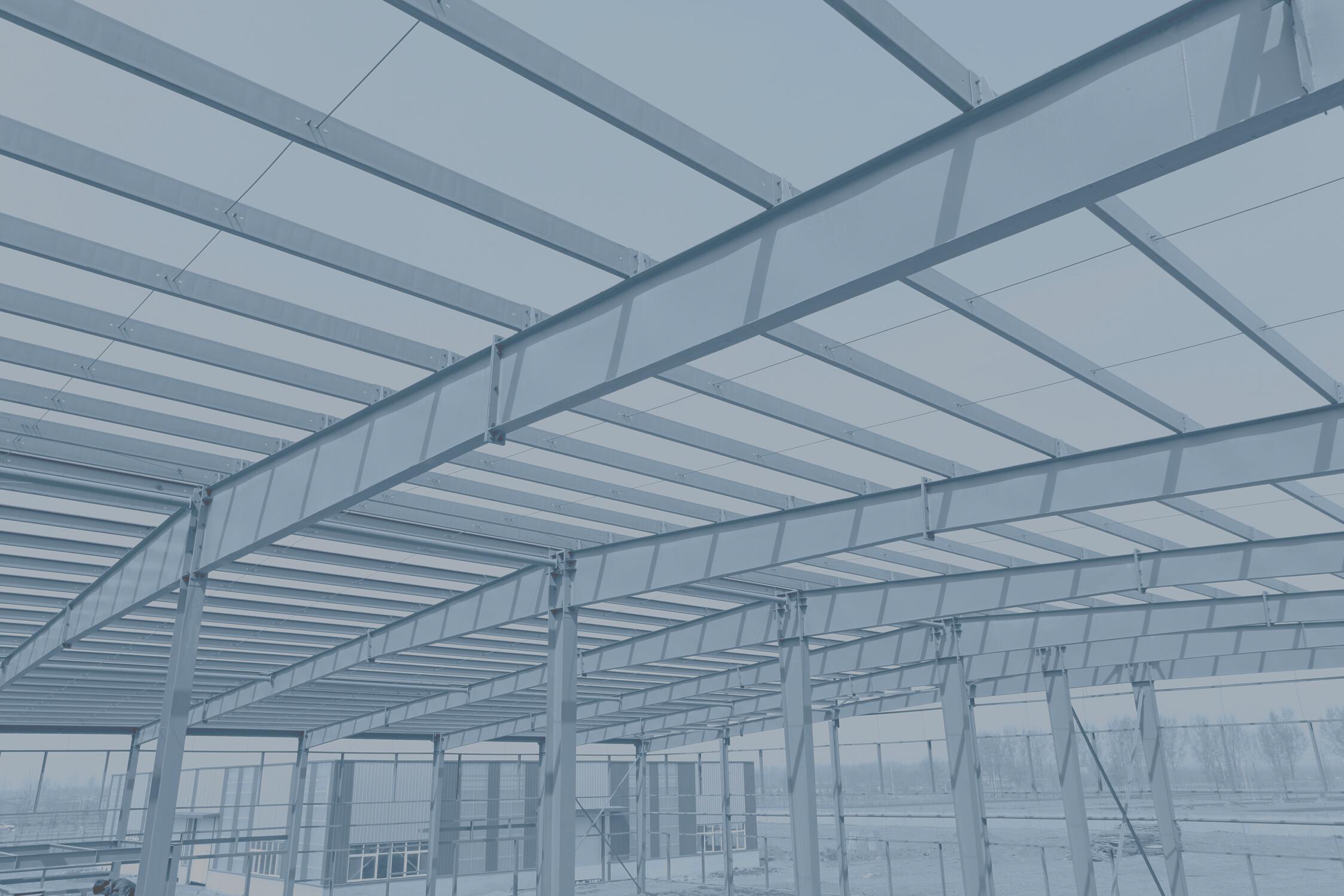
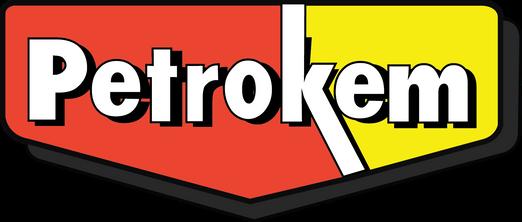
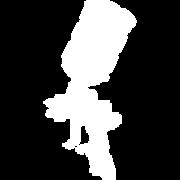
Since our modest beginnings in 1989, Petrokem® has grown to become one of Sri Lanka's leading chemical companies. Over the last three decades, Petrokem® has seen an impressive 8% average annual growth rate, and we now operate through a nationwide dealer network spanning over 2500 Stores. We believe in combining economic success with a commitment to environmental sustainability and social responsibility.
