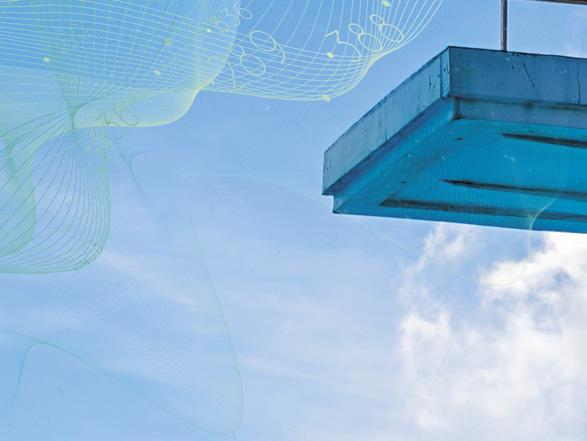
7 minute read
One platform for data

Steffen Zendler, Heavy Industry - Strategy and Marketing Manager, EMEA, Rockwell Automation, Germany, illustrates the implementation of a new automation system for onboard LNG applications.

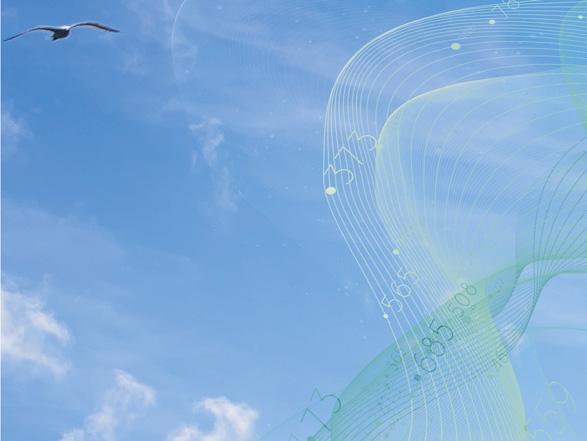

The LNG Portovenere and LNG Lerici are two ships designed for the transportation of LNG. Built in 1997 by Fincantieri and having reached the middle of their lifespan, their owner, in collaboration with their management company, the Belgian firm EXMAR Ship Management, made the ships the object of a significant, total renovation project to prolong their lifespan by at least 15 years.
In addition to revamping the boilers, pumps, and turbines, the project also included modernisation of all the control systems, from the central management system to the system used for the turbines and turbopumps. The design and