4 minute read
Meet the team behind SCM's Software and Digital Services
Manuela Adreani, SCM software product manager (Image is credited to SCM)
By Szeto Hiu Yan
The woodworking industry may be undergoing an inevitable digital transformation, but it is a game that is still in its early stages. Many companies are still exploring the many possibilities of digitalisation.
“But this is also an exciting stage to be at,” said Manuela Andreani, SCM software product manager, whose team takes care of Software and Digital Services.
How do Andreani and her team assess and decide on their customers’ digital needs?
“Our digital services are customercentric, each product development always starts from the customers. We nourish customer relationships by listening to their needs. We visit them, talk to them, watch and listen to them to truly understanding what they need. We believe this is the only rewarding approach. For example, we learnt what type of information they needed to improve performances, or experienced the importance of integrating data coming from the machines and transmitted to external, diff erent software to turn them into useful information of value”, explained Andreani.
"Eventually, all these inputs from our customers become our products’ specifi cations. This is how we develop our digital services based on IoT technology: turning data into useful and relevant information,” she said.
“We gave up talking about IoT as this is not about the technology itself. It is about what the technology enables, that is value-added services. Today we off er our customers a fast growing portfolio of digital services, aiming either to keep their machine in good health or to improve the performance and productivity of the machine. Isn’t this gorgeous? ” Andreani said with a smile.
SCM’S DIGITAL INNOVATIONS
SCM’s Maestro Digital Systems is made up of two main product groups — Software and Digital Services.
SCM Software, consisting of Maestro office and Maestro active, covers all the SCM technologies throughout the different stages of woodworking processes - from design to production. Maestro offi ce embodies software that is used in the office for the different machine technologies — from design, optimisation, simulation stages to before production. Maestro active refers to the diff erent HMI software of the SCM machines, which share a common look, feel and interaction modes.
SCM’s Digital Services are enabled by the IoT technology, which connects the machines to centralise and share data and information among diff erent users, thus providing customers with a wide range of benefits which can support and assist them to move forward and transform their business operations.
Named Maestro connect, customers can access the IoT platform to better understand their machines’ operations and efficiencies. For example, now that customers can be notifi ed in real time when an alarm occurs and have access to smart, troubleshooting documentation as well as get an immediate contact with the SCM service; customers can seek faster service intervention and reduce troubleshooting time; finally, Maestro connect’s full kit of sophisticated sensor devices can easily detect and warn machine operators in case critical conditions arise in the machine; real time access to spare parts inventories and availability also shorten down time. “The IoT solution offers several monitoring, maintenance and performance services. This technology was launched as a proof of concept in 2015 and today, it has been elaborated in terms of services."
DEVELOPED ENTIRELY BY SCM
Andreani is very proud of the fact that Maestro connect is entirely “made in SCM”, having been developed by the people at SCM.
