with minimised resource and energy consumption by closed loop systems
ECO SOLAR FACTORY
Argon purge gas
Silver
crucibles Si ingot DI water process chemicals DI water use by rinsing
process organics
Aluminium
crucibles break Argon purge gas is vented Si-kerfloss is unutilized wafering process efficiency
low process efficiency difficult disassembly
crystallization
IMPACT
re-use DI water re-use Argon purge gas
40% plus eco-efficiency gains in the photovoltaic value chain with minimised resource and energy consumption by closed loop systems
European Union
re-use crucible re-use Si-kerf loss easy disassembly component re-distribution
use Si-kerfloss in Li-ion batteries
reduced resource consumption
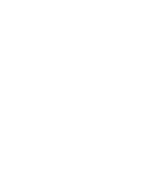
This project received support from the European Union in the Horizon 2020 programme
innovative module design
sealing modules
cell processing module assembly energy efficiency copper recycling re-use of glass
installation end of life repair testing diagnostics
no material degradation reduced energy consumption
ECOSOLAR
Eco-Solar Factory – 40% plus eco-efficiency gains in the photovoltaic value chain with minimised resource and energy consumption by closed loop systems
Duration: 2015-2018
H2020 project
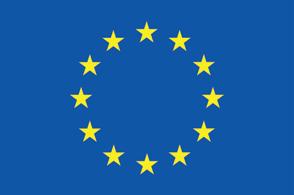
Grant agreement no: 679692 H2020-FoF-2015
FoF-13-2015 Re-use and remanufacturing technologies and equipment for sustainable product lifecycle management
Document date: January 2023
Eco-Solar Factory
40% plus eco-efficiency gains in the photovoltaic value chain with minimised resource and energy consumption by closed loop systems
ABSTRACT MULTIPLE PROBLEMS, INTEGRATED SOLUTIONS 1
BACKGROUND
THE “PHOTOVOLTAIC WASTE” ISSUE
ECOSOLAR
ACHIEVEMENTS
ACHIEVEMENTS
10-11
14-15
9 16-19 20-21 22-23 24-25 26-27
2 I II III IV V VI
CHAINS OF EFFECTS: APPROACHES IN DETAIL
28-29
CRYSTALLIZATION
RECOVERING ARGON, RE-USING CRUCIBLES
WAFERING
UTILIZING KERF LOSS
CELL PROCESSING
REDUCING SILVER CONSUMPTION, RE-USING DI WATER, EFFICIENT CHEMICAL PROCESSING MODULE ASSEMBLY INNOVATIVE MODULE DESIGN FOR DISASSEMBLY AND RECYLING
CELL REPARATION
ECOLOGICAL AND ECONOMIC ASSET
LIFE CYCLE ASSESSMENT
PROCESS ANALYSIS AND ENVIRONMENTAL IMPACT
IMPRINT
PROJECT PARTNERS
30-37 38-41 42-47 48-51 52-55 56-59 62-63
ABSTRACT
EcoSolar envisions an integrated value chain to manufacture and implement solar panels in the most ecologic way by maximising resource efficiency, taking into account reuse of materials during production and repurposing solar panel components at end of life stage. EcoSolar demonstrated that during the lifetime of a solar electricity producing field, individual panels can be monitored, allowing to identify defaulting panels at an early stage, replacing or repairing them and thus to increase the overall energy yield.
In WP1, SINTEF and Norsun worked on recovery & reuse during silicon ingot crystallisation, addressing recovery of argon purge gas and work with Steuler on reusable crucibles. In WP2 Garbo recovered Si-kerf-loss during wafering, and worked with SINTEF on potential reuse applications, like Si-feedstock in crystallization processes, or as resource in crucible manufacturing or lithium ion battery production. In WP3, ISC and SoliTek looked into potential for re-using process water; reducing material resources, like chemicals and silver, by smarter solar cell design, more efficient processes and recovery and reuse of chemicals; AIMEN developed solar cell monitoring and repair for inline processing, to enable remanufacturing.
In WP4, Apollon used a module design that results in reduced bill of materials, enables remanufacturing and reuse of components from modules that showed failures after assembly or have been identified as malfunctioning in operating PV installations, based on integrated diagnosis techniques for the detection of failure modes. will collected data from all previous WPs to assess environmental impact of the intended innovations (WP5). bifa identified waste streams that are costly and hard to recycle and find opportunities to repurpose those waste products. BCC disseminated results and supported the partners with the exploitation and replication potential of the results (WP6).
ABSTRACT (continued)
At the end of the Eco-Solar project, the consortium wishes to demonstrate economic viable PV-modules that have been designed and manufactured for re-manufacturing. Following the different lines of research we will demonstrate Eco-Solar PV-modules that have been produced with optimised recovery, reuse and resource efficient production methods. These demonstrator modules will:
> be industrial size (60 cells) PV-modules
> show less than 2% degradation of module performance after IEC 61215 degradation tests
> have a mono-facial STC power of 260 Wp for multi-crystalline silicon (mc-Si) cells and 285 Wp for mono (solo)-crystalline silicon (sc-Si) cells
> show that individual panels within a solar electricity producing field, can be monitored, so that defaulting panels can easily be spotted and repaired or replaced
> be cost-competitive aiming for 5-8 ct/kWh
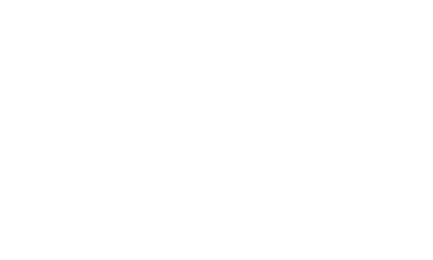
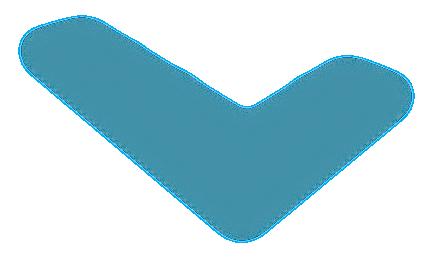
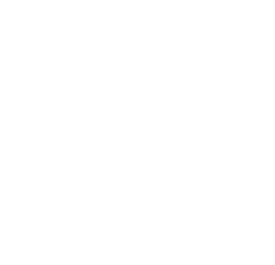
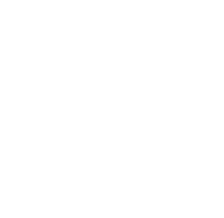
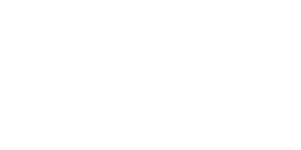
1
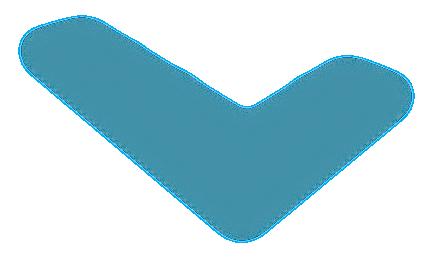
MULTIPLE PROBLEMS, INTEGRATED SOLUTIONS
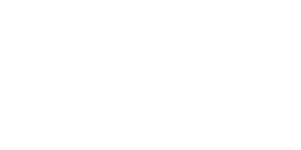
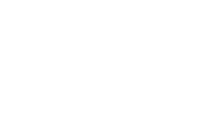
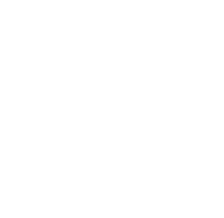
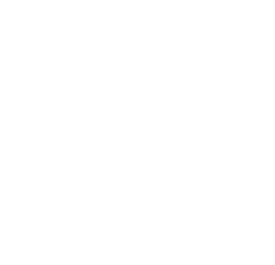
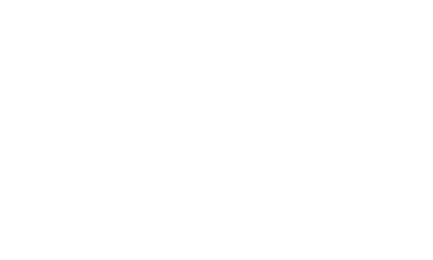
BACKGROUND
THE “PHOTOVOLTAIC WASTE” ISSUE
As a result of global efforts to reduce CO2 emissions and dependence on fossil fuels, the photovoltaic industry is focused on creating products that generate solar electricity. As such, it is one of the fastest growing economic sectors, following an exponential growth curve since 1992 until now. Projections for photovoltaic growth are difficult and burdened with many uncertainties, and official agencies, such as the International Energy Agency, consistently increased their estimates over the years, still falling short of actual deployment.
