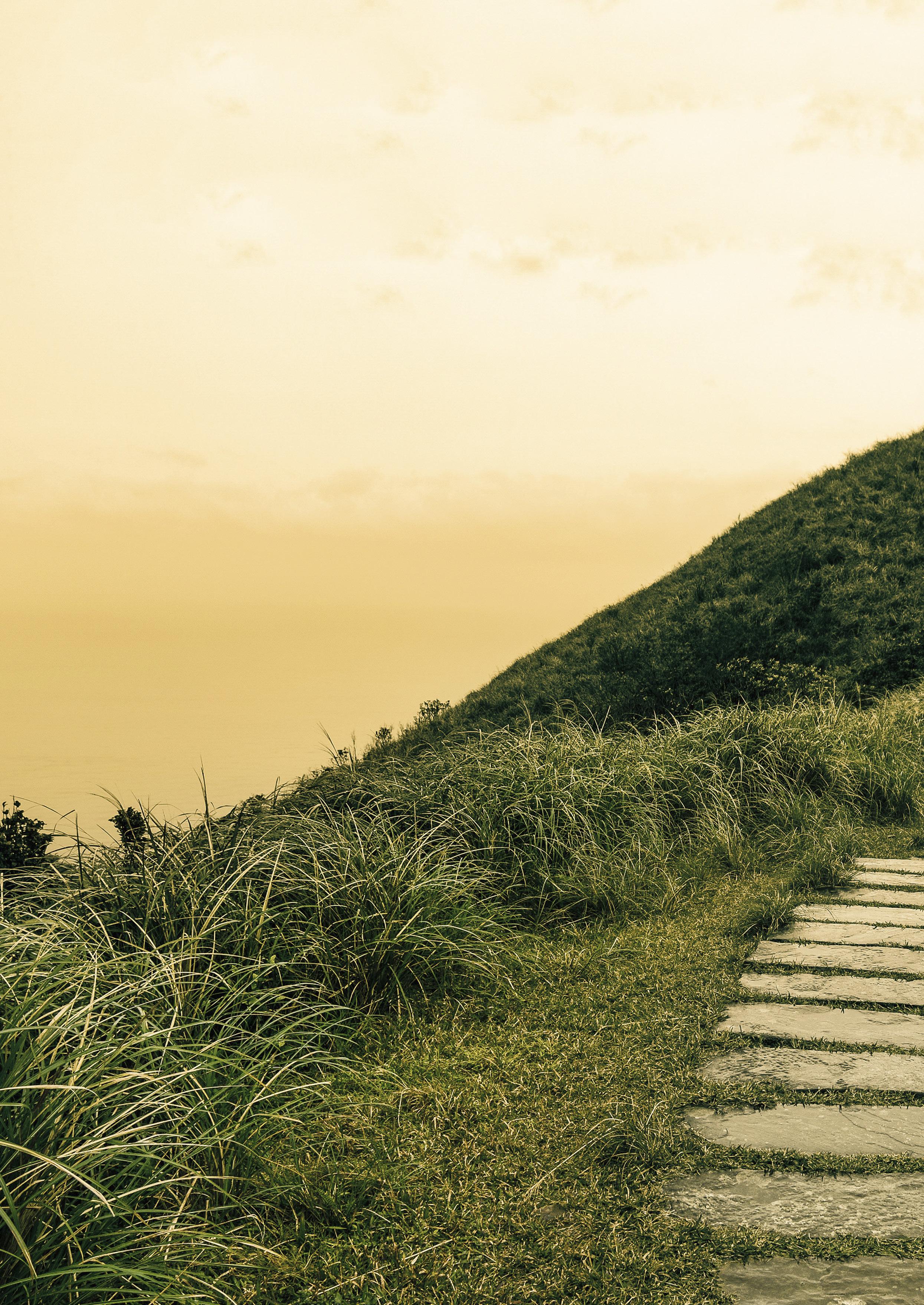
10 minute read
Stepping stones on the path to sustainability
Lucas Vergara, Axens, France,
presents catalytic solutions to help tackle the challenges associated with co-processing sustainable feeds.
