You’ll never believe what these
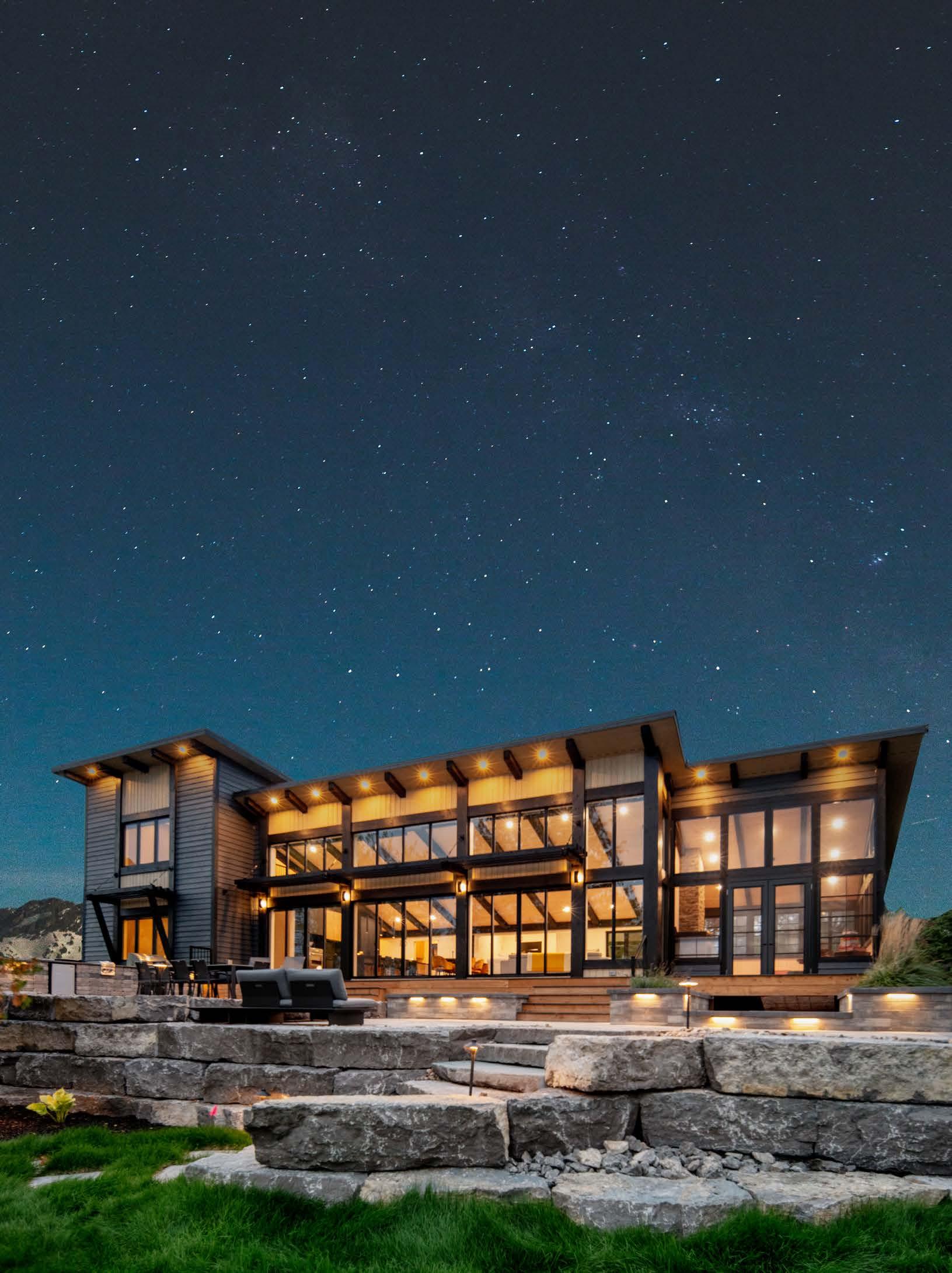
You’ll never believe what these
Five spectacular builds and the challenges they entailed
We recognize the important work done by builders and developers across Ontario. We strive to be your energy provider of choice and are committed to ensuring that Enbridge Gas adds value to every builder’s experience. The Savings by Design program promotes best practices, innovation, energy-e ciency programs and training opportunities to support the building of higher performance homes.
Connect with your regional representative today to get started.
Visit enbridgegas.com/savingsbydesign to learn more.
Stay ahead of upcoming code changes. Get customized design advice and assistance.
financial incentives.† Support your sustainability goals.
Build-to-rent is taking root in Ontario
9 Association News
Queen’s Park Day makes invaluable connections, a deep dive into Ontario’s spring legislative push, and taking in Swiss sights (and lessons) during OHBA's international housing tour.
17 Frame of Mind
A New York mid-rise project shows just how well pre-fab can stack up.
19 Inside Storey
The questions and opportunities of Enerquality’s carbonconcious demo project.
23 Trending
Great Escapes
Five luxury cottage retreats that checked all the clients’ boxes
55 Building Buzz
Lanterra makes time for a unique art form, improving access to construction defibrillators, falling land size deals, OHBA earns national honours, and more.
This R&M Smith / Discovery Dream Homes project in The Kawarthas has no shortage of rooms with a view. P38 Purpose-Built Solution
From indoor/outdoor stone and copper-toned shingles to builder insurance and insulation advice, here's what’s new in industry products and services.
62 Chapter Spotlight
Simcoe County HBA CEO Sandy Tuckey on weathering storms and finding sunnier skies for a youth initiative.
THE COVER
Innovative and user-friendly form for sustainable and resilient design
No tying required Built-in rebar holders eliminate tying
FormLock™ interlock
Patented interlock with moisure drain system
Embedded cross-ties
Two diagonal cross ties which virtually eliminate the chance of blow out.
Multiple block types available Including straight, 90° corner, 45° corner, taper top, brickledge, t-block, and radius blocks
Summer 2025| Vol. 41 Issue 4
EDITOR
Ted McIntyre ted@laureloak.ca
ART DIRECTOR Ian Sullivan Cant
CONTRIBUTORS
Tamara Aspeling, Avi Friedman, Tracy Hanes
ADVERTISING
Cindy Kaye, ext. 232 cindy@laureloak.ca
PUBLISHER
Sheryl Humphreys, ext. 245 sheryl@laureloak.ca
PRESIDENT Wayne Narciso
PUBLISHED BY
Laurel Oak Marketing Ltd. laureloak.ca
ohba.ca
Take a photo of our QR code and sign up for digital updates and news!