implementation of the new automation system was assigned to the Safety Systems and Information Division of the Italian company Leonardo. A high-tech global company and one of the main players in the aerospace, defence, and security sectors, the company is a leader in the design and provisioning of high-integrity security systems and process safety systems.
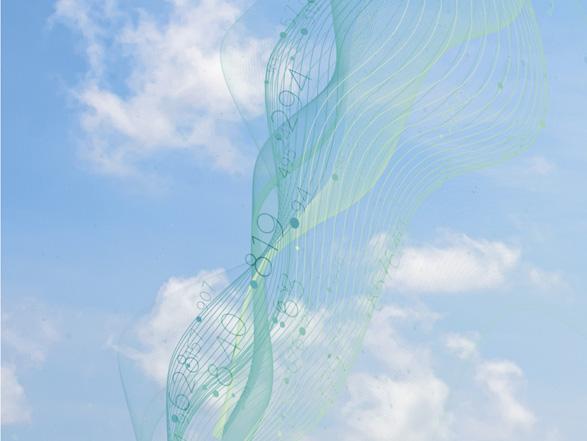

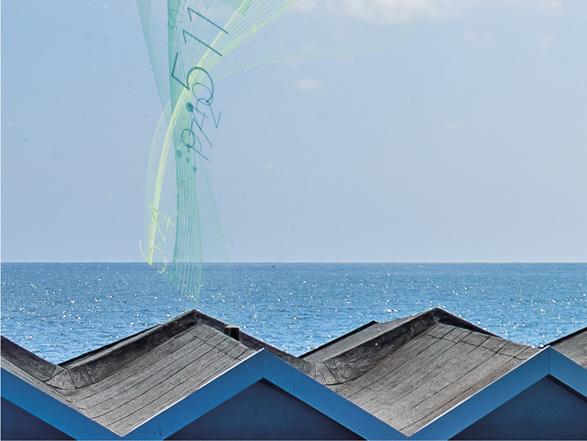

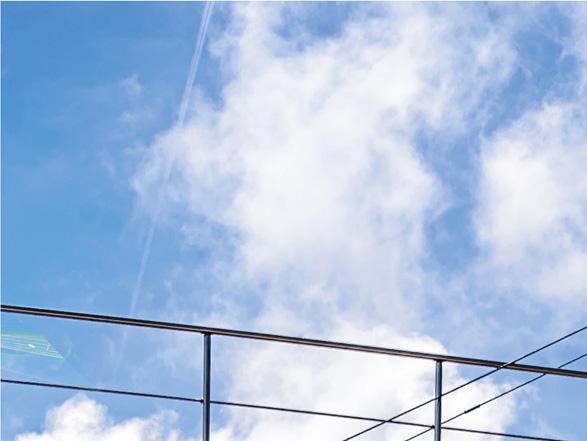
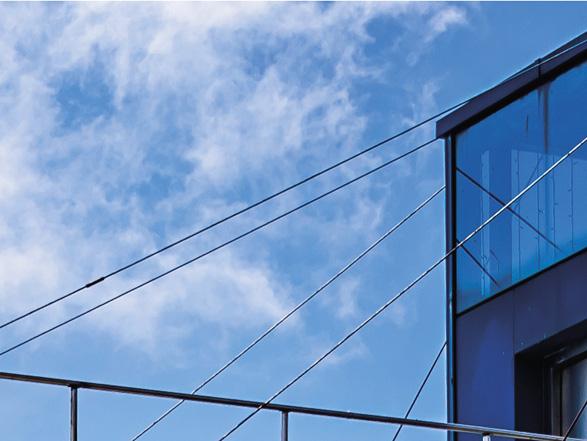
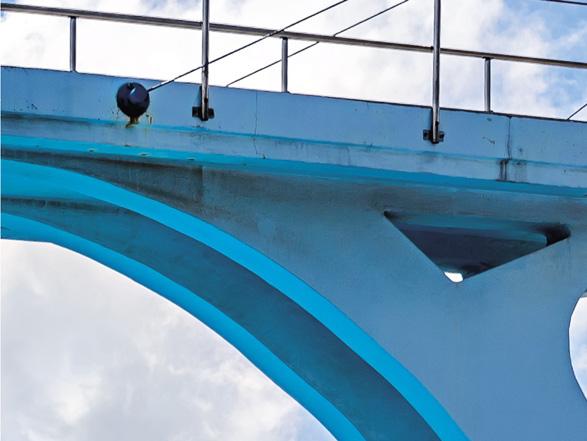
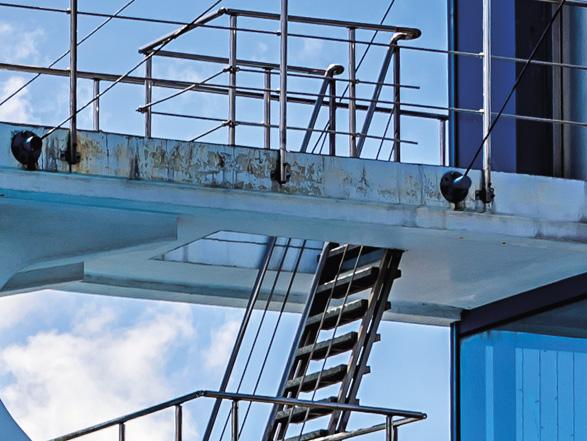
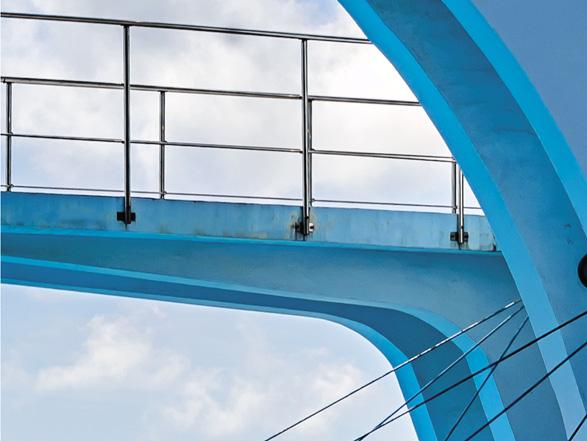
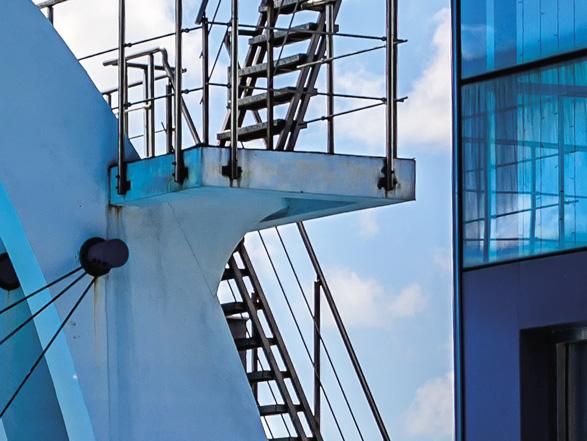
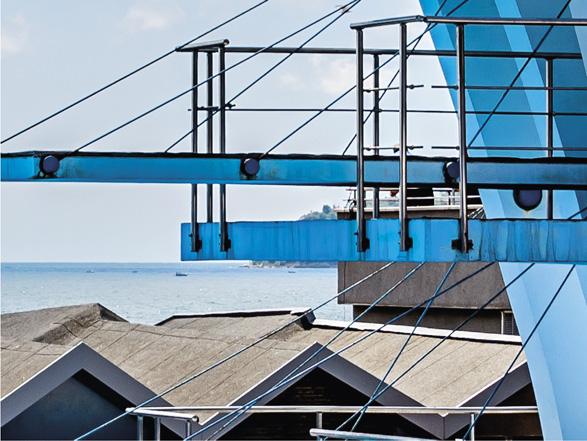
Based on its in-depth knowledge of Rockwell Automation solutions and a long-term collaboration with its team, Leonardo opted for the deployment of a new infrastructure controlled by the PlantPAx® DCS.
