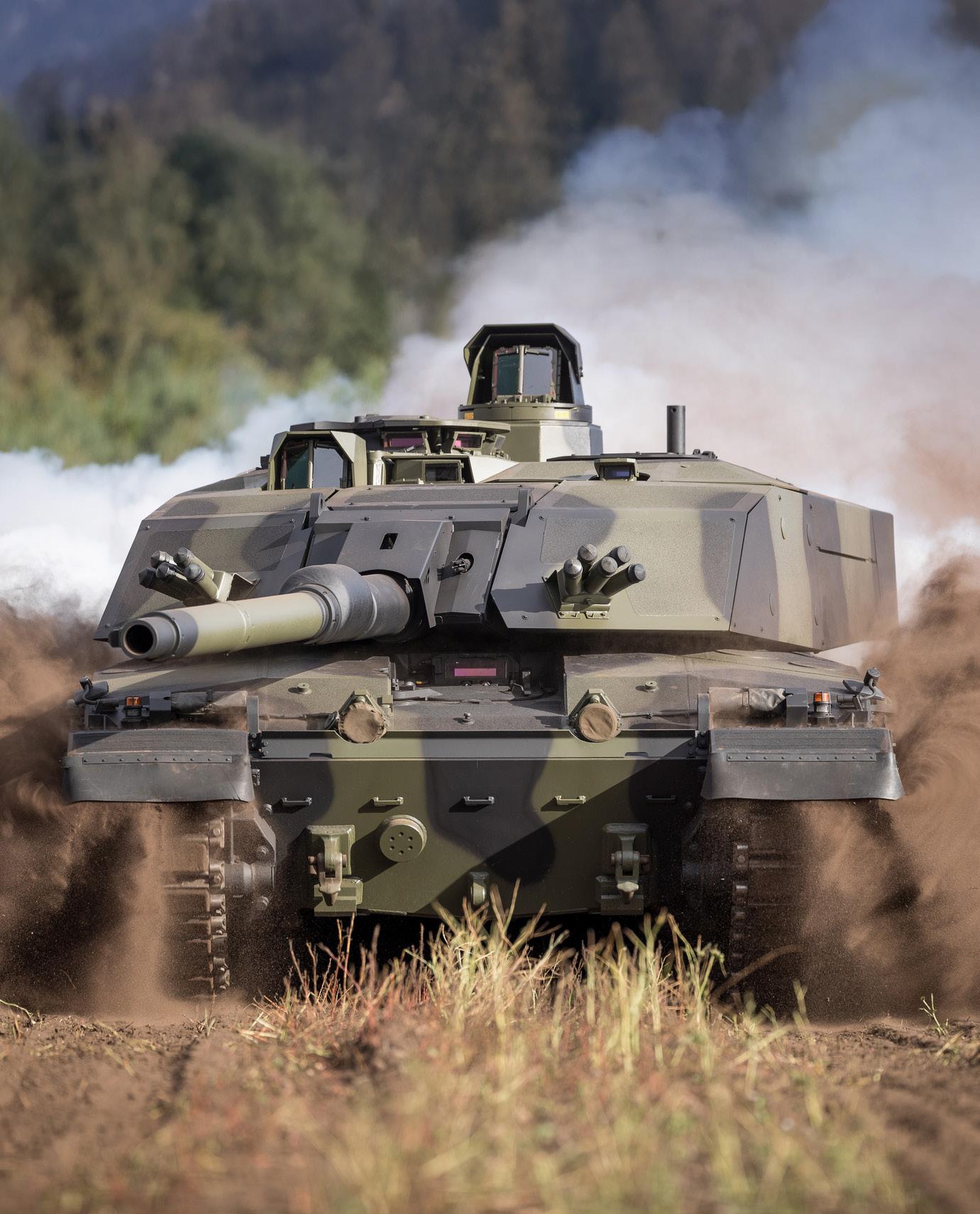
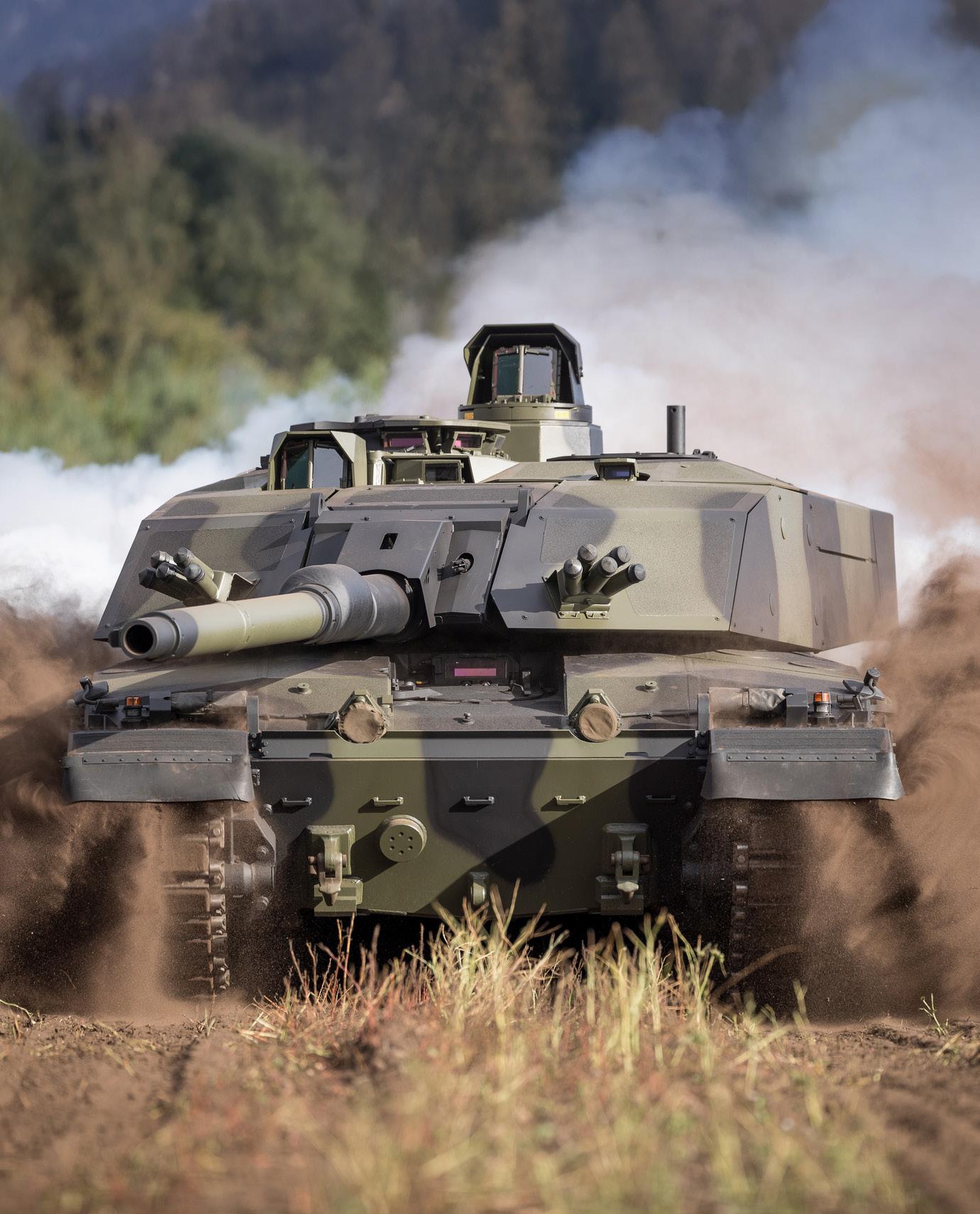
CAPABILITY SOVEREIGN

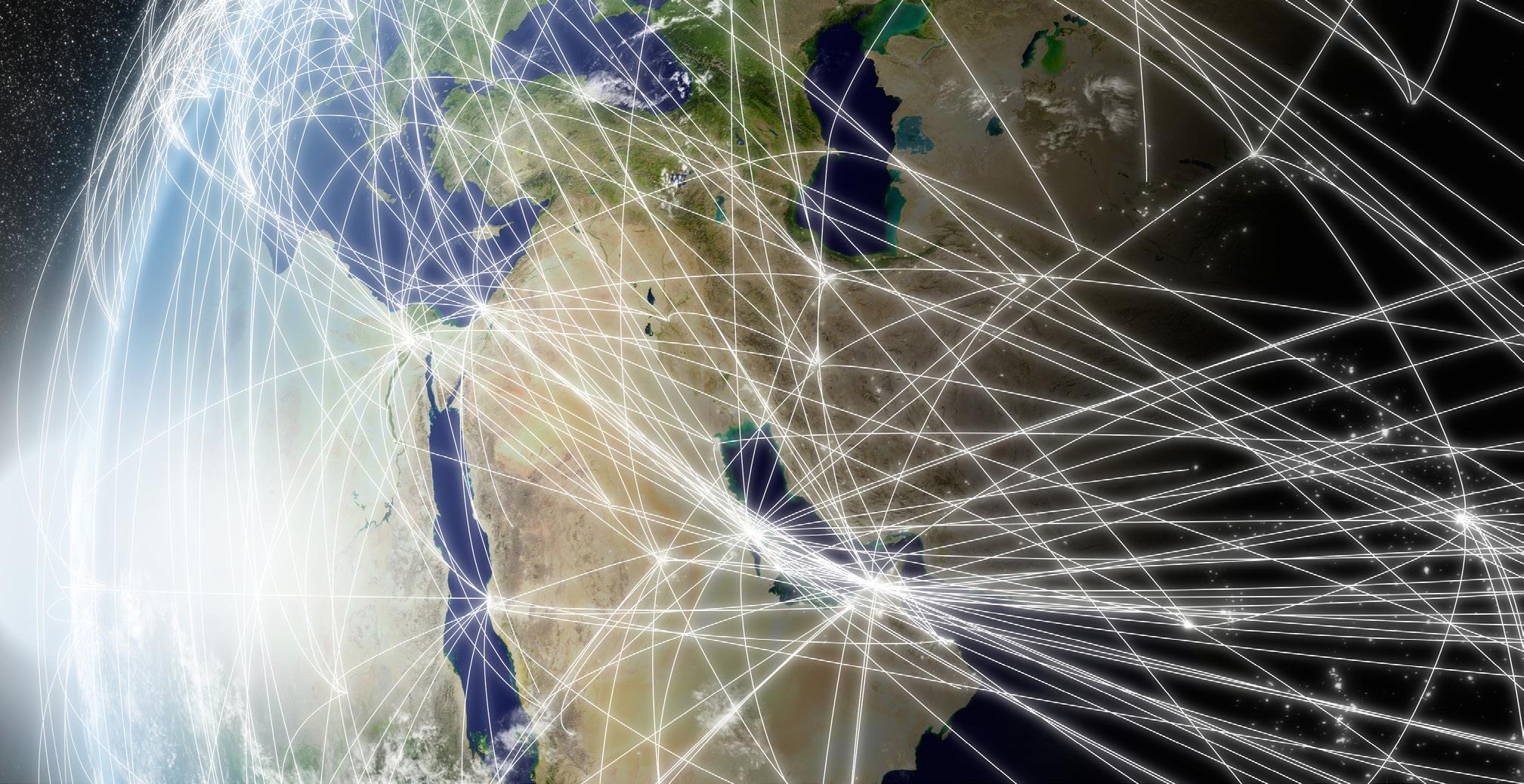


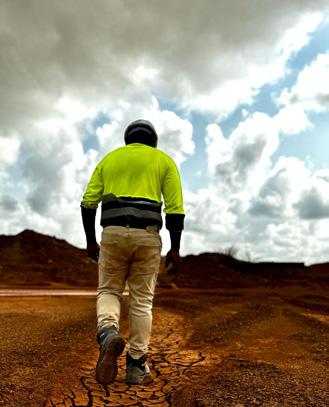


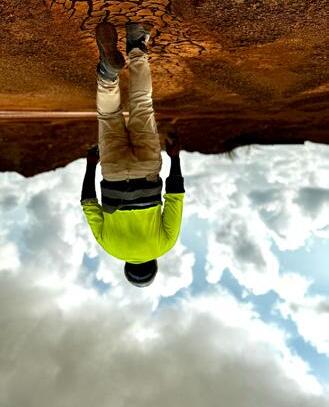
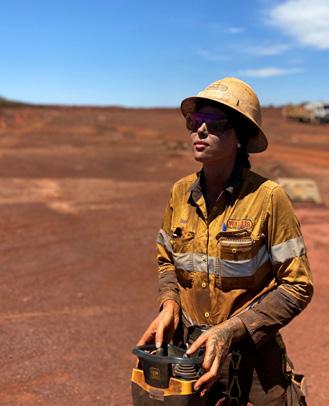

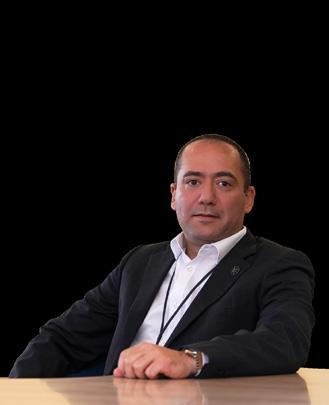

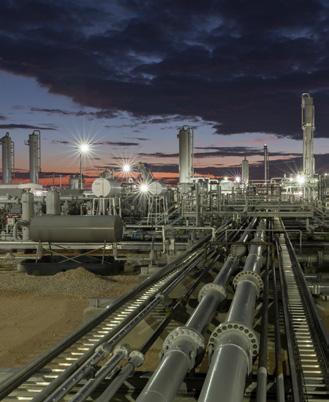
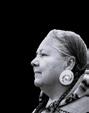
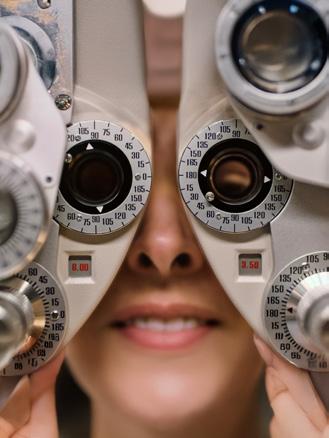

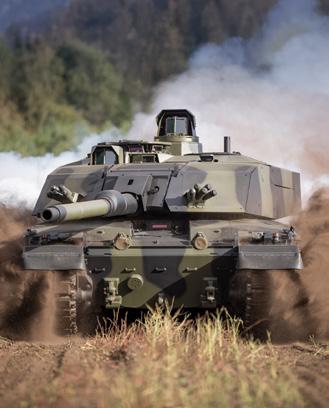


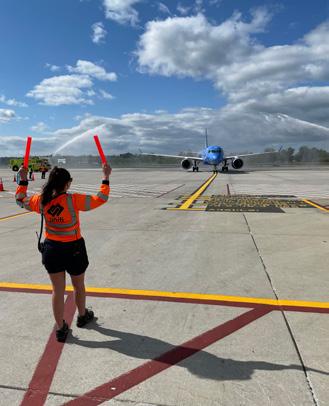

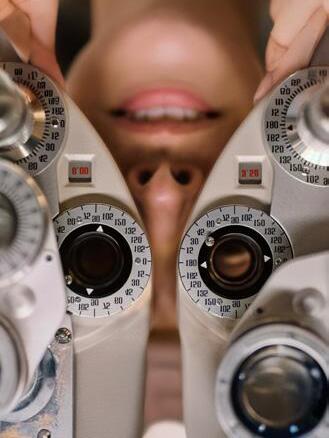


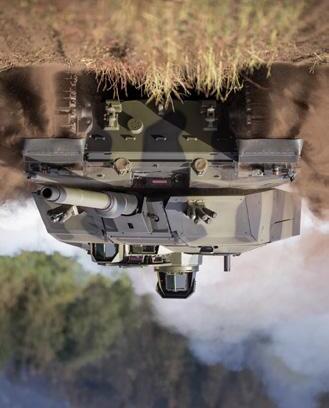

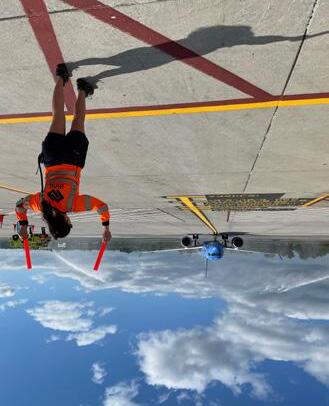



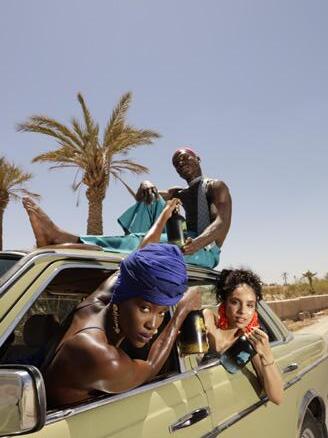
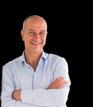
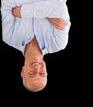
Africa Outlook, APAC Outlook, EME Outlook, North America Outlook, Mining Outlook, Healthcare Outlook, Manufacturing Outlook, Supply Chain Outlook, and Food & Beverage Outlook are digital publications aimed at boardroom and hands-on decision-makers, reaching an audience of more than 800,000 people around the world.

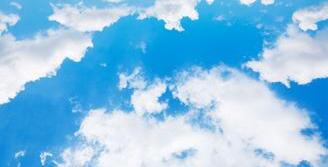
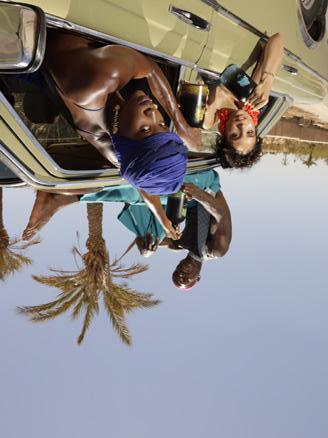
With original and exclusive content compiled by our experienced editorial team, we look to promote the latest in engaging news, industry trends, and success stories from across the globe.
Your company can join the leading industry heavyweights enjoying the free exposure we provide across our platforms with a free marketing brochure, extensive social media saturation, enhanced B2B networking opportunities, and a readymade forum to attract new investment and help you grow your business.
Visit www.outpb.com/work-with-us for details on how your company can feature for free in one of our upcoming editions.
EDITORIAL
Head of Editorial: Jack Salter jack.salter@outpb.com
Deputy Head of Editorial: Lucy Pilgrim lucy.pilgrim@outpb.com
Senior Editor: Lily Sawyer lily.sawyer@outpb.com
Editor: Ed Budds ed.budds@outpb.com
Editor: Rachel Carr rachel.carr@outpb.com
Editor: Lauren Kania lauren.kania@outpb.com
PRODUCTION
Art Director: Stephen Giles steve.giles@outpb.com
Senior Designer: Devon Collins devon.collins@outpb.com
Designer: Louisa Martin louisa.martin@outpb.com
Production Manager: Alex James alex.james@outpb.com
Digital Marketing Director: Fox Tucker fox.tucker@outpb.com
Website Content Manager: Oliver Shrouder oliver.shrouder@outpb.com
Social Media Executive: Jake Crickmore jake.crickmore@outpb.com
BUSINESS
CEO: Ben Weaver ben.weaver@outpb.com
Managing Director: James Mitchell james.mitchell@outpb.com
Chief Technology Officer: Nick Norris nick.norris@outpb.com
ADMINISTRATION
Finance Director: Suzanne Welsh suzanne.welsh@outpb.com
Finance Assistant: Victoria McAllister victoria.mcallister@outpb.com
CONTACT
Manufacturing Outlook
Norvic House, 29-33 Chapelfield Road
Norwich, NR2 1RP, United Kingdom
Sales: +44 (0) 1603 804 445
Editorial: +44 (0) 1603 804 431
SUBSCRIPTIONS
Tel: +44 (0) 1603 804 431 jack.salter@outpb.com www.mfg-outlook.com
Follow us on Linkedin: @manufacturingoutlook
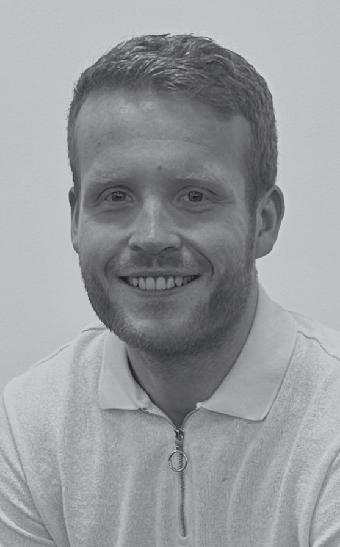
MORE IN THE TANK
Welcome to our eighth edition of Manufacturing Outlook magazine.
The role defence plays in ensuring national security has always been vital, however its importance has only intensified in today’s increasingly complex and uncertain global landscape.
This issue’s front cover features the Challenger 3, the most advanced Main Battle Tank (MBT) ever fielded by the British Army.
It has Rheinmetall UK’s advanced technology at the core, delivering nextgeneration firepower, survivability, and digital capability.
A champion of British engineering, Rheinmetall UK is committed to ensuring the country remains a global leader in defence innovation.
The company is a multi-domestic prime contractor, generating intellectual property, creating jobs, and driving economic growth within the UK defence sector.
“We’re playing an active role in shaping the future of land warfare by driving innovation, building strategic partnerships, and delivering mission-critical solutions at pace,” observes Deputy CEO, Rebecca Richards.
DOK-ING’s comprehensive and transformative robotics solutions are also saving countless lives and evolving industries throughout Europe.
Headquartered in Zagreb, Croatia, the company is leading the charge in heavy-duty robotics and autonomous systems and has established itself as a manufacturing powerhouse, renowned for producing world-class unmanned vehicles that protect people in otherwise hazardous and harmful environments.
“The technology already exists, but at DOK-ING, we’ve made a deliberate choice to apply it where it matters most – in the world’s most dangerous and demanding jobs,” outlines Davor Petek, COO of DOK-ING Security and Defence.
Morbern, meanwhile, creates innovative vinyl upholstery fabric solutions with a long-term focus on sustainability, digital transformation, and market expansion.
The Canadian company is North America’s leading designer and manufacturer of decorative vinyl upholstery fabrics, with this year marking its 60th anniversary.
“Our products are used for pretty much everything we sit on, whether it’s chairs for an office, airport, cinema, cruise ship, boat, jet ski, recreational vehicle (RV), car, or truck,” shares Eric Lamontagne, President of Morbern. There’s even more in this issue’s tank with the latest manufacturing advancements and innovations from Defy Appliances, Nurol Makina, Emirates Glass, and many more.
We hope that you enjoy your read.
Jack Salter Head of Editorial, Outlook Publishing
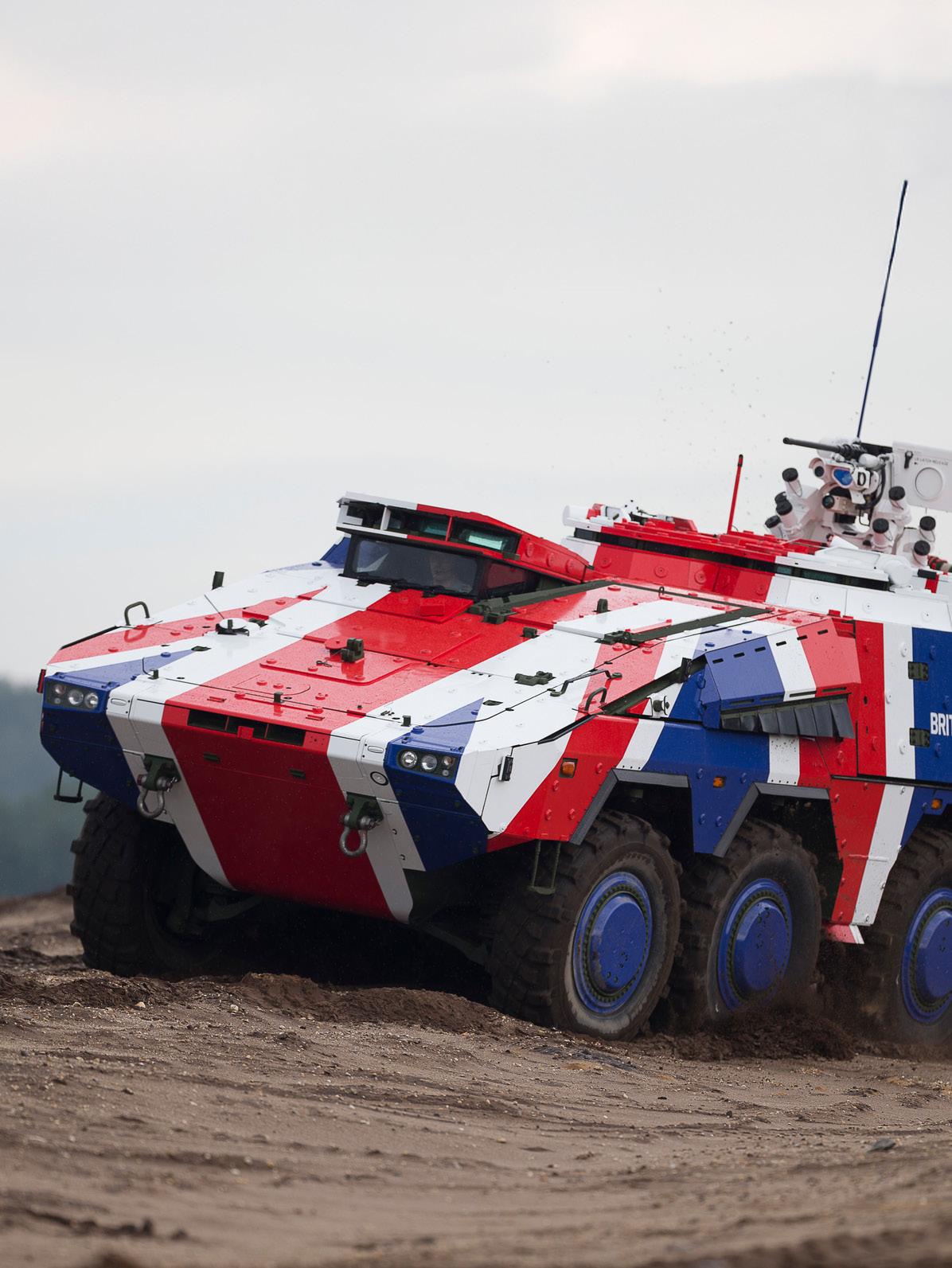
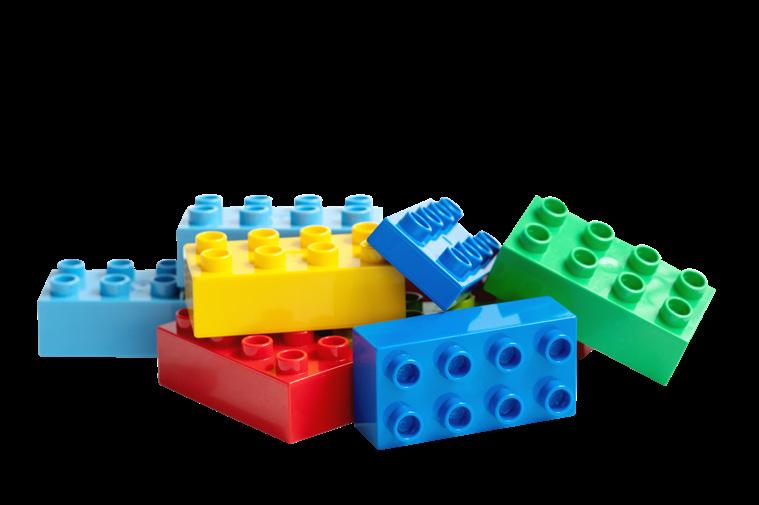
FEATURES
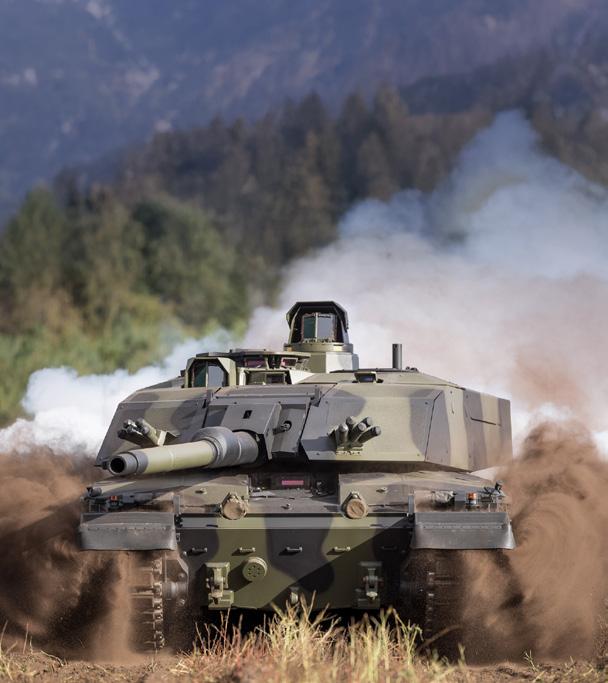
EUROPE & MIDDLE EAST
50 Rheinmetall UK
Sovereign Capability
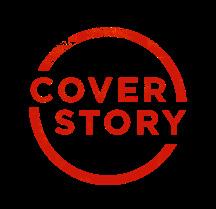
A champion of British engineering
68 DOK-ING
Robotics That Save Lives
Don’t send a man to do a machine’s job
86 Nurol Makina
Over 40 Years of Excellence
Fortifying European defence capabilities
96 Emirates Glass
An Unbreakable Commitment to Excellence
An innovative architectural vision
106 Resonac Graphite
Business Unit
Leaders in an Evolving Electrode Industry
An innovative and sustainable approach
114 Martin-Baker
Safety When it Matters Most Ejection seats that have saved thousands of lives
120 Dunlop Aircraft Tyres
Tread on the Runway
Committed to reliability
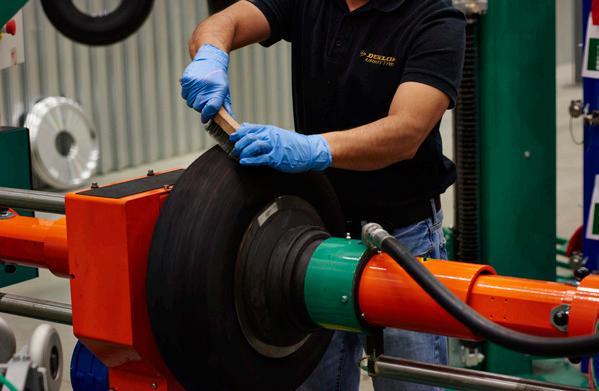
NORTH AMERICA
126 Saulsbury
Getting the Job Done Right
A trusted partner, employer of choice, and leader in safety
166 Morbern
Sit in Style
Innovative vinyl upholstery fabrics
174 Aero Industries
Top-Tier Tarp
Generations of transportation innovation
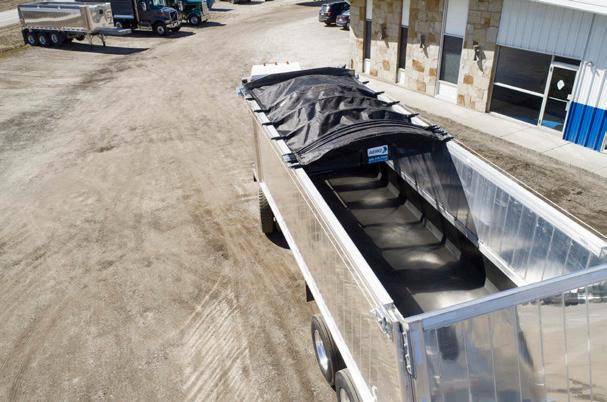
186 Aquila Power Catamarans
Embodying the Eagle
High-performance and innovative catamarans
194 Johnson & Johnson
Vision Care for Every Stage of Life
Delivering on the eye health needs of patients around the world
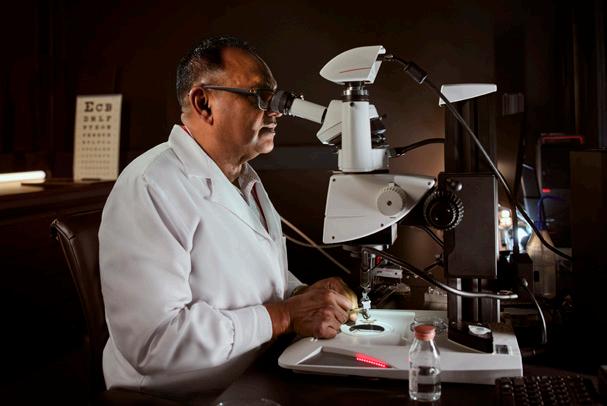
AFRICA
202 Defy Appliances
Elevating the Domestic Equipment
Experience
Leveraging cutting-edge technology to enhance everyday living
212 Saab Grintek Defence
Innovation at the Core of Operations
Empowering advanced systems for enhanced security
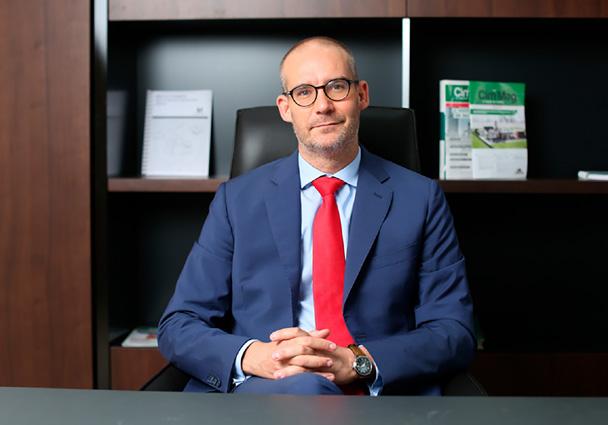
222 Cimencam
Cementing a Place in History
Constructing Cameroonian excellence
230 LafargeHolcim Côte d’Ivoire
Cementing a Sustainable Future
High-quality, sustainable construction solutions
236 Sulzer South Africa
Powering Partnerships Beyond Pumps
Maintaining certainty through customer partnerships
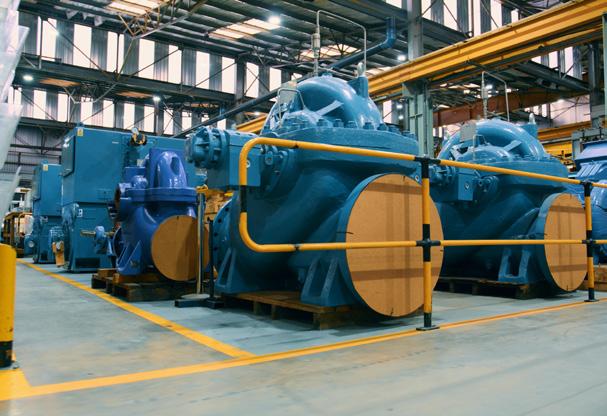
242 NewSpace Systems
Rocketing to Success
Enabling a galaxy of possibilities
250 Trotech
Think Tanks, Think Trotech
Leading the way in construction excellence
ASIA PACIFIC
256 Leonardo Australia
Protecting Australia Since 1885
Technologically advanced defence products, services, and solutions
264 ASSA Abloy Vietnam
Unlocking the Door to Manufacturing Excellence
An integral manufacturing hub unlocking key markets
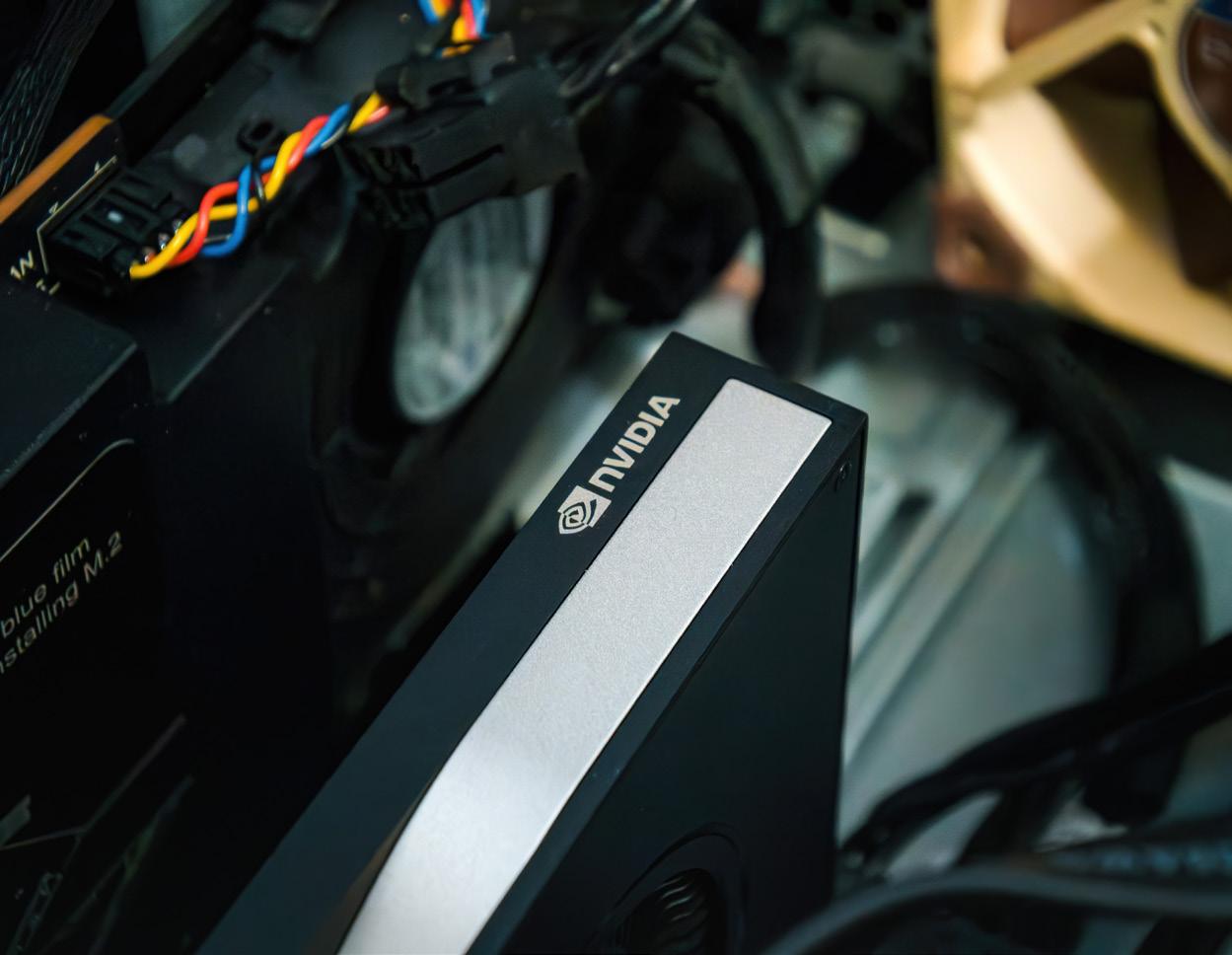
AN INTELLIGENT INVESTMENT
COMPUTER MANUFACTURER NVIDIA is helping to build an artificial intelligence (AI) factory in Germany that will support industrial AI workloads for a host of European manufacturers.
The state-of-the-art facility will feature 10,000 graphics processing units (GPUs) and be built following the framework highlighted in the NVIDIA Omniverse Blueprint for AI factory design and operations.
As part of this blueprint, Cadence’s reality digital twin platform will be used to simulate and optimise the entire factory in a physically accurate virtual environment, enabling engineering teams to build a smarter, more reliable facility.
This exciting investment will serve as a launchpad to accelerate AI development and adoption for numerous European manufacturers in anticipation of future AI gigafactories.
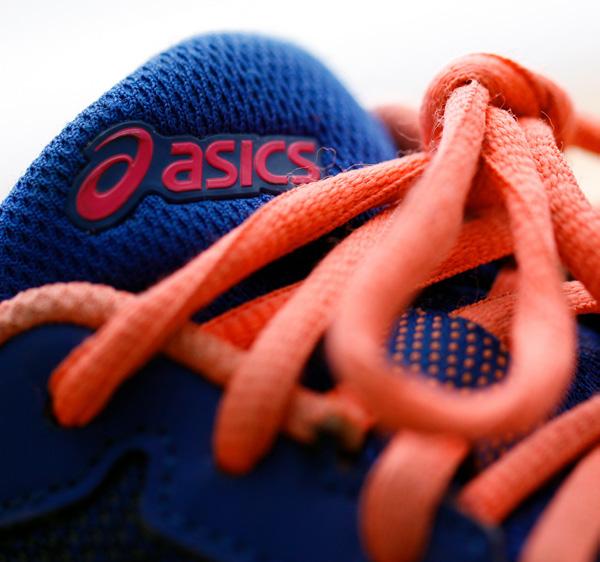
ASICS ACCELERATES INDIAN MANUFACTURING
JAPANESE SPORTSWEAR BRAND ASICS has announced plans to ramp up its Indian manufacturing capacity from 30 to 40 percent.
This decision from the athletic apparel company aligns with the current regulatory environment
PROUDLY SHOWCASING AFRICA
THE ORGANISERS of the 2025 edition of Manufacturing Indaba, Africa’s premier industrial event, have announced the confirmed participation of a large delegation of exhibitors from Kenya, who will be showcasing their manufacturing capabilities under the “Made in Africa” brand.
Held from 15th-16th July at the Sandton Convention Centre in Johannesburg, South Africa (SA), the event has become the continent’s primary platform for advancing industrialisation, innovation, and trade.
The strong Kenyan presence reflects a shared continental vision to unlock intra-African trade and industrial development in alignment with the African Continental Free Trade Area (AfCFTA).
As one of East Africa’s leading economies, Kenya is experiencing a renewed focus on manufacturingled growth and its participation in this event will showcase its industrial ambitions moving forward.
in India, which has compelled international brands to halt footwear imports due to new quality standards.
Alongside plans to enhance its manufacturing capacity, and with approximately 125 stores operated through franchise partners, ASICS is preparing to launch its first companyowned store in India this year, with potential sites being evaluated near Delhi and Mumbai.
NINTENDO CONTEMPLATES
SWITCHING
MANUFACTURING STRATEGY
THE HIGHLY ANTICIPATED Nintendo Switch 2 sold over 3.5 million units worldwide in the four days following its release on 5th June, marking the highest global sales for any Nintendo hardware.
However, despite this huge victory, Japan-based Nintendo currently manufactures many of its US-bound goods in Vietnam, with some other production facilities located in China.
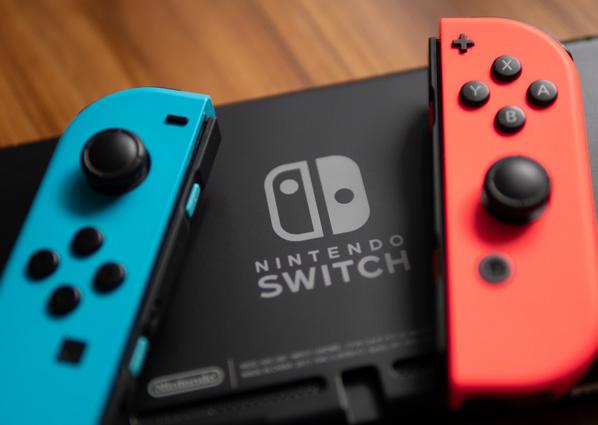
Under the Trump administration’s original announcement, exports from Vietnam to the US were hit with a 46 percent reciprocal tariff, amongst the highest rates of any country worldwide.
Despite a 90-day suspension on the tariff, Nintendo is pondering whether to pivot and enhance its manufacturing capabilities in the US instead.
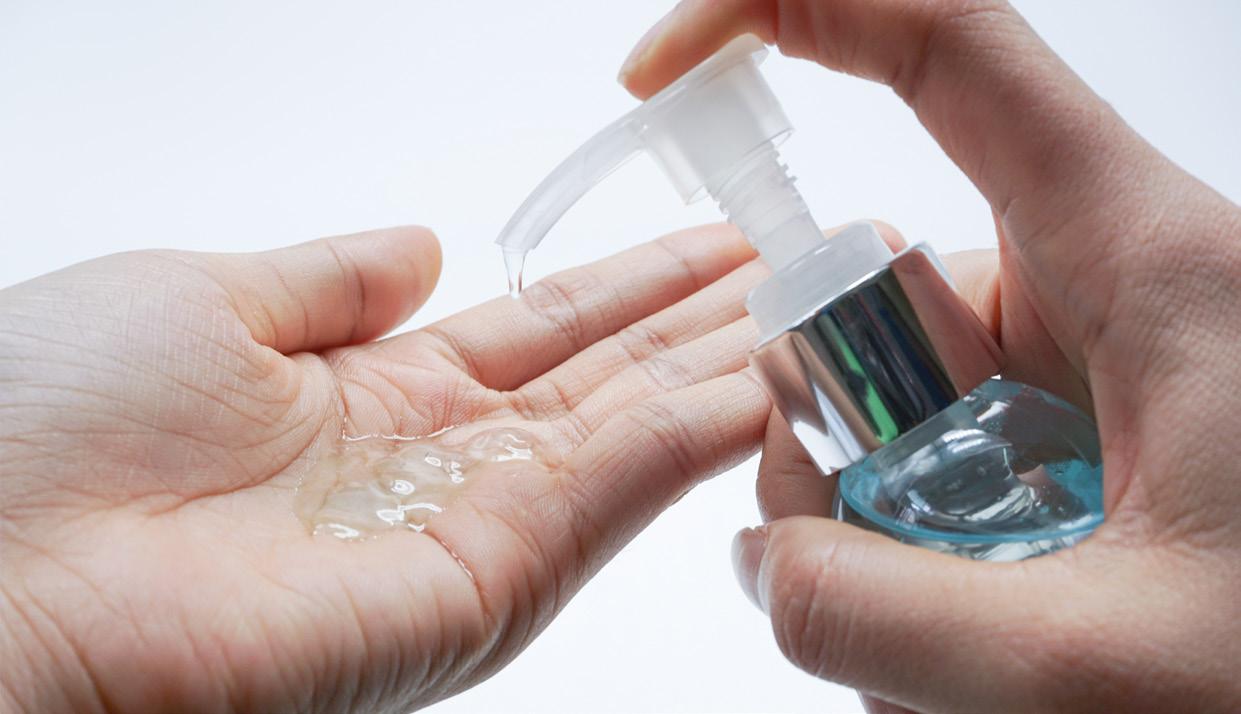
WHITELY ENHANCES PRODUCTION PROWESS
WHITELEY, A LEADING global innovator in medical infection prevention and professional hygiene solutions, has officially unveiled its new AUD$25 million human therapeutics plant in Tomago, New South Wales.
The facility is an exciting move for the company that represents a crucial development for regional
manufacturing and healthcare supply capabilities across Australia and New Zealand.
It is the first plant of its kind in the state and will produce alcohol-based hand rubs and over-the-counter medicines for use in hospitals and healthcare settings.
The investment reflects Whiteley’s long-term commitment to strengthening domestic capability in Australian science, jobs, and manufacturing.
CELEBRATING THE BEST OF BRITISH
THE INNOVATION AND achievements of the UK’s finest manufacturers have been celebrated at Insider’s Made in the UK Awards.
The event, held at the Titanic Hotel in Liverpool, is now in its third year and celebrates the international growth of the UK’s most dynamic manufacturing businesses.
Whilst the awards naturally reflect the sectoral diversity of British innovation, this year’s winners signal a global appetite for UK leadership in two high-growth areas – sustainability and AI.
Each prestigious category included one winner and up to three highly commended businesses.
UNLEASHING AFRICA’S POTENTIAL
CHINESE AUTOMAKERS ARE seeking to unlock Africa’s underdeveloped manufacturing potential with a new focus on hybrid and electric vehicles (EVs), as fresh restrictions on exports to the US and Europe send them on a global quest for new markets.
Despite being home to over a billion people, a combination of low incomes and high import duties have historically hampered manufacturers’ efforts to sell more cars in Africa.
On top of this, unreliable power availability and a lack of charging infrastructure have held back EV uptake across the continent.
Nearly half of the 14 Chinese automotive brands currently active in SA launched only last year, with more set to enter the market soon.
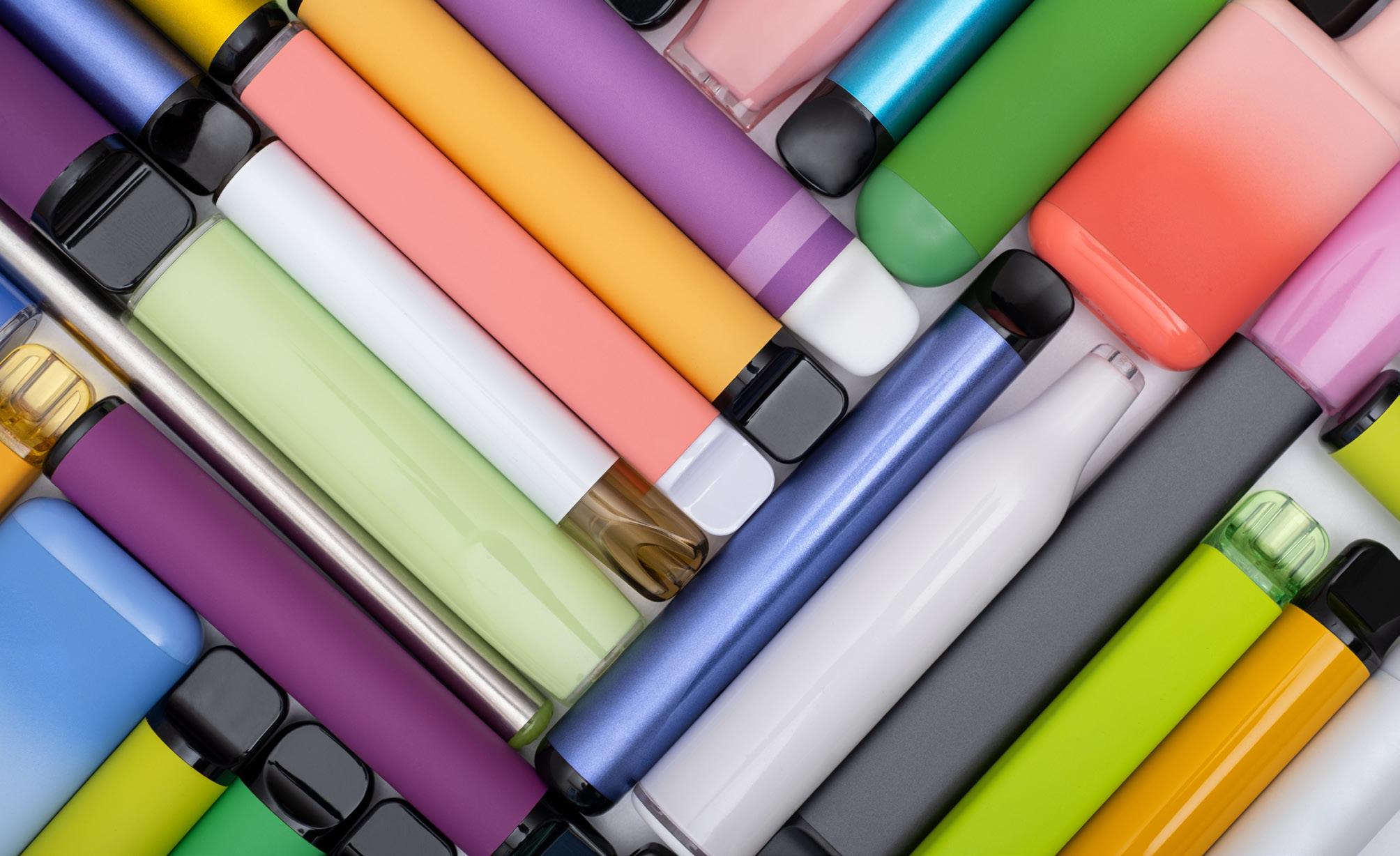
EPR Compliance in Vape Production
Millions of disposable vapes, packed with lithium batteries and toxic materials, end up in landfills each year. With the ban on single-use vapes in the UK, the industry is being forced to clean up its act. John Redmayne, CEO of European Recycling Platform UK, taps further into this topical issue
Writer: John Redmayne, CEO, European Recycling Platform UK
We’ve all seen them – the telltale glint of discarded vape devices littering our streets and parks.
As the environmental impact of the vaping boom unfolds across the UK, the disconnect between rapid market growth and proper end-of-life management has become impossible to ignore.
The UK vape industry is experiencing unprecedented growth, with consumers purchasing an estimated 13.5 million vapes weekly in 2024 – a staggering 37 percent increase year-on-year.
Alongside this commercial success comes a mounting environmental
crisis and regulatory landscape that many manufacturers, retailers, and waste supply chain professionals are dangerously unprepared to navigate.
FROM PUFF TO PROBLEM
Since 1st June 2025, a ban on singleuse vapes has been in place.
In parallel, environmental agencies are intensifying the enforcement of extended producer responsibility (EPR) regulations across the vape sector – regulations that have been in place but largely overlooked until now.
This enforcement shift creates significant challenges for manufacturing and supply chain
management, particularly for smaller producers who may lack dedicated compliance resources.
Under the Waste Electrical and Electronic Equipment (WEEE) regulations, vape manufacturers and importers bear responsibility for the entire lifecycle of their products.
This means not just designing, manufacturing, and selling vapes, but also ensuring proper collection, transportation, and recycling at end-of-life.
With approximately 8.2 million single-use vapes discarded weekly in the UK, the environmental implications are substantial, and regulators are taking notice.
The Environment Agency, supported by local authority trading standards, the Department of Environment, Food, and Rural Affairs (DEFRA), the Office for Product Safety and Standards (OPSS), and the Medicines and Healthcare products Regulatory Agency (MHRA), is now actively targeting non-compliant vape producers.
Every brand, regardless of size,
must register with an approved compliance scheme and accurately report on its waste or face serious consequences, including financial penalties, public investigations, and significant reputational damage.
HAZARDOUS JOURNEY
For supply chain professionals, this regulatory shift introduces complex logistical challenges. Vape recycling isn’t simply a matter of conventional waste management – it requires specialised handling throughout the collection and transportation process due to the hazardous materials involved.
Lithium-ion batteries present particular challenges, with fire risks during transport being a serious concern. Proper vape recycling demands ADR-licensed transport for hazardous materials, specialised containment systems (sometimes using vermiculite for added safety), and carefully managed logistics to prevent environmental contamination.
Once collected, vapes must be transported to specialised facilities where they undergo a complex dismantling process. Components are separated – plastics, metals, electronic elements, and batteries –with each material stream requiring different recycling pathways. The e-liquids themselves must be safely extracted and disposed of according to hazardous waste protocols.
For retailers, the responsibilities are equally significant. Those left with stock of single-use vapes they can no longer sell must seek a responsible recycling method or risk hefty fines, and under WEEE regulations, businesses selling vapes must provide recycling options for consumers.
If retailers have small amounts of stock, they may be able to dispose of them in the single-use vape bins they are legally required to provide in-store for customers.
However, for larger quantities, a specialist waste company will need
to be engaged for ethical, safe, and legal clearance.
In these cases, retailers must arrange for the secure transportation of these collected materials to appropriate recycling facilities – a process that demands careful planning and often specialised logistics partners.
BEYOND COMPLIANCE
Smaller manufacturers and brands face particular vulnerability in this changing landscape. Without dedicated compliance teams, many remain unaware of their legal obligations until enforcement action begins. By then, the financial and reputational damage can be severe. However, within this regulatory challenge lies a strategic opportunity. Forward-thinking manufacturers are recognising that robust EPR compliance can become a market differentiator.
As consumer awareness of environmental issues grows, brands demonstrating responsible end-oflife management for their products can build stronger customer loyalty and brand reputation.
Looking ahead, the regulatory landscape will only become more demanding. A new specific WEEE category for vapes (including replacement coils) will be introduced in 2026, bringing even greater scrutiny to the sector. Manufacturers who establish compliant supply chain processes now will be better positioned to adapt to these future changes.
For supply chain professionals in the vape industry, the message is clear – EPR compliance is becoming a fundamental business requirement that demands strategic attention.
This means conducting thorough audits of current practices, engaging with approved compliance schemes, and developing robust systems for tracking products throughout their lifecycle.
HELP AT HAND
The transition to full EPR compliance requires expertise and guidance. Organisations like European Recycling Platform UK can provide essential support in navigating these complex regulations, helping manufacturers and retailers develop compliant processes whilst minimising disruption to their operations.
From registration and reporting to developing effective take-back schemes, specialised compliance partners can transform a potential regulatory headache into a streamlined part of business operations.
Vapes aren’t disappearing in a cloud of regulatory smoke any time soon – quite the opposite. The industry will continue to evolve, innovate, and grow – but those that thrive will be the manufacturers and retailers who embrace their environmental responsibilities with the same enthusiasm they’ve shown for market expansion.
The most successful players will be those who see WEEE compliance not as a burden, but as an integral part of building a sustainable, responsible business model that resonates with increasingly eco-conscious consumers.
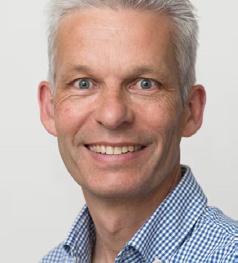
ABOUT THE EXPERT
John Redmayne is the CEO of European Recycling Platform UK and a senior environmental executive with over 20 years of leadership and management experience spanning the public, private, and third sectors.
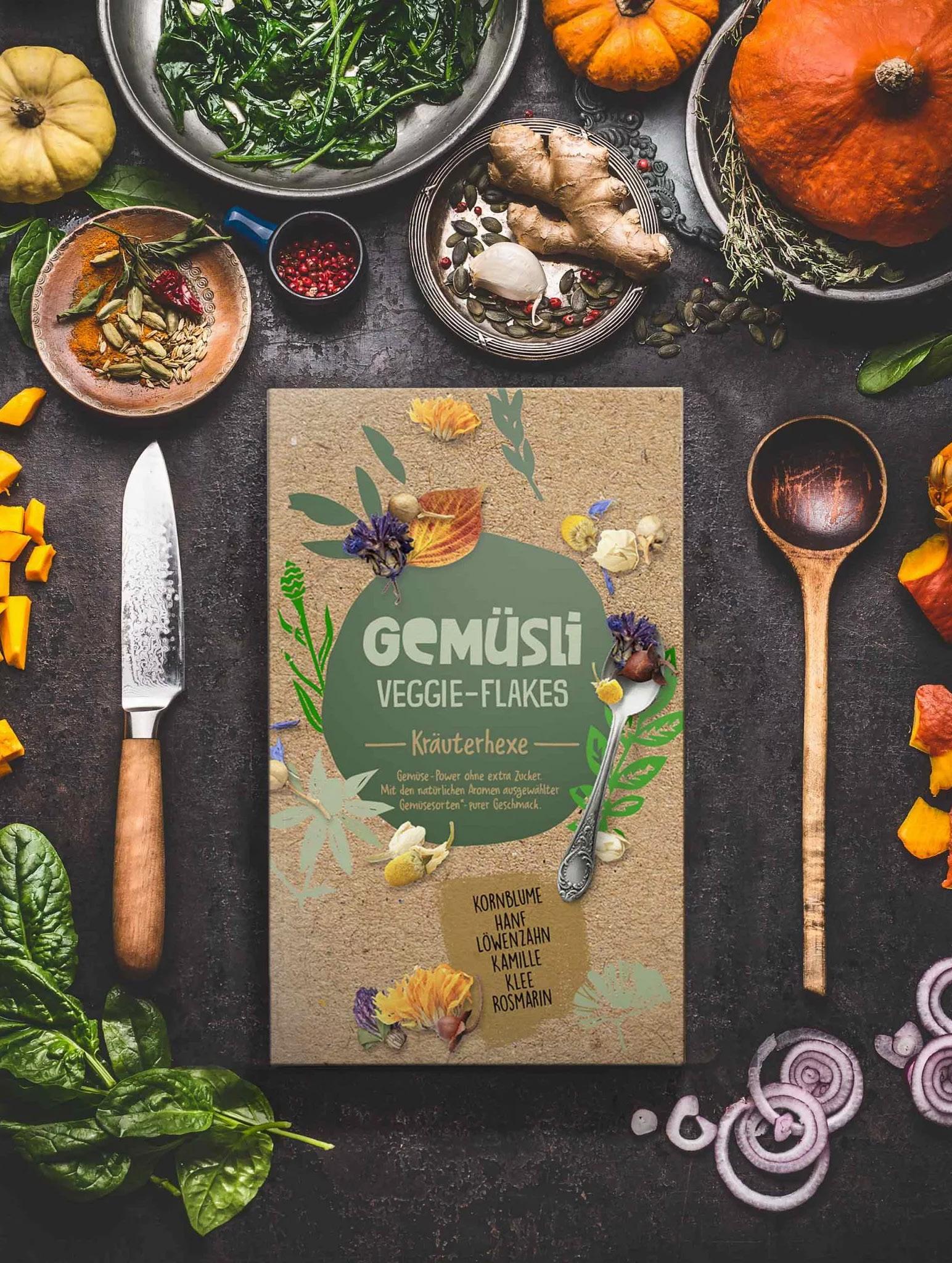
FOR THE LOVE OF FOOD
As a food branding and packaging design agency with a passion for all things delectable, MILK. brings brands to life through each of the senses. Eleonore Eisath, Innovation Lab Lead and Business Development Manager, tells us more
Writer: Lauren Kania
Developing pioneering designs that harmonise functionality, aesthetics, and sustainability, MILK. is more than just a design agency – it’s a driving force for sustainable and future-oriented brand management.
With an aim to create packaging that not only looks good but also offers real added value for brands, consumers, and the environment, the company is the ideal partner for those seeking innovative and sustainable packaging solutions.
Based in Frankfurt, Germany, MILK. offers comprehensive brand and packaging development services, from selecting the optimal materials to creating a standout shelf presence at the point of sale.
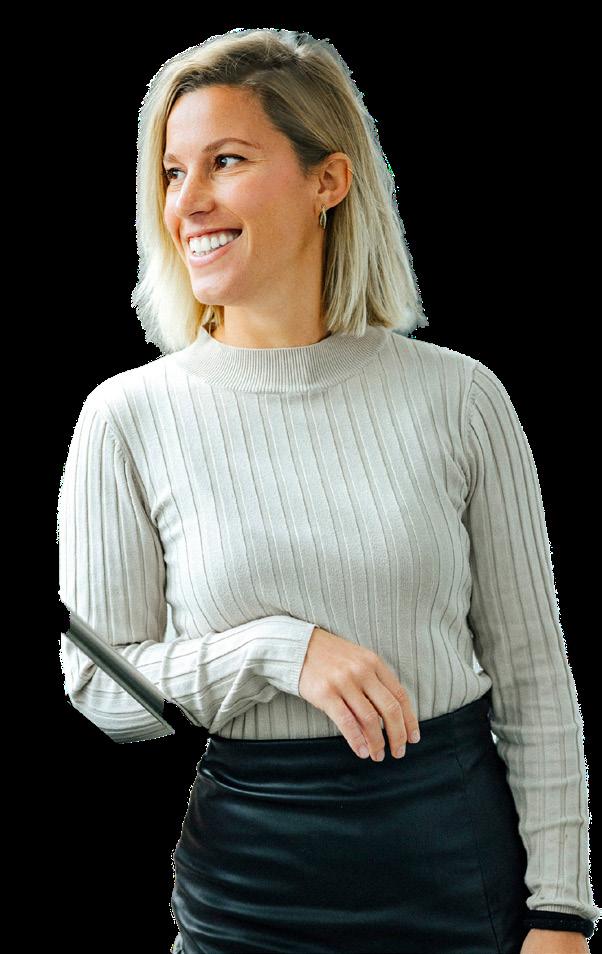
“Our core clients are in the food and beverage industry across all German-speaking countries in Europe, ranging from small startups to major brands like Nestlé and Ferrero,” introduces Eleonore Eisath, Innovation Lab Lead and Business Development Manager.
Currently, Eisath finds it an exciting time in the packaging industry, with significant changes on the horizon.
Specifically, the EU market is set to undergo a major transformation driven by new regulations, the most notable of which is the upcoming Packaging and Packaging Waste Regulation (PPWR), alongside lesser-known initiatives such as the Green Claims Directive.
Eleonore Eisath, Innovation Lab Lead and Business Development Manager
“Together, these regulations will substantially impact how companies design and communicate their packaging,” she details.
As the company specialises in developing sustainable packaging and helping clients navigate these new requirements, this moment presents a unique opportunity for it –and the industry at large.
MILK. differentiates itself from the competition in various ways, most predominantly through its unparalleled passion and innovation.
“With our in-house Innovation Lab, we think beyond the conventional –and beyond the present,” prides Eisath.
CAN YOU EXPAND UPON THE NEED TO RETHINK FOOD PACKAGING AND MARKETING IN A NEOECOLOGICAL APPROACH?
Eleonore Eisath, Innovation Lab Lead and Business Development Manager:
“The neo-ecological approach goes beyond traditional sustainability efforts. It reflects a deeper, systemic shift in how consumers, businesses, and regulators view the relationship between people, products, and the planet. In this context, packaging is no longer just a functional layer or marketing tool – it becomes part of a product’s ethical and ecological footprint.
“After years of greenwashing and overly ambitious promises, it’s time for a shift towards authenticity and accountability. That means being honest with consumers about what’s possible, what still needs work, and where real progress is being made.
“The transition won’t be easy, but it’s achievable. Brands that embrace
The company scouts for new materials, compiles them into its open-source glossary, and collaborates with machine manufacturers to test scalability. Additionally, its Trend Radar offers a clear view of food and packaging trends – today, tomorrow, and in the future – whilst serving as a strategic tool in the company’s Innovation Workshops.
“Whilst most packaging design agencies focus primarily on aesthetics, we go further. We guide our clients through the entire journey and encourage them to be bold,” she establishes.
this mindset won’t just meet the new regulatory standards – they’ll build stronger, more lasting relationships with their consumers grounded in trust and transparency.
“At MILK., we believe this is the future of packaging design – and it’s the path we’re committed to every day.”
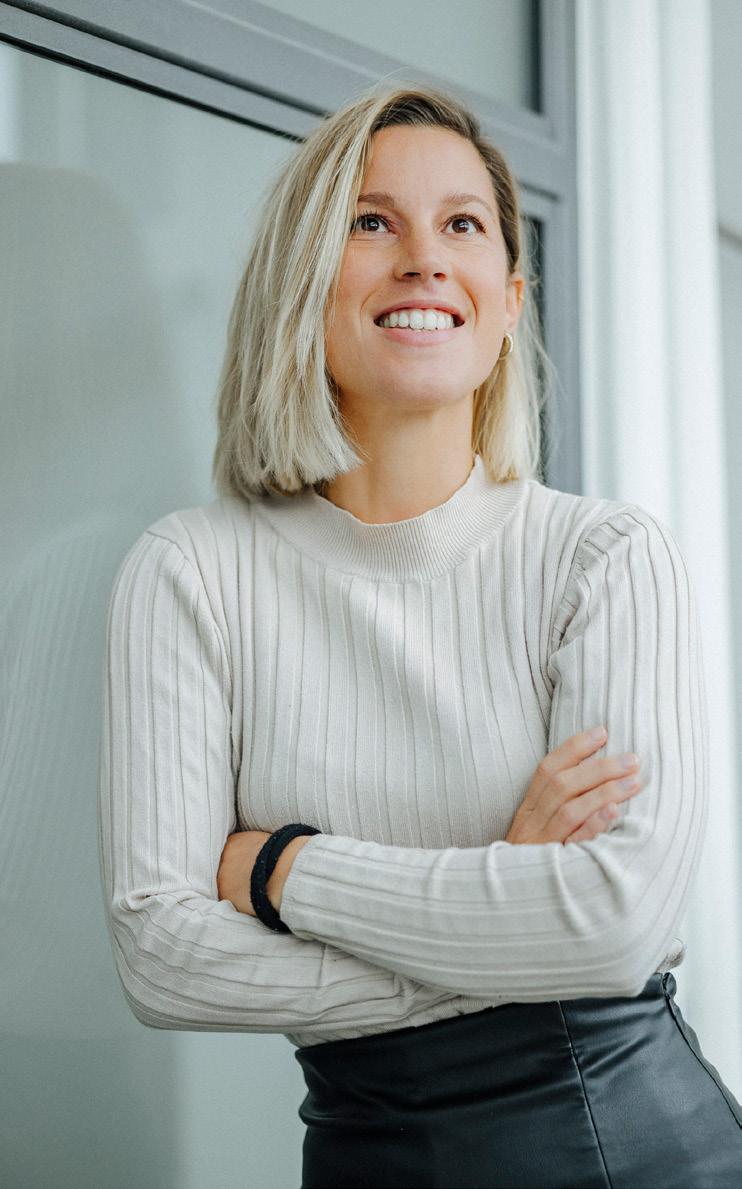
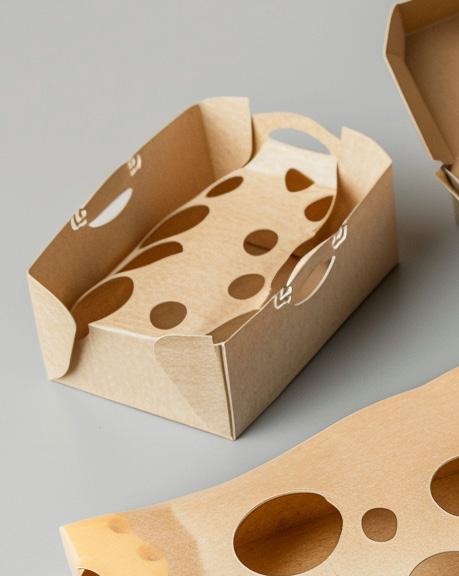
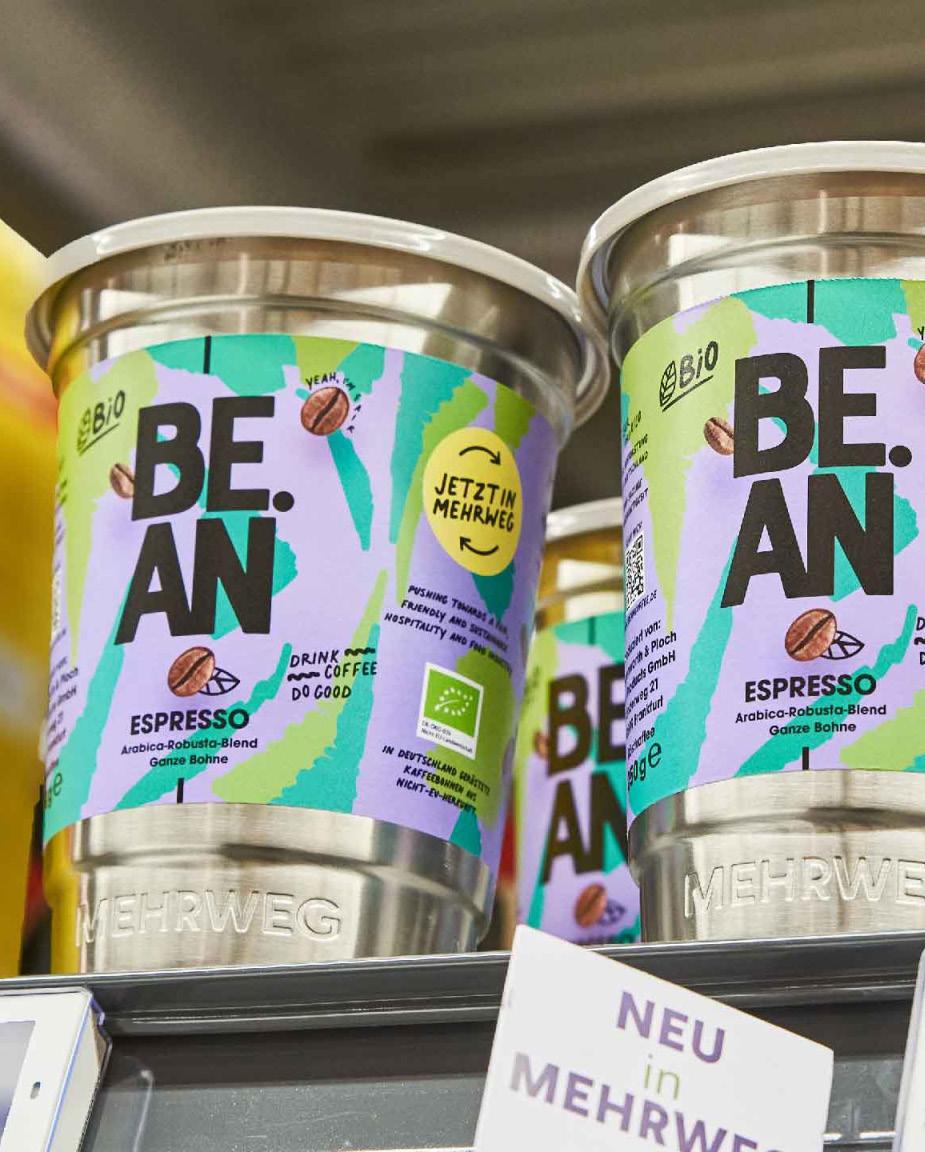
MORE THAN JUST PACKAGING
Although the world may be changing rapidly, the packaging industry tends to move at a slower pace.
This means that introducing innovative designs into existing fast-moving consumer goods (FMCG) infrastructure entails altering highly optimised and standardised processes, sometimes in production lines that operate around the clock. Hence, many players in the food and beverage industry struggle with new regulations and often respond with hesitation.
“Our mission as partners in change is to make this transition easier by
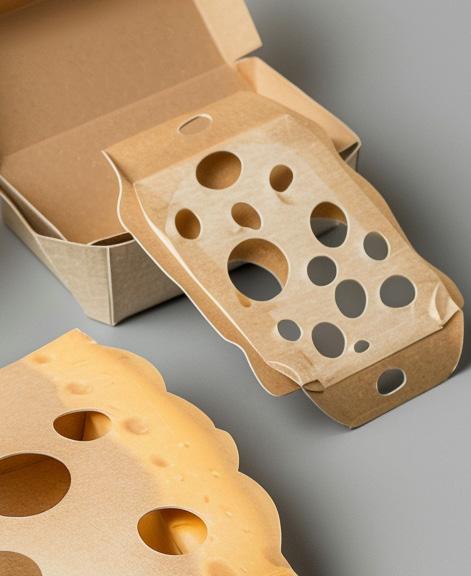
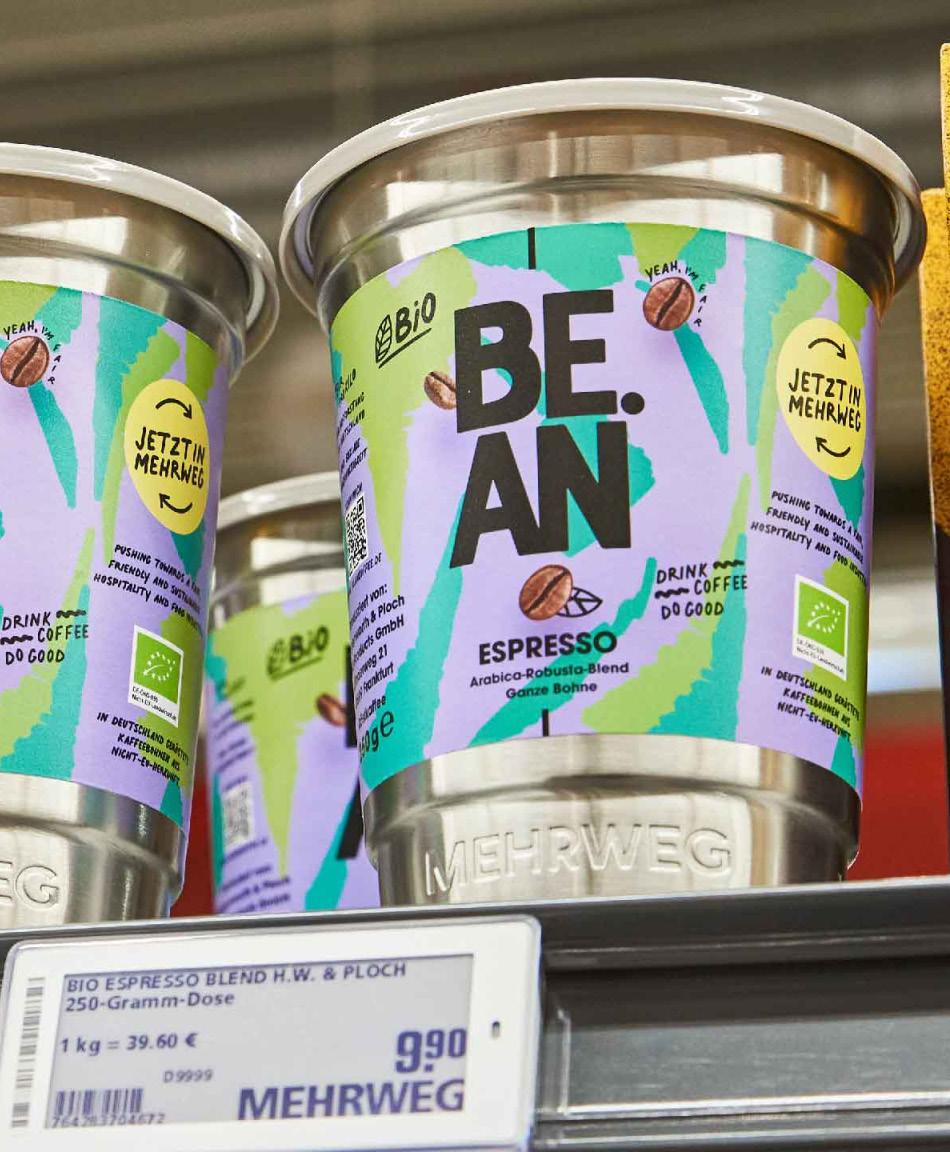
developing innovative yet pragmatic solutions, because the best idea is worthless if it can’t be implemented,” insights Eisath.
Beyond the push for sustainability, another major shift is the move towards digitalised packaging, particularly through the Digital Product Passport (DPP).
This initiative will require all EU products to have a digital twin of their physical counterpart, which means that packaging design must now be approached in a more integrated, cross-functional way.
“To make this vision a reality, we’ve partnered with a start-up called
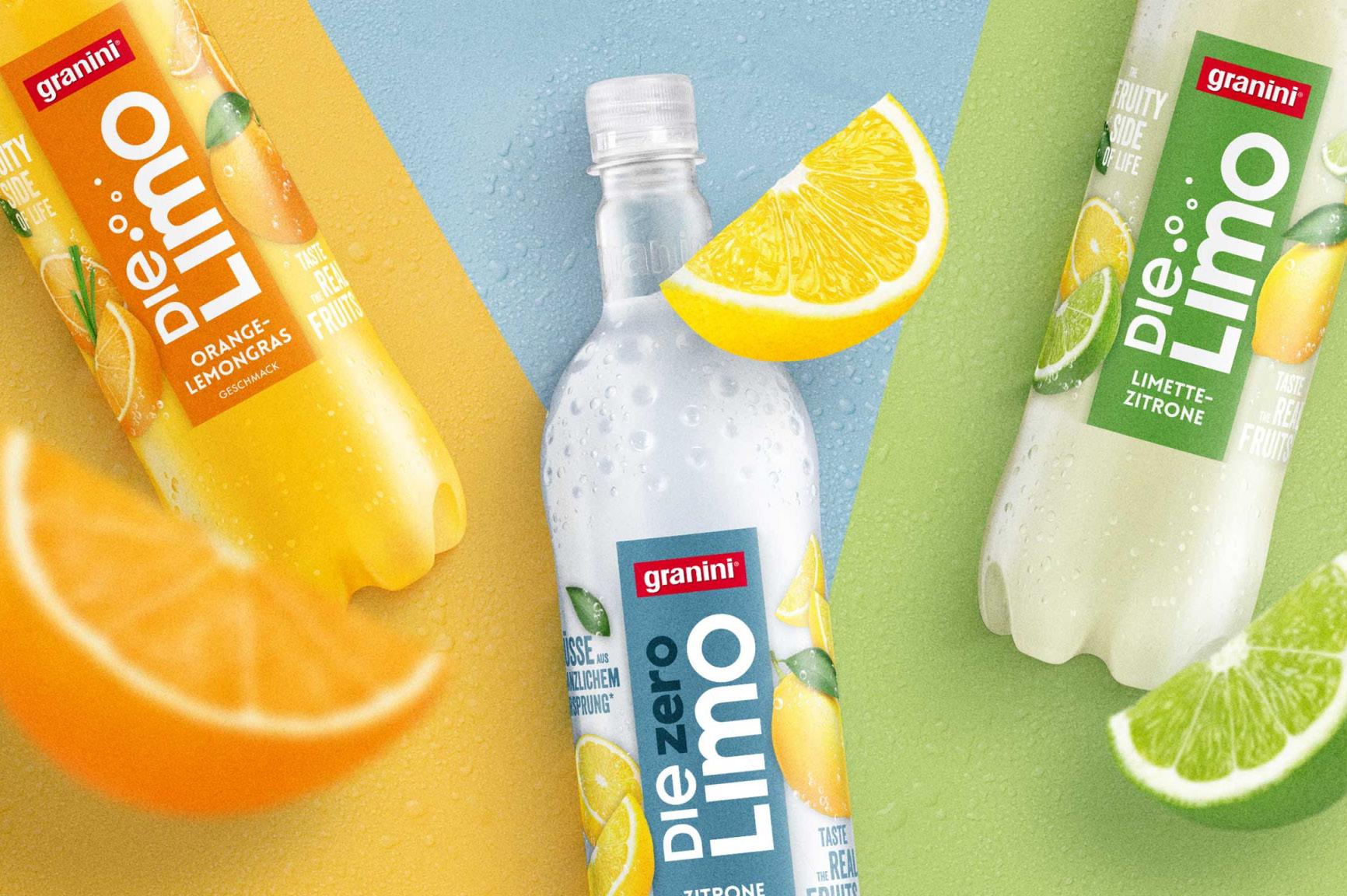
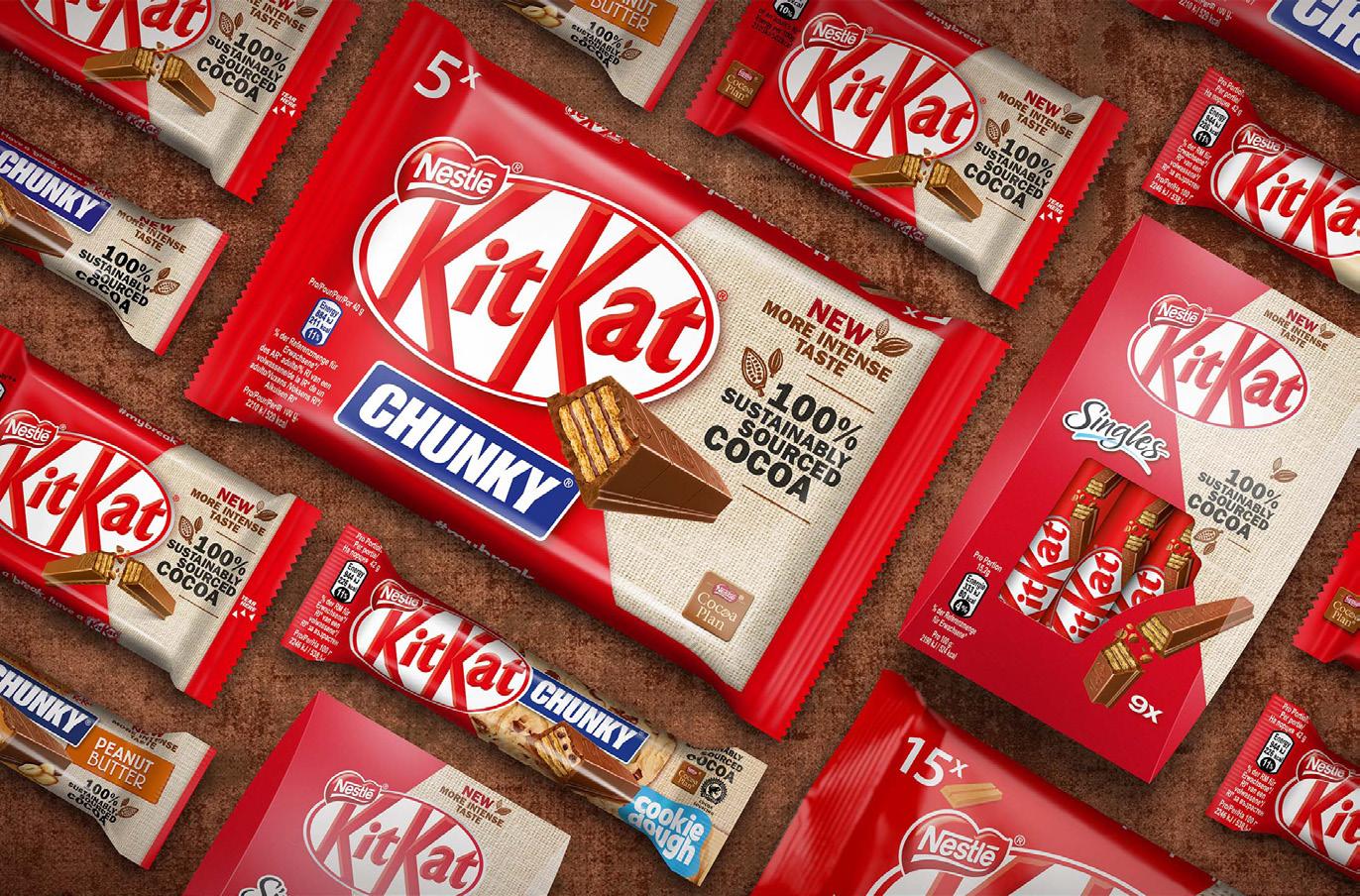
info.link, which focuses on the tech infrastructure whilst we ensure the visual and structural adaptation of the packaging artwork is on point,” expands Eisath.
In addition to MILK.’s design expertise, it is using artificial intelligence (AI)-powered tools to predict packaging performance on the shelf.
“Digitalisation is unstoppable, but we see it as a powerful tool to elevate and enrich a product that, at its core, remains an analogue touchpoint.”
A great example of how a wellestablished, traditional brand can successfully launch an innovative
new product is Reoat – a mealreplacement drink designed by MILK. and one of Germany’s leading oat brands.
The brand has not only entered a new product category but also tapped into a growing, healthconscious target group, clearly demonstrating how smart product and communication design can breathe fresh life into a legacy brand whilst telling a compelling story.
Elsewhere, MILK. is currently working on a comprehensive, fullpicture project with a German tea brand.
After defining a clear packaging
MILK.’S VISION AND MISSION
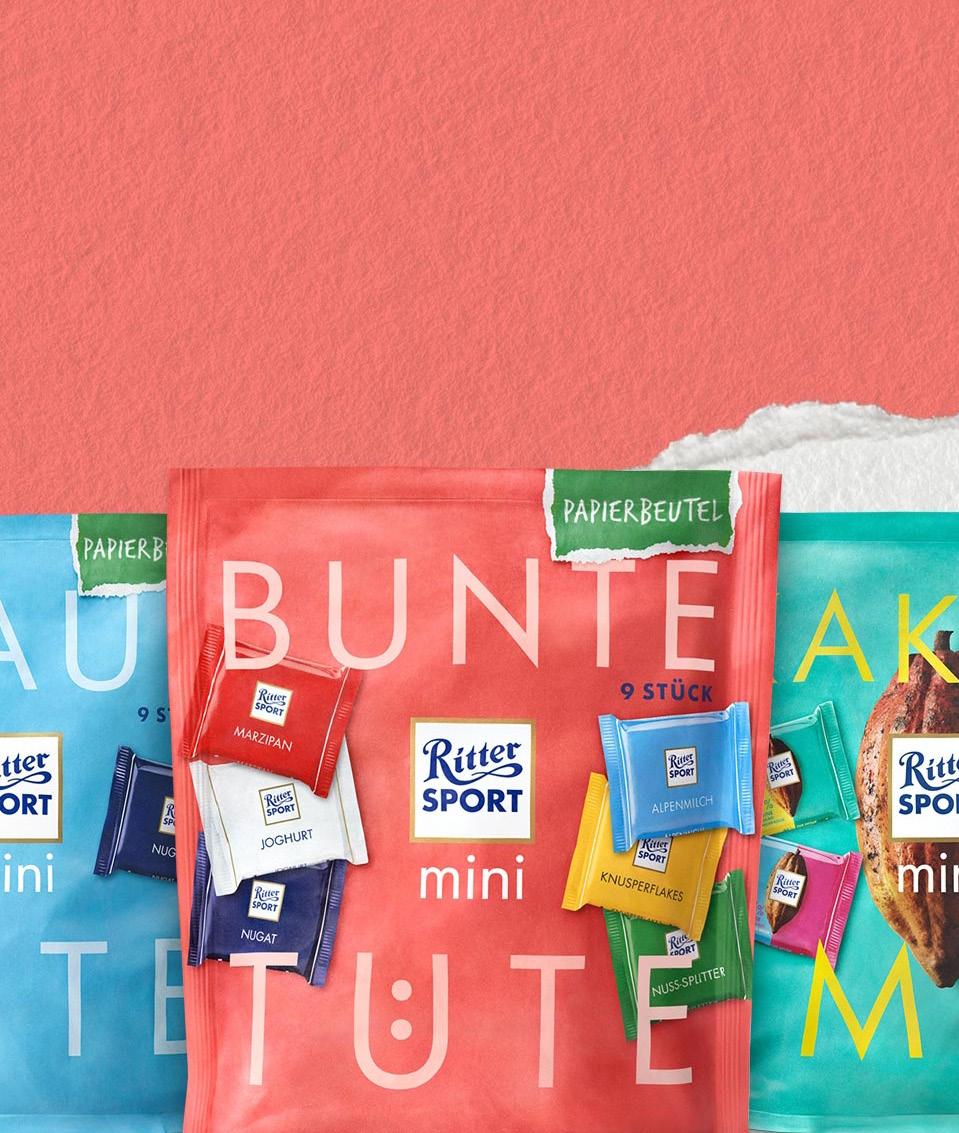
As partners in change, MILK. sees its future in the synergy between increasing digitalisation and a renewed appreciation for analogue products.
The company’s unique expertise lies in gaining a deep understanding of food and applying this insight to its designs, drawing on its craftsmanship and specialised knowledge of the food and beverage market to do so.
Clients find MILK. though a shared passion for food and the company’s belief in creating real value through design.
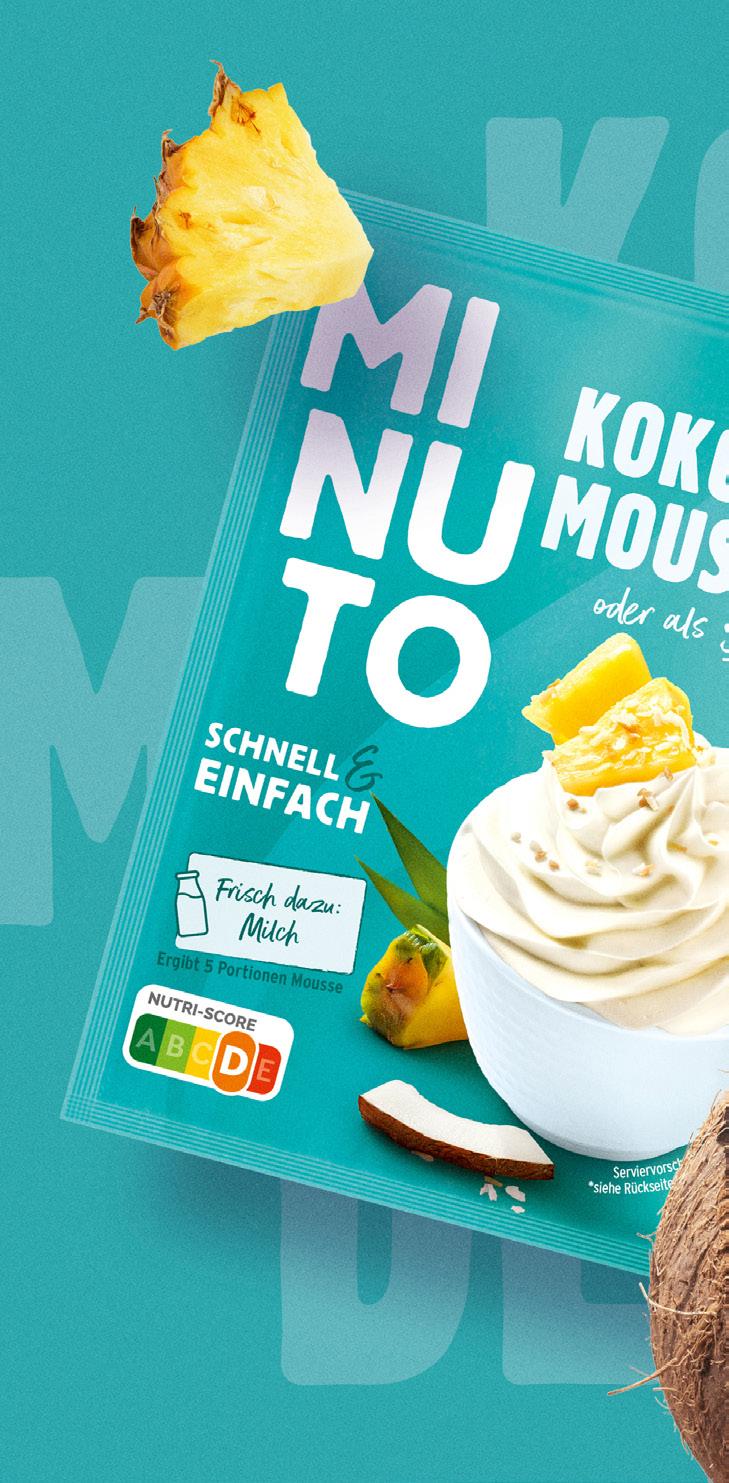
“WITH OUR IN-HOUSE INNOVATION LAB, WE THINK BEYOND THE CONVENTIONAL –AND BEYOND THE PRESENT”
– ELEONORE EISATH, INNOVATION LAB LEAD AND BUSINESS DEVELOPMENT MANAGER, MILK.
strategy and technical guidelines, the company is now developing a communication campaign that will share this journey with the consumer.
“True to our belief in authenticity, the campaign will be transparent and honest, highlighting challenges the brand faces and how they plan to tackle them, rather than relying on polished claims and empty promises,” expands Eisath.
DESIGNING AN AESTHETIC FUTURE
As MILK. continues to look at a creative future in the packaging industry, it aims to take a leading role by creating holistic product experiences that engage all the senses.
“We see food, packaging, and branding as one experience which cannot be developed in silos,” imparts Eisath.
MILK.’s Innovation Workshops address all three areas and work to craft a compelling story rather than just another consumer product.
Specifically, the senses play a crucial role in consumer decisionmaking, no matter how digital the world becomes. Food products and their packaging must look, feel, and smell engaging, otherwise they won’t be chosen.
“We’re constantly exploring new ways to excite the senses – for example, by replacing traditional labels with textures that reflect the characteristics of the food inside,” explains Eisath.
In parallel, MILK. prides itself on
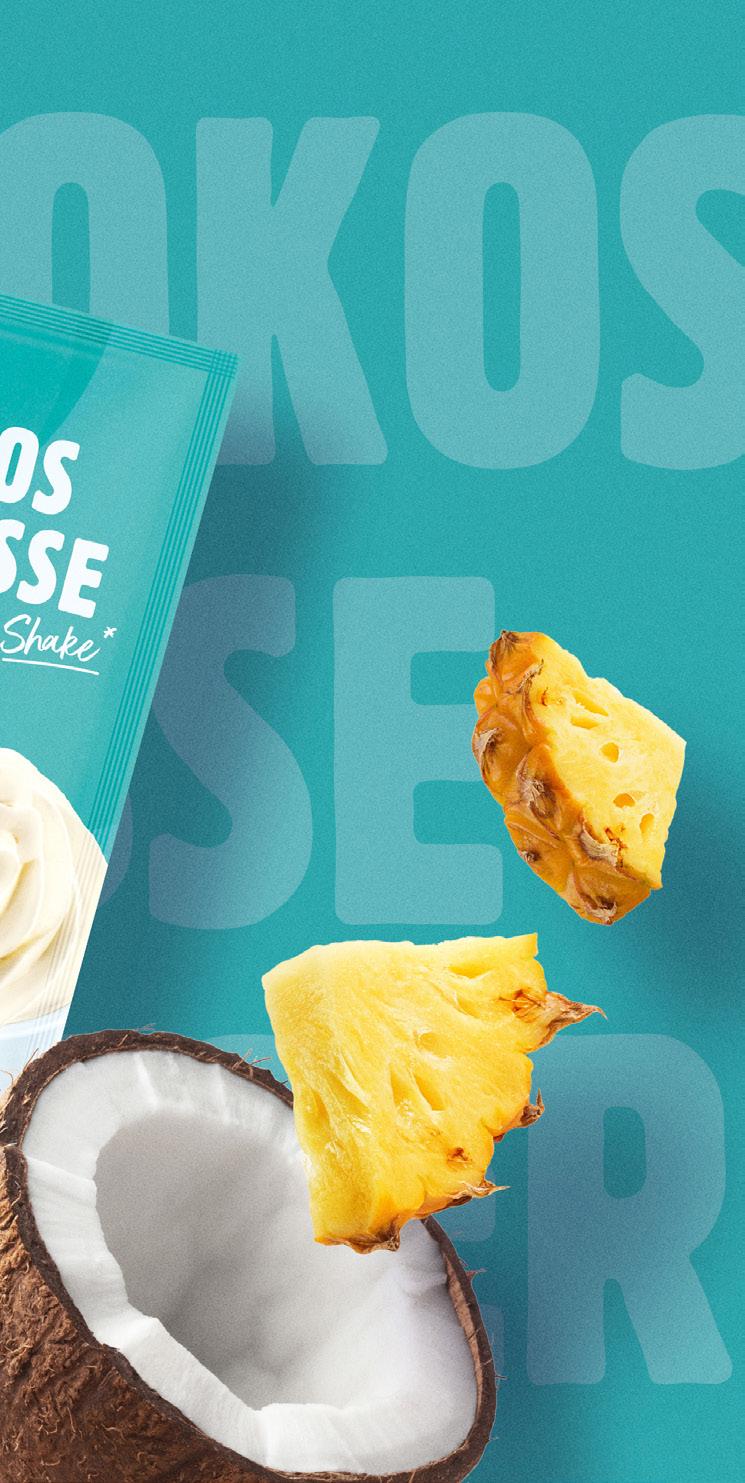
its ability to transform clients’ future scenarios into a personalised brand radar whilst producing innovative products and packaging solutions aligned with their vision.
The company’s Trend Radar is a dynamic pool of developments across four key categories – food, packaging, production, and kitchen. It spans today, tomorrow, and the future, offering a broad yet focused perspective on the evolving food industry.
“By tailoring the Trend Radar to a client’s specific needs, we can strategically fill their innovation pipeline,” informs Eisath.
“We identify and prioritise relevant
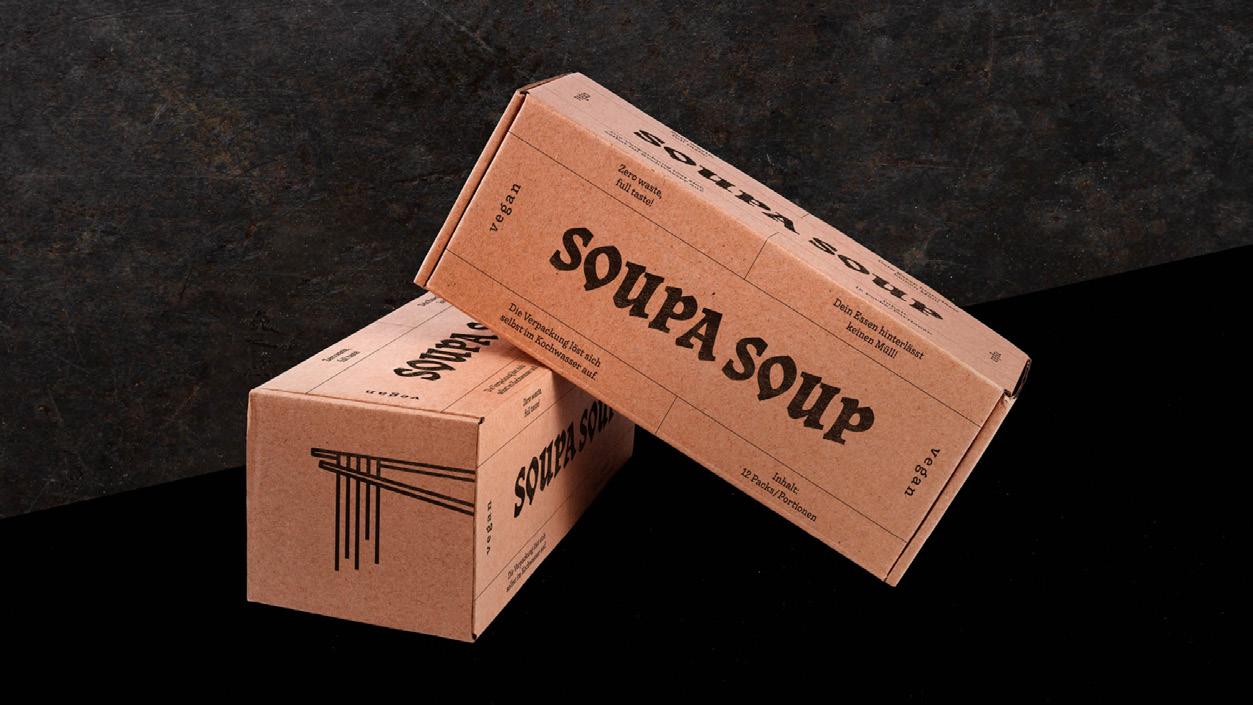
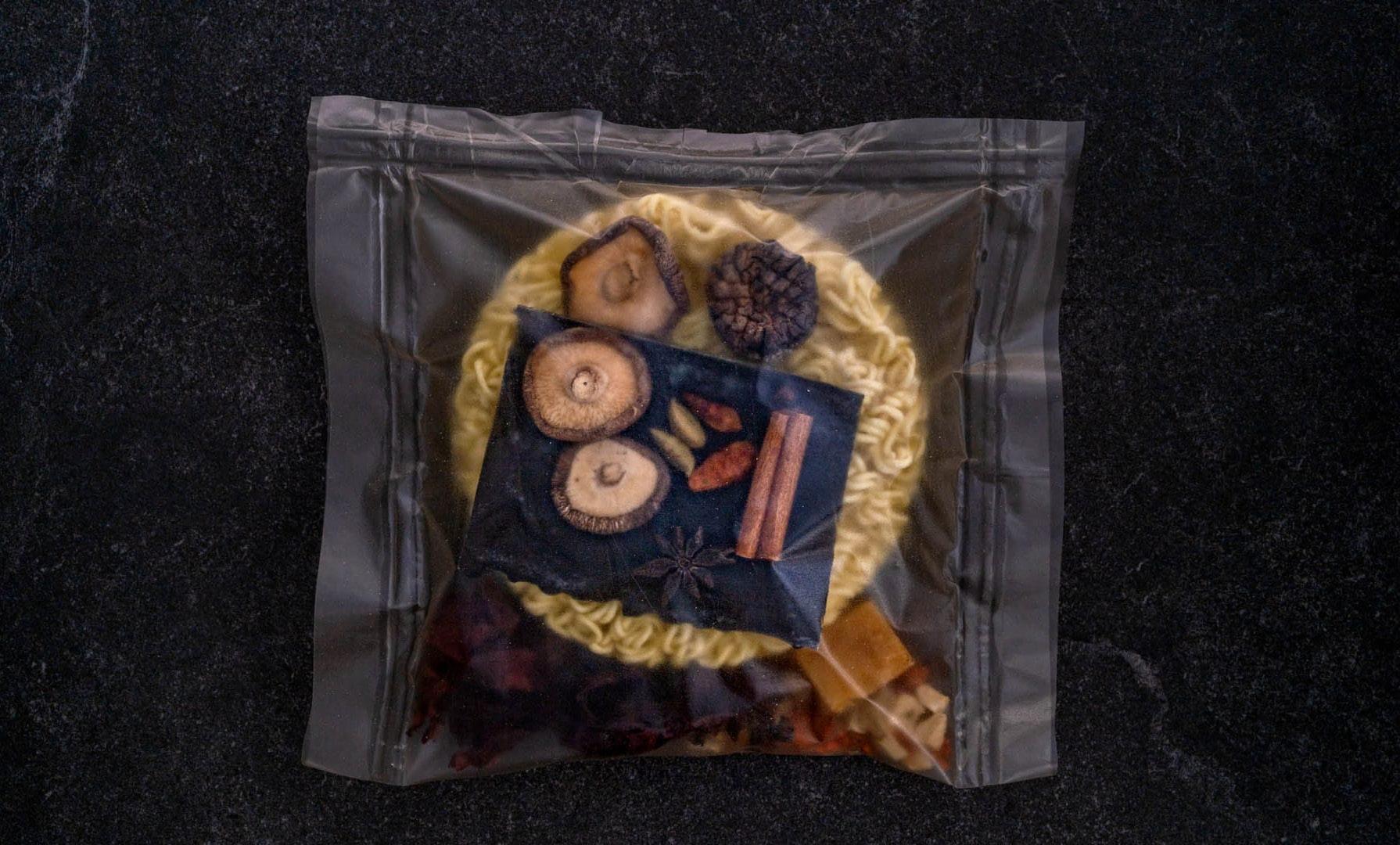
trends, align them with the brand’s identity and target group, and combine them in unexpected ways to create customised trend scenarios, which serve as a strategic framework.”
By thinking across three time horizons, MILK. covers the full spectrum of innovation, from quickwin solutions implementable within the next two years to speculative product visions looking ahead to 2040.
To implement this vision and endless creativity further, MILK.’s goal is to establish more partnerships across Europe and be a significant driver of the transformation the entire industry faces.
“We ultimately want to expand the work of the Innovation Lab and convince even more conservative clients that sustainability and innovation are key to being successful in the food business,” Eisath confidently concludes.
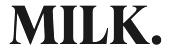
Tel: 49 (0) 69 8008717 0
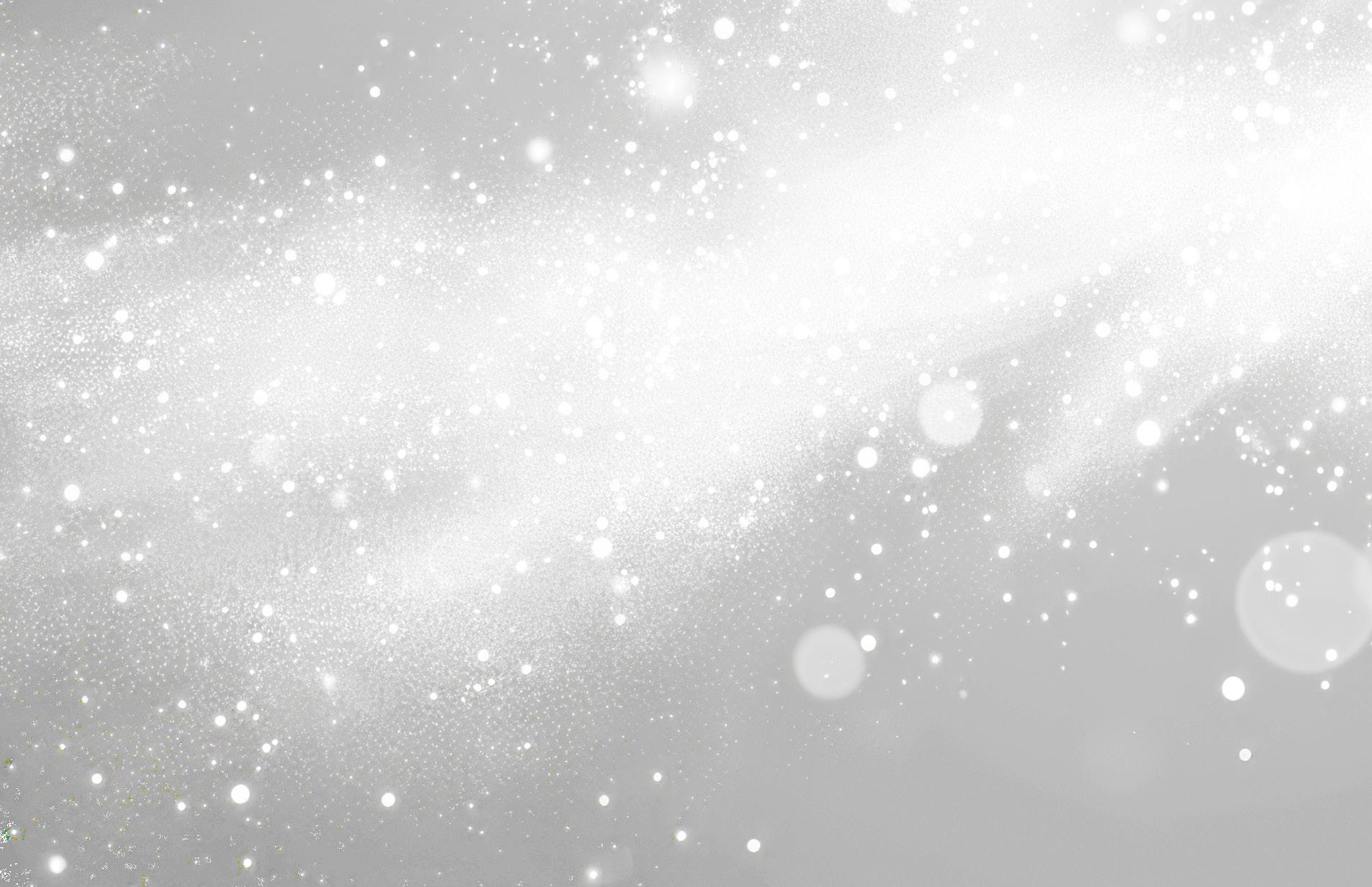
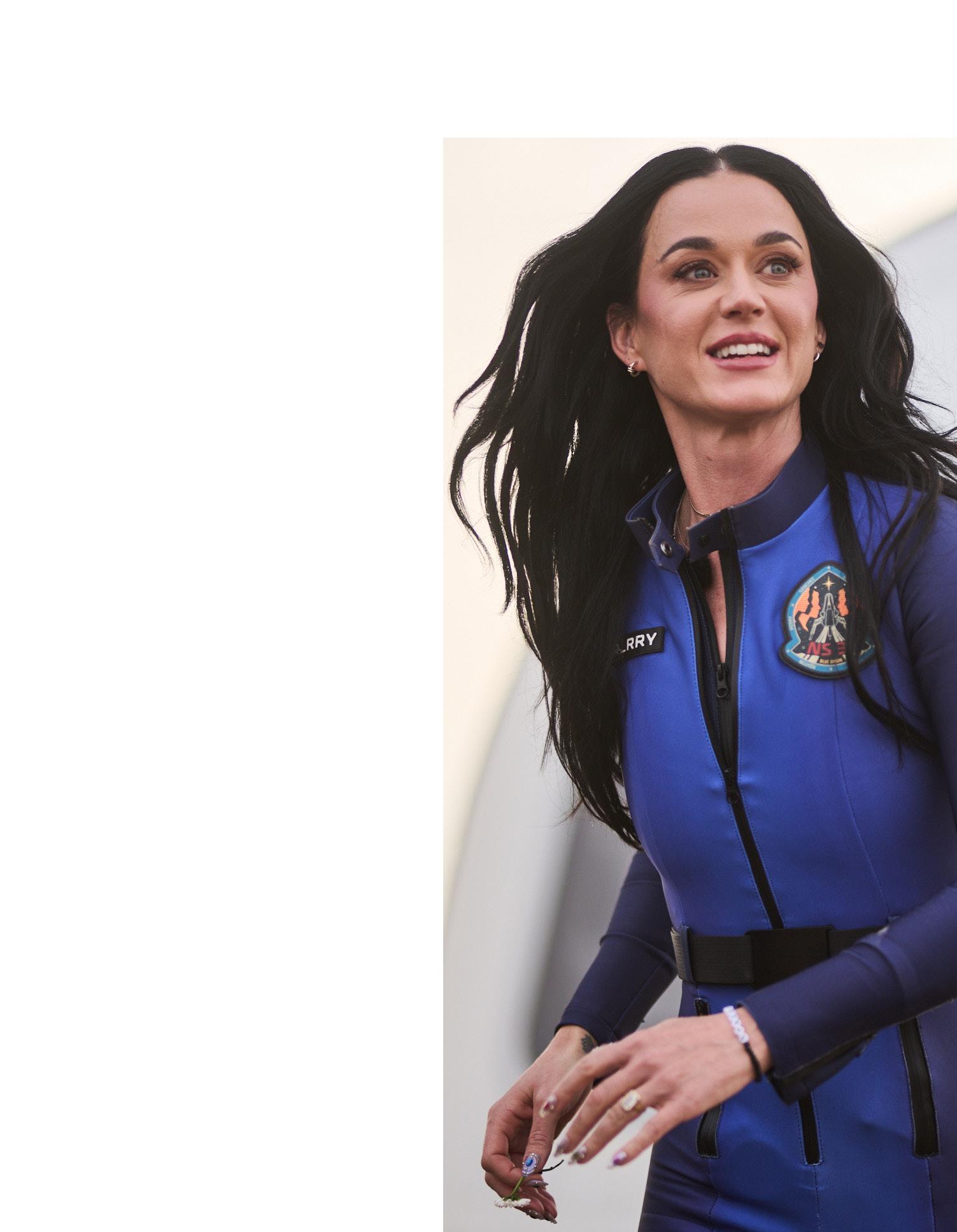
SPACE SPACE
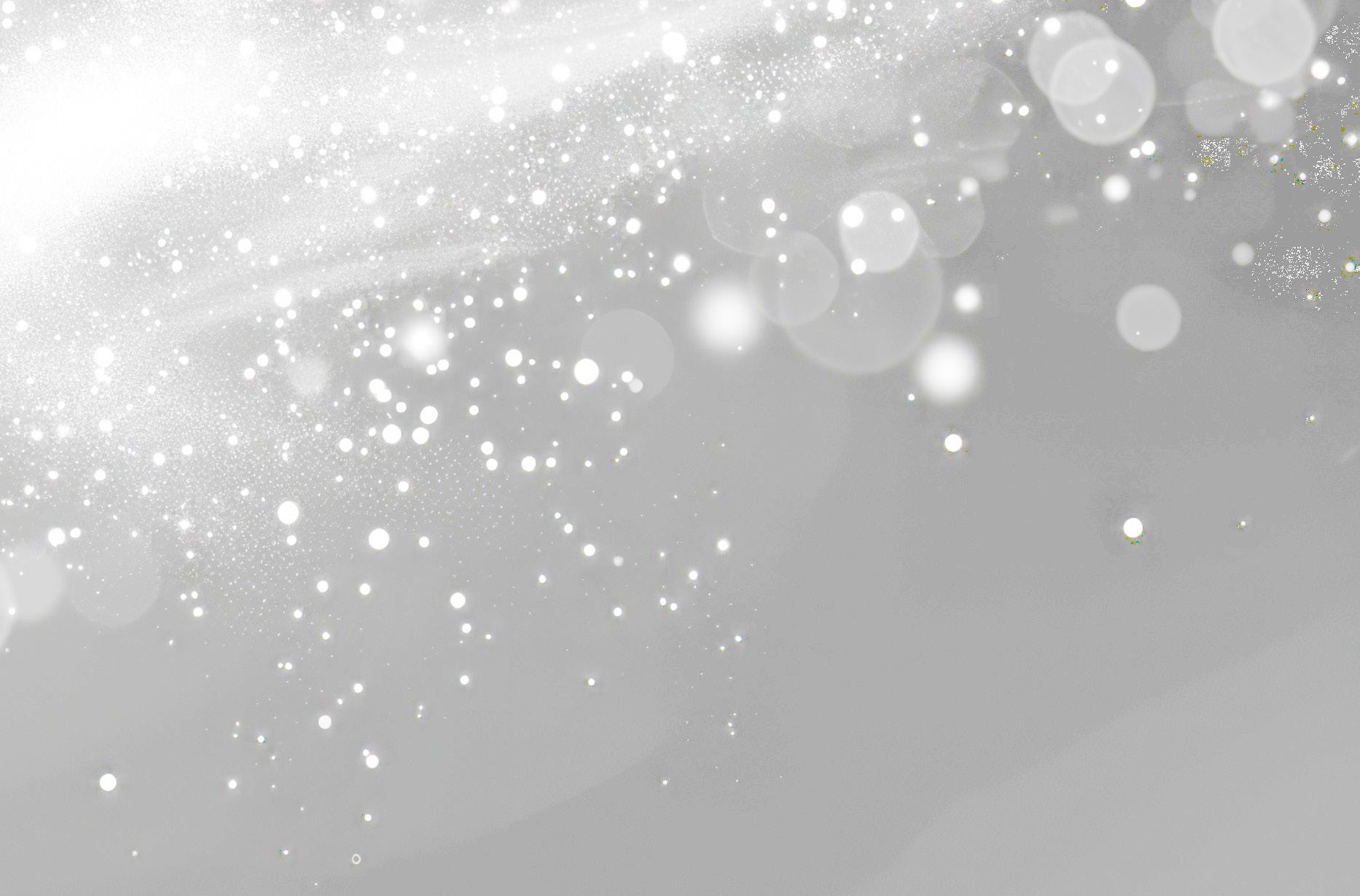
GIRLS GIRLS
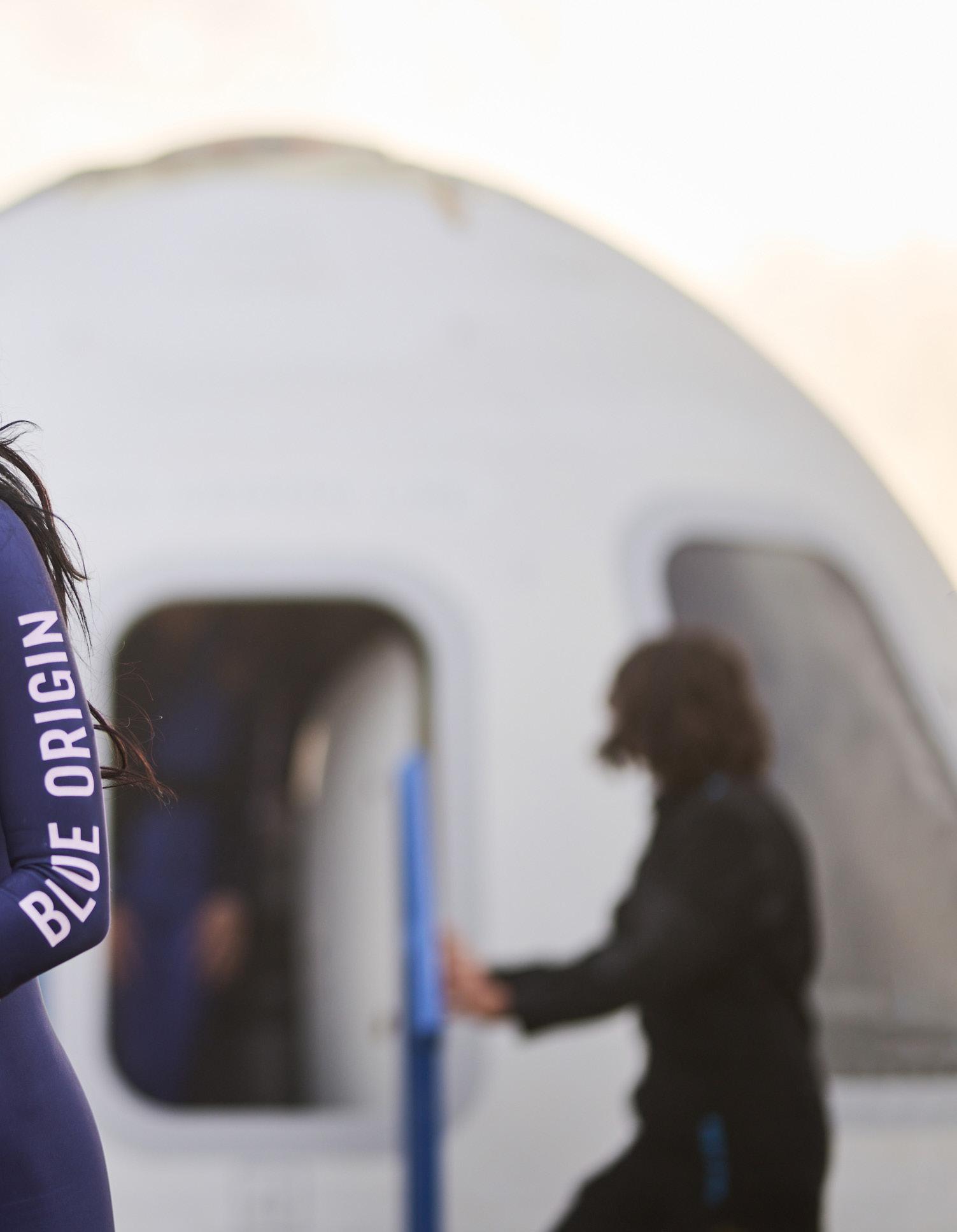
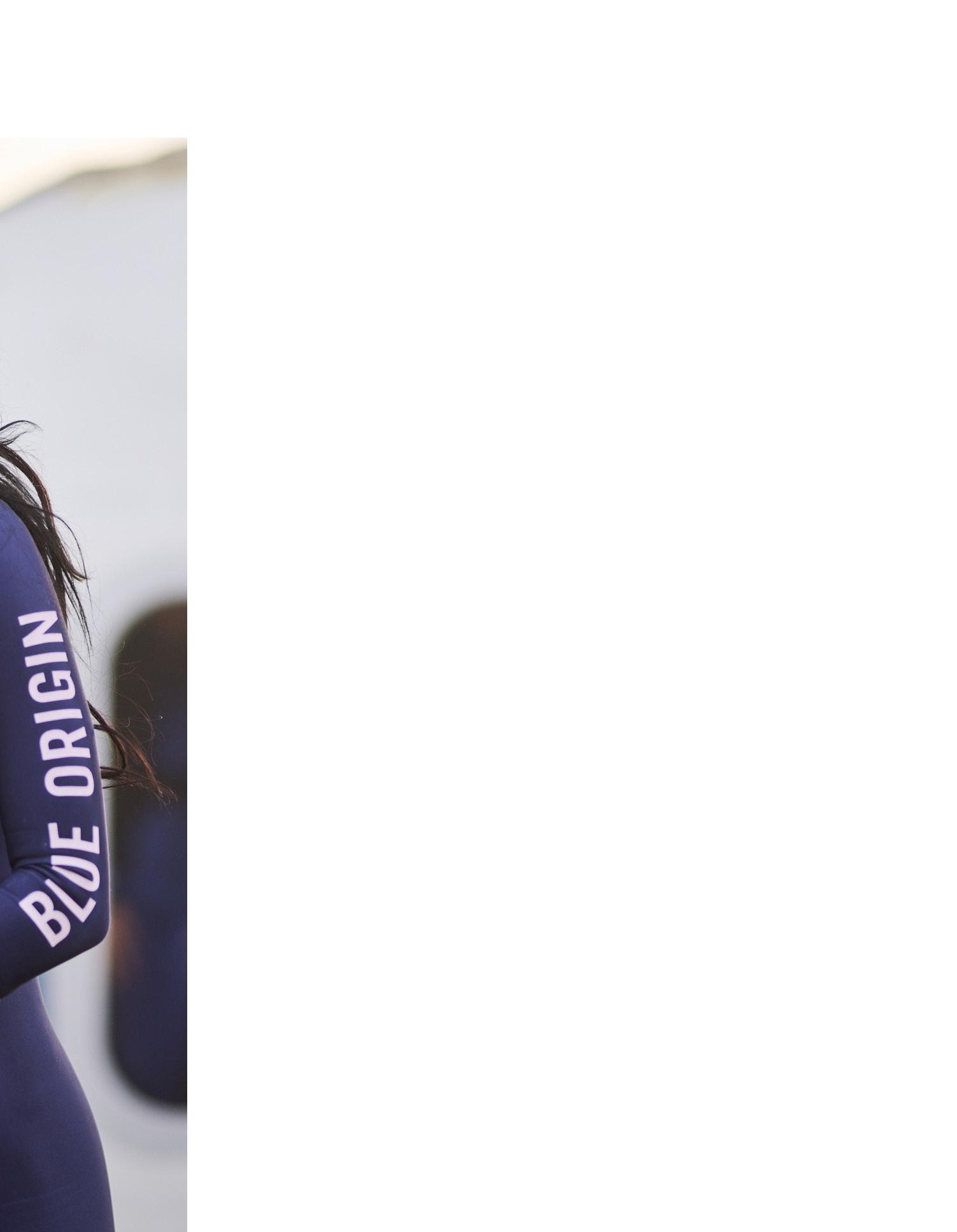
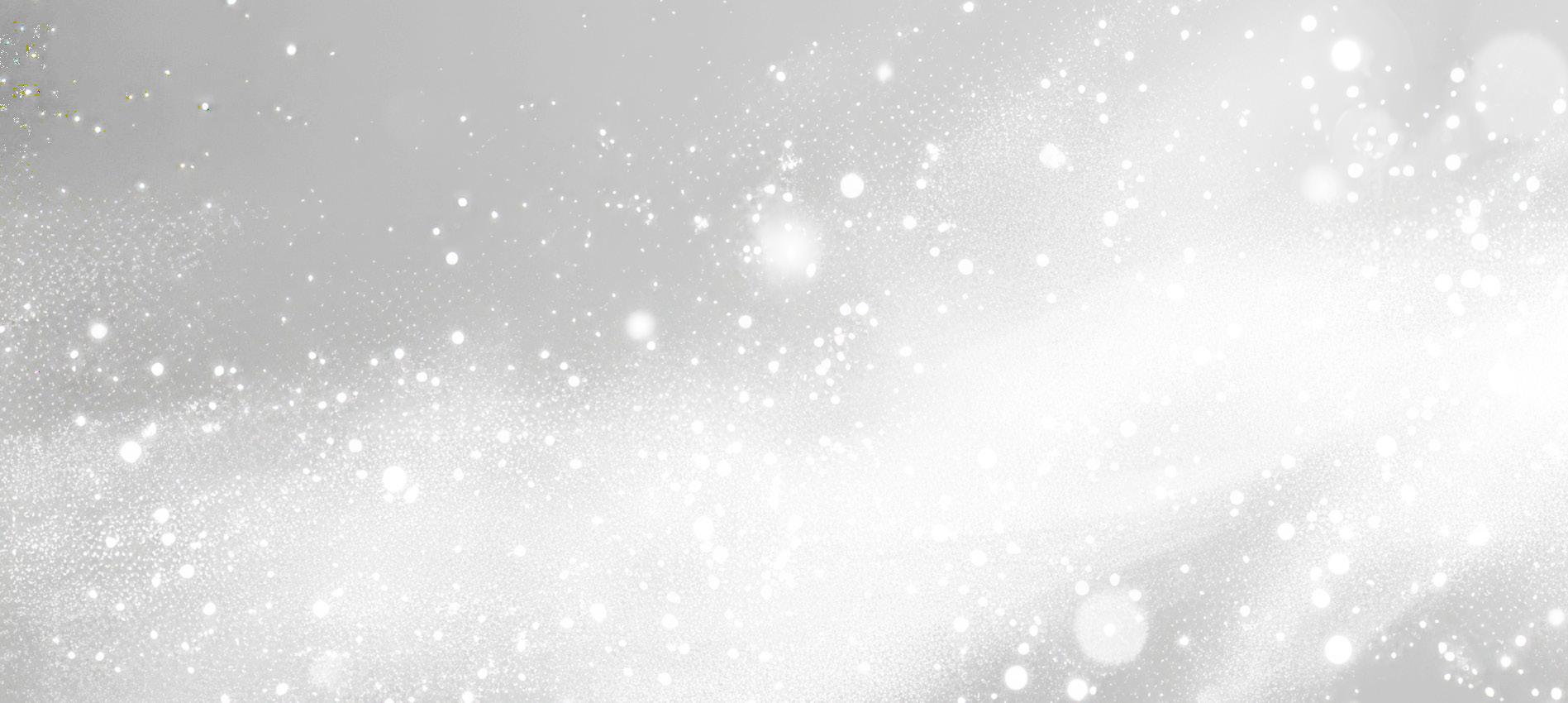
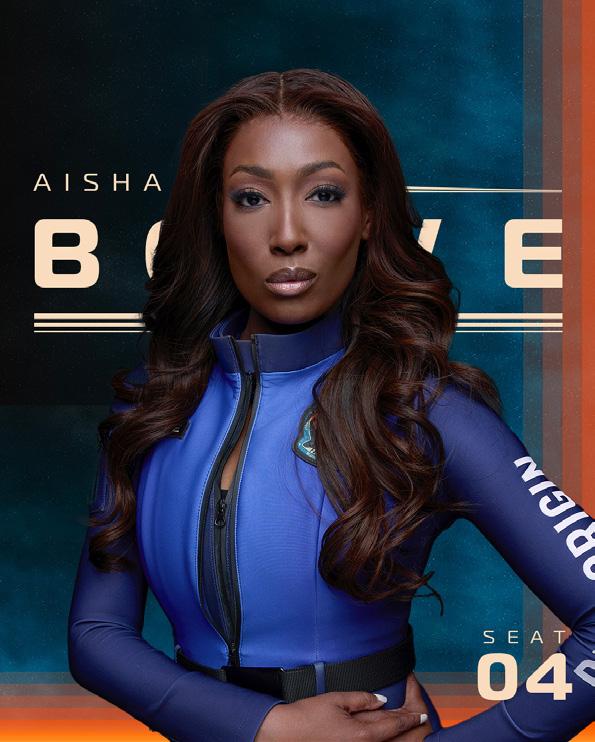
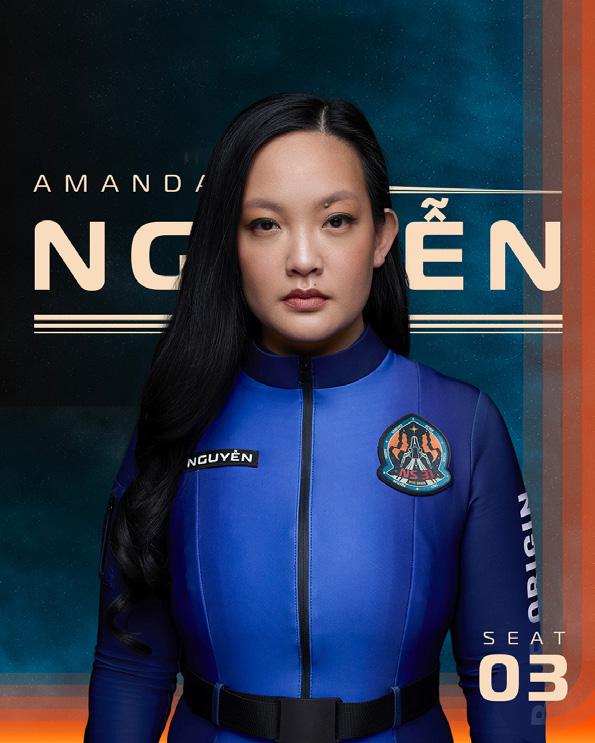
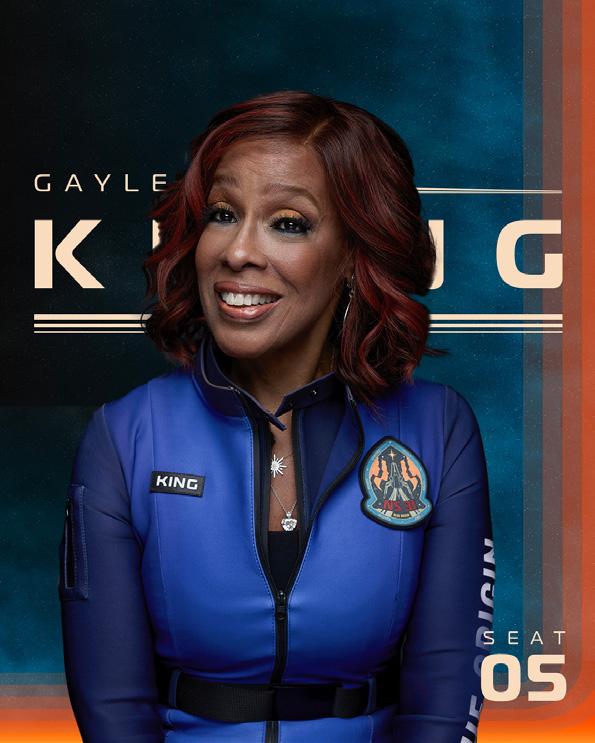
MEET THE NS-31 MISSION CREW
Aisha Bowe – A former NASA rocket scientist, entrepreneur, and global STEM advocate, Aisha Bowe is the CEO of engineering firm STEMBoard and Founder of EdTech company, LINGO. She became the first person of Bahamian descent to visit space as part of the mission.
Amanda Nguyễn – Bioastronautics research scientiest Amanda Nguyễn graduated from Harvard University in 2013. As the first Vietnamese and Southeast Asian woman astronaut, her flight was a symbol of reconciliation between the US and Vietnam and highlighted science as a tool for peace.
Gayle King – Award-winning journalist Gayle King is recognised as a gifted, compassionate interviewer capable of breaking through the noise and creating meaningful conversations. She is a co-host of CBS Mornings, editor-at-large of Oprah Daily, and host of Gayle King in the House on SiriusXM radio.
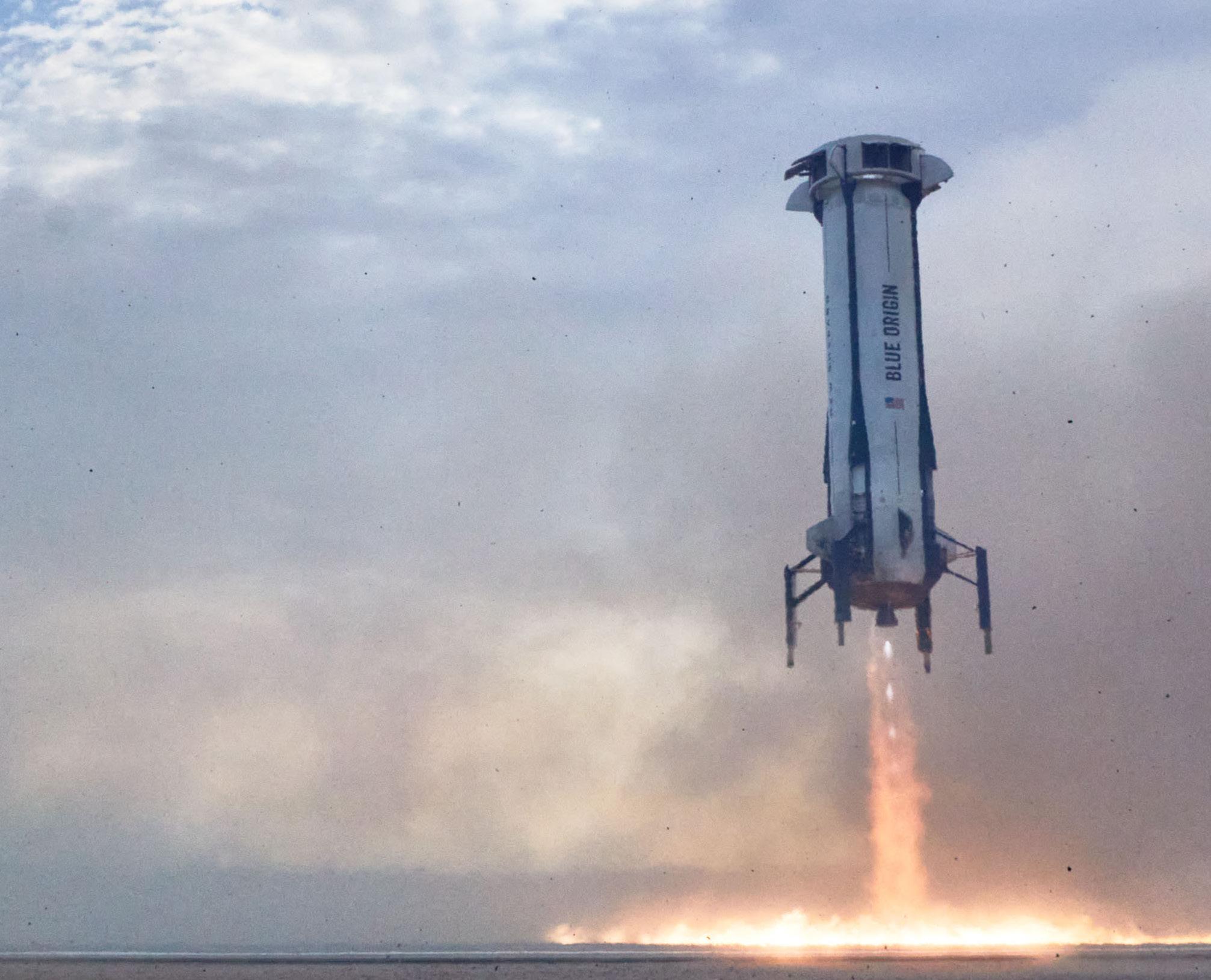
Katy Perry – The biggest-selling female artist in Capitol Records’ history and one of the best-selling music artists of all time with over 115 billion streams, Katy Perry is a global pop superstar.
Kerianne Flynn – Following a successful fashion and HR career, Kerianne Flynn has spent the last decade channelling her energy into community-building. She is passionate about the transformative power of storytelling and has produced thoughtprovoking films such as This Changes Everything and Lilly.
Lauren Sánchez – Emmy award-winning journalist Lauren Sánchez founded Black Ops Aviation, the first female-owned and operated aerial film and production company, in 2016.
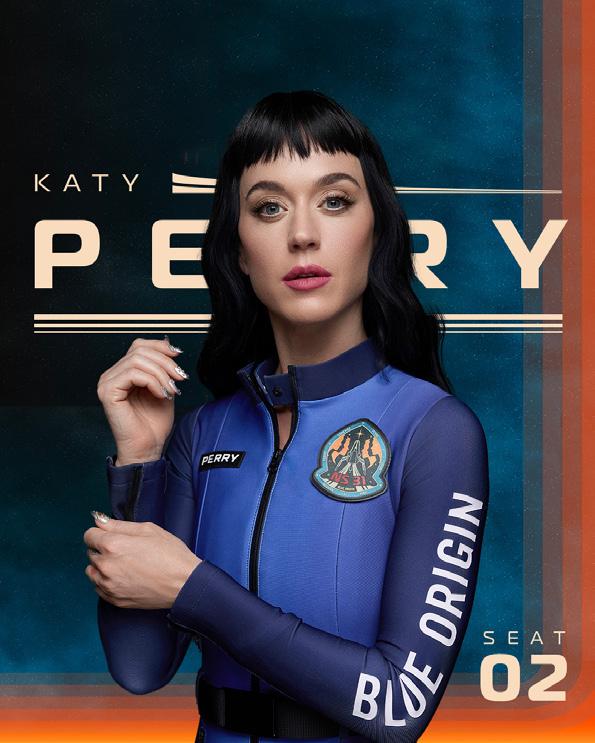
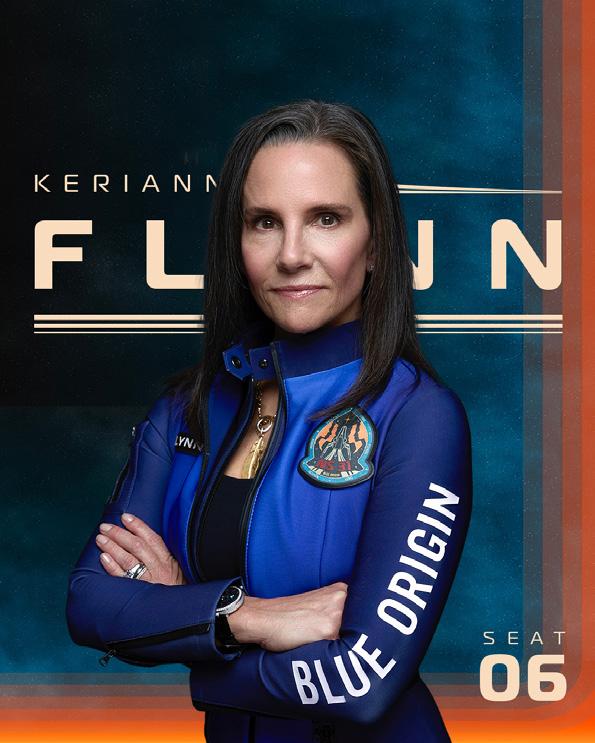
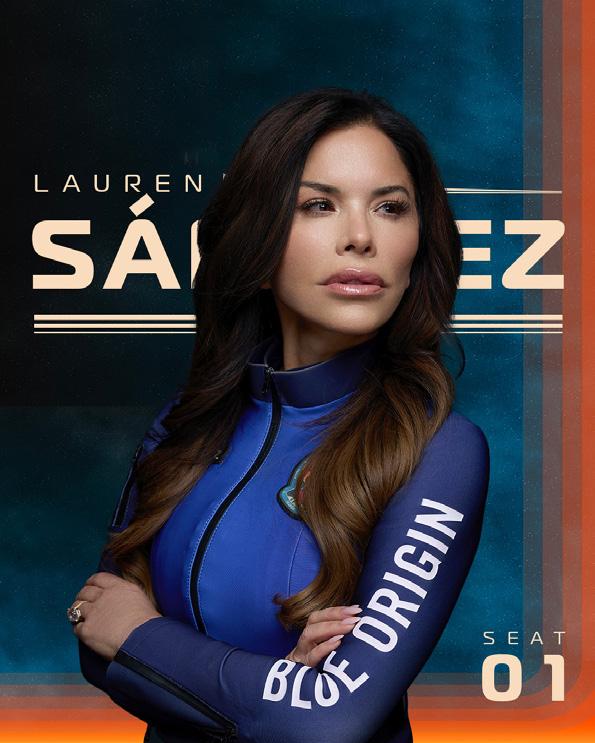
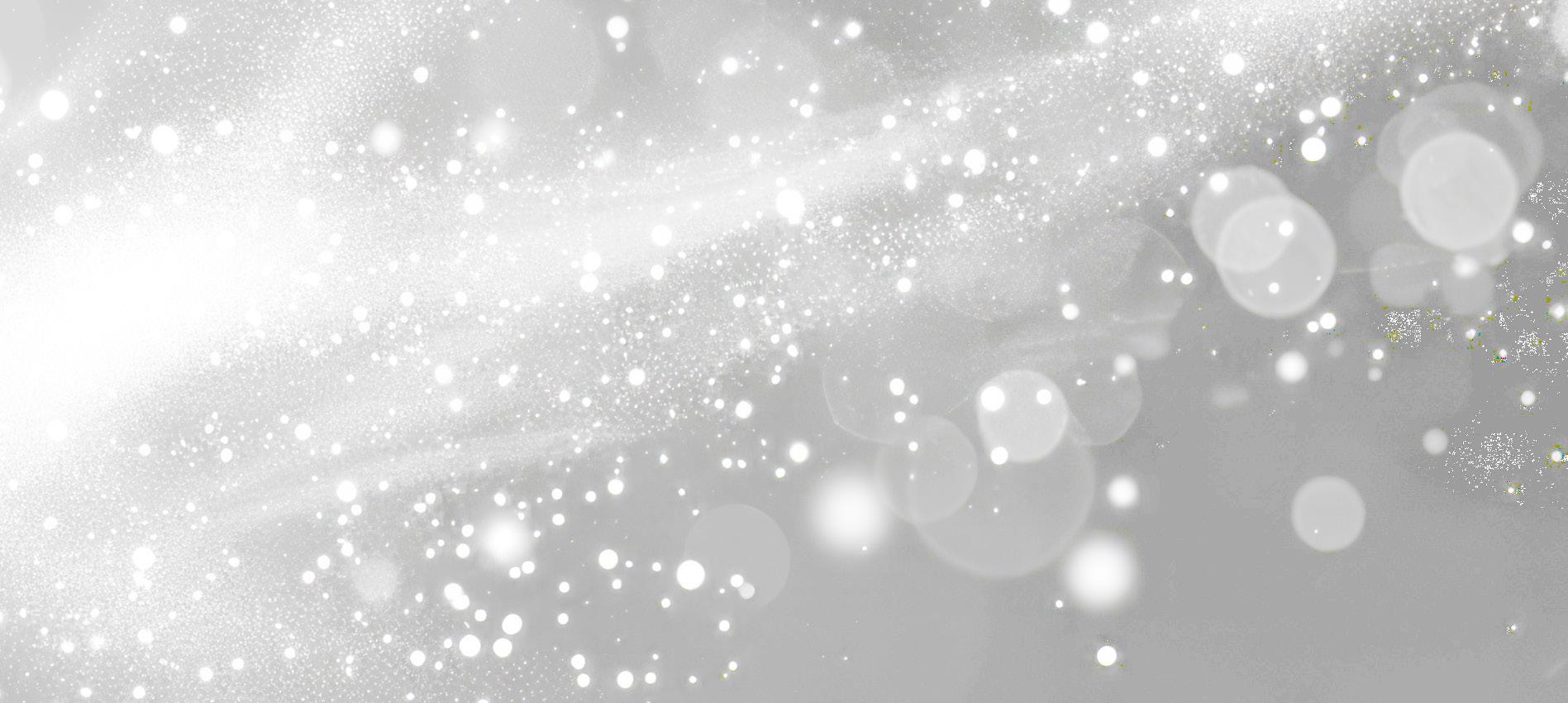
The vehicle features a vertical takeoff and landing architecture, enabling booster reuse up to 25 times with minimal refurbishment.
Its reusable, throttleable, and liquidpropellant BE-3PM engine, meanwhile, is fuelled by highly efficient liquid oxygen and hydrogen.
During flight, the only byproduct of New Shepard’s engine combustion is water vapour, with no carbon emissions emitted.
The rocket system has also been designed to ensure minimal maintenance between flights, lowering the cost of access to space and reducing waste.
LADIES HAVE LIFT-OFF
On the 11-minute journey, New Shepard astronauts ascend towards space from Launch Site One, nestled in the Guadalupe Mountains near Van Horn, Texas.
At more than three times the speed of sound, they soar past the Kármán line – the internationally-recognised boundary of space – before unbuckling to experience several minutes of weightlessness and enjoy breathtaking views of Earth.
Though the vehicle is fully
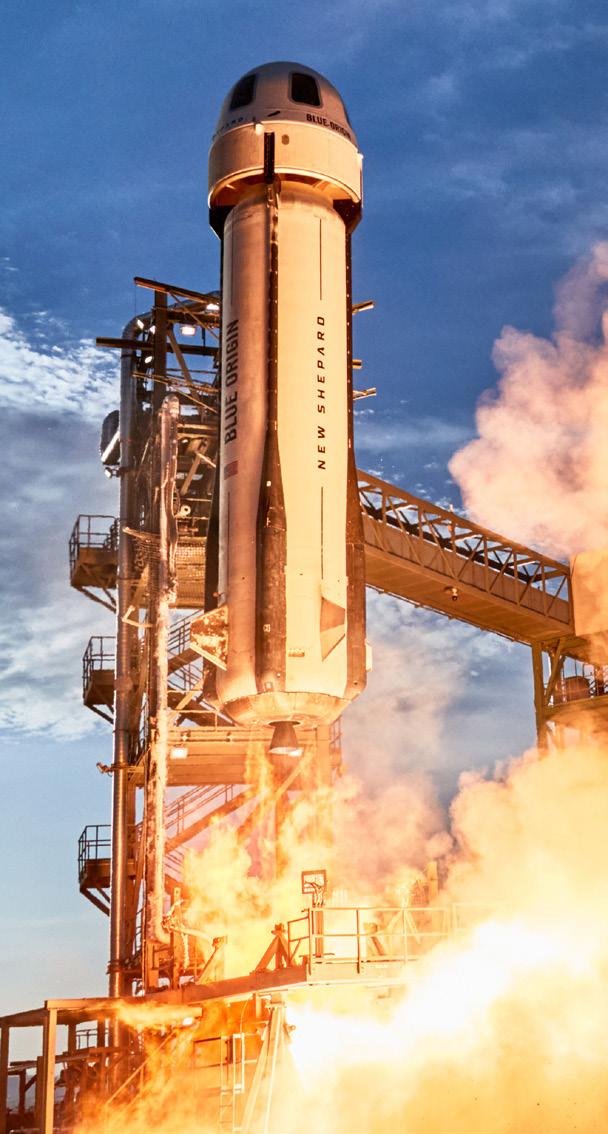
autonomous, meaning there are no pilots, New Shepard’s pressurised crew capsule has enough room for six people and is environmentally controlled for comfort.
In this spacious capsule, each
astronaut gazes upon the planet from their own giant windows, among the largest to have ever flown in space, which comprise one third of the capsule’s surface area.
Uniquely, on the NS-31 mission, the six astronauts – Aisha Bowe, Amanda Nguyễn, Gayle King, Katy Perry, Kerianne Flynn, and Lauren Sánchez – were all women, heralding the first all-female spaceflight since Valentina Tereshkova became the first woman in space in 1963.
The mission challenged their perspectives of Earth, empowered them to share their own stories, and created lasting impact that will inspire generations to come.
PRIORITISING SAFETY
New Shepard began flying humans in 2021 following the conclusion of a rigorous flight test programme.
This included several successful flight and capsule escape tests, demonstrating that the crew escape system, which separates the capsule from the booster in the unlikely event an issue is detected, can safely activate during any phase of the flight – whether from the launch pad, midflight, or in the vacuum of space.
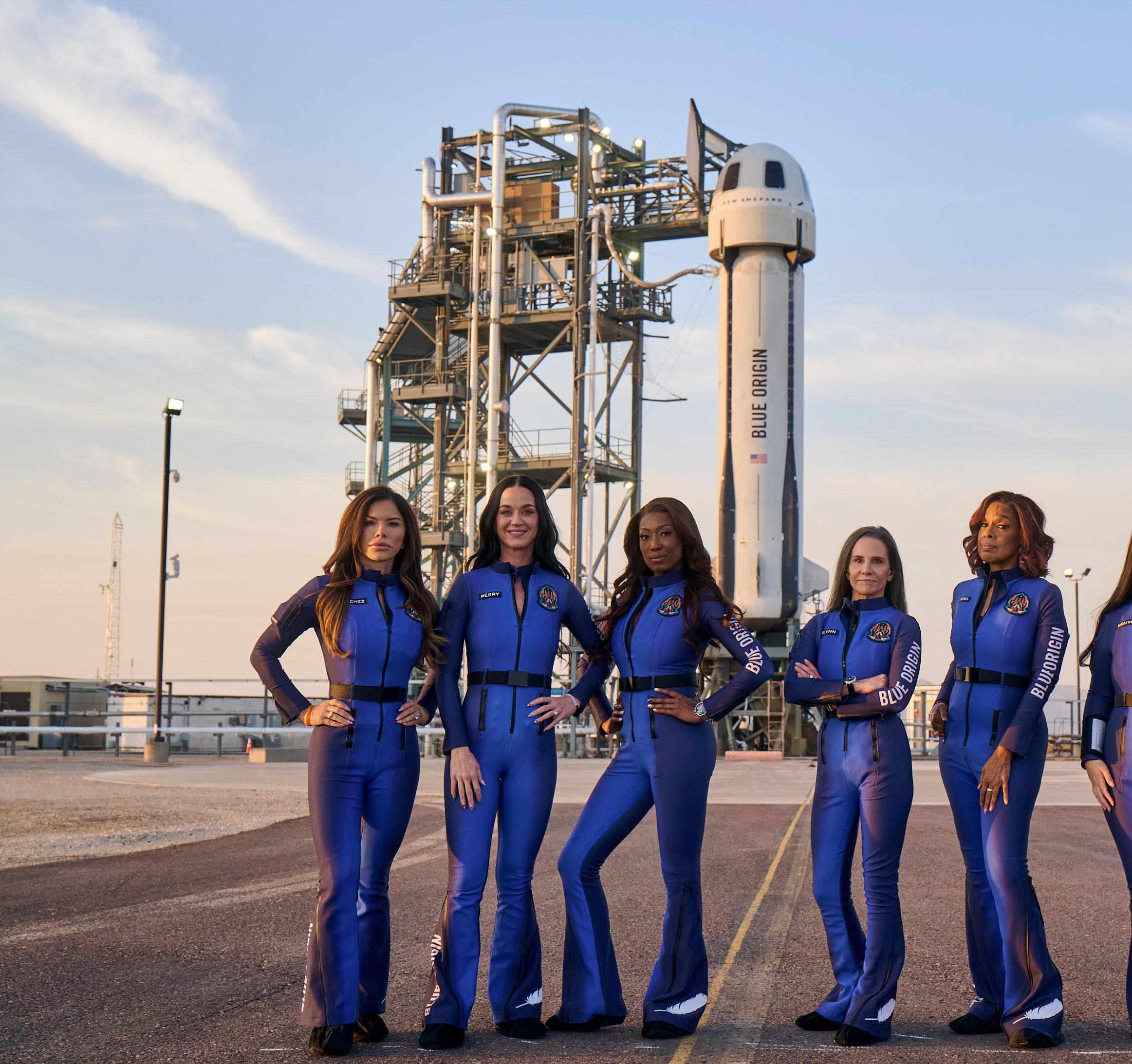
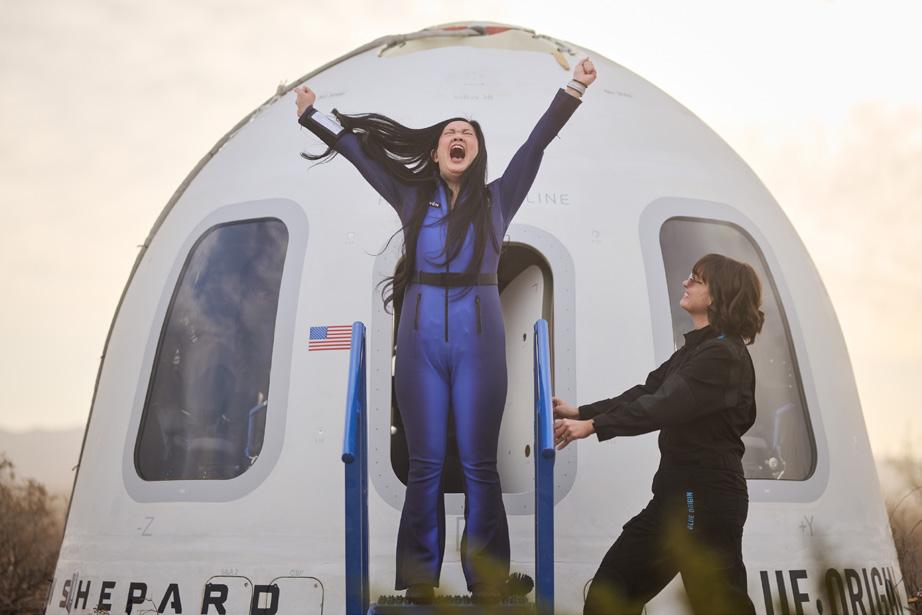
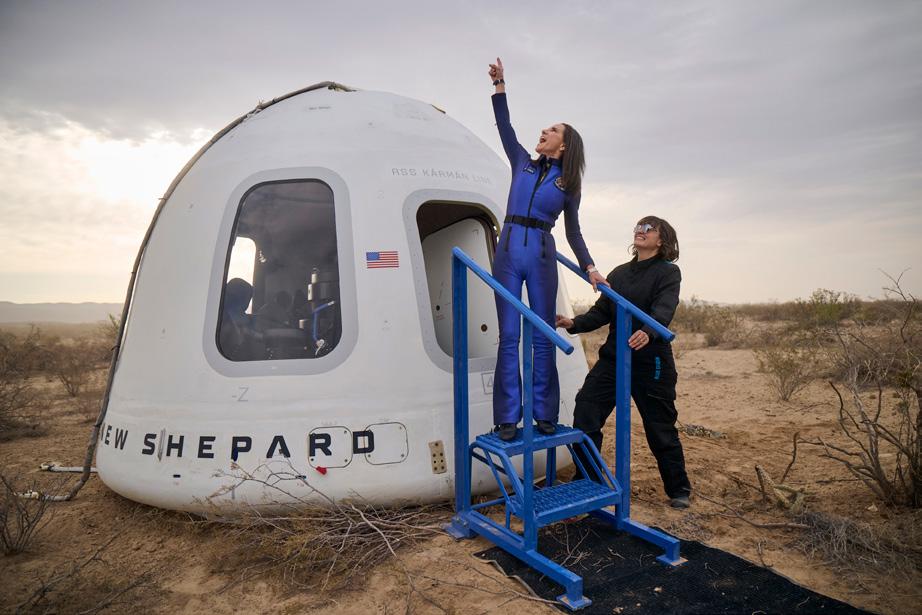
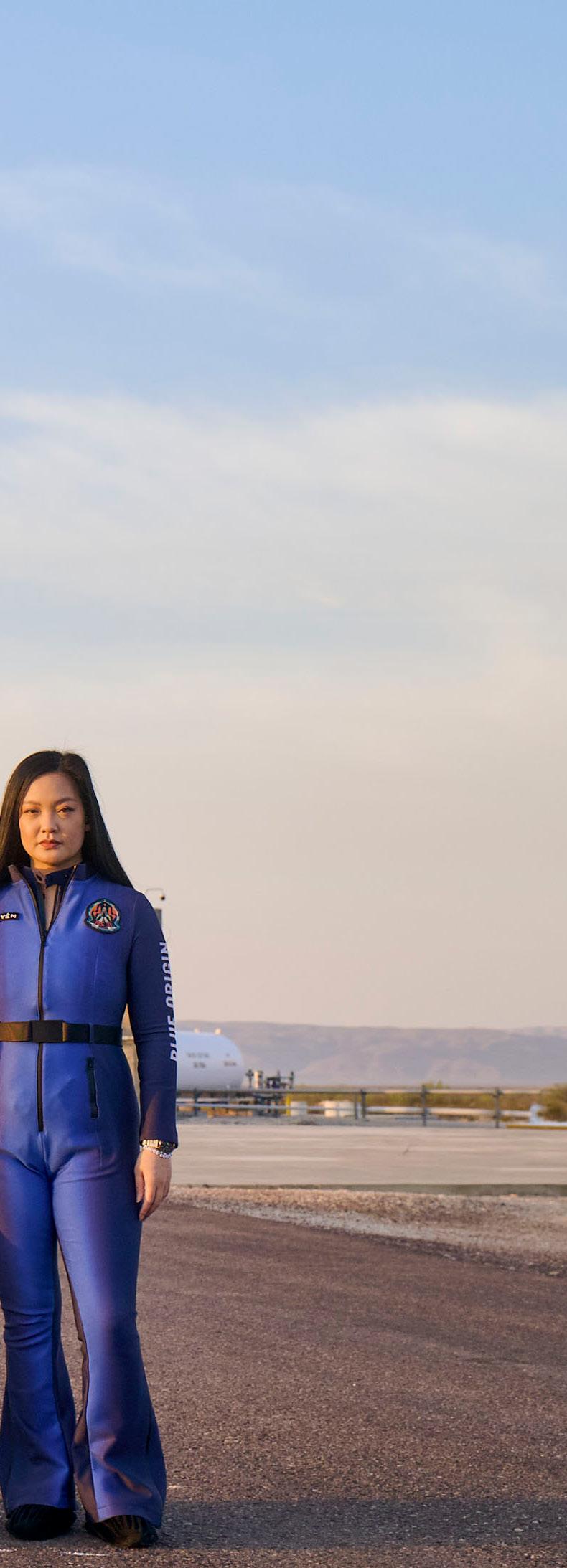
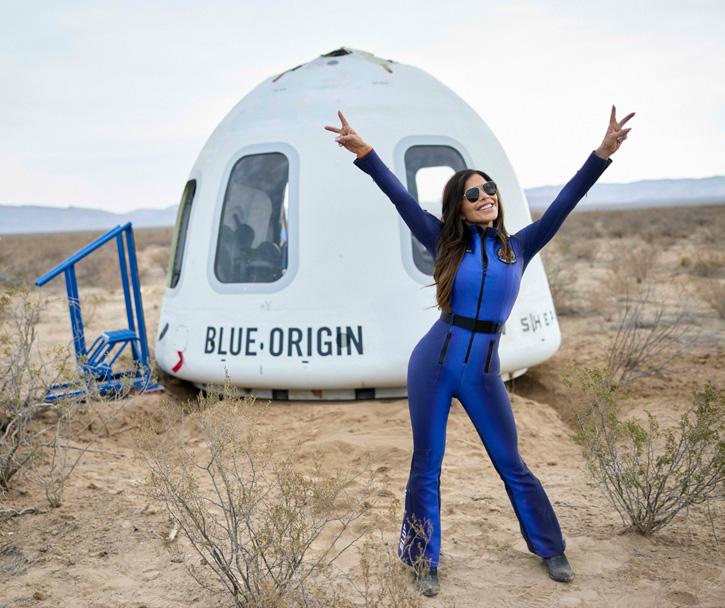
NS-31 MISSION PATCH – KEY SYMBOLS
• Target star – Aisha Bowe’s ambition for setting big goals, passion for STEM, and commitment to inspiring future generations.
• Scales of justice – Amanda Nguyễn’s efforts to advocate for civil rights, break barriers, and empower everyday people to create change.
• Shooting star microphone – Gayle King’s commitment to sharing important stories with the world.
• Firework – Katy Perry’s global influence across music, pop culture, and philanthropy.
• Film reel – Kerianne Flynn’s passion for filmmaking, storytelling, and crafting beautiful narratives.
• Flynn the Fly – The main character in Lauren Sánchez’s best-selling children’s book, The Fly Who Flew to Space.
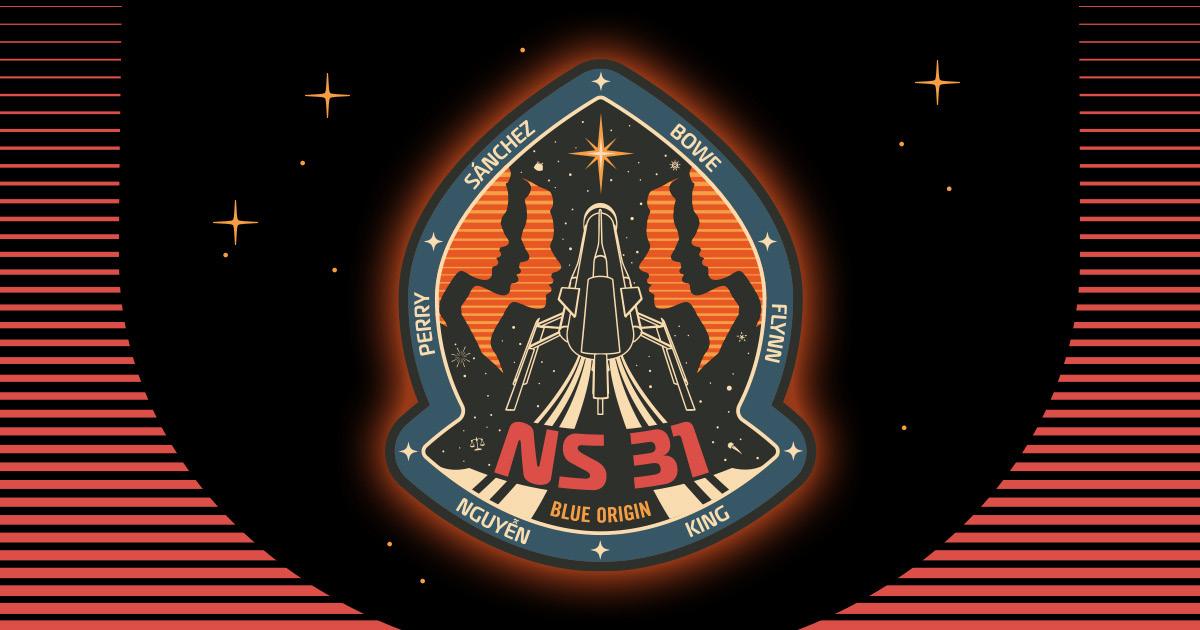
The crew capsule also has numerous redundant safety systems, including a retro-thrust system that expels a burst of nitrogen gas to slow the landing to around two miles per hour.
Additionally, the capsule can land with only one of its three parachutes deployed, whilst the seats and a crushable ring on the bottom of the capsule are designed to absorb g-forces.
Blue Origin’s on-site training programme is also meticulously designed to teach astronauts everything they need to know for a safe spaceflight onboard New Shepard, from the mission profile
and safety systems to zero-gravity protocols.
These measures ensured the historic NS-31 mission was safely executed and created history with the first all-female spaceflight in over six decades.
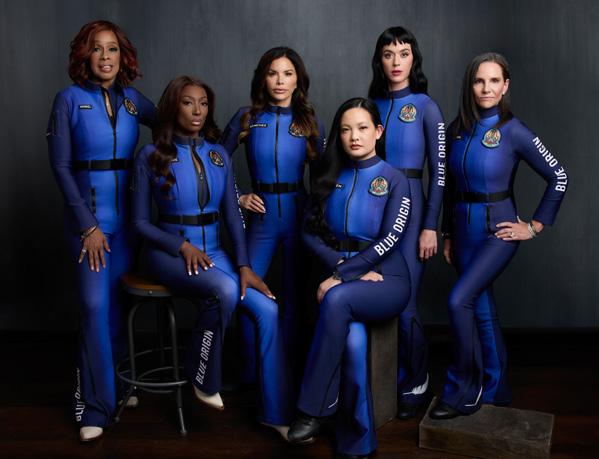
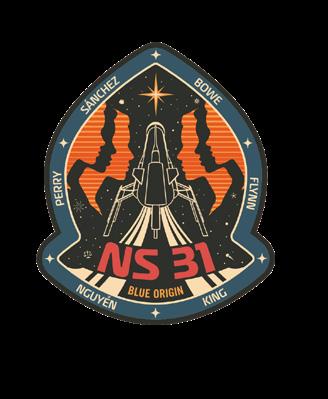
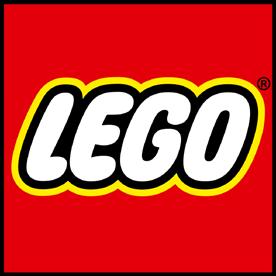
In a breathtaking feat of design and engineering, the drivers’ parade at the recent Miami Grand Prix was taken over by fully driveable LEGO big build cars representing every team on the Formula 1 grid
Writer: Jack Salter
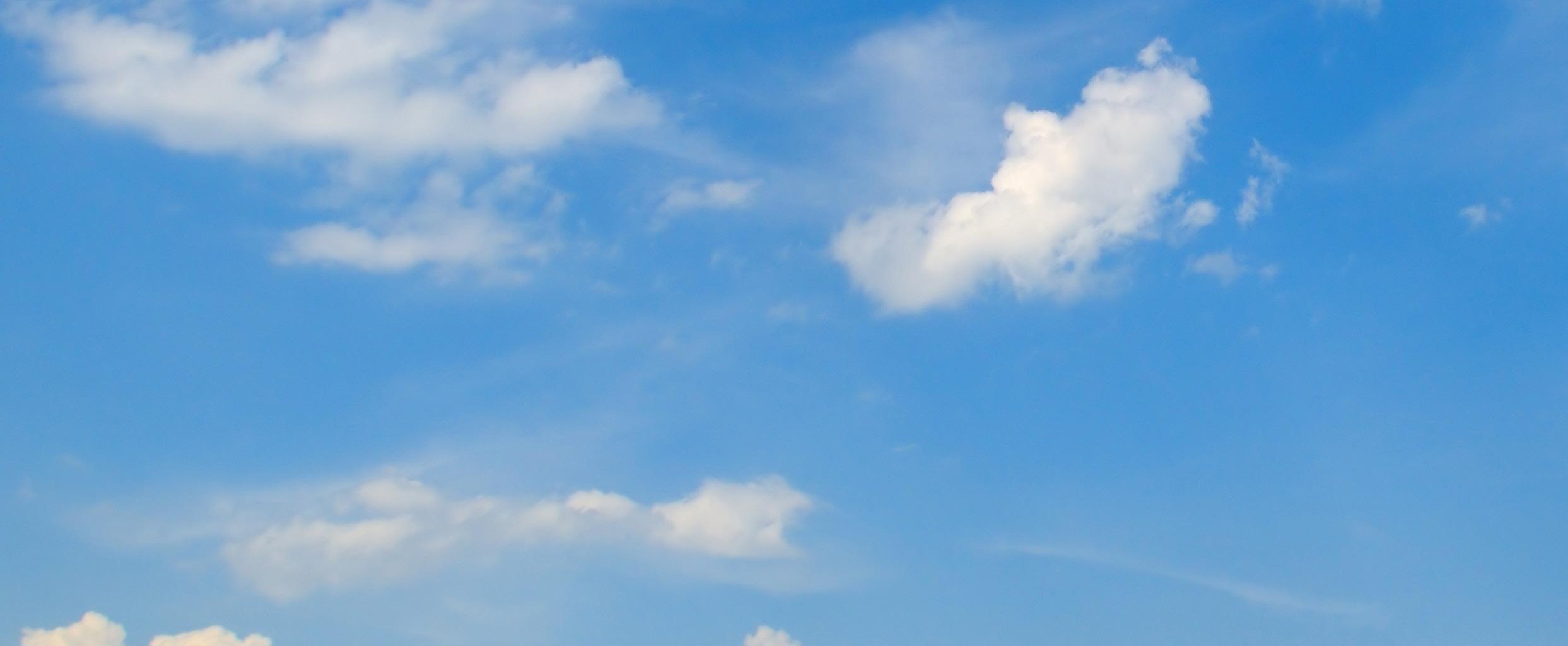
BUILD THE
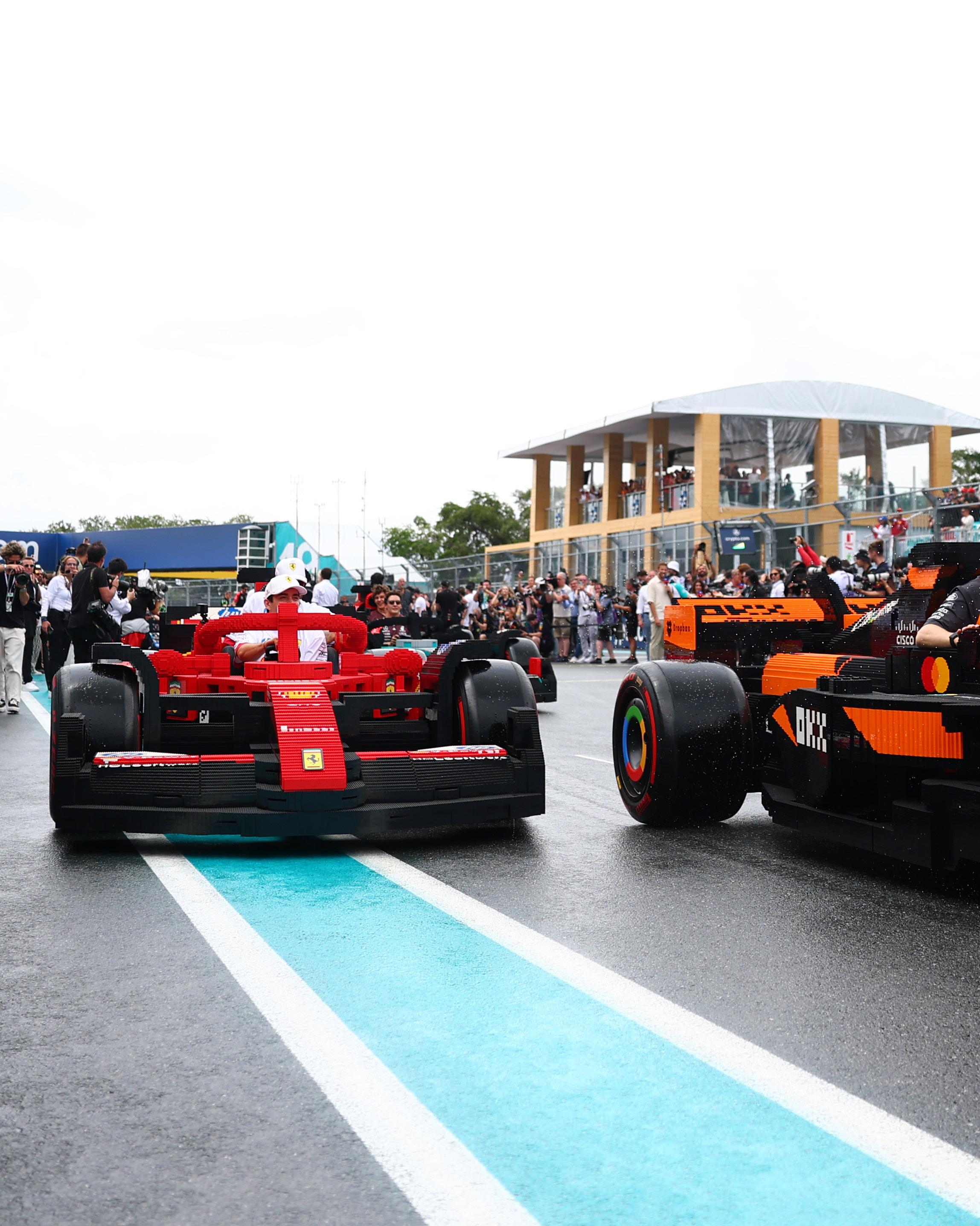
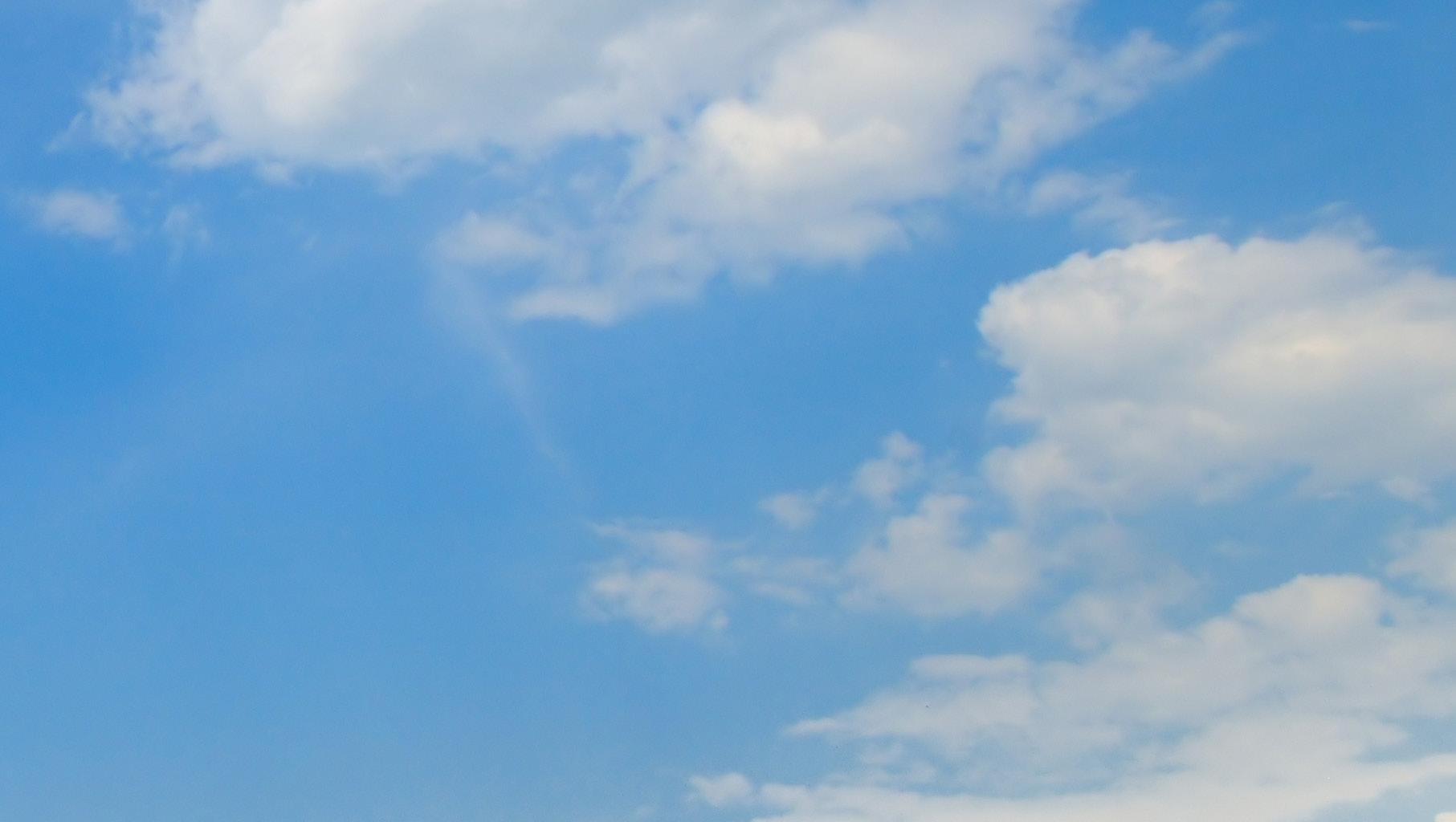
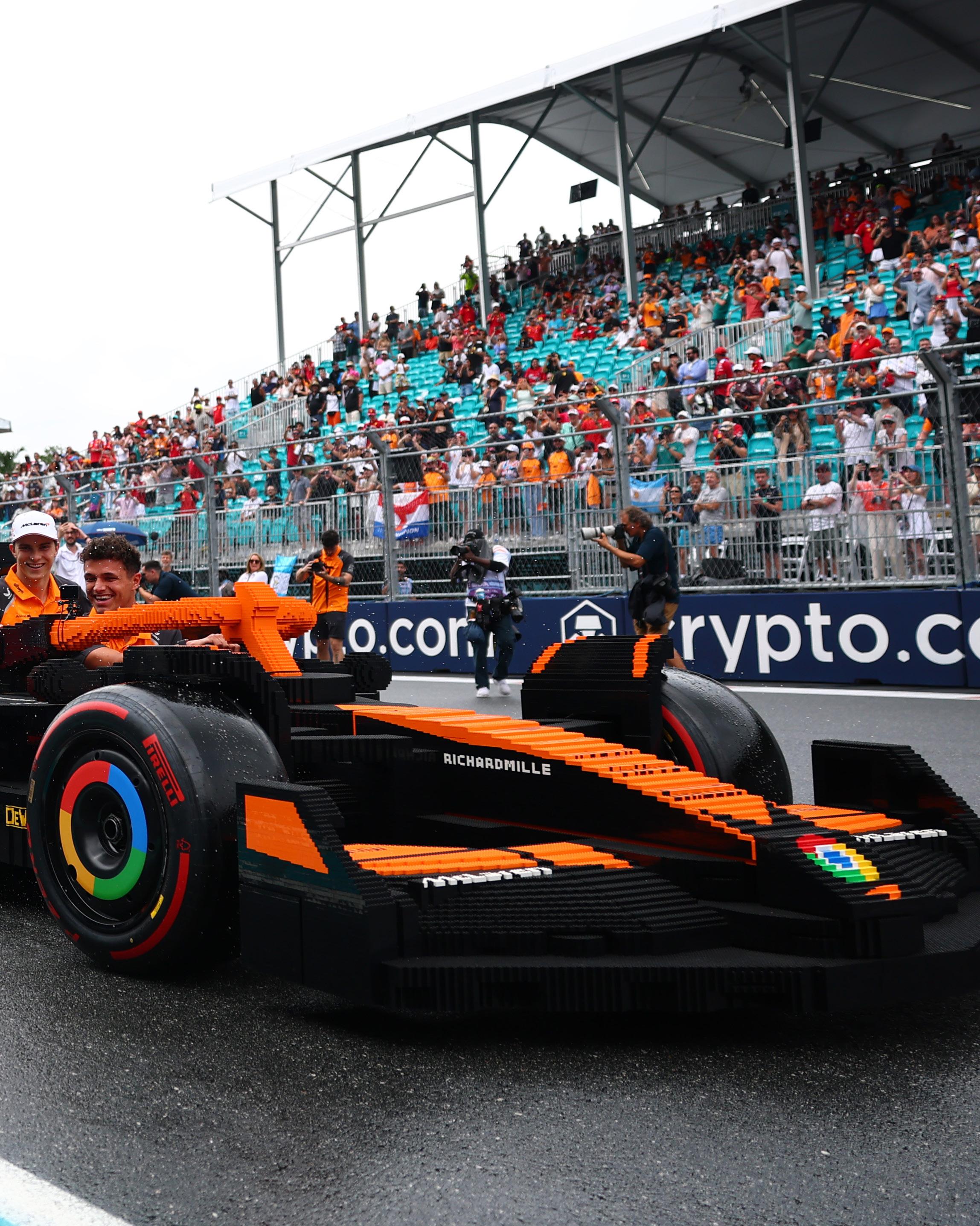
Ahead of the Miami Grand Prix, there was a fresh take on the Formula 1 (F1) drivers’ parade.
Rather than touring the track on the back of a truck, all 20 drivers had the chance to get behind the wheel of fully drivable LEGO big build cars, lapping the 5.4-kilometre Miami International Autodrome whilst waving to fans before the race.
Over 22,000 hours, a skilled team of 26 design, engineering, and building specialists from the LEGO Group created these incredible two-seater vehicles at its Kladno factory in Czechia, where the idea initially emerged, marking the first time multiple drivable big builds have been produced by the company at the same time.
The cars are based on the LEGO F1
DID YOU KNOW?
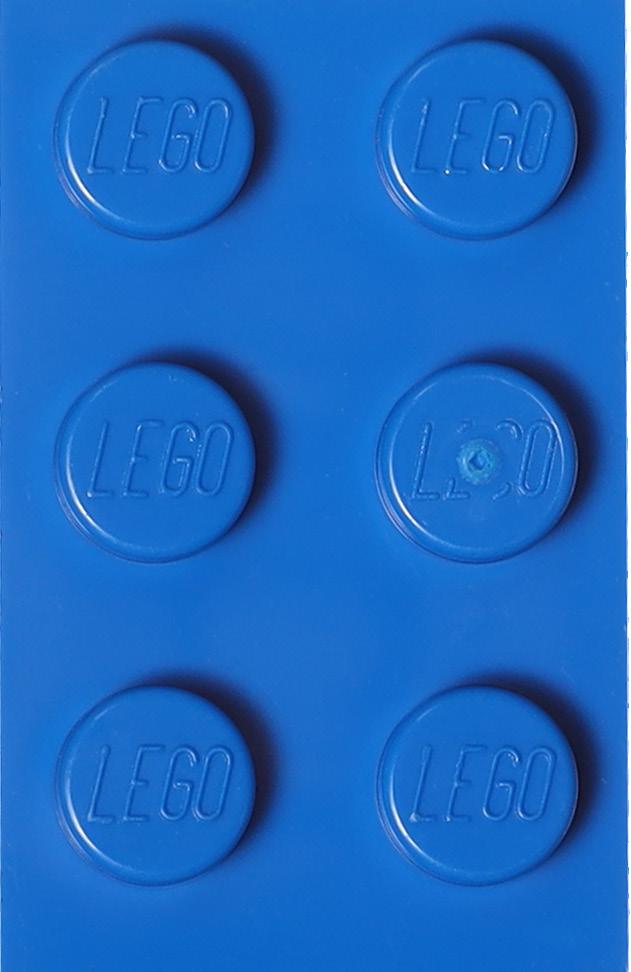
• The Miami Grand Prix is located 7,626km from the LEGO Group’s headquarters in Billund, Denmark – equating to 1,412 laps of the track.
• The inaugural Miami Grand Prix in 2022 coincided with the 90th anniversary of the LEGO Group, which was founded in 1932 by Ole Kirk Kristiansen.
• 40,000 LEGO bricks would be needed to cover the longest straight at the Miami International Autodrome, which stretches 1.28km.
Speed Champions range and bespoke to each team’s colours and liveries, capturing intricate and unique details such as sponsor logos, and even fitted with authentic Pirelli tires.
Each vehicle is made of nearly 400,000 LEGO bricks and able to reach speeds of 20 kilometres per hour (kph) – a fraction of the ~375kph top speeds that can be achieved by an actual F1 car, which the LEGO big builds are at a near 1:1 scale with.
However, the slower speeds didn’t stop stars such as Max Verstappen, Lewis Hamilton, and Lando Norris from racing – and humorously, crashing into – each other on the parade, to the amusement and excitement of fans and drivers alike as the track was littered with LEGO debris.
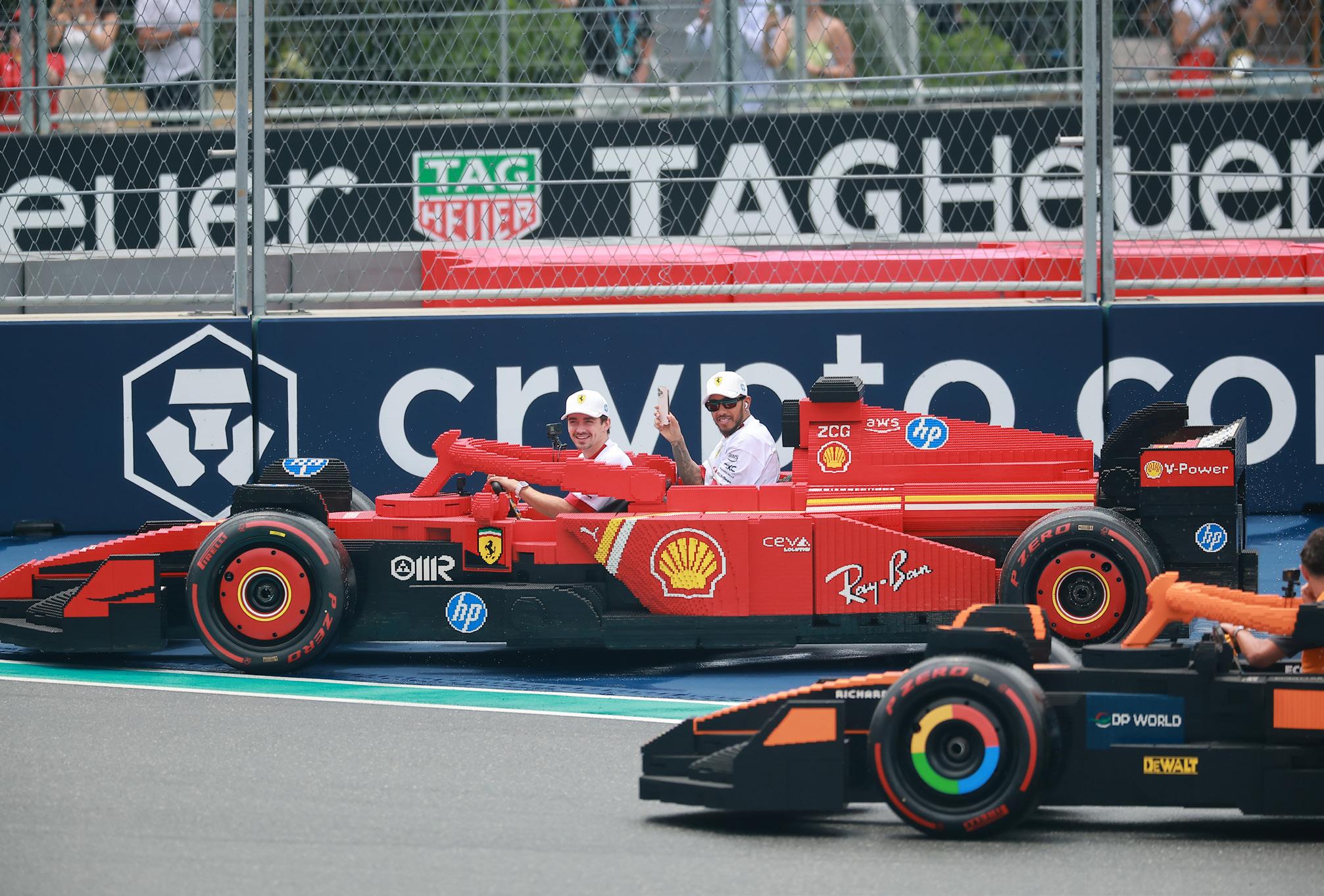
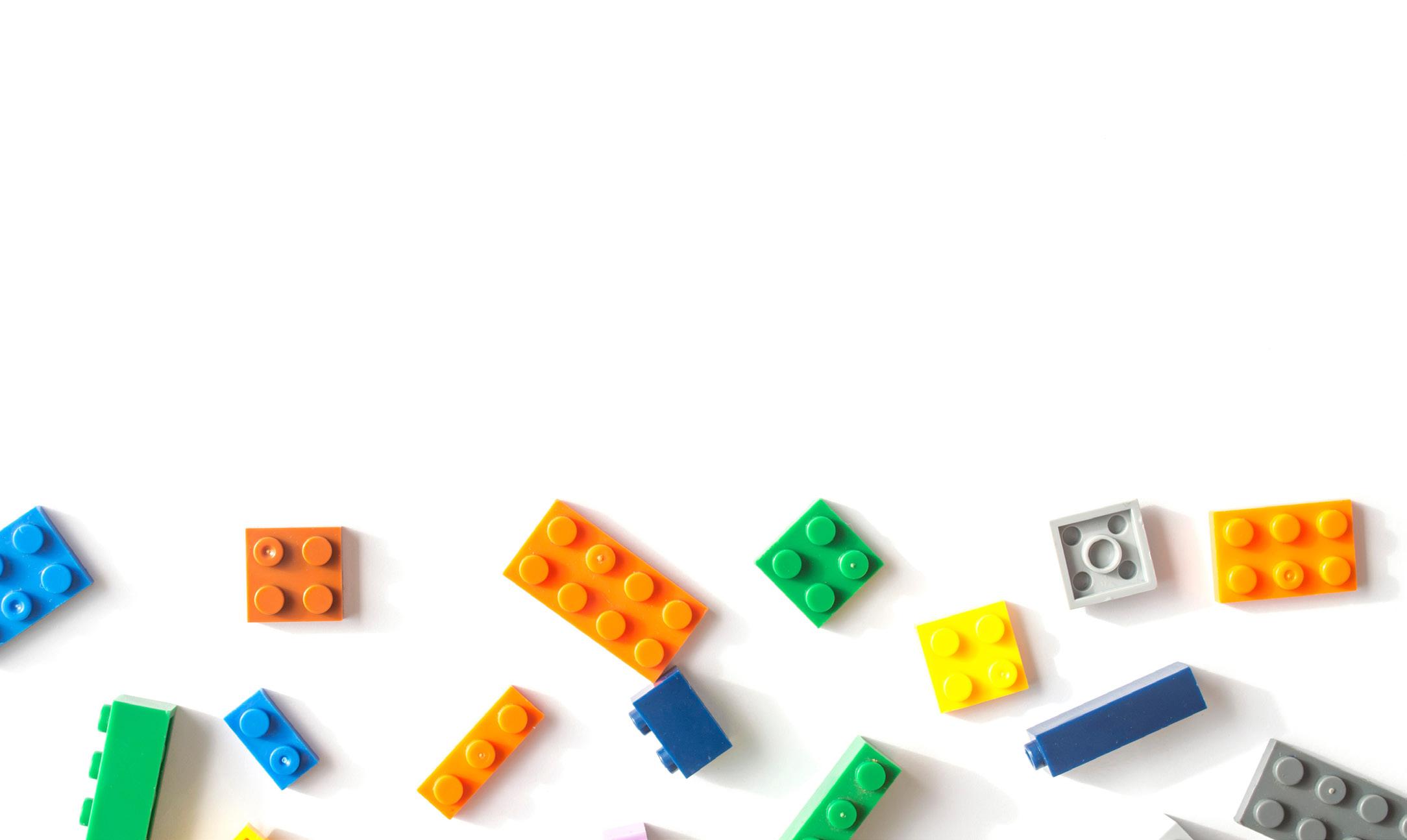
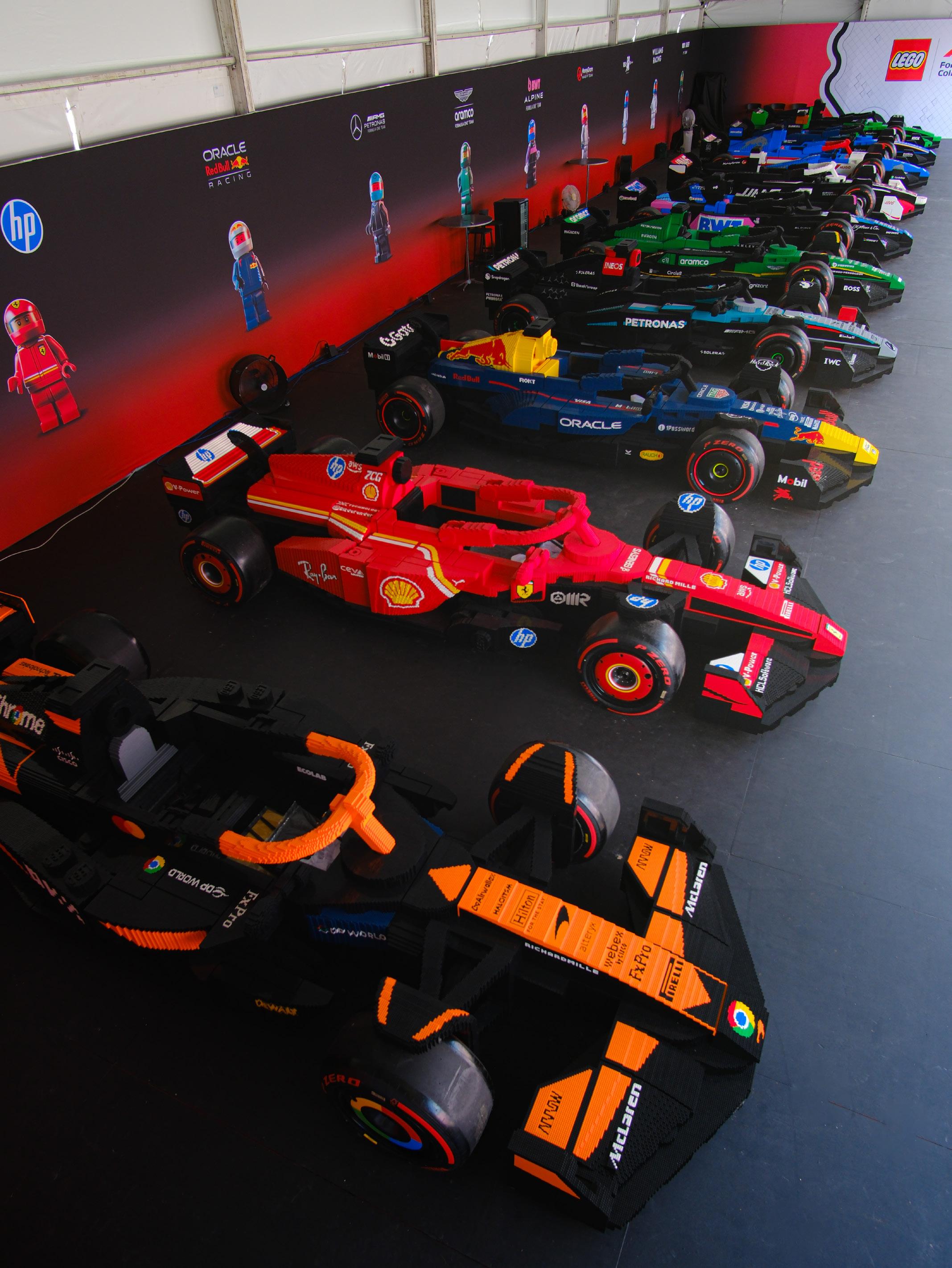
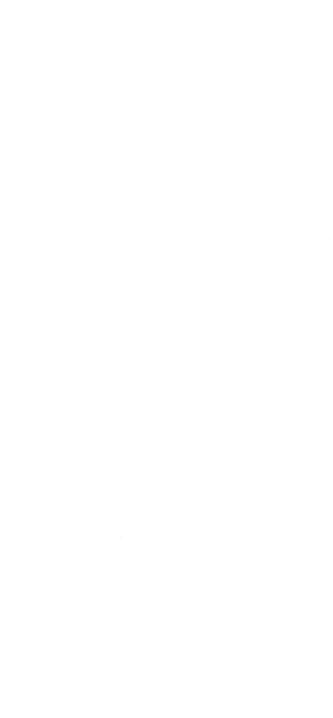
LEGO BIG BUILD CARS – FACTS AND FIGURES
• Each car was built using almost 400,000 LEGO bricks, along with a selection of other components to make them capable of driving.
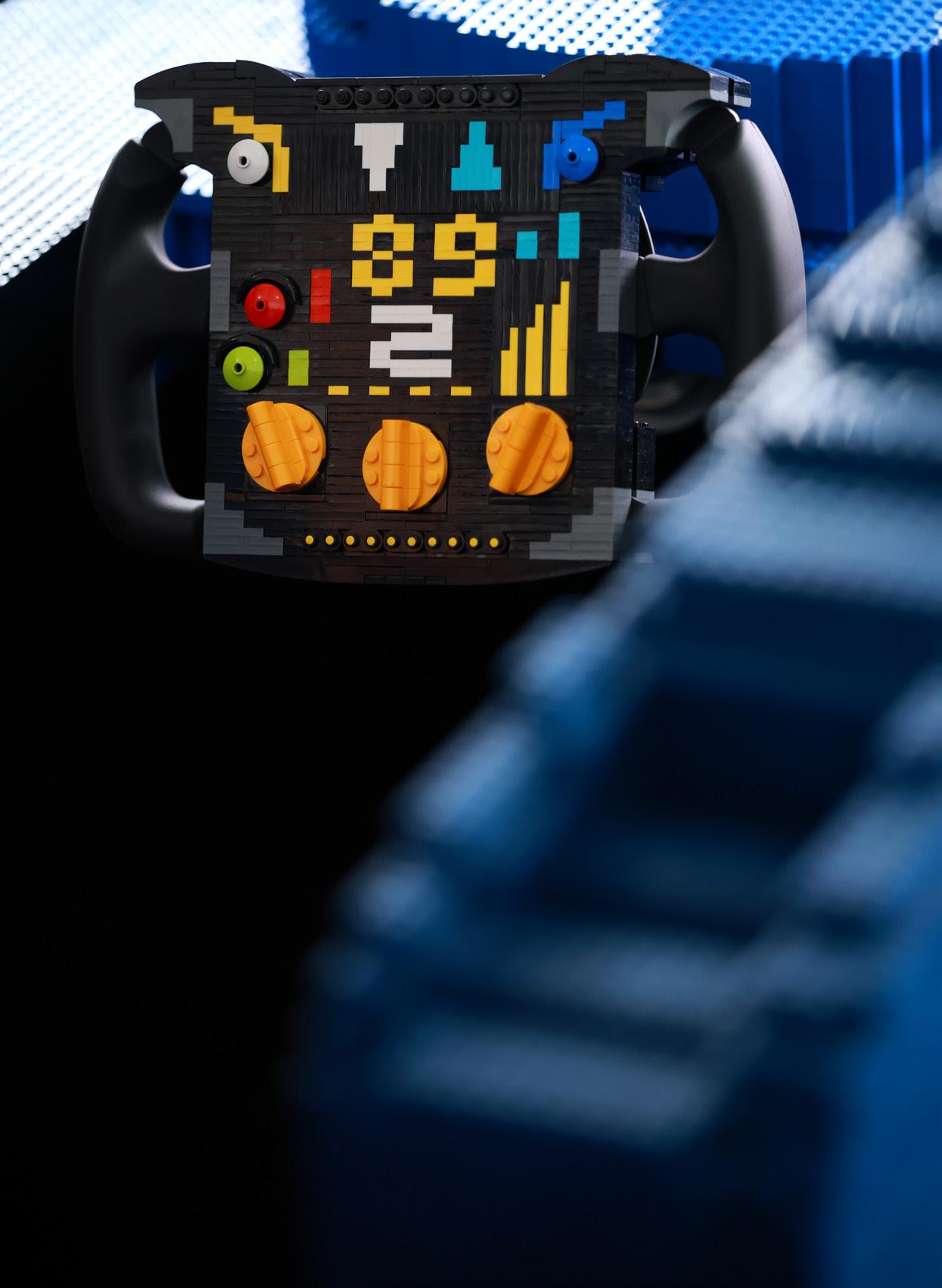
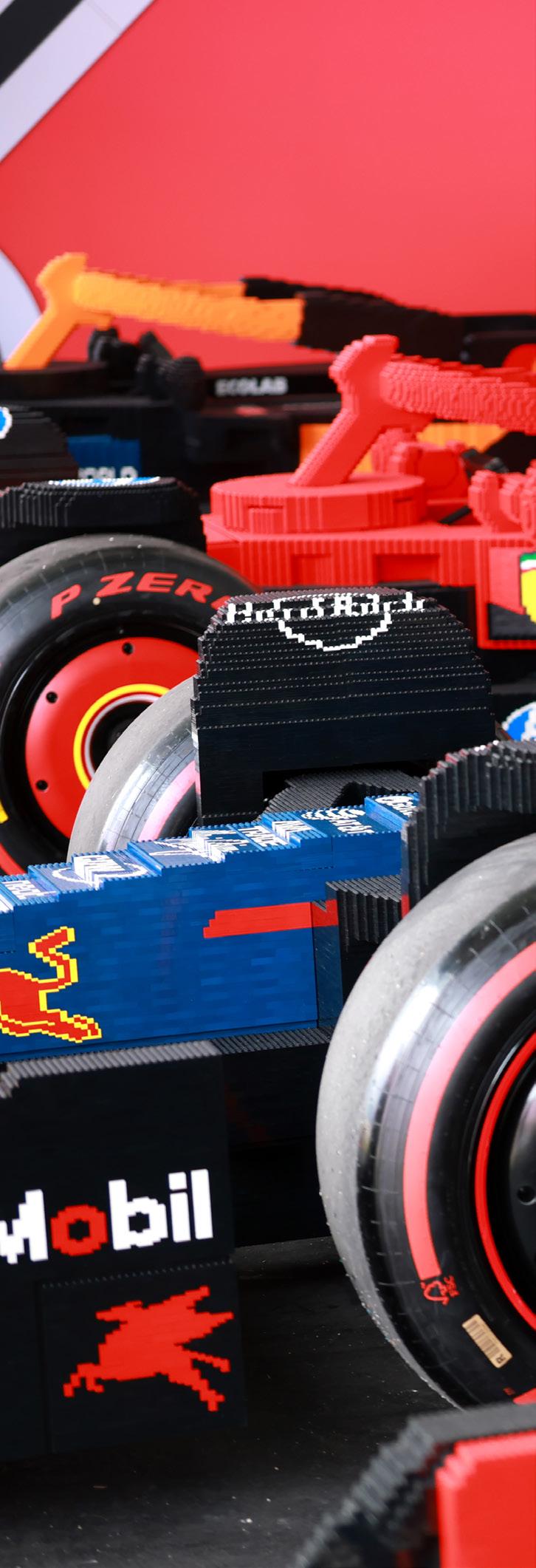
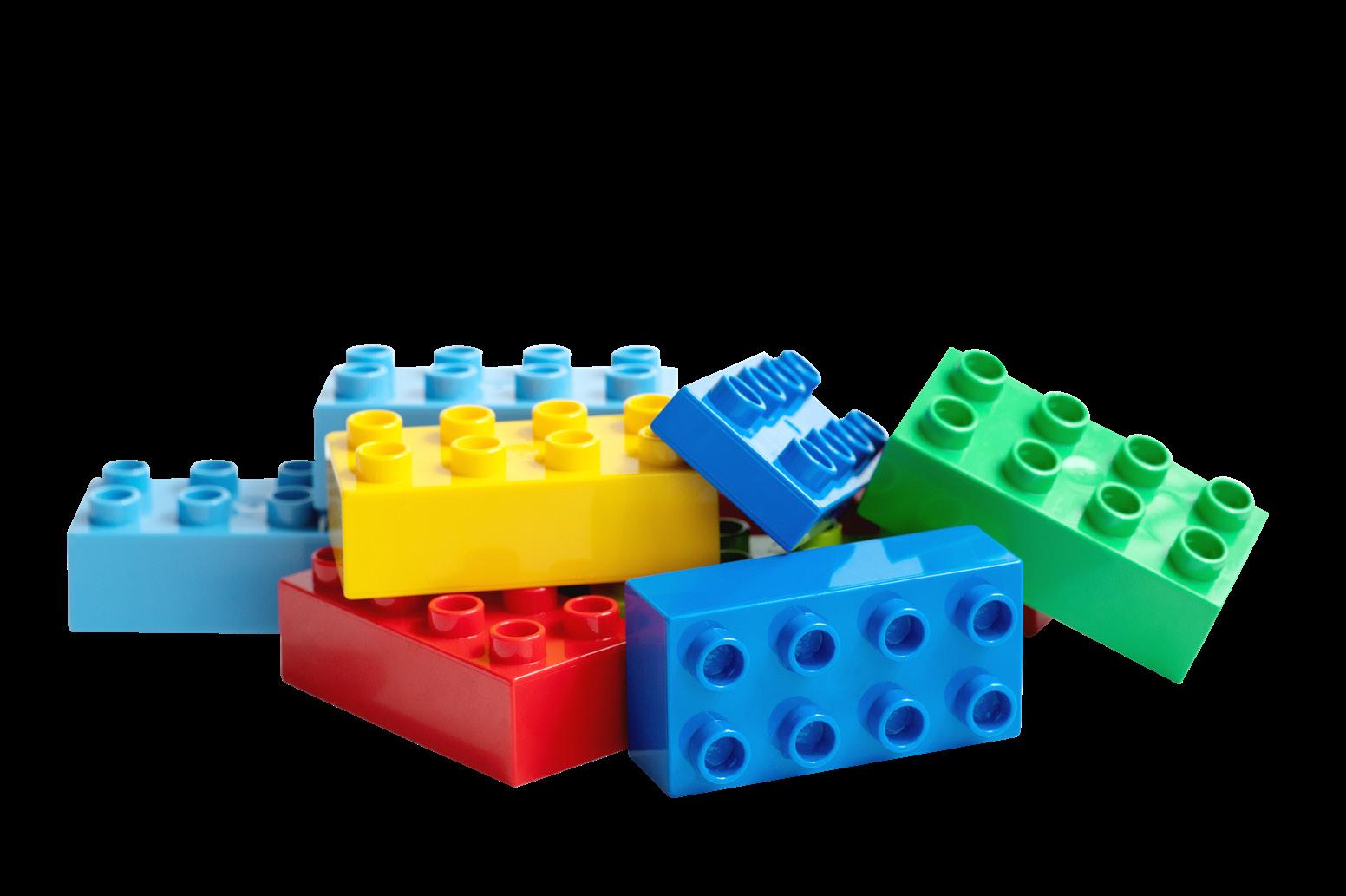
Gasly and Jack Doohan ahead of the 57-lap showpiece.
PUSHING THE BOUNDARIES
Both F1 and the LEGO Group are synonymous with pushing the boundaries, and this latest challenge was a true testament to that.
between the two that was first announced in September 2024, bringing together two passionate global fanbases and engaging new audiences.
This partnership will make the sport more accessible to families around the world at a time when F1 has seen
a huge surge in growth with younger
Indeed, data shows that across the US and European Union (EU), over four million children between the ages of eight and 12 now actively follow the pinnacle of motorsport, whilst 40 percent of Instagram followers are under 25.
It will also promote innovation,
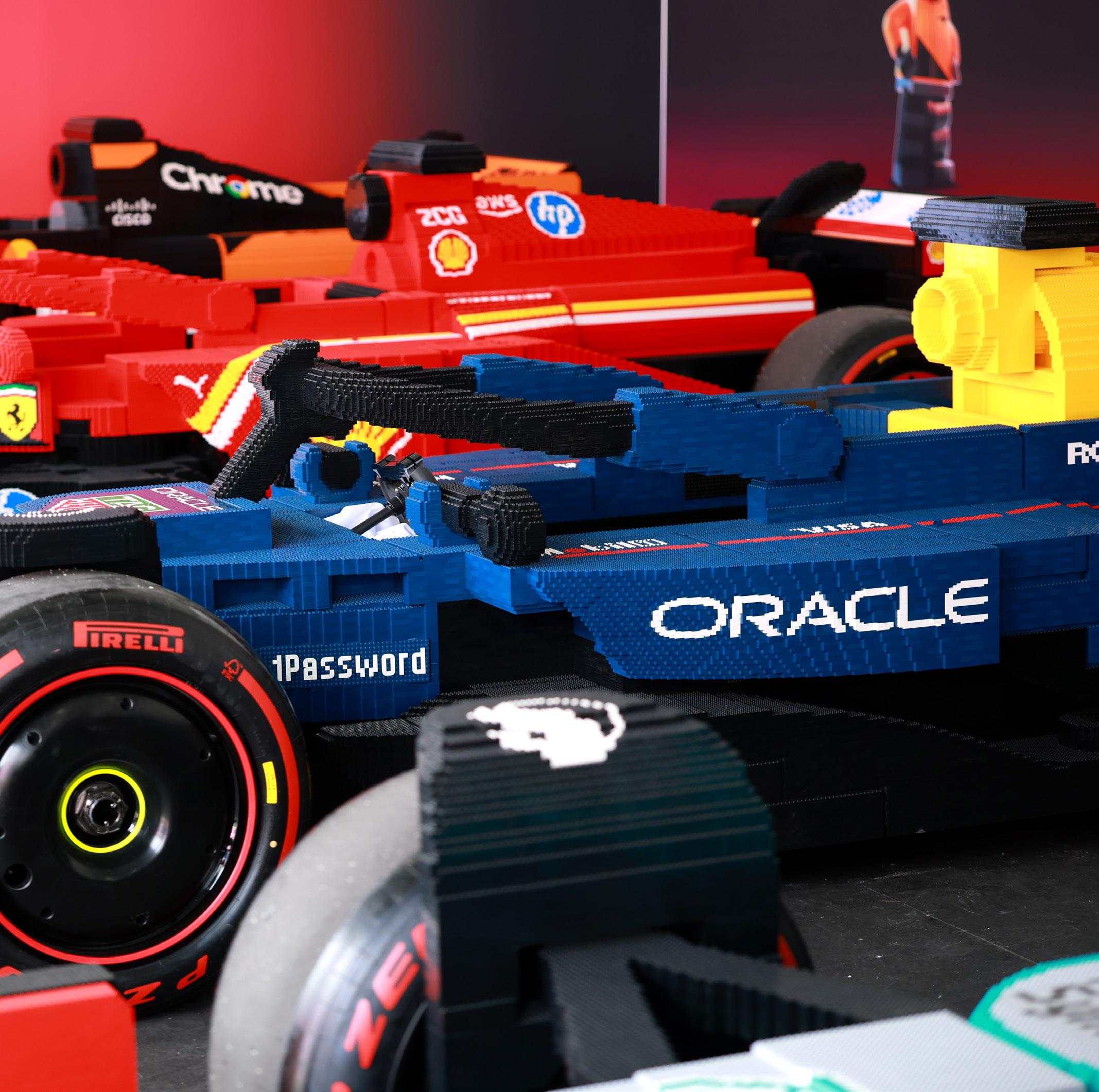
technology, and engineering – which have defined the sport for 75 years –as exemplified by the LEGO big build cars in Miami, along with stronger inclusion and representation.
As well as the driveable big builds, there are a number of other at-race experiences that will ramp up the fun during the 2025 season for people of all ages.
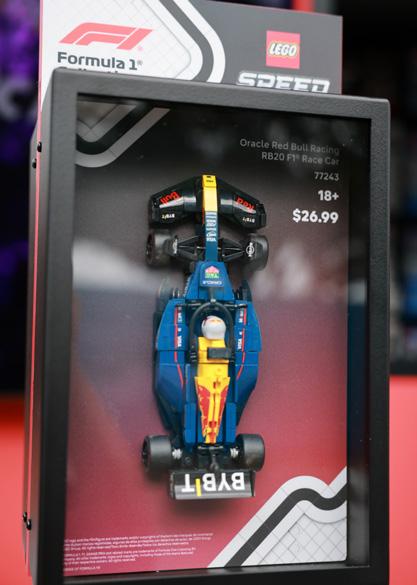
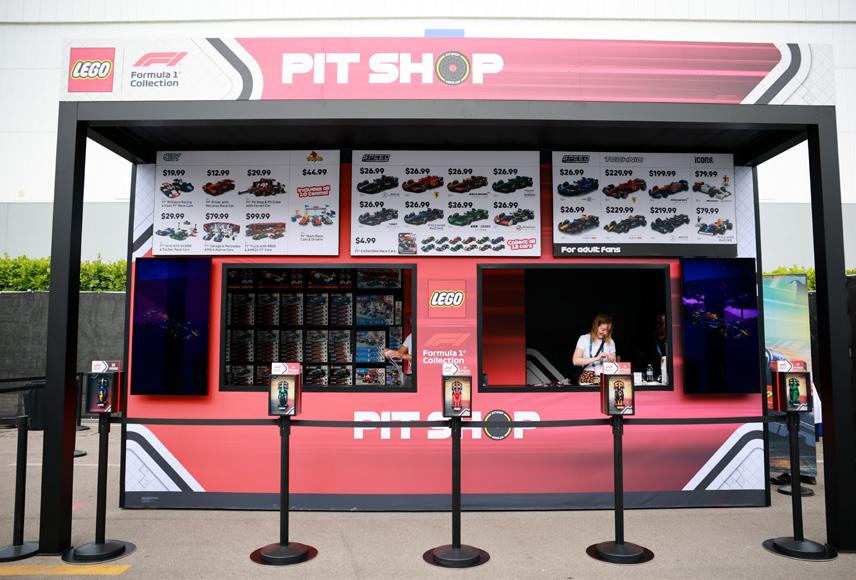
Fans are set to be immersed in the world of F1 by the LEGO Group with interactive activities and challenges designed to celebrate the sport’s engineering and technical heritage.
At select events, the experience of being at an F1 track will also be heightened by brand-new LEGO Fan Zones, where fans can enjoy exclusive make-and-take builds, photo
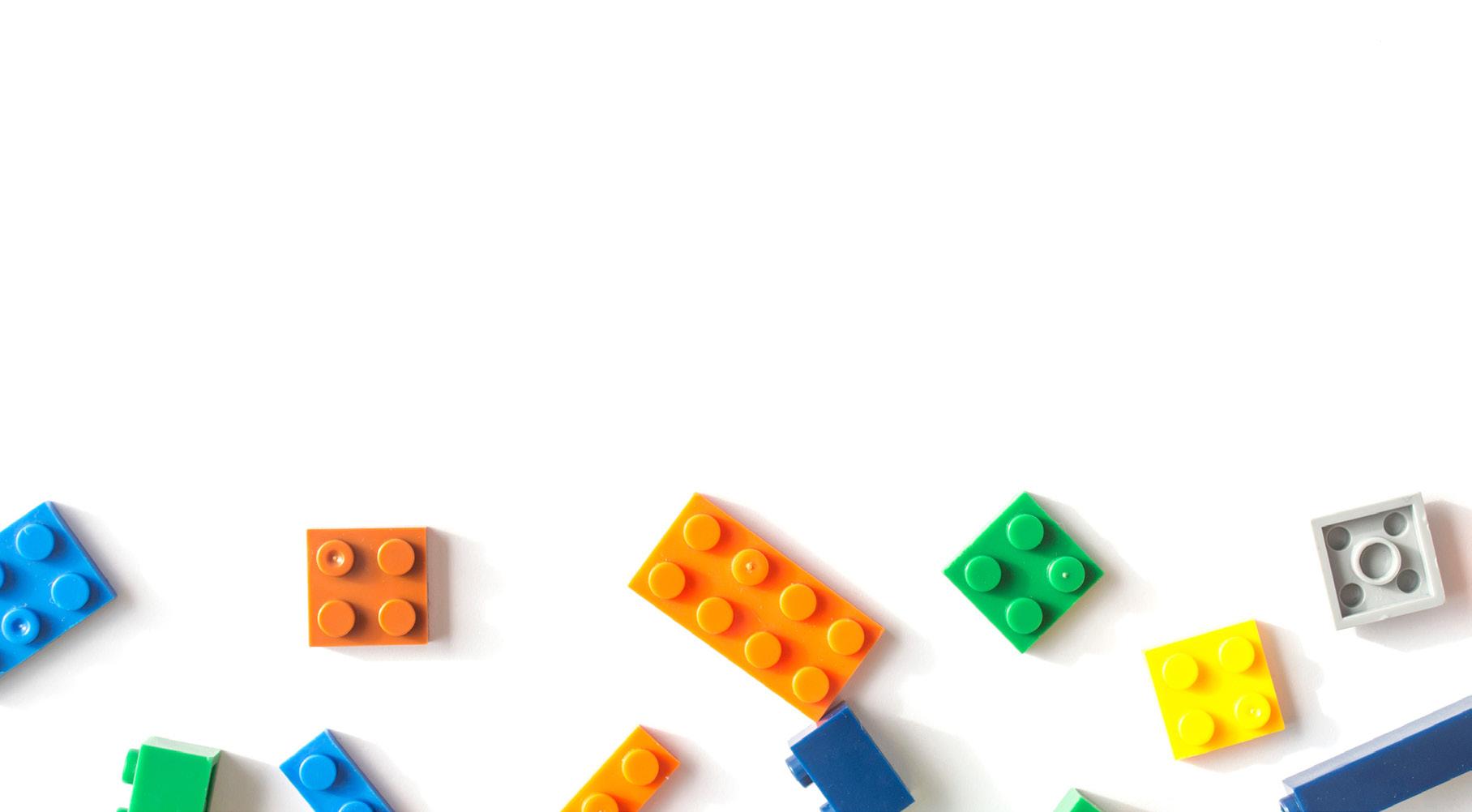
opportunities, and a chance to see the LEGO Group’s entire F1 product range featuring all 10 teams for the first time.
Following the conclusion of the Miami Grand Prix, all 10 LEGO big builds are now embarking on a world tour with appearances at future races.
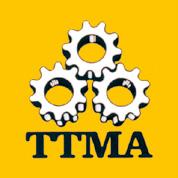
SPOTLIGHT ON TRINIDAD AND TOBAGO MANUFACTURING
Thriving with untapped potential, Trinidad and Tobago’s manufacturing landscape is a significant economic driver for the country thanks to both regional and national governmental support and steadfast dedication across the industry
Writer: Lucy Pilgrim | Project Manager: Krisha Canlas
Most avidly known for its vibrant mixture of cultures, bustling carnival atmosphere, and welcoming locals, Trinidad and Tobago lies at the heart of the Caribbean.
Emerging as a key player in the global industry landscape, the dual-island nation’s burgeoning manufacturing sector is a critical economic driver, with its GDP contributions reported to be TTD$16.1 billion in 2023, marking a 350 percent increase since 1999.
As a result, manufacturing has experienced significant foreign direct investment thanks to the country’s stable and reliable infrastructure, numerous bilateral trade agreements, and continued government support.
Regarding the latter and the efforts of the then Ministry of Trade and Industry (MTI) specifically, numerous impactful initiatives have been introduced in recent decades to help foster manufacturing growth across
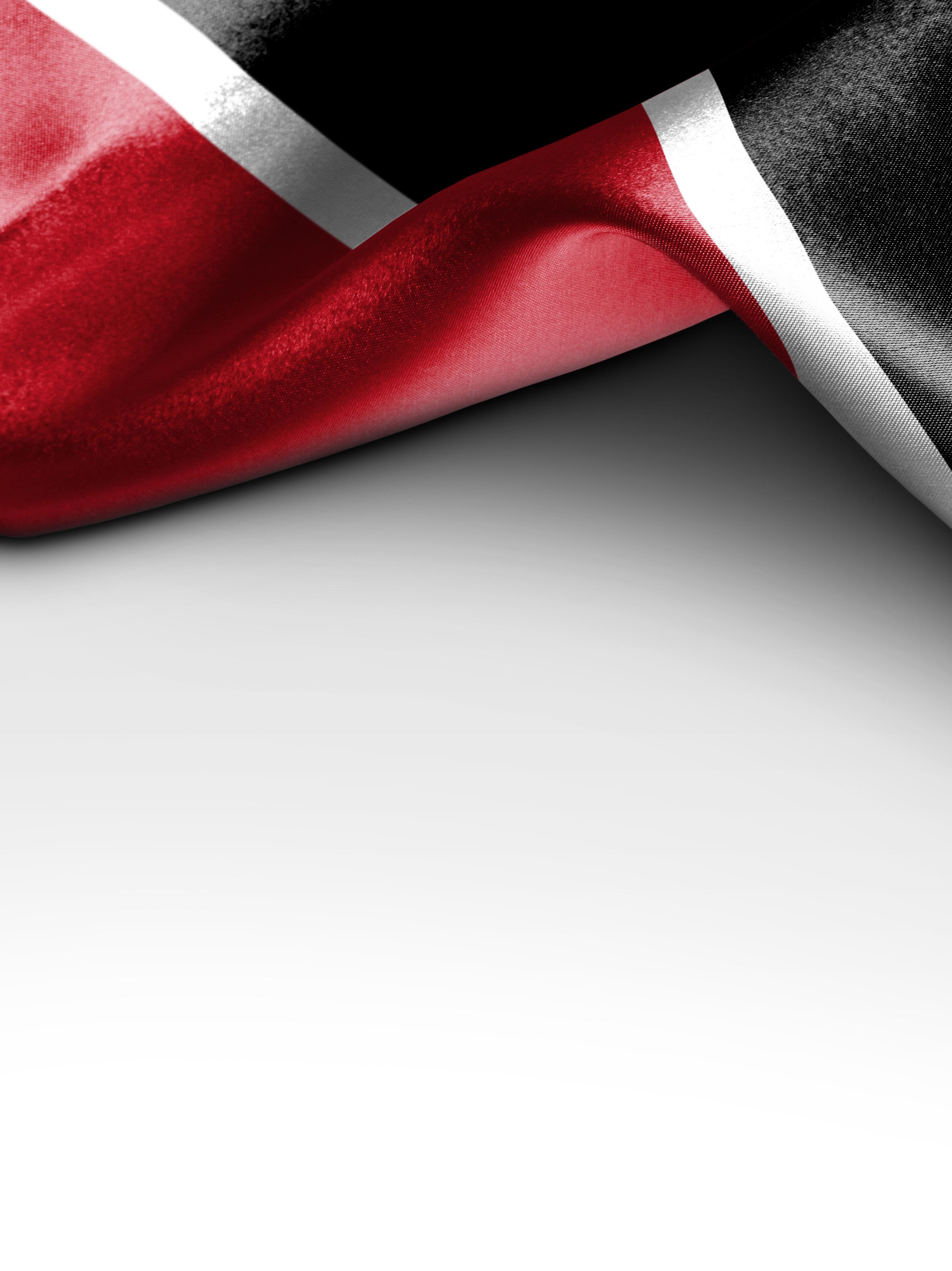
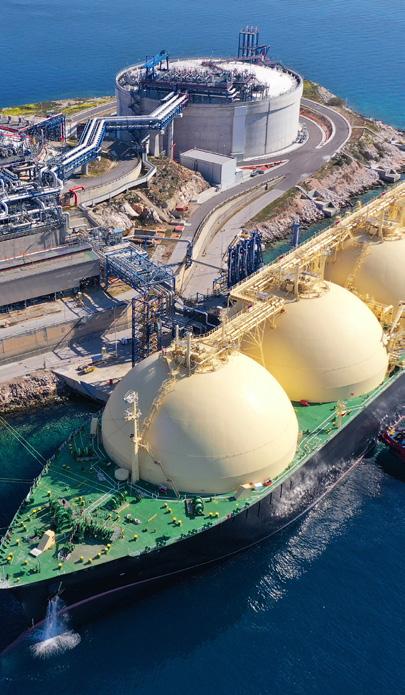
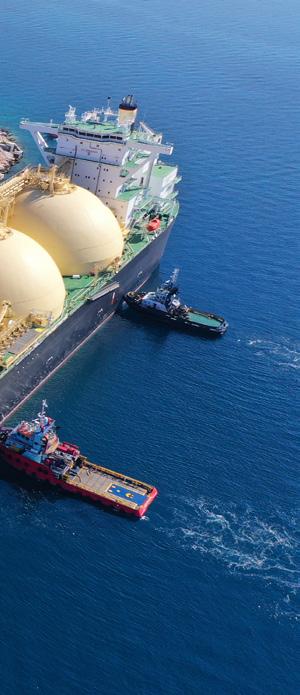
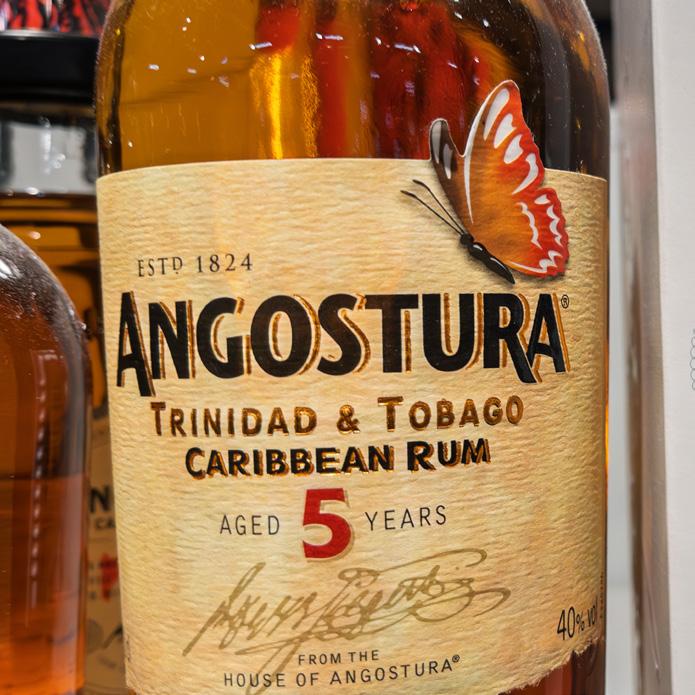
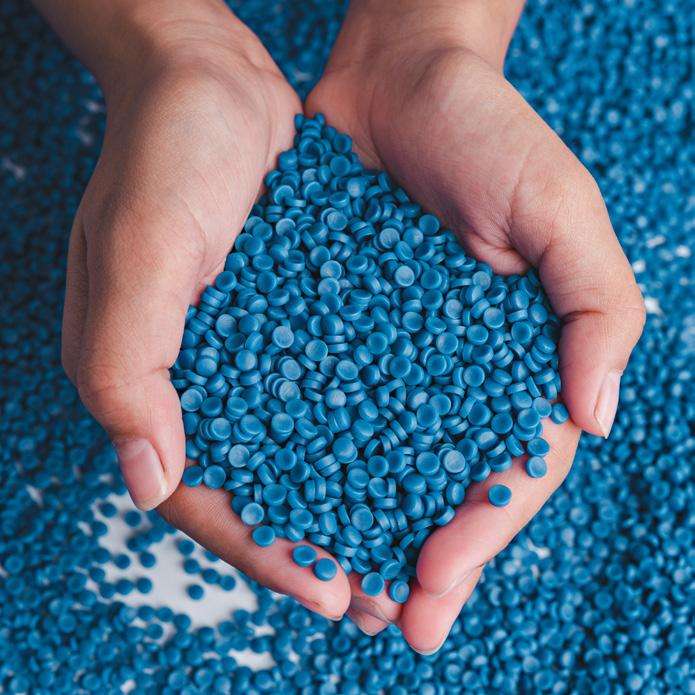
the islands. These include fiscal incentives, grants, additional funding arrangements, achievable targets, and more.
Equipped with these subsidies and government aids, manufacturers across Trinidad and Tobago have had greater access to myriad benefits such as duty-free raw materials and extensive plant and machinery investments. Consequently, the country’s manufacturing output is toptier and able to meet stricter requirements, opening the door to greater regional and international export potential, particularly in the realm of non-energy manufacturing exports.
More broadly, given manufacturing is the most active industry in the English-speaking Caribbean, the support of the Caribbean Community (CARICOM) market has also been invaluable to the sector’s evolution, as it has helped to
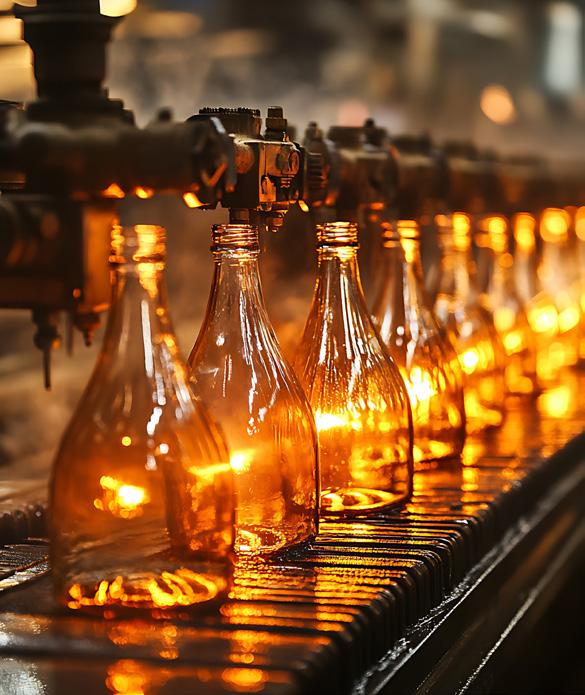
protect the landscape from international export competition while also allowing key players to expand into global markets.
The future of Trinidad and Tobago’s manufacturing sector seems bright as the country is prepared to create an environment that fosters growth and encourages innovation. In light of this, manufacturers are focused on expanding the workforce and entering into an era of sustainability.
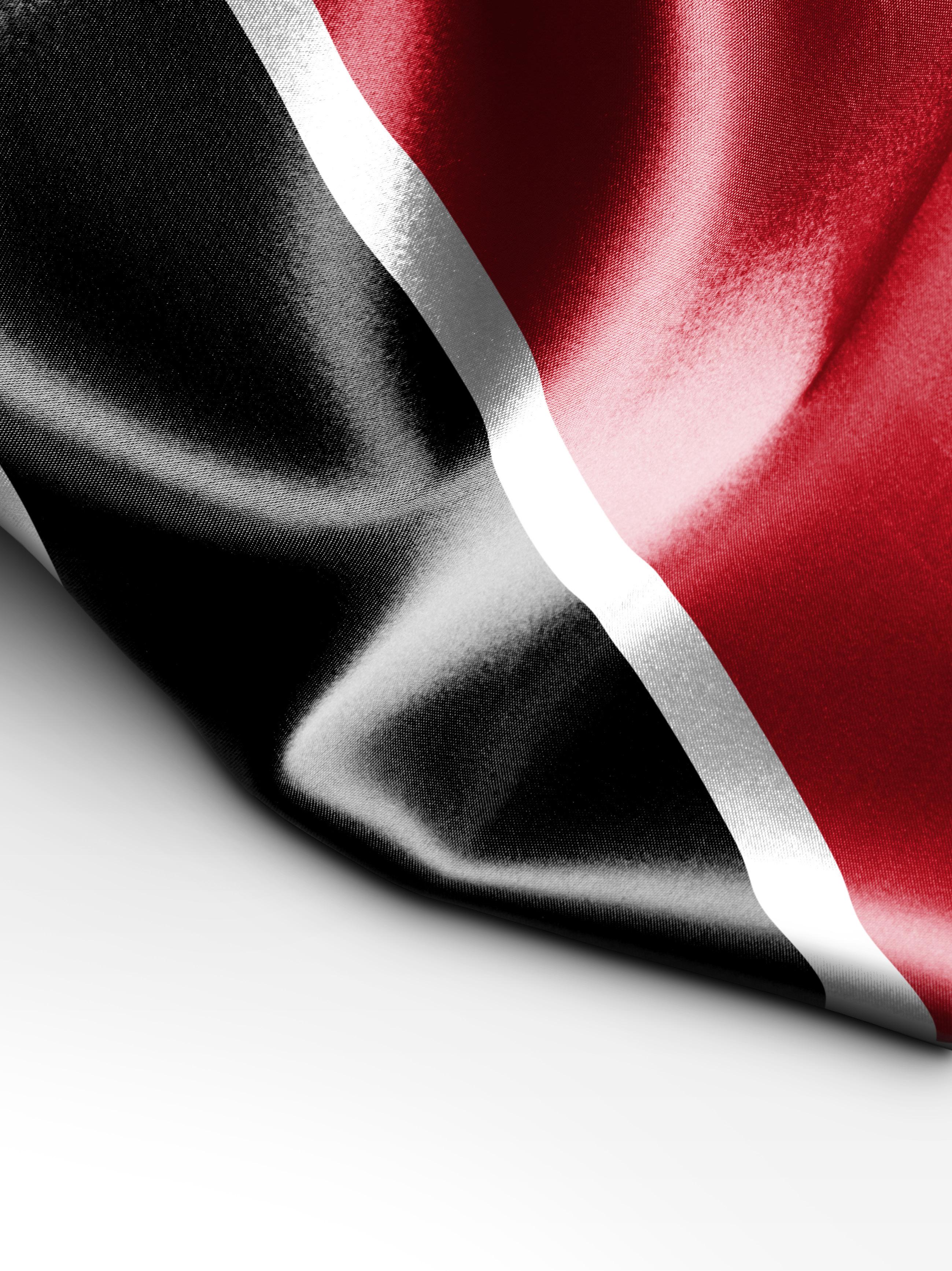
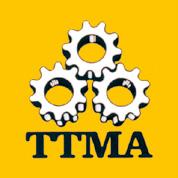
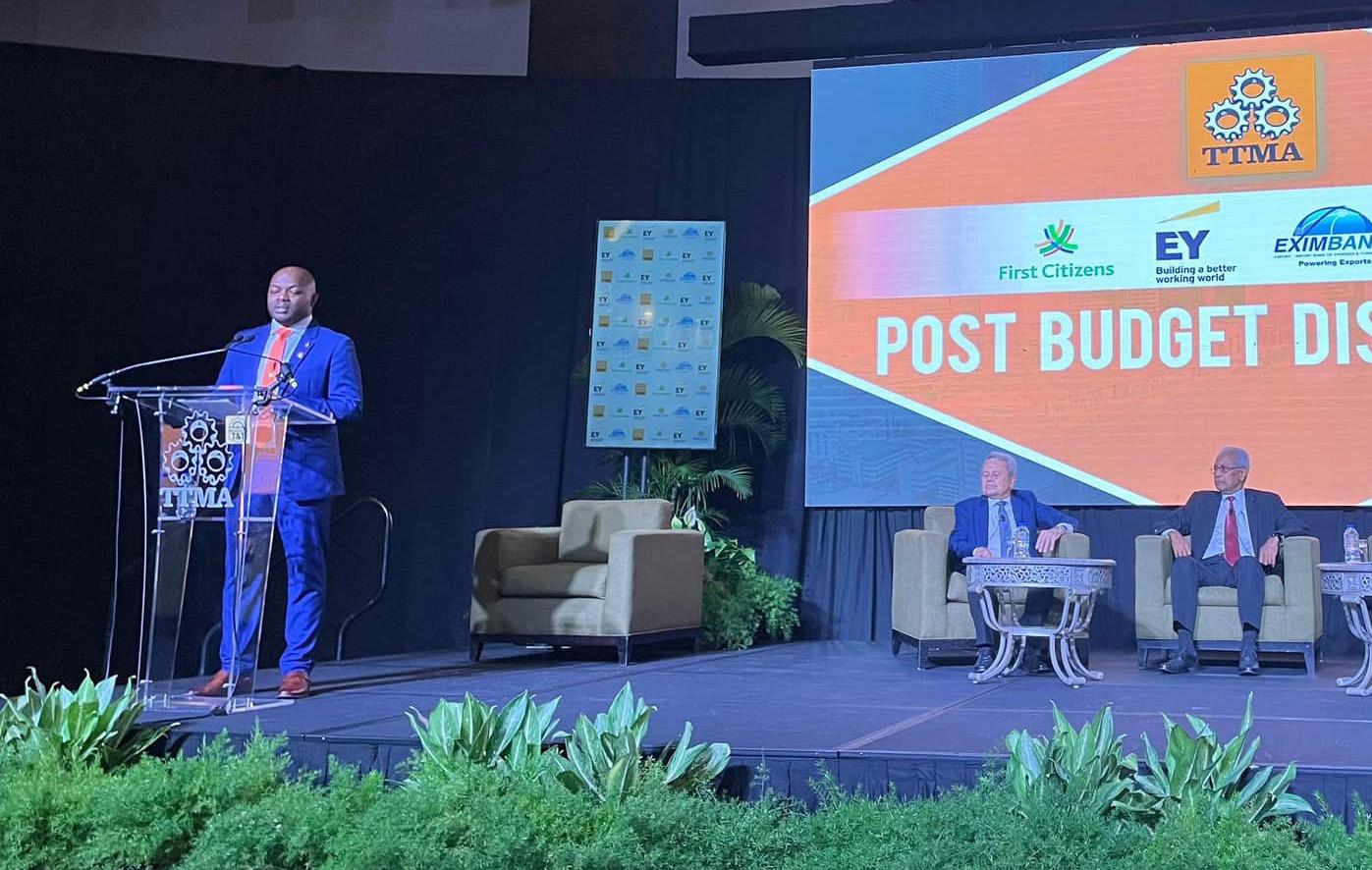
INTERVIEW: TRINIDAD AND TOBAGO MANUFACTURERS’ ASSOCIATION
Dr. Mahindra Ramdeen, CEO of the Trinidad and Tobago Manufacturers’ Association, talks us through its mission to foster market expansion across the industry and emphasizes the importance of local entities
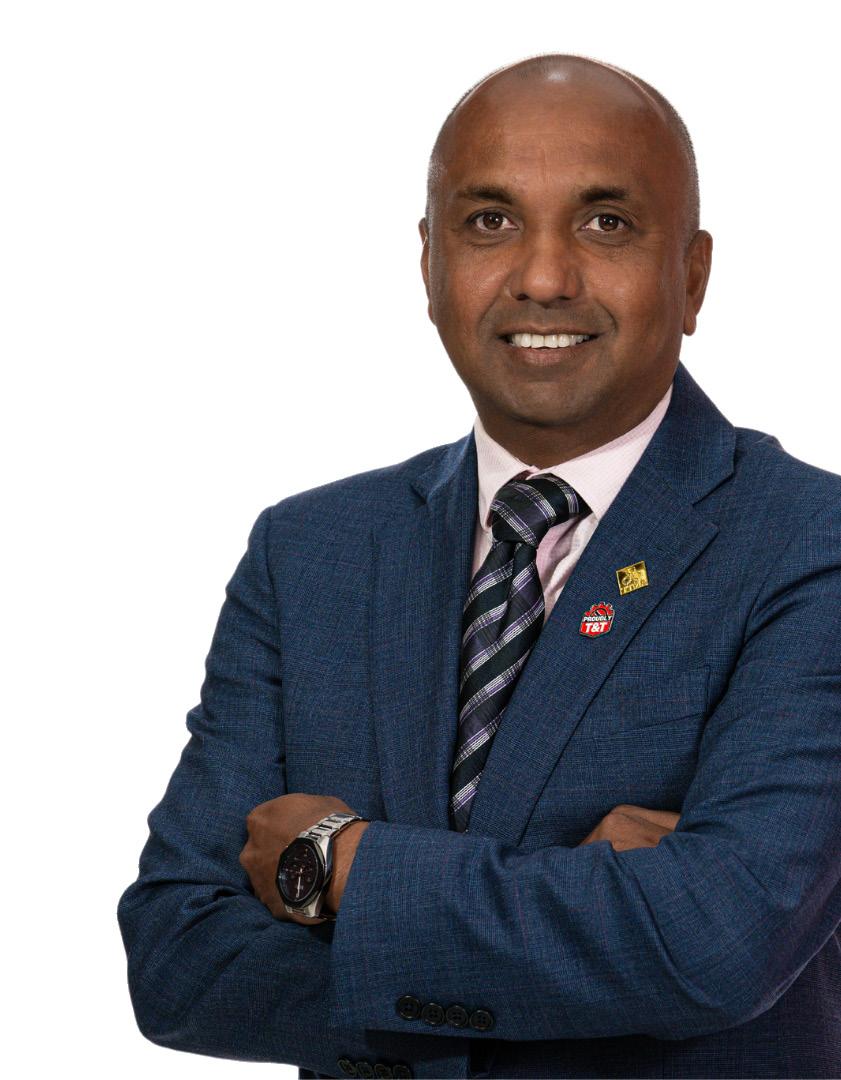
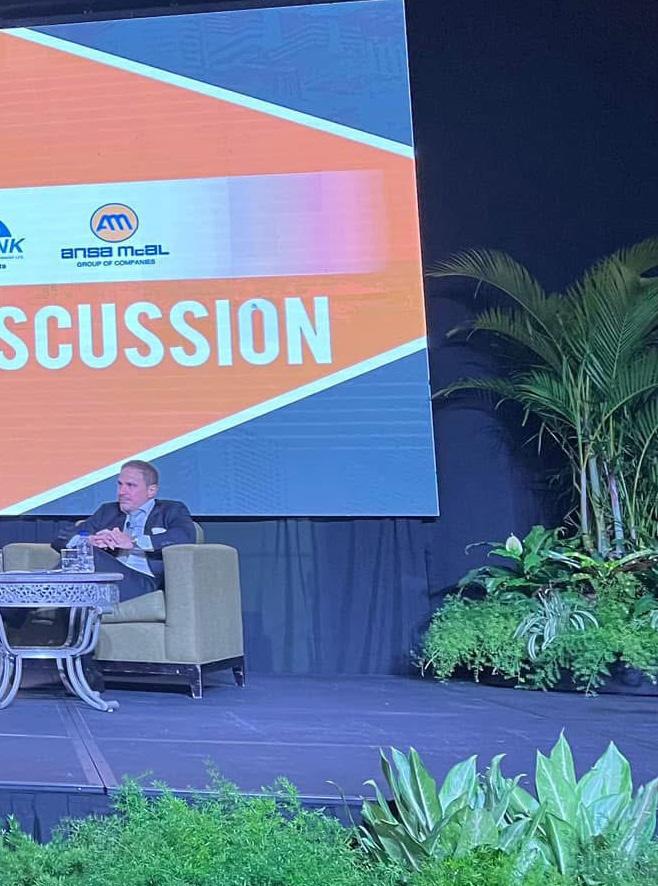
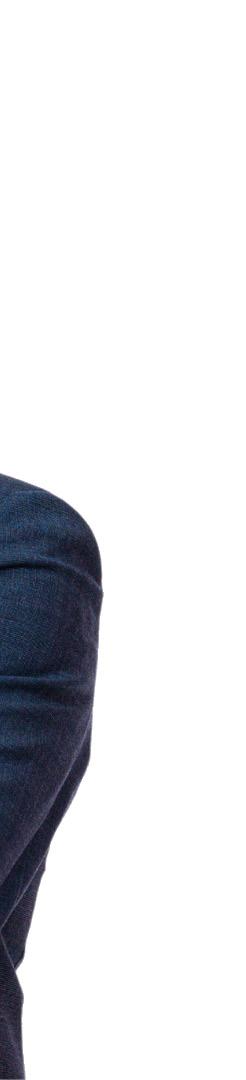
Manufacturing Outlook (MO): Could you introduce the Trinidad and Tobago Manufacturers’ Association (TTMA) and provide an overview of your purpose, values, and founding mission?
Dr. Mahindra Ramdeen, CEO (MR): TTMA promotes, encourages, and assists the growth and development of manufacturing industries in Trinidad and Tobago. The Association also acts as a representative for industries when dealing with the government and monitoring legislation affecting manufacturers.
TTMA is additionally responsible for generating market expansion both regionally and internationally through the mounting of local, regional, and global trade fairs, exhibitions, and foreign trade missions. The Association promotes the use of modern methods in manufacturing and the education of all its members. TTMA also focuses on assisting local manufacturers in maintaining required standards of safety, labor relations, wages and benefits, communications, public relations, and advertising. Moreover, the Association provides assistance in the securing of markets for both raw materials and finished products, as well as in the sourcing of investment partners
MO: What is your take on Trinidad and Tobago’s manufacturing sector at the moment? What are the current challenges and opportunities facing the industry?
MR: The non-energy manufacturing sector remains a pillar of Trinidad and Tobago’s economic growth. According to the MTI’s 2023 Year in Review, the non-energy sector’s total exports from the country increased by 54 percent from the year before; exports in 2022 were TTD$55.3 billion and increased to TTD$89.1 billion a year later. Energy exports, meanwhile, increased by 15 percent from TTD$15.6 billion in 2022 to TTD$17.9 billion in 2023.
Trinidad and Tobago’s exports continue to grow due to excess capacities in domestic operations. Thus, local manufacturers are able to meet the demand once it occurs, and if demand outstrips supply, they are prepared to invest in plants and machinery. Presently, on average, most factories operate at approximately 80 percent capacity, meaning that manufacturers can immediately grow by 20 percent if needed.
In the period between 2014 and 2023, exports from the manufacturing sector amounted to over TTD$134 billion, with the contribution to non-energy exports averaging around 94 percent annually.
Several other subsectors of manufacturing have recorded positive growth, including:
• Food and beverages – Valued at TTD$3.2 billion in 2023 (increased by TTD$1.2 billion or 58 percent).
• Plastic and rubber products – Valued at approximately TTD$532 million (increased by TTD$262 million or 97 percent).
• Paper and paper products – Valued at approximately TTD$753 million (increased by TTD$293 million or 64 percent).
• Glass products – Valued at approximately TTD$165 million (increased by TTD$55 million or 50 percent).
• Other chemical products – Valued at approximately TTD$515 million (increased by TTD$158 million or 44 percent).
These gains align with TTMA’s 2020–2025 Non-Energy Manufacturing Export Strategic Plan, aimed at doubling exports and enhancing industry resilience. The plan is supported by key government strategies such as the Export Booster Initiative (EBI), National Apprenticeship Program, Exim Bank’s Foreign Exchange Facility (FX Facility), SME Stimulus Loan Facility, and the Single Electronic Window TTBizLink platform.
Due to the decline in the energy sector, the supply of foreign exchange (FX) to the non-energy sector has been curtailed. Without the reliable source of FX that
“THROUGH STRATEGIC INITIATIVES, COLLABORATIVE EFFORTS, AND A COMMITMENT TO INNOVATION, WE ARE CONFIDENT IN OUR ABILITY TO DRIVE ECONOMIC DIVERSIFICATION AND CONTRIBUTE MEANINGFULLY TO THE NATION’S PROSPERITY”
– DR. MAHINDRA RAMDEEN, CEO, TRINIDAD AND TOBAGO MANUFACTURERS’ ASSOCIATION
would have come from the energy sector, the only other way to realize it is to export. The business community needs FX to purchase raw materials and machinery and engage in international trade. Fortunately, Exim Bank’s FX Facility offers some relief to manufacturers. However, it is imperative that companies earn their own FX to sustain and grow their operations in the non-energy community.
Trinidad and Tobago produces some very high-quality goods and services, and the certification for entry into markets has been met in most instances, meaning our world-class goods and services can compete in many global markets. The potential and capacity are there to meet the needs and standards of entry to all international markets, and TTMA is continuously working with its members so that they can earn their own FX. This also means there is less reliance on the government and the energy sector.
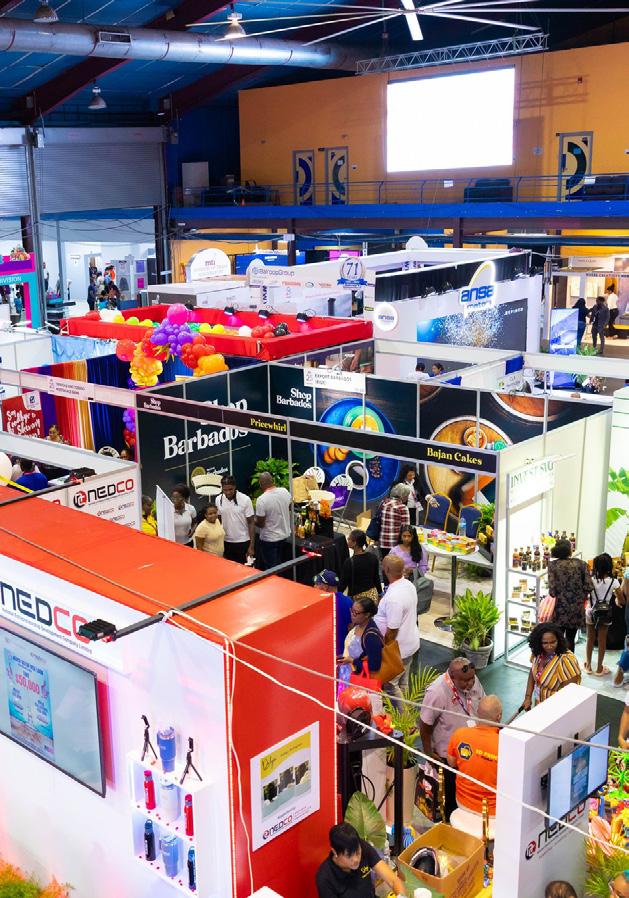
TTMA has continued to work hard over the last couple of years to improve its offerings in education and training, statistical information and data, and member development, allowing them to prepare themselves for exports and earn their own FX.
For example, a major focus has been executing trade missions for companies of all sizes, benefiting over 100 businesses in 2024. These trade missions are done in partnership with the MTI under the EBI and target specific markets with existing trade
agreements. Partnering with CARICOM nations is also a priority, as the trade missions result in increased exports, the security of new or additional orders, and the inclusion of first-time exporters or new market entries.
Additionally, the Trade and Investment Convention (TIC), TTMA’s annual hallmark event, seeks to promote businesses of all sizes to earn FX by providing a platform for them to display their products to regional and international buyers, as well as setting up business-tobusiness (B2B) meetings which may result in export orders.
TTMA also works with the MTI to negotiate trade agreements and, in so doing, creates market opportunities for our members to export. Currently, there are partial scope negotiations with Curaçao taking place, while negotiations with Chile were recently concluded.
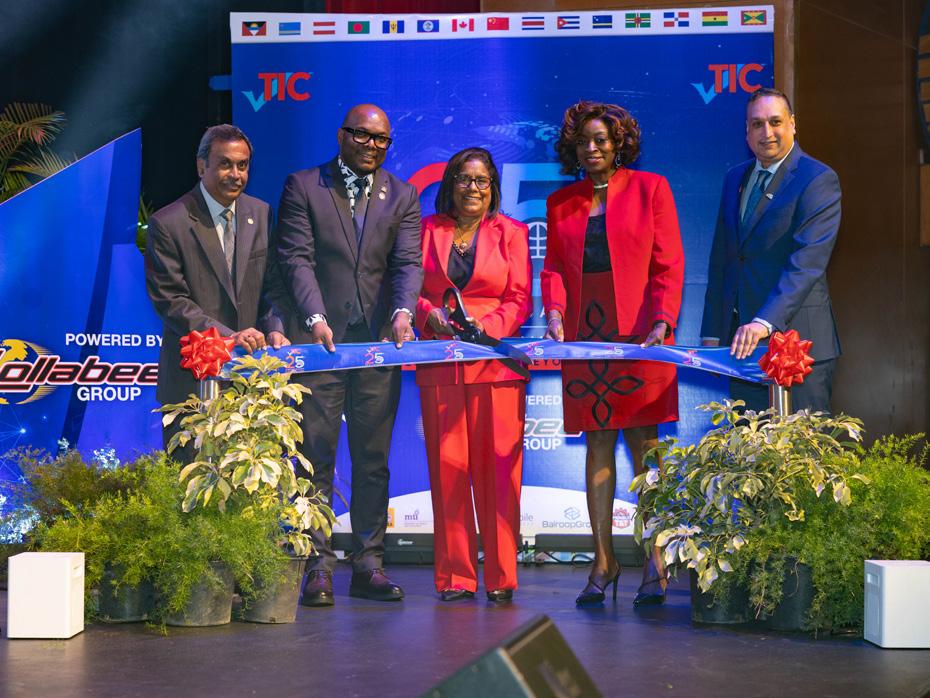
MO: What strategies does TTMA deploy to develop and promote local industries?
MR: TTMA has been instrumental in trade policy, advocacy, and market expansion. Through the former, the Association has secured private sector representation in CARICOM’s Front-of-Package Nutrition Labeling (FoPNL) Scheme and engaged extensively in trade negotiations, opening doors in markets of TTD$19 million and 150,000 people.
By representing CARICOM’s Council for Trade and Economic Development (COTED), we have shaped regional trade rules. Through regulatory collaboration, we also worked with the Trinidad and Tobago Bureau of Standards (TTBS) and the National Quality Council (NQC) on 10+ regional standards. The Association has additionally collaborated with commercial attachés in the UK, US, Panama, Jamaica, and Guyana, hosting over 30 traderelated webinars.
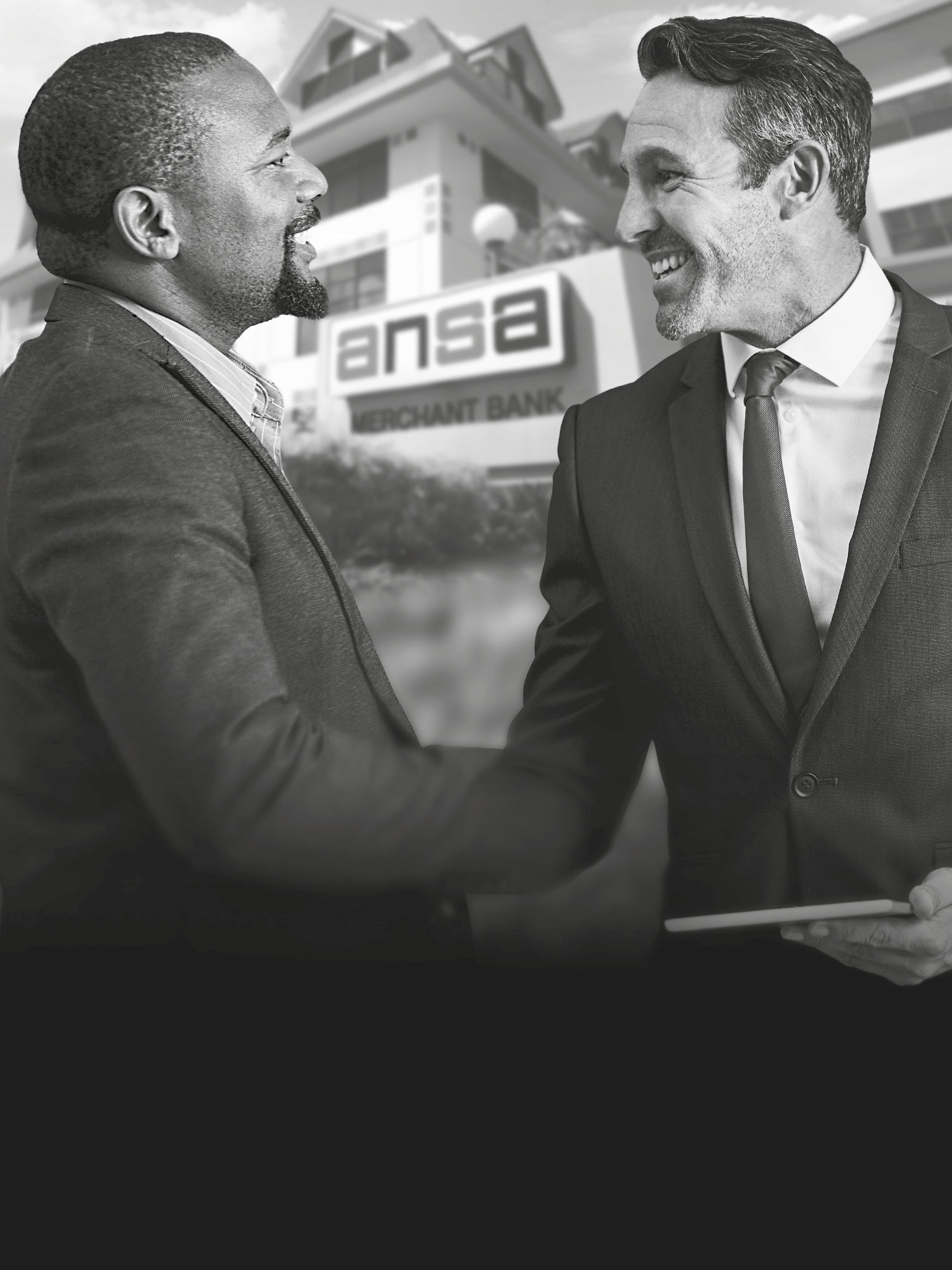
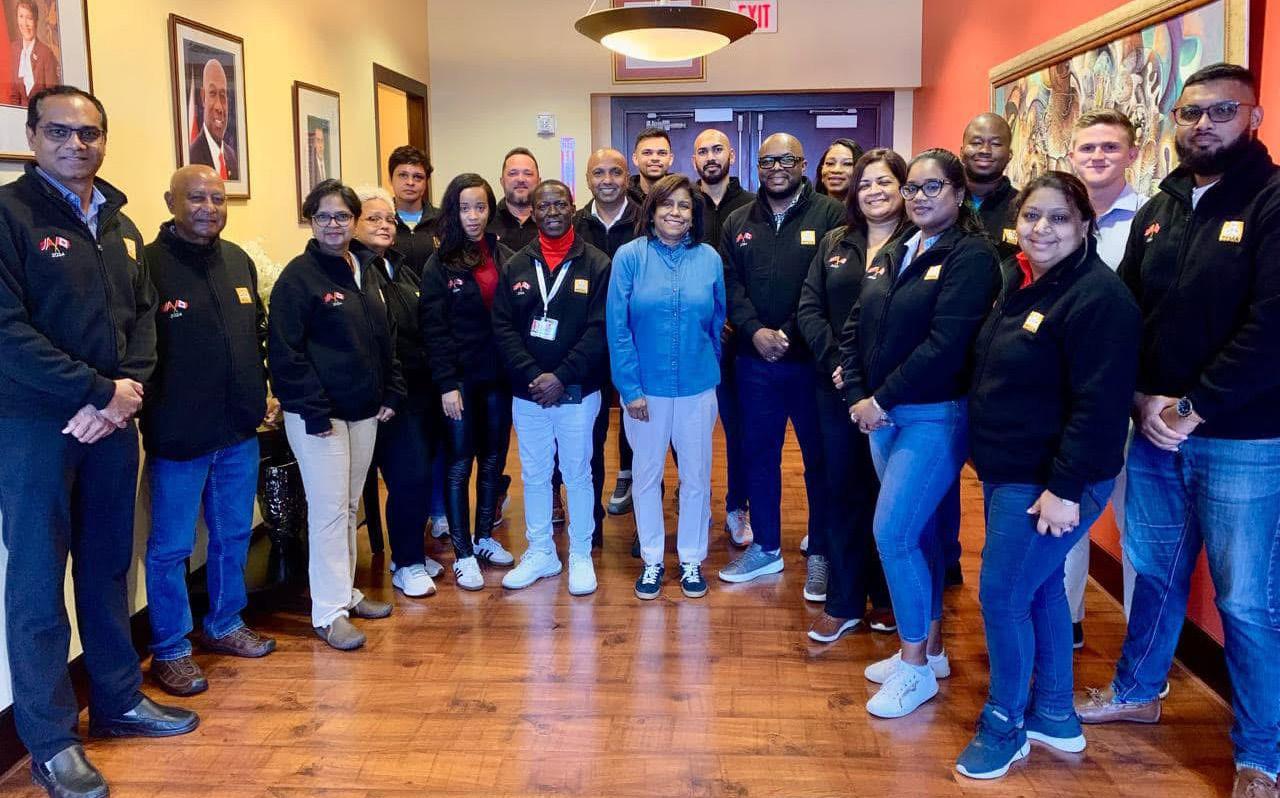
TTMA also addressed duty removals and common external tariff (CET) increases in partnership with the MTI. The Association continues to drive international expansion through strategic trade missions. Our outreach has evolved from virtual-only in 2021 to full-scale physical missions across the Caribbean, Latin America, and North America. Key highlights include:
• 2021: Virtual format – Three trade missions in Curaçao, Antigua and Barbuda, and Grenada – 136 B2B meetings.
• 2022: Return to physical missions – Three missions in Suriname, Guyana, and Jamaica – 216 B2B meetings.
• 2023: Expanded reach – Six missions in Grenada, the Dominican Republic, Suriname, St. Lucia, Guyana, and Antigua and Barbuda – 588 B2B meetings.
• 2024: Six missions in Ghana, the Bahamas, Suriname, Canada, St. Vincent, and the Grenadines, along with the first regional mission in Belize – 812 B2B meetings.
• 2025: Completing trade missions in Dominica with additional missions planned for Jamaica, China, New York, Chile, Guyana, and Suriname.
In total, TTMA-led trade missions have facilitated over 1,800 business connections, resulting in millions of dollars in trade opportunities for local manufacturers.
“TTMA
HAS CONTINUED TO WORK HARD OVER THE LAST COUPLE OF YEARS TO IMPROVE ITS OFFERINGS IN EDUCATION AND TRAINING, STATISTICAL INFORMATION AND DATA, AND MEMBER DEVELOPMENT, ALLOWING THEM TO READY THEMSELVES FOR EXPORTS AND EARN THEIR OWN FX”
– DR. MAHINDRA RAMDEEN, CEO, TRINIDAD AND TOBAGO MANUFACTURERS’ ASSOCIATION
Furthermore, our annual TIC is another way TTMA promotes local industry and has evolved significantly over the years. For instance, in 2021, we hosted a virtual event with 21 webinars and over 1,200 participants. In 2022, the TIC partially returned to a physical format, featuring 134 exhibitor booths, eight exhibiting countries, and 8,000 visitors. In 2023, we hosted a full-scale physical event featuring 276 exhibition booths and 20,719 visitors, including 380 B2B meetings, 35 participating countries, and 12 webinars.
Trade mission to Canada
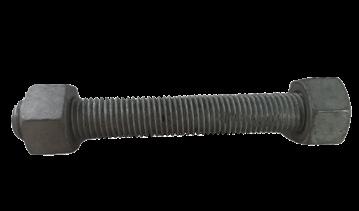
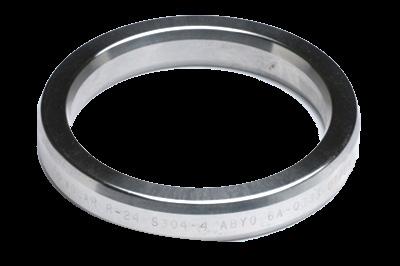
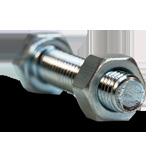
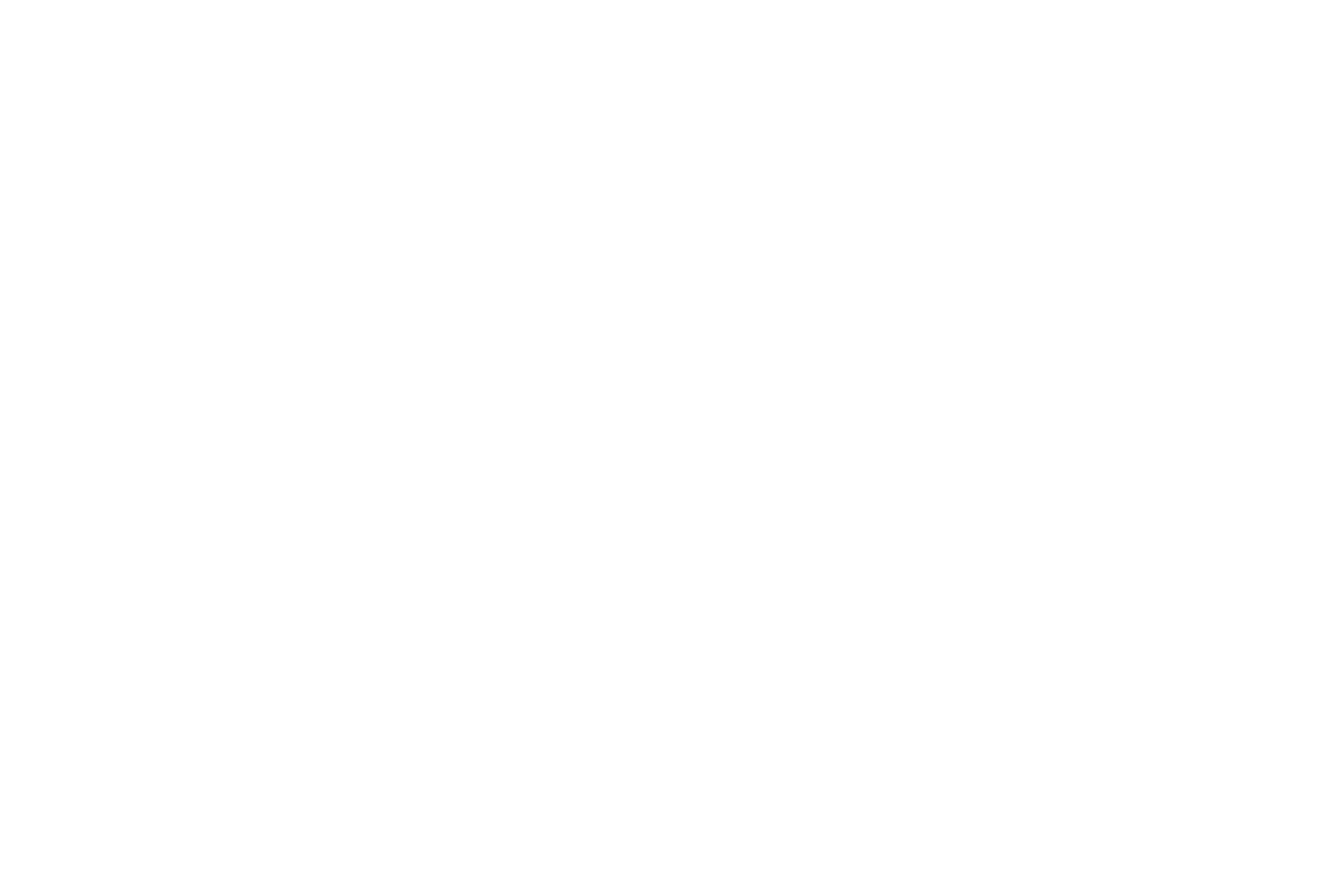
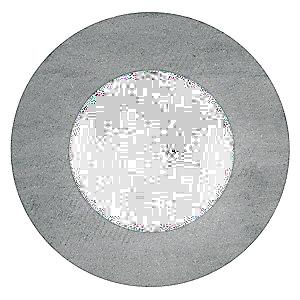
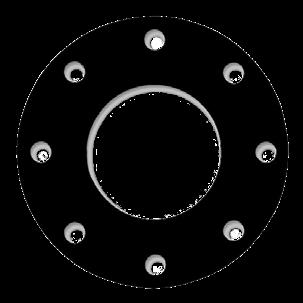
PRECISION IN EVERY SEAL, STRENGTH IN EVERY STUD
Dumore Enterprises Ltd. (Dumore) has grown to become a trusted manufacturer and supplier of premium-quality studs and gaskets for critical industrial applications, now boasting advanced manufacturing capabilities, unrivalled industry expertise, and a firm commitment to precision and reliability.
Dumore offers world-class service for procurement managers, engineers, and operations executives in the oil and gas, petrochemical, energy, construction, and industrial sectors.
Alongside this, the company expertly services a multitude of businesses requiring high-performance gaskets and studs for demanding applications.
Today, Dumore is a leading manufacturer and supplier of studs and gaskets for industrial applications.
As a licensed manufacturer of high-performance gaskets, the company ensures quality and compliance with industry standards.
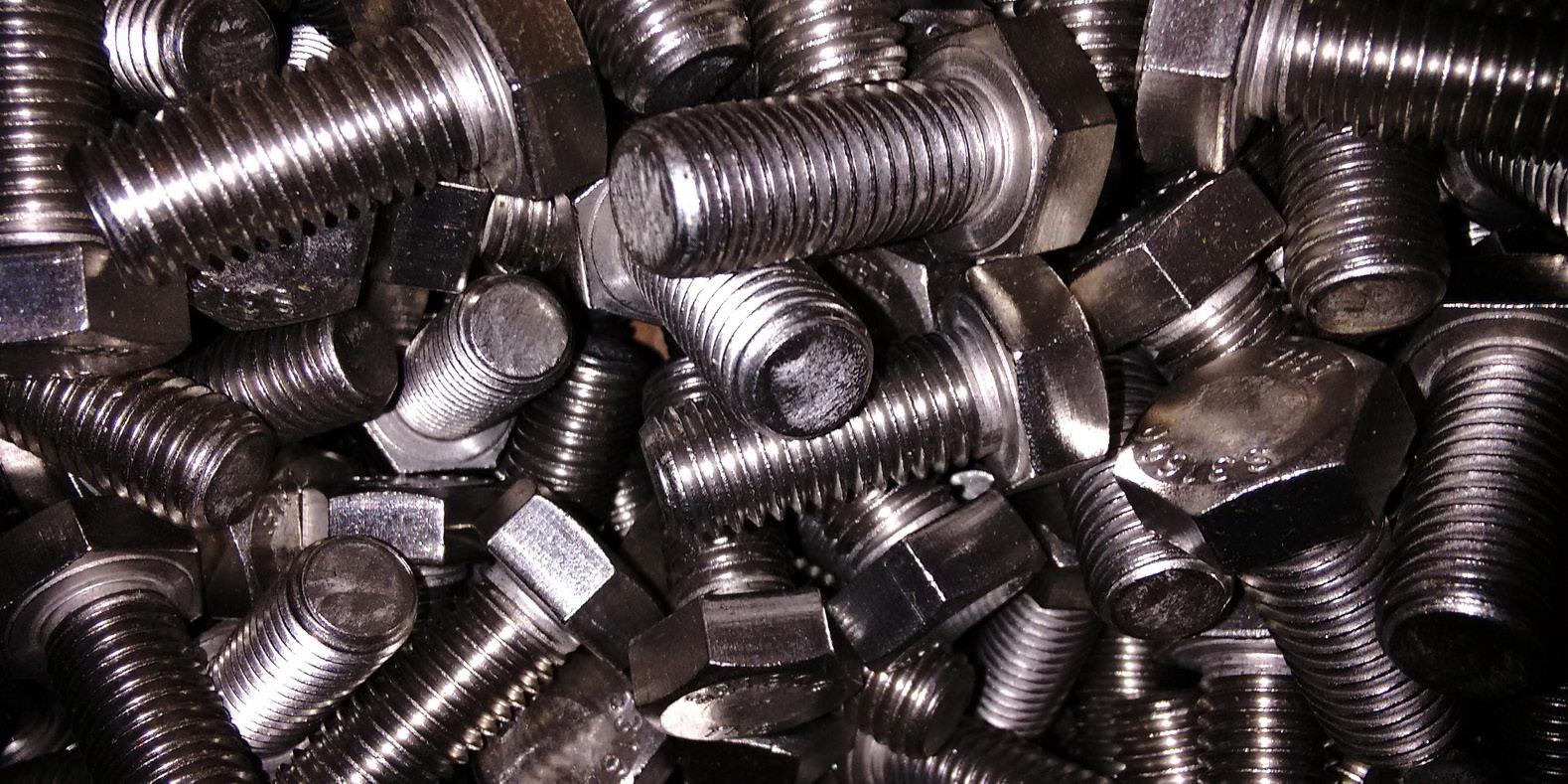
Dumore specializes in manufacturing and supplying:


SOFT GASKETS – Ring type, full-face and custom shapes (Flexible Graphite, PTFE/Teflon, Rubber: Neoprene, EPDM, Insertion)
SEMI - METALLIC GASKETS – Kammprofile, spiral wound (S, GS, GSI in SS, PTFE, Alloy 20, Graphite), heat exchangers (ARMCO Iron, SS)

LATEST IN GASKET TECHNOLOGY – Ring joint gaskets (Oval, Octagonal, RTJ to RF Adaptors), specialty kammprofile gaskets, isolation gasket kits for buried and offshore piping

STUDS AND FASTENERS – Manufactured for heavy-duty industrial applications
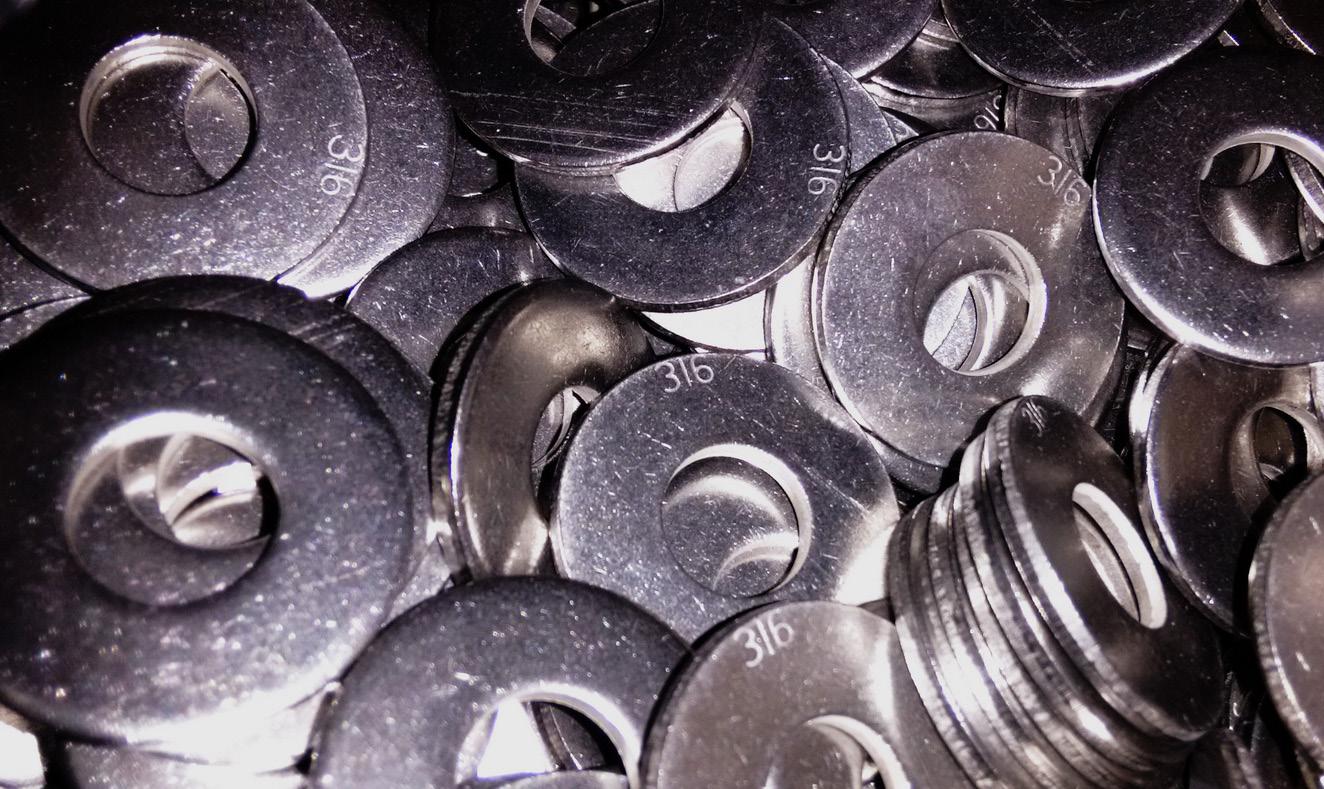
Contact us today for reliable gasket and stud solutions:


industrial@dumore.com
225-4440

https://www.dumore.co/



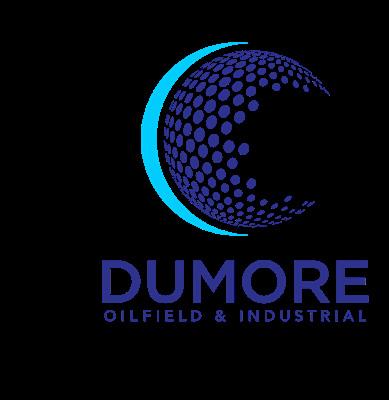
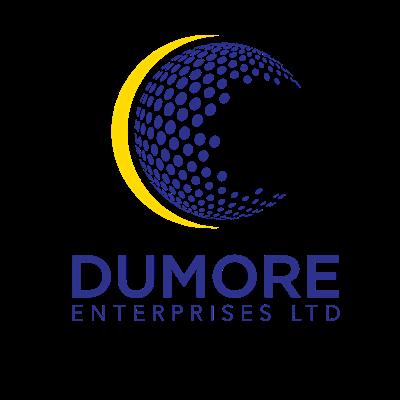
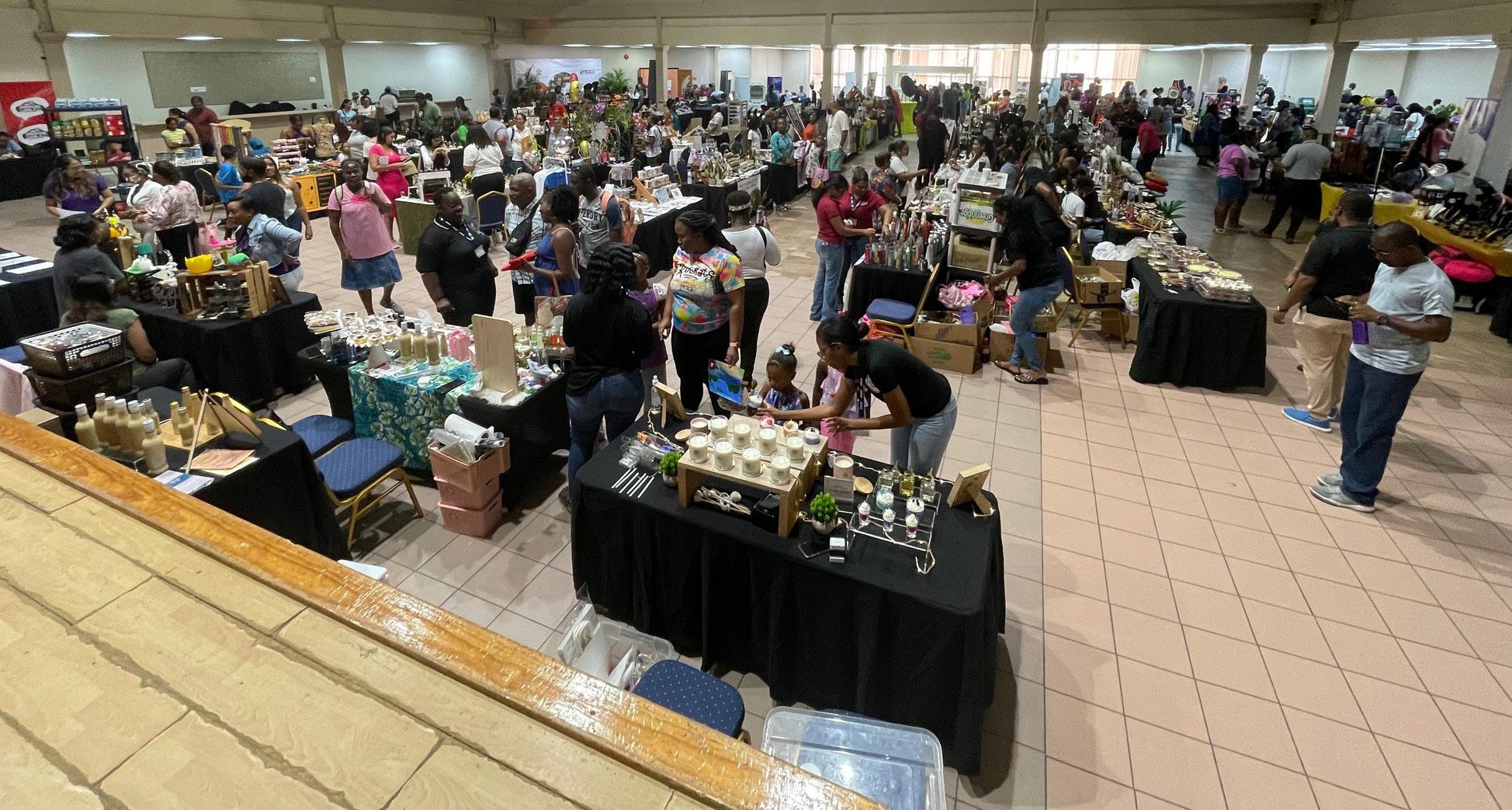
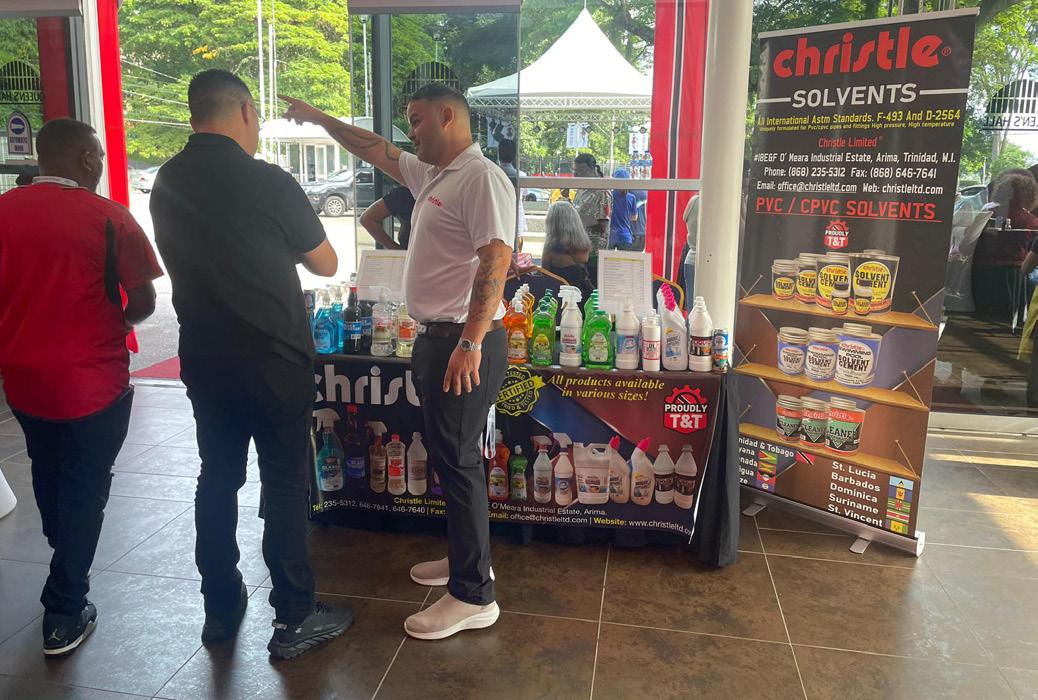
TIC 2024 featured the largest exhibition floor plan in the convention’s history, with a total of 20,757 participants and 320 booths representing 38 countries, 13 webinars, and 427 B2B meetings.
TTMA has also been instrumental in supporting small and medium-sized enterprises (SMEs) – defined as companies that employ between six and 25 staff – through initiatives such as SME Pop-Up Shops since 2022. Hosting two per year, we have given an average of 300 SMEs the opportunity to expose their products, enhance brand visibility, and engage directly with consumers.
Further to this, we host a specific SME pavilion within the TIC framework to give export-ready companies the opportunity to gain exposure and participate in B2B meetings that are integral for the growth of their business. Such initiatives are part of TTMA’s broader commitment to fostering SME growth.
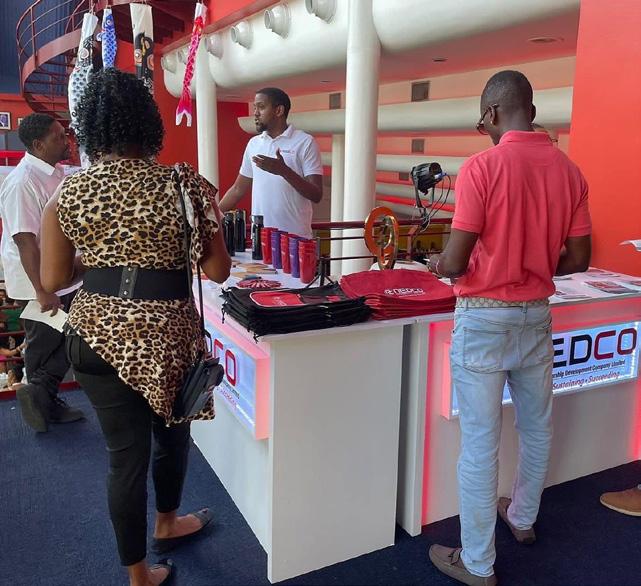
MO: How does the Association promote innovation and modern methods across the country’s manufacturing sector?
MR: TTMA has a productivity committee that focuses on promoting strategies to boost productivity among manufacturers. Its primary goal is to drive technologydriven productivity, particularly in areas such as ICT (Digital 4.0), labor, and the improvement of manufacturing efficiencies.
This is achieved using a platform offered by the TIC to host digital webinars and physical seminars with manufacturers exposed to technology, done in collaboration with industry experts under the TIC Business Education Series. Another avenue is via our Learning Factory project – a collaboration with the MIC Institute of Technology and the University of the West Indies’ (UWI) St. Augustine Campus. An injection of funding totaling TTD$1 million has been allocated for Phase 1 and this year’s equipment purchases.
MO: How does TTMA encourage training and skills development among its members?
MR: Over the past four years, TTMA has formed strategic partnerships to encourage training and skills development among its members. The Association is an industry partner lending support to the development of programs in collaboration with the MTI and the MIC Institute of Technology.
SME Pop-Up Shops
Discover the Excellence of DSB Marketing Limited
Your Premier Partner in Manufacturing and Supply
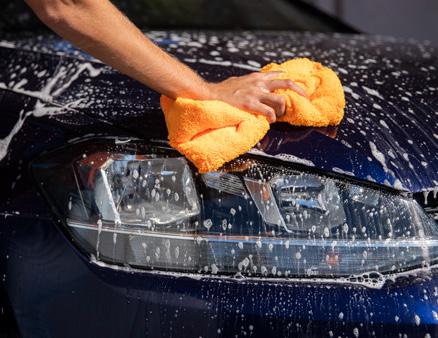
Your Reliable Source
Raw Materials: We are your dependable source of raw materials, supporting similar businesses and providing specialty chemicals to our esteemed partners.
Why Choose Us?
• Extensive Inventory: Over 100 products in stock.
• Large Production Capacity: Efficiently meet varying demands.
• Rapid Turnaround: Fast production runs and timely delivery.
Join Our Family
Welcome to DSB Marketing Limited!
As a proud family-owned and operated enterprise, we extend an invitation to join our growing family. We specialize in creating superior products in diverse sectors, ensuring unparalleled quality and service.
Our Expertise:
• Personal Care: Hair food, gel, pomade, shampoo, conditioner, body lotion, and cream.
• Household: A wide range of household essentials.
• Institutional: Products tailored for institutional use.
• Industrial: Specialty blends for industrial applications.
• Automotive: High-performance automotive products.
• Para Pharmaceutical: Specialty chemicals for para pharmaceutical needs.
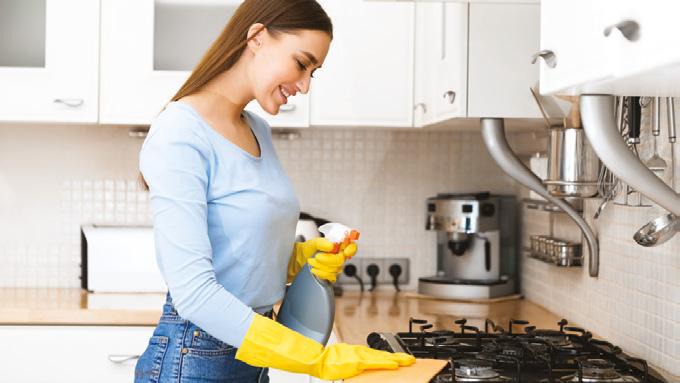
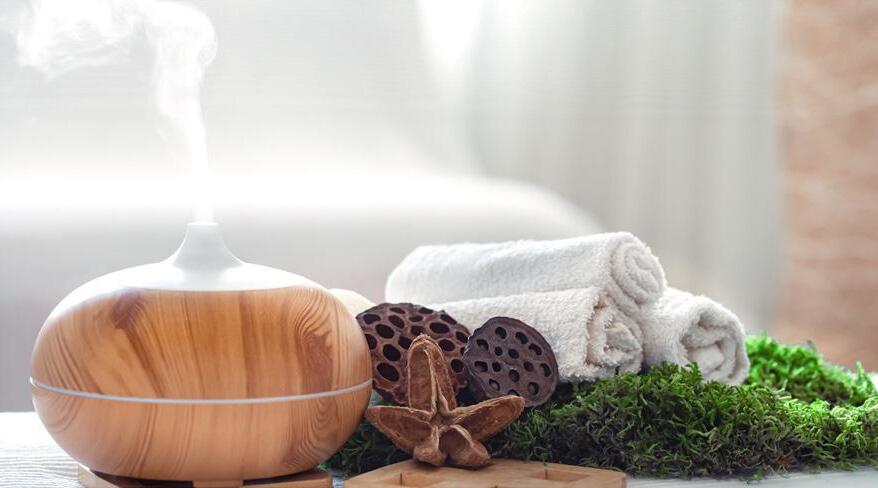
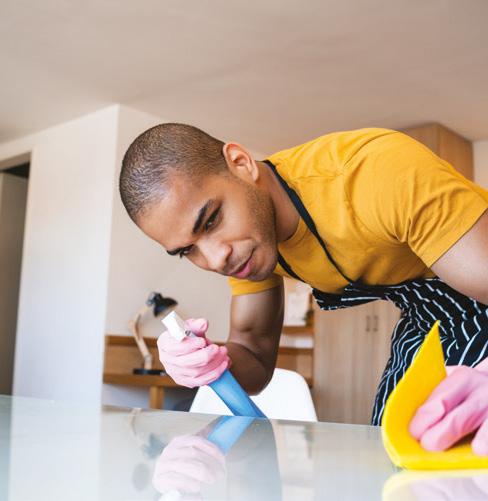
From its inception, DSB Marketing Limited has been dedicated to contract manufacturing. Our commitment to quality and service has allowed us to expand our product portfolio, ensuring we meet the evolving needs of our customers.
Experience the DSB Difference
Contact us today to learn more about how we can help your business thrive. Trust in DSB Marketing Limited – where excellence is a tradition.
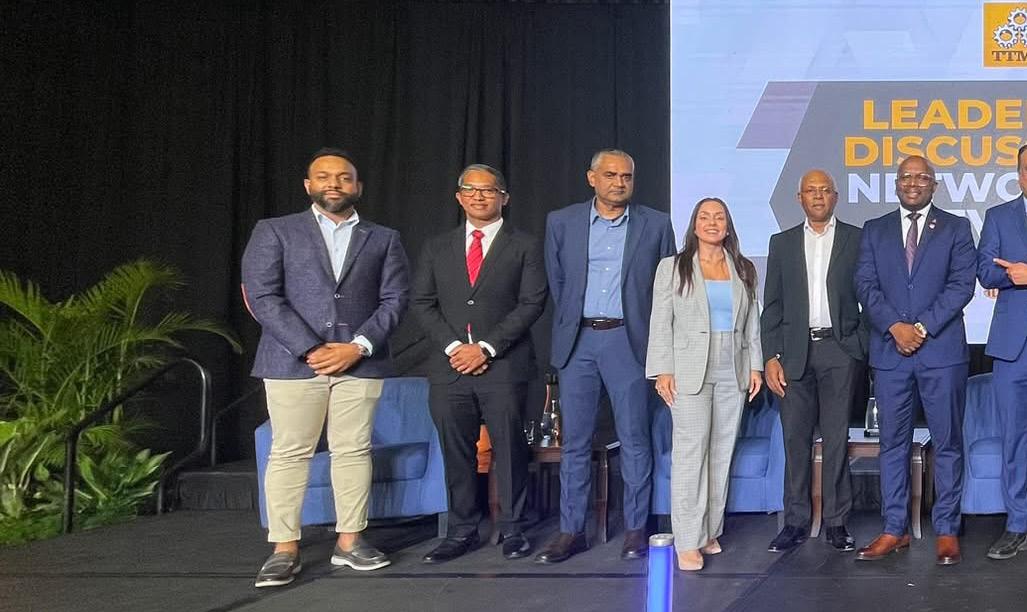
Over 200 new trainees have been enrolled in the Manufacturing Apprenticeship Program, along with 100+ in the Woodworking Apprenticeship Program (WOODAP). Similarly, TTMA partnered with UWI, where over 70 university students were placed in the manufacturing industry under the TTMA and UWI Summer Internship Program.
Furthermore, SMEs were granted access to free expert-led sessions under a newly established mentorship program, starting with the ‘She Leads’ session, where women-owned SMEs were able to gain invaluable insights and build connections to take their business to the next level.
MO: Looking ahead, how do you see the industry developing over the next five to 10 years?
MR: I am proud to share a forward-looking vision for our manufacturing sector over the next five to 10 years – one rooted in resilience, innovation, and strategic growth.
These include:
Strengthening our contribution to the national GDP
The manufacturing sector has shown commendable growth, with its contribution to Trinidad and Tobago’s GDP increasing from 18 percent in 2021 to 19.2 percent in 2022. In the same year, manufacturing value-adding reached 22.24 percent of GDP. This upward trend underscores the sector’s pivotal role in the nation’s economic landscape.
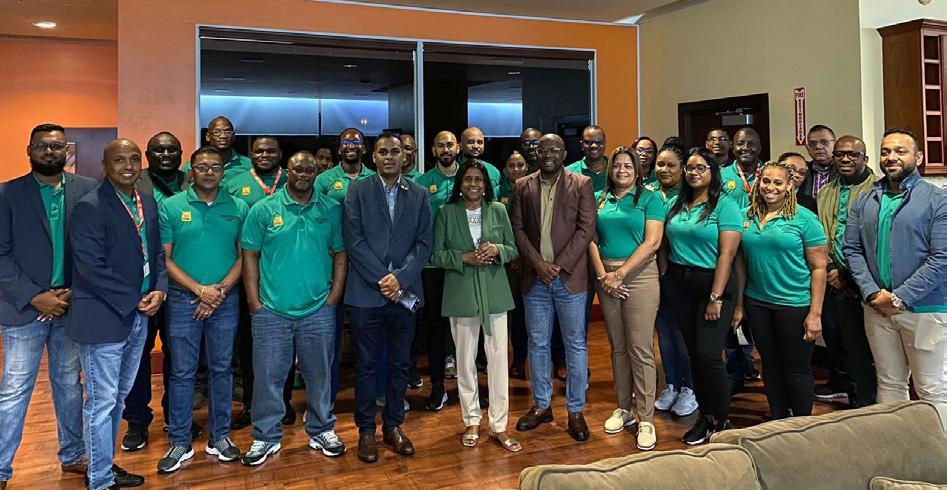
Driving economic diversification
Our sector is central to Trinidad and Tobago’s diversification strategy, reducing reliance on the energy sector. TTMA has launched a comprehensive manufacturing strategy aimed at producing 40 large manufacturers by the end of 2025, with a target of TTD$3.6 billion in export value, which we are on the way to achieving.
Strategic initiatives and collaborations
To support these ambitions, TTMA is actively engaging in:
1. Trade missions.
2. Infrastructure development, supporting the establishment of special economic zones to attract investment and boost exports.
3. Policy advocacy.
Annual General Meeting 2024
Trade mission to Ghana
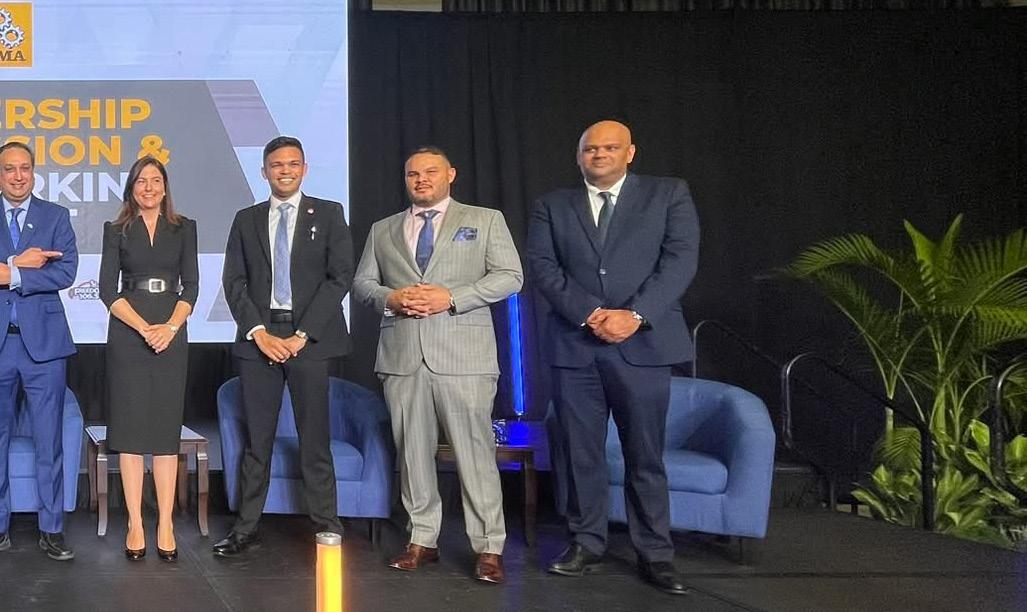
Embracing innovation and sustainability Looking ahead, TTMA is committed to fostering innovation, sustainability, and digital transformation within the manufacturing sector. By leveraging technology and sustainable practices, we aim to enhance productivity and competitiveness on a global scale.
In summary, the manufacturing sector in Trinidad and Tobago is poised for significant growth and transformation. Through strategic initiatives, collaborative efforts, and a commitment to innovation, we are confident in our ability to drive economic diversification and contribute meaningfully to the nation’s prosperity.
MO: With this in mind, what are TTMA’s key future priorities in order to continue representing the interests of its industry members?
MR: Firstly, and perhaps most significantly, our new strategic export goal is to grow non-energy exports from TTD$6.2 billion at the close of 2024 to TTD$10.6 billion by 2030, reflecting a conservative 71 percent increase in non-energy exports over the next five-and-a-half years. We continue to work with those in authority to create an enabling environment that will allow non-energy exports to reach this target.
We will also continue to foster the growth of SMEs in Trinidad and Tobago, which account for over 85 percent of local businesses and employ 200,000+ people directly. Most SMEs in the country have hindrances in engaging in
trade, with some of these challenges including registering their business, creating product barcodes, developing export plans, sourcing financing for equipment, and advocating for their interests, thus curtailing the advancement of their operations. We invite SMEs to reach out to us and join TTMA with lowered membership fees so we can help them grow their business.
The Association would also like to work with the government to acquire a 20-acre parcel of land in a centralized area with highway access to construct a 200,000-square-foot Caribbean trade and convention center to host our TIC and other events that foster global trade. This will assist our vision to position Trinidad and Tobago as the regional manufacturing powerhouse for the next 25 years.
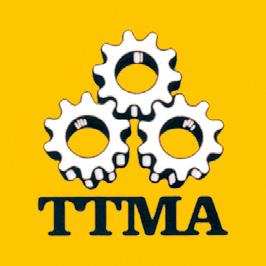
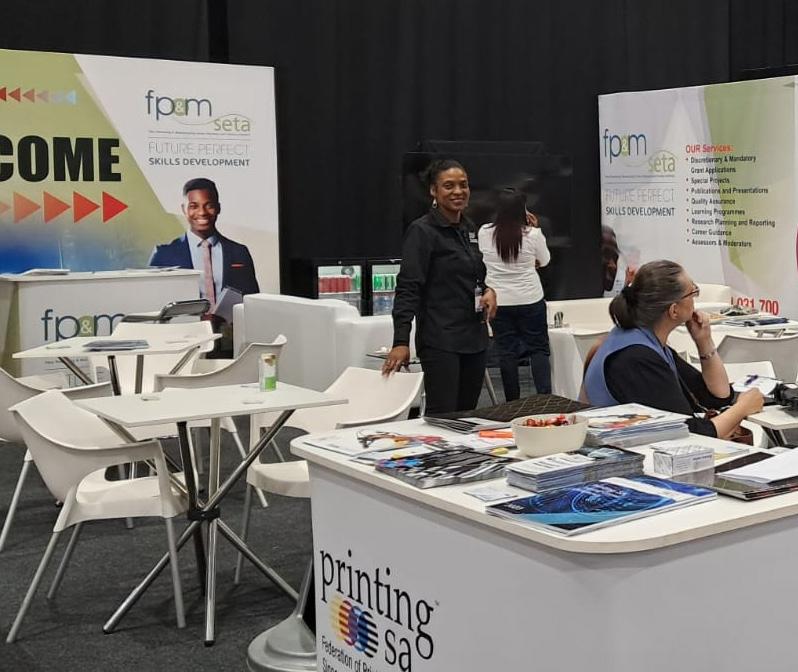
SOUTH AFRICA PRINTING AND PACKAGING SPOTLIGHT
RFrom an economic contribution perspective, the printing and packaging industry plays a vital role in South Africa, where technology and sustainability also present exciting opportunities
Writer: Jack Salter | Project Manager: Joseph Perfitt
ecent research published towards the end of 2024 confirms that two key elements of the packaging sector – plastic and paper packaging – have an estimated market value of ZAR65 billion in South Africa, whilst printing is worth an additional ZAR25 billion.
This combined market value of ZAR90 billion creates jobs for approximately 40,000 to 45,000 employees across the sector. Printing and packaging also feed into retail, food and beverage, pharmaceuticals, and logistics, creating additional jobs in these spaces.
Alongside its significant contributions to a developing economy, the industry is impactful on many different fronts. In education, for example, printing and packaging provide
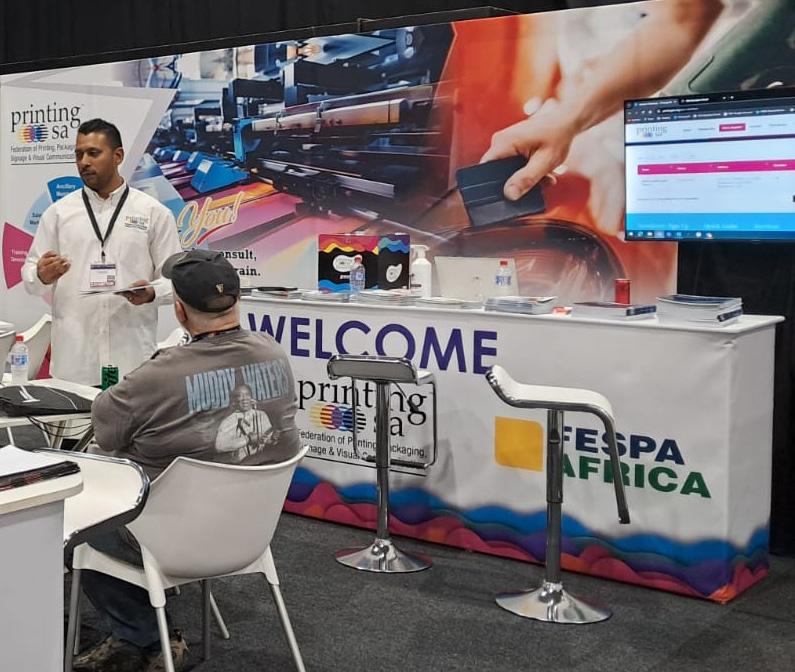
PRINTING SPOTLIGHT
the vast majority of scholars with crucial learning materials.
In the consumer goods market, the industry plays a vital role in growing the brand equity of company owners. In the print packaging space, meanwhile, the industry profoundly impacts a wide gamut of safety, security, and product primary and enhancement features.
In the security segment, the industry is core to maintaining tactile security features that satisfy a plethora of commercial business requirements, including passports, ID cards, ballot papers, and more.
However, these fast-evolving product demands come with other exciting opportunities in terms of technology and sustainability.
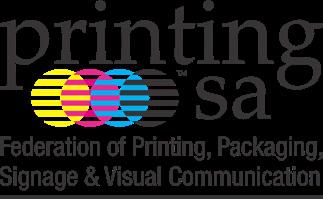
In the dynamic landscape of South Africa’s commercial printing and packaging industry, the need for efficient, cost-effective, and sustainable solutions has never been more pressing.
The challenge for the sector is to implement eco-friendly practices and invest in printers and similar equipment to contribute meaningfully to a healthier planet.
There is also now a more concerted drive from the industry to adopt sustainable practices to improve South Africa’s export ability and reduce the country’s trade deficit.
This means dealing with the likes of Europe, North America, and Asia, where sustainability is at the forefront and subsequently being adopted in South Africa.
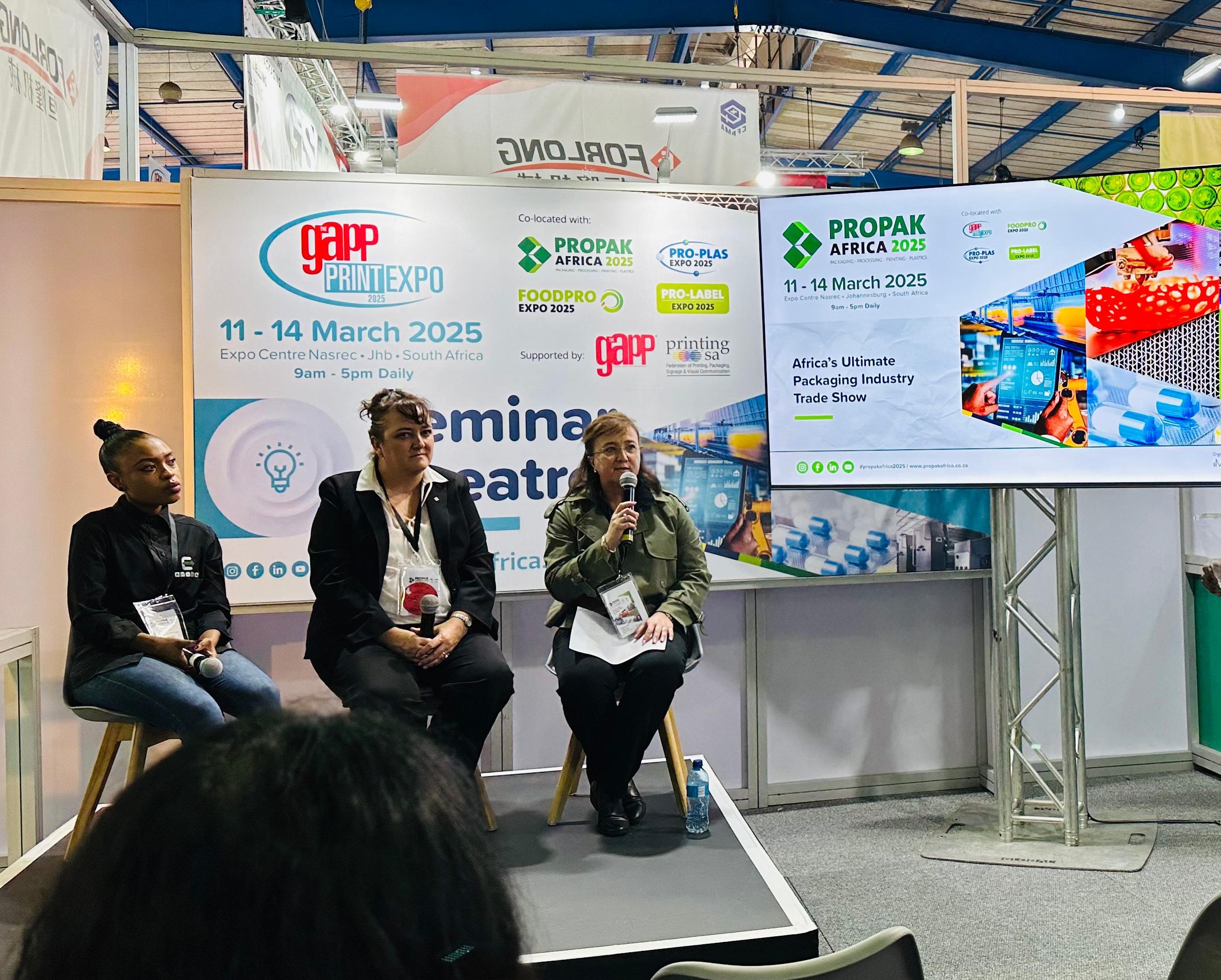
PRINTING SA INTERVIEW:
Printing SA is the official voice and representative body of the printing, packaging, signage, and visual communications industries in South Africa. Jermaine Naicker, Managing Director, goes to print with his perspective on the sector’s socioeconomic impact
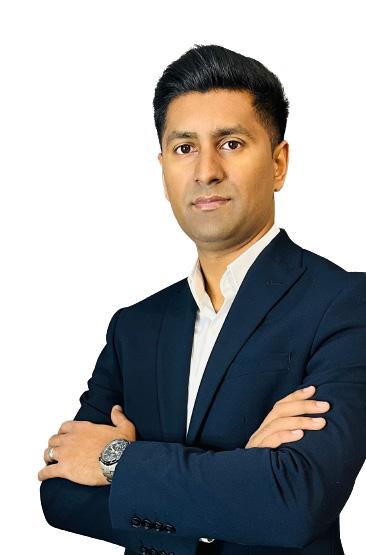
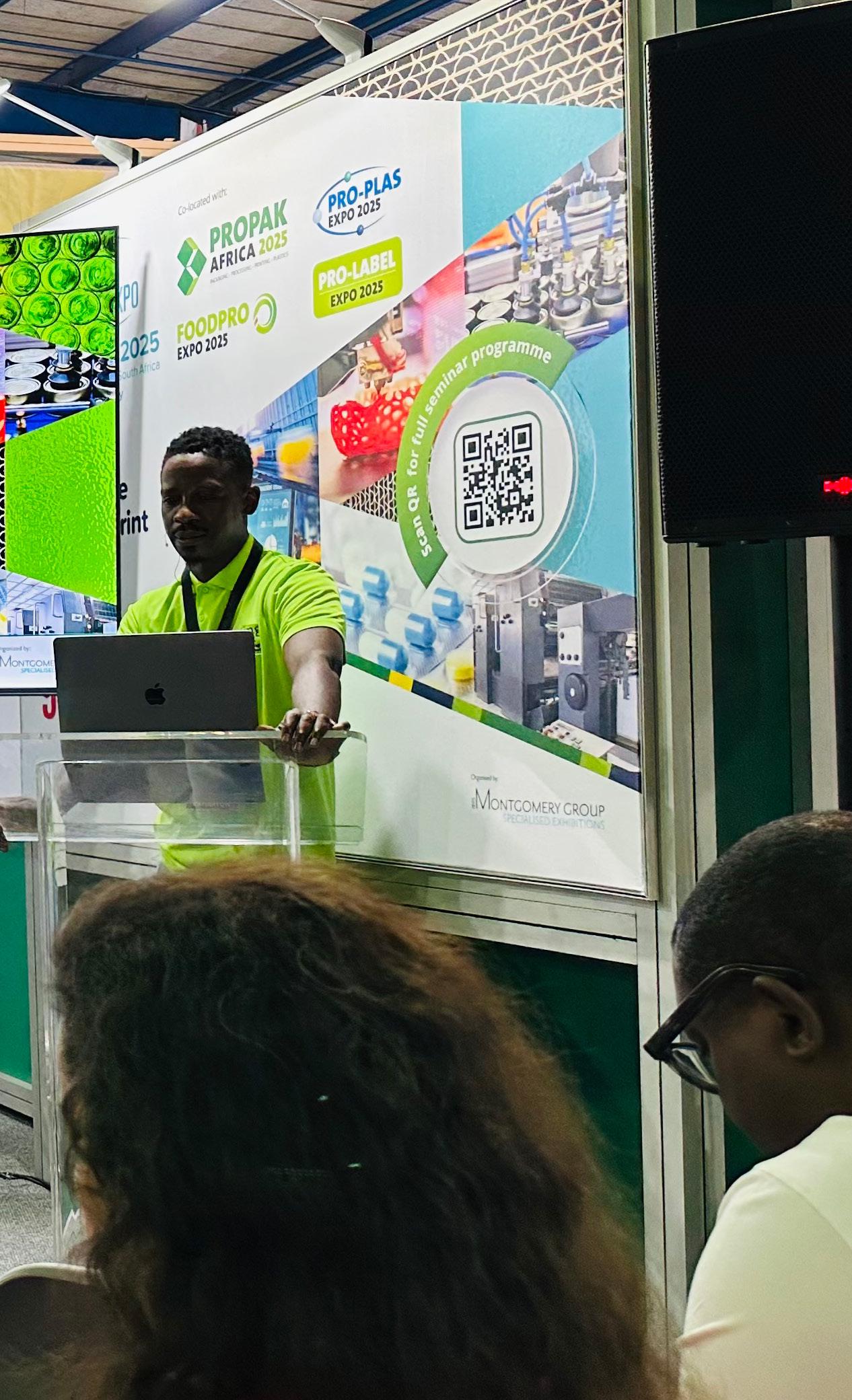

Manufacturing Outlook (MO): Firstly, please introduce us to Printing SA as the official voice of the South African printing and packaging industry.
Jermaine Naicker, Managing Director (JN): Printing SA’s vision is to support, preserve, and grow the printing, packaging, signage, and visual communications industry.
Those three words encapsulate why we exist – we’re here to fundamentally ensure we provide support, preservation, and growth opportunities for the industry through conferring, consulting, campaigning, and training.
Whilst you may have various speciality industry associations, Printing SA broadly covers the printing and packaging industry. This includes specialisations in print, whether it’s digital printing, graphic design, lithographic printing, gravure printing, or flexographic printing.
Then, the packaging element segues into components of our industry that do printing for packaged goods, so it’s not mainstream packaging per se, but the actual printing that goes onto it.
Our core objective is to ensure the industry is sustainable in the future, and we do that in several ways. The first pillar we focus on is the commercial and technical aspects, i.e. the policy and advocacy role that we play.
From an advocacy perspective, we liaise and deal with government institutions and organs of state to ensure that when policy is developed for our industry, it is much more favourable from a business environment point of view than it would originally be without our intervention.
We’ve recently been working on some of the Employment Equity Act amendments impacting South Africa that will put sectoral targets into place, which could adversely impact the industry.
Then there’s the Air Quality Act where, from a sustainability perspective, there’s been some legislation touted by government that we’ve represented the industry on. It could have had serious financial implications for the industry and lead to a large demise of smaller players in the market, so we operate heavily in that space.
On that front, we’re working on the establishment of an industry master plan which serves as a strategic blueprint to drive growth, sustainability, and competitiveness in an evolving landscape. It would involve collaboration between industry stakeholders, government, trade unions, and training institutions to address key challenges and unlock opportunities for industry.
We do both human resource and technical consulting for the industry, and one of the bigger things we do is training and development, which speaks to the industry sustainable growth agenda of Printing SA. At the moment, we offer in excess of 70 courses, ranging from accredited to short, administrative, and technical programmes.
The last thing we do as the voice of the industry is assume a thought leadership responsibility. We host a plethora of seminars and disseminate information to keep our members abreast of the latest movements in both the industry and peripheries of the economy impacting the sector.
MO: What is your current take on the printing and packaging industry in South Africa? Is it particularly exciting or challenging to work in?
JN: Our industry is both exciting and challenging to work in. There are different perceptions of what printing and packaging are about in the minds of people, which creates a challenge for us. In this way, we, as an industry association, also play a pivotal part in educating society about its various integrations and relevance.
“THE INTEGRATION OF SMART PACKAGING TECHNOLOGIES AND FAST-CHANGING CONSUMER PREFERENCES INTO THE DIFFERENT ADAPTATIONS AND APPLICATIONS OF PRINT HAS BECOME PHENOMENAL”
– JERMAINE NAICKER, MANAGING DIRECTOR, PRINTING SA
We’re seeing the greatest opportunities with the advent of technology and how we adopt all these technological changes to evolve as an industry.
Looking at the workforce coming in, nobody necessarily wants to operate manual machines, so the integration of technology gives us a new challenge in how we develop skills and change the perceptions of people coming in, which is exciting.
The integration of smart packaging technologies and fast-changing consumer preferences into the different adaptations and applications of print has become phenomenal.
MO: What socioeconomic role does the printing and packaging industry play in South Africa, and how do you promote awareness of this?
JN: Up top is the employment and skills development aspect. The unemployment rate in South Africa currently sits at about 32 percent, which is significantly higher than other emerging and developed economies across the world.
We, therefore, focus very heavily on skills development as a conduit to creating employment opportunities.
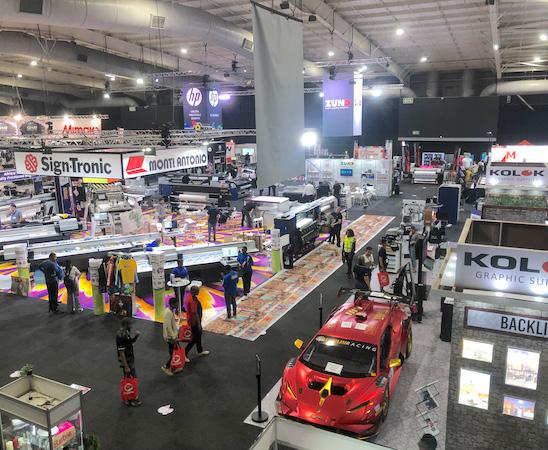
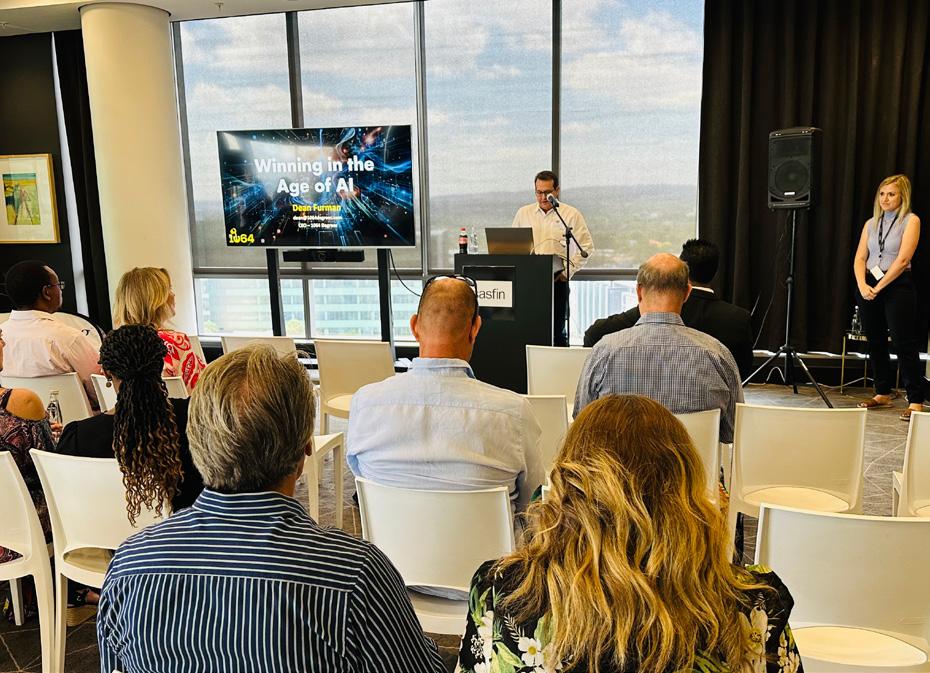
That also comes with a key partnership with the Fibre Processing and Manufacturing (FP&M) Sector, Education, and Training Authority (SETA), which works very closely with us to fund opportunities and interventions that we can use to narrow the skills gap and unemployment rate in South Africa. Through that funding, we provide unemployed people with upskilling, experiential learning, and internship opportunities.
Another programme that we still offer is the Foundational Learning Programme. Once this has been completed, we thrust learners into the industry and allow them the opportunity to gain first-hand experience of the wide gamut of complexities that the industry is comprised of, and how integrated this industry is in the daily lives of people.
Over the years, about 20 percent of learners have been absorbed by the sector and become qualified artisans, which is an impactful story to tell from a socioeconomic perspective.
Sustainability is another area we want to get heavily involved in to support the industry and provide information to centre operations and activities around eco-friendly business practices. That’s going to be our core focus over the next few years.
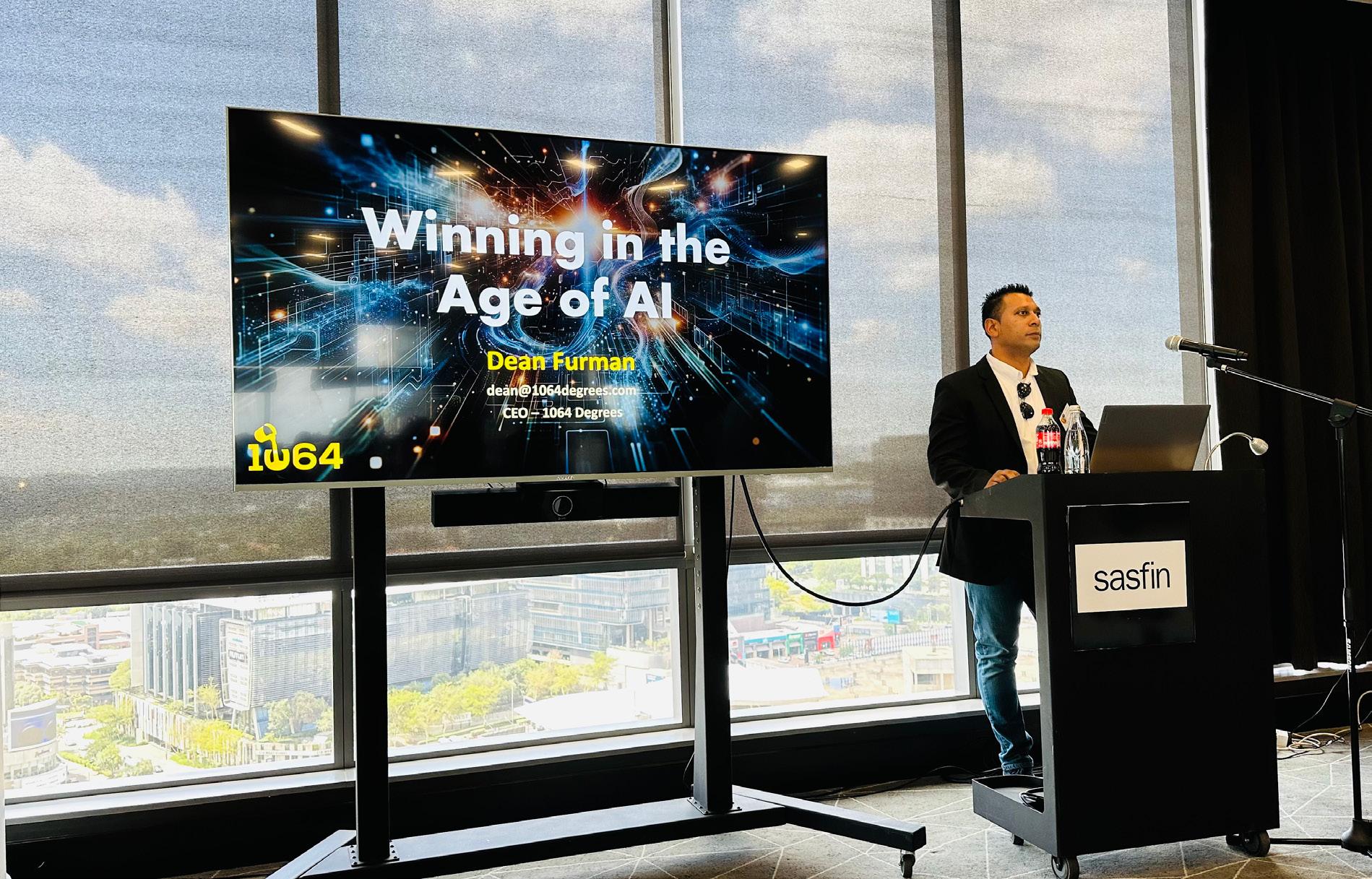
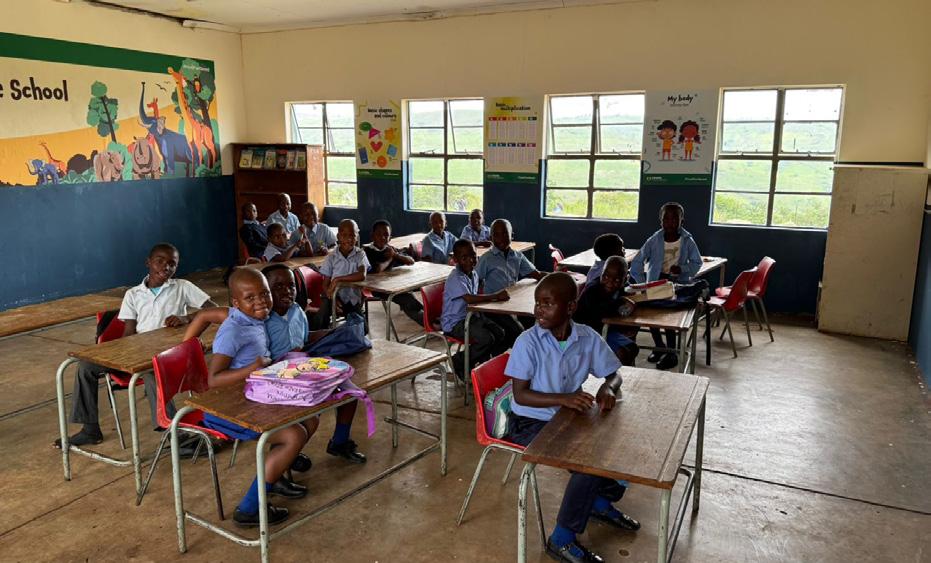
MO: How does Printing SA represent industry interests and ensure all stakeholders and members prosper?
JN: As an industry association, everything we do is fundamentally driven by our members’ needs and what they require us to do for them.
Take training and development, for example – they would come to us with a skills gap that is having a downstream economic impact as these skills become more expensive, and say we need to arrest the situation. Typically, we would come up with solutions for the
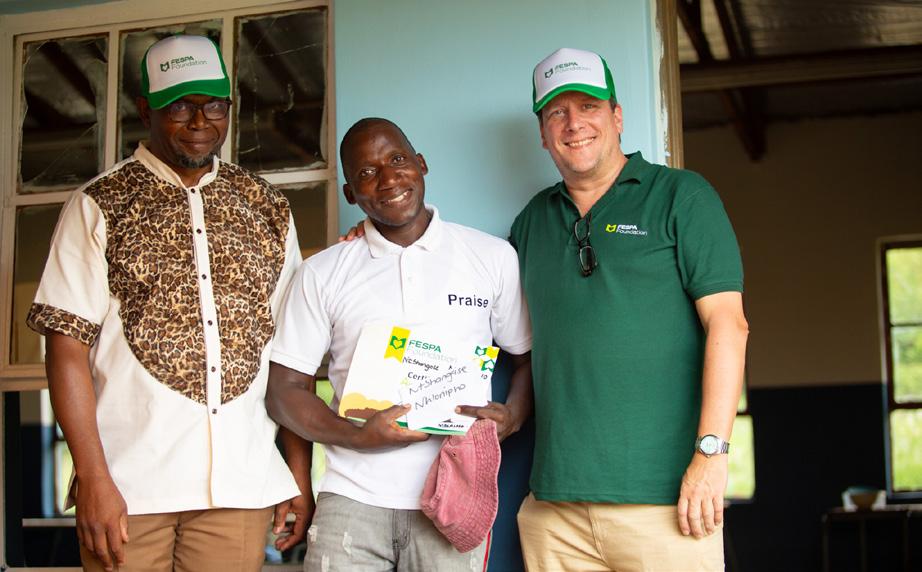
industry to ensure we can close the skills gap and make more skills available to the industry.
Another example is if there’s a huge evolution and proliferation of technology and artificial intelligence (AI) impacting the industry, we’re asked to integrate AI into our training courses and develop new ones that are more aligned with technological advancements.
Or, perhaps members come back to us and say there’s a piece of legislation touted by government and it’s going to be unfavourable for the industry based on plausible reasons. In the recent case with the Employment Equity
CSI initiative by FESPA
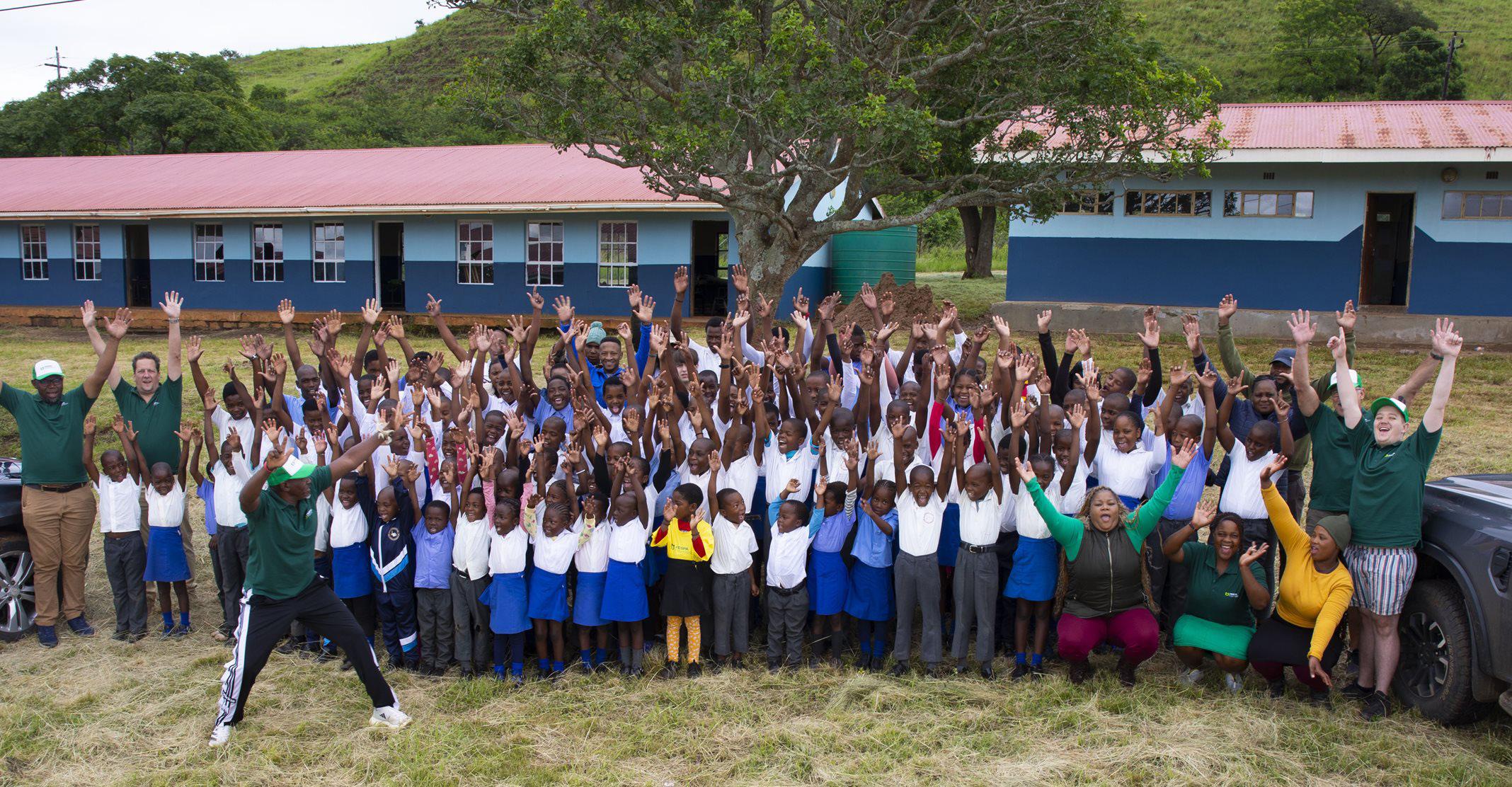
“THERE ARE DIFFERENT PERCEPTIONS OF WHAT PRINTING AND PACKAGING ARE ABOUT IN THE MINDS OF PEOPLE, WHICH CREATES A CHALLENGE FOR US. IN THIS WAY, WE, AS AN INDUSTRY ASSOCIATION, ALSO PLAY A PIVOTAL PART IN EDUCATING SOCIETY ABOUT ITS VARIOUS INTEGRATIONS AND RELEVANCE”
– JERMAINE NAICKER, MANAGING DIRECTOR, PRINTING SA
Act, there were sectoral targets put into place.
The government argued that because South Africa is such a diverse country, there are certain inclusion targets that need to be met in order to be compliant with operating a business. This came as a negative because the rationale behind the act and the practicality around it created significant complexities when operating a business in South Africa.
Printing SA had to take that, understand it, and spend money with attorneys and legal firms to fight this for our industry to represent its interests. Members drive what we do as an industry association, and those are just some of the ways in which we represent their interests.
MO: Equally, how does Printing SA act as the first port of call for government and other important local and international bodies wanting to engage the industry?
JN: As we are the collective voice for the printing and packaging industry, a lot of players around the globe
approach us to access our members and the market.
From a government perspective, if we look at policy development, we are approached to engage on whether initiatives that are being developed are realistic and in line with the industry’s needs. If we determine that a policy has merit, based on member consultation, we refine it with them so that it doesn’t adversely impact the industry.
That’s how we engage with government on various fronts; it could be from a labour, sustainability, training and development, or even financial perspective.
Not many international bodies engage the industry except the various ones that Printing SA belongs to. For example, we belong to the World Print and Communication Forum (WPCF), a global conferencing forum that convenes annually and talks about the printing and packaging trends in particular countries. It also positions and communicates on a global front what industries around the world are doing and creates a core message around that.
Rural project by FESPA
MO: How do you see the South African printing and packaging industry developing over the next five years?
JN: More than ever, we’re seeing significant momentum being created as far as sustainable and eco-friendly products are concerned.
If you look at global statistics, South Africa is an emerging market and we have a higher population of youth and educated young people. Their inclination to understand and procure sustainable and eco-friendly practices is a lot greater, so the market is adjusting to that.
In e-commerce and packaging solutions, with the advent of online shopping, there’s demand for durable, lightweight, and cost-effective packaging. Different packaging solutions around protective, tamper-proof, and sustainable shipping materials are also being driven by e-commerce.
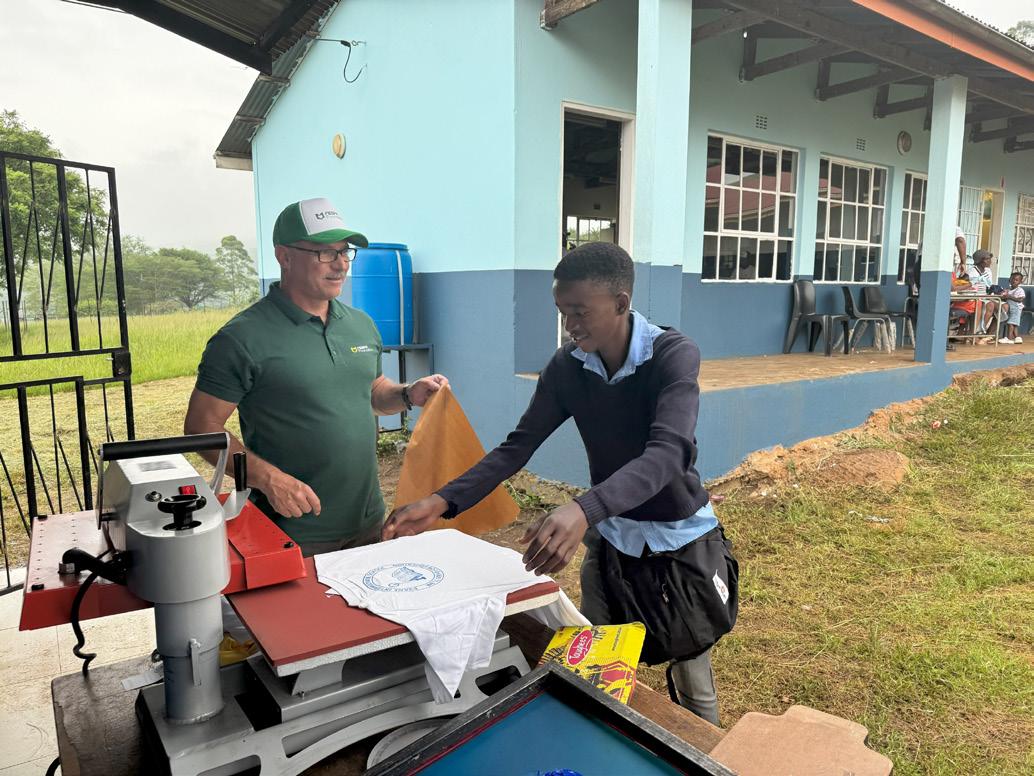
Digital transformation and smart packaging are now starting to gain a lot of traction in South Africa, and I believe in the next five years we will realise an increased presence of this in the market with the integration of automation, AI, and robotics.
Localisation and industry growth opportunities speak to the industry master plan that I mentioned earlier. South Africa is looking to expand local production to reduce the reliance on imported materials and supply chain disruptions.
We’re also looking at growth in the export of packaging products, and government is now showing some interest in incentives for local manufacturers. There’s a drive towards the localisation of manufacturing capabilities in South Africa so that we can convert our raw materials into value-adding goods for the export market.
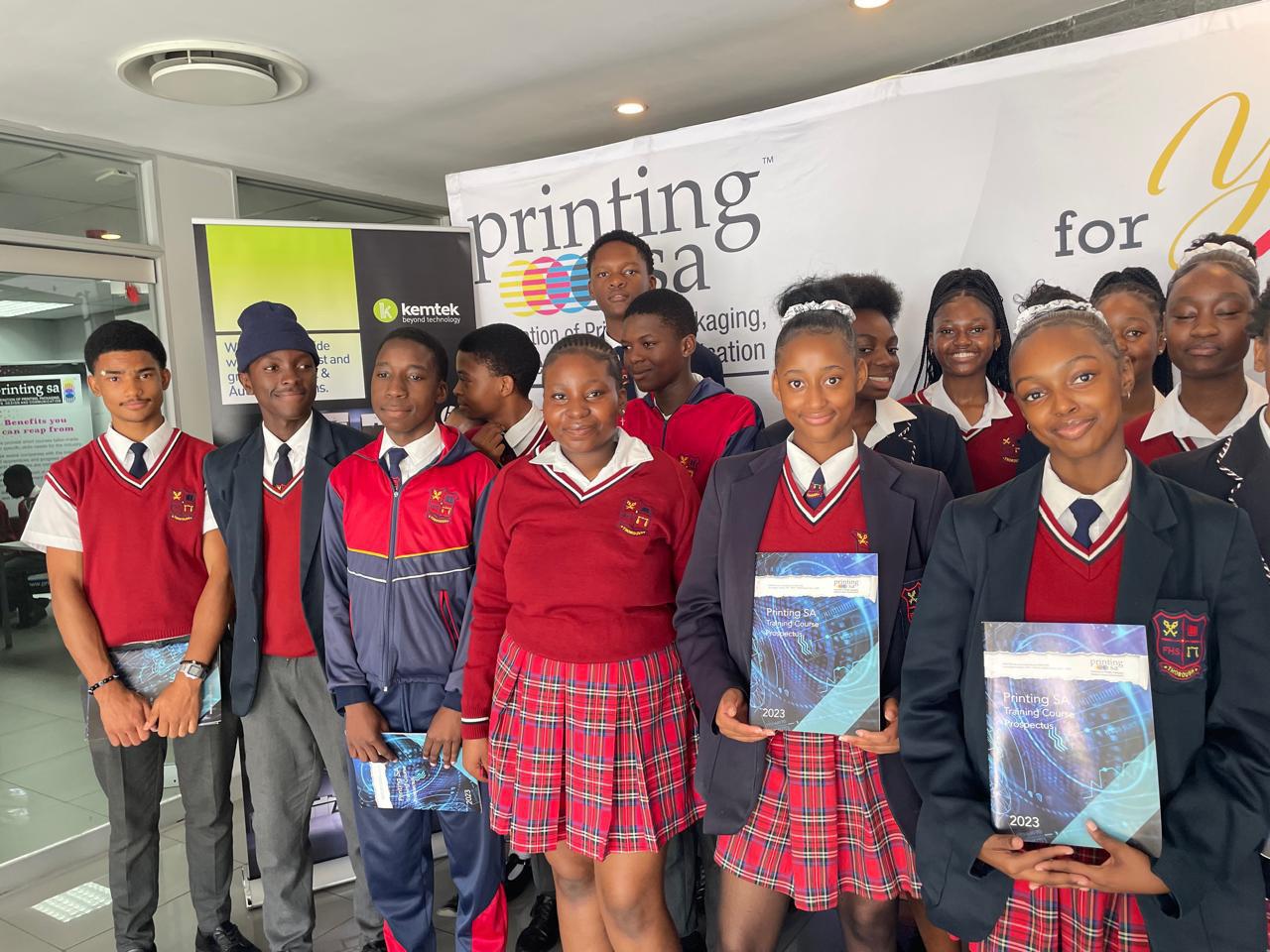
Lastly, skills development and job creation will be high up on the agenda for the industry and a core focus over the next five years. Technical and vocational education and training (TVET) colleges are being given targets to ensure their courses are aligned with industry demand and they are creating employment opportunities.
MO: Finally, what are Printing SA’s key priorities in order to continue representing the South African printing and packaging industry?
JN: Firstly, the establishment of an industry master plan to protect the local industry, inject spending into it, and close the skills gap.
A lot of R&D support will be available for the industry so it can make informed decisions, and sustainability is going to be a core focus of ours.
The last one is thought leadership and how we keep the industry abreast. This will come in many forms, including thought leadership events to bring international knowledge exchange to South Africa so we’re well aware of what’s going on in the industry and can make informed decisions.
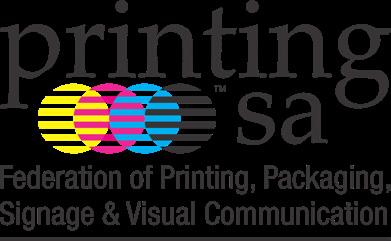
Tel: 011 287 1160 asamuel@printingsa.org printingsa.org
Career day
Rural project by FESPA
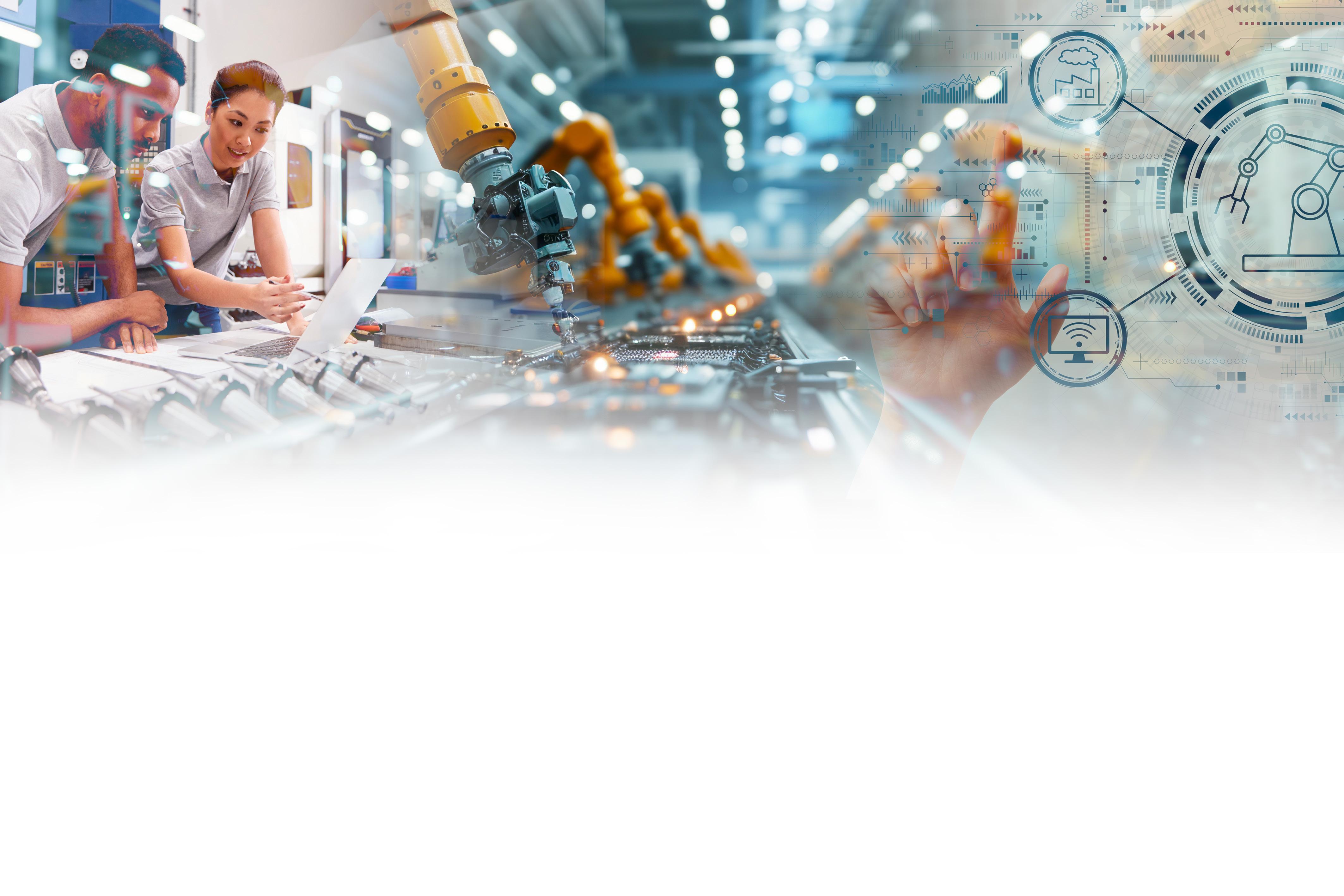
A production-line of exclusive content, delivered straight to your inbox
As manufacturing organisations worldwide confront unprecedented change, embracing technological innovations and incorporating critical environmental sustainability agendas, now more than ever is the time to showcase the strides being taken in this dynamic sector.
A multi-channel brand, Manufacturing Outlook brings you the positive developments driven by organisations across the global manufacturing industry through its various platforms.
Discover exclusive content distributed through its website, online magazine, social media campaigns and digital dispatches, delivered straight to your inbox with a bi-weekly newsletter.
Through these compelling media channels, Manufacturing Outlook will continue to foreground the movers and shakers of the industry.
To participate as a featured company and join us in this exciting endeavour, contact one of our Project Managers today.
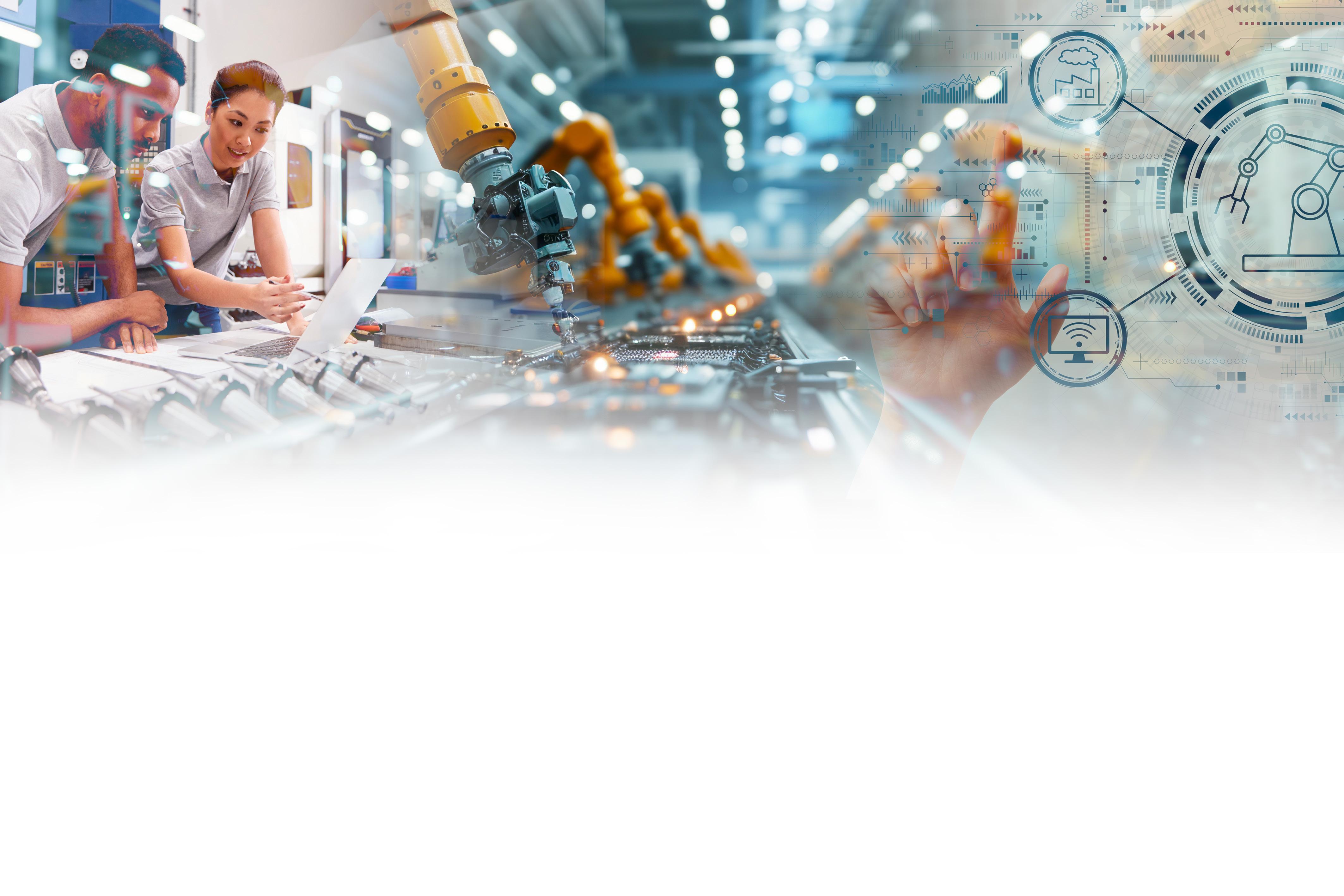
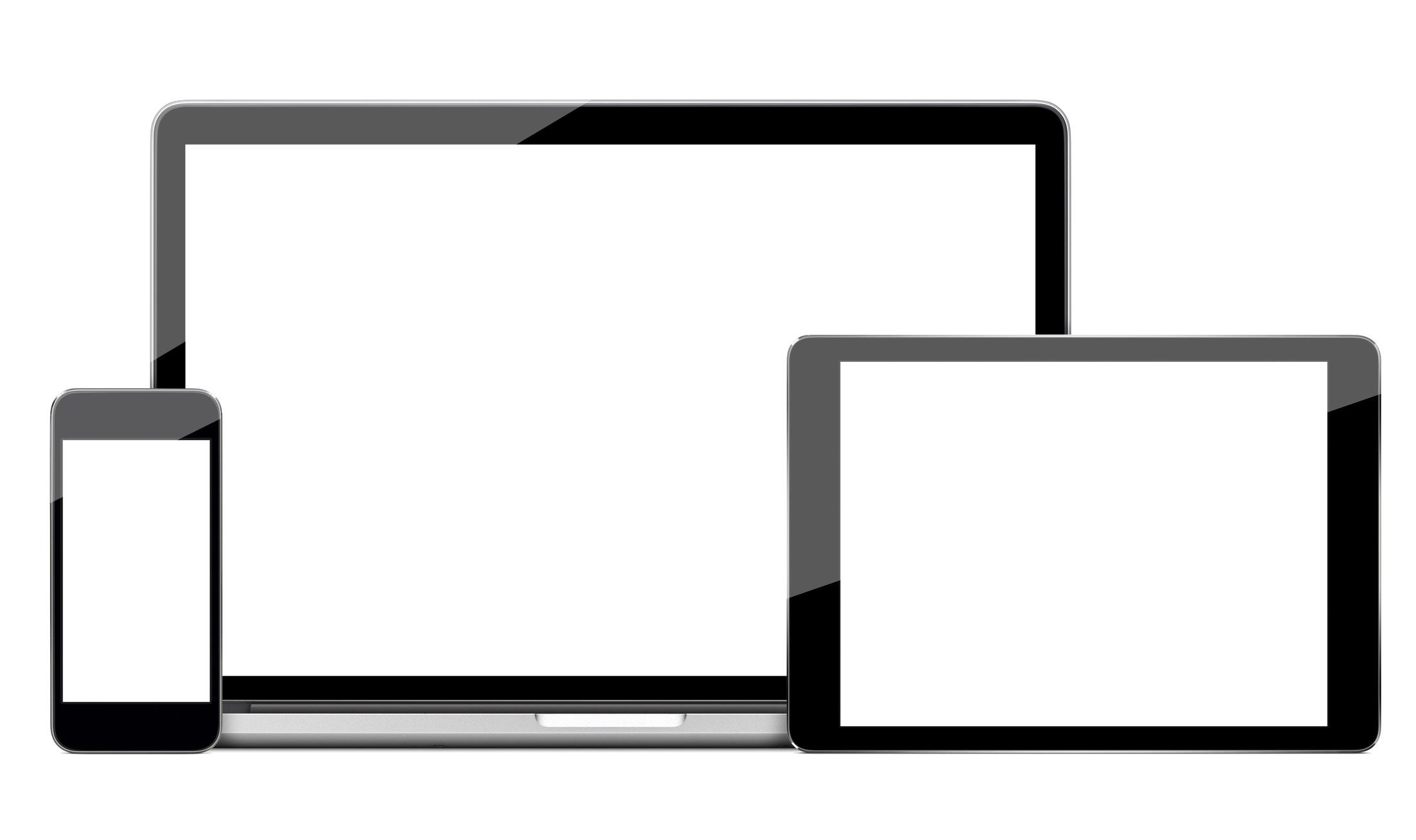
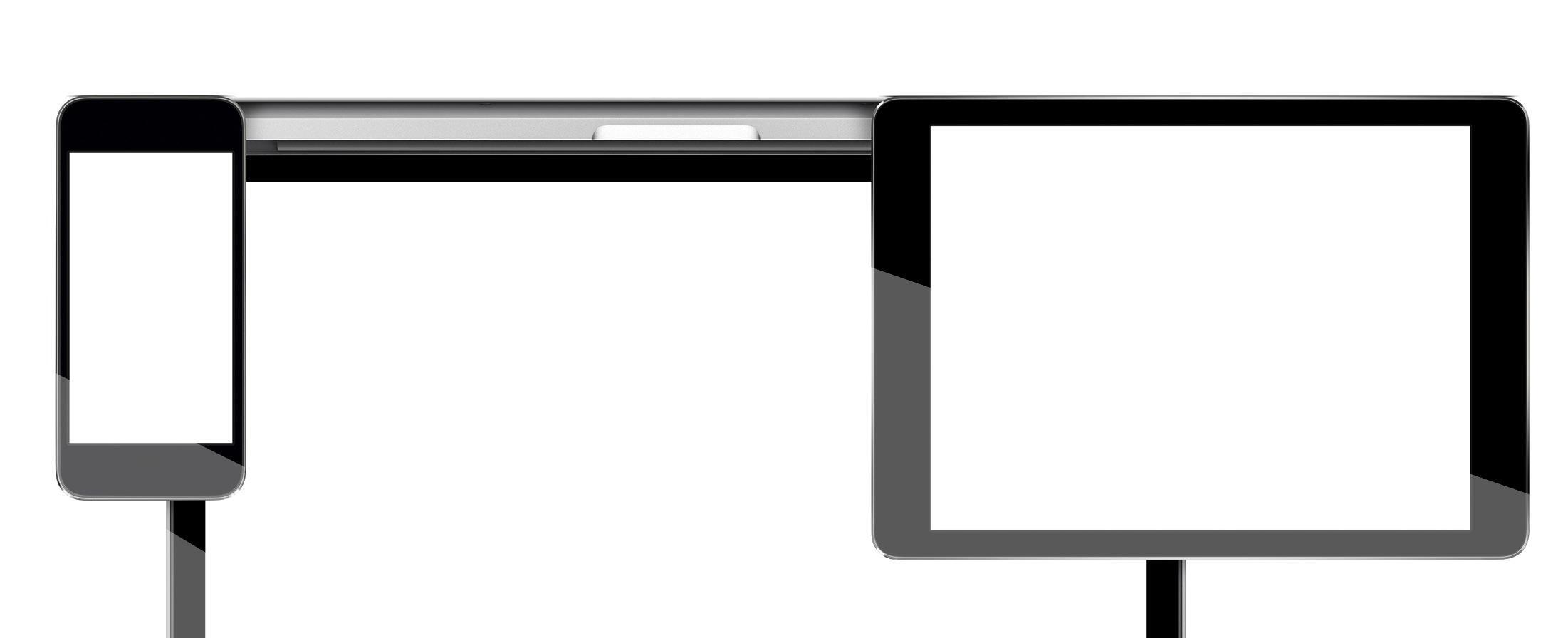
CAPABILITY SOVEREIGN
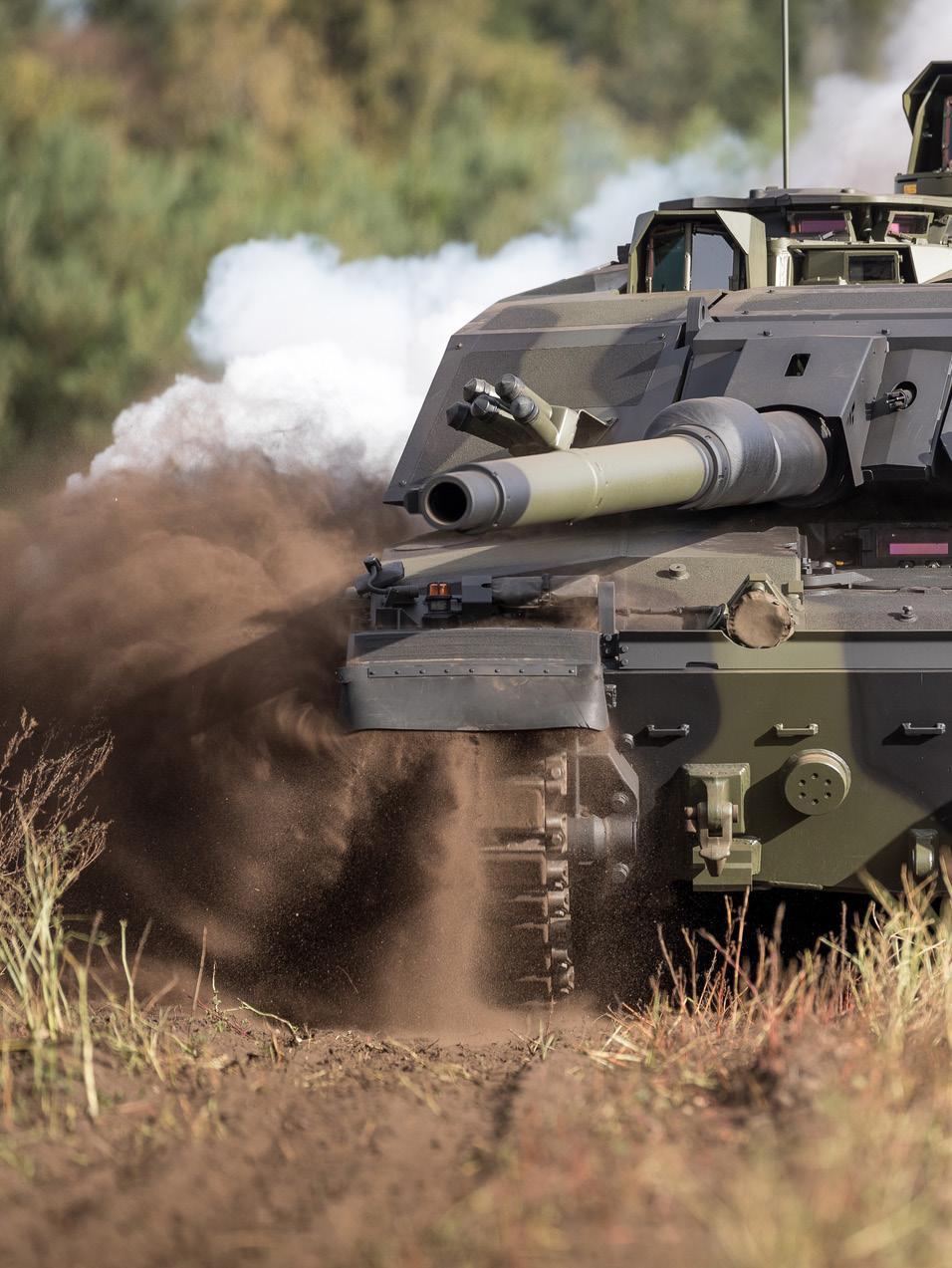
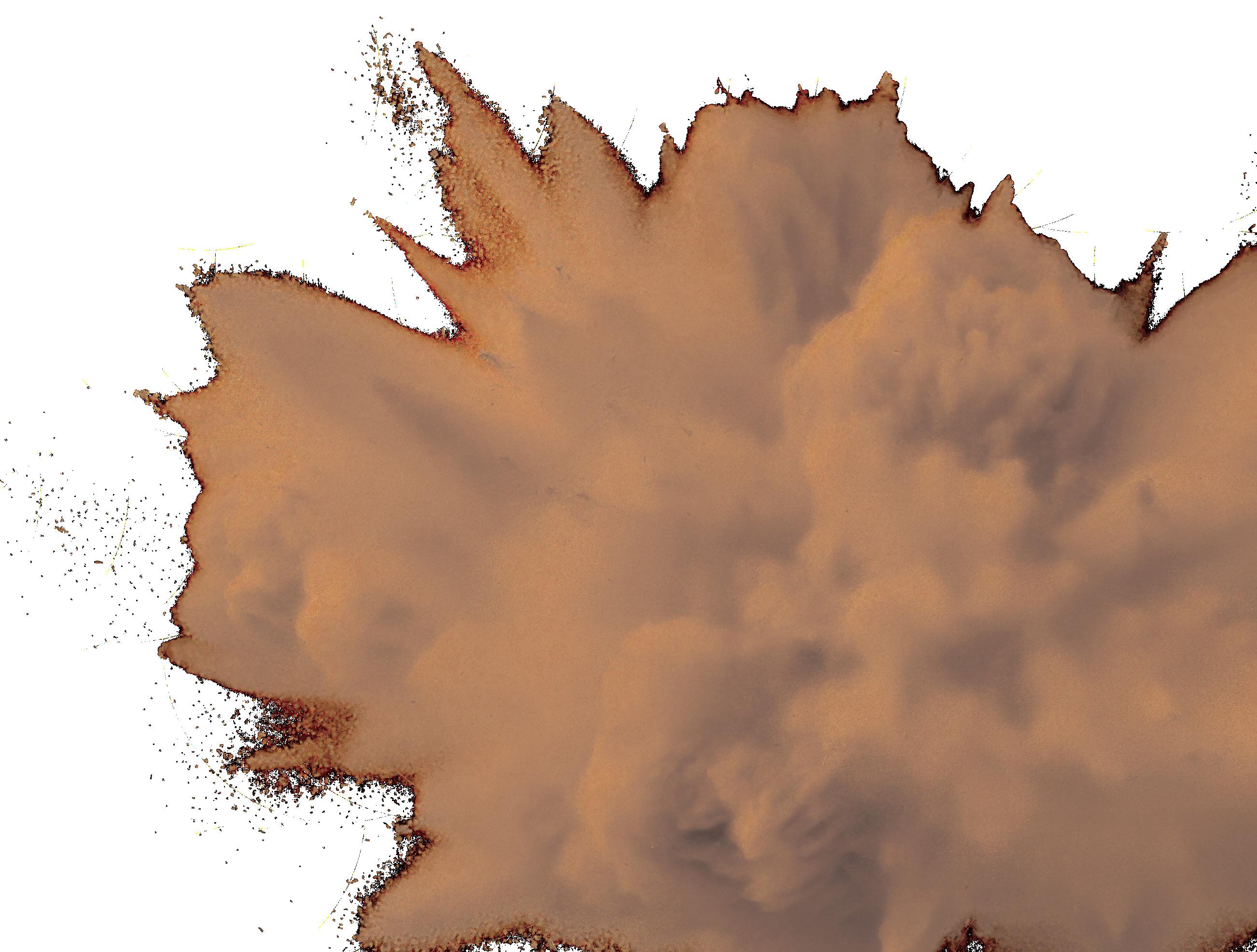
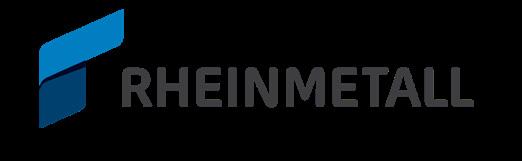
A champion of British engineering, Rheinmetall UK is committed to ensuring the country remains a global leader in defence innovation as we find out from Deputy CEO, Rebecca Richards Writer: Jack Salter | Project Manager: Cameron Lawrence
CAPABILITY CAPABILITY
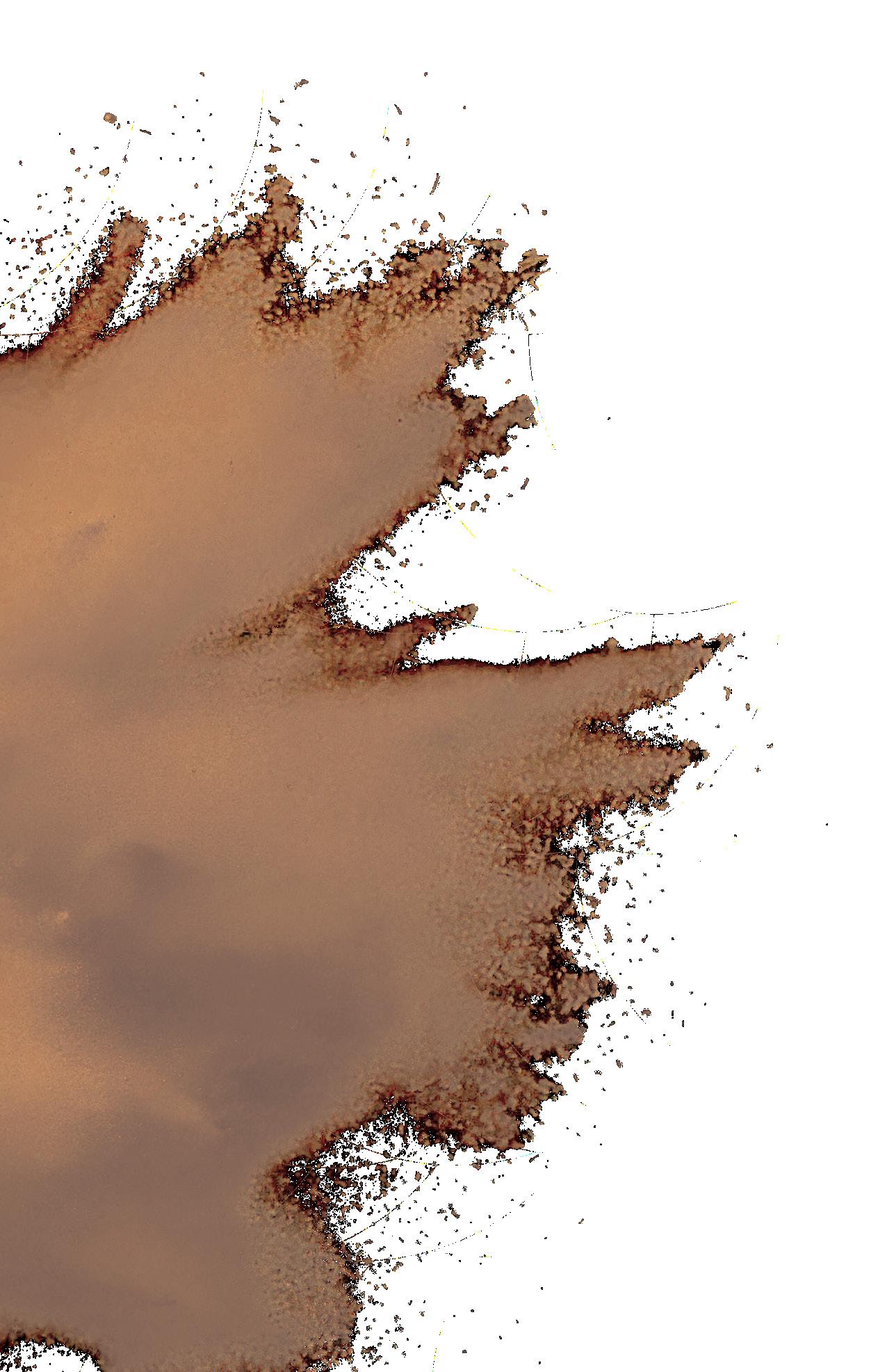
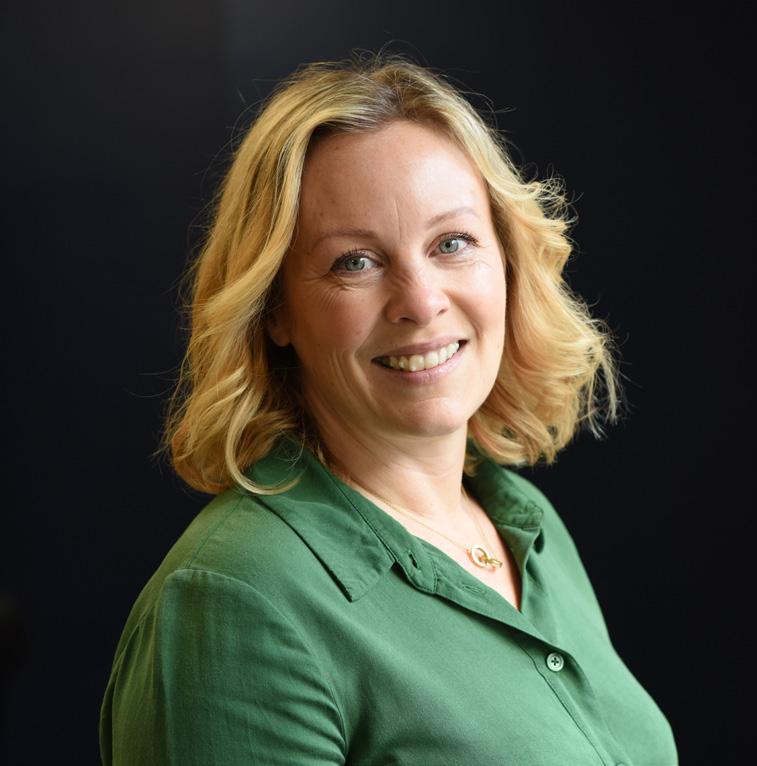
Rebecca Richards, DeputyCEO
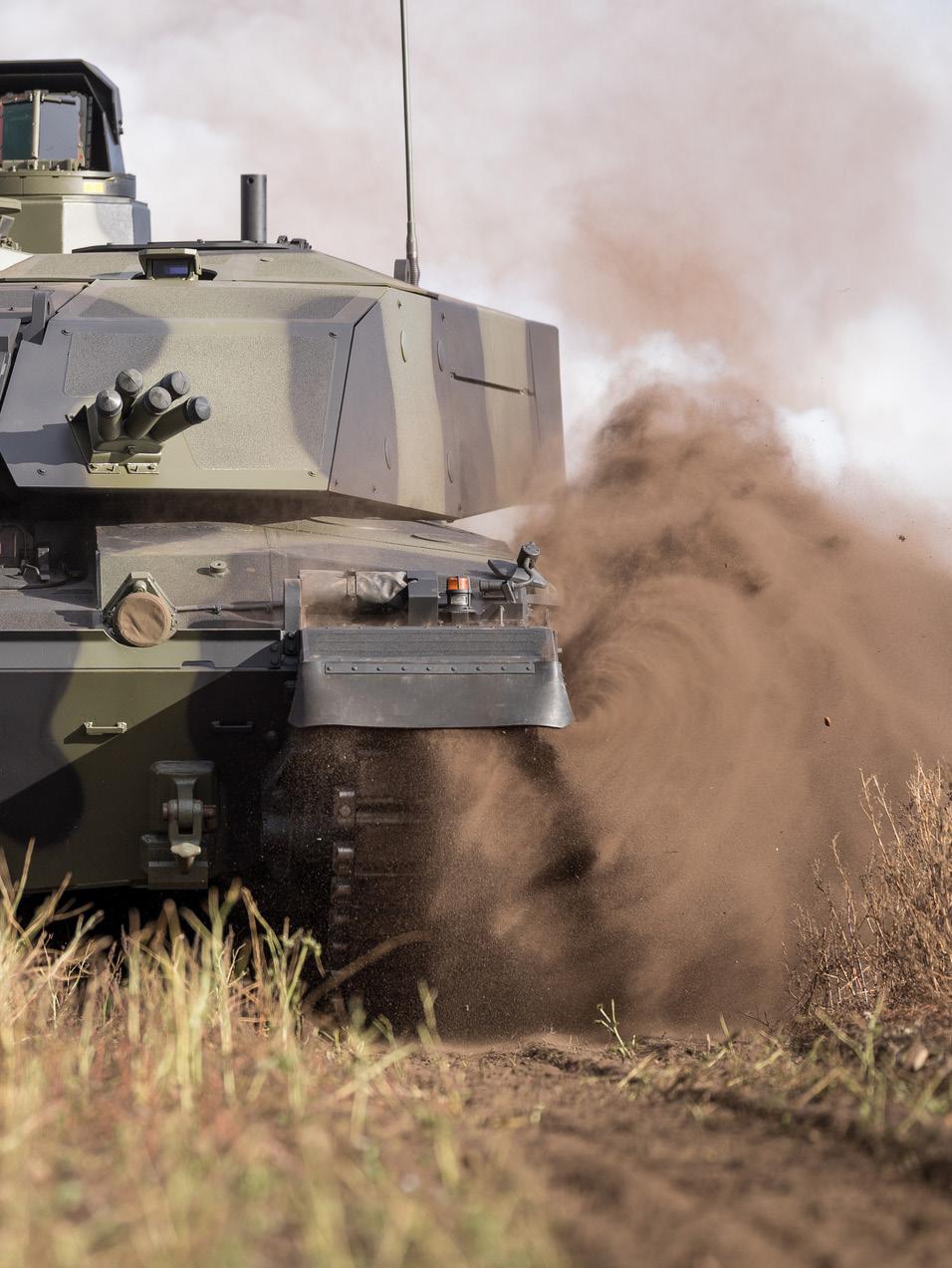
Defence has always played a vital role in ensuring national security, but in today’s increasingly complex and uncertain global landscape, its importance has only intensified.
That said, the value of defence extends far beyond security alone; it’s a catalyst for economic growth, innovation, and regeneration, particularly in areas that benefit from long-term investment, skilled employment, and industrial revitalisation.
In Europe and the Middle East (EME) specifically, modernisation and innovation across the sector is being driven by increased defence spending, evolving security threats, and a renewed emphasis on NATO collaboration.
“It’s a truly dynamic environment – one that’s pushing boundaries, advancing technologies, and fostering stronger partnerships between
governments and industry,” notes Rebecca Richards, Deputy CEO of Rheinmetall UK (Rheinmetall).
Proud to be at the forefront of this shift, Rheinmetall is delivering next-generation capability through programmes like the Boxer Mechanised Infantry Vehicle (MIV) and Challenger 3 Main Battle Tank (MBT).
These systems will not only enhance the British Army’s capabilities but also strengthen interoperability with NATO and allied forces.
Another of the key changes in the region has been the growing need for speed and agility in procurement; today, responding quickly to operational requirements is critical.
A great example of this is Rheinmetall’s delivery of 500 HX 8x8 military trucks to the UK Ministry of Defence (MoD) in just seven months – demonstrating the company’s efficiency and unwavering focus on readiness and mission success.
“With significant investment flowing into the sector, increasing cross-border collaboration, and a strong focus on capability development, this is a genuinely exciting time to be working in defence,” Richards observes.
“At Rheinmetall, we’re playing an active role in shaping the future of land warfare by driving innovation, building strategic partnerships, and delivering mission-critical solutions at pace.”
INVESTING IN THE UK
Rheinmetall is a multi-domestic prime contractor, generating intellectual property, creating jobs, and driving economic growth within the UK defence sector.
From concept and design to production and long-term sustainment, the company offers a full-spectrum capability, ensuring mission-ready solutions.
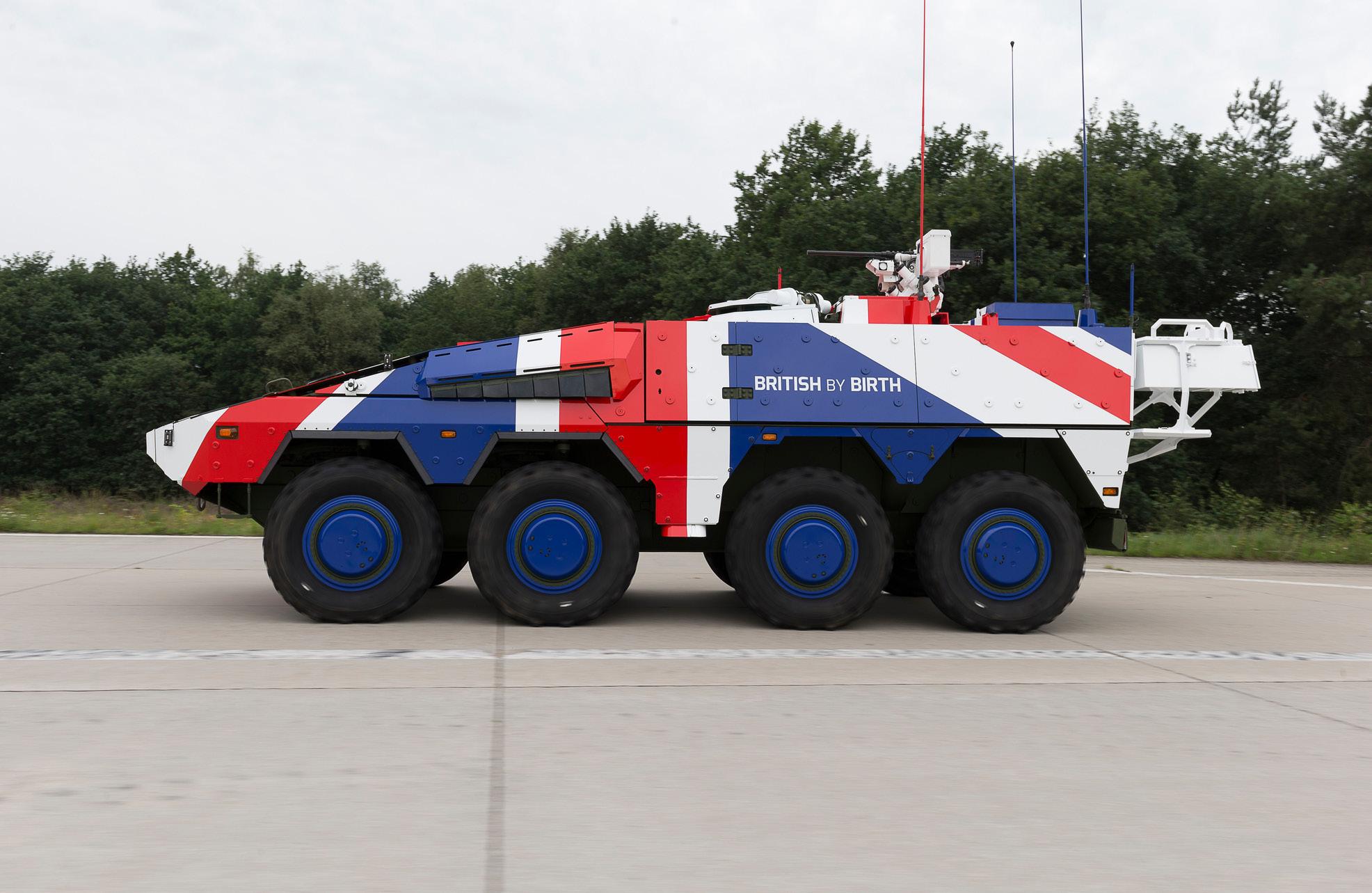
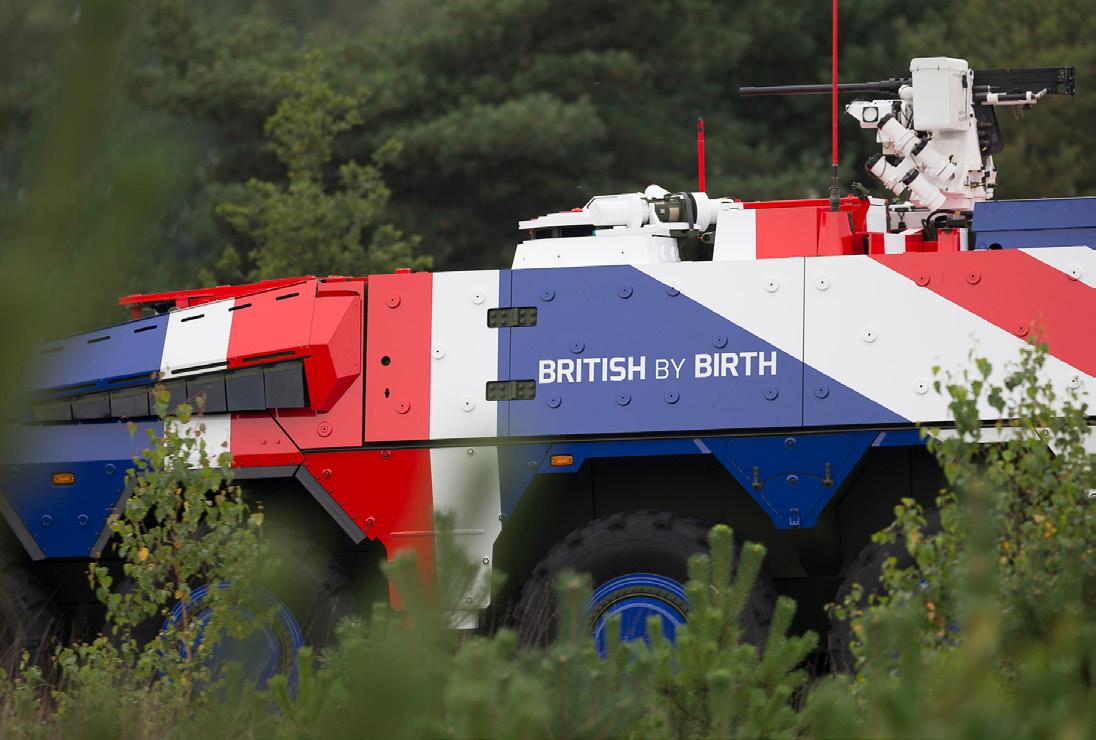
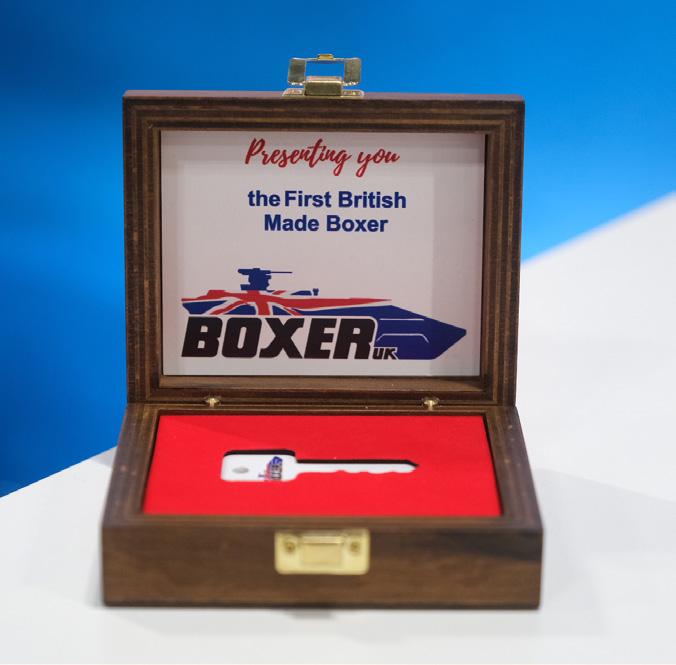
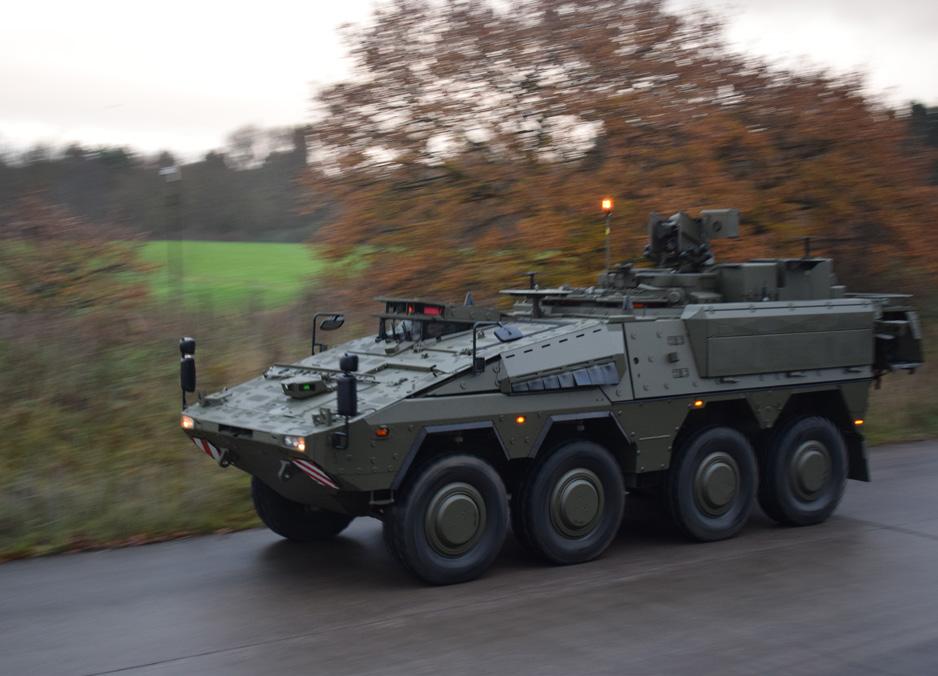
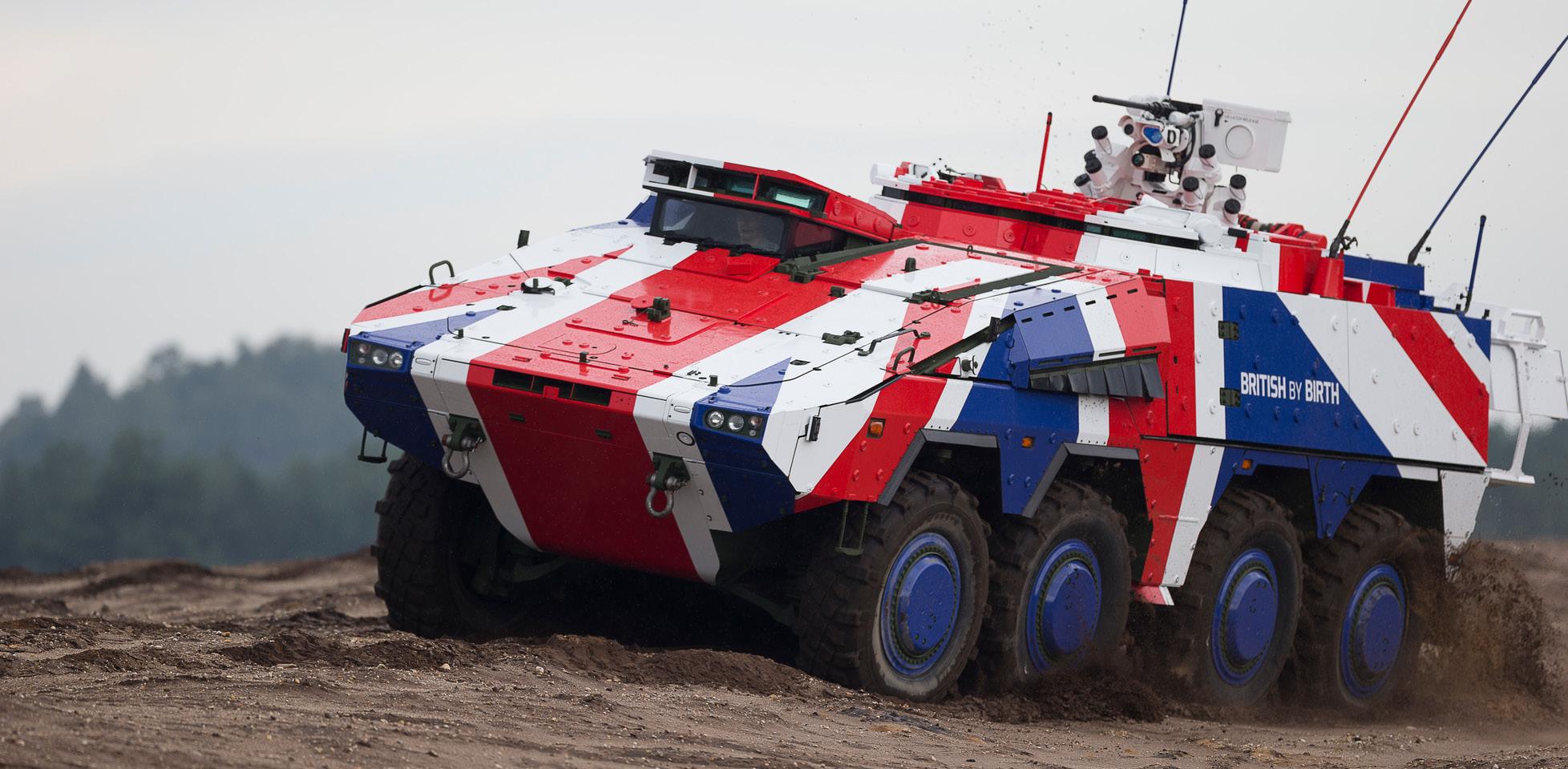
“WITH A STRONG INDUSTRIAL FOOTPRINT AND COMMITMENT TO DEVELOPING SOVEREIGN DEFENCE SOLUTIONS, RHEINMETALL IS ENSURING THE BRITISH ARMED FORCES AND OUR ALLIES ARE EQUIPPED FOR THE FUTURE BATTLEFIELD”
– REBECCA RICHARDS, DEPUTY CEO, RHEINMETALL UK
It has been operating in the UK for nearly two decades across seven sites in Telford, the Isle of Wight, Newcastle, Bristol, London, Bovington, and Southampton.
Rheinmetall House, the Rheinmetall UK headquarters in Bristol, includes the Collaboration and Innovation Centre, a hub for advancing battlefield technology through partnerships with the UK MoD, small to medium-sized enterprises (SMEs), and academia.
Its Telford facility, meanwhile, is home to Rheinmetall BAE Systems Land (RBSL), a defence engineering
joint venture, and has undergone a £56 million investment to support major UK defence programmes, including Boxer and Challenger 3 production.
“With a strong industrial footprint and commitment to developing sovereign defence solutions, Rheinmetall is ensuring the British Armed Forces and our allies are equipped for the future battlefield,” Richards tells us.
The Telford site has been transformed into a world-class armoured vehicle manufacturing hub, ensuring the UK retains a leading role in land defence systems.
END-TO-END EXPERTISE AND WORKFORCE DEVELOPMENT
From concept and design to production and long-term sustainment, Rheinmetall offers a full-spectrum capability, ensuring mission-ready solutions.
With over 1,000 highly skilled employees and strong investment in apprenticeships, graduate schemes, and industrial placements, the company is securing the future of defence engineering and long-term sustainability of defence skills in the UK.
“Our approach not only sustains critical skills but also supports defence exports by integrating British SMEs into our global supply chain, reinforcing the UK’s position in global security,” outlines Richards.
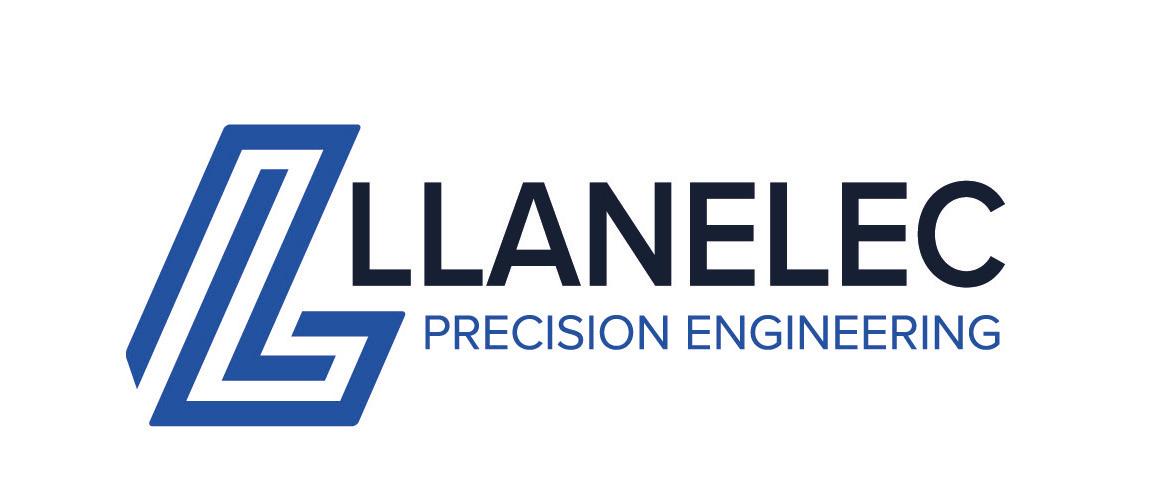
PRECISION ENGINEERING
Llanelec is a precision engineering company which specialises in manufacturing integral parts for vehicles operating in defence and high-precision titanium parts for aerospace.
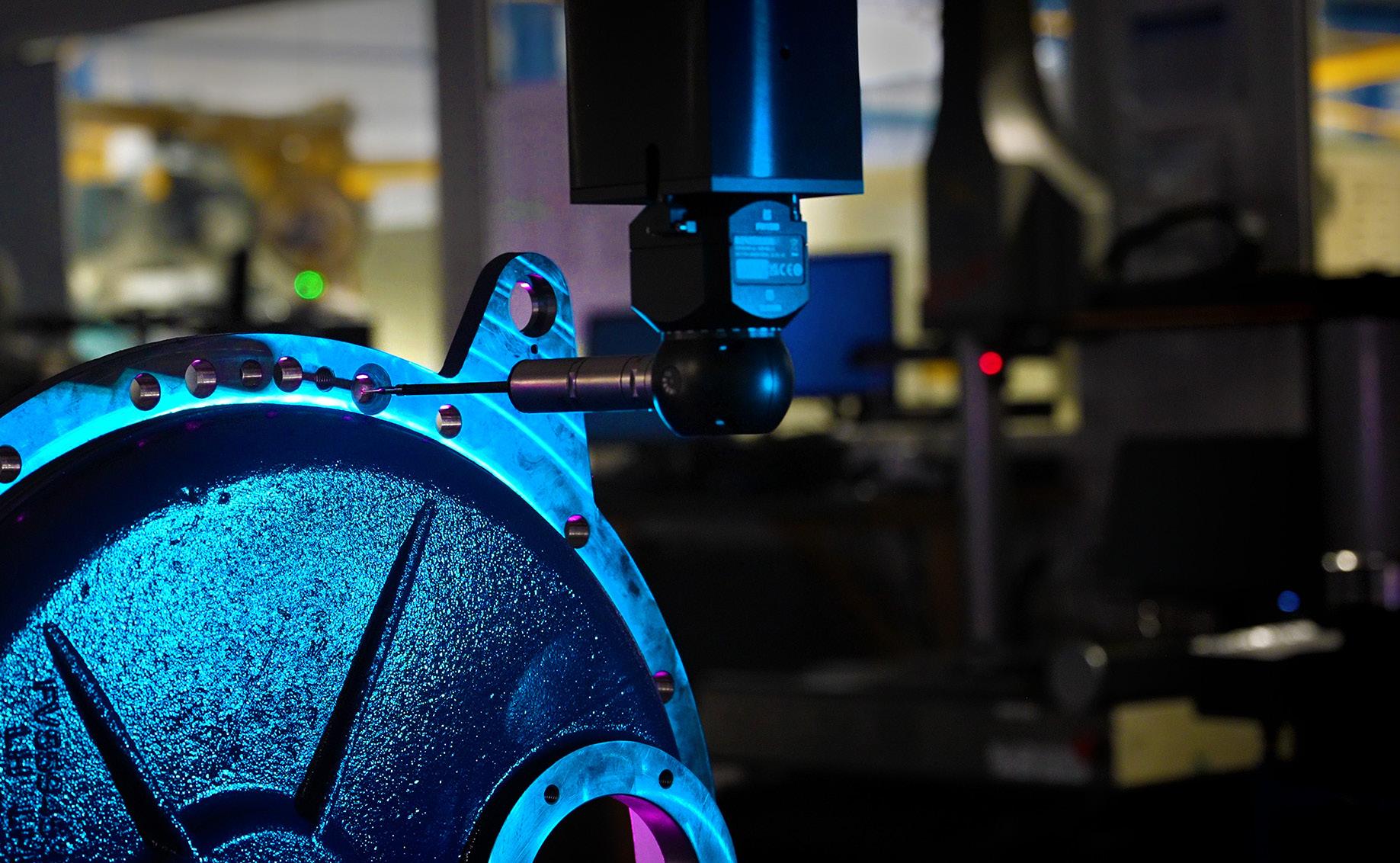
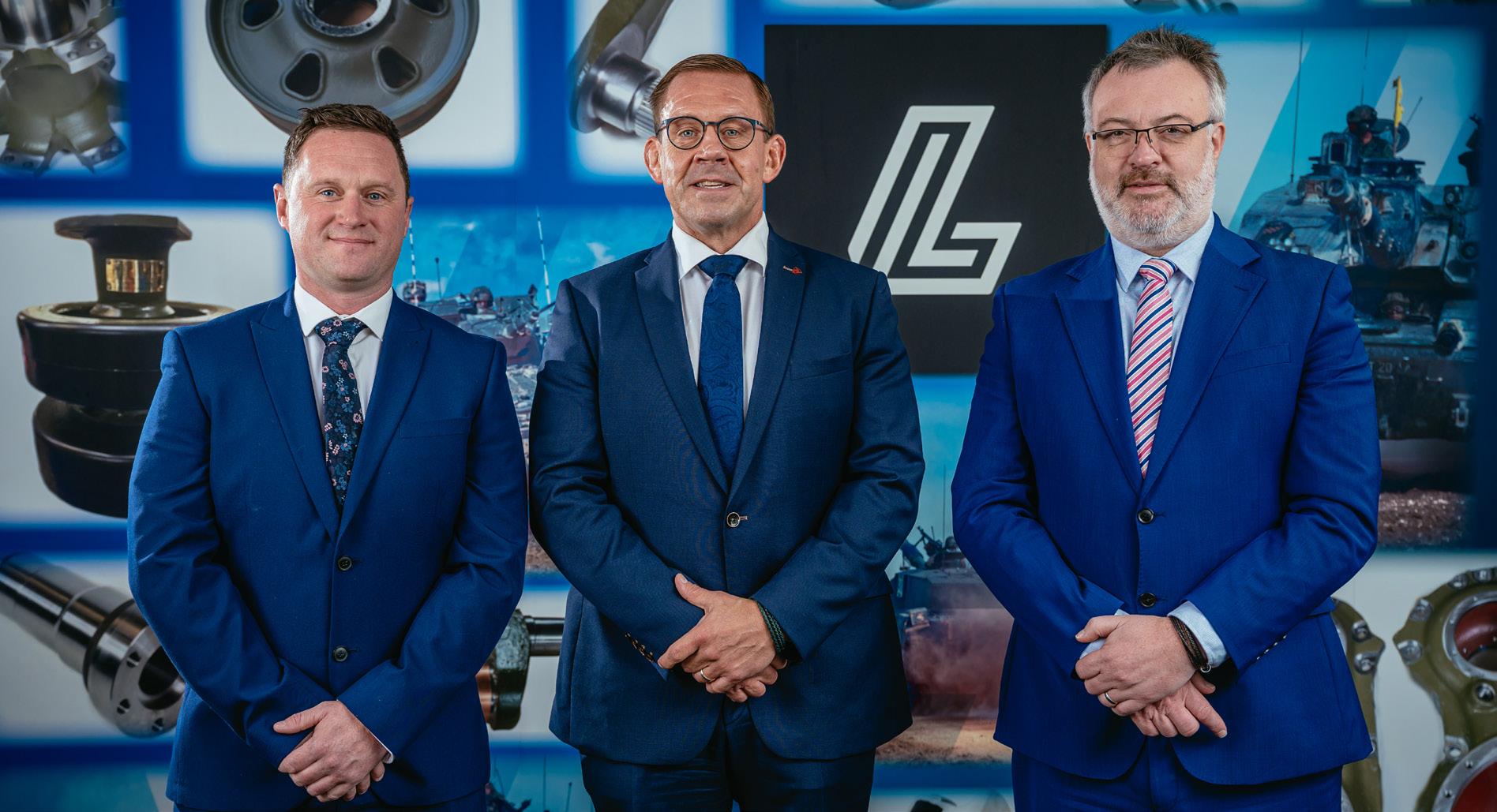
I understand Llanelec specialises in precision CNC machining of running gear and the supply of solid compound wheels for military vehicles. Could you provide a brief overview of your day-to-day activities, locations across the UK, and the client base you typically serve?
Founded in 1984 in Neath, South Wales, we pride ourselves on our commitment to quality and reliability. Our state-ofthe-art facilities and dedicated team of experts allows us to deliver products that meet the rigorous requirements of the sectors we work in. Our reputation is built on a foundation of reliability, precision, and a relentless commitment to excellence.
With a global customer base and diverse product portfolio, we are proud to be recognised as the partner of choice for many leading manufacturers. We have also been a trusted supplier for the Ministry of Defence for more than 35 years. Our expertise lies in crafting vital products for military vehicles and solid compound wheels, with our extensive product portfolio covering everything from road wheels and gears to final drive components and potential capacity to undertake armour plating for vehicles.
We use advanced CNC machinery and the latest software to produce precision components with exceptional reliability. Our commitment to continuous improvement and innovation ensures that we stay ahead of industry trends and consistently meet our customers’ evolving needs. This guarantees that we not only meet but exceed our customers’ demands in quality, delivery, and cost efficiency.
By partnering with leading manufacturers and using cuttingedge technology, we deliver solutions that enhance the performance and durability of military vehicles and the aerospace market.
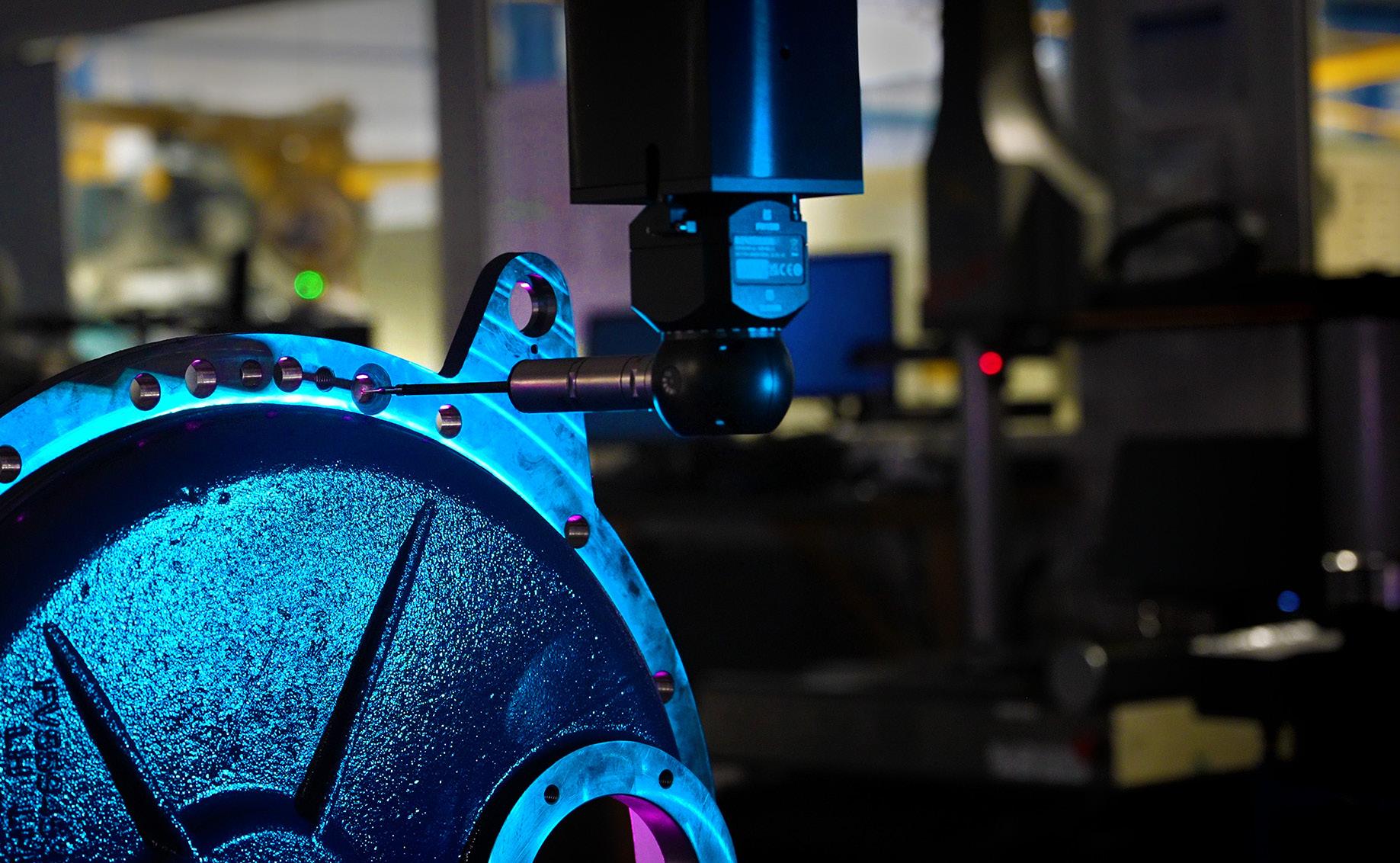
Our dedicated team of engineers and technicians work tirelessly to refine our processes and develop new techniques, ensuring that every product we create is of the highest standard. Through rigorous testing and quality control measures, we ensure that our components withstand the most demanding environments.
Our customer-centric approach and strategic investments in research and development enable us to provide innovative and cost-effective solutions, solidifying our position as a trusted leader in the industry
Having been in business for more than 40 years, how have you seen the UK’s industrial machinery manufacturing landscape evolve? How has this impacted your business?
Llanelec have endured over 40 years in the defence sector and witnessed the highs and lows that coincides with the industry. We have seen many changes in that period, a major one being the advances in technology, not only in the plant that is used for milling and turning but the significant improvements in our measuring capacity as implements become more sophisticated. This has in effect led us to drive back into the design phase the requirement for tighter tolerances and more complex interfaces to be achieved.
Another major shift over the years has been the dramatic change in manpower and personnel skill level. We saw the move from traditional apprenticeships being very attractive to the youth of that day to a desire to have more officebased job roles around the millennium years. This had an impact on the engineering and manufacturing pipeline, causing a shortage in the system. Whilst this trend is starting to change with manufacturing again coming to the fore, the infrastructure to support the development will need to keep pace.
“The Iron Triangle is what Llanelec prides itself on: quality, cost, and delivery.”
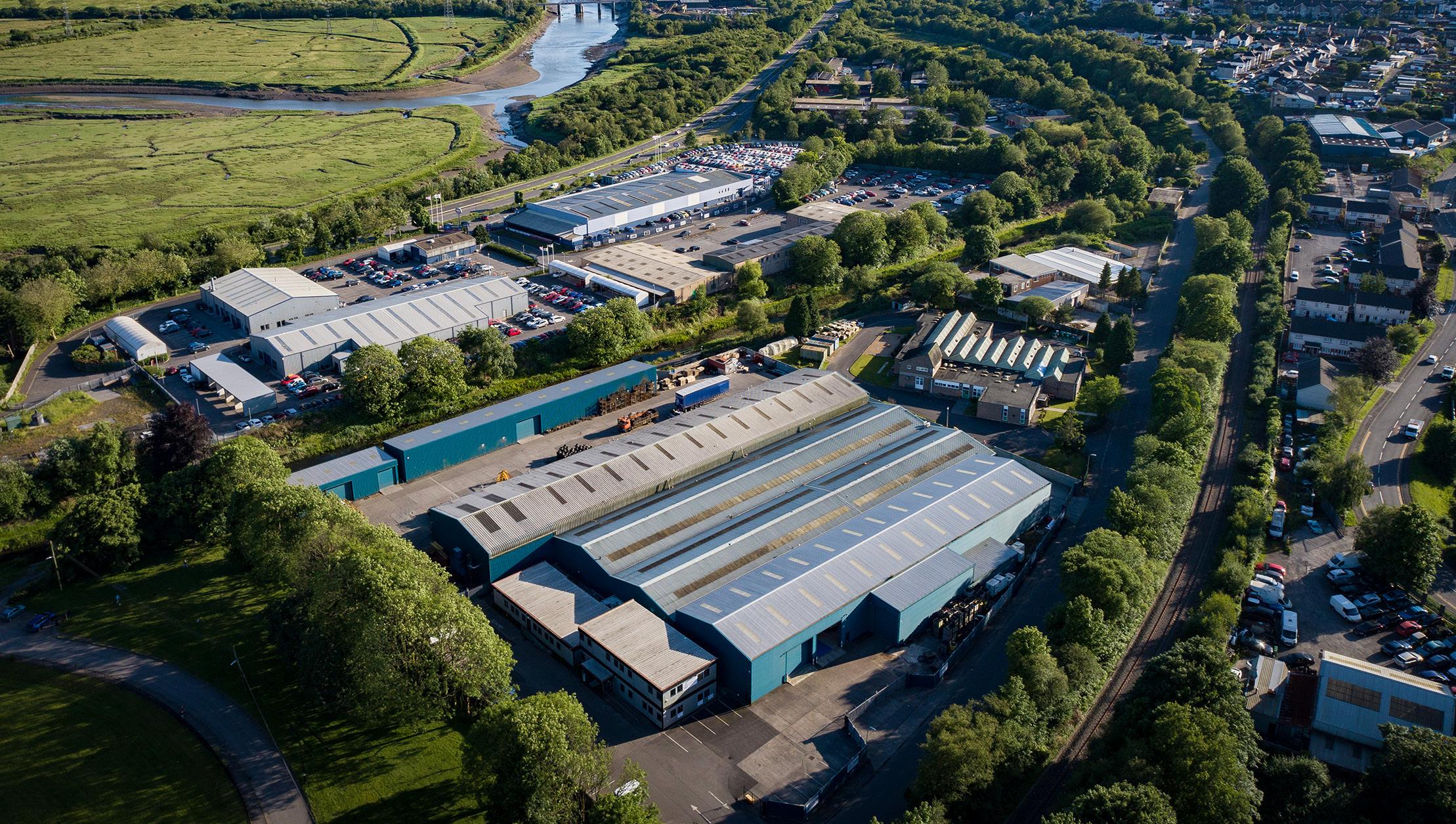
We see this point as fundamental and key, and as such we have a strategic goal to support.
Finally, as the defence sector can be quite niche, we have been subjected to the ebb and flow of defence needs.
We have worked through defence thinking and shrinking during the 80s and 90s post-Cold War with less reliance and need for heavy armour, through the 90s and 00s with the Gulf Wars requiring more agile vehicles, to the recent RussiaUkraine conflict that has stretched defence manufacturing capacity to its limits.
What, in your opinion, is the company’s key differentiator? What do you do to stand out from the competition?
Whilst our company absolutely recognises the need for agreements, contracts, and agreed terms and conditions as the framework to do business, at Llanelec we place a great deal of importance on how we manage a change to the plan. We believe that it is more important for customers to have a supplier who will collaborate, and problem-solve effectively without reaching for the contract in the first instance. We welcome a close relationship with both our customer and supply base and have a long-standing track record of keeping calm under adversity, with a laser focus on solving
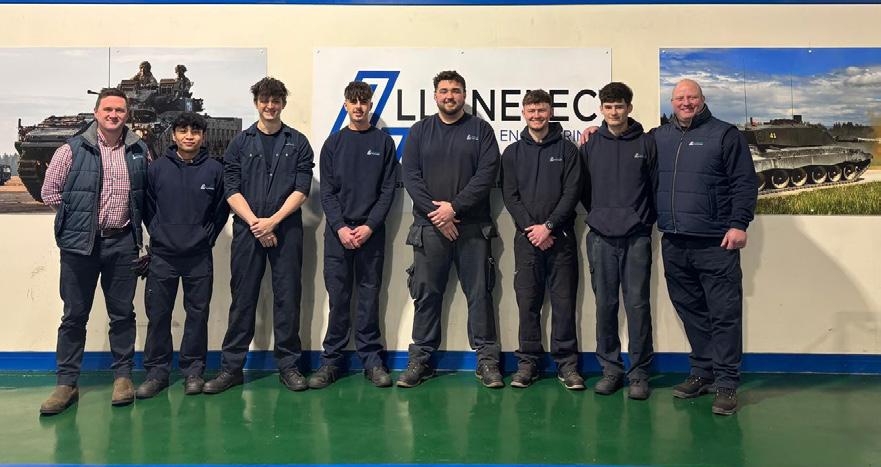
the problem to achieve the aim. We think that is the essence of engineering and manufacturing. To have the solutions to the problems, Llanelec has built up a strong capability over the years. This means that we have a broader scope within the value chain and can deliver most projects as a turnkey solution, keeping the links in the chain to a minimum and having more control.
Llanelec prides itself on being a problem solver to OEMs and prime defence and aerospace companies.
Can you talk about your work with Rheinmetall Vehicle Systems International, and any recent projects or jobs you have collaborated on?
The first project that comes to mind was a recent problem that RVS International had with a component that was required for a high-profile programme to deliver a vehicle which, without the component, would have compromised the planned roll-out. Llanelec were contacted at the beginning of December 2024 with the notion that it was probably impossible to source the component from anywhere other than the current supplier. Technical specifications were shared which identified that it would be unachievable to source the required raw material in the timeframe.
Llanelec identified a suitable alternative material that was available, RVS International assessed the request and issued approval within 24 hours and the material was sourced.
Llanelec expedited the request, whilst carrying out other operations out of sequence, to benefit the overall delivery time of the finished component. The result was that the components were delivered to RVS International by midJanuary, successfully meeting their need date. From original enquiry to delivery was no more than six weeks, quite remarkable in the current manufacturing sector where there is a real lack of widespread capability and capacity. This is a classic example of how Llanelec solves problems for OEMs and prime defence companies.
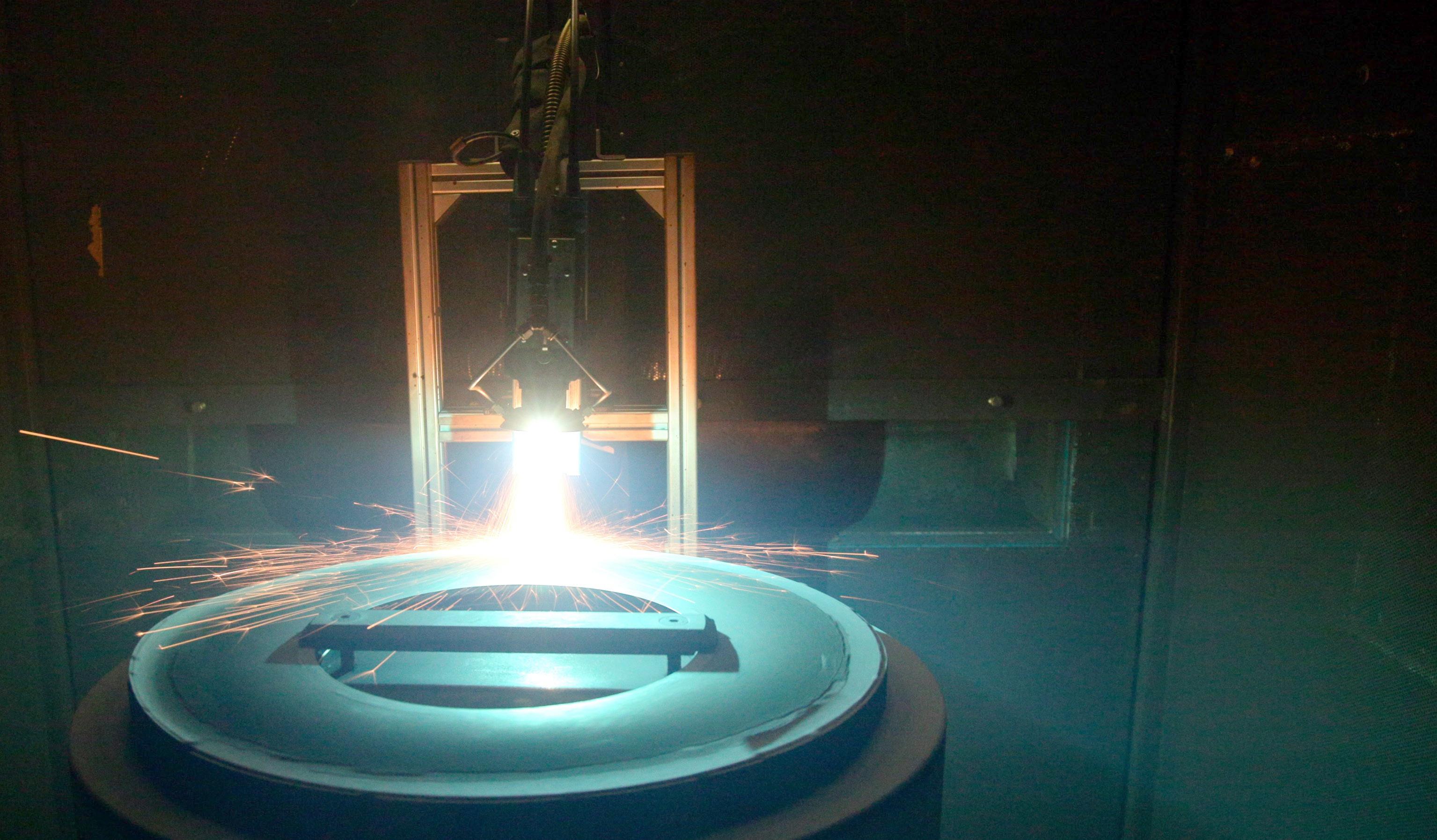
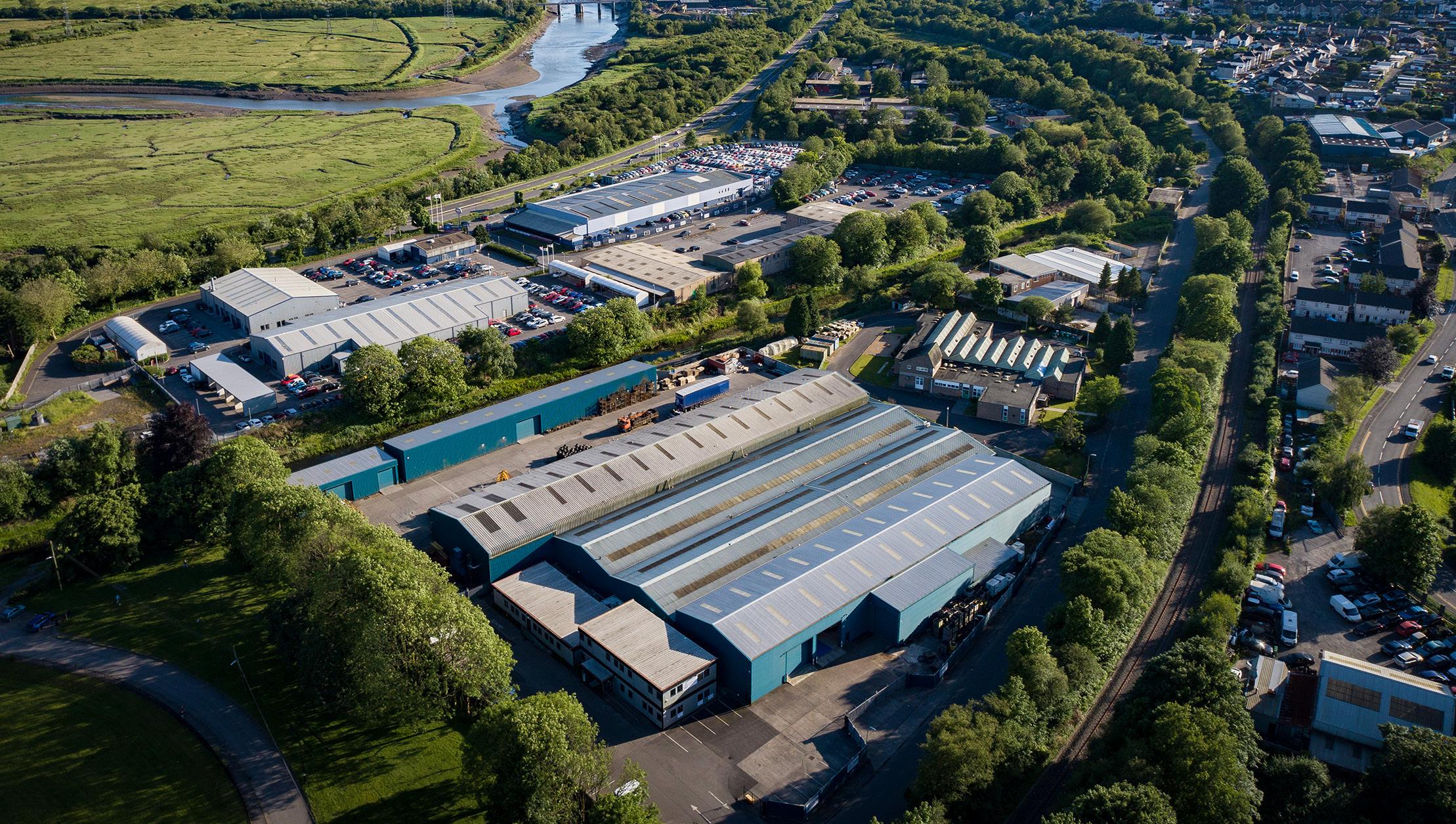
How do your values of reputation, quality, flexibility, reliability, expertise, and cost-effectiveness allow you to consistently provide precise, high-quality solutions that surpass expectations?
Almost all business and project plans will change. We believe that embedding our values throughout our organisation, at all levels, is a key facilitator to our ability to deliver consistently to our customers. The values we set and actively reinforce daily basis are what set our high standards. It creates a sense of pride in what we do and for whom we do it.
Throughout all our organisation, individuals and teams challenge themselves and others to go that extra step.
The values are there as the standard to remind the business what we stand for and how we have all agreed to operate.
The Iron Triangle is what Llanelec prides itself on: quality, cost, and delivery.
Could you tell us more about your long-held vision to grow the business, and how being awarded contracts such as UK MOD Land Forces and Babcock International Group have endorsed recent investments in resources, infrastructure, capability, and capacity?
Being awarded contracts provides an element of certainty, which is crucial to support business cases, particularly in a small to medium-sized enterprise (SME) family-owned business.
Our vision is to grow the business year on year, and to achieve this the business must invest in Llanelec and its infrastructure. The contracts awarded to us provide that stability to not only invest in our equipment but also our staff. We also look to use the contracts to leverage the political desire to level up the surrounding areas, rejuvenating what once was.
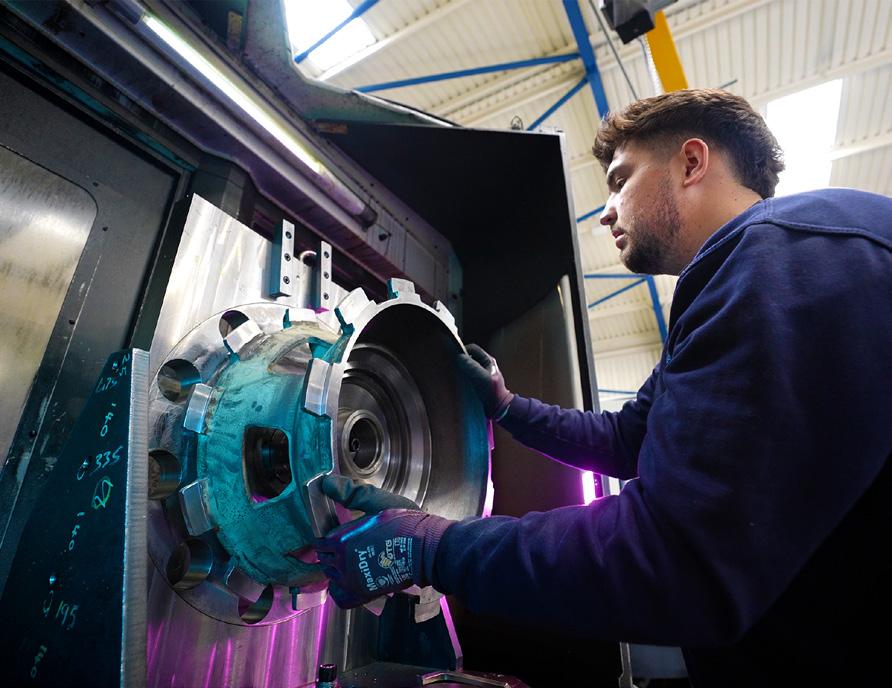
The area was once a hotbed of engineering and manufacturing, and the company’s vision is to play an active part in developing that once again.
Llanelec has grown 400% 0ver the past 5 years in revenue, size and capabilities; the new 8.5 acre site, with a state-ofthe-art 120,000 sqft multi-disciplined manufacturing facility allows a further 400% for future growth.
A truly one-stop shop servicing aerospace and defence.
Finally, what are your key priorities, targets, and goals for the year ahead?
Our Strategic Plan describes how we wish to continue to grow the business whilst continuing to maintain our standards. We have several goals contained within, but the one we are most focused on and will be proud of when we deliver is our plan to create an Engineering Training Centre.
Llanelec have planned a new engineering school for both young apprentices and local skills; it will provide quality labour, which is key to our growth, whilst supporting the local community in replacing jobs lost from Tata Steel - Port Talbot.
This will not only support the development of our growing number of apprentices but also provide an opportunity for local people to retrain and attain new skills. We believe that this opportunity will not only benefit the affected people but also increase the manufacturing capability and capacity in the area supporting the defence requirement for many years.
In addition, Llanelec plans to expand its product range internationally in supporting all NATO countries within defence. Our aim at Llanelec is to become a centre of excellence within the defence and aerospace industry!
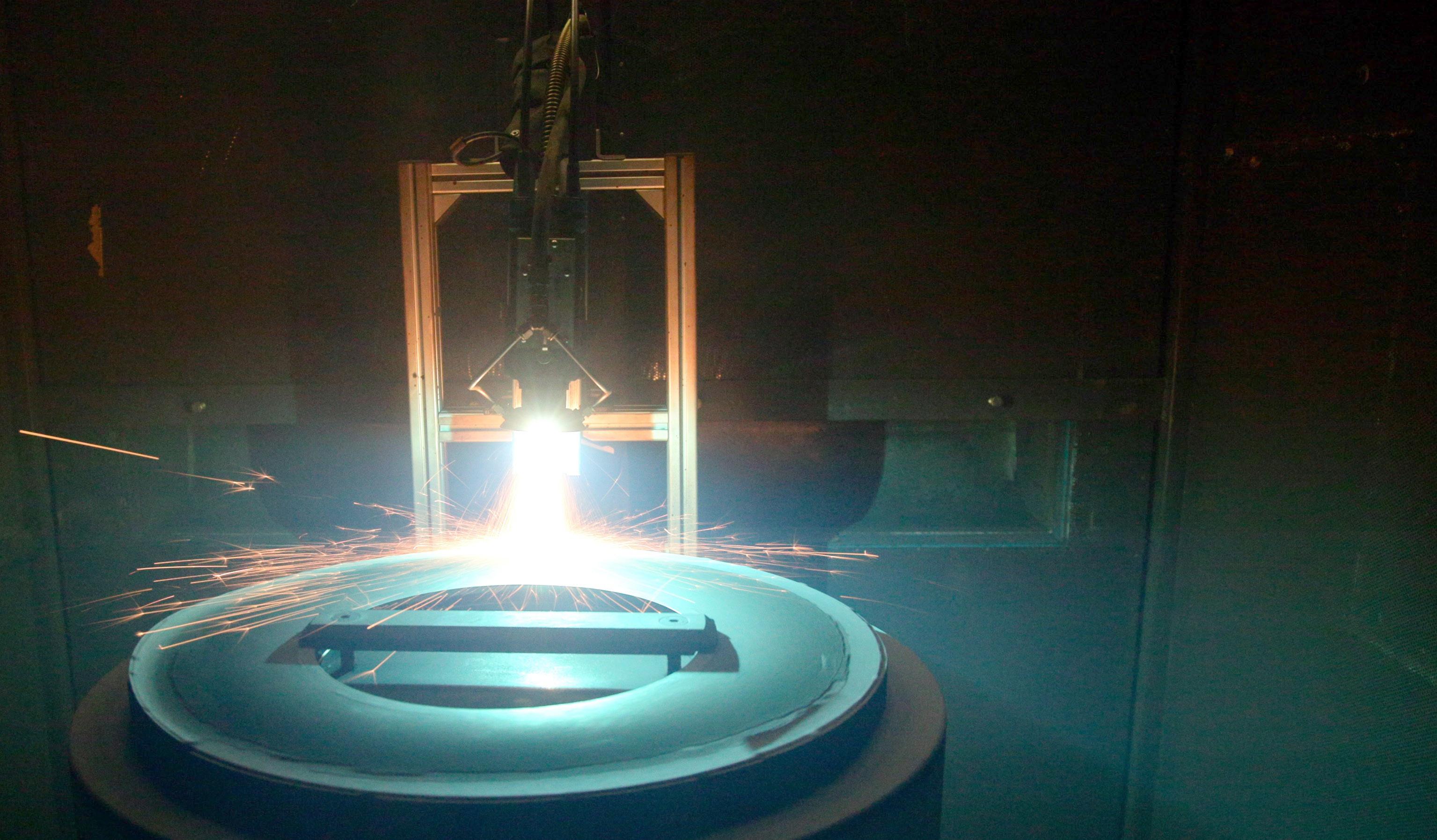
“Our
aim at Llanelec is to become a centre of excellence within the defence and aerospace industry!”
COMMUNITY ENGAGEMENT
Rheinmetall encourages and supports employees who give back to their communities, whether by mentoring, coaching local sports teams, or volunteering as scout leaders.
This commitment to community engagement is an integral part of the company’s culture.
“Through strategic partnerships with universities and STEM initiatives, we are helping to shape the next generation of engineers and innovators, thereby strengthening the UK’s defence talent base,” Richards sets out.
One key partnership is with the University of the West of England’s Formula Student team – a group of skilled STEM students who design and build a race car for international competitions.
Rheinmetall’s sponsorship not only strengthens its relationship with a leading academic institution but also connects the company with talented engineers and innovators who may become part of its future workforce.
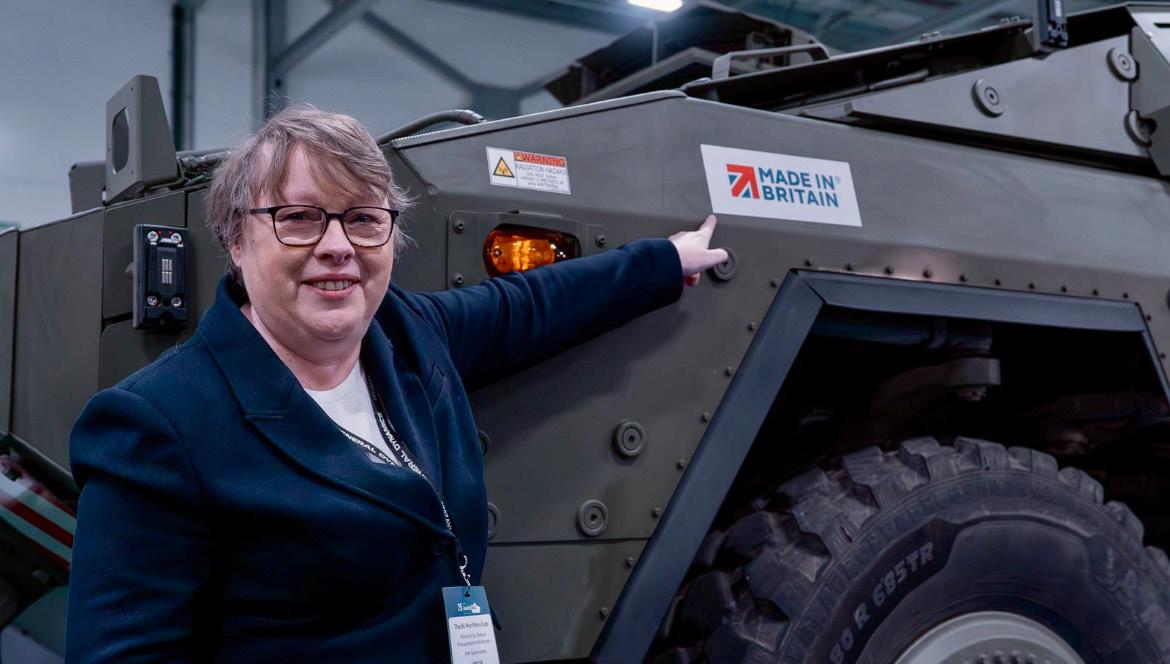
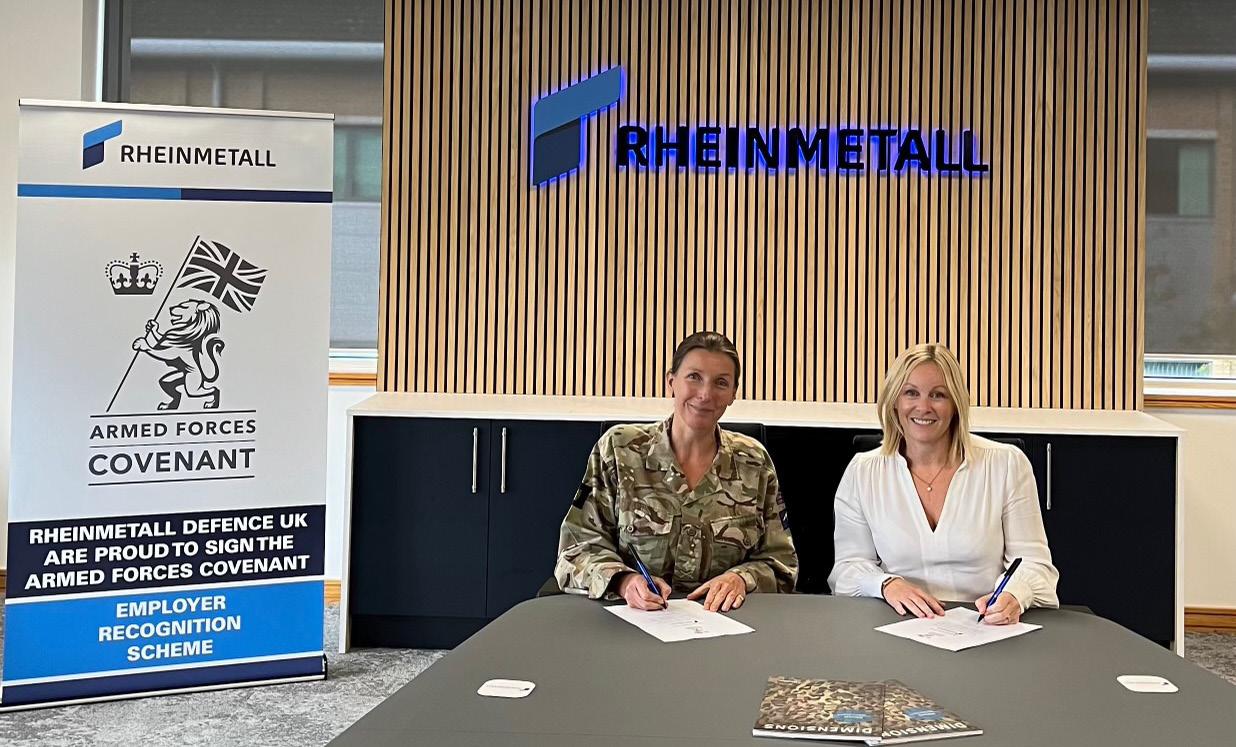
Rheinmetall stands out through its sovereign manufacturing capability and has strategically invested over £70 million in its UK production facilities, demonstrating the company’s commitment to British-designed and manufactured military vehicles.
In addition to Rheinmetall House and the Telford facility, key areas of this investment include a new largecalibre gun hall and expanded military vehicle production.
“These underpin critical defence programmes and position the UK as a global leader in land defence manufacturing,” adds Richards.
In May 2025, Telford was confirmed as the home of Rheinmetall’s new gun hall, marking a bold step in re-establishing sovereign defence manufacturing in the UK.
BUILT IN BRITAIN
The unveiling of the first British-made Boxer at the International Armoured Vehicles Conference in January 2025 by Maria Eagle, Minister of State for Defence Procurement and Industry, marks a major milestone for Rheinmetall and the UK defence industry, signifying the return of armoured vehicle manufacturing to the UK.
Built at its Telford facility, the achievement highlights Rheinmetall’s investment in sovereign capability, industrial growth, and long-term defence manufacturing.
“It also reflects our commitment to skills, infrastructure, and cutting-edge manufacturing, underscoring the importance of industry-government collaboration in delivering worldclass military capability,” Richards highlights.
One of the world’s most advanced wheeled armoured vehicles, the Boxer offers unmatched mobility, protection, and modular adaptability.
“Its reconfigurable design allows for multiple mission roles, ensuring the British Army’s evolving operational requirements are met whilst
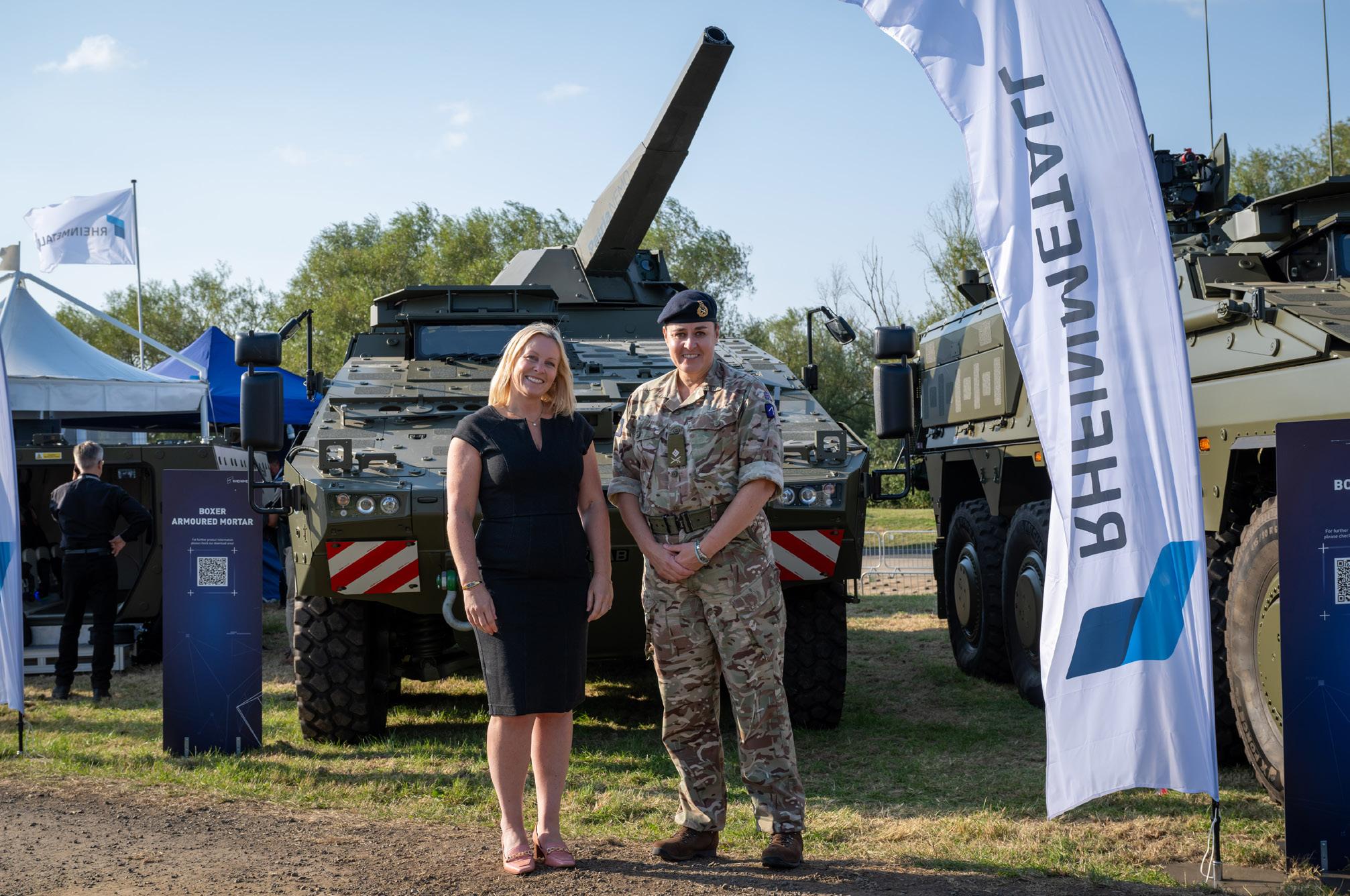
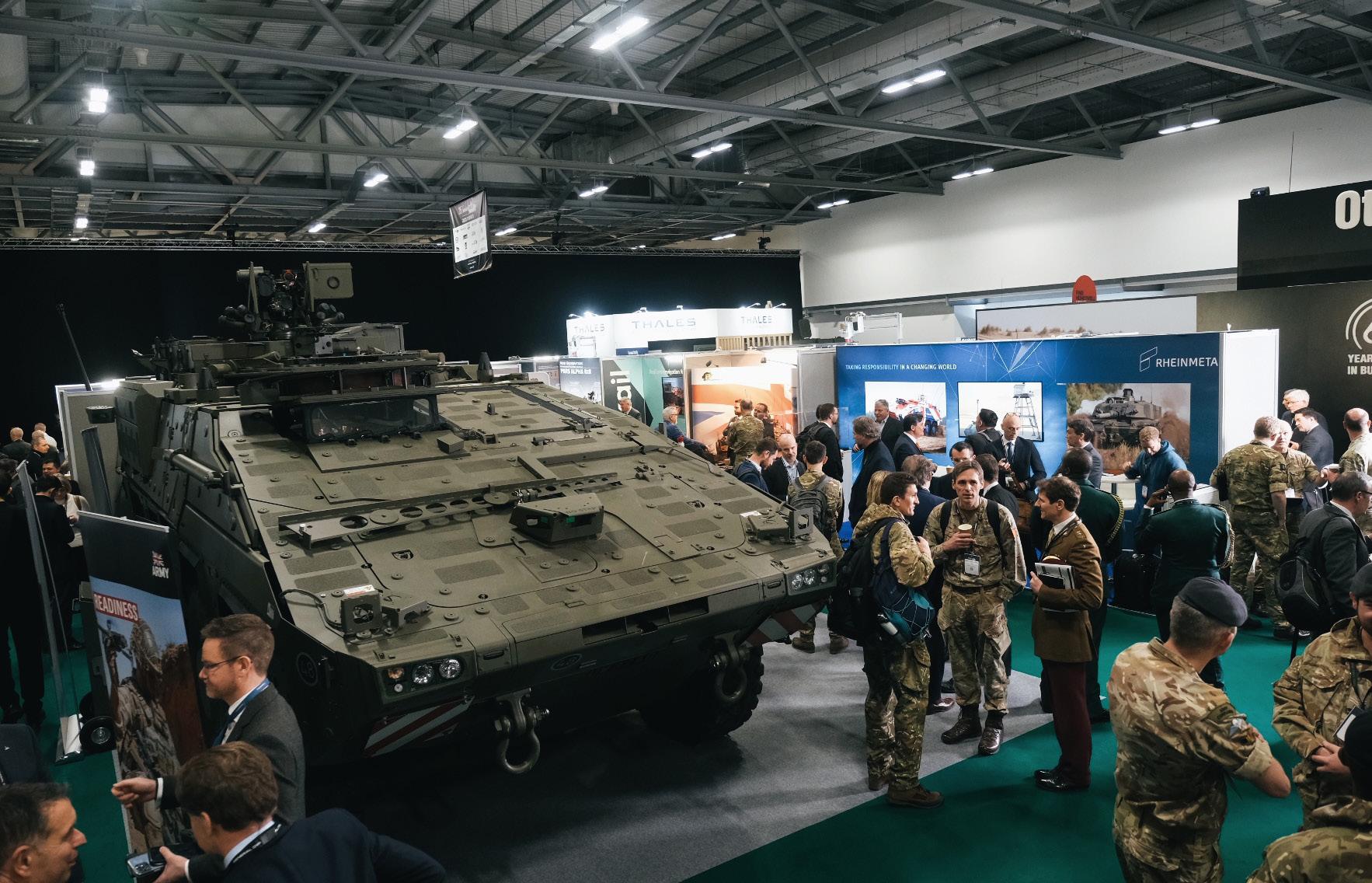
delivering battle-proven survivability,” she acclaims.
The Boxer has undergone extensive live-fire exercises, mobility trials, and extreme environment testing to ensure peak combat effectiveness. By exceeding performance benchmarks, the Boxer will deliver
game-changing capability to the UK Armed Forces.
The country’s defence industry and economy have been strengthened as a result of this milestone with over 1,000 domestic jobs created, reinforcing its manufacturing base and engineering expertise.
75 percent UK supply chain integration also ensures British SMEs play a central role in Boxer production, whilst its export potential positions domestic suppliers for international contracts.
As production scales up, the Boxer MIV programme will continue to strengthen UK industrial sovereignty, defence capability, and economic prosperity, solidifying Britain’s leadership in global armoured vehicle manufacturing.
A NEW CHALLENGER
Equally, the Challenger 3 MBT programme represents a major leap forward in armoured warfare, ensuring the British Army remains equipped with a world-class tank for decades.
Under an £800 million contract, Rheinmetall is leading the design, development, and production of 148 Challenger 3 tanks through RBSL, with full operational capability targeted for 2030.
Put innovation in motion
Curtiss-Wright Defense Solutions is a leading provider of comprehensive solutions for various rugged applications, with a complete portfolio of cost-effective engineering and support services.
Modular and scalable motion control solutions, built and designed in the company’s facility in Switzerland, are used in a wide range of military platforms, from Remote Weapon Stations (small-calibre solutions) and Infantry Fighting Vehicles (medium-calibre solutions) to Main Battle Tanks (large-calibre solutions).
Our high-speed, highly precise solutions are also used in applications such as train tilting systems and Hollywood camera crane drive and stabilisation systems.
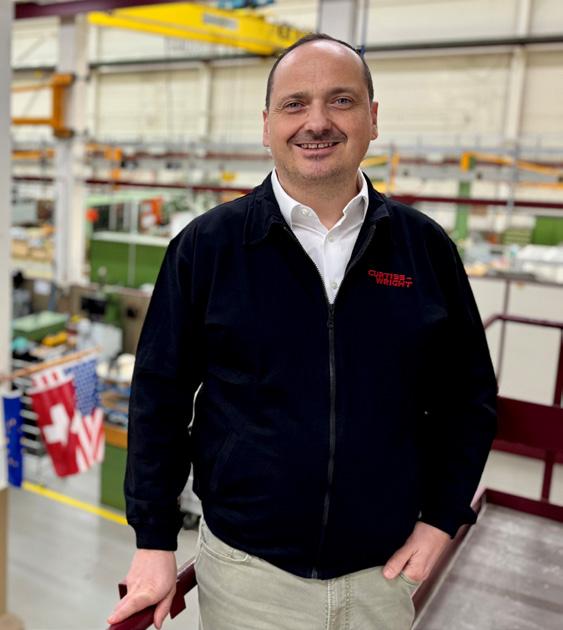
Tell us about Curtiss-Wright’s motion control business.
We have been a trusted and proven partner in the field of motion control for over 70 years. In the last 30 years, we have become a global leading supplier of electromechanical drive systems for the industrial and defence industries. A significant part of our business is focused on turret drive stabilisation. We are a one-stop shop system integrator with excellent customer and field integration support.
Turret Drive Stabilisation System (TDSS) solutions are globally recognised for their high performance, quality, and reliability. When customers require a high-speed motion control solution that must operate in harsh environments, we provide a single point of contact to solve their problem. Examples include ammunition flow systems, auto-loader systems, and missile launchers, which our customers integrate into their overall solution. On the industrial side, examples include the tilting train system for the Swiss inter-city railway that enables higher speeds and better performance on the track. Another application is a motion picture camera crane drive and stabilisation system, which is used on different vehicles during the production of numerous feature films.
What are some recent projects the company is proud of?
We are proud to be a preferred supplier of Rheinmetall BAE Systems Land (RBSL) and were selected by them to provide the TDSS for the British Army’s Challenger 3 main battle tank. We have long been a leading supplier for medium-calibre system infantry fighting vehicles, but this represents our first electro-mechanical TDSS on a main battle tank. What’s more, this business provided the foundation for our recent selection to support the development of Germany’s next-generation main battle tank.
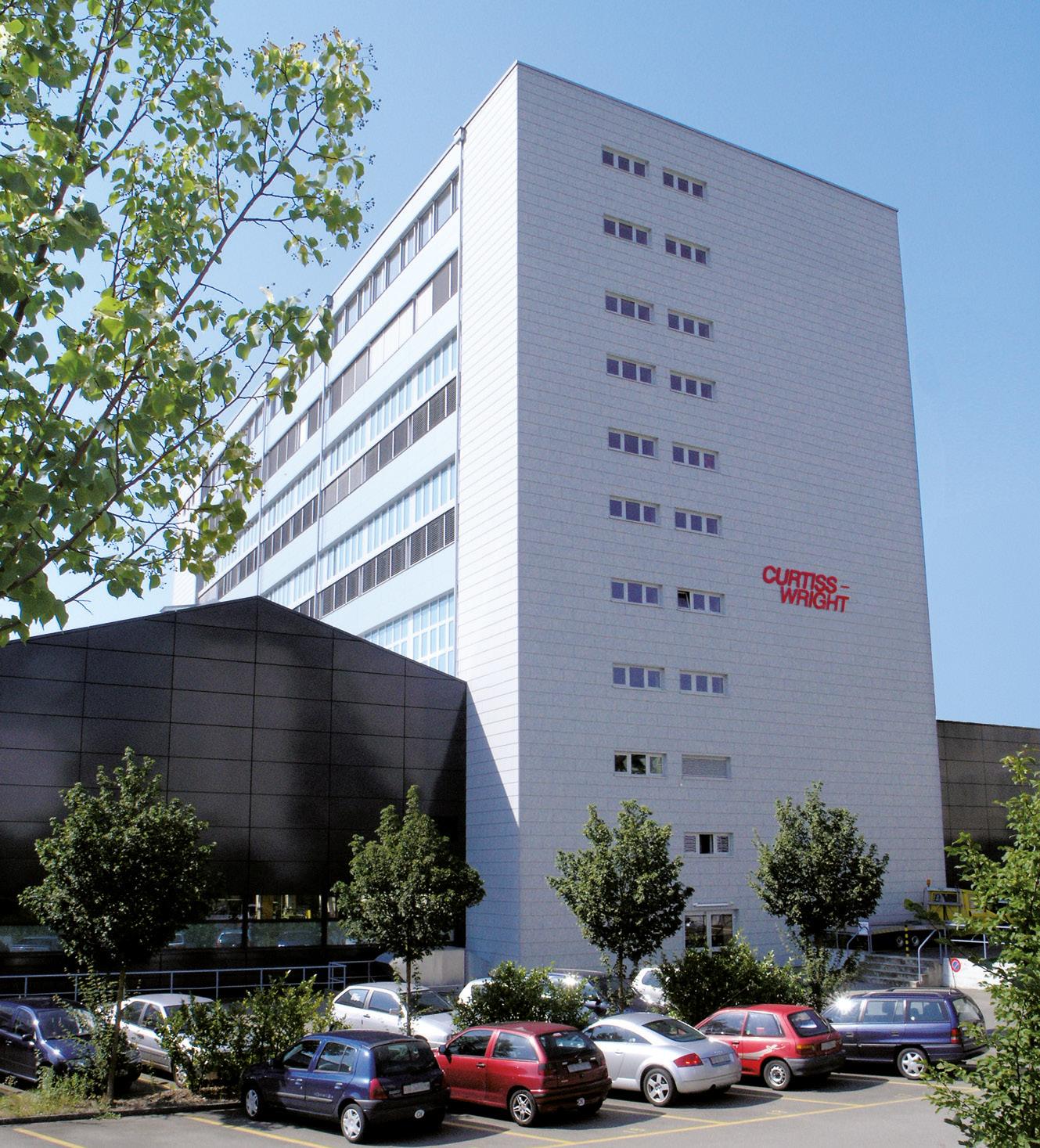
Looking forwards, what are the key priorities and goals for the year ahead?
Our highest priority in 2025 is supporting the development phase of Germany’s new main battle tank, with the critical design review at the end of this year. We have invested significant IRAD to support the tank’s high weight and load turret within the platform’s limited space. Our innovative, modular approach uses two parallel azimuth drives. Compared to a single large drive, this saves weight, helps balance the payload, and enables operation in limited performance mode if a single drive fails.
What is the company’s vision?
We are committed to being the number one preferred TDSS supplier and integrator in the world. The market for armoured fighting vehicles is growing. With strategic uncertainty and growing international tensions fuelling the need to bolster military capabilities, this trend is likely to continue beyond 2025. We also see growing opportunities in the power management market. Examples include the DC/DC converters with energy power packs we developed for an Air Defence System and opportunities for our DC/DC converters with intelligent safety power management, ruggedised with an EMI filter, on platforms such as UUVs.
What differentiates you?
Having delivered over 5,000 electromechanical turret systems in the last two decades, we have unmatched experience in the design, development, and production of ruggedised solutions that meet military specification for use in harsh environments. Our renowned field support customer service team consults with customers to find better solutions and ensure flawless integration. We also have expertise in meeting requirements to enhance local economic benefits for customers. We have partnered with Rheinmetall and other customers in multiple countries to support local content programmes, such as our successful participation in Australia’s Land 400 Phase 2. We are especially proud to be known as one of the most supportive, forward-thinking, and agile suppliers.
“We are committed to being the number one preferred TDSS supplier and integrator in the world.”
Christian Kopp, Managing Director, Curtiss-Wright Antriebstechnik GmbH
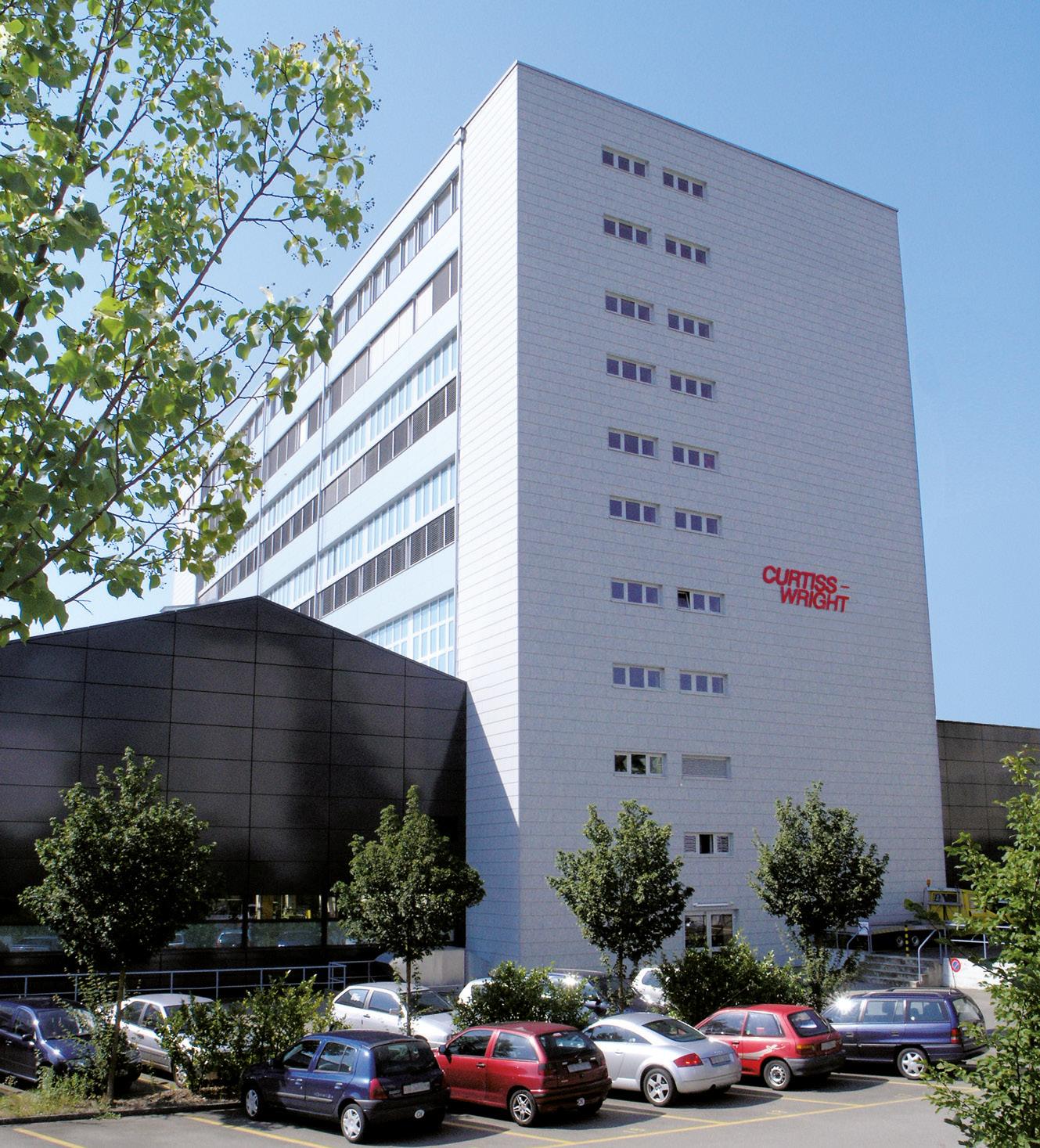
Tailored to Meet Mission Needs
Precision Target Location and Shot Stabilization
Single Axis Gyroscopes
Rotary Gear Drive
Two Hand Controller
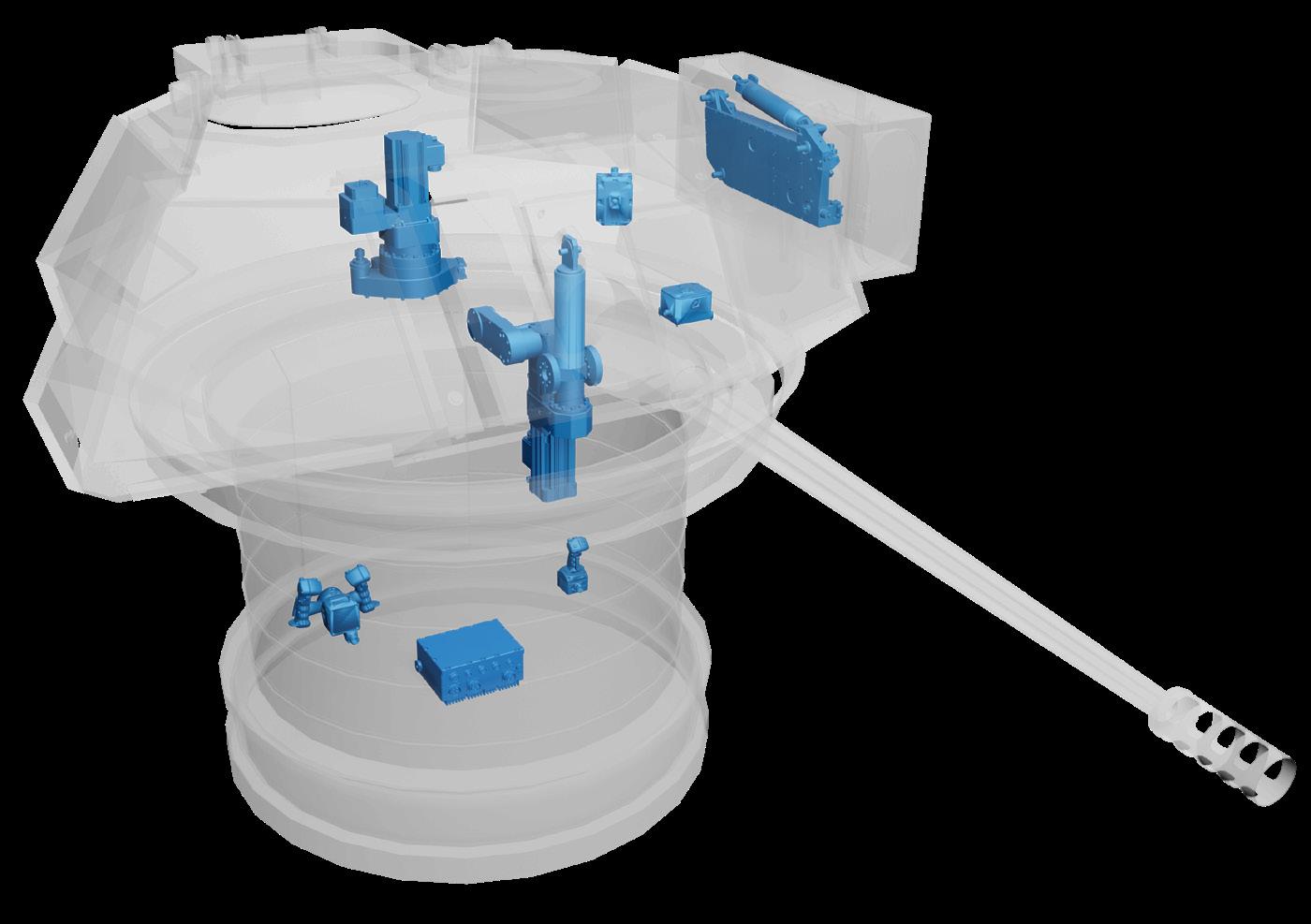
Electrical Motion Actuator
Dual Axis Gyroscopes
Linear Gear Drive
One Hand Controller
Motion Controller
Motion Controller

Suited for use on weapons stations or main battle tanks and designed for the most demanding dynamics and precision requirements.
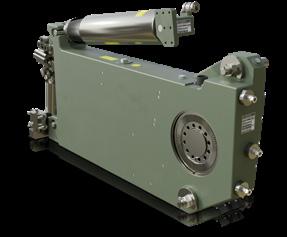
Electrical Motion Actuator
Designed to meet the demanding requirements for future and legacy land systems for missile launchers and radar applications.
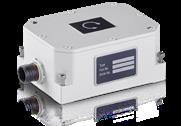
Single Axis Gyroscope
Ultra-fast and low noise fiber optic gyro developed for high-performance military applications.
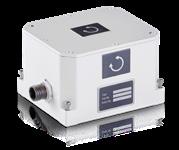
Dual Axis Gyroscope
Equipped with ultra-low noise sensors and engineered to withstand extreme environmental conditions.
curtisswrightds.com/motion-control
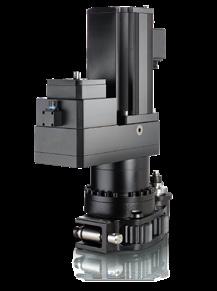
Rotary Gear Drive
Define system performance with a configurable gearbox while maximizing stiffness and minimizing friction and backlash.
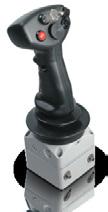
One Hand Controller
One-handed operation optimized for user comfort. Connector handles can hold up to 12 independently sealed switches.
Linear Gear Drive