Ontario Home Builder is published six times per year (Winter, Early Spring, Late Spring, Summer, Fall, Awards).
A l l rights reserved. No part of this magazine may be reproduced without the written consent of the publisher. © 2025
For address corrections please email info@laureloak.ca or phone: (905) 333-9432, ext. 245.
Si ngle copy price is $6.00
Subscription Rates: Canada $14.95 + HST per year, USA $29.95 USD O rder online at https://www.laureloak.ca/subscribe
C A NADIAN PUBLICATION MAIL AGREEMENT NO. 42011539 ISSN No. 1182-1345 The
DURABLE AND LOW-MAINTENANCE VINYL AND ALUMINUM CONSTRUCTION
ALUMINUM-CLAD EXTERIOR, OFFERED IN AN ATTRACTIVE SELECTION OF COLOURS
SLEEK, 26% LOW-PROFILE FRAME AND HARDWARE DESIGN
ENERGY-EFFICIENT DUAL-PANE AND TRI-PANE LOW-E GLASS OPTIONS
UP TO 22% BETTER ENERGY EFFICIENCY
JELD-WEN® of Canada proudly introduces the groundbreaking JWC8500 series window —a perfect blend of style, performance, and energy savings, meticulously engineered to exceed expectations. Our newest JWC8500 hybrid option exceeds performance, in all regions of Canada, offering an aluminum-clad exterior finish with an exquisite selection of colours to choose from.
Discover the advantages of JELD-WEN of Canada’s most energy-efficient window. Our 8500 series windows are 2030-rated to meet Canada’s U-Factor 0.14 (U.S./I-P) / 0.82 (Metric/SI) or ER 44 building codes, and are designed to significantly reduce energy costs while ensuring year-round comfort in your home.
Tailored to meet the regional needs of homeowners, our windows are the perfect fit when planning a renovation or new home build, seamlessly blending functionality and style to suit any project.
Discover the JWC8500 series window from JELD-WEN of Canada—and experience the future of home comfort and efficiency.
OHBA’s 2025 Queen’s Park Day marked a standout moment for our association, one that underscored the power of collaboration, the value of informed advocacy and the importance of having a strong, unified voice in the provincial policy conversation.
With a record-setting 28 meetings held throughout the day with provincial ministers, MPPs and senior government staff, this year’s Queen’s Park Day marked OHBA’s most impactful advocacy day yet. This achievement was made possible by
the dedication, expertise and commitment of our board of directors, chapter chairs, executive officers and members, who showed up with purpose and clarity to champion the issues that matter most.
The day began with a focused morning program dedicated to provincial advocacy. This strategic session was designed to prepare attendees with the latest policy insights, key messaging and practical tools to ensure every conversation that followed would be impactful. From housing and affordability to regulatory frameworks and economic development, participants were well-equipped to speak to the challenges and opportunities facing our industry today.
The afternoon was devoted to faceto-face meetings with government decision-makers. These direct engagements were more than just meetings; they were crucial conversations that brought real issues to the forefront. They provided a forum to highlight the priorities of our members and offer constructive, solutions-focused input on shaping the policy environment in which we operate.
Beyond the formal agenda, Queen’s Park Day also offered invaluable opportunities for informal dialogue and in-person
connection. These moments, over coffee, between meetings and in hallway conversations, reinforced our shared goals and deepened the relationships that drive our work forward. They reminded us of the value of face-toface interaction in building trust, strengthening collaboration and energizing our collective efforts.
As we reflect on this memorable day, we are inspired by the momentum we’ve built and the path ahead. Our advocacy does not stop here. The groundwork laid during Queen’s Park Day will continue to inform and fuel our efforts in the coming months as we work to shape policy, support our members and advance the interests of our industry. OHB
The Ontario government kicked off its spring legislative session at Queen’s Park on April 6 with a Speech from the Throne, unveiling a bold agenda aimed at driving economic growth amid ongoing global uncertainty. With tariff threats from the United States looming large, Premier Doug Ford’s government is doubling down on fostering development—particularly in housing and construction—as a strategic means of strengthening the provincial economy.
Three key pieces of legislation introduced early in the session could have far-reaching implications for Ontario’s housing and construction sectors. Together, they mark a significant shift toward pro-growth, pro-trade and pro-housing policies that promise to remove barriers, cut red tape and increase the pace of development.
The first major bill, Bill 2, aims to boost economic integration by eliminating interprovincial trade barriers. By promoting freer trade with provinces such as Nova Scotia and New Brunswick, Ontario is positioning itself as a leader in Canadian economic cooperation. The bill looks to enhance labour mobility, streamline regulations and diversify supply chains—critical steps in bolstering local businesses and creating jobs.
“Free trade within Canada should be the baseline,” said one industry observer. “This legislation is a long overdue step toward maximizing our internal market.”
The second legislative initiative is a sweeping reform package designed to streamline approvals for major infrastructure, resources and housing projects. Bill 5 introduces special economic zones and a “registration-first” approval model to speed up development without compromising environmental standards.
For the home building industry, these changes could be transformative. Faster project approvals mean reduced costs and greater predictability for builders, while the broader economy stands to benefit from job creation and accelerated growth.
“This bill recognizes that Ontario can be both pro-development and pro-environment,” noted
a sector advocate. “It’s about building smarter and faster.”
The most groundbreaking development is Bill 17. Hailed by many as the province’s most consequential housing legislation in years, it received Royal Assent on June 5 and is now law. The bill takes direct aim at two of the biggest contributors to high housing costs: development charges and permitting delays. These factors have long been cited by builders as significant impediments, often adding hundreds of thousands of dollars to the final price of a new home.
This legislation responds directly to concerns OHBA has been raising with the provincial government for several years. For instance, Bill 17 makes it clear that municipalities cannot create their own municipal building standards that are above and beyond the Ontario Building Code. The bill also makes development charges payable at occupancy rather than when a permit is applied for, and limits municipal study requirements for development applications, among many other progressive measures.