Challenge
Dedicated to transporting LNG, the ships, with a capacity of 65 000 m3 each, underwent an extensive refit project, in which Leonardo was involved for automation control, sensors, and field instrumentation.
At the time of their construction, both the LNG Portovenere and the LNG Lerici were equipped with a Bailey Infi 90 system, popular at the time, which became a legacy system at the end of its lifespan, maintained by the Leonardo service department. The desire to replace the legacy system with a modern, high-performing system was at the heart of the project assigned to Leonardo.
In addition to the central system, in itself already a challenge because it represents the heart of these ships, Leonardo was also contracted for the modernisation project covering the automation systems for the turbopumps and turbines, which up to that point had been managed by separate systems. The replacement of all field instrumentation was also necessary, as it had become obsolete and at danger of imminent breakdown, especially in light of the difficult conditions in which these ships operate.
The greatest challenge, however, was related to the timeframe given by the owner. For understandable economic reasons, the stoppage time for the ships had to be as brief as possible. This required perfect co-ordination with the other contractors in order to proceed with installation of the hardware and software in parallel with the revamping of the boilers, turbines, pumps, and other equipment – reducing the subsequent commissioning phase to a minimum.
It was also necessary to consider that all internal inspection activities would also have to be scheduled during the time period. External certification by certifying bodies also had to be factored in as the ships have dual registry: specifically, RINA – Registro Italiano Navale (the Italian Naval Registry) and ABS – the American Bureau of Shipping.
“In this context, with so many variables and rigid timetables, selecting the best solution and suppliers was a key factor,” explains Stefano Baccelliere, Homeland Security and Critical Infrastructure LoB/Project Manager of Leonardo. “On the one hand, our time was very restricted, but on the other we wanted to take advantage of the occasion offered by these large scale works to offer our client a solution that was decisively better than the incumbent solution, to allow for possible future developments.
“We had to lean towards a solution that did not have hidden surprises of any kind and one that we knew very well that could satisfy the requirements for modernity, scalability, and flexibility,” he continues. “We also wanted a system that had high performance levels associated with the management of functional safety, while also being simple to implement, in terms of hardware and software, ultimately delivering fluid migration of the legacy system to the new system. We could not take for granted the importance of finding a supplier that could bring proven experience from three diverse markets – naval, oil and gas processing, and energy – and above all, one with the capacity to make these vertical skills a common thread throughout the project.”
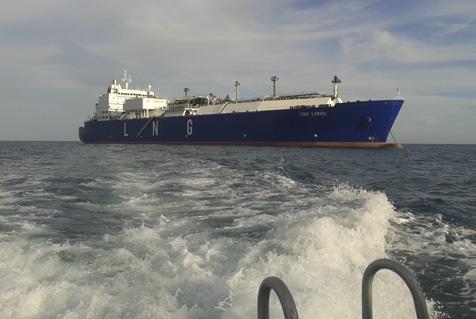
Figure 1. In addition to revamping the boilers, pumps, and turbines, the project also included modernisation of all the control systems.
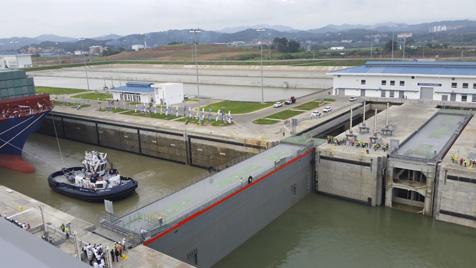
Figure 2. Navantia shipyard in Ferrol, Spain.
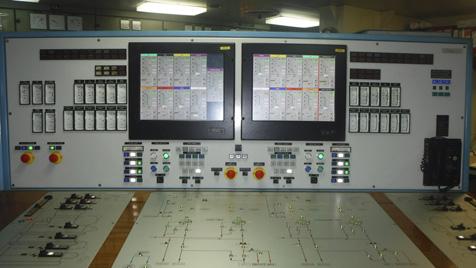
Figure 3. Having combined all the systems into a single platform also means having a single supervision and control system.