The drawback of this fast deployment of photovoltaic products (like solar modules) is, that even though solar power is pollution-free during use, production of PV-modules consumes considerable energy and natural resources. The fast growth of the PVindustry entails similar fast growth in resource consumption with growing production capacity: currently modest amounts of use can become very high.
Moreover, recycling is hardly considered during module production, and therefore still cumbersome and inefficient. Therefore, it is necessary to design modules for end-of-life recycling to allow recovery and recycling of glass, wafers/cells in whole pieces, which will result in a much more (energy-) efficient method for harvesting and especially reusing the secondary raw material, in addition to sustainable improvements in each process step.
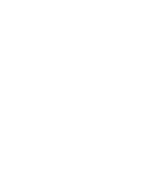
ECOSOLAR THE HOLISTIC APPROACH
The EcoSolar project aims to maximise resource productivity and reduce pollution in PV, through minimising use of critical resources like energy, water, chemicals, aluminium, silver and lead, while simultaneously maximising recycling possibilities, by introducing design for recovery, reuse and recycling in this sector. To realise this, collaborating over the value chain is imperative.
EcoSolar’s concept for improvements in waste reduction is to increase remanufacturing potential, including repair of PV-modules, while simultaneously improving reuse of resources and components and increasing resource efficiency, over the whole value chain. EcoSolar focused on multiple processing steps, where ecologic impact and economic gain are expected to be realised through the intended innovations. As shown in the figure, the project includes the monitoring of PV-modules after installation and their reuse and recycling potential within the PV-value chain and beyond.
A pan-industrial approach has been chosen to identify by-products, recycled and recovered wastes. With this information, the best possible ecological and efficient utilisation of raw materials and solutions for poorly recovered and reused materials can be presented. The results for the individual process steps, and their impact over the integrated value chain have been assessed with a LCA and eco-efficiency analysis methods to provide proof of their success in reducing the environmental footprint.
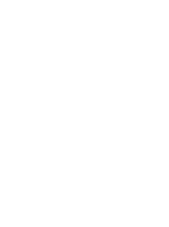
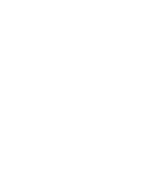
FIVE DOMAINS INPUTS, PROBLEMS, PRODUCTION, STRATEGIES, IMPACT
Improvements in waste reduction have been assessed over the whole value chain, by looking at the major process inputs: in terms of (near) scarcity, in terms of easy recyclability and in terms of large volumes of waste.
Based on this assessment, the major problems have been identified: the reasons why industry has not adapted remanufacturing, re-use or recycling options in their production process, which have led to strategies to solve these problems. By adapting the production processes, the impact will be created:
module disassembly recycling/ re-use
VI
FOCUS INTERVENING IN THE PRODUCTION PROCESS
The most important bottleneck for eco-friendly solar panels is the PV-module design. Current modules encapsulate the solar cells using EVA (Ethyl Vinyl Acetate) which, due to the high temperatures involved, acquires a dense cross-linked structure, and becomes hard and chemically resistant, complicating recycling of PV modules. Modules must be destroyed and treated under extreme conditions such as extended treatment at high temperatures to recover the component pieces as impure fragments. Without a design where the module can be reopened after assembly, repair, recovery of components and hence remanufacturing will be impossible. Therefore, the project will use Apollon Solar’s design of PV-modules that can easily be disassembled and separated into their different components. From this starting point, the whole value chain, from silicon feedstock to modules has been assessed for improvements without losing competitive edge.
The process from Si feedstock to wafering should ideally recover and reuse an maximum amount of consumables, such as crucibles and argon. Moreover, it should recover a maximum amount of resource materials (like Si-kerf) to be reused within the feedstock process or within another market, leading to the consumption of minal energy, but resulting in a high yield.
Solar cell processing should ideally use a minimum of (near) critical materials such as silver. Moreover, it should Avoid using of chemicals in cell processing steps, such as during texturisation and cleaning, emitter formation and etch isolation. In addition, it should recover and reuse a maximum amount of water and chemicals within the production process. It should also enable an option for automated repair of defective silicon cells and wafers, within the manufacturing line, combined with a high yield and throughput.
Solar modules should ideally be easy to open after sealing, so that they can be repaired if rejected at failure control or when sent back from PV-fields. Moreover, this would also allow salvaging of glass, solar cells and copper tabs, and allow for avoid using aluminium frames.
Ar 18 Ag 47 A l 13
Ceramics (kg)
2.55 0.46 0.23 baseline project target value
Argon gas (kg) Silver (g) Aluminium (kg)
1,5
1,0
0,0 0,5 1,0 1,5 2,0 2,5 3,0 0 1 2 3 4 5 6 7 8 0,0
0,4
0,3
0,2
0,1
0,0
2,0 24
0,5
2,0
1,5
1,0
0,5
2,0 0,0
project result value 6.47 2.90 3.34 1.73 1.00 0.08
Silicon (kg)
DI water (kg)
2,5
1,5
1,0
0,5 0 50 100 150 200 250 300 0,0
0.43 0.06 0.06 279 14 7.08a 2.44 0.20 0.32 1.99 0.88 1.6
0,5
ACHIEVEMENTS PROJECTED AND REDUCED RESOURCE CONSUMPTION
Through the different solutions and strategies EcoSolar reduced the waste generation within the PV-industry, but also beyond. Our overall impact on non-renewable materials is shown in the figures, where we have visualised the impact of our resource efficiency, reuse and reducing amounts of waste within the PV-value chain.
The seven resources depicted on the left could be used more effectively during the production process, resulting in significant reductions in consumption and costs. Each graph depicts the baseline measurement or estimation, the project target value and the results that have been obtained.
These numbers apply to mono-Si and multi-Si modules. The values given here are based on a mono-Si PV module of 1.62 m2
ACHIEVEMENTS CARBON FOOTPRINT AND GLOBAL WARMING
The combination of different strategies that has been implemented in the production process results in significant reductions in the carbon footprint of the PV-module production process. In turn, this reduction contributes to the reduction of global warming. In each of the production steps, measurements have been made and models have been used to calculate or approximate the respective carbon footprint reduction.
