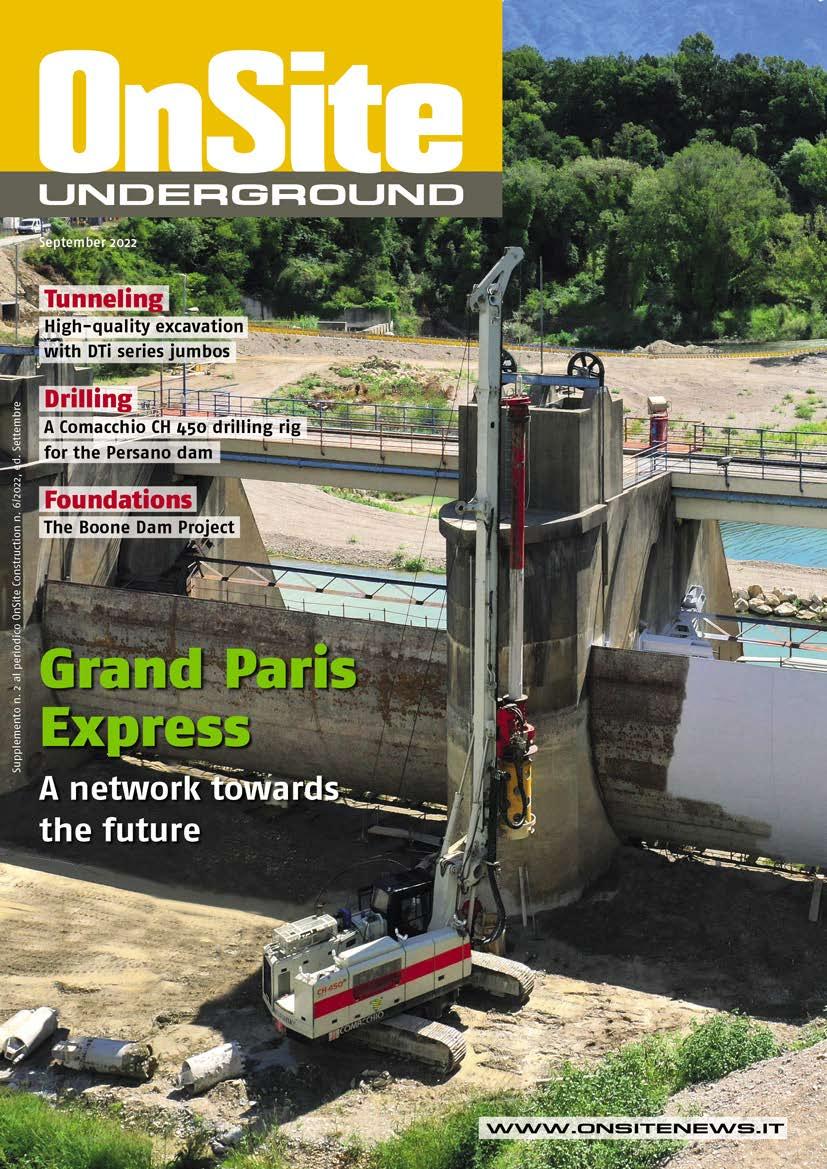
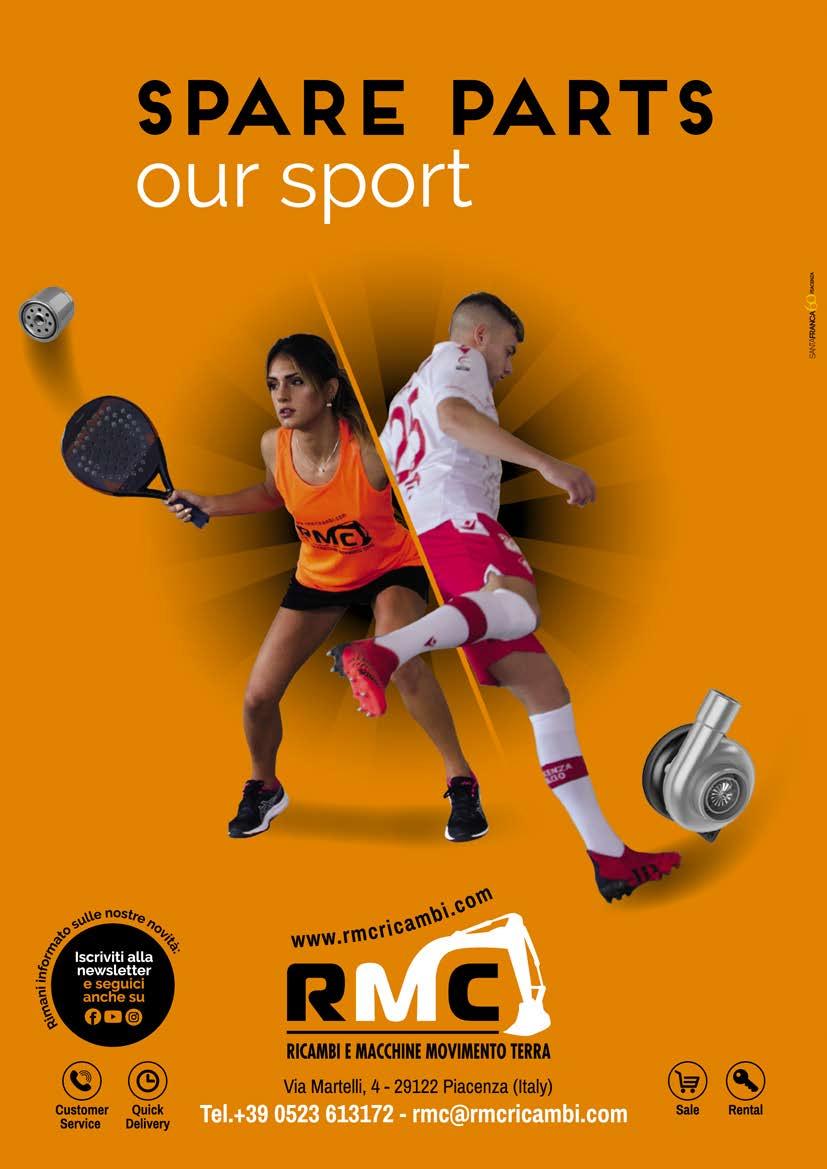
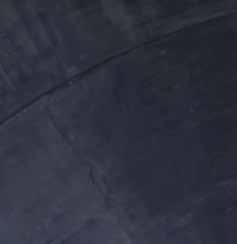


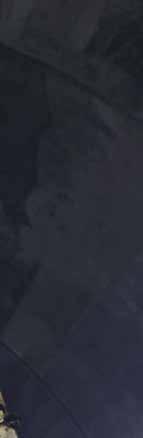
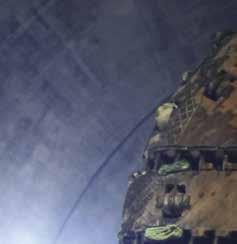
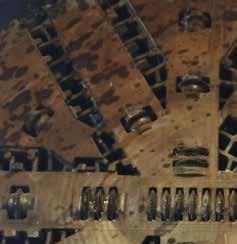
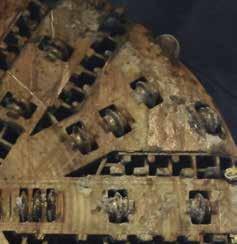
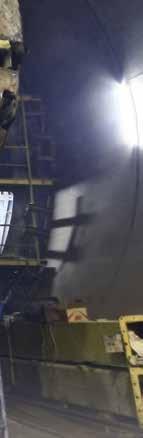
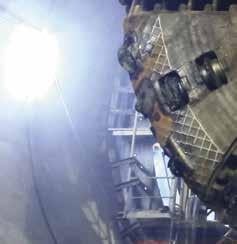
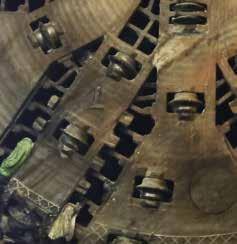
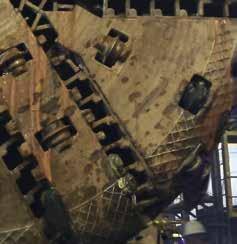
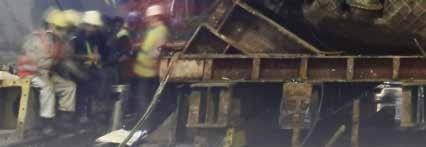
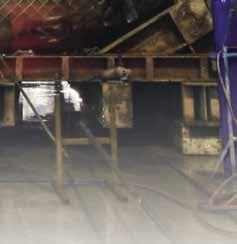

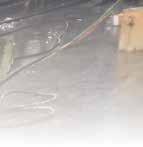
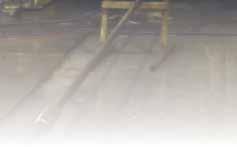
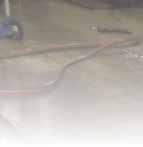





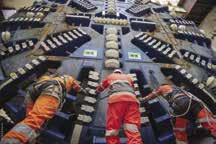
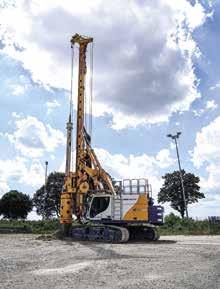
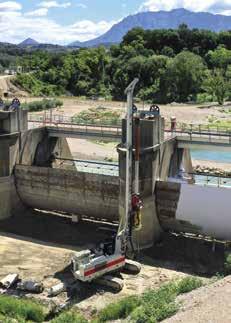
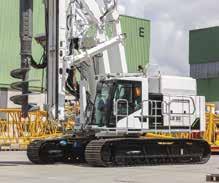
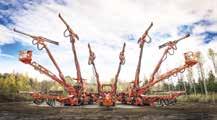
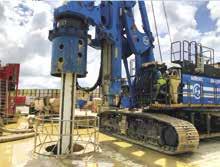
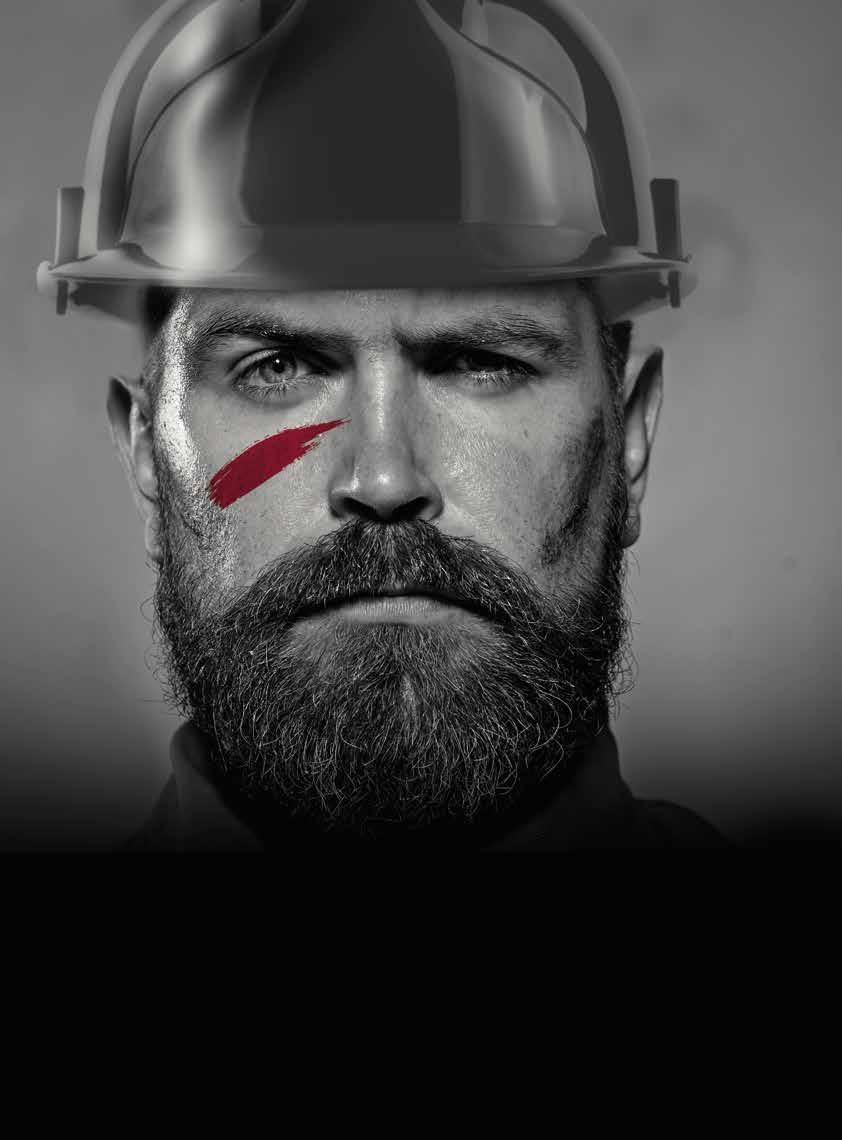
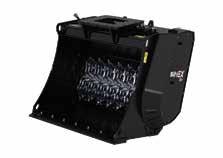

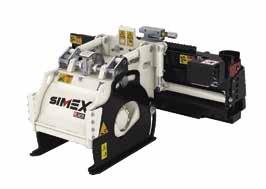

On July 25, 2022, a crowd gathered as a large Robbins Main Beam TBM, dubbed ‘Big Tex’, broke through in Dallas, Texas, USA. The machine and its continuous conveyor system, for the Mill Creek Drainage Relief Tunnel, successfully bored 8 km (5 mi) in chalk and shale at up to 498 m (1,634 ft) advance in one month. “I think when you step back and look at what was accomplished by this team as whole…the overall length and size of this tunnel, the TBM conversion, the everyday grind to keep moving forward…it truly is something to be proud of, professionally and personally. No single individual
could reach this milestone. It took a great team of skilled individuals. I am fortunate to be a part of it,” said Nick Jencopale, Sr. Project Manager for contractor JV Southland/Mole. Good advance rates were not the only cause for celebration: the unique project required a planned in-tunnel diameter change of the TBM from its original 11.6 m (38 ft) to a more compact 9.9 m (32.5 ft). The firstof-its-kind conversion process was undertaken 2.8 km (1.7 mi) into the bore and was not done inside a shaft or pre-excavated portal. “ The TBM conversion was a unique challenge that we were excited about, and
ultimately provided a more efficient method for the desired product compared to the alternative options. Hopefully the successful conversion proved that this option can be considered for future tunnel projects,” said Jencopale.
