Human Resource Professionals on the Front Lines
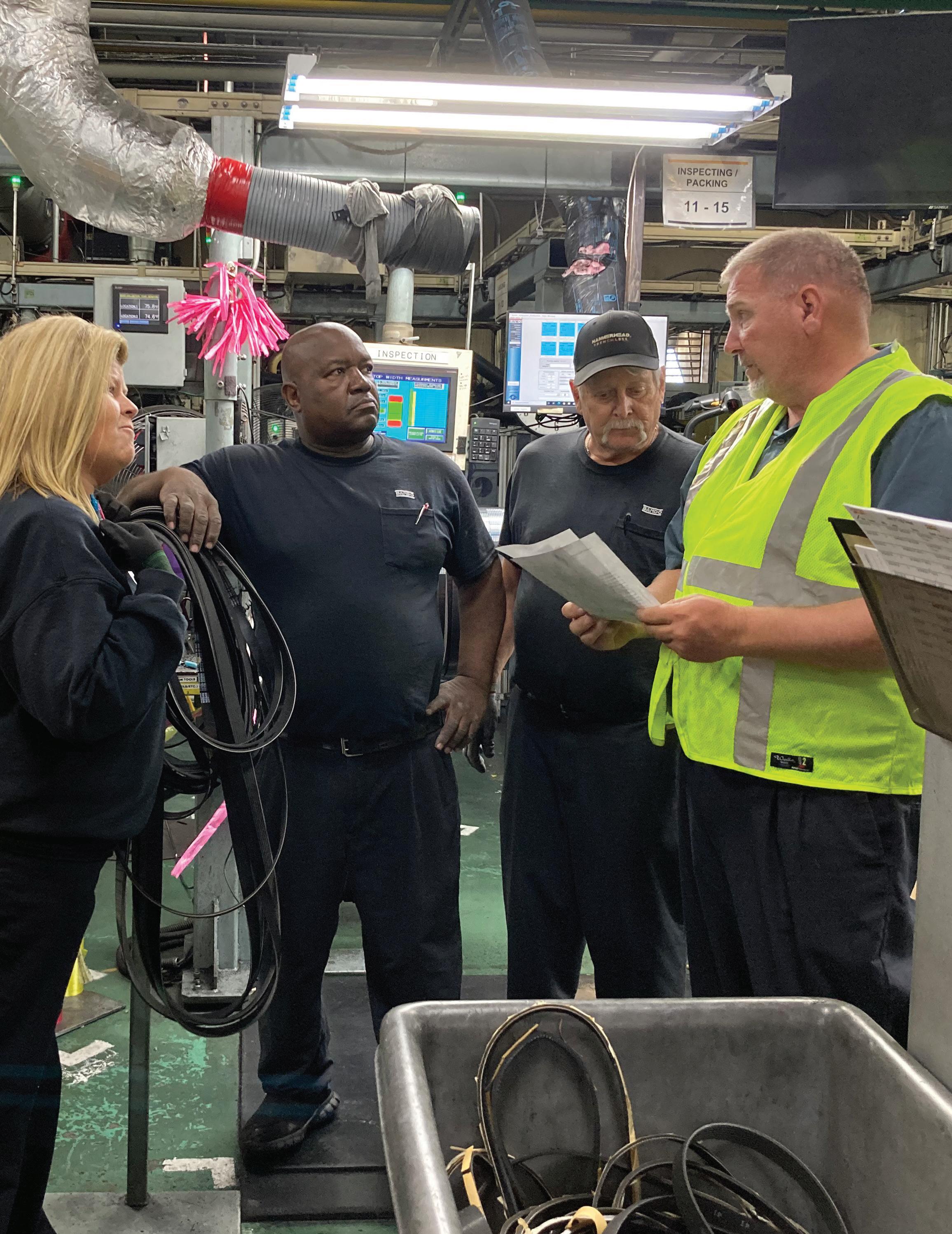
Robotics with the Sense of Touch
Four Key Pillars to Developing Internal Talent
Solving Design Problems Through Simulation
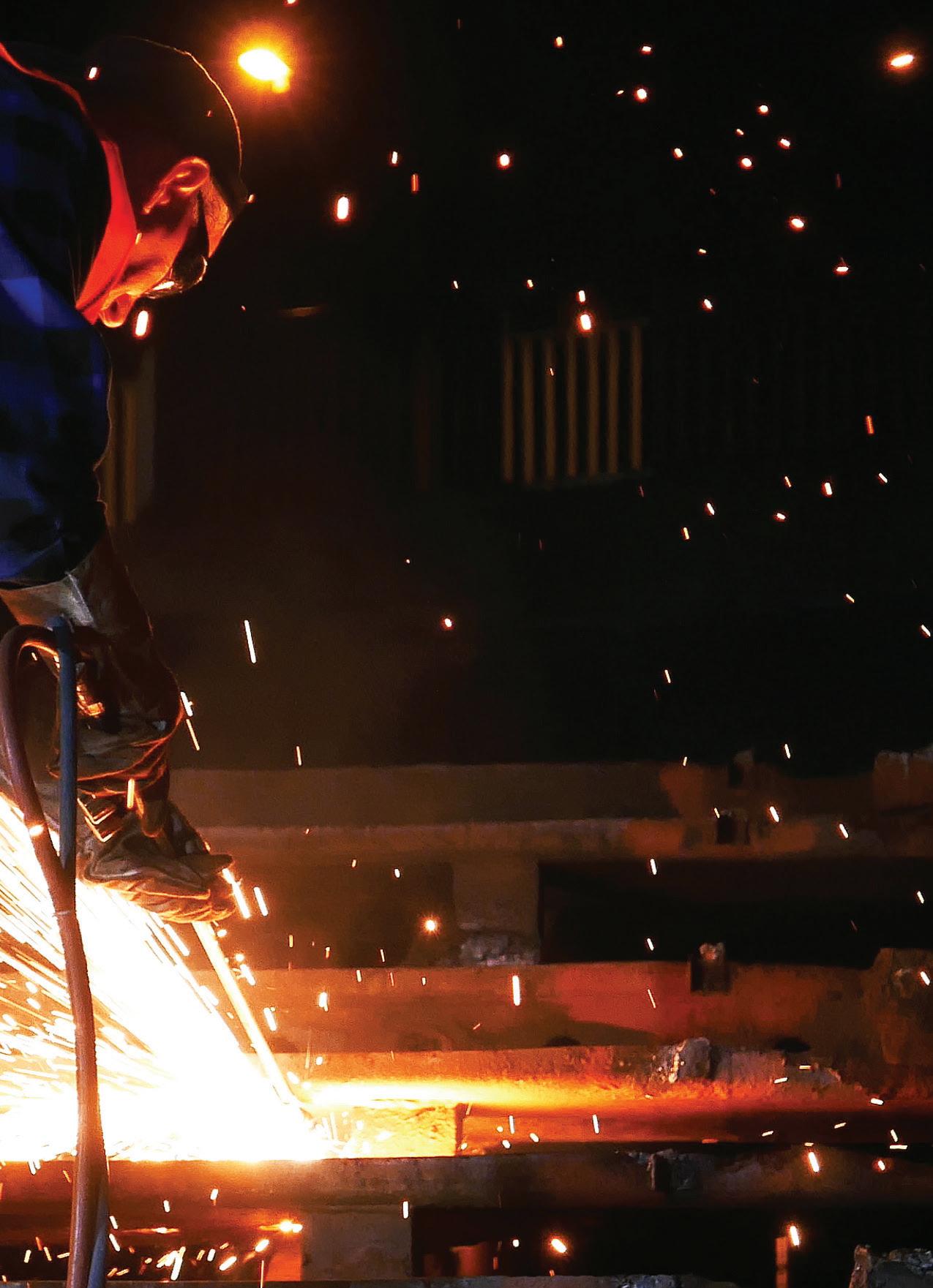
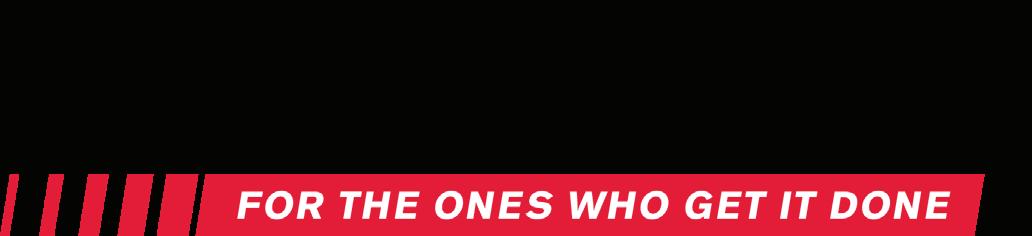
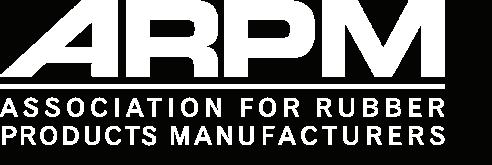
Robotics with the Sense of Touch
Four Key Pillars to Developing Internal Talent
Solving Design Problems Through Simulation
One of the wonderful things about living in this great country of ours is witnessing how people support each other in times of crisis. TV news scenes of great destruction caused by natural disasters or other unfortunate circumstances almost always are countered by human acts of heroism, generosity and unbelievable kindness. Those who have survived such situations often reflect upon the ways that the spirit and support of the community in which they live were the driving factors in getting their lives back on track.