2
CHAINS OF EFFECTS: APPROACHES IN DETAIL
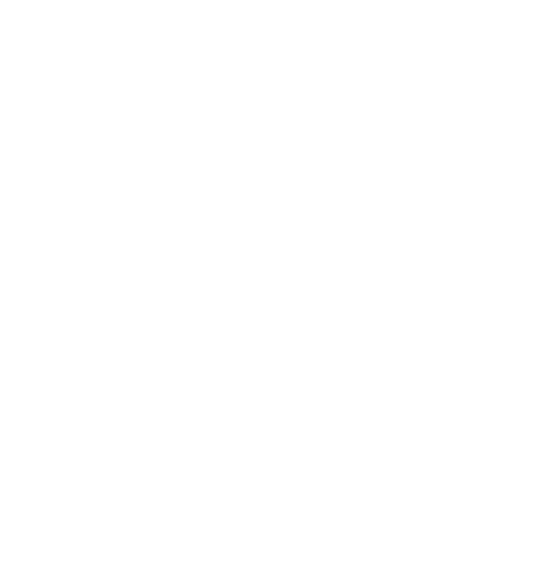
PROCESS INPUTS
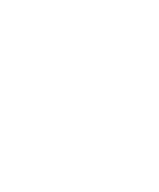
PROBLEMS
Si feedstock use Si-kerfloss in Li-ion batteries
purge gas crucibles Si ingot DI water process chemicals DI water use by rinsing
process organics
crucibles break Argon purge gas is vented Si-kerfloss is unutilized wafering process efficiency
crystallization
re-use DI water re-use Argon purge gas
Silver Aluminium re-use crucible re-use Si-kerf loss easy disassembly component re-distribution
innovative module design
no material degradation reduced energy consumption reduced resource consumption
low process efficiency difficult disassembly installation end of life enhanced disassembly recycling repair testing diagnostics
cell processing external use
sealing modules
module assembly energy efficiency copper recycling re-use of glass
CRYSTALLIZATION RECOVERING ARGON RE-USING CRUCIBLES
During crystallization, pure argon gas, used to remove contaminants, is currently being vented into the air. The effluent argon gas is typically composed of argon and a few contaminants at the particles per million (ppm) level, chiefly composed of carbon monoxide, hydrogen, methane and other hydrocarbons.
Though perhaps argon is abundantly available in the earth’s atmosphere (approximately 1% of mass), there are still (ecological and financial) costs involved in the production of pure gas. For instance, NorSun’s wafer facility with an equivalent output of ~350 MWp of wafers per year, requires ~1.4 million Nm3 argon, resulting in a typical bill of 0.7–1.4 million EUR per year, accounting for 3–5% of the wafer cost.
Though in other industries, argon gas recycling has become state of the art, in PVproduction this was not yet the case. However, Gas Recovery and Recycle Ltd. (GR2L) has developed a relatively simple and cost efficient technique for argon-gas-recycling, providing a recovered gas stream of around 99.9999% purity. This method is based on a chemical looping combustion process to convert combustible species in the exhaust gas stream to carbon dioxide and water, followed by efficient of carbon dioxide and water in re-generable reactor beds. Such a recycling system has been integrated in NorSun’s factory collecting and recycling exhaust gas from 8 crystal pullers. First results from crystals grown with argon recycling show similar material performance as grown by standard process without recycling. In the near future, solar cells and modules will be manufactured from this material to confirm the technological potential and qualify for customers.
Savings of over 95% could be realised if the wasted argon is purified and re-used, as has been assessed by bifa in an LCA.
single Si crystal ingot (so-called monocrystalline silicon ) for optimum conductivity
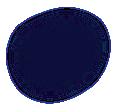
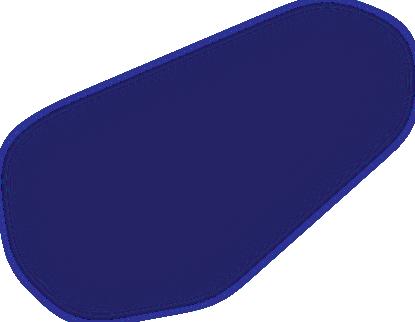
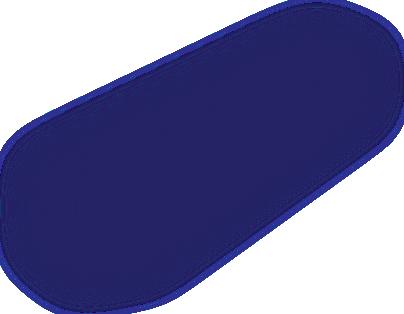
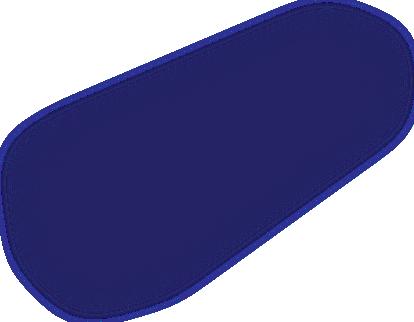
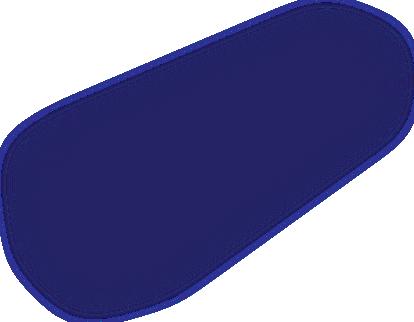
Argon atmosphere
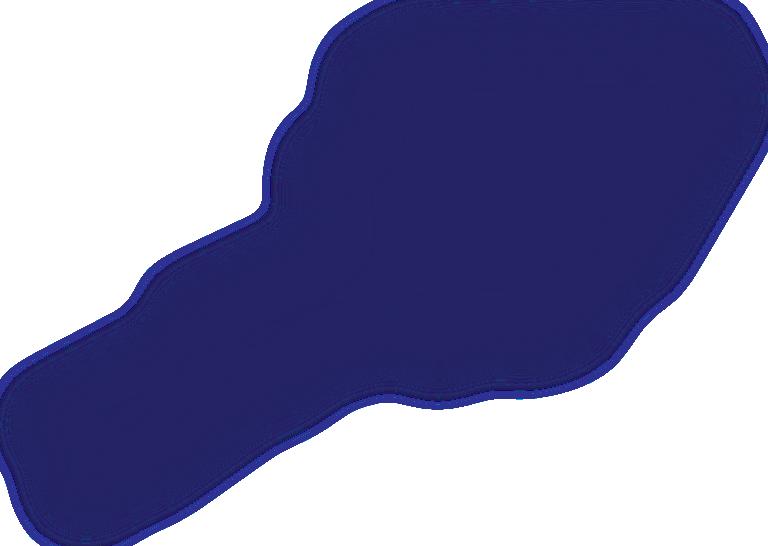
The Argon is recirculated and re-used
1 ingot is 1 crystal made under a special atmosphere
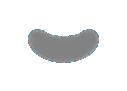
seed crystal is slowly pulled through liquid Si
ongoing crystallization (from liquid Si to solid single Si crystal)
ingot is wafered into single cells
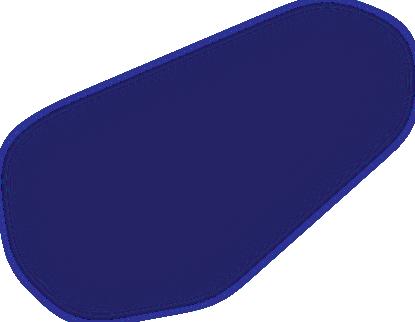
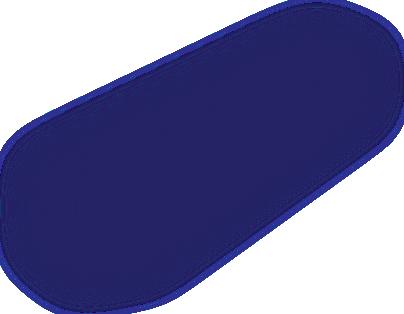
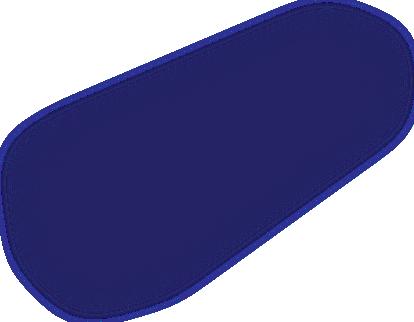
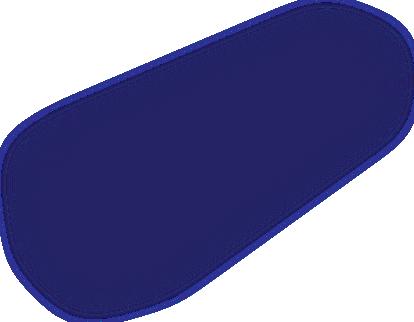
CRYSTALLIZATION
Argon gas will be catched
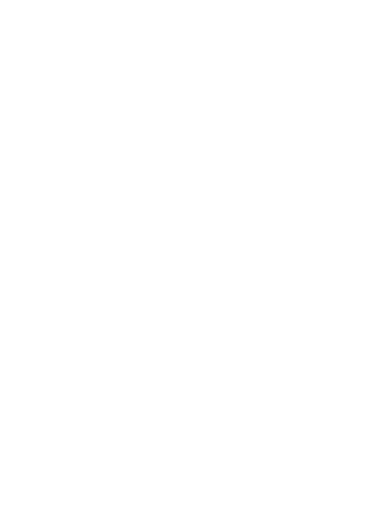
this gas can be re-used in a second round inert atmosphere
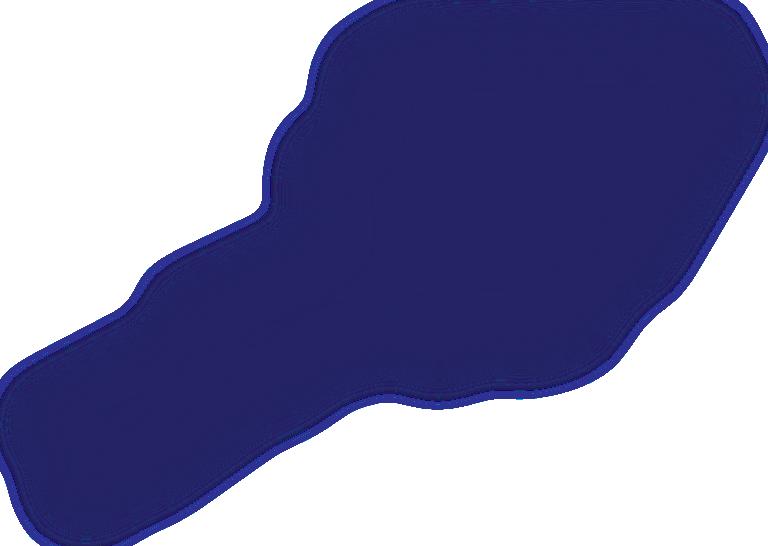
CRYSTALLIZATION (continued)
