the beginning, things have gone smoothly, and with their unique approach, SEC Catering has gained many satisfed clients. “Whether it’s for 25 or 5,000 guests, our added value makes the difference,” explains René Willems. “We are a genuine Zeeland company and, where possible, use regional, preferably organic products. Our organisation is entirely designed for fexibility. The core of our company is compact, and where needed, we have access to a fexible pool of skilled hospitality staff. Additionally, we beneft from the fact that many of our suppliers are located close to our company, allowing us to act quickly. Even if we need to prepare a meal for dozens of people on the same day, that’s no problem. We never shy away from a challenge and always maintain the high quality we stand for.” Martijn van de Woestijne adds, “René and I are the face of the company, and without a fxed division of tasks, we handle whatever comes our way. We have a great team we can rely on, and our role is mainly to keep an overview where necessary and maintain contact with both existing and potential clients.”
This year marks the ffteenth anniversary of SEC Catering, and although the company has never actively pursued clients, it has have become a regular caterer for various institutions and companies such
as the municipality of Vlissingen, the province of Zeeland, DB Cargo Vlissingen, De Ruyter Training & Consultancy, Verbrugge and Shipyard Reimerswaal. “At the moment, the labour market is tight, making it diffcult to fnd and retain employees. Keeping personnel satisfed plays a big role in this. It may sound simple, but a good, tasty, and varied selection of meals, from a simple
sandwich to a delicious hot meal, certainly helps, and no one is better equipped than SEC Catering to unburden businesses, including those in the port area of North Sea Port, in this regard!” concludes René Willems.
Luctor Belting Europe is an independent supplier, installer, and service provider of conveyor belts. As an expert with over 50 years of experience, the company offers tailor-made solutions and a 24/7 maintenance service to ensure smooth operations and an effcient production process.
Founded in 1970, Luctor Belting is a family-owned business with over 50 years of experience producing and installing conveyor belts for any type of business or product.
Conveniently located in Hulst, near the Belgian border, the company services many companies in North Sea Port, the Port of Antwerp-Bruges and the Port of Rotterdam.
“Conveyor belts are used in all sorts of businesses and for a variety of products,” says Bianca Morcus, managing director and Owner. “In the port, you have for instance the loading and discharging of vessels or value-added services such as bagging. We also supply and maintain belts for the food industry, the recycling industry, agriculture and the packaging sector, to name just a few. Basically, we operate anywhere any product must be moved from point A to point B by conveyor belt. Not only do we supply rubber and plastic conveyor belts,
we also deliver round & V-belts, drive belts, modular belts, metal gauze belts, and belt scrapers. Our rubber and plastic belts are manufactured here in Hulst, where the heart of our operations is located. Our divisions in Sint-Denijs-Westrem, Belgium and Paris, France enable us to supply and serve customers throughout Belgium and in France, from the Port of Dunkerque to Calais. As suppliers, we also ship our belts worldwide.”
“We handle all sorts of products in North Sea Port,” Bianca Morcus says, “from chemical and petrochemical products to foods and breakbulk. We also supply and maintain belts for dredging vessels, textiles, wood panels and furniture, the automotive industry, agriculture, the paper industry, parcel frms, and many more. This dazzling variety in products transported by our belts means we manufacture various types of belts and
optimisation solutions, the latter being often tailor-made for a specifc product or customer. In fact, we have over 400 different types of belts currently in stock, as well as many accessories and components such as drums and rollers, trough idlers, seal rubber and cover materials, and many more, basically all things necessary to transport the product as effciently as possible. Your product, our solution, that is our motto.”
Although the company sometimes delivers belts for new installations, its core business is replacement, maintenance and optimisation, Bianca Morcus explains. “Most new installations come with the conveyor belts already installed, so we are usually called in when replacements or adjustments to the installation are needed. Most installations are standard or at least multipurpose, which is not always the best solution for your company or product. That is where we come in: we collaborate with and offer optimisation for any product, whether it is the transport of candy, fries or concrete, horizontal or vertical transport, inside a factory or between vessels for transhipment. Of course, everything starts with good quality. We pride ourselves in making conveyor belts of the highest quality. This results in a longer lifespan for the belts as well as fewer incidents with the conveyor system.”
“We think of conveyor belts as the arteries of a company,” Bianca Morcus adds, “they have to keep running. Issues with conveyor belts can cause unwelcome interruptions in production processes or delays in the loading of international transport, resulting in high costs. That is why we offer a 24/7 maintenance and repair service to our customers. Our aim is peace of mind for our customers, at least regarding their conveyor belts. As many of our solutions are tailor-made, this also implies we have to be able to pinpoint problems before they happen. That’s where our team of representatives comes in.”
“Even though we have an enormous stock with over 400 different types of conveyor belts and their accessories, the high level of customisation means replacements could require a few days of production time. Of course, when one of your conveyor belts is out of service, waiting a couple of days for a new one is unthinkable. We understand that and always try to
Our representatives are more than just partners of our customers, they are an extension of the technical department.
stay one (or more!) step ahead. For instance, when installing a tailor-made or special accessory-optimised belt we always propose purchasing at least one replacement, so it can be produced and stored until needed. This is no unnecessary luxury when your installation suffers damage and replacement is needed quickly.”
“More importantly, our representatives visit each of our customers regularly. They are more than just partners of our customers, they are an extension of the technical department. Through regular visits, inspecting the installation, and talking to the customer’s technicians, our representatives truly know the specifcations of the customer’s operations, allowing them to both timely signal any maintenance needs that may occur as well as propose further adjustments to optimise the transport by conveyor belts.”