The rubber industry is experiencing a time of crisis, and the ARPM community is reacting.
International entities are proposing to ban more than 10,000 PFAS substances in the REACH Restriction Dossier, despite the fact that a substantial body of scientific data already has demonstrated that fluoropolymers do not pose a risk to human health or the environment. To remove PFAS from the world of rubber would take extraordinary measures and ultimately would endanger the sustainability of many companies in the North American rubber industry.
The North American rubber industry is dangerously vulnerable due to its dependency on the overseas chemical supply chain, and this represents a security threat to our country and North America. Currently, over 40% of all critical rubber chemicals needed in the US – those used for curing (vulcanizing) and those used to protect rubber –are controlled through China’s manufacturing dominance. In some cases, we do not even possess the capability of producing some of these key ingredients, such as MBTS or dicumyl peroxide.
The current chemicals market for curing and protecting rubber represents nearly 1,995,000 tons, and a whopping 850,000 tons are controlled directly by China. If China unexpectedly slows production (name any reason), the current capacity infrastructure remaining within North America would not be capable of supplying the rubber industry’s growing needs,
Letha Keslar, ARPMand this would have devastating consequences both in the US and North America.
ARPM is working to change the perception of the rubber marketplace and raise the awareness of government representatives that these critical issues must be addressed. Senators, Congressmen and all leaders in DC must understand the importance of the rubber products industry.
No matter the size of your business, as rubber products business leaders, we are responsible for educating these decision-makers. Please set aside 15 minutes to connect with your state representatives and contact those who serve on your behalf. Contact the MADE IN THE USA office in Washington, DC (https://www.whitehouse.gov/contact/) and tell them the impact the broad ban on PFAS would have on your business and on the rubber industry, as well as the industry’s vulnerability because of the foreign supply chain.
If each rubber products company acts today, there will be an ocean of influence to positively impact the industry for tomorrow. n
“THE NORTH AMERICAN RUBBER INDUSTRY IS DANGEROUSLY VULNERABLE DUE TO ITS DEPENDENCY ON THE OVERSEAS CHEMICAL SUPPLY CHAIN, AND THIS REPRESENTS A SECURITY THREAT TO OUR COUNTRY AND NORTH AMERICA.”
By Lindsey Munson, editor, Inside Rubber 10
By Greg Vassmer, technical coordinator, ARPM
By Andrew
An interview with Gustavo Mosquera, vice president of operations, SIGMASOFT®
ARPM’s EHS Summit Scheduled for May 2023
ARPM Team
Executive Director Troy Nix – tnix@arpminc.org
Managing Director Letha Keslar – lkeslar@arpminc.org
By Kuehl, By Rick Arnold, By By Liz Stevens,Marketing Director Marcella Kates – mkates@arpminc.org
Analytics Director Tony Robinson – trobinson@arpminc.org
Analytics Lead Andrew Carlsgaard - acarlsgaard@arpminc.org
Director of Publications Susan Denzio – sdenzio@arpminc.org
Membership & Events Director Kaitlyn Krol – kkrol@arpminc.org
ARPM Officers and Board of Directors
President
Travis Turek, Bruckman Rubber Corporation
Vice President
James Wideman, MBL (USA) Corporation
Treasurer
Marel Riley-Ryman, Southern Michigan Rubber
Secretary
Joe Keglewitsch, Ice Miller LLP
ARPM Board of Directors
Rich Balka, Home Rubber Company
Bill Bernardo, Ebco, Inc.
Kirk Bowman, The Timken Company
Russ Burgert, Maplan Rubber Machinery
Aaron Clark, Danfoss
Joe Colletti, Marsh Bellofram
Randy Dobbs, Sperry & Rice
Ryan Fleming, Freudenberg-Nok Sealing Technologies
Doug Gilg, Continental ContiTech
Diya Garware Ibanez, Fulflex, Inc.
Seth Johnson, Zochem LLC
Donovan Lonsway, BRP
Jon Meigan, Lake Erie Rubber & Manufacturing
Mike Rainey, HBD Industries Inc.
Mike Recchio, Zeon Chemicals L.P.
Brandon Robards, Ace Extrusion
Vice President, Editorial: Dianna Brodine
Editor: Lindsey Munson
Vice President, Design: Becky Arensdorf
Graphic Designer: Hailey Mann
Published by: 2150 SW Westport Dr., Suite 101 Topeka, KS 66614 Phone: 785.271.5801
The rubber industry over the past four years has settled into its post-Covid-19 routines and protocols but, overall, it has remained a challenging time for human resources professionals who stand on the front line of recruiting and retaining the industry’s most valuable asset – its employees.
HR professionals are the first to connect with a potential employee who walks through the front door. They conduct and implement the onboarding process, set the tone for the company brand, trends and culture, build a sustainable workforce, and positively and proactively enforce a peoplecentered workplace – from management to the entry-level worker on the shop floor.
What was once known by HR professionals slowly is becoming a thing of the past. Loosening up on fixed job titles and specific job descriptions now has turned into a goal of not hiring just to fill the position, instead, it’s about creating employee balance, protecting customer needs and fighting for the future of the industry – all of which affect the bottom line. HR is leaning into a creative mix of old-school ways with new market trends when it comes to recruiting and retaining – from yard signs, partnering with the community and referral programs, to employee cross-training in job roles, flexible scheduling and bonus incentives.
The five HR professionals interviewed for this article have two things in common – to be front-line workers that inspire within their communities and company, and to innovatively build a strong employee base. All of them believe that if an employee has a reason and a “why” to perform the job every day, then nine times out of 10, the company retains its talent and skilled workers not for just a job to perform but for a career.
From the shadows of the back office to the front line, these HR professionals are sharing approaches and insights to attracting the attention of new employees, ways to handle onboarding and incentives, combating attendance woes, encouraging safety and, lastly, building a company culture that sticks.
From La Habra, California, VIP Rubber & Plastic Company has been manufacturing custom rubber extrusions, plastic extrusions, rubber sheet products, molded rubber products, plastic pipe and tubing in the US since 1961. Albert Levalle, VIP Rubber’s human resources manager, leads the company in its “old school” ways of recruiting and retaining employees with a company culture based on hard work, safety and respect. Levalle won’t be found at his desk but rather walking the plant facility, engraining himself in the action and connecting with employees. “I want to be on the floor where the action is at, always available to employees, accessible and within reach, my door is open,” he said.
Daniel Gifford, human resources manager for Bando USA, Inc., Bowling Green, Kentucky, and Sandy Burnett, human resources generalist and seasoned employee of more than 25 years, are proactively and methodically working to recruit and onboard quickly while strategically working closely with the 125 employees that are in it for the long haul. Gifford and Burnett do most of their hard days’ work from what they call “the heart of the facility” – their office, which resides right by the break room that has an influx of employees coming and going every day. Bando’s facility has been in operation for over 35 years and is a supplier of automotive and industrial power transmission and conveyor belts.
Garware Fulflex USA, Inc. (Fulflex), Brattleboro, Vermont, is a manufacturer of rubber sheets and elastic tapes, positioned in a small town along the Connecticut River where Anne Meyer, human resources manager, and her team of one, Pamela Savory, HR administrator, passionately work tackling labor market trends and setting aside time, no matter the hour, to give employees their full attention. Meyer spoke keenly about the labor struggles not just for Fulflex, but also for the community.
“We’re the only rubber manufacturer in the area. Not just our company but all businesses are struggling to hire and retain employees,” she said. “Between the companies in Brattleboro, we have a rotationalemployee base where one leaves us and goes to another company. It’s hard. But there are positive times when an employee leaves and we get to do an exit interview and understand it was not about Fulflex, but more about that employee being closer to family or just needing to make a living situation easier. There are times I get to guide employees to other companies of interest to get them where they need to be. The job can be challenging, although can be rewarding.”
Fernando Gauna is a human resource recruitment specialist at R.E. Darling Co., Inc. (REDAR), a composite manufacturing company in Tucson, Arizona, that prides itself on its employees and their dedication to producing quality products “because someone’s life depends on it.” Gauna said employees’ dedication is important to daily operations, so people who are recruited and hired are a critical piece to creating a company based on “quality over quantity.” Gauna said, “It’s important to REDAR to have data but also a culture that allows for sound decision-making when it comes to employees and the future of their employment. We benchmark ourselves with top-performing companies and want to be competitive in this tight labor market.”
Residing in Elgin, Illinois, Ebco, Inc., is a family-owned and engineered-driven company supplying OEM customers with elastomer solutions since 1951. Bill Bernardo, CEO, knows Ebco is a large company with a lot to offer new hires and current employees, and he believes in operating with flexibility and close communication. He said, “We try to maintain a small business atmosphere. We want employees to share the good and the bad, and we want those in the C-suite as well as myself to be available to listen.”