Epoxy-based products are a cornerstone of our business. Today, these products are integral to many of our most common applications, such as paints and coatings, flooring, automotive, water delivery, food packaging, electronics, energy and sports. As one of Sri Lanka's leading epoxy manufacturers, we are proud to be part of the driving force behind many of the country's premier industries. Our corporate culture is best summed up in our motto:
'Formulating The Future®'.
At Petrokem, our technical staff are experts in the field of manufacturing epoxy-based products for both local and foreign markets. We have been providing epoxy-based protective coatings for various industrial applications since 1989 in Sri Lanka and are proud to have established ourselves as a leader in this field.
Petrokem is proud to operate three state-ofthe-art production facilities located in Sri Lanka. Our headquarters can be found at 240 Galle Road in Katubedda, and our main facility boasts 80000 square feet of production space in Kahathuduwa, Sri Lanka.
The Petrokem R&D team is dedicated to combining homegrown technology and sustainably sourced engineered raw materials to provide customers with a truly world-class product. We are committed to maintaining the highest standards of production while also being conscious of our environmental impact To offset our building footprint, we have installed roof gardens in all of our facilities, which provide a variety of produce for our workforce to enjoy. As one of Sri Lanka's premier chemical manufacturers, Petrokem has set a prime example of sustainability practices. To learn more, please visit www.petrokemlanka.com
What is Corrosion -
Corrosion TypesCorrosion Prevention -
Corrosion Categories -
Petrokem Performance Coatings -
Alfa Series Coatings -
Delta Series Coatings -
Paint System Guide -
Paint System Illustration -
Corrosion is a naturally destructive phenomenon that occurs when some metals are exposed to the environment. The reaction between air, moisture (containing dissolved salt) and the metal substrate gives rise to specific chemical reactions that cause the metal to convert to its more chemically-stable oxide, hydroxide or sulfide form. In ironbased metals, such as steel, corrosion comes in the form of iron oxides, also known as rust.
Sri Lanka has made a significant development in the design and construction sector during the last 10 years. The use of steel is one of the governing construction materials in the industry. One of the major concerns of existing steel structures is the durability. Corrosion and deterioration have become major challenges in the lifetime of the steel or metal structure.
Galvanic corrosion
Stress-corrosion cracking (SCC)
General corrosion
Localized corrosion
Caustic agent corrosion
Galvanic corrosion refers to corrosion damage that occurs when two different metals are in electrical contact in an electrolyte, where the more noble metal is protected and the more active metal tends to corrode.
Stress corrosion, also known as stress corrosion cracking, is a type of corrosion that occurs due to the simultaneous action of a corrodent and a sustained tensile stress. This mechanism is characterized by corrosion in the microscopic granular composition of a metal's surface. The introduction of stresses (either applied or residual) causes the boundaries to open, introducing fine cracks on the metal's surface.
General corrosion is normally characterized by an attack that appears to be uniform in nature. The uniformity is normally spread on the whole surface of the metal, resulting in a smooth appearance. The attack that leads to corrosion on the surface of the metal is the result of the material being subjected or exposed to a medium that is corrosive in nature. For this reason, the corrosion rate is therefore defined as the loss of mass per unit of surface area. In other words, the corrosion rate can be expressed as mean loss of metal per unit over time, or units of mm per year.