While there were many detailed steps to the conversion process, precision design of the machine was a key aspect. “We started with a smaller machine, then we made a kit or second skin that was slightly larger. And then when the time came, we just took that skin off. It was essentially that simple,” said Evan Brinkerhoff, Robbins Field Service Manager. The conversion took about four months and was completed in April 2021.
“ The Robbins Main Beam TBM (‘Big Tex’) performed consistently throughout the duration of the tunnel excavation. There were very minor issues and little overall downtime as a result of theTBM itself,” said Jencopale. Due to the relatively favorable ground conditions in much of the tunnel, including low rock strength and low abrasivity, only eight disc cutters were changed during the length of tunnel bored at the larger diameter. At the time of diameter change the full dress of cutters was changed, and since that change only 14 cutters have needed replacing. Crews did encounter some fault zones, and installed rock bolts and wire mesh in the tunnel crown as needed. With the TBM-driven portion of the tunnel now complete, work can commence to remove the machine from the tunnel and install a final lining. The tunnel is a designated critical infrastructure project for the City of Dallas, providing 100-year flood protection for areas of East Dallas that have experienced severe flooding in the past. Construction work is expected to be complete in late 2024/ early 2025.
technologies, dewatering and groundwater, energy transition, the sustainable exploitation of sources and geoengineering, new materials for transporting fluids, digitization of processes and machinery for the construction of new infrastructures linked to utilities with particular reference to the water crisis are the themes that will underpin the exhibition part of Geofluid 2023. New construction vehicles, equipment and technologies already available for the construction industry have always been the added value of the event, which boasts the certified status of “international
Piacenza Expo launches the promotional campaign for the next edition of Geofluid, scheduled from 13 to 16 September 2023 at the Piacenza exhibition centre, boosted by the push for environmental, energy and infrastructure works generated by new investments. The important international trade fair for the drilling & foundations sector finds new incentives from the precise moment in history related to the recovery. In the European Union’s 2021-2027 budget, a large part of the European Regional Development Fund’s (ERDF) resources, amounting to billions of euros, will be channelled into renewable energies, decarbonisation and energy efficiency.
The NRDP funds are structured in line with the European Green Deal. The planned interventions are aimed at investment and research programmes for renewable energy sources, initiatives to combat hydrogeological instability, efficient water use, and the improvement of inland water quality. The Plan devotes considerable resources to land safety, understood as the mitigation of hydrogeological risks (with prevention and restoration
measures), the elimination of water and soil pollution, and the availability of water resources such as primary infrastructure and purification. The theme of water and new energies is the dominant feature of the next Geofluid. It remains quite clear that the decisive impulse will come from EU funds to ensure construction sites on both large-scale works and punctual interventions, and to make a greater impact on the issues of environmental protection, hydrogeological instability and alternative sources.
Geothermal energy, underground construction sites 4.0, new trenchless
exhibition”. The 2021 edition was a success with the specialized public coming from over 50 foreign countries. The survey conducted by Piacenza Expo on 1000 trade visitors showed that 96.5% found Geofluid fulfilling and useful for their profession. 59% visited Geofluid to find out about equipment, technologies and services useful for planned works while the motivation for visiting that prompted 26% of the operators interviewed was to make a decision on new purchases in machinery and plants. The rate of topicality and proximity to the market was confirmed by 30% of new visitors. Geofluid 2023 aims to reconfirm the numbers of the last edition with 280 direct exhibitors and ten thousand professional visitors for an edition that will involve, thanks to the favourable season, the entire territory in order to offer a complete and unforgettable exhibition experience.
Wimmer has been a supplier in tunnel construction for 30 years. Above all, the quick-change systems A-Lock, as well as the attachments from the tunneling bucket to milling cutters and drilling rigs, are in demand products for tunnel excavators from 14 to 60 tons. Above all, the Tunnel A-Lock is now standard when it comes to excavator equipment in tunnel construction.
The quick coupler not only impresses with its robustness, but above all it is safe to use. Recently, this has also been confirmed by a type examination certificate from SUVA (Swiss accident insurance).
The type examination of the wellknown and extremely precise Swiss
testing institute was successfully issued in June 2021. The Wimmer A-Lock system is the only quick coupler system in Europe to date with the
required two-handed operation of the quick coupler (press the button and operate the hydraulics) is another guarantee for a secure locking of the quick coupler.
coveted inspection sticker. With the Wimmer A-Lock, security is guaranteed by integrated sensor technology and an acoustic and optical signal. The
“ A manufacturer who only meets minimum requirements is not going far enough ”, says Andreas Wimmer, Managing Director of Wimmer Hartstahl from Austria. “ As important players in the construction industry we proactively think ahead and like to set the bar higher. Requirements in tunnel construction are very high. The forces that act on the quick coupler during propulsion are enormous. Wimmer only delivers top quality and has done so for many years”.
The partnership between Doosan and Geax, a company based in Montefano (MC) and an international industry lead er in the design and construction of drilling and boring machines, is now well established. Geax was founded in 2006 on the initiative of Eng. Adriano Pesaresi, who, after gaining 20 years of experience as a designer in the indus try, wanted to create a new business project with the aim of producing inno vative, compact and very high perfor mance drilling machines, thanks to the fact that they are mounted on excava tors. In 2019, the difficulty of sourcing from regular suppliers prompted Geax to look for a new partner who would be able to support the company globally. Geax’s choice fell on Doosan to sup ply excavators from 6 to 24 tons (DX63, DX140, DX180, DX210 and DX225), in the three Tier III, Stage IV Epa and Stage V engines, so they can be marketed in the Italian, American and Asian mar kets. The excavators are supplied by Doosan without the boom so that they can be converted by Geax into a drill ing machine for foundation piles up to 30 meters̀ deep and up to 1.5 meters in diameter. The complex drilling setup, for the machines distributed world wide, is strictly made from scratch in Italy, at Geax’s Montefano facility. The machine is then completely re-certified and distributed by the Marche-based
company in its target market. Alessandro Baldazzi, Geax Sales Man ager, says, “We needed a supplier that was known worldwide, reliable, and had a service center on an internation al scale. We conducted a survey with our customers to identify the preferred brand, and Doosan turned out to be the best choice.”
The use of Doosan excavators as a base to the functions of drills has the advantage of being able to use engine, cab, tracks and hydraulics that guaran tee maximum reliability, robustness, high performance and ensure supe rior quality in ergonomics, comfort and quietness. In addition, Doosan is able to guarantee excellence and widespread service, thanks to its glob al distribution network that can inter
vene for any routine and extraordinary maintenance, repairs and warranty needs. These compact drilling rigs, in addition to the important advantage of being easily transported without spe cial permits, make it possible to work where classic drills and large-diameter pile machines fail, namely in confined spaces, on slopes, inside buildings or in the vicinity of power lines. These machines are especially successful in large cities such as Los Angeles, Sid ney or Seattle, where every inch has a significant cost, and it is particularly profitable to be able to perform con struction work in confined spaces, avoiding wasted time and resources due to oversized machines. Geax com pact drilling machine distribution mar kets are mainly Italy and the United
States, but demand is also growing in Australia, England, France, Germany, the Middle and Far East.
The first Doosan deliveries began in 2020, and in as early as 2021 the first machines were sold. To date, about 80 machines have been made of which more than 60 have been ordered and delivered worldwide.
Christian Randi, Doosan Infracore Af ter Market Manager for Southern Eu rope, as well as responsible for the de velopment of the partnership with Ge ax, says, “The Geax machines, based on Doosan, were presented to our dis tribution network, first of all as a great opportunity to develop more and more our presence on the international mar ket and to put our image side by side with that of another established com pany and world leader. In addition, this partnership represents an important opportunity to make our excellent ser vice network available worldwide. The prospect is to continue to be a relia ble partner for Geax, coming to supply
80 percent of the machines needed for their annual production, thanks also to the continuous support of our Service Manager, Antonino De Carlo, and one of our Korean engineers, who are fun damental in order to identify, the best configuration of the machines.”
Marco Buratti, Doosan Infracore Sales Director for Southwest Europe, adds, “The partnership with Geax responds
to the company’s strategic direction to strengthen our presence in socalled special applications, important market niches that help the process of continuous improvement of the relia bility and durability of our machines, also thanks to the continuous ex change of information and feedback with a qualified and market-appreci ated company like Geax.”
Leister Technologies Italia Srl Via T.A.Edison, 11 | 20054 Segrate (Mi) Tel.: 02-2137647 | info@leister.it
La saldatrice automatica TWINNY T è adatta per la saldatura di geomembrane spesse o sottili, come ad esempio PVC, TPO e PE in opere di ingegneria civile e sotterranea. La saldatrice di materiale termoplastico può essere inoltre utilizzata per l’impermeabilizzazione di laghetti artificiali e discariche.
Saremo CHRISTIAN RANDI DOOSAN INFRACORE AFTER MARKET MANAGER FOR SOUTHERN EUROPE MARCO BURATTI DOOSAN INFRACORE SALES DIRECTOR FOR SOUTHWEST EUROPEThe Grand Paris Express is the new metro that will connect the main places of life and activity in the suburbs without going through Paris. This project, which will contribute to the transformation of Île-de-France, will become a reality from 2024
by Gianni GennariToday, metros and RER form a star-shaped network of which Paris is the centre. The new great infrastructure project “Grand Paris Express” completes this system with the construction of four new metro lines around the capital (new lines 15, 16, 17 and 18), serving
the nearby and outer suburbs. Added to this is the extension of line 14 to the north, from Saint-Ouen-sur-Seine to Saint-Denis, and to the south, between Paris and Orly airport. This future transmission network will be gradually brought into service between 2024 and 2030. Its management is provided by the Société du Grand Paris.
Every day, between two and three mil lion passengers will travel on the entire Grand Paris Express. With 200 km of lines, i.e. as much as the current metro, and 68 stations, 80% of which are con necting trains, the Grand Paris Express will bring Ile-de-France residents clo ser to employment, education, health facilities and cultural venues and hob
bies. It will relieve certain public tran sport lines which, without it, would be saturated. For its travelers, the daily ti me savings will be substantial, someti mes exceeding more than 30 minutes on a trip.
