FLSMIDTH
Trailblazing comminution that doesn’t cost the Earth, we speak with Oscar Malpica, CEO and co-Founder of the Canadian mining innovator, Rockburst Technologies
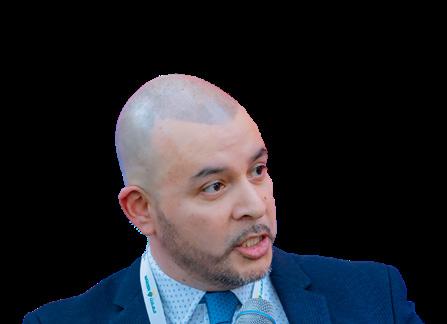

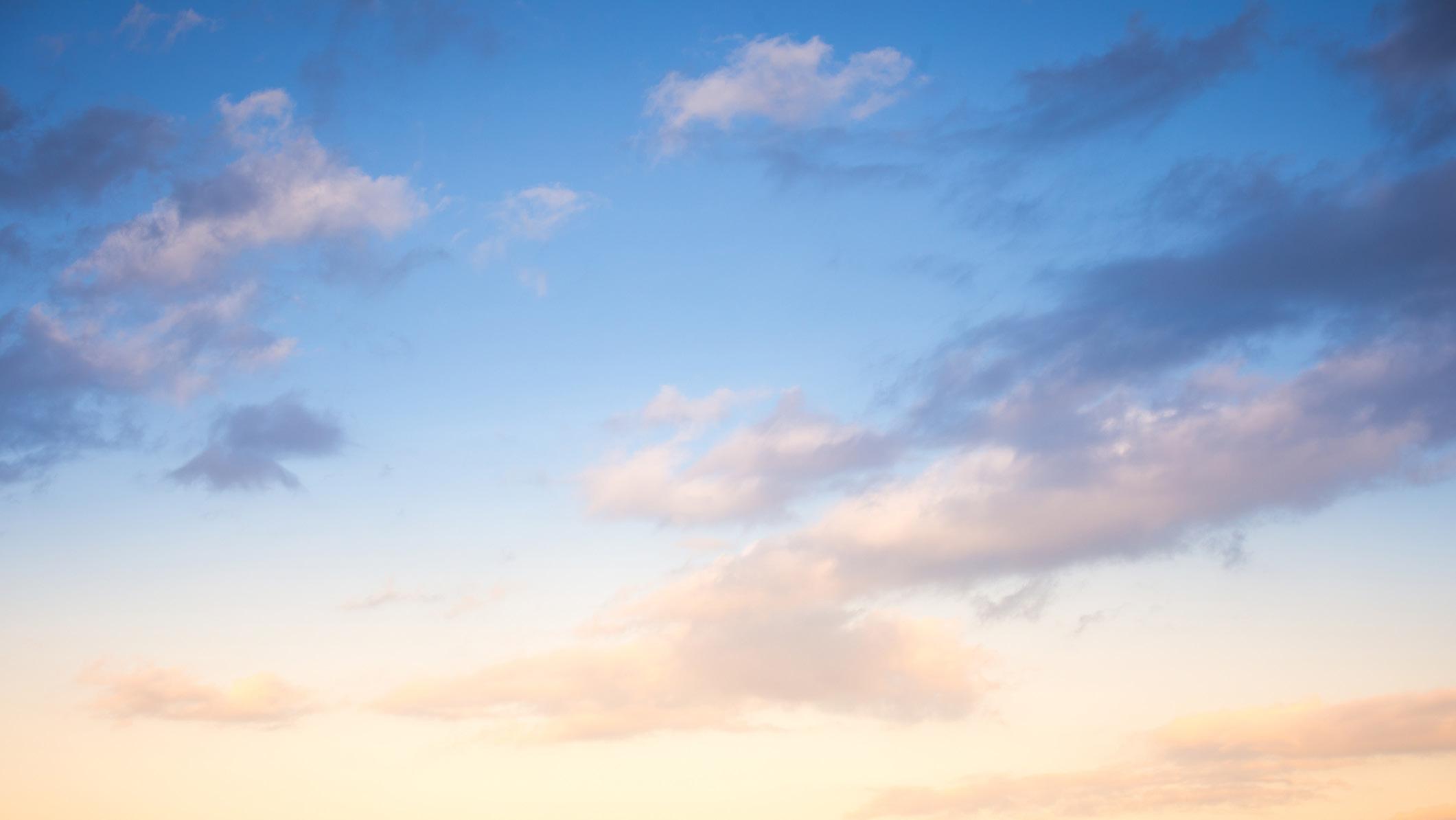

Trailblazing comminution that doesn’t cost the Earth, we speak with Oscar Malpica, CEO and co-Founder of the Canadian mining innovator, Rockburst Technologies
For over a decade, our portfolio of in-house magazines has been lovingly produced, printed, and distributed to our esteemed subscribers across the globe from our headquarters in the UK.
But now we are moving with the times, adopting a digital-first approach by producing online-only publications. A major factor in this decision is to minimise our environmental footprint, reducing the carbon emissions involved in the logistics of print magazine distribution and the resources required therein.
“We always planned that when our digital subscribers consistently accounted for 85% of our total magazine subscribers, we would cease printing our publications in-line with our environmental and sustainability goals.”
Going forward, we will provide print orders of any magazine in-line with the requests of our featured companies, subscribers, and conference & expo partners.
Please get in touch for a print-on-demand quote or visit our website to find out more.
– Ben Weaver, CEO, Outlook Publishing Ltd
EDITORIAL
Editorial Director: Phoebe Harper phoebe.harper@outlookpublishing.com
Senior Editor: Marcus Kääpä marcus.kaapa@outlookpublishing.com
Editor: Jack Salter jack.salter@outlookpublishing.com
Editor: Lucy Pilgrim lucy.pilgrim@outlookpublishing.com
Junior Editor: Ed Budds ed.budds@outlookpublishing.com
Junior Editor: Rachel Carr rachel.carr@outlookpublishing.com
PRODUCTION
Production Director: Stephen Giles steve.giles@outlookpublishing.com
Senior Designer: Devon Collins devon.collins@outlookpublishing.com
Designer: Sophs Forte sophs.forte@outlookpublishing.com
Junior Designer: Louisa Martin louisa.martin@outlookpublishing.com
Production Assistant: Megan Cooke megan.cooke@outlookpublishing.com
Digital Marketing Manager: Fox Tucker fox.tucker@outlookpublishing.com
Social Media Executive: Bria Clarke bria.clarke@outlookpublishing.com
Web Editor: Oliver Shrouder oliver.shrouder@outlookpublishing.com
BUSINESS CEO: Ben Weaver ben.weaver@outlookpublishing.com
Managing Director: James Mitchell james.mitchell@outlookpublishing.com
Sales Director: Nick Norris nick.norris@outlookpublishing.com
Regional Director: Joshua Mann joshua.mann@outlookpublishing.com
TRAINING & DEVELOPMENT MANAGER
Marvin Iseghehi marvin.Iseghehi@outlookpublishing.com
BUSINESS DEVELOPMENT DIRECTOR
Thomas Arnold thomas.arnold@outlookpublishing.com
HEADS OF PROJECTS
Callam Waller callam.waller@outlookpublishing.com
Deane Anderton deane.anderton@outlookpublishing.com
Eddie Clinton eddie.clinton@outlookpublishing.com
Josh Hyland josh.hyland@outlookpublishing.com
Ryan Gray ryan.gray@outlookpublishing.com
PROJECT MANAGERS
SALES MANAGERS
SALES & PARTNERSHIPS MANAGER
Donovan Smith donovan.smith@outlookpublishing.com
Alfie Wilson alfie.wilson@outlookpublishing.com
Krisha Canlas krisha.canlas@outlookpublishing.com
ADMINISTRATION
Finance Director: Suzanne Welsh suzanne.welsh@outlookpublishing.com
Finance Assistant: Suzie Kittle suzie.kittle@outlookpublishing.com
Finance Assistant: Victoria McAllister victoria.mcallister@outlookpublishing.com
CONTACT
Mining Outlook
First Floor, Norvic House, 29-33 Chapelfield Road
Norwich, NR2 1RP, United Kingdom.
Sales: +44 (0) 1603 363 631
Editorial: +44 (0) 1603 363 655
SUBSCRIPTIONS
Tel: +44 (0) 1603 363 655
phoebe.harper@outlookpublishing.com www.mining-outlook.com
Like us on Facebook: facebook.com/miningoutlook Follow us on Twitter: @MiningOutlook
Did you know, that to enable the transition towards a net zero society, we need the same amount of copper in the next 40 years as we have mined in the history of humankind? And that we will need three times as much lithium than what is currently being explored? It is an indisputable reality that the mining industry is the bedrock on which the clean energy future that we all envision rests.
Welcome to our second edition of Mining Outlook magazine. This issue, we’re foregrounding responsible mining as the topical issue which the global sector must adhere to or face the consequences of falling behind.
As an early adopter of responsible mining, our cover star, FLSmidth, positions itself as the ultimate enabler by facilitating other mining companies on their journeys to comply with the industry’s carbon neutrality targets by 2050. In an exclusive interview with members of the FLSmidth executive team, we delve into the company’s unsurpassed portfolio as it advances its ‘MissionZero’ initiative, which was set out way ahead of the curve in 2019. This culminates in the company’s ultimate vision of the MissionZero Mine, a concept that is elegantly defined by FLSmidth’s APAC President, Jason Elks, as, “a global example in the art of the possible.”
Pursuing an equally groundbreaking vision – in the most literal sense – we showcase the newcomers on the block, Rockburst Technologies – as the Canadian innovation start-up proposing comminution technology that is set to slash two percent of the world’s electricity consumption. CEO and co-Founder, Oscar Malpica, explains the advantage of using carbon dioxide within a closed loop circuit to blast rock more efficiently.
Elsewhere, this issue presents a host of corporate stories from some of the most exciting players in mining from around the globe, including Ravenswood Gold, Tietto Minerals, Storm Mountain Diamonds, and Bowen Coking Coal.
We hope that you enjoy your read.
Phoebe Harper Editorial Director, Outlook Publishing6 NEWS
Around the mining sector in seven stories
8 EXPERT EYE
Enhancing the value chain through digital transformation
INDUSTRY INSIGHTS
10 Quickfire Q&A
Helder Santos, dss+
12 Explosive Innovation
Comminution that doesn’t cost the Earth
TOPICAL FOCUS
1 6 Keeping the Mining
Workforce Safe
Protecting people in one of the world’s most dangerous industries
EVENTS
154 AIMEX
Australia’s longest-running mining event
82
114 Howden
Pioneering
122
Laying the Tracks of the Cargo Corridor Setting the benchmark for logistics solutions in Southern Africa
134 Storm Mountain Diamonds
Pinks Amid the Peaks
144
WORLD-LEADING UNDERGROUND MINING company, Aramine, has announced the opening of its newest subsidiary in Poland.
After operating in the industry for 45 years, Aramine’s expansion follows its previous subsidiaries in Mexico, Niger, Burkina Faso, and Armenia, with Poland representing the beginning of the company’s European strategy. Thus, the company is focused on meeting the demands and proximity of an international customer base.
AUSTRALIAN GOLD PRODUCER Bellevue Gold Ltd has secured the final permits for its namesake project based in Western Australia (WA).
The Australian Department of Water and Environmental Regulation has granted the company’s tailings facility and water storage permits, meaning the Bellevue Gold Project
RECENT WILDFIRES IN Canada’s provinces of Quebec and Labrador have forced mining activities to halt. In the face of over 160 forest fires, mining companies operating in the regions have turned to evacuate employees while pausing exploration work.
Osisko Mining, the owner of the Windfall gold project in the
in the region is now fully permitted, drawing the company closer to minting its first gold bar from the site this year.
The announcement is a key achievement for Bellevue Gold Ltd, and the company is set for commissioning and operation, ready to deliver carbon-neutral gold foreseen to attract a premium price.
On top of building its presence in Europe, Aramine Poland will carry the innovative and technical strengths of the company while also creating jobs in the local area. The subsidiary will be led by Piotr Bakowski, a mining expert with almost two decades of industry experience and in-depth knowledge of the Polish mining market.
Eeyou Istchee James Bay region of Quebec, has suspended activities, and withdrawn its workforce while
continuing to monitor the situation. Similarly, Patriot Battery Metals, which operates a lithium project in the same area, has halted its drilling and exploration operations in light of the wildfires.
The fires have so far cut off transport networks between Quebec and Labrador (West), causing damage to digital and communications infrastructure and continue to rage with 145 considered out of control.
Around the mining sector in seven stories
MINING INDUSTRY GIANT BHP states that it has underpaid current and former workers for 13 years, while 28,500 employees are said to have received less holiday than entitled, as well as 400 workers not receiving additional allowances, according to a review conducted by the company.
MULTINATIONAL MINING
COMPANY
Anglo American plc, has reported its latest valuation of rough diamond sales for De Beers’ fourth sales cycle this year.
It has been announced that De Beers, an international name in diamond mining and exploitation, industrial diamond manufacturing, and diamond retail and trading, of which
THE PORTUGUESE ENVIRONMENTAL regulator, Agência Portuguesa do Ambiente (APA), has issued a Positive Declaration of Environmental Impact (DIA) to Savannah, the European lithium development company, in light of the firm’s Barroso Lithium Project in northern Portugal.
The declaration was given as a result of the project’s optimisation and revised design that was based on stakeholder feedback aimed to minimise environmental impact. This stands as a significant milestone for Savannah, and the first positive DIA regarding raw lithium supply in the country, that collaboratively advances
Anglo American plc is the majority shareholder, boasted rough diamond sales of approximately USD$480 million. However, the number is subject to final completed sales.
According to Al Cook, CEO of De Beers, the company’s rough diamond sales saw a small decrease from its previous sales cycle following the industry entering a seasonally quieter period, as well as other international market factors.
This error caused some of the impacted employees to receive leave deductions on public holidays, with the average worker owed six days of annual leave. BHP has reported the findings to the authorities, as the incident costed the firm up to USD$280 million before taxes.
In an apologetic statement, BHP’s Australia president Geraldine Slattery said: “We are sorry to all current and former employees impacted by these errors. This is not good enough and falls short of the standards we expect at BHP.”
European environmental, social and governance (ESG) practices.
Following this positive development, the Barroso Lithium Project can move forward to the next stage of the environmental licensing process (RECAPE).
RIO TINTO’S OPERATIONS in Boron, California have successfully transitioned from fossil fuels to renewable diesel to fuel the company’s heavy machinery.
This milestone marks out Rio Tinto’s site as the very first open pit mine on the globe to achieve such a feat, with the transition bringing promising change to company operations. It is estimated that the change will bring about a CO2 equivalent reduction of around 45,000 tonnes per annum (tpa), amounting to approximately 9,600 cars.
Chief Executive, Sinead Kaufman stated that the site is: “The first open pit mine to operate a fleet running entirely on renewable diesel. This is an excellent example of what happens when internal and external partners collaborate toward a carbon reduction goal.”
To date, the greatest single obstacle to addressing water-related challenges within the scope of the mining sector’s environmental, social and governance (ESG) response has been the almost exclusive focus on carbon emissions using up much of the sector’s ESG bandwidth, drowning out conversations around water.
The problem is exacerbated by the fact that water is a critical resource for all life, and the missteps in the mining sector where issues around extraction, beneficiation and disposal impact geographic areas of both scarce and abundant water resources. Polluting entire water systems can and in most cases does have dire longterm consequences unless adequate solutions to mitigate these disasters are adopted immediately.
Much the same as with carbon emissions, we are running out of time to simply talk about water risk management. The conversation around water is already lagging behind topics of carbon emission reduction, and having acknowledged the issues, we can now move toward finding meaningful, viable and costeffective solutions.
At Acrux Resources, we are con-
scious of our ESG responsibilities and those of our entire industry. That is why we are already thinking – and talking –about water. We believe that technology holds the key, but also that there is no magic wand we can wave to solve the water issue. Instead, we maintain that the answer will be found in taking incremental steps – a drop by drop approach to improved water stewardship. These solutions will need to focus on resource efficiency, smarter usage and water preservation.
By achieving, or at least coming closer to, these three goals, mining companies can do a great deal of good. Not only will they boost their own ESG scorecards, thereby attracting investment, but they can also help to reposition the entire mining sector towards a more sustainable trajectory.
Negative perceptions around mining must be weighed against the fact that the sector plays a vital role in the transition to a low-carbon economy through the metals and minerals that it produces. Becoming water stewards is therefore essential and will involve increased awareness of the downstream impacts of water extraction, use and effluent disposal. Improved efficiencies in the
circular use of water could well play a role in repurposing and reusing water. In addition, avoiding further contamination by protecting existing sources, reducing mine tailings and tailings dam seepage and the risk of tailings dam failure while investing in technology or innovations that do not use water are some of the possible solutions to adopt.
At Acrux Resources, we believe that it is our collective responsibility as the mining industry to set a replicable model of global good practice standards in water stewardship. The scale of mining’s water problem does have at least one advantage: it gives the sector the opportunity to be proactive and to take the lead on the movement to protect our most precious resource. In taking the lead, we can authentically reposition mining as a water-positive industry, thereby helping to avoid environmental liabilities, reputational damage and the diminution of social license to operate. In essence, mines must be not merely water users but water stewards.
As the first port of call, we need to reduce the sector’s dependence on water. This will necessitate focusing on the thirstiest mining processes, specifically ore processing, which accounts for some 90 percent of the waste-stream mass. Urgent measures are also needed to mitigate the most significant threats to water, for
“NEGATIVE PERCEPTIONS AROUND MINING MUST BE WEIGHED AGAINST THE FACT THAT THE SECTOR PLAYS A VITAL ROLE IN THE TRANSITION TO A LOW-CARBON ECONOMY THROUGH THE METALS AND MINERALS THAT IT PRODUCES. BECOMING WATER STEWARDS IS THEREFORE ESSENTIAL AND WILL INVOLVE INCREASED AWARENESS OF THE DOWNSTREAM IMPACTS OF WATER EXTRACTION, USE AND EFFLUENT DISPOSAL”
– SEAN BROWNE, EXECUTIVE DIRECTOR, ACRUX RESOURCESexample, by reducing tailings and the risk of tailings dam seepage and failures.
Again, this is where we believe that innovative technology can make a material difference. By employing dry sorting techniques, the industry has the ability to extract greater value from tailings. Attributing greater value to tailings will incentivise finding disposal methods other than on-site accumulation, which comes with multiple water-management risks.
Mining has made an outsized contribution to the problem; but now, as an industry, we must step up and lead the development of solutions. Our portfolio company, Acrux Sorting Technology (AST) has developed and successfully deployed dry sorting technology solutions that use multiple sensors to accurately process and retrieve economic mineral from both low grade discard dumps and run-ofmine ore flows.
Mineral sorting and processing usually account for much of the water usage in mining operations, but dry
sorting technologies such as those offered by AST are one of the single most impactful ways to address high water consumption, by reducing water in this process entirely.
A major obstacle to improved ESG impacts has been limited access to funds and resources. AST enables resource owners to sidestep this hurdle by offering a fully-funded dry ore sorting solution. The AST model has proven to reduce water usage without the need for capital investment.
Not only do AST’s solutions deliver cost-free water usage reduction, but
they help resource owners extract maximum value from their mineral resources, thus creating a more environmentally and economically sound operation.
This is the holy grail of mining: improved ESG impact plus an increase in saleable product. Historically, these two outcomes have been mutually exclusive. The positive ESG impacts of AST’s solutions extend beyond more responsible water management to a reduction in carbon emissions (which will always be part of the ESG conversation) and a reduction in tailings generation. This last outcome can in turn mitigate water-related risks.
At Acrux Resources, we are throwing down the gauntlet of water risk management to the entire mining industry, in South Africa and beyond. We have given examples of technological fixes that can reduce water consumption and prevent contaminated water entering the environment. These solutions not only enhance ESG impact, but actually improve the profitability of mining operations.
Never before have we had a more urgent need to manage water more effectively, nor a more compelling economic case for doing so. Will you join us in talking about water – and
Sean Browne is an Executive Director at Acrux Resources with 19 years’ experience in investment banking, commodity derivative sales, structuring and trading, FX and rates trading, debt capital markets, structured mining finance and deal origination. Browne has worked at Deutsche Bank, Standard Bank of South Africa and Standard Chartered Bank. He holds a BA in Law and English and a Postgraduate diploma in Finance, Banking and Investment Management.
www.acruxresources.co.za
As the leading provider of operations management consulting services with the purpose of saving lives and creating a sustainable future, dss+ enables businesses to build organisational and human capabilities, manage risk, improve operations, achieve sustainability goals and operate more responsibly.
By leveraging its deep industry and management expertise and diverse team, dss+ consultants are on the ground and in the boardroom helping clients work safer, smarter and with purpose.
dss+ was one of the associate sponsors at this year’s Mining Indaba, where the company presented a range of expert insights throughout the event. We speak to Helder Santos, Mining and Metals Director for Europe, the Middle East and Africa, about this exciting occasion and the company’s viewpoint on current industry trends.
Mining Outlook (MO): What did it mean for the company to be one of the associate sponsors of the Mining Indaba event?
we have long been involved with investing in African Mining Indaba. We believe that the event is not only a rare opportunity for the mining industry, government and private sector to come together to share ideas, but also a way to expedite progress in the sector. This is needed more than ever at the moment as the sector faces global challenges of volatility, economic uncertainty and climate change. Given our global footprint in the mining industry, we believe that sharing our views and lessons learned from the challenges companies are facing in Africa, as well as best practices across the world, will benefit the industry as a whole.
MO: How can the Mining Indaba bring value to the business?
HS: For us, the Mining Indaba is always about connecting with our network and industry professionals in a space that allows us to take a step back from daily operational tasks, learn from each other, and envision future solutions. At this year’s event, we focused on a number of important discussions about the future of resilient, sustainable mining, and
what it might look like as the sector prepares to address the demand for more metals and minerals to meet the needs of the energy transition.
MO: Is it rewarding to be involved in delivering enhanced operational practices to so many people across different workplaces?
HS: As a business, we exist to save lives and create a more sustainable future, so helping mining and metals organisations enhance their operations to enable both safer working environments and increased efficiency is at the heart of what we do. We are increasingly finding that an integrated risk management approach focusing on operational risks, efficiency and sustainability is the best way to help operations lay the groundwork for future prosperity, and a critical aspect to ensure the move of the industry into sustainable mining.
MO: What vital insights did the company deliver at the event?
HS: As a team, we took part in four important discussions that linked
– HELDER SANTOS, MINING AND METALS DIRECTOR FOR EUROPE, MIDDLE EAST AND AFRICA, DSS +
essential issues of employee and community safety, and environmental sustainability. The sessions that our team participated in include:
• From intent to impact – how to activate the journey towards sustainable mining of the future
• Security of supply – threat or opportunity in Africa’s metals and minerals supercycle context?
• Mining and the circular economy
• Tailings, safety and mining’s ‘zero harm’ approach: are people and communities being prioritised and what frameworks are in place to assure transparency?
MO: How do you assess the future of mining in Africa?
HS: We believe that there is a great opportunity for the future of mining in Africa – there will be significant demand for minerals and metals that not only meet growing energy transition needs but also increased imperative to extract these resources in a sustainable and ethical way. Within these new ways of operating, there are significant opportunities to reduce costs and increase income streams, through energy efficiency
and utilising by-products through circular economy programmes, by reducing waste in any form or shape across the full value chain, for example. We believe that if companies lay the foundations now for safe, efficient and sustainable operations, they can leverage these opportunities well into the future.
“AS A BUSINESS, WE EXIST TO SAVE LIVES AND CREATE A MORE SUSTAINABLE FUTURE”
On course to slash two percent of the world’s electricity consumption through its unique comminution technology, we dig deep with the company breaking new ground in mining – Rockburst Technologies
Writer: Phoebe Harper
Did you know that comminution – the process of rock breakage in mining to liberate valuable minerals – currently accounts for between three to four percent of global energy consumption? Startlingly, this process stands out as the largest energy consumer of all facets of the mining industry across milling, smelting and refining.