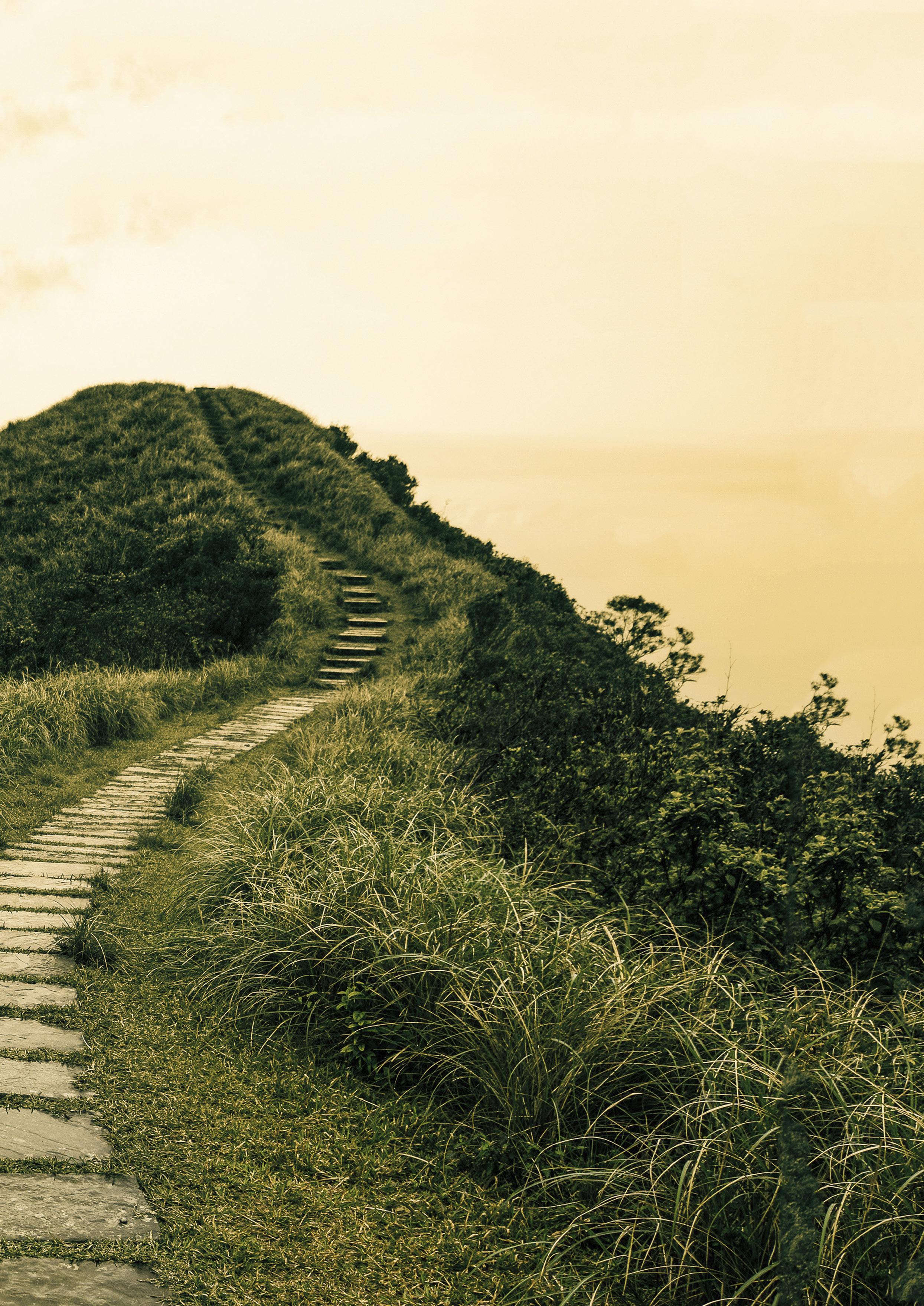
Recent changes in legislation and mandates have propelled a sharp rise in global demand for sustainable fuels, challenging refiners to rapidly integrate hydroprocessing renewable feedstock solutions into their existing infrastructure. While large investments in dedicated oils and fats processing facilities are still years away from coming onstream, a drop-in co-processing solution presents an immediately-available, low-CAPEX stepping stone on the path towards decarbonisation. Moreover, driven by RFS/LCFS and RED II policies, the significant expansions recently announced in the US and
Europe will soon place a massive constraint on the global bio-based feedstock market. Not only is it crucial for refineries to be an early adopter, but it is also paramount that the best strategic approach is taken to widen feed options and consider other unconventional advanced alternatives that are not in direct competition with food, such as bio-oils and pyrolysis oils. Although the refining industry has extensive experience in producing fossil fuels, the simultaneous processing of renewable material along with fossil-based blendstock presents new technical challenges related to catalyst and process design which require new competences, and need to be addressed with a robust approach.
