
11 minute read
From molecular-level engineering to enhanced aromatics economics
Roy van den Berg and Richard Mauer, Shell Catalysts & Technologies, discuss how an innovative zeolite technology is unlocking business value.
Growing demand for high-value aromatic products means that many refiners and petrochemical companies are keen to maximise paraxylene (PX) and orthoxylene (OX) yields. Doing so cost effectively, however, is not straightforward. This is because more than 75% of PX and OX production costs originate from an increasingly expensive feed.
An innovatively-engineered, new zeolite catalyst system could significantly improve the economics of aromatics conversion. This article will reveal how Shell Catalysts & Technologies’ researchers unlocked significant activity and selectivity gains by deploying a dual-bed catalyst configuration, ground-breaking passivation technology, and a highly-selective novel metal function.
Owing to the evolution of the chemical industry, PX demand has risen steadily at 6%/yr since 2009. A key driver is its use in polyester plastics such as polyethylene terephthalate, or PET, which is widely used for food and beverage packaging. Sustained demand is forecast for the next five years, with a 3% compound annual growth rate for xylene isomerisation predicted.1 Consequently, the ability to leverage oil to chemicals will be on the radar for many refiners. The challenge that emerges is to maximise PX and OX yields, per unit of refinery feed, while using the lowest amount of energy.
Much of the growth in this area is concentrated in xylene isomerisation ethylbenzene dealkylation (XI-EBD) type processes within an aromatics plant. In such a plant, C6-C10 aromatic molecules from a reformer or a steam cracker are processed further. Via distillation, benzene (C6); toluene (C7); PX, metaxylene (MX), OX and ethylbenzene (C8); and C9+ aromatic molecules are separated. Pure PX is the most valuable of the C8 molecules because it is a feedstock for the manufacture of PET plastics.
The boiling points of the C8 molecules are too alike to allow separation by distillation. Instead, PX is removed from the stream via adsorption or crystallisation. The remaining C8 stream is then passed over a xylene isomerisation catalyst to form PX from MX and OX, after which the stream is recycled to extract further PX. To avoid the build-up of ethylbenzene in this cycle loop, ethylbenzene can be dealkylated to ethane and benzene (ethylbenzene dealkylation [EBD]) or reformed to xylenes (ethylbenzene reforming [EBR]). This is typically carried out in the same reactor as the xylene isomerisation. ZATARIS-21, Shell Catalysts & Technologies’ latest generation XI-EBD catalyst, has improved selectivity and is optimised to maximise PX or OX production yields, from a PX-lean and OX-lean xylene mixture. It is used in aromatic complexes, as shown in Figure 1. A typical aromatic complex takes a catalytically-reformed, heavy naphtha feed from refinery streams, or alternatively it takes pyrolysis gasoline (or pygas), which is a byproduct of making ethylene in a steam cracker. As PX is removed, using separation technology, the EBD and isomerisation unit restores an equilibrium mixture of para-, meta-, and ortho-xylenes. In this way, the other aromatic molecules are steadily converted to PX upon each pass through the EBD unit. As a drop-in upgrade, with no increase in plant footprint compared to industry standard catalysts, ZATARIS-21 provides exceptional preservation of the aromatic content of the feed, while offering high activity for reduced energy consumption. Requiring lower temperatures to keep the process running, the catalyst can also offer carbon dioxide (CO2) emission reductions. Additionally, as aromatic hydrogenation is limited, less hydrogen is consumed.
