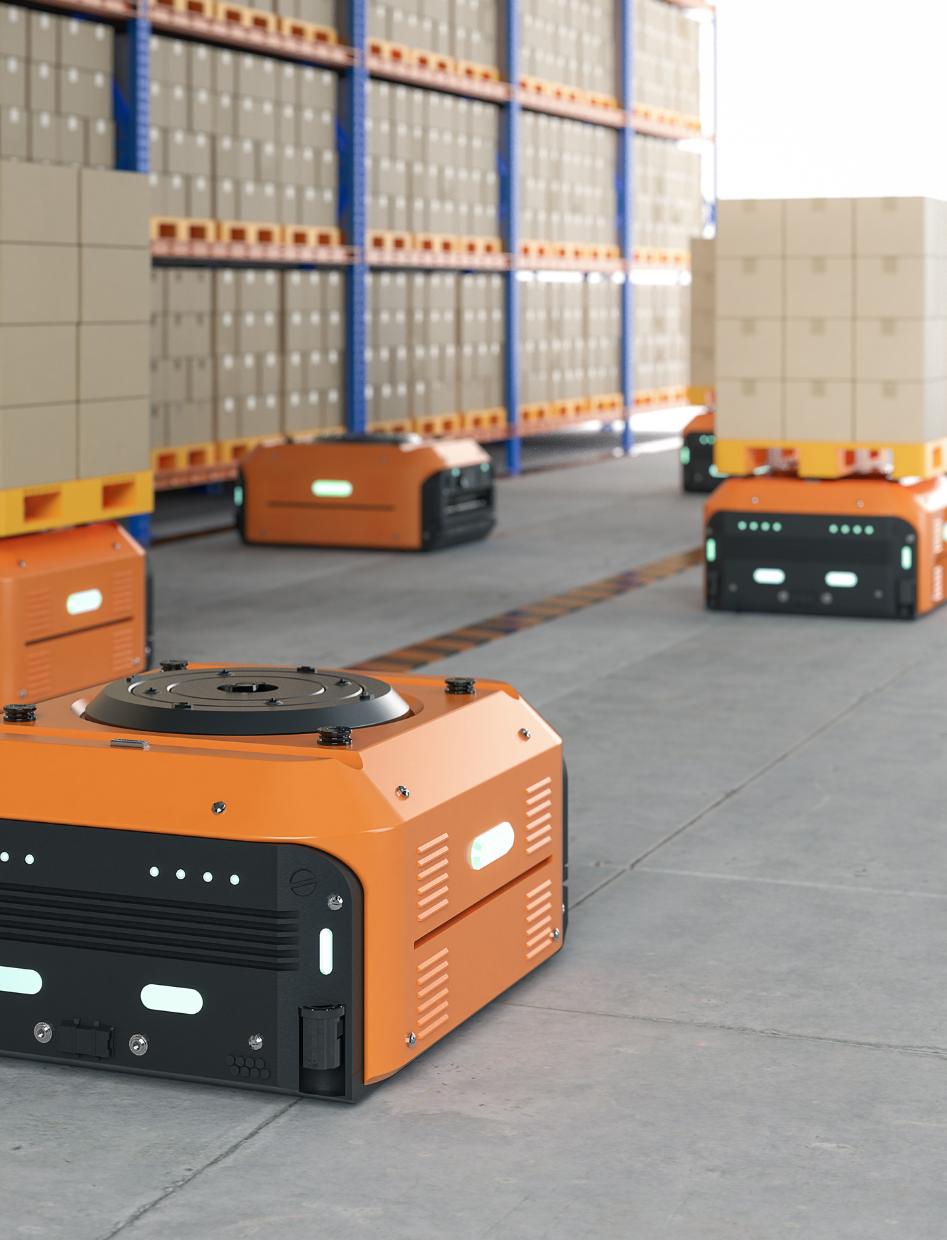
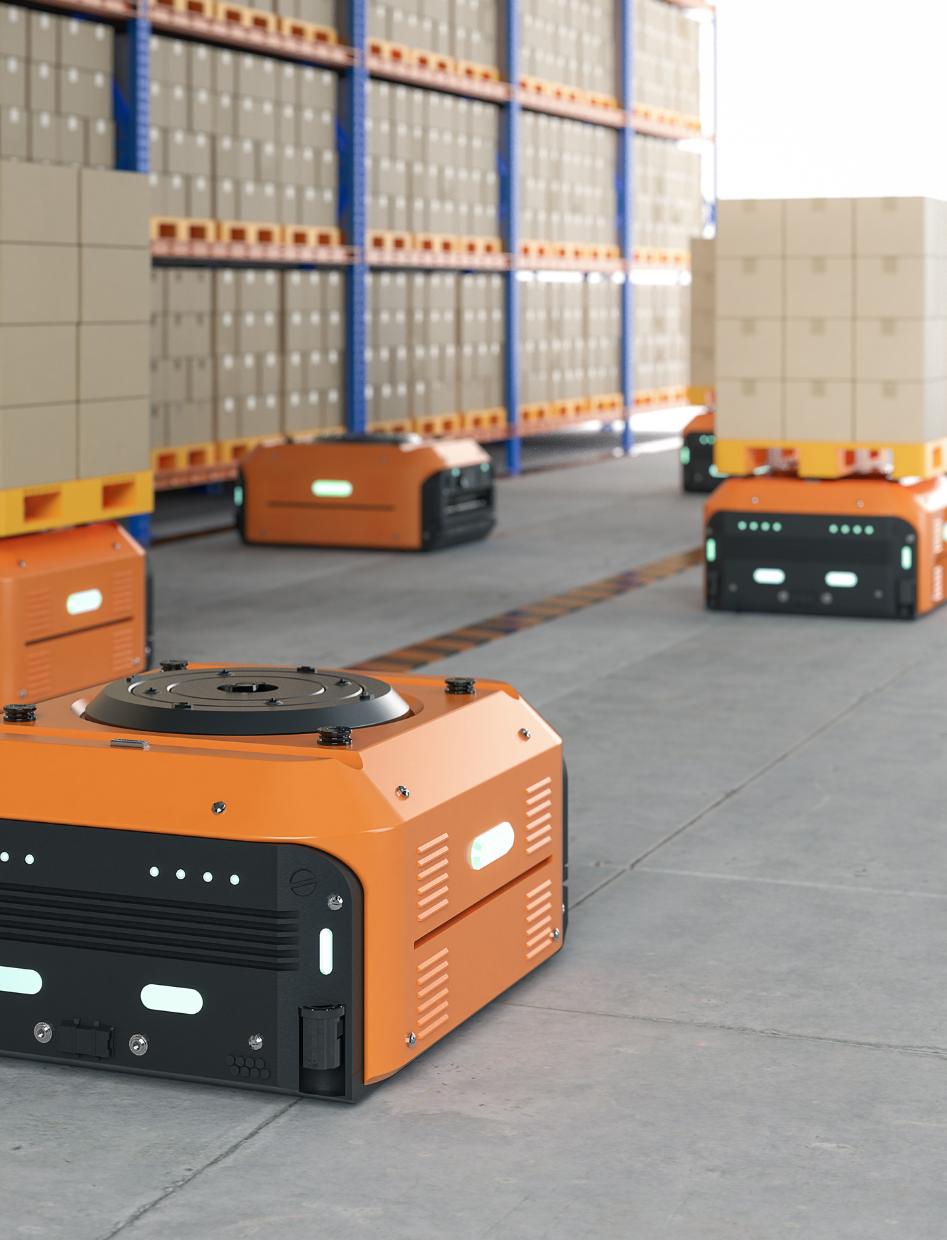
Welcome
About The Magazine
Published quarterly to a circulation of 20,000 + industry professionals across Australia, New Zealand and the wider Asia-Pacific region, Supply Chain Insights Magazine is focused on helping you solve the complexities of today's supply chain. The digital magazine highlights the latest trends, operational strategies, technology advancements and best practice within the supply chain and logistics industry.
Welcome to Supply Chain Insights Magazine
your primary source of industry news, focused on innovation, technology and knowledge-sharing in the logistics sector.
In this edition, we address the pressing challenge facing Australian businesses as the rapid evolution of technology in supply chain operations collides with the persistent shortage of skilled workers. Delving into this, features editor Mel Stark investigates the critical question: ‘While the skills gap and labour shortages are undoubted challenges, could adversity pave the way for innovative and streamlined processes between man and machine?’.
We also share insights from Bastian Consulting’s new report, 'Supply Chain Challenges: What Leaders Forecast for
2024', which highlights the perspectives of diverse industry executives on the complex challenges in supply chain management and the necessity for resilience and adaptability over the coming year.
Meanwhile, Terry Smagh of Infor emphasises the critical impact of robotics in elevating manufacturing and supply chain efficiency and ROI. And we also spotlight Toll Group's transformative adoption of low-code solutions with Mendix.
We hope that you enjoy this edition of our magazine and look forward to hearing your feedback!
For more information or story suggestions, please contact: editor@supplychain-insights.media
For advertising enquiries, please contact: advertising@supplychain-insights.media
Visit our website: www.supplychain-insights.media
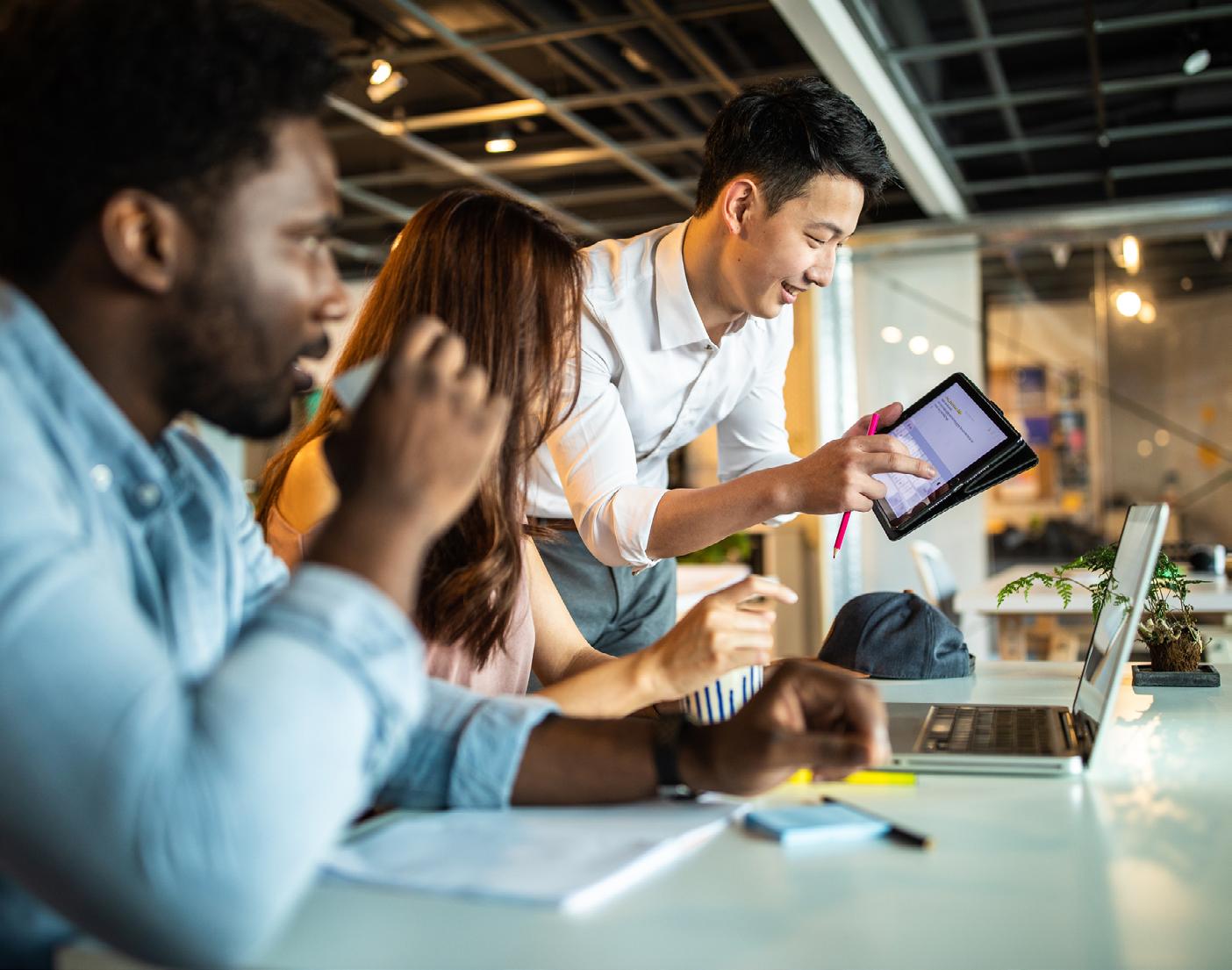
News & Insights
Manhattan Debuts the First and Only Fulfillment Experience Insights Dashboard for Retail
Realtime capability enables retailers to compare key fulfillment metrics against their peers
Manhattan Associates, the global leader in supply chain commerce, has launched the Fulfillment Experience Insights dashboard to give retailers a realtime assessment of how their omnichannel fulfilllent performance stacks up against the industry. Fulfillment Experience Insights provides continuous benchmarking of fulfillment performance, proactively informing retailers how they compare against a large pool of peers and competitors. This realtime ‘actuals versus actuals’ comparison avoids the inherent latency of most benchmarking tools.
Included in Manhattan Active® Omni, this new capability gives retailers a single view of digital order fulfillment KPIs like store pickup conversion, shorts and abandonment, time to fulfill and more. Retailers can evaluate, measure and adjust their supply chain execution strategies using aggregated and anonymised data from the Manhattan Active cloud ecosystem. This unique analytical
tool, which includes the ability to quickly pivot between various timeframes, provides detailed insight into the experience a retailer is delivering for their customers.
“Introducing cutting-edge innovation like the Fulfillment Experience Insights Dashboard is one of the reasons Manhattan continues to be ranked the only leader in omnichannel order management,” said Amy Tennent, Senior Director of Product Management at Manhattan. “For the first time ever, retail operations teams can see exactly how they are performing against the rest of the industry. This is a complete game changer, because they now have a starting point to begin creating more efficiency and improving fulfillment performance for their customers.”
Manhattan is uniquely capable of developing this solution because hundreds of the world’s top brands use its fulfillment execution tools to process millions of orders every week. Drawing upon this extensive knowledge and experience, the company has skillfully identified the key performance indicators crucial to fostering growth and maximising revenue.
Last year, Manhattan launched the firstof-its-kind Unified Commerce Benchmark which measured 286 customer experience capabilities across four segments. Of these four primary segments, ‘Promising & Fulfillment’ returned the lowest scores by a significant margin. Manhattan's new dashboard gives retailers their real-time performance in this critical area, helping them become unified commerce leaders.
Further enhancing its commitment to providing comprehensive solutions for the retail industry, Manhattan also announced a strategic alliance with Shopify (NYSE, TSX: SHOP), a leading global commerce company. This collaboration combines Shopify’s commerce platform with Manhattan’s omnichannel order management capabilities, offering a more cohesive and enriched shopping experience for customers.
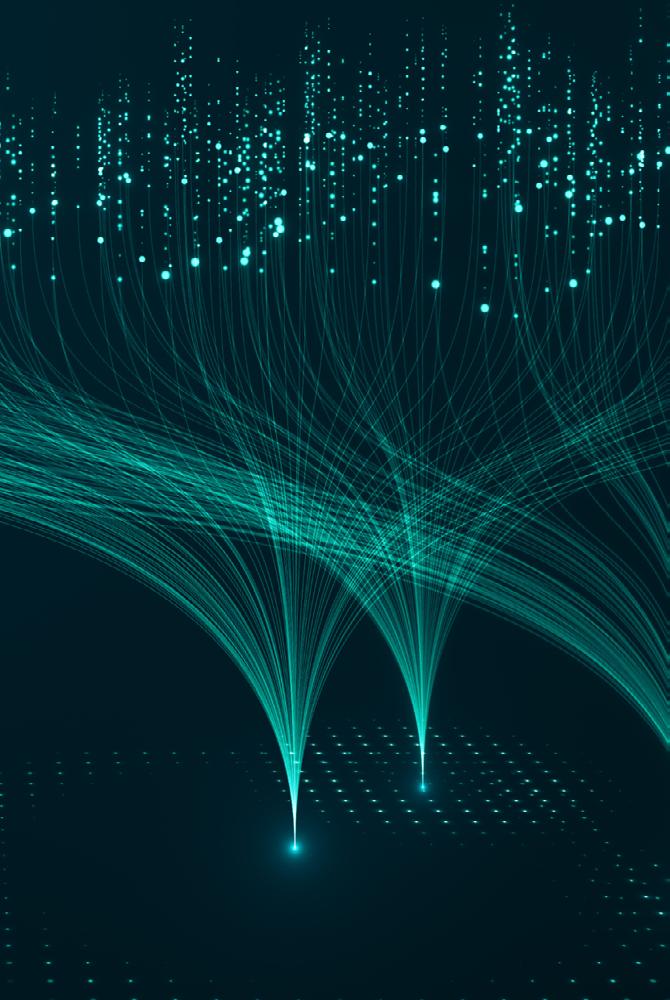
The combined solution will also include Manhattan’s post-purchase customer service tools, including digital self-service solutions that provide the visibility, flexibility and convenience required by today’s consumers.
Nautica, part of SPARC Group, is set to be the first to leverage this synergy.
“By offering our customers the combination of Shopify’s fast and reliable commerce platform with Manhattan’s powerful order promising and post purchase offerings, we are providing them unparalleled visibility and the industry’s premier endto-end online shopping experience,” said Mike Dupuis, Chief Digital Officer for SPARC Group. “For SPARC, we believe the combined solution will result in improved sales, reduced shipping costs, fewer returns, and improved margins and profits overall.”
The integration with Shopify will provide consumers with more precise product location and delivery information, a critical aspect in today’s ecommerce landscape. Additionally, it offers global inventory visibility for brands, encompassing items in stores, warehouses, and transit, thereby streamlining the supply chain process.
Bobby Morrison, Chief Revenue Officer at Shopify, expressed enthusiasm about the partnership. “We’re thrilled about teaming up with Manhattan as it's a major leap forward in transforming supply chain operations for enterprise commerce. This is a game-changer in today's fiercely competitive landscape, and we're excited to provide commerce solutions that will ultimately enhance unified shopping experiences for consumers.”
Receive up-to-date product, customer and partner news directly from Manhattan Associates on X (formally Twitter), LinkedIn and Facebook ●
Zebra Study: Nearly Six in 10 Warehouse Leaders Plan to Deploy RFID by 2028
Zebra Technologies today released the findings of its 2023 Global Warehousing Study, which confirmed 58% of warehouse decision-makers plan to deploy radio frequency identification (RFID) technology by 2028 to help increase inventory visibility and reduce out-of-stocks.
Over the next five years, a majority of warehouse decision-makers plan to deploy fixed, passive or handheld RFID readers and fixed industrial scanning solutions that can better track assets, workers, and goods
Device Technologies’ New 17,000 sqm Distribution Centre Fully Operational in Sydney’s Northwest
The 15,000 sqm facility is five-star green rated and equipped with 300kw solar array.
The warehouse boom in Sydney’s northwest is seeing more finished products, with Device Technologies’ new 17,000 sqm distribution centre achieving practical completion in Marsden Park in November last year.
Developed by Sydney Business Park, Prime Constructions built the customised facility, which is targeting 5 Star Green Star rating, has 300kw solar array, and has three temperature-controlled chambers. Reid Campbell is the project architect.
The site is on track to be the largest hub for medical device supplier Device
throughout the warehouse environment. This year marks the 50th anniversary of the invention of RFID which has become a problem-solving tool for front-line workers in warehouses and other industries.
The survey also showed 73% warehouse decision-makers globally have or will be accelerating timelines of modernisation projects. This should help with returns management which climbed to the top operational challenge cited by nearly half of the respondents —an increase of 10 percentage points year-over-year.
“The significant growth of returns aligns with e-fulfillment growth over the last several years, and it is a mandate for change across every part of the supply chain,” said Andre Luecht, Global Strategy Lead for Transportation, Logistics and Warehouse, Zebra Technologies. “This means warehouse leaders must modernise their operations with technology solutions to handle returns and increase agility, inventory visibility and demand forecasting in order to improve efficiency and make better decisions in real time.” ●
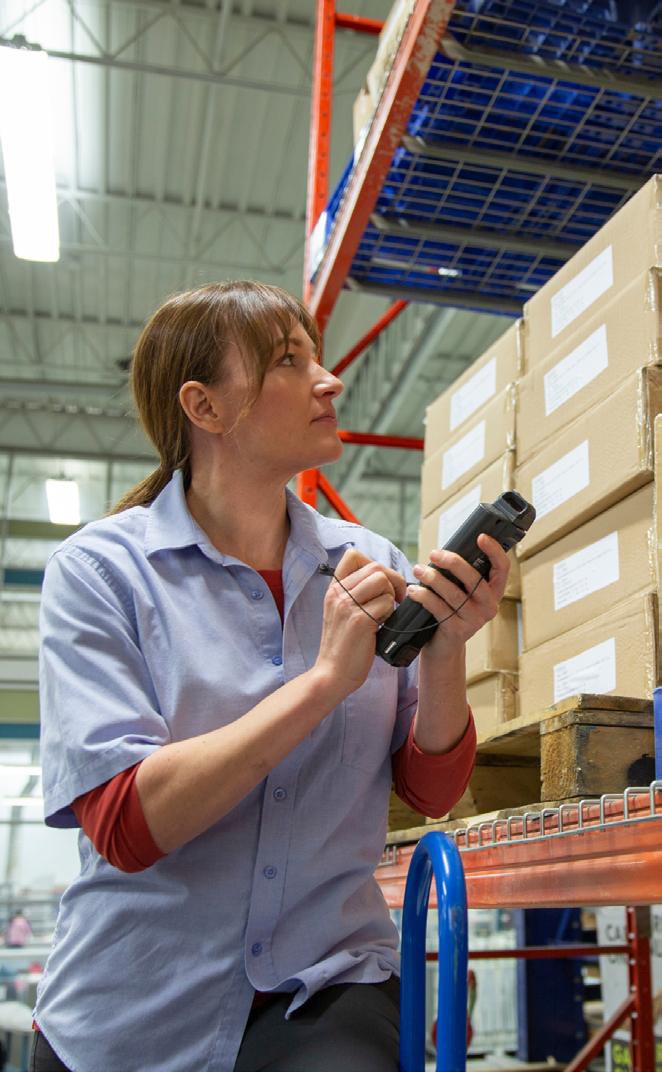
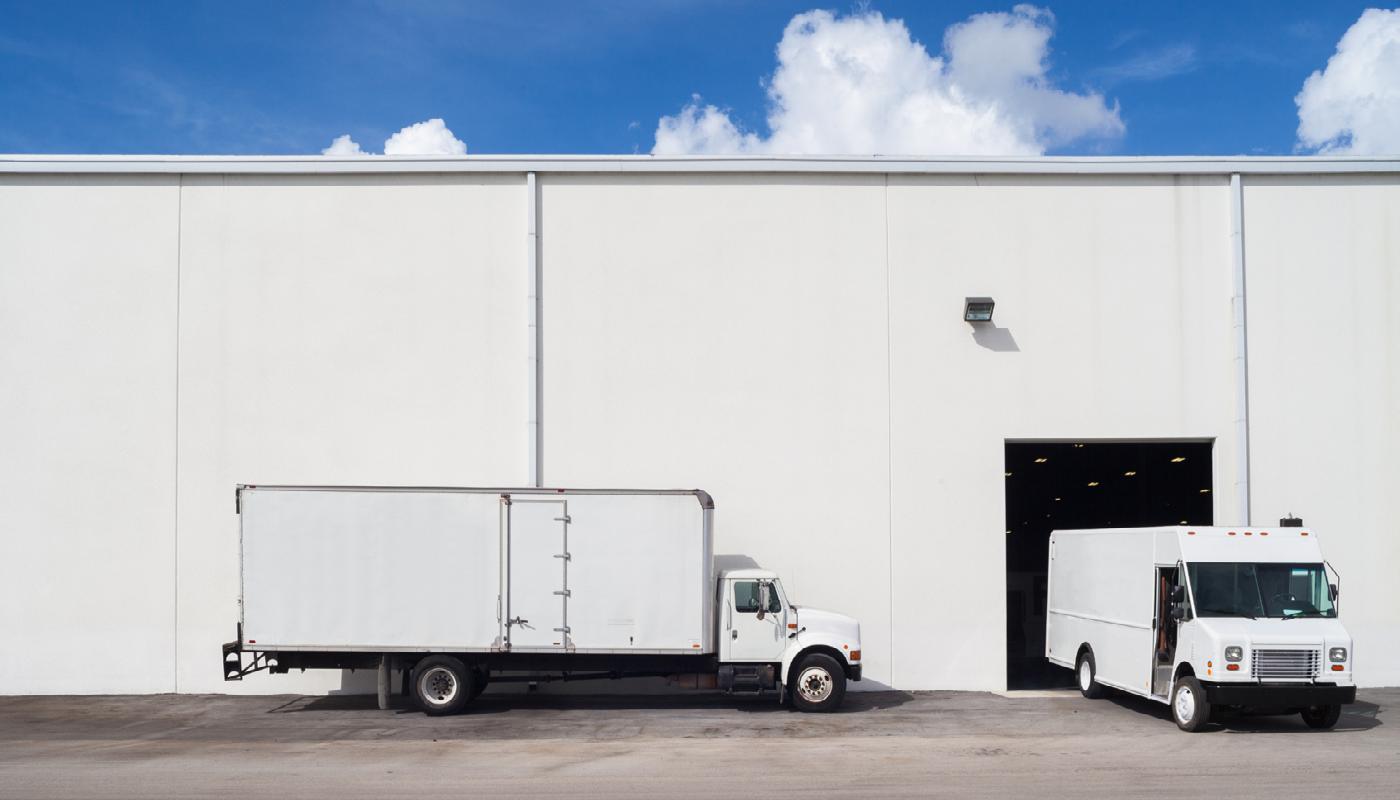
Technologies’ operations, warehousing, and logistics, which operate throughout Australia, New Zealand, and Asia.
“This state-of-the-art distribution facility serves as the cornerstone for optimising our operational efficiency and elevating customer service standards for hospitals and healthcare professionals,” Meredith Archibald, Director of Operations at Device Technologies, said.
“As well as warehousing, this facility will cater to our reverse logistics and technical service’s needs, ensuring a seamless experience. Positioned as the central hub, it will orchestrate the warehousing and logistics operations for Device Technologies.”
TMX Transform provided end-to-end supply chain advisory, property procurement,
and project management services.
“It was our privilege to assist Device Technologies transition into their new custom-built distribution centre,” TMX Senior Project Manager, Matt Logan, said.
“Being involved with the project endto-end, across supply chain, property, and project services meant we could optimise our assistance to Device Technologies, including tenant representation and racking superintendent supply and install.”
Sydney Business Park is filling up quickly with new distribution centres, with tenants including Hitachi, Garmin, and Australian Pharmaceutical Industries (API).
Despite the limited industrial space in Sydney, there are still site vacancies advertised in the park. ●
Dematic following up on previous Success at AS Colour’s New Zealand Headquarters with automation at its Melbourne distribution centre
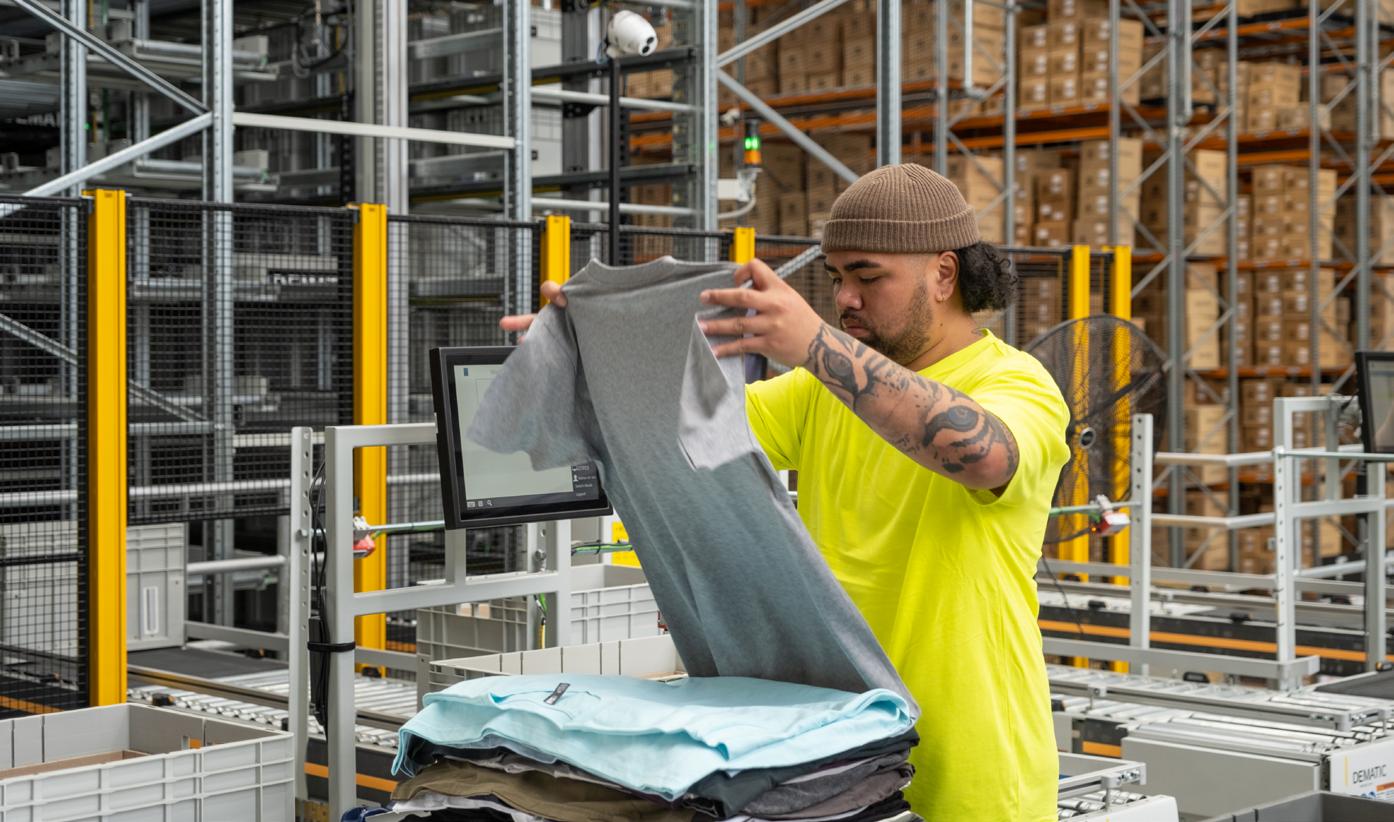
Dematic today announced that AS Colour, a leading global wholesaler and retailer that designs, manufactures, and distributes premium apparel, will transform its Melbourne distribution centre (DC) with automation featuring a Dematic Multishuttle® goodsto-person (GTP) solution.
Starting out in New Zealand in 2005 as a supplier of quality blank apparel for sportswear, music industry and events merchandise, and company promotional wear, AS Colour now operates from five DCs in Auckland, Melbourne, Los Angeles, North Carolina, and Leighton Buzzard (Bedfordshire, UK), plus 25 retail stores across New Zealand, Australia, and the UK.
“Dematic has been a really strong technology partner, helping us from a global perspective, and we see this as a long-term partnership as we continue to expand as a business in the future,” explains Lawrence Railton, Managing Director, AS Colour. “We’re excited to again partner with Dematic on the Melbourne chapter of our automation.”
As a compact, high-throughput automated storage and picking system, the Dematic solution features high-density tote storage and sequenced order picking for better productivity. The system is capable of processing varied order types, including small e-commerce orders, medium and large B2B orders, as well as retail store fulfilment.
The modular, scalable Dematic Multishuttle at the Melbourne DC will be 18 levels high and four aisles storing over 55,000 totes, with additional capacity built in for projected future growth. Product and
order totes will be retrieved and delivered in the required sequence to GTP picking workstations for efficient, ergonomic, and accurate order picking.
The system will be capable of sustainably delivering up to 1,500 product totes per hour across the five GTP picking workstations (an average of 300 product totes per hour to each independent picking workstation). After orders are fulfilled at GTP workstations, order totes will be temporarily buffered within the Dematic Multishuttle before being released and conveyed to the packing sorter in precise order sequence to support efficient packing processes.
Dematic Warehouse Control Software (WCS) will be an optimisation layer between the AS Colour’s Warehouse Management Software (WMS) and the automated equipment that provides the most efficient picking tasks and transportation of goods throughout the system.
The Melbourne GTP system will be roughly 2½ times larger than the GTP system at AS Colour’s Auckland DC. To support future growth after outgrowing its previous warehouse, AS Colour went live with a brand new 7,500 square metre DC in Auckland in 2021.
“Due to our growth over the last 5–10 years, we have outgrown many distribution facilities. Rising demand led us to building a brand-new facility with the focus on automation,” says Railton.
“AS Colour was the first company to choose the Dematic Multishuttle GTP solution in the New Zealand market,” says
Seth van Dijk, Business Development Manager, Dematic. “The Auckland system has 18 levels and features two aisles storing just under 20,000 totes with four ergonomic GTP workstations.”
manual RF processes to pick orders, with operators walking up and down aisles pulling trolleys. Stock was replenished with forklifts and other equipment.
Auckland facility has increased throughput per worker by 344% – from an average of 45 lines per hour to an average of over 200 lines per hour. Other benefits include decreased labour costs and a vast improvement in order accuracy, which reduces the number of unnecessary customer returns and leads to greater customer satisfaction.
be accurate and arrive very quickly. ,” says Railton. “With our automated facility, the speed, efficiency, and accuracy with which we’re able to get orders to customers differentiates us. Orders placed online can be picked within 30 minutes of being received, and then packed and out the door within a few hours.”
Multishuttle GTP solution has been a game changer for our business, and we’ve actually seen a big increase in sales in New Zealand – our customers can see how quickly and accurately we get their orders to them.”
and the throughput is 5,000 lines per day (6am–5pm) over the six days a week the DC operates, with the capability to process 8,000+ lines per day. The previous DC achieved 2,700 cycle counts. The current DC has dramatically increased to 13,000 cycle counts per month.

