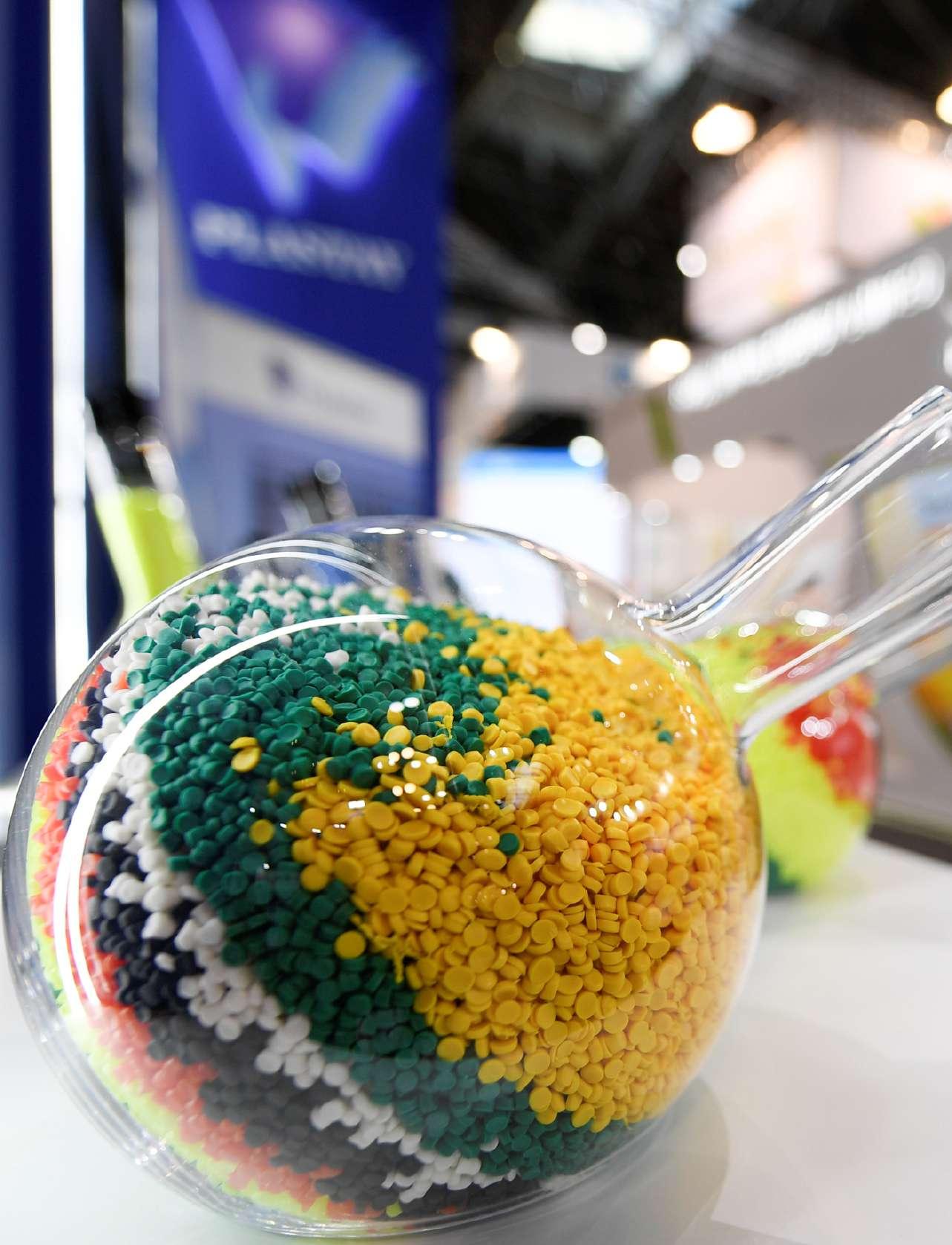
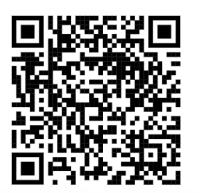

9th to 11th December 2025
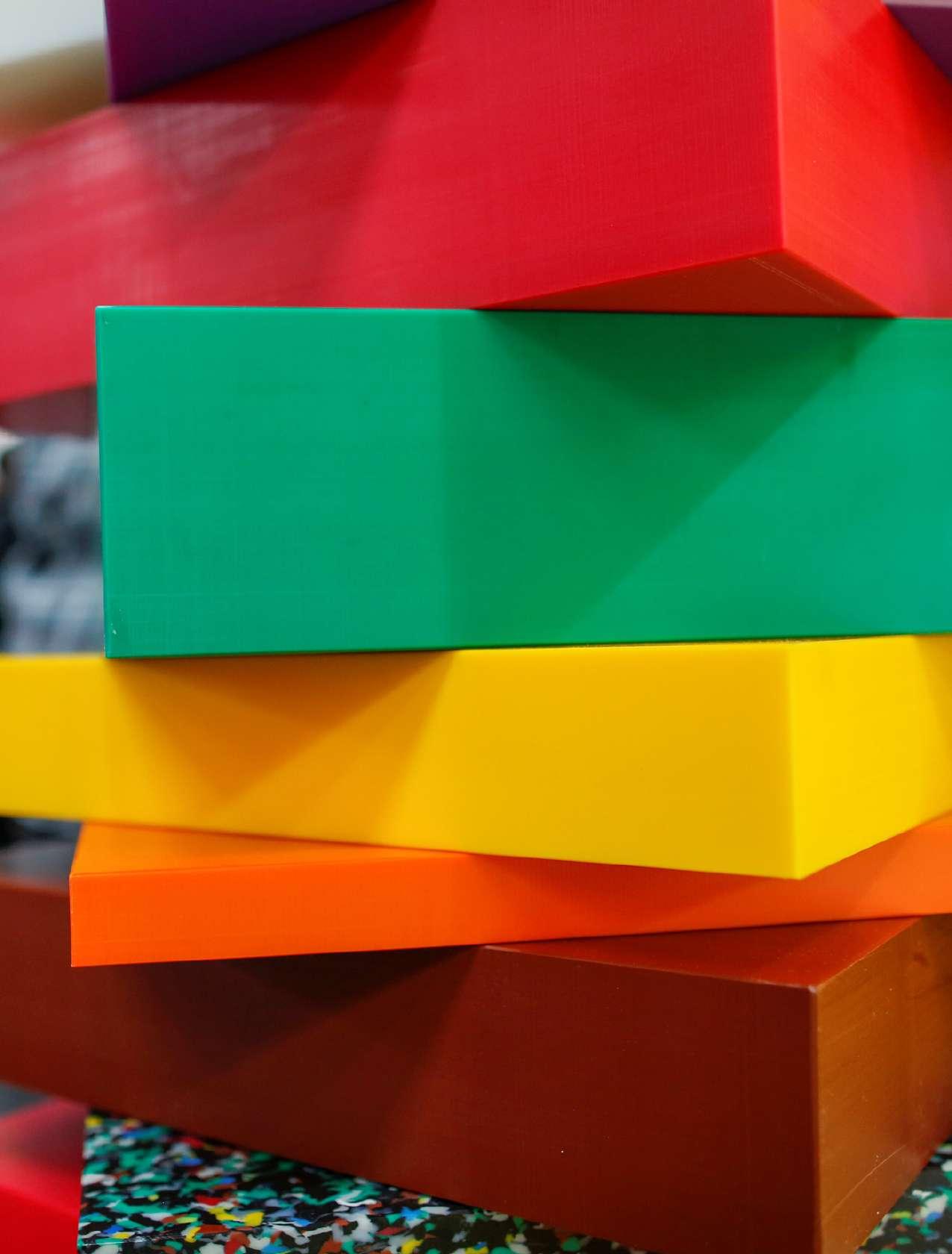
9th to 11th December 2025
Advanced Recycling will Process 20-25 Million Tons of Plastic Waste Annually by 2030, Representing Approximately 5-7% of Global Plastic Production
The report offers in-depth insights into the rapidly expanding chemical recycling sector, driven by rising plastic waste, sustainability mandates, and policy support. Covering technologies like pyrolysis, gasification, solvolysis, and depolymerization, the report forecasts up to 25 million tons of plastic waste processed annually by 2030. It includes market dynamics, LCA analysis, investment trends, and profiles of 193 companies. Regional forecasts, technology comparisons, and end-product analysis position this report as an essential guide for stakeholders in circular economy and advanced plastics recycling.
Advanced recycling, sometimes referred to as chemical or feedstock recycling, is a process that breaks down waste to the molecular level so it can be converted to new raw materials. The advanced recycling market is experiencing major growth as stakeholders seek solutions for previously unrecyclable plastic waste. Unlike mechanical recycling, which primarily reshapes polymers, advanced recycling breaks materials down to molecular building blocks, enabling true circularity for a wider range of plastics and other materials.
The market is driven by increasing regulatory pressure, corporate sustainability commitments, and technological maturation across multiple conversion platforms. Leading technologies include pyrolysis, gasification, solvolysis, and depolymerization, each targeting specific polymer streams or end-product applications. Investment flows into the sector have accelerated dramatically, with over $7.5 billion committed since 2020. This integration of advanced recycling with conventional petrochemical infrastructure creates deployment advantages through existing distribution networks and technical expertise.