“On top of this, we also provide tailor-made training for our customers, teaching them how to take good care of our premium quality belts so they stay in good condition. It’s just one more step in the optimisation process.”
“We invest, not only in our customers but in our employees as well,” Bianca Morcus states. “There’s no such thing as an education in conveyor belt mechanics, as there is in woodor metalwork. Even if there was, we offer such a diversity in conveyor belt solutions that thorough in-house training would remain necessary. We therefore provide an in-house, oneyear education programme for all new mechanics, teaching them all the specifcs of the different materials, welding methods for each type of belt, and so forth, to become an all-round mechanic. Upon completion, our mechanics will frst accompany our more senior technicians to learn the ropes in the feld. We provide regular internal and external training courses for all our employees to keep our knowledge up to date, and we are VCA-P and ISO 9001 certifed. Furthermore, we have a monthly toolbox meeting about safety issues. Safety for our employees is our number one priority.”
“Our mechanics encounter all sorts of diffculties and safety hazards in the feld. That is why we strive to make everyone, mechanics, representatives and customers, aware of our philosophy: no work can be done if it cannot be done safely. This is an absolute priority. It seems harsh but it is of such importance. We cannot guarantee the quality of the work if our mechanics cannot work safely and no customer is served by an accident on their premises. Furthermore, we think of our company as one big family, the Luctor Belting family, and our family members need to be protected, meaning all necessary safety measures have to be in place. That is why everyone is instructed to perform an extensive last-minute risk analysis before starting any job. Every assignment fled by our representatives is accompanied by a list describing the conditions in which the work will be performed.”
The phrase “Luctor Belting family” can be taken quite literally, as it has always been family-owned. “Although it was founded by my father, I initially had no interest in working for the family business,” Bianca Morcus says. “I did receive an education in electrical engineering, but I went on to the hotel school Spermalie in Bruges and got a bachelor’s degree in hotel and hospitality management at TIO Den Bosch. However, after spending 6 months in Nice to perfect my French (French Language school), my father asked if I was interested in helping out as a representative for the French customers. I was, I did, and I was lucky enough to be accompanied by someone who was incredibly experienced in the matter and the feld, and I never left. I bought the company in 2016, a few years before my father’s retirement, and I’m proud to say that the company is thriving. I believe our employees are very happy here as well, as we recently looked up the statistics and noticed that 55% of our employees have worked here for over ten years! Having happy personnel is really important here. We don’t believe in an extensive and rigid chain of command, but rather strive for a tightly-knit team and an open-minded culture where there’s room for growth and opportunity.”
“That our philosophies are carried and embraced by our employees is obvious in the details. For instance, we strive to work as paperless as possible, with iPads provided for all our mechanics and the reuse of cardboard boxes for shipping. We see that actually, many employees now bring reusable cardboard boxes from home to help reduce the ecological footprint of our shipping services.”
Bianca Morcus adds, “Of course, that is not all we do to improve the sustainability of our company. For instance, we go to great lengths to make our waste management as green as possible. Not only do we rigorously separate our own waste fows, we also handle the environmentally compliant disposal of the old conveyor belts of our customers. We have also started a project to electrify our feet. Everything that can be done to improve our environmental footprint, we do. It is an inherent part of our philosophy: we strive to work sustainably and effciently in keeping your company moving.” I. LUCTORBELTING.COM
Many organisations contribute to strengthen the position of the companies in and around the port area of North Sea Port. One such organisation is Zeeland Connect.
Zeeland Connect is an independent knowledge and innovation network that supports Zeeland’s logistic sector in and outside the region by means of collaboration, sharing of knowledge, and facilitating of projects. Mariko Rouw, program manager at Zeeland Connect since October of last year, explains, “In our activities, focus lies on four innovation lines. The first one is Logistic Flows and Connections, the second one is Zero Emission Logistics, the third is Digitalisation and Robotising, and the fourth line aims at Autonomous Transport. It is obvious that these four lines are closely related and overlap in various
ways and our goal is to maximise the opportunities within these four subjects. For this we closely work together with industry, governments, such as the province of Zeeland, and knowledge institutes, such as HZ University of Applied Sciences and Scalda. By jointly initiating and executing projects we look for sustainable and innovative solutions for the future of the logistic industry in Zeeland.”
Today, the network consists of over 50 partners. “Since our origin we have managed to attract a growing number of companies,” Mariko Rouw states. “We started with a small group that today form the strategic partners: the province of Zeeland, Impuls Zeeland, Kotra Logistics, HZ University of Applied Sciences, Lineage Logistics, Wielemaker Transport, and North Sea Port. Representatives of the strategic partners form the steering committee that is responsible for the overall policy
of the network. Last year we organised a congress for everyone interested in logistics. With this congress we showed that our network is of added value for companies that are operating in logistics or that are heavily depending on good logistics. We emphasised that, to completely profit from this added value, one should join Zeeland Connect and this really helped to expand our network with valuable partners. The more partners join Zeeland Connect, the stronger the synergy within our network will become, and the more everyone will fully profit from the enhanced collaboration and added value. Apart from logistic companies we now see a growing interest from companies that are not focusing on logistics but for which logistics form a vital component in their operation.”
In the early days, Zeeland Connect acted more or less on a part time basis, using capacity of their strategic partners, and this limited their possibilities, but today the network has a team that can operate on a more full-time basis. “With the growing number of partners, our financial strength grew too, enabling us to invest in people and developing our programme. Now, we have a cluster team responsible for the daily overall organisation of Zeeland Connect. Think of the management, the communication and the development and organisation of our annual programme of activities. The managers of these four innovation lines, and our communication colleague Lotte de Kam, are part of the cluster team and together we are responsible for our strategic plan 2024-2027,” Mariko Rouw explains.