The legislation is the result of extensive consultation with industry leaders, including the Ontario Home Builders’ Association (OHBA), whose data-driven insights helped shape its provisions. By addressing these systemic issues, Bill 17 seeks to restore housing affordability and ease Ontario’s ongoing housing crisis.
“This legislation is a strong step towards boosting supply, restoring affordability, and protecting jobs in the residential construction sector,” said OHBA CEO Scott Andison.
Collectively, these legislative efforts demonstrate a collaborative and forward-thinking approach to Ontario’s most pressing economic and housing challenges. By fostering interprovincial trade, accelerating development timelines and reducing housing costs, the Ford government is laying the groundwork for a more prosperous and livable province.
For stakeholders in the construction and housing sectors, this legislative session may mark a turning point—one that blends opportunity with long-overdue reform.
APPLIANCES FOR YOUR
DO IT RIGHT WITH ONTARIO’S HOME TEAM.
Doing appliances right with a partner in your own backyard has never been easier. Founded in Stoney Creek, Ontario, we’re 100% dedicated to removing the appliance burden from your projects. Our responsive team will be there every step of the way from qualifying your needs, to dealing with your clients, to facilitating a smooth onsite delivery and quickly correcting issues. Do appliances right with Goemans and scan the code to connect with an experienced Commercial Account Manager.
By Michael Collins-Williams CEO, West End Home Builders’ Association
In May, an OHBA delegation embarked on a four-day tour of Zürich, Switzerland, as part of the ninth OHBA International Housing Tour. The mission: to explore the city’s forward-thinking approach to housing, urban design and sustainable development. Zürich, often ranked among the world’s most livable cities, offered compelling examples of how thoughtful planning and architectural excellence can meet the needs of a growing urban population while preserving quality of life.
Zürich presented a compelling case for balancing density with livability. With its strong emphasis on sustainability, mixed-use development and efficient public transportation, it offers valuable
lessons in creating compact yet comfortable urban environments. We visited several transit-oriented developments, including the celebrated Zürich-West district—a former industrial zone that has been transformed into a thriving neighbourhood combining housing, office space, cultural venues and green infrastructure. Delegates were particularly struck by the seamless integration of new construction with the city’s historical character, demonstrating that high-density development need not come at the expense of community or heritage.
Our tour included ETH Zürich University, where we had the opportunity to spend the day at
an ETH
Thank you to our sponsors: Reliance Home Comfort, Building Knowledge Canada and Design Plan Services.
the National Centre of Competence in Research (NCCR) for Digital Fabrication, a Swiss initiative aimed at leading the development and integration of digital technologies within the field of architecture. The visit began with an overview of the centre’s groundbreaking work, followed by in-depth presentations on digital timber and concrete construction. These sessions, led by Oliver Bucklin and Benjamin Dillenburger, offered valuable insights into how digital tools and automation are revolutionizing the way we build, enabling greater precision, material efficiency and design flexibility.
We also had the chance to hear from a dynamic group of startups at the forefront of innovation, including Vaulted AG, Contouro GmbH, SAEKI Robotics AG and Foldcast Limited. Each presentation showcased novel applications of robotics and AI that have relevance to the future of Canada’s housing and construction sectors. A guided tour of the Robotic Fabrication Lab further demonstrated how these technologies are moving from research to reality, while the visit to Zürich’s Anergy Grid provided a compelling look
Best-in-Class performance for both Dual and Triple glazed windows
Modern and slim design with improved functionality
Triple perimeter weatherstrip for best air/water leakage resistance
Some of the best builders choose Pollard Windows & Doors for their projects. A proud Canadian manufacturer of quality products, with more than 75 years in business. Pollard has earned the ENERGY STAR Most Efficient mark for Best-in-Class performance. With expert installation, exceptional service and an industry-leading 20-year warranty, you can trust Pollard to be the right choice for new home construction and multi-level buildings.
Aluminum reinforced mullions for larger window configurations For a free estimate today, call 1.800.263.6616 or visit pollardwindows.com
at scalable low-carbon energy solutions. The exchange of ideas, hosted in part by the Canadian Embassy, left our delegation inspired and equipped with fresh thinking about how to bring these global innovations home.
As part of our delegation’s tour through Switzerland, we had the privilege of visiting the remarkable City Lounge – Red Square in St. Gallen, an ambitious and imaginative approach to public space design. This bold urban intervention, featuring a striking red carpet-like surface that unites the entire square and surrounding streets, challenges our conventional thinking about how public space can foster community identity, vibrancy and accessibility. We were inspired by how the design integrates commercial, residential and civic elements into a cohesive and inviting environment that encourages pedestrian activity and social interaction. The visit sparked valuable conversations among our group about the role of placemaking in building livable, human-centred cities, and offered a compelling example of how creative public realm design can contribute meaningfully to the housing and urban experience.
Zürich demonstrated a hyperfocus on transit-oriented development, placing livability at the core of urban planning. The city’s integration of housing, transit and high-quality design offered an inspiring framework for Canadian cities grappling with affordability and intensification challenges. With OHBA’s International Housing Tour continuing to be a valuable platform for sharing global best practices and fostering professional development, delegates returned to Canada energized and equipped with practical ideas and policy insights that can help shape better, more inclusive communities at home.
We extend sincere thanks to Canadian Ambassador and Canadian Trade Commissioner Hauke Harms in Bern for joining us and sharing his insights on Swiss-Canadian collaboration. This tour would not have been possible without the generous support of our sponsors: Reliance Home Comfort, Design Plan Services and Building Knowledge Canada. Their commitment to supporting innovation in housing continues to drive important conversations and action. Stay tuned for information on the 2026 OHBA International Housing Tour! OHB
The Navien NWP500 is built for efficiency, performance and durability with a stainlesssteel tank and aluminum refrigeration coils... no anodes needed.
The Navien NWP500 is built for efficiency, performance and durability with a stainlesssteel tank and aluminum refrigeration coils... no anodes needed.
To learn more about all the advantages of the NEW NWP500, visit navieninc.com or scan the QR code.
To learn more about all the advantages of the NEW NWP500, visit navieninc.com or scan the QR code.
Energy Star rating: up to 4.05 UEF.
Energy Star rating: up to 4.05 UEF.
Top and side connection options.
Top and side connection options.
Built-in Wi-Fi powered by NaviLink® with over-the-air software updates.
Built-in Wi-Fi powered by NaviLink® with over-the-air software updates.