During the crystallisation step, crucibles are the main containers for the (molten) silicon feedstock. As silicon at high temperature reacts easily with almost everything, there are only a few crucible materials that will meet purity requirements for manufactures. One of the main drawbacks of using silica, as is current standard practice, is the (ecologic and financial) cost due to single use. Silica crucibles contribute up to ~30% of the conversion cost from Si-feedstock to the as-grown ingot.
STEULER has developed a concept for reusable silicon nitride crucibles, for both crystallization processes, DS and Cz.
In Eco-Solar the technical potential of these crucibles for crystallisation of multicrystalline silicon has been investigated at SINTEF. Currently, one silicon nitride crucible has been used for 5 subsequent crystallisation runs. The obtained silicon material quality is similar to material crystallized from Electronic Grade HighPurity Quartz crucibles. It is aimed for at least 10 times reuse. The near future plan is to scale it up to larger silicon ingots and then to manufacture solar cells and modules out of the silicon grown in this material in order to demonstrate that this technique is suitable for PV applications.
Savings of more than 85% can be realized with this novel technology.
1 ingot costs
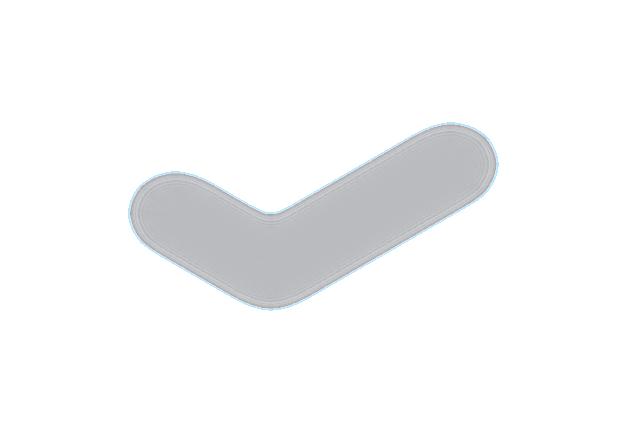
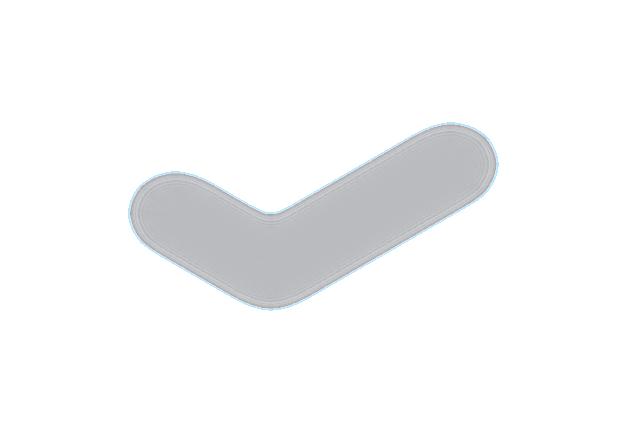
1 crucible
6 ingots cost
1 crucible
1 ingot costs
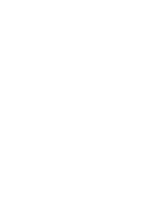
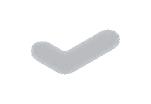
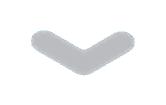
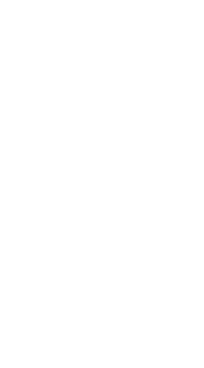
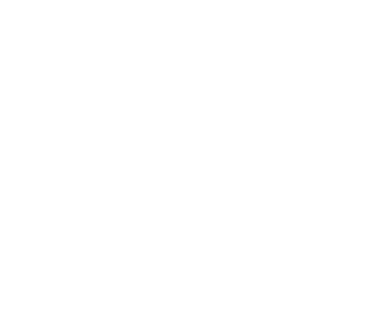
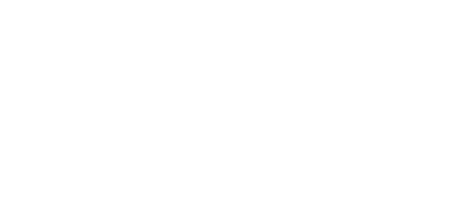
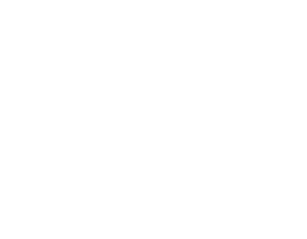
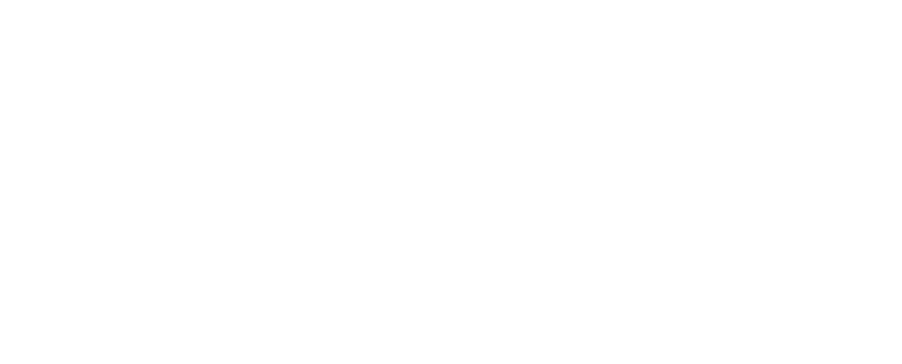
1 crucible
Si ingot production is expensive, as each crucible breaks
crucibles are as of yet not recycled
crucibles break through attachment of the Silicon to the crucible material
attachment leads to material degradation, cracks and breaking
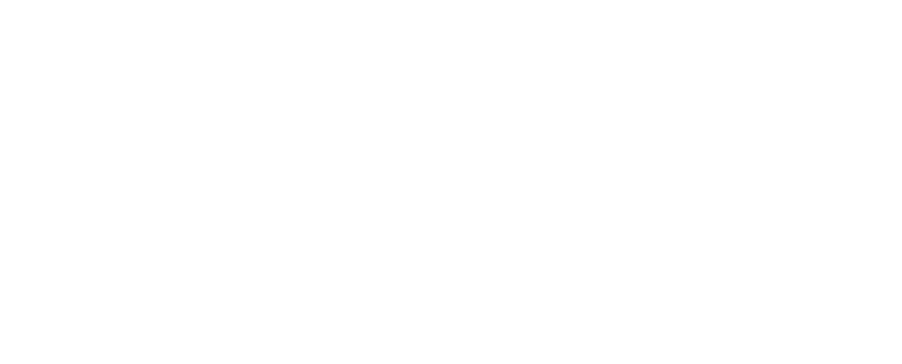
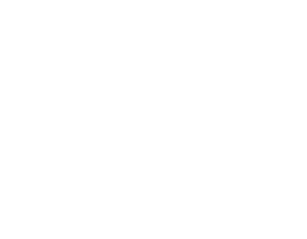
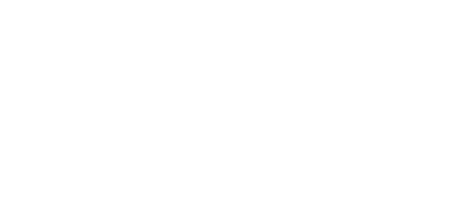
PROCESS INPUTS
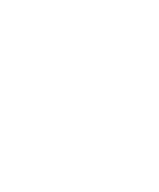
PROBLEMS
feedstock use Si-kerfloss in Li-ion batteries
purge gas crucibles Si ingot DI water process chemicals DI water use by rinsing
process organics
crystallization
crucibles break Argon purge gas is vented Si-kerfloss is unutilized wafering process efficiency
cell processing
re-use DI water re-use Argon purge gas
innovative module design
Silver Aluminium re-use crucible re-use Si-kerf loss easy disassembly component re-distribution
no material degradation reduced energy consumption reduced resource consumption
module assembly energy efficiency copper recycling re-use of glass
sealing modules
low process efficiency difficult disassembly installation end of life enhanced disassembly recycling repair testing diagnostics
use
II
WAFERING UTILIZING KERF LOSS
After crystallization, side-, top- and bottom-parts are removed before the ingot is cut into blocks and then wafered. A considerable amount of silicon is lost in form submicron powders (kerf-loss) during the cutting processing of silicon ingots to obtain wafers: up to 50% of starting silicon goes into the coolant used during the sawing of silicon wafers. The ability to recycle the kerf-loss for solar ingot production will have beneficial effect in terms of savings of precious poly-silicon consumption and of waste reduction.
Therefore, Garbo has patented and implemented a silicon recycling process which removes contaminations and brings silicon to ‘five nines’ (or 5N), i.e. 99,999% purity. Purified silicon is then dried, compacted and packed under vacuum in order to obtain a stable silicon powder, that however needs to undergo a high temperature oxygen degassing process before being used as feed material in the standard production of solar ingots and cells.