Reaction pathways in lipids conversion
Despite the availability of many different types of oils and fats on the market today, they are all essentially chemically-analogous, as they are mostly composed of free fatty acids (FFA) and glycerides, with different degrees of unsaturation and chain lengths, as shown in Figure 1.
Since the sulfur and nitrogen content of these feeds is naturally low compared to fossil feedstocks, the fundamental challenge when hydroprocessing them is to produce the deoxygenated bio-sourced hydrocarbon products that not only fall in the same boiling range, but are also fully compatible with the existing fuel platform.
Under typical hydroprocessing operating conditions, the rapid saturation of double bonds will be followed by the disconnection of the paraffinic chain from the glyceride backbone. This last step can take two different dominant reaction pathways (see Figure 2): n The hydrodeoxygenation (HDO) pathway consists of hydrogenation to produce water, propane, and a normal paraffin that has the same length as the corresponding fatty acid chain. n The decarboxylation (DCO) pathway, in turn, involves a
C-C bond break to produce carbon dioxide (CO2), propane, and a normal paraffin that is one carbon atom shorter than the corresponding fatty acid chain.
These simultaneous deoxygenation routes produce CO2 and water (H2O), which undergo further methanation and water gas shift reactions that define the final balance between the carbon monoxide (CO)/CO2/H2O/methane (CH4) species in the reactor effluent.
Selectivity towards HDO is normally desired, as it maximises paraffin mass yield, while simultaneously minimising CO/CO2 production. Mastering these
mechanisms at play requires the best catalytic design and process configuration solutions.
Renewable lipid feeds co-processing challenges
When considering repurposing an existing hydroprocessing unit to perform co-processing, it is critical to first evaluate the potential risk factors and consequences (see Table 1), in order to mitigate them with the best process design practices and catalytic solutions.
Due to its nature, renewable lipid material has new and different quantities of contaminants, such as FFAs, phospholipids, chloride and metals, as well as a larger amount of highly-reactive species. Even though the content of impurities can be, to some extent, controlled by feed selection and level of pre-treatment, some remaining quantity is always present.
Consequently, processing this type of material results in additional difficulties that are mainly related to the control of the reactor pressure drop and the very exothermic reactions, as well as increased corrosion in the feed and effluent sections: n Phospholipids, which are naturally present in lipid biogenic material, tend to precipitate at high temperatures, leading to fouling concerns at the level of feed and reaction section. n FFAs are the carboxylic acid product of the chains that have broken off from the glycerol backbone of the triglycerides, by degradation of the feed. Even though their corrosive effect is reduced by dilution with mineral oil feed, rich FFA feeds can still cause damage to pipes and equipment in the feed system. n Localised high consumption of hydrogen, in rapid exothermic double bounds saturation and deoxygenation reactions, may lead to accelerated pressure drop build-up and premature catalyst ageing. n At the same time, deoxygenation results in significant amounts of propane, water, CO, CO2 and methane byproducts which need to be removed from the recycle loop to avoid having a negative impact on hydrogen partial pressure and recycle gas compressor performance. n CO in particular, which is not effectively removed by amine gas treating systems, is known to also selectively inhibit CoMo hydrotreating catalyst promoters’ activity by blocking access of sulfur and nitrogen-containing species to the catalytic sites. n Additionally, in the reactor effluent train, some of these reaction byproducts may accelerate piping and equipment corrosion rates, and increase the formation of ammonium salts.