Designed to meet NEEA AWHS Tier 4 requirements.
Designed to meet NEEA AWHS Tier 4 requirements.
Quiet operation, less than 45dBA.
Quiet operation, less than 45dBA.
Ambient operating range of 41°F–113°F.
Ambient operating range of 41°F–113°F.
WITH GROWING DEMAND for higherdensity housing, mid-rise prefabricated apartment buildings are emerging as a compelling solution. Their scale allows them to integrate more seamlessly into existing neighbourhoods than towering high-rises, offering both density and compatibility. When paired with sustainable materials, energy-efficient systems and public transit access, these buildings can deliver not only affordability but also environmental and social benefits.
A key challenge with prefabrication is avoiding monotonous design. This is especially critical for larger buildings, as their facades significantly influence the character of streetscapes. Fortunately, variations in materials, colours, rooflines, balconies and facade elements like shutters can address that challenge. Additionally, when prefab units are modular, their arrangement can result in unique, stacked compositions, helping to dispel the perception that such buildings are uniform. Interior variety is another advantage of prefab mid-rises. A flexible modular system can accommodate a diverse mix of unit types—from compact studios
and micro-units to spacious multibedroom apartments for families. This diversity responds to evolving urban demographics and lifestyle needs, allowing buildings to serve a broader range of residents without compromising on speed or construction efficiency.
A prime example of this innovative approach is The Stack in New York City—the Big Apple’s first prefabricated steel and concrete multi-unit residential building. Developed by Gluck+, The Stack meets the demand for moderateincome housing while also acting as a pilot for cost-effective and adaptable urban infill development.
The eight-storey building was strategically designed to maximize its narrow site. Its construction began with a resident-focused design, which was then divided into modules for off-site fabrication. While these modules were being built, the on-site team prepared the foundation and infrastructure. Once delivered, the modules were assembled in just four weeks by a crew of eight, who bolted the units together, connected utilities, completed finishing work and installed the facade.
The Stack features a ground-floor
commercial space and six residential levels. Its 56 modules include 28 apartments: six studios and six one-bedroom, 14 two-bedroom and two three-bedroom units. Rather than compromising the architecture to suit module sizes, Gluck+ adjusted the modules to suit their optimized apartment layouts, with some units and rooms spanning multiple modular sections.
Attention to detail extends throughout the building’s design. Durable materials such as sealed concrete floors and high-performance aluminum windows ensure longevity. Residents enjoy features such as tenant-controlled climate systems, Corian countertops, stainless steel appliances, maple cabinetry and WaterSense fixtures.
Beyond aesthetics and function, 35% of units have private terraces, and all residents share access to a communal outdoor space. Notably, a virtual doorman system adds an extra layer of security and convenience. And its location—close to parks, transit and major roads—supports urban living.
By merging design flexibility, construction speed and thoughtful urban integration, The Stack offers a blueprint for the next generation of sustainable, inclusive and efficient city living OHB
AVI FRIEDMAN IS AN ARCHITECT, PROFESSOR, AUTHOR AND SOCIAL OBSERVER. AVI.FRIEDMAN@MCGILL.CA
By Ted McIntyre with Rose Benedetto
“THE URGENCY to reduce carbon emissions in the building sector has never been greater—and Ontario’s building community is uniquely positioned to lead,” says Enerquality Managing Director Rose Benedetto. “Buildings are one of the largest contributors to greenhouse gas (GHG) emissions, both through operational energy use and the embodied carbon in materials and construction. As climate change accelerates, regulatory and market pressures are converging.”
To that end, Enerquality has initiated its Carbon-Conscious Construction Project. Focused on operational and embodied carbon in new residential construction, the project examines materials analysis and energy consumption, highlighting best practices and innovative solutions that reduce emissions and support climateresilient construction. The goals
include educating builders, developers and homeowners about the carbon impacts of residential construction and how they can make informed, lower-carbon choices, driving market demand for these types of products and systems, providing a cost-benefit analysis of using low-carbon materials and identifying financial incentives or lifecycle savings; and supporting better design decisions through lifecycle assessment.
The demo project has been brought to life through two core storytelling pieces: a video featuring interviews with manufacturers and product installers, and a webinar where industry experts and project participants shared insights, findings and recommendations, including a live house tour.
Chatting with Ms. Benedetto, we explored the potential benefits—and costs—of pursuing this path.
OHB: What was the genesis of the Carbon-Conscious Construction Project?
RB: “The idea was sparked by one of our manufacturer partners whose building material is often criticized for its carbon intensity during production. They wanted to demonstrate how, over the full lifecycle of a home, their product significantly reduces operational carbon emissions—ultimately offsetting its embodied carbon footprint. We found several building material suppliers who wanted to share what their companies were doing to offset carbon.
“The demo project launched in October and was completed in March. One of our Energy Advisors, who was already active in this space, connected us with Bill Hasso, a construction manager at Lakeview Homes, who saw the value and enthusiastically stepped forward to join the project.”
Did anything come out of this project that caught you by surprise?
“Yes. One was how quickly the builder team embraced the carbon-conscious mindset once the data was presented in a practical, performance-based context. What began as a technical demonstration evolved into a deeper conversation about material choices and long-term energy performance, and how these decisions align with climate goals and customer expectations. Another unexpected insight was the potential for collaboration across the value chain. From the supplier to the Energy Advisor to the builder, each partner brought a unique perspective that enriched the project and highlighted how meaningful carbon reduction is achievable when stakeholders align.”
How can you allay builder fears of added costs of going down this road?
“This project highlights the kind of support builders will need if carbonrelated requirements are eventually mandated in the building code. That includes financial incentives or subsidies to help offset costs, especially
during the transition phase. Without meaningful cost relief, even wellintentioned policy can become a barrier rather than a catalyst for progress.”
Will there be a universally accepted system to track the carbon footprint of each product?
“Working through this demo project, we can say that we are not quite there yet—but we’re getting close. Tools like Environmental Product Declarations (EPDs) and platforms like EC3 are helping track the carbon footprint of materials, but we still need a simpler, universal system. The goal is clear: make it easy for builders to choose low-carbon options without needing a PhD. And we’re working with industry partners to make that a reality.”
Each of the subtrades and suppliers would need to know the numbers for these various components.
