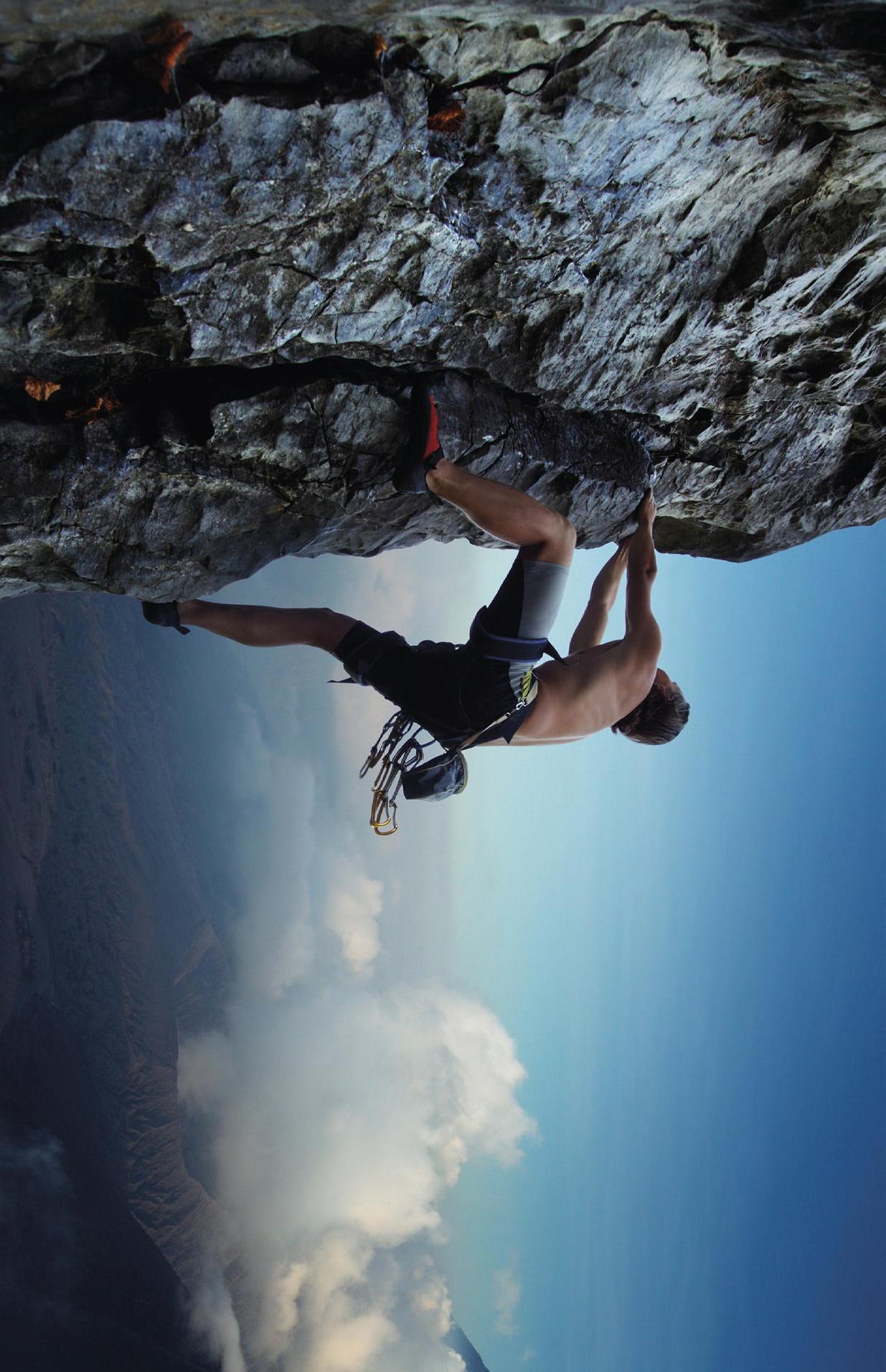
7 minute read
Motors in beast mode
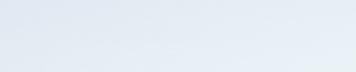
Marek Lukaszczyk, kaszczyk, WEG, UK, explains how optimising motor performance can contribute to more efficient and effective production processers in the oil and gas industry.