Localized corrosion refers to the hastened attack of passive metals in corrosive environments. It is characterized by an intense attack at confined areas on surface components, while the remaining area of the surface corrodes at a much slower rate. This can be due to environmental effects or the component material’s inherent properties, like in the creation of protective film oxide.
Caustic corrosion is a type of corrosion that occurs in metal equipment (e.g., boilers) in certain environmental operating conditions that have a high pH water level, resulting in an operating medium that is highly alkalized (i.e., a high concentration of sodium hydroxide (NaOH)
Preventing corrosion on structural ste essential to the overall integrity and aesthetics of the structure. Whether t structural steel supports a bridge, commercial building or plant, asset ow must be able to count on the infrastructure for the long haul.
Asset owners and their corrosion engi or project manager should evaluate th best ways to implement corrosion protection for the steel supporting th asset. Petrokem, in this document, aim provide information on corrosion protection and then describe design methods and coating systems that wil ensure the structural steel is protecte from corrosion for decades to come.
Before a coatings team applies a singl application, asset owners can implem corrosion prevention methods with informed steel and design choices.
Coatings alone are not effective at protecting structural steel from all for of corrosion. For instance, coatings ar effective at controlling uniform corros but are less effective at controlling localized attacks such as pitting.
Use the following advice on steel sele and design considerations to set up a coating system for success.
The quality of the steel itself can have a impact on corrosion prevention. High-alloy steel is naturally more corrosion-resistant than low-alloy steel (though it should still have a protective coating applied) and is more expensive. If asset owners choose a more affordable low-alloy steel, it will likely need a more comprehensive coating system to effectively fend off corrosion.
Corrosion control is just one part of the steel selection process. Asset owners should balance those needs with the steel component's end use, its initial cost and its future maintenance costs.
The design of structural steel can also prevent corrosion. These design factors won’t play a part in coating or re-coating a built structure, However they are important to consider because failing to follow them leads to an increased risk of corrosion.
For a new structure, keep these design considerations in mind early in the process.
Reduce exposure to the atmosphere. Any areas where exposure to the atmosphere can be limited (especially when the environment is particularly corrosive) will aid the overall corrosion prevention system. Stay away from dissimilar metals. Galvanic corrosion (explained above) is possible when two or more dissimilar metals are used in a structural steel system. Be conscious of metal choices to prevent this type of corrosion. Prevent water from building up. Water traps are intrinsically corrosion-prone because moisture accelerates corrosion. They are even more problematic if the environment contains dirt and debris, because when trapped, they tend to retain moisture. Ensure no areas cause unnecessary water build up or stagnation. Avoid surface irregularities. These include crevices, sharp edges and inaccessible areas that are difficult to coat and inspect. However, not all irregularities can be avoided. For those that remain, pay careful attention to them while coating.
ion is the essential first stage treatment of a steel substrate before the y coating, and is generally accepted as being the most important factor al success of a corrosion protection system.
elements in new structures are usually either hot rolled sections or fabricated e initial steel surfaces normally comply with rust grades A or B according to BS Material that is pitted, i.e. rust grades C or D, should be avoided if possible, t to clean all corrosion from the pits during surface preparation. Descriptions to D are as follows :
ace largely covered with adhering mill scale, but little if any rust. ace which has begun to rust and from which mill scale has begun to flake. ace on which the mill scale has rusted away or from which it can be with slight pitting under normal vision. face on which the mill scale has rusted away and on which general pitting der normal vision.
and grades of cleanliness are presented in BS EN ISO 8501-1. At Petrokem we below systems, however would only certify with abrasive blast cleaning it blasting for the guarantee periods to apply.
significant and important method used for the thorough cleaning of mill-scaled ces is abrasive blast cleaning. This method involves mechanical cleaning by the ct of abrasive particles at high velocities on to the steel surface either in a jet essed air or by centrifugal impellers. This is the only method recommended by rface preparation.
by hand tools such as scrapers and wire brushes is relatively ineffective in ale or adherent rust. Power tools offer a slight improvement over manual ese methods can be approximately 30% to 50% effective but are not usually steelwork fabrications. Where it is not possible to clean by abrasive blasting, tool methods may be the only acceptable alternative method.