“Yes, each will increasingly need to quantify the carbon footprint of their products and systems. As carbon accounting becomes more common, builders may begin factoring this information into procurement decisions. In other words, the carbon performance of a product or system could influence which materials, manufacturers or trades are selected—right alongside cost, quality and availability. This shift could drive greater transparency and innovation across the supply chain, as everyone from insulation suppliers to HVAC installers looks to demonstrate lowcarbon value to stay competitive.”
Are the products involved readily available and cost-effective?
“Many used in carbon-conscious building, such as advanced insulation, low-carbon concrete mixes, highefficiency HVAC systems and low-GWP (global warming potential) refrigerants, are already available in the market, though availability and pricing can vary by region and volume. While some options currently come at a premium, costs should decrease as demand grows.”
Is there a fear that policymakers might determine thresholds and essentially dictate the supply chain?
“Yes, there is certainly apprehension this could happen. It could feel like a loss of flexibility, especially for smaller builders who may struggle to adapt quickly. The key is ensuring
that policymakers work collaboratively with industry to set achievable, phased targets that allow time for adaptation, provide financial incentives and technical support to ease transitions, and foster market transparency around product carbon footprints.”
How significant a difference can builders make vs. standard practices?
“Builders adopting carbon-conscious practices can achieve meaningful reductions in both operational and embodied carbon, often in the range of 20%-40%— and sometimes significantly higher when pursuing Net Zero or advanced certification programs. From an ROI perspective, these improvements translate into the following: lower energy costs for home owners, which boosts market appeal and resale value; stronger differentiation in a competitive market, attracting increas ingly eco-conscious buyers; access to incentives and rebates that help offset upfront costs; reduced risk of future retrofit expenses as codes tighten and regulations evolve; and the potential for premium pricing on high-performance homes, depending on market demand. While some upfront investment may be required, the long-term financial benefits and reputational gains often outweigh the costs, especially as sustain able building becomes mainstream.”
Might there be unintended conse quences of selecting products with low embodied carbon?
“Some low-embodied-carbon products or materials may have different perfor mance characteristics than traditional options, which could lead to issues like air or moisture leaks if not properly integrated into the building system. However, this risk can be managed through careful design, proper instal lation and rigorous quality control. It’s essential to follow best practices and work closely with architects, energy advisors and building scientists to ensure system compatibility. And many low-carbon products are, in fact, designed specifically to maintain or improve building durability and indoor air quality. The key is not to compromise performance for carbon reduction but to pursue solutions that deliver both. By investing in training and oversight, builders can avoid unintended conse quences and deliver homes that are both low carbon and high performance.”
NOVEMBER 2024
JANUARY 2025
Our streamlined precast solution helps you build faster without sacrificing quality. From planning to install, every step is optimized to save time and keep your project on track. When timelines are tight, FastTrack delivers. Example shown
Rinox stands out for its strong commitment to sustainability. Our products emit, on average, 31 % fewer greenhouse gases than the competition. Since 2015, this reduction has helped prevent 34,000 tons of CO2 emissions. That's equivalent to driving 140 million kilometers, or about 16,000 times around the Earth. In environmental terms, it equals the CO2 absorption of over half a million trees. Choosing Rinox means making a real impact on the planet while maintaining exceptional quality and design. A
Rinox stands out for its strong commitment to sustainability. Our products emit, on average, 31 % fewer greenhouse gases than the competition. Since 2015, this reduction has helped prevent 34,000 tons of CO2 emissions. That's equivalent to driving 140 million kilometers, or about 16,000 times around the Earth. In environmental terms, it equals the CO2 absorption of over half a million trees. Choosing Rinox means making a real impact on the planet while maintaining exceptional quality and design.
Continuing your brick or stone to the back of the house sets a dramatic stage for outdoor living while saving clients from future expense. Arriscraft’s calcium silicate brick and stone offer a unique fine-grain texture. And since it’s natural stone, made from just sand and lime, it will never fade, chip or require maintenance. Choose from a vast range of styles, colours and custom blends (pictured: Cashmere tone of Citadel Building Stone). ARRISCRAFT.COM
Copper brown roofs are making waves in 2025, echoing the popular back-to-nature trend with their earthy, timeless appeal. These warm hues—copper, tan and orange—are transitioning from interiors to exteriors, offering a cozy, organic look that suits diverse architectural styles. BP Canada highlights Signature Mesquite, Toscana and Dublin shingles (pictured) as top picks, with the latter blending copper tones with grey for added visual depth. BPCAN.COM
More stringent building code requirements are making continuous insulation (CI) an increasingly popular method to meet and exceed codes and help achieve Net Zero performance. CI offers thermally effective assemblies that can help provide external air barriers and weather-resistive barriers, along with enhanced control of concealed condensation, while allowing for an economical construction compared to other high-RSI (thermal-resistant) wall alternatives. Builders can create a high-performance building envelope using Tyvek HomeWrap and flashings. DUPONT.COM/CONSTRUCTION-MATERIALS.HTML
The new Hawa Concepta III from Häfele’s is a versatile “pivoting pocketing” door system designed to bring efficiency, flexibility and sleek design to contemporary interiors. Featuring a straightforward, tool-free installation process and intuitive push-to-open functionality, it allows for both single and bi-folding doors to pivot open and smoothly glide into an ultranarrow pocket of just 2-3/16” wide. Ideal for kitchens, offices, closets and more, it creates multifunctional, customized spaces while concealing clutter and effortlessly partitioning off rooms. HAFELE.CA
The new Bosco Collection by Rialux features lightweight, rustproof aluminum siding panels with the warm, textured look of natural wood. Easy to install and built to last, these panels offer a stylish, low-maintenance alternative for exterior cladding—ideal for elevating the look of any project while complementing a wealth of home exterior surfaces. RIALUX.COM
Schluter’s new Kerdi-Line-A adaptor kit upgrades older shower drains to work with Kerdi-line linear drains. It joins Kerdi-Drain-A— now redesigned to fit more drain types—and is compatible with tileable grates. It transforms traditional two-part liner drains into modern bonded flange drains, creating a more durable and longer-lasting waterproof system. With adaptor rings, installers can upgrade withouttearing out the old setup, saving time and money. SCHLUTER.CA
While fire and water damage remain top risks for home builders, there are many more—from slips and falls to cyber-attacks to equipment theft. Download the latest whitepaper by Federated Insurance on these risks and see how Federated can help home builders protect against these ongoing hazards. Take a look to better understand your potential exposures and take steps to help keep your projects moving forward on time and on budget. FEDERATED.CA
Helping to extend outdoor living beyond the summer, Napoleon’s Phantom Freestand Electric Heater is crafted for exceptional versatility. It features a foldable cantilever design, providing precise, multi-directional warmth wherever it’s needed. Using infrared technology, it effectively heats people and objects directly rather than the surrounding air, ensuring efficient and targeted warmth. Its lightweight, portable frame ensures easy repositioning, while the eight-foot cord offers flexibility for greater placement options. NAPOLEON.CA
Featuring a 10-in. bar and chain and a telescoping shaft that extends to 11.5 feet, the rugged new brushless, cordless DeWalt 60V Max Pole Saw kit delivers the reach, power and efficiency to make demanding, hard-to-reach cuts. Engineered to meet the needs of professional arborists, it’s easy to assemble and use, cutting through an 8” log 2.7 times faster than a 28cc gas pole saw. DEWALT.CA
By Jonathan Oke
With the world in such flux, cottage country provides a most welcome retreat for tens of thousands of Ontarians. But some new projects— customized to the clients’ every wish and packed with dazzling views—go far beyond mere cabins in the woods.