Based on the innovation lines, Zeeland Connect organises a broad range of activities for its partners. Mariko Rouw elaborates, “First of all, the network itself offers ample opportunities for the partners to meet like-minded professionals, experts and policy makers. Collaborations initiated by the network open doors to new opportunities, projects and markets. Apart from this, we offer a varied annual programme of activities and events, such as a CEO dinner, an annual congress, innovation tables, company visits and masterclasses. With our programme we always keep the challenges in our sector in mind.”
Jennifer Vermaas has recently joint Zeeland Connect, as manager of this innovation line. “Within the upcoming years,” Jennifer Vermaas explains, “connected vehicles such as teleoperated or remotely operated vehicles will be introduced in the Netherlands, followed by completely autonomous trucks. We look how companies can use these kind of technologies and what changes are necessary at the companies and in the infrastructure for a successful implementation. Recently, there have been tests in autonomous transport in the port area at the terminal of our partner Lineage Logistics. In the end, autonomous transport should not be restricted to internal transport, such as on a terminal, but cover the entire port area and even public roads. However, to continue, we have decided
to take small steps as we believe that this enlarges the chance to be successful. In the third quarter of this year we want to have our agenda ready with new projects.”
Digitalisation and Robotising
Manager of this innovation line is Rutger van der Male.
“Because of the growing shortages in the labour market and the introduction of robotised and self-learning logistic systems, innovation in digitalisation and robotising has become inevitable,” he elaborates. “Of course there are many solutions available in the market that can be used and the challenge is to find out what solutions are suitable for our partners and how to implement them. Another challenge lies in the fact that some of our partners are operating in niches and therefore have not enough volume to earn back the high investments. Finally, developments in IT go very fast and the challenge lies in how to see these developments in time, to learn what developments are useful, and how to be able to implement them in the right way. One of our first goals is to develop an innovation toolbox with tips and tricks for our partners. Also, we organise visits to our partners. This way everyone can learn from each other. Another point of interest in our innovation line is research: where do we stand with regards to digitalisation? What are the trends in the logistic sector, and what can Zeeland Connect do, to help? Also, we have initiated the collaboration with HZ University of Applied Sciences and educational institutes in Flanders. With this cross-border initiative we hope to connect the border regions based on a longer term collaboration. As one of the first steps we have submitted a request for subsidy and we hope that this project can take off next year in September.”
hinterland connections and new destinations strengthen the
Logistic Flows and Connections Manager of this innovation line is Remco de Rijke. “Efficient hinterland connections and new destinations strengthen the competitiveness of transporters and logistic companies, and it improves the business conditions in Zeeland. This counts for the port related cargo flows as well as for the flows to and from trading and producing companies around the port area, the so-called continental flows of goods. The challenge lies in combining as many as possible cargo flows to and
from Zeeland to be able to offer higher frequencies and more destinations. Apart from this, it is of utmost importance to be able to adapt the transport network fast to changing demands. This innovation line in fact started with the so-called Verladerskring (network of shippers) in the Terneuzen port area and soon we extended this network to Vlissingen. We have been organising network meetings and company visits for quite some time now and we act as intermediate with Topsector Logistics, for example for subsidies. I think we all can be proud with what we have already have achieved and this innovation line shows what can be done with good collaboration.”
Rick Suurmond is manager of this innovation line. “To prevent the earth from warming further than is sustainable,” he says, “it is becoming increasingly clear that CO2 emissions must be reduced. Combined with technical developments in the field of zero-emission transport, this offers many companies a lot of challenges, but at the same time a lot of opportunities. What we aim to achieve with this innovation line is that we logistically prepare Zeeland for a zero-emission future. And that starts with awareness. At the intersection of the energy transition and social innovation, we have developed a number of projects to sketch a picture of the zero-emission future together with the sector.”
Rick Suurmond continues, “An excellent example of our efforts is the successful Zero Emission Truck Academy. With this academy we share knowledge and expertise that help companies to make their truck park more sustainable. To date, we have helped more than 50 partners this way. Based on this success we also started this academy for owners of vans.
These are not only logistic companies, but also, for example, smaller and mid-size trading companies and contractors owning a van for their own use. For us, this is a completely new group of companies that become partners of our network. Another successful example is our CSRD masterclass, which started in September. Here we tell our partners everything about the new CSRD regulations and how they can adapt to these.”
“Now that our organisation has become more structured, our next organisational step is that the four innovation lines become more independently organised and managed with more room for a longer term strategy,” Mariko Rouw concludes. “It is good to see that everyone involved in Zeeland Connect, supported by our chairman Ronald Wielemaker of Wielemaker Transport who really has put ample efforts in helping our network to become a success, is very dedicated to our goals. Our partners are all willing to collaborate. In the beginning companies were quite hesitant to share knowledge and expertise but now our partners see that working together, instead of competing, can be helpful in many situations. Of course, it is evident that collaboration works best in urgent situations and it is our objective to make our partners aware of these. Take for example the Zero Emission innovation line. Within this line we explain that reaching the level of zero emission is relevant for everyone and that it is easier for all partners to succeed when you help each other to find the right solutions.”
I. ZEELAND-CONNECT.NL
Zeekanaal Ghent - Terneuzen: The depth of water in the canal is 13.5 m and there are no currents or tides. Inside the port there are fve large docks and three smaller docks, offering a total quay length of 31 kilometres for vessels up to 92,000 DWT. 22 kilometers with a depth of water of at least 12.5 metres. All the docks have direct access to the canal.