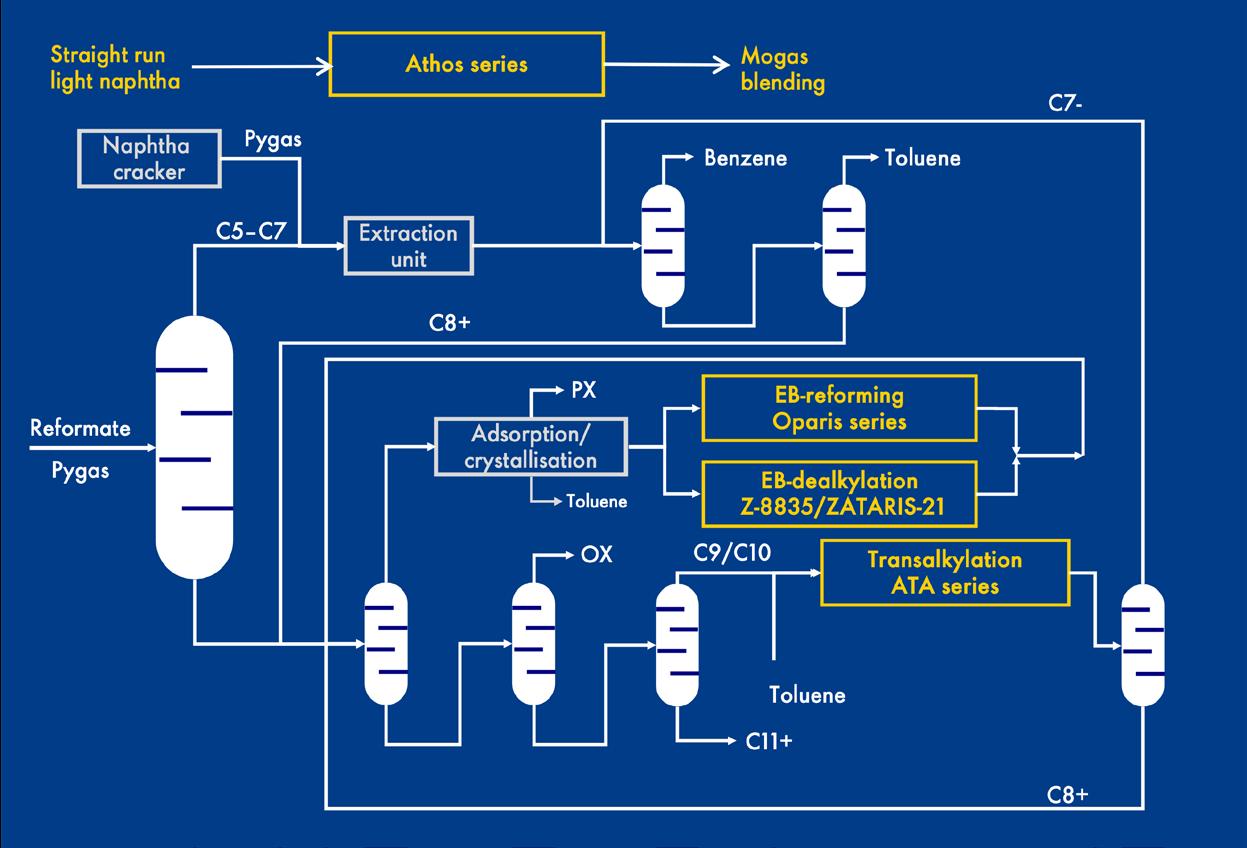

Figure 1. Typical aromatic complex.
Figure 2. EBD catalyst technology timeline.
Figure 3. EB and PX concentration variation in separate catalyst beds.
EBD catalyst timeline
Historically, EBD catalysts, such as Z-8835 and its successor ZATARIS-20 (Figure 2), were single-bed that could be used for feeds with relatively high PX levels. Typically, these catalyst systems would last for a very long time – sometimes up to 20 years. As these legacy-generation catalysts offer robust performance, refiners are typically reluctant to try something new. Compared with the 1980s and 1990s, the mode of operation for these catalysts has changed substantially. Separation technology has improved