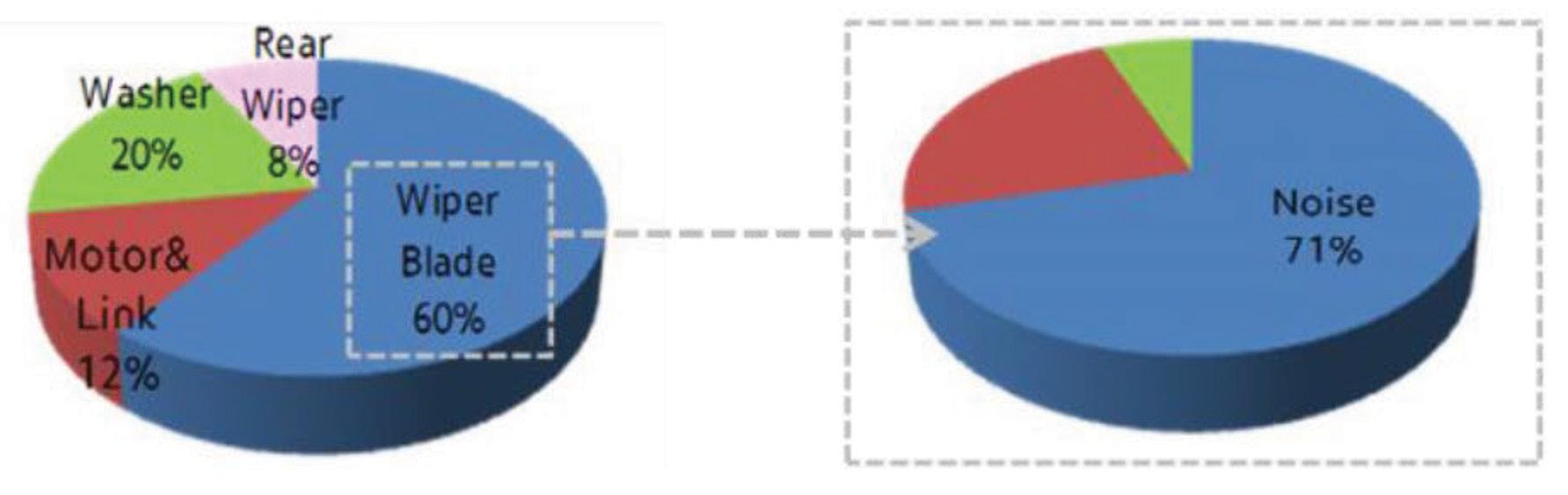
15 minute read
Technical – Study on Basic Principles of Operation Noise of Wiper System on Vehicle
from VTE March 2022
by Possprint
Nak Kyoung Kong, Kihong Lee, and Jongmin Park, Hyundai Motor Company
Citation: Kong, N.K., Lee, K., and Park, J., “Study on Basic Principles of Operation Noise of Wiper System on Vehicle,” SAE Technical Paper 2019-01-1421, 2019, doi:10.4271/2019-01-1421.
Introduction
The wiper system consists of a motor, linkage, arm, and blade, which provides a clear front view to the driver by removing rain, snow, and foreign matter from the windshield glass. It is a system component that requires a robust design to meet system rigidity, scrubbing performance, and operating noise in any external environment to provide the driver with a front view. However, after analyzing the customers’ complaints about the wiper system, it was confirmed that the customers were most dissatisfied with the noise / vibration of the wiper blade. As a result of analyzing the customer complaints by car class, it was confirmed that the noise of the luxury car was more complaining than the small and medium sized passenger car. We have confirmed that our evaluation criteria focus on emotional evaluation that is not sufficient to improve the various wiper operating noises that customers are dissatisfied with. Therefore, this paper proposes a quantitative analysis method that can analyze various noise that can occur in wiper system. The human auditory system consists largely of the outer ear, the middle ear, and the inner ear. The sound transmission path consists of the cranium -> outer ear canal -> eardrum -> Ossicle -> cochlea. The basement membrane of the cochlea is called the basal membrane, which is made up of hard, short fibers, but it is made up of long, soft fibers going to the end of the cochlea. Due to this structural difference, the basement membrane of each part reacts to different frequencies. That is, since the basement membrane at different positions along the frequency of the sound is bent, the activated hair cells are different. The treble in the near basal membrane resonates well in the remote basement membrane. Important physical quantities of sound are frequency and intensity. A person can distinguish a sound by the difference between frequency and intensity. The difference in frequency can be determined from what type of hair cells the vibration is detected, and the difference in frequency is recognized by the pitch of the sound. The intensity of the sound can be determined by the magnitude of the signal detected by the hair cell, and the intensity of the sound is divided by the amplitude. In other words, due to the structural form of the human ear, it is impossible to recognize the quality of sound simply based on the size of the sound. While we still manage the wiper noise based on the noise level only for the wiper noise, other competitors who recognize the need to improve the noise quality manage the wiper noise by introducing psychoacoustic quality standards using Zwicker parameters have. Competitors’ evaluation criteria for noise evaluation are based on evaluation of sound quality for emotional, as well as performance evaluation criteria of blades that meet various environmental conditions that have the greatest influence on wiper noise. In this paper, we propose quantitative emotion noise discrimination for wiper blade noise and establishment of verification method considering environmental impact.
Noise Measurement and Evaluation
For this study, we recorded the wiper operating noise by clas-sifying large
ABSTRACT
The wiper system consists of a motor, linkage, arm, and blade, which provides a clear front view to the driver by removing rain, snow, and foreign matter from the windshield glass. It is a system component that requires a robust design to meet system rigidity, scrubbing performance, and operating noise to any external conditions to provide the driver with a front view. In recent years, however, customer complaints about wiper noise have increased as automobile engine and noise levels have decreased. Based on the analysis of wiper noise, this paper presents quantitative judgment criteria for various wiper noises. In addition, we predict the change of wiper noise to environmental factors through the sound field analysis and propose the solution.
/ medium / small / small / small / RV vehicles. The sensory evaluation was carried out by 82 customers using data recorded in the interior of the vehicle to classify the preferred / non-preferred vehicles for wiper noise. Based on the above results, we analyzed the outdoor / indoor noise characteristics, the influence analysis according to the applica-tion of the sound insulation film, the noise of the motor & linkage, and the noise trend of the new / aged blades. As a result, it was possible to distinguish the non-preferred vehicle group in which the quality of the wiper noise was rapidly deteriorated. Table 2 shows the results and examples of preference group and non-favored group vehicle classification. Based on the results of this evaluation, we conducted a comparative analysis with the vehicles clas-sified as the preferred group for the vehicles classified as non - preferred wiper noise. Visualization Noise Analysis We compared the operating noise of new and aged wiper system for the preferred and non - preferred vehicles. The aged wiper system was used for comparative evaluation after confirming satisfaction of blade pressure, attack angle, overrun specification after 300,000 cycles of continuous oper-ation according to the durability evaluation specification without replacing the wiper blade. Visualization noise measurements were performed in indoor and outdoor of the car under the engine off and wet windshield condition in the anechoic room for the preferred and non - preferred group vehicles.