Regulatory frameworks increasingly support advanced recycling adoption. The European Union's Circular Economy Action Plan and Plastic Packaging Levy create direct economic incentives for recycled content, while the U.S. EPA and state-level legislation increasingly recognize chemical recycling as legitimate recycling rather than waste disposal. Challenges persist despite these advances. Capital intensity remains high at $1,500-4,000 per ton of annual capacity, creating economic barriers to rapid scaling. Process yield and energy efficiency improvements continue through catalyst development and process integration, gradually improving economics. Feedstock quality and consistency represent operational challenges, with contaminants potentially affecting catalyst performance and product quality.
Market forecasts suggest advanced recycling will process 20-25 million tons of plastic waste annually by 2030, representing approximately 5-7% of global plastic production. While still a modest fraction of total plastics volume, this represents significant growth from current levels (<1%) and creates meaningful circular pathways for materials previously destined for landfills or incineration. The sector's evolution increasingly focuses on specialized applications where advanced recycling provides unique value rather than competing directly with mechanical recycling for clean, homogeneous streams. This complementary approach addresses the full spectrum of plastic waste while optimizing environmental and economic performance across different material qualities and contamination levels.
The Danish company Dansk Emballage, located in Vamdrup, specializes in the collection and reprocessing of Intermediate Bulk Containers (IBC). The containers are sorted, washed, and recycled on-site. A significant role in this process is played by a WEIMA W5.18 single-shaft shredder.
Dansk Emballage brings over 30 years of experience in trading new and reconditioned industrial packaging such as IBCs, drums, jerrycans, and pallets. The company collects these packages, cleans, repairs, and recycles them in an ISO 9001 and ISO 14001 certified process.
When reconditioning is not possible, the bottles from the IBCs are subjected to material recycling. The same concept applies to plastic drums and cans. The containers come from companies in the chemical and food industries throughout Scandinavia.
"Every day, our employees work on a mission: to do something good for the environment. With our
customized and intelligent solutions, we continuously optimize the recycling cycle for the benefit of our planet. Plastic is not a bad material but a good one when it is recycled and not burned or disposed of in nature," says Martin Schack Staffeldt, Managing Director of Dansk Emballage in Vamdrup, Denmark. Heart of the Recycling Line: The WEIMA W5.18
The WEIMA W5.18 single-shaft shredder is ideal for shredding large volumes of plastics. It features a Vrotor with a diameter of 500 mm and a rotor length of 1,800 mm. The Siemens PLC control system with an intuitive touch panel makes the shredder easy to operate. A generously sized inspection hatch ensures convenient access for maintenance work. The owners are also impressed with the material feed:
"The swing ram transports the IBC containers very quickly and thoroughly to the rotor. These are partly 16-kilogram IBCs, and within a short time, shredded plastic pieces measuring 60 mm come out. We are
very satisfied with the result," says Martin Schack Staffeldt. Innovative Additions for Maximum Results
The shredding process at Dansk Emballage is optimally tailored to plastic applications. Before shredding, all grids, pallets, and valves are removed from the cans, drums, or IBCs, leaving only pure plastic.
Thanks to an integrated and automated water injection system in the shredder's cutting chamber, the containers are pre-washed during shredding. This cleans the containers of coarse residues and significantly reduces the risk of fire.
Dansk Emballage has also opted for additional rotor wear protection. This ensures the rotor is wellprotected against foreign objects and abrasive materials. A camera installed inside the shredder allows for continuous monitoring of the process.
The pre-shredded material is then transported to a granulator for further size reduction. This is followed by a friction washer. The combination of granulator and friction washer enables effective shredding and cleaning of plastic waste. The granulator ensures further reduction of material size, while the friction washer removes contaminants to provide clean granules for further processing. These two processes are crucial for the quality of the recyclate and the efficiency of the entire recycling process.
Dansk Emballage uses 35% of the
recycled material to produce new IBCs – a closed-loop system that is highly appreciated by customers. The decision to choose WEIMA was made after a thorough evaluation of various suppliers. "We looked at many different potential suppliers for the shredder and ultimately chose WEIMA. And we are very satisfied with it," says Martin Schack Staffeldt. The comprehensive service and support from the local WEIMA representative in Denmark have significantly facilitated the implementation and operation of the shredder.
We are WEIMA:
More than 40,000 machines sold worldwide. WEIMA has been manufacturing robust shredders and briquetting presses for the disposal and processing of all types of waste for more than four decades. Our machines include single-shaft shredders, four-shaft shredders, cutting mills, briquette presses, packaging and draining presses. The popular blood orange machines are used in the wood, plastics, paper, metal and waste-to-energy industries.
Made in Germany. Built for the world.
Shredders, briquette and draining presses from WEIMA are exclusively made in Germany and come from production plants in Saxony-Anhalt and Baden-Wuerttemberg. Every year, more than 320 employees work on around 1,200 customer solutions from around the globe. We have long-standing sales and service locations in the USA, Italy, India, and China. More than 80 representatives supplement this global presence.
9th Oman Plast 2025
9-11 December 2025
Silver Star is organising the 9th INTERNATIONAL PLASTICS, RUBBER, PETROCHEMICALS, CHEMICALS, FERTILIZERS, PLASTIC RECYCLING, PRINTING AND PACKAGING INDUSTRY EXHIBITION
2025 at the Oman Convention & Exhibition Centre, Muscat from 9th to 11th December 2025.
OMAN PLAST 2025, in its 9th edition will showcase the latest technology and machineries used in manufacturing of international plastics, rubber, petrochemicals, chemicals, fertilizers, plastic recycling, printing and packaging industry exhibition. It will be an ideal platform for Oman and its neighbouring countries to source new technology and products through this knowledge forum. As the petrochemical industry is one of the main components of the Omani economy, the event will give great impetus to further diversify its growth. Noteworthy gains
In fact, the plastics industry per sector has seen sustained growth levels in the region as Middle East and African markets are expected to deliver noteworthy gains right up to 2026. An annual growth rate of around 25 percent has been projected. This region is emerging as a leading global plastic production resin hub with capacities expected to double in the coming years.
Largest source
The Middle East remains the largest source of plastic raw materials; upto
16 per cent of the region's abundant petroleum supply that is not used for energy production is converted into other materials such as plastic products. While sustaining growth in the plastic industry is of prime importance, Oman has made sure they maintain a green outlook.
The world produces and uses 20 times more plastic today than it did 50 years ago. Ordinary plastics can take up to 400 years to break doom. Given plastic is a fundamental part of our day-to-day lives, Oman also made sure that it has earth-friendly product like degradable plastic.
Mr. P.D. Nath, Chairman & Managing Director, Silver Star, explained that the, “9th OMAN PLAST 2025 is perfectly timed for the continuing boom in Oman’s plastics, rubber, packaging and petrochemical industry”, added, “This event will offer a perfect gateway to reach this highly potential market and will provide excellent business opportunities and new collaborations”. The participating countries are China, Egypt, France, India, Italy, Iran, Oman, Taiwan, Turkey, and U.A.E. etc.
Silver Star is one of the leading organisers of large-scale exhibitions and Event Management Company in Oman and has organised quite a lot of exhibitions across the country and outside.
The exhibition timings of 9th OMAN PLAST 2025 is from 10.00 am to 6.00 pm on all three days. The
exhibition is exclusively for traders and businessmen. Entry for children below 15 years are not allowed.
Please be informed that many countries are participating in our 9th OMAN PLAST 2025 as on today and many more going to join. We are also pleased to inform you that the countries which had visited our 8th OMAN PLAST 2024 is Austria, Bahrain, Bangladesh, Belgium, Egypt, Germany, Greece, India, Iran, Iraq, Italy, Latvia, Lebanon, Lithuania, Netherlands, Pakistan, Qatar, Saudi Arabia, Singapore, Srilanka, Sultanate of Oman, Taiwan, Tanzania, Turkey, UAE, UK, USA and Zambia. We expect more visitors from much more countries than last year as per the present trend of visitor registrations going on for our 9th OMAN PLAST 2025.
Last but not the least, we take this oppor tunity in giving below the early bird discount offer for the last few stalls left on this special category.
1. Four days single room free of cost in a three/four-star hotel including breakfast.
2. Free pick-up and drop to and fro to Oman Convention and Exhibition Centre on daily basis at 9.00 a.m. and 6.00 p.m. respectively.
3. Free visa for the 9th OMAN PLAST 2025 by Silver Star.
4. Free pick-up and drop from the airport to the hotel provided the
exhibitor inform the complete travel arrangement minimum three days in advance.
5. One complimentary full page colour ad in our exhibitor catalogue for the participating company as part of our anniversary celebrations.
Please note that the above facilities are offered for a minimum booking of 9 sq.m. for one person only and the same is applicable for multiples of booking accordingly. The cost of 9 sq.m. stall with two sides open is U.S $ 3,150/- i.e. @ U.S. $ 350/-per sq.m. which includes one table, two chairs, one double socket, one LED light, carpet and fascia including electricity.
Furthermore, if you would like to avail the above five freebies which we have explained you may kindly fill, sign, stamp and send back to us the registration contract which can be downloaded from our website so as to send you the invoice immediately and arrange the payment by you before 31st March 2025 which is the last date for early bird discount offer.