As a company, attracting candidates that fit the brand right from the start is crucial to getting them through the onboarding process and retaining them for years to come.
Meyer is versed in just how important company branding is. “The history is interesting,” she said. “Fulflex is owned by the parent company in India and is a woman-owned business. When I attend job fairs, I share the history and story of Fulflex with job seekers and post a stand-up sign that features our owner in an article on women in the tire and rubber business. It’s interesting because when this is mentioned to candidates, they say in question, ‘It’s a woman-owned business?’ It piques interest and gets the conversation flowing, a valueadded benefit for our company when recruiting.”
Meyer also pushes company-wide employee engagement in the community. She said it’s a win-win for creating company awareness and being visible to possible candidates, but also gives employees value outside of the facility and allows managers and teams to bond.
“Last August, we sponsored the 200 Backpack Challenge partnering with Brattleboro Auto Mall. It was a massive event with the community. The backpacks were filled with various school supplies and handed out to kids in the community who could not afford to buy supplies for back-to-school. Kids could also get a free haircut at the event. It was an outstanding public event with the Auto Mall, the community and our company,” she said “In addition, this past fall, Fulflex donated money to a food drive where every seat at the theater in downtown Battleboro housed a bag full of food. These community events are big for Fulflex!”
With the population thinning in Battleboro, Meyer looks to the surrounding states of New Hampshire and Massachusetts for a recruitment base, focusing on the gap between high school graduates and seasoned employees. She said, “Right
now, I’m targeting high school graduates and believe they’ll be the segment that will fill the entry-level machine operator positions. We’ll be partnering with the Brattleboro Development Corporation, which has the Pipelines and Pathways Program as they closely work with the high schools Windham County, Vermont.”
Through that partnership, Meyer will attend fairs in May and June and will step into several high schools to tap local talent and spread Fulflex’s story. As part of Meyer’s efforts, there has been a significant return for the company in finding graduate hires through an event on life skills held in the village of Townshend, Vermont, where students are hands-on learning and adapting to life scenarios, from changing a car tire to budgeting for car insurance – all of which shows that a career and being financially responsible are necessities in life. Meyer said, “Then we get to share the job opportunities right in their backyard, such as an entry-level position with Fulflex.”
REDAR saw an opening and decided to make a few minor adjustments to its new hire policy. “We increased our referral bonuses and changed our policy to allow immediate family members to work here,” Gauna said. “Our data shows us that the referral bonuses and hiring immediate family members has increased retention, and productivity also has increased.”
Gifford shared similar thoughts, “Bando saw the light when it came to the referral program including referrals from family, friends, relatives and current seasoned employees – we saw a difference in work performance, attendance and culture. But it doesn’t stop with referrals, Bando will continue working closely with the Chamber of Commerce in Bowling Green.”
Ebco, being a family-owned company, knows firsthand how important recruiting from local and state talent is to get depth across the company’s platform. Bernando said, “For new hires, we are very active in going to college recruiting events and when seeking a position that requires experience past an entry-level position, we sell our culture and benefits. Those two things must be buttoned up and sound to attract top-skilled talent.”
For years VIP Rubber has been recruiting through temp agencies, hiring walk-in candidates, placing ads in the local newspaper, posting signs in the front of the building and looking deep into its community for talent – methods that are still working well for the company. Levalle said, “We’re old school from newspaper ads to yard signs. We’ve had so many people coming in the front door, averaging three people a day, along with phone calls inquiring about job opportunities. And for us, it’s also financially better because, at this point, the temp agencies are a thing of the past. It’s all working.”
Similar to REDAR’s focus on a referral program, Bando relies heavily on its current employees to refer friends and relatives. For example, a tenured employee recruits his son to work for the company – it is with a high percentage that this referral sticks vs. a temp employee. Gifford said, “We’ve had a ton of success with the referral bonus program.”
On the flip side, even though temp employees aren’t where Bando would like to spend its time or investment currently is housing 12-15 company temps who have an opportunity to grow into a production position. Gifford said, “Bando has an amazing tenure of 20-30 years to retirement with several of its employees. At some point, we’re going to start feeling the effects of a lot of people retiring and we’re trying to build up that middle band of people with experience who could eventually become the future managers.” It’s the middle-aged employment gap that Bando would like to fill immediately. And, to fill the gap, Bando works closely with Bowling Green’s Chamber of Commerce.
Bando’s recruitment strategy is based on two approaches:
● Fill entry-level temp positions – These positions do not take a lot of training; the job role and responsibilities are easy to learn, and temp employees can step into the job quickly. The goal for the temp employee when the job hours expire is to move into a direct/full-time position.
● Fill direct, full-time positions – These positions are for employees directly hired for a production or general role, where they are onboarded, trained and released within a month to do the job on their own. These positions could earn incentive bonuses, attendance awards and safety certificates.
“Bando recently had an employee who referred three of his friends, and they all work for the company in full-time indirect positions. The employee referral bonus program has been our best source of candidates over the past six months,” Gifford said.
It is important not to undervalue the need for a benefits package for full-time and part-time employees. A wellrounded benefits package including healthcare, wellness, dental, vision, life insurance, disability and retirement drives employee behavior the moment an employee is recruited and continues to be a driver through the years. Benefits make up about 30% of an employee’s compensation according to the U.S. Bureau of Labor Statistics. It is the benefits package that gives employees a work-life balance.
Lavelle said a full benefits package is essential in recruiting. He continued that benefits heavily weigh on a candidate’s decision to accept an offer from a company or to leave. “We give a full benefits package with insurance, vision, dental
and life insurance,” he said. “VIP pays out the majority of it. We used to pay 100% but noticed that when you pay 100% employees don’t have a stake in their job and the company. So, in turn, we decided that it was important to add immediate value to the position an employee is being hired for and requested a small buy-in to the benefits package. If the employee buys in, they will use the benefits appropriately and feel valued in the process. We invest in the employee; the employee invests in us.”
Ebco is competitive among other manufacturing companies in Illinois when it comes to its wage rates and benefits package. Bernardo shared, “We pay at or above published pay rates, with the opportunity for employees to earn bonuses through their 90-day reviews.”
REDAR is staying ahead of the curve by conducting compensation analysis against other manufacturing companies in Arizona, helping to stay competitive in pay and benefits for all positions. “We have increased our starting pay to $16-$17 per hour,” said Gauna, “and the minimum wage for Arizona is $13.85. We benchmark ourselves with top-performing companies and want to be successful in this tight labor market.”
As for Illinois-based, Bando, Gifford said, “We try to get new hires in the door quickly, streamline several items such as background checks and drug screenings and I believe that’s helped us keep from losing a few people. We get new employees trained and, in their roles, allowing them to start feeling valued and earning a wage along with benefits.” For Bando, it takes an estimated one month to get a new hire fully in the door and trained to do the job on their own.
Recruitment is key for human resources because finding and acquiring talent is essential in meeting company goals and succeeding as an organization. By building a recruitment strategy and a competitive benefits package, companies can ensure a workforce that improves company culture, adapts to changing environments, reduces turnover and positively hits the bottom line. Together, the rubber industry will continue to make improvements and find solutions to the volatile labor market. “It’s how you treat people from the moment you meet them. It’s a simple recruiting strategy – a smile and a conversation can give a person the extra push to where they are meant to be,” Meyer said. n
Last issue, the column discussed the connection between dynamic oil seals and the (mostly) metal shaft surfaces they contact. In one corner is the seal – which, through the magic of rubber formulation, design and wear characteristics – acts like a small pump. In the other corner is the surface on which the seal slides, either helping or hindering this sealing magic. Rubber processors need this two-part system to act to keep oil inside and air outside.
There is a long list of enemies to this arrangement, but the focus is on one: the shaft lead. Can can indirectly manufacturers affect the quality of the shaft since it is provided by someone else, but rubber processors can measure and understand some vital characteristics; one of them, the “lead” or “twist,” is the most important. Unfortunately, this characteristic is measured in a non-analytical way, using a piece of quilting thread and a weight. Using the thread method is a lot like defining a “meter” as one ten-millionth of the shortest distance from the North Pole to the equator passing through Paris, assuming an Earth flattening of 1/334, which is, in fact, the original 1790 definition of a meter. 1 The method could use some improvement.
There are more modern ways to measure lead. Contact profilometers drag a diamond tip across the shaft surface while recording how it moves vertically. If the resulting graph is wavy like a screw thread, chances are good there is lead on the shaft. Single-trace contact methods are not enough. Seals leaked on shafts even when there was no wavy trace. If several traces are taken close together, it is possible to match the peaks from one trace to the next and see if a given peak moved slightly left or right. That catches a few more bad shafts, but not all. Only the thread and weight technique seemed to catch all types.