TABLE 1. Sensibility Quality Evaluation Table
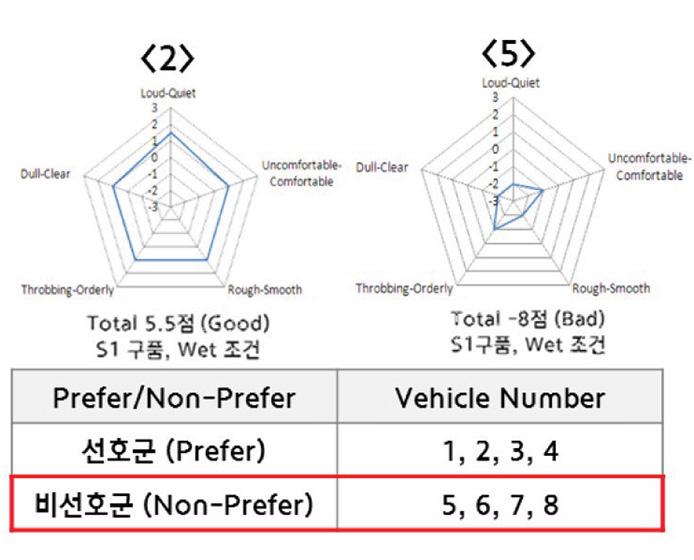
TABLE 2. Classification result FIGURE 3. Spectrum and visualization noise analysis
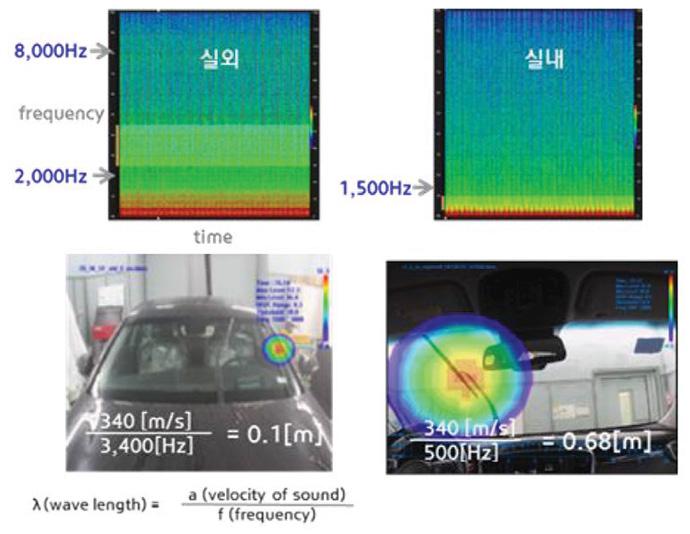
Figure. 2 shows the results of noise visualization analysis for the preferred and non-preferred vehicles. The vehicle of preference group has no change of noise position between new and aged at outdoor measurement and low frequency inversion noise increases at indoor measurement. In the non-preferred group, noise position of aged wiper is changed compare with new at outdoor measurement, low frequency inversion noise increases at indoor measurement. The frequency of the highest noise of the wiper occurs mainly at 1.5 ~ 3Khz outside and at 1KHz or less inside, regardless of the division between vehicles and the durability of the wiper system. In addition, the wiper noise is larger at the upper and lower reversal positions than the moving range, and is larger at the upper reversal than the lower reversal. As the wiper system ages, the magnitude of the transmitted noise is signifi-cantly affected at frequencies below 500 Hz. Considering the influence factors of various noise, it is not possible to know the noise position and the cause of the noise change only by the above result. Therefore, it is necessary to analyze the char-acteristics of wiper noise by analyzing wiper transmission noise and wiping operation. Noise Characteristics Analysis The characteristics of outdoor noise and indoor noise during wiper operation were analyzed. Figure. 3 shows the outdoor and indoor wiper noise spectra when the wiper speed is low in the glass wet state when the engine is off. The outdoor noise has a spectrum ranging from 2,000 to 8,000 Hz, but the noise heard mainly in the room is mainly in the band below 1,500Hz. As a result of the visualization analysis of the noise characteristics, the wiping noise is distributed outdoors in the band of more than 3000Hz. On the other hand, wiping noise transmitted through the interior of the vehicle is mainly present at less than 500 Hz. As shown in Figure. 