So is the market for luxury lakeside estates more resilient than for more modest cottages?
“This market remains robust and unwavering, with a steady stream of clientele investing in cottages, boathouses, bunkies and more,” says Andrew Hall, Project Manager, Luxury Homes & Cottages, at Bachly Construction. “These homeowners belong to a distinct niche where demand for new builds remains consistently strong—driven
by a fast-moving market and a desire for refined, high-end finishes. Full-scale rebuilds and luxury renovations are increasingly becoming the standard.”
Andrew Burtch, engineering and operations director at Haliburton’s G.J. Burtch Construction, says he has observed “a considerable increase in the renovation market, including upscale projects. Our ability to undertake both renos and smaller projects is proving to be a definite advantage in the current economic climate.”
But there are still awe-inspiring new builds to be had. Consider Burtch’s brand-new 5,000 SF project in the Haliburton Highlands as well as these four other recent OHBA member-built waterside wonders.
Lake Joseph, Port Carling (7,231 SF)
BUILDER: Bachly Construction
COMPLETION DATE: Summer 2022
The mesmerizing vistas from this Port Carling property come with the territory, but what Bachly did on the inside rivals those views. Consider the two-storey circular library with its ultra-high-gloss paint finish, or the winetasting room and cellar, replete with a flat-topped and polished granite boulder for display, or the pebbled and leather flooring to protect dropped wine bottles. And then there’s the spa, with its sauna, cold plunge, shower and massage room, with handpicked, quarry-sourced Fantastico Danby marble flooring.
Beyond the sprawling cottage itself—7,231 SF including basement—there’s an additional 990 SF above the 3,000 SF boathouse. (Although current regulations allow for a maximum of 650 SF for an upper boathouse, Bachly was permitted the extra room based on the previous structure that was torn down.) While a second boathouse is in the design phase, the main boathouse has a capacity for eight vessels. Above, there’s a rooftop patio, arcade room and bar. Below, a helicopter pad and expansive custom deck adorn the water.
Construction on an island always adds logistical challenges due to limited access, and this project was no different. The hovercraft used for transporting materials had size and weight limits, requiring multiple trips and careful planning to move heavy or bulky items. Transporting tradespeople and workers daily was also complex, often needing boats or other watercraft to shuttle teams back and forth. Winter construction added further difficulty, affecting transportation schedules, deliveries and storage, while requiring additional safety measures.
(Location withheld) (10,764 SF)
BUILDER: True North Log & Timber Homes COMPLETION DATE: 2023
This extraordinary log home, spanning nearly 11,000 SF of living space, draws inspiration from the bold, rustic architecture of Montana, Wyoming and Colorado. Its grand scale and distinctive silhouette offer undeniable curb appeal, with an exterior that artfully blends cedar shake, log and rustic channel siding beneath varied rooflines.
Inside, the soaring great room immediately impresses with expansive views and a dramatic 16-foot stone fireplace. Overhead, handcrafted pine timber trusses, 10”x16” ridge beams and 8”x12” rafters elevate the space, continuing seamlessly into the primary suite for a unified architectural aesthetic.
The primary ensuite is a luxurious retreat, featuring spa-like finishes, rich tilework, gold accents and generous windows that bathe the space in natural light.
Downstairs, the lower level is designed for both relaxation and entertaining, complete with a curated wine collection, a private theatre, games room and a wellappointed bar and kitchenette.
Haliburton Highlands (5,000 SF)
BUILDER: G.J. Burtch Construction
COMPLETION DATE: May 2025
This 5,000 SF home was built for a masonry products supplier. As such, even more attention than usual was paid to the selection of stone, architectural details and installation. The intricate work is exemplified by a trio of hand-built fireplaces and a striking stone feature wall that spans the entire three-storey stairwell.
The dark tree bark of the surrounding oaks inspired the colour of the bricks, which were produced in kilns that date to the 1800s. Employing a Frank Lloyd Wright style, the 2 ¼”x16” bricks provide a plank siding effect.
An abundance of floor-to-ceiling windows offers dazzling panoramic views of two lakes and a distant ski hill. The lower level is a destination for wellness and recreation, including a lake-facing workout room, family music studio, wine cellar and walk-out lounge.
Accessibility was a central focus, with extra-wide hallways on all levels, a barrier-free ensuite bathroom featuring a walk-in steam shower, motion-activated lighting throughout, and a centrally located custom elevator that provides access to all levels.
Integrating a building of this scale into a 22m natural elevation change from the road to the lake required relocating excavated foundation material toward the lake. That enabled Burtch to effectively terrace and reshape the landscape, complementing the architectural design. That included creating a sub-basement level with a garage door to store recreational vehicles and cottage equipment.
A key innovative feature is the state-of-the-art double boiler system, which provides heating and domestic hot water. Monitored by personal computer and phone, it is fuelled by hardwood pellets, combining efficiency with environmental consciousness. Superheated glycol is then pumped through underground insulated pipes to the main mechanical room, where it’s used for the radiant floor and forced air systems. Along with being insulated far above code, the structural framing is wrapped with vapour-permeable sheathing and 1” of rockwool to reduce thermal bridging.