In the context of Canada, the home of mining innovation company Rockburst Technologies (Rockburst), this equates to a staggering 17 percent of the national electricity consumption exclusively being
used to break rock. For Rockburst’s team led by Oscar Malpica, CEO and co-Founder, this mining energy dilemma called for a solution.
“Comminution is a huge energy hog and a major cost. By extension, it’s also a significant contributor to greenhouse gas (GHG) emissions,” he introduces.
When Natural Resources Canada proposed an open innovation challenge to the public in 2019 with the target of decreasing energy consumption in mining by 20 percent or more, Malpica and his business partners Cliff Edwards and Chuck
Lee, knew they had an answer based on the idea of using CO2 to blast rock from within. As a result, Rockburst was born.
“At the time, this was just a concept, but we were lucky enough to be selected as one of the finalists and we received the initial financial support to build a prototype,” he recounts. Proving the viability of the Rockburst model, it was quickly established that using gas as opposed to mechanical means minimised energy consumption considerably.
“We have now evolved our technology to a point where it’s still
in an experimental stage and not yet commercial. However, we are already showing early evidence of energy savings of up to 89 percent, compared to traditional comminution methods currently being used in the mining industry,” shares Malpica.
Rockburst’s flagship comminution process is referred to as transcritical CO2 pulverisation (tCO2) technology. tCO2 promotes tensile breakage by fracturing rock from within, using CO2 as the working fluid to achieve a grinding process within a closedloop, pressurised vessel. Under certain thermodynamic variations of temperature and pressure, the CO2 penetrates the rock pores and results in tensile pulverisation as the gas expands after it is released.
“We know that rock is 10 times weaker under tension than it is under compression, and that it is simply easier to break rock from within rather than the external forces that the industry exclusively relies on,” Malpica elaborates. “As a result, right off the bat, we’re taking advantage of a lower energy threshold.”
Since the CO2 is used within a closed-loop cycle, tCO2 brings not only energy savings but also “tremendous” decarbonisation potential. A source of major excitement for the Rockburst team was revealed recently in experiments that proved the potential for carbon sequestration in certain ores, accelerating carbon mineralisation as the gas is permanently locked away in waste streams.
The third key advantage of the tCO2 process is how it negates the need for any traditional grinding media, such as steel rods, balls or liners.
“The grinding media used in current comminution needs to be changed every so often, which translates to more operational expenditure. With tCO2 you’re not only saving costs,
“THE ELEGANCE OF OUR SOLUTION IS THAT WE’RE BREAKING ROCK FROM WITHIN – THAT’S THE FIRST LEVER IN TERMS OF OUR COMPETITIVE ADVANTAGE IN USING LESS ENERGY”
– OSCAR MALPICA, CEO AND CO-FOUNDER, ROCKBURST TECHNOLOGIES
but also energy, since you no longer need to move those mechanical parts within your process. This also applies to ancillary GHG emissions, as you don’t need to produce the grinding media in the first place,” he explains.
Looking ahead, Malpica sets out a clear strategy for Rockburst’s ambitions with two key streams defining the future evolution of tCO2.
“Firstly, we are running the experimental stream whereby we are analysing which types of rock are the most susceptible to our technology and under what conditions as we investigate the right parameters of our process.
“The second stream which we are working on in parallel, is the pilot stream. This involves building a demonstration plant where we can work on the engineering involved in
scaling this technology to industrial sizes,” he shares.
To achieve this ambition, Rockburst has an ongoing fundraising campaign which aims to raise approximately USD$10 million over the next three years to develop the two streams.
“To build our pilot demonstration plant, we are currently reaching out to large international mining companies that are looking to adopt new technologies,” Malpica tells us.
As a new, breakthrough technology with proven potential and major ambitions, a significant amount of capital is inevitably required if tCO2 is to realise its full effect across the global mining industry. But for Malpica, the outlook is optimistic as all mining players are awakening to the need for environmentally friendly processes.
“Although we’re still in the technology development phase, many mining companies are
interested in what’s around the corner in terms of next-generation mining equipment, as the whole world looks towards the race to net zero for 2050,” he says.
“Everyone is trying to figure out ways of decarbonising the industry, but we want to electrify the future – moving from fossil fuels to electrification and clean energies. To do this, you need more minerals, especially copper and lithium, which obviously demands more mining production.
“It’s a total oxymoron if that production simply creates more pollution. To meet the future demands of those industrial processes, you need clean technologies such as ours.”
Watch this space.
Incredible work has been done across the global mining industry to improve safety standards for workers. The CDC, through the National Institute for Occupational Safety and Health (NIOSH), has kept records on US mining injuries and fatalities since 1983, and the fatality rate per 100,000 equivalent full time employees has thankfully fallen dramatically between then and now. Despite this progress, mining is still considered one of the most demanding and dangerous work environments, with the third highest fatality rate of any industry, creating a challenge for organisations to provide reassurance to workers and to recruit the highly skilled staff
needed to operate efficiently under ever-increasing demand.
Each worksite presents its own unique set of obstacles and threats, and requires investment in a specialist tailored approach based on the specific circumstances to deliver exceptional healthcare and health and safety practice. At RMI our specialist teams develop and deliver bespoke health and medical services, from risk assessments to permanent on-site medical teams, to hazardous client work sites across the world.
Managing an occupational health programme can be challenging within the mining industry due to
Natalie Henley, Sales Associate at RMI, explores best practice in protecting the workforce of one of the world’s most dangerous industries
the remoteness and demanding nature of the work. The requirement for workers to be in good physical condition is crucial to efficient operations and therefore ensuring each staff member has obtained medical clearance before starting work can create high administrative demands on an organisation and push
it beyond its domain of expertise. To manage this demand organisations can implement an occupational health service to minimise the risk of medical issues causing operational delays. RMI has for many years offered outsourced support to mining companies, including travel vaccine administration, physical examinations,
health history assessments, drug alcohol testing to clinical laboratory testing, among other services.
Our medical facilities, which can be temporarily or permanently integrated into a site, or operate in mobile structures, offer care for both occupational and non-occupational injuries and illnesses, together with
“AT RMI OUR SPECIALIST TEAMS DEVELOP AND DELIVER BESPOKE HEALTH AND MEDICAL SERVICES, FROM RISK ASSESSMENTS TO PERMANENT ON-SITE MEDICAL TEAMS, TO HAZARDOUS CLIENT WORK SITES ACROSS THE WORLD”
– NATALIE HENLEY, SALES ASSOCIATE, RMI
RMI delivers technical, medical and security solutions to companies and governments around the world. The company has offices in the Americas, UK and Africa, and has been recognised six times by Inc. 5000 as one of the fastest-growing companies in the US. RMI works with Fortune 100 corporations and governments.
around-the-clock services providing telemedicine support and case management. This all helps to limit the number of cases that require referral for further off-site medical care, saving time and resources, as well as increasing efficiency by enabling the worker to return to work as soon as possible.
For mining sites, health clinic solutions must be tailored to reflect the physical demands of every site. An on-site clinic should be considered an essential aspect of any project, with the cost-benefit of being able to prevent operational delays due to workforce health issues far outweighing the set up and staffing costs. A clinic is much more than a medic with a first aid kit, in enables advanced procedures be handled on site, and the provision of care through a broader scope of practice. For example, many of RMI’s onsite medics play a vital role in reinforcing healthy lifestyle among workers and ensuring early intervention through patrolling the job site to provide education and training. This can take the form of smoking cessation advice, tailored health awareness campaigns, first aid, and CPR training. This support helps to improve the day-to-day awareness of health and safety practices among
the workforce, reduce the risk of injuries and illness, and ensure that workers feel valued. Without access to a medical clinic available onsite, operators need to ensure that suitable transport options are available for emergency vehicles to both quickly exit and access wherever a member of staff may be, which can be particularly challenging in the tricky terrain. One solution for this is Mobile Treatment Centres (MTCs), four-wheel drive clinics staffed by RMI medics which can move with the site as it expands and changes, allowing our medical staff to provide treatment in the types of remote environments standard emergency vehicles are unable to reach. In addition to a treatment area, storage and hand washing facilities, each MTC is equipped with first aid supplies and emergency response equipment, meaning that our medics are well prepared to respond to any type of medical emergency.
All mining sites, even those located within reach of a hospital, should have a regularly reviewed Medical Emergency Response Plan. This plan outlines the accessible referral facilities and their respective capabilities to treat a wide variety of health emergencies and should
specify how to transport patients to these places, which could be either by road or by air. Clinicians working on site also need to be capable of monitoring unwell patients and liaising with the company’s Topside team of physicians to discuss any concerns, all of which ensures that no time is lost in the event of an emergency medical situation.
Skilled and robust medical and safety support is absolutely essential in enabling safe and cost efficient mining operations, and while progress towards improving safety has been significant having the right support in place to reassure workers can improve recruitment pipelines, as well as make operations more efficient and profitable. Through a partnership with RMI, operators can have medical expertise embedded into their teams, working to reduce the consequences of illness-related absences and confidently tackle the unique challenge of working in remote locations.
MINING OUTLOOK is a quarterly digital publication and media brand showcasing the latest innovations, industry insights and corporate stories from across the international mining and resources sector. Its world-class team collaborates with the biggest and most exciting brands to craft engaging and authoritative content for a global audience of industry players. As mining organisations worldwide confront unprecedented change, embracing technological innovations and incorporating critical environmental sustainability agendas, now more than ever is the time to showcase the strides being taken in this dynamic sector.
The expertise of our in-house design and production teams ensures delivery to the highest standards, as we look to promote the latest in engaging news, industry trends and success stories from the length and breadth of the global mining sector.
As a multi-channel brand, Mining Outlook reaches an international audience through various platforms, with exclusive content distributed through our website, online magazine, social media channels, and bi-weekly newsletter.
Through this compelling venture, we intend to foreground the movers and shakers of the industry. To participate as a featured company and join us in this exciting endeavour, contact one of our Project Managers or our Managing Director, James Mitchell, today.
Uniquely positioned as an early adopter of sustainable mining practices, we foreground the full flowsheet solution provider at the vanguard of an evolving industry. Members of FLSmidth tell us more
We are proud to offer the solutions of tomorrow, for the early adopters of today.”
A giant of the modern mining industry, FLSmidth (FLS) is the full flowsheet technology and service supplier driving sustainable productivity. In terms of both its portfolio and geographical footprint, few can rival its sheer scope and reach with the amount of both plants and equipment captured under the FLS banner.
Indeed, as a global leader in a high number of its total product portfolio, FLS has either equipment or services in practically every major mine site across the APAC region, regardless of the operator.
Although a Danish company with a presence worldwide, this particular geography is a dynamic area of operation for FLS with over 500 technical, services, product development, sales, project management and R&D teams serving the entirety of Australia, whilst also supporting countries such as Papua New Guinea and New Zealand.
For Jason Elks, FLS’ APAC Regional President and orator of the opening statement, it is a region undergoing a “significant transformation”, as the industry navigates a shifting global outlook influenced by the choppy currents of macroeconomic and geopolitical issues, regional instability and high inflationary pressures, all while answering the resounding demand for the green transition and sustainable economies.
“Whether in terms of government policy or resource sector implementation, APAC is a late adopter to the movement,” shares Elks. “However, we have a significant push here because it’s a region where the International Monetary Fund (IMF), the World Bank, and others are more than aware that sustainable mining builds education, healthcare, infrastructure, and essentially develops countries.”
As FLS’ Head of Sustainability, Wouter de Groot acknowledges the shortcomings of the wider industry in articulating mining’s relevance and necessity in driving the transition to net zero.
“As an industry, we haven’t done
Mikko Keto, Group CEO: “We know that we are one of the best in the market for our technology, but when we evaluated our portfolio, we saw gaps that could be filled with acquisitions. HPGR is one such area that is going to become increasingly important as a future technology. As the market leader for HPGR, TK Mining was an obvious choice for us. The company also had other products to advance our sustainability journey including
a very good job in making it visible just how instrumental mining really is,” he admits. The reality is stark and demands action from responsible players.
“To put it simply, to enable a transition towards a net zero society, we need the same amount of copper in the next 40 years as we have mined in the history of humankind, and about three times as much lithium as we are currently exploring,” de Groot continues.
In advancing the green transition of the mining industry, FLS established itself as a frontrunner in the space by taking a stance on accelerating sustainability in 2019 with its MissionZero commitment.
“While we are on an exciting journey with some of our early adopting partners, by and large the industry has not embraced the evolution,” echoes Elks. “FLS is wellpositioned, since for the past five years we have moved in a space that differentiates us as a market leader in innovation for sustainable practices.”
As the hotly anticipated target years of both 2030 and 2050 steadily approach, the pressure is on as mining players must meet escalating demand while remaining current and competitive, or face the consequences of being late adopters with a backlash of taxes, tariffs, and negative community perception.
In this charged environmental context, combined with the industry-specific demands of declining ore grades, cost pressures, and increasing demands on raw materials, FLS stands out as comprehensive solutions provider on hand to meet evolving customer needs.
“Major innovators such as FLS have the products available today to meet the objectives of 2030 and 2050,” Elks attests.
Speaking with FLS Group CEO, Mikko Keto, two core advantages transpire as the company’s most competitive differentiators.
Mikko Keto, Group CEO: “Through evaluating our portfolio, we identified that we add the most value to our customers through our products and technology. We are not an EPCM house – our core competency is technology and integrating it to give our customers a performance guarantee. This led us to exit certain parts of the business under this strategy that didn’t fit with where we add the most value.
“As part of this review, we decided to focus our portfolio on core technology, our products and our aftermarket service. Equally, we want to be the best partner for the full life cycle of a mine, which can last for decades. We provide our technology and support our customers from the mine’s design and build and throughout its life.
“The third pillar of CORE’26 is our sustainability commitment –MissionZero – where we help our customers to reach net zero targets. Within this, we also want to become a leader in environmental, social, governance (ESG), health and safety, and diversity. Our final fourth pillar is performance, since we need healthy financial performance to continue investing in the technology that ultimately supports our customers.”
Supplying all industries in Australia and overseas for over 30 years.
Are you looking for a high-quality engineering company that can provide reliable machining for your plastic parts? Look no further than our team at Polymer Engineering!
With over 30 years of experience in the industry, our skilled engineers and technicians have the expertise and equipment necessary to create precision parts for a variety of applications. We specialise in machining plastic parts for use in industries such as automotive, aerospace, mining, medical, and consumer products.
Our state of the art facilities are equipped with the latest machinery, allowing us to tackle even the most complex projects efficiently and effectively. We are committed to providing our clients with personalised services and flexibility, ensuring that their projects are completed on time and to their exact specifications.
At Polymer Engineering, we pride ourselves on our commitment to excellence and our dedication to customer satisfaction. Whether you’re looking for a custom part or need help with a large-scale production run, we’re here to help. Contact us today to learn more about our services and how we can help your business succeed.
Contact our Sales Team: sales@polymerengineering.net.au www.polymerengineering.net.au
02 9979 8645
Unit 12/No 2 Apollo Street, Warriewood NSW 2102
“Over the years, we have built a position of having the most complete portfolio in the industry, combined with our full flowsheet competency which allows mines to be configured in an optimal way,” he introduces.
As an original equipment manufacturer (OEM), FLS is in a rare position by operating across the entire mining flowsheet, offering its customers a full set of solutions from pit to plant. This comprehensive technological prowess thrives alongside a commitment to driving sustainable productivity that cements FLS’ status as a true industry leader and innovator.
“We see a significant opportunity and believe we have a responsibility to enable the green transition,” comments de Groot.
Running parallel to this core aim is FLS’ unrelenting commitment to delivering quantifiable value over the life cycle of a mine through its core service offering as a partner to its customers. In both sustainability and productivity, Qasim Abrahams, Head of Spare Parts and Aftermarket Service, recognises FLS’ standout strengths.
“Due to our expertise and the technology, we are uniquely equipped and positioned to create this value by increasing asset life and throughput, reducing downtime, and mitigating emissions, energy and water usage through process solutions,” he says.
The process solutions that FLS have developed seek to combat the most environmentally damaging facets of mining, with energy and electricity consumption, comminution, flotation, tailings and water as the problematic areas calling for the most improvement across the flowsheet. By seeking to minimise these contributors as much as possible, FLS preserves essential mining business in a responsible way.
“The global green transition depends on minerals, and to achieve climate targets, we need more commodities and processing plants. Our commitment is to help our customers do that in the most sustainable way possible,” states Keto.
By leveraging its well-advanced expertise and comprehensive product range to drive environmental footprint mitigation, the inception of MissionZero placed FLS firmly ahead of the curve in this regard.
“MissionZero was born from the recognition that we needed to use our expertise to help mining companies meet their targets and move the overall industry to a more sustainable production set up,” says de Groot. This entails a commitment to reaching zero energy waste, water waste and zero emissions by 2030, in line with the wider industry’s pledge for carbon neutrality by 2050.
“FLS will essentially be a shop where any mining operator can find all the competencies, people, and technologies that will enable you to operate with zero emissions by 2030,” he continues.
“Our MissionZero efforts and end to end flowsheet technology for lithium and other battery and critical minerals is at the forefront, but we are also focused on the traditional core and have innovated considerably in gold, copper and iron ore flowsheets to assist and fast track those commodity groups’ achievements for a sustainable future,” adds Elks.
MissionZero’s success is intrinsically bound to the technological solutions designed to enable the fruition of that ambition across the flowsheet.
This is evidenced by FLS’ vision of the MissionZero Mine and its flowsheet of the future which highlights the impact of solutions and optimisations across the mine site. With progress well underway, Elks elegantly describes the future MissionZero Mine as, “a global example in the art of the possible.”
The site leverages key technologies including in-pit crushing and conveying, low impact grinding, coarse flotation, eco-beneficiation, dewatering, tailings management, and digitalisation, all of which combine to keep energy consumption to a minimum.
“At FLS we take a holistic approach to our sustainability solutions to ensure they always have a net positive impact as we work towards our net zero targets,” shares Abrahams.
Such solutions include a market leading high pressure grinding roll (HPGR) - the HPGR Pro - which has been proven to optimise energy efficiency in milling circuits by up to 30 percent.
“WE SEE A SIGNIFICANT OPPORTUNITY AND BELIEVE WE HAVE A RESPONSIBILITY TO ENABLE THE GREEN TRANSITION”
– WOUTER DE GROOT, HEAD OF SUSTAINABILITY, FLSMIDTH
GLOBAL PROVIDES COMPLETE DESIGN AND MANUFACTURING SOLUTIONS
In water management, FLS’ automation filtration process can recycle 90 percent of the water used, offered in combination with a dry stack tailing solution. With many mines located in water-starved areas, the reuse of this precious resource is critical in minimising freshwater consumption.
Elsewhere, state of the art flotation technologies have been introduced
For Vice President, Head of Digital Services, Rebecca Siwale, the innovation of FLS’ flotation advanced process control (APC) system “pushes the envelope” of technology by leveraging deep learning to drastically enhance applications.
“Our APC systems mimic how the human brain processes visual input. These deep learning technologies bring machine vision into an application where highly subjective decisions become instantaneous,” she tells us.
As reflected by Siwale’s role at FLS, the company’s digital offerings of connected equipment and expertise in analytics are fundamental in providing value to customers through remote monitoring, predictive maintenance, and support services.
“The digital transformation effort requires working with the customer across the mineral processing value chain to identify opportunities for improvement and implement
– QASIM ABRAHAMS, HEAD OF SPARE PARTS AND AFTERMARKET SERVICE,
“AT FLS WE TAKE A HOLISTIC APPROACH TO OUR SUSTAINABILITY SOLUTIONS TO ENSURE THEY ALWAYS HAVE A NET POSITIVE IMPACT AS WE WORK TOWARDS OUR NET ZERO TARGETS”
FLSMIDTH
solutions that drive business value,” she says.
Digital services are deployed across the mineral processing flowsheet in comminution, sizing, flotation, separation, and dewatering to positively impact productivity, cost, and environmental footprint through real-time data, analytics and algorithms.
“We leverage such technologies where systems will self-train themselves from the continual analysis of data and create models for effective sustainable decisions,” Siwale continues.
“We are confident that building solutions on such innovative and breakthrough technologies for continuous and real-time optimisation and health monitoring of mining assets will greatly lower the impact and make our environment safer - be it through operational efficiencies, reduction in emissions and carbon footprint, savings in energy usage or protecting our water reserves.”
To uphold this industry-leading position at the forefront of technological innovation, FLS maintains an emphasis on performance to guarantee the steady
stream of investment that fuels the R&D necessary for future endeavours.
“If we don’t make sufficient profit, then we can’t invest anything back into the business,” says Keto. “Without healthy financial performance, there is no R&D, innovation, or new develop ment. This is extremely beneficial to our customers since it is this continual investment into R&D that makes us a leading technological supplier.”
In terms of delivering customer benefit, FLS prides itself on working in partnership with its customers,
“WE ARE PROUD TO OFFER THE SOLUTIONS OF TOMORROW, FOR THE EARLY ADOPTERS OF TODAY”
– JASON ELKS, APAC REGIONAL PRESIDENT, FLSMIDTH
optimising operations and supporting their growth as an end-to-end process solution partner.
“By working directly in partnership with our clients, rather than through an engineering, procurement and construction management (EPCM), they can see and understand so much more of our product range,” elaborates Elks.
Aside from the environmental advantages, partnership with FLS simply makes good business sense.
“The value that we deliver has a direct positive impact to our customers’ bottom line,” affirms Abrahams.
Siwale highlights one particularly effective example of this, where FLS’ use of advanced analytics, machine learning (ML) and artificial intelligence (AI) can increase a customer’s mill efficiency by up to 10 percent, an advantage which improves their bottom line tremendously.
“We use digital technologies that
quickly and efficiently to improve the uptime of our customers’ assets, but also to support improving their supply chain and optimising their capital committed on inventory levels. Having the right critical parts available with little or no lead time is crucial to ensure profitability,” she continues.
FLS continues to grow and develop the business through its partnerships, approaching acquisitions as a means to fill in any gaps or make improvements in areas within its already impressive portfolio as per its CORE’26 strategy “It’s always a win/ win relationship if both parties commit and align on the overall goals of a partnership,”
Incorporating a range of technological firsts for minerals grinding, HGPR Pro achieves higher throughput with less energy, maintenance, and environmental impact than similar technologies.
As a committed partner to its clients, FLS provides comprehensive aftermarket services including workshop, maintenance, repair, upgrades and overhaul, spare parts, retrofitting, and performance optimisation services.
“The most important factor for the customer is that we can support them over the full life cycle of the mine,” Keto says.
These run alongside the digital support solutions that are fundamental to modern mining, including remote monitoring, analytics, predictive maintenance, process control and automation solutions.
REBECCA SIWALE, VICE PRESIDENT, HEAD OF DIGITAL SERVICES, FLSMIDTH“As technology develops, so too do customer expectations of what service should be delivered. Gone is the era of service merely keeping mines up and running and minimising downtime,” says Siwale. “We are committed to innovative aftermarket service offerings to meet the evolving needs of our customers.”
Such needs range from improving maintenance efficiency, equipment reliability and overall uptime to maximising the lifespan of assets resulting in increased production and optimised operational expenditure. With customer needs integral to the company’s operations, the entire structure of the FLS group has
been formatted to emphasis its dedicated service organisation, thereby elevating its focus on this specific area.
“Our strategic service priorities and initiatives have been developed using a customer-centric lens, getting feedback from our customers looking forward to improving their journey and experience, while creating more value than before,” says Abrahams.
This crucial customer feedback is the fuel that drives new product development, continually innovating and improving based on their demands.