*Notepleasereadpagenumber27foracompreheisive guideon surfacepreperationgrades
Coatings, the first line of defence, play a major role in protecting structural steel from corrosion. The surface preparation standards, coating systems and coating application methods are the key for an effective corrosion protection system.
The preferred surface preparation standards for structural steel are SA 2 to SA 3. Hand tool cleaning or wire brush cleaning are always options, however, strict standards (ST 2, ST 3) for this type of surface preparation need to be followed for desired system performance. (Please refer page 27)
The best-fit coating system is dependent on the corrosiveness of the environment (Corrosion category). Understanding the appropriate corrosion category will aid in the selection of the correct coating system.
,C4,C5i) y and reas t. A zinc hoice. r the steel bstrate. an epoxy en be or color eries s of ts (C3) oderate al areas y of ervice on risk. ng they g rusted n to bare the m Alfa ese paints can 1,C2) on. In with little , a basic lly coating m Alfa se
Petrokem was founded in 1989 and has grown to be one o companies that manufacture specialty chemicals, industri both local and foreign markets.
At Petrokem we have studied the effects of corrosion in s understood the unique challenges specific to Sri Lanka th face on a daily basis. Our research and development has led us to develop two coating systems for a wide array of protective application
RECOMMENDED FOR CORROSION CLASS : C3, C4, C5I
C3 - Urban and industrial atmospheres, moderate sulphur dioxide pollution; coastal area with low salt content.
C4 - Industrial areas and coastal areas with moderate salt content.
C5i (CX) - Industrial areas with high humidity with aggressive atmosphere and coastal areas with high salt content.
Petroprime® 100 is a two t, high quality universal ive primer developed to meet sing demand for high quality ive primer. The product is a on of a high quality epoxy a polyamide activator. e® 100 is recommended for tion and maintenance of all ctures in civil engineering ns, storage/ballast tanks, ship ks, metal pipe lines, cargo oil dges, off shore structures, es, chemical plants and oil ns. The product should be mmediately after the cleaning the metal. Petroprime® 100 high quality anticorrosive all metals such as steel, , zinc, copper, etc. the ill protect the surface against rosive elements such as umes, diluted alkali solutions d acid solutions. Petrokem e® 100 is also resistant to pray, therefore is nded for coastal areas and ent re-coatability. Overcoat e with Petrokem Petrocover® st results.
Developed to prime harsh corrosive environments. 100 microns per coat. Resistant to salty sea spray and chemical fumes. Adheres to concrete, cement, fiberglass & metal surfaces including steel, aluminum, zinc and copper. Overcoat with alfa series petrocover 240 for maximum protection.
Developed to coat harsh corrosive environments such as ship decks. 240 microns per coat. Resistant to salty sea spray and chemical fumes. Adheres to concrete, cement, fiberglass & metal surfaces including steel, aluminum, zinc and copper. Prime with alfa series Petroprime 100 for maximum protection.
Petrokem Petrocover® 240 is a high build two component non-toxic epoxy paint developed to meet the increasing demand for high quality anticorrosive painting systems and is specially designed for highly corrosive industrial and coastal environments. The product is recommended as an anticorrosive coating for the protection and maintenance of metal structures, ship decks, fiber glass, wooden boats, metal pipelines, bridges, off shore structures, radial gates, chemical plants, beverage factories, oil installations, storage tanks & house hold applications. Petrocover® 240, once fully cured, achieves maximum DFT of 240 microns and is extremely resistant to salty sea spray, abrasion and other highly corrosive elements.