New Zealand, so we had a goal of reducing building size. The Dematic solution helped us achieve a smaller footprint at the Auckland DC and reduced our construction costs by about 30%,” says Railton. “Additionally, we’ve been able to increase our product storage capacity by about 35%, which has brought in more revenue and given us a buffer for supply chain issues.”
Another big goal for AS Colour was to completely remove single-use plastic from its supply chain.
“Traditionally apparel is packaged in plastics or paper, but what’s quite unique to AS Colour is they store the product loose and unpackaged within totes, which is the final package that is shipped to customers. This is a more sustainable approach that the Dematic solution facilitates by keeping products clean and tidy,” adds van Dijk.
To find out more about the automation that is at the heart of AS Colour’s Auckland DC watch the video ●

Wi-Fi 6E enabled
• Unmatched scanning range (up to 30.5m)
• Biometric facial recognition
• Industry-leading drop/tumble ratings
• Freezer model for reliable cold chain operations
• Best-in-class battery power
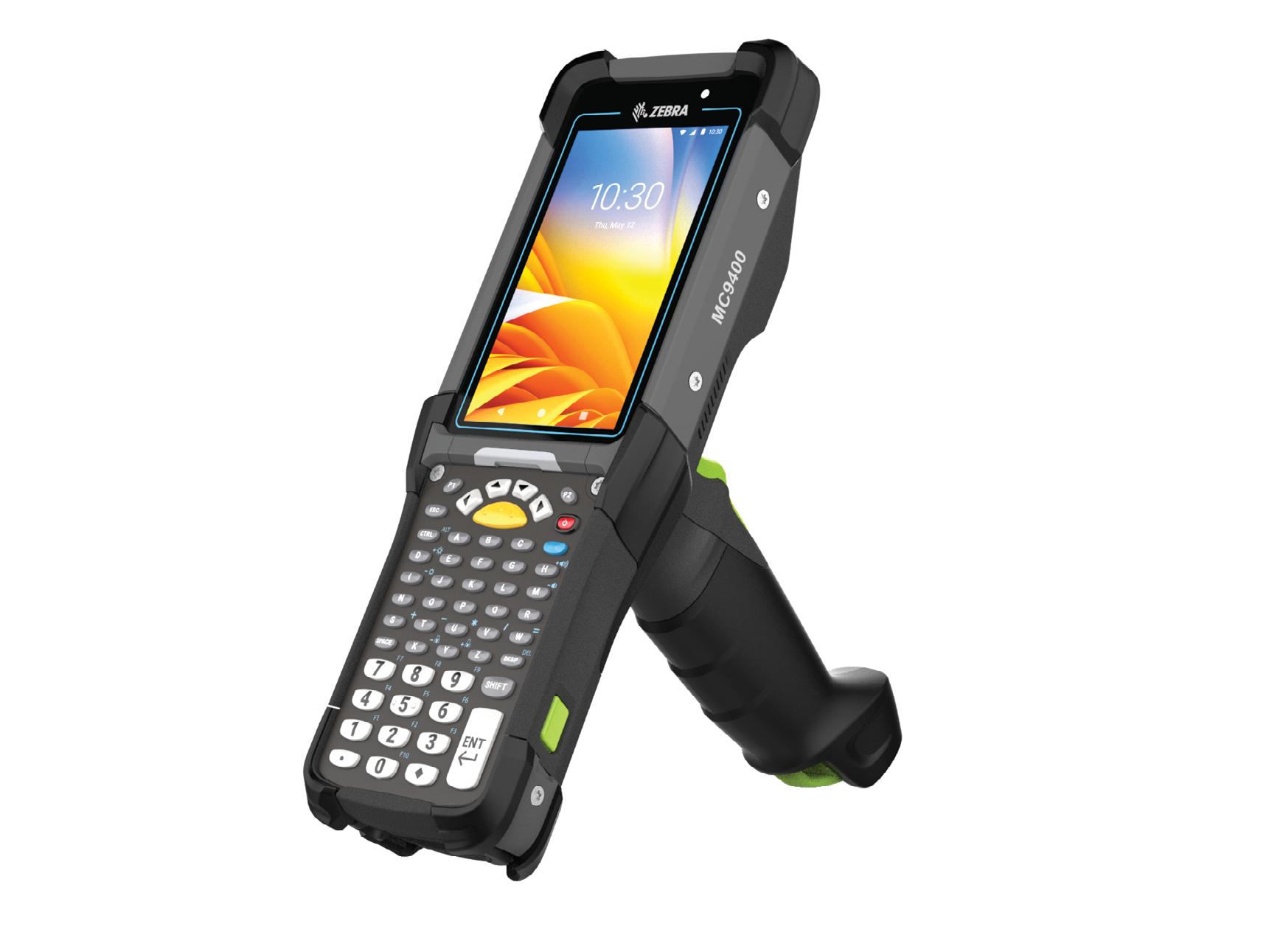
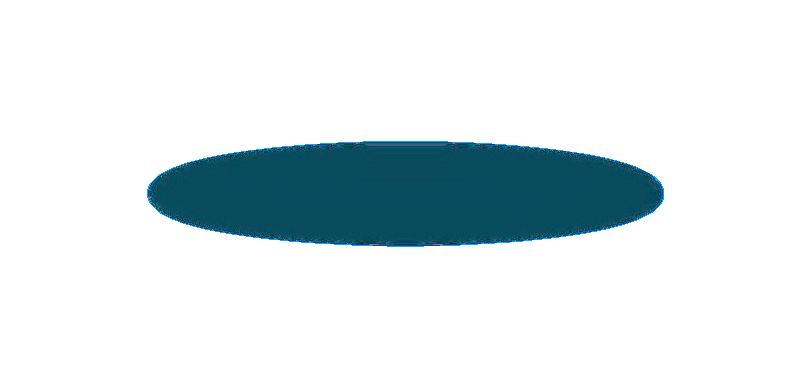
How Wearable Technology is Fast-tracking Employee Training Across the Supply Chain
It’s hard to believe in this digital world that a warehouse operator (or any organisation) is struggling to onboard front-line workers.
Yet, over half of decision-makers surveyed in Zebra’s latest Warehousing Vision Study said that training workers was their second biggest struggle. It’s taking an average of 4.7 weeks to get employees to full productivity! The fastest time reported was four weeks for receiving. The longest was five weeks for cross-docking and 5.1 weeks for put wall.
Retailers are reporting similar challenges. In the 15th Annual Global Shopper Study from Zebra, released in late 2022, three-quarters of retail decision-makers said reskilling or upskilling current employees is a challenge.
Why is this happening? There is so much technology – and even more on-demand content –available to guide employees through new tasks. You would think workers would be able to clock in and make an immediate impact in their first hour.
Well, by digging deeper into the data from the Global Shopper Study, we can see two key stats standing out:
• Nearly nine-in-10 retail decision-makers and employees say training and learning could be improved by technology. This statement rings true across the whole supply chain. In many organisations,
there’s often a missed opportunity for self-directed on-the-job training via mobile technology.
• Three-quarters (76%) of retailers said they will invest time and money in training employees on technology in 2023. As opposed to general onboarding/training, which is a given with any new job, the majority of organisations recognise they need to invest more resources into training employees on how to use the specific technology they rely on to do their jobs efficiently. No wonder onboarding times are extending out for a month or longer!
This last statistic is quite staggering. Technology shouldn’t be so complicated that organisations have to spend a lot of resources teaching people how to use it – at least not when it comes to tools used by front-line workers. We know turnover can be high in front-line roles, and a common reason why new workers get frustrated and quit so quickly is because they don’t feel they are contributing to their organisations fast enough. Or perhaps they get frustrated with how complicated their job seems to be because the technology is difficult to learn and use.
If your business processes are simple, but the technologies used within those processes are not – at least not from a user experience (UX) perspective – that’s a problem. And it’s one you must solve immediately.
The Case for Wearables
Warehouse, distribution, transportation, logistics, retail, and manufacturing operations functioned just fine before technology existed.
That’s not to say they functioned perfectly, but the simplicity of paper checklists, inventory lists and job aides reduced friction in workers’ days. If they didn’t know how to do something, they would shadow a colleague for a while to learn or just ask for help.
Today, it seems like new employees are having to spend a lot of time learning how to use technology in addition to learning how to do their jobs because they are expected to be autonomous. According to a recent Microsoft study, 55% of front-line workers report they’ve had to “learn new tech on the fly, with no formal training or practice”. If being inherently tech-savvy is a prerequisite for front-line work, then it will be difficult for companies to survive in the ondemand economy.
While a growing percentage of the labour pool is comprised of digital natives, and 64% of front-line workers are excited about the job opportunities technology creates, nearly half of front-line workers
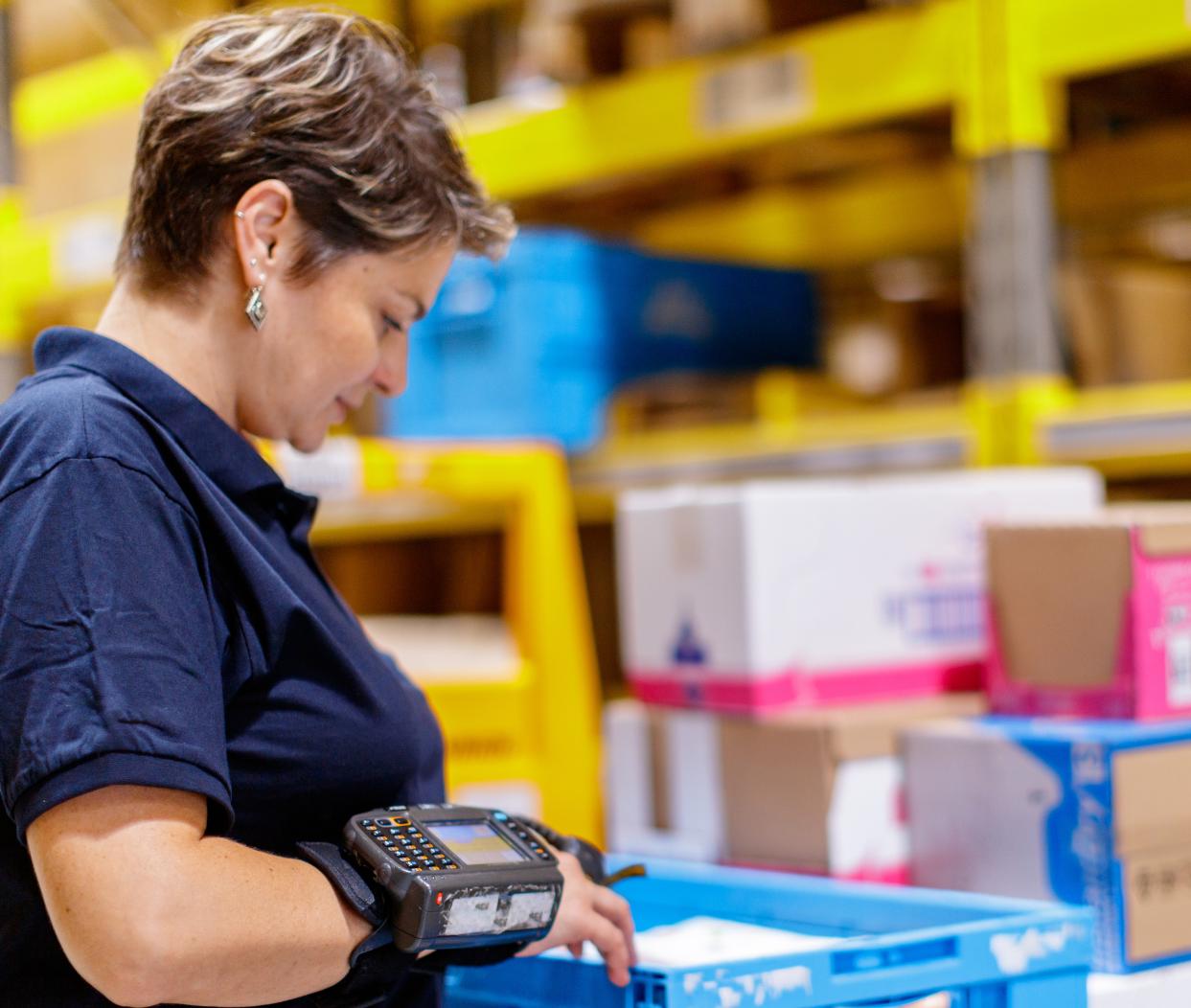
(45%) “feel pressure to adapt to new technology over fear of losing their jobs”.
You cannot allow technology – or the fear of technology – to complicate an employee’s first day, week or month (and eventually scare them away.) You must give them technology that facilitates on-thejob training in a way that is simple, straightforward, and familiar rather than forcing them to learn complicated new technology to complete new tasks. The tech you give them should be self-explanatory as much as possible. That’s one of the reasons why wearables must become a staple in your warehouse: to maximise productivity and operational efficiency and to simplify user training.
Though there are plenty of mobile devices you could use, such as a mobile computer or tablet, the reality is that any device that must occupy someone’s hand could be adding friction to those workflows.
The only way people can move as fast as humanly possible in a warehouse is if they have their hands totally free to pick items, operate equipment and more.
With wearables, staff don’t have to worry about picking up and putting down a device every time they need to do something else, they can just flow through their tasks. And because the device can essentially show – or audibly tell – them where to go and what to do next, they don’t necessarily need a
large screen device for direction. They can also get up to speed quickly, which means they can reach full productivity faster.
Take for example the average smartwatch, which many people own today. Wearable computers like the Zebra WS50 look and function a lot like the consumer smartwatches employees may already use (even though the WS50 is an enterprise-grade device built specifically for business applications used across the supply chain.) So, when workers put on the WS50, which runs on the Android operating system (OS) like many consumer devices, there won’t be much of a learning curve, if any. They’ll have to learn the software on the device just like they may have to learn a new app on their personal devices. But familiarising themselves with that software won’t be overly difficult.
In fact, one of the reasons wearable computers like the WS50 have become so popular with business leaders and front-line workers alike is because Zebra designed the WS50 and Ivanti’s Velocity software application to enable day-one productivity. The device essentially coaches the user through their job, facilitating on-the-job training that expedites time-to-productivity and aids with worker retention – without layering on a secondary tech training requirement during onboarding. Instead of asking another team member to hold a new employee’s hand, you can give them a WS50 loaded with stepby-step guidance software to wear on their hand (or wrist) and send them on their way. The WS50 even comes in an RFID model, packing even more functionality into the world’s smallest all-in-one enterprise-class wearable computer.
The Bottom Line Technology will remain pivotal to your business operations, so you must find a way to make it work better for your front-line workers.
They need to be able to jump into a new job and feel productive from day one – or fill a new role at a moment’s notice. They no longer have the luxury of month-long onboarding periods. Neither do you.
So, make sure you are only investing in technology that offers highly immersive, microlearning experiences for all employees rather than choosing technology that requires a lot of extra training investment. If anything, allocate that money to the creation of snackable, on-demand visual or audible guides that can give front-line workers the full autonomy they want and the confidence they need
to
be
a valued
member of your team. ●
Learn more about the WS50 and Zebra’s range of wearables.
From Blind Spots to Insights: New SOTI Research Highlights the Demand for Real-Time Device Visibility
The number of devices in organisations has increased globally by 37% in the past year. However, Australian supply chain organisations often do not have full visibility into what those devices are doing and the data they are collecting.
How do device location, poor signal strength and late deliveries impact business operations and what can supply chain organisations do to overcome these challenges?
Supply Chains Need a Transparent View of Frontline Operations
According to global Enterprise Mobility Management (EMM) solutions leader, SOTI, businesses lacking a transparent view of frontline operations can experience increased operational costs, inefficiencies and e-waste in workforce management. Additionally, blind spots in these areas expose supply chains to vulnerabilities and risks in compliance, cybersecurity, and quality.
“In 2024, organisations need to make visualising business operations a priority by consolidating business and device data in real-time. They need to view all critical mobile and app data immediately

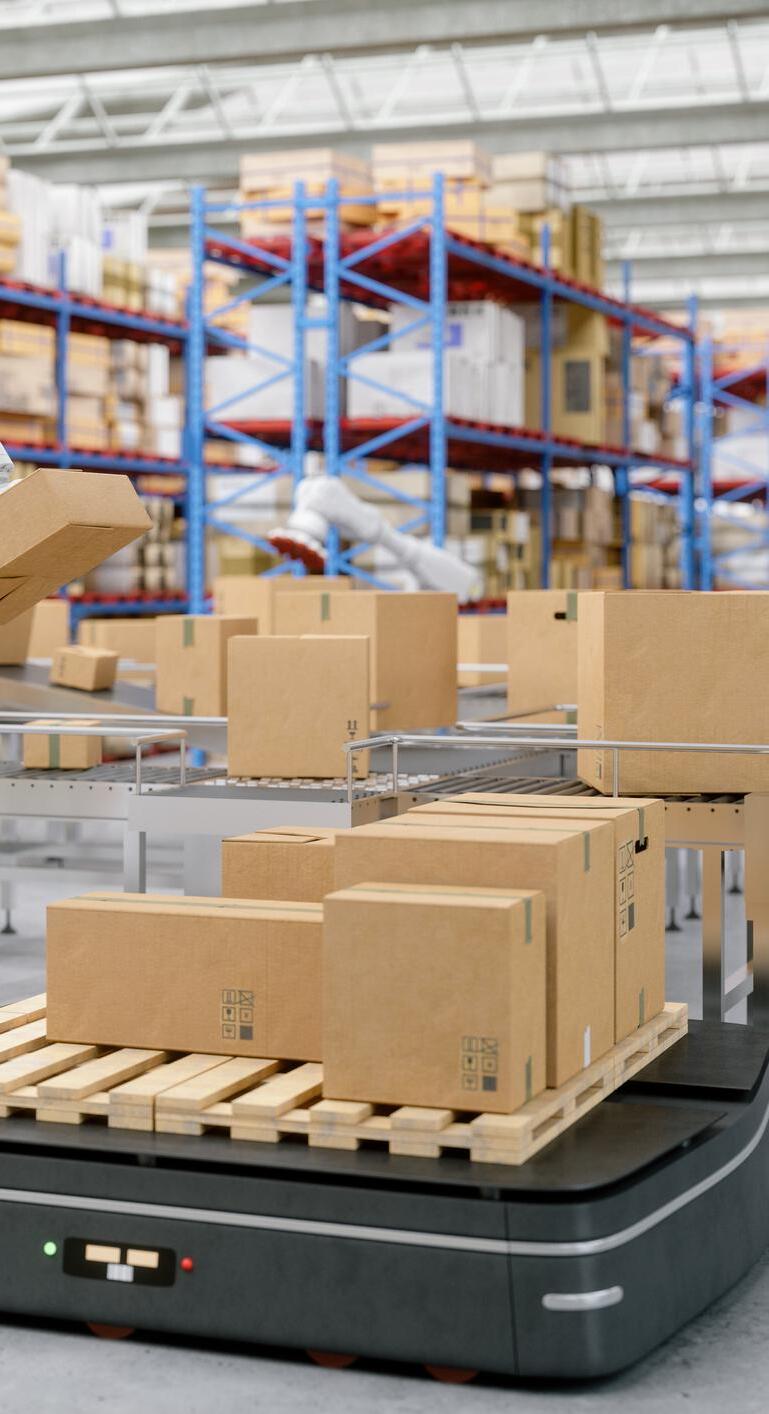
and then leverage that data to make faster and smarter decisions to improve their operations. As devices in the field are on the move, data such as signal strength and battery health, can be merged with critical business data collected via apps. In supply chain settings, that could be using an app to confirm inventory levels as deliveries are made,” said Carl Rodrigues, President, and CEO at SOTI.
To enable Australian supply chain organisations to visualise their operations in real-time, SOTI recently launched SOTI XSight Live View, the first tool of its kind to visualise business mobility.
Live View offers immediate detection and reaction to operational challenges by consolidating device and business data in real-time. Live View maps and visualises metrics such as location and signal strength alongside business data such as inventory levels, delivery status and any other priorities required by the business. It also allows IT professionals to go back and study situational data at specific times to resolve issues and keep the business running smoothly.
In a supply chain environment, organisations are able to get real-time answers to questions about mobility coverage, the status of deliveries, inventory status and driver behaviour. Live View does this through providing visibility into the real-time location of devices, access to device data for informed decision-making regarding device fleets and access to business data to improve operational efficiencies.
Retail Supply Chains Must Meet Real-Time Demands
The health and performance of technology and devices in the supply chain is critical today, as these technologies are requried to help meet consumer demands for real-time information, efficient product availability and rapid delivery in-store and online. According to a new industry research report from SOTI called, Techspectations: Consumer Demand for Digital Transformation in Retail, 77% of consumers expect to always know the status of their orders, highlighting the need for efficient supply chain visibility.
Today, 30% of Australian consumers have considered shopping with a different retailer to get a better in-store tech experience.