According to McKinsey, most oil and gas operators have not maximised the production potential of their assets and offshore platforms are, on average, running at only 77% of maximum production potential. Industrywide, this shortfall represents a considerable US$200 billion in annual revenue.
Energy efficient oil and gas processing begins with efficient facility design, and this includes the choice of each piece of equipment in each individual process. More and more, an increasing number of oil and gas companies are being seen adopting a wider range of technologies that are helping them become more efficient and minimise costs. From the automatic monitoring of steam traps in LNG processes, to embracing advanced analytics, it is clear that this sector is stepping up its efforts to optimise its processes.
While efficiency improvements should be considered as a facility-wide strategy instead of limited to one individual asset, electric motors play a key role in the oil and gas production and distribution infrastructure. They are widely used to drive equipment such as pump and compressor systems and thus offer great potential for efficiency gains. This article will explore five considerations to improve the efficiency of motors in the oil and gas industry.

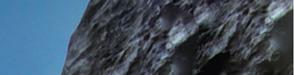
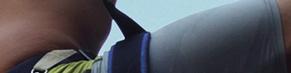
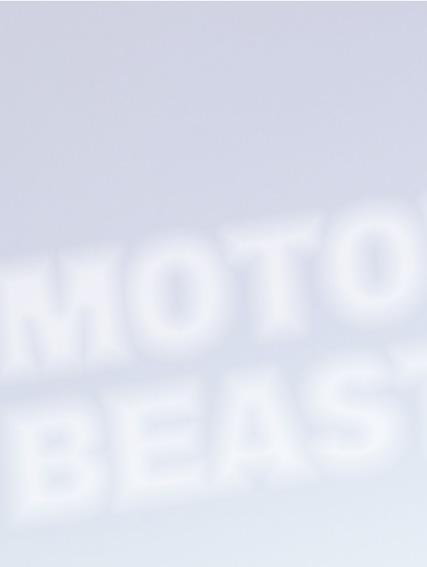
High efficiency motor upgrades
Europe has over 8 billion electric motors in use across industry, consuming approximately 63% of the electricity generated across the continent. Many of the electric motors in use in oil and gas applications are either low-efficiency or not properly sized for the application. Incorrect motor sizing can result in the performance of the motor not being at its most efficient, especially below 50% of rated power output.
Similarly, older motors may have been rewound a few times during maintenance, lessening their efficiency. For this reason, a cost benefit analysis should be completed prior to rewinding any motor to determine if purchasing a new, higher efficiency motor is economically advantageous. Today it is possible to purchase a hazardous area motor with highefficiency ratings up to IE3 or IE4.
Because energy consumption accounts for 96% of the total lifecycle cost of a motor, paying extra for a premium efficiency motor will result in return on investment over its lifespan. The recent introduction of stricter ecodesign requirements (EU 2019/1781) for electric motors has accelerated this trend, not only in Europe, but worldwide.
Until recently, some motors, including those designed for hazardous areas, were exempt from energy efficiency regulations. This will no longer be the case under the latest regulations. Additionally, these regulations will also be imposed on variable speed drives (VSDs) for the first time. The legislative changes will impact many industries, but sectors with high energy usage or using ATEX motors, such as the oil and gas industry, may see the greatest transformation.
The new regulations replace the regulation EC 640/2009 and are expected to bring huge reductions in the energy consumption related to motor use, while maintaining the required level of safety. It is estimated that by 2030, this will deliver extra energy savings of 10 TWh/yr and greenhouse gas (GHG) emission reduction of 3 million tpy CO2 equivalent.
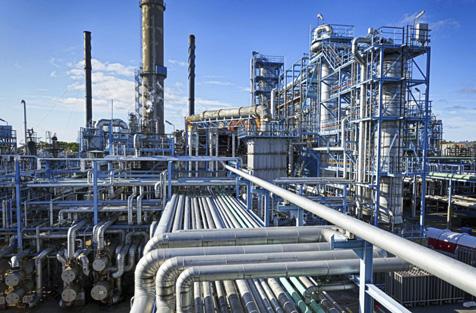
Figure 1. Industrial pipelines at an oil and gas refinery.