The Grand Paris Express represents an investment of 36.1 billion euros (at 2012 economic conditions). The Société du
Grand Paris is financing the construc tion of the new metro through tax reve nue from the Ile-de-France region, bor rowing from public investors and fun draising on the financial markets as part of “green” labeled programs. It also be nefits from European subsidies. More than a transport network, the Grand Paris Express is a major project
for many reasons. First Social, because it will open up towns whose inhabitants are currently far from employment and trai ning opportunities. More than half of the stations will be located on the outskirts of urban policy priority districts. Then Urban: in fact its realization accompa nies and drives many development ope rations around stations, mixing housing, offices, shops, services, public spaces
and green spaces in the right propor tions. Also Environmental, because it represents a real alternative to the car on certain journeys. The new metro will help reduce traffic congestion and pol lution. Its arrival will also promote the emergence of facilities dedicated to envi ronmentally friendly mobility (walking, cycling). And last, Economic, since the number of jobs created with the com
With their unique architecture, the stations of the Grand Paris Express will become emblematic places of the cities served. Their design emphasizes passenger comfort and accessibility. Each of the Grand Paris Express stations will have an emerging building whose unique architecture will blend into its urban environment. All of them will
share a common ambition in terms of durability, comfort and eco-design: resistant floors, noble materials, natural light, optimization of volumes and materials, energy savings, etc. All of these approaches are defined in the architecture charter for Greater Paris stations, produced by Jacques Ferrier and Pauline Marchetti, and are implemented by some thirty architectural firms.
missioning of the Grand Paris Express is estimated at 115,000. The construction of the metro will also have an effect on the attractiveness of Île-de-France.
The idea of a ring road metro around Paris dates back to the early 1990s, but only within a broader urban planning law for the global metropolitan area. The law defines Greater Paris as “an urban, social and economic project of natio nal interest” which aims to promo te “sustainable, inclusive and job-crea ting economic development in the capi tal region” (Art. 1). It specifies that this project must be based on the creation of a public passenger transport network whose infrastructure is financed by the State: the Greater Paris public transport network.
The Grand Paris Express was born from the merger of two projects: the “Grand Paris public transport network”, suppor ted by the State, and “Arc Express”, sup ported by the Île-de-France Region. The project took shape after four months of intense discussions, which between
Much more than access to the metro, the stations will house shops, services and collaborative spaces, which will make them lively places open to the city. Travelers and residents will have access to both local and consumer products. The programming of these commercial activities will be done in particular according to the existing local offer.
In 2030, four new automatic metro lines will bypass Paris and serve the nearby and outer suburbs. Thus, thanks to its many services and its multiple connections to existing transport lines, the Grand Paris Express will transport people quickly from one place to another in Île-de-France.
• Line 15 will form a loop all around Paris and will cross the bordering departments: Seine-Saint-Denis, Val-de-Marne and Hauts-de-Seine. It will also pass in Seine-et-Marne, in Champs-Sur-Marne.
• Line 16 will serve Seine-SaintDenis, from Saint-Denis to ClichyMontfermeil before stopping in Seine-et-Marne at Chelles then at Champs-sur-Marne.
• Line 17 will head north of Île-deFrance from Saint-Denis to MesnilAmelot via Le Bourget and Roissy - Charles de Gaulle.
Saint-Denis Pleyel, to the north, and to Orly airport to the south, will complete this new transport network. NEW METRO LINES
2010 and 2011 brought together mo re than 22,000 people during 67 mee tings. Following extensive public deba te, the State and the Region recorded its birth with a historic agreement signed on January 26, 2011. The implementing decree approving the overall public tran sport plan for Greater Paris was publi shed on January 24 August 2011. Since then, a long way has been covered: the first civil engineering works started in 2016 on the southern section of line 15. In 2017, all the lines of the new net work were declared of public utility. By the end of summer 2022, more than 80 km of tunnels had been dug. To manage this large-scale project and ensure its financing, the State created, by the law of June 3, 2010, a public in stitution dedicated to its realization: the Société du Grand Paris. In barely 10 years, the company has structured itself to support the ramping up of construc tion sites. Composed of around thirty experts when it was created, it now has more than 900 employees.
On the strength of the steps taken, from the first studies to the laying of the rails,
• Line 18 will mainly serve Essonne and Yvelines, from Orly airport to Versailles via the Saclay plateau.
• The extension of line 14 to
the Société du Grand Paris has beco me a benchmark contracting authori ty. Since the start of the project, it has worked in close collaboration with its partners: the State, local authorities, the Greater Paris Metropolis, regio nal transport players (Île-de-France Mobilités, RATP, SNCF, etc.).
Automatic, the new metro will meet tra vellers’ need for reliability. Its frequency will be adapted according to particular events (cultural or sporting events) and changes in the rhythm of life of Ile-deFrance residents (weekdays, weekends, school holidays, etc.). Thanks to its de sign and the distances between the sta tions, the trains will run at an average speed of between 55 and 65 km/h, with a maximum speed of 110 km/h. By way of comparison, the Paris metro curren tly travels between 21 and 27 km/h on average. The RER A runs at an average speed of 49 km/h.
The optimal driving of the metro, ena bled by automatic piloting, will ma ke it possible to reduce its energy con sumption. The modern design of the trains, 100% electric service braking and the generalization of LED-type lighting will contribute to making the Grand Paris Express the least energy-consu ming mode of transport possible. Fully accessible, the new metro will offer a large number of priority spaces iden
tifiable by a specific colour. Spaces for strollers and wheelchairs will be present in each car. All access doors to metro cars, without exception, will be wheelchair ac cessible. To ensure passenger comfort, the metro trains will be equipped with efficient ventilation, air conditioning and heating systems. Lighting will also vary in intensity depending on the time of day. The light under the seats will reinfor ce the perception of a secure space and the metro will be equipped with a video surveillance system.
The choice of design for the trains on lines 15, 16 and 17 and 18 is the result of collaborative work between Alstom, the manufacturer, Île-de-France Mobilités and Société du Grand Paris .
Up to 15,000 jobs could be mobilized to build the new metro. Many trades are already involved in the construction of the Grand Paris Express: construction of tunnels, laying of rails, development and equipment of stations, etc.
The commissioning of new metro lines in the suburbs will stimulate the realization of real estate projects in Île-de-France. This dynamic will contribute to creating a neighborhood life around the stations served, where local services, shops, offices, co-working places and green spaces will mingle. Already, more than 180 urban projects have been undertaken in the neighborhoods surrounding the stations, which will be delivered in 2024 and 2025, and 84,000 housing units are planned there. In these new station areas, priority will be given to cycling, walking, bus and car-sharing.The development projects planned with the arrival of the Grand Paris Express are part of an environmental approach with low carbon impact constructions (biosourced materials, thermal requirements, eco-design).
The most impactful construction works of the project are certainly those for the construction of the underground tun nels. The Grand Paris Express tunnels are made using TBM – Tunnel Boring Machines, gigantic factory trains more than 100 meters long. At the height of its activity, the construction site of the new metro has already mobilized around twenty tunnel boring machines, some of which are used on several sections of line. Since the start of underground work, 28 Tunnel Boring Machines have been baptized. Today, seven of them are being excavated on lines 16, 17 and 18.
The Tunnel Boring Machines of the Grand Paris Express are introduced un derground thanks to an entrance shaft, then extracted from the underground by an exit shaft. As far as possible, these shafts are built on the site of the futu re service structure in order to pool site facilities and limit the number of work sites. Given its size, the Tunnel Boring Machine is transported piece by pie ce, by exceptional convoy, to the shaft, before being assembled underground. During excavation, the entrance shaft is used to supply the materials necessary for the proper functioning of the tunnel boring machine and the manufacture of the tunnel. It also allows the evacuation of excavated soil.
As is the tradition of Saint Barbara, pro tector of miners and tunnel builders, each Grand Paris Express tunnel boring machine is baptized and bears the name of its “godmother”. For the most part, the names were attributed following citi
zen votes carried out in schools, colleges, and even in municipal youth councils.
90% of the new metro lines are built underground. To limit dust emissions, powdery materials are transported in covered trucks and stored away from
the wind, work areas are sprayed or mi sted, and vacuum equipment is regularly used. The client also implemented dedi cated measures to protect natural envi ronments and local biodiversity during the construction of the metro. From the definition of the route to the construction of the works, an attempt is
made to avoid or reduce the impact of the construction of the new metro on the environment and on the territories crossed. Innovative solutions are put in place for the recovery of cuttings, the de sign of structures and the reduction of greenhouse gases. ■
Photo credits: archive Société du Grand Paris
“Grand Paris Express” è il nuovo sistema di linee della metropolitana che col legherà i principali luoghi di vita e di attività della periferia senza passare per Parigi. Questo progetto, che contribuirà alla trasformazione dell’Île-de-France, diventerà realtà a partire dal 2024.
Oggi metro e RER formano una rete a forma di stella di cui Parigi è il centro. Il nuovo grande progetto infrastrutturale “Grand Paris Express” completa que sto sistema con la realizzazione di quattro nuove linee metropolitane intorno alla capitale (le nuove linee 15, 16, 17 e 18), a servizio della vicina periferia ed esterna. A ciò si aggiunge l’estensione della linea 14 a nord, da Saint-Ouensur-Seine a Saint-Denis, e a sud, tra Parigi e l’aeroporto di Orly. Questa futura rete sarà gradualmente messa in servizio tra il 2024 e il 2030. La sua gestione è assicurata dalla Société du Grand Paris. Con 200 km di linee, pari all’attuale metropolitana, e 68 stazioni, di cui l’80% sono treni di collegamento, Grand Paris Express avvicinerà i residenti dell’Ilede-France al lavoro, all’istruzione, alle strutture sanitarie e ai luoghi culturali e per il tempo libero.
Located in the municipalities of Campagna and Serre (in the Province of Salerno), the Persano dam is a fluvial barrage built for irrigation purposes following the damming of the Sele River in the 1930s. In addition to having a historical and monumental value (it is still considered an important example of the architectural legacy of Fascism), it plays a strategic role in the economy of the entire region, one of the main agricultural areas in Italy.
The dam is managed by the Reclamation Consortium of the Right bank of the Sele River. The Italian Ministry of Infrastructure and Transport has awarded the Consortium a total of 10 million euros for the hydraulic and seismic upgrade and extraordinary maintenance of the dam. The funding will allow improving the safety of the
dam whilst increasing the reservoir capacity and contributing to the overall efficiency of the irrigation network, especially in drought conditions. The intervention was arranged as part of a national plan of interventions focused on dam security worth 293 million euros. The dam covers a total area of approximately 57,000 square meters. The barrage consists of a sill placed in the riverbed at an altitude of
40.5 m a.s.l., with four aligned metal gates closed between five piers, surmounted by a reinforced concrete walkway. The barrage extends towards the left bank with a masonry structure. To seal the dam, a concrete diaphragm wall was built downstream of the barrage with an area of 2500 square meters. Surveys conducted in recent years have highlighted critical issues related to the hydraulic safety of the plant, involving the structure of the dam itself. To assure the dam safety in case of flood events, the General Directorate for Dams and Water Infrastructures has established that the dam must be upgraded to increase its outlet capacity, thus allowing to maintain 100% storage capacity of the reservoir. Another important goal of the upgrade is the seismic and structural adaptation of the dam.
The project design was developed by engineering firm Technital.
The Italian Ministry of Infrastructure and Transport has awarded the Consortium a total of 10 million euros for the hydraulic and seismic upgrade and extraordinary maintenance of the Persano damConstruction was awarded to the Consortium “Research” (Research Consorzio Stabile Società Consortile), which has entrusted company Gorrasi Cost with the execution of the works. These involve, in particular: construction of an upstream cut-off and downstream filter, with 19.3 and 6.55 m depth respectively; surface repair of the existing sill plates; surface repair of the dam body; expansion of the upstream piers to allow the installation of the stop-log grooves for gate maintenance; reinforcement of some profiles building the metal gates; seismic adaptation of the reinforced concrete walkway; surface repair on the bottom outlet tunnel; seismic adaptation of the guard house, the control building on the right bank and the transformer cabin; adaptation of the lighting system; construction of a new fish ladder. As far as the dam foundation is concerned, the proposed design solution envisages two cut-off walls consisting of cased secant piles with a diameter of 800 mm spaced at 600 mm. Using two cut-off walls both upstream and downstream of the dam will help decrease seepage, hydraulic gradient, and uplift force. The upstream wall will be built of 206 piles with 18 m depth, the downstream filter will consist of 144 piles, installed to approx. 4 m depth.