4, wiper scrubbing noise when passing through the room from outside shows the attenuation of the high frequency band and the increase characteristic of the low frequency band as a whole. It can be seen that the windshield glass acoustic PVB film which blocks the wind noise in the high frequency range applied to the luxury car cannot have a great effect on the wiping noise. When the wiper noise is transmitted to the room and transmitted to the low frequency noise, the noise can be largely divided into two. The first is the friction noise of the wiper blade and glass, and the second is the transmitted noise due to the operation of the motor & linkage. Table 3 shows the results of analysis of the transmission noise of the motor and linkage in the off-state of the wiper blade when the engine is off. As a result, the transmission noise of the wiper motor and the linkage can be divided into two types. It can be divided into a low frequency structure noise of less than 300Hz, and around 500Hz band, which corresponds to noise generated by the motor. Especially, #8 and #2 are similar design to each other. However, #8 is well transmitted with motor operation noise, whereas #2 is characterized by transmission of struc-tural sound. #2 is a vehicle belonging to the group of preference result of customer’s emotional evaluation, and #8 is a vehicle belonging

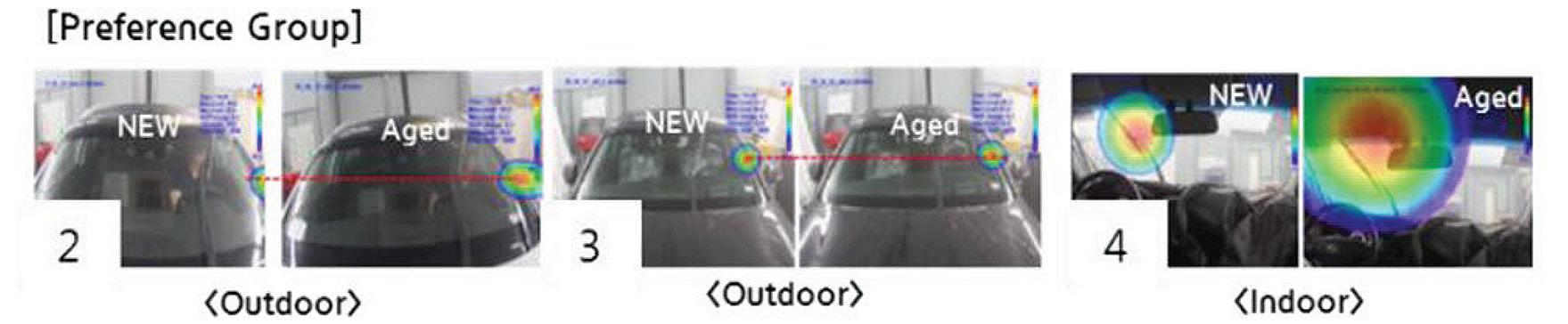
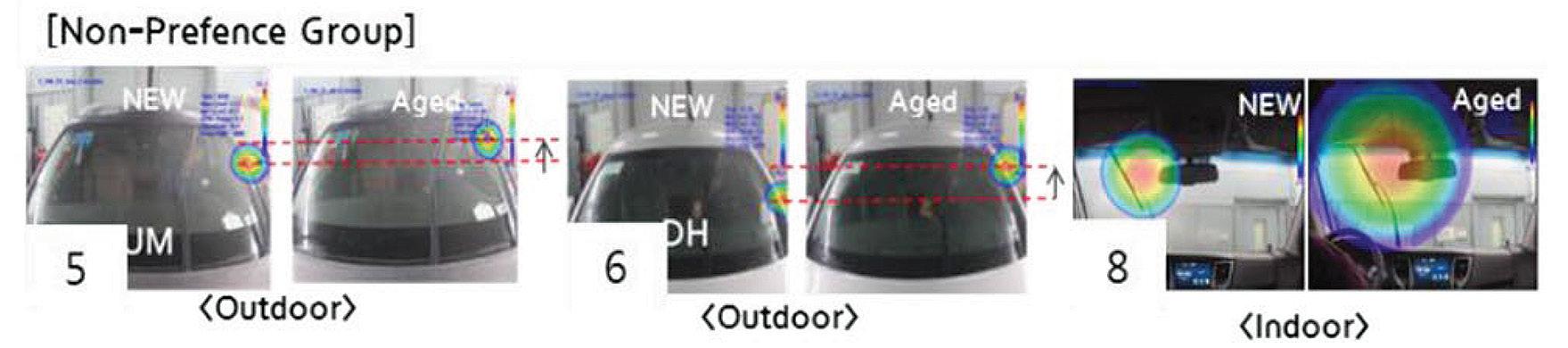
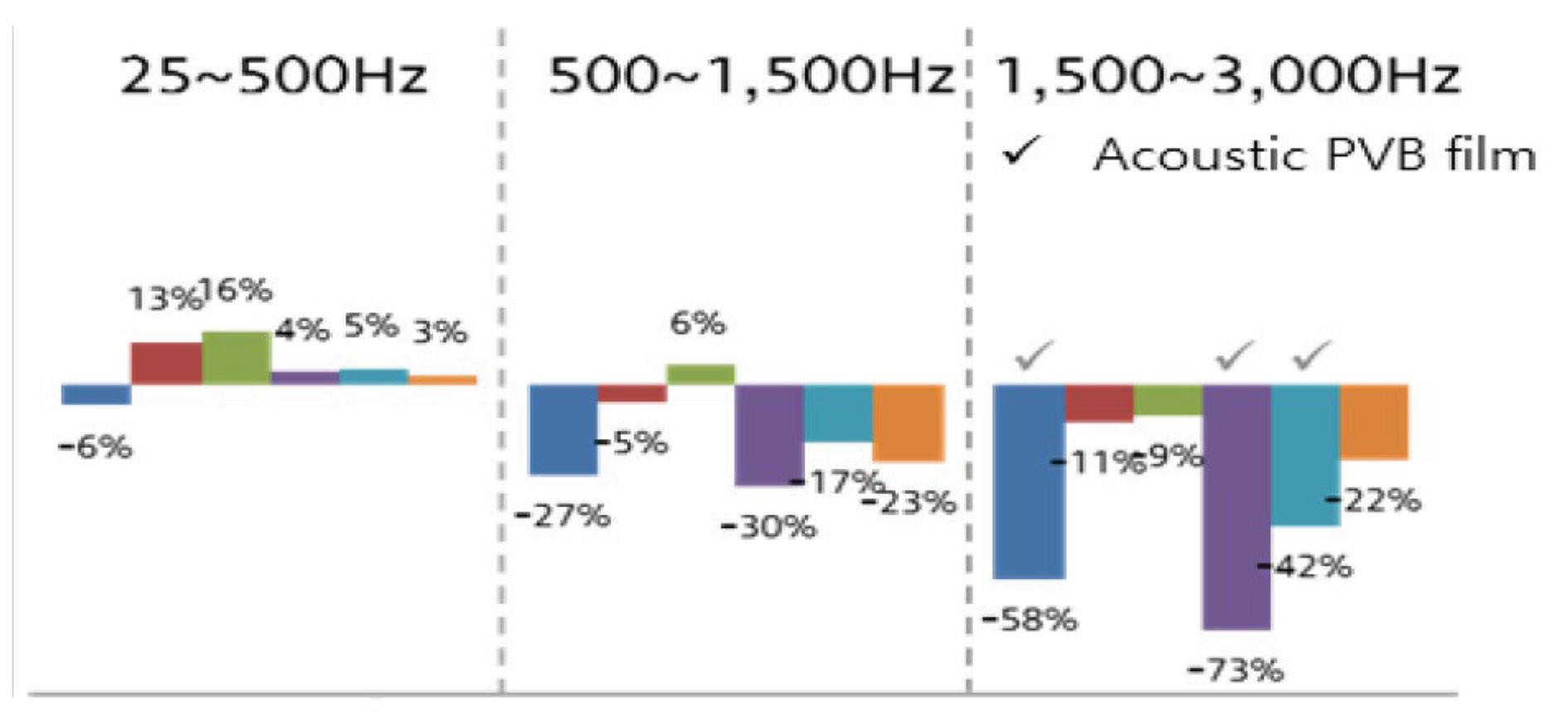
FIGURE 4. Noise transmittance

TABLE 3. Motor & Linkage Transmission Noise
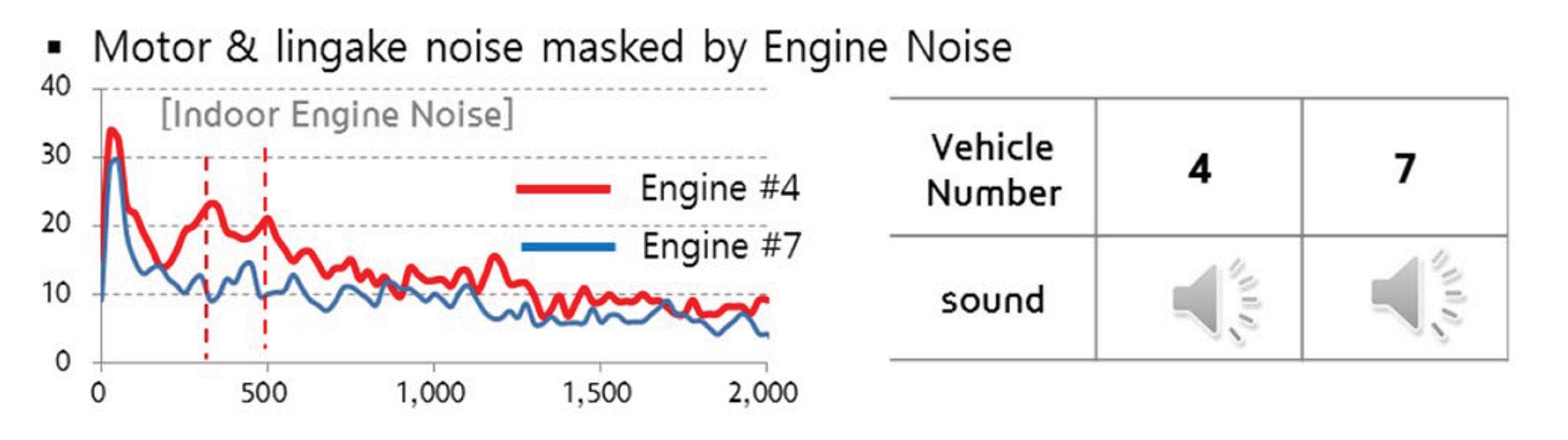
TABLE 4. Masking Effect of Motor & Linkage Noise
TABLE 5. Noise Difference (New/Aged Blade)
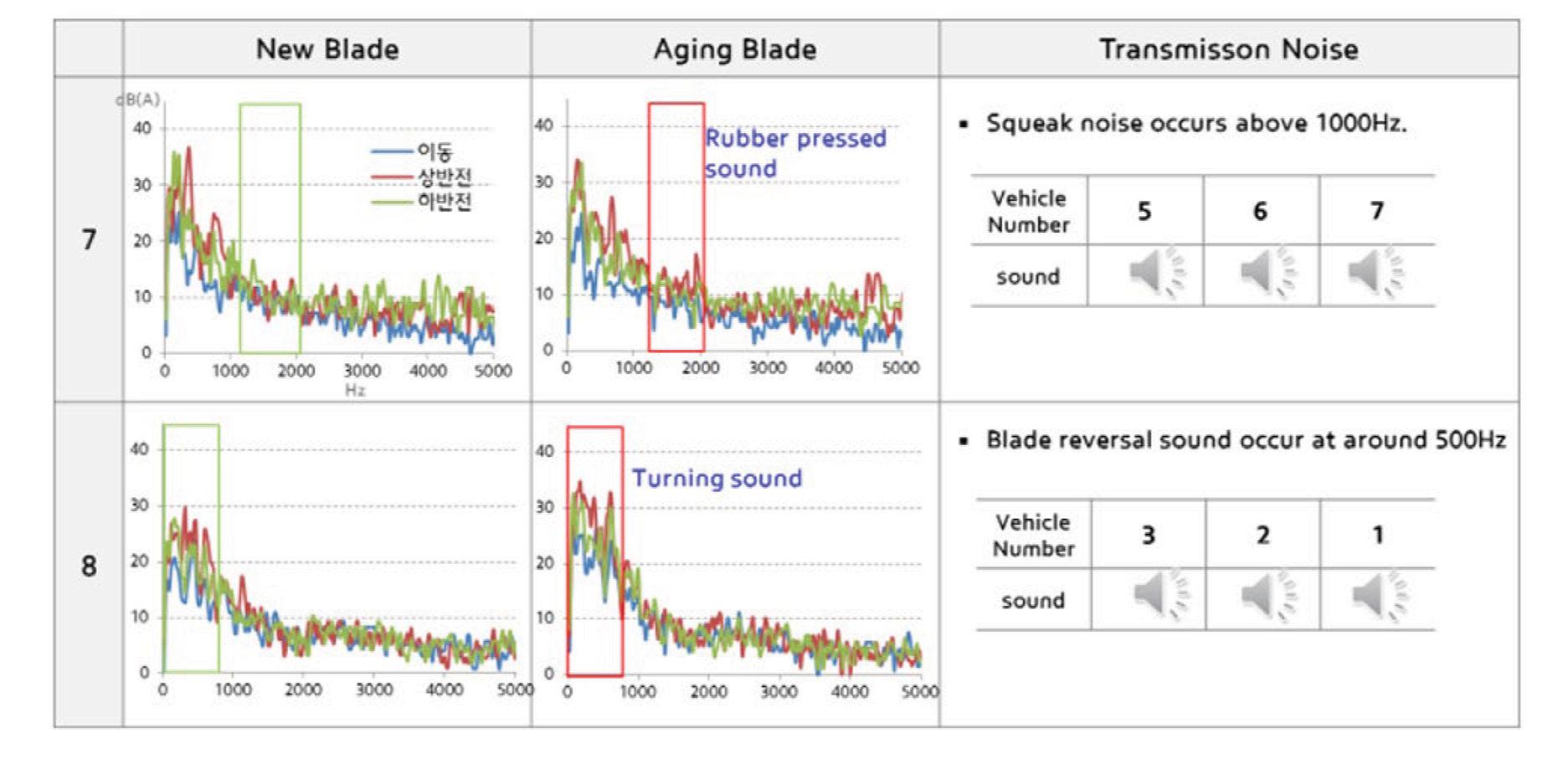
to the non-preferred group as a result of the noise evaluation of the customers. This allows us to deduce what kinds of noise are sensitive and uncomfortable with customer. Wiper motor & link operation noise of # 4 of the preferred group shows a peak at about 300 and 500 Hz in the room, which shows the same peak as engine #4 noise of Table 4. It can be seen that this noise masking effect actually causes the wiper motor & link noise to be smaller than the other vehicle noise. In other words, it was confirmed that the transmission characteristics of the wiper motor & linkage noise are affected by the characteristics of the engine noise, the body structure, and the sound insulation performance.