in its efficiency to the extent that there are very low levels of PX in most feeds now. This requires the use of a redesigned catalyst that is fit for purpose, with very high selectivity.
To keep in step with advances in separation technology, ZATARIS-21 operates within a dual-bed configuration. The first bed contains a zeolite-based catalyst where
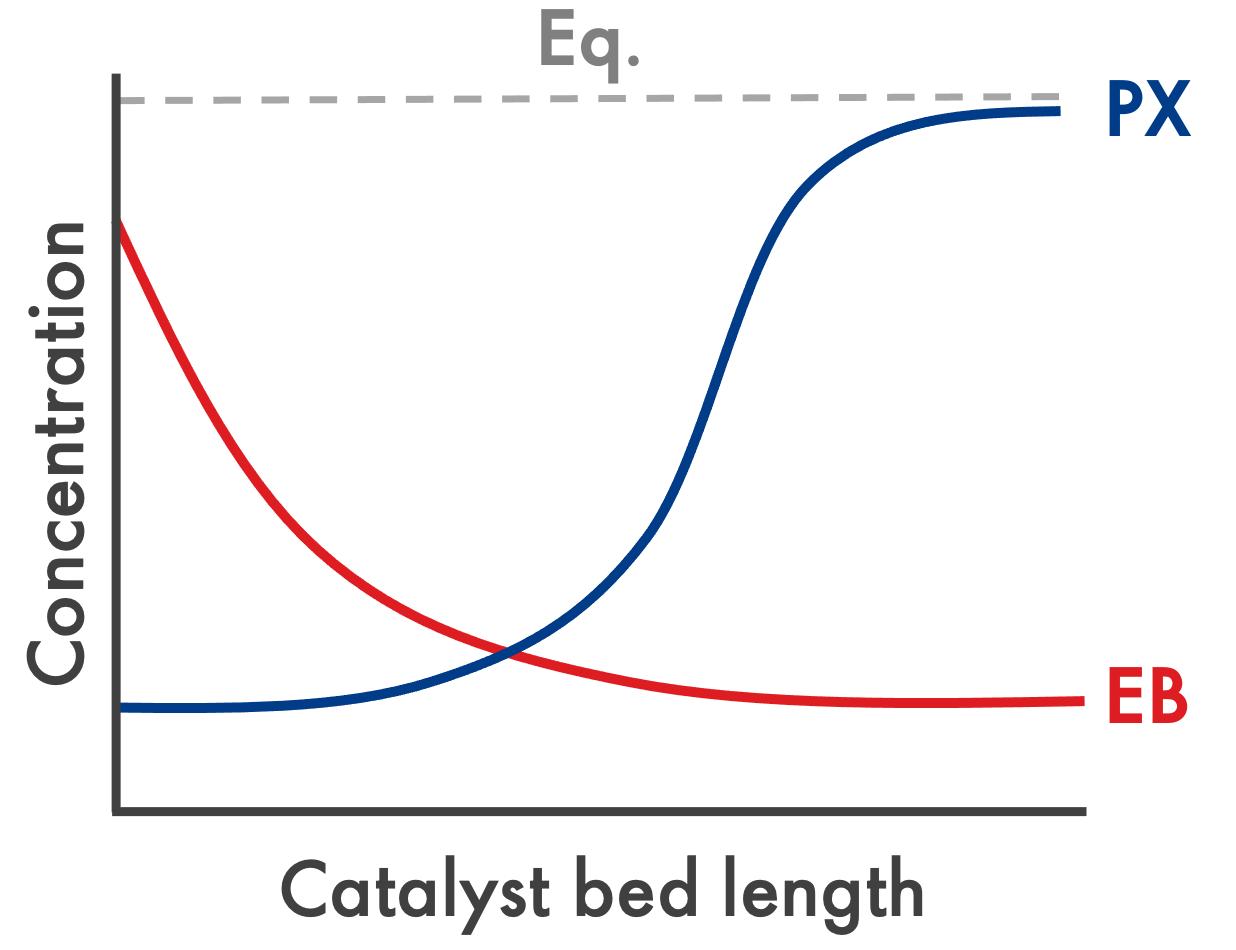
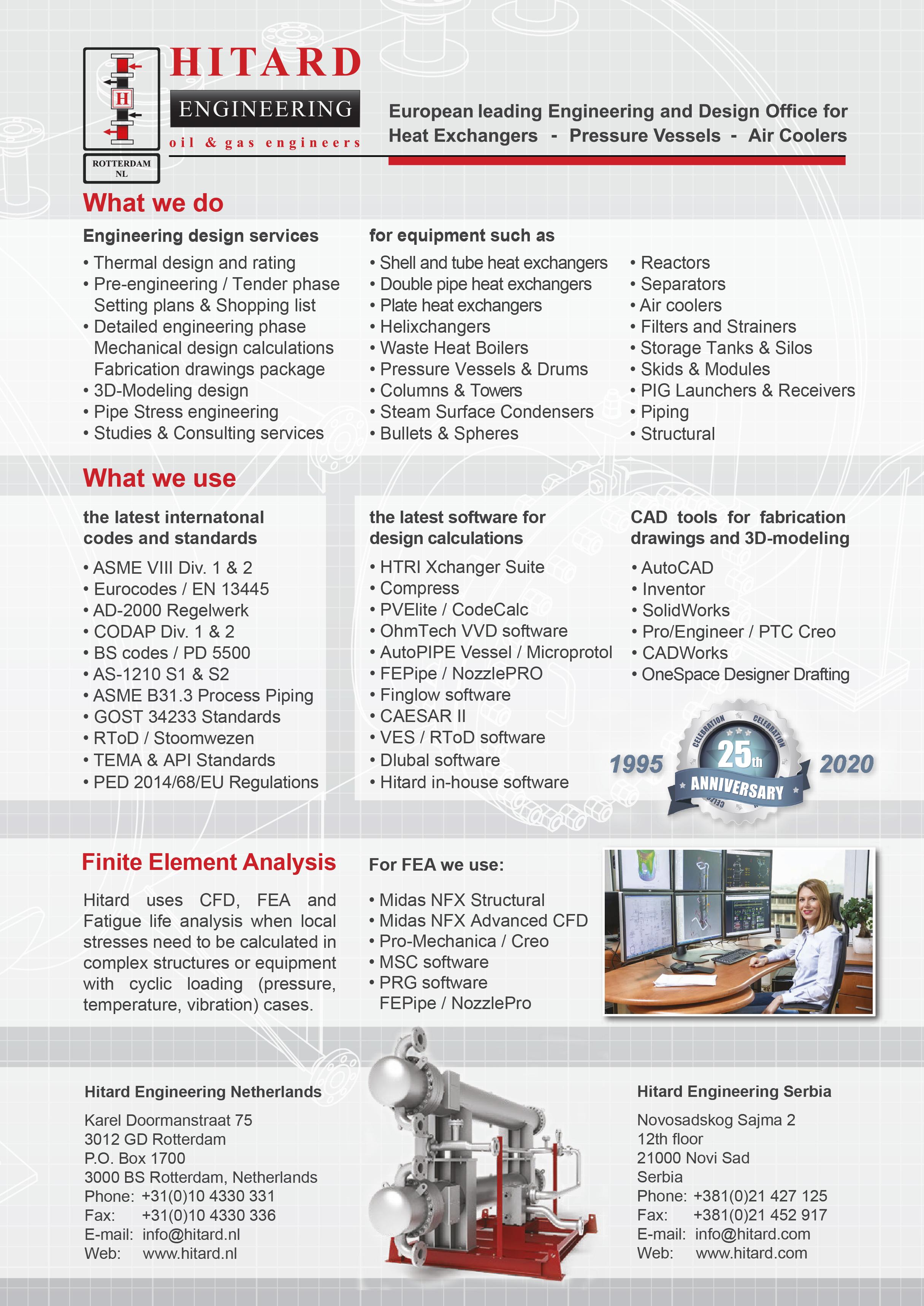
EBD occurs. At this stage, the concentration of EB in the feed is rapidly depleted, indicated by the red curve on the graph in Figure 3.
The second bed contains a catalyst that facilitates isomerisation reactions, converting xylenes to PX. As the isomerisation reactions take place in the second