Zeekanaal Ghent - Terneuzen: The depth of water in the canal is 13.5 m and there are no currents or tides. Inside the port there are five large docks and three
smaller docks, offering a total quay length of
31 kilometres for vessels up to 92,000 DWT. 22 kilometers with a depth of water of at least 12.5 metres. All the docks have direct access to the canal.
• Kluizendok: Is a brand-new dock. Has a total quay length of 4,300 metres with a depth of water of 13.5 metres and a width of 350 metres.
• Kluizendok: Is a brand-new dock. Has a total quay length of 4,300 metres with a depth of water of 13.5 metres and a width of 350 metres.
• Rodenhuizedok: Quay on the southern side is 790 metres long with 13.5 metres of depth. Width of 270 metres.
• Rodenhuizedok: Quay on the southern side is 790 metres long with 13.5 metres of depth. Width of 270 metres.
• Mercatordok: Quay is 1,800 metres long with 13.5 metres of depth. Width of 250 metres.
• Mercatordok: Quay is 1,800 metres long with 13.5 metres of depth. Width of 250 metres.
• Alphonse Sifferdok: Quay is 4,800 metres long, with 12.5 – 13.5 metres depth. Width of 300 metres.
• Alphonse Sifferdok: Quay is 4,800 metres long, with 12.5 – 13.5 metres depth. Width of 300 metres.
• Grootdok, Noorddok, Middendok and Zuiddok:
• Grootdok, Noorddok, Middendok and Zuiddok:
Total quay length of 6,855 metres. 6,575 metres with 13 metres depth of water, and 280 metres with 8.5 metres depth of water.
Total quay length of 6,855 metres. 6,575 metres with 13 metres depth of water, and 280 metres with 8.5 metres depth of water.
Width: Grootdok: 150 metres
Width: Grootdok: 150 metres
Noorddok: 200 metres
Noorddok: 200 metres
Middendok: 250 metres
Middendok: 250 metres
Zuiddok: 220 metres
Zuiddok: 220 metres
Zelzate • Ghent •
• Terneuzen Western Scheldt
• Hoek
Ghent-Terneuzen channel (Kanaalzone)
Ghent-Terneuzen channel (Kanaalzone)
• Noorderkanaalhaven: North quay: 170 metres; South quay: 192 metres.
• Noorderkanaalhaven: North quay: 170 metres; South quay: 192 metres.
• Zuiderkanaalhaven: North quay: 225 metres; South quay: 230 metres.
• Zuiderkanaalhaven: North quay: 225 metres; South quay: 230 metres.
• Massagoedhaven: 978 metres.
• Massagoedhaven: 978 metres.
• Zevenaarhaven: North quay: 421 metres and 555 metres; South quay: 259 metres.
• Zevenaarhaven: North quay: 421 metres and 555 metres; South quay: 259 metres.
• Axelse Vlaktehaven: 290 metres.
• Axelse Vlaktehaven: 290 metres.
• Autrichehaven: 850 metres.
• Autrichehaven: 850 metres.
Braakmanhaven
Braakmanhaven
Braakmanhaven is part of North Sea Port, located directly on Western ScheIdt with no locks. Four berths for seagoing vesseIs and three berths for inland vessels.
Braakmanhaven is part of North Sea Port, located directly on Western ScheIdt with no locks. Four berths for seagoing vesseIs and three berths for inland vessels.
• Scheldt Jetty: 0ne berth for vessels up to 22,500 dwt or 200 metres LOA.
• Dow’s Scheldt Jetty: One berth for vessels up to 22,500 dwt or 200 metres LOA.
• Oceandock: North and south berths.
• Dow’s Oceandock: North and south berths.
• Zeeland Container Terminal: 185 metres.
• Zeeland Container Terminal: 185 metres.
• 0iltanking Jetties: Jetty 0tter 1 and Jetty 0tter 2.
• EVOS Terneuzen.
• Braakman: Docks A, B and C.
• Dow’s Braakman: Docks A, B and C.
• Philippine •
•
• Westdorpe
• Middelburg
• Middelburg
Lewedorp •
Lewedorp •
• Nieuw- en Sint Joosland
• Nieuw- en Sint Joosland
• Oost-Souburg
• Oost-Souburg
• Vlissingen
• Vlissingen
• Ritthem
• Ritthem
W es t ers c he lde
es t ers c he lde
• Nieuwdorp
• Nieuwdorp
’s-Heerenhoek
’s-Heerenhoek
•
•
• Borssele
• Borssele
• Sloehaven: Suitable for alI kinds of transshipment including LPG and chemical bulk 920 metres of quay. Cobelfret RoRo jetties: Four berths.
• Sloehaven: bulk 920 metres of quay.
• Sloehaven: Suitable for alI kinds of transshipment including LPG and chemical bulk 920 metres of quay. Cobelfret RoRo jetties: Four berths.
• Bijleveldhaven: 1,980 metres of quay. North bank is 300 metres long.
• Sloehaven: Suitable for alI kinds of transshipment including LPG and chemical bulk 920 metres of quay. Cobelfret RoRo jetties: Four berths.
• Bijleveldhaven: 1,980 metres of quay. North bank is 300 metres long. Can accommodate largest reefer vessels.
• Bijleveldhaven: 1,980 metres of quay. North bank is 300 metres long.
• Bijleveldhaven: 1,980 metres of quay. North bank is 300 metres long.
• Westhofhaven: 475 metres of quay. Can accommodate largest reefer vessels. East side jetty for discharging peat and general cargo quay.
• Westhofhaven: 475 metres of quay. Can accommodate largest reefer vessels. East side jetty for discharging peat and general cargo quay.
• Westhofhaven: 475 metres of quay. Can accommodate large offshore vessels.
• Kaloothaven: 1,130 metres of quay.