Wiper Noise Classification
The effect of deterioration of the wiper blade affects the blade, glass friction coefficient and frictional force, and causes direct transmission noise. This analysis analyzed the noise of new blades and internal parts under the condition of wiper low and glass wet condition with the engine turned off. As shown in Table 5, the aging blade noise is larger than that of the new blade. However, the frequency range in which the noise of the vehicle is increased is different. The customer’s preferred wiper noise is in the frequency range of 20 ~ 500Hz in the wiper reverse section and the low-frequency sound tends to increase. However, wiper noise, which is not preferred by customers, shows a tendency to increase squeak noise in the high frequency band of 1,500 to 2,500 Hz. Although the size of the sound is not large, it can be confirmed that the squeak noise in the high frequency band causes dissatisfaction with the sense of listening to the customers. As a result of analyzing the wiper noise characteristics of the preferred group and the non-preferred group based on the result of the auditory evaluation of the customer, the charac-teristics of the noise can be analyzed by frequency as shown in Figure 5. In addition, we were able to distinguish the noise-sensitive customers of each frequency band. Customers responded sensitively to high-frequency rubber squeaks and motor transmission noise. Wiper Noise Simulation Theoretically, the factors affecting the wiper noise are rubber section and physical prop-erties, change of friction coefficient, pressing pressure, and contact angle as shown in Figure 6. In order to determine the influence of these theoretical parameters, the fundamental duration factors affecting the wiper noise were identified and classified as shown in Table 6. Typical durability factors that can cause noise are push pressure change, operating speed change, rubber property change, friction coefficient change, blade wear, glass contamination, low temperature / high temperature environment change. Figures a, b, and c in Table 6 represent cross sections of the blades used in our company. a, b, and c have different shapes,