Within Eco-Solar, the consortium investigated 3 factors that will give both environmental and monetary gain. Garbo will look at reducing chemicals consumption in Si kerf cleaning step and improving compact density of powders, while NorSun carried out sawing tests with increased kerf-loss saturation level in sawing coolant, for Garbo to study if the saturation level in the coolant affects the coolant recycling process and the recycled coolant quality, even if no variations are expected in this respect.
In total, the impact from the innovations could be saving more than 70% of the silicon kerf-loss, which has been assessed by bifa.
towards crystallization
part of the kerf loss is re-used in the feedstock for the production of new ingots
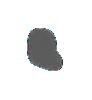
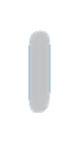
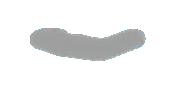
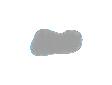
the overall impact of this strategy is to reduce resource consumption, notably Silicium (Si)

wafers are used in cell processing
part of the kerf loss is re-used in the Lithium (Li) batteries
diamond sawing wire ingot
process step: wafering
WAFERING
solar cells are made by wafering ingots
while cutting, the dust is extracted for recycling
dust is utilized in batteries or feedstock
resource: kerf loss impact: reduce resource use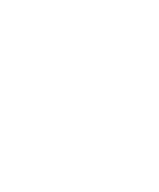
III
CELL PROCESSING REDUCING SILVER CONSUMPTION RE-USING DI WATER EFFICIENT CHEMICAL PROCESSING
In crystalline solar cell manufacturing, when wafers are being processed into solar cells, several wet chemical etching and cleaning steps are implemented, which have negative impact on the environmental footprint. By reducing and avoiding certain chemicals or metals (e.g. HF, Pb, Ag, Al) and using less pure or recycled chemicals, waste can be reduced and the ecologic footprint of solar cells and panels can be improved.
Especially silver is an important element, as it is used in most solar cells (over 98%) currently produced, providing the metal contact that ‘collects’ and ‘drains’ the current from the solar cell, resulting in todays silver consumption for PV of about 15% of the total silver market with the expectation to rapidly grow further.
In the Eco-Solar project, ISC-Konstanz experimented with different solar cell architectures, to minimize the use of Ag. In addition, an innovative interconnection scheme enabled by Apollon’s module design, allows us to avoid soldering of a contact tape onto the rear side Ag pads and the front side busbars. Only the small contact fingers on the front side are needed.
In addition, ISC-Konstanz and SoliTek tested an alkaline saw damage removal and texturization to replace the current state of the art concentrated HF:HNO3 mixture, HF reduction in cleaning process is also investigated. Advanced processes for emitter formation are developed that will enable higher throughput, resource efficiency and avoid the needs for chemical phosphorous glass layer removal (PSG-removal).
AIMEN further developed advanced laser treatment, in order to minimize the cut-off area at the wafer edges to a negligible fraction of the whole wafer area, to avoid the wet chemistry normally used to separate the front and rear of the solar cells.
CELL PROCESSING (continued)
During the processing of wafers in to solar cells, water is mainly used for cleaning: after each chemical processing step, the wafers are rinsed with de-ionized, ultra-clean, water.
Afterwards, the water that goes down the drain, is often of higher quality than the water contracted from the tap.
One of the cornerstones of environmental protection in Europe, is the protection of water resources, of fresh and salt-water ecosystems and of the water we drink and bathe in.
With the example of Solitek, where solar cell processing with a production capacity of 80MW, consumes about 54.000m3 of de-ionized water per year, it becomes clear that recycling systems for waste water can have a large impact.
Therefore, ISC-Konstanz looked into industrial viability of recycling systems for waste water, and investigate its potential for saving more than 90% in solar cell processing, while bifa will assess the environmental benefits via an LCA.
