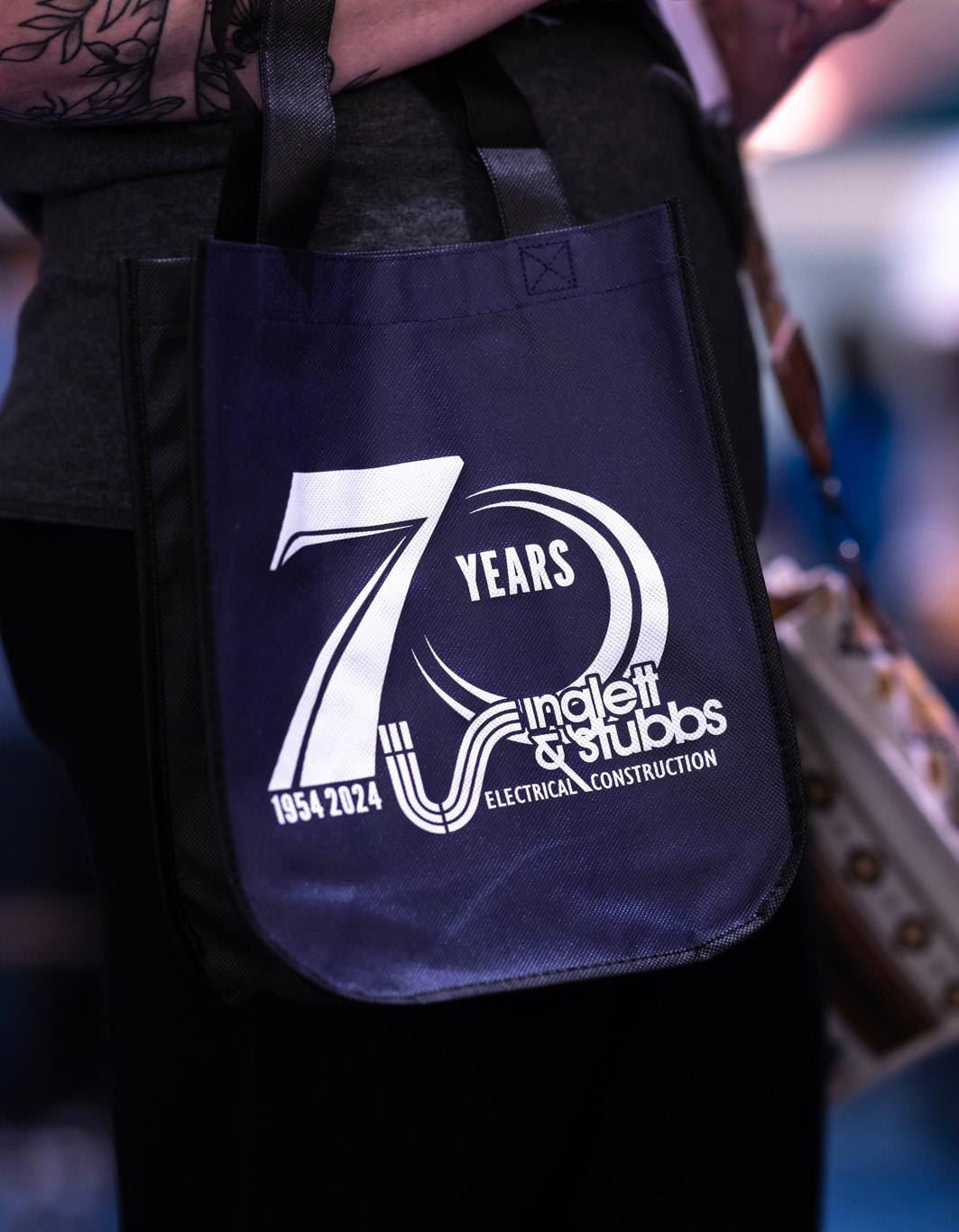
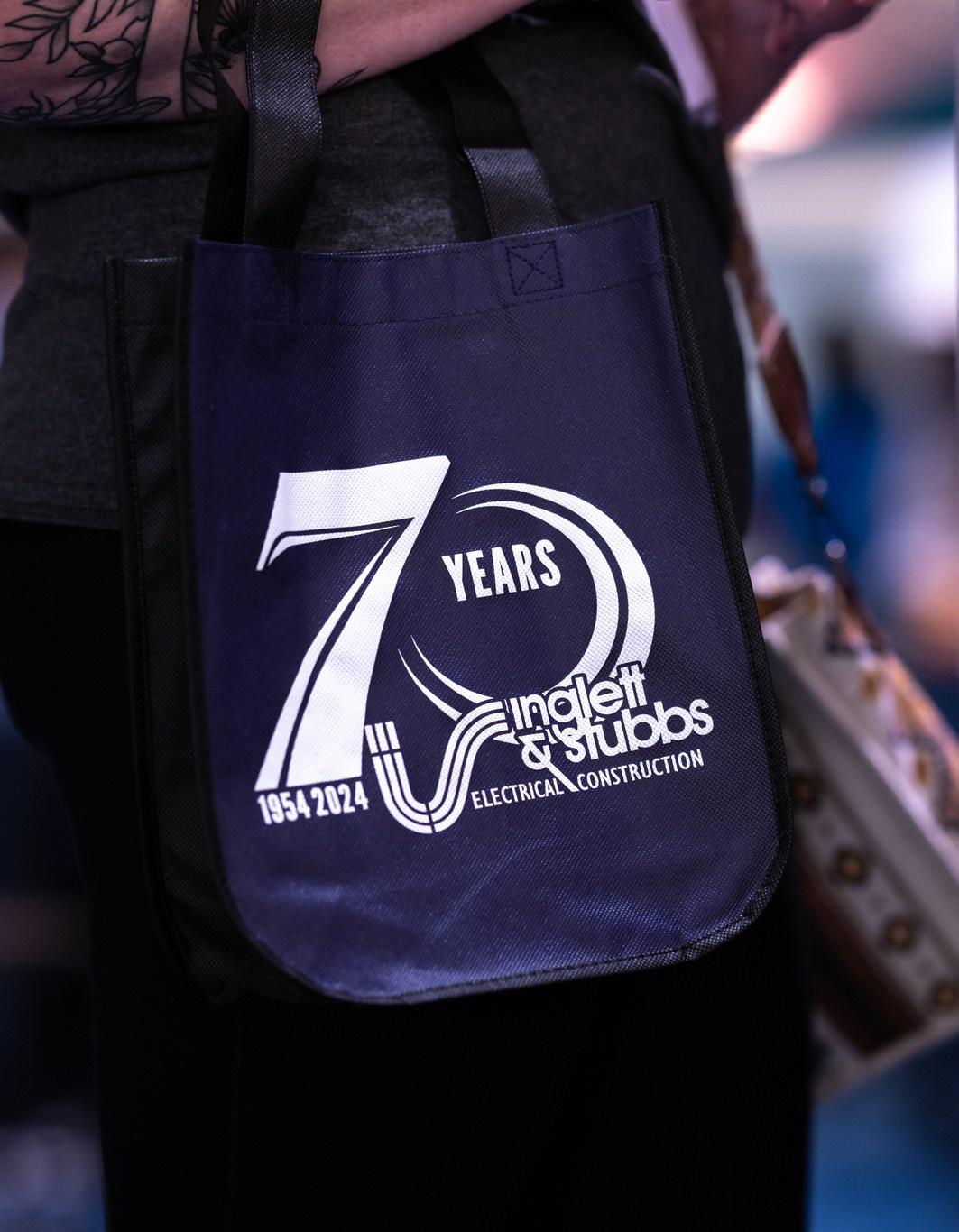
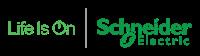

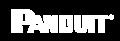
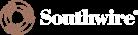


It is the ongoing mission of Inglett & Stubbs to be the contractor that consistently exceeds its clients’ expectations. No matter the size of the job, the company has the resources to complete the work in a professional, thorough, timely, and cost-effective manner. We catch up with President, Miller Chalk, about its latest developments and strategy for the future
Writer: Ed Budds
Project Manager: Michael Sommerfield
Our business is as strong as ever, and I’m told by our people that all the problems we are experiencing now are the kind that we have been looking to solve in our first seven decades of business.
“We celebrated our 70th anniversary this year, and the demand for our services is overwhelming, while our target markets are booming in Atlanta, and we are in a great position to begin work on a lot of exciting upcoming projects.”
As Miller Chalk, President, alludes to in his opening statement, Inglett & Stubbs is a recognized leader in the electrical construction industry.
Indeed, the company is consistently ranked in the top 50 electrical contractors in the US by EC&M magazine.
Remarkably, with a history of successful electrical construction projects spanning more than half a century, Inglett & Stubbs also enjoys the advantages of a dynamic team of young and seasoned professionals made up of electricians, technicians, foremen, engineers, project managers, and more.
“Our tradition of accomplishment and the sustained growth of our people have secured our position in the market and ensured a promising future for both Inglett & Stubbs and our customers,” Chalk sets out.
Founded in 1954, Inglett & Stubbs has since developed into one of the most progressive and innovative electrical contractors in Atlanta.
Historically, the company’s focus has been on the city’s metropolitan area, specializing in healthcare, commercial, industrial, institutional, telecommunications (telecoms), information technology (IT), and co-generation projects.
