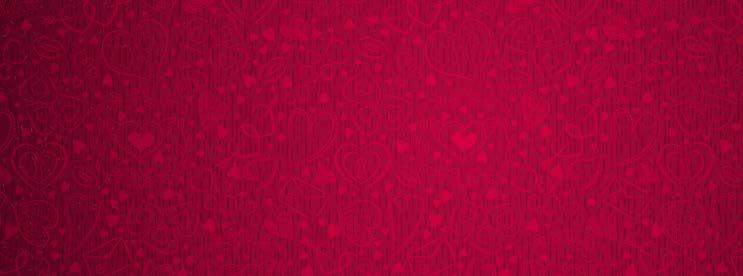
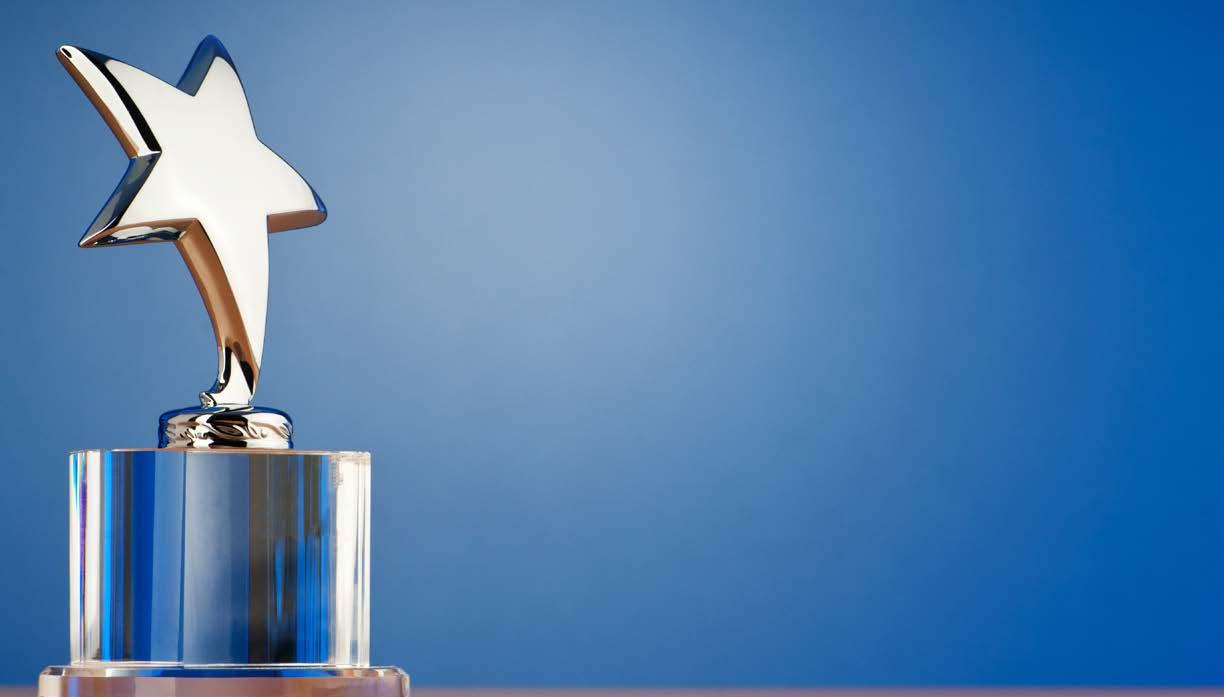
P1 Safety Earns 2024 MCAA/CNA Safety Excellence Award
The P1 Safety Team has done it again, winning the 2024 MCAA Safety Excellence Award for contractors logging more than 1,000,000 hours.
IT’S ONE OF THE WORST THINGS TO BEHOLD...
“The reason for our success is because we remain focused on our most important resources: the human ones.”
From field to office, the award also belongs to all the P1 associates who dedicate themselves to our P1 Safety culture, ensuring that Safety is not just a priority at P1, it’s truly a core value.
The annual awards honor MCAA member companies’ successful safety programs and innovative safety initiatives.
To be eligible to win, a company had to submit an application describing their safety and health program in 2024, why they believe it deserves the award, and innovation/s that helped them achieve a high degree of safety excellence during the year.
Companies were divided into five categories by number of hours worked in 2014, and a winner was chosen in each category.