DI water used for rinsing is recycled
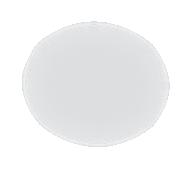
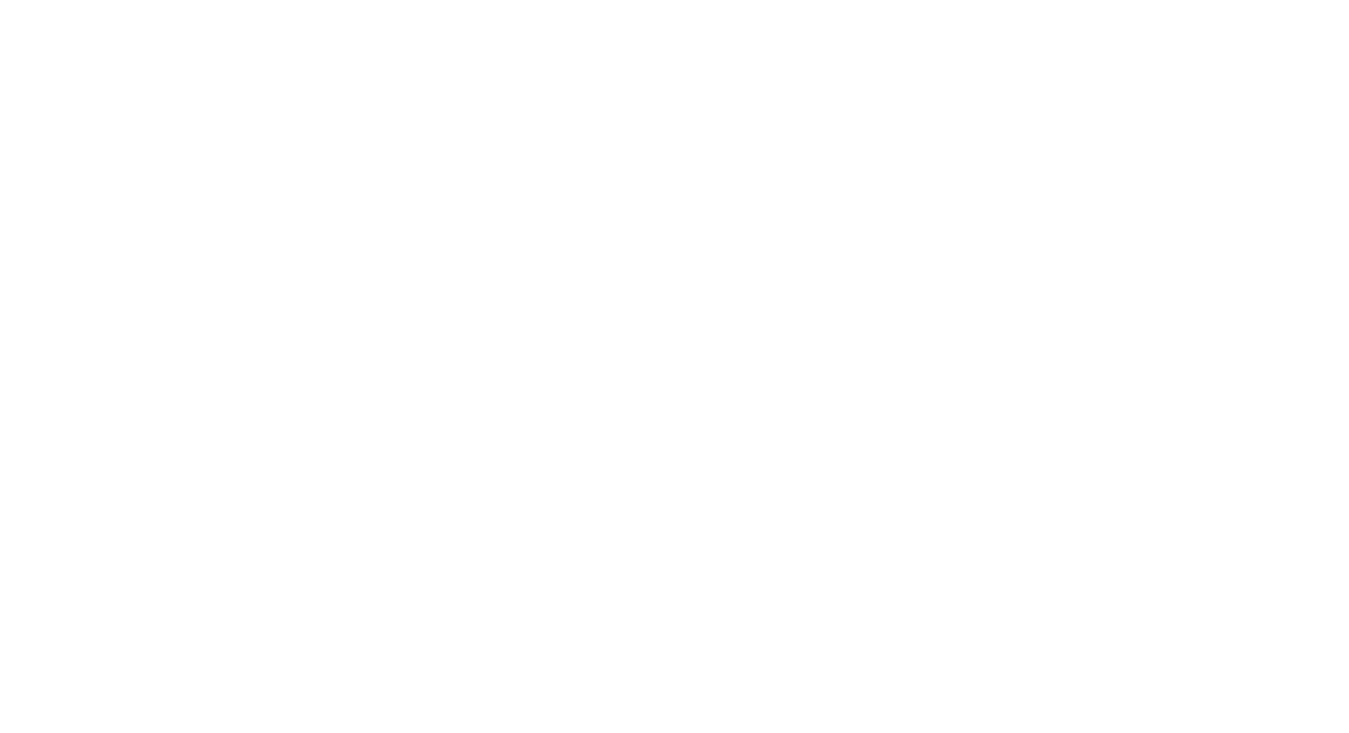
CELL PROCESSING
efficient cleaning and damage removal to reduce the use of process chemicals
new contact need less silver due to new printing technology
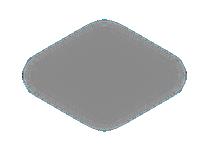
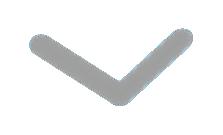
new technology allows for printing smaller silver fingers
efficient processing reduces required chemicals
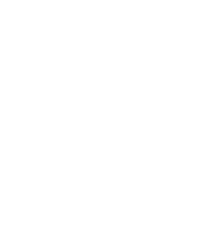
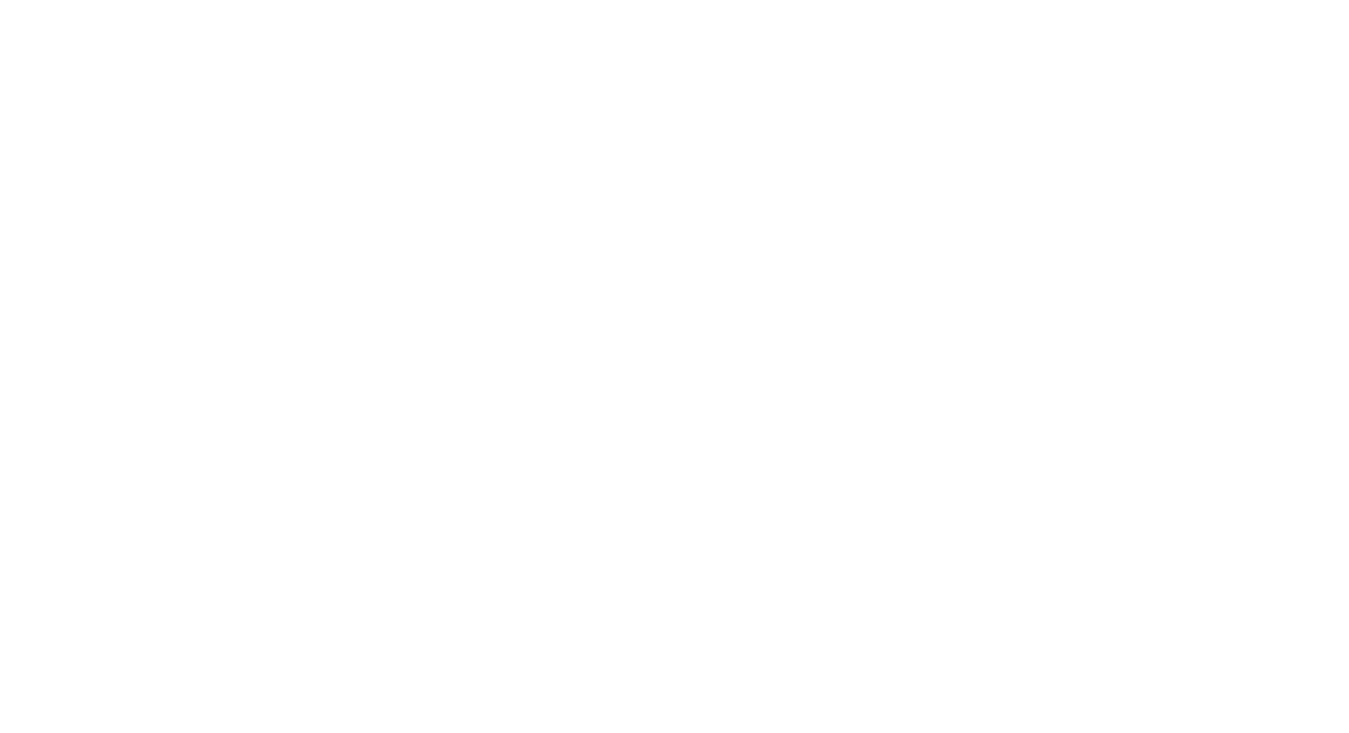
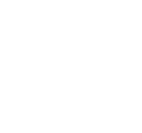
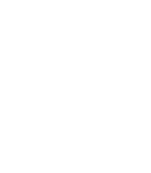
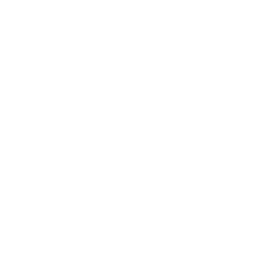
resource reduction silver fingers are expensive
resource reduction process chemicals are polluting new printing technology allows for thinner fingers
resource reduction DI water is lost during rinsing
DI water is recycled within the process
resource: kerf loss impact: reduce resource use process step: wafering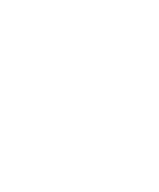
IV
MODULE (DIS)ASSEMBLY INNOVATIVE MODULE DESIGN FOR DISASSEMBLY AND RECYCLING
After completion of the cells, they are electrically series connected and assembled into a solar module. Moreover, a junction box is attached that will ensure suitable power output. Within current solar modules technology, one big eco-challenge is the fact all module components are physically linked to each other by lamination and soldering.