“WE ARE CONFIDENT THAT BUILDING SOLUTIONS ON SUCH INNOVATIVE AND BREAKTHROUGH TECHNOLOGIES FOR CONTINUOUS AND REAL-TIME OPTIMISATION AND HEALTH MONITORING OF MINING ASSETS WILL GREATLY LOWER THE IMPACT AND MAKE OUR ENVIRONMENT SAFER”
–
For Keto, the service area will be the focus of much investment in the years ahead through continued exploration into digital technologies to enhance FLS’ capabilities and offerings, particularly by improving on its strengths in consumables and wear parts.
“On the service side of the business, our immediate priority is to strengthen our technological position and grow,” he tells us.
Looking ahead, FLS’ overriding ambition across the whole group is one of rapid growth, to facilitate the equally rapid transition required to champion a more sustainable resources sector, working with and influencing policy and governmental considerations on a wider scale.
“I am confident that we will grow rapidly,” affirms Elks. “Our end-toend flowsheet solutions and product range will revolutionise the transition
and rapid growth that sustainable mining demands to keep up with the early adopters.”
Within the APAC region, this growth has seen FLS open a new office in Indonesia in April of this year, a country that Elks identifies as a “thriving resources hub and economy” poised to become the powerhouse of Southeast Asia and the broader region. In addition, the company seeks to develop its existing presence in Vietnam where there are great opportunities for critical minerals and metals of the future.
Continually perfecting its technology portfolio, FLS will simultaneously pursue growth through the strong and innovative partnerships that the green transition demands.
“As an industry, we need to increase the speed of adaptation to bring new technologies on board, working together to develop
them in joint fashion,” concludes de Groot.
With a recent rebrand in place reflecting the group’s reputation as a united company and provider of full flowsheet solutions with everything needed for productivity and sustainability, FLS continues the journey to 2030 one step ahead.
Phoenix Lining Services (PLS) is the leading specialist in industrial rubber lining and protective coating services and processes. Working closely with major global mining companies and engineering firms, the experienced team at PLS also engages with a range of Tier 2 and Tier 3 organisations.
Established in 2017, PLS has swiftly garnered a reputation for delivering excellence in its results while successfully achieving robust quality, safety and environmental management systems. Currently, PLS is one of the few companies in its field to have completed a comprehensive assessment and to be independently certified. This achievement further demonstrates the company’s commitment to maintaining the highest possible service, quality, environmental and safety standards. This is achieved through a fully qualified and well-equipped team that is reliable and trustworthy. No matter how complex a project is, the PLS team of experts has the resources and expertise required to execute and meet client requirements successfully. In this way, the company is fully adaptable with mobilised equipment to work in the most extreme climate conditions, and the PLS team is always ready to undertake jobs at the most remote sites, both within Australia and overseas.
PLS adheres to a specific set of crucial core values, upon which the ethos of the entire company is built and held together.
Most importantly, the company regards safety as its main priority. PLS consistently complies with industry safety standards as a highly safety-driven organisation. Every team member has completed comprehensive training in health and safety procedures within the organisation and off-site.
The highly motivated and expert team employed by PLS consistently achieves outcomes of the highest quality whilst also continuing to strive for improvements in its products. It is this premium quality of service that is at the very heart of everything PLS does and stands for.
Additionally, accountability is another crucial element of PLS’s success. Reliable and trustworthy, its team is committed to delivering what it promises, ensuring high-quality outcomes for any project undertaken.
Never satisfied and always striving for growth, PLS aims for continuous improvement. In this way, the company takes customer feedback seriously to continually provide excellent service and outstanding results.
Elsewhere, PLS champions integrity as a key element to achieving ongoing success. The company believes in open and honest discussions with both its clients and suppliers.
As PLS updates its clients on issues or problems, it simultaneously works towards achieving a solution. This is because it is a company that aims to do the right thing even when no one is watching.
In order to outperform the competition, a meticulous approach is employed alongside attention to detail for every project. This ensures that PLS exceeds all project requirements. Finally, trust and respect remain foundational elements of the PLS core values. The entire team believes respect is vital and promotes healthy relationships, fosters empathy and understanding, and creates a more inclusive and harmonious work environment. Employing teamwork as a core value promotes a culture of collaboration, mutual support, and shared success. It helps to build strong and resilient teams that can achieve more together than they could as individuals, as is the case at PLS.
Our mission is to provide end-to-end project management, exceeding our client’s requirements for their rubber lining and specialised protective coating application requirements, regardless of location or climate conditions to protect and extend the lifespan of industrial equipment. We strive to be a reliable partner for our clients, delivering innovative and costeffective solutions that meet their specific needs and exceed their expectations.
To be the industry leader in Australia and overseas by delivering results with the highest standards set by our comprehensive ISO accreditation in safety, environmental management and quality. Here at Phoenix Lining Services, we have a clear and compelling vision of our purpose and values. Our Management Team are passionate and visionary leaders who inspire and empower their fellow employees to achieve greatness. Innovation and creativity are encouraged and rewarded. Our company is constantly exploring new ideas and technologies to improve its offerings and stay ahead of the competition. All our employees are proud to come to work each day and are motivated to contribute their best efforts to achieve the company’s goals.
PLS works closely with many of its major clients such as FLSmidth, to achieve positive outcomes and to guarantee customer satisfaction. Additionally, by working closely with customers and suppliers to understand their needs and challenges, the company has gained valuable feedback and insights that have helped drive innovation and improvement. This feedback has also been used to develop new products and services that better meet the needs and requirements of customers and help PLS stay ahead of its competitors. By striving for customer satisfaction and repeat business, the company has built customer loyalty and brand recognition, which has ultimately contributed to fantastic levels of long-term success.
www.phoenixlinings.com.au
In a country that is estimated to host the world’s largest gold reserves, the last decade has seen Australia become the second largest global gold producer, second only to China. Current gold prices on the Australian market are at a record high, and despite ongoing economic and geopolitical volatility, the outlook is strong after the country managed to maintain a steady stream of production throughout the turbulence of the COVID-19 pandemic.
With Australia’s gold mining industry generally defined by opportunity, thanks to high levels of investment in exploration and a swathe of various projects in the pipeline, the prospective outlook of the country is reflected in the dynamic microcosm of junior Australian Stock Exchange (ASX) listed minerals exploration and development company, Talisman Mining Limited (Talisman).
From the company’s headquarters in Perth, Western Australia (WA), Talisman’s CEO, Shaun Vokes, maintains an astute perspective of the opportunities currently facing the industry, but equally, the challenges that all mining players are forced to navigate.
“The easy deposits have already been found and exploration to find economic deposits is becoming harder, both by having to look deeper or in locations which carry additional risks,” Vokes introduces.
“Furthermore, all of the input costs have escalated, applying cost pressures to every facet of the industry from exploration through to production.”
This current state of play makes players such as Talisman key in unlocking new areas of exploration and driving the industry forward.
For Vokes, another prevailing challenge that the entire industry must confront is the promotion of mining’s social value, particularly if it is to maintain relevance and importance in the environmentally and socially sensitive context of the present day, and remain competitive in the face of other potential land uses.
The Lachlan Copper Gold Project
• Located in the Lachlan Fold Belt region of Central West NSW.
• Covers approximately 6,400km2 of highly prospective base and precious metals tenure.
• Comprises four sub-projects – the Central Lachlan CopperGold, Dandaloo Copper, Elvis Copper-Gold and Hillston Copper-Gold projects.
The Mabel Creek Iron-OxideCopper-Gold (IOCG) Project
• Located in the Gawler Craton of South Australia.
• Provides approximately 1,000km of highly prospective IOCG tenure in the same prospective corridor as BHP’s world class Olympic Dam mine and the OZ Minerals Carrapatena and Prominent Hill mines.
“Although it is possible to draw a clear nexus between the mining of base metals and the topical social themes of decarbonisation and electrification, the social value of mining gold is more difficult to quantify,” he observes. As such, a steadfast commitment to promoting the positive benefits of the mining industry to all stakeholders is crucial in order to sustain social licenses to operate.
Complementing a board of directors boasting extensive experience across all facets of minerals exploration and development, Talisman’s exploration team prides itself on working in close communication with local landowners throughout its areas of operation.
“Wherever possible, we also
utilise suppliers and contractors based in regional locations which brings economic benefits for local communities,” adds Vokes.
The company’s entire modus operandi is encapsulated by a value-driven mission, as evidenced by Talisman’s proven track record of generating value for shareholders and its ongoing business development programme.
“Our objective is to maximise value to our shareholders through exploration, discovery and development or commercialisation of opportunities in base and precious metals within Australia,” he emphasises.
In its pursuit of generating value, Talisman stands out from other junior ASX listed exploration companies in
Munro Geological Services is a family-owned business operating since 2013. Munro Geological Services provides contract Geological Field Staff, Environmental Technicians and Geologists to the minerals exploration and mining industries throughout Australia.
www.munrogeological.com.au
admin@munrogeological.com.au
0427298357
terms of funding, since the company benefits from a regular income stream generated by one percent gross revenue royalty from Mineral Resources’ Wonmunna Iron Ore Mine, located in the Pilbara region of WA. For the past two years, this revenue has been instrumental in enabling Talisman to undertake “substantial and sustained” greenfield exploration programmes in excess of AUD$5 million every year.
“We are constantly on the lookout for potential base and precious metals growth opportunities in Australia (and elsewhere) with the aim of identifying quality assets with the capacity to create long-term shareholder value,” surmises Vokes.
In terms of seizing current opportunities, Talisman’s flagship undertaking and main area of focus is the Central Lachlan Copper-Gold Project. Located within the richly
mineralised region of Cobar/Mineral Hill, the site covers an extensive strike along the Gilmore Suture and is considered by Talisman to have significant potential for the discovery of substantial base metals and gold mineralisation.
Last year, the company proved the potential and lack of modern systematic exploration on this land package by collecting evidence of its base and precious metals endowment. To do so, Talisman
leveraged its aforementioned income stream to complete two regionalscale airborne geophysical surveys (both electromagnetic and gravity) to “unlock a new generation of discoveries” in the Lachlan Fold Belt by indicating the concealed presence of blind mineralisation.
The investment has been pivotal in allowing Talisman to acquire highquality datasets that can potentially shorten the discovery timeline on its tenure by several years by directing
“WE ARE CONSTANTLY ON THE LOOKOUT FOR POTENTIAL BASE AND PRECIOUS METALS GROWTH OPPORTUNITIES IN AUSTRALIA (AND ELSEWHERE) WITH THE AIM OF IDENTIFYING QUALITY ASSETS AND WITH THE CAPACITY TO CREATE LONG-TERM SHAREHOLDER VALUE”
– SHAUN VOKES, CEO, TALISMAN MINING LIMITED
Shaun Vokes, CEO: “Our third concurrent workstream is an auger drilling campaign, comprising approximately 5,500 holes over seven exploration licences using Talisman’s in-house auger drill rig. To allow for rapid target generation based on these auger drilling programmes, Talisman has partnered with Portable PPB Pty Ltd, an Australian private company holding the exclusive global licence to the CSIRO developed low-level gold by pXRF technology known as detectORE™.
“The technology is a fast, simple and robust process currently used by a number of Australian mineral explorers and producers to enable the leaching, concentrating and detection of gold from a bulk sample at parts per billion levels with high precision using conventional hand-held XRF instruments. Talisman’s use of this system provides a fast (less than 12-hour turnaround) on-site preliminary gold and multi-element geochemistry result to guide realtime exploration, while still allowing follow-up geochemical analysis via commercial assay laboratories.”
its exploration efforts to the areas with the highest chance of returning economic discovery.
“These surveys generated over 50 anomalies and, after extensive delays due the extraordinary weather events in New South Wales (NSW) and the East Coast last year, we were finally able to get on the ground in January 2023 and kick off a major drilling programme,” Vokes shares.
The programme entails three key exploration workstreams operating concurrently across the Central Lachlan Project – reverse circulation (RC) drilling, ground geophysical surveys and soil geochemistry utilising auger drilling – which are interlinked and designed to rapidly test priority drill targets while screening areas below cover for
further geochemical and geophysical anomalies.
“Together, the workstreams aim to identify, prioritise, and systematically test exploration targets, ensuring that Talisman’s exploration strategy is provided with up-to-date targeting data from multiple sources,” he explains. “At present we are halfway through the programme and results have been encouraging with a number of assays awaited.”
Thanks to the solid progress of Talisman’s ground based moving-loop electromagnetic (MLEM) and PoleDipole Induced Polarisation (PDIP) geophysical surveys in identifying prospect areas indicative of base metal sulphide mineralisation, several new targets have been revealed with plans for RC drilling to follow.
MINING OUTLOOK: COULD YOU TELL US MORE ABOUT THE AUGER DRILLING WORKSTREAM UNDERWAY AT THE LACHLAN COPPER GOLD PROJECT?
Another significant undertaking for Talisman was announced in January this year, following its acquisition of the Mabel Creek Iron-Oxide-CopperGold (IOCG) Project located in the under-explored region of the northern Gawler Craton of South Australia (SA).
Comprising three granted exploration licences covering a contiguous region of 1,048km2, the project area was initially identified as part of the SA Government’s “Gawler Challenge” in 2020 and subsequently recognised as one of the most significantly prospective areas in SA for IOCG and Gawler Craton-style gold mineralisation.
With recent aeromagnetic data published by the Geological Survey of South Australia suggesting the presence of a fluid conduit potentially hosting mineralisation within Mabel Creek’s deep-seated east-west trending fault system, the previously under-explored site has rightfully become an area of significant interest.
“The project is surrounded by exploration licences held by other major mineral companies, including recent tenements granted to Fortescue Metals Group (FMG) and Rio Tinto Exploration, as well as the exploration ground held by Oz Minerals and the BHP Group with its existing Tier 1 mining and development projects,” Vokes tells us. “The regional presence of these significant mining companies highlights the exploration opportunity for additional significant copper-gold discoveries in the Gawler Craton.”
Poised to capitalise on future developments, Talisman’s Mabel Creek Project benefits from a centrally located position with the Prospective IOCG Corridor where the moderate depth of the Moho boundary beneath the continental crust and its significant potential for IOCG discovery awaits.
“We are very excited by the potential of the Mabel Creek project and once the exploration licence transfer process is completed, we will immediately progress discussions with traditional owners to facilitate land access. We are hopeful that we can commence on-ground exploration activities before the end of this year,” shares Vokes excitedly.
With extensive exploration programmes underway or in the pipeline at both Mabel Creek and the Lachlan Copper Gold Project in NSW, 2023 is shaping up to be a busy year for Talisman.
“As exploration in NSW progresses,
we are constantly improving our understanding of the geological setting and continually refining and improving our targeting methodology.
“Meanwhile, at our Mabel Creek Project, we envisage that we will run some geophysical surveys ahead of planned drilling to refine our existing targets and build on our existing knowledge of the area,” Vokes tells us.
Leading with a strategic approach to exploration and an unrelenting pursuit of delivering value, the untold future potential of Talisman is yet to be unearthed.
“We would like 2023 to be the year that Talisman makes a significant mineral discovery.”
We speak to the Executive Chairman of Bowen Coking Coal, Nick Jorss, about the company’s successful acquisitions and its tenacious efforts in sustainability
Lucy Pilgrim | Project Manager: Eddie Clinton
Australian mining is a highly significant contributor to the country’s exports, whilst also providing substantial opportunities for national employment and local infrastructure. Regionally, Queensland is one of the most prosperous mining states in the country, and the Bowen Basin in central Queensland offers an abundance of coal mining opportunities, which are plentiful and low-cost.
As one of the newest operators in the Bowen Basin, Bowen Coking Coal (Bowen) has taken full advantage of the resource and has grown rapidly via several acquisitions over the previous four years. In the last 12 months, the organisation has brought two of the acquired coking coal mines into production with a third underway, producing over 1.5 million tonnes of run-of-mine (ROM) coal to date. And yet, despite its recent prosperity, the company still feels
the effects of the challenges that face many mining companies across Queensland, such as regulation, increased government intervention, and environmental activism. However, Bowen is working as a team to overcome these challenges, which is one of the most important parts of the job, according to Executive Chairman, Nick Jorss.
“The industry is cyclical and has faced greater headwinds recently from increased government intervention and environmental activism. The flipside is that, as the
We are a locally owned and operated business who have operated out of the Mackay region for over 20 years and are committed to providing the highest quality training and services to support local industries. We constantly work with our clients to develop the most safe, practical, efficient and effective solutions that meets your safety needs and exceeds industry standards.
industry becomes hard for some players to exist in the market, it sometimes creates opportunities for smaller, nimble operators like Bowen,” he opens.
As the industry flourishes, coal demand continues to grow, driven by industrialisation and urbanisation. Subsequently, there is an increased need for steel and low-cost energy, both of which are supplied by highquality Queensland coal.
“We are resolute that steelmaking coal has a climbing demand trajectory. To make the new steel required for economic growth and decarbonisation we will need more coking coal in the future, and there’s no economical substitute on the near horizon,” Jorss highlights.
Steel is widely regarded as an
essential component in electrification, and more steel requires more coking coal. Meanwhile, supply is constrained by an effective capital strike, with regulatory and approval pressures having an additional impact.
These dynamics are favourable, however, to coal as an investment commodity. “With the increasing demand for coal and other minerals, Queensland can be a world leader if we encourage investment.
“We maintain some of the world’s highest environmental and safety standards, best geology, and lowest emissions export coals,” Jorss proudly comments.
Every major investment decision made at Bowen is supported by
Nick Jorss, Executive Chairman: “My career started as a construction engineer in the early 1990s where the highlight was the construction of Melbourne’s Bolte Bridge, which was considered a bold architectural statement at the time. It’s a landmark for me in part because its architectural simplicity belies the complex engineering and hard work that underlies it.
“I then transitioned into corporate finance which built my commercial understanding of mergers, acquisitions, and financing of large projects. This experience across these sectors served my entry into the mining industry in 2008 when I formed Stanmore Coal, later Stanmore Resources, with a couple of long-term colleagues. I have always been interested in business and bulk commodities caught my eye because of the ability to leverage returns on very large volumes. Highly successful coal companies such as Felix, Whitehaven, Excel, MacArthur Coal and New Hope provided inspiration on what could be achieved.”
“WE DON’T MAKE ANY BIG CALLS LIGHTLY AND WE DON’T CHASE GROWTH FOR GROWTH’S SAKE. AS SUCH, WE REJECT MANY ACQUISITION OPPORTUNITIES IF THEY DON’T FIT OUR STRATEGIC GOAL”
– NICK JORSS, EXECUTIVE CHAIRMAN, BOWEN COKING COAL
Project delivery specialist AB Power prides itself on the ability to deliver a range of turnkey solutions from temporary power installations for greenfield projects through to large site project works and ongoing maintenance and breakdowns. It is the go-to company for premium mine site project results throughout the Bowen Basin.
The locally owned and operated enterprise specialises in delivering projects from start to finish, in-house. AB Power is unique in the mining and projects arena across Queensland, providing end-to-end services with cost effective solutions that ensure projects are delivered on time and on budget.
While maintaining flexibility and competitiveness within the industry, AB Power continues to deliver services and expertise without relying on external contractors, through a highly trained staff group offering a highquality service, in-depth knowledge and reliability.
Comprised of three divisions, AB Power is an established business in the mining sector, spread across AB Power Electrical, AB Power Civil and AB Power Generation.
Essential Services for all Three Specialist Divisions:
• Plant maintenance and project works
• Temporary power stations
• Mining camp power and maintenance
• Plant electrical operators
• U/G HV distribution systems
• Lighting and power distribution
• Communication systems
• Water treatment plants
• Raw and fire water systems
• HVAC cooling systems
Whilst the loss of power can be inconvenient and debilitating, AB Power has various solutions for mining projects that require power generation.
Offering more than just standard generator hire, the high-quality back-up service provided by AB Power is an insurance policy for project owners that require uninterrupted and reliable temporary power supply. AB Power offers a various range of generators, in customisable sizes to suit all requirements.
All AB Power equipment complies with international and Australian electrical standards to ensure all safety compliance specifications are upheld.
• Multi-megawatt, HV power stations
• Power station installation and operation
• Purpose built switch-room facilities
• HV power: 1000V, 3.3kV, 6.6kV, 11kV and 22kV
• Temporary power solutions: 20kVA to 1400kVA
• Contingency power plans
• 24/7 breakdown support
• End to end project management
• Contract maintenance
• Rental, purchase or flexible ownership options
• On-site refuelling solutions and management
• Engineering design and remote monitoring
One of the benefits of AB Power Electrical services is guaranteed customer satisfaction.
The AB Power Electrical team provides a range of mine site electrical works from switchboard upgrades and maintenance to electrical outages, shutdowns and more by understanding the complexities of working in remote locations .
• CHPP project and operations electricians
• Experienced surface and underground electricians
• End-to-end project management
• Switchboard and maintenance upgrades
• Competent and authorised electrical supervisors
• Complete mine maintenance
• Power pole inspections and maintenance
• HV switching operators and coordinators
• Data and communications networks
• Sub-division underground electrical works
• Earth grid design and installation
• Full HV reticulation
AB Power Civil contractors handle small to mid-size mine site projects and civil works which include haul roads, build pads, concrete pads and more.
No matter the size or the complexity of the project, from temporary power installations to supplying civil contractors for large site project works, the high-quality level of service remains the same.
The team can effectively manage anything from ongoing plant maintenance to complete project delivery and sign off.
• Mine site civil maintenance and repairs
• Hardstand infrastructure
• New building construction
• Hardstand infrastructure
• Bulk and detailed construction
• Bulk and detailed earthworks
• Operator equipment hire
• Detailed concrete construction
• Construction of roads and drains
• Concrete removal and remediation
• Project management and supervision
AB Power believes in a strong safety culture, high client productivity standards and a flexibility to adapt to clients’ needs with consistent cost management procedures.
Maintaining integrity, especially surrounding honest and transparent client relationships, are just some of the attributes that the AB Power team possess. Partners and employees alike enjoy being involved with AB Power. This is evidenced by high employee retention rates, as AB Power understands the quality and safety benefits of having a long-term workforce in place.
The AB Power team provides 24/7 support to guarantee your operation continues to run smoothly.
A wealth of knowledge and experience can be applied to the entire life cycle of your project as well as a range of temporary power solutions, along with a team of over 75 highly qualified technicians to provide and advise the path forward according to your needs.
www.abpower.com.au
info@abpower.com.au
1300 422 769
significant prior work to ensure that assets are well positioned across the pricing cycle. The company never takes any big acquisition lightly, and doesn’t chase growth for growth’s sake. Rather, Bowen rejects acquisition opportunities if they do not align with the specific strategic goal of building more near-term, high-quality and low-cost production assets. Timing is also critical to an investment decision to ensure any assets are acquired at the right time in the cycle, which helps drive long term shareholder value.
Examples of such criteria are evidenced in some of Bowen’s most recent acquisitions, including the Burton Complex, which comprises multiple open pit deposits at Broadmeadow East, Burton and Lenton. The complex, with an annual ROM production target of 3.5 to 4.5 million tonnes, includes a 5.5 million tonne coal handling and preparation plant (CHPP), train loadout facility,
350-person camp, haul road, offices and workshops. The site is located near Moranbah in Burton, central Queensland, producing high-quality coking coal and secondary thermal product.
The company has successfully opened the first low-cost mine within the Burton complex named Broadmeadow East, and is currently opening the second. The first module of the CHPP has been refurbished and is now operating at above the nameplate capacity.
Bowen’s other operating asset is the Bluff Mine which is ramping up to
an annual ROM production target of over one million tonnes and produces ultra-low volatile pulverised coal injection (UVPCI). This is located 20 kilometres (km) east of Blackwater in central Queensland.