“We develop our products internally by ourselves. We have digital specialists who are totally dedicated to these products and they work closely with the machine production and technical offi ces. They also worked with the servicing teams who know our customers and the worst pains they face. To have all these people
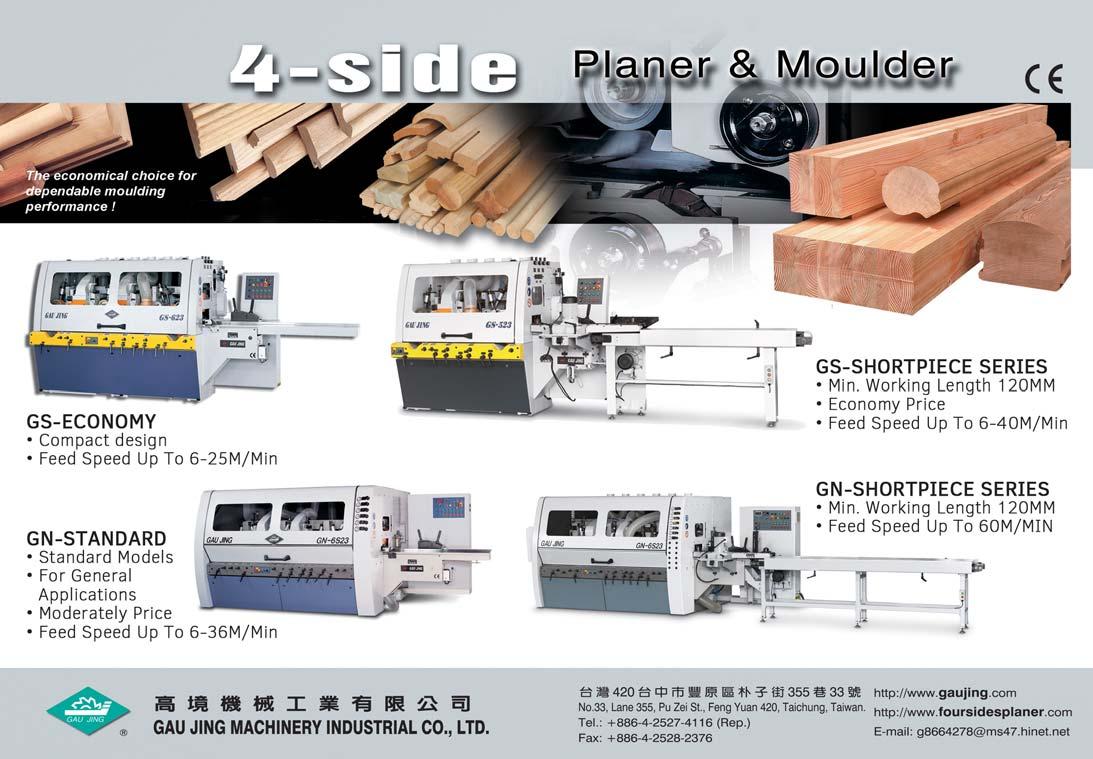
stick around the table to create excellent digital products, it is very exciting and humbling. We are determined to help our customers solve issues and fi x their machines in better ways than before.” There are at least 15 people currently working on the development of the IoT platform. The software product department, which is in charge of the IoT platform, started the product development process in 2018, with research and innovation starting even earlier, back in 2015. Andreani herself joined the team in 2018.
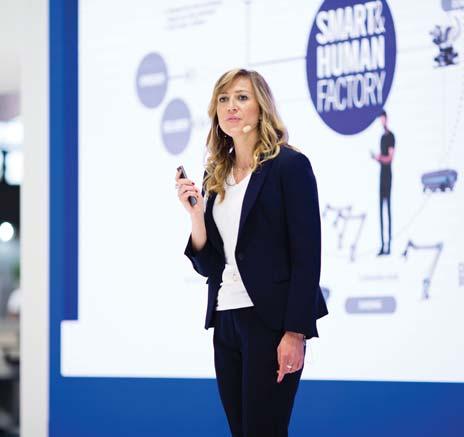
As a company, SCM has long understood the importance of innovation and thinking ahead, which is why SCM reinvests 7 per cent of the company’s total turnover annually into R&D. “This is a continuous improvement and reinvestment that SCM places great priority in,” said Andreani.
Ultimately, it is about adding value to SCM machines by enhancing the interaction between customer and service. “In fact, Maestro connect helps to bring about improvements in many aspects of machinery operation and efficiency — instant notifi cations and insights optimise productivity and improve availability and use of the machines; maintenance costs are cut down while effi ciency can be improved by drastically reducing errors, time and costs; Service can improve performance by carrying out tasks faster and an immediate access to the Smart Parts e-shop reduces customer downtimes. Reports and KPIs allows further data analysis and customer awareness. Finally, Maestro connect off ers machine learning services, to allow forward looking maintenance and prevent failures before they occur,” said Adreani.
“What the IoT platform provides, is actually full awareness, and with that, users will easily see an overall productivity and performance improvement.” ℗
