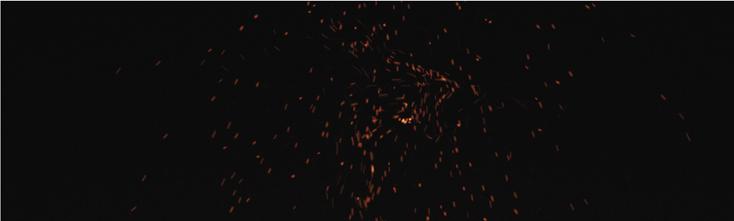
8 minute read
Keeping an eye on the transfer of heat
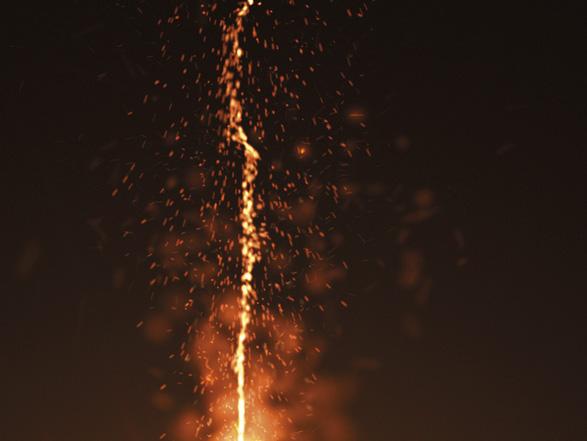
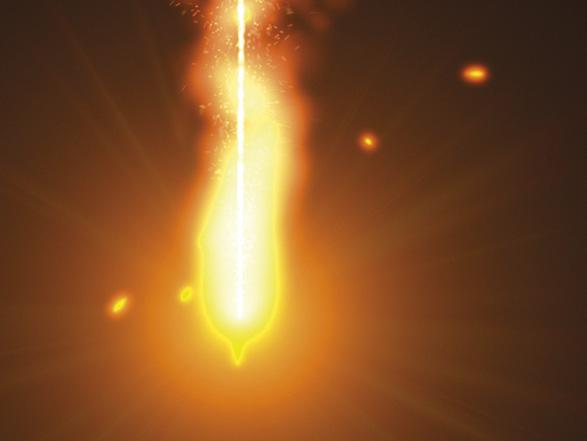
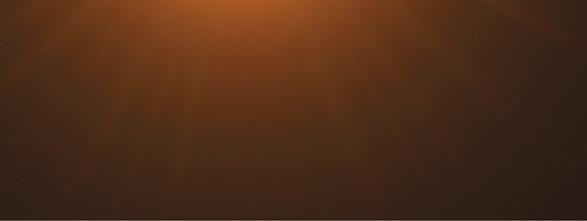
Paul Heinz and Christoph Heckmann, Linde Engineering, Germany, explain how digital twins are being developed for plate-fin heat exchangers.
Every industrial plant is unique, as are the plate-fin heat exchangers (PFHE) at the heart of many of these plants. PFHEs can be found in cryogenic processing plants such as air separation units, petrochemical and natural gas treatment facilities, as well as helium and hydrogen liquefiers. They transfer heat between various fluids in different phase states. Linde’s PFHEs measure up to 8 m in length. Their compact design belies their strong performance. With a heat duty of up to 20 MW, a single core is as powerful as a small natural gas power plant. Moreover, a single PFHE can handle up to 20 process streams simultaneously.
Design considerations
Heat transfer performance is one of the key factors in determining PFHE size. In Linde’s PFHEs, the surface-to-volume ratio can measure up to 2000 m2 per m3. This exceptionally high specific heating area maximises heat transfer efficiency, helping


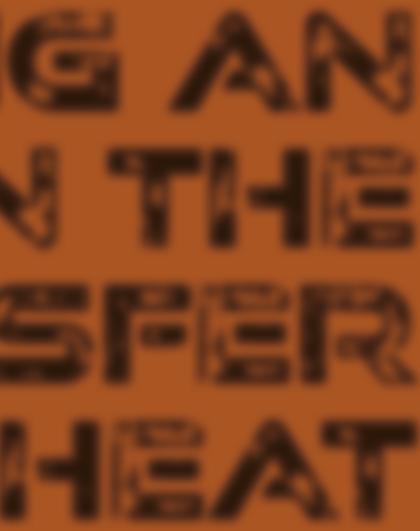
to limit investment costs by reducing the column height and weight. Optimised heat transfer performance also enables very small temperature differences – down to 1 K. Other design highlights of Linde’s PFHEs include low-pressure drops and fast responses to flow and temperature changes. These factors combine to maximise operational efficiency, making PFHEs the most economical exchangers available.