Figure 2. WEG provides high-efficiency motors and drives for the oil and gas industry such as the WG20, W22X, and CFW ranges.

Motor sizing
Significant improvement to motor design can be achieved without incurring substantially increased costs. However, the use of high-energy class IE motors must not replace a fundamental rule: the electric motor must be properly dimensioned according to its real load. If a motor is oversized, with the actual load less than 50% of the rated load, it will reduce efficiency and power factor values. For this reason, it is important that efficiency and sizing considerations go hand in hand.
There may also be additional factors to bear in mind when choosing ATEX motors for oil and gas applications. As a result of safety requirements, explosion proof motors (Ex db, Ex dc) may face design constraints such as derating for VSD operation or reduced starting current. This may sometimes result in a larger frame size, which could lead to additional considerations when retrofitting equipment with a need for motor interchangeability.
Installing a VSD or soft starter
Although very few oil and gas applications require 100% flow continuously, many of the motors employed in oil and gas applications, such as pumping systems, are started at full speed and remain running at full, fixed speed while in use. VSDs can effectively control rotating equipment such as fans, compressors, and pumps in industrial processes and offer the best efficiency advantages in variable torque applications. In fact, according to the European Committee of Manufacturers of Electrical Machines and Power Electronics (CEMEP), a 20% reduction in speed could lead to a 50% reduction in energy.
For example, in LNG compressors, VSDs can offer many efficiency benefits. The majority of LNG plants feature refrigeration compressors driven by industrial gas turbines. However, if plants opt for a full electric solution by using an electric motor and a VSD, this increases the production flexibility, reduces emissions, and decreases the maintenance costs.
To deliver the maximum energy saving potential, VSDs must be commissioned and installed correctly. Following the manufacturer’s guidelines can make the difference between installations that run reliably for years and those with much
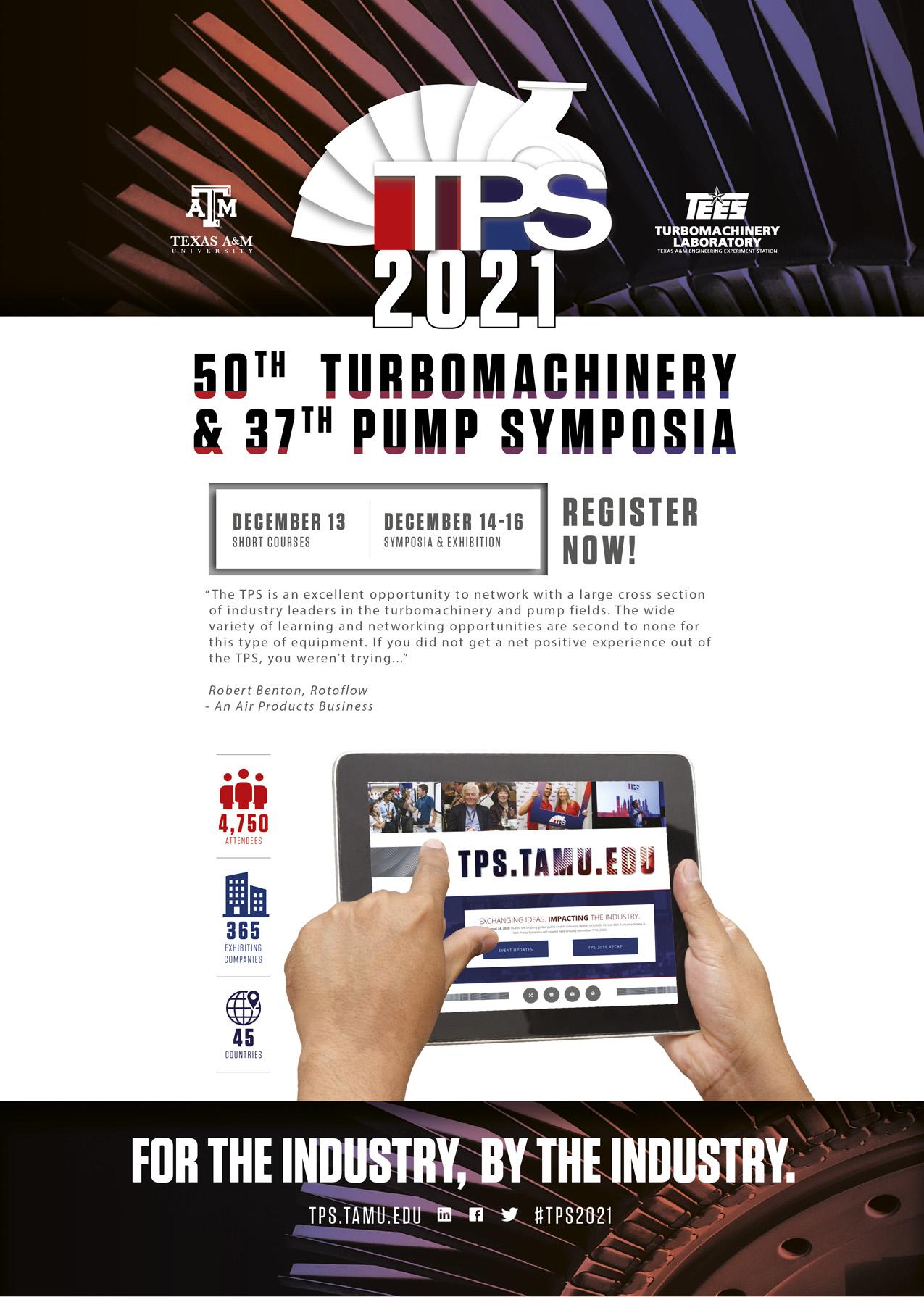
shorter lifecycles. This is where partnering with an expert such as WEG can pay off. If the VSD has not been properly configured this can have a real impact on the performance of the system. To maximise the reliability of the installed VSDs, start by considering the application conditions and the speed at which the motor is required to run. Parameters usually have a ‘default’ setting which will probably be adequate for most applications. However, these should be checked and adjusted for optimum operation.