Enter optical systems – shining a light source on the shaft and recording the reflection (or perhaps the diffraction) of the light, the user will get a two-dimensional “patch” of
shaft surface to analyze. Do that enough times around the full circumference of the shaft and it is possible to generate a very complete picture of the segment of shaft along which the seal slides. The two primary optical methods are white light interferometer and scatterometry. These methods provide an image of part of the shaft surface and can provide depth and statistical surface structure information. To convert this height data to the shaft twist requires some mathematics and software. The vendors of these systems have taken the images generated and applied Fourier transform techniques that extract embedded screw-thread-like features and calculate their direction and depth. From this can be derived the volume of anticipated fluid movement, also known as leakage, for the most part, but not completely.
So here is where a good standards organization can get involved. There are four to five vendors providing equipment promising to measure lead using these techniques. The mathematical techniques mostly are unique to each vendor, and each has strength in identifying a specific type of lead. But the techniques do not always correlate with the original, trusty thread and weight method. Rubber processors have new technology that is less subject to error and more repeatable attempting to replace a well-tested but error-prone technique, but so far, without finding correlation in the results between the two, ARPM cannot yet recommend it as a standard. But rubber processors can do something about it.
In December last year, the ARPM Seal Committee began a project aimed at testing the more modern, optics-based shaft lead devices and software to determine whether there is a correlation with the thread method and their repeatability. Vendors of the new techniques have been pulled in and will provide sample shafts made with techniques known to provide both good and bad shafts for them to test. Along with establishing the validity of the new techniques, the goal is to provide a broad background of how the analysis algorithms work and how to properly prepare samples. Once concluded, an update will be given to OS-1-1 with a valuable addition representing a more robust, less error-prone technology. n
References
1. https://en.wikipedia.org/wiki/History_of_the_metre#
How do industry executives view the US rubber industry – a diverse sector that produces a wide range of rubber products, generates billions of dollars in revenue and supports thousands of jobs – going into 2023? ARPM’s 2023 State of the Rubber Industry Report aimed to answer this query by surveying leaders across 86 rubber processors for their thoughts on various topics, addressing 2022 fourthquarter results and optimism for 2023. One of the critical factors influencing the outlook of the US rubber industry in 2023 is the state of the global economy at the end of 2022. As the world continues to recover from the pandemic, there is hope that the demand for rubber products should increase as specific industries return to pre-2020 levels of production, especially in segments such as automotive and construction.
At this time last year, rubber processing executives viewed 2022 with optimism, accompanied by solid momentum in several major business performance indicators at the end of 2021. Fortunately, the rampant supply chain issues from 2021 began to subside in the second half of 2022, allowing the industry to see continued growth and forward progress throughout the year. However, although most Q4 performance metrics vaulted the sector across the finish line a year ago,
several Q4 2022 indicators related to sales and operations may cause processors to temper expectations for 2023.
Growth potential for the next year likely is to be strongly influenced by 2022 sales performance, with momentum coming from how it ended the year before. Compared to the end of the previous year (2021), where 54% of respondents reported increased sales going from the third to the fourth quarter, 2022’s final quarter only saw 41% experience a sales increase from the prior quarter. The sales increase in 2021 primarily was due to new programs or increased volume in current programs from existing customers. In 2022, most increases came from new customers – potentially signaling an expansion of the industry’s client base over the past year. Despite the decline in sales momentum at the end of 2022 compared to how 2021 ended, executives still forecast optimism, as 89% of respondents indicated sales increased overall in 2022, and 78% anticipate growing sales in 2023. Also, 85% reported 5% or higher profit margins in the past year, an improvement compared to 77% in 2021 (Chart 1).
On a less optimistic note, rubber processing business leaders also face continued labor issues – a consistent struggle even before the pandemic, and one that may impact the industry’s performance in 2023. Participants reported some red flags in the fourth quarter regarding labor, particularly around rising cost pressures on entry-level wages (partly due to scarcity and doubledigit inflation). However, the number of open positions and turnover rates stabilized slightly compared to the fourth quarter of 2021. Though processing leaders have realized some stabilization with logistics and raw material challenges, the costs of having
enough employees to perform the work likely will cut their bottom line (Chart 2).
Other factors influencing the outlook of the US rubber industry in 2023 are technological innovation and strategic investments. Developing new materials, manufacturing processes and automation could improve the rubber
segment’s efficiency and quality, making the sector more competitive globally. According to the survey respondents, these remain topics at the top of the list of potential investments over the next 12 months, along with expanding their production capacity and capabilities. Environmental regulation also may play a role in shaping the future of the US rubber industry as concerns about climate change and pollution continue to grow. As a result, rubber manufacturers may be pressured to adopt more sustainable practices and reduce their environmental footprint –another area where processors expect to see innovation (Chart 3).
Overall, the outlook for the US rubber industry in 2023 will depend on various factors, though the state of the global economy is the most important. From a sales perspective, an underwhelming end to 2022 signals there may be headwinds going into the new year. However, improvements in the supply chain and the labor market could help boost profitability for producers if economic conditions improve and inflation slows down compared to the previous year’s highs. Regardless of the economy’s direction, the industry must remain resilient as it navigates this “new normal” full of uncertainty and speculation to take full advantage of more prosperous times that hopefully are around the corner. n
To discover the latest outlook of the US rubber industry, obtain ARPM’s 2023 State of the Rubber Industry Report at www.arpminc.com/publications.
Flow analysis simulation allows engineers and designers to test, diagnose and improve the injection molding process, with the end result of optimizing production output. The simulation shows how the resin will fill the mold during the injection molding process. By understanding how the resin fills into the mold, designers can be in a better position to react quickly and anticipate mold specifications that may be problem areas – issues affecting the mold construction during production. Taking a mold from good to great is the basis of the simulation, with the result of producing a high-quality product, saving time and reducing overall mold cost.
Virtual molding simulation allows a realistic 3D simulation of flows, heat flow and material characteristics for injection molding processes, creating reliable information that gives a base for reliable decision-making. Here are five common questions that arise among rubber processors.
Simulation has an impact on manufacturers – it allows them to work out ideas, problem-solve and resolve any potential issues that occur while designing the part and the mold. Knowing where to put a gate or heaters to help reduce filling or curing issues can be very helpful before molding. The simulation process helps and assists manufacturers in getting away from “hoping” that the project will work to “knowing” that it will. The goal in simulation is to get to first-shot success so that tooling doesn’t need to be reworked during the production cycle.
The biggest factor for rubber manufacturers is confirming the design criteria that is very hard to change or alter after cutting the tool steel. One of the design factors is the gate location, especially on molds that are made up of multiple cavities. Once the gate has been placed and the runner designed, it’s very difficult to change these criteria without starting over. Making sure manufacturers know where the vents need to be placed, where the weld lines are located and how the parts fill can be very important in any mold design.
Secondly, being able to understand the size of the runner would be optimal. If the runner can be reduced in size, then rubber manufacturers can save material and the overall cost of each part. From the mold design, it is critical for manufacturers to select the right mold materials and to get heaters laid out correctly with proper wattages, which in turn produces an even temperature distribution and consistent curing times.
Three main inputs should be assessed when evaluating a simulation: geometry, material and process.
From the geometry side, rubber manufacturers should locate the area where the gate should be placed in the part to reduce
air bubbles. Locating where to gate the part is navigated by aiming to push the air to areas that easily can vent the air out of the mold.
Flow analysis simulation can evaluate how easy or how hard a material is to push through the cavity, and how the material cures. In a simulation, it’s easy to change the viscosity of a material and make a material cure faster or slower. This information can be used to develop a material that will fit a specific need. On the flip side, there’s an opportunity during the simulation to create a process that helps to utilize existing material to fit specific needs.
Process in the mold flow simulation allows molders to see if there’s the use of too much pressure, which can lead to longer fill times or exceed the clamp force. With longer fill times, it is important to make sure that the part is not cured too much, which would lead to scorching or no fills. Temperature and fill speed can be adjusted to understand this better.
The inputs are very important to get good results from simulation, and that goes back to material data, geometry and process. In order to replicate an existing mold in production, a high level of detail on all these topics is needed so that no assumptions are made. While in the design stage, more assumptions can be okay since there might not be a worry about considering every little detail.
SIGMSOFT® offers training to support manufacturers in how to use a simulation and merges it with how to make good decisions once data analysis is available from the simulation. The main point is that not every simulation needs the highest level of detail to get what a manufacturer wants out of it.
For example, if a manufacturer is worried about its mold curing time, a design of experiments can be run with different mold temperatures to understand the change it has on the curing time. Knowing the range can be important when quoting, while simulation software may be used to evaluate the legitimacy of a project. Later, the manufacturer and simulation software team can work on designing the tool to be able to meet the temperatures observed earlier in the process and match the desired curing time from when quoting occurred.