bed, the concentration of PX rises to an equilibrium concentration, as indicated by the blue curve on the graph in Figure 3.
In contrast to a historic one-bed system, a stacked bed, as illustrated in Figure 4, contains independent catalysts and can be optimised. Depending on the feed, operating conditions, product requirements, and profit considerations, the ratio of each catalyst per bed can be tailored to provide greater feed flexibility. By decoupling the EBD and xylene isomerisation functions to a large degree, the overall performance of the catalyst system is significantly improved.
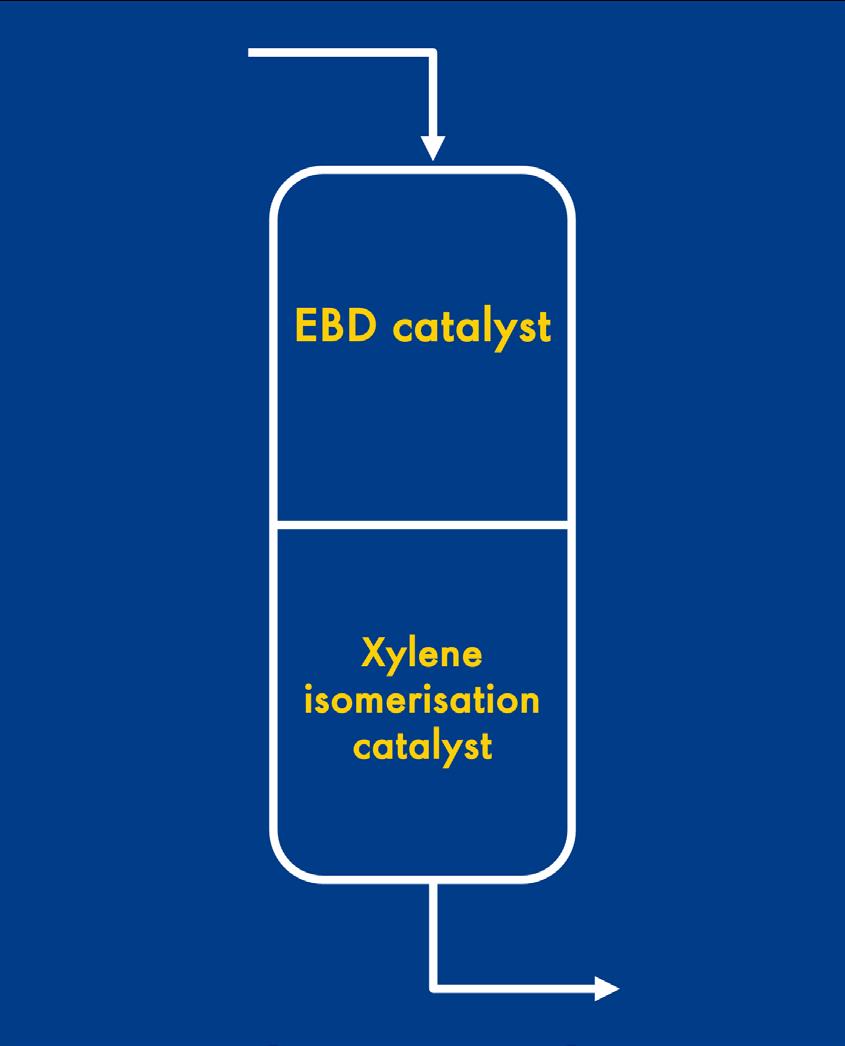
Figure 4. Typical EBD/xylene isomerisation catalyst configuration employed per reactor bed.