Why settle for less? For beauty, convenience, durability and ease of installation, ALIGN® Composite Cladding from Gentek® is the best of all worlds while delivering the distinctive look of real wood.
Vinyl, wood and fiber cement siding don’t match up. ALIGN never needs painted. It’s moisture resistant, so it won’t swell or warp. It’s impact resistant against dents, dings and hail. Its insulating performance prevents energy loss.
ALIGN gets an upgrade. A full suite of accessories like J-channel, trim and corner post profiles, colour-matched to ALIGN 7" plank and 12" vertical Board & Batten.
These accessories are part of the full ALIGN solution that creates a seamless, high-end finish with fewer crew members and no caulking, sealing or painting required.
More cost savings
Increased time savings
Efficient jobsite handling
Better quality
Longer durability
Beautiful results
Find ALIGN Composite Cladding and ALIGN accessories at your closest Gentek retailer. gentek.ca/align
Lake Muskoka, Port Carling (3,134 SF)
BUILDER: Confederation (1867)
Log & Timber Frame
COMPLETION DATE: 2023
Listed in June for $5,755,000, this residence towers over Lake Muskoka on a 2.3-acre lot with 205 feet of pristine eastern-facing frontage.
A steep incline to the driveway and limited space made material deliveries a challenge during construction, as did the winter (and Covid) timing of this build—one in which the homeowner served as the general contractor. But the finished product was well worth the effort.
The angled garage, dormer windows and vaulted ceilings create striking rooflines, while timber accents tie everything together in this marriage of log and timber-frame styles. But it’s the colour palette that makes this home unique. Speckled stone-hued shingles complement the dark exterior stain, while whitewashed timbers brighten the interior.
It features a huge front deck, lakeside hot tub, screened Muskoka room, ample outdoor entertaining space with a fire pit, and a fullhome generator.
Additional upper-level space provides room for games, media or extra sleeping quarters.
Take curb appeal to backyard bliss, by designing with outdoor living in mind. Extending character-rich masonry to the back of a home delivers the ideal backdrop for stunning backyard spaces that perform for generations. Arriscraft’s unique calcium silicate brick and stone never fades, damages or requires maintenance. Our distinct masonry products help retain the beauty and value of homes for a lifetime. Now that’s thinking ahead.
Chemong Lake, Selwyn (2,900 SF)
BUILDER/SUPPLIER: R&M Smith Contracting / Discovery Dream Homes
COMPLETION DATE: June 2022
The clients, one a retired doctor and the other still working at Toronto Sunnybrook Hospital, wanted a cottage to enjoy evening campfires and waterfront fun with their family. They sold their ski chalet in Collingwood, found a property on a former trailer park in the Kawartha Lakes, and selected Discovery Dream Homes as their company of choice. Discovery design consultants worked with the clients to develop a site-specific timber frame design, while sourcing one of their preferred builders, R&M Smith Contracting.
While excavating, Smith found lake water at a depth of just over four feet, requiring them to build at a depth above this with an engineered reinforced pad foundation.
The clients desired a modern millwork finish and drywall return windows with no trim, although they agreed with Smith to include a minimalistic baseboard and door trim.
Despite challenges of delays during Covid, Smith polished off the project within the 12-13 month timeframe the clients had requested.
The four-bedroom modern design is highlighted by the striking façade of west-facing, floor-to-ceiling, wall-to-wall glass. OHB
Could build-to-rent be a practical housing model in Ontario?
By Tamara Aspeling
While there’s no debate that Canada has a housing problem, the solution is complex. Affordability remains the highest hurdle. Although Ontario’s average salary has increased to $69,068, according to a December 2024 report from Statistics Canada, the average home in Ontario costs $860,000, which means buyers would need a downpayment of $172,000 and minimum earnings of nearly $190,000 per year to qualify for a mortgage on that home. That means even dual-income households will likely fall far short of the required numbers in most cases.
That leaves investors, who so far have driven the property market in many parts of the country. However, with recent reports of demand for condos dropping in hot markets like Toronto and vacancy rates increasing, there’s clearly something up among the buy-to-rent demographic, too.
So it seems there’s a gap in the market, and a model known as build-torent (BTR), or sometimes purpose-built housing, could be poised to fill it.
No one knows for sure when the first project of this type was constructed, and there’s a good chance its earliest origins are lost in the mists of time. But we do know exactly when it started gaining ground in North America.
In 2008, immediately following the Great Recession, property developers in the United States, constrained by lower demand for new homes, pivoted to BTR in response to the economic climate. By 2022, there were about 350,000 BTR units in the U.S. In 2023, another 27,500 were added, and in the first quarter of 2024, construction on another 18,000 commenced.
It’s not just apartments, either.
According to the U.S. Census Bureau’s Survey of Construction Data, 90,000 single-family BTR homes were started in 2024, up from 60,000 the year before. Although exact statistics about BTR inventory in the U.S. are hard to pin down, it’s safe to say that this type of development is well entrenched in our neighbours to the south. And while build-to-rent homes might be a newer concept in Canada, the current economic conditions would appear to support this kind of development.
David Gerrard and Adam Peaker
certainly think so. Both come from construction backgrounds. David worked as a project manager at Graham for several years before moving on to management roles at Melloul-Blamey Construction. Adam’s experience ranges from founding an energy company to industrial sales for CGT (a global leader in hightech plastics) and several years in the investment side of the development world with Brookfield and TD Bank. In November 2022, the duo chose to go all in on build-to-rent development with the founding of Livwell Developments. And things have progressed quickly. Despite a core team of just four people, they’re on track to have over 600 BTR units completed, rented or ready for tenants in the near future. They certainly seem to have cracked the code, and according to Gerrard, it’s all about the mindset. “I see a lot of people, predominantly condo builders, kicking tires on this model because they have many projects that can be switched over to rental. But I haven’t seen too many actually pull the trigger
“I see a lot of people, predominantly condo builders, kicking tires on this model because they have many projects that can be switched over to rental. But I haven’t seen too many actually pull the trigger yet.”
yet. When you get entrenched in a way of doing things, it’s sometimes hard to make the switch.”