1. 0 - 100,000 hours
2. 100,001 – 250,000 hours
3. 250,001-450,000 hours
4. 450,001 – 1,000,000 hours
5. Over 1,000,000 hours
“The 0.61 incident rate P1 held in 2023 was impressive, especially after a year of growth and adding a lot of new field personnel,” Vice President Don Campbell said.
In 2024, P1 lowered that number to 0.57, adding not only more field personnel, but 504,000 more hours worked than the previous year for a total of 2,474,519 hours worked.
“The reason for our success is because we remain focused on our most important resources: the human ones,” Don added.
“While P1 will always have a commitment to embracing technology, we recognize our actual human resources are the most critical components to a world-class safety record and culture,” Don explained.
“Through rigorous daily checklists, mental health resources, training, and mentorship, P1 leadership is committed to ensuring associates show up mentally and physically prepared to make the best decisions, every day, at every job site,” Don said.
According to Safety Director Greg Sweeney, the P1 Safety team makes a concerted effort to build rapport and relationships with each and every employee on a jobsite.
“Our field associates are actually happy to see us (most of the time) because they know and trust our safety staff,” Greg said.
P1 Safety works to ensure the entire organization can get behind safety as a core value, adopting our expectation of zero accidents.
On the following page are some of the new and existing initiatives that make P1 deserving of the MCAA award.
P1 is developing a second safety orientation to help mitigate injury numbers. All new associates will receive the standard safety orientation when hired. In 60 days, after getting some on-the-job experience and exposure to P1’s high expectations for safety, they will be re-trained on the same topics they initially learned to ensure they understand, and buy in to, P1 safety standards.
A Peer Connector is someone an employee can talk to and know that they will not be judged, and all will be kept confidential. The Peer Connector is identified by a hard hat sticker (or laptop sticker, if they are not a field employee) as a safe person to talk to.
The P1 Safety Committee continues to help mentor new associates by placing a red sticker on the hard hat for all apprentices, new employees, and traveling/visiting employees. The red sticker identifies an employee that may not be familiar with P1’s safety culture, so our experienced P1 workers can take the opportunity to mentor them as needed.
P1 continues promotion of suicide awareness with a “mental health stand down” in the month of September. The event is for all P1 associates to talk about suicide in the construction industry, that it’s “ok to not be ok”, and how to get help. In addition, a suicide awareness Tool Box Talk has been added to address suicide prevention and mental health issues for our associates and workers.
P1 developed a branded “Don’t Lose Hope” campaign that includes signage around the offices and jobsites, as well as a sticker for hard hats that reminds everyone they are not alone, they can talk to our Safety professionals any time, and that includes the 988 national suicide hotline number.
SOI is the P1 system for all workers to implement safety in every task. It is a trifold checklist that is distributed to each crew on the jobsite. It is that crew’s responsibility to fill out and complete an SOI for each task. This SOI will be completed and reviewed by the whole crew, each day, before starting the task.
QR codes are placed not only on the checklist, but hard hats and other accessible areas of job sites that link immediately to a list of P1 Safety professionals. Associates are encouraged to call any time, day or night, if there is an issue or incident.
Since 2003, P1 has emailed every employee a monthly Accident Prevention Bulletin (APB). It discusses any accidents or near misses for the month, including the root cause and corrective action. This ensures that all employees nationwide are aware of corrective actions that need to be made to prevent a re-occurrence of the accident at another jobsite.
P1 has built an inclusive Safety Committee that meets monthly to discuss safety issues and changes that should be made. The committee is made up of executives, project managers, foremen, field staff and the Safety Department, with a monthly “visiting” employee to provide a new perspective.
It may be frigid outside, but golf season is just around the corner.
P1 Marketing does not have golf or other similar swag at this time, so be sure to place your orders soon to ensure you have what you need on hand for those last-minute tee times!
THERE ARE SEVERAL WAYS TO ORDER ITEMS.
1. P1 COMPANY STORE: Most golf-type swag is located in the Promotional Quick Ship section. STORE QUANTITIES ARE LIMITED, so be sure you leave enough time in case items are out of stock.
2. Contact Beth Martens for specific items not available on the store, or if using the store doesn’t fit your needs.
THE COMPANY STORE:
To access the COMPANY STORE, use your full email address (joe.smith@p1group.com) with password "p1store". BE SURE you are in the P1 Company Store, and not the Safety Incentive store. The URL should look like this: https://store.allcustomwear.com/ p1groupstore
The sheer size and weight of the materials made this mezzanine project the largest mezzanine P1 Millwrights have fabricated and installed to date.