With its main headquarters located in Mableton, Georgia, the company now also specializes in hospitals, mission-critical projects, sports and entertainment, fiber and copper
cabling, off-site construction, and preventative maintenance.
“In recent years, our expertise on high-end, technically challenging projects has resulted in securing contracts on both a national and international basis, and we emphasize cost efficiency within all of our work,” Chalk acclaims.
“Paired with our past performance and superior quality, this has resulted in a high percentage of our workload being negotiated,” he adds.
A team of expert foremen that are experienced in all aspects of electrical construction make up the heart of the company’s field operations, and many of these proficient professionals have been with Inglett & Stubbs for their entire careers.
As such, the company operates on the conviction that the electrical contractor is a key member of the construction team on any project.
“We know that all team members must work together to provide the best finished projects in the most cost-effective manner for the end user. We work with the most prominent architects, engineers, and general contractors in the US, and we constantly strive to maintain excellent relationships with our customers,” Chalk elaborates.
After acquiring vast levels of electrical experience, Inglett & Stubbs now impressively maintains a 0.69 experience modification rate (EMR) which gauges past injuries and future risk.
“We are proud that this rating lies well below the 1.0 EMR industry average,” Chalk shares.
“Our rating is kept low by maintaining safety as a priority and the main focus of our daily business.
“We recognize that electrical power work remains within the Occupational Health and Safety Administration’s Focus Four Outreach Program and is consistently listed in the top 10 most dangerous occupations by the Bureau of Labor Statistics, so we strive every day to promote a safe work environment,” he details.
This relentless diligence begins with Inglett & Stubbs’ safety directors, instructors, and coordinators, and trickles down through each and every employee.
“Our proactive approach makes Inglett & Stubbs one of the safest contractors in the industry.”
The company is also now hosting training classes for its customers and others in the industry who are interested in understanding arc flash risks and the requirements of NFPA 70E and 70B.
Without a doubt, it’s the people at
“OUR TRADITION OF ACCOMPLISHMENT AND THE SUSTAINED GROWTH OF OUR PEOPLE HAVE
SECURED OUR POSITION IN THE MARKET AND ENSURED A PROMISING FUTURE FOR BOTH INGLETT & STUBBS AND OUR CUSTOMERS”
– MILLER CHALK, PRESIDENT, INGLETT & STUBBS
Inglett & Stubbs that continue to set the company apart and define its ongoing success.
“We have an incredible team and they have gotten even stronger over the past year through formal and informal development and strategic additions to the team. Alongside this, our alignment with our vision and values has grown as well,” Chalk tells us.
Drawing on a firm sense of unity in its senior leadership team, Inglett & Stubbs now finds itself a year and a
half into working within its “System and Soul” business operations framework, which has helped the company to both become and stay aligned.
This successful framework is designed to support and grow both the system and the soul of a business to create key breakthroughs.
Growth creates complexity, and even the best teams struggle to be effective without a clear structure, direction, and collective goals.
Born during the first Industrial Revolution, Schneider Electric boasts over 180 years of enduring dedication, expertise, and the combined strength of acquired business.
Developing innovative, connected technologies and solutions for safety, reliability, efficiency, and sustainability, the company continues to deliver success and technological breakthroughs at every level.
Throughout history, we have led the way in strategic choices and innovative solutions, with business acquisitions that have built our unique position and time-tested technology portfolio.
Our company’s purpose is to create impact by empowering everyone to make the most of our energy and resources, bridging progress and sustainability for all.
At Schneider Electric, we call this Life Is On.
With a mission to be the trusted partner in sustainability and efficiency, we are proud to be a global industrial technology leader bringing world-leading expertise in electrification, automation, and digitalization to smart industries, resilient infrastructure, future-proof data centers, intelligent buildings, and intuitive homes.
Anchored by our deep domain expertise, Schneider Electric provides integrated, end-to-end lifecycle artificial intelligence (AI), enabling the company to offer comprehensive industrial Internet of Things (IoT) solutions with
connected products, automation, software, and services, delivering digital twins to enable profitable growth for our customers.
We are proud to be a people company with an ecosystem of 150,000 colleagues and more than a million partners operating in over 100 countries to ensure proximity to our customers and stakeholders.
At Schneider Electric, we embrace diversity and inclusion in everything we do, guided by our meaningful purpose of a sustainable future for all.
We don’t make energy; we make you save it.
“We believe that access to energy and digital is a basic human right”
– Schneider Electric
We believe that access to energy and digital technologies is a basic human right.
Our generation is facing a tectonic shift in energy transition and industrial revolution, catalyzed by a more electric and digital world, which is key to addressing the climate crisis.