Designed to provide smooth linear motion to defense applications operating in harsh environments.
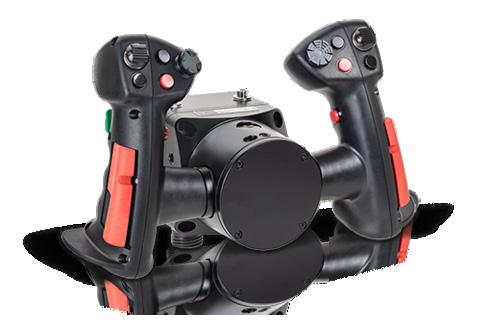
Two Hand Controller
Engineered for both horizontal and vertical handling, ensuring precise control and a firm grip over challenging terrain.
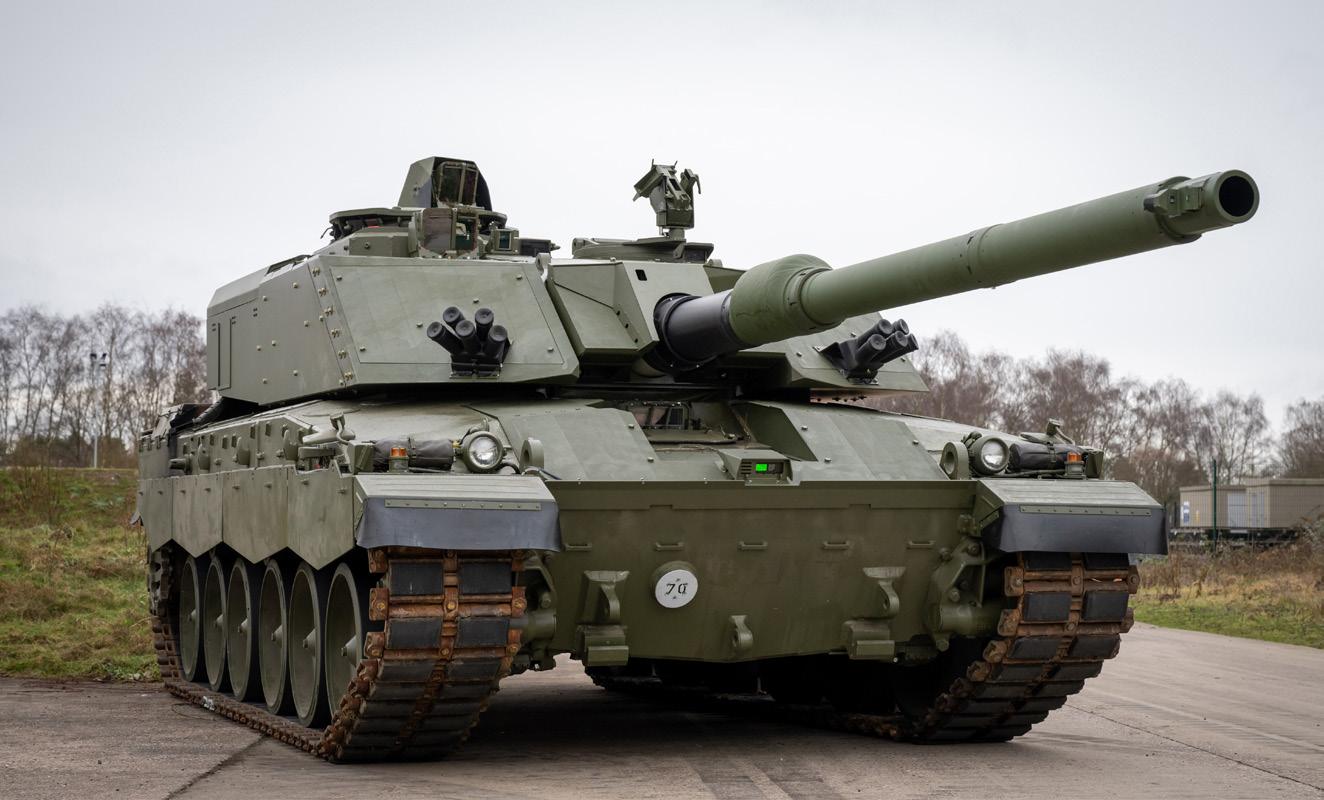
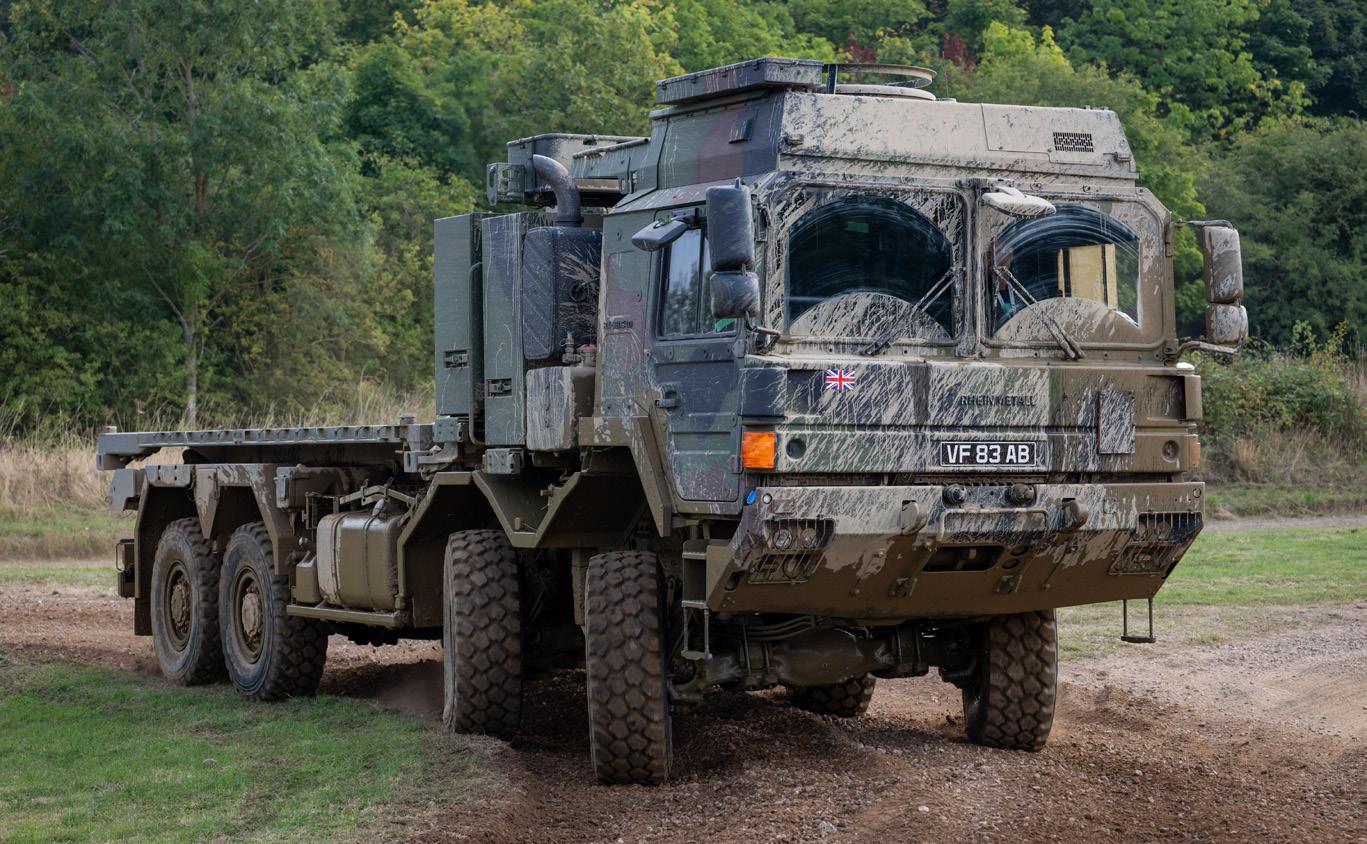
RHEINMETALL KEY PROJECTS – AT A GLANCE
• Boxer MIV – Over 600 vehicles for the British Army, strengthening the UK’s armoured fleet.
• Challenger 3 MBT – The most advanced tank ever operated by the British Army, providing unmatched lethality and survivability.
• HX trucks – 500 delivered in under five months, adding to the 7,000 already in UK service.
• Large-calibre weapon production – Investment under the Trinity House Agreement to enhance UK and NATO capabilities.
• Electronic systems and digitisation – Rheinmetall is expanding its capabilities, ensuring future armoured vehicles are fully networked and interoperable with cutting-edge battlefield technology.
• Autonomous revolution – The company is launching three brand-new Advanced Land Autonomy Centres of Excellence in Germany, the Nordics, and the UK, whilst also expanding its current Canadian Autonomy Centre of Excellence.
“Manufacturing is underway at our advanced facility in Telford, reinforcing our commitment to sovereign UK manufacturing and industrial capability,” reveals Richards.
The Challenger 3 is the most advanced MBT ever fielded by the British Army, with Rheinmetall’s advanced technology at the core, delivering next-generation firepower, survivability, and digital capability.
It features a state-of-the-art, 120-millimetre smoothbore gun capable of firing the latest NATOstandard ammunition for enhanced range, accuracy, and firepower.
It also boasts modular armour, developed in collaboration with UK defence experts, offering superior protection whilst maintaining high mobility.
A fully digitised turret and fire control system provides real-time battlefield awareness and precision targeting, whilst advanced survivability systems ensure crew protection in high-threat environments.
Beyond its battlefield superiority, the Challenger 3 MBT programme delivers long-term benefits to the UK.
These include sustaining and creating highly skilled jobs across engineering, manufacturing, and systems integration; strengthening the country’s defence supply chain with key components sourced from British industry; and enhancing the UK’s defence export potential, positioning the Challenger 3 as a next-generation MBT for allied nations.
“With prototype vehicles undergoing rigorous trials, the programme remains on track, ensuring the British Army retains cutting-edge armoured capability for the future,” Richards details.
INNOVATION AND COLLABORATION
Along with its sovereign manufacturing capability, Rheinmetall’s competitive edge is defined by technological innovation
We protect those who protect us.
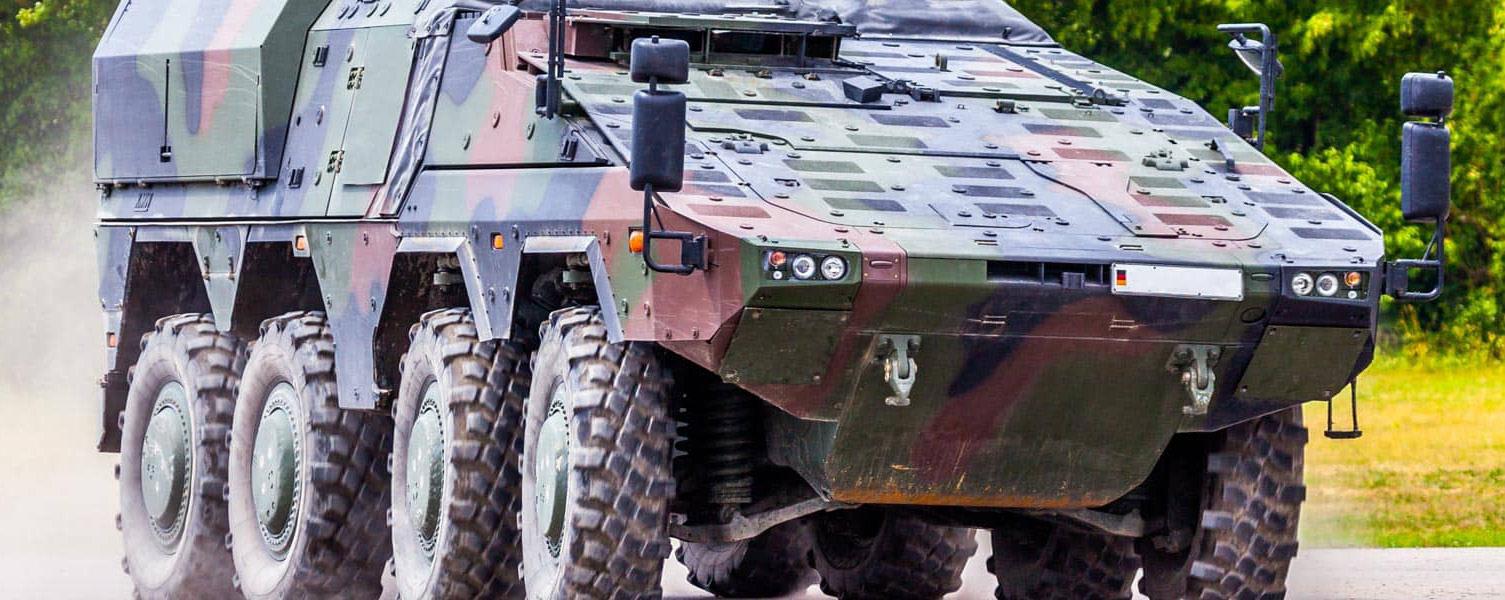
EXPERTS IN MILITARY PERISCOPE TECHNOLOGY
GuS Periscopes Ltd (GuS UK) is a UK-based defence company with extensive expertise in Military Periscope Technology. Based in Cwmbran, South Wales, within an 11,000 sqft facility, GuS UK specialises in the design and manufacture of both standard and custom observation systems, including periscopes, hybrid electronic periscope systems, episcopes, and vision blocks for armoured fighting vehicle applications.
As the only UK manufacturer of both PMMA (acrylic) and optical glass periscopes, GuS UK is passionate about providing the best performance and value solutions to its end users, actively engaging and encouraging end user input during the design and development process. GuS UK’s talented team of engineering, manufacturing, and supply chain management specialists are agile and reactive, using the latest 3D CAD software, in-house optical simulation tools, and rapid prototype techniques to produce products quickly and effectively for customer delivery and end user feedback. This design and supply chain expertise also allows GuS UK to reverse engineer and repair legacy OEM products that can no longer be sourced new.
Significant investment is planned for 2025, including a £250,000 CNC polisher and extensions to the bonding department and engineering offices. This investment supports the unique GuS UK bonding process that provides near-glass optical quality and superior environmental quality to traditional laminated PMMA (acrylic) periscope.
GuS UK has developed strategic alliances with companies who offer complementary, specialist capabilities - such as optical coatingsto ensure GuS UK can offer a true “one-stop shop” service and is
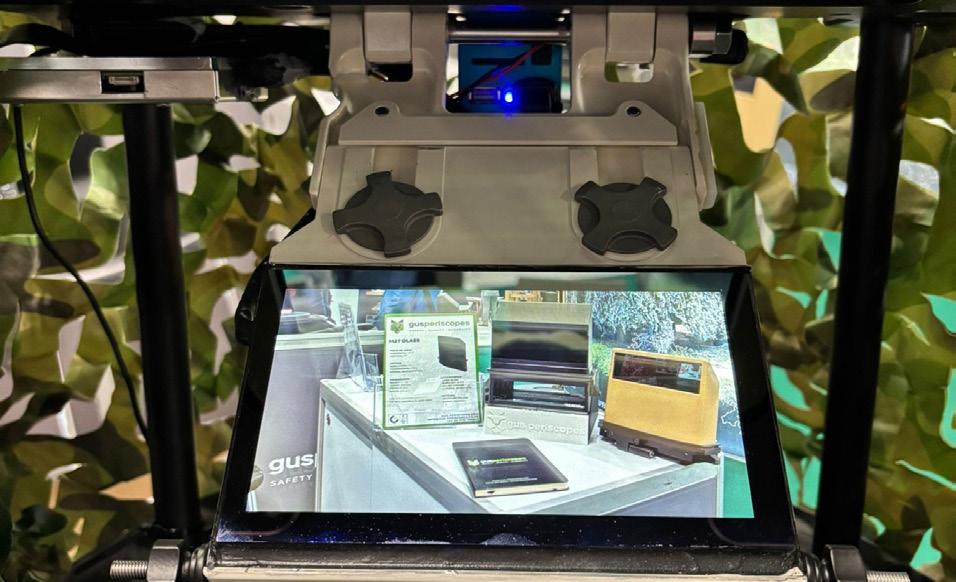
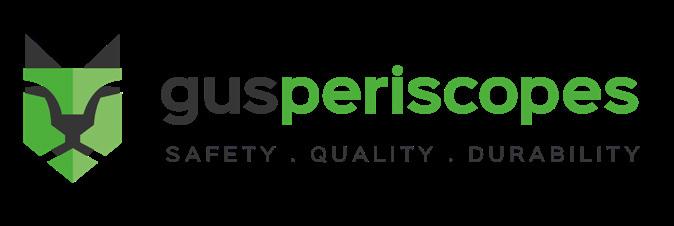
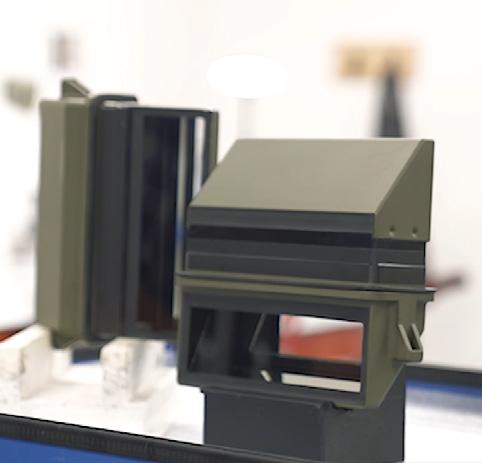
continually adapting to meet the evolving technological demands of the modern defence landscape. GuS UK provides a comprehensive service that spans the entire design and manufacturing process.
The GuS Family
GuS UK is proud to be a part of the GuS family. The GuS brand is synonymous with safety, quality, and durability. Leveraging the 45-year heritage of the GuS family, GuS UK can offer ballistic windows using the ballistic glass manufactured at GuS Glass and Safety in Germany and acts as a distributor of fully ruggedised electronic display screens from the sister company Lucius and Baer in Munich.
Working with the electronics capability within the GuS group, new design electronic hybrid periscopes have increased the scope of GuS UK’s offering, allowing the end user to integrate the camera feed into the the company’s state-of-the-art hybrid periscope systems.
The systems combine the standard periscope technology with new innovative digital technology, offering the end customer enhanced reversionary mode in the digital age. The GuS EP range of hybrid periscopes includes IR, day, lowlight, and fusion capability alongside the direct view vision. GuS UK can work with the end user to offer the optimum system for each customer requirement.
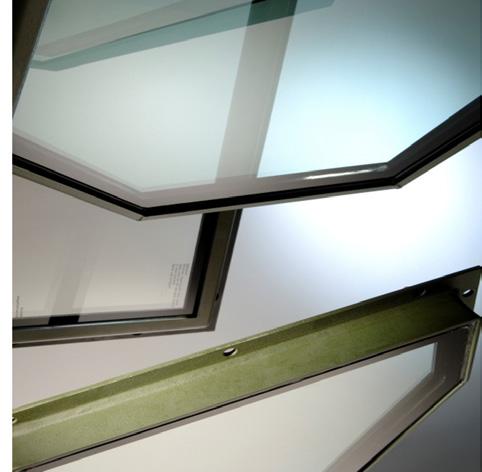
GuS UK’s Mission.
GuS UK’s mission is to “protect those who protect us” and the team is dedicated to fulfilling this.
GuS Periscopes UK is proud to be the periscope supplier to Rheinmetall for the Boxer programme in the UK and the Land 400 Boxer programme in Australia.
+44 (0) 1633-495043

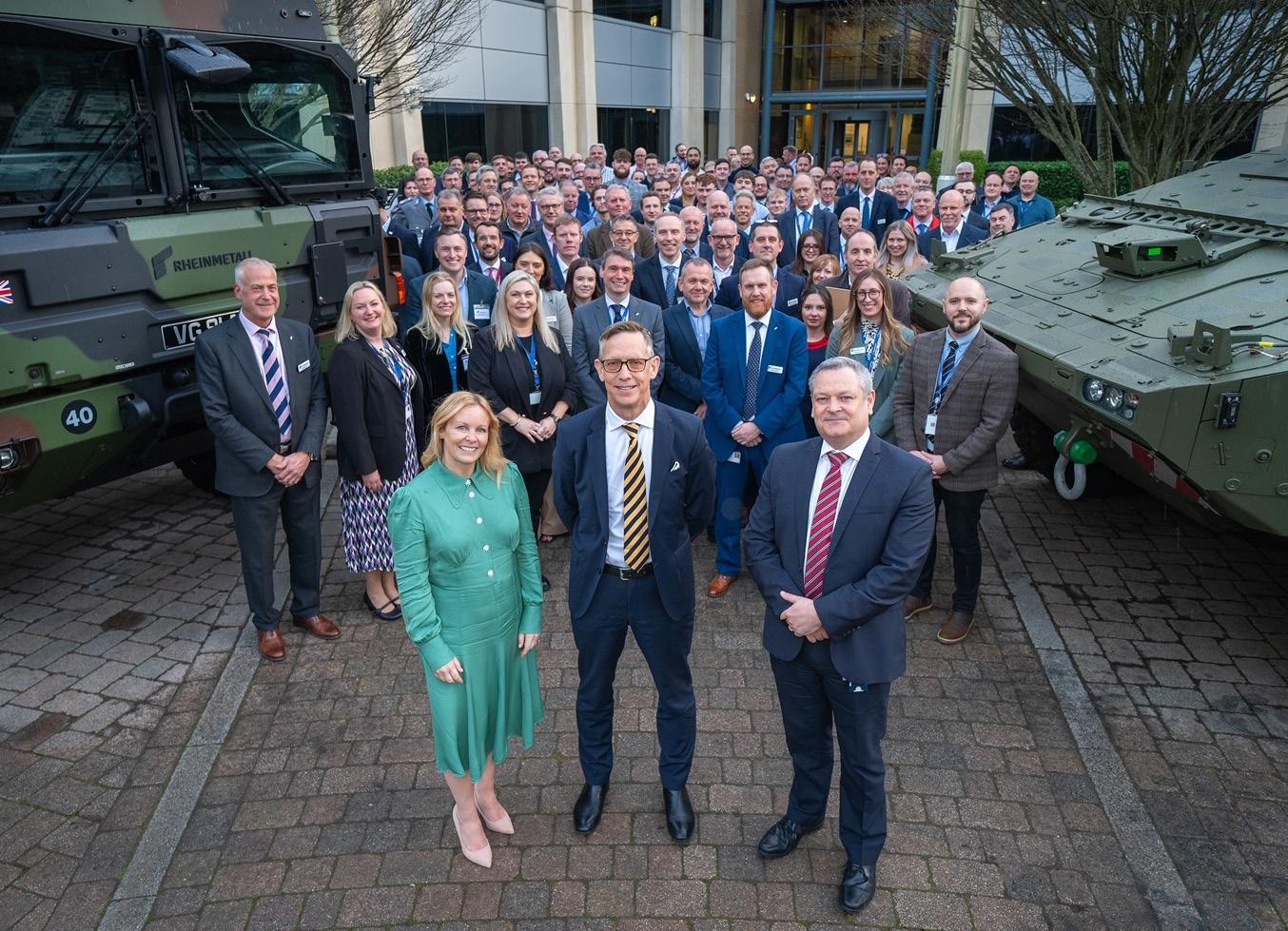
and deep-rooted partnerships.
The company is pioneering the future of armoured warfare, investing in lethality, survivability, and digital systems integration.
“We are expanding our capabilities in electronic systems and digitisation, ensuring future armoured vehicles are fully networked and interoperable with cutting-edge battlefield technology,” Richards informs us.
“This focus on digitisation is critical to enhancing command-and-control capabilities and supporting the integration of artificial intelligence (AI)-driven decision-making tools.”
The company is also launching its Advanced Land Autonomy Centres of Excellence in Germany, the Nordics, and the UK, whilst additionally expanding its current Canadian Autonomy Centre of Excellence.
These pioneering hubs will serve as the core of Rheinmetall’s autonomous systems strategy, providing advanced


“I BELIEVE STRONGLY IN BEING VISIBLE, NOT ONLY FOR MY DAUGHTERS BUT FOR OTHER WOMEN LOOKING TO BUILD SUCCESSFUL, FULFILLING CAREERS IN DEFENCE. I’VE BEEN TOLD I’M LOOKED UP TO FOR MY PERSONAL STYLE – BRIGHT COLOURS AND BOLD PRINTS IN A WORLD OF DARK SUITS; IT’S ALWAYS BEEN A CONSCIOUS DECISION”
– REBECCA RICHARDS, DEPUTY CEO, RHEINMETALL UK
integration, testing, and national control over next-generation solutions, with a strong focus on the PATH Autonomous Kit.
Close collaboration, meanwhile, ensures future-proof solutions, as demonstrated by the company’s Challenger 3 modular armour system which was co-developed with the Defence Science and Technology Laboratory (DSTL) and Defence Equipment and Support, an
arm’s-length body of the MoD.
“Additionally, the Trinity House Agreement, signed in 2024, further strengthens UK-Germany defence industrial ties by expanding largecalibre weapon production,” shares Richards.
DRIVING DEI
Aside from the Boxer MIV and Challenger 3 MBT programmes, Rheinmetall takes great pride in its
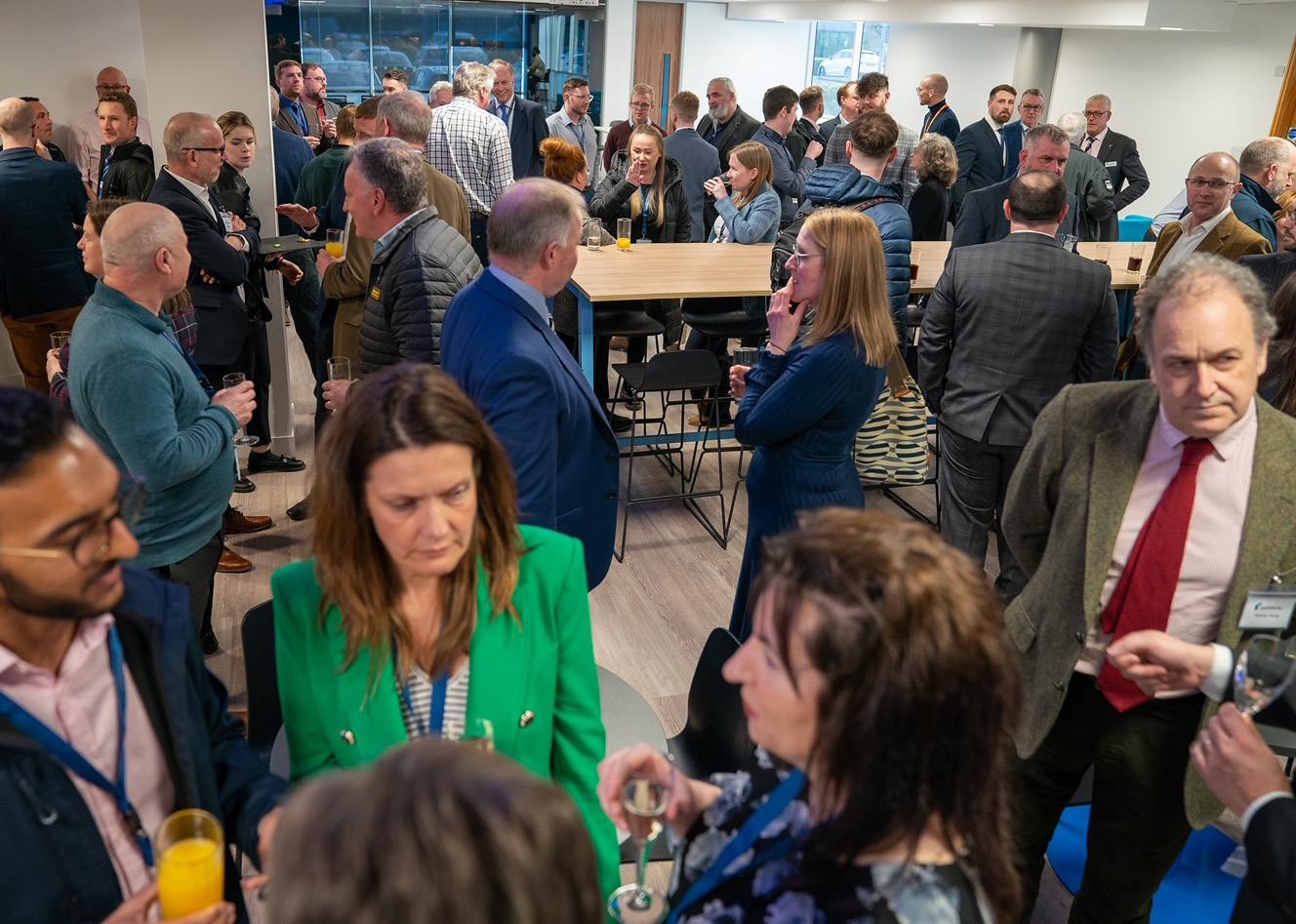
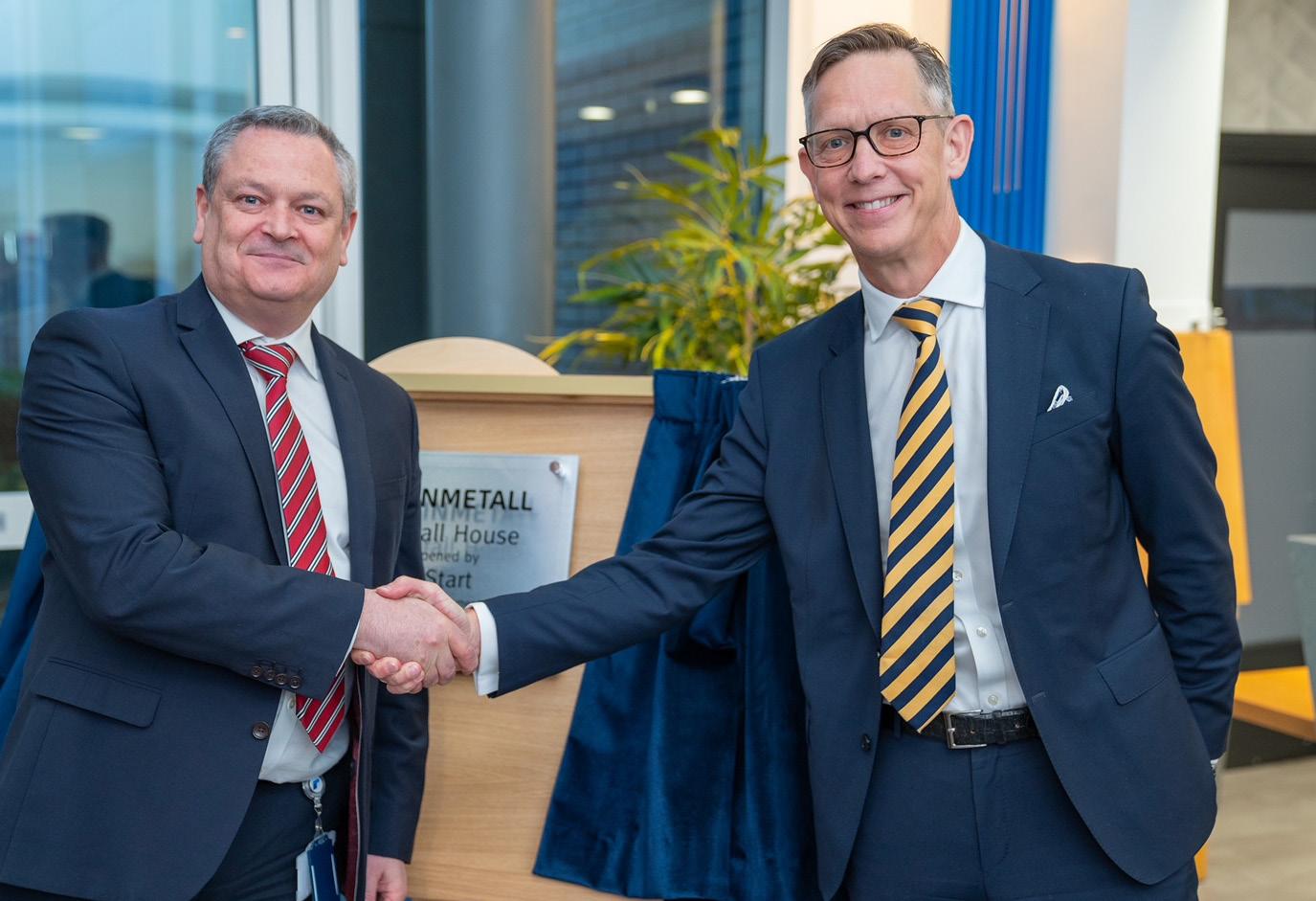
commitment to the Armed Forces community and fostering diversity, equity, and inclusion (DEI) in the workplace.
The company actively recruits veterans and works closely with specialist organisations to help ex-service personnel transition into civilian careers.
“In 2024, we formalised this commitment by signing the Armed Forces Covenant, providing additional leave for reservists and Cadet Force Adult Volunteers and supporting military families through flexible employment opportunities,” Richards confirms.
Beyond employment, Rheinmetall is a proud corporate friend of SSAFA, the Armed Forces charity, engaging in fundraising and initiatives that support veterans, service personnel, and their families.
On driving DEI, Richards firmly believes diversity is essential for
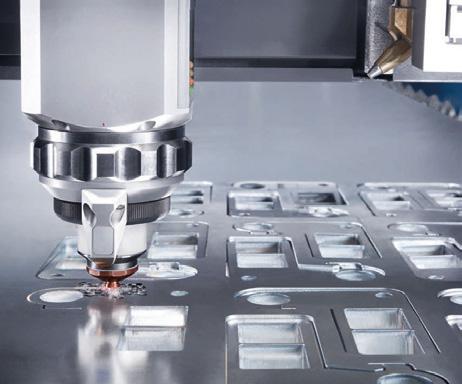
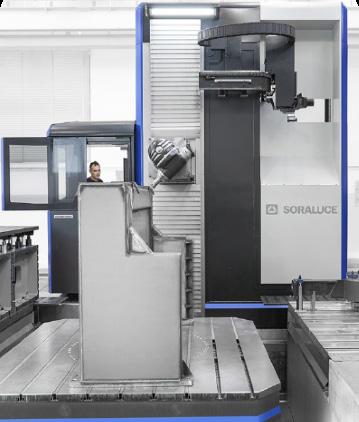
Oldham Engineering is a UK Premier manufacturing service provider for all Industrial Sectors, including Nuclear, Defence, Oil and Gas, Subsea, Aerospace, Rail and Renewables.
Operating from it’s UK manufacturing site based in Oldham and Sheffield, the company has premium engineering facilities totalling over 150,000 sqft. The business is ISO9001 certified and holds the ‘Investors in People’ accolade. Oldham Engineering’s Competitive Advantage is driven by three key elements;
• a highly skilled and competent workforce,
• investment in the latest machining technology, and
• a business culture of continuous improvement.

better decision-making, broader perspectives, and innovative problemsolving – critical factors in today’s defence industry.
“Different viewpoints lead to stronger outcomes, and we must foster new ways of thinking to address the evolving challenges we face,” she emphasises.
Rheinmetall’s progress in DEI wouldn’t be possible without the full support of its executive leadership, who continue to champion and drive this work forwards.
“We are committed to creating a workplace where every individual feels valued, empowered, and supported.”
As part of this commitment, the company is developing a comprehensive well-being strategy that aims to enhance its focus on employee health, resilience, and an inclusive culture that promotes work-life balance and family-friendly policies.
The strategy will build upon existing support structures to ensure Rheinmetall’s workforce remains motivated, engaged, and equipped to succeed.
“Beyond the workplace, I am deeply passionate about driving gender diversity and inspiring future talent. I want to show my daughters that they can achieve anything they set their minds to, even in traditionally male-dominated industries,” Richards affirms.
“To help achieve this, I volunteer at local schools, mentor young people, and encourage more females to pursue STEM careers. I am also dedicated to raising aspirations in deprived communities.”
As part of its broader commitment to gender diversity, Rheinmetall has signed the Women in Defence Charter, pledging to increase female representation in senior leadership roles.
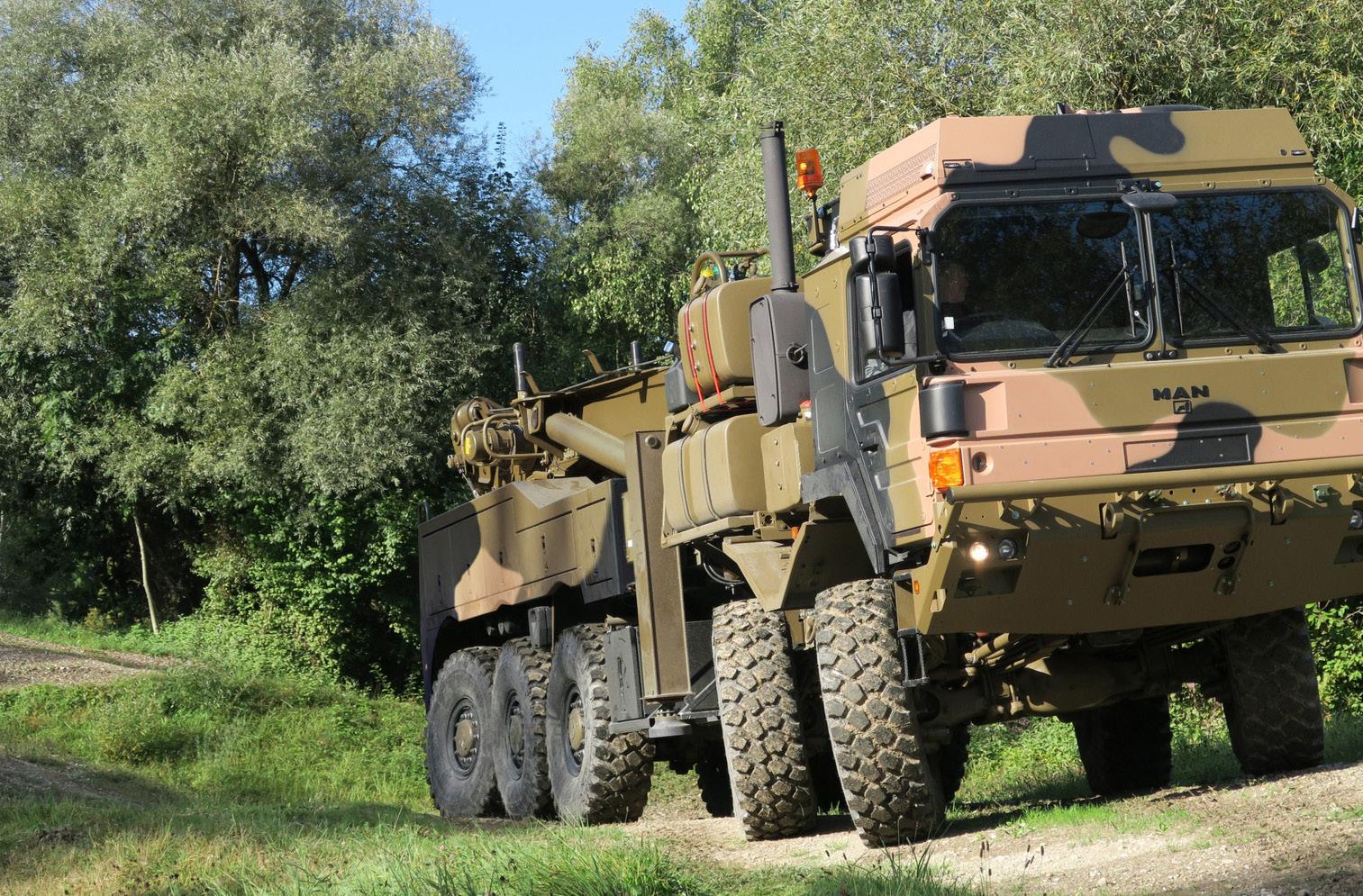
The company has made great strides in ensuring women are wellrepresented at all levels, creating a culture where everyone has the opportunity to thrive and contribute.
It is also proud to have recently been endorsed by Work180, which recognised the company’s commitment to gender equality – a milestone that reflects the impact of policies such as 26-week paid parental leave and flexible work options that support parents in returning to the workplace after the birth of a child.
Additionally, the company invests in STEM engagement, apprenticeships, and graduate programmes, ensuring it nurtures a diverse pipeline of future talent for the defence sector.
“I’ve worked closely with schools, universities, and STEM outreach initiatives to help inspire the next generation – especially young women – to consider careers in a sector that has traditionally been male-dominated. Over time, I’ve seen greater diversity emerging across the
defence industry, and I’m proud to be part of that shift,” she impassions.
“I believe strongly in being visible, not only for my daughters but for other women looking to build successful, fulfilling careers in defence. I’ve been told I’m looked up to for my personal style – bright colours and bold prints in a world of dark suits; it’s always been a conscious decision.”
Evidently, Rheinmetall recognises the importance of actively engaging with communities that have historically been underrepresented, prioritising initiatives that support veterans, promote STEM opportunities, and address gender equality in a meaningful way.
PASSIONATE PEOPLE
With DEI deeply embedded in its values and how the company operates every day, the greatest strength of Rheinmetall is its people, including some of the most talented engineers, technicians, and defence
specialists in the country.
These individuals are not only highly skilled but also deeply passionate about innovation and excellence.
Whether developing cutting-edge military technology, supporting the Armed Forces, or strengthening Britain’s sovereign defence capability, everyone at Rheinmetall plays a vital role in delivering real-world impact.
“I’ve come to appreciate that every member of the team brings unique strengths. High-performing teams are built on diversity of thought and experience; it’s about understanding, balance, and compromise – not oneupmanship,” acknowledges Richards.
“We’ve built a genuinely supportive and friendly workplace culture. It’s the small, thoughtful moments –people checking in, sharing a laugh, or showing a genuine interest in one another – that make a big difference. We’re a motivated, passionate team, and that positive energy is what makes it such an inspiring and
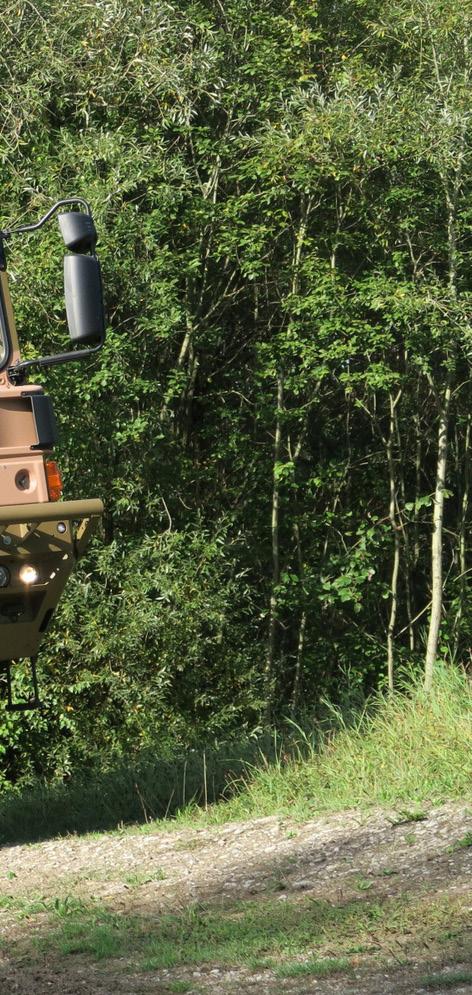
dynamic place to work.”
As a growing business, Rheinmetall is investing heavily in the UK and planning for the future, not just in military capability but also in creating high-value jobs and meaningful careers.
With that growth comes the opportunity to help shape the company culture, ensuring it remains a place where people want to work, develop, and stay.
“Being part of that journey is incredibly rewarding. Early in my career, I believed everything in work had to be perfect – contracts had to be flawlessly negotiated and bids had to be won – but as I progressed, I realised that true success comes from building long-term, fair partnerships,” Richards reflects.
“It’s not about winning but achieving the right outcomes for everyone involved. No two days are the same, especially in defence, and even with years of experience there’s always something new to learn.”
THE JOURNEY INTO DEFENCE
Despite having this extensive experience in the industry, Richards’ journey into defence was an unconventional one.
She initially studied law and began her career in a solicitor’s firm before moving in-house to the legal department of an iron and steel company.
When the opportunity arose to move back home, Richards came across a role at military vehicles and communications company General Dynamics, which opened the door to the world of defence.
“That role marked my first real exposure to the industry, and I was immediately drawn in by the scale and complexity of the programmes,” she recalls.
“Defence enabled me to contribute to significant projects whilst remaining rooted in my local community.”
As her career progressed, Richards became increasingly passionate about the wider impact of the industry – not just on national security, but on local economies and social mobility.
Indeed, it plays a valuable role in supporting regional development, particularly in areas that benefit from skilled jobs and long-term investment.
Having progressed to Commercial Vice President of General Dynamics in 2016 – a milestone Richards believed would be the pinnacle of her career – a new chapter soon opened at Rheinmetall when she joined as Managing Director in 2019.
Initially tasked with overseeing key programmes and strategic partnerships across the UK, Richards is now proud to serve as Deputy CEO.
“My focus is on strengthening sovereign manufacturing capability and delivering world-class military vehicle systems to the British Army,” she summarises.
“I have been fortunate to work on some of the UK’s most
significant defence programmes, which has provided me with a deep understanding of defence procurement, manufacturing, and the supply chain landscape –knowledge that is instrumental in shaping Rheinmetall’s future.”
PIVOTAL PRIORITIES
The future includes a number of priorities for the company, with 2025 being a pivotal year as Rheinmetall expands its operations and advances key defence programmes.
These priorities include scaling Boxer production capacity, advancing Challenger 3 trials, and operationalising its new large-calibre gun hall.
Rheinmetall is also investing in advanced defence technologies and expanding both the UK defence supply chain and the autonomous revolution.
By 2030, the company aims to be the nation’s leading armoured vehicle manufacturer, not just meeting domestic defence needs but also positioning Britain as a key exporter of advanced military vehicles.
“Our long-term investment in workforce development, infrastructure, and sovereign defence capabilities will be instrumental in achieving this vision.
“Through continued collaboration with the UK government, industry partners, and international allies, we remain focused on delivering world-class defence solutions that strengthen Britain’s strategic position on the global stage,” Richards closes.
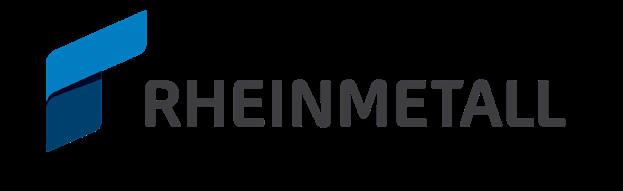
Tel: 07707853374
uk.communications@rheinmetall.com https://www.rheinmetall.com
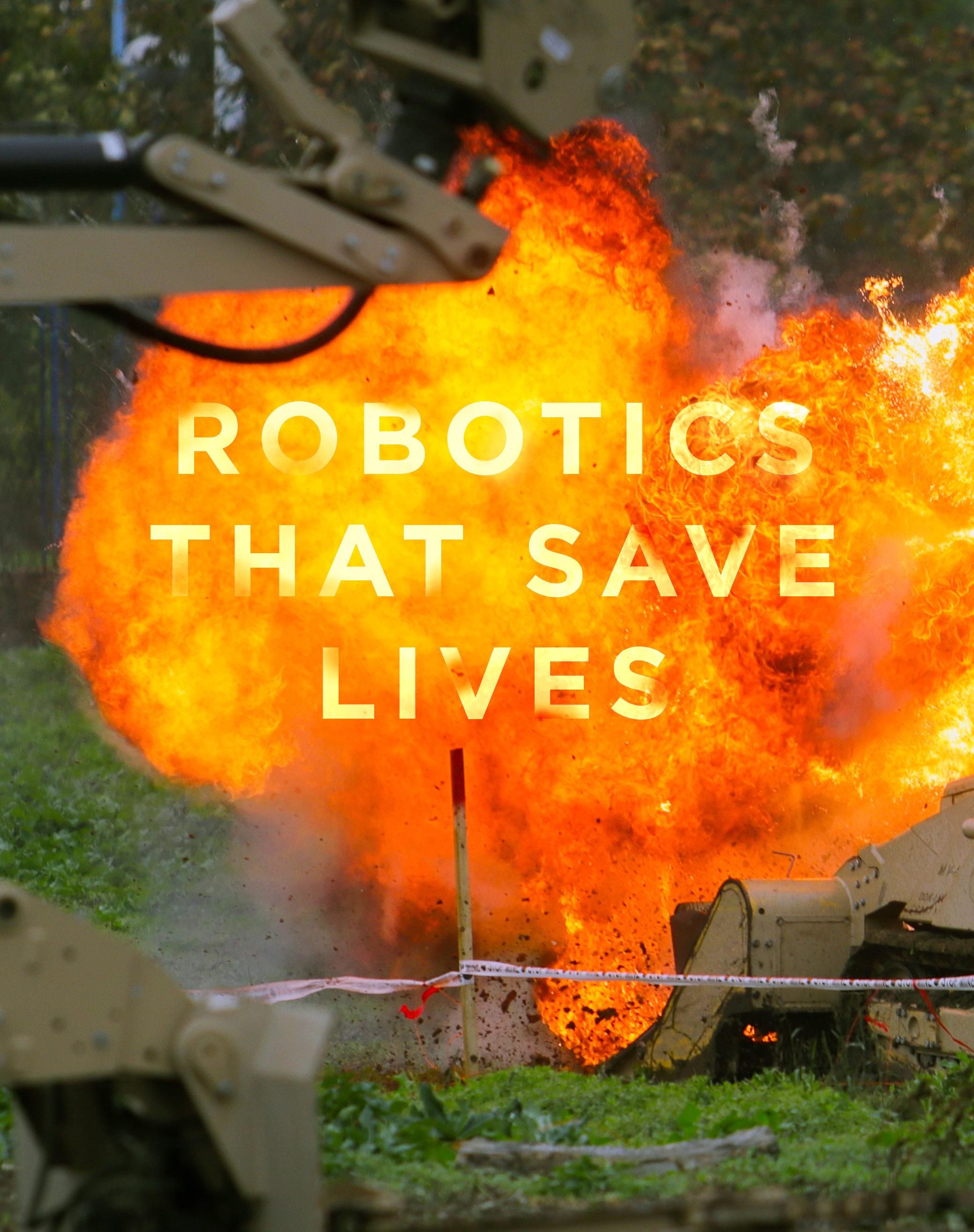
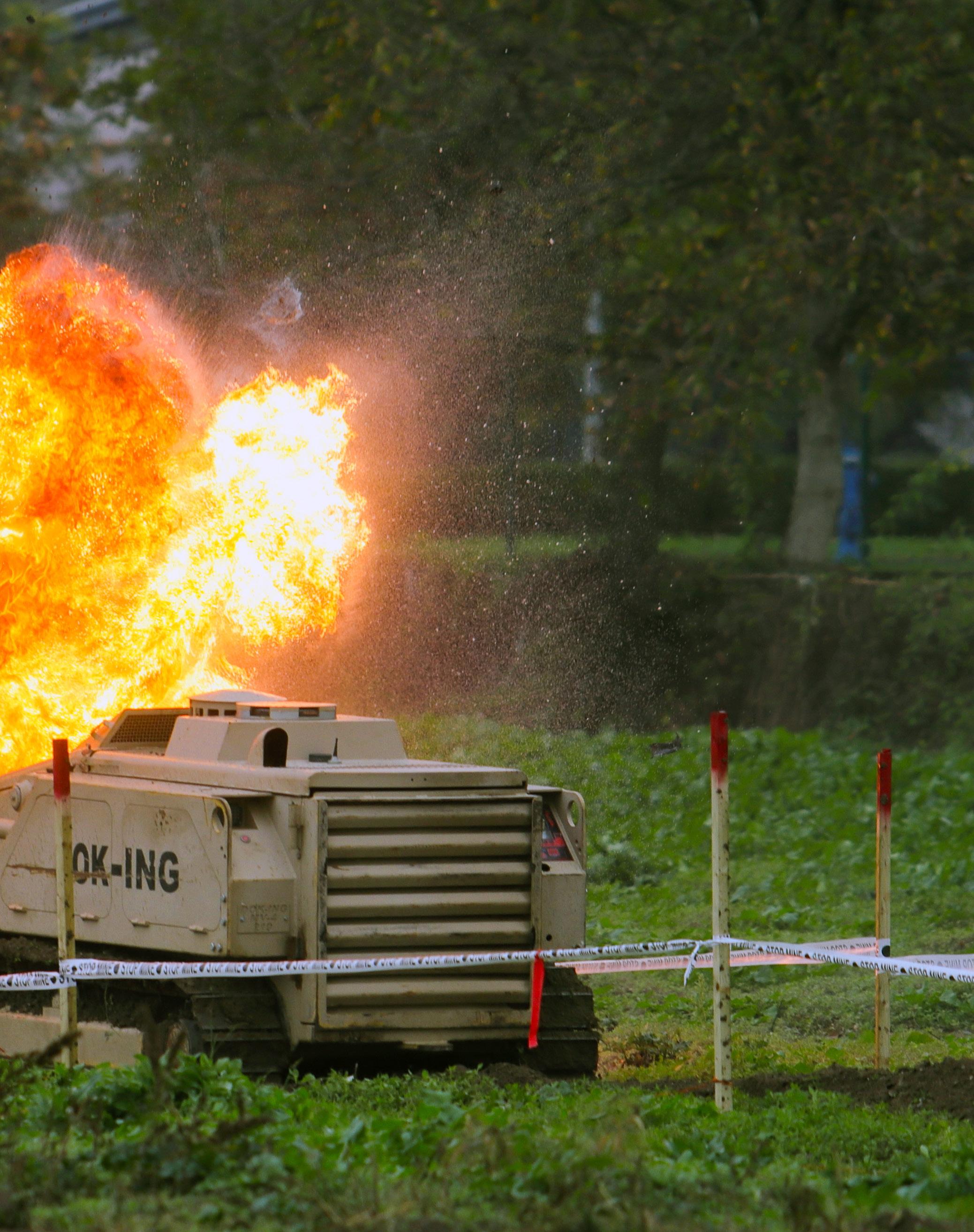
Equipped with the steadfast mantra of ‘don’t send a man to do a machine’s job’, we learn about DOK-ING’s comprehensive and transformative robotics solutions that are saving countless lives and evolving industries throughout Europe. The company’s leadership team across its three divisions tell us more
Writer: Lucy Pilgrim | Project Manager: Cameron Lawrence
Leading the charge in heavyduty robotics and autonomous systems, DOK-ING has established itself as a manufacturing powerhouse, globally renowned for producing world-class unmanned vehicles that protect human lives in otherwise hazardous and harmful environments.
Headquartered in Zagreb, Croatia, the company operates across 40
countries and diligently meets the needs of the security and defence, underground mining, and energy sectors through three proactive divisions.
DOK-ING strives to produce forward-thinking applications that deliver a step-change in both safety and efficiency.
Indeed, the company first emerged from the mission to find a mechanical
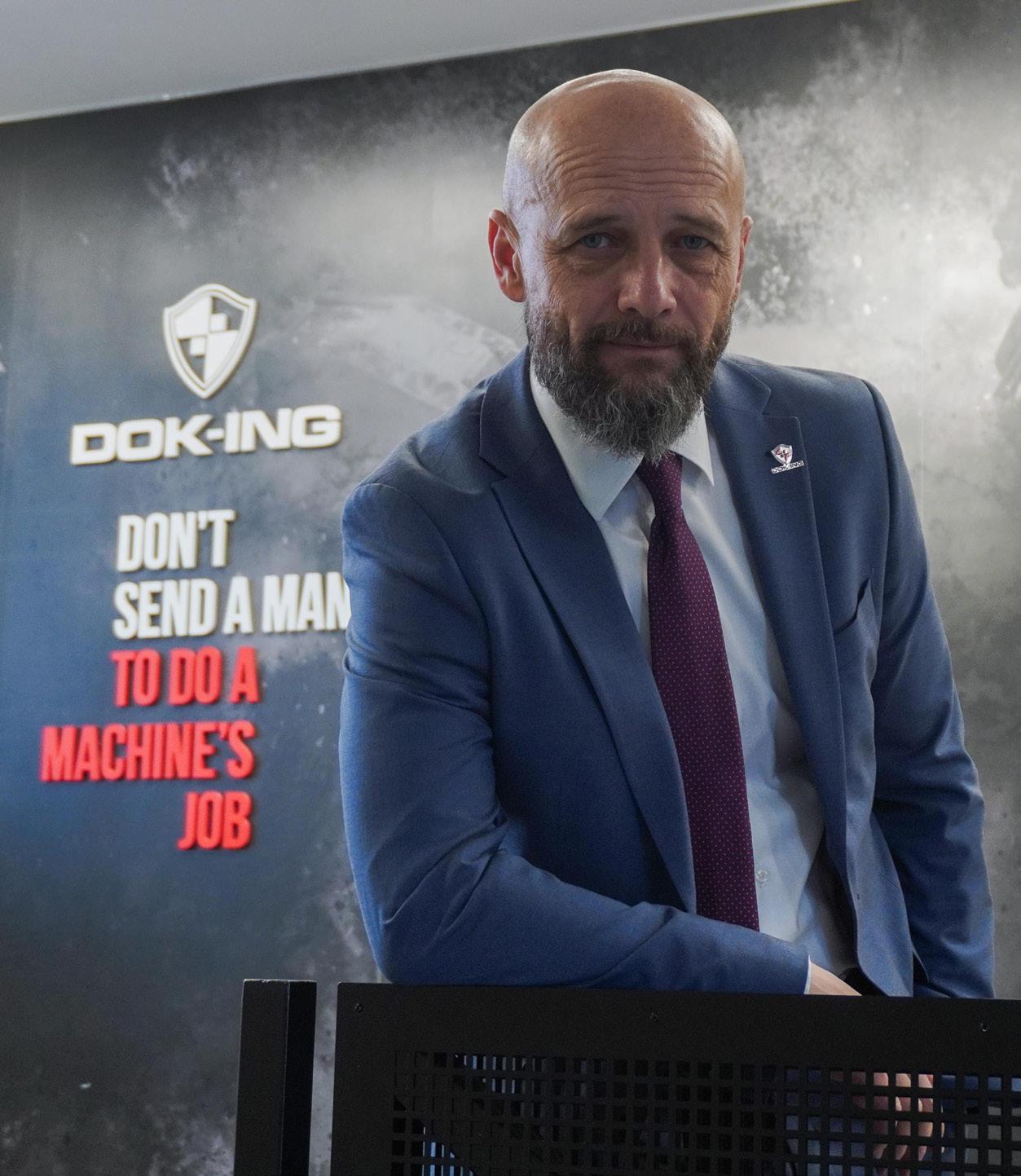
“WHEN WE DESIGNED THE KOMODO, WE HAD ONE GOAL IN MIND: TO INCREASE EFFICIENCY AND REDUCE COSTS FOR THE END USER”
– DAVOR PETEK, COO, DOK-ING SECURITY AND DEFENCE
solution to take humans away from dangerous and labour-intensive environments during the demining effort in Croatia in the early 1990s.
Since then, DOK-ING’s focus has remained on operating in hazardous and dangerous areas where conventional first responders are incredibly limited, particularly in the extreme conditions often experienced in the military and during underground mining.
“The technology already exists, but at DOK-ING, we’ve made a deliberate choice to apply it where it matters most – in the world’s most dangerous and demanding jobs,” introduces Davor Petek, COO of DOK-ING Security and Defence.
“By targeting high-risk environments, we create real impact, reducing exposure for frontline workers whilst improving operational performance. This is where innovation truly proves its worth, and it’s the path we’ve committed to,” echoes Luka Petro, COO of DOK-ING Mining.
“Bottom line, our systems are designed to thrive where humans would otherwise die,” Petek adds.
DELIVERING THE COMPLEX NEEDS OF DEFENCE
As one of the company’s key focus divisions, DOK-ING Security and Defence delivers critical unmanned systems for the harshest military situations.
Due to ongoing political conflicts across Europe and further afield, alongside the rise of chemical, biological, radiological, and nuclear (CBRN) environments, the division’s unmatched capabilities are at the top of development and procurement priority lists due to an increasingly complex global security situation.
Croatia’s defence capabilities in particular are shifting into a higher gear, as demonstrated by the recent establishment of an inter-ministerial commission for the nation’s defence capabilities and
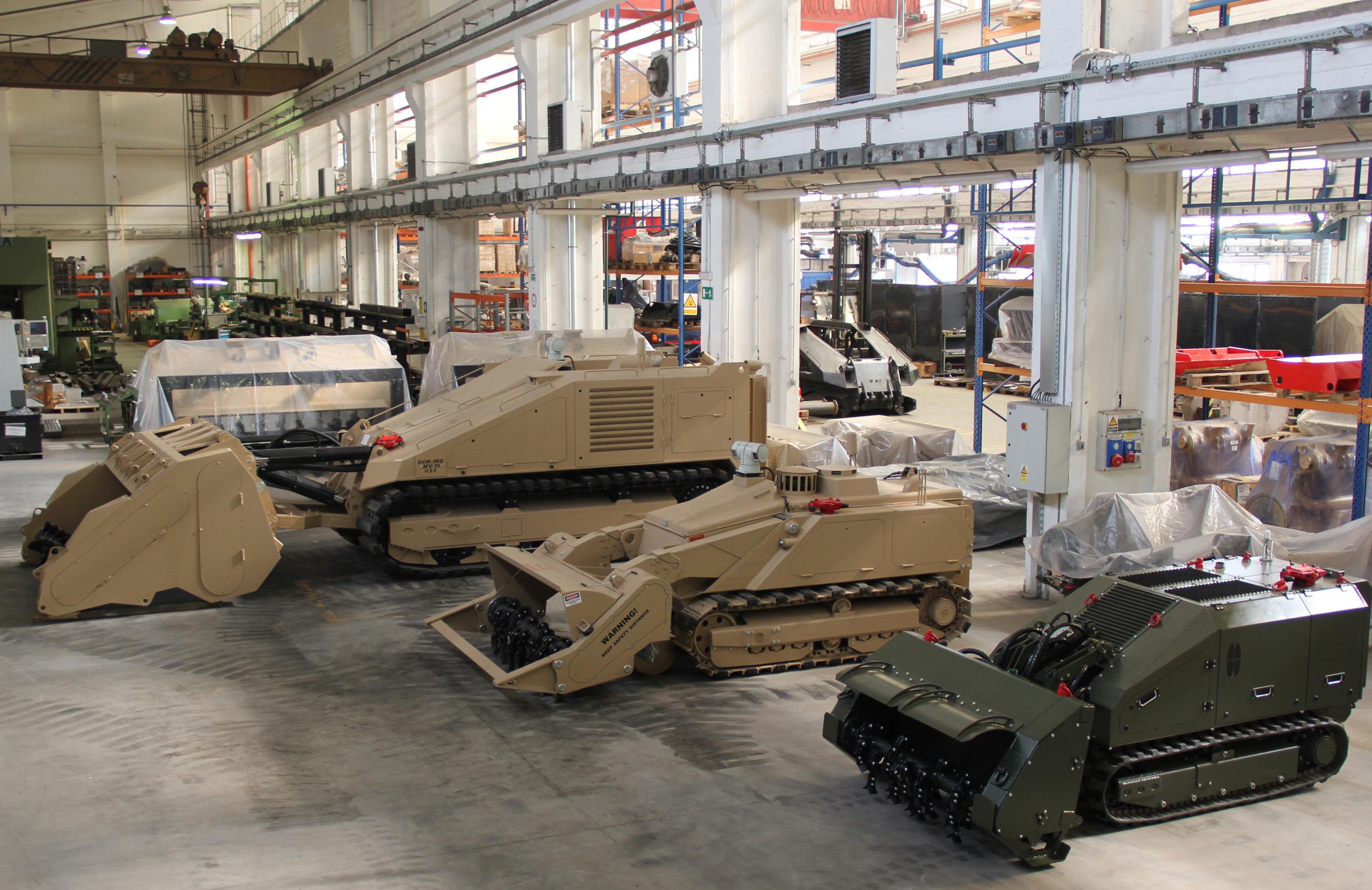
industry development, paving the way for improvements in business-togovernment (B2G) activities.
However, it will still be some time before the appropriate policies and initiatives are fully operationalised to effectively close Croatia’s capability gap when compared to other European countries.
“The financial aspect is there and our production capacity is increasing, but without long-term contracts and orders from governments, industry cannot close the gap,” Petek discusses.
“We also still have a very slow and complex procurement process that was maybe acceptable in peace time, but we are now operating in a different, more demanding environment that requires a serious change in EU procurement policies.”
This is particularly pertinent given the recent conflict between Russia and Ukraine, which has increased the significance of secure defence capabilities.
With this in mind, DOK-ING Security
and Defence’s advanced systems designed for mobility operations and demining and humanitarian demining, such as the MV-4 Scorpion and MV-10 Bison, are preferred systems in Ukraine due to their high survivability and reliability.
The continual targeting of the country’s critical infrastructure has also highlighted the demand for the division’s crisis response systems, including the MV-3 Hystrix, MV-5 Tusk, and MV-8 Komodo (Komodo) CBRN.
A NEXT-GENERATION UNMANNED PLATFORM
As DOK-ING Security and Defence’s latest modular platform, the Komodo is proving to be a critical capability for the increasing operational use of unmanned vehicles.
“When we designed the Komodo, we had one goal in mind: to increase efficiency and reduce costs for the end user whilst maintaining the same – or similar – level of capability, all with a strong focus on protecting human
lives and property. I truly believed we have succeeded in that mission,” Petek states.
Therefore, as unmanned ground vehicles continue to be integrated into the capabilities of military forces, the Komodo aims to provide the same levels of combat support as manned vehicles.
“Combining manned and unmanned platforms with same or mutually supporting capabilities increases combat power and force protection whilst ultimately lowering cost,” Petek explains.
Given the Komodo is a payloadagnostic platform, its users are able to integrate payloads that are either lacking on conventional platforms or more efficient and acceptable due to unmanned aspects.
Furthermore, providing a single platform with multiple payloads simplifies operations, maintenance, and logistics support, enabling users to utilise the same platform with combined capabilities for multiple tasks.
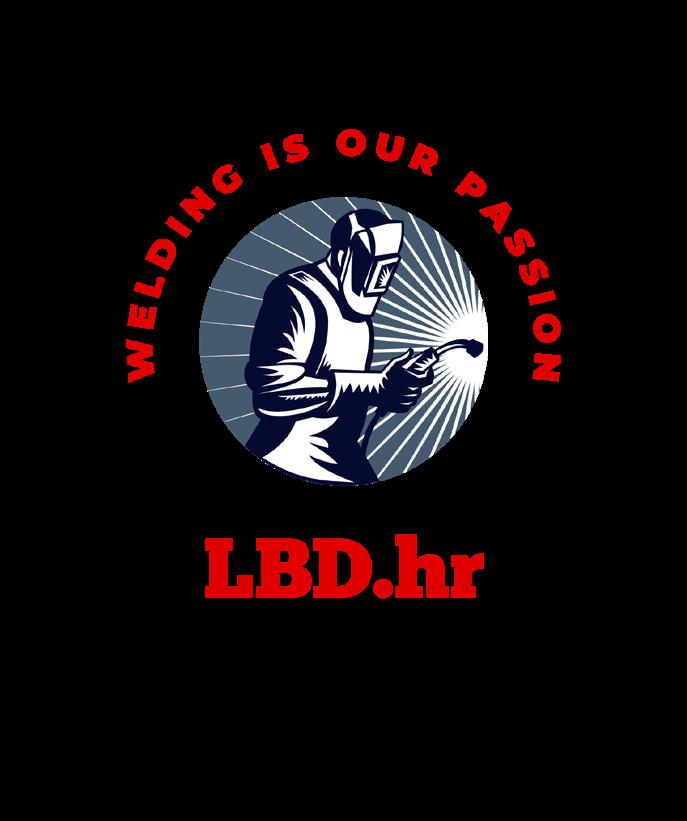
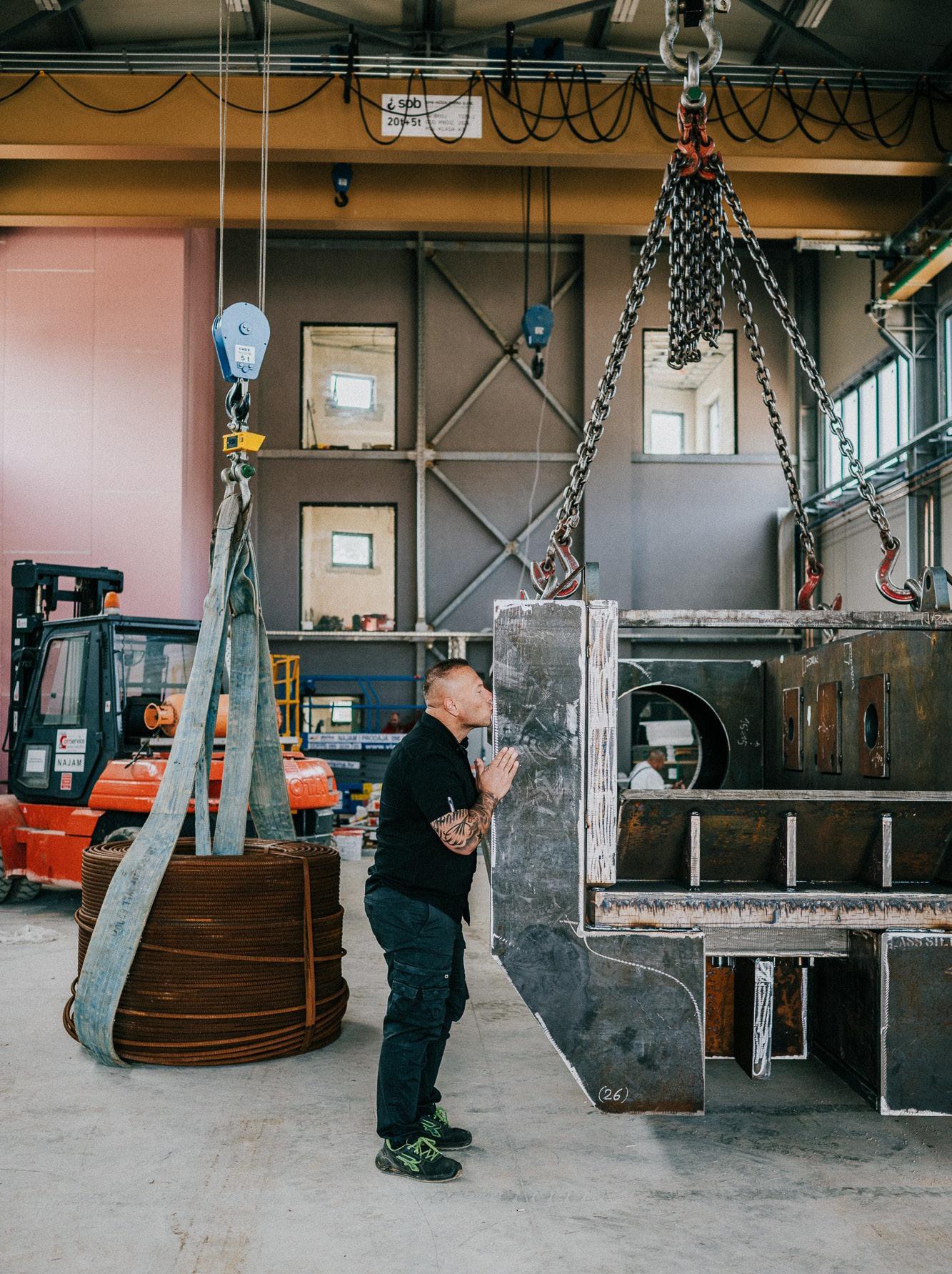
FUSING QUALITY WITH EXPERTISE
With a proud 20+ year history of welding all types of metal for various structures, LBD d.o.o. is a company driven by customer satisfaction and service excellence
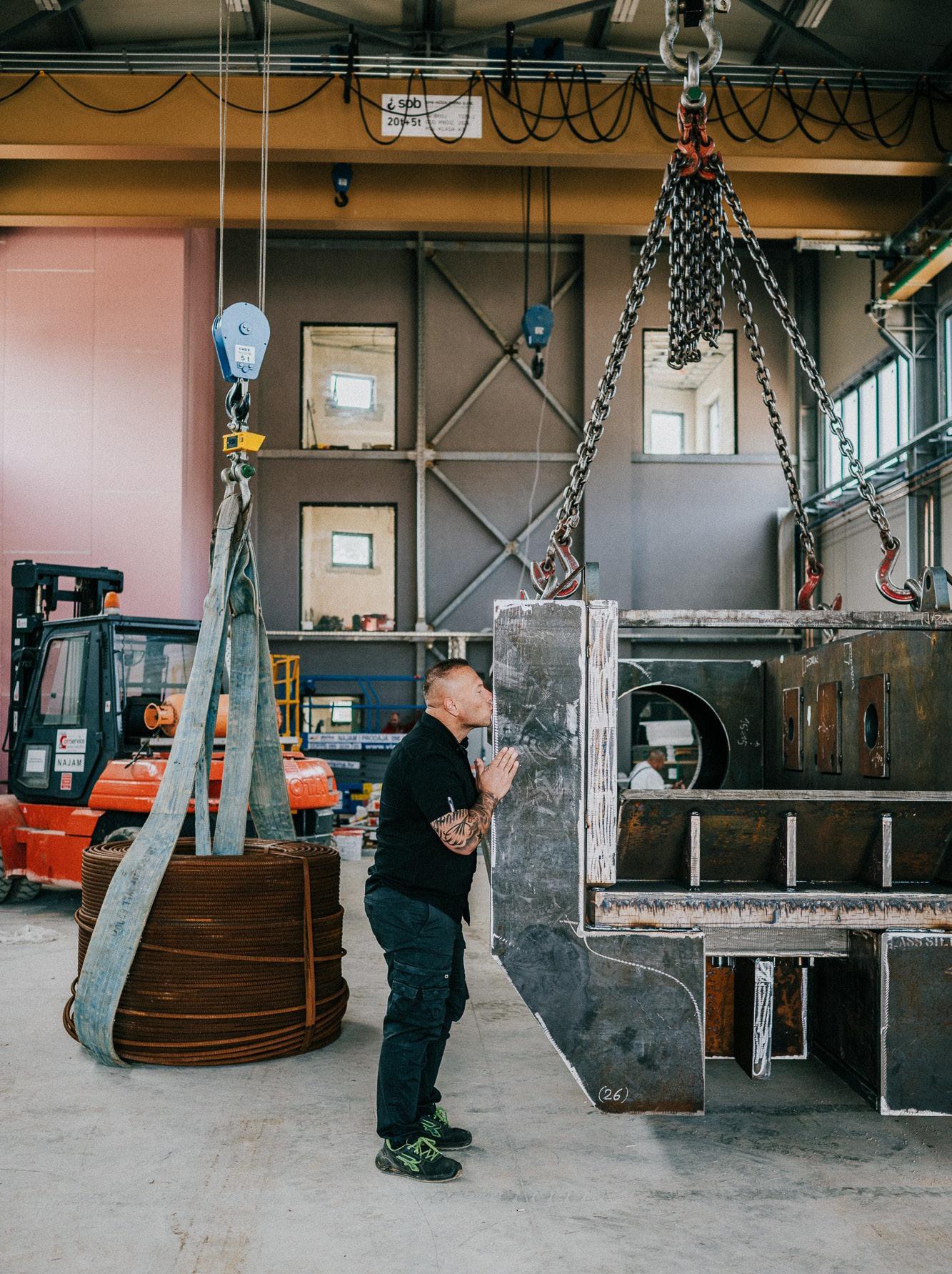

Headquartered in the city of Rijeka, Croatia, LBD d.o.o. (LBD) offers a wide range of welding, processing, and assembly services for all types of metals.
Having evolved from humble beginnings as a small Croatian business, the company has grown rapidly and is today recognised across Europe for its firstrate services.
With a newly established branch in Trieste, Italy, and a vision for continued expansion, LBD draws on its two decades of industry experience and team of dedicated and qualified personnel to ensure welding excellence every time.
Its staff base consists of engineers, certified welders, structural fabricators, managers, and administrative employees, each of whom are offered comprehensive training and professional development opportunities.
Well-versed in complex projects where various tests of welded joints are required, LBD’s knowledge of the metalworking industry guarantees consistent quality, regardless of the thickness of the material or purpose of the finished product.
FIRST-CLASS SERVICES
Metal inert gas (MIG) and metal active gas (MAG) welding, also known as gas metal arc welding (GMAW), are versatile welding processes that enable fast and efficient results, applicable to various metals.
LBD utilises MIG and MAG alongside two other welding processes, Tungsten inert gas (TIG) and remote exothermic welding (REL).
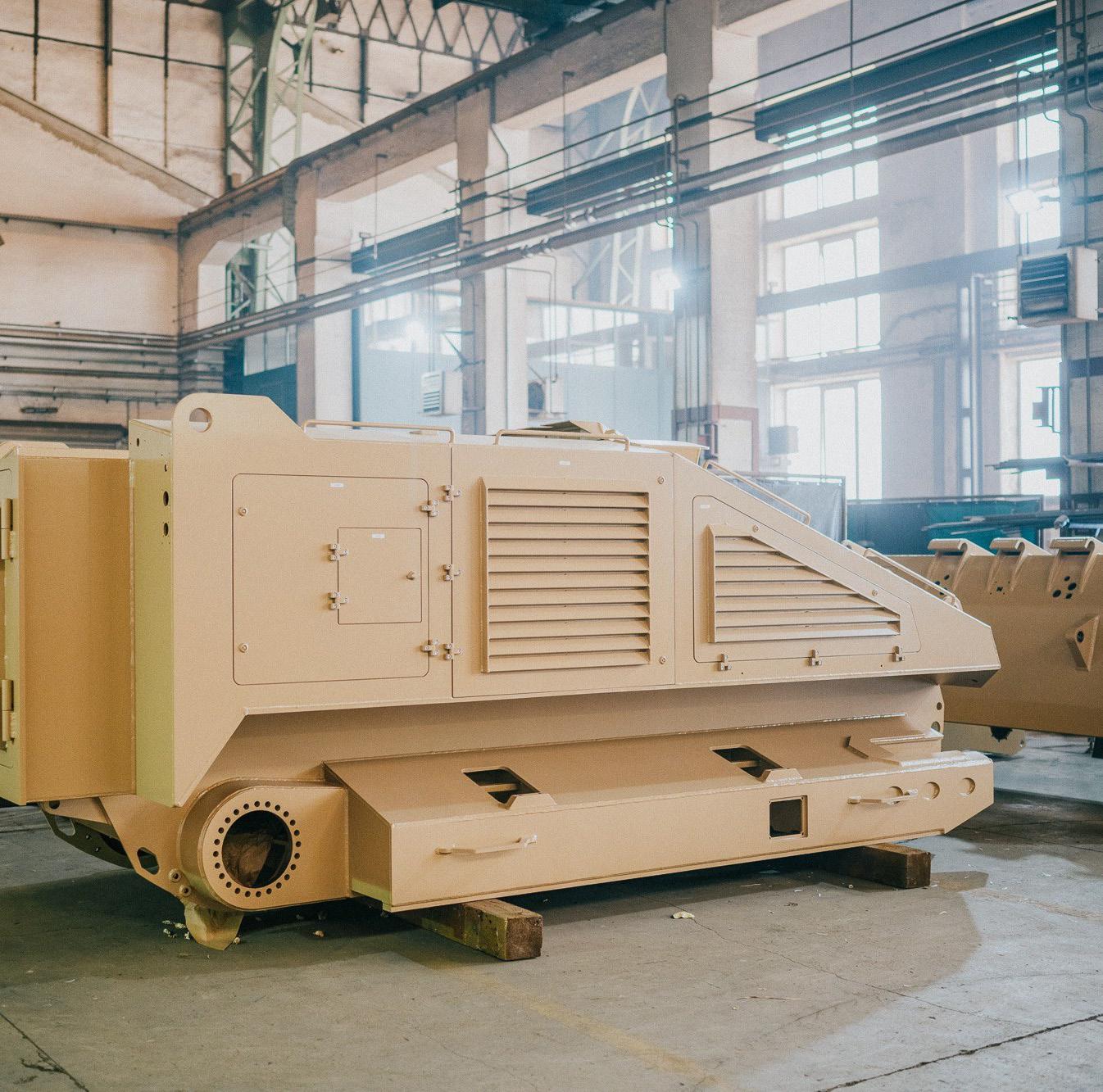
The method selected depends on the type of material being welded, alongside its thickness and the environment in which it must perform.
Offering a comprehensive range of supplementary services, including magnetic particle testing (MPT), non-destructive testing (NDT), and ultrasonic testing (UT), the company conducts its activities in a workshop fitted with cranes which have capacities of 10, seven, or five tonnes.
It also offers construction services and technical support solutions throughout the entire project life cycle, from the initial design stages to the finished product.
Utilising top-of-the-range 2D and 3D modelling programmes alongside appropriate methods and specifications helps LBD produce a precise and defined final product.
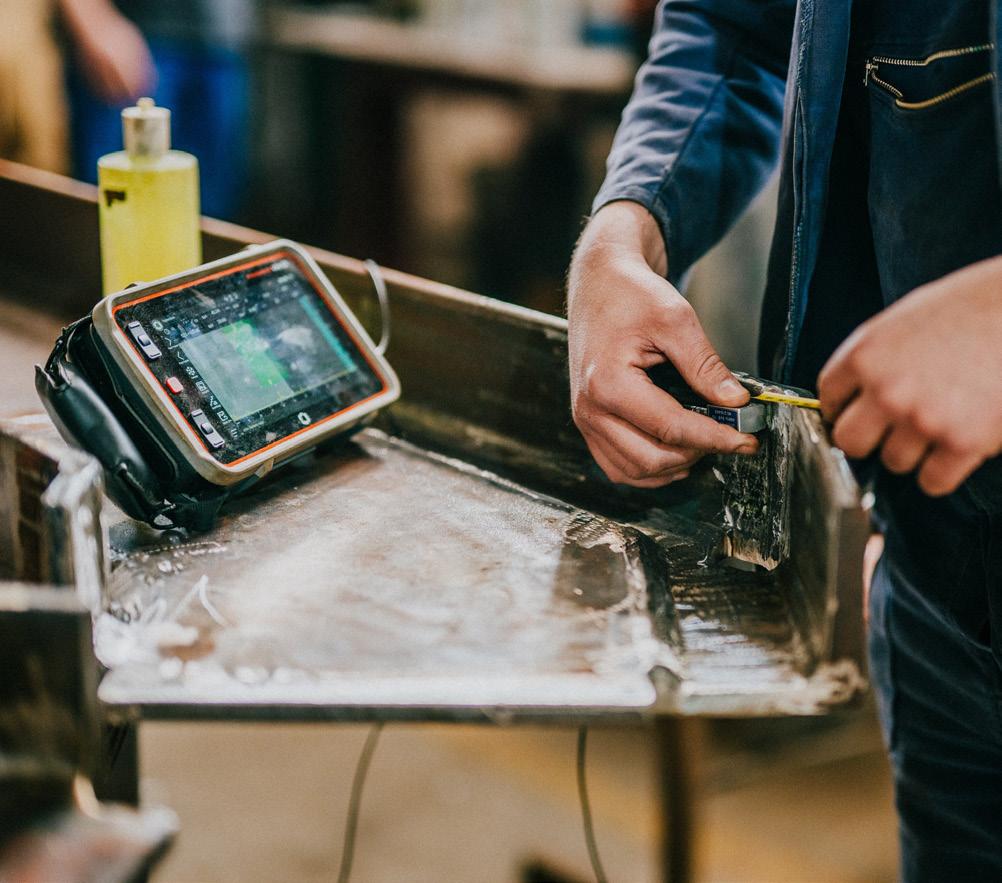
PROJECT OF NOTE
LBD is currently working on the MV-10 BISON (MV-10) demining machine for DOK-ING, a leader in the development and production of robotic and autonomous systems and equipment.
An industry stalwart for over three decades and present in 40 countries, DOK-ING is known for its innovative approach and state-of-the-art technologies, which have earned it a superior status in international markets.
LBD is therefore committed to its responsibility of welding and manufacturing the machinery to a high quality.
A crucial piece of equipment, the remote-controlled MV-10 uses a rotating appendage to detonate landmines at mine sites across the world.
Made entirely of HARDOX 450 steel, the MV-10 benefits from the resilience and endurance of the material, making it ideally suited to operate in challenging terrains.
Proud to showcase its involvement in the development of this product, LBD demonstrates its ability to deliver the highest standards of quality and workmanship.
LBD d.o.o. has a Non-Destructive Testing (NDT) department. NDT of welds and base materials is a critical process used to evaluate the integrity and quality of components without causing damage. It ensures that welds are free from defects such as cracks, porosity, or incomplete fusion, and that the base material meets structural and safety requirements. LBD d.o.o. and its employees are certified in the following NDT methods: visual testing (VT), ultrasonic testing (UT), radiographic testing (RT), magnetic particle testing (MT), dye penetrant testing (PT), holiday test and hardness test. Each of the methods is suited to different types of materials and flaw detection. These techniques help prevent failures, improve reliability, and maintain compliance with industry and state standards.
Visual Testing (VT) is the most basic and widely used non-destructive testing method. It involves

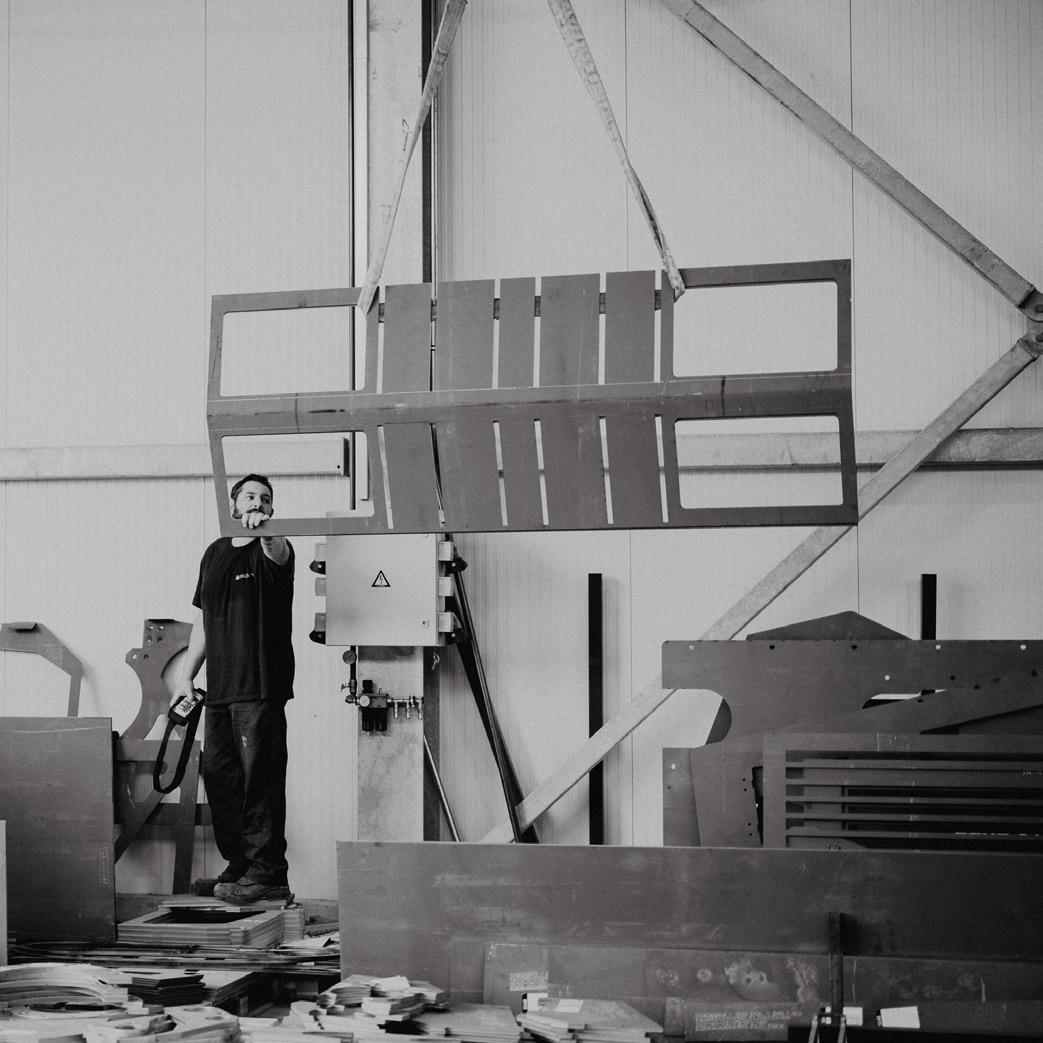

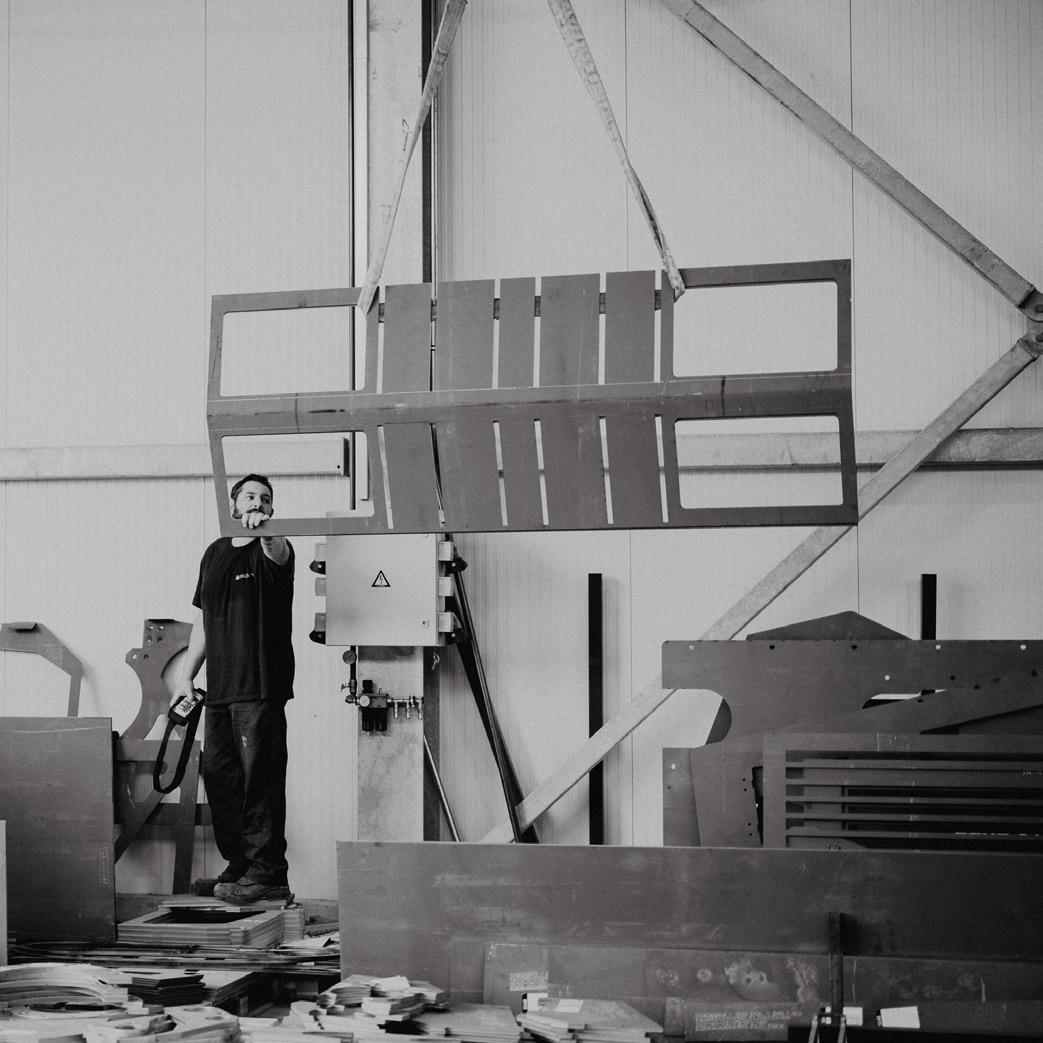
inspecting the surface of welds and base materials with the naked eye or with the help of tools like magnifying glasses, borescopes, or cameras. VT is used to detect surface defects such as cracks, undercuts, porosity, misalignment, and incomplete welds. It is often the first step in quality control and is cost-effective, quick, and easy to perform, but limited to surface-visible flaws.
Magnetic Particle Testing (MT) is a non-destructive testing method used to detect surface and nearsurface defects in ferromagnetic materials like carbon steel. The process involves magnetizing the part and then applying fine magnetic particles (either dry or suspended in liquid). If there are any discontinuities such as cracks or laps, they create leakage fields that attract the particles, forming visible indications. MT is highly effective for detecting surface-breaking flaws but cannot be used on non-magnetic materials like aluminum or austenitic stainless steel.
Penetrant Testing (PT), also known as Dye Penetrant Testing, is a non-destructive method used to detect surface-breaking defects in nonporous materials, both metallic and non-metallic. It involves applying a liquid dye penetrant to the surface, allowing it to seep into any cracks or flaws, then removing the excess and applying a developer to draw the penetrant back out. This creates a visible indication of defects such as cracks, porosity, or seams. PT is especially useful for materials that are non-magnetic, unlike MT, but it only reveals surface defects.
Radiographic Testing (RT) is a non-destructive testing method that uses X-rays or gamma rays to inspect the internal structure of welds and materials. The radiation passes through the component and exposes a film or digital detector on the opposite side. Variations in material thickness or internal flaws like porosity, slag inclusions, or lack of fusion appear as differences in density on the radiograph. RT provides a permanent record of the inspection and is highly effective for detecting internal defects, but it requires strict safety precautions due to radiation exposure.
Ultrasonic Testing (UT) is a non-destructive testing method that uses high-frequency sound waves to detect internal flaws, measure thickness, and evaluate material properties. A transducer sends sound waves into the material, and any reflections from discontinuities - such as cracks, voids, or lack of fusion—are recorded and analyzed. UT is highly sensitive, capable of detecting very small internal defects, and can be performed from one side of the component. It is widely used in weld inspection, corrosion monitoring, and thickness measurement, especially in materials where radiographic testing cannot be used.
Hardness testing is a non-destructive method used to measure a material’s resistance to deformation, typically by indentation. It provides valuable information about the mechanical properties of welds, base materials, and heat-affected zones (HAZ), such as strength and wear resistance.
MISSION, VISION, AND VALUES
As a person-centred organisation, LBD’s mission is to prioritise customers’ needs and demonstrate its investment in people.
Meanwhile, by constantly educating its employees and introducing new services, it strives to deliver best-in-class products to meet even the most stringent customer requirements.
The company’s relentless dedication, enviable precision, and high level of execution are evident in its products, which are supported by its continuous investment in new machines, devices, and technologies.
LBD’s vision to establish, develop, and maintain business relations with domestic and foreign partners is built on ensuring high standards of delivery for optimum welding, structural fabricatoring, and assembly services.
Paying special attention to the safety of its workers across construction sites, the company stands out from the competition due to its team of professional, trained, and highly motivated staff, whose impeccable knowledge and discipline are secondto-none.
Additionally, the quality and timeliness of LBD’s work help to distinguish it, with strict compliance and delivery deadlines in place to ensure it remains ahead of the curve.
Cell: 00385 91 554 2468
E-mail: info@lbd.hr
Website: www.lbd.hr
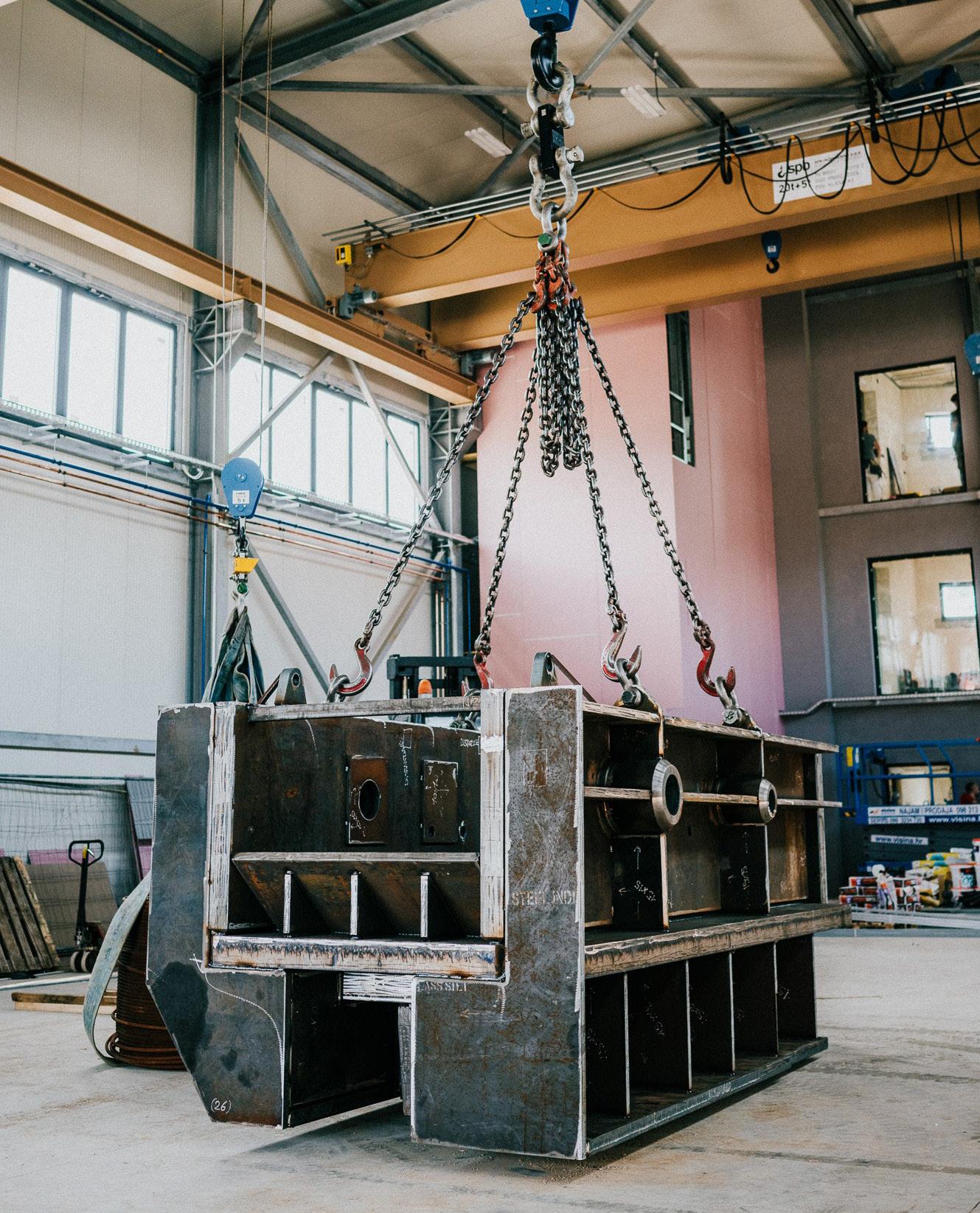
As such, the Komodo provides immeasurable benefits to ongoing conflicts, offering versatility in response to threats and a vast range of payload capabilities. This is particularly advantageous given the current combat systems in service are either outdated, very expensive, or there are too few pieces of equipment for it to be considered for expansion.
“We aim to tackle these challenges but in the unmanned vehicle domain. We plan to roll out unmanned and programable systems for both hasty and planned counter mobility operations.
“At the same time, we will provide solutions for mobility operations that are currently only available on manned platforms,” Petek sets out.
Elsewhere, DOK-ING Security and Defence is heavily involved in EU and NATO technology development
HOW DOES DOKING DIFFERENTIATE ITSELF FROM THE COMPETITION?
Luka Petro, COO, DOK-ING Mining: “The culture at DOK-ING is truly one of a kind – a rare blend of relentless, goal-driven focus and a deeply-rooted, family-like atmosphere. It’s a place where people care just as much about the mission as they do about each other.
“Over time, this culture becomes visible in everything we create. You can see it in the precision of our engineering, the purpose behind our designs, and the pride our teams bring to every machine we deliver.”
projects that define current and future industry trends, from critical infrastructure protection to a varied defence portfolio.
For example, the EU has recently focused on the development of robotic systems and capabilities that support the civilian structures responsible for critical infrastructure protection and response operations.
DOK-ING Security and Defence’s unmanned support to first responder units aligns with this goal and ensures the division is well positioned to provide innovative solutions that not only support these units but drastically increase their response capabilities.
BREAKING THE MINING PARADIGM
DOK-ING’s reputable capabilities also
has pioneered a state-of-the-art fleet of narrow reef equipment (NRE) for the South African and global underground mining market.
The narrow reef mining sector has undergone significant challenges in the last 20 years, as businesses have had to choose between limited methods, including more conventional and labour-intensive methods that are difficult to scale in a cost-effective manner and have significant safety risks, and lowprofile mechanisation that often leads to dilution, high costs, and limited adaptability to changing reef inclinations.
“With the development of the NRE fleet, we’re breaking that paradigm and delivering a solution that enables the safe, efficient, and truly scalable mechanisation of narrow reef
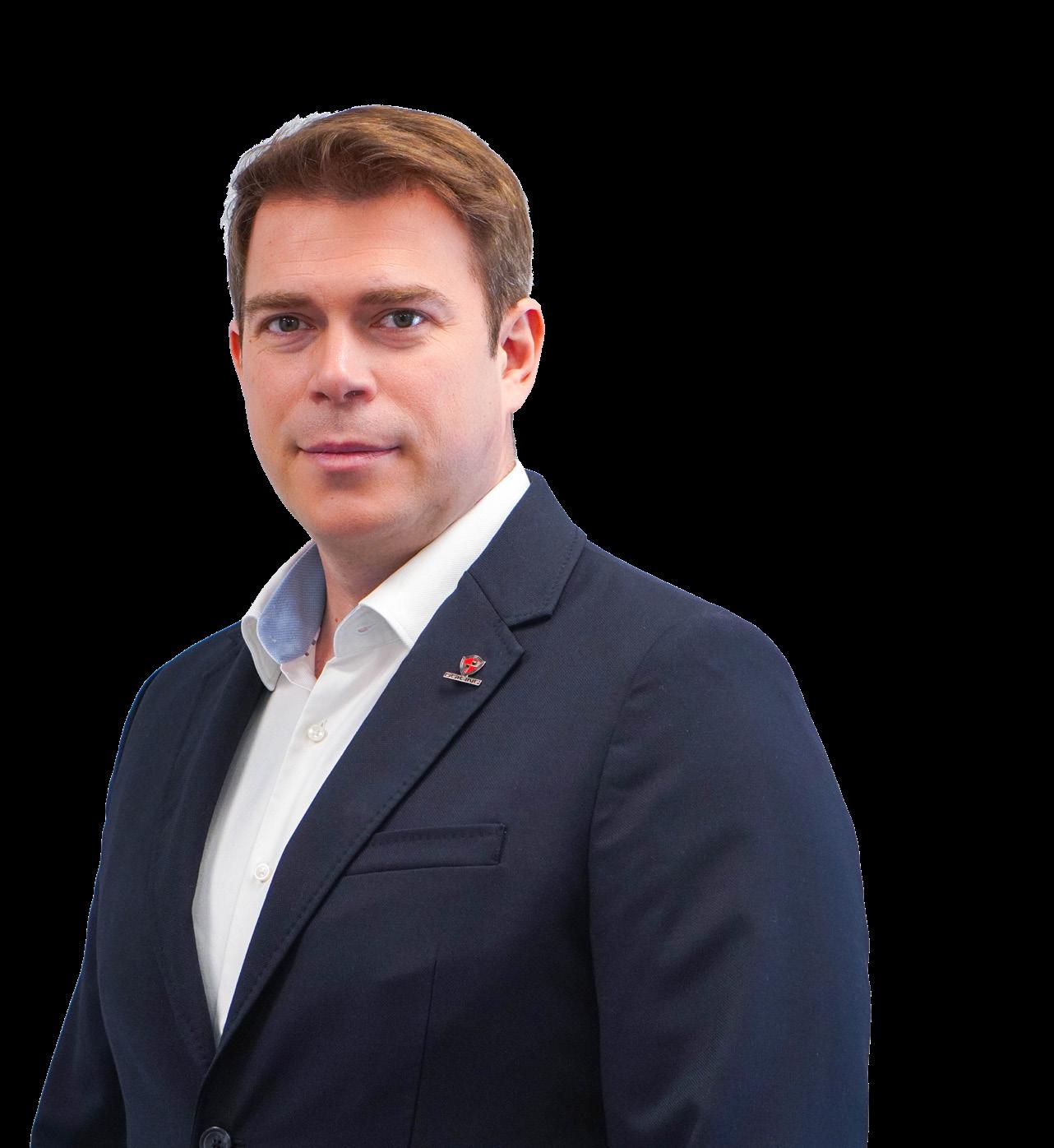
“This isn’t just an incremental improvement – it’s a game-changer for sub-horizontal, thin orebodies like those found in South Africa’s platinum group metals and gold sectors. It’s a bold step towards unlocking value that was previously trapped by
DOK-ING Mining’s NRE fleet stands out in particular due to its facilitation of mechanised mining in ultra-narrow
Furthermore, the fleet has continually demonstrated it can consistently achieve optimum performance, be maintained effectively, and deliver the required output, thus shifting the industry’s response to the equipment from cautious interest to genuine enthusiasm. This is evidenced by DOK-ING Mining’s recent application of its NRE for Bokoni Platinum Mines, which demonstrated the extent to which
“BY TARGETING HIGH-RISK ENVIRONMENTS, WE CREATE REAL IMPACT, REDUCING EXPOSURE FOR FRONTLINE WORKERS WHILST IMPROVING OPERATIONAL PERFORMANCE. THIS IS WHERE INNOVATION TRULY PROVES ITS WORTH, AND IT’S THE PATH WE’VE COMMITTED TO”
– LUKA PETRO, COO, DOK-ING MINING
the fleet can consistently meet production targets, thus representing the future of narrow reef mining.
“This success gave us the confidence to scale our NRE to the global stage,” Petro prides.
With recognition and support from EIT Rawmaterials, a consortium in the European raw materials market, DOK-ING Mining’s NRE fleet is on an accelerated path and poised to
become the global benchmark in mechanised mining.
“What began as a bold idea is now setting the standard for what’s possible in some of the world’s most challenging underground environments,” he insights.
GURANTEEING CONTINUOUS SAFETY
DOK-ING Mining further stands
out due to the plethora of safety benefits that its robotic systems provide, primarily due to the introduction of remotely operated machines that have transformed what was once a highly hazardous environment.
Using NRE technology not only removes personnel from dangerous to supported environments but also allows the operator to achieve the same output as a dozen miners at the face, without being exposed to the risks.
DOK-ING’s ultra low-profile Dozer, for instance, addresses one of the most pressing safety challenges in narrow reef mining – replacing the scraper winch, which historically results in many injuries and fatalities.
More than a mechanical upgrade, this equipment represents a step-change in how safety and productivity can co-exist.
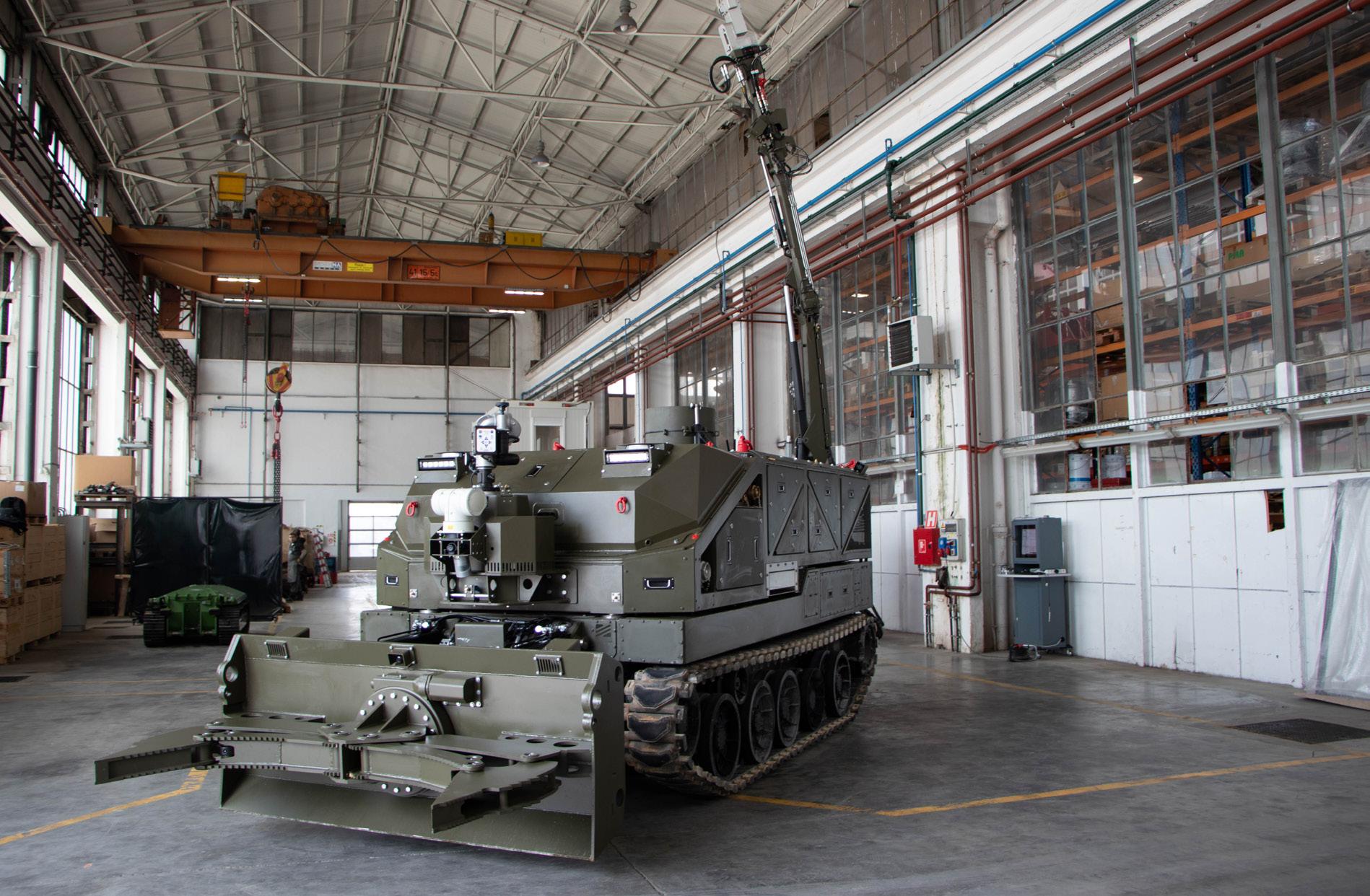
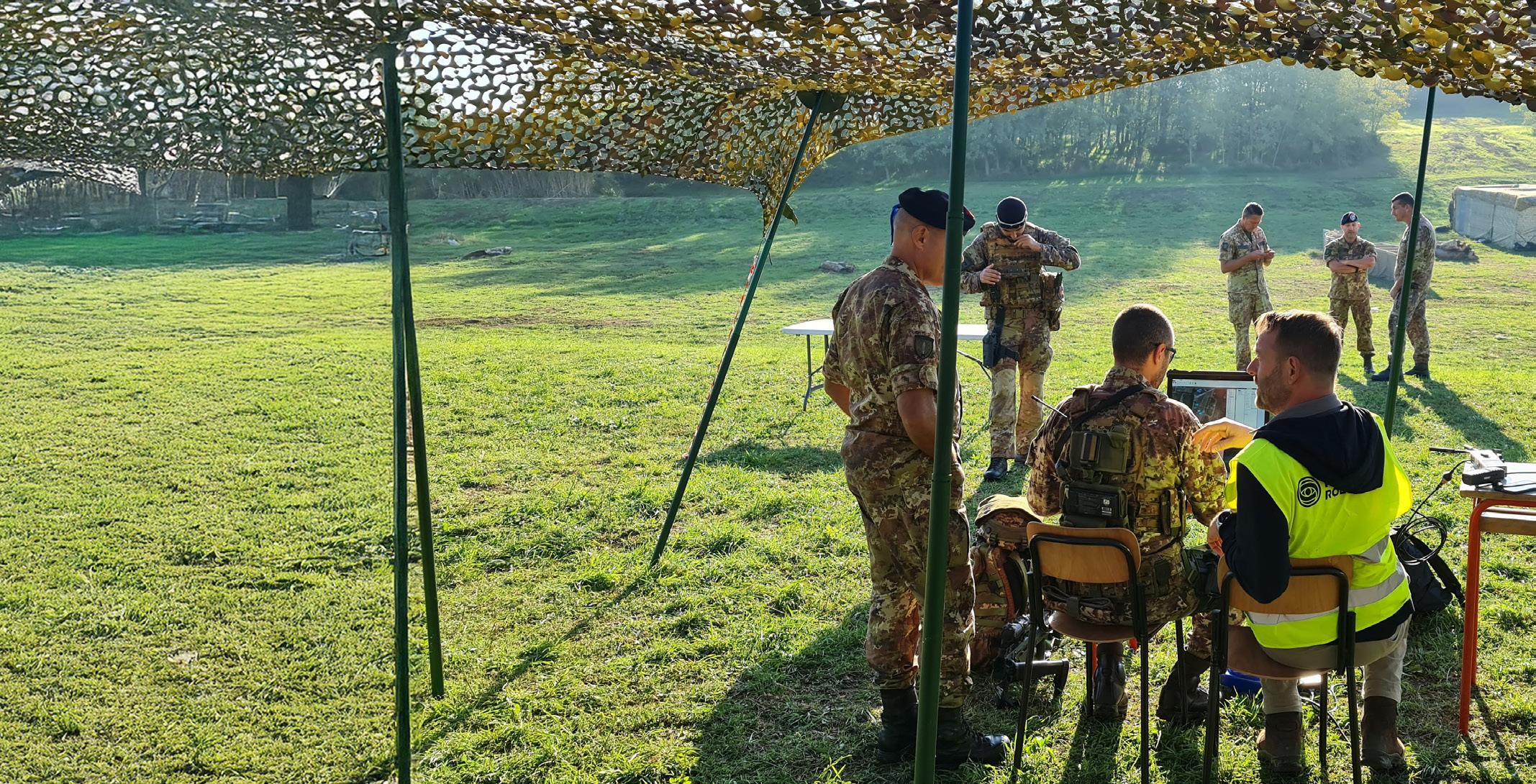
WHEN YOU DON’T SEND A MAN TO DO A MACHINE’S JOB .... AND THEN WHAT?
A practical insight into integration of robotic assets into a tactical operations (and C4I / C2 software).
Theage of autonomy isn’t coming - it’s here. But the real winners will be those who go beyond the hardware and make their systems smarter through integration. Done right, unmanned assets won’t just support the mission - they’ll shape it.Yet for all the promise they hold, these tools often remain underused, misused, or siloed in operations that have yet to catch up with their potential.
The central issue? We’re still sending men to do a machine’s job - and not integrating those machines properly when we do.
Small Tools, Big Missions
Robotic assets generally fall into two categories. The first: compact, personal drones like the DJI or FLIR Black Hornet, often wielded by individuals or tight-knit teams. The second: larger, more autonomous systems, like the MQ-9 Reaper or DOK-ING Komodo UGV. Here, operators are more like service providers, delivering tactical capabilities to other personnel.
But what both categories often share is isolation from the broader tactical picture.
The Grill Team Conundrum
In military slang, the “grill team” refers to drone operators who set up shop safely behind the lines, out of the fray. Whilst their systems collect critical intel, these teams often remain disconnected from the command staff or field units who need that data most.
Most UxV platforms are delivered with proprietary Ground Control Stations (GCS) — typically bundled as software-hardware suites “off the truck” — providing basic functionality for direct control and limited mission planning. Whilst effective for localised task execution, these GCS solutions operate in isolation from the overarching command infrastructure. They are not battlefield management systems.
Bridging the Gap: Integrating Robotic Systems into C4I/C2 Battlefield Management
Despite growing interest in robotic systems, their integration into command, control, communications, computers, and intelligence/command and control (C4I/C2) environments remains limited. As a result, unmanned ground and aerial assets are frequently excluded from standardised digital frameworks used for operational planning, resource allocation, and mission reporting. This disconnect impedes the seamless employment of robotics in contemporary military operations.
UGV System scenario evaluation results
While AI has demonstrable utility in reducing operator cognitive load and automating routine surveillance functions, the reality is that full autonomy remains aspirational. Current systems lack the robust situational awareness and adaptive decision-making necessary to navigate dynamic battlefield environments without human intervention.
“And then what?”
Start by being real. Understand the tools. Experiment. Expect a few metaphorical smashed thumbs along the way. Real tactical value begins when unmanned systems are integrated with the C4I command & Control at every phase of the mission: from planning and logistics to execution and review.
True integration requires a C4I/C2 platform capable of incorporating UxV tasking into the broader operational context — where unmanned missions are treated as integral components of the overall scheme of maneuver. This means the ability to plan, assign, and synchronize UxV missions within the same digital environment that governs maneuver elements, fires, ISR, and logistics.
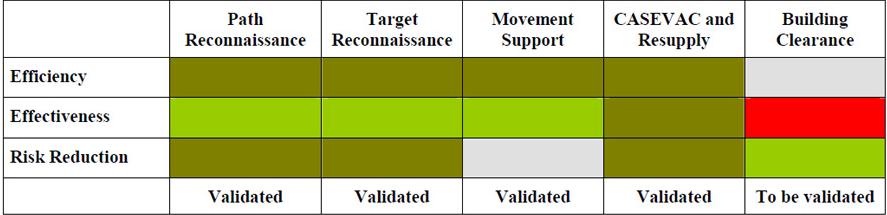
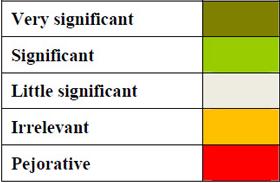
Without this, robotic systems risk being employed as tactical one-offs rather than as force-multiplying assets within a coordinated, multi-domain operation.
UxV mission planning software (not BMS) Source: carmenta.se
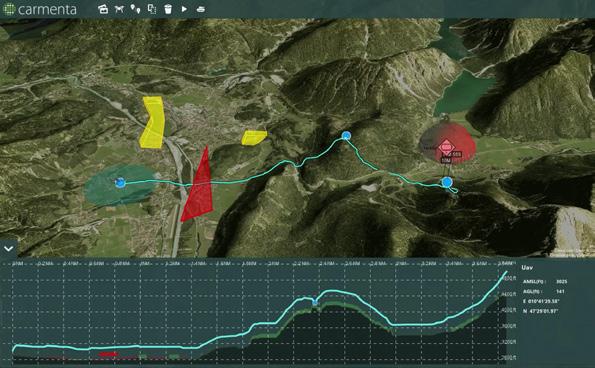
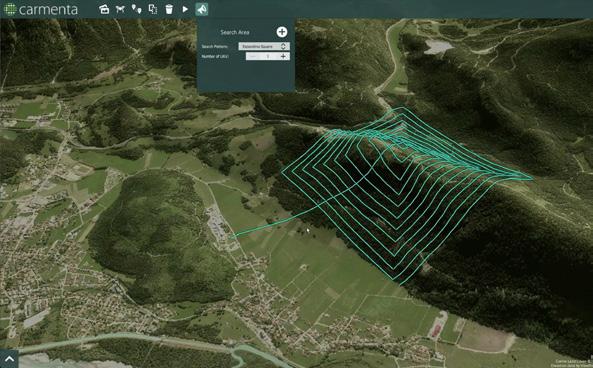
Including the UxV resources in mission plans will assure their availability to the intended (planned) users according to the schedule prepared. By sharing mission order over the communications (SATCOm, VHF, LTE etc.), users will always know what type of robotic assets with what capabilities are at their disposal at any given time.
Users can use the BMS to request “eyes on” a certain location or object on the map displayed on their EUD (End User Device). Not only does video feed gets directed to them, but they also get an option to take over drone gimble control and control the camera directly, all from a safe distance whilst a UAV is automatically flying in a pattern above the target.
PES Battlefield management software, supporting UAV operations by showing the tactical situation, sensor coverage and video feed. Source: Mil Sistemika
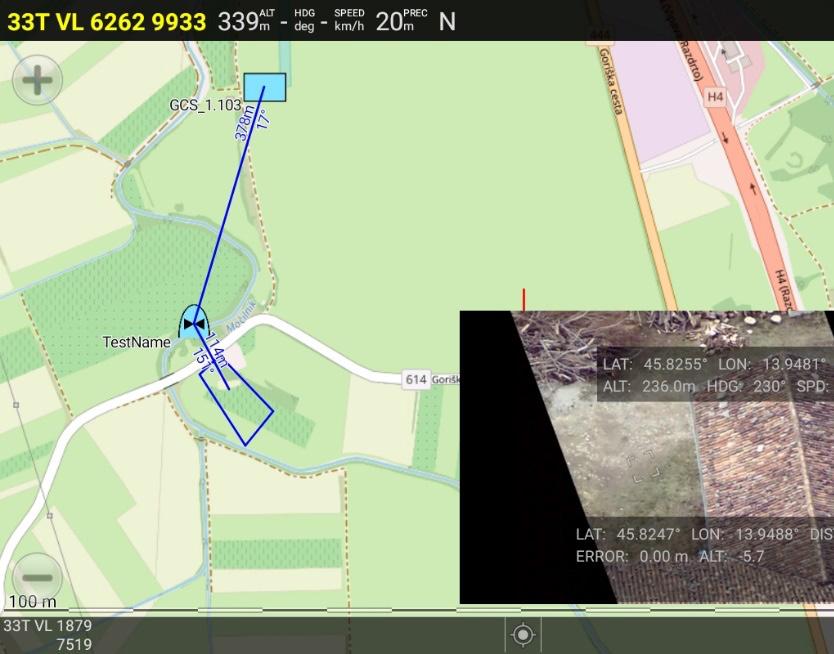
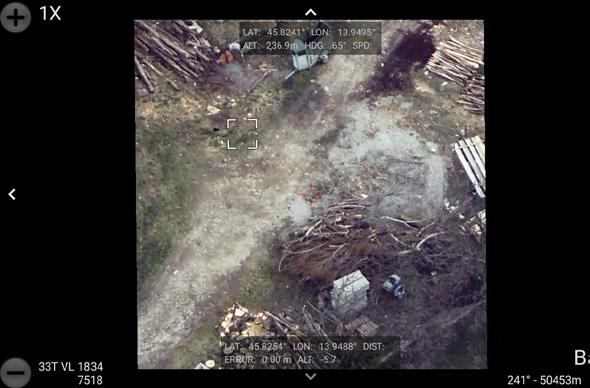
About Mil Sistemika
Powering Autonomy with Smart, Mission-Ready Software
When high-quality unmanned platforms are paired with robust, interoperable software integrated into the broader C4I/ C2 ecosystem, the result is more than just operational efficiency — it is a true force multiplier. As advancements in artificial intelligence and sensor technologies continue to push the boundaries of autonomy, the functional role of UxVs on the battlefield will expand accordingly.
Successful integration is as much a human challenge as a technical one. Embracing new operational paradigms, refining workflows, and adopting a systems-level mindset are essential steps towards harnessing unmanned systems not as niche tools, but as integral components of future combat operations — enhancing mission safety, simplicity, and effectiveness across the force
And what of the once-detached grill team? They’ve evolved. Now known as “UxV mission specialists,” they are fully embedded in fire brigades, civil defence, and frontline units. No longer watching from afar, they’re integral to the mission - just like any other soldier, medic, or technician.
From military-grade control systems to industrial robotics, Slovenia’s Mil Sistemika enables smarter, safer unmanned operations across industries. Based in Slovenia and with over two decades of experience in mission-critical software development, Mil Sistemika is a trusted partner to organizations operating in complex and often hazardous environments. From battlefield command platforms to mining robotics and disaster response systems, Mil Sistemika provides the software backbone that makes high-stakes operations both smarter and safer.
In addition to DOK-ING, the company supports a growing roster of partners in Europe, Asia, and North America - ranging from defence ministries and government agencies to private robotics developers and industrial equipment manufacturers.
www.milsistemika.com
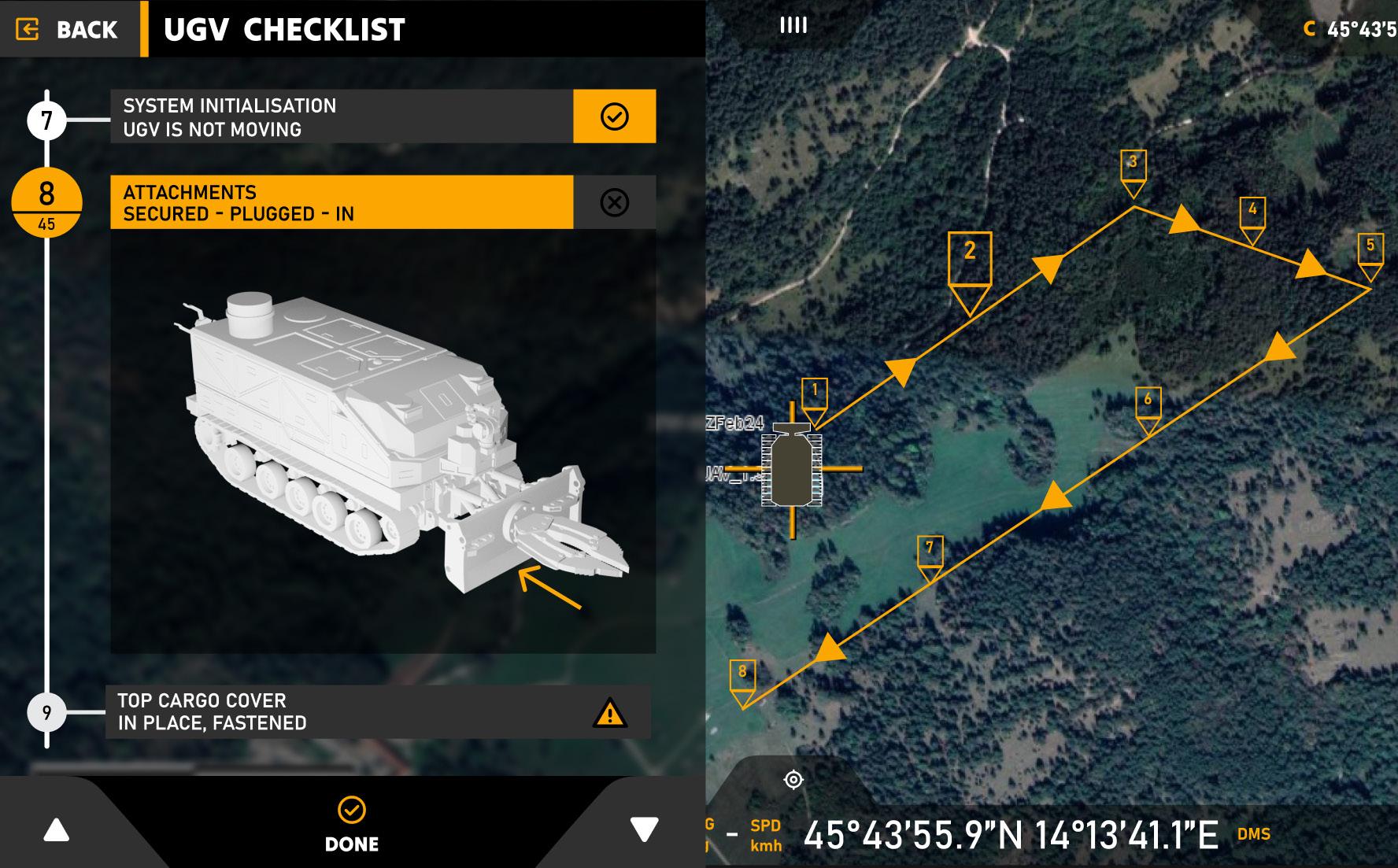
PES Battlefield management software, showing the STANAG 4609 full screen geo located video feed. Source: Mil Sistemika
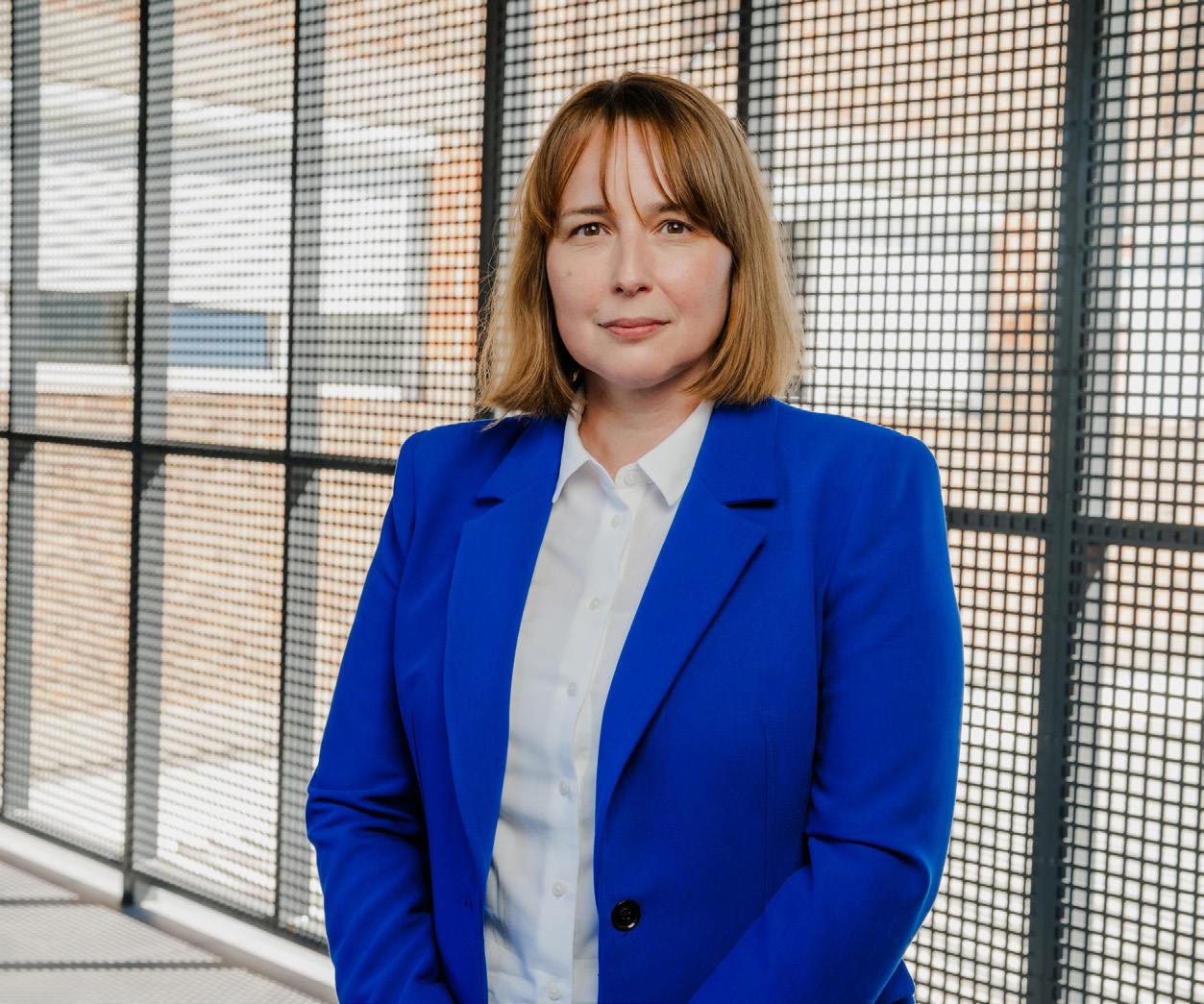
“I BELIEVE OUR MIX OF ENGINEERING TALENT, DEDICATED R&D, AND COURAGE TO DEVELOP WHAT DOESN’T YET EXIST WILL ALLOW US TO SHAPE A MORE SUSTAINABLE, CIRCULAR, AND RESILIENT FUTURE – BOTH IN WASTE MANAGEMENT AND GREEN ENERGY PRODUCTION”
– DR DANICA MALJKOVIĆ, HEAD OF BUSINESS DEVELOPMENT, DO-KING ENERGO
“Even in the best-run operations, underground working conditions remain extreme – that’s why the shift to electric machinery is so critical. It’s not just about reducing toxic fumes and noise levels, but cutting the cost and complexity of ventilation infrastructure,” Petro highlights.
No longer viewed as a mechanism of the future, electric machinery in mining is already proving to be smarter, more reliable, efficient, and eco-friendly.
Accordingly, the division’s NRE fleet is fully electric and emission-free,
indicating an industry-wide departure from diesel-based equipment.
“I firmly believe it is only a matter of time before electric becomes the standard and not the alternative. The mine offers a perfect environment to accelerate this transition,” Petro asserts.
Indeed, a mine site provides a long-term construction site with fixed infrastructure which is ideally suited for electric heavy machinery.
“It’s a natural symbiosis – the mine needs cleaner, quieter, smarter tools, and electric technology needs
a proving ground. This is where innovation meets opportunity, and transformation becomes inevitable,” he expands.
As part of the development of its remote-controlled technology, DOK-ING Mining is taking the next step towards teleoperation and semi-autonomous systems in order to achieve its ultimate goal of zero personnel underground.
Although this is a unanimous vision across the industry, the division is dedicated to leading the way by pushing boundaries with further automation.
“It won’t happen overnight, but with each innovation, we move closer to a safer, smarter, and fully mechanised future; just as we’ve done so far, we’re ready to keep leading that journey.”
SET FOR MINING EXPANSION
Equipped with a steadfast mission, DOK-ING Mining is now recognised as a leader in innovative ultra-low and extra-low profile mining solutions, expanding the division’s presence rapidly across the globe.
With its eyes set on South America as a new frontier and its extra lowprofile technology gaining traction in Canada, DOK-ING Mining’s solutions are ready to deliver on the complex demands of international mining markets.
Such targets will be reached by staying true to its founding mission, expanding its product portfolio, and delivering new technologies designed specifically for the world’s hardest-toaccess ore bodies.
“R&D has always been at the core of DOK-ING, and we’re committed to carrying that legacy forward by pushing the boundaries of what’s possible, one breakthrough at a time,” Petro states.
As such, DOK-ING Mining is building a future where mining is no longer seen as dangerous or outdated, but as a space of innovation, safety, and high efficiency.
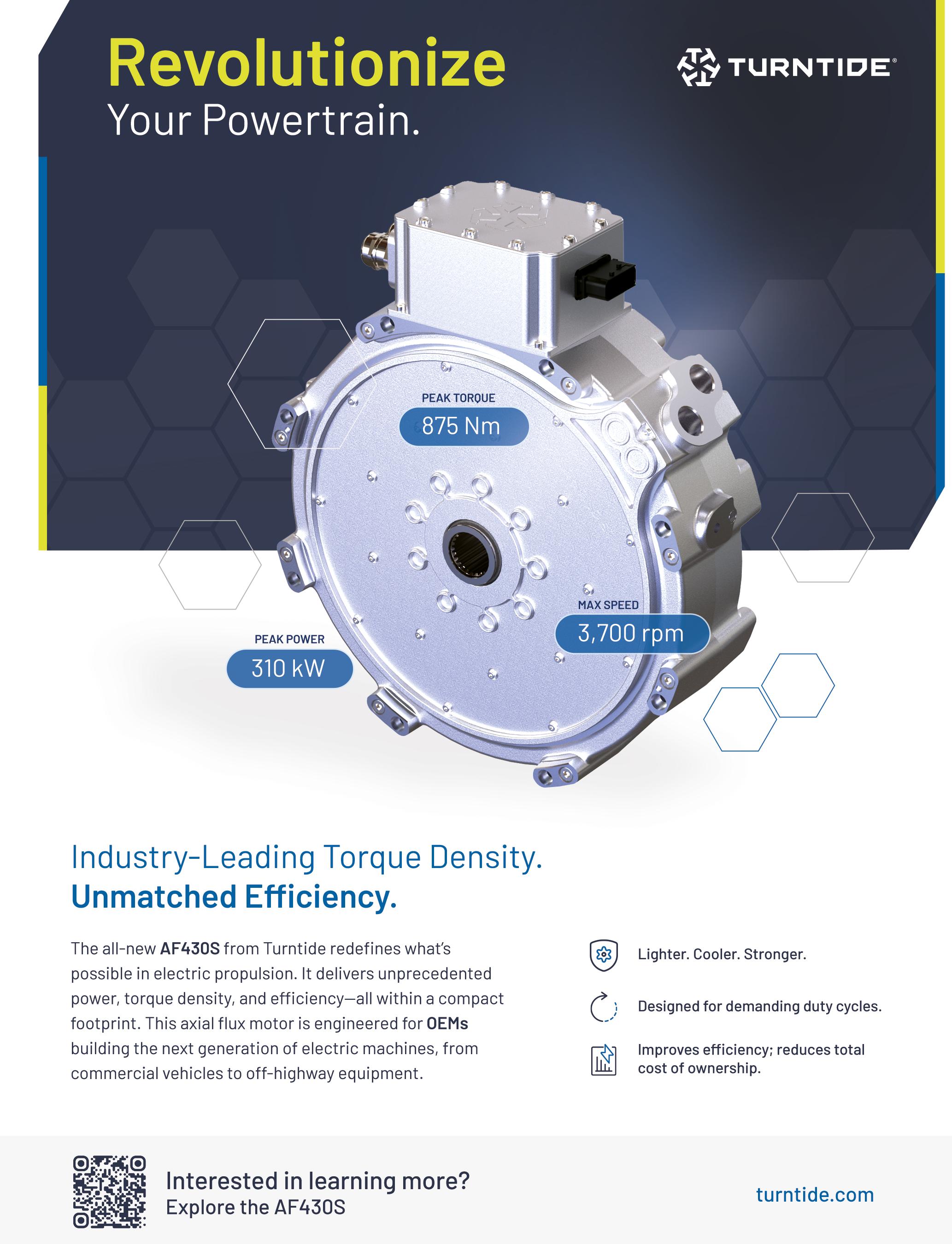
OVERCOMING ENERGY OBSTACLES
Another subsidiary of the organisation, DOK-ING Energo endeavours to tackle Europe’s energy and waste challenges.
The division’s initial focus revolved around helping cities solve their waste management problems. However, as the use of hydrogen gained prominence, DOK-ING Energo broadened its approach to cater to industry evolutions.
Case in point, the EU is working hard to accelerate its hydrogen economy, facilitating strong research networks, funding programmes, and ambitious climate targets.
A number of industry-wide steps are needed to develop this further, such as a robust market network, clear regulations, targeted incentives, and strategic support for small to medium-sized enterprises.
Croatia specifically requires greater cooperation between industry, academia, and policymakers if its hydrogen use is to take centre stage.
Although the nation’s regulatory framework for such is still being developed – creating market uncertainty – platforms including the Croatian Chamber of Commerce’s Croatian Hydrogen Group indicate a domestic hydrogen ecosystem that can contribute meaningfully to the broader European strategy.
In light of this, DOK-ING Energo operates across both the energy and waste sectors in order to combat these adversities.
During the hydrogen production process, the division discovered a carbon-rich by-product of its system could be used in industries such as brick production, which improves the properties of bricks.
DOK-ING Energo has also developed water purification systems for water used in the Looper system – which converts non-recyclable waste into clean hydrogen – because it wants to follow circular economy principles in every aspect.
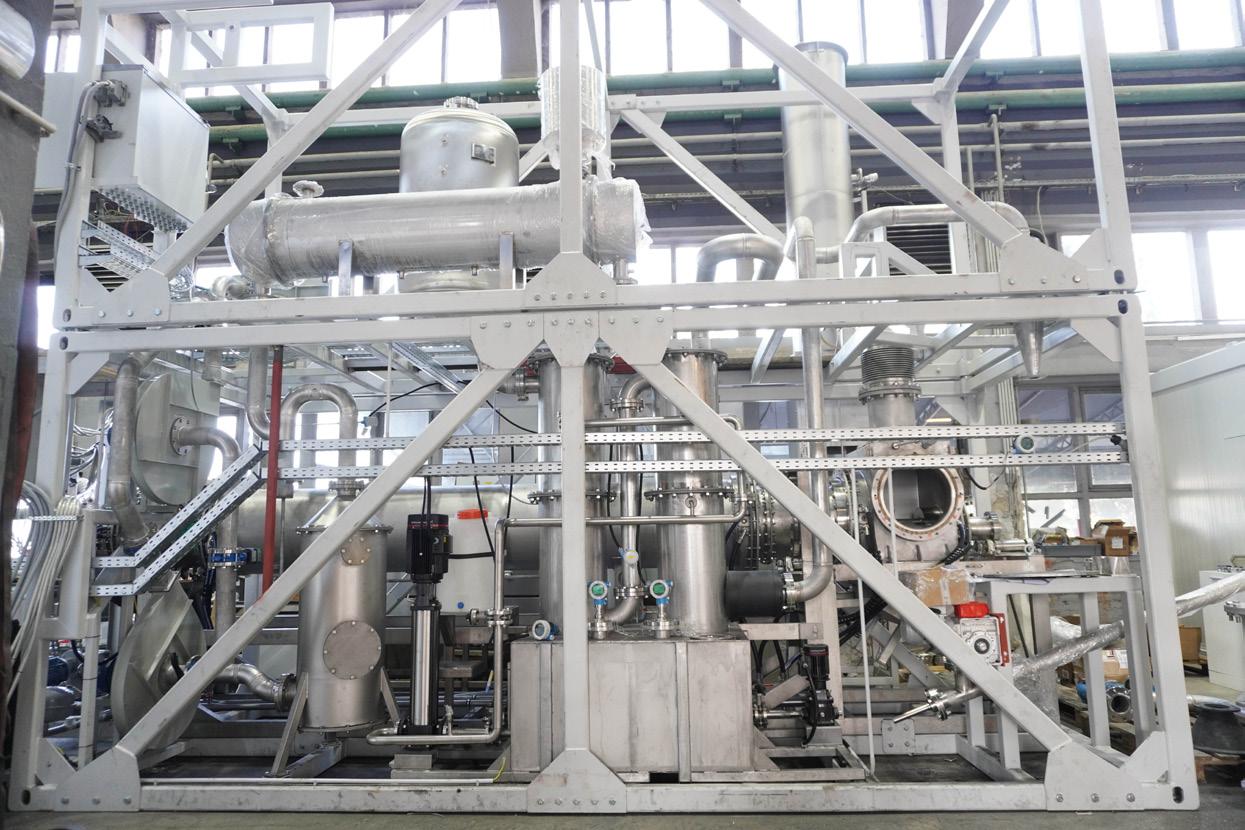
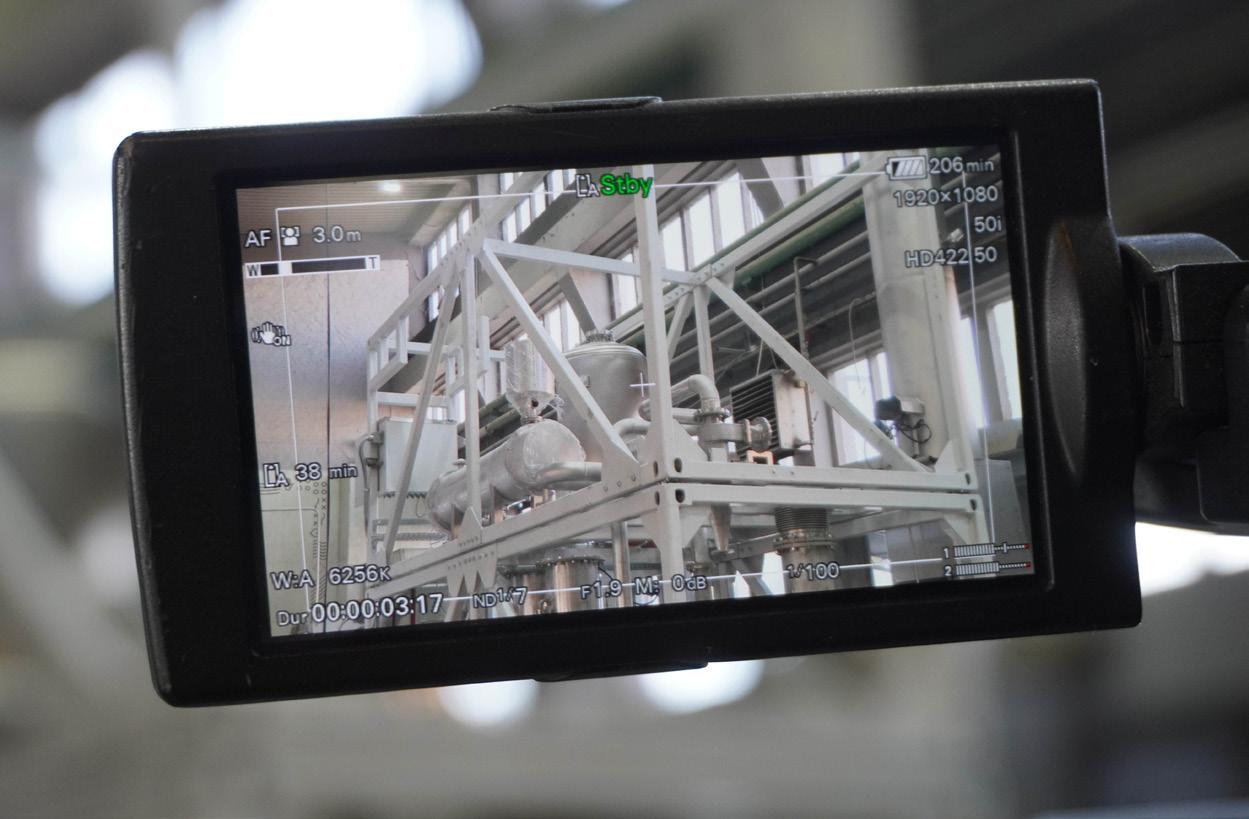
“Ultimately, we are working towards creating a system that can power itself, therefore contributing to its own energy self-sufficiency.
“This circular approach focuses on energy, waste, water, and materials, and is what sets us apart from other energy tech companies,” outlines Dr Danica Maljković, Head of Business Development at DOK-ING Energo.
FACILITATING CLEAN ENERGY
A landmark technological innovation, DOK-ING Energo’s Looper system
can process non-recyclable waste such as textiles and other contaminated organic matter through a thermochemical process that generates synthesis gas.
From this gas, the division extracts hydrogen whilst carbon from feedstock remains trapped in solid residue.
“As such, Looper is a unique technology because it simultaneously addresses two major global challenges – waste management and clean energy production,” Maljković voices.
DOK-ING Energo’s Looper system
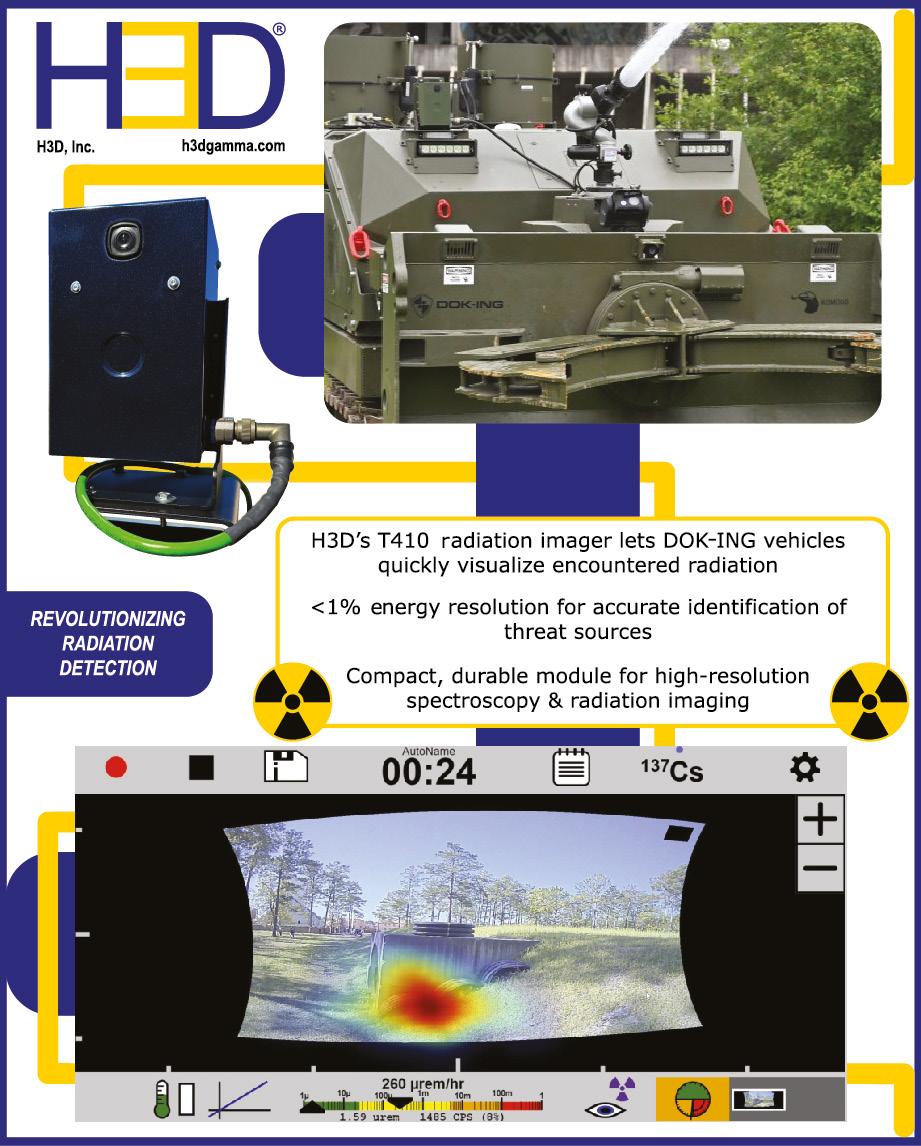
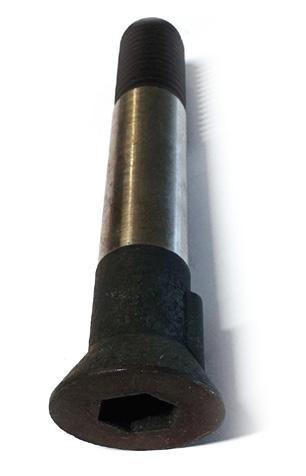
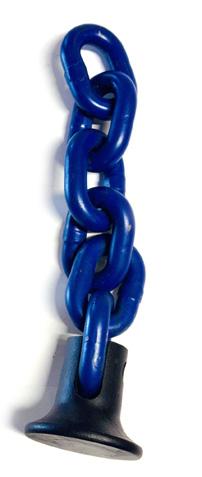
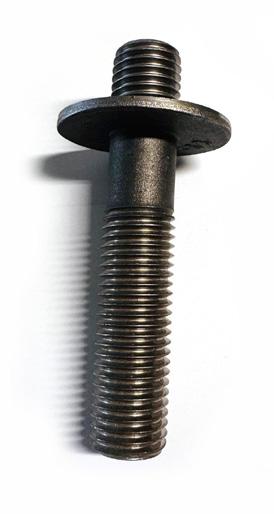
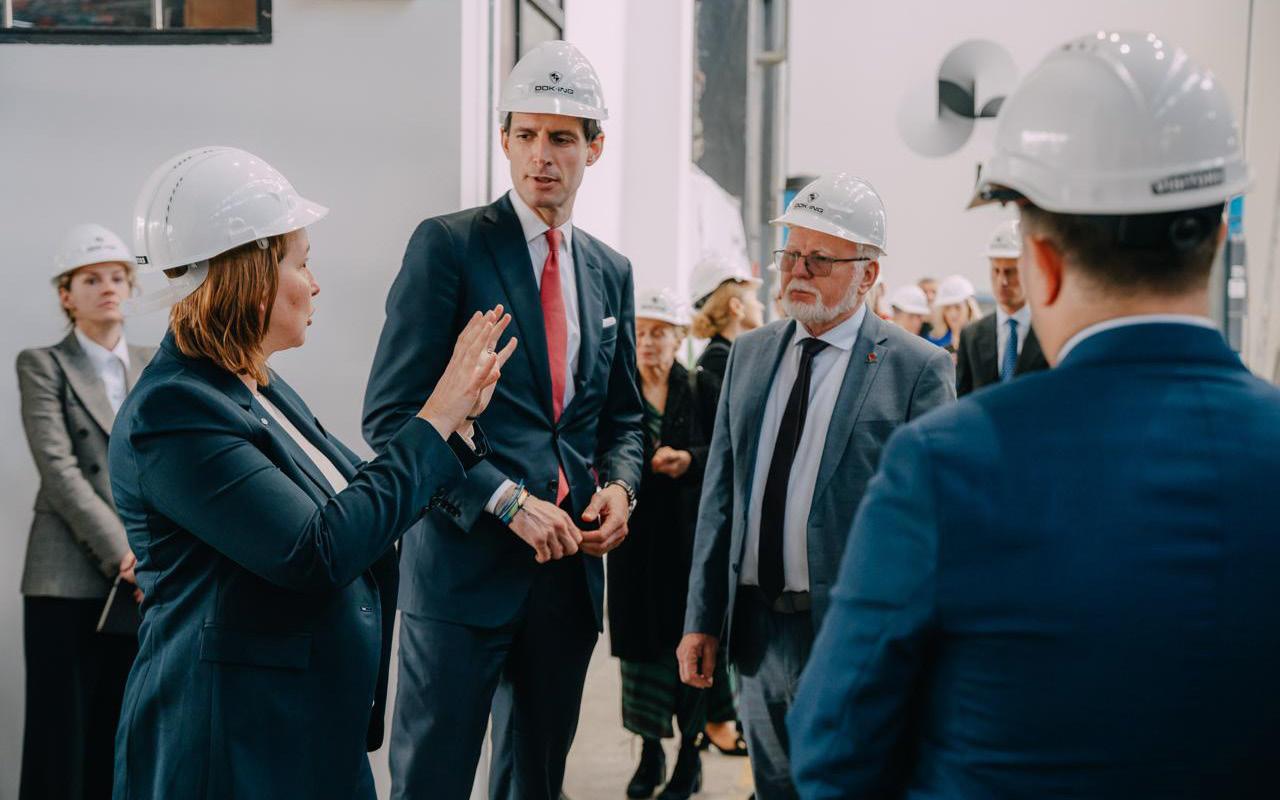
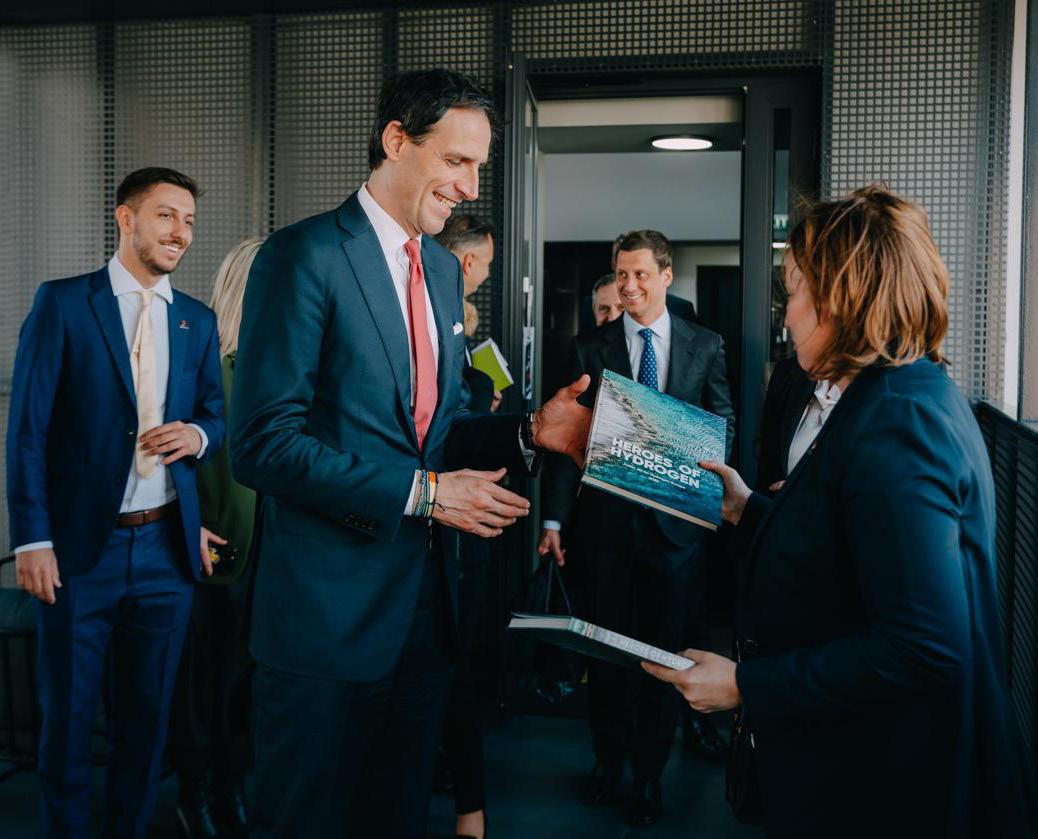
During his recent visit to its facility, Wopke Hoekstra, European Commissioner for Climate, Net Zero, and Clean Growth, acknowledged the technology’s strategic value and praised its commercial and geopolitical potential in the energy sector.
“This kind of recognition is vital for us as it confirms Looper is not just a scientific innovation, but a technology with real market relevance and societal value,” she points out.
Indeed, the system’s modularity, mobility, and scalability make it highly appealing across multiple sectors. In fact, Looper offers a potentially more cost-effective alternative to hydrogen via electrolysis, particularly when waste reduction is taken into account.
DOK-ING Energo has already explored Looper’s implementation in waste management systems, wastewater treatment facilities, the textile industry, military camps, utility
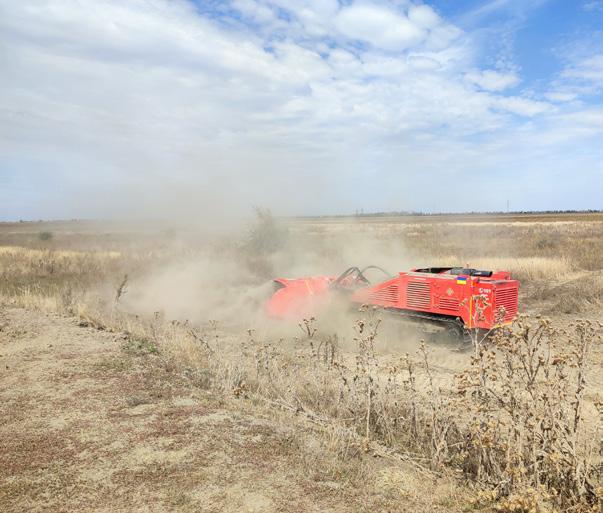
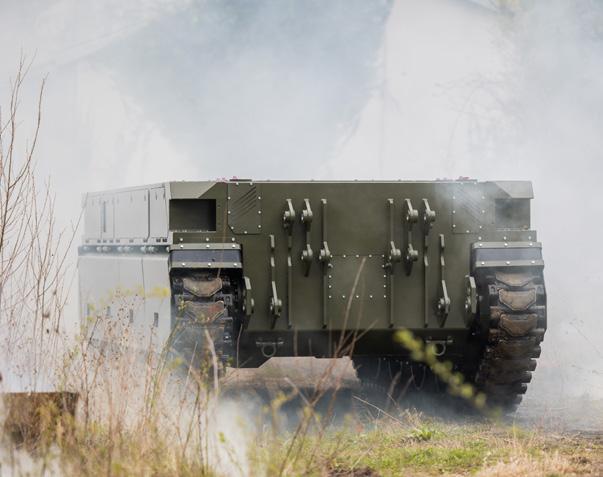
companies, airports, and remote locations, alongside many other uses.
“Basically, wherever people generate organic waste, which is nearly everywhere, Looper has the potential to be implemented.”
Notably, the technology also has the ability to create real societal impact, reflected in the Humana Nova cooperative in Čakovec, where Looper was deployed to convert textile waste for heating.
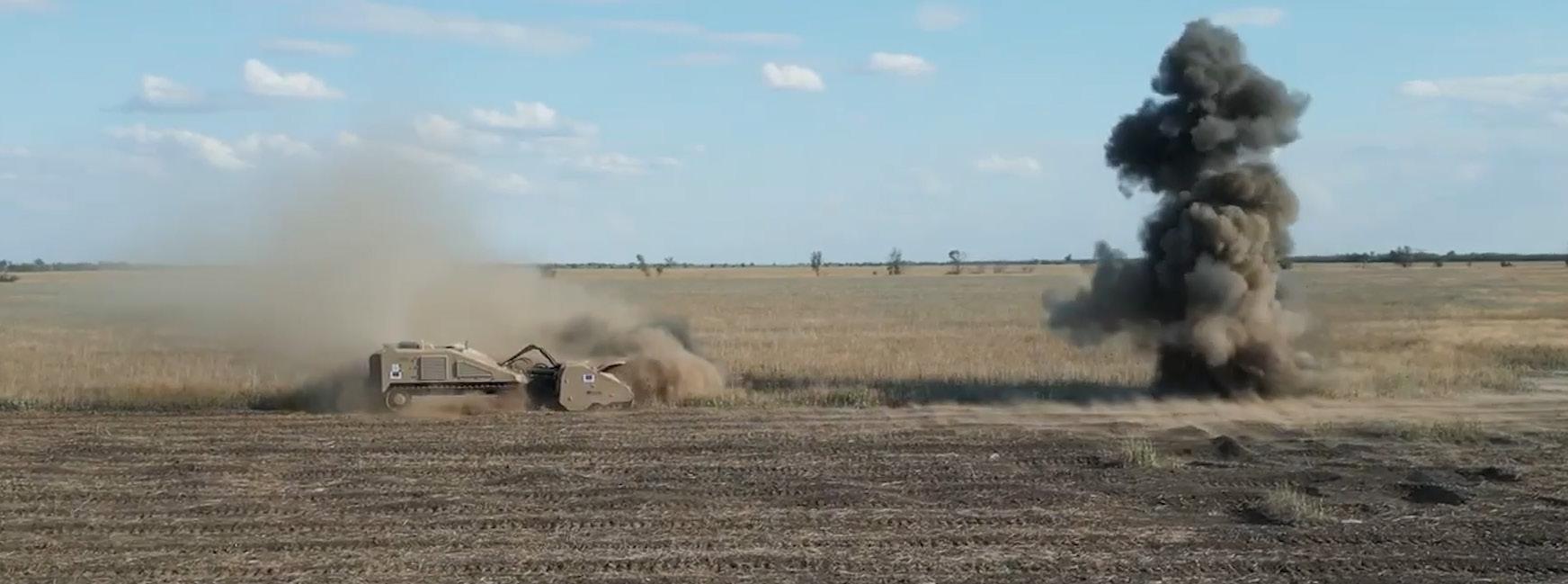
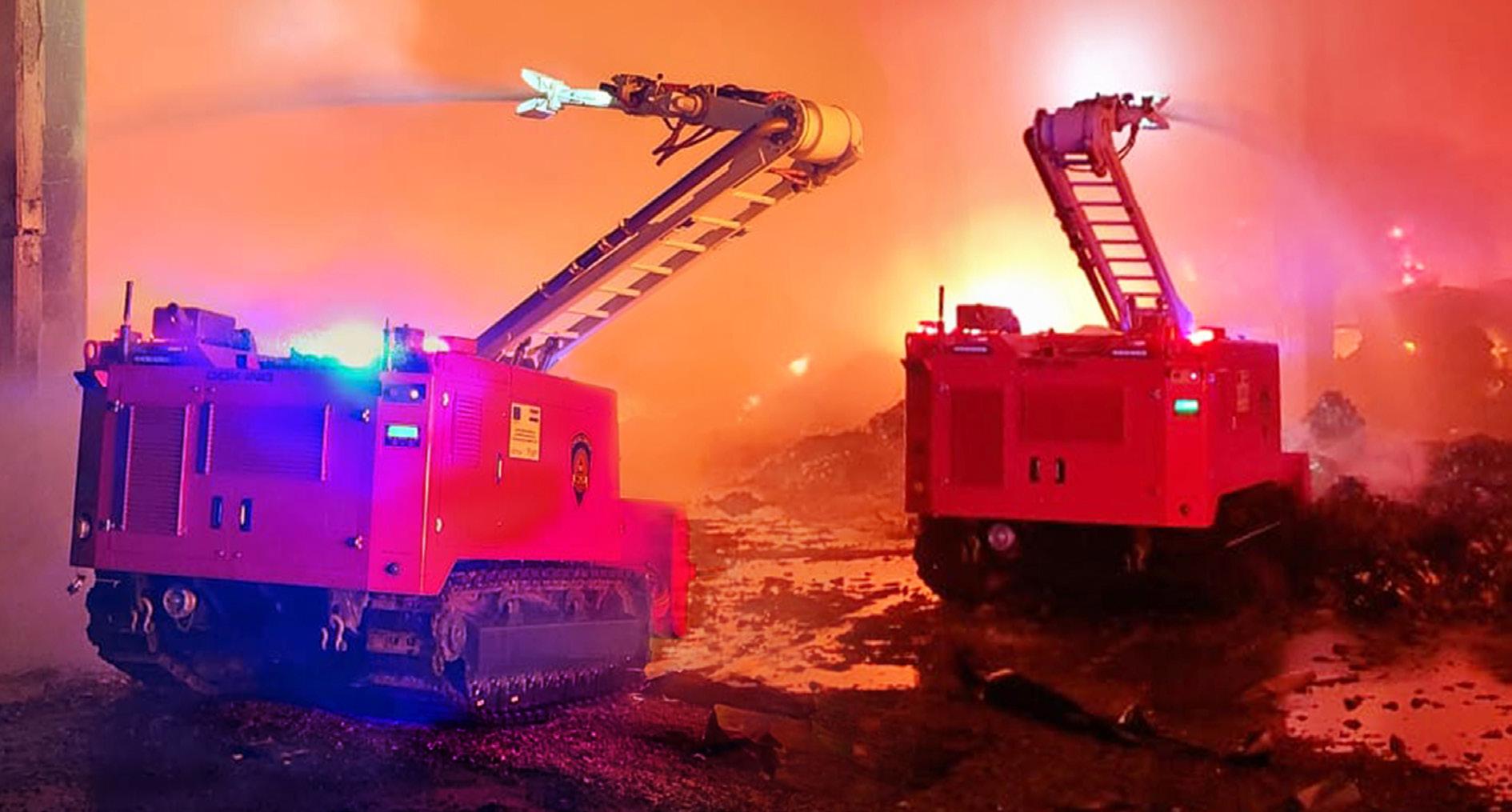
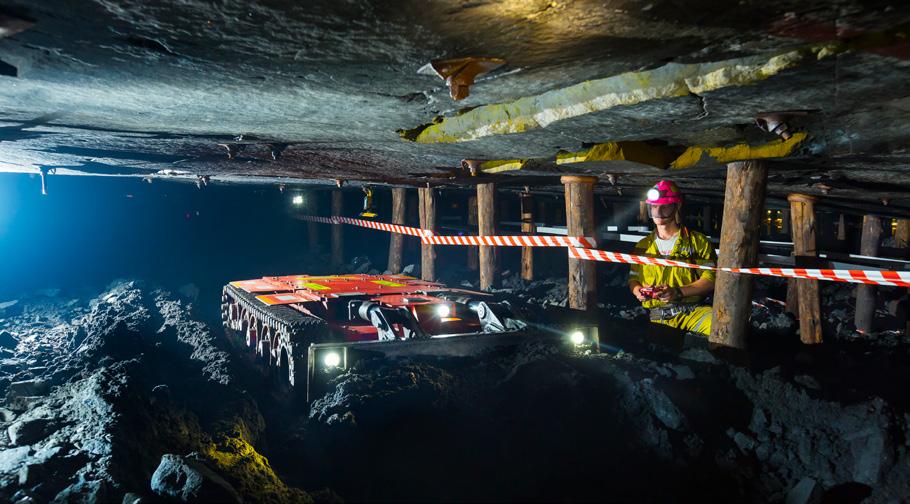
“This project was particularly meaningful because it showed how our technology could directly benefit vulnerable groups in society. It’s a powerful example of how innovation can serve environmental and social goals at the same time,” Maljković tells us.
FACILITATING CLEAN ENERGY
In the next five years, DOK-ING Energo strives to become a recognised name in Europe’s green transition, particularly in the field of waste to hydrogen process solutions.
“Our goal is to not only bring technologies like Looper to the market but also demonstrate that
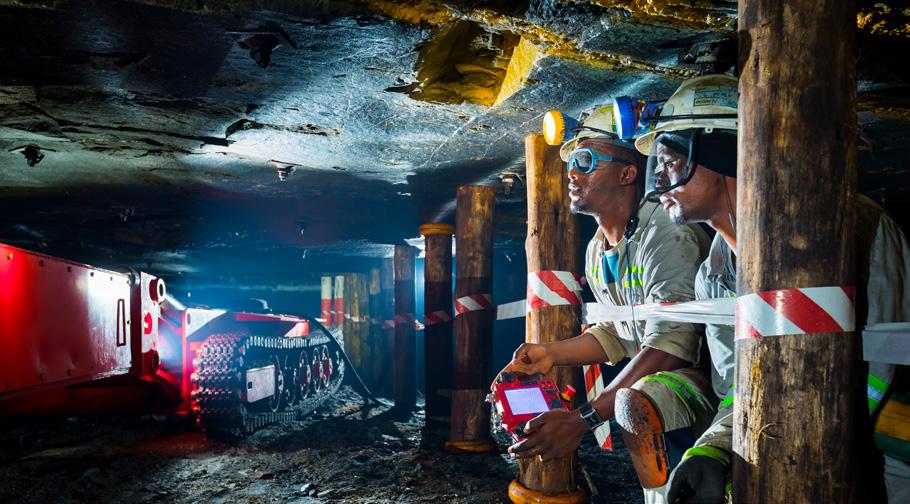
a company from Croatia can play a serious role in solving some of the world’s most complex environmental challenges,” Dr Maljković emphasizes.
The division is already experiencing an increased interest from international partners and institutions, which is essential for mutual learning, knowledge sharing, and global market visibility.
However, Maljković believes there is still room for the greater promotion of Croatian energy production across Europe.
“I believe our mix of engineering talent, dedicated R&D, and courage to develop what doesn’t yet exist will
allow us to shape a more sustainable, circular, and resilient future – both in waste management and green energy production,” she concludes.
Equipped with a strong union of three powerful divisions, DOK-ING is ultimately set to achieve significant growth and become an international market leader in robotics and autonomous systems.
Tel: +385 1 2481-300
info@dok-ing.hr
dok-ing.hr
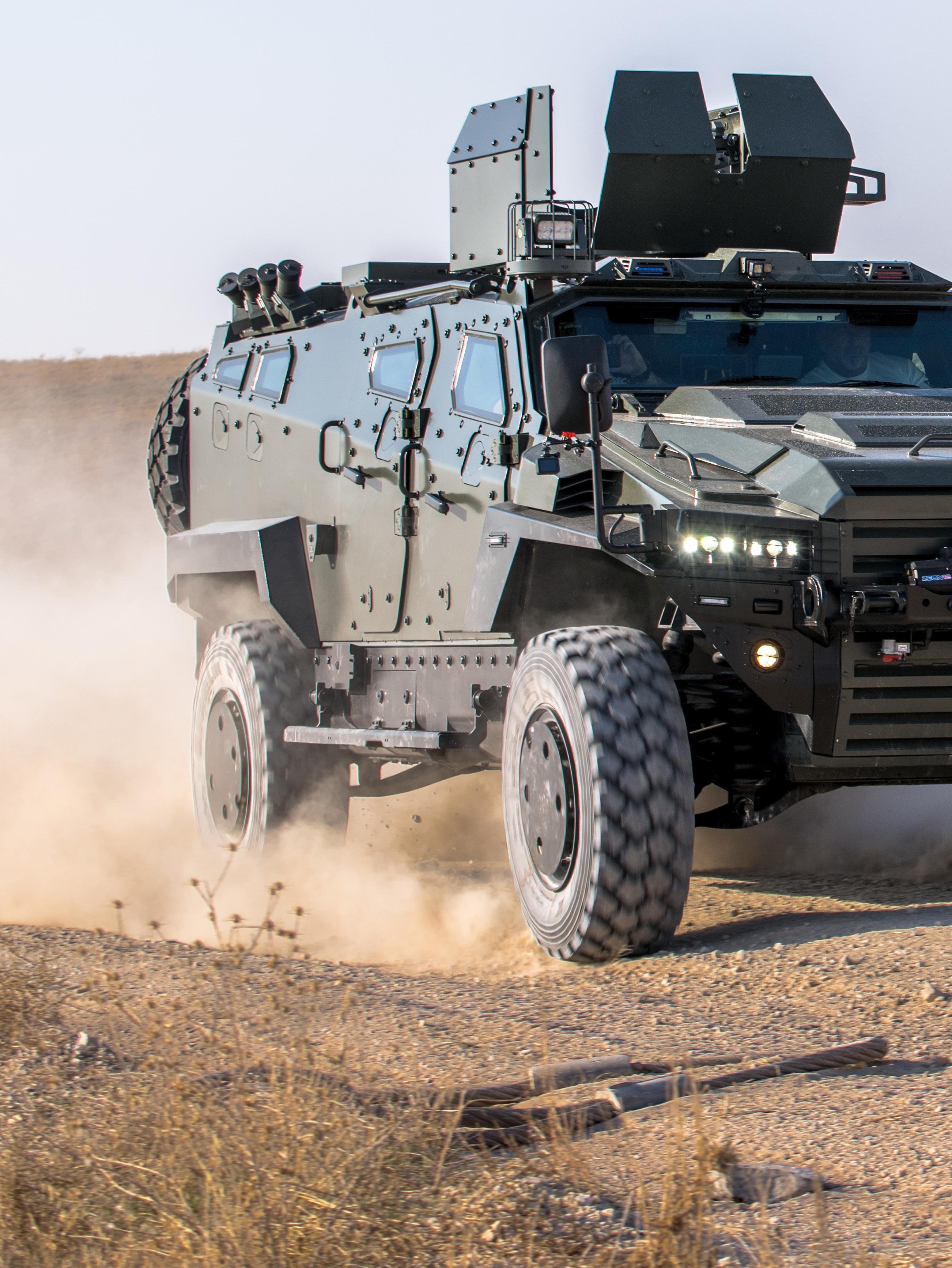
Headquartered in Ankara, Türkiye, and with a burgeoning presence in the UK, Nurol Makina is on a mission to fortify European defence capabilities in an era of increasing conflict with its best-in-class armoured vehicles.
Emre Akin, Chief Operating Officer, Europe, tells us more Writer: Lily Sawyer | Project Manager: Cameron Lawrence
OVER 40 YEARS OF EXCELLENCE
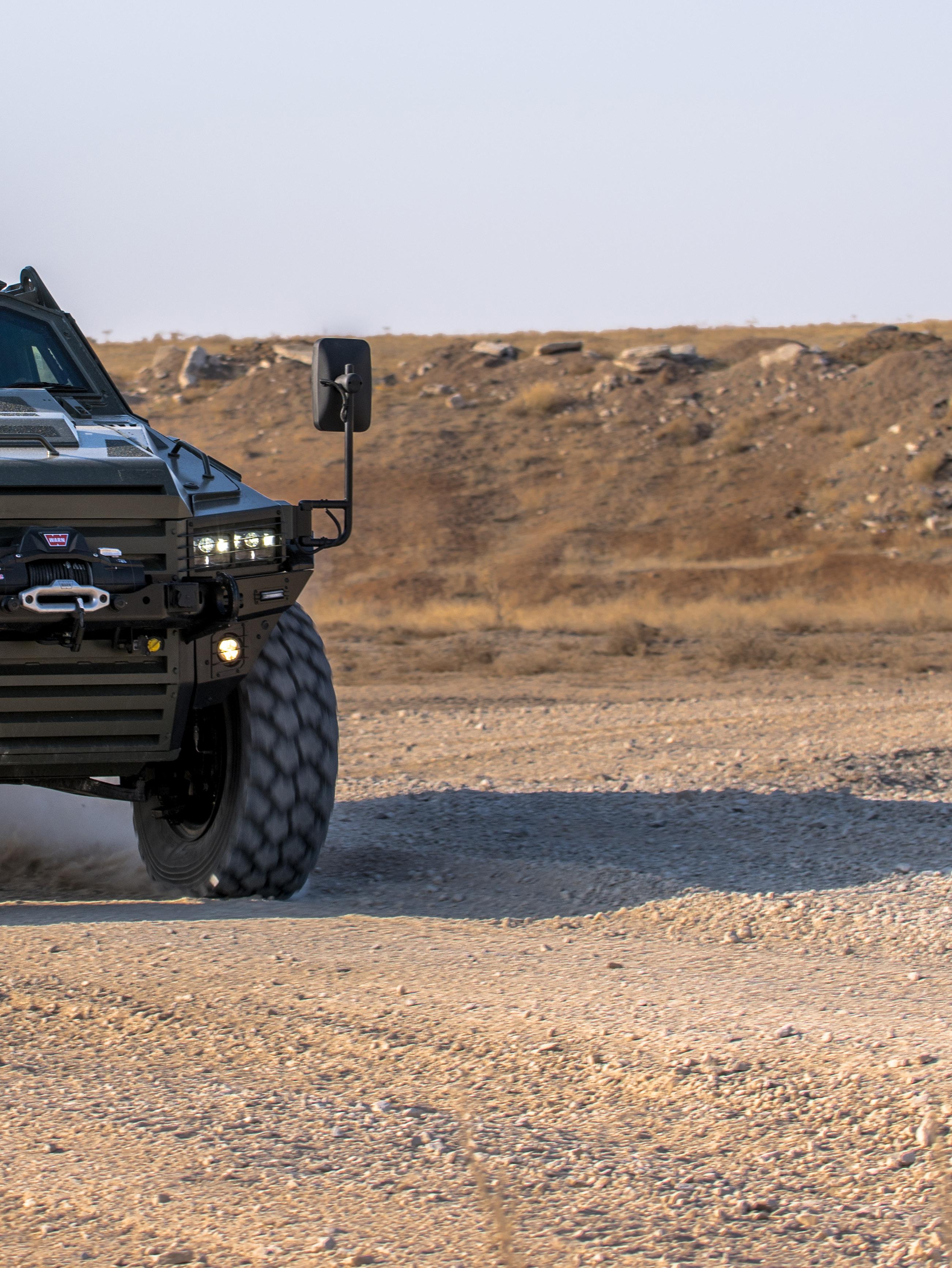
Driven by increased military spending and a focus on innovation and technological advancement, the European defence industry has experienced significant growth in recent years, particularly due to shifts in the geopolitical landscape.
For instance, EU initiatives like the European Defence Fund (EDF) have ramped up funding, and this year, the European Commission proposed
a €150 billion Security Action for Europe (SAFE) loan instrument to bolster the defence capabilities of EU member states.
However, despite this apparent influx of funding, questions remain about whether the authorities managing these programmes are distributing financial support equitably.
“One of my observations regarding some policies declared by EU
authorities is that they can be overly restrictive and favour existing market players,” says Emre Akin, Chief Operating Officer, Europe of Nurol Makina, a Turkish defence company with over 40 years of experience.
Nurol Makina, which has generated almost 90 percent of its revenue in recent years from international trade, has been utilising all major subsystems from NATO and EU countries for its armoured vehicles.
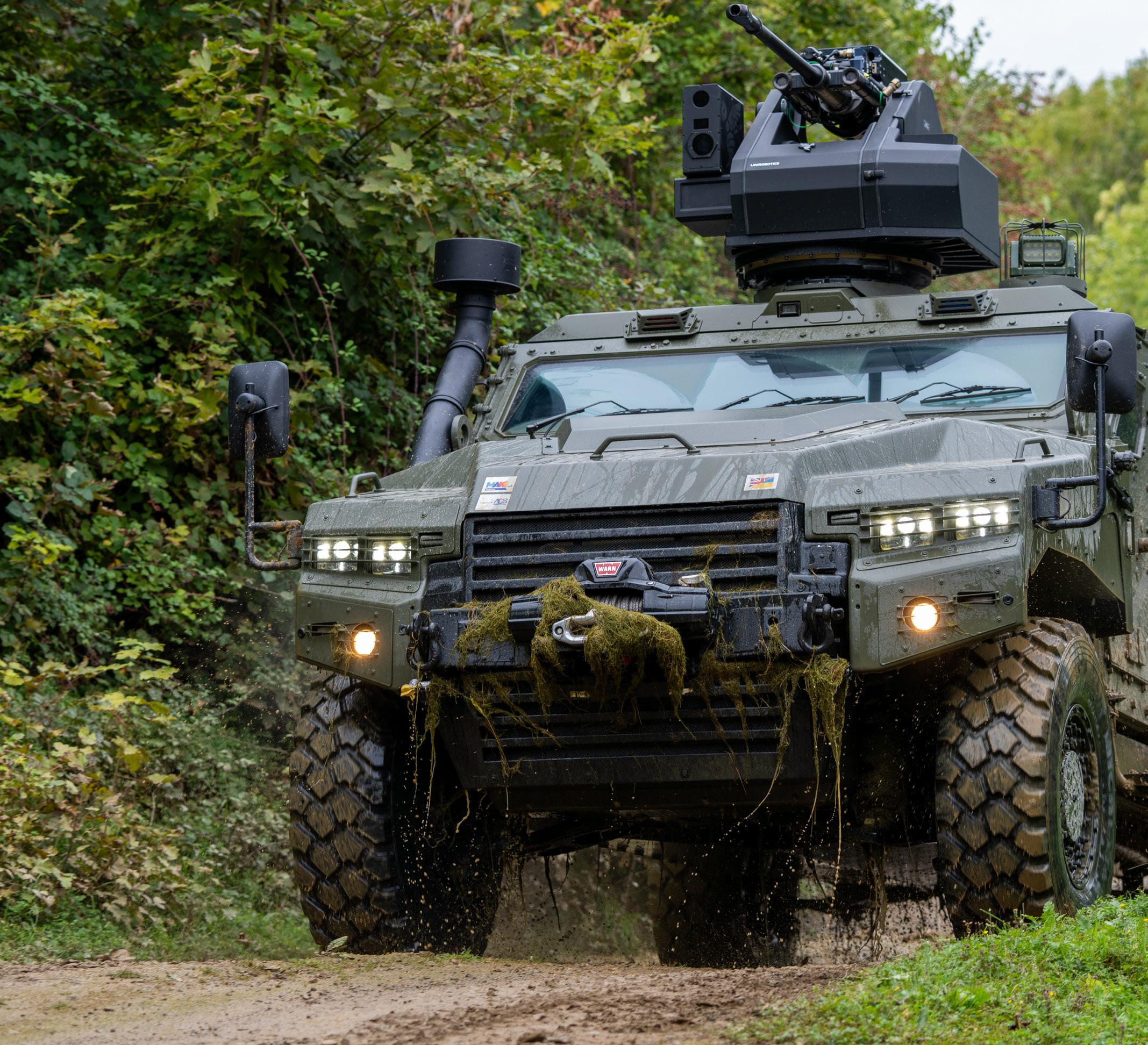
Having already demonstrated its export maturity, Nurol Makina anticipates continued participation in European defence markets. With sites across Hungary and, more recently, the UK, the company aims to further increase its utilisation of the European supply chain.
“We invested in the UK because it’s a liberal and welcoming business environment, which creates a win-win situation for both the investor and the host country. In today’s hypercompetitive business world, everyone competes for talented workforces and
business know-how.
“We excel in protected mobility solutions and have proven our commercial success in global markets. Here in the UK, we offer our business expertise to grow alongside the British defence ecosystem, and by investing in the country, we demonstrate our confidence in the strength of the UK defence industry and our commitment to being a vibrant member of it,” Akin states.
“I believe it would be beneficial for the entire European defence base to adopt a similarly liberal approach.
“I think EU policies could be more encouraging towards international players from non-EU countries – as long as they’re creating value for the EU, of course. The implications for the defence industrial base caused by the ongoing war between Ukraine and Russia underscore the need for this industrial integration,” he adds.
PROTECTIVE MOBILITY SOLUTIONS
A specialist in manufacturing protective mobility solutions and 4x4 armoured vehicles for a wide
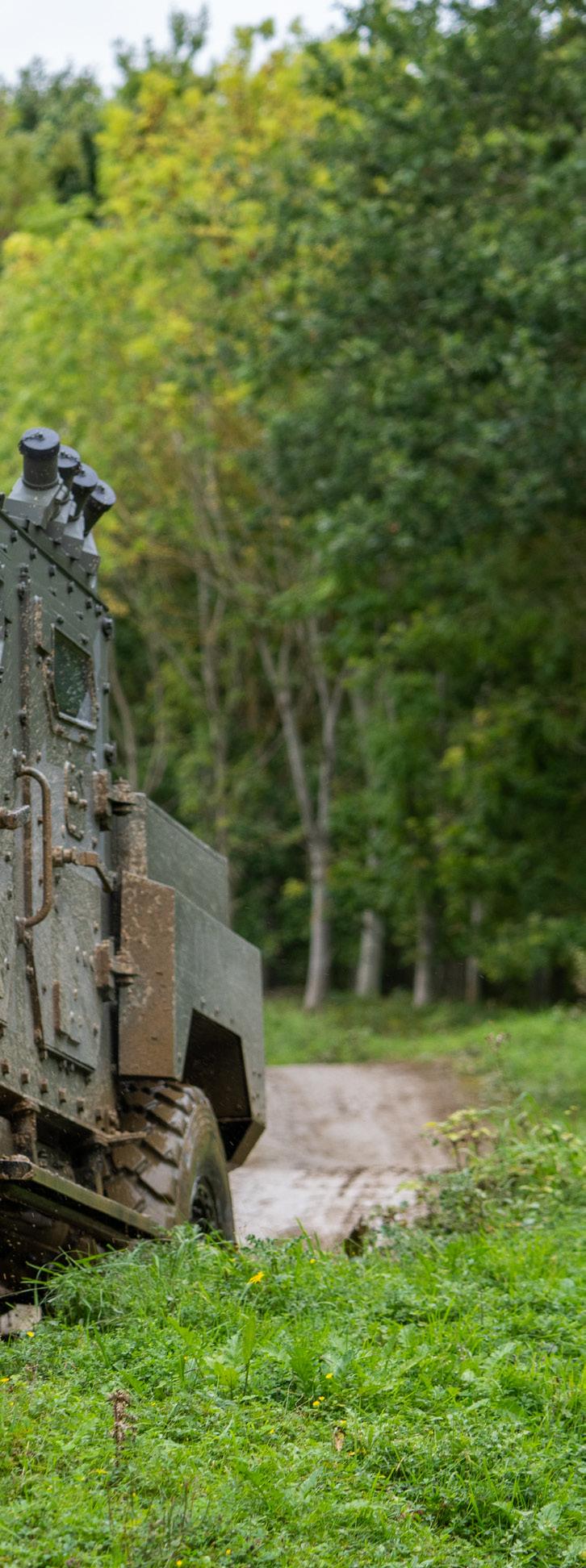
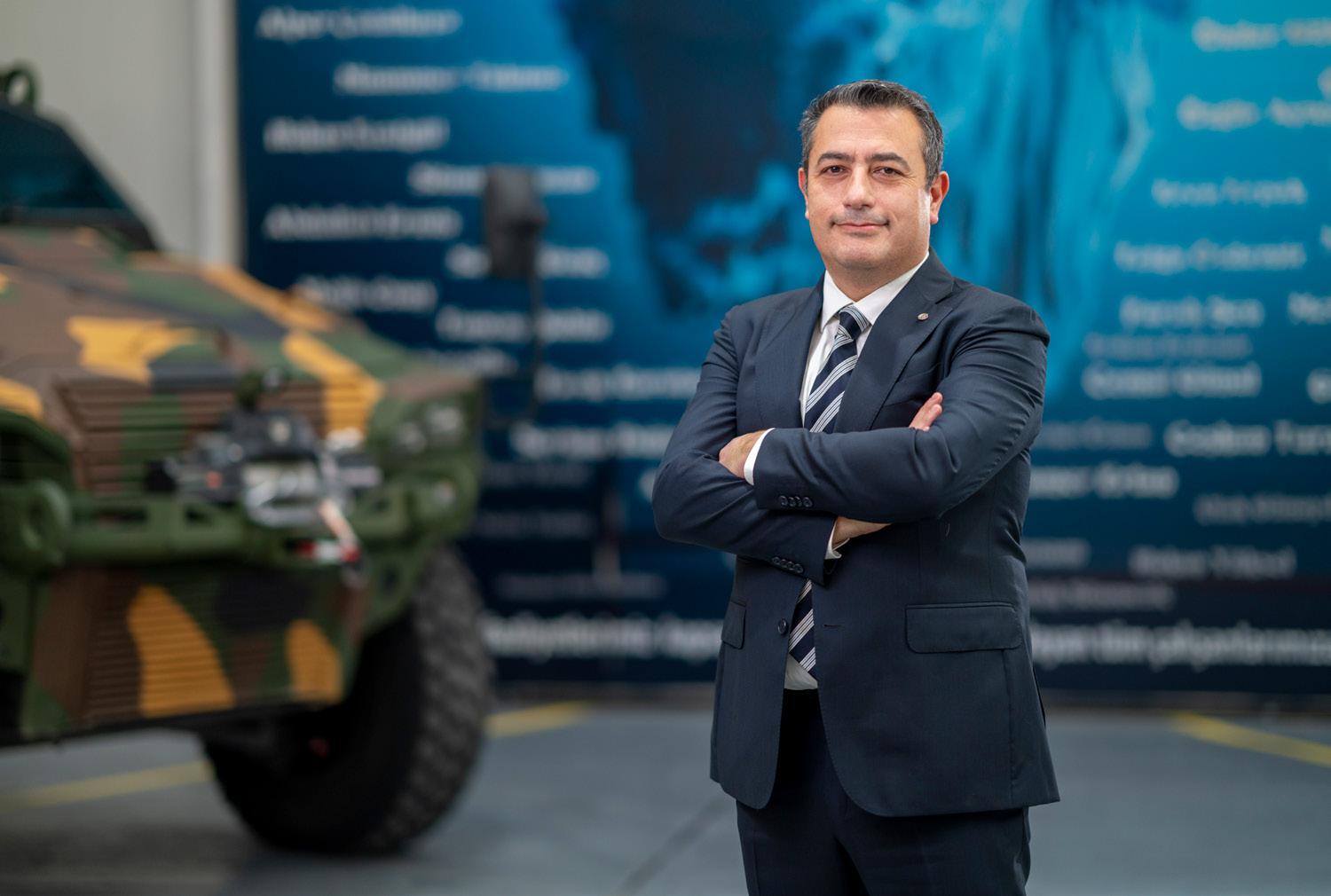
“AS A PEOPLE-CENTRIC ORGANISATION, WE ALWAYS SUPPORT OUR TEAM MEMBERS – ESPECIALLY THOSE WHO ARE WILLING TO TAKE INITIATIVE – TO GROW AND EMPOWER THEM”
– EMRE AKIN, CHIEF OPERATING OFFICER, EUROPE, NUROL MAKINA
range of users worldwide, Nurol Makina differentiates itself through its combat-proven superior vehicle performance.
By continuously utilising bestin-class commercial and military hardware systems from NATO and EU countries, its products consistently maintain high quality.
Furthermore, as an original equipment manufacturer (OEM) with a full spectrum of capabilities starting from authentic designs, the company is able to offer competitively priced products.
“We generate most of our revenues from international sales because we excel in what we do; all of our 4x4s are developed from our own designs,” Akin confirms.
Having established its first global operation in Hungary in 2021, Nurol Makina subsequently identified the British defence market as an ideal business environment where it can contribute and create value within the existing defence ecosystem through its export capabilities and proven technical and commercial expertise.
The company commenced its activities in the UK three years later at a 120,000-square-foot facility, NMS UK, in Leamington Spa.
“As an export-oriented company, the aim of our UK operations has not just been to provide competitive solutions to the British Army but also to serve export markets,” he tells us.
Meanwhile, the country’s liberal business environment has facilitated a positive start for the company.
“The UK is a very business-friendly environment, and we already feel
part of the team in the British defence industrial base,” Akin observes.
As such, Nurol Makina has successfully participated in industry events and conferences across the nation, including Defence IQ’s International Armoured Vehicles Conference (IAVC) in Farnborough and the annual Defence and Security Equipment International (DSEI) expo in London.
A COMBINED LEGACY
Keen to position itself as an investor creating positive synergies in the UK’s business environment, Akin highlights the many ways in which Nurol Makina will contribute to the British defence sector.
“We’re not a competitor to the existing UK defence industrial base – we’re simply here to increase the engineering and manufacturing work for protective mobility vehicles in the UK. We aim to create positive synergies in terms of job creation and strengthen the broad defence ecosystem needed for the entire product life cycle,” Akin tells us.
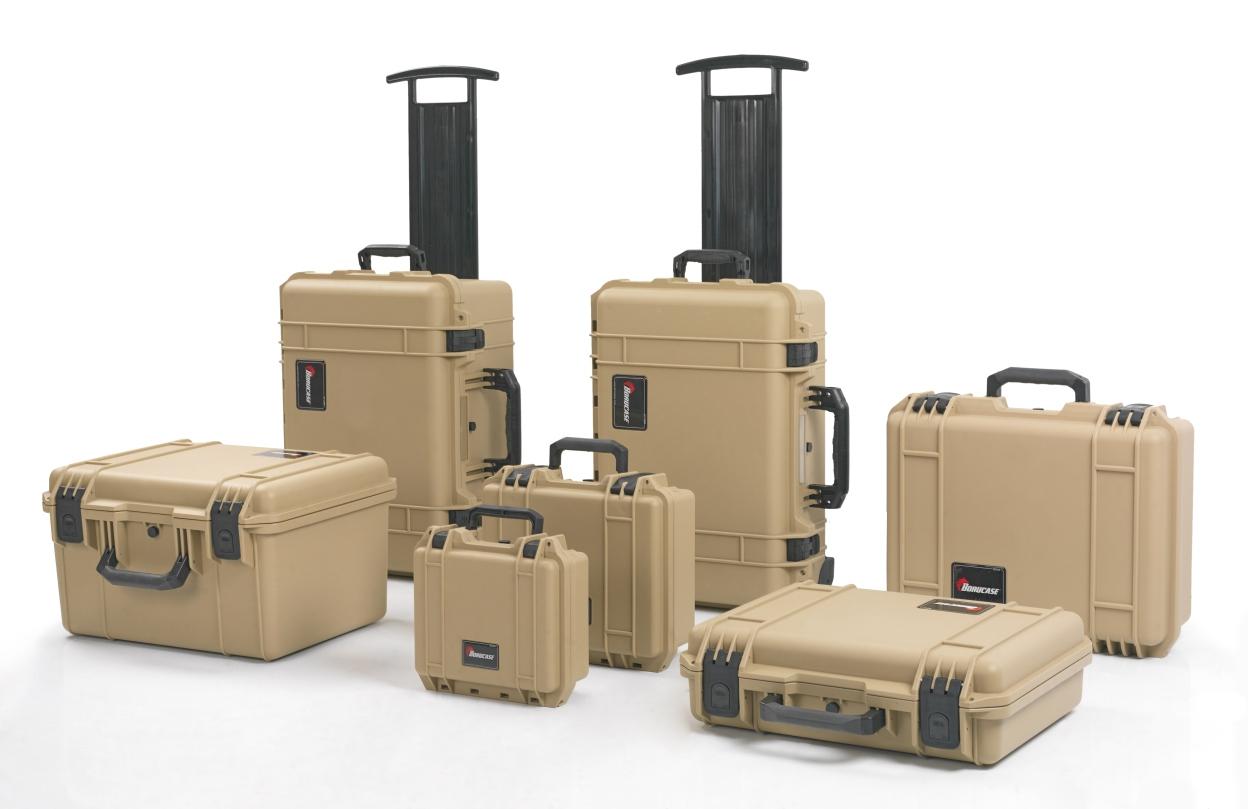
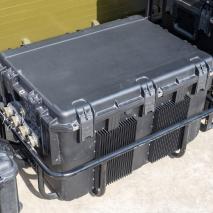
Br e y ntroduce us to Gökçeler Mak na.
Gökçeler Mak na LTD. T . (Gökçeler Mak na) s a company w th many competenc es located n a 3,000 square metre closed area n the S vas organ sed ndustr al zone.
In 2011, Gökçeler Mak na wh ch des gns and manufactures wagons, locomot ves, parts for ndustr al mach nery and systems, spec al mach nery des gn, and product on changed ts customer base w th the product on of Boe ng 787 Ram A r Turb ne structural parts, sw tch ng to the defence ndustry and produc ng body form ng moulds for Ta wan and armoured veh cle parts for FNSS.
In 2012, our company began to work w th Nurol Mak na A. . (Nurol Mak na), produc ng structural parts such as
bulldozer system parts, alum n um fenders, and water tanks used n Soc al Inc dent Response Veh cles (SIRV). Today, we produce prec s on armoured veh cle parts on computer numer cal control (CNC) mach nes for our customers and manufacture parts nclud ng h nges, locks, and r ng guards used n veh cle doors n all Nurol Mak na projects, such as Ejder Yalç n, Yörük, NMS 4x4, and STA, accord ng to the techn cal requests g ven, del ver ng them as coord nate measur ng mach ne (CMM)-controlled.
In add t on to armoured veh cle parts, Gökçeler Mak na manufactures plast c carry ng cases (hardcase) w th the BörüCASE brand.
We carry out product-mould des gns, plast c nject on moulds, and parts product on, ofer ng complete solut ons
by produc ng foam accord ng to customer des gns. Through our plast c carry ng cases, we prov de serv ces to many defence ndustry compan es. Add t onally, our products are used n countr es such as the USA, Germany, Denmark, Czech a, Ukra ne, and Qatar
What d st ngu shes Gökçeler Mak na from ts compet tors?
Our pr or ty at Gökçeler Mak na s not to make a pro t from every job; t s to del ver the ordered parts n accordance w th the del very schedule al gned w th customer requests and cons stent qual ty.
Wh ch completed, ongo ng, or recently completed projects would you l ke to showcase?
We have recently produced and del vered a large number of parts for Ejder Yalç n alongs de Yörük veh cles for Nurol Mak na. We are also prepar ng for new projects that start mm nently and w ll prove prom s ng for our future.
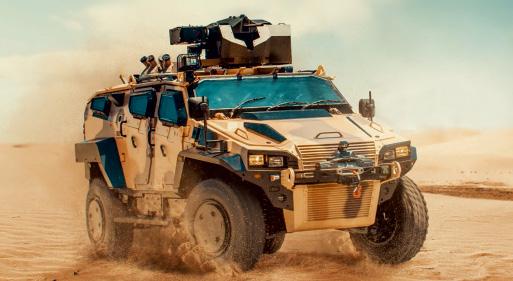
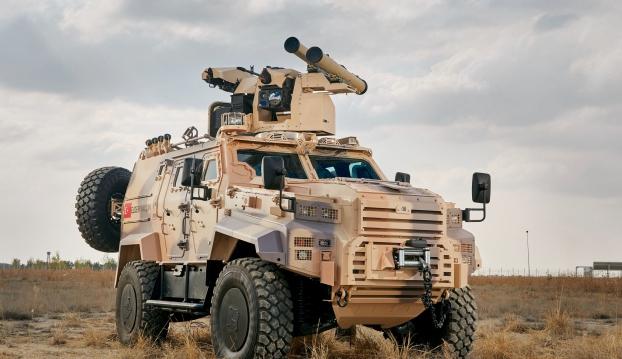
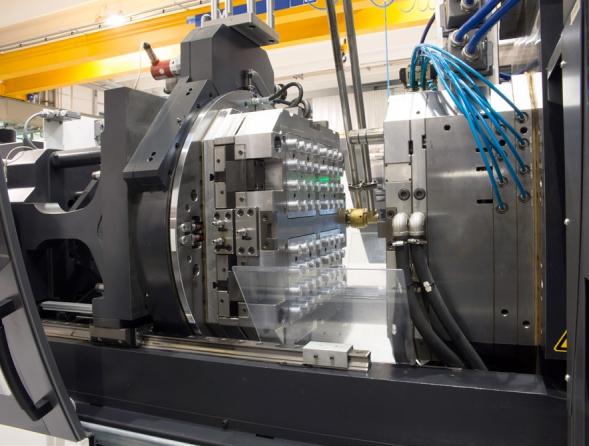
Look ng ahead, what are your ma n pr or t es for the com ng year? Do you a m to reach certa n targets, grow, or d vers fy?
We are plann ng to ncrease our CNC mach ne capac ty and are target ng new technolog cal nvestments n d ferent features.
For plast c carry cases, our r e carry case des gns come n three d ferent s zes and are expand ng rap dly. In 2025, we a m to present them to our customers.
Could you tell us about your relat onsh p w th Nurol Mak na?
We have been proudly work ng together for 13 years w thout nterrupt on.
Nurol Mak na s a very valuable bus ness partner for us. The company has ncreased the qual ty of our understand ng by prov d ng support n many areas to ncrease our product on process competence w th n the framework of the orders prov ded to us.
A hmet Turan G azi OS B. MH. OS B-9 S k. No:8
5 8060 S İVA S - TÜRKİYE
www.borucase.com
+90 346 218 1 444
ahmetnazmi@borucase.com
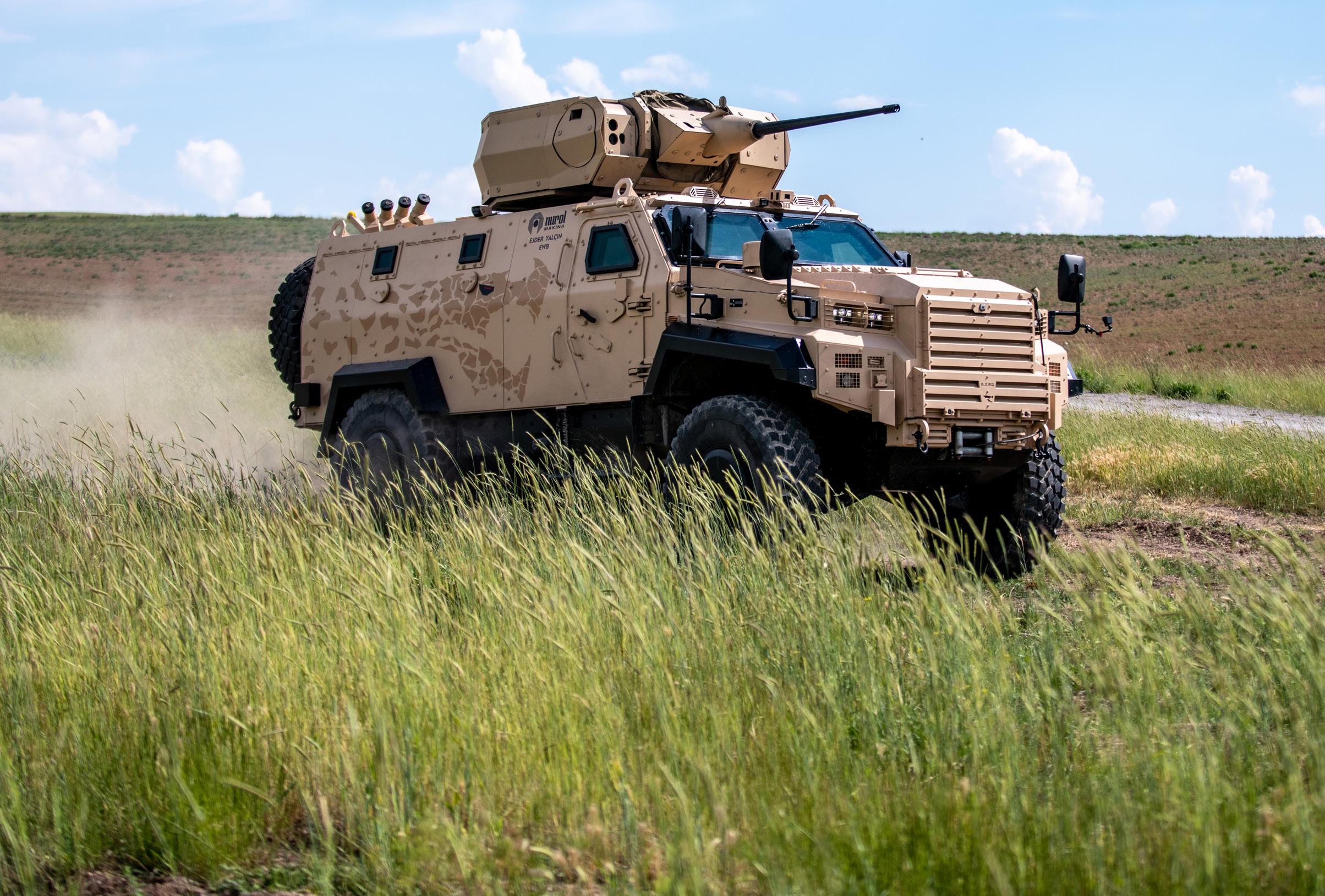
On a mission to expand its global presence within a wider defence ecosystem, Nurol Makina has already been in discussions with local companies to model its supply chain.
“We’re benefitting from the engineering and innovation capabilities of the UK and look forward to carrying these services to export markets alongside our products and services,” he explains.
In turn, the company is working on various export programmes that will enhance the UK’s status as an influential exporter of protected mobility vehicles.
“I think NMS UK is going to be a very positive example of how something that initially began as foreign direct investment (FDI) can evolve into a successful, self-sustaining UK business,” Akin reflects.
In service in more than 20 countries and with over 10 years of experience in protected mobility vehicles, the company is proud to showcase its
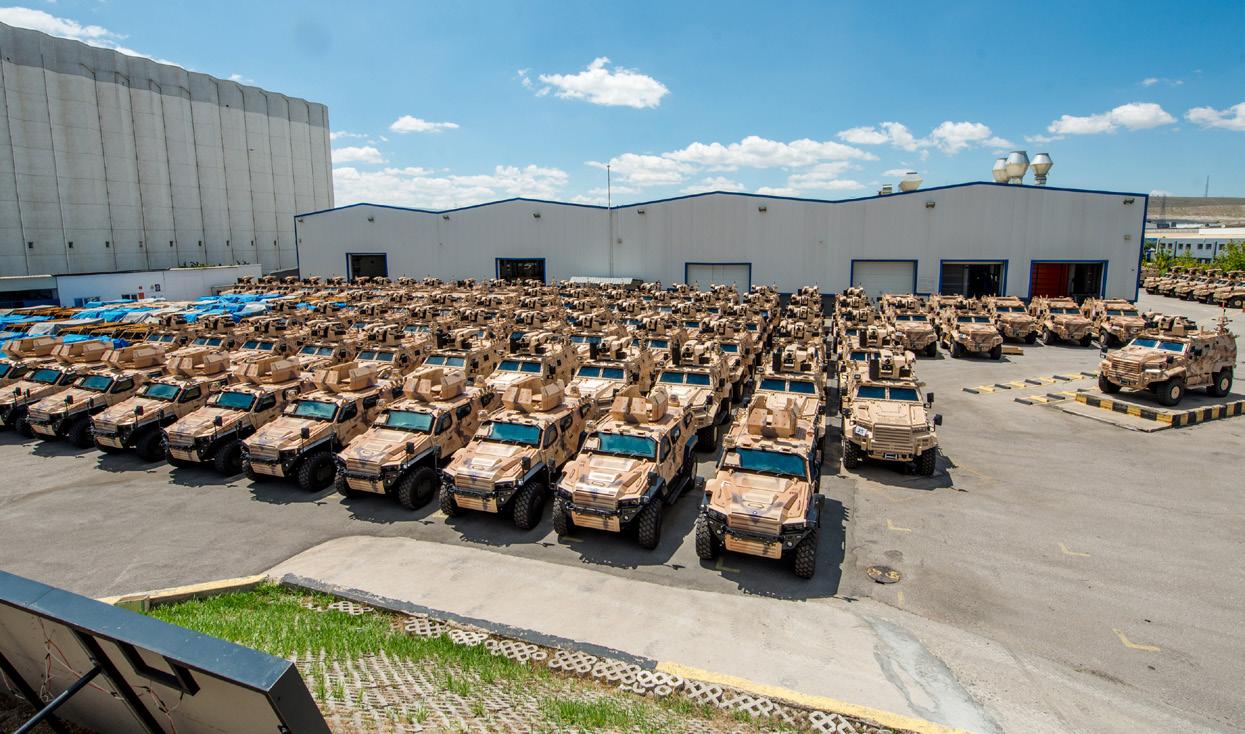
combat-proven 4x4 vehicles in the UK.
“They are competitive, highly reliable vehicles, and we are proud to bring this expertise and know-how to be locally manufactured and enhanced.
“We believe we can further grow our brand value within the UK defence industry and contribute to the nation’s economy. That’s our sincere aim and the source of our excitement about investing in the country,” he adds.
AN EMPLOYER OF CHOICE
As it progresses beyond its initial stages of expansion in the UK, Nurol
Makina has deployed some of its most highly qualified and educated engineers to work on product development and manufacturing.
The company also proudly collaborates with educational institutions for recruitment purposes, whilst an agreement with the British Armed Forces Covenant encourages the employment of veterans and ex-forces personnel.
When its facility in the UK reaches full capacity, Nurol Makina will employ approximately 150 staff, creating thousands of indirect jobs as well.
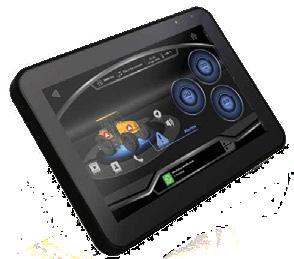
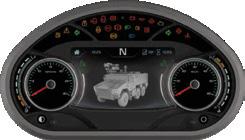
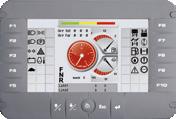

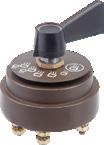
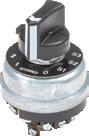
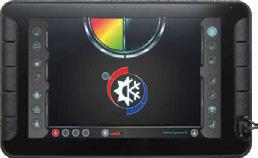
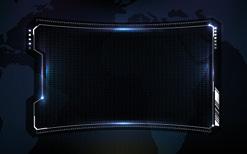
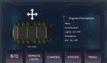
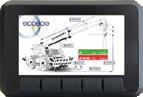

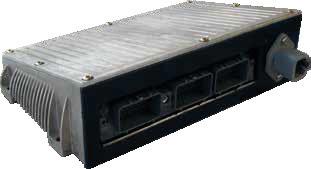
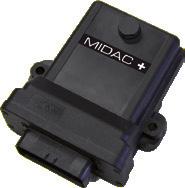
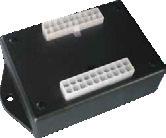
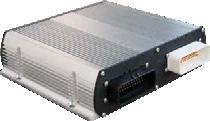
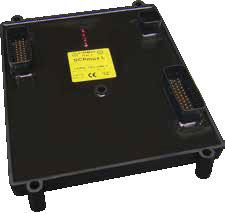

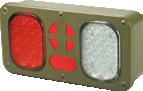

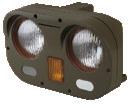

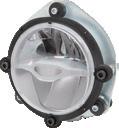
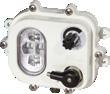
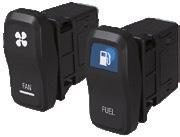
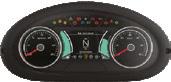
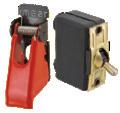
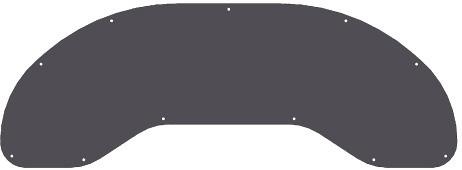


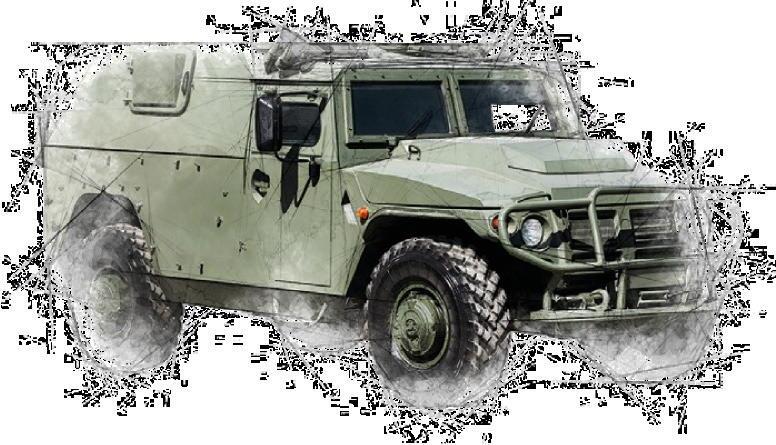
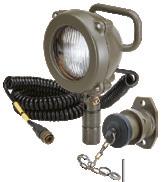
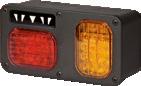

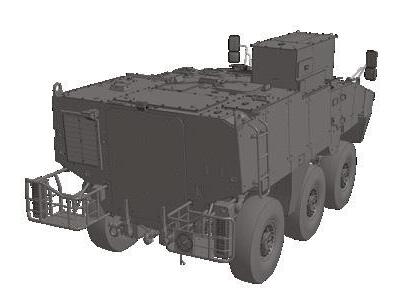
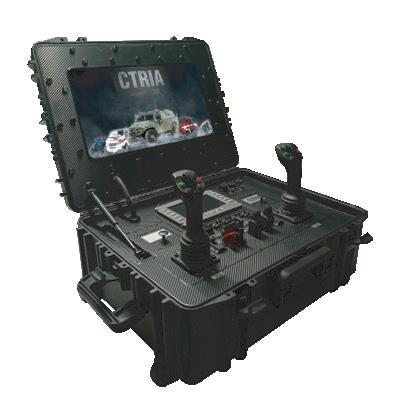
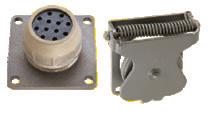
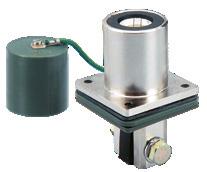
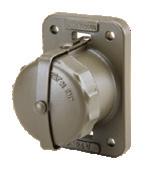
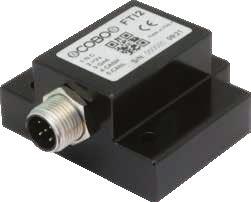
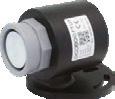
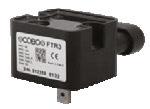
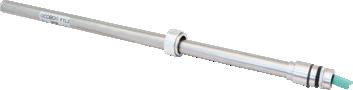
NUROL MAKINA’S PRODUCT RANGE –AT A GLANCE
• EJDER YALÇIN 4X4 – Developed to meet the operational requirements of military units and security forces across both rural and urban settings, offering mine resistant ambush protected (MRAP)-level protection.
• NMS 4X4 – Nurol Makina’s most recent design features a V-shaped monocoque body, making it both fast and highly manoeuvrable.
• NMS-L 4X4 – Incorporates high levels of protection and modularity in its lightweight class.
• PARS 4X4 – Featuring an amphibious design, this vehicle is purpose-built to undertake specialised operational roles such as advanced surveillance, antitank, and command and control.
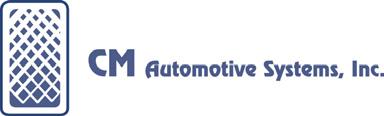
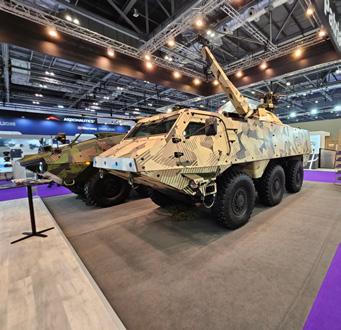
We at CM Automotive believe in quality, performance, and reliability. Using the CM Automotive operating system, we have been in business for over 35 years, manufacturing and designing the best Central Tire Inflation Systems in the world. With over twenty thousand units in the field today across a diverse array of applications that include military trucks, fire engines, and commercial buses. Each has benefited from the use of our all terrain mobilizer, robust R&D capabilities, and ongoing customer support.
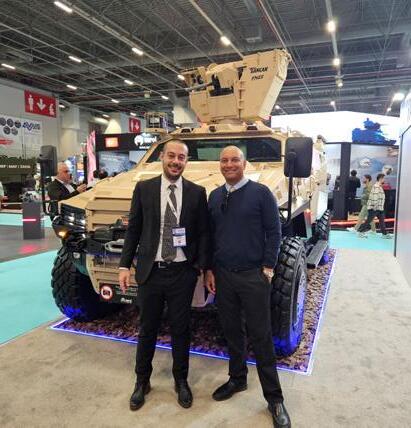
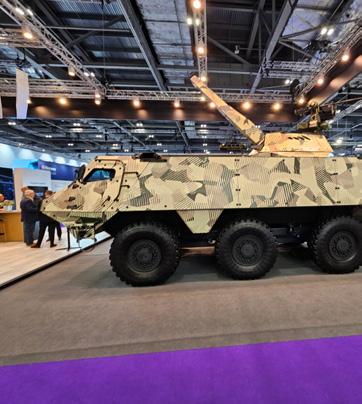
www.cmautomotive.com
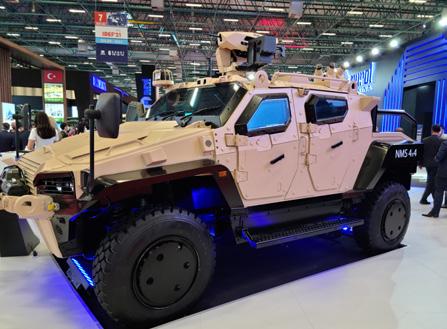
“IN TODAY’S HYPER-COMPETITIVE BUSINESS WORLD, EVERYONE COMPETES FOR TALENTED WORKFORCES AND BUSINESS KNOW-HOW. WE EXCEL IN PROTECTED MOBILITY SOLUTIONS AND HAVE PROVEN OUR COMMERCIAL SUCCESS IN GLOBAL MARKETS. HERE IN THE UK, WE OFFER OUR BUSINESS EXPERTISE TO GROW ALONGSIDE THE BRITISH DEFENCE ECOSYSTEM”
– EMRE AKIN, CHIEF OPERATING OFFICER, EUROPE, NUROL MAKINA
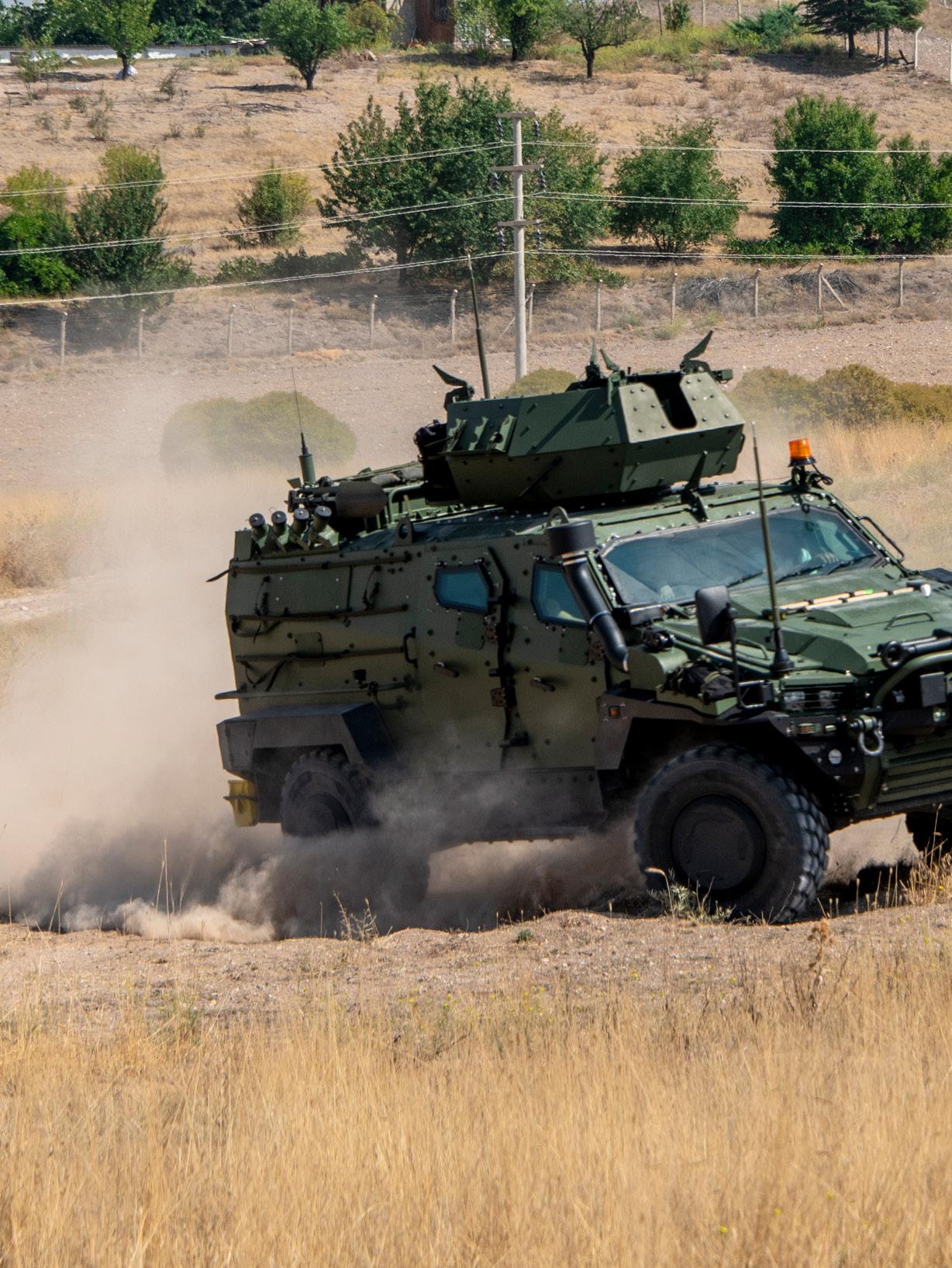
“In recognition of the importance of a skilled and highly dedicated workforce, we need to reach young people who have a positive aspiration for self-improvement, contributing to society and the security of their country,” Akin asserts.
He points out that universities and high schools are excellent sources for this kind of talent. As such, the company has made agreements with
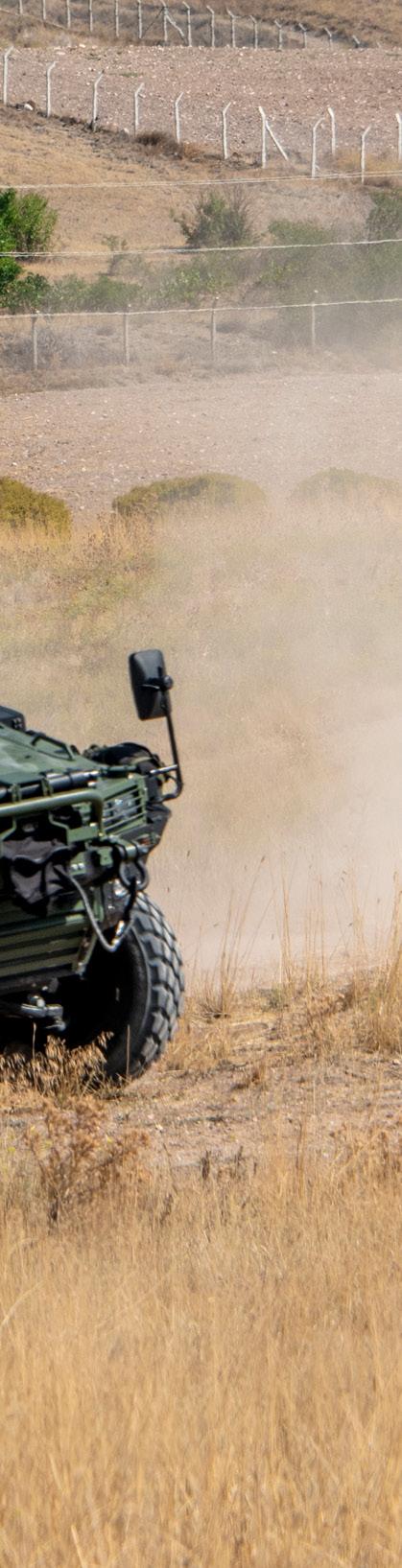
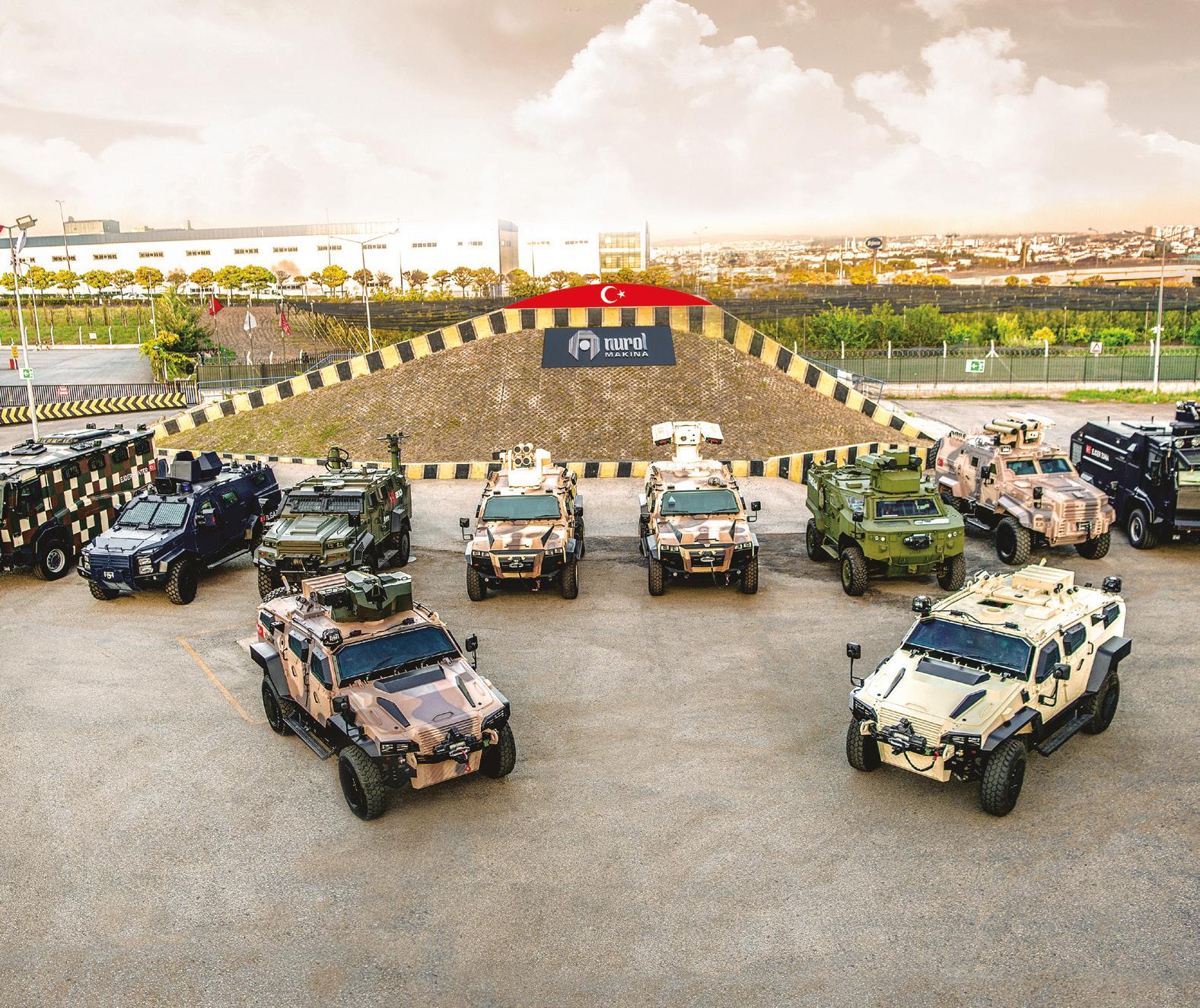
LOOKING AHEAD
Going forwards, Nurol Makina aims to meet a range of targets primarily within the UK business environment, the most important of which is its export programme.
local universities and educational institutions to promote practical programmes for students, offering them clear insights into the industry and NMS UK’s activities.
“As a people-centric organisation, we always support our team members – especially those who are willing to take initiative – to grow and empower them,” Akin passionately concludes.
“We are in discussions with some major international customers and expect to begin export work and sign international contracts from our NMS UK facility by the end of this year.”
The company is also collaborating with engineering firms to redesign parts of its armoured vehicles, including advanced mission systems.
Additionally, Nurol Makina will continue to participate in local and global defence events such as DSEI 2025 and IAVC 2026.
In terms of international events, NMS UK recently took part in the International Defence and Security
Exhibition of Spain (FEINDEF) in Madrid and the DSEI Japan Exhibition in Tokyo this May.
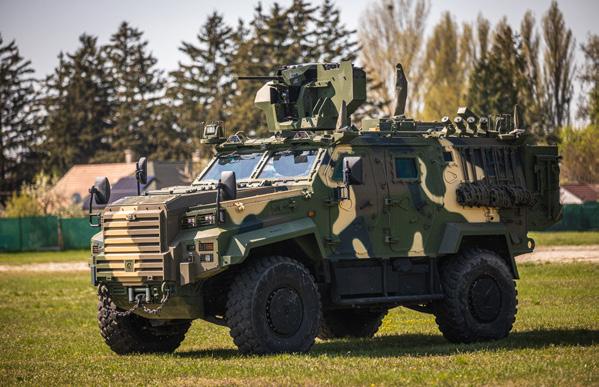
Tel: +90 (312) 480 30 00 - 05
info@nurolmakina.com.tr
www.nurolmakina.com.tr/en
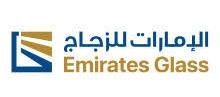
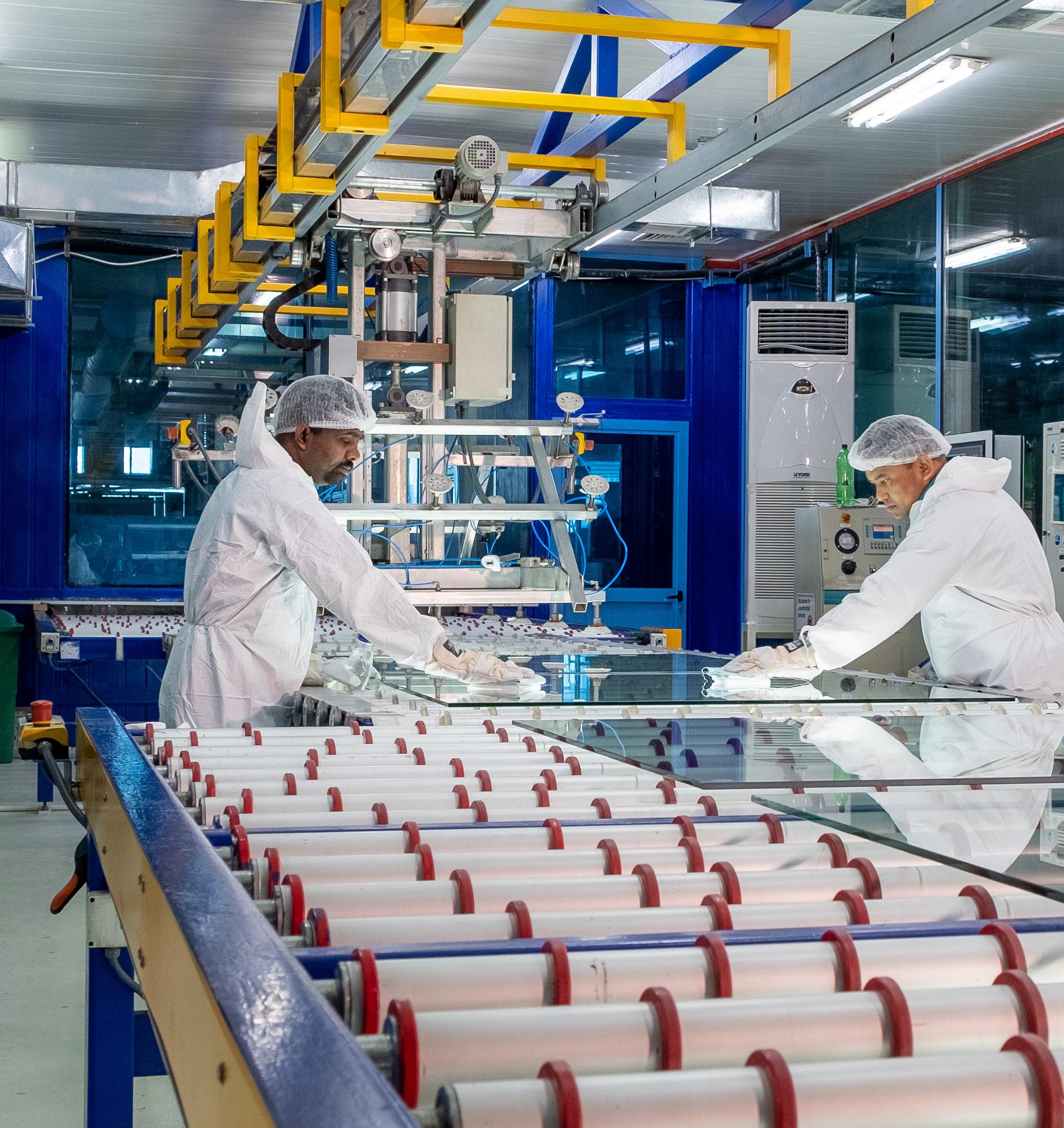
With a visually striking landscape comprising towering skyscrapers and luxurious, futuristic buildings, Dubai’s opulent architecture is both captivating and unique.
The construction industry in the city is thriving, with many buildings
primarily composed of glass and some even featuring fully glazed façades. Glass manufacturing companies are flourishing as they adapt to the high demand for energyefficient and innovative products.
As we revisit Emirates Glass, the company demonstrates a keen
awareness of the increased industry requirements.
“We have been proactive in enhancing our production capacity to meet the surging demand for high-performance architectural glass, targeting a market share of 27 percent this year,” introduces Rizwanulla Khan,
AN UNBREAKABLE COMMITMENT TO EXCELLENCE
With a crystal-clear objective of meeting evolving customer needs, Emirates Glass has undergone a significant transformation since we last spoke with the company in 2018. Executive President, Rizwanulla Khan, highlights its leading position in the architectural glass industry
Writer: Rachel Carr | Project Manager: Josh Whiteside
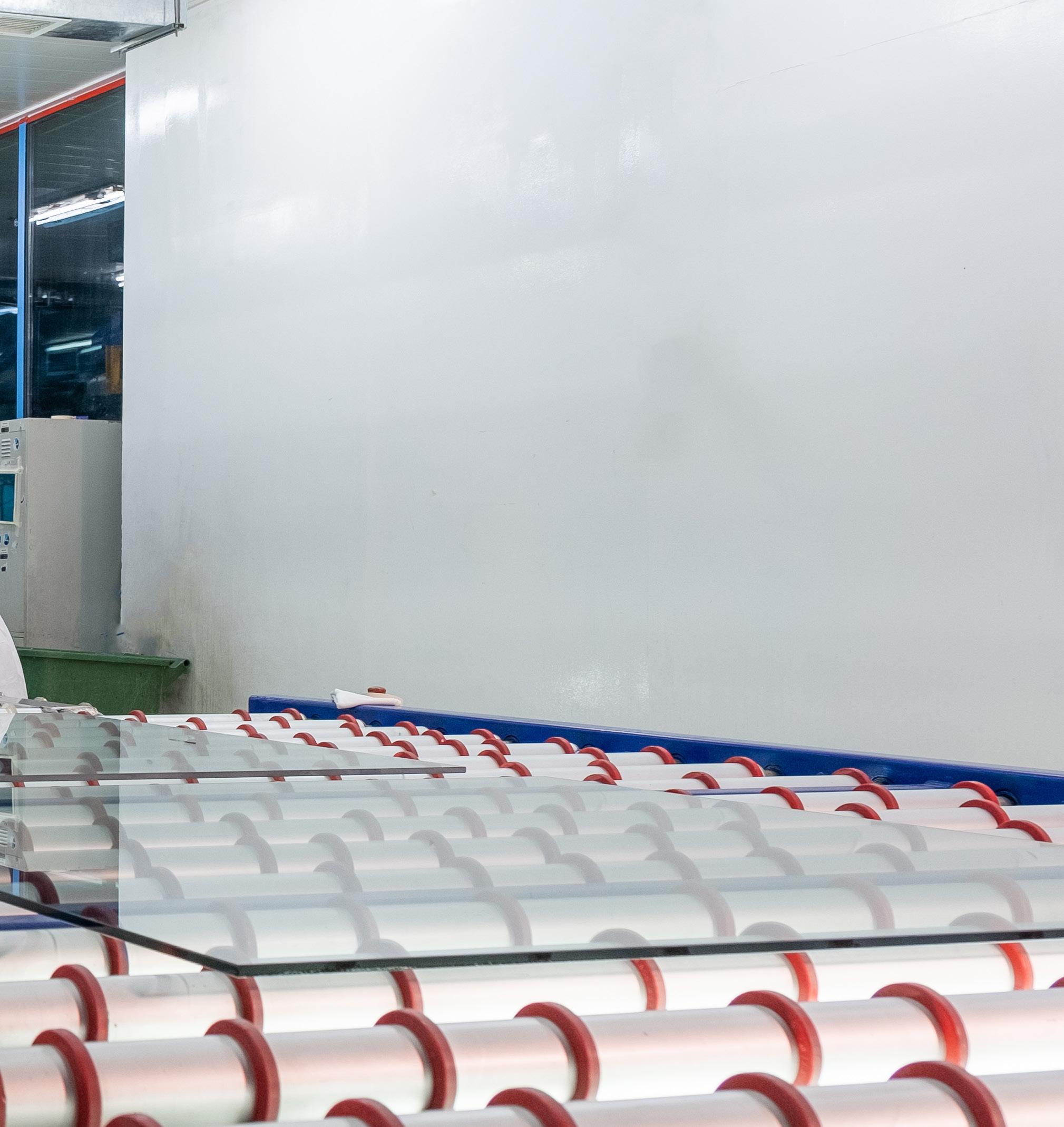
Executive President.
“In 2024, the company achieved its highest revenue and profit to date, contributing over 1.3 million square metres (sqm) to our total production – an eight percent increase year-on-year.”
The growth was propelled by the
commissioning of state-of-the-art machinery, including a jumbo glass panel processing system and a glass digital printing line, as well as scaling up bullet-resistant glass production by 15 percent.
Additionally, Emirates Glass successfully launched its fire-related
glass product line, Emfire, cementing its position in the passive fire protection sector.
The company has also embraced diversification, with notable expansions into fire-rated glass and architectural and automotive bulletresistant glass, ensuring alignment
with market trends and sustainability goals whilst developing its portfolio.
“Our bulletproof glass segment had a productivity boost last year, providing unparalleled safety solutions for high-security projects. Meanwhile, the newly installed jumbo glass processing line caters to specialised projects requiring oversized panels, offering both aesthetic and functionality for iconic architectural structures,” he adds.
CAPABILITIES AND FACILITIES
In 2024, Emirates Glass integrated cutting-edge technologies into its manufacturing processes, with key highlights including advanced tempering and lamination systems, as well as a sophisticated digital printing line which enhances the decorative glass segment.
The technologies ensure precision, quality, and efficiency whilst meeting diverse customer requirements.
“We have invested in equipment to bolster the company’s capabilities, enabling increased productivity and thereby expanding our portfolio with innovative products, such as fire-rated and bulletproof glass,” notes Khan.
HOW DOES EMIRATES GLASS ENSURE CUSTOMER SATISFACTION AND MAINTAIN STRONG CLIENT RELATIONSHIPS?
Rizwanulla Khan, Executive President: “At Emirates Glass, we prioritise customer satisfaction by fostering strong, trust-based relationships and delivering innovative solutions tailored to our clients’ needs.
“By maintaining open communication channels and providing technical expertise, we ensure seamless project execution and customer confidence. Our commitment to quality, timely delivery and precision reinforces these relationships, making Emirates Glass a reliable partner for both standard and specialised projects.
“Our continuous improvement and responsiveness to market demands further enhance the customer experience.”
“In addition, we are in the process of setting up a curve tempering facility, which will further expand its specialised offerings and allow for greater flexibility in high-performance architectural applications.”
This strategic addition reinforces Emirates Glass’ commitment to technological advancement and market leadership.
The investments reflect a key approach to growth, diversification, and operational excellence.
Whilst the commissioning of stateof-the-art jumbo-sized processing equipment has enhanced production capacity, there have also been substantial investments beyond
“We recognise that innovation is driven by expertise and have actively invested in human resources, tapping
workforce. By fostering a dynamic and skilled team, we ensure its ability performance architectural glass and
This focus on both technological
long-term industry
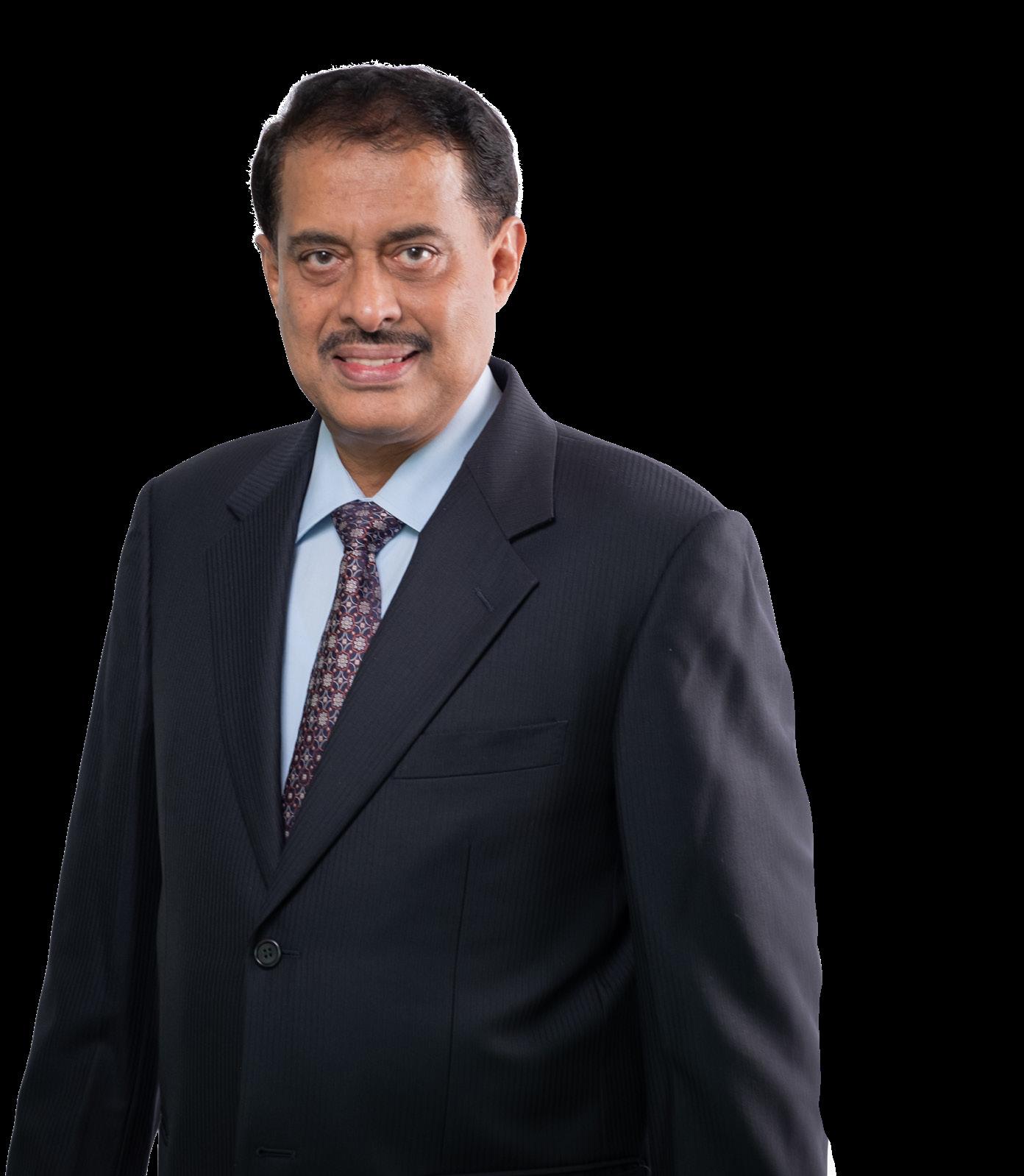
STRATEGIC AND SUSTAINABLE PARTNERSHIPS
partnerships have been fundamental to Emirates Glass’ success, driving excellence, and market expansion.
“Collaborating with globally
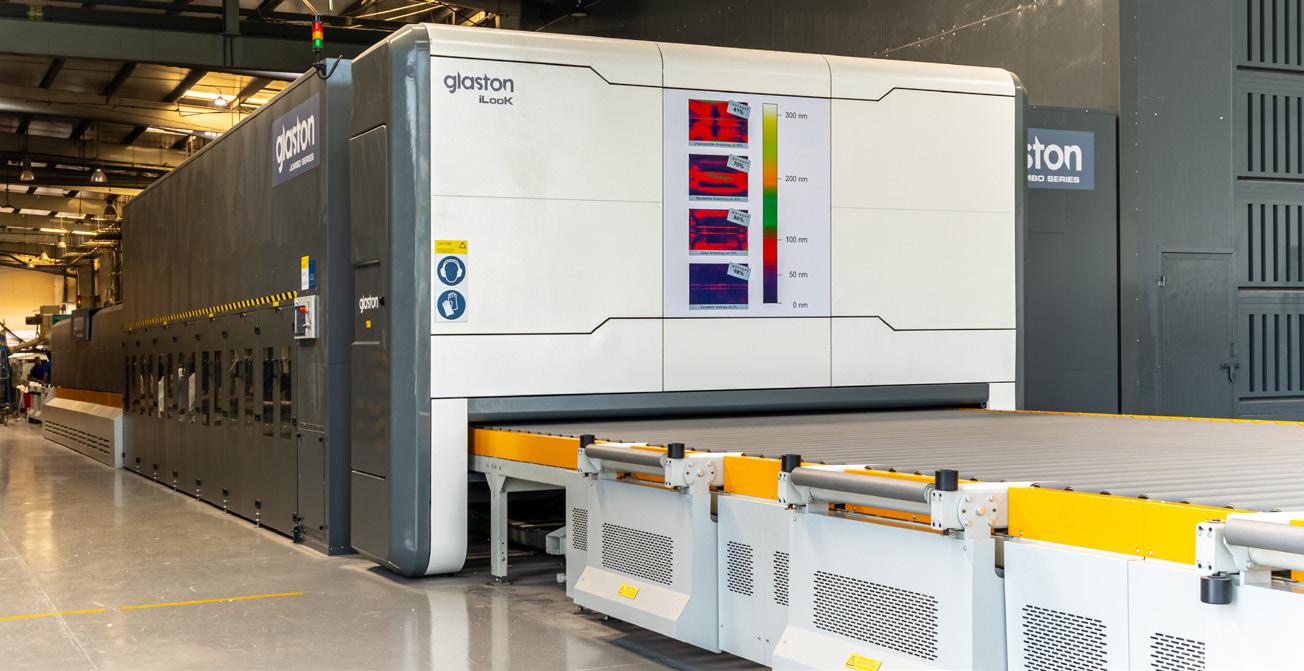
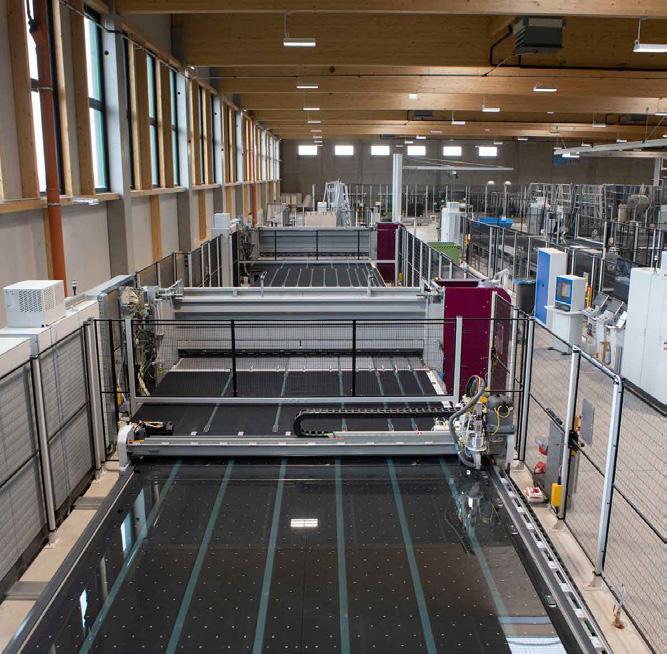
recognised certification bodies such as Intertek ensures rigorous product testing and compliance, reinforcing industry credibility and customer trust,” Khan emphasises.
“We have also established strong relationships with leading industry players, including Schott, Vetrotech Saint-Gobain, Aluprof, Kuraray, and Tremco. Our partnership with the latter has been long-standing, playing a vital role in advancing high-performance glazing solutions, particularly in fire-rated and speciality applications.”
These alliances have significantly contributed to Emirates Glass’ ability to deliver cutting-edge architectural and safety glass solutions.
Furthermore, the company maintains robust supplier relationships, ensuring operational efficiency, consistent material quality, and seamless production workflows. These strategic collaborations continue to fuel its growth, innovation, and leadership in
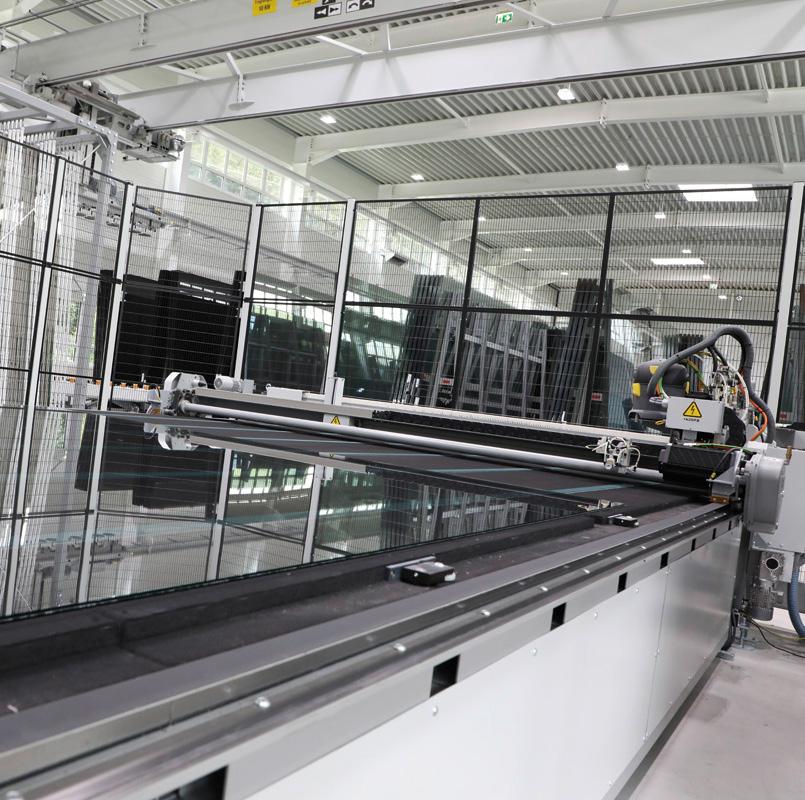
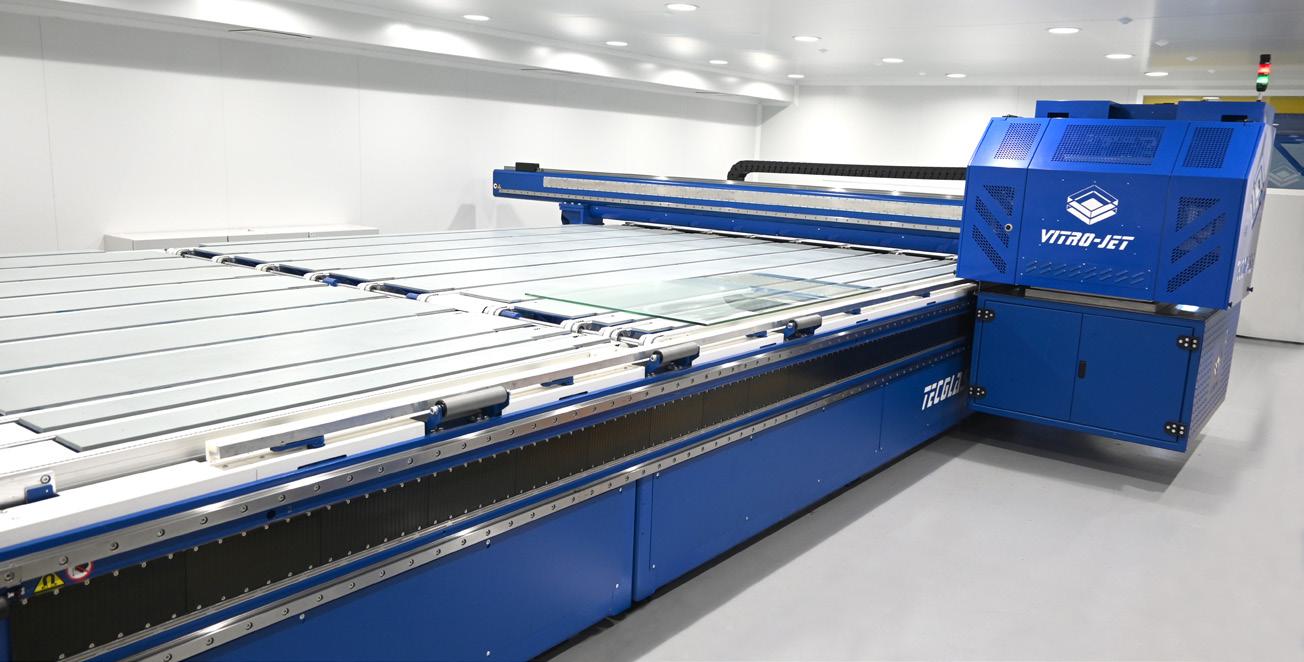
“WE HAVE INVESTED IN EQUIPMENT TO BOLSTER THE COMPANY’S CAPABILITIES, ENABLING INCREASED PRODUCTIVITY AND THEREBY EXPANDING OUR PORTFOLIO WITH INNOVATIVE PRODUCTS, SUCH AS FIRERATED AND BULLETPROOF GLASS”
– RIZWANULLA KHAN, EXECUTIVE PRESIDENT, EMIRATES GLASS
the global glass industry.
“By fostering long-term relationships with suppliers, we ensure consistent material quality, timely production, and enhanced customer satisfaction – key factors in maintaining our market leadership. We emphasise efficient supply chain management to meet growing demands,” explains Khan.
Sustainability is also a fundamental pillar of Emirates Glass’ operations, with a strong focus on reducing environmental impact through advanced glass solutions. The
company has developed energyefficient glass products that optimise thermal insulation, minimising energy consumption in buildings.
“We actively promote sustainability by integrating Total Solar panels into our product offerings, enhancing energy efficiency and supporting renewable energy initiatives,” he assures.
Total Solar is the name given to the solar panels installed by TotalEnergies in partnership with Emirates Glass as part of a joint effort to harness the sun’s natural energy and reduce carbon emissions.
Covestro TPU films set new standards in security glazing
We are a world-leading manufacturer of high-quality polymer materials. With innovative products, processes, and methods, we improve quality of life and drive our vision of becoming fully circular.
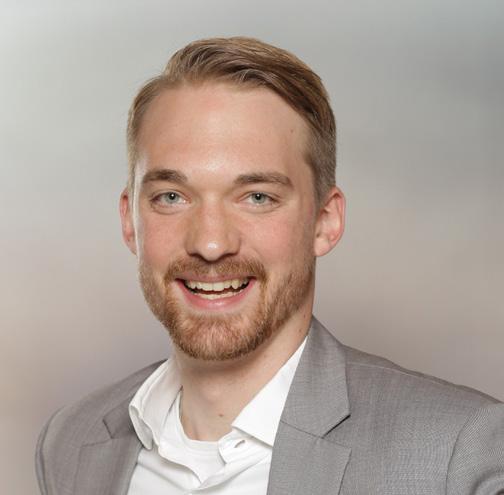
Kaiser, Director of Commercial Operations Specialty Films
Briefly introduce us to Covestro Films GmbH (formerly Epurex).
Covestro Films GmbH (Covestro) is a subsidiary of Covestro AG - a global leader in high-performance polymer materials. Headquartered in Leverkusen, Germany, Covestro operates 46 production sites worldwide and employs approximately 17,500 people.
Covestro specialises in manufacturing and developing advanced thermoplastic polyurethane (TPU) films under Platilon® and Dureflex® brands for industries such as mobility, construction, electronics, and healthcare. These solutions support technical performance with a focus on sustainability and innovation.
Committed to becoming fully circular, Covestro targets for climate neutrality for Scope 1 and 2 emissions by 2035, and for Scope 3 emissions by 2050, driving long-term sustainable growth and a resource-conserving economy.
What differentiates Covestro?
Covestro sets itself apart through its vertically integrated raw material production, global manufacturing footprint, and decades of technical expertise. These strengths enable us to deliver consistent, high-quality TPU film solutions tailored to unique customer requirements.
One key application area for Covestro’s film solutions is security and bullet-resistant glazing. These applications require materials that deliver robust protection without compromising appearance.
Covestro’s aliphatic TPU film portfolio is designed to meet the high demands of the bullet-resistant glazing market, offering excellent durability, UV resistance, and optical clarity. These films are used in adhesive applications for glass-clad and glass-plastic laminates, including polycarbonate (PC) and acrylic (PMMA). Free from plasticisers, the films maintain long-term stability, while the lightweight construction of glass-plastic laminates helps reduce overall weight. This innovative solution particularly excels in addressing ballistic threats. The film’s properties effectively slow bullet penetration and retain glass shards, making it ideal for security glazing that protects against debris.
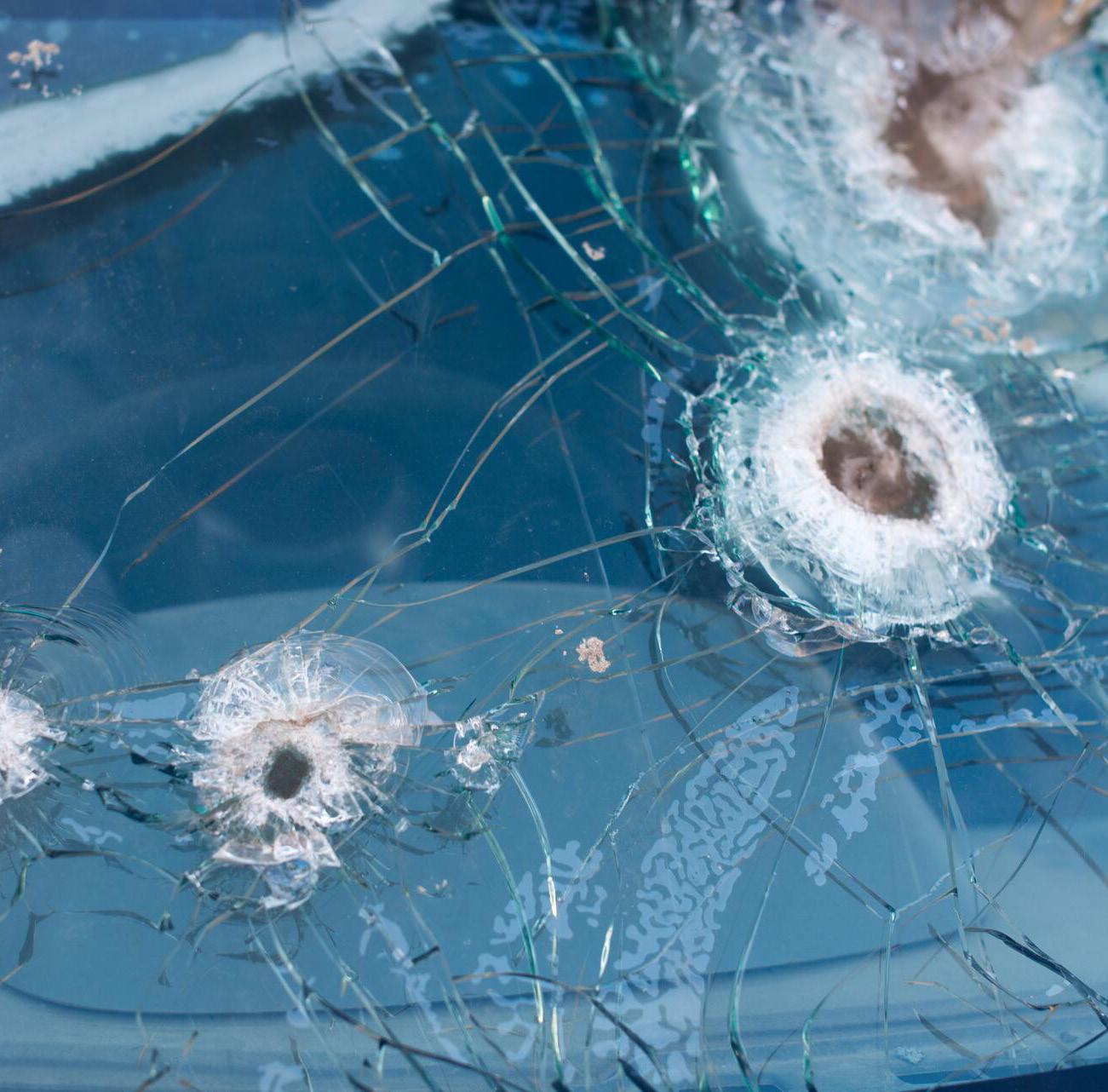
How does Covestro push for the circular transformation of the industry by developing new ideas?
In line with our vision to become fully circular, we expanded our Specialty Films portfolio by partly consisting of bio-based content or partly recycled raw materials, as well as ISCC PLUS-certified films, where recycled and renewable feedstock has been attributed via a mass balance approach.
As a result, our innovation strategy follows two complementary paths: we actively develop pioneering solutions that set industry trends and shape the future direction of sustainable film technology, positioning ourselves as thought leaders in the industry.
Simultaneously, we maintain close partnerships with industry leaders, collaborating to create sustainable, tailor-made solutions that precisely address their specific challenges and requirements.