The mezzanine was fabricated to support production equipment at the new Heartland Coca-Cola bottling facility in Olathe, KS.
The 11,000 sq. ft. project was a comprehensive Millwright effort, including the fabrication, painting, and installation of large, heavy pieces that included more than 377,000 lbs. of processed steel.
The Millwrights worked long hours to meet a tight schedule.
Senior Project Manager Marques Nisely says the sheer size of the project presented some challenges when it came to painting and install, but the P1 team was up to the task.
“The 3/8-inch deck plate included pieces measured 5’ x 10’, each weighing several hundred pounds,” Marques said. “The team had to rig and set multiple large pieces like this up on the mezzanine.”
The field team, led by Millwright Foreman Rich Staples, had a big space to fill. (continued)
“The guys did a great job working through the project. It was the largest mezzanine we’ve installed, and the most paint we have ever used.”
-Marques Nisely, Senior Project Manager
“The amount of work and effort it took to make such a large project happen in a short amount of time was extremely impressive,” Rich said.
“Millwright Foreman Andy Lister and his crew started us off with an excellent layout and an exceptional beginning to the structural steel, which was in place when I got on site,” he added.
Rich says truck shortages in Kansas City made getting materials to the site a challenge.
“We requested any components and materials we could get to be loaded at night and delivered first thing in the morning so we had a chance to inspect, sort, and prep all materials for installation,” he said.
The team worked through scheduling with the P1 warehouse to keep things rolling.
“The large and complex platform meant there were many components close to the same dimensions, and the fact they were laser engraved meant it took a little longer to identify them and install them accurately.” Rich explained.
Contract Value: $2,700,000 (including change orders)
GC: Sidel Construction
Owner: Heartland Coca-Cola
Senior Project Manager: Marques Nisely Field Foremen: Andy Lister (early); Rich Staples
Fabrication Foreman: Tyler Ranes
Approximately 1,300 ft. of fabricated handrail
Approximately 6,000 fabrication hours and 3,700 field hours
More than 377,000 lbs. of steel processed
Nearly 400 gallons of paint/ paint thinner used
“Working closely with other contractors at the Coca-Cola plant, we had lots of planning and scheduling to work through daily.”
After the heavy lifting there was still plenty to do in the fab shop.
Painting all of it was another challenge. Nearly 400 gallons of paint and paint thinner were used in total.
“We had to get creative by making our paint space a little bigger,” Marques said. “The fabrication team worked night shifts and 20-hour days. They did a great job utilizing the space at the Haskell fab shop, as well as creating some space in our new North Lawrence shop.”
When the fabrication team, led by Millwright Foreman Tyler Ranes, found out just how much painting the project would entail, they made the necessary adjustments to ensure on-time delivery.
“One of the main challenges we encountered during this project was maintaining organization and ensuring consistent quality standards between the two fabrication shops,” Tyler said. (continued)
“To address this, we implemented daily completion checklists and QA/ QC forms, which were essential for tracking progress and maintaining project specifications. These tools played a critical role in ensuring the project was completed efficiently and to our high standards.”
Marques says the guys in the field and the shop were the reason the project went so well.
“The guys did a great job working through the challenges – it was the largest mezzanine we’ve installed, and the most paint we have ever used on a project,” he said.
Most of the fabrication and install was executed July-August of 2024, with the main part of the mezzanine completed in September.
The total project took 6,000 fabrication hours and 3,700 field hours to complete, and the team is now working on completing change orders.
“It was a fun and exciting project, and we enjoyed the challenges it brought because it helped us get outside our normal wheelhouse and learn new ways to overcome,” Rich added.
Marques notes that in addition to the change orders, the Millwrights continue to receive new opportunities due to the excellent performance and professionalism of the team.
Congratulations to our Millwright field and fabrication rock stars!
“We implemented daily completion checklists and QA/QC forms, which were essential for tracking progress and maintaining project specifications. These tools played a critical role to ensure the project was completed efficiently and to our high standards.”