Drilling works are currently underway upstream of the dam. The construction of the cut-off was entrusted to the company Fondsistem, based in Gricignano di Aversa (CE). “The piles
are installed at a depth of less than 20 m from the base of the opening of the bottom outlets of the dam”, explains Giuseppe Della Gatta, Owner and Technical Director of the Company founded in 1979 and specializing in foundation construction and ground improvement works. “ The main challenge of this project is that construction work is carried out in the riverbed of the Sele and is dependent on hydro-meteorological conditions. To hold back the water and protect the construction site, we had to build an embankment and install some sheet piling.”
The dam is situated in the upper part of the Sele River plain. From a geological point of view, the area features a plateau landscape, resulting from late Quaternary floods that caused the forming of wide deposits, composed of rounded to sub-rounded pebbles in a silt matrix. “The soil is gravelly, sandy and silty; there are parts of cemented sand and gravel. For the installation of the cutoff wall, we are using a Comacchio CH 450 piling rig equipped with a drilling
Fondsistem was born following the expansion of the company founded in 1979 by Della Gatta Venanzio, father of Della Gatta Giuseppe. It has its core business in foundation construction, both for civil and industrial applications. Thanks to a massive modern equipment fleet, the company provides a diverse scope of geotechnical solutions including deep foundations, bridge construction, earth retention, tunneling, ground improvement, marine drilling and all types of ser vices that require the use of specialized foundation equipment.
For the installation of the cut-off wall, Fondsisem is using a Comacchio CH 450 piling rig equipped with a drilling bucket of 800 mm diameter Fondsistem team members: Pasquale Gentile (driller), Khattab Abdelghani (assistant driller) and Salvatore Della Gatta (driller)bucket of 800 mm diameter. Due to the particular site conditions, we are working with 880 mm casings. Casing installation is carried out up to 16 m deep using a driver mounted on the rotary head .”, continues Della Gatta. “We found that the use of this technique has logistical and economic benefits, allowing the production of a 20m pile per day.”
The CH 450 is the first and best-selling model of the Comacchio CH range of piling rigs. “The machine has a transport weight of about 43 tons with the rotary head and kelly bar installed, it is easy to transport and fully self-erect: once on site, the machine can be offloaded from the truck and easily set up without the
need for service crane. This is of great help on construction sites with limited spaces and difficult access conditions such as this one”, explains the driller Pasquale Gentile. The CH 450 in the Fondsistem fleet features a CPD (Cylinder Pull Down) system. It can be equipped with different kelly bars reaching a max. pile depth of 57 m with self-mounting Kelly bar (64 m with non-self-mounting 14x5 bar). The bored piles max. diameter varies from 1500 mm (cased) to 2000 mm (uncased).
The rotary head offers 190 kNm nominal torque and can be operated both with manual gear change and in “constant power” mode, where speed and torque are adjusted automatically. The rotary head, just like all machine functions,
is connected to the Comacchio Controlling System (CCS).
“
The cabin is roomy and fully glazed; it has a sliding door and panorama roof as well as four cameras, allowing excellent visibility of the site. The workplace is adjustable and uses capacitive levers and manipulators as well as a large 12” color touch screen display connected to the CCS system that controls all drilling parameters and on-board diagnostics. The machine entered our fleet in 2019 and in 4000 engine hours, it has never had a breakdown. It is proving to be a valid choice in terms of performance, efficiency and consumption, which is reduced compared to other machines.
The motors used for the rotary head have the advantage of performing drilling
Situata nei comuni di Campagna e Serre, la diga di Persano è una traversa flu viale realizzata a scopo irriguo negli anni Trenta. Di grande valore storico e mo numentale, questa struttura svolge un ruolo strategico nell’economia della re gione. Le indagini condotte negli ultimi anni hanno evidenziato delle criticità le gate alla sicurezza idraulica dell’impianto. Il Ministero delle Infrastrutture e dei Trasporti ha dunque assegnato al Consorzio di Bonifica in Destra del Fiume Sele complessivi 10 milioni di euro per consentire l’avvio di interventi di ristruttura zione e miglioramento della sicurezza idraulica della diga, che prevedono tra le altre cose la realizzazione di una diaframmatura a monte della traversa e di un taglione a valle della soglia, realizzati mediante una paratia di pali secanti. I la vori di perforazione sono stati affidati alla ditta Fondsistem, che sta utilizzando per questo progetto una perforatrice Comacchio CH 450, scelta che si è rivelata vincente sia in termini logistici che economici.
The CH 450 in the Fondsistem fleet features a CPD (Cylinder Pull Down) system. It can be equipped with different kelly bars reaching a max. pile depth of 57 m with self-mounting Kelly bar (64 m with non-selfmounting 14x5 bar). The bored piles max. diameter varies from 1500 mm (cased) to 2000 mm (uncased). The rotary head offers 190 kNm nominal torque
with a reduced noise level. The rotation speed of the engine cooling fan adjusts electronically to the actual operating requirements, thus reducing the impact in terms of noise, emissions and fuel consumption. The rig is also easy to maintain, some small details, such as the replaceable drive sleeve and keys are certainly of great advantage”, Pasquale Gentile confirms.
■
The German company will present numerous innovations at the Bauma 2022. This year, the particular focus of the equipment exhibited as well as the CO 2-neutral exhibition stand of the Bauer Maschinen Group is one main topic: Sustainability Maschinen Group
by Linton S. DawsonIn the field of multifunctional rigs, the Bauer BG 45 and BG 23 H will give a small insight into the variety of applications
Bauer is presenting at Bauma 2022 a small selection of the various possible applications and equipment lines, with a total of four large rotary drilling rigs. In the area of multi-function equipment, the BG 45 and BG 23 H offer a small glimpse into the range of applications, kinematic systems and base carriers available. The BG 45 is the largest drilling rig at the Bauer stand. Thanks to V-kinematics, where the mast is shifted to the front in transport position, it offers a high level of rigidity for difficult applications, and above all, excellent versatility in the mobilization phase. As a result, a transport weight of around 35 tons for the heaviest individual components can be achieved with high efficiency. The flexible mobilization process is supported by the wireless remote-controlled mobilization package featuring hydraulic actuation of the main connection bolts for the mast and kinematics. At Bauma, the unit is exhibited with an equipment package for soil mixing technology: the Single Column Mixing-Double Head (SCM-DH). Two mixing tools with reverse rotation achieve thorough soil mixing and column quality due to this contrary motion. The smallest drilling rig on display is the BG 23 H, a compact machine with H-kinematics. This equipment can be completely mobilized and loaded using wireless remote control. With this model, the mast is stored on the machine in transport position, and the counterweight can be removed by the machine itself if necessary. This facilitates rapid and easy mobilization from one construction site to another. The complex undercarriage allows for a transport width of just 2.5 m and a transport height of just 3.1 m when the rotary drive is dismantled. This makes it easier to pass through narrow entrances and gates, as often found on urban construction sites. Thanks to a divided mast, the equipment is also prepared for work with restricted heights. Using the appropriate expansion kit, it is possible to work on construction sites with a working height of less than 9 m. But compact does not mean weak: In
Kelly operation, a powerful capacity of 235 kNm is available for installing the casings, and with the Crowd Plus assistant it is possible to activate a retraction force of up to 400 kN for retracting the casings. The compact BG 23 H is equipped with a new assistance system. This system provides the operator with a considerably extended range of outreach for work with continuous monitoring by the control system. Thanks to the powerful 225 kW CAT diesel engine, there is also enough power for applications with two rotary drives. The Bauer base carrier BT 65 for
the BG 23 H is equipped with important safety details: It features integrated service platforms for easy, convenient and safe access for maintenance work. The practical scaffold can be pulled out like a drawer, transforming the engine cladding into fall protection. The cladding concept also provides excellent noise protection. In combination with the EEP drive concept, very good sound pressure levels are achieved during normal operation. All of these elements underscore the excellent suitability of the BG 23 H for site requirements in urban areas.
In 2021 the Bauer Maschinen Group presented the new eBG 33 during its in-house exhibition “Bau Erleben”. Bauer is now introducing a new chapter and presenting the next generation of electric drilling rigs in the top torque classBauer’s ValueLine equipment is specially optimized for Kelly drilling. The BG 36 is the latest development in this line. EEP technology is now the standard for the upper end of the ValueLine range of equipment. For the toughest applications with large drilling diameters of up to 3 m and drilling depths of up to 115 m, the V-kinematics provide a solid and robust foundation with large bearing width. The feed cylinder with a length of 8.5 m and a retraction force up to 50 t enables the use of long casings as well. The B-Tronic system has also arrived for the special Kelly equipment. Apart from the large-scale display of drilling data and equipment parameters, the drilling assistant system allows for low-fatigue work during long drilling processes. The adaptive Kelly speed assistant is available for the new BG 36. This modern assistant enables fully automated, safe, fast and gentle extension and retraction of the heavy Kelly bars with up to five thrusts in places. The configuration exhibited at Bauma with a BV 1500 casing oscillator, automatic turning table and a long Kelly
bar is specifically coordinated to the requirements for reworking existing wells.
Cut-off walls, which are used for retaining structures, sealing off dams or as a foundation element, can be constructed using a variety of methods and equipment. One option is the cutter soil mixing method (CSM), which is applied particularly at great wall depths or final depths. It combines features of the diaphragm wall technique and the soil mixing method. The CSM equipment that Bauer is presenting on an RG 21 T at Bauma enables a maximum mixing depth of 20 m. A new model of the BCM mixing unit delivers enhanced performance for narrow soil mixing walls. In the area of diaphragm wall technology, Bauer is presenting a BC 48 cutter with turnable HDS-T hose drum system and a new cutting tool at Bauma. The base carrier is a MC 96 duty-cycle crane. But that’s not all: visitors can also experience the innovative Bauer Cube System, which will be transported directly
from the test site to the Bauma stand. The complete cutter including hose drum system fits in three conventional 20-foot-tall high cube containers. As a result, the system can be easily used in 3 x 3 m diameter tunnels, a major advantage for cutting projects in densely populated large cities. This means that large-scale closures of urban areas could potentially be a thing of the past. The impact of construction sites on traffic, businesses, and residents (in particular) are minimized, even during daytime use. The electric drive system considerably reduces the ecological disturbance of a cutting site. When it comes to logistics, the system’s compact dimensions are another major advantage. Instead of expensive heavy haulage, individual elements of the system can be easily transported to their place of deployment as conventional containers.
The RTG Rammtechnik GmbH also has multiple innovations to display. For example, the exhibited RG 21 T has a newly developed BCM 5 cutting
Klemm Bohrtechnik GmbH presents a total of four drilling rigs of the KR series at Baumaand mixing unit. Particular features include the expanded cutting width and a markedly increased performance capacity. This results in a highly efficient CSM unit with low noise emissions and an excellent CO2 footprint: after all, the CSM method eliminates the need to remove excavated material because the existing soil is used. The RG 21 T is equipped with the latest B-Tronic version and can be operated entirely using “Operate” remote control. A true world first is the RG 19 T on display, which is setting standards as the first hybrid model in the telescoping leader segment. The system capacity is achieved with a diesel engine and an additional electric drive, which considerably reduces the CO2 and noise emissions. All RTG models on the BS55RS and BS65RS base carrier can be offered with this hybrid technology in the future. The fitted vibrator features the SilentVibro package and the sheet pile assistant, which enormously increases occupational safety while also enhancing productivity. In addition, the “Operate” remote control is also available in the hybrid version. All equipment and attachments including the BCM 5 are equipped with the ACS clutch system for rapid change of attachments. The RTG Pile Driver app enables the operator to operate the equipment quickly and safely. In addition, complete service can be carried out on the equipment with the help of the app.