• Kaloothaven: 1,130 metres of quay. Two jetties on south bank, one for inland barges.
Westhofhaven: 475 metres of Can accommodate largest reefer vessels. East side jetty for discharging peat and general cargo quay.
• Kaloothaven: 1,130 metres of quay. Two jetties on south bank, one for inland barges.
• Scaldiahaven: Over 1,700 metres of quay. South side used by Verbrugge for handling and storage of cellulose and metals. Transverse quay is 250 metres long.
• Scaldiahaven: Over 1,700 metres of quay. South side used by Verbrugge for handling and storage of cellulose and metals. Transverse quay is 250 metres long.
• Kaloothaven: 1,130 metres of quay. Two jetties on south bank, one for inland barges.
• Scaldiahaven: Over 1,700 metres of quay. South side used by Verbrugge for handling and storage of cellulose and metals. Transverse quay is 250 metres long.
• Van Citterskanaal/haven: Six jetties for inland vessels and coasters. 0n south bank, 275 metres. 0n north bank, 200 metres. Heerema quay: 230 metres and 220 metres.
• Van Citterskanaal/haven: Six jetties for inland vessels and coasters. 0n south bank, 275 metres. 0n north bank, 200 metres. Heerema quay: 230 metres and 220 metres.
• Van Citterskanaal/haven: Six jetties for inland vessels and coasters. 0n south bank, 275 metres. 0n north bank, 200 metres. Heerema quay: 230 metres and 220 metres.
• Scaldiahaven: Over 1,700 metres of quay. South side used handling and storage of cellulose and metals. Transverse quay is 250 metres long.
• Quarleshaven: Extension of Sloehaven to NNE, 315 metres of quay. Set of two mooring buoys on east bank with a span of 320 metres. Zalco quay: East bank, length of 150 metres. Vopak Terminal VIissingen: Four LPG jetties.
• Quarleshaven: Extension of Sloehaven to NNE, 315 metres of quay. Set of two mooring buoys on east bank with a span of 320 metres. Zalco quay: East bank, length of 150 metres. Vopak Terminal VIissingen: Four LPG jetties.
• Quarleshaven: Extension of Sloehaven to NNE, 315 metres of quay. Set of two mooring buoys on east bank with a span of 320 metres. Zalco quay: East bank, length of 150 metres. Vopak Terminal VIissingen: Four LPG jetties.
• Van Citterskanaal/haven: Six jetties for inland vessels and coasters. 0n south bank, 275 metres. 0n north bank, 200 metres. Quay: 230 metres and 220 metres.
• Zeeland Refinery Pier: Located on Western Scheldt. Accommodates tankers up to 100,000 dwt with maximum LOA of 280 metres.
• Zeeland Refinery Pier: Located on Western Scheldt. Accommodates tankers up to 100,000 dwt with maximum LOA of 280 metres.
• Zeeland Refnery Pier: Located on Western Scheldt. Accommodates tankers up to 100,000 dwt with maximum LOA of 280 metres.
• Quarleshaven: Extension of Sloehaven to NNE, 315 metres of quay. Set of two mooring buoys on east bank with a span of 320 metres.
• Buitenhaven: Located outside lock system with direct access to sea, 300 metres of quay. Northern basin has area for coasters and Iighters. Vesta also operates an oil jetty for tankers.
• Zeeland Refinery Pier: Located on Westernscheldt River. Accommodates tankers up to 100,000 dwt with maximum LOA of 280 metres.
• Buitenhaven: Located outside lock system with direct access to sea, 300 metres of quay. Northern basin has area for coasters and Iighters. Vesta also operates an oil jetty for tankers.
• Buitenhaven: Located outside lock system with direct access to sea, 300 metres of quay. Northern basin has area for coasters and Iighters. Vesta also operates an oil jetty for tankers.
• Buitenhaven: Located outside lock system with direct access to sea, 300 metres of quay. Northern basin has area for coasters and Iighters. Vesta also operates an oil jetty for tankers.
for
The Promotion Council North Sea Port is pleased to welcome new members. Founded in 1993, the Promotion Council North Sea Port represents members located in North Sea Port. Together they offer a complete range of the best possible port facilities and all the logistics solutions you need. See pages 61-64 for a complete list of members.
Aertssen Cranes is a 100% family-owned business specialising in heavy lifting, SPMT transport, jacking and skidding activities. You can rely on their extensive feet of mobile lifting cranes worldwide, of which about 200 are in the Benelux. Aertssen Cranes offers you mobile telescopic cranes up to 800t capacity and crawler cranes up to 1,350t. For your transport requirements, road trucks and SPMT axle lines with a combined capacity of more than 3,000t are at your disposal. The company’s own jacking system has a capacity of 1,000t. As working area, Aerssen Cranes concentrates mainly on
North-Western Europe and the Middle East and on sectors with high safety requirements such as offshore, oil & gas (refning/tank storage terminals), (petro)chemicals (new construction/conversion/shutdowns/site management), energy production and distribution (wind turbines, power plants, high-voltage lines), large-scale infrastructure projects (bridges/tunnels, and so on. All its activities are supported by the company’s own engineering team and maintenance service.
I. AERTSSEN.BE
Independent energy knowledge partner COMCAM is market leader in Energy portfolio management. They help companies maintain control over the increasingly complex energy market through an integrated, long-term energy strategy. COMCAM operates in nine countries and assists organisations in keeping strategic energy management manageable and affordable. COMCAM’s consultants are all specialists with extensive experience in the energy market. They now use their expertise and experience to help companies advance in
Global Port Training (GPT) is specialised in training machine operators and port and terminal workers worldwide. With its global presence, GPT can share its in-depth knowledge and extensive experience with various port companies and communities. Global Port Training introduces an innovative approach through a mobile crane simulator, brought directly to your location.