There has been an increased interest in what is happening to the mold – not just looking at the temperature of the mold but the stresses that are being observed and how those can impact the longevity of a tool. If components of the mold are breaking, evaluating the part is important – but only part of the question is being asked. This is a great direction for the industry because molders are being more considerate of everything that is important in a successful project. n
Since 1998, SIGMA, headquartered in Aachen, Germany, has been the pioneer and pacemaker of injection molding simulation technology. SIGMASOFT® Virtual Molding is developed in cooperation with MAGMA. SIGMASOFT® modules allow injection molders the ability to simulate their process and leave traditional trial-anderror in the past, using an intuitive graphical user interface and integrating multiple process-specific models and 3D-simulation technologies. For more information, visit www.sigmasoftvm.com
Alpha Technologies, Hudson, Ohio, a leader in polymer testing and analysis, announced its collaboration with The University of Akron (UA) in a multifaceted program that includes scholarship support, equipment donation, training and participation in the University’s co-op program. Alpha Technologies will donate a $10,000 scholarship each year for the next five years to the UA School of Polymer Science and Polymer Engineering. Additionally, the company will donate a new Premier® Rubber Process Analyzer for the University’s use. Alpha Technologies also will participate in the University co-op program and offer free rheometry training once per year to students. These initiatives are part of Alpha Technologies’ strategy of delivering deeper material insights for its customers and gaining new insights from academia. For more information, visit www.alpha-technologies.com
DESMA, Hebron, Kentucky, is a complete systems provider in North America for rubber injection molding solutions. DESMA is setting new standards for horizontal rubber injection molding machine capability with the release of its SEALMASTER+ machine series. This new machine series was unveiled to the market in late 2022, specifically for precision elastomer seals that have unique requirements benefitting from the machine’s stability, speed and precision. The SEALMASTER+ series is offered in 335 and 450 US tons and revised with optimal operator access and ease of maintenance utilizing top-quality materials and components. For more information, visit www.desma-usa.com.
Orion Engineered Carbons (OEC), Senningerberg, Luxembourg, a specialty chemicals company and global supplier of carbon black, has announced it signed new distribution agreements with Divsa and Terrachem S.A. to represent OEC in Central America and the Caribbean. Divsa, a Barentz company based in Guatemala, will represent OEC’s specialty and rubber carbon black products in Central America from Belize through Panama. Terrachem S.A. is based in the
Dominican Republic and represents OEC’s specialty and rubber carbon black product lines throughout the Caribbean. For more information, visit www.orioncarbons.com
ASTM International, West Conshohocken, Pennsylvania, is committed to serving global societal needs with impacts on public health and safety, consumer confidence and quality of life, and has released an approved standard from its recovered carbon black committee (D36). This standard provides a test that will help to differentiate products and provide a quality control tool for producers and users. Recovered carbon black (rCB) is a recycled product made from end-of-life tires. The new standard (to be published as D8474) describes a thermogravimetric (TGA) technique to determine the amounts of organic residue, overall fixed carbon content and ash content in recovered carbon black. This effort directly relates to the United Nations Sustainable Development Goal No. 12 on responsible consumption and production. For more information, visit www.astm.org
Grand River Rubber and Plastics, Ashtabula, Ohio, a manufacturer of lathe cut washers, tubular gaskets, flat drive belts and wastewater treatment membranes, has acquired the lathe cut gasket and seal division of ASC Engineered Solutions, LLC. All orders are set to be produced and shipped out of Grand River Rubber’s facility starting July 1, 2023. For more information, visit www.grandriverrubber.com.
H.M. Royal, Trenton, New Jersey, a provider of raw materials and specialty chemicals, has hired Quinn Wierckz as a technical sales manager covering North Carolina, South Carolina and Virginia. With more than 10 years in the rubber industry, Wierckz will work to strengthen current customer and supplier relationships, while also aiding in identifying new opportunities to expand customer and supplier bases. A graduate of Ferris State University, he has an A.A.S. in industrial chemistry technology and a B.A. in chemistry with a minor in polymer material technologies. For more information, visit www.hmroyal.com n
The Environmental, Health & Safety (EHS) Summit is designed to share best leadership and safety practices with industry professionals hoping to achieve world-class safety within their companies.
This one-of-a-kind learning and networking conference will focus on uniting manufacturing executives from across the United States. Attendees will focus on best practices in environment, health and safety along with becoming a better leader. This Summit promises to provide high-level safety professionals with implementable ideas they can take back to their facilities to improve their operations and achieve world-class safety.
A full schedule is available at www.arpminc.com/ehs.
"This was my first safety summit. Expectations were unknown, but from the opening greeting, the Summit made me look at myself for my 'why' and the ways I lead safety at my organization. It provided me with new insights and ideas to what is happing in the industry, and the opportunity to meet and discuss with peers on similar topics. The resources and networking at the EHS Summit is one of the greatest assets."
Safety is not a one - person job, It is a commitment from each person at your company. Therefore, the EHS Summit is open to everyone.
Why EHS?
Safety should be a top priority at your organization, and continuously improving your safety program is essential to protect your employees.
When is it?
Columbus, OH
Bruce Whitney is the program director for Integrated Community Solutions to Active Violence Events, an Arizonabased charitable foundation dedicated to traumatic event prevention and preparedness training. As one of the founding members of Arizona’s Disaster Medical Assistance Team (AZ DMAT-1), he also presently serves as its deputy team commander. A passionate educator, Whitney has been actively teaching public safety to healthcare professionals, military personnel and the community for over twenty-five years.
Visit www.arpminc.com/ehs
Don’t Miss the Safety Awards Recognition!
George Hupp is a retired criminal investigator, who currently volunteers for Integrated Community Solutions to Active Violence Events and runs a small life-safety consulting and tactical training company, Heloderm LLC. Hupp, an avid public speaker, shares his life experiences and knowledge on subjects as diverse as first aid, crime prevention, active shooter response and government ethics. He is an ASHI/HSI certified instructor, an NAEMT-certified Tactical Emergency Casualty Care and Tactical Combat Casualty Care instructor and a nationally registered EMT. Hupp has been teaching civilians, police and the military since the 1980s.
The 2023 Safety Awards recognize companies in the manufacturing industry that have achieved excellent safety techniques that go beyond the average regulations. The awards will be given out based on OSHA 300's Log of WorkRelated Injuries and Illness statistics and Safety Best Practices.
The industry likely has seen more upheaval in commercial contracts in the past five years than it did in the 20 years that preceded that period. It is no coincidence that recent history has seen an economy beset by unprecedented challenges: pandemics, labor shortages, energy crises, transportation challenges and a supply chain that has come unhinged. The risks and uncertainties that these circumstances have created have had a ripple (or, perhaps more accurately, a tidal wave) effect on the landscape of commercial contracts, as businesses attempt to adjust to both the short-term and long-term ramifications that have resulted. How companies document commercial relationships has shifted in a number of important ways.
Not surprisingly, one key contracting objective is locking down mission-critical commercial partners. One would presume that this always has been a goal but, frankly, it recently has taken on a newfound importance and fewer businesses are asleep at the wheel on this front. Longer-term agreements (with thoughtful renewal provisions) increasingly are common. Termination provisions are receiving more scrutiny as the need to terminate for performance issues increases and, ironically, the desire to actually end a relationship decreases as viable alternatives become harder to find.
Those on the vendor or supplier end of the equation are experiencing unparalleled leverage to increase prices. Buyers in no position to lose a supplier are finding it difficult to flex contractual muscles and resist increases in prices. The axiom seems to be that a more expensive supply is better than no supply at all. Sellers either are negotiating deals to boost prices or entering into contracts that contemplate the ability to increase pricing in order to pass through the volatile nature of labor, raw material and utility inputs. Similarly, agreements more frequently shift shipping and transportation costs to the purchaser as those variables become ever more expensive and volatile.
More forgiving delivery schedules and quantity terms also are progressively becoming more common. Many sellers historically stuck with “requirement” contracts or similarly onerous quantity terms are seeing a heightened ability to wriggle out of those arrangements.
Forecasting needs rather than preset quantities or unilaterally determined purchase order quantities is one strategy to reduce exposure to quantity targets that just may not be doable. And, either by shifting transportation obligations to the buyer or
loosening obligations, sellers are reducing risks to a highly uncertain logistics environment. Passing through increases in shipping costs to customers or shifting that financial obligation altogether are potential avenues.
A less lenient payment environment also is increasingly on display. Paralleling the heightened ability and willingness to raise prices, suppliers also are less reluctant to insert late payment provisions and the ability to suspend work or change payment terms (to COD, for instance) if customers fail to timely pay (or otherwise improve such terms that existed but which historically were ignored).
These challenges seen in the current sales environment have been destabilizing (and even destructive) forces from an operational standpoint and also have created an assortment of legal challenges. There has been unprecedented uncertainty as to a business’s ability to perform, its vendor’s ability to perform and whether its customers actually are ready for it to perform. As a consequence, force majeure provisions have crept way out of contractual boilerplate and regularly are front and center in commercial relationships (and disputes).
Force majeure provisions, representing a shield against contractual nonperformance when unexpected circumstances present themselves, proved to be worth the weight in gold as the marketplace progressively became more squirrely over the past several years. Some businesses were shocked to find those provisions did not give an “out” for which the business had hoped. Other businesses were thrilled with the “get out of jail free” card it offered, and still other businesses were left scratching their heads trying to sort out if (and how) such terms fit their situation, if at all. Ill-conceived and rarely considered force majeure provisions are the rule, not the exception, exacerbating consternation over the pragmatic meaning of these provisions.