Within the Bauer Maschinen Group, Klemm Bohrtechnik GmbH is the competence center for compact drilling rigs in specialist foundation engineering. At Bauma, the company is presenting a total of four machines from its KR series: The mini drilling rig KR 606-3 with full anchor kinematics is perfectly suited for use in cramped urban conditions. The power packs are available in a diesel version or electrohydraulic version; the smallest drilling rig in the Klemm portfolio is optionally available on a crawler, tire chassis or in a steel frame. With an operating weight of less than 10 tons and a total width of 1.8 m, the exhibited KR 800-3G is the smallest universal
Bauer MAT Slurry Handling Systems is presenting its BE 300-C, the most compact desanding plant of its capacity class worldwide. This is installed in a 20-foot container frame. In two stages, the plant separates solids up to a particle size of d 50 = 30 µm (known as the cut point) from rinsing fluid (known as slurry)
drilling rig with anchor kinematics and rollover. Its smart feed function with divisible feed is designed for lowheadroom applications. The KR 8053GW is a drilling rig for probe drilling involving near-surface geothermal heat. This makes it possible to reach drilling depths of up to 200 m using the doublehead drilling method. A crane and drill string manipulator as well a hydraulic pulling mechanism in the clamping and breaking device are included on this
Il prossimo ottobre si terrà un’altra manifestazione fieristica dai toni “superla tivi”: il Bauma di Monaco. “Dopo gli ultimi anni, in cui i contatti personali so no stati possibili solo in misura molto limitata a causa della pandemia, siamo particolarmente impazienti di accogliere presso il nostro stand molti clienti, partner e amici provenienti da tutto il mondo”, afferma il Dr. Rüdiger Kaub, amministratore delegato di Bauer Maschinen GmbH. All’interno dello stand FN 520 (area esterna nord) saranno esposte macchine e attrezzature Bauer e delle consociate Klemm, RTG e Bauer MAT. “Ai nostri ospiti saranno riservate alcune anteprime molto speciali che presentiamo per la prima volta in assoluto agli operatori del settore”, continua Kaub. Quest’anno l’attenzione del Gruppo Bauer Maschinen sarà incentrata su un tema principale: la sostenibilità. In par ticolare, all’interno dello stand saranno esposti, tra gli altri: gli impianti di per forazione multifunzionali Bauer, inclusa una novità “elettrificata”; gli impianti di perforazione ValueLine; nuove tecnologie destinate alla costruzione di pa reti divisorie e diaframmi; gli impianti di perforazione compatti e universali di Klemm; nuove tecnologie di miscelazione e separazione.
■
equipment weighing nearly 20 tons. The series of Klemm exhibits is rounded off by the KR 806-3E. This features proven technology from the KR 806-3GS, yet as an electrohydraulic, emission-free variant. The intelligent control system enables the use of batteries as a booster for drilling operation to reduce the required electricity load. Compared to the diesel-hydraulic variant, there are no restrictions when it comes to power and application.
Since the alternative drive of the LB 16 unplugged quickly established itself on the market as a Gamechanger, the design has been extended to further product areas. Today, the electrified unplugged series comprises crawler cranes as well as piling and drilling rigs. An outstanding feature of the battery-powered unplugged units is zero emission. They do not produce any exhaust fumes and are extremely quiet. This strikes the right note especially in noise-sensitive regions and finds favour with construction site personnel and residents. Whether London, Paris or Oslo - the concept has already been successfully applied in these metropoles. The battery is charged using a conventional jobsite electric supply. Operation can continue as normal while charging. In order to change to battery operation, you just need to pull out the plug, therefore: unplugged. Whether attached to the electric supply or not, the performance and range of application remains unchanged. All six models are available in both conventional and battery-operated versions and have identical performance specifications.
Liebherr-Werk Nenzing
GmbH will launch at Bauma six new models for lifting, drilling and piling operations have charged their batteries to electrify with zero emissionThe new Liebherr crawler crane type LR 1130.1 is available as electro-hydraulic and conventional version
The LRH 200 has been completely newly developed and closes the gap between the proven LRH 100 and LRH 600 in the series of piling rigs. A 200-kWh battery pack ensures that the unplugged models can operate in battery mode for 4 to 5 hours in average pile driving applications. Optionally, it can be upgraded to 400 kWh for 8 to 10 hours of operation. The new design of the LRH 200 extends the range of applications and makes if even more versatile in use. In addition to piling, the machine can be used for continuous flight auger, full displacement and down-the-hole drilling, as well as for soil mixing work. A torque of 250 kNm provides the necessary power. When equipped with the hydraulic hammer H 6 from Liebherr, the LRH 200 and the LRH 200 unplugged can lift piles up to 24.5 m long and weighing 16 tonnes. The machine especially excels with its large working range. A radius of up to 8.7 m has the advantage that the machine does not have to be constantly moved. The design of the leader enables inclinations of up to 18° in all directions.
Furthermore, it is also possible to raise or lower the leader by 6.5 m (e.g., when working in a foundation pit), which makes the machine even more flexible.
The Ground Pressure Visualization of the new LRH model calculates the current ground pressure in real time and compares it with the specified safety limits of the respective construction site. The ground pressure is displayed in the operator’s cabin. This means the operator is permanently aware of whether the machine is situated in, or is approaching, a critical area.
The operation of the new piling rig LRH 200 is based on the proven concept of the LRH 100 and is therefore very user-friendly. The integrated data recording makes the analysis of the pile data extremely easy and saves a huge amount of time.
Over many years, the drilling rigs LB 25 and LB 30 have proven themselves in the conventional version. The new battery-operated unplugged versions are identical with regard to application possibilities, weight
or transport; however they have the additional advantage of zero emission. The drilling rigs can be used for all common applications in the field of deep foundation. Thanks to the optional extension of the drilling axis, the machines can be deployed for drilling diameters of up to 3.4 m. The optional rear support and the new design of the modular rear counterweight ensure higher stability and longer service life.
In addition to the standard design, both machines are available in a Low Head version with a total height of 14.1 m, or as Ultra Low Head with only 7.7 m. For battery operation, the charging cable only needs to be unplugged and, for unlimited operation, reconnected to the construction site power supply.
The battery is designed for a working time of 4 hours in Kelly operation. Whether in battery or plugged-in operation, the drilling performance remains unchanged.
LR 1130.1 and LR 1160.1
The new machines LR 1130.1 unplugged and LR 1160.1 unplugged extend the range of crawler cranes from Liebherr-
The new piling rig from Liebherr: LRH 200 unpluggedWerk Nenzing GmbH. The electrohydraulic drive of the new cranes has the same performance specifications as the conventional version. Both versions are operated in the same way, which is especially practical if the crane driver
has to often change between machines in one fleet.
The capacity of the battery is designed for an average lifting operation of eight hours. Alternatively, the main boom with luffing jib can be completely erected.
Una caratteristica unica delle macchine Liebherr “unplug ged” alimentate a batteria è la “Zero Emission”: non pro ducono gas di scarico e sono silenziose. Le batterie ven gono caricate utilizzando l’alimentazione elettrica del cantiere (durante il processo di ricarica il funzionamento può continuare come di consueto). Tutti i sei nuovi mo delli proposti da Liebherr sono disponibili sia in versione convenzionale che a batteria e presentano performance identiche. La LRH 200 è stata rielaborata e colma il diva rio tra le collaudate LRH 100 e LRH 600 nella serie delle palificatrici: un pacchetto di batterie da 200 kWh assicura che i modelli “unplugged” possano funzionare in moda lità batteria per quattro-cinque ore. In opzione, l’attrez zatura può essere portata a 400 kWh per otto-dieci ore di funzionamento. Questa macchina può essere utilizza ta anche per lavori di perforazione con elica continua o martello a fondo foro, nonché per la miscelazione a umi do. Una coppia di 250 kNm fornisce la potenza necessa ria. Equipaggiata con il martello idraulico Liebherr H 6, la LRH 200 o la LRH 200 “unplugged” possono trivellare pali fino a 24,5 m di lunghezza e un peso di 16 t.
The battery can be recharged within only 2.5 to 4.5 hours. As an option, the performance can be increased by 20 to 60 per cent using additional batteries. In idling mode, the sound pressure level of three unplugged cranes is equivalent to that of a normal conversation on the jobsite. This corresponds to a value of only 60 dB(A). If it is taken into account that a crawler crane is in idling mode for 60 % of the time on the jobsite, this low noise level is an advantage with great resonance. The designers of the crane laid great emphasis on the safety concept. As with all crawler cranes from LiebherrWerk Nenzing GmbH, the new batteryoperated models are also available with all proven assistance systems. The latest system is the Gradient Travel Aid for the safe negotiation of slopes and inclines. The crane’s control system automatically calculates the centre of gravity and warns the operator before the crane leaves the safe area. While travelling, the operator receives information about the permissible and actual gradient, and the crane’s overall centre of gravity at all times. ■
Lo sbraccio di 8,7 m offre il vantaggio di non dover spostare la macchina durante il lavoro. Il design dell’asta guida-palo consente inclinazioni fino a 18° in tutte le direzioni. Inoltre, è possibile sollevare o abbassare l’asta guida-palo di 6,5 m. Gli impianti di perforazione LB 25 e LB 30 hanno invece già dato prova di sé per molti anni come versioni convenzionali. Le nuove versioni “unplugged”, alimentate a batteria, sono identiche in termini di possibilità di applicazione, peso o tra sporto, ma hanno l’ulteriore vantaggio di essere “a emissioni zero”. Le nuove LR 1130.1 “unplugged” e LR 1160.1 “unplug ged” ampliano invece la gamma di gru cingolate di LiebherrWerk Nenzing GmbH. L’azionamento elettroidraulico delle nuo ve gru ha le stesse prestazioni della versione convenzionale: entrambi vengono azionati nello stesso modo, il che è pratico quando gli operatori delle gru passano spesso da una macchi na all’altra in una flotta. La capacità della batteria è progettata per un’operazione di sollevamento media di otto ore; in alter nativa, il braccio principale può essere allineato con il braccio ausiliario. La batteria può essere ricaricata in 2,5-4,5 ore; in opzione, le batterie aggiuntive possono aumentare la poten za dal 20% al 60%.
Liebherr once again electrifies the drilling rig series with the LB 30 unpluggedPreparations for Bauma China 2022 are in full swing. Despite the challenging circumstances, about 3,000 exhibitors are expected to occupy the exhibition space of 300,000 m². As Bauma China celebrates its 20 th anniversary in China, it will continue to provide the key platform for Chinese construction machinery companies to showcase its capability to the world, and the ‘gateway’ for international companies to enter the Chinamarket. As of 28 June 2022, the quarantine measures for inbound travelers to Mainland China have been reduced to 7 days of centralized quarantine, followed by 3 days of home monitoring for most cities. Additionally, the embassy of China in France, Australia, Indonesia, Norway, Spain and the United States have also relaxed the Chinese visa application requirements since June 20, 2022. To date, international pavilions from Germany, Italy, Spain, and South Korea have confirmed their participation. Major international brands like Caterpillar, Komatsu, Isuzu, Bonfiglioli, Bosch Rexroth, Danfoss and Parker have applied to participate in Bauma China. As Asia’s leading trade fair for the construction and mining machinery industry, Bauma China provides the best platform for industry players to meet again in person, to exchange information, and to network. Catching up the cutting-edge construction machinery and equipment. To achieve the country’s dual carbon goals of getting CO2 emission speak by 2030, reducing them progressively and finally arriving at carbon neutrality by 2060 through planting trees, saving energy, and reducing fossil fuel output to offset carbon emissions, automation, digitalization, artificial intelligence, energy conservation, and emission reduction have become the main drivers for industrial transformation and upgrading. Key construction machinery manufacturers have since introduced new products to meet the China IV emission standards for non-road machinery –a series of standards that aim to transit all heavy-duty vehicles to soot-free emission levels.
Epiroc has entered an agreement with Skanska Industrial Solutions AB to trial the first ever tophammer battery-electric rig in Sweden. Also, at Bauma 2022 the company will show other important solutions for the drilling market
by Ettore ZanattaThe recent trial between Epiroc and Skanska Industrial Solutions
AB marks a significant milestone in the journey towards zero emissions drilling in surface mines and quarries all over the world. “This is a proud day. For many years we have been leading the development in lowering fuel consumption within tophammer drilling. With this new
solution we are taking a giant leap in the low emissions field – we are practically removing emissions from the actual drilling process”, says Ulf Gyllander, Product Manager tophammer drill rigs, Epiroc Surface division.
The new SmartROC T35 E
The design of the rig is based on the well-proven SmartROC T35 surface drill rig. In combination with invaluable
experience gained from the development of Epiroc underground battery rigs, this SmartROC T35 E is designed to enhance the environmental standards of quarries and larger construction sites. Besides the low emissions, this rig comes with a range of smart features, options and enhanced automation solutions for high safety, reliability, and performance. “With this achievement we show that the innovations of Epiroc
will play a significant role in the shift to low-carbon operations within quarries and large construction applications,” says Jose M. Sanchez, President Epiroc Surface division. “As our sustainability agenda goes hand in hand with those of our customers, we are very pleased to be collaborating with Skanska Industrial Solutions AB in the trials of this important solution.”
The tests will commence in September 2022 in one of Skanska Industrial Solution’s quarries in the Stockholm area: “A milestone has been reached and a new opportunity has come to reduce our climate impact. I am very happy about the long collaboration between Epiroc and Skanska, and it is exciting to be able to do this project together. Both companies have set bold environmental goals – this project really takes a great step towards Skanska´s goal of being completely climate neutral by 2045, which is an important part of our promise to build a better society”, says Johan Eliasson, Project Manager, Skanska Industrial Solutions AB.