Figure 5. Density maps for aromatic molecules of different sizes, within (L-R) large, medium and small ZSM-5 crystals.
Figure 6. The molecular sizes of the aromatic molecules of interest.
Zeolite crystal size effect
ZSM-5, a synthetic zeolite with a pore diameter range of five to six angstroms, was used as the basis of the ZATARIS-21 catalyst system. The crystal size of the EBD catalyst is highly important in determining which molecules diffuse all the way to the centre of the individual zeolite structures.1 Shell Catalysts & Technologies’ research revealed that large ZSM-5 crystals facilitate the diffusion of smaller molecules, such as EB, compared with larger molecules such as MX and OX. The large ZSM-5 crystals are therefore used in the ethylbenzene dealkylation catalyst, found in the first bed.
Conversely, small ZSM-5 crystals are better for the conversion of larger molecules which diffuse slowly, such as MX and OX, so these crystals are used in the xylene isomerisation catalyst located in the second bed. The impact that crystal size has on the activity and selectivity of the catalyst is an important feature of the ZATARIS-21 system.
Figure 5 shows cross-sections of ZSM-5 crystals with different sizes. Within the crystals, regions containing a high density of large aromatic molecules are represented by areas shaded in red. The blue areas indicate regions where a higher concentration of smaller aromatic molecules is found. For reference, the molecular sizes of the aromatic molecules of interest are indicated in Figure 6.
Even though the catalyst in the first bed is highly size-selective, PX is small enough to fit into the zeolite and this will result in some unwanted side reactions (Figure 7). For this reason, a feed with low PX is both desirable and commonly encountered, given the modern separation technology used in most aromatic complexes today.
Passivated zeolite development

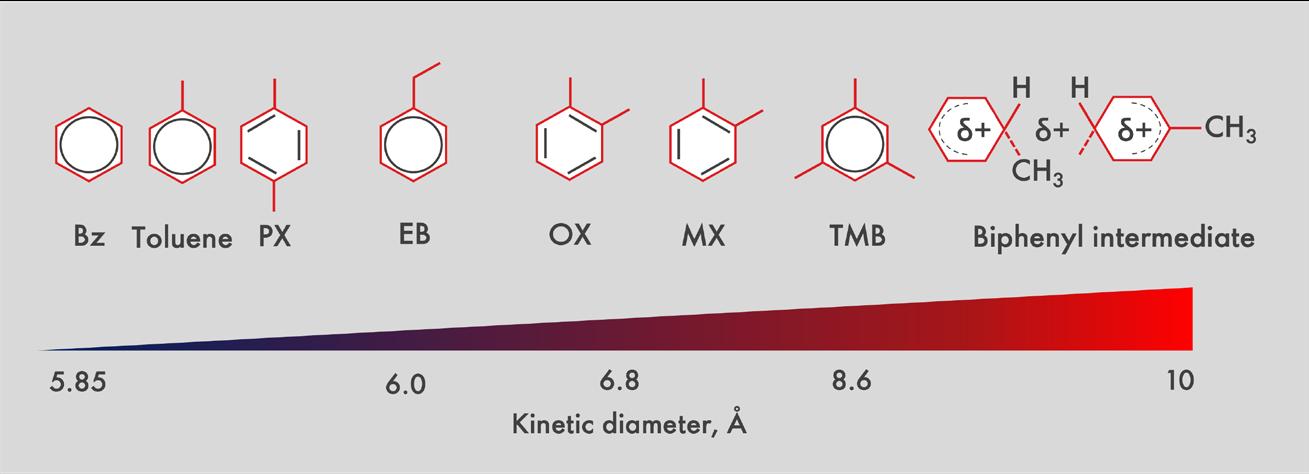
Researchers developed the catalyst in the first bed from a proprietary zeolite, ZSM-5, which was passivated to enhance selectivity.2 The passivation was achieved by depositing a thin layer of silica on the surface of the zeolite crystal, which further restricts molecular access to the pores.
