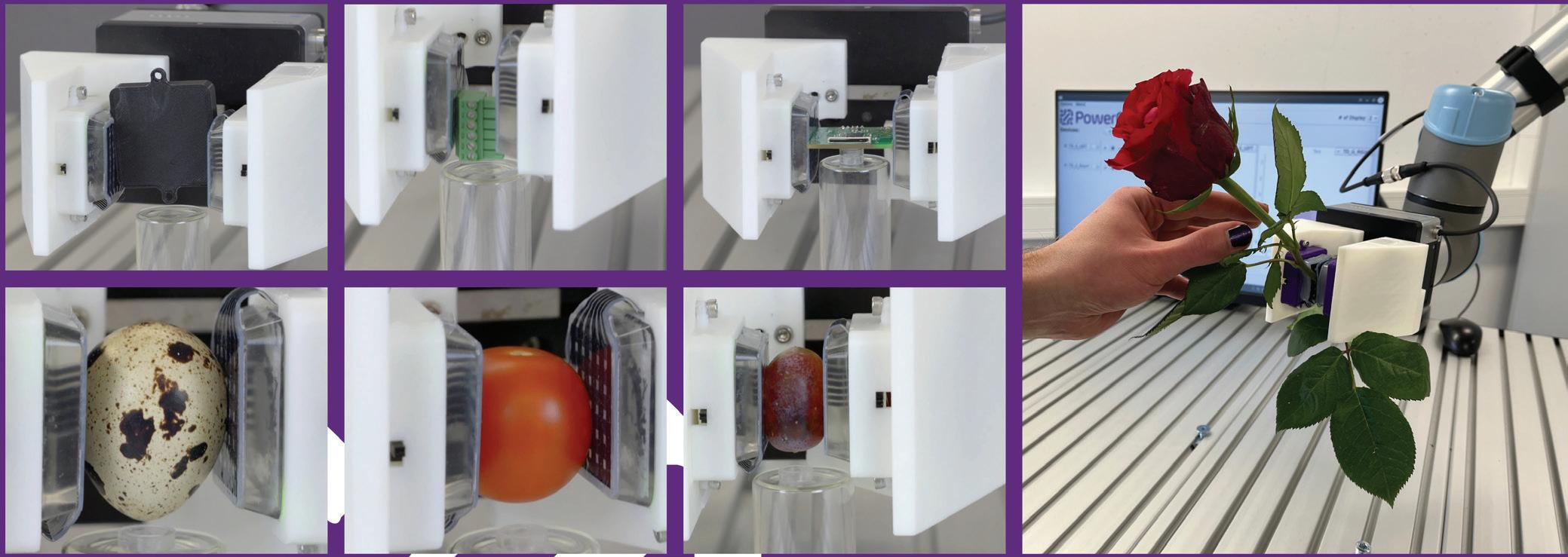
2 minute read
Robotics with the Sense of Touch – The Future for Rubber Injection De-Molding?
By Liz Stevens, writer, Inside Rubber
Automation continues to improve rubber injection molding, making production more efficient, more economical and safer. PowerON, a startup in Germany that resulted from a collaboration between TU Dresden and the University of Auckland in New Zealand, has created a type of sensory fingertip for industrial robots that could be used for handling fragile items, for harvesting produce or for removing rubber products from injection molding machines.
Advertisement
Dr. Markus Henke, CEO of PowerON, shared information about the company’s first demonstration model – a gripper, “forearm” and actuator – and about TouchDetect, the “tactile skin” material that gives the company’s gripper fingertips their sense of touch.
“Our demonstrator (Figure 1) showcases the ability of our smart elastic technology to revolutionize the way we design, think about and collaborate with robotic structures,” said Henke. The demonstrator device is controlled by printed artificial muscles that drive and move the upper part, a prototype of a bio-inspired gripper. The muscles are made of soft polymer materials that were laminated in layers. “The gripper (uppermost in Figure 1) does not possess any conventional joints or hinges,” Henke explained. “It has been 3D printed from flexible TPU materials and can achieve a large continuum of deformation and movement caused by contraction and elongation of the muscles.”