Peter Beckman, Business Line Manager, Epiroc Customer Center Sweden comments: “Skanska is a perfect partner for this trial as they have their own quarries which are fitted with the infrastructure required to handle the operation of this new technology. I am looking forward to following this exciting project during the coming months.”
The SmartROC T35 E rig is equipped with both a battery and an electric cable, which improves flexibility considerably. You can choose to drill with the most suitable alternative for the location and occasion. It also allows for quick and smooth transportation in and between sites. The surface drill rig is fitted with the same type of well-proven batteries and subcomponents as in the Epiroc underground battery solutions. This streamlines spare parts handling and service for customers with several different operations.
At Bauma 2022 Epiroc will launch the latest range of 5” DTH hammers, a complete, new innovative platform. Each customer has unique circumstances in
their operations; whether it’s the rock condition, type of rig used, length to be drilled, or even the altitude at which you are operating. Epiroc wants to provide a tailormade solution for each of his customers. The COP 57P platform is a wide range of hammers, fine-tuned to specific customer needs. This versatile new platform will replace the existing 5” hammer platform from Epiroc with which we have been market leaders for the past 20 years. Then, if you thought the handheld drilling market consisted only of rock drills based on century old pneumatic technology that is very inefficient from an air consumption perspective, Epiroc announces good news: The HRD 100 system consists of the rock drill, power pack and a selection of pusher legs. Together
they have two missions: The first is to provide hydraulic drilling that helps you exceed your production targets in a safe way. Thanks to the hydraulic system, you don’t have to worry about losing production time due to poor air pressure at large depths. The company has also gone out of his way to design a system that helps avoid heavy lifting and wasting precious energy. The second mission is to provide good value for money, over a long period of time. To succeed, Epiroc uses only the best parts and materials available and combine them with active security systems that protect both you and the equipment. At Bauma, Epiroc will also showcase a selection of the EssentialLine tophammer range consisting of bits and rods mainly used in surface applications.
Epiroc has frequently been a pioneer in the world of hard materials for drilling. Now the company is introducing Powerbit X rock drilling tools with diamond-protected buttons – the technology is called PCD (polycrystalline diamond). Changing drill bits is a safety risk. The diamond layer of Powerbit X gives the drill bits a longer service life, which means fewer changes and less exposure to danger for operators. The two-millimeter diamond layer can help improve workplace safety, reduce downtime and minimize CO₂ emissions.
The SmartROC T35 E is designed to enhance the environmental standards of quarries and larger construction sites
tuned to meet tunneling construction needs. Knowing that all personnel are in a safe location is key in all conditions but especially during blasting, danger, or an evacuation. What you can measure, you can stabilize; what you can stabilize, you can improve. The new digital tunneling solutions make the tasks of planning and following up on progress much smoother. A digital workflow can help to drastically improve efficiency. Go from monitoring work orders to becoming operational, and report progress in real time at the face. An extra
bonus with this way of working is that there is no need for manual reporting after the shift. The Mobilaris Tunneling Intelligence suite includes the following software products: Mobilaris Situational Awareness, Mobilaris Planning and Scheduling, Mobilaris Operator Client and Mobilaris Productivity Analytics
My Epiroc is a digital platform for Epiroc customers where they can manage their daily business. The platform is role based and allows operators, fleet managers,
Based on the successful use of Mobilaris Mining Intelligence products in mines globally, these solutions have been fine-
Epiroc ha concluso un accordo con Skanska Industrial Solutions AB per speri mentare il primo carro di perforazione top-hammer a batteria in Svezia. Questo test costituisce una pietra miliare significativa nel percorso verso la perforazione a emissioni zero nelle miniere di superficie e nelle cave di tutto il mondo. Il pro getto si basa sul collaudato carro di perforazione da superficie SmartROC T35: facendo tesoro della preziosa esperienza acquisita con lo sviluppo dei mezzi da galleria a batteria, questo SmartROC T35 E è stato progettato per migliorare gli standard ambientali delle cave e dei cantieri. Oltre alle basse emissioni, questo carro è dotato di una serie di funzioni intelligenti, opzioni e soluzioni di automa zione avanzate per garantire sicurezza, affidabilità e prestazioni elevate. I test inizieranno nel settembre 2022 in una delle cave di Skanska Industrial Solution nell’area di Stoccolma. Il carro di perforazione SmartROC T35 E è alimentato sia da una batteria che da un cavo elettrico, il che ne migliora notevolmente la fles sibilità. È possibile scegliere di perforare con la soluzione più adatta al luogo ed alle condizioni del cantiere. Inoltre, consente un trasporto rapido e senza proble mi all’interno del cantiere e tra i diversi siti. La macchina è dotata dello stesso tipo di batterie e sotto-componenti collaudati delle soluzioni elettriche dei mez zi da sottosuolo Epiroc. Questo semplifica la gestione delle parti di ricambio e l’assistenza per i clienti che operano in diversi tipi di cantiere.
buyers, technicians, managers and other personnel to work more smoothly and efficiently. With My Epiroc they not only have the tools needed to keep track of the fleet and its status, they also get insights to its service needs, and simple ways to track orders and follow up on any support requests as they arise. This increases confidence in making the right decisions based on information reported by machines and colleagues. My Epiroc allows access to the information from any modern web enabled device at any location. My Epiroc is designed as “mobile first”, i.e., designed for mobile devices first and then for desktops. ■
The construction of a new bridge is always synonymous with connecting people. With this new project based from ShirsadMasvan section of Vadodara Mumbai Expressway, Casagrande is drilling to connect and building an eight lane access controlled expressway. The foundation work project consists of a total of 856 piles with diameters ranging from 1200 to 1500 mm up to 25 m depths. 520 piles are on land, and 336 piles are in water, all drilled for socketing in hard rock – Basalt - from 3.5 m to 5 m.
B250XP-2 and B300 XP-2
This site is employing two drill rigs: the Casagrande B250XP-2 and B300 XP-2. GR Infra Projects Ltd has selected the two rigs for their specific features: high torque of rotary head to encounter hard rock, weight of rig according to the weight limitation on pontoon, extraction force of rig suitable for bigger height of tools (i.e. core barrel with rollers of 3 m height) to achieve better productivity.
“This project is one of the critical projects for GR Infra Projects Ltd which have to be completed within the time period of 1 year and in this jobsite, they have to
drill thru very hard rock having UCS value ranging from 80 to 150 Mpa”, said Mr. Dharmendra Singh - Piling Head GR Infra Projects Ltd. The two drill rigs, top tier models in the Casagrande’s range with outstanding performances in the 80 and 100 t classes, are arranged here in bored piling mode with interlocking kelly bars and crowd ram feed system. Thanks to its excellent stability, wide tracks, reduced swing radius and high working radius, the B300XP-2 has been chosen to operate from a pontoon in the middle of the river. The basement of the new bridge will bear on piles
A Casagrande B250XP-2 drill rig and a B300XP-2 version are working in India for building an eight lane access controlled expressway in Mumbaiø1500 mm diameter and up 17-19 m deep in weathered rock and hard rock. The casings are installed by a vibrator mounted on auxiliary crane to get inside about 10 m of water. The B250XP-2 is piling ø1200 mm diameter piles up to 20-23 m depth in softer soil, weathered rock and hard rock. The combination of optional main winch with 335 kN nominal line pull, the powerful H26 rotary head, the heavy-duty crowd ram
system, 3 and 4 elements interlocking kelly bars and the Casagrande experience in supplying the proper drilling tools makes the operation easy and fast. Casagrande has provided the tooling best suited for this project to tackle hard rock. The tools used are 3 m long Core Barrel with Rollers, Double Layer Core Barrel with Rollers, Special Rock Auger for hard rock (UCS up to of 100 Mpa) and Cross Cutter.
The Casagrande B250 XP-2 equipment consists in: rotary head with 263 kNm max torque and up 38 rpm rotation speed and the crowd cylinder 350 kN / 220 kN extraction / crowd force make the rig ideal for casing operations (crowd winch version is available with up to 16 m stroke of rotary head and 420 kN extraction/crowd force; the crowd winch version allows rapid-cfa drillings up to
24 m depth); a powerful 336 kW diesel engine complying with the latest EU Stage V emission regulations or EU Stage IIIA equivalent, drives all the working functions of the ~85 t rig. The B250XP-2 is multifunction rig designed to drill Bored Piles diameter 2700 mm max up to 78 m drilling depth or up to 32 m CFA drilling depth and ø1200 mm diameter. The rig is ready for easy conversion in other piling modes as displacement piles, soil mixing as well as diaphragm wall equipment with heavy duty hydraulic suspended hydraulic grabs.
The Casagrande B300 XP-2 The Casagrande B300 XP-2 equipment
GR Infra Projects Ltd has selected the two rigs for their specific features: high torque of rotary head to encounter hard rock, weight of rig according to the weight limitation on pontoon, extraction force of rig suitable for bigger height of tools
consists in: rotary head with 300 kNm max torque and the crowd cylinder 400 kN / 250 kN extraction / crowd force make the rig ideal for casing operations (crowd winch version is available with up to 19 m stroke of rotary head and 535 kN extraction/crowd force and allows easy conversion in rapid-cfa drillings up to 27 m depth). A powerful 400 kW
The two drill rigs are the top tier models in the Casagrande’s range with outstanding performances in the 80 and 100 t classes
diesel engine complying with the latest EU Stage V emission regulations or EU Stage IIIA equivalent, drives all the working functions of the ~100 t rig. The B300xp-2 is multifunction rig designed to drill Bored Piles diameter 3100 mm max up to 89 m drilling depth or up to 32 m CFA drilling depth and ø1200 mm diameter. The rig is ready for easy conversion in other piling modes as displacement piles, soilmixing as well as diaphragm wall equipment with heavy duty hydraulic suspended hydraulic grabs. The rigs have been designed to make rigging/derigging and transport operations easy and safe thanks to the remote control and modular design of the machine. The cabin has been designed with improved ergonomics for comfort and soundproofing, both inside and outside. The fan speed is related to the oil temperature in the smart oil heat exchangers, thus reducing fuel consumption and the overall noise level of the cooling system.
The XP-2 series hydraulic and electronic systems directly control the performance of the hydraulic pumps to achieve efficient, precise and rapid execution of all operations. The powerful diesel engine uses a highly efficient coupler to transmit the required power to the latest generation of hydraulic pumps, whilst ensuring reduced pollutant emissions and minimal fuel consumption. The rig body has hydraulic openings for quick and easy access for inspections and maintenance. Optional Stairs, platforms and railings provide excellent and safe accessibility where required. Optional cameras and display monitors give the operator full visibility of the winches, the sides and rear of the machine. The XP-2 control system offers several advantages for the operator including monitoring of all working functions and parameters, diagnostics of the working systems to ensure constant monitoring of the sensor and component status, easy conversion to any drilling arrangement using the control system and customization of the working parameters. The two rigs are equipped with the
CFM “Casagrande Fleet Master” that is the Casagrande online platform that allows remote control from any device, PC, Tablet or Smartphone. By accessing a dedicated web page, you can monitor the activity, the location of the machine, the active alarms and their history, all the significant data recorded as well as use and maintenance manuals and hydraulic and electrical
diagrams. The CDR “Casagrande Data Recording” is available for both B250 xp-2 and B300 xp-2. The CDR is the system for recording and monitoring working parameters and drilling data. The monitor in the cabin displays the working parameters and stores the data according to the drilling technology. The data are available for download and post processing. ■
Una perforatrice Casagrande B250XP-2 e una B300XP-2 sono attualmente im pegnate in India. Qui, infatti, è in corso d’esecuzione il progetto di realizzazione di una superstrada a otto corsie nel tratto tra Shirsad - Masvan di Vadodara a Mumbai. Esso prevede un totale di 856 pali di fondazione con diametro 1.200 mm e 1.500 mm e profondità massima di 25 m. Tra questi, 336 pali vengo no realizzati in acqua posizionando le perforatrici su un pontone. La GR Infra Projects Ltd ha scelto queste due macchine per le loro caratteristiche specifi che. Entrambe, infatti, offrono un’elevata coppia della rotary, ideale alla per forazione in roccia (la massa è in linea con il limite del pontone e gli argani hanno una forza di estrazione elevata che consente di sollevare utensili specia li di 3 m di altezza, ottenendo quindi una migliore produttività). “Questo pro getto è uno dei più critici per GR Infra Projects Ltd, in quanto la tempistica per la realizzazione è di un anno e la perforazione coinvolge strati di roccia molto dura, con valore UCS che va da 80 a 150 Mpa”, dichiara Dharmendra Singh, ingegnere presso GR Infra Projects Ltd. Le due perforatrici si distinguono per le loro prestazioni nelle classi 80 e 100 t del range Casagrande. Nell’occasione sono disposte in modalità “bored piling”, con aste telescopiche a incastro con martinetto “pull down”.