You may kindly refer our website www.omanplast.net in case you may require any further information in this regard.
You are most welcome to 9th OMAN PLAST 2025 either as a sponsor, exhibitor or visitor as you feel free.
How much energy could you save with a Yizumi D1 machine? What other efficiencies could you get? Call our engineers today for a chat on 01933 27 27 47 or visit us at:
With the rise in the consumption of raw materials, plastic processors are facing higher political and social demands to use a greater proportion of recycled materials. Companies such as MultiPet GmbH, a recycling company that processes used PET materials into flakes, make this transition possible. Along with their sister company Multiport, which specializes in making HDPE compounds from packaging waste, they are considered important suppliers of secondary raw materials for the plastics processing industry.
MultiPet GmbH is part of Veolia, a
globally active environmental service provider. MultiPet processes discarded PET bottles and trays into high-quality recycled PET flakes that are pure enough to be used by plastic processors to create new products and containers.
How does the PET recycling process work?
MultiPet receives pressed bales of pre-sorted PET waste. After the bales are broken up, plastics are first checked for impurities, then ground into flakes and intensively washed.
The FLAKE PURIFIER+ multi-sensor sorting systems from Sesotec come into play directly after the ground material has undergone a two-stage
density separation process involving two rounds of hot washing. At this stage, the sorting systems separate discolored materials, foreign plastics, and metals from the flakes.
Sesotec FLAKE PURIFIER+ units are designed especially for use in plastic flake processing and are characterized above all by the ease of operation and heightened throughput capacities.
At MultiPet, the FLAKE PURIFIER+ systems are equipped with multiple sensors for color and material recognition. This enables MultiPet to produce PET flakes in batches of different colors and qualities for use as raw materials in the plastics
processing industry. By using recyclates produced by MultiPet, plastic processors are reducing their CO2 footprint, contributing to climate protection and conserving resources.
“Sesotec’s processing technology enables us to keep the loss of good material to a minimum”, says Herbert Snell, Managing Director of MultiPet GmbH. “This makes our sorting processes even more efficient.“ Sesotec‘s scope of delivery was complemented by a turn-key material handling setup which included steelwork platforms and material conveyance systems, simplifying integration into the overall system.
Interview with Anders Nybäck, Sales Director Technical Moulding, ENGEL AUSTRIA
8000 tons in weight, a good 30 meters long – how do you manage to ship such a gigantic injection moulding machine across the big pond? In an industry where logistics and size present special challenges, ENGEL has managed to master them with expertise and a cooperative approach.
In an interview with K-MAG, Anders Nybäck, an expert from ENGEL, sheds light on the successful delivery of two massive 8,000-ton injection molding machines from Austria to the United States. What is the significance of these machines, and how is the future outlook for injection molding machines with such high clamping forces?
Mr. Nybäck, ENGEL recently delivered two 8,000-ton injection moulding machines to the USA. How did that happen exactly? And how long did it take from order to handover?
Anders Nybäck: ENGEL received the order in November 2020 and the first machine could already be handed over in February 2022. Now, one year later, a second identical machine has been delivered.
What must be considered when supplying machines of this size?
Nybäck: Logistics is a special challenge. Before delivery, each
machine is completely assembled and tested at the ENGEL plant. Such large machines then have to be disassembled again for transport. The weight of the individual components plays a major role in logistics planning. The mould fixing platens for these two 8000-ton machines, for example, were transported on barges on the Danube.
What challenges did you face and how did you overcome them?
Nybäck: From the initial idea to completion, the project was a close team effort across company boundaries. Our long collaboration with Infiltrator, mutual trust, and not least the fact that everyone knows what is important to the other were key success factors here. This is the only way to deal with the risks that naturally come with the size of the machines, the degree of innovation and the immense investment volume. We are thrilled to see what we have achieved here together. When we develop solutions together with our customers, we do everything we can to make them even more successful with innovative and forward-looking concepts.
What makes injection molding machines with such high clamping forces necessary?
Nybäck: Injection molding enables particularly resource-efficient processing of plastics and also a high degree of process integration and automation. As a result, more
and more very large components are being produced by injection molding for which other processes were previously used or which were previously assembled from several individual components - for example, large containers and underground tanks, but also more and more large-area vehicle components such as structural components and lightweight body components or glazing. We see a lot of potential in the automotive sector in particular. Hyundai-Kia in Korea, for example, recently took delivery of a particularly large injection molding machine from us.
Why did Infiltrator approach ENGEL specifically with its request? What makes your machines special?
Nybäck: ENGEL has a great deal of experience and expertise in building large-scale machines and also a global production network, which simplifies logistics, shortens time-to-market and makes the overall project more costeffective. ENGEL already has a long business relationship with Infiltrator. This was the deciding factor in this particular case. All previous projects for Infiltrator were completed by ENGEL on time, and costs were not exceeded either. Therefore, Infiltrator also placed the necessary trust in us for this particularly challenging project.
To what extent does ENGEL contribute to sustainability with these injection molding machines (e.g. in this specific case)?
Nybäck: The large machines make it possible to produce components that previously consisted of several individual parts and had to be assembled in a single process step and in one piece. This saves process steps and thus a lot of energy and raw material. Infiltrator also says that with the new machines they can manufacture the products even more cost-effectively and efficiently. Sustainability played a major role in the overall project. Infiltrator produces innovative water management products that have a high percentage of recycling. The company recycles more plastic than any other in North America.
How will the demand for injection molding machines with such high clamping forces develop in the future and how is ENGEL preparing for these developments?
Nybäck: We see an increasing need and an increasing demand. However, it is important to realize that injection moulding machines with clamping forces of over 5500 tons are a niche market and will remain that way. However, this niche is very interesting for ENGEL because we are one of the injection moulding machine manufacturers with the greatest experience and competence in the field of large machines. Not to forget: With our worldwide production network, we have the capacity to efficiently build and deliver such machines.
How can the economy be restructured to lower carbon emissions? What steps towards decarbonisation have nations already taken and how successful have they been? These are the questions to be addressed in a research project whose participants include scientists from the Institute for Political Science at Heidelberg University. Prof. Dr Jale Tosun will head up the work in Heidelberg which will start at the beginning of 2021. The work is part of a project based at the University of East Anglia (Great Britain), which the European Research Council
(ERC) is funding with an ERC Advanced Grant for leading researchers. A total of nearly 2.4 million euros has been granted for the project. Approximately 530,000 euros is earmarked for the research in Heidelberg.
In the “Deep Decarbonisation: The Democratic Challenge of Navigating Governance Traps” (DeepDCarb) project, coordinated by Prof. Dr Andrew Jordan of the University of East Anglia, the researchers first want to gain a fundamental understanding of climate policy action throughout the world. Datasets from the past 30
years that depict the activities of 41 countries with different levels of economic development will be used as a basis.
The researchers will then look more closely at the processes that have already brought about the passage of climate policy laws and enactments in the past. “Further on, we will link political science research with approaches from the behavioural sciences. The central question is how should decisionmaking situations be set up to achieve long-term goals, like reducing global warming to 1.5
degrees,” explains Prof. Tosun. The researchers in Heidelberg will be creating empirical models to measure climate policy action and thus explain how climate policy is developed. “In past projects, we already developed approaches to measure legislative activities in this area for a large number of nations and over long periods of observation,” adds Prof. Tosun. “With our research activities in the DeepDCarb project, we plan to continue this work and facilitate insights that can be implemented in practice and thus benefit policy and public administration.”
The coronavirus has only helped to underscore the importance of plastic packaging when it comes to keeping food contamination-free and to preserving its freshness and usability for longer. This is particularly vital now, given how millions of people worldwide are sheltering in place, and doing their best to make their provisions stretch. But the COVID-19 pandemic has also accelerated another trend that has a major impact on product packaging -- e-commerce. Online shopping already was showing strong growth, but the current stayat-home phenomenon has only increased demand. An even broader awakening to the convenience of delivery to your doorstep may forever reshape parts of the retail sector.
In North America, it reported, the number of online orders for webonly online retailers soared 52% year-over-year in the United States and Canada for the period of March 22 through April 4, according to an online tracker from marketing
platform Emarsys and analytics platform GoodData. Revenue for web-only retailers in the U.S. and Canada was up 30% year-over-year for the period.
In the Asia-Pacific (APAC) region during the same two-week period, year-over-year transactions for webonly retailers grew by 23%, according to Emarsys/GoodData. During the same period, year-overyear revenue was up 19% in the region.
Virus or not, retail e-commerce is rising sharply. New York-based consumer research firm Statista Inc. said that U.S. online retail sales of physical goods amounted to $365.2 billion in 2019, and projects that will rise to nearly $600 billion in 2024.
Consider also that China’s annual, 24-hour online shopping spree known as Single’s Day -- last held on Nov. 11, 2019 -- generated record sales estimated at some $38 billion. The darker side of such a sales boom relates to the impact on the environment of so much product
packaging. China’s State Post Bureau reported that e-commerce giants delivered 1.88 billion packages from Nov. 11 to Nov. 16 last year, an annual increase of almost 26%. Greenpeace estimated that the waste generated exceeded 250,000 tonnes. The volume of packaging material used by China's ecommerce and express delivery sectors hit 9.4 million tonnes last year, and is on course to more than quadruple to 41.3 million tonnes by 2025 if they keep up the rate of increase, according to Greenpeace and other non-government bodies.