This means that the engineered zeolite system in the first bed selectively denies access to aromatic molecules that are larger than ethylbenzene, which has a kinetic diameter of about 6 angstroms. The size of the ethylbenzene molecule, relative to other aromatic molecules of interest, is shown in Figure 6.
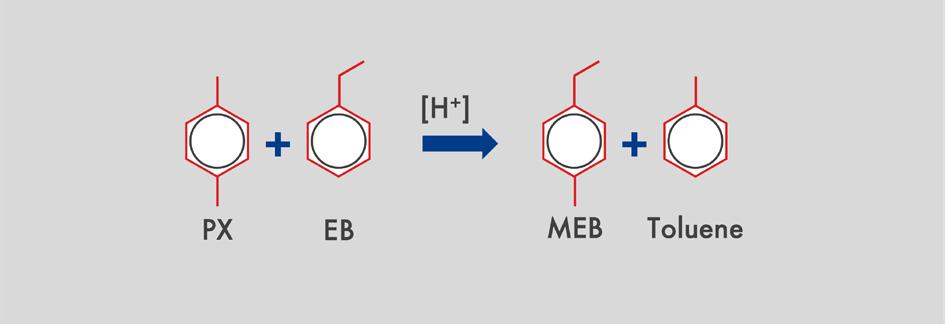
Figure 7. The main side reactions that occur.
Figure 8. STEM-EDX image of the passivated zeolite crystals.
Figure 9. Binding of aromatic rings to a conventional platinum metal catalyst, facilitating hydrogenation.
Figure 10. Activity, selectivity, and ring retention data for ZATARIS-21, vs industry standard catalyst.
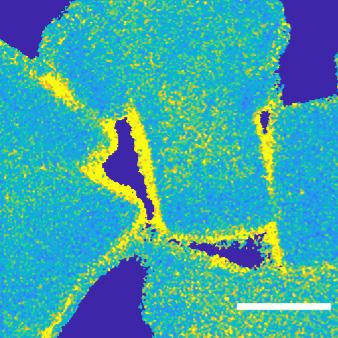
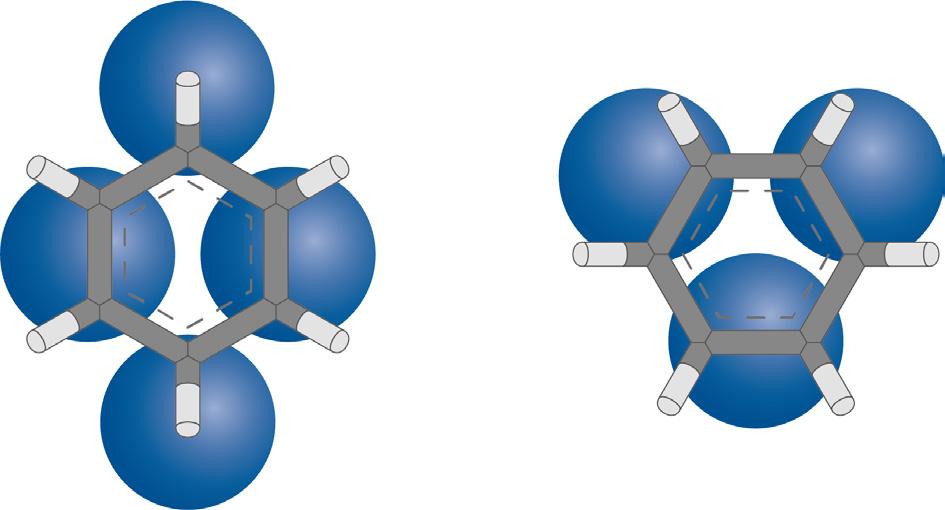
Without the silica layer passivation, larger aromatic molecules can enter the zeolite crystal.
The silica layer is characterised in Figure 8, which shows a scanning transmission electron microscope (STEM-EDX) image of the passivated crystals. The silica layer is seen in yellow, whereas the light blue region is the ZSM-5 zeolite material.
Owing to their smaller molecular size, benzene, toluene, PX, and EB can reside, and react, in the zeolite. The larger molecules (such as OX and MX) that cannot fit into the zeolite remain almost unreacted throughout the first catalyst bed. Consequently, the effective EB concentration in the zeolite, and hence the reaction rate, is increased by an order of magnitude, while at the same time xylene-loss side reactions are significantly reduced.
When ethylbenzene reacts in the first catalyst bed, the ethyl group is removed from the benzene ring, producing benzene and ethylene. It is important that the reactive ethylene byproduct is hydrogenated to prevent re-alkylation and the formation of undesirable heavier molecules. This is where the metal function is highly important.