-Tyler Ranes, Millwright Foreman/Fabrication
AKIN
BRUCE BELCHER
MASON HILGENKAMP
SHANA WALLACE
KALEB YOUNG
KALE KRUM
MARK MCGLONE
JAKE GARDNER
COLE JENKINS
BOBBY SHANDS
KEELAN DAVIS
ZACHARY JOHNSON
KALEN LESPERANCE
RONALD ROETTGEN
VINCENT VEGA 4
MIKE GORDY
KAYLA HICKS
CADEN MARTINEZ
HAROLD MUMPOWER
JASON ECK
JEFFREY RATHBONE
JEREMY AVERSMAN
JOHN COBB
KERRY AYRES
VICTOR HANLEY
STEVE OTTER
7 TYLER BRENN
CODY STEINER
HARRISON HUBBARD
DUSTIN MCDONALD
TAYLOR TEETERS
JEFF WELLS
8 KEVIN CARPENTIERE
FELIX ALBINO
BRYAN BARROW
MEGAN BERRY
NATHAN LITTLEJOHN
KELLY MCBRIDE 9 DEREK WOODS
JOE SORRELLI
BRYAN BEACH
JAYDEN HERNANDEZ
TROY WILSON
10 ED FITZWATER
KYLE BABCOCK
BRYAN PRICE
PERLIE TREVINO
11
MATTHEW STRANATHAN
COLE RAYMOND
JACOB BRAMBLE
MONTANA LEONARD
ED LONGSTAFF
MICHAEL WEISBENDER
12
13
14
CLINTON GECHTER
VERNON BROOKS
GEORGE DEDRICK
CHRISTOPHER WILLIS
BLAKE MARTIN
AARON CURRENCE
CHERIE NICHOLS
KEITH STANSBERRY
KARLEY PEARL
KRISTI BROWN
AARON CAMPBELL
GEOFF COLLINS
LOWELL SHORT 15 AUSTIN WIEBLER
AARON BUDGETT
DAMON FLOURNOY 16
LUCAS SLOAN
BRANDON FINLEY
RUBEN AMADOR
GREGORY DURANT
CARSON LUTZ
DYLAN SPARKS
JAMES
O’BRIEN
YARBOROUGH
AARON JANUS
JERRETT PENCE
THOMAS CARDER
RYAN DOWELL
JASON ESPELAND
IVAN KOLOSIEJ
DIANA KORBE
BAKER LALLY
ERIK RONEY
THOMAS SMILEY
KATHLEEN SMITH
TRISTAN STICKLEY
NICK JONES
ANDRES CABRAL-MALDONADO
CHAVEZ
MCCONNELL
KESSLER
MEDINA
MOBERG LINDSEY PATRICK
RICHARDS-ST CLAIR MITCH CAMPBELL
LASSITER
BOXBERGER JARED BRADEN PARKER CORNELIUS
KELLER JASON KOELZER KENNY LIEFFRING
SAVEA
BRYANT MATT DAMON
BLAKE DENKERS HAYLEY LEONARD
OSHEL
JOSEPH ELDER
HINES JUSTIN SOREM
GRAHAM DAVE BEEBE PAM FRAZEY
KALEB LEMEN
MATTHEW BELT
JOSHUA KING
NOAH NOCE
SUSANNE BLAUKAT
TUCKER AUSTIN
THOMAS COULTER
BLAKE WINGERT 28 KASEY O’CONNOR
TERRY JENKINS
SEAN HAWKINS
WILLIAM BENAKA
PETE DOWD
COOPER JONES
TODD MIHALCHIK
RENNOLDZ SOARES 29 CLINTON CALHOUN
5 YEARS: ERIC WOODS, TOM SPARKS, PARKER CORNELIUS, SUSAN WATSON, CHRISTIAN SMOOT
10 YEARS: BEN GANNAWAY
Anna Schnacker has been with P1 Service for less than two years, and she’s already moving up, forging a path to success at age 23.
Anna started as an HR Coordinator, and was recently promoted to HR Generalist in May of 2024. The promotion came as she was completing her master’s degree in business administration.
Like many college students, Anna didn’t stick to her original career plan.
She considered both journalism and bakery science, neither of which ended up being the right fit.
“Before even stepping on campus, I changed my study focus from journalism to bakery science in the School of Agriculture,” Anna said. “But studying the layers of a wheat kernel in the Introduction to Grain Science class made me think, maybe this was a mistake!”
An elective course in entrepreneurship got Anna interested in business.
“I always thought people chose business as a major because they didn’t know what they wanted to do, and I didn’t want to be that person,” she recalled.
“Then I discovered that I was genuinely enjoying business classes, so I changed my major to business,” Anna said.
Associate Profile on P1 Service Human Resources Generalist Anna
While working on her bachelor’s degree, she took an internship with Yellow Freight, where she specialized in FMLA (Family Medical Leave Act) cases.