One of the ways in which Schneider Electric is facing this change headon and building a more sustainable future is through our Electricity 4.0 initiative.
Together with our customers, we are building the new electric world by providing smart energy across homes, buildings, data centers, industries, infrastructure, and grids.
Schneider Electric is uniquely positioned to join the dots
With a story written by generations of people who have transformed Schneider Electric, and the world, for almost two centuries, our company’s heritage empowers us to innovate at every level, ensuring Life Is On.
• 1836 – The Schneider brothers acquire mines and forges at Le Creusot, France. Two years later, Schneider & Cie. is created.
• 1891 – Having become an armaments specialist, the company launches itself into the emerging electricity market.
• 1919 – The business expands into Germany and Eastern Europe via the European Industrial and Financial Union.
• 1949 – In-depth restructuring takes place after World War II.
• 1981 – 1997 – The company divests from steel and shipbuilding and focuses mainly on electricity through strategic acquisitions.
• 1975 –The Schneider Group acquires an interest in Merlin Gerin, one of the leaders in electrical distribution equipment.
• 1999 – The group develops installation, systems, and control with the acquisition of Lexel and adopts its current name.
• 2000-2009 – The company goes through a period of organic growth and acquisitions in new market segments.
• 2003 – The Square D by Schneider Electric brand celebrates 100 years of know-how and innovation in electricity and automation management, now focusing on electronics through strategic acquisitions.
• 2010-present – Schneider Electric further reinforces its position in software, critical power, and smart grid applications.
between them all for a future that promises more sustainability, resilience, and efficiency. Specifically, we believe that electricity makes energy more ecofriendly.
Proven to be three to five times more efficient than other sources, electricity is the most promising energy and the best vector for decarbonization. By 2040, the share
of electricity in everything we do will double, reaching approximately 40 percent of final energy consumption, with six times more electricity being generated from solar and wind. Additionally, utilizing digital innovation allows the invisible to become visible by eliminating waste and driving efficiency. Digital technology such as metering and monitoring enables us to see how
we are using our energy. Smart devices, apps, analytics, and software allow us to go a step further and deploy smart energy more efficiently, meaning we can address a huge amount of untapped potential for energy savings.
Schneider Electric is proudly accelerating the pace at which we can address climate change through agile digital innovation and efficient electricity solutions.
Having recently been named the 2024 Most Sustainable Company by TIME Magazine, we are going further, faster, by boosting innovation whilst expanding our digital, end-to-end solutions in all stages of the lifecycle.
Schneider Electric is proud to partner with channel partners, such as contractors, in order to better serve its customers’ various needs.
We help grow businesses by providing direct access to exclusive resources and technical support through our Electrical Contractor
Portal that helps companies boost productivity and expand their footprint even further.
Recent events have shown us that relentless, even turbulent change, is the new normal, and despite the wide variety of different jobs electrical contractors perform, their businesses still face remarkably similar challenges in the face of accelerating technological change.
Schneider Electric is here to help you embrace emerging trends and build a relationship of mutual trust and benefit with clients in order to boost competitiveness, gain recurring revenue, and grow your company to its full potential.
Additionally, we help customers put electrical safety first by providing access to our technology, tools, and expertise. Explore how our solutions contribute to hazard reduction and develop a safety plan to reduce, eliminate, and control the risks and consequences of electrical and nonelectrical incidents.
At Schneider Electric, we recognize
“Our mission is to be your trusted partner in sustainability and efficiency”
– Schneider Electric
that our customers have an array of codes, standards, and regulations that impact their safety, energy efficiency, and day-to-day business operations. As our products and services are designed to help meet the challenges often posed by these regulations, we boast a team of professionals who dedicate themselves to the codes and standards needed to fully comprehend what is changing and how these changes will impact customers.
To provide even further solutions for customers, our experts have produced numerous technical papers and bulletins that help businesses better understand the codes and standards systems as well as many of the technical requirements for these procedures. We work within the system to make sure that the new technologies and approaches to resolving customer’s energy needs are properly addressed in the codes and standards.
Alongside working with customers on the appropriate regulations,
Schneider Electric offers useful online tools, calculators, and visual configurations to make selecting the right product faster and easier. This includes the DigestPLUS online catalog, product selectors, cross reference tools, power system design and selection, industrial and original equipment manufacturer (OEM) tools, and data center tradeoff tools, alongside many others.
Making the most of our energy and resources, Schneider Electric is here to bridge progress and electricity for all, ensuring Life Is On by being the trusted partner in sustainability and efficiency.
Contact Details
Customer Care Centre: 0330 587 8030
Website: se.com
INGLETT & STUBBS
Using this method of working, Inglett & Stubbs believes in helping its teams design clear structures and develop cadences for their most important activities.