Smart businesses have reviewed their form contracts and those of their vendors and customers to refine them to fit challenging new environments – ensuring pandemics, national health crises, governmentally imposed shutdowns and alike were covered. Efforts were made to be certain businesses actually knew what it meant as a practical matter if a force majeure provision was triggered (and to rework if the business was landing on the wrong result).
Another recent phenomenon that has impacted commercial contracting has been a spike (at least in interest, if not in
actual repositioning of operations and supply chains) of reshoring. Businesses have been forced to consider more holistically where they and their suppliers are located and the potential benefits of relocation domestically. But taking advantage of reshoring requires a revisiting of contractual relationships to accommodate any reworking of supply chains. And, as a forward-looking matter, it increasingly has become imperative to ensure that the contracts one has in place are flexible enough to actually allow for reshoring if and when any such initiative is rolled out.
On the most basic level, this business climate has required that companies scrutinize how they view their contracts and contractual affairs. The upheaval has been great, and business as usual just will not cut it anymore. Template or form contracts must be reviewed and reworked to ensure they pass muster and accommodate the challenges presently faced. Businesses also are pushing back on problematic terms that lock them into assumed circumstances that recent history tells us are not safe to assume for long. The once sleepy arena of commercial contracting is more regularly the subject of keen attention and vigorous activity.
It cannot be denied that the past several years have been challenging in the variety and scope of uncertainties presented to the marketplace. That said, where there is uncertainty there is opportunity; in this case, the opportunity to ensure that contractual relationships are state-of-the-art and ideally positioned – positioned to quickly and painlessly accommodate changes, recognize the volatility of pricing, alleviate the risk of an unpredictable supply chain and maneuver around governmental regulations and restrictions. The wisdom of taking action to stay ahead of this changing environment, including developments businesses cannot forecast today, is perhaps the only inevitable feature of commercial contracting in a new world. n
Josef Keglewitsch is a partner with Ice Miller handling complex corporate and business law issues for both private and public companies, with a focus on and extensive experience in mergers and acquisitions, general corporate counsel, complex commercial relationships and entrepreneurial legal issues. Keglewitsch graduated from Kalamazoo College in 1993 with his Bachelor of Arts, magna cum laude In 1996, he earned his juris doctor from Case Western Reserve University, cum laude. For more information, email Josef. Keglewitsch@icemiller.com or call 614.462.2279.
Led by Industry Expert Instructors with Over 140 Years of Experience
Seals Product Design and Manufacturing
If you are involved in the design, quality, sales, or manufacturing of rubber articles, and would like to know why it works not just when it works, this is for you!
June 5-9, 2023
Columbus, OH
Training includes:
comprehensive training in rubber science, product seal design, and reproducibility
one-week intensive course not available anywhere else copies of ARPM Product Standards and MO-1 The Rubber Handbook
Space is limited for this in-person class. Register today!
Moods are shifting as 2023 gets underway. At this juncture, it is as easy to find a pessimist predicting a deep and long recession as it is finding an optimist asserting the downturn will be mild. Why the variability?
The easy answer is that some very significant motivators for the overall global economy have started to change, and nobody is quite sure how real these changes are. The fundamental question through all of 2022 was what to do about inflation. The rate had exploded to levels not seen in 40 years and, at this stage, these numbers still are high – but not as high as they have been. The assertion is that global inflation started to peak in the fourth quarter of last year, and the data suggests that this is true. The latest CPI showed inflation down to 6.5% and, just about a year ago, it was at 9.2%. The wholesale inflation rate fell by 0.06% when the expectation was for a fall of about 0.1%. There have been declines in the producer price index, commodity prices and even shipping rates. The inflation rate is by no means low –the Federal Reserve watches the performance of the Personal Consumption Expenditures (PCE), and it has dropped to around 4.4% (the target is 2.0 to 2.5%).
Why does all this matter to the manufacturer? Beyond the obvious reason that it means that prices for inputs are slightly lower, there is a connection between inflation and the interest rates that are set by the central banks. The Fed has indicated that it will slow and even halt hiking rates when it determines it has done enough to break the back of inflation.
Has that point been reached? The latest statements from the Fed suggest it is looking at no more than a quarter-point hike at the next meeting, and it was just a month ago when the consensus view was for a half-or even three-quarter-point hike.
Generally, the central banks (including the Fed) use employment as their indicator, but the job market has been skewed by the chronic worker shortage. This has been obvious in the manufacturing sector. By this point, many in the industrial community would have been laying people off, but they are reluctant to lose the trained and skilled people they had to work so hard to find. This has meant a delay in the employment gauge, and the banks are looking at other indicators to determine whether enough has been done.
One of these is the performance of the Purchasing Managers’ Index, and the US is now down to 46.6. Globally, there now are 22 nations that have fallen below that 50 line. Two of the most notable exceptions have been Mexico (51.3) and India (57.8). Canada is not all that far from expansion with a reading of 49.2. India has been the big winner of late. It always has been understood that India can make whatever China can make; its Achilles heel has been the country’s transportation infrastructure and the notorious bureaucracy. The supply chain mess that has overtaken China has allowed nations like India to grow their export business despite those inhibitions.
Obviously, interest rates matter, and now there is considerable debate over what they might look like in the months to come. There still are those that predict rates at 5.0% or even 5.5%, but many are asserting they will not go that high. The trigger for this reassessment has been the erosion of inflation, with many indicators pointing toward that easing. Wholesale inflation fell more than expected, the Germans have seen their Producer Price Index fall, energy prices are down and so are shipping rates. Inflation still is high and at levels not seen in close to three decades, but the trend has been in a direction that has the markets believing central banks are close to halting interest rate hikes. If past patterns hold, that means rates could start heading down again as soon as the coming summer.
Manufactoring is very sensitive to the developments in the oil and gas sector, and here the news has been better as well. The US is set to produce between 13 and 14 million barrels a day –this would be a record. The US level of consumption is now at about 20 million bpd, which is down from 24 million bpd just a few years ago. Gas production likewise is up, and prices are expected to fall and stabilize. The Energy Information Agency predicts West Texas Intermediate prices to be in the high 70s and low 80s. That translates into gasoline at around $3.60 a gallon nationwide and diesel at around $4.00. This is down from the averages in 2022. Natural gas prices have been falling for weeks and reached the lowest levels since 2021, due to the warmer winter weather and the reduced demand from Europe.
Canada and Mexico also are looking to their central banks for guidance. The Bank of Canada is hiking rates to a peak of 4.5% – the highest seen in years. At the time BoC set this new rate, it also commented it was not going to hike any further (unless
additional inflation pressure is seen). The message from the BoC is that Canada’s economy still is close to overheating and still has the resilience to handle more hikes, but the BoC thinks that enough has been done to slow the economy down. The commodity surge has faded a little, but oil prices still are high relative to what they had been. Natural gas prices are falling quickly. The unemployment rate remains very low, and this still is a marker as far as the BoC is concerned. Until the jobless number climbs, there is a sense that rates can go up a bit higher. This hike is expected to be followed with a pause. Inflation fell to 6.3% in the last reading, but that still is three times higher than would be preferred.
Mexico is seeing higher inflation in contrast with the US and Canada and that has Banxico considering another rate hike in February. The inflation rate had been dropping but has risen to 7.85% – well past the target rate of 3.0%. The interest rates have been shoved past 10% and may jump a bit more at the next meeting. Three factors seem to have been driving inflation and certainly are familiar to the US and Canada. Labor rates are climbing for skilled and trained workers and have spurred consumer spending. Then there is the rise in commodity prices (especially food). Finally, there has been supply chain pressure
even as reshoring and nearshoring accelerate. Many items remain in short supply, and that results in more price pressure. There is some concern regarding housing. The drop in demand for single-family housing has been dramatic – permits are off by over 20%. At the same time, demand for multi-family has expanded, with permits up 11%. The demand for plastic often ebbs and flows with construction, and that has been good news for the last few years but now is threatened by the single-family slowdown. The good news is that commercial construction has started to see a rebound – even for the muchmaligned office building – as more businesses demand a return to the office. n
Chris Kuehl is managing director of Armada Corporate Intelligence. Armada executives function as trusted strategic advisers to business executives, merging fundamental roots in corporate intelligence gathering, economic forecasting and strategy development. Armada focuses on the market forces bearing down on organizations.
More information: www.armada-intel.com
May 24-25, 2023 – EHS Summit
June 5-9, 2023 – Seals Product Design and Manufacturing Training
June 7-8, 2023 – Sales and Marketing Forum
August 2-3, 2023 – Human Resources Forum
September 18, 2023 – Building Leaders of Character
October 4-6, 2023 – Benchmarking and Best Practices Conference
November 9, 2023 – Stockwell Elastomerics Plant Tour
November 15-16, 2023 – Finance Forum
For the most up-to-date information and to register for events, visit www.arpminc.com/events.
ARPM’s Annual Environmental, Health and Safety Summit is being brought back in person in 2023!
The EHS Summit held May 24-25, 2023, in Columbus, Ohio, will highlight best safety practices that attendees can take back and implement in their organization.