In addition, increases in heat transfer efficiency speak to the current trend towards larger process equipment designs. In recent decades, plants and equipment have grown steadily larger and have to handle more and more operational scenarios. Natural gas liquefaction plants are a case in point here. As a result of this, mass flows have also increased, as has the volume of heat that PFHEs have to handle. This calls for higher specific heating surfaces inside a PFHE.
Linde designs and builds its PFHEs for industrial plants based on the individual process requirements of every customer, factoring in variables such as heat transfer targets and the permissible pressure drop. In short, every PFHE is tailor-made. Plant operators are presented with a PFHE that aligns perfectly with their overall process flow.
Optimising performance through detailed data analyses
From the outside, all of these plant components look the same. Inside, however, the temperature profile of every PFHE is unique. For a long time, heat exchangers were like black boxes, providing limited or no insights into temperature behaviour. It was therefore practically impossible in the past for plant operators to assess process conditions. Yet this information plays a vital role in efforts to optimise performance and maintain long-lasting, reliable, robust operations. To close this information gap, Linde’s experts have been developing methods to optimise PFHE efficiency and extend its service life for many years. Linde now offers a service that provides valuable insights into what is happening inside heat exchangers. The operator of Australia’s largest LNG plant is one of the first customers to award Linde in 2020 with a contract for the continuous remote monitoring and diagnostics of Linde-supplied PFHEs. The objective of this service is to identify and avoid potentially critical operating conditions beyond the specifications and thus minimise the risk of costs due to unexpected downtime. As part of this service, Linde continuously monitors PFHE operations and warns the plant manager if the on-site team creates operational conditions with the potential to reduce PFHE lifetime. Furthermore, Linde experts support the on-site team in optimising operational efficiency and avoiding these situations.

Figure 1. Linde manufactures plate-fin heat exchangers (PFHEs) at its sites in Germany and China.
Figure 2. Aluminium PFHE, proven technology in a variety of designs.
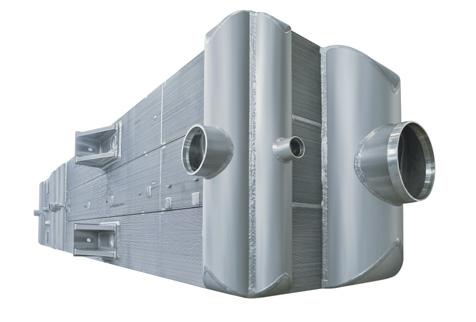
The best way to avoid material fatigue
PFHEs can be prone to thermal stress, resulting from localised temperature fluctuations, which can be as high as 200˚C. This causes thermal shrinking and expansion inside the heat exchanger, placing the unit under increased mechanical stress. Over time, microscopic damage and small cracks can develop into localised leaks. Changes in the metal’s microstructure ultimately lead to material fatigue, which can shorten the operating life of these exchangers.
Linde’s PFHEs are designed with a high stress margin. When operated within their design specification and in compliance with industry best practices, they offer a long lifetime. However, repeated thermal loads beyond specification can have a major negative impact on PFHEs in the long-term, as confirmed by countless studies under real-life process conditions run by Linde’s experts. The studies revealed that occasional excursions from optimal operating parameters were not a major problem but that repeated excursions are a very different matter.
This challenge can be solved by monitoring PFHEs remotely. Combined with advanced diagnostics, remote monitoring gives operators the insights they need to track thermal conditions inside the heat exchanger, detect potentially critical instances of thermal stress, and take corrective action.
Insights into the inner life of PFHEs
For Linde, this process starts with a detailed temperature profile of the metal wall. One tried-and-tested solution here involves installing sensors on the surface of the heat exchanger. Benefits include the fact that these can be retrofitted to existing plants and heat exchangers. These sensors collect temperature readings to assess the possibility of thermal stress. The more sensors that are installed, the more accurate the findings. However, design constraints can limit the number and placement of sensors
on the PFHE and this, in turn, can compromise the insights possible with these sensors.