The Blue Gate Training Center, located at the Petroleum-Zuid site in Antwerp, serves as
the energy transition. Additionally, COMCAM is an independent knowledge partner in the energy market, providing services without conficts of interest like those of an energy supplier or intermediary.
COMCAM’s Energy Portfolio Management provides insight into and access to all energy markets. This is why COMCAM offers its clients the best of both worlds, guiding them in developing a long-term energy strategy.
I. COMCAMENERGY.COM
GPT’s training hub, where both theoretical and practical training is provided to machine operators. Here, the company offers reachstacker and empty container handler courses, as well as training for all other types of machines used in the port. Additionally, the Blue Gate Training Center specialises in lashing & securing and stuffng & stripping training.
I. GLOBALPORTTRAINING.COM
Hendrik Veder Group is a European company, operating worldwide from its locations in the Netherlands, the UK, France, Norway and Poland. It is headquartered in the Port of Rotterdam. The company provides products and services in the feld of steel wire rope and synthetic rope, which play an important part in the offshore and maritime industries around the world. It also offers all-in-one solutions and services in many other industries.
Hendrik Veder Group’s ambition is to make the offshore and maritime sectors more sustainable. The company works alongside its forward-thinking clients to achieve sustainability through innovation. The result is new, cost-effective solutions based on inventory management, maintenance and a circular approach to raw materials.
I. HENDRIKVEDERGROUP.COM
MEDIA58 is not about the fuss, but straight to the point. Whether it’s eye-catching signs, printed materials, sleek websites, or producing books about Zeeland, at MEDIA58 they simply get it done. No hassle, just effective and high-quality work. The company’s team is small and skilled. Together, they ensure your business shines in a no-nonsense way. MEDIA58 values direct communication. Its swift communication ensures a smooth business experience. Its
involvement goes beyond just giving advice; they are there from start to fnish. In the down-to-earth strength of collaboration with MEDIA58, professionalism and results come together without any frills. Together, MEDIA58 elevates your company’s presentation to new heights, from Vlissingen to Ghent, with the powerful image that suits the maritime character of North Sea Port.
I. MEDIA58.NL
meet | connec t | promot e
5G Multimodal
www.5gmultimodal.com
A.C. Rijnberg transportservice B.V. www.rijnberg.com
Aannemingsmaatschappij Van Gelder B.V. www.vangelder.com
ABAB Accountants en Adviseurs www.abab.nl
ABN AMRO www.abnamro.nl
Access World Terminals B.V. www.accessworld.com
Adriaanse & van der Weel Advocaten www.avdw.nl
Aerssens & Partners www.aenpmakelaars.nl
Aertssen Kranen N.V. www.aertssen.be
Agro Minne www.agro-minne.be
AmSpec PMI B.V. www.polarismarineinspections.nl
ASD Group / Vervaeke www.industrial.vervaeke.be
Atlas Professionals www.atlasprofessionals.com
AXXAZ www.axxaz.nl
Baker Tilly N.V. www.bakertilly.nl
BMD Advies www.bmdzuid.nl
Boels Rental B.V. www.boels.com
Boluda Towage Europe www.boluda.eu
Bouwgroep Peters B.V. www.bouwgroep-peters.nl
BOW Terminal www.bowterminal.nl
Brandwacht Huren België www.brandwachthuren.be
Brandwacht Huren Nederland www.brandwachthuren.nl
Cemminerals N.V. www.cemminerals.be
CLdN www.cldn.com
COMCAM International www.comcamenergy.com
Competence Development Center www.bbeu-cdc.org
Control Union Belgium N.V. www.petersoncontrolunion.com
Cordeel Nederland B.V. www.cordeel.nl
C.T.O.B. Transport & Logistics www.ctob-logistics.com
Customs Support Terneuzen www.customssupport.com
Damen Shiprepair Vlissingen www.damen.com
Danser Group www.danser.nl
DB Cargo Belgium B.V. www.dbgargo.com
DB Cargo Nederland N.V. www.nldb.cargo.com
De Baerdemaecker N.V. www.stukwerkers.com
De Pooter Personeelsdiensten www.depooter.nl
De Ruyter Training & Consultancy www.drtc.nl
De Zeeuwse Alliantie Notarissen www.dezeeuwsealliantie.nl
Delta Safe Security Services B.V. www.delta-safe.nl
DEME Environmental N.V. www.deme-group.com
DFDS Belgium N.V. www.dfds.com
DHG www.dhg.nl
dNM www.dnm.nl
DOC Logistics B.V. www.dutchcontractors.com
DOW Benelux B.V. www.dow.com
Draftec B.V. www.draftec.nl
DRV Accountants & Adviseurs www.drv.nl
Dutch Marine B.V. www.dutchmarinebv.com
E.I.B. Insulation N.V. www.eib-group.eu
Elloro www.elloro.nl
Elopak B.V. www.elopak.com
ELTEN Benelux B.V. www.elten.com
Embedded Coaching & Consultancy www.ecc-coach.nl
EP NL Sloe centrale B.V. www.epnl.nl
Epesi B.V. www.epesi.nl
Equans www.equans.be
Euro-Mit Staal B.V. www.euro-mit-staal.com
Euro-Rijn Global Logistics www.eurorijngroup.com
Euro-Silo N.V. www.eurosilo.be
Evolution Terminals B.V. www.evoterminals.com
Evos Ghent N.V. www.evos.eu
meet | connec t | promot e
Evos Terneuzen B.V.