Bullet-resistant glass is essential for vehicle safety and protection against attacks. ©alex-stock. adobe.com
Glass-clad polycarbonate employs TPU film to bond glazing layers together, where polycarbonate provides protection from flying glass in the interior of a building.
(Photo courtesy of Covestro)
Justus
EMEA, Covestro

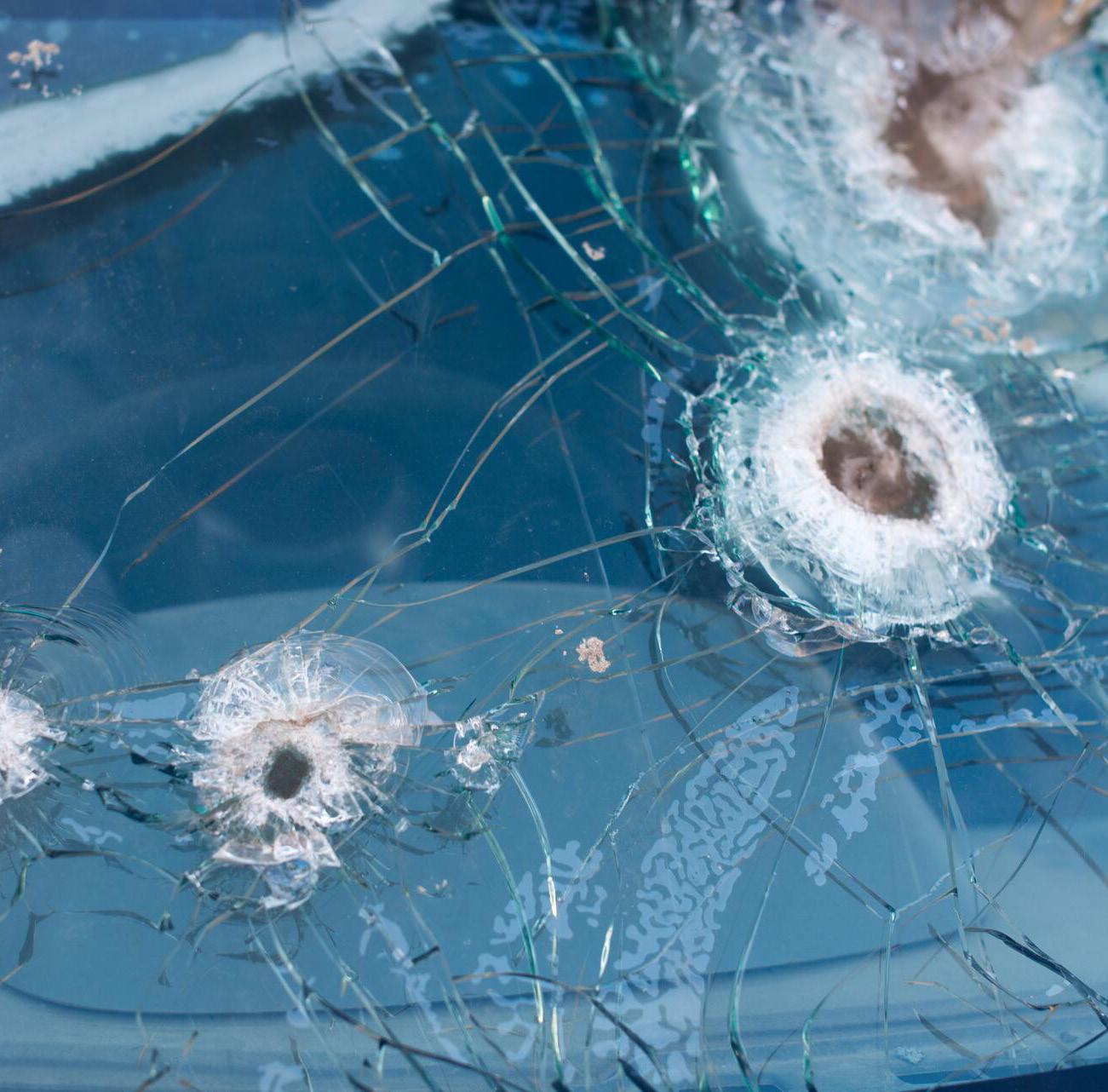
This balanced approach of driving innovation independently and co-creating with partners ensures we deliver cuttingedge solutions while meeting real-world market demands for sustainability.
What projects would you like to showcase?
We recently collaborated with Emirates Glass, a leading manufacturer of energy-efficient architectural glass in the Middle East. This partnership aims to elevate safety and performance standards in architectural glazing. This collaboration reflects a shared commitment to innovation, quality, and sustainability in the construction industry. By combining Covestro’s material expertise with Emirates Glass’s regional market leadership, the project demonstrates how collaborative innovation can drive the development of safer, more efficient, and environmentally conscious building materials.
The incorporation of Covestro’s TPU films into Emirates Glass’s products has led to significant advancements:
• Enhanced Safety: Improved resistance to impact and ballistic threats, ensuring occupant protection.
• Durability: Increased longevity of glazing systems due to superior UV and weather resistance.
• Design Flexibility: Ability to create complex, multi-layered glazing solutions that meet specific architectural requirements.
Beyond technical benefits, the project aligns with both companies’ sustainability goals. Covestro’s TPU films are designed to reduce environmental impact without compromising performance.
Please tell us more about the materials that you provide and how they serve key sectors on their transformation journeys towards circularity and climate neutrality.
Our films play a vital role in enabling key industries to the transition toward more sustainable practices:
• Textiles: Our TPU films provide excellent bonding, flexibility, durability, and recyclability for breathable, long-lasting fabrics.
• Automotive: We deliver advanced UV-resistant, lightweight films that enhance design and support fuelefficient, electric vehicles.
• Construction: Our films support sustainable solutions for sanitary applications and insulation, boosting building durability and efficiency.
An excellent example of our contribution to circularity and performance is the use of aliphatic TPU films in laminated glass applications. Architectural and automotive glazing demands have become more complex. Traditional interlayer materials like polyvinyl butyral (PVB) have shown limitations. This is especially true when paired with thermoplastics such as polycarbonate.
To meet these new requirements, next-gen aliphatic TPU films, such as Dureflex® A4700, offer an excellent alternative:
• Optical clarity: Maintains transparency over time without yellowing, ensuring clear visibility.
• Impact resistance: Provides robust protection against ballistic threats by absorbing and dissipating energy.
• UV stability: Resists degradation from ultraviolet exposure, extending the lifespan of glazing systems.
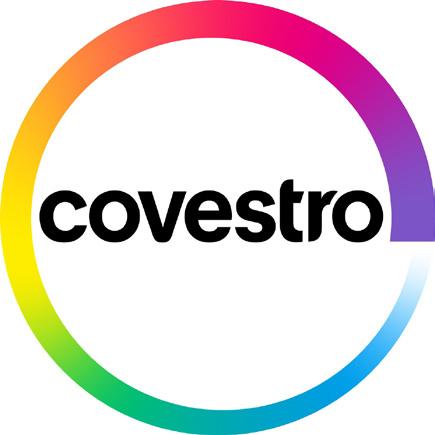
• Flexibility: Accommodates thermal expansion differences between glass and polymers, preventing delamination. These advanced materials enable high-performance, sustainable glazing, helping customers achieve safer, more circular, climate-neutral solutions.
Looking
ahead, what are your key priorities for the coming year?
Our future vision at Covestro is built on three fundamental pillars.
First, we will continue excelling at developing innovative materials that create real value for our customers. Second, we aim to maintain and strengthen our position as a trustworthy, long-term partner, just as we have done throughout our history. We firmly believe that true innovation and value-adding products come from lasting, trust-based partnerships.
This brings us to our third crucial objective: sustainability. As products increasingly need to meet stringent environmental standards, we are committed to making a significant contribution to this global challenge.
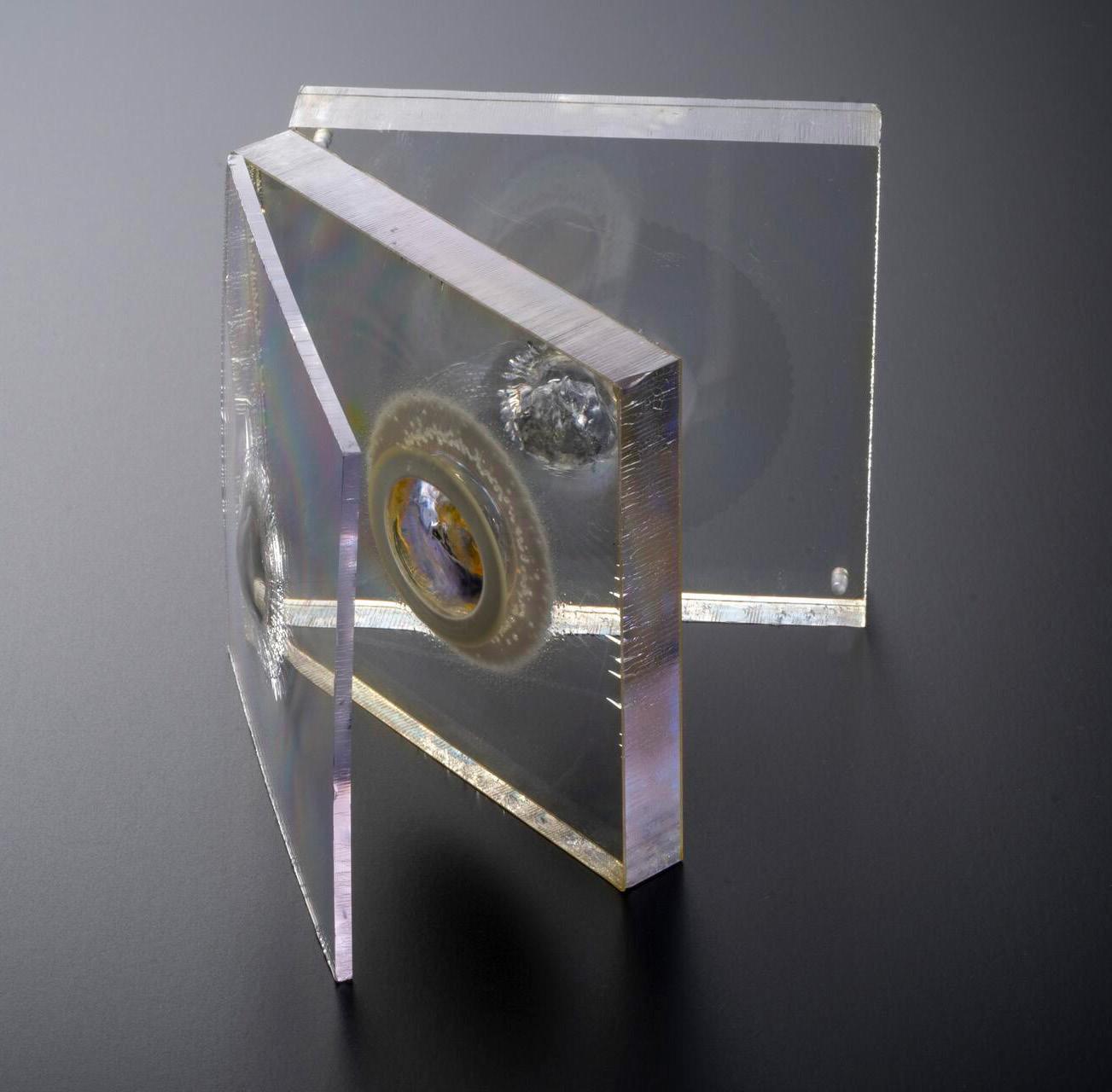
Multilayer polymer laminates using TPU interlayers provide bullet resistance with reduced weight and ease of fabrication.
(Photo courtesy of Covestro)
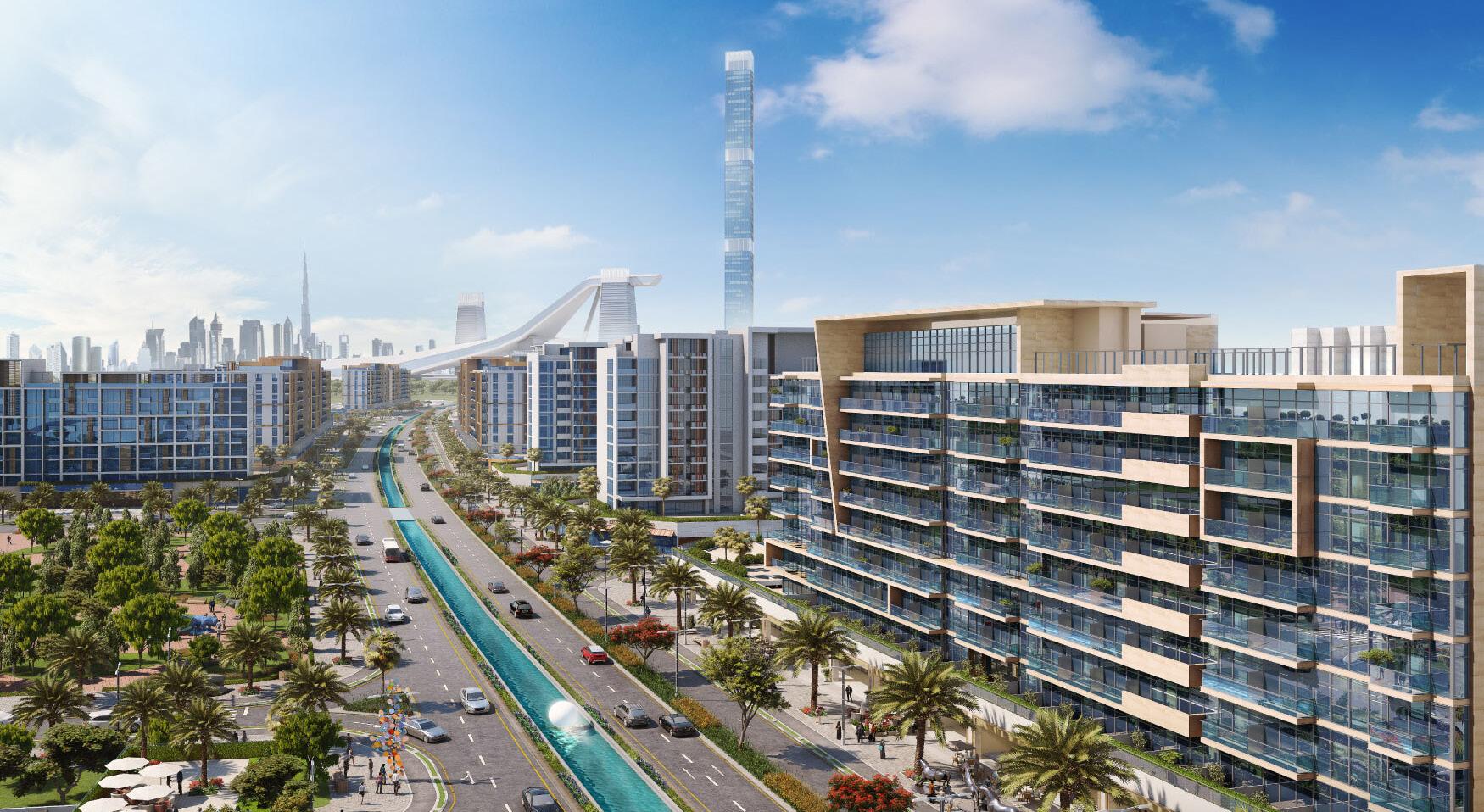
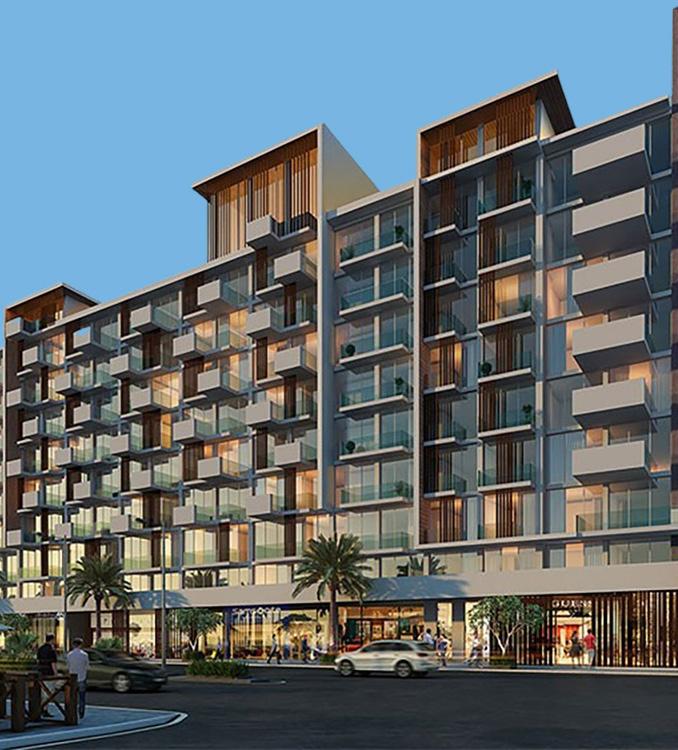
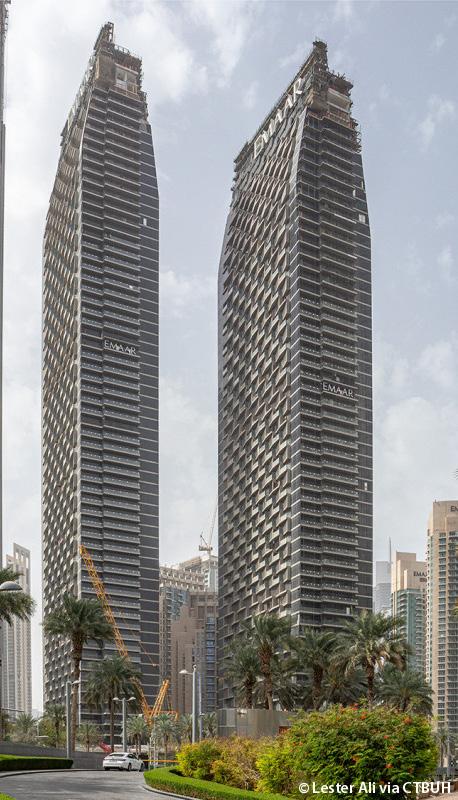
“Additionally, we prioritise responsible sourcing and raw glass processing, ensuring material optimisation whilst reducing waste. A key initiative includes our recycling programmes, where excess glass is repurposed, contributing to a circular economy and minimising our environmental footprint,” Khan informs.
Emirates Glass further reinforces its commitment to transparency
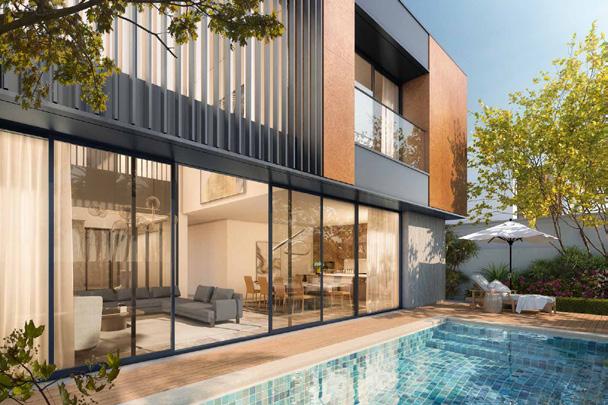
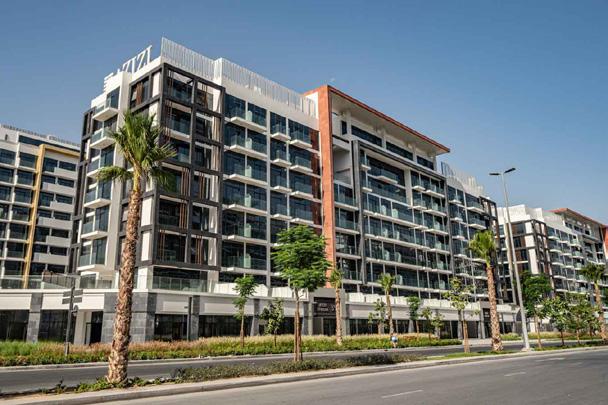
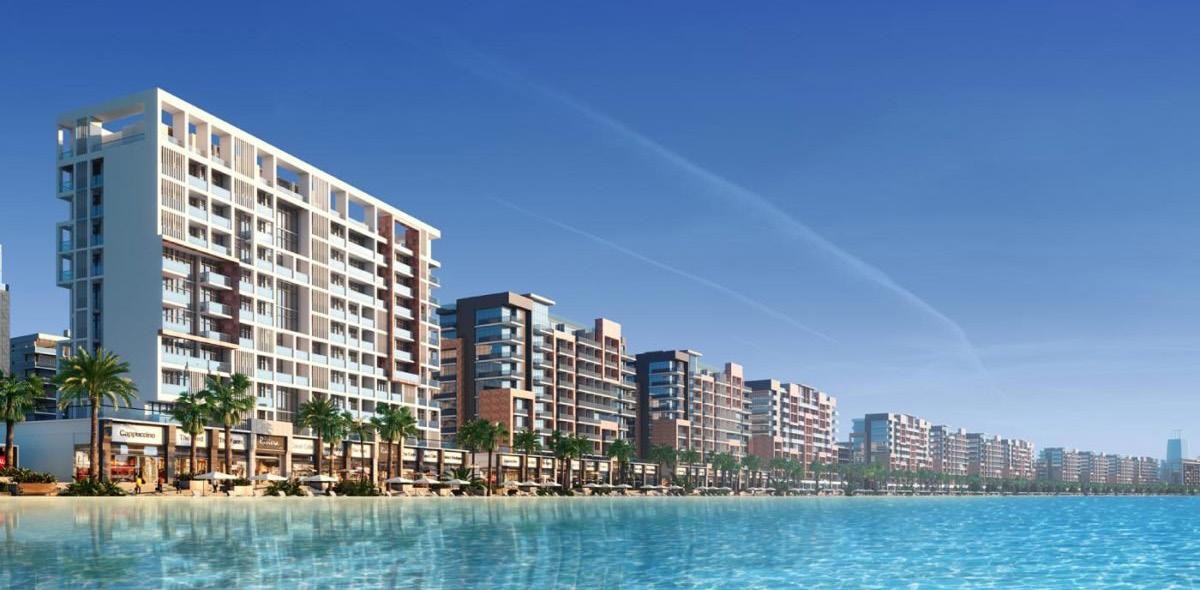
and sustainability through Environmental Product Declaration (EPD) certifications, demonstrating compliance with global environmental standards and providing clients with data-driven insights into the impact of its products.
“Through these efforts, we continue to lead the way in sustainable innovation, aligning with industry advancements,” he highlights.
GLOBAL GOALS
Looking ahead, Emirates Glass is focused on the continuous development of existing products and the introduction of new innovations to meet evolving market demands.
The company is seeking to expand its footprint beyond current markets and remains dedicated to broadening its international presence.
“With a strategic focus on meeting the global demand for
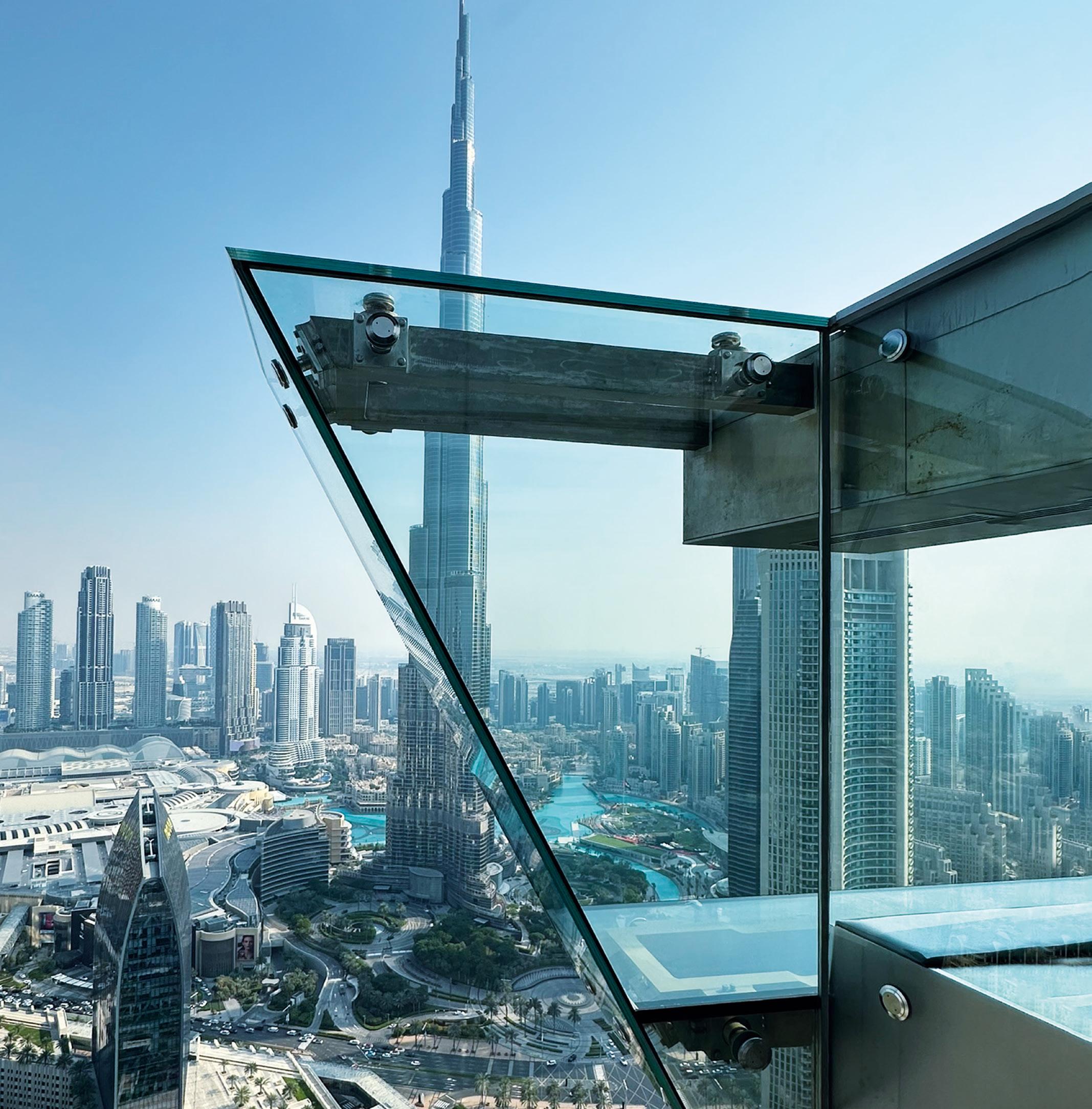
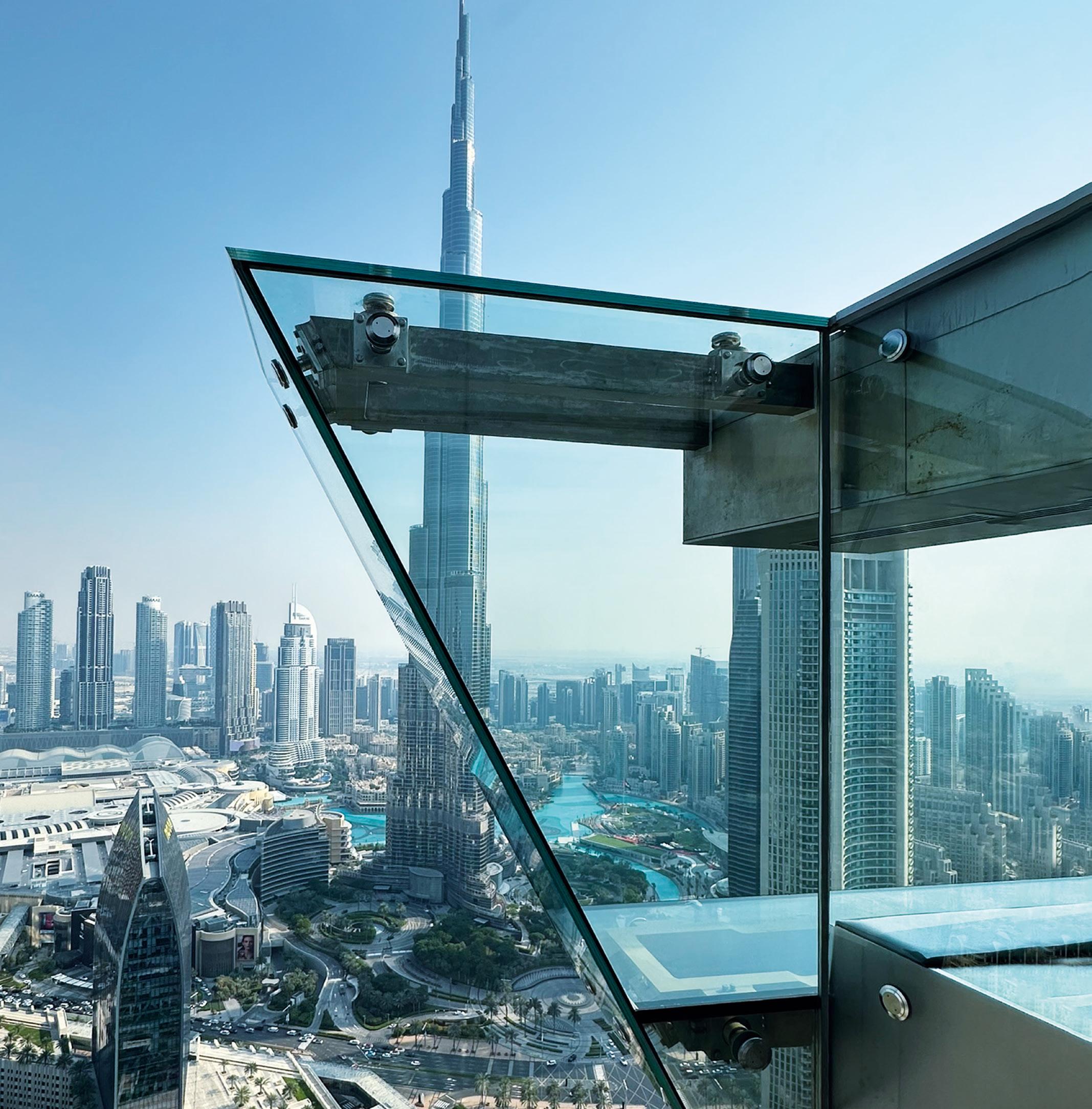
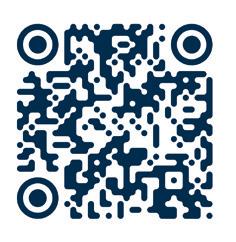
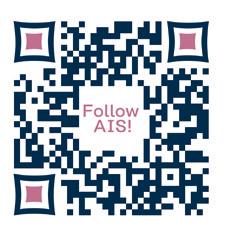
Photo: © Kuraray
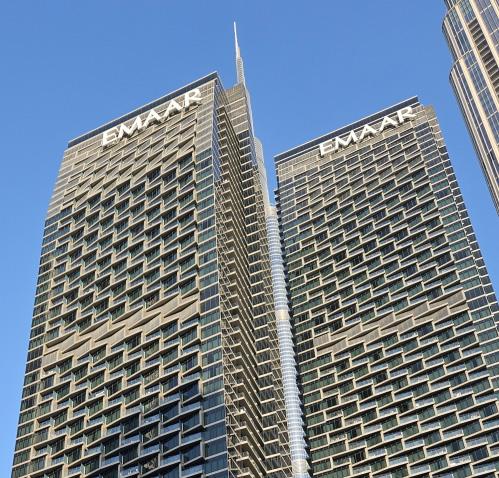
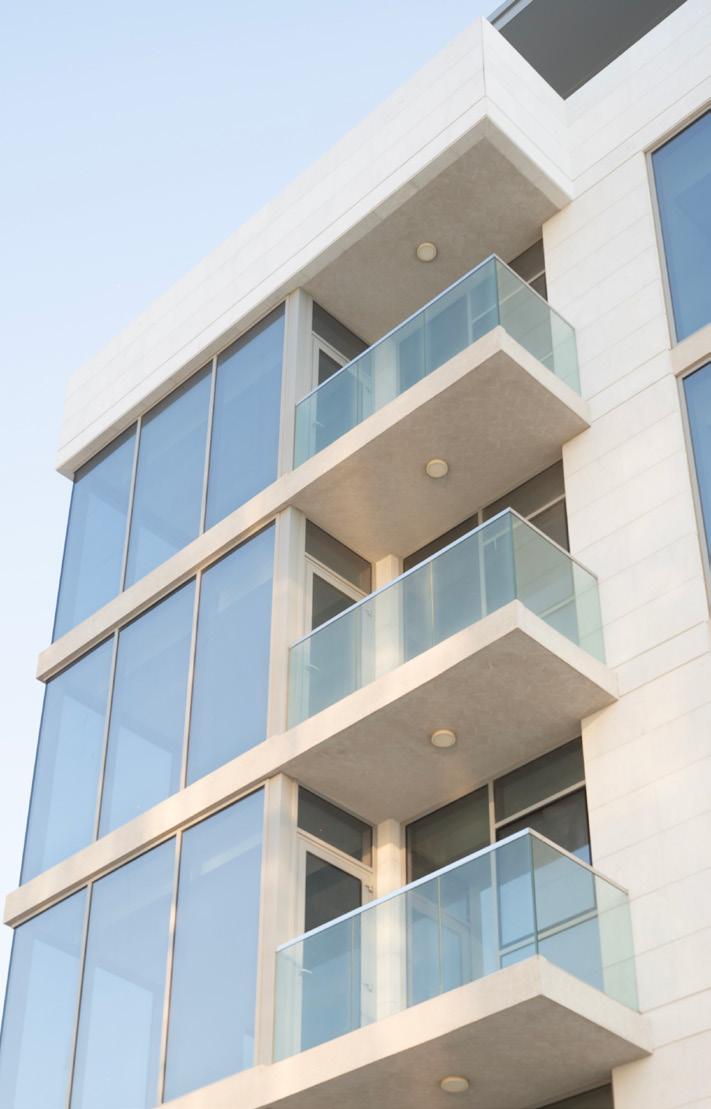
high-performance architectural glass, we are exploring new opportunities in emerging and established markets alike,” shares Khan.
Through innovative product offerings, state-of-the-art production facilities, and strategic collaborations, the company aims to reinforce its position as a global leader in the industry whilst ensuring adaptability to regional needs and trends.
“We aim to scale up production capacity even further, targeting
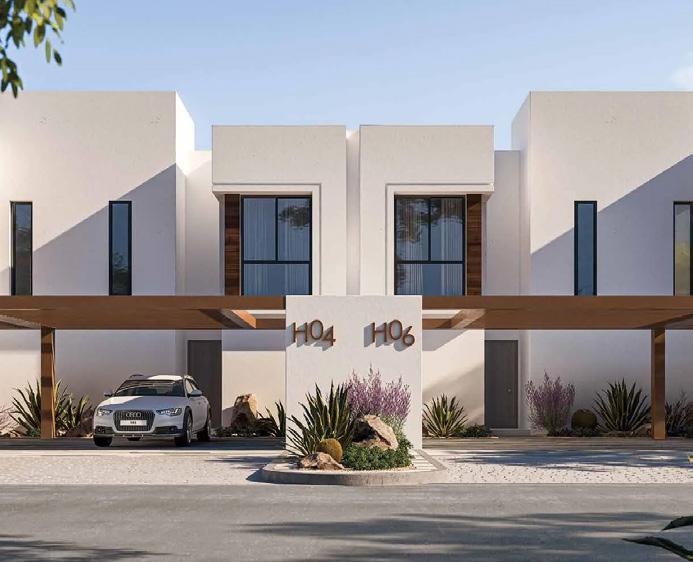
ICONIC PROJECTS
ONGOING
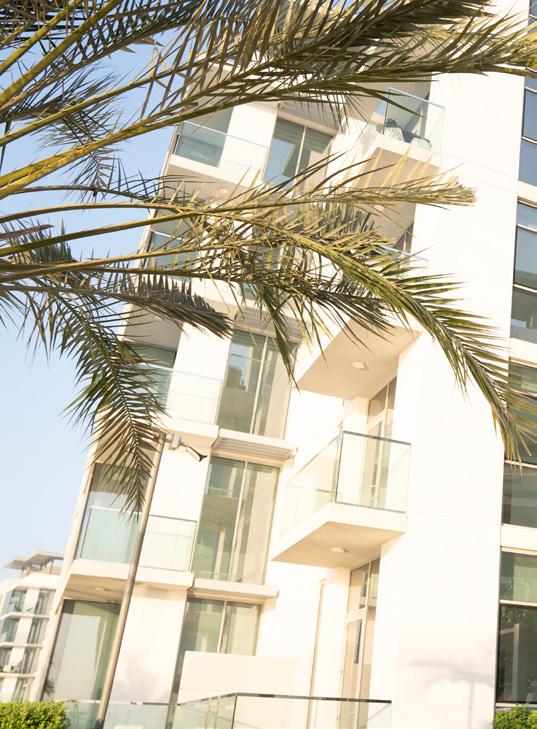
• SAADIYAT LAGOONS – EmiCool Sun NN30 DSL coating ensures enhanced performance in solar control and thermal insulation.
• DISTRICT ONE – Supplied EmiCool DSR II coating, offering superior energysaving capabilities whilst complementing modern architectural designs.
• OPAL GARDEN – Provided EmiCool Sun NN40 coating on clear glass substrates, combining solar control with architectural brilliance.
• ELORA – Integrated EmiCool Super Vision 60/32 coating, ensuring optimised daylight management and energy efficiency.
COMPLETED
• IMPERIAL AVENUE – Supplied EmiCool Sun NN30T coating on clear glass substrates, ensuring superior solar control and thermal performance.
• ADDRESS RESIDENCES – EmiCool Superlite 70/40 coating on grey glass substrates enhances the façade with its excellent light transmission and solar protection.
• MOHAMMED BIN RASHID CITY – Provided EmiCool NN35 coating, delivering optimal energy efficiency and visual clarity.
• GOLF HEIGHTS TOWER – Contributed EmiCool Super Vision 50/25 coating, striking a balance between solar performance and elegant aesthetics.
• NOYA VILLAS – The EmiCool Solite Jar coating offers outstanding insulation and durability, providing a refined residential experience.
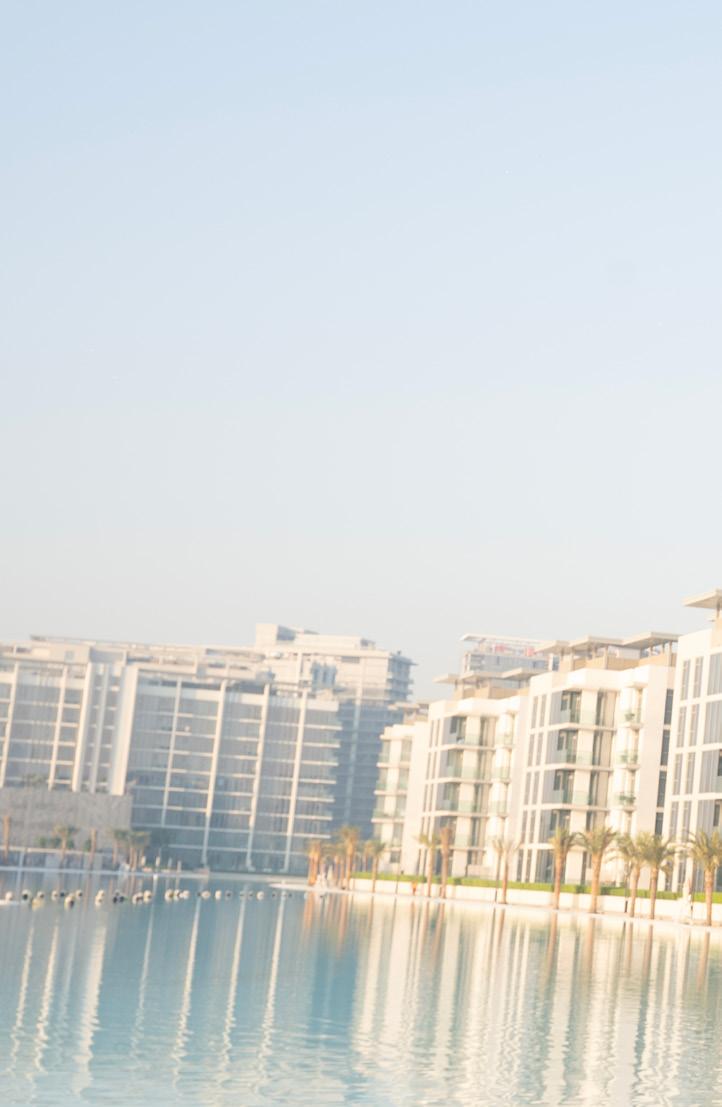
• AZIZI RIVERA – Supplied EmiCool DSR II coating on grey glass substrates, reinforcing sustainability and thermal regulation in this iconic waterfront development.
“At Emirates Glass, we take pride in delivering high-performance architectural glass solutions tailored to the unique demands of prestigious developments across the region. Our expertise and commitment to excellence have positioned us as a trusted partner in shaping modern skylines, providing innovative coated glass solutions that enhance aesthetics, energy efficiency, and durability in landmark projects,” Khan impassions.
“Each of these projects reflects our commitment to delivering innovative, high-quality glass solutions that redefine modern architecture and enhance sustainability. As we continue to expand our portfolio, we remain dedicated to excellence, ensuring our products contribute to the future of the built environment,” he adds.
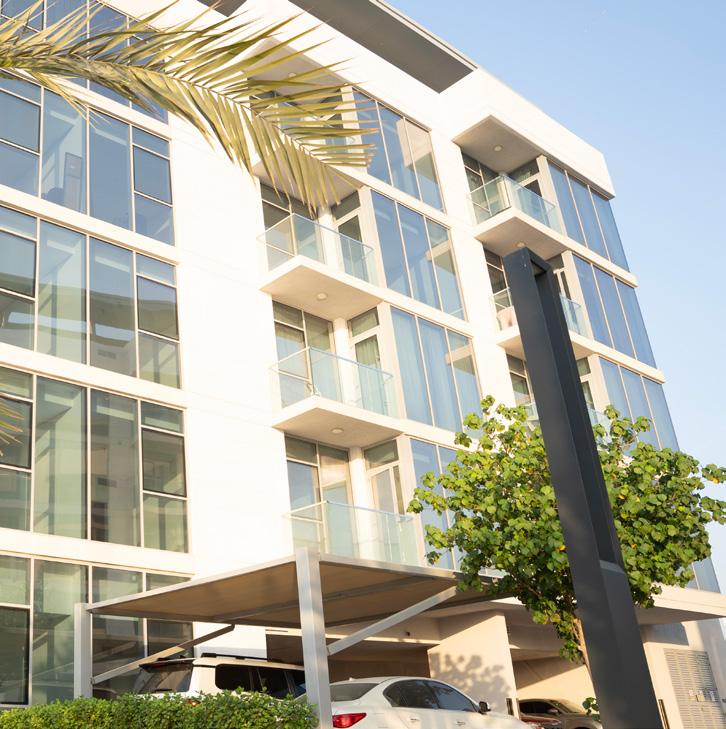
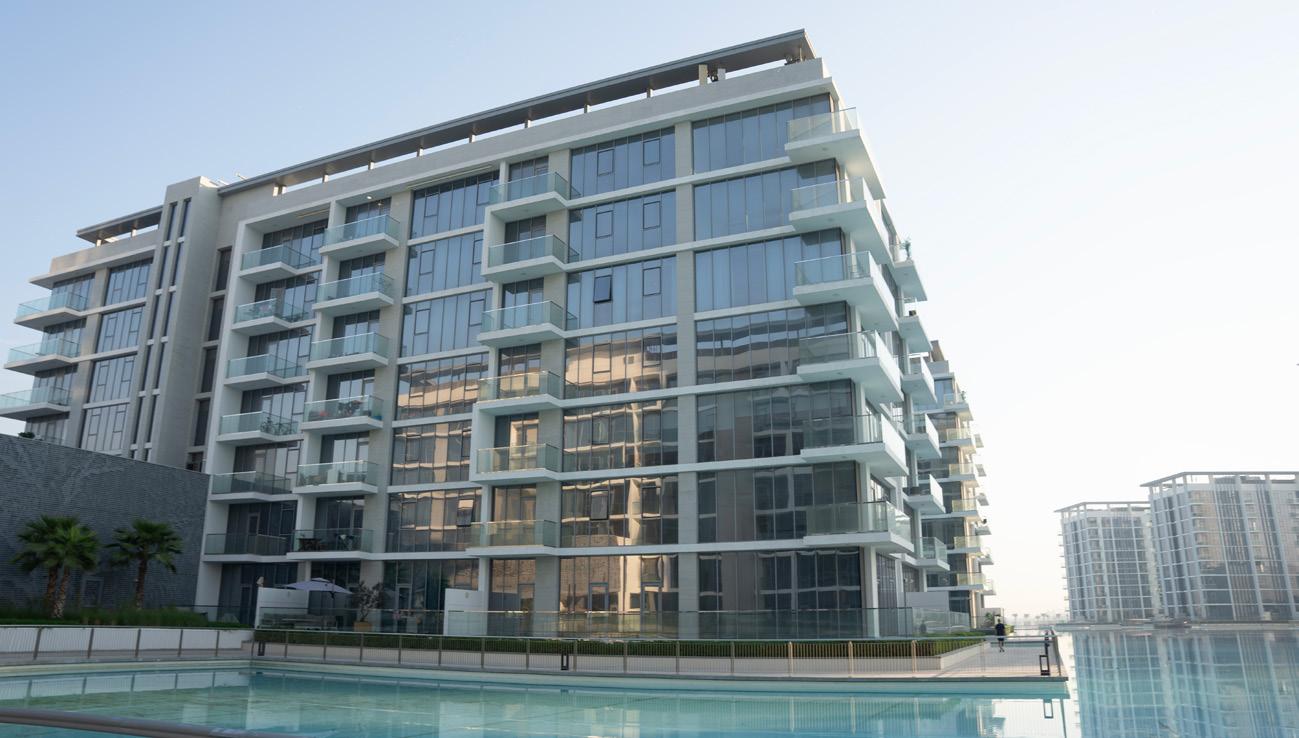
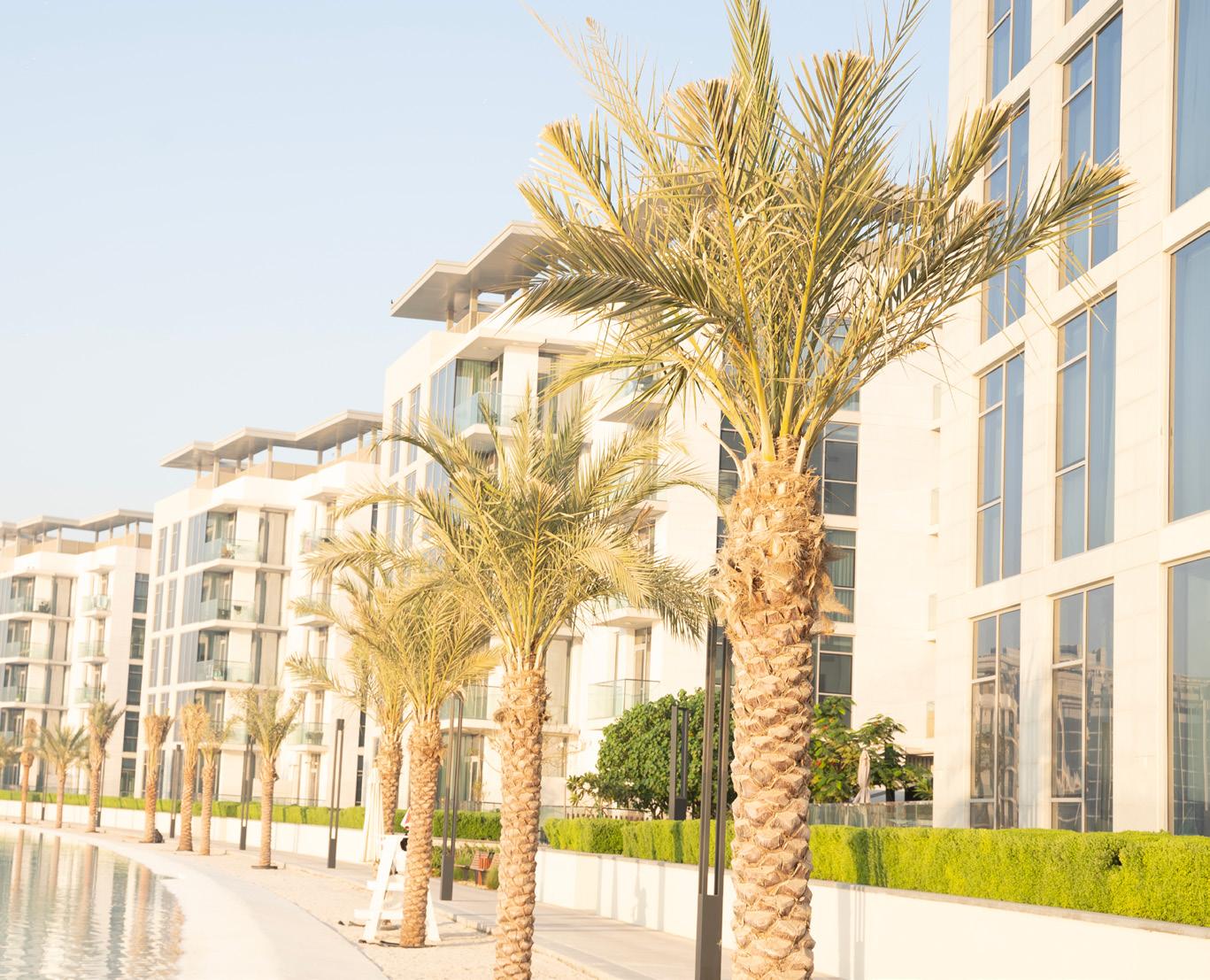
27 percent of the market share. Our plans include expanding our fire-rated glass segment, investing in additional cutting-edge machinery, and reinforcing our commitment to sustainability through energy-saving solutions.
“These priorities reflect Emirates Glass’ strategic vision for growth, technological advancement, and industry leadership,” Khan concludes emphatically.
As Dubai undergoes a remarkable transformation, marked by ambitious construction projects and a strong emphasis on energy efficiency,
Emirates Glass is strategically poised to expand its market presence by providing exceptional highperformance architectural glass solutions.
The company’s unwavering commitment to cutting-edge technological advancements, combined with its strategic alliances with esteemed global certification bodies, positions it at the forefront of industry standards and innovation, ensuring it remains a leader in the dynamic glass manufacturing landscape.
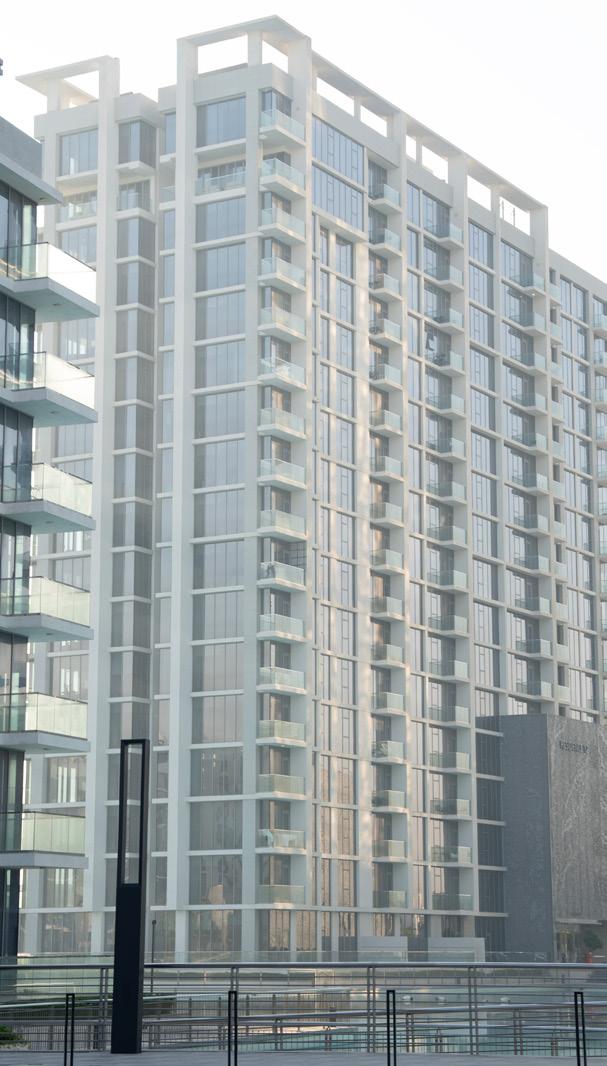
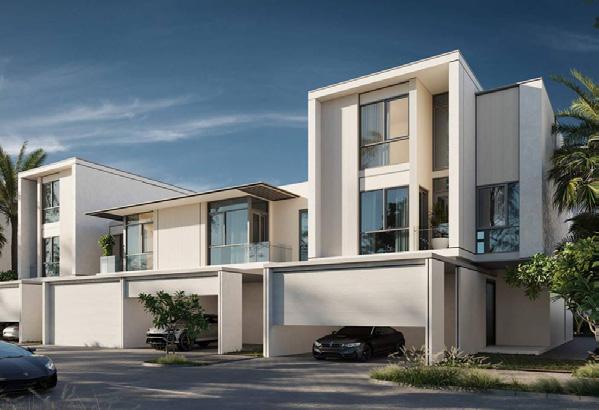
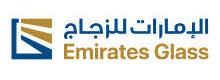
Tel: 00971 4 709 4700
info@emiratesglass.com
emiratesglass.com
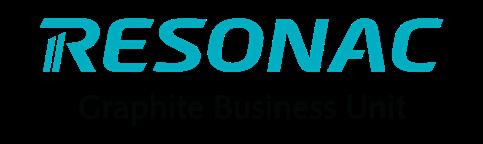
LEADERS IN AN EVOLVING ELECTRODE INDUSTRY
In a world marked by trade tensions and economic uncertainty, Resonac Graphite Business Unit is redefining its approach to sustainability, innovation, and customer partnerships. Tim Saxon, CMO, reflects on the current challenges as we revisit the company
Writer: Rachel Carr | Project Manager: Nicholas Kernan
Today’s headlines are filled with discussions about tariffs and trade wars, making the future of global commerce a topic of widespread concern.
We reconnect with Resonac Graphite Business Unit (RGBU) to explore how these developments have affected the company since we last spoke a year ago.
“Regardless of the outcomes in the current trade discussions, I believe this period will have a lasting impact on how businesses think about their suppliers, operations, and customers in the future,” introduces Tim Saxon, CMO.
The last year has been challenging for the graphite electrode (GE) industry, with most major competitors finishing 2024 in a financial deficit, and worryingly, Q1 2025 has not seen much improvement.
“Much like the steel producers we serve, we operate in an industry where China manufactures over half of the world’s supply.
“With enough capacity to meet its domestic needs four times over, China exports its ‘subsidised overcapacity’ to other global markets. This puts significant downward pressure on domestic pricing and harms the local suppliers and regions where they
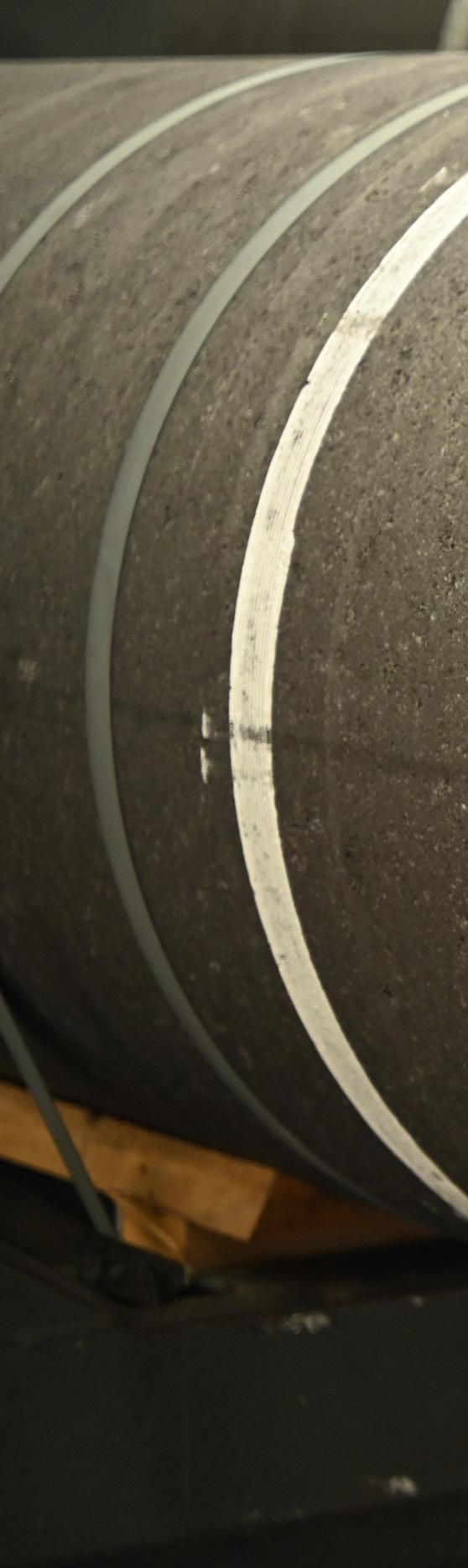
operate,” Saxon points out.
Fortunately, various government and trade organisations have begun understanding the need for a healthy domestic electrode industry, as demonstrated by tariffs and anti-dumping duties on Chinese electrodes in the EU, US, and Japan, which just announced their preliminary duties in February this year.
“80 percent and 75 percent of the total spend of our Japanese and US electrode plants stayed inside the respective countries. These funds will support domestic energy suppliers, local and regional governments in
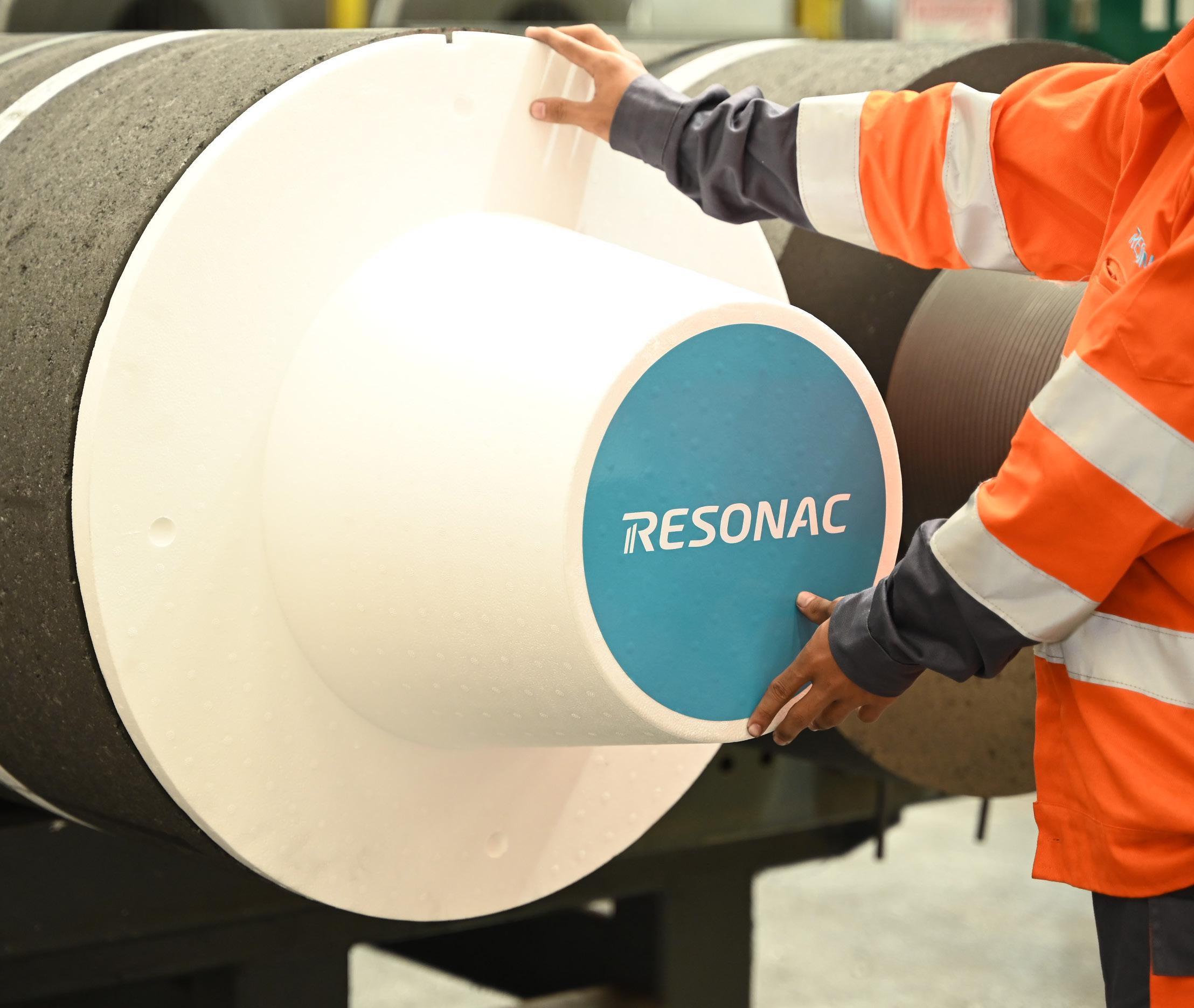
the form of taxes, domestic workers, and the communities where they live,” Saxon explains.
EVER-EVOLVING ELECTRODES
As with all industries, the GE market is continuously evolving, and RGBU primarily services customers who use electric arc furnaces (EAFs) to melt scrap steel into new products, creating 75 percent less carbon dioxide emissions than the traditional blast furnace method of steel production.
One of the many advantages of an EAF is its flexibility and agility. Depending on customer orderbooks,
the furnace can run to maximise production volumes or run to maximise efficiency and minimise energy consumption.
“We are very excited to be a critical part of the circular economy, in that our electrodes are essential for this type of steel recycling. It is widely agreed that the future is bright for the EAF industry, and we are glad to be partners with electric steelmakers worldwide,” Saxon enthuses.
A GE is needed to make every tonne of EAF steel, and the product is becoming increasingly commoditised. This is the primary contributor to the current global challenge of balancing
supply and demand.
“We are optimistic that the proper authorities are addressing those challenges in places where they are needed most.
“Regardless of the outcomes in trade cases or geopolitical conflicts, we understand our responsibility is to be innovative and continuously add value to our customers’ operations. Like many industries, we believe future success in the steel and GE business is moving towards digitalisation and value-added services,” he acknowledges.
Though the electrode is an essential part of melting steel, it is
“OUR EMPLOYEES ARE OUR FOUNDATION, AND WE ARE COMMITTED TO FOSTERING A SAFE, SUPPORTIVE WORKPLACE FOR THEIR GROWTH. ESG IS NOT JUST PART OF OUR STRATEGY; IT IS OUR STRATEGY”
– TIM SAXON, CMO, RESONAC GRAPHITE BUSINESS UNIT
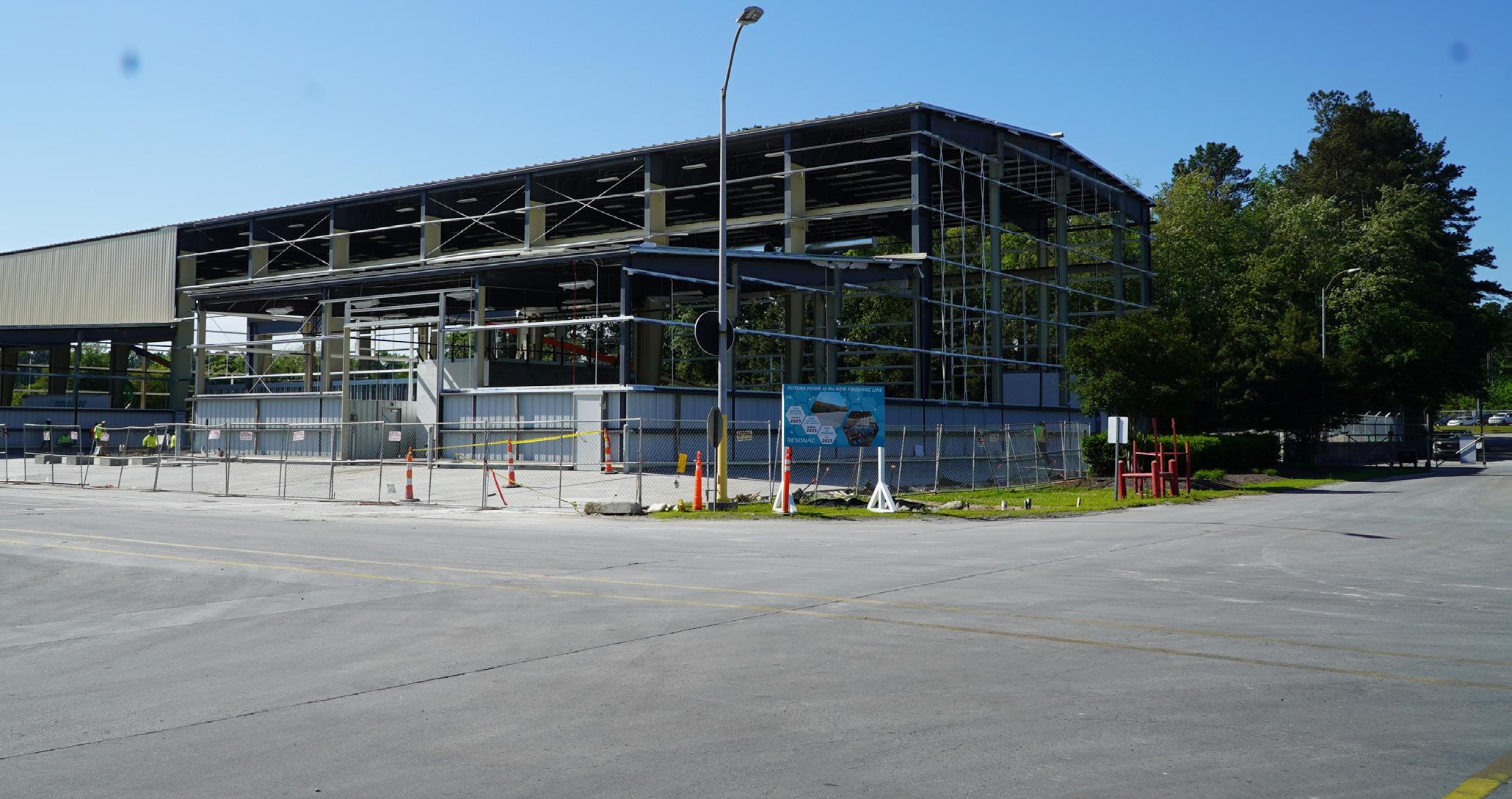
just one instrument in the orchestra that makes up the symphony of an EAF operation. The electrode’s performance is impacted by how the furnace operates, which is ultimately determined by the customer’s needs.
A SYMBIOTIC SYMPHONY
By acquiring AMI Automation (AMI), RGBU can help customers meet their business needs in real time through EAF optimisation.
“This acts as a ‘digital conductor’ of the orchestra (the EAF) to achieve the optimum symphony (the EAF performance), with the electrode as the instrument,” Saxon analogises.
When RGBU acquired AMI, many people viewed it as a paradox that a large, traditional electrode supplier would purchase an innovative technology company known for helping customers reduce their electrode consumption.
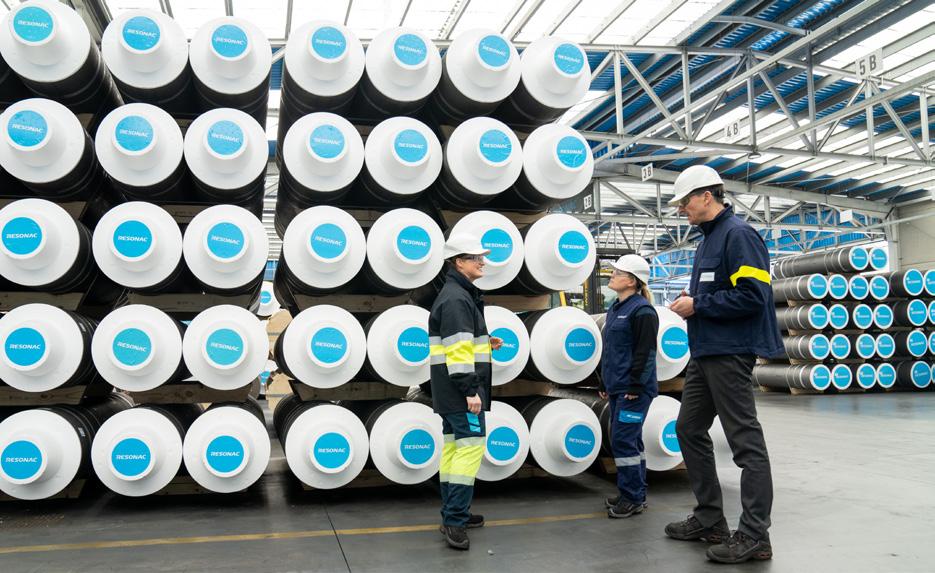
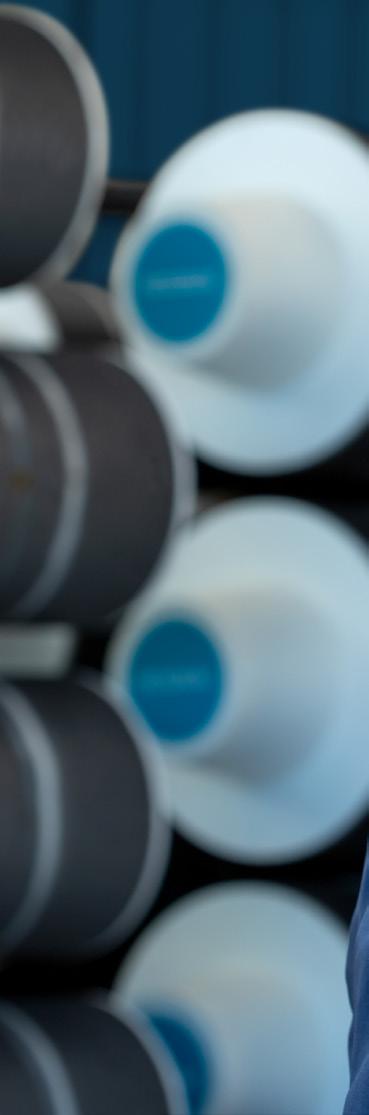
“We view our role as a way to serve our steelmaking partners better. As an electrode supplier for 80+ years, we have continually invested in R&D to manufacture the best products on the market. By utilising AMI’s products and services, our customers can achieve peak performance from their EAF, including the electrode,” Saxon expresses.
“For decades, RGBU has manufactured premium GEs, but
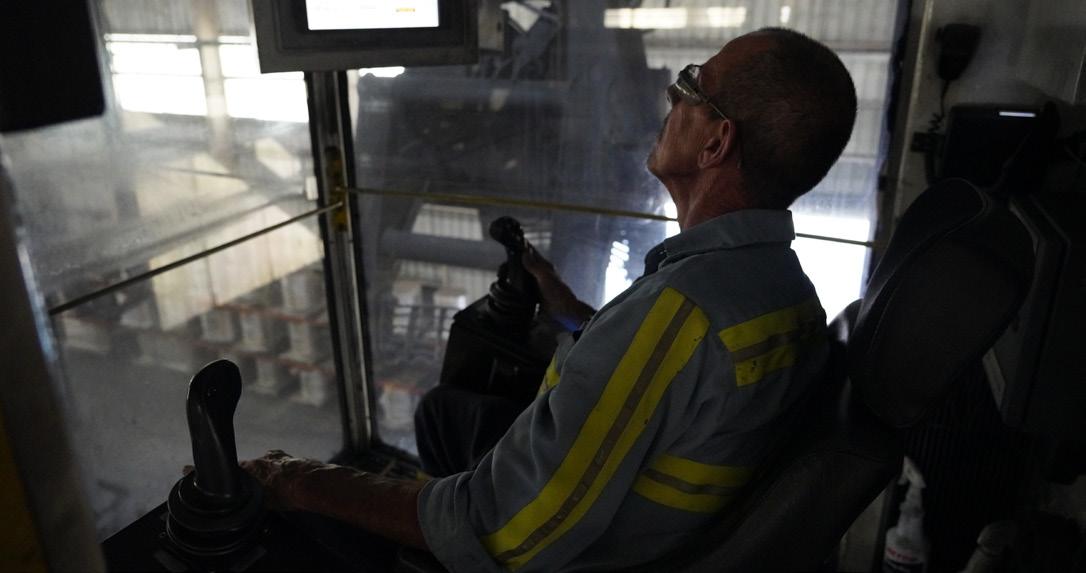
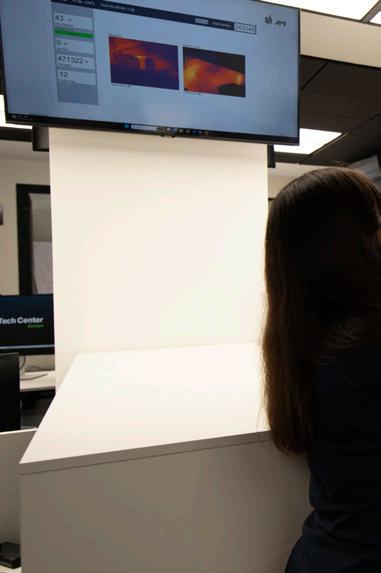
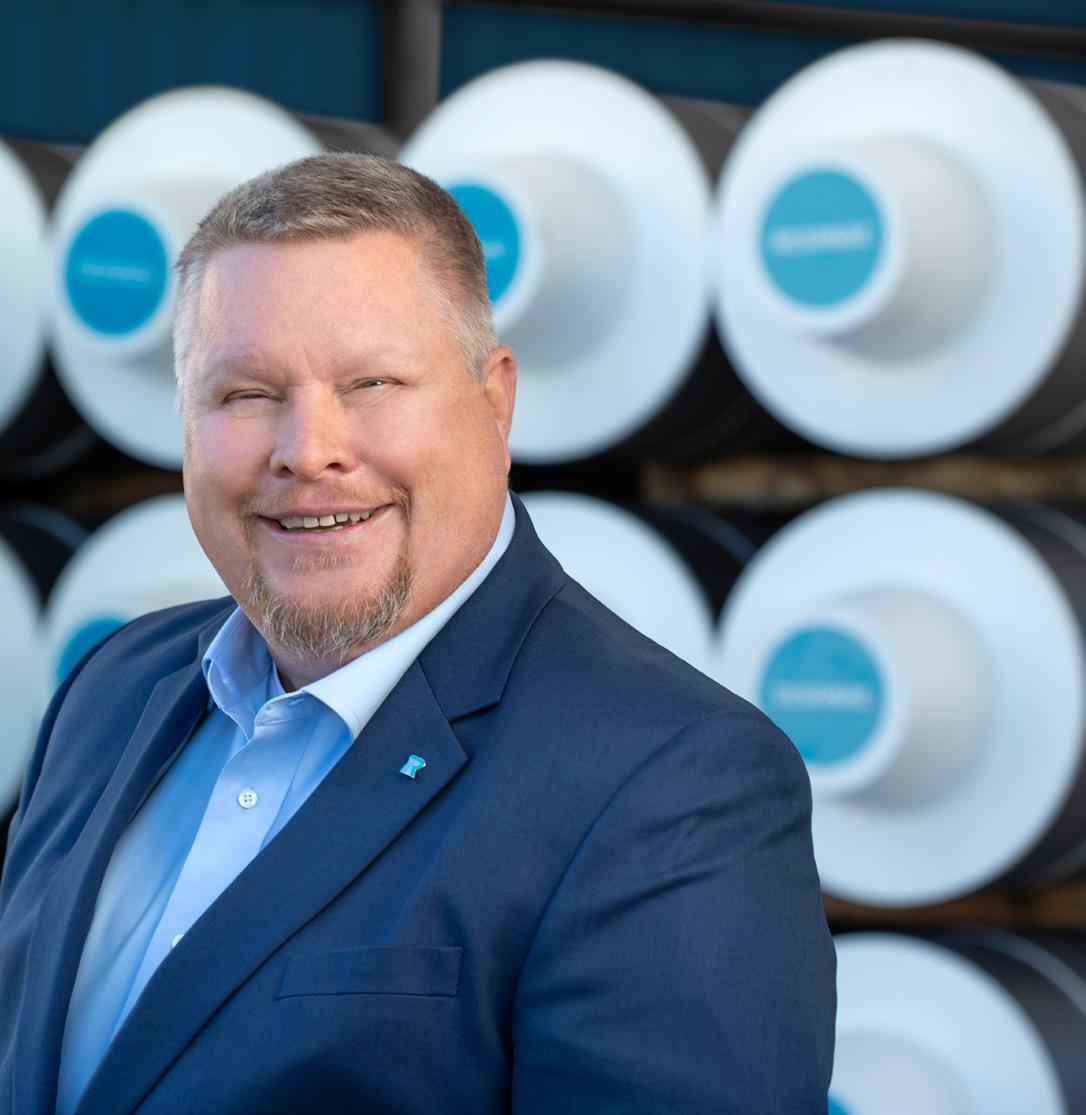
their performance can be hindered by factors unrelated to the electrode in the furnace. Imagine a skilled, firstchair violinist playing a Stradivarius being drowned out by a novice in the back, honking on a cheap trumpet. The true quality of an electrode shines in a fully optimised EAF; thus, we see the RGBU and AMI partnership as a fusion of tradition and innovation.”
Within this partnership, RGBU can now work with customers in
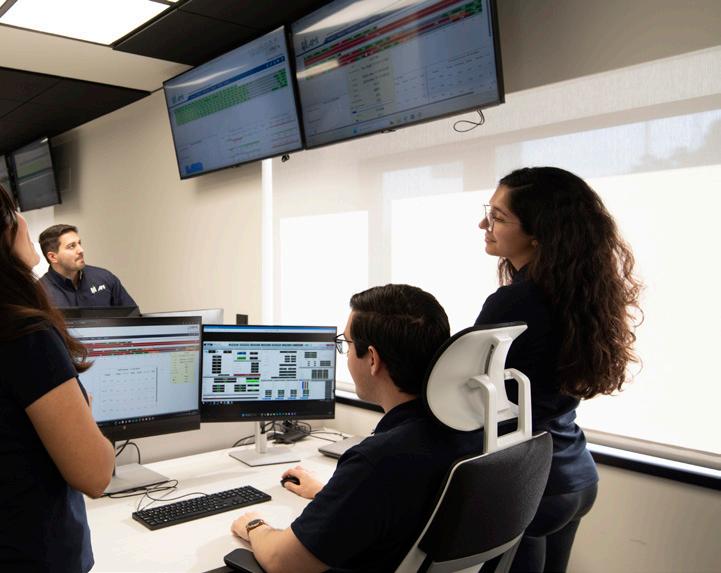
WHAT SIGNIFICANT PROJECTS IS RGBU CURRENTLY UNDERTAKING?
Tim Saxon, CMO: “For years, AMI has benefitted from its AMITech Center (ATC) in Monterrey, Mexico, where engineers monitor customer furnace performance in real time. This 24/7 service has become integral to customers’ operations, often alerting them to issues before their internal teams do.
“AMI has officially opened an ATC in A Coruña, Spain to provide our global customer base with enhanced support from top EAF optimisation engineers.
“Additionally, we’ve introduced AMITech Talks, which are customerfocused events aimed at optimising the EAF steelmaking process through interactive workshops on cutting-edge technologies, with the inaugural talk scheduled for May 20th-21st in A Coruña. These efforts reflect our commitment to innovation and collaboration within the global electric steelmaking community.”
other areas such as employee safety, supply chain management, and decarbonisation.
Through collaborating with RGBU, AMI has additionally developed digital tools designed to detect potential issues with the furnace and electrodes.
These early warning indicators not only allow the furnace crew to react and mitigate issues but also provide an opportunity to clear the furnace floor, ensuring the safety of operators.
TRANSITIONING TO A NEW MARKET
After laying out a prudent and measured approach, RGBU has entered the electric vehicle (EV) battery business through its pilot plant in Spain.
Whilst the GE and EV battery industries rely on synthetic graphite, they have different views on global supply and demand. The latter in particular recognises the strategic importance of graphite and is taking steps to reduce dependence on one region.
The EU and US classify graphite as a critical mineral essential for modern technologies and national security. In contrast to the locally rooted global steel and GE industries, which have consolidated over decades with over half of production in China, the EV battery market has rapidly expanded due to surging demand for EVs and synthetic graphite.
“The early, long-term projections for EVs resembled a modern-day gold rush, and China had the resources, capacity, and economic environment that allowed it to become the dominant supplier, producing 97 percent of the world’s battery anode materials by 2018,” Saxon comments.
As the COVID-19 pandemic exacerbated geopolitical stability and supply chain resiliency, EV battery producers began diversifying their supplier base, particularly in the US and Europe, with the optimistic growth forecast suddenly leading to the same artificial gold rush in these regions.
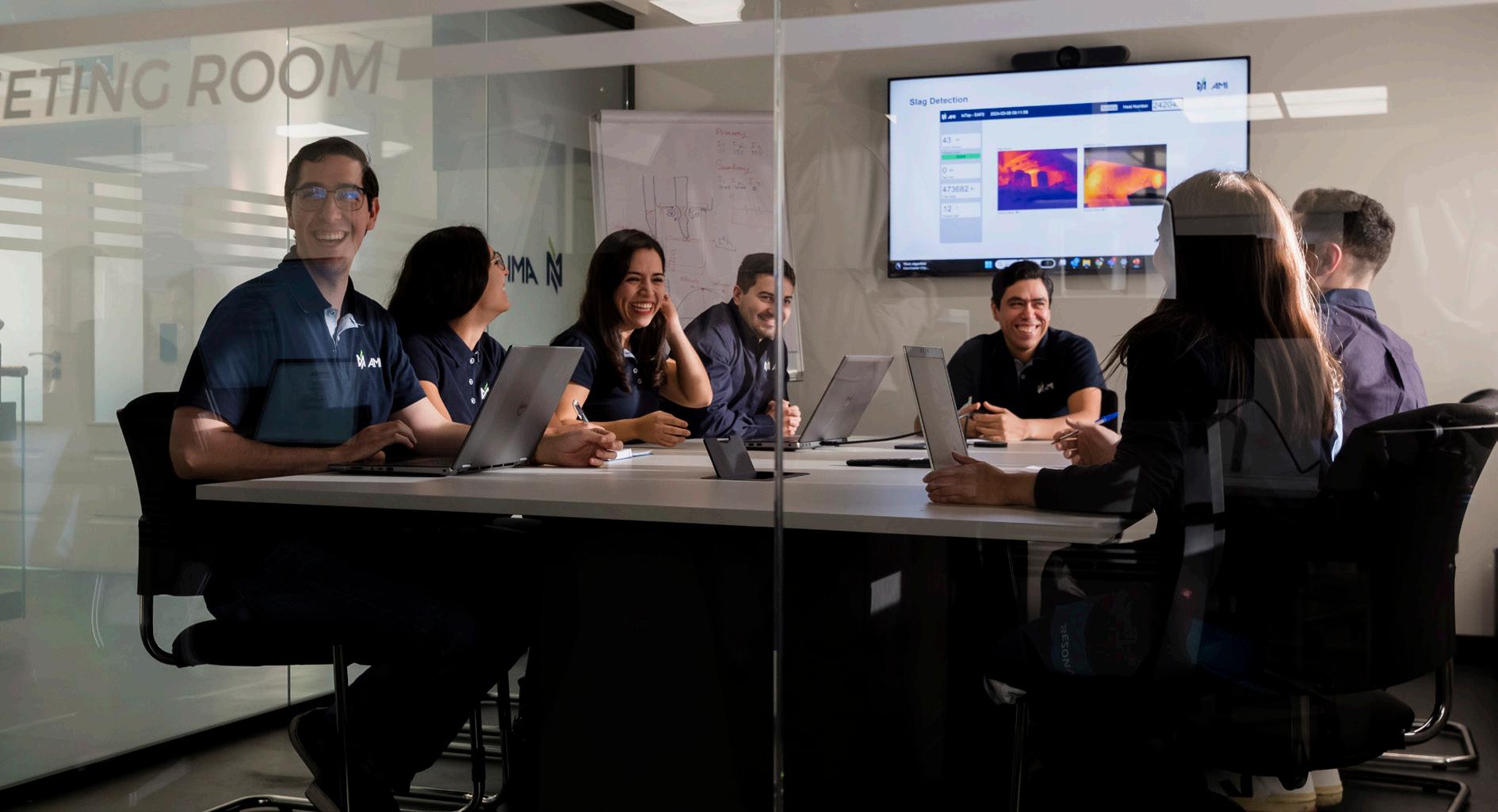
“The projections for EVs have softened a bit, but at RGBU, we are not necessarily disappointed. We had a plan from the beginning and are taking a prudent, measured approach to that market. This softening could benefit us because we are not overleveraged whilst implementing our plan,” he reports.
GREEN AND CLEAN
As a Resonac company, RGBU prioritises environmental considerations and decarbonisation in its mission to “change society through the power of chemistry.”
“We harness the power of graphite to enhance societal well-being by enabling steel recycling with our GEs
A SPELLBINDING SUSTAINABILITY STORYBOOK
Recycling is Like Magic is a series of children’s books and educational materials designed to teach young minds about the importance and benefits of recycling metal. It aims to engage readers in eco-friendly practices to encourage them to make sustainability part of their daily routine.
“If you are interested in learning more about steel recycling, look out for the third book from the Recycling is Like Magic series. I’m told the main character, Ellie, and her friends are going to visit one of Nucor’s steel mills to learn more about remelting scrap steel. If you look closely, you might even see an RGBU GE!” Saxon informs us.
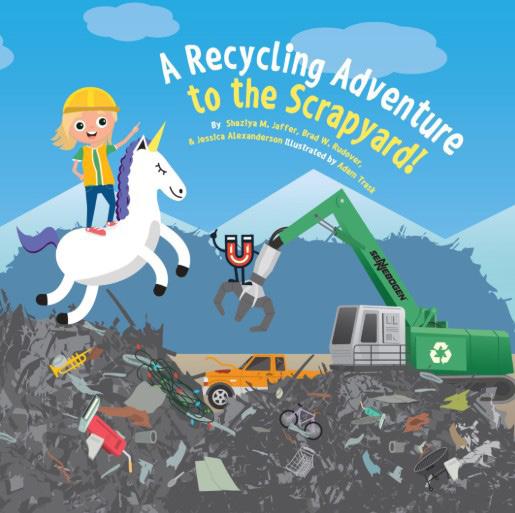
and supplying graphite for renewable energy storage in batteries,” urges Saxon.
It’s crucial for RGBU to differentiate between sustainability and decarbonisation; the latter focuses on production processes and emissions, whilst the company highlights the significance of environmental, social, and governance (ESG) factors.
“Our employees are our foundation, and we are committed to fostering a safe, supportive workplace for their growth. ESG is not just part of our strategy; it is our strategy. We are dedicated to continuously improving, lowering our carbon footprint, and ensuring a resilient supply chain,” he highlights.
“Long before it was trendy, our plants in Austria and Japan utilised renewable energy from hydropower, and our facility in A Coruña, Spain invested in local wind energy.”
At the inaugural Global Steel Climate Council® Member Forum in Brussels, Belgium, discussions around green steel highlighted the need for clear definitions and the complexities
PROVIDING MOLDING SOLUTIONS FOR GROWING MARKETS
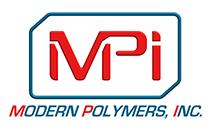
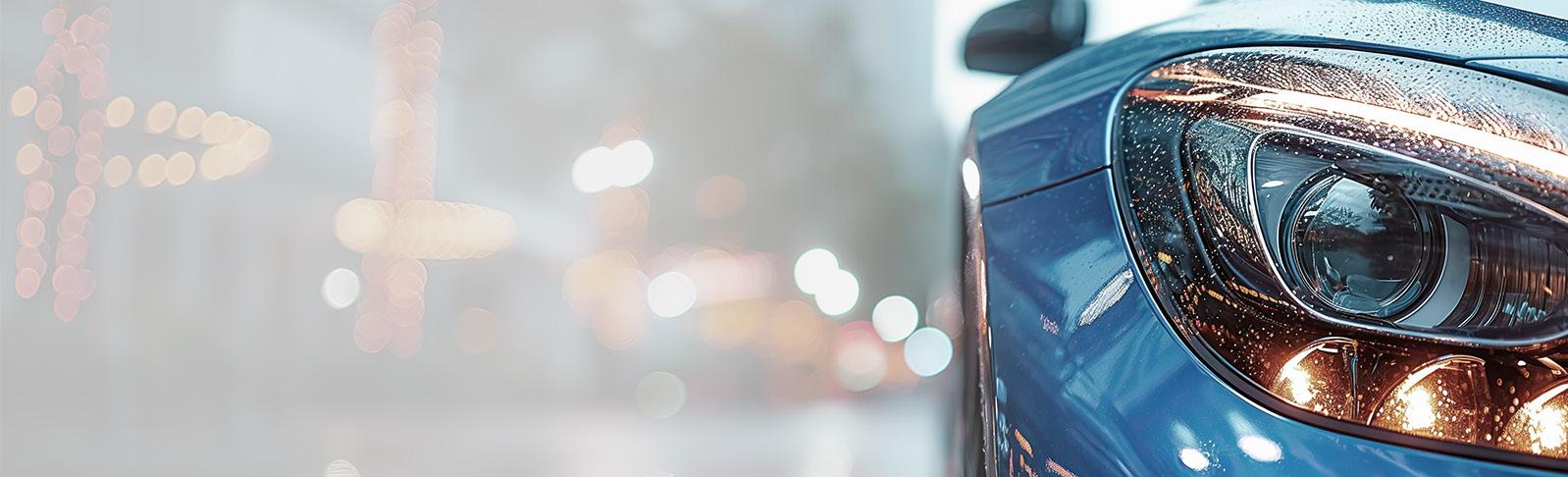
WHO WE ARE:
• Established in 1970 and headquartered in Cherryville, North Carolina.
• A family-owned and operated business with a strong emphasis on family values.
• Second-generation ownership since 2019.
• Recognized nationally and internationally as in industry leader in Expanded Polystyrene. (EPS) and Expanded Polypropylene (EPP) Technology.
• State-of-the-art EPS and EPP moulding facility.
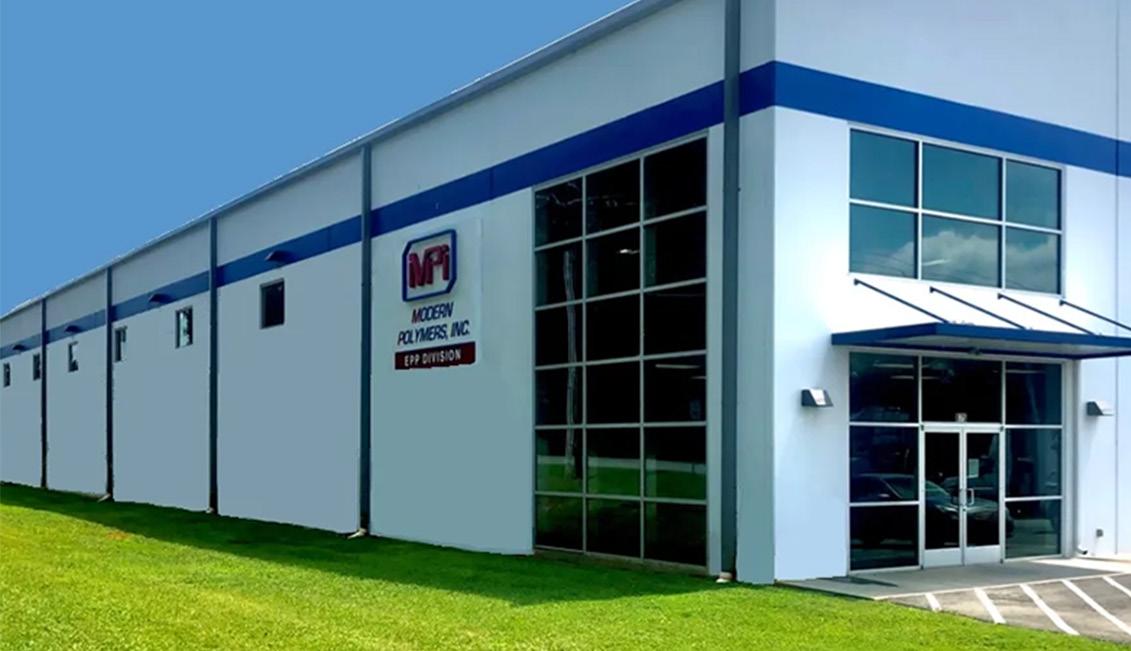
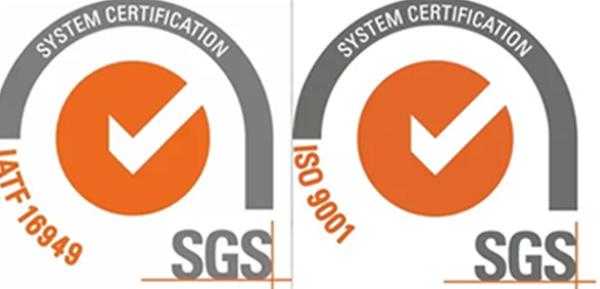
WHAT WE DO:
Modern Polymers manufacture lightweight, durable, and energy-absorbing materials used for safety protection in automotive applications such as bumper assemblies, crash pads, and carpet inserts, as well as in child safety seats. We also produce customized packaging solutions tailored to precise customer specifications, offering nearly unlimited shapes and sizes. Our impactresistant packaging is designed to protect products with specific requirements for impact transfer.
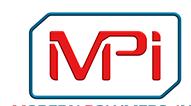
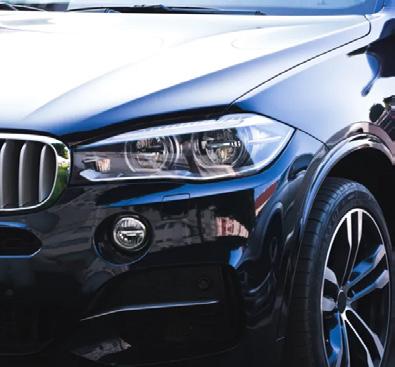
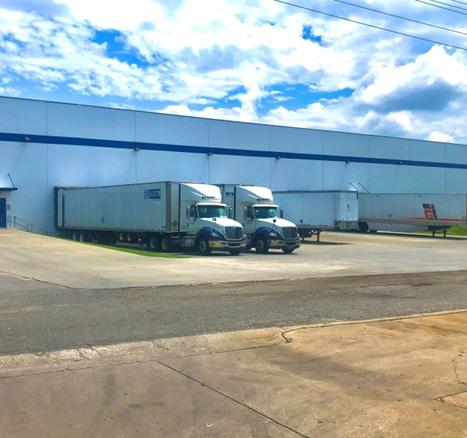
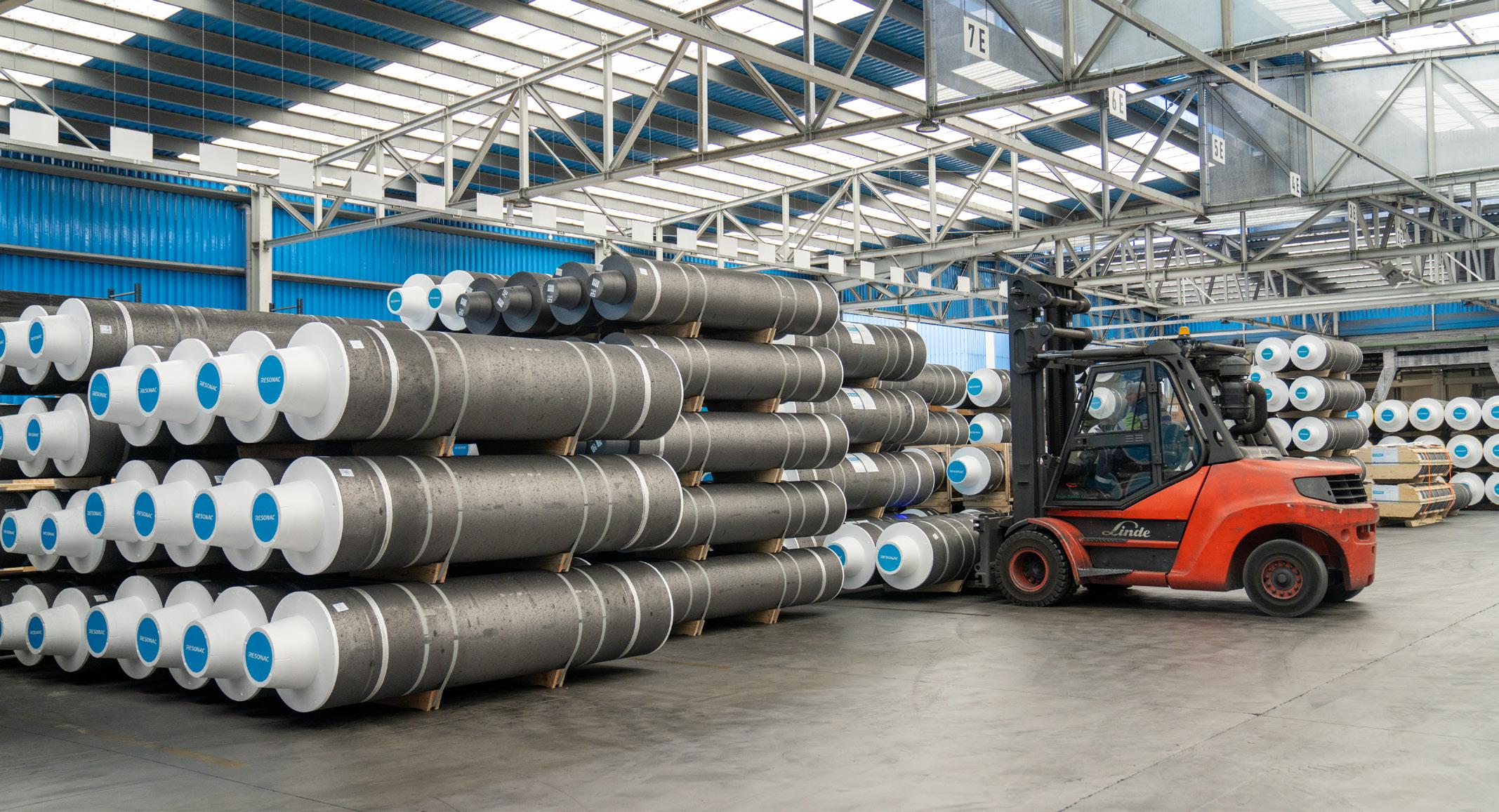
of monetising sustainable products.
“It’s evident that the future is green, yet the term is overused. Therefore, manufacturers must scrutinise investments carefully,” Saxon warns.
Indeed, whilst many support clean products, real investments require consumer willingness to contribute to the extra expense, or they just end up benefitting less responsible players.
“WE VIEW OUR ROLE AS A WAY TO SERVE OUR STEELMAKING PARTNERS BETTER. AS AN ELECTRODE SUPPLIER FOR 80+ YEARS, WE HAVE CONTINUALLY INVESTED IN R&D TO MANUFACTURE THE BEST PRODUCTS ON THE MARKET”
– TIM SAXON, CMO, RESONAC GRAPHITE BUSINESS UNIT
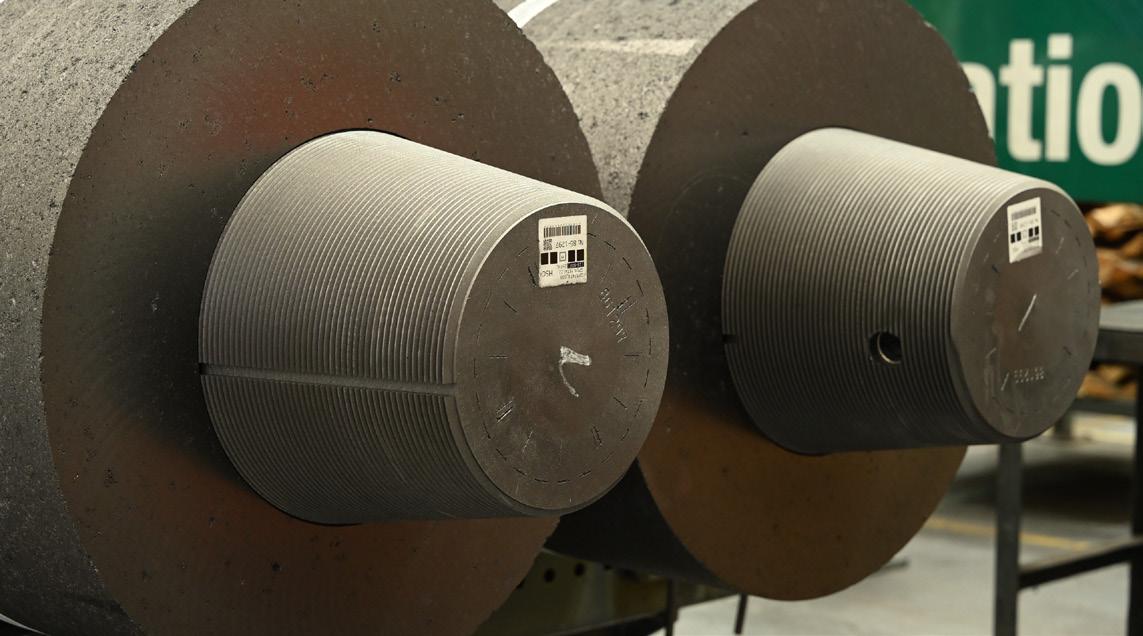
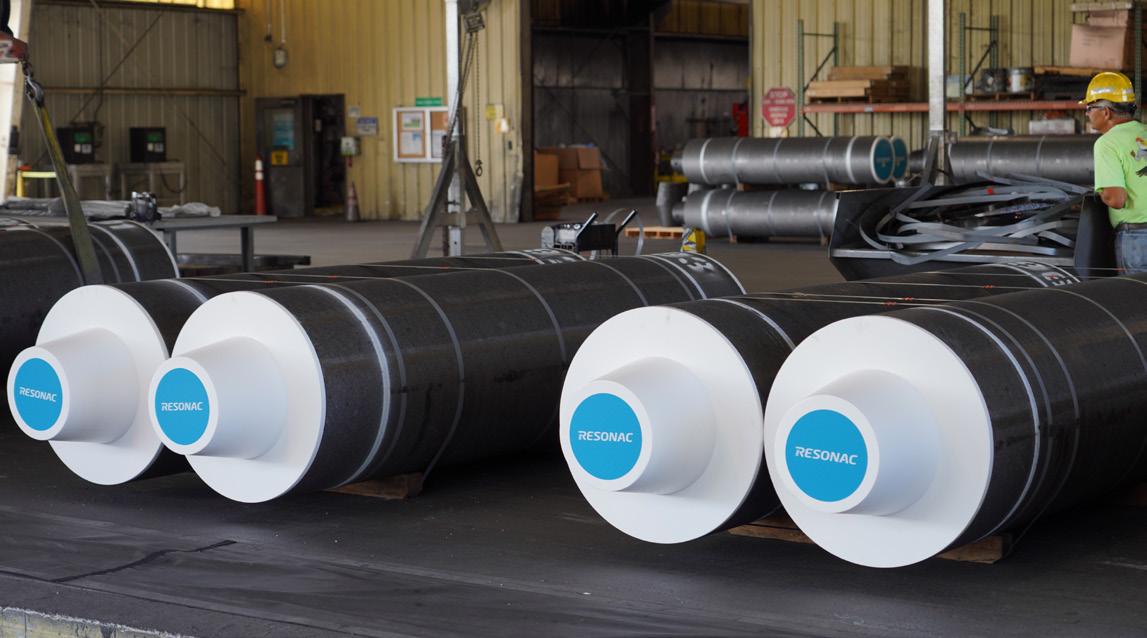
JFE Chemical Corporation
JFE Chemical Corporation is a supplier of coal chemical products, offering unique basic chemicals and various performance products. Our performance products include:
• Fine Chemicals (indene derivatives, fluorene derivatives, acenaphthylene, phenol derivatives, special olefin polyimide raw materials, polyimide varnish, special phenolic resins, benzoxazine, bismaleimide)
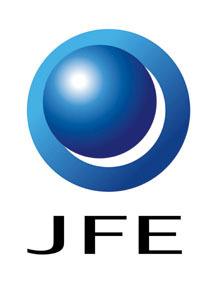
• Battery Materials (hard carbon, natural graphite anode materials, artificial graphite anode materials)
• Magnetic Materials (iron oxide powders, soft ferrite powders, ferrite cores)
• Thermoformable Composite Sheets (KP-Sheet)
4F JFE Kuramae Bldg., 2-17-4 Kuramae, Taito-ku, Tokyo 111-0051, Japan
Contact us: www.jfe-chem.com/en/contact
“Decarbonisation is more of a regional than a global effort. We anticipate that supplying a GE with an Environmental Product Declaration (EPD) will soon be as standard as providing a safety data sheet, and RGBU is ready for this shift,” he states optimistically.
ENHANCING MARKET OPPORTUNITIES
An area where RGBU has wisely invested in its future is its Ridgeville location in the US, where a new, stateof-the-art GE machining line is set to be operational this summer.
This investment focused on the challenges of the US steel industry, hinging on the need for preciselymachined electrodes for new EAF furnaces.
“The project utilised US-made steel, ensuring the same customers using these electrodes to turn scrap steel into building materials were
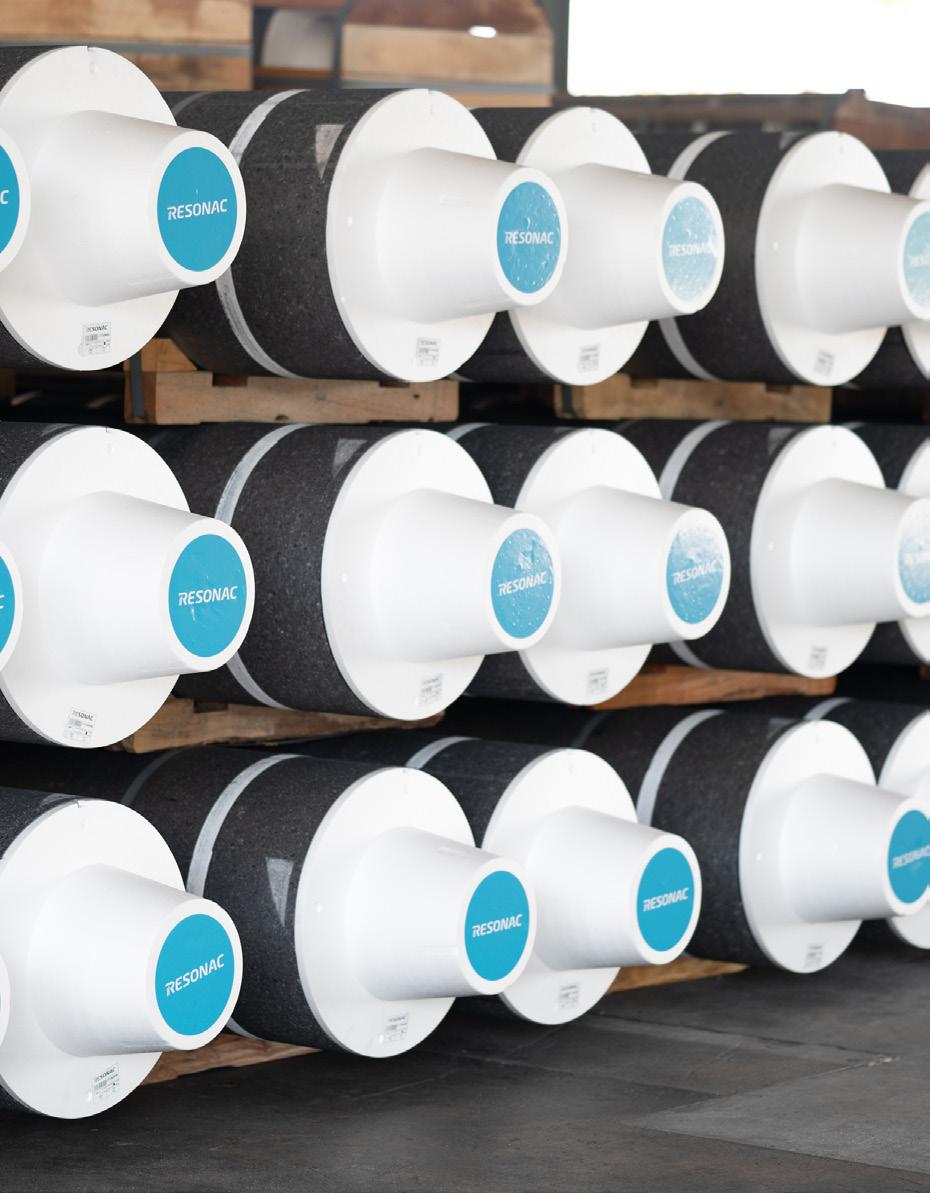
involved in creating the structure that machines them,” Saxon observes.
Recognising the complexities of modern EAF steelmaking and having the country’s newest advanced electrode machining line, alongside cutting-edge EAFs, will ensure RGBU remains the benchmark of the US steel industry.
“Considering the current state of our industry, our priorities for the coming year are straightforward. We aim to establish ourselves as a responsible and respected leader in the synthetic graphite sector,” he impassions.
“Whilst factors such as critical mineral designations, regional outlooks, tariffs, anti-dumping duties, and unfair competition are relevant to our industry, it is essential to understand that these issues alone will not make us a true leader.”
With this in mind, RGBU is committed to being the supplier
of choice in synthetic graphite by delivering maximum value for its customers and aiding them in challenging business environments by striving to offer competitive products and services, ensuring sustainability and value in the marketplace.
“Looking ahead, we aim to keep our business sustainable for our colleagues, customers, suppliers, and stakeholders. This involves being economically, environmentally, and managerially sustainable whilst upholding our core values – these are our priorities for the future,” Saxon concludes.
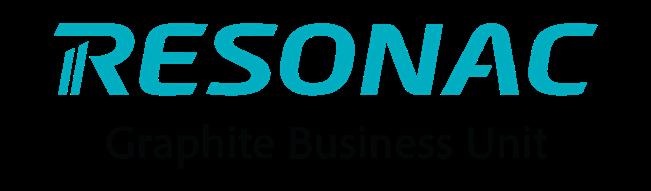
www.graphite.resonac.com
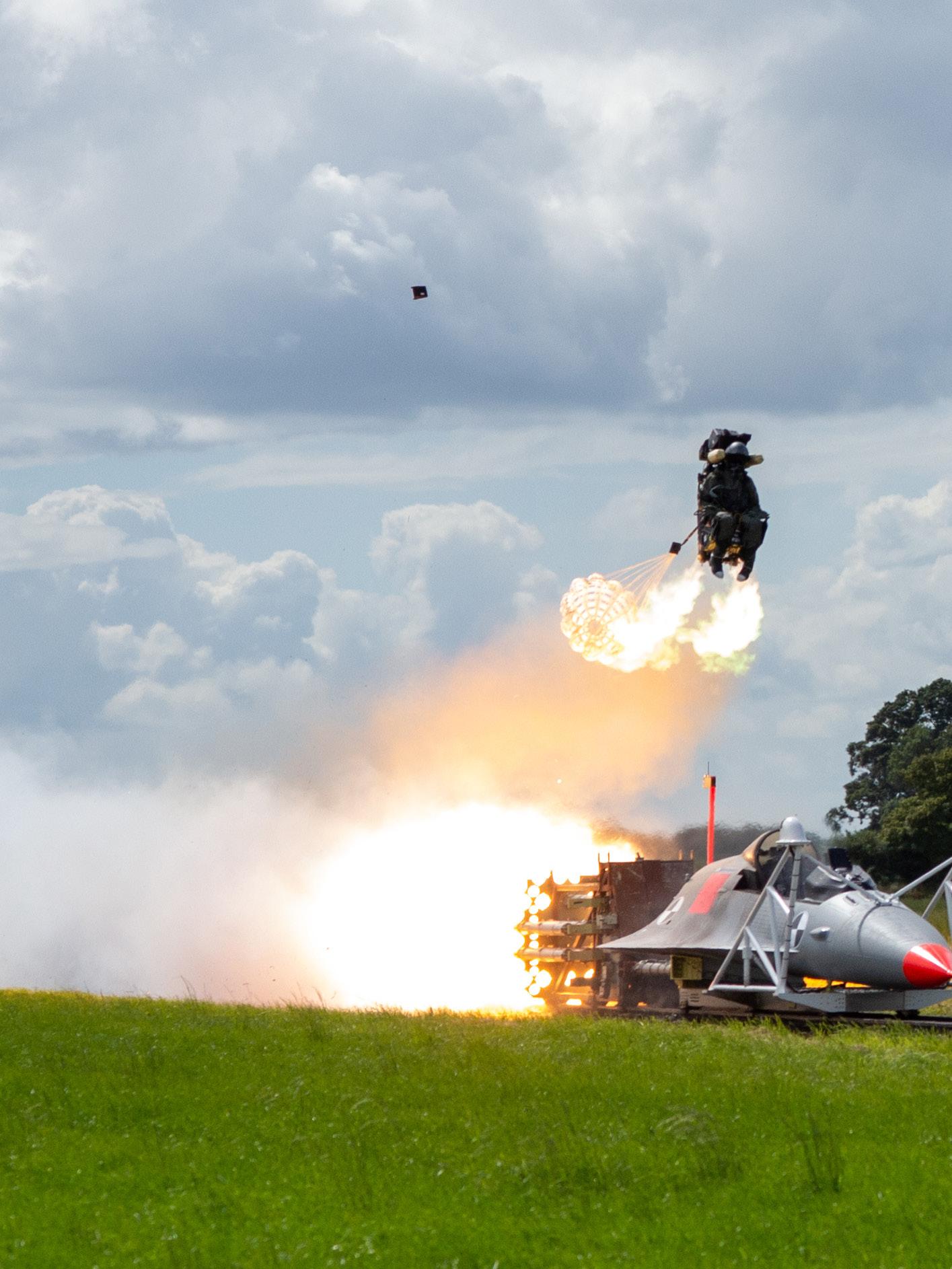
SAFETY WHEN IT MATTERS MOST
Saving lives since 1946, Martin-Baker has honed a unique set of ejection seat capabilities that are at the cutting-edge of aircraft safety. Mark Cooper, Vice President of Sourcing, delves into the company’s commitment to technological and operational excellence
Writer: Lucy Pilgrim | Project Manager: Cameron Lawrence
Due to ongoing geopolitical conflicts, nations around the world are increasingly turning their attention to defence equipment procurement and operational availability, making it both a fascinating and challenging time to operate in the aerospace manufacturing sector.
As a result, organisations across the industry are working hard to develop capabilities and processes that respond and deliver products with shorter lead times and increased rates. However, the innovation needed to achieve these capacities and stay ahead of global conflicts means that manufacturing development cycles are under considerable pressure.
On top of this, defence budgets continue to tighten following
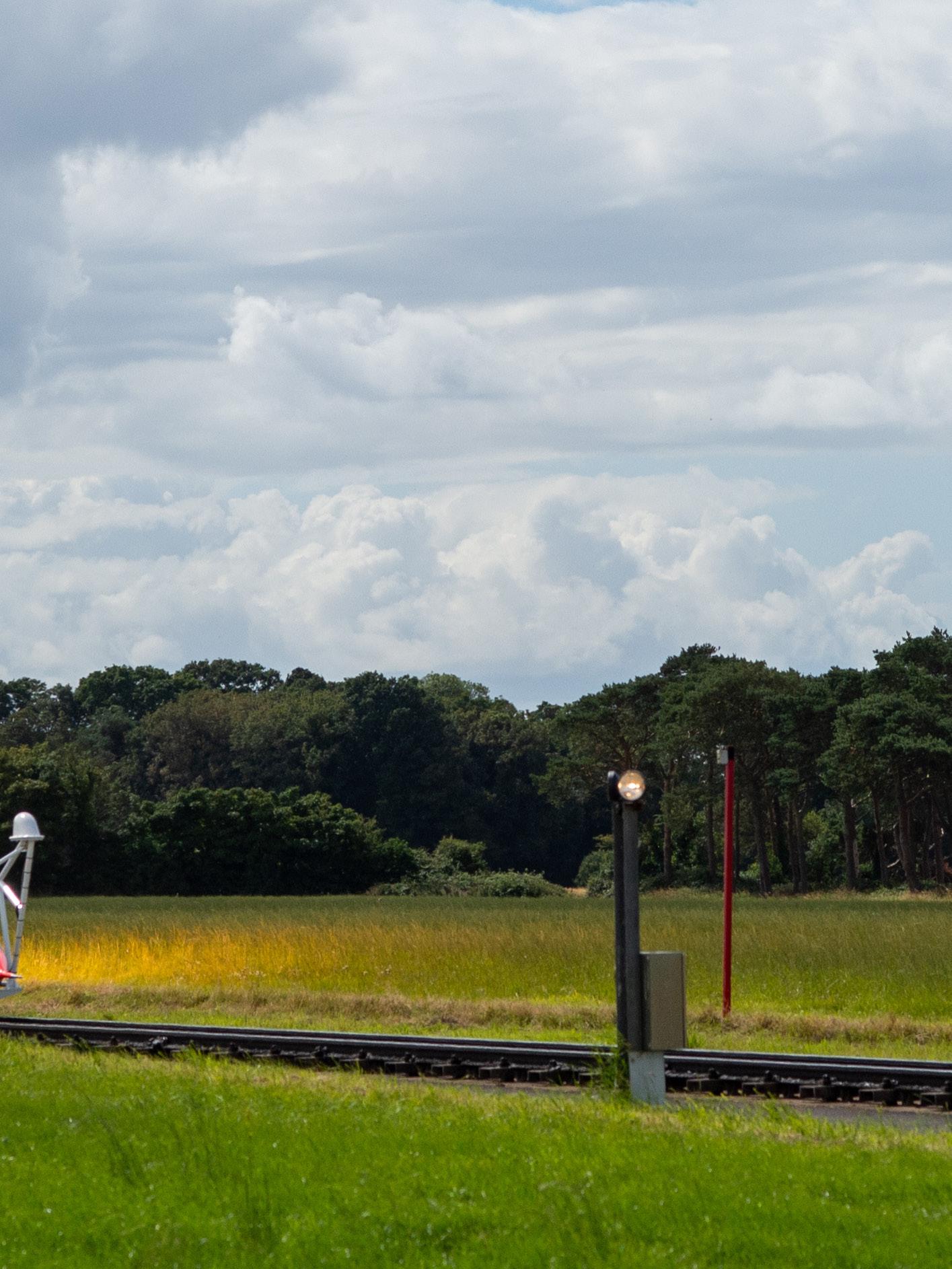
successive international economic challenges, which is pushing the industry towards more cost-efficient solutions.
“All these are central to defence sector procurement, and we are constantly working to optimise the quality, cost, and delivery performance using technology and supply chain improvements,” introduces Mark Cooper, Vice President of Sourcing at MartinBaker, the world’s leading manufacturer and supplier of ejection seats.
“Our job is now significantly more complex and challenging than it was five years ago, but my team has shown multiple times that they can rise to ever higher levels and mitigate crises whilst also driving improvement,” he adds.
INNOVATIVE AND LONG-LASTING
Operating at the forefront of the seat ejection subsector, Martin-Baker is proud to support the global aerospace industry with cutting-edge products that have helped save over 7,700 lives and counting.
“A passion for the life-saving nature of the job that we do runs through the business, it’s what grounds you when you are having a bad day and boosts you when you see the reports of successful ejections,” Cooper reflects.
The company supports over 60 aircraft across 106 operators in 85 countries, offering a range of seats that are both innovative and long-lasting. Accompanied by a strong team of experts in the field, Martin-Baker retains the knowledge and skills required to develop complex integrated escape systems.
Furthermore, its status as a familyowned and operated company, which is rare for a business of its size, is a key driver of Martin-Baker’s strong position.
Its role as an ejection seat frontrunner is further upheld by the company’s significant investment in technology and processes, strategically making decisions that have an impact over decades.
“Our ultra-long-term thinking helps us keep focused on sustainable strategies and approaches rather than chasing short-term tactics,” Cooper affirms.
Case in point, Martin-Baker recently recorded an ejection from a product over 40 years old, demonstrating the longevity of a seat in service.
The company also aims to control the intellectual property (IP) and manufacturing expertise of its solutions by developing in-house capabilities that ensure it serves its
customers for as long as they are flying.
Additionally admirable is the strength of Martin-Baker’s supply chain and the part it has played over the last few decades. As such, the combination of a diverse network of suppliers and extensive internal capabilities is a key component of the company’s success and resilience.
AT THE FOREFRONT OF AIRCRAFT SAFETY
Martin-Baker has developed an enviable reputation for state-of-theart equipment and manufacturing capabilities, which call for significant investment and capital expenditure (CapEx).
“Our products can be extremely complex and are designed at the limits of technology, so our strategy is to control manufacturing know-how to ensure we support our customers long into the future,” Cooper assures.
The COVID-19 pandemic and the subsequent energy crisis highlighted a need for the company’s longterm strategy, as the increased obsolescence issues faced by customers in recent years reinforce the resilience of Martin-Baker’s products.
On account of this, the company’s factory is capable of manufacturing almost any part of the ejection seat, brought about by significant and thoughtful investments.
Martin-Baker also firmly believes in offering the highest quality product at the most competitive price point, which consequently drives its investment in the latest technology, most recently demonstrated by the acquisition of computer numerical control (CNC) machining cells and cartridge assembly lines.
“We have a factory deployed with the latest milling and turning centres and have also invested in automated
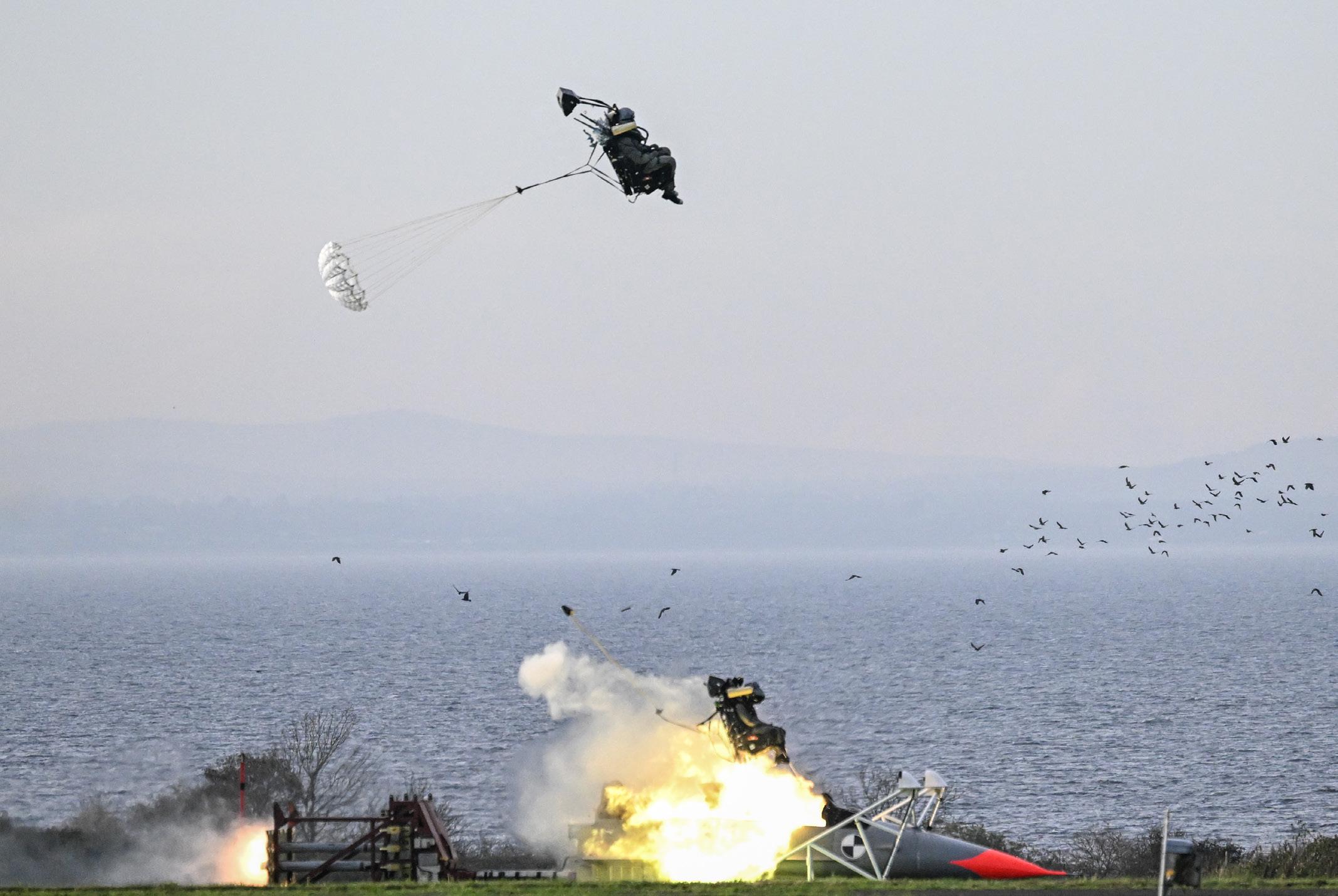
inspection and verification with vision systems and computed tomography (CT) scanning to aid equipment inspectors and eliminate defects,” Cooper expands.
The company’s latest technological investments go hand-in-hand with Martin-Baker’s commitment to safety.
“Product safety is our core focus and guiding principle. The ejection seat is the last line of defence in the event of aircraft failure. Although it sits dormant for many years, the seat must be operational when needed,” he asserts.
With this in mind, the company regularly conducts quality assurance (QA) and quality check (QC) processes for the business and its supply chain.
In the last two years, Martin-Baker has additionally been initiating and driving a zero-defects culture throughout its supply chain, in aid of its product safety goals.
“This seeks to create openness and transparency in terms of supplier defects so that we can collaborate on preventative solutions,” Cooper adds.
PASSIONATE AND SKILFUL
Alongside its operational safety targets, Martin-Baker is further committed to investing in its people.
“Personally speaking, I believe that the core asset of any business is a strong team, and we work very hard to create a company where people are engaged,” Cooper reflects.
Indeed, employee development and recognition are important for the retention of staff and therefore the business, whether that is developing competence within its roles to improve employee efficiency, or through promotions.
Martin-Baker’s strong companywide dedication to improvement is exemplified by the recent restructuring of Cooper’s team to create more specialised management roles, facilitate progression routes, and introduce early career pathways.
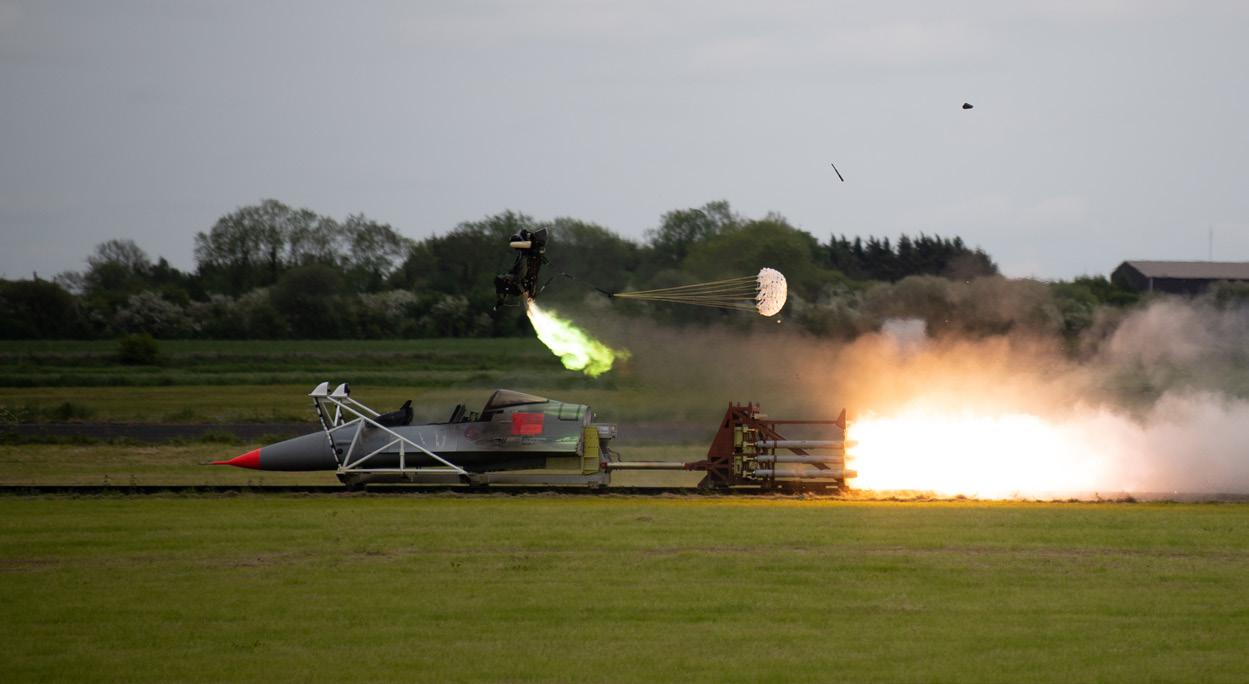
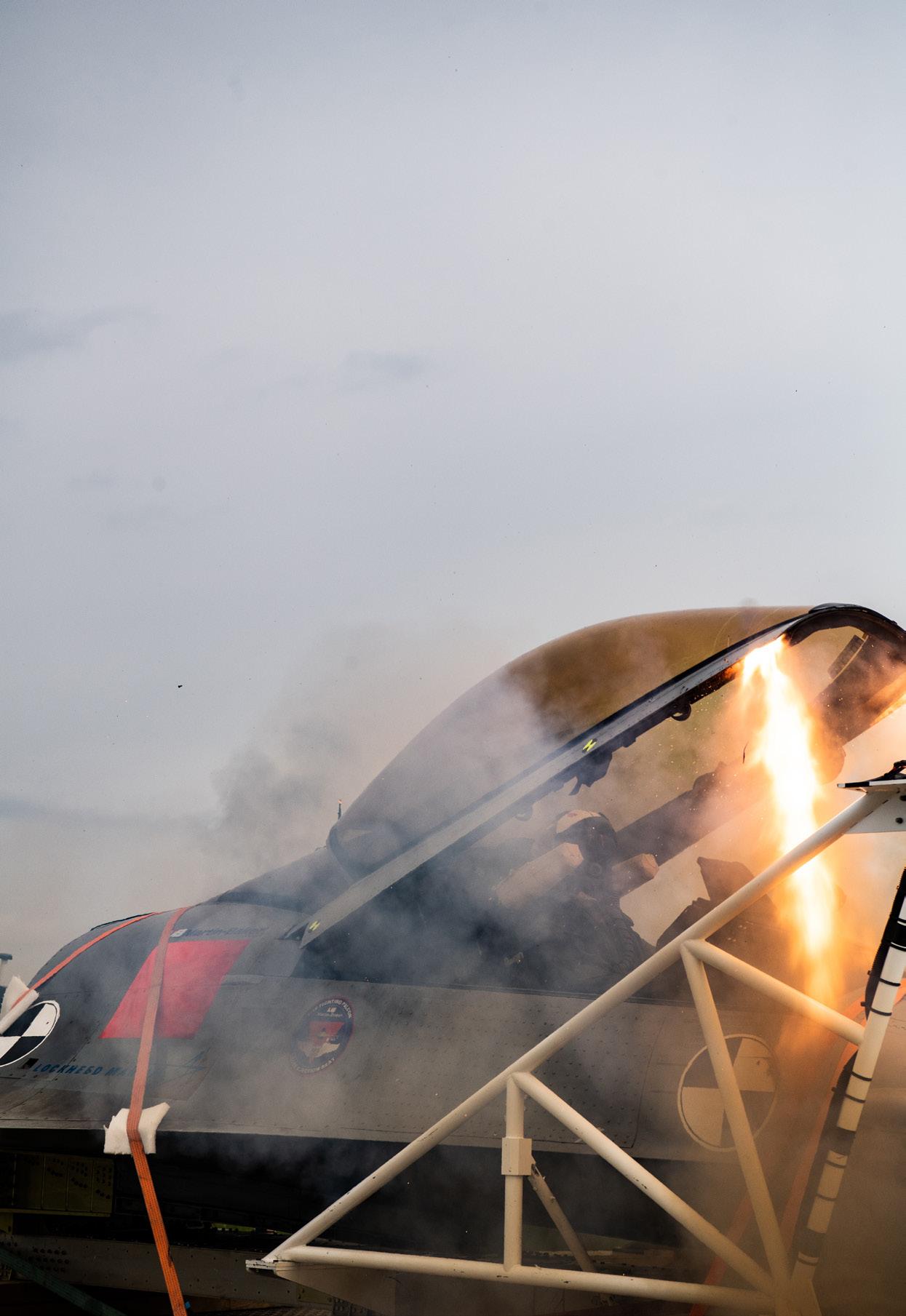
MARTIN-BAKER’S VALUES - AT A GLANCE
• Professionalism – The company strives to always achieve the highest possible standards in every task.
• Understanding – Martin-Baker is sympathetically aware of others’ viewpoints and works to comprehend why they might come into conflict with one another.
• Teamwork – The company works to eliminate functional silos, align all activity with strategic objectives, and be honest, open, and factual.
• Humility – Martin-Baker endeavours to understand when and why it is wrong and uses failure positively in everything it does.
• Accountability – The company accepts responsibility for any problems and works proactively to solve them.
• Integrity – Martin-Baker acts honestly, ethically, and without prejudice with everyone at all times.

Martin-Baker also strives to promote internally before reaching out to external applicants.
“We do this for two key reasons; firstly, it is a complex and unique business where the learning curve as an external hire is steep. Secondly, we want to reward our existing staff for high performance.
“I have been lucky enough to experience this and see various areas of the business, and this is a common theme through them all,” he reminisces.
“PRODUCT SAFETY IS OUR CORE FOCUS AND GUIDING PRINCIPLE. THE EJECTION SEAT IS THE LAST LINE OF DEFENCE IN THE EVENT OF AIRCRAFT FAILURE. ALTHOUGH IT SITS DORMANT FOR MANY YEARS, THE SEAT MUST BE OPERATIONAL WHEN NEEDED”
– MARK COOPER, VICE PRESIDENT OF SOURCING, MARTIN-BAKER
Indeed, Cooper has enjoyed a diverse array of roles at Martin-Baker, including positions in production engineering, procurement, factory management, and environmental testing, highlighting how the organisation encourages career development across its departments.
“Throughout my time with the company, I have been privileged to work with excellent people, and within my role of Vice President of Sourcing, I have inherited a fantastic team who are highly capable and engaged.”
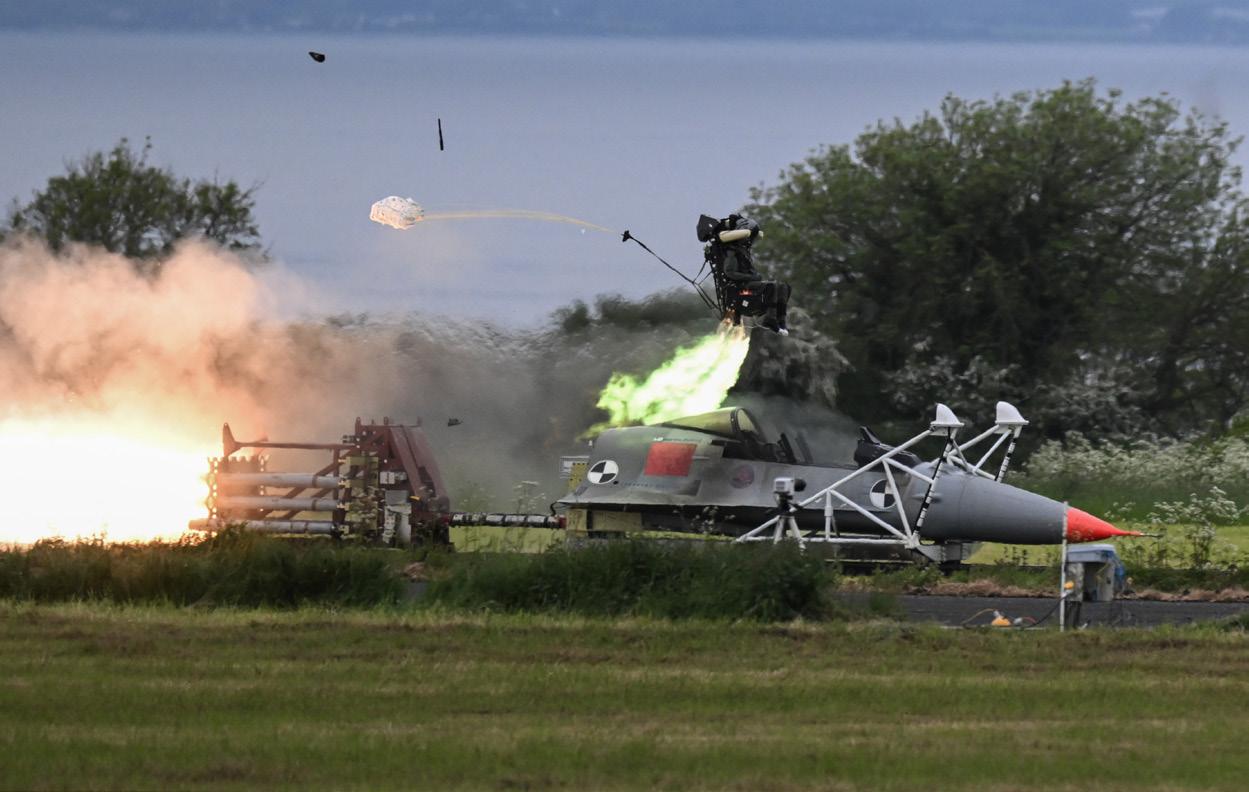
Looking ahead, Martin-Baker is focused on continuously improving its product quality whilst ensuring its on-time delivery fully recovers following recent global and national events such as the pandemic and energy crisis.
As such, its priorities remain on operational resilience, safety, and staff engagement, which filter across the entire business.
“We have made really great progress over the last year through a lot of hard work and determination, and we will push for even better in the future.
“There are some risks on the horizon with tariffs and trade complications, so managing and mitigating these will become a growing part of our roles over this year,” Cooper concludes.
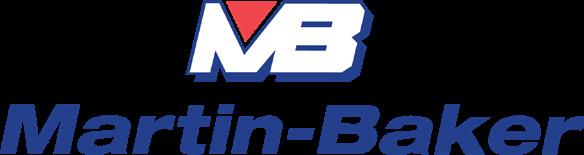
Tel: 01895 832214
information@martin-baker.co.uk www.martin-baker.com
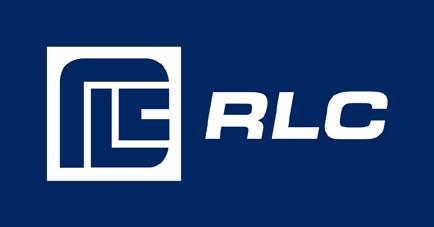
www.rlc-group.com
SHAPING THE FUTURE OF AEROSPACE
For 70 years, RLC is proud to have worked with leading operators in the Civil and Defence Aerospace sectors including Martin-Baker. Our dedication to offering our valued customers a vertically integrated supply chain solution encompassing CNC machining, aircraft textiles, heat treatments, and ground support Equipment is the core of who we are as a company.
RLC is a trusted supply chain partner for engineered solutions to the Civil and Defence Aerospace sectors. We have an intimate understanding of our customers’ expectations, and manufacture detailed high specification components to their requirements. RLC’s capability offers the market an end-to end solution and is viewed by our customers as an extension of their overall production capability. RLC is shaping the future of the aerospace sectors; we deliver on our commitment to provide the highest standards of machined components for the civil and defence aerospace spares and aftermarkets.
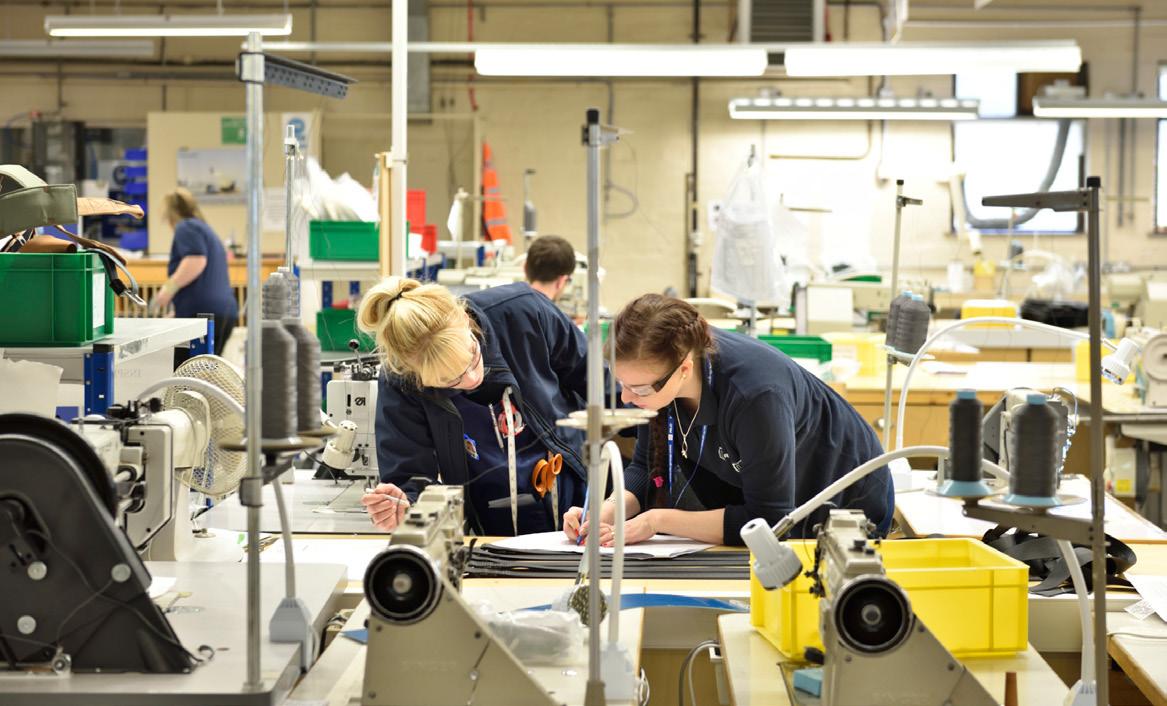
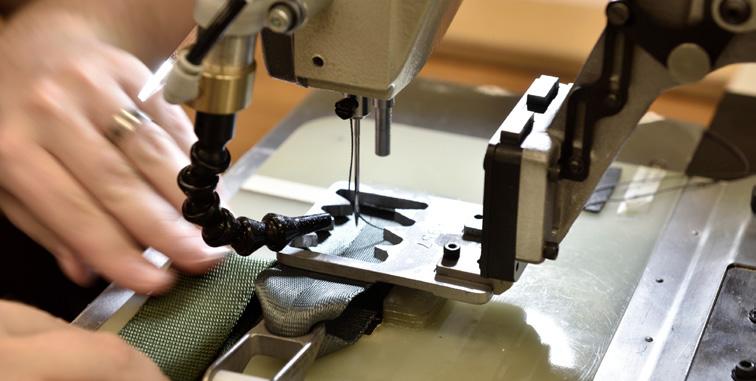
CRITICAL CAPABILITIES
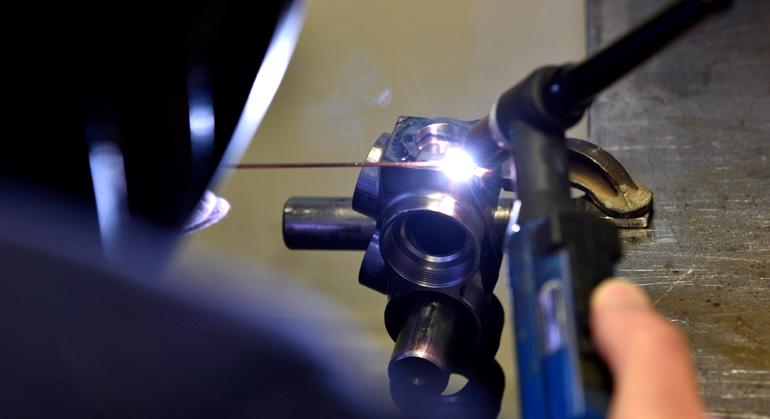
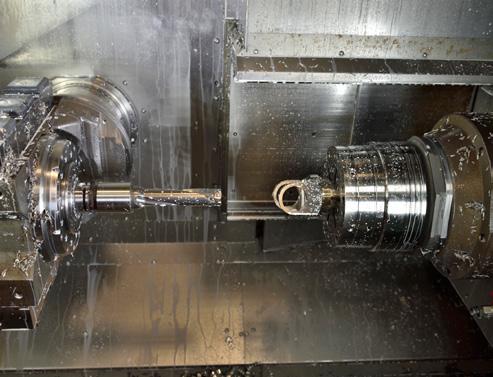
RLC offers a full range of services, including: Machining, aircraft textiles, heat treating, plating, painting, and extensive testing. We provide a complete supply chain solution from prototyping to full life cycle support. We have quality approvals including AS9100 and NADCAP certifications in areas like welding, heat treatment, and non-destructive testing.
Providing Electronics Manufacturing Services and Design Support for Over 30 Years
Martin-Baker’s recent product lines include its latest generation of ejection seats, the Mark 18, recently qualified for the F-16 and F-21 aircraft, complemented by several other programmes in the pipeline.
Elsewhere, the company is highly anticipating the exploration of automation and artificial intelligence (AI) to streamline processes and upskill staff.
“Almost all jobs come with the burden of administrative tasks that distract from high value-added activities, but now technology exists to automate and streamline these administrative processes so that people can spend more time doing the intellectually challenging, valuable, and interesting tasks,” Cooper imparts.
“Just imagine what you could do in the time saved by reducing administrative processes and answering emails. I want to see how we can harness AI to improve our supply chain management and, in turn, provide better service to our customers,” he impassions.
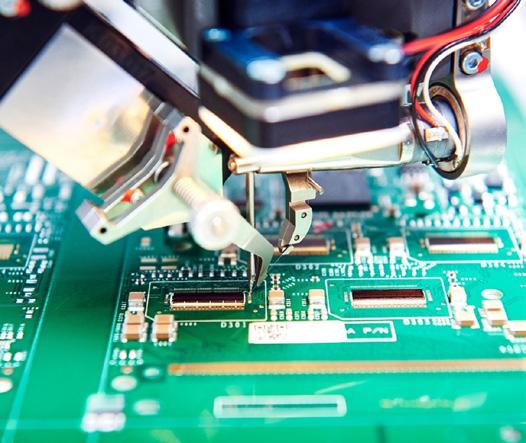
Axis Electronics is an established UK EMS partner within international supply chains for Prime, Tier 1 and Tier 2 market leading companies. In November 2021 it became part of the Cicor Group.
Axis has been proud to supply Martin Baker with manufacturing and design support services for over a decade. Producing lifesaving electronic sub-systems for use in the harshest environments means quality manufacturing comes first.
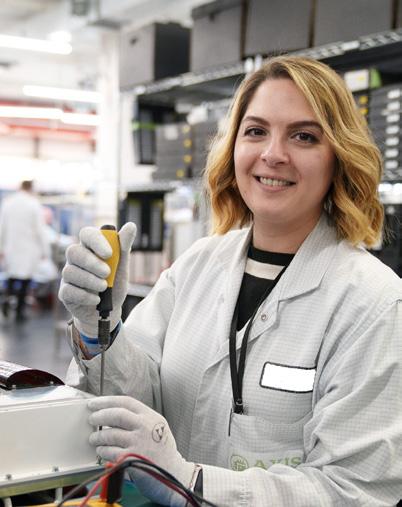
Focused on delivering life, mission and system critical hardware on time, and with zero defects drives our passion – to be our customers’ best supplier.
enquiries@cicor.com www.axis-electronics.com
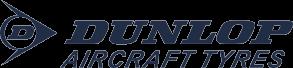
Designed and built to be strong and reliable, Dunlop Aircraft Tyres provides the perfect products for a multitude of planes across the commercial, cargo, passenger, and military spectrum. We learn more from CEO, Susan McKenna
Writer: Ed Budds
Project Manager: Cameron Lawrence
The story of Dunlop Aircraft Tyres (Dunlop) began with a spark of innovation when, in 1888, John Boyd Dunlop invented the pneumatic tyre in Belfast, Northern Ireland.
Since that groundbreaking moment, Dunlop has become synonymous with advances in tyre technology and high-performance products.
“As someone from Belfast, this history carries a special sense of pride and nostalgia,” introduces Susan McKenna, CEO.
“Within our industry, Europe finds itself at a fascinating crossroads. We’re seeing increased demand for regional and narrowbody aircraft, driven by both passenger recovery and cargo,” she sets out.
Throughout the sector, sustainability, supply chain resilience, and digital transformation are not just trends – they are necessities, providing agile businesses such as Dunlop space to lead where other competitors might be slower to pivot.
“We are smaller, more specialised, and more agile than our global competitors. Whilst Michelin, Goodyear, and Bridgestone dominate in size, we compete in speed, focus, and technical innovation.”
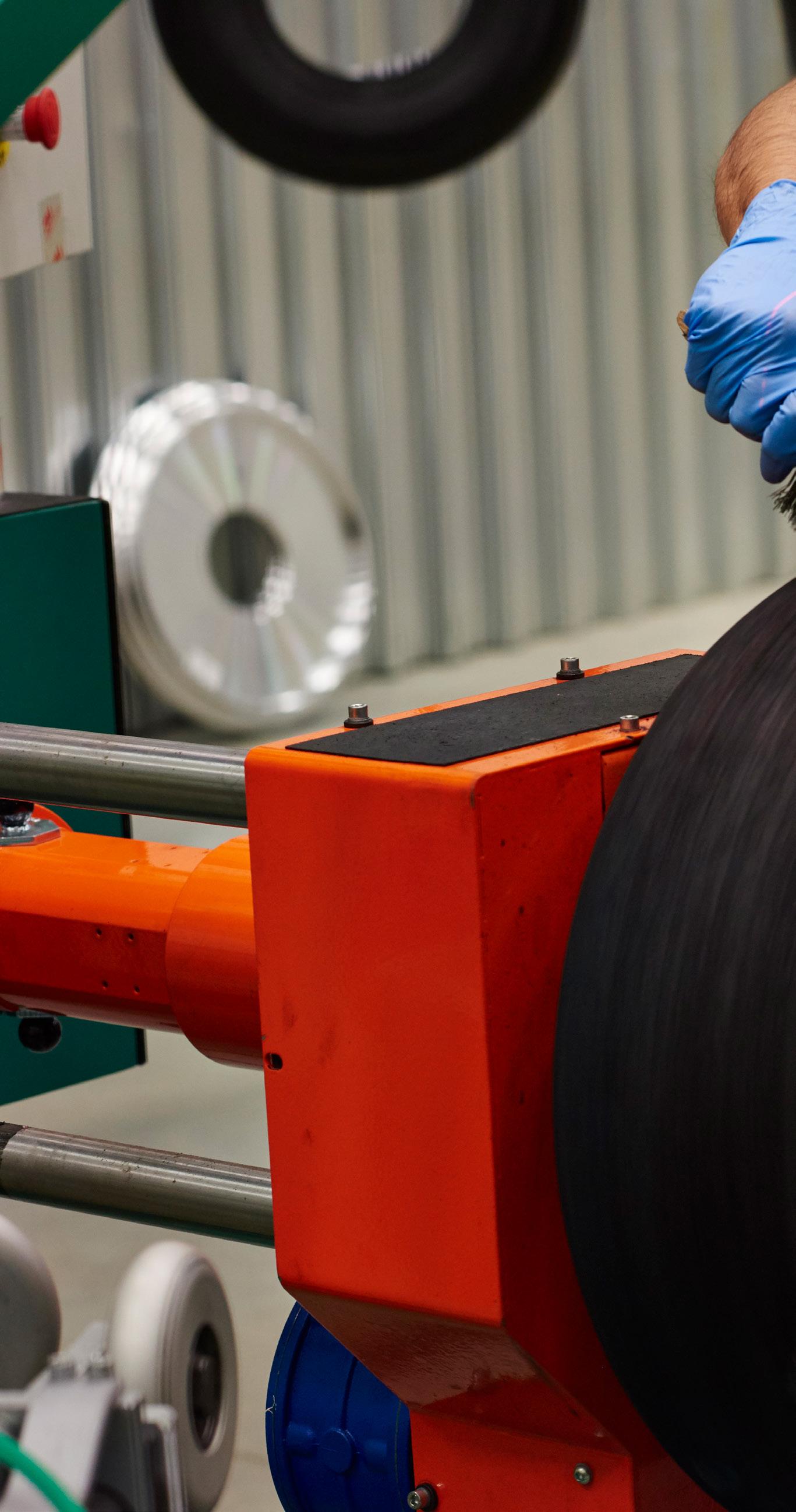
TREAD ON THE RUNWAY
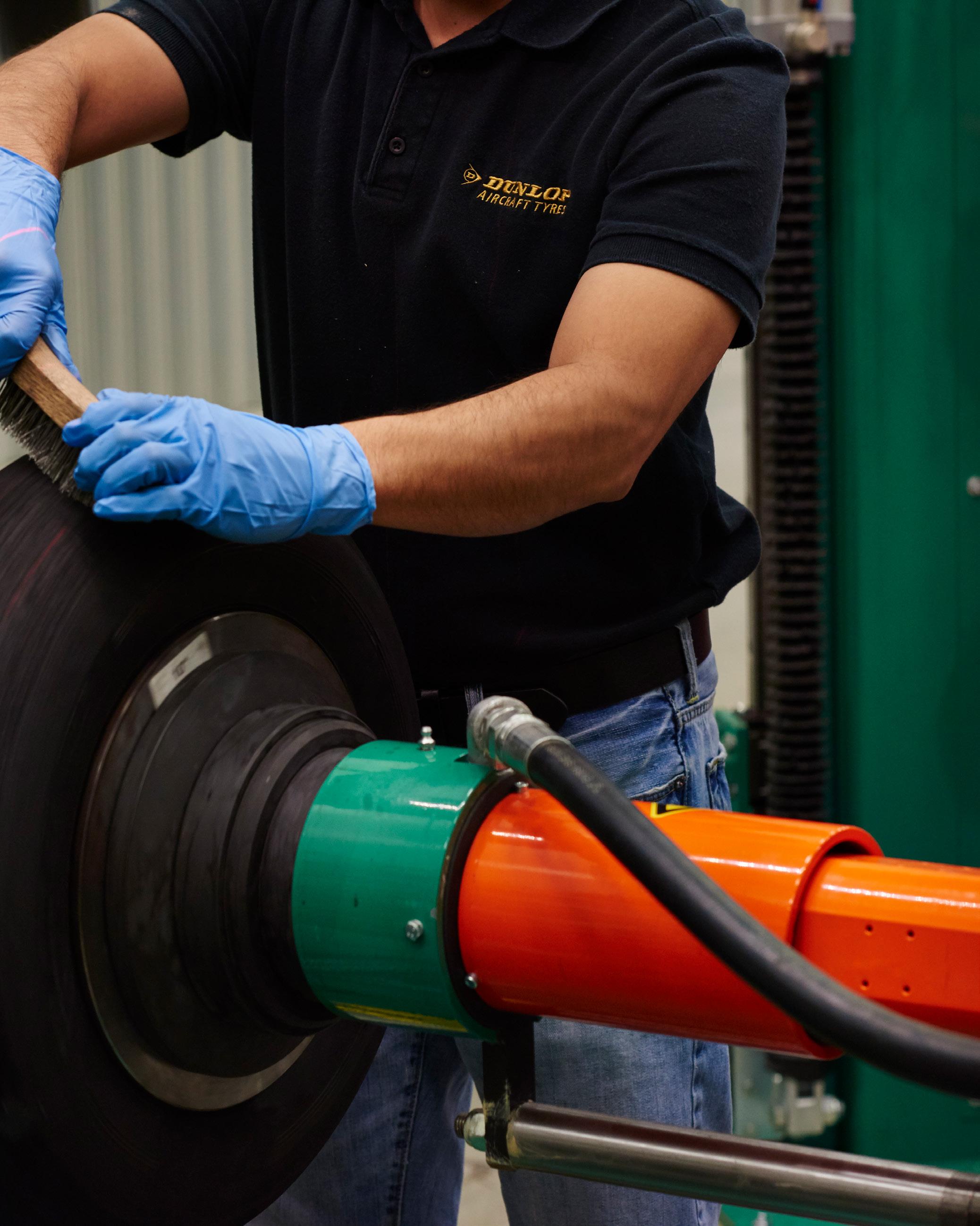
Most importantly, Dunlop is 100 percent focused on designing, manufacturing, and retreading worldclass aircraft tyres.
ÖZKA TYRESA VALUED PARTNER
Özka Tyres (Özka) has been a valued partner in broadening Dunlop’s manufacturing base and helping to meet demand surges. The collaboration has allowed Dunlop to test new supply chain models whilst maintaining high standards.
Recognised for its excellence in manufacturing and innovation, Özka continues to expand its presence across global markets, with particularly strong and growing sales figures in Europe.
Operating with an extensive international footprint and delivering products to over 90 countries, the company stands out for its commitment to high performance, durability, and continuous development.
Özka’s production facility supports a daily capacity of 260 tonnes, establishing it as one of the leading players in the global tyre industry. Its integrated R&D centre drives innovation in tyre engineering, creating solutions tailored to agricultural and industrial needs.
The company offers one of the industry’s most comprehensive product portfolios, including VF (Very High Flexion) and radial tractor tyres, flotation and implement tyres, as well as products for harvesters, irrigation equipment, forestry, industrial and off-the-road (OTR) vehicles, forklifts, compactors, light trucks, and minibuses. Özka embraces sustainability as a core strategic pillar, investing in environmentally responsible materials, energy-efficient production, and advanced waste management systems, actively shaping a future where highperformance tyres and environmental responsibility coexist.
A BROAD PORTFOLIO
What sets Dunlop apart is that it is currently the only tyre company in the world solely dedicated to aircraft tyres.
“Our core focus is on designing, manufacturing, and retreading tyres for both fixed-wing and rotary aircraft. Headquartered in Birmingham, UK, with service facilities in the US and China, our global presence spans over 80 countries,” explains Susan.
“We supply tyres to a diverse range of customers, including commercial passenger airlines, military forces, recovery services, and freight operators.”
With over 300 product approvals, Dunlop’s tyres support a wide array of aircraft, from AgustaWestland helicopters to the massive Antonov AN-124 transporter.
“Our tyres are fitted on everything from regional aircraft like the Bombardier Q400 to narrow-body jets such as the Boeing 737 and freight carriers including the Airbus
A300, Boeing 757, Boeing 747, and McDonnell Douglas MD-11.”
In the military sector, Dunlop provides tyres for advanced platforms such as the Lockheed Martin F-35B fighter jet and BAE Systems Hawk trainer aircraft, as well as large transport aircraft like the Boeing C-17 and Airbus A400M.
As air transport continues to evolve rapidly, the company is now also actively engaged in the emerging unmanned aerial vehicle (UAV) and air taxi sector.
RELIABLE SERVICE
For Dunlop, nothing is more important than the customer.
“The operator is always at the heart of everything we do because each tyre we make or retread earns its right to be called a Dunlop,” states Susan.
“This means our drive for everimproving product performance and tyre safety is as determined as it is relentless,” she affirms.
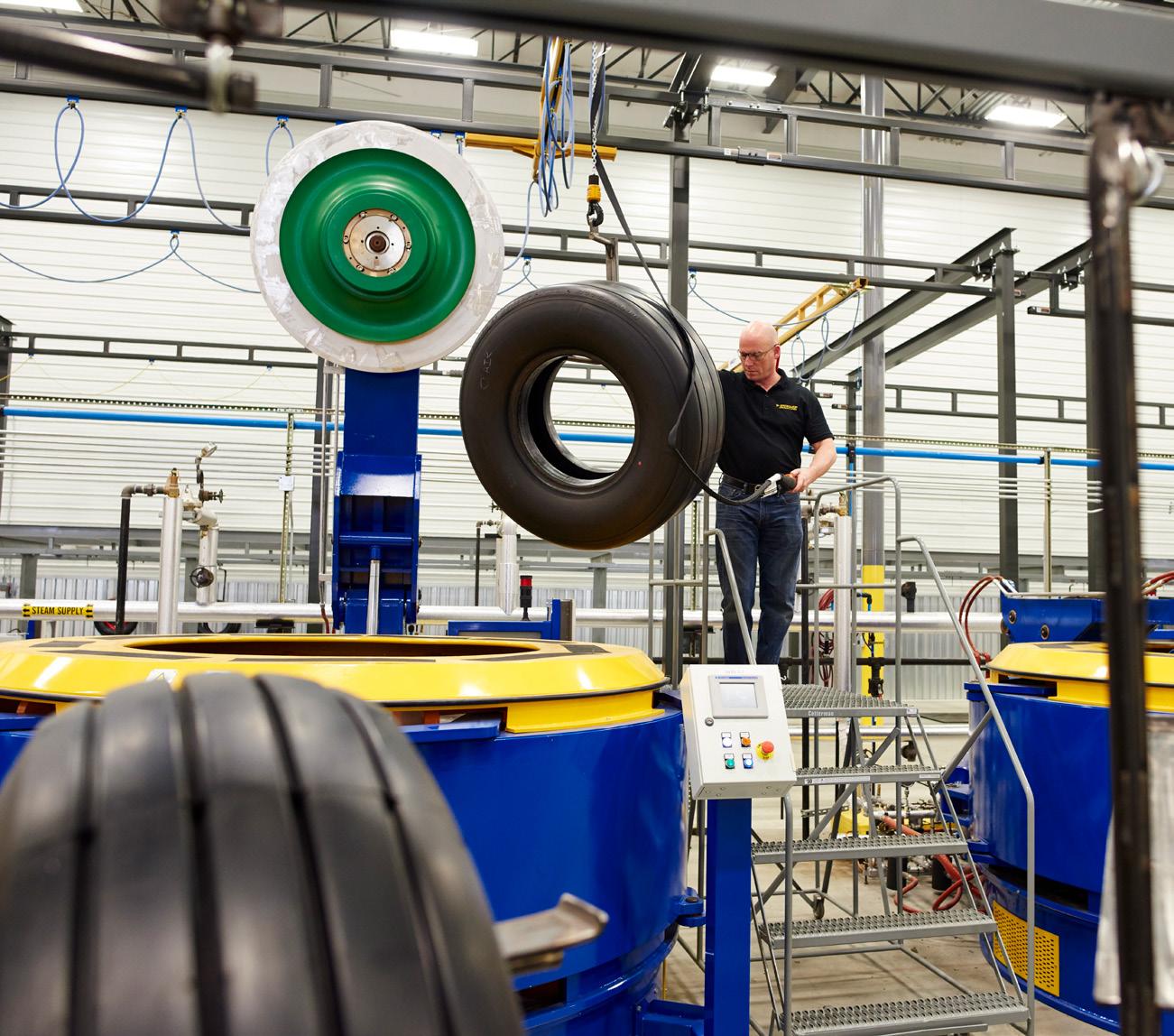
“WE ARE SMALL, BUT THAT’S OUR STRENGTH – WE’RE FOCUSED, HUNGRY, AND HAVE THE COURAGE TO DO THINGS DIFFERENTLY”
– SUSAN MCKENNA, CEO, DUNLOP AIRCRAFT TYRES
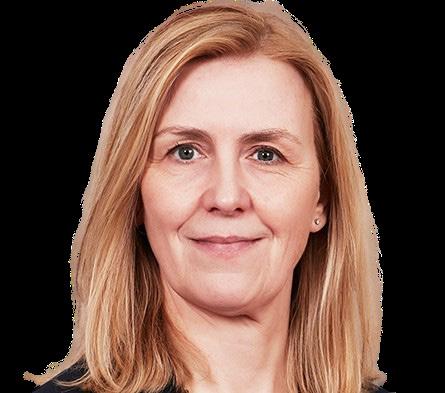
As a true aviation specialist, Dunlop understands better than any the crucial contribution of both performance and service to dispatch reliability.
“With the operator at the heart of everything we do, dispatch reliability is our focus.”
Now standing as a globally recognised brand and symbol of quality, working in partnership with airframers and industry stakeholders, it’s no surprise Dunlop also meets the world’s most exacting aviation standards, approvals, and certifications.
CONTINUOUS GROWTH
Dunlop has recently completed several successful expansions of its retreading capabilities, supporting circular economy objectives by extending tyre life without compromising safety.
“Parallel to this, we’ve invested in digital inspection tools and
data analytics to enhance lifecycle forecasting for operators. In 2023, we also introduced policy deployment to align our long-term vision with actionable goals,” Susan prides.
This approach enables the setting of annual targets that support Dunlop’s medium and long-term
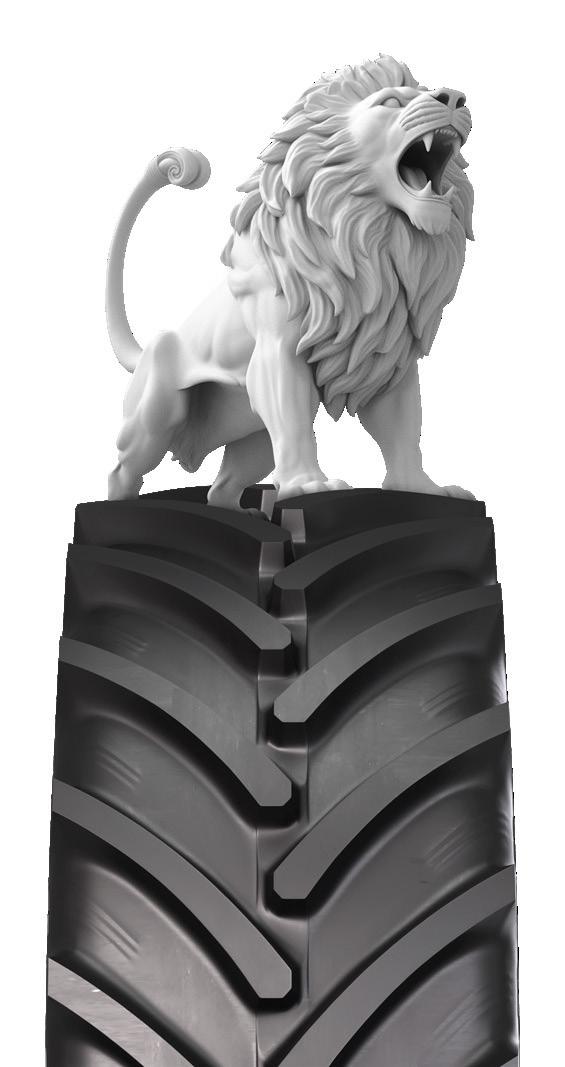
strategies, with goals cascaded across departments to ensure alignment and accountability.
“In addition to our ongoing attention on new products, improvements, and infrastructure, I’d say our most significant investment today is in our people.
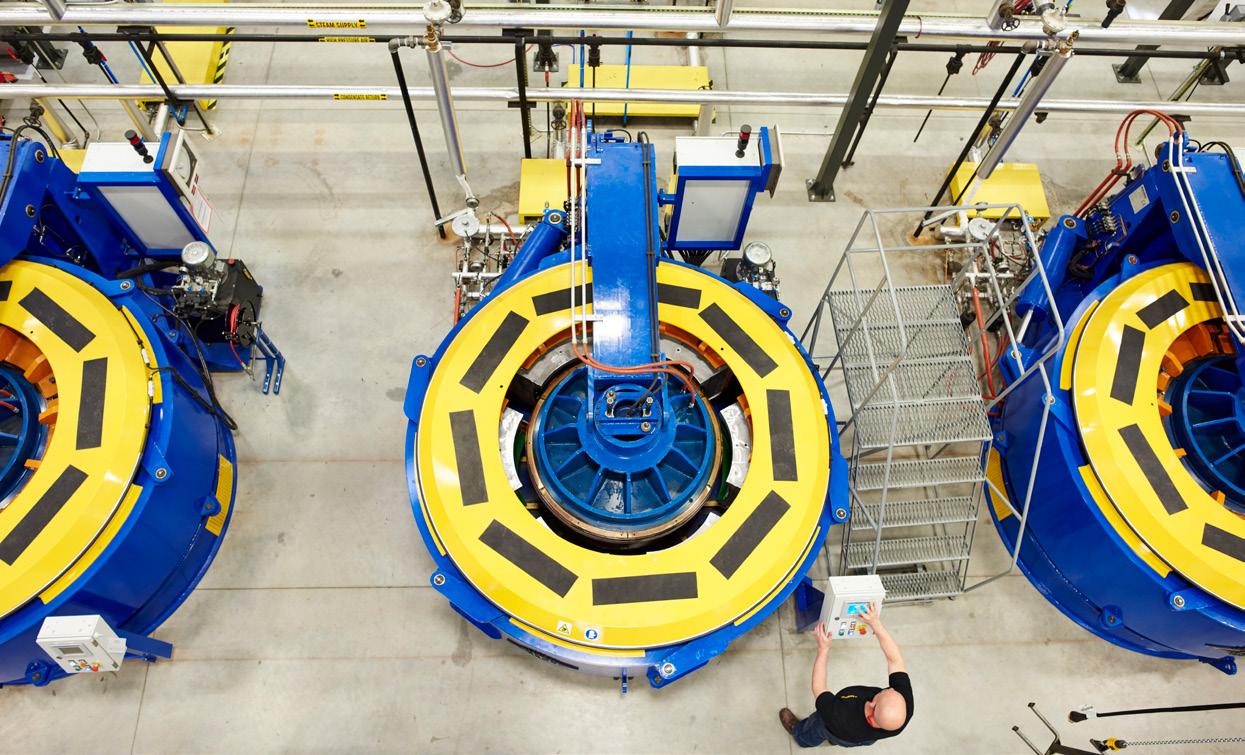
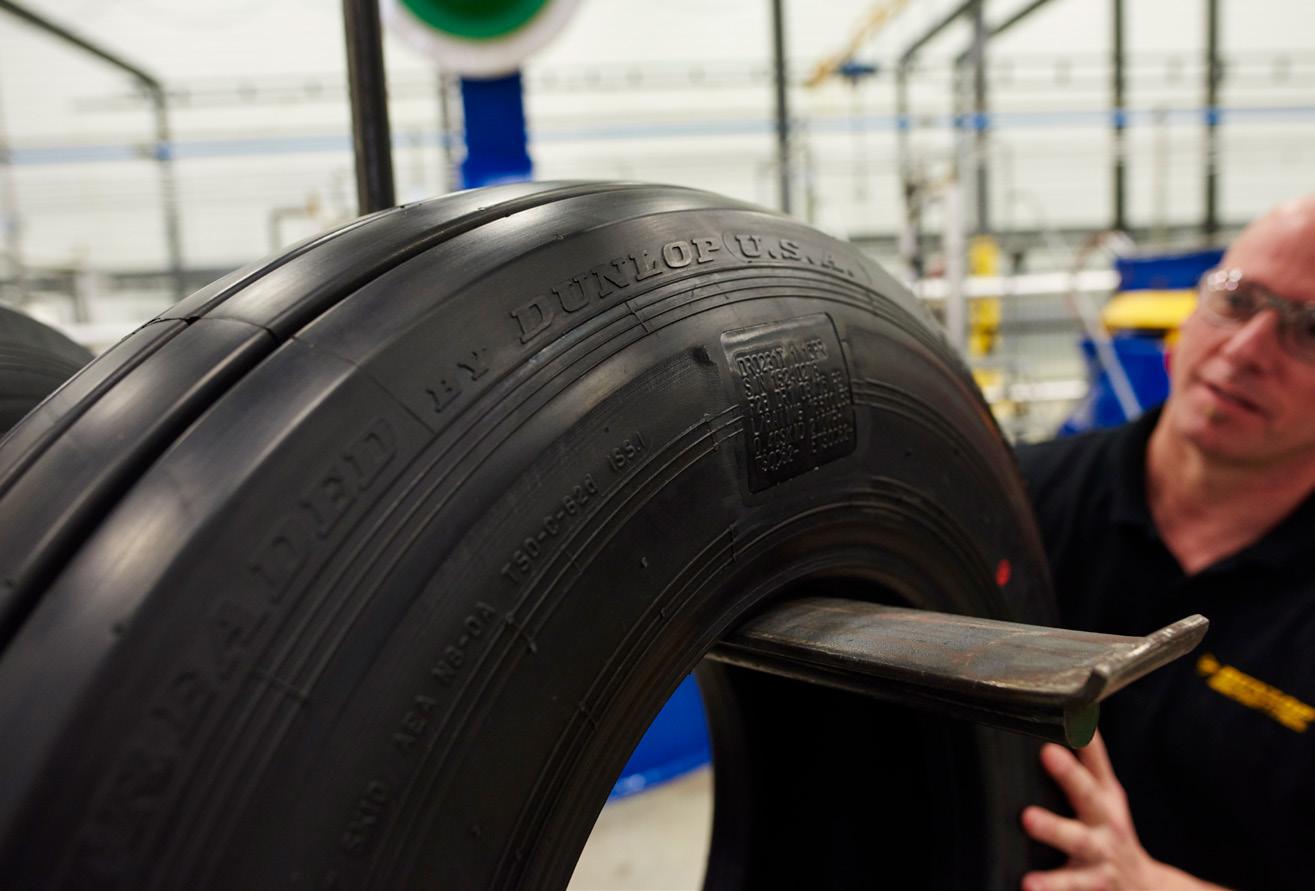
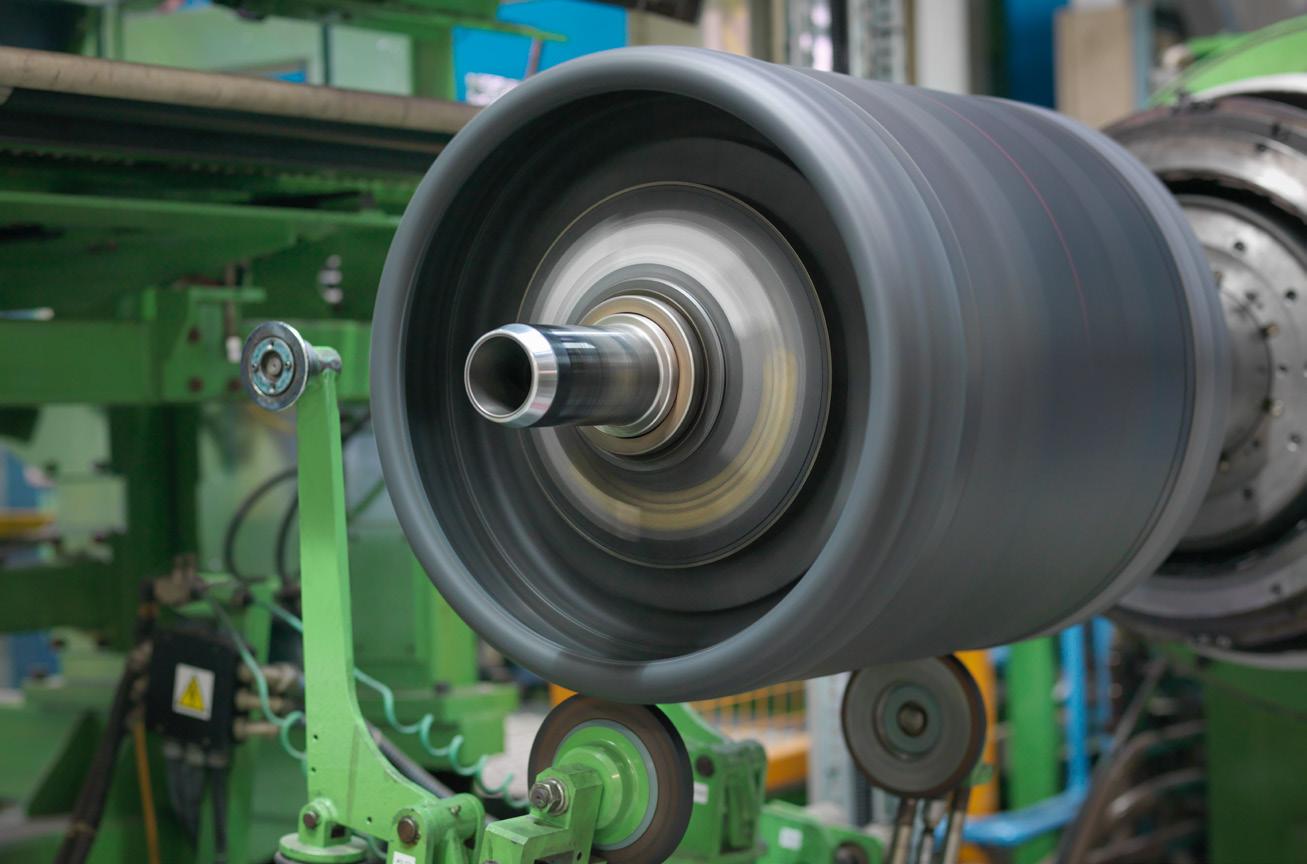
DUNLOP’S KEY PRIORITIES FOR THE COMING YEAR
The company is laser-focused on:
• Delivering growth despite a tough cost environment.
• Continuing its leadership development programme.
• Enhancing digital capability in operations.
• Expanding its reach in strategic markets, including defence and in Asia.
• Becoming more investment-ready by driving performance and clarity in everything it does.
“We’re currently implementing a multi-year transformation strategy that prioritises leadership development, technical training, and rethinking how we embed innovation at every level of the company,” she tells us.
Undoubtedly, Dunlop recognises the future lies in empowering its team to drive progress, which is why it remains focused on nurturing talent and fostering a culture of continuous growth.
“We believe leadership is visible in the agency of others; that’s why we give our people space to grow. We’ve implemented weekly, monthly,
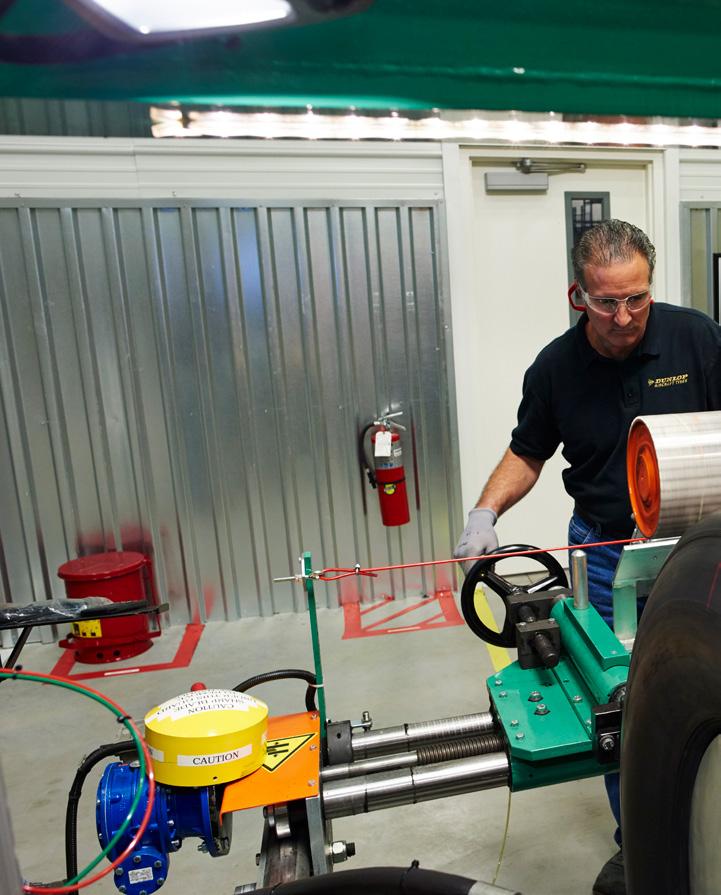
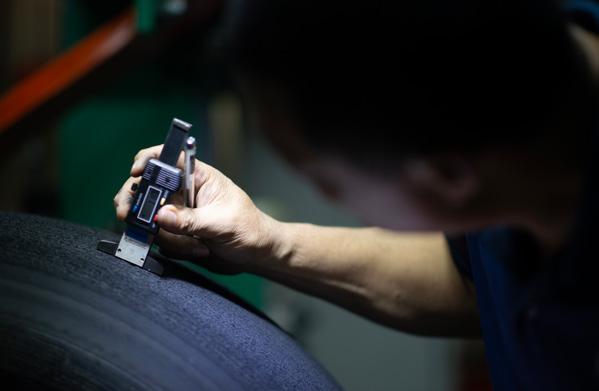
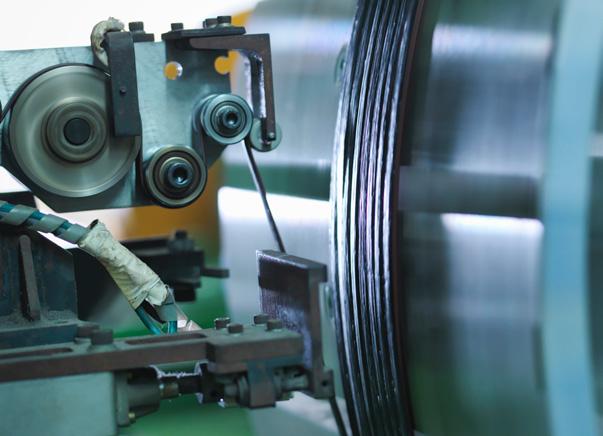
and quarterly check-ins focused on behaviours, not just tasks.”
For Dunlop, it’s about unlocking the best version of someone each day and celebrating progress, not just outcomes.
“Alongside this, we’re investing in developing new compounds to further enhance performance and sustainability, ensuring we stay at the forefront of technological advancement and environmental responsibility,” Susan acclaims.
RESILIENT TO THE CORE
At Dunlop, company culture is built on quiet resilience.
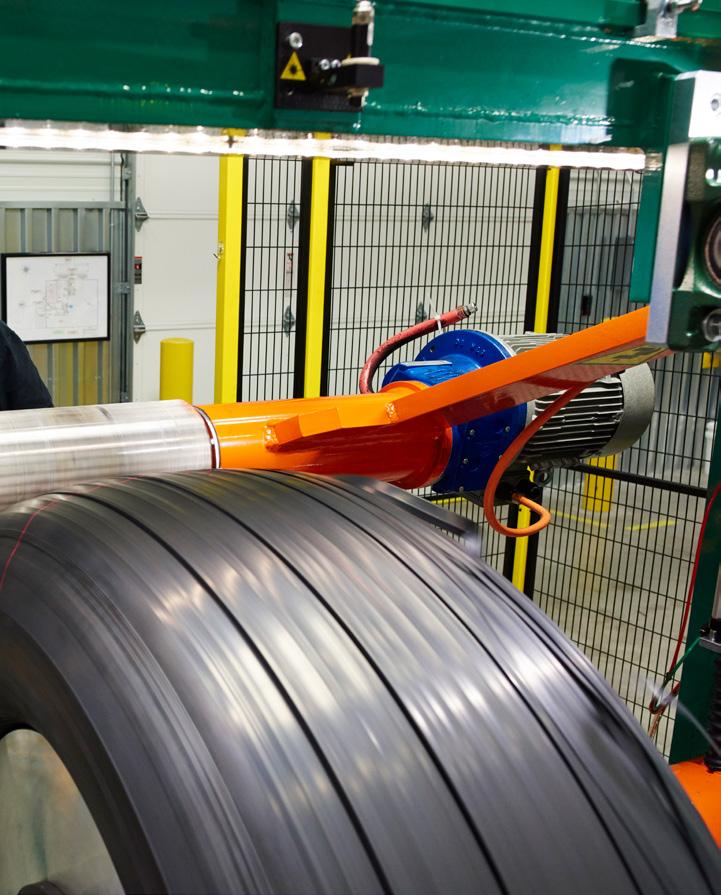
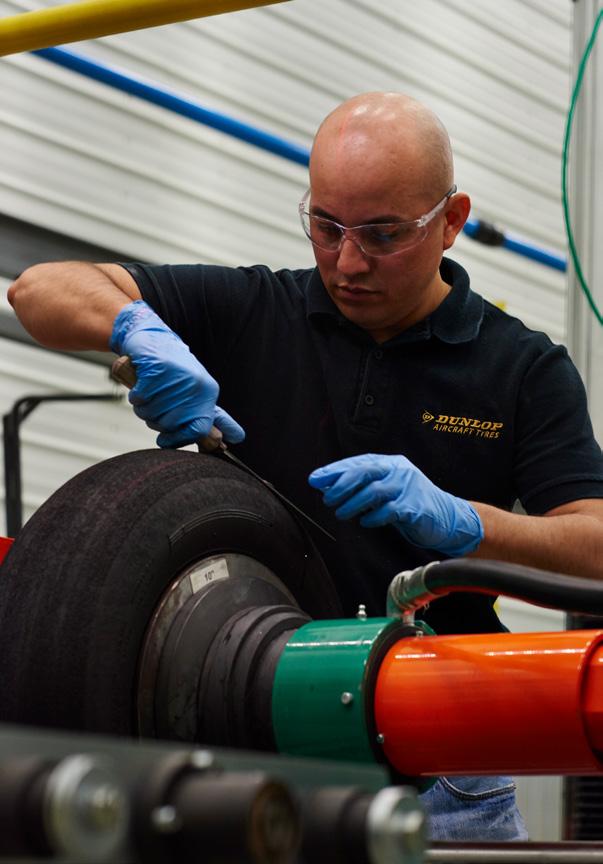
“There is a deep sense of pride in the craftsmanship of what we produce. We are still operating on the tyre factory site built in 1916, and many of our employees have been with us for years, contributing to our strong sense of continuity,” Susan posits.
“We’re able to give tailored, responsive service, something that makes a real difference to operators who can’t afford downtime. We’re also proud of our UK-based manufacturing legacy and close relationships with our customers.”
Resilience is a core value for the company; Dunlop always stays the course. It also values collaboration
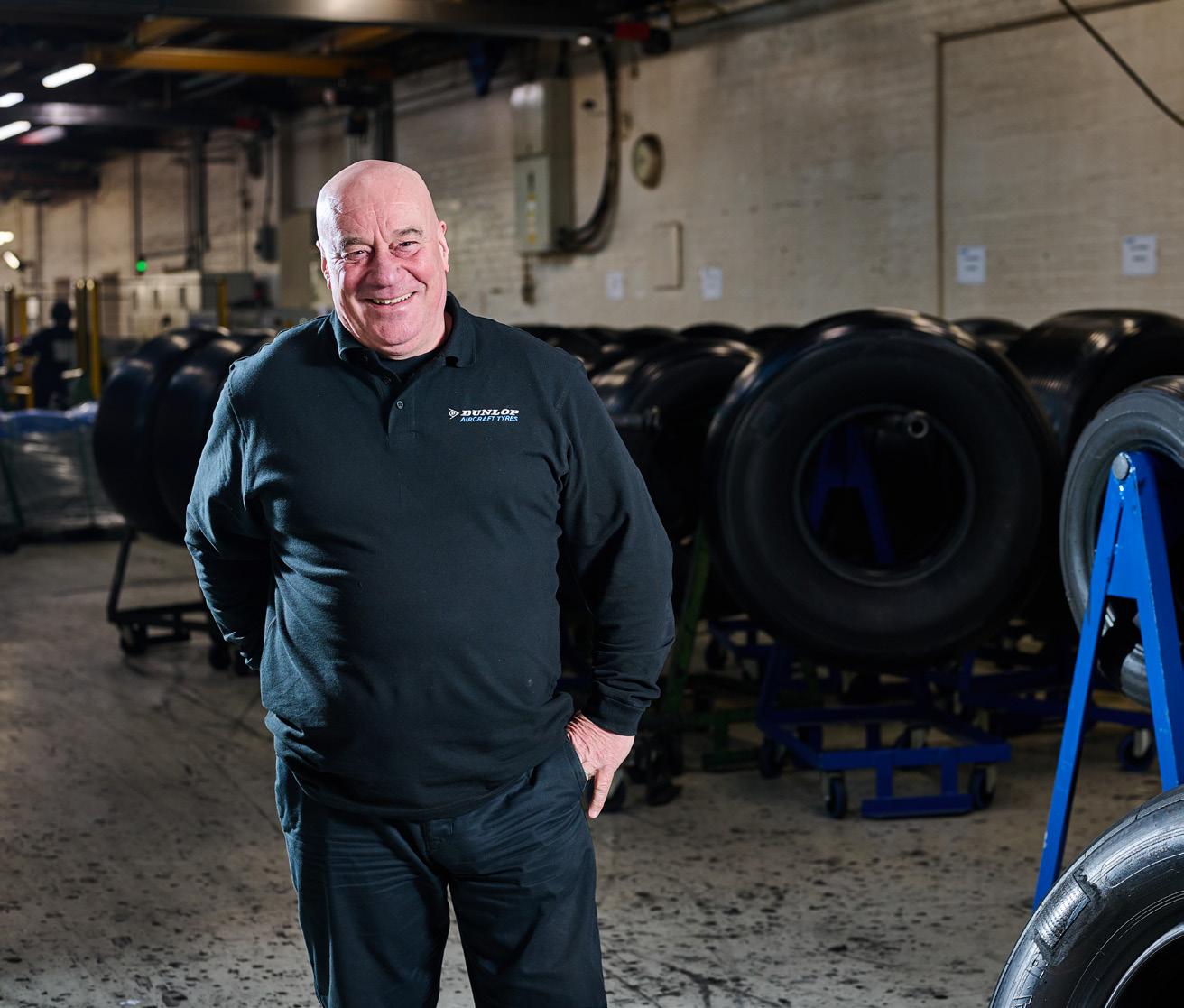
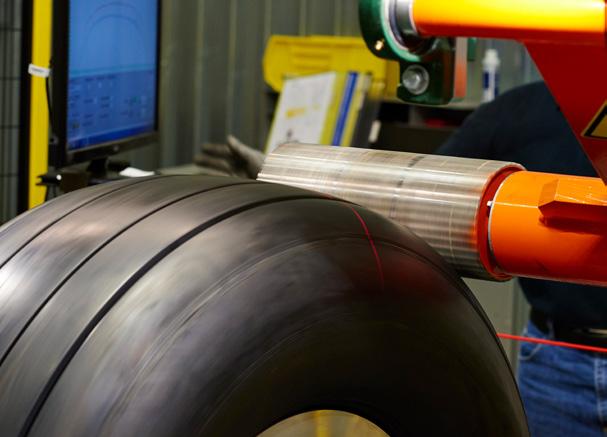
and open-mindedness and, above all else, remains entirely responsible, never sacrificing the quality or safety of its people, products, or customers.
Alongside this, the company operates a tightly-controlled, highlycompliant global supply chain. Strong relationships with partners are critical – Dunlop can’t deliver safety-critical products without total trust and performance transparency.
Moving forwards, Dunlop is working to nearshore some aspects of its supply chain to mitigate risk and improve responsiveness.
“I believe this is a pivotal moment for the company. We are small, but
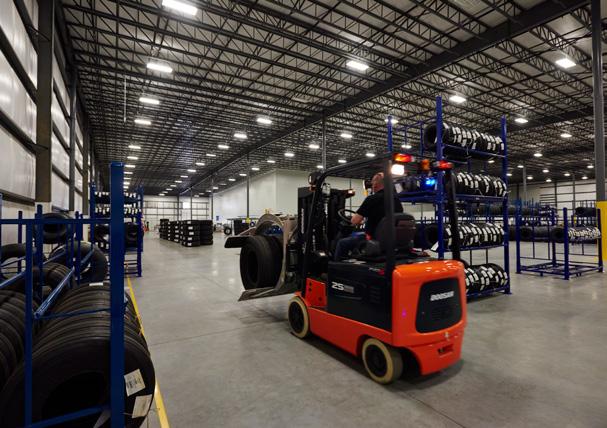
that’s our strength – we’re focused, hungry, and have the courage to do things differently.”
“We’re not trying to be our competitors – we’re trying to be the best version of Dunlop,” Susan concludes proudly.
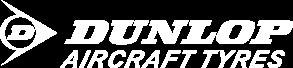
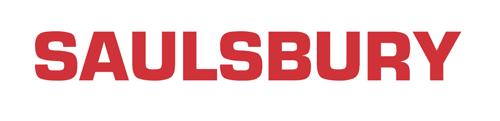
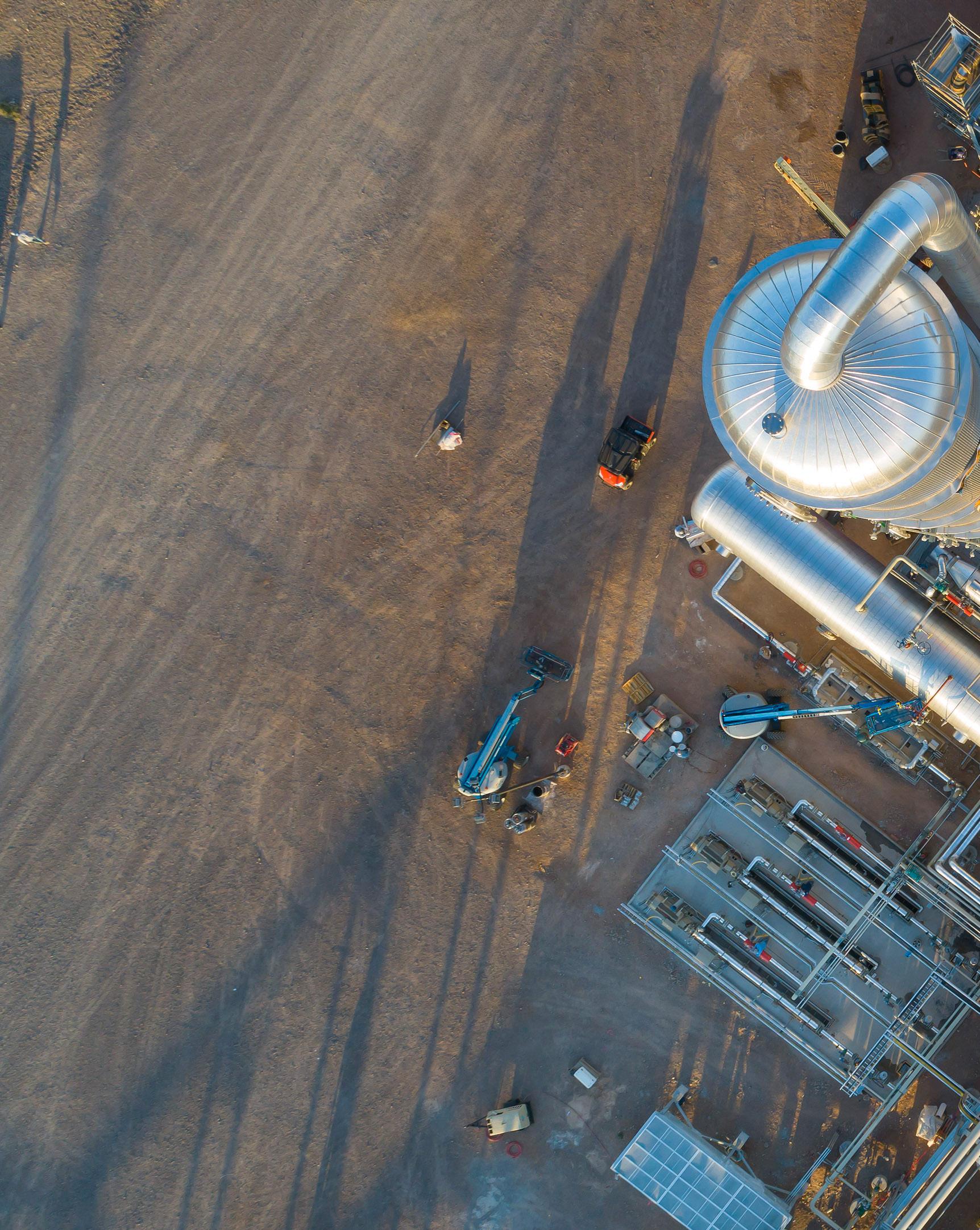
GETTING THE JOB DONE RIGHT
With safety, integrity, excellence, relationships, and community at its core, Saulsbury is more than just an award-winning engineering, procurement, and construction contractor – it is a trusted partner, employer of choice, and a leader in safety. We sit down with CEO, Matt Saulsbury, who is sustaining his father’s legacy as he leads the company toward continued success
Writer: Lily Sawyer | Project Manager: Scarlett Burke
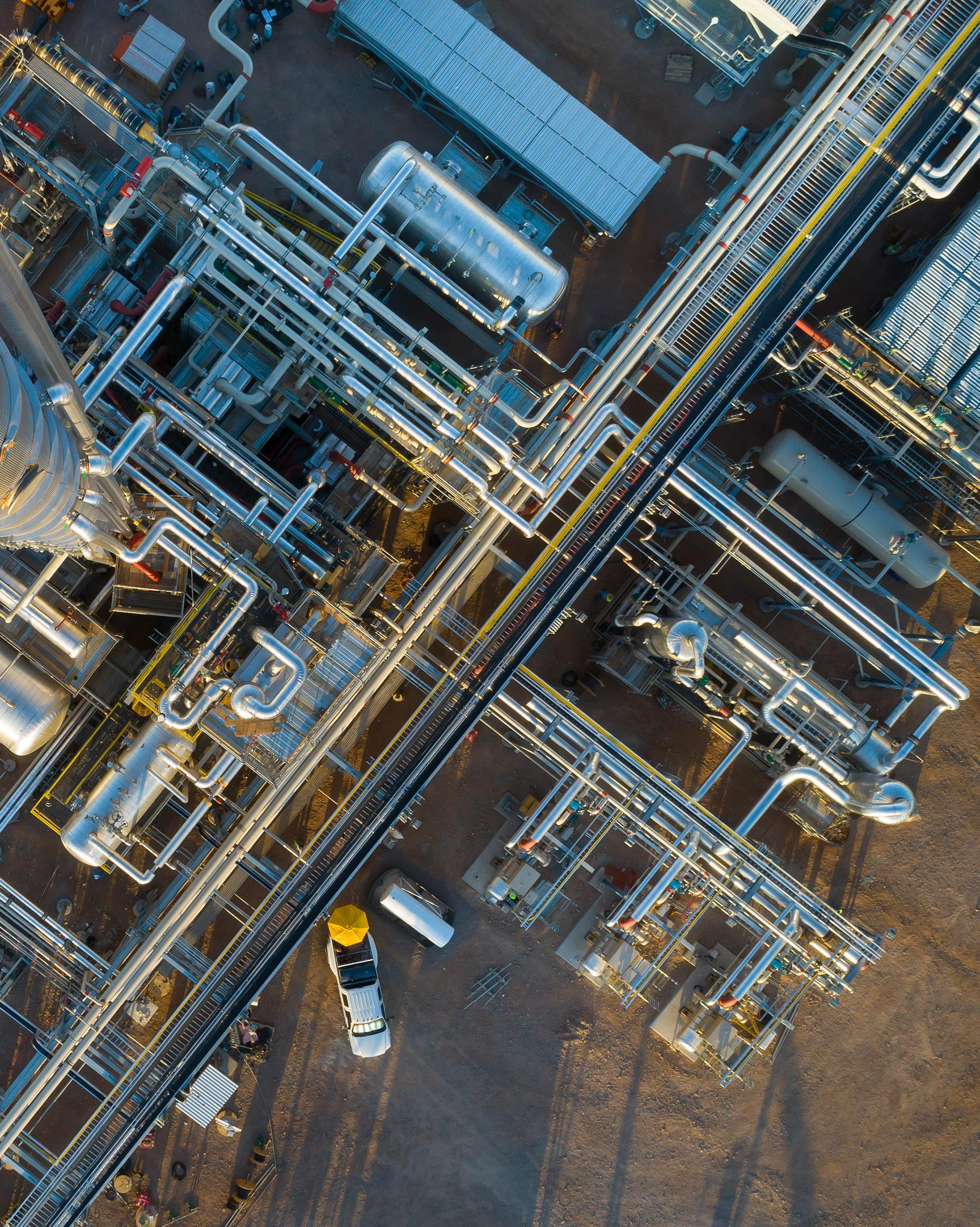
Adominant force in North America’s oil and gas industry, Texas has long been responsible for a significant portion of the nation’s crude oil and natural gas production, contributing considerably to socioeconomic development in terms of job creation and revenue generation.
More widely, the US’ abundance of affordable and reliable energy resources continues to strengthen national security and bolster the country’s overarching goal of achieving energy independence by reducing its reliance on imports and increasing export potential.
“Continuous innovation across the sector has fueled a surge in domestic production, positioning the US as a leading global exporter,” introduces Matt Saulsbury, CEO of Texas-based full-service engineering, procurement, and construction (EPC) company, Saulsbury, a market leader with a proven history of expert project execution in the oil and gas sector.
As the son of Founder, Dick Saulsbury, Matt was appointed as CEO in February 2023, and his deeprooted industry expertise, particularly in Texas, is second to none.
Playing a crucial role in the company’s operations for over three decades and having previously held the position of Vice President of Project Services, Matt is uniquely qualified to lead Saulsbury toward a bright future.
“Over my 30-year tenure at Saulsbury, I’ve witnessed a dramatic transformation in North America’s oil and gas industry, largely driven by technological advancements such as horizontal drilling and hydraulic fracturing,” he insights.
Matt’s wealth of experience, vision for the future, and dedication to the company’s core values has helped Saulsbury continue to deliver on its modus operandi – ‘getting the job done right’.
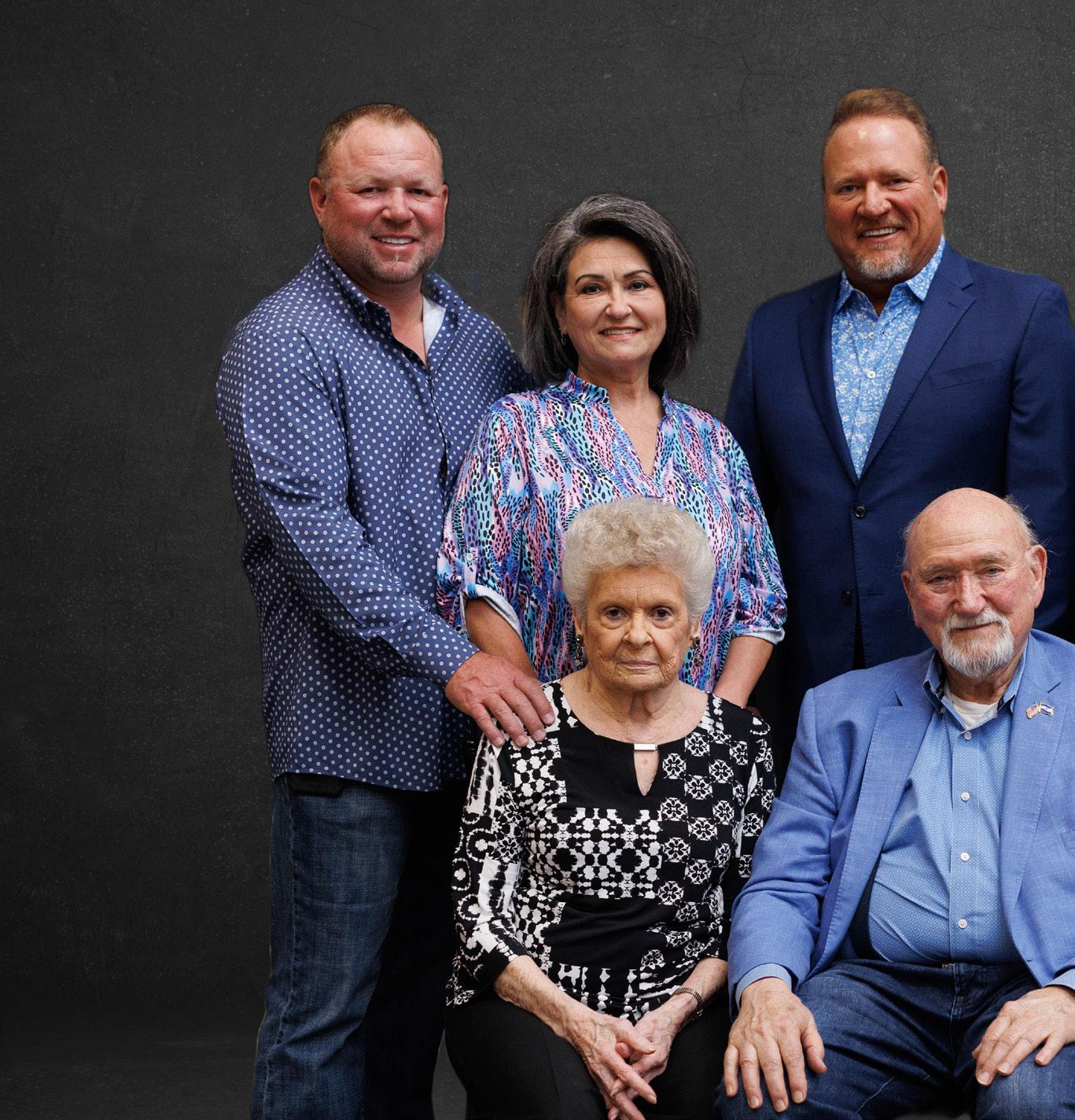
AN EVOLVING INDUSTRY
Despite the historic successes and benefits of the oil and gas sector, those operating within it today must navigate a complex landscape of challenges.
For example, regulatory changes at both federal and state level have prompted a shift away from traditional fossil fuels, necessitating the implementation of robust compliance strategies to minimize environmental impacts, promote air quality, and protect natural water sources.
Market instability also persists, caused by international supply chain disruptions and variable demand.
“Industry challenges are ongoing, particularly oil price volatility driven
by global supply and demand dynamics, geopolitical events, and economic fluctuations,” Matt confirms.
Therefore, in the face of continuous adversity, many oil and gas companies are increasingly partnering with EPC contractors such as Saulsbury to help deliver their projects and achieve their objectives.
By utilizing a fast-track designbuild approach to minimize costs and maximize the efficiency of its clients’ schedules, the company has seen much success thanks to its ability to make timely decisions and react promptly to industry changes.
“Our core values of safety, integrity, excellence, relationships,
The Saulsbury family
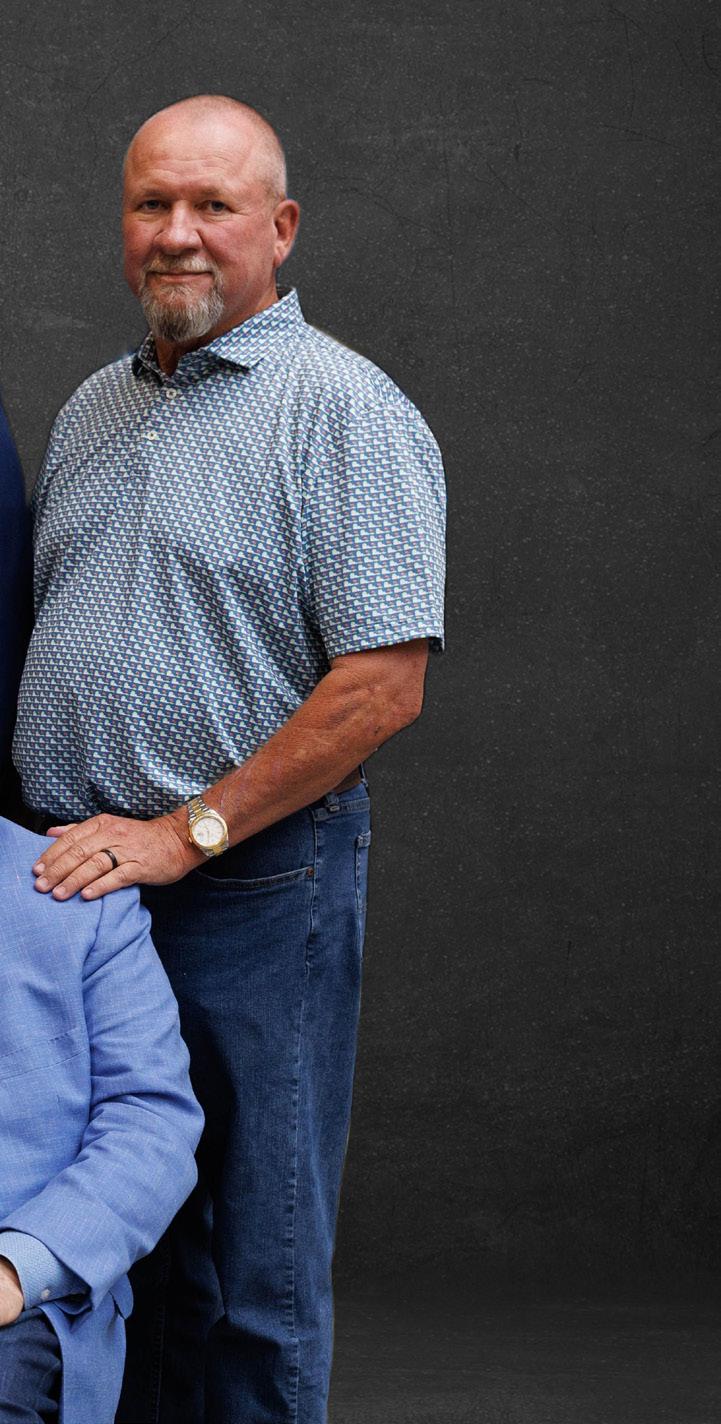
and community guide our operations,” he asserts.
A FAMILY AFFAIR
As a family-owned company, Saulsbury takes pride in maintaining over 90 percent repeat business with a large proportion of its clients.
Founded as Saulsbury Electric Co. in 1967, the company underwent rapid initial evolution from its humble beginnings.
By the 1980s, client demand eventually led to the business expanding into general construction through Saulcon General Construction, before evolving into a full EPC provider in the 1990s with Saulsbury Engineering and Construction.
INDUSTRIES SERVED BY SAULSBURY
As a leading full-service EPC company, Saulsbury provides its services to heavy industrial and renewables clients nationwide, delivering comprehensive integrated solutions.
With over five decades of expertise across a broad range of projects, the company can achieve maximum efficiency and minimum downtime for clients. The industries it serves include:
OIL AND GAS – Saulsbury’s bread and butter, it has established an outstanding reputation for effective execution and project delivery in the oil and gas sector with expertise in terminals, compression, tank batteries, pipelines, slug catchers, pump stations, and more.
GAS PROCESSING AND TREATMENT – Many clients look to Saulsbury for turnkey EPC support as well as focused services in cryogenic gas processing, amine gas treating, dehydration, condensate stabilization, and more.
CARBON DIOXIDE (CO2) – Saulsbury provides industry-leading support to the design and construction of CO2 processing facilities, covering the entire lifecycle from the source field through to transportation, injection, and recovery.
REFINING AND PETROCHEMICALS – The team offers turnkey support for plant reliability, productivity, and process safety projects in the petroleum refining industry with capabilities from engineering and design through to start-up and commissioning.
RENEWABLES – Saulsbury strategically collaborates with key partners to offer EPC solutions in this space, constructing renewable resource or alternative fuel projects including solar power generation, battery storage, hydrogen, carbon capture, and renewable natural gas facilities.
AGRICULTURAL AND FOOD PROCESSING – Whether clients require small modifications to existing facilities or full integration of new process units and grassroots facilities, Saulsbury offers support from balance of plant engineering through to start-up support.
MINING AND METALS – The company provides client support for ore processing, cement, aggregate, and crushing - including auxiliary-related projects such as acid plants, water treatment, control systems, and related infrastructure.
CHEMICALS, SPECIALTY CHEMICALS, AND FERTILIZERS – Saulsbury offers a complete range of EPC solutions, working in close collaboration with industryleading partners for the technology and process integration requirements for these complex projects, including polymers, olefins, and agricultural chemicals and fertilizers, to name a few.
WATER TREATMENT – Comprehensive industrial water treatment services are tailored to client requirements, inclusive of oil and gas field applications and municipal projects.
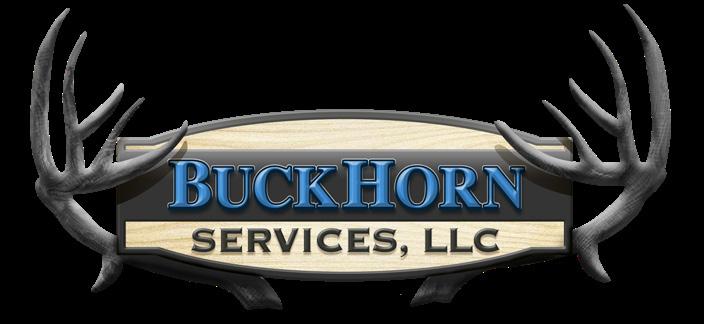
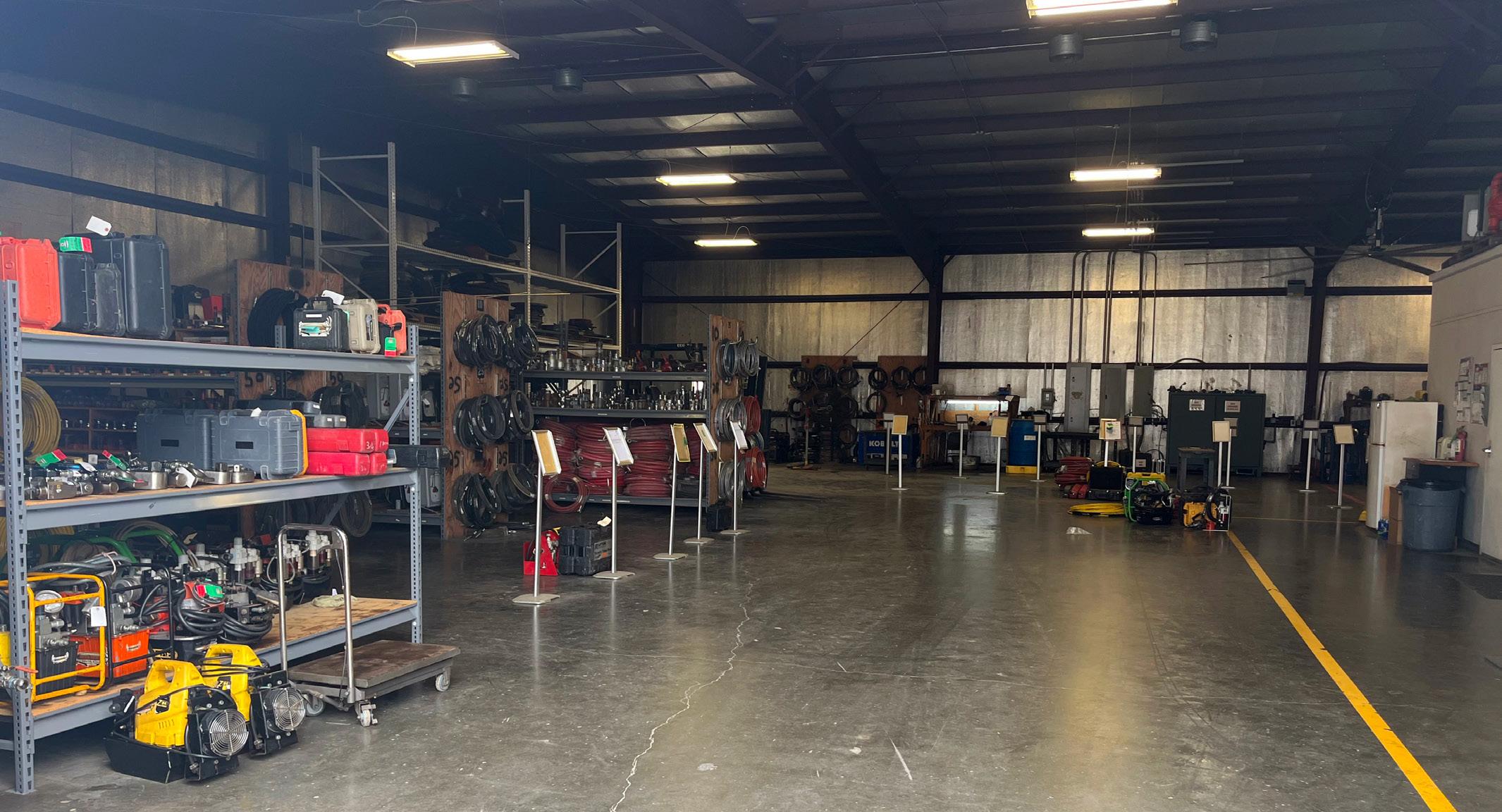
QUALITY PRIDE EXCELLENCE
INTRODUCTION TO BUCKHORN
BuckHorn Services and BuckHorn Rentals are here to provide you with unparalleled expertise in technical bolting, pressure testing, field machining, pipeline maintenance, valve repair services, and so much more for a truly seamless and reliable experience
Buckhorn Services started with very humble beginnings as a small rental company owned and operated by two good ole boys from the bayous of South Louisiana.
What started small soon grew into a multimillion-dollar business that now spans two states with locations in Houma, LA, Gonzales, LA, and Midland, TX.
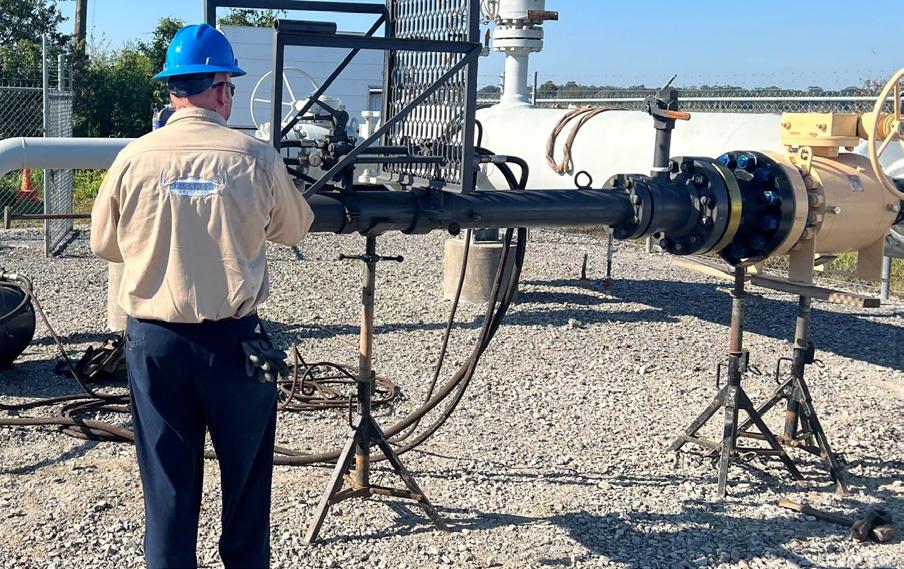
Within Buckhorns’ three locations, they have created multiple business units. These business units are experienced in providing technical bolting, pressure testing, field machining, Hot Tapping, pipeline maintenance, and valve repair services in the Upstream, Midstream, and Downstream Markets.
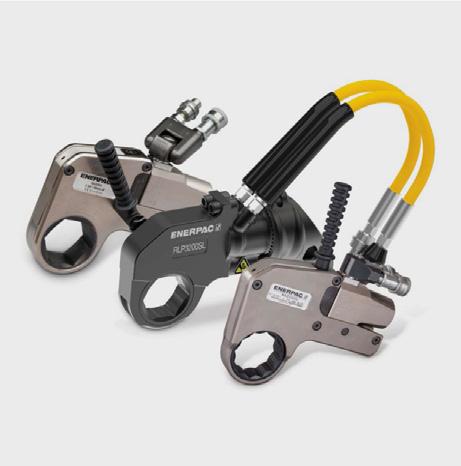
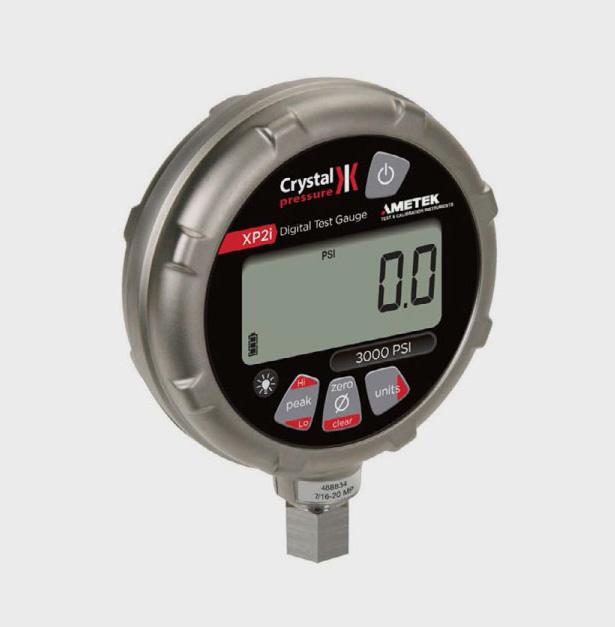
Buckhorn can provide experienced professionals to manage your project from inception to commissioning, providing traceable data to meet any QA specification.
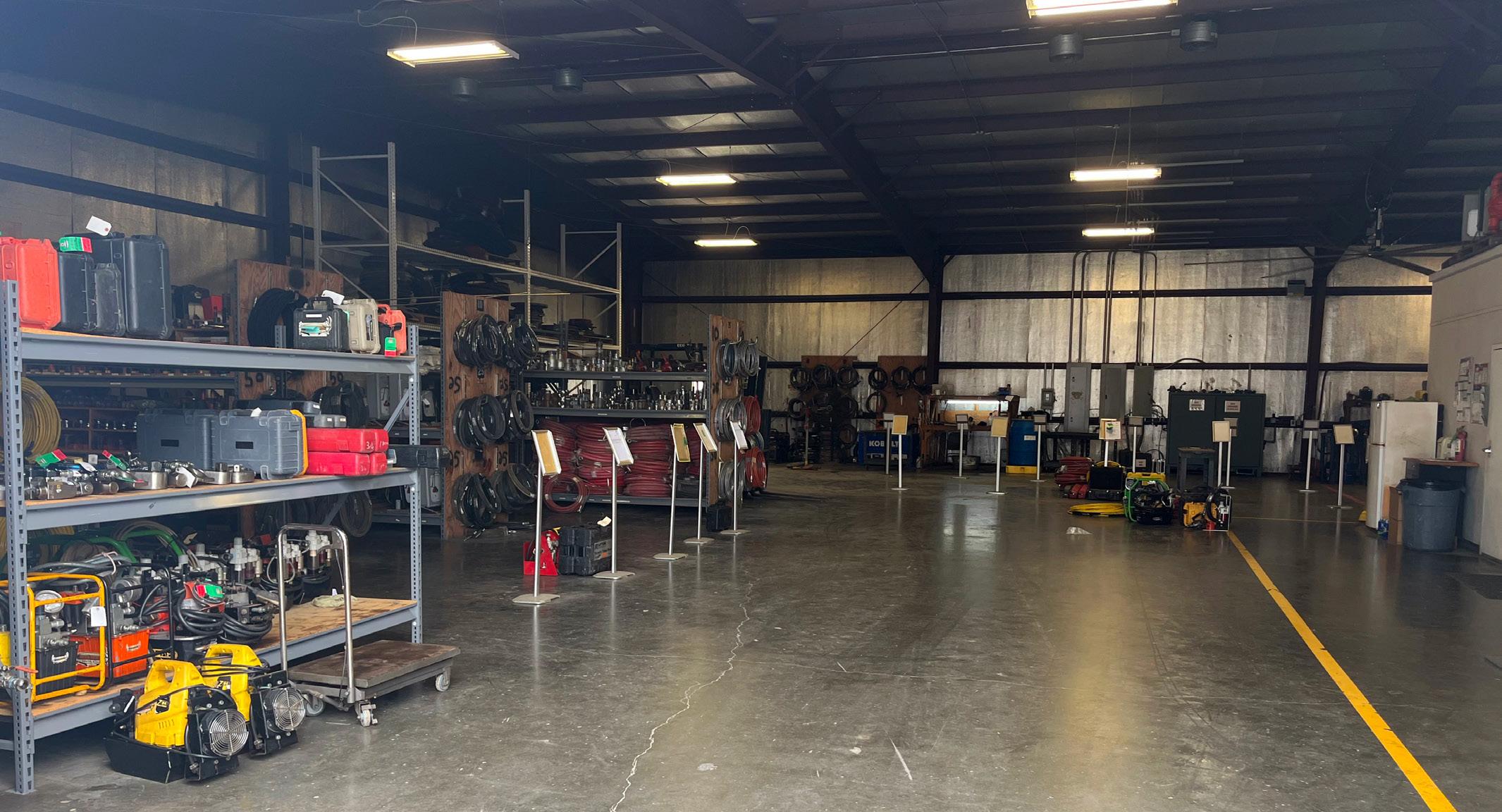
BUCKHORN SAFETY
Buckhorn has established a process for involving employees at all levels within the organization, measuring health, safety, and environmental (HSE) performance, reviewing issues, identifying improvement areas and best practices, managing incidents and their resulting actions, and communicating the effectiveness of the Health, Safety, and Environmental Management System.
Communication is critical to the overall success of our process, providing quality engineering and management practices and maintaining a safe working environment.
SKILLS AND KNOWLEDGE
Every Buckhorn employee undergoes extensive training in specialized areas, safety and accident prevention, followed by competency tests/operator qualification testing, to ensure that each new hire meets Buckhorn standards. Buckhorn employees specialize in Hydro and Pneumatic Testing, Double Block and Bleed Isolation and Localized Weld Testing, Field Machining, Flange Refacing, Line Boring/ Shaft Turning, Key Groove Cutting, Drilling and Tapping/ Stud Removal, Portable Milling, Hot Tapping/ Line Stop and Line Freezing, Metal Disintegration, Pipe Cutting and Beveling, Controlled Bolt Torquing and Tensioning, Millwright Services, Valve Repair and Preventative Maintenance, and Hydraulic Flushing.
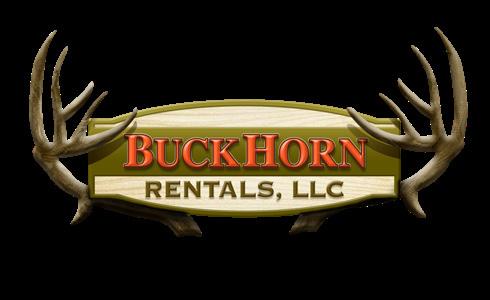
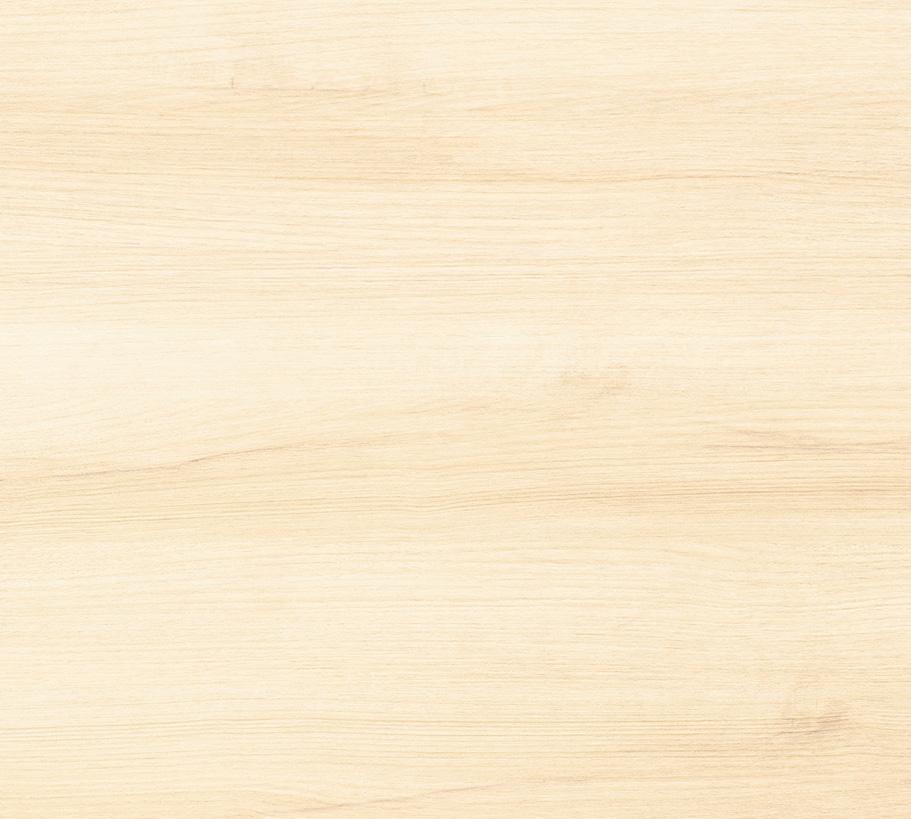