Further projects under development in Bowen’s portfolio include the Isaac River project, located 30km to the southeast of Moranbah, next to BHP’s giant Daunia mine. Isaac River recently received its important final federal government environmental approval to allow the grant of the mining lease. The Hillalong project, 150km
“WE MAINTAIN SOME OF THE WORLD’S HIGHEST ENVIRONMENTAL AND SAFETY STANDARDS, BEST GEOLOGY, AND LOWEST EMISSIONS EXPORT COALS”
– NICK JORSS, EXECUTIVE CHAIRMAN, BOWEN COKING COAL
ABOUT US:
WMT Transport is a family owned and operated company with over 40 years’ experience in the transport industry. Trucks are our family’s passion and lifelong business. Specialising in a wide range of transport solutions, we operate a fleet of over 100 units of equipment. We are proud of our trucks and take the utmost pride in maintaining our fleet.
DAILY SERVICE:
24/7 hot shots and general freight to the Bowen Basin, Mackay to Brisbane and all throughout.
WEEKLY SERVICE:
Brisbane, Toowoomba, Dalby, Miles, Banana, Middlemount, Nebo, Mackay and Whitsundays
OUR EQUIPMENT CONSISTS OF:
• Drop-decks
• Road trains
• B doubles/tautliners
• Liquid tankers
• Flat top trailers
• Oversize
• Container trailers
• Body trucks
• Utes
Geared Engineering has been in Mackay for seven and a half years.
Locally owned offering quality, economical repairs to Mobile and Fixed Plant transmissions
WMT Transport Pty Ltd
Phone: 07 4829 4700 | admin@wmttransport.com.au
www.wmttransport.com.au
Mackay Depot: 25170 Peak Downs Hwy, Greenmount, QLD, 4751
Brisbane Pick up and Drop off Depot: 62 Randolph Street, Rocklea, QLD, 4106
For rapid and reliable service contact
Geared Engineering Mackay.
T: (07) 49524448
E: adminqld@gearedeng.com
www.gearedeng.com
In mid-October 2022, Bowen Coking Coal contacted us to see if we could overhaul 11 different items from the Burton Coal Plant that they were starting back up after many years of sitting idle. The pressure was on as they wanted them back as soon as possible before Christmas. The first item arrived on the 25/10/2022 and the last one left our workshop on the 20/11/2022. It was a huge effort from our team to complete this work in the required time frame.
HBF Box Rebuiltsouthwest of Mackay, has 87 million tonnes of Total JORC Resource, consisting of low ash coking coal and secondary thermal coal and will form an important extension to the Burton mining complex.
In line with its strategic acquisition choices, Bowen’s employees must also have their hearts in mining.
“There isn’t a lot of ego in the team, just good people wanting to work to create value and have some fun whilst doing it. The ability to work
in this collaborative and fast-paced environment to strive for the best result is probably the most important criteria in our team.
“We aim to be nimble and able to respond to opportunities as and when they arise,” he tells us.
Most recent developments in the global mining industry include an appreciation of mining’s
environmental footprint. The Australian mining landscape is no different, as being environmentally and socially responsible is not just perceived as good business, but the core of business.
Responsible mining solutions for safety, economic development of communities, efficient extraction techniques and technologies, comprehensive environmental safeguards, and community engagement are all part of the
company’s planning and operations from the development of mines to their end of life.
Such a commitment is a key driver for Bowen, as guaranteeing a sustainable industry with a minimal environmental footprint is central to the company’s approach. Regional communities around the Bowen mines rely on mining for their existence and benefit from Bowen’s operations through economic development, opportunities and employment.
To date, more than 700 direct jobs and thousands of additional indirect positions have been generated in Queensland, due to Bowen Coking Coal projects. This includes apprentices and trainees, as well as opportunities with very competitive salaries in regional areas.
In addition, efficient extraction of mining resources is important in supporting sustainable operations.
“Queensland is blessed with great
to 250 tonnes together with a fleet of heavy haulage equipment and various types of height access and material handling equipment.
The business prides itself on providing services across a variety of industries in Central Queensland and Bowen Basin regions including mining, construction, rail, sugar mills, marine and ports.
Sarina Crane Hire is pleased to be associated with Bowen Coking Coal in the rebuild of existing Burton Coal Handling and Preparation Plant (CHPP) at Burton Coal Mine/Lenton Joint Venture, supplying crane and transport services in the assembly of new mining equipment.
The business has a modern fleet of Equipment which can either be wet or dry hired, depending on project requirements. SCH has a large number of resources available which clients can call on at any time. The business maintains its fleet of equipment to the highest standards to minimise lost time from breakdowns to maximise productivity and utilisation. www.sarinacranehire.com.au
coal resources, and because of this, our industry underpins the global seaborne metallurgical coal market. Our coal quality is high, and our emissions profile is typically low,” Jorss highlights.
Evidently, mining produces sizeable economic benefits to the local communities, despite only ever occupying a small area of land. In Queensland, mining occupies approximately less than half a percent of the land but produces half of the export revenue that supports employment and growth in the community.
“The small amount of land we do occupy is returned to mainly productive uses when mining is completed. Progressive rehabilitation of our sites is critical to Bowen’s approach, and this is built in from the beginning of the mine’s planning.”
In continuation of supporting the local community, Bowen works closely with localised suppliers and
contractors. For example, the recent CHPP refurbishment was conducted on time by a highly motivated labour force, who were supported by supplier partners in the local region.
Looking ahead, Bowen’s nearterm focus is on safely and efficiently transforming assets acquired in the last five years and reaching the five million tonnes per annum ROM production target by next year.
“We will continue to grow with acquisitions at the right time, but for now we have a fantastic set of assets we need to work hard on to unlock shareholder value,” Jorss concludes.
Sarina Crane Hire is a privately owned, family operated business supplying cranes, heavy transport and height access services across Central Queensland. The company commenced in 2007 and under the ownership of Scott Goode, the fleet has grown to approximatively 140 pieces of equipment including Franna cranes, Rough Terrain, All Terrain and Crawler Cranes ranging from 13 tonnes
The mining industry has always been a prosperous asset to Australia, and the industry is booming now more than ever. At the forefront of such sector-wide success is Hallett Group (Hallett), which stands as the largest business of its type in South Australia (SA), with 24 operational sites.
Hallett currently employs over 500 people who work to supply everything from cement, quarry products and concrete to timber, steel, and building supplies. With such a variety of products, Hallett’s customer base ranges across sectors, including mining, heavy infrastructure, renewables, defence, and civil and residential construction.
Hallett is positioning itself to meet the demands of the evolving industry. Although Australia has traditionally
been a global powerhouse in iron ore, coal and gas, it also has a huge potential to grow its capacity in the materials of the future, such as copper, lithium and rare earth metals.
“With some of the best renewable energy sources anywhere in the world, and the scale and stability of our industry, Australian mining is well positioned to provide key resources to the world with the lowest carbon footprint,” introduces Kane Salisbury, CEO of Hallett.
Salisbury has had a varied career path prior to his position as CEO at Hallett, taking his initial steps in the manufacturing space. Here, he was a manager in charge of overseeing the manufacturing of paper bags, beer and biscuits, through to pipe fittings and car parts.
“As I worked in manufacturing,
“I had a really strong interest in driving continuous improvement and was lucky enough to gain some great training and mentoring in LEAN manufacturing methodology, which I was able to successfully implement in a number of workplaces,” he explains.
“That was 14 years ago, and I have absolutely loved my time in the industry ever since. No two days are the same, there is always a new project or challenge just around the corner and I have greatly enjoyed being able to shape our strategy and achieve some great results.”
As a privately owned company, Hallett possesses a distinct drive to succeed. The company’s leadership has a strong and intimate involvement in the business to ensure its growth.
“We are clearly aiming to be the very best in our industry and if you are the best at what you do, growth will follow. A lot of companies have agility as a value, but then have a whole range of hierarchies and systems that slow down agility.
“Hallett’s flat structure, clear
strategy and purpose, plus the connectivity of its leadership team, allow us to act with speed and agility in our market like no other,” highlights Salisbury.
Hallett is further set apart from competitors by its trajectory of growth. Having tripled in size over the past decade, the company is making its biggest ever investments to support a further doubling of the business in the next three to four years.
Through key investments, the company is establishing a green cement manufacturing and distribution business to supply SA and surrounding regions. This is a real catalyst for Hallett, as it expands its footprint in the mining supply sector
KANE SALISBURY, CEO: “Whilst Hallett has a diverse set of internal capabilities, we cannot be successful without great supply partners. We greatly appreciate those suppliers that have stuck with us through our growing pains, and we have enjoyed many of these partners growing with us.
“We are always looking for suppliers to innovate and bring their ideas to the table and we love to share the wins when genuine value is created. We are in an industry that values service and reliability very highly. We like to think we do this better than the rest and our suppliers and partners do as well.”
whilst giving itself and its partner customers access to the lowest carbon cementitious products in the market.
Furthermore, the company has been a significant component of many crucial and remarkable across SA, as it continues to supply many major infrastructure projects and key building projects including hospitals, schools, bridges and roads.
More specifically, Hallett has proudly supplied the Osbourne Tech Port Shipyard project, which is becoming the centre of naval ship construction in Australia. This has become more pertinent with the commitment to build future submarines at Osbourne, which is one of the most exciting investments in SA’s history.
Whilst Hallett is proud of its achievements in major projects, it does not lose sight of its base foundation customers which consist of residential, civil and commercial builders throughout Adelaide and SA, as well as the families that are building homes.
“These are the people and businesses that have supported Hallett through thick and thin over the past 40 years and helped us to get to where we are today,” Salisbury acknowledges.
SA is the global leader in the uptake of renewable energy with over 70 percent of its electricity usage coming from renewable sources. As such, Hallett has become an expert in incorporating environmentally
“HALLETT’S FLAT STRUCTURE, ITS CLEAR STRATEGY AND PURPOSE, PLUS THE CONNECTIVITY OF ITS LEADERSHIP TEAM, ALLOW US TO ACT WITH SPEED AND AGILITY IN OUR MARKET LIKE NO OTHER”
– KANE SALISBURY, CEO, HALLETT GROUP
In just four years, we’ve built over 20 pieces of plant equipment for some very picky customers, hailing from Katherine to Kununurra, to Callington.
Together, we’ve created tailored solutions to suit their needs.That’s over 20 mobile and fixed batch plants, silos, specialty bins and transit mixers on time, on budget and unique to each customer’s needs.There’s no cookie cutter approach at Delmix and just like our customers, we’re picky too.
We’re driven by quality and results, maybe that’s why picky customers pick us!
If you’re looking for someone to assist you with any of your concrete production or delivery needs, pick up the phone and call us.
“WE ARE CLEARLY AIMING TO BE THE VERY BEST IN OUR INDUSTRY AND IF YOU ARE THE BEST AT WHAT YOU DO, GROWTH WILL FOLLOW”
– KANE SALISBURY, CEO, HALLETT GROUP
Providing solutions through our equipment, people and services:
• Vacuum Loading Liquids, Solids, Tank Cleaning
• High Pressure Water Blasting Concrete Demolition, Surface Preparation, Plant Cleaning
• Non Destructive Digging Pot Holing, Trenching, Service Locating
• Drain Cleaning and CCTV
“SpryCrete is a family owned and operated business supporting Murray Bridge, South Australia and the surrounding districts. Our focus is not only on supplying our customers with a quality product, but also on providing reliable delivery and outstanding customer service. With a versatile and capable fleet, no job is too big or too small.”
Providing industrial cleaning solutions that help support these objectives in the government and commercial sectors.
conscious projects into its agenda, as it has been proud to supply most of the recent and current wind farm developments right across the state.
A noteworthy case is the green cement transformation project, which is the most significant carbon reduction innovation project ever undertaken in the Australian cement and concrete industry.
The transformative project will witness Hallett construct a sovereign manufacturing capability to process and distribute two streams of Australian-generated industrial waste by-products into low-carbon green cement products, utilising established renewable energy resources.
The project will have an employment creation investment of AUD$125 million, split across the regional city of Port Augusta, along with new infrastructure in Port Adelaide. In total, the project will reduce Australian CO2 emissions by 300,000 tonnes
per annum immediately, growing to approximately one million tonnes per annum in years to come. This amounts to approximately one percent of the entire Australian 2030 CO2 reduction target.
Sustainability permeates other areas of the company, seen in the use of waste materials, water harvesting as well as planting trees and native vegetation.
“We are really pushing the boundaries on cement substitution in concrete, and we take pride in offering closed loop systems where every waste stream we generate is beneficiated into products that are consumed again,” Salisbury tells us.
As SA enters a key decade with generational investment, Hallett means to continue on its course for greater success, through a flurry of ambitious projects that tap into opportunities across renewables, defence and mining.
Hallett perceives great growth potential in the circular economy
and plans to continue investing in the enhancement of its offerings, well beyond what it is already doing in construction materials.
“Hallett is focused on positioning itself to maximise its share of these opportunities and importantly provide the construction material capability to ensure they are delivered,” concludes Salisbury.
Tel: 08 8366 7777
hallett.com.au
Yuxin Holdings Pty Ltd is a key producer and explorer of gold in the land
Down Under. We speak to Gary Goh, General Manager, about the company’s Pajingo Gold Mine and the community-centric mission that lies at its core
Despite certain challenges, the gold industry is going through an exciting and critical phase with opportunities that Yuxin Holding Pty Ltd’s (Yuxin) Pajingo Gold Mine is well-positioned to capitalise on.”
Gold has always been a source of awe. Unaffected by oxidisation and many harmful chemicals, cultures throughout history have associated gold with immortality, godhood and, by the nature of mortal aspiration, royalty. To this day, gold still carries many of these connotations and because of its relative rarity in comparison to other metals, beauty and valuable properties, is the classic representation of national wealth. Indeed, most countries across the globe hold gold reserves as insurance
against their primary currencies.
With such perpetual importance in our society, it is no surprise that there are many in the industry bringing gold to the surface; Yuxin is one such key player.
In November 2022, Yuxin acquired Pajingo Gold Mine, a mine with a longstanding history of operation dating back to the 1980s. The company owns 100 percent of the Pajingo Gold Mine operation in Northern Queensland.
Yuxin currently works with over 300 employees and contractors, and takes
pride in its work culture that promotes a positive, engaging workforce, offering career progression and training development within the mining industry.
Gary Goh, General Manager of Yuxin, has spent the majority of his career in the Australian underground hard rock mining sector with a brief stint abroad. Since his return to the country, Gary accepted the position of Group Manager of Operations and Technical Services at Minjar Gold, a company that Yuxin recently acquired, and recognises gold as a metal of key and immutable significance.
“Gold has always been a consistent source of interest due to the longterm sustainability of precious metals as well as the collective properties that make the element so unique,” Gary says. “The gold mining space is one of great activity, but despite that, it is not without its challenges.”
According to Gary, the mining industry is experiencing a significant boom whilst simultaneously undergoing difficulties in recruiting and retaining employees, with labourhire shortages and increased burnout of skilled and experienced workers in the industry. In the face of this, Yuxin offers its employees autonomy and the ability to be innovative. The company’s career progression opportunities are available to all
Yuxin is an equal employment opportunity (EEO) employer that is committed to diversity. The company’s Pajingo Gold Mine offers residential and FIFO opportunities on flexible rosters, a competitive salary, and entitlements that are above the industry award standards. Yuxin’s entitlements include bonus schemes, parental leave schemes, and EBA staff accrue 13 weeks of service leave upon completion of 10 years’ service.
The site recruits from communities in Charters Towers and the Northern Queensland region wherever possible, offering a positive worklife balance, and Yuxin supports indigenous employment, providing employment opportunities to apprentices, trainees and graduates.
Yuxin’s workplace culture embraces five core values:
staff and are truly outstanding, offering mentoring, training and development, as well as a study assistance programme to help bolster the number of skilled workers in the industry.
In order to be closer to its Pajingo Gold Mine site, Yuxin decided to set up its headquarters in Townsville (Queensland) rather than the Minjar Gold office which is located in Western Australia (WA). Yuxin also acquired NQM Gold 2 Pty Ltd (NQM), who operates the Pajingo Gold Mine in the Charters Towers region, from Minjar Gold in late 2022.
“Yuxin’s exploration strategy is to realise the full value of its extensive tenement holdings in North Queensland,” Gary elaborates. “Initially, this means focusing on targets within the mining leases, to maximise the return on capital that has been invested in the Pajingo Gold Mine infrastructure and development, and to generate revenue to fund future exploration. However, it also includes a smaller but significant commitment to identifying and testing targets beyond the mine.”
In order to achieve this, Yuxin has assembled a team of experienced exploration geologists and support personnel with a track record of discovery, both at the Pajingo Gold
Minetruck MT65
Minetruck MT65 is designed for fast productive haulage in large mining and construction operation. With smart system and robust component the Minetruck MT65 ensures productivity, reliability, operator safety and comfort along with ease of maintenance.
GARY
“As a key management staff member of an Australian company invested in by a Chinese company, managing the operations requires a unique set of skills and strategies. I have been playing a key role in bridging the communication between the board, corporate and the workforce. I believe that the key to effectively managing such a diverse workforce is to promote crosscultural understanding and respect while fostering a sense of common purpose and teamwork.
“To achieve this, I encourage open communication, promote cultural awareness, and organise cultural exchange programmes to help employees understand and appreciate each other’s cultural differences in communication. We also must ensure that key management members, both Chinese and Australian, speak the same “mining language”. Additionally, I ensure that the company’s policies and procedures comply with local laws and regulations.
“In summary, managing an international company with a blend of Chinese and Australian workers requires a sensitive and culturally aware approach. By promoting respect, understanding, teamwork, diversity, and a global mindset, I am confident that I can effectively manage the company and create a positive work environment for all employees.”
Mine and elsewhere. To support this team, Yuxin is funding exploration at levels not reached in the last 20 years; the company’s board has approved AUD$20 million in combined exploration and resource definition for 2023. In response, the exploration team are working with a local drilling contractor to increase the number of operational drill rigs on site, to achieve the estimated 50,000 metres of surface drilling to be completed this year.
As part of Yuxin’s strategic plan, the company is committed to expanding its business operations in Australia and maximising value for its stakeholders, including its dedicated staff. Yuxin’s focus on growth will not only create new opportunities for the business, but also enable it to provide additional benefits and incentives to its employees, ensuring they share in the success of the company, an aim that is communicated to all staff.
“The Pajingo Gold Mine operation is the only active mine under Yuxin at present,” Gary adds. “The
company’s procurement goal as always is to achieve the most costeffective solutions to the mine. With 62 percent of the supplier base in Queensland and the majority of them from Charters Towers, our strategy is to support the local economy, particularly small businesses, as much as we can.
“The company has the confidence to build a harmonious and ecological economic relationship with the local community. However, due to regional supply limit, a number of major mining services are sourced extensively to other states such as WA.”
For Gary, the approach to growth can vary depending on the company’s financial situation, strategic goals, and regulatory environment, however Yuxin is in a fortunate financial position thanks to its continuous outstanding operational performance.
“On top of this, the stable political environment, skilled workforce, and supportive government policies make
“WE ARE ACTIVELY SEEKING OPPORTUNITIES TO ACQUIRE OTHER MINING COMPANIES OR MINERAL DEPOSITS TO EXPAND OUR GEOGRAPHIC REACH”
– GARY GOH, GENERAL MANAGER, YUXIN HOLDINGS PTY LTD
the mining investment environment in North Queensland and the whole of Australia highly attractive to us,” he remarks. “In this way, Yuxin is able to pursue growth through a combination of approaches.”
The first of these is exploration; 2023 is the 40th year since the Pajingo Gold Mine was discovered. The mine has produced over 3.5 million ounces of gold to date, and
over two million metres of drilling have been completed, which equates to approximately AUD$245 million of drilling expenditure. Again for 2023, Yuxin has a huge exploration budget to continue its success in the region.
“We are actively seeking opportunities to acquire other mining companies or mineral deposits to expand our geographic reach,” Gary notes. “We are also open to forming
joint ventures with other companies if it benefits both parties better.
“On top of this, our operational team always pursues growth by optimising the existing operations. This involves investing in new equipment and technology to increase efficiency, reduce costs, and improve safety and environmental sustainability.”
Lastly, Yuxin is focused on
streamlining operations while remaining sustainability centric. The company has a strong willingness to invest in new technologies and infrastructure to improve sustainability for long-term success in a low-carbon economy.
“WE PRIDE OURSELVES ON EFFECTIVE PERFORMANCE MANAGEMENT SUPPORTING OUR WORKFORCE TO TRULY SUCCEED AND ACHIEVE OUR BUSINESS GOALS AND OBJECTIVES”
– GARY GOH, GENERAL MANAGER, YUXIN HOLDINGS PTY LTD
“The transition to renewable energy sources like solar farms has been seriously considered, as has engaging with manufacturers that help convert the traditional dieselpowered vehicles and equipment to the electric form,” Gary adds.
Yuxin is set to embark on an exciting year for the rest of 2023, as a 100 percent subsidiary owned by Shandong Yulong Gold (Shandong), a public company listed on the
Shanghai Stock Market. Shandong is seeking to grow and expand in both the gold mining sector and the new energy sector, and aims to become a truly international gold mining company which embraces a global vision, cultural diversity and highquality management. The acquisition of the Pajingo Gold Mine is part of this overall strategy, and Yuxin’s ultimate goal is to assist Shandong to achieve this success.
into exploration and tenement development, expanding the project’s productivity to generate better welfare for its workforce, and exploring other acquisition opportunities.
“Yuxin fosters a strong commitment to leadership, and we pride ourselves on effective performance management supporting our workforce to truly succeed and achieve our business goals and objectives.”
“This mission is challenging and exciting at the same time,” Gary reveals. “As a start, from this year, Yuxin will focus on a few key tasks, including investing more YUXIN
www.minjargold.com.au
After three years of expanding operations, Ravenswood Gold is geared towards a longterm future in gold mining. We speak to CEO, Brett Fletcher, as the company celebrates the end of phase one of the project
Now that the project is established, we are looking at steady and stable operations while improving the business and growing mine activities - it is the end of the beginning stage at Ravenswood Gold.”
Gold is a distinctive and precious metal. It is unique in its combination of malleability, boiling point, conductivity and ductility, while also being prized for its evident beauty. Across the world, gold is a very real representation of wealth and, outside of trade and commerce, plays an important part in industry, such as the circuitry of computers, phones, detectors and many more modern pieces of technological hardware.
Australia is home to a huge gold mining industry, one that is embedded in its history and has been pivotal in the development of the nation. In 1851, Queensland saw the first recorded discovery of alluvial gold deposits –gold able to be extracted from water sources such as rivers and streams - at the Darling Downs, leading to a swiftly growing region of industry by the end of the decade. Today, Queensland sees multiple players bringing the region’s deeply rooted legacy of gold to the surface.
Ravenswood Gold is one such company, a gold mining and processing facility located in the town of the same name in North Queensland. Ravenswood town has a long history of mining dating back to 1868, with the modern mine operating continuously since 1987. Ravenswood Gold acquired ownership of the mine in April 2020, including around 160 permanent employees. Since then, the company has expanded its number of permanent staff to support the expanded operations and grow the gold resources.
Ravenswood Gold is a private company owned by EMR Capital (EMR) and SGX-listed Golden Energy and Resources Limited (GEAR). EMR and GEAR established a joint venture
Ravenswood Gold is committed to responsible and community-centric operations through:
- Acknowledging the Birriah people as the traditional owners of the land on which operations occur.
- Respecting the historic heritage of the town of Ravenswood and its surroundings.
- Compliance with all applicable laws, regulations, statutory obligations and agreements.
- Maintaining effective heritage management systems and practices.
- Taking all practicable steps to prevent or minimise the impacts of its operations on heritage aspects.
- Identifying and implementing opportunities to conserve or interpret local heritage.
- Ensuring all persons working on site are aware of and executing their responsibilities associated with heritage management.
- Continuous improvement of heritage management systems and practices.
- Considering community aspects and impacts in all stages of operations and development.
- Taking all practicable steps to prevent or minimise the impacts of its operations on the local community.
- Maintaining effective community and stakeholder engagement and management systems and practices.
- Compliance with the Strong and Sustainable Resource Communities Act 2017 by maintaining a principally local and regional residential or drive-in, driveout workforce.
- Working to maintain a positive and open relationship with the local community and stakeholders through effective communication.