On the inner sides of the gripper’s fingers, the company’s tactile skin, TouchDetect, was applied. Similar to the muscles, the skin also was printed and laminated from polymer materials. It can detect how and where an object is gripped and can sense if the object moves, tilts, slips or falls out of the gripper.
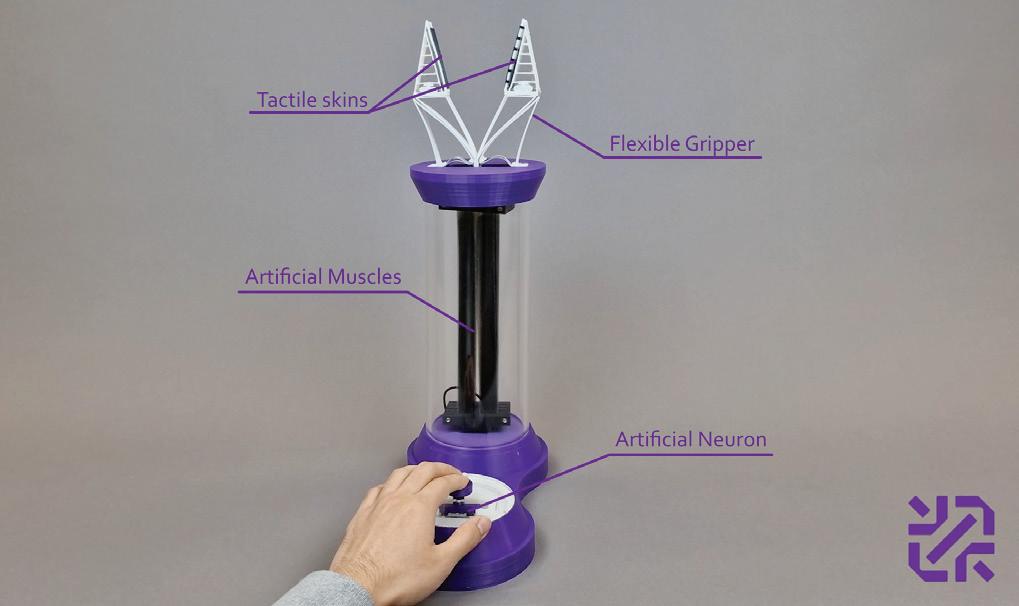
“The control of the muscles and fingers is done by a structure that we like to call an ‘artificial neuron’,” said Henke. “In principle, it is a kind of switch that can be compared, in function, to a biological neuron that detects mechanical inputs and controls biological muscle contraction accordingly.” Over time, PowerON aims to produce soft robotic structures that possess reflexes which no longer rely on conventional semiconductor electronics.
By integrating this type of device into robotic systems, industrial robots would be able to handle a variety of diverse objects. “The devices would be able to adjust their gripping force dynamically,” said Henke, “and they would not scratch the surfaces of sensitive objects.”
As of now, PowerON offers a tactile sensation fingertip as a retrofit device for standard industrial robotic grippers. Although it does not possess the artificial muscles seen in the demonstrator device, TouchDetect consists of a tactile skin and a soft fingertip. TouchDetect allows conventional industrial grippers to handle random, soft and brittle objects. Figure 2 depicts how TouchDetect can be integrated into standard industrial grippers connected to a collaborative robotic arm.
PowerON’s final vision is to develop fully soft, bio-inspired robotic structures that are only made up of compliant materials and supporting structures like skeletons. “These structures will possess bio-inspired reflexes and tactile sensitivity throughout their entire surface, and will be powered by artificial muscles,” Henke said. With devices such as these, functionality will be distributed throughout an entire system in which the individual parts of a robot can merge into one structure.
“Based on discussions with our partners in the gripper manufacturing business,” said Henke, “we know that handling injection-molded rubber parts is a challenging task for conventional robotic grippers. With the current version of TouchDetect, it already is possible to safely handle soft, bendable and sensitive parts, with no need to develop a completely new gripper technology.” n
For more information, visit www.poweron.one. To see TouchDetect and PowerON in videos, visit https://youtu. be/ph-_1kuhHZI, https://youtu.be/ntflFrB0-WE and https:// youtu.be/0Hw1VYDZE4o. For a comprehensive video on the demonstrator, visit https://youtu.be/ph-_1kuhHZI.