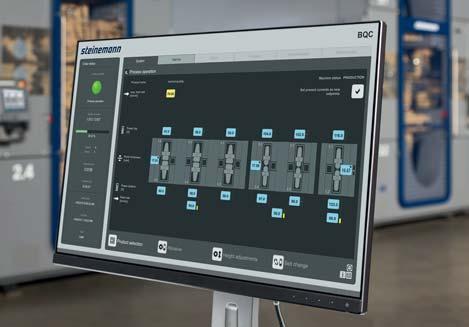
6 minute read
BQC from STEINEMANN - Another milestone in sanding line automation
The Swiss technology leader calls its new development "BQC Board Quality Cockpit". Together with BQC, the brand-new satos TSQ wide belt sanding machine makes it possible to implement a fully integrated, automated sanding process. Steinemann also off ers a range of upgrade packages for existing machine installations like satos.
With the introduction of its nextgeneration satos TSQ machine, Steinemann has completed the technical groundwork for integrating an innovative process control system.
Advertisement
OPTIMAL SURFACE QUALITY WITH THE RIGHT SANDING RECIPE
Surface quality depends on a great many factors, all of which have to be perfectly coordinated in every sanding process. As a system provider, Steinemann not only provides its customers with comprehensive process expertise but also advises users about choosing the ideal abrasive and making sure that parameters are optimally adjusted. The goal here is to ensure customers have the perfect sanding recipe on hand for every new job.
Success depends on the interplay of the factors of sanding machine, sanding belt, and sanding platen, with the quality of the fi nal sanding result depending directly on the coordination of all three of these factors. Since Steinemann has its own tried and tested range of abrasives and abrasive accessories, which is also under continuous development, the company can provide customers with a complete, integrated sanding system. Segmented sanding belts are produced in-house, which ensures that the machine and tool can be coordinated optimally to the respective production process.
Steinemann customers benefi t from an integrated portfolio of services and all-round process expertise. At its Swiss headquarters, Steinemann operates a state-of-the-art Technology Centre that holds seminars for professionals and user training courses on a regular basis. Alongside satos TSQ, the newest generation of sanding machines from Steinemann, company HQ is also home to the very latest equipment for surface analysis. This means customers can send in panel samples to Steinemann and have them analysed by experienced specialists. The insights gained by this analysis are then shared and made available to the customer.
BQC – THE KEY TO A FULLY AUTONOMOUS SANDING PROCESS
Developed by Steinemann, Board Quality Cockpit (BQC) is a process control system that turns sanding into a fully integrated and automated process. Independent of the machine's own software, this is a standalone software suite that is used to network all of the peripherals in the sanding line. Interfaces to external and internal systems are provided to ensure the straightforward collection of all relevant information. The system also integrates order, product, and abrasives management. BQC fi rst analyses all of this data, and then derives recommendations for action that result in improved quality and effi ciency, plus cost savings.
BQC Board Quality Cockpit - the process control system for a fully integrated and automated sanding process to achieve Total Surface Quality
As an integrated solutions provider, Steinemann strives for "Total Surface Quality" to ensure consistent, reproducible panel quality. Total Surface Quality depends on ensuring standardisation and automation along the entire process chain: this, in turn, not only improves production quality, boosts productivity, and makes material fl ows more effi cient, but also reduces the reject rate and achieves signifi cant optimisations in setting processes. With BQC deployed in the machine pre-setting process, an 80 per cent increase in A-quality panels produced can be achieved. Steinemann works closely with its customers to achieve this goal, with the focus here being on the continuous optimisation of the sanding line and the sanding process. With BQC, Steinemann customers can preset the machine automatically when changing jobs, increase machine availability, and signifi cantly reduce the consumption of sanding belts and energy.