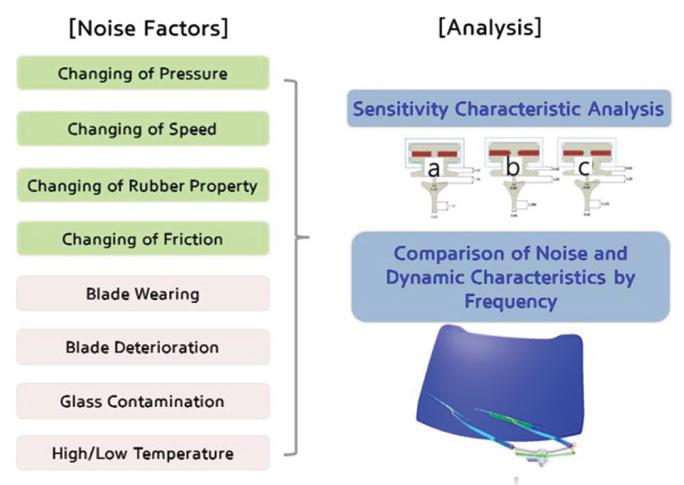
TABLE 6. Wiper Noise Factor
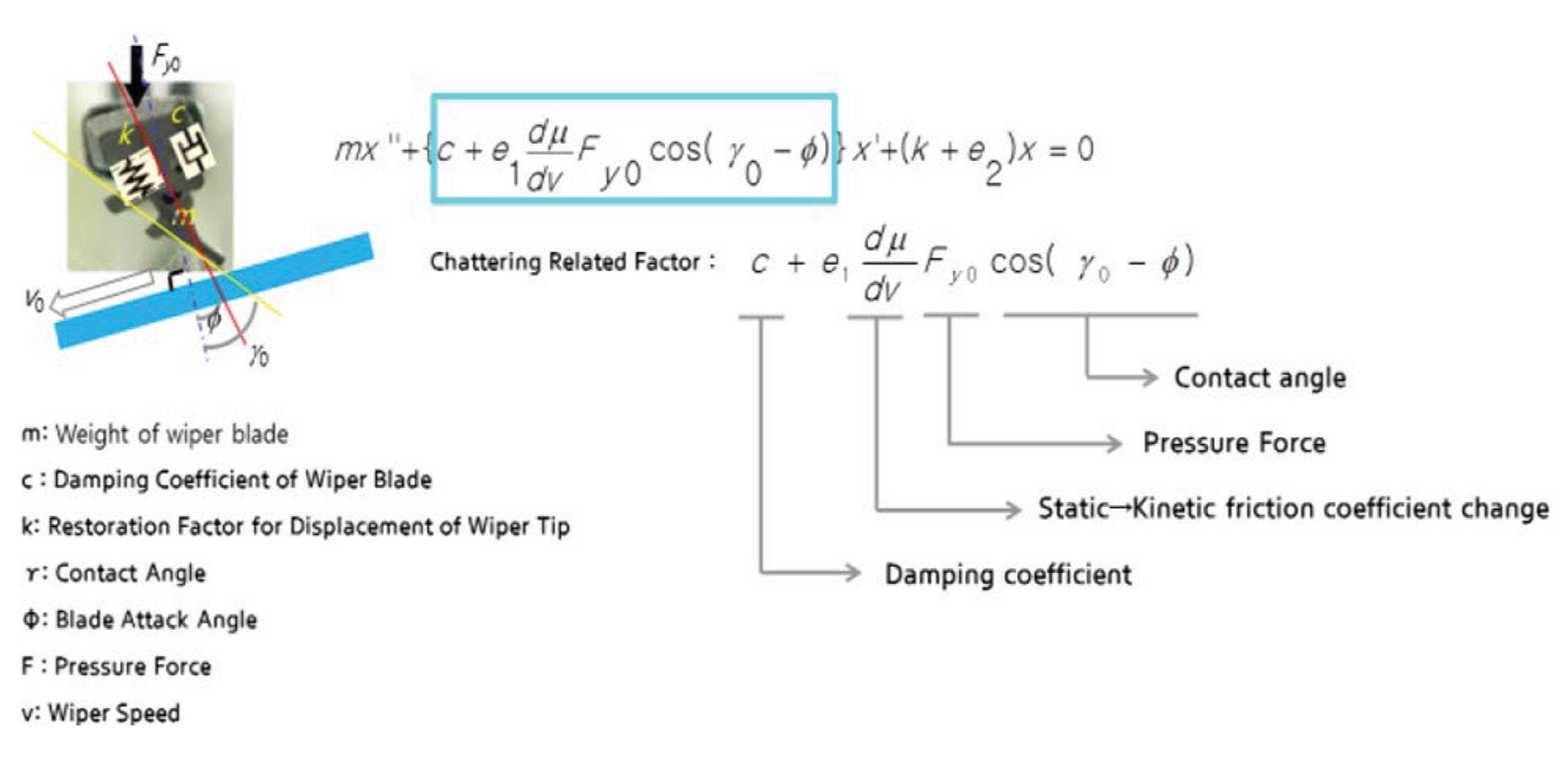
friction coefficient, and rubber properties. Therefore, in this paper, the Mooney-Rivlin parameters were obtained through rubber hardness evaluation, tensile test, and shear test of each of a, b, and c, and noise analyzes were conducted for a, b, and c. A sound field analysis technique is applied to implement the classified noise factors. The sound field analysis method is a method of converting the surface speed of the wiper on the glass measured by the structural analysis of the wiper system into the sound pressure using Ohm’s acoustic law. This makes it possible to construct wiper environment conditions with various conditions and to predict the noise of the wiper through actual sound field analysis. The sound field model was constructed using the surface velocity obtained from the durability analysis and the noise analysis according to the durability change was performed. The results of this analysis were compared and analyzed for frequency - specific noise through analysis of durability and dynamic characteristics of wiper blade. As a result of comparison of sound pressure (SPL) value, loudness, sharpness, roughness, and fluctuation intensity of the wiper blades using the sound quality analysis parameter of Zwicker, Figure. 7 shows the sensitivity analysis results. The horizontal axis of the graph represents defects of the blades that can occur according to changes in the environmental conditions. The sound field analysis was performed to deter-mine how the sound pressure (SPL) value, loudness, sharpness, roughness, and fluctuation intensity change when blade defects occur. The higher the slope on the graph, the greater the noise variation between the new and aging blades. The analysis shows that the ‘a’ and ‘c’ blades show a large slope of the graph under both deteriorating and cold-deforming conditions, which may indicate that noise is poor for degrada-tion and low-temperature deformation conditions. The ‘b’ blade also exhibits high noise fluctuations in glass contamination and low temperature conditions. In addition, as shown in Figure. 