Sustainability still important
So, booming e-commerce offers sales growth for key sectors as well as greater convenience (and safety) now for many, but it clearly comes at a cost. While public health trumps sustainability concerns at the moment, it’s clear that the packaging sector cannot afford to take its collective eye off the ball when it comes to being eco-conscious. As Dow Inc. CEO Jim Fitterling mentioned in ANTEC 2020 virtual
conference on March 31: The COVID-19 crisis is going to end, "but the air we breathe, our water and the land we live on is here forever. And we can't afford to lose the momentum that we've started to gain already to safeguard the environment and help us move to a more circular economy." Leaders in the European Union also are concerned that the current virusdriven economic slump will cause the focus on sustainability to wane, writing in a joint statement in midApril, “We should withstand the temptations of short-term solutions in response to the present crisis that risk locking the EU in a fossil fuel economy for decades to come.” These conditions offer both extreme challenges and enormous opportunities for brand owners, consumer packaged goods (CPG) companies, and for those designing and manufacturing the packaging. Multiple approaches being pursued Such firms are exploring and advancing multiple strategies to address these issues, including increased plastics recycling, more reusable packaging, greater use of
biomaterials, reduced material use, and design for circularity. Package designers also need to take into account the different priorities for on-shelf vs. e-commerce products. Eye-catching package design is less vital for products sold online than in the store, but ensuring the shipped product arrives at its destination undamaged is vital. Advances in these areas take diverse forms, but consider the efforts being by CPGs to redesign the e-commercefriendly and highly popular –– but largely unrecyclable –– flexible pouches to make them more ecofriendly. This mostly involves finding a way to convert those pouches’ multilayer, multimaterial constructions, which till now have been needed to protect the contents from such unwelcome factors such as moisture, oxygen, and ultraviolet light, into recyclable, mono-material structures.
For example: mono-material pouches
Mondi helped develop this fully recyclable, all-PE pouch
Several advances are happening in
this area. Austria’s Mondi Group, for just one example, worked with several partners for four years to develop an all-polyethyelene, stand-up pouch for Germany’s Werner & Mertz GmbH to use with its Frosch-brand detergent. This patented pouch features detachable decorative panels on both sides, to help enable easier recycling.
Another new technology, called AeroFlexx and developed by Procter & Gamble Co., enables liquid packaging in a flexible yet rigid package. Made with coextruded flexible film, the product leverages compressed air to inflate specific portions of the pouch, specifically along the edges, to bring a degree of rigidity not otherwise possible in a flexible package.
An AeroFlexx package uses half the plastic needed to blow mold a traditional bottle and can be delivered as roll stock to a filling facility, meaning it is easier to ship throughout the supply chain. In addition to significantly reducing
plastic at the source, the Chicago-based company’s vision is to be 100% recycle ready by 2025. While enabling seamless, edge-to-edge artwork, AeroFlexx also features a no-leak, self-sealing valve that offers easy, onehanded operation by the consumer.
Loop platform touts reusability
New Jersey recycler TerraCycle Inc., meanwhile, is taking a completely different approach with its Loop circular shopping platform. Loop has gained support from many of the world’s best-known brands, ranging from Unilever, PepsiCo, and Nestlé to Danone, Procter & Gamble, and UPS.
The Loop circular shopping platform aims to get brand owners to develop durable, reusable packages that get picked up, sanitized and reused over and over again. The Loop system uses UPS to ship a variety of food, household cleaning, and personal-care products in a reusable and collapsible, padded container called the Loop tote.
The products are dispensed from reusable containers, which are returned in the same reusable tote when empty. Some have dubbed it “the milkman model,” in a nod to the old days when milk was delivered to your doorstep in glass bottles, which were later collected, cleaned, and reused. “Loop,” maintains TerraCycle founder and CEO Tom Szaky, “is an engine for CPGs to shift from disposable products that consumers own to durable ones they borrow.” The brand owners, meanwhile, actually own the package, which is meant to be reused at least 100 times.
The impact on packaging is obvious – instead of trying to make the cheapest possible disposable package or container, the brands are incented instead to design handsome, reusable containers out of durable materials. Numerous companies are also investing in initiatives and technologies to advance both mechanical and chemical recycling, and to develop biocompatible and compostable materials.
The Streamrunner ® is an additively manufactured hot runner with maximum design freedom. Through the free three-dimensional design of the runners, completely new possibilities are created in multi-component injection moulding.
• New possibilities for product designers
• Distribution of different plastic components or colours over a very small area
• Channels can be intertwined with each other
www.hasco.com
Interplas,Birmingham 26-28September2023 Booth 4/A12
Eight to ten times on average a wooden pallet is used in the handling area of logistics before it shows a defect and has to be sorted out. This is neither particularly economical nor good for the environment. Pallets made of plastic offer a more sustainable solution.
In an interview with K-MAG, Wolfgang P. Albeck talks about the switch from wood to plastic and the concrete advantages of plastic pallets for companies and the environment.
Mr Albeck, how did the decision to use plastic pallets instead of wood come about?
Wolfgang P. Albeck: In 2019, we started using plastic pallets as loading aids in our long-distance transports, i.e. in the transport between our 36 sorting centres in Germany. Pallets are a long underestimated production factor in logistics. Many companies assume that the use of wooden pallets and the exchange option are without alternative, cheap and sustainable, but on closer inspection all that is not the case.
In what way?
Albeck: We have analysed the use of our wooden pallets in detail and found three structural points at the
core. Firstly, the low durability. In the handling area of logistics, wooden pallets have a defect after only a few turns (8 to 10!), are no longer safe and have to be sorted out and booked out as broken pallets. Moreover, in pallet exchange you do not always receive flawless, but already damaged loading aids. Secondly, wooden pallets are heavier than the H1 pallets we use, absorb more and more moisture over time and thus become even heavier. Thirdly, the wooden pallets become darker due to the absorption of moisture and dirt. Then they are no longer considered hygienic and may no longer be used according to the EU rules for the transport of pharmaceuticals (GDP), which trans-o-flex adheres to.
How could the plastic pallets solve these problems?
Albeck: The 30,000 plastic pallets we have been using since 2019 have reduced the annual number of broken pallets by 240,000. On the other hand, we hardly have any breakage with H1 pallets. They are predicted to have a service life of more than seven years.
At 18 kilos, H1 pallets are a quarter lighter than wooden pallets. These weigh 24 kilos when new and also absorb more and more moisture in the course of their life, making them even heavier. As a result, a full
articulated truck with freight on wooden pallets has to carry over 200 kilos more load on each journey. Finally, the plastic pallets are GDP-compliant throughout their entire service life.
How do you as a company benefit from the changeover?
Albeck: We have been able to increase productivity because we have less work with the plastic pallets. In addition, they are cheaper on balance. Although they have higher acquisition costs, they save money in the end in a full cost calculation. And the prices for wooden pallets have at times tripled in the last two years.
Recently, you have also started making the pallets available to your customers. How does that work exactly? And what are the advantages for the customers?
Albeck: After the advantages in internal transport have clearly been proven, we wanted to make these advantages directly available to our customers as well. We have therefore now started to provide our customers with plastic pallets for so-called mixed pallets. These are consignments on which the customer stacks parcels for different recipients.
We collect these mixed pallets from the customer and bring them to one of our sorting centres. There, the parcels are taken off the pallet, distributed to the different relations and the pallet can go back to the customer. In order to ensure that there are always enough pallets on hand at the customer's premises, even in the event of fluctuations in quantity, we can assume as a rule of thumb that the customer needs about three times the number of pallets that he sends as mixed pallets every day. The benefit for the customer is also less breakage, easier handling for the employees, less administrative effort.
To what extent can plastic pallets make logistics more sustainable?
Albeck: By being more economical and environmentally friendly. The durability, the lower weight and the GDP conformity clearly speak for the plastic pallet. According to a Fraunhofer study, an H1 pallet causes 50 per cent less CO2 emissions over its entire life cycle than an equivalent number of wooden pallets in the same time. What's more, the pallets we use can be completely recycled if they ever break down. The plastic is regranulated and can be used to make new pallets again.
The all new eQ-SERIES raises the benchmark in energy savings in its category. Its advanced regenerative servo drive reduces energy consumption. The eQ-Series also allows to handle a wider range of applications. The eQ-Series maximizes acceleration and provides ultimate precision and repeatability throughout the cycle, thanks to its best-in-class servo drives. The eQ-Series delivers better shot weight and cycle time consistency throughout its cycle. It’s a new industry standard for an All-Electric Injection Molding Machine.
InterviewwithMauritiusSchmitz, ScientificDirector,Institutefor Plastics Processing (IKV) in Industry and Craft at RWTH Aachen University
Plastic packaging made from recycled material? Yes, but please as high quality as possible – and recyclable! This poses great challenges for manufacturers, because the use of recycled materials still often leads to downcycling. One key to more sustainable plastic packaging lies in digitalisation. This is also where the KIOptiPack project comes in.
