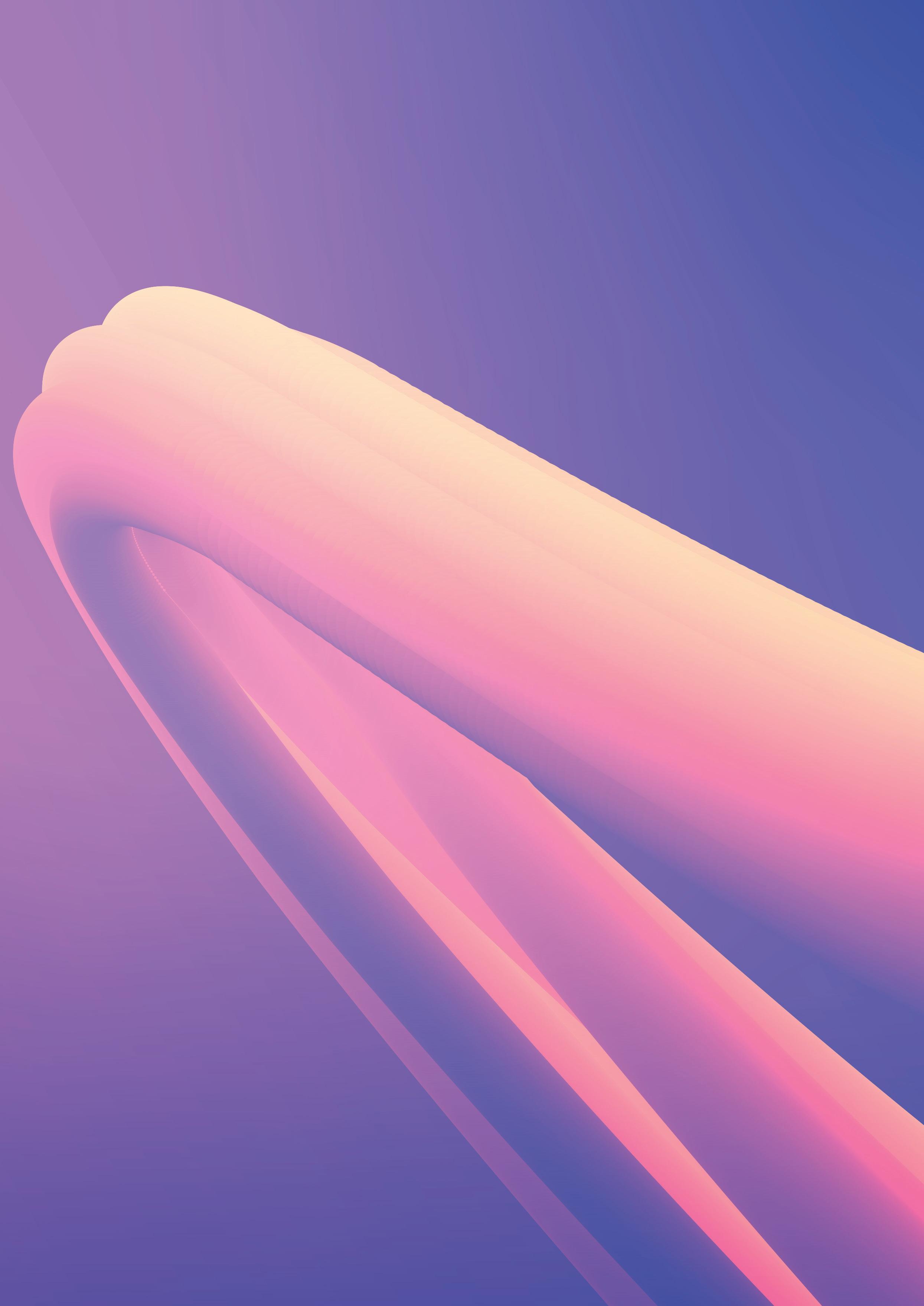
6 minute read
Rising to the unpiggable challenge
Rod Lee, Pipetel Technologies Inc. (an Intero company) presents an overview of key milestones in Pipetel’s journey of providing certainty and safety to challenging and unpiggable pipelines around the world.
Although Pipetel (which recently became an Intero Company) began operations in Canada and the US in 2010, the development of EXPLORER inline inspection robots for transmission natural gas pipelines started in 2003 with InvoDane Engineering under the leadership of NYSEARCH. Part of the Northeast Gas Association, NYSEARCH is a member-funded organisation that focuses on technology research for the benefit of the natural gas industry and its customers in the US. This article presents an overview of key milestones in Pipetel’s journey of providing certainty and safety to challenging and unpiggable pipes from the company’s beginnings in North America to its current expansion worldwide.