The only potential for recycling are destructive processes that result in lower grade materials in form of granules. Current PV modules also contain a vast amount of organic materials (EVA for encapsulation, PVF in back sheets).
As Apollon Solar’s NICE-modules are already designed for disassembly, in Eco-Solar Apollon focused on further reduction of the module BOM (Bill Of Materials) focusing on a frameless version of the PV module, and integration of electronics in the junction box, to monitor the performance in the field. Moreover, Apollon demonstrated that module assembly of the Eco-Solar cells will result in comparable module output as with current non-eco-friendly state of the art module technology.
Finally, Apollon Solar demonstrated the disassembly of modules into their major components (glass sheets, copper wires, cells) allowing for their recovery as entire pieces with a high added value and strong potential for re-use (in PV or other industries).
The benefits of material savings will be demonstrated via the LCA carried out by bifa.
controlled disassembly prevents high energy consumption and material degradation
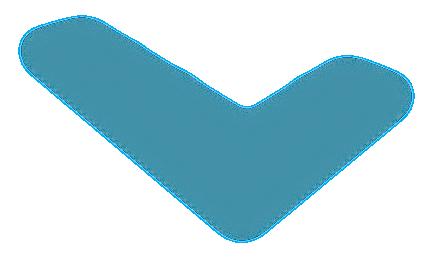
module can be easily disassembled due to underpressure technology
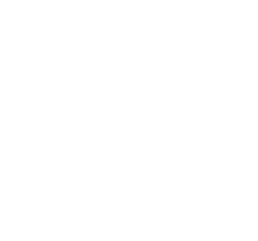
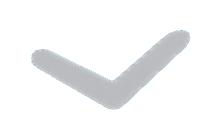
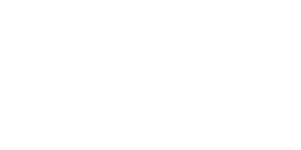
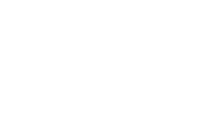
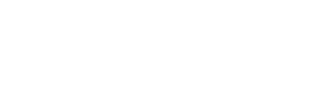
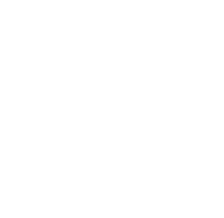
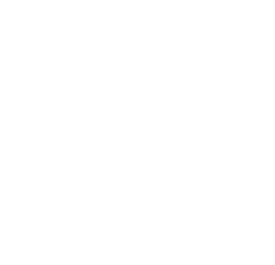
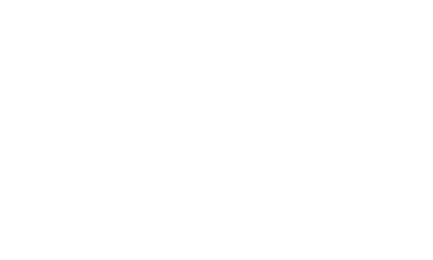
front glass, re-used in new modules
no Aluminium frame due to glass/glass and double edge sealing
cell contacts, silver is re-used
pure copper wires, copper is re-used cells can be scanned, repaired and re-used cells can be etched or melted no encapsulant, neutral gas instead
MODULE (DIS)ASSEMBLY
process step: module (dis)assembly
resources: Aluminium, Copper, Silver, glass, cells
impact: reduce resource use/ degradation/ energy consumption
back glass, re-used in new modules
modules are closed by encapsulants individual components are sorted and re-used
this leads to high energy consumption and material degradation
modules are vacuum sealed
modules can easily be taken apart
hazardous encapsulants are not needed
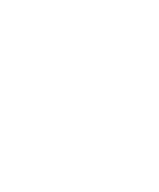
V
CELL REPARATION ECOLOGICAL AND ECONOMIC ASSET
A small fraction of the finished solar cells (about 2%) contains electrical defects and can therefore not be used for module assembling. There is in practice no solution available for such cells, other than scrapping. Besides that an additional 2% contain hidden defects, which will develop cracks and other defects early in their use, probably during their handling and mounting in the modules, or early in their service.
Another approximate 4% of cells initially produced as prime or class B, have to be downgraded to their selling due to small fabrication defects. These cells are fully functional, but have lower efficiency and lifespan, hindering their lifecycle ecological balance: energy produced over energy, carbon, material and chemicals used in producing it.
Therefore, to capitalise on the value a solar cell represents, repair of defect solar cells within the solar cell process can represent a significant financial and ecological impact. AIMEN coordinated the EU-funded project REPTILE, in which ISC and INGESEA participated as beneficiaries. The project provided preliminary work on a system that is able to automatically select and cut out or isolate non-defective areas in defective cells and wafers, called the CellDoctor.
ISC evaluated rejected solar cells with an automated system for defects recognition. AIMEN and INGESEA further developed the accuracy of the Cell-Doctor prototype, aiming to avoid 50% scrapped cells. Moreover, this technology can be used to evaluate solar cells after end-of-life modules return to the factory for recycling and reuse.
In an LCA, bifa assessed the environmental benefits of the repair process for solar cells.
2 54
cells are diagnosed to identify the scope and location of the damage
solar cell supply
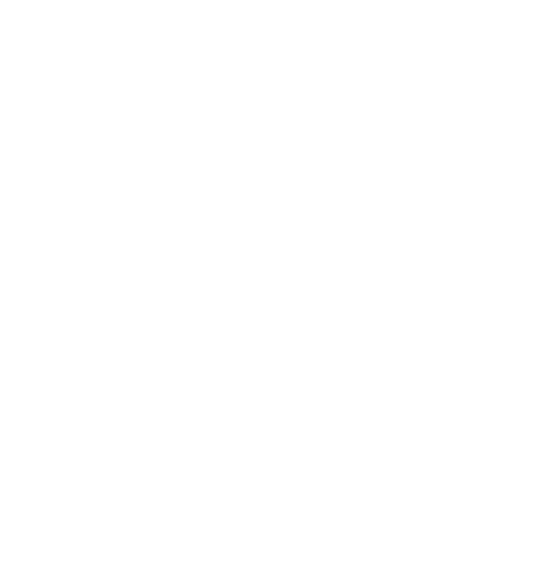
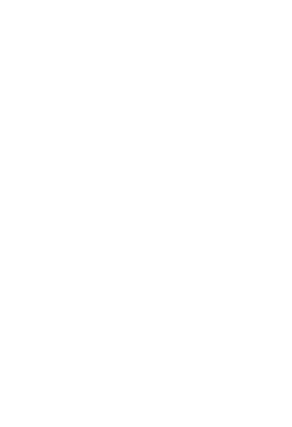
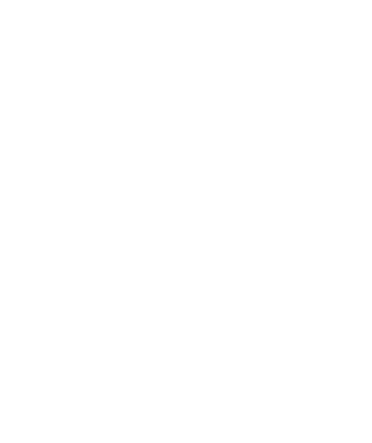
robot arm carefully transports individual cells
a laser treats the affected spots, removing damage
3 4
a flash test determines how succesful the treatment has been
CELL REPARATION
solar cells are checked for defects
laser treatment is used to remove defective spots
repaired cells can be re-utilized
fully integrated reparation and testing process
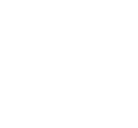
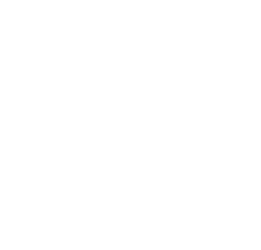
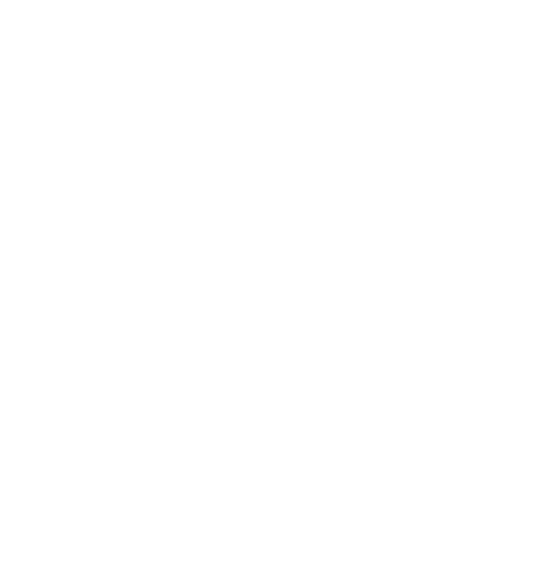
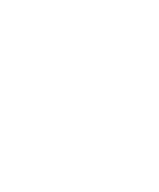
VI
LIFE CYCLE ASSESSMENT PROCESS ANALYSIS AND ENVIRONMENTAL IMPACT
To be able to determine the actual environmental impact of the Eco-Solar results, a thorough ecologic validation is necessary. Moreover, the only chance for implementing eco-friendly production methods is when they are economically viable. Therefore, it is of crucial importance that all processes are assessed for their economic viability and that the recovered waste products find (new) markets, where they can purposefully be introduced as (new) resources.