BUCKHORN’S CORE VALUES FOR SERVICES AND RENTALS
Our core values are at the center of everything we do. Buckhorn is committed to conducting business with a high moral standard.
Each value is equally important to the success of the company. Safety and the protection of our most important asset –our employees are at the core of our beliefs.
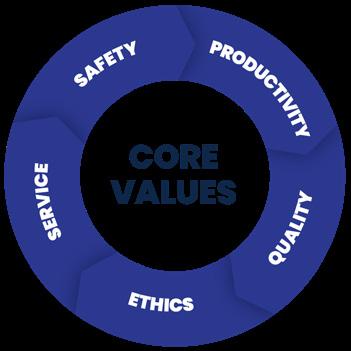
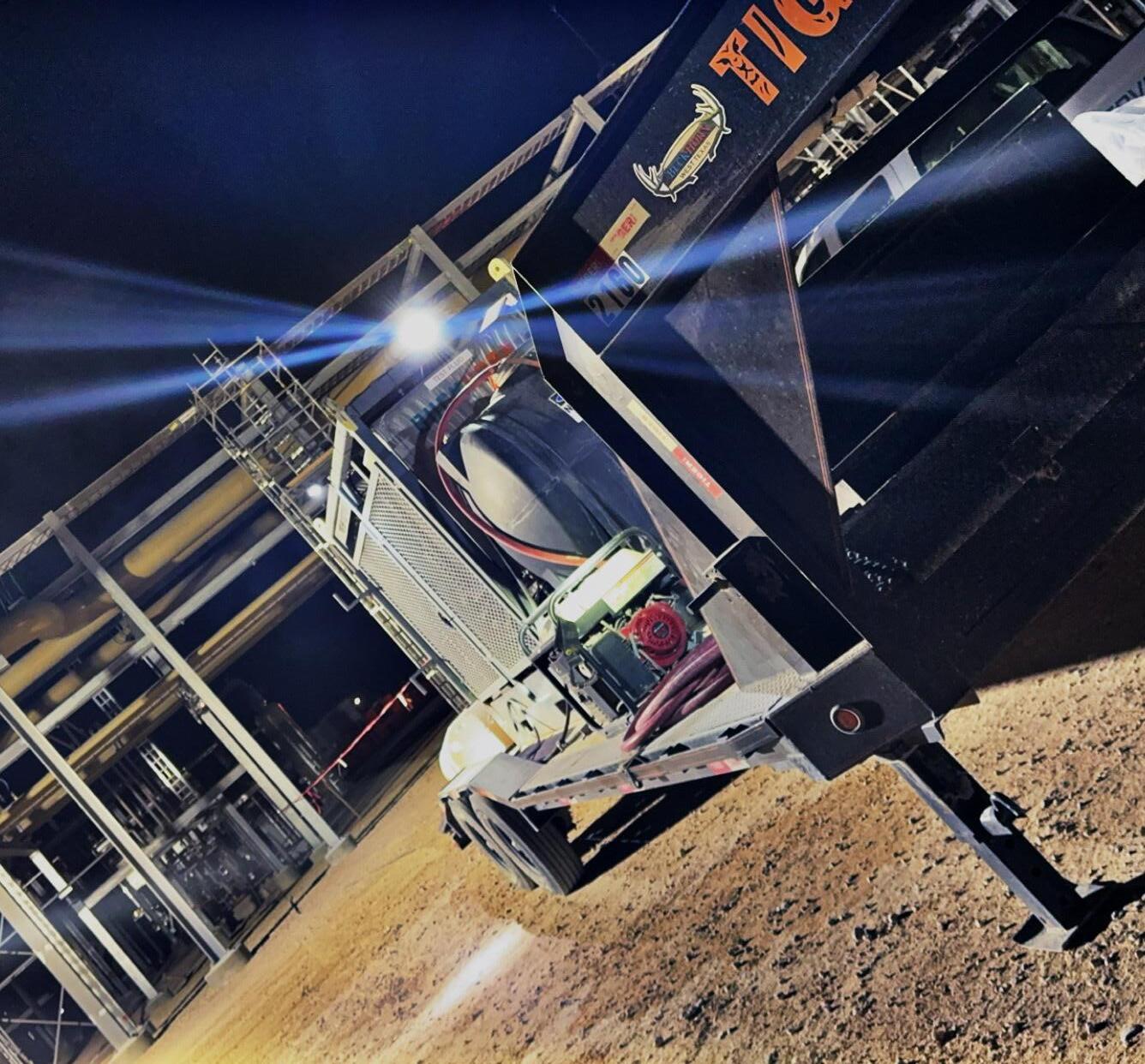
THE FUTURE OF BUCKHORN
Buckhorn’s goal moving forward is to create partnerships with all of our customers and contractors to pursue long-term projects and provide support, as well as grow our footprint in the Midland/Odessa area and beyond.
Buckhorn’s pledge is to perform at a high level with efficiency and integrity. Buckhorn looks forward to exceeding your expectations soon!
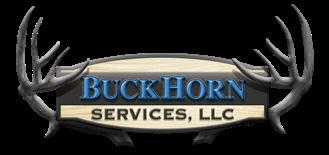
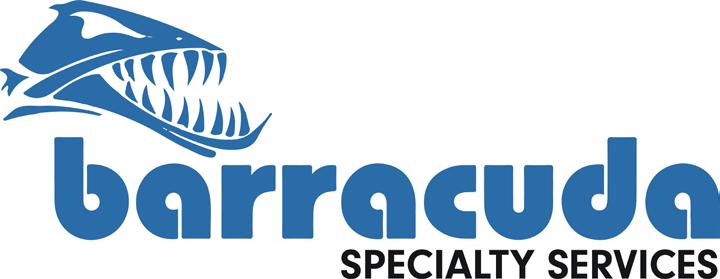
INSPECTION IS ONLY HALF OF THE JOB
AtBarracuda Specialty Services, we believe inspection is just the beginning. Our mission is to provide our clients with innovative inspection solutions while nurturing an environment that advocates safe, proficient, and virtuous performance. This drives our commitment to delivering comprehensive, actionable solutions that go beyond simply identifying problems. We combine elite technical expertise with cutting-edge technology to support critical infrastructure, minimize downtime, and enhance operational safety.
WHAT WE DO
Non-Destructive Testing (NDT)
Our certified technicians utilize proven NDT methods to evaluate materials and structures without causing damage. From pipelines to pressure vessels, we deliver precise assessments that help clients maintain asset integrity, ensure regulatory compliance, and achieve operational excellence across demanding industries.
Advanced Inspection Services
Barracuda sets the standard for advanced inspection with state-of-the-art tools and deep technical expertise. Our advanced services include:
• Phased Array Ultrasonic Testing (PAUT) and Time of Flight Diffraction (TOFD) for highprecision flaw detection and sizing
• Corrosion Mapping to visualize wall loss and monitor asset health over time
• 3D Laser Scanning for high-resolution spatial analysis and deformation monitoring
• Eddy Current Applications for surface and nearsurface crack detection in conductive materials
• Computed and Digital Radiography (CR/DR) for detailed internal imaging with minimal exposure risk
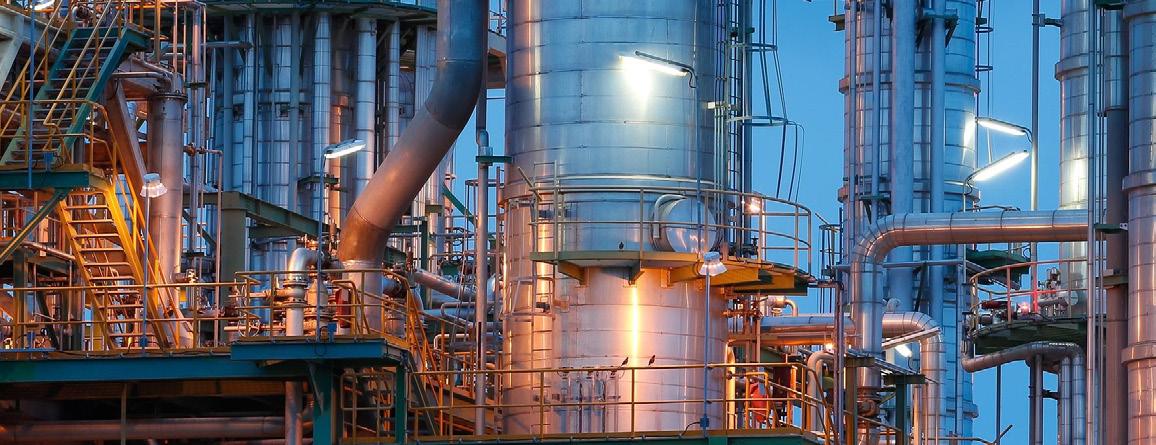
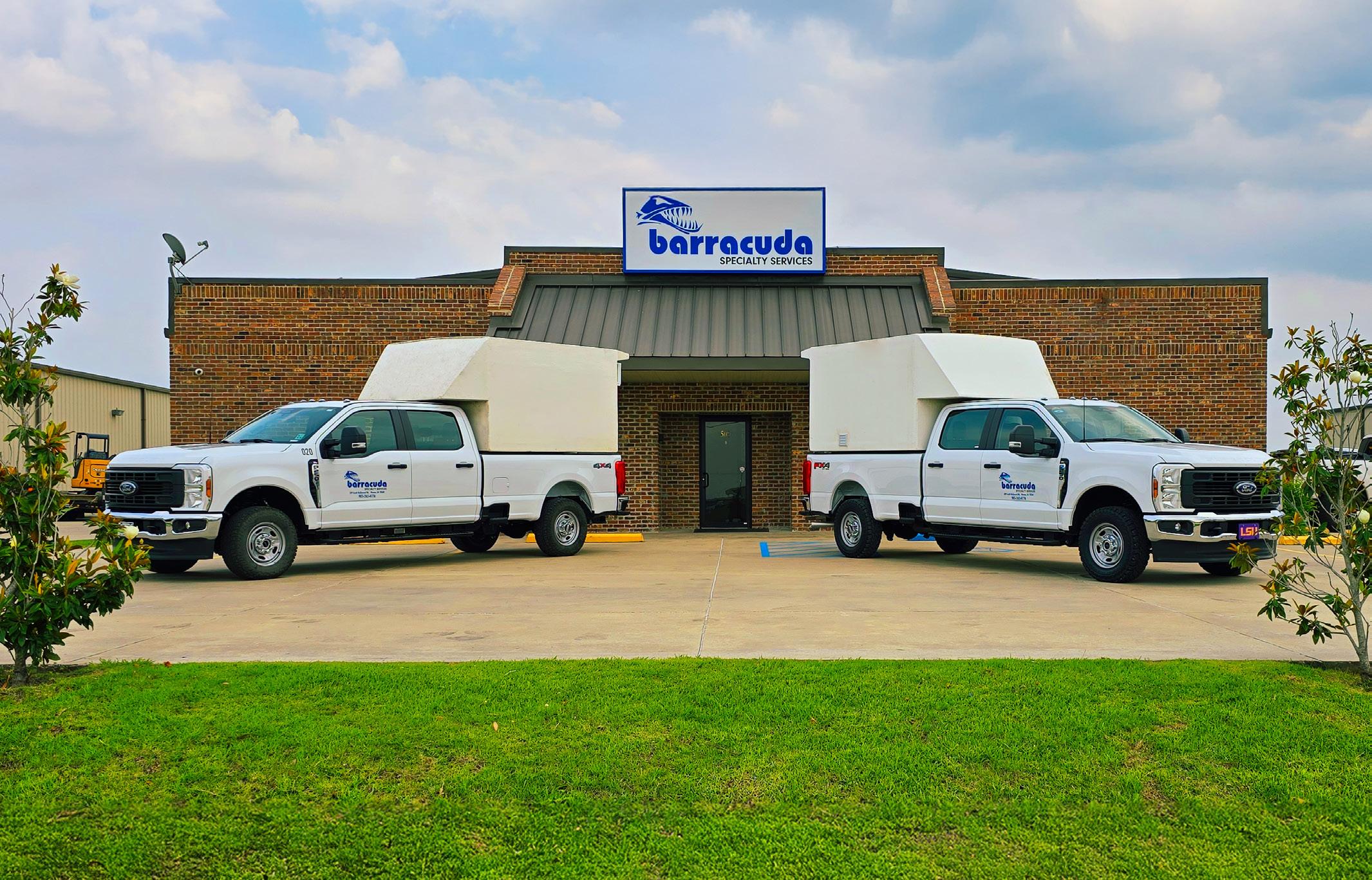
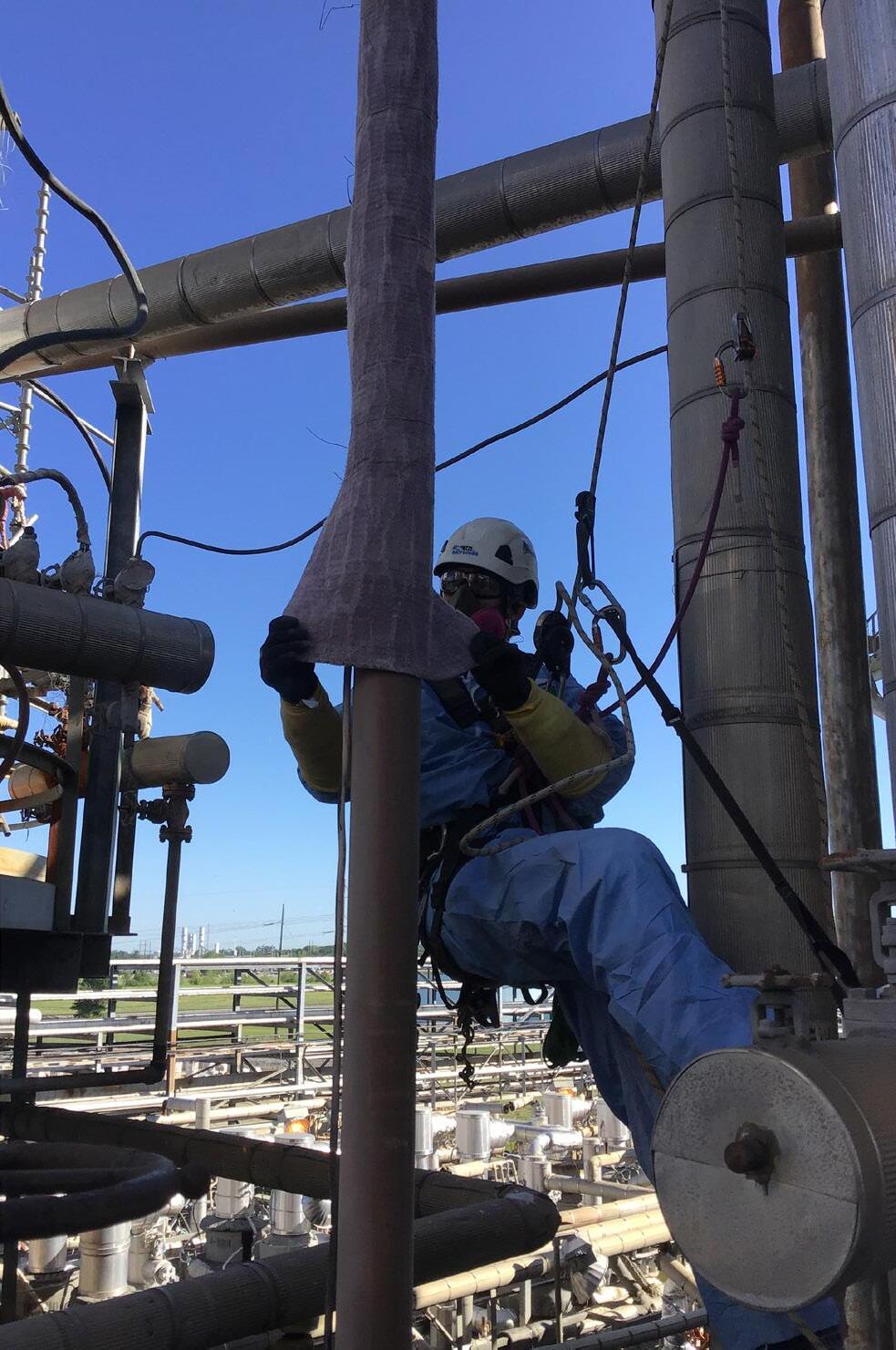
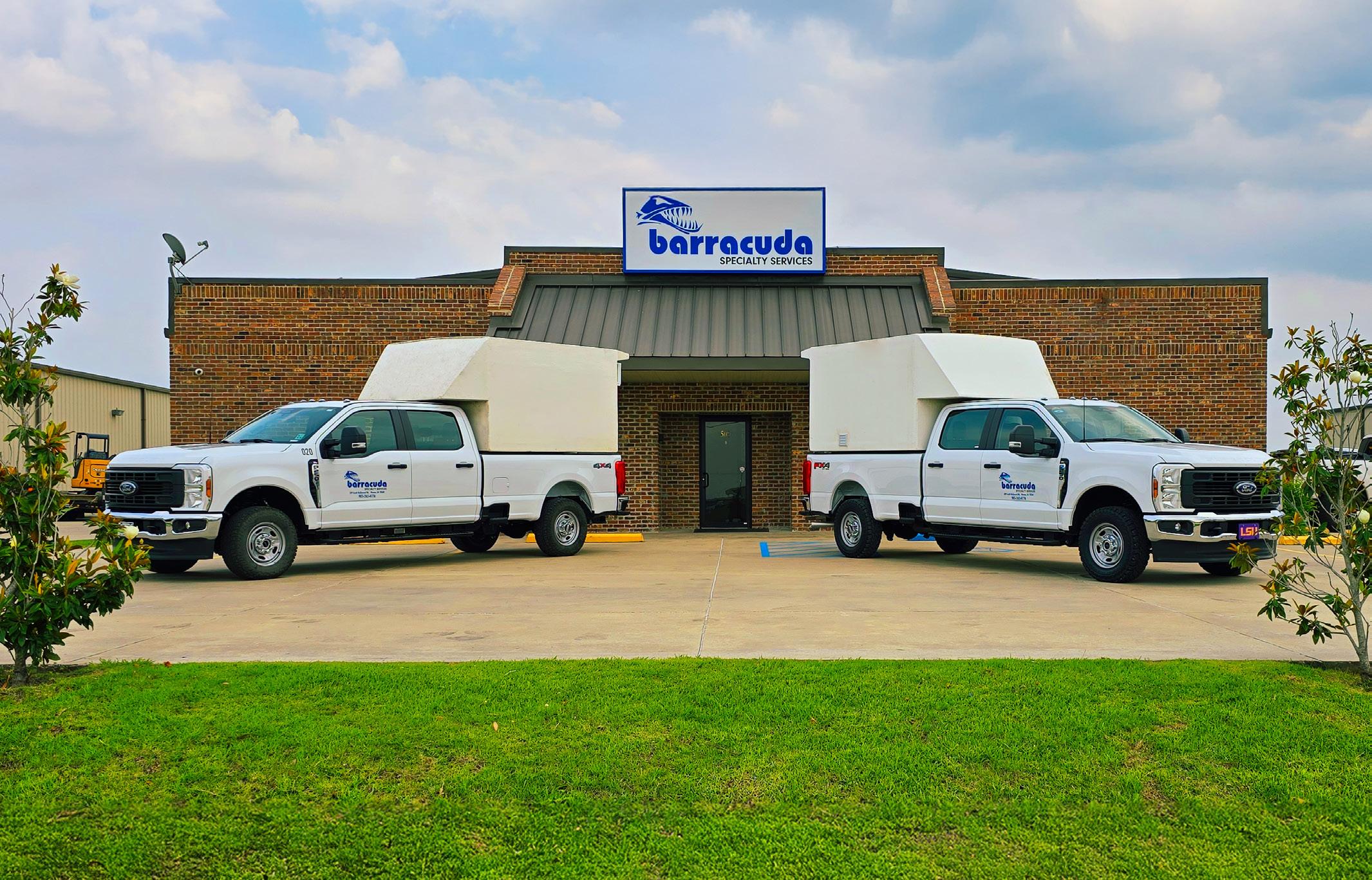
Rope Access Services
We specialize in delivering safe, efficient solutions for hard-to-reach and high-risk environments. Our rope access capabilities include:
• Rope Access Inspections
• Rope Access Maintenance
• API Visual Inspections (internal and external)
• Insulation and Painting
• Welding (R-stamp certified)
• Pipe Fitting
• Torquing of Piping and Equipment
• Ironwork
• Steam Leak Repairs
• Piping Demolition
• Electrical Services (wire pulling and cable tray installation)
• Bull Rigging (handling all types of assets)
• Sandblasting and Painting
Our rope access teams are highly trained to perform inspection and maintenance work with minimal disruption and rapid setup, eliminating the need for scaffolding or heavy lift equipment. On average, rope access solutions deliver cost savings of 40% to 80% compared to traditional methods.
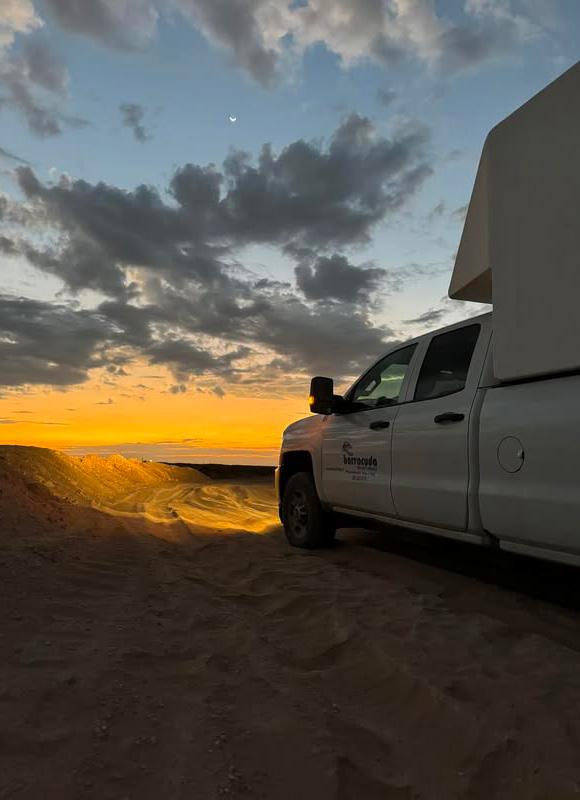
Why Barracuda?
At Barracuda, we don’t just find problems—we solve them. From top-tier inspections to hands-on support, we’re more than a service provider; we’re your solutions partner. Whether it’s a conventional inspection or a complex corrosion analysis, we have the experience, equipment, and expertise to get the job done right.
At BSS, we understand that your work is missioncritical. We proactively manage our operations and resources to ensure shared success. You can count on us to deliver the highest standards of quality, efficiency, and reliability, even on the most complex projects and most demanding production schedules.
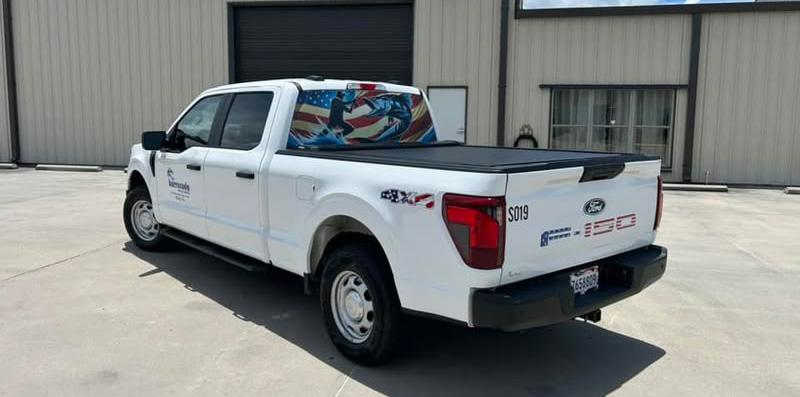

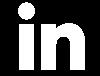
“In 2012, we unified these entities under the Saulsbury banner to streamline our operations,” Matt informs.
Today, the company supports clients across the country by providing expert services in engineering, general construction, electrical and instrumentation work, field services, structural and piping module fabrication, insulation, and scaffolding.
Saulsbury supports a broad scope of industries, including oil and gas, gas processing and treatment, nitrogen rejection, CO2 management, renewable energy and infrastructure, water treatment, liquified natural gas (LNG), power, refining and petrochemicals, agriculture and food processing, mining and metals, chemicals, specialty chemicals, and fertilizers.
Headquartered in Odessa, Texas, the company operates across multiple locations in the state, including
“THE WORLD WE LIVE IN TODAY IS A FAR CRY FROM WHEN MY FATHER RAN HIS BUSINESS WITH JUST A HANDSHAKE. EVEN NOW, HE SHARES STORIES AND ADVICE FROM THOSE EARLY DAYS AND OFTEN FOLLOWS UP WITH – ‘IF I HAD KNOWN BACK THEN WHAT IT TAKES TO DO BUSINESS THESE DAYS, I PROBABLY WOULD’VE CLOSED UP SHOP A LONG TIME AGO’”
– MATT SAULSBURY, CEO, SAULSBURY
Corpus Christi, Abilene, Houston, and Port Arthur, as well as a fabrication facility in Henderson.
Elsewhere, it also operates in Bismarck, North Dakota; Carlsbad, New Mexico; and Tulsa, Oklahoma, with a staff base of over 2,000.
“We self-perform the majority of our work and are licensed across most of the US,” he shares.
With a strong track record of
delivering integrated solutions for complex capital projects, Saulsbury stands out from the crowd.
Its comprehensive portfolio of in-house functions eliminates the need for extensive subcontracting, meaning the company not only provides customers with direct access to its 50+ years of expertise but also the ability to control the safety, quality, schedule, and cost of projects.
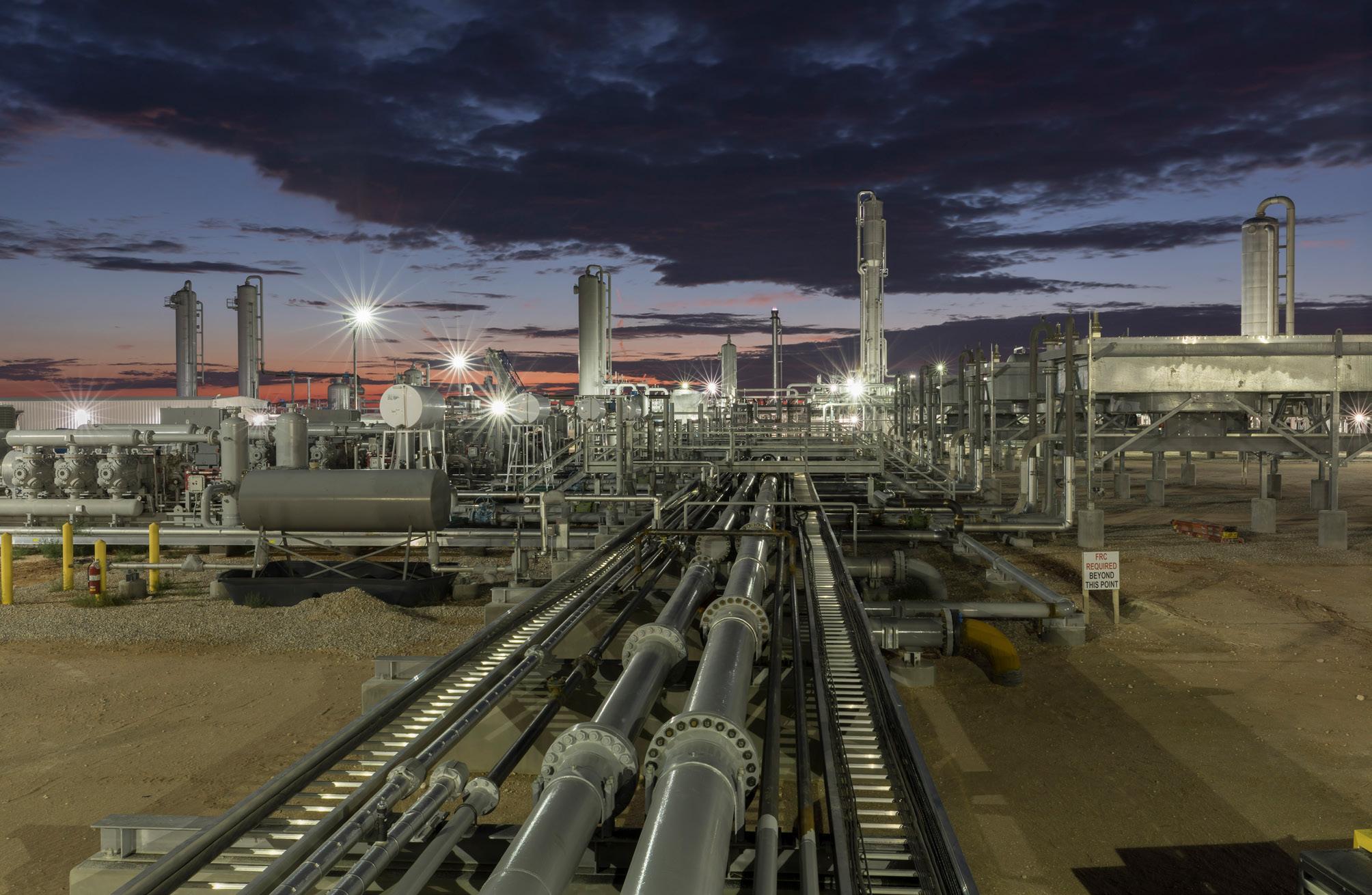
Proudly recruiting the best talent in the industry, Saulsbury’s experienced teams are known for maintaining the highest standards and delivering exceptionally safe projects on an accelerated timetable.
While the company’s roots are in oil and gas, it has also begun to strategically diversify its portfolio.
“Our increased focus on renewables and non-oil and gas sectors has strengthened our resilience against industry downturns,” Matt reveals.
As such, Saulsbury’s expertise in industrial construction has enabled the company to successfully enter new and emerging markets by applying proven, transferable skills and methodologies.
SAULSBURY’S AWARDS
A frontrunner in more than one area, Saulsbury is honored by the awards it receives. The company has recently been recognized not only for its work in renewable energy infrastructure, but also the core value that it places above all else – safety.
• Saulsbury was recently listed on Solar Power World’s Top Solar Contractors list, ranking 32nd nationwide. These accolades celebrate the top solar installers in the utility, commercial, and residential sectors, and are based on the kilowatts installed in the preceding year.
• In 2024, Saulsbury was recognized on Engineering News-Record’s 2024 Top 400 Contractors and Top 20 Petroleum Contractors lists.
• The company was proud to receive the Safety Merit Award, Safety Milestone Award, Safety Improvement Award, and Community Advancement Award from the North Dakota Safety Council in 2025.

BOLSTERING THE NATION’S OIL AND GAS
In the early 2000s, Saulsbury experienced a period of significant growth as shale development took off in the region, allowing it to support the industry with natural gas cryogenic processing facilities, power generation infrastructure, turbine and reciprocating compression facilities, and various gathering and production assets.
“Despite industry downturns, including the 2008 financial crisis, we remained disciplined and resilient,” Matt recalls.
The 2010s saw the US emerge as a dominant oil and gas producer and, by 2018, it regained its status as the world’s largest oil and natural gas supplier.
At the time, Saulsbury was executing major projects across the Permian, Midland, Eagle Ford, Bakken, Haynesville, Barnett, Niobrara, Anadarko-Woodford, and Utica Basins, further bolstering the nation’s impressive oil and gas footprint. Since then, the industry has faced
persistent challenges, with the onset of the COVID-19 pandemic serving as a particularly significant setback.
However, the company’s resilience and its commitment to retaining talent allowed it to recover from the aftermath of COVID-19 swiftly, returning to business as usual within a year.
Having said this, post-pandemic supply chain disruptions continue to be a challenge for Saulsbury –particularly where procuring critical equipment and electrical components is concerned.
Elsewhere, industry consolidation through mergers and acquisitions has presented opportunities, with the company’s strong financial position, leading safety programs, operational expertise, and world-class field teams enabling it to maintain and expand beneficial relationships in this regard, such as those with supermajors.
“As we move forward, we are also diversifying our portfolio to support emerging markets and new opportunities beyond traditional oil and gas,” Matt reminds.
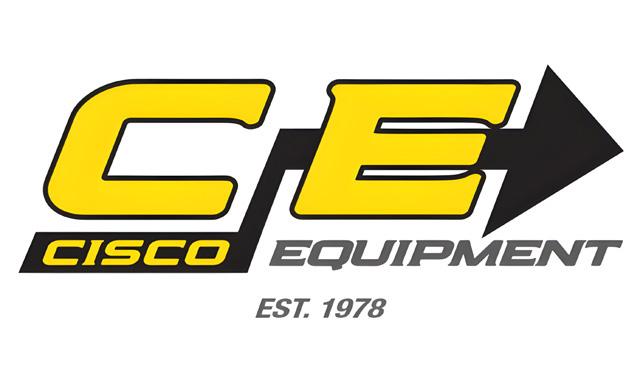
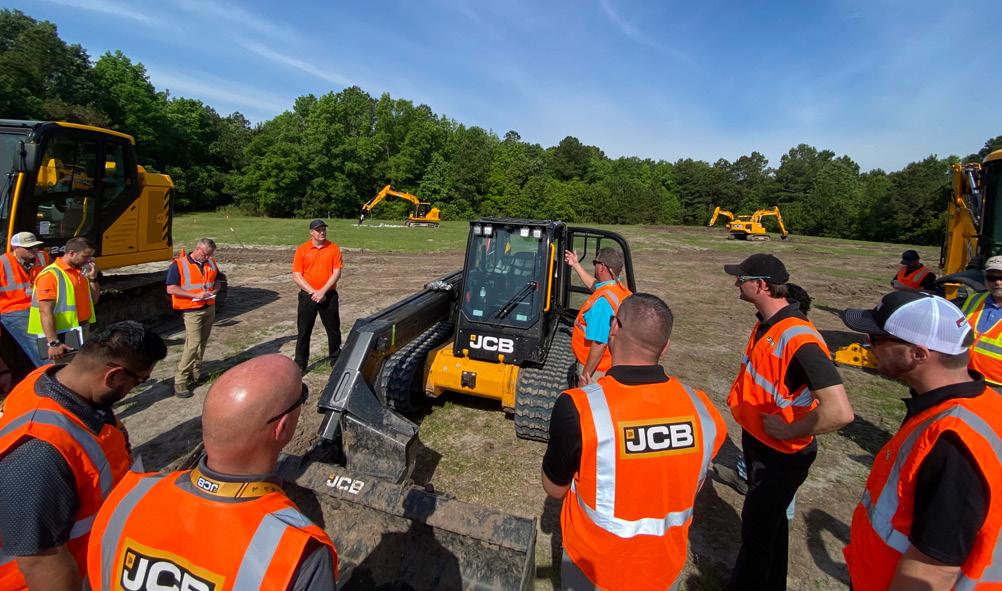
Global Expertise Local Solutions
1. Briefly introduce us to Cisco Equipment.
Cisco Equipment (Cisco) is a trusted provider of heavy equipment rentals, sales, service, and parts, with operations focused in West Texas and Southeastern New Mexico. Headquartered in Odessa, Texas, with administrative support co-housed in Dallas, we are strategically positioned to support the energy, construction, and infrastructure sectors at the heart of the Permian Basin.
In January 2025, we made the strategic decision to close our Fort Worth and Austin branches. This decision was driven by a renewed focus on our core customer base and long-term partners in West Texas. With deregulation and oil-friendly conditions under the current administration, we felt it essential to ensure none of our customers were waiting on the parts, service, or equipment they’ve come to expect from
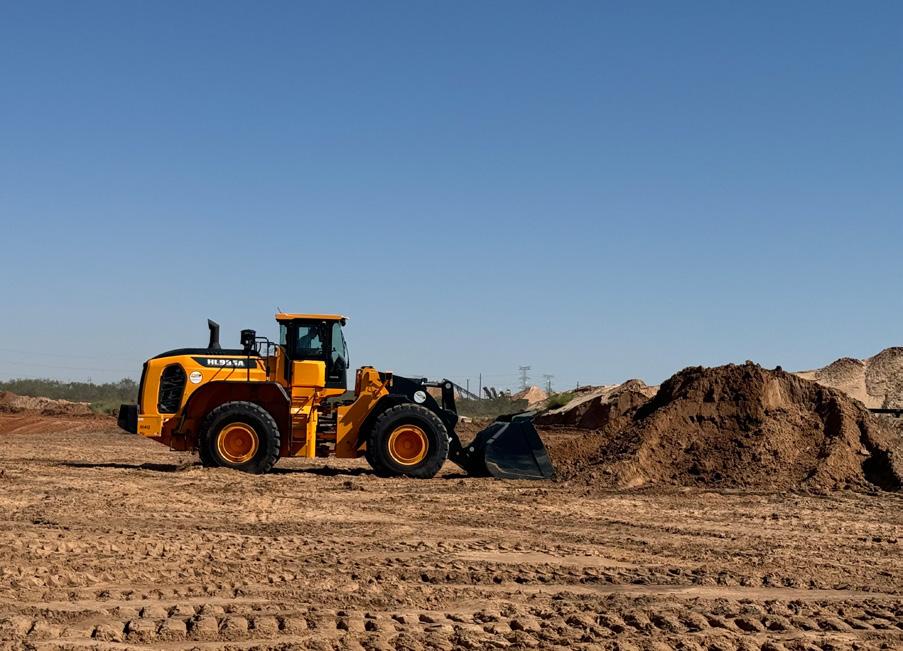
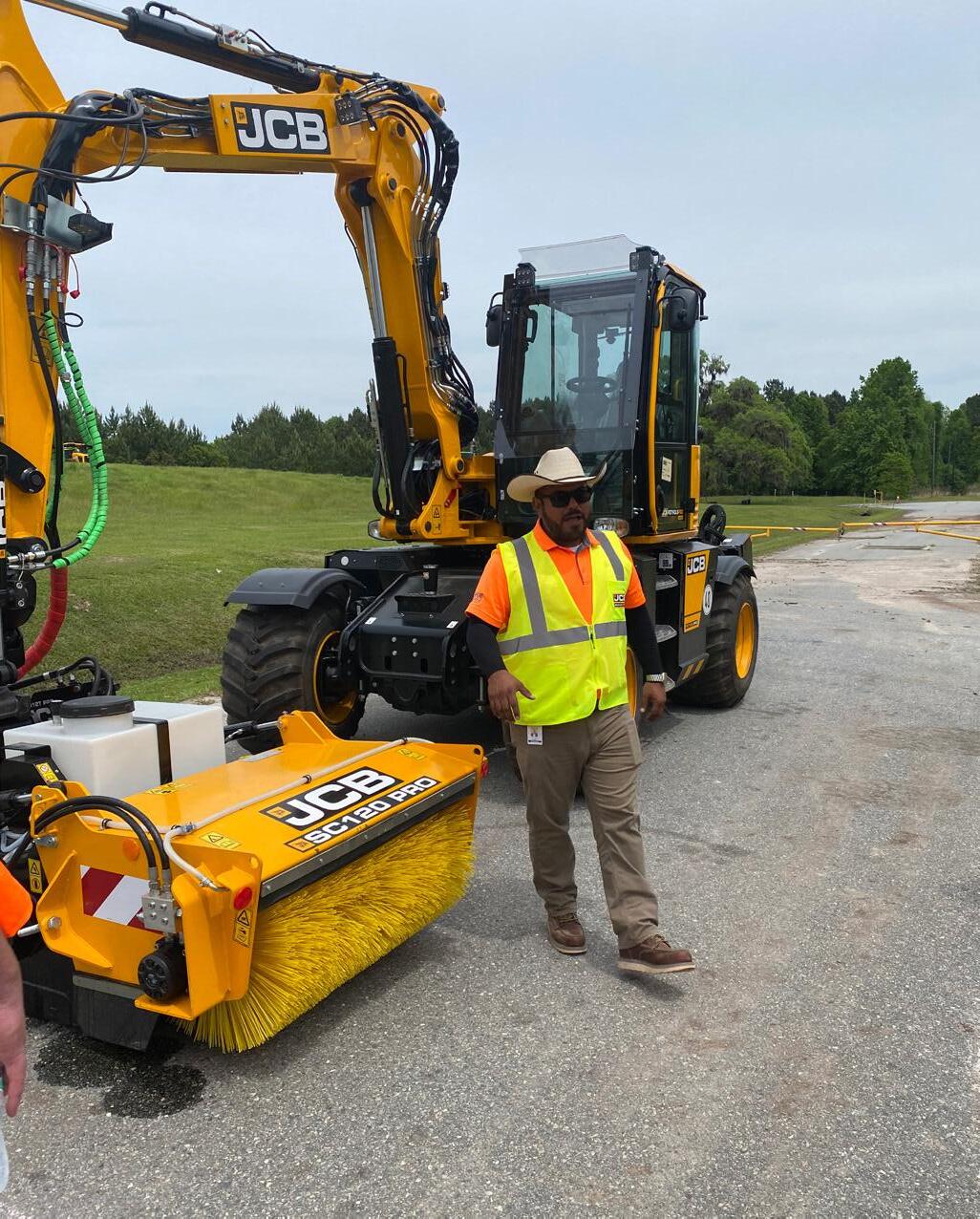
Cisco. Concentrating our assets locally has allowed us to deliver even stronger, faster, and more personalized service.
Cisco employs professionals dedicated to delivering uptime-focused solutions, backed by a rental fleet that includes excavators, loaders, telehandlers, backhoes, and specialty machines.
Our team is deeply experienced and locally engaged, working closely with clients ranging from contractors and municipalities to energy EPC leaders like Saulsbury.
2. What are some of the ongoing or recent projects that you are most interested in showcasing?
We are proud of our role in supporting large-scale energy and infrastructure projects across West Texas, particularly those led by key companies like Saulsbury.
Our team has played a central role in providing tailored rental solutions, field support, and maintenance programs for high-priority projects where reliability and responsiveness are critical.
We’re also showcasing our investment in predictive fleet return technologies, which allows us to anticipate equipment availability more accurately and redeploy assets without delay. Preventative maintenance has become a cornerstone of ourapproach - keeping machines in top shape and minimizing unplanned downtime in the field.
Additionally, Cisco has made a significant technological leap through our partnership with CDK Global and the
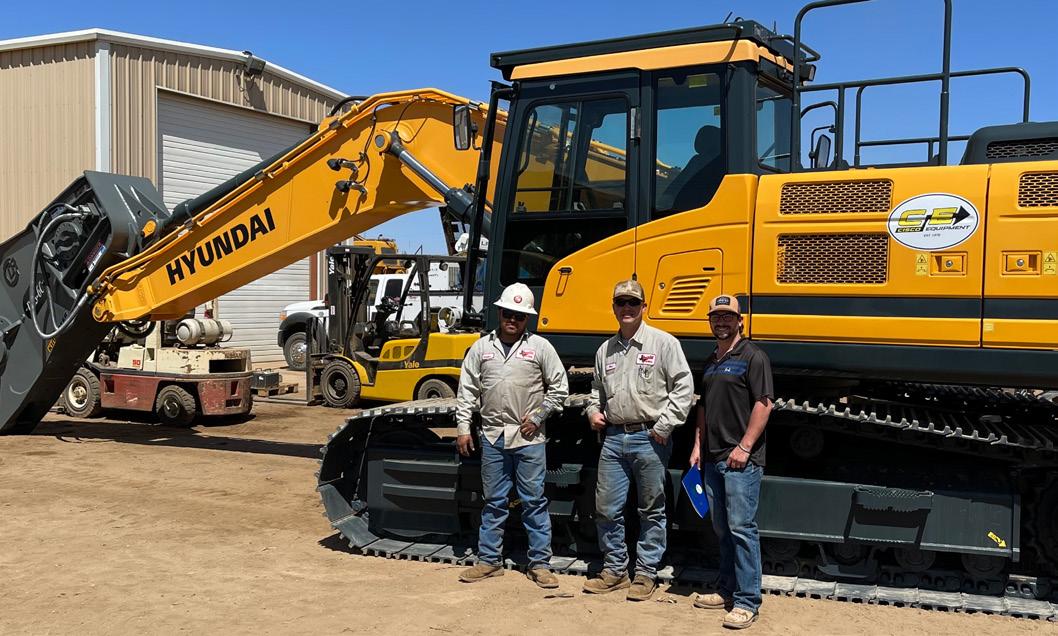
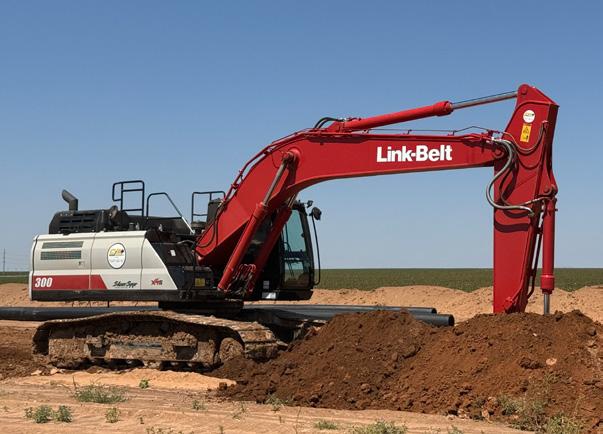
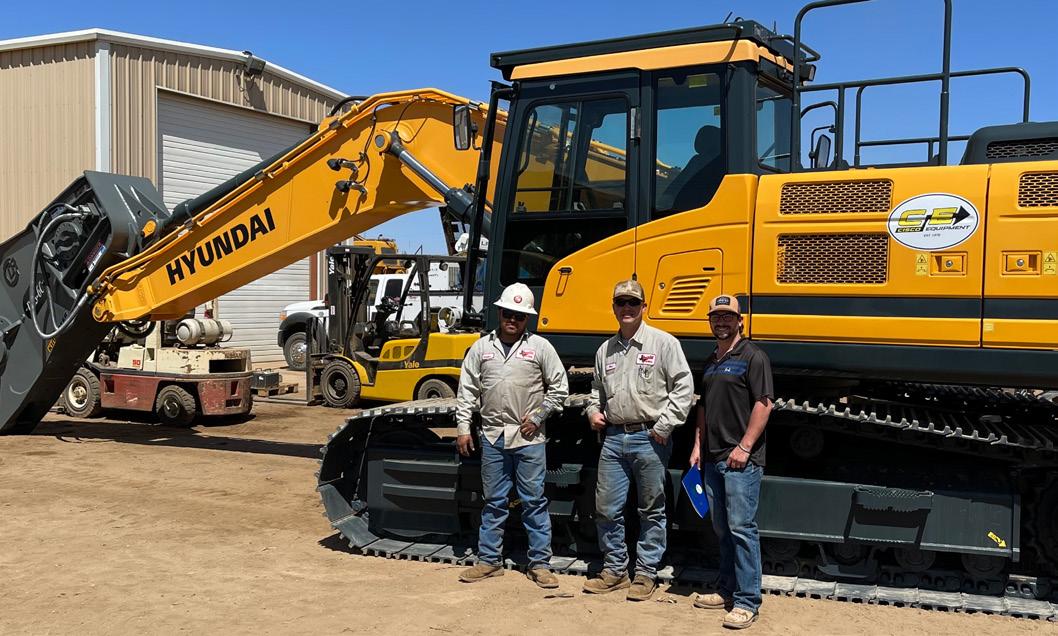
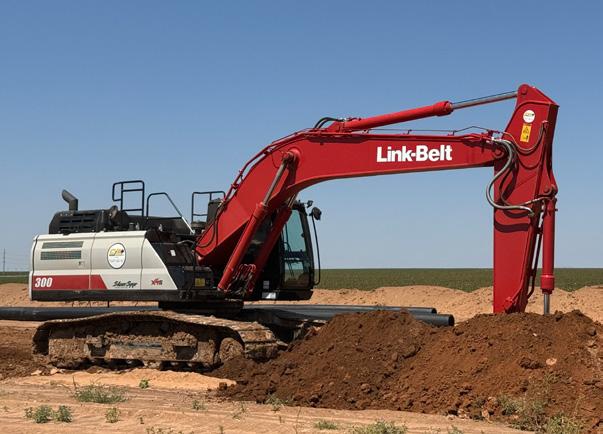
launch of the MyDealer portal. This system provides our customers with a user-friendly interface to manage their entire Cisco experience - from viewing telematics data across all manufacturers, to requesting services, paying invoices, renting or off-renting machines, and ordering parts. Whether on a jobsite or in the office, our customers now have seamless digital access to the support and information they need.
3. What, for you, differentiates your business from the competition?
Cisco’s biggest differentiators are our mindset and our methods: we focus on prevention, prediction, and true partnership. Our service model is designed to proactively identify issues before they cause downtime. We’re committed to keeping machines running, and our field technicians are strategically deployed to ensure fast, expert service in remote or high-demand areas. While our physical footprint is now centered in West Texas, our operational reach remains broad.
Through our partnerships with trusted dealers across the state, along with telematics-enabled fleet management and mobile field service capabilities, we can support customers throughout Texas when needed. Our strength lies in being locally focused and regionally capable. Most importantly, we work hand-in-hand with our customers to find customizable solutions. Whether it’s structuring custom rental packages, managing utilization data, or providing flexible terms on sales and trade-ins, we operate like a true business partner - not just another dealership.
4. Could you tell us about some of the major challenges faced within the industry and the business itself and then detail how these have been overcome?
One of the most persistent challenges in our industry has been the global shortage and delay of critical parts. Cisco has taken proactive steps to navigate this by building stronger relationships with OEMs, establishing
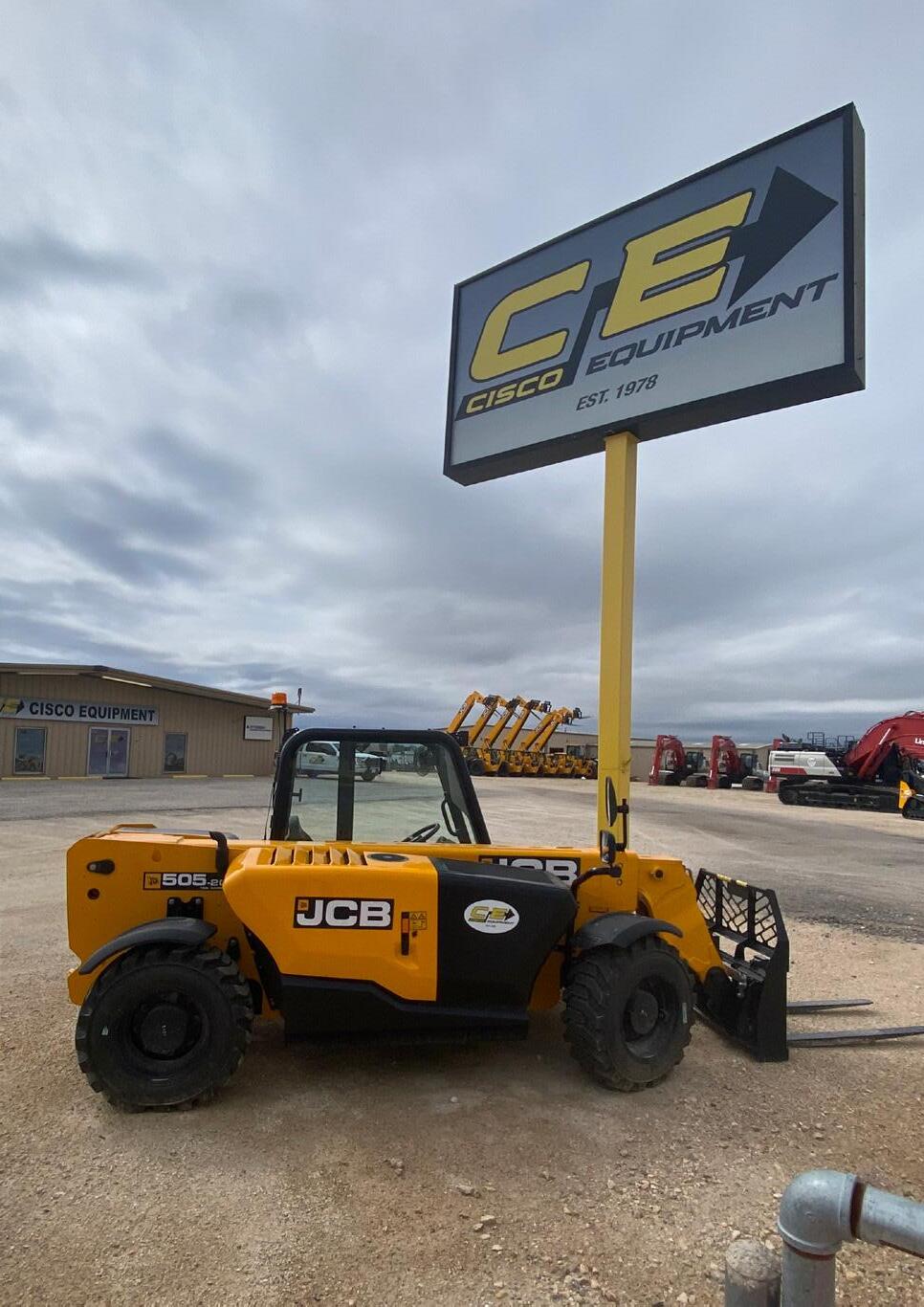
direct lines to critical components, and even pulling parts from our own fleet when necessary to keep customer equipment running. We’ve also expanded our collaboration with dealers outside of our core area, allowing us to source needed parts faster and support customers with minimal disruption.
Another key challenge has been the volatility of used equipment values, which can impact both our customers’ ability to trade or resell machines and our ability to structure long-term plans. Cisco addresses this by helping customers maintain strong residual value through preventative maintenance, proper utilization, and smart lifecycle planning. We offer tailored options for trade-ins and work closely with each client to transition them into a new fleet that better fits their evolving needs - often in ways that minimize cost while maximizing return on investment.
Rising interest rates have also created pressure for businesses that rely on financing. To ease that burden, we’ve centralized our retail finance efforts under a dedicated director, who works across multiple lenders to negotiate competitive rates by combining deal volume. This approach allows us to pass savings directly to our customers and structure more favorable financing operations - helping them continue to grow their operations even in a tighter financial climate.
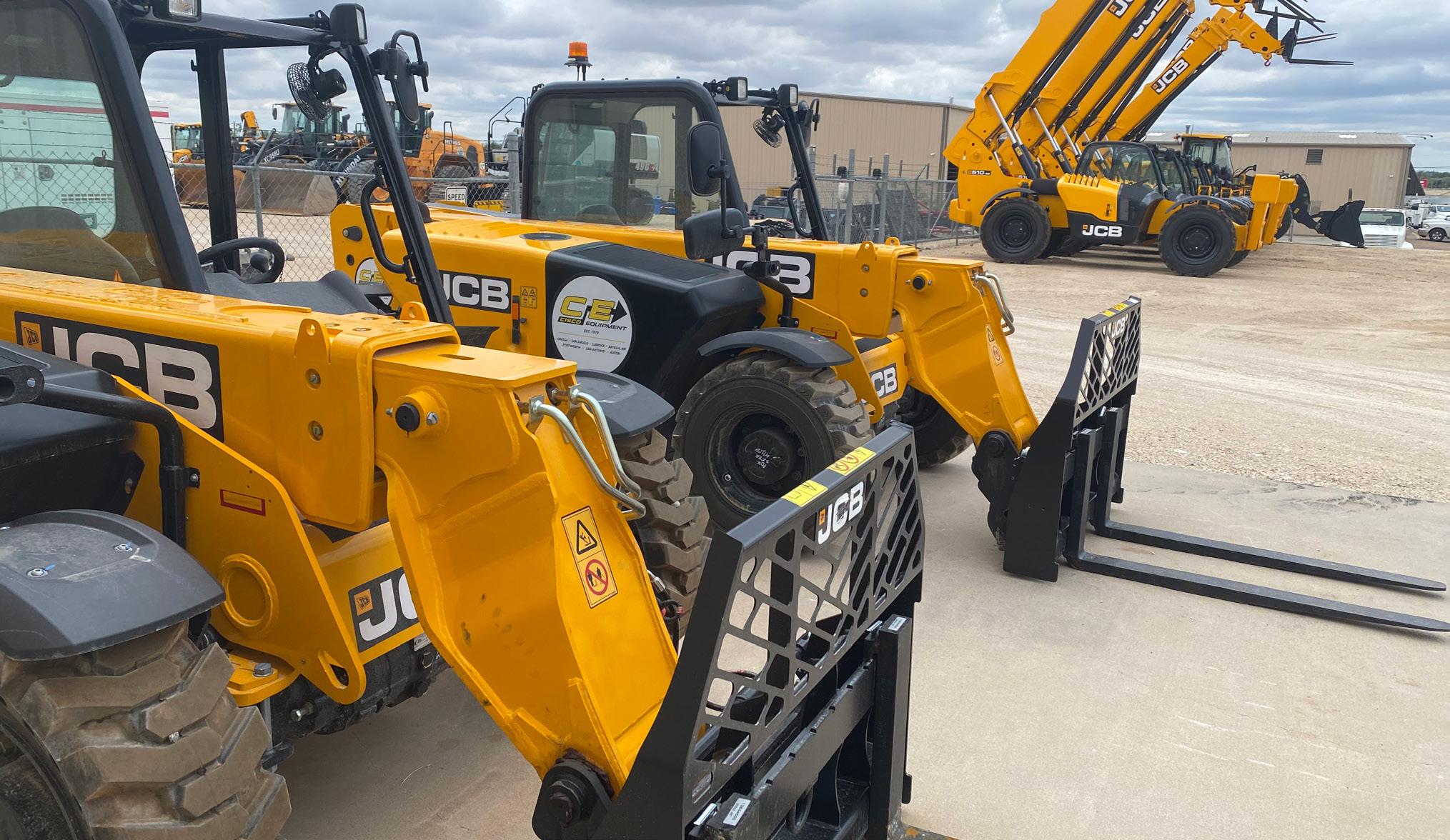
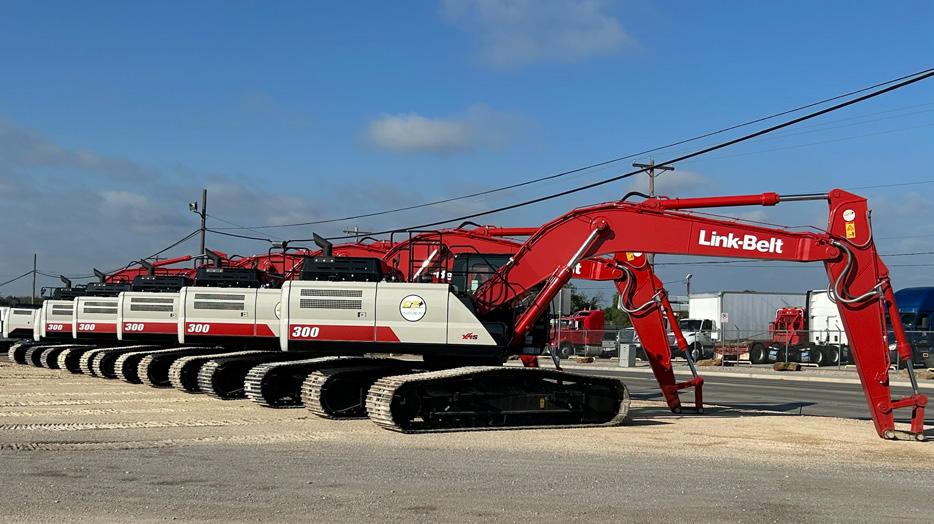
5. What are your major future ambitions going forward and how will these goals be achieved?
Looking ahead, our primary ambition is to deepen our commitment to West Texas and expand our influence in the broader Texas equipment landscape through strategic partnerships, better technology, and a laser focus on customer uptime.
We are investing in our digital infrastructure, with tools like MyDealer offering more visibility, more control, and more convenience to our customers.
We also plan to continue enhancing our technician network by participating in CTE and Apprenticeship Programs. By investing in people and tools that directly impact equipment performance, we’re ensuring our service capabilities remain best-in-class.
Our strong alignment with OEMs like JCB gives us the product support, warranty coverage, and inventory flexibility we need to stay competitive.
And by working with financial institutions like Comerica to explore refinancing and capital realignment, we’re positioning ourselves to make smart, long-term investments in our fleet and facilities.
6. Could you tell us more about any environmental or CSR initiatives that you have in place?
Cisco Equipment is proud of the role we play in supporting our communities and protecting the environment. On the environmental front, we operate a modern fleet that meets or exceeds Tier 4 final emissions standards and continually invest in newer, more fuel-efficient models. We also monitor machine idle time and promote emission-conscious practices for customers, helping them run greener job sites. All oils, filters, and fluids are recycled responsibly through trusted environmental vendors.
On the social side, Cisco is actively engaged in programs to support local trade schools, veterans’ programs to employ exiting military personnel with technical skills, and charitable initiatives with customer participation throughout West Texas.
7. What are you most proud of in relation to the company overall?
Above all, we’re proud of our people - the technicians, coordinators, sales professionals, and support staff who bring our commitment to life every day. Their dedication, expertise, and focus on doing the right thing for the customer is what keeps Cisco running at the highest level.
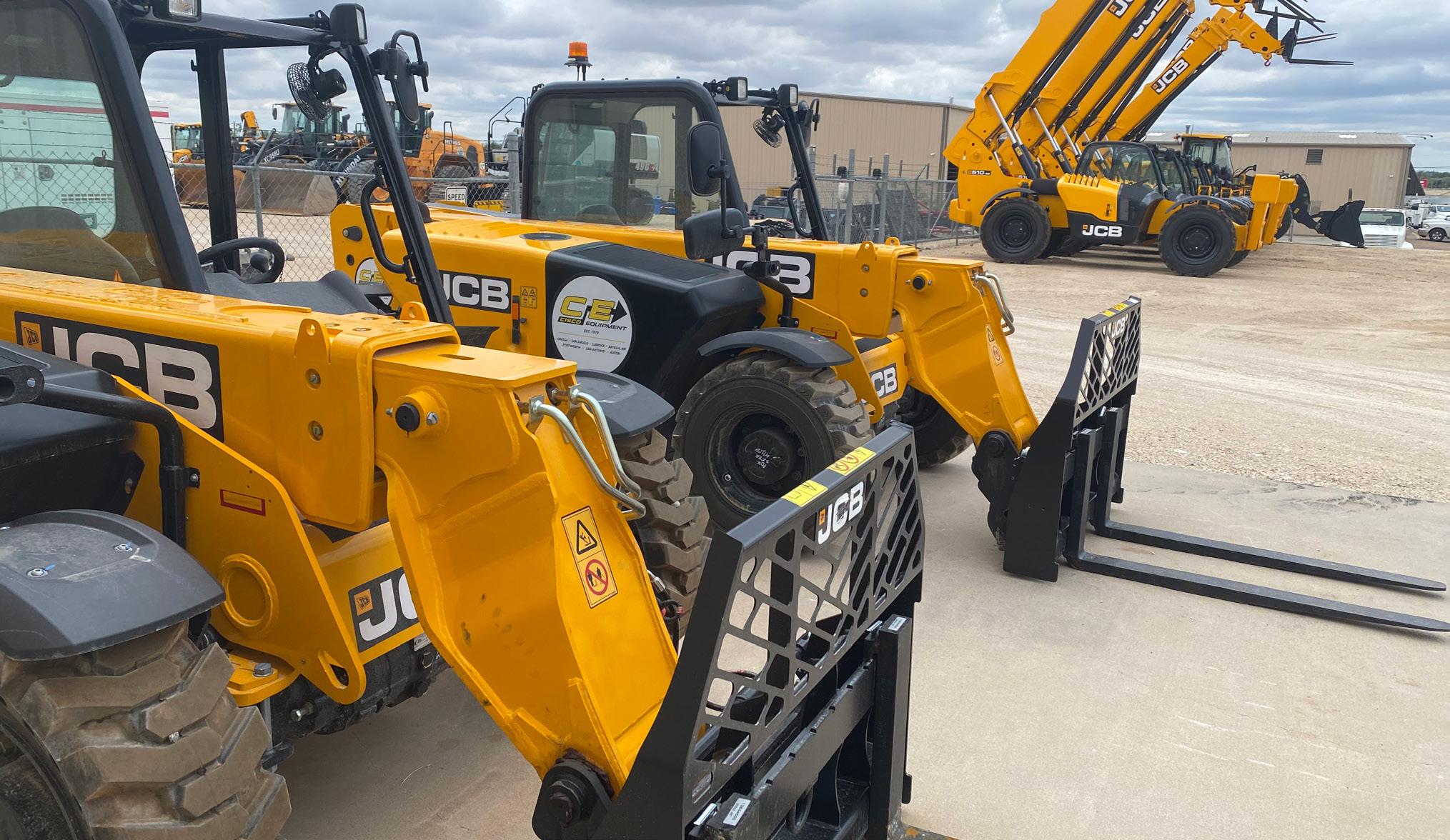
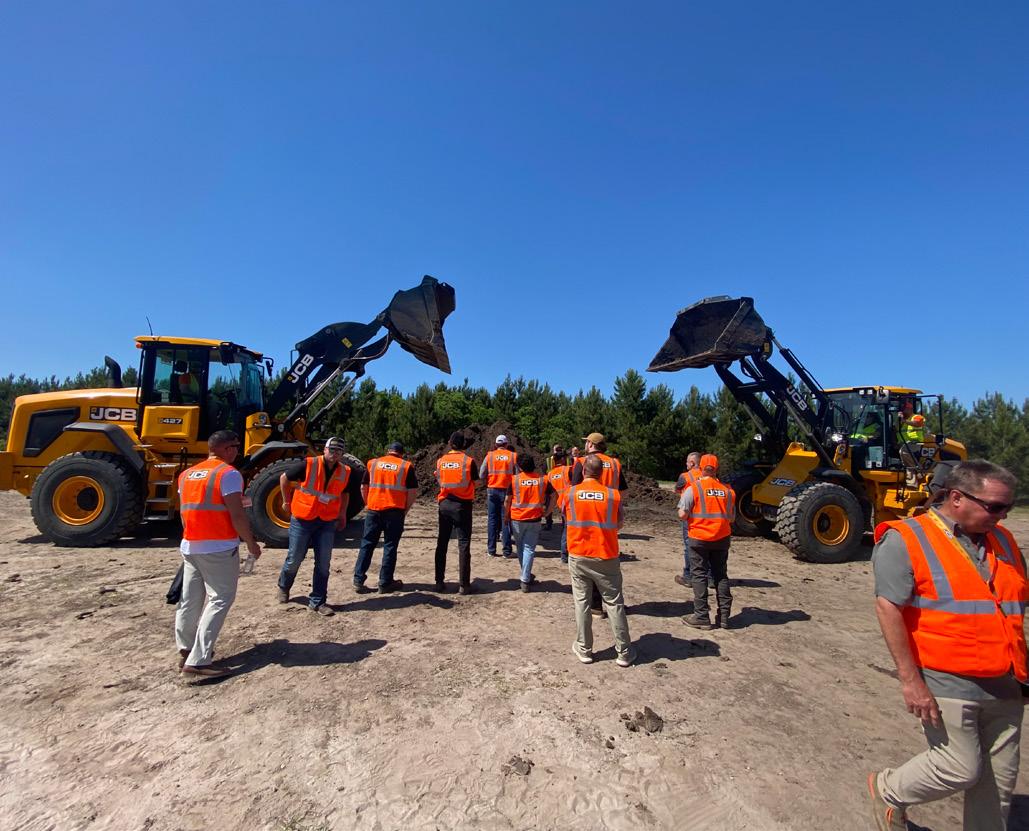
We’re also proud of the long-standing customer relationships we’ve maintained. Our clients know we’ll be there when they need us, whether it’s to deliver a machine in a pinch or troubleshoot a complex service issue. That trust is something we’ve earned over time and continue to build on every day.
Finally, we take great pride in continuing to build on the legacy of our founder, Scott Sibert. His vision of integrity, service, and hands-on leadership remains at the heart of Cisco. Scott continues to play a respected and active role in the business, helping guide strategy while staying closely connected to both our team and our customers. His presence ensures that our core values are not just preserved - but lived out.
8. What does the next 12 months look like for the business?
The coming year will be focused on solidifying our position in West Texas while modernizing how we serve customers. We’re actively working with OEMs for fleet expansion and product support improvements, advancements, and upgrades.
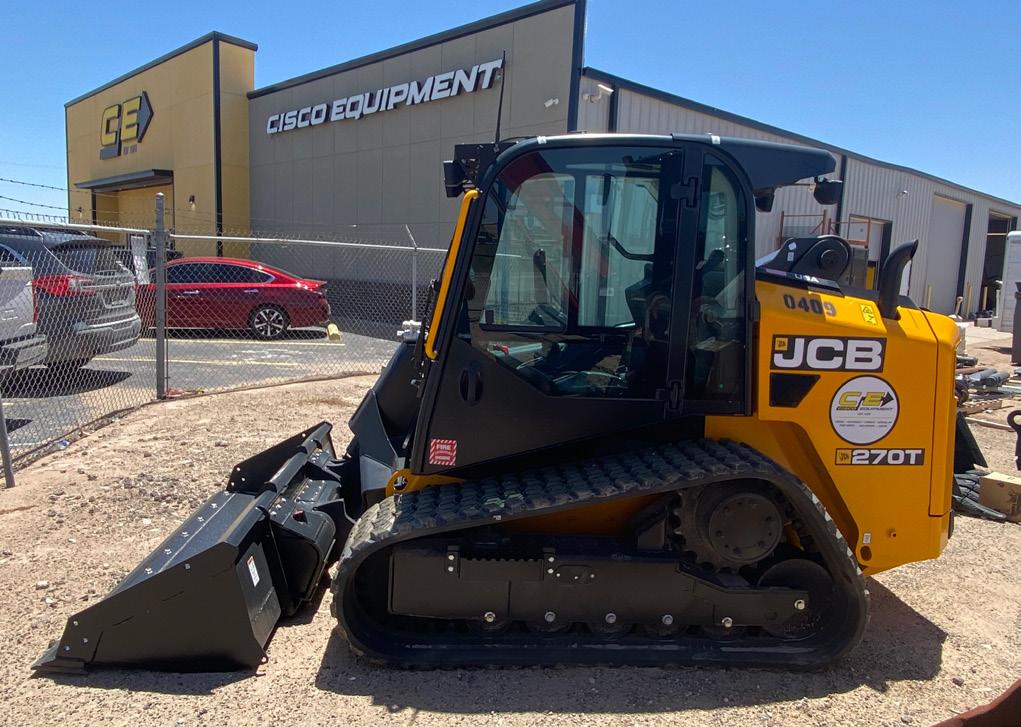
We’re expanding our use of the MyDealer platform to streamline communication, automate transactions, and improve how we deliver support in the field.
Internally, we’re strengthening our field service department with new customer facing support rolesincluding a Technical Coordinator position - to improve technician support and efficiency. We’re also increasing alignment with customers and OEM partners, ensuring stronger warranty programs, better parts access, and flexible purchasing options.
All of this is driven by one simple goal: to make sure our customers are never waiting for the equipment, service, or support they need. With a focused strategy and a committed team, Cisco is positioned to thrive in 2025 and beyond.
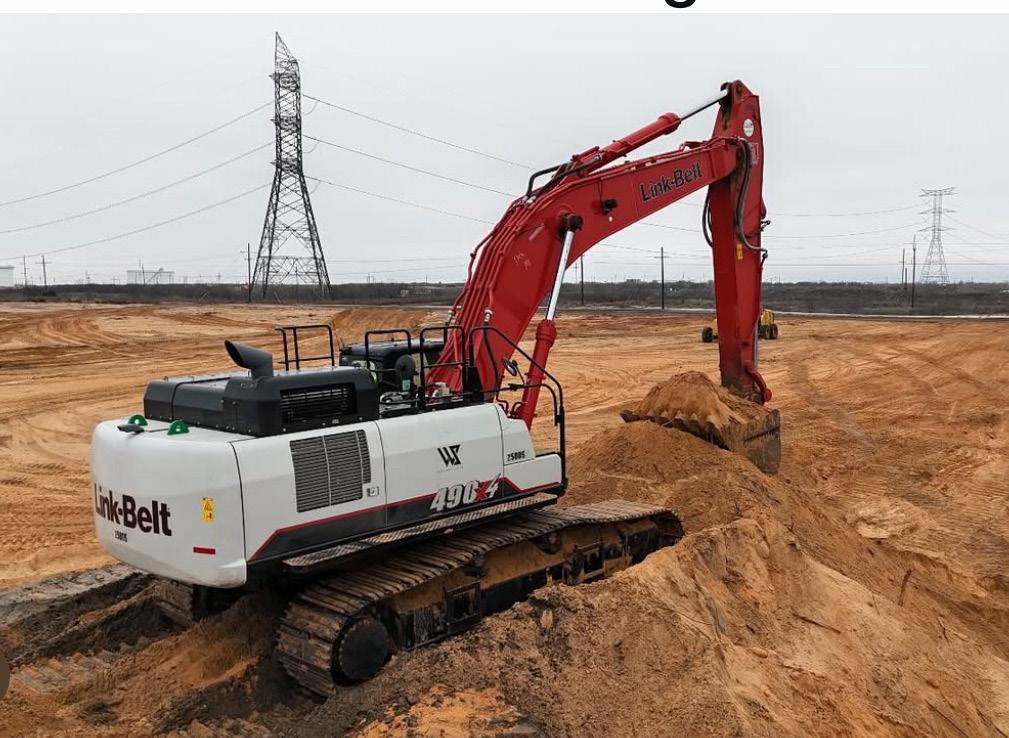
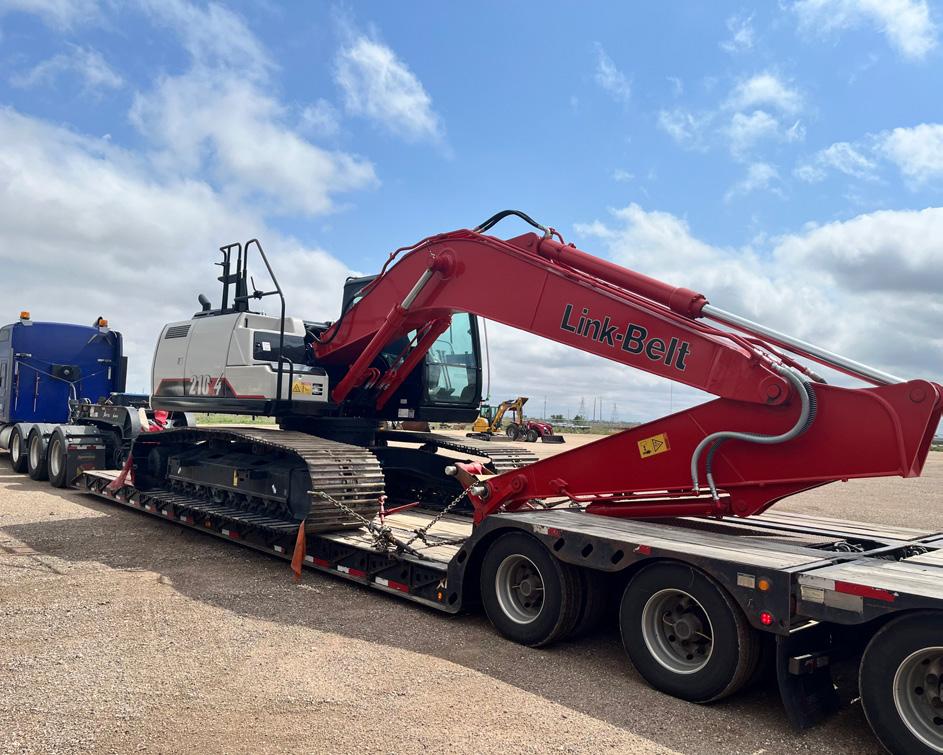
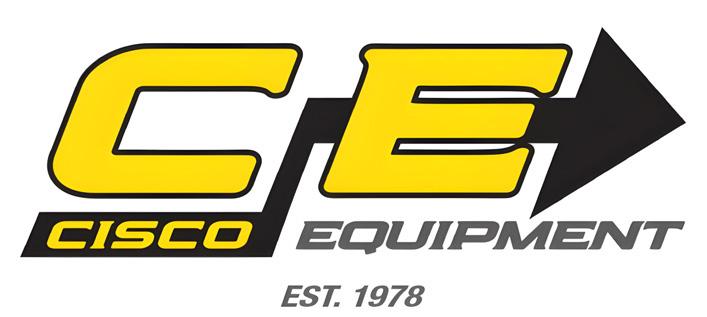


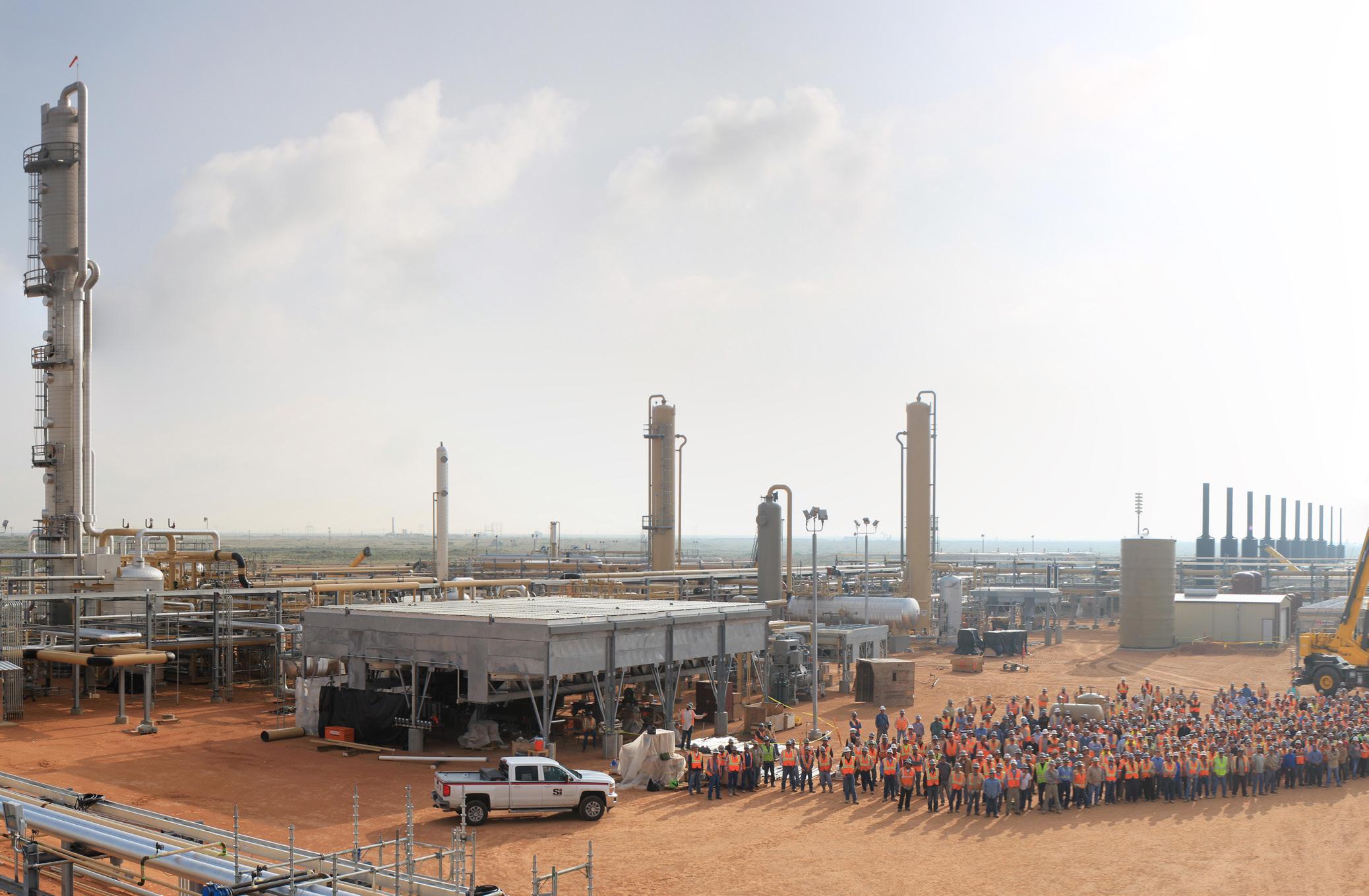
DIGITAL DEVELOPMENTS
Beyond the ongoing enhancements it continues to make to its automated fabrication and welding technology, Saulsbury actively invests in emerging technologies such as artificial intelligence (AI), Microsoft Power Business Intelligence, cloud platforms, and advanced communications systems to remain ahead of the curve.
“These investments drive operational efficiency, reduce costs, and foster innovation across our projects,” Matt excites.
By leveraging AI-driven cybersecurity systems, for example, Saulsbury has been able to improve threat detection and protection, ensuring its digital infrastructure is safeguarded against evolving risks.
Elsewhere, intelligent workflows and real-time data analytics provide customers with granular end-to-end visibility into every aspect of the company’s operations.
“WE DON’T PRIORITIZE SAFETY JUST BECAUSE OUR CLIENTS EXPECT IT — WE DO IT BECAUSE WE GENUINELY CARE ABOUT OUR EMPLOYEES AND IT’S SIMPLY THE RIGHT THING TO DO”
– MATT SAULSBURY, CEO, SAULSBURY
“This allows us to proactively manage risks, adapt to changing demands, and maintain seamless project execution for our customers,” he adds.
To further enhance transparency, Saulsbury utilizes digital signage at job sites, intranet communication, secure video streaming, and realtime quality tracking mechanisms.
As such, it ensures teams and clients have access to up-to-date project metrics that are measured against company and projectspecific key performance indicators (KPIs), fostering a more connected
and well-informed workforce while delivering consistent and reliable customer experiences.
Saulsbury also proudly utilizes advanced technology within its safety practices, leveraging cutting-edge, data-driven software to track every accident, incident, near miss, or good catch.
“By analyzing trends related to incident types, severity, affected body parts, and seasonal fluctuations, we are able to develop targeted safety training programs at company-wide, project-specific, and individual levels,” Matt says.
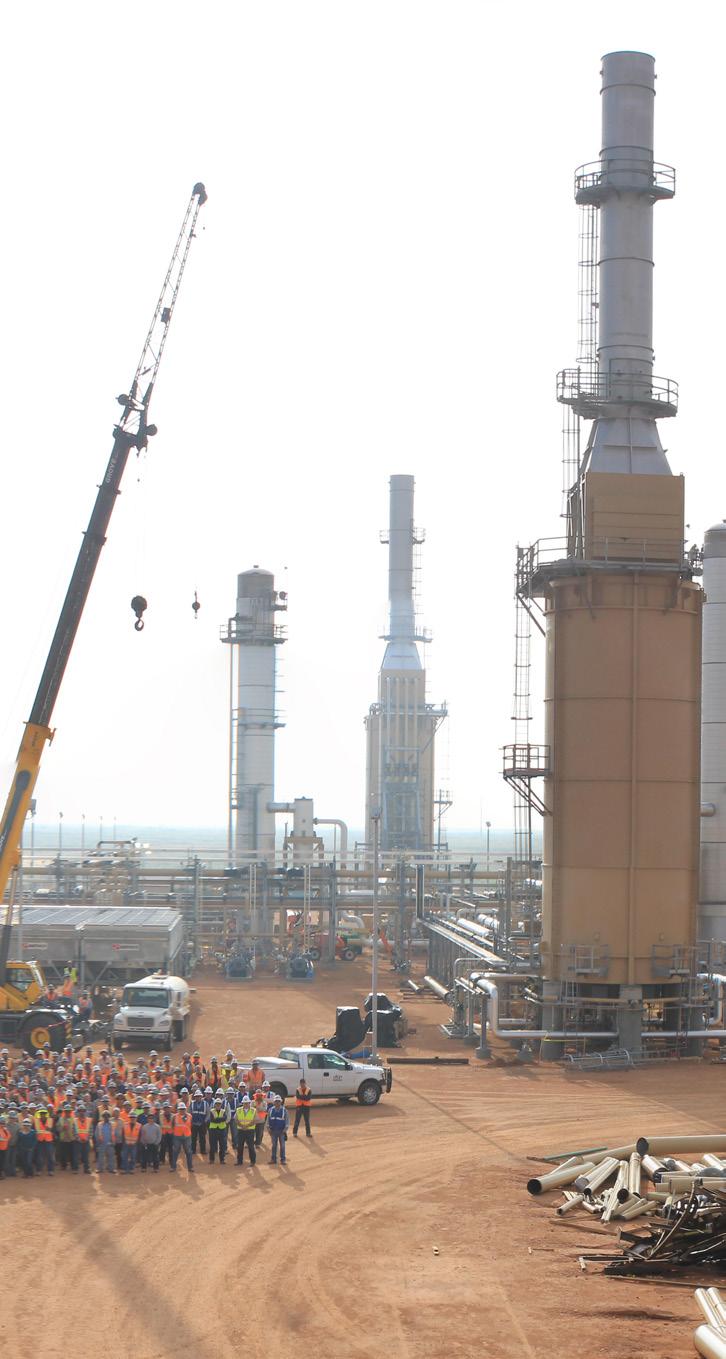
This comprehensive approach to safety extends across the organization, with key trends and issues communicated through emails, weekly meetings, and digital video boards at every project site.
At Saulsbury, embracing a safety-first culture is a fundamental requirement for all employees.
A PROACTIVE APPROACH
Saulsbury’s deep commitment to safety is compounded by its overarching culture of accountability and continuous improvement, through which it promotes safety as more than just a policy but a way of life.
“Embedded in our culture as a fundamental obligation to our employees, safety is something we live and breathe every day. Every team member is their brother’s keeper, and our collective duty is to ensure that each employee goes home in the same – or better – condition than when they arrived at work,” Matt prides.
A UNITED COMMUNITY
Dedicated to aiding, honoring, and giving back to the communities in which it operates, Saulsbury has been involved in countless community and employee initiatives over the past year.
• The incredible women who work for the company were recognized and honored for their talent, dedication, and hard work during Women in Construction Week.
• Saulsbury attended Western North Dakota Honor Flight’s pre-flight meeting to demonstrate its financial support and engage with veterans. The organization’s mission is to transport veterans to Washington DC to visit memorials dedicated to those who have served and sacrificed.
• The company was honored to be the presenting sponsor for XTO Energy’s annual golf tournament in 2024, which helped to raise more than $225,000 for the Midland Rape Crisis and Children’s Advocacy Center.
• Saulsbury sponsored Military Appreciation Weekend at Momentum Bank Ballpark, home of the Midland RockHounds baseball team, where it was grateful to honor military service members, veterans, and their families.
• The company holds an annual Vitalant blood drive at its headquarters in Odessa, Texas, through which employees donate units of blood to be used in life-saving medical procedures throughout the local community.
• Saulsbury partners with the West Texas Food Bank to help toward their goal of a West Texas without hunger. In 2024, employee volunteers sorted and boxed 850 cases (13,600 pounds) of food for distribution to the surrounding community.
• Employees at a project site in Wyoming held a school supply drive for the local elementary school, providing much needed supplies for young students as they headed back to school.
• The company provided funding to support a nearby volunteer fire department in Arizona, enabling the purchase of essential life-saving equipment and gear.
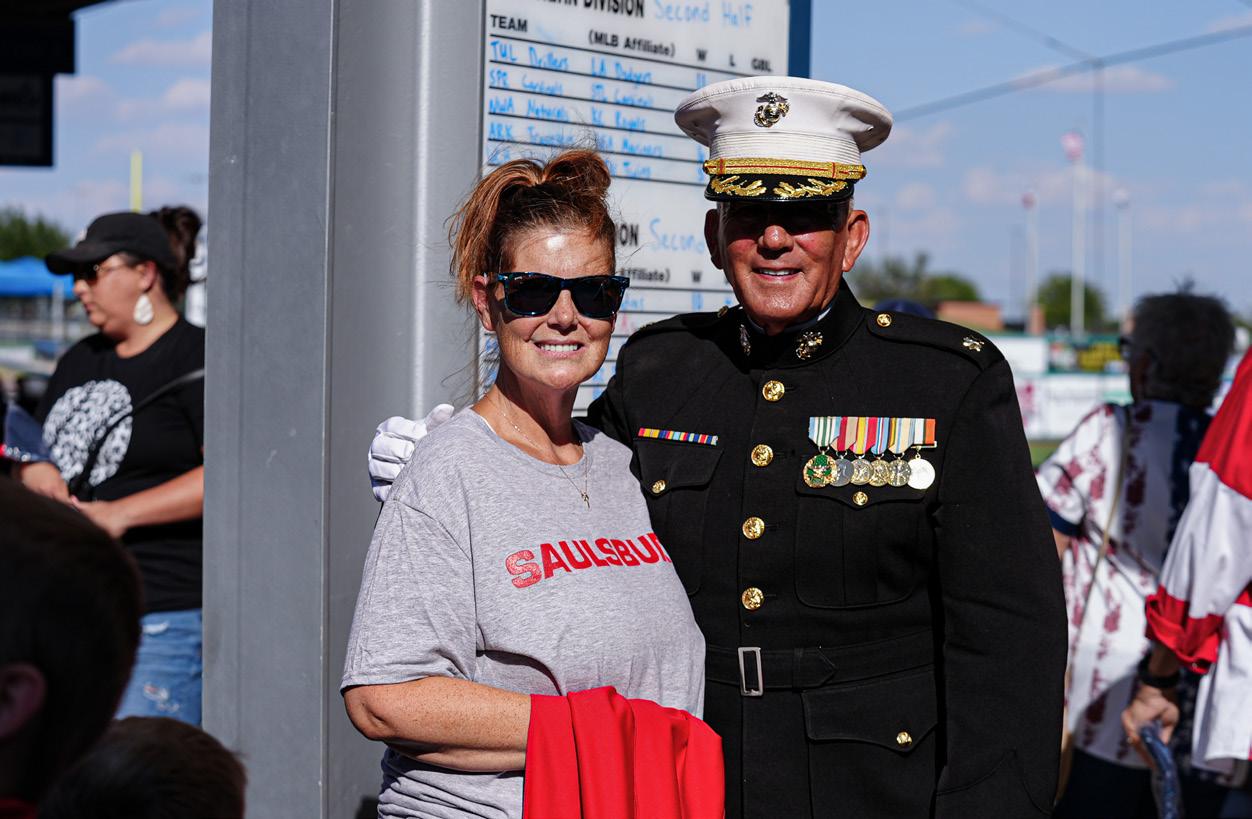
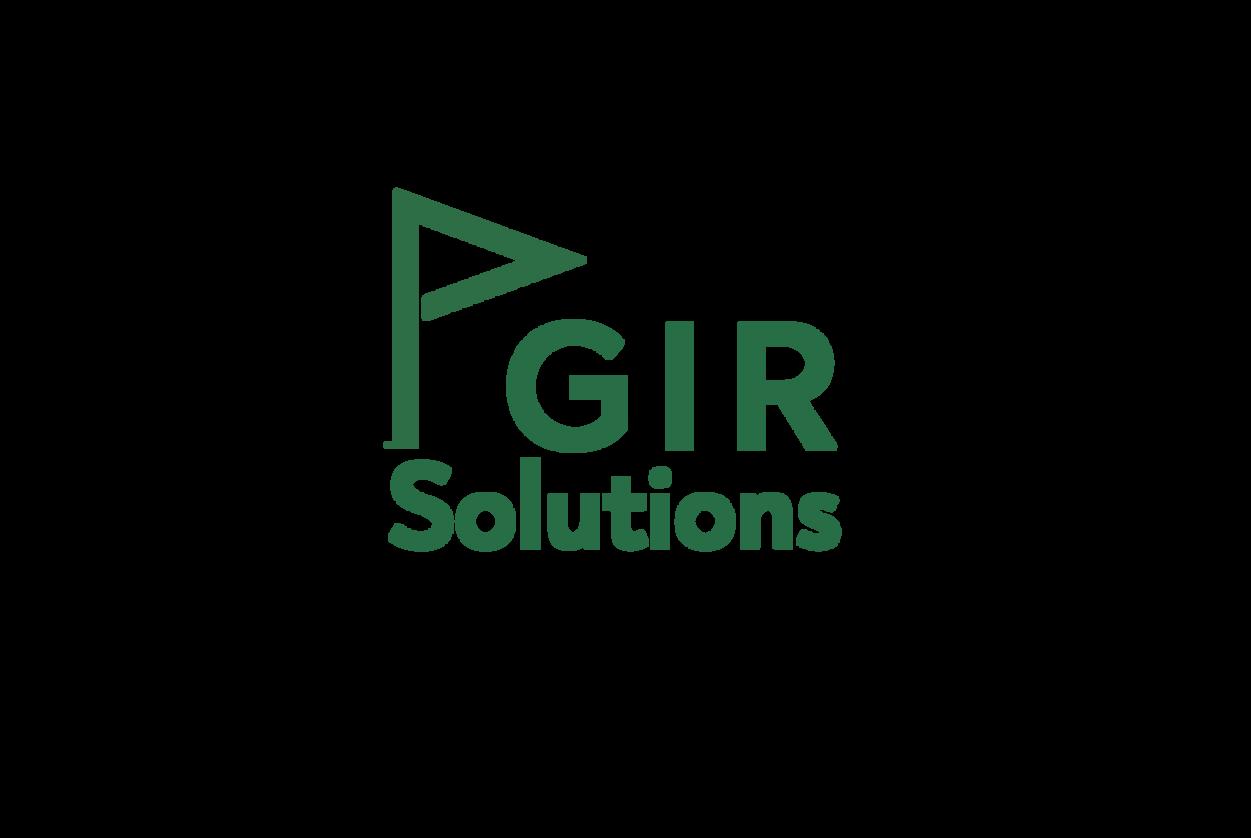
DRIVING ASSET
INTEGRITY
THROUGH INNOVATION:
How GIR Solutions MI is Advancing the Future of Inspection in Energy
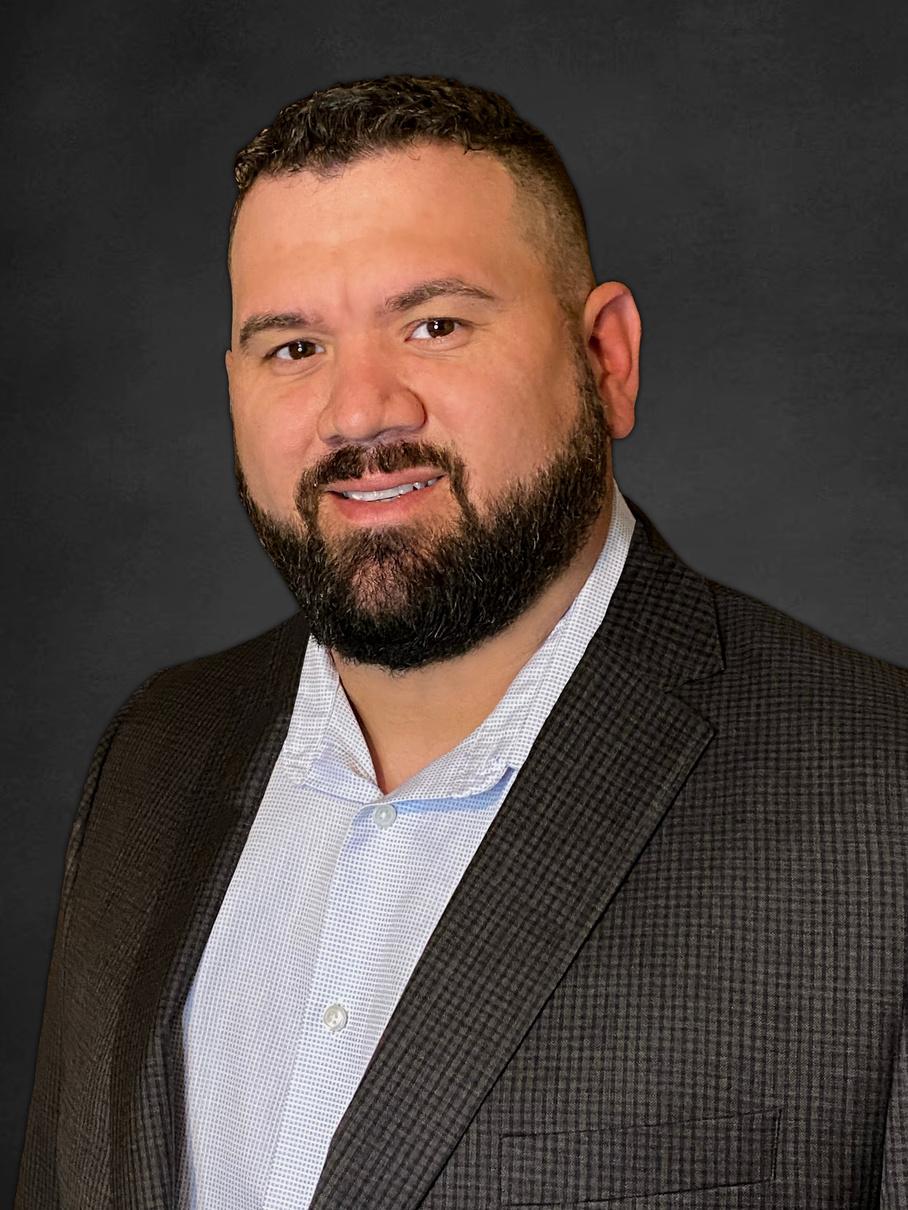
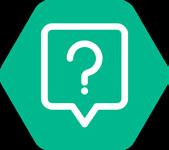
WHO IS GIR Solutions MI?
“As the President of GIR Solutions MI, I’m proud to stand alongside Saulsbury in supporting them on this major carbon capture project. This collaboration between GIR Solutions MI & Saulsbury demonstrates a shared commitment to safety, quality, and innovation in advancing clean energy solutions Together, we ’ re helping build a more sustainable future one inspection at a time ”
Trevor Doucet,
President, GIR Solutions MI
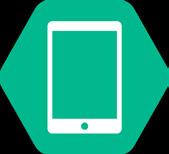
INTEGRATED TECH & CLIENT-FOCUSED DELIVERY
In an industry where precision, safety, and data integrity are paramount, GIR Solutions MI stands out as a forward-thinking energy services company. Specializing in Non-Destructive Testing (NDT), Mechanical Integrity Inspection, Level 1 Topside Inspection, Construction Inspection, and advanced data management, GIR delivers the tools and insight required to protect critical assets and maintain operational excellence. Founded to bridge the gap between fieldwork and data-driven decisionmaking, GIR has grown into a trusted partner for some of the energy sector’s most demanding clients At the center of its approach is a belief that technology, innovation, and personalized service must go hand-in-hand to create truly effective solutions.
From scope planning to final deliverables, GIR Solutions MI takes a streamlined, modern approach to inspections. Their tablet-based system automates data flow from field to office, cutting processing time and reducing manual errors At the core of their workflow is the Client-Data Management Suite a cloudbased portal offering clients 24/7 access to reports, dashboards, KPIs, and historical records. It supports legacy data imports, CAD isometric drawings, and fully customized reporting to align with operational goals and compliance needs This flexibility makes GIR a standout offering real-time visibility into asset health and enabling smarter decisions
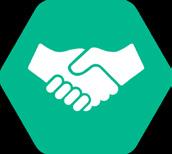
PARTNERSHIP WITH SAULSBURY
As the energy industry continues to evolve toward a more sustainable future, successful partnerships like the one between GIR Solutions MI and Saulsbury are proving that collaboration is key to innovation and impact The recently completed carbon capture project in the Niobrara region stands as a shining example of what can be achieved when two industry leaders align their strengths and values toward a shared mission
GIR Solutions MI was honored to provide specialized Non-Destructive Testing (NDT) services in support of Saulsbury’s execution of this critical carbon capture infrastructure. From the earliest phases of fabrication through final commissioning, GIR Solutions MI worked hand-in-hand with Saulsbury to ensure that every weld, pipeline, and pressure system met the highest standards of integrity, reliability, and safety The Niobrara region, known for its rich energy resources, is now home to one of the most forward-thinking carbon capture installations in the area Designed to significantly reduce CO₂ emissions from active production facilities, this project exemplifies the type of strategic environmental investment that is reshaping the energy landscape The successful delivery of this initiative highlights how experienced partners can drive real progress toward emissions reduction and energy transition goals.
Throughout the project lifecycle, GIR Solutions MI provided a full suite of NDT services including radiographic testing (RT), ultrasonic testing (UT), magnetic particle (MT), and liquid penetrant (PT) inspections By utilizing the latest inspection technology and deploying highly trained technicians, the team was able to proactively identify potential issues, maintain quality control, and support Saulsbury in keeping the project on schedule and in full compliance with regulatory standards. Saulsbury's role as the EPC leader ensured seamless project management, efficient coordination among vendors, and unwavering focus on safety and quality Their trust in GIR Solutions MI to perform these critical inspections was a reflection of their deep commitment to partnering with specialists who deliver consistent, highperformance results Together, both teams navigated complex logistical and environmental challenges to bring the project across the finish line safely, on time, and with excellence The results speak for themselves: a fully operational carbon capture system, built to last, and designed to serve as a benchmark for future sustainability-focused developments. It’s a win for the region, a win for the environment, and a proud achievement for everyone involved.
The collaboration between GIR Solutions MI and Saulsbury is more than just a project success story it’s a model for how strategic partnerships can drive meaningful change in an evolving energy landscape As both companies look ahead, the lessons learned and the standards set during this project will continue to shape the way they approach innovation, quality, and environmental responsibility This project may be complete, but its impact and the strength of this partnership will endure for years to come.
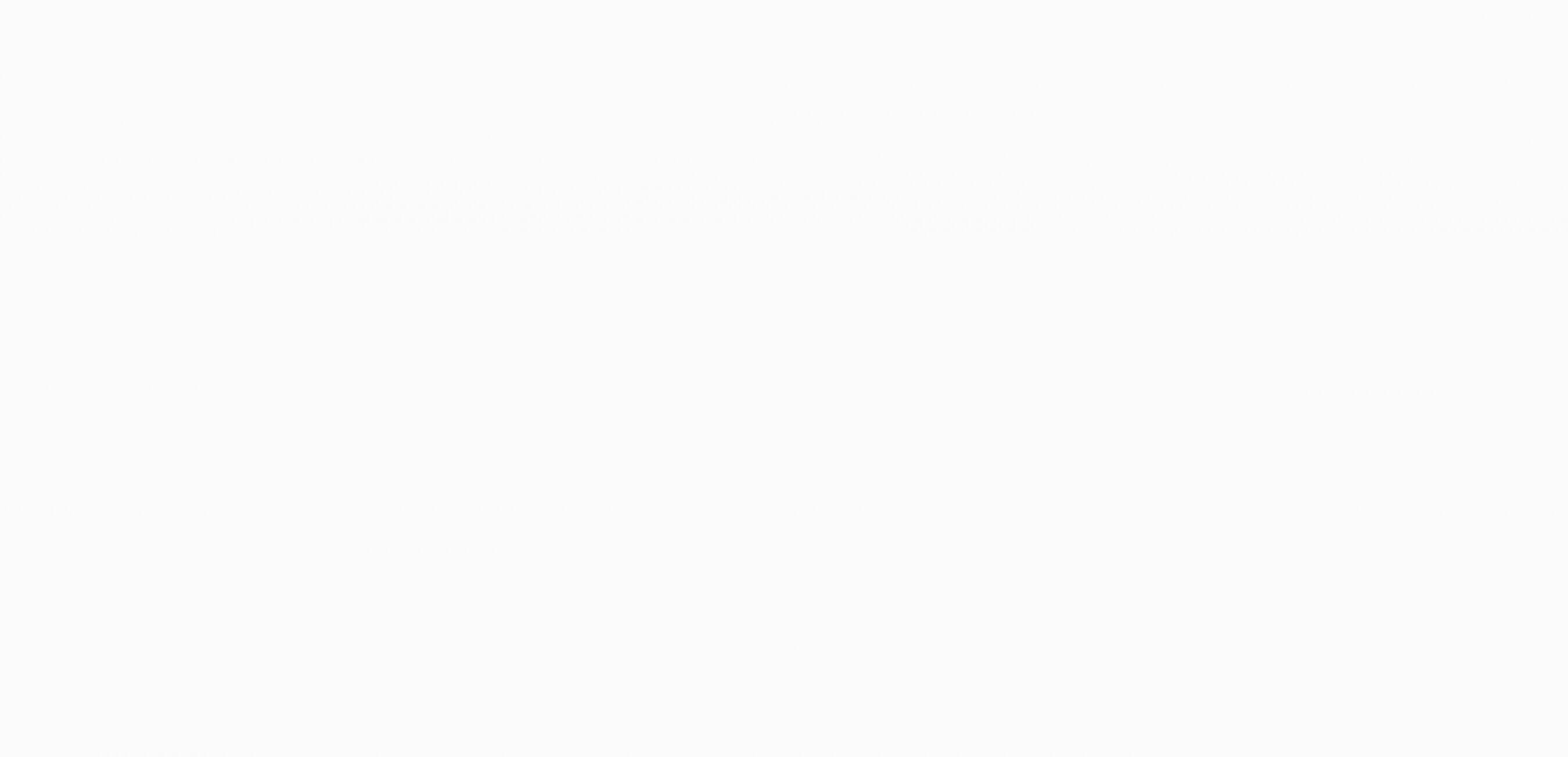
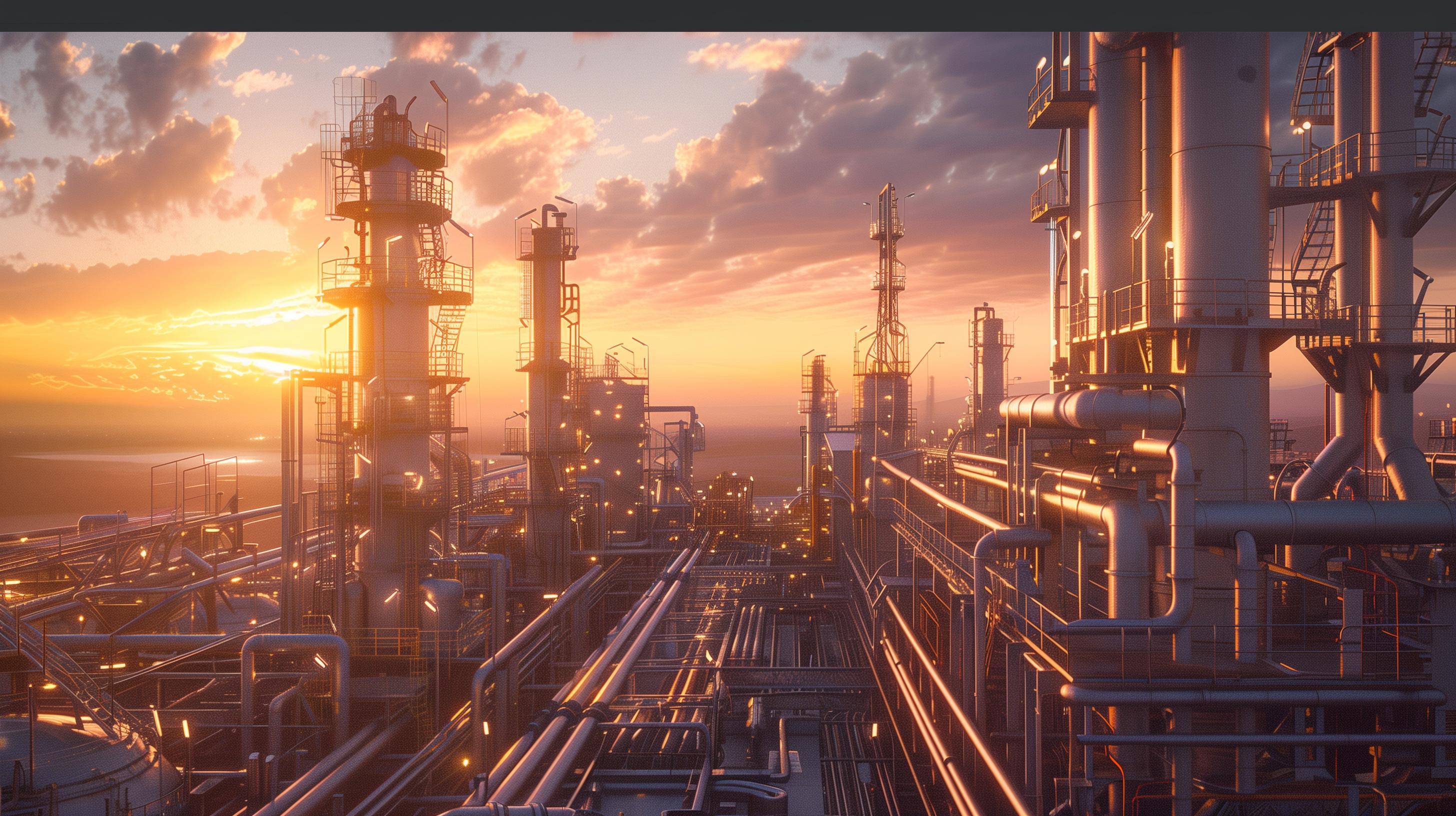
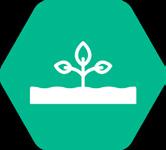
ORIGINS AND VISION FORWARD
GIR Solutions MI was founded with a clear mission: to transform the way inspection and integrity services are delivered in the energy sector Drawing on years of firsthand experience in the field, the team recognized the inefficiencies in traditional workflows and set out to solve them using modern tools and processes.
Today, GIR operates with a forward-thinking mindset investing in automation, training, and innovation to stay ahead of industry demands The company ’ s commitment to continuous improvement doesn’t stop at technology It extends to its people, partnerships, and pursuit of excellence in every job they undertake.
As the company continues to grow, its focus remains fixed on solving realworld problems with scalable, adaptable, and intelligent solutions
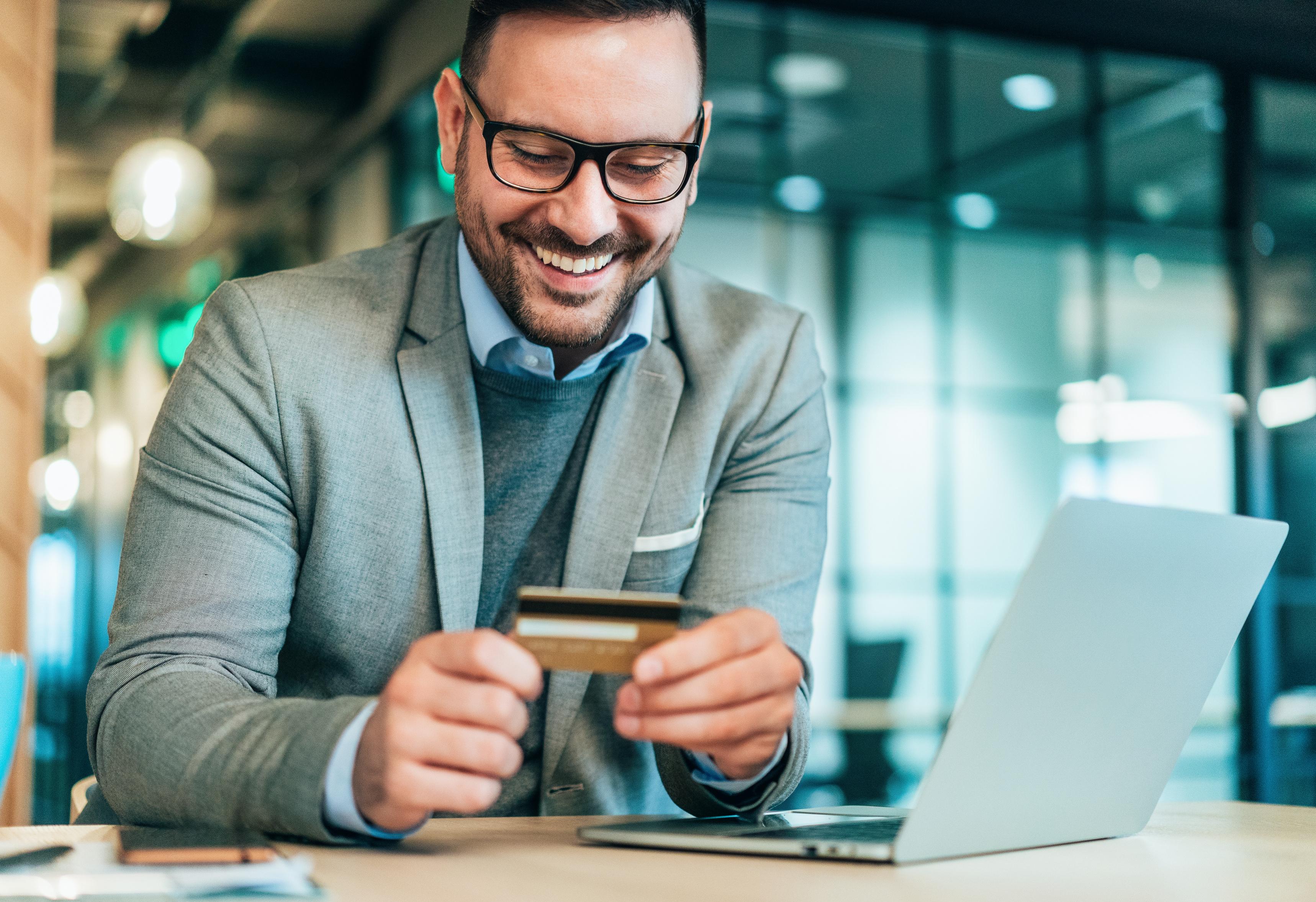
Inspection & Integrity Solutions for the Energy Sector
Non-Destructive Testing (NDT)
Rope Access Inspection
Construction Inspection
CAD-Based Isometric Drawings
Tablet-Based Inspection Systems
Client-Data Management Suite with 24/7 Access
Custom Reporting, KPIs & Alarm Logic
Trusted by industry leaders. Built for the field.
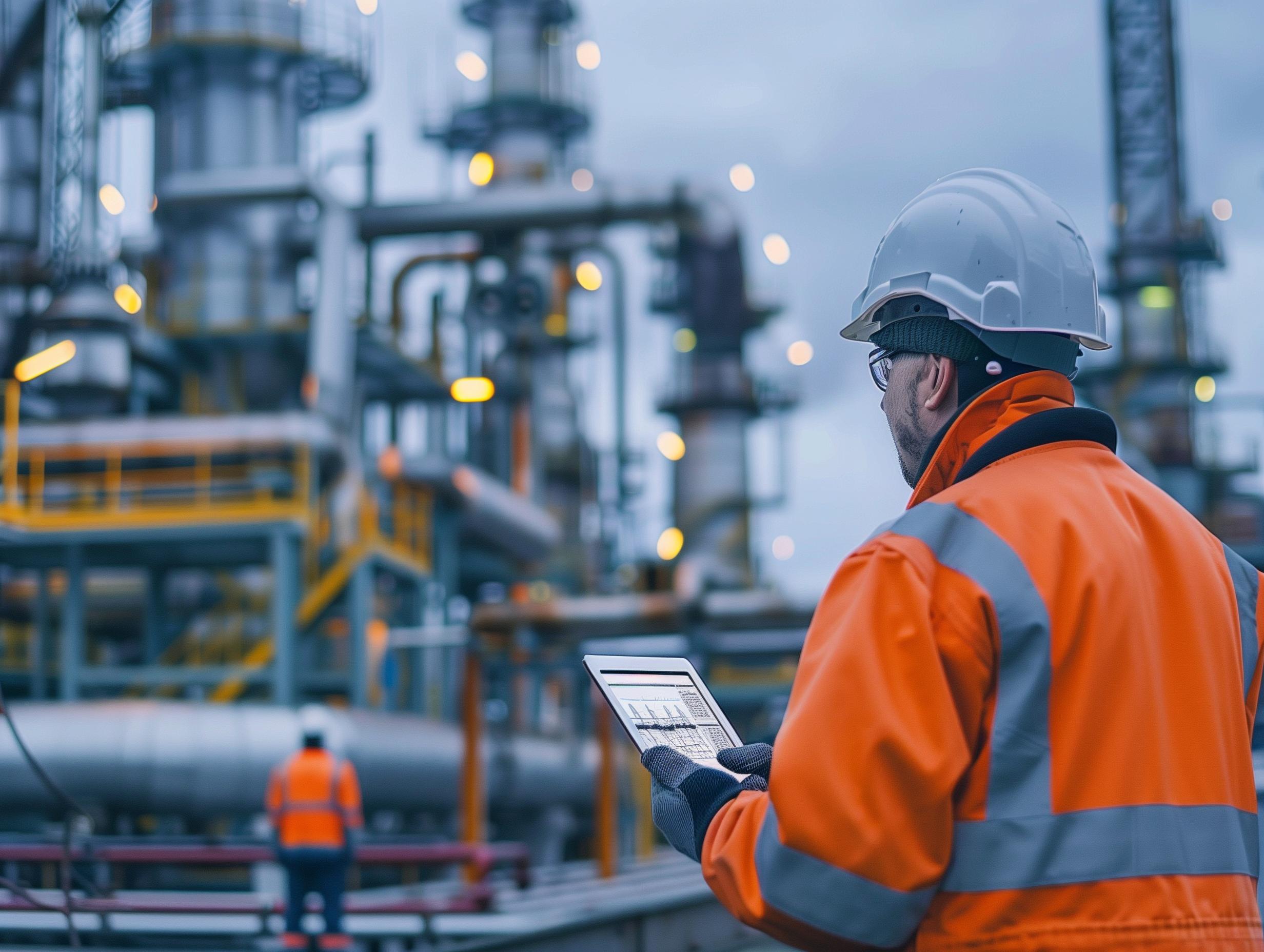
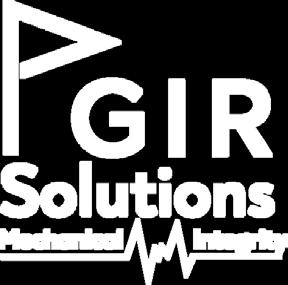
Capabilities
Asset Integrity Program Support
Data Processing, CAD & Analysis
Construction & Engineering Inspection
Training & Technical Staffing
Real-Time Field-to-Office Reporting
Import & Mapping of Legacy Inspection Data
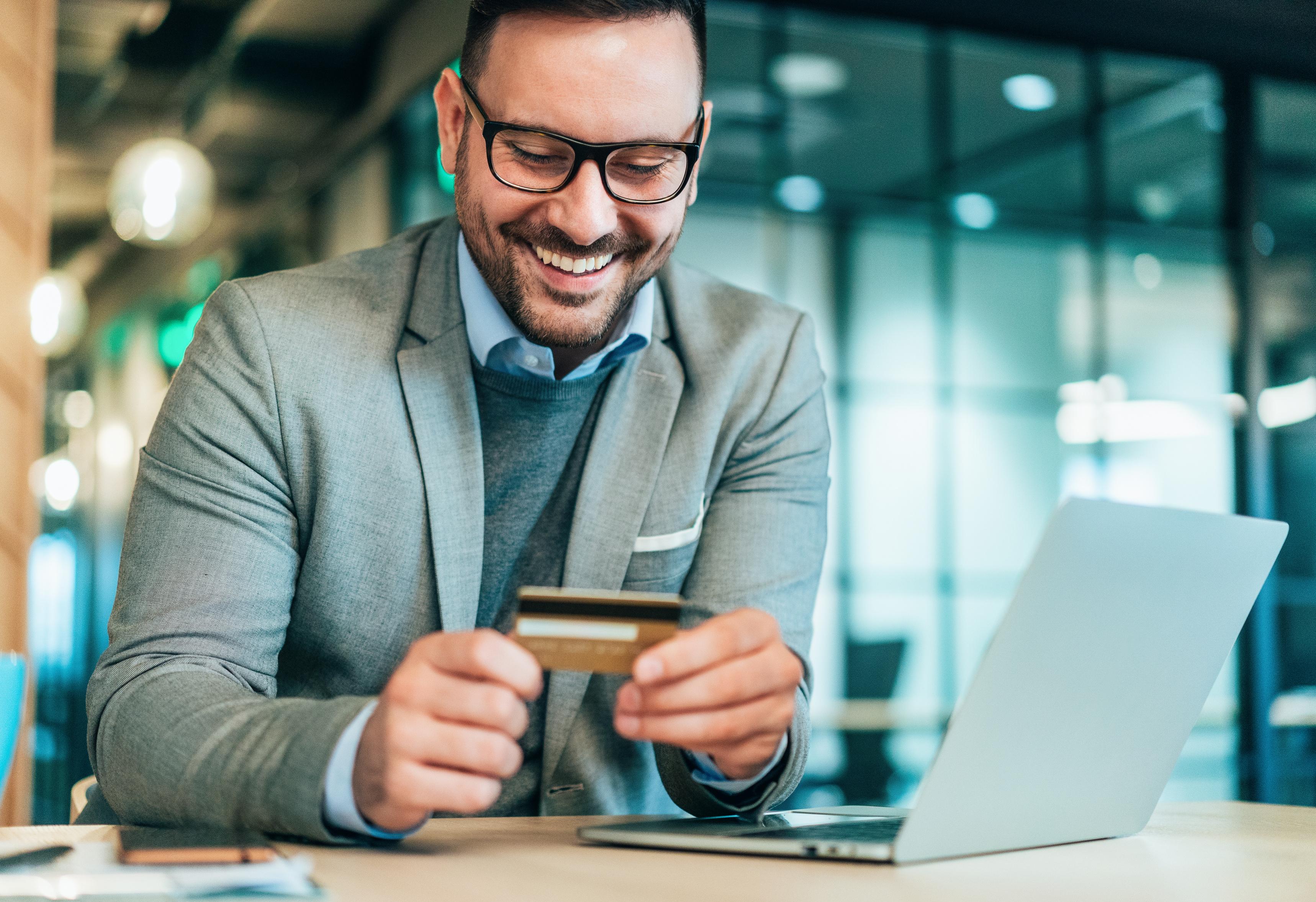

INDUSTRY INSIGHTS & FUTURE OUTLOOK
The oil and gas industry is undergoing significant change Rising environmental standards, evolving safety regulations, and the growing demand for digital transformation are reshaping expectations Companies must do more with less without compromising safety or compliance.
GIR Solutions MI meets this challenge head-on By combining automated inspection technology, cloudbased data delivery, and a client-first service model, the company enables operators to reduce downtime, improve forecasting, and increase asset longevity
As asset integrity becomes more complex, GIR remains committed to simplifying the path forward delivering clarity and control through every inspection.
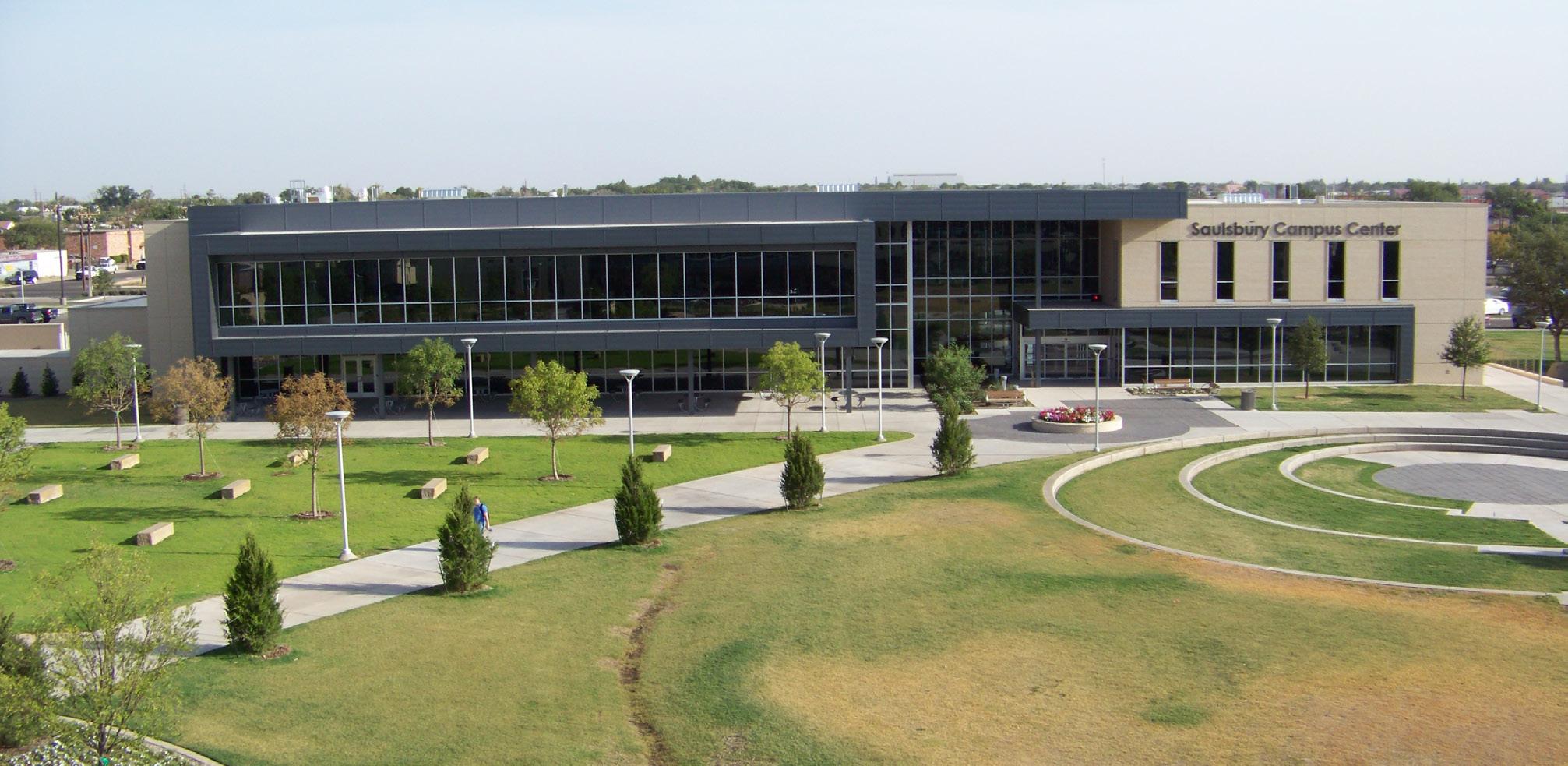
SAULSBURY’S EDUCATION INITIATIVES
Engaging with future engineers and industry leaders has always been a top priority for Saulsbury. As such, it has countless academic engagement and education charity initiatives in place to shape the workforce of tomorrow.
• Connecting classroom learning to real-world applications, Saulsbury recently presented to the Institute of Electrical and Electronics Engineers (IEEE) at the University of Texas Permian Basin (UTPB), contributing to its belief in educating tomorrow’s industry leaders, today.
• Last year, Saulsbury participated in Abilene Christian University’s career fair, hosted by the College of Business Administration and Department of Engineering and Physics, where it was on the search for top talent.
• The company is proud to be involved in the Education Foundation of Odessa’s Bookworms Literacy Program, in which Saulsbury’s volunteers counted and sorted 66,000 books last year. Designed to help increase literacy and foster a life-long love of reading, the program is closely linked to Saulsbury’s love of learning and its philanthropic efforts.
• Partnering with the IEEE at UTPB, Saulsbury hosts lunch-and-learn sessions for engineering students. Last year, Pedro Alejandro Mancilla, P.E, PMP, Saulsbury’s Director of I&E Controls Engineering, presented during one of the sessions, allowing the company to cultivate close working relationships with higher education institutions in the hope of eventually recruiting and training stand-out students.
Key to the company’s approach is transparency, through which it requires the reporting of every incident regardless of how minor it may seem.
This open reporting system reinforces Saulsbury’s allencompassing approach to safety, providing learning and training
opportunities that help prevent future incidents.
“Achieving this level of safety awareness requires rigorous reporting, extensive training, weekly company-wide meetings, and daily project site discussions,” he conveys.
With a proactive attitude in this regard, Saulsbury’s unwavering
commitment to health, safety, and environment (HSE) emerges as a key cornerstone of the company.
Indeed, Saulsbury believes safety should be a proactive effort built on continuous improvement, accountability, and engagement at every level of the company – as opposed to a reactive or retrospective approach.
As such, one of the pillars of Saulsbury’s safety management system is its weekly company-wide safety teleconference, which is attended by over 250 personnel from across the organization – from site managers to the CEO.
Setting the tone for the week ahead, the meeting begins with a ‘safety moment’ that comprises discussions and a thorough review of the previous week’s incidents, analysis of safety performance metrics, industry trends, and key safety takeaways.
Employee achievements are also recognized at the end of the meeting, reinforcing Saulsbury’s culture of teamwork, dedication, and appreciation for hard work, while an open round table fosters collaboration.
“Importantly, this is the only company meeting without a set end time, underscoring our
steadfast dedication to safety,” Matt emphasizes.
STELLAR SAFETY CUTLURE
In a bid to further bolster its stellar safety culture, Saulsbury has implemented several proactive programs.
Engaging in the JSA Leader Program, for instance, transforms employees from passive participants to driven leaders in safety.
It helps them to plan work steps, identify hazards, implement mitigation strategies, and communicate these to all affected workers.
In addition, supervisor engagement sessions have provided those at management level with the opportunity to reflect on and improve their approach to safety.
“These forums provide supervisors with a space to discuss program changes, offer candid feedback, and explore ways to enhance their leadership in safety,” Matt outlines.
Saulsbury also encourages open and honest feedback at all levels of management, ensuring employees clearly understand expectations and feel empowered to contribute to the company’s safety policies and programs.
A reflection of Saulsbury’s core value of integrity, this transparency has fostered trust and alignment across the organization.
Elsewhere, continuous training and development has helped the company to analyze key indicators that highlight potential knowledge retention gaps among staff.
“We continuously refine our training programs to ensure employees, supervisors, and management receive relevant and up-to-date safety education,” he adds.
This feeds into Saulsbury’s mantra that safety is about more than just compliance, but a shared responsibility among employees, contractors, and stakeholders.
By adopting a culture of proactive engagement, continuous learning, and open communication, the company ensures that its workforce remains protected and empowered to maintain the highest standards.
“Our commitment to safety isn’t just reflected in policies and programs – it is ingrained in our everyday actions. Safety is one of Saulsbury’s core values and a defining pillar of our success,” Matt asserts.
COMMUNICATION IS KEY
Fostering engagement through communication and recognition, Saulsbury emphasizes employee satisfaction by promoting a
transparent and positive workplace culture.
A key initiative supporting this regime is SiteCast – a company-wide platform that keeps employees informed about the latest business updates, safety initiatives, and key developments.
Having launched in 2024, its cutting-edge visual communication capabilities have improved workforce connectivity across the organization, enhancing Saulsbury’s communication and safety awareness.
In addition, SiteCast’s ability to bridge language barriers and streamline the delivery of critical information has proven invaluable.
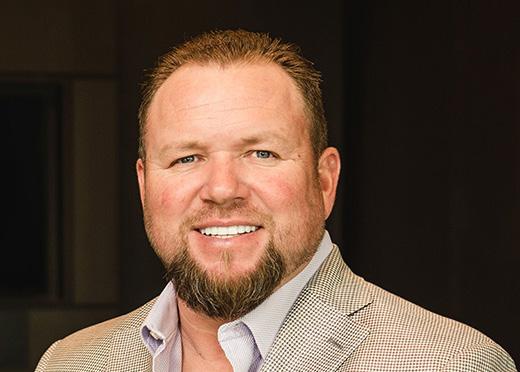
“EVEN WITH ALL THE GROWTH WE’VE EXPERIENCED OVER THE YEARS, SAULSBURY HAS MANAGED TO MAINTAIN A FAMILY ATMOSPHERE — A PLACE WHERE PEOPLE FEEL COMFORTABLE AND VALUED. MY FATHER ALWAYS SAID TO DO THE RIGHT THING, EVEN WHEN NO ONE IS WATCHING, AND THAT MINDSET IS SOMETHING OTHERS RECOGNIZE AND WANT TO BE A PART OF”
– MATT SAULSBURY, CEO, SAULSBURY
Industry Leaders in Control System Solutions
Innovative Control Solutions (ICS) is a Texasbased corporation established in 1997, headquartered in Plano, TX. The company specializes in delivering critical process and safety control system solutions tailored for the oil and gas, petrochemical and refining, utility power, cogeneration, renewables, and various other industries.
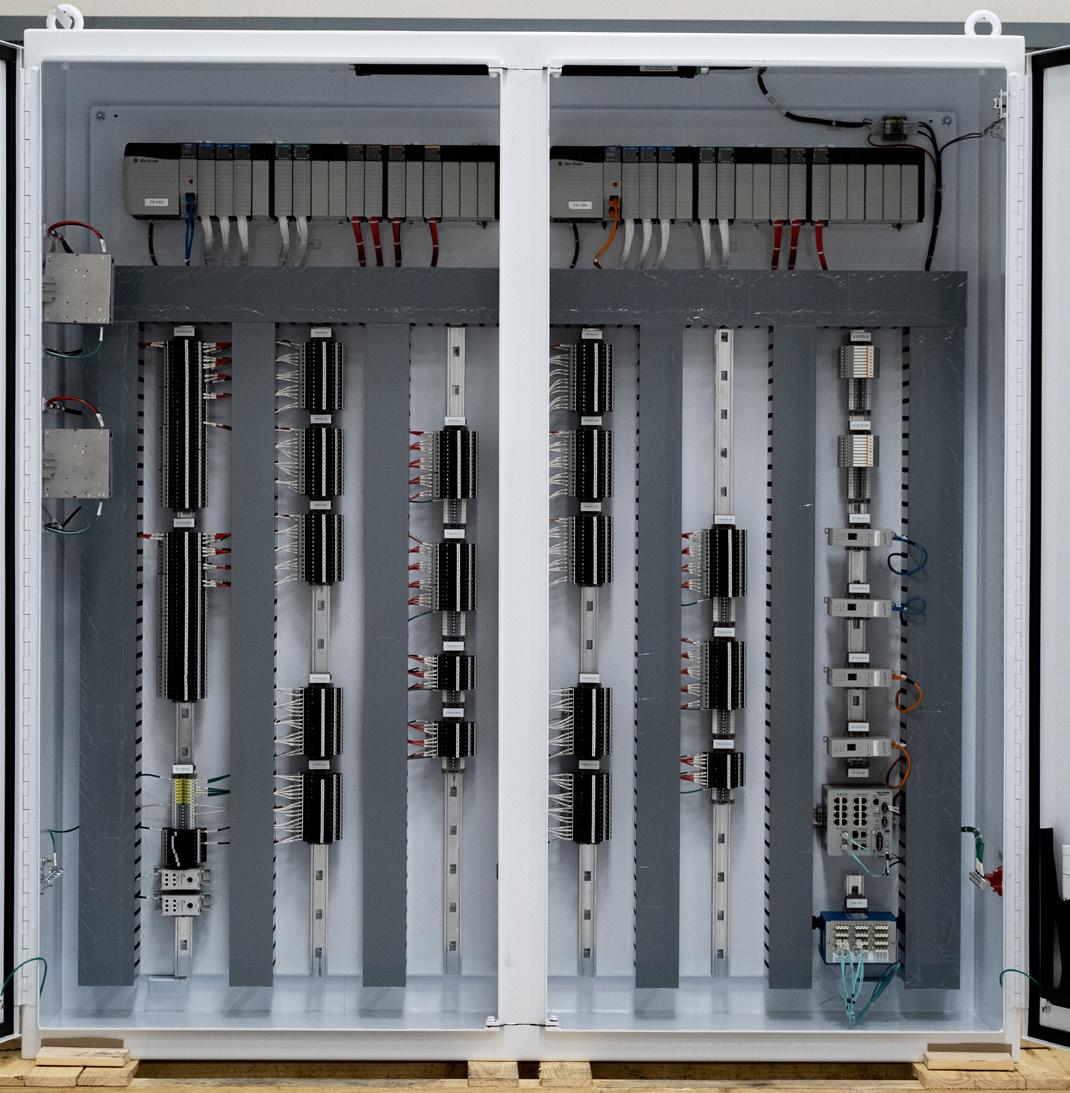
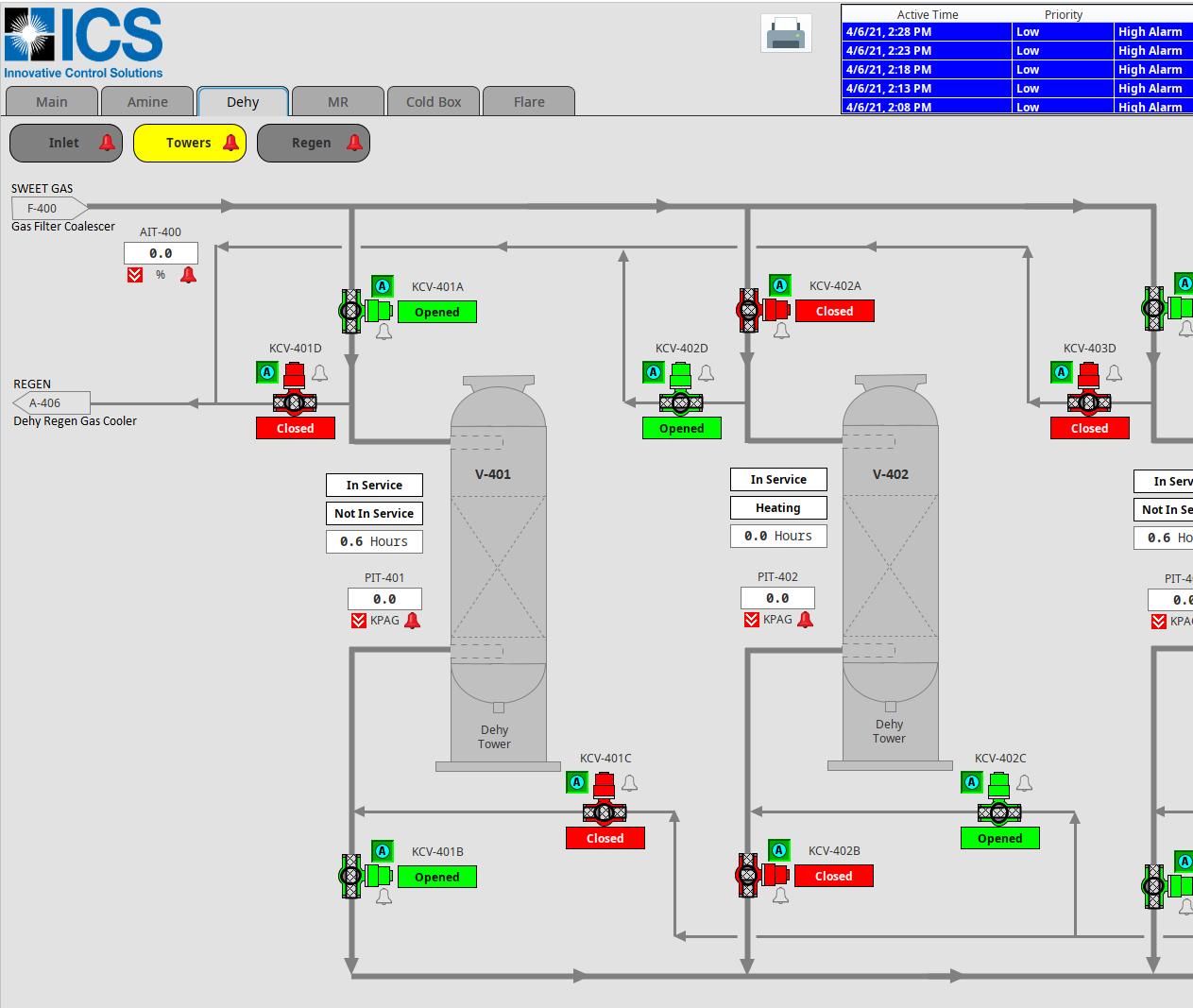
As a premier controls systems integration company, we have built a proven track record of nearly 30 years in delivering superior performance and results to our customers. ICS has successfully completed projects in over 30 countries globally and is one of the few Texas-based control system integration firms that has the technical and commercial expertise to execute projects around the globe.
Some of the offerings ICS can provide include:
ICS Integrated and Packaged Turnkey Solutions:
• PLC Programming and Configuration
• HMI & SCADA Design and Configuration
• Control System Hardware and Architecture Design
• Control System Migration and Upgrade Solutions
• Network and System Topology Design and Configuration
• Remote Monitoring and SCADA Solutions
• Start Up and Commissioning Support
• Control System Staging and Testing
• Control Panel Integration (UL-508A Certified)
• Design Adherence to Meet Agency Standards (NFPA/ FM/UL/CE/NEC/IEC/ATEX)
• Modular MCC/PDC/Control Room Buildings
• Switch Racks
• Control Room HMI Workstation Configurations
• Server Cabinet HMI Configurations
• Intelligent “Smart” MCC Solutions
• LV-MCC / MV-SWGR / VFD / Soft Start Line-ups
• Internal Raceway Design and Power Distribution
• Uninterruptable Power Supply Solutions
ICS OEM Platform Expertise and Certifications:
• Rockwell Automation (Factory Talk SE/ME and Plant PAX)
• Emerson DeltaV, PACSystems
• Sensia Safety Systems
• Ignition
• Wonderware System Platform
• Schneider Electric Triconex
• Red Lion
ICS is also equipped with dedicated engineering and design staff, a UL-508A panel shop, and a field service department. We handle turnkey projects, offering both mechanical and electrical installations, and ensure full business insurance and bonding coverage for our projects.
ICS has consistently met the challenges of meeting the “speed to market demands” of customers while still delivering high-quality control systems with superior performance. Whether your company is an end user in need of a plant wide control system, an EPC firm, or OEM packager that self-performs, ICS can provide solutions that will exceed your project expectations.
What makes ICS an industry leader in control system solutions and a premier systems integrator?
From the beginning, ICS has been driven by innovation in the design and delivery of critical process and safety control system applications while providing superior customer service during and after the project. Since our creation in 1997, ICS has been committed to providing products and services that achieve our customers’ project goals while adhering to high standards of safety and ethics.
Our automation and design team have decades worth of experience in the applications and industries we serve. Additionally, we are extremely proficient on many OEM programming platforms, making us an attractive option for customers who have a wide variety of projects. Lastly, we have no geographic boundary constraints. We will travel anywhere in the world to start up a project.
How do your control system solutions make operations as efficient, productive, and safe as possible?
Safety is a major focus for us when building and designing a control system. Before we start a project, we make sure we are on the same page as our customers on which agency approvals and area classifications are required. Additionally, our control systems are fully simulated and debugged prior to shipment. We go through two rounds of checks (internal and customer-witnessed Factory Acceptance Test) before our systems are shipped, which helps ensure a safe operation in the field. When we get to site, we know that our control systems have been thoroughly checked out. Lastly, we can help train our customers’ operations teams on using our supplied HMIs, which will ultimately improve efficiency and drive productivity.
Can you outline ICS’ Oil & Gas application expertise?
Oil & Gas is the primary industry served by ICS. As a premier systems integration firm, we have proven application expertise in the Oil & Gas and LNG industries. For nearly 30 years, we have successfully delivered control systems for all of the following applications:
Cryogenic Gas Plants
Natural Gas Fractionation Facilities
· LPG/NGL Process Plants
· Natural Gas Compressor and Gathering Stations
· Salt Water Disposals (SWDs)
· Reciprocating Gas Compressors
· Balance of Plant (BOP)
Amine Treating Plants
OEM Third-Party Process Applications
What core technologies does ICS utilize?
We offer a wide range of technologies to help serve every industrial sector we work in. When talking with customers
about their projects, we listen to what their needs are to come up with a solution that’s custom-fit to their situation. Below are some of the technologies we offer:
• Process Control Systems (PCS)
• Emergency Shutdown/Safety Systems (ESD/SIS)
• Fire and Gas Systems (FGS)
• BOP Control Systems
• SCADA and Remote Monitoring Solutions
• Remote Monitoring of Well Pad and Process Subsystems
• Third-party OEM Solutions
• Burner Management Systems
• Historian and Reporting Solutions
• Network and Communications Solutions
• Edge and Cloud Computing
• Server Virtualization
• Data Protection and Back-ups
• Industrial Cyber Security
Finally, how have you supported Saulsbury with your innovative control solutions and contributed to their success?
ICS has delivered dozens of automation solutions for Saulsbury’s projects for over a decade, which includes providing integrated control panels, HMI/PLC programming, loop check support, and the supply of various hardware offerings.
The engineers and project managers at Saulsbury and ICS have developed a close working relationship over the years built on trust, high-quality deliverables, and excellent customer care.
ICS and the Saulsbury automation team have worked closely with one another to successfully achieve one of Saulsbury’s goals of building cryogenic gas plants across West Texas and New Mexico.
It has been a pleasure to witness Saulsbury’s success and watch them grow. ICS is proud to be a trusted partner in that process.
We are extremely proud of the work we have done together in the past and look forward to many more years of success together!
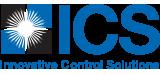
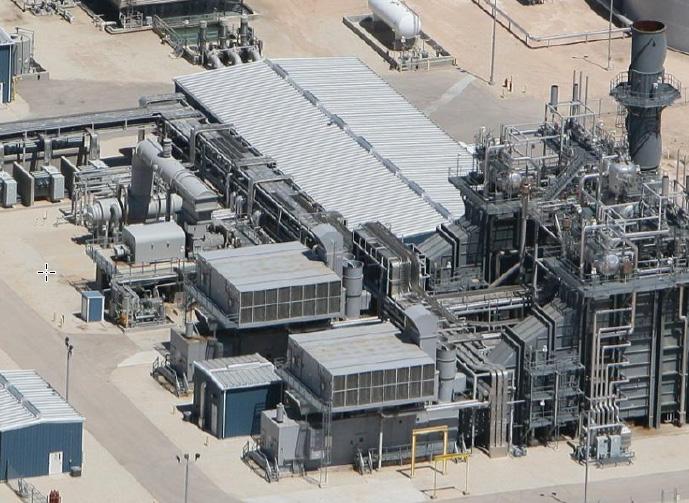
A STAND-OUT EMPLOYER
With a reputation founded in honesty and integrity, Saulsbury’s promise to its staff includes a continuous commitment to safety, quality, growth, and mutual profitability.
Offering employment stability alongside career advancement and a devotion to work-life balance, the company emerges as an employer of choice.
Moreover, its core value of safety has yielded one of the preeminent records for incident and injury-free operations in the construction sector.
To ensure it is attracting and retaining the best of the best in the industry, Saulsbury offers competitive benefits to its employees, including:
INDUSTRY STABILITY – As a company that has seen the sector evolve over 50 years of peaks and troughs and remained resilient throughout, staff can rest assured that their employment is stable with Saulsbury.
COMPETITIVE PAY – Rewarding its staff through competitive pay is just the beginning – employees are also eligible for paid time off.
HEALTH INSURANCE – The company is proud to offer competitive and comprehensive medical, dental, and vision coverage for employees and their dependents.
401K – A retirement plan is available to help employees build an income source for their future.
OPTIONAL BENEFITS – Employees may opt into a variety of additional health and wellness benefits, including identity theft protection and critical illness insurance.
PERKS – Discounts on phone plans, car rentals, hotel stays, and work apparel are just some of the many benefits Saulsbury’s employees are offered.
LOCATION OPTIONS – The company has offices located throughout the US, offering several options.
“SiteCast strengthens our safety culture through a number of features,” Matt sets out.
Safety alerts and announcements, for example, keep teams informed about potential hazards and preventative measures.
Weather-related notices provide real-time updates on conditions which may affect job sites, while positive recognition and good catches highlight the daily safety successes and major milestones of personnel.
“By showcasing employees who exemplify Saulsbury’s core safety values in action, SiteCast gives us the opportunity to celebrate their success.”
Project photos, meanwhile, offer a visual narrative of operational progress and complexity, and ‘Why I Work Safe’ videos feature employee insights into their commitment to safety.
Safety trivia quizzes with monthly winners engage employees in interactive safety education, while lifesaving rules and actions reinforce the company’s critical safety guidelines.
SiteCast also aligns with broader industry safety initiatives through national campaigns and reinforces Saulsbury’s hazard prevention efforts via departmental updates.
“While SiteCast is currently the gold standard in safety, we will continue to evolve the platform to meet the needs of our teams and projects,” he updates us.
MAXIMUM FLEXIBILITY, MINIMUM DOWNTIME
As a company that takes pride in its ability to customize project execution and meet the unique needs of its clients, Saulsbury’s services are flexible and seek to accommodate all kinds of requirements.
It understands how each project can present distinct challenges, whether related to commercial commitments, complex technical requirements, geographic constraints, or other factors.
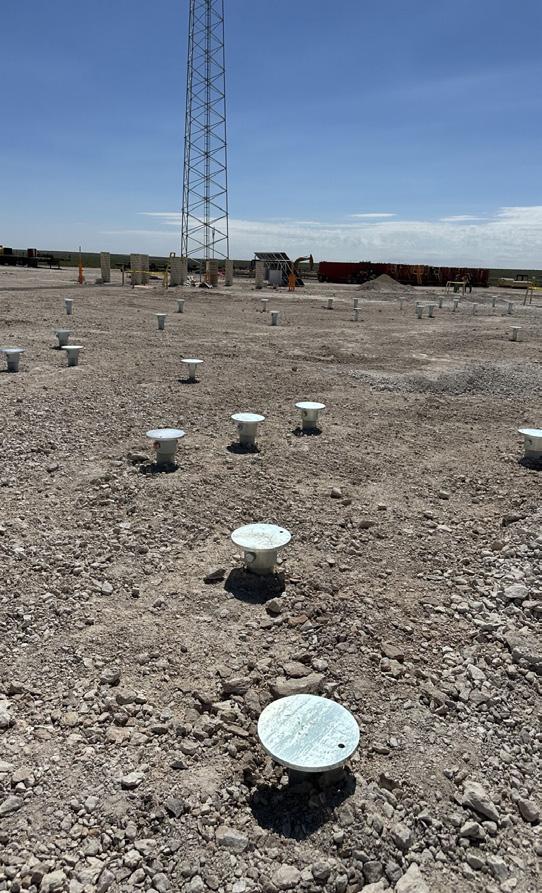
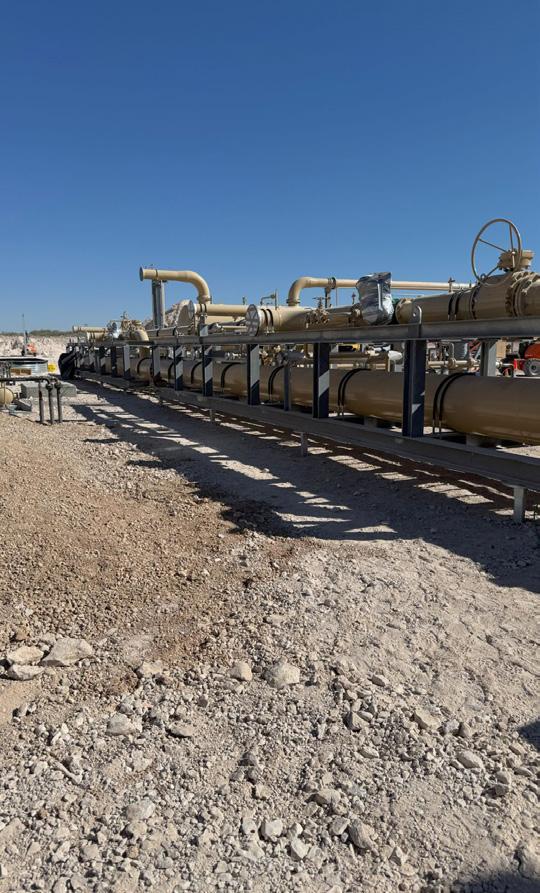
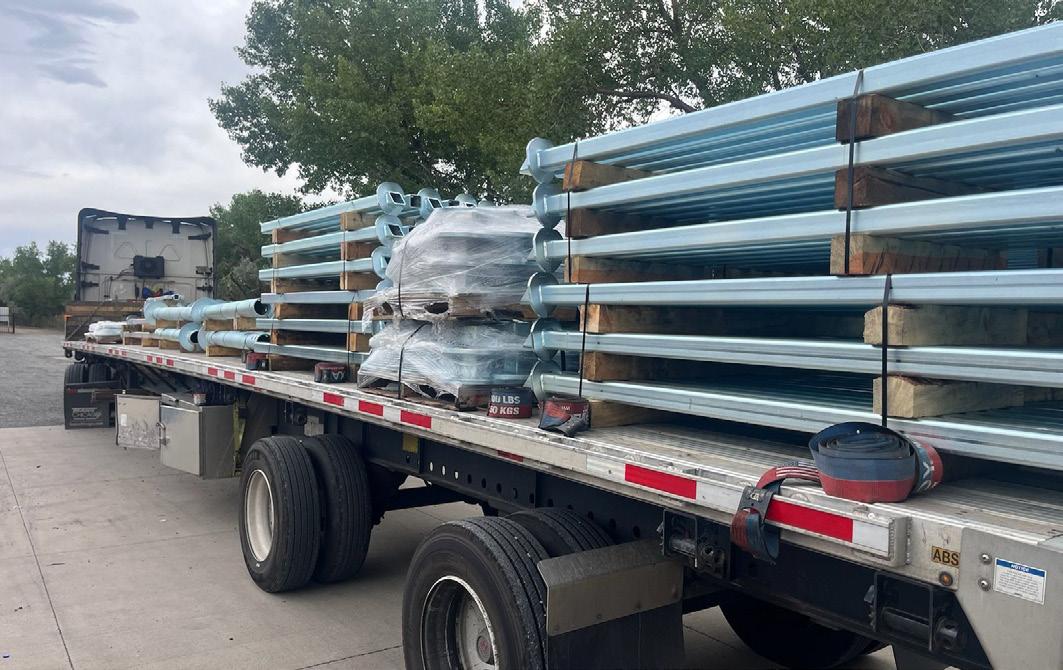
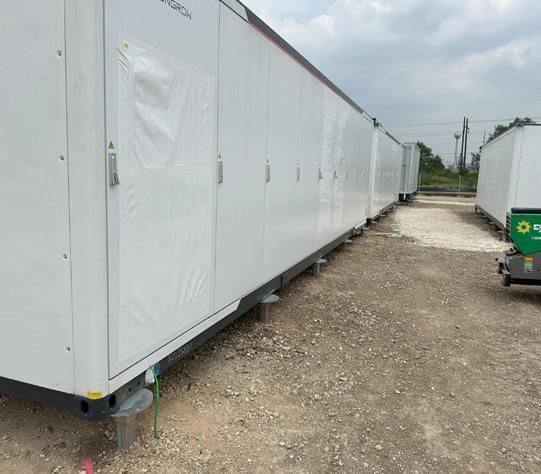
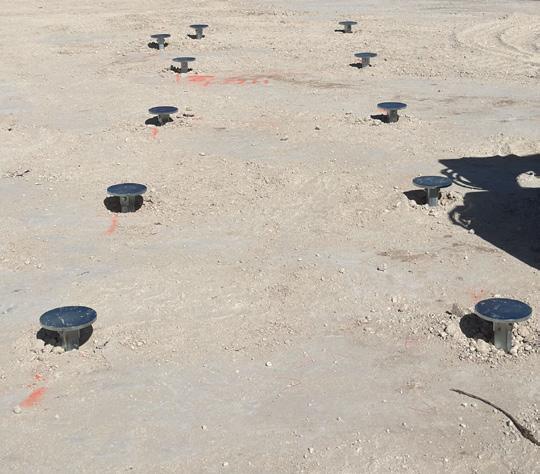
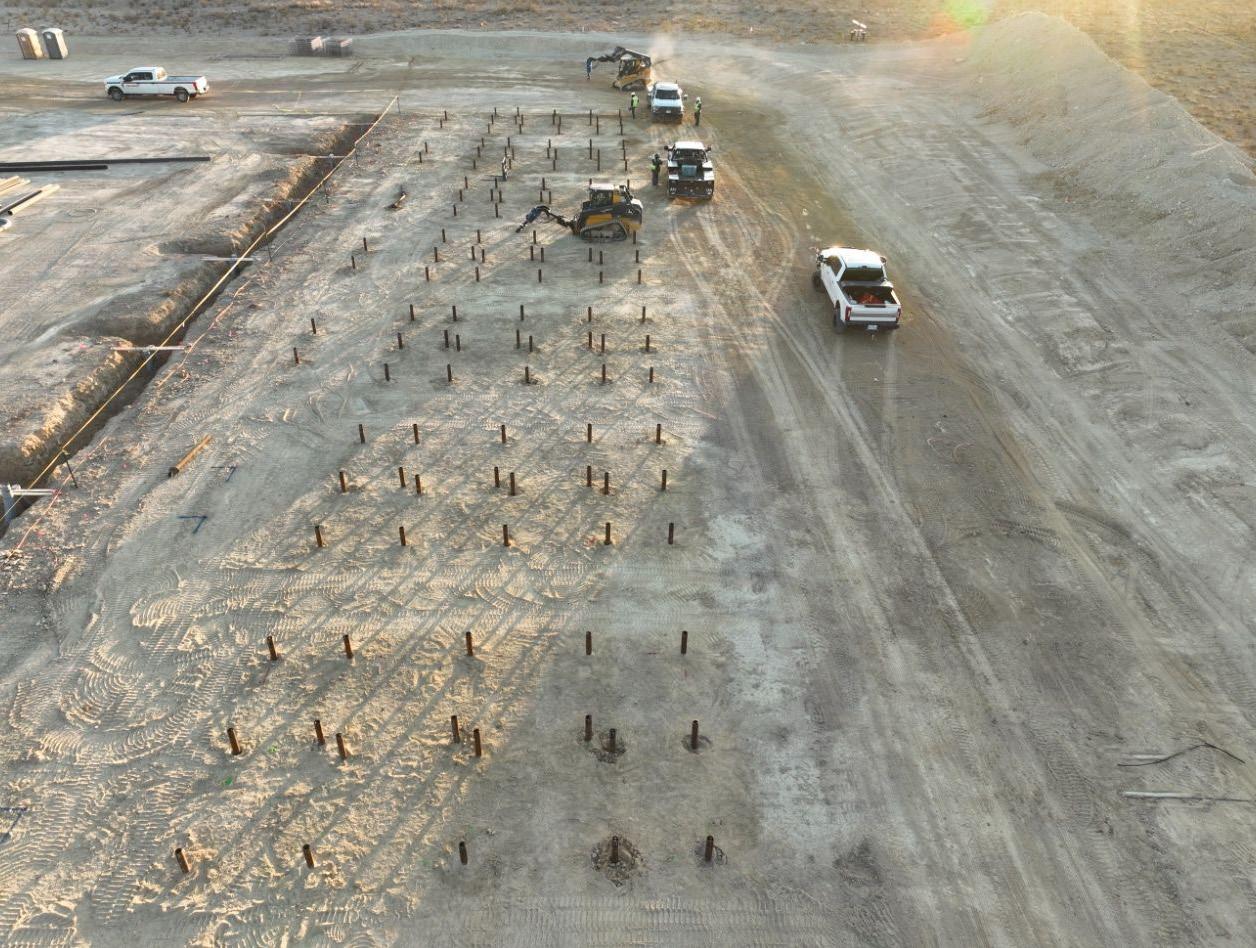
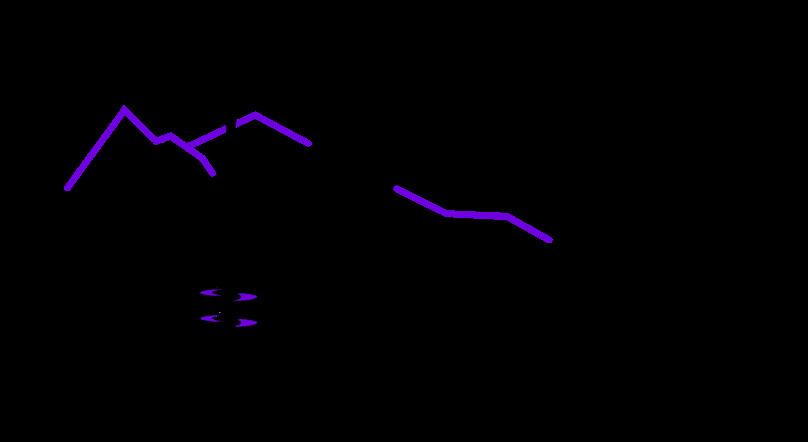
Helical piles are a premeditated innovation for this generation. Concrete, meanwhile, is as it sounds – firm, reliable, and has long been the go-to for curbs, light pole foundations, gas pumps, homes, and businesses.
But if you’ve ever owned assets, you know the panic that sets in when your concrete foundation starts splitting, cracking, or breaking. It’s doomsday – expensive, emotional, and exhausting.
This leads us to all ask the same thing: why isn’t there another way? There is, it’s Alterrus LLC (Alterrus).
While some companies jumped on the helical pile trend chasing profits, Alterrus was founded on something more enduring – a vision.
For Casey Palenshus, President and Owner of the company, this wasn’t about following a market wave, it was about solving a problem that plagued every industry. As a seasoned expert in structural solutions, he saw past the steel and torque, identifying an opportunity to build better, smarter, and safer.
Palenshus’ mission? To provide immaculate engineering, industry-leading product delivery, and uncompromising quality – all at a fair and honest price. He didn’t want to just support structures, he wanted to elevate industries.
Alterrus was formed for two clear reasons: integrity and service. We recognized not just the environmental edge of helical piles but the human aspect, as people deserve answers, reassurance, and a partner they can count on.
The Alterrus difference is our customer experience and that presence is felt in every call, on-site visit, and handshake.
Why did our team choose helical piles over other solutions? Easy – because anything that withstands the test of time is built on a solid foundation. Whether you’re a business owner, an oilfield operator, or a battery storage developer, we all can agree that strength and resilience begin at the base.
With helical piles, there are no cracks in the foundation.
Each pile is installed with surgical precision, real-time feedback, and to the exact depth and torque required, with engineering data confirming it can bear the designed load.
With no guessing or waiting, helical piles can also be loaded immediately, involving no curing, delays, or early-age concrete risk.
They are built to thrive in any soil – strong or weak, dry or saturated. Each pile is manufactured under strict quality standards, weld-checked, and tested. Our tech teams train for months or years before ever stepping on site. As such, we don’t cut corners, we anchor them.
Unlike concrete, which relies on on-site workmanship, weather, and other factors, our work is measurable, reliable, and futurefocused. This isn’t a trend, it’s a transformation.
At Alterrus, we don’t just install foundations, we build trust, elevate industries, and strengthen communities.
Because at the end of the day, our foundation is where your future begins.
Deep Earth Work – Alterrus
Phone: 281-516-5797
Email: projects@alterrusllc.com

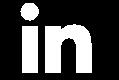
The company’s approach therefore begins with in-depth planning and strategy sessions to identify the best path to success.
“Careful preparation and shared objectives are the key differentiators that drive project efficiency and minimize downtime,” Matt outlines.
By aligning its success metrics with those of its clients, Saulsbury continues to ensure reliable project execution.
Furthermore, by maximizing a project’s operational uptime, the company is able to deliver a strong and profitable return on investment (ROI) for stakeholders.
“Our reputation is built on providing solutions that enhance efficiency, mitigate risks, and create long-term value for all,” he tells us.
SUPPORTING A BALANCED ENERGY STRATEGY
One project that demonstrates Saulsbury’s dedication to a comprehensive energy mix is the completion and commissioning of a large-scale water treatment plant designed to support a direct air capture (DAC) facility.
“Being part of initiatives like this is always inspiring as it allows us to contribute a broad range of energy solutions,” Matt enthuses.
Saulsbury often partners with major oil and gas clients who are integrating renewable energy solutions.
“Their dedication to innovation aligns with our mission to deliver highquality solutions that support both industry advancement and energy efficiency,” he points out.
SHAPING THE FUTURE OF ENERGY
On a mission to support clients with their expanding portfolio of projects, the company has significantly extended its presence in the renewable energy sector.
Its expertise in this area spans across multiple clean energy technologies, including utility-scale solar power, battery energy storage systems (BESS), and carbon capture facilities – some of the largest in the US.
“We also recently completed a major hydrogen production facility in Nevada, further strengthening our commitment to supporting a diverse mix of energy solutions,” Matt confirms.
Well-versed in the requirements set forth by the Inflation Reduction
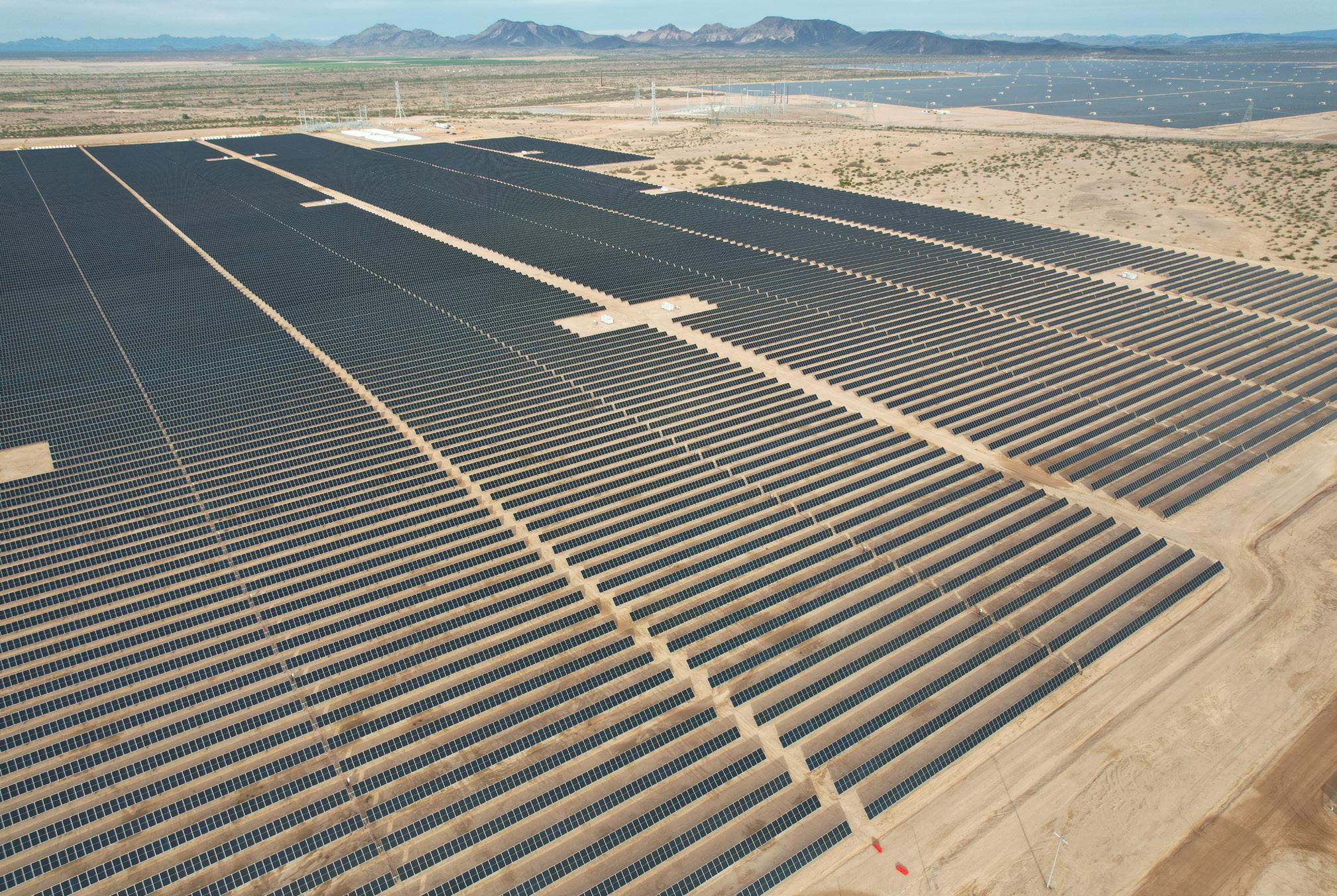
With a 50,000 square foot production facility on 9 acres and a capacity of 200 to 250 tons per month, Fab-Worx Industrial LLC, supplies fabricated industrial structural steel to our clients in the Oil, Gas and Chemical markets. FabWorx system of estimating, procurement and project tracking provides our clients with the information needed to manage delivery schedules and project milestones.
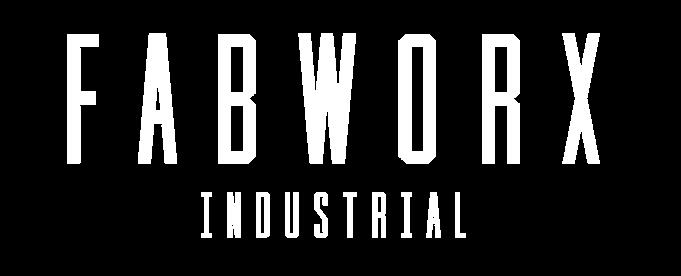
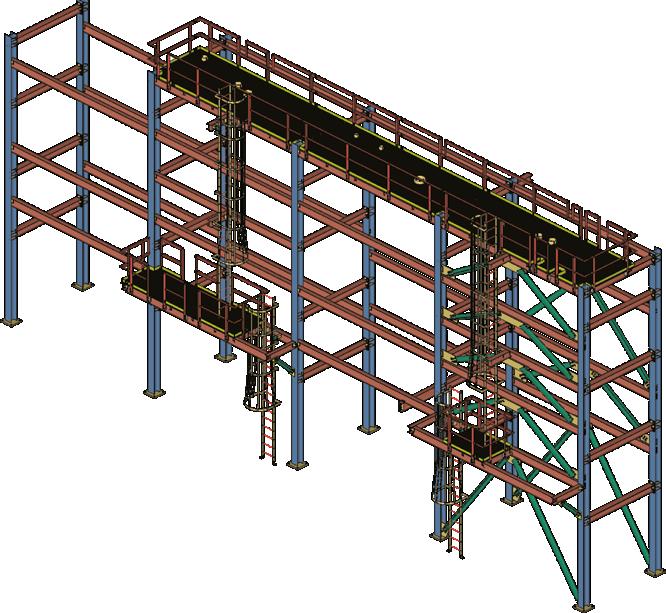
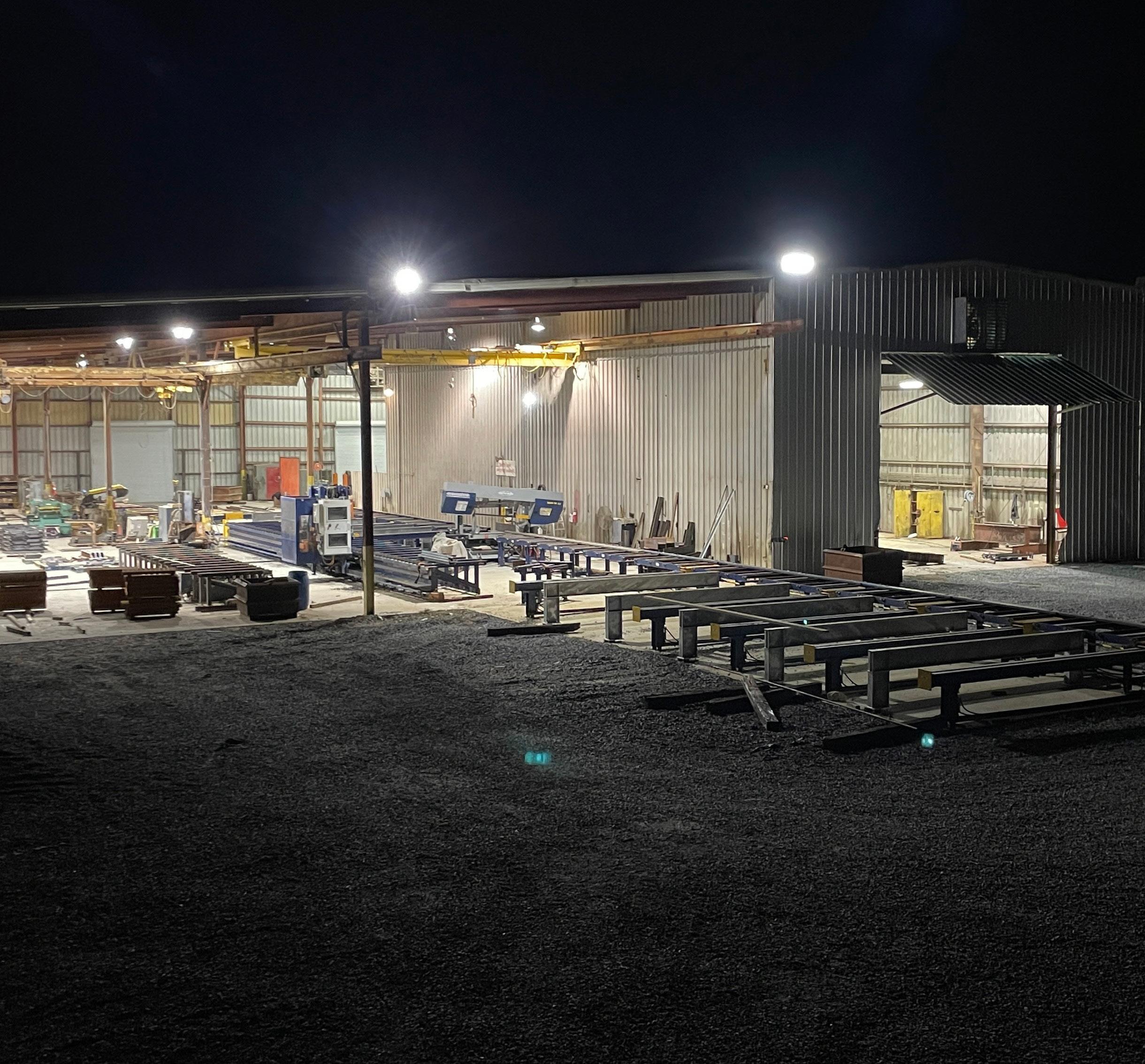
Services provided by FabWorx include:
1. Engineering Resources when required.
2. In-house detailing (SDS, Tekla and DWG formats).
3. Quality Control.
4. Project Fabrication and Delivery Tracking.
5. Structural Steel fabrication includes Pipe Rack, Platforms, Stair Tread, Grating and Handrail.
6. Engineered/Fabricated Pipe Supports.
a. CL Clamps
b. Clamps and Shim Blocks
c. Adjustable Supports
d. Pipe Shoes, Guides, Anchors etc…
e. Custom Designed Supports.
7. Automated CNC cutting and drilling for steel and pipe.
8. Plate roller and press break.
9. Galvanizing and Painting Resources.
Our goal at FabWorx is to be the one stop shop for meeting all our clients’ structural and custom fabrication needs.
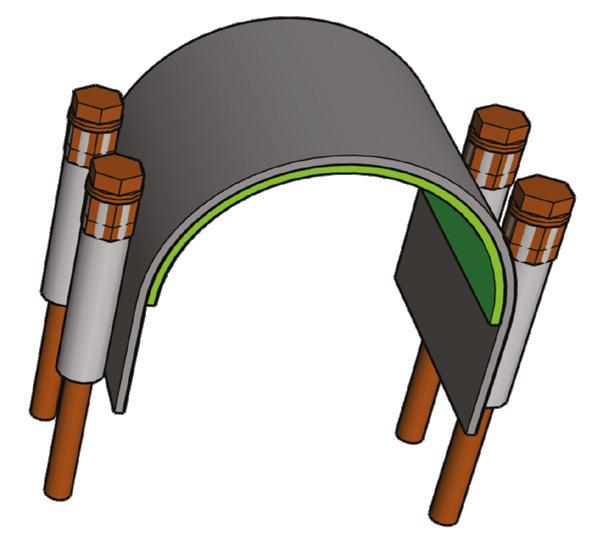
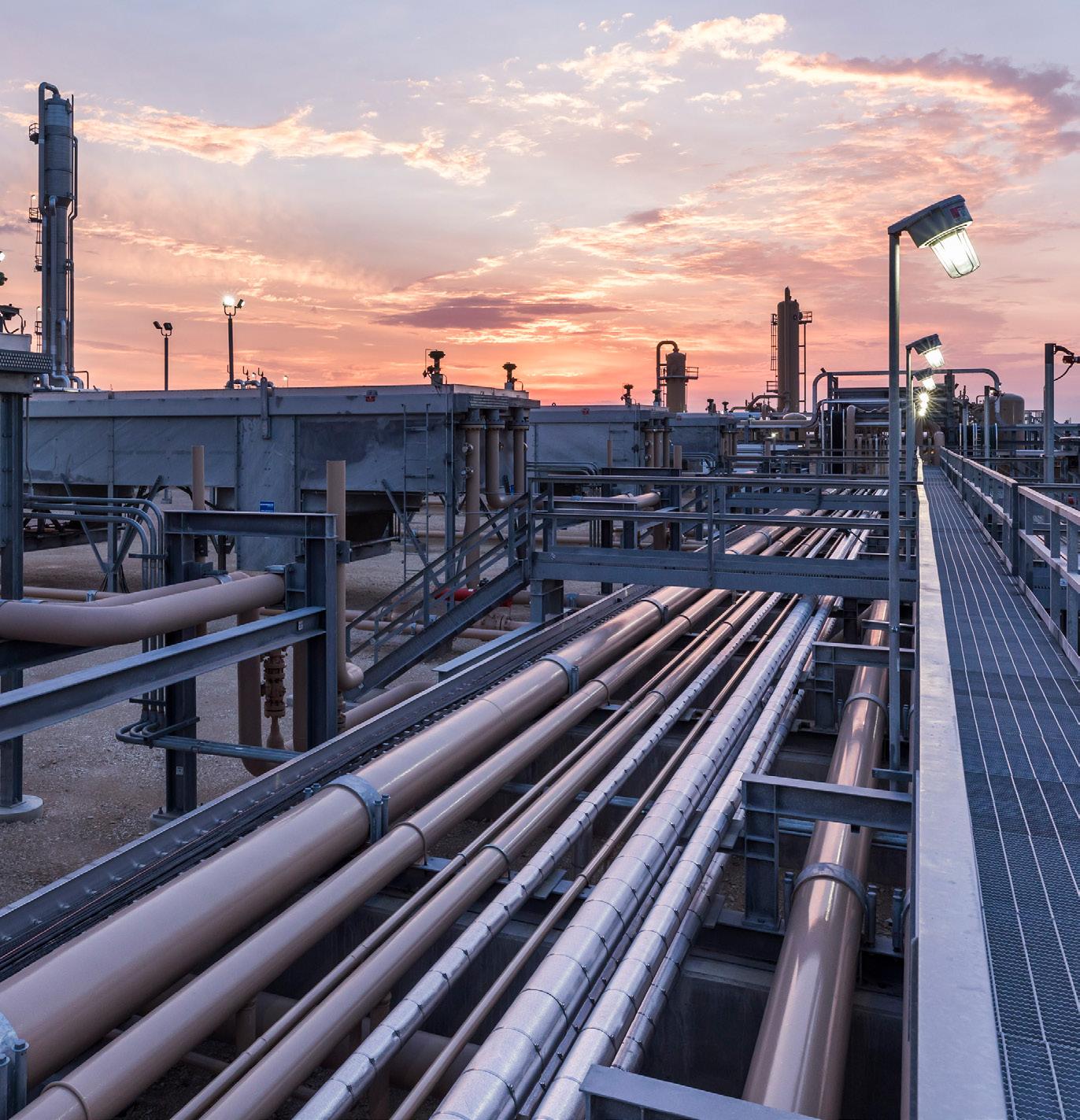
CORE COMPANY VALUES
Assisting Saulsbury in ‘getting the job done right’, the company’s core values are central to everything it does, ensuring expectations continue to be exceeded time and time again. They comprise:
SAFETY – An overarching goal of safety is evident across all operations, with the company striving to send employees home safely to their families every day in the same condition they arrived at work. As such, safety among employees, clients, and partners remains the number one priority.
INTEGRITY – With honesty and accountability at the heart of everything Saulsbury says and does, consistently cultivating integrity means it always does the right thing.
EXCELLENCE – Providing only the highest level of quality and performance, the company’s unsurpassed value alongside its dedication to client satisfaction continue to guarantee excellence.
RELATIONSHIPS – Proudly creating positive, lasting partnerships with its clients, Saulsbury sets itself apart through long-standing relationships with both employees and stakeholders.
COMMUNITY – With a deep-seated belief in supporting the communities in which it lives and works, the company takes pride in its commitment to community success and sustainability.
Act (IRA), Saulsbury has established compliance programs to ensure that both the company and its clients are able to capitalize on the benefits of these regulations.
“In recognition of the increasing demand for renewable energy solutions, we have launched a dedicated Utilities and Infrastructure business line, with a primary focus on solar power, BESS, and substation project delivery across the US.”
Thus, by leveraging its deep industry expertise and commitment to innovation, the company is helping to shape the future of energy.
“We ensure long-term, multi-source solutions while meeting the evolving needs of the US energy market,” he clarifies.
PROJECT SOLUTIONS IN ALL SIZES
Through its Field Services division, Saulsbury supports small and midsized capital projects by offering a comprehensive range of construction services for in-field gathering systems, pipelines, tank batteries, wellhead hookups, field modifications, and facility construction and maintenance.
“By embedding ourselves within our clients’ operations, we create long-term stability and continuity, ensuring seamless execution across multiple projects,” Matt insights.
In establishing a predictable pipeline of work with specific clients, Saulsbury is able to manage the workload effectively by allocating key resources over extended periods, as opposed to sporadically deploying personnel.
“For our clients, this model provides highly productive teams that are familiar with their operations and aligned with their people and specific requirements,” he adds.
By integrating deep-seated expertise into client workflows, Saulsbury effectively reduces the daily support required on each project, improving overall efficiency and execution.
Quality Metal Building Construction
HPB Construction, Inc. is a turnkey building contractor, that is family-owned and operated and was established in 1988. We employ experienced and talented tradesmen, as well as second-to-none field supervision, for every project.
We are looking forward to working alongside Saulsbury for all of their building needs with excellence, energy, and enthusiasm in the years to come. Here is a glimpse at some of the building packages/services we offer:
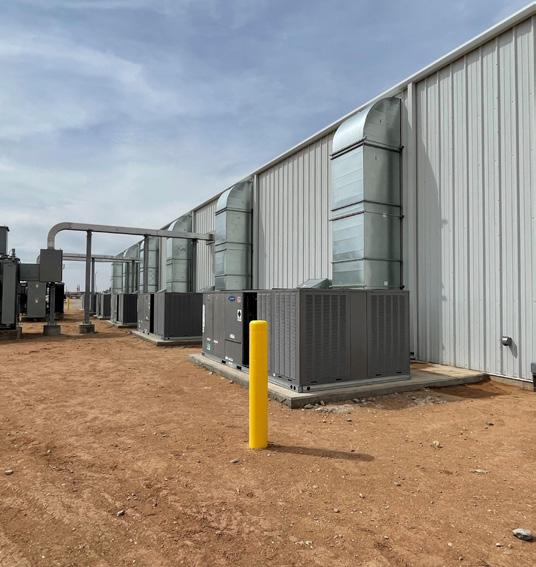
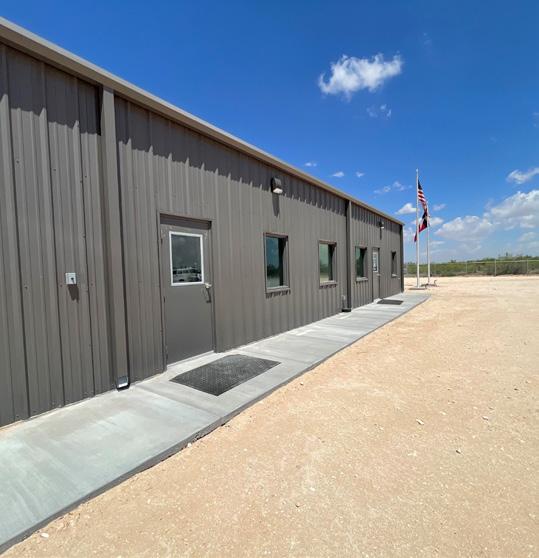
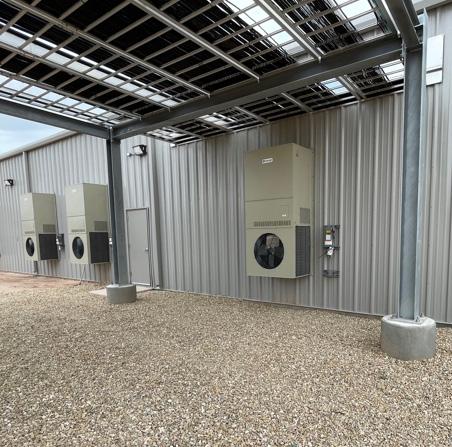
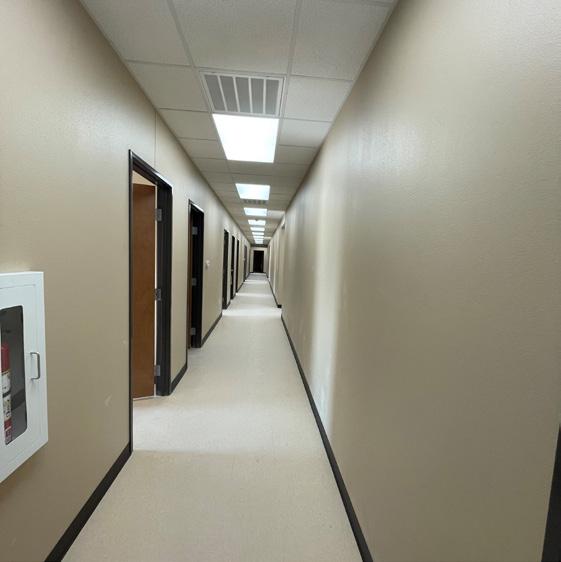
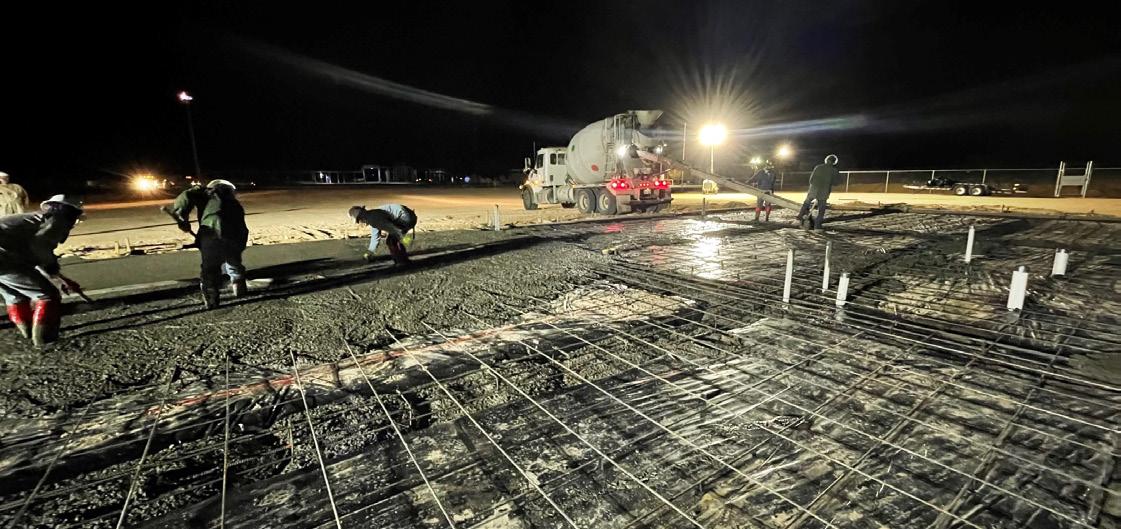
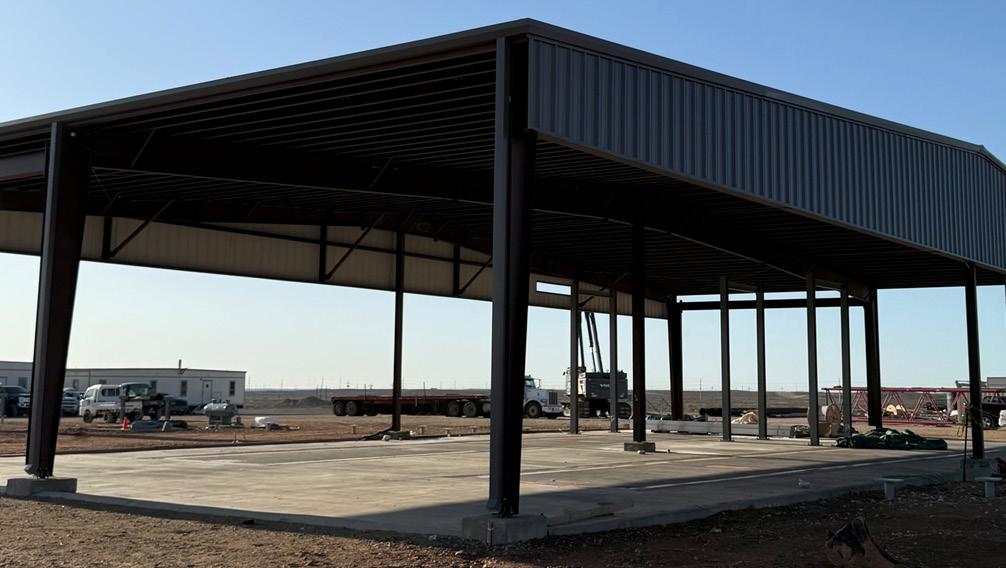
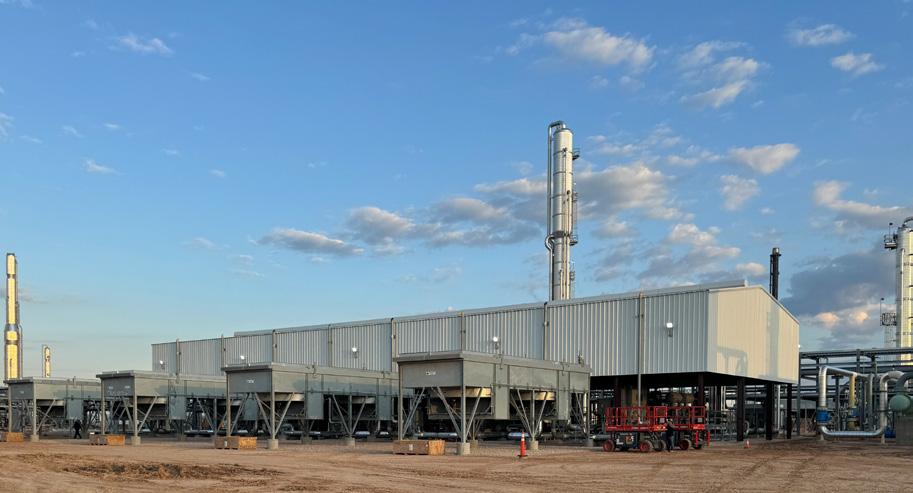
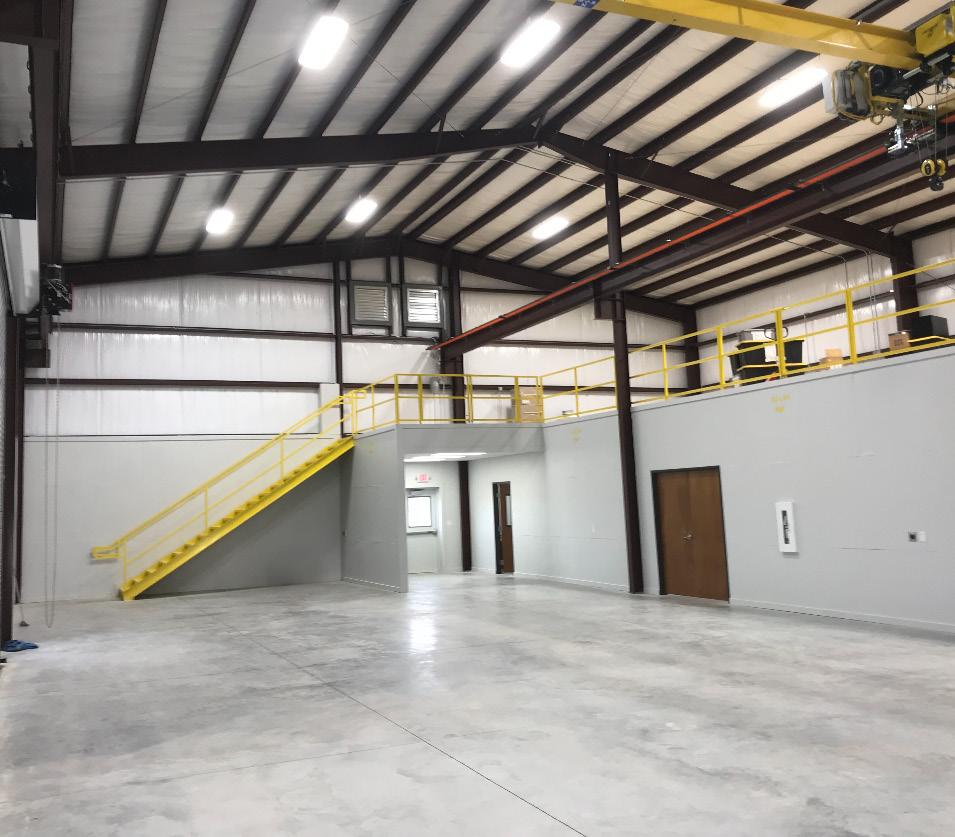
Saulsbury consistently proves itself to plan early, enabling the construction process to run smoothly in the field. Saulsbury’s team of highly qualified engineers, project managers, superintendents, and safety experts work hand in hand with HPB Construction to ensure we have everything we need to be successful.
Truck Canopies
Compressor Canopies
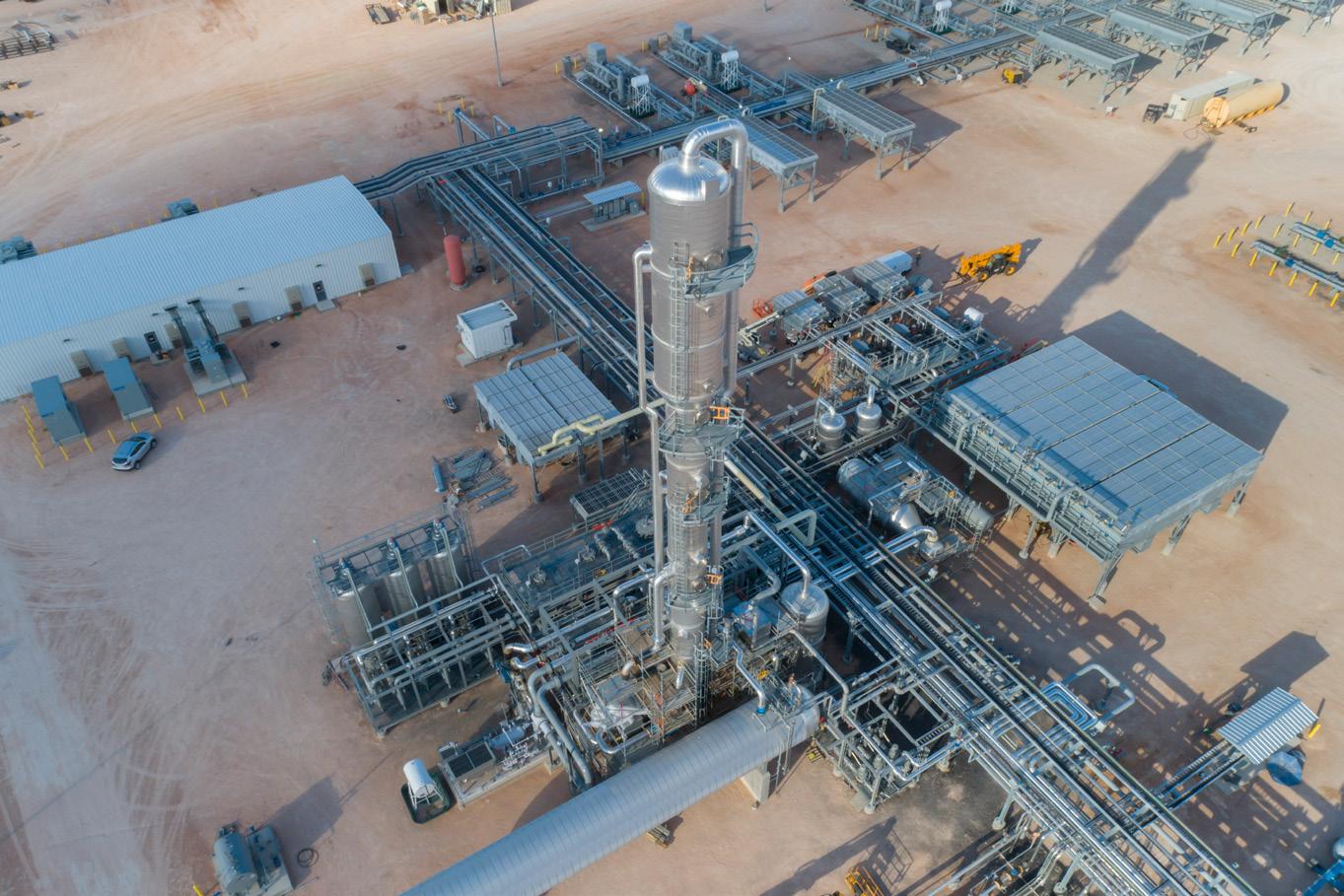
“EMBEDDED IN OUR CULTURE AS A FUNDAMENTAL OBLIGATION TO OUR EMPLOYEES, SAFETY IS SOMETHING WE LIVE AND BREATHE EVERY DAY. EVERY TEAM MEMBER IS THEIR BROTHER’S KEEPER, AND OUR COLLECTIVE DUTY IS TO ENSURE THAT EACH EMPLOYEE GOES HOME IN THE SAME –OR BETTER – CONDITION THAN WHEN THEY ARRIVED AT WORK”
– MATT SAULSBURY, CEO, SAULSBURY
The contracts it undertakes for this type of work vary but are typically structured around KPIs that measure its performance in critical areas.
“These KPIs ensure we meet or exceed expectations in schedule adherence, productivity, safety performance, cost control, and quality,” Matt assures.
Saulsbury’s dedicated project control teams are on hand to meticulously track these metrics, providing transparency and accountability to the company’s clients while demonstrating its dedication to operational excellence.
A WORKPLACE OF CHOICE
Committed to employee growth and engagement, Saulsbury seeks to actively build a workplace of choice.
A strong, family-oriented culture, alongside a set of core values, creates a supportive environment and contributes to staff feeling inherently valued.
“We believe in fostering a workplace where accountability, fair compensation, and personal development go hand in hand,” Matt sets out.
As such, team members feel empowered to build long-term careers with Saulsbury, with many having spanned decades.
“Employees are not just numbers to us – we take an active interest in their well-being, ensuring they feel protected, heard, and appreciated.”
Striving to enhance the quality of life of those that work at the company, Saulsbury’s commitment to employee empowerment extends beyond business operations.
The company invests in the future of its employees and their families through scholarship and education support, including the Dick and Amelia Saulsbury Scholarship Program.
Administered by Scholarship America, the program was established to assist the children of Saulsbury employees who plan to continue their studies into higher education, such as in college or vocational school programs.
“This initiative reflects our commitment to education by providing financial assistance to employees’ children, helping them to pursue their academic goals,” Matt reflects.
Likewise, the company supports staff who are in active pursuit of higher education, reinforcing its belief in the next generation of leaders while strengthening the skill set of its current workforce.
Committed to promoting from within, Saulsbury’s career advancement and internal mobility initiatives offer employees opportunities to progress across departments.
In the past two years alone, it has successfully transitioned employees into new roles within accounting, supply chain, operations, and HSE, allowing top performers to broaden their expertise and contribute to the business in new ways.
“This internal mobility is complemented by ongoing professional development, including both internal and external training programs, to prepare employees for future leadership roles,” Matt explains.
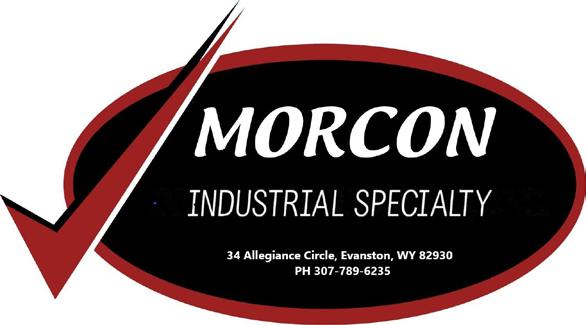
INDUSTRIAL SPECIALTY
Founded in Evanston, a small boom town in SW Wyoming, in October 1987. Operations began in a small 2,500 sqft facility offering a large variety of industrial supplies to the local oil and gas industry. With fast growth and emerging industry needs, our selection of products grew quickly, necessitating a move to a 15,000 sqft facility in 1991.
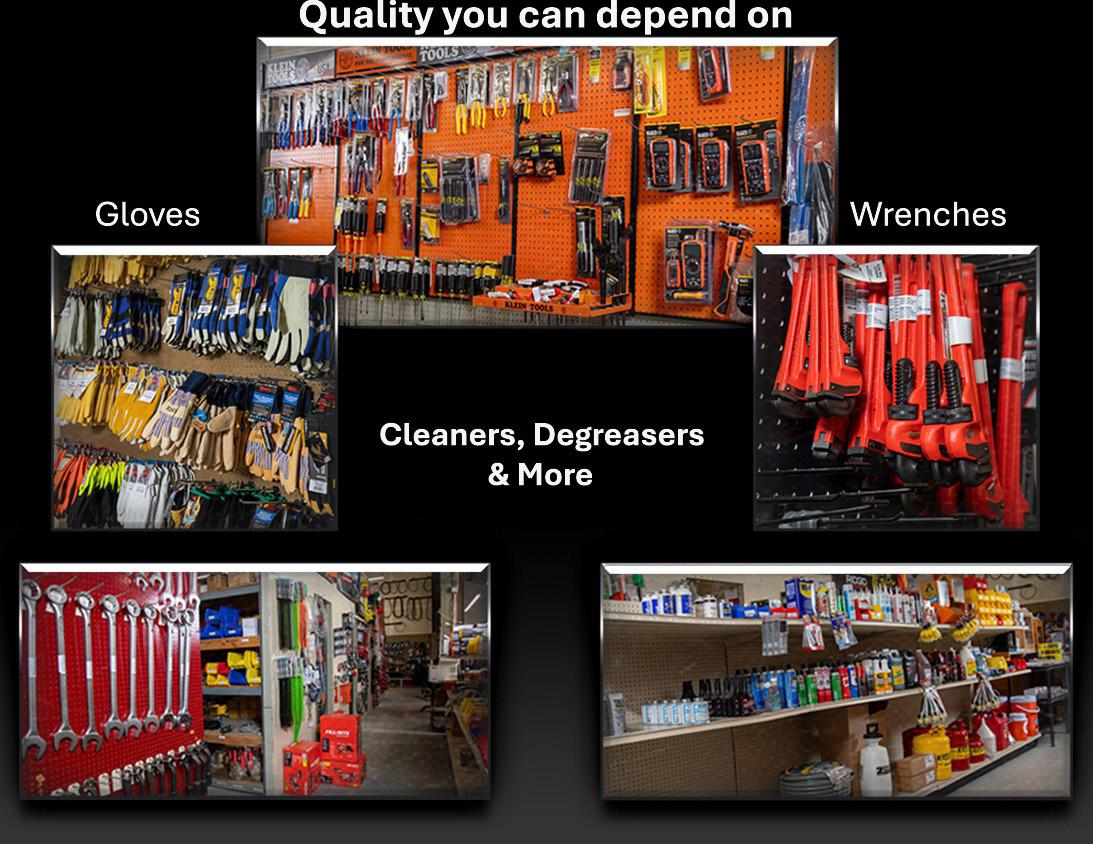
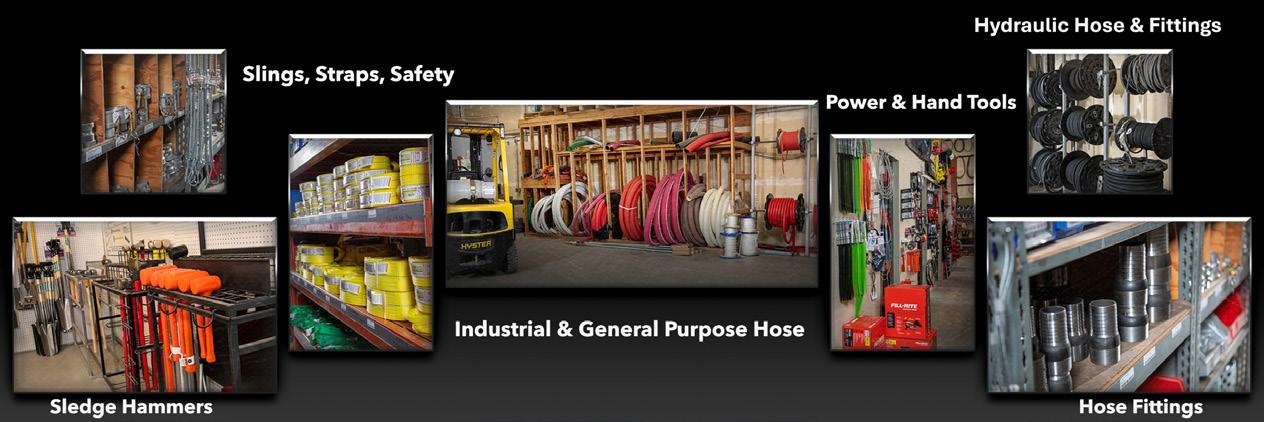
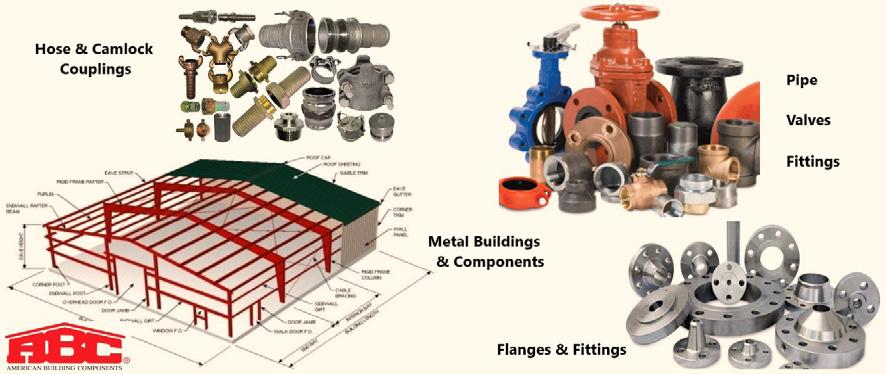
Our experienced team provides high-quality products and exceptional customer service to help you achieve your business needs. From large projects to small tools and parts, we have everything you need to keep your operations running smoothly.