“We do a great job at giving people the room and resources to empower themselves to make changes. We spend a lot of time trying to figure out new and improved ways to show recognition and appreciation, and we can and will do better in acknowledging and appreciating our teams that continue to make us shine,” he gushes.
Over the past 40 years, the Atlanta area has experienced heavy growth and expansion of its cultural centers, educational facilities, entertainment hubs, and sports venues.
Inglett & Stubbs has been honored to participate in the construction of many of these major iconic projects throughout the region.
“WE CELEBRATED OUR 70 TH ANNIVERSARY THIS YEAR, AND THE DEMAND FOR OUR SERVICES IS OVERWHELMING, WHILE OUR TARGET MARKETS ARE BOOMING IN ATLANTA, AND WE ARE IN A GREAT POSITION TO BEGIN WORK ON A LOT OF EXCITING UPCOMING PROJECTS”
– MILLER CHALK, PRESIDENT, INGLETT & STUBBS
“We have worked on constructing galleries and sports facilities, as well as the modernization of many of the best-known stadiums, museums, and performing arts centers statewide,” Chalk outlines.
“We at Inglett & Stubbs are continuously innovating, with stateof-the-art products and installation methods which allow us to meet the demands of building an array of unique signature facilities. We hold our construction methods, management systems, and field workforce to the highest standards so that we are prepared for the challenges that come with highprofile projects,” he confirms.
With a history that is unquestionably proven, the company has positioned itself to be a superior electrical contractor in the field of sports, entertainment, and cultural building construction for years to come.
Healthcare is a critical and everpresent division of the electrical construction market.
Since its inception, Inglett & Stubbs has worked diligently to make this market segment a focal point of its business and has completed a wide variety of projects ranging from new hospitals to small one-room MRI additions.
Inglett & Stubbs works in most of the key medical facilities in metropolitan Atlanta and the surrounding areas, and on many hospital campuses the company maintains a full-time workforce to perform maintenance duties as well as ongoing construction projects.
In this way, the company has been maintaining several facilities for over 30 years, making customer satisfaction its highest priority.
As working in a healthcare facility requires a high level of expertise with
Inglett & Stubbs is proud to support charitable organizations in the Atlanta community as part of the company’s increasing corporate social responsibility (CSR) efforts.
As successful professionals, Inglett & Stubbs truly believes that it is the duty of the company to give back through interoffice fundraisers, community events, and organizational involvement. Some of the causes that have been supported over the years include:
• Adopt a Mile
• Alzheimer’s Association of Georgia
• American Heart Association
• Children’s Healthcare of Atlanta
• Habitat for Humanity
• JDRF
• Mattie Freeland House
contamination control measures, Inglett & Stubbs therefore keeps facilities fully functional during invasive renovations and works with existing electrical distribution systems to minimize downtime.
“We take great pride in our ability to perform and succeed in these highly technical and clinical environments,”
Chalk affirms.
“We have developed long-standing relationships with our healthcare partners built on trust, respect, and confidence. We at Inglett & Stubbs take pride in that and continue to expand our medical capabilities in order to exceed client expectations,” he follows.
Firstly, could you provide a brief insight into MEI Rigging & Crating’s service offerings?
MEI Rigging & Crating (MEI) is a national provider of rigging, machinery moving, millwrighting, mechanical installation, storage and warehousing, and crating and export packaging services. MEI can move, install, and relocate machinery or equipment of any size. Whether it’s a single piece, a complete process line, or an entire plant, we are able to move it. MEI manages significant storage and warehousing capacities for longterm or just-in-time delivery.
Operating across North America for over 30 years, how would you say the rigging and machinery sector has evolved since the inception of the company?
Historically, rigging and equipment installation were often viewed
as discrete activities within an established project schedule. However, changes in construction methods and trends — including prefabrication and modularisation, decreased just-in-time delivery to job sites, rising demand for secure long-term storage and equipment monitoring, and an emphasis on collaborative delivery methods — have made rigging a more strategic function than it was 30 years ago. The most successful projects now engage riggers early and often in the design phase to unlock significant scheduling and cost efficiencies.
Positioned as one of the largest providers of rigging and machinery moving in the region, how does the business differentiate itself from other players in the industry?
MEI operates 18 locations across
14 states, has three decades of experience across a wide range of industries, and has a relentless focus on safety and quality. We provide over three million square feet of storage space nationwide. Through a superior portfolio of services and problem-solving capabilities, we minimize complexity and provide outstanding value to our customers.
Finally, how do the collective brands of the organization ensure that the needs of its customers across the US are met?