Finally, the linear paraffins in the end product result in the significant improvement of some key diesel properties, such as density and cetane number, as shown in Figure 3, but
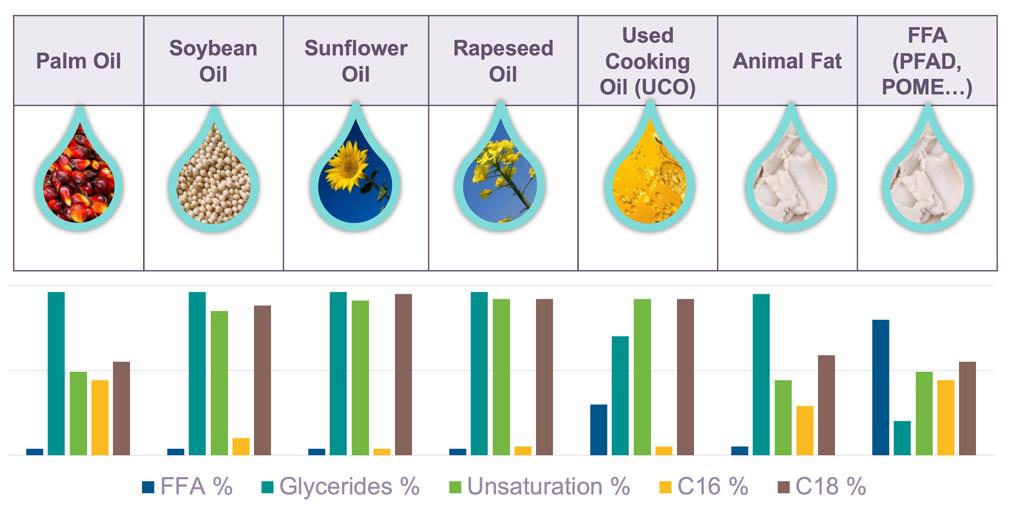
Figure 1. The wide spectrum of lipid feeds.
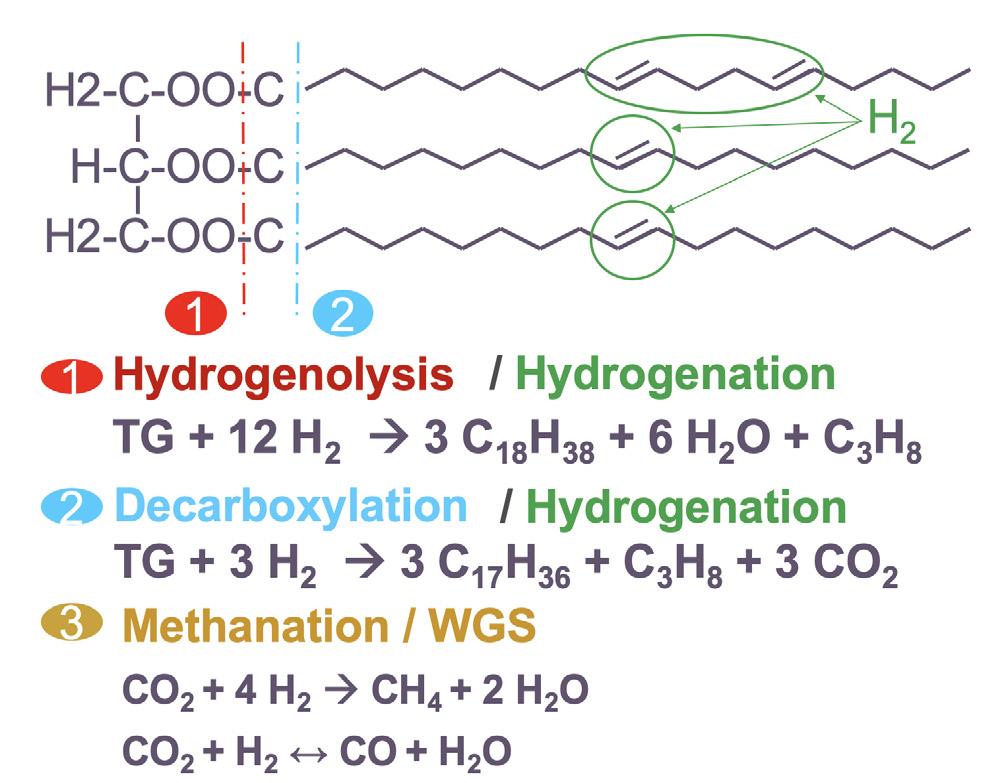
Figure 2. An example of C18 triglyceride conversion pathways.