C1 - Buildings with clean atmospheres, e.g. offices, shops, schools, hotels
C2 - Atmospheres with low level of pollution: mostly rural areas, buildings where condensation can occur, e.g. depots, sports halls
Petrokem Epoxy Iron Oxide Primer is a two component, high quality anticorrosive primer developed to meet the increasing demand for high quality anticorrosive primers. The product is a combination of a high quality epoxy resin and a polyamide hardener. Epoxy Iron Oxide Primer is recommended for the protection and maintenance of all metal structures in civil engineering applications, storage tanks, ship hulls, metal pipe lines, bridges, off shore structures, radial gates, chemical plants, oil installations etc. The product should be applied immediately after the cleaning process of the metal and will act as a high quality anticorrosive primer for all metals such as steel, aluminum, zinc, copper, etc. Petrokem Epoxy Iron Oxide Primer will protect the surface against highly corrosive elements such as chemical fumes, acid fumes, and is also resistant to salty sea spray and therefore recommended for coastal areas. Overcoat the surface with Petrokem Epoxy Marine Paint, Petrokem Epoxy Gloss Paint or Petrokem Coal Tar Epoxy Paint for best results.
Adheres to all metal including steel, aluminum, zinc, copper etc. Non toxic when fully cured. Resistant to salty sea spray and chemical fumes.
Adheres to GI (low sheen) steel, hard plastics and glass.
Excellent adhesion to most substrates.
Resistant to salty sea spray and chemical fumes.
Petrokem 3Dot® 2K Auto Primer is a two component, high quality isocyanate free primer specially designed for refinishing vehicles. Recommended to use over all metal surfaces (steel, aluminium, zinc, copper etc.) as a high quality anticorrosive protective primer. The product can also be used as a high quality protective primer for hard plastic, wood, Fibreglass or over most other similar surfaces. 3Dot® 2K Auto primer is resistant to salty sea spray and therefore recommended to use in coastal areas. The product should be applied immediately after the cleaning process of the metal. The product can be over coated with 3Dot® 2K Auto Filler, Petrokem Carpach Metal Filler or 3Dot® Polyester Putty Fine.
Prevents rust and resistant to moisture. Acts as a bonding agent to help the topcoat adhere more strongly to the body of the vehicle. Isocyanate free system.
Adheres to all metal including steel, aluminium, zinc, copper etc. Resistant to salty sea spray and number of chemical fumes. Recommended for coastal areas. Non toxic when fully cured.
® is an anti l tar eveloped highly duct is osive d res, wood, bridges, etal pipe ns, storage ) and product ovide long ressive ing is over han black. ations s.
Developed to be used on underground pipework and similar applications.
Used on ship hulls as a protective layer.
Tough long lasting coating when not exposed to UV.
Resistant to salty sea spray, abrasion and other highly corrosive elements. Recommended as an anticorrosive and decorative coating for the protection and maintenance of metal structures. Non toxic when fully cured.
3Dot 2K Epoxy Marine Pa quality two component n paint developed to meet demand for high quality painting systems and is s designed for highly corro and coastal environment is recommended as an a and decorative coating fo protection and maintena structures, concrete floo glass, wooden boats, me bridges, off shore structu gates, chemical plants, b factories, oil installation & house hold application Epoxy Marine Paint is als recommended for swimm ponds, concrete and cem tanks as a decorative pro and once fully cured is re sea spray, abrasion and corrosive elements.
Adheres to all metal including steel, aluminum, zinc, copper etc. High build epoxy paint. Resistant to salty sea spray.
Non toxic when fully cured. Resistant to salty sea spray and certain chemical fumes. Adheres to concreate/cement, fiberglass/metal surfaces including steel, aluminum, zinc and copper.
