
9 minute read
Improving level reliability
Tai Piazza, VEGA Americas Inc.,
USA, discusses the use of gamma instrumentation to improve level reliability in the delayed coking unit.
Delayed coking is a thermal cracking process used in petroleum refineries to upgrade and convert petroleum residuum into liquid and gas product streams. The delayed coker is the only main process in the petroleum refinery that is a batch-continuous process. Primarily, vacuum flasher bottoms, atmospheric/distillation tower bottoms, and heavy cat-cracked oil feed the delayed coker. Since the feed stream is regularly switched between drums, a cycle of events will occur at regular intervals, depending on the delayed coking unit feed rate, drum size, and throughput capacity. The residuum feed into the coke drum is quickly heated to approximately 1000°F, and then charged into the bottom of the coke drum. It is at these temperatures that thermal cracking occurs. As the residuum sits in the insulated coke drum, it keeps cooking. The lighter streams crack in vapour form and rise to the top of the coke drum where they are drawn off to the fractionator for separation. The heavier product fills up the coke drum until nearly all of the molecules of hydrogen are cracked off. Once cooled, mostly carbon is left behind in solid form, and this is called coke. High-pressure water jets cut up the solidified coke into smaller sizes that drop out of
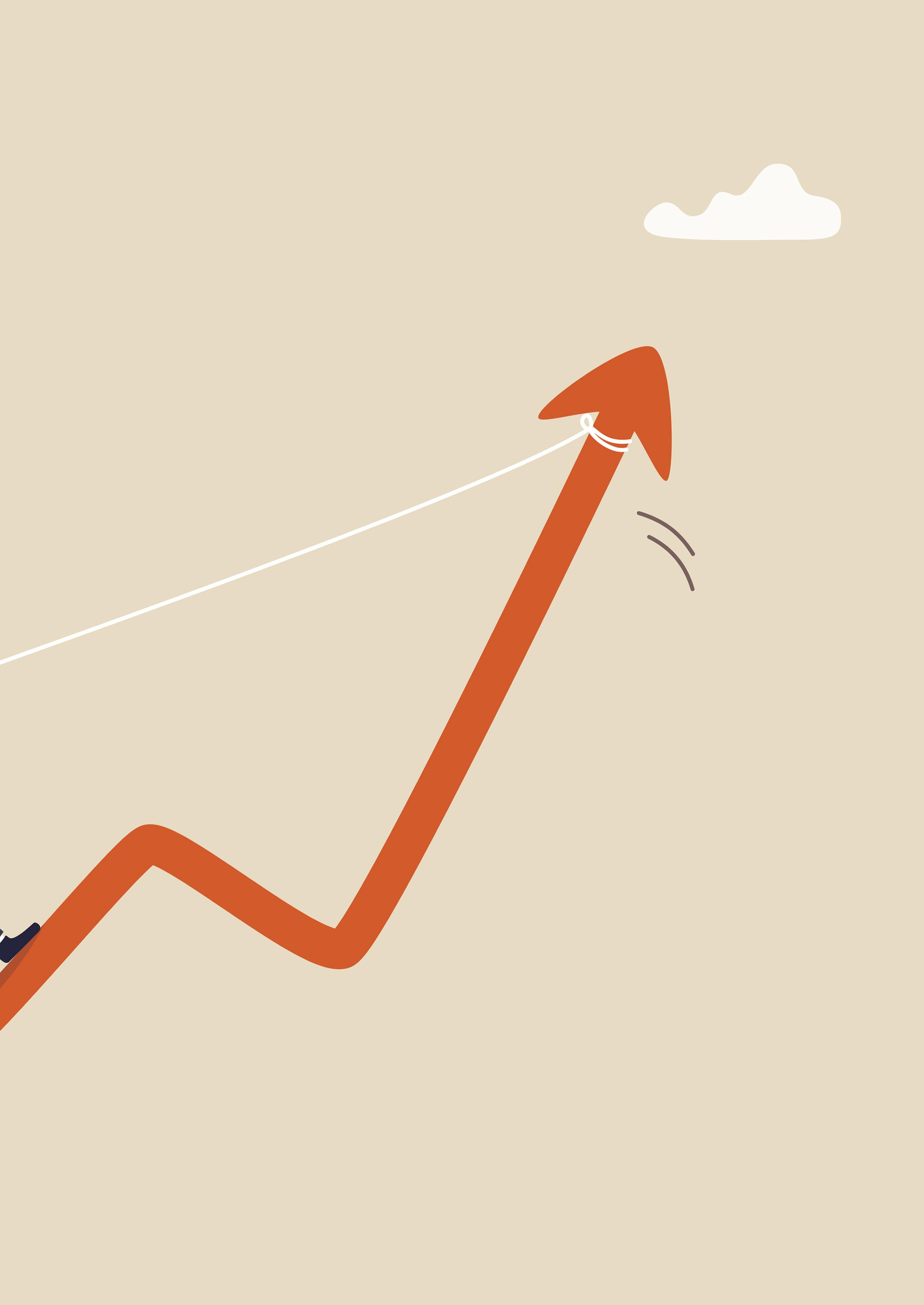
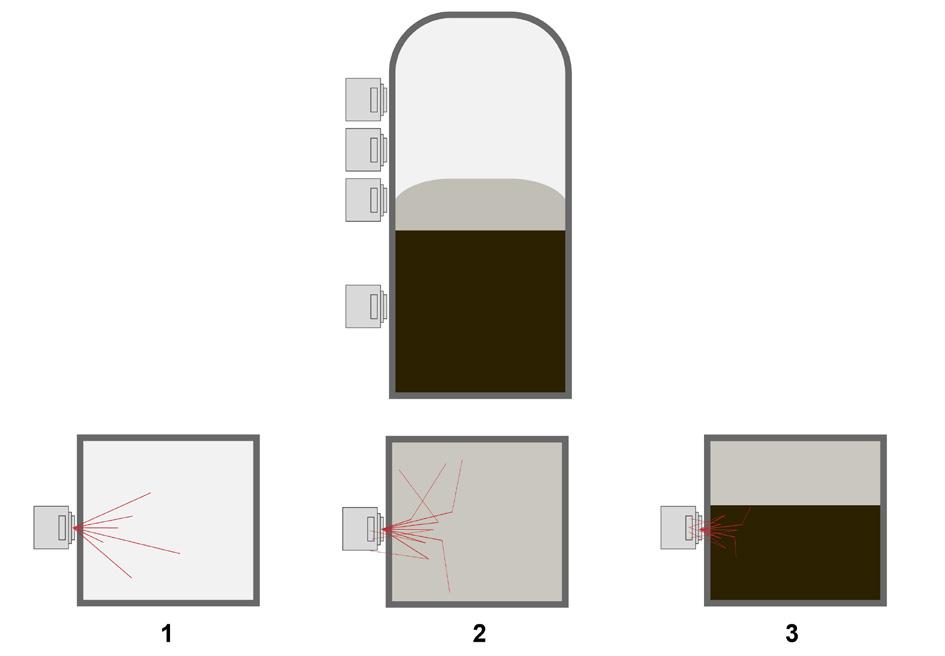
Figure 1. Top: general arrangement. Left: vessel empty – very little hydrocarbon, almost no backscattered neutrons = ‘zero’ or ‘low’ pulse rate. Middle: filling – hydrocarbon vapour, some backscattered neutrons = intermediate pulse rate. Right: coke present – heavy hydrocarbon, many backscattered neutrons = ‘high’ pulse rate.
Figure 2. Left: vessel empty – entire length of detector exposed = ‘high’ pulse rate. Middle: filling – part of detector exposed = intermediate pulse rate. Right: full – none of detector exposed = ‘low’ or ‘zero’ pulse rate.
Figure 3. A gamma target switch (VEGA POINTRAC31). the coke drum into a bunker from which the coke is loaded onto trucks, railcars, or barges for shipment. Depending on the physical structures and chemical properties of the coke, the material can be burned as fuel, calcined for use in the aluminium and steel industries, or gasified to produce electricity.
