‘GRACE,
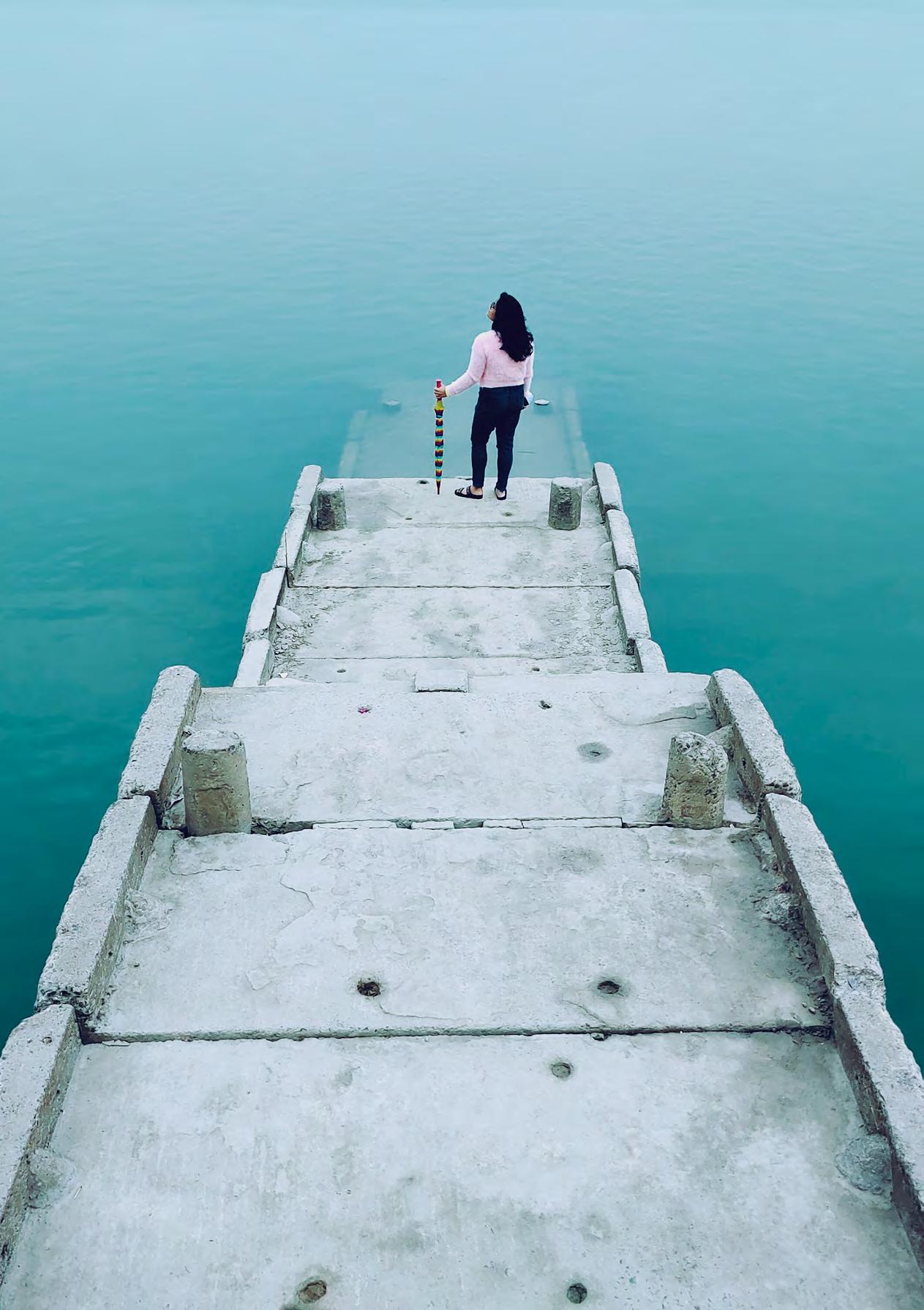

Golden Jubilee Hospital Surgical Centre, Glasgow
Client
NHS Golden Jubilee Foundation
Architect
IBI Group
Consulting engineer
Curtins
Cost consultant
AECOM
M&E engineers
TUV SUD/NG Bailey
Main contractor
Kier Construction Scotland
Specialist frame contractor
PCE
PCE’s precast concrete
supply chain
Techcrete/Explore/FP McCann/
Flood Precast
Ready-mixed concrete supplier
Breedon
Reinforcement supplier
Central Rebar
Steelwork
Peikko/Harris Manufacturing
MAIN IMAGE: Careful lift plan co-ordination was required to safely rotate the brick-faced façade panels.
Norman Brown, considers the future use of concrete structures and façades in the health sector.
There has been a lot of political ‘noise’ since the announcement in 2019, before the onset of Covid-19, about many new buildings required within the NHS sector throughout Great Britain. Whether it is new hospitals, new wings to existing hospitals, or other healthcare buildings, quantities and timings are, many would say, still subject to confirmation and interpretation. However, what is clear is that this will be an important new-build growth sector going forward and that concrete is the ideal construction material to meet the NHS’s needs.