Petrokem Epoxy Gloss Paint is a high quality two component non-toxic epoxy paint developed to meet the increasing demand for high quality floor and wall painting systems. The product is specially designed for house hold and industrial environments. Epoxy Gloss Paint is non-toxic when fully cured and therefore is recommended as a decorative, water resistant coating for the protection and maintenance of bathroom floors/walls, concrete/cement floors, metal drinking water tanks, kitchen floors/walls, wooden/fiber glass boats, metal pipe lines and other house hold applications.
uard 353 WB is a single ater-base anti-corrosive d on acrylic polymer veloped to be applied ints to withstand UV xposed environments. The hly recommended to be xy painted metal steel pipelines, bridges, ctures, radial gates, ts, beverage factories, oil storage tanks & house ons. The product will ecorate all metal surfaces over epoxy painted
UV resistant. Decorate all metal surfaces when applied over epoxy painted systems.
P E T R O K E M C - G U A R D 3 5 3
P l e a s e r e q u e s t t e c h n i c a l d a t a s h e e t s f r o m o u r s a l e s e x e c u t i v e s u s i n g c o d e s o r u s i n g p r o d u c t n a m e s .
Petroprime 100 - PP100 LIT
Petrocover 240 - PC240 LIT
Petroprime ZNR - PPZNR LIT
Petrokem epoxy marine paint - EMP LIT
3Dot 2k epoxy marine paint - D2KMP LIT
Petrokem epoxy Gloss Paint - PEGP LIT
C-Guard® marine paint - CGMP LIT
Petrokem epoxy iron oxide primer - PEIOP LIT
Petrokem 3dot® 2k auto primer - 2KAP LIT
Petrokem mpg primer - PMPGP LIT
C-Guard® 353 - CG353 LIT
2K Coal Tar Epoxy - 2KCOALE LIT
PLEASE READ TECHNICAL PAINT GUIDE (0034APA) AS A GENERAL PROTECTIVE COATING GUIDE TO BETTER NAVIGATE PETROKEM'S TECHNICAL PAINT PORTFOLIO
The lifetime of a paint system is assumed to be the period of time which passes until maintenance is required for the first time after application. ISO 12944 specifies a range of time frames to categorise durability:
LOW—L Upto7years
MEDIUM M 7to15years
HIGH—H 15to25years
VERYHIGH—VH Morethan25years
Standard surface preparation grades for primary surface preparation by abrasive blasting method
Whenviewedwithoutmagnification,thesurfaceshallbefreefromvisibleoil,greaseanddirt,andshallbe freefrommillscale,rust,paintcoatingsandforeignmatter.Itshallhaveauniformmetalliccolour.
Whenviewedwithoutmagnification,thesurfaceshallbefreefromvisibleoil,greaseanddirt,andfrom millscale,rust,paintcoatingsandforeignmatter.Anyremainingtracesofcontaminationshallshowonly asslightstainsintheformofspotsorstripes.
Whenviewedwithoutmagnification,thesurfaceshallbefreefromvisibleoil,greaseanddirt, andfrommostofthemillscale,rust,paintcoatingsandforeignmatter.
Whenviewedwithoutmagnification,thesurfaceshallbefreefromvisibleoil,greaseanddirt,andfrom poorlyadheringmillscale,rust,paintcoatingsandforeignmatter.
Standard preparation grades for primary surface preparation by hand cleaning (power tool cleaning)
AsforSt2,butthesurfaceshallbetreatedmuchmorethoroughlytogiveametallicsheenarisingfrom themetallicsubstrate.
Whenviewedwithoutmagnification,thesurfacesshallbefreefromvisibleoil,greaseanddirt,andfrom poorlyadheringmillscale,rust,paintcoatingsandforeignmatter.