- Ensuring the local community is kept up to date on operations and any changes that may affect them.
- Fostering sustainable social and economic initiatives through the Tourism Directions plan, supporting local organisations and providing local sponsorship opportunities.
- Sourcing local and regional supplies and services where practicable.
- Ensuring all persons working on site are aware of and executing their responsibilities associated with community aspects.
- Involving the community, employees and business partners in continuous improvement of community and stakeholder engagement and management systems and practices.
to acquire, operate and develop the Ravenswood Gold Mine which is located approximately 130 kilometres (km) south of Townsville and 90km east of Charters Towers in north-east Queensland.
For Brett Fletcher, CEO at Ravenswood Gold, this historic industry has always been familiar.
“I come from a long line of people involved in mining; I was born in New South Wales (NSW) at Broken Hill,
Eagle Drilling QLD provides specialist hard-rock drilling services across Queensland. We operate on the surface and underground, offering diamond drilling and multipurpose drilling solutions. Our clients range from large mining companies to smaller, independent prospectors.
Eagle Drilling QLD services areas between Regional QLD and surrounds. Our head office is strategically located in Charters Towers, where we have an extensive fleet, including
our own aircraft, to allow us to work across Queensland with ease.
We employ some of the best professionals in the industry – skilled, capable and experienced in all aspects of surface and underground exploration drilling. As drilling specialists, we pride ourselves in leading the industry, using the best in technology, systems and equipment to get the job done safely, on time and within budget. Learn more
a well-known mining town, and my father worked for the multinational mining giant Rio Tinto for 35 years, one of many family members on both sides who worked in the sector,” he tells us.
“Naturally, I went into the industry myself and worked at a variety of mines, from being Mine Manager at Broken Hill and working on the west coast of Tasmania as General Manager of the Rosebery operation, to working the Century Mine in Townsville (Queensland) and managing at a large zinc smelter in Hobart. I have held numerous corporate roles travelling to mines around the Pacific region and have been with the Ravenswood Gold project from day one.”
Now, Fletcher has the privilege of watching Ravenswood Gold move forward with a long and productive future. The company has undertaken significant expansion in recent years to increase production capacity. Initially, investment had been a concern due to its timing alongside the outbreak of the global COVID-19 pandemic which made way for certain challenges in the industry. However, according to Fletcher, Ravenswood Gold’s management team was very effective when it came to pandemicrelated challenges.
“Over 95 percent of Ravenswood Gold employees commute from the local region, and we partner with suppliers from North Queensland
Greenstone is a leader in the design, engineering and manufacturing of material handling solutions for the C&D recycling, concrete batching, quarrying and mining industries.
Our approach is simple. Listen to our customers and their needs, call on our years of strong industry experience and the knowledge and technical expertise of our comprehensive team of engineers, technical staff and wellrespected project managers.
The result is first-grade equipment and plant solutions brought in on time and on budget to industry leading clients who keep returning to a team they trust.
Greenstone is proud to be the company of choice for many industry leading organisations, both nationally and internationally. Our quality of work and outstanding reputation has led to some of the most recognised names in C&D recycling, concrete batching, quarrying and mining industries turning to Greenstone.
Reliability, innovation, quality and a willingness to go the extra mile, are all values that Greenstone is noted for today. We continue to grow and are proud to partner each step of the way with our clients.
Greenstone has built a well-earned reputation as the one-stop shop for making your material handling vision a reality, providing its clients with clear and transparent communication to achieve your company goals.
With its wide range of services across design and engineering, fabrication and full project management through to construction, the Greenstone team of industry experts can tailor a solution for your specific industry and company needs. We are there for you every step of the way.
Greenstone is also ISO certified, which assures the highest industry standards recognised internationally. www.greenstoneindustries.com
“WE ARE LOOKING AT STEADY AND STABLE OPERATIONS WHILE IMPROVING THE BUSINESS AND GROWING MINE ACTIVITIESIT IS THE END OF THE BEGINNING STAGE AT RAVENSWOOD GOLD”
– BRETT FLETCHER, CEO, RAVENSWOOD GOLD
Greenstone is a leader in the design, engineering and manufacturing of crushing and screening solutions for the C&D recycling, quarrying and mining industries. Our approach is simple. Listen to our customers and their needs, call on our years of strong industry experience and the know-how and technical expertise of our comprehensive team of engineers, technical staff and well-respected project managers.
The result is first-grade equipment and plant solutions brought in on time and on budget to industry leading clients who return again and again to a team they trust.
We are ISO certified, which assures the highest industry standards recognised internationally.
LEARN MORE
where possible,” Fletcher explains. “In 2022, over 70 percent of Ravenswood Gold’s procurement expenditure was spent in Queensland, with around 23 percent directly in the local region. This translates to tens of millions of dollars invested back into our local area.
“We were quite lucky in the sense that we have been able to get the
project built and operational without major disruption because we have such a local workforce - even our contractors are locals. As for the supply chain, there have been challenges in this area. However, most of our supplies are manufactured in Australia, making transportation at a time of restrictions relatively straightforward.”
Ravenswood Gold is committed to safe and sustainable operations through:
- Providing visible leadership and never walking past an unsafe condition or unsafe act.
- Continually placing the health and safety of workers as a priority over production.
- Maintaining clear and open communication lines for safety-related information between all levels of the business
- Demonstrating a commitment towards achieving an injury-free workplace.
- Involving all employees and business partners in the improvement of occupational health and safety performance, through open communication and consultation.
- Ensuring all employees and business partners are aware of their responsibility for the safety of themselves and their colleagues.
- Ensuring all individuals carry out their work safely and are provided with the resources to do so.
- Implementing risk management systems to identify, assess, monitor and control hazards in the workplace.
- Providing adequate health care to all workers and the Ravenswood community.
- Continuously aiming to improve safety-related performance.
- Meeting or exceeding all relevant legal obligations.
- Maintaining robust environmental management systems and practices.
- Complying with all applicable laws, regulations, and statutory obligations.
- Taking all practicable steps to prevent or minimise the environmental impacts of its operations.
- Managing natural resources, particularly water, in a responsible and sustainable manner.
- Considering life of mine aspects, including rehabilitation, in planning processes.
- Progressive rehabilitation of areas no longer required by the operations.
- Ensuring all persons working on site are aware of and executing their environmental responsibilities.
- Involving all employees and business partners in the continuous improvement of environmental management and performance.
- The promotion of a proactive environmental culture.
Powertx Pty Ltd specialises in the design and construction, modification and testing of high voltage electrical systems and related LV reticulation/infrastructure including earth modelling, design and testing. RPEQ design certification can be provided by our in-house engineering and engineering consultants.
Powertx fosters strong and lasting relationships with other construction industry leaders and OEM suppliers. This brings synergies and economies producing a broader scale of capabilities and resources, capturing all installation and commissioning requirements including MDR’s and critical spares.
Associated industries include:
• MV and HV Primary and Secondary Equipment Providers
• Switchroom Providers
• Civil Contractors
• Overhead Powerline Contractors
• National Electrical and Communications Association
• Energy Network Providers
Example Project
66kV METERING STATION, 66/11kV (20MVA) SUBSTATION AND 66/11kV(10MVA) SUBSTATION
As part of the mine’s HV power infrastructure upgrade, Powertx was engaged by Ravenswood Gold for the design, manufacture, and installation of three separate 66kV stations, undertaken on both greenfield and brownfield sites. The three installations consisted of:
• Design, Construct and Commission a 66kV Metering Station including the design and implementation of N.E.R compliant revenue metering.
• Design, Construct and Commission a 66/11kV 10MVA Substation including 4.5MVAR Power Factor Correction (Nolan Substation).
• Design, Construct and Commission a 66/11kV 20MVA Substation including design, installation, and commissioning of point on wave switching and Inter Substation IEC61850 GOOSE communications (ER 4 Substation).
Whilst on site, Powertx has been involved with HV protection testing and temporary HV distribution and has recently been engaged to design, construct and commission a 66/11kV 3MVA Substation to supply the Accommodation Village and Water Treatment Plant.
www.powertx.com.au
Ravenswood Gold is unique in its localisation. According to Fletcher, 95 percent of the company’s employees are locals from the region, with Ravenswood Gold’s entire employee count standing at 420 – with an additional 240 permanent contractors - where in 2020 it was 160 – proof of the mine’s expansive and productively sustainable operations.
Similarly, it is also the use of localised contractors that is helping shape Ravenswood Gold’s success. On top of major growth in its own workforce, Ravenswood Gold has seen an increase in business partnerships, which are key for the company and have been supporting its growth since its establishment.
“Our relationships provide critical
support for the project in the present and into the future, and include Cater Care, who run our village for us and the catering on site; Roc Drill, who has the production drilling contract in the pit; Orica, who support us with blasting and explosive services; Pensar, who have undertaken the civil earthwork for our Tailings Storage Facility; and SimmCo, our local earth moving contractor,” Fletcher elaborates.
“Thanks to our collective partnerships, our workforce reaches approximately 660 permanent longterm employees, and at times we have seen an additional 1,500-2,000 contractors come in to help build the project.”
Ravenswood Gold boasts productive business relationships with
During 2021 and 2022, ECG Engineering (Queensland) was proud to provide electrical design capability to the Ravenswood Gold project, located 130km south of Townsville, Queensland and owned by EMR Capital and Golden Energy and Resources Ltd.
Responsible for the electrical, instrumentation and control systems design, ECG has played a significant part in the project which involved upgrading capacity of the 5 mtpa plant by more than doubling the output to 12 mtpa.
Commissioning was completed in late 2022, with full production to start in early 2023.
www.ecg-engineering.com
A key supplier for Ravenswood Gold’s Conveyor Expansion Project, Fenner Conveyors was contracted to streamline operational processes and reduce overall down-time, with a focus on improving site efficiency.
This was done through the supply of specially engineered rollers and pulleys, alongside conveyor alignment, belt cleaners, rubber lining, and belt installation services.
Fenner is a long-standing supplier for Ravenswood Gold; from its Engineering Teams assisting with component design and system improvements, to detailed scoping and inspections from Service Teams.
From years of demonstrated performance and built trust, Fenner was also contracted to supply belt spares for the Conveyor Expansion Project featuring its impact resistance compound and carcass combination for gold mining applications: Tuff AsTM & Crows Foot Weave.
www.fenner.com.au
From our offices in Australia, The Philippines and Canada, ECG services the electrical needs of Mining, Utilities and Material Handling clients across the globe. Our electrical engineering expertise covers feasibility studies, system audits, design, project management, procurement, construction management and site support. ECG has the expertise and key staff experience to deliver Electrical and Control solutions for:
• Mining and mineral processing facilities
• Power systems, grid connections or power stations
• Non-process Infrastructure
Our guiding philosophy of engineering innovation and integrity in partnership has allowed us to develop strong and successful relationships with our mining partners.
Electrical & Controls Global
E info@ecg-engineering.com
W www.ecg-engineering.com
Engineering innovation & integrity in partnership
OUR OFFICES
PERTH - WESTERN AUSTRALIA
T +61 (0) 8 6164 3400
BRISBANE - QUEENSLAND
T +61 (0) 7 3568 8840
MANILA – THE PHILIPPINES
T +63 2 7091 7469
T +1 905 206 6319
the likes of AUSENCO, the company’s engineering, procurement and construction management (EPCM) contractor, a partner who has helped design, engineer and manage the expansion project. On top of this, the company has multiple construction partners based in the Queensland area; this localisation has given Ravenswood Gold an advantage in overcoming the challenges caused by the COVID-19 period. Additionally, Ravenswood Gold’s incorporation of the latest technology has helped the company establish itself in the field, especially during a period of global challenges.
“We have this Chrysos
PhotonAssay™ machine which is a pretty unique piece of technology that helps us analyse our gold content, owned and operated by Chrysos Corporation,” Fletcher says. “All of our drill results, metallurgical samples, tests and more are now run through the high-tech machine which rapidly analyses and determines the grade of gold that’s in the pit or being processed.”
The advantage of such technology is multifaceted, including providing more accurate test results faster, and improving the overall profitability of gold mining operations through streamlining gold analysis.
Pensar challenges established thinking to deliver innovative solutions and works hand-in-hand with our clients to achieve their vision and build critical infrastructure for the future.
We customise our approach to best suit the needs of each individual project, ensuring we use leading edge solutions to deliver the best results for every client. We create clarity of purpose, alignment of all stakeholders, and ensure the safety and accountability of everyone involved across process water infrastructure, non-process water infrastructure, specialist infrastructure, electrical infrastructure and infrastructure rehabilitation.
pensar.com.au
Since 2021, Wilson Security and Ravenswood Gold have partnered to create a customised, broad security strategy.
From welcoming visitors through to asset protection and traffic and flood management, Wilson Security works closely with Ravenswood Gold, using its Integrated Security Solution Model to protect and support the northeast Queensland mining community. A national leader in security, Wilson Security is rapidly expanding and sharpening its operations across the resources sector. To learn how we can protect your future, call 1300 945 766 or email us at marketing@wilsonsecurity.com.au.
www.wilsonsecurity.com.au
Further proof of Ravenswood Gold’s success is embodied by its milestones. With the Olympics coming to Brisbane in 2032, there are exciting prospects on the horizon for the company. For example, Ravenswood Gold is proud to have commenced discussions with the Queensland government about an opportunity to provide gold for medals at the Olympics.
“Although we are currently working through this process and it may take some time, we see this as a recognition opportunity for the Birriah people, the traditional owners of the land on which we operate, who are very supportive of this as well,” Fletcher explains.
There is no doubt that there are exciting times ahead at Ravenswood Gold. While the Olympics remains a plan for the future, the company’s current activities include the opening of the expanded processing plant and new tailings storage facility expansion. This opening will showcase the company’s completion and full operation of the Buck Reef West pit mine, the completion of the process plan expansion, and the fully functional tailings storage facility.
“We are very proud to be opening
our doors to some of the many people that have helped us execute the various aspects of the Ravenswood Expansion Project since 2020,” Fletcher says. “The official opening ceremony is a way for us to thank everyone that has played a part, from our owners to our business partners, government representatives, local community and, of course, our hardworking employees.”
This marks a milestone and shows that Ravenswood Gold is a company of opportunity, supported by employees, partners and the wider community who have been paramount to the project’s success over the past three years. The ceremony will see state and federal politicians of various departments, foreign ambassadors and representatives from over 30 supplier groups gather to celebrate the completion and future prospects of the Ravenswood Gold project.
For Fletcher, the next six to 12 months will revolve around ensuring a steady and stable operation, making sure that the project is delivering on what is promised, and looking for ways to improve the business.
“We are definitely at a turning point at Ravenswood Gold,” Fletcher concludes. “We originally picked
“Our roots lie in engineering and design.”
RJE Global has a reputation for delivering innovative, client-focused solutions.
With a diverse and dynamic team of over 350 permanent employees, we can provide turnkey solutions both within Australia and internationally. We have specific expertise in the design, manufacture, fit-out, installation and commissioning of transportable switch rooms and skid mounted electrical equipment to support a large range of surface and underground mining projects.
Our unique manufacturing techniques allow for the efficient construction of high integrity transportable buildings and skid mounted structures for harsh conditions. www.rjeglobal.com
up the asset and had a very clear strategy on what needed to be built to transform the business into a longlife, low-cost, large-scale operation, looking at a production rate of around 200,000 to 250,000 ounces a year.
“There was a lot of project work to be done, but as I sit here three years later it’s fair to say we have finished that construction phase and are ramping the plant up to its new full capacity. We are going to focus on improvement: how can we achieve more production? How do we reduce costs? How can we increase the life of the mine? That is very much our medium-term focus, with the longterm being consistency and growth.”
TerraCom is an Australian-based mining resources company encompassing an impressive portfolio of operating assets and exploration projects within the national coal sectors of Australia and South Africa. We learn more about this global operation with a community-centric core from Managing Director, Danny McCarthy
A South African owned mineral processing company with 52% black shareholding based in Emalahleni Mpumalanga Province.The company was incorporated in 2006 to service the mining industry in contract mineral processing.
Coal is a cornerstone of Australian industry. Built on the efforts of hardworking Australians across regional operations, the sector has a strong future which promises to meet all the requirements of a modern economy.
Despite the ongoing negative rhetoric concerning coal, Danny McCarthy, Managing Director of TerraCom, believes that the resource will remain at the forefront of Australian industry for a long while yet.
“Whilst alternate energy sources are discussed and strategised over, the coal industry will continue to keep the lights on in Australia and indeed around the globe until a like-for-like
DANNY MCCARTHY, MANAGING DIRECTOR: “At TerraCom, we are focused on motivating and empowering our employees, resulting in higher job satisfaction, improved work performance, and a greater commitment to the company.
“As Managing Director, I am deeply committed to making a positive difference and it is important that our vision, purpose, and values are known, understood, and lived by all employees.
“Our vision sets out what the future will look like, our purpose outlines why we exist, and our values are the fundamental shared beliefs and internal code of conduct which inform and inspire the ethics, behaviour, communication style, and culture within our company.”
energy source can eventually replace it,” he introduces.
Coal mining in Australia is a highly sophisticated and high-tech process. Continuous improvements in mining technology, occupational health and safety and environmental performance have ensured Australia’s standing as an efficient and reliable producer of high-quality, low-cost thermal and metallurgical coal for the domestic and international markets.
Regarding South Africa (SA), TerraCom’s other major operational market, coal mining underpins the nation’s economy and is an important contributor to its success and longevity. Coal usage is integral to SA’s energy sector and over the course of the past decade, the nation’s public-owned utility, Eskom, announced the construction of the Medupi and Kusile coal-fired power plants to enable continued electricity supply for its people for decades to come.
Growing up in Central Queensland, McCarthy’s interest in the mining industry commenced at a young age. His father was an underground miner who transitioned to surface mines in the late 1970s, and it was this early exposure to the industry that ultimately led to McCarthy forging his own path within it.
“I was intrigued by the sheer size and complexity of the mining process,” he recalls.
Fast forward through 27 varied years in the mining, minerals processing and resources sector within Australia, and McCarthy started working with TerraCom as Chief Executive Officer in December 2018, as the company was poised to start implementing an improvement agenda focused on long-term sustainability for employees and shareholders.
Having grown significantly to now boast a global footprint, TerraCom is
an Australian-based mining resources company, comprising a large portfolio of operating assets in Australia and SA with an impressive suite of exploration projects within the vast coal sectors of these two nations.
“We are a renowned low-cost producer focused on delivering exceptional outcomes from our highyielding diversified asset portfolio for investors,” explains McCarthy.
On a combined basis, via both direct and contractor engagement, TerraCom now employs approximately 3,600 people worldwide.
“Our people are our business, and their continued dedication allows us to consistently deliver products to our customers every day of the week, and every day is the chance to better the achievements of yesterday,” he continues.
The Australian business unit of TerraCom comprises the flagship Blair Athol coal mine located in Clermont, Queensland, as well as a large portfolio of exploration and evaluation assets predominantly located in the Northern Galilee coal region.
The life of the Blair Athol mine is projected at more than eight years at the current run rate of 2.2 million tonnes for export, and TerraCom continues to explore several potential near-mine expansion opportunities which could see the facility utilised as a processing precinct for many decades to come.
In SA, TerraCom, via its 100 percent ownership of Universal Coal Plc, holds an interest in a portfolio of producing, development and exploration assets located across the nation’s major coalfields. There are currently three operational mines including the North Block Complex, New Clydesdale Colliery and Ubuntu Colliery.
The SA operations provide domestic quality coal to Eskom, and also supply high quality export coal to customers via the Richards Bay and Maputo coal terminals.
Customer focus is our priority. In line with our motto of ‘Operational and Maintenance Partner of choice’ operate 12 coal-processing facilities for different clientele: Universal coal, Thungela coal, Menar, Canyon coal, Salungano, Overlook, Ikwezi and ArnotOpco. In 15 years, Ingwenya Mineral Processing (Pty) Ltd has completed 13 Coal Processing and Handling Plants Capital projects, and seven retrofits and modifications. Ingwenya specialises in contract mineral processing consulting services with a specific focus on the coal industry.
Our areas of expertise comprise:
• Operations and maintenance
• Design and build of plants
• Engineering design and fabrication
• Feasibility and due diligence studies, trouble shooting and optimisation
We operate different types of DMS plants of varying capacities incorporating the following beneficiation equipments: Drum, Cyclone or 3-Product Cyclone, Larcodem, to produce Powerstation coal, RB1/RB2/ RB3, and metallurgical sized products according to client needs. We rely on our dedicated, competent and efficient teams to produce coal that meets required specifications and targets. A group of specialist process engineers, mechanical and electrical engineers supports the operations with expertise to ensure seamless production.
Our modular plants can be summed up as cost effective, simple, flexible and easy to operate and maintain. This reduces fabrication time and erection costs and also ensures that projects are delivered at short lead times.
The modules are designed to accommodate future expansion by just adding onto the existing module sharing the peripherals. Our plants are tailor-made to suit client specific needs, flexible to treat different seams and to produce single or multi products to cater for different markets. Our modular plants are easy to dismantle and relocate elsewhere.
Ingwenya has developed strategic partnerships with OEMs, which assists in acquiring expertise in leading technology to ensure efficiency from the design phase straight into production.
We design and build Slew stackers suitable for Eskom products. It can rotate 220° to build five conical stockpiles of 5,500 tons each. Slew stacker can build one 5,500 tons stockpile in nine hours. We also build smaller product stackers capable of building two stockpiles of 3,000 tons each for smaller operations or crush and screening operations.
Ingwenya is committed to the highest standards of safety, health and environmental performance and fully supports the SHEQ management standards and systems of our clients.
Our advantage point: Bomax Engineering Workshop
Ingwenya has a fully equipped in-house 4,000m2 engineering workshop located in Hendrina, Mpumalanga, where we fabricate our own steel structures and platework. The workshop has a well-qualified and experienced team in Fabrication, Construction and Maintenance. The workshop supplements the operations in terms of upgrades, installations, maintenance and shutdowns.
In the future, Ingwenya intends to diversify into other commodities and grow its portfolio beyond local borders.
TerraCom currently finds itself in a unique position whereby it does not have the bureaucracy that some larger organisations in the industry have.
“We are flexible and agile, and this allows us to quickly adjust to meet the changing demands and parameters of the market, internal business requirements and stakeholders,” McCarthy outlines.
The main ethos of the company is “we do what we say”, which is extremely important both within the organisation and when dealing with external stakeholders. TerraCom strives to maintain a high level of leadership and show accountability for everything it does, and this subsequently inspires its entire team to remain committed to goals, be attentive during all tasks, and crucially, never lose sight of opportunities to grow.
“Our mantra is simple yet compelling – be better than our peers, deliver reliable and consistent products, and be cost-conscious with every dollar spent. There is no ‘done’ or finish line; our sights are continually honed on being better at every turn. With each interaction, every movement and motion, we aim higher and higher and higher, and we do it at every chance we get,” he adds.
This is critical in building positive community relationships. Indeed, the strength and success of TerraCom, whilst founded on its people, is underpinned by long-term business partnerships with several key equipment and contracting partners.
“As part of our everyday actions, we strive for continuous improvement. We know there’s always something to learn from what we’ve done; whether that be the way we act, the choices we make, how we live out our cultural values or how we treat each other and the wider community,” McCarthy says.
Monandi Group was established in 2015 by Kriven Maharaj (Director) who has experience in the mining industry since 2013.
The company has been working with major mining groups within the Mpumalanga region providing material handling services and stockpile management. We strive for excellence service delivery so our clients can meet their targets on a monthly basis. We are a Level 1 B-BBEE company which focuses on creating job opportunities for the locals around the Mpumalanga region.
www.monandigroup.co.za
• Loading and hauling 350,000 tons of Export and Eskom Coal
• Material handling and Stockpile Management
Shape and level ROM, crushing boulders, compaction and road maintenance.