In 2007, after years of painstaking development, we saw the first deployment of the original EXPLORER 6/8, for inspection of 6 and 8 in. diameter pipes, in a live natural gas pipe for testing. Further refinement over the next few years allowed us to finesse the technology and commercialise the robot into a service offering that solves a major problem in the oil and gas industry – the inline inspection of unpiggable pipes.
Pipeline integrity leaders and professionals with challenging and unpiggable pipeline assets need reliable and accurate data to determine the state of their assets as part of a well-rounded integrity management programme. In order to reduce risk and exposure to incidents, inline inspection provides the most comprehensive data to develop a safety programme that meets or exceeds mandated standards and significantly reduces the probability of incidents. However, traditional inline inspection methods may not be suitable for all unpiggable pipes. Unpiggable inspections In 2010, Pipetel officially formed, with its sole mission to provide certainty and reduce risk in unpiggable pipes. In the next year, we completed our first inspection of an 8 in. diameter pipe, embarking on the journey to make unpiggable pipes safer. EXPLORER 6/8 at the time had a camera for visual inspection and a remote field eddy current sensor for detecting corrosion. That year, we inspected pipes for a Canadian operator and a US operator as well as successfully completed our first ever, robotic inline inspection of otherwise unpiggable pipes that were in service without shutting down the natural gas pipes. EXPLORER 6/8 entered and exited through an industry-standard hot tap fitting.
In 2012, we added the EXPLORER ILI 10/14 to our fleet, to inspect pipes in the diameters of 10, 12, and 14 in. This was the first EXPLORER ILI robot featuring tri-axial sensing and a high-resolution Magnetic Flux Leakage (MFL) sensor. The following year, due to popular demand of our first robotic MFL service, we released the EXPLORER ILI 20/26 to provide a much-needed service to keep larger diameter pipes of 20, 22, 24, and 26 in. safer.
By developing self-propelled, robotic inline inspection tools, Pipetel became an industry leader in the inspection of unpiggable pipes by providing the best visibility of imminent threats. EXPLORER ILI robots capture high quality, accuracy, and quantity of data for industry-leading operators to achieve certainty and reduce risk of incidents in challenging to inspect pipes. By reducing imminent and future risks with comprehensive integrity data, operators will experience a reduction in operational,

liability, and property damage costs. They will also see better protection of their reputation as a safe and reliable operator. Additional benefits for operators include enhanced uptime and the potential to increase product throughput which can result in increased revenue while also maintaining high safety standards.
Inspecting longer pipelines One of the most common demands from operators we began to receive, after having a fleet of three EXPLORER robotic tools, was to extend our service to include the ability to inspect longer pipes. In 2014, Pipetel responded by introducing a proprietary inline charging (ILC) process and technology. The ILC technology recharges EXPLORER inside the pipe to extend the range of inspection and expanded our service offering to no longer be limited by the inspection distance capable with a single battery charge. This technology is also able to be used with no interruption to gas service. Since the introduction of our ILC technology and process, Pipetel’s longest continuous inspection conducted is 4 km.
In that same year, we introduced our Laser Deformation Sensor (LDS) onto each EXPLORER ILI to add the collection of deformation data by all EXPLORER robots. It was at this time that EXPLORER robots became a combination tool with visual, MFL, and laser deformation sensors. This additional data has proven to provide vital information to operators, revealing common threats due to third party damages to unpiggable pipes. Collecting this multipoint data better reveals imminent threats and thus keeps unpiggable pipes safer.
Terminals and facilities In 2015, we began inspecting liquid pipes in terminals and facilities, extending the benefits of robotic inline inspections to not only natural gas pipeline operators but liquid pipe operators as well. We also continued to expand our inspection capabilities to include 16 and 18 in. diameter pipes by introducing EXPLORER ILI 16/18. The next additions to our fleet included the EXPLORER ILI 30/36 to inspect pipes of 30, 32, 34, and 36 in. in diameter and the development of a new and improved EXPLORER ILI 8 to replace the original EXPLORER 6/8 with an inline inspection robot that collects multipoint data. Finally, we completed our lineup of multipoint data collecting robotic tools in 2020 by adding the smallest robot in our fleet – EXPLORER ILI 6. This expansion to our fleet allows us to inspect pipes from 6 - 36 in. in diameter.
Focusing on pipeline safety Over the years, our teams have worked tirelessly to improve pipe safety across the US and Canada. The longest project, with multiple sections of inspection, that we have inspected was 14 km. Relentlessly and strategically focused on pipeline safety of difficult-to-inspect pipes, we lead the industry in the ability to navigate unpiggable pipes. Our team conducts inspections safely and accurately to collect the highest quality and breadth of data possible so that pipeline operators can make the most informed decisions about their assets.