8, As a result of analyzing the sound field, it was confirmed that the ‘a’ blade generates chatter and squeak noise at the deteriorated and low temper-ature condition, and the ‘b’ blade shows that the reversible noise is increased in the glass contamination condition where the glass friction coefficient is not constant there was. In addition, the ‘c’ blade was found to have large reversal noise and chattering noise under deteriorated and low temperature conditions. Figure 8 shows the noise levels for the five environmental conditions of ‘a’, ‘b’, and ‘c’ blades. In the chattering, inversion, and squeak noise frequency regions, noise magnitudes of blades were analyzed by environmental conditions. As a result, ‘a’ and ‘c’ blades exhibited higher noise levels under blade deformation and cold conditions. However, the ‘a’ blade showed a high squeaky noise while the ‘c’ blade showed a tendency to show a large reversal noise. The ‘b’ blade had a large
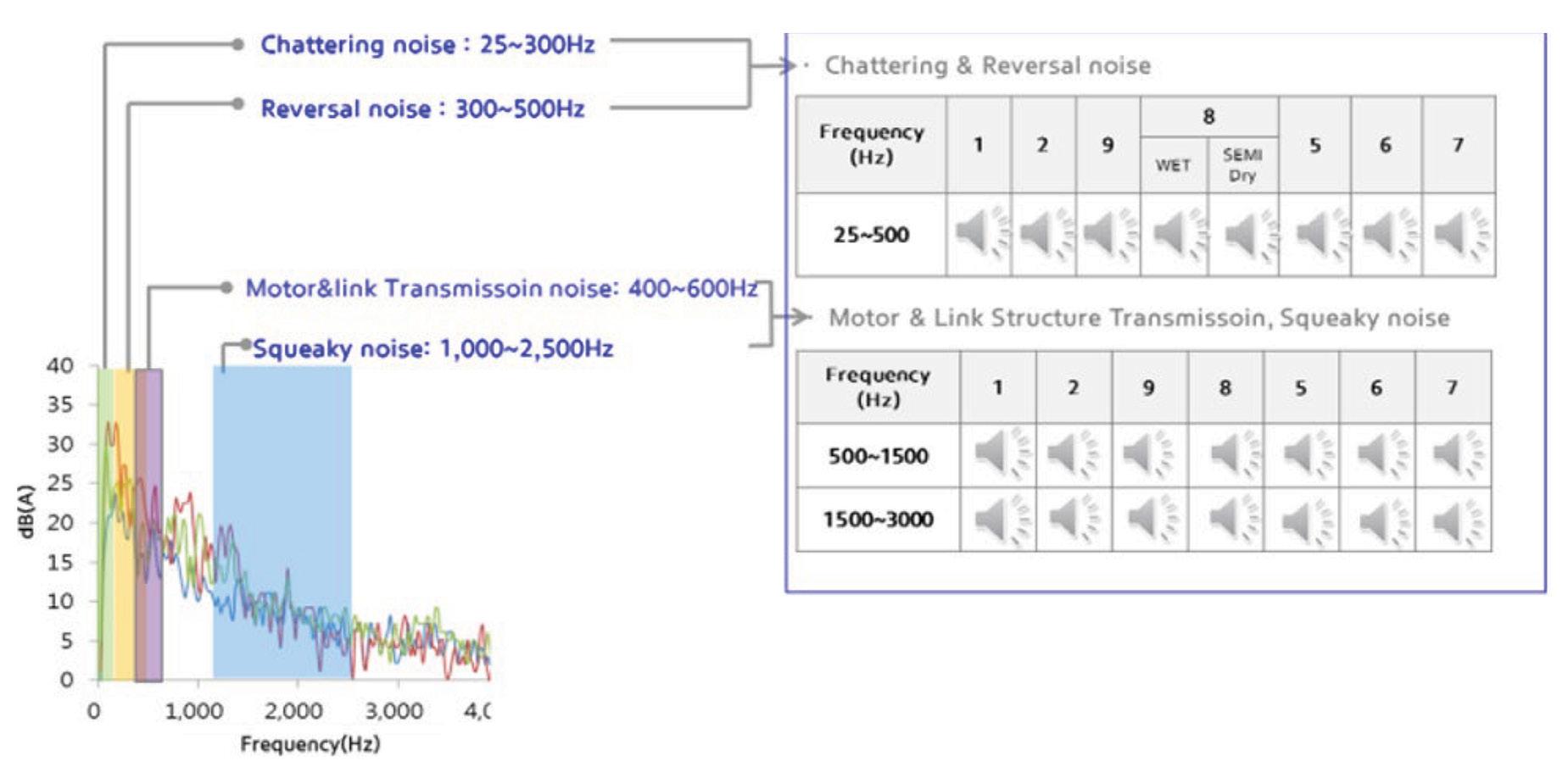
FIGURE 5. Noise Difference (New/Aged Blade)
FIGURE 6. Theoretical background of wiper chattering
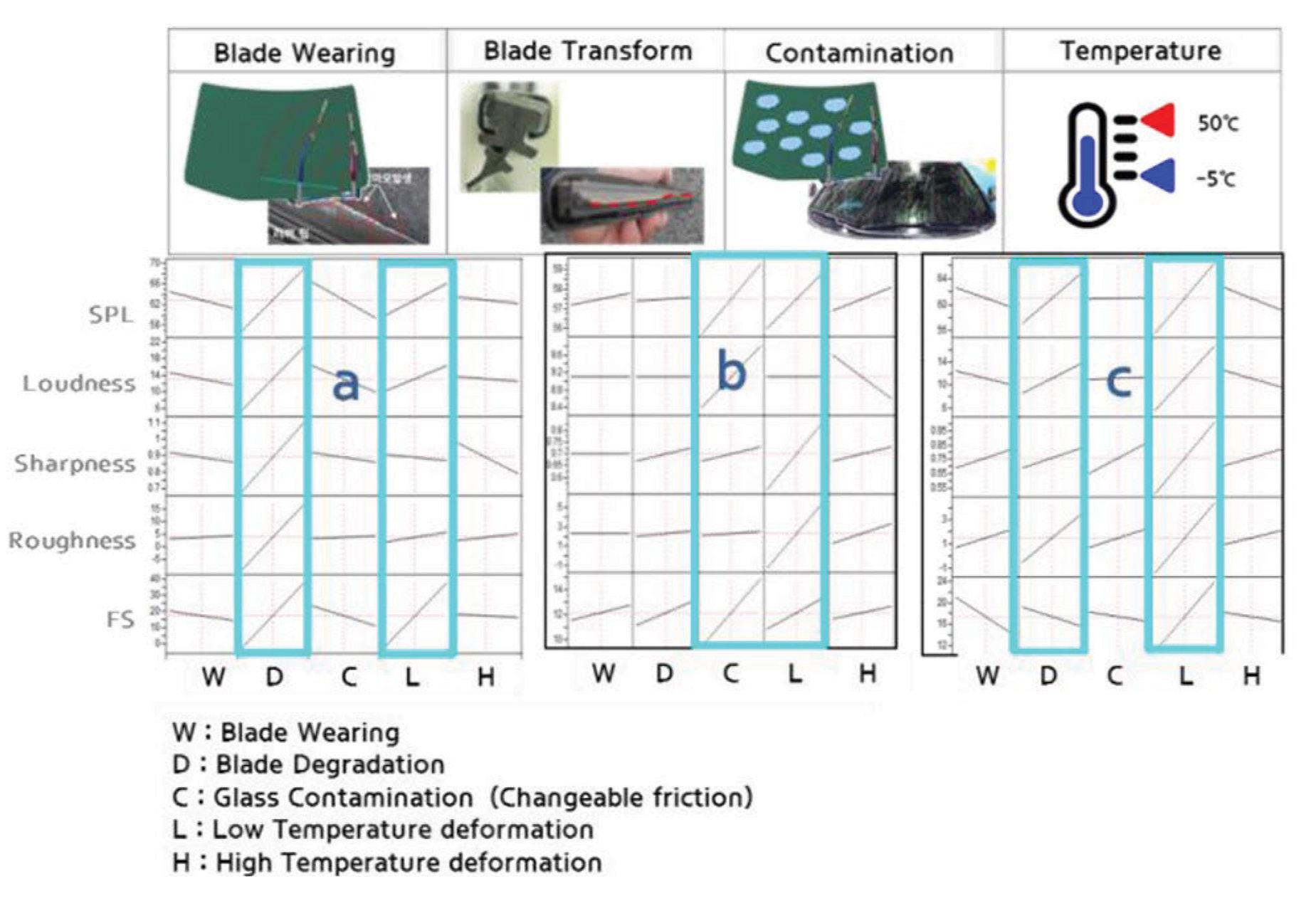
FIGURE 7. Wiper Blade Sensitivity Analysis
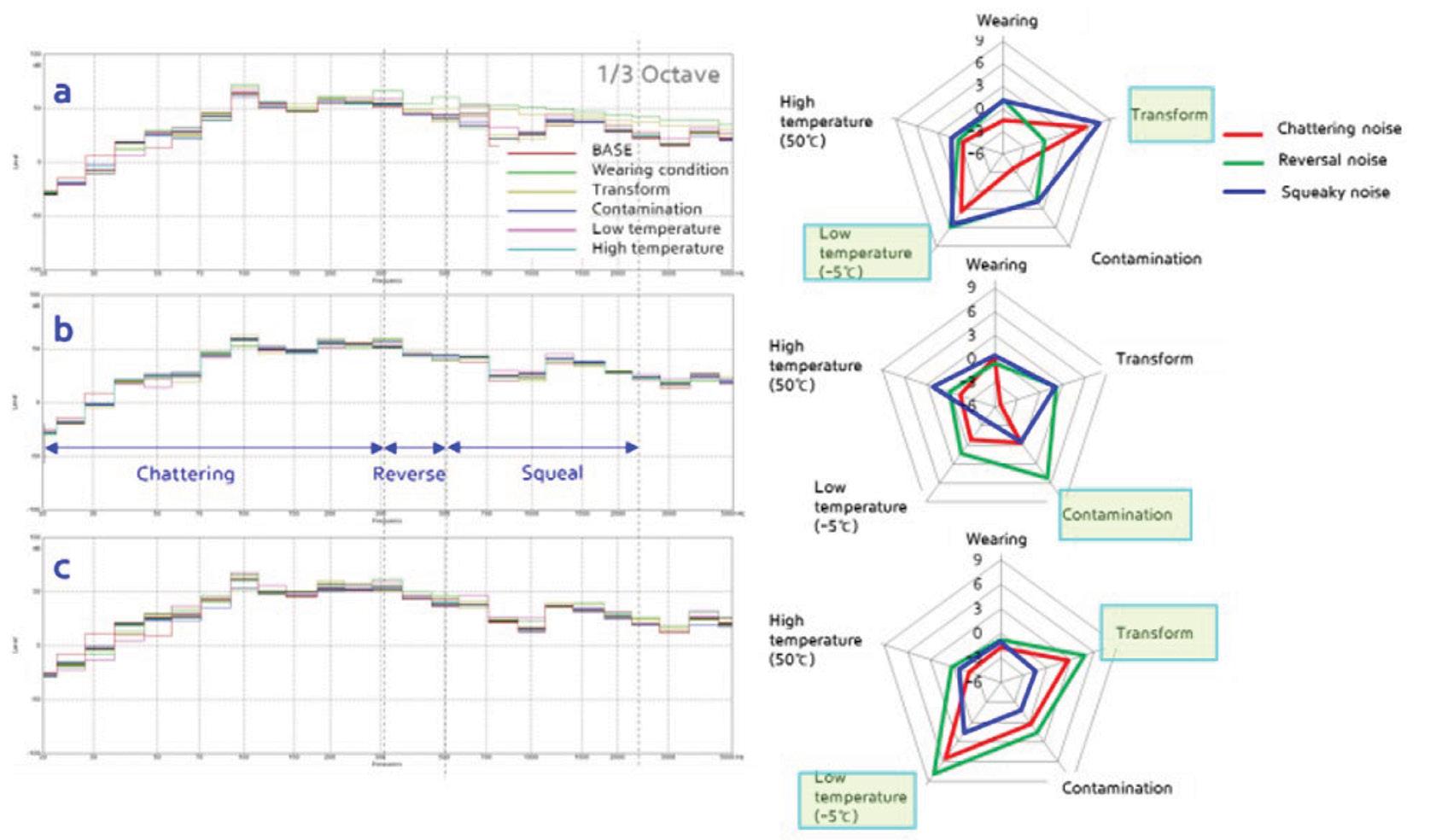
FIGURE 8. Wiper Noise by frequency
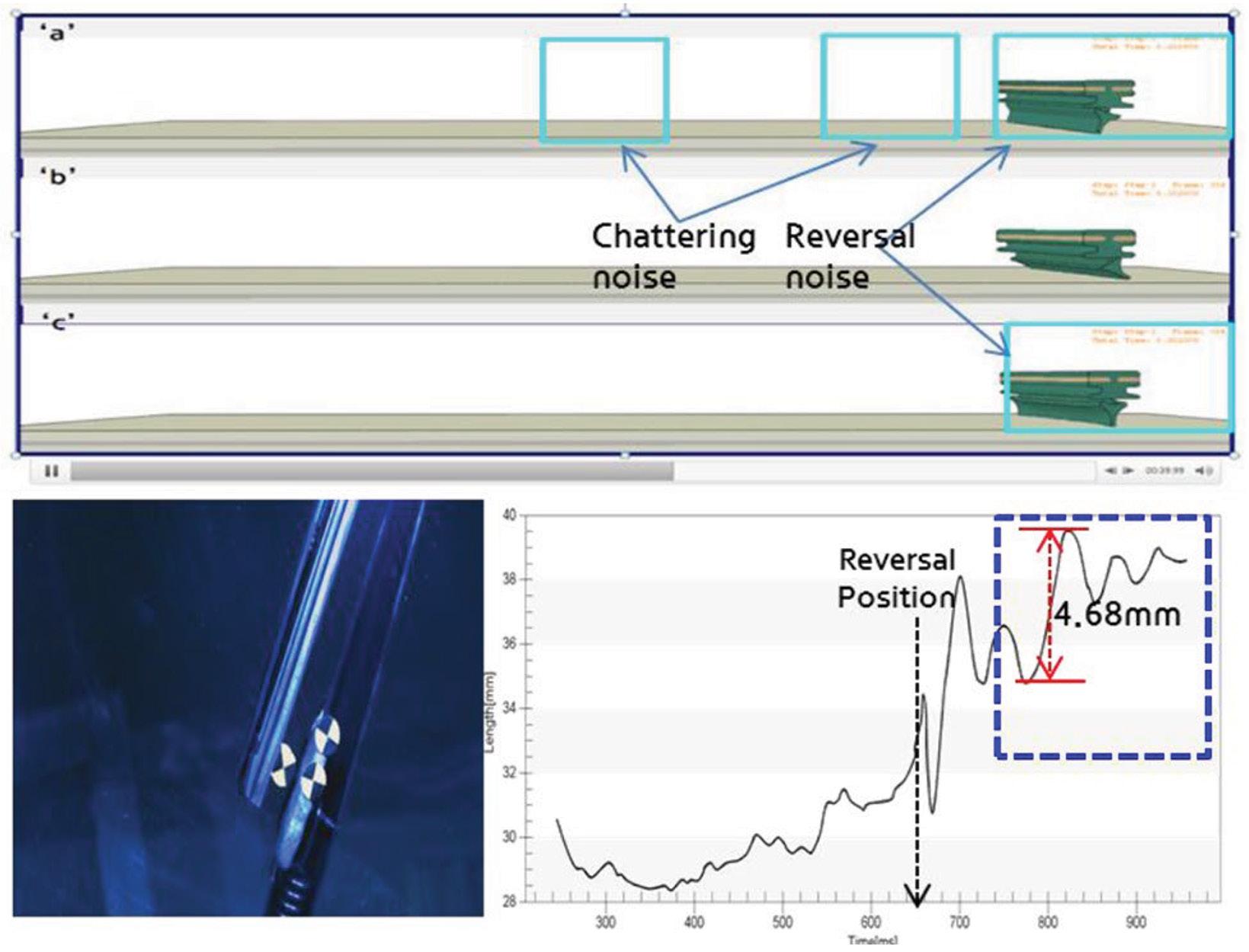
FIGURE 9. Dynamic Analysis and high-speed camera simulation Summary/Conclusions
This paper is to investigate the weakness of our wiper noise criterion through basic research on wiper noise and to study its improvement direction. The following conclusions were obtained through this study. 1. Qualitative criteria for wiper penetration noise were established in accordance with customer standards. Frequency range and noise characteristics for chatter, reversal, and sweep noise of wiper are presented. 2. We analyzed the influence factors of the wiper noise and analyzed the frequency - specific noise of the wiper system through sound field analysis technique and Zwicker noise sensitivity evaluation. 3. We propose to introduce the sound field analysis technique that reflects deterioration of wiper, wear condition, high temperature / low temperature condition, and glass pollution condition as our preliminary problem prevention technique. 4. In addition, we introduced a method to build a quality control process for the wiper noise problem by introducing our reliability evaluation standard considering the same blade deterioration condition as the above analysis considerations.