Fertilife Benelux B.V.
www.evos.eu
Feyter Group www.feyter.com
FincoEnergies Marine www.fncofuel.com
Firma Klouwers Terneuzen www.klouwers.nl
Flushing Shipping Agencies www.fsagencies.com
FMJ E & I Zeeland B.V.
www.fmj.nl
Geodetics Construction Maintenance www.gcm.be
Ghent Transport & Storage N.V. www.gtsghent.be
Global Port Training B.V. www.globalporttraining.com
Gould services www.foundgould.com
Green Blue Ofshore Terminal www.greenblueot.nl
H4A www.h4a.nl
Havenwerk B.V. www.havenwerk.nl
Hendrik Veder Group Vlissingen www.hendrikvedergroup.com
Henk Kramer Communicatie www.henkkramer.nl
Heros Sluiskil B.V. www.heros.nl
Heylen Warehouses www.heylenwarehouses.com
Holland Shipyards www.hollandshipyardsgroup.com
Hoondert ‘s-Heerenhoek www.kampsstraalbedrijf.nl
Hoondert Services & Decommissioning www.hsd.nl
HR Expat Services www.hrxpats.com
Hudig & Veder Chartering B.V. www.hudigveder.nl
IBS Staalbouw B.V. www.ibs-hallenbouw.nl
ICL-IP Terneuzen B.V. www.iclip-terneuzen.nl
IGL B.V. www.igl.nl
Impuls Zeeland www.impulszeeland.nl
ING Business Banking www.ing.nl/zakelijk
Ingenieurbureau Walhout Civil B.V. www.walhoutcivil.com
Interface Terminal Gent (ITG) www.stukwerkers.com
Interlashing B.V. www.interlashing.com
IPC Services België B.V. www.ipc-services.be
Istimewa Electrotechniek B.V. www.istimewa-elektro.nl
Jonkman Opleidingen B.V. www.jonkmanopleidingen.nl
Justion Advocaten www.justionadvocaten.nl
Juust B.V. www.juust.nl
Kamps Straal- en Industriële Spuitwerken www.kampsstraalbedrijf.nl
Katoen Natie Westerschelde B.V. www.katoennatie.com
Koch adviesgroep Ingenieurs & Architecten www.kochadviesgroep.nl
Koolwijk Shipstores B.V. www.shipstores.nl
KWS Infra/Aquavia www.kws.nl
Labojuice B.V. www.labojuice.nl
Lalemant N.V., Lalemant Trucking N.V. www.lalemant.com
Legrant Freight Management B.V. www.legrant.eu
LGH BVBA www.lgh.eu
Liftal Hijstechniek www.liftal.com
Lineage Logistics Vlissingen www.kloosterboer.nl
Lion Storage Netherlands B.V. www.lion-storage.nl
Loodswezen Regio Scheldemonden www.loodswezen.nl
Luctor Belting Nederland B.V. www.luctorbelting.com
Maaskade Bevrachters Belgium www.maaskade.com
Maaskade Group www.maaskadegroup.com
Mammoet Nederland B.V. www.mammoet.com
Maritiem & Logistiek College de Ruyter www.scalda.nl
Maritiem Muzeeum Zeeland www.muzeeum.nl
Martens Renewables www.martenscleaning.nl
MasChem B.V. www.musimmas.com
Media58 B.V. www.media58.nl
Mervielde N.V. www.mervielde.be
Meyland N.V. www.meyland.be
MMPS www.mmps.nl
meet | connec t | promot e
Montis Mooring- and Boatservice B.V.
www.montismooring.com
Multraship Towage & Salvage www.multraship.com
Municipality of Borsele www.borsele.nl
Municipality of Middelburg www.middelburg.nl
Municipality of Terneuzen www.terneuzen.nl
Municipality of Vlissingen www.vlissingen.nl
Navonus N.V. www.navonus.be
North Sea Port www.northseaport.com
Northfreeze N.V. www.northfreeze-group.com
N.V. Westerscheldetunnel www.westerscheldetunnel.nl
Oceanwide Personnel Services B.V. www.oceanwidecrew.com
Oliehandel Dekker B.V. www.oliehandeldekker.nl
OMC Services B.V. www.linkedin.com/in/chvdo
Onilio | Hotels – Appartementen – Vakantieparken www.onilio.nl
Ørsted Nederland www.orsted.nl
Outokumpu Stainless B.V. www.outokumpu.com
Ovet B.V. www.ovet.nl
Ovet Shipping B.V. www.ovetshipping.com
Pantank www.pantank.be
Pfauth Logistics B.V. www.pfauth.nl
Premier Modular B.V. www.premiermodular.nl
PreZero www.prezero.nl
Prior Group www.priorgroup.nl
Projectontwikkeling Herengracht B.V.
