12 minute read
Wood Clinic: Common problems seen in solid wood louvered door after assembly
Hello, Mr Shen!
I am a reader of PANELS & FURNITURE ASIA. I am in charge of making wooden doors and interior decoration in a small wood factory. The company purchased a second-hand louvered door making facility days ago, using Red Meranti wood and Nyatoh wood for small batch production of solid wood shutters. There are many quality defects encountered during production. For example: The slats near the transom above the louvered door are slanted, damaged or loosened. (As shown in fi gure) • Some slats become bent. (As shown in fi gure) • Cracks or damage on the doorpost Mr Shim (Shen Yuxin) • The louvered door can be packaged only after repairing by hand sanding several times, resulting in low production effi ciency. • In the warehouse with fi nished products, the doorposts of the louvered doors made from Nyatoh wood are found to be out of shape and poorly glued. I hope you can help to evaluate these issues and provide some suggestions for improvement.
Yours sincerely, Lin Yongkang 17/7/2019
Common problems seen in solid wood louvered door after assembly
Based on your descriptions, I have provided the reasons for the common problems seen in solid wood louvered door after assembly and solutions for improvement:
1. Slanted slats on the louvered door
It is often found that the slats on the upper transom are not parallel after assembling the louvered door, the main reason is: • Improper operation of the automatic slotting machine: when two doorposts enter the automatic slotting machine to be slotted and one of the doorposts is not pressed tightly, it may shift during milling, resulting in some non-parallel slats.
It is recommended to ensure that both doorposts are tightly pressed and that both milling cutters are sharp during the operation of the automatic slotting machine. 1. When the automatic slotting machine is not properly aligned, the accuracy of the automatic slotting machine will decline from wear and tear for a prolonged time.
A thorough check and maintenance is recommended to ensure the accuracy of the automatic slotting machine.
2. Damaged slats
If there are broken grains or knots on the slats of the louvered door, or the wood grains are not straight, the pressure created when assembling and pressing will cause damages to the slats, in which case, the slats need to be replaced.
It is recommended to strictly control the quality of the slats when preparing materials to ensure they are free of the defects listed above, and that the chamfering on both ends of the slats is in place.
3. Loose slats
After assembly of the louvered door, slats are often found loosened (as shown in the fi gure), the two main reasons are as follow: • Mismatched automatic slotting specifi cations: if the milling cutter with a metric diameter of 6.0mm is used with the milling cutter with a diameter of 1/4 inch (1/4" - 6.35mm), slats will not be tight after assembly.
It is suggested that the worker set the specifi cations of the milling slot according to the louvered door design drawing, making sure that the milling cutter diameter is 6.0mm when replacing it.
• Inconsistent specifi cations of slats: when the setting of the slat manufacturing machine is not in place, the slats may come out too thin, or with irregular thickness, resulting in inconsistent thickness after sanding. Any of these reasons will lead to inconsistent slat tightness throughout the louvered door. It is suggested that the workers set the thickness of slats after sanding to 6.0mm, and follow the specifi cations on the drawings of the louvered door.
4. Bent slats
Slats become bent if the milling cutter of the automatic slotting machine is blunt, or the milling slot depth has been pushed beyond limit, or the slat arch is too tight because some of the slats are too long.
It is suggested to check the sharpness of the milling cutter regularly and ensure that the milling slot is deep enough. The length of slat must be strictly controlled in sawing, and both ends should be at right angle.
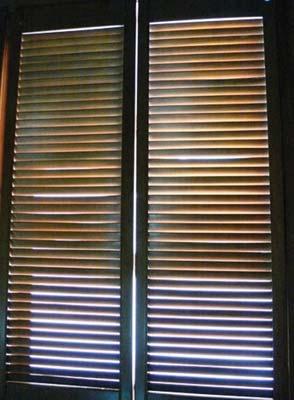
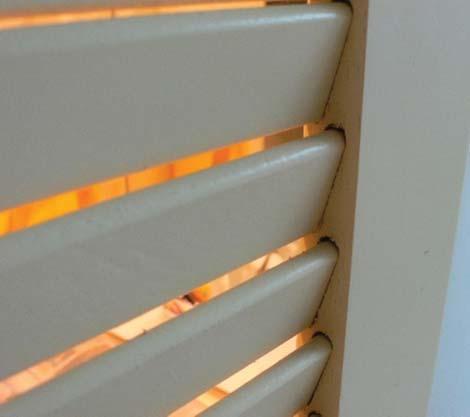
Figure 1: After spraying white paint on the louvered door, there is an obvious loose seam between the slat and the milling slot.
5. Damaged doorpost
There are three main reasons why the doorpost is often damaged when assembling the louvered door: - Improper setting of automatic slotting machine: this leads to milling slots that are too short. When dozens of slats are pressed into the milling slots of the doorpost at the same time, the milling slots crack.