When writing the grant application, it became obvious that current literature does not provide consistent data to fully calculate ecologic impact of reducing materials in certain process steps. Moreover, different market forecasts for PV-growth give additional uncertainty. Therefore, within the Eco-Solar project, bifa carried out a Life-Cycle Inventory, based on data from the partners and published data. bifa will monitor and validate the achievements, using state of the art LCA and LCI methodologies.
Moreover, bifa supported partners in finding alternative uses for their waste products. This recycling and repurposing of advanced materials will address argon purge gas, graphite hot-zone parts from the crystallisation furnaces, Si-kerf-loss, silica crucibles, water, steel wires from the saw, silicon nitride crucibles, solar cells and modules. A strength of the eco-efficiency analysis is the simultaneous optimization of economic and ecological aspects that can be used to identify the most promising development routes and products.
It will also be applied to develop recycling processes that allow the highest possible recycling yield and quality that will be feasible from an economic point of view for the individual materials used in production and products. The eco-efficiency analysis starts with setting the system boundaries and defining the processes. After that the collection of environmental and economic data starts, the life cycle inventory is built up and the LCA is carried out on the impact categories agreed on in the definition phase. Environmental key performance indicators can be calculated after normalization and weighing. This will also be used together with the cost analysis to build the eco-efficiency portfolio,
no need for Aluminium frame due to sealing technology
front glass, re-used in new modules
cells can be etched or melted
cells can be scanned, repaired and re-used
crystallization wafering cell processing
recycling Argon re-using crucibles
cell contacts, silver is re-used
module assembly
recycling Si kerf re-using in batteries re-using components recycling components
reducing use of Silver reducing use of process chemicals re-using Di water repairing cells wires, copper is re-used
encapsulants are no longer needed
module can be easily disassembled due to vacuum technology
recycling
recycling and re-using source materials
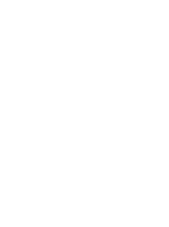
IMPRINT
SINTEF
Martin Bellman (coordinator) Anu Schei Nils Peter Wagner
NORSUN
Gyou Seong Park
SOLITEK
Valius Čyras Julius Denafas Povilas Lukinskas Lina Petrèniené
ISC KONSTANZ
Florian Buchholz Stephan Eisen Elina Schmid Eckard Wefringhaus
APOLLON SOLAR
Roland Einhaus Frédéric Madon
GARBO Gianluigi Noja Ilaria Lombardi
BOUKJE.COM
Karen van den Bos Boukje Ehlen Otto Paans
BIFA
Iris Fechner Boris Mertvoy René Peche Matthias Seitz Karsten Wambach
AIMEN Tamara Delgado García Francisco Rodriguez Lorenz Pablo Romero Romero
STEULER Arjen Ciftja Rune Roligheten Jan D. Sandmo
INGESEA
Axier Bollar Ane Miren Iriondo
Graphics by Boukje.com Consulting BV
(c) 2016–2023
IMPRINT
This project has received funding from the European Commission in the H2020 program.
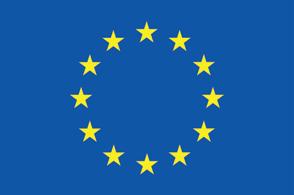
2015–2018
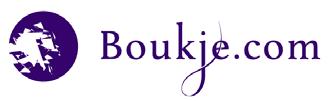
Grant agreement no: 679692
H2020-FoF-2015
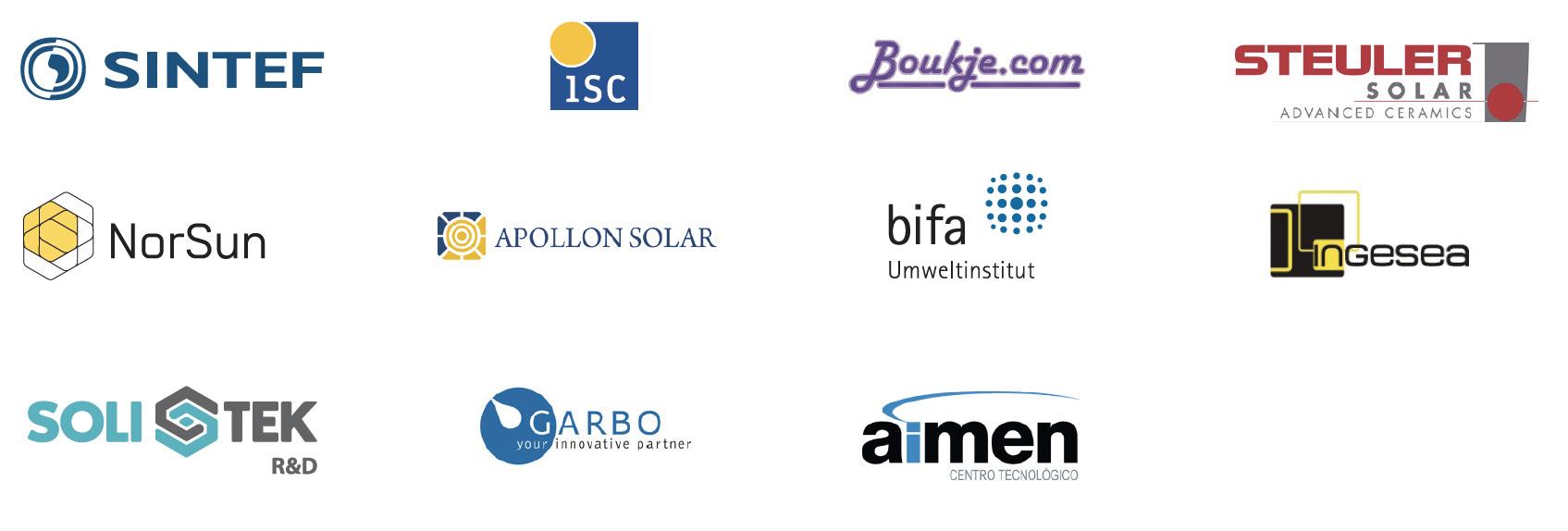
FoF-13-2015 Re-use and remanufacturing technologies and equipment for sustainable product lifecycle management
project partners