Metal function development: metal centre selectivity
The selectivity of the metal function is critical to ensuring that the right molecules are hydrogenated. Ethylene must be quickly hydrogenated, whereas aromatics should not be hydrogenated because that would consume additional hydrogen and create naphthenes and gas with much lower value. By incorporating innovative design elements, the metal featured in ZATARIS-21 offers exceptional selectivity, with almost 100% aromatic ring retention.
Researchers developed a metal catalyst based on a platinum surface alloy for the second bed, which is where the isomerisation takes place. In a conventional platinum catalyst, multiple metal atom centres are located close together, which facilitates the binding of aromatic rings across three or four platinum atoms (this is illustrated in Figure 9). As a result, unwanted hydrogenation of aromatics can take place.3 The technology developed in ZATARIS-21 places the active metal atoms in the matrix further apart by spacing inert atoms in between them. Olefins, requiring only one platinum atom centre, are selectively hydrogenated, thus preserving the valuable aromatic molecules.
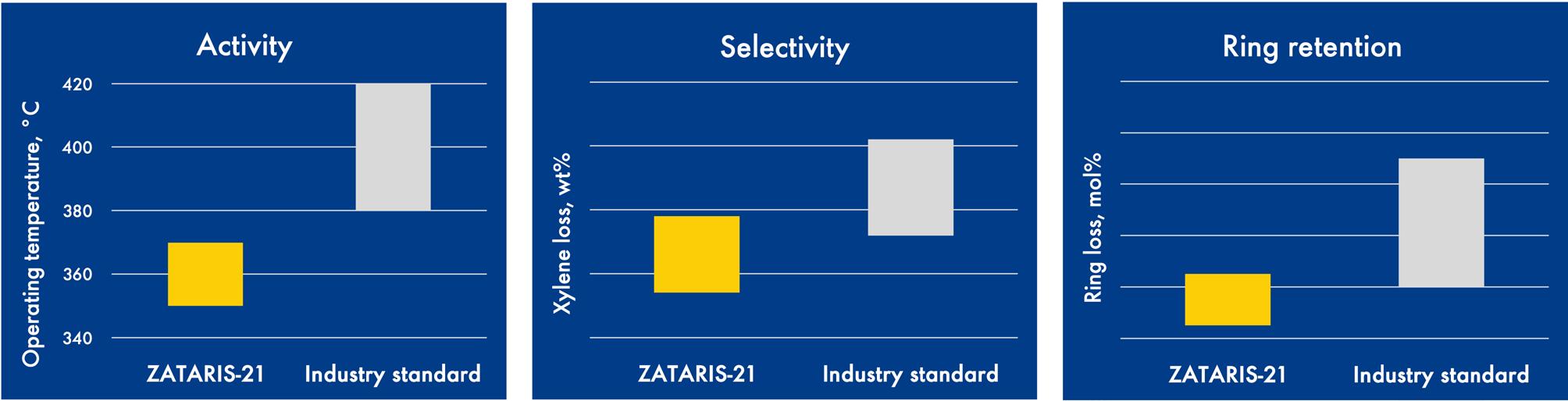
Performance benefits
ZATARIS-21 offers impressive performance in terms of activity and selectivity. This results in lower operating temperatures, reduced CO2 emissions, and lower xylene losses (see Figure 10).
To quantify the benefits of the new catalyst, compared to incumbent EBD catalyst systems, performance data can be compared using a modelling system. The refinery used for this comparison has a PX capacity of approximately 1 million tpy. The results reveal that PX production can be increased by approximately 67 tpd (from 3072 to 3139 tpd) by replacing the incumbent catalyst with ZATARIS-21.
Economy of operation is improved by US$19 million/yr, due to the higher activity and selectivity of the new catalyst system.
As a result of the lower operating temperature of the new catalyst, subject to catalyst load and EB conversion, energy savings of US$208 000/yr can be realised. This would correspond to a reduction in CO2 emissions of approximately 4900 tpy.