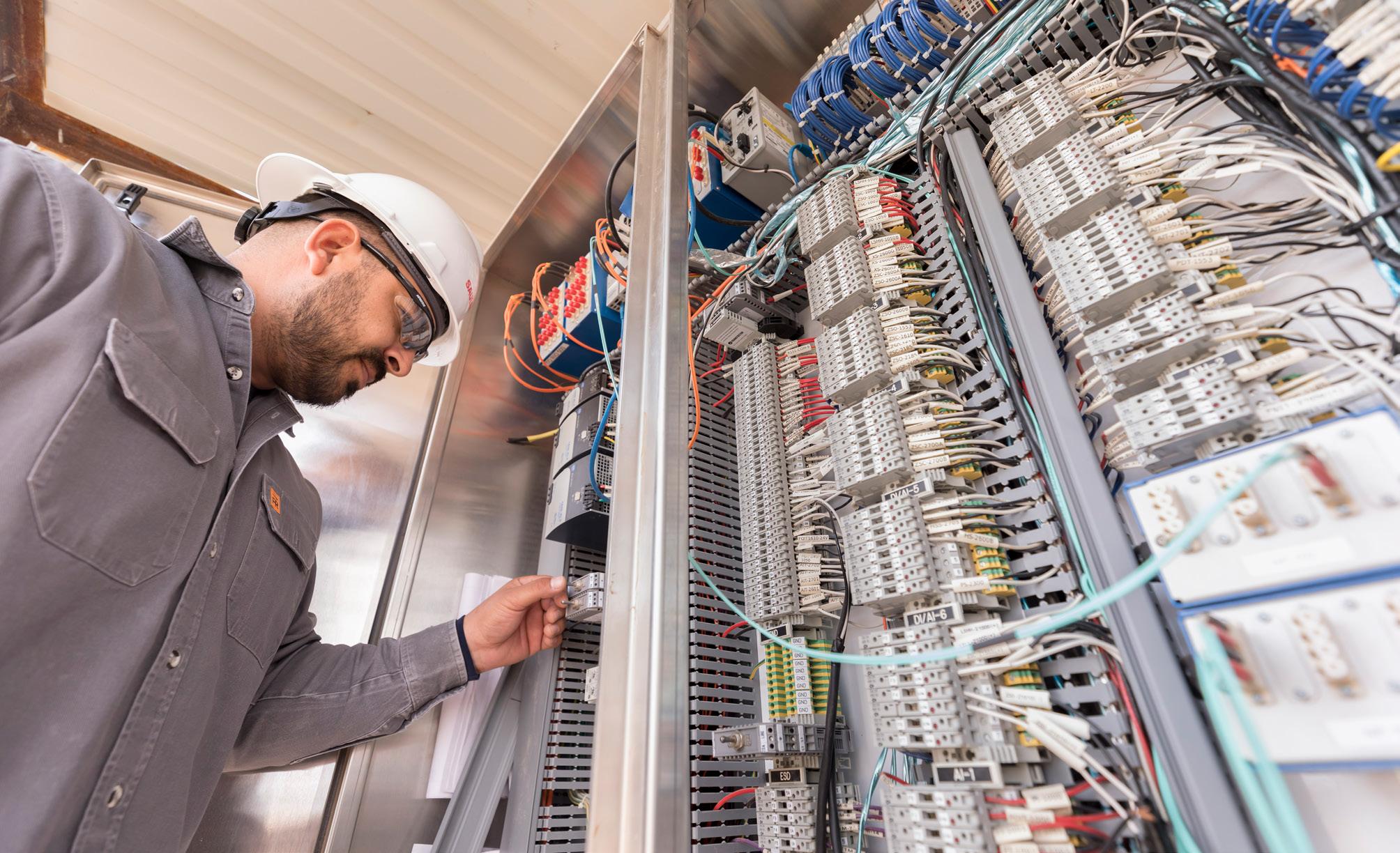
As such, Saulsbury continues to build a workplace that supports career development by investing in its employee growth, fostering a culture of transparency, and reinforcing its overarching commitment to education and community.
“Our people are the foundation of our success, and we remain dedicated to providing the resources, opportunities, and recognition they deserve,” he divulges.
SOCIALLY RESPONSIBLE
Beyond the workplace, Saulsbury is deeply engaged in the communities in which its employees live and work.
Through charitable contributions, volunteer initiatives, and corporate partnerships, it provides opportunities for everyone across the organization to make a meaningful impact beyond their day-to-day roles.
Community engagement is therefore not just a priority for Saulsbury, but part of who the company is.
Saulsbury was involved in the repair of the spring-fed pool at Balmorhea State Park (BSP) in West Texas – a long-held favorite leisure site among local residents.
A BRIEF HISTORY
Dick and his wife Amelia left their home in South Arkansas in 1961 to join the booming oil industry in West Texas.
Having worked as an electrician for his own electrical construction company for a number of years, Dick segued into EPC when he established Saulsbury Electric Co. in 1967 in Odessa, Texas.
Dick’s exceptional work ethic and dedication to ‘getting the job done right’ set the company apart from the competition and quickly led to it becoming the foremost electrical contractor in the Permian Basin with a commitment to safe and high-quality projects.
The continued growth and success of Saulsbury Electric Co. led to Dick establishing Saulcon General Construction in 1980, whose turnkey construction services included civil, structural, mechanical, and electrical instrumentation.
As Dick’s suite of services continued to evolve and expand, so did the local oil and gas market. This became particularly prevalent in the mid-1990s, when a distinct shift towards EPC projects became apparent.
As a result, Dick added Saulsbury Engineering and Construction to his repertoire in 1994, distinguishing the business as a full-service EPC firm that supported both engineering and construction projects.
Over the subsequent two decades, he continued to undertake larger projects, add additional services, enter new markets, and open new offices under the Saulsbury name. In 2012, the three companies officially merged to become Saulsbury.
From its humble beginnings to its status today as a premier EPC company with over 2,000 employees, the foundation of Saulsbury’s success is built on its five core values of safety, integrity, excellence, relationships, and community.
Stewards of Dick’s nearly 60-year legacy, Saulsbury’s current leadership team continue to exceed customer expectations and deliver project excellence.
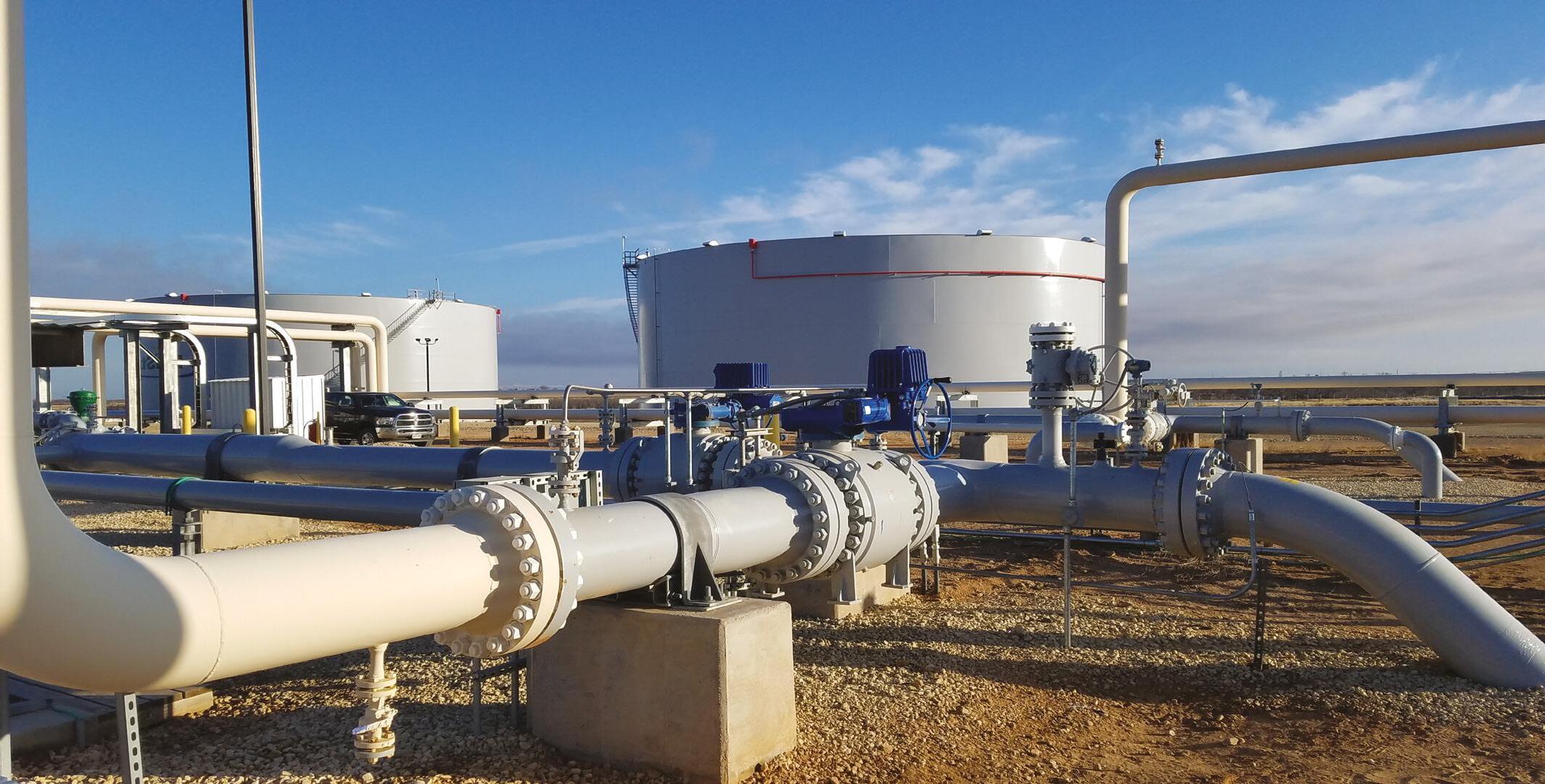
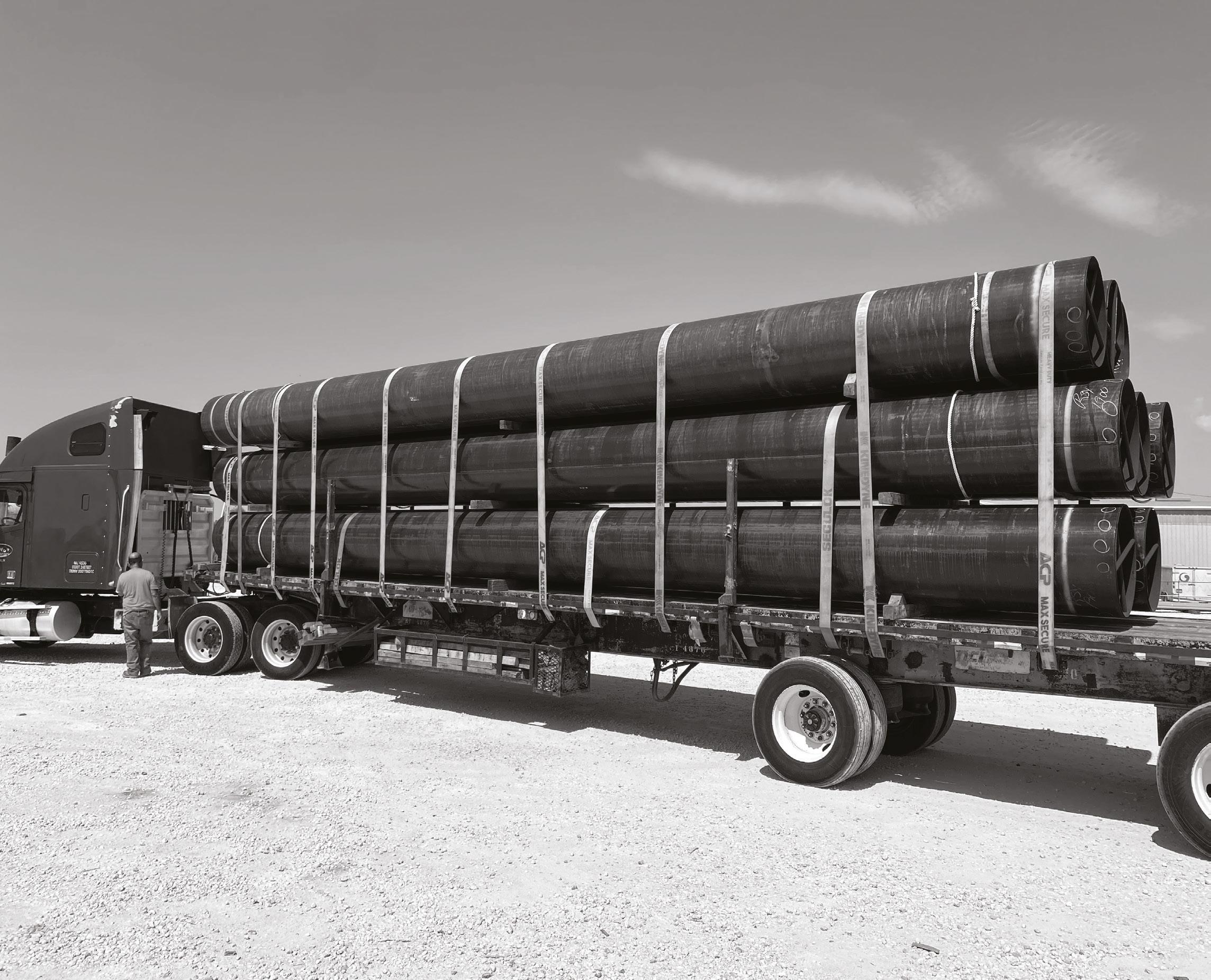
With a generous donation of $100,000 to the Texas Parks and Wildlife Foundation, the company was proud to contribute to the repair, as many of its own employees have enjoyed the cool, clear waters at BSP for generations.
Following a lengthy fundraising drive and a comprehensive ‘topto-bottom’ renovation, the pool reopened in June 2021.
“Our commitment to making a positive impact is deeply rooted in our culture and reflected in the way we support the communities where we live and work,” Matt affirms.
Through the Saulsbury Family Foundation and an internal charitable giving committee, the company also
contributes to a wide range of nonprofit organizations, each of which have a strong emphasis on employee involvement.
“Our dual approach to community engagement ensures that each of our team members have a voice in directing funds toward causes that matter to them personally and are local to the regions we serve,” he insights.
Saulsbury is a proud supporter of numerous organizations focused on education, health, family services, and community development, including Court Appointed Special Advocates (CASA), High Sky Children’s Ranch, the West Texas Food Bank, Meals on Wheels, the Harmony Home
“MY LEADERSHIP STYLE IS A BLEND OF DEMOCRATIC AND SERVANT LEADERSHIP. I BELIEVE IN COLLABORATION, ACCOUNTABILITY, AND EMPOWERING TEAMS TO MAKE INFORMED DECISIONS. NO ONE HAS ALL THE ANSWERS, AND I VALUE INPUT AND HEALTHY DEBATE”
– MATT SAULSBURY, CEO, SAULSBURY
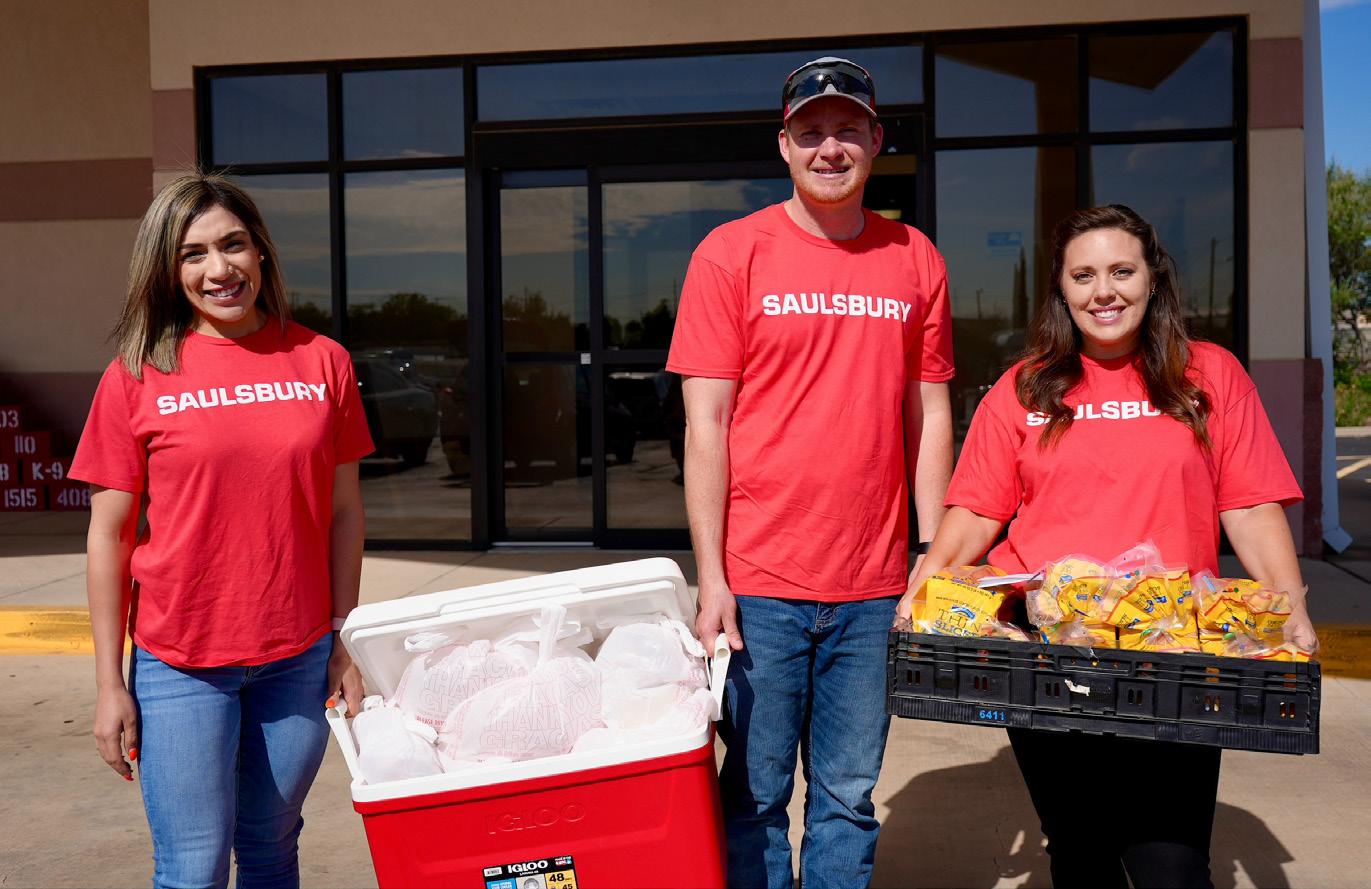
Children’s Advocacy Center, the Aphasia Center, Odessa College, and UTPB, to name a few.
Furthermore, the company’s culture of giving extends beyond financial contributions through its Saulsbury Serves program.
“Through Saulsbury Serves, employees are encouraged to roll up their sleeves and get involved,” Matt expands.
Whether volunteering at the local food bank, supporting Meals on Wheels deliveries, or participating in Christmas in Action projects, its teams are active participants in improving the lives of local people.
Every year, Saulsbury Serves volunteers dedicate hours of their time and resources to support the local causes closest to their hearts.
Meanwhile, with a strong commitment to honoring and supporting veterans, the company proudly partners with organizations such as Trinity Oaks Outdoors, a charity on a faith-based mission to make a difference in the lives of veterans through outdoor activities.
“To us, corporate philanthropy means more than writing checks – it’s about building lasting relationships, giving our time, and being a true community partner. That’s the Saulsbury way,” he proudly states.
COMMITTED TO CONTINUOUS IMPROVEMENT
Last year, Saulsbury was recognized on Engineering News-Record’s 2024 Top 400 Contractors and Top 20 Petroleum Contractors lists.
However, while industry recognition is always appreciated by the company, it is not what drives it forward.
“While such awards affirm our standing in the industry, our true motivation lies in something deeper – a relentless commitment to excellence and continuous improvement,” Matt reflects.
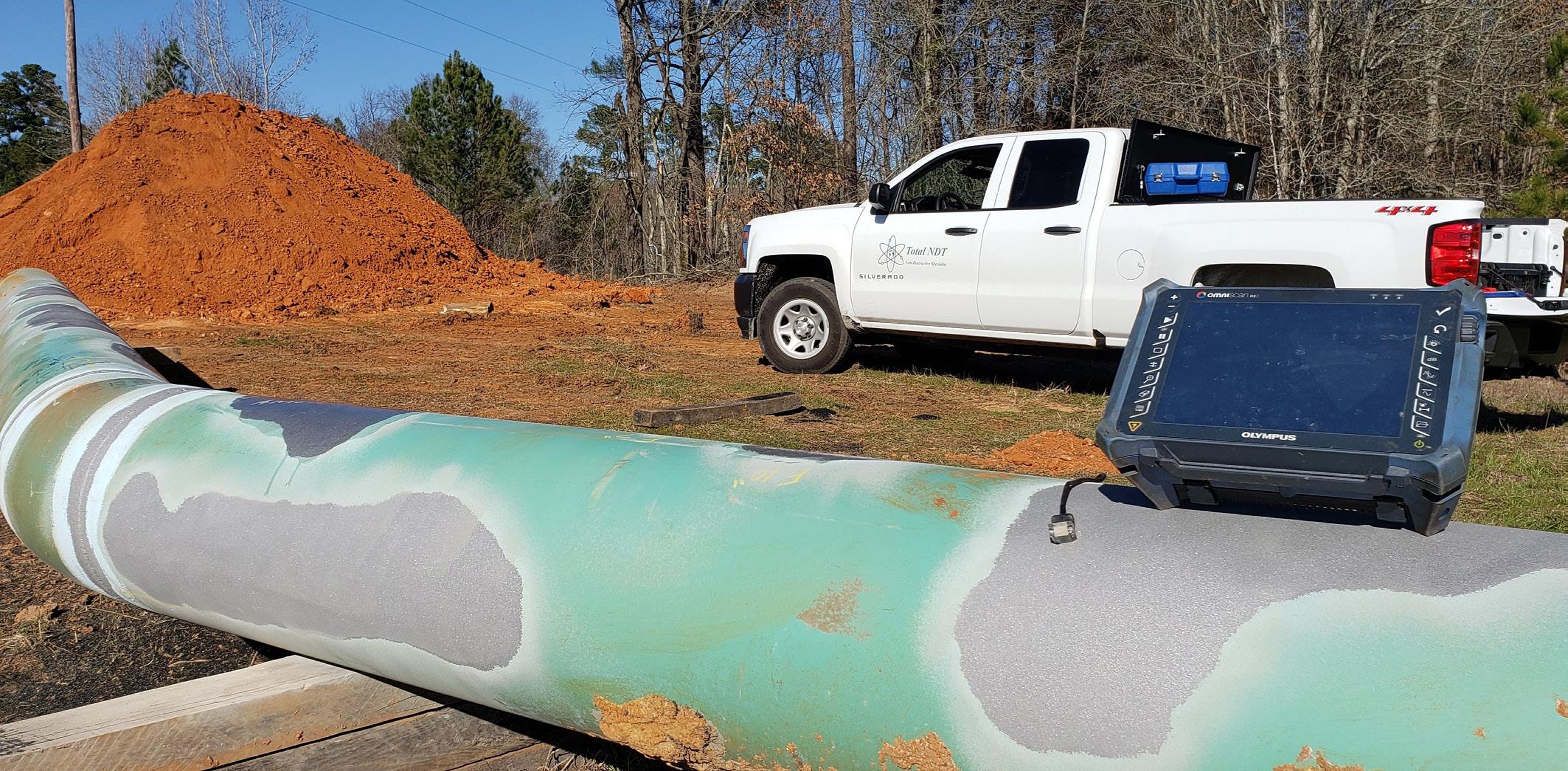
Safety is our #1 Priority
Our Mission Statement
Here at Total NDT, our goal is to provide non-destructive testing to an array of sectors from energy to food industries. Total NDT gives the highest level of quality, customer service, and safety on every task. Total prides itself on doing it right the first time, every time.
We will provide a safer environment giving our customers peace of mind by inspecting their components in a safe, reliable, and cost-effective manner without causing damage to the equipment or shutting down the operations of the plant.
Quality
By using Total NDT, you are choosing a company with a proven record of reliable service. Each of our employees take pride in their work, giving you the repeatability of inspection with integrity. Our knowledge of codes and standards make sure that you are getting the quality you deserve.
We continue to train and invest in each and every employee from their hire date to advance them in the industry. Each of our technicians are trained to a minimum of ASNT SNT-TC 1A to meet your needs.
Quality, Safety, Integrity
Total NDT, LLC. provides each customer with qualified technicians, certified as a minimum to ASNT SNT-TC-1A, along with vast knowledge and years of hands on experience. Each member of the team is trained by an outside agency to provide superb safety standards to meet your needs. Total NDT provides the customer with the integrity you can trust.
Our Promise
Total NDT, LLC. will provide each and every customer with a personalized level of care with 24/7 on-call. We promise a quality job the first time, every time.
Our Goals
• No one gets hurt
• No environmental damage
• Enhance our business through continuous improvement of HSE
• World-class HSE performance
Our employees are trained in-house and through outside agencies for meeting high safety standards which comply with all regulations from the state as well as customer specifications.
We belong to multiple agencies consisting of ISNetworld, Veriforce, Browz, and more. Your people and our people are the number one priority.
Our Team
Our management Team is highly trained, skilled, and possesses over 125 years of combined experience, while our field technicians are here to make your experience and daily routine easier for you.
We are here to answer all your questions and provide all your NDT needs.
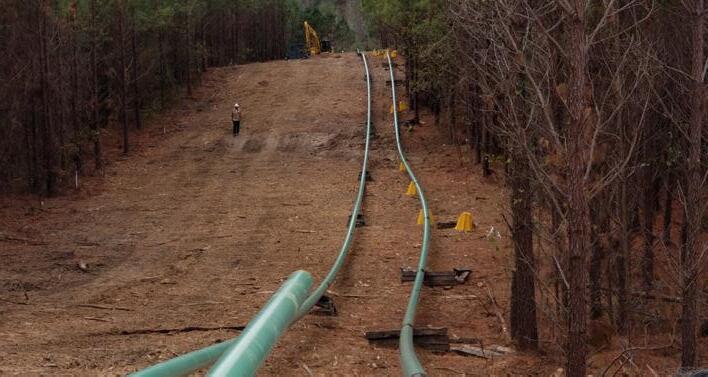
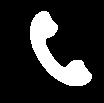
Our Culture
Total NDT has the culture of a team-based environment. Each and every employee has impact on our decisions and customer satisfaction.
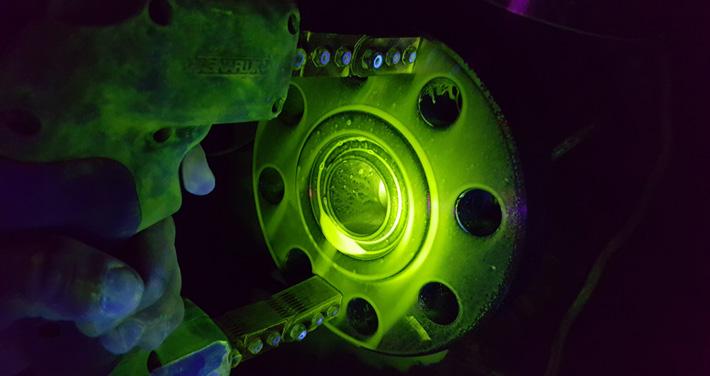
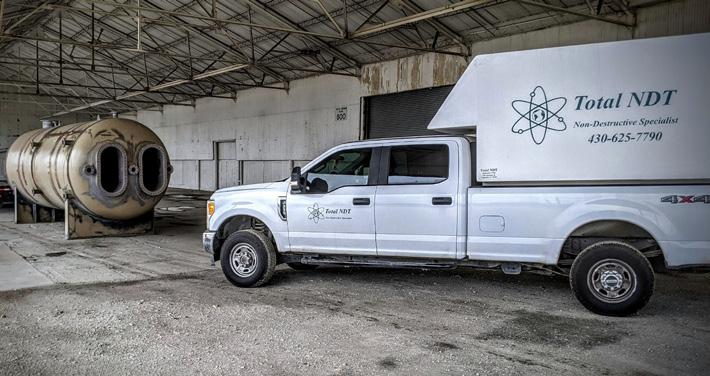

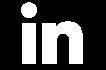
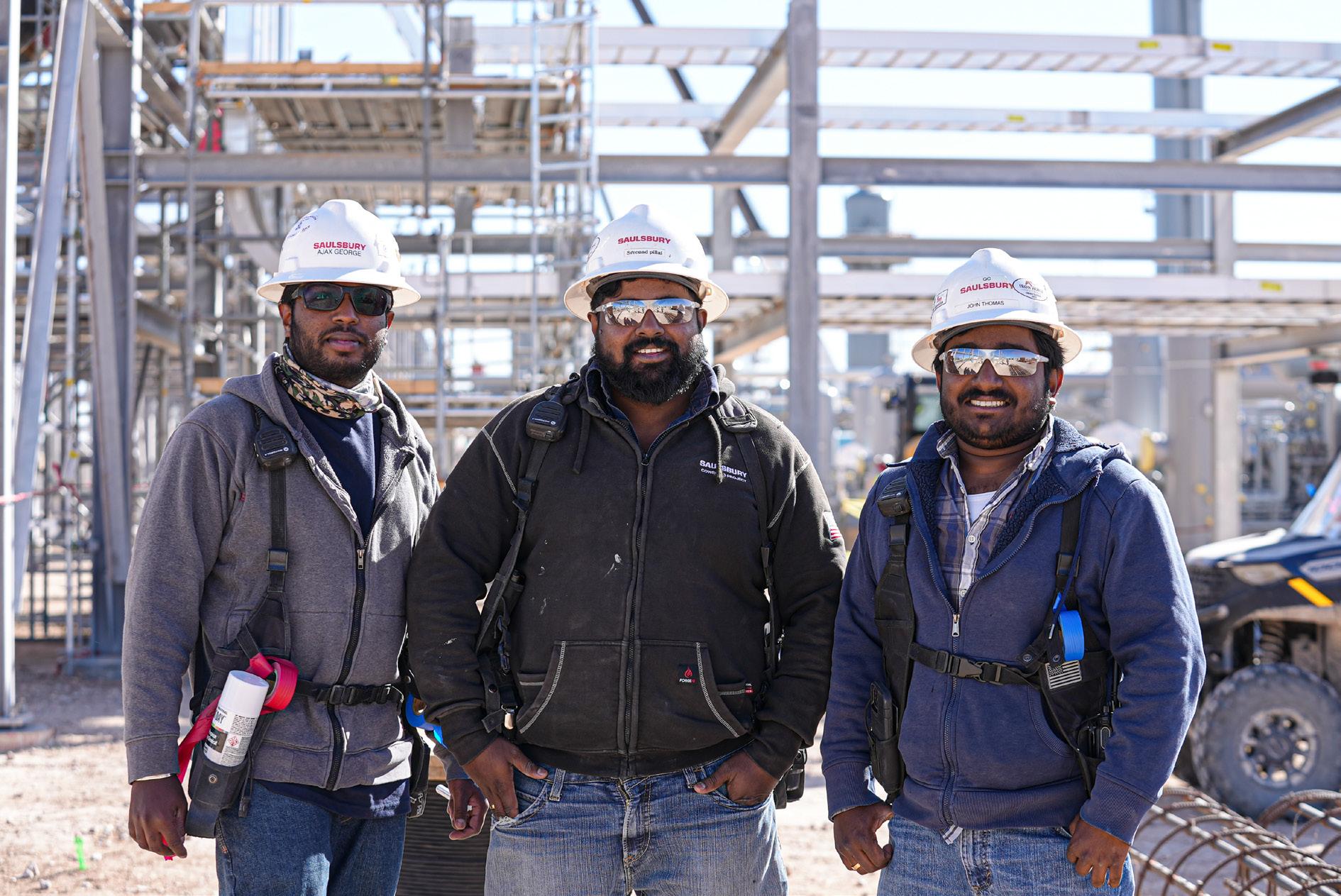
Fostering a culture that constantly challenges the company to be better than it was the year before, Saulsbury measures its success not by comparing itself to others but with its own internal benchmarks – always setting the bar higher.
“We’re our own toughest critic, constantly evaluating how we can improve through enhanced training, streamlined processes, and the integration of new technologies,” he says.
As a privately held company, Saulsbury’s focus is on long-term sustainability and strategic growth rather than short-term accolades.
While recognition may follow, it’s the result of staying true to its principles that is most important.
INVESTING IN TOMORROW
By investing in future engineers and young people interested in energy
and infrastructure, Saulsbury recognizes the critical role that the next generation of leaders will play, not only in shaping the evolution of the company but driving progress across industries nationwide.
Therefore, engaging with students and young professionals is more than just a recruitment effort – it is a commitment to fostering innovation, leadership, and excellence in the field.
As such, the company has cultivated strong partnerships with higher education institutions across Texas, such as its long-standing relationships with Odessa College and UTPB.
“Our involvement extends beyond traditional recruitment – we actively support capital campaigns to expand and modernize campuses, ensuring students have access to state-of-theart facilities that prepare them for the
workforce,” Matt explains.
With a dedication to community and education that is deeply rooted in the areas in which it operates, Saulsbury representatives serve on local school boards.
“These efforts reflect our belief that investing in education at all levels benefits not just our company, but the industry and society as a whole,” he states.
DEDICATED TO LEARNING
Further to its work in communities and with young people, Saulsbury believes in the power of uniting academia with industry and bridging the gap between the two.
In this way, it actively collaborates with UTPB, Odessa College, and other academic institutions to provide learning opportunities for both current and future employees.
Cherokee Measurement & Control delivers innovative analytical & measurement solutions for hydrocarbon, clean energy, & industrial markets—through custom integrations & expert technical field services.
We Integrate & Service
Gas Chromatographs & Contaminant Analyzers
Sample Conditioning Systems
Gas & Liquid Flow Meters
Natural Gas Regulation (Control Valves & Regulators)
Liquid Control Valves
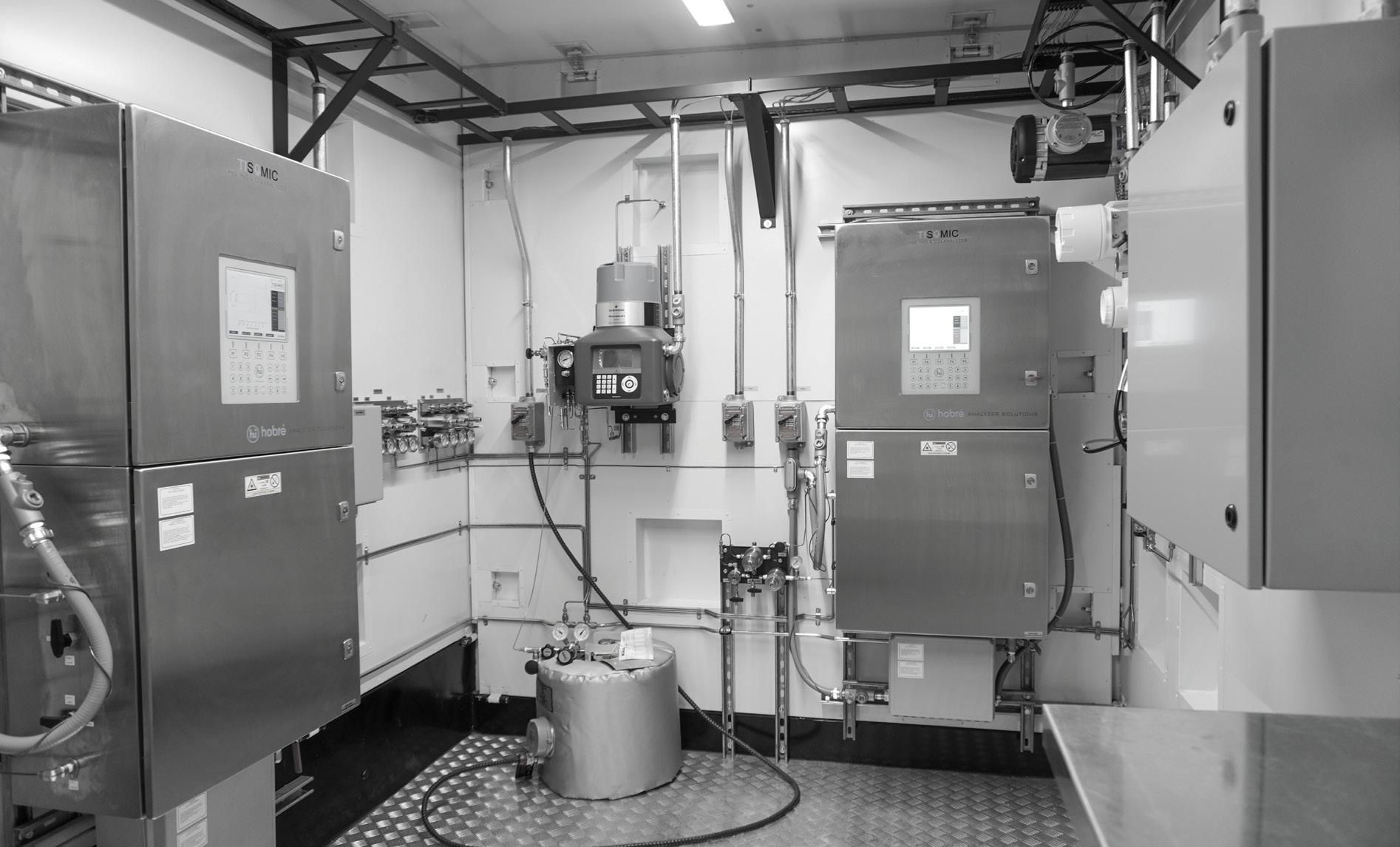
sales@cherokeetulsa.com CHEROKEETULSA.COM
Why CM&C
Analytical & Measurement Experts
20+ Years of Experience
Avetta, ISNetworld, & Veriforce Certified Technicians
Certified National Minority Supplier Distributors
Trusted EPC Partner
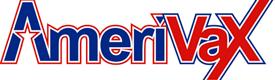
Ph: (432) 634-3587
Email: travisjones@amerivax.com
Website: www.amerivax.com
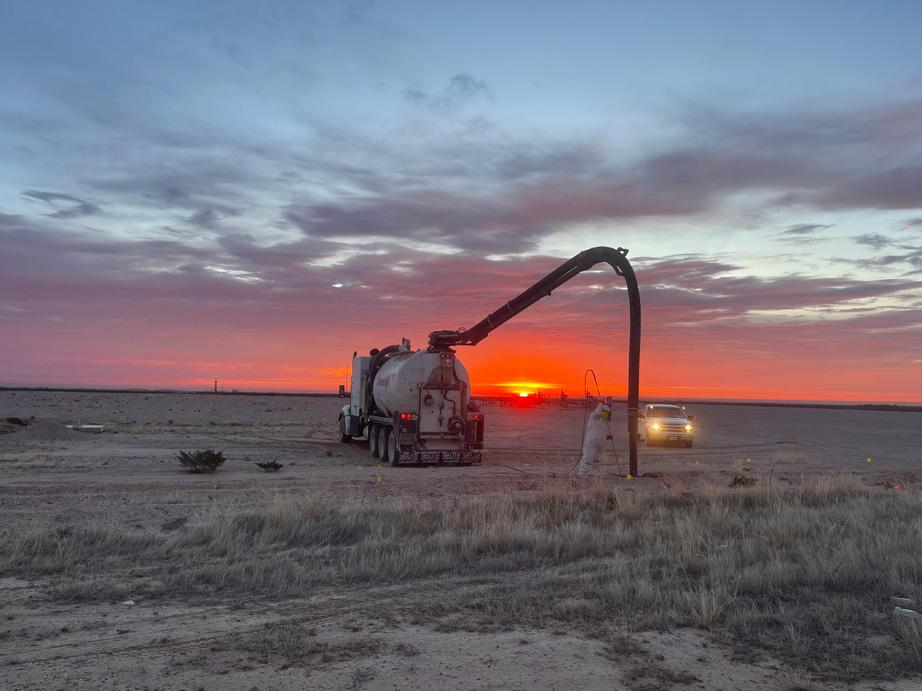
With a fleet of 30+ Hydrovac trucks and over a decade of industry experience, Amerivax delivers safe, precise, and efficient excavation services across Texas and beyond.
We offer comprehensive solutions including sanitation, environmental cleanup, line locating, and hydro testing. Our commitment to safety, innovation, and client satisfaction sets us apart in the field. Whether supporting construction, utility, or industrial operations, we provide turnkey services with unmatched reliability.
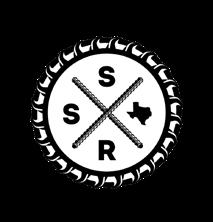
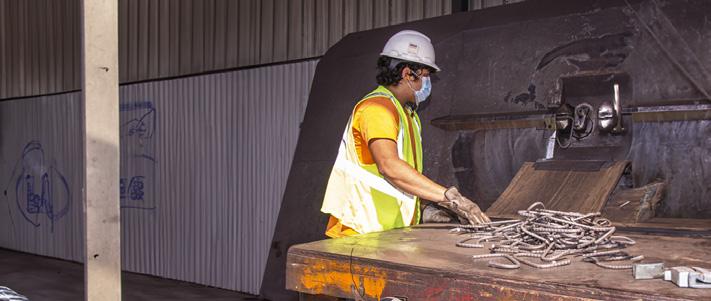
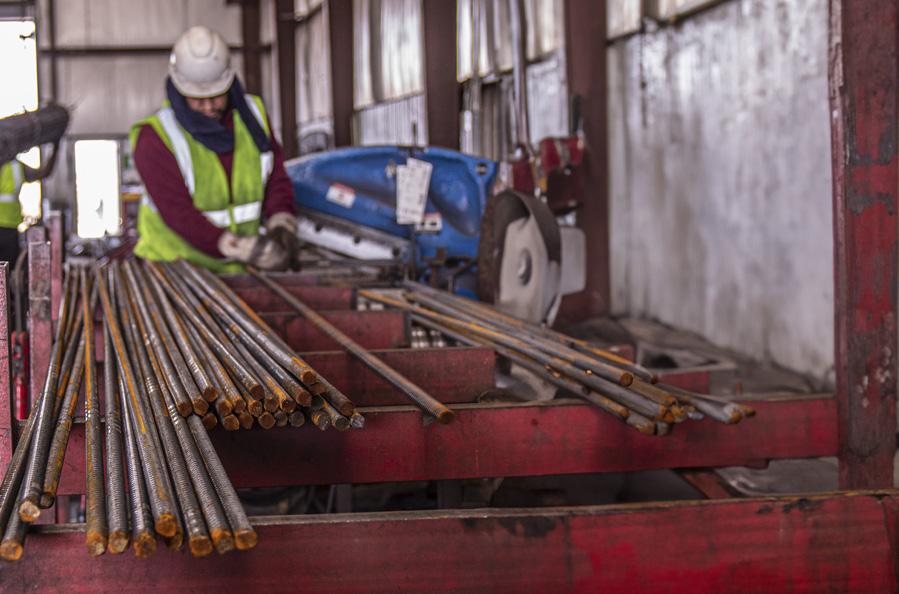
THE COMMERCIAL REBAR EXPERTS
Southern State Rebar’s team has 43 years of experience in the reinforcing steel industry.
We strive to provide superior customer service and execution on all rebar fabrication projects from water treatment plants, foundations, petroleum construction, highways, and beyond.
Located in Alvarado, TX, we are equipped to handle estimates, detailing, and delivery of jobs both small and large. Our sister company, Eldorado Steel, can also help you with all of your structural and miscellaneous steel needs.
We are here and ready to assist you with your projects across Texas and beyond.
817-779-6960 | cameron@southernstaterebar.com | southernstaterebar.com
SCAN ME
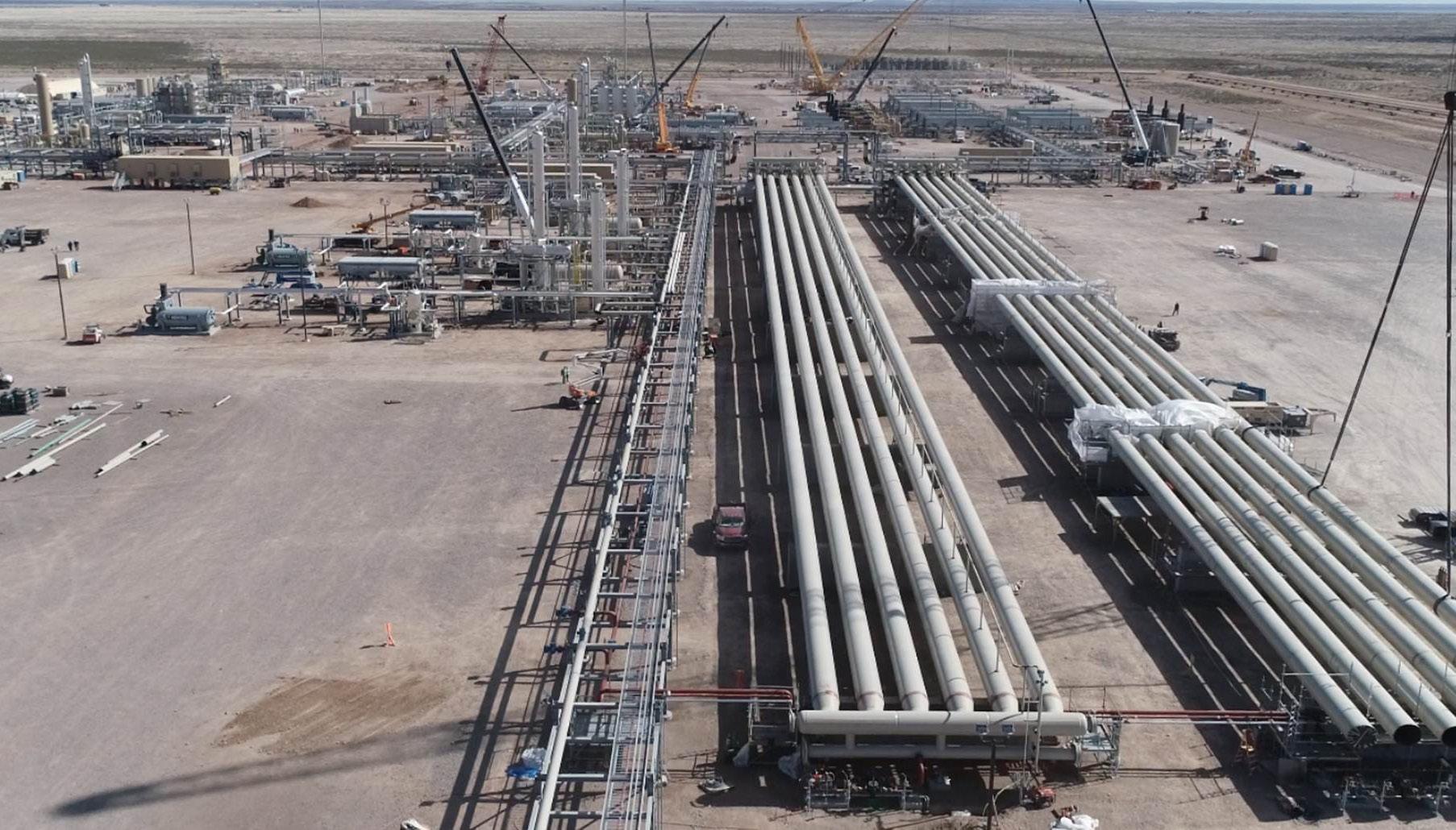
“We facilitate lunch-and-learn programs, tuition reimbursement initiatives, and on-site learning at Odessa College,” Matt outlines.
Through continued professional development, the company ensures its workforce remains at the forefront of industry advancements and ahead of the curve.
Its dedication to learning aligns with its core value of excellence, recognizing that innovation and technical expertise are key to staying competitive in an evolving industry.
Additionally, Saulsbury facilitates professional certifications for its employees on the understanding that career development doesn’t stop after graduation.
For this reason, the company invests in team members who are seeking technical certifications and professional licenses – whether it be young engineers pursuing a professional engineer (PE) certification or electricians working toward a master electrician’s license.
“We support the training, costs, and time necessary for employees to achieve these milestones, reinforcing our commitment to building a highly
skilled and capable workforce,” Matt informs.
By engaging with higher education institutions, supporting lifelong learning, and championing professional growth, Saulsbury is actively shaping the next generation of industry leaders.
“We take pride in playing a role in their journey, ensuring they are well-equipped to drive innovation and excellence for years to come,” he sets out.
A SIMPLE PHILOSOPHY
Going beyond its role as a mere contractor, Saulsbury strives to be a true partner to its clients on every project.
It takes full ownership of project execution, working collaboratively across the value chain to ensure success from inception through to commissioning.
“Our philosophy is simple – if a project isn’t successful for our clients, it isn’t successful for us,” Matt shares.
Transparency is at the core of Saulsbury’s approach as it works closely with clients to determine the best contracting strategy and integrates constructability
engineering to optimize costs and improve schedule efficiency.
It has the flexibility to adapt to complex project challenges, providing innovative solutions that align with clients’ evolving needs.
“This commitment to partnership fosters long-term relationships and has led to a high percentage of repeat business with nearly all our clients.”
By prioritizing collaboration, adaptability, and shared success, Saulsbury continues to build strong, trusted alliances that drive excellence in every project it undertakes.
Reflecting on his own style of leadership, Matt understands that teamwork and collaboration are integral to his success.
“My leadership style is a blend of democratic and servant leadership. I believe in collaboration, accountability, and empowering teams to make informed decisions. No one has all the answers, and I value input and healthy debate,” he asserts.
As such, Matt’s leadership style is not about authority, but fostering a culture where people feel valued, challenged, and motivated to achieve success together.
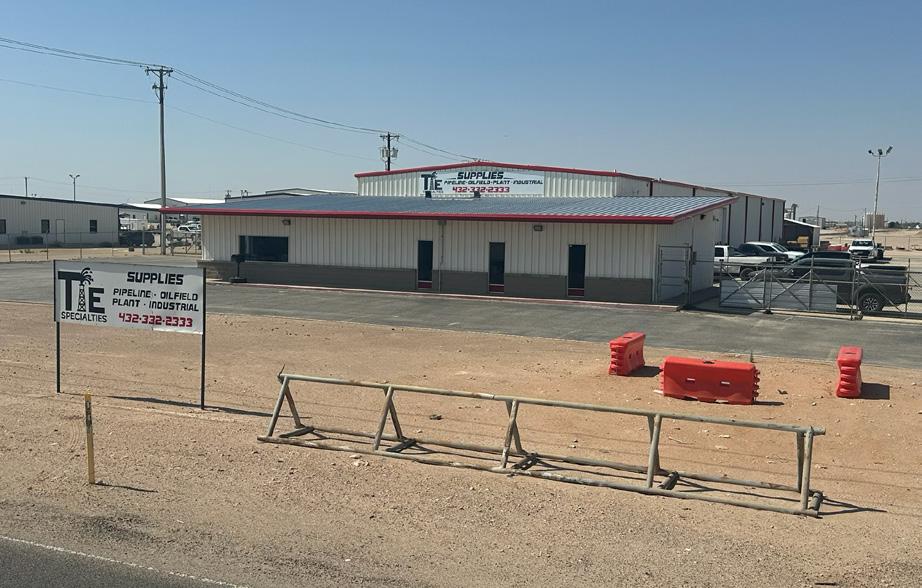
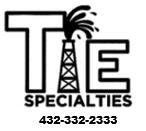
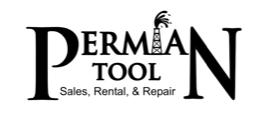
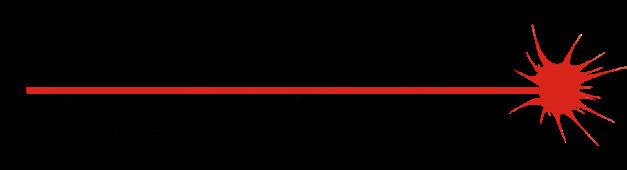
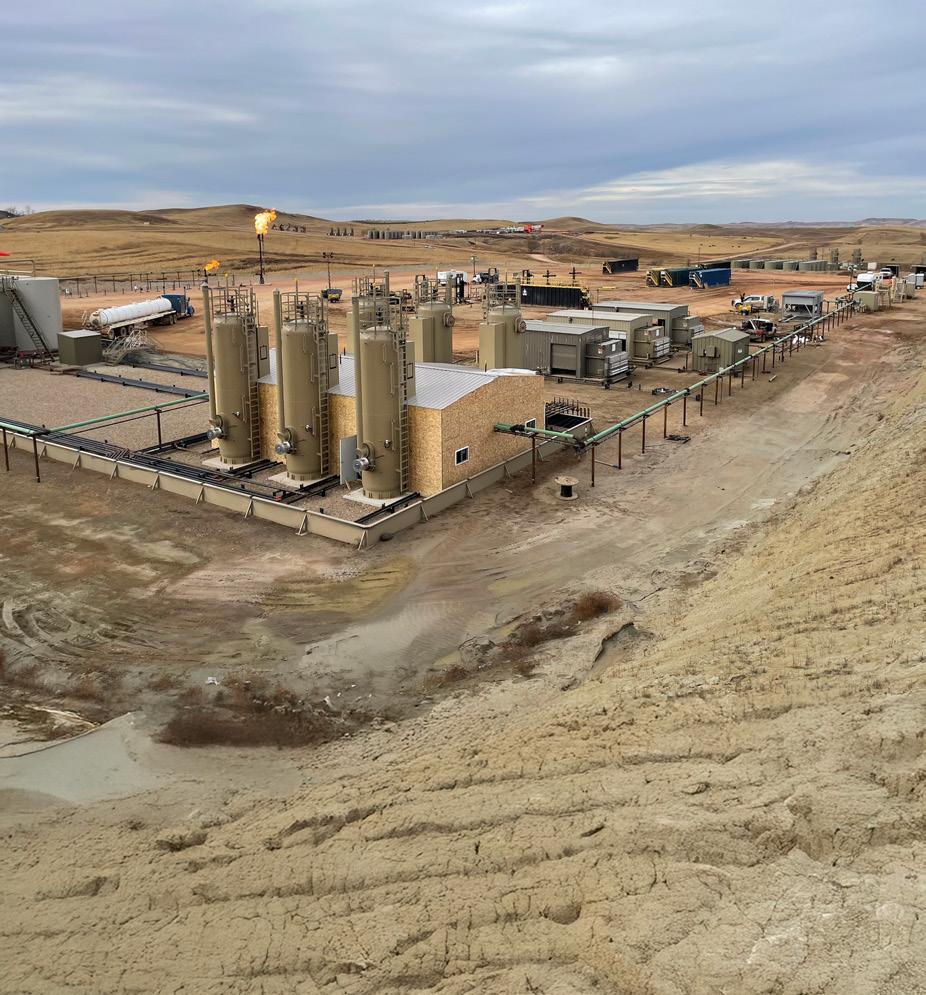
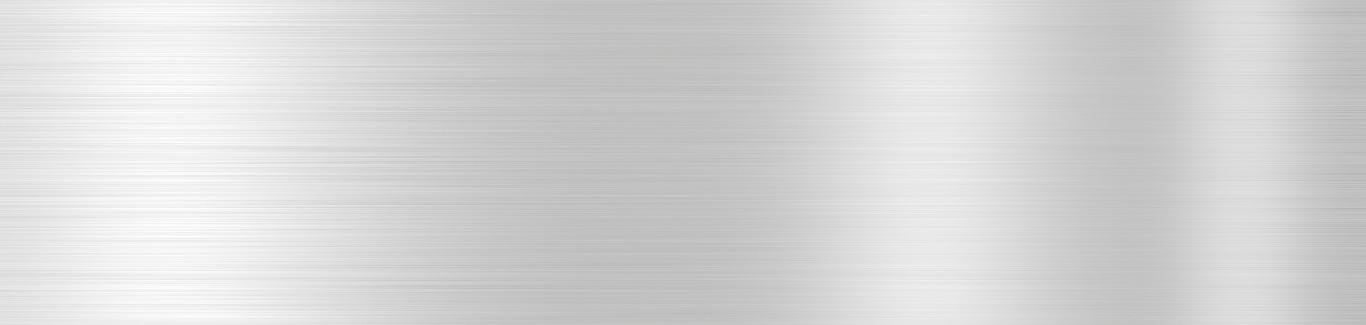

A BRIGHT FUTURE
Looking to the future, continuous improvement remains Saulsbury’s guiding principle as it strives to be a stronger, more agile organization year on year.
It has the unique advantage of setting strategic goals that align with long-term stability as opposed to short-term shareholder expectations.
“This allows us to stay focused on what’s best for our business, people, and clients,” Matt confirms.
Strategic diversification is also a key priority which the company has been actively pursuing for several years and will continue to do so moving forward.
Indeed, while Saulsbury’s legacy and foundations are deeply rooted in the oil and gas sector, it recognizes the volatility that can accompany the industry.
“We’ve strategically expanded into renewable energy and infrastructure, focusing on key growth areas such as utility-scale solar power, BESS,
substations, and power delivery.”
These sectors complement the company’s core strengths and capabilities while offering long-term and less cyclical opportunities that align with global energy transition trends.
Having recently surpassed a significant milestone in constructing its 70th cryogenic gas plant, equaling over 14 billion cubic feet of processing capacity to date, it is ideally positioned for continued success.
“Surpassing that milestone is a symbol of the trust we’ve earned, partnerships we’ve built, and Saulsbury’s story of relentless progress. We’ve built a reputation as a trusted leader in the industry – one project, one partnership, and one milestone at a time,” he prides.
Looking ahead, Saulsbury will continue a managed growth trajectory into emerging markets while exploring additional industries that can benefit from its proven track
record in complex project execution.
“Our goal isn’t just to grow – it’s to grow with purpose, delivering value and additional opportunities for our employees while remaining adaptable in an ever-changing energy landscape,” Matt confidently concludes.
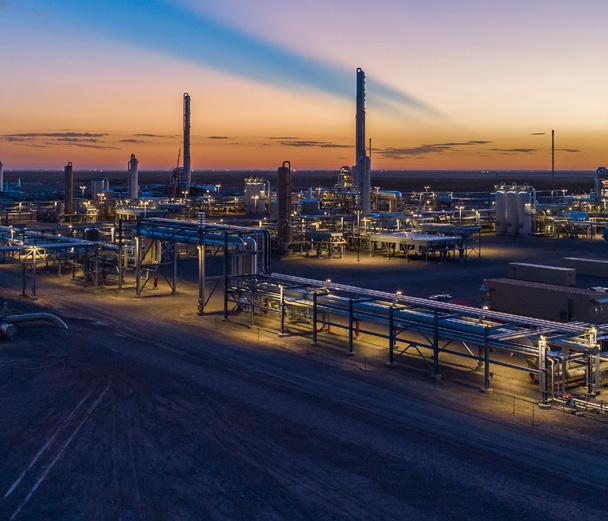
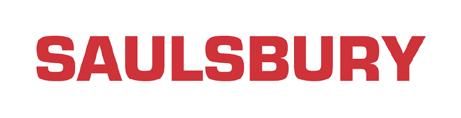
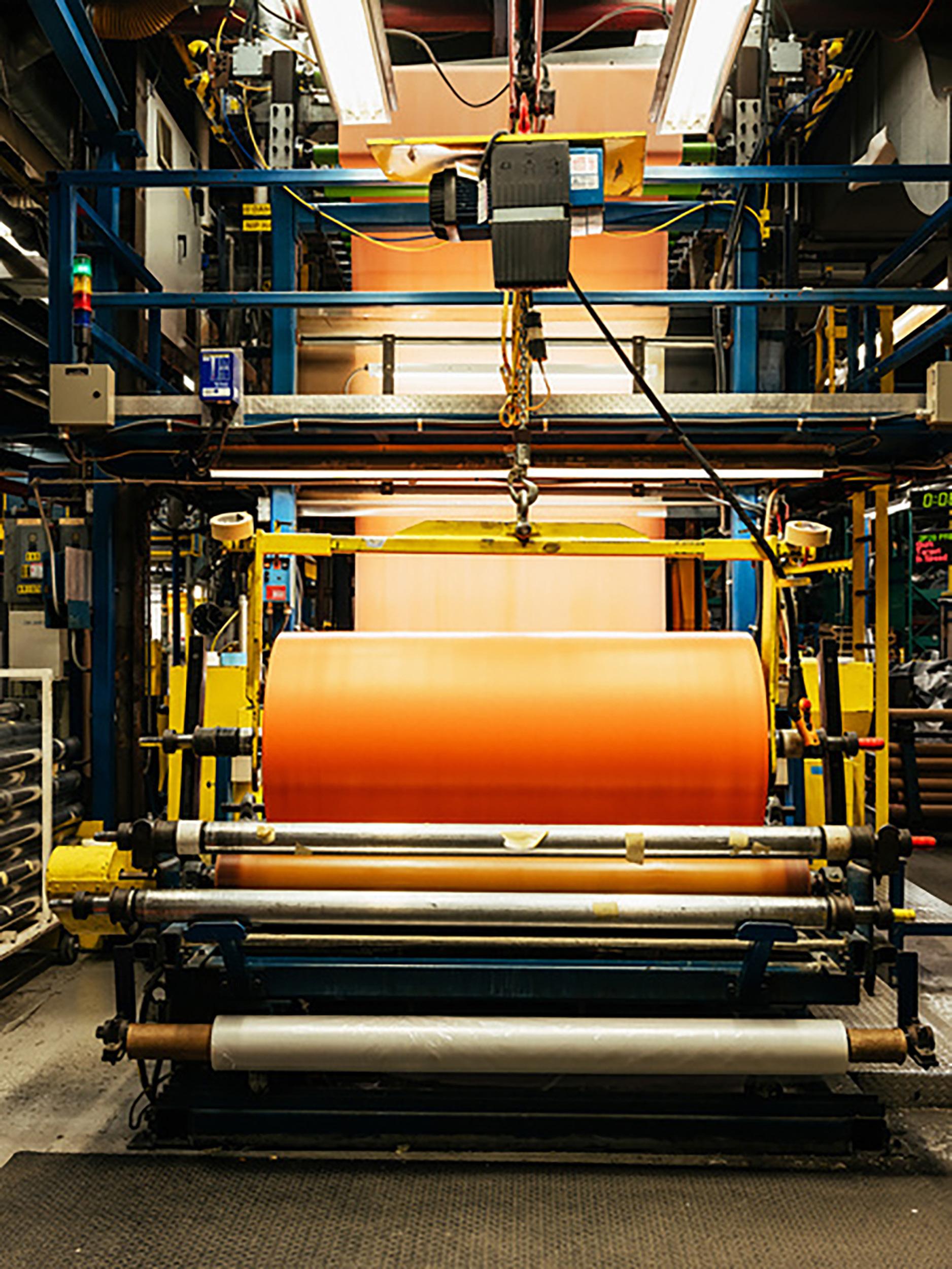
SIT IN STYLE
Morbern creates innovative vinyl upholstery fabric solutions with a long-term focus on sustainability, digital transformation, and market expansion. We take a seat with President, Eric Lamontagne
Writer: Jack Salter | Project Manager: Michael Sommerfield
Established in 1965, this year marks the 60th anniversary of Morbern, North America’s leading designer and manufacturer of decorative vinyl upholstery fabrics.
The Canadian company creates innovative vinyls for a wide variety of industries, including automotive, trucking, healthcare, marine, hospitality, and more.
This cross-sector reach allows Morbern to share learnings across industries, strengthening its product development capabilities.
“The quality of what we make and our ability to develop solutionfocused products are our strengths. We don’t produce seats – we produce the material that we offer to companies making seats for all these markets,” opens Eric Lamontagne, President.
“Our products are used for pretty much everything we sit on, whether it’s chairs for an office, airport, cinema, cruise ship, boat, jet ski, recreational vehicle (RV), car, or truck.”
Morbern’s head office in Cornwall,
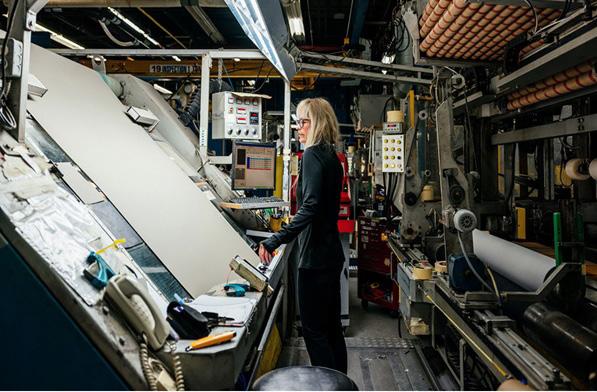
Ontario is complemented by plants in Montréal, Québec and High Point, North Carolina.
Together, these locations form a vertically integrated operation, producing Morbern’s vinyl fabric solutions from end to end.
LONG-TERM OUTLOOK
As a family-owned company, the longterm outlook is extremely important to Morbern, prioritized above shortterm gains for shareholders.
“When we make decisions, the long term is the most important criterion
because there are no external shareholders,” emphasizes Lamontagne.
“That reflects our credibility in the market with customers because that’s what they want. When we supply material to a customer for decades, they rely on our stability, quality, and ability to supply.
“We’re in the middle of a supply chain where we transform raw materials into finished products. If we stop supplying, the impact on our clients can be significant,” he adds.
CEO, Mark Bloomfield, represents the second generation of the Bloomfield family to run the company, whose ability to retain many employees for over 40 years and make quick decisions stems directly from this family ownership. Jake Bloomfield, the third-generation rising star, did not fall far from the tree.
Lamontagne works directly with Morbern ownership on a day-to-day basis, ensuring close collaboration and togetherness.
“It’s not like a group of investors are sitting in an office somewhere. I find it interesting and very rewarding to work in the kind of environment where decisions are made quickly and always for the long-term benefit,” he adds.
Morbern was named one of Canada’s Best Managed Companies in 2020 and 2021, acknowledging the organization’s dedication to innovative, world-class business practices.
SUSTAINABLE SEATS
Last year, Morbern invited top leadership – including Mark – to join its Green Council.
The council meets monthly to define sustainability strategies and objectives across product development, manufacturing, and materials.
“It’s very interesting what can come up from these meetings because it’s a multidisciplinary audience where
HOW DID YOU END UP IN YOUR CURRENT POSITION AT MORBERN?
ERIC LAMONTAGNE, PRESIDENT:
“When I was a kid, I always enjoyed figuring out how things are made and how they work. I was also interested in aviation, so I had two choices from there – either becoming an engineer or a pilot.
“I became an engineer, so I’ve always been involved in manufacturing processes. The first part of my career was in composite manufacturing; I managed and developed different operations in Canada, the US, and China.
“In 2017, I was contacted by Morbern to lead their operations and become President, so I made that change after a long career in composite manufacturing.
“Morbern is a beautiful local manufacturing company very close to where I live, so that attracted me.”

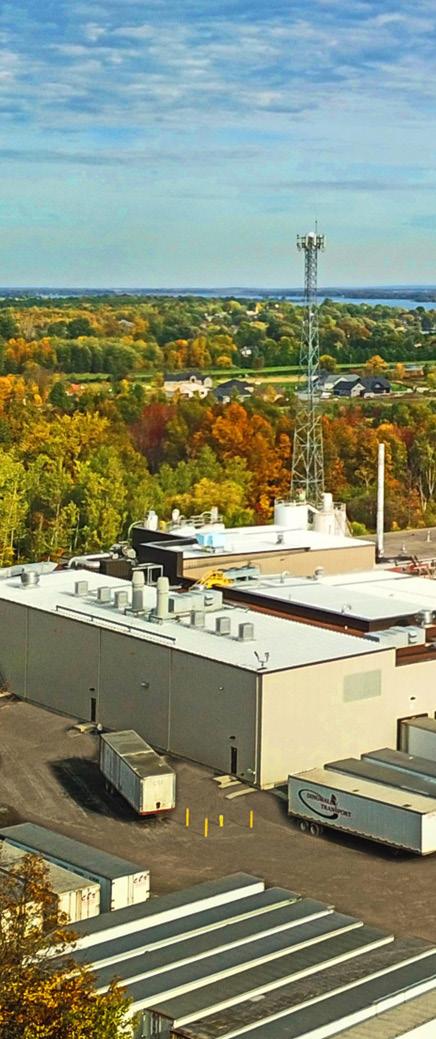
everybody has their say and we generate exciting ideas for sustainable products,” says Lamontagne.
“The demand for these products is getting bigger and bigger, which is very exciting. I’m proud to be part of the Green Council, and I’m certain Morbern is a leader in sustainable vinyl-coated fabric manufacturing.”
Morbern’s products are designed not only to meet client needs but also minimize environmental impact.
As such, the company is committed
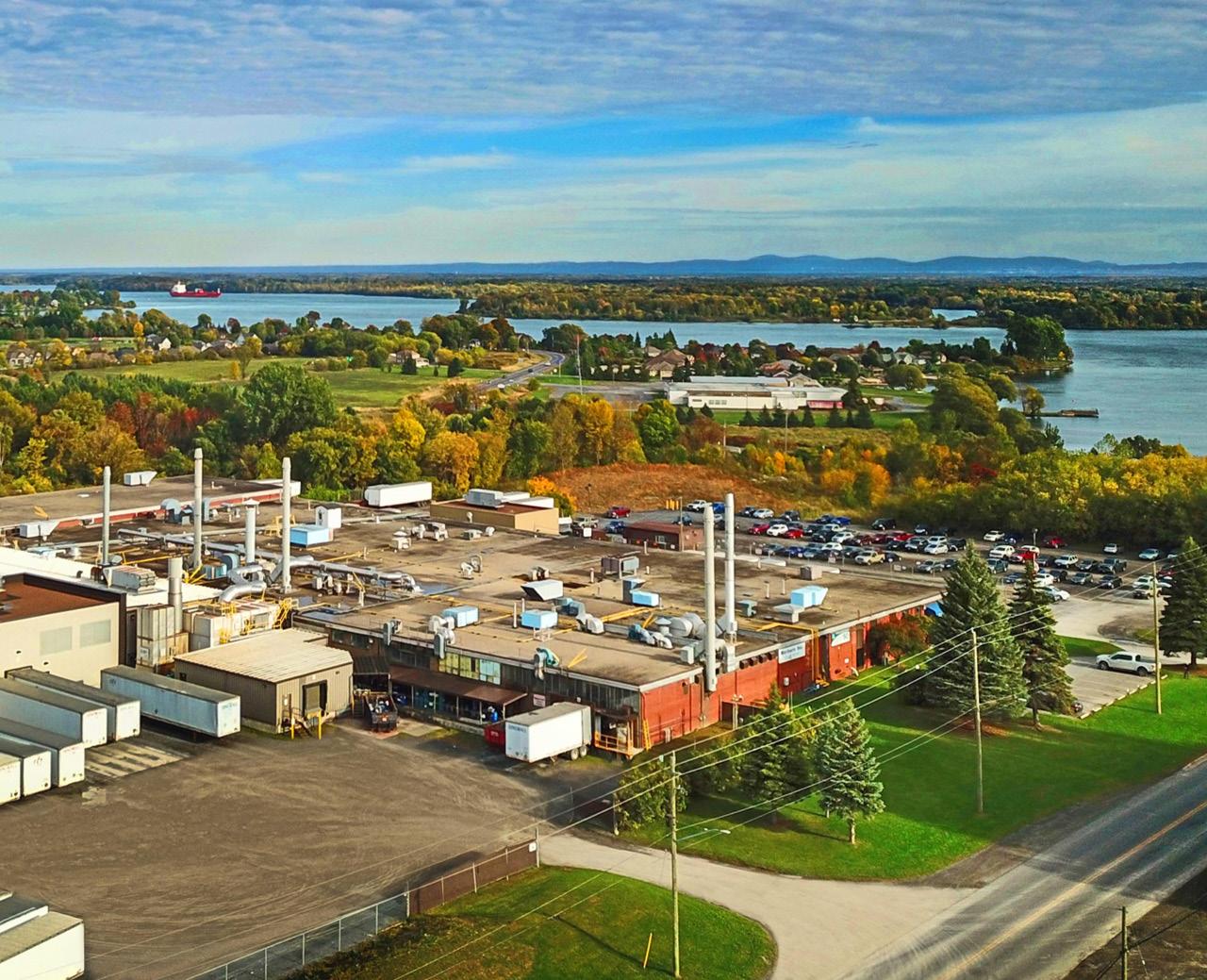
to sustainability in all areas and ISO 14001-certified, with an Environmental Management System (EMS) that governs how it addresses its environmental responsibilities.
“We’re very proud of developing this EMS to remain a good corporate citizen and focus on continuous improvement of the environmental aspects of the business,” notes Lamontagne.
Morbern focuses on everything from reducing waste and
using bio-based materials to sourcing renewable energy like hydroelectricity.
“Every time we improve a process in the plant or add new equipment, we focus on using electrical energy instead of gas. Today, 100 percent of the electricity we consume at our plant now comes from hydroelectricity,” he informs us.
Morbern also takes steps to increase carbon neutrality and reduce greenhouse gas (GHG) emissions
– making sustainability a core principle of the business.
By embedding it into operations, the company is building a better future for customers, employees, and the planet.
QUEST FOR DIGITAL TRANSFORMATION
Along with prioritizing sustainability, there has been a large focus on digital transformation at Morbern over the last few years.
“THE QUALITY OF WHAT WE MAKE AND OUR ABILITY TO DEVELOP SOLUTION-FOCUSED PRODUCTS ARE OUR STRENGTHS. WE DON’T PRODUCE SEATS – WE PRODUCE THE MATERIAL THAT WE OFFER TO COMPANIES MAKING SEATS FOR ALL THESE MARKETS”
– ERIC LAMONTAGNE, PRESIDENT, MORBERN
After six decades of operations, several legacy processes required updating and many long-standing employees were accustomed to traditional methods.
Morbern has therefore embraced change and is currently implementing Microsoft Dynamics 365 as its new enterprise resource planning (ERP) system.
“We’re in the implementation phase right now, and this will support our quest for digital transformation going forward,” affirms Lamontagne.
SAFETY, QUALITY, CAPACITY
“We have three priorities at Morbern, which are in a specific order. The first is safety, the second is quality, and the third is capacity.
“When we make a decision in the plant, they are in that order. For example, you can’t try to produce faster by increasing safety risks, and you shouldn’t focus on increasing output but producing low-quality products.
“It’s like a triangle, but they’re stacked on top of each other. We keep repeating and focusing on these things in the plant, and I think it serves us quite well.
“That’s why we’re a safe place to work and make quality products at a competitive price.”
- Eric Lamontagne, President
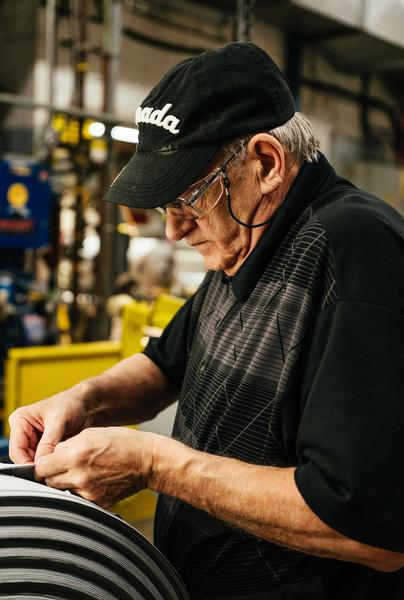
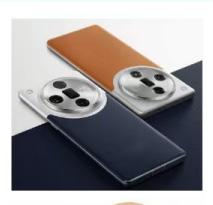
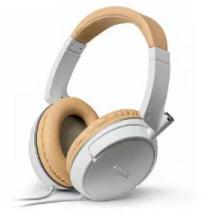
Global Certifications and Quality Assurance
B.T.F adheres to stringent international standards, holding certifications such as:
- IATF 16949 (Automotive Quality Management)
- GRS 4.0 (Global Recycled Standard)
- ISO 14001(Environmental Management)
- ISO 45001(Occupational Health and Safety)
- ISO 50001 (Energy Management)
- ISO 27001 (Information Security).
- ISO 14097:2018 (Carbon Footprint Certification)
- Regular Knitted Leather Substrate: 4.48 kg CO2e/kg
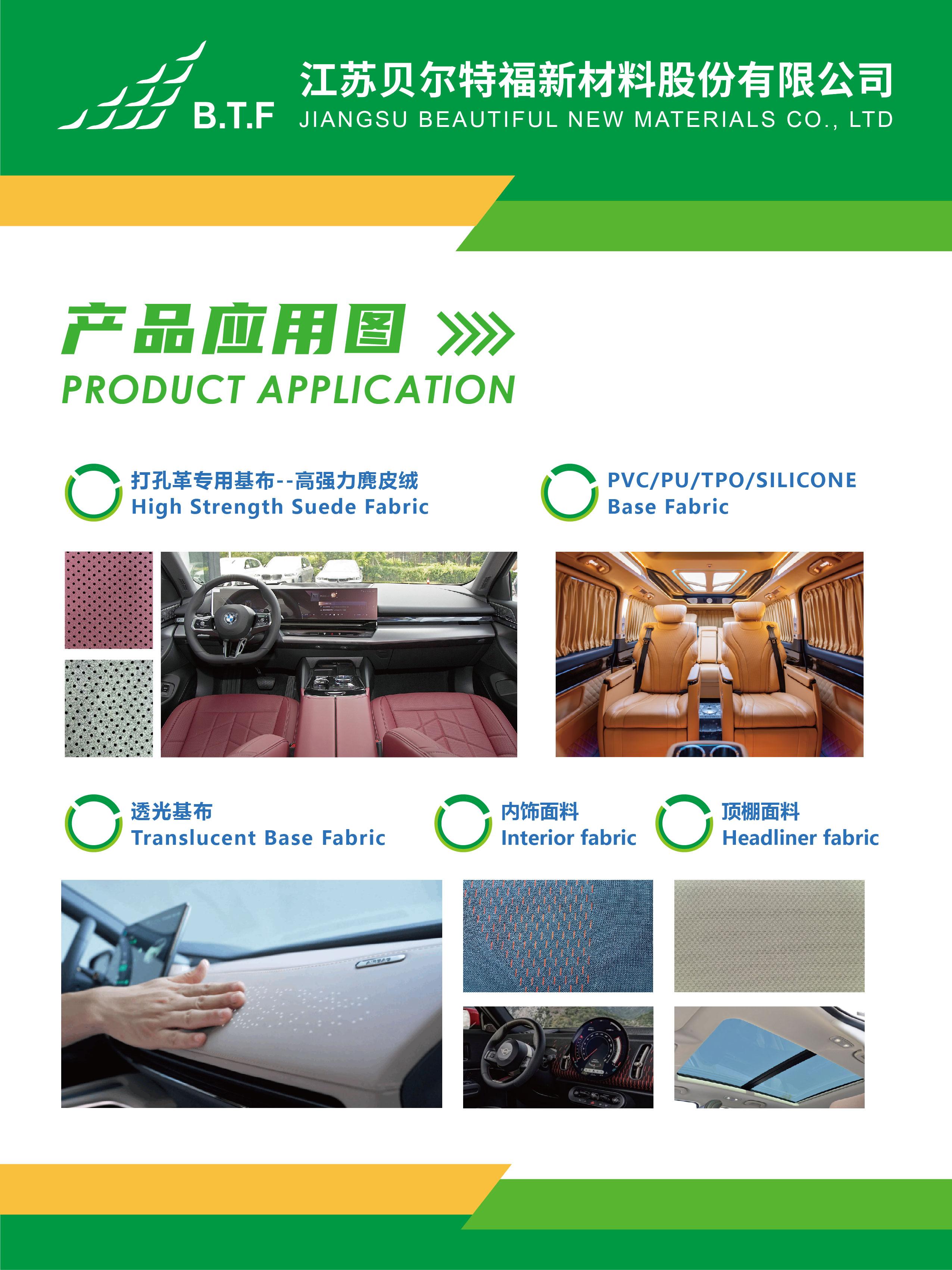
- Recycled Leather Substrate: 2.86kg CO2e/kg (50% reduction vs. conventional PET).
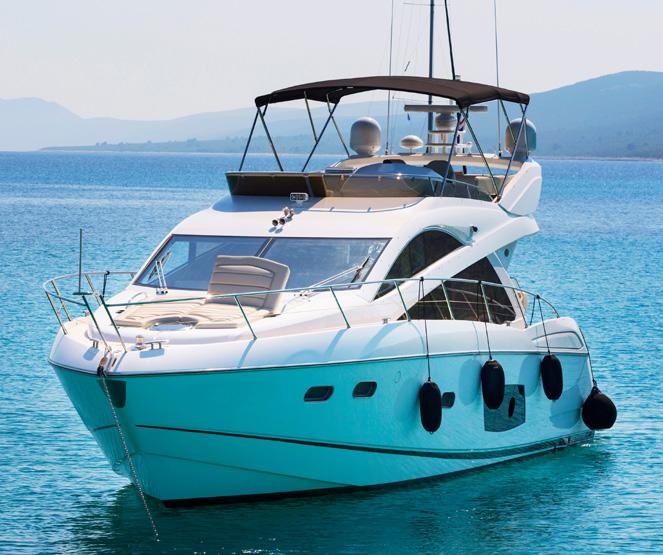
Ultra-thin PU leather base fabric
3C Electric Fabric
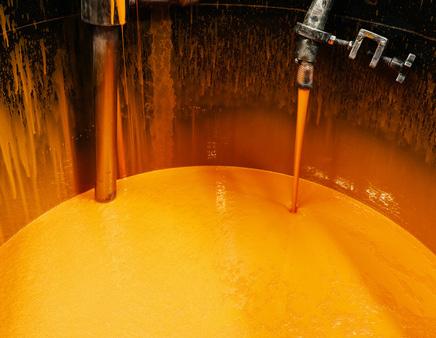
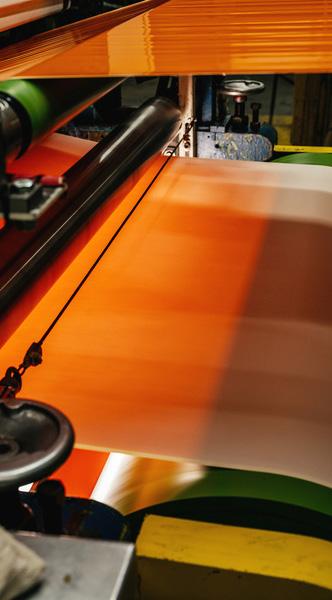
As well as digital transformation, product development is another priority target for Morbern in order to provide the market with appealing, high-value offerings.
It is also heavily focusing on expansion outside of North America, with the company committed to developing its presence across Europe.
Last year, its Morbern Europe subsidiary celebrated a significant milestone with its 10th anniversary on the continent, where its products have had to be adapted to European market requirements.
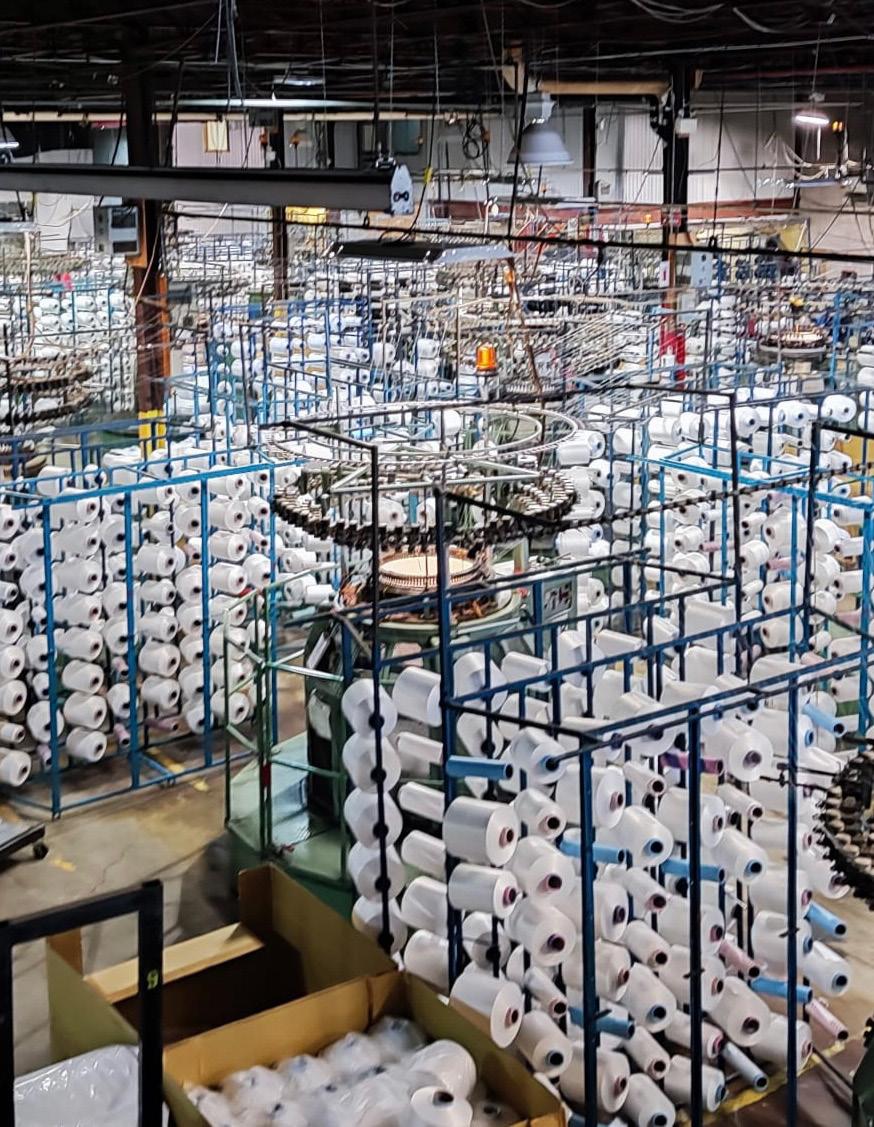
The company started its European sales operations in 2014, underpinned by a dedicated warehousing and logistics platform in Amsterdam, which relocated to Belgium in 2022.
From there, over 500 stockkeeping units (SKUs) are sold through a wide distributor network and shipped daily across Europe and beyond.
Morbern’s enthusiasm for developing innovative products is therefore supported by incredible teams of people on both sides of the Atlantic Ocean.
“We love North America, and it’s a very good market for Morbern, but Europe is also an important focus.
“We’re growing very well over there, so I would say market diversification is very important,” Lamontagne closes.
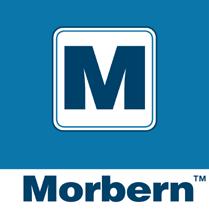
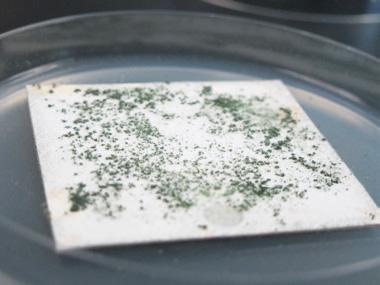
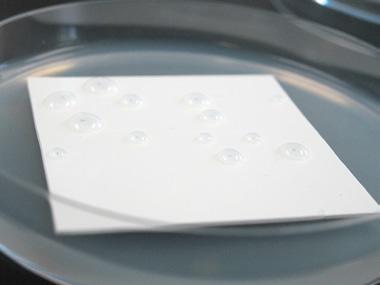
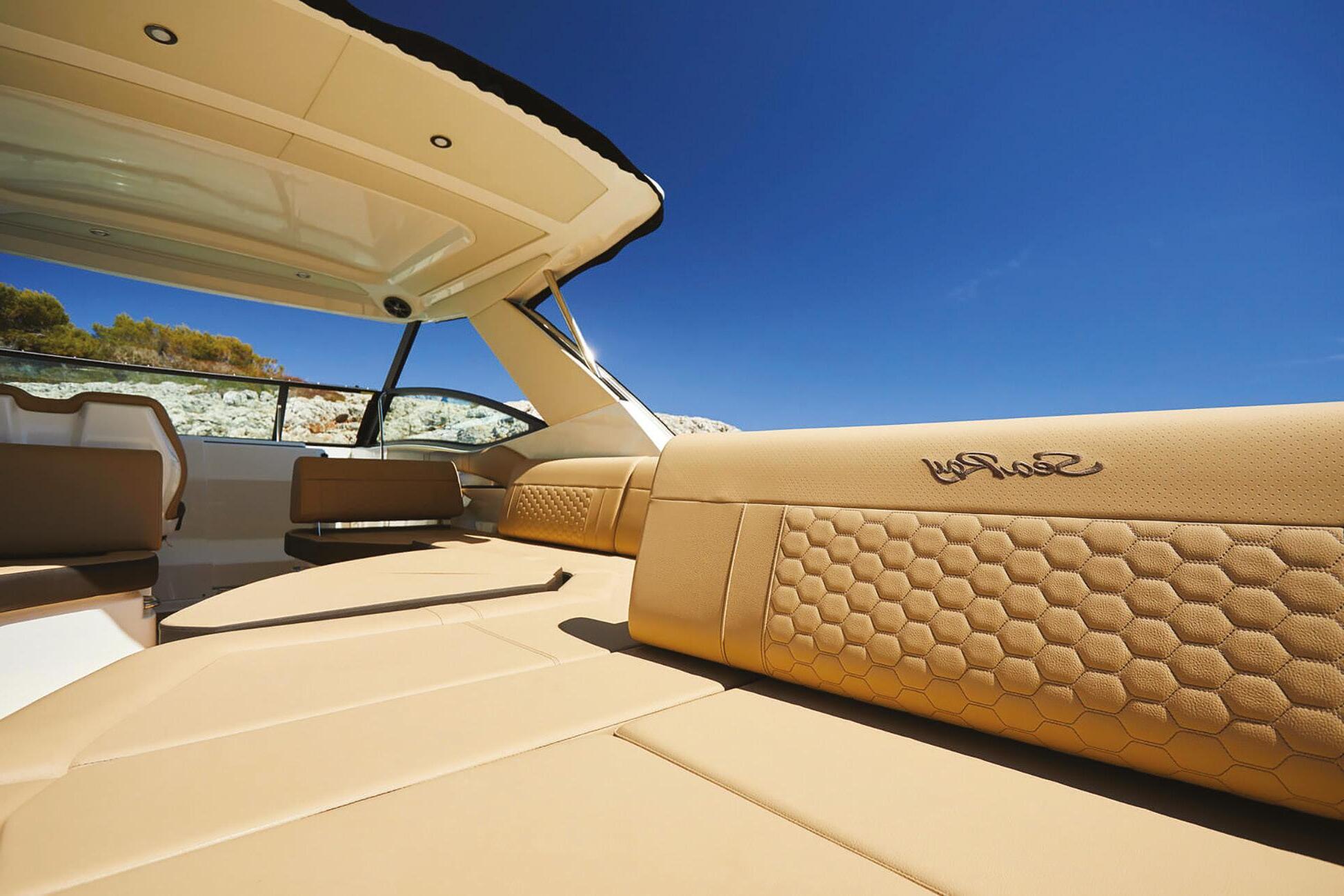
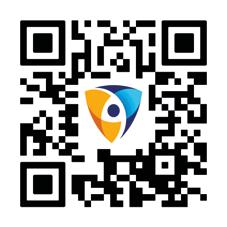
Polyrol is a leader in manufacturing durable paper tubes and cores tailored to meet the diverse needs of industries. With its expertise, the company ensures high-quality products that adhere to the strictest standards. In collaboration with its partners, Corrupal - specialists in cardboard packaging, and Manubois - experts in wooden solutions, Polyrol delivers a comprehensive and innovative range of packaging solutions.
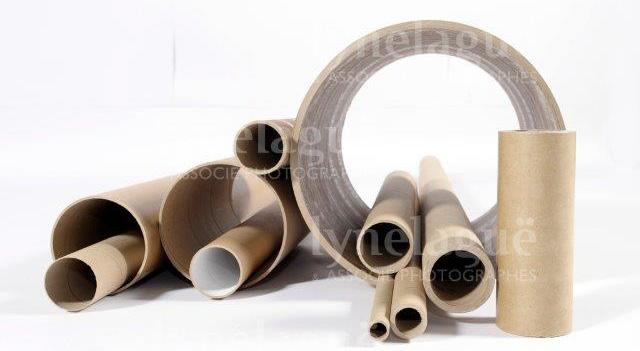
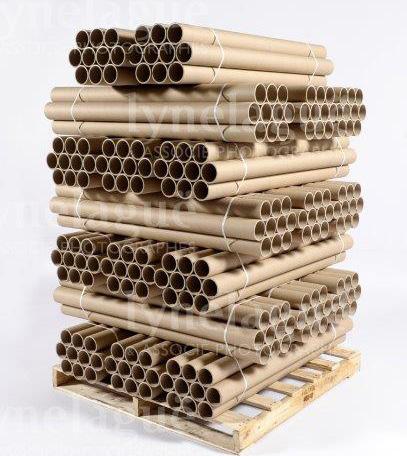
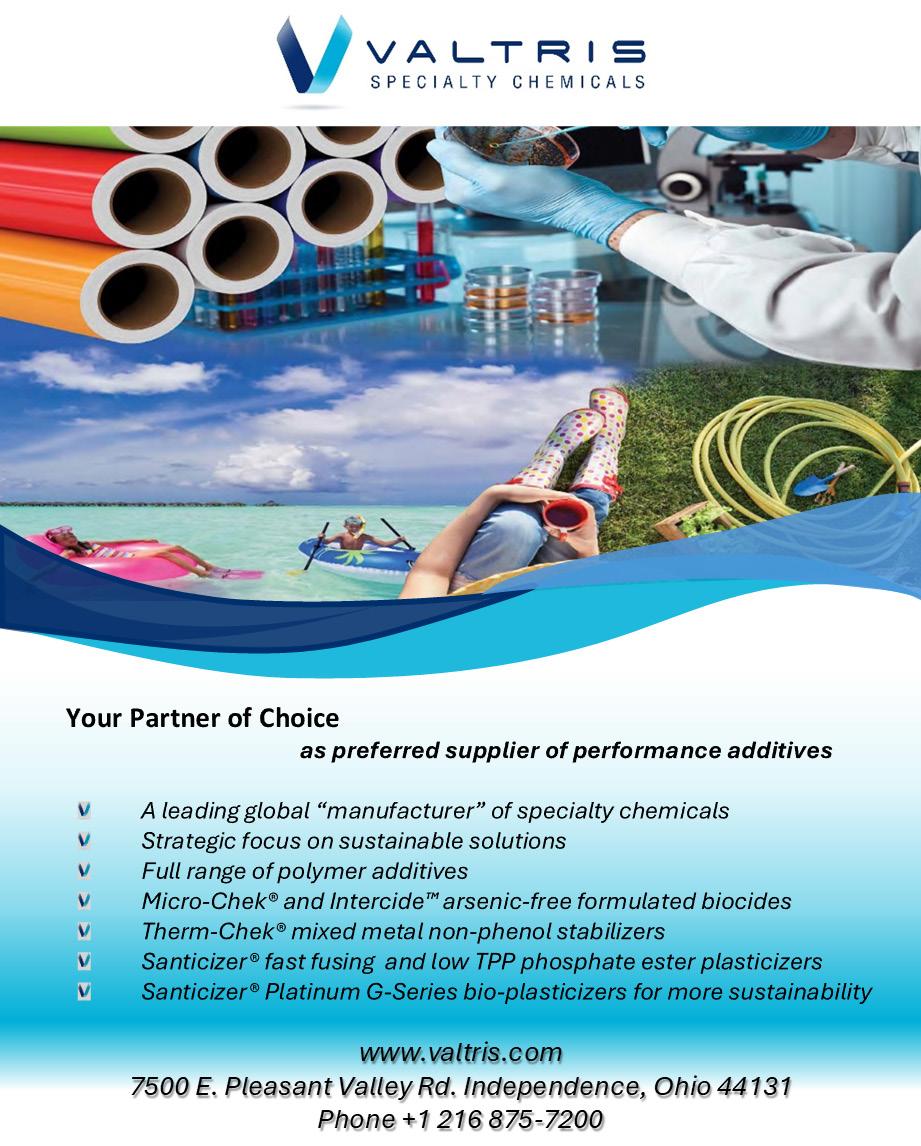
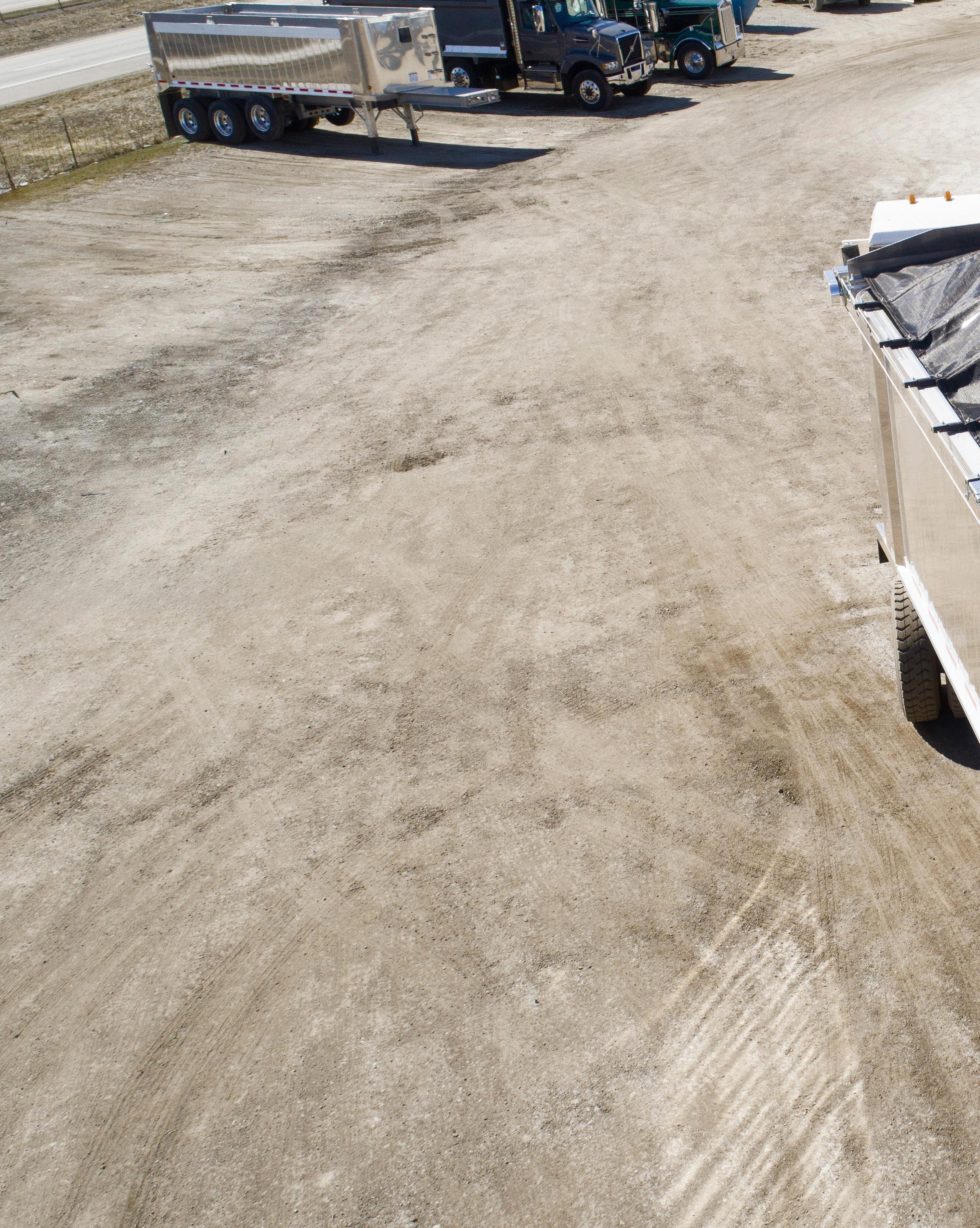
TOP-TIER TARP
Renowned throughout the transportation industry for its advanced tarp system manufacturing, Aero Industries boasts a rich legacy and illustrious history. John Rodgers, Vice President of Operations, provides insight into the legendary company
Writer: Rachel Carr | Project Manager: Michael Sommerfield
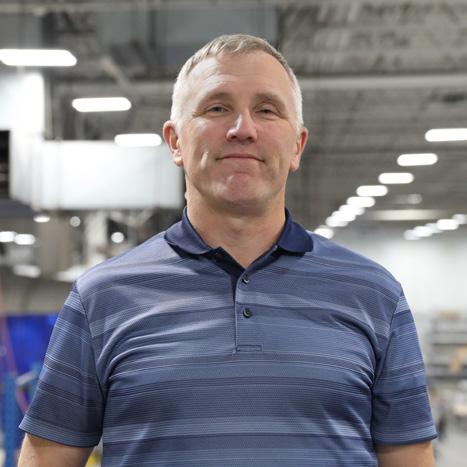
John Rodgers, Vice President of Operations
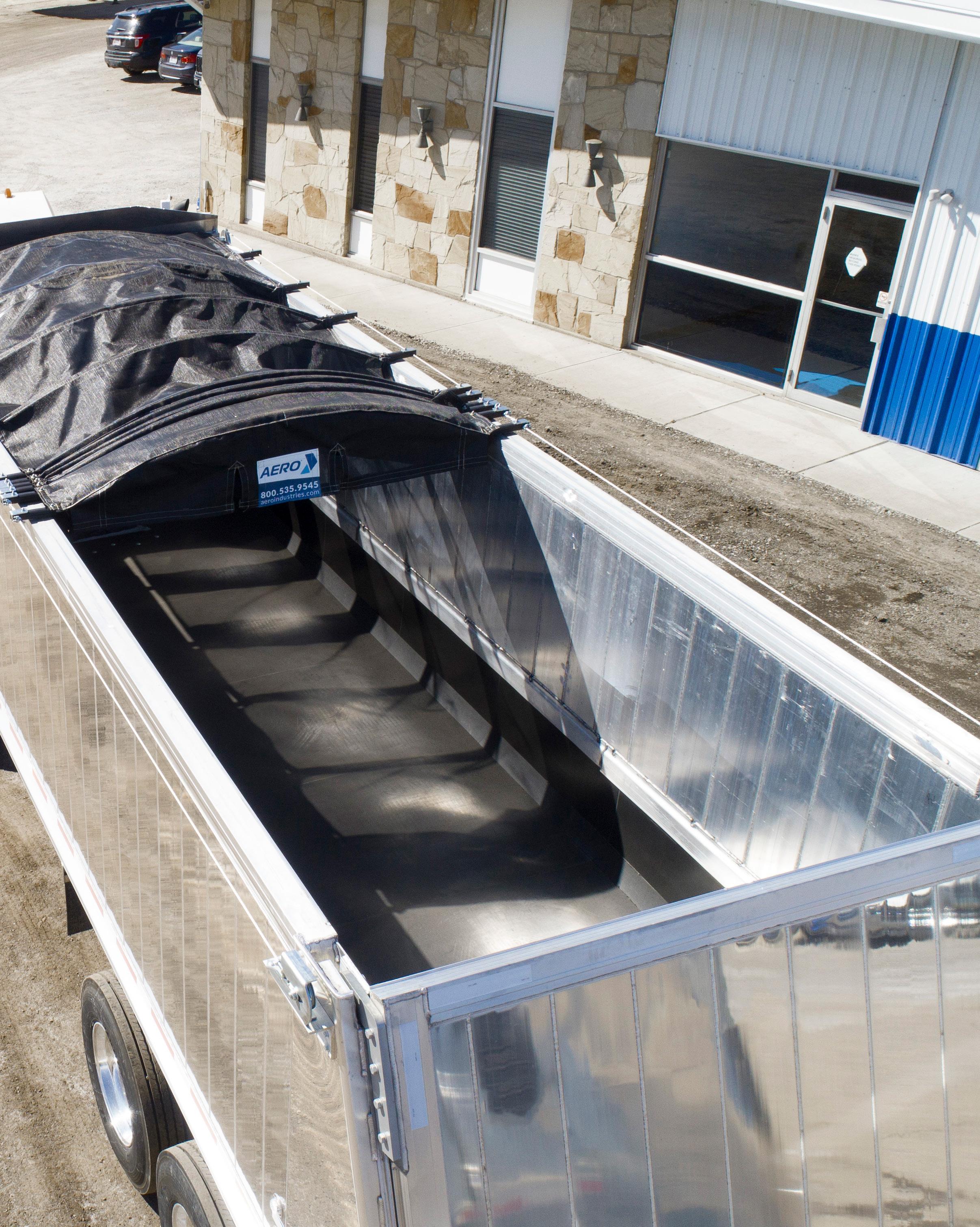
In 1944, innovative tarp systems and trucking accessory manufacturer Aero Industries opened its doors, originally as Aero Canvas Products.
Founded by Paul Tuerk after a brush with death, ingenuity and persistence in the face of adversity have come to define the company.
Indeed, the tarp industry would have been a very different space if Paul had boarded the RMS Titanic in 1912, which was initially planned as part of his voyage to emigrate from Germany to the US.
Fortunately, a late train interrupted the journey, allowing Paul to form Aero Industries, which has been granted over 100 patents to date.
“Many of our design ideas come from customer requests and their
A FAMILY FIRMLY AT THE FOREFRONT
The DataCo vision is to improve and expand the availability of affordable internet access to all people of PNG, by partnering with the government and surrounding communities. It ensures the company is a responsible entity championing safe and sustainable development.
Connect my District Initiativeparamount to its core values is connecting PNG to the digital world and driving development and growth.
Environment Safety - ensuring that local communities benefit from services in a way that the environment is safe.
New Triplex Units - were handed over by DataCo as part of its community social responsibility initiative.
confidence in our ability to solve engineering problems,” introduces John Rodgers, Vice President of Operations.
To establish itself as an innovative industry leader in the competitive manufacturing market, Aero Industries has demonstrated a remarkable ability to think creatively with new materials, design breakthroughs, and cutting-edge patents.
Beginning in the lingerie business during the Great Depression, Paul was determined to provide for his family. This drive led him to Indiana, where he bootstrapped his business while working at Hoosier Tarpaulin, manufacturing army tents.
His experience in fitting lingerie
proved valuable for his next venture, selling customized tarps. The early logic was simple – “if Paul could fit a woman, he could fit a truck.”
Today, Aero Industries employs 215 people across Indiana, Ohio, Nebraska, and Oklahoma, operating in the dump, flatbed, agriculture, refuse, and work truck sectors.
After overcoming many obstacles, the company is now in its third generation of ownership by the Tuerk family.
A LEGACY OF LONGEVITY
Last year, Aero Industries celebrated its 80th anniversary, a testament to the company’s resilience which is rooted in family values.
Built on a foundation of community,
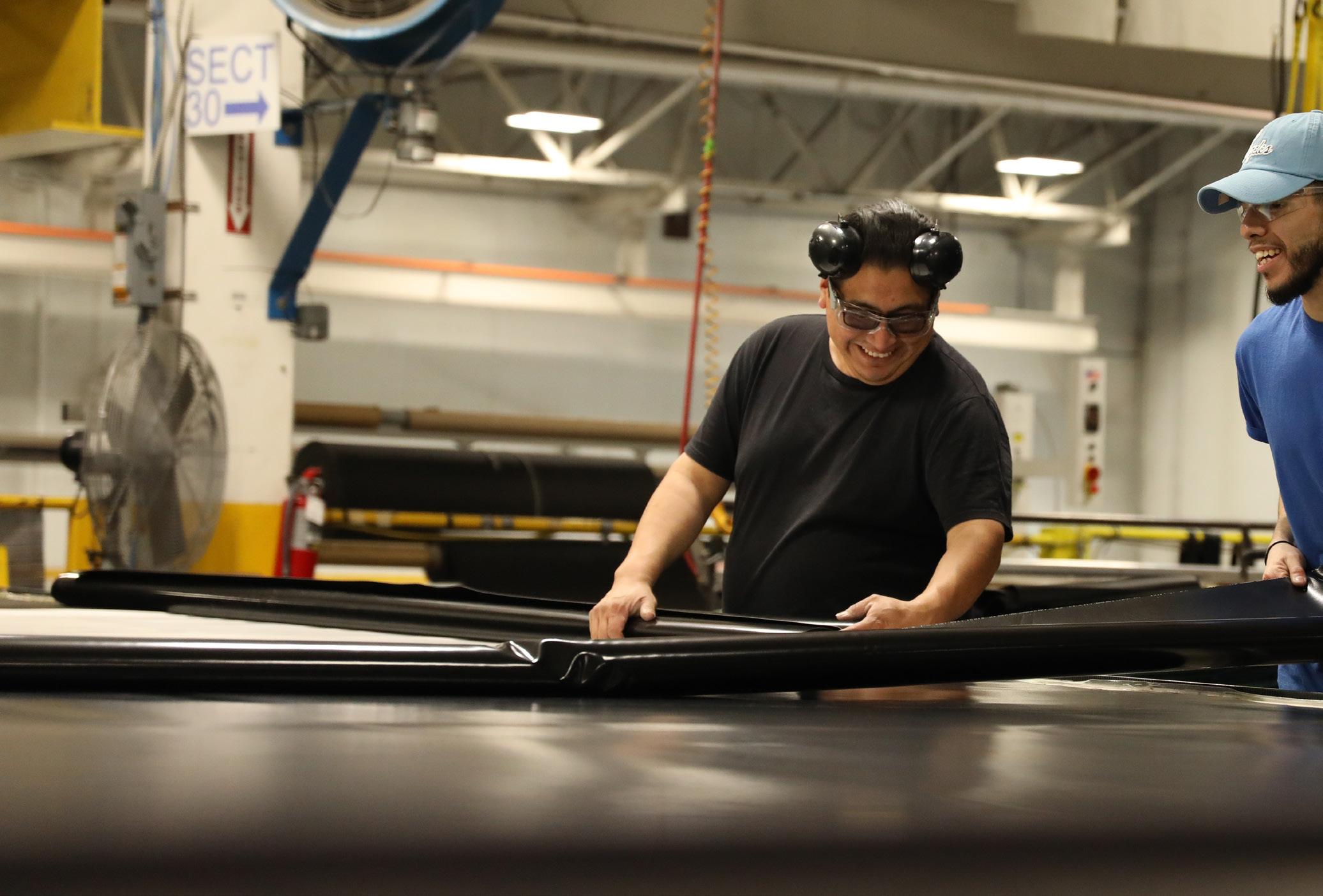
Aero Industries has made a lasting impact on generations of employees and customers.
Fortunately, an entrepreneurial spirit is embedded in the Tuerk family’s DNA, allowing the company to continue innovating to this day.
“We celebrated the anniversary at all our locations, hosting cookouts, games, and team activities. We also marked our packaging and labelling with ‘80’ and ‘1944-2024’ logos to communicate the event with our customers,” Rodgers enthuses.
The company has introduced significant innovations throughout its history. As an industry leader, it developed the Neoprene-Hypalon Tarp in the 1950s, replacing traditional canvas and vinyl tarps.
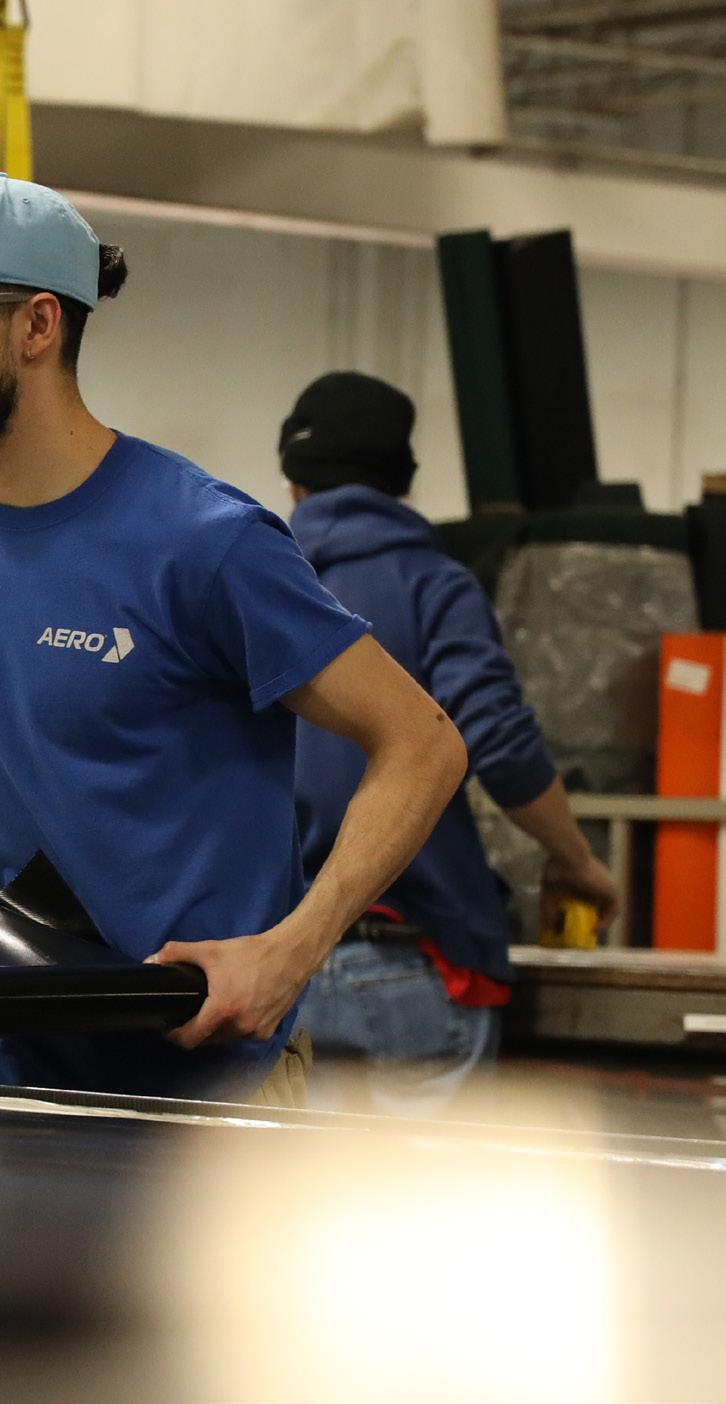
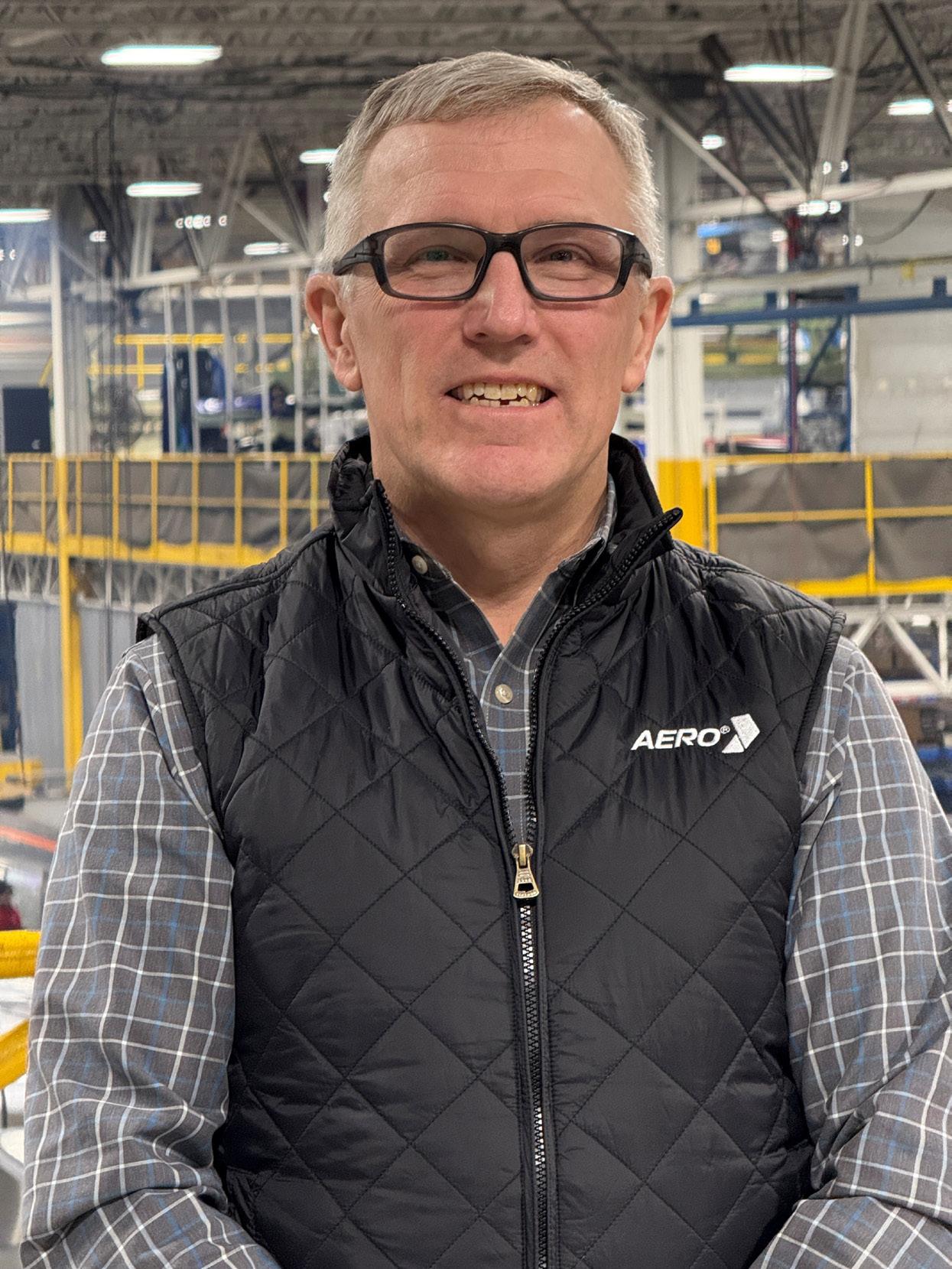
“OUR REPUTATION IN THE INDUSTRY IS FOR PRODUCTS THAT OUTLAST THE COMPETITION AND QUALITY THAT IS SUPERIOR”
– JOHN RODGERS, VICE PRESIDENT OF OPERATIONS, AERO INDUSTRIES
In the 1960s, other major innovations were introduced, starting with the One-Minute Roll-Away Tarp, followed by the Shortie Roll Tarp.
“Of special note is Aero Industries’ pioneering rolling tarp system, the Conestoga,” he acknowledges.
The Conestoga has long been one of the company’s top products. However, in the late 1990s, it faced challenges related to the width of the tarping systems.
After a demanding four-year effort by the Aero Industries team, led by Paul’s grandson, Jim Tuerk, the issue was resolved in conjunction with new regulations that benefited the entire US trucking industry.
Looking ahead to the next 80 years, Aero Industries has a guiding mission and an ambitious vision that will further solidify its position at the forefront of the industry.
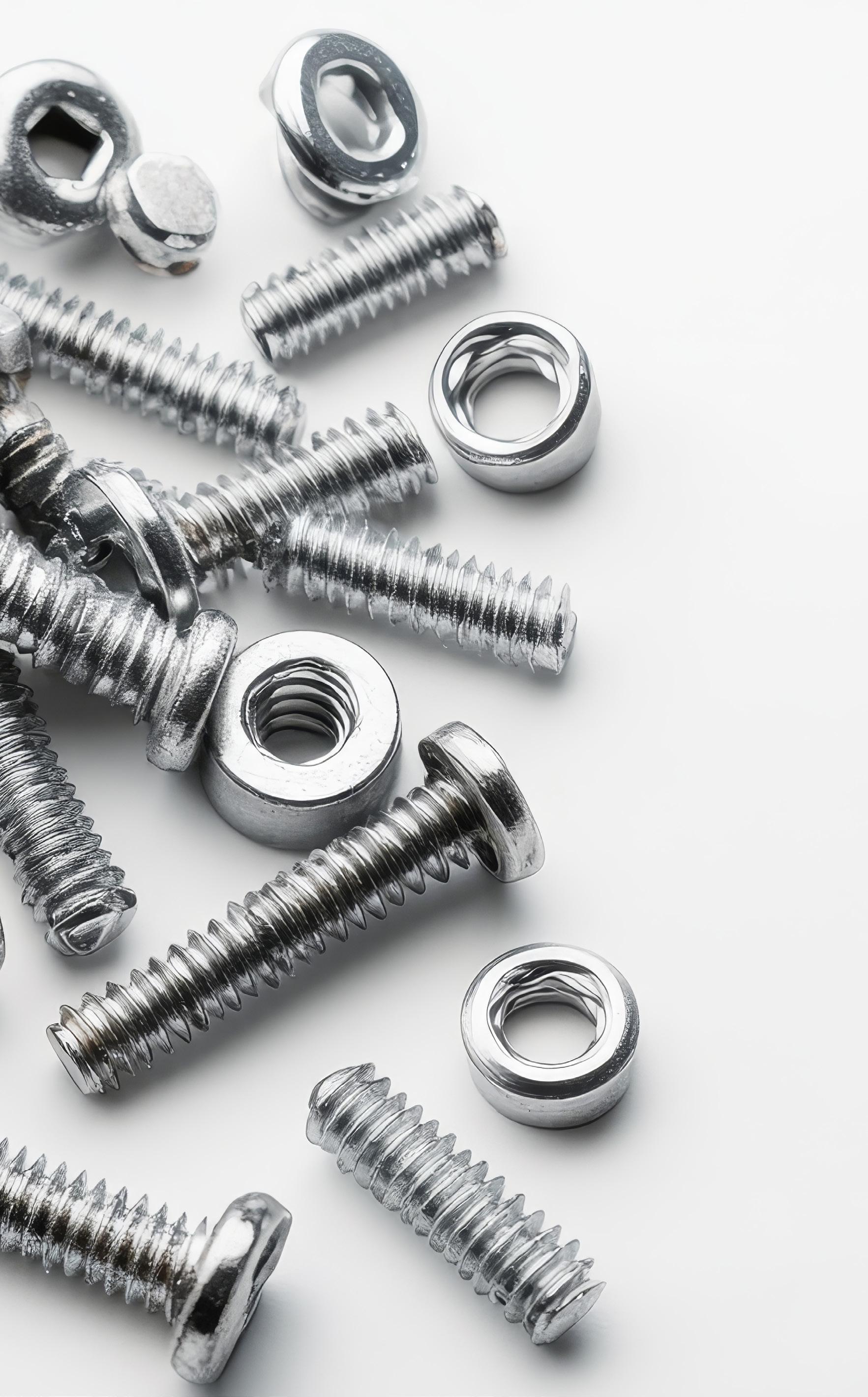
A Model Supplier
Leaders in the burgeoning North American fastener sector, Crown Screw & Bolt has grown from humble beginnings to become a trusted supplier of bolts, nuts, washers, and more
Crown Screw & Bolt (Crown) has evolved over the last 50 years to diligently meet the needs of a vast range of industries, including construction, automotive, aerospace, manufacturing, and many more.
In fact, the North American fastener industry has experienced substantial levels of growth, driven by the upward trajectory of key end-user industries and is expected to be worth over $25 billion by 2030.
In this context, the company understands its customers’ diverse requirements in an evolving sector, having come from humble beginnings and adhering to a simple philosophy ever since: ‘Work hard for your customers and offer the best services available’.
Moreover, thanks to a steadfast dedication to industry requirements, Crown has garnered an outstanding reputation for its second-to-none products, best-in-class technical assistance, and most competitive pricing in the market.
Its expert ability to serve customers stems from a worldwide network of supply partnerships, highly comprehensive inventory, professional sales team, and an all-encompassing commitment to excellence, which each help the company stand out in a saturated field.
ONE-STOP SOURCE
Crown boasts a diverse fastener inventory and unsurpassed product availability for its customers, providing them with everything they need to get the job done.
Namely, it is the go-to supplier for all types of nuts, bolts, washers, screws, pins, and specialty fasteners, available in both metric and imperial measurements.
Additionally, Crown also supplies standard and custom brackets, clamps, fittings, metal stampings, and extruded products, offering personal attention to customers’ fastener needs.
The company promotes both quantity and quality, stocking world-class brands in its inventory to guarantee the best solutions for businesses across the US.
CUSTOMIZED AND SPEEDY SHIPPING
Delivering an unmatched repertoire of products across the country, Crown’s central distribution facility in Indiana – situated at the crossroads of the US – offers fast and easy shipping to every corner of the nation. The company is committed to maintaining a dynamic and world-class delivery fleet, which guarantees the efficient and reliable delivery of products.
Crown also offers custom packaging and bin stocking services to ensure orders arrive safely in the hands of customers, further guaranteed by the highly accurate packaging and labelling of all products according to strict customer specifications.
The company’s delivery services also extend to end user assembly assortment and the option to have items sent bagged or boxed, thus optimizing the entire delivery process. Crown’s customers can also rest assured that purchased items are of the highest quality, as the entirety of the company’s product list ardently meets industry standards and is ISO 9001:2000 certified.
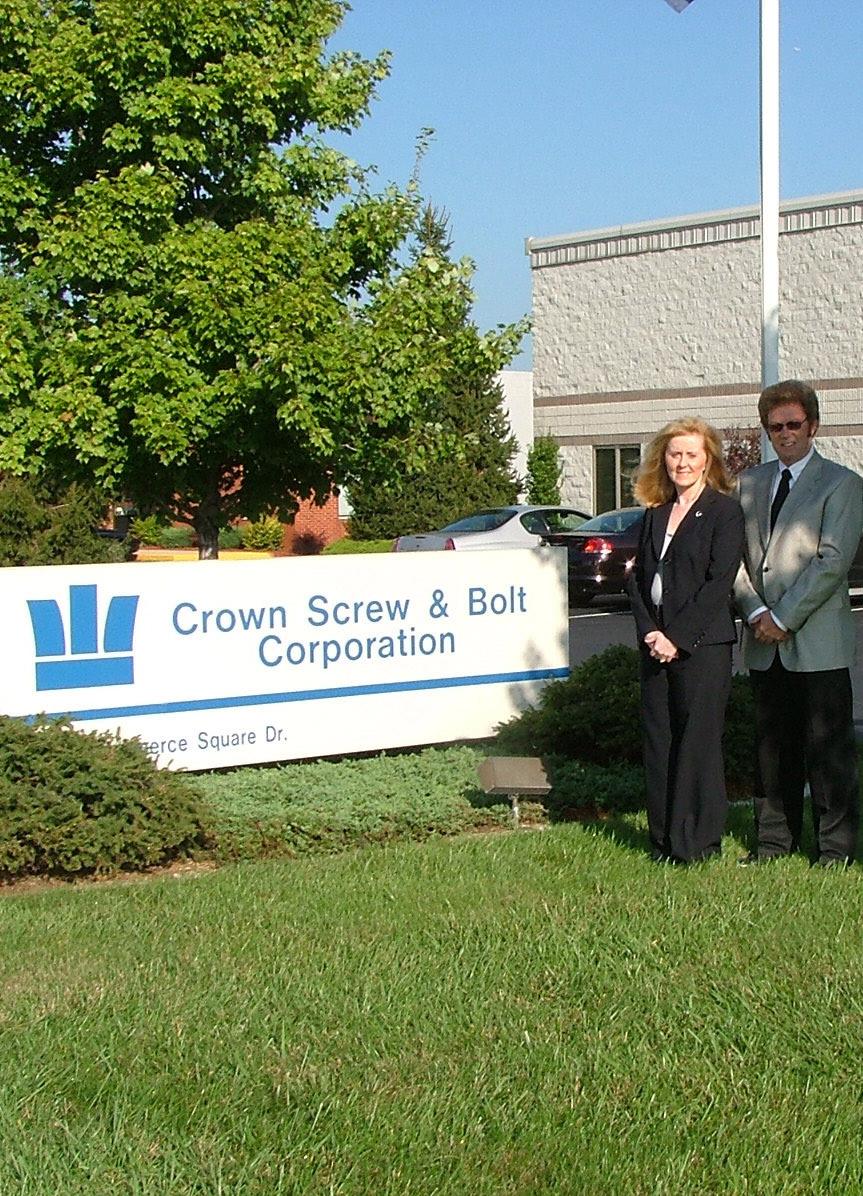
Crown’s product lines
Top-of-the-range companies that Crown has in its inventory include but are not limited to:
• Rotor Clip/Clamp
• Tinnerman
• Oetiker
• Allen
• Universal Metal Products
• E-Z LOK
• Engineered Components Company (ECC)
• Avdel Cherry Textron
• Huck® Fastening
• DimcoGray
• RAF Electronic Hardware
• Holo-Krome
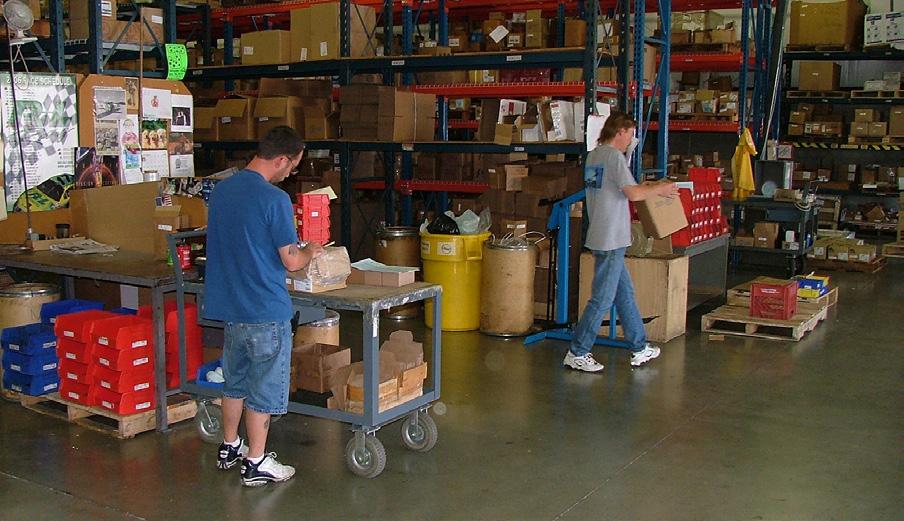
The company also offers the Fastener Locator – an easy-to-use online tool that lets businesses find the best product to fit their needs.
After customers complete a short form to describe what they are looking for, Crown’s experienced team conduct a thorough search of their nationwide supply chain to find the most suitable product, before getting in touch with the customer with the best price and availability.
As such, this unique tool grants customers access the best of what the US fastener industry has to offer, all at the click of a button!
Evidently, customers can rely on Crown to provide the best solution as quick as possible.
CROWN SYSTEM BUYING
Crown additionally provides guidance and support with its turnkey Crown System Buying option, which offers each client endto-end and highly personalized services. Through the system, the company is able to make a note of customers’ buying patterns,
which are then closely analysed by professional sales personnel.
As a result, Crown can compile a list of products that it thinks would be useful for meeting future challenges. Such items are subsequently stocked in the company’s warehouse, ready to deliver to customers at a moment’s notice.
This unparalleled service alleviates many logistics and warehouse obstacles for customers. For instance, it greatly reduces the burdens of limited inventory space whilst maintaining areas for working capital, therefore allowing businesses to focus more on what matters.
On top of this, Crown System Buying eliminates waiting times for specialist products and large-scale orders, further reducing stress for customers and fostering a more pleasant buying experience.
Most significantly, the service helps facilitate future planning opportunities by preempting challenges and providing advanced solutions.
Businesses can make the most of this allencompassing service by selecting Crown System Buying at the website checkout, creating an easy shopping experience.
A HIGHLY EXPERIENCED TEAM
Crown’s success is built on an encouraging family culture, as its employees strive every day to promote the quality nature of its products through a close-knit workforce. Indeed, the company’s experienced team work for their customers, offering an
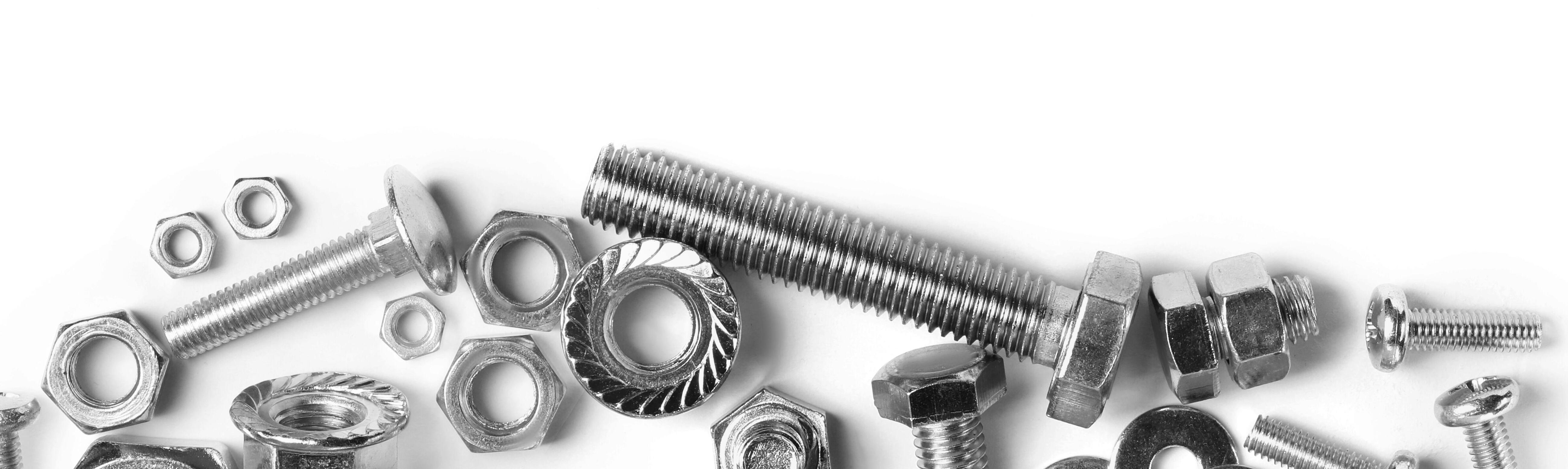
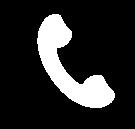
Crown’s nuts and bolts
Nuts:
• Acorn nuts
• Cap nuts
• Flexloc nuts
• Hex nuts
• Heavy hex nuts
• Jam nuts
Bolts:
• Anchor bolts –concrete and foundation
• Askew head bolts
– Grades 1 and 2
• Castle nuts
• Coupling nuts
• KEP nuts
• Left-handed nuts
• Machine-screw nuts
• Locking nuts
• Pal nuts
• Security locknuts
• Serrated flange nuts
• Structural nuts
• Square nuts
• T-slot nuts
• Tinnerman nuts
• Weld nuts
• Wing nuts
• Plow bolts
• Eye bolts
• Cap screws
• Hexagonal flange bolts
attentive and personal service to ensure that every obstacle is overcome.
Its highly vigilant team of professionals are on call around the clock to provide each customer with a complete service, regardless of its complexity.
By liaising directly with each customer, businesses across the US have easy access to the company’s extensive inventory. In addition, Crown can provide guidance and pricing quickly and efficiently without timewasting follow-up calls.
Furthermore, the sales team can be trusted to provide the best and most up-to-date advice on the latest developments in the
• Hex machine bolts
• Lag bolts
• Structural bolts
• Square head bolts
• T-slot bolts
• Tap bolts
• Spring toggle bolts
fastener industry thanks to a diversified pool of experience and the full range of merchandise at their disposal.
This specialist know-how permits them to inform customers of fluctuating product prices and advise customers on any potential changes that may affect their business.
As such, the Crown team works hard to exceed customer expectations, meeting the fastener needs of the nation.
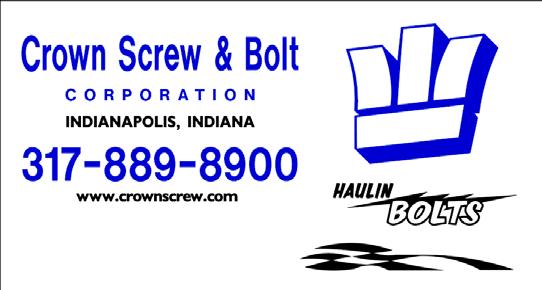
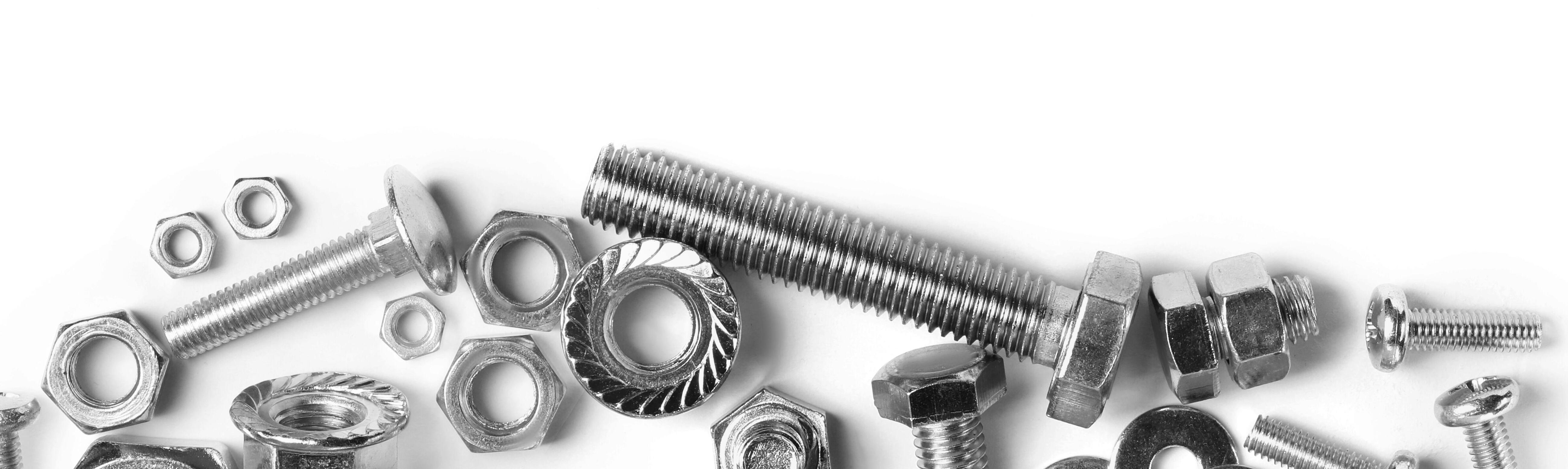
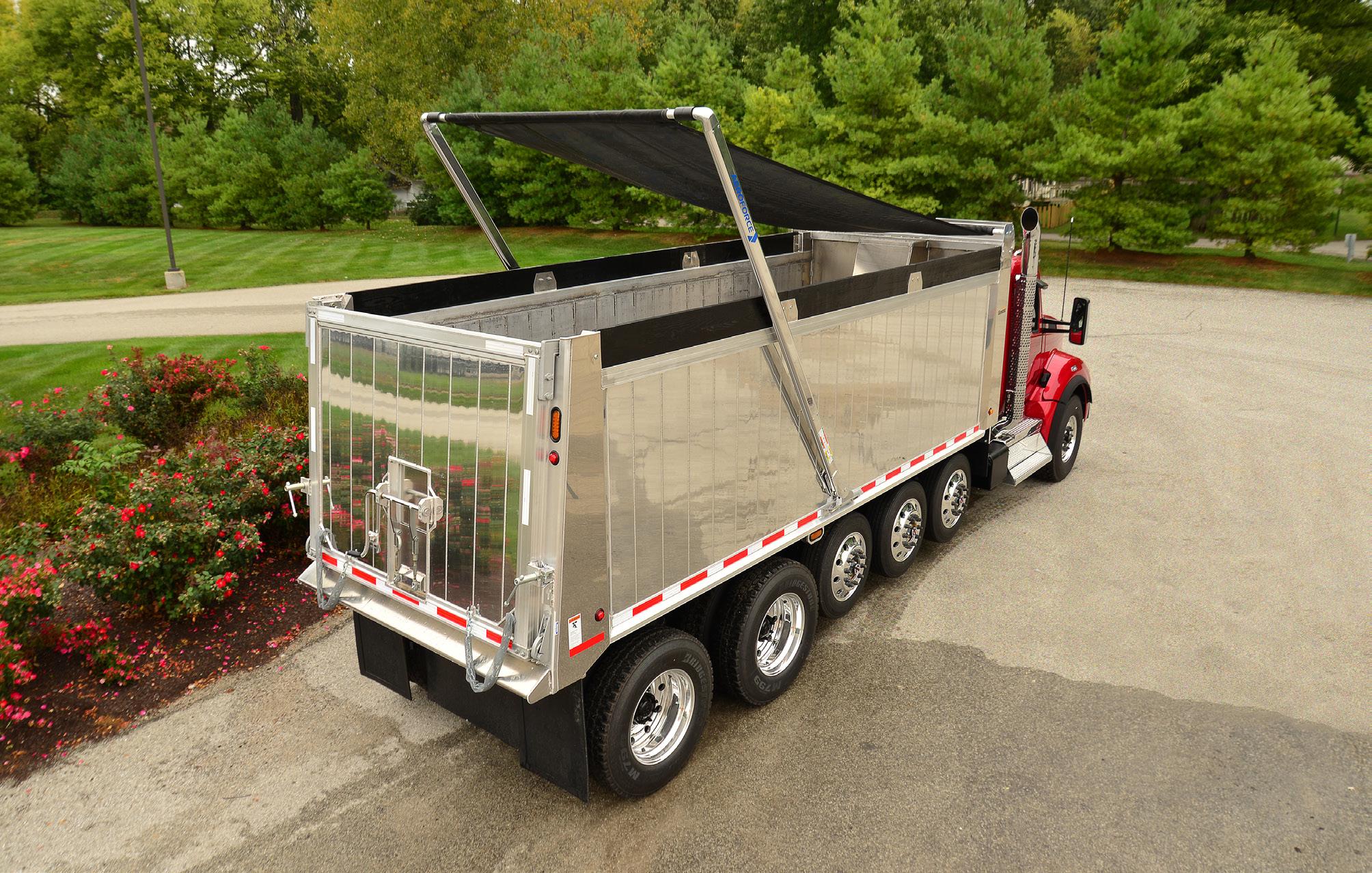
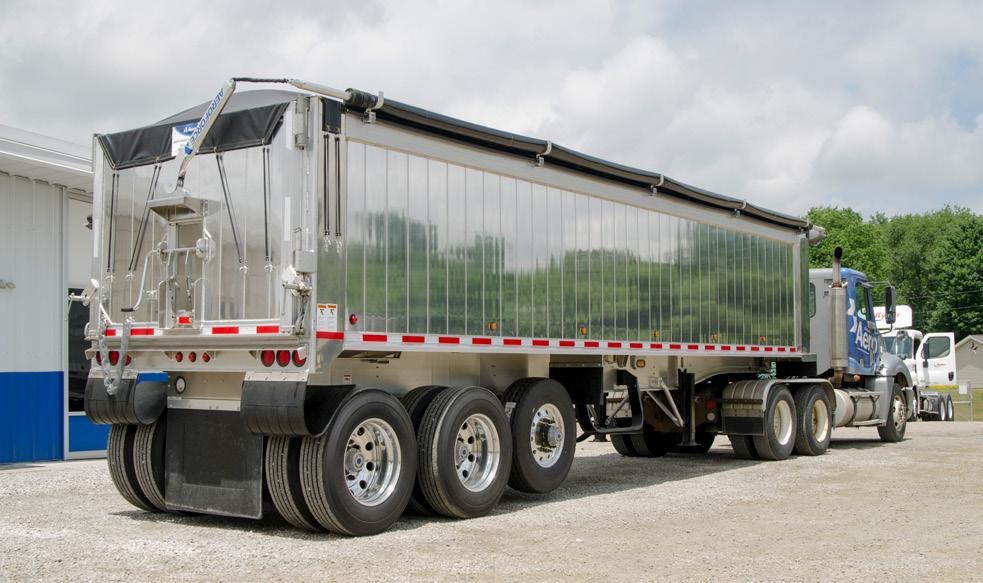
“Our mission is to provide innovative and quality solutions that enhance the lives of customers and employees; our vision is that Aero Industries’ transportation accessories and tarp systems are the solution above anything else; and finally, our values are that we innovate and persevere as we create and grow relationships while continuing to build our legacy.
“What differentiates us from our competitors is our people and the relationships we have both internally and externally,” expresses Rodgers.
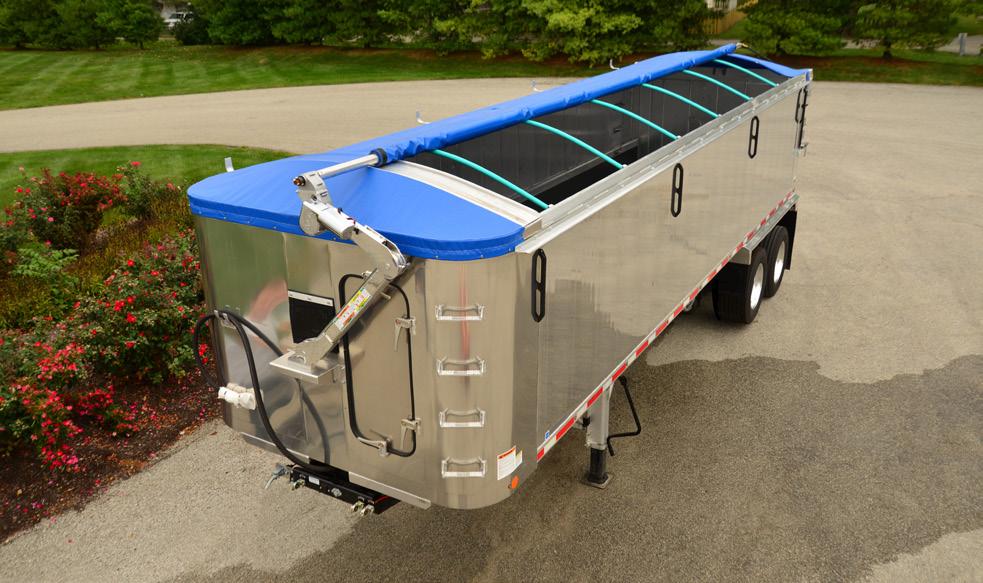
PIONEERING PRODUCTS AND EVOLVING EQUIPMENT
Aero Industries boasts state-ofthe-art facilities and a top-tier team that contributes to the innovative products it has developed over the years.
“Our reputation in the industry is for products that outlast the competition and quality that is superior,” Rodgers prides.
The recent projects undertaken by the company provide clear evidence of its innovation. In 2021, the design of the Crank-N-Go system was updated
and rebranded as the Aero TopGlide. This new version combines advanced drive cable and bow-end technology with a pleat system that has been reimagined and re-engineered to meet industry demands, ensuring reliable movement of the bow and tarp.
The AeroForce ROC 700 series, meanwhile, addresses the need for a lightweight roll-off container cover system suitable for Class 4 and 5 chassis. Additionally, the enhanced slide design improves serviceability and maintenance.
AERO INDUSTRIES’ HISTORY AND HERITAGE
1900S – 30S – Paul journeyed from Germany to New York and later Illinois. While living in Chicago, he married Viols Mueller and started a family. In 1939, he went to work for Hoosier Tarpaulin & Canvas Goods Co., which changed the course of his life.
1940S – 50S – Aero Canvas Products opened and, with successful sales leading to continuous growth, introduced rubberized tarps.
1960S – 70S – The company introduced the aluminum stake side kit and the use of vinyl tarps. It also opened a manufacturing and installation facility in Omaha, Nebraska, and the first Side-to-Side Roll Tarp was developed.
1980S – 90S – Aero Industries launches the first cable tarp system in the US – the Crank-N-Go – along with launching the Easy Cover, which is the industry’s leading front-to-rear flip tarp system and introducing the first rolling tarp system – the legendary Conestoga.
2000S – 10S – The SideKick 2 is developed, and the Conestoga 2, the industry’s most advanced rolling tarp system, is launched. The company also introduced StorMor storage boxes.
TODAY – Aero Industries is still growing and innovating, instilling a deep sense of pride in those committed to its future.
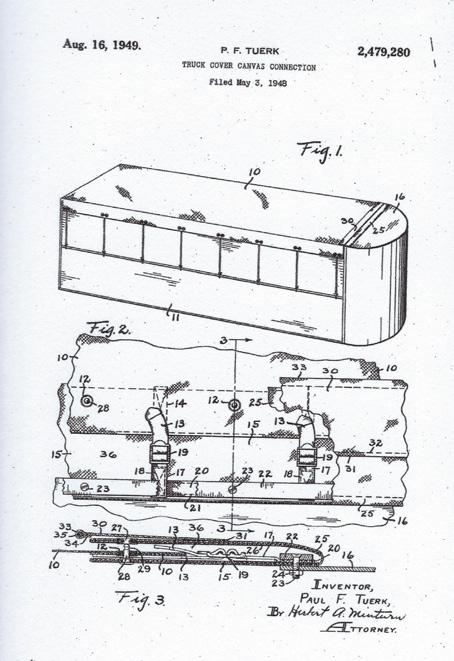
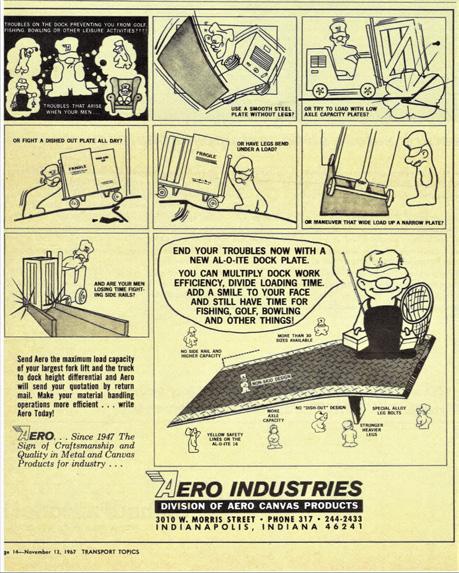
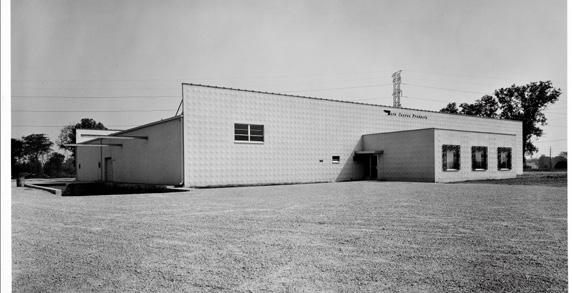
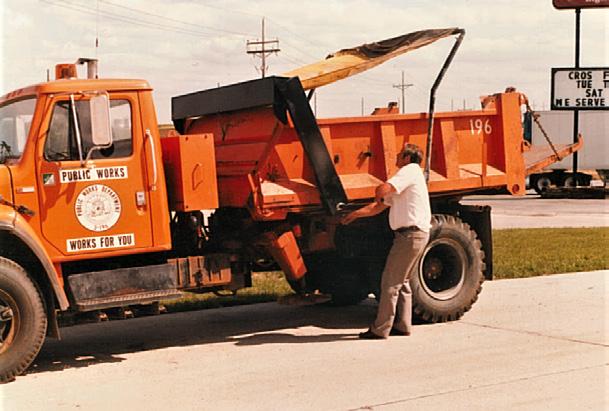
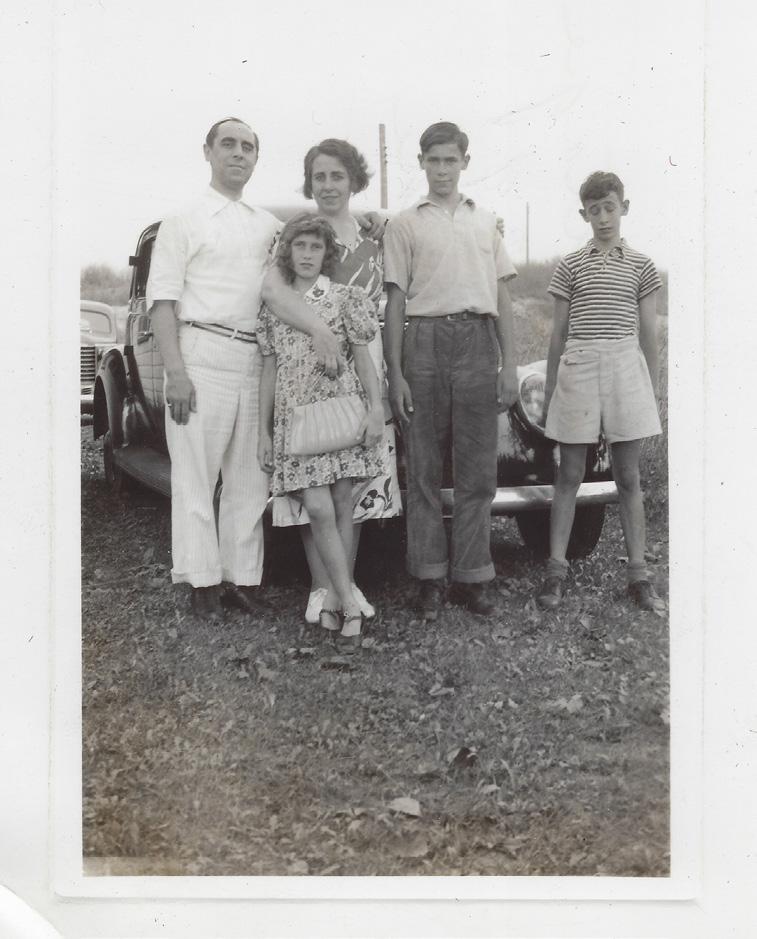
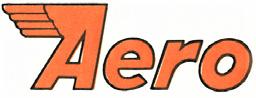
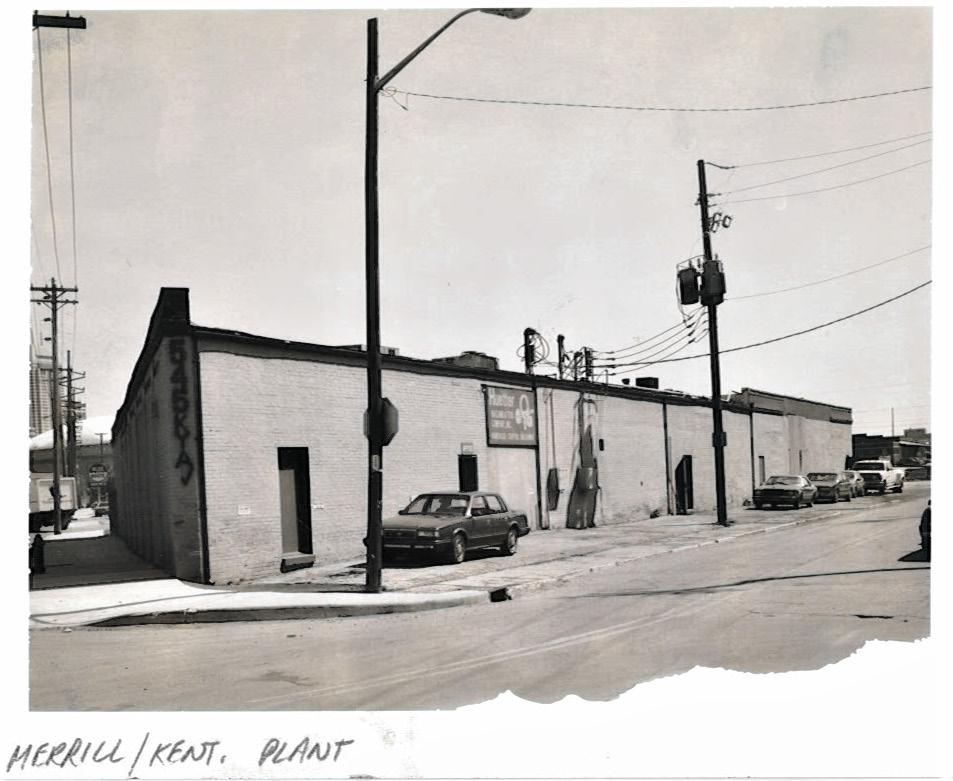
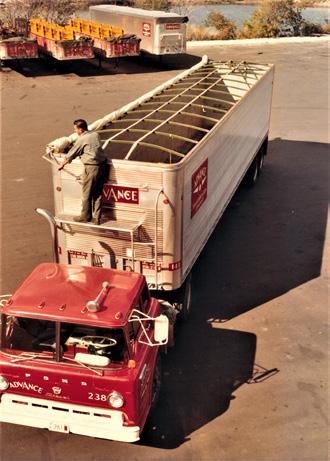
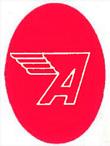
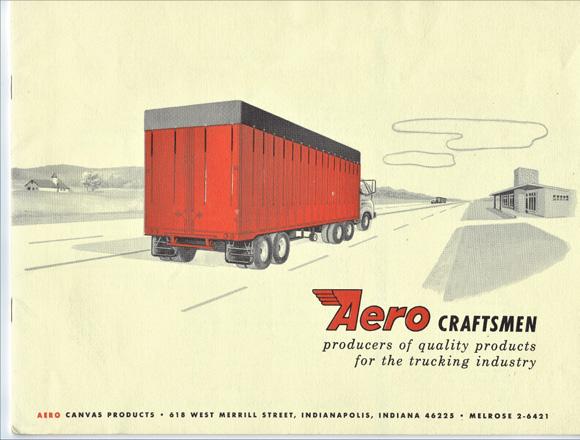
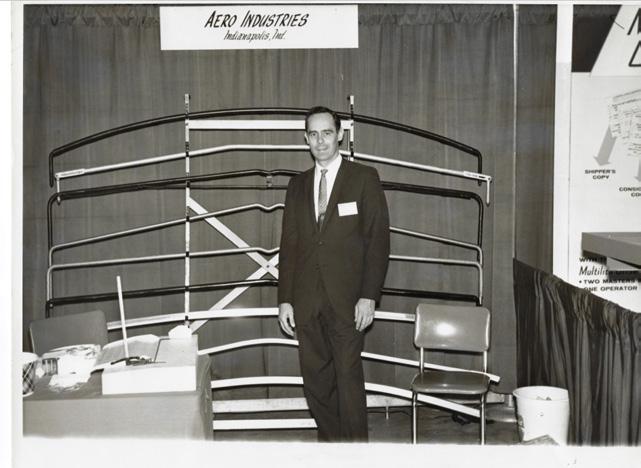
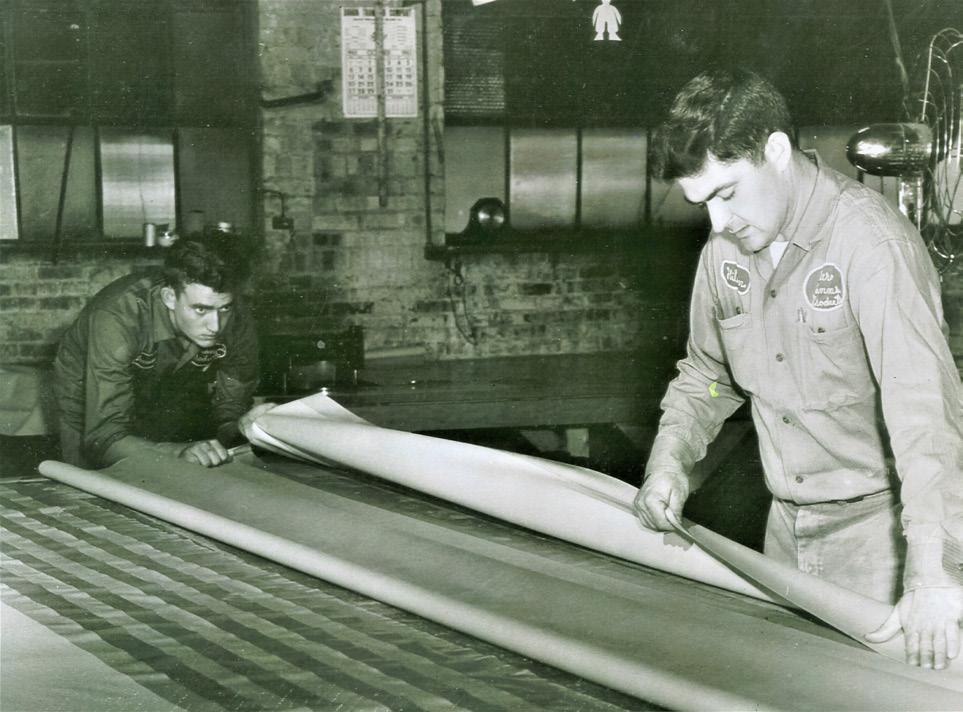
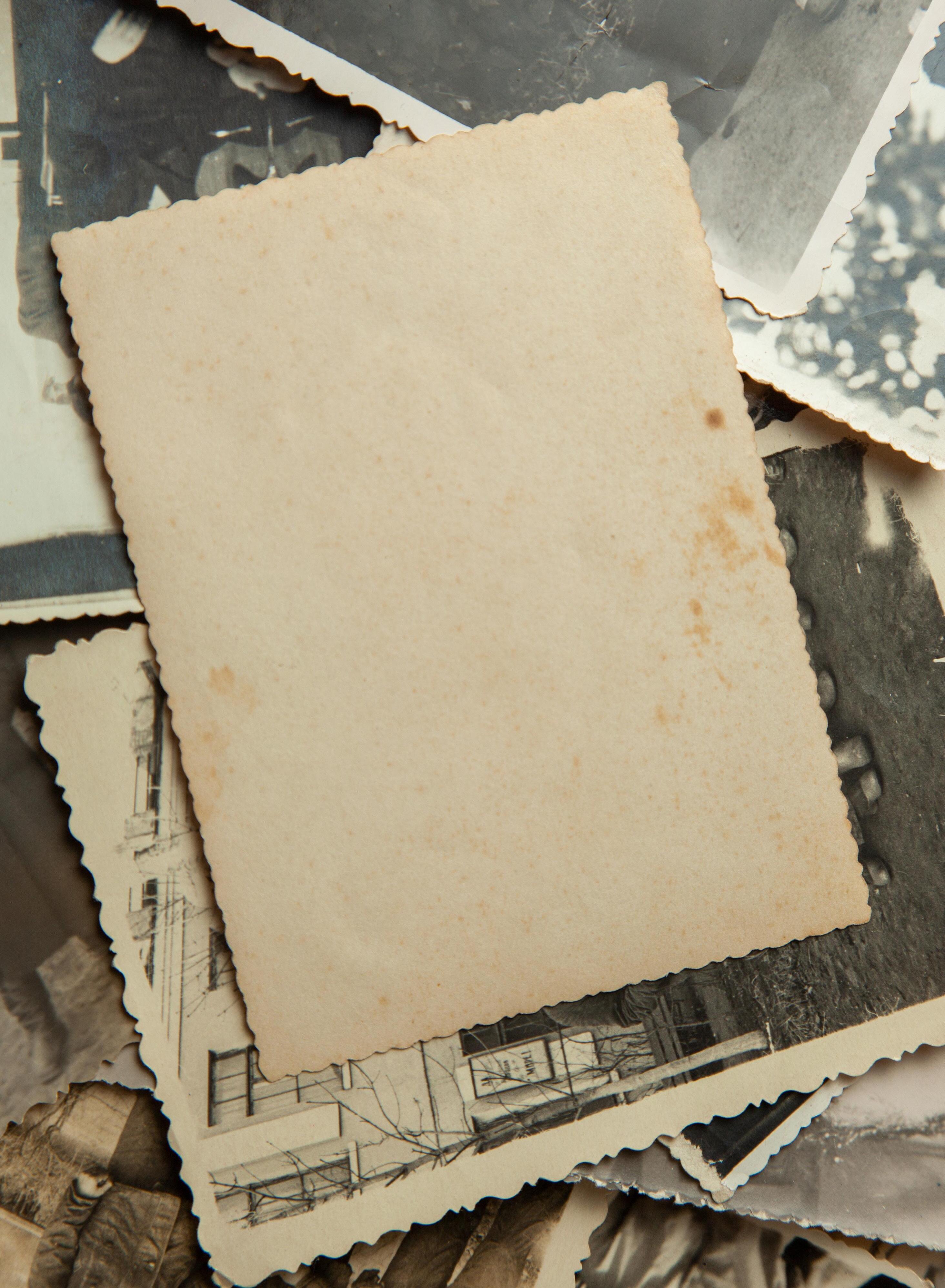
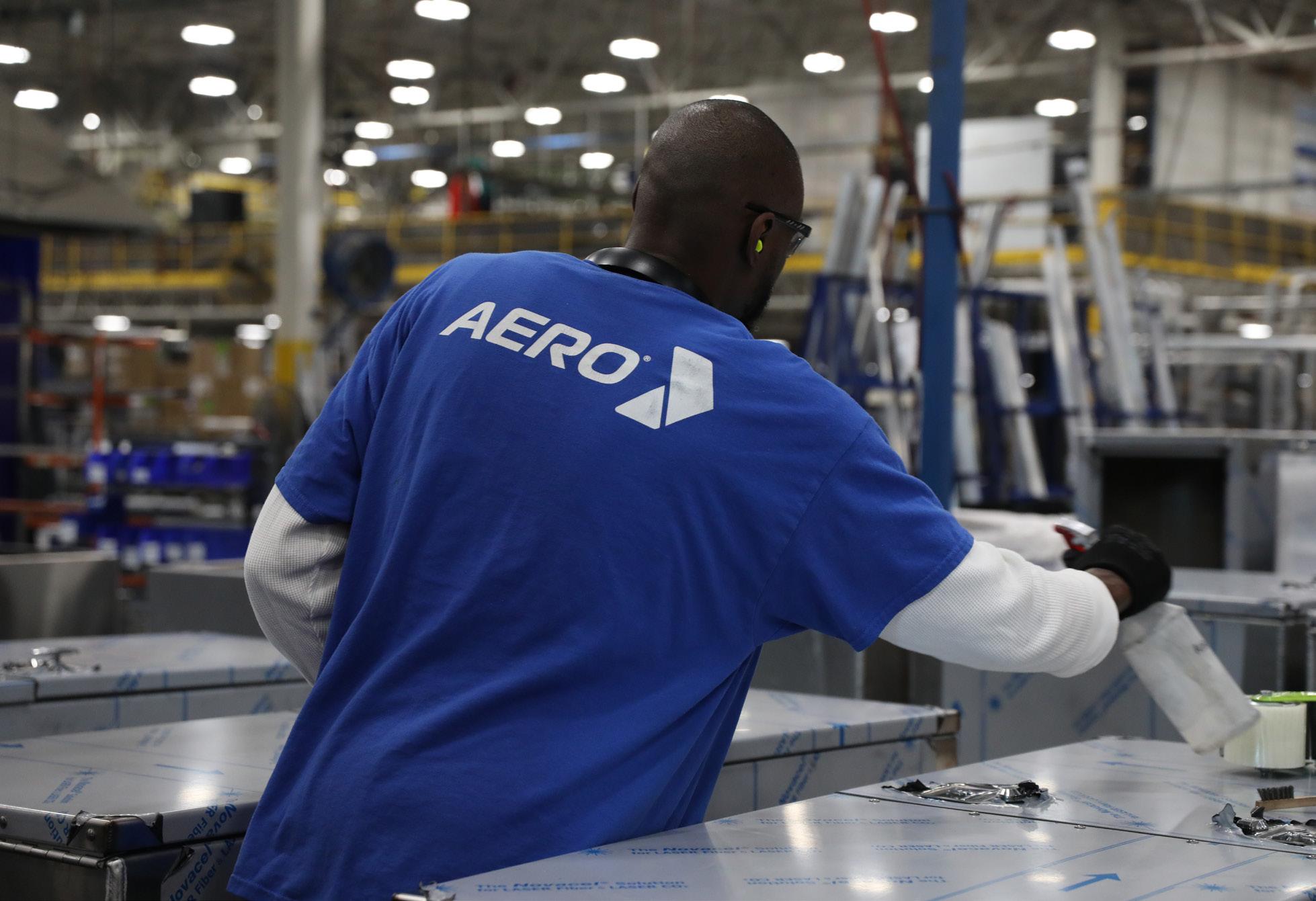
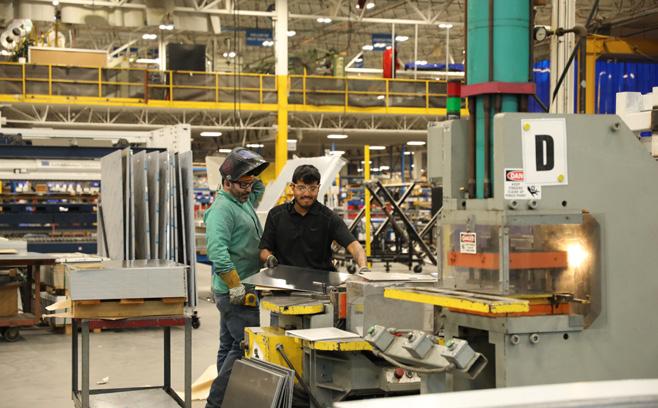
“We are very fortunate to have excellent relations with our customers, and we have found a few key opportunities to provide some significant product improvements for 2025 to our flatbed accessories products.
“In addition to product improvements, we have seen a consistent increase in demand for our AeroForce F2B and S2S products, so much so that we are now expanding production into a second facility to support growing customer demand,” shares Rodgers.
AERO’S DYNAMICS
Aero Industries has built a strong reputation over the past eight
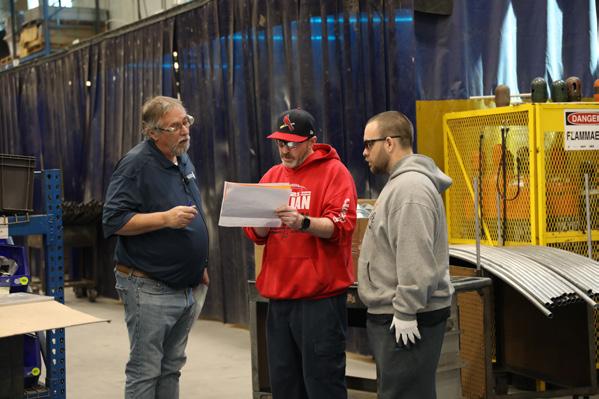
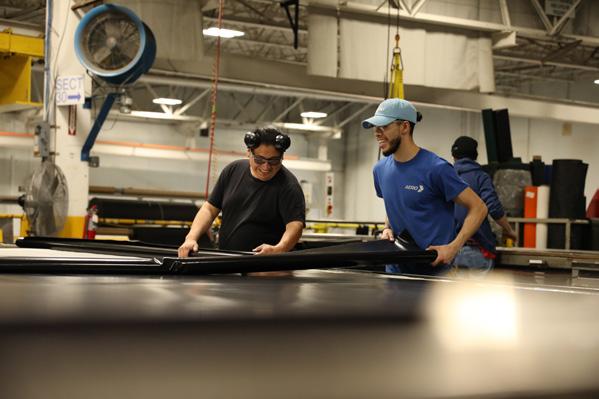
“MANY OF OUR DESIGN IDEAS COME FROM CUSTOMER REQUESTS AND THEIR CONFIDENCE IN OUR ABILITY TO SOLVE ENGINEERING PROBLEMS”
– JOHN RODGERS, VICE PRESIDENT OF OPERATIONS, AERO
INDUSTRIES
decades, recognizing that its employees, customers, and suppliers contribute significantly to its success.
“The culture here is special; we genuinely care about and look after each
other. I like to say – “we get to do this!” – which means that we are blessed to be able to come to work at a place like Aero Industries alongside fantastic team members,” Rodgers prides.

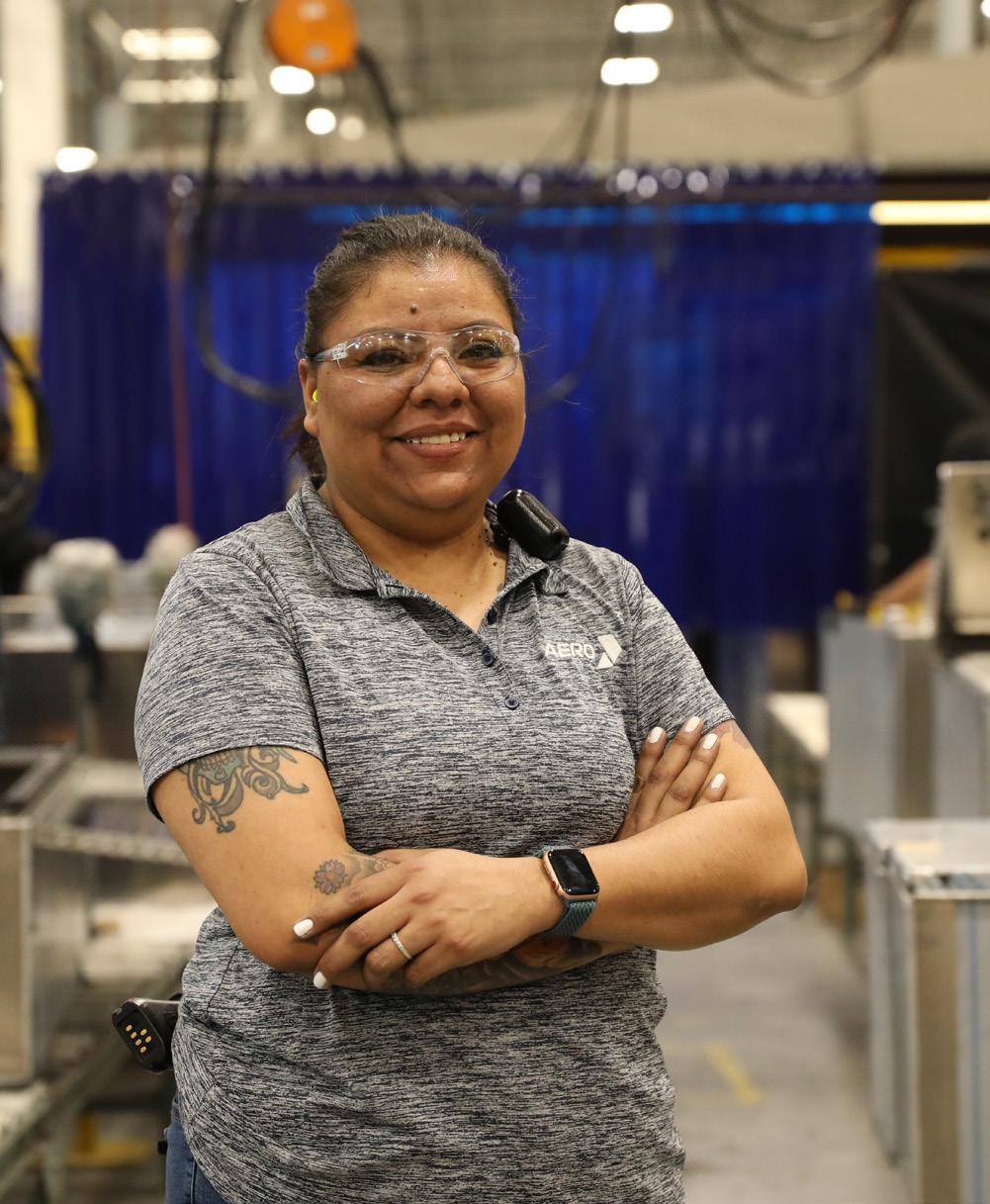
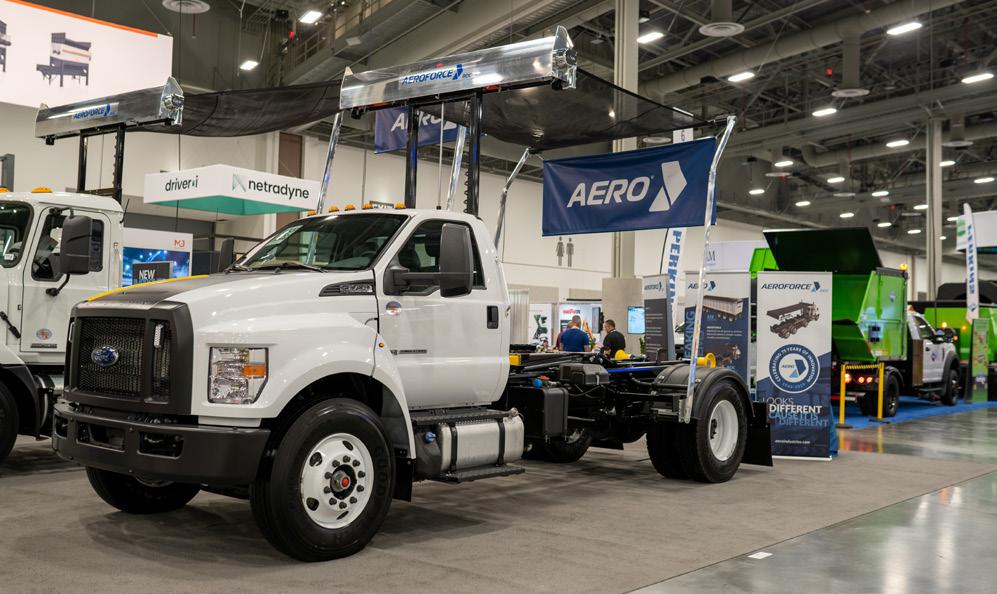
Supplier relationships are also vital for smaller companies such as Aero Industries, whose supply chain has a mix of centralized and decentralized elements.
“With Indianapolis being our primary production location, components and assemblies are distributed to our Nebraska, Ohio, and Oklahoma sites for installation, where we have some of their own established product-specific supply chains.
“We are reliant on a handful of international suppliers for fabrics, motors, castings, and extrusions to support us. We also have several
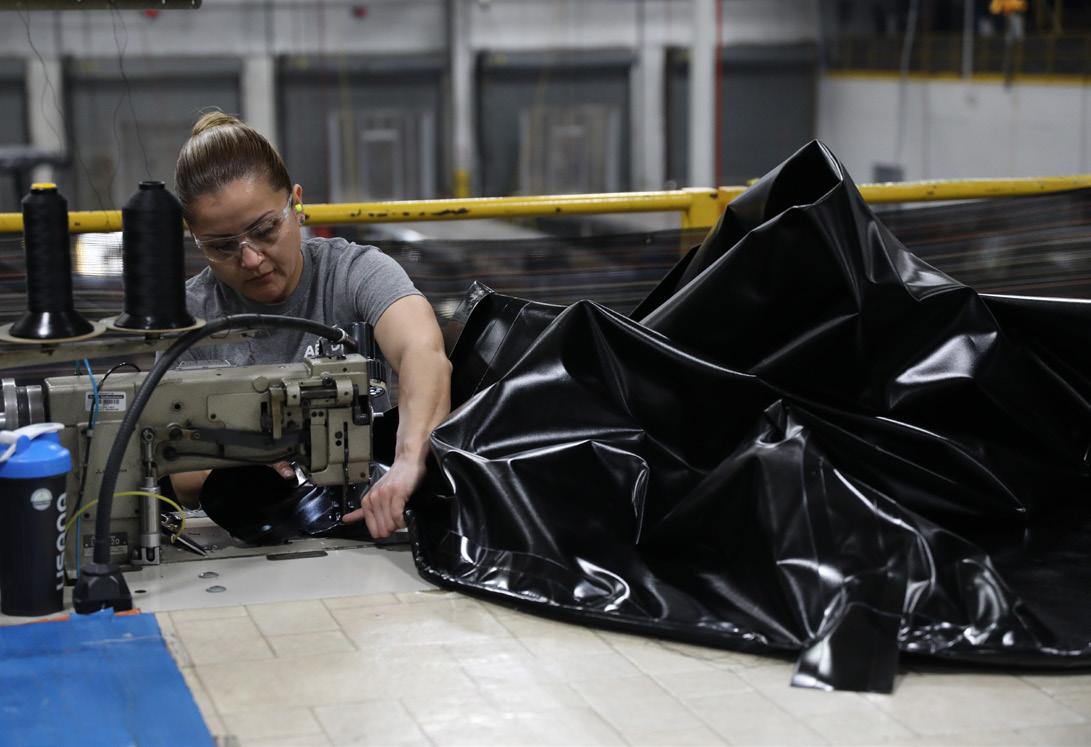
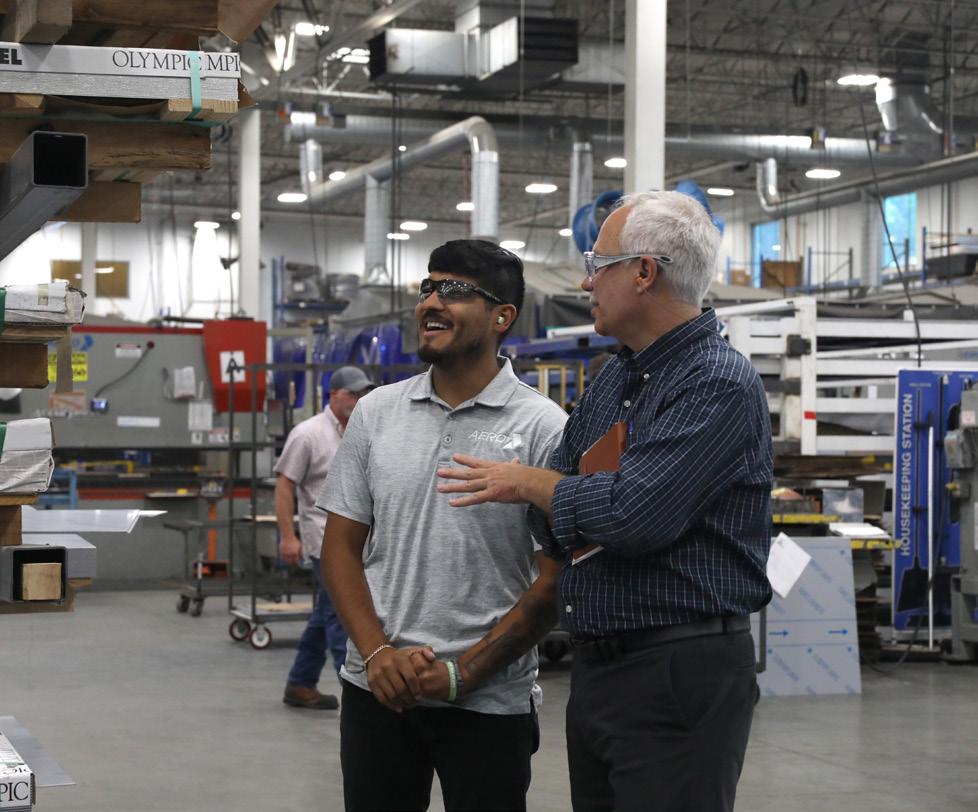
local supplier partners for polishing, printing, painting, and more, with whom we have had long-standing relationships.”
As Aero Industries continues to innovate and introduce new products to the market, the company seeks new opportunities while overcoming challenges – a mindset it was built on and will sustain for decades to come.
“The flatbed industry is currently in a recession, while dump products remain stable. Our focus during this time is to grow our market share by expanding into adjacent regional markets, playing offense against our competitors, and improving service
and delivery,” finishes Rodgers. Despite the challenges the market may present, Aero Industries will boldly forge ahead as a leader in innovation and excellence, poised to embrace the next chapter in its story.
Tel: 800 535 9545
info@aeroindustries.com www.aeroindustries.com
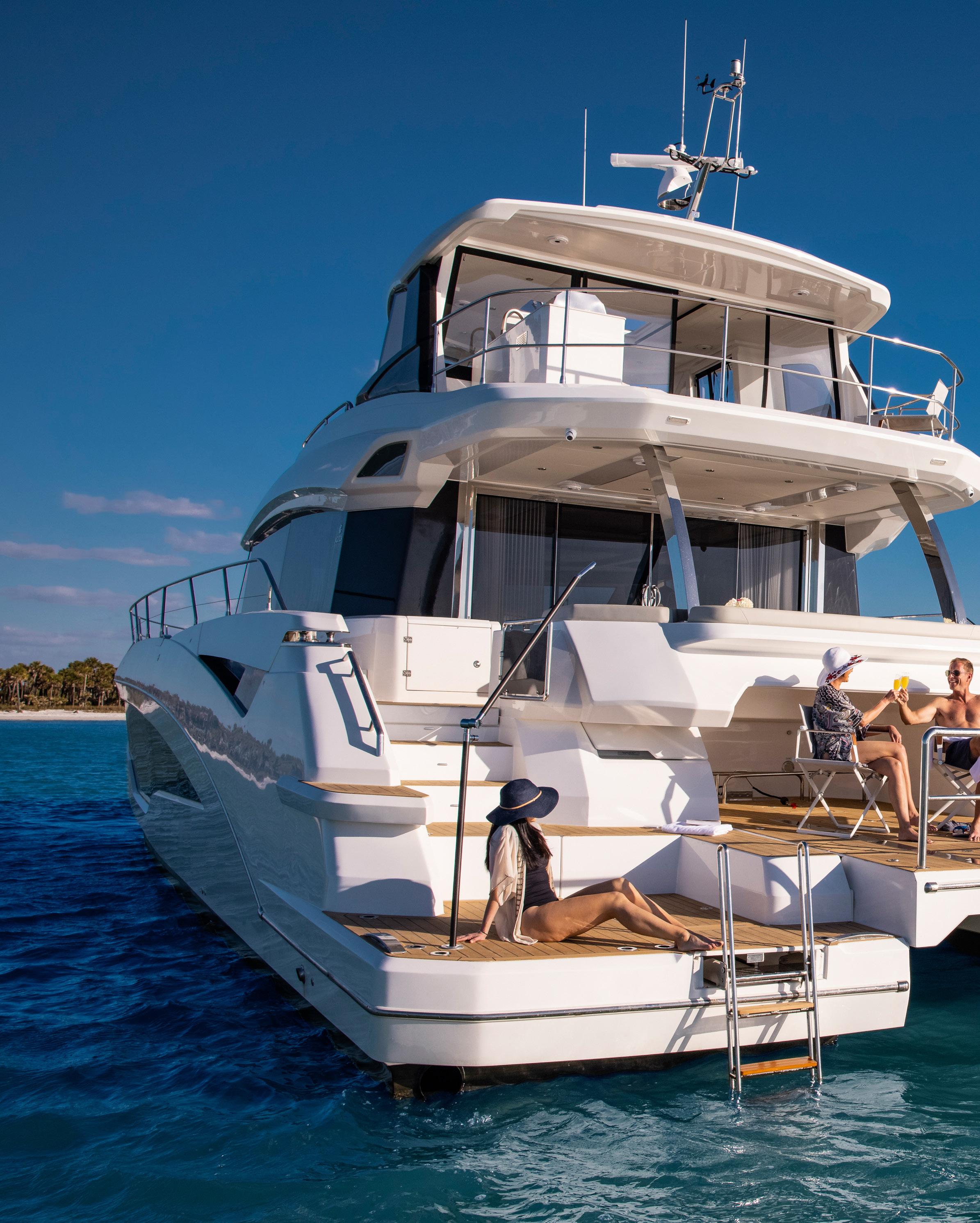
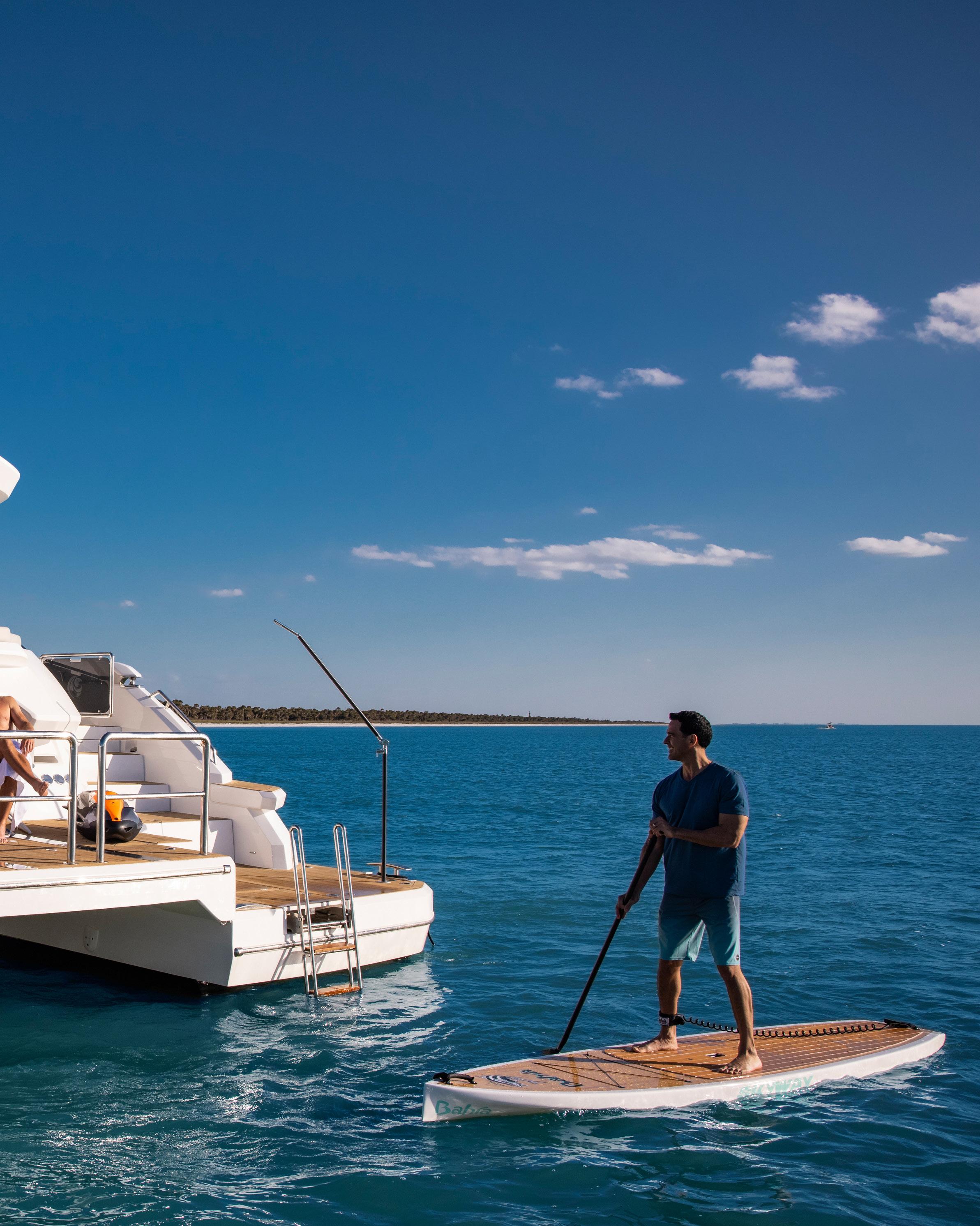
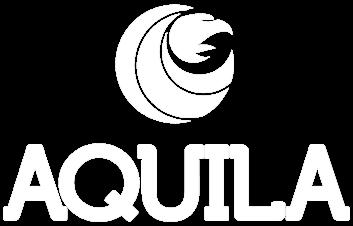
EMBODYING THE EAGLE
Bringing high-performance and innovative catamarans to boating lovers across the world, Aquila Power Catamarans is one step ahead in the recreational marine sector. Lex Raas, President, highlights the company’s world-class offerings
Writer: Lucy Pilgrim | Project Manager: Michael Sommerfield
North America’s marine industry continues to be one of the most dynamic in the world.
Despite going through a period of success in the last five to six years, recent geopolitical events have caused the market to soften.
As the world’s foremost recreational power catamaran manufacturer, Aquila Power Catamarans (Aquila) understands these challenges but remains optimistic, consequently evolving to facilitate numerous exciting projects.
“We believe in the tremendous strength of the marine industry in North America, and Aquila is not holding back in bringing new models and technologies to the sector,” opens Lex Raas, President.
Derived from the Latin word for “eagle”, Aquila embodies the very essence of power, grace, and majesty.
The company’s power catamarans
range from 14 feet tender catamarans to the semi-custom Aquila 70 Luxury power catamaran, emphasizing Aquila’s focus on purpose-built power vessels.
Based in Hangzhou, China, the company is immensely proud of its one million square foot, state-of-theart manufacturing shipyard that rivals many leading boat manufacturers across the world.
“Fundamental to Aquila’s philosophy is offering our owners, new and old, a path in their boating lifestyle.
“Whether you are new to boating and buying your first vessel or a seasoned boater that knows exactly what fits your lifestyle, we have a model to grow or downsize with you,” prides Raas.
The company’s boating segments include Offshore, Sport, Coupe, Yacht, and Luxury.
Making the most of this diverse
range, the majority of Aquila’s client base comprises private owners, alongside other charter companies and private charter programs.
“Our most notable charter customer at this time is MarineMax Vacations, whose extensive fleet of Aquila catamarans is located in the British Virgin Islands,” Raas notes.
Meanwhile, the company also boasts a global dealer network of world-class retailers, representing Aquila across the Americas and the Caribbean with a presence in the US, Canada, Mexico, Panama, Dominican Republic, Puerto Rico, Peru, Chile, and Saint Lucia.
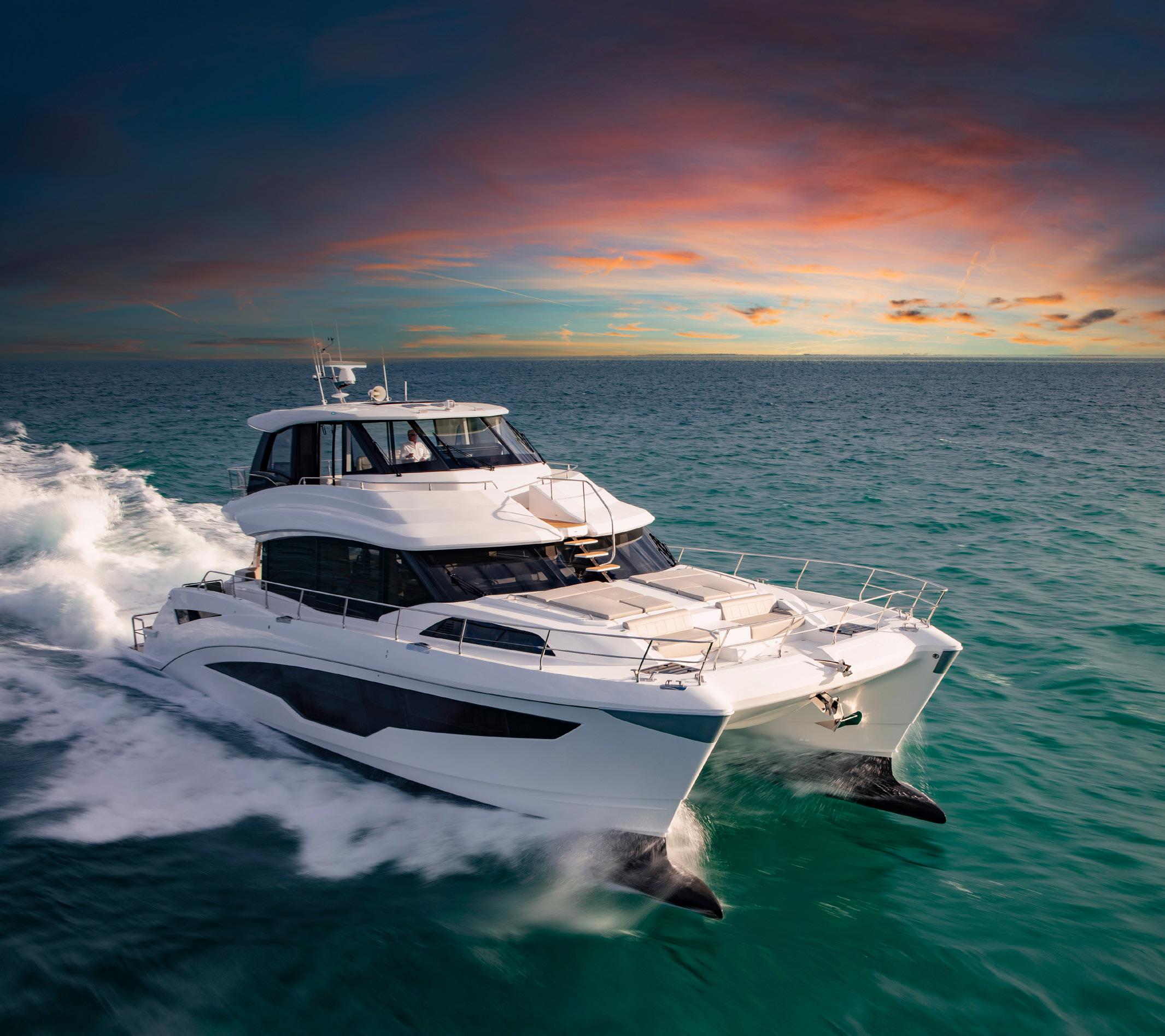
Further afield, the company is represented by the best dealers across Europe in Finland, Denmark, Poland, Germany, the UK, France, Portugal, Spain, Italy, Greece, Turkey, Croatia, as well as elsewhere in Dubai, Australia, Thailand, Malaysia, the Philippines, China, and Mauritius.
AS THE WORLD’S LEADING POWER CATAMARAN MANUFACTURER, WHAT IS THE SECRET TO AQUILA’S SUCCESS?
Lex Raas, President: “There are many factors that go into making Aquila the leading power catamaran manufacturer in the world. To be successful, one needs a world-class builder (Sino Eagle Group) and a powerful distributor (MarineMax), with a leading global dealer network to tie everything together.
“For all those aspects to come to fruition, there is nothing more important than having a dynamic team behind the brand. Our original equipment manufacturer (OEM) partners are also critical to the success of the company, supporting ours and our owners’ needs.
“The core secret to Aquila’s success, however, is quite simple. Like a stool, the company needs three legs to stand up - innovation, manufacturing, and distribution. You need all three, and we have these.”

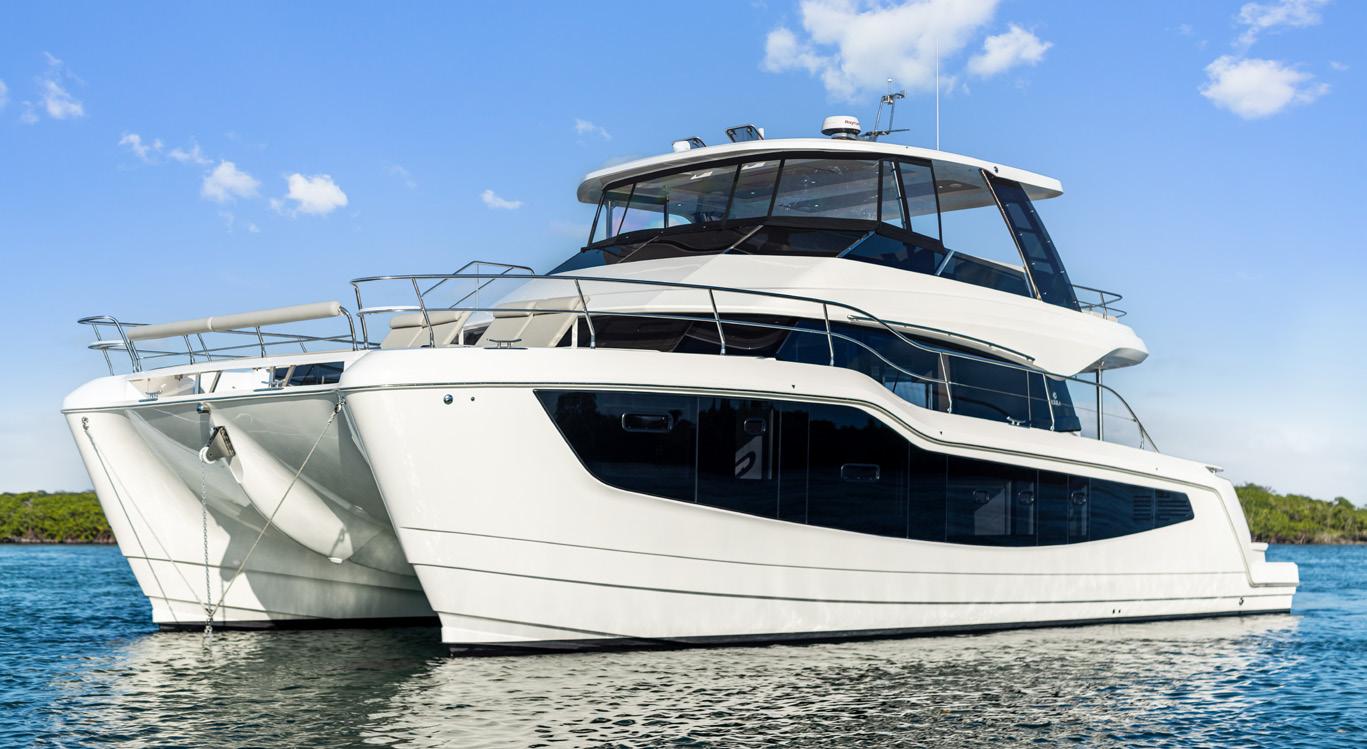
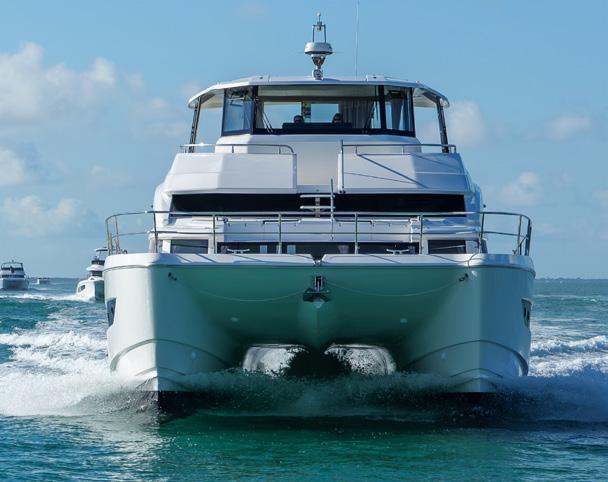
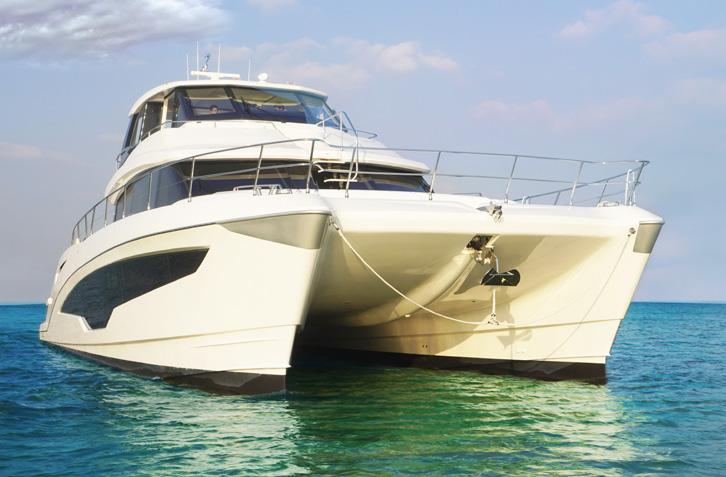
BOATING BRILLIANCE
Aquila emerged from Raas’ lifetime of experience on the water, building and selling boats through his own businesses before working with Groupe Beneteau and later The Moorings as CEO.
Following his departure from the latter in 2010, Raas had a vision of creating a power catamaran brand that at the leading edge of enhancing an owner’s life on the water.
Two years later, he brought two boating powerhouses together –Sino Eagle Group and MarineMax – marking the establishment of the company and laying strong foundations for growth.
“The first Aquila vessel out of the shipyard was an Aquila 37, which allowed our teams to understand the dynamics of a true purpose-built power catamaran,” Raas recalls.
The Aquila 48 was subsequently launched with great success, and since that time, the company has evolved to offer a vast range of powerful catamarans, with many new models forthcoming.
Aquila’s continued progress over the last decade has been achieved by its commitment to innovation and pushing boundaries.
Case in point, the company was the first production builder to include hydrofoils on power catamarans, which remains one of the most forward-thinking and impactful projects in the sector.
“Prioritizing the design philosophy of ‘KISS’ (Keep It Simple, Stupid), we have developed the user-friendly Aquila Hydro Glide Foil System™, which requires no pushing buttons or seat belts for the foil assist system to function.
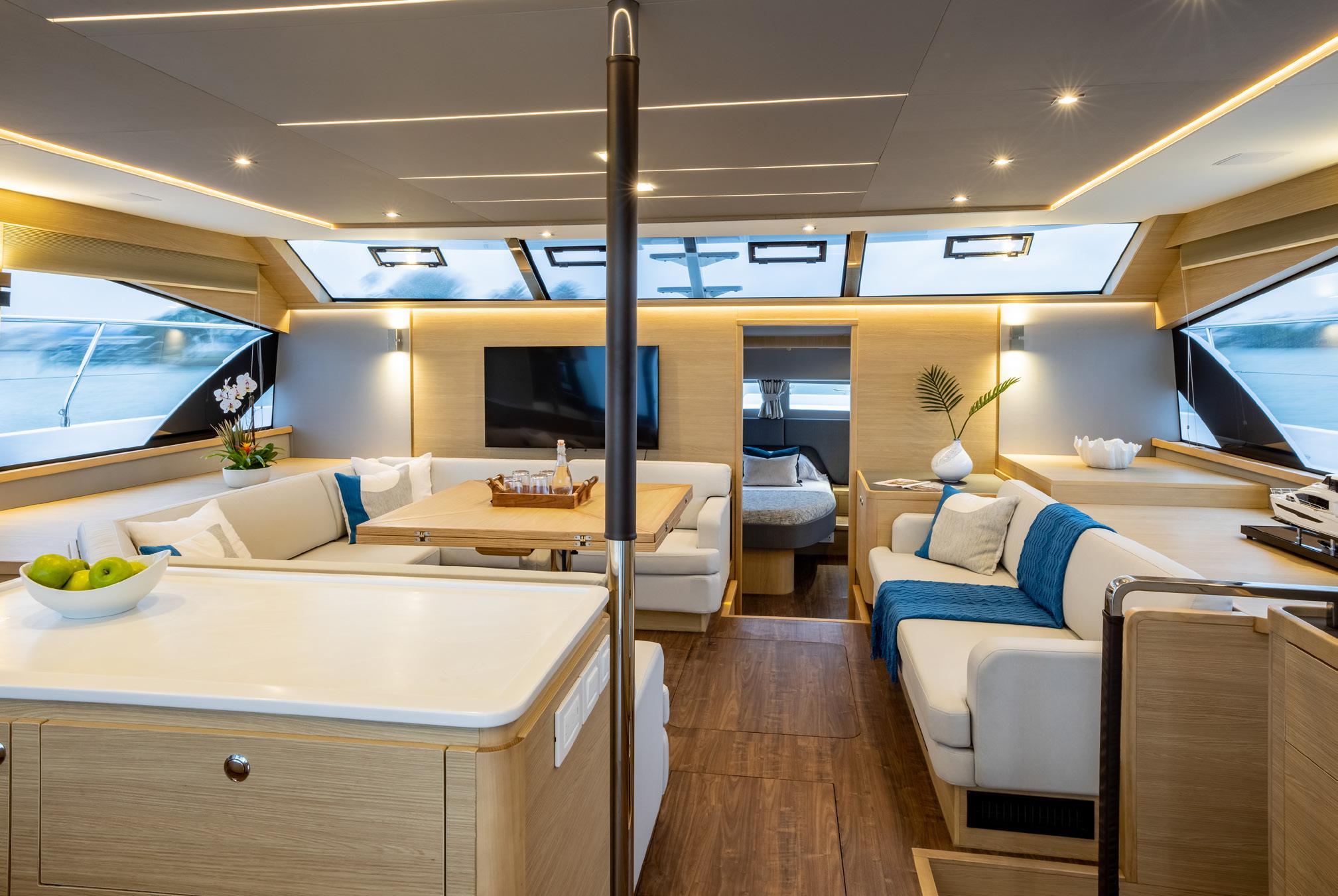
“This was no easy feat and required lots of engineering hours and failures before we achieved success on our first model,” Raas emphasizes.
The company embraces its failures as it provides an opportunity to learn and build stronger solutions. For example, the latest generation of the foil system has become a standard offering on the recently-launched Aquila 42 and 46 Coupe models, resulting in significant performance and efficiency.
This has also allowed Aquila to run its vessels on less horsepower while maintaining the same cruise and top-end speeds as boaters with more engines and horsepower.
“This is a game-changer when it comes to efficiency and the environmental aspects of the marine industry as we produce less carbon emissions due to less engines and cover more miles with less fuel,” he informs us.
The Aquila Hydro Glide Foil System™ is now available on the company’s 36 Sport, 42 and 46 Coupe, and 42, 46, and 50 Yacht models.
AQUILA’S CORPORATE SOCIAL RESPONSIBILITY COMMITMENTS
Corporate social responsibility (CSR) remains a key pillar of the business, materialized by following a steadfast ethos of manufacturing boats in a responsible manner.
With this in mind, Aquila’s manufacturing facility revolves around CSR, as demonstrated by its:
CLOSED MOLDING – Limits styrene emissions.
AIR FILTRATION SYSTEMS – Filters grinding and cutting dust to protect both the planet and employees.
WATER FILTRATION SYSTEM – Recycles run-off water and filters exhausted water.
SOLAR POWER – 70 percent of the factory’s rooftop is covered by solar panels, providing a large part of the consumable power required by the facility to manufacture boats.
WASTE REDUCTION – Aquila has a development strategy that focuses on efficient build technologies to reduce overall waste.
Elsewhere, Aquila has supported several causes, most recently during the 2023 Hawaii wildfires which directly impacted communities and families. As such, the company continues to work with communities in times of need.
Isotherm is ready to supply all your refrigeration requirements with a broad range of sizes and sophisticated styles.
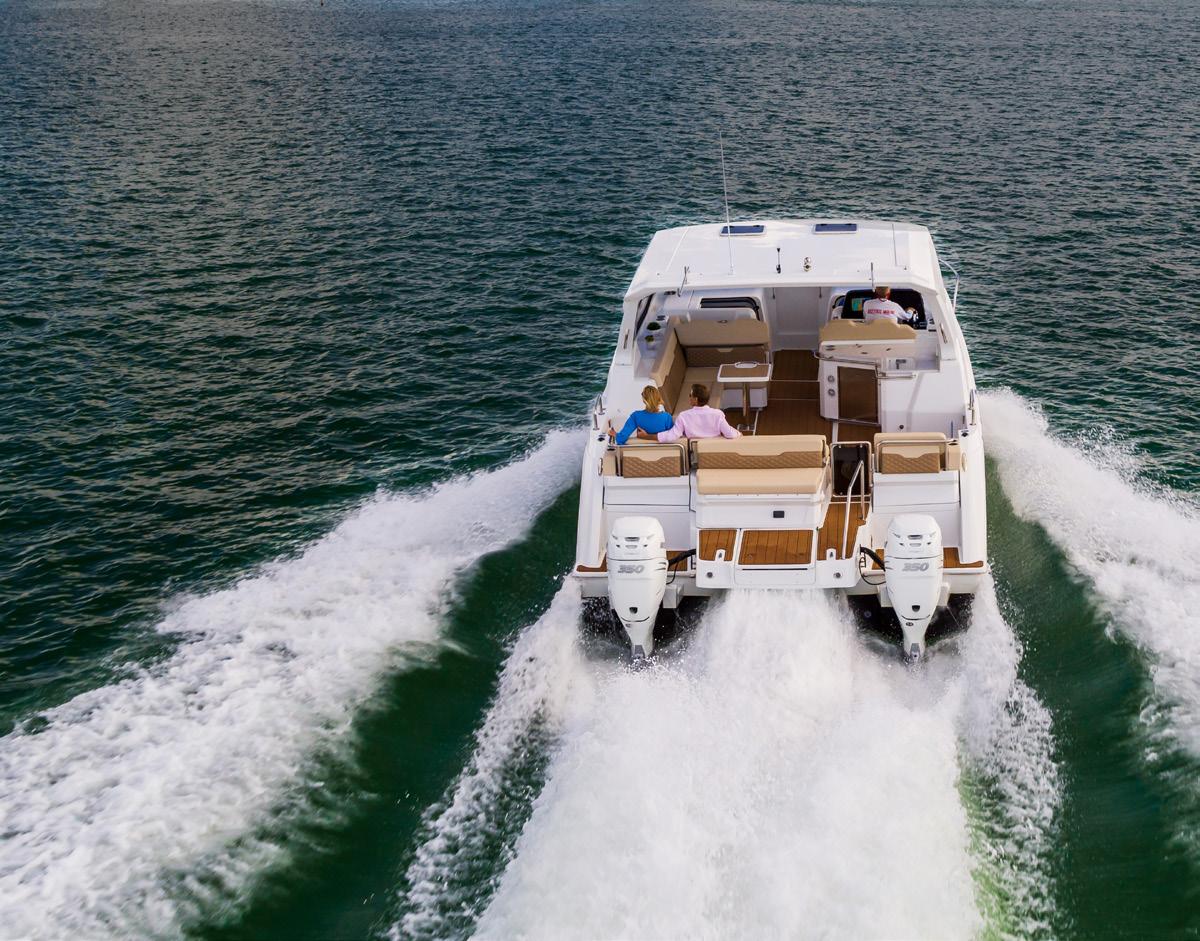
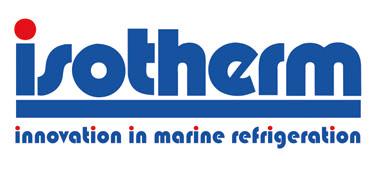
Phone: 954-984-8448 | Email: info@iwmarine.com
Website: www.indelwebastomarine.com/us/ Instagram: isotherm_indelwebastomarine
LUXURY COOKING
AT SEA: ELEVATE YOUR AQUILA YACHT EXPERIENCE WITH KENYON
Imagine savoring a perfectly grilled steak or fresh seafood while cruising on your Aquila yacht, with the open water as your backdrop With the Kenyon Signature Grill and Cooktop, you can turn every meal into a five-star dining experience right on deck
Designed for effortless, smokeless, and flame-free cooking, Kenyon’s premium stainless steel appliances are weather-resistant, easy to clean, and built for the open sea No charcoal, no propane just the push of a button for instant heat and precision cooking
Whether you're hosting a sunset dinner or preparing a casual breakfast before a day of adventure, Kenyon delivers gourmet results with no hassle Elevate your yachting lifestyle with the best in marine cooking
Kenyon Luxury Cooking, Anywhere Anytime
Discover more at www CookWithKenyon com
Isotherm Marine Refrigerators and Isotemp Marine Water Heaters are well known for their technological innovation, with sophisticated yet practical designs. Our products are specifically designed for dependable service in tough marine environments.
Our product range consists of Cruise fridges, drawers, built-in boxes, wine cellars, water heaters, and safes. All Isotherm Refrigerators and Isotemp Water Heaters are ignition protected by IMANNA Laboratory INC.
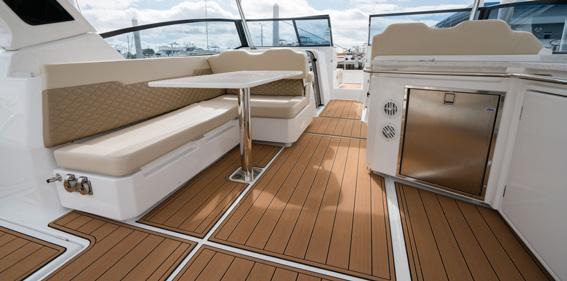
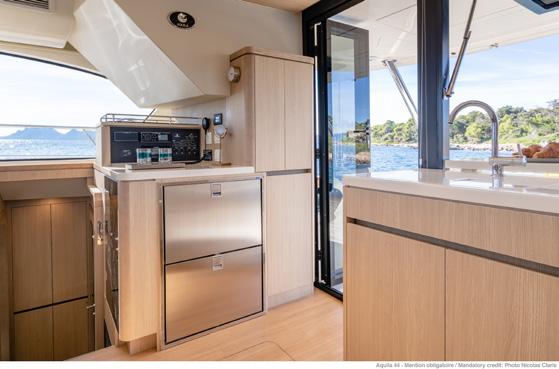
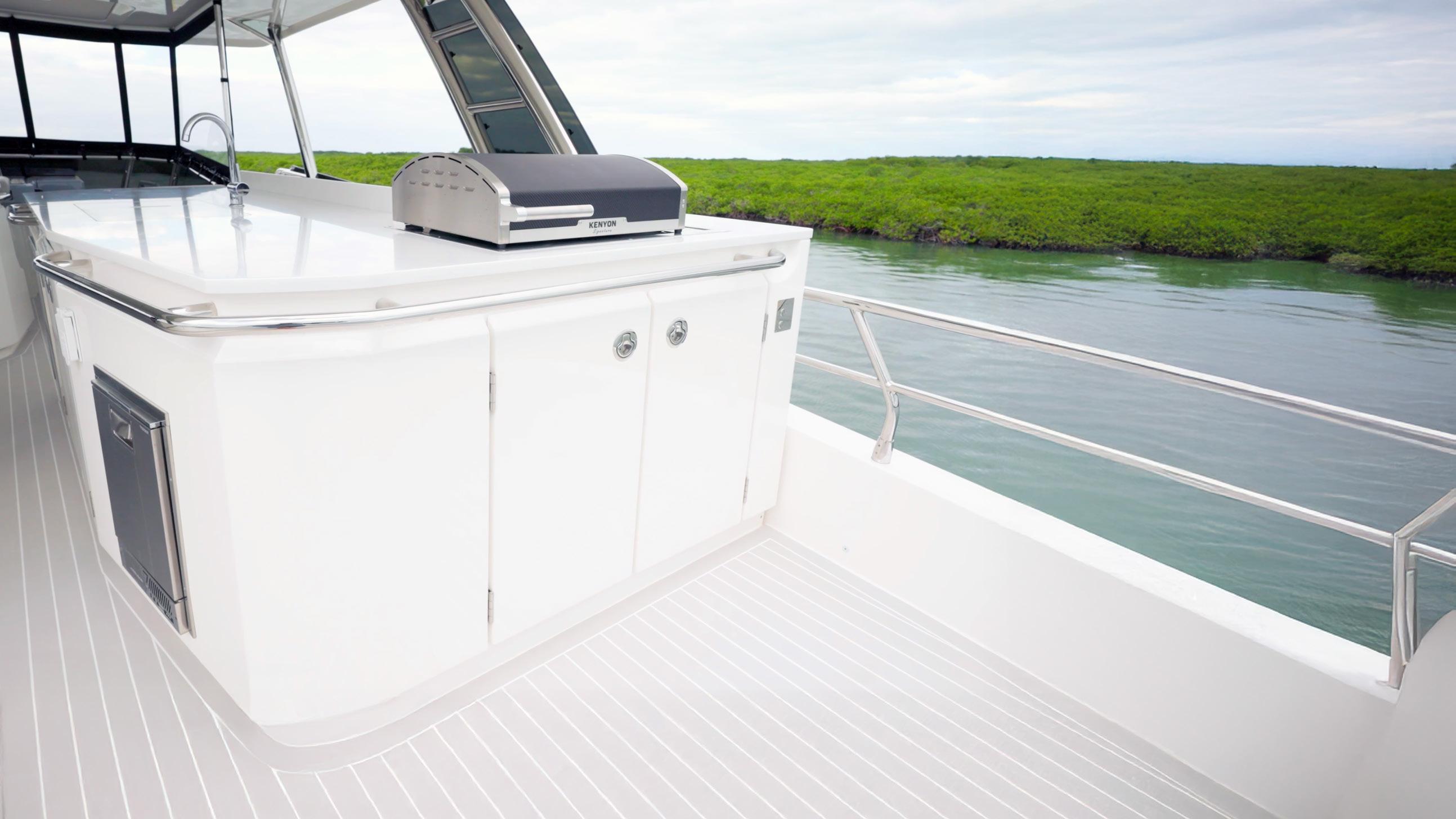
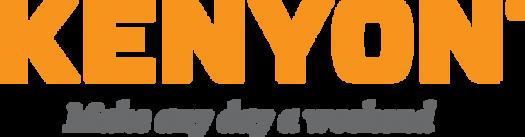
CUTTING-EDGE AND DIVERSE MODELS
Aquila continues to develop new models at a rapid pace. For instance, the company successfully launched the 50 Yacht in October 2024 at the Fort Lauderdale International Boat Show, which resulted in immediate acclaim and success.
The introduction of this product marked a new era in the design of power catamarans, featuring an explorer-look aesthetic, high freeboard, a single-level, full-beam owner’s suite, an enhanced flybridge, and options for both diesel and hybrid power.
Hot on the heels of the 50 Yacht, Aquila launched its game-changing 42 and 46 Coupes in February this year at the Miami International Boat Show.
The Coupe product segment was developed from the renowned success of the Aquila 36 Sport with the cruiser package.
“Our clients were telling us they wanted an enclosed salon outboard catamaran that offered the features of a yacht but the versatility and speed of an outboard-powered boat. We also went a step further with our Coupe models, which now come with our fixed foil system made out of carbon fiber as standard,” outlines Raas.
At the Cannes Yachting Festival in September this year, the company will be introducing its 46 Yacht, shortly followed by the new 36 Molokai at Fort Lauderdale.
“We have been quite busy, and this is only the beginning. We have a completely new project well
underway which will be introduced very soon and will open Aquila catamarans to a completely new market segment.
“The introduction of both the 46 Yacht and the 36 Molokai will also continue bringing new innovations to the power catamaran segment within the marine industry,” Raas expands.
The company’s impressive product portfolio wouldn’t be achievable without its manufacturing plant in Hangzhou.
“About 60 percent of what goes into building our boats originates from the US and European Union (EU), so we are constantly having supplies sent to our shipyard.”
Following their construction and assembly, the boats are then shipped from regional freight ports close to Hangzhou to all corners of the world.
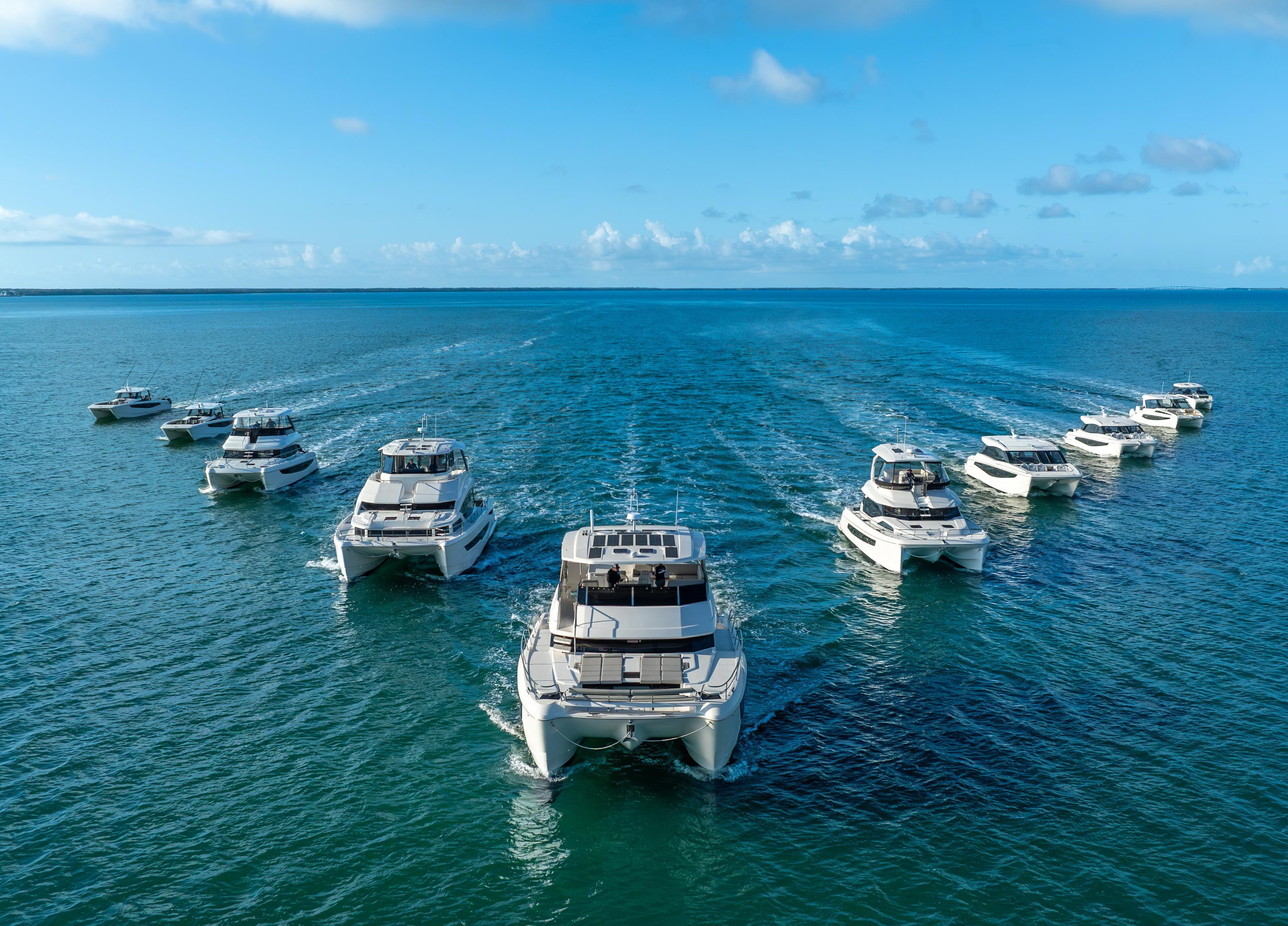
“WE BELIEVE THAT WHEN AQUILA SUCCEEDS, WE ALL SUCCEED TOGETHER – AS A FAMILY. OUR VISION IS CLEAR, AND AS MANY OF US ARE LIFE-LONG BOATERS, WE ALL WORK IN A DYNAMIC AND FAST-MOVING ATMOSPHERE WITH A PASSION FOR BOATING”
– LEX RAAS, PRESIDENT, AQUILA POWER CATAMARANS
“We are fortunate that the US, EU, and China all have exceptional supply chain capabilities. Having such a robust network in these regions provides Aquila with a tremendous ability to supply our shipyard and distribute our products to dealers,” Raas highlights.
THE FOUNDATION OF SUCCESS
Comprising a dependable workforce of approximately 1,000 employees, Aquila possesses a dedicated international team, with many staff members based at its manufacturing plant as well as across Europe, Asia, and the US.
Aquila’s team has expanded significantly since it was founded in 2012 through hard work and determination.
The design, marketing, and service and warranty headquarters are located in Clearwater, Florida, accompanying Aquila’s global headquarters and manufacturing shipyard in Hangzhou.
“Our team members are provided with an abundance of support. We are all a family with the singular goal of making Aquila the number one catamaran manufacturer in the world,” Raas smiles.
Furthermore, the company has a flat internal structure and creates a strong team environment, which helps promote fresh ideas and facilitates forward-thinking, rapid, and constant progress toward building a worldclass brand.
This is also reflected by Raas’ leadership style, as he endeavors to hire passionate individuals and remain humble in his role, promoting success as a team.
“We believe that when Aquila succeeds, we all succeed together – as a family. Our vision is clear, and as many of us are life-long boaters, we all work in a dynamic and fastmoving atmosphere with a passion for boating,” he enthuses.
The company’s key priority for
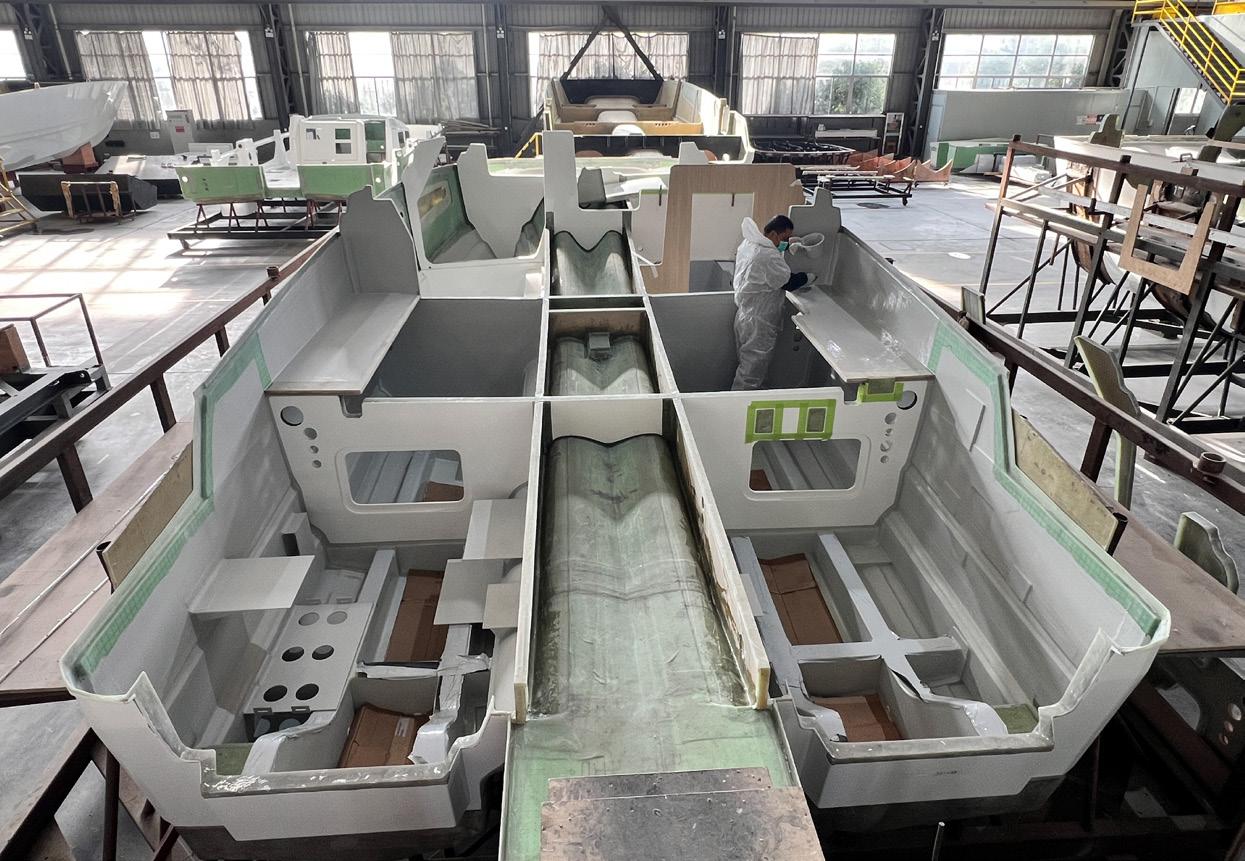
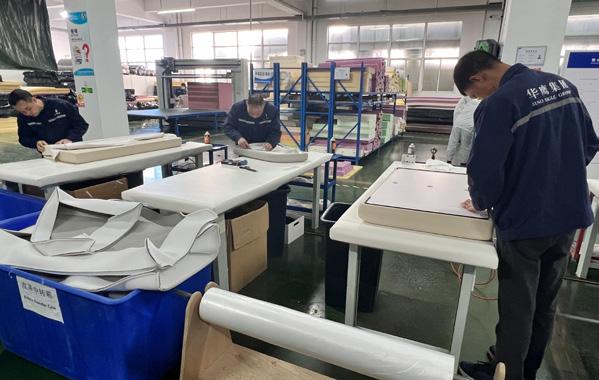
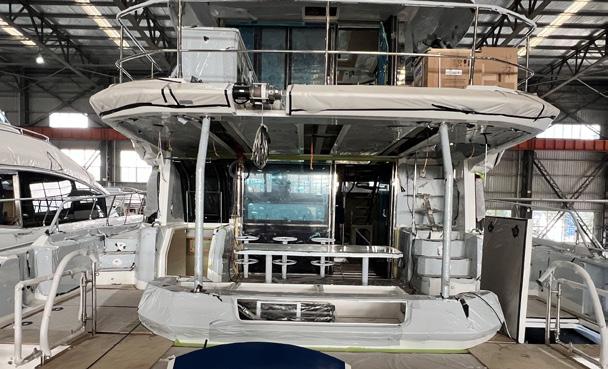
this year is to continue to grow and develop its brand, with the goal of increasing production by approximately 20 percent over the next 12 months as well as introducing several new models and projects currently in the pipeline.
This will significantly expand Aquila’s product offerings in a new market segment, helping it overcome industry hurdles.
“The current geopolitical climate is proving to be a challenge in achieving our goals; it is in times of hardship that
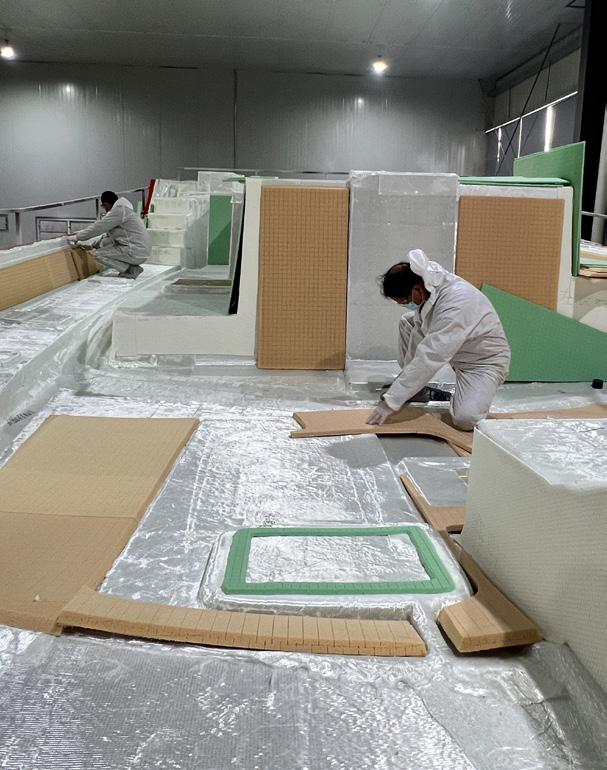
true success can be measured.
“We are entrenched in meeting our targets and will pivot as necessary to continue to drive Aquila’s success,” Raas concludes.

