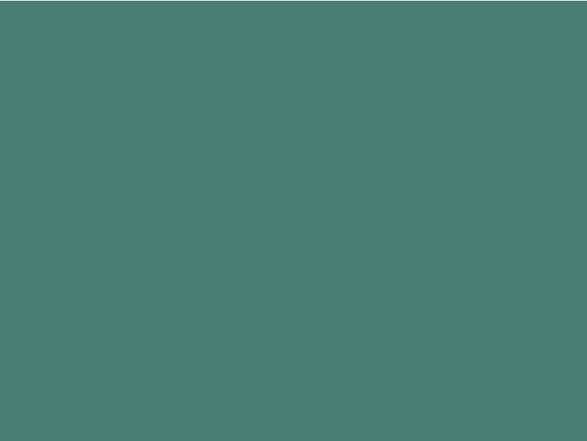
8 minute read
Sustaining LNG growth
Richard Bowcutt, Heatric, UK, indicates how heat exchangers are fundamental to realising the benefits of LNG and cleaner energy.

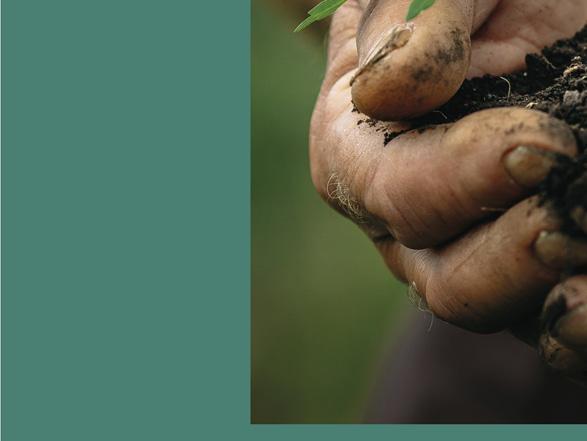

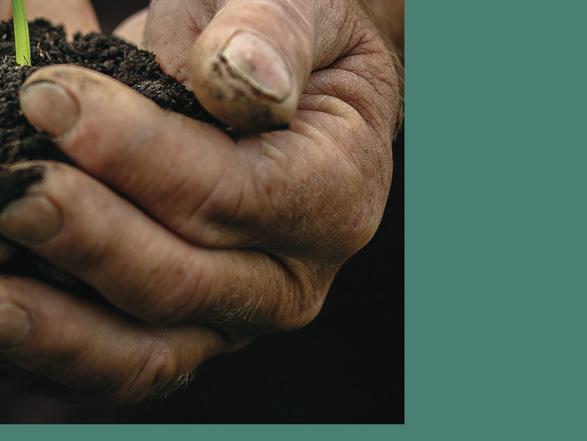
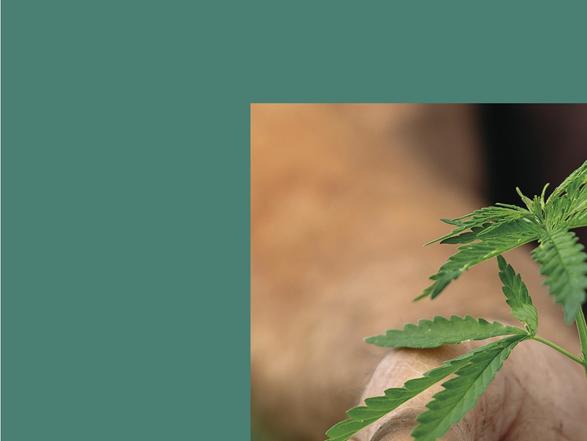
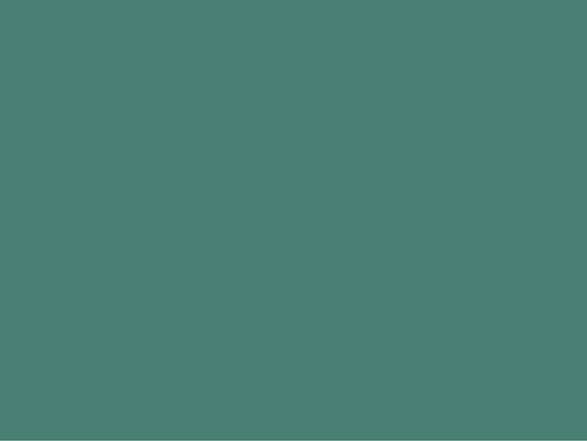
As governments look to overhaul their energy systems and their economies in support of the green agenda, an increasing number of renewable energy, carbon capture, and biofuel sources are entering the supply grid. Against this backdrop, LNG is an energy source with the potential to support countries’ green ambitions.
LNG is the fuel of the future. However, with a complicated and lengthy value chain, from source processing to liquefaction, transport, regasification, and onshore infrastructure, significant investment and expertise is required to scale LNG to support emissions targets being set by governments around the world. The climate change race, and transition to clean energy, is well underway. Countries around the world have adopted goals for net-zero emissions by 2050, and hundreds have joined the 2015 Paris Climate Accord, which aims to limit global warming to below 2˚C.
Clean-burning and low-carbon, natural gas is an effective, proven, and more sustainable alternative to gasoline and diesel, releasing 45% less carbon dioxide than coal and 30% less than oil. With the clock ticking for businesses, and the gas industry itself to become compliant with environmental legislation, natural gas is playing an increasingly vital role in reducing the