Table 1. The challenges presented by renewable lipid feeds
Renewable feed challenges Impacts Vegetable oil Waste oil (UCO) Animal fats POME/FFAD Tall oil
FFA Corrosion on feed section/preheat train/ reactor
Phospholipids Pressure drop build-up and catalyst poisoning
Metals
Pressure drop build-up and catalyst poisoning Chloride Corrosion on effluent side
Poly-unsaturates Hydrogen consumption, exotherm, risk of fouling
they may also end up detrimentally affecting cold flow properties.
Given that, in this service, the use of improvers and modification of product cut points have a limited effect on end product cold flow properties, operators ultimately consider implementing dedicated catalytic dewaxing solutions to produce different commercial diesel grades.
Depending on the original plant configuration, the combination of all of these factors imposes diverse constraints with regards to the amount of renewable feed that can be successfully co-processed in a given unit. In this context, refiners have followed a progressive approach to this problem, by incrementally investing in catalyst and hardware upgrades to provide access to better economics through improved co-processing rates.
Catalyst technology as a keystone to tackling the challenges of co-processing Case study
Grading technology to maximise run length
Proper management of all previously-mentioned factors requires the use of top performance catalyst systems and a careful selection of the reaction conditions. After extensive pilot testing and industrial experience, Axens developed a robust, comprehensive solution that can cope with these extreme challenges and help producers to achieve a stable operation during long runs, while meeting all product specifications.
To begin with, feed pollutants and hydrogen depletion, due to double-bond saturation at the top part of the catalyst bed, can pose the associated risks of fouling, pressure drop build-up, and premature loss of activity. Tackling these challenges requires the installation of a dedicated grading design that provides not only a mild hydrogenation activity but also includes a demetallisation catalyst, to guarantee that the impurities will not break through and reach the active catalyst.
When aiming to process lightly pre-treated renewable material with conventional fossil feeds, this grading solution can also be complemented with a Hy-Clean® bypassable smart filtering distributor tray system, allowing for optimal control of the pressure drop build-up.
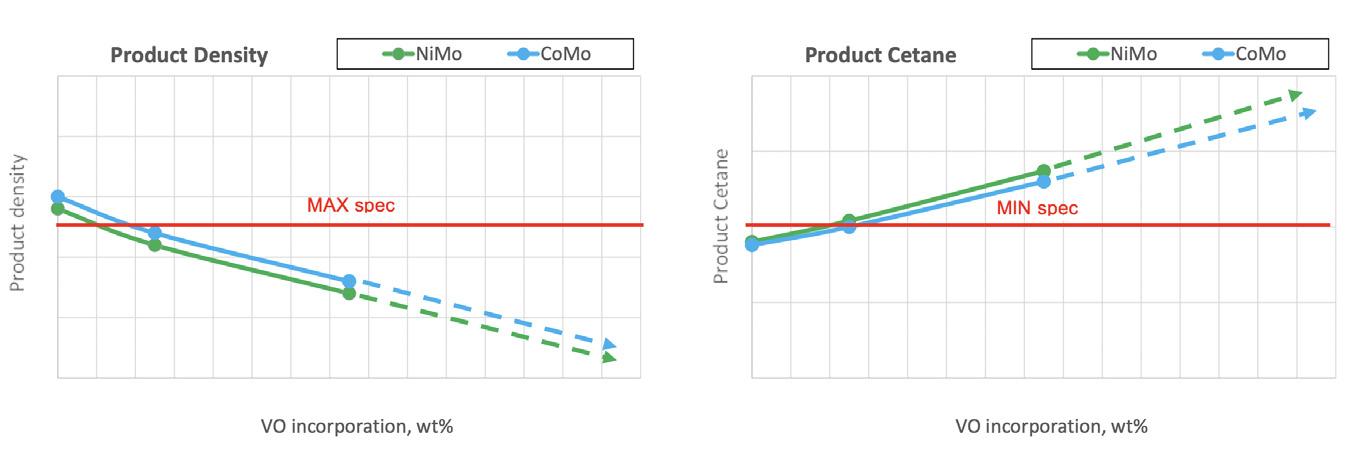
To illustrate the relevance of having a proper grading system in place, even at low levels of co-processing, Figure 4 presents the industrial feedback of a diesel hydrotreater unit in a European refinery, and shows the evolution of the normalised pressure drop across the reactor beds. Motivated by the changes in legislation, and after two years of stable operation processing mineral feed, this refinery decided to start co-processing a maximum of 3 vol% of vegetable oil along with the existing fossil diesel, using its original grading system. After introducing the bio-feed, the reactor pressure drop quickly began to increase, reaching – within a few months’ time – the point where the unit had to be briefly shut down for Figure 3. The impact of the co-processing of lipid feeds on final diesel two consecutive skimming operations density and cetane. to replace the top layers of the grading arrangement. A comprehensive analysis of the recovered material allowed Axens to design the optimum reactor loading configuration, which was later installed, and remains to this day in stable condition, after 18 months in continuous co-processing service. Figure 4. The impact of the co-processing of lipid feeds on reactor pressure drop. Hydrotreating catalyst technology: a matter of balance
Both the HDO and DCO reaction mechanisms for renewable feed conversion described in the previous section are catalysed by the same types of metal sulfide catalysts used for conventional hydrotreating. At the same time, the high sulfur content of the fossil feed ensures that the active phase remains in the sulfide form.