The keynote presentation, Stop the Bleed, will welcome trainers Bruce Whitney and George Hupp to the stage. During this two-hour, hands-on training course, attendees will learn to recognize life-threatening bleeding and act quickly and effectively. Attendees will leave this course empowered to make a life or death difference when a bleeding emergency happens, a course completion certificate and the opportunity to earn continuing education credits.
To read more about the keynote presentation, view the agenda and register for the event, visit www.arpminc.com/ehs. Registration is limited.
ARPM is excited to announce one-week intensive training courses through its new program, the ARPM Training Academy. The Seals Product Design and Manufacturing course is the first session and will be held June 5-9, 2023, in Columbus, Ohio.
This one-week intensive course provides comprehensive and consistent training in rubber science, product seal design (for static and dynamic sealings) and producibility. This course on in-depth principles of design is not available anywhere else in the industry and is taught by industry professionals with over 140 years of combined experience. For more information or to register, please reach out to Letha Keslar at lkelsar@arpminc.org
ARPM’s next plant tour will be on Nov. 9, 2023, in Philadelphia, Pennsylvania. Stockwell Elastomerics is an employee-owned business, and the leadership team will discuss its ESOP, continuous improvement initiatives and safety best practices.
To learn more about this event and to register, visit www.arpminc.com/events Come and meet fellow ARPM members and improve your business’s bottom line!
ARDL
Akron Rubber Development Laboratory (ARDL) is a leading international laboratory dedicated to providing testing, development and problem-solving services to all facets of the rubber industry. ARDL always is looking for ways to help impact ROI; therefore, all ARPM members receive preferred pricing on services. Discounts may include, but are not limited to:
● Physical and Mechanical Testing
● Chemical Analysis
● Shelf-Life Predictions/Fluid Aging
● Automotive Specification/Compliance Testing
● Dynamic/DMA Testing
● Electrical Testing
● FEA
● Flex-Fatigue Testing
● Compression Stress Relaxation
● Failure Analysis
● Formula Reconstruction
● Chemical Analysis
● Microscopy
For more information, visit www.ardl.com.
DESMA is a supplier of rubber injection molding machines, tooling, automation and turnkey systems. DESMA’s Hebron, Kentucky location is its headquarters and the home of its North American Manufacturing Center (NAMC).
The NAMC is part of the DESMA Global Mold Shop. This is a key advantage to customers in search of custom-designed- and-built molds and cold runners for the efficient production of injection molded rubber products. Unique DESMA, the in-house mold design and optimization capability allows its team to look at customer projects wholistically and propose the best complete solution for the application.
DESMA extends the following offers to ARPM members:
● Process development: 15% courtesy discount off the daily rate for R&D trials in DESMA’s demonstration laboratory for up to five days
● Preventative Maintenance: 15% courtesy discount off PM contracts for all 968, 969, Alpha and Sigma machines
● Training: 15% courtesy discount off DESMA Academy training programs held at the Hebron, Kentucky, facility
● Training: 15% courtesy discount off DESMA Academy training course BC-1 or MSC-2 packages conducted at the customer site. (Note: discount does not apply to relevant travel costs.)
For more information, visit www.desma-usa.com
Please join ARPM in welcoming the following new members!
Rainbow Rubber Extrusions
D&D Global ConMet
LaurSilicone n
With an ever-evolving labor market and high demand for industry experts, many companies are struggling to find and retain quality talent, especially for leadership roles that require technical expertise. One effective strategy an organization can deploy is to prioritize the development of its current employees.
There are many benefits to developing leadership talent pipelines within an organization. First, employees in these pipelines already are well-versed in company culture and know the processes and systems used. In addition, they have established relationships with other employees, which gives them a head start on building trust as a leader.
The Smithers global leadership team has a proven track record of individuals who began in entry-level roles and, through gaining multiple experiences, have accelerated their career paths. This includes multiple examples of people who entered the organization as bench chemists, sample preparation technicians or entry-level engineers and now are lab managers or members of the executive leadership team.
Another example – and one of my favorite stories – is Amanda Cool. Cool started working at Smithers in 2015 as a physical and chemical testing technician in the rubber testing labs in Akron, Ohio. Today, she is the chemistry and tire services supervisor in Akron, a critical role in the company’s Materials Science & Engineering division.
Cool’s career trajectory is a prime example of what happens when a talent development strategy is invested in and executed. Her story will be used to illustrate four fundamental tactics and cultural touchstones that have contributed to the company’s success with prioritizing internal development opportunities.
Success profiles have been created for critical leadership roles within the organization. Each profile is built around four main pillars: Technical leadership, business leadership, operations leadership and sales and marketing.
Each profile includes durable skills and competencies that will enable success, such as agile and strategic thinking, openness to feedback, enabling a culture of accountability and courageous communication. These profiles are fantastic to have when creating and managing talent pipelines and identifying future leaders. Knowing what the company is looking for makes it easier to find excellent current or future leaders within the existing talent pool.
It was clear that Cool had a penchant for leadership, but she did not have the experience necessary to immediately be placed into a leadership role. Through coaching and investment from her direct leader, the company identified a few potential career paths and used that information to identify areas for her to further develop, which set Cool on a path to success.
One of the tenants of a talent development strategy is the basic concept of a 70-20-10 development model. Briefly, this model explains development in three areas:
● 70% of development happens on the job, encouraging people to stretch outside their comfort zones.
● 20% comes from direct feedback from others, including having a good coach and/or mentor.
● 10% comes from formal education, such as continuing education, seminars or leadership summits.
Placing job experience at the forefront of a talent development strategy is a fundamental principle for Smithers leaders. Challenging assignments, as an example, build leadership capabilities and deepen expertise across an enterprise while fulfilling self-directed learning for an individual.
Cool’s career trajectory demonstrates the efficacy of a career ladder in practice. As an example, she briefly left the rubber lab to work in the company’s Medical Device Testing division as a quality assurance specialist. After time in quality assurance, she also gained two years of experience specializing in dynamic mechanical analysis (DMA), a new technical area for her. Her technical knowledge and leadership skills grew in those roles, providing Cool with the additional skills she needed to step seamlessly into her current leadership role. A critical component of this process was her manager’s full support and mentoring during the process.
Employees are encouraged to think like entrepreneurs – to come up with bold ideas and take ownership of new projects and assignments. Of course, there are business benefits to this approach, but it’s also a valuable strategy for identifying future leaders, for two reasons:
1. It reveals how people think. Someone who leverages the freedom and possibilities of an entrepreneurial environment is likely to show similar initiative and creativity in a leadership role.
2. It shows how people handle multiple expectations and their resiliency to bounce back from occasional failure. Having advocates to help leaders learn from their mistakes while improving performance is a vital part of an organization’s talent ecosystem.
From day one, Cool has done all the right things, from taking on new assignments to learning from her setbacks. Now, as a senior leader, she has ample experience to coach and guide her team to achieve results through open and honest communication that creates better alignment.
When identifying those who aspire to be future leaders, I always look for people who are open to feedback and
coaching. It’s not difficult to find people who are open to positive feedback, but being open to receiving critical feedback is an invaluable part of the growth process.
In an ideal workplace, ongoing coaching and feedback are embedded in company culture. From entry-level employees to senior leaders, early exposure to receiving coaching on both effort and results makes for a stronger and more sustainable organization overall.
Cool had a strong, trusting relationship with her first supervisor from the beginning, which meant she was able to accept feedback, understanding that it was delivered with positive intent. Because she aspired to be on a leadership track, Cool listened to the advice she received from the leaders she admired, and she worked hard to apply it to her daily work activities. This willingness to learn has made her transition to a senior role much smoother, and now, as a leader herself, she can pay it forward by offering constructive feedback to her team.
Creating the type of environment that fosters internal development, as well as creating coaching and feedback opportunities takes time, but success stories like Amanda Cool and many others make it well worth it. n
Rick Arnold is the human resources director for Smithers and an experienced global human resources leader with a history of working in the specialty chemicals, transportation and financial services industries. Founded in 1925 and headquartered in Akron, Ohio, Smithers is a multinational provider of testing, consulting, information and compliance services. With operations in North America, Europe and Asia, Smithers supports customers in industries essential to human lives, including transportation, materials and components. For more information, visit www.smithers.com.
Automation continues to improve rubber injection molding, making production more efficient, more economical and safer. PowerON, a startup in Germany that resulted from a collaboration between TU Dresden and the University of Auckland in New Zealand, has created a type of sensory fingertip for industrial robots that could be used for handling fragile items, for harvesting produce or for removing rubber products from injection molding machines.
Dr. Markus Henke, CEO of PowerON, shared information about the company’s first demonstration model – a gripper, “forearm” and actuator – and about TouchDetect, the “tactile skin” material that gives the company’s gripper fingertips their sense of touch.
“Our demonstrator (Figure 1) showcases the ability of our smart elastic technology to revolutionize the way we design, think about and collaborate with robotic structures,” said Henke. The demonstrator device is controlled by printed artificial muscles that drive and move the upper part, a prototype of a bio-inspired gripper. The muscles are made of soft polymer materials that were laminated in layers. “The gripper (uppermost in Figure 1) does not possess any conventional joints or hinges,” Henke explained. “It has been 3D printed from flexible TPU materials and can achieve a
large continuum of deformation and movement caused by contraction and elongation of the muscles.”