In an interview, Mauritius Schmitz talks about the requirements for plastic packaging, the role that design plays in the sustainability of packaging and the extent to which artificial intelligence can support this.
To make plastic packaging more sustainable, the entire value chain must be considered. The KIOptiPack innovation lab deals with the beginning of the value chain - design and production. What role does design already play in sustainability?
Mauritius Schmitz: Product design plays a central role in the sustainability of products. It defines the choice and consumption of materials and thus the types and quantities of plastic introduced into the cycle. It also influences functionality and suitability for (packaging) use, manufacturability and production efficiency. Furthermore, product design can facilitate or complicate the sorting, separation and reprocessing processes – which in turn determine the quality of the resulting recyclates.
Schmitz: Even with sustainable
packaging design, the same, or at least comparable, expectations and criteria must be fulfilled for the product as for products made of virgin material.
This is about product functionalities, such as barrier properties, purity and mechanical stability, and about subjective requirements from the consumer's point of view, such as appearance, smell and safety. But also the processability of the chosen material in the production process plays a decisive role for a functioning product design, by this I mean, for example, the thermal or flow properties of the plastic.
AI can be used to take these complex and diverse influences into account and make them optimisable. By using AI, these influences can be made quantifiable and packaging designers can get a better idea of how their designs affect the different requirements and how they can optimise them to create more sustainable packaging.
Graphic: Illustration of the support provided by AI throughout the entire plastic packaging cycle;
Copyright: Institute for Plastics Processing (IKV) in Industry and Craft at RWTH Aachen University
Copyright: Institute for Plastics Processing (IKV) in Industry and Craft at RWTH Aachen University
How can AI make production more sustainable?
Schmitz: To improve the quality of plastic packaging, AI is used in different production phases. AI is already used at the material receiving stage to detect material fluctuations and adjust the processing accordingly. During the processing stages, neural networks are used to
generate and optimise process models. In this way, correlations between material characteristics, process settings and quality can be recognised and used for correct process adjustment. In the KIOptiPack project, the processing methods compounding, flat film and blown film extrusion, injection moulding and thermoforming are specifically considered.
Graphic: Goals of KIOptiPack; Copyright: Institute for Plastics Processing (IKV) in Industry and Craft at RWTH Aachen University
Copyright: Institute for Plastics Processing (IKV) in Industry and Craft at RWTH Aachen University
Why is cooperation with industry – i.e. companies like Brückner, Reifenhäuser or Pöppelmann – important?
Schmitz: Cooperation with industry is of great importance and depends in its way on the respective industry. However, an important aspect that has not been sufficiently considered so far is the consideration of the entire value chain. In order to achieve optimal sustainability, changes have to be made at various points in the value chain, which may not be initiated and implemented out of their own motivation. For example, the responsibility for more sustainable plastic packaging could be shifted to the collection and reprocessing process alone, but this would certainly not be the most effective and sustainable approach. Instead, it makes more sense to develop incentives and business models that enable global change and load-sharing along the entire value chain.
To achieve this goal, it is essential to understand the hurdles and
potentials for each participant. Through the AI Application Hub, which networks project partners from established machine manufacturers to technology start-ups, as well as from research institutes to food manufacturers and distributors, the possibility of a direct exchange along the entire value chain is created. Only in this way can we achieve a common understanding of the potentials of more sustainable packaging production.
What will the plastic packaging of the future look like?
Schmitz: It is difficult to predict what packaging will look like, because we will also be able to develop and produce sustainable plastic packaging in great variety in the future.
These will be individually tailored to the specific application, so that they fulfil minimal material consumption and at the same time reliable suitability for the application. At the same time, however, this packaging will have to be returned to the cycle with the minimum possible losses.
What can already be predicted with great certainty, however, is that the packaging of the future will contain a maximum proportion of recyclate. It will preferably contain only one type of polymer and be easier to handle when sorting and separating.
In order to improve and simplify the sorting processes, digital – and at best global – product or material passports, which are currently being developed through various initiatives, will play a decisive role.
And in this area, we will not make progress without digitalisation and artificial intelligence methods.
Even at a low dosage of 5 %, UHMW-PE Lubmer reduces the friction coefficient of engineering plastics much more efficiently than PTFE. © Mitsui Chemical
Lubmer UHMW-PE grades from Mitsui Chemicals offer highperformance solutions where applications for engineering plastics place increased demands on sliding, abrasion and wear behaviour. In many cases, these materials, which are suitable for both injection moulding and extrusion, can replace the previous standard solution PTFE, which will no longer be produced in Europe in the future, if its high heat resistance is not required. In addition to their excellent tribological properties, they are characterised by good chemical resistance, low density, very low water absorption and high flexibility and impact strength at low temperatures. Another advantage is the low noise development during sliding movements. Dreyplas, Meerbusch, is the distributor for Lubmer materials in the DACH region.
The Lubmer granulate range includes the highly abrasion-resistant types L3000, L4000 and L5000, which
differ in terms of their molecular weight. In addition, the special grade L5220, which contains a low oil content, offers self-lubricating properties. Lubmer TM-80B is a weather-resistant grade that was specially developed for glass running channels (GRC) in motor vehicles. These granules are the only UHMW-PE products in the world that are suitable for traditional thermoplastic processing methods. They allow the use of hot runner technology and tunnel sprue systems for injection moulding technical parts, and they are also suitable for the extrusion of sheets, profiles and hoses. In both cases, their opaque, light inherent colour facilitates colouring with masterbatches.
Unlike the granules suitable for direct processing, Lubmer LY1040 is a masterbatch based on the standard grades that is compatible with most engineering plastics and can replace PTFE as an additive. As a PFAS-free engineering plastic modifier, it
exhibits better sliding properties than PTFE or molybdenum disulphide even at low addition levels of 3 % to 5 %. It can also significantly improve the wear resistance of PA6 and many other materials without affecting the substrate properties. Typical applications include bearings and gear parts for electrical equipment and automotive interior parts as well as mechanical components for lifts and escalators.
Mitsui Chemical has developed the PA Lubmer alloys LS4140 and LS4120 for applications that require increased mechanical strength. The PA masterbatch LY4100, which can be added during extrusion or injection moulding without compounding, rounds off the portfolio.
At their end of life, all Lubmer product types can be returned to the PE recycling loop thanks to their thermoplastic processability. Another plus in terms of sustainability is the fact that injection moulding produces little to no waste, unlike the machining of conventional UHMW-PE products. And due to its density, which is half that of PTFE, LUBMER has proven to be advantageous for use in lightweight components with increased durability.
Together with customers, Dreyplas and Mitsui Chemicals Europe develop solutions for the substitution of PTFE as well as special grades with application-specific properties that go beyond those of the standard grades available.
Details of Mitsui Chemical's UHMWPE and PFAS regulations can be found at:
https://jp.mitsuichemicals.com/en/ special/uhmw-pe/index.html and https://jp.mitsuichemicals.com/en/ special/uhmw-pe/pfas_regulations/ .
Mitsui Chemicals Europe GmbH is the European subsidiary of the Mitsui Chemicals Group, which is a Japanese, global operating chemical manufacturer and supplier of value added specialty chemicals& plastics. Since mor than 100 years, Mitsui provide products and services to enrich people's activities in a wide range of fields such as cars, electronics/information, health/ medical care, packaging, agriculture, construction/materials, environment/ energy.
DREYPLAS GmbH, founded in 2010, is a distributor with its registered office in Meerbusch, Germany. Its portfolio covers high-performance additives and polymers as well as adhesive raw materials, mainly from major Asian manufacturers, and focuses on technically high-quality alternatives to established products. Its customers are polymer manufacturers, compounders, coating producers and plastics processors in Europe.
Further information:
MITSUI CHEMICALS EUROPE GmbH, Oststrasse 34, D-40211 Düsseldorf
Claus Hartmann, Technical Sales Manager EMEA
Tel. +49-151 2219 8806, claus.hartmann@mcie.de
DREYPLAS GmbH , Meerbuscher Str. 64-78 Haus 6A, D-40670 Meerbusch
Norbert Hodrius, Technical Marketing Director
Tel. +49-2159-815 31-11, hodrius@dreyplas.com
LyondellBasell integrates KARO® 5.0 from Brückner Maschinenbau to boost R&D Capabilities
LyondellBasell, a prominent player in the chemical industry, has recently integrated the stateof-the-art KARO® 5.0 laboratory stretching machine from Brückner Maschinenbau into its research and development facilities at the LYB Technical Center in Akron, Ohio. This strategic enhancement is set to significantly advance the company's ability to develop and test masterbatch solutions tailored for various oriented film applications.
The KARO® 5.0 machine marks a pivotal advancement in LyondellBasell's research capabilities, allowing for more precise and efficient development and testing of masterbatch solutions. "This advanced technology will allow us to accelerate the development of new and improved masterbatch solutions, ultimately helping our customers bring their products to market faster and with greater confidence," stated Tiago Piccoli, LYB Director of APS PAD for Consumer & Industrial Markets in the Americas.
Benefits of KARO® 5.0
The KARO® 5.0 stretching machine is equipped with multiple cuttingedge features that enhance the testing and development process:
required to bring new products to market. It enhances LyondellBasell's speed-to-market process, offering customers the ability to rapidly identify and select the optimal masterbatch for their specific needs.