Therefore, main hydrotreating catalyst selection for co-processing operation presents a unique challenge as it is required to find the right balance between high desulfurisation/denitrogenation activity, and a gradual conversion of the highly-reactive renewable feed components that otherwise would provoke hydrogen starvation, leading to coke formation and pore-mouth plugging.
Considering all of these factors, Axens developed HDO-selective NiMo catalyst formulations that are highly tolerant to CO inhibition (Axens’ 700-series catalyst) and that, in a synergetic arrangement with the tailor-made grading solution, maximise run time. Figure 5 reveals the different expected effects of CO in standard hydroprocessing NiMo and CoMo catalyst activity.
Furthermore, by performing a controlled conversion of the renewable feed with a highly active HDS catalyst, not only are the cycle lengths extended, but the lower operating temperature required to meet the sulfur product specification also favours the catalyst selectivity towards the hydrogenolysis pathway, providing better overall product yields. Dewaxing catalyst technology to meet the most stringent cold flow specifications
As previously discussed, a high linear paraffins content in the final product will result in cold flow property degradation and may dictate the need for a dedicated catalytic dewaxing solution to comply with the most severe market requirements. Currently-available catalytic dewaxing solutions on the market can be generally categorised into two different types of bi-functional catalysts: n Catalysts based on noble metals, which selectively isomerise the linear paraffins to produce multi-branched iso-paraffin molecules. n Catalysts based on base metals, which improve the cold flow properties by a combination of isomerisation and hydrocracking of the normal paraffins.
While the first type can show better yields by retaining product molecules in the diesel boiling range, their catalytic activity is highly sensitive to inhibitors, thus requiring a separate reaction stage. In turn, the second family of catalyst can be placed at the bottom of an existing reactor, providing a low-cost solution with the flexibility to produce different grades of refined products (e.g. winter and summer diesel) by adjusting its operating temperature with the use of quench gas. Although slightly lower diesel yields are obtainable, there is an increasing market interest in bio-LPG and bio-naphtha products.
Hydrocracking catalyst technology for optimum product slate
In the hydrotreating process, the renewable material deoxygenation reactions take place on active metal sites, whereas in the hydrocracking catalyst the acid sites of the zeolite carrier promote cracking and isomerisation of the normal paraffins. Lately, this particular feature has brought focus to the hydrocracking technology, as it provides an economical pathway to produce sustainable aviation fuel (SAF).
Axens’ zeolite-based hydrocracking catalyst can be grouped into two distinct families: one that provides maximum viscosity index improvement for the unconverted oil (Cracken Flex® product line), and one that guarantees maximum middle distillate yields with improved product cold flow properties (Cracken D® product line).
By selecting the appropriate hydrocracking catalyst formulation, it is possible to preserve similar unit performance while achieving an attractive yield of isomerised bio-paraffins that not only fall in the jet fuel boiling range, but also contribute to meet most stringent commercial product cold flow specifications.