• AshDam Project
Supply machinery for material handling
Our Assets
• Front-End loaders
• Dozers
• Packers
• Excavators
• 10-Cube Tipper Trucks
• Diesel Bowsers
• Compactors (All machinery is well maintained through OEM)
DESIGNING WITH PASSION. BUILDING WITH PURPOSE.
The Outlook Creative Services Division provides a complete web design, build and delivery service that leverages the expertise of our in-house production team. Complementing Outlook Publishing’s portfolio of esteemed global publications, our specialist skills cater to clients around the world with a fully bespoke service.
If you would like us to bring your digital story to life with passion and purpose, visit www.outlookcs.com or email hello@outlookcs.com
Elsewhere, TerraCom also works cooperatively with local communities to progress its projects both in Australia and internationally, and is committed to a positive programme of engagement in every community in which it operates.
In Australia, the Blair Athol mine plays an integral part in the Clermont community. In addition to providing community group support, TerraCom has recently completed the onboarding of 16 local traineeships and is launching an apprenticeship programme providing careers in mining and skills pathways to further support the future of Clermont and the wider central highlands region.
Further to these communitybuilding initiatives, TerraCom is also a well-regarded supporter of CQ Rescue, a community-funded rescue helicopter service based in Mackay, Queensland. CQ Rescue is an instrumental service across Central
and North Queensland, providing the community and stakeholders with a sustainable and supported, worldclass aeromedical and emergency helicopter rescue service available to anyone, anywhere at any time.
For the South African strand of the business, TerraCom, via its subsidiaries, has identified education as a key area that will change the lives of the youth in the company’s host communities and will therefore continue to offer skills, training programmes, internships and funding for higher education and donations to local schools across its operations.
TerraCom transports products from its mining facilities to customers by rail, train, truck and ship. The business partners that provide the company’s supply chain services are wellestablished, reputable firms that are
deeply engrained in the industry.
It is TerraCom’s preference to always work with local suppliers, in order to promote local community growth and support the availability of skilled labour, goods, and services from stakeholders near its operations in both Australia and South Africa.
The reality is, successful partnerships don’t just happen, and TerraCom recognises the genuine relationships that it has built with its customers and valuable business partners who have supported the company along the way.
“These highly reputable and established relationships emphasise accountability across all areas of our business; we focus on priorities and gauge business metrics to track and measure performance which help us to thrive, creating more value than we otherwise would,” ensures McCarthy.
Of equal importance to TerraCom is protecting the unique environment of the areas in which the company
operates and managing social responsibilities with immense sincerity.
“Our commitment is being responsible to minimise our impact, to progressively rehabilitate areas disturbed during our operations, and preserve or restore the longterm health and sustainability of the environment where we operate,” McCarthy tells us.
The advancement of this rehabilitation is being completed progressively at TerraCom’s Blair Athol mine in Clermont and its South African
operations, with the aim of significantly reducing rehabilitation activities at the end of the mine’s life. The mine currently has dedicated rehabilitation equipment and resources to undertake the necessary rehabilitation works with additional support from the production dozer fleet.
It is now TerraCom’s immediate focus to continue to ensure dividends flow to shareholders and the company remains open to the right growth
opportunities that pass its strict investment criteria.
“Ensuring responsible management of capital within our recently developed framework is a key focus, and our growth agenda is governed by responsible decision making for opportunities that add value to our story,” wraps up McCarthy.
The story of TerraCom is one that looks set to continue unwinding in exciting new directions and promises to deliver a highly satisfying overarching narrative for all characters involved, in line with the company’s relentless ambition for forward progress.
Tel: +61 7 4983 2038
info@terracomresources.com
www.terracomresources.com
“OUR PEOPLE ARE OUR BUSINESS, AND THEIR CONTINUED DEDICATION ALLOWS US TO CONSISTENTLY DELIVER PRODUCTS TO OUR CUSTOMERS EVERY DAY OF THE WEEK”
– DANNY MCCARTHY, MANAGING DIRECTOR, TERRACOM
Buried beneath Africa’s earth is a wealth of natural resources. Hugely valuable and readily extractable commodities, such as coal, make the continent one of the most important places in the world with regard to mining opportunities. The mining industry has a
long history in Africa, with its cornucopia of mineral, metal, and gemstone reserves. In the past, the continent has experienced gold rushes, diamond discoveries, and is currently the world’s third largest coal exporter, with the commodity concentrated in the Mpumalanga
province in South Africa.
Coal mining in South Africa has its roots in the late 19th century, occupying a similar timeline to gold mining, and in the same area of Witwatersrand. Coal was extracted in large quantities, close to the nascent gold mines. However, as
demand for fossil fuels started to grow, South Africa began to build its industrial future.
Not only is South Africa’s past rooted in coal, but its future is too, as its energy resources are still dominated by the resource. Despite its negative perceptions in the era
of climate change, coal remains the most widely used primary fuel on an international scale, accounting for over a third of the world’s total fuel consumption for electricity production.
Major mining countries in Africa include Namibia, Zimbabwe, the
Democratic Republic of the Congo (DRC), and South Africa. The latter is home to Msobo Coal, based in the Breyten and Carolina area of Mpumalanga province. This particular location is situated within South Africa’s coal belt, with more than 100 coal mines and a dozen
As an industry, coal mining is thriving in South African provinces. We extract answers from Yacoob Mansoor, CEO of Msobo Coal
coal-fired plants that punctuate the industrial landscape. In fact, Mpumalanga produces around 80 percent of the country’s entire coal supply.
Around 40 percent of South Africa’s coal is used for power production, and approximately 77 percent of the country’s energy needs are provided by the commodity. It therefore makes sense that South Africa’s largest energy supplier, Eskom, accounted for 38 percent of Msobo Coal’s clientele in the last financial year.
The remainder of the company’s business includes 27 percent export and 34 percent inland, which produces coal for various markets. Msobo Coal owns many assets to accommodate the demand in production.
The clientele breakdown for the export market centres on RB1 and RB2 products (types of coal known for their high thermal content), whereas the inland market is concerned with 5000Kcal, RB1 peas (used for agriculture and generating electricity), nuts, and RB1 low
phosphorus small nuts. Finally, Eskom primarily deals with Msobo Coal for the supply of washed middlings with future crush and screen products.
“We have nine opencast and two underground coal mining operations, four coal washing plants and four railway sidings,” begins Yacoob Mansoor, CEO. The sidings can handle 200,000 tonnes of coal per month.
“Coal is transported from the mines to the company’s processing plants. Msobo Coal prides itself on managing all its key operations including its coal washing plants and four sidings,” he adds.
As a qualified geologist, Mansoor joined Middelburg Mine Services in 1994, a neighbouring coal mine located nearby in Mpumalanga province. After working for various opencast and underground coal operations, he was stationed as a senior geologist for Matla Colliery,
Dabmar, established in 1966 by Otto Martin, has been a world leader in screening machines for sorting, sizing, and feeding material for over 50 years. Today, Josef Martin, son of Otto Martin, leads Dabmar with the same unstinting commitment to delivering the most optimal process solutions and the best possible ongoing service and support for which Dabmar is so well known. Dabmar’s continued innovation focuses on solutions in reducing, or eliminating altogether, the use of water in processing sticky, near-size materials, prone to pegging and blinding of conventional screening systems.
Dabmar offers screening solutions to the bulk material processing industry.
• Non – Blinding system
• 100% spare parts availability
• Handles difficult to screen materials
• Smaller machine footprint
• Negligible dynamic loading to support structure
• 95% screening efficiency
• Proven reliability
• 24/7 support, 365 days a year
• Higher amplitudes for better efficiency
• Low wear on moving parts
which was subsequently taken over by Eyesizwe Coal.
Mansoor has a plethora of experience in the mining industry gained from his time spent as a Projects Manager and General Manager with Liketh Investments. Working on coal processing operations until 2021, he was subsequently appointed CEO at Msobo Coal.
Established in 2012, Msobo Coal is headquartered in Breyten within the Msukaligwa Municipality. Its subsidiaries include Northern Coal and Estrapade.
“The mining sector has great potential to expand further and lead the African commodities sector. We need to improve our rail and access to ports in order to take advantage of the current commodities demand in South Africa,” Mansoor informs us.
With six million tonnes of
“WE HAVE MANAGED TO PROCURE MORE FUEL-EFFICIENT FRONT-END LOADERS AND DOZERS AND WILL CONTINUE TO REPLACE OLDER MACHINES FOR MORE FUELEFFICIENT MODELS”
– YACOOB MANSOOR, CEO, MSOBO COALRun-of-Mine (ROM) coal produced annually, the final product is transported to clients using both rail and road, but moving the product by train has not been without issues.
As recently as last year, mining companies in South Africa have resorted to trucking coal to ports to meet a surge in demand in Europe. Due to poor maintenance and a lack of parts for trains, logistics have been disrupted, and as a consequence, coal exports have fallen.
Considering 27 percent of Msobo
Coal’s business is exported, the lack of freight rail services has had a significant impact on business, as South Africa is the sixth largest producer of coal in the world.
With 900 employees and 1,500 contractors, 90 percent of whom are local, Msobo Coal is orientated towards investing in people. In fact, 70 percent of the company is Blackowned, which also includes 33.5 percent women.
• Four processing plants
– Spitztop Plant
– Tselentis Plant
– Northern Coal Plant
– Umlabu Plant
• Five collieries
• Eight opencast mines
• Two underground mines
RESOURCES:
• Verkeerdepan Opencast
• Hammerkop/M16 Opencast
• Mimosa/Koppie Opencast
• Sara Buffels Opencast/ Underground
• Tselentis Mooiplaats
Underground/Mini Pits
• Jaglust/Roets Opencast –Northern Coal
• Weltevreden Opencast
• Black Diamond Opencast – for Eskom only
SKILLS PROGRAMMES INCLUDE:
• Driving licenses
• Plumbing
• Welding
• Operator training
• Bricklaying
• Iron ore beneficiation
In addition, the company offers 52 skills programmes, 74 learnerships, seven university bursaries, and five high school bursaries, alongside more than 23 schools on the Ligbron E-Learning Project.
Skills and development are crucial to the Msobo Coal workforce, ensuring the uplift of livelihoods amongst local communities and employees, providing opportunities to build a future through gaining the necessary knowledge and work readiness programmes.
Msobo Coal’s partnership with the Department of Basic Education is designed to achieve the goal of educational outcomes for learners in the community. Msobo Coal also provides financial support to the needs of students and educators of the local Adult Basic Education and Training (ABET) Centres, which support adult education in South Africa and enable adult learners to gain new skills, knowledge and attitudes.
“Our employees have been empowered to manage and take ownership of their area of responsibility. More than 85 percent of our employees are from the local communities around our mining operations.
“We continue to support and invest in our local schools, small, medium, and micro enterprises (SMMEs) and community projects,” Mansoor says proudly.
In addition to the learnerships and internship programmes, there are bursaries and other education programmes available which are designed to assist employees beyond the life of a mine. The employees can enjoy individual career development programmes. Moreover, it is not only employees which benefit from such schemes but also members of host communities.
“Our employees are incentivised with both safety and production bonuses; we also have seasonal safety programmes in place that reward employees for achieving zero accidents or incidents.
“Training is an ongoing process at the operational level, and we offer bursaries to our employees so they can further upskill themselves to fill vacancies within the company,” outlines Mansoor.
The pressure is building on the mining industry to practice more environmentally and socially responsible methods.
As the world moves towards green energy, and with coal accounting for around 50 percent of the global mining market, South Africa is the biggest centre of mining activity on the African continent, therefore the future of mining practices is seen as a guide for the broader African industry.
Choosing mining pit locations in relation to geology and the environment requires experience
and knowledge based on geological reports with mine planning and scheduling. Known as geologic mapping, it is an important task in exploration.
“Once these are found to be economically sound, we then apply for all the necessary licenses for environmental approvals and water use. Once these are received, mining operations are planned and commenced. Any area that is sensitive in terms of the environment is not considered for mining. Areas that are mined are fully rehabilitated and restored back for the commercial agricultural sector,” Mansoor explains.
To conduct mining operations in South Africa, a mining permit from the Department of Mineral Resources and Energy (DMRE) is required. This is to promote environmental sustainability as well as economic growth and development, and social equity.
Coal has entered a new phase of abatement and as such, up to 99
percent of all coal emissions will be eliminated through technologies and processes. Therefore, mine rehabilitation is an important restoration process to ensure a site is safe and stable for future use after mining activity.
“We have rehabilitated in excess of 1,181 hectares (ha) and seeded in excess of 581 ha in the last three years. Our social initiatives are working with the local SMMEs, as well as schools and local municipalities in providing infrastructure for sustainable projects,” he adds.
Earlier this year, Msobo Coal completed the expansion of the Spizkop processing plant to handle 180,000 ROM tonnes. It includes a spiral section as well as fines recovery with two new filter presses installed. However, Mansoor is looking to the year ahead. “We have managed to procure more fuel-efficient front-end loaders and dozers and will continue to replace older machines with more fuel-efficient models.”
Alongside mining activities, Msobo Coal is involved in more societybased ventures. By immersing itself in community projects, the company is involved in the KwaChibikhulu Thusong Service Centre, which has a multi-purpose community hall and a library staffed by Msukaligwa Municipality employees. The project was handed over to the community
in April 2021 as a social and labour plan (SLP), at a cost of R10.07 million.
“The building will provide a base for the community to launch various development programmes and projects,” states Mansoor.
Another worthy project that Msobo Coal was a party to was delivering 7,213 textbooks to Masizakhe Secondary school, and in late 2022 the company partnered with Gert Sibande District Municipality to resurface the Breyten roads.
The thought process behind donating stationery to community learning centre (CLCs), in the Gert Sibande District, is to assist students in gaining their Grade 12 senior certificate.
Msobo Coal wants to encourage youths to return to school because there is a strong possibility of employment at its mines after completing the grade. It was an initiative started by the company after noticing the level of poverty and illiteracy in the townships of the Gert Sibande District.
The mine also has a programme in place where it awards bursaries to deserving students who have completed studies at the various CLCs. The aim is to motivate students to work in the mining industry.
The initiative assists students from the disadvantaged Breyten community with a full bursary which includes fees, hostel uniform, and stationery. “We currently have five students from grade eight to grade 12 on the Ligbron Learner Support,” notes Mansoor.
Msobo Coal’s continuous drive to develop local businesses is evidenced in its management training and mentoring, alongside supporting emerging farmers with seeds and machinery. The company not only invests in its employees, but it cares about its local communities too. MSOBO
We offer
the following:
Caliwe Group has been working with Msobo Coal since 2016 to date, offering consulting services. We have also been involved in project management of the SLP projects on an adhoc basis.
The Barberry Group offers the market and our customers a unique value proposition, and one which we believe is not matched by any of our competitors.
Our value proposition – SMART RAIL IN MOTION - is primarily focused on lowering the customer’s costs of logistics, while ensuring a safe, reliable and consistent service is provided. info@barberry.co.za
Mining Outlook Issue 2 | 107 MSOBO COAL (PTY) LTD MINING
Tietto Minerals is the newest gold producer in West Africa, marked by its first successful gold pour this year. We speak to Managing Director Caigen Wang about the company’s Abujar Gold Project and its exciting potential moving forward
Project Manager: Joshua Mann
Africa is a continent of precious gems and metals.
In the west, Ivory Coast is home to a diverse range of mineral commodities and hosts a mining sector set to attract foreign investment from all over the world. The national government has helped in this regard, establishing measures to simplify the process surrounding obtaining mining permits, as well as providing tax incentives to those companies and bodies seeking to invest in sector operations. On top of this, there exists a national agency for the promotion of investments, established by the government to help develop investor projects in the field.
As Managing Director, Wang has significant experience in the mining minerals sector. On top of having obtained a Master’s and PhD in Mining Engineering, Wang is also the Founder of Tietto, a Fellow of the Australasian Institute of Mining and Metallurgy (AusIMM), and a chartered professional engineer of the Institution of Engineering, Australia.
Wang has over 30 years of practical experience in mining engineering and mineral exploration in Australia, China, Africa and Canada, with recent professional experience including Managing Director for an Australian Stock Exchange (ASX) listed junior mineral resources company, and senior technical and management roles in various mining houses (St Barbara, Sons of Gwalia, BHP Billiton and China Goldmines PLC and more). He has been working on a variety of mineral commodities including coal, gold, nickel, iron, copper, lead and zinc, molybdenum and oil sands and many others.
Backed by this government assistance, it is no surprise that Ivory Coast is rapidly growing in recognition as a country with substantial mining potential.
“Ivory Coast is one of the best locations for gold mining investment in the world. When it comes to jurisdiction, it is certainly the best in Africa. The government is very transparent, and the mining industry operates under the New Mining Code, working with safety at the fore,” introduces Caigen Wang, Managing Director of Tietto Minerals (Tietto).
Tietto is West Africa’s newest gold producer, achieving its first gold with the Abujar Gold Project (Abujar) in Ivory Coast in January of this year. With an estimated life of mine (LOM) revenue of USD$2.87 billion at a USD$1,700/oz gold price, Abujar can deliver a pre-tax cashflow of USD$1.28 billion and achieve payback within a year of first production post-ramp-up. On top of this, Abujar gold production is unhedged and free of debt.
Abujar exemplifies the rich potential of mining in Ivory Coast. According to Wang, the country has a lot to offer in terms of resources in the mining sector and is currently one with less focus continentally, leading to a lot of untapped opportunities across the nation.
“Importantly, Ivory Coast is underexplored resource-wise compared to neighbouring countries,” Wang explains. “Ivory Coast also has fantastic infrastructure and when it comes to transport, power and supply, these are all available. Power
is very cheap for the mining industry nationally, and on top of all this, the government is very ambitious to escalate the mining sector’s contribution to overall GDP.
“The government is aiming to increase this from two to five percent of the country’s GDP, and the economic and supplier support proves this.”
For such a new and established company, Tietto has a bright future ahead of it. Tietto’s 2021 definitive feasibility study (DFS) for Abujar demonstrated the project can produce 260,000 ounces (oz) of gold in its first year of production postramp-up at an all-in-sustaining-cost (AISC) of USD$651/oz and produce 1.2 million ounces of gold over the first six years of operation, averaging 200,000 ounces per year at an AISC of USD$804/oz.
“Tietto started in 2010 with a focus on gold exploration in West Africa,” Wang tells us. “The company originated in Liberia, and two years later we expanded into Ivory Coast. This expansion gave rise to the Abujar project, located in the central west of the country.”
Tietto is positioned to continue building its resource inventory at Abujar while ramping up gold production in the first half of 2023. Abujar itself is comprised of three contiguous tenements: Abujar South, Abujar Middle, and Abujar North, totalling over 1,114 kilometresquared (km2) and features a
“IT IS NOW TIME TO DRILL WIDELY ON THIS PROJECT AND EXPLORE ITS POTENTIAL FURTHER TO PRODUCE THE GREATEST YIELD OF GOLD POSSIBLE WHILE KEEPING AN EYE OUT FOR FURTHER EXPANSION OPPORTUNITIES WITHIN IVORY COAST”
– CAIGEN WANG, MANAGING DIRECTOR, TIETTO MINERALS
Global Earthmoving Contractor for Mining and Infrastructure Projects, serving the industry for more than 60 years, committed to a Sustainable Life Impact for Today and Future Generations.
www.epsagroup.com
70-kilometre-long gold corridor. Less than 10 percent of the project area has been explored, providing plenty of exploration upside for Tietto to further grow its resource inventory.
Ivory Coast is home to diverse mineral resources, and key among these is gold. However, the country boasts significant reserves of other minerals that are used for a wide variety of purposes, such as manganese, nickel and bauxite etc.
On top of gold, Ivory Coast’s diverse mineral resources include:
- Diamond
- Manganese
- Bauxite
- Iron ore
“Starting from scratch, we began exploring Abujar in 2014. We explored the potential of the project extensively, gaining a mining licence in 2020, and started building the mine at the beginning of 2022, completing in December of last year,” Wang says.
“Since then, Abujar has operated full steam ahead, leading to its successful first gold pour at the beginning of this year, a significant and celebratory milestone for Abujar and all of us at Tietto.”
Abujar is strategic in its location, being 30 kilometres from the major regional city of Daloa and close to excellent regional and local infrastructure including grid electricity to make the most of Ivory Coast’s cheap power costs.
Abujar has a current LOM of 11 years with scope for Tietto to extend this with further near-mine and regional exploration success. With this in mind, Tietto is investigating the viability of a second site, the AbujarPischon-Golikro (APG) gold deposit, seven kilometres from its Abujar CIL operations.
Tietto’s investigation into the viability of a second gold mine at the APG deposit has led to a promising
find; the scoping study has identified potential for a heap leach operation that could deliver an additional 850,000oz of gold over 10 years.
In addition, Tietto has opportunities to improve on DFS gold production by increasing project output via infill diamond drilling targeting the delineation of measured resources, deep drilling targeting underground potential below the ore reserve pit design at Abujar Gludehi (AG) core, aggressive regional exploration drilling and APG heap leach potential, which is currently being assessed. Tietto is planning to complete 120,000m of drilling in CY2023. An Abjuar resource update was released in mid-April CY23 for 3.83 million oz, an 11 percent increase from 3.45 million oz delivered in April 2022.
“We are constantly undertaking explorations to increase our resource base, which will give us very good opportunities to extend the LOM, that is currently over a decade. We aim to extend the LOM substantially, and we have a very good drilling capacity so we will up our resources via aggressive drilling,” Wang adds.
“We employ drillers – those that
“IVORY COAST IS ONE OF THE BEST LOCATIONS FOR GOLD MINING INVESTMENT IN THE WORLD”
– CAIGEN WANG, MANAGING DIRECTOR, TIETTO MINERALSTailings slurry discharging into TSF
operate our drill rigs – ourselves, so our drilling costs are very low compared to other mining operations in the industry.”
Tietto’s operations at Abujar included the use of a 4.5 million tonnes per annum carbon-in-leach (CIL) processing system that was constructed within budget and on schedule, completed after 12 months with no debt and zero hedging – a monumental achievement for the company.
“We have a very unique in-house mine building capacity led by our Executive Director and COO Matt Wilcox,” Wang elaborates. “Abujar is the fifth gold mine that Matt has built in the past 12 years in West Africa, and it is through his lead on the production side of things that we have succeeded to the extent that we have today.”
Prior to his time at Tietto, Wilcox
directly managed the construction of gold producer West African Resources’ (West African) 300,000oz per annum Sanbrado Gold Mine, which was completed in March 2020, ahead of schedule and under budget.
He is highly experienced in the gold mining construction industry in West Africa, having spent the prior eight years working for Nord Gold, which operates nine gold mines globally, including three mines in Burkina Faso and one mine in Guinea.
“Abujar was built during a very
challenging COVID-19 pandemic period, which shows the capacity, professionalism and efficiency of Tietto when it comes to project management and completion,” Wang concludes.
“It is now time to drill widely on this project and explore its potential further to produce the greatest yield of gold possible while keeping an eye out for further expansion opportunities within Ivory Coast.”
Tel: +61 8 9420 8270
admin@tietto.com
www.tietto.com
Abujar Mine Camp Abujar Mine Camp Abujar Mine CampAs Howden offers high-end ventilation solutions to the mining sector, we discover more about the company’s evolutionary leap forward in engineering equipment with Managing Director Kudzai Nyangoni
Writer: Rachel Carr | Project Manager: Joshua Mann
Revolutionary engineering in the 19th century paved the way for various technologies that everyone is familiar with today. In 1854, James Howden founded a marine engineering company, and it was his early inventions which enabled the steamships of the era to
reduce their energy consumption by nearly 50 percent.
As industrial innovations increased, and the engineering industry expanded into homes with efficient appliances such as refrigeration and air conditioning, the company began to grow. Almost 100 years after the initial steps into
marine engineering, James Howden & Company Africa Pty was formed in 1952. After its recent acquisition by Chart Industries, the company has since rebranded as Howden.