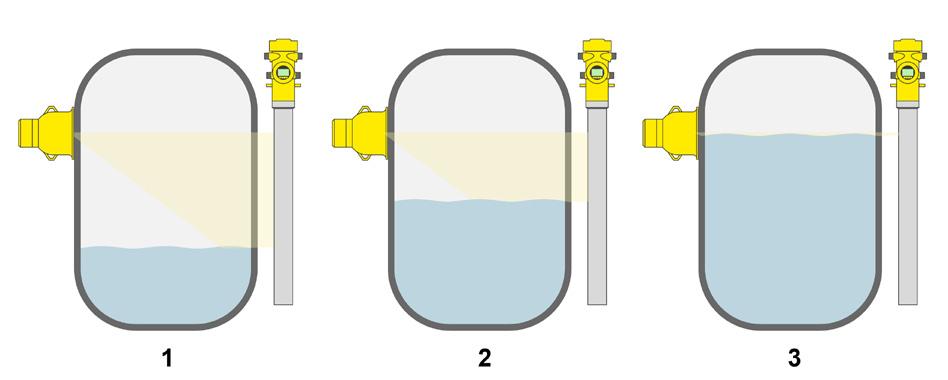
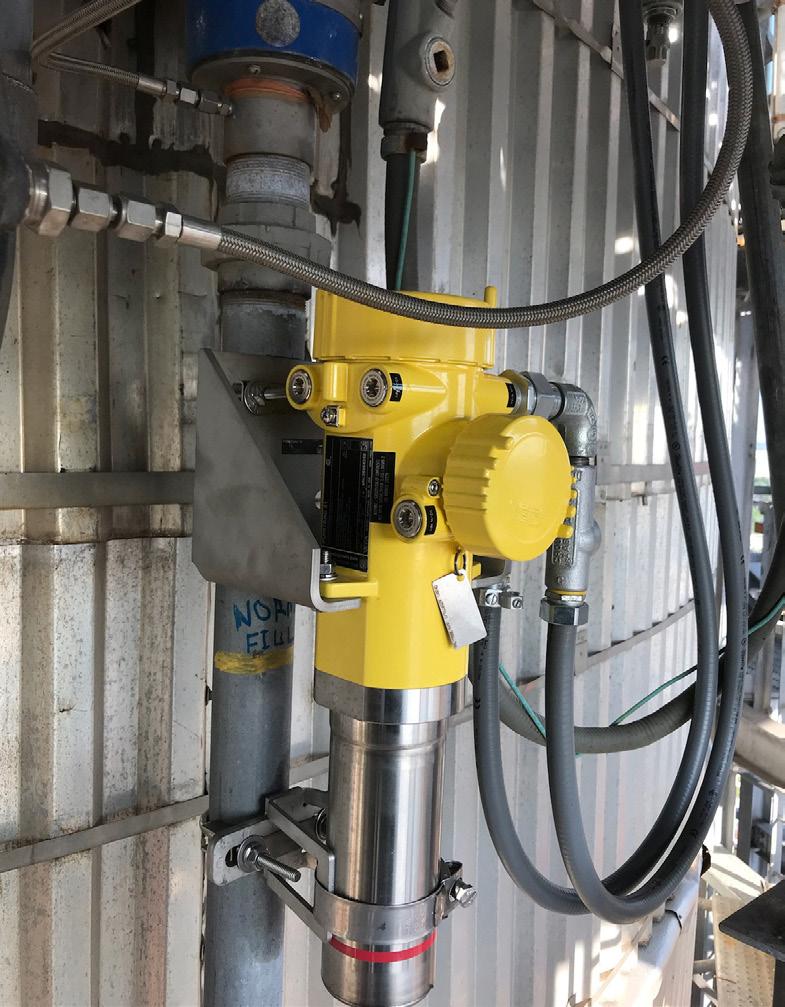
Why is level so important?