emissions of pollutants. LNG can also power low-polluting modes of transport, and as such, is becoming an increasingly popular marine fuel to support clean shipping.
With the green energy transition accelerating, demand for natural gas is growing. As more countries increase their usage of natural gas as an efficient source of energy, structural global LNG demand could rise 14% by 2025 from 2020, resulting in a 26 - 34 million tpy call on balancing markets over 2022 - 2025, of which Europe would be the biggest driver, with China, South Asia, and Southeast Asia as key growth regions. Indeed, there is potential that use of LNG could overtake the supply of natural gas through pipelines. Therefore, it is critical that LNG processes are as efficient and sustainable as possible. Heat exchangers, which perform fundamental and essential heat transfer operations for numerous oil and gas applications, can support the reduction of emissions in LNG processes to enable the drive to net-zero.
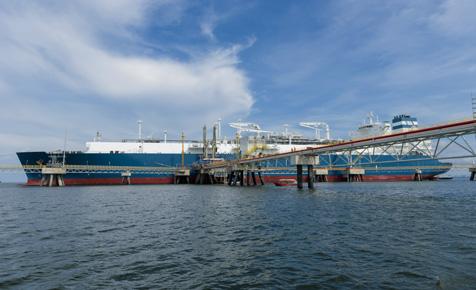
Figure 1. Höegh Grace FSRU. Image courtesy of Höegh LNG.
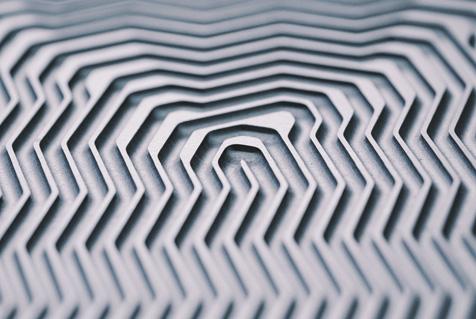
Figure 2. A close-up of Heatric’s chemically-etched plate channels.
Figure 3. A fully-constructed Heatric printed circuit heat exchanger (PCHE) awaiting final testing.