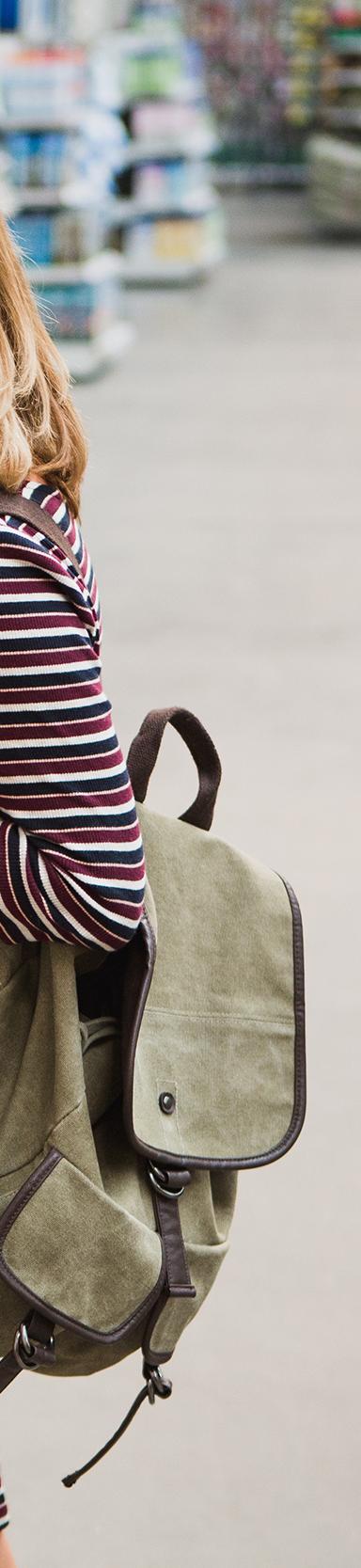
Unfortunately, poor tech functionality along with disjointed supply chains have forced many consumers to shop elsewhere.
Many of these issues can be resolved with a more seamless, intuitive, and automated supply chain operation designed to ensure real-time, reliable visibility of items: to both the consumer and in-store staff. This supply chain optimisation is especially important, given that majority of Australians (57%) now expect to be able to pick up an item ordered online from a physical store that same day. Additionally, almost two-thirds (62%) of global consumers confirmed they have continued shopping with brands that deliver goods the fastest. Quick delivery can only be achieved with AI-driven forecasting and inventory management solutions to ensure availability of items.
Optimised connectivity of solutions between the warehouse, distribution channels and the store ultimately guarantee timely fulfillment and consumer satisfaction. “Consumer supply chain needs are centred around a few key areas – speed, visibility, and reliability. All of these needs require a supply chain that is seamlessly connected and visible in real-time to both the retailer and consumer, and only possible with effectively managed mobile device fleets,” said Rodrigues.
Trek Bicycle Corporation Transforms Device Management With SOTI
The challenges of increasing the effectiveness of mobile devices to help meet consumer demands and operate an efficient supply chain were not lost on leading bicycle retailer, Trek Bicycle Corporation (Trek).
Operated for over 45 years and expanded operations to more than 80 countries, Trek had the need for increased device visibility and management to support surging production and shipping demands.
Previously, Trek struggled with troubleshooting mobile device issues, device security and gaining insight into the performance of its rugged devices. The team experienced hours of unnecessary downtime and several other mobility challenges due to a lack of visibility into its device fleet. As a result, Trek sought a solution that could increase efficiency across the hundreds of devices operating in its manufacturing warehouses.
Leveraging the SOTI ONE Platform – specifically SOTI MobiControl and SOTI XSight – Trek has been able to gain clear visibility into all its devices and can monitor how, when and where they are being used.
“Using the SOTI ONE Platform, we can quickly solve and prevent issues, limiting the amount of stoppage time for our warehouse staff. It’s safe to say we are seeing 15-20% time savings on new
employee onboarding. We highly depend on SOTI MobiControl and SOTI XSight because these products drastically decrease downtime and secures our devices,” said Tom Spoke, Director of Global IT at Trek Bicycle Corporation.
The simplicity of SOTI MobiControl’s drag and drop feature allows Trek to seamlessly roll out critical updates as its IT team easily sets up and configures devices.
With the addition of SOTI XSight, the team can quickly diagnose, support, and troubleshoot issues remotely. This ensures its distribution facilities can ship same-day orders, so stores have available stock for all cyclists needs.
“Visibility into the location of a device fleet is essential, especially as consumers expect their favourite brands to ship out orders the same day. With SOTI, Trek can now monitor when and where a device is being used and quickly troubleshoot device issues, remotely and in real-time,” added Rodrigues.
Maintain a Competitive Advantage Through New Technology
The rapid advancement of technology in supply chains is central to meeting the heightened demands of today's consumers. However, the increase in device usage within organisations necessitates an advanced approach to device management and data utilisation.
“The ability to seamlessly integrate device data with crucial business metrics is now indispensable in achieving faster delivery times, increased customer satisfaction and overall supply chain optimisation. As the landscape of consumer expectations continues to evolve, the role of technology in supply chains will undoubtedly grow, making it essential for Australian supply chain organisations to embrace these advancements to maintain a competitive advantage,” concluded Rodrigues. ●
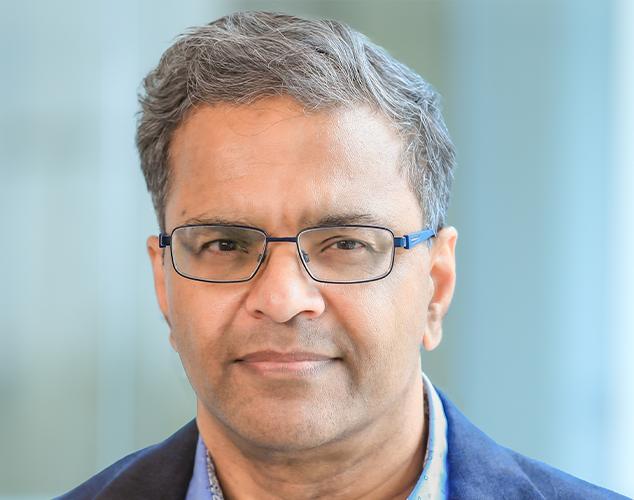
Welcome to supply chain commerce
Unify ware h ouse manageme nt, t ransportation management and o rder management
With all your sup p ly chain a pplications on a s ingle p latform, you can b reak down silos, unlock efficie n cies, boost p rofitability and transform execution. Set your most a mbitious goals, Ma n hattan will make them poss ible.
To learn more, visi t m anh.co m.au

How Simulation Changes the Game End-to-End in Supply Chain
Simulation is getting more attention in supply chain, given the compounding global impact of geopolitical, technological, and environmental disruption.
The mandate has never been clearer for organisations to transform their supply chains, and simulation, which replicates realworld environments in a digital environment, is one way they’re doing it.
Companies can visualise, validate, and test designs for distribution centres, warehouses, and supply chain optimisation prior to any implementation, according to TMX Transform, a pioneer in the simulation space.
“Simulation is an incredible technology, but it is not an ‘offthe-shelf’ product or a ‘slap-on’ service."
"The value and impact of simulation always depends on the client and what business problems they need to solve. We always start with the problem – not the solution,” Glen Borg, Head of Simulation at TMX, said.
“Like most advanced technology, simulation is valuable when it is created and operated by subject matter experts, who know the technology in and out, but can also contextualise and interpret the outputs and scenarios to clients, because they have been on the warehouse floor themselves.” This pairing of industry expertise with advanced technology is what differentiates TMX as a supply chain consultant, according to Mr Borg.
While a broad term, simulation pinpoints and scales variables that impact the whole supply chain, such as picking speeds, stock allocation, and staff behaviour and movement on the floor.
The complexity of supply chains has been increasing for years, but the solutions and ways clients can tackle that complexity may not necessarily get the same attention.
Nonetheless, businesses need a datainformed approach to DC design that reflects real operations, rather than using averages to predict requirements.
Simulation, along with augmented reality (AR) and virtual reality (VR), equip clients with
insights into DC operations and greenfield facilities. Simulation can be used for:
• Network performance optimisation: identifying efficient network configurations that minimise costs and maximise service levels through simulation modelling and synthesising demand.
• DC optimisation and operations validation: creates virtual representations of manual and automation DCs to assess performance and to identify gaps, potential issues, and effectiveness of operations.
• Automation feasibility validation: creates models of real-world processes through simulation to evaluate the impact of automation on productivity, efficiency, and cost. ●
For more information on How Simulation Changes the Game Endto-End in Supply Chain, click here.
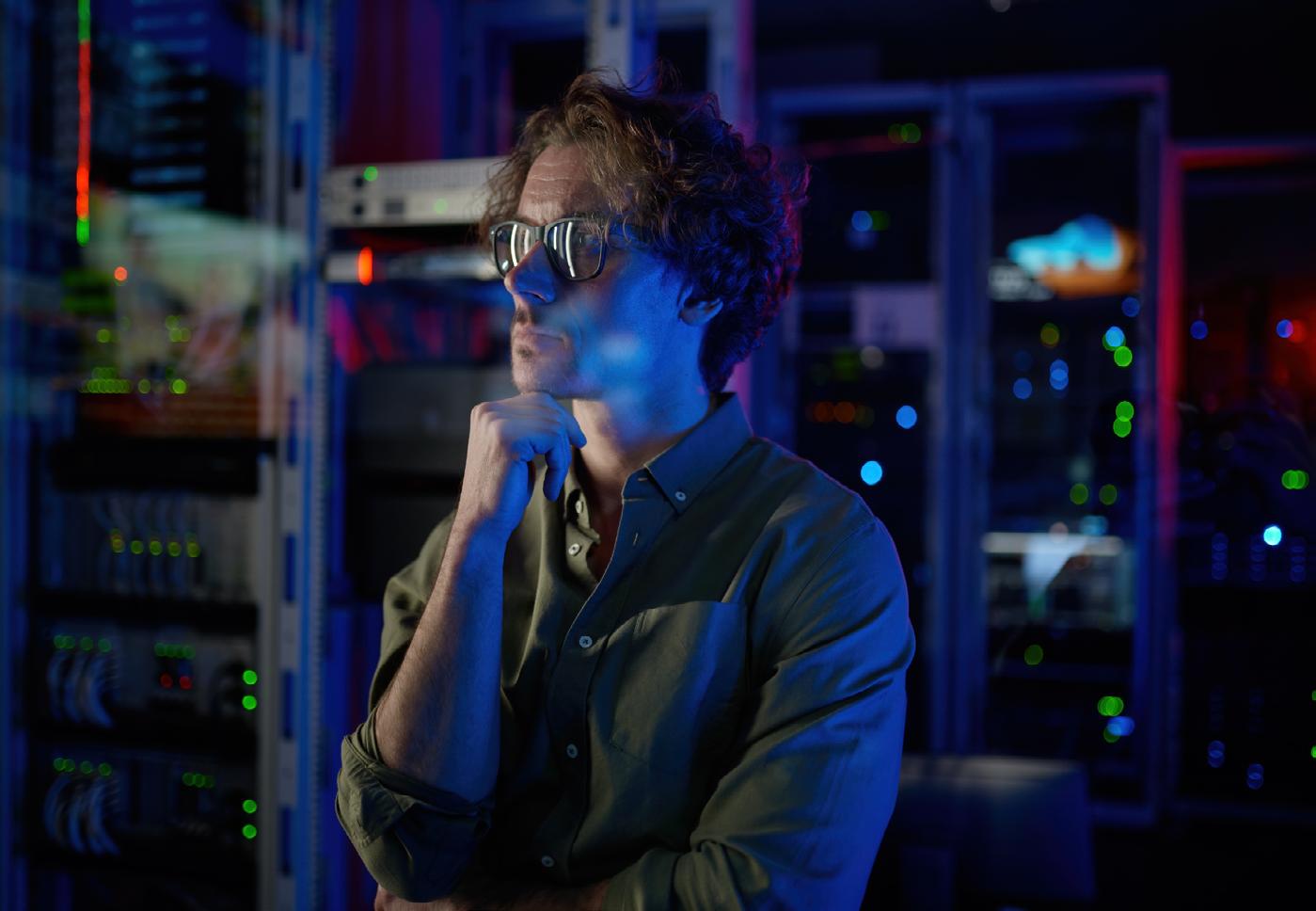
Low-Code Solutions for Logistics: A Toll Group Case Study
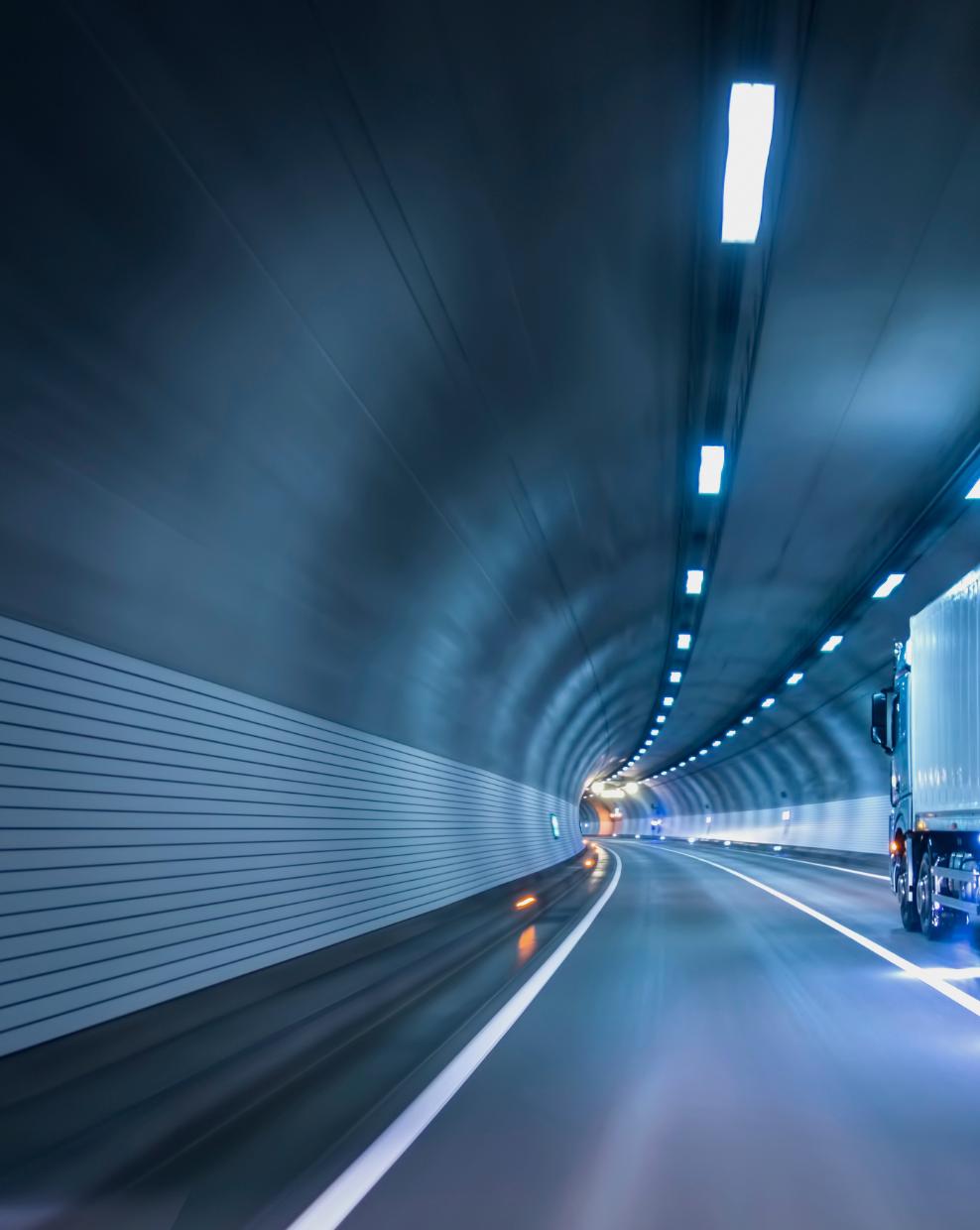
Ecommerce has undergone unprecedented growth over the last five years, forcing logistics organisations to adapt by fast-tracking their digital transformation in an effort to better support employees and customers. For Toll Group, a subsidiary of Japan Post and one of the largest integrated logistics companies in the world, this meant modernising its IT landscape to provide a better experience for its 20,000 customers across 150 countries.
However, within Toll Group’s IT landscape, numerous systems of record were in place, catering to processes such as warehouse and logistics management to serve its customers globally. New software development requests at Toll Group underwent the traditional programming and waterfall delivery route. This created significant challenges as prolonged software development timelines and
constraints on IT talent were not conducive to the rapid pace of change required by the industry.
The need to rapidly modernise its IT infrastructure to fortify its competitive edge and rapidly adapt to evolving customer needs was clear, and in 2021, Toll Group embarked on its IT modernisation journey. At the centre of this transformation effort was low-code development, with Toll Group seeing its potential to streamline processes and optimise operational efficiency and profitability, ultimately leading to securing its competitive advantage quickly and cost-effectively.
Evaluating Low-Code Solutions: A Collaborative Approach
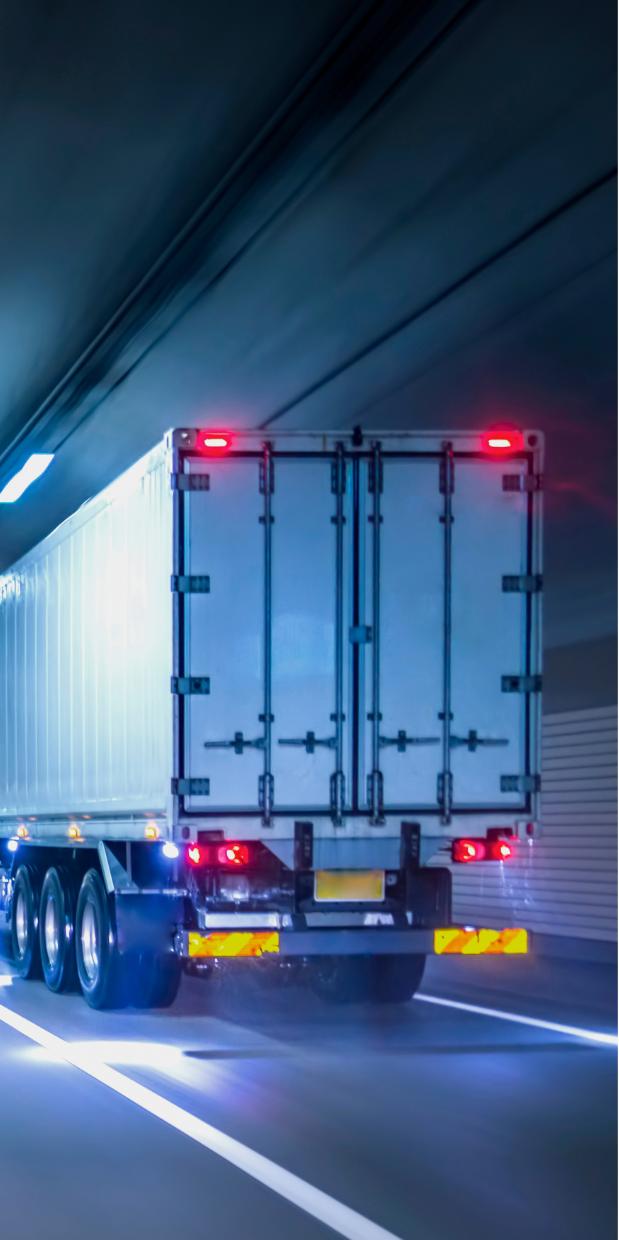
concepts engaged key stakeholders from IT security, enterprise architecture, development, and business units, fostering a comprehensive understanding of lowcode development's potential for Toll Group.
Structuring a Low-Code Capability
Toll Group ultimately selected Mendix as the preferred vendor for its low-code capability. After partnering with Mendix, Toll Group assembled a team to collaborative on initiatives with divisional IT teams and business counterparts. Central to this effort was a key focus on governance to ensure consistency and quality across applications. Additionally, Toll Group emphasised establishing reusable architecture and making early investments in a standardised design system to streamline development processes effectively while maintaining a unified brand identity.
Measuring Value
Transport and logistics businesses operate with thin profit margins, prompting careful review of every element from a cost perspective.
Deliverables ultimately must be commercially viable, addressing both customer and employee experience objectives, with a key focus on differentiation. Google Analytics was integrated to provide valuable insights into application usage, ensuring low-code initiatives aligned with broader organisational goals and key metrics such as revenue, efficiency, and productivity.
These insights revealed that Toll achieved an impressive 40% reduction in both project delivery time and costs. This integration facilitated continuous improvement and optimisation efforts, contributing to the overall success of Toll's strategic objectives.
Quick Wins Demonstrate Tangible Value
During the evaluation phase, Toll identified diverse business areas that could benefit from low-code development and careful consideration was given to selecting the team’s first projects.
A range of use cases required new solutions, including customer-facing web apps, progressive web apps (PWA) for field staff, and eventual mobile applications. These applications spanned global logistics in Asia to global forwarding in 28 countries and 500 sites.
In mid-January of 2021, Toll Group’s risk and audit team was undergoing a significant update to their audit process, rendering a longstanding legacy risk management and audit application obsolete. The team initiated low-code development in early February and was able to deliver the application in just six weeks at a cost of less than $30K. This application was used by operations managers to effectively document specific risks and implement mitigations while routing these to relevant management levels.
A notable success was a PWA for the automotive logistics division in Singapore. Traditionally, when Toll Group vessels arrived in a port, vehicles were
unloaded, and employees manually recorded VIN numbers, took photos of damage, and compiled documentation. The new PWA built with Mendix transformed this process, allowing employees to use their mobile devices to scan VIN numbers, take pictures, and submit documentation in real-time, eliminating the need for paperwork and creating a more efficient process.
In early September 2023, Toll Group launched their legal capital review application, utilising a reusable module built by Toll Group for delegation of authority (DOA). This module, though complex due to varying approval workflows, mirrors the organisation's various approval levels. This emphasis on reusability at the onset of Mendix adoption paid dividends with a 40% reduction in project delivery time and costs.
Education and Communication
Continual education and communication were pivotal to Toll Group's success in transitioning from waterfall to agile software delivery with Mendix. The organisation hosted global hackathons to promote low code application potential, exposing participants to different working methods and showcasing platform capabilities. This commitment to education extended to the recruitment of new graduates to become Mendix developers, with a focus on a 9-month timeline for them to become productive contributors.
Looking Forward: Innovation and Differentiation
As Toll Group looks to the future, innovation and differentiation remain key objectives. The organisation recognises that low-code development with Mendix is not just about addressing current needs but also about preparing for future challenges. The ability to rapidly prototype and test new ideas positions Toll Group as an innovative player in the logistics industry. ●
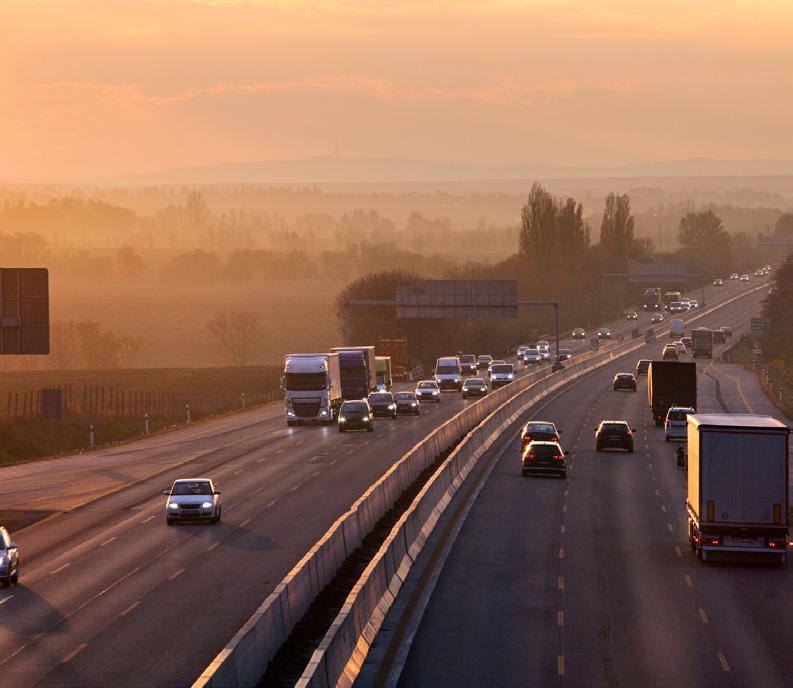
New Standard for Warehouse Racking in Australia: Ensuring Safety and Quality
WRITTEN BY DR MURRAY CLARKE, DIRECTOR STRUCTURAL ENGINEERING, DEMATICSafety in warehouse environments is of the utmost importance. Each year in Australia, warehouse employees are injured as a result of
accidents involving forklifts and warehouse racking.
With steel storage racking systems forming the backbone of warehouse operations, it is essential to ensure racking safety, quality, and structural integrity over the long term.
Following recent developments globally and calls from local industry, the racking Standard in Australia has undergone a significant update, with revisions aimed at enhancing structural design, safety measures and operational procedures.
Evolution of the Standard: The New vs. the Old
The Standard for selective racking in Australia has recently been updated, with the previous AS 4084:2012 being superseded by:
• AS 4084.1:2023 Steel storage racking.
Part 1: Design
• AS 4084.2:2023 Steel storage racking.
Part 2: Operation and maintenance
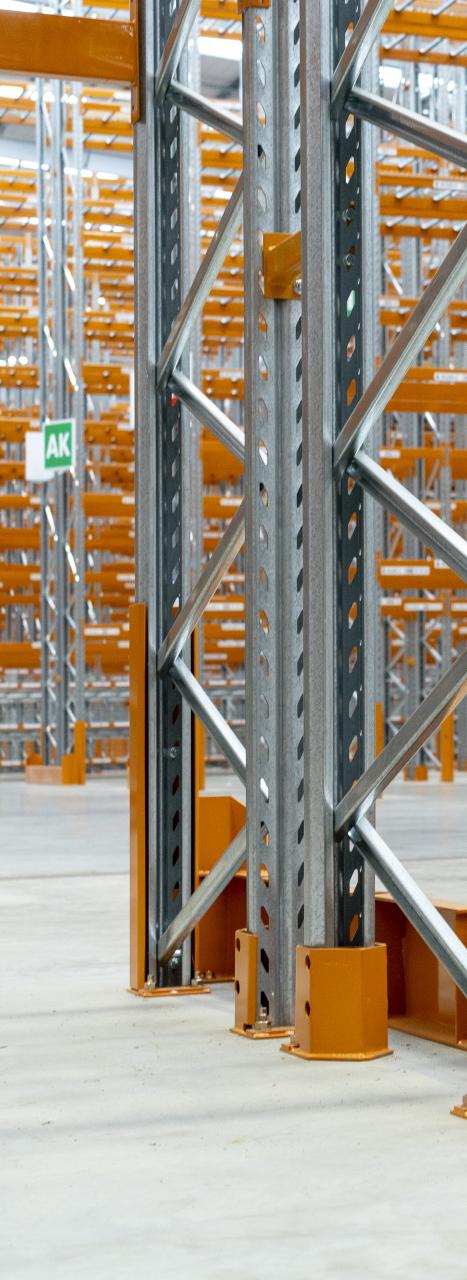
The subdivision of the Standard reflects a more comprehensive approach, addressing both design and operational aspects. Expanded and improved guidance is provided to end users and those carrying out inspections of racking systems, particularly in relation to damage assessment and This change reflects global advances in the industry, since the last update in 2012, where developments in seismic design, testing methods, and structural analysis have set new benchmarks. This is because the field of storage racking has been the subject of extensive research and development, notably in
With the European and North American Standards already adopting these advancements, Australia recognised it was time to align itself with global best practices. The recent integration of seismic design considerations into the new Standard follows similar developments in
Previously, it was not standard industry practice to design racking for seismic loads. Consequently, little guidance on seismic design was provided in the previous Australian Standard, and it was not requested nor enforced by building certifiers. On the occasions when seismic design was carried out, the detailed calculations were largely at the discretion of the racking supplier rather than an industry Standard.
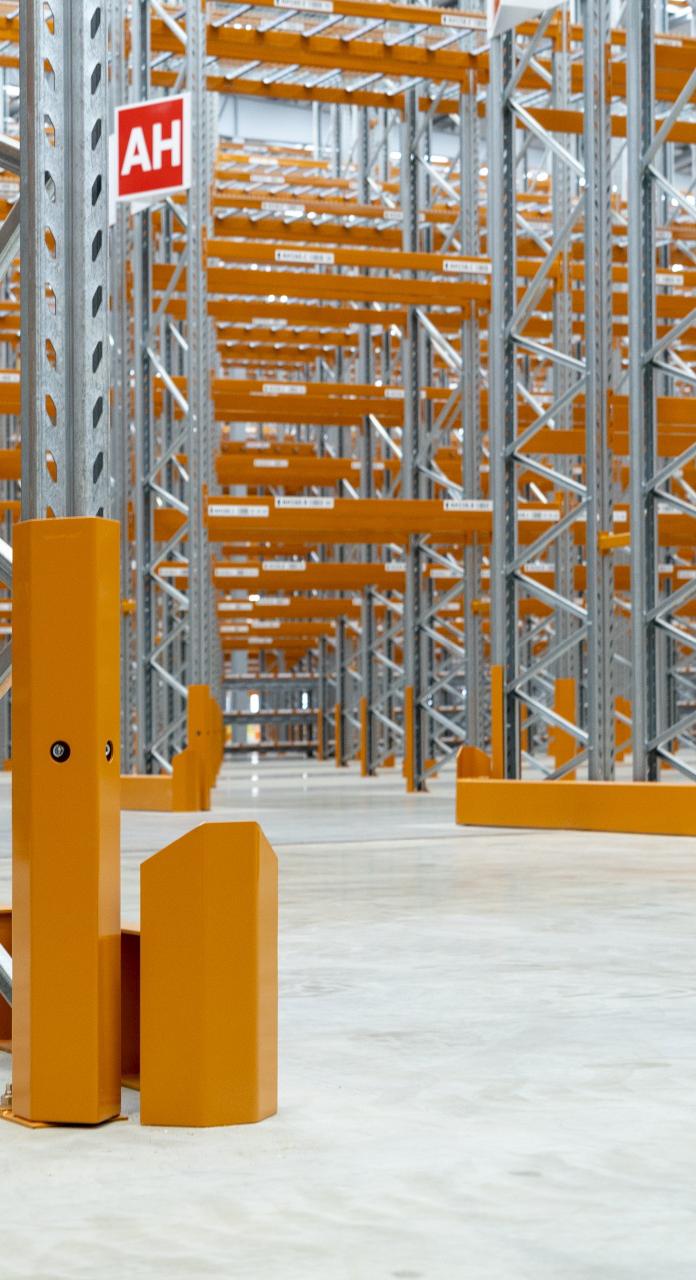
Approximately five years ago, seismic design of racking (as well as other non-structural building elements) started to receive increased focus from building certifiers.
Consequently, the mandatory requirements for seismic design of racking have been included and clarified in the new Standard to remove any ambiguity around the need for seismic design and the relevant design inputs. This ensures, as far as possible, that all racking suppliers in Australia are operating on a level playing field.
The Major Changes
At a high level, the changes in the Standard cover:
Modification of existing racking systems: While the new Standard does not apply retrospectively to existing racking installations, if those systems are reconfigured, modified or extended then they should be upgraded to the current Standard.
Clarification of seismic design: Previously, designing racking systems with seismic considerations wasn't common in Australia. The new Standard, however, mandates the seismic design of selective racks, ensuring all racking systems can withstand earthquake-induced forces, aligning with global best practice. The updated Standard provides clearcut inputs for seismic design, ensuring consistent adherence across suppliers.
Operational and maintenance focus: The inclusion of operation and maintenance as a separate part to the Standard addresses the industry's requests, specifically supporting and guiding damage assessment and repair methodologies.
Testing methods: Enhanced methods for testing racking components, ensuring they provide reliable data for safe design of racking.
Structural analysis: Advanced methods of structural analysis, providing a more accurate and reliable evaluation of racking systems.
Direct strength method: Introduction of the direct strength method for designing perforated cold-formed steel racking uprights, aligning with Australian and North American best practices for cold-formed steel design.
Dematic Moves Quickly to Meet Industry Needs for its Colby Products
While seismic design has only recently found its way into the Australian Standard, this is old news for the Colby pallet rack range, engineered and manufactured by Dematic in Australia. With a history that traces back to the 1990s, Colby rack has been designed for seismic loads for many years – particularly for clients in New Zealand, where seismic considerations