reversal noise in the glass contamination condition. In other words, it was confirmed that the type of noise can be changed according to blade characteristics even under the same environmental conditions. In order to verify the above results, dynamic character-istics analysis and behavior of the actual vehicle wiper blade were compared and analyzed. The aged blade was attached to the glass of the actual vehicle and the glass was contaminated to change the coeffi-cient of friction. The analysis conditions were simulated similar to the actual conditions by varying the coefficient of friction of the glass and distributing the blade pressing pressure unevenly. As a result, ‘a’ and ‘c’ blades exhibited SLIPSTICK and chattering phenomenon after reversing. Figure 9 shows the results of real vehicle evaluation and the results of highspeed camera imaging and measurement of blade vertical vibration. As a result of the analysis, the vibration position and vibration phenomenon of the blade on the glass were confirmed as the same as the analysis result. This can be prevented by pre-simulating noise problems that can occur in the wiper, using sound field analysis that reflects the physical properties and environmental conditions of the wiper system.
References
1. Lee., S.-B., “A Study on Finite Element Analysts and Aging Test for Automotive Grommet,”
Elastomers and Composites 47(3):201-209, 2012. 2. Kuk, J.-H. and Yun, J.-H., “Sound Quality of Water Turbing Generator Noise using Zwicker
Parameter,” Won-Guang University, 2012. 3. Wileman, J., Choudhury, M., and Green, I., “Computation of Member Stiffness of Bolted
Connections,” Transactions of ASME 113:432-437, Dec 1991. 4. Kang, H.-S., “Study Concerning Preference for Noise Quality of Automotive Horn for
Improvement of Perceived Quality and Improvement of New Noise Metric,” Inha
University, 2015. 5. Zolfagharian, A., Md Zain, M.Z., Abu Bakar, A.R., and Hussein, M., “Particle Swarm
Optimization Approach on Flexible Structure at Wiper Blade System”, World Academy of
Science, Engineering and Technology, 2011.