It is recommended to thoroughly check the accuracy of the automatic slotting machine and train skilled workers to set milling slots according to the specifi cations on the drawings.
• Improper specifi cations of slats: the thickness and width tolerance of slats is too large. Suppose an 80-inch-high door requires about 64 slats. If the slat is 0.30mm larger than the milling slot, the door post will crack. It is suggested to follow strictly the thickness and width of slats specifi ed on the drawing.
• Improper chamfering of slats: due to improper chamfering of slats, where the chamfering is not in place on one side or one end of the slat, it will be stuck at the edge of the milling slot when pressed and installed to the doorpost, resulting in crushed milling slots.
It is recommended to check the chamfering equipment and reset it to ensure that the chamfering at both ends of the slats is even and in place.
• Improper setting of assembly press: the assembly press mold setting is not accurately enough, diff erent parts of the louvered door are not centred uniformly,on the same horizontal surface, or the centre line of the doorpost of the louvered door, the wood mortise of the transom and the milling slot are not aligned. When the centre line is not accurately aligned during assembling and pressing, this will lead to crushed milling slot of the doorpost, or distorted louvered door.
It is recommended to re-check the mold setting of the assembly press to ensure that the setting is in place, and strictly control the positions of the wood mortises of the louvered door post and the transom, as well as the milling slot centre line.
According to the information you have provided, regarding the problem that the louvered doors need many repairs by hand sanding after assembly and thus aff ecting production effi ciency, the suggestions for improvement in the process are as follows: 1. Quality control of materials
• The grade of wood purchased should meet the requirements of the louvered door order. Wood with too many defects such as knots, wormholes and discoloration are not acceptable. When purchasing wood, such defects should be avoided as much as
Figure 2: Some slats on the louvered door are not straight and become arched.
possible to reduce the screening and repair work, thus indirectly improving the production effi ciency.
2. Four-side planer
• When using four-sided planer, doorposts and louvered door transoms should follow the specifi cations on the louvered door design drawing, the linear speed of the planer should be kept at 10 m/min (planer tool mark at 12/inch). The planing tool should be sharp at all times to reduce fuzzing and roughness on the some areas of the surface, thus reducing the use of putty and hand sanding.
3. Multiple louver door slat machine
• Slats should be produced according to the specifi cations of the louvered door design drawing. The arcs on both sides of the slat should be kept symmetrical (r = 6.0mm). Linear speed should be kept at 8 m/min and the planing tool should be kept sharp to reduce fuzzing and roughness in some areas on the surface, thus reducing the puttying and hand sanding work.
4. Fixed length
• When using the radial arm saw to trim diff erent parts of the louvered door, the most ideal sequence is to start from large louvered doors to the smaller louvered doors. Make sure the saw blade is sharp and at a right angle. If the linear speed of the saw is too high, the surface will become rough and fuzzy.
It is recommended to use an appropriate linear speed when trimming parts of the louvered door, and replace the saw blade and the bottom plate regularly to reduce fraying edges, thus reducing the need for puttying and hand sanding.
5. Automatic louver slotting machine
• Following the louvered door design drawing, set the inclining angle of the automatic louver slotting machine and the specifi cation of the milling slot. Check to make sure that the milling cutter of the automatic louver slotting machine is sharp, the clamping pressure of the fi xed doorpost and the accuracy of the milling slot are in place.
6. Wide-belt sander
• The wide-belt sander can be used to sand fl aws such as the planer tool marks, burrs and putty on the fl at louvered door post, upper, middle and lower transoms and the slat; and the wide-belt sander can also be used to achieve equal thickness.
7. Drilling machine
• The drilling of the louvered door set and transom’s log mortises should be set according to the specifi cations on the drawings. The operator will check the accuracy of the mortises regularly with a special mold to make sure it is in place.