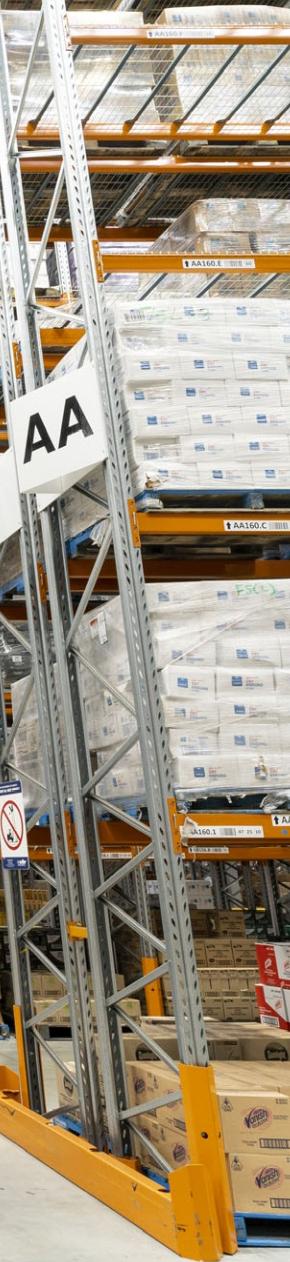
are of heightened importance. As part of Dematic’s commitment to quality design, we collaborate with New Zealand engineers who have a high level of expertise in seismic design. This wealth of experience not only reflects Dematic's dedication to safety, but also enables its ability to move quickly in response to industry requirements.
How Does the New Standard Impact Rack Design?
The new Standard brings changes that will influence the design of new racking systems and upgrades to existing systems.
While selective pallet racking is the primary focus of the updated Standard, Dematic employs a consistent approach to structural safety and applies seismic design principles to all types of Colby rack including drive-in, high bay, satellite and Multishuttle/miniload systems. A detailed Dematic project on the seismic behaviour of drive-in racks from 2012 to 2015 jointly with Sydney University produced detailed analysis that supports Dematic's approach and preparedness for the new Standard.
Dematic has also carried out extensive structural testing at the component level to provide the required data to support our Colby racking designs.
These tests notably include cantilever tests on welded beam end connectors to simulate the cyclic load coming from earthquakes. Additionally, testing has been undertaken on base plates under uplift loading conditions that arise in seismic analysis.
ColbyRACK: A Testament to Dematic’s Unwavering Commitment
Dematic's commitment to safety and quality, and its ability to consistently meet the Standard, means that its Dematic and Colby products are not only compliant but also set the benchmark for what should be expected in the industry.
Dematic takes the certification of its racking systems seriously. In-house developed structural software ensures that every Colby racking system that is delivered meets the stringent requirements of the new Standard, providing customers with peace of mind.
Dematic’s advanced software and extensive experience ensures that every Colby rack system complies with the new Australian racking Standard. Dematic’s proposals include detailed calculations around seismic design. There are many parameters that go into the calculation; not just the hazard factor and soil type, but also the importance level of the structure, the design life, the rigid mass factor, the ductility factor, and more.
The rigid mass factor, previously unspecified in the code and subject to individual interpretation or reference to international Standard, is now clearly defined.
The ductility factor, crucial for measuring a structure's capacity to handle deformation and absorb seismic forces, allows for design beyond a fully elastic response.
Meeting the New Standard with Key ColbyRACK Features
Colby beam connectors, designed for both seismic and non-seismic conditions, stand out due to their length at 280mm with four hooks and a thickness of 4 mm in high strength steel. Their robust design can usually withstand seismic forces without the need for extra cable or vertical bracing which is common in other designs. Colby rack's seismic design strategy prioritises minimising additional bracing, only utilising it for structures where it's essential, such as high bay and drive-in racks – but not for selective racks.
Ongoing Safety Adherence
Customers need to be vigilant and ensure that their racking solutions comply with the updated Australian racking Standard.
In addition to meeting the new Standard by installing properly designed warehouse racking, it’s also essential for every warehouse to install safety signs and conduct yearly audits and safety inspections. The new Standard requires rack load signs to contain additional information, in particular the ‘tolerance grade’ of the racking system and the name of the firm responsible for the structural design.
The Future of Warehousing
The new Standard for warehouse racking in Australia marks a significant step forward in improving the safety and efficiency of storage solutions across the industry. As a leader in this space, Dematic embraces these changes, continuing its long history of providing reliable and economical solutions that meet the required Standard.
As the warehousing industry in Australia brings in the new Standard, companies like Dematic are positioned to lead the way. With a longstanding commitment to safety, quality, and innovation, Dematic and its Colby range of storage products are ready to help shape the future of warehousing, ensuring that customers have access to the best the industry has to offer. ●
Robotic Integration and the Future of Supply Chains
WRITTEN BY TERRY SMAGH SENIOR VICE PRESIDENT AND GENERAL MANAGER, ASIAPACIFIC AND JAPAN AT INFORRobotics has captured headlines for its role in manufacturing and final assembly operations, with some of the world’s largest manufacturers reporting massive robotics-led return on investment (ROI) in their efforts to automate and innovate across the factory floor.
Robots vary significantly in size, functionality, mobility, dexterity, artificial intelligence, and cost. They can be fixed, mobile or fly, in the form of drones, and increasingly, they are programmed to recognise and learn from their surroundings. Their ability to capture information and make decisions independently means they can often perform tasks with little to no human intervention.
Robotics-as-a-service
Robotics’ deployment in the warehouse was, until recently, restricted to only the largest of organisations as they typically came in the form of fixed assets with high price tags. The emergence of robotics-as-a-service has, however, changed the
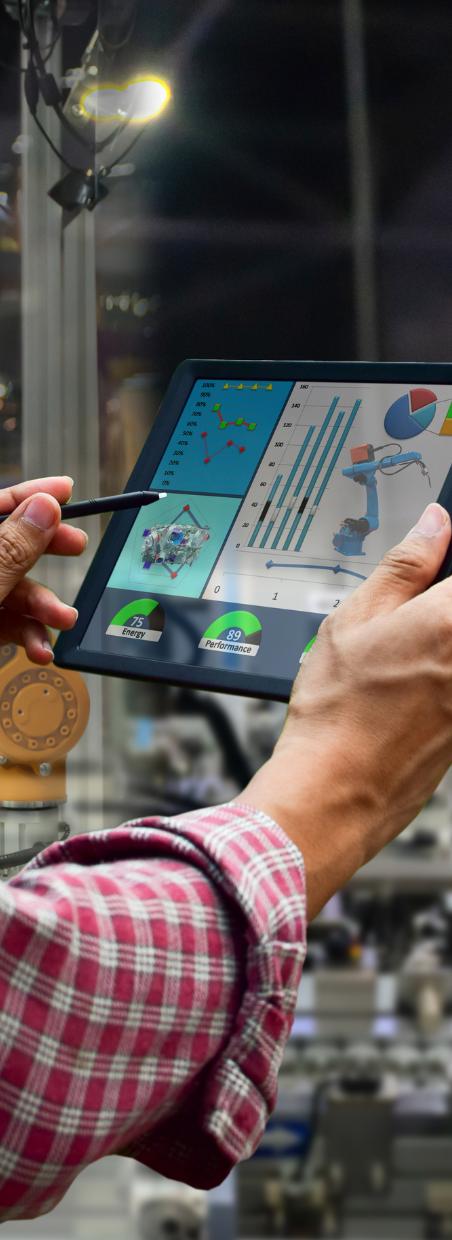
game somewhat, bringing robotics-led innovation to warehouses of all different sizes and profiles. Testament to this, is that robotics is expected to see strong growth over the next five years, particularly
As many organisations bring their warehouse operations back in-house to regain control in a time of unprecedented complexity, robotics can instil flexibility.
In a similar vein, it can give third-party logistics (3PLs) an advantage as they move complex merchandise mixes across numerous categories for high volumes of customers.
Cyber Physical Automation
While robotics present a potential game changer in automation and efficiency – allowing people to shift to more strategic, less dangerous, and higher value work – a WMS platform is the core foundation of the warehouse. Without such a system – which can be easily integrated via APIs, and seamlessly talk to the robots, interpret data, and inform workflows, robotics can only extend so far, limiting potential and impeding ROI.
In fact, according to Gartner, 95% of supply chain organisations have either invested, or plan to invest, in cyber-physical automation, with a significant proportion of those planning on using intralogistics smart robots (ISRs).
And against a backdrop of a global labour shortages, organisations are look for even more creative ways to bridge skills gaps, and robotics
In the wake of a rise in online shopping, and associated SKU proliferation, merchandise has increased in both volume and diversity. Robots in the warehouse make it simpler and more efficient to move both batches and individual picks, not only reducing reliance on labour, but mitigating risk through increasing
Similarly, drones can undertake detailed stock counts at night, eliminating the need for people to physically check inventory.
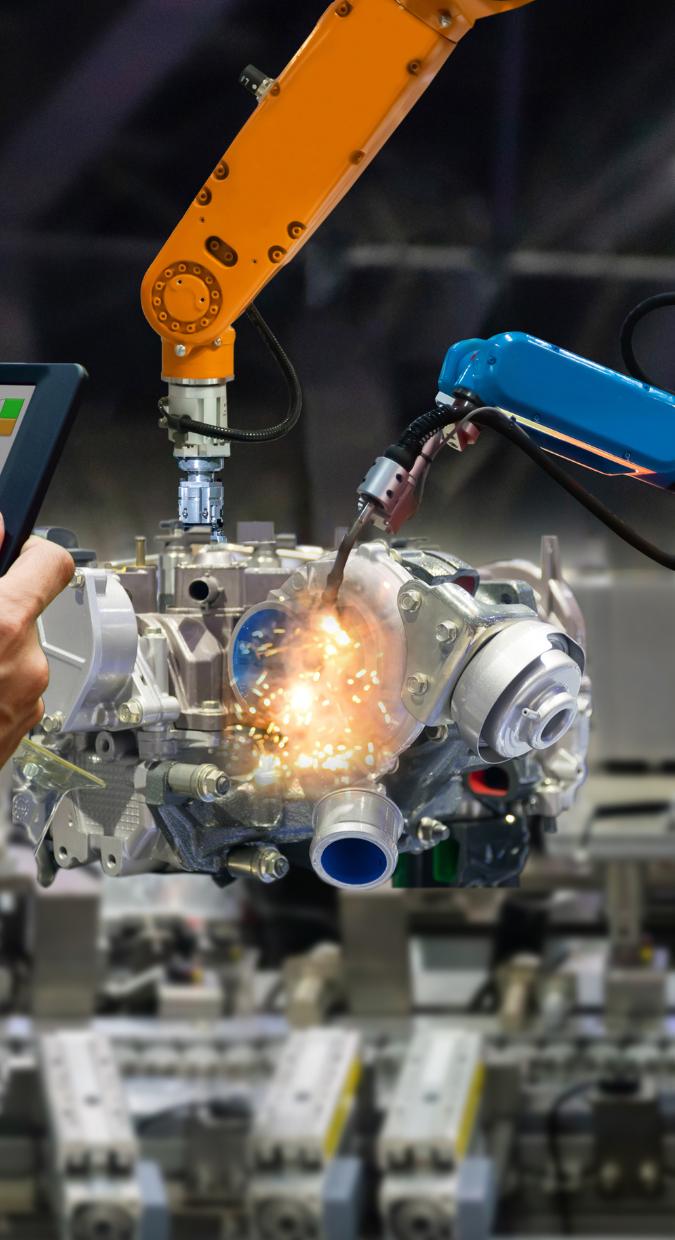
Labour availability constraints are the primary driver behind investments in robotics according to 66%. As technology continues to improve, roboticsas-a-service gains further momentum, and prices decrease, the question is no longer whether to capitalise on robotics, but in what way, and how soon. What is certain, is that its success will depend largely on the extent to which a modern WMS is leveraged to integrate and optimise workflows.
A Robotic-Centric Future for Supply Chains
There is no doubt that the supply chain of the future is likely to see continued growth of autonomous robots. Those who get it right will not only improve the speed and accuracy of routine operations right now but ensure flexibility and agility to adapt in the future as market conditions and dynamics dictate. ●
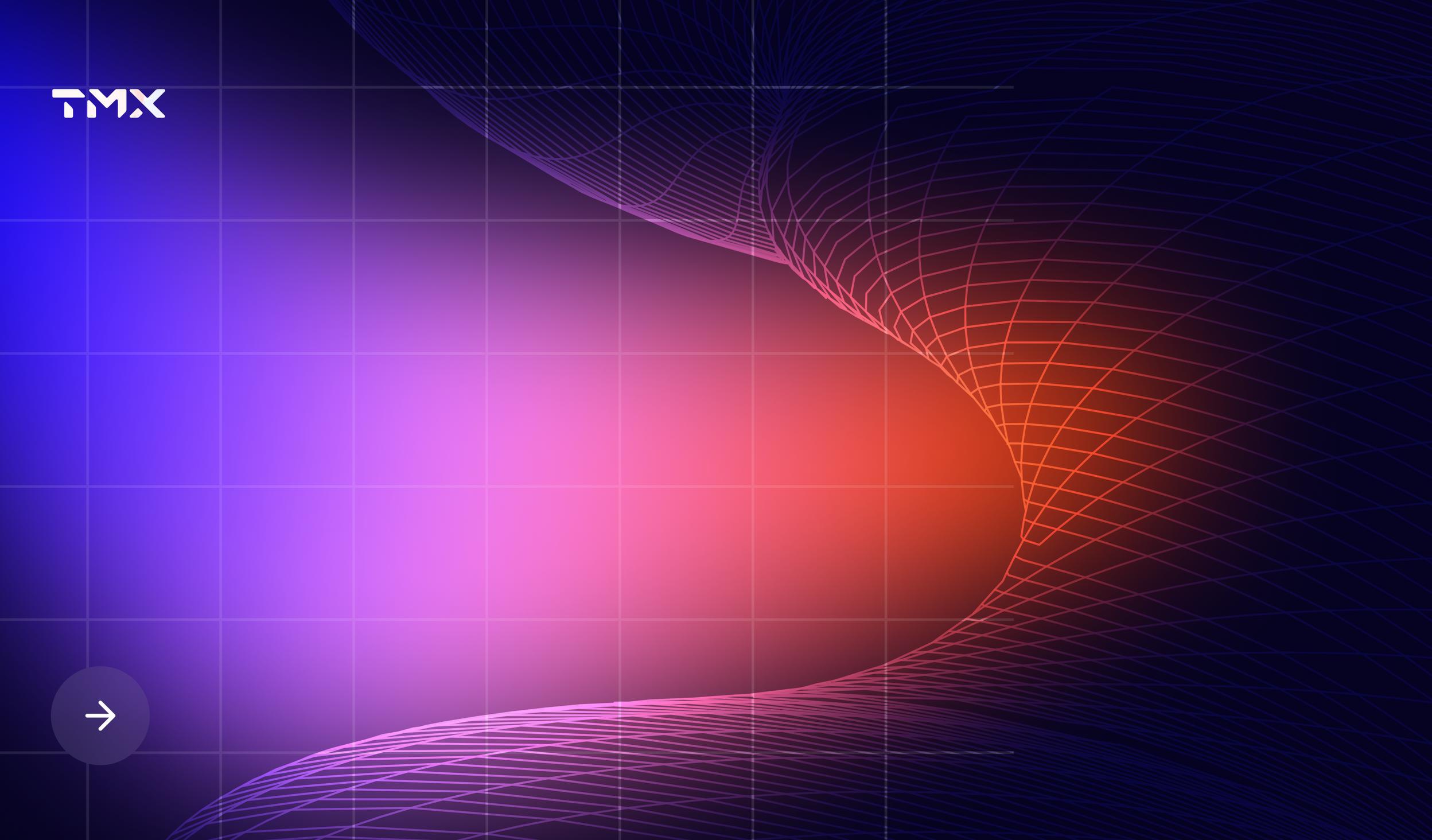
Meet the World’s Most Trusted and Powerful Enterprise Mobile Computer
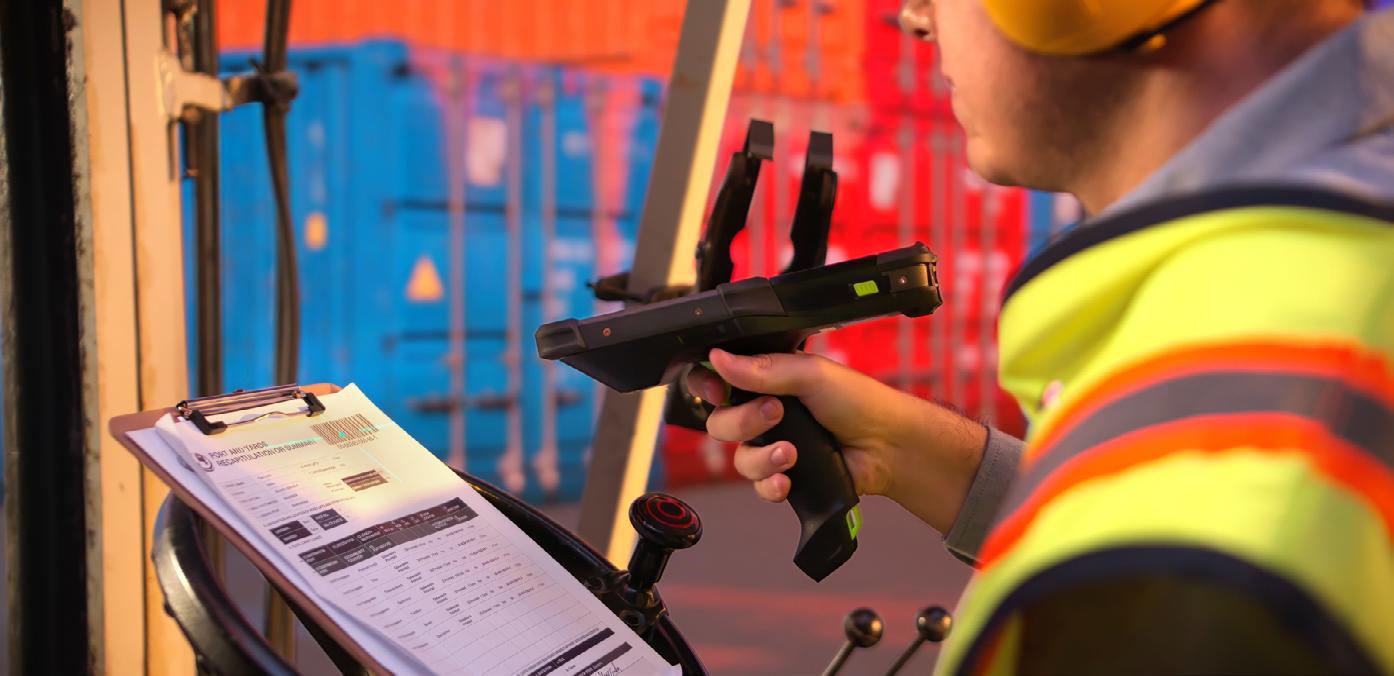
Zebra Technologies have sold nearly five million MC9000 Series ultra-rugged mobile computers – and for good reason. The devices have helped streamline and errorproof processes in the toughest outdoor and indoor environments — in ports and yards, on the manufacturing floor, in the warehouse, and in the back of retail stores.
Zebra has just released the next evolution in this highly successful handheld mobile computer family, the MC9400/MC9450.
Loaded with all the latest mobile technologies, these devices are faster, ready to power the new generation of industrial applications.
The MC9400 and MC9450 offer the latest in wireless connectivity, with the flexibility to cost-effectively connect anywhere and everywhere. Private and public 5G provide new affordable wireless networking options in the most expansive outdoor and indoor environments. And Wi-Fi 6E delivers the fastest available Wi-Fi connections.
The new devices also offer the best in data capture. The SE58 Extended Range
Scan Engine with IntelliFocus™ delivers an unmatched scanning range, enabling workers to scan barcodes as far as 100 ft./30.5 m away.
Its innovative green laser aimer is seven times more visible than the typical red aimer dot, making it easy for workers to scan at a distance.
Biometric facial recognition provides easy access for workers and peace of mind that only pre-authorised users can access devices. Workers can resolve issues quickly with the video-based collaboration, enabled by the high-resolution front-facing camera. And with the 16 MP high resolution rear camera, it’s easy to capture highly detailed photos to document the condition of incoming shipments, quality checks and more.
With OCR Wedge, workers can capture shipping container identification numbers, tire identification numbers (TINs), vehicle identification numbers (VINs) and more with the press of one button — ideal in manufacturing plants, yards, ports, and depots. And with seven keypads to choose from, you can choose the keypad that is best suited to the data utilised in your facility, enabling workers to enter data faster and more accurately.
Compared to the previous generation, the MC9400 and MC9450 offer 2.5x more processing power, 50% more RAM, 4x the
Flash and 8x the storage. Whether you’re running simple ‘green screen’ apps or apps powered by augmented reality and artificial intelligence, you can power them all at once.
Not only are these devices faster, but they’re also more rugged and ready for just about any environment — including a model dedicated to the freezer area. They easily survive 12 ft./3.65 m drops to concrete as per military standards. Meanwhile, Corning Gorilla Glass protects the display and the scanner exit window, and a double IP65 and IP68 sealing rating means you can drop it in water or mud, and even hose it off.
When it comes to flexibility and value-add extras, these devices deliver more. With Device Tracker and the new BLE battery, you can quickly and easily find devices, even if they are turned off or low in power.
The large 4.3 in. display is easy to see indoors and outside in bright sunlight, and also works when wet or with thick gloves.
When you buy a Zebra Android device, you also get features that give you the enterprise control you need. With support to Android 17, you don’t need to worry that your operating system (OS) will become outdated. You choose when and if you want to update — and when you’re ready for an OS update, you can do it automatically via LifeGuard™.
This latest evolution in the ultra-rugged MC9000 Series can power your enterprise to the next level of productivity and efficiency in your most demanding environments. ●
How to Manage Fuel Adjustment Factor (FAF) in an Unstable Market
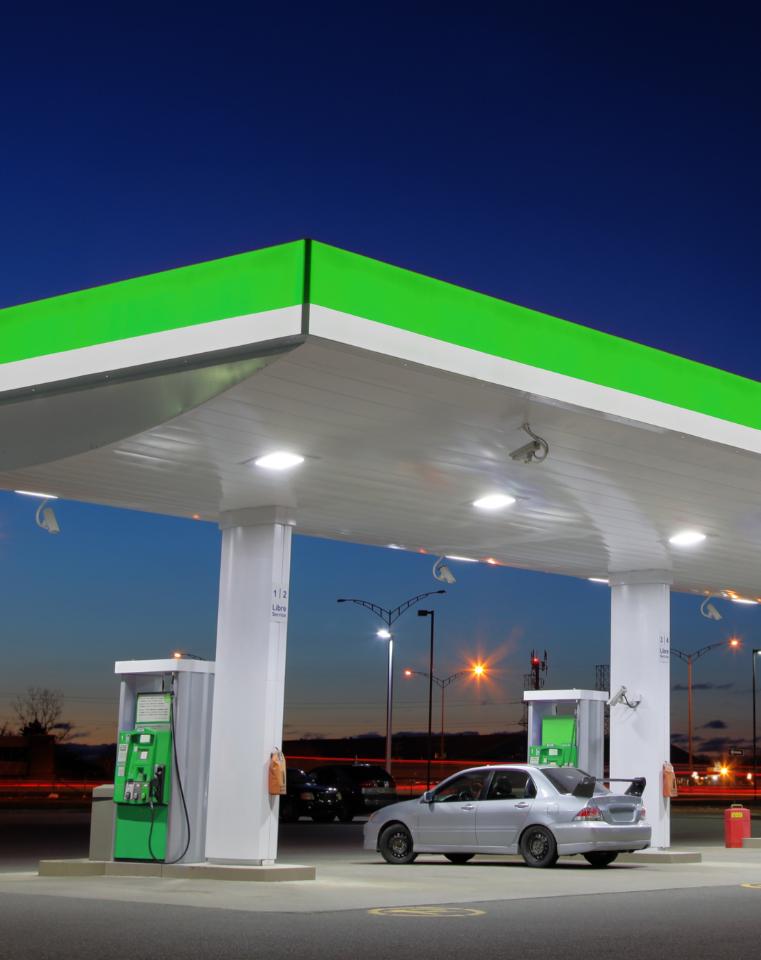
Average fuel prices in Australia hit record highs in October 2023 at $2.11 per litre, while data from the Australian Institute of Petroleum shows prices have remained volatile for the past two years.
Fluctuations in fuel prices can have a substantial impact on the operating costs of transportation companies which is why so many include a Fuel Adjustment Factor (FAF) in their pricing structure – typically calculated as a percentage of the base rate for shipping which varies depending on fuel costs and other factors.
In a market that’s increasingly becoming difficult to keep pace, managing FAF in a way that ensures fuel surcharges are fair for the customer while protecting the bottom line can be a real headache for businesses in the transport space.
Here are some tips and techniques that will help make your FAF calculations and processes more accurate and less painful.
Determine the Frequency of Updates
According to historical year-on-year data, the rise and fall of fuel prices have become increasingly drastic. Taking a ‘set and forget’ approach to FAF is risky in a volatile market. While there is a possibility the business will absorb sudden increases in transportation costs due to jumps in fuel prices, customers will quickly become disgruntled and lose trust if surcharges remain high despite price falls.
To ensure your company or customers don’t lose out, it’s important to keep a close eye on market trends to decide how often it will be necessary to reevaluate and potentially update your FAF rate.
Consider Regional Variations
If operations are spread over a large geographical area, there may be regional variations in fuel price trends to justify setting a different FAF for each area. Importantly, compared to applying one nationalised rate, responding to regional economic conditions and other diverse factors when calculating an individual FAF for operational areas can result in more competitive pricing for customers, who may be considering localised transport providers as alternatives.
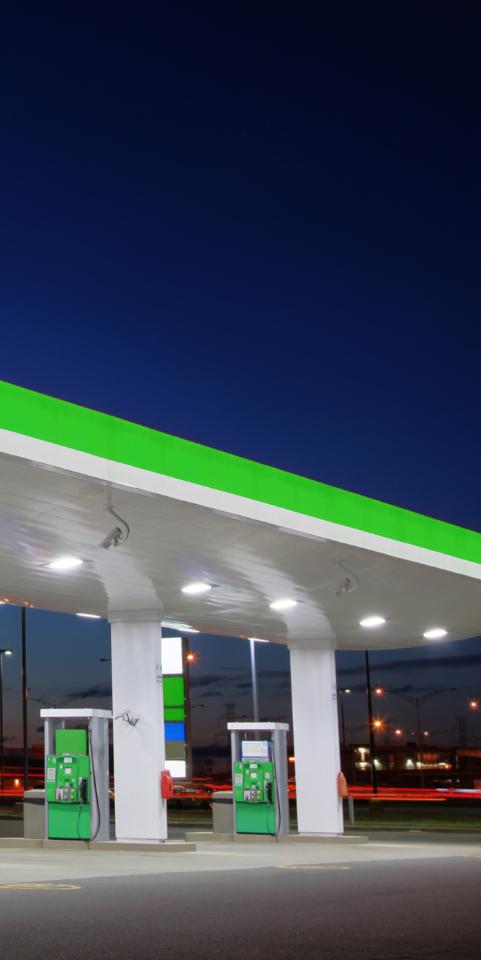
While fuel prices can vary significantly from one region to another, other localised factors to consider include the costs of transporting goods across challenging terrains as well as the quality of infrastructure – both of which can impact fuel consumption. Meanwhile, regardless of the hard costs associated with fuel prices and consumption, ensure you evaluate every regional FAF calculation in the context of local market expectations to remain competitive.
Be Transparent About Changes
Naturally, customers are unlikely to question any reductions in fuel surcharges, but when it comes to raising FAF, it’s best practice to communicate with customers about how the new FAF rate has been calculated. To maintain loyalty and build trust with your customer base, be transparent about how trends in fuel prices have impacted the calculation as well as any other ‘less obvious’ factors that may have been taken into consideration, such as those associated with specific geographical areas or transportation routes.
Take a Proactive Approach
Waiting for fuel prices to increase before starting the process of adjusting FAF is almost certain to leave your business out of pocket for a period of time. Plus, the bigger the operation, the higher the price will be for any delay. Conversely, if fuel prices drop, customers will expect to see this reflected in your surcharges very quickly.
Continuous monitoring of market conditions, forecasts, and any influential factors affecting fuel prices will ensure the business stays on the front foot, ready to implement an adjusted FAF when the time is right. Effective ways to proactively monitor the market might include using logistics management technologies that integrate with fuel price databases and provide real-time updates, evaluating the activities and rates of competing transport providers, and developing and continually refining internal forecasting models.
Utilise Automation to Improve Accuracy and Minimise Risk
Some transport operators have many potential FAF variables to consider across their network – from geographical location and route to the vehicle type and final journey length. Manually calculating and adding the right FAF to every customer invoice can be hard work, time-consuming, and fraught with risk, requiring impeccable record keeping.
A dispatch solution that integrates with invoicing software can solve these problems by automatically
adding the correct pre-programmed FAF surcharge for each journey. For example, different FAF rate percentages can be set across multiple transport line items which feed through to customer invoices once jobs are recorded as completed by the dispatch software.
Automating FAF can benefit transport companies in several ways. When employees spend less time crunching numbers and completing documentation, they have more time to redirect to other strategic or revenue-generating tasks.
By removing the risk of error, employees will also spend less time responding to customer queries or complaints, or even re-generating invoices. Another key benefit of automating FAF calculations is that any changes to the rate will be automatically recognised and called out on the invoice, supporting the need for clarity and transparency with customers, guaranteeing that you’re not just raising prices. ●
For more information, please click here.
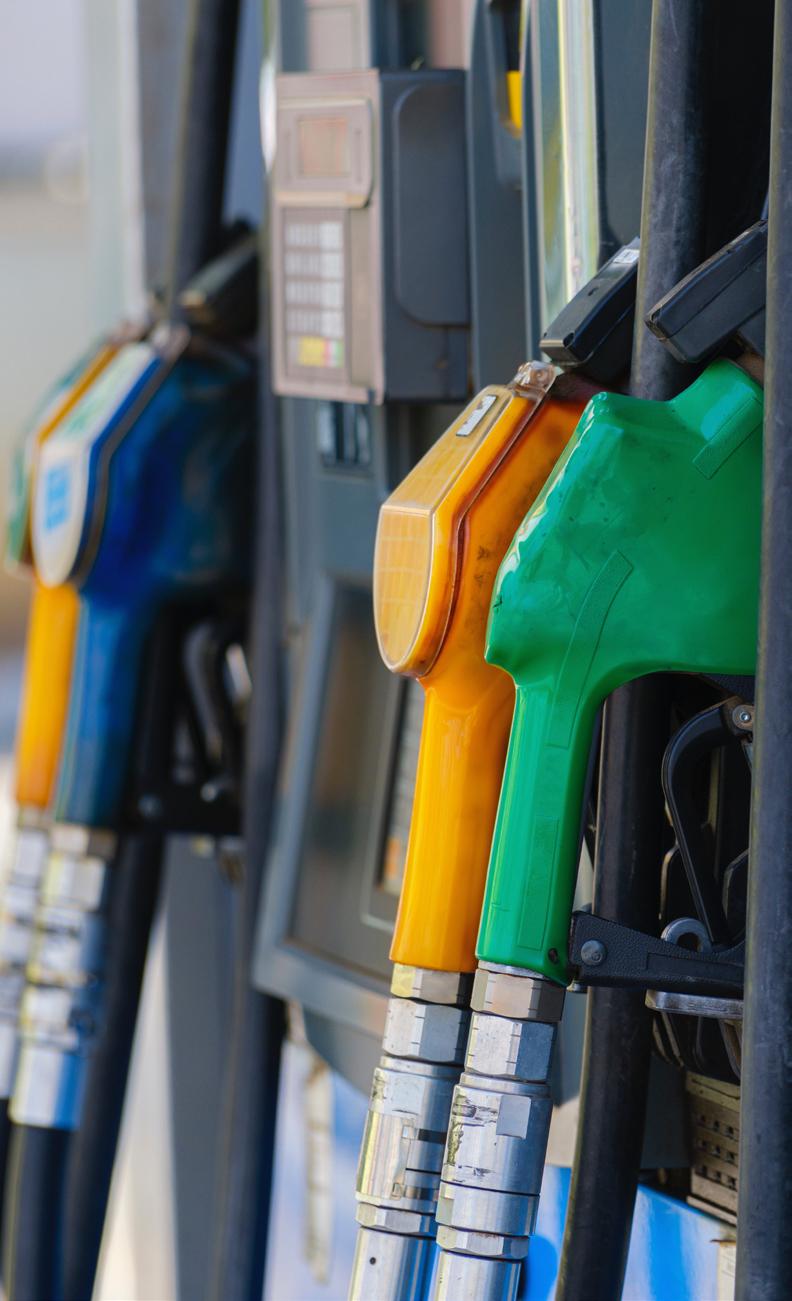