Solution
In light of all of this, Leonardo chose Rockwell Automation and its modern PlantPAx DCS, because both could satisfy all the requirements.
The PlantPAx DCS made it possible to combine all of the control systems in a single platform. Now the central control system for the ships is managed by the Automated Integrated System (AIS), as are the turbines and turbopumps.
Leonardo’s technicians are already very familiar with the hardware elements of the PlantPAx solution, meaning that the migration project could be completed without the need for
any field rewiring. Furthermore, in collaboration with the Rockwell Automation team, an identical mock-up of the software solution destined for the ships was created on land. This created the opportunity to undertake in-depth functional tests to check that the new system’s functionality was identical to previous levels, therefore making it possible to study possible improvements in the solution and new functionalities with the help of Rockwell Automation specialists.
The land-based inspection phase was fundamental because it made it possible to arrive at the commissioning phase with the onboard software operationally ready, and it also overcame the problem of working with two ships located in two different shipyards. For the LNG Portovenere, commissioning took place in January 2016 at the Navantia shipyard in Ferrol, Spain, while the commissioning of the software on the LNG Lerici took place in 2018 at the Keppel shipyard in Singapore.
The decision to use the PlantPAx DCS also made it possible to include the emergency shutdown system for safe functioning. A remote service line was installed with a satellite internet connection, to deliver continuous customer support during navigation. It also gave Leonardo the opportunity to offer continuous assistance during operations, along with troubleshooting support for maintenance personnel.
Results
“Today the ships are equipped with a modern system with better performance than the former system, and all the advantages that come with that. Energy consumption was also reduced thanks to the new generation-control system. Basically, using the PlantPAx DCS, we enjoy double advantages: in addition to progressing from a legacy system to a modern one, today we also have a single system instead of three separate systems, with improved performance and speed,” remarked Baccelliere.
Having combined all the systems into a single platform also means having a single supervision and control system, which in this case is based on FactoryTalk® View SE, and provides a faster solution in respect to refresh times for the graphic pages and more intuitive for operators.
From an assistance and maintenance standpoint, the ships are now equipped with a remote service system with a satellite internet connection; therefore, operators can count on continuous assistance as needed. Another advantage stems from the fact that if it becomes necessary to secure a spare part, a global company such as Rockwell Automation has a better chance of having spares available in the many different countries where the ships dock. This is especially true in light of the changes in operating area for these ships, from the Mediterranean basin to the Far East, and in particular between China and Indonesia.
“We selected an open system like PlantPAx to give us the possibility of providing the client with additional functionalities backed up by Rockwell Automation, with which we have been developing successful projects for over 10 years, and whose mission is to continue to invest in R&D to improve the level of service to the client. All of these factors are the basis for further development of this specific project and future collaborations with other clients,” concluded Baccelliere.
• More efficient heat transfer • Requires significantly smaller footprint • Environmentally friendly system easily meets the toughest regulations Electrify Your Thermal System
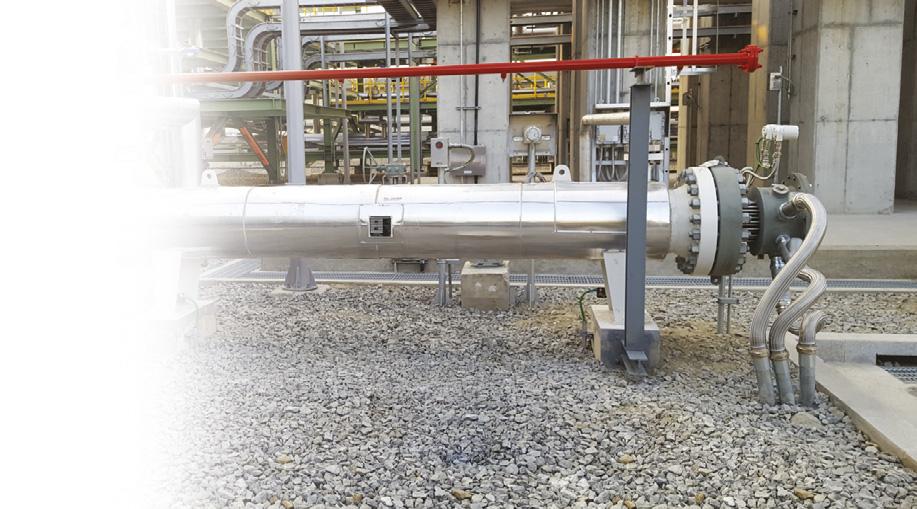
Powered by Possibility