FULL AUTOMATION AND INTEGRATION FOR THE ENTIRE SANDING LINE
The latest generation of wide belt sanding machines, the satos TSQ, off er an ideal starting point for implementing a fully automated sanding line. Out of the box, satos TSQ already meets all of the technical requirements involved in integrating a modern process control system like BQC. When combined with BQC, satos TSQ can be linked to all of the sanding line peripherals needed. The ultimate aim is horizontal and vertical integration of the entire sanding line. Horizontal integration involves connecting selected sanding line units with BQC: BQC collects data from these machines to provide real-time process monitoring. Potential benefi ts increase with every unit that is
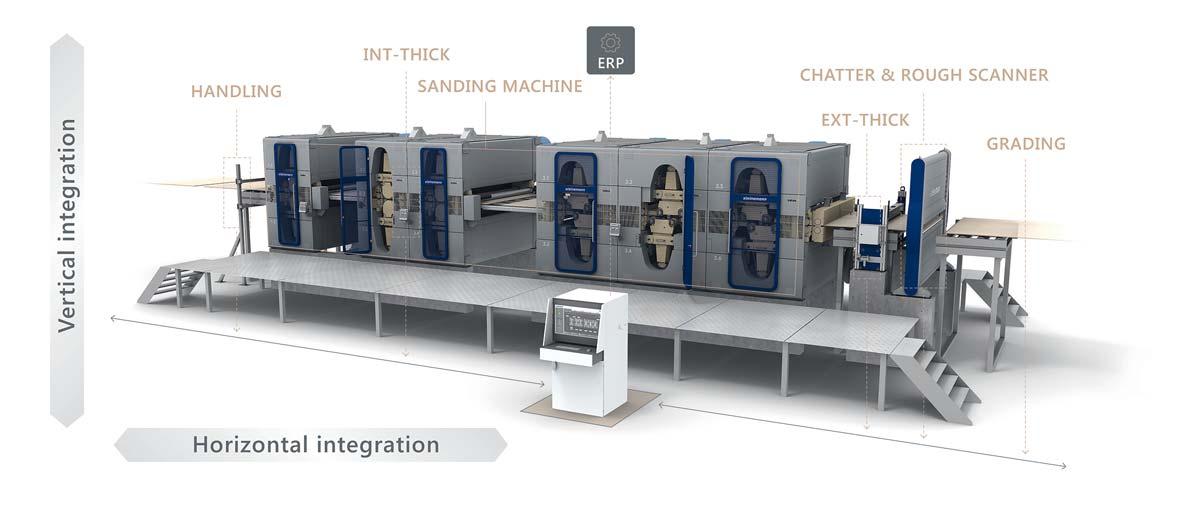
The interlinking of the sanding line peripherals off ers a high level of process transparency, results in real-time process monitoring and improves production quality signifi cantly (All images are credited to Steinemann)
added to the BQC network. A thickness measuring interface, for example, means optimum sanding machine settings can be monitored based on the panel's actual thickness before entering the sanding machine, while being processed and after exiting the machine.
Steinemann off ers various BQC modules and packages for implementing an automated and fully integrated sanding process, which work together like building blocks to steadily increase the degree of automation available in the sanding line. The basic module, “BQC BASIC”, provides the important initial connection to the sanding machine. Other add-on modules provide additional interfaces: "BQC ERP" for the ERP system, "BQC HANDLING" for the handling system, "BQC EXT-THICK" for the external thickness measuring unit, and "BQC INT-THICK" for the internal thickness measuring system.
These add-on modules handle all of the steps required to achieve full automation. For example, the interface to the handling system means operators no longer need to make entries in this system manually. The ERP interface also ensures that details of the various products can be transferred. Within BQC, each product is linked to a matching sanding recipe, which enables automatic machine presetting in the event of a job change.
By choosing appropriate add-on modules, the sanding process can be almost entirely automated. The "Basic Package" (BQC-BASIC + ERP + HANDLING) includes automatic machine pre-setting
Level of automation - Steinemann off ers various BQC modules and packages for implementing successively a fully integrated and automated sanding process

after a job change as well as guided recommendations for action in the event of alarm handling being necessary. This leads to cost savings in both setup and operations. The "Total Thickness Control (K)" package (BQC-BASIC + ERP + HANDLING + INT-THICK + EXT-THICK) offers a fully automated calibration process, ensuring reproducible, constant panel thickness and parallelism. As a result, this means that the calibration unit can operate as part of a closed loop system (control plus regulation). At the end of 2020, Steinemann plans to release the "Total Surface Control (N)" package (BQC-BASIC + ERP + HANDLING + INT-THICK + EXT-THICK + CHATTER & ROUGH) for complete automation of the sanding process, calibration sanding, and fi ne sanding.
Alongside solutions for its latest generation of machines, Steinemann also off ers solutions for previous models such as the "satos". Upgrade packages can be used to retrofi t these machines as needed and make them capable of integrating the new BQC process control system.
The next few years will see major changes in practice in the sanding industry. The automation and networking of the entire machine pool therefore forms an essential part of ensuring a smart, successful production line, in which the overall system can apply machine learning to derive new knowledge from the vast volumes of data produced. Steinemann's technological quantum leap marks the beginning of a new and modern age of sanding process automation and process data handling. As always, the key focus here is on human-machine interaction and the performance capabilities of a fully automated, integrated sanding process. The automated replacement of actual sanding belts is one feature that will take a while to implement, however. ℗