As refiners continue to process a complex mix of crude slates, including blends of sour and high-sulfur crudes, an increase of residuum is created and fed to the delayed coker. These higher sulfur crudes may produce foaming conditions that create challenges for traditional instrumentation, and thus make it difficult for operators to understand exactly where the level is within the coke drum. Ideally, operators would like to make use of as much remaining drum capacity as possible to maximise liquid yield to the fractionator. However, with foam height uncertainty, frequently filling the coke drums beyond well-established limits and time sequences can present a higher-than-acceptable risk of foam-overs or solids carryover, and pose possible safety risks. The consequences of a foam-over range from high back pressure due to plugging in outlet lines, to a required 10+ day shutdown to remove coke from the fractionator and coke blowdown system.
Neutron backscatter technology
Historically, many existing coke drums included neutron backscatter (NBS) technology for point level density indication. These devices are installed onto the coke drum at specific elevations recommended by the coke drum process licensor, or prescribed specifically by the end user. These instruments transmit ‘fast’ (high energy) neutron particles into the coke drum vessel, which is approximately 18 in. Neutron radiation particles that impact hydrogen nuclei transfer some energy to that nuclei and reflect off with less energy. Some of these reflected ‘slow’ neutrons interact with a sensor in the instrument and are counted and filtered.
As the concentration of hydrogen increases, more slow neutrons are reflected and detected (see Figure 1). Through calibration and interpretation, the NBS detector can indicate the process state immediately in front of the device. When in proper calibration, the instruments can indicate vapour, foam, coke and water conditions (see Figure 1), and this has proven value to operational control. This is useful for prompting operators to start injecting anti-foam, switch out to the other drum, or stop quench water feed.
When properly maintained, NBS technology provides operations with an effective means of level control in a very challenging process. However, the technology does have some limitations. Since these instruments are, in effect, hydrogen density gauges, they can be influenced by extraneous sources of hydrogen. This could be from rain/quench water accumulating on the device or in the vessel insulation, or from an operator or technician carrying out maintenance on the device. With direct connection to the vessel, the instrument can be exposed
to higher-than-acceptable temperatures. As seen in Figure 1, the instrument arrangement is such that it can offer a point density indication at specific elevations, but is limited in defining level position in the areas between those elevation. When operators are trying to optimise drum capacity, this can often mean that liquid yield is not being maximised.
Gamma technology and continuous level measurement
Level measurements using gamma transmission have a proven track record for use in very difficult industrial measurements. First developed in the 1950s, gamma instruments for level and density have been used in the refining, petrochemical, mining, and pulp and paper industry for decades. It is in the last 25 years that gamma instruments have been used to provide coke drum level indication.
With gamma transmission, gamma rays emitted from the source holder travel towards the detector. In this configuration, the source holder and detectors are 180˚ opposed. The mass of material between the source and detector affects the number of gamma rays that reach the detector. In the case of an empty coke drum, the vessel walls block a fixed/known amount of energy. The source activity is specified in a way that allows some energy to pass through the vessel walls and reach the detector. The amount of radiation reaching the detector in an empty drum state would be quantified as the highest radiation field or maximum counts. As process material mass increases (i.e. coke level rises), more energy is blocked by the process, resulting in relatively lower numbers of gamma rays reaching the detector. When the drum is completely full, no gamma rays reach the detector, resulting in no counts. The detector counts and filters the number of received gamma rays to produce a pulse rate (or rays received per second), which is the primary measured value (see Figure 2).
In most level conditions, process material (including foam) completely blocks gamma rays from reaching the detector. Detector material below the process level stops producing signals to be counted, while detector material above the level continues to produce signals. As level rises, the detector’s pulse rate falls. Through a careful calibration process, the detector can be taught how to correlate measured radiation intensity (pulse rate) to process conditions such as level or density. It is important to note that gamma transmission when used for delayed coke drum levels will always track the leading edge of the process based on the aforementioned principal of operation. Additionally, one of the limitations of gamma transmission is its natural vulnerability to x-ray interference from non-destructive examination (NDE) or radiography. There are proven methods to mitigate these influences via hardware and software solutions within the instrument solution that offer operators reliability through these events.