Transforming the Australian Supply Workforce:Chain
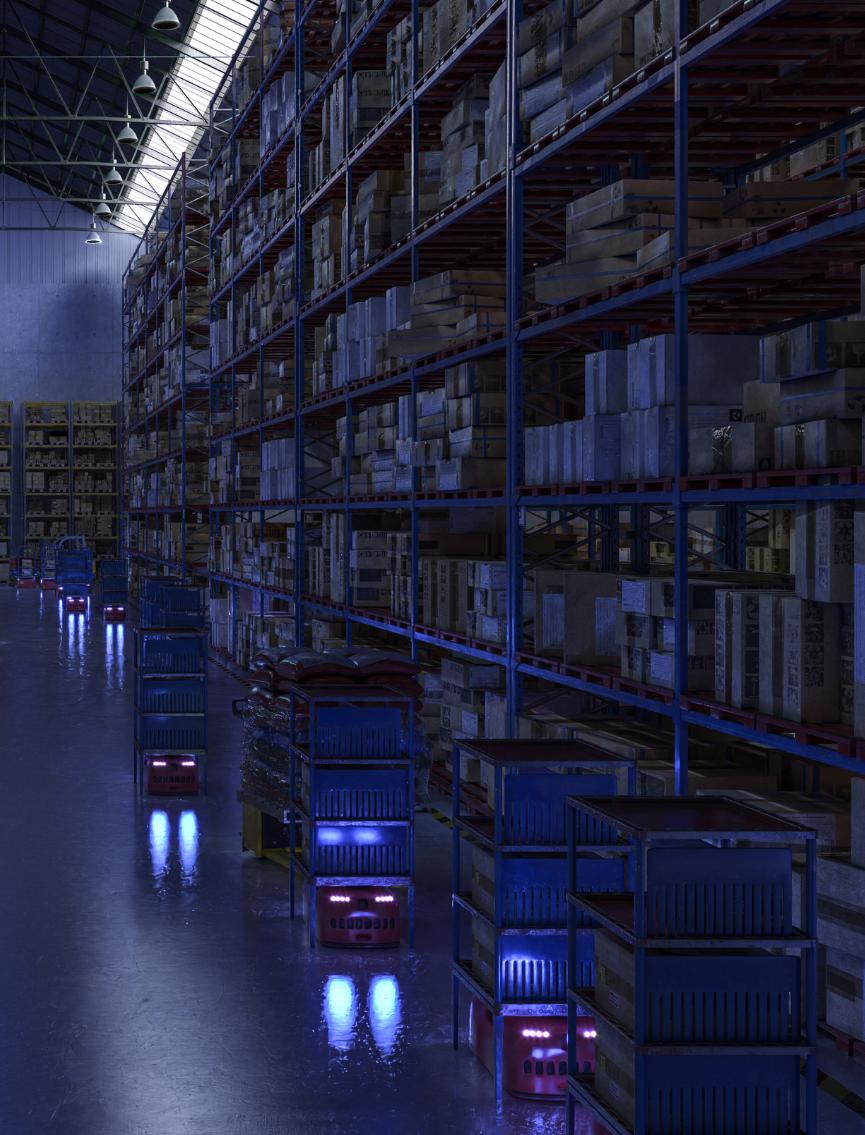
A Deep Dive into the Skills Gap and AdoptionTechnology
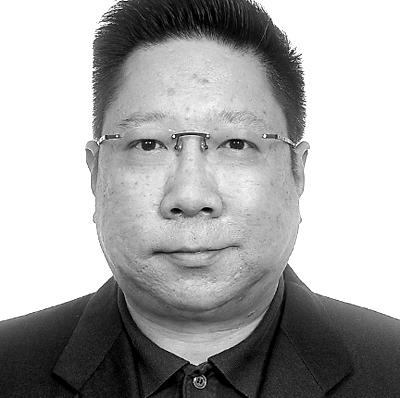
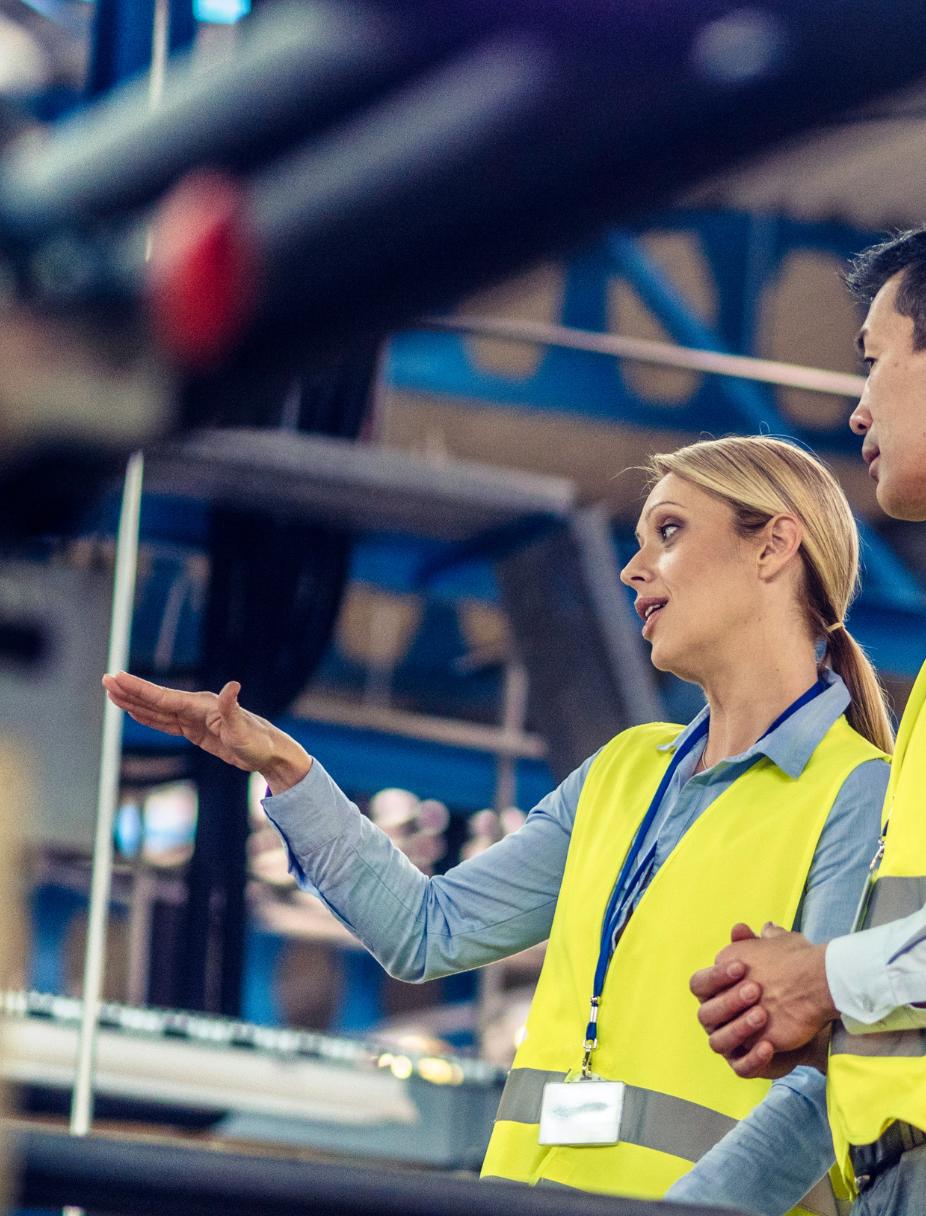
"As labour shortages continue to plague the industry, businesses are exploring and adopting mixedlevel sensors like radio frequency identification tags (RFID) to enhance their operations."
ROYSTON PHUA, VERTICAL PRACTICE LEAD, APAC SUPPLY CHAIN, ZEBRA TECHNOLOGIES

As technology in supply chain rapidly evolves, the persistent shortage of skilled workers looms large for Australian businesses. Supply Chain Insights explores: While the skills gap and labour shortages are undoubted challenges, could adversity pave the way for innovative and streamlined processes between man and machine?
Australia, much like most of the world, has a labour shortage problem. The closure of Australia’s international borders to stem the spread of COVID-19 left almost half a million jobs unfilled in 2022, with 28% of businesses reporting vacancies according to the Australian Bureau of Statistics. As of August last year, 388,800 jobs remain unfilled and no improvement is being felt in the supply chain.
From sourcing to production, logistics, and delivery of goods and services, supply chains are profoundly impacted by skills and labour availability. Industries such as warehousing and distribution face a critical shortage of manual labour, making it challenging to find and retain workers to run warehouse floors. Pasquale Tomasiello, Senior Regional Director at Dematic, says customers have significant concerns around the inability to find and retain warehouse labour. The shrinkage of workers within the warehousing and distribution segments of the supply chain has a flow-on effect to increased competition and higher wage costs.
On top of a general labour shortage, a skills shortage presents itself as a broader industry challenge. According to Pasquale, a dearth of control engineers and qualified engineers puts greater pressure on the industry to train and develop these skills internally.
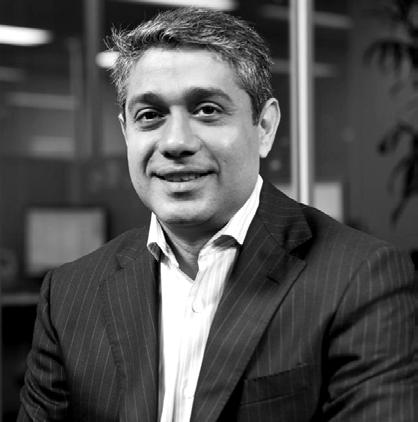
“The problem of a lack of skilled workers has lingered over the last few years, which in a way is getting worse because the demand on supply chain is increasing.”
RAGHAV SIBAL, MANAGING DIRECTOR, ANZ, MANHATTAN ASSOCIATES
“Organisations, like Dematic, who have invested in staff training and development over a sustained period of time benefit from having a strong, longtenured pool of resources to draw upon to help train young graduates and attract qualified engineers to oversee automation projects. This is particularly important as more and more businesses compete for these few and far between resources which is why more and more companies are prioritising automation experts,” says Pasquale.
According to Raghav Sibal, Managing Director, Australia & New Zealand at Manhattan Associates, the Australian supply chain industry is yet to recover from the effects of border closures over the COVID-19 pandemic which prevented skilled workers from entering the country.
“The problem of a lack of skilled workers has lingered over the last few years, which in a way is getting worse because the demand on supply chain is increasing. The skills gap is widening, which is adding to the overall problem. The number of logistics jobs that are open and unfilled is very high,” Raghav notes.
The labour shortage impact extends beyond operational constraints, influencing overall supply chain productivity, cost structures, and the ability to adapt to evolving market demands. To counter this, Australian supply chains are embracing technology solutions in a transformative wave, with industry leaders looking to invest in cutting-edge tech because of the amalgamation of rising labour costs and workforce scarcity. David Sim, Supply Chain Director at TMX Transform, says to successfully usher in the automation era, experienced and highly intelligent operations managers and industry leaders are needed.
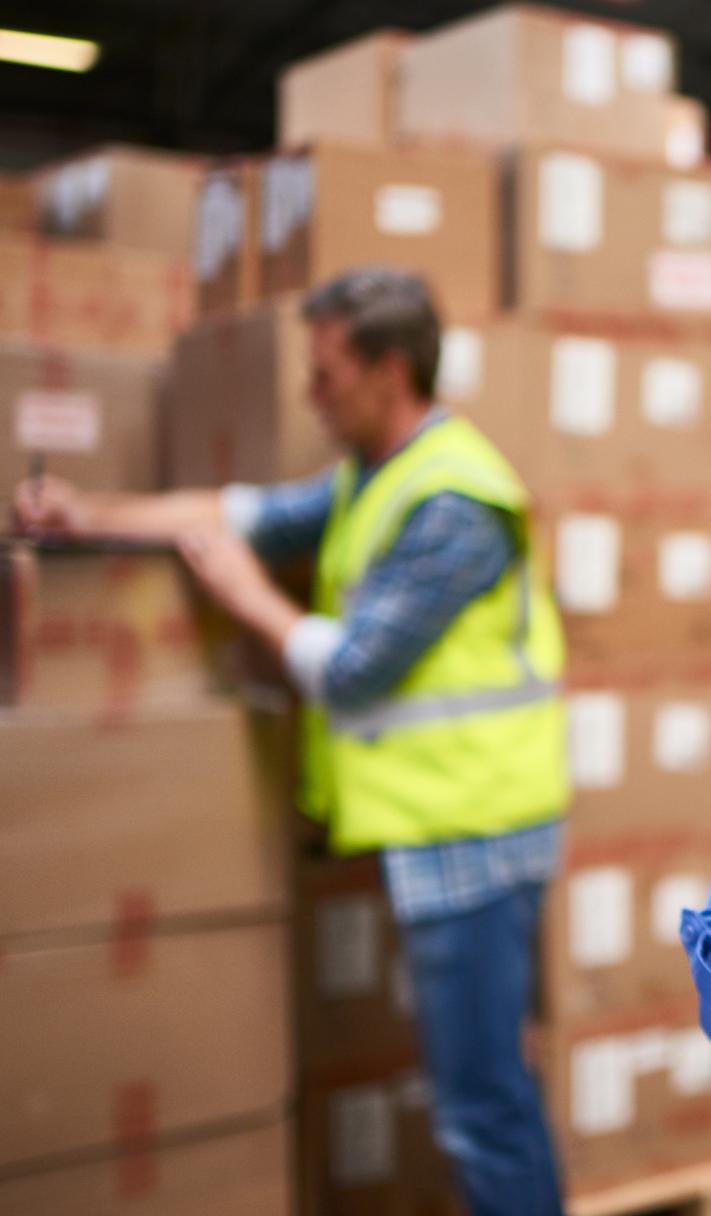
“The skillsets haven’t caught up to the direction the industry is trying to reach in automation, data science, and data-based decision making,” he says. “Working in fulfilment, omnichannel or retail environments is extremely demanding for operations leadership roles and requires stamina and an ability to absorb stress.
Filling these roles with people who aren’t equipped to deal with the speed of innovation and technology can cost businesses millions, but the opportunity to get it right is exciting.”
Warehouse Opportunities
The warehouse landscape is changing quickly. Initially, labour costs pushed the needle towards more automation, and the recent shortages in workers have piled on the pressure. The critical challenge, according to Raghav Sibal, lies in finding the right balance between automation and manual labour. Warehouse technologies are proving essential in streamlining operations, from unloading trucks to efficiently managing assets, ensuring adaptability to fluctuating demands.
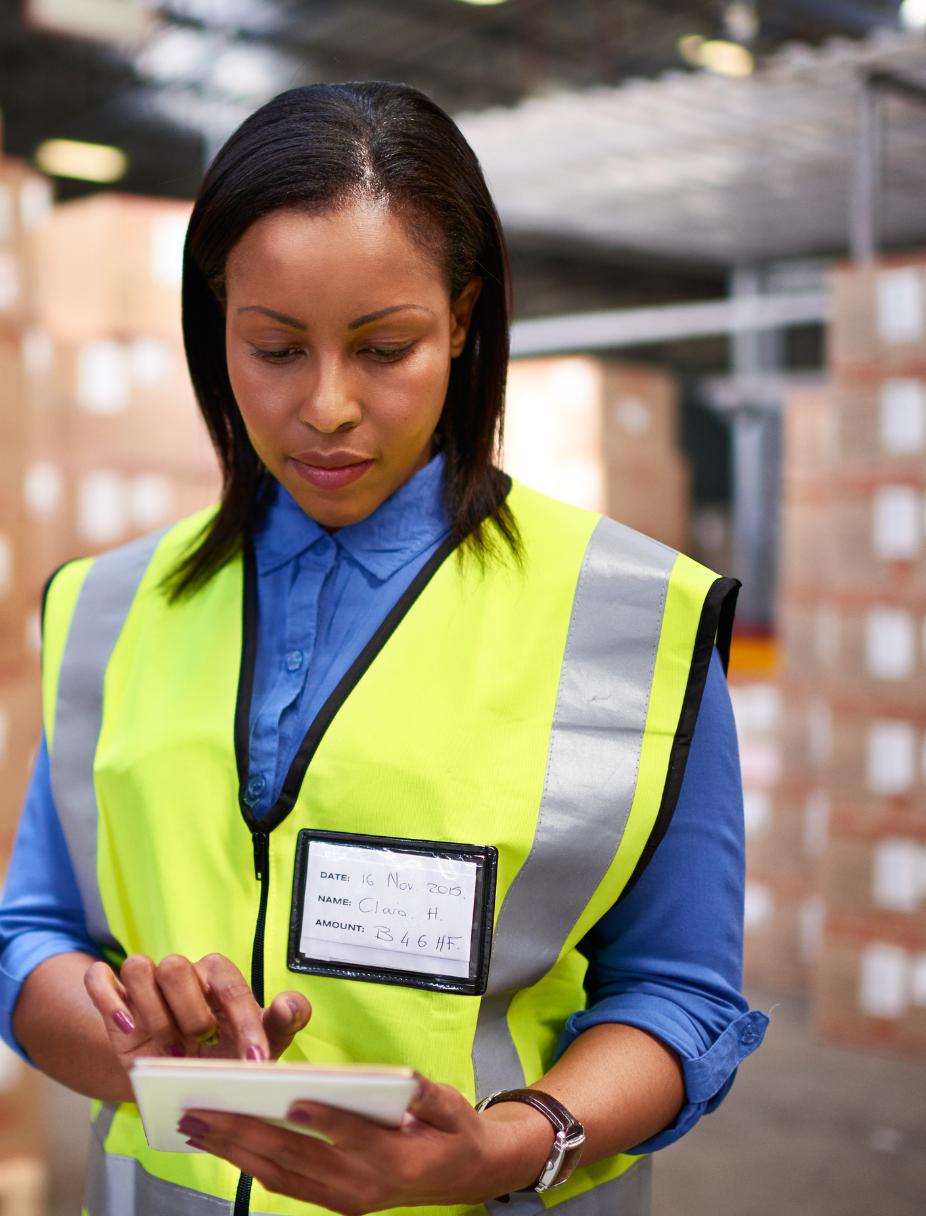
“Using sophisticated labour planning and forecasting technology has become critical,” he says.
“Software gives visibility into the forecast of orders, but also an indication of what labour requirements would be needed to meet those requirements. If the order forecast is set to increase because of an upcoming sales event, how do you prepare and adjust to the hours needed from your workforce?”
Dematic’s Pasquale Tomasiello echoes this sentiment, emphasising that embracing new technology is not just a choice, but a necessity.
“The skills gap has made it imperative for companies to explore automation across various levels of warehouse and distribution functions. Technology adoption is no longer solely about addressing the skills shortage; it is now a strategic move to gain competitive edge.”
One technology making strides is Automatic Storage and Retrieval Systems (ASRS), helping to buffer and sequence pallets and cases, optimising processes for picking stations and sortation systems.
“The automatic storage and retrieval of pallets and cases can reduce huge amounts of labour,” Pascal says. “The combination of the storage and retrieval system with a very clever and ergonomically designed pick station creates this methodology called Goods-to-Person.”
More and more, robotic solutions are taking centre stage in warehouse operations. Autonomous Mobile Robots (AMRs) and Automated Guided Vehicles (AGVs) handle transport functions to articulated armed robots for pick and pack operations. The integration of robotics not only simplifies transport tasks – replacing manual labour – but brings a new level of efficiency to pick and pack operations.
Importantly, the adoption of robotics is not limited to specific industries, it’s extremely versatile, making it a viable solution for warehouses across various sectors.
Despite the widespread adoption of technology in organisations, particularly in automation, businesses can struggle to transition seamlessly from implementation to benefits realisation. For organisations with substantial capital investments and comparatively smaller workforces, a lack of leadership makes it difficult to bring transformations to fruition. As organisations navigate their own transformation journeys, workforce planning, training, and effective leadership becomes paramount in ensuring the successful integration of technology into daily operations.
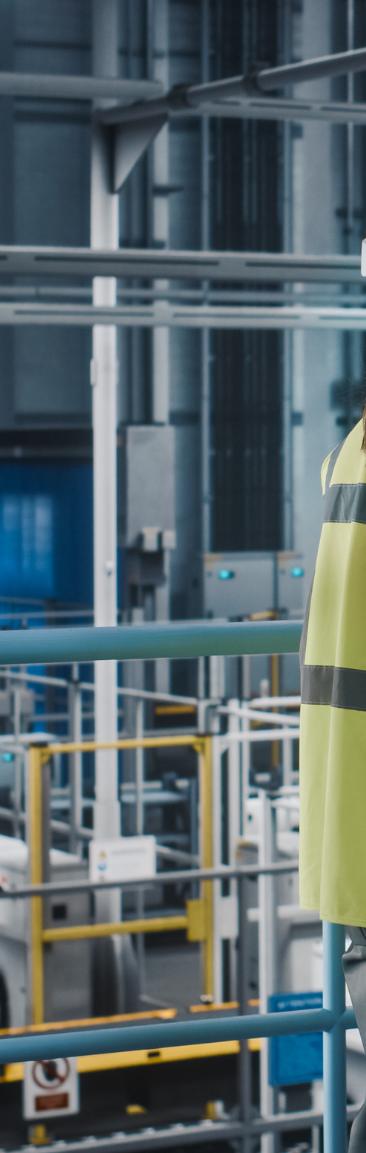
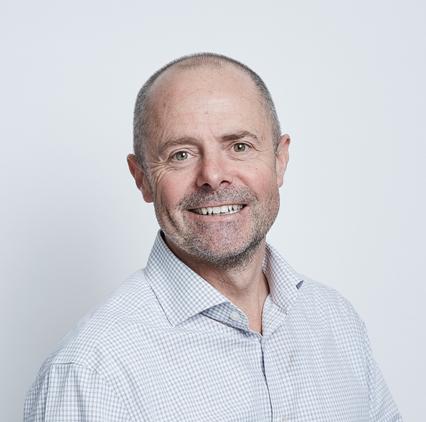
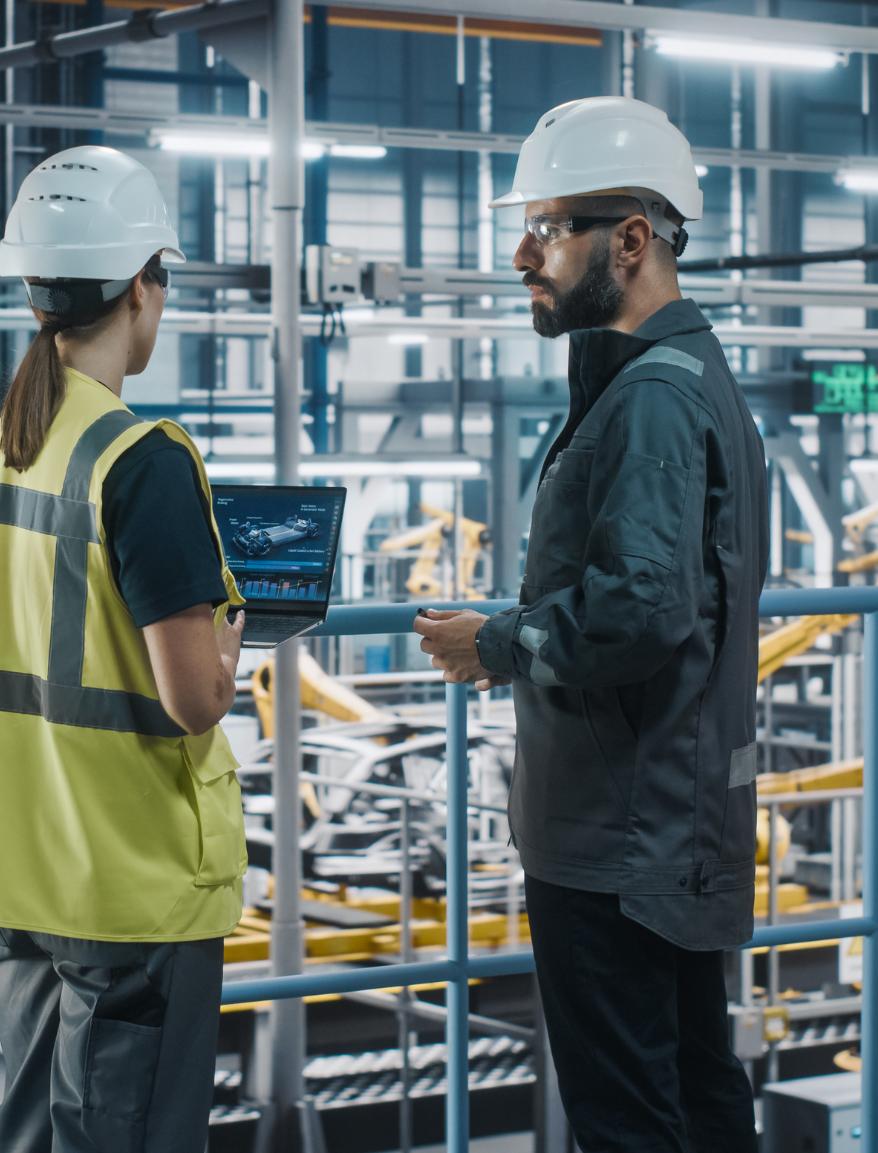
“Organisations are usually very excited and energised by a shiny, new automation tool, but the initial buy-in can fade away as the fatigue factor sets in."
DAVID SIM, SUPPLY CHAIN DIRECTOR AT TMX TRANSFORM
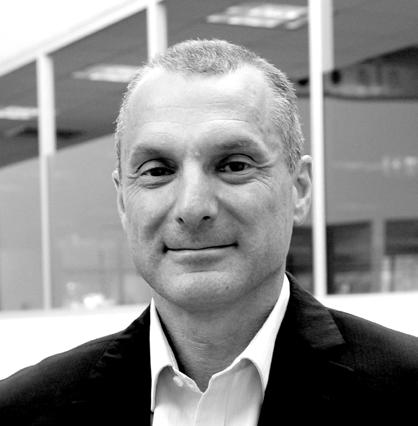
“Organisations, like Dematic, who have invested in staff training and development over a sustained period of time benefit from having a strong, long-tenured pool of resources to draw upon to help train young graduates and attract qualified engineers to oversee automation projects.”
PASQUALE TOMASIELLO, SENIOR DIRECTOR – INTEGRATED SYSTEMS, DEMATIC
David Sim points out the challenges encountered at the middle and supervisory levels are felt the most, where skilled managers are becoming scarce due to the increased utilisation of automated systems. On top of this, David highlights that much of industry grapples with maintaining a robust continuous improvement framework and structure around automation changes.
“Organisations are usually very excited and energised by a shiny, new automation tool, but the initial buy-in can fade away as the fatigue factor sets in,” David says. “It’s not just about spending millions of dollars of capital, it’s also crucial to drive and maintain the smaller improvements.
Once the gloss wears off, organisations need to have a plan around making the new technology sing for sustained benefits long term.”
Wearable Technologies
Tracking solutions, barcode technology, and wearable devices are emerging as key players in addressing the persistent challenges associated with labour shortages. Royston Phua, Vertical Practice Lead APAC Supply Chain at Zebra Technologies, sheds light on the innovative ways