“It was during COVID, so I got a lot of experience,” she said. “It turned out to be the catalyst for deciding I wanted to take the Human Resources path for my career.”
Anna finished her degree in three years, earning a Bachelor of Science in Business Administration with an emphasis in human resources and a minor in entrepreneurship.
University gave her more HR experience, and she finished her bachelor’s and started working towards a master’s.
to move away from the college town, so I moved to the KC area.”
with Yellow Freight,
Celebrating graduation
“What’s nice about HR is you can stay in HR without having to stay in the same role.”
-Anna Schnacker
Working in HR is one of the best way to support employees, as a liaison between the employee and the company.
-Anna Schnacker
Anna saw a post for an HR coordinator with P1 Service, and thought it might be a good fit.
So far, it has been.
“What's nice about HR is you can stay in HR without having to stay in the same role,” Anna said.
“There are so many different avenues, so if you decide you need a new challenge, there is another area you can try. There are also many levels available for promotion, so I can keep learning and advancing in my career.”
Anna says she enjoys the challenges that being in HR brings, but her favorite part is being able to help other employees in the company.
“I ultimately ended up choosing HR because I like working directly with people,” she said.
“Working in HR is one of the best way to support employees, as a liaison between the employee and the company.”
During her full time tenure at P1, Anna completed her master’s degree in December of 2024.
“I am thrilled to have a master’s in business administration, and look forward to continuing a long and rewarding career in Human Resources.”
In her free time, Anna likes to read and hang out with her 25 lb. cat Apollo. She has recently started sewing, completing a quilt and Christmas tree skirt this past year.
She has also become interested in traveling, and took her first trip abroad last year, visiting Lisbon (Portugal), and Barcelona (Spain). She is currently planning a trip to London (England) and Copenhagen (Denmark) this year.
Nacional d’At de Catalunya
Young artists from across our P1 families competed for a spot in the colorful 2025 Safety Calendar. Look for the calendars in your office or on your desk! Winning entries were selected, making up the “12 months of safety” + cover art. Here are a few highlights, with a full list of this year’s winners.
Cover: Liam Kittle, 14 (Zach Kittle)
January: MaKenna McDonald, 8 (Jeff McDonald)
February: Macey Bishop, 12 (JD Bishop)
March: Grayson Kittle, 12 (Zach Kittle)
April: Elise Goodwin, 12 (Jessica Goodwin)
May: Skylynn Harris, 9 (Victoria Walkowiak)
June: Jessina Price, 10 (Nesha Board)
July: Melanie Denkers, 13 (Blake Denkers)
August: Braden Hollis, 14 (Steven Hollis)
September: Charlie Bugg, 7 (Kayla Hicks)
October: Kaydi Klamert, 13 (Mike Myers)
November: Layken Luthi, 9 (Zac Luthi)
December: Kendall Spresser, 10 (Danae Damon)
P1 Pop-up Store Helps Feeding America: The fall pop-up store sponsored by P1 generated $650 in donation funds for Feeding America. P1 matched that amount for a total donation of $1,300. Thank you to those who purchased from the store! Feeding America is a nationwide network of more than 200 food banks that feed more than 46 million people through food pantries, soup kitchens, shelters, and other community-based agencies.
SMG Recognizes P1 Commitment to Safety Culture: The P1 team working at Elanco was recently recognized for safety excellence by SMG (Safety Management Group), the company hired to oversee all construction safety at a current Elanco jobsite. Foreman Zach Rever was given the award in the form of a gift card to a local restaurant. According to P1’s contact with SMG, he was impressed with the detail in P1’s pre-task analysis (PTA) – the equivalent of the “SOI/Stop. Observe. Implement. checklist” - especially the fact every crew member could tell him what was on it. He also noted that on several occasions, P1 associates approached him to ask the best way to safely access areas in a crowded ceiling. P1 would also stop work and add to the PTA/SOI before beginning unforeseen changes. “We earned this award by simply getting all our employees to buy into P1’s safety culture,” Zach said. “We never allow a schedule or production to get in the way of working safely. For P1, this is nothing above and beyond our safety standards, we just hold ourselves to a higher standard than many other contractors.”
Safety QR Code: Safety has created a QR code that links immediately to a list of P1 Safety and Fleet contacts. The QR code is placed on the SOI checklist, hard hats, and other accessible areas of job sites. Associates are encouraged to call any time, day or night, if there is an issue or incident.