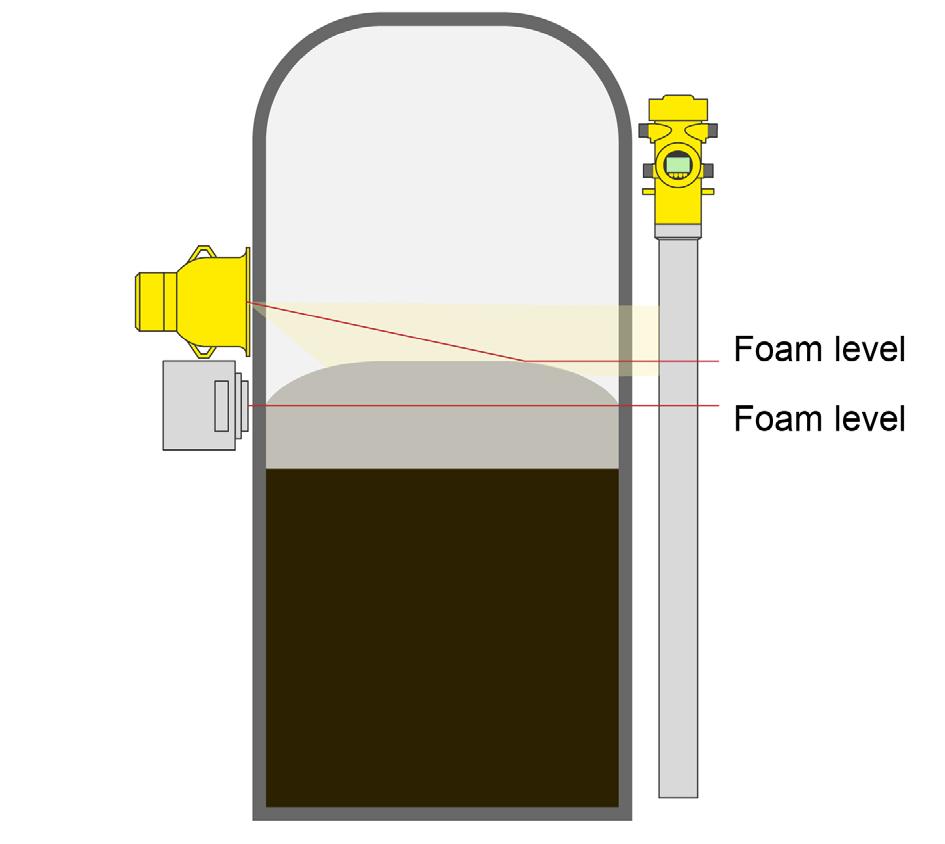
Figure 4. Gamma level indication vs NBS level indication.
Figure 5. VEGA’s continuous level system for delayed coking.
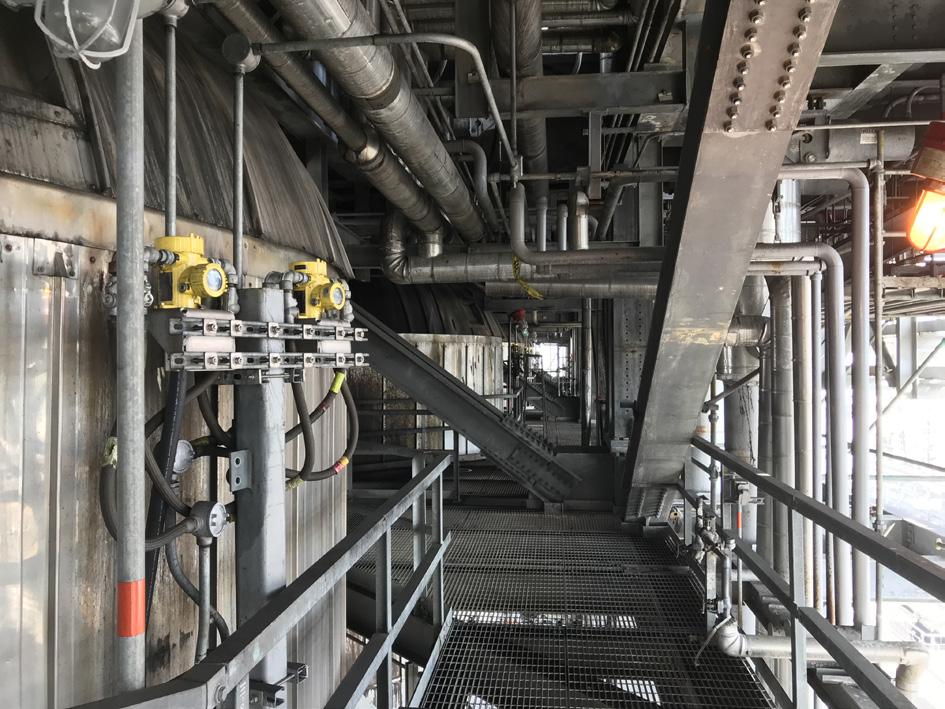
Point level
In some cases, end users would like their level system to emulate the NBS functionality in respect to level indication/position. Adding gamma target switches to an existing gamma continuous level system is an excellent way to provide discrete signals for operators to recover process control. Gamma target switches can trigger anti-foam injecting, drum switch out, or quench water feed stoppage. These can be very easily mounted in the radiation beam of the existing level system and mounted directly next to or onto the continuous level devices. Both 4…20 mA HART for analog indication, and 8/16 mA HART or SPDT relay for discrete indication are available. The addition of these target switches can be an economical way to reliably improve operational control of strategic trigger actions, while providing plenty of flexibility to adjust these target switch points in the future (see Figure 3).
Differences between NBS and gamma continuous
NBS and gamma transmission are often utilised for common level control in the same coke drum. Intuitively, operators would expect to see the NBS indications
CATALYSTS
INTRODUCING KF 774 PULSAR™
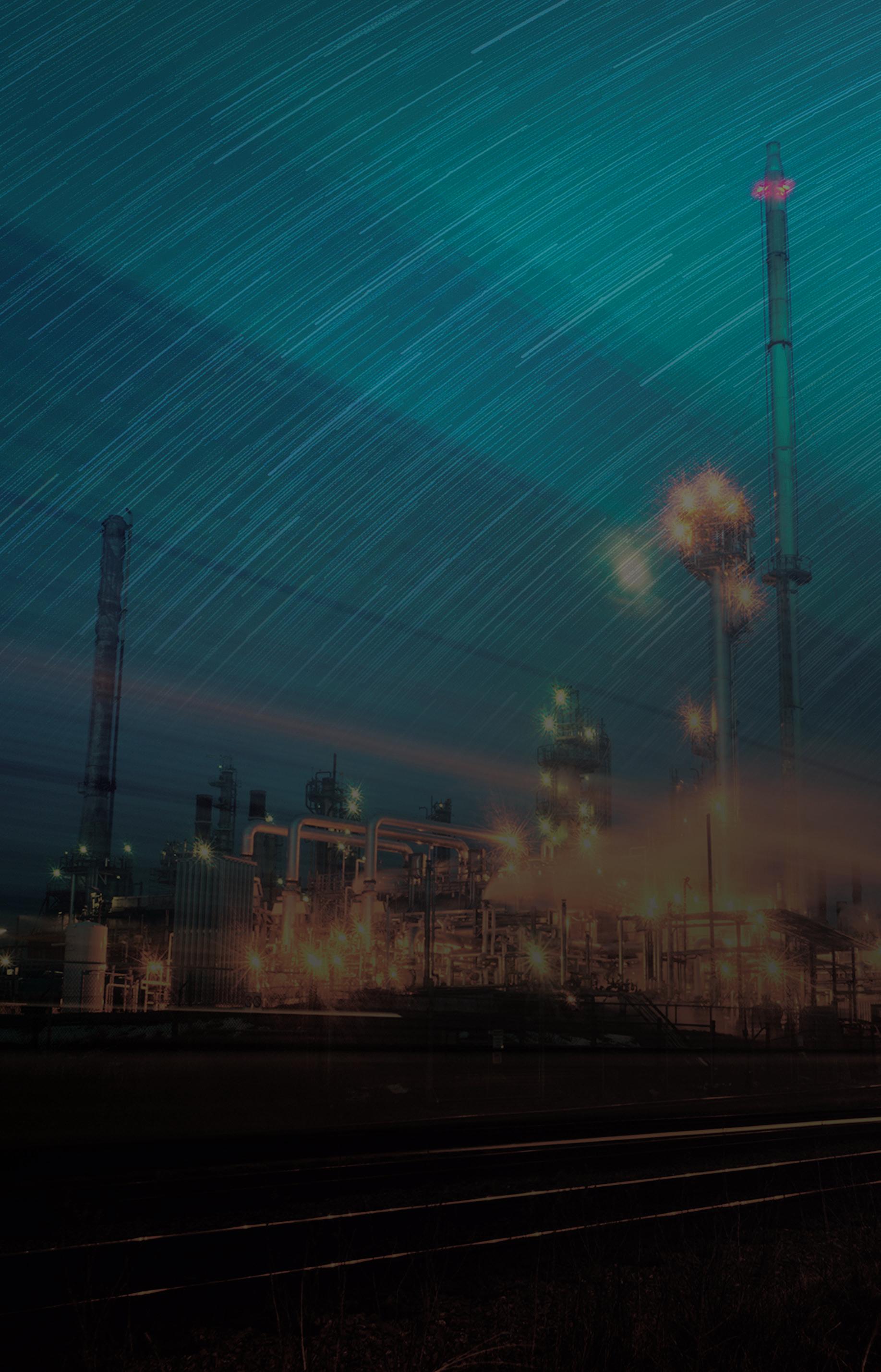
KF 774 joins KF 787 in Albemarle’s growing PULSAR™ Catalyst Platform