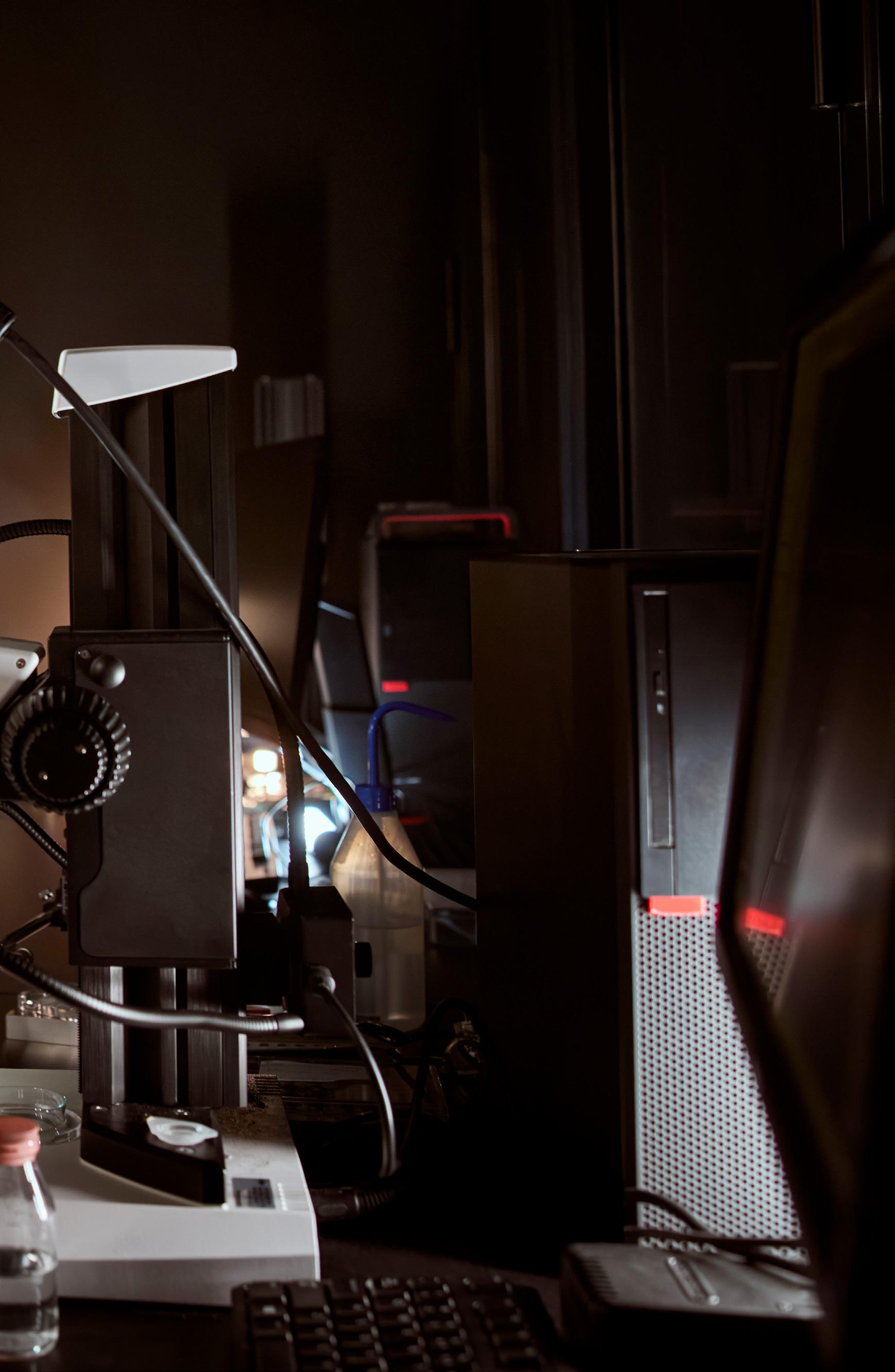
VISION CARE FOR EVERY STAGE OF LIFE
Committed to delivering the eye health needs of patients around the world, Johnson & Johnson has vision solutions for patients at every stage in their lives. Ryan Reinhardt, Vice President, Supply Chain, Johnson & Johnson, Vision tells us more about how the company collaborates, innovates, and works seamlessly together to care for patients at every stage in their eye health journey
Writer: Lily Sawyer | Project Manager: Michael Sommerfield
Fueled by innovation at the intersection of biology and technology, Johnson & Johnson (J&J) prioritizes delivering on the eye health needs of its patients around the world.
“We understand that eye health evolves over a lifetime, from contacts to cataracts,” introduces Ryan Reinhardt, Vice President, Supply Chain, Johnson & Johnson, Vision.
As such, J&J has built a unified, global organization that collaborates, innovates, and works seamlessly together to care for patients at every stage of their eye health journey.
Providing vision solutions for patients throughout their lives, the company’s portfolio is vast.
Its ACUVUE® contact lens portfolio is the most trusted by eye doctors
globally (1) and is the number one selling contact lens brand in the world (2)
Meanwhile, J&J’s refractive surgery solution, iLASIK, has been used in over 25 million patients worldwide, delivering exeptional visual quality with a patient satisfaction rate exceeding 96 percent.
Having started his career journey in engineering in Buffalo, New York, Reinhardt’s own journey into healthcare is an interesting one. His strong foundation in the industry sparked a hunger to pursue an MBA to broaden his skillset – sponsored by his company at the time.
This led to him moving abroad to lead aftermarket, spare parts, and distribution operations, which turned out to be a transformative move both
professionally and personally.
“I took this as an opportunity to not just deliver on the work I was undertaking but also enrich my life; I wanted to immerse myself in the culture and committed to learning the local language. What began as a three-year assignment evolved into a decade-long journey,” he smiles.
EVOLUTION AND GROWTH
During Reinhardt’s time working abroad, he held several leadership roles, expanding his scope beyond his initial work overseeing aftermarket, spare parts, and distribution operations.
“I led a factory before transitioning to a healthcare company, where I took on new challenges,” he shares.
While working with at the
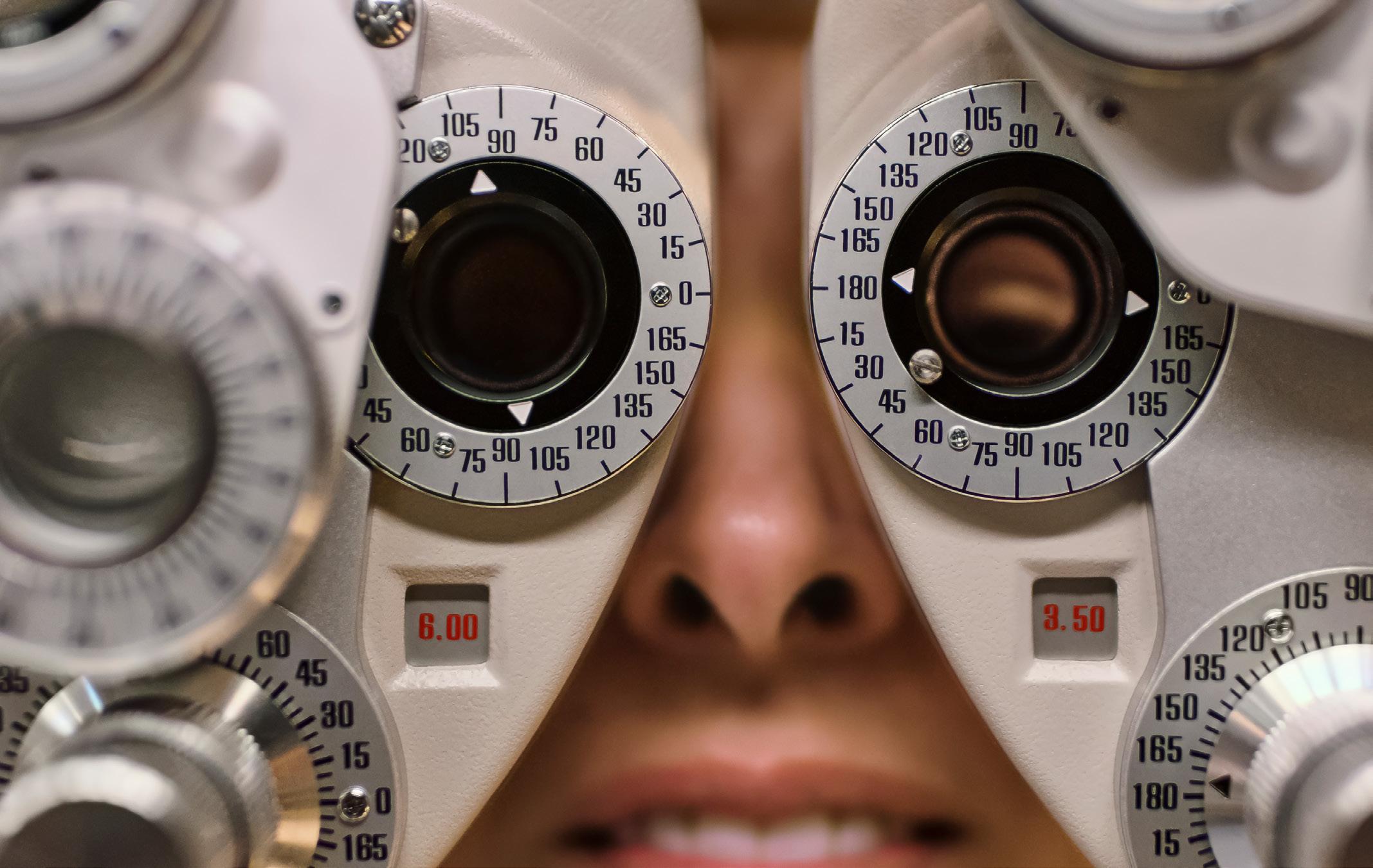
WAS IT AN INTENTIONAL MOVE WHEN YOU TOOK ON THE ROLE AT J&J TO LEAD THE VISION SUPPLY CHAIN BUSINESS?
Ryan Reinhardt, Vice President, Supply Chain, Johnson & Johnson, Vision: “I’ve always seen J&J as one of the great American companies, with a unique position in both the pharmaceutical and medical technology sectors.
“This dual presence across such critical industries is what sets J&J apart and makes it an exciting place to work. The opportunity to step into a leadership role within one of their MedTech businesses, where I could truly make a meaningful impact, was incredibly appealing.
“I saw this as a chance to not only contribute to a company with a rich legacy but also to shape my career trajectory within an organization that offers immense growth potential.
“The combination of J&J’s strong reputation, its broad reach in healthcare, and the opportunity to lead in the MedTech space were key factors that motivated me to make this move.”
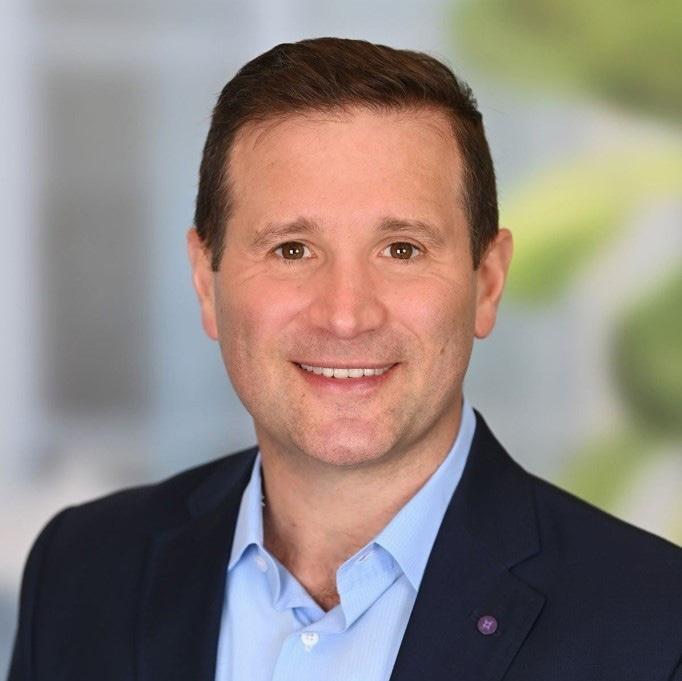
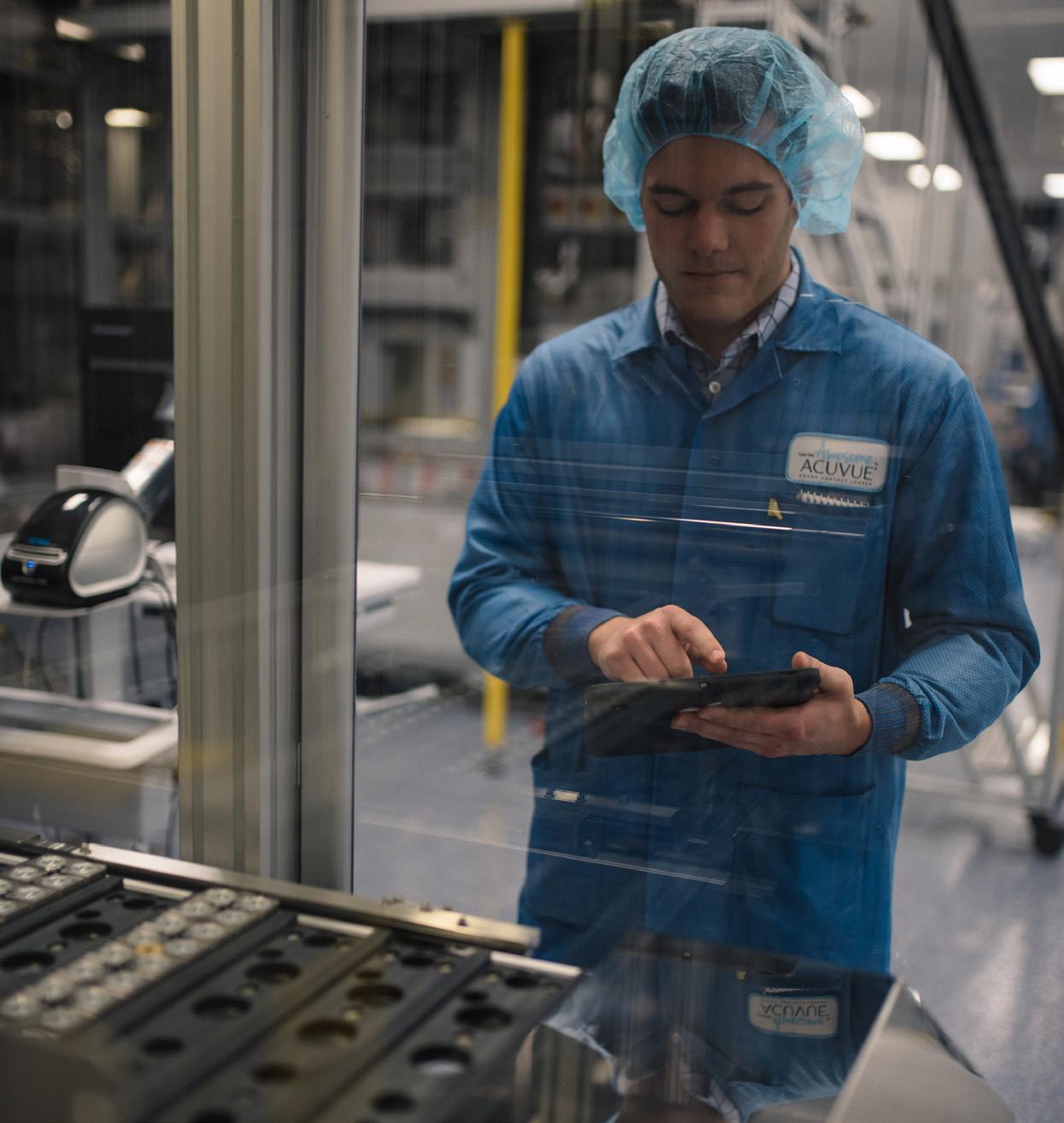
healthcare company, Reinhardt became responsible for larger sites. As such, this period of his career became defined by leading and managing factories and supply chains, providing an opportunity to glean insights into the intricacies of a global logistics operations.
After 10 years working abroad, Reinhardt had the opportunity to return to the US, assuming a new role in Seattle.
“Here, I led the end-to-end supply chain for the ultrasound business. My responsibilities continued to evolve,
and from that point on, I focused on overseeing end-to-end supply chains for different business sectors,” he explains.
Two years ago, Reinhardt assumed his role at J&J, where he now leads end-to-end supply chain operations for vision.
While his technical roots in engineering have always played an important role, Reinhardt’s focus has shifted over the years toward business leadership – particularly in the realm of managing complex supply chain functions.
“IT’S NOT EVERY DAY YOU GET TO BE PART OF A COMPANY THAT PRODUCES BILLIONS OF CONTACT LENSES A YEAR. THE SCALE IS PHENOMENAL, AND IT’S INCREDIBLY EXCITING TO BE INVOLVED IN A SUPPLY CHAIN THAT OPERATES AT SUCH HIGH VOLUMES”
–
RYAN REINHARDT, VICE PRESIDENT, SUPPLY CHAIN, JOHNSON & JOHNSON, VISION
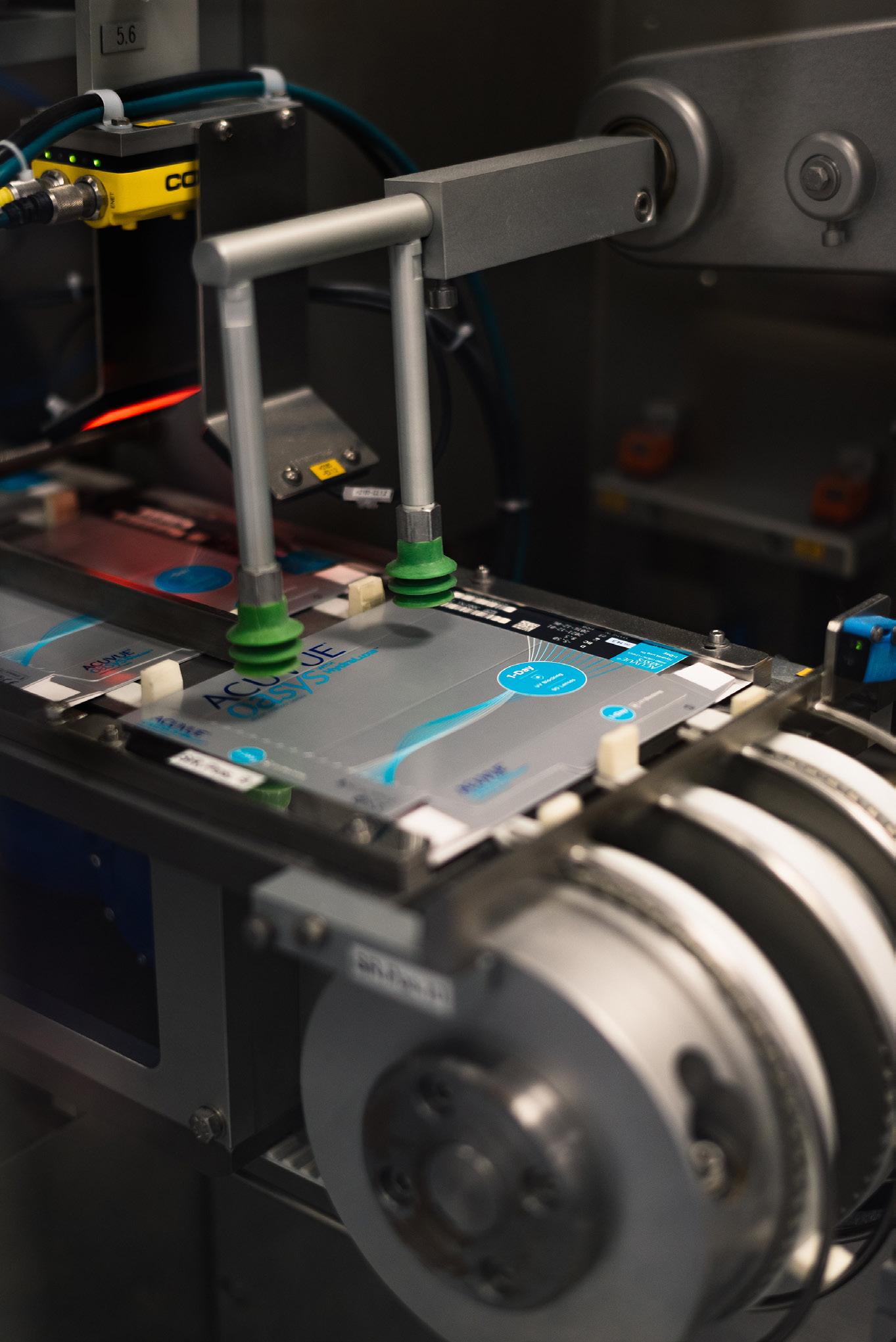
J&J’S STEPS TOWARD SUSTAINABILITY
As the company continues to advance its sustainability efforts, J&J is tackling climate change by reducing its carbon footprint and increasing the use of renewable energy across facilities.
It is also reducing waste, optimizing packaging, helping customers and patients recycle more, and protecting natural resources by finding alternative solutions to protect the environment.
J&J’s manufacturing plant in Jacksonville, Florida was awarded Leadership in Energy and Environmental Design (LEED) status, recognizing its sustainable design.
Meanwhile, the company’s intraocular lens manufacturing sites recycle wherever possible, including its product boxes, cardboard cartons, and swabs, with its Dutch manufacturing facility receiving Zero Waste to Landfill certification.
“This evolution reflects my growth from an engineer to a business leader overseeing global supply chain operations,” he prides.
DELVING DEEPER
Having always been drawn to processes, science, and math, engineering seemed the perfect way for Reinhardt to channel his passions.
“It helped me to develop strong problem-solving skills and allowed me to work in a field that matched my analytical mindset,” he observes.
However, after gaining more experience in the workforce, Reinhardt’s interests began to shift. He realized he had a growing passion for business leadership – specifically gaining an understanding of how a business operates at a larger level.
“I wanted to focus on driving outcomes that benefited the business, employees, shareholders, and ultimately its customers or patients.”
This small shift in focus led him to explore new avenues where he could merge his technical background with leadership and strategy.
Thus, Reinhardt’s decision to move into the healthcare supply chain was deliberate and thoughtful.
“Before joining the healthcare industry, I worked in the capital equipment manufacturing sector, where we sold products to healthcare companies,” he informs.
Reinhardt found this intersection of business and healthcare intriguing, and with several friends already working in the healthcare industry, the opportunity to make a noticeable difference in patients’ lives piqued his interest even further.
Today, Reinhardt also wants to be part of an industry that has a direct, positive impact on the world.
Whether improving the health of children, adults, or anyone along the healthcare continuum, the ability to make meaningful contributions to people’s well-being is a daily motivator.
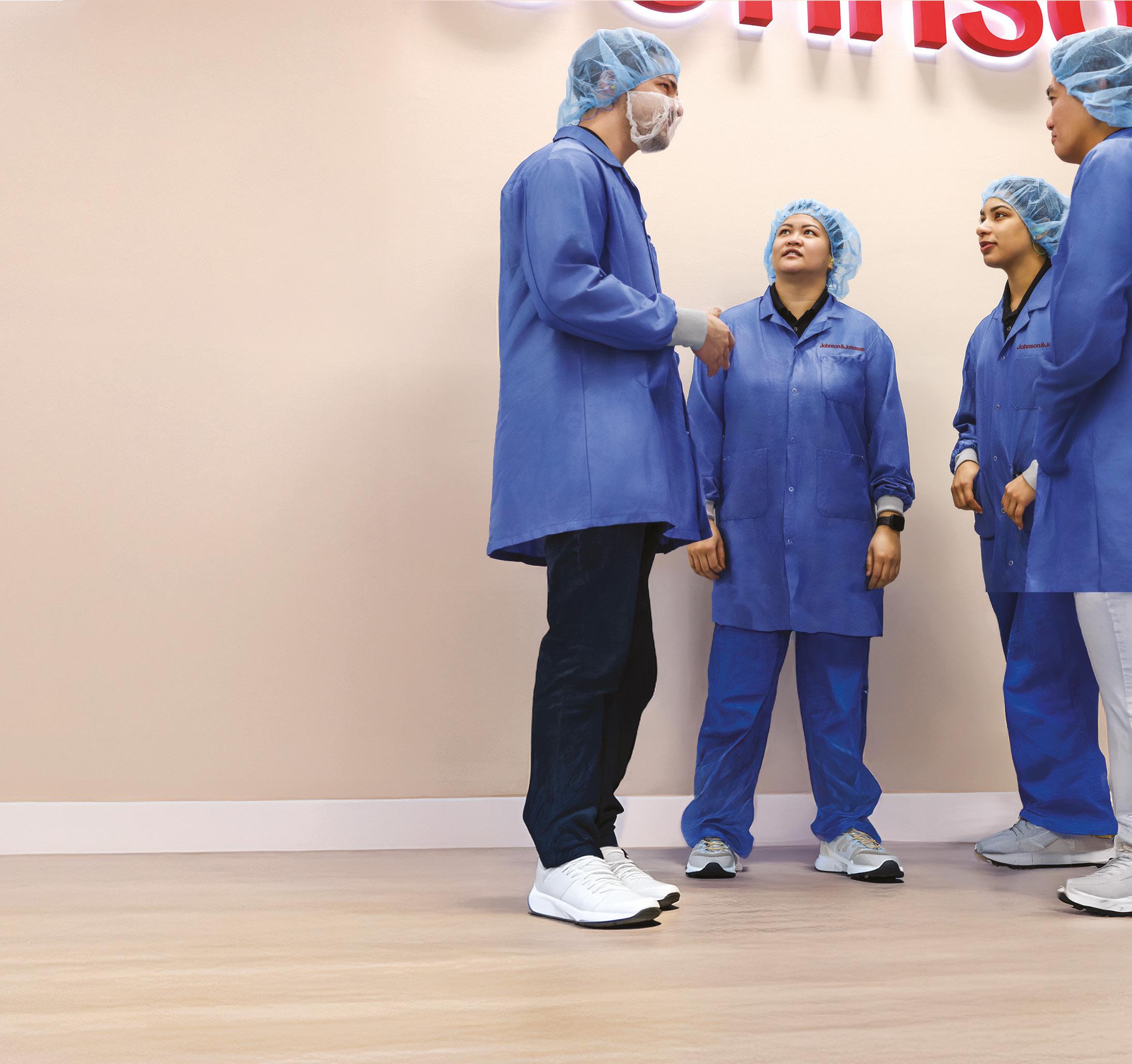
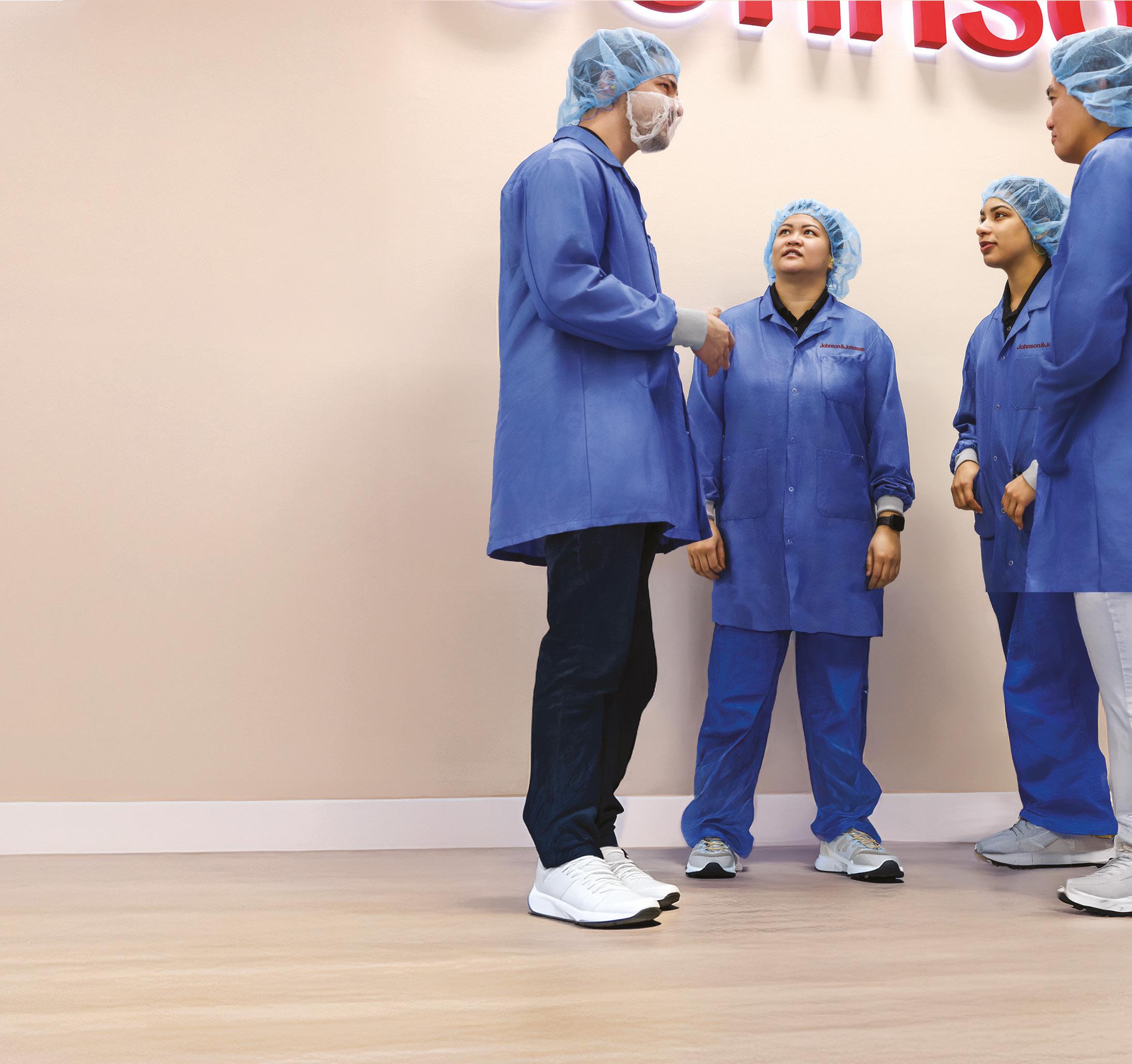
Our engineers drive innovation in eye health by turning patient insights into advanced products. Help us pave the way:
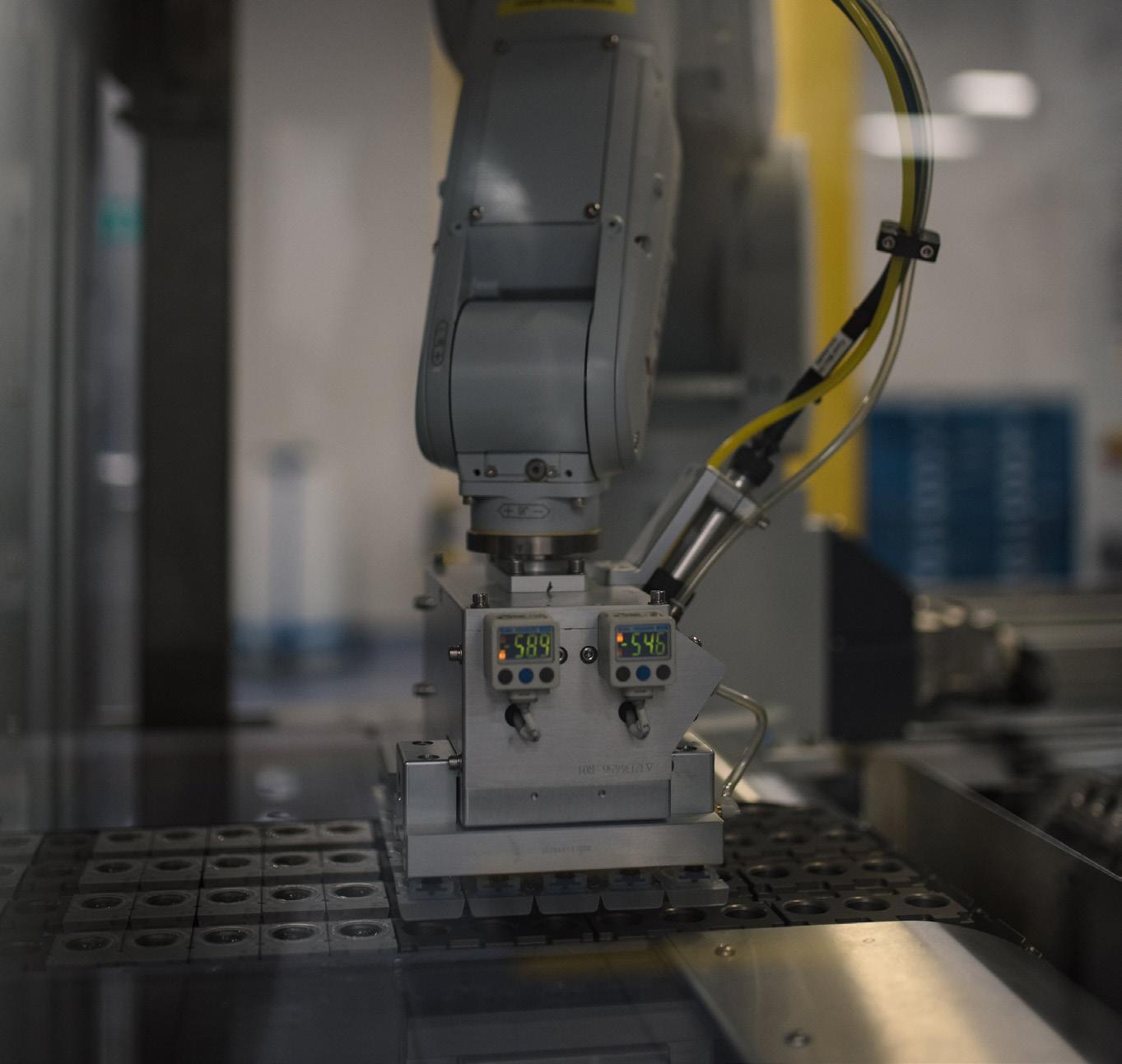
“KNOWING THAT THE DECISIONS I MAKE IN MY ROLE CAN HAVE SUCH AN IMPORTANT IMPACT MAKES IT INCREDIBLY FULFILLING, AND THAT’S WHAT ULTIMATELY DREW ME TO THIS PATH IN HEALTHCARE”
– RYAN REINHARDT, VICE PRESIDENT, SUPPLY CHAIN,
JOHNSON
& JOHNSON, VISION
“Knowing that the decisions I make in my role can have such an important impact makes it incredibly fulfilling, and that’s what ultimately drew me to this path in healthcare,” Reinhardt states.
KEY LEARNINGS FROM ACROSS THE GLOBE
Working in various roles across different regions throughout his career has provided Reinhardt with invaluable personal and professional insight.
“Each step along the way has broadened my understanding of the role that manufacturing and supply chain play within a business,” he tells us.
In the early stages of his career, Reinhardt’s focus was very much on optimizing individual factories or distribution centers, ensuring operations were running smoothly and driving the right outcomes at a micro-level.
As his career progressed, he began to see how all these roles fit into the larger picture.
Transitioning from leading a factory to overseeing end-to-end supply chains allowed him to view how these functions tied into broader business objectives.
“My thinking evolved and moved up the value chain as I assumed more responsibility and began to
IMPORTANT INFORMATION FOR CONTACT LENS WEARERS
ACUVUE® Contact Lenses are available by prescription only for vision correction. An eye care professional will determine whether contact lenses are right for you.
Although rare, serious eye problems can develop while wearing contact lenses. To help avoid these problems, follow the wear and replacement schedule and the lens care instructions provided by your eye doctor.
Do not wear contact lenses if you have an eye infection, or experience eye discomfort, excessive tearing, vision changes, redness or other eye problems. If one of these conditions occurs, remove the lens and contact your eye doctor immediately.
For more information on proper wear, care and safety, talk to your eye care professional and ask for a Patient Instruction Guide, call 1-800-843-2020, or visit www.acuvue.com
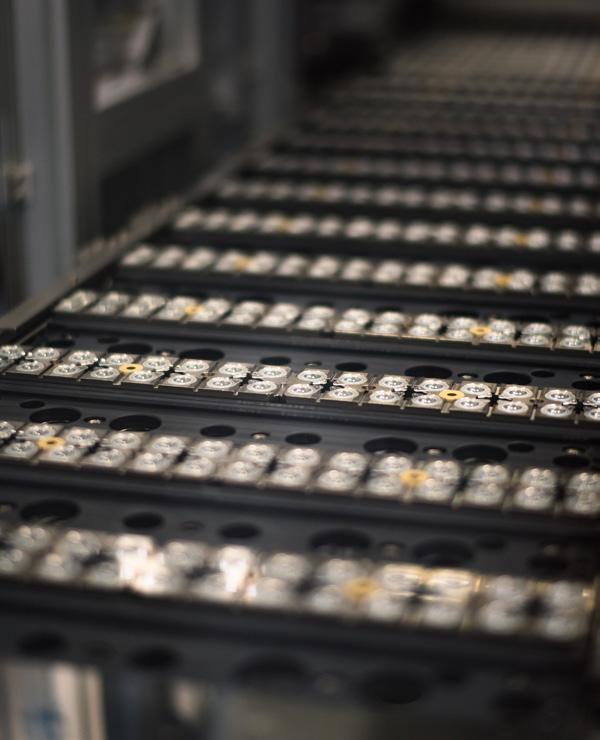
understand the deeper connections between the supply chain and overall business success,” he recalls.
One of the most important things Reinhardt learned from living and working abroad was the value of understanding and connecting with local culture.
“I spent a lot of time immersing myself by learning the language, forming friendships with local people, and understanding what motivated them,” he passions.
This led to a deep belief that relationship building is key to achieving desired outcomes and that these connections often transcend geographic boundaries.
Being open, curious, humble, and willing to learn from different cultures was essential to Reinhardt navigating his time working and living in different regions and leading teams successfully across continents.
When he returned to the US, he was able to apply this broader worldview, approaching problems and devising strategies in new ways.
“This cross-cultural exposure expanded my horizons, allowing me to think more creatively and strategically when facing challenges,” he informs.
Ultimately, it was these experiences that shaped the way Reinhardt approaches leadership and problemsolving today.
STANDING OUT FROM THE COMPETITION
With its approach to bridging the gap between two very different industries – fast-moving consumer goods (FMCGs) and medical devices – working in vision presented an opportunity to tackle a unique set supply chain operations.
“It’s not every day you get to be part of a company that produces over five billion medical devices a year. The scale is phenomenal, and it’s incredibly exciting to be involved in a supply chain that operates at such
high volumes,” he excites.
J&J’s process starts with getting products off the production line, directly into its warehouses, and then swiftly to customers around the world.
On the other end of the spectrum, the equipment side of the business involves a much more assemblydriven process and is focused on electromechanical assembly.
This is the typical medical device approach when dealing with lowvolume, high-complexity products sold to the likes of surgeons and hospitals.
Two distinct models – one focused on high-volume FMCGs and the other on more specialized medical devices – demand very different supply chain solutions.
“We have these models existing alongside each other within Johnson & Johnson Vision. Being able to manage and optimize both in one supply chain is truly special,” he says.
J&J also has a high level of automation on site which, in Reinhardt’s opinion, is world-class.
AN ADVANTAGEOUS MODEL
With significant advantages afforded by J&J’s end-to-end supply chain network model, especially in terms of alignment with the organization, there’s no ambiguity when it comes to its end goal.
“We all know what we’re working toward, and this clarity enables us to develop strategies that drive business outcomes rather than just functional ones,” Reinhardt confirms.
Everyone at J&J works together to achieve these goals, and this unified approach allows for quicker, more effective decision-making.
Because the whole company is aligned in terms of its understanding of business objectives, it can make decisions more closely linked to customer needs.
“Ultimately, this leads to better outcomes for the eye care professionals we work with, as well
as the patients who rely on our products,” he outlines.
One of the key benefits of J&J’s model is that it helps executives understand and respond to customers better.
“We can link our decision-making directly to customer needs, which strengthens our ability to deliver the right products at the right time.”
However, with such a contained business model, Reinhardt notes how important it is to be mindful of what’s happening outside the immediate vicinity.
“We have to make sure we’re not overlooking best practices or innovations happening in other parts of J&J,” he explains.
To mitigate this, it focuses on creating centers of excellence through which J&J teams can collaborate with other parts of the company to share insights and learn from each other.
“This approach allows us to bring best practices from across the organization into our supply chain processes, ensuring we’re always striving for continuous improvement while still maintaining full ownership of our mission to deliver the best possible outcomes for customers, patients, and the business,” Reinhardt confidently concludes.
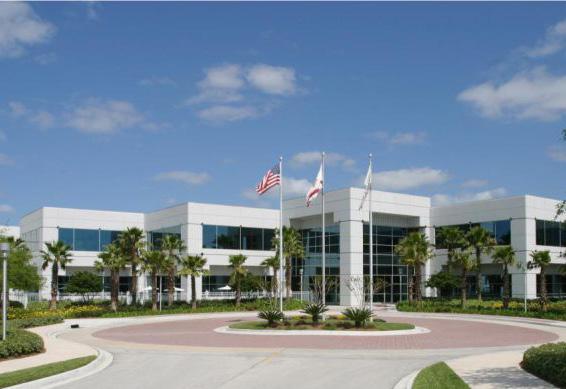
Tel: (904) 443-1000 sa-visus-viseyesite@its.jnj.com www.clearvisionforyou.com
ELEVATING THE DOMESTIC EQUIPMENT EXPERIENCE
As the home appliances sector in South Africa evolves to meet modern demands, Defy Appliances stands at the forefront of innovation and sustainability. Hugo Coetzer, Regional Director of Manufacturing and Technology, discusses how the company spearheads efforts to enhance everyday living
Writer: Rachel Carr | Project Manager: Josh Whiteside
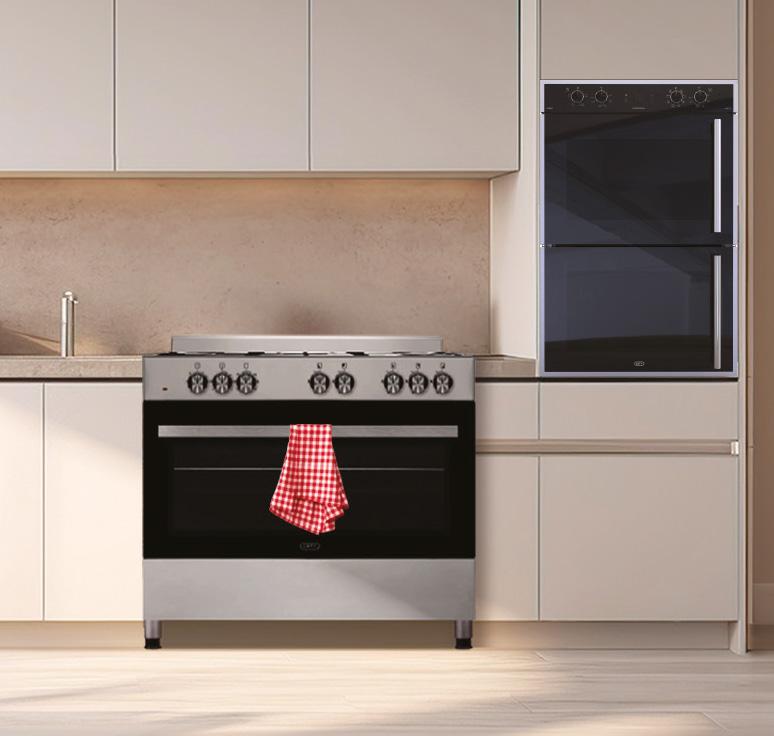
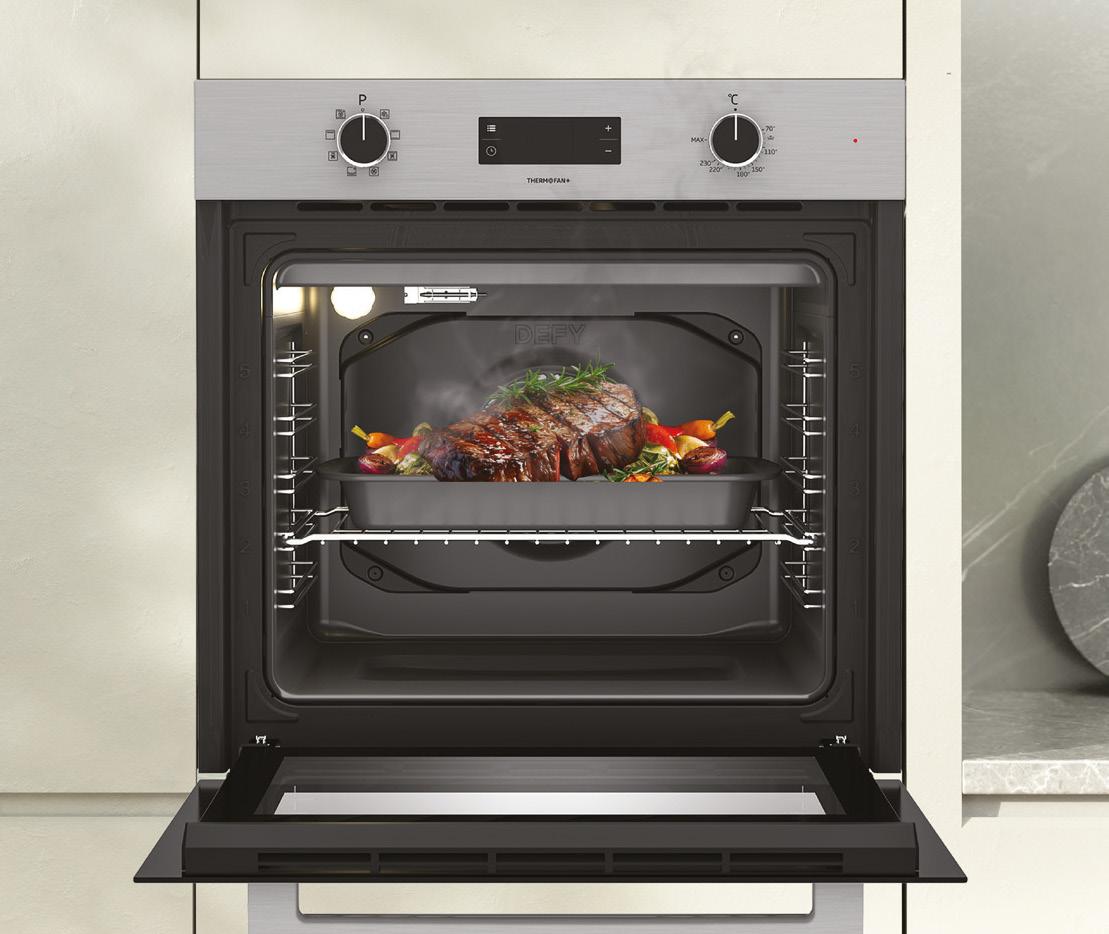
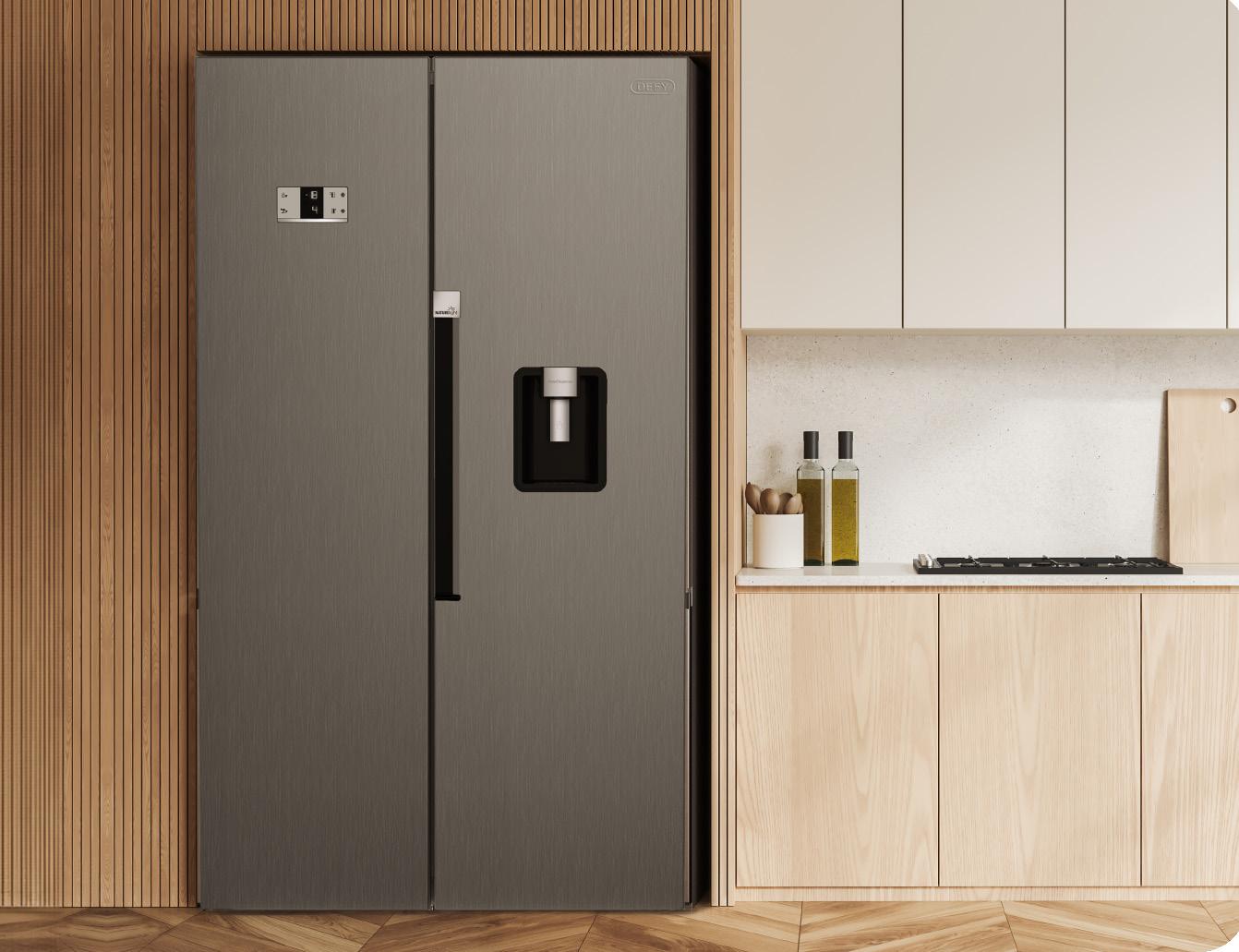
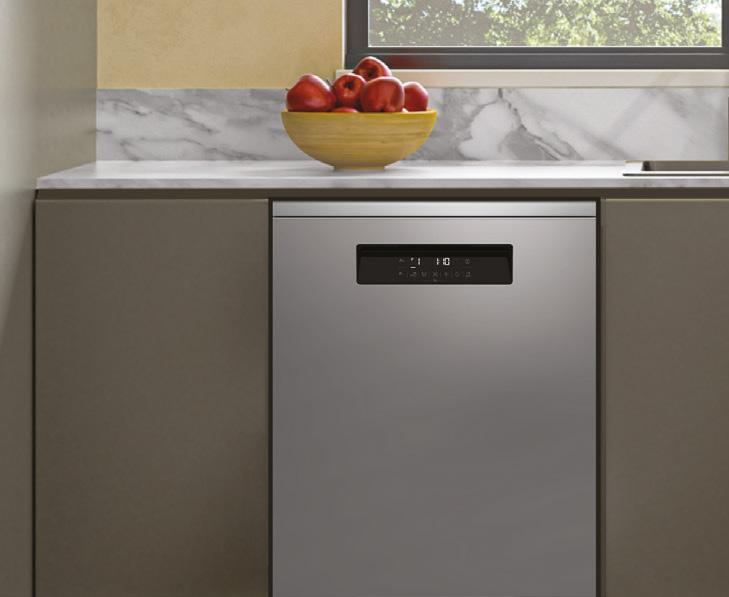
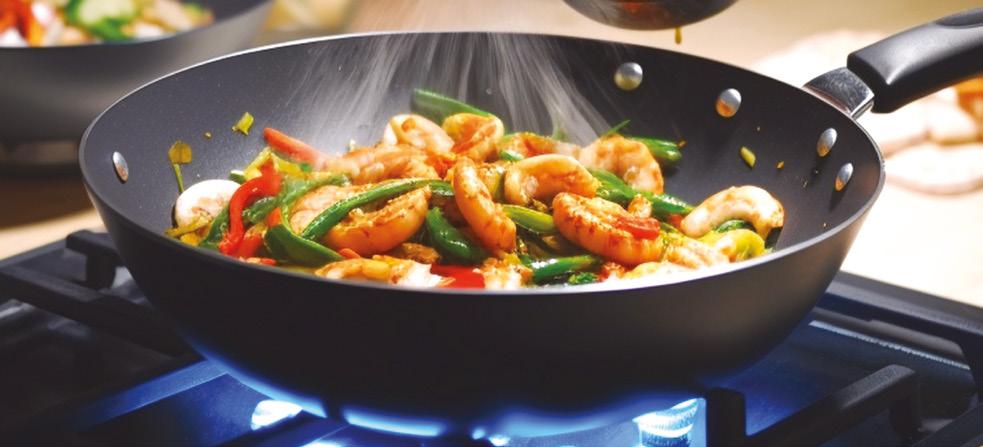
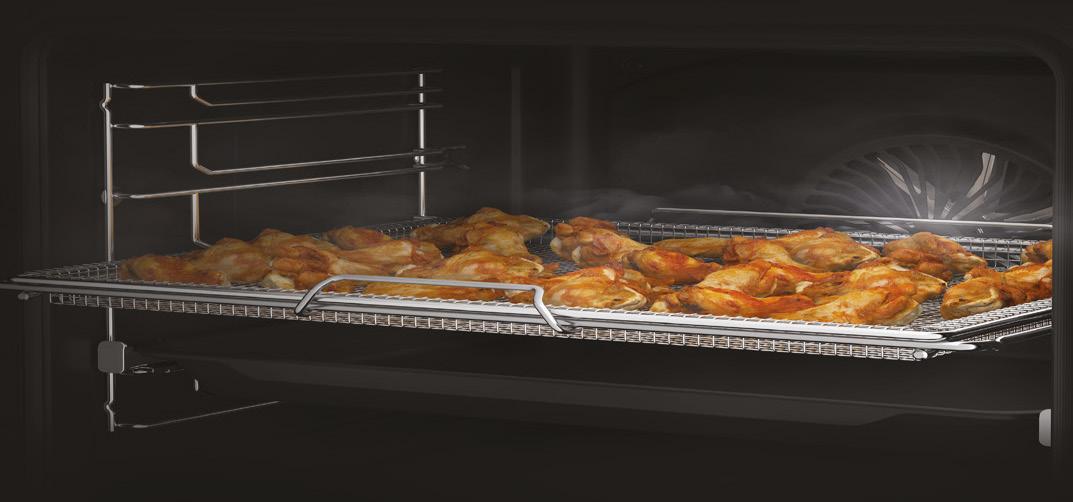
The history of domestic appliance manufacturing in South Africa (SA) reflects both the technological advancements of the time and the evolving needs of households.
In the early 20th century, the local manufacturing sector was relatively nascent, with few companies engaged in the production of household appliances.
However, as electrification spread across the country, the demand for electric appliances increased significantly and manufacturers began to emerge, focusing on essential items such as refrigerators, stoves, and washing machines.
Towards the end of the 1900s, SA’s appliance manufacturing industry featured a combination of established local brands and international companies. The sector evolved as manufacturers embraced advanced technology and energy-efficient designs to meet the needs of ecoconscious consumers.
Recently, there has been a focus on the rise of sustainability and smart technology, with products that integrate into modern smart home systems. The arrival of multinational corporations has also increased competition, driving local companies to innovate and improve production standards.
Standing out as a key player in the industry is Defy Appliances (Defy), a prominent manufacturer of domestic equipment in SA. Established in 1905 as a producer of hollow building blocks and cast iron parts, the company has a long history and is well-known for producing a range of products, including refrigerators, washing machines, stoves, and other kitchen appliances, focusing on innovation and quality.
Aiming to provide reliable and efficient solutions for everyday household needs, Defy has become a trusted brand amongst consumers in the region since it was acquired
CAN YOU ELABORATE ON DEFY’S PARTNERSHIPS WITH UNIVERSITIES FOR TRAINING AND GRADUATE PROGRAMMES? HOW DO THESE CONTRIBUTE TO THE WORKFORCE?
Hugo Coetzer, Regional Director of Manufacturing and Technology:
“We’ve built strong partnerships with several tertiary institutes across SA to create a pipeline of future-ready talent through tailored training and graduate programmes.
“These collaborations aren’t just about recruitment – they’re co-designed initiatives that bridge academic theory with real-world application. Together, we shape curricula, offer hands-on industrial exposure, and host joint research or innovation projects that align with our future skills roadmap.
“For example, we host annual career fairs, offer student vacation programmes such as Fresh Start and WE-inTech, and engage in conversations with tertiary institutes about Industry 4.0 skills – whether that’s manufacturing, sustainability, or automation. These efforts not only help graduates transition smoothly into the workforce but also ensure our teams remain agile and innovative.
“Ultimately, this investment strengthens our talent pipeline, enriches our teams with fresh perspectives, and contributes to a more resilient, future-ready workforce.”
by Arçelik, now rebranded as Beko Global, in 2011.
“Thanks to this investment, which has gone into three factories and products, we have launched new pioneering innovations such as the Solar Off-Grid refrigerator, allowing us to solidify our leadership in the domestic appliances industry,” opens Hugo Coetzer, Regional Director of Manufacturing and Technology.
“We operate factories located in Jacobs, Durban and Ezakheni, Ladysmith, and employ more than 2,600 permanent staff members with a presence in 13 countries, where we export and sell our products.”
AN EVOLVING INDUSTRY
As the continent with the greatest potential for exponential growth, the manufacturing sector in Africa is currently experiencing significant transformation and substantial progress as various countries have invested in the industry in recent years.
“Our holding company has also opened a manufacturing plant in Egypt, which shows that Africa is currently a market where people can invest, and existing businesses will continue to invest further to see more growth,” Coetzer confidently states.
Many countries across the continent are currently witnessing economic developments which will boost demand for goods, especially household appliances. Furthermore, like elsewhere in the world, there is a need to adapt to new technologies such as automation and robotics.
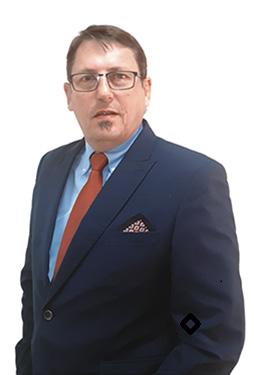
“Remember that no one has closed borders anymore, and we all compete with other African nations that had a head start in automation,” affirms Coetzer.
The continent also has a large
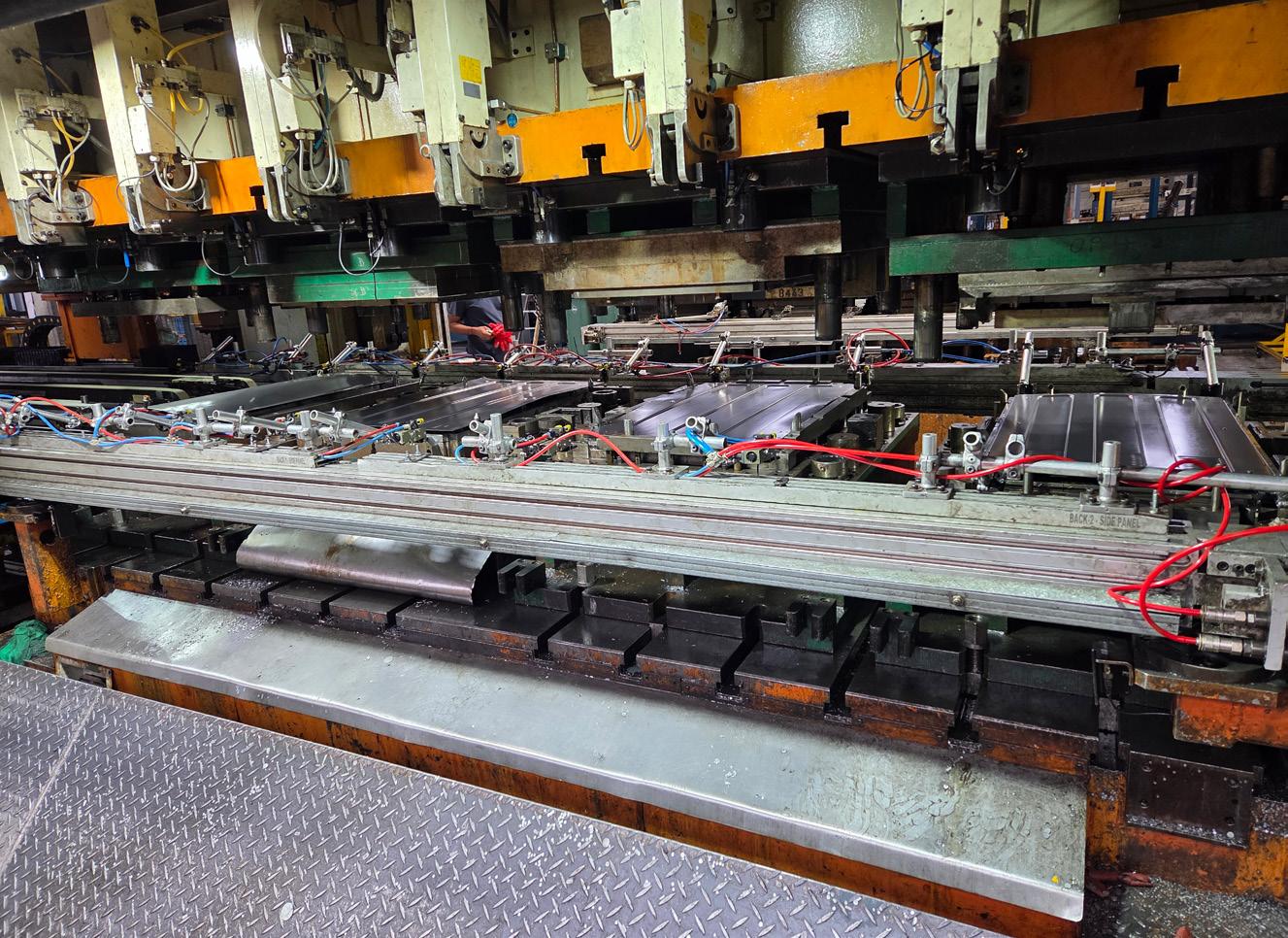
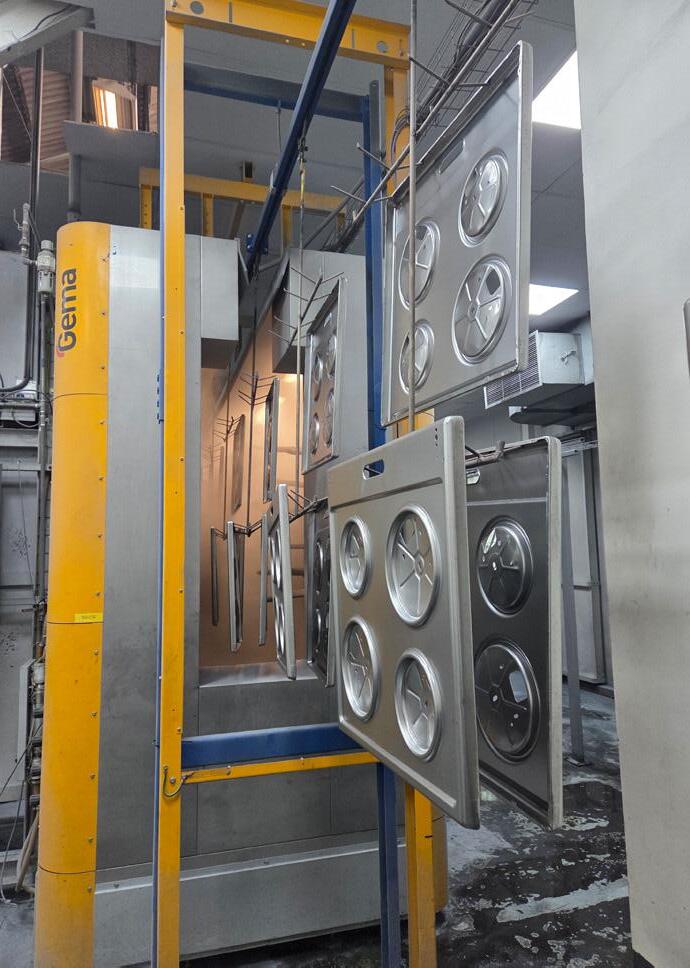
and youthful population, which presents significant opportunities for a dynamic workforce. As this demographic offers a wealth of fresh ideas and energy, particularly in conjunction with the rapidly evolving manufacturing industry, Coetzer is optimistic about the future.
“Given the constant change in consumer trends and needs, the appliances industry is always an exciting space to work in.
“Having an accredited lab on site
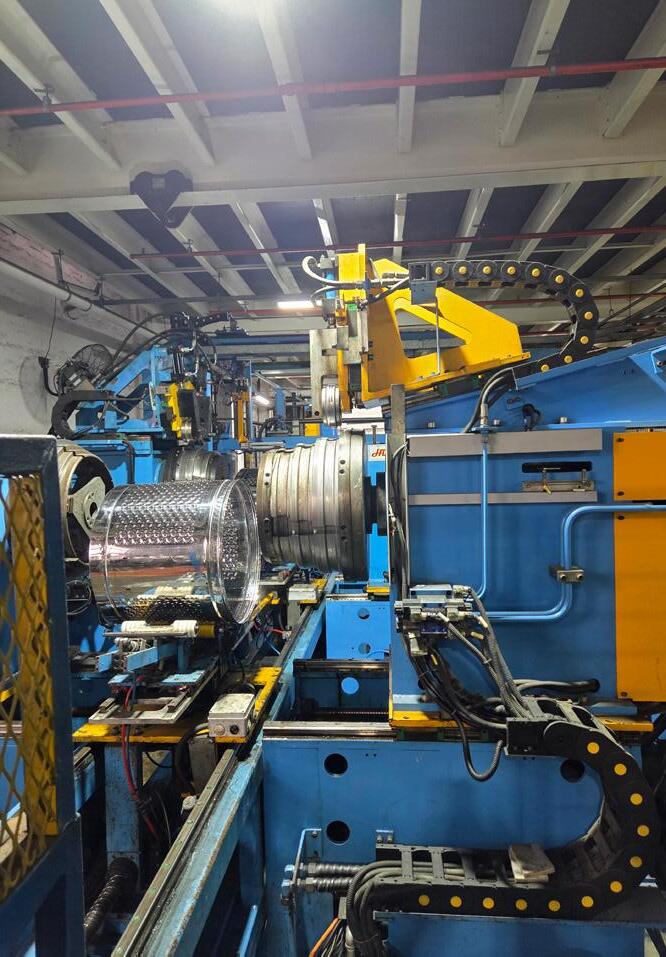
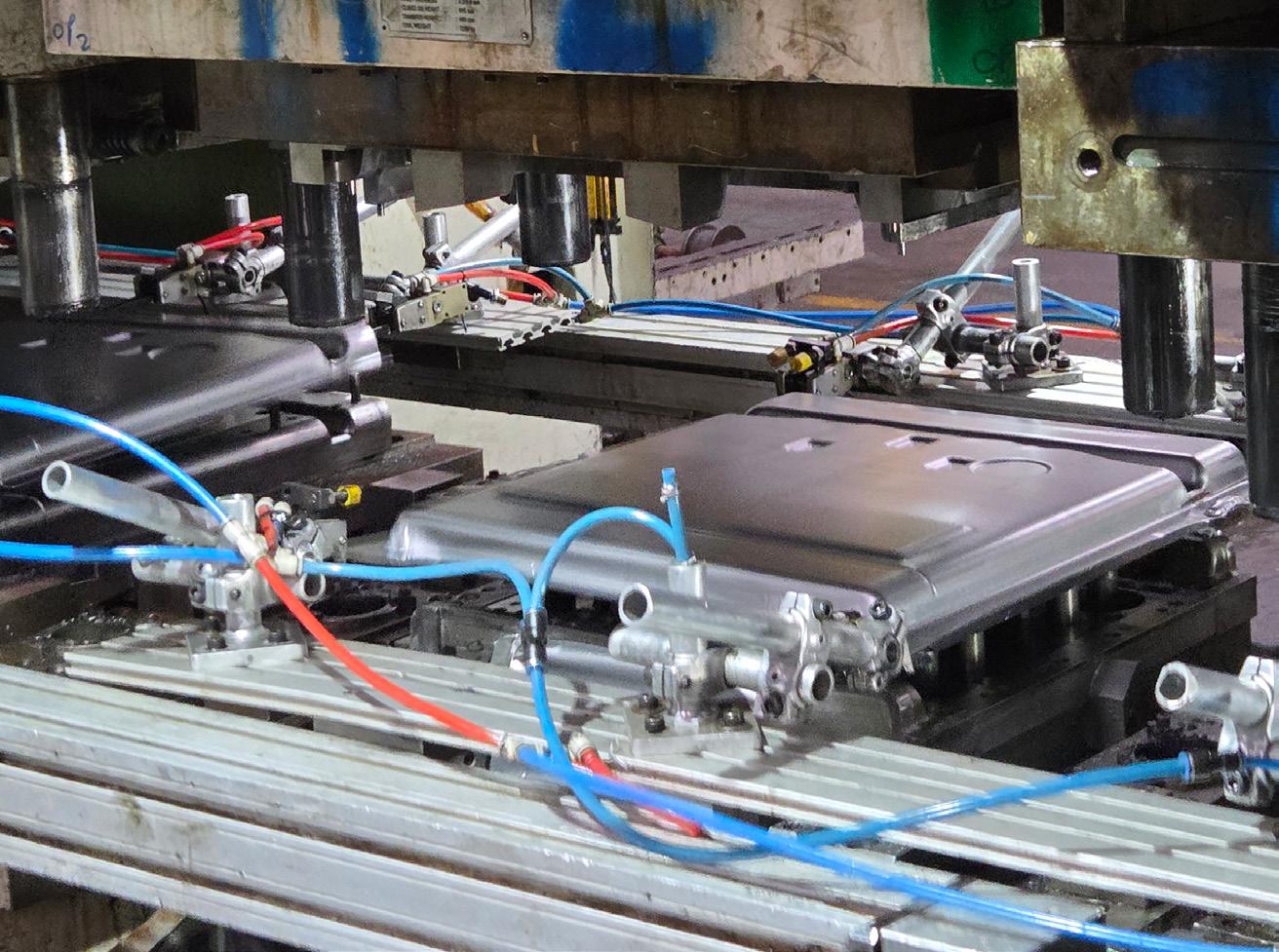
allows us to develop new products that are not only improving people’s lives but also ensure we lead in energy efficiency and conform to our group’s sustainability targets,” he continues.
Coetzer opines that artificial intelligence (AI) is the future and, when implemented correctly, will not only reduce man-hours but also ensure quality improvements, especially when paired with robotics.
“Given our products and processes, there are many
opportunities to automate and use AI, so we are actively adapting it into manufacturing. Companies that don’t follow suit will not survive the next five to seven years.
“The challenge of a poor exchange rate means the local currency has less purchasing power when the technology you are after comes from countries with stronger currencies. So, it makes the financial calculations on payback much more difficult to justify.”
Maintaining these systems, obtaining spare parts, and receiving technical support can be difficult, whilst the continuous emigration of skilled professionals to developed countries results in a significant brain drain in Africa.
“However, this situation compels us to invest more in our own people and address these challenges.
A DEFIANT HISTORY OF EXCELLENCE
1905 – Defy was founded in Durban by John Skinner and Sir Benjamin Greenacre and originally named Hollow Block Syndicate.
1922 – Coal stove manufacturing commenced.
1955 – SA’s first gas stove was manufactured and branded as Defy.
1988 – Produced the first microwave oven at the Jacobs site, becoming the only company to do so in SA.
2007 – The company was acquired by Franke Holding AG.
2011 – Turkish company Arçelik, part of the Koç Group, acquired Defy.
2015 – The company celebrates 110 years in existence.
2019 – Defy opens the top loader plant in Jacobs.
PRESENT DAY – After pioneering the SA landscape with the firstever electric stove, winning the company awards for innovation and technology, Defy has evolved into the leading appliance brand with 80 percent of its product range sold in Africa and at least one dealer in each of the 34 subSaharan countries.
Unfortunately, developing these technicians is not a quick process; it takes time to equip them to support the business effectively,” Coetzer elaborates.
DYNAMIC DEVELOPMENT
As Defy’s parent company, Beko Global has manufacturing facilities in Africa, Turkey, Romania, Russia, Thailand, India, Pakistan, Egypt, and Bangladesh, creating a collaborative environment where innovation is fostered and shared amongst all.
“Our various internal R&D facilities help us to foster continuous learning and have a pool of mentors that shape the future of this company across the globe. These various departments working together also fosters a diverse perspective and innovative solutions,” Coetzer impassions.
Indeed, Defy offers a dynamic
space that cultivates and encourages creativity using brainstorming, hackathons, and innovation labs, with collaboration being the key.
“The recent launch of our solar fridge shows our dynamic approach leads to a tangible result.”
Despite the company’s positive outlook, several challenges remain across Africa, including inadequate infrastructure, limited access to financing, and a shortage of foreign exchange in many countries. Additionally, there is often a lack of political will to support local manufacturing and recognise its benefits to reduce unemployment in the country.
“Addressing all relevant issues is critical for our sustainability and growth. Overall, however, I would say that manufacturing in Africa is a dynamic space full of opportunities for innovation,” Coetzer acknowledges.
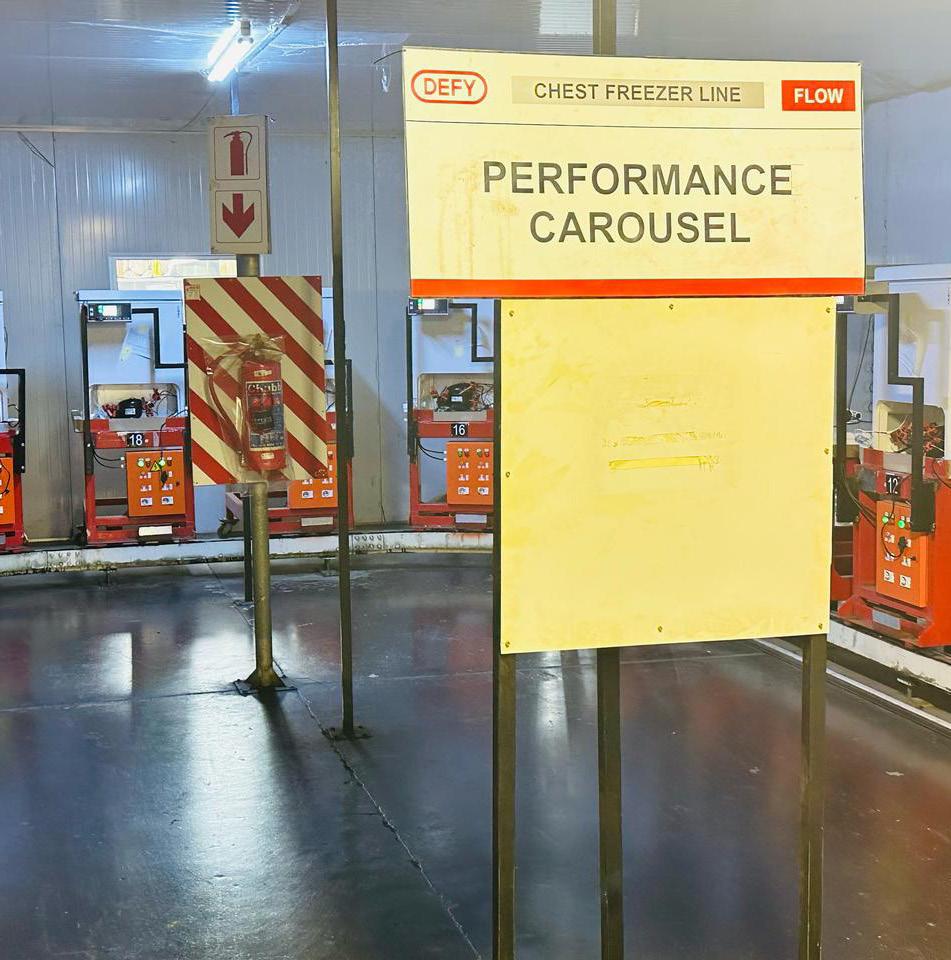
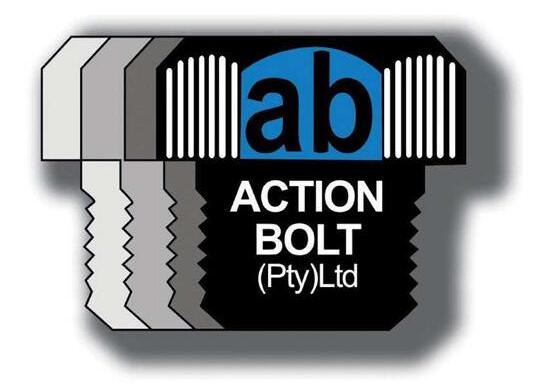
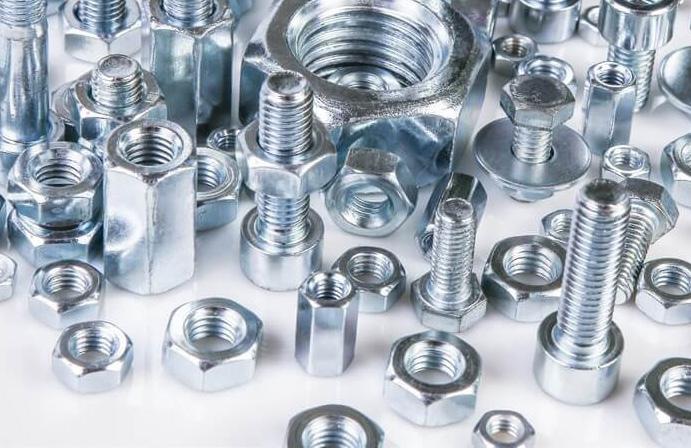
C-PARTS MANAGEMENT - WE SELL SECURITY!
Wurth Industry, Action Bolt’s Holding company, presents itself to industry customers as a world class partner in C-Parts Management with a complete range of over 420,000 items. We offer customized supply concepts for handling your requirements in manufacturing, maintenance and servicing primarily in the fields of:
• All Categories of Fastener and assembly techniques
DIN/ISO and standard parts
• Manufactured according to technical drawing specifications
• Automotive engineering supply and component supplies
• All forms of Mechanical fitting components
• Rivet Technology
Action Bolts C-Parts-Management System is a process management concept for:
• Procuring and Stock Control of the complete range of C-Category Parts.
• Creating customer-individual supply and service concepts.
Bringing significant and quantifiable savings to our customers
Objectives
• Cost Optimization Supplier Reduction
• Standardization Stock Reduction
• Allowing more time to focus on A-Category procurement activities
• Lean processes Benefits
Lower Capital commitment by inventory reduction
• Maximise process security and protection of supply chain management
• No tracing of goods or deadline monitoring
• Our inventory management system tracks stock levels, automates orders, and integrates with systems to maintain real-time accuracy.
Process simplification
Action Bolt is now trading as “Würth Industry South Africa (Pty) Ltd”, as part of our continued integration with the Würth Group.
We’re proud to be aligning fully with the global Würth Industry network.
• Same team
• Same service
• Stronger brand
• Stronger global alignment
We’re embracing innovation and global best practices to serve you better.
Expect smarter solutions, seamless service, and world-class excellence— with the same trusted team.
New name. Bold future. Same commitment to excellence.
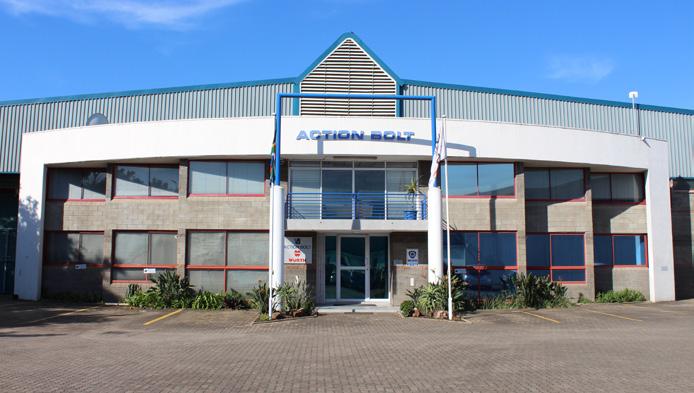

Since the acquisition of Defy in 2011, nearly ZAR2 billion has been invested in the company, with an additional commitment of ZAR500 million over the next five years. A significant portion of these investments has gone into manufacturing facilities and new product development.
“Our refrigeration factory has production lines equipped with the latest technology, matching that of our other global factories. Additionally, our cooking and laundry factory has received upgrades, bringing our equipment and technology in line with European standards,” he notes.
“These investments serve not only to modernise our factories but also reduce our environmental impact, addressing both our processes and the energy efficiency of our appliances.”
Investing is crucial for Defy’s future, and these enhancements will enable the company to withstand
“OUR VARIOUS INTERNAL R&D FACILITIES HELP US TO FOSTER CONTINUOUS LEARNING AND HAVE A POOL OF MENTORS THAT SHAPE THE FUTURE OF THIS COMPANY ACROSS THE GLOBE”
– HUGO COETZER, REGIONAL DIRECTOR OF MANUFACTURING AND TECHNOLOGY, DEFY APPLIANCES
the competition faced from imports and help mitigate the environmental effects of its products.
“Our strategic investments not only position us favourably in the market but also reinforce our commitment to sustainability, ensuring long-term success in a highly competitive landscape,” summarises Coetzer.
TRANSFORMING ENERGY ACCESS IN AFRICA
The new Defy Solar Off-Grid refrigerator marks the beginning of an important phase for the
company, reinforcing its position as an innovative market leader dedicated to sustainable development and social impact.
By harnessing solar energy, this cutting-edge appliance addresses the critical energy challenges faced in SA and across the continent, where limited or unreliable electricity access hinders food preservation and the safe storage of essential supplies.
“The Smart Control Box, which serves as the product’s brain, features USB ports that allow for phone charging or powering lights, providing
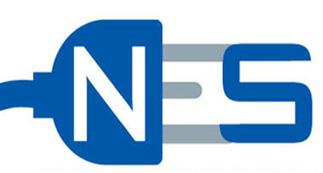
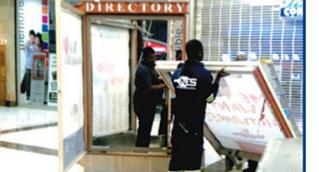
NES Electrical Services cc is a construction and maintenance services enterprise. Our company started and is based on passion, drive and an everlasting effort to strive for being the best. We boast offices in KZN, Gauteng and the Western Cape thus allowing us to have a national foot print. Each branch is utilised to send a wave throughout the industry.
We are a 100% black Owned Company that was developed in 1992, which started as purely a maintenance company but we realized that there was a demand for other specialized service such as:
• Hazardous Areas Installations
• Temporary Installations
• New Installations
• Maintenance of existing installations
• Transformer & Switchgear Installations
• Transformer & Switchgear Maintenance
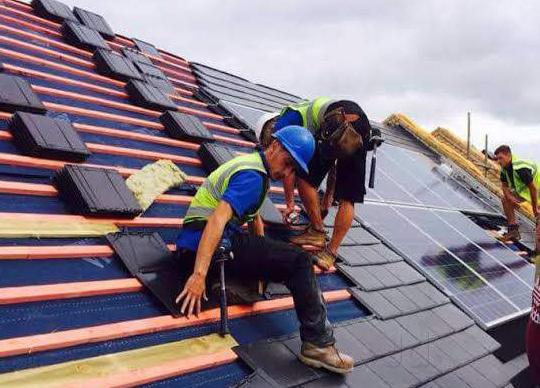
Compliance
and Certification
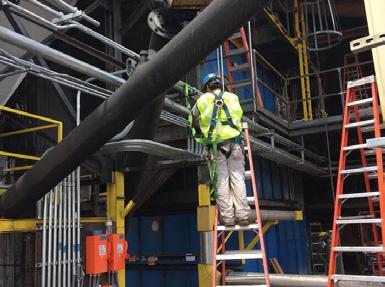
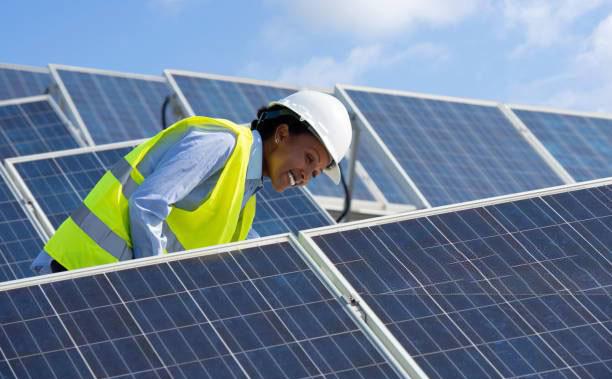
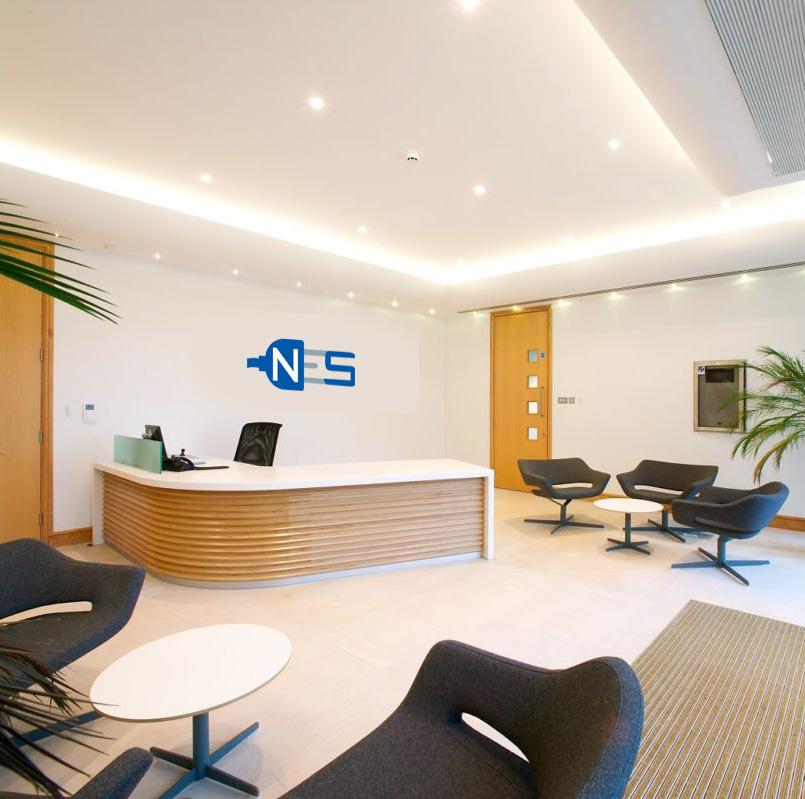
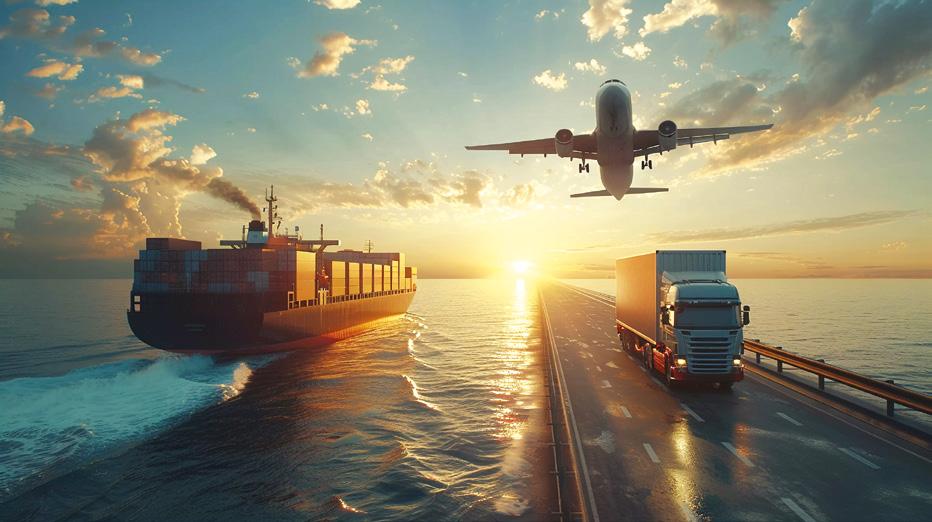
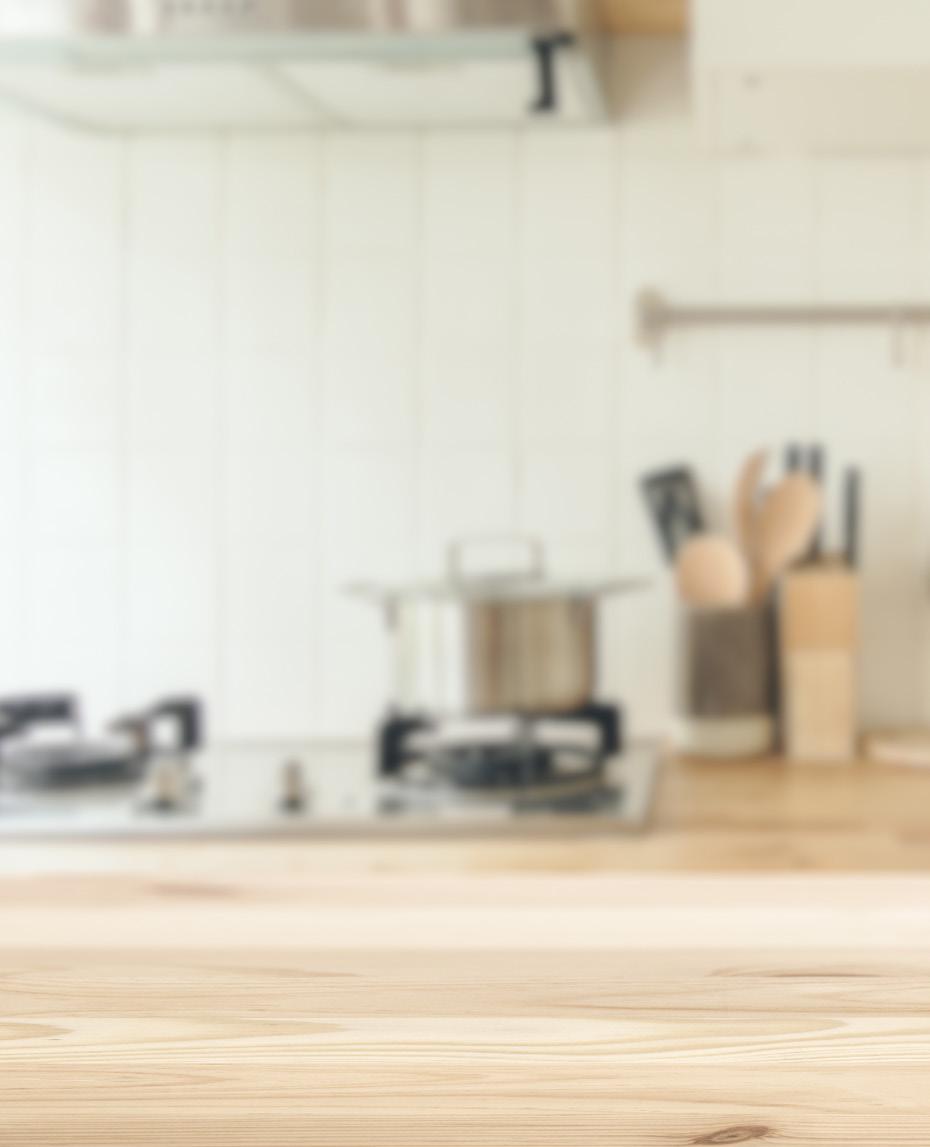
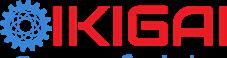
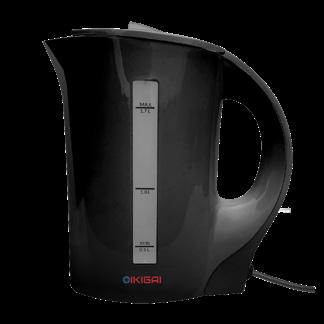
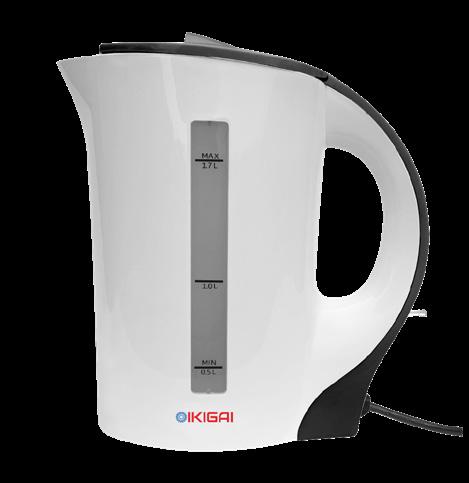
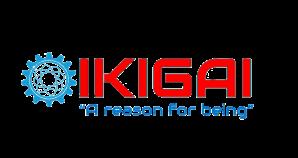
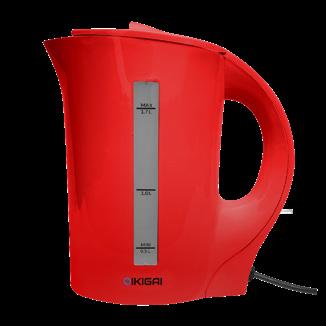
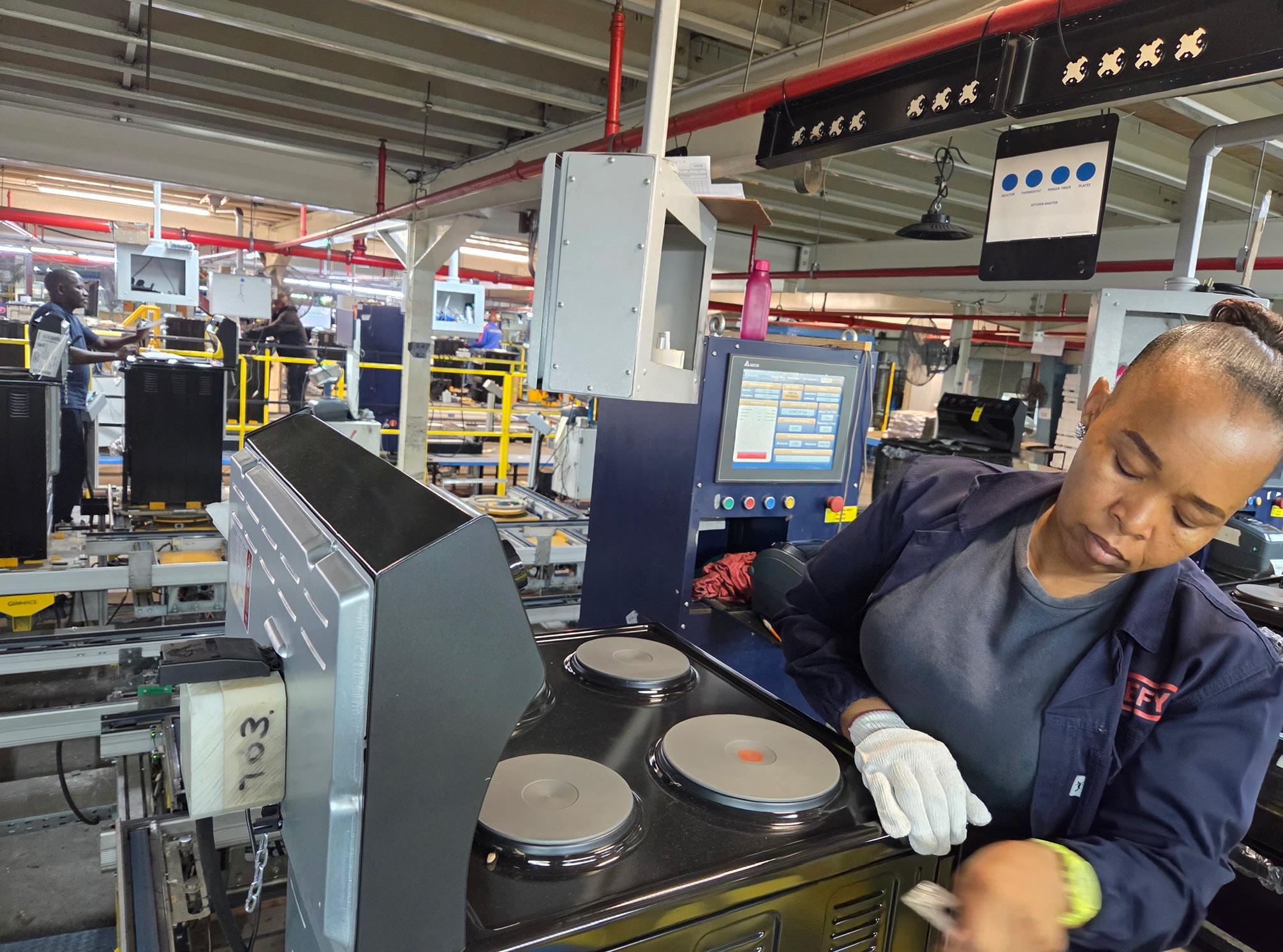
“HAVING AN ACCREDITED LAB ON SITE ALLOWS US TO DEVELOP NEW PRODUCTS THAT ARE NOT ONLY IMPROVING PEOPLE’S LIVES BUT ALSO ENSURE WE LEAD IN ENERGY EFFICIENCY AND CONFORM TO OUR GROUP’S SUSTAINABILITY TARGETS”
– HUGO COETZER, REGIONAL DIRECTOR OF MANUFACTURING AND TECHNOLOGY, DEFY APPLIANCES
added flexibility for users. When fully charged, the product can operate for up to three days during periods of low sunlight or no sun,” explains Coetzer.
“Additionally, the refrigerator is equipped with phase change material, an advanced technology which helps maintain its temperature for extended periods. As climate change poses challenges to traditional energy systems and infrastructure, solutions like our Solar Off-Grid refrigerator offer a resilient and eco-friendly
alternative that supports both environmental goals and human development.”
Defy is also developing an off-grid cooker aimed at providing a transformative solution for communities lacking stable access to electricity or clean cooking energy. Designed to function independently from electricity, it seeks to provide a safe, affordable, and sustainable option.
“Amongst its key benefits, the offgrid cooker will significantly reduce
household air pollution, lower the risk of fires, and eliminate fuel costs over time. It also promotes sustainable living by decreasing deforestation and carbon emissions associated with traditional cooking fuels.
“Once completed, this innovative appliance will empower households with a cleaner, safer, and more efficient cooking method, enhancing everyday life whilst contributing to long-term environmental and economic sustainability,” he urges.
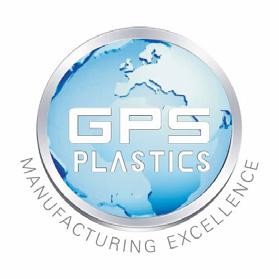
Industries we specialise in are:
• Small Appliances
• Houseware
• Engineering
• Medical
• Hardware
• Forestry
• Mining
• Farming
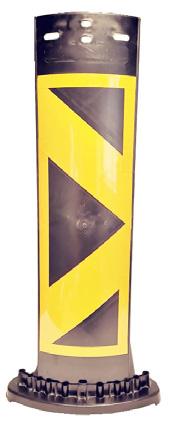
MANUFACTURING AT ITS BEST!
Specialists in plastic injection moulding, we have a team of experts focused on creating and manufacturing end-to-end solutions that help businesses to innovate and create maximum addition for its customers.
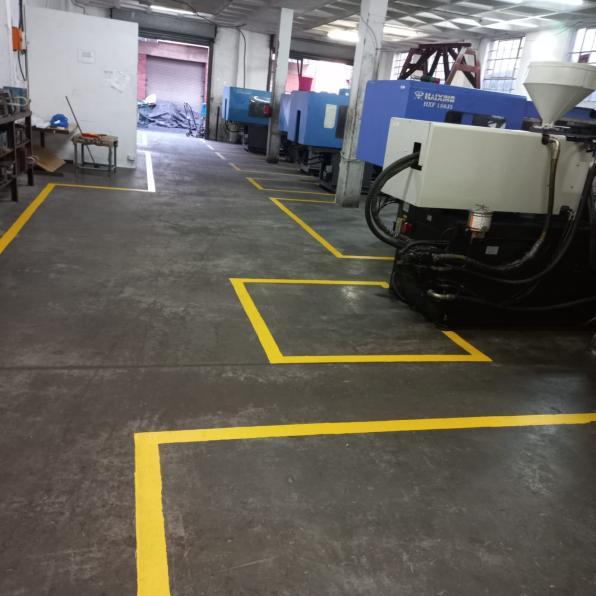
To keep our business competitive and marketable, we created value-added services to be able to offer a complete manufacturing solution of products:
• Research, Development and Design
• Toolmaking
• Assembling of components/ parts
• 4 Colour Pad printing
• Screen printing
• Complete supply chain of product
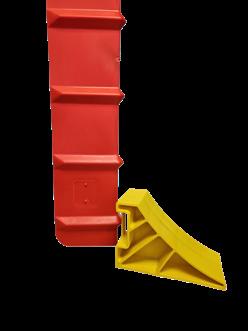
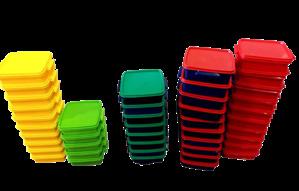
Telephone: +2731 7006900
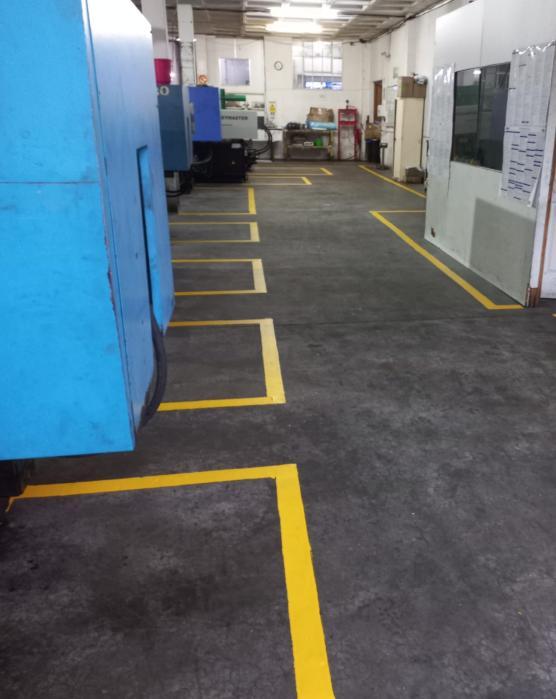
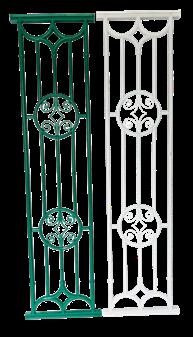
Email: kevingov@gpsplastics.co.za | sales@gpsplastics.co.za
Website: www.gpsplastics.co.za
HONOURING HERITAGE WHILST EMBRACING TOMORROW
What truly differentiates Defy from its competitors is its commitment to local manufacturing, innovation, and quality.
“As a company, we invest heavily in R&D to ensure our products are competitive, have the latest innovations and quality with the lowest possible consumption of natural resources, and are safe for our consumers,” Coetzer prides.
“We are also focused on environmentally-friendly practices. For example, we use solar energy to help power our factories and limit our water consumption through rainwater harvesting and water recycling plants that form part of our infrastructure.”
Additionally, Defy provides comprehensive after-sales service and support, offering peace of mind to customers with locally-sourced parts and service capabilities across
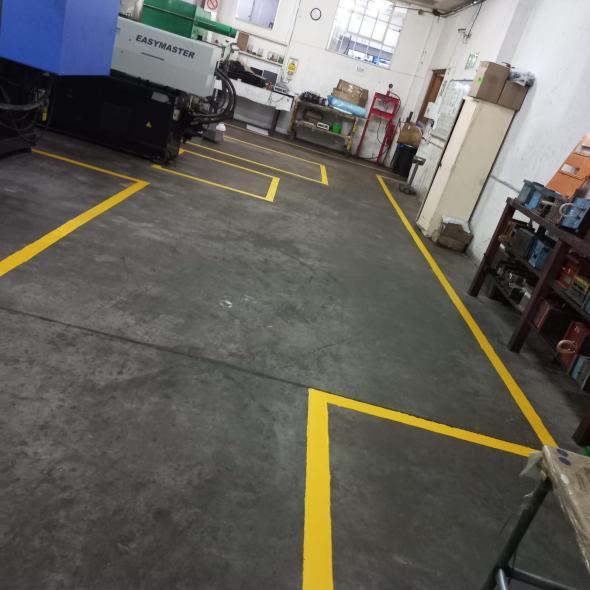
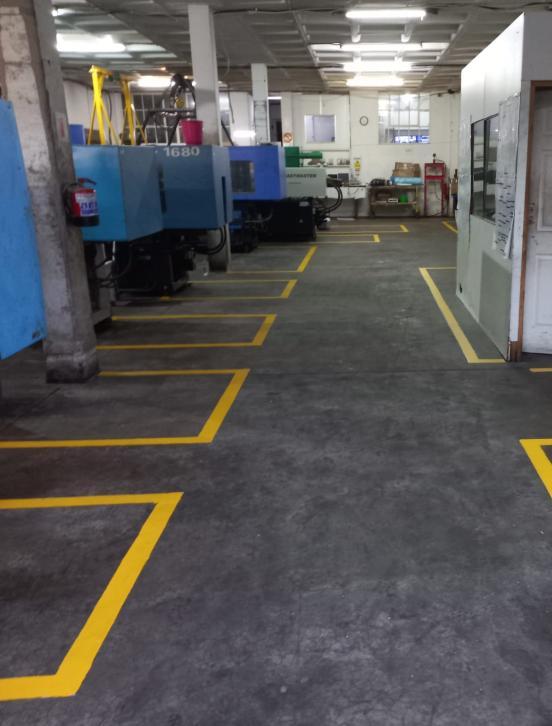
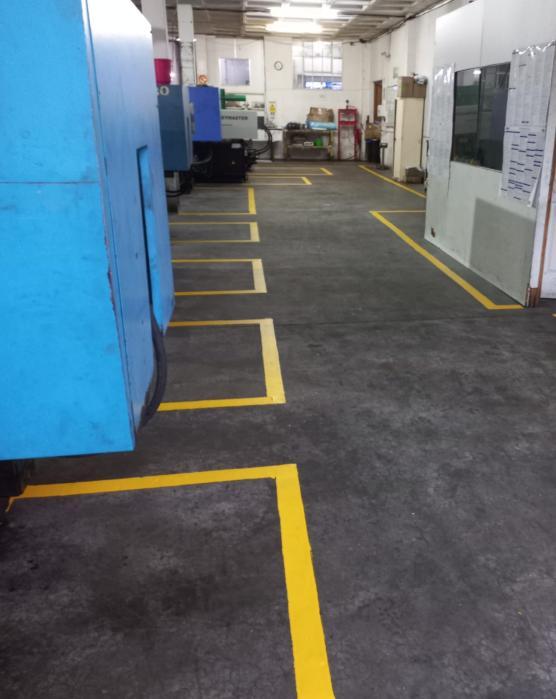
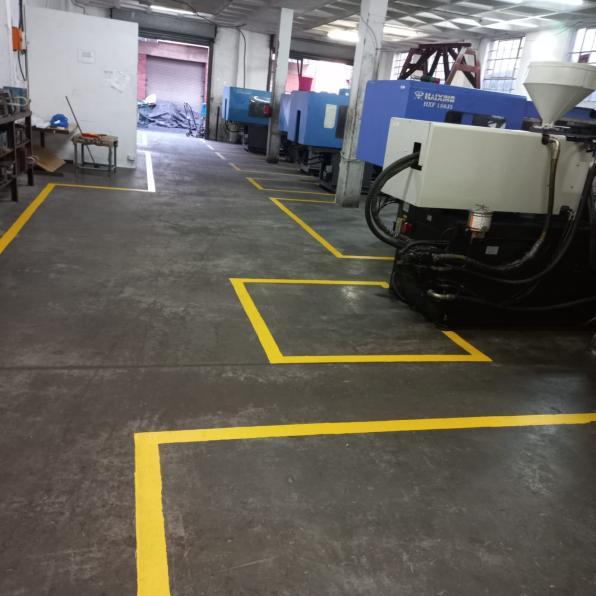
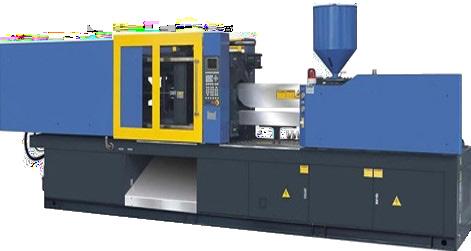
SA, as well as agents in the African countries it exports to.
As such, the company’s commitment to embracing modern technology and sustainable practices positions it well to meet the demands of an evolving market.
With a focus on fostering collaboration across its global manufacturing network, Defy is poised to continue leading the way in enhancing everyday living, ensuring its products meet consumer expectations and contribute positively to the environment.
This year is remarkable for Defy as it proudly celebrates its 120th anniversary – a significant milestone that highlights its enduring legacy.
“We are excited to celebrate this momentous occasion through a PR campaign, which will launch in June or July,” Coetzer emphatically concludes.
The future remains bright for Defy
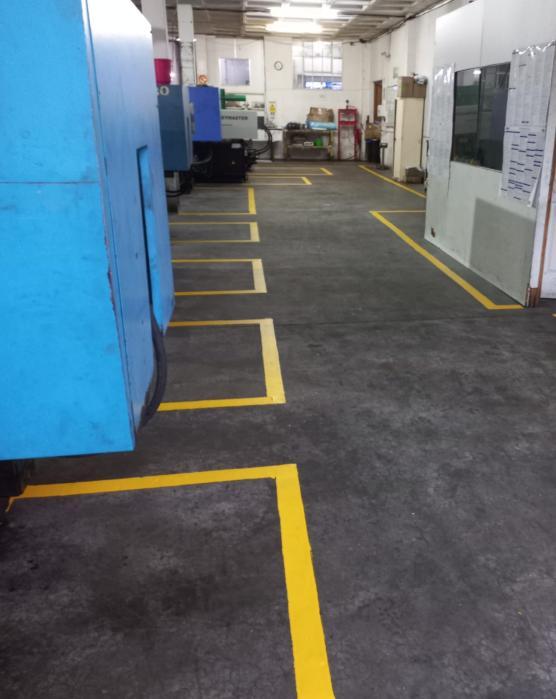
as the industry navigates the rapid changes in consumer behaviour and technological advancements. The company’s adaptability and forwardthinking approach will undoubtedly sustain its legacy of excellence.
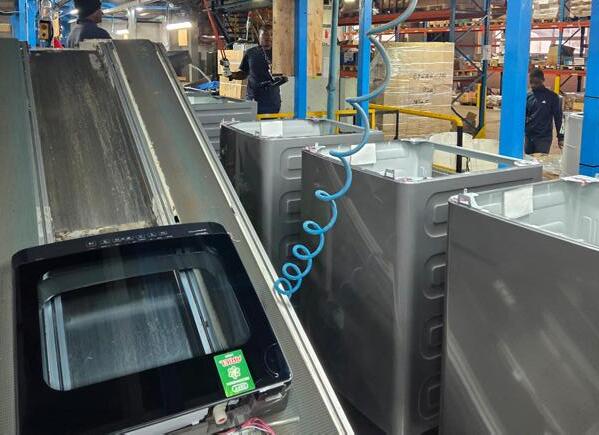
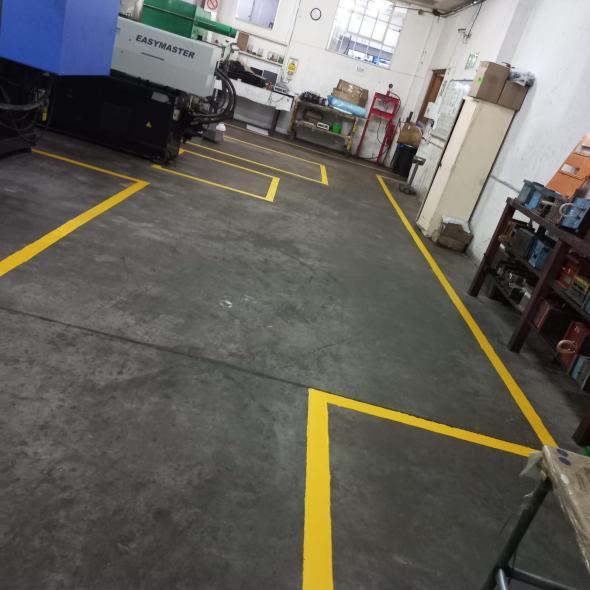
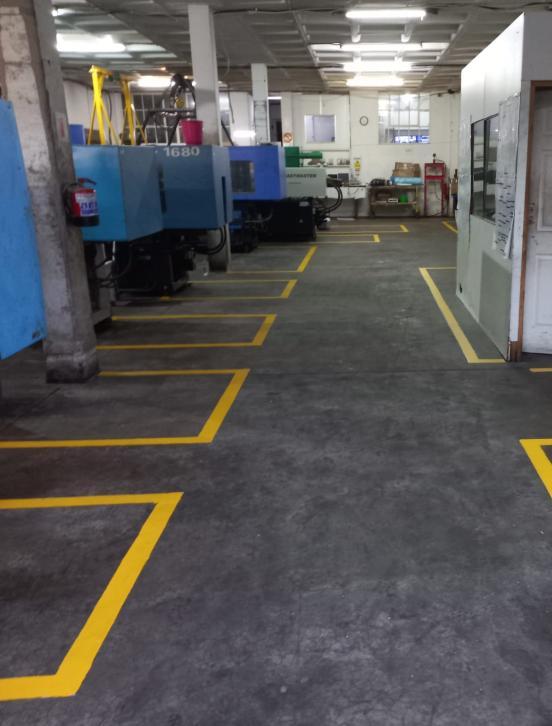
www.defy.co.za
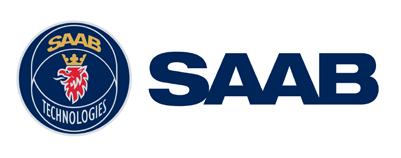
INNOVATION AT THE CORE OF OPERATIONS
With a long-standing legacy in electronic warfare, Saab Grintek Defence is developing advanced technologies to aid with detecting, deceiving, and countering threats. President and Managing Director, Jan Widerström, discusses recent developments as we reconnect with the company
Writer: Rachel Carr | Project Manager: Josh Whiteside
As a subsidiary of Saab, known for its unique design and engineering innovations, Saab Grintek Defence (SGD) stands at the forefront of the South African defence industry, specialising in electronic warfare (EW) systems, sensor technology, and avionics.
Its expertise in technology design, development, and specialised manufacturing remains unmatched as SGD delivers innovative solutions and services across air, land, and sea domains.
The company offers a fully integrated, multispectral EW selfprotection suite and is a global leader in optical and laser sensors, digital processing, microwave components, and antenna technology.
SGD solutions are trusted to protect
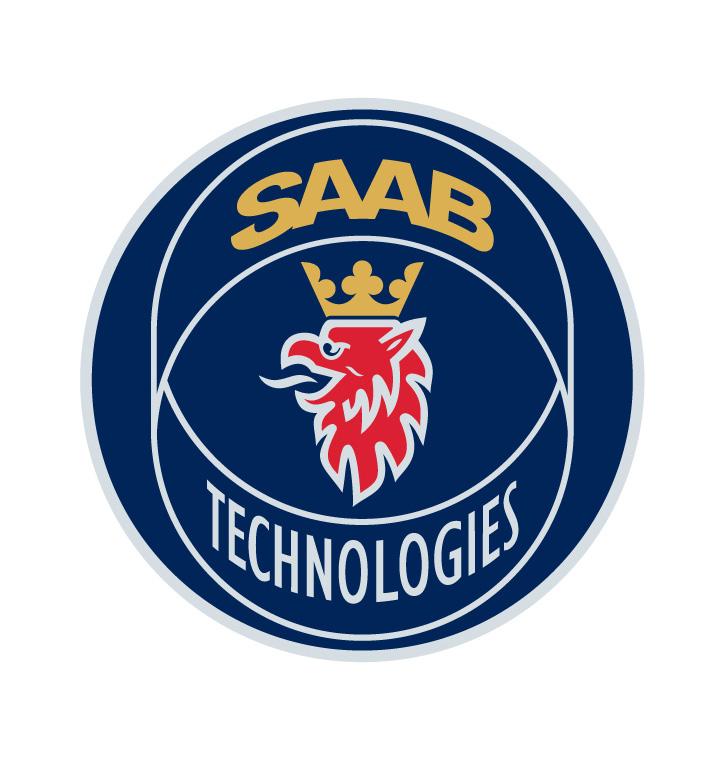
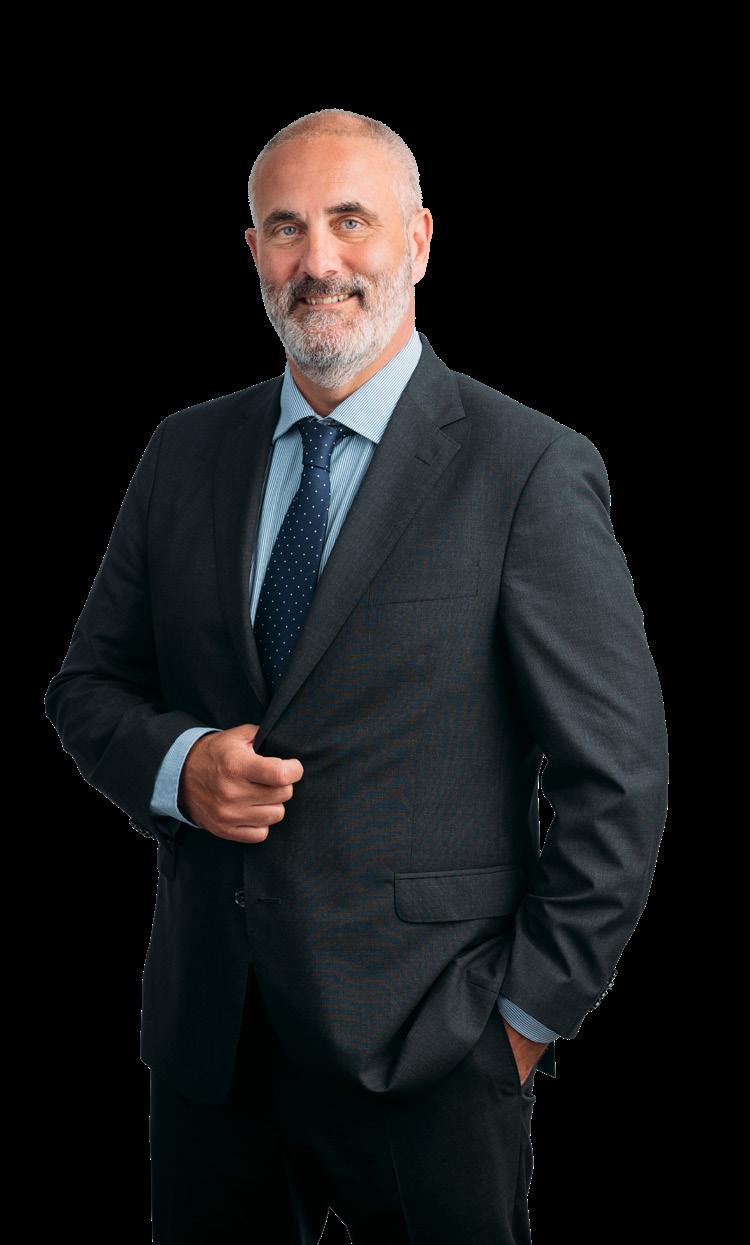
aircraft, helicopters, land vehicles, naval vessels, and submarines, as well as provide signals intelligence systems for radar and communication interception.
Since we last spoke to SGD, the EW sector has been experiencing substantial development, fuelled by the demand for advanced capabilities and their integration into various defence platforms.
“We are experiencing strong and consistent growth in most of the global markets where we operate. Currently, Europe is our largest market, and we are concentrating on expanding our capacity. This involves recruiting new personnel and optimising our production processes,” introduces Jan Widerström, President and Managing Director.
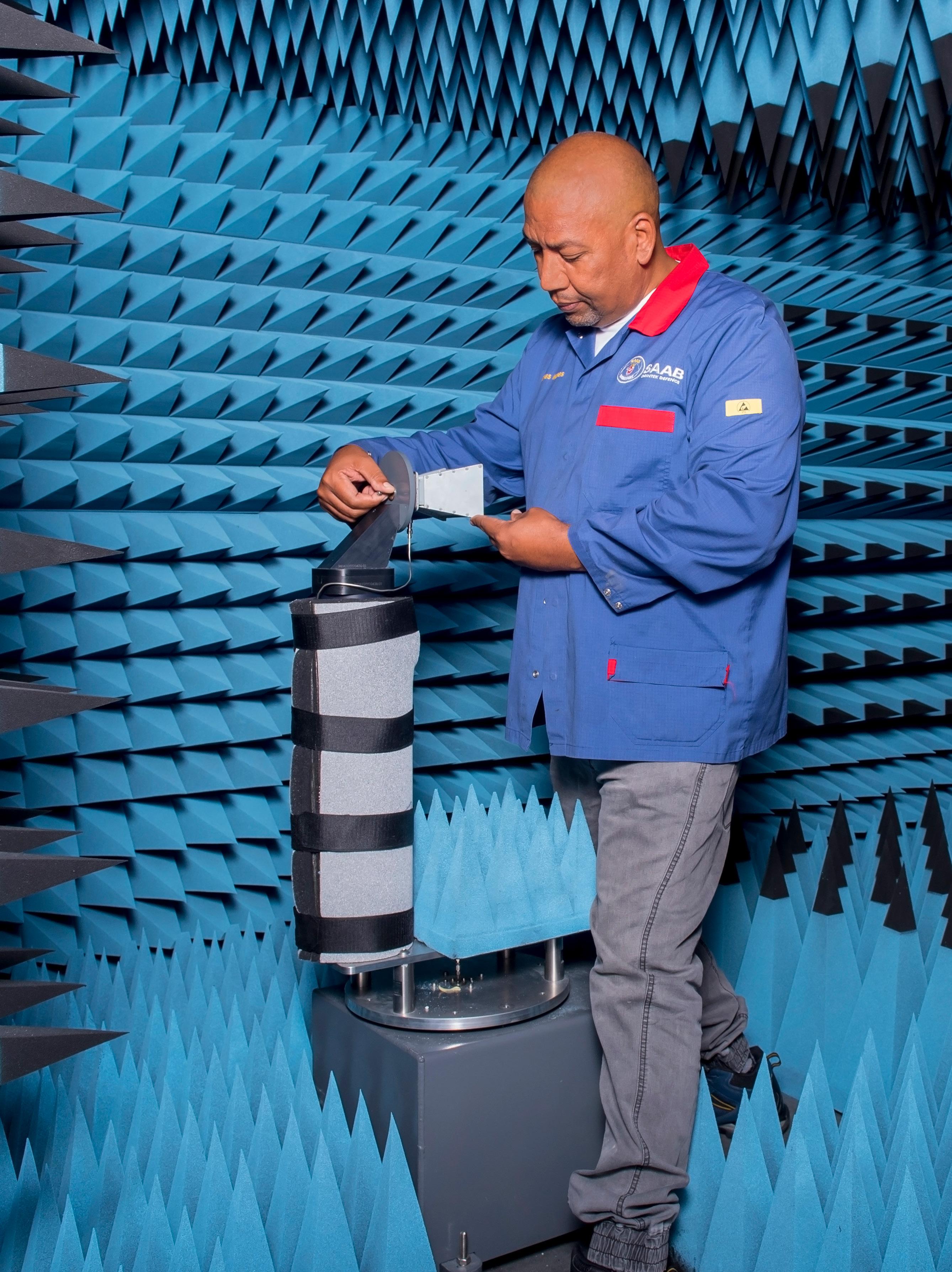
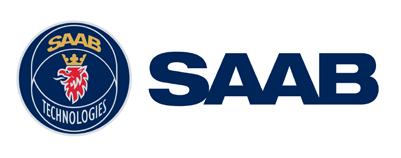
“OUR SUSTAINABILITY INITIATIVES EXTEND TO OUR COLLABORATIONS WITH LOCAL COMMUNITY SCHOOLS, AS WE ARE DEDICATED TO ENSURING ACCESS TO KNOWLEDGE IN THE COUNTRY”
– JAN WIDERSTRÖM, PRESIDENT AND MANAGING DIRECTOR, SAAB GRINTEK DEFENCE
“Our main emphasis right now is on execution, which aligns with the priorities of our colleagues in Europe, but that’s where our key focus currently lies.”
CONFRONTING CHALLENGES
South Africa (SA) faces capacity challenges due to a shortage of skilled labour, reductions in government funding for product development, and global demand that exceeds local capabilities, resulting in backlogs for companies trying to meet local and international needs effectively.
“The biggest challenge currently facing the industry is expanding capacity to meet growing demand, not only in Europe but worldwide. The current global situation puts us under significant pressure,” Widerström acknowledges.
“We export our systems to various regions, including Europe, Asia, and Latin America. Whilst restrictions exist on where we can export, we have a significant presence in the open market overall; currently, the local market represents a small portion of our total sales.”
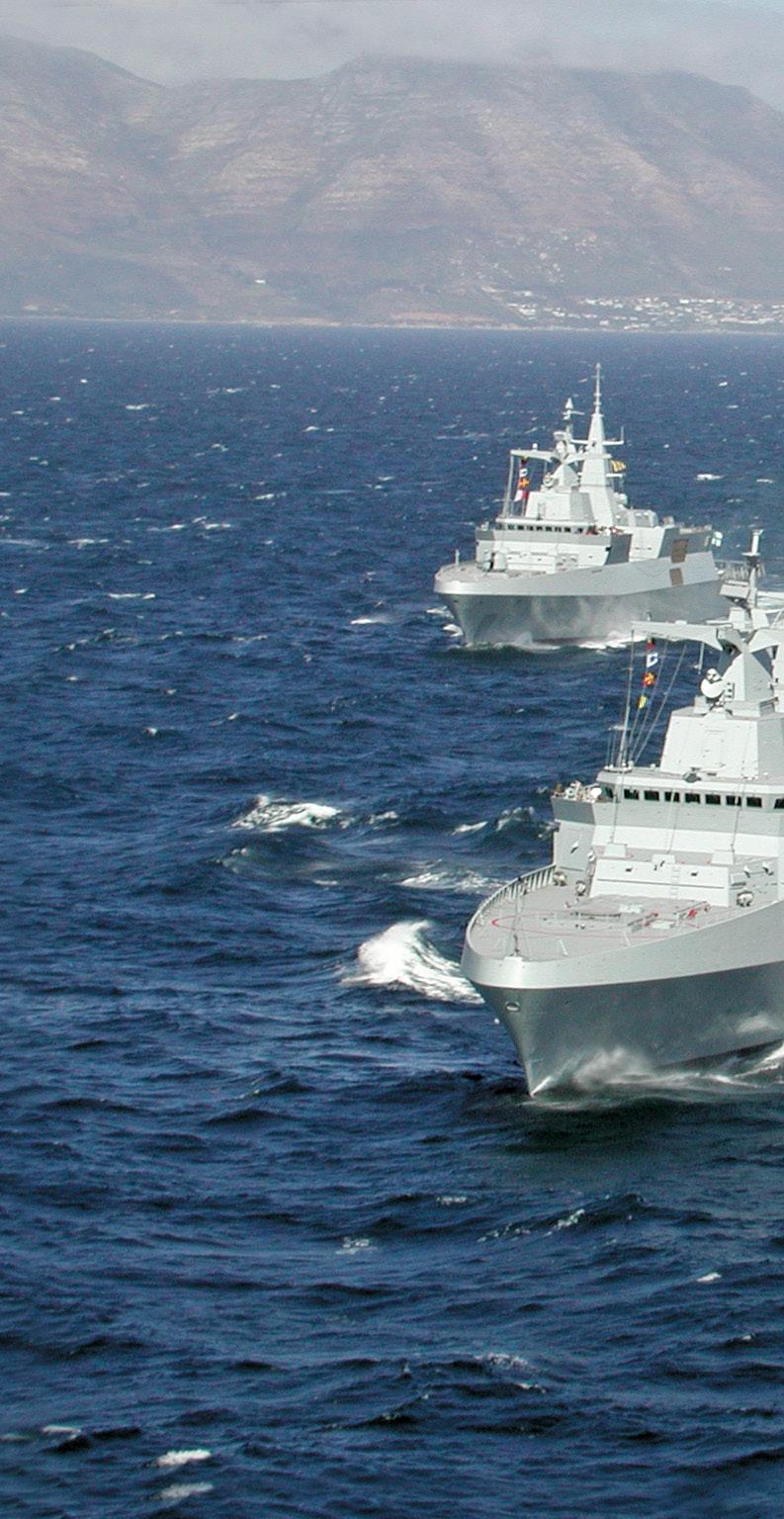
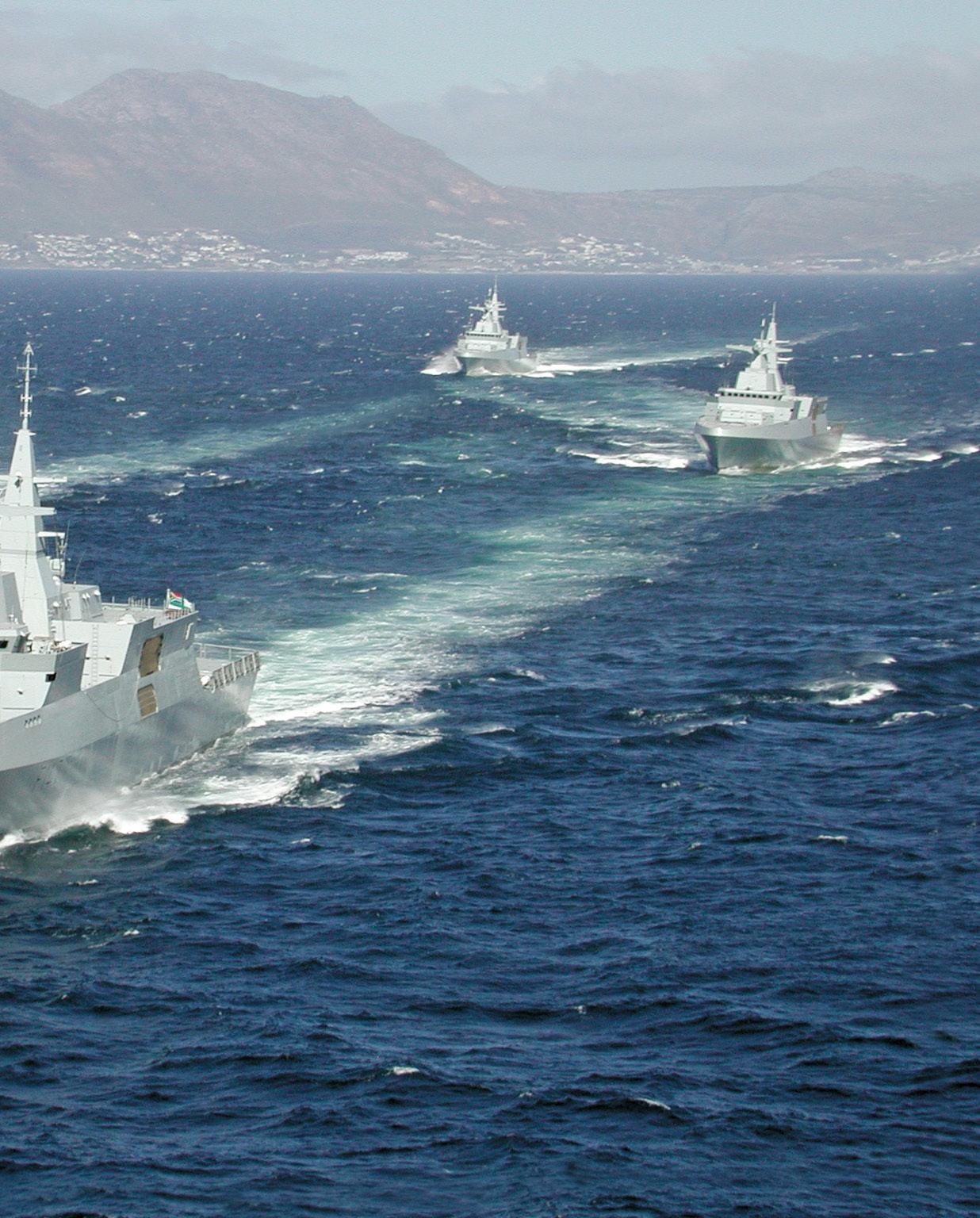
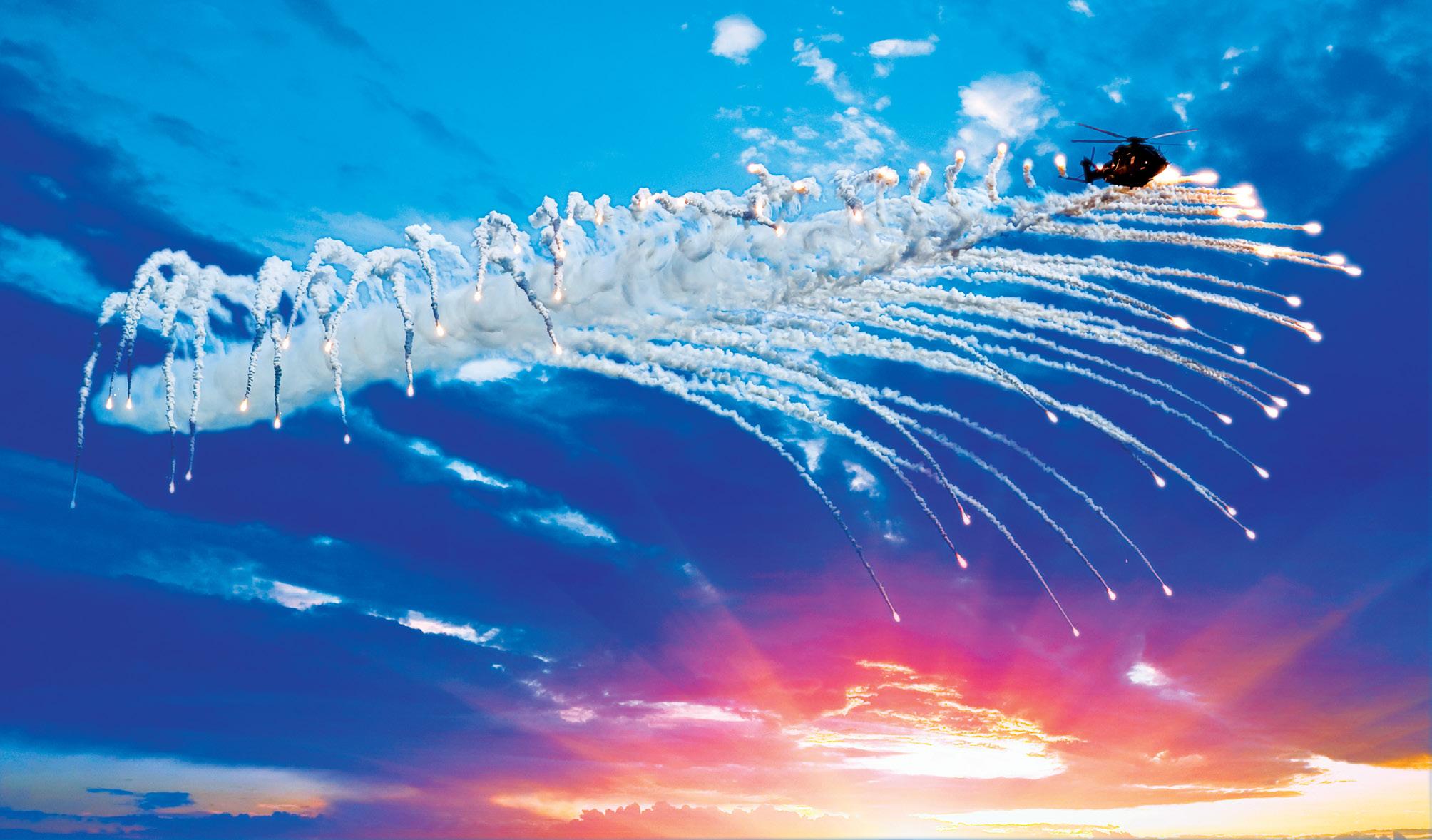
Therefore, SGD’s primary focus is on building capacity in product development and production to cope with this growth. Indeed, the company has entered into an agreement with Omnigo to expand production, in which the supplier will cover manufacturing for selfprotection systems across the air, land, and sea domains.
This strategic decision will significantly support SGD’s growth and help the company meet the increasing global demand. Additionally, the contract will further commit Omingo to continue providing comprehensive electronic services to SGD, building on their long-standing and mutually beneficial partnership.
“We’ve seen a quadrupling of order backlogs, highlighting this challenge. Finding people with the correct skills is crucial, and we need to create an environment that prevents us from overworking and exhausting our employees to retain them,” Widerström notes.
However, there is an urgent requirement for skilled engineers and technicians, with many companies competing to attract these resources.
ALLIANCES AND ASSURANCES
SGD’s culture is built on its ‘#Ubuntu Together As One’ philosophy, reflecting a belief in collaboration and shared success.
Guided by the core values of drive, trust, expertise, and diversity, the company strives for excellence in
SGD PRODUCTS DEVELOPED AND PRODUCED IN SA
• Integrated Defensive Aids Suite (IDAS)
• Land Electronic Defence Systems (LEDS)
• Naval Laser Warning Systems (NLWS)
• Electronic Support Measures (ESM)
• Electronic Intelligence (ELINT) for surface vessels and submarines
• Radio frequency (RF) components and EW antennas
• AviCom communications management system
everything it does, from advancing cutting-edge technology to fostering an inclusive, high-performance workplace.
This commitment is further demonstrated through the company’s partnerships. To navigate the recent surge in growth effectively and successfully, it is essential to foster collaboration with suppliers.
“On the one hand, we are focused on expanding our supply chain, which primarily consists of local partners. This involves providing suppliers with more work and supporting them in their development. In doing so, we can assign greater responsibilities to our supply chain, allowing us to concentrate on the areas where we excel,” explains Widerström.
Additionally, SGD is exploring strategic partnerships in Europe and Asia to increase capacity and address the current political climate.
“The issues of security, cybersecurity, and supply chain integrity are becoming increasingly important. We recognise the need to be close to our customers to ensure they feel confident in our suppliers and the overall security of our operations.”
Partnership. Progress.
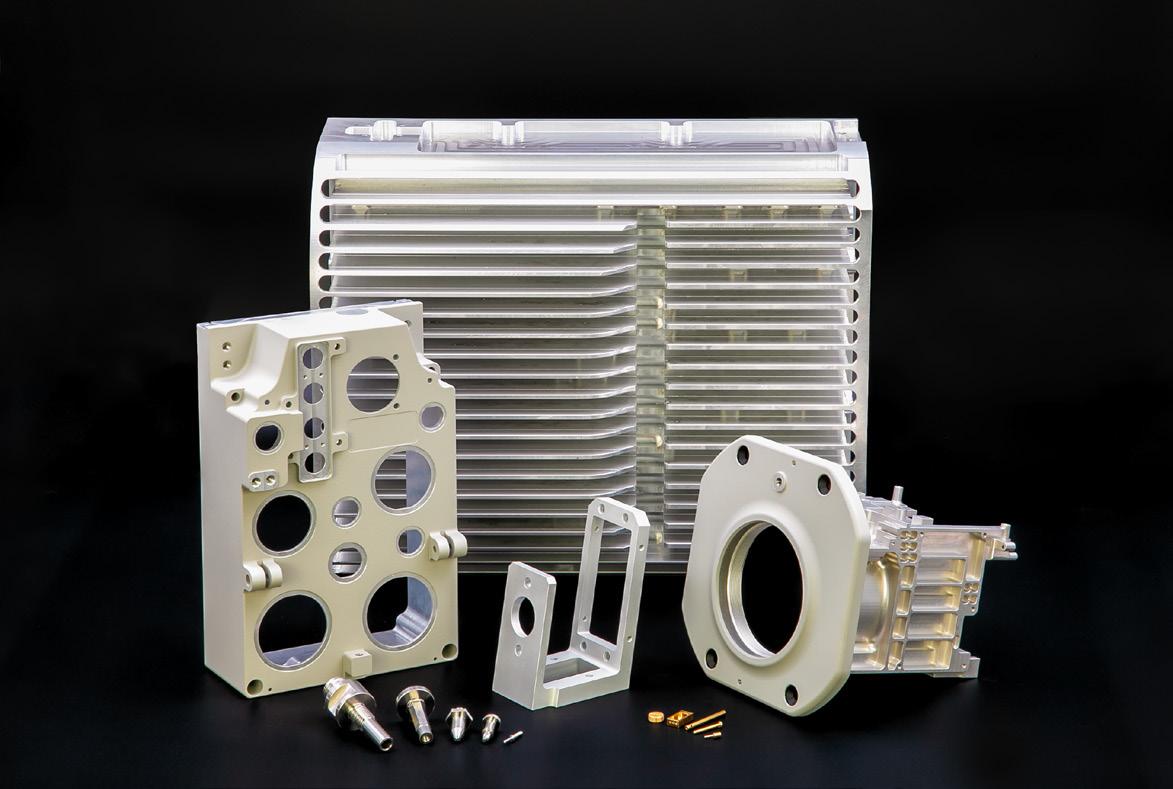
Since 1986, Acu-Turn has been enabling manufacturing excellence across South Africa. What began as a small workshop producing mechanical components for the defence sector has evolved into a trusted manufacturing partner across a wide range of industries, including precision engineering and instrumentation.
Guided by a clear vision “to be a leading force in enabling manufacturing excellence across diverse sectors in South Africa,” Acu-Turn focuses on delivering real-world value through precisionengineered components. Its mission is simple: “to exceed client specifications through a commitment to exceptional quality, cost-efficiency, and timely delivery—empowering clients to achieve operational excellence and maintain a competitive edge.”
Based in Pretoria, Acu-Turn is led by Rupert Stander, alongside a team of skilled engineers and tradespeople who bring decades of technical expertise to every project. The company’s strength lies not only in its machines or materials—but in the way it partners with clients and continually reinvests in its own capabilities to meet their evolving needs.
“At Acu-Turn, we don’t just manufacture parts—we solve problems,” says Rupert. “We see ourselves as an extension of our clients’ operations. When their needs change, we invest to keep pace.”
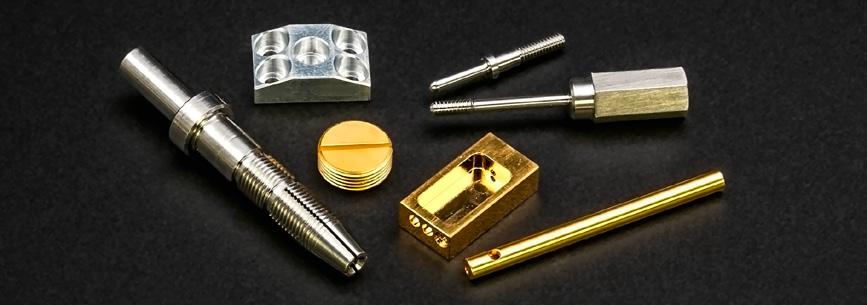
This investment mindset is reflected in Acu-Turn’s modern CNC milling, turning, and EDM equipment, capable of handling a wide variety of materials and tolerances. The company’s largest milling capacity—1000 x 500 x 500mm—makes it well-suited for everything from delicate gold-plated tubes to large, high-precision components.
The value Acu-Turn delivers extends beyond machining. Through a curated network of suppliers and subcontractors, the company offers turnkey solutions including surface treatments, electroplating, specialized painting, and heat treatments.
This integrated approach ensures that even the most complex projects are delivered with consistency, quality, and efficiency.
The company’s culture is built around three pillars: meeting and exceeding customer quality standards, a commitment to cost-efficiency, and delivering on time. That focus, paired with a deeply relational approach to doing business, has made Acu-Turn a vital contributor to South Africa’s manufacturing landscape.
“Our commitment is long-term,” adds Rupert. “We don’t just serve a client—we grow with them. That’s why we continue to invest in our people, processes, and equipment: so we can help our clients stay competitive, agile, and successful.”
With nearly four decades of experience, Acu-Turn remains grounded in its purpose: enabling excellence. Through partnership, precision, and a commitment to continuous improvement, the company continues to shape the future of manufacturing.
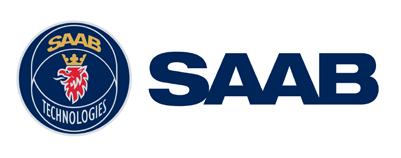
Although these topics are a growing concern for SGD, as a subsidiary company, it has rigorous and centralised management of its tools and IT systems.
“We are undertaking significant work to strengthen all our security systems, which extends to considering big risks and increasingly incorporates cybersecurity within our products. This is particularly relevant as we develop more advanced airborne systems, amongst other products,” Widerström expands.
For political reasons, cyber and supply security are becoming increasingly critical as SGD must comply with such aspects and be close to its customers to ensure they are comfortable with the company’s suppliers.
“Sometimes, we need to be physically located where the customer is, especially for certain parts of our products and support services, as they often want full control over the location of their logistics and equipment,” he outlines.
COMBATTING CLIMATE CHANGE
At SGD, sustainability is a core aspect of its business strategy. Indeed, the company intertwines safety and security with its mission to keep people safe, aligning with broader environmental and socioeconomic progress.
“Sustainability is increasingly important; we need to establish a robust framework for the future as we face significant challenges with power supplies, electricity, and water,” Widerström states.
“We have made a major investment in solar power, and whilst we are not entirely autonomous or independent, we are close to achieving that goal. This step is vital for ensuring we can sustain operations, even during grid failures.”
In a significant stride towards a greener future, SGD completed the
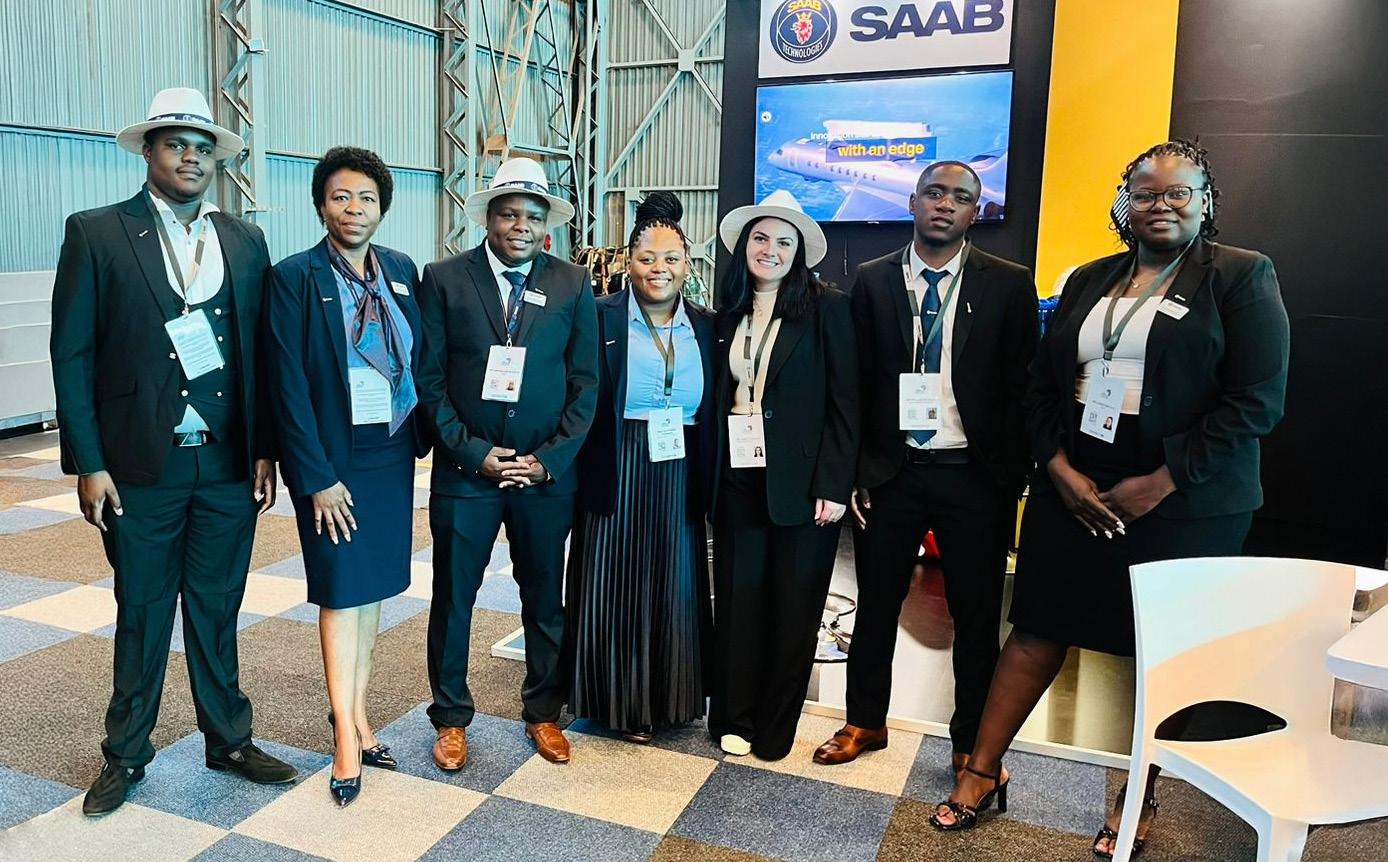
TRAINING AND SKILLS DEVELOPMENT
As continuous learning is crucial for employee growth and business success, SGD offers a variety of workshops and resources to equip its team with the skills needed to thrive in a dynamic and innovative workplace. This ongoing development helps the company stay competitive by enhancing talent attraction and retention.
Employees have access to e-learning platforms, including Pluralsight and LinkedIn Learning, with 40 dedicated learning hours per year available during working hours.
INVESTING IN FUTURE TALENT
SGD is dedicated to nurturing young talent through collaborations with local universities and schools, promoting community engagement and leveraging academic resources for mutual benefits.
• Bursary Programme – Supports students in critical fields to cultivate future leaders whilst addressing the critical skills gap.
• Graduate Programme – Offers hands-on workplace experience and mentorship, with 60 percent of participants in 2024 securing permanent positions.
• Learnerships – Aims to provide essential skills to unemployed youth, including individuals with disabilities, by equipping them with job-ready skills for greater inclusion in the labour market.
CORPORATE SOCIAL INVESTMENT (CSI)
SGD strives to positively impact its communities through CSI initiatives focused on poverty alleviation, education, and unemployment reduction. These initiatives include:
• Partnering with schools, like Ribane-Laka Secondary School, to empower high-performing students, some of whom have gone on to join SGD. This creates a full-circle approach; by investing in learners, the company not only uplifts communities but also strengthens its internal talent pipeline.
• Collaborating with the Department of Basic Education to celebrate excellence by recognising top-performing schools and districts at national awards across SA.
• The Small, Medium, and Micro Enterprises (SMMEs) Programme supports local businesses, such as Solve Direct Electronics, Kutleng Engineering Technologies, and Sparcx, contributing to their technical skills and engineering growth.
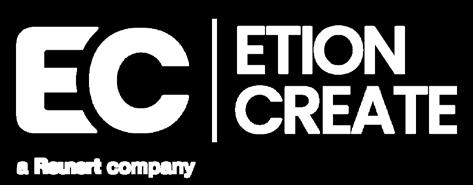
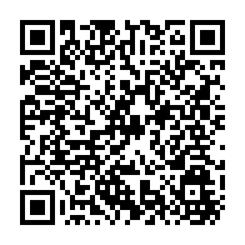
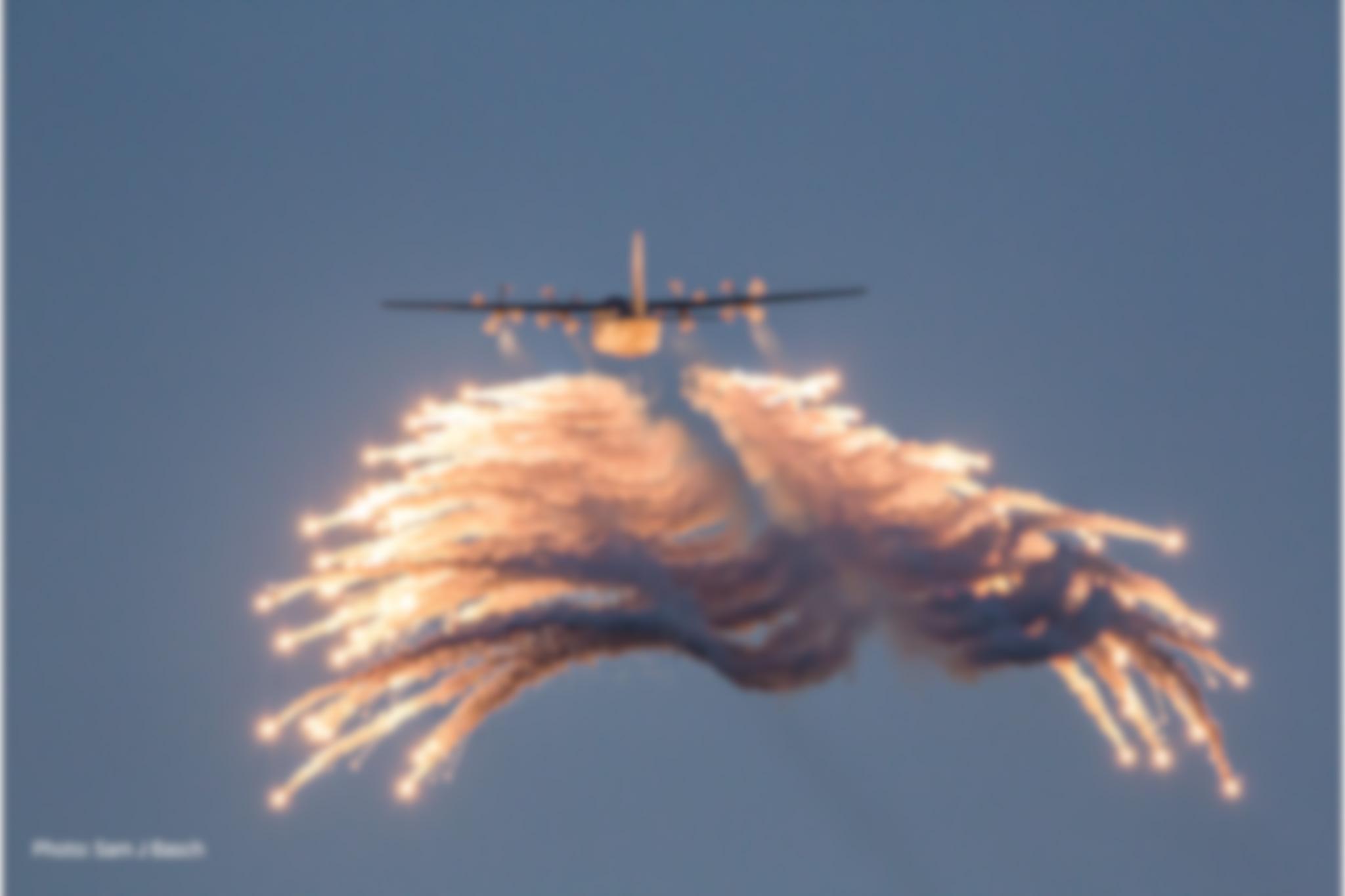
High-Performance Processing in Compact Form Factors
Etion Create (EC) is an Original Design Manufacturer that partners with clients to deliver complete, customised electronic solutions By leveraging proprietary IP and engineering expertise, EC integrates modular technology into client-specific systems Its VF370 and VF365 3U OpenVPX modules exemplify EC’s capabilities in high-performance embedded applications
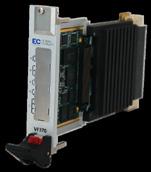
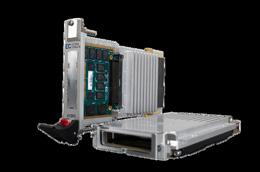
VF370 – 3U VPX SBC with Intel Atom® The VF370 is a versatile 3U OpenVPX SBC featuring Intel Atom® E3900 CPU, Altera® Cyclone® V FPGA and FMC support for scalable I/O in compact, SWaP-optimized environments Its rugged reliability suits aerospace and industrial use. Proven in Saab’s IDAS-310 EW systems, the VF370 is rated at the highest Technology Readiness Level TRL9 “Etion’s innovative VF370 has extended our product’s life and capability,” says Harry Schultz, Saab Product Manager
The VF365 combines Altera Arria® 10 SoC FPGA and TI KeyStone® DSP technologies to deliver ultra-high bandwidth processing ideal for Radar, SIGINT, EW, SDR, and video-intensive systems Its dual-core ARM Cortex-A9 processor and highspeed AXI bus ensure tight integration between software and hardware
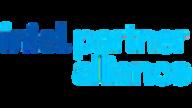
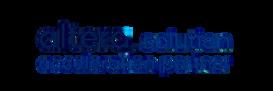
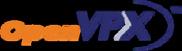

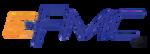
www etioncreate co za
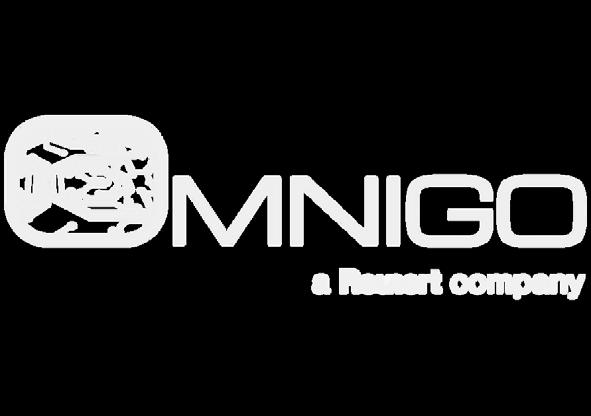
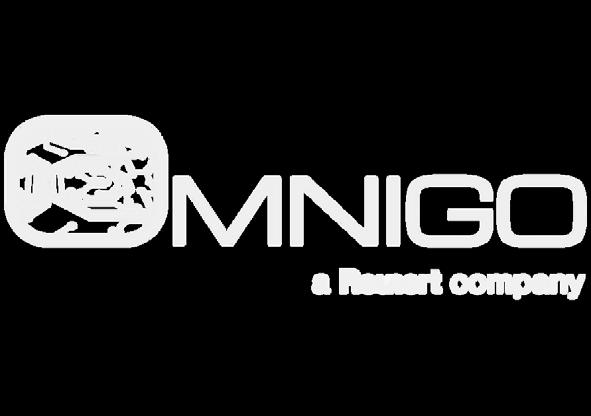
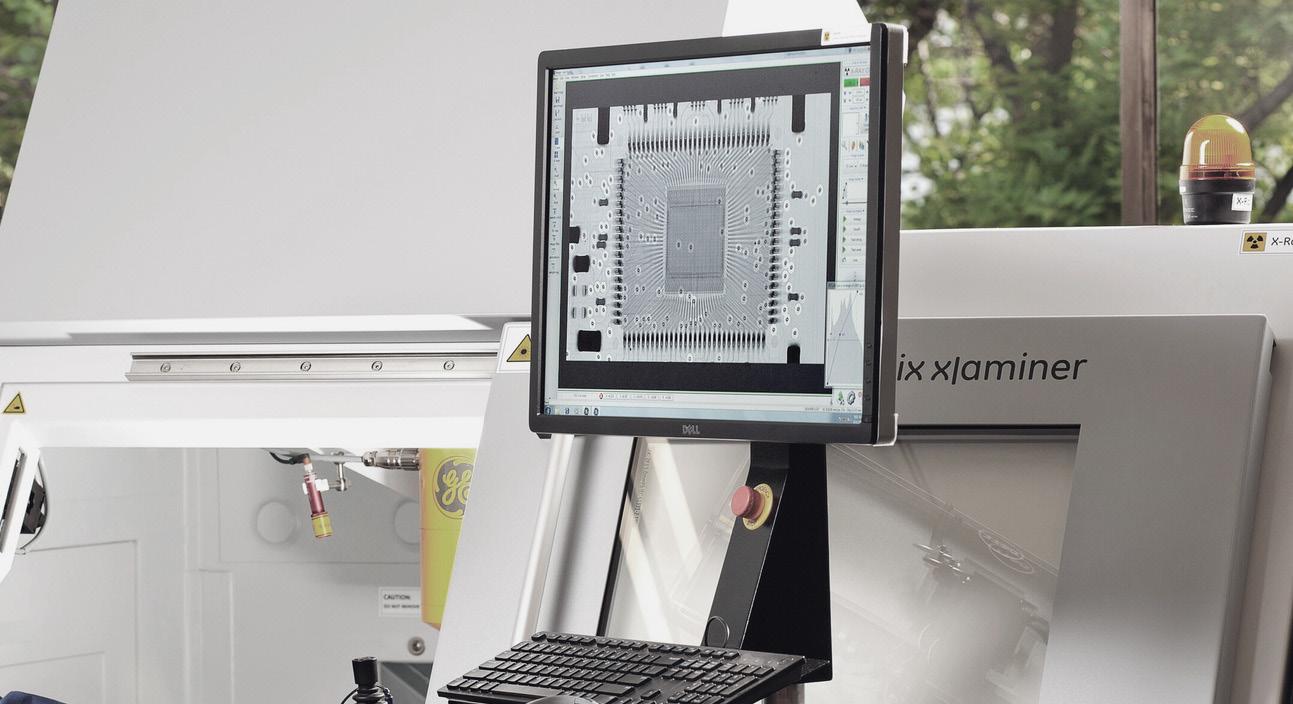
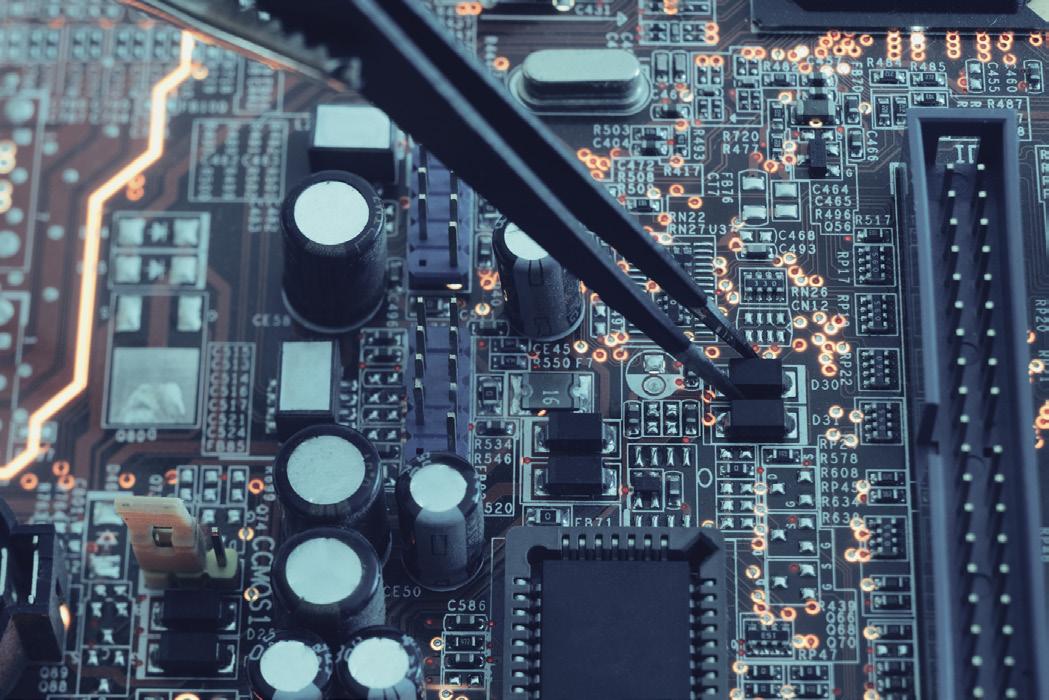
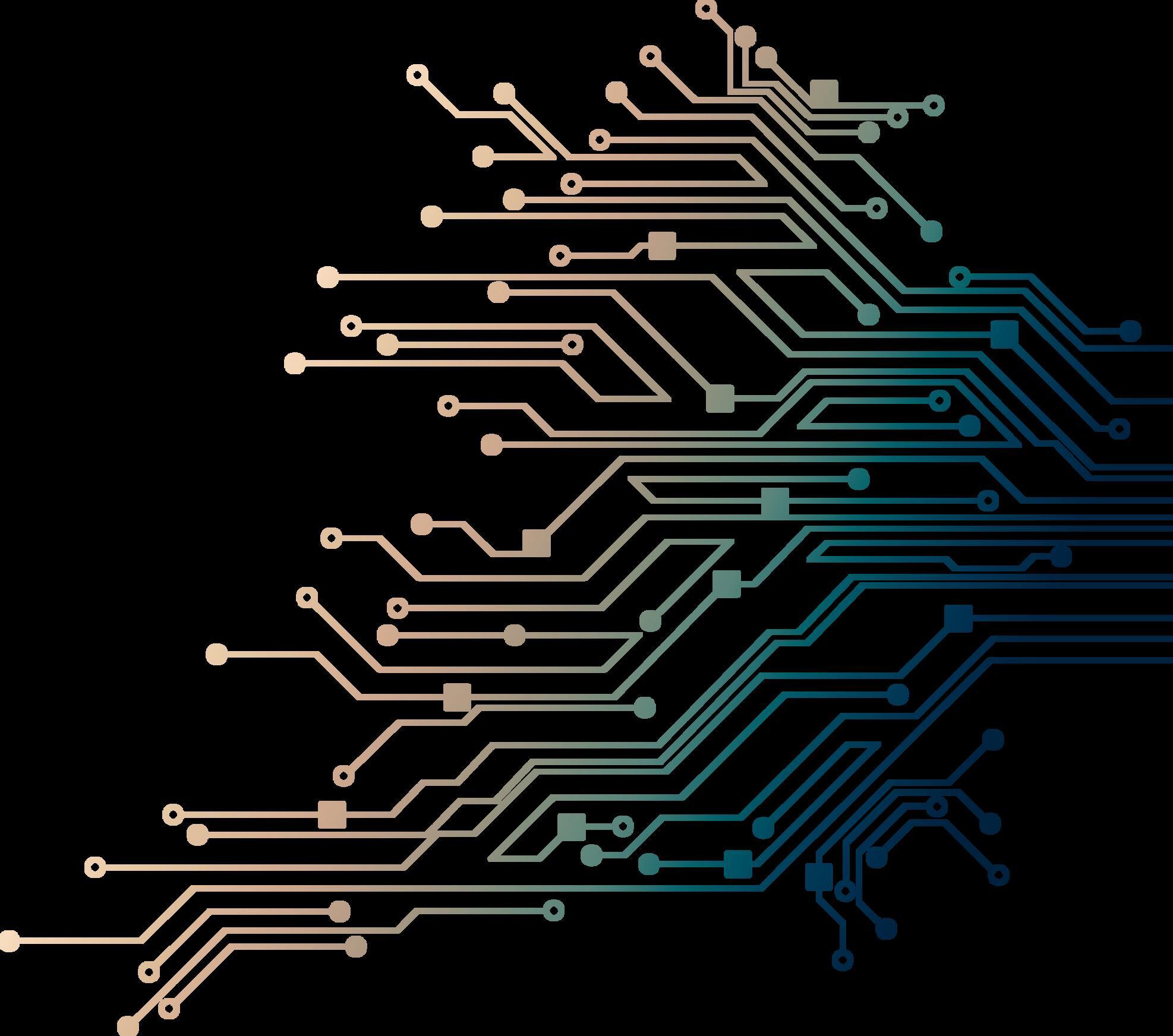
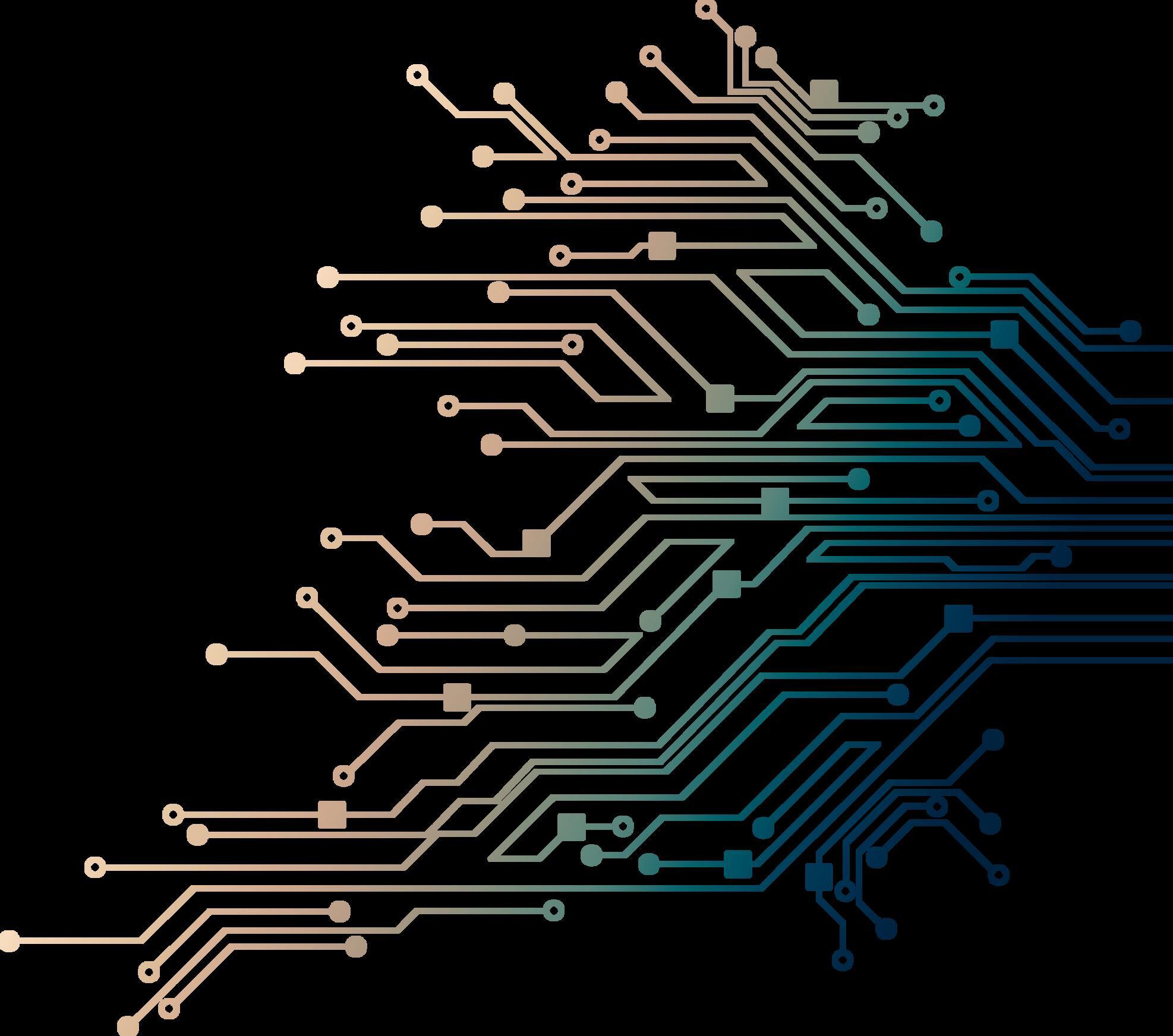
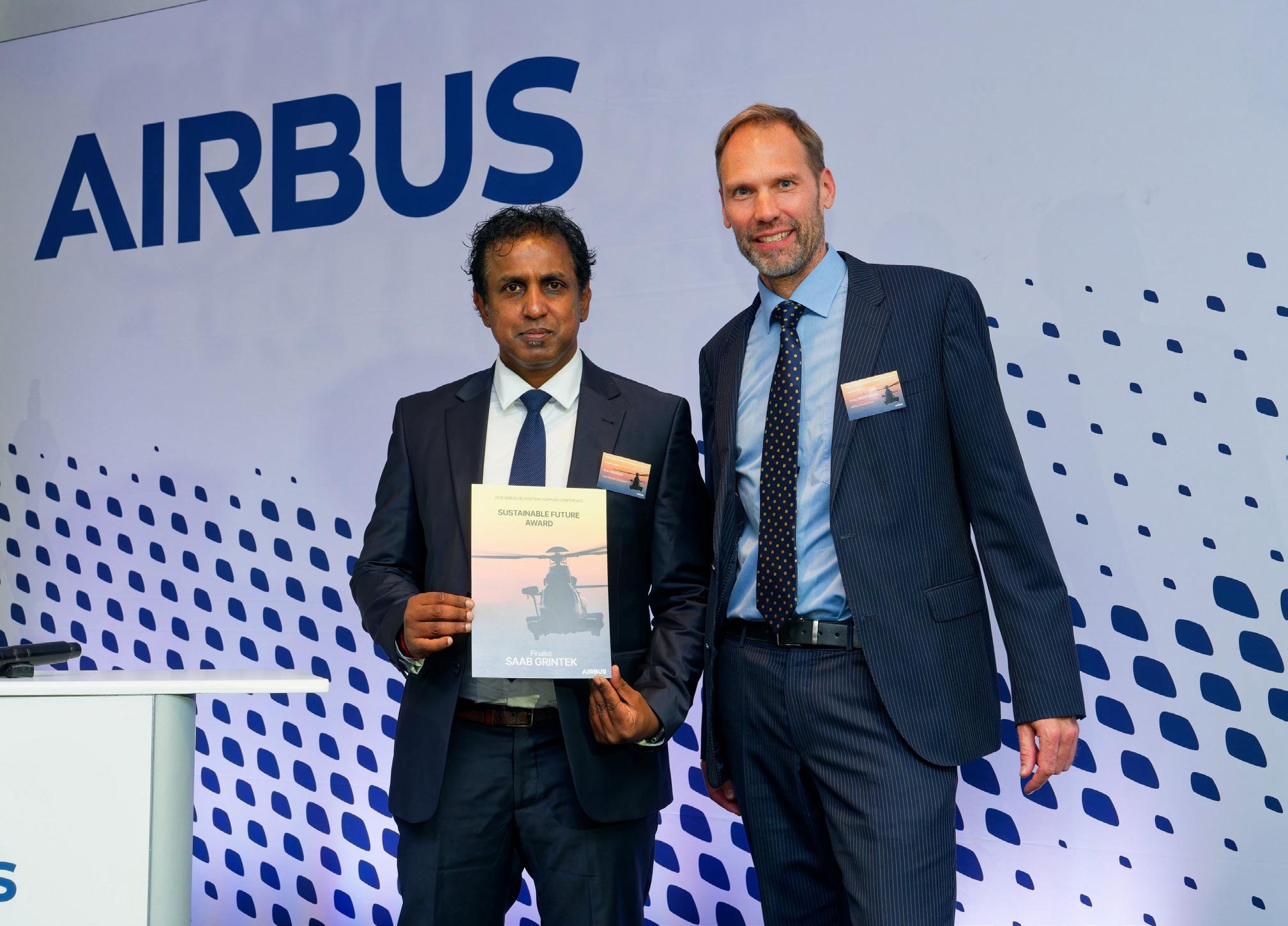
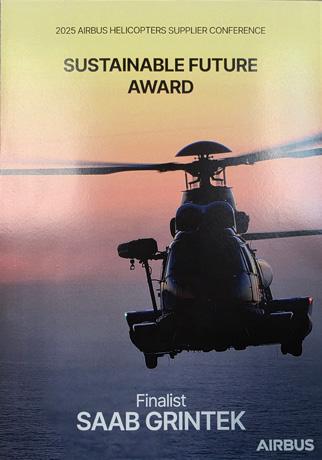
CELEBRATING ENVIRONMENTAL ACCOLADES
SGD recently achieved second place in the Sustainable Future category at the 2025 Airbus Helicopters Supplier Conference, highlighting its commitment to sustainable business practices within Airbus Helicopters’ global supply chain.
The award reflects SGD’s alignment with the Airbus Supplier Code of Conduct, strong EcoVadis and Carbon Disclosure Project scores, and active initiatives such as substance substitution and local investment, with 87 percent of procurement spending directed to local businesses.
Moreover, sustainability is integrated into SGD’s products and, in collaboration with Airbus, the company received an accolade at the Sustainable Future Awards.
By embedding sustainability into operations and supporting local enterprises, SGD contributes to a safer and more responsible world.
installation of a one megawatt (MW) solar power plant at its Centurion office in SA. This project will enable the company to achieve 70 percent self-sufficiency from the national grid. Aligned with the global Race to
Zero campaign and the company’s broader sustainability goals, the solar plant is complemented by a state-ofthe-art 1MW battery back-up system. This advanced set-up utilises JA Solar 550-watt (W) modules
and cutting-edge battery storage technology, ensuring efficient and reliable on-site energy generation.
The installation embodies SDG’s vision of a sustainable future where innovation and environmental consciousness seamlessly merge, underscoring its commitment to reducing environmental impact whilst ensuring energy reliability for operations.
“Our sustainability initiatives extend to our collaborations with local community schools, as we are dedicated to ensuring access to knowledge in the country. Furthermore, we continuously enhance our facilities and long-term capacity,” Widerström prides.
FORTIFYING THE FUTURE
SGD invests significant effort and resources into its future. This includes focusing on its local product portfolio and contributing to the organisation’s broader vision, emphasising
Left: Nivan Moodley, Vice President and Head of Business Development and Strategy, SGD at the 2025 Airbus Helicopters Supplier Conference
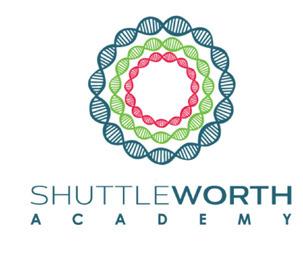
Let us 10x your staff and ensure your company is well-prepared for the future world of work.
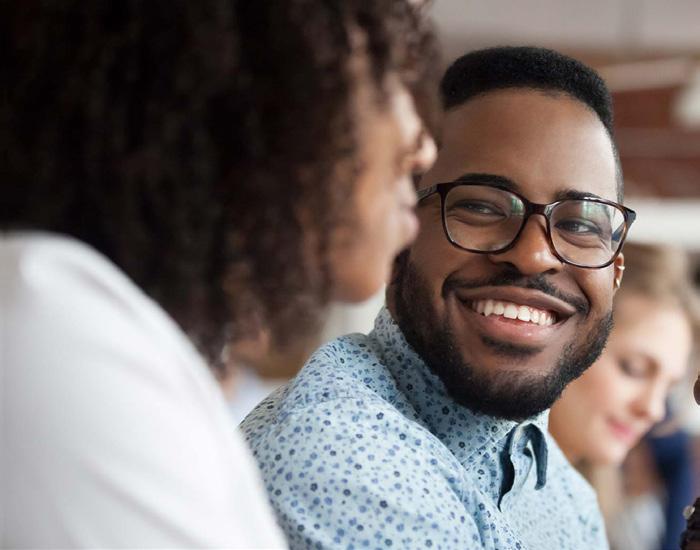
As a proud SETA accredited education and corporate training institute. 10x your-self and company. World-Class Technologies, Latest AI Methodologies, Cosmic and Neuroscience Insights, Local and UK Accreditation!
We use Artificial Intelligence, IT, Neuroscience and a Business School that train individuals, and companies, to deal with change to achieve ROI, be sustainable and manage risk in a VUCA World. Neurons that fire together wire together, and this embeds the learning.
At Shuttleworth Academy, our mission
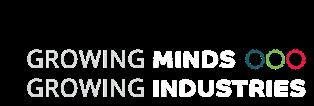
is to inspire growth in minds, hearts, and organisations through our innovative product offerings. We leverage cutting-edge technology and advanced methodologies to enhance skills and transform mindsets.
Our approach incorporates digital training methods that ensure superior learning outcomes, making education accessible and engaging.
We specialise in Artificial Intelligence Games-Based learning, which is designed to captivate learners whilst equipping them with essential skills for the modern workforce.
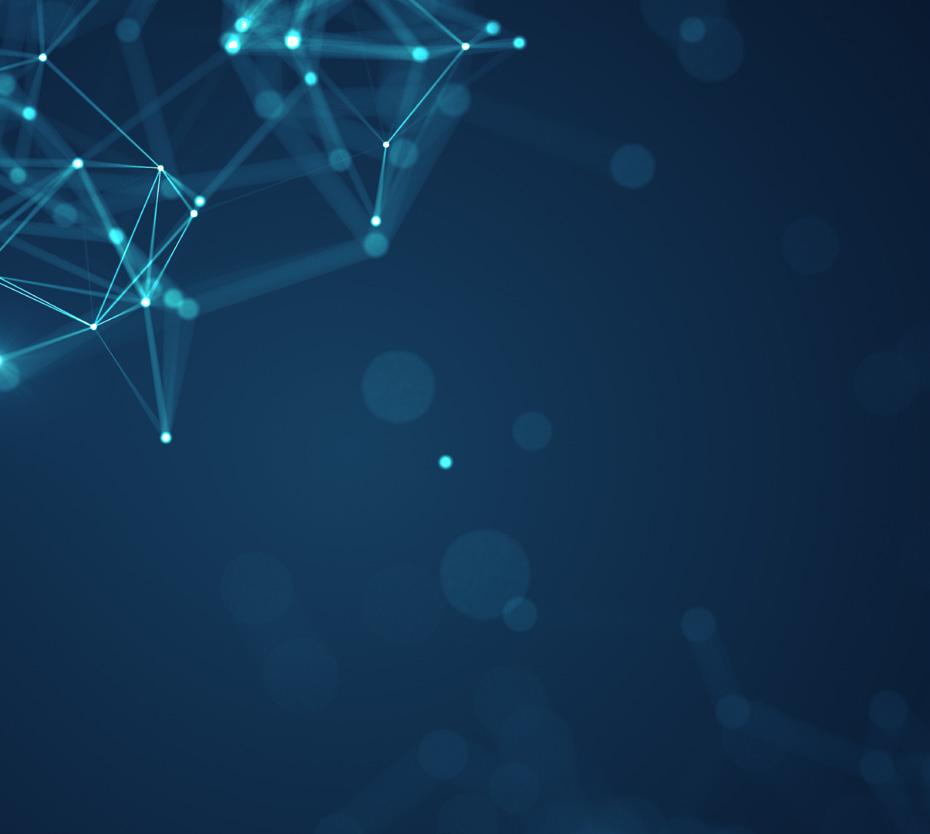
Contact us now: info@ShuttleworthAcademy.com www.ShuttleworthAcademy.com
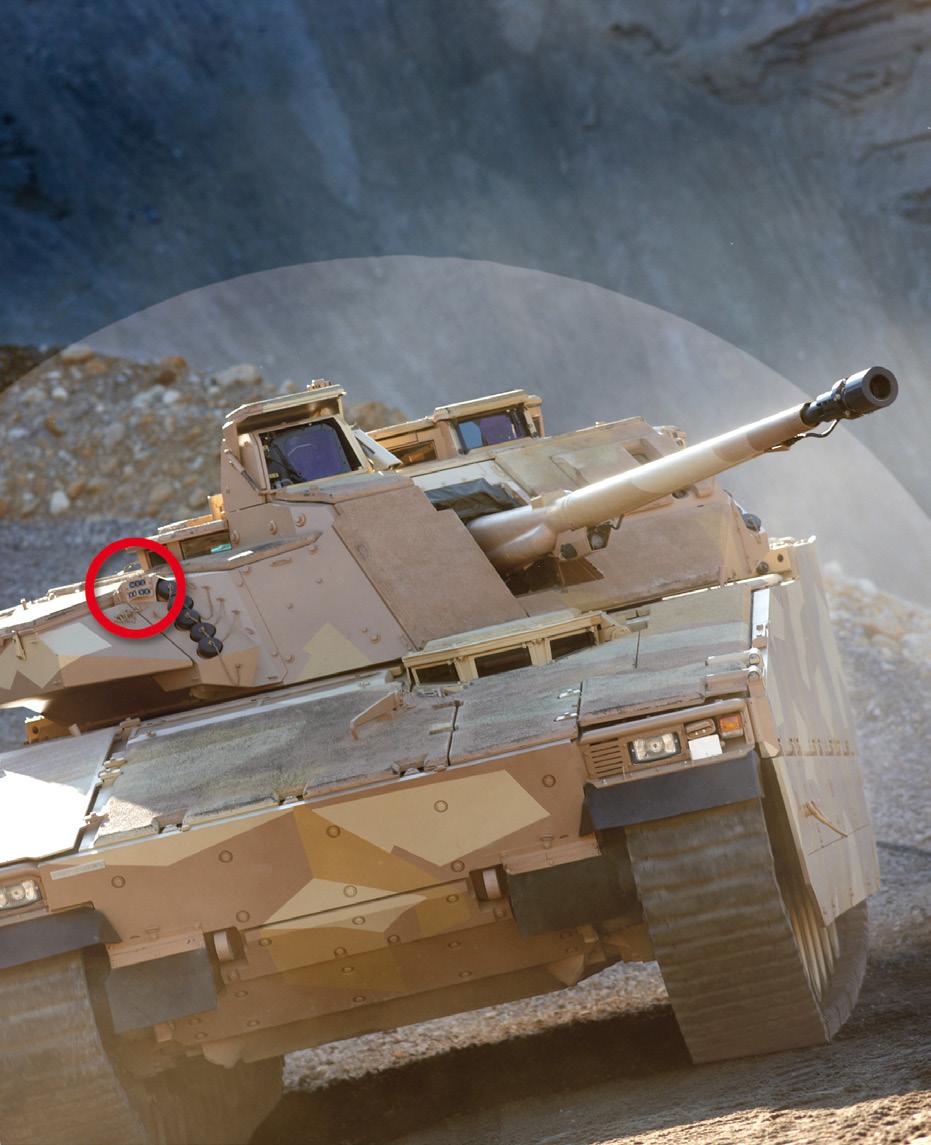
“MUCH OF OUR R&D IS CONDUCTED LOCALLY, AND WE ARE COMMITTED TO INVESTING HEAVILY IN DEVELOPING NEXTGENERATION SYSTEMS”
– JAN WIDERSTRÖM, PRESIDENT AND MANAGING DIRECTOR, SAAB GRINTEK DEFENCE
tomorrow’s technologies.
“We are focused on capacity building and technological advancement by investing in machinery and resources to increase output and improve efficiency. We also prioritise funding R&D for future products to stay at the forefront of technology,” informs Widerström.
“In collaboration with our parent company, Saab, we are proud to be one of the centres of excellence in the EW domain. Much of our R&D is conducted locally, and we are committed to investing heavily in developing next-generation systems,” he sets out.
This will strengthen SGD’s position in the industry, whilst integrating cutting-edge technologies such as artificial intelligence (AI) into its systems will be crucial in maintaining a competitive edge.
“Our goal is to meet current demand whilst planning for the future and identifying where we need to be in the next five to 10 years. The challenge lies in balancing both objectives, but we are actively working to achieve this.”
“Our top priority is to increase capacity whilst recruiting the right candidates – we are actively working to identify new talent. This is essential
for effective project execution and everything that comes with it,” Widerström concludes.
The future of SGD is evidently one of innovation, growth, and a firm commitment to excellence in defence solutions.
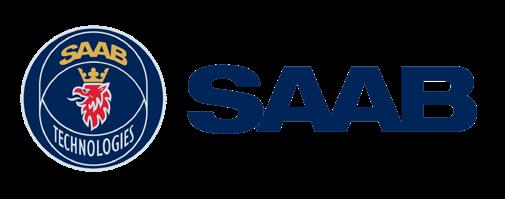
CEMENTING A PLACE IN HISTORY
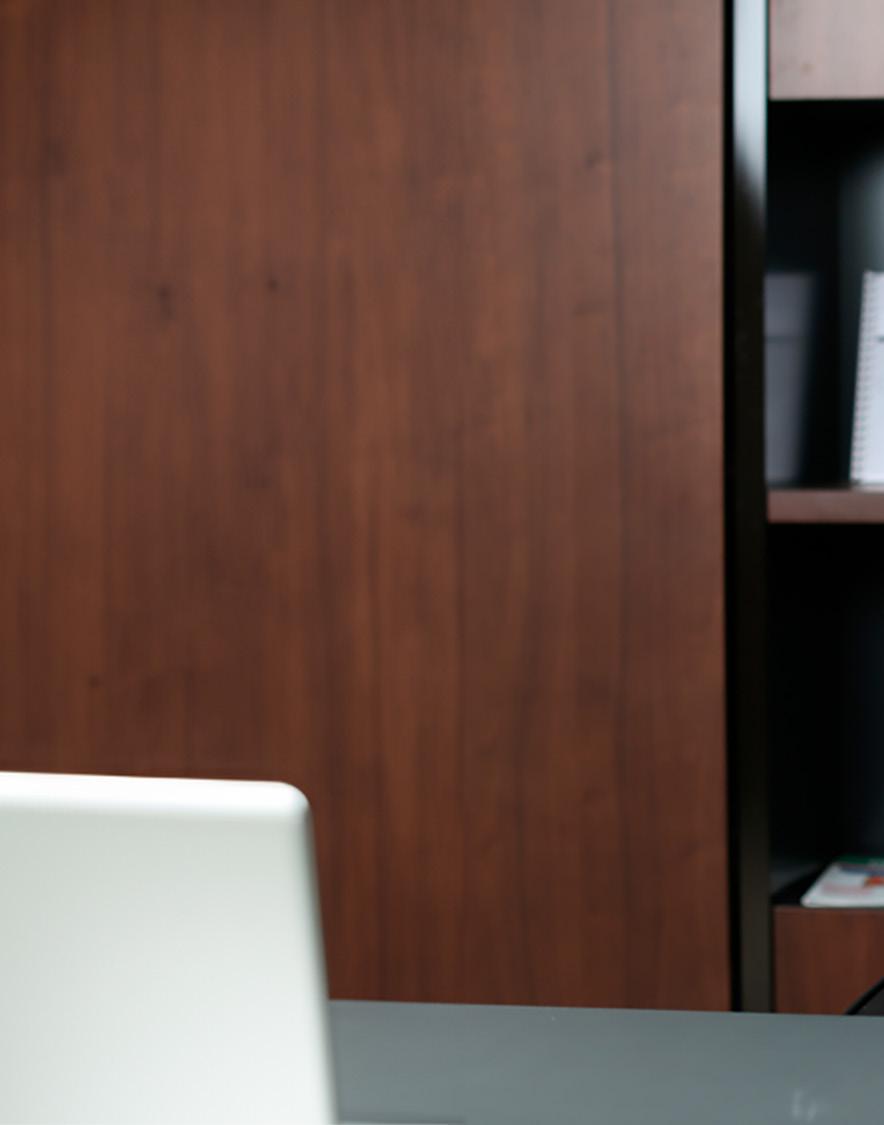
Cimencam has been operating in the construction materials sector since 1963 and is now proud to be one of the largest cement and concrete companies in Cameroon. CEO, Xavier Legrand, gives us all the details of this impressive success story
Writer: Ed Budds | Project Manager: Josh Whiteside
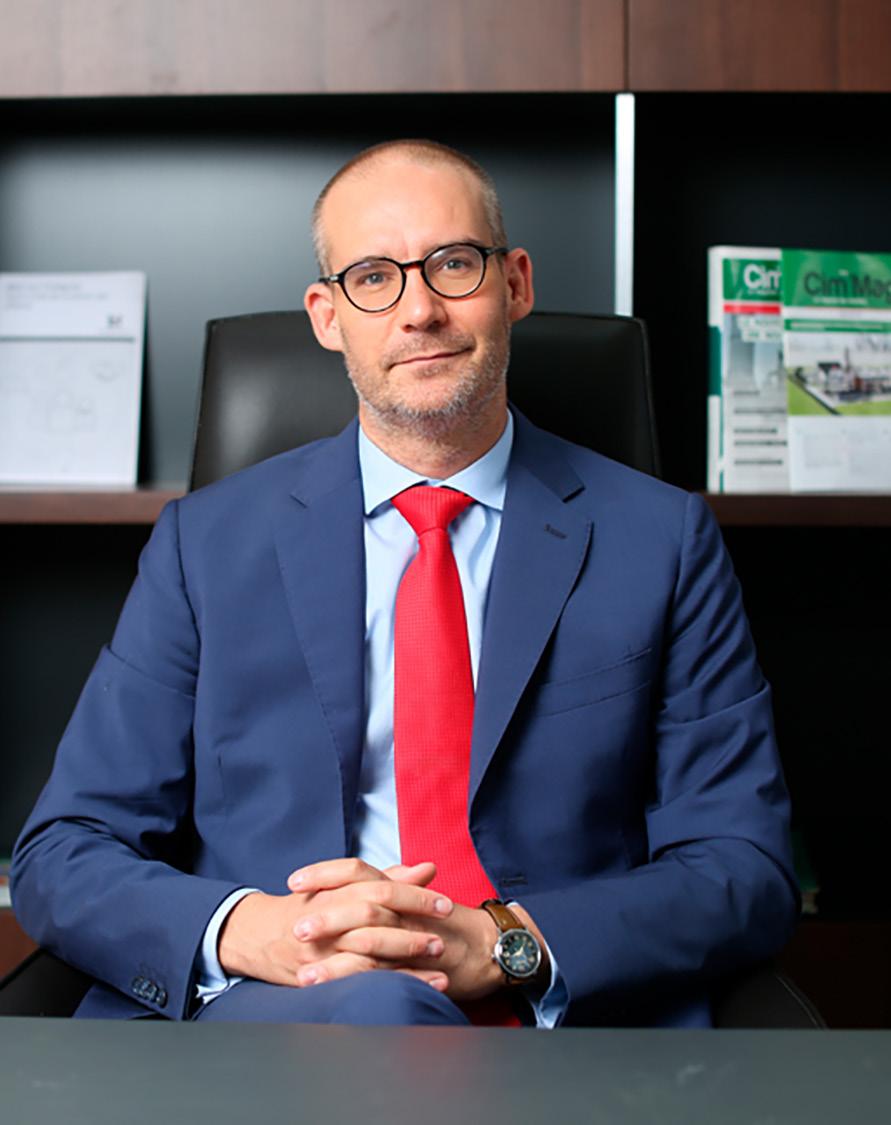
The African manufacturing and construction industries are currently more strategic and exciting than ever.”
The opening words of Xavier Legrand, CEO of Cimencam, reflect the surging nature of these vast, everexpanding sectors.
He believes these closely linked industries sit at the intersection of enormous economic, technological, and environmental change for the entire continent.
“At Cimencam, we are actively engaged in this evolution firsthand – the digitisation of our processes, integration of circular economy principles, and increasing sustainability demands are
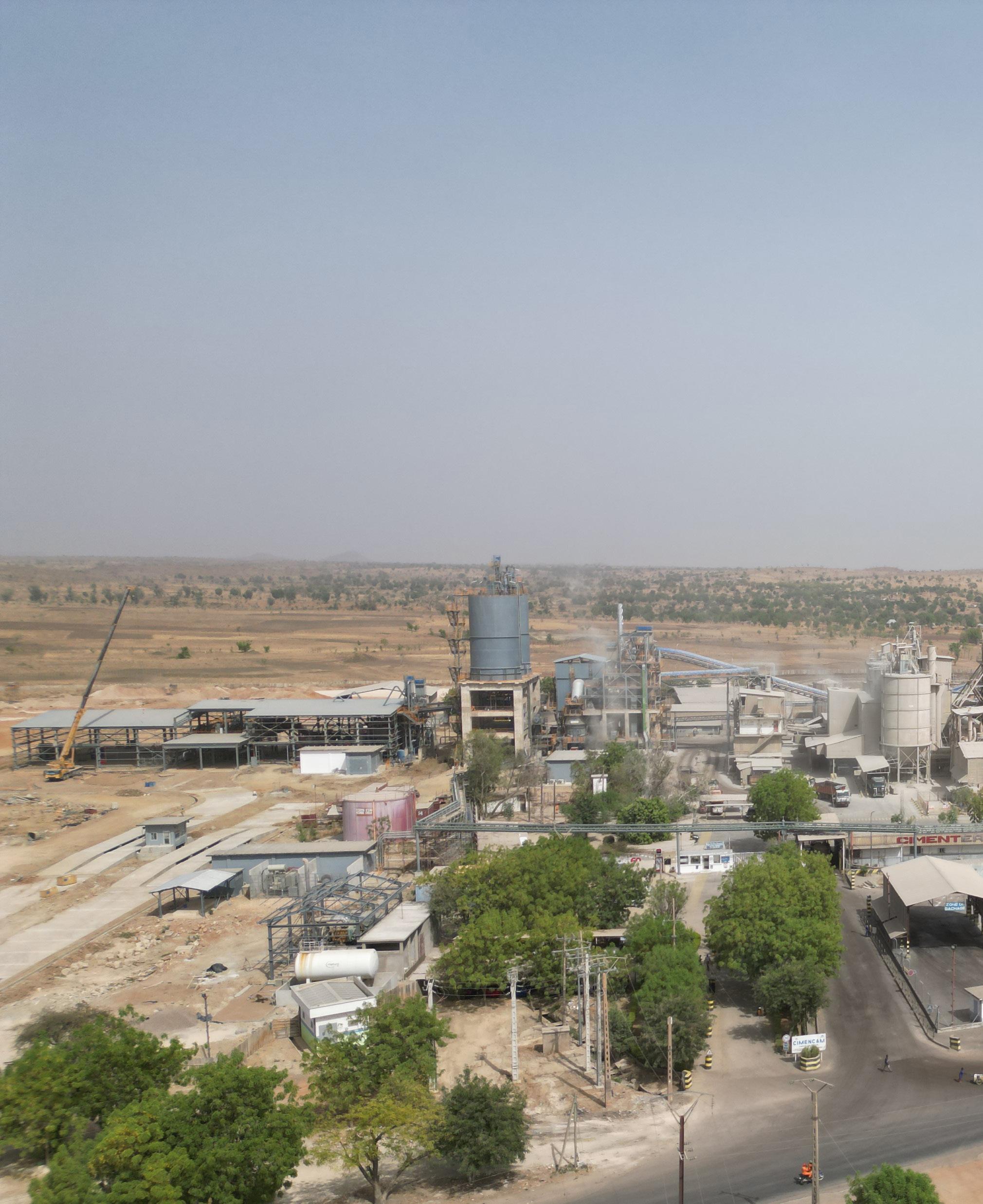
profoundly reshaping our operations,” he introduces.
“These immense challenges make our work even more stimulating as they push us to innovate, adapt, and anticipate the expectations of our clients and stakeholders.”
Across Africa, innovative and resilient companies such as Cimencam continue to thrive within this burgeoning industry transformation and rise valiantly to overcome the many obstacles that follow.
THE PRIDE OF THE NATION
At present, the increased demand for housing, infrastructure projects, and commercial developments continues to fuel the expansion of the African
cement market.
Cimencam is a pioneer of Cameroon’s cement industry, operating proudly across the nation since 1963.
As a subsidiary of the Holcim Group, the company is a part of what has become a global leader in construction solutions.
“Our mission is to provide innovative, high-quality building solutions across Cameroon and the wider region,” Legrand sets out.
Today, Cimencam’s production sites include the Bonaberi plant in Douala, its oldest site to date, the Nomayos plant near Yaoundé, and most recently, a new, state-of-the-art subsidiary in Figuil, located in the
“AT CIMENCAM, WE DON’T JUST PRODUCE CEMENT – WE SUPPORT OUR CLIENTS WITH TAILORED SOLUTIONS AND A STRONG SENSE OF LOCAL PROXIMITY”
– XAVIER LEGRAND, CEO, CIMENCAM
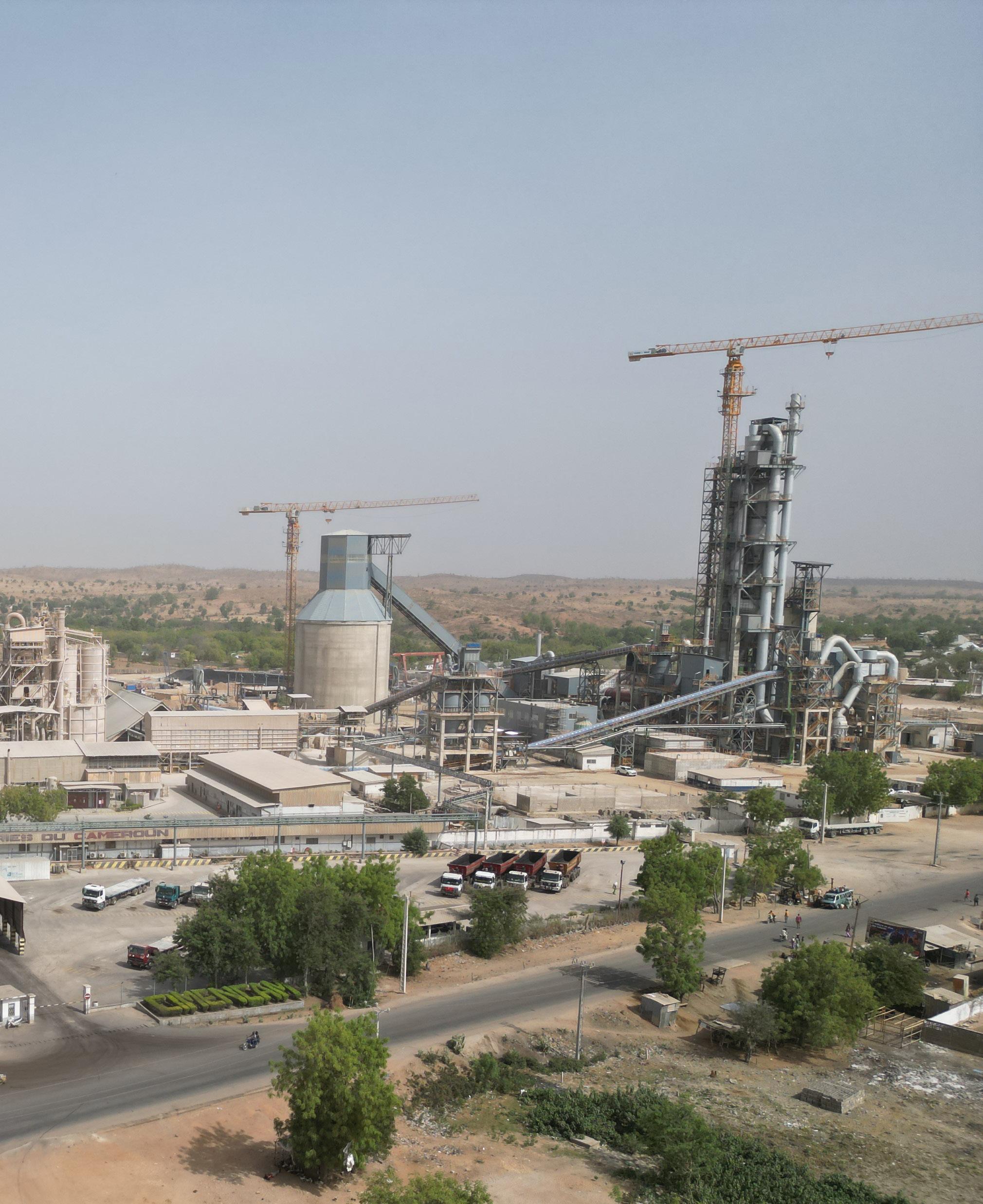
North Region of Cameroon.
“We produce and market a wide range of solutions, tailored for various uses, including individual houses, public works, buildings, and major infrastructures,” he lists.
SUSTAINABLE SUPPLY AND DEMAND
Undoubtedly, the company’s greatest strength lies in its ability to combine operational excellence, product innovation, and social responsibility.
“At Cimencam, we don’t just produce cement – we support our clients with tailored solutions and a strong sense of local proximity,” Legrand affirms.
Alongside this, the company’s connection to the Holcim Group allows it to benefit from global best practices whilst remaining deeply rooted in local realities.
Equally vital to Cimencam’s success is the smooth operation of its meticulously crafted supply chain, which stands as a key pillar of its exceptional performance.
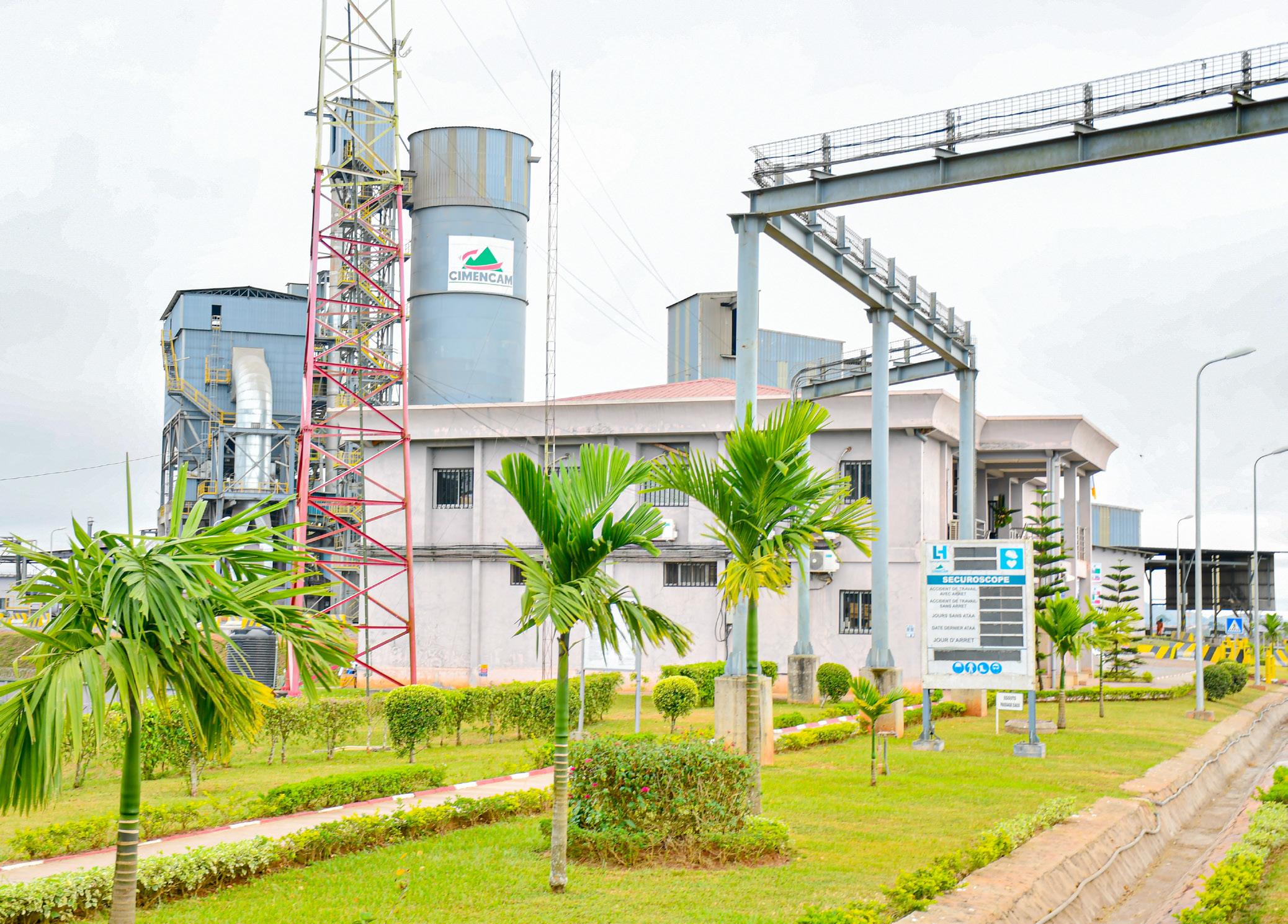
CIMENCAM’S KEY PRIORITIES
• Strengthening market leadership, particularly with the support of the company’s new plant and expanded product range.
• Advancing its digitalisation strategy, particularly in logistics and commercial operations.
• Accelerating the environmental transition by increasing the use of alternative fuels.
• Focusing on building stakeholder relationships.
• Further developing staff skills through targeted, high-impact training programmes.
“I’M ALWAYS KEEN TO HIGHLIGHT A KEY DRIVER OF OUR SUCCESS - THE REMARKABLE COMMITMENT OF OUR EMPLOYEES”
– XAVIER LEGRAND, CEO, CIMENCAM
“We place strong emphasis on building long-term, ethical relationships with our partners, utilising regular meetings as opportunities to review progress and identify areas for improvement,” he says.
Furthermore, an impressive territorial footprint, committed human capital, and contribution to sustainable development truly set the business apart.
CIMENCAM FIGUIL PLANT
One of Cimencam’s most significant projects is its new Figuil plant, which was inaugurated on 12th June.
“The opening of this facility represents a major milestone that strengthens our presence in Cameroon’s North Region. The plant is fully aligned with our strategy of industrial proximity and reduced logistical costs,” Legrand prides.
Cimencam Figuil is the company’s newly created subsidiary, and its integrated plant has been established to meet the growing demand in Northern Cameroon and neighbouring Chad, with a production capacity of approximately 500,000 tonnes of cement per year.
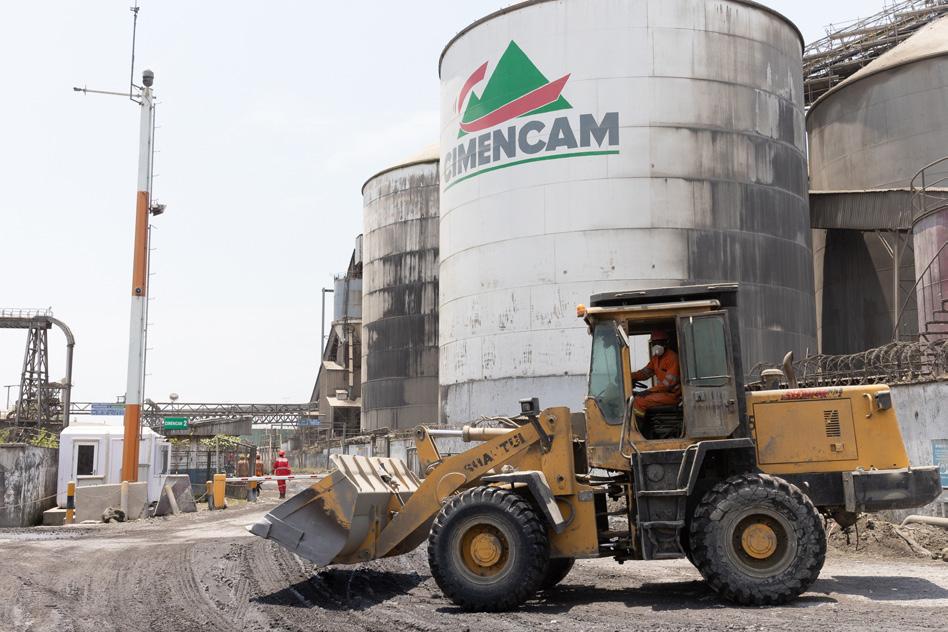
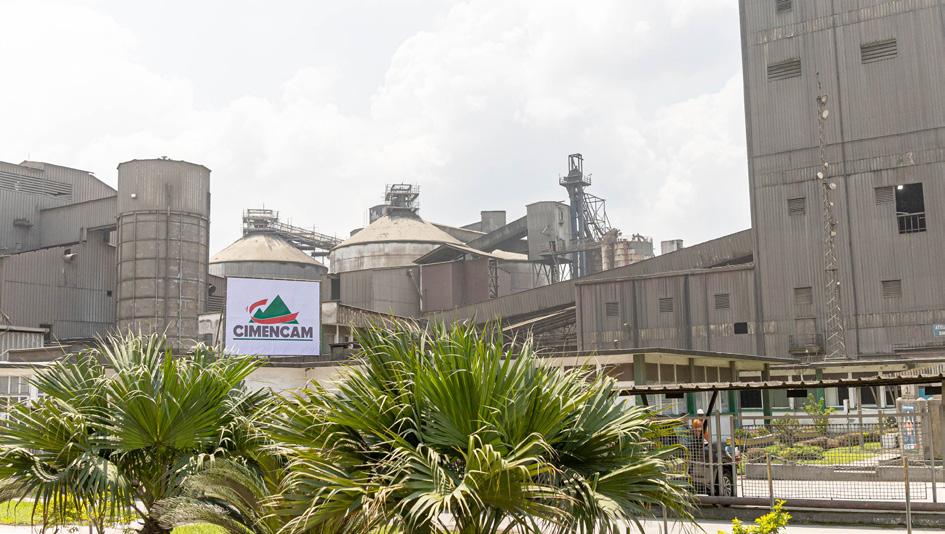
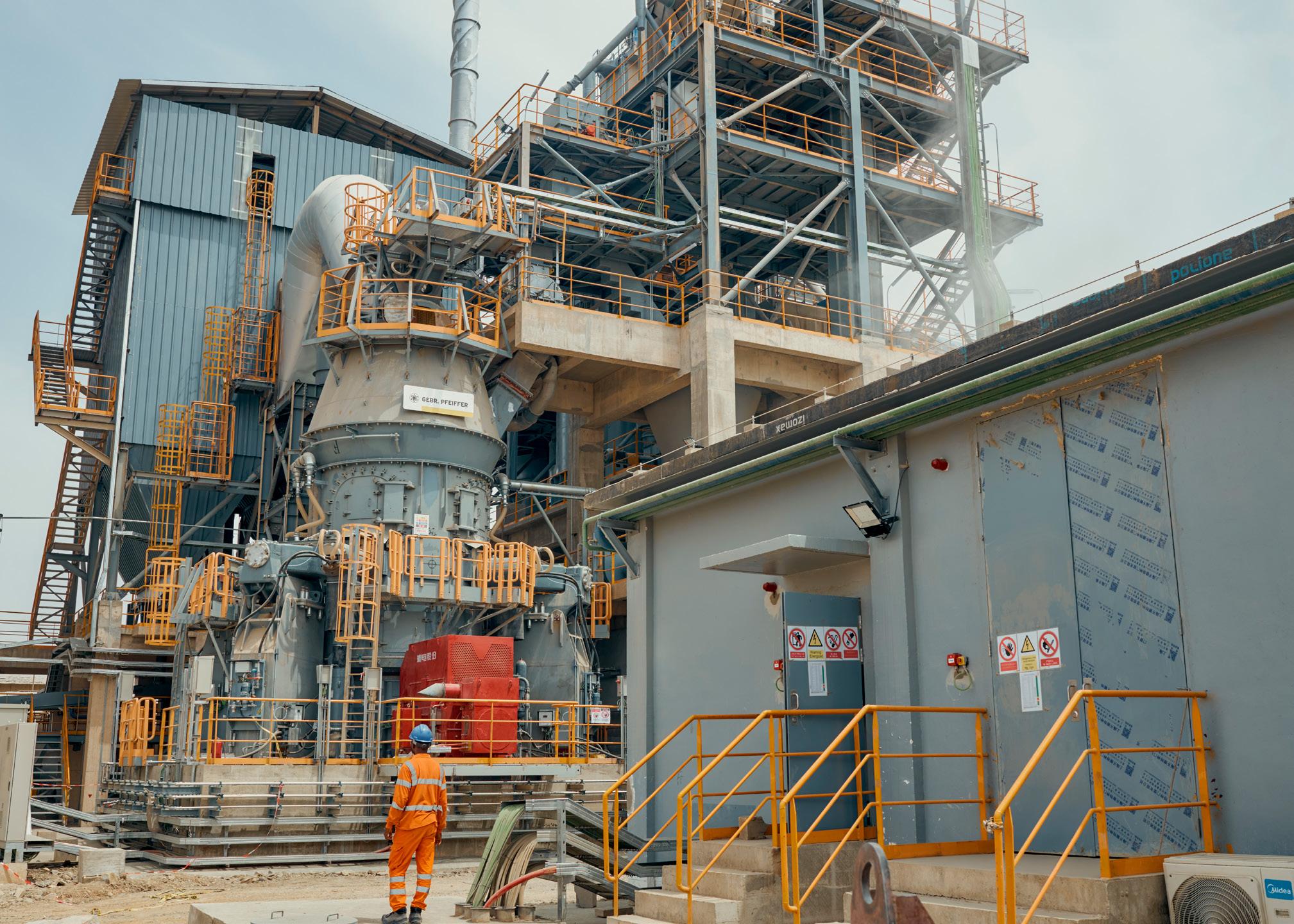
CIMENCAM’S VALUES – AT A GLANCE
• The health and safety of its teams, subcontractors, and families is Cimencam’s top priority. In conducting its business, the company is committed to ensuring a safe and healthy working environment for all its employees, with an overarching goal of achieving zero accidents on its sites.
• Cimencam builds partnerships with its suppliers. This dedication to collaboration ensures the company can guarantee the highest and most consistent quality of its products and services. As part of its ongoing efforts to strengthen relationships with its subcontractors and service providers, Cimencam considers a multitude of criteria other than performance, price, and quality.
• Rigorous health and safety standards have been integrated into every action across each facet of the company’s operations. In addition, staff must have a deep understanding of Cimencam’s health and safety rules.
Impressively, the project has seen more than three million hours worked without a single major accident.
Legrand believes its impact on the region will be significant, creating an estimated 900 new sustainable jobs
both directly and indirectly.
“The plant will also facilitate new business opportunities for local entrepreneurs, improve socioeconomic and cultural conditions in the region, and grow
support for the completion of infrastructure projects,” he excites.
MAINTAINING SOCIAL RESPONSIBILITY
The overarching corporate social responsibility (CSR) strategy at Cimencam aims to balance economic performance with positive social impact by creating value for its stakeholders. To date, the company has consistently ranked amongst the top five socially responsible companies in Cameroon.
“Regarding our social aspect, we act across three key areas – education, health, and employability. One standout initiative is our road safety programme for motorcycle taxi drivers, designed to improve road behaviour and reduce the number of accidents,” Legrand voices.
“Environmentally, we are actively working on reducing our carbon footprint, managing dust emissions, and ensuring a positive impact on nature
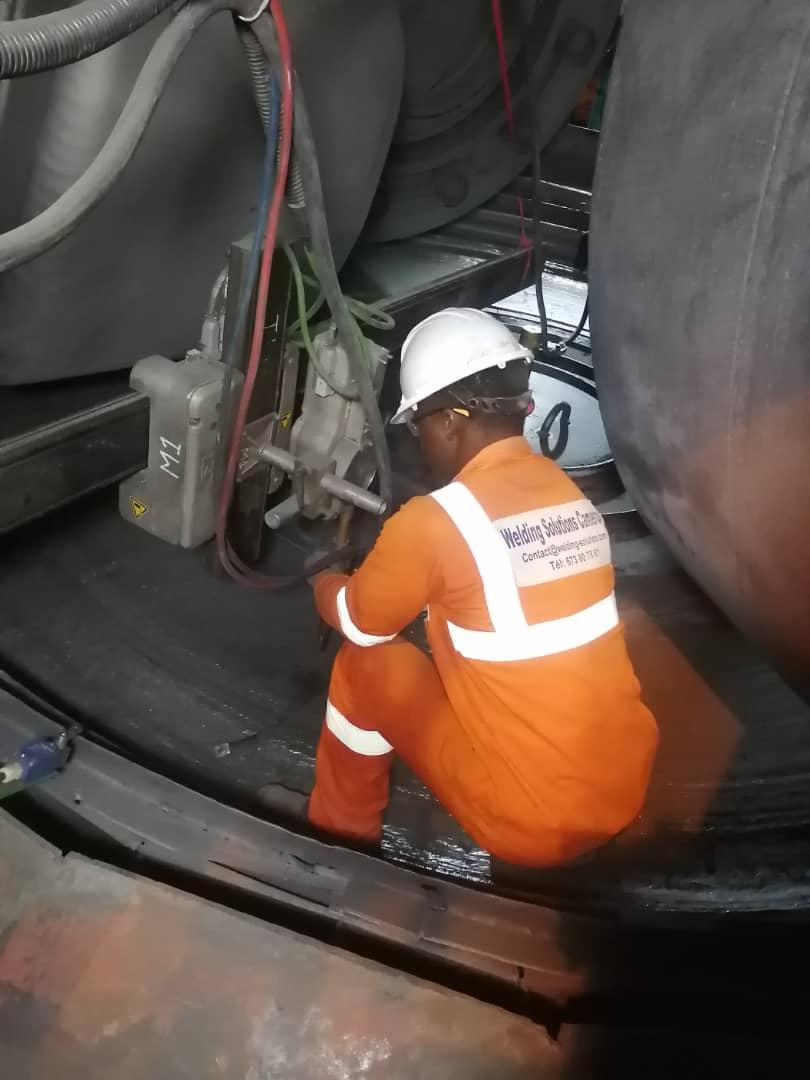
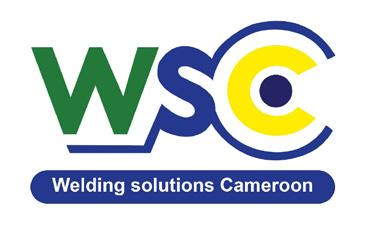
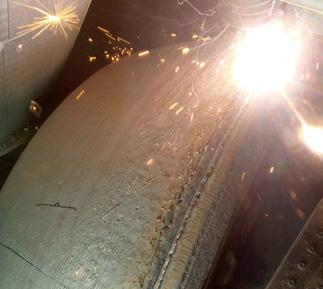
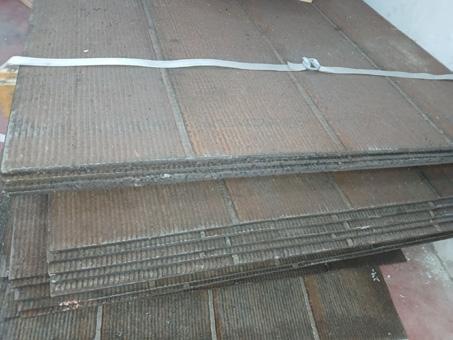
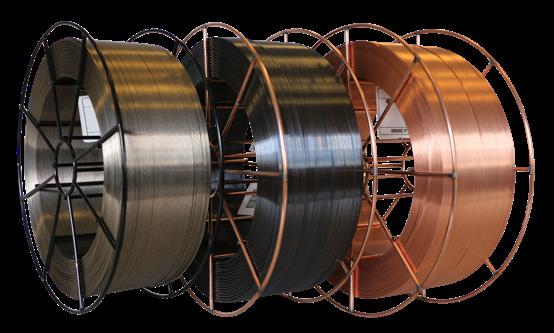
through multiple initiatives such as replacing fossil fuels with biomass and recycled oils, reusing wastewater, and planting trees in communities near our sites,” he follows up.
Parallel to these initiatives, Cimencam proudly supports local wealth creation by collaborating with agricultural cooperatives, offering financial assistance for fertiliser purchases, and training in farming techniques.
“We have also launched a textile training programme to promote community empowerment through sewing and tailoring skills,” Legrand confirms.
Meanwhile, over the past three years, Cimencam’s staff have volunteered more than 2,000 hours to help local communities, raising awareness amongst young students and school children about the dangers of and ways to prevent HIV and AIDS, malaria, poor sanitation, cholera, and domestic accidents.
The wear phenomenon affects many industries. This is a progressive deterioration through loss of material due to prolonged or overly frequent use. For grinding equipment, wear degrades the condition of a part, leading to a loss of performance.
Due to its experience and solid know-how, Welding Solutions Cameroon is the central africa leading provider of advanced anti-wear products (hardfacing wire, electrode, overlay wear plate, ceramic, …) and in-situ hardfacing services (Refurbishment of grinding parts.)
Welding Solutions Cameroon’ mission is to improve quality of life of maintenance teams through high performance anti-wear materials.
THE HEART OF THE BUSINESS
At Cimencam, the employees are the driving force behind the company’s excellent performance and formidable track record.
“Through ambitious training programmes, ongoing social dialogue, and a strong recognition policy, we place people at the heart of our strategy,” Legrand tells us.
Furthermore, the company’s development programmes, such as its comprehensive talent review and commitment to diversity and inclusion, reflect a firm desire to create a fulfilling, fair, and empowering workplace for all.
“I’m always keen to highlight a key driver of our success – the remarkable commitment of our employees. Thanks to their dedication, professionalism, and team spirit, we achieved outstanding results in Q1 2025, both industrially and commercially,” he explains.
From meeting production targets and maintaining operational discipline to implementing strategic projects, each team within the company has played a vital role in achieving its shared success.
“This positive momentum stems from a healthy work environment, a culture of continuous improvement, and a shared sense of purpose. It’s a great source of pride and a powerful lever for driving us forward, together,” Legrand concludes proudly.
CEMENTING A SUSTAINABLE FUTURE
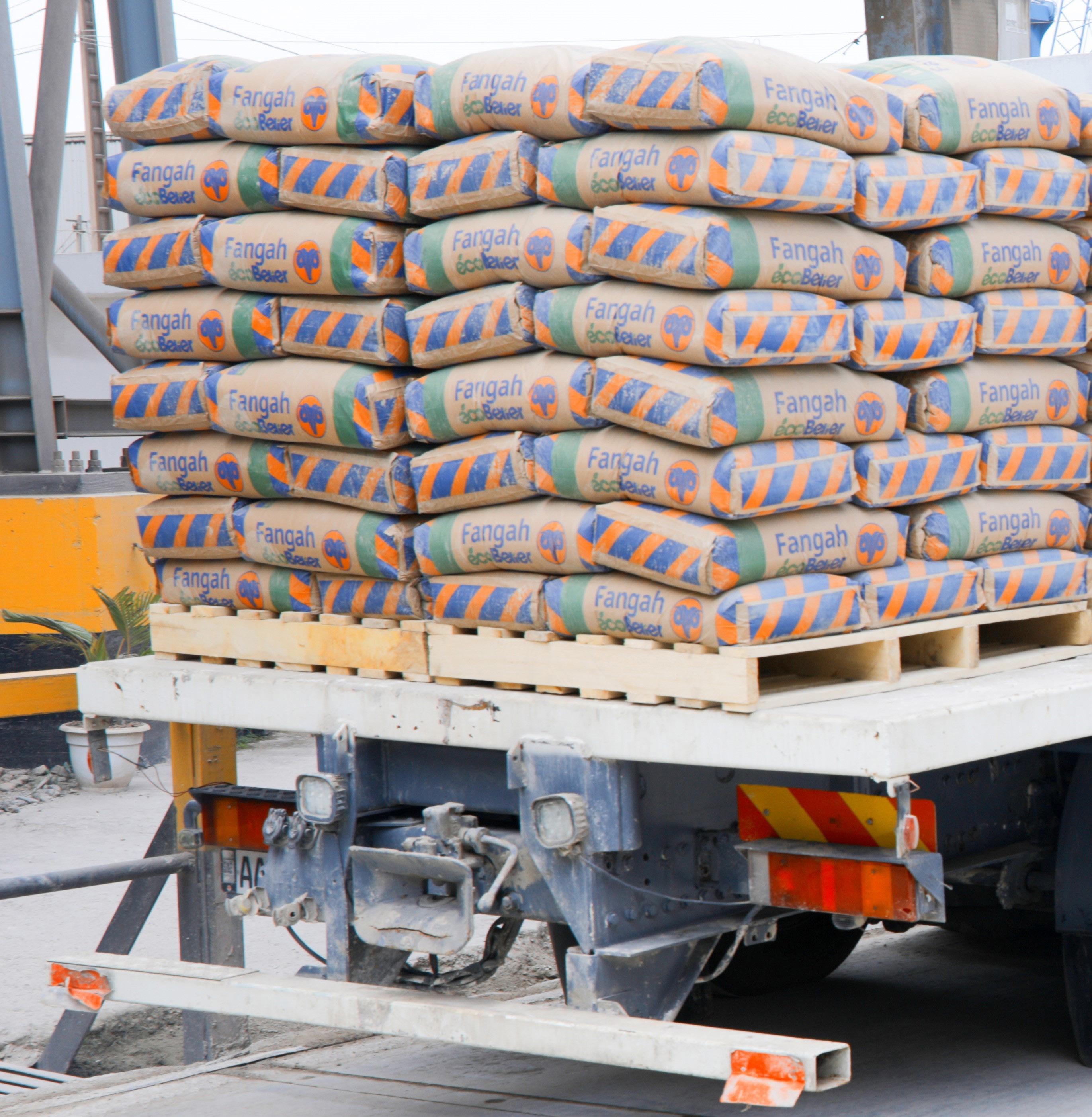
As it seeks to reshape West Africa’s cement sector, we reconnect with LafargeHolcim Côte d’Ivoire, who is on a mission to provide highquality, sustainable construction solutions whilst actively contributing to the socioeconomic progress of the region. Rachid Yousry, Country CEO, tells us more
Writer: Lily Sawyer | Project Manager: Josh Whiteside
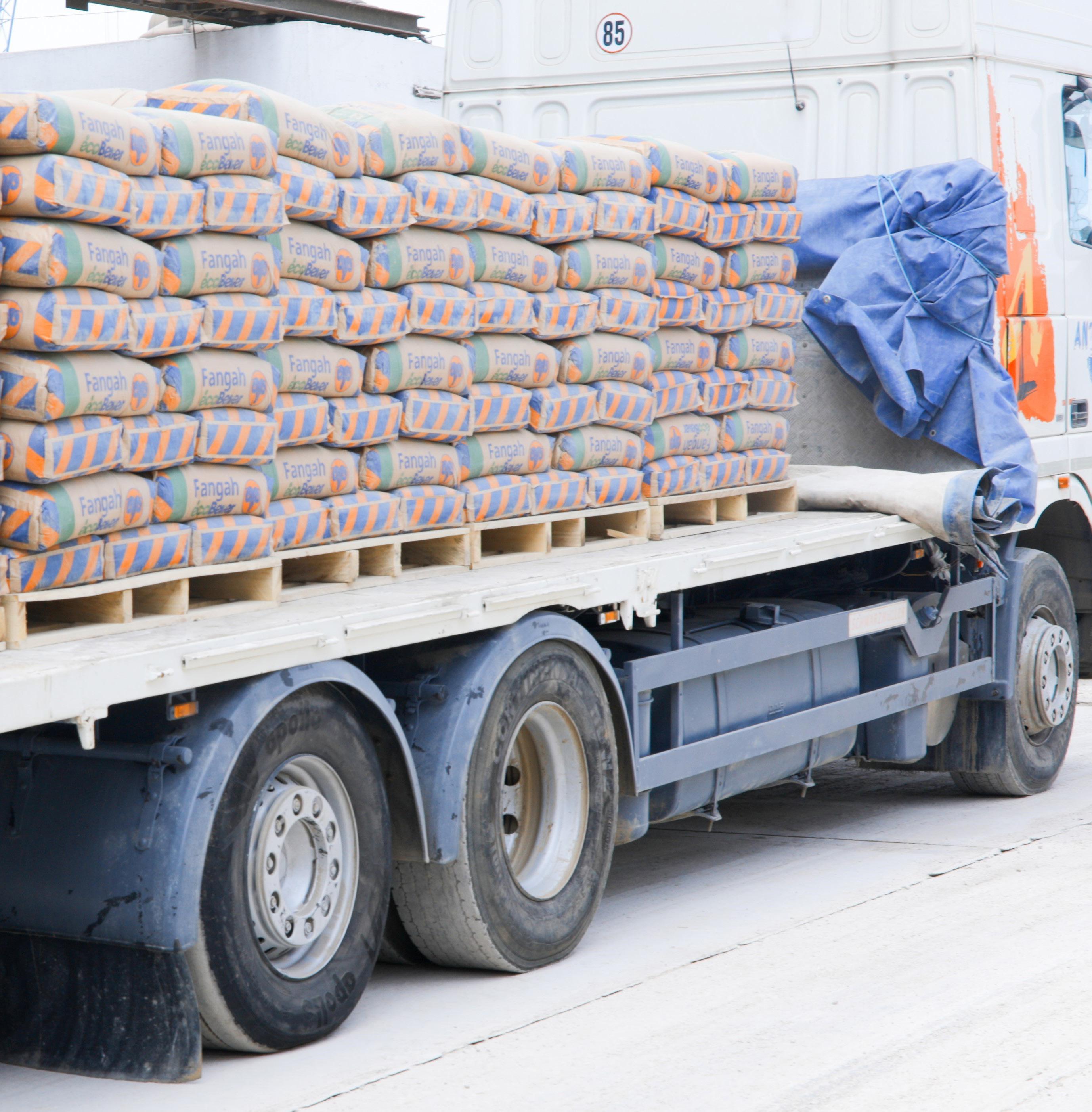
Asubsidiary of the Holcim Group, LafargeHolcim Côte d’Ivoire (LafargeHolcim CI) has embodied excellence and innovation in the country’s cement industry since 1952.
Committed to sustainable development and research, the company has emerged as a key player in the sector, currently employing 150 staff members and over 200 subcontractors.
“Ciment Bélier, our flagship
product, has played a crucial role in the construction of major infrastructure and buildings across the country and continues to drive the growth of construction projects in Côte d’Ivoire and beyond,” introduces Rachid Yousry, Country CEO.
With an annual production capacity of two million tonnes (t), LafargeHolcim CI ensures continuous, efficient distribution and a marketresponsive supply.
Operating from its headquarters in Abidjan and with a manufacturing plant, quarry, and raw materials storage facility at its disposal, the company remains true to its mission.
“Demonstrating our expertise and industrial heritage, we are on a mission to provide high-quality, sustainable construction solutions and actively contribute to the socioeconomic progress of the region,” he confirms.
A SUSTAINABLE OPERATION
Standing out from the competition as the only company producing six different types of cement, LafargeHolcim CI considers itself a market transformer.
Its slag cement is highly praised for a low carbon footprint and its exceptional resistance to the most aggressive environments. As pioneers of white cement in West Africa, the company also supplies builders and architects with premium raw material that meets the highest standards.
“In an industry where the proliferation of products exposes users to major risks, we have maintained the trust of our customers through our unwavering quality and unmatched stability,” Yousry tells us.
As such, every bag of Ciment Bélier embodies LafargeHolcim CI’s absolute commitment to sustainability and reliability.
With environmental preservation and sustainable construction at its core, the company is also launching its own pozzolana cement quarry – a low-carbon cement product designed to combine performance and environmental responsibility by reducing carbon dioxide (CO2) emissions by 40 percent across the construction sector.
As an end-to-end managed site with an annual production capacity of 300,000t, LafargeHolcim CI’s pozzolana quarry in Sokouamékro has so far enabled a cumulative reduction of over 500,000t of carbon emissions since its commissioning.
“This breakthrough aligns perfectly with our goal of offering increasingly innovative and ecofriendly materials,” he prides.
LafargeHolcim CI also invested F. CFA 3.5 billion in 2018 to install a cement bag palletiser,
significantly reducing manual handling which is known to be a primary source of dust emissions during loading operations.
“In 2021, we also commissioned a new clinker silo, backed by an F. CFA18 billion investment,” Yousry adds.
COULD YOU PROVIDE US WITH SOME INSIGHT INTO YOUR CAREER TO DATE?
Rachid Yousry, Country CEO: “I am a trained computer science analyst and hold an MBA from École des Ponts Business School in Paris.
“With over 30 years of experience in commerce and logistics, I have held major leadership positions across various markets.
“In July 2011, I joined Holcim Group as Cement Supply Chain Director in Iraq, where I later took on commercial and logistics leadership roles.
“My career then expanded across the Middle Eastern region, where I served as Logistics Director for Africa and the Middle East, defining key strategies and standards to support regional operations in achieving their logistics objectives.
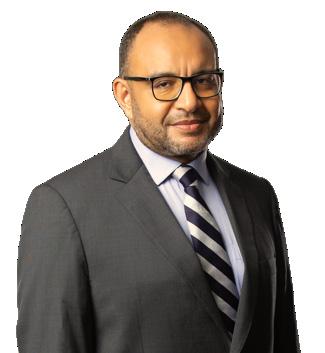
“I then transitioned to Jordan, where I held the position of Commercial and Supply Chain Director for three
“In June 2021, I was appointed CEO of LafargeHolcim CI, and since December 2023, have also served as President of the Cement Producers Association.”
This strategic infrastructure reduces truck unloading operations by 90 percent, which led to a significant drop in dust emissions from raw materials transport, and helped decongest the port area, eliminating the equivalent of 18,000 trucks per year.
POWERED BY PEOPLE
With strength that goes beyond its products, LafargeHolcim CI’s dedicated, innovative, and passionate teams are at the heart of its success, giving their best every day to build the future.
“Our employees are the driving force behind our success. We foster a culture of respect, inclusion, and wellbeing, where every team member is valued for their dedication and expertise,” Yousry outlines.
Celebrating loyalty and excellence through dedicated events, such as the recent Honorary Work Medal Ceremony which recognised the contributions and commitment of employees over the years, LafargeHolcim CI is dedicated to staff development.
“We invest in training and skillbuilding programmes, enabling our teams to acquire new expertise and advance their careers” he details.
The company seizes every opportunity to prioritise internal candidates who demonstrate strong engagement and a clear willingness to develop the organisation when it comes to recruitment.
“We also continuously strive to improve working conditions, integrating modern infrastructure and initiatives that enhance safety and well-being,” Yousry continues.
LafargeHolcim CI firmly believes that respect, recognition, and inclusion are essential to building a high-performing and sustainable company.
Through these commitments, it creates an environment where everyone has a place and can actively contribute to collective progress.
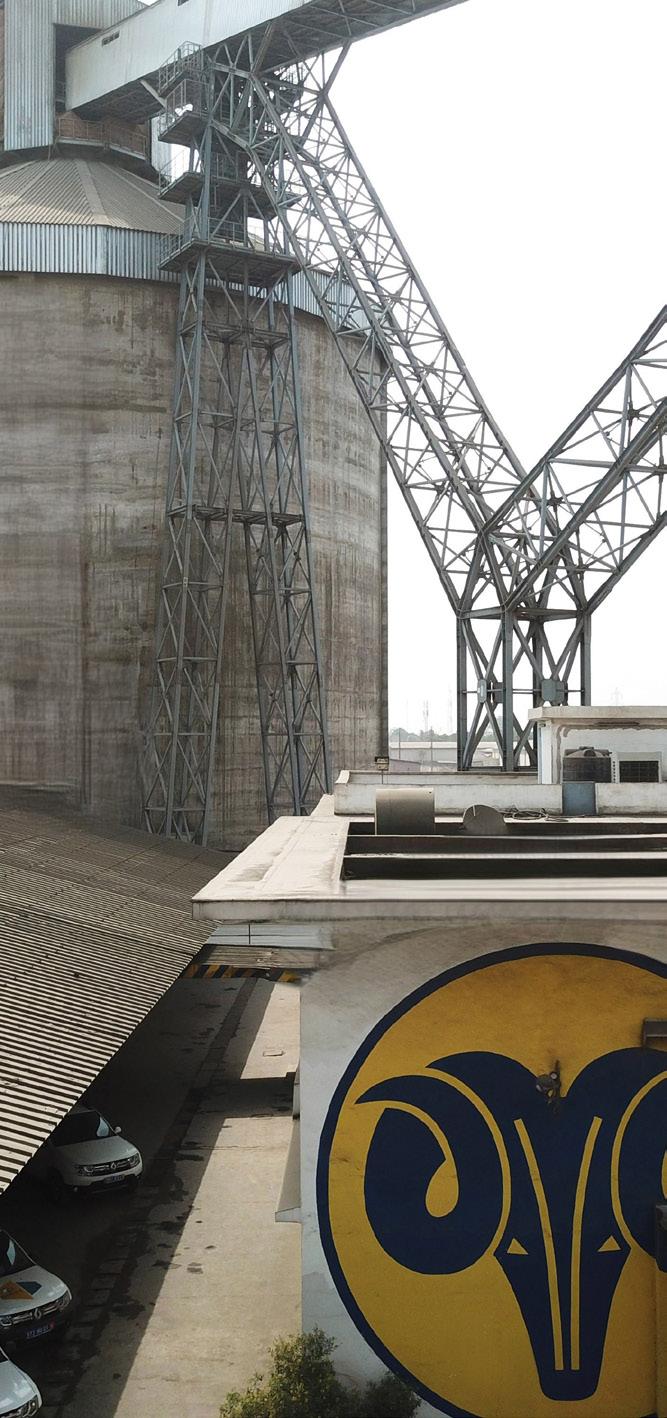
SOCIALLY RESPONSIBLE
Dedicated to transforming the construction industry by integrating innovative and sustainable solutions, LafargeHolcim CI’s initiatives reflect its ambition to build responsibly and contribute to community development.
Fuelled by the momentum of its pozzolana cement launch in 2024, the company took a decisive step forward with the launch of Bélier Blanc cement – the first white cement produced in West Africa that is fully compliant with international standards.
“This product provides construction professionals with a high-quality local alternative, reducing reliance on imports and ensuring consistent availability,” Yousry explains.
LafargeHolcim CI’s commitment to progress extends beyond industrial innovation and into education and community development.
“With a total of F.CFA200 million
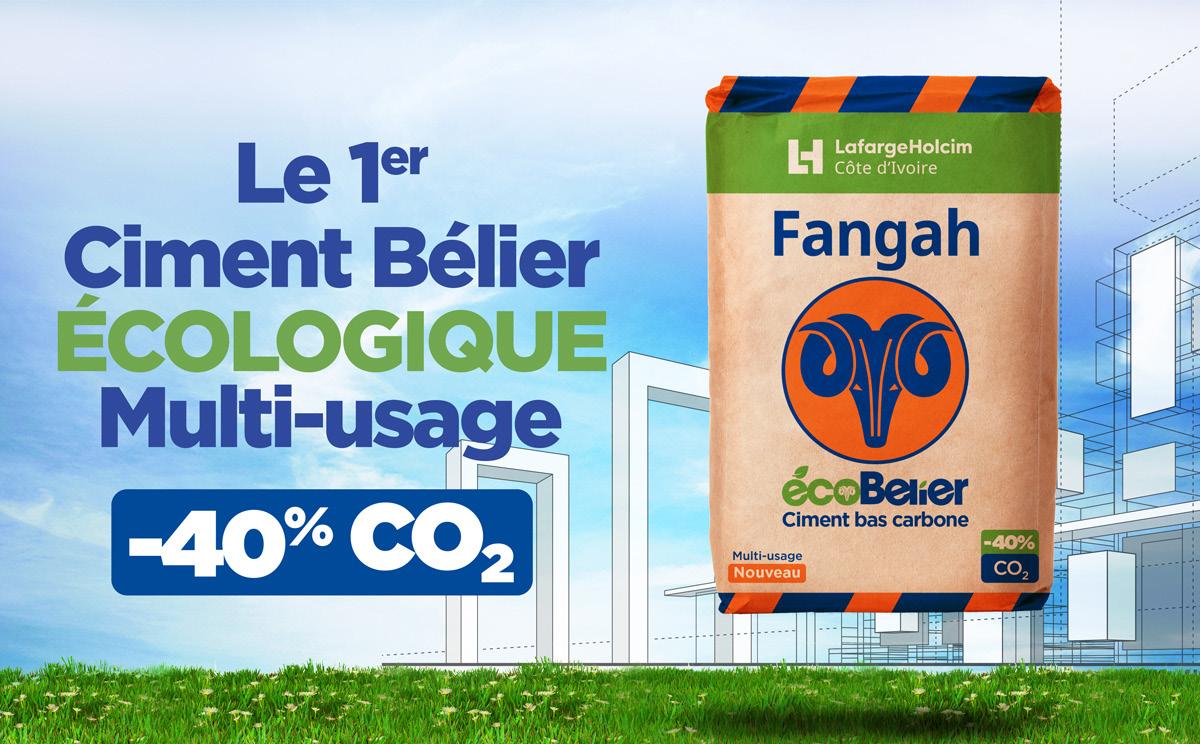
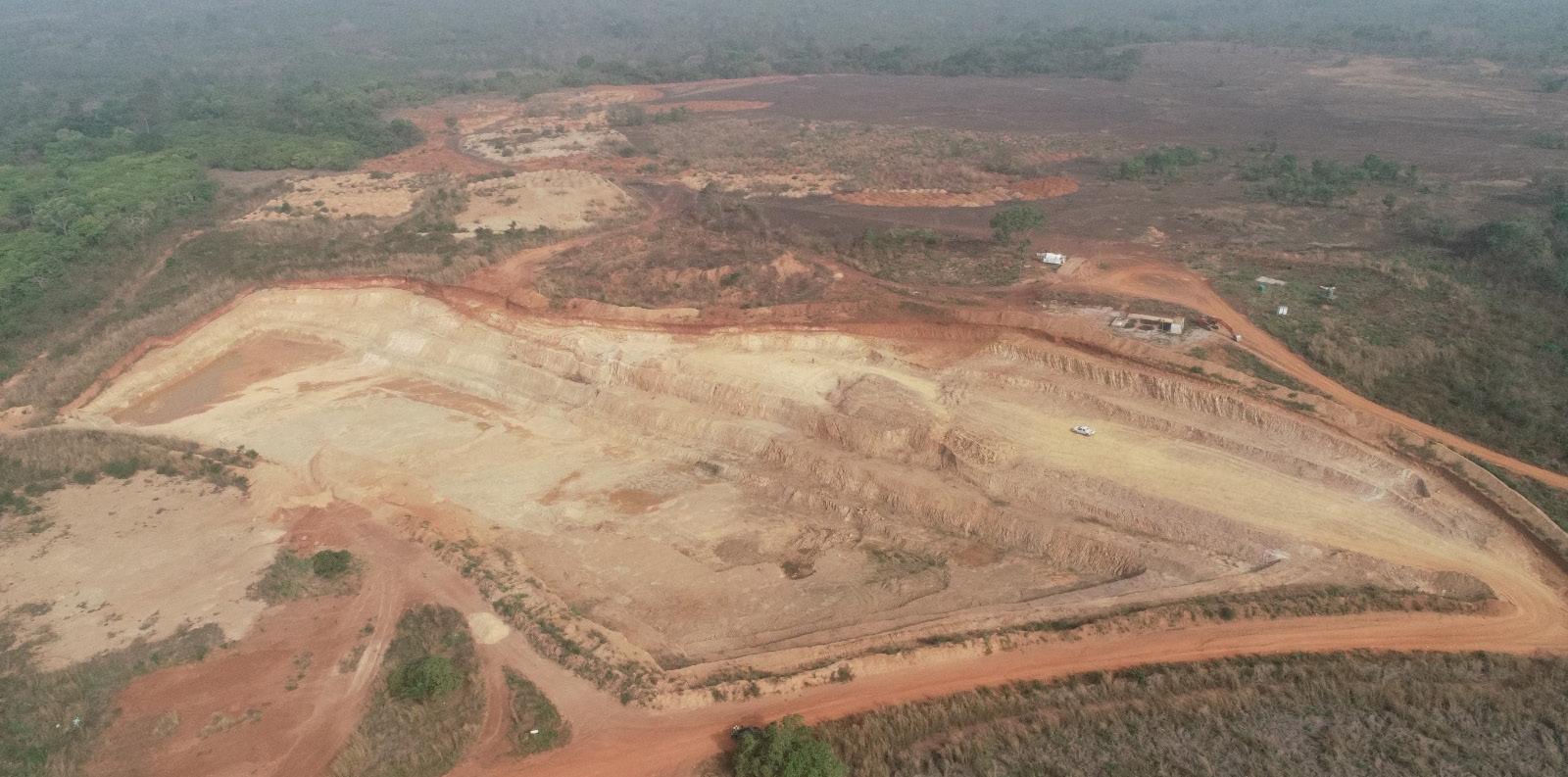
“THESE INVESTMENTS GO BEYOND TECHNOLOGICAL AND FINANCIAL ADVANCEMENTS – THEY REFLECT A BROADER VISION OF AN INDUSTRY CAPABLE OF COMBINING PERFORMANCE WITH ENVIRONMENTAL RESPONSIBILITY”
– RACHID YOUSRY, COUNTRY CEO, LAFARGEHOLCIM CÔTE D’IVOIRE
invested in École Primaire Publique (EPP) Kouamekro , a local primary school, we are providing a modern and secure educational environment for the children of Sokouamékro,” he impassions.
Following the official handover of the classrooms in October 2023, the company is continuing its initiative with the construction of a school canteen, library, and six housing units for teachers.
“By delivering these essential infrastructures on a 1.5-hectare site, we are helping to create an optimal learning environment, whilst enhancing the school’s appeal for both teachers and students.”
LafargeHolcim CI is also investing in environmental measures to improve its processes and minimise its ecological footprint.
“Reducing dust emissions by utilising innovative equipment,
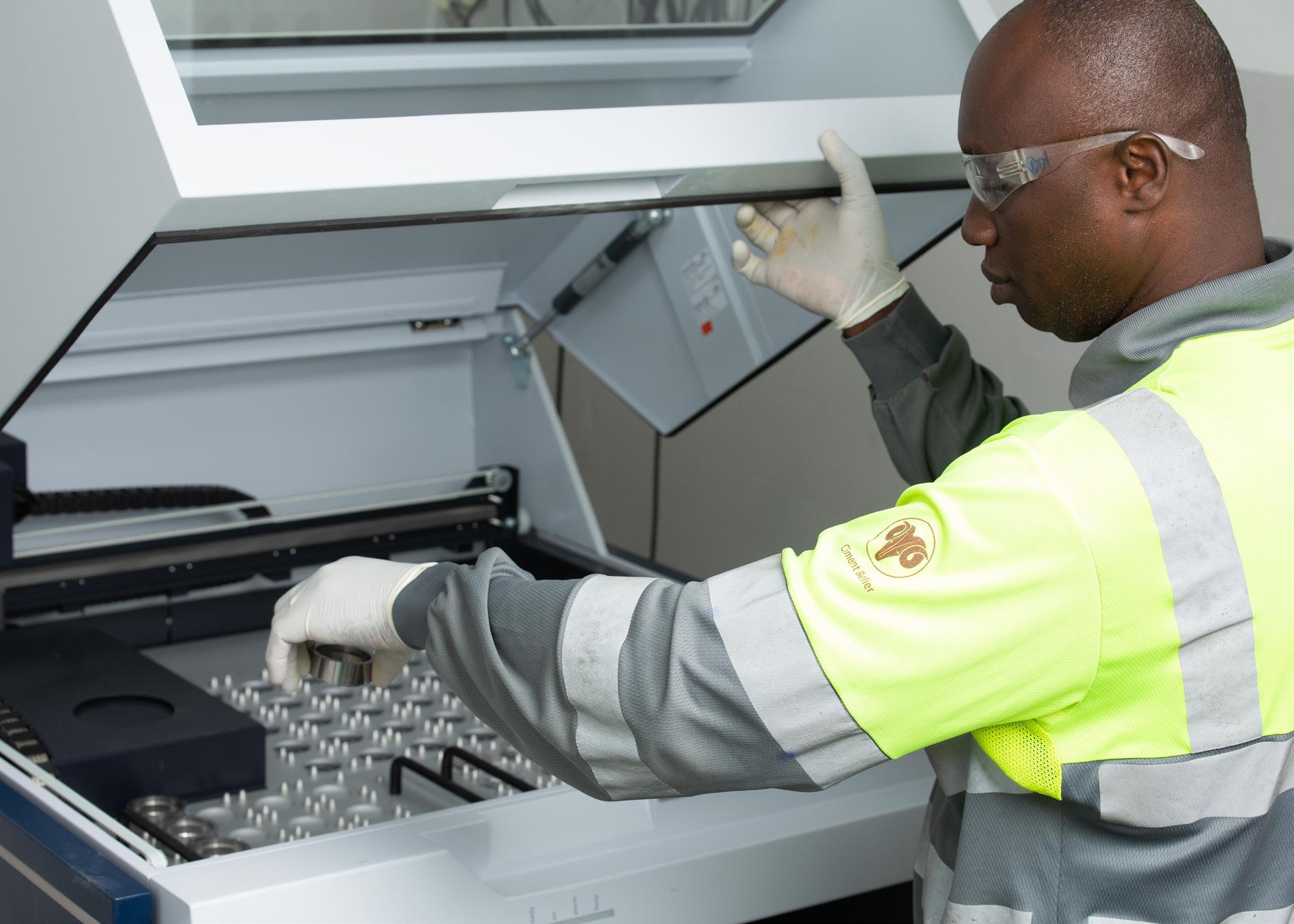
COMMITTED TO HEALTH AND SAFETY
LafargeHolcim CI places HSE at the core of its daily commitments, far beyond mere priorities. With a clear ambition to achieve zero incidents by 2030, the company has implemented a structured programme that is already delivering results.
This programme is built on six strategic pillars, developed in collaboration with subcontractors to ensure a comprehensive and sustainable approach:
• On-site safety – Implementation of the strictest HSE standards, including critical control management, ensure effective risk management for major hazards.
• Zero-risk culture – Deployment of the BootsOnGround (BOG) innovation, a mobile application that encourages managers and supervisors to increase their presence on-site and promote a proactive safety culture.
• Health – Upholding a preventive approach with rigorous monitoring of occupational risks, ensuring the well-being of employees.
• Road safety – A globally recognised programme, structured around three strategic pillars designed to protect employees and partners.
• Environmental excellence – Initiatives focused on preserving natural resources and reducing CO2 and dust emissions, contributing to a more sustainable future.
• Systems and processes – Use of cutting-edge tools certified by ISO 14001 and ISO 45001 standards, integrating digitalisation and artificial intelligence (AI) to optimise HSE performance.
optimising raw material transportation, and enhancing working conditions with safer and more sustainable infrastructure are just a few of the initiatives that demonstrate our commitment to responsible construction,” Yousry shares.
In July 2024, meanwhile, the company further strengthened its environmental initiatives with an F.CFA360 million investment in an innovative covering system for one of its plant’s shipping areas.
“This pioneering project underscores LafargeHolcim CI’s commitment to providing a healthier and more comfortable work environment, benefiting both employees and surrounding communities,” he adds.
Through these undertakings, the company reaffirms its ambition to build a sustainable and inclusive future, contributing to progress for both people and the planet.
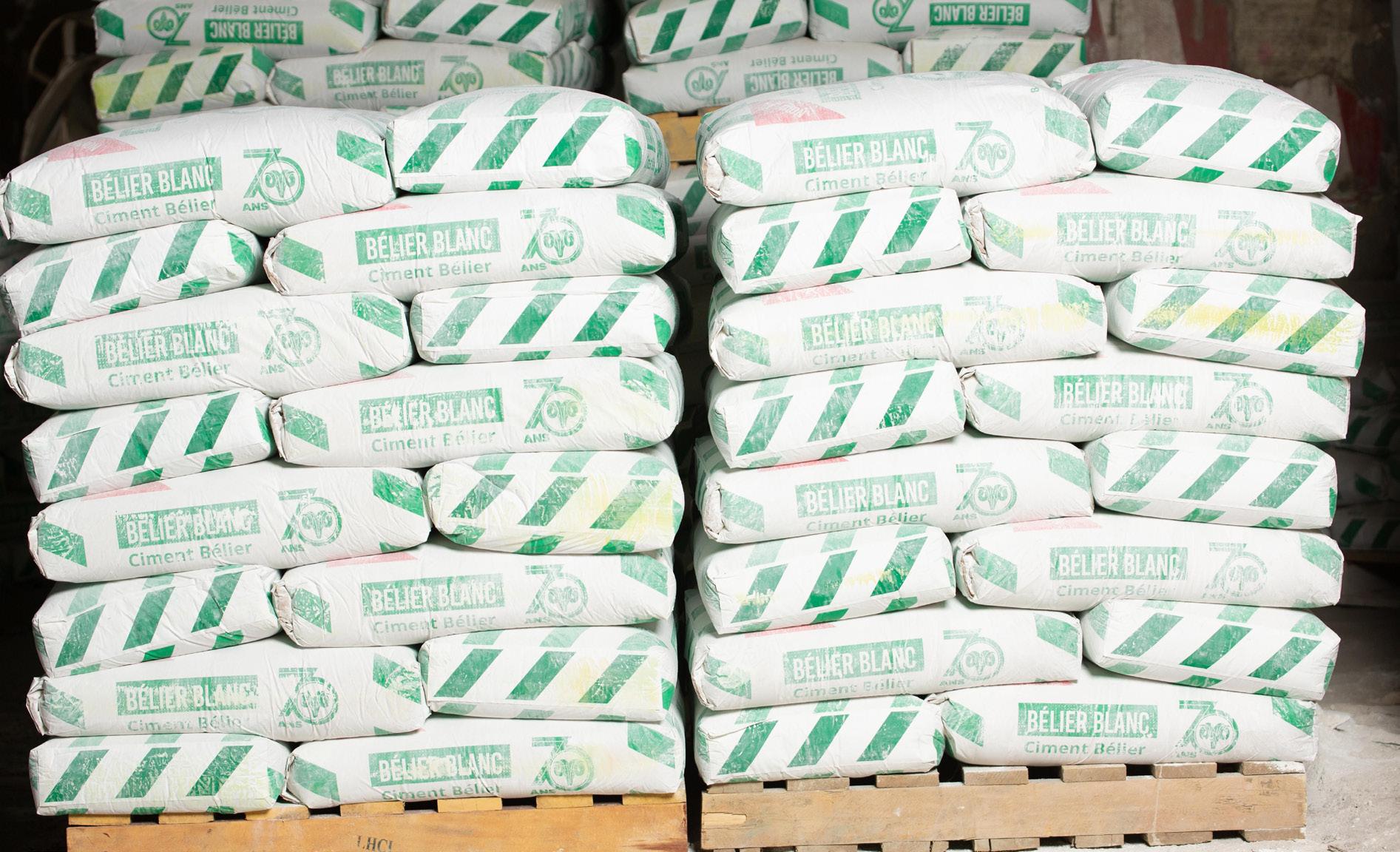
A BRIGHT FUTURE
Through an ambitious and structured approach based on six strategic pillars, LafargeHolcim CI reaffirms its commitment to building a safer, healthier, and more environmentally responsible workplace.
“Health and safety are no longer seen as a set of rules to follow. Our employees increasingly understand and believe that processes and safety standards are there to protect them — not to constrain them,” Yousry reflects.
A testament to the company’s ongoing commitment and tangible progress in health, safety, and environment (HSE) protocols, LafargeHolcim CI is proud to announce its official status as part of Holcim Group’s Excellence Club for HSE, earning the distinguished silver status.
“This recognition reflects our continuous efforts to uphold the highest safety standards, foster
a proactive safety culture, and implement innovative solutions that protect our employees, partners, and communities,” he smiles.
The accolade also reinforces the company’s dedication to making workplace safety a priority and striving for excellence in every aspect of its operations.
Elsewhere, LafargeHolcim CI has recently reinforced its commitment to the circular economy by installing a cement recycling station on-site, representing an investment of F.CFA19.7 million.
“These investments go beyond technological and financial advancements – they reflect a broader vision of an industry capable of combining performance with environmental responsibility.”
Going forwards, LafargeHolcim CI has set a clear ambition to continue to significantly reduce the clinker factor in its cement formulations to increase the sustainability of its
products, having already achieved a 3.89 percent decrease between 2022 and 2024.
By 2030, the company’s goal is to achieve a global clinker factor of just 61 percent, aligning the African cement industry with a sustainable trajectory that promotes the circular economy and preservation of natural resources.
“This commitment reflects our dedication to innovation by integrating more responsible solutions whilst maintaining leading industrial performance,” Yousry passionately concludes.
Tel: +225 27 20 25 22 50 nadia.yace@holcim.com www.lafargeholcim.ci