The progressive and energy efficient solutions continue to this day, in fact, with the company and the team deeply rooted in sustainability. Its environmental, social and corporate governance (ESG) efforts are a fundamental characteristic of the Howden brand.
For more than a century, Howden has supplied ventilation systems and equipment to global mining companies from the Arctic to Africa. Whatever the type of mine, whether it is coal, mineral, or base metal, Howden’s technology offers a superior ventilation performance.
“In the last 14 years that I have been with Howden, I have overseen the design, manufacture, installation
“Our employee onboarding process is strategic, as it is designed to build and establish engagement earlier in the employment stage. We have developed a five-step framework that starts from the day the new employee accepts the offer. We also utilise our buddy system that provides socialisation into the organisation as well as promoting team integration in the first three months of the onboarding process.
“The hiring process is comprehensive and varies according to the expertise required. At Howden, we believe in talent management as a strategic and holistic process for the business and for the individual. We look for candidates with a hunger for success and with relevant skills and knowledge in their chosen field, who also demonstrate good behaviour with a capability and potential to fulfil roles that are more complex and specialised.
“We also have a graduate programme for those who want to gain industry experience and build their careers at Howden.”
commissioning and maintenance of mine ventilation and mine cooling plants for some of the world’s deepest mines located in South Africa,” opens Kudzai Nyangoni, Managing Director of Howden.
As a supplier of diverse gas handling equipment such as air heaters, mine ventilation fans, industrial process compressors, and a wide range of air pollution control equipment such as bag filters, scrubbers, industrial and medical waste incinerators, heating, cooling systems and more, Howden offers a fully integrated suite of expertise.
“For the mining sector, Howden offers products and services under the Total Mine Ventilations Solutions (TMVS) strategy, ranging from pre-feasibility engineering studies, ventilation and cooling solutions and aftermarket services for installed equipment. The products and services are flexible, efficient and safe, and consequently, TMVS is a one-stopshop,” Nyangoni informs us.
FIELD SERVICES AND ENGINEERING
Facilities include a 25,000m2 workshop with a 20,000m2 laydown area.
- Overhead cranes
- Two GM technical services cranes – 100 ton per crane with 15 metre clearance
- 2x 35 ton cranes
- 9x 10 ton cranes
- 4x 5 ton cranes
FIELD SERVICES AND ENGINEERING
All employees from each division are tested and certified to all relevant standards and specifications.
Engineering and manufacturing capabilities include:
• Sub arc welding
• Flux-cored arc welding
• Gas metal arc welding (GMAW)
• Shielded metal arc welding (SMAW)
Offering a 24-hour breakdown service to minimise downtime and production loss.
FSE has core engineering and field service solutions with the following engineering and manufacturing services available:
FSE PIPETEC
Facilities include two dedicated 4,000m2 under roof workshops
- 4x overhead cranes
• General fabrication for the medium to large industrial sector, for example, ducting, fan casings, motor housings and structures
• Sand blasting and painting completed to meet customer requirements
• Reconditioning of gearboxes, pumps, hydraulic cylinders, etc.
• Manufacture of shredding machinery for the recycling industry
• Specialised welding of carbon steel, hardened and tempered steel, stainless steel, duplex stainless steel, aluminium and boilerplate
• General fabrication for the medium to large industrial sectors include, but are not limited to, structural steel, platework, and machining
FSE PIPETEC
• Skid manufacturing
• Ducting manufacturing
• Light/medium structural steel manufacturing
• Equipment manufacturing – tanks, vessel, cyclones etc
• Small and large bore pipe spool fabrication – carbon, stainless, duplex stainless, etc.
BPI
Facilities include
- 2x 10 ton overhead cranes
- 1x 25 ton mobile crane
- 1,500m2 light sheet metal workshop with a 4.5 ton overhead crane
BPI
• Sandblasting and glass bead blasting
• Painting
• Insulation and cladding – hot, cold and acoustic
Plate sizes range from 0.5mm to 2mm - aluminium, galvanised, and stainless steel
BPI is an approved applicator for Stonecor, Jotun and PPG/Sigma
Field Services and Engineering is the proud preferred supplier to Howden. Our group’s certifications include ISO 9001 and ISO 3834, and we have implemented ISO45001 and ISO 14001 management systems into the core of our business. B-BBEE Level 2 certified.
Howden has a solution for most gas handling processes with highend engineered solutions often supplied into industrial processes as packaged solutions or installed on a turnkey basis. The company also supplies ventilation systems and equipment to major mining companies in global settings.
“In recent years, we have added to our suite of air handling technologies. Ventsim™ software optimises underground mine ventilation and Ventilation on Demand (VoD) software to help mines save energy and reduce operating costs.”
The future of mining lies in the Ventsim™ initiative, a suite of solutions which comprises two software packages – Ventsim™ DESIGN and Ventsim™ CONTROL. Introduced in 1993, it is now licensed to over 1,500 mining sites, consulting and research agencies, universities, and governments worldwide. Ventsim™ DESIGN is the ultimate 3-D mine ventilation design system.
“It allows users to create a 3-D model of their tunnels, shafts and underground workings. This enables our customers to simulate, and animate, air flow and fan behaviour in
Howden is focused on sustainability, reflected in its vision of a sustainable world. Commitments for 2030 in a 2021 ESG report include:
• 50 percent - reduction of Scope 1 and 2 carbon footprints, becoming carbon net zero by 2035
• 50 percent - of zero waste to landfill
• 30 percent - reduction in mains water usage
• 40 percent - increase female representation on the Management Committee
• 35 percent - increase in female representation in senior roles
• 30 percent - increase in female representation overall
• 25 percent - employee volunteer participation through a community services programme
Impact explained by a case study at a Canadian Operation, where the following results were achieved:
• 43 percent - reduction in mine heating costs
• 56 percent - in underground ventilation electricity costs
• 76 percent - decline in surface ventilation electricity costs through VoD implementation
Another exciting prospect is the hydrogen movement, along with natural gas liquefaction. Following Howdens’ acquisition by Chart Industries, customers are offered a suite of products, along the value chain, to support a transition to renewable energy.
real time and analyse mine ventilation within a rich and dynamic visual environment,” details Nyangoni.
“Ventsim™ CONTROL enables the remote, and autonomous, control of ventilation devices as doors, fans and regulators. The technology combines ventilation modelling with a flexible control system and advanced control strategies. It is tailored for monitoring, control and optimisation in ventilation of underground mines,” he continues.
Fundamentally resting on the four pillars of Ventsim™ Engineering Services Turnkey Engineering Solutions: Mine Ventilation, Turnkey Engineered Solutions: Mine Cooling, and the Aftermarket Services, the TMVS is a single point of contact solution, focused on providing a fully integrated approach to mine ventilation, cooling and conditioning monitoring.
“It is aimed at creating work environments which are safe and risk free to the health of the employees, whilst protecting the environment. Through our products and services, we support our customers along the value chain, to achieve zero harm and ESG commitments.”
Engineering studies in the prefeasibility and feasibility stages of the project undertaken using Howden’s proprietary Ventsim™ software is the first part of the TMVS strategy, taking leading mine ventilation modelling software and applying it extensively across most mines globally.
“Mine ventilation and cooling studies offered under our consulting arm, Ventsim™ Engineering Services, lead to optimisation of mine ventilation and cooling systems that help our mining customers to comply with strict ESG requirements in most jurisdictions,” Nyangoni assures.
“The second part of the TMVS strategy is mine ventilation equipment ranging from the small 37 kilowatts (kW) auxiliary fan to the mighty 4 megawatts (MW) fans mixed flow primary ventilation fans. Howden has supplied the largest proportion of
fans on Africa’s mines in the past eight decades,” he explains.
After securing a contract for a Ventsim™ CONTROL system at Gold Fields South Deep gold mine (South Deep), the collaboration with Howden is to implement the state of the art ventilation optimisation system.
“The solution will support a safe working environment as well as reduce the mine’s energy consumption, which will contribute towards South Deep’s environmental and operational goals. Our ventilation
optimisation solution offers varying levels of control to suit the needs of the mine,” Nyangoni notes.
Level one and two allows for manual remote control and scheduling of ventilation devices. Meanwhile, the level four VoD, the solution employed by South Deep, allows ventilation devices to react based on feedback from environmental and operational goals.
Furthermore, it will adjust mine airflow in real time based on vehicle and personnel position, the solution also offers a 3-D modelling capability within the software, which helps users
to better predict, and control air flows based on what is evidenced in the simulation.
“The installation of Ventsim™ CONTROL will improve the operability and flexibility of the mine’s ventilation system to ensure a safe, healthy and efficient ventilation solution. Ventsim™ CONTROL will further reduce energy consumption and associated tonnes of carbon emissions,” he says.
As the system allows the mine to optimise its ventilation based on fully remote vehicle and personnel monitoring, it directly contributes to
“BY EMPLOYING OUR OPTIMISATION SOLUTIONS, WE HAVE SUPPORTED NUMEROUS MINES TO ACHIEVE THEIR DESIRED OBJECTIVES”
– KUDZAI NYANGONI, MANAGING DIRECTOR, HOWDEN
achieving the emissions reduction targets, “something which the Howden team is very proud of.”
The mine is a world-class bulk mechanised mining operation reaching depths between 2,800 metres (m) and 3,300m below surface, located in the Witwatersrand Basin, near Westonaria 50 kilometres (km) southwest of Johannesburg, South Africa.
Sustainability and carbon footprint reduction have come under the spotlight in recent years, especially regarding mining practices, however, the savings and carbon reduction depends on the maturity of the solution.
“Ventsim™ CONTROL is a product we are extremely excited about.
Power consumption for ventilating the works of underground mines forms a substantial percentage of the operational expenditure for running
the mine,” states Nyangoni.
The percentages typically range between 30 and 50 but can be more in extreme cases. These high costs, and the associated impact on the environment, drive demand for solutions that offer operational efficiencies for ventilation systems.
“By employing our optimisation solutions, we have supported numerous mines to achieve their desired objectives.”
Priorities for the year ahead include remaining focused on helping customers across highly diversified end-markets and geographies, increasing the efficiency and effectiveness of their air and gas handling processes, and enabling sustainable improvements with regards to health, safety and environmental impact.
The mining industry’s value chain is very extensive. Engineering services
are required throughout the life of a mine from feasibility studies to mine development, mining operations, mineral extraction and processing as well as the reliable maintenance of equipment.
Therefore, it is difficult to find an industry that does not, one way or another, intersect with the mining value chain both upstream and downstream, therefore ensuring Howden’s success for centuries to come.
Abhay Mishra, CEO of Nacala Logistics, introduces the logistical mega-enterprise connecting almost 1,000 kilometres of railway across Southern Africa
In the landlocked nation of Malawi a lifeline of connectivity is being forged, creating a vital link between the northern regions of Mozambique, the coastal gateway of the Nacala-àVelha Port, and onward to Zambia.
The ongoing development of the Nacala Corridor represents a megaenterprise that is set to revolutionise the efficient transportation of coal,
general cargo, passenger services and port management through integrated logistics solutions across Southeast Africa.
Combining the powerful trifecta of the Nacala-à-Velha Port, the Northern Railway, and the Malawian Railway System, the corridor will channel the synchronicity of major forces of transport working in unison to
provide unrivalled safety, quality, and efficiency with rail as its backbone.
Today, the best interests of all logistics companies operating along the corridor – namely Northern Development Corridor (CDN), Integrated Logistics Corridor of Nacala (CLN), Africa Logistics Company (CLA), and Central East African Railways (CEAR) - are consolidated
and represented under one enterprise and trading name - Nacala Logistics (NL).
“This is undoubtedly one of the largest logistics infrastructure projects built in Southern Africa.”
The opening words of Abhay Mishra, CEO of NL, encapsulate the sheer magnitude of this colossus of logistical solutions. Indeed, encompassing the multi-user terminal port of Nacala-àVelha, 1,600 kilometres (km) of railway system between the port and Cuamba (Mozambique), with two branches at Cuamba-Entre-Lagos and CuambaLichinga, plus the 912km stretch of rail from Nacala- à-Velha to Moatize (Mozambique) via Malawi, NL’s remit is vast.
As a logistics partner of the major
coal exporter Vulcan Mozambique, NL specialises in coal logistics, general cargo, and passenger transport in addition to port operations.
Its coal logistics are expedited by trains made up of four locomotives and over 120 wagons that carry coal from Moatize to Nacala-à-Velha, which has an annual capacity of 18 million tonnes and three coal yards of one million tonnes each.
In terms of general cargo transport, NL has a capacity of four million tonnes a year for transporting containerised, bagged, bulk and liquid cargo – primarily fuel – alongside a variety of products including fertilisers, wheat, tobacco, cotton, soybeans, peas, tea, sugar, clinker, salt, gypsum, soap, and containers.
Empowering Growth and Resilience in Key Industries.
As Mozambique continues to experience economic growth and diversification, several critical industries, including agriculture, energy, and health, are playing a crucial role in driving the country’s progress and creating employment opportunities. However, with expansion comes a range of complex and dynamic risks that necessitate bespoke insurance solutions.
At Hollard Mozambique, we understand the unique challenges and opportunities facing businesses in these sectors. We work closely with our clients to create customized insurance solutions that meet their specific needs, foster resilience, and provide peace of mind in the face of uncertainty.
Hollard Mozambique’s agriculture solutions include named-peril crop insurance, index-based livestock insurance, and agriculture assets and liabilities. These policies protect against natural disasters, disease outbreaks, market fluctuations, and other risks uniquely identifiable within Mozambique’s geo-economy. In the energy sector, Hollard Mozambique leads the way in Mozambique’s insurance coverage of integral assets such as power plants, pipelines, and offshore rigs, while specialized coverage reinforces the foundational reliability of renewable energy projects, including wind and solar farms, hydroelectric infrastructure, and bioenergy manufacturing.
Hollard Mozambique takes pride in collaborating with businesses in essential industries to attain their maximum in-market potential with focused, tailored insurance solutions, ensuring a better future for Mozambique.
Protect your business from risks and uncertainties, contact Mozambique’s favourite insurer today.
Better Insurance. Better Futures.
www.olahollard.co.mz
“NACALA LOGISTICS IS 100 PERCENT COMMITTED TO BEING AN ECO-FRIENDLY SOLUTION AND PROVIDING THE BEST TRANSPORT ALTERNATIVE WITHIN THE NORTH CORRIDOR”
– ABHAY MISHRA, CEO, NACALA LOGISTICS
MILLION TONNES OF COAL TRANSPORTED 18
MILLION TONNES OF COAL SHIPPED FOUR MILLION TONNES OF GENERAL CARGO TRANSPORTED
480,000 TRANSPORTED PASSENGERS
“We generate a value chain for more than 500 suppliers that serve an entire structure of 912km of railway, from maintenance services, works and infrastructure, food, accommodation and various consumables,” Mishra outlines.
“Our mission is to provide integrated logistics solutions with safety, quality and efficiency, and our vision is to be a reference in the supply of logistics solutions in Southern Africa, adding value to our clients and customers, through engaged people and sustainable processes.”
As Mishra suggests, the concept of ‘adding value’ is central to NL and this is seen across the board – whether in reference to its customers and clients, its staff, or by contributing to the socio-economic upliftment of the countries in which it operates. It was this foundational purpose – to add value – that initially drew Mishra himself to the role.
“After the recent change in management, I saw this position as
a great opportunity to lead a multicultural international team and add value,” he recalls. Since that takeover, significant improvements have ensued, with NL overcoming major operational and maintenance issues within a short space of time.
“I am happy to share that the NL team has broken all previous operation records of the railways and port within the first four months after being taken over by the present company,” Mishra states proudly.
As a railway network with worldclass assets, NL offers undeniable value to its clients through the facilitation of an indispensable transport link for goods and services. Serving a diverse roster of clients from around the world, approximately 70 percent of NL’s market is based in Asia as the majority share. Meanwhile, Africa represents the company’s second largest market at five percent.
Despite this international outlook, NL maintains an explicit emphasis on adding value to its countries of operation – primarily Malawi
We have a staff of more than 100 dedicated professionals, including specialist doctors, senior paramedics, experienced nurses, pharmacy and laboratory technicians, aided by a solid logistics and management team. Our health professionals have further certified training on the critical areas of emergency, prevention of infections and occupational health.
SEPRI is ready to provide a service of excellency, following international health standards, to our current and future customers. The recognized quality of our processes is currently certified under the ISO 9001:2015 standard.
Occupational Health medicine
Emergency Medical Service and Air Evacuation
Medical services at remotes sites
First aid training
Assembly of modular clinics
Medical consultancy
Operation of the first (and only!)
rail-road ambulances in Mozambique comercial@sepri.co.mz
In the district of Nacala, where NL’s port infrastructure is located, the majority of local communities practice fishing for their livelihood. To guarantee food security, NL has a fishing programme that currently directly benefits around 600 fishermen and indirectly 3,000 members of the families of the beneficiaries. This support for fishermen includes training, infrastructure, providing motorboats and the funding of income generation projects.
This programme has helped beneficiaries to increase their ability to capture different species, but also to practice more environmentally sustainable fishing, abandoning artisanal fishing practiced along the coast, which captures developing species to use semi-industrial techniques.
NL supports a school lunch programme across three districts where it operates, which consists of distributing meals to local children enrolled in schools. This programme benefits around 32,000 children, with meals served in 26 schools in the districts of Nacala-a-Velha, Ribaue and Malema.
Generally, in low-income communities, many children have dropped out or missed school because of hunger or to help their parents produce family income, selling in the streets or practicing agriculture. The school meal distribution programme has helped to keep children in school, reducing the rate of school dropouts and school absenteeism, thus simultaneously contributing to children’s education and food security.
and Mozambique - through its contribution to the local economy. This is primarily in the form of paying taxes directly to the government.
“To give you an idea, from 2019 to the end of the third quarter of 2022, NL paid approximately USD$540 million in taxes, including corporate taxes, concession fees, and others,” Mishra tells us.
Equally important, however, is the means of connection that NL’s rail system provides for local agricultural producers throughout Mozambique, who rely on the transport of their produce across provinces for commerce and financial income.
“Agricultural products from Niassa, for example, travel more than 500km using NL trains, to be marketed in the northern province of Nampula. This has a very positive impact on the local economy, helping small family producers to market their production in a country where there are still major infrastructure challenges,” he explains.
“In other words, if it weren’t for the NL trains, much agricultural production could rot due to lack of a market.”
For Mishra, the ultimate culmination of the company’s emphasis on adding value and positively contributing to its local surroundings, is the myriad employment opportunities that NL creates.
“We believe that our biggest contribution to the economy of Mozambique is through job creation,” he says. “By employing 2,000 people, NL is helping an equal number of households and around 12,000 people, since an average household here has five members.”
In addition, providing jobs for workers from subcontracted companies has the multiplier effect of generating income for thousands of households.
“Across our human resources structure, almost 100 percent of our
Civil Lda., based in the province of Maputo, Matola Rio, brings more than 10 years of experience working in the maintenance and civil construction field, with a reputation for executing projects on time, always maintaining quality, health and safety and the best environmental management practices certified in ISO 9001, 45001 and 14001 by Bureau Veritas.
Investing recently in dust management in exploration mines, MCC is and ambitious company with young and talented staff all over Mozambique.
employees are local labour, with over 80 percent local leadership. We are a reference company in terms of the dream of employability of several professionals in the country and aspiring Mozambican students from the northern region,” Mishra shares.
Throughout its history, NL has maintained a strong support programme for local development throughout its regions of operation. Several initiatives are key in this regard, reflecting the positive impact that NL hopes to have on its surrounding communities.
Through its sustainability programmes, NL effectively supports 14,000 households and approximately 4,000 people in agriculture, as the cornerstone of regional economic
activity. By distributing 4,000 tonnes of crop seeds to local communities, NL helps households to improve the production and productivity of the main crops produced locally, including peanuts, rice, maize, sesame, beans and vegetables.
“The impact of this programme has been very positive, with the beneficiary family producers adopting new environmentally friendly production techniques and increasing productivity above the local average,” Mishra observes.
Efforts such as this, pertaining to food security, are becoming increasingly important in the face of climate change, as Southern Africa is one of the many regions across the world to be severely impacted by extreme weather events as a result of climate change. In recent years, this
has included cyclones, strong winds, severe rains and flooding. As such, NL’s support for local families is a welcome contribution to guarantee a vital food supply.
Elsewhere, NL participates in supporting local fishermen in the Nacala district and providing school lunch support to further food security across the region.
“All our actions are based on the values that guide us and one of them is undoubtedly respect for the communities and our environment,” Mishra states.
In terms of how NL demonstrates its commitment to the environment as a responsible corporate citizen, by its very nature, rail is one of the greenest solutions for transport at scale. As
Outlook Publishing’s awardwinning in-house team is now utilising its extensive production skills to offer a full and bespoke range of editorial, design and marketing services via its new Outlook Creative Services division.
ASSOIIIMAT has been created with the main goal of diminishing and fighting against malnutrition in the communities.
• Removal of weeds
•
•
Providing international and specialised services in the area of Information Technologies (International Information Technology Enabled Services – ITES) and Business Process Outsourcing – BPO in Mozambique.
Our values:
Integrity Commitment Excellence Growth Diligence Teamwork
Serving both national and international clients.
MISSION
Sell products and services that transmit a professional image of our customers, always acting in a sustainable and cost effective manner.
VISION
Innovate, promoting the best solutions for customers and become a reference throughout the region in professional clothing and PPE.
VALUES
• Integrity - Inspiring trust and confidence through ethical and professional standards.
• Focus on results - Striving to fulfil our commitments taking into account our customers’ needs, within the estimated time frame, and in highest quality standard.
• Openness - Favouring a collaborative working environment, sharing information, actively listening, and allowing constructive challenges.
www.howardjohnson.co.mz +258 21080193 info.howardjohnson.co.mz
LEARN MORE
‘Things Become Hard in own Hands’
such, the company can be considered an advocate for green logistical solutions.
“In a nutshell, Nacala Logistics is 100 percent committed to being an eco-friendly solution and providing the best transport alternative within the North Corridor,” surmises Mishra.
The company’s efforts towards becoming an increasingly environmentally friendly solution are best embodied by the NL ‘Go Green’ initiative. The demand for the scheme was identified within the NL customer base, and the company was quick to respond.
“This has pushed our actions in a way to improve our services in order to position the railway as the best alternative for moving cargo. Major companies (shipping lines, fertiliser
and cement suppliers, etc.) are evolving their strategies to engage with “Go Green” as a flagship for enhancing their businesses,” he shares.
Several initiatives are currently in motion as NL continually strives to mitigate its greenhouse gas (GHG) emissions. This includes a reduction in the number of locomotives to pull while trains are manoeuvring in
the yard and loading coal to reduce diesel consumption and the carbon monoxide (CO) emissions caused by burning that fuel.
In addition, NL has reduced the number of locomotives used during the unloading of coal in the port from two to just one engine. Throughout these coal yards, NL has begun sprinkling the piles of coal during the unloading process in order to avoid the emission of harmful particulates.
To further reduce diesel consumption across both the port and railway operations, NL now reverts to using its power generator system exclusively in emergency situations. Simultaneously, the company is now in the process of exploring transitioning its air conditioners from chlorofluorocarbons (CFC) gases
to less polluting, environmentally friendly 410 A Gas.
Finally, NL is championing a greener environment in the most literal sense through the revegetation of degraded areas along its railway and port systems and improving the development of mangrove forests at the Nacala-à-Velha Port.
With his eyes on the future, Mishra endeavours to ensure that the Nacala Corridor reaches its fullest level of potential.
“Looking at our commercial footprint, the natural vocation for the corridor is to reach its full extension. In the short-term, this will entail taking the railways to operate up to the border of Zambia,” he details.
In order to attain this, NL may look to diversify into other transport modes and will explore the possibility of integrating with a road model in order to optimise flows whilst supporting the growth of the corridor in its full capacity.
Despite these major ambitions, the number one focus for the immediate future is to get NL back on track in the wake of turbulence.