8. Nail dowels
• One must ensure that the dowels on the upper, middle and lower
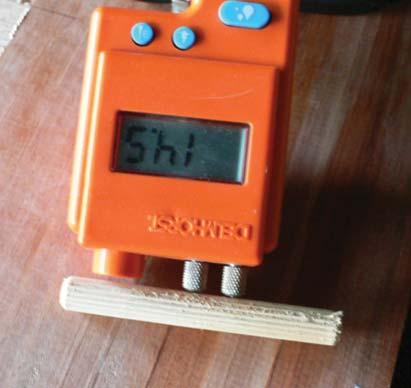
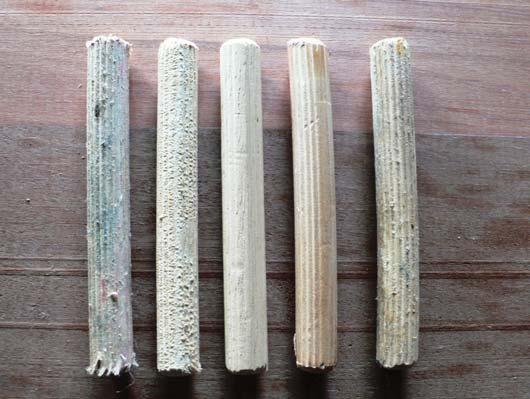
Figure 3: Common shortcomings of homemade dowels. Figure 4: Diagram showing the measuring of moisture content of dowels at 14.5% using a moisture meter
transoms of the louvered door are uniformly glued and of the same height. The quality of dowels should be strictly controlled and the chamfering of both ends of the dowel should be in place. This can reduce the chances of pressure damage to the door post when assembling the louvered door.
Colour matching of the louvered door components
• The colour of the components of each louvered door and the number of slats (tied in a bundle) should be allocated before assembling the louvered door. It will improve the effi ciency of the louvered door assembly.
9. Louvered door assembly press
• Skilled workers are required to accurately set the template of the louvered door assembly press. When laying out the parts of the louvered door on the template of the assembly press, one must make sure that the centre lines of the parts are on the same horizontal plane without any dislocation. When assembling and pressing the doors, it is common to see cases where the milling slot of the doorpost are crushed or the assembled louvered door is distorted when the centerlines are not aligned.
• There are two stages of pressing when operating the louvered door assembly press. At the fi rst stage, one must confi rm that the dowels of the louvered door transom are aligned with the doorpost mortises, and that there is no dislocation between the slats and the milling slot. The second stage of pressing is to make sure that there is no crack between the post and the transom of the louvered door, and to remove any spilled glue. After that, pressure can be released upon the assembly of the louvered door.
It will also reduce the repair work and improve the effi ciency of the louvered door assembly.
According to your description, regarding the problems of distortion of the doorpost and weak gluing strength of the Nyatoh wood louvered door in the fi nished product warehouse, reasons are analysed and solutions are given as follows:
1. Distortion of the doorpost of the Nyatoh wood louvered door
• The moisture content of Nyatoh wood is 12%-20%, and the equilibrium moisture content in the warehouse is 10%-14%. When other lumber with high moisture content in the warehouse continues to release moisture, wood shrinkage will lead to deformation of the doorpost of the Nyatoh wood louvered door, and will aff ect the gluing strength of the log nail.
Reason for uneven moisture content: Due to non-standardised operation of the drying kiln -- the materials used for the doorpost and the transom are dried in the same drying kiln, the material used for the doorpost is high in moisture content due to its greater thickness, which results in the deformation of the doorpost. Suggested improvement solutions: in addition to stacking materials with 1-inch square stickers for wood drying in the kiln, make sure the wood is of the same thickness, and avoid mixing with other tree species as possible. Before drying, it is necessary to confi rm the hot air circulation of drying kiln is uniform without short fl ow.
2. Weak gluing strength of the Nyatoh wood louvered door after assembly:
• Non-standard, uneven or insuffi cient glue is applied on the log mortises. It is common to apply glue only on one side of the mortise or only on its bottom, which will result in weak assembly gluing strength.
It is recommended to use a small brush, or a pneumatic glue gun with a nozzle diameter of 8.0m and a small hole in the periphery. It will help coat the glue evenly around the perimeter and ensure there is suffi cient glue.
• Mortise glue fi lm crusts. After the glue for the doorpost mortise has been applied but left untouched for too long, the glue the mortise turns into glue crust in a semi-dry state, which will lead to insuffi cient gluing strength after the door is assembled.
It is recommended that assembly should be fi nished within 3 to 5 minutes after application of Europe D3 water-based white latex.
• The dowel is unstable in quality. Shortcomings of the dowel such as fuzzing, diff erent diameters, diff erent length, uneven chamfering at both ends (as shown in Figure 3), and high moisture content (as shown in Figure 4) will aff ect the gluing strength of the door after assembly.
It is suggested to strictly control the specifi cation of dowel and its screw thread quality. Diameter tolerance ≤0.1mm and moisture content control at 8%±2% are the most ideal.
• The log mortise is unstable in quality. Diff erent size and depth of the log mortise will also lead to insuffi cient gluing strength after assembly of the louvered door.
It is suggested to strictly control the specifi cation of the log mortise and ensure that the mortise diameter tolerance is ≤0.1mm, and the drill bit should be checked regularly and stays sharp.
The above explanation and suggestions are provided for your reference. I hope it will help you deal with the shortcomings of the louvered door, and improve the production effi ciency. ℗
Yours sincerely, Mr Shim