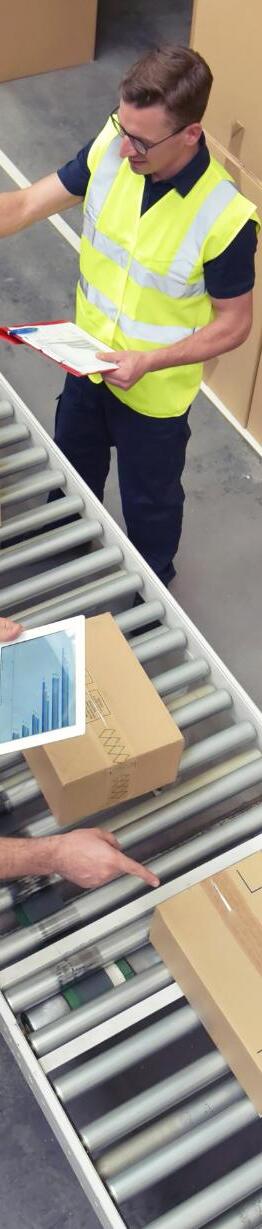
these technologies are transforming warehouse operations and bridging the skills gap.
"As labour shortages continue to plague the industry, businesses are exploring and adopting mixed-level sensors like radio frequency identification tags (RFID) to enhance their operations. Despite the initial cost, these technologies prove to be costcompetitive and justified over time because of the ongoing scarcity of skilled labour."
Usability needs to be a priority for those looking to invest in new technology, according to Royston.
“If the new technology doesn’t have a big learning curve, users can implement it right away. User-friendly tech with an interface similar to a smartphone makes it more comfortable for workers to embrace a new process.”
Royston emphasises the need for a strategic combination of labour and various automation solutions, dispelling notions of full autonomy in warehouse operations.
The integration of ‘barcode and sensor-based technologies, coupled with mobile computing apparatuses’, plays a crucial role in augmenting labour resources. These technologies support businesses in boosting productivity, retraining workers, and enticing them to stay within the organisation.
“A shift on a warehouse floor can be brutal, physical work,” he says. “Wearable technology emerges as a game-changer in enhancing flexibility and efficiency within warehouse operations.
It frees up the hands of operators, enabling them to execute tasks on the spot with the highest level of productivity. Not only is this resulting in financial gains, but it’s taking care of workforces who engage in monotonous, frankly sometimes exhausting manual labour.”
By minimising unnecessary tasks such as excessive walking, bending, and reaching, wearable tech helps workers concentrate on more valueadding functions, which creates a sense of team and job satisfaction.
Software as the Backbone for Automation
Much like automation, warehouse management systems (WMS) are fast evolving. According to Raghav Sibal, there is a common misconception that a large kit of automation can fulfill all warehouse
requirements. Instead, more sophistication is required to bring out the benefits of automation, especially in warehouses with a combination of human and machine labour. Raghav notes that Warehouse Execution Systems (WES) have become crucial to be used as part of the WMS for warehouses with diverse automation pieces and control systems. More warehouse automation –often from different vendors which provide distinct control systems – brings its own complications and has only increased the requirement to bring different software systems into one.
The transition to Software as a Service (SaaS) and cloud-native applications is helping businesses reduce previously troublesome integration challenges and provide seamless data flow in realtime across applications.
“Integrated software from years past have been individual applications interfaced together with data and messages flowing back and forth. There are still multiple points of failure and information delays between applications with this approach. With this new technology stack available with native cloud technology, there is no need for integration, which gives a true unification between a warehouse solution and a labour solution,” he said.
"Cloud-native technology has really made unification possible in the supply chain."
Collaboration is Key
Collaboration within the supply chain industry can help to address the skills gap. By working collectively, the industry can influence authorities to increase skilled migrant visas and implement consistent skill sets and training standards. The current surge in re-skilling and re-tooling needs a unified approach to maintain a minimum training standard, so there’s consistency as professionals transition between businesses.
“There’s a difference between doing things quickly and doing things properly,” David says.
“Collaboration can help avoid those hasty decisions which lead to bigger problems down the line, such as capital blowouts, delayed timelines or the souring of relationships.”
Royston Phua also sees huge value in collaboration, considering the gravity of catalytic events such as the COVID pandemic, geopolitical tensions, and climate events.
“Slowly but surely, more collaboration will happen,” he says. “It must, because the world has changed. Businesses need to move away from siloed operations – which is admittedly a huge challenge – to find ways to collaborate within their supply chains.” ●
Understanding the Consumer Shift: Adapting to Economic Pressures
WRITTEN BY RICHARD WRIGHT MANAGING DIRECTOR, SEA, AT MANHATTAN ASSOCIATESThe retail landscape is undergoing a dramatic transformation, primarily driven by shifting consumer behaviours in response to the escalating cost-of-living challenges. Recent research from Manhattan Associates has revealed that 89% of consumers are modifying their spending habits to cope with these economic strains. This shift has a significant impact on retail dynamics, creating a divide between those who adapt and those who falter in meeting evolving consumer expectations.
Retailers' Response to Changing Demands
In an era where mediocre shopping experiences are increasingly unacceptable, retailers are under pressure to not just serve, but to impress. They are doubling down on digital transformation, recognising that digitalisation is not just a trend but a necessity. About 26% of retailers are now focusing on upgrading to modern, omnichannel-capable point of sale (POS) systems, viewing this as a top priority for the coming year. This shift signifies a broader trend of integrating digital technologies across both front and back-end processes.
The way that retailers connect and engage with shoppers is evolving.
While email remains the dominant channel, younger consumers are showing a growing inclination towards engaging through social media. This trend is in line with the broader move towards starting the buying journey online, with 84% of consumers beginning their search digitally.
The New Role of Retail Associates
With the added financial burden on consumers, the expectation for a seamless, personalised shopping experience has intensified. Retail staff are increasingly required to provide an experience beyond what can be achieved through online shopping. This trend is particularly pronounced in nonfood retail sectors, where staff must engage customers with unique and memorable experiences. To meet these expectations, store associates are being equipped with digital tools and skills, transforming their roles from traditional customer service to tech-enabled brand ambassadors.
However, digitalisation brings its own set of challenges. Retailers reported only having accurate inventory data 70% of the time, a decline from previous years. This lack of inventory accuracy hinders the ability to deliver seamless omnichannel activity, which can lead to negative shopper perceptions as customers expect consistent and reliable information across all retail touchpoints.
Customers are increasingly looking for frictionless, interconnected retail experiences. For instance, when faced with out-of-stock scenarios, they prefer store associates to provide immediate solutions, such as checking product availability in nearby stores or arranging for home delivery. This need has led to the adoption of mobile POS devices and other technologies that facilitate retail store associates to deliver on-the-spot customer service and sales.
The Sustainability Challenge
While there is growing industry focus on operating sustainably, research suggests that only 45% of consumers now consider sustainability a critical factor in their shopping decisions, a notable decrease from previous years most likely tied to economic pressures becoming more prominent.
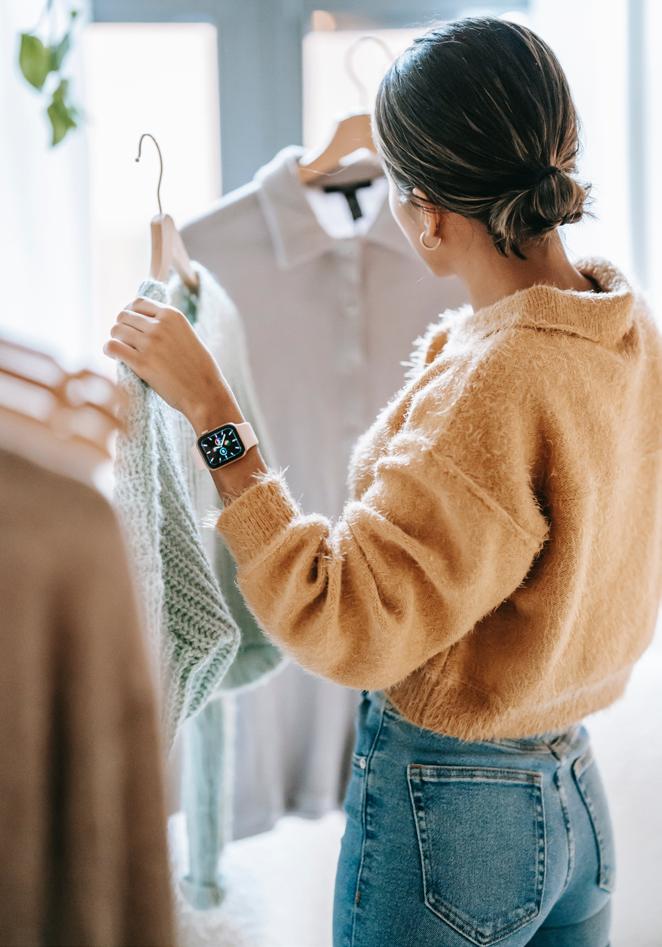
Despite these findings, retailers need to find innovative ways to incorporate sustainable practices into their operations, recognising that this will be a critical factor in long-term customer loyalty, especially among younger generations of shoppers.
Adapt and Succeed
The retail sector is at a crossroads, facing both economic and digital challenges. The most successful retailers will be those that can adapt swiftly, integrating digital capabilities with a deep understanding of customer needs. This approach will not only meet the immediate challenges of today’s economic climate but also set the foundation for future growth and success in an increasingly digital world. ●
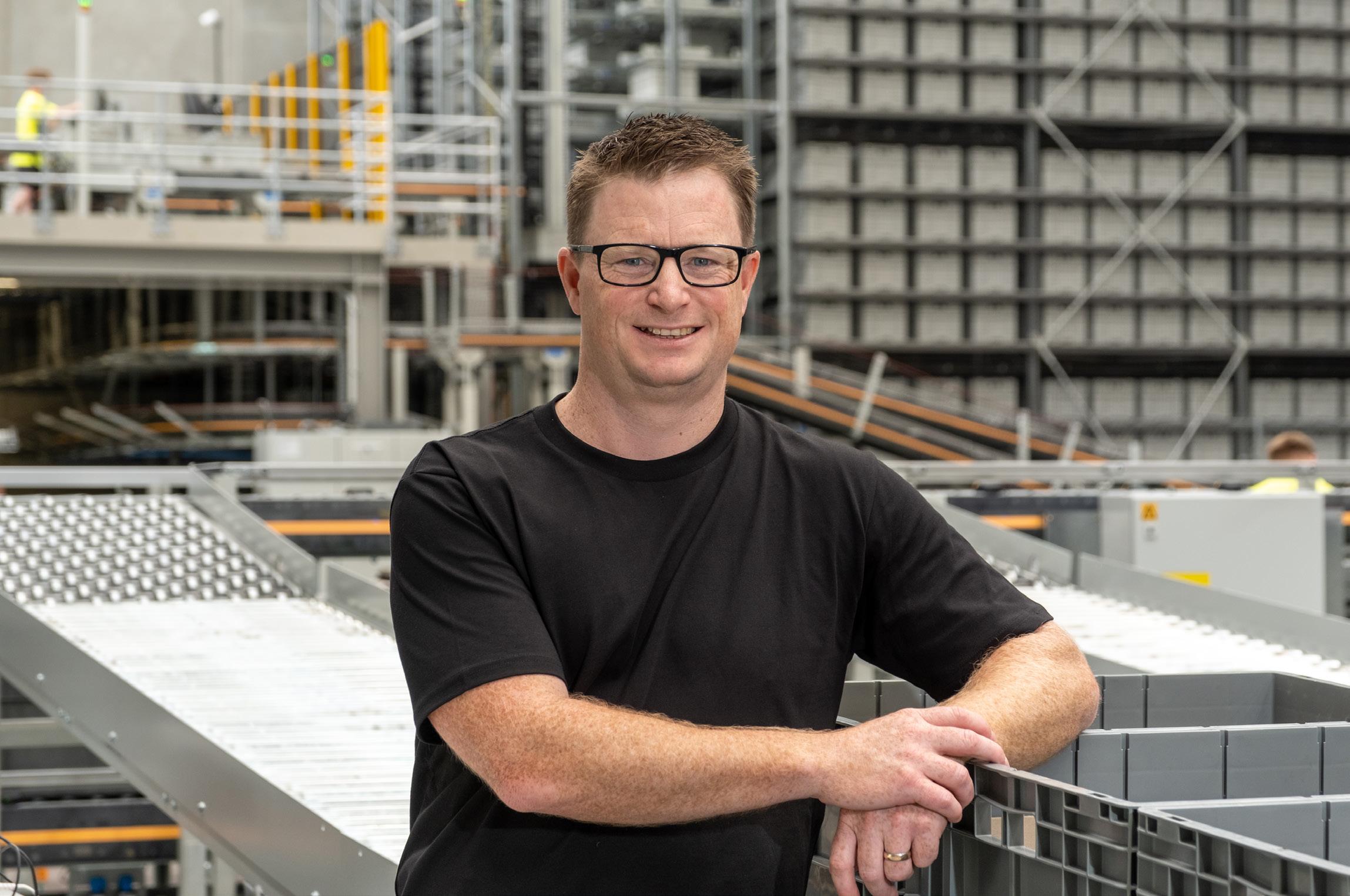
Order Fulfilment Down to a Tee
When AS Colour started out, the trend was for tight tees and baggy pants. But while clothing fashion trends come and go, the trend that doesn’t change is that customers want their orders delivered on time and accurately.
Dematic’s Multishuttle Goods-to-Person (GTP) fulfilment system enables AS Colour to process orders with higher productivity, faster and with increased accuracy, down to the sequence of items in the package. As a result, AS Colour has seen a big increase in sales as customers see how fast and accurately their orders reach them.
Learn more at dematic.com/as-colour


Dematic.com/as-colour
Top Retail Tech Trends Set to Transform Customer Experience in Australia in 2024
Manhattan Associates Inc. predicts four key technology trends that will impact the Australian retail market in 2024.
As retailers continue to innovate and adapt offerings and experiences in 2024, they are becoming increasingly reliant on technology and consumer behaviour to improve not only what they sell, but how they sell. Key retail technology trends for 2024 to watch include:
Old Tech, New Applications: Bridging the Inventory Accuracy Gap with RFID
As the retail industry continues to evolve, the integration of physical and online shopping experiences has shifted from a luxury to a necessity. In this context, RFID technology, an established but often underutilised tool, is set to redefine retail inventory management in 2024. Despite being a well-known technology, it is predicted to play an increasingly important role in the current retail landscape.
A recent Manhattan survey sheds light on a significant challenge: only 4% of retailers in Australia and New Zealand are confident in their inventory accuracy across their stores and distribution networks. RFID technology emerges as a solution, transcending its traditional use for item tagging. In
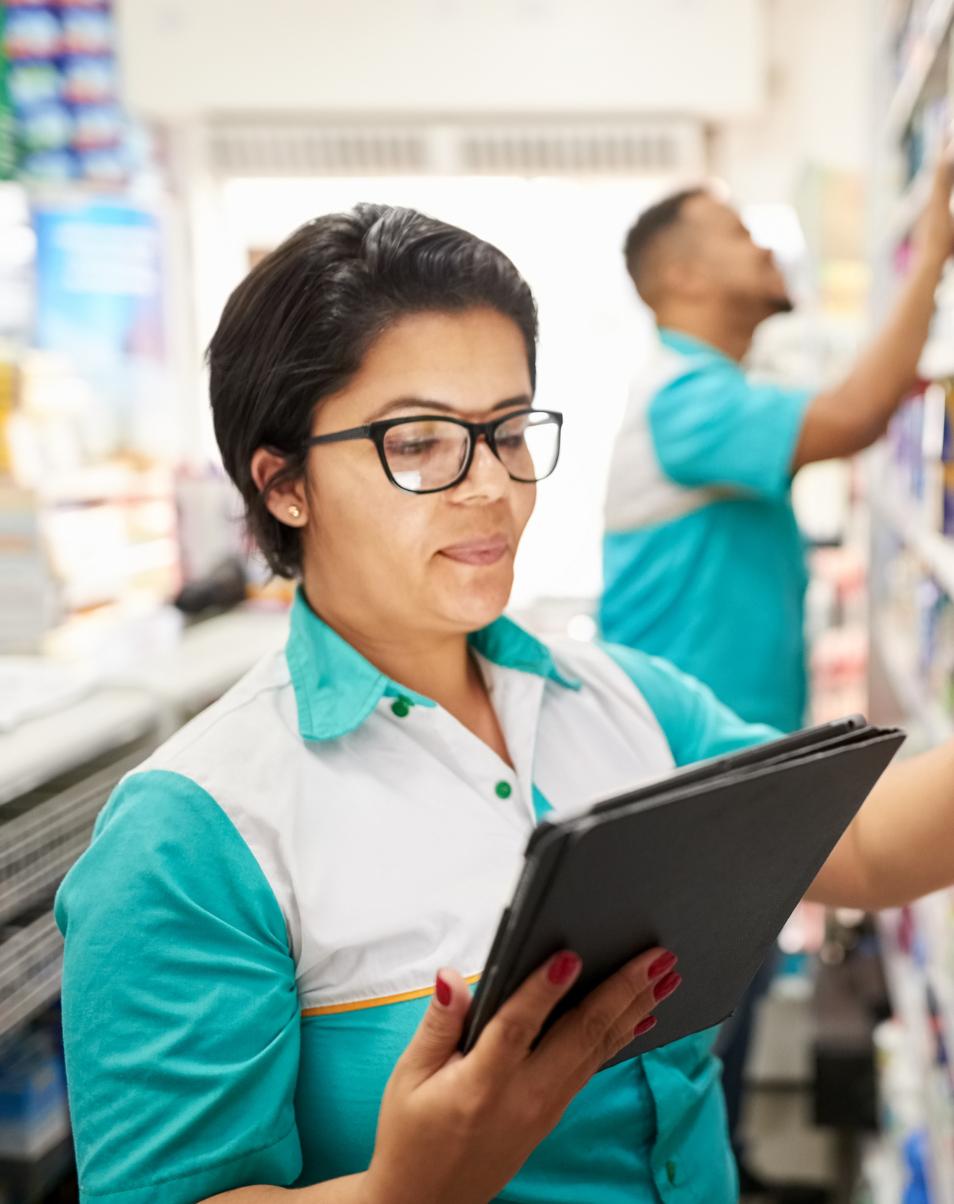
2024, an increasing number of retailers are set to utilise RFID’s capabilities by automating tracking and replenishing processes, enhancing data analytics for better insights into customer behaviour, and seamlessly integrating in-store and online operations.
Shifting Interfaces: The Convergence of Generative AI and Voice Commerce
In the coming year. the retail landscape will continue to be transformed by the integration of generative AI and voice commerce.
Large Language Models (LLMs) are at the heart of this transformation, enabling computers to understand and respond in human languages, thereby creating a two-way, intuitive interaction.
In 2024, Australian retailers are set to integrate voice-activated shopping experiences. This allows customers to use voice commands for purchases, simplifying the buying process and opening new avenues for engagement. The combination of voice commerce with AI-driven assistants like Siri, Google Assistant, and Alexa offers a hands-free, efficient shopping experience, meeting the demands of modern consumers.
“The synergy of Generative AI with voice commerce represents a trend towards more human-centric,
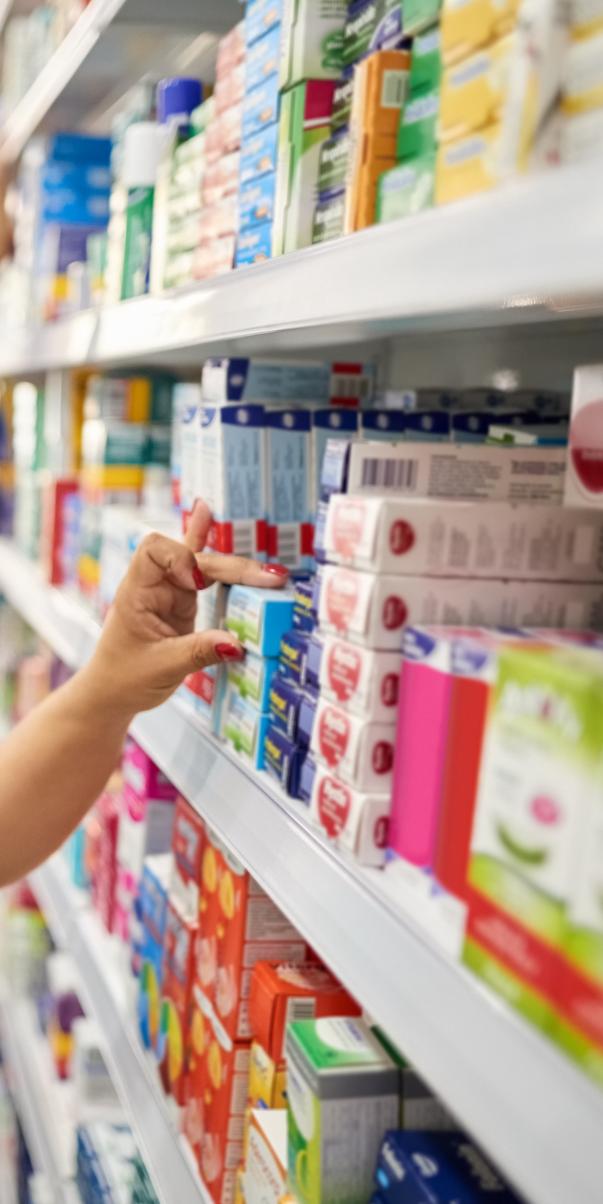
versatile technology in retail,” explained Raghav Sibal, Managing Director, ANZ, at Manhattan Associates. “This shift is transforming customer interactions, making them more natural and integrated, much like RFID's impact on inventory management. Together, they are shaping a more responsive, personalised retail environment for 2024.”
Streamlining Supply Chains: The Push for End-to-End Unification
Heightened customer expectations mean retailers must deliver inbound and outbound efficiency, optimising dock resource planning, reducing labour interactions and travel times, and cutting detention expenses. Traditional integration approaches are giving way to a more unified strategy, where systems like Transportation Management Systems (TMS) and Warehouse Management Systems (WMS) operate in sync, allowing continuous adjustment and optimisation in response to real-time changes.
This integrated approach leads to improved visibility, and cost reduction for shippers, logistics firms, and retailers. Organisations are therefore becoming more transparent about their supply chains, offering time-poor customers greater control over their orders. This transparency extends to having complete visibility into inventory and customer purchase history, facilitating a unified, personalised, and intuitive experience across all channels, functions, and devices. Retailers will be able to provide shoppers with accurate real-time availability view of products online.
The use of cloud technology is identified as key to achieving this unification, enabling a more dynamic and realistic optimisation of the entire supply chain process, rather than relying on estimates.
“Embracing end-to-end unification in supply chains allows businesses to create more efficient
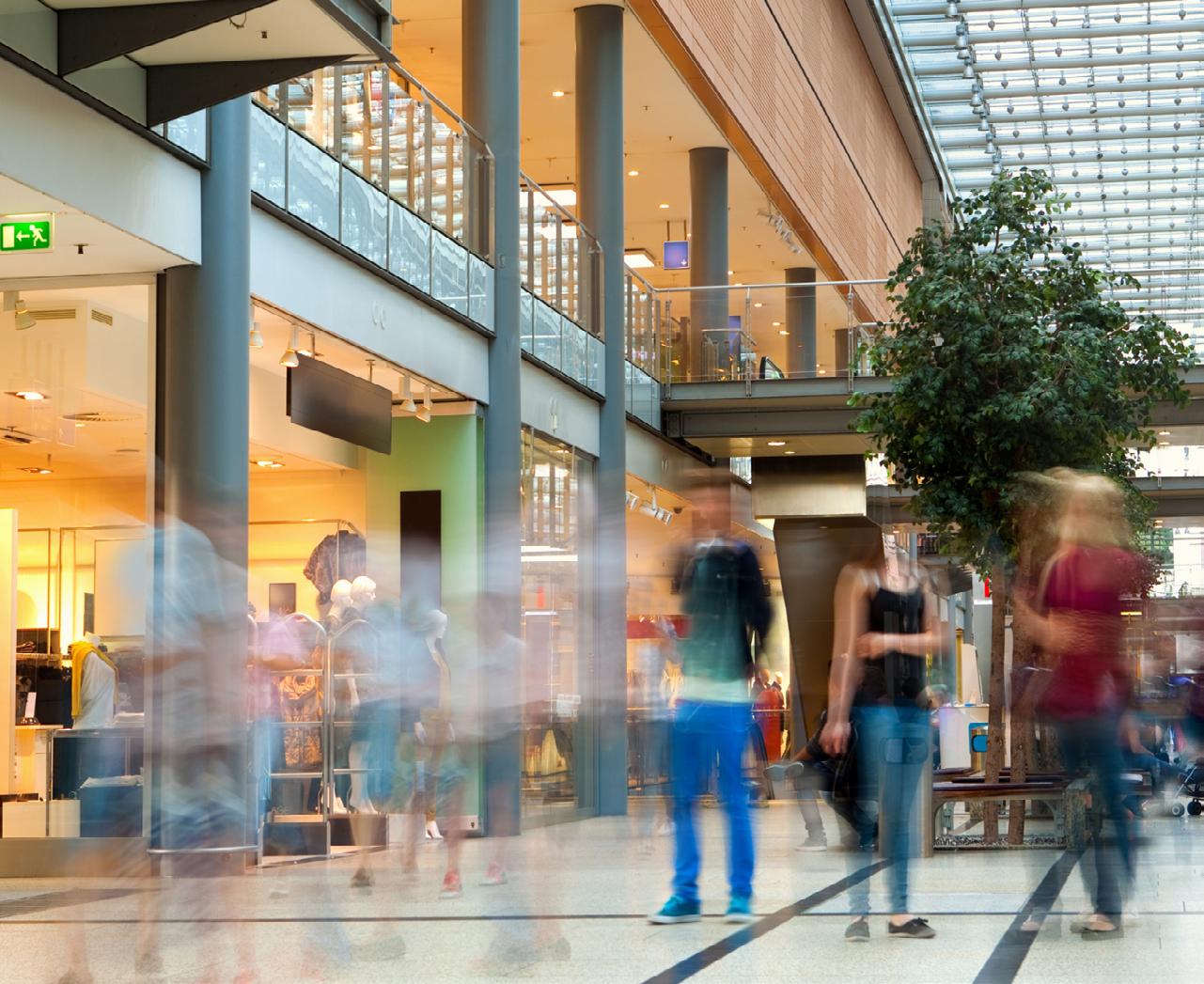
and responsive logistics plans, enhancing customer experience and driving revenue growth."
"This shift towards a unified system underscores the evolving nature of supply chain management in an increasingly interconnected and digital world,” added Sibal.
Augmented Reality (AR) Shopping Experiences: Bridging the Gap Between Virtual and Physical Retail
In 2024, Augmented Reality (AR) is not just a futuristic concept, but a tangible tool predicted to reshape the retail industry in Australia. This technology is revolutionising the way customers interact with products, offering a seamless blend of the virtual and physical shopping realms.
Australian retailers are increasingly adopting AR to enhance customer engagement and satisfaction. AR allows customers to virtually try on clothes, view furniture and home decor in their actual space before purchasing and explore products in a highly interactive manner.
This immersive technology is not limited to highend retailers; brands across various segments, including fashion leaders like Oroton, Zara, and ASOS, are integrating AR into their customer experience strategies.
“The impact of AR in retail is more than just a novelty; it addresses core consumer needs. For example, in fashion retail, AR try-on significantly reduces the uncertainty around fit and style, which has been a major hurdle in online shopping. This not only improves the customer experience but also minimises returns, a costly aspect of online retail,” Sibal explained. “AR is also paving the way for a new form of customer data analytics. Retailers can gain insights into customer preferences and behaviours based on their interactions with AR features.
This trend signifies a shift towards more experiential and personalised shopping. It not only enhances the customer's buying journey but also provides retailers with valuable insights and a new approach to customer engagement,” he concluded. ●
AI in the Business Operations of Supply Chain
Artificial Intelligence (AI) is changing the business world, transforming operations across industries.
However, while it shows promise, 70% of business implementations fail due to a lack of understanding, poor data quality, and a lack of total-business buy-in.
Business leaders globally face the same challenges – turbulent economic conditions, skilled labour shortages, cyber threats, and pressure to enhance the customer experience. AI can alleviate some of these pressures through its ability to mimic human decision-making.
It is not about replacing people – on the contrary, it returns time to employees to focus on strategic and value-adding activities. Additionally, embedding AI offers cost-saving opportunities, freeing up capital to reinvest elsewhere.
From enhancing customer experience and building connectivity, to forecasting demand, and optimising inventory management, AI is reshaping how businesses operate in today's digital age.
Connecting the Dots
Firstly, AI enhances operations through its ability to make fast decisions, based on data, improving efficiency and productivity.