KF 774 leverages PULSAR™ active phase technology, with superior HDS/N/A activity for medium and medium-to-high pressure ULSD production. The PULSAR™ Catalyst Platform provides outstanding activity, stability and flexibility in operation for all middle distillates hydrotreaters.
Albemarle delivers tomorrow’s catalyst technology solutions today.
activate at the same elevations as the gamma continuous level. However, since the measurement principal between NBS and gamma transmission is different, there is a scenario where these readings will not match. Gamma transmission is tracking the leading edge of level, regardless of density. In this way, the level reading would remain the same whether the foam is of high or low density. The NBS instruments are indicating process density, which is irrespective of the level position of the process. This would be an example of where the NBS and gamma continuous instruments would be in disagreement.
In addition to this, during normal coking conditions, foam level is higher toward the middle of the drum due the infeed characteristics, and lower along the walls. If this foam level is high enough in the centre, there is a circumstance where the NBS instrument would not indicate density, as there is none at the vessel wall, but the gamma continuous would indicate level. This is another scenario where the NBS and gamma continuous level may not always match. See Figure 4.
Process improvement opportunities with gamma continuous level
Getting the most out of your delayed coker requires innovative solutions. High-temperature, aggressive environments make getting accurate level measurements challenging. A non-contacting continuous gamma solution does not interfere with the process. Rather, it makes it safer and allows for more efficient operation, while providing operators with improved process control (see Figure 5).
Installing continuous gamma level measurement instruments will help to address a number of the deficiencies of NBS point density instrumentation. A coke drum solution using a gamma continuous level will ensure better control over this ever-changing and dynamic process. Continuous level indication will provide operators with the ability to more accurately estimate the actual level in the coke drum, allowing for the level to be safely run higher in the drum.
With this additional utilisation, operators can expect to realise an additional percentage of drum filling height, which allows for increasing feed rate and utilised capacity, while maintaining the current cycle times. Using the continuous or point level outputs for automatic anti-foam control will result in less anti-foam and improve/extend downstream catalyst life. This will help to increase operator confidence and greatly reduce the risk of unplanned shutdowns.
Bibliography
• ELLIS, P. J., and PAUL, C. A., ‘Tutorial: Delayed Coking
Fundamentals’, Great Lakes Carbon Corp., (8 March 1998). • LEFFLER, W. L., ‘Petroleum Refining in Nontechnical
Language, 4th Edition’, (2008).