PTC B.A. www.ptcba.nl
Rabobank Oosterschelde www.rabobank.nl/oosterschelde
Rabobank Walcheren-Noord Beveland www.rabobank.nl/wnb
Rabobank Zeeuws-Vlaanderen www.rabobank.nl
Royal HaskoningDHV Nederland B.V. www.royalhaskoningdhv.com
S.T.T. B.V. www.agency-stt.com
Sagro Aannemingsmij. Zeeland B.V. www.sagro.nl
Sarens Nederland www.sarens.com
Saybolt Nederland B.V. www.corelab.com/rd/saybolt
Schelde Exotech www.exotech.nl
Schipper Groep www.schippergroep.nl
SEA-invest www.sea-invest.com
Seatrade Rotterdam B.V. www.seatraderotterdam.nl
SEC Catering www.seccatering.nl
Secil Cement www.secil.pt
SFP Zeeland www.sfp-group.nl
SGS Nederland B.V. www.sgs.com
Shipyard Reimerswaal www.shipyardreimerswaal.com
Simons Bouwgroep B.V. www.simonsbg.nl
Smulders Projects Netherlands B.V. www.smulders.com
Solinoor B.V. www.solinoor.com
Sorteerbedrijf Vlissingen B.V. www.sorteerbedrijfvlissingen.nl
SPIE Nederland B.V. www.spie-nl.com
Stukwerkers Havenbedrijf N.V. www.stukwerkers.com
Supermaritime Nederland B.V. www.supermaritime.com
Swagemakers Intermodaal Transport B.V. www.swagemakers.nl
Sweco Nederland B.V. www.sweco.nl
T.I.M.E. Service Catalyst Handling B.V. www.ts-cat.com
Tanido B.V. Sworn Marine Surveyors www.tanido.com
Tank Terminal Sluiskil www.tankterminal-sluiskil.nl
Tauris B.V. www.tauris.be
Terberg Tractors Belgium www.terbergspecialvehicles.com
Terneuzen Port Service www.terneuzenportservice.nl
Terneuzen Processing Technologies www.tpt.nl
The Safety Network www.thesafetynetwork.nl
Timmerman Industrial Repairs www.ltimmerman.nl
TOS Port & Logistics B.V. www.tos.nl
| connec t | promot e
Transuniverse Group N.V.
www.transuniverse.be
Tri-Modal Containerterminal Terneuzen www.vlaeynatie.eu
TSA Safety Services B.V. www.tsa-bv.nl
UWV EURES Goes www.uwv.nl
Van Ameyde Marine Vlissingen www.ameydemarine.com
van Hoorebeke Timber N.V. www.vanhoorebeke.com
Van Keulen Transport B.V. www.vankeulentransport.nl
Vandeputte Safety Experts www.vdp.com
Verbrugge Internationale Wegtransporten B.V. www.verbruggeinternational.com
Verbrugge Marine B.V. www.verbruggeinternational.com
Verbrugge Terminals B.V. www.verbruggeinternational.com
Verenigde Bootlieden B.V. www.bootlieden.nl
Vlaeynatie B.V. www.vlaeynatie.eu
Vlissingse Bootliedenwacht B.V. www.vlb.vlissingen.nl
VoltH2 Operating B.V. www.volth2.com
Wagenborg Agencies B.V. www.wagenborg.com
Water-Link www.water-link.be/industry
Westerschelde Ferry B.V. www.westerscheldeferry.nl
Wielemaker B.V. www.wielemaker.nl
Wilhelmsen Port Services B.V. www.wilhelmsen.com/port-services/
Witte-Boussen Assurantiën B.V. www.witteboussen.nl
XL Group Vlaanderen www.xlgroupvlaanderen.be
Yellow & Finch Publishers www.ynfpublishers.com
Zeeland Connect www.zeeland-connect.nl
Zeeland Cruising B.V. www.zeelandcruising.nl
Zeeland Maritime Cleaning www.zmcleaning.nl
Zeeland Refnery www.zeelandrefnery.nl
Zeeland Sugar Terminal www.vlaeynatie.eu
Zéfranco Communicatieservice Frans www.zefranco.com
ZTZ Logistics B.V. www.ztzlogistics.com
Covering the port area of North Sea Port, PortNews is the offcial publication of the Promotion Council North Sea Port and port authority North Sea Port.
Circulation and subscriptions
Distributed to a wide international audience, the high quality quarterly magazine promotes the activities of companies active in the ports to key customers, business partners, stakeholders, as well as at major international trade events. PortNews is available in hard copy as well as a digital version. Each issue has approximately 10,000 readers.
Editorial Committee
P.O. Box 132 4530 AC Terneuzen, The Netherlands T +31 (0)115 647 400
John Kennedylaan 32, Harbour 3000A, 9042 Ghent, Belgium T +32 (0)9 251 0550 E contacteer@northseaport.com I www.northseaport.com
Follow us on: meet |
P.O. Box 5130 4380 KC Vlissingen, The Netherlands T +31 (0)118 491 320 E info@pc-nsp.com I www.pc-nsp.com
Follow us on:
OMC SERVICES BV
• Henk de Haas, Chairman, Promotion Council North Sea Port
The content of PortNews is the responsibility of the Editorial Committee. Contact:
• Michael Moreau, Communication Manager, North Sea Port
• Charles van den Oosterkamp, Director, OMC Services BV
Special thanks to everyone who kindly contributed their time and expertise to put together this issue of PortNews. Find out more about contributing to future issues of PortNews by contacting Charles van den Oosterkamp, info@omc-services.com, tel. +31 (0)6 10 979 655.
Free subscription or additional copies?
Would you like a free subscription to PortNews, or would you like to receive additional copies of PortNews free of charge for promoting the port and your organisation to your business relations? Please contact the publisher at info@pc-nsp.com or contacteer@northseaport.com.
Copyright 2024. All rights reserved. The contents of this magazine may not be reproduced in whole or in part without the express written consent of the publisher(s). PortNews is a production of OMC Services BV on behalf of the Promotion Council North Sea Port and North Sea Port. The opinions expressed in PortNews are not necessarily those of the Editorial Committee or the publishers. While every effort has been made to ensure the accuracy of information in PortNews, no liability can be accepted for any errors or omissions.
Management
Charles van den Oosterkamp
Contributing editors
Arno Dirkzwager
Ben Littler
Tamara De Maesschalck
Jean-Louis Vandevoorde
Contributing photographers
Foto-atelier De Rammelaere BV
Limit Fotografe
Mark Neelemans Fotografe
Contact E info@omc-services.com
T +31 (0)6 10 979 655