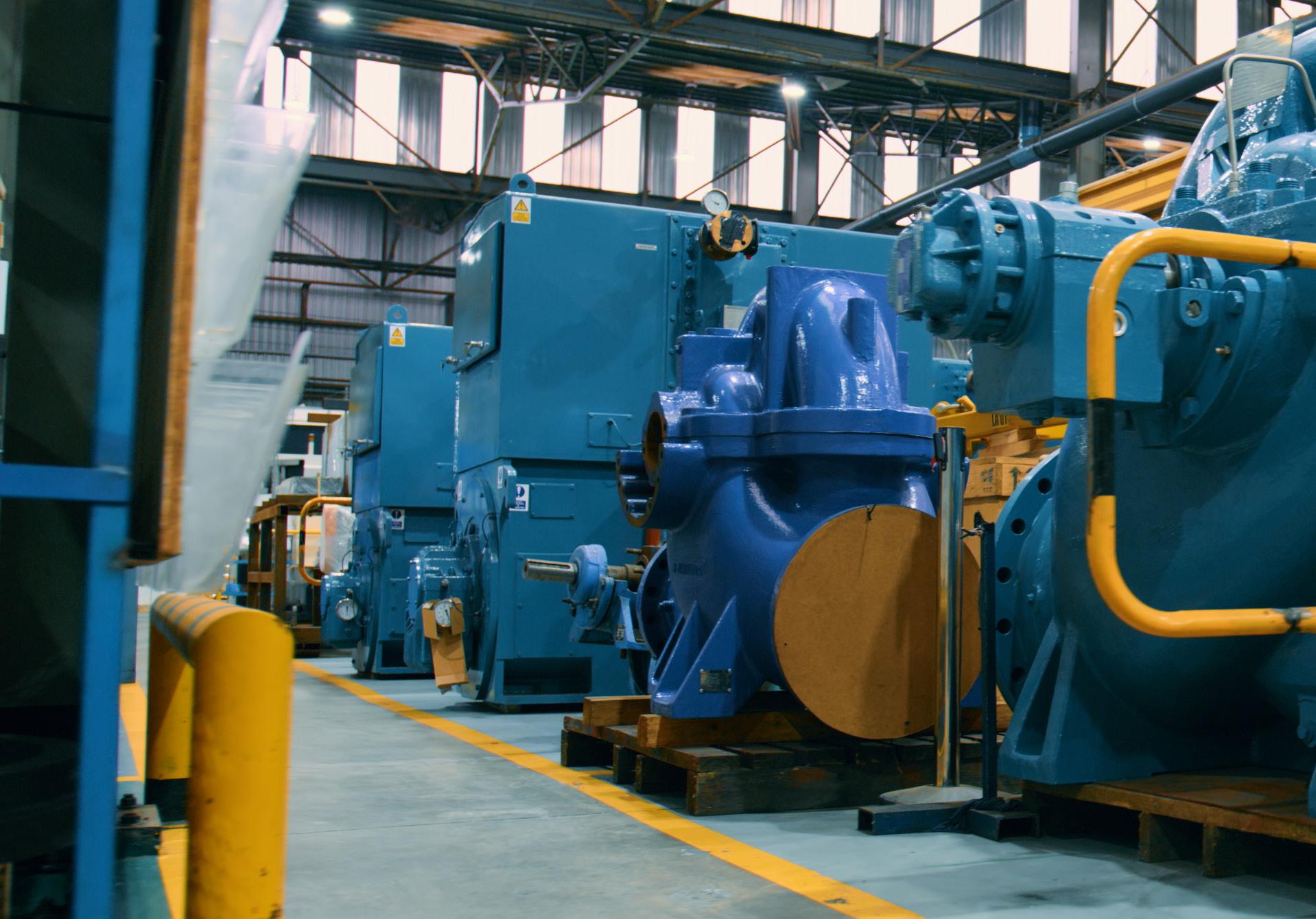
POWERING PARTNERSHIPS BEYOND PUMPS
We revisit Sulzer South Africa and Managing Director, Henry Craukamp, who enlightens us about the company’s ability to maintain certainty through its partnerships with customers in an uncertain business environment
Writer: Lucy Pilgrim | Project Manager: Poppi Burke
Established in 1922, Sulzer South Africa (Sulzer) quickly grew to become a highly established original equipment manufacturer (OEM) of pumps across the country. Since last featuring the company in 2023, Sulzer has continued to deepen its focus on developing maintenance and repair solutions around its customers’ rotating equipment needs, something which Managing Director, Henry Craukamp, has been passionate about since his appointment to the
role three years ago.
“By focusing on our customers’ needs, we started employing a preventative technology that transitioned our service orientation from reactive to proactive,” he opens.
Indeed, Sulzer supports customers across the entirety of their operations by providing cutting-edge maintenance and repair solutions for pumps, turbines, compressors, motors, generators, and high-speed gearboxes.
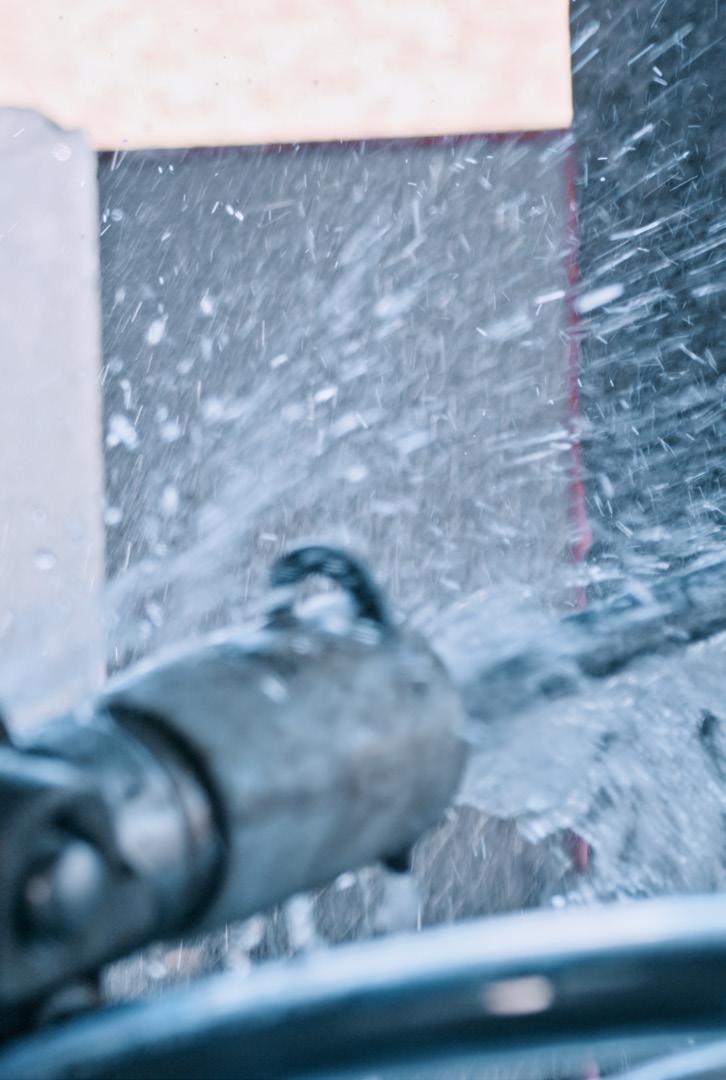
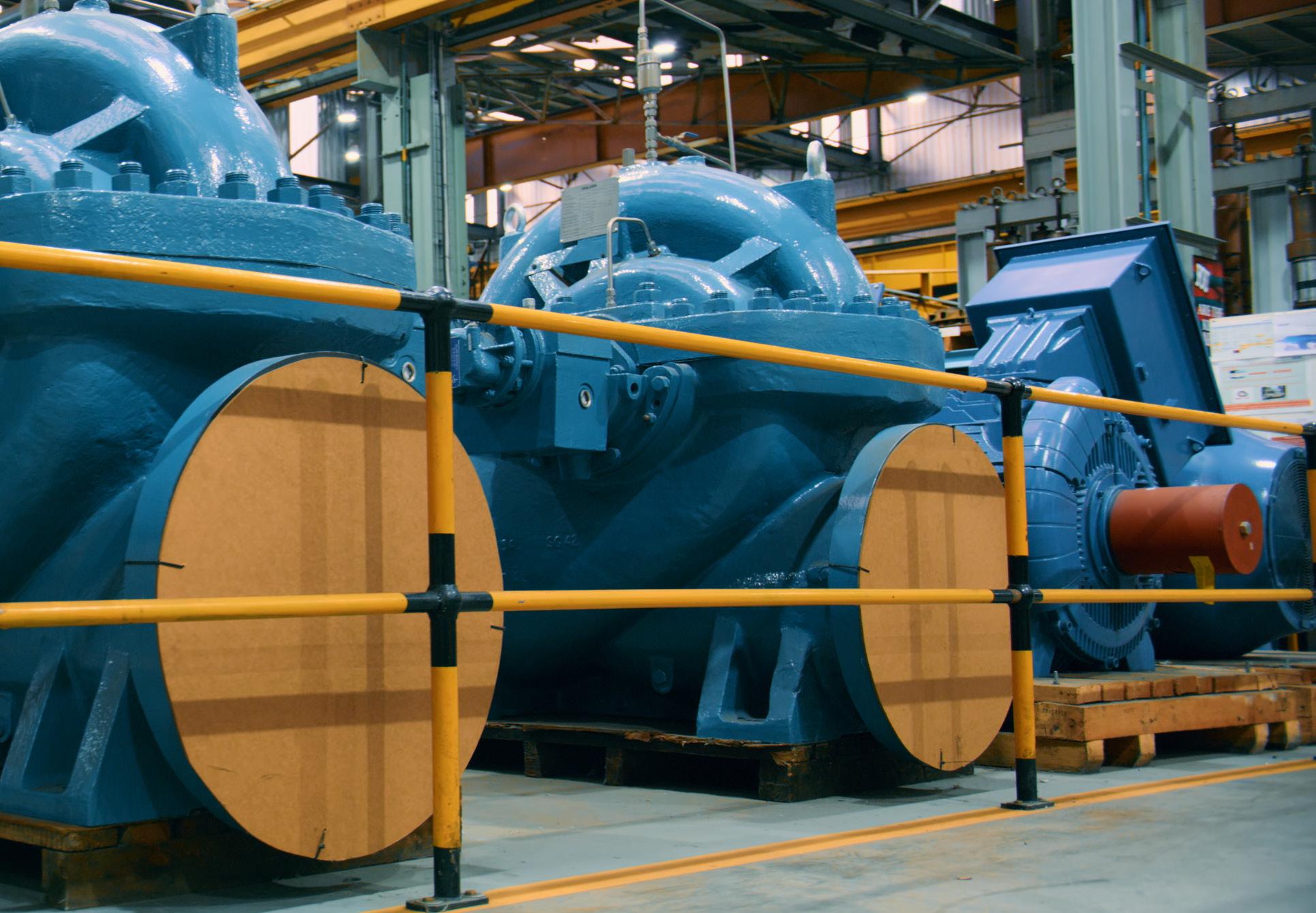

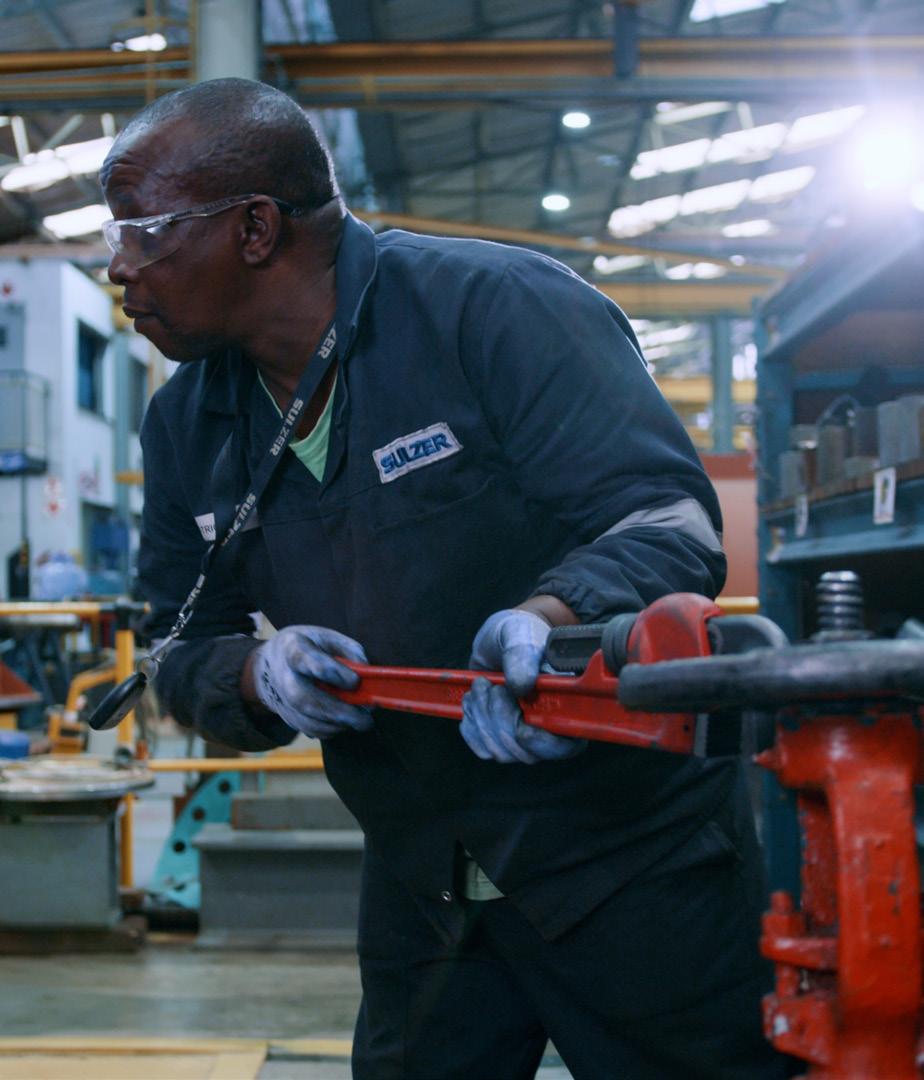
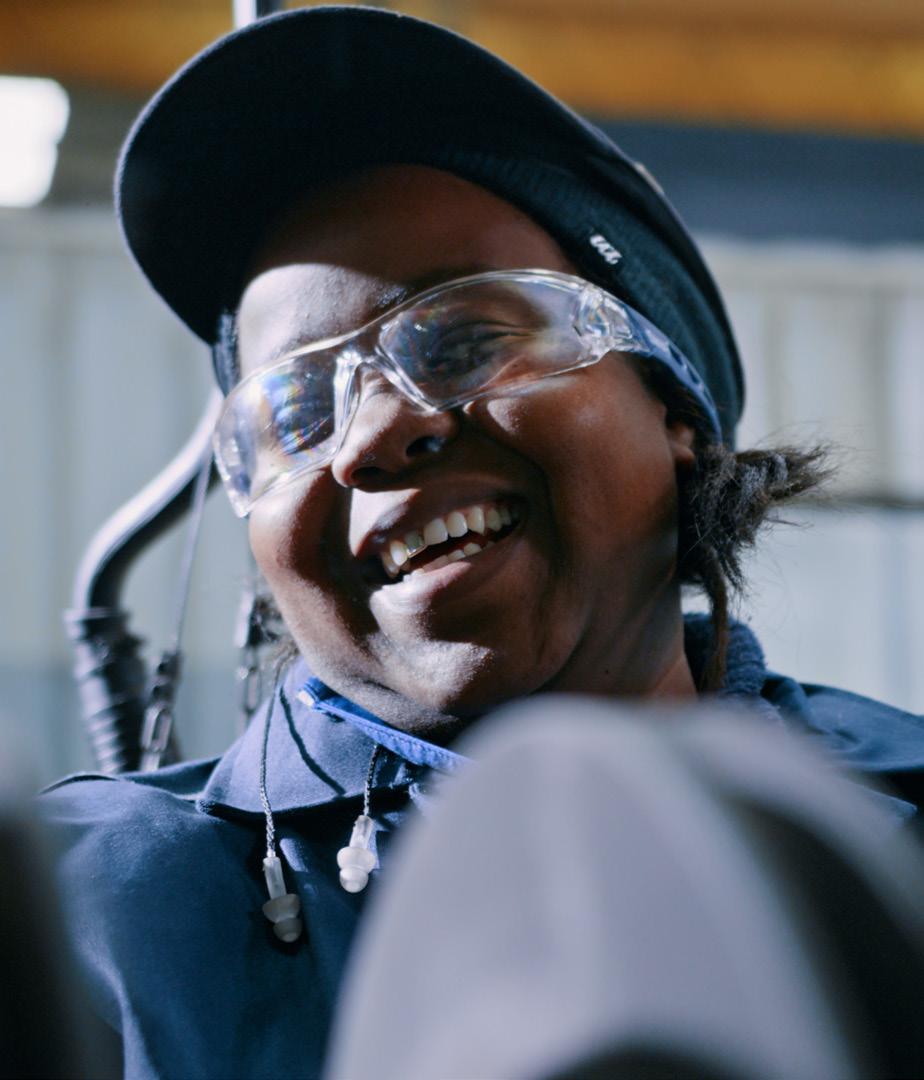
“The next phase of our support will target predictability using digital tools powered by machine learning (ML) technology. I believe this will enable us to unlock further potential in partnership with our customers,” Craukamp adds.
An additional key initiative for the company is the implementation of a track and trace platform that creates a digital footprint for every asset made, supporting customers with effective lifecycle management and leveraging real-time data to benchmark asset performance.
Sulzer is therefore able to maintain a complete record of its customers’ equipment from the moment it is added to the main database. The data can subsequently be accessed instantly by the field services team by simply scanning a QR code, enabling faster and more informed responses and decisions.
This capability significantly reduces downtime, minimising costs for customers and safeguarding their critical infrastructure.
“Real-time data is essential for digital tools to be effective, but this may not be feasible for some highsecurity industrial customers who could be at risk of malicious activity. In these cases, we deploy secure, on-site monitoring tools that operate independently of the customer’s control system,” he highlights.
This allows Sulzer to safely gather the data needed for its artificial intelligence (AI) platform to assess equipment risk accurately.
“Since every customer is at a different stage in their digital transformation, it’s vital that we work closely with them to offer tailored recommendations that suit their unique needs.”
END-TO-END SUPPORT
Sulzer serves a broad range of industries across South Africa (SA), such as oil and gas, chemical, water infrastructure, wastewater, power generation, and mining, with its Flow and Services divisions.
The former specialises in delivering engineered solutions, which includes the supply of pumps, mixers, compressors, and other fluid handling equipment.
The Services division, meanwhile, deploys a lifecycle approach to maximise equipment uptime, efficiency, and longevity for both Sulzer and its equipment. This is achieved through the company’s comprehensive maintenance, repair, and upgrade solutions for rotating equipment.
“We also operate several specialised facilities across SA to support our customers with localised expertise and service,” Craukamp states.
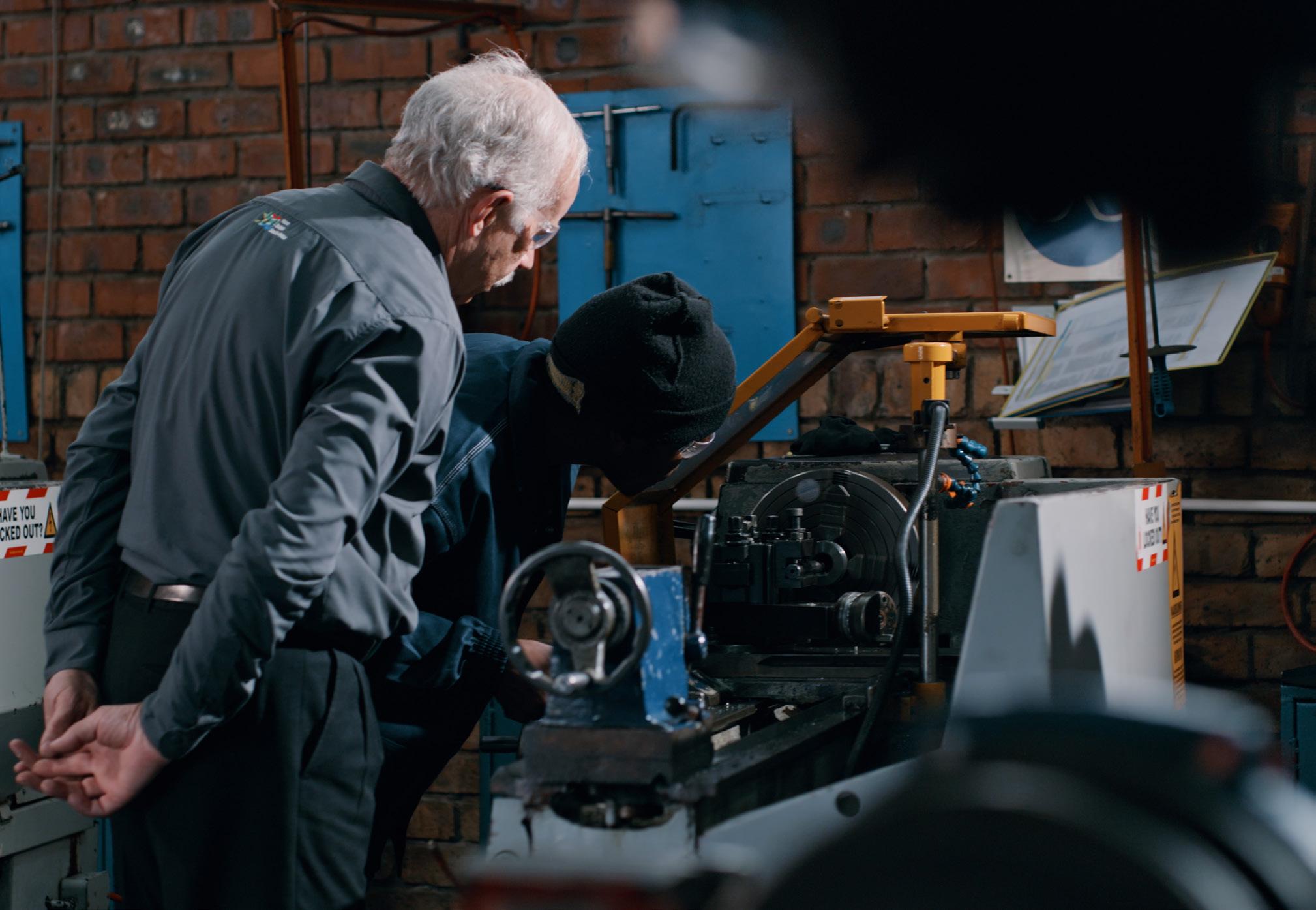
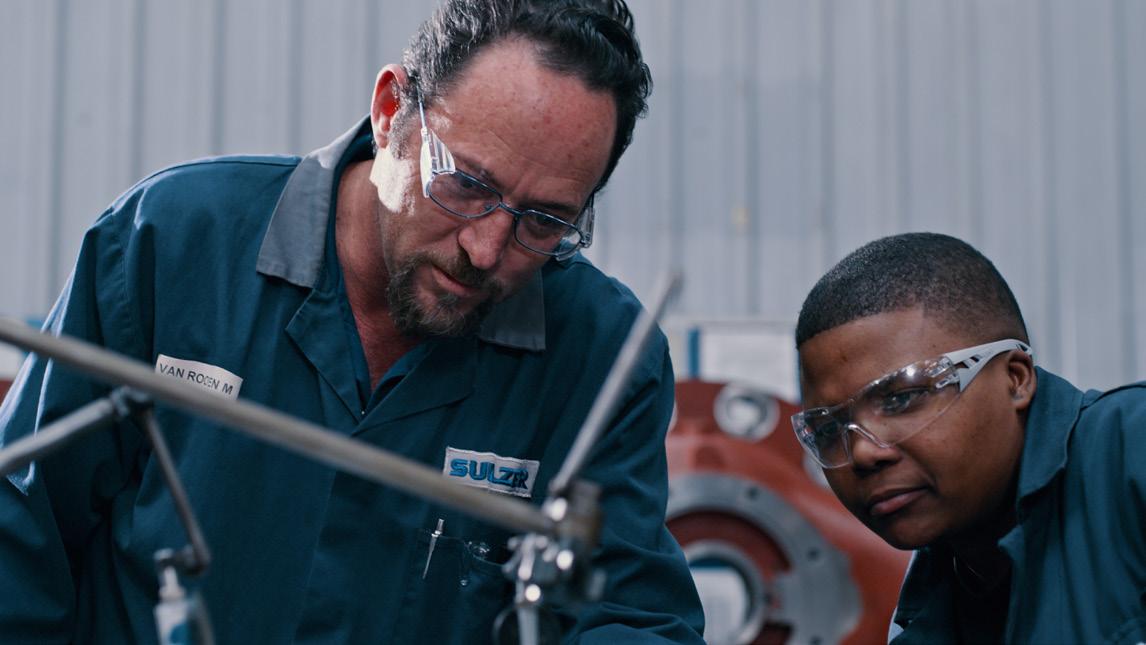
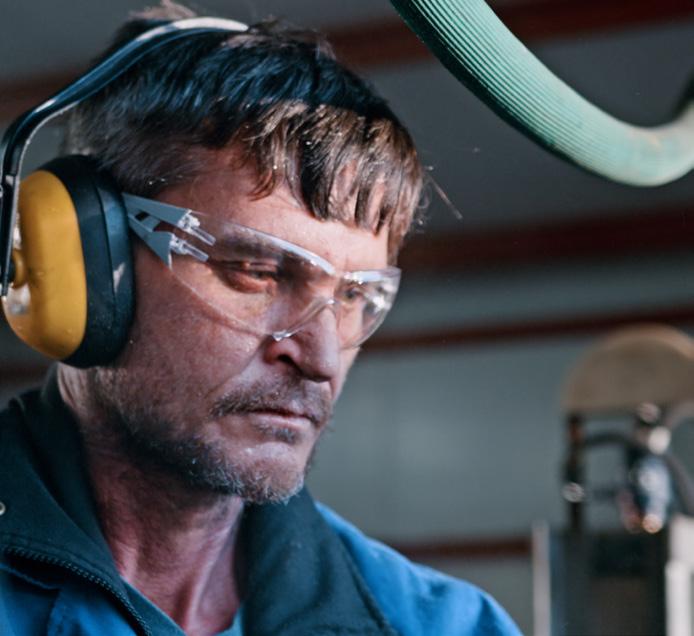
SULZER’S DIVISIONS –AT A GLANCE
FLOW – Wherever fluids are treated, pumped, or mixed, the company delivers highly innovative and reliable solutions for the most demanding applications.
SERVICES – Sulzer is the go-to partner for ensuring uptime and enhanced performance for a vast range of rotating equipment. The company’s committed services team provides unrivalled service and expertise to meet customers’ operational needs.
CHEMTECH – Sulzer recognises that superior chemical processing and separation technologies matter most. Therefore, the company enables its customers to operate world-class plants and produce high-value products.
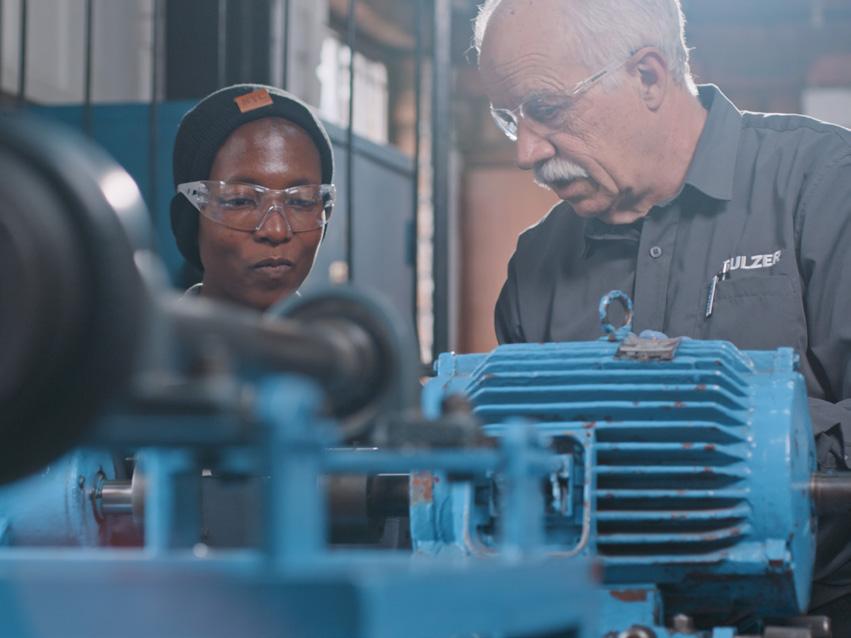
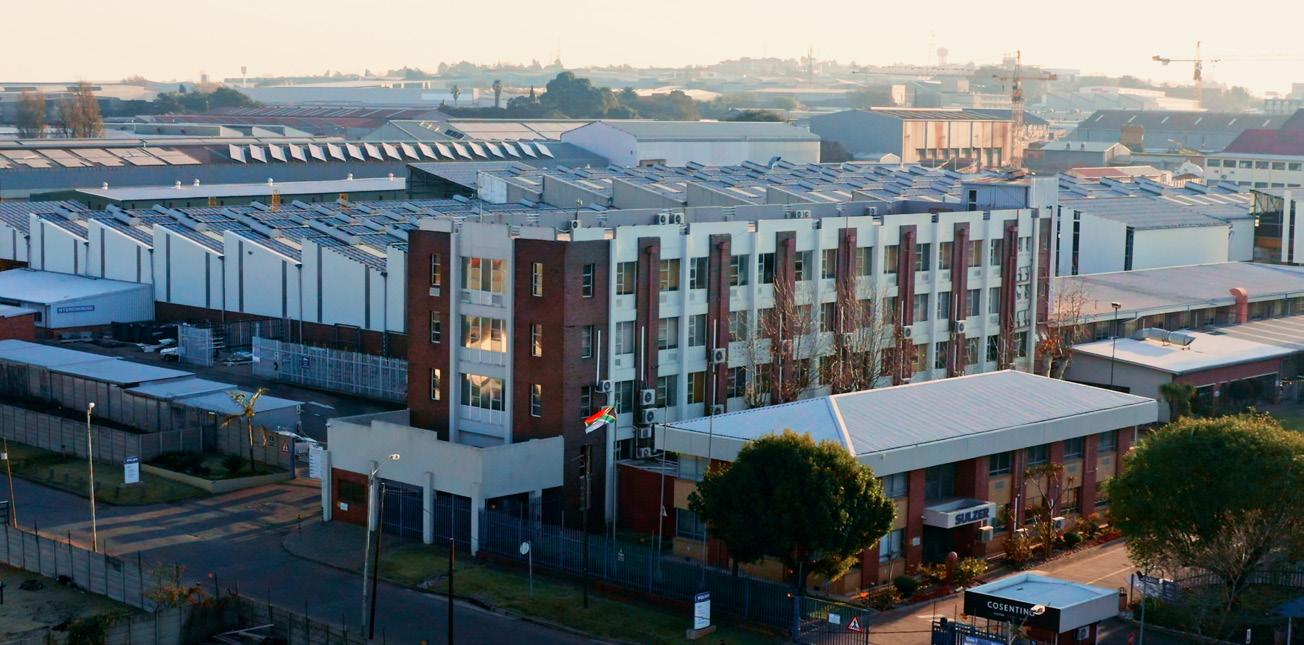
“WE LIVE BY OUR PRINCIPLES EVERY DAY, AND AS A RESULT, WE’VE REMAINED A RELIABLE, LONG-TERM PARTNER TO OUR CUSTOMERS. IN A WORLD OF CONSTANT CHANGE, SULZER OFFERS SOMETHING INCREDIBLY RARE – STABILITY”
–
HENRY CRAUKAMP, MANAGING DIRECTOR, SULZER SOUTH AFRICA
In Johannesburg, for instance, Sulzer has its Advanced Manufacturing Centre (AMC), a dedicated Service Centre for pumps, and a separate facility for electromechanical equipment.
The AMC in particular utilises stateof-the-art machinery and tooling equipment combined with rigorous quality control processes to produce world-class parts.
Its Service Centre meanwhile, is able to repair, overhaul, and improve all types of rotating machinery, allowing the company to support the complete drivetrain system, whilst the
electromechanical centre is uniquely equipped for the refurbishment of high-speed, complex gearboxes.
“These bespoke facilities ensure Sulzer exceeds market requirements amidst the country’s skills shortage,” Craukamp points out.
Elsewhere in Durban, the company has another new Service Centre dedicated to the pulp and paper and industrial water sectors, whilst an additional facility in Welkom focuses on supporting gold mining operations, energy recovery systems, and large vertical turbine services.
“With sales offices in both Johannesburg and Durban, alongside our extensive footprint across the country, we effectively serve customers throughout SA and the broader sub-Saharan Africa region.”
ENACTING CHANGE
Operating nationwide, Sulzer strives to be a good corporate citizen and consistently makes a positive difference across SA.
For example, the company is proud to be a Level 2 Broad-Based Black Economic Empowerment (B-BBEE) contributor, reflecting its ongoing commitment to transformation, empowerment, and inclusive economic growth.
“This status not only strengthens our partnerships with customers and suppliers but also demonstrates our active role in supporting SA’s socioeconomic development goals,” Craukamp asserts.
Sulzer is likewise dedicated to developing critical skillsets that will benefit the country as a whole.
“In a recent conversation, someone asked me why it’s so difficult to fill positions when unemployment is so high. The reality is a persistent skills gap, and it is therefore our responsibility to engage with people across society to help close that gap,” he impassions.
This approach includes actively participating in industry initiatives and partnerships that promote skills development, as the company believes that it can have a far greater impact by collaborating across companies and communities rather than operating on its own.
In a similar vein, Sulzer also prioritises creating teams comprised of the local workforce, as evidenced by its regional engineering team that has been integrated into the company’s global R&D network.
As a result, Sulzer has access to a vast pool of international expertise, ensuring its capabilities remain
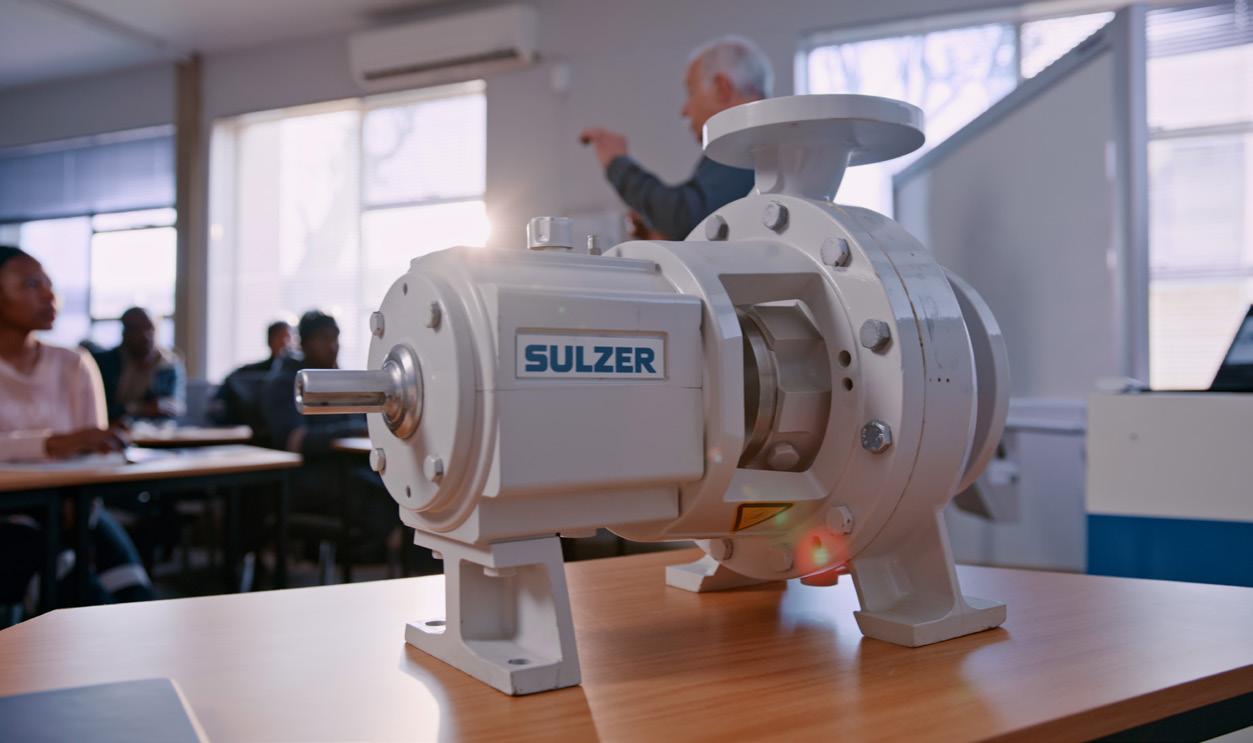
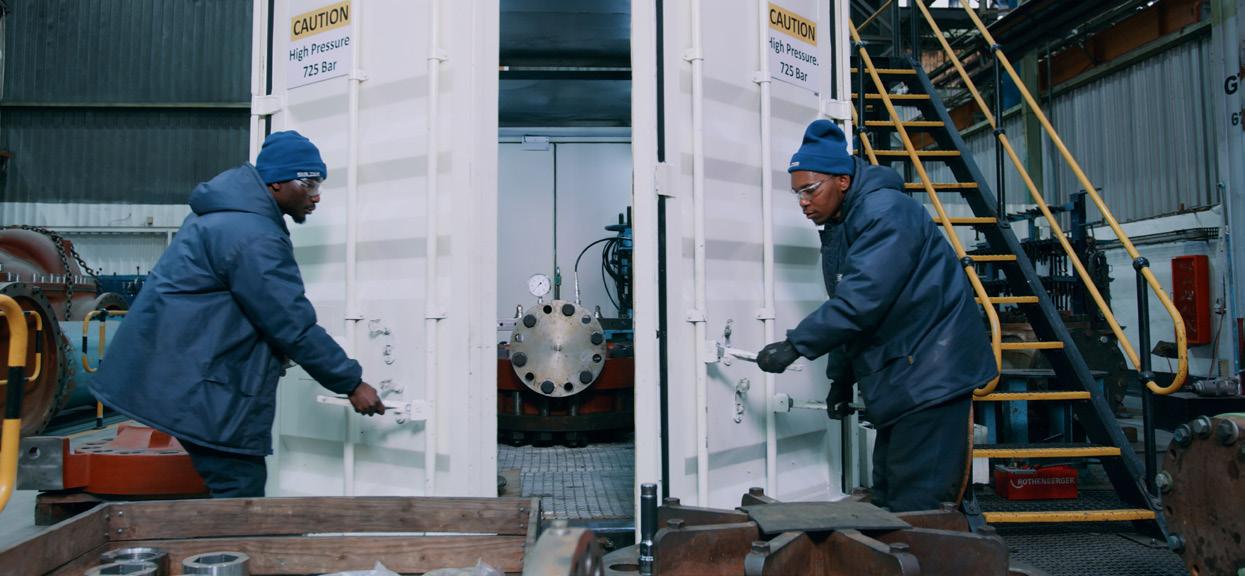
“SINCE EVERY CUSTOMER IS AT A DIFFERENT STAGE IN THEIR DIGITAL TRANSFORMATION, IT’S VITAL THAT WE WORK CLOSELY WITH THEM TO OFFER TAILORED RECOMMENDATIONS THAT SUIT THEIR UNIQUE NEEDS”
– HENRY CRAUKAMP, MANAGING DIRECTOR, SULZER SOUTH AFRICA
world-class.
A prime example is its HydroMining division, which specialises in underground drilling equipment for mining applications. Notably, all R&D for this division is conducted locally in SA.
“Our continued investment in R&D has positioned us as a leader in
several areas. For example, we are the only company offering both air drills for higher-level mining operations and pneumatic drills capable of functioning at depths greater than 1,000 metres – an essential capability given the depth of many South African mines,” Craukamp remarks. Beyond technical innovation,
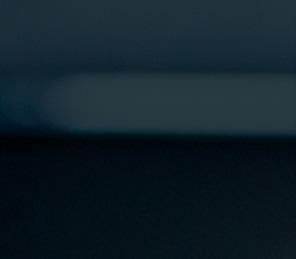
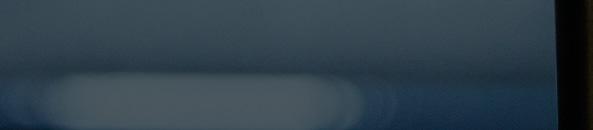
INDUSTRY LEADERS IN
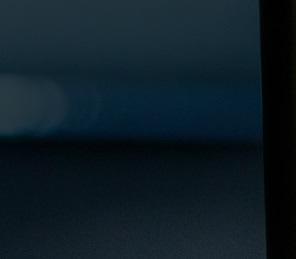
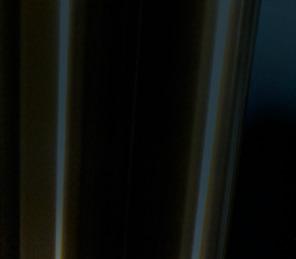
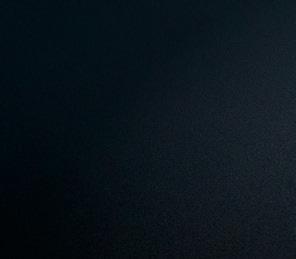
• TURBO MACHINERY
• GEAR TECHNOLOGY
• PRECISION MANUFACTURING
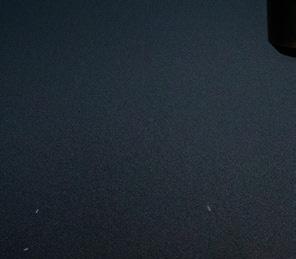
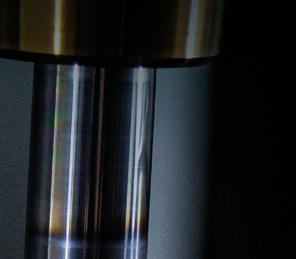
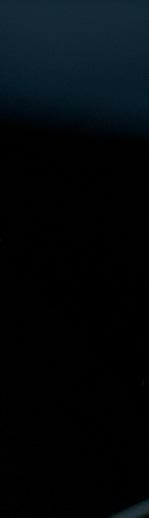
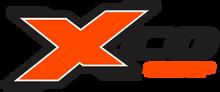
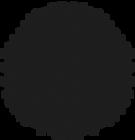
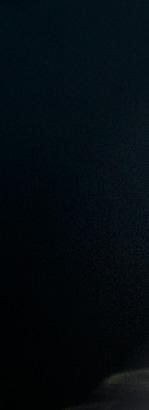

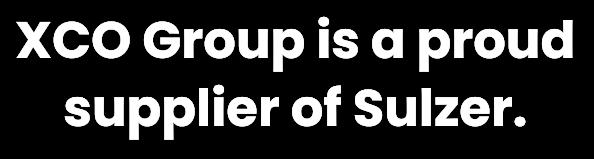
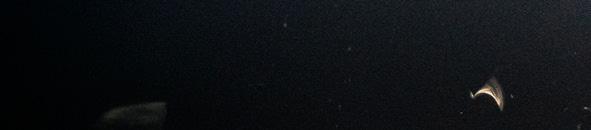
• REVERSE ENGINEERING
• DESIGN
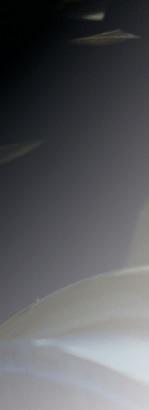
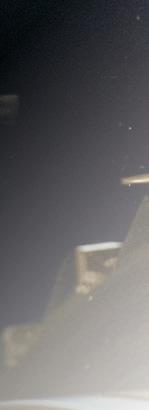
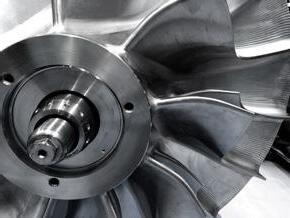
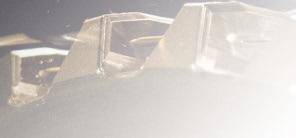
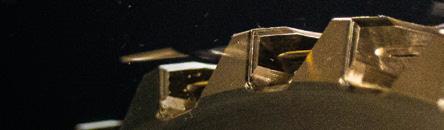
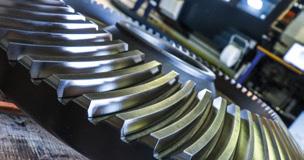
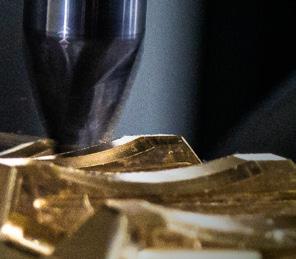
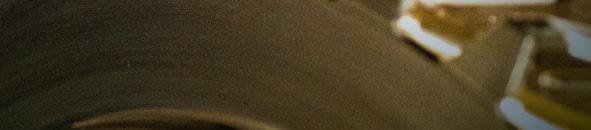
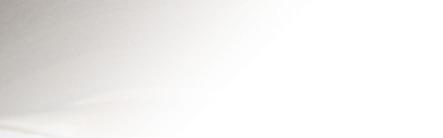
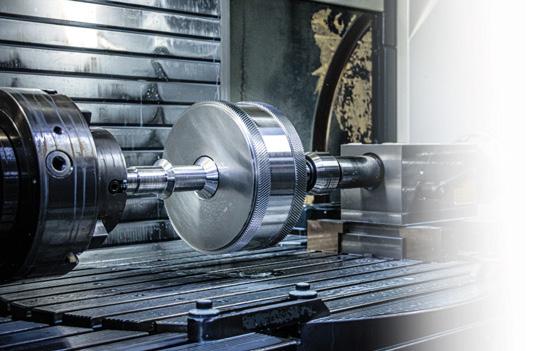
Tel: +27 (0) 12 644 2005
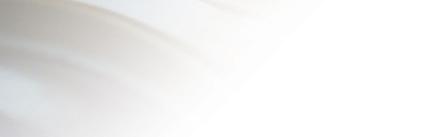
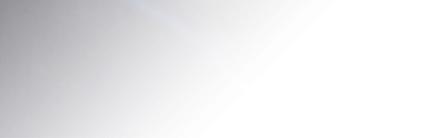
Email: info@vceng.co.za www.vceng.co.za
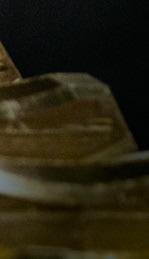
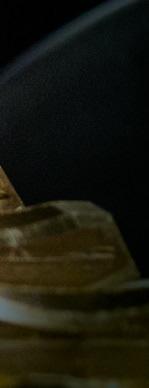

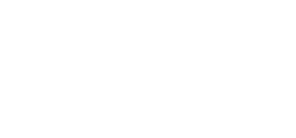
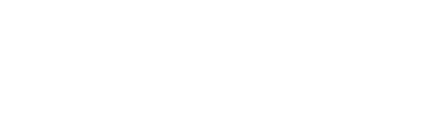
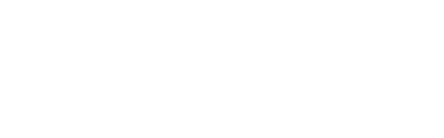
Sulzer’s R&D efforts have far-reaching and meaningful social impacts. For instance, its team recently developed a drill that is six kilogrammes lighter than the industry standard, reducing physical strain on users.
“This advancement not only promotes better health outcomes but also opens the door to greater gender inclusivity in mining roles – an industry traditionally dominated by men.”
CENTENARY CELEBRATION
Sulzer is proud to have recently celebrated its 100th anniversary, having grown alongside SA’s key sectors as an integral pillar in the development of infrastructure, energy, mining, water, and industry.
From humble beginnings to becoming a trusted leader in engineered solutions and services, the company’s journey has been marked by resilience, transformation, and a meaningful contribution.
“Our centenary is more than a
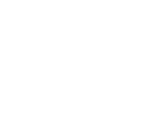
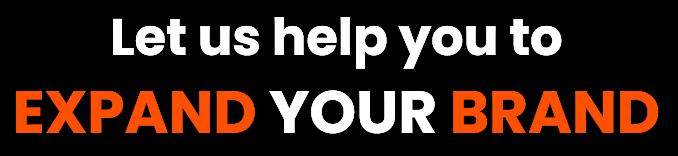
milestone – it’s a testament to the enduring strength of our brand, role as a responsible corporate citizen, and the positive impact we’ve made in local communities.
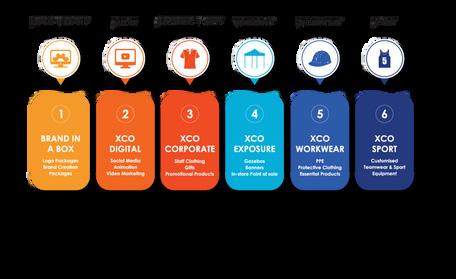
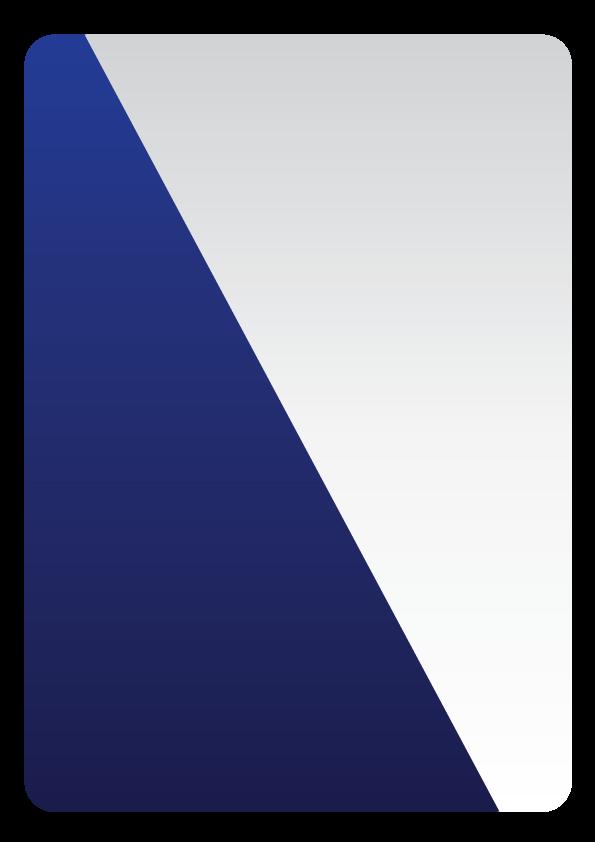
“It reflects a century of commitment to innovation, service excellence, and partnership across the industries we proudly serve,” Craukamp insights.
This achievement also speaks volumes about the people behind the company’s success. Indeed, with an average employee tenure exceeding 15 years, Sulzer’s team loyalty and dedication are well above the industry norm, underscoring the strength of its culture and shared purpose.
“We live by our principles every day, and as a result, we’ve remained a reliable, long-term partner to our customers. In a world of constant change, Sulzer offers something incredibly rare – stability,” he prides.
Going forwards, the company’s focus remains firmly on three core
priorities; namely customer centricity – truly understanding what keeps its customers up at night; an outcomebased mindset – ensuring its solutions are directly aligned with its customers’ needs; and its people – engaging a highly-skilled and committed team.
This will allow Sulzer to continue delivering cutting-edge technologies, developing local talent, and contributing to the sustainable progress of SA.
“Our approach is brought to life by continuously maintaining our principles – seize opportunities, own it, team up, and create value,” Craukamp concludes.

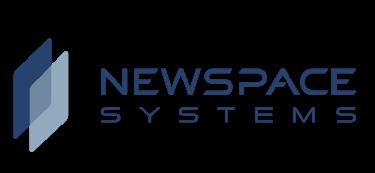
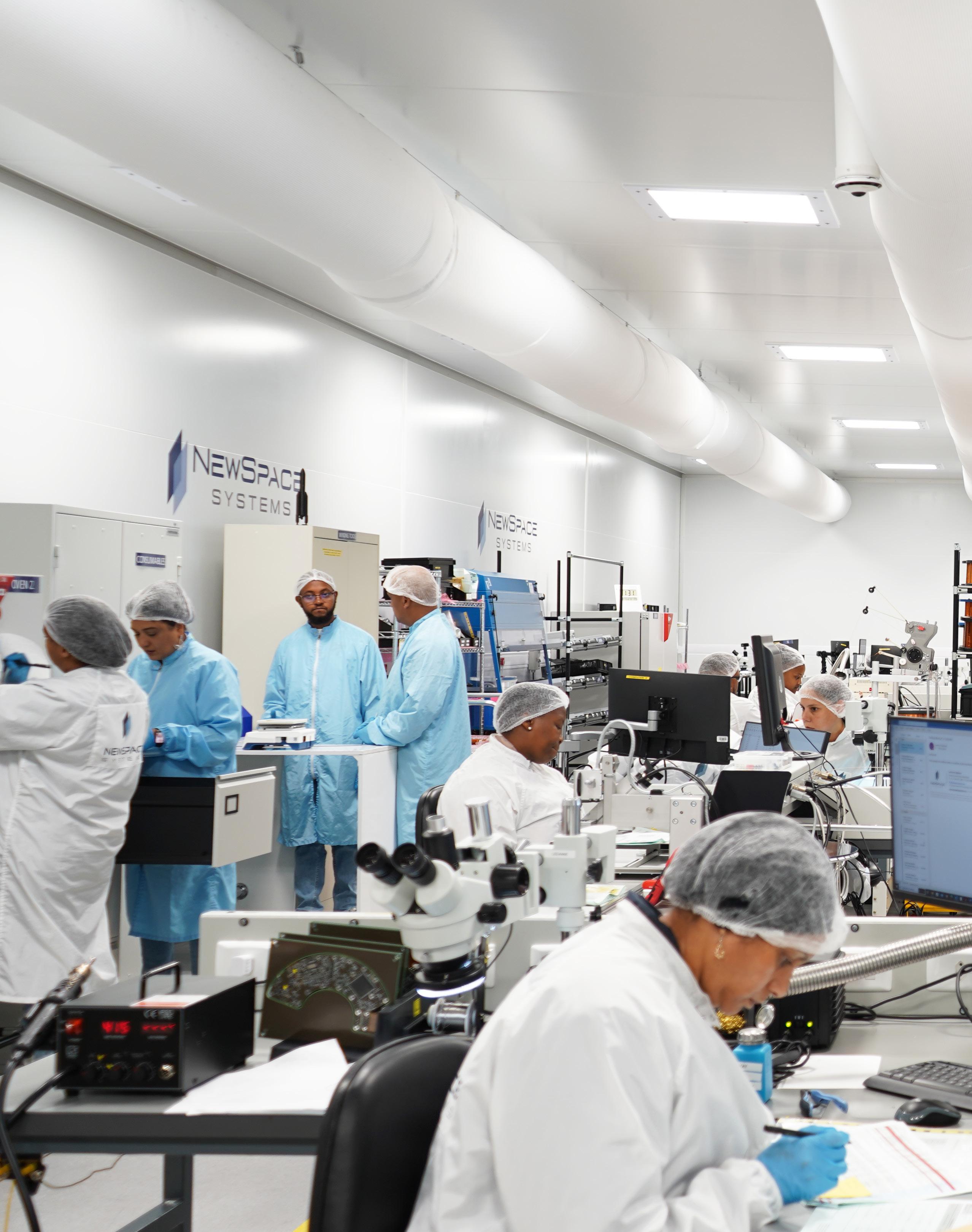
ROCKETING TO SUCCESS
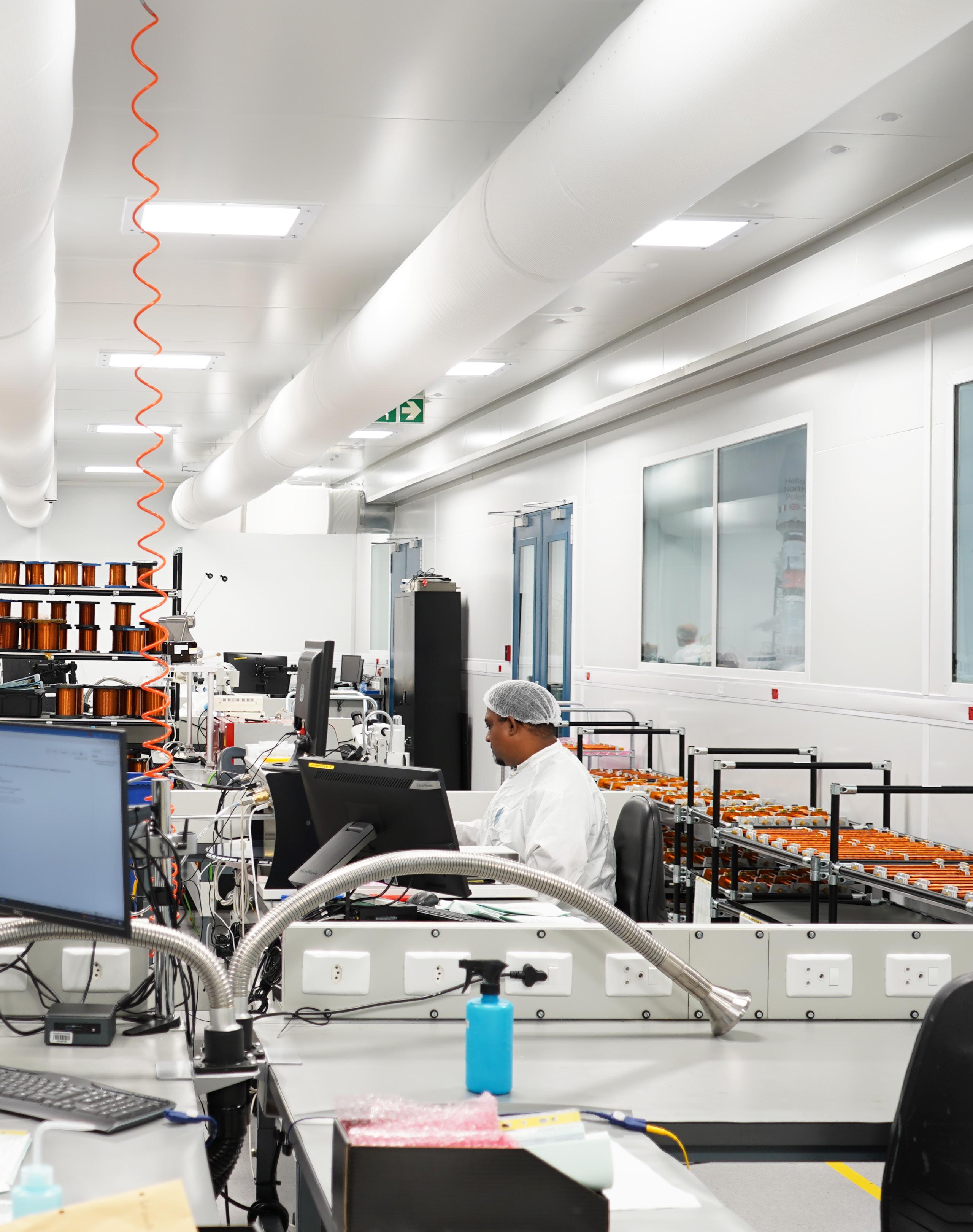
Headquartered in South Africa, NewSpace Systems is a trusted multinational manufacturer of spacecraft components and subsystems. CEO, Tanya Lerm, updates us on the burgeoning African space industry and what the company has been up to since we last spoke
Writer: Ed Budds | Project Manager: Josh Whiteside
For companies like NewSpace Systems (NSS), it is an incredibly exciting time to be part of the African space industry.
The continent is undergoing a remarkable transformation, with momentum accelerating in both the public and private sectors.
“We’re seeing increasing investment and collaboration across African nations, with more countries launching their own space programmes or establishing national space agencies,” introduces CEO, Tanya Lerm.
“This translates into rising demand for locally developed space capabilities, which is exactly where NSS fits in,” she elaborates.
The company is witnessing a key trend in the growing emphasis on sovereignty in space technology. Indeed, there’s a strong drive amongst African governments to develop local capability, not only for economic reasons but also to ensure independent access to critical services like climate monitoring and disaster response, as well as communications infrastructure.
“A further milestone for the industry this year was the launch of the African Space Agency in April 2025, set to play a pivotal role in coordinating space activities across the continent, followed by the NewSpace Africa Conference in Cairo, which I had the privilege of attending.
“This growing institutional support fosters a dynamic environment for innovation, partnerships, and longterm impact,” Lerm impassions.
DEDICATED TO RELIABILITY
Today, NSS is uniquely positioned as a high-reliability manufacturer of satellite subsystems, capable of supporting both customised missions and large-scale constellation programmes.
“Being headquartered in South Africa allows us to deliver spacegrade quality at a significantly more
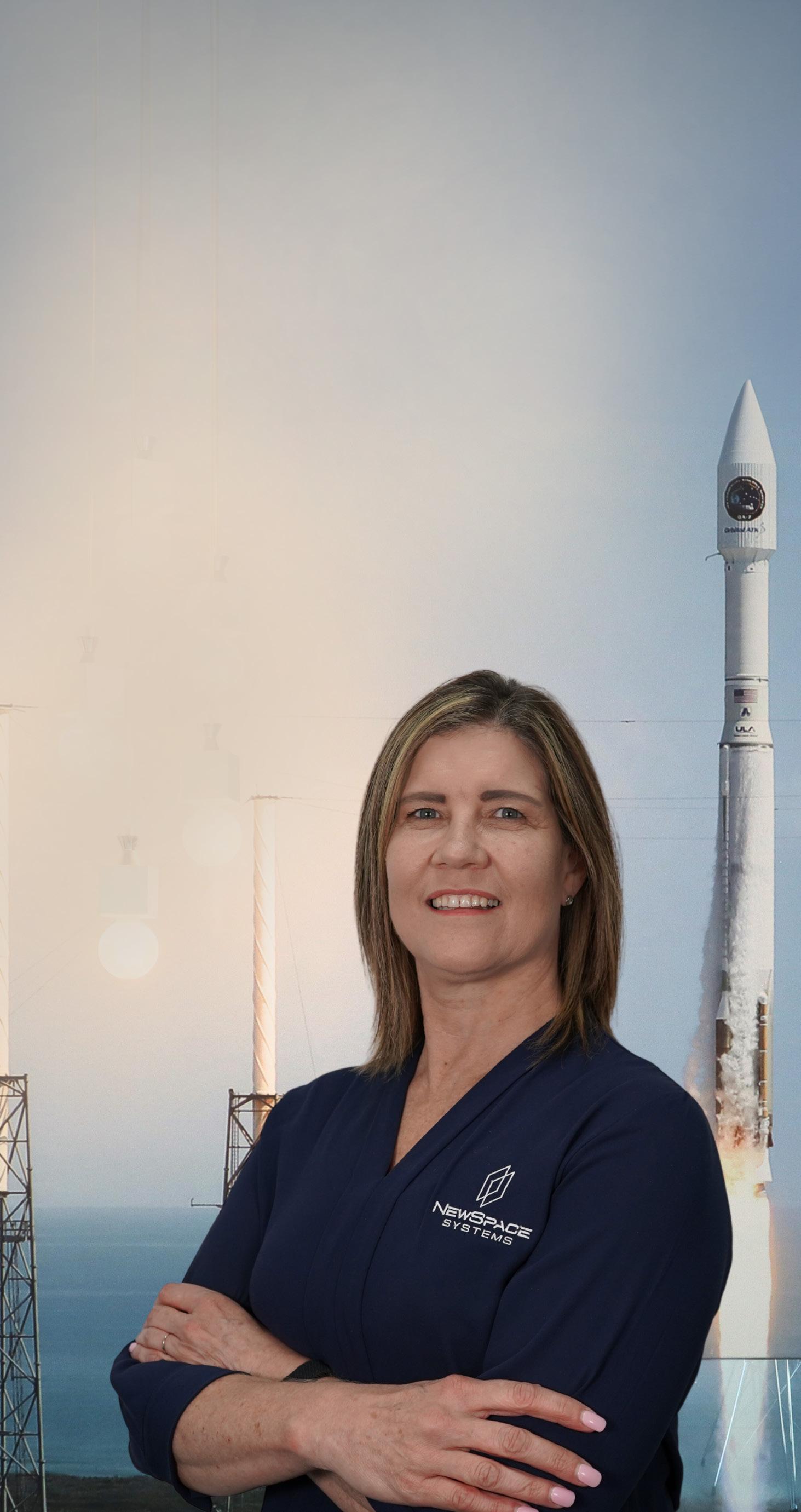
HOW DID YOU ARRIVE AT YOUR CURRENT ROLE AT NSS?
Tanya Lerm, CEO: “I studied engineering at university before beginning my career in manufacturing, working across a range of industries. Over time, I became increasingly drawn to environments where quality, precision, and reliability were nonnegotiable, naturally leading me towards the aerospace sector.
“My first exposure to the industry came at a company specialising in composite manufacturing, where we designed and produced components for airline seating. It was a fascinating space that combined complex engineering with the highest safety and performance standards.
“Nearly seven years ago, I met James Barrington-Brown, the Founder and Chairman of NSS, when the company was still in its start-up phase.
He had a bold vision to build a business that could serve not just the local or continental space sector but become a respected global player. His passion deeply resonated with me, and I joined as COO.
“In August 2024, I stepped into the role of CEO. Leading a fast-scaling company comes with immense opportunities and challenges. My focus has been on maintaining momentum whilst ensuring we grow sustainably and strategically. We’re doubling revenue annually, building a new state-of-the-art cleanroom facility, and scaling our team to position us for the next phase of our global journey.”
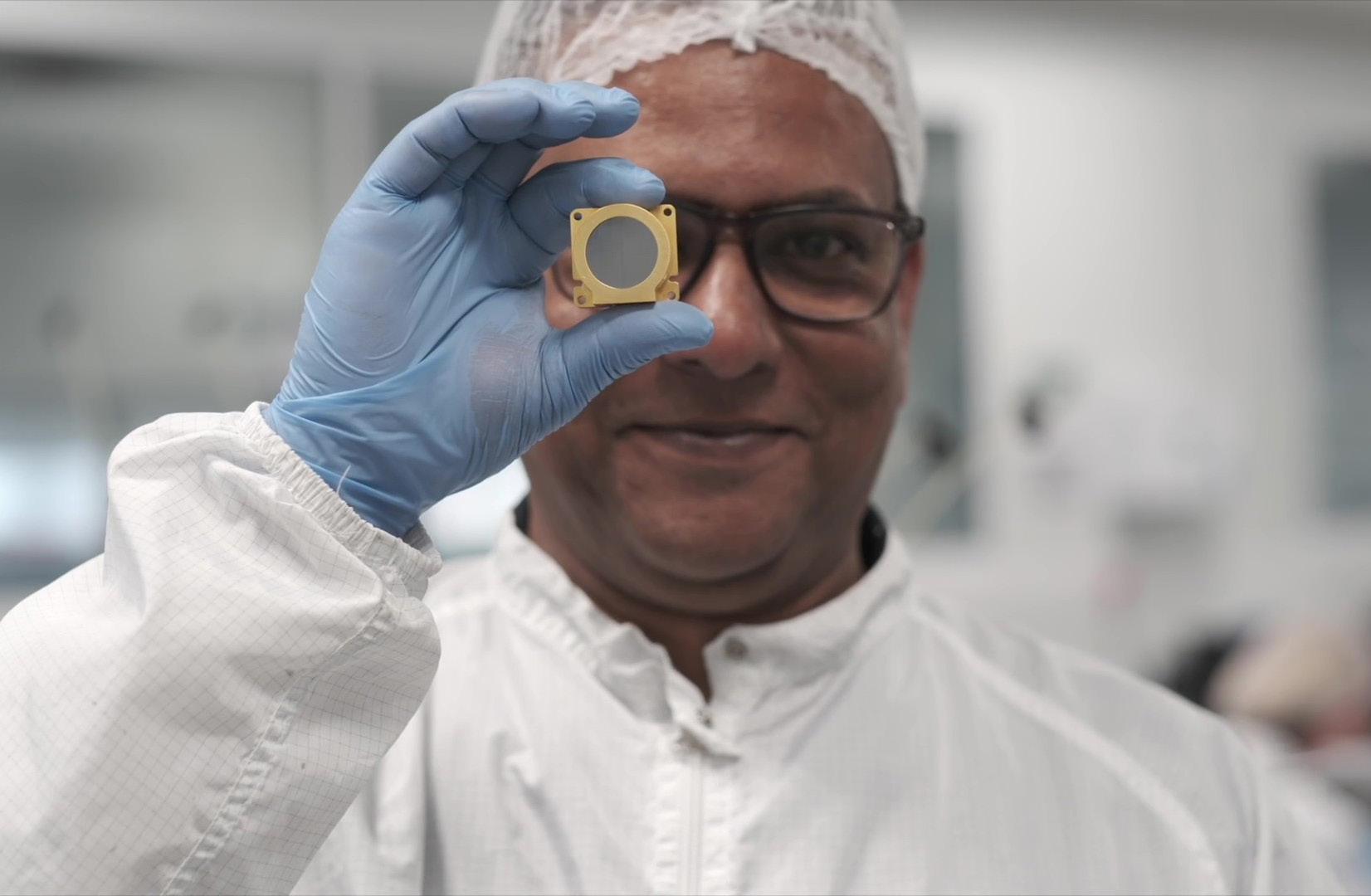
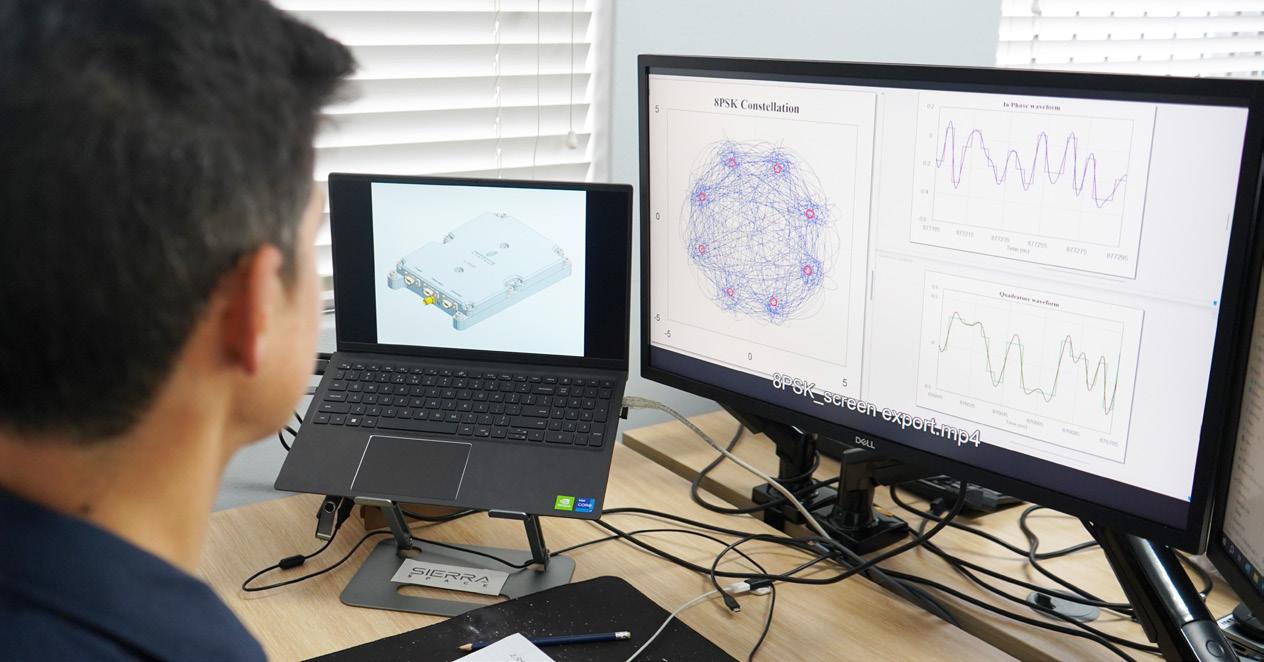
“I’VE STAYED IN AEROSPACE BECAUSE OF THE DISCIPLINE IT DEMANDS, THE GLOBAL PERSPECTIVE IT OFFERS, AND THE SENSE OF PURPOSE THAT COMES FROM CONTRIBUTING TO MISSIONS THAT QUITE LITERALLY REACH BEYOND OUR PLANET”
– TANYA LERM, CEO, NEWSPACE SYSTEMS
competitive price point than many international players, but what truly sets us apart is our customer-centric approach,” explains Lerm.
“We treat our clients as long-term partners, providing exceptional support throughout the mission lifecycle, from engineering collaboration to post-launch support,” she expands.
The company’s growing global presence – with offices in the US, UK, and New Zealand – also enables it to
support customers across time zones and regulatory environments, further reinforcing NSS’s commitment to accessibility and responsiveness.
For Lerm, the journey has been both challenging and deeply rewarding.
“Since joining the business, I’ve witnessed the company grow from a small team of 20 to nearly 160 employees, and we’re still expanding!
“I’ve stayed in aerospace because of the discipline it demands, the
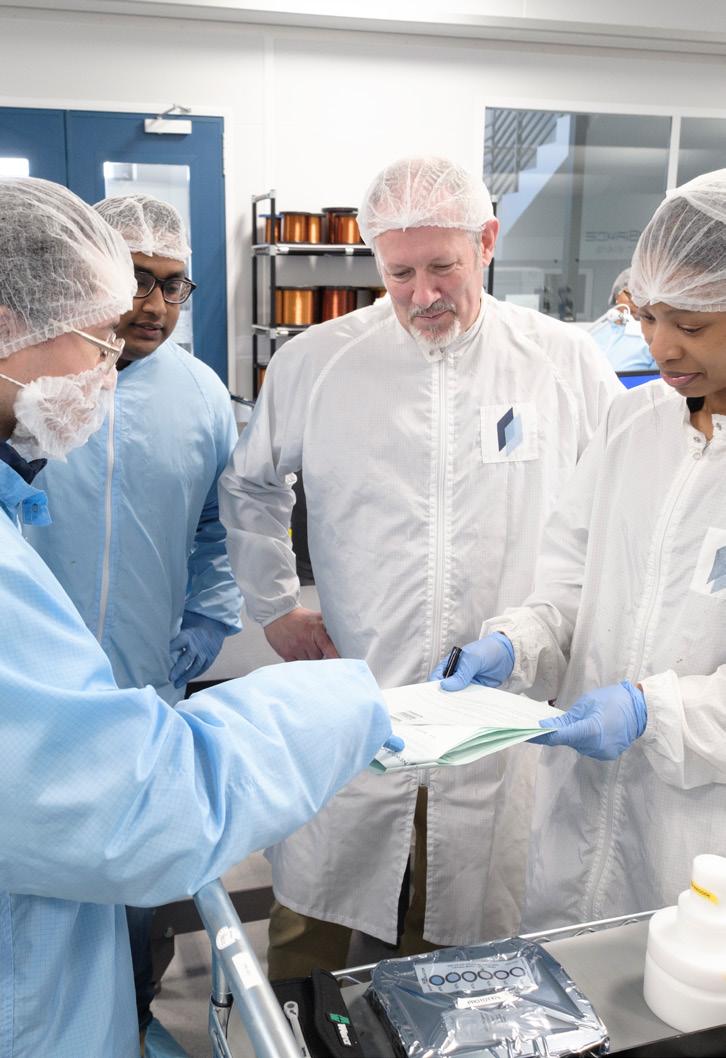
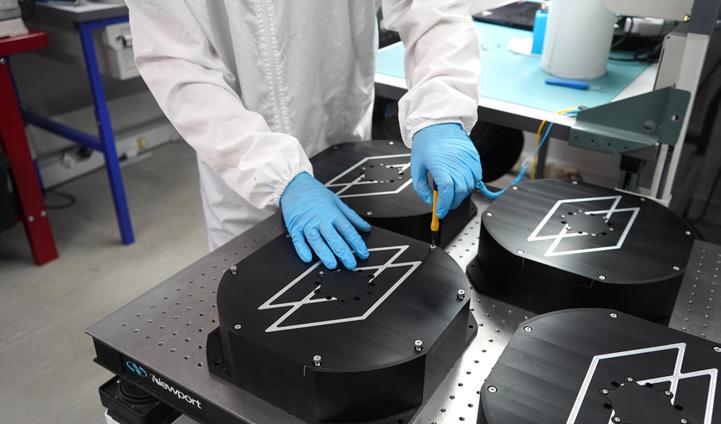
global perspective it offers, and the sense of purpose that comes from contributing to missions that quite literally reach beyond our planet,” she enthuses.
STRATEGIC EXPANSION
2025 has been a pivotal year for NSS, marked by strategic clarity as the company prepares for the next growth phase.
“We are investing heavily in the future – not only in terms of our people but also the infrastructure, systems, and products that will enable us to scale sustainably and lead with impact,” Lerm excites.
One of the most significant projects currently underway is the construction of NSS’s new 1,270-square-metre, state-of-the-art cleanroom facility, which will see the company’s operational space grow to more than 5,000 sqm.
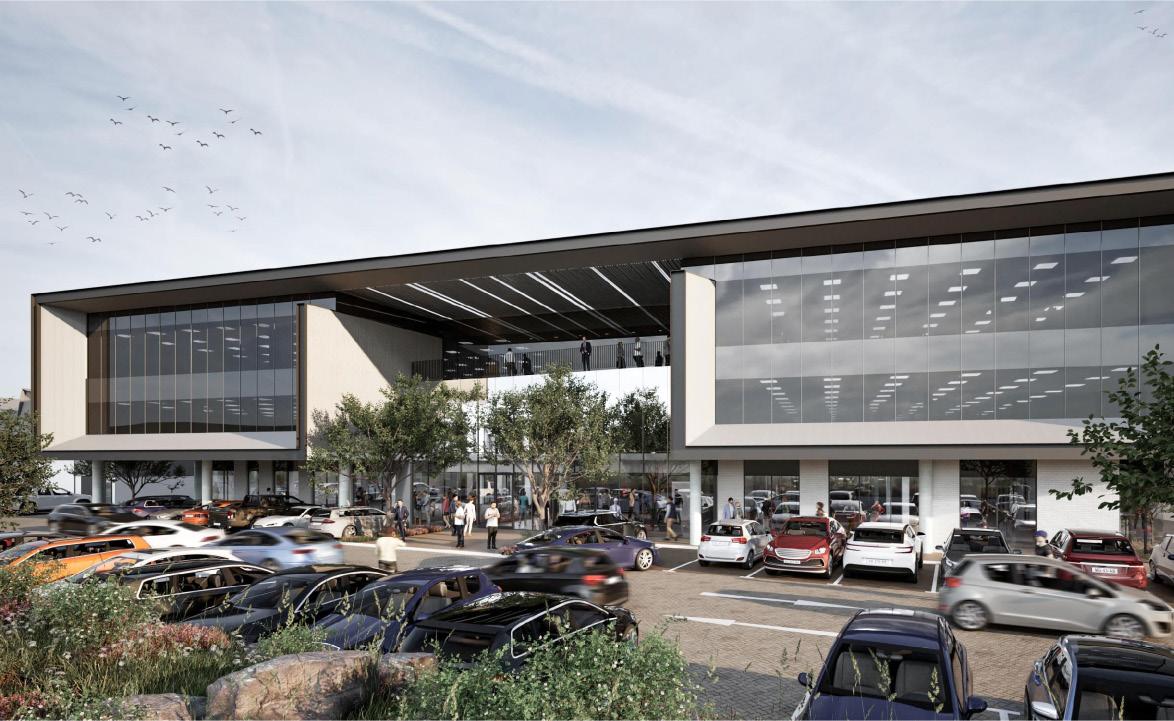
“This exciting expansion will dramatically increase our manufacturing capacity, allowing us to meet rising global demand whilst continuing to deliver high-reliability space technology.
“It’s not just a physical upgrade –it’s a strategic enabler that will mean we can take on larger, more complex projects and higher production volumes without compromising on quality,” she predicts.
The company plans to move into the facility before the end of the year.
EXCITING INNOVATION
On the product front, NSS is developing the next generation of its existing flight-proven product lines, including an even more efficient sun sensor, a radiation-hardened magnetometer, a new GPS receiver, and an expanded reaction wheel range.
These redesigned systems will retain their trusted heritage but are being enhanced for easier manufacturability and higher-volume production, enabling the company to meet customer needs more efficiently
“WE ARE INVESTING HEAVILY IN THE FUTURE – NOT ONLY IN TERMS OF OUR PEOPLE BUT ALSO THE INFRASTRUCTURE, SYSTEMS, AND PRODUCTS THAT WILL ENABLE US TO SCALE SUSTAINABLY AND LEAD WITH IMPACT”
– TANYA LERM, CEO, NEWSPACE SYSTEMS
without compromising performance.
“Parallel to this, we’re expanding into the space radio frequency communications domain, representing an exciting growth area for us.
“This diversification allows us to support the rising demand for in-orbit connectivity and opens new markets and partnership opportunities,” details Lerm.
“Internally, we are upgrading our IT and digital systems, enhancing data visibility, integration, and operational efficiency. These upgrades are essential foundations for scaling and managing increasing complexity across the organisation.”
Collectively, these projects reflect NSS’s commitment to continuous innovation, operational excellence, and long-term relevance in the global space industry.
TO INFINITY AND BEYOND
Future facing, NSS’s key priorities are focused on scaling operations in a way that ensures long-term success whilst preserving the innovation, quality, and agility that continue to define the company.
“One of our most immediate goals is ramping up production to meet the growing demand from new constellation contracts,” Lerm sets out.
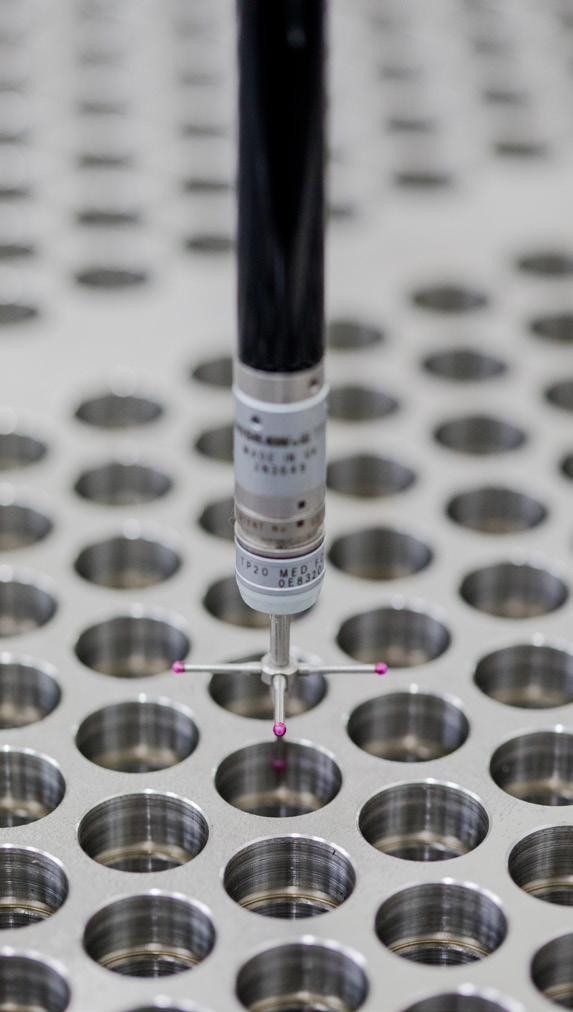
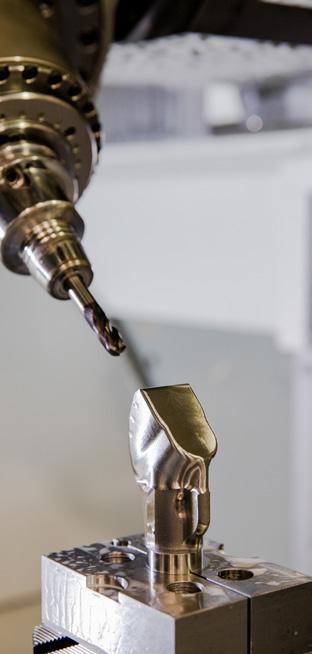
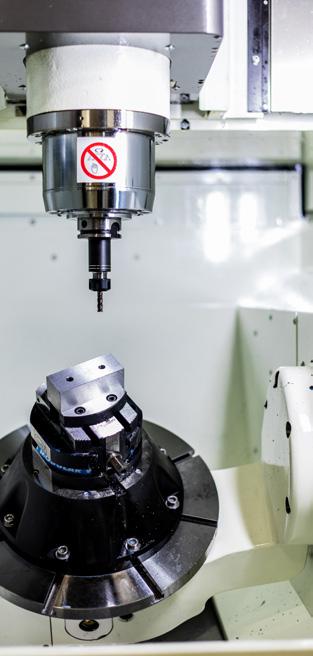
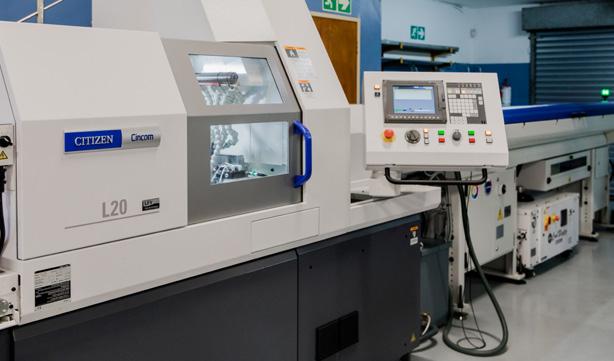
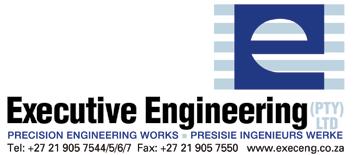
of
Executive Engineering is proud to celebrate over three decades as one of South Africa’s premier precision engineering companies.
We provide fully integrated, end-to-end component manufacturing solutions, specialising in highprecision machined components. Our commitment to accuracy, consistency, and innovation ensures we meet the most demanding engineering specifications across a wide range of industries. With a fleet of over 60+ CNC machines and the capability to work with a wide range of materials, we pride ourselves on our ability to adapt to evolving requirements and consistently deliver high-quality, reliable results. ISO 9001 certified, Executive Engineering continues to invest in cuttingedge equipment, software and expertise to deliver engineering solutions defined by accuracy, efficiency and excellence.
Jurie Swart (Managing Director)
Cell: +27 71 334 2939
Office: +27 21 905 7544
info@execeng.co.za jurie@execeng.co.za www.execeng.co.za
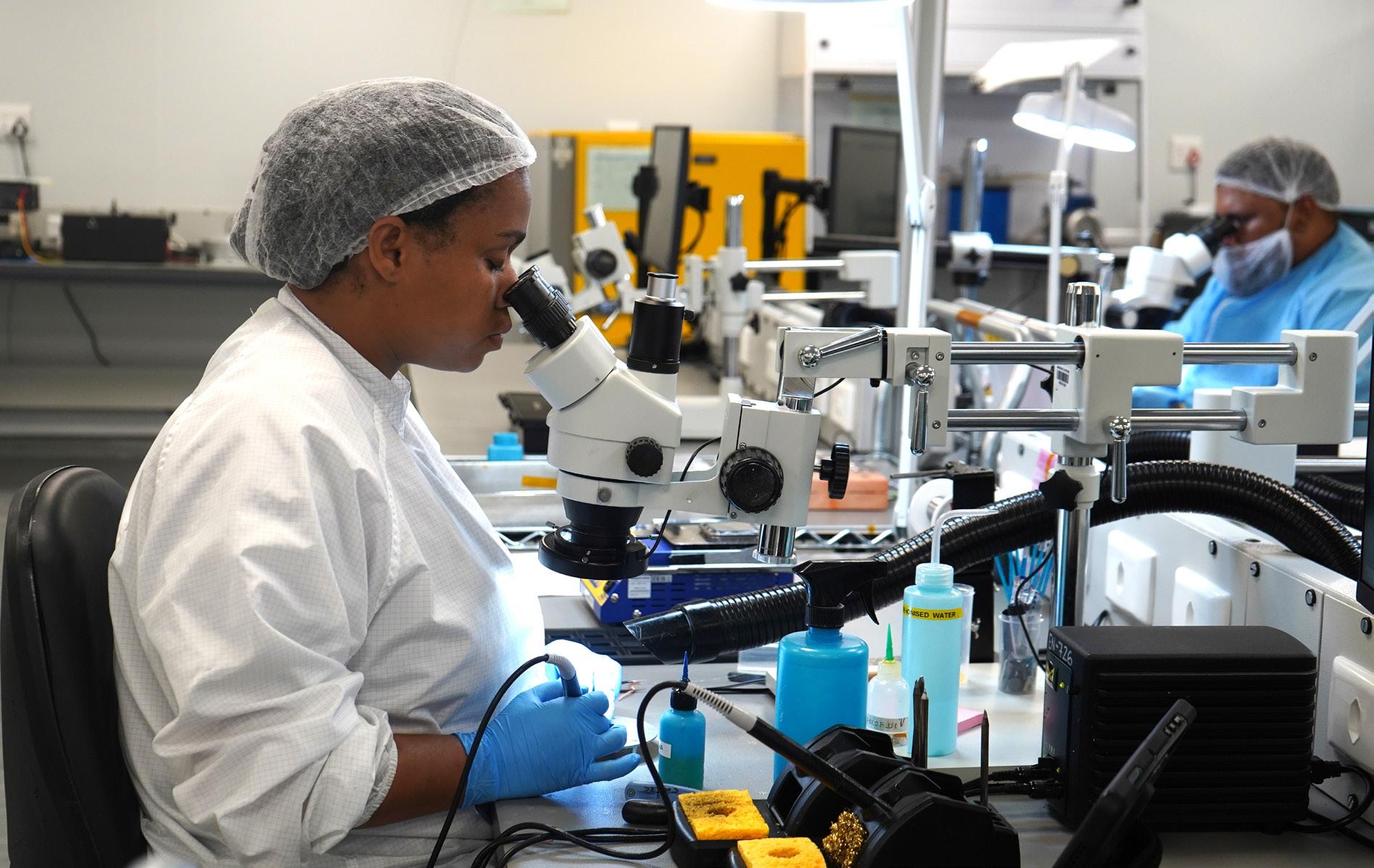
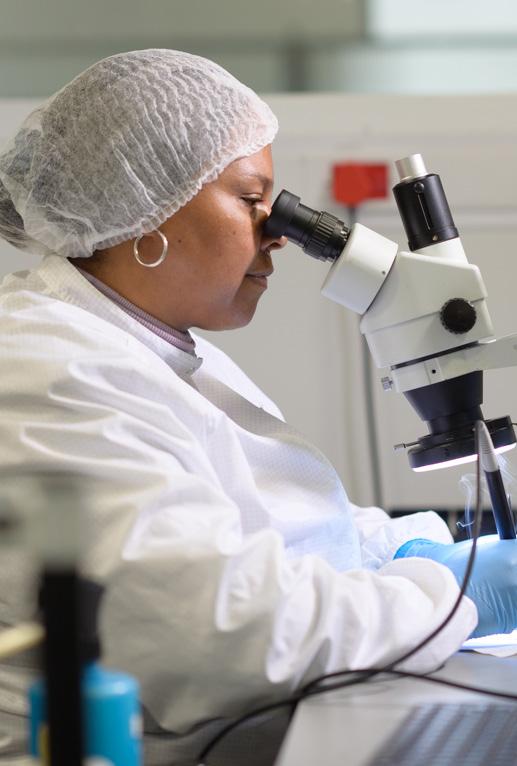
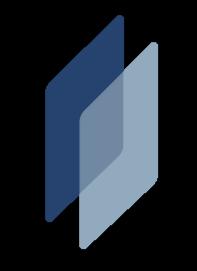
INSPIRING WOMEN IN SPACE
One aspect Lerm is keen to highlight is her role as a female CEO in an industry that has traditionally been largely male-dominated.
“The space industry is evolving rapidly, yet leadership positions, especially at the top, are still predominantly held by men. Being in this position is not just about leading a growing company – it’s also about challenging the norm and inspiring more women to take on leadership roles in technology and space.
“I believe that diversity – whether in gender, background, or perspective –is a catalyst for innovation. The more varied voices we have in decision-making and leadership, the stronger and more
dynamic our companies and industries become.
“Whilst the numbers are still low, it’s encouraging to see a gradual shift in the corporate world. As of 2025, there are 31 female CEOs leading S&P 500 companies, a sign that the corporate landscape is slowly becoming more inclusive.
“We’re not there yet, but I see my role as an opportunity to pave the way for more women to step into leadership positions within the space industry and beyond.
“I hope my journey will inspire other women to consider top roles in typically underrepresented sectors, showing that leadership is about skill, vision, and determination, not gender.”
- Tanya Lerm, CEO
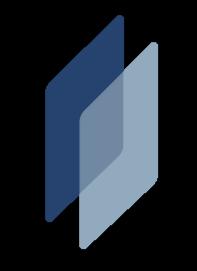
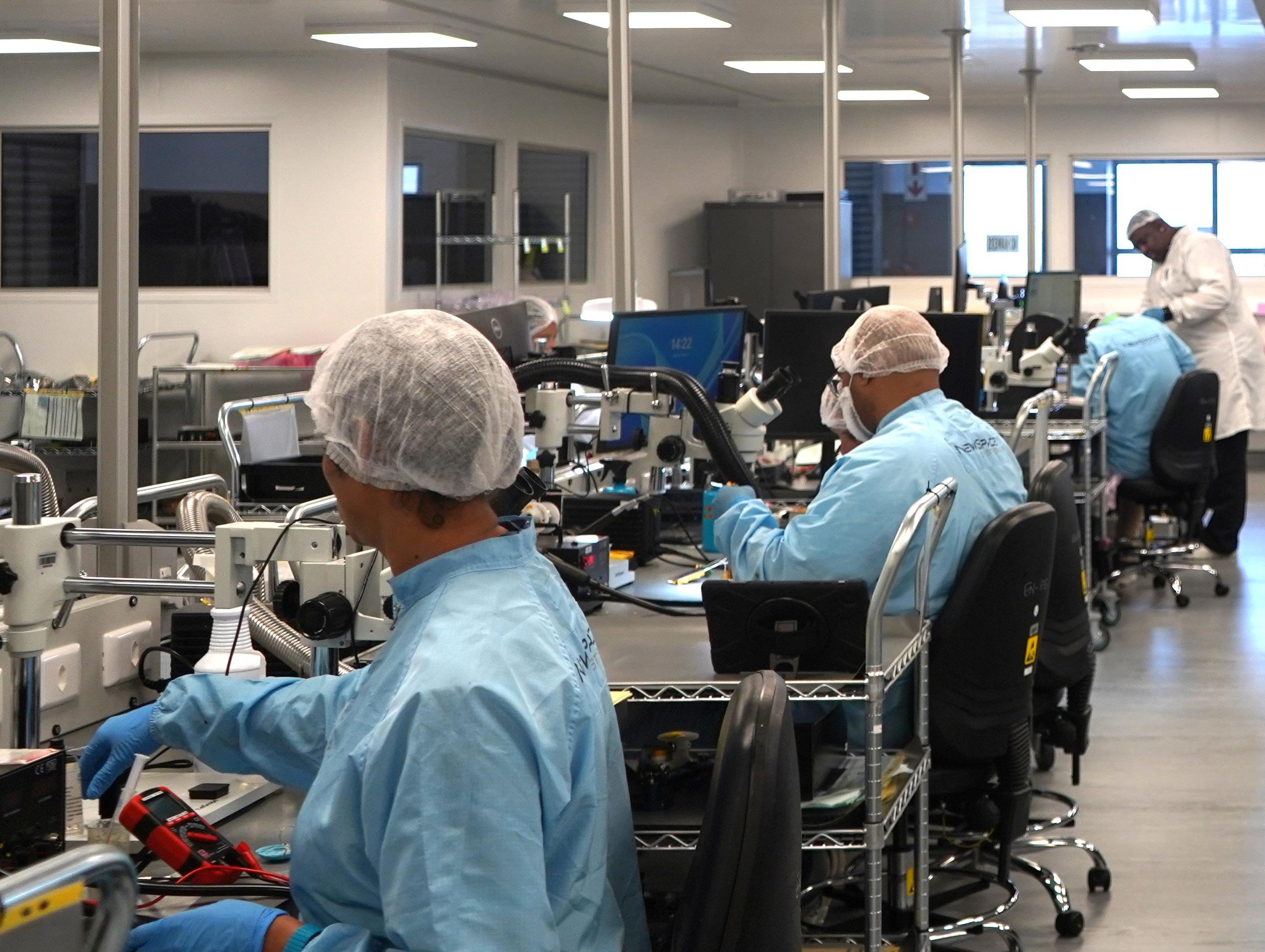
This includes completing a facility expansion – most notably NSS’s new cleanroom, alongside optimising internal systems to support higher-volume, high-reliability manufacturing.
“We’re also strengthening our international footprint by deepening our presence in strategic markets such as Europe and Asia. Expanding our global partnerships will be key to unlocking new opportunities and serving customers in regions with strong growth potential,” she adds.
On the technology front, NSS is continuing to push the boundaries with its next generation of intelligent subsystems, introducing features like built-in diagnostics and artificial intelligence (AI)-driven capabilities to meet the evolving demands of the space sector.
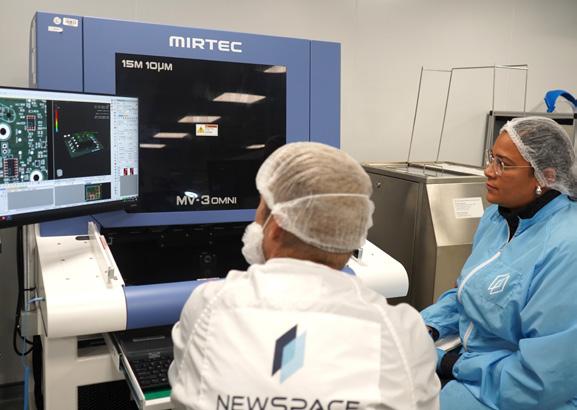
Alongside this, the company is exploring complementary technologies that will allow it to diversify and stay ahead in an increasingly competitive landscape.
“Investing in our people remains a top priority. We’re focused on expanding our talent and leadership pipeline, developing skills at all levels, and growing our internship programme to build a strong foundation for the future.”
For NSS, maintaining its culture of excellence, efficient collaboration, and high performance will undoubtedly prove to be essential.
“Ultimately, our aim is smart, sustainable growth, achieved by balancing operational excellence, global expansion, and continuous innovation to ensure we remain a trusted leader in delivering cutting-edge space technology to a connected and informed world,” Lerm finishes proudly.
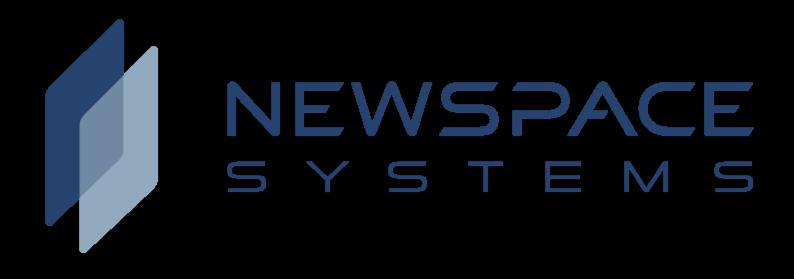
Tel: +27 21 300 0160
www.newspacesystems.com
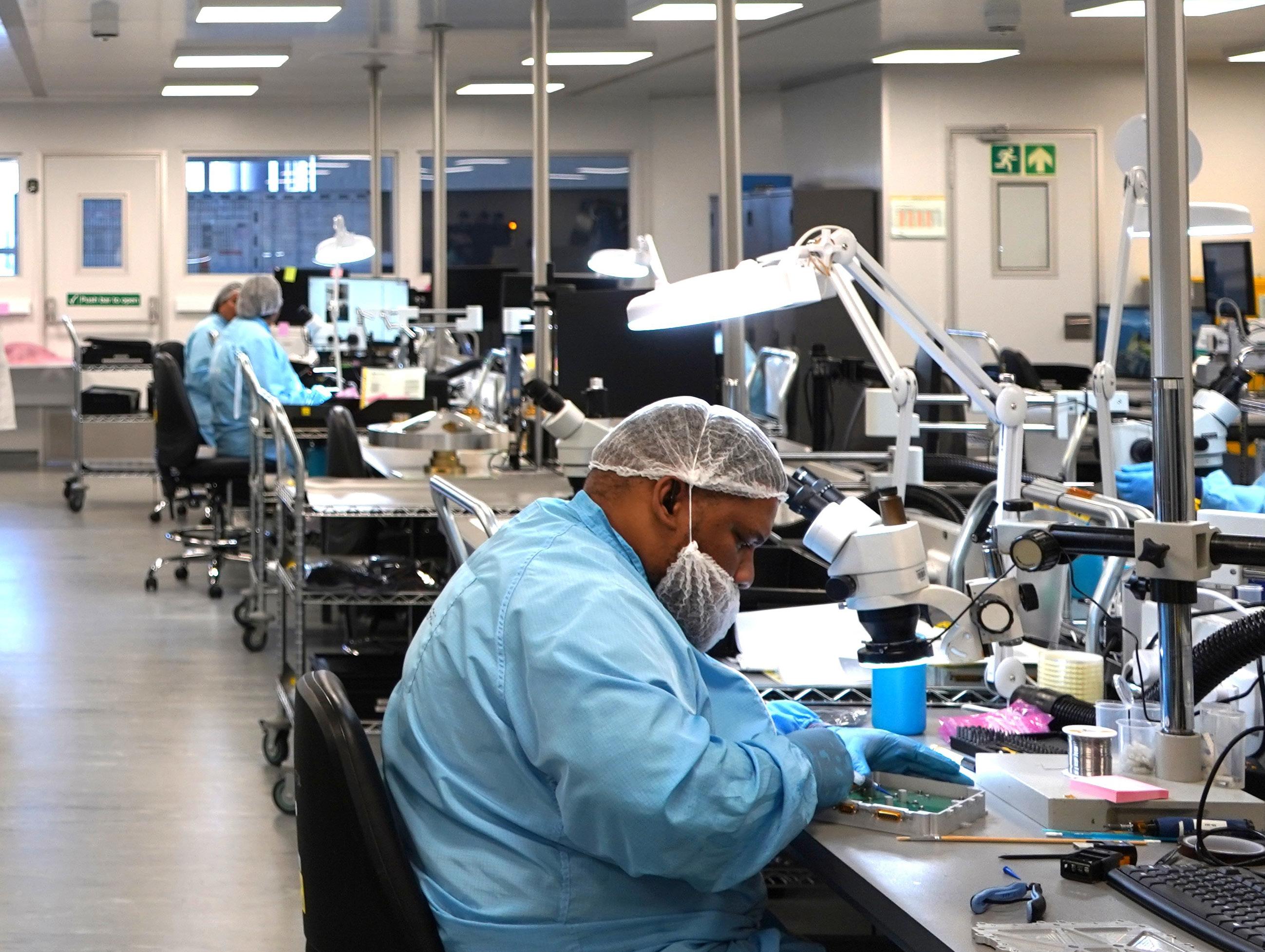
Tailored to ensure efficiency, quality, and safety, underpinned by 30 years of established experience, Trotech engineers, procures, and constructs above-ground bulk storage tanks and auxiliaries. Lukas Brink, Managing Director, takes us on a journey through the company’s myriad offerings
Writer: Lauren Kania | Project Manager: Josh Whiteside
Established in 1993 in South Africa (SA), Trotech has made a reputable and reliable name for itself by offering specialist services in the field of engineering, design, manufacture, and installation with operations that extend across the country and abroad.
Boasting over three decades of experience delivering bulk storage tank solutions safely, on time, and with the highest quality standards, the company serves clients across the oil and gas, chemical, and mining sectors alongside other heavy industry entities.
“We build large storage tanks primarily on-site for a variety of customers,” introduces Lukas Brink, Managing Director.
“Approximately 95 percent of our business is local to SA. With many companies entering the market utilising international labour and materials, we are proud to be local and connected with our surrounding communities.”
Trotech’s main focus is on new build tanks; however, the company’s other core capabilities include rebuilding and repairs, geodesic dome roof tanks, cryogenic tanks, pressure tanks, and tank design, jacking, and semi-automatic welding.
In August 2024, the company began a new depot services division to expand its services, which it
anticipates will comprise 20 percent of its business going forth.
“In the first six months of starting the division, we’ve already secured enough work to make 20 percent of our turnover,” Brink excites.
This success can be seen directly in Trotech’s continued substantial growth. Specifically, the company doubled its turnover in 2024, and this trajectory is on track to continue for the coming financial year.
Brink began his career at a small business conducting sales before taking a role as a project mechanical specialist at a large oil company in SA. From there, he joined a consulting engineering firm where he oversaw as many as 18 fuel installation and field depot service projects at any one time.
With vast experience as a professional mechanical engineer involved in the design and project management of large-scale construction operations, he felt he needed a new challenge, thus joining Trotech in its vision to lead the way in construction excellence.
AT THE FOREFRONT OF INNOVATION
Brink has observed the industry taking an interesting turn over the past few years, primarily due to the rapid advancement of technology and focus on commercial safety.
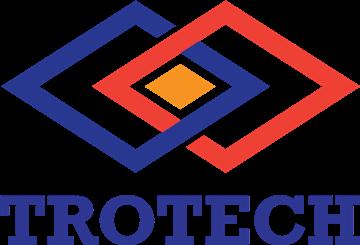
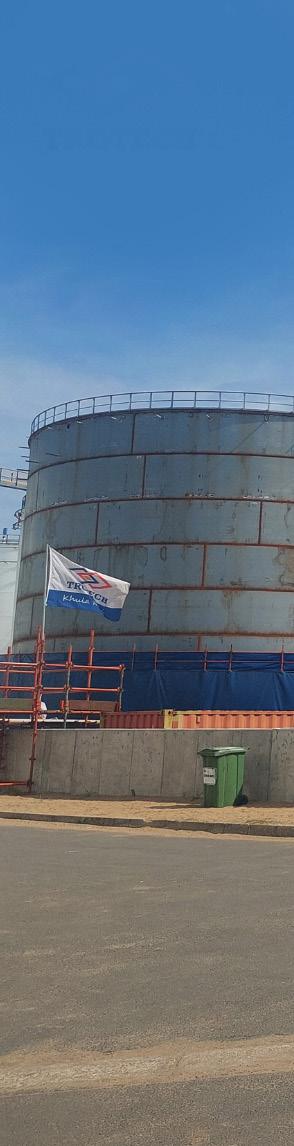
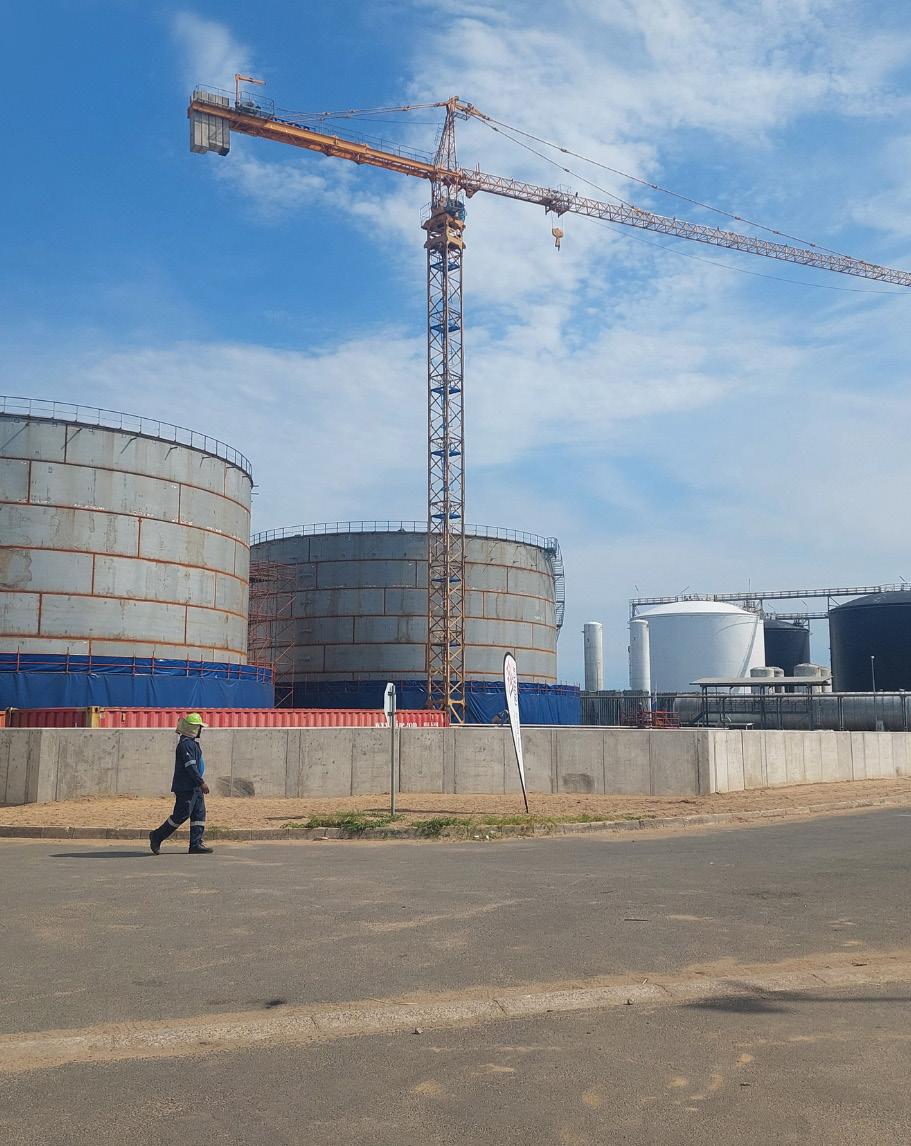
THINK TANKS , THINK TROTECH
“The sector has gone from very straightforward to much more competitive and intricate,” he notes.
“Despite it being a tough environment at the moment with the SA market being very touch and go, Trotech is continuing to succeed in doing what it does best – providing unparalleled service.”
What serves to distinguish the company and allow it to remain an industry leader is its hands-on nature and flat organisational structure.
A wholly-owned subsidiary of the Murray and Dickson Construction Group (M&D), the company is not only able to be agile and make quick
decisions but is also afforded the ability to operate in a broad sphere of construction activities, many of which are specialist in nature.
Additionally, Trotech has adopted the international entrepreneurial operating system (EOS), which it has customised as its own management system, MDOS, aligning with M&D. This system is rigorously applied company-wide, enabling it to have clear strategic planning, ongoing performance monitoring, and immediate identification of issues necessitating urgent attention.
These procedures allow Trotech to work seamlessly between teams,
clients, and locations.
Specifically, construction projects are executed by various operational divisions. This structured approach not only creates an integrated network but also enhances performance management across all divisions.
Equally, the company’s core values and unwritten ground rules (UGRs) help to define how it functions with integrity on a daily basis.
“We prioritise growing the people within our organisation alongside our partners. It’s all about looking forwards together and seeing how we can all benefit from collective teamwork,” Brink dictates.
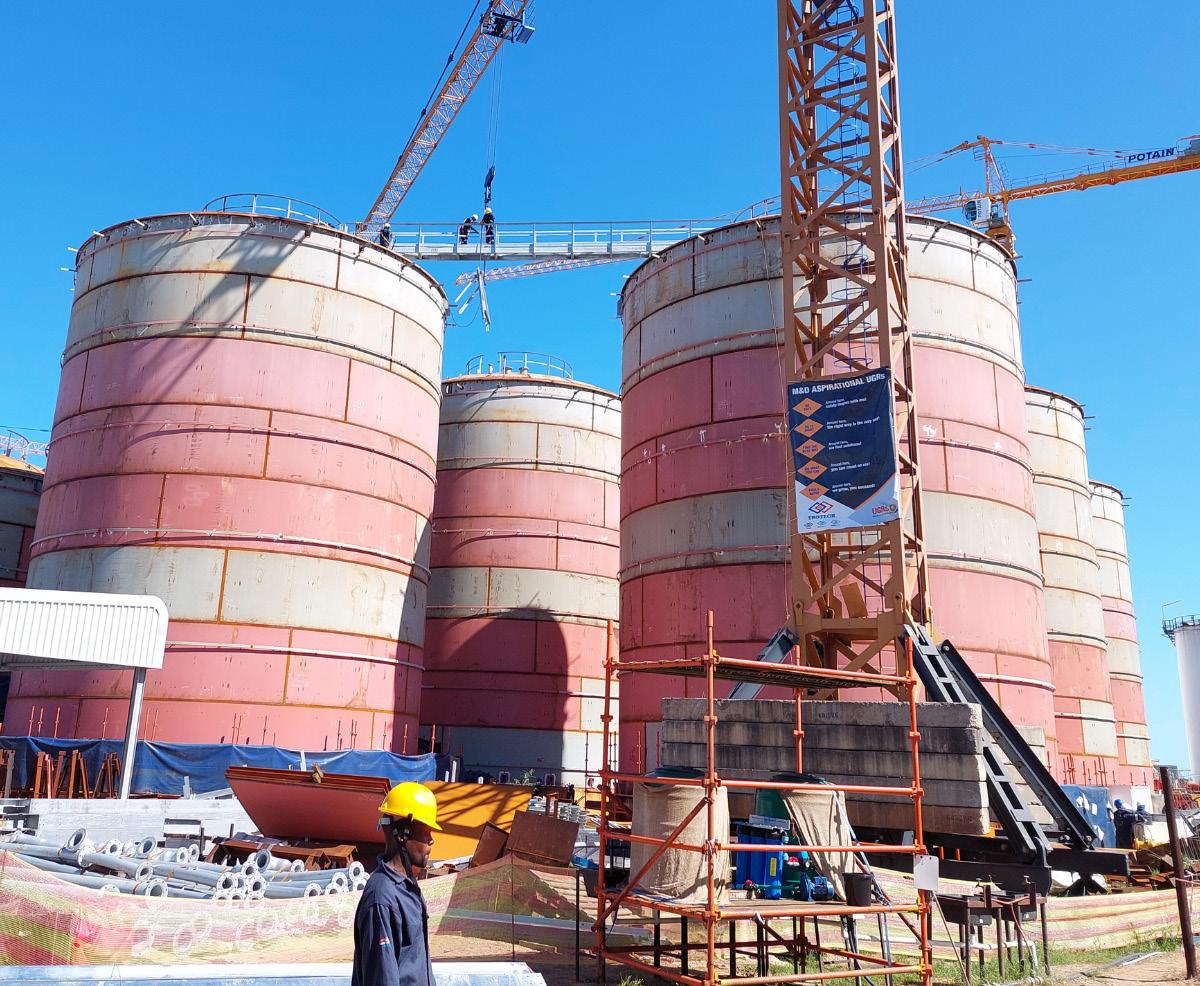
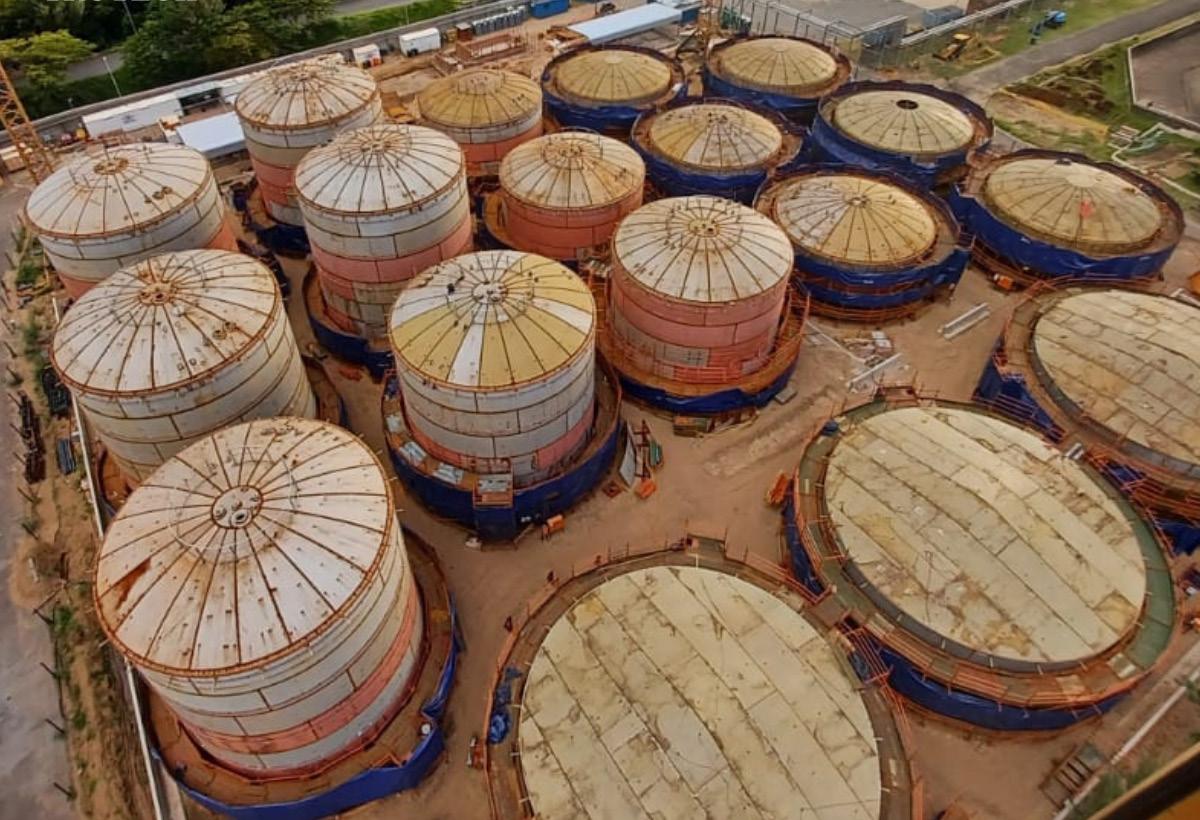
Trotech’s core values and UGRs
• Be safe – Safety begins with the individual.
• Do it right – The right way is the only way.
• Find the best way –Trotech always finds the best way.
• Do what you say – Businesses can count on Trotech.
• Khula Nathi – An African phrase for ‘around here, we
“WE ALWAYS STRIVE TO PROVIDE OUR CLIENTS WITH THE BEST SERVICE. OUR MAIN DRIVER, AND WHAT WE SEEK TO CONSISTENTLY ACHIEVE, IS BEING THE BEST CONTRACTOR AVAILABLE”
– LUKAS BRINK, MANAGING DIRECTOR, TROTECH
STREAMLINING TANKAGE NEEDS
Currently, Trotech is working on a variety of projects across the African region, with one comprising the construction of four new tanks for Botswana Oil Limited and the national government – an operation that is ahead of schedule and running successfully.
by bringing their projects to life much more quickly and efficiently,” Brink expands.
“We always strive to provide our clients with the best service. Our main driver, and what we seek to consistently achieve, is being the best contractor available.”
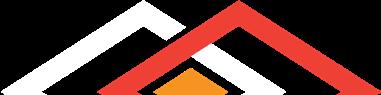
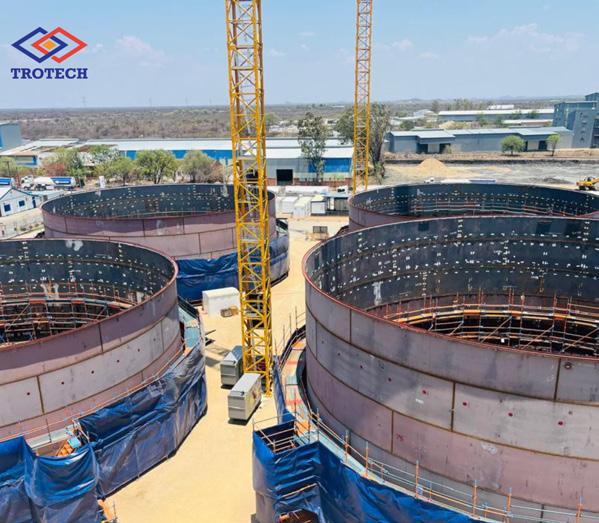
Additionally, the company achieved a massive feat in 2024 when it completed a total of 18 tanks in just 10 months – aptly displaying its ability to not only construct high-quality tanks but also do so in a timely manner.
“We benefit the client substantially
One example of Trotech’s advanced technical capabilities is its specific method of building called tank jacking, which few companies in SA are able to do.
“Tank jacking is a much safer and faster method of construction,” he details.
This specialised method consists
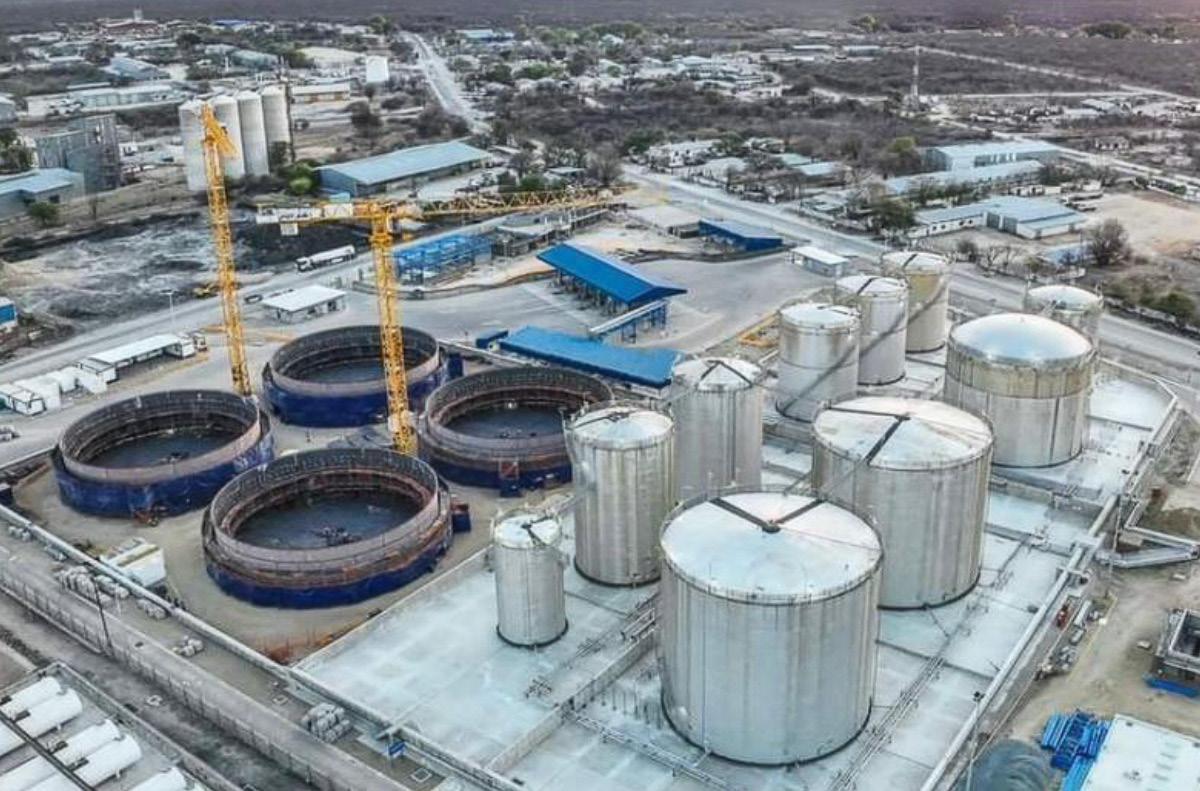
of constructing a tank from the top down, using hydraulic jacks to lift and support plates as they are welded into place, as opposed to the traditional method of starting with the bottom plates and working upwards.
In addition to being much safer and more efficient, tank jacking is ideal for erecting steel tanks, repairing tank floors, and enlarging storage capacity.
Crucial to producing results such as these is Trotech’s relationships with its partners and suppliers. The company has a significant level of trust in these relationships and ensures both contributors find mutual benefit in the long term.
Trotech’s supply chain is mainly from SA, with all raw materials coming from inside the country.
“In Africa, a local mindset is monumental because it’s all about how you can grow your country and
“WE PRIORITISE GROWING THE PEOPLE WITHIN OUR ORGANISATION ALONGSIDE OUR PARTNERS. IT’S ALL ABOUT LOOKING FORWARDS TOGETHER AND SEEING HOW WE CAN ALL BENEFIT FROM COLLECTIVE TEAMWORK”
– LUKAS BRINK, MANAGING DIRECTOR, TROTECH
Trotech’s track record
• 250+ tanks constructed
• 1,116,869 cubic metres of tankage
• 11 countries
• 31 years in the industry
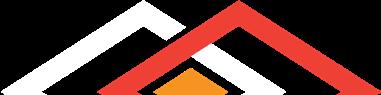
uplift the communities around you, creating jobs and opportunities for everyone,” Brink insights.
CONSTRUCTING A SAFER FUTURE
As Trotech continues to look towards the future of tank construction in the region, it is emphasising a few key initiatives, including securing another anchor project, continuing its upward growth, and ensuring its depot services and maintenance division
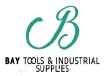
The Professional’s Choice
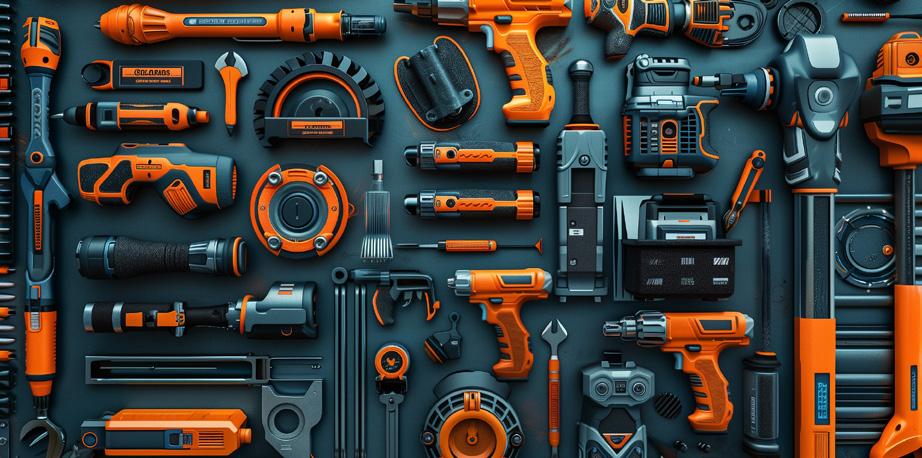
• Industrial Tools
• Engieering Tools
• Abrasives
• Safety Wear
• Electrical Supplies
• Lifting Equipment
• Welding Machinery
Our mission is to build an empowered company that will be capable of ensuring quality and service excellence in everything we do.
Our vision is to establish and maintain a reputation of integrity, hard work, and professionalism. By giving our best at all times, we can take pride as the trademark of Bay Tools and Industrial Supplies.
• Building Material
• Hardware
• Cleaning Supplies
• Bolt, Nuts and Consumables
• Fabrication
• Pump Impellers Casting
becomes stable and self-sustaining.
Equally, the company has a broader 10-year target of becoming the most significant bulk storage tank builder in Africa.
It is working to accomplish this by expanding its footprint into the Southern African Development Community (SADC) – a regional economic community comprising 16 member states.
“We want to expand further into Botswana, Namibia, Angola, and so forth to provide our cuttingedge services to more regions and communities who have the potential to benefit from it,” Brink explains.
Just as crucial to Trotech as it evaluates where it wants to be in the coming years is its work with corporate social responsibility (CSR) programmes.
The company engages with
• Pump Recon
• HDPE Piping – Steel/ Engineering
• Minor Fabrication
• General Building and Maintenance
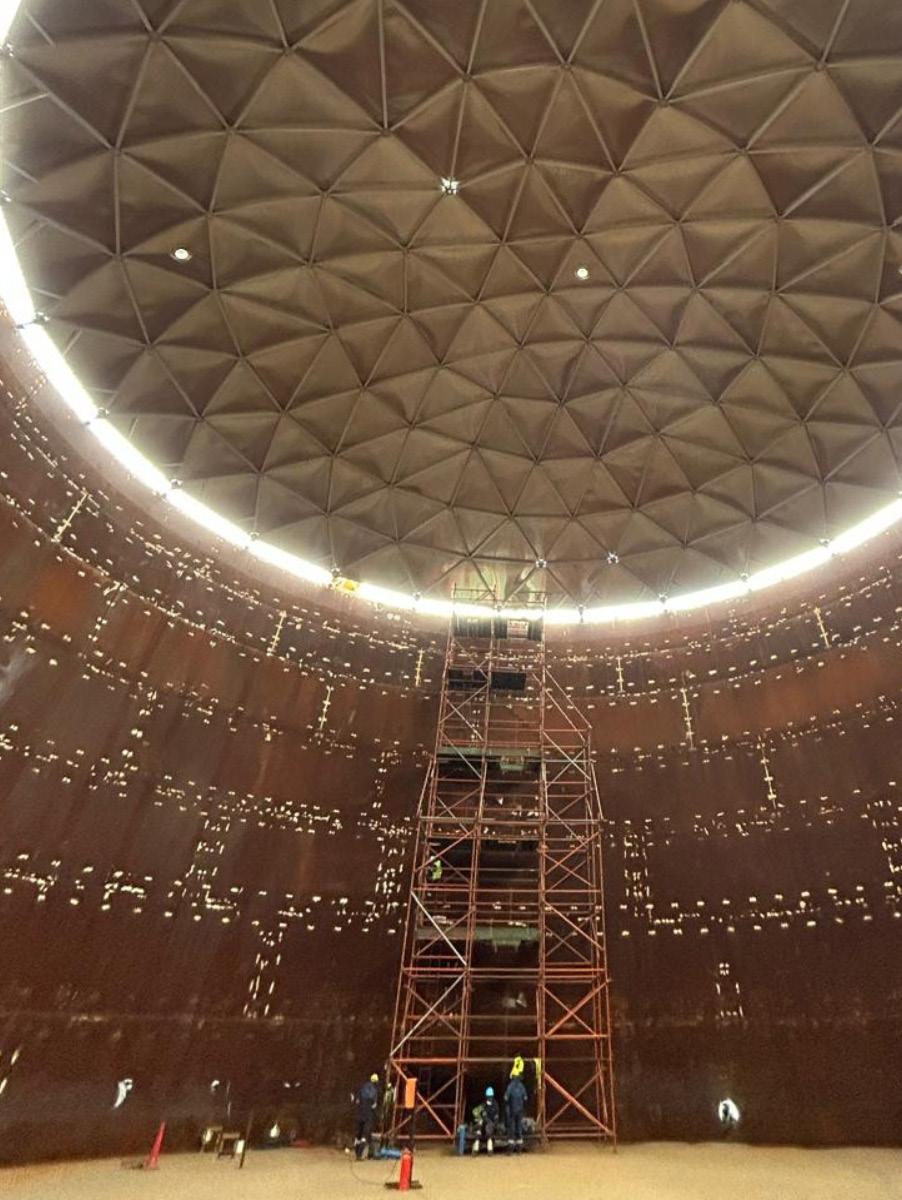
the communities it works in by making considerable contributions, supporting local sports teams, and even donating some of its project containers to local schools to be used as additional classrooms.
“We also train artisans to help them gain skills for careers such as boiler making and welding. After two to three years of training, they become absorbed into the company and are able to improve their livelihoods,” Brink details.
Trotech is, therefore, determined to continue its impressive track record and commitment to safety.
Proudly, in March 2025, the company’s maintenance team for Astron Energy (Astron) – an industryleading fuel brand – achieved 1,000 days of injury-free performance at its state-of-the-art refinery in Cape Town. This impressive feat reaffirms
Trotech’s unwavering dedication to health and safety. This is a significant accomplishment for a construction company doing high-risk work,” proudly concludes Brink.
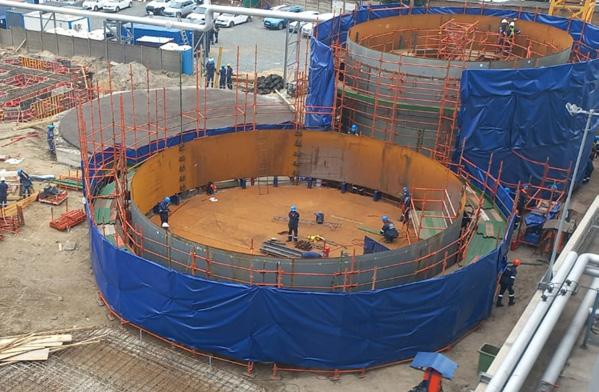
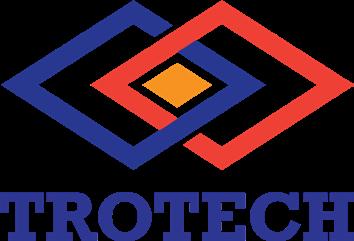
trotech.co.za
The company has experience in supplying the following services:
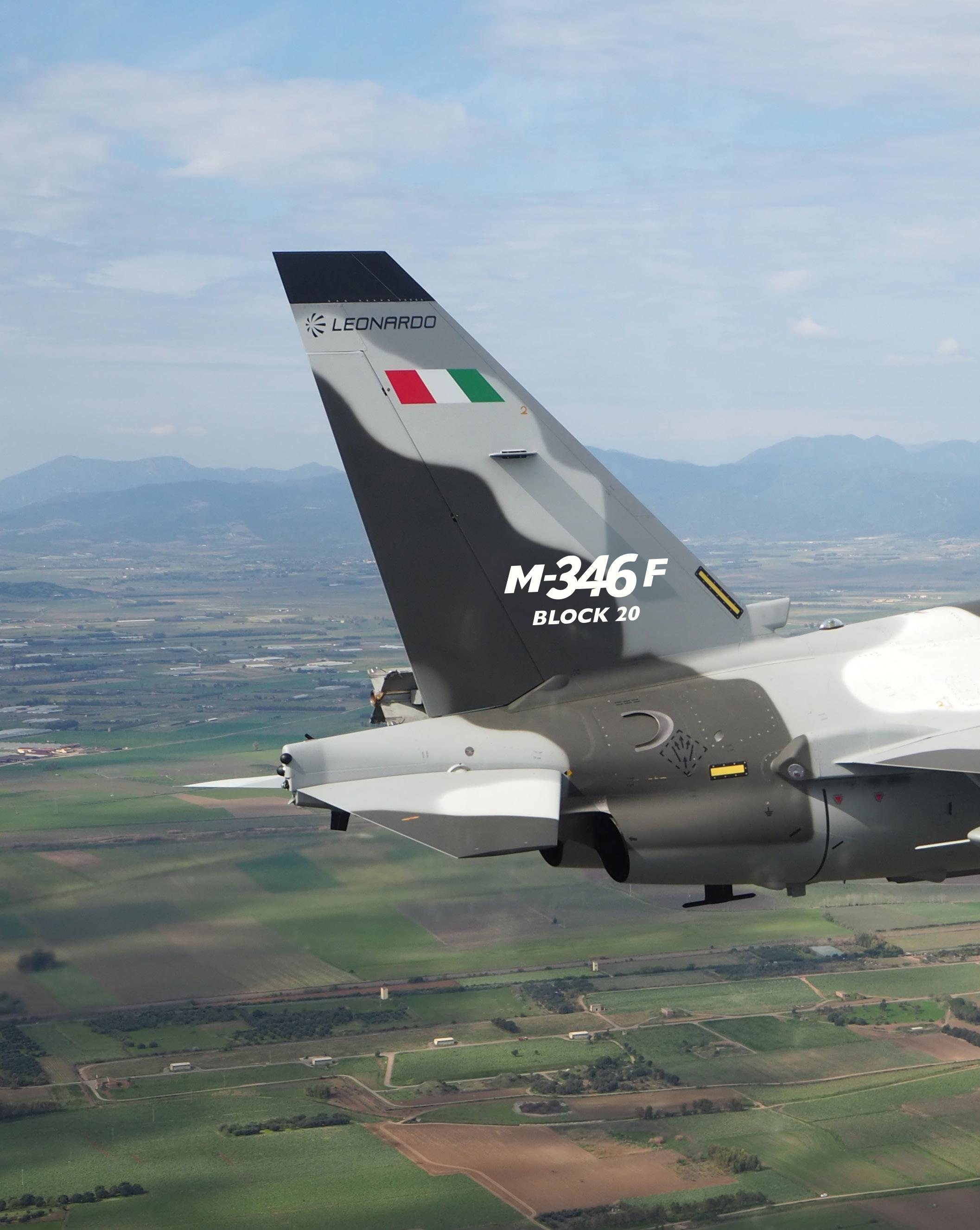
PROTECTING AUSTRALIA SINCE 1885
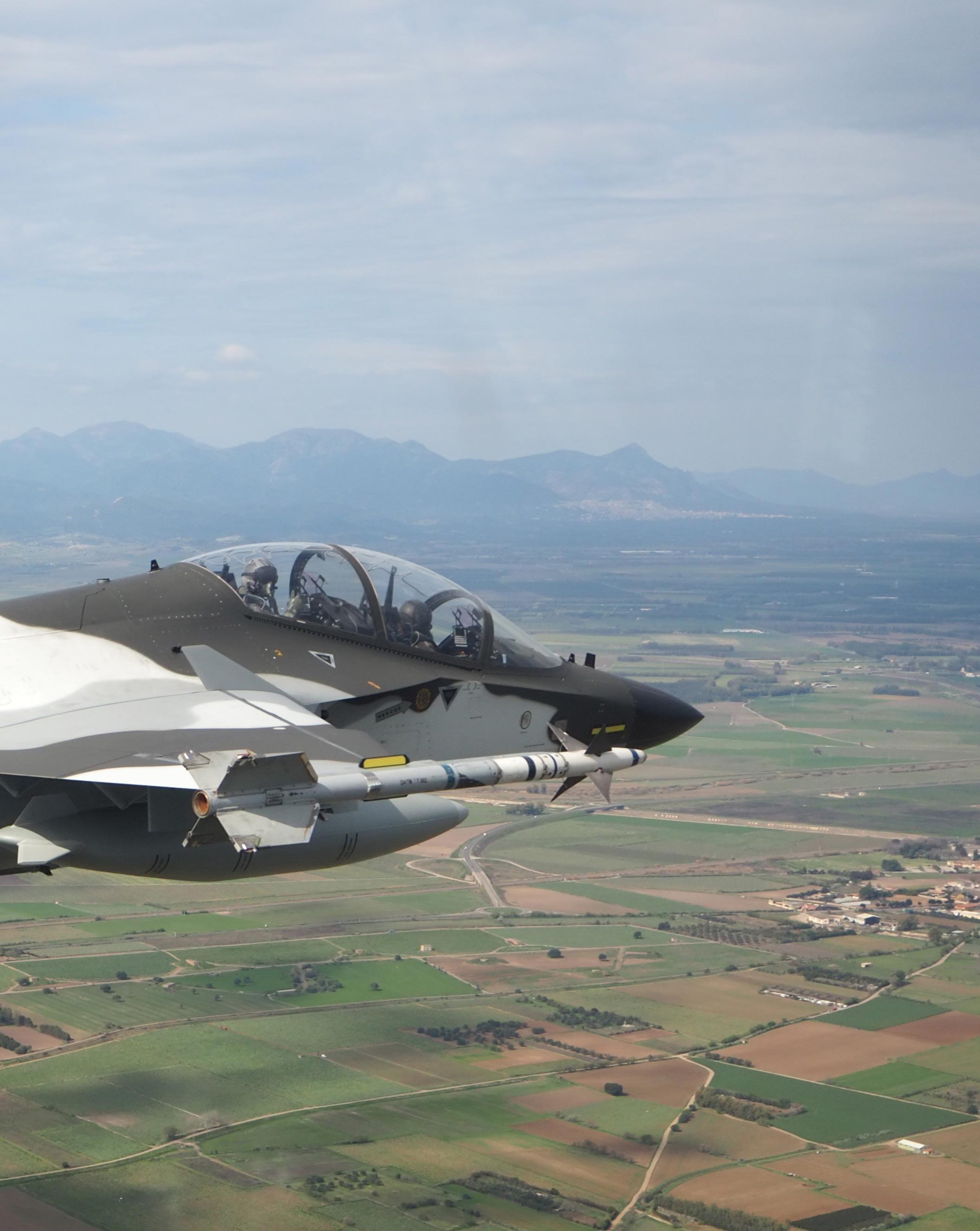
Advancing the country’s sovereign defence capability, Leonardo Australia delivers technologically advanced products, services, and solutions to the nation’s land, air, and sea domains.
Giorgio Mantegazza, Chairman of the Board, discusses the company’s unparalleled impact
Writer: Lucy Pilgrim | Project Manager: Cameron Lawrence
The defence manufacturing landscape in Australia has significantly evolved in recent years, making it both a challenging and exciting environment.
This is primarily due to a number of industry regulatory reviews from the government that have greatly impacted the future of the country’s defence capability.
Namely, the Defence Industry Development Strategy and Sovereign Defence Industrial Priorities (SDIPs) offer clear guidance around key sovereign defence requirements. Thus, major industry players have had to carefully assess their future strategies to ensure they meet these evolving national requirements.
As a subsidiary of the global industrial group, Leonardo Australia identifies niche areas in which it can contribute to the requirements
of defence across the country and broader Commonwealth.
The group plans to transfer technology, production, and sustainment for its products and services in Australia to effectively provide a comprehensive sovereign defence capability, as well as leveraging its UK and US network to boost capabilities as per the AUKUS defence partnership between the three nations.
“This will translate into an increase in manufacturing capabilities that will also support the rise in demand for defence products in line with the recently-launched rearmament programmes,” opens Giorgio Mantegazza, Chairman of the Board at Leonardo Australia.
The company has been active Down Under since 1885 with the delivery of 30 torpedoes across Australia to Victoria (VIC), South Australia, and
Tasmania. It subsequently grew as a systems integrator and partner with both defence and civil customers.
Today, Leonardo Australia is a key player in the aerospace, defence, and security solutions sectors, with a significant in-country base of installed equipment and sites operating in Melbourne, Perth, and the capital, Canberra.
MISSION-READY AIRCRAFT
Leonardo Australia has cultivated a renowned reputation across the nation, with its primary product lines of business in helicopters and electronics.
“We are able to draw on the full capabilities of the global Leonardo group. With a broad portfolio spanning helicopters, aeronautics, electronics, space, and cybersecurity, we are uniquely positioned to deliver comprehensive, turnkey solutions for
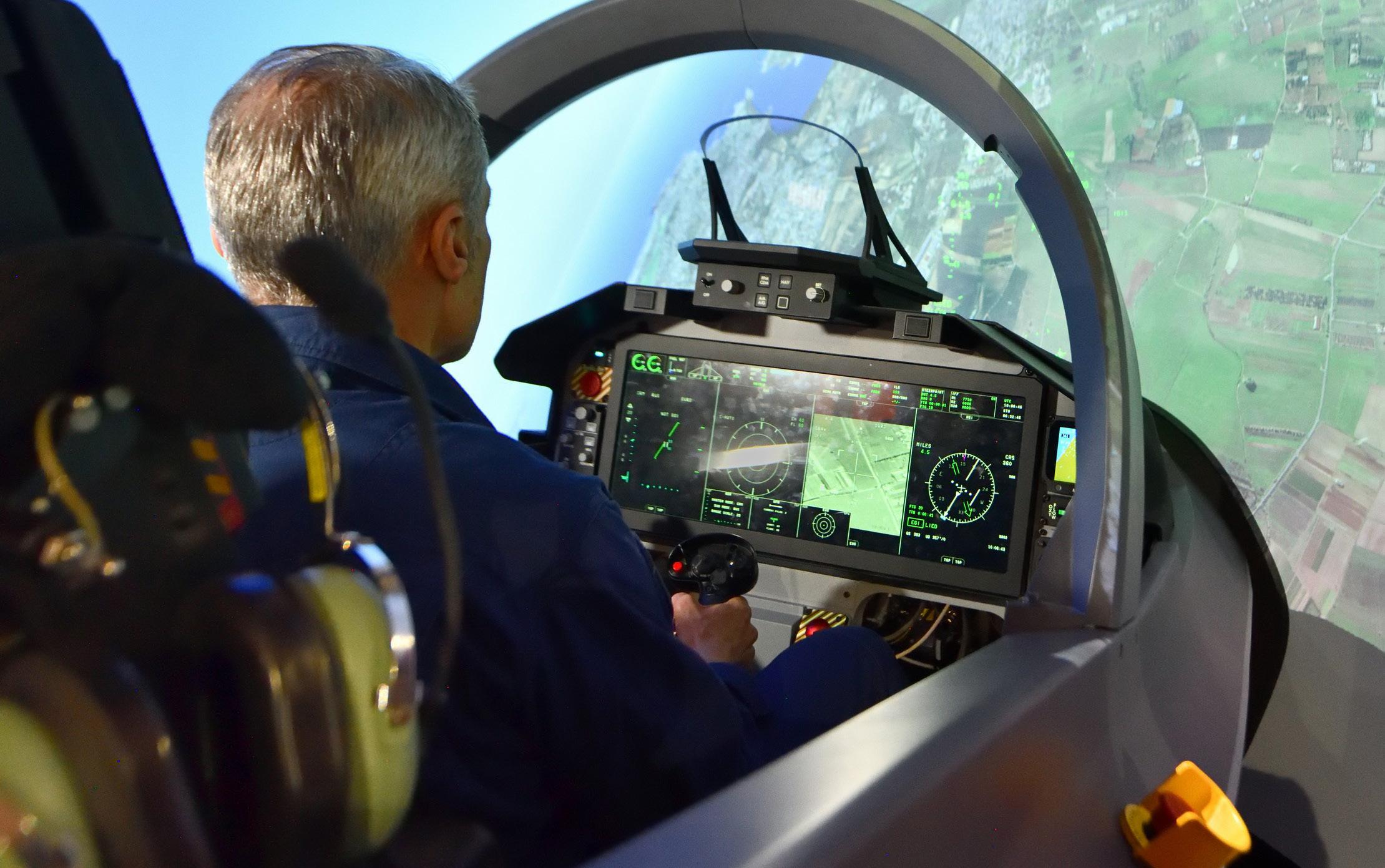
complex and sophisticated services,” Mantegazza insights.
Leonardo Australia has over 150 helicopters across Australia and New Zealand for a range of applications, namely military, civil, health and emergency services, VIP, and transport and training.
Its services, meanwhile, include aircraft maintenance, maintenance, repair, and overhaul (MRO), customer support and account management, and material and product support engineering.
Primarily operating from Port Melbourne and Essendon Fields (EF) in Melbourne, its helicopter services in particular include everything from aircraft painting and component replacement to full helicopter assembly, as well as pre-purchase, pre and post-lease evaluations, and condition inspections.
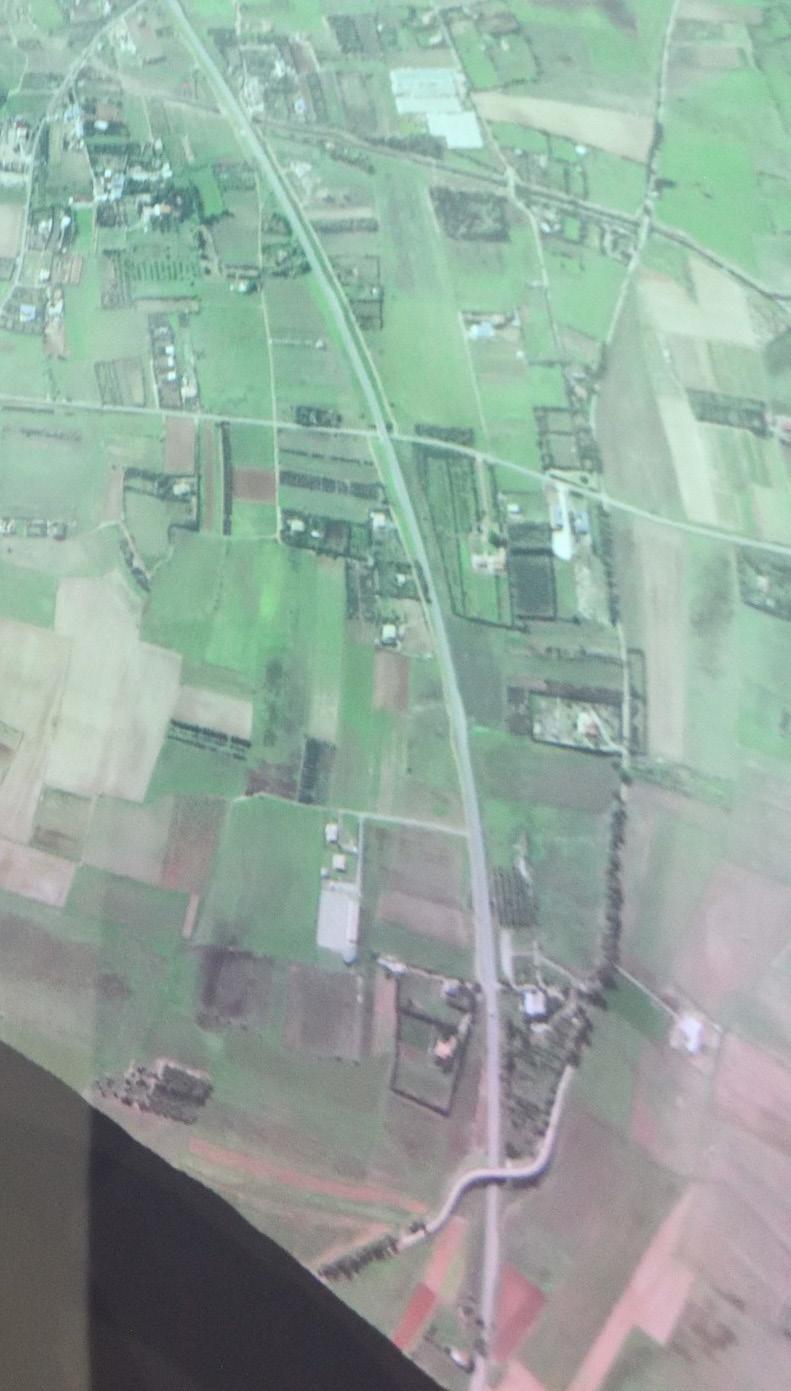
“These end-to-end services ensure aircraft remain mission-ready, safe, and fully compliant with operational requirements,” he asserts.
The company’s headquarters and core capabilities allow it to deliver defence technologies that facilitate flexible technology transfer and local industrial participation in Australia.
This provides significant advantages for manufacturing and production processes, helping to build Australia’s sovereign capability.
Leonardo currently has C-27J Spartan military transport aircraft in service with the Royal Australian Air Force (RAAF). The logistics support and sustainment for the aircraft is provided from Richmond, New South Wales and Amberley, Queensland.
“In collaboration with Leonardo Germany, our electronics capabilities
also continue to install new weather radars for the Bureau of Meteorology across the country, including many remote and regional locations,” Mantegazza informs us.
In addition, Leonardo Australia’s cybersecurity technology, automatic number plate recognition (ANPR) technology, and supervisory control and data acquisition (SCADA) systems have been deployed for the Queensland Police Service and Perth Transport Authority of Western Australia, respectively.
UNPARALLELED CAPABILITIES
Created in collaboration with the Commonwealth, Leonardo Australia’s helicopter main gearbox MRO facility in Port Melbourne is one of three across the world and is the only facility of its kind in the Southern Hemisphere.
LEONARDO AUSTRALIA’S STAFF BASE
The company’s people are at the heart of its success, bringing deep technical knowledge, professionalism, and a commitment to excellence to the forefront.
“We empower them by investing in continuous learning and development and offering both local and international training opportunities, including specialised technical programmes at Leonardo’s global headquarters in Italy.
“This ensures our teams stay at the cutting edge of innovation and capability, whilst also building sovereign expertise here in Australia,” Mantegazza shares.
Leonardo Australia works hard to foster a collaborative and inclusive work environment where staff are trusted with their responsibilities, encouraged to contribute ideas, and take ownership of outcomes.
Their contributions are subsequently recognised through direct engagement, open communication, and opportunities to grow within the business.
The company also creates equal opportunities for its people, encouraging fair treatment for all regardless of race, nationality, political creed, religion, gender, age, physical ability, or sexual orientation.
As such, Leonardo Australia continuously respects the dignity of each employee.
“Ultimately, we aim to ensure our people feel supported, respected, and proud to play a role in delivering critical capability for Australia.”
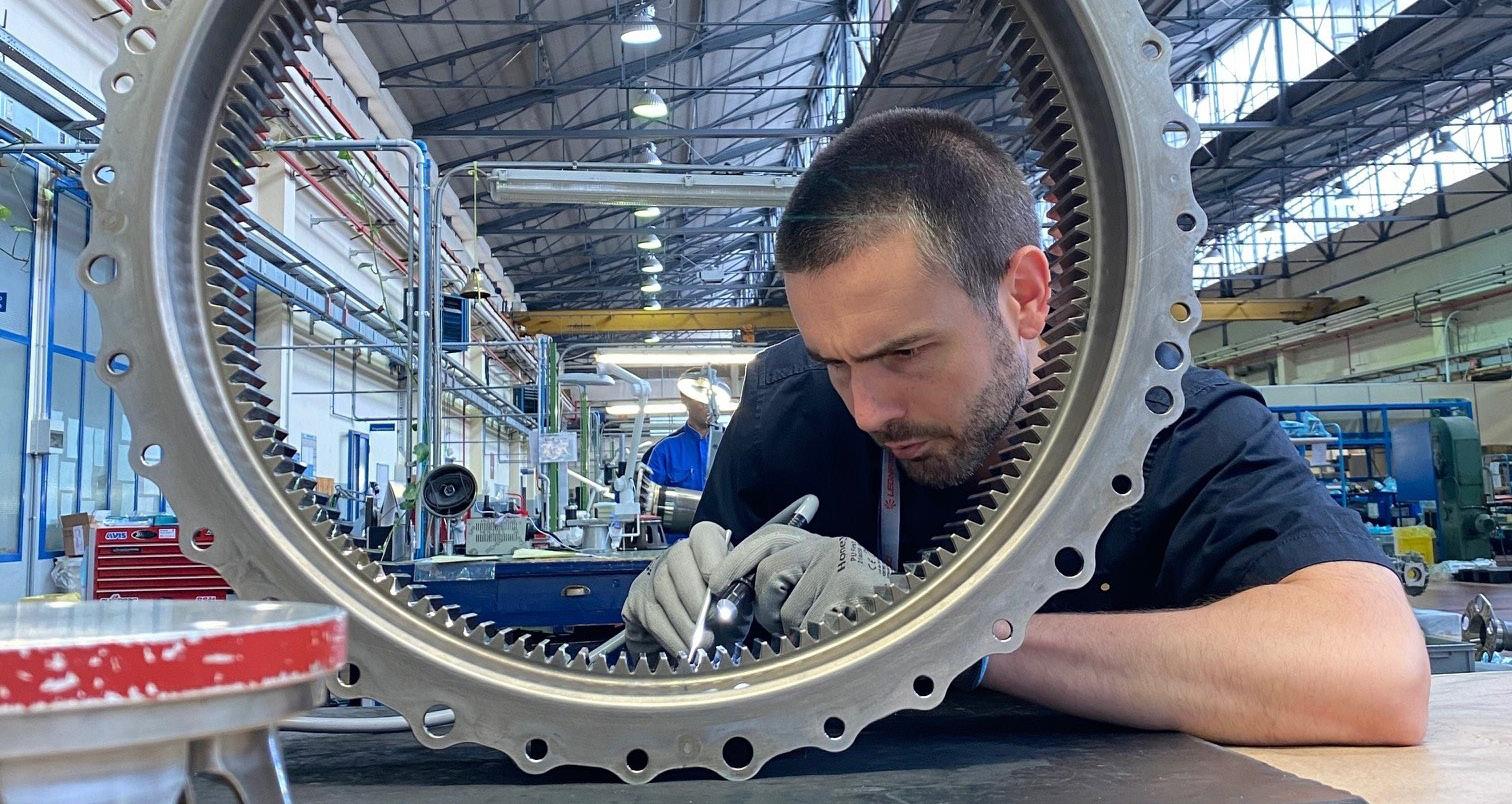
A ROBUST SUPPLY NETWORK
A localised and resilient supply chain is central to Leonardo Australia’s strategy and directly supports Australia’s SDIPs.
“In-country repair, overhaul, and component sustainment are not just operational enhancements – they are critical to maintaining platform readiness, reducing turnaround times, and easing the logistical burden on defence in an increasingly volatile global environment,” Mantegazza urges.
In addition, Australia is the first country to implement a global supply chain optimisation programme. Developed by Leonardo Italy, the model is designed to boost sustainment capabilities and customer proximity across the APAC region.
Key support functions, as well as logistics capabilities such as helicopter MRO, SEA1442 Phase 4, and ANPR are also being transitioned from overseas to Australia, enabling a faster local response and greater control over critical systems.
Pointedly, the facility conducts the complete overhaul and testing of Leonardo’s AW139 and NH90 main gearboxes, certified by the aviation safety authorities in Australia and Europe.
The MRO facility’s core capabilities are unlocked by a custom-designed and manufactured 120-tonne test bench capable of autonomously operating gearboxes by reproducing and simulating the dynamics of flight conditions in helicopter transmissions.
The cutting-edge bench is also able to accommodate the various gearbox types of a range of helicopters.
“With complex electrical power, hydraulic, lubrication, and rotor systems, it can simulate dual jet engine inputs at 21,000 revolutions per minute, ensuring each gearbox meets the operational specifications for high performance and guarantees product safety,” Mantegazza explains.
The MRO facility has extended Leonardo Australia’s industrial aerospace proficiency with capabilities including non-destructive testing, an aerospace-grade paint booth, an electroplating facility, sophisticated surface finishing and cleaning equipment, a machining shop, and a state-of-theart parts warehouse.
It is overseen by an all-Australian
team of 15 aviation technicians and engineers who have undertaken more than 12 months of dedicated transmissions training in both Australia and Italy.
“The MRO capabilities afforded by the facility will primarily support emergency medical services in Australia and the defence sector throughout the Asia Pacific (APAC) region with the overhaul of main gearboxes locally,” he elaborates.
ENHANCED ELECTRONICS
On the electronics side of the business, the ANZAC Communications Upgrade Programme is particularly important to Leonardo Australia as it upgrades the communications systems on eight ANZAC-class frigates utilised by the Royal Australian Navy.
“This is the first defence electronics programme for Leonardo Australia and has provided the local capability to expand our electronics services,” Mantegazza tells us.
In light of its long history of providing torpedoes to Australia, the company has also been selected to support the integration of the torpedo launch system for the Australian government’s SEA5000 Hunter-class frigates.
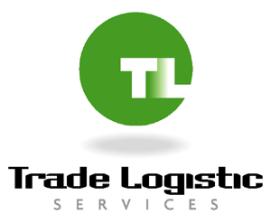
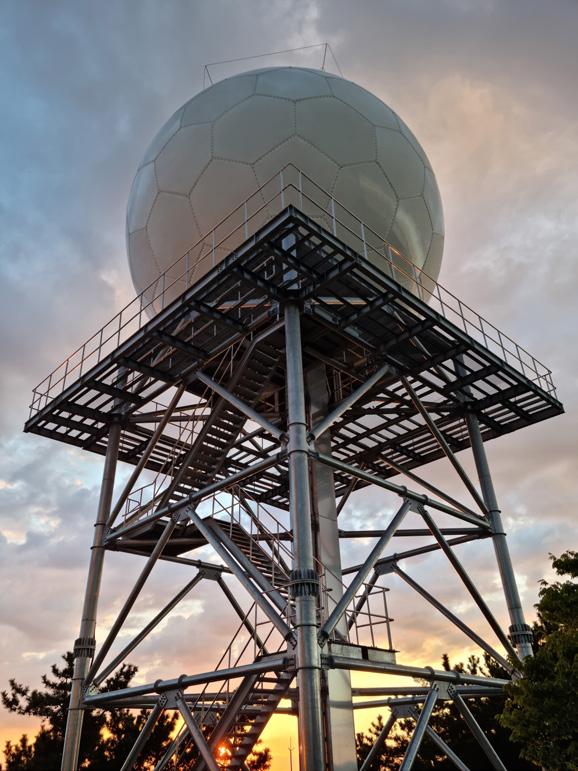
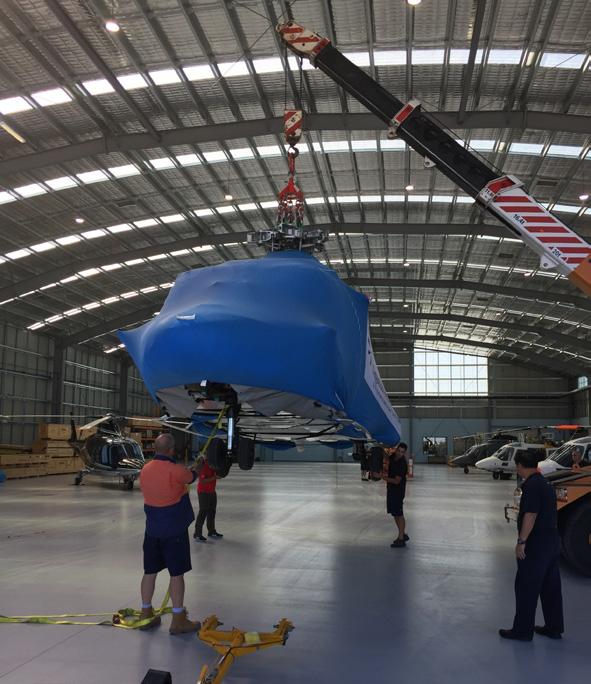
Leveraging these capabilities, Leonardo Australia is actively pursuing other defence electronics opportunities such as communications, combat systems, armaments, ammunition, and guided weapons.
With this in mind, the company is engaged in F-35 Lightning II
Proudly Australian-owned and operated, Trade Logistic Services PTY LTD has been delivering smart, tailored logistics solutions for over three decades.
With a legacy of trust and excellence, we specialize in managing the complexities of modern supply chains so you can focus on growing your business.
Industry Expertise You Can Count On
From Meteorology Equipment to Technology, Industrial, Agricultural, Automotive, and Recreational & Building Equipment, we have the experience and capability to move your goods safely, efficiently, and on time.
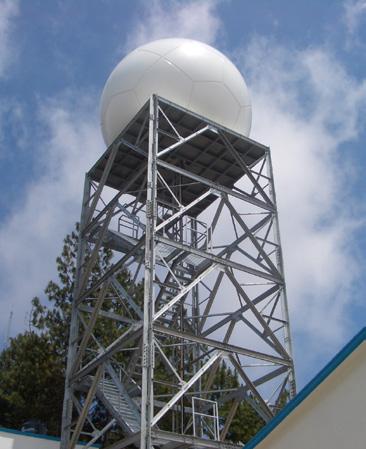
End-to-End Logistics Solutions
Whether you need warehousing, distribution, international & domestic freight forwarding, or customs brokerage, we provide seamless logistics services customized to your specific needs.
Odran Lipscombe Managing Director
Email: sharon@tradelogistic.com.au Mobile: +61 400 104462 www.tradelogistic.com.au
Simplify Your Supply Chain Today Connect with us to discover how we can make a difference in your logistics journey.
Email: odran@tradelogistic.com.au Mobile: +61 417 585359
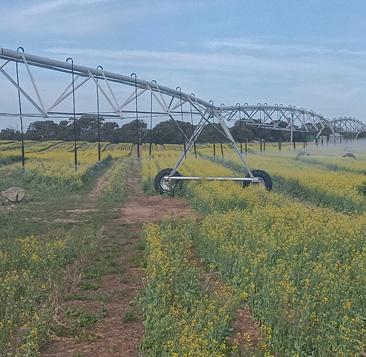
Why Choose Trade Logistic Services?
• 30+ Years of Proven Experience
• Personalized Service for Businesses of All Sizes
• Cost-Effective, Scalable Solutions
• Commitment to Delivering Value and Satisfaction
Sharon Lipscombe
Managing Director
“IN-COUNTRY
REPAIR, OVERHAUL, AND COMPONENT SUSTAINMENT ARE NOT JUST OPERATIONAL ENHANCEMENTS – THEY ARE CRITICAL TO MAINTAINING PLATFORM READINESS, REDUCING TURNAROUND TIMES, AND EASING THE LOGISTICAL BURDEN ON DEFENCE IN AN INCREASINGLY VOLATILE GLOBAL ENVIRONMENT”
– GIORGIO MANTEGAZZA, CHAIRMAN OF THE BOARD, LEONARDO AUSTRALIA
electronics and avionics maintenance, SEA3000 general purpose frigates, LAND 8710 landing craft, and the Guided Weapons and Explosives Ordinance Enterprise.
Leonardo Australia is additionally well-positioned to support upcoming infrastructure programmes across airports, ports, and metro systems
with its integrated technologies. These include advanced air traffic management systems for both manned and uncrewed aircraft, airport surveillance and cyber solutions, baggage handling automation, port management information systems, and SCADA systems.
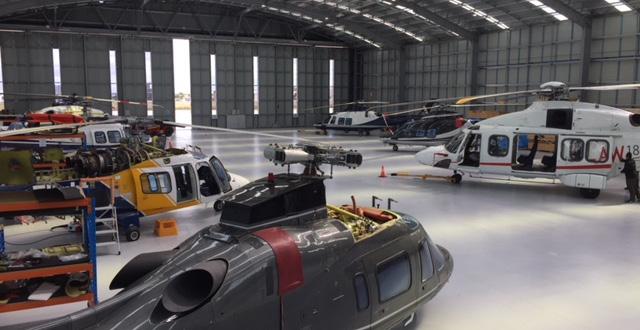
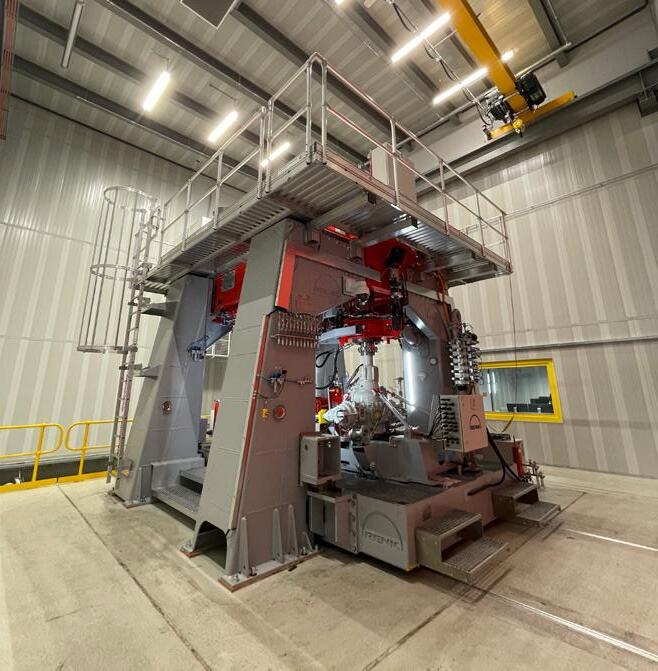
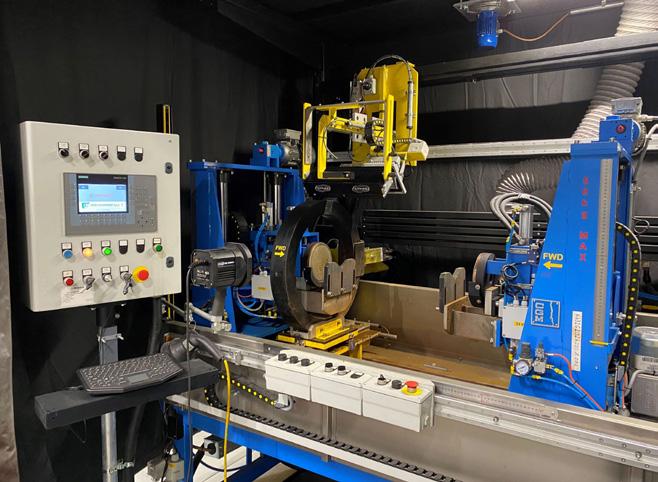
“We’re excited to grow into these new areas as we can draw on Leonardo’s global expertise and flexible technologies to deliver smart, effective solutions that improve operations and help keep communities safe across the aviation, transport, and maritime sectors,” Mantegazza prides.
STEADFAST SOCIAL COMMITMENTS
Leonardo Australia contributes to the socioeconomic development of the communities in which it operates by transferring its technologies and expertise.
This is evidenced by its active participation in local bodies to support and grow its communities, such as FB IDEAs, a new not-for-profit that promotes a collaborative culture in Fishermans Bend, Australia’s largest urban renewal project in Melbourne.
VicWorx, a proposed innovation hub at Fishermans Bend, aims to bring together small to medium-sized defence enterprises and research institutions to provide a reliable means for fostering innovation, collaboration, and problem-solving.
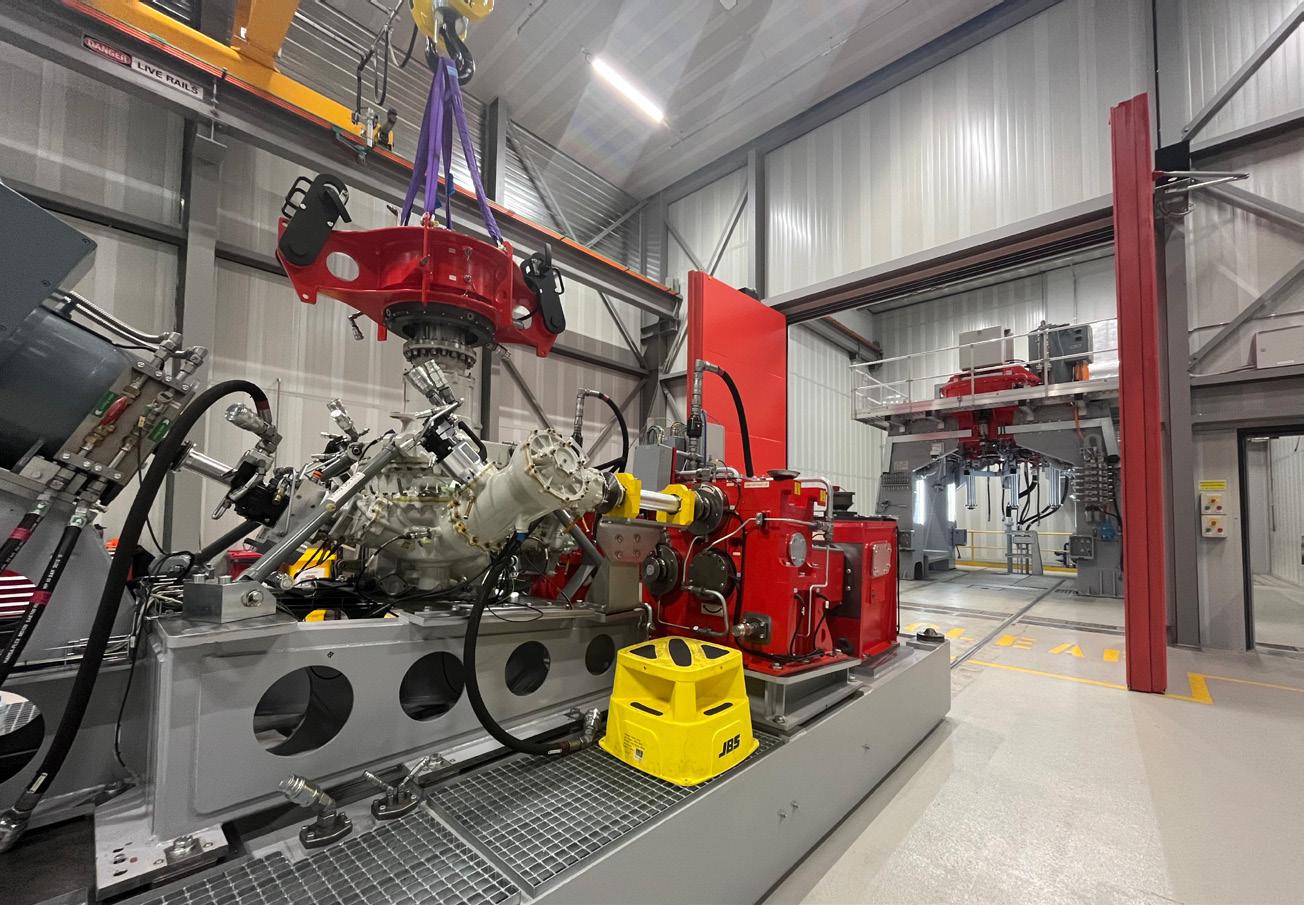
“WITH A BROAD PORTFOLIO SPANNING HELICOPTERS, AERONAUTICS, ELECTRONICS, SPACE, AND CYBERSECURITY, WE ARE UNIQUELY POSITIONED TO DELIVER COMPREHENSIVE, TURNKEY SOLUTIONS FOR COMPLEX AND SOPHISTICATED SERVICES”
– GIORGIO MANTEGAZZA, CHAIRMAN OF THE BOARD, LEONARDO AUSTRALIA
“The long-term vision is to develop a collaborative hub designed to bolster Victoria’s advanced manufacturing and defence technology sectors,” states Mantegazza.
In addition, Leonardo Australia offers guided tours of its MRO and hangar facilities in order to share its
industry knowledge and operational expertise with universities and flight academy students.
“These visits provide students with a real-world perspective on aircraft maintenance, engineering practices, and the day-to-day workings of a professional aviation environment,” he comments.
MRO test bench gearbox
MRO test bench
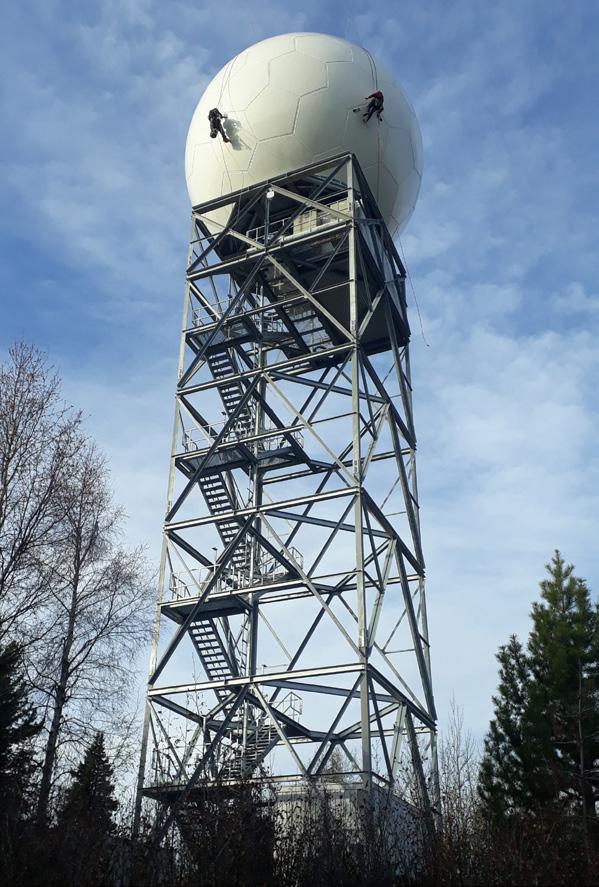
In support of its Indigenous engagement commitments, Leonardo Australia additionally celebrates Aboriginal and Torres Strait Islander peoples as traditional custodians of the land and recognises the present and future generations of the Kulin Nation.
As an equal opportunity company, Leonardo Australia is likewise committed to increasing its engagement with Indigenous enterprises and their communities and works hard to develop these longterm relationships.
“We have successfully built relationships with Indigenous communities, as well as employment agencies and businesses in Melbourne and Perth where we have a significant technical employee base comprising maintenance, repair, installation, and engineering capabilities,” he outlines.
ON THE HORIZON
Leonardo Australia is proud to have technologies and innovative solutions that are trusted to satisfy the Australian government in critical sectors such as defence, cybersecurity, infrastructure, and mobility.
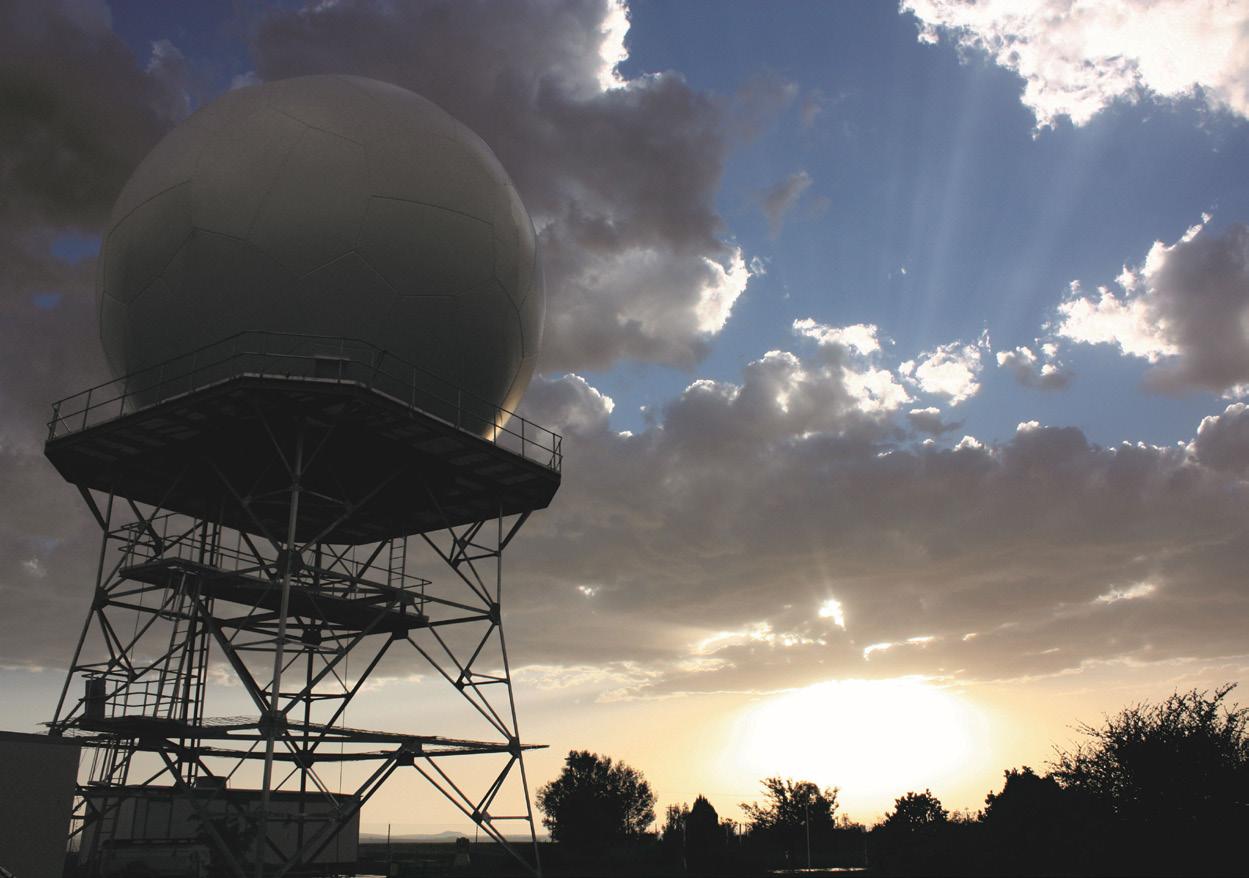
Leonardo Australia is therefore focused on the continued improvement and enhancement of its ongoing programmes, including the ramp-up of the AW139 main gearbox, SEA1442 Phase 4 and 5, weather radar installations for the Bureau of Meteorology, and its ANPR system.
“Besides our ongoing programmes, we are following with great attention the development of the Australian market and the new requirements expressed in the various reviews issued by the Ministry of Defence,” Mantegazza sets out.
Indeed, Leonardo Australia is proposing its M-346 jet aircraft to respond to the AIR6002 programme for the replacement of RAAF’s Hawk training aircraft with a new lead-in fighter training system.
“This is the most advanced jet trainer present in the market, and the new Block 20 version will grant the full ability to train pilots for decades to come,” he explains.
In the naval sector, meanwhile, Leonardo Australia is promoting the 127-millimetre (mm) gun used for Project Sea 3000 and the 30mm gun used for the Project Land 8710.
“These guns, together with their
guided and pre-fragmentated ammunitions, will provide unique capabilities to the Australian Armed Forces and represent the best valuefor-money solution.”
The company is also working with local agencies and universities to develop solutions in the aerospace sector, working in the areas of earth observation, satellite sensors, and payloads.
Leonardo Australia is additionally involved in several initiatives concerning cybersecurity and automation, working with its local partners to provide valuable solutions for airports, ports, and border control.
“Our cutting-edge technologies are ideal to satisfy Australian requirements, and with the dedicated transfer of technology programmes, we will be able to assure strategic sovereign capabilities in all these critical sectors,” Mantegazza concludes.

UNLOCKING THE DOOR TO MANUFACTURING EXCELLENCE
The Vietnamese division of ASSA ABLOY, a global leader in access solutions, is an integral manufacturing hub for the production of smart door locks, hardware, and more. Alison Astarita, Vice President of Operations, highlights the company’s two cutting-edge facilities and commitment to innovation
Writer: Lucy Pilgrim | Project Manager: Josh Whiteside
Renowned across the globe for producing outstanding smart locks, doors, keys, gates, and automatic entrances, to name a few, ASSA ABLOY products are utilised by billions of people across the world.
The inception of the company’s Vietnamese manufacturing hub occurred when its greenfield factory was established in 2020, solely dedicated to producing smart door locks for the residential segment.
Fast forward four years, the company’s journey continued with a USD$30 million investment in a second state-of-the-art facility that specialises in door closers, which is expected to ramp up production to two million units per year once it reaches full capacity in the near future.

Alison Astarita, Vice President of Operations
“Vietnam plays a key role in ASSA ABLOY’s growth strategy, so we can expect to continue expanding our manufacturing footprint in this
fast-growing nation,” introduces Alison Astarita, Vice President of Operations.
Indeed, Vietnam is ripe with potential for manufacturing companies thanks to its favourable business climate, strategic location, and highly skilled workforce, making it an attractive destination for organisations looking to expand.
Additionally, nationwide government initiatives to improve infrastructure and support industrial growth further enhance its appeal.
“As technological advancements and market needs converge, Vietnam presents new opportunities for innovation and service delivery, creating a vibrant and dynamic environment for manufacturing companies,” she expands.
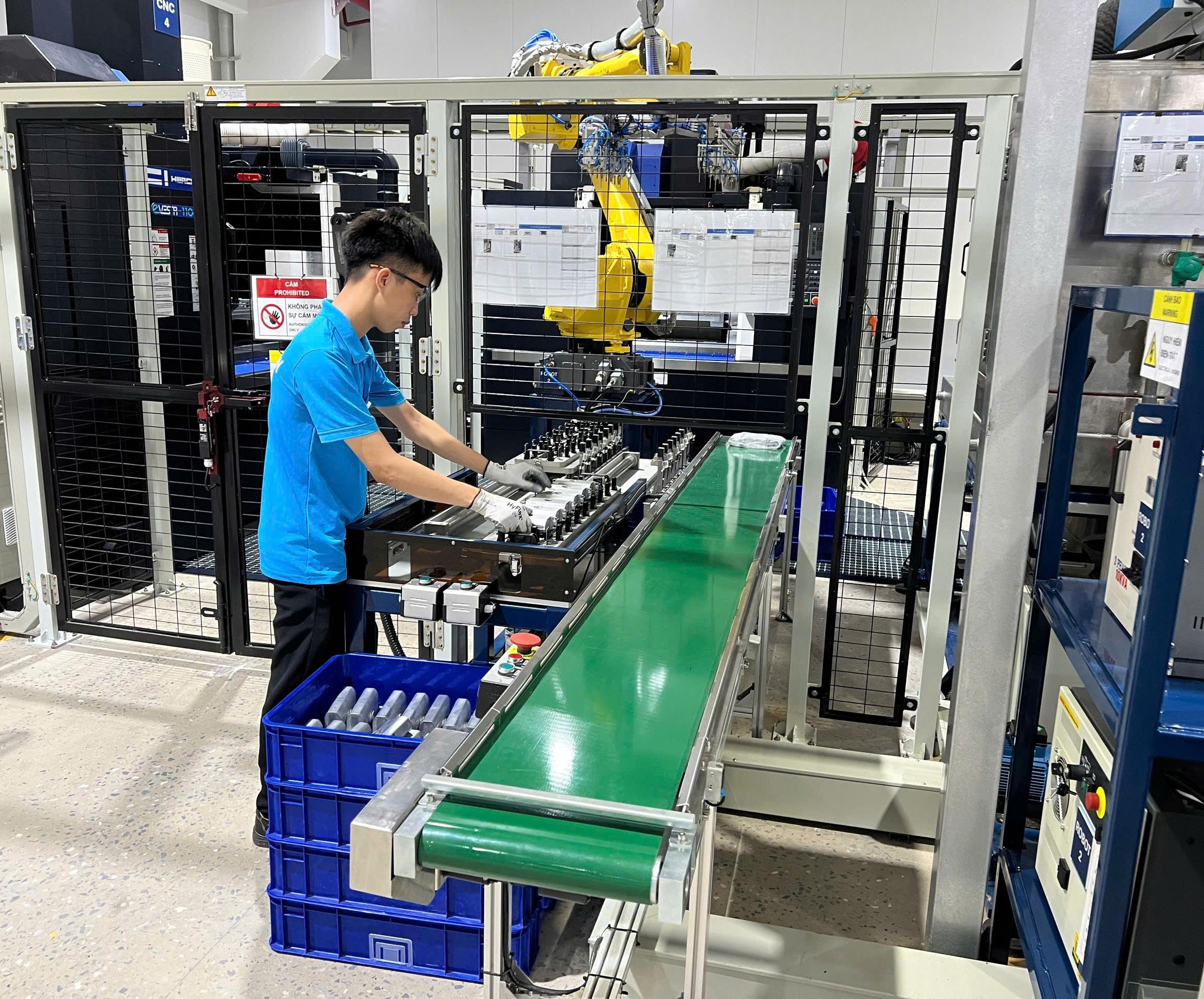
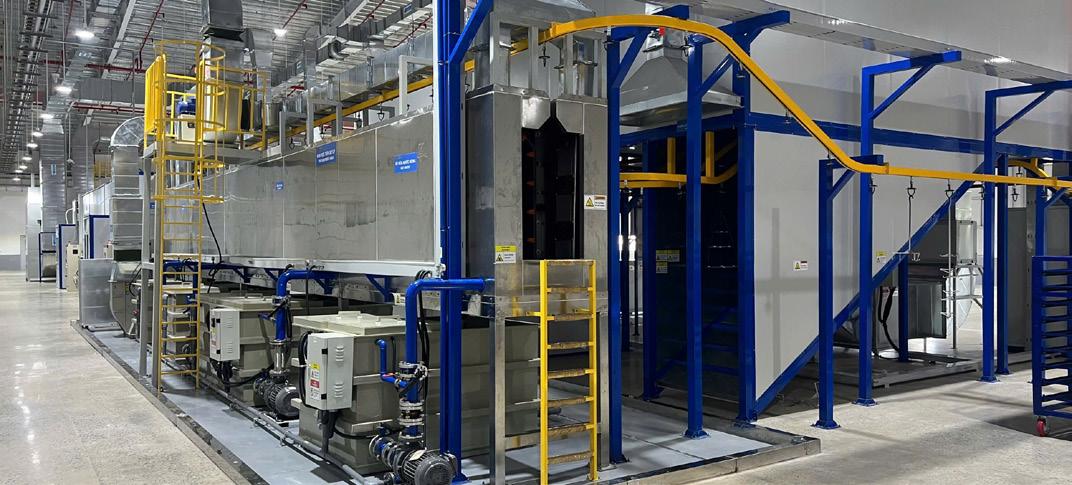

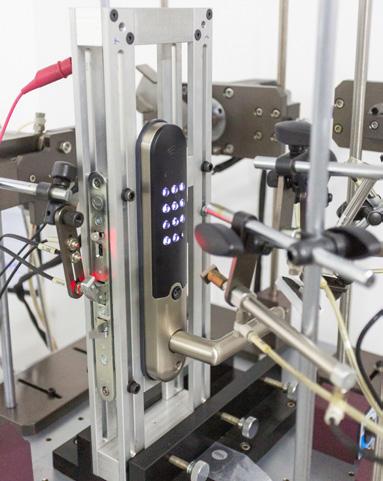
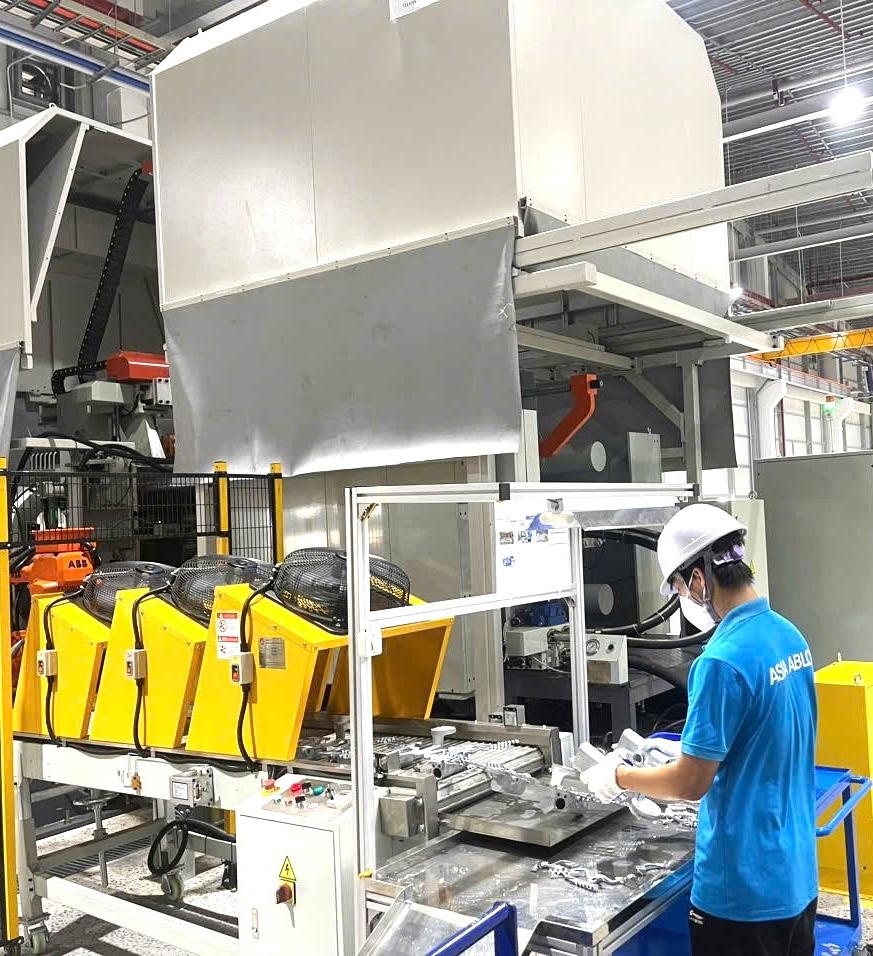
“AS
TECHNOLOGICAL ADVANCEMENTS AND MARKET NEEDS CONVERGE,
VIETNAM PRESENTS NEW OPPORTUNITIES FOR INNOVATION AND SERVICE DELIVERY, CREATING A VIBRANT AND DYNAMIC ENVIRONMENT FOR MANUFACTURING COMPANIES”
– ALISON ASTARITA, VICE PRESIDENT OF OPERATIONS, ASSA ABLOY VIETNAM
CONTROL AND EFFICIENCY
ASSA ABLOY’s presence in Vietnam makes it a key manufacturing hub for smart locks and door closers, exporting high-quality products to customers around the globe, with Europe and Asia Pacific in particular being key markets.
One of the company’s two factories across the country, ASSA ABLOY Smart Technology Vietnam (AASTV),
is strategically located north of Noi Bai International Airport in Hanoi and has produced state-of-the-art smart locks since 2020.
ASSA ABLOY’s second facility, meanwhile, situated in Haiphong – the principal port city of the Red River Delta – opened its doors in September last year and is equipped with nextgeneration machinery and technology that ensure precision manufacturing and high-quality output.
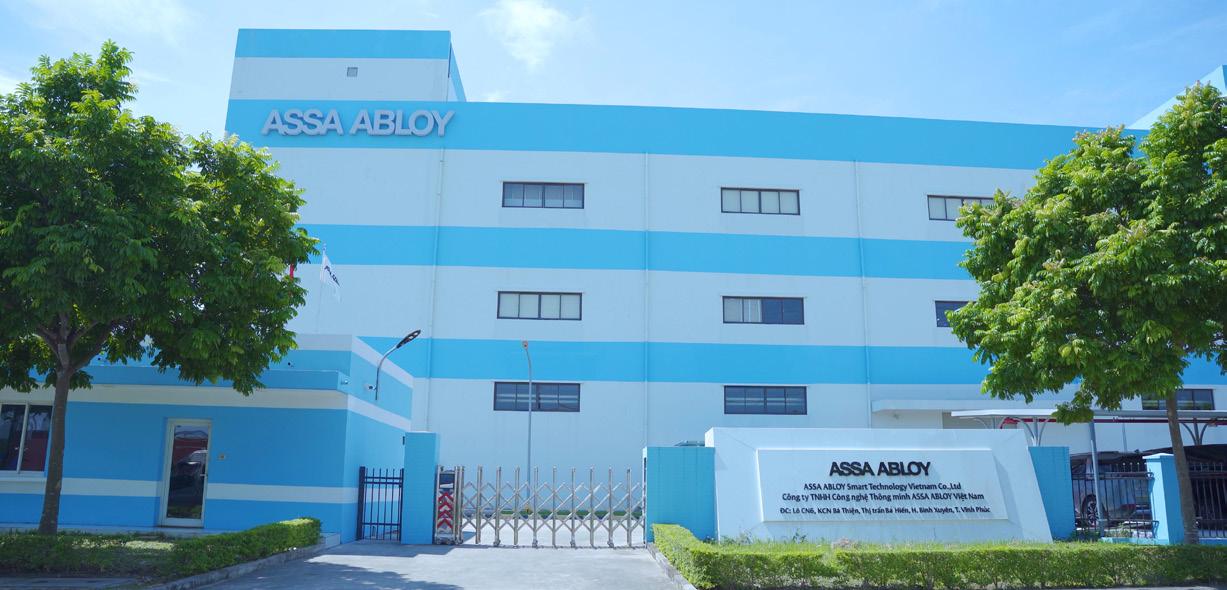
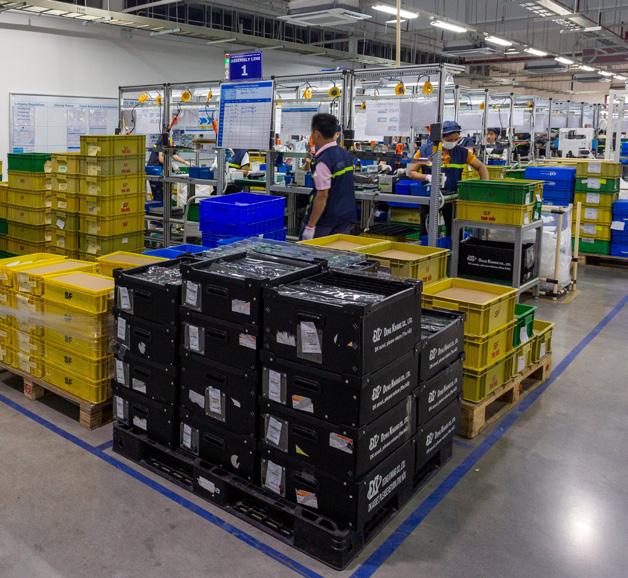
“These locations not only enhance our logistical efficiency but also position ASSA ABLOY’s Vietnamese operations at the heart of industrial growth in the region,” Astarita insights.
Both of these world-class facilities are specifically designed to support large-scale production with an emphasis on control and efficiency.
Alongside its facilities, ASSA ABLOY is further distinguished by its commitment to innovation, quality, and customer service.
Indeed, the company’s focus on integrating cutting-edge technology with a user-centric design ensures that its products are not only advanced but also practical and reliable.
ASSA ABLOY’s smart locks, for example, incorporate the latest in biometric and connectivity technology, making them secure and user-friendly.
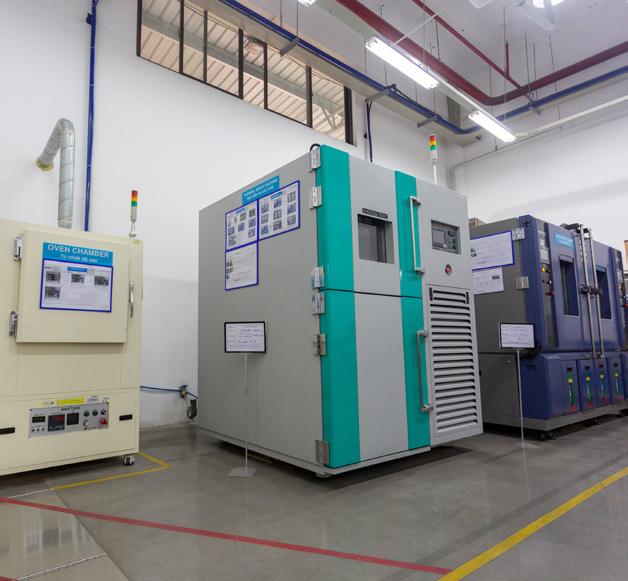
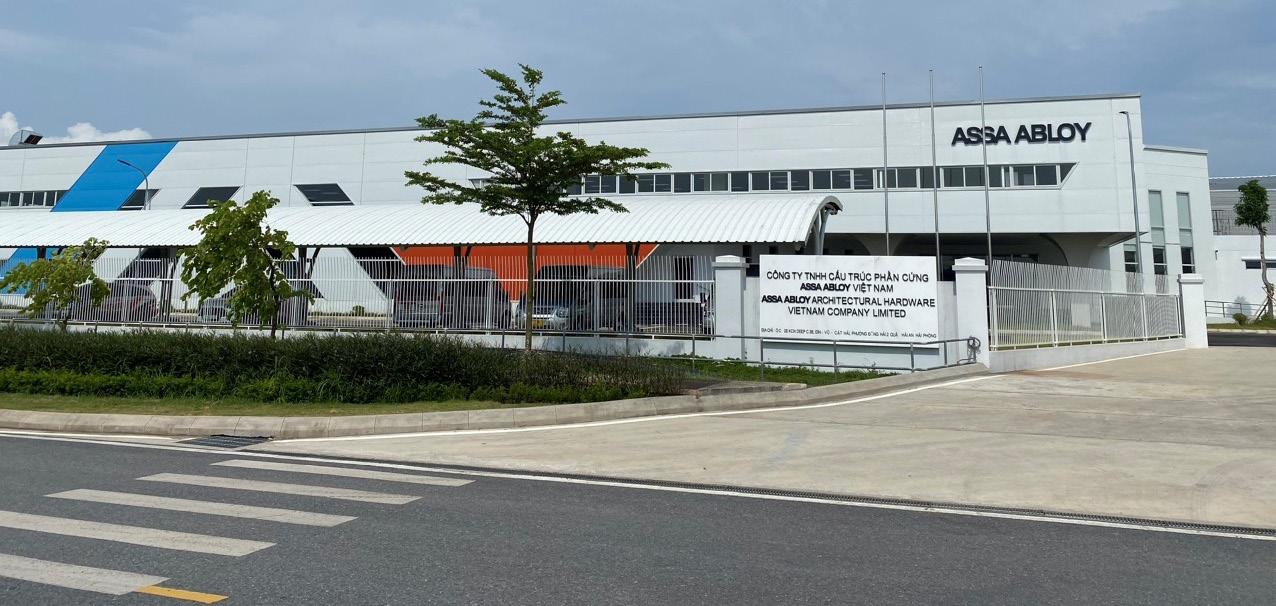
Test lab
AASTV building AASTV shop floor
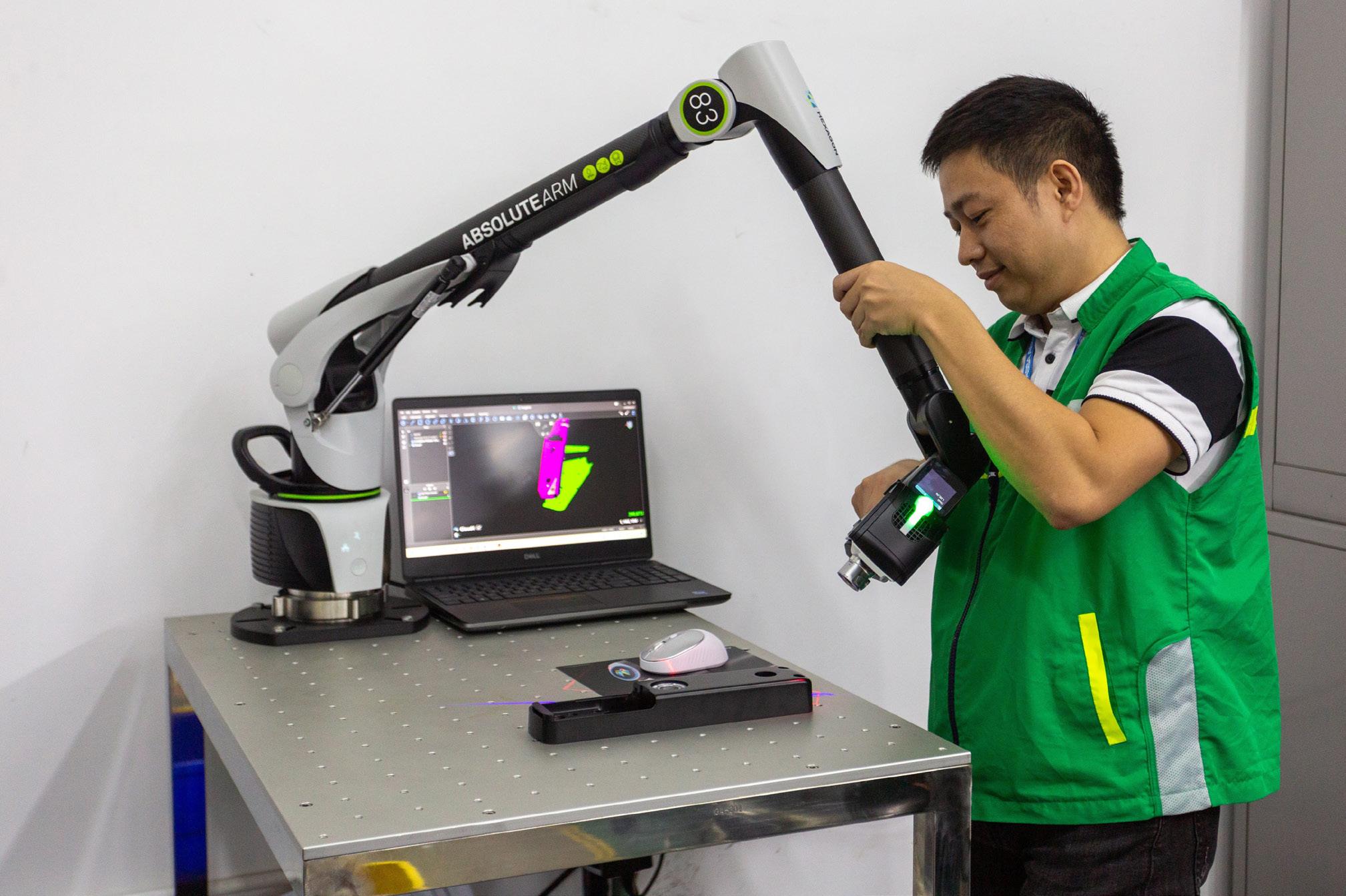
GREEN INITIATIVES
The company has made significant investments to ensure its factories operate as sustainable and ecofriendly facilities.
These include implementing energy-efficient technologies such as LED lighting, eliminating the use of plastics, reducing waste through recycling programmes, and adopting sustainable practices throughout its manufacturing process.
For example, its brand-new door closer facility has been designed to minimise its environmental impact and align with ASSA ABLOY’s global commitment to sustainability.
MAINTAINING A PRESTIGIOUS POSITION
ASSA ABLOY continuously expands its product portfolio to not only improve its own capabilities but also meet evolving market needs.
Recent additions to the product line include advanced access control systems, smart video doorbells, and high-security locking mechanisms. This approach allows the business to stay ahead of industry trends, offer comprehensive solutions that cater to a wide range of security requirements, and address new market segments.
“The introduction of new products provides opportunities for crossselling and upselling to existing clients, further enhancing customer satisfaction and loyalty.
“By constantly innovating and expanding its product range, ASSA ABLOY ensures it remains a leader in the security solutions industry,” Astarita points out.
This prestigious position is further
cemented by strong local partner and supplier relationships, allowing the company to secure a steady supply of high-quality materials and components.
“ASSA ABLOY’s supply chain strategy focuses on collaboration, transparency, and mutual benefits, building long-term supplier relationships. This approach keeps the company competitive and efficient with a flexible supply chain that quickly adapts to market changes and customer needs,” she affirms.
The company’s local partnerships and deep understanding of various markets likewise enable it to offer tailored solutions specific to regional challenges.
“The rapid ability of our Vietnamese operations to adapt to market changes and customer feedback also differentiates us,” Astarita highlights.
EMPOWERING STAFF
In Vietnam, ASSA ABLOY’s dedicated
STV incoming inspection
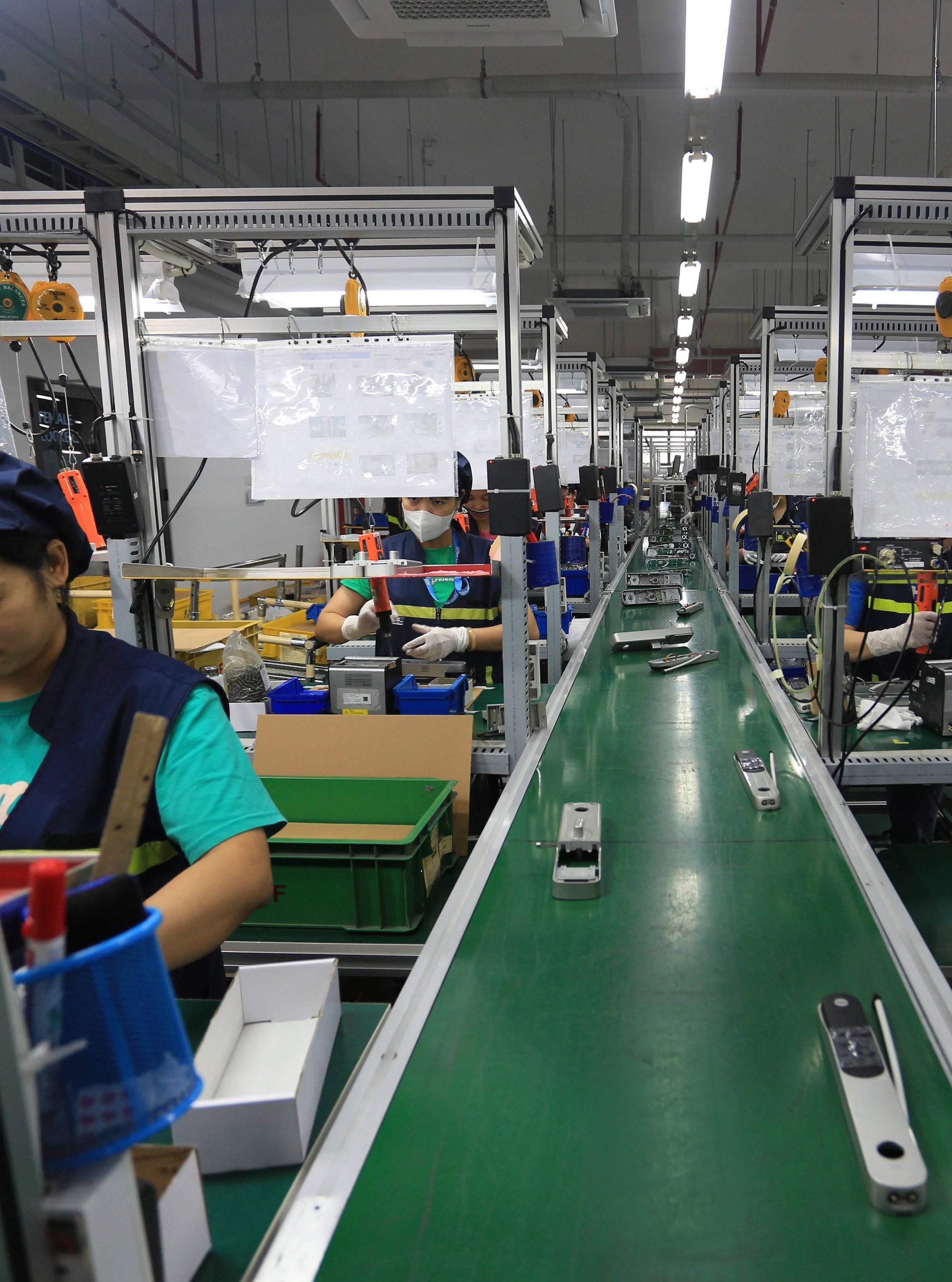
“BY CONSTANTLY INNOVATING AND EXPANDING ITS PRODUCT RANGE, ASSA ABLOY ENSURES IT REMAINS A LEADER IN THE SECURITY SOLUTIONS INDUSTRY”
– ALISON ASTARITA, VICE PRESIDENT OF OPERATIONS, ASSA ABLOY VIETNAM
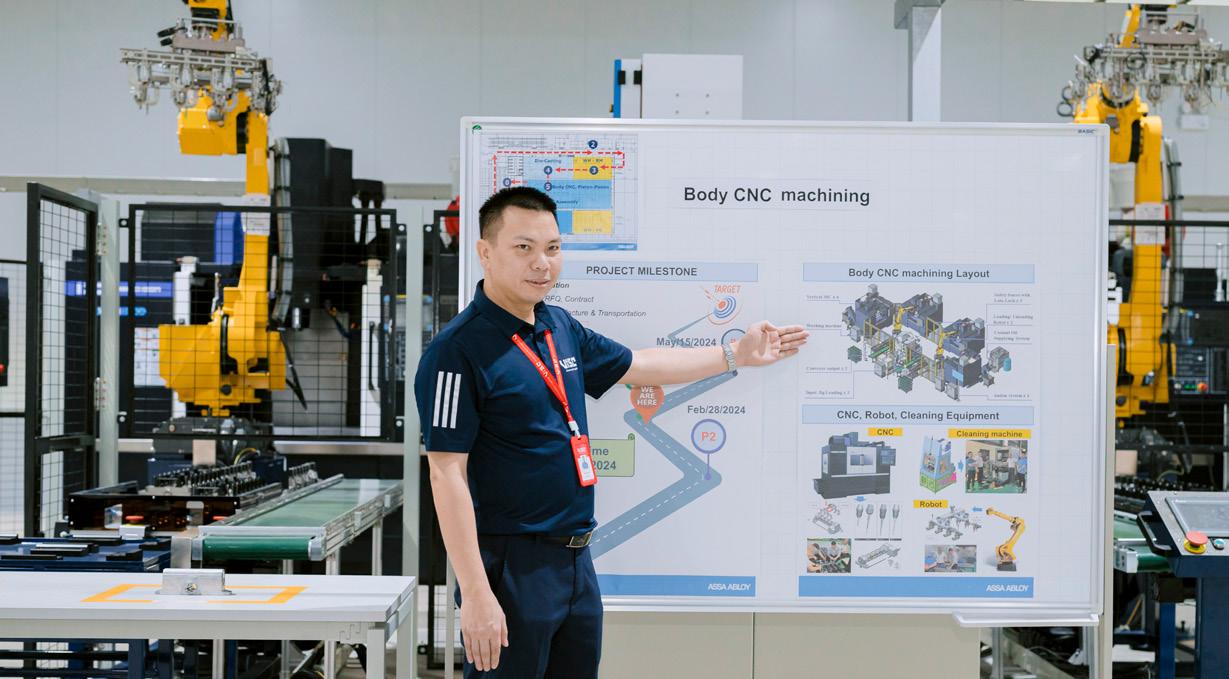
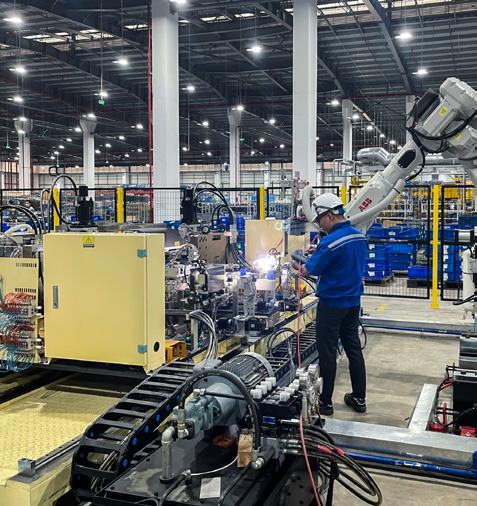
VISC – Precision Engineering & Automation Solutions for Industry
With over 15 years of expertise, VISC delivers world-class automation systems and highprecision machining services tailored for Vietnam’s dynamic manufacturing sector.
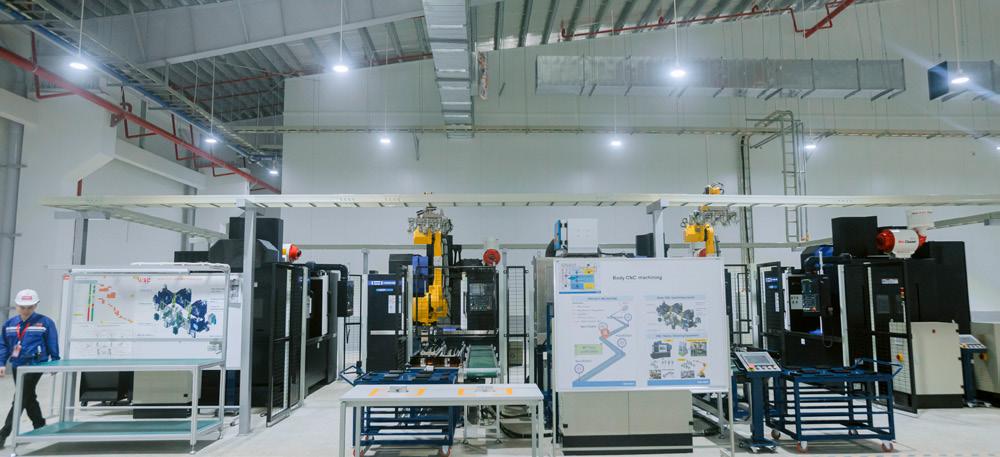
From CNC machining to custom-built automation lines, we empower factories with innovation, reliability, and local support.
+84-904338606
info@machines.com.vn www.machines.com.vn
Partner with VISC – where engineering meets efficiency.
ASSA ABLOY’S GLOBAL VISION AND MISSION
VISION
To be the global leader in innovative access solutions that help people feel safe and secure, enabling them to experience a more open world.
MISSION
• Building sustainable shareholder value.
• Providing added value to customers, partners, and end users.
• Being a world-leading organisation where people succeed.
• Conducting business in an ethical, compliant, and sustainable way.
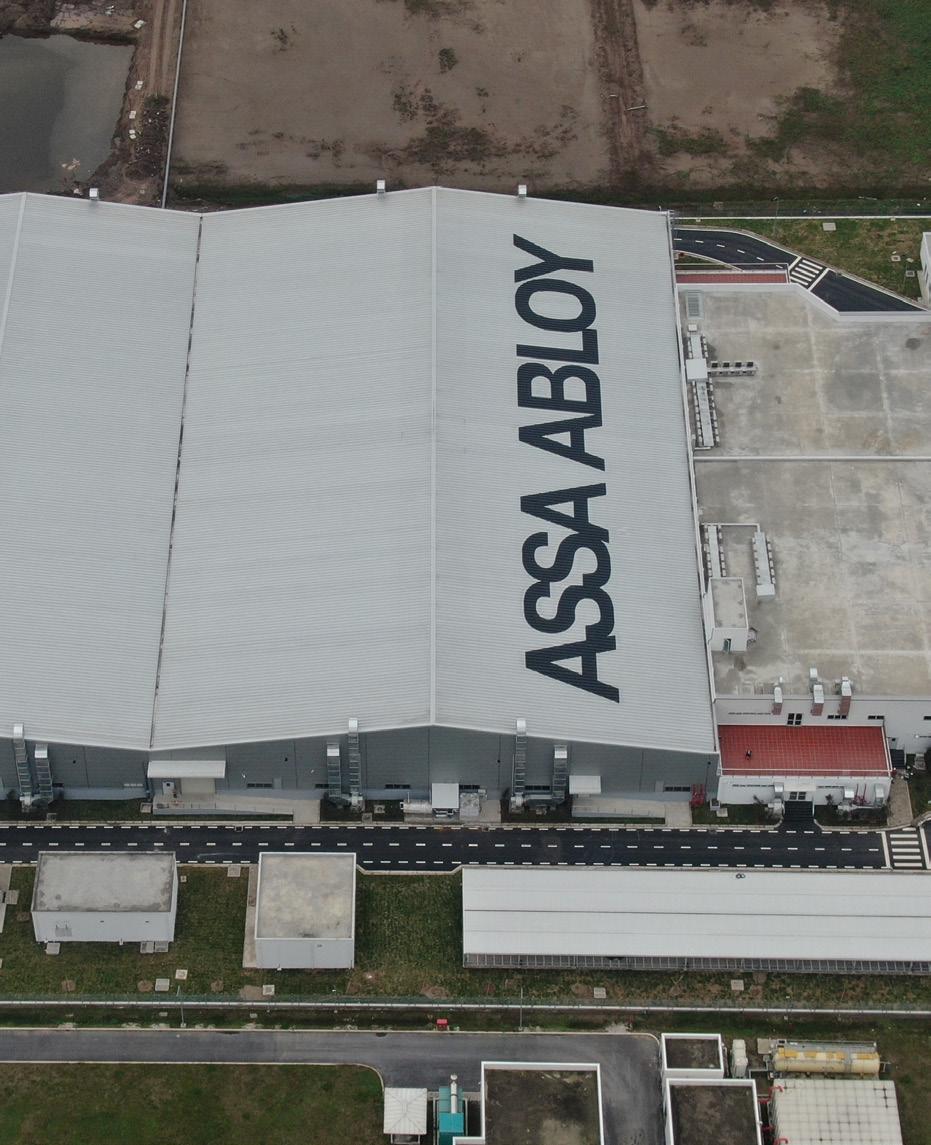
workforce comprises approximately 300 steadfast individuals, each integral to maintaining high standards of manufacturing and innovation.
With this in mind, the company places great importance on empowering its staff and recognising their contributions.
This is evidenced by the various initiatives implemented to support employee development, including training programmes, career advancement opportunities, and a variety of communication channels that create a positive working environment.
More specifically, ASSA ABLOY regualrly offer workshops and seminars on the latest technologies and industry and leadership trends, helping employees enhance their skills and stay updated.
The company also has a comprehensive recognition programme that regularly celebrates staff achievements and milestones.
Therefore, by valuing and investing in its employees, ASSA ABLOY fosters a motivated and committed workforce that drives the company’s success.
ASSA ABLOY’s culture of continuous improvement and collaboration ensures employees feel valued and engaged in their work.
“As the business continues to flourish, we have ambitious plans for further expansion, promising new opportunities and major advancements within our teams,” Astarita closes.
As a manufacturing hub still relatively in its infancy, ASSA ABLOY’s main aim is to continually grow the business whilst keeping a competitive edge through its talented workforce and commitment to operational excellence.

Tel: +84 211388 8286
www.assaabloy.com
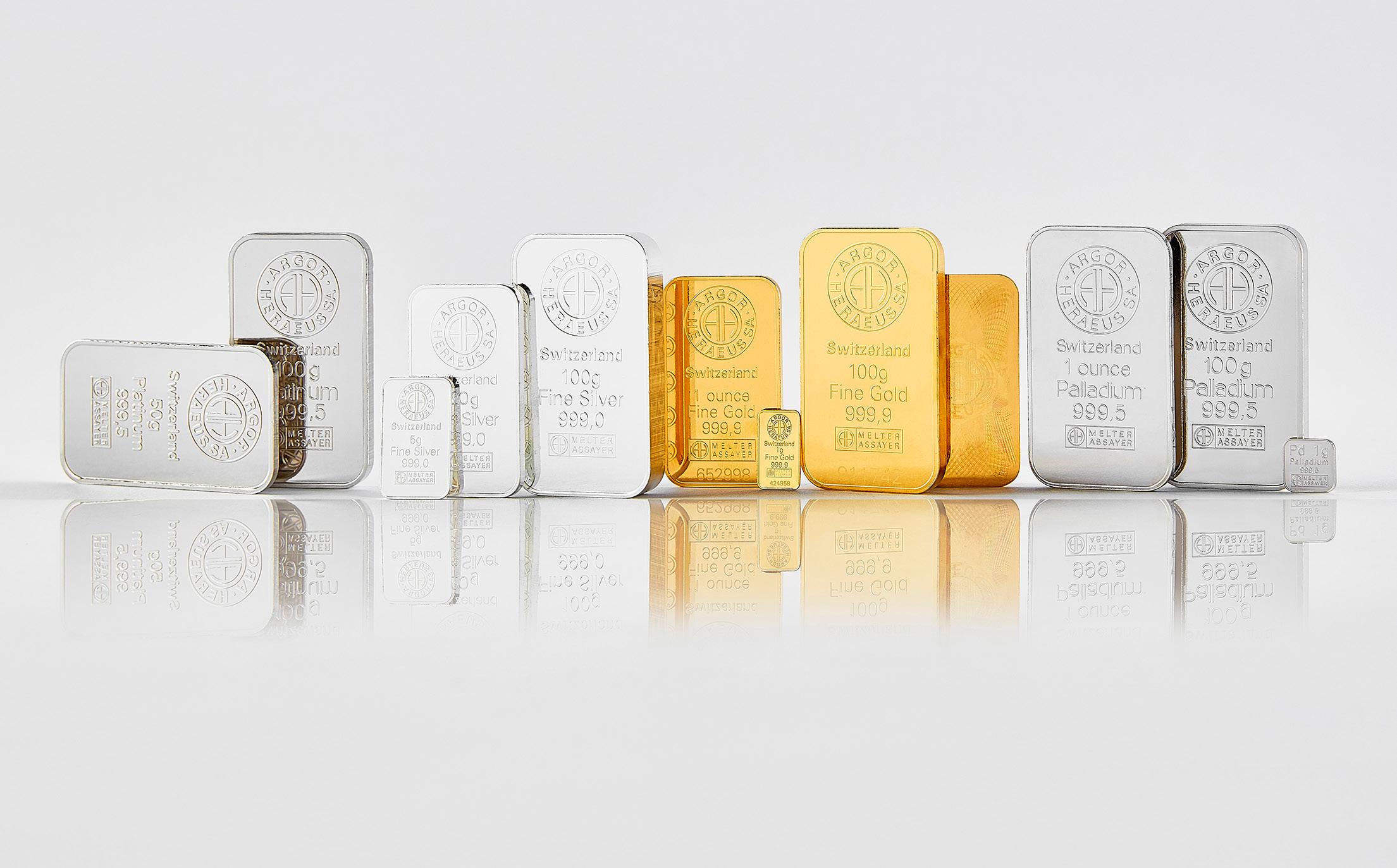
YOU CAN TRUST
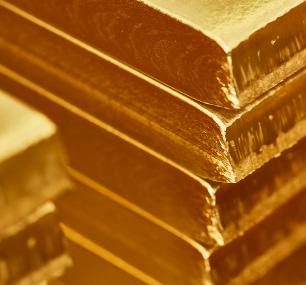
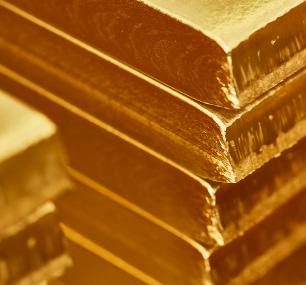
chain, from sourcing to final product. As part of Heraeus Precious Metals, we are one of the world’s leading companies in the industry.
Argor-Heraeus is the preferred choice for all your precious metal needs, offering comprehensive solutions and a longstanding dedication to trust and excellence. Established in 1951, and located in Mendrisio, Switzerland, Argor-Heraeus has been for decades at the forefront of the precious metals industry, covering the entire precious metal supply chain, from sourcing to final product. As part of Heraeus Precious Metals, we are one of the world’s leading companies in the industry.
Focusing on responsibility, with cutting-edge technology and strict compliance frameworks, we are able to to provide full traceability of precious metals, to meet your specific needs and ESG goals. With our expertise in delivering personalized 360° precious metal services, we can accommodate varying production volumes and provide precious metal trading services for a complete solution that will suit the most demanding requirements.
ARGOR-HERAEUS SA
Via Moree 14 | CH-6850 Mendrisio +41 091 640 53 53
Focusing on responsibility, with cutting-edge technology and strict compliance frameworks, we are able to to provide full traceability of precious metals, to meet your specific needs and ESG goals. With our expertise in delivering personalized 360° precious metal services, we can accommodate varying production volumes and provide precious metal trading services for a complete solution that will suit the most demanding requirements.
info.argor@heraeus.com | www.argor-heraeus.com
As a confirmation of our high standards, Argor-Heraeus is one of the five LBMA “Approved Good Delivery Referees” worldwide.
We offer a comprehensive product range that extends to investment bars, minted bars and coins, bespoke alloys, raw materials and both semi-finished and high-precision finished products crafted specifically for the luxury and watchmaking industries.
Our longstanding reputation as a trusted refinery is built upon our core values of responsibility, excellence, trust and innovation. These values resonate through every product and service we offer, assuring you of our commitment to not only meet but exceed expectations.
As a confirmation of our high standards, Argor-Heraeus is one of the five LBMA “Approved Good Delivery Referees” worldwide.
Our longstanding reputation as a trusted refinery is built upon our core values of responsibility, excellence, trust and innovation. These values resonate through every product and service we offer, assuring you of our commitment to not only meet but exceed expectations.
ARGOR-HERAEUS DEUTSCHLAND GMBH Ostendstrasse 12
D-75175 Pforzheim +49 7231 139360