*Non exposed to UV radiation
Surface
Delta Series Alfa Series
C1C2.1
MEDIUM—M
Mild Steel
C1C2.2
HIGH H
GI Low Sheen
C1C2.3
MEDIUM M
C1C2.4
C1C2.5
HIGH—H
HIGH H
Outdoor Applications
Petrokem epoxy iron oxide primer - PEIOP
Petrokem epoxy marine paint - EMP
TOTALDFT
Petrokem mpg primer - PMPGP
Petrokem epoxy marine paint - EMP
TOTALDFT
Petrokem epoxy iron oxide primer - PEIOP
*PC - Primer Coat | IC - Intermidiate Coat | TC - Top Coat PC IC TC
Petrokem epoxy marine paint - EMP c-guard® 353 - CG353
30 microns 60 microns 90 microns
Coat PC IC PC IC 60 microns * 2 = 120 microns
30 microns 150 microns
30 microns 60 microns 30 microns
TOTALDFT
120 microns
Petrokem epoxy iron oxide primer - PEIOP
Outdoor Applications 60 microns * 2 = 120 microns
PC IC TC
30 microns
Petrokem epoxy marine paint - EMP c-guard® 353 - CG353
Outdoor Applications 30 microns
Mild Steel Mild Steel 180 microns
TOTALDFT
GI Low Sheen
Petrokem mpg primer - PMPGP PC IC TC
Petrokem epoxy marine paint - EMP c-guard® 353 - CG353
TOTALDFT
60 microns * 2 = 120 microns
30 microns 30 microns 180 microns
SystemNo LifeTime
*Non exposed to UV radiation
Surface
GI Low Sheen
C3.5 C3.2 C3.3 C3.4 C3.5
MEDIUM—M
MEDIUM—M
Mild Steel
MEDIUM—M
HIGH—H
Delta Series Alfa Series
PaintName
DFT
GI Low Sheen
Petrokem epoxy marine paint - EMP
Petrokem mpg primer - PMPGP 30 microns 150 microns
TOTALDFT
Petroprime 100 - PP100
Coat PC IC PC IC 60 microns * 2 = 120 microns
Petrokem epoxy marine paint - EMP
TOTALDFT
Petroprime 100 - PP100
*PC - Primer Coat | IC - Intermidiate Coat | TC - Top Coat PC IC TC
Petrokem epoxy marine paint - EMP c-guard® 353 - CG353
100 microns 220 microns
100 microns 30 microns
TOTALDFT
HIGH—H
Outdoor Applications
Mild Steel Mild Steel
Outdoor Applications 60 microns * 2 = 120 microns
PC IC TC
Petroprime 100 - PP100 Petrokem epoxy marine paint - EMP c-guard® 353 - CG353
TOTALDFT
250 microns
60 microns * 2 = 120 microns 60 microns * 2 = 120 microns 100 microns * 2 = 200 microns
Outdoor Applications 30 microns
350 microns
Petroprime 100 - PP100 PC IC TC
Petrocover 240 - PC240 c-guard® 353 - CG353
TOTALDFT
240 microns
100 microns 30 microns 370 microns
SystemNo LifeTime PaintName
C4C5.1 C4C5.2 C4C5.3 C4C5.4
MEDIUM M
*Non exposed to UV radiation Surface Mild Steel
System Delta Series Alfa Series
DFT
HIGH—H
HIGH H Outdoor Applications
GI Low Sheen Petrocover 240 - PC240
Mild Steel Mild Steel
GI Low Sheen
Petrocover 240 - PC240
TOTALDFT
*PC - Primer Coat | IC - Intermidiate Coat | TC - Top Coat TC c-guard® 353 - CG353
Petroprime 100 - PP100 340 microns
Petroprime 100 - PP100
Coat PC IC PC IC 240 microns
100 microns 30 microns
100 microns * 2 = 200 microns
MEDIUM M Outdoor Applications 30 microns
PC IC TC
TOTALDFT 470 microns
240 microns 100 microns * 2 = 200 microns
Outdoor Applications 240 microns * 2 = (Use second IC diluted with 221)
Petroprime 100 - PP100 Petrocover 240 - PC240 c-guard® 353 - CG353
TOTALDFT IC 2k Coal Tar Epoxy - 2KCOALE 60 microns
Petroprime 100 - PP100 PC IC TC
590 microns
100 microns 240 microns * 2 = 880 microns
Petrocover 240 - PC240 c-guard® 353 - CG353 30 microns Approx 1MM
TOTALDFT