“The key priority for NL is to stabilise its operations. After the transition from our shareholding restructure and the huge effects that have come from two cyclones passing through Mozambique and Malawi, we have had to practically recover from scratch,” says Mishra.
Although a significant setback for NL’s progress, such natural
events are a poignant reminder of why the company’s continued efforts in contributing to the local community through economic uplift, implementing food security, and sustainable initiatives, are so vital.
Resolutely committed to adding value, with engaged people behind operations centred on sustainable processes, NL will continue to lay the tracks of Southern Africa’s largest infrastructural advantage.
NACALA LOGISTICS
Tel: +258 84 321 5880
https://nacalalogistics.com
Owned and operated by Storm Mountain Diamonds, the Kao mine is renowned for the production of rare, precious pink diamonds.
Mohale Ralikariki, CEO, highlights the exceptional prospects of the deposit
Writer: Jack Salter | Project Manager: Joshua Mann
Irrespective of location, mining remains one of the key drivers of national economies and the backbone of industrialisation.
In Lesotho, the mining industry is predominated by diamond mining, with the landlocked mountain kingdom considered one of the most important diamond-producing countries in Africa.
A continent blessed with abundant resources, Africa remains a key destination for investment, but the geopolitical risk needs to be well understood.
Lesotho, for instance, has one of the highest number of kimberlite bodies per square kilometre in the world, meaning the full mineral prospectivity of the country has not yet been determined.
“It is up to the African governments to create a conducive environment for attracting investment by developing a consistent, predictable and enabling legal framework,” outlines Mohale Ralikariki, CEO of Storm Mountain Diamonds (SMD).
Ralikariki grew up in a small village in Lesotho, where for decades labourers have been migrating to neighbouring South Africa to work in the mines. Lesotho has thus been heavily reliant on remittances from migrant mine workers.
Mining, although in its infancy stage, is a popular sector in Lesotho for this reason, and there has been a shift in government policy direction since the beginning of the 21st century to unlock the country’s mineral wealth potential. New diamond mines continue to open up, with the latest two new mines at the development stage.
By intensifying efforts to promote and attract investment into the domestic mining industry, the Lesotho government has successfully translated its sheer comparative advantage inherited from mineral resources endowment to a national competitive advantage, which marked the beginning of large scale commercial mining operations in Lesotho.
“I was then awarded a scholarship by the government to pursue a degree in mining engineering, as part
of the initiative to create a sustainable pool of talent to support the emerging mining sector,” Ralikariki elaborates.
“That is where my illustrious career in mining started. It has been quite an exciting and challenging journey, which I continue to cherish to this day.”
Despite the increasing global challenges, the mining industry remains a dynamic and exciting environment to work in.
Africa, like other continents across the world, is shifting to align and respond to internal and external shocks, with mining companies such as SMD generally flexible enough to adapt to the changing environment in order to remain competitive and profitable.
Jointly owned by Namakwa Diamonds Limited and the Lesotho
“We are leaders in Mechanical Engineering”
Based in Lesotho and entirely Basotho-owned, MS Fabrications and Engineering Pty Ltd (MSFE) is a mechanical engineering company defined by its people-centric professionalism and commitment to its customers.
With operations starting up in 2016, MSFE has always strived to provide the professional machining and welding services that Lesotho’s economy needs. The company’s original aim was to provide such services to the local agricultural industry, earth-moving equipment and logistics companies. Yet with time, MSFE recognised that there were four revenue streams that it services in its drive towards “moving the industry forward”, namely; mining, construction and logistics, and lastly, individual customers in the agricultural industry.
Today, MSFE’s central mission is to provide maintenance, fabrication, construction and manufacturing services within an acceptable quality standard in the interest of all stakeholders through transparency and consistency, employing a professional, committed and wellmotivated workforce.
Other MSFE Services:
• Coded welding compliant to ISO 3834-2
• Parent material identification-PMI
• Non Destructive Testing - NDT
• Mechanical Engineering design and consultancy
Every company is motivated by their vision for the future. For MSFE, the aim is to become a leader in the provision of mechanical fabrications and maintenance solutions and services in sub-Saharan Africa, a goal backed by its professionalism.
www.msfabrications.co.ls
“WE PRODUCE GEM QUALITY DIAMONDS, AND WE ARE FAMOUSLY KNOWN FOR THE PRODUCTION OF TOP QUALITY PINK DIAMONDS”
– MOHALE RALIKARIKI, CEO, STORM MOUNTAIN DIAMONDS
MS Fabrications and Engineering Pty LTD (MSFE) is a mechanical engineering company registered in Lesotho over half a decade ago and is owned entirely by Basotho.
• Coded welding services (SMAW, TIG, MIG)
• Automated oxy-acetylene cutting
• Fitting and Machining (employing conventional machines: Turning, Milling, Drilling, Line boring)
• Repairs on pumps and pumping systems
• Fabrications and erections of steel structures
• Supply and Installations of wear plates and hard facing materials
• Condition monitoring
It started operations to provide maintenance, fabrication, construction and manufacturing services within an acceptable quality in the interest of all stakeholders. Simultaneously, MSFE co-creates value with stakeholders through transparency and consistency, while employing a professional, committed and well-motivated workforce. The company is aware of the interconnectedness of the global economy and it intends to become the major player as it realises its growth. Hence, there is an aggressive drive to acquire certification for International standards such as ISO 3834, ISO 45001, ISO 14001 and ISO 9001.
government, SMD owns and operates the Kao diamond mine, the fourth biggest kimberlite in Southern Africa and the largest in Lesotho.
With a remaining resource base of approximately 6.6 million carats, it has been explored to a depth of 500 metres and is located in the kingdom’s picturesque Botha Bothe district.
“The mine is situated in the heart of Lesotho’s mountain range, a spectacular landscape with
breathtaking views,” smiles Ralikariki. As well as the typical shades of yellow, pale brown and white, Kao yields diamonds in a glittering array of rare colours such as blue, purple and pink, the latter of which it has become a primary producer across the globe. Indeed, over the last couple of years, some remarkable pink stones have been recovered from the mine, including the Pink Storm, the Rose of Kao and the Pink Palesa. What’s more,
MOHALE RALIKARIKI, CEO: “The management culture at SMD is to recognise its people for innovation, a job well done, and going the extra mile.
“It is prudent as a business that we recognise our employees’ efforts and celebrate milestones as a means of appreciating and valuing their contributions.
“The guiding principle to management is the SMD recognition framework, which was developed to ensure consistency. We believe that our corporate culture is empowering and improves employee morale.”
Buhrig Southern Africa is proudly associated with Storm Mountain Diamonds through our roller mounted scrubber that provides 24/7/365 robust dependability.
Installed over 10 years ago, we appreciate the long-term loyalty of the mine and hope to provide the best possible levels of support for the next decade.
Our scrubbers have been sold throughout Africa and into North America over the past 40+ years.
Located in Benrose, Johannesburg, South Africa.
+27-11-614-6674
www.buhrig.co.za
The Mendi Group of companies focuses on the transport and energy sectors.
The group was founded on the appreciation of the extractive nature of the African economy, with minerals being mined in Africa, transported by road and rail to the nearest port, stockpiled and shipped to customers at the port of destination.
Whilst historically, each of these functions have been performed by independent role players in each sector, Mendi has an appreciation for the holistic and consolidated approach that future supply chains are geared towards. Accordingly, Mendi companies have been structured to provide each of these services holistically and in an integrated manner under the Mendi banner.
1956 – 2005 – The Kao kimberlite was discovered by Colonel Scott and his exploration team in the mid to late 1950s. After this discovery, Kao was mined by artisanals and organised co-operatives. Various commercial mining enterprises dabbled with the prospects of developing the mine, however, their exploration results showed that while the kimberlite body was diamondiferous, the grade and value of the diamonds were too low to make the development of the mine economically viable.
2006 – 2009 – Despite this, Kao Diamond Mines (KDM), a subsidiary of Global Resources Inc. acquired the mining lease for Kao from the Lesotho government in 2006. However, KDM struggled with poor production, failed to pay royalties during the period that it held the mining lease, and was eventually in debt to creditors without the cash flow or funding to service these debts.
2010 – SMD took over the mining lease at Kao in 2010 following the liquidation of KDM, and has been instrumental in redeveloping the mine to create an attractive financial environment for investors as well as employment opportunities and local development. SMD’s success is one of the unique memoirs in the history of diamond mining in Lesotho.
most of the Kao pinks do not have secondary colours, and those that do are dominated by purple.
With the closure in 2020 of the Argyle diamond mine, the world’s number one pink diamond mine situated in the remote north of Western Australia, Kao is well poised to become a major player in the world of rare pink diamonds.
Further confirmation of Kao’s role as a leading producer of pink diamonds came in October 2022 when SMD announced the recovery and sale of the Pink Eternity, an exceptional 47.8 carat pink diamond, the largest recovered at Kao to date.
“We produce gem quality diamonds, and we are famously
known for the production of top quality pink diamonds and other fancy colours,” Ralikariki tells us.
Unique in the market, SMD’s pink diamonds are of the highest quality and come in a range of sizes, giving buyers unrivalled access to premium goods that no other mine produces.
Products are sold through an international trading platform in Antwerp, Belgium, with buyers coming from across the globe.
“We pride ourselves on the quality of our diamonds and the resilient nature of our 800 employees, who are the key asset to our operations,” notes Ralikariki.
Although competition is high for specialised technical and engineering expertise, due to a scarcity of skills in Lesotho, SMD remains an employer of choice in the country and has extensive skills development programmes in place.
Equally, employee retention schemes keep the Kao mine ahead of its competitors, whilst SMD’s low turnover of staff is symptomatic of the management’s efforts to implement a people-focused human resources (HR) Strategy.
“SMD currently has an employee turnover of less than 0.5 percent, which is significantly lower than the industry norm of around 3.5 percent,” Ralikariki informs us.
Employee engagement, increased business communication, and continuous improvement of employee morale are benchmarks of the company’s HR Strategy, which is informed by the outcome of engagement surveys periodically
conducted across the business.
The HR Strategy therefore represents the voices of staff members, aims to mitigate turnover risks, and ensures a conducive working environment within the business.
A vibrant Community Investment Strategy, meanwhile, drives all of SMD’s projects, aimed at improving the livelihoods of the surrounding communities.
“We have done a lot for communities, such as building health posts, schools, supporting agricultural projects and local businesses through localised procurement, and developing skills by providing sponsorships and internships to host communities,” explains Ralikariki.
“All of these efforts have played a pivotal role in creating a positive image for the company, to remain attractive to the buyers of the product as well as the employees.”
SMD has managed to increase its processing capacity by an impressive 40 percent over the past five years, as a result of the additional processing capacity created by a plant expansion project in 2017, and will continue to look for opportunities to expand.
Following the expansion of SMD’s processing plant, the company undertook various initiatives to stabilise production at the upgraded capacity.
“I believe that the key for us to maintain such impressive production figures lies in the motivation and dedication of our people, along with very sound maintenance practices,” affirms Ralikariki.
Since 2017, the company has also continued to invest in Kao through projects that both improve the safety of its people and increase the efficiency of the mine.
For example, SMD has recently invested in stormwater management
due to increased rainfall over the years in Lesotho, as well as installed efficient crushers at the existing plant to improve diamonds liberation.
“We are currently assessing the viability of adding even better technology to our crushing circuits that could decrease the risk of breakages, with the added benefit of better liberation,” Ralikariki reveals.
Approximately, the Kao mine has more than 18 years of operation left, which has positively influenced the facility’s operational processes.
“Having the benefit of a large resource in Lesotho (compared to other mines) definitely has a positive influence on both the mine and the people.
“Kao is, nonetheless, a low-grade primary kimberlite pipe and thus will remain marginal, hence we are constantly looking at our cost structures, especially with the high inflation that we are currently experiencing. More importantly,
however, we have to look for continuous improvement in our efficiencies on the production side, whether through higher throughput or better extraction and quality or a combination of both,” concludes Ralikariki.
By pursuing its own aggressive production targets for the year ahead, SMD hopes to convince all stakeholders to continue to invest in a rosy future for this great resource.
Guinea is the home to one-third of the best bauxite reserves on the globe. We take a look at world-leading bauxite producer, Compagnie des Bauxites de Guinée, and the importance of aluminium on an international level
Bauxite has an important role to play in modern society. It is a resource key to the production of aluminium, a material used across the globe and in a multitude of industries, from automotive production and aeronautics to electricity, packaging, and the construction of buildings, infrastructure and more.
When it comes to production, bauxite requires various steps including prospecting, planning, stripping, drilling and blasting, transportation, crushing and drying.
It takes approximately four tonnes of bauxite to make two tonnes of alumina, which in turn produces roughly one tonne of aluminium. Meanwhile, aluminium is present in more than 35 percent of modern materials and equipment used around the world, making bauxite a highly sought-after resource critical to our modern way of life, and bauxite mining companies key to keeping our world turning. One such player in the bauxite mining space is Compagnie des Bauxites de Guinée (CBG).
CBG supplies its customers with bauxite that has a moisture content significantly lower than or equal to seven percent. This low level of humidity gives the bauxite a superior quality, facilitating, among other things, its transport by boat as well as unloading and transformation
The Republic of Guinea holds one-third of the best bauxite reserves in the world, which contain a high content of extractable alumina (45-60 percent) and a level of silica below two percent.
The production of bauxite on Guinean territory began in the 1930s on the island of Tamara and continued in the 1950s in the Loos Islands by French company Société des Bauxites du Midi. In 1963, CBG was created, with a shareholder base made up of the Guinean state (49 percent) and the Harvey Aluminum consortium (51 percent), bringing together the firms Alcoa (US), AlCan (Canada) and Péchiney (France).
In order to optimise CBG’s contribution to national development, the Guinean government the Boké Development Office (OFAB) which will build and manage the infrastructure required for the production of the ore, in particular industrial handling and processing facilities, a railway, and modern cities in Kamsar and Sangarédi.
Bauxite exports started in 1973, with the first ship, the Coronia, leaving the port of Kamsar with 19,000 tonnes on board. Since then, CBG has experienced considerable industrial growth which makes it a key player in today’s global bauxite market.
Specialised in the distribution of industrial spare parts, we offer over 15,000 references. In our warehouses across Africa, we have all kinds of bearings, belts, gears, joints, ball joints, pneumatic, hydraulic, protective equipment and many other items. Our boiler making and foundry also allows us to make and repair all kinds of mechanical parts for industrial clients.
the company the renowned position of world leader in bauxite provision.
CBG operates a series of bauxite deposits in the prefectures of Boké, Télimélé and Gaoual in Guinea. The most important of these is the Sangarédi plateau (Sangarédi), with an alumina content unique to the region. The process involved on the Sangarédi plateau includes going from the Sangarédi mine to the Kamsar plant via a 135-kilometre (km) railway line.
At Sangarédi, bauxite is produced according to a well-executed mining plan. The process involves drilling holes in the mine, loading them, then blasting them with the explosive ammonium nitrate fuel oil (ANFO). The configuration of such holes is designed to achieve the optimal fragmentation of the ore. Following this operation, the bauxite is loaded into 77- to 100-tonne trucks and transported to the homogenisation stocks, where it is then placed onto trains (120 wagons at 82 tonnes
1819 - Realisation of the first bauxite analysis on the Boké site.
1963 - Creation of CBG.
1973 - First bauxite exports aboard an ore carrier from the port of Kamsar.
2007 - Shipment of the 100 millionth tonne of bauxite.
2010 - First appointment of a Guinean citizen as General Manager of CBG.
each) and taken to the company’s Kamsar plant. The production flow is maintained continuously thanks to a rotation loop, ensuring a consistently streamlined operation throughout.
In Kamsar, the raw material is crushed in a workshop and handled towards production control stocks or the drying ovens. The crushed and dried bauxite is then sent to be loaded onto ships with capacities averaging 50 to 70,000 tonnes.
With the expansion of CBG’s operating capacities, the company will produce up to 19 million tonnes per year in the first phase, 25 million tonnes in the second, and an estimated 28 million tonnes in the third phase. By doing this under
‘IT TAKES APPROXIMATELY FOUR TONNES OF BAUXITE TO MAKE TWO TONNES OF ALUMINA, WHICH IN TURN PRODUCES ROUGHLY ONE TONNE OF ALUMINIUM’
Our world depends on the mining industry to extract precious metals and minerals to be used in all kinds of technology and devices, including aluminium, which is helping to drive lower waste and better electric transmission.
VERMEER Terrain Leveler® surface excavation machines (SEMs) help to precisely mine the desired ore while reducing dust, noise and environmental disturbance caused by traditional mining methods, such as drilling and blasting. This also manages the impact on our precious natural resources and the environment that we all enjoy and need for a life well lived.
BEREMAT GUINEE teams are providing on site maintenance and operators with KPIs, as an availability guarantee and fixed budget cost, which allows the customer to focus on his core business.
Health, safety and sustainability are constant objectives for our whole team, to protect individuals but also to avoid any damage to the environment.
the best possible health and safety conditions, CBG positions itself as one of the biggest and best bauxite producers in the world.
It is an exciting time for CBG. Financed by loans from major international financial institutions, including the International Finance Corporation (IFC), the Development Bank of the United States (DFC) and UK Finance, CBG is looking towards an expansionist future. Such growth will enable CBG to not only increase the production capacities of the Sangarédi mine as well as surrounding infrastructures such as the railway, processing plant, port, power plants, and cities, but also generate jobs and increase the company’s contribution to the internal revenues of the Guinean state.
Above all, CBG is committed to respecting international standards and this is reflected in its adherence to the highest standards in the world in this area, placing great focus in its corporate social responsibility (CSR), the promotion of the health and safety of its employees, and the protection of the environment.
CBG recognises the importance of increased sustainable mining practices and consequently operates responsibly in one of the largest
bauxite reserves in the world. The company’s activities contribute to sustainable growth for the benefit of a healthier environment, more resilient communities, and fulfilled employees.
Bauxite mining generates considerable challenges, including social, environmental and human rights-related issues. While very aware of this fact, CBG has placed the question of sustainability at the heart of its corporate strategy. To do this, CBG makes every effort to comply with all national and international
‘CBG POSITIONS ITSELF AS ONE OF THE BIGGEST AND BEST BAUXITE PRODUCERS IN THE WORLD’
Manutention Services understands the unique challenges that come with operating in a mining environment, which is why our forklifts are designed to be versatile enough to handle a variety of tasks. From warehouse and workshop operations to mining equipment maintenance, our forklifts are up to the task. We offer equipment for heavy-duty applications in mining sites in Africa, designed to operate in extreme conditions and offer a large load capacity for handling heavy materials. We are proud to support the use of forklifts in mining operations in Africa with a dedicated team of professionals, we strive to make sure that our clients have everything they need to succeed in their challenging industry.
legislation applicable to the industry as well as the highest performance standards in terms of environmental and social management. These standards include those of the IFC, the Aluminum Stewardship Initiative (ASI) whose certification is in progress, ISO standards as well as the United Nations Guiding Principles on Business and Human Rights.
CBG’s approach is based on the support, involvement and active participation of its stakeholders in the initiation and implementation of projects and activities, particularly in favour of local communities and the environment. It is a matter of ensuring that they work with them appropriately to guarantee the success and sustainability of the achievements.
National and international practices and standards are also adhered to by CBG, to manage and mitigate environmental and social risks and impacts in order to promote and enhance
‘IN COLLABORATION WITH LOCAL AUTHORITIES, CBG HAS SUPPORTED THE CREATION OF 10 MICRO-ENTERPRISES RUN BY YOUNG PEOPLE. SINCE 2010, THIS HAS RESULTED IN THE CREATION OF NEARLY 3,000 DIRECT AND INDIRECT JOBS WITH A TURNOVER OF AROUND USD$3 MILLION’
sustainable development.
On top of this, the preservation of biodiversity and ecosystem services remains a key priority. So much so, that this component is a key performance indicator for operational excellence. To materialise this commitment, CBG has voluntarily subscribed to the Performance Standard (PS) Six of the IFC, which is the most demanding in this area.
Local communities, particularly those neighbouring company operations, are at the centre of CBG’s prioritiesthis is a societal commitment that the company has imposed on itself.
At CBG, the management of community relations is the result of a skilfully thought out and mature process which has enabled it to establish an appropriate
framework governed by a certain number of principles. These include establishing and maintaining lasting relationships based on mutual trust and respect; promoting the culture of responsibility at the level of all actors; practicing the spirit of active and independent partnerships; and establishing a mechanism for handling complaints and grievances from local communities.
Community development has always been one of CBG’s highest priorities. To date, the company has invested more than USD$60 million in the development of infrastructure and basic social services for local communities. Since 2017, CBG has been investing up to USD$2.5 million in the socio-economic development of communities, and on top of this, the company has supported the construction of some 220 infrastructure developments based on various local development plans.
CBG also invests in the development of income-generating activities, particularly for young people and women. They aim to improve their income with a view to their economic empowerment. Launched in 2017 with a start-up fund of approximately USD$3 million, this programme is showing positive results with an average increase in community income of more than 100 percent.
In collaboration with local authorities, CBG has supported the creation of 10 micro-enterprises run by young people. Since 2010, this has resulted in the creation of nearly 3,000 direct and indirect jobs with a turnover of around USD$3 million.
In 2010, CBG promoted the creation, training and supervision of a set of ‘Very Small Enterprises’ (VSEs) in collaboration with the local authorities. These VSEs mainly operate in the sectors of sanitation,
construction, rehabilitation and reforestation, and market gardening. To date, this policy has made it possible to create about 10 VSEs in Sangarédi and Kamsar, which employ more than 950 people. This initiative has greatly contributed to establishing social peace.
Promoting and respecting the traditional and cultural heritage as well as the human rights of local communities remains a top priority in this approach. The company is committed to developing and maintaining trusting and lasting relationships with local communities, based on mutual respect, transparency, active partnership and long-term commitment. CBG ensures that its community investments are aligned with community priority areas such as health, education and basic infrastructure, to name a few.
AUSTRALIA’S LONGESTRUNNING mining event returns in September this year. Asia-Pacific’s International Mining Exhibition (AIMEX) 2023 is a destination for decision-makers, experts and suppliers determined to change the face of the mining industry through technology, collaboration and radical improvements in productivity and sustainability.
With over local and international 250 exhibitors, AIMEX provides an unmatched opportunity to connect and do business with some of the best mining suppliers from around
the world. The event will also feature a free-to-attend conference, with themes including decarbonisation, technical innovation, and waste management. New at AIMEX are the Transformative Technology Pavilion, showcasing exponential technologies, such as augmented reality, virtual reality and data utilisation, and the Decarbonisation Zone, featuring smart and sustainable solutions that meet the sector’s environmental, social, and governance (ESG) obligations.
For further details please contact aimex@reedexhibitions.com.au
AIMEX is the destination for the mining sector to collaborate and hear from industry thought leaders. AIMEX provides an unmatched opportunity to connect and do business with some of the best mining suppliers from around the world, while sourcing solutions to boost productivity and meet sustainability goals. New at AIMEX this year are the Transformative Technology Pavilion and the Decarbonisation Zone.
6,000+ local and international suppliers
industry connections
250+ expert speakers
50+
Adding to its growing family of regional titles – APAC Outlook, Africa Outlook, EME Outlook, North America Outlook, and its sister sector title, Mining Outlook – Outlook
Publishing is proud to announce the birth of a dedicated platform for the healthcare sector. As organisations worldwide must navigate a new healthcare landscape defined by technological innovation in the wake of the COVID-19 pandemic, now is the time to showcase the strides being taken in this critical sector.
A multi-channel brand, Healthcare Outlook will bring you the positive developments driven by organisations across the healthcare industry through its various platforms. Discover exclusive content distributed through its website, online magazine, social media channels, and dispatches delivered straight to your inbox with a bi-weekly newsletter.
Through this compelling new venture, we intend to foreground the movers and shakers of the industry. To participate as a featured company and join us in this exciting endeavour, contact one of our Project Managers today.
www.healthcare-outlook.com