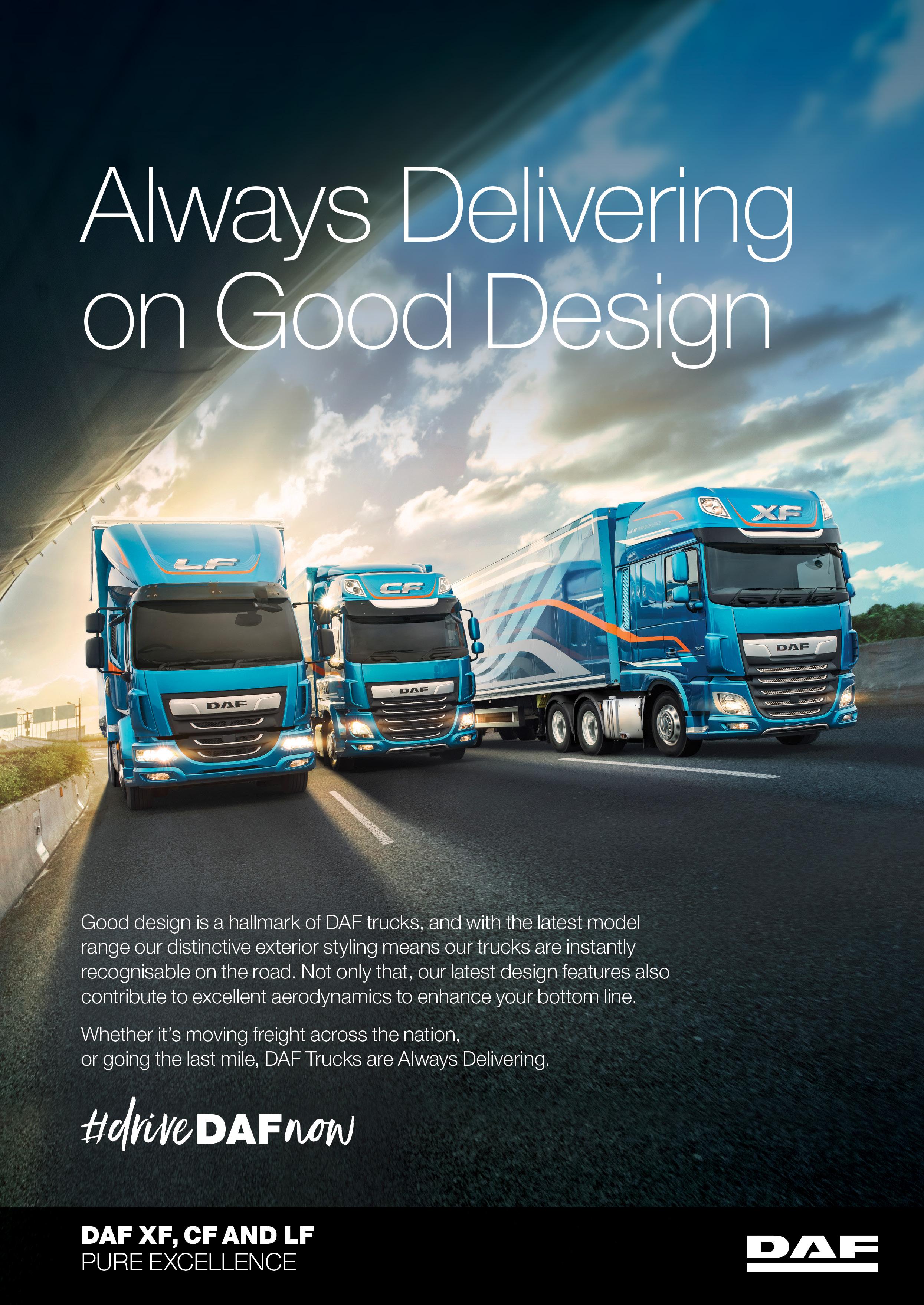
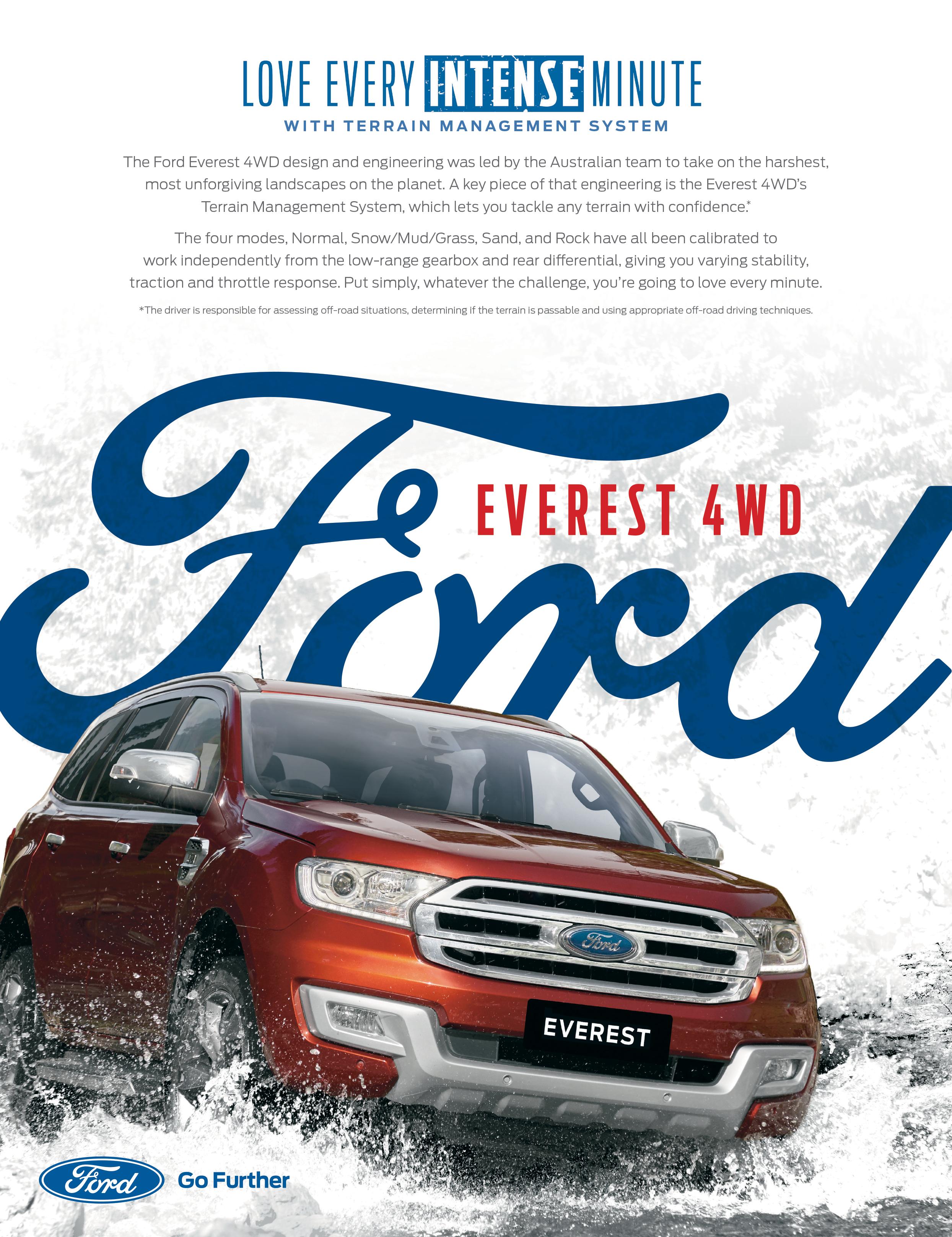