MEI strategically seeks to merge with rigging providers that not only enhance our technical expertise and delivery capabilities across the nation but also share our vision of excellence, market leadership, and enduring value. The strength of our family of brands – MEI, A&A Transfer, A&A Machinery Moving, Able Machinery Movers, Dunkel Bros Machinery Moving, and Harnum Industries – enables us to expertly meet the needs of our local customers, while pooling our resources and equipment to deliver the same exceptional service across a national footprint.
“WE WORK WITH THE MOST PROMINENT ARCHITECTS, ENGINEERS, AND GENERAL CONTRACTORS IN THE US, AND WE CONSTANTLY STRIVE TO MAINTAIN EXCELLENT RELATIONSHIPS WITH OUR CUSTOMERS”
– MILLER CHALK, PRESIDENT, INGLETT & STUBBS
To date, Inglett & Stubbs’ healthcare facilities include hospitals, cancer treatment, radiology, surgical, and women’s centers, emergency departments, central energy plants, and medical office buildings.
Inglett & Stubbs prides itself as a multifaceted electrical contractor, and due to the variety of construction opportunities that exist within colleges and universities, these facilities have been identified as further optimal places to display and
enhance the company’s construction knowledge.
As such, because of its dedication to being part of this burgeoning environment, Inglett & Stubbs has sought and completed numerous successful projects on many campuses in North Georgia.
The company’s long history of higher education projects varies widely, from site lighting contracts and electrical utility infrastructure to sports stadiums, teaching and laboratory buildings, research facilities, student centers, and more.
“Inglett & Stubbs has developed project managers who specialize in this field,” Chalk prides.
“We are very proud of our excellent reputation and work every day to earn repeat customers with each institution. We do this by always increasing our project diversity and adding value to the overall construction team,” he continues.
Inglett & Stubbs has been working in the data center construction industry for almost 40 years.
“Our first major project was built in 1985 in Alpharetta, Georgia, where we also constructed the first major Tier 4 data center in 1994 for UPS,” Chalk recalls.
“Since then, we have worked on numerous major data center projects in Georgia and across the US. Our expertise in this field has also led us to collaborate on projects in South America,” he adds.
Technology revolutionizes hospital design with Belden as the central nervous system enabling the transformation of smart systems into truly intelligent ones.
Our unique combination of people, products and perspective is why healthcare systems have known and trusted Belden for decades. Let’s collaborate to build a space that sets new standards in enhancing patient experiences, inspiring staff satisfaction, and optimizing facility efficiency.
Use this QR code to access literature, applicable products and more information on Belden’s healthcare solutions.
• 12-story tower
• State-of-the-art cafeteria and new kitchen
• New patio for patient use
• New lobby space
• Retreat areas and greenspace
• 200 day patient beds
• Diverse surgical staff from a range of specialties
• Innovative new imaging capabilities and technology
• A new parking deck with 1,800 spaces
• Added slip ramp
• ICU beds to replace critical care rooms
Inglett & Stubbs acts as a designassist team member in many of its projects, lending its experience to owners, engineers, and general contractors. This collaboration leads to long-term relationships in the form of renovations, upgrades, expansions, and maintenance contracts.
“We attribute the majority of our success and knowledge to the collaborative nature of these projects. Our experienced team can assist with all aspects of data center design, construction, and maintenance.”
Inglett & Stubbs works on all project sizes, from small computer rooms to large, dedicated facilities.
“Some of our customers work with us to design a small single generator system, while other clients utilize large, dedicated utility services paired with dozens of generators and UPS modules. We work to meet the needs of our customers, whatever they may be,” Chalk emphasizes.
Across the board, Inglett & Stubbs’ modular approach brings innovation to the way that its clients design, build, and maintain electrical and low voltage systems.
“Our in-house design team can customize and optimize electrical set-ups so that each component fits precisely and seamlessly interconnects with other systems. We can engineer products that drive efficiency and enhance productivity within the project footprint,” Chalk excites.
As such, the company uses the latest technology and its construction expertise to design solutions that meet specific needs. Meanwhile, its expert team leverages the latest virtual reality (VR) technology to create immersive design experiences.
“Our modular manufacturing services help gain a competitive advantage in rapidly changing markets. Our modular solutions will
Artificial intelligence is revolutionizing data center operations. With 70 years of innovative experience, the Panduit team will be your trusted partner throughout your AI journey and is ready to assist with the seamless integration of products and solutions to enable your AI network. With strategic alliances and a focus on sustainability, we’re committed to delivering quality infrastructure products and solutions that will resolve high-power, high-density requirements and prepare you for tomorrow’s challenges.
Discover how together we can transform your infrastructure to support your AI initiatives by visiting www.panduit.com/AI .
TRUSTED DATA CENTER PRODUCTS AND SOLUTIONS FOR YOUR AI NETWORK
allow our customers to optimize resources, minimize waste, and improve production capabilities.”