On the inner sides of the gripper’s fingers, the company’s tactile skin, TouchDetect, was applied. Similar to the muscles, the skin also was printed and laminated from polymer materials. It can detect how and where an object is gripped and can sense if the object moves, tilts, slips or falls out of the gripper.
“The control of the muscles and fingers is done by a structure that we like to call an ‘artificial neuron’,” said Henke. “In principle, it is a kind of switch that can be compared, in function, to a biological neuron that detects mechanical inputs and controls biological muscle contraction accordingly.” Over time, PowerON aims to produce soft robotic structures that possess reflexes which no longer rely on conventional semiconductor electronics.
By integrating this type of device into robotic systems, industrial robots would be able to handle a variety of diverse objects. “The devices would be able to adjust their gripping force dynamically,” said Henke, “and they would not scratch the surfaces of sensitive objects.”
As of now, PowerON offers a tactile sensation fingertip as a retrofit device for standard industrial robotic grippers. Although it does not possess the artificial muscles seen in the demonstrator device, TouchDetect consists of a tactile skin and a soft fingertip. TouchDetect allows conventional industrial grippers to handle random, soft and brittle objects. Figure 2 depicts how TouchDetect can be integrated into standard industrial grippers connected to a collaborative robotic arm.
PowerON’s final vision is to develop fully soft, bio-inspired robotic structures that are only made up of compliant materials and supporting structures like skeletons. “These structures will possess bio-inspired reflexes and tactile sensitivity throughout their entire surface, and will be powered by artificial muscles,” Henke said. With devices such as these, functionality will be distributed throughout an entire system in which the individual parts of a robot can merge into one structure.
“Based on discussions with our partners in the gripper manufacturing business,” said Henke, “we know that handling injection-molded rubber parts is a challenging task for conventional robotic grippers. With the current version of TouchDetect, it already is possible to safely handle soft, bendable and sensitive parts, with no need to develop a completely new gripper technology.” n
For more information, visit www.poweron.one. To see TouchDetect and PowerON in videos, visit https://youtu. be/ph-_1kuhHZI, https://youtu.be/ntflFrB0-WE and https:// youtu.be/0Hw1VYDZE4o. For a comprehensive video on the demonstrator, visit https://youtu.be/ph-_1kuhHZI.
Electric vehicles, new lines for rail travel, material development and increasing safety standards – as the markets change, flexible companies must react with new resources, from machinery investments to investments in their people. While Akron Rubber Development Laboratory (ARDL) has had an engineering department for more than 25 years, it recently launched an initiative to expand the department, growing not only its equipment and capabilities, but also its staff.
Capital expenditures often are made to increase production capacity, whether adding new equipment to run alongside existing assets or replacing older technology. ARDL – a provider of provides characterization for material, small parts and full-scale parts – chose to follow both paths, growing through the acquisition of load frames, actuators, thermal chambers, shakers and other assets from Experimental Services, Inc. (ESI) in the fall of 2020 and with the addition of new controllers and a video extensometer. ESI, based in Akron and in operation for 30 years, specialized in engineering testing and provided static, dynamic, fatigue and vibration testing.
“ARDL’s engineering department,” said Chelsye Dailey, engineering manager, “focuses on standard and custom testing for quality control, qualification, engineering, research and development, proof of concept, and more. We offer dynamic mechanical analysis, fatigue and durability, vibration, FEA support testing and various life prediction.” With the ESI assets, ARDL has gained equipment that increases its testing volume capacity, its load capacity and its vibration/frequency testing abilities.
“These equipment acquisitions,” she continued, “have significantly expanded our capabilities for larger-scale part testing and more customizable options for mechanical and dynamic characterization.” The equipment includes large temperature chambers as well as specialized structural actuators which allow for simultaneous testing and facilitate a great range of directions and orientations for testing. “ESI had controllers that allow for synchronization of multi-axis testing,” she explained, “and that do other, more sophisticated
analysis behind the scenes. We also purchased a new MTS controller that is state-of-the-art.” The controller features upgraded software and includes more processing power for controlling frames and actuators.
As a result of the expansion initiative, ARDL now can offer services for a wider range of projects and at any point in a project’s life cycle. “It doesn’t matter what stage of the project the customer is in,” said Dailey, “we can help. We have engineers on staff who can interpret specifications, help design tests and design the fixturing necessary for testing.”
Without human expertise, the additional equipment would sit idle – so ARDL has invested in growing the engineering knowledge base as well. Dave Houk, who holds a BS in mechanical engineering, has been at ARDL for 24 years and has a wealth of historical knowledge that has been valuable as new team members have been added to the department. “He has an amazing memory for the projects conducted here over the years,” Dailey said. “He has so much experience that when a customer needs a custom-designed test, Dave can almost always recall a similar test done in the past, allowing us to address our customers’ unique testing needs.”
Seth Glasgow was hired when the company acquired ESI’s assets. Glasgow also has a BS in mechanical engineering and has QC experience from his work with a firm specializing in bushing and large-scale dynamic testing. “I’ve held roles in R&D and manufacturing,” said Glasgow. “These roles included exposure to rubber and plastics but, in particular, my prior experience with hydraulics made for a seamless transition to learning about the hydraulic nature of the test equipment we use at ARDL.”
“The consultants from ESI,” said Dailey, “have spent a lot of time mentoring Seth. We felt that acquiring the vault of knowledge from ESI was just as important as acquiring their testing equipment.
Another recently hired department engineer is Joe Fiocca. “Joe came from the rubber industry,” said Dailey. “He has 30-plus years of experience in rubber manufacturing
as well as mechanical design experience. He is an expert in designing tests and designing test fixturing, and he has a great understanding of the material itself.” With his rubber industry background and his BS in mechanical engineering, Fiocca can make suggestions from the test perspective.
Dailey herself joined ARDL in 2021 with a BS in mechanical engineering from Youngstown State and a Master’s in engineering and industrial management from Ohio University. She came to the role with a decade of experience in stress analysis and structural design, as well as project and personnel management experience. An assignment in Denmark gave her an opportunity to work with EN specifications.
ARDL has expanded its engineering department for a variety of reasons. “ARDL serves 11 of the 12 essential industries,” said Dailey, “so we have a huge range of customers, many of whom have increasing testing requirements.” New materials are being introduced for some products, and many products now need to be more durable than ever. “We see customers push the limits in every direction all the time,” she explained. “We are seeing new materials that require testing and we also are seeing more stringent safety requirements. Demand for re-vetting is on the rise for customers who have launched new applications for an existing material or for material that now is seeing different loads.”
Dailey pointed to the automotive market as an example. “As we move toward electric vehicles,” she said, “a lot of revetting must occur; we are seeing an uptick in electric vehicle testing across our company.”
The rail travel industry is another area where testing demand is expected to grow. “Rail travel,” said Dailey, “has changed over the years and a lot of extra rail line coverage is being added, especially in countries that we serve outside of the US.” Glasgow noted that the acquisition of ESI’s testing equipment allows ARDL to expand into these markets. “One example of this,” said Glasgow, “is the testing of railroad
elastomeric pads, also known as DFF’s (direct fixation fasteners), which provide the noise and vibration mitigation for the entire rail support system in the railroad industry.”
In other markets, products have been tested for roomtemperature operation; nowadays, ARDL is seeing testing requests for extreme temperatures as well. “And defense and aerospace,” said Dailey, “are always pushing the envelope. Our expanded load capacity allows us to do more large-scale testing and perform more of the testing in-house.”
As Dailey sees it, ARDL is unique in the breadth of services it can offer to customers and the depth of knowledge that its engineering department contributes to R&D and testing projects. “We now have the equipment, the ability and the staff to go far beyond what we offered customers in the past,” said Dailey. “We are focused on being a start-to-finish resource.” n
Akron Rubber Development Laboratory (ARDL), Barberton, Ohio, is an international laboratory established in 1962 that provides testing, development and problem-solving services for the rubber and plastics industries. For more information, visit www.ardl.com.
Ice Miller focuses on meeting the needs of our clients quickly, efficiently and cost-effectively. Ice Miller attorneys with rubber industry experience can assist with your greatest legal challenges. Contact Josef Keglewitsch at 614-462-2279 or josef.keglewitsch@icemiller.com for more information.
300+ lawyers in Columbus and
icemiller.com
A S S O C I A T I O N F O R R U B B E R P R O D U C T S
M A N U F A C T U R E R S
B e n c h m a r k i n g | I n d u s t r y S t a n d a r d s |
T r a i n i n g | N e t w o r k i n g | a n d m o r e . . .
L i s t e d i n R u b b e r a n d P l a s t i c s N e w s " T o p 5 R u b b e r
I n d u s t r y A s s o c i a t i o n s Y o u S h o u l d K n o w . "
V i s i t a r p m i n c . c o m f o r m o r e .