We always encourage our team to be innovative, customerfocused, responsive, flexible, and have integrity to provide operators with the best experience and assurance that they will receive the most complete information to utilise as part of their asset integrity programmes.
In January 2021, we extended our mission of keeping unpiggable pipes safer all over the world by merging with Intero Integrity Services. This strategic alignment means that the benefits of a multipoint MFL, LDS, and visual inline inspection are no longer limited to North America, but are now available worldwide. Both companies have the same focus on difficultto-inspect pipes, high service levels, state-of-the-art technology including robotics MFL as well as free-swimming Ultrasonic Transducer (UT) tools to provide a plethora of integrity solutions and options for all pipeline operators. As pipe assets age, all of us at Intero and Pipetel strive to continuously help operators improve the safety of pipelines globally.
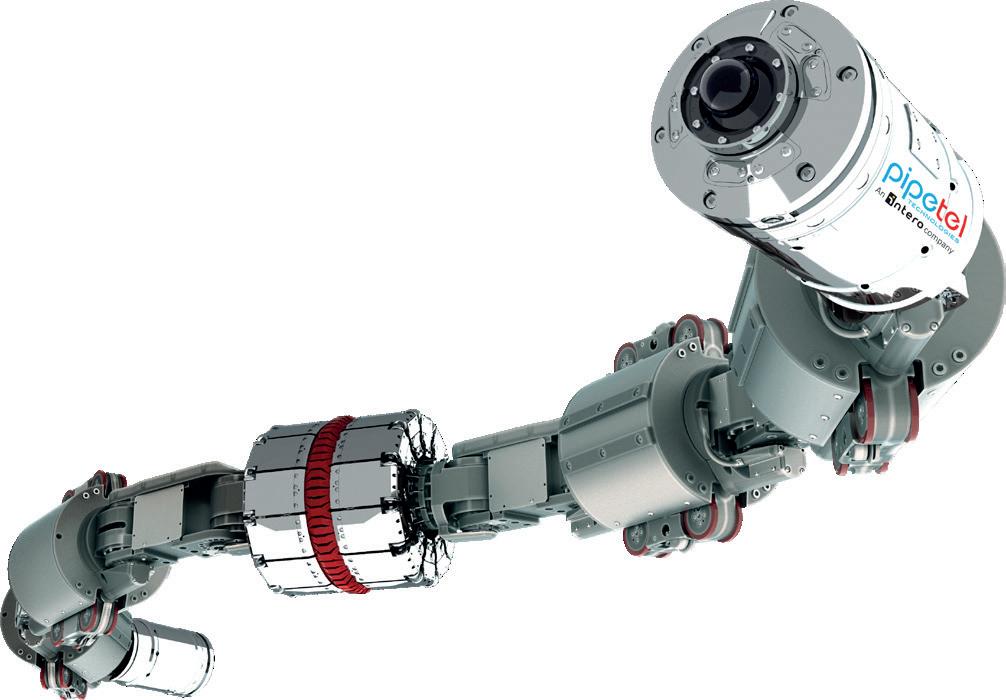
Figure 1. company Tetherless, self-propelled, remotely controlled EXPLORER ILI robot with multiple data collecting sensors.
2007 Explorer 6/8 with video and eddy tested in live gas pipes sensor
2010 Pipetel formed to provide certainty and reduce risk in unpiggable pipes
2011
1st inspection of 8" diameter pipe in service, inspected pipes for 1 US operator and 1 Canadian operator
2012 Explorer 10/14 first deployed for inspecting 10"-14" pipes with tri-axial MFL
2013 Explorer 20/26 deployed to expand MFL inspections to 20"-26" pipes
2014
2014
In-line Charging (ILC) technology developed to extend inspection range beyond a single battery charge
Laser Deformation Sensor (LDS) added onto Explorer MFL robots, giving them the ability to collect MFL, LDS, and video data
2015 Began inspecting liquid pipes in and facilities terminals
2015 Introduced Explorer 16/18, Explorer 30/36, and new MFL Explorer 8
2020 Introduced new Explorer 6
2021
Extended mission of keeping unpiggable pipes safer worldwide by merging with Intero Integrity Services
Figure 2. Historical timeline of Pipetel’s technology.
CANADA 44 Metropolitan Road, Toronto, ON M1R 2T6 + U.S.A. 300 International Drive, Suite 100, Williamsville, NY 14221 Main: 416-510-8588 pipetelone.com Toll free: 1 855-747-3835