"The addition of the KARO® 5.0 reinforces our technical leadership and commitment to innovation in the masterbatch industry," commented Chuck Hampton, LYB Director of Masterbatch and Colors U.S. & Canada. The new technology not only complements LYB's testing
assets in Europe but also extends its advanced R&D capabilities to the Americas, benefiting global customers with innovative masterbatch solutions.
The KARO® 5.0 supports LYB's Advanced Polymer Solutions (APS) and Olefins and Polyolefins (O&P) business segments by enhancing product development for applications such as protective films and food packaging. Testing with the new equipment is already underway, showcasing LyondellBasell's dedication to creating advanced solutions that cater to a diverse range of industry needs.
In the era of rapid technological advancement, where connectivity is king, the demand for highspeed internet has never been greater. With this surge in demand comes the need for robust and efficient infrastructure to support it. Enter microduct pipes for optical fiber, a groundbreaking solution that is revolutionizing the telecommunications industry.
Microduct pipes are small, flexible conduits designed to house optical fibers, protecting them from environmental factors while facilitating easy installation and maintenance. Their compact size and flexibility make them ideal for various applications, from urban environments to rural areas, and even within buildings.
One of the key players in this burgeoning market is Tecnomatic, a company at the forefront of innovation in extrusion technology. Tecnomatic's groundbreaking lines,
specifically engineered for microduct pipe production, have set new standards in terms of speed, efficiency, and quality.
At the heart of Tecnomatic's innovation lies its die-head, meticulously designed to achieve unprecedented production speeds. Capable of reaching up to 400 meters per minute for diameters of 7/3.5 and up to 200 meters per minute for diameters of 14/10, this die-head stands as a milestone in microduct pipe manufacturing.
The secret behind Tecnomatic's remarkable speed and precision lies in its innovative geometries, precise line adjustments, and profound understanding of the production process. By optimizing these factors, Tecnomatic has been able to push the boundaries of what was once thought possible, achieving production speeds that were previously unimaginable. One of the most remarkable achievements of
Tecnomatic's die-head is its ability to maintain impeccable sizing results even at such high speeds. With minimal tolerance and ovality, the microduct pipes produced are of the highest quality, meeting the stringent standards of the telecommunications industry.
Moreover, Tecnomatic's die-head is engineered for efficiency and flexibility, allowing for fast skin and colour changes with the adoption of special valves and multiple extruders. This feature not only enhances productivity but also enables manufacturers to meet the diverse needs of their customers with ease.
The implications of Tecnomatic's innovative die-head extend far beyond the realm of microduct pipe production. By enabling faster, more efficient manufacturing processes, it paves the way for accelerated deployment of fiber optic networks worldwide. This, in turn, translates to improved connectivity, economic growth, and quality of life for millions of people around the globe.
As the demand for high-speed internet continues to rise, so too does the importance of robust and efficient infrastructure. With Tecnomatic's groundbreaking die-head leading the way, the future of fiber optic connectivity has never looked brighter.
The new standardised E 2600 chill vents save you time and money during design, production and procuring spare parts.
Sophisticated geometry for optimal venting and fast cooling
Three sizes available with 3D data
Cost-effective delivery from stock thanks to standardisation
AVAILABLE IMMEDIATELY
Algorithms are supporting the
Artificial intelligence is revolutionising modern industry. Thanks to it, complex processes can be automated, efficiency increased and further innovations made possible. In the plastics industry, AI not only plays a decisive role in the optimisation of production processes and the development of new materials. It also enables more precise waste sorting and therefore better recycling – a win for the environment!
brief history of AI
Ideas about artificial intelligence date back to the early 20th century, when scientists began to consider the possibility of developing machines that could exhibit human-like intelligence. The modern era of AI began in the 1950s with the development of the first models, including Alan Turing's Turing test and Frank Rosenblatt's neural network. In the 1960s and 1970s, some successes were achieved in AI, including the development of expert systems. However, disappointments also followed when many early approaches failed to deliver the expected results. In the 1980s, AI experienced a boom with the development of algorithms such as the backpropagation algorithm for neural networks and the support vector machine algorithm. Knowledge-based systems and expert systems became popular in the 1990s. These systems used rules and databases to make human-like decisions in specific domains. The algorithms make it possible to recognise patterns in large data sets and to model complex relationships. From the 2000s onwards, AI experienced a further boom due to advances in machine learning and data analysis. Today, advanced AI technologies such as machine
learning, image recognition and natural language processing are used in various areas of daily life. Companies are using AI to increase efficiency, reduce costs, drive innovation and develop sustainable solutions.
Artificial intelligence has a wide range of applications in the plastics industry: Process optimisation: AI can be used to optimise production processes and reduce energy consumption and waste. By analysing operating data and sensor data, algorithms can recognise patterns and make recommendations to improve efficiency. Material development: AI can help in the development of new materials and compositions by applying simulation-based design methods and analysing large amounts of data to identify optimal material properties.
Quality control: AI can be used in quality assurance to detect defects or irregularities in plastic products by analysing images or sensor data. This can help to identify faulty products at an early stage and improve production quality. Production planning and management: AI can be used in production planning and management to improve demand forecasting, optimise supply chains and manage stock levels. This helps to avoid bottlenecks and increase the efficiency of the entire production process. Waste management: AI can help with the sorting and identification of plastic waste by using image recognition technologies and machine learning. This enables more efficient sorting and recycling of plastics, which helps to promote the Circular Economy.
Artificial intelligence can support the
promotion of the Circular Economy in various ways: Recycling optimisation: AI can make the recycling process more efficient, for example by controlling robots in recycling plants to sort and process plastics more effectively.
Material identification: With the help of AI, plastics can be precisely identified, making it easier to sort recyclable materials and improving the quality of the recycling process.
Design optimisation: With the help of AI, plastic products can be designed in such a way that they are easier to recycle or can be made from recycled materials. This helps to reduce waste and promote a closed Circular Economy. Sustainable production processes: AI can be used in production facilities to minimise energy consumption and material waste by optimising processes and using resources more efficiently. Forecasting and analysis: By analysing large amounts of data, AI can help identify patterns in the consumption of plastics, predict trends and make informed decisions to reduce the use of plastics and promote the Circular Economy.
Another obstacle is the lack of skilled labour with the necessary knowledge of AI and plastics technology. Finally, employee acceptance poses a challenge, as the use of AI changes work processes. Employees may first need to be trained in the use of AI technologies. AI in the plastics industry: an outlook Overall, the future of AI in the plastics industry looks promising. There is great potential to significantly increase efficiency and sustainability. AI is expected to continue to optimise processes, from material selection to end-of-life processing, and promote innovative recycling methods. The develop-
ment of smarter, self-learning systems could improve the adaptability of production and contribute to the realisation of a fully circular economy. Despite challenges in terms of data, integration and skilled labour, the increasing focus on sustainability and technological advances is expected to drive the adoption and implementation of AI in the industry.Artificial
Intelligence in the Plastics Industry: Sustainability through Technology.
Artificial intelligence is revolutionising modern industry. Thanks to it, complex processes can be automated, efficiency increased and further innovations made possible. In the plastics industry, AI not only plays a decisive role in the optimisation of production processes and the development of new materials. It also enables more precise waste sorting and therefore better recycling – a win for the environment!
“ACROSTAR”
Single, Twin Parallel or Conical, Multi -start and mixing, we offer a wide choice in Nitride and hardened alloy screws.
Single or Twin Barrels for extrusion and barrels for injection and blow moulding Nitride and Bimetallic that meet and exceed OEM standard
Fast Track Services for refurbishment, on site wear check surveys and technical support, full in -house design facilities...and much more.
To discover more about our products and service, please contact us: Tel 01920 465201
E.mail enquiries@magog.co.uk www.magog.co.uk
The versatility of plastic is one of its strongest characteristics, and it makes it particularly popular amongst designers. Once you have found the right plastic for a project, you have endless design possibilities. Plastic is also a favored material for BASF's design team: in collaboration with Citroën, the chemical company rethought the classic carwith plastic as the central building block that made the implementation of the innovative concept possible in the first place.
Alex Horisberger: In many aspects, the concept car answers questions that are directed at the mobility of tomorrow: How can I simplify my commute? Can a vehicle save resources and be fun at the same time? How can it look good at the same time? The result is a particularly lightweight yet robust and durable automobile - without frills, unnecessary luxuries and well thought out down to the smallest detail.
What challenges arise in such a development? What requirements have to be met?
Horisberger: Durability, recyclability
and simplicity play a crucial role in the novel concept. At the same time, the aim was to make sustainability look good. And in terms of production technology, the simplification principle was also consistently implemented; for example, the driver and passenger doors are identical. During development and design, we worked closely with Citroën to select the right materials from BASF's broad portfolio.
To what extent can plastics help meet these challenges?
Horisberger: Plastics are incredibly versatile and can therefore contribute to the functionality and functional integration of many vehicle components. Our polyamides have also proven their longterm durability many times over under typical automotive conditions without aging or corrosion. Of course, the sustainability aspect is also crucial: BASF is developing plastics that enable both mechanical and chemical recycling to support the industry in its transition from a linear to a circular economy. In addition, these engineering plastics
can be made from renewable or recycled raw materials.