The use of concrete and modern methods of construction (MMC), enable the development of construction that meets the NHS health technical memoranda (HTMs). These give comprehensive advice and guidance on the design, installation and operation of specialised building and engineering technology used in the delivery of healthcare projects. With design drivers accommodating differing uses such as clinical wards, theatres, M&E plant etc, a flexible structural grid approach can be achieved allowing for future changes. The use of digital techniques in the design, build and subsequent use is paramount, as well as ensuring the most sustainable options especially in terms of reducing the carbon footprint and achieving net-zero carbon, as the NHS has committed to completely eradicating its core carbon footprint by 2040.
One healthcare building structure that was constructed during the pandemic using a concrete MMC approach was the Golden Jubilee Hospital Surgical Centre extension in Glasgow, with Kier Construction Scotland being the main contractor. This new building, a three-storey structure, includes additional operating theatres, a day case surgery admission unit, an outpatient preoperative assessment area, diagnostic space and supporting accommodation. The Surgical Centre needed to be built alongside the live hospital structure, while also being close to a housing estate and all site deliveries were required to pass through the hospital’s existing ground-level car park. The original Stage 3 design intent was for a post-tensioned in-situ concrete structure with traditional brickwork façade. Kier Construction Scotland approached
PCE to develop a design-and-build scheme using the PCE HybriDfMA Frame System, to replicate the layout, performance characteristics and usage flexibility of the posttensioned in-situ design, together with a modular non-load-bearing brick-faced precast concrete panel façade.
It was of particular importance in the design process to ensure that the floor areas of the
ABOVE: The structure was assembled very close to the existing hospital building.
LEFT: Reinforced composite concrete/ structural steel beams with prestressed concrete floor units gave an uninterrupted soffit for M&E installation.
operating theatres had a very low susceptibility to vibration due to the sensitive equipment that would be used within them. Based on previous experience of using the HybriDfMA Frames System within the biosciences sector, where such requirements are common, the floor-plate design resulted in reinforced precast concrete edge beams and internal composite concrete/steel Deltabeams
supporting 200mm-deep solid prestressed concrete floor units acting compositely with 200mm of in-situ reinforced concrete topping. Following construction, a full-scale test of a floor was carried out using an array of shakers and accelerometers, with the results showing that the vibration response was lower than the design predicted.
The use of the composite construction concrete/steel Deltabeams gave a flat soffit for the floor plate, resulting in no beam downstands and with the precast floor components having channels cast into their soffits, the fixing of M&E services was made faster and simplified, as will be any subsequent change of use requirements. Precast concrete twinwall components together with precast stairs and landings form the lift and stair cores, which give the building stability and provided safe access and egress for site personnel during the assembly phase. Other precast concrete components include columns, parapet beams, lift core capping slabs, ancillary walls and roof plinths to take M&E plant.
A total of 612 off-site-manufactured units were delivered on a preplanned just-in-time basis, with the units being lifted direct from the delivery vehicle to their intended position in the structure, thus not requiring a site storage area and the double handling that would be required, giving time savings and reducing the risk of damage. Apart from the off-site-manufactured components, a total volume of
1350m3 of in-situ reinforced concrete was also used to form composite concrete/steel beam construction and floor structural toppings. To clad the structure, a further 177 off-site-manufactured façade panels were manufactured using Himley Black Wirecut Dragfaced facing brick between ground- and firstfloor level with Sandlewood Wirecut Dragfaced facing brick for the upper two levels and units having complementing reconstructed stone bandings and mullions as required. During the design process,
the façade units were maximised in line with the lifting capacities of the project’s two CTL430 tower cranes, together with the structural grid and storey height, to minimise the number of external joints. The resulting panel dimensions were up to 4.5m high, with a maximum weight of 16.13 tonnes. All glazing and vent units were installed at the façade panel manufacturer’s factory prior to delivery, saving time and the need for external access to the envelope, and keeping to a minimum the number of operatives working on-site. Delivered in ‘landscape’ orientation, these units needed to be rotated through 90° prior to their installation, which was achieved by careful use of a combination of one of the site’s tower cranes and a 90-tonne allterrain mobile crane, configuring them to comply fully with all the legislative guidelines for complex lifting operations.
Assembly on-site of the structure and façade, including the in-situ concrete operations, took PCE’s skilled, multi-disciplinary workforce only 15 weeks. The superstructure assembly was completed 12 weeks quicker than the Stage 3 design was expected to take, which is a
significant achievement considering operational difficulties including the pandemic. It has been estimated that the off-site-manufactured solution resulted in over 350 fewer delivery vehicle movements through the hospital’s car park, while the reduced on-site workforce and programme reduction saved over 50,000 on-site operative hours. This dramatically reduced disturbance at the hospital location, waste disposal from the site and health and safety risks.
Adam Clark, PCE’s project manager for the Golden Jubilee Surgical Centre, says, “A great working relationship was developed with Keir Scotland and the other parties involved. The quality of the finished structure is the result of a great team effort including our supply chain and I am pleased with the added value we have given the client, as well as the reduced hospital and neighbourhood disruption. This project proves that concrete can be very successfully
and advantageously used in new healthcare buildings, especially using modern methods of construction.”
ABOVE LEFT:
Brick-faced precast concrete panels including reconstructed stone finishes, preglazed at the factory.
ABOVE:
Off-site precast concrete components assembled adjacent to the existing hospital, enabled ease of construction with minimal disturbance.