Linde’s LINEX® sensor system was developed to take measurement accuracy and speed to the next level by overcoming the design constraints of other sensor systems. It is the first solution of its kind to provide detailed, real-time insights into the inner workings of a PFHE. To achieve this, multiple sensors are installed at various points of interest inside the PFHE. The technology is integrated seamlessly into Linde’s engineering and fabrication process and does not affect the thermal performance or size of the PFHE. Depending on the size and operational requirements, PT100 sensors or glass fibre sensors can be used to take high-resolution measurements of temperature profiles and material strain.
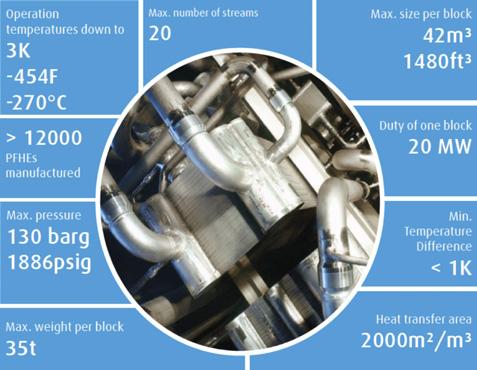
Figure 3. PFHEs in numbers.
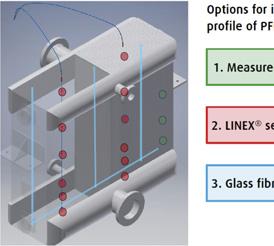
Figure 4. Options for measuring temperature.
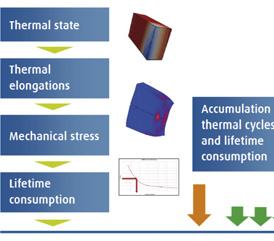
Figure 5. Thermal stress fatigue mechanism.
Predicting the future with digital twins
The data collected by the PFHE sensors is transmitted directly to Linde’s Industrial Internet of Things (IIoT) cloud using a ‘Smart Box’, which transmits data via Ethernet, WLAN, or a SIM card. Linde’s experts have already verified this set-up using a test rig and integrated it into the company’s own plants. One of the great benefits of the system is that it is compatible with any plant control system and can even be shipped preconfigured to customers. Local technicians can then install it on-site, significantly reducing implementation costs and time. The system can easily be retrofitted into existing plants.
The quality of the simulation model is ultimately what determines the extent to which the digital PFHE twin matches its real-life counterpart. Linde’s tool is able to simulate the thermal status of a heat exchanger in detail together with all relevant correlations for heat transfer and pressure drop as well as dynamic conditions. It then uses this information to generate predictions. Linde’s experts also work with computational fluid dynamics (CFD) to provide detailed analyses of flows inside PFHEs. For larger scale analyses, Linde has developed a model that can simulate the complete geometry of a PFHE using the company’s proprietary performance and pressure drop correlations. This three-dimensional CFD/FE analysis can be used to evaluate the impact of rapid warm-ups or cooldowns, for example.
Extending lifetime and improving performance
Linde’s vision is to create a complete digital replica of a PFHE based on its precise properties, the customer-specific process technology, and the instrumentation in use. The idea is for this twin to be able to respond dynamically. In other words, actual data from the heat exchanger and/ or its process values will be fed into an algorithm, which will then use this information to continuously simulate and evaluate the thermal status of the unit and make predictions.
For the Australian reference customer mentioned earlier, the temperature and flow data from the process streams are transmitted to the Linde cloud at regular intervals, along with surface temperature readings from the heat exchanger. A digital twin calculates temperature distribution, etc. and displays the health of the plant 24 hours a day, also sending alerts to Linde experts if any issues arise. Plant operators can monitor the operational status via a special online dashboard and also assess the impact of current conditions on the performance. Linde experts support this process with consulting on the resulting impact on the operating life of heat exchangers.
Digital twins are thus paving the way for nextgeneration PFHE operations, offering enhanced transparency and continuous monitoring. In addition to prolonging the service life of heat exchangers, digital twins also provide options for improving overall plant performance by visualising PFHE operations.