The manufacturing teams of Inglett & Stubbs are made up of skilled union labor workers that ensure the highest level of quality for the finished product. This process involves design and coordination, schedule planning, manufacturing control, production quality assurance, and testing.
After the manufacturing process is complete, the company’s logistics services team manages the delivery to ensure a seamless and efficient transition from production to site location. This process also involves strategically planning for just-in-time delivery to help minimize storage fees and requirements.
“We can self-deliver locally and have strategic partnerships with top-notch logistics providers to offer flexible delivery options. Our team will handle all modular components with the utmost care during transportation,
“WE ARE VERY PROUD OF OUR EXCELLENT REPUTATION AND WORK EVERY DAY TO EARN REPEAT CUSTOMERS WITH EACH INSTITUTION. WE DO THIS BY ALWAYS INCREASING OUR PROJECT DIVERSITY AND ADDING VALUE TO THE OVERALL CONSTRUCTION TEAM”
– MILLER CHALK, PRESIDENT, INGLETT & STUBBS
and design and plan packaging to ensure that it arrives safely and ready for installation,” states Chalk.
Regarding the multifaceted management of a project, Inglett & Stubbs splits this process into the three key areas of budget, schedule, and material cost.
“We believe that quality begins in the pre-construction stage, which is used to accumulate information into
a format effectively managed and accessed by the field,” says Chalk. This information is managed using work packets and tradesman manuals to bridge the gap in quality standards.
Each manual consists of equipment-specific drawings, specifications, and approved submittals, the latter of which are condensed to only include information pertinent to the installation. These manuals are
At Eaton, we believe that power is a fundamental part of just about everything people do. That’s why we’re dedicated to helping our customers find new ways to manage electrical, hydraulic and mechanical power more efficiently, safely and sustainably. To improve people’s lives, the communities where we live and work, and the planet our future generations depend upon. Because this is what really matters. And we’re here to make sure it works.
To learn more go to: Eaton.com/whatmatters
We make what matters work.
Miller Chalk, President: “Our Pre-Construction Director, Holly Wilson, joined us in the spring of 2023 and has taken that team to the next level. They have been very busy this year pricing new work and leading us through a successful software transition.
“We worked with Mark Wojcik of East Park Avenue Talent Consulting to build a talent acquisition plan, which led to the hiring of our first ever recruiter, Natalie Armstrong. She has been a great addition to the team and is doing a good job of adding much-needed talent to our field teams.
“Additionally, we brought Kyle Crossfield into the office as our Electrical Services Consultant, with the task of educating our customers. I felt a great responsibility to help our customers understand the risks and requirements of working on and maintaining their electrical equipment, so I’m proud of how our safety team jumped in to lead in teaching a class that we are now hosting quarterly as well as on location where needed.
“Elsewhere, our modular team continues to grow and add value to our projects, and we are seeing a lot of exciting new opportunities.
“Finally, we hired a former long-time employee, Thomas Alexander, to come back and lead our quality assurance group. He has updated our policies, developed our software, and built a team to support the highest possible quality across all projects.”
updated with common issues and best practices throughout the project,” he continues.
Inglett & Stubbs provides all parties with a full plan of activities and durations to be plotted on the master construction schedule. Critical
milestone dates such as equipment delivery, equipment energization, system testing, and system checkout are all plotted.
“We develop a load schedule to monitor the work progress on a week-by-week basis, which allows
us to address all scheduling issues immediately to ensure on-time project delivery.
“Our project management team also develops a cost accounting structure broken down by systems and phases. This enables us to monitor the budget, delivery, and installation of each critical component of the project,” says Chalk.
By tracking costs, Inglett & Stubbs is able to identify budget changes quickly and accurately, whilst savings can be identified so that the owner can spend resources on other items or areas. If overruns are anticipated, the company provides alternatives to bring the project back within budget.
Inglett & Stubbs regularly tracks current market conditions for commodities including copper and aluminum (wire), steel (conduit, cable tray, boxes, and fittings), electrical devices and equipment, and PVC (conduit).
In this way, the company issues a request for proposal (RFP) to major vendors of these products to support acquiring and supplying them, and to offset and mitigate extreme price increases.
One of the company’s greatest sources of pride is how it has supported many charitable organizations.
Over the years, Inglett & Stubbs has supported many charities in the Atlanta region, raising funds and awareness as part of a deliberate endeavor to increase its CSR practices. These include interoffice fundraisers, local community events, golf tournaments, and other initiatives.
“We set up a charity team to steer our decisions around the organizations we give to and volunteer with. In the past, we would select one charity a year to support; this year, we are financially
Inglett & Stubbs has a plan in place to deliver a successful project before even being awarded it.