Horisberger: We are dealing here with the reversal of the normal approach to a product, because often the prevailing principle is 'form follows function'. But when we look at a car from a sustainability perspective, materials and manufacturing technologies have to come first. In this project, the boundaries were pushed further and further, whether by using materials in unusual ways or by fundamentally rethinking the design of a component.
Which plastics are used in the concept car and why exactly these?
Horisberger: To make Citroën's vision of reusability and simplicity a reality, BASF relied on the material of a single TPU product family for the interior, for example, thereby facilitating mechanical recycling at the end of the product life cycle. Thanks to their versatility, our TPU grades enable different functions in the process. One visionary highlight of the concept, for example, was the production of a 3D-printed seat
made of TPU material that is both highly flexible and functional. The iconic storage compartment (Elastollan®) and the vehicle floor (Infinergy®) are made from the same product family. The exterior features lightweight yet robust plastic components that on the one hand reduce energy consumption while driving, but on the other hand leave design managers with all the design options they need. The hood, roof and pickup-like trunk made of Elastoflex® are strong enough to be used as ladders, roof tent bases or for transporting Christmas trees.
How do you assess future developments as far as the use of plastics in design objects is concerned?
Horisberger: In the numerous customer projects we carry out as BASF Creation Center, we see that the versatility of plastics, combined with the right sustainability concepts, offer designers endless possibilities to design clever products that really make consumers want to act sustainably. Just as oli impressively demonstrates: Modesty and sustainability can look good!
One day in the not-toodistant future, the plastics in our satellites, cars and electronics may all be living their second, 25th or 250th lives
New research from the Colorado University Boulder, published in Nature Chemistry, details how a class of durable plastics widely used in the aerospace and microelectronics industries can be chemically broken down into their most basic building blocks and then formed once again into the same material.
It's a major step in the development of repairable and fully recyclable network polymers, a particularly challenging material to recycle, as it is designed to hold its shape and integrity in extreme heat and other harsh conditions. The study documents how this type of plastic can be perpetually broken down and remade, without sacrificing its desired physical properties.
"We are thinking outside the box, about different ways of breaking chemical bonds," said Wei Zhang, lead author of the study and chair of the chemistry department. "Our chemical methods can help create new technologies and new materials, as well as be utilized to help solve the existing plastic materials crisis."
Their results also suggest that revisiting the chemical structures of
other plastic materials could lead to similar discoveries of how to fully break down and rebuild their chemical bonds, enabling the circular production of more plastic materials in our daily lives. In the mid20th century, plastics were ubiquitously adopted in almost every industry and part of life as they are extremely convenient, functional and cheap. But half a century later, after exponential demand and production, plastics pose a major problem to the health of the planet and to people. The production of plastics requires large amounts of oil and the burning of fossil fuels.
Disposable plastics create hundreds of millions of tons of waste every year, which ends up in landfills, oceans and even in our bodies, in the form of microplastics.
Recycling, therefore, is key to reducing plastic pollution and fossil fuel emissions this century.
Conventional recycling methods mechanically break down polymers into powders, burn them or use bacterial enzymes to dissolve them. The goal is to end up with smaller pieces that can be used for something else. Think shoes made from recycled rubber tires or clothing made from recycled plastic water bottles. It's not the same material anymore, but it doesn’t end up in a landfill or the ocean.
But what if you could rebuild a new item from the same material? What if
recycling didn't just offer a second life to plastics, but a repeat experience? That's exactly what Zhang and his colleagues have accomplished: They reversed a chemical method and discovered they can both break and form new chemical bonds in a particularly high-performance polymer. "This chemistry can also be dynamic, can be reversible, and that bond can be reformed," said Zhang. "We are thinking about a different way to form the same backbone, just from different starting points." They do this by breaking the polymer –"poly" meaning "many"– back into singular monomers, its molecules, a concept of reversible or dynamic chemistry. What's especially novel about this latest method is that it has not only created a new class of polymer material that, like Legos, are easy to build, break apart and rebuild over and over, but the method can be applied to existing, especially hardto-recycle polymers.
These new chemical methods are also ready for commercialization and can plug and play with current industrial production."It can really benefit future design and development of plastics to not only create new polymers, but it's also very important to know how to convert, upcycle and recycle older polymers," said Zhang. "By using our new approach, we can prepare many new materials—some of which could have similar properties to the plastics in our daily life."
This advance in the closed-loop recycling of plastics is inspired by the natural world, as plants, animals and human beings alike are currently part of a planetary-level, circular system of recycling, said Zhang. "Why can't we make our materials the same way?"
UV Absorbers
AA Reducers
Anti Yellows
IV Enhancers
Optical Brighteners
Blowing Additives
Process Aids
Xpansor Foaming Additives
EFFICIENT SUPPLY CHAIN FOR PROMPT DELIVERIES
PRODUCTION CAPACITY
14,000 MTPA (18,000 MTPA BY 2021)
IN-HOUSE WELL EQUIPPED TESTING LABORATORY HIGH STANDARDS OF QUALITY & TRACEABILITY
CABLES
General Purpose Insulation and Sheathing (Power / Flexible / Flat cables)
Low Temperature PVC Compounds (-550)
Heat Resistant Insulation / Sheathing (850 - 1250)
Insulation for Building Wires
Control Cables: RDSO
REACH & RoHS Compliant Compounds
FR & FRLS Compounds
NBR PVC Compounds
UV & Oil Resistant & UL Grade PVC
Data Cable Compounds
Anti Rodent & Anti Termite Compounds
Moulding Grade
AUTOMOBILE COMPOUNDS (JIS-DIN STANDARD)
SHOE GRADE COMPOUNDS
PVC MASTERBATCHES
Fine Products Pvt. Ltd.
Works: H 938 - 939 - 940, RIICO Industrial Area, Chopanki
M: +91 9810541068 T: +91 72318 60009
E : fpplindia@gmail.com info@fineproducts.co.in
W: www.fineproducts.co.in
YOUR LOCAL EREMA CONTACT LEEVAMS INCORPORATED Makarpura Vadodara | INDIA www.leevams.in
Whether it is inhouse, postconsumer or bottle recycling: you can only close loops in a precise and profitable way if machines are perfectly tuned for the respective application. Count on the number 1 technology from EREMA when doing so: over 6000 of our machines and systems produce around 14.5 million tonnes of high-quality pellets like this every year –in a highly efficient and energy-saving way.
launched in October 2020, aims at creating circular foodgrade recycled polypropylene (FGrPP) from post-consumer packaging. LyondellBasell (NYSE: LYB), one of the largest plastic and chemical companies in the world, has recently joined the initiative that brings more than 40 major industry players together.
"To unlock the full value of plastics, critical gaps must be addressed so these valuable resources can be circulated back into the economy after use. The development of innovative, new solutions and the increase of recycling rates is key to addressing plastic waste and climate change," says Richard Roudeix, Senior Vice President Olefins & Polyolefins EMEAI at LyondellBasell. "In the area of post-consumer polypropylene for food packaging, we are eager to join and support the research of the NEXTLOOPP project, together with other industry players, to help find new solutions." Polypropylene is the most widely used plastic in food packaging. NEXTLOOPP is able to close
the loop on polypropylene (PP) by using a combination of cutting-edge technologies, developed by Nextek Ltd. It does this by separating foodgrade PP from the rest, and by decontaminating the polymer to ensure compliance with food-grade standards in the UK, EU and the U.S. Following outstanding results of its innovative tracer-based sorting trials, Nextek Ltd recently started production trials of food-grade compliant recycled PP, making over 60 different products from NEXTLOOPP's four grades of PPristine food compliant and INRT rPP grade resins.
Professor Edward Kosior, founder and CEO of Nextek Ltd and NEXTLOOPP said, "We are delighted to welcome LyondellBasell to our project. As we continue to build momentum, LyondellBasell’s expertise on delivering technologies that advance solutions to our world’s biggest challenges will be key."
just launched the Kalix® 10000 series, an ideal structural material for precision electronics components used in smart devices, to complement its Kalix® product line. The newest HPPA-based material is set to take both performance and sustainability to the next level.
The Kalix® 10000 series, a partially bio-based material made with renewable feedstock from non-food competing sources, is produced with 100 percent renewable electricity. Available with a wide range of recycled content alternatives for diverse customer needs, it also has a lower global warming potential (GWP) than traditional polyamides. Additionally, it offers higher heat resistance, stain resistance, and lowest moisture absorption in the Kalix® families, making it suitable for use in electronic applications with more demanding customer requirements.
"Our Kalix® portfolio has seen high demand, as it delivers the highest elongation and weld line strength of all HPPA, as well as great stiffness and chemical resistance. It also shows low moisture absorption, which makes it an ideal structural material for precision electronics components," said
Andrew Lau, Senior Executive Vice President of Solvay Materials. "The Kalix®10000 series further strengthens the Kalix® family as it not only exceeds the performance demands of structural and cosmetic frames for smartphones, but it also is a more sustainable solution that meets evolving customer needs."