As an example, AI can:
• Reduce human errors.
• Speed up processes.
• Automate repetitive tasks.
• Optimise planning decisions and delivery routes.
Plus, much more. But what does it all mean for business success? The answer – enhanced customer experience, ongoing brand loyalty, and an opportunity to reinvest in your customer.
How? By enhancing how customers interact with your business. Customer experience (CX), from the first point of interaction, is essential to business success as it impacts sales, operations, retention, and value. According to Deloitte, customers who have positive interactions with a brand spend 140% more than those who report a negative experience.
However, a good customer experience isn’t just framed by marketing, it’s a total business effort across product, price, promotion, online experience, and on-time delivery – all of which are underpinned by supply chain efficiency, from manufacturing, to logistics, to end customer.
“Customers are influenced by their experience of the supply chain – even in the simplest terms, it’s easy to see that a late delivery can disappoint, whereas an expedited delivery can delight,” Lisa Callinan.
Digitising the supply chain and leveraging AI can revolutionise supply chain operations and management, directly influencing customer experience. This means the supply chain becomes a strategic enabler for growth and a competitive point of difference – offering ways to grow, optimise costs, and remain agile. Many household names such as Amazon and Apple use supply chain expertise to enhance customer experience.
When done well, a digitised supply chain can offer significant cost savings. These savings offer another avenue to reinvest in the customer, whether it be in price, promotion, or business expansion.
While the benefits of digital transformation using AI are justifiable, the challenges presented by AI must not be overlooked. Queries of ethics, transparency, cyber security, and talent remain a concern. However, to fully embrace the future of AI in business, companies need to overcome these challenges. This involves investing in AI talent,
creating a culture of innovation, and integrating AI into existing business processes. By doing so, businesses can unlock the full benefits of AI, transforming their operations, and staying ahead in an increasingly competitive marketplace.
The TMX whitepaper, ‘AI: an Indispensable Ally’, not only outlines ways businesses can approach these challenges, but reviews ways AI can be embedded into the supply chain, addressing where to start, how to initiate business change, and the employee landscape.

Supply Chain Challenges 2024

“Attracting experienced and competent talent is challenging and continues beyond COVID-19.
With the unemployment rate at 3.8% in Australia and 3.9% in New Zealand, and international migration recording the largest declines in arrivals during the pandemic, the cycle of migration has not returned to the pattern seen prior. As a result, we are seeing high turnover in the workforce, retraining of new staff is impacting productivity, new starters are demanding higher salaries, and the learning curve to gain the skills for the job is slow.”
Bastian Consulting, an Australian Supply Chain and Technology Recruitment firm, sheds light on key concerns among executives, including the ongoing challenge of hiring and retaining skilled talent in their recent one-question survey report 'Supply Chain Challenges: What Leaders Forecast for 2024'.
The report, capturing insights from diverse industry executives, navigates the complex challenges in supply chain management.
While highlighting how economic uncertainty and inflation impact cost strategies, executives also discuss the rising customer expectations and geopolitical issues, contributing to the sector's unpredictability. The report also stresses the need for AI integration and robust cybersecurity. Serving as a guide, it reflects on the evolving challenges and the necessity for resilience and adaptability in supply chain management over the coming year.

“In 2024 global conflict in Gaza, Red Sea and Ukraine will increase volatility of shipping lead times and rates.
This will have an adverse impact on cost of imports, whether that be product or equipment to support infrastructure growth, and also to the supply and cost of fuel. Local inflationary pressures continue to slow down spending and this will mean more focus on supply chain cost reduction to offset sluggish revenue. Aside from the global market conditions, supply chain’s biggest challenges will be scope 3 emission management, building a circular supply chain, pressure to electrify heavy vehicles with limited supporting government-funded infrastructure, rapid digitisation to take advantage of generative AI and blockchain opportunities and ongoing skills shortages across transport and warehousing.”
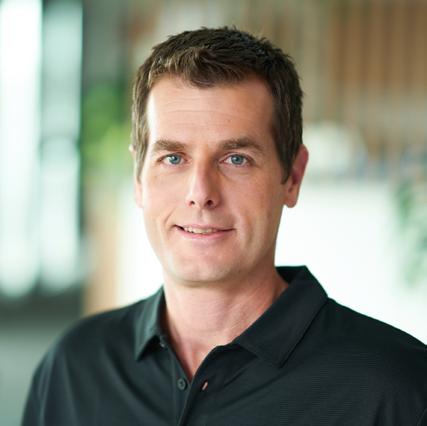
“One of the biggest challenges for supply chains in 2024 will be establishing a new operating normal. This will include but not limited to revised Inventory levels (post COVID yet still factoring in various ongoing global conflicts).
Whilst some of this decision making will be driven by the customer, it’s critical that supply chain professionals manage expectations in this space given they know the market and the various challenges that still remain. The other area of concern is in regards to pricing of some key commodities. We’ve seen pricing impacted by shortages, then inflation. With some of those factors now correcting, it will be a challenging year to establish a new baseline for pricing. I also believe that the “war” for talent won’t let up, keeping employers on their toes and supply chain professionals in strong demand.”

“The challenges I’m seeing are to some extent sectordependent, but there are a couple of common themes. The first is access to capital to develop next generation supply chains.
For example, for those with significant customer fulfilment operations, the development of a costeffective last mile solution that meets customer service expectations and competes effectively with industry leaders remains elusive. In many cases, securing the investment required to do this is proving a difficult hurdle to get over without outside support. The second is the latent threat posed by a lack of supply chain resilience and wae’re doing an increasing amount of work to help our clients prepare to operate in a “compromised state” in the event of a cyber-attack or similar major disruption. In contrast from normal business continuity planning, this acknowledges that the compromised state may persist for several weeks within the four walls of the organisation without the availability of core IT systems.”
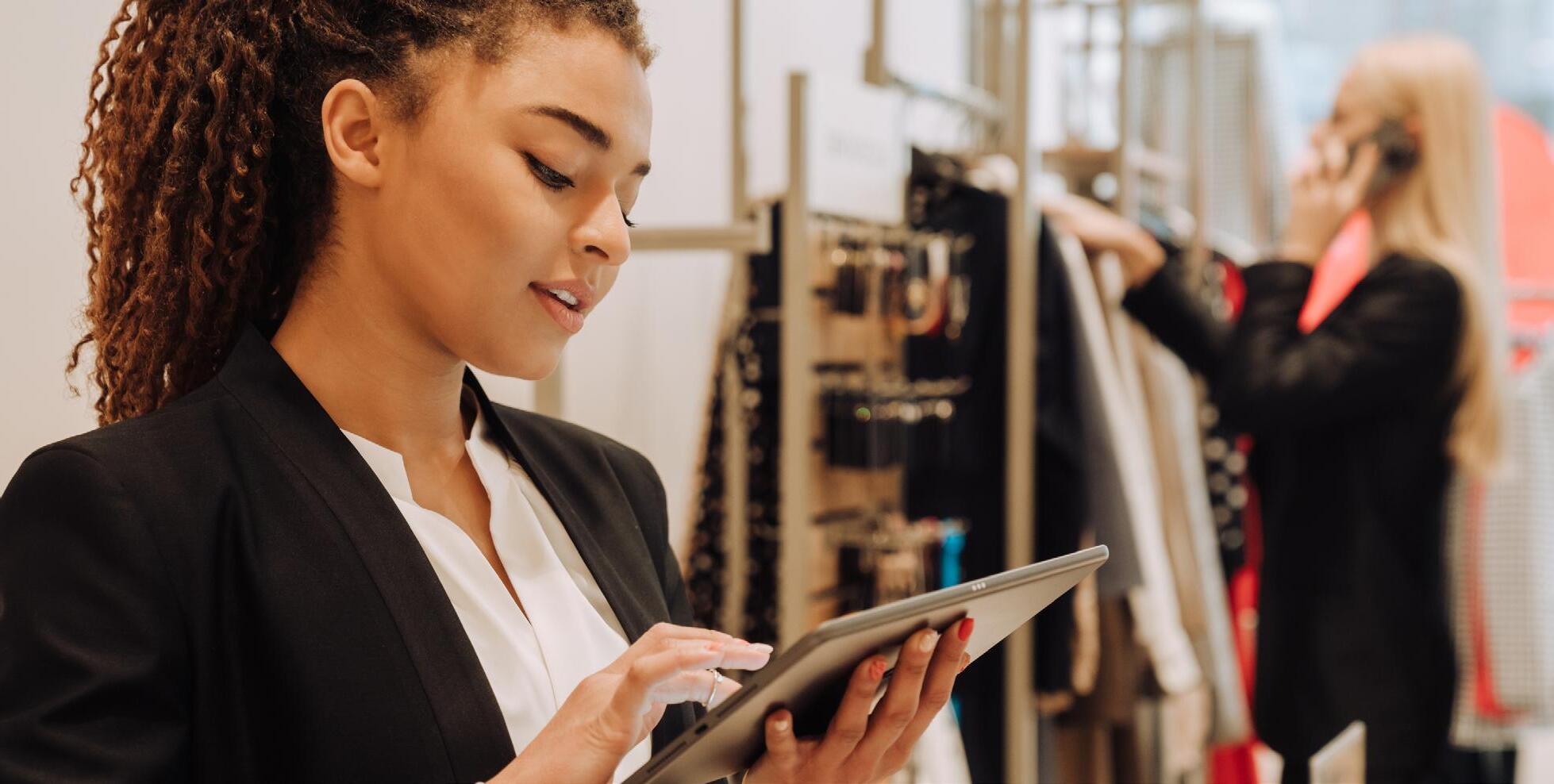

“In 2024, APAC supply chains confront the pivotal challenge of harmonising a renewed focus on operational excellence, geopolitical resilience, and futureready capabilities. Firstly, reinstating operational efficiency and sustained investment in supply chain resiliency are paramount.
Executives can unlock immediate short-term returns through targeted investments in transformative technologies, with a focus on supply chain planning and analytics capability, ensuring agility and adaptability. Secondly, navigating global geopolitical uncertainties demands initiative-taking supply chain risk management reviews and extensive multi-tier supplier visibility. Short-term gains hinge on strategic measures, leveraging technology for real-time insights and informed decision making.Prioritising immediate visibility and risk mitigation measures lays the foundation for long-term supply chain resilience. Thirdly, building future organisational capability across people, process, and technology is critical.
Short-term returns are achievable by investing strategically in talent, process optimisation, and transformative technologies like Advanced Planning Solutions embedded with Generative AI.
This dual-pronged approach not only delivers immediate results but ensures sustained success and competitiveness in the evolving landscape of APAC supply chains.”
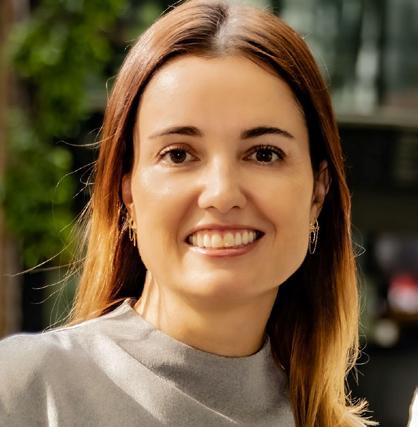
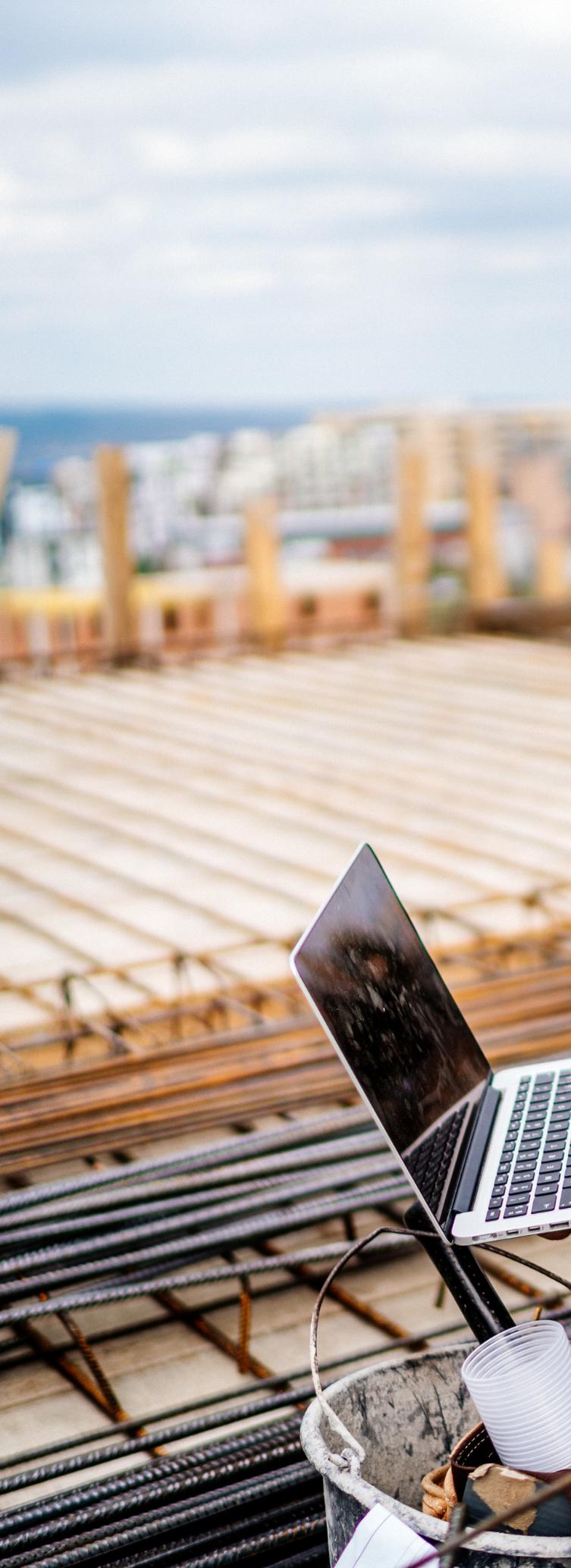
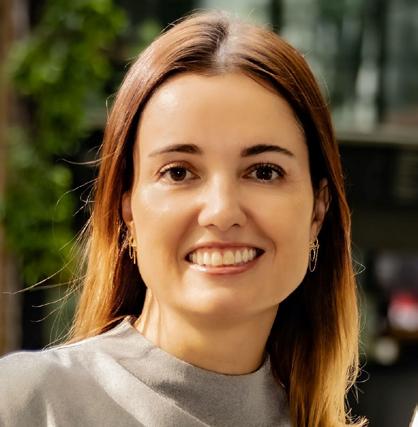
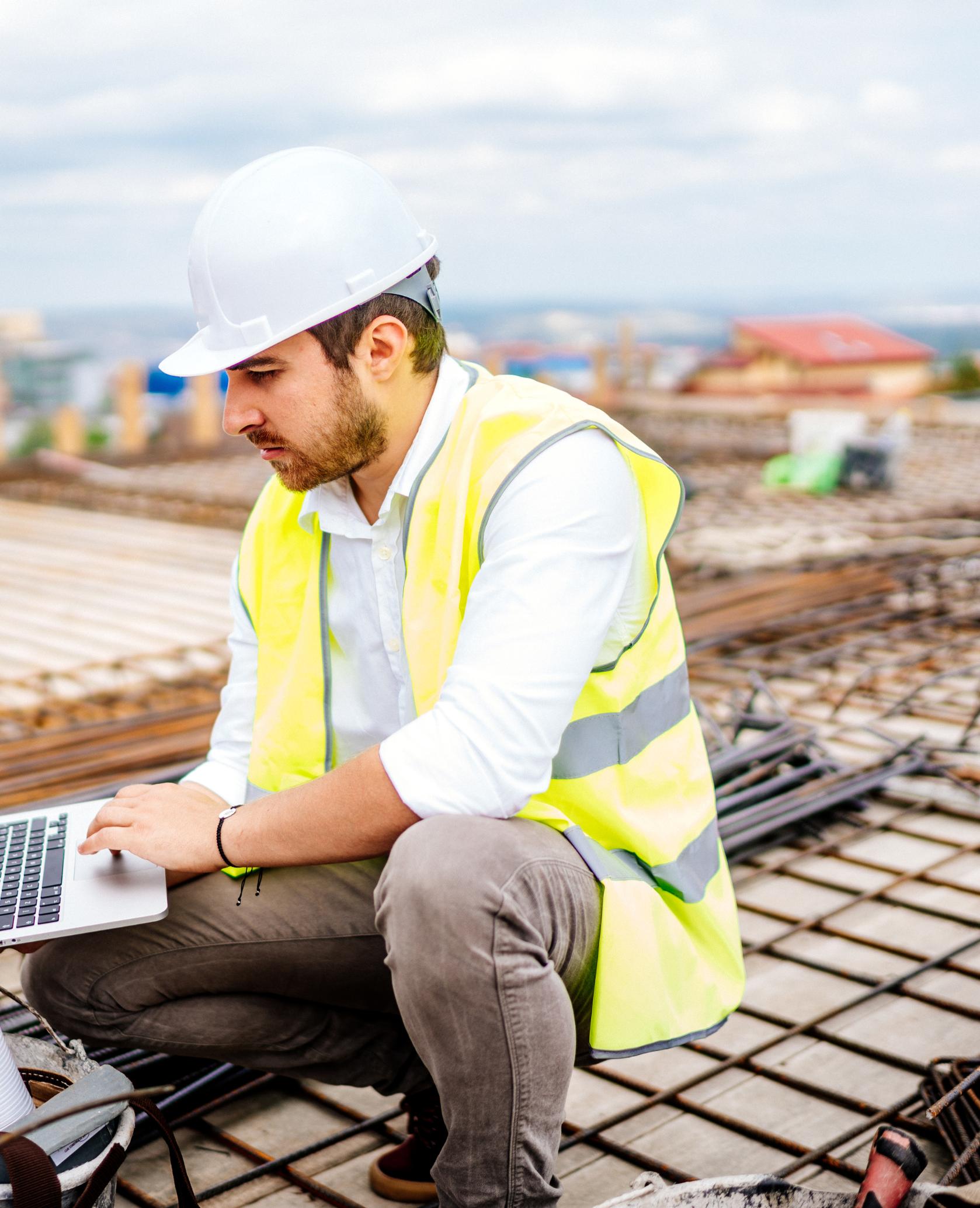
A focus on ESG and scope 3 emissions is top of mind, showing our dedication to leaving a cleaner planet for future generations. Supply continuity, driven by natural disaster and geopolitical disruptions (hopefully, without the recurrence of a public health crisis) will have to be managed by strong risk mitigation plans; we will also thrive to integrate more AI and data-driven decisions into our daily operations. Amidst economic uncertainty, we anticipate heightened demand volatility and a shift in customer priorities influenced by their consumers' preferences for healthier, more sustainable, and tastier products. We will continue to partner with our
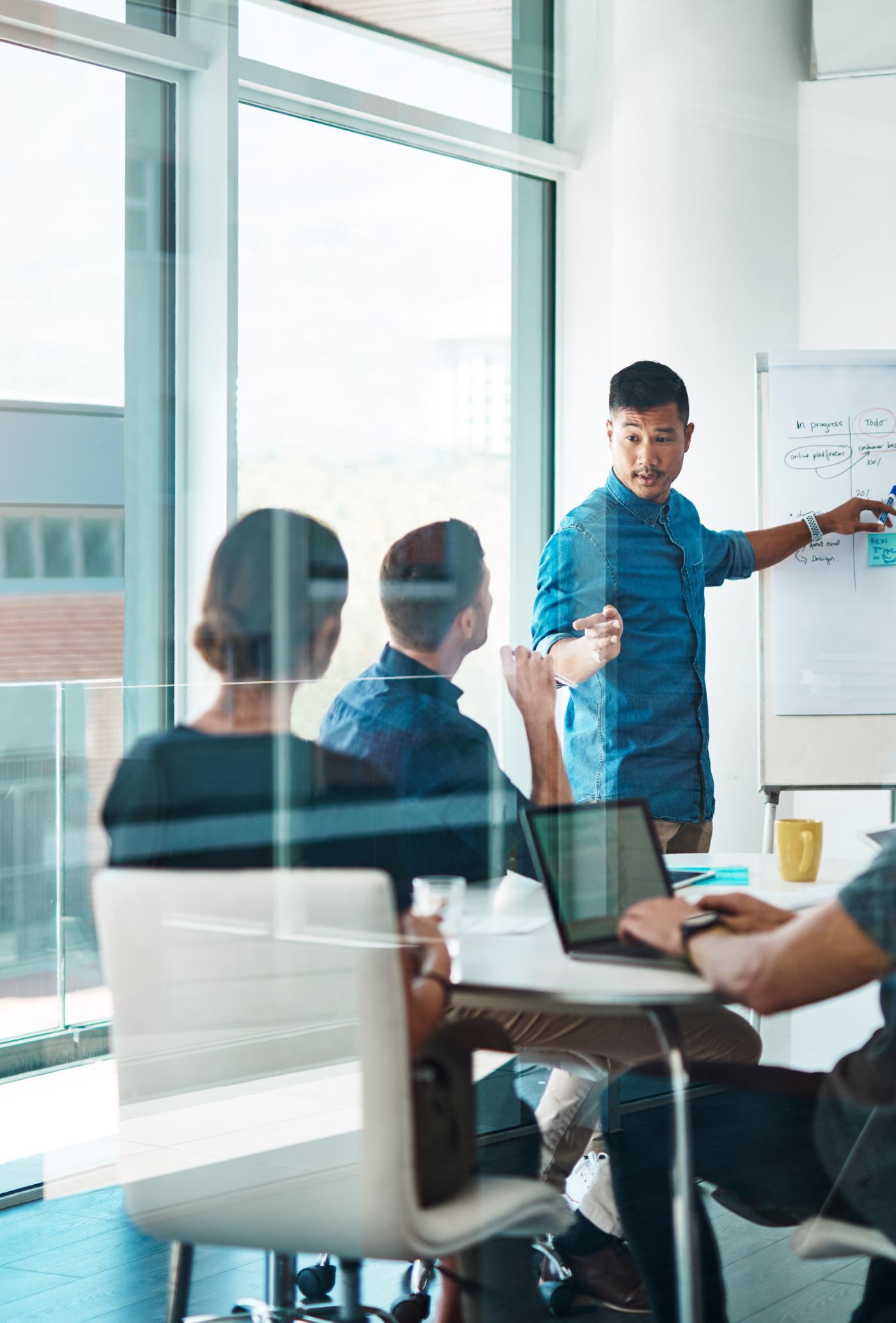
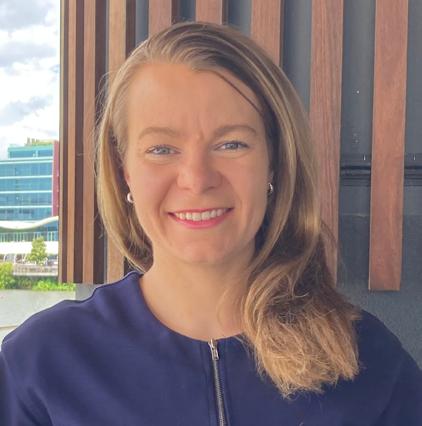
industry confronts a triad of challenges that significantly
Firstly, sustaining effective freight partnerships while concurrently addressing inventory management and cost concerns poses a complex task when planning service and managing freight relationships in declining volumes – Balancing commercial and service viability requires strategic collaboration and the adoption of sustainable new methods. Keeping your service providers loyal when you have lowering volumes, and remembering it’s a two-way relationship will be core to success in this challenge.
Secondly, the sector grapples with inventory management pressures as it navigates the delicate equilibrium between maintaining optimal stock levels and meeting dynamic consumer demands, particularly when they are in the decline. The challenges are compounded by the evolving ecommerce landscape and global supply chain disruptions, continuously
Thirdly, labour market dynamics present hurdles characterised by ‘the right’ skilled labour shortages and the need for a flexible and specialised workforce. Adapting to changing workforce demographics and fostering talent development emerge as critical components for sustaining efficiency and reliability in the Australian logistics industry. Addressing these challenges demand innovative solutions and a holistic approach to ensure resilience and adaptability in this crucial sector. Finally, remember to serve your customer under cost pressure should always be

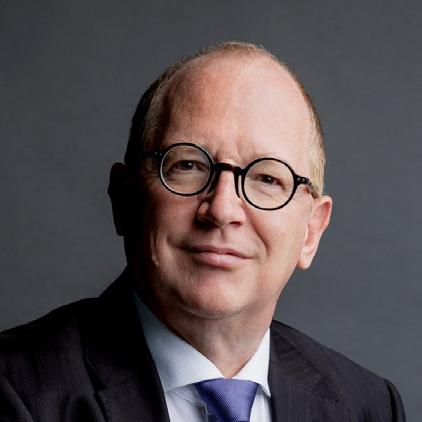
“In supply chain, the usual “statement of the obvious” is to say that supply chain networks are getting more and more complex. This will obviously remain.
More recently, we saw big shift towards near shoring decisions after the COVID episode, impact of political instability in Ukraine, Middle east, and Gulf of Aden due to Yemen’s rebels’ groups now. Everything is pretext for abusive price increase. This situation is also true for the healthcare supply chain among life science companies, wholesalers, healthcare providers and patients. Efficiency is finally becoming important to reduce costs. But much more important in healthcare is the topic of patient safety, where counterfeiting is increasing, product recalls have to be handled effectively and efficiently, and medication errors have to be reduced.
Hopefully, some good news is around the corner: increased visibility of operations through data mining, AI, introduction of Cloud systems, synchronisation between systems help to control what we buy, and how we buy.
Regulators as well are quickly progressing in their data protection regulations, allowing soon data transfers between countries and severs, as long as confidentiality can be maintained. This increased control on data gives better visibility on gaps and inefficiencies not captured previously. More than ever, the triangle between people, technology and process is moving towards digitalisation and technology, taking the lead against people and process to compensate traditionally unperfect processes and improve people’s skills.” ●
Enhancing PepsiCo's Production and Logistics Safety, Efficiency, and Accuracy with Dematic's Automated Storage and Retrieval System