LNG process challenges
Whilst LNG serves as an important component of a more sustainable energy and fuel supply, liquefaction and LNG transportation create greenhouse gas (GHG) emissions. In a nutshell, the liquefaction and regasification processes require significant energy, with associated parasitic losses due to boil-off during storage and transportation. Pure LNG or dual-fuel engines also release GHGs from methane slip but still offer an overall reduction compared to conventionally fuelled engines from between 14 - 23% for two-stroke and 6 - 14% for four-stroke.
Alongside environmental efficiency challenges, there are complications involving the regasification process and distribution of LNG once it has reached the shore. For projects where space and cost make a land-based facility unfeasible, floating storage regasification units (FRSUs) can be a more practical, economic, and environmentally friendly alternative for converting LNG that has been shipped from the offshore platforms back to its gaseous state for piping inland. However, as with offshore oil and gas platforms, these units have very specific requirements and space is much more compromised vs land platforms.
Heat exchanger developments to support reduced emissions
Heat exchangers play an essential role in all stages of the LNG value chain. The design of heat exchangers has evolved to meet the demands of the LNG industry; with enhanced efficiency, energy savings, ease of maintenance, and increasingly, modularity. Designing heat exchangers to withstand high pressure and large temperature spans can often lead to heavy and bulky equipment. On FRSUs, where space is extremely limited, it can be challenging to find a suitable and effective solution to enable the liquefaction and regasification processes.
Meggitt’s Heatric division has designed printed circuit heat exchangers (PCHEs) to meet the specific requirements of high-productivity, space compromised platforms such as FRSUs, by providing space and weight savings, high thermal effectiveness, low pressure drop, and high design pressure capability. Capable of operating with a very close temperature approach, PCHEs enable higher thermal efficiencies throughout the LNG value chain to reduce waste energy and emissions by enabling optimum process conditions to be met. Manufactured to be 85% smaller and lighter than traditional technologies, Heatric PCHEs’ unit size provides significant space and construction savings due to the elimination of extra pipework and associated equipment. This reduces the overall weight impact on FRSUs and therefore the fuel impact, with significant cost and emissions savings.
As with any oil and gas offshore platform, safety is paramount, meaning equipment has to be extremely robust. PCHEs are not susceptible to vibration and do not suffer from catastrophic failure modes. Heat exchangers manufactured using a specialised solid state joining process known as ‘diffusion bonding’ are extremely durable, capable of
withstanding temperature shocks and mechanical damage, to both optimise system up-time and ensure the highest safety levels.
Greener shipping: LNG – the fuel of the future
In the climate change fight, LNG is not just being used as a cleaner energy supply. Demand for LNG is also being driven by the marine industry. Shipping is the fundamental facilitator of global trade and is under growing pressure to reduce its carbon footprint. As a result, LNG is increasingly being seen, at least as an intermediate solution, as a cleaner fuel to help power shipping. Traditionally the shipping industry uses variants of marine diesel oil (MDO) for power and propulsion. LNG produces up to 30% less carbon dioxide than diesel equivalents used in the industry. LNG-fuelled ships also emit almost zero sulfur oxide emissions.
A small percentage of ships globally have made the transition to run on LNG, with most having dual-fuel capability, enabling the switch between MDO and LNG. However, the number of ships powered purely by LNG is increasing exponentially, and is expected to increase as existing LNG infrastructure grows and comparative cost approaches other fuel solutions.
The effort to reduce carbon footprint is being partly driven by a deadline set by the International Maritime Organization (IMO), the United Nations marine regulator, to cut carbon emissions in half by 2050 compared with 2008 levels. Several IMO regulations have already been imposed on vessel owners to reduce several key emissions such as SOx and NOx, in an attempt to kick-start a green revolution in global shipping. It is also being driven by consumer and therefore logistics customer demands for cleaner supply chains. Shipping companies know that if they want a long-term chartering contract with a big client, they will be assessed on how green their ships are. Royal Dutch Shell plc and Australian miner BHP Group have, for example, been offering long-term charters to shipowners willing to build natural gas-fuelled tankers and bulk carriers over the past 18 months.
Bulk tankers that transport LNG across the seas have been using LNG for many years. Even with sophisticated storage tanks, a small amount of LNG turns back to gas while it is being transported, rather than wasting it, the boil-off gas (BOG) can be used as a fuel source for the engines or reliquefied and returned to the LNG storage tank using specialised BOG reliquefaction systems. Other LNG powered ships require a fuel gas supply system (FGSS), which is a complete system comprising of an LNG storage tank, LNG process system, and control and safety system that turns the LNG into gas to power the ships. Incorporating this infrastructure onto cargo ships has significant space efficiency and weight ramifications. PCHEs are an integral part of both BOG reliquefaction systems and FGSSs, delivering space and weight benefits which make them a vital component to delivering on the emissions promises of LNG.
The LNG value chain needs optimised equipment and systems at every process stage, to give the market the best opportunity at maximising impact through reducing emissions whilst demand growth is highest. Current gas prices are volatile and demand is expected to fluctuate for the short-term in the UK for example, where a long, windless summer has prompted the start-up of coal plants to cover energy recesses from offshore wind. LNG remains the critical transition fuel whilst development of alternatives such as hydrogen are matured and become economically viable. In the meantime, the imperative is to sustain the growth in LNG applications as a key aspect of delivering the sustainable energy mix required for global emissions reductions. Otherwise, LNG will miss the boat altogether.

Figure 4. A painted Heatric PCHE for a gas processing application.
Figure 5. An ‘exploded’ digital view of a Heatric PCHE, showing how the exchanger core is encased.
Figure 6. Alternating hot and cold fluid core plates.
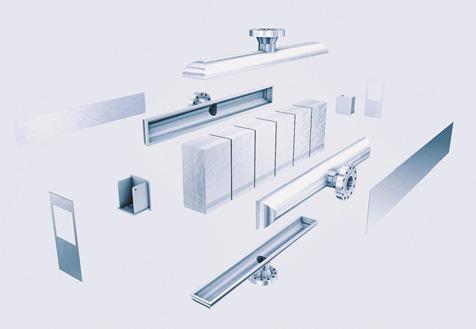
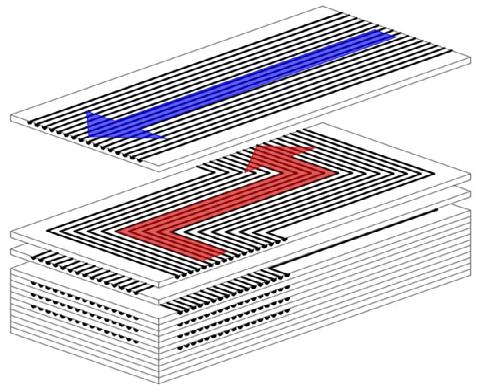