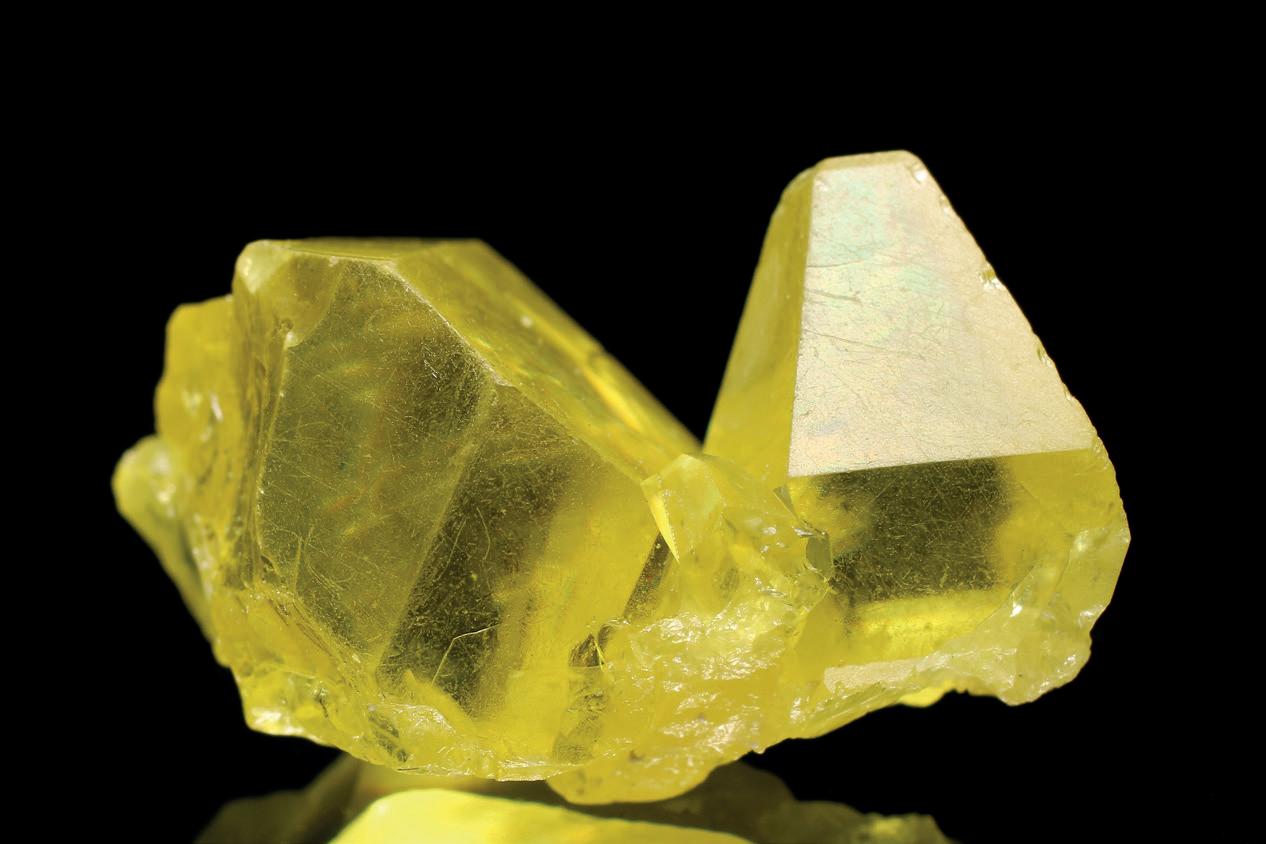
Conclusion
The ZATARIS-21 catalyst system achieves significant activity and selectivity gains by deploying a dual-bed catalyst configuration. Novel design features include engineered ZSM-5 crystals containing groundbreaking passivation technology and a platinum metal function where the metal centres are optimally separated for aromatics preservation.
Intensive research and development means that refiners can improve their feed efficiency, enabling more PX to be produced for a given amount of fresh feed. Fewer side products produced, along with lower gas and heavies, means that less hydrogen is consumed.
The robust catalyst system offers flexibility because the two-bed configuration facilitates tailoring of the two catalysts used. Owing to efficient dealkylation of EB and isomerisation of xylenes, minimal aromatic losses occur. The very limited xylene losses that do occur tend to result in the formation of toluene and C9+ aromatics, which can be recycled by routing to the transalkylation unit. The catalyst system therefore avoids the formation of significant amounts of low-value gases that cannot be recovered as an aromatic product.
By using lower operating temperatures, refiners can realise improved process economics from a drop-in solution that requires no process modifications.
References
1. DEMIKHOVA, N. R., RUBTSOVA, M. I., VINOKUROV, V. A., and GLOTOV, A.P., ‘Isomerisation of xylenes (a review)’,
Petroleum Chemistry, (November 2021). 2. ZHENG, S., JENTYS, A., and LERCHER, J., ‘Xylene isomerisation with surface-modified HZSM-5 zeolite catalysts: An in situ IR study’, Journal of Catalysis, (2006), 241, pp. 304 – 311. 3. DENG, Y., GUO, Y., and JIA, Z., et al., ‘Few-atom Pt ensembles enable efficient catalytic cyclohexane dehydrogenation for hydrogen production’, Journal of the American Chemical
Society, (2022), 144, pp. 3535 − 3542.
SulphurPro®
Native Sulphur
The ULTIMATE in Sulphur Plant Simulation
Optimized Gas Treating, Inc
212 Cimarron Park Loop, Buda, TX 78610 www.ogtrt.com +1 512 312 9424