PepsiCo is proud to be one of the world’s leading convenient foods and beverages companies. Pepsico’s products are enjoyed more than one billion times a day in more than 200 countries and territories around the world.
Pepsico’s portfolio – including Lay’s, Doritos, Cheetos, Gatorade, Pepsi-Cola, Mountain Dew, Quaker, and SodaStream – consists of many iconic brands that generate more than US $1 billion each in estimated annual retail sales, helping to deliver more than US $79 billion in net revenue in 2021.
PepsiCo aims to become a stronger, more unified company by transforming its capabilities and costs, and by using new technologies to its advantage. This includes developing and scaling the company’s core capabilities through advanced technology in logistics.
Optimising Through Expansion
In today’s competitive business landscape, global companies like PepsiCo are constantly seeking ways to optimise their operations for increased productivity, efficiency, and accuracy.
PepsiCo’s Rojana facility in Thailand is a critical regional hub for the company. With a growing demand for its products in Thailand, PepsiCo recognised the necessity to build capacity in both production and logistics.
Colin Matthews, Supply Chain Senior Director –IndoChina Foods, PepsiCo, says, “Rojana is one of our biggest plants with production lines for a number of different products. The products made at Rojana are not only distributed nationally across Thailand, but we also send products internationally to Vietnam and other neighboring countries.”
One of the key strategies employed by PepsiCo to support growth was the expansion of its production and logistics capacity at the Rojana site. This expansion project has been driven by the vision of a digitalised future, where automation plays a pivotal role in addressing challenges and enhancing overall operational performance.
Charan Techapattaraporn, Logistics Manager, PepsiCo, says “Automation is the perfect solution to take on these challenges, whilst also improving our facility operations across the board.”
Integrating Automation
As part of its expansion and automation goals, PepsiCo turned to its global partner Dematic, a world leader in providing automated solutions for materials handling and logistics.
“I've now worked with Dematic across two business units, firstly here in Indochina and also in Australia and New Zealand,” adds Matthews.
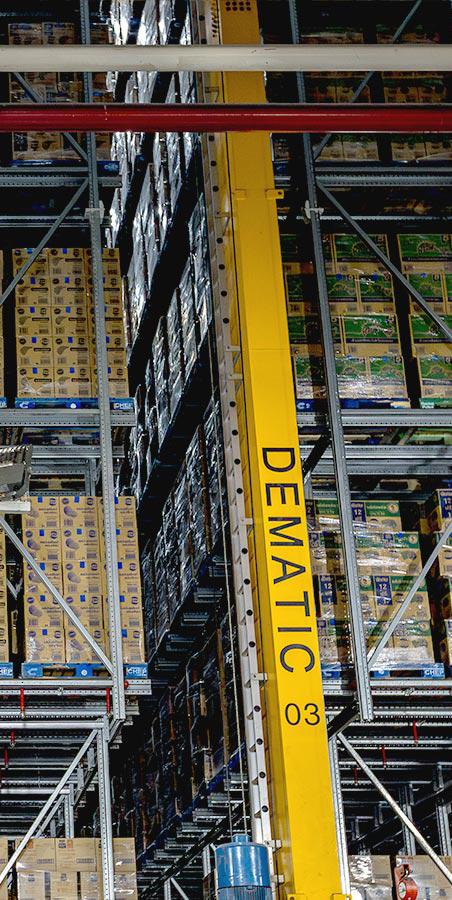
“I've seen Dematic really lean into providing a customised response based on the tailored needs of individual problems.”
Dematic took a collaborative approach to the Rojana facility system design, understanding PepsiCo’s key business and operational objectives, and aligning the solution with PepsiCo's forecasted business growth. To address the need for increased capacity, space constraints and other challenges, Dematic worked closely with Pepsico to develop an automation solution for their logistics operations. The solution centred around an Automated Storage and Retrieval System (AS/RS) with a direct link to both the production and order fulfilment areas.
“Dematic has a strong track record of successfully implementing AS/RS solutions across the Asia Pacific region and globally, catering to diverse industries and applications,” says Phamondate Rukdee, Sales Manager, Dematic Thailand. “The AS/RS is at the heart of PepsiCo's strategy to enhance its production and logistics efficiency at the Rojana facility."
“The AS/RS aids in storing products before they are delivered to customers. It provides an extremely space efficient way to store products in between when they are manufactured and when they need to be assembled and dispatched for delivery to customers.”
The AS/RS stores pallets within five aisles of double deep high bay racking, with a total capacity in excess of 16,000 pallet locations. A network of pallet conveyors and Rail Guided Vehicles (RGVs) receives pallets automatically at the end of the production lines and transports them for storage, then directs them from storage to dispatch docks or to automatically replenished pick locations for fullcase order picking. The system includes Dematic's Warehouse Control System (WCS) software to manage all of the automation, the material flow and inventory and to provide real time tracking and visibility of all transactions.
Dematic's commitment to quality and reliability is exemplified through the deployment of top-ofthe-line equipment including Dematic RapidStore Storage and Retrieval Machines (SRMs), Dematic pallet conveyors and RGVs for automated pallet handling. The equipment, controls and software are all designed and engineered in-house by Dematic and serviced and supported 24/7 by the experienced local Dematic team of engineers and technicians.
The Dematic AS/RS not only provides PepsiCo with the capacity to meet their forecast demand but has been designed in a modular way to provide the flexibility for expansion so that the system can be scaled and adapted to their changing needs in the future.
Roll-out, Support, and Training
Dematic was on the ground at the Rojana facility during implementation, testing and go live phases to ensure the success of the project, which was delivered on time for PepsiCo, despite the challenging conditions of a pandemic.
“The system was completed on schedule. We are also well supported by both domestic and international Dematic teams who are ready to quickly aid PepsiCo in terms of both hardware and software,” says Techapattaraporn.
The success of any new automated system is ultimately in the hands of the system operators. That’s why training is essential for providing an understanding of not only the automated equipment, but also the procedures for ensuring its safe and efficient operation. To achieve this, Dematic followed a “train the trainer” approach to helping PepsiCo develop a good working knowledge and understanding of the system so that PepsiCo supervisors and lead operators can train their teams on an ongoing basis.
“Our team really embraced the solution that we've put in at Rojana and they really value the investment that we've given them, as we've trained them to get new skills. That training of new skills has helped us with people retention, which is another benefit,” says Matthews.
The complexity of the automation installed for PepsiCo makes it essential to have service and support in place to optimise system uptime, continuity of throughput, and production efficiency. The benefits of ongoing support include a reduction in downtime due to component failure, lower overall system maintenance costs, optimisation of system lifespan and knowing that Dematic as the system designer and builder are also available to service the system.
“Dematic takes care of PepsiCo’s AS/RS and machinery 24 hours a day, 7 days a week,” says Nipat Kummu, Service Engineer, Dematic Thailand. “We have Dematic staff on-site to make sure any issues are responded to and resolved quickly.”
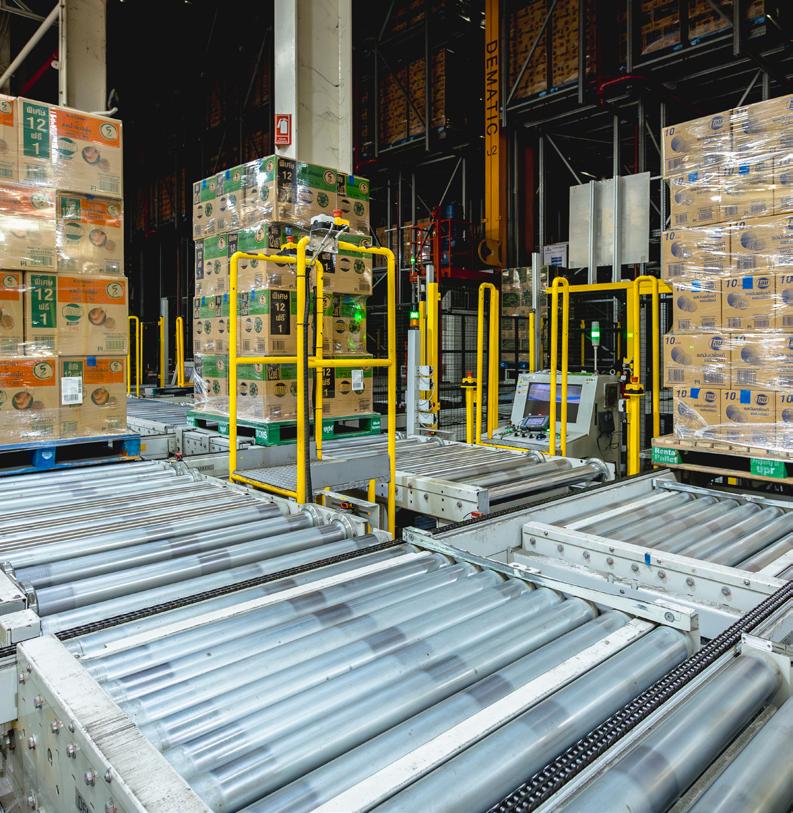
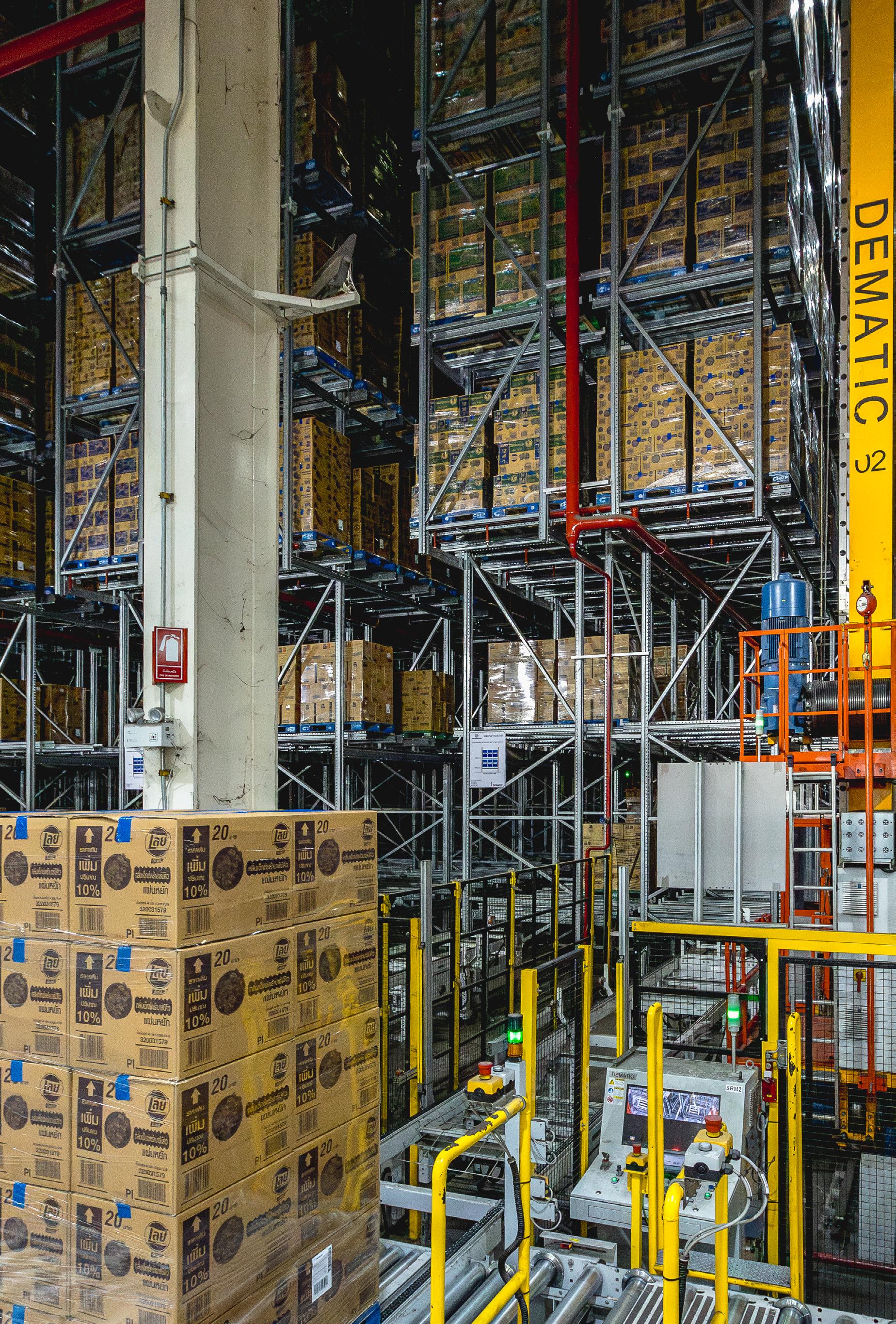
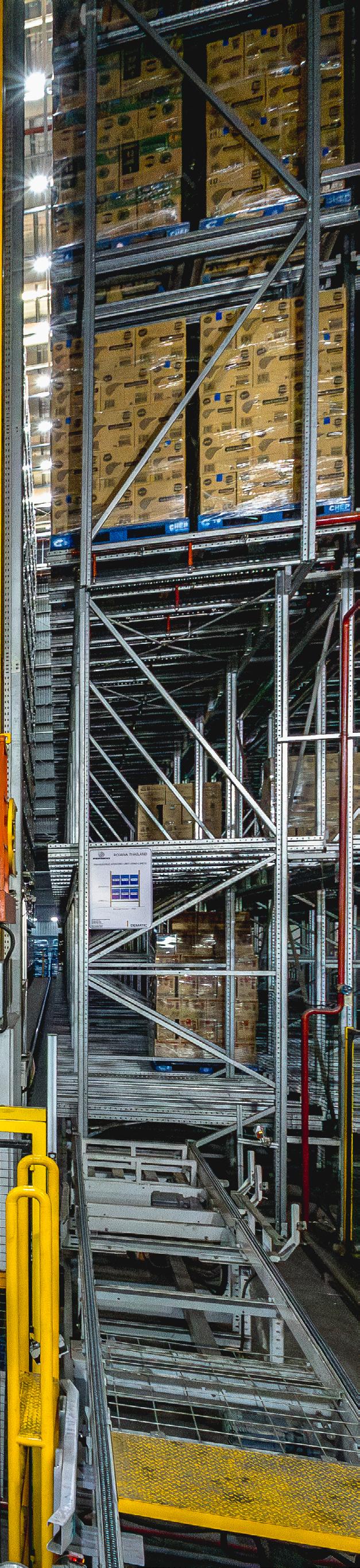
Key Benefits of the Solution
The AS/RS provides fully automated high-density, high-throughput storage for pallets. With an AS/ RS, stock cannot be lost or forgotten, as the system provides complete and real-time visibility of overall inventory, delivering the highest level of accuracy. With minimum manual handling needed, product damage and the associated cost and waste are also significantly reduced.
“Previously we had a very manual solution that took a lot of time for people to go around and understand exactly what products we had in the warehouse. In contrast, the Dematic system is very intuitive. It enables our team to look across the whole of the AS/RS and understand exactly where we have the stock, and they can intuitively and quickly make any adjustments they need. The AS/RS has more than doubled our capacity and the automation takes us away from the very manual operation we had before. This allows us to supply goods to customers with greater efficiency, leaving them very satisfied,” explains Matthews. The Dematic solution has delivered a multitude of benefits to PepsiCo, including:
• Improved space efficiency: The AS/RS has more than doubled storage capacity, making the most of the available footprint, which is important in highly urbanised regions.
• Improved productivity: Automation streamlines processes, reducing reliance on manual labour and increasing throughput.
• Fast responsiveness: Automation allows for quick and efficient responses to customer orders and to changing demands.
• Accuracy and tracking: Precise tracking of inventory ensures accuracy in order fulfilment.
• Inventory security: Enhanced security measures inherent to the AS/RS protect valuable stock.
• Modularity and scalability for expansion: The system can grow with PepsiCo’s needs.
• Redundancy: Built-in redundancy ensures continuous operation and avoidance of costly downtime.
• Reduced facility energy consumption: Automation helps to minimise overall warehouse energy usage.
• Low maintenance, reliable, and locally supportable: Dematic provides ongoing local support for trouble-free operation.
• Life cycle value: A long-term investment that continues to provide value over time.
The superior high-density storage capability of the AS/RS allows PepsiCo to store much more within the warehouse building cube than would be possible within a conventional warehouse environment. Beyond the benefits described above, the AS/ RS also improves warehouse operator safety by dramatically reducing the amount of manually-
operated forklift trucks, pallet movers and other materials handling equipment, helping to prevent accidents in the facility.
“Our first priority was safety, and the AS/RS plays a crucial role in reducing the occurrence of accidents. Secondly, we were focused on efficiency gains, and this was achieved through reducing the storage footprint. Thirdly, PepsiCo wanted increased accuracy and traceability of products so that the warehouse throughput could be increased,” explains Techapattaraporn.
Long-term Automation Goals
PepsiCo’s Rojana system has been designed with the future in mind, offering the potential for the system to be expanded to accommodate additional growth and to adapt to changing business requirements.
Dematic and PepsiCo have already been exploring additional automation possibilities for future stages, including truck-sized outfeed lanes, paperless picking technology, and Automated Guided Vehicles (AGVs) for various tasks within the production and warehouse areas.
“Dematic and PepsiCo collaborated closely to achieve outstanding results. This system will bolster PepsiCo’s growth, enabling it to become bigger and stronger, and provide PepsiCo with a solid foundation to build on for the future,” concluded Kummu. ●

Retail Resilience: How Australian Businesses Can Thrive Despite Economic Headwinds and Supply Chain Strain
WRITTEN BY RYAN MCGRATH GROUP MANAGING DIRECTOR AT PEACOCK BROSAustralian consumers are under pressure.
Cost- of-living challenges and interest rate increases have stretched household budgets, with new research from Pattern Australia indicating that 65% of people are expecting their online shopping to be flat, or
lower in 2024 compared to previous years.
As a result, the barrier to sale is higher than ever for retailers who need to offer seamless experiences to convert shoppers into customers.
While it’s easy to get wrapped up in marketing campaigns or attractive discount offers to win business this year, a central factor in being able to meet heightened customer expectations is anchored in an efficient supply chain operation.
At a time when consumers are looking for any excuse not to make a discretionary purchase, any hiccup in the supply chain can have cascading consequences, affecting sales, tarnishing reputation, and jeopardising consumer trust.
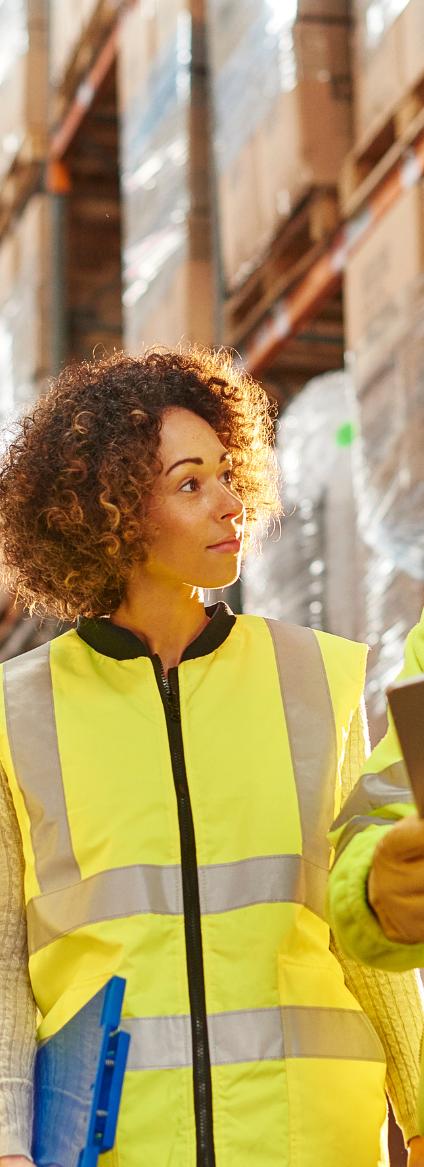
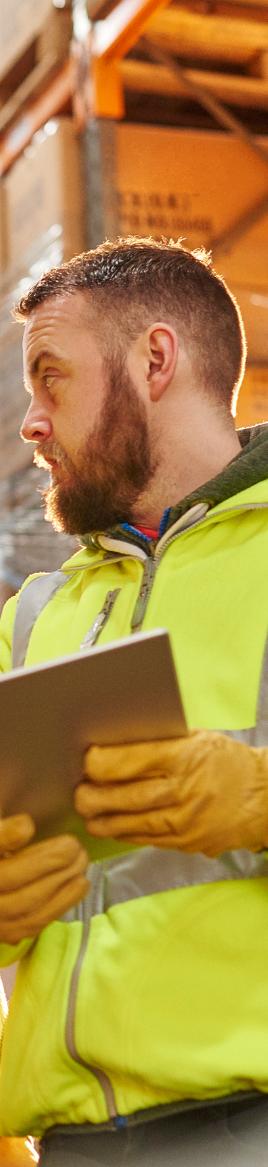
Considerations for Achieving an Efficient Supply Chain
Inventory Management:
Effective inventory management is paramount. Accurately predicting the demand levels for particular products can be daunting. By leveraging advanced label printing, scanning, and in-warehouse RFID solutions, like those offered by Peacock Bros., businesses can enhance accuracy in demand forecasting. This approach not only guards against stockouts but also precludes excessive inventory accumulation, subsequently lowering holding costs.
Swift Deliveries:
Rapid delivery expectations can peak throughout the year, especially during sales periods. To cater to such anticipations, retailers should invest in systems that allow intelligent mobile scanning, facilitating improved stocktake processes and fluid stock movement. For example, Peacock Bros.’ Electronic Proof of Delivery (ePOD) solution enables real-time data communication between businesses and their fleet, ensuring everyone is always on the same page. These technologies enable agile supply chains ready to meet heightened consumer demands through seamless coordination among suppliers, warehouses, and transport systems.
Returns and Exchanges:
Seamless purchasing experiences must be mirrored by seamless return and exchange processes. By integrating efficient mobile printing and scanning solutions, retailers can guarantee a swift and effective response to these returns, ensuring products are promptly vetted for resale standards.
Cost Efficiency and Sales Process:
Not only are Australian consumers under pressure with cost-of-living challenges and interest rate increases but so are retailers. By utilising state-of-the-art in-store mobile computers which can process sales anywhere in the store, retailers can not only keep escalating costs in check but also enhance the efficiency of the entire sales process.
The Risk of Being Unprepared
Retailers today are not just grappling with the usual challenges of managing inventory or ensuring swift deliveries; they're navigating the maze of global supply chain intricacies. These complexities are heightened by communication barriers among various stakeholders, from suppliers in diverse geographical locations to transport systems adapting to ever-changing conditions. Add to this the dynamic fluctuations in demand — based on a variety of factors from global events to local celebrations — and it's clear that retailers have their work cut out for them.
However, with challenges come opportunities. Understanding potential pitfalls is the first step toward effectively managing them. And, in the modern retail landscape, data has emerged as the North Star guiding retailers through these choppy waters. It's no longer enough to rely on intuition or traditional methods. The key lies in harnessing data for strategic decision-making.
Retailers armed with robust analytics capabilities are in a powerful position. They can dig deep into sales data, unearth patterns from past seasons, anticipate emerging trends, and craft strategies that are rooted in data-driven insights. It's like having a crystal ball; but instead of vague predictions, retailers get actionable intelligence. For instance, tools that dissect and analyse consumer behaviour aren't just ‘nice to have’ add-ons; they're essential. They empower retailers to predict which items will be the season's hot sellers, allowing them to stock up proactively.
But it's not just about anticipating demand. It's also about real-time responsiveness. Modern systems, coupled with advanced, fit-for purpose hardware solutions like barcode label printers, barcode scanners, mobile computers, and RFID technology, enable real-time supply chain monitoring, empowering all team members to make informed and strategic decisions to achieve their goals. In the fastpaced world of retail, reacting after a problem has snowballed is a recipe for disaster. These systems allow retailers to identify potential issues at their nascent stage, tackle them head-on, and ensure that the supply chain operates seamlessly.
So, what's the risk of not being adequately prepared? The consequences can range from stockouts of popular items (leading to immediate lost sales and disgruntled customers) to more long-term damage like a tarnished brand reputation. In the age of social media, a single supply chain hiccup can become a viral story, impacting a brand's image and bottom line.
Preparedness: The Key to Retail Success
Preparation is crucial to retail success today. With the right strategies and tools, retailers can proactively address potential pitfalls. By being ready and having a responsive and resilient supply chain in place, they can navigate the dynamic retail landscape and meet heightened customer needs. ●
For more information, please click here.
Look out for the next issue
For all of your latest supply chain industry news, be sure to join our community on LinkedIn
Look out for the next edition of Supply Chain Insights, where we take a detailed look at the complexities and opportunities of “Reverse Logistics: How to Drive Efficiency and Customer Satisfaction”.
Traditionally viewed as a cost centre, the process of returning goods from consumers to retailers or manufacturers is now being recognized for its potential to drive value creation, environmental sustainability, and customer loyalty. We'll investigate how companies are leveraging advanced
technologies to streamline processes, enhance visibility, and improve decisionmaking around reverse logistics. Featuring insights from industry leaders, this edition promises to equip you with knowledge and strategies to transform your reverse logistics from a necessary cost to a strategic asset.
For all of your latest supply chain industry news, be sure to join our community on LinkedIn
For more information or story suggestions, please contact: editor@supplychain-insights.media
For advertising enquiries, please contact: advertising@supplychain-insights.media
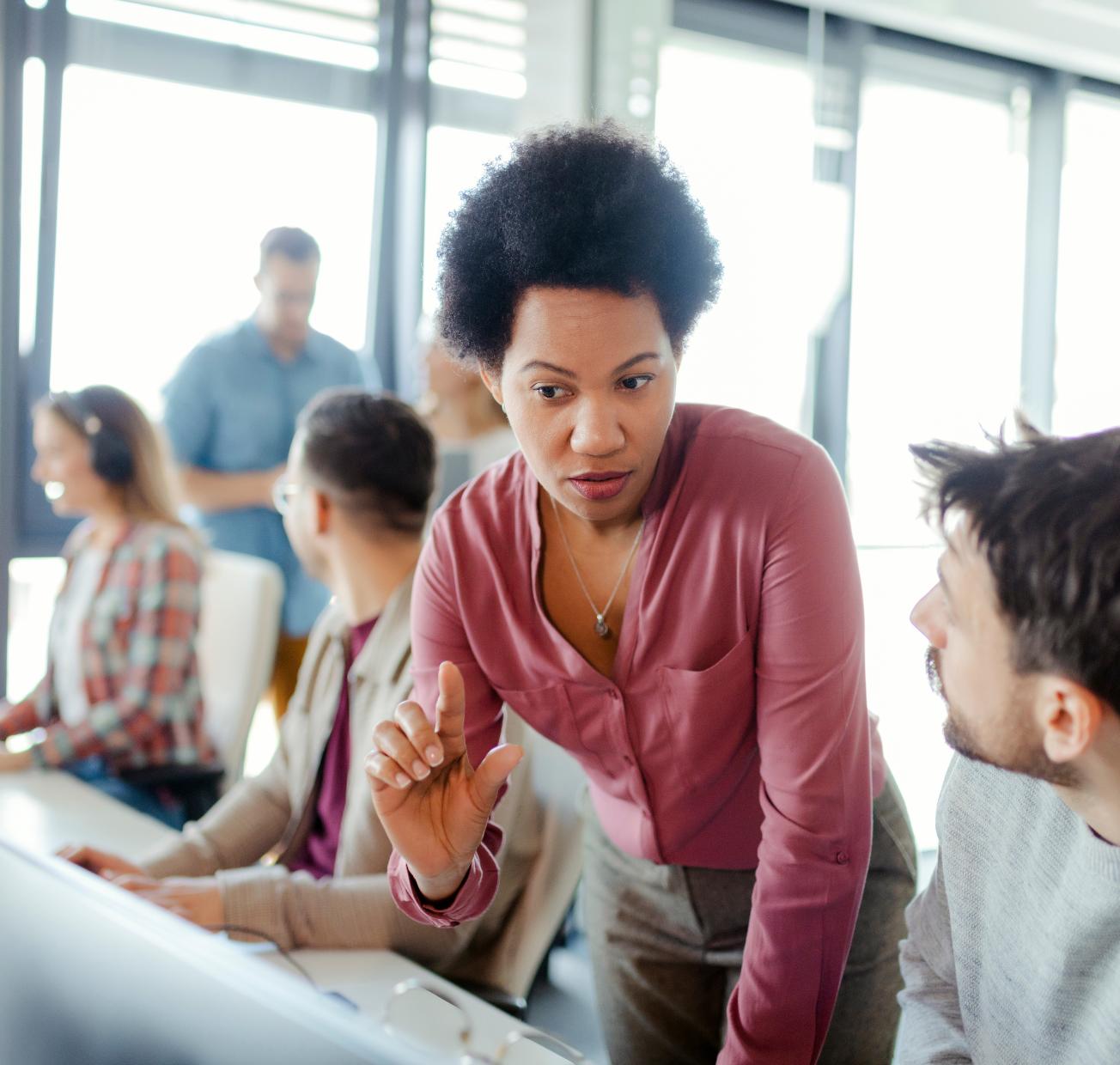