The average lifespan of consumer devices, and the parts that go into them, have been rapidly decreasing. Vast amounts of waste will continue to be generated and cause sustainability challenges. Solvay has developed advanced technologies to help manufacturers close the loop between product design and production execution on the factory floor. With a multitude of sustainable materials solutions that address various market needs, the company is working to put our society on a fast track towards more circular solutions.
Many enzymes promise to break down plastic. But what works well in the lab often fails on a large scale. Now a new study by Gert Weber, Helmholtz-Zentrum Berlin (HZB), Uwe Bornscheuer, University of Greifswald, and Alain Marty, Chief Scientific Officer of Carbios, shows how raising the bar for laboratory experiments could help identify promising approaches more quickly. The team demonstrated the new standards on four newly discovered enzymes.
PET recycling: lots of alleged breakthroughs
From time to time, media reports of major advances in the recycling of polyethylene terephthalate (PET). This is thanks to newly discovered enzymes, breaking down plastic into its constituent parts. However, the success story from the academic laboratory is usually followed by silence. PET accounts for 18% of the world's plastic production, making it one of the most important plastics in terms of volume. Biotech company Carbios, for example, is building a plant in the north east of France by 2025. This plant will be able to recycle 50.000 tons of PET per year. They are interested to find the best possible enzymes for their industrial setup and have realised that many results from laboratory research cannot be
transferred to a larger scale.
Upscaling experiments on PET recycling is difficult
"Some enzymes work great in laboratory experiments for a few hours, but they lose their activity very quickly and the substrate is not completely degraded," says HZB expert Gert Weber. This is not a problem in the test tube in the laboratory, but it is when used in a large bioreactor. Together with the biotech company Carbios, Uwe Bornscheuer and Gert Weber show how new enzymes for PET degradation can be better compared with each other.
"In order to allow upscaling later, many parameters must be within a narrow range even in laboratory experiments. The starting material must be precisely defined and the test protocols must be more standardised in order to better assess the performance of the enzymes and their application on an industrial scale," explains Bornscheuer.
The researchers have therefore developed a standardised PET hydrolysis protocol that defines reaction conditions relevant for hydrolysis on a larger scale. In particular, two PET materials were used, firstly a defined PET film and secondly PET granulate from waste
bottles, as used by Carbios on a technical scale. They used these materials to test four recently discovered PET-decomposing enzymes: LCC-ICCG, FAST-PETase, HotPETase and PES-H1L92F/Q94Y.
When experimenting under this protocol, they found that two of these enzymes, FAST-PETase and HotPETase, were less suitable for large-scale use. This is mainly due to their relatively low depolymerisation rates. PES-H1L92F/ Q94Y performed better. The fourth candidate, LCC-ICCG, outperformed the other enzymes by far: LCC-ICCG converts 98% of PET into the monomeric products terephthalic acid (TPA) and ethylene glycol (EG) in 24 hours. "In addition, we were able to reduce the amount of enzyme required for LCCICCG by a factor of 3 and the reaction temperature from 72 to 68 °C, which makes the use of this enzyme more economical," says Bornscheuer.
"We should think about industrial applications already in our laboratory research," says Gert Weber. After all, we are dealing with one of the really big problems of our time. Plastics are still being produced again and again from fossil raw materials, recycling rates are low and so far, it has mostly been a case of "downcycling" to inferior quality. Plastic waste can now be found in all bodies of water and soil and thus in the food chain. Progress is therefore urgent. "With these standards, we can do something to separate the wheat from the chaff more quickly."
Mid-January sees the exhibitor database for K 2025 go online. Now completely booked up, this leading trade fair of the plastics and rubber industry will once again stand out with its participation of international market leaders along the value chain and industry know-how and information galore well before the start of the trade fair.
From 8 to 15 October 2025 K in Düsseldorf will again become the central business hub for the global plastics and rubber industry. It sets clear accents with its motto “The Power of Plastics! Green – Smart –Responsible”. This slogan reflects the industry’s current values and targets and emphasises that plastics are an indispensable component of many sectors that contribute significantly to innovation and progress. Especially in today’s
challenging times K once again proves its outstanding relevance as a world-leading trade fair. It is the place where the entire value chain unites to present top performances and where the challenges of this industry are addressed. No other event boasts such international flair, extraordinary innovative power and such a rich variety of product launches as does K in Düsseldorf.
K 2025 stands for the open dialogue and exchange on innovative solutions and sustainable developments that forge connections across national borders and continents. Exhibitors from 61 countries will take part in K in Düsseldorf and more than 3,000 exhibitors are expected in the 18 exhibition halls. The fairgrounds are fully booked once again.
The exhibitor database of K 2025
can be accessed at www.konline.com/2410. At present, all principal exhibitors can already be found there and the database will gradually fill up with their coexhibitors.
At www.k-online.com K not only provides details on the event in October already at this early stage but also offers numerous opportunities via other channels to obtain indepth information about the industry’s current developments and to benefit from the global K Community:
K-Mag is the name of K’s online magazine. It targets all K-related industries and delivers facts, news, stories, interviews and trends from the international plastic and rubber industry in German and English throughout the year. K-monthly is K’s Newsletter in Düsseldorf. Subscrib-
ing to it you will not only receive the most interesting news and stories from the K-MAG by e-mail every month but also current information revolving around K in Düsseldorf and the international trade fairs of the KGlobal Gate family of products.
You can subscribe via the K-website or the K-MAG.
What’s up in plastics and rubber? is K’s new Newsletter on LinkedIn. It provides concise and up-to-date information on the latest news from K and the international trade fairs of the K-Global Gate family.
In addition, the K LinkedIn Newsletter focuses on industry highlights and strengthens the K community in this international network.
Not to be missed: the Ticketshop for K 2025 opens in April 2025.
Innovativemindspresentpioneering ideas for the plastics and rubber industry
After its successful debut at the previous K the Start-up Zone will also form an integral part of the trade fair again in 2025 – this time located in the direct proximity of the Science Campus. Celebrating a premiere will be the Start-up Pitch as part of the Special Plastics Shape the Future.
By organising the Start-up Zone K in Düsseldorf, the world-leading trade fair for the plastics and rubber industry, intends to once again offer young companies a dedicated stage from 8 to 15 October 2025. After all, it is especially start-up companies that play a decisive role for the plastics and rubber industry since they introduce innovations and fresh ideas into an industry increasingly faced with such challenges as sustainability, efficiency and
digitalisation. Especially start-ups are characterised by great pioneering spirit, risk affinity and high flexibility.
At K 2025 the Start-up Zone will be situated in Hall 7.0 and, hence, in the immediate vicinity of the Science Campus. At the Science Campus universities (of applied sciences) and institutes will present the latest results of their plastics research. Both K Specials ideally complement each other. The immediate vicinity of the Start-up Zone and Science Campus will make Hall 7.0 a unique science and innovation hub.
Young companies still have the chance to register for the Start-up Zone thereby leveraging the opportunity of presenting their developments at the world’s most relevant industry trade fair and making valuable international business contacts. A special participation package has been prepared for them minimising the obstacles and organisational expenses associated with participat-
ing in such a large trade fair.
Participation criteria:
The company is younger than 10 years
It employs less than 100 employees
Annual sales do not exceed € 10 million
The registration form can be downloaded at: www.konline.com/Start-up Zone
T
he contact person for the Start-up Zone is Katharina Kolissnyk, Kolissnyk@messe-duesseldorf.de .
In line with the Start-up Zone the official Special Plastics Shape the Future, organised by Plastics Europe, will also offer the newcomers in the industry a dedicated forum at K for the first time – the Startup-Pitch Towards Zero. Here, start-ups whose innovations and technologies, solutions or new business
models for a circular economy with plastics, for the decarbonisation of the plastics industry or the reduction of so-called Scope-3 emissions, are given the opportunity to showcase their pioneering technology projects and network with partners worldwide.
The Startup-Pitch Towards Zero will take place at K 2025 on Monday, 13 October, as part of the Special Plastics Shape the Future in Hall 6 of the Düsseldorf Exhibition Centre. The deadline for applications is 1 March 2025: TOWARDS ZEROStartup Pitch at K 2025.
In 1952 K was held by Messe Düsseldorf for the first time and is held in a 3-year cycle. The latest K in 2022 registered 3,020 exhibitors from 63 countries on over 177,000 m² net exhibition space and 177,486 trade visitors, 71% of these from abroad. For more information go to www.k-online.com.
perfectly tailored to your needs FOR ALL
Stäubli Fluid Connectors o ers a new End-of-Arm-Tooling range, along with consultation for customized robotic material handling solutions. Through our partner FIPA, we can now provide a broad portfolio. Stäubli Fluid Connectors therefore makes gripping, suction and cutting available for all robots worldwide from a single source - including manual or automatic robotic tool changing systems.
Always a customized solutions for your requirements Broad technology portfolio for Material handling from a single source
Flexible and durable systems for lasting productivity Worldwide on site with highest consulting and service quality
KraussMaffei helps you gain the purest recyclates in a „like new“ quality that seemed unimaginable a few years ago. We implement your formulations in a way that costs little in terms of money, energy and CO2 emissions. Our groundbreaking technology in compounding and recycling gives you the critical edge in the competition for sustainability – for your company‘s figures and our children‘s future.
DISCOVER MORE ABOUT OUR INDUSTRIES www.kraussmaffei.com