Since Livwell has been a BTR developer from day one, they haven’t had to make any big changes to their way of thinking, which has allowed them to focus on the most important things to ensure success in this kind of property development. One thing they have clearly mastered is speed of delivery. They constructed their first 50-unit building in just nine months, which is, by any metric, a blistering pace. To achieve this, Livwell collaborates with municipalities that are committed to expanding rental inventories, which in turn accelerates the permitting and approval processes.
However, Livwell has also focused heavily on systems and uniformity, often in collaboration with Stubbe’s, whose precast systems they use on many of their developments.
“What we’ve tried to do is standardize and limit the customization of the units,” Gerrard explains. “So where a standard condo development might have 15 different layouts, we try to aim for five. And we try to make the designs repeatable across projects too.”
It’s a system that enables the Livwell team to procure materials in bulk, establish a network of tradespeople who are familiar with the designs and specifications, and stockpile
- UP TO 17.2 SEER2
- UP TO 17.5 SEER2 / 8.5 HSPF2
•True Inverter experience that provides the ultimate in comfort for a homeowner.
•40% smaller, and 53% lighter than traditional cube style units.
•Environmentally friendly - Now available in R-32, using less refrigerant.
•Ultra quiet and best in class humidity control.
• Available in Air Conditioner, Heat Pump, and Dual Fuel (Hybrid) applications!
“We think of it as the Ikea of apartment buildings.”
replacement parts and materials for the rental phase of the project.
These new, purpose-built developments aren’t what you would expect from rental housing either. Rather than builder-grade finishes and notorious ‘landlord-grade’ repairs and maintenance, tenants in these developments enjoy secure, luxurious lobbies, indoor and outdoor communal areas, on-site gyms and other lifestyle amenities that you wouldn’t normally expect in a rental community.
Design-wise, these new rentals are also head and shoulders above most of what is out there, with sleek modern designs and quality materials that look more like a high-end condo than a typical rental unit.
If Livwell is the new kid on the block, at least as far as the company itself is concerned, Stubbe’s is a true veteran. The company has been in operation since 1982, when it began producing precast products for the Ontario agricultural industry. They later transferred their precast concrete experience into hollow core floors, adding wall panels, beams
and other structural concrete components over the years. They even built a ready-mix plant and acquired a rail terminal to grow their precast concrete business. So it was probably no surprise when this seasoned innovator got involved in build-to-rent, nor that their chosen method of construction was precast concrete.
Stubbe’s builds rental communities, but they also sell their Fast Track precast system to other developers working in BTR and traditional construction. And like Livwell, they’re committed to systems and standardization. Or, as Jason Stubbe says, “We think of it as the Ikea of apartment buildings.”
He means it in the best possible way. By standardizing their Fast Track building system in partnership with BIM Studios, they can deliver completed projects faster and at a significantly lower cost than traditional builders. A recent development delivered 130 units in nine months at a cost of $224 per square foot. When you consider that comparable quotes from traditional builders in the same area are about $300 per square foot, that’s an astonishing cost savings.
And there is more good news. “Unlike
traditional building where prices are volatile, we can typically lock in prices for six months to a year,” says Stubbe. While Livwell is laser-focused on purpose-built housing, Stubbe’s is involved in many different areas of construction, from materials to construction and nearly everything in between. Still, the message about BTR is the same. You need to do it at scale, standardize as much as you can, and keep it simple.
While many companies involved in BTR projects focus on high-density developments, such as apartments and low-rise, some are expanding into the single-family space. Toronto’s Core Development Group invests in renovating single-family homes specifically to keep them as rental housing, but they have also started to develop single-family BTR properties, duplexes and townhomes.
In fact, between Core Developments and its subsidiary Avanew, this purpose-built housing investor is betting big, with $1 billion planned for rental housing investment. But Core’s approach to BTR is, by their own admission, unique. On its Avanew page, the company describes itself as a pioneer in single-family rentals, or SFR.
Not that it’s all sunshine and roses in the SFR space. In fact, ACORN, a prominent anti-poverty group, is concerned that this kind of investment in rental housing might harm rather than benefit would-be renters in Ontario. Clearly, there is a misalignment between what renters want and need and what developers like Core are proposing, but the fact remains that based on its own research, 81% of Ontario renters don’t want to live in condos or apartments.
When you consider that statistic and the enormous investment Core has planned for this sector of the BTR market, there’s certainly room for a lot more of this kind of development.
Younger people, starting out and unable to manage those eye-watering homeownership figures, are, expectedly, well represented among renters. But both Livwell and Stubbe’s have experienced considerable interest from
a surprising market segment: empty nesters who have sold their too-large family homes and are embracing these high-end, lock-up-and-go developments for their retirement years.
That’s good news for the housing market, too, because there are tens of thousands of family homes occupied by senior singles and couples, and when they choose to sell, that stock becomes available to the next generation of families.
While companies like Livwell and Stubbe’s are doing something relatively new in Canada— building properties with the goal of retaining them long-term—they’re still running into some of the same issues. Occasionally, the bottleneck is with city engineers, as Stubbe experienced when they ran afoul of an engineer who would not approve a precast concrete project, permanently mothballing it. (The City of Toronto has since approved Stubbe’s Total Precast system.)
Sometimes, municipal planners are less enthusiastic about building rental homes in certain areas. But the simple solution, as Gerrard says, is to “work with the communities that want this kind of development.”
Often, the biggest problem is programs that are put in place with good intentions but need some tweaking to deliver maximum benefit. Livwell found that while the Canadian Mortgage and Housing Corporation’s
MLI Select multi-unit mortgage loan insurance financing program helped fund their developments, the criteria changed frequently, making it much harder to standardize designs in the way they are critical for this kind of development. This type of funding also prohibits developers from holding condominium titles on their developments, meaning they can’t sell individual units while retaining others as rentals, which could be a roadblock for risk-averse developers.
Stubbe’s, who chose to use CMHC’s Rental Construction Financing initiative—now the Apartment Construction Loan Program (ACLP)—found the biggest hurdle to be the time from application to funding, which in their case was close to six months.
However, despite the hurdles and roadblocks, governments recognize rental housing as a critical part of the Canadian property puzzle. The CMHC’s ACLP has already invested nearly $22 billion, which has facilitated the construction of nearly 57,000 units,
Furthermore, CMHC notes that the processing time for ACLP applications decreased to an average of 60 days in 2024, while those who qualify for the MLI Select program can expect processing in approximately 44 days.
It’s not only