The company’s pre-construction teams are then already working on identifying the correct deliverables for the project and establishing a detailed milestone schedule.
Inglett & Stubbs’ pre-construction team works hand-in-hand with building information modeling (BIM) and prefabrication methods to ensure that the critical first phases of the project always stay on track.
The company then develops an overall strategy to support a wellplanned path for construction. High level goals for pre-construction include several crucial steps:
• Establish the right deliverables to be successful.
• Complete the deliverables on a planned milestone schedule to ensure the information and tools are available as needed to support construction.
• Align contractor-furnished and owner-furnished equipment to support the construction schedule.
• Coordinate the prefabrication efforts with owner-furnished equipment.
supporting three organizations and working on additional volunteering opportunities,” Chalk informs us.
“We are blessed, but the needs around us are great and we are excited to partner with Children’s Healthcare of Atlanta, Free Bikes for Kids, and Sunrise Ministries to help those in need in our community,” he tells us passionately.
The company has given its unwavering support to the former for many years, as the charity continues to complete crucial work in the Atlanta community and benefits people across the world with its research.
Inglett & Stubbs has also been honored to support the Alzheimer’s Association of Georgia, and through its incredible fundraising efforts has donated over $400,000 to help stamp out this pervasive disease.
Fundraising efforts have equally supported Atlanta’s Children’s Hospital, with over $100,000 donated to help fund cancer research efforts.
Furthermore, Inglett & Stubbs’ field and office staff have previously volunteered through both financial donations and boots on the ground to assist in building three Habitat for Humanity homes for deserving local community members.
On top of this, the company is also working with several high schools that offer work-based learning and was previously named Newton County Schools’ Work-Based Learning Employer of the Year.
“We have supported high schools through conduit bending and other electrical classes, careers fairs, and hiring graduates. This has been a great program for us to be part of because it provides a workforce that is motivated and interested in the trade, and we have had many of these students join our team full-time after graduation,” Chalk explains.
One project that perfectly surmises the company’s beliefs and achievements is its work on the new Arthur M. Blank Hospital.
Made possible through a generous $200 million donation from the Arthur M. Blank Family Foundation, the hospital is part of a transformative $1.5 billion project that will be a huge leap forward in how it cares for children in Georgia.
The 1.5 million square foot (sqft) facility, slated to open in late 2024, will be located at the northeastern corner of the North Druid Hills suburb.
Southwire’s SIMpull ® Coil PAK™ Wire Payoff and SIMpull BARREL™ Cable Drum are changing the way electrical contractors install branch circuits.
We proudly team up with our distributor partners to deliver solutions like these and many more to contractors across the country like Inglett & Stubbs.
To connect with our field team and see for yourself, reach out to contractorsolutions@ southwire.com to schedule a site visit with one of our Contractor Solutions Professionals.
These innovative solutions are key components to the SIMpull ® Circuit Management system that allow the user to maximize productivity while minimizing the risk of injury on the job.
They are designed to make wire pulling easy, by reducing the amount of labor required to get the job done by up to 50 percent compared to traditional methods.
Designed to take advantage of research-proven healing views of nature, the Arthur M. Blank Hospital will include one tower with two wings and additional operating rooms, specialty beds and diagnostic equipment to meet anticipated patient needs, and space for clinical research, clinical trials, and overall patient care.
The North Druid Hills Campus, where the new hospital will be located, also includes the Center for Advanced Pediatrics, support buildings, and plans for more than 20 acres of greenspace and walking trails.
“Construction on the vastly impressive new hospital began in 2020 when we partnered with one of our largest competitors, Cleveland Electric (Cleveland), in a joint venture agreement to take on the project. It is the largest hospital to be built in Georgia,” notes Chalk.
The company was able to incorporate prefabrication into all areas of the project, and the prefabricated
headwalls were built in a warehouse, with the Inglett & Stubbs and Cleveland team working alongside plumbers and the drywall contractor.
“We prefabricated mixed trade racks with the sheet metal, plumbing, and mechanical piping contractors,” he enthralls.
Inglett & Stubbs has now established its reputation and prominent standing within its field of electrical construction expertise.
“In terms of the future of the company, our focus remains on off-site construction, from preconstruction and virtual design and construction (VDC) to prefabricated and modular methods. We will continue to grow that side of the business, which truly sets us apart from others in the market.
“We take a lot of pride in our history and the people who built the foundations that we are privileged to
start from. The recent anniversary was a great time to stop and celebrate,” Chalk finishes.
“Bringing our people and their families together is something that we plan to do more regularly. 70 years on, our team has more energy and willingness to change and innovate than ever before.”
Tel: 404-881-1199 mchalk@inglett-stubbs.com www.inglett-stubbs.com