Motors are often left to idle, as some operators believe that it is more economical than stopping and restarting the motor. Idling motors use energy unnecessarily and should always be shut down if they will not be needed. This is where soft starters should be considered. As the name suggests, soft starters allow the motor to start the load more gradually by limiting the voltage to the motor and providing a reduced torque. In addition to reducing energy consumption, a reduced voltage soft starter helps protect the motor and connected equipment from damage by controlling the terminal voltage.
Digitalisation and motor performance sensors
Correctly implemented data analytics systems and tools can overcome the operational complexity of oil and gas operations. While most oil and gas companies have vast volumes of data, they are typically using less than 1% of it. By combining advanced engineering, the latest data science, and computing power, there is the real potential to make production optimisation improvements across the board.
Instead of replacing conventional methods of asset operation, digitalisation will supplement them. For example, to keep motors running optimally in LNG plants, managers can install retrofit sensors. With important metrics such as vibration and temperature monitored in real-time, built-in predictive maintenance analytics will identify future problems ahead of failure, preventing shutdown of processors.
Correct maintenance practices
Regular maintenance should be carried out on the entire motor system. Performance will naturally decrease after prolonged heavy-duty use or the exposure to harsh conditions. This can be as a result of erosion, corrosion, or chemical attack. Engineers should firstly opt for products – such as those provided by WEG – that can provide energy efficient operation in harsh oil and gas environments.
For example, voltage in-balance, where the voltage of power supplied to the motor does not match the voltage at which the motor is rated, can cause vibrations and mechanical stress, increased losses, and motor overheating. These issues increase the maintenance costs of running the motor and shorten its life.
Like many energy-intensive industries, the oil and gas sector is exploring new solutions to increase production and energy efficiency. As the sector continues to evolve its processes and infrastructure, it will continue to rely on high-efficiency motors and drive control technology as a reliable pillar in the wider energy efficiency drive.
Need a reprint?