Conclusion
A combination of a rapidly rising demand for sustainable fuels with the significant lead time and investment associated with dedicated production units makes co-processing the perfect fast-to-market leap, providing refiners access to an ever-growing market with maximum use of existing assets. In addition to this, with great versatility to process feeds of a diverse and complex nature, co-processing technology may well co-exist to complement and expand refineries’ future operation on alternative circular economy feeds. Axens, with extensive knowledge of process design and corrosion engineering, reaction chemistry and catalyst technology, paves the way with innovative pragmatic drop-in solutions that provide producers with customised and cost-effective options to co-process a wide range of sustainable feedstocks with minimum investment and quick returns, while Figure 5. The impact of the co-processing of lipid feeds on reactor WABT. maintaining excellent operating performance throughout the cycle.
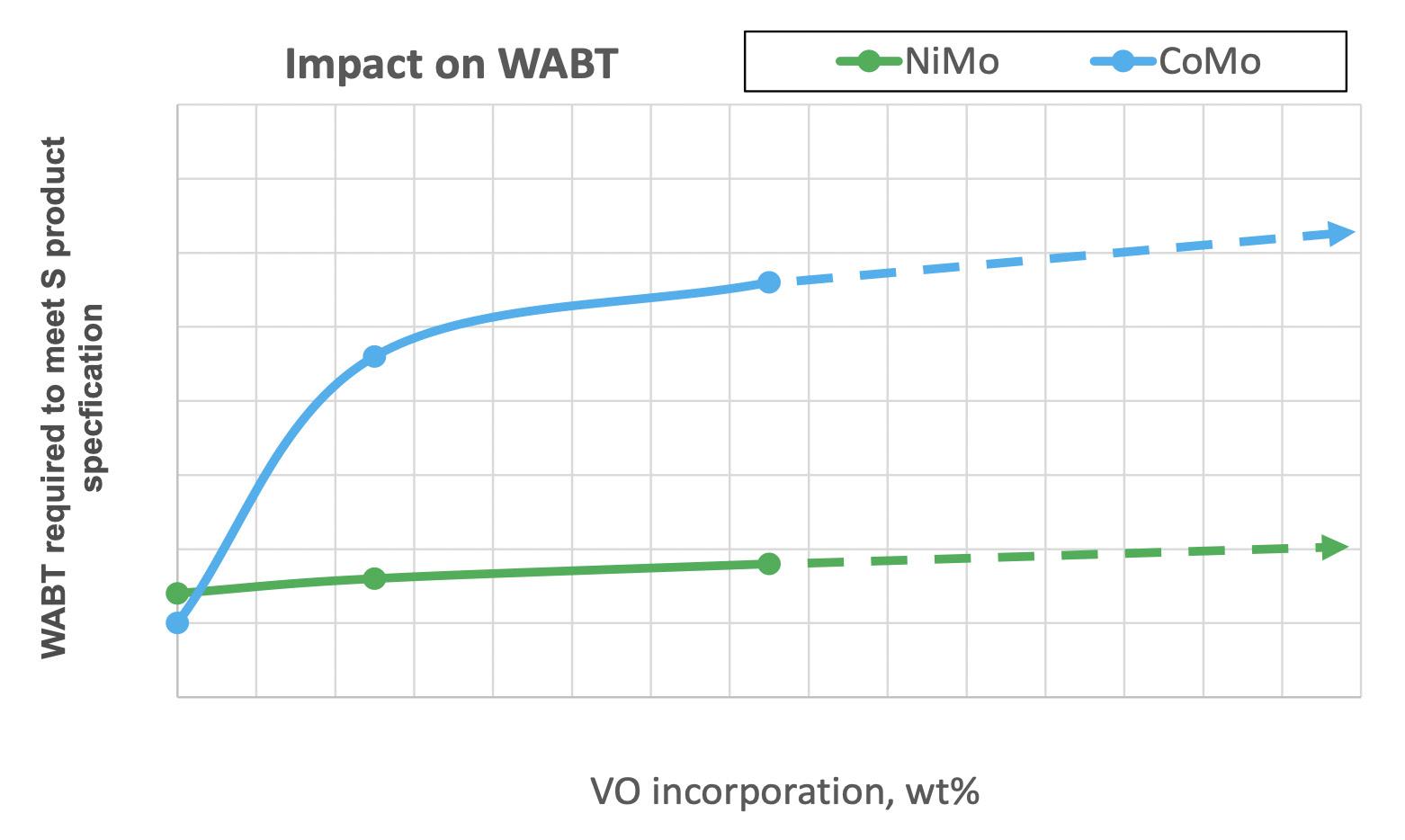