The B250XP-2 is multifunction rig designed to drill Bored Piles diameter 2700 mm max up to 78 m drilling depth or up to 32 m CFA drilling depth and ø1200 mm diameterBoone Dam, located upstream of Kingsport, TN (USA) is owned and managed by TVA. Built in 1953, the barrier has an 850-ft long concrete gravity dam section, and an 850-ft long earthen embankment dam. The resulting Boone Lake has a capacity of 75,800 acre-feet. A sinkhole was discovered near the downstream toe of the dam
in October 2014, and soon after TVA observed turbid discharge exiting from the riverbank downstream of the dam, indicating potential dam safety issues. In July 2015, TVA announced plans to construct the Boone Dam Internal Erosion Remediation Project, an erosion barrier through the dam and its foundation, consisting of works aimed to mitigate the risk of potential dam failure due to internal erosion and safely
return the dam and reservoir to normal operations. The program included five components: Low mobility grouting, high mobility grouting, stability berms, cutoff wall, crest floodwall.
After the completion of the preliminary enabling grouting works, in 2018 TNJV, a Joint Venture formed by Treviicos and Nicholson, was awarded the contract for the installation of the cutoff wall. With the working platform at approximately elevation 1,400 feet and the bottom elevation of the cutoff wall as low as 1,230 feet, the wall has a resulting maximum depth of approximately 170 feet, and is formed by a single row of secant
by Ettore Zanatta
Tennessee Valley Authority (TVA) has completed a seven year US$326M (£259M) project to remediate the Boone Dam in the US state of Tennessee
piles extending through embankment, foundation soils, and weathered rock into intact rock up to 170 feet below crest, including tie-in of wall on sloping face of existing concrete dam.
The technology of the secant piles was chosen after consideration of a number of cutoff wall construction methods for having lower dam safety concerns, and to maintain strict alignment and overlap requirements while penetrating through a challenging mixture of soil and highly weathered rock within the upper portions of the dam’s foundation.
The cutoff is keyed into the sloping face of the existing concrete dam, forming a continuous composite seepage barrier could along the entire alignment of the earthen dam. Over 300 50-in dia. secant piles were installed to create 850-ft long secant pile barrier, totaling 113,000 square feet of cutoff wall, and 27,000 cubic yards of concrete for backfilling. Verification of the verticality, embedment and concrete quality of each element forming the wall was critical. The secant piles were installed using a combination of equipment and techniques: piling rigs were used to drill through the embankment and the alluvial, to depth of approximately 100 ft, using segmental casings. Reverse
circulation top pile rigs then completed every pile, to a total maximum depth of circa 170 feet, into a rock with peak UCS values as high as 36,000 psi (240 MPa). The concrete for the piles was manufactured in an onsite batch plant operated and controlled by TNJV. The quality of the joints between the elements was of paramount importance for the integrity of the wall. An extensive quality control program provided TVA with an accurate validation of the installed final product for their acceptance. This, in conjunction with an equally extensive quality assurance program, ensured that the cutoff wall was installed meeting or exceeding the stringent requirements of the Project. For instance, as part of this program, vertical deviation was check by measuring with different instruments and piles were brushed to grant quality joints.
Longitudinal section of the cutoff wall Schematic of the full Boone Dam Internal Erosion Remediation Project, including item 4, performed by TNJVThe cutoff wall project started in 2019 and was completed in February 2021, allowing TVA to restore normal operations of the reservoir to pre2014 levels, 17 months ahead of schedule. The Boone Dam Project was a further achievement in the decades-long experience established by the Trevi Group in the field of Dams and Levees rehabilitation where, in the US alone, TREVIICOS has successfully completed tens of projects using several technologies such as secant piles, cutoff walls, soil mixing, jet grouting, etc. Among these projects several were first of its kind applications: W.F. George (AL), the first secant pile cutoff wall under water ever constructed; Herbert Hoover Dike (FL), fist time installation of cutoff wall by selfhardening-slurry by hydromill for a total of over 8 million square feet; LPV 111 (NOLA - LA), the biggest deep mixing projects ever done outside Japan for the stabilization of approximately 5.5 miles of levee; and Wolf Creek Dam (KY), the largest Dam Rehabilitation project ever done in North America for the installation of a concrete cutoff wall to depths exceeding 280 ft. ■
TREVIICOS, filiale americana di Trevi, si è aggiudicata in joint-venture con Nicholson Construction Company i lavori per la messa in sicurezza della diga Boone Dam, nello stato del Tennessee (USA). La diga è di proprietà della società TVA la qua le, nel 2014, ha individuato alcune problematiche strutturali causate dall’erosione interna e ha dovuto necessariamente ap prontare un intervento di messa in sicurezza per poter riportare il bacino idrico alle normali operazioni. La joint-venture tra TREVIICOS e Nicholson Construction Company ha riguardato la realizzazione di una barriera continua realizzata tramite un’unica fila di pali secanti, tecnologia scelta dopo aver preso in considerazione altri metodi di costruzione. Sono stati in stallati oltre 300 pali da 50” di diametro, al fine di creare una barriera lunga 259 m, per un totale di circa 11.000 m2 di parete e 27.000 m3 di calcestruzzo utilizzati per il suo riempimento. I pali secanti sono stati installati utilizzando una combinazione di attrezzature e tecniche: sono stati utilizzati impianti di trivellazione per perforare il terrapieno fino a una profondità di cir ca 30,5 m; gli impianti di trivellazione a circolazione inversa hanno poi completato ogni palo, per una profondità massima totale di circa 52 m. Il progetto del muro di separazione è iniziato nel 2019 ed è stato completato nel 2021, consentendo alla TVA di ripristinare le normali operazioni del bacino ai livelli precedenti al 2014, con 17 mesi di anticipo rispetto alla tabella di marcia. Il progetto della diga Boone Dam è stato un ulteriore risultato dell’esperienza maturata dal Gruppo Trevi nel campo del ripristino di dighe e argini dove, solo negli Stati Uniti, TREVIICOS ha portato a termine con successo decine di progetti utilizzando varie tecnologie come pali secanti, muri di cutoff, miscelazione del terreno e jet-grouting.
Since its founding in 1969, Soilmec has always focused on developing sound engineering solutions for the foundation world by building product lines designed to improve quality, safety, productivity and profitability on the construction site. In this edition of Bauma, the Company has decided to present itself with a completely revamped exhibition format by putting the customer and his needs at the center.
Based on the experience and success of the first generation, the new SR machines of the Blue Tech line have been designed to improve their productivity and operational flexibility to an evergreater extent, reducing operating costs and emissions as well as dedicated care on comfort, ergonomics and safety of operator and staff on site. The design of the Blue Tech Lines is based on the optimization of power transmission
and on the minimization of energy dissipation. Special focus has been placed on the main parts of the machine normally involved during the work cycle. The range will be represented at the fair by the most successful models for medium-sized machines, including the SR-65, and the new SR-125 platform, which was previewed at Bauma in its Blue Tech guise. The SR-65 will be configured in the LDP version, appreciated especially for its
by Ettore Zanatta At Bauma 2022 the Company from Cesena will present a completely renewed display layout, focusing on customers and their needsperformance in segmental casing piles, equipped with segmental mast and LHR mast. The choice of this configuration is to highlight its multifunctionality and ease of conversion not only between different technologies but even between different solutions within the same technology. The SR65 Blue Tech in LDP version is the maximum expression of its dynamic and aggressive character. In fact, the machine was built with a compact design that boasts high mechanical performance that is agile on site and transportable complete with Kelly bar. The SR-125 has been updated to the Blue Tech version which includes a redesigned operator cab, new hydraulic and mechanical systems improved for greater efficiency. The machine has improved characteristics compared to the previous model, HIT, mainly in terms of the performance of the rotary head, with an increased torque value and in the main winch thanks to the adoption of a closed circuit. The machine will be exhibited in CAP/CSP, a technology developed by Soilmec to build diaphragms of piles where the size of the construction site did not allow traditional methods.
The SC-135 Tiger is Soilmec’s flagship. The Hydromill the way it should be: designed to be as productive as the situation demands, unfailingly reliable and able to minimize downtime and maintenance costs. The SC-135 Tiger is equipped with a Caterpillar C27 engine capable of delivering the 708kW power required to work in demanding conditions in terms of depth and panel size. The power unit offers a complete package of solutions aimed at reducing consumption and pollution. The “start & slow” system, the automatic and independent control of the radiator fans and the optimized air flows inside the machine allow the customer to work in the most extreme temperature conditions and with severe work cycles. The excellent reliability of the SC-135 is ensured by the double hydraulic system featuring lines dedicated to the excavation module and the base machine, high-pressure filters for each return line, and an accurate drainage unit with dedicated tank. This over 200 t machine was designed for modular assembly, with a single load transport weight of 45 t. The Bauma 2022 version of the SC-135 Tiger is
equipped with the new Soilmec SH-35 excavation module. With an operating weight of between 30 and 38 tons, the SH-35 is assembled on a frame that allows for a wide range of panel thicknesses, from 650 mm to 1500 mm. To ensure a precise verticality and allow correction of any deviation there are 12 instrumented flaps. A new mud pump, hydraulic compensators with improved flow rate and new hydraulic fittings for connecting the motors are some of the developments installed on the equipment.
The Soilmec line of micropile machines will be represented at Bauma 2022 by two SM-22 and the new electric machine developed with kinematics capable of guaranteeing an extreme variety of angles and positions in different construction site conditions and with different drilling methods. The Cummins B6.7 engine, available in Stage V version, can deliver the necessary power to offer the correct support for various applications. The machine is equipped with openable hydraulic cages, ROM and SPM operating modes and all accessories / devices to ensure the
Soilmec SR-125 in North Americahighest level of accessibility, visibility and safety in compliance with the latest safety standards. The Soilmec SM-22 is truly a multi-function micro-drilling rig. Thanks to its modular design it can be easily set up in different configurations such as single rotary, double rotary, tophammer and vibro-rotary to perform consolidations, micropiles and anchors with different drilling technologies, direct circulation, reverse circulation, DTH, CFA and jet grouting.
The novelty of the line, exhibited in preview, will be the SM-13e. The project was born with the aim of creating the first electric drilling machine, evolving that path started decades ago, with the advent of the first electric motorized rigs for internal environments and in tunnels (ST-20, ST -60, SM-5E, etc..).
This is not simply a “engine replacement” to avoid the emission of exhaust gases in closed environments by connecting the
machine to an electric power cable. Infact the power transmission operates thanks to permanent magnet electric motors, lithium batteries, alternatives to cable power supplies, and control inverters. Hence a real leap forward from previous technologies. In essence this represents the first step in the development of a whole range of electrified Soilmec machines, which we call zero Emission of the E-TECH line.
Fin dal 1969, anno di fondazione, Soilmec si è sempre concentrata sullo sviluppo di valide soluzioni ingegneristiche per il mondo delle fondazioni costruendo linee di prodotti progettate per migliorare la qualità, la sicurezza, la produttività e la redditività del cantiere. Per quest’edizione del Bauma l’azienda di Cesena ha deciso di presentarsi con una veste espositiva completamente rinnovata mettendo al centro il cliente e le sue esigenze: dalla classica “sfilata” di perforatrici a un’esposi zione ad aree tematiche, che riprendessero la quotidianità dei clienti attraverso approfondimenti su macchine, tecnologie e campi di applicazione. Le attrezzature esposte andranno a sottolineare le caratteristiche distintive dei prodotti che caratte rizzano l’attuale gamma Soilmec, razionalizzata e implementata agli ultimi aggiornamenti tecnici. Tra le soluzioni proposte spiccheranno la linea “Blue Tech” di macchine da palo, sviluppata con un’architettura a risparmio energetico per garantire il miglior utilizzo prestazionale attraverso soluzioni mirate a ridurre perdite di carico e consumi, e la linea di idrofrese, sarà rappresentata dall’ammiraglia SC-135 Tiger, esposta per la prima volta a Monaco. La versatilità delle macchine per micro palo avverrà attraverso l’esposizione di modelli in differenti configurazioni e la prima macchina elettrica a batteria. Infine ci sarà un’area dedicata a digitalizzazione, controllo e formazione.
■
Soilmec SC-135 hydromill in ChinaAtunneling project is a race against time and costs. Getting it right from the very beginning requires true knowledge and experience, as well as a proper range of equipment that work whenever and wherever needed. Sandvik specialists are continuously exploring the possibilities for process and technology development. Our aim is to create machines that meet the needs of modern day tunneling, today and tomorrow.
Designed to be fast, accurate and userfriendly, the DTi series jumbos produce excavation results of the highest quality with the lowest costs. The computercontrolled tunneling jumbos include five different models for excavation of 12–231 m2 cross sections, including face drilling, bolt hole drilling, and mechanized long-hole drilling. To produce the highest repeatability and the best possible excavation predictability, the DTi series is designed for automatic use. Still, a range of practical features will allow the operator to fine-tune the process online, if the rock conditions so require. This means that a single operator
can easily manage the jumbo and all its drilling booms. The DTi jumbos utilize a valuable tunnel planning software, Sandvik iSURE, which offers an efficient way to work with blasting and drilling pattern simultaneously. The iSURE ensures optimized blasting according to plan and supplies better pull-out, decreased need for scaling, increased rock loadability and smoother collaring in the following round.
The drilling speed and exceptional accuracy of the DTi jumbos stems from the combination of high-performance
RD525 rock drills, robust booms, advanced drill string guides and an advanced iDATA control system. The control system features a variety of automation functions from full-round drilling automatics to boom positioning according to plan. Even though, the drilling process can be manually finetuned online in terms of drilling power, feed and rotation speed – still keeping the accuracy of automation in place.
The DTi series features total station navigation, an automated way of positioning the rig in the tunnel, which decreases the risk of human errors and significantly improves accuracy. One of the many accuracy-improving features of the DTi is its boom control, based on proven and tested deflection compensation. It has been improved further with ingenious features such as rollover joint and boom location compensation model. The latter also accommodates the degree of any possible boom position.
Equipped with high-frequency Sandvik RD525 (25 kW) hydraulic percussive rock drills, the DTi series jumbos can offer 10–30 % higher penetration rates. In addition to this, it can reach 17 % longer bit life and 40 % more meters per shank than the previous model in its class, thanks to the advanced patented stabilizer that dampens harmful shockwaves. The drill’s simple body structure, modular construction and
visual wear indicators guarantee ease of use and maintenance. Furthermore, excellent lubrication of the rock drill reduces part wear. Since the robust and reliable RD525 drill is built to last,
it features only few pressurized seams between functional modules. To top up the DTi’s drilling accuracy, it is equipped with a new type of front centralizer guaranteeing the best possible drill
steel guidance in the collaring phase. Keeping the drill bit inside the front guide in the collaring, it offers excellent rock contact.
The rigs’ modern FOPS-certified 3i cabin has an extra-large window surface, providing excellent visibility in every drilling application, even when the cabin is not elevated. High-power xenon-lights for drilling and tramming, an operator seat close to the windshield, and effective windshield wipers further add to it. An ergonomically designed workstation, where sophisticated controls are integrated with arm rests, offers the operator a truly comfortable and productivity-boosting working environment.
The Sandvik DTi design focuses on ease of service: The components are damageprotected, and all daily service points are accessible from the ground level. Rock drill modules can be serviced on the feed beam, and all hoses on the booms are well organized. The DTi jumbos have a built-in self-diagnostics system, which
includes e.g. real-time self-check of all computer modules, boom movement comparison, and drilling pressure and function monitoring. The diagnostics system shows where the fault is and greatly helps service personnel in identifying the actions needed.
The Sandvik DTi series utilizes Sandvik iSURE tunneling excavation management tool, which offers an efficient way of designing blasting and drilling pattern together. ISURE uses the most critical spot, the blast plane, as the basis for the whole planning process. As the drill plan is implemented to fit the blasting plane, the hole bottom
spacing and the burdens will be adjusted accordingly, the used charge defined and the cracking zone examined. As a result, hole locations and blasting are optimized. With iSURE, the whole project can be managed in concert, not just one tunnel at a time. Once good design parameters are found and defined, they can easily be imported into other drill plans. ISURE is available in four different levels: I basic, II Plus, III Premium, IV Pro. One level is different from the others in terms of functionality, from a basic to a more complete and premium experience. One of iSURE’s unique features is pull-out analysis: It combines information on two sequential rounds, accurately showing the pullout of the round under investigation. The results are then traced back to the drilling pattern, and the plan can be modified accordingly if needed.
Un progetto di scavo in galleria è una corsa contro il tempo e i costi. Per ese guirlo in maniera ottimale sono necessarie adeguate conoscenze ed esperienze, oltre a una gamma affidabile di macchine e attrezzature che funzionino quando e dove necessario. Sandvik esplora continuamente le possibilità di sviluppo di processi e tecnologie, con l’obiettivo di creare soluzioni che soddisfino le esi genze del moderno lavoro in galleria. Progettati per essere veloci, precisi e fa cili da usare, i jumbo Sandvik della serie DTi producono risultati di scavo della massima qualità con costi contenuti. La gamma di jumbo computerizzati per lo scavo in galleria comprende cinque modelli per lo scavo di sezioni trasversali di 12-231 m2. Per ottenere la massima ripetibilità e la migliore prevedibilità di sca vo possibile, la serie DTi è progettata per l’uso automatico. Tuttavia, una serie di pratiche funzioni consente all’operatore di mettere a punto il processo in linea, se le condizioni della roccia lo richiedono. Ciò significa che un solo operatore può gestire facilmente il jumbo e tutti i suoi bracci di perforazione. I jumbo DTi utilizzano peraltro un efficace software di pianificazione delle gallerie, il Sandvik iSURE, che offre un modo efficiente per lavorare contemporaneamente con lo schema di brillamento in base al piano e di perforazione.
■
The DTi jumbos utilize a valuable tunnel planning software, Sandvik iSURE®, which offers an efficient way to work with blasting and drilling pattern simultaneouslyDiaphragm walls are concrete or reinforced concrete walls constructed in slurrysupported, open trenches below existing ground.
Concrete is placed using the tremie installation method or by installing precast concrete panels (known as a precast diaphragm wall). They can be constructed to depths of 100 meters and to widths of 0.40 to 1.50 meters.
Diaphragm wall construction methods are relatively quiet and cause little or no vibration. Therefore, they are especially suitable for civil engineering projects in densely populated inner city areas. Due to their ability to keep deformation low and provide low water permeability, diaphragm walls are also used to retain excavation pits in the direct vicinity of existing structures. If there is a deep excavation pit at the edge of an existing
excavation, only small amounts of residual water will penetrate.
During production of cast in situ concrete diaphragm walls, the most important factor, especially to achieve a watertight joint, will be the use of the right stop end elements. They contain the concrete on the lateral
structure and groundwater is present, diaphragm walls are often used as the most technically and economically favorable option. They can be used for temporary supporter as load-bearing elements of the final building, they can be combined with any anchor and bracing system. Diaphragm wall panels are also used in deep, load-bearing soil layers as foundation elements to carry concentrated structural load in the same way as large drilled piles do. These foundation elements are known as “Barrettes”. If diaphragm are socketed into impermeable soil layers of sufficient thickness or if they are combined with seal slabs (grout injection or tremie concrete slabs) almost waterproof excavation pits are created. After reducing the initial groundwater level within the
side meanwhile they create a particular casting profile that offers a high seal against water infiltration. Stop End Elements are coupled together through special steel shafts even better special “o-ring” ensure a perfect seal between the areas of the diaphragm. They are made of sheet metal welded and its special profile is achieved by a process of press bending and finally an internal reinforcing structure increases its strength and avoids the risk of deformation. The excavation of a follow-up panel is carried out by clamshell grab, with the help of a special flat chisel if needed, both guided by the channel in the pipe. While digging, these tools clean the exposed side of the pipe. The trapezoidal design of the Stop End Elements, and its constructive characteristics, allows a spontaneous
Element Trapezoidal shape with rubber seal (water stop) groove and clamshell grab guide channellateral movement after the excavation, making a delayed extraction very easy. The continuity of two following panels is guaranteed even in the presence of small vertical deviations, because the excavation is guided along the stop-
end element. With this method as opposed to other working system, there is no urgency to remove the stop end element. It can be left in place for days or even weeks before extraction. A water stop can be added to the stop-
end element to improve water tightness between joints. For this purpose, a special rubber seal will be mounted on the side of Stop End Element which will come into contact with the concrete. The lateral movement of the stopend element during extraction leaves the water-stop fixed in the concrete.
SIP&T can supply Stop End Elements in various widths, lengths and profiles. They are easily jointed each other through special steel connection pin. The Stop End Elements are composed with a head element that is used for their lifting and extraction, intermediate elements and element shoe (Starter).
In addition, to facilitate the use of Stop End Elements, SIP & T manufactures a chisel cleaner kit (dedicated to the cleaning of the channel guide) and a Platform Suspension Jig/Clamping Devices (dedicated to the support of Stop End Element during installation).
L’esperienza maturata in oltre 25 anni di attività permette a SIP&T di distinguer si nella produzione di utensili per perforatrici di grosso diametro e di attrezza ture per le fondazioni verticali. La sua gamma prodotti comprende soluzioni per soddisfare le esigenze delle aziende operanti nel settore delle fondazioni speciali per la realizzazione diaframmi, pareti in cemento armato costruite in trincee aperte e sostenute da liquame o da elementi meccanici noti come tubi spalla sotto il terreno esistente. Il calcestruzzo viene posato utilizzando il me todo di installazione tubi getto o installando pannelli prefabbricati in calce struzzo (noti come diaframmi prefabbricati). I diaframmi possono essere co struiti a una profondità di 100 m e a larghezze da 0,4 a 1,5 m e sono adatti per progetti di ingegneria civile in aree urbane densamente popolate. Durante la produzione di diaframmi in calcestruzzo gettato in opera il fattore più impor tante, soprattutto per ottenere un giunto a tenuta stagna, è l’uso di adeguati tubi spalla che contengono il calcestruzzo sul lato laterale e offrono un’elevata tenuta alle infiltrazioni d’acqua. SIP&T è in grado di fornire tubi spalla in va rie larghezze, lunghezze e profili, composti da un elemento di testa che serve per il loro sollevamento ed estrazione, elementi intermedi ed elemento finale chiamato “scarpa”. Per facilitare l’utilizzo dei tubi spalla, SIP&T realizza poi un kit pulisci/scalpello (dedicato alla pulizia della guida del canale) e un disposi tivo di bloccaggio dedicato al supporto del tubo spalla durante l’installazione. Non appena il calcestruzzo inizia a fare presa, gli estrattori idraulici progettati e prodotti da SIP&T estraggono i vari elementi. Gli estrattori possono essere usati per estrarre elementi larghi da 400 a 1.500 mm e lunghi fino a comporre una colonna di 100 m. Gli estrattori SIP&T sono azionati da una centralina in dipendente composta da un telaio di base e pistoni idraulici. Come dotazione opzionale è disponibile anche un sistema a controllo remoto per il funziona mento dell’unità.
As soon as the concrete begins to set, hydraulic extractors pull out the stop end elements. They have been designed for the extraction of diaphragm wall stop-end-element having a width from 400 to 1500 mm and length up to 100 meters. SIP&T unit is operated by an independent power pack and it is composed of heavy-duty base frame with two trapezoid sliding columns maneuvered by four hydraulic rams. The system is complete with locking system pins to ensure the stop end element to the sliding frames and to prevent dropping of the column. A remote control panel to operate the unit is also available as an optional supply.
Prodotti commerciali da ufficio
Biglietti da visita, carta intestata, buste intestate, agende, calendari, planning, cartelline, raccoglitori, fatture e documenti fiscali a due o a tre copie a modulo continuo.
Espositori di tutti i tipi, varie tipologie di confezioni, shoppers, box e raccoglitori e cofanetti.
Depliants, brochures, manifesti, cartelline, locan dine, roll-up, pieghevoli, banner, tele, volantini, pannelli e striscioni.
Cataloghi e Listini Prezzi
Cataloghi di tutti i tipi e misure, con rifiniture particolari di stampa, brossura e lavorazioni specia li. Listini prezzi con varie tipologie di lavoro sia di stampa sia di cartotecnica.
Libri, volumi d'arte, riviste e manuali Libri di varie misure e lavorazioni come incollatura, brossura, punto metallico, volumi d'arte e libri.
Etichette adesive e in bobina Varie tipologie e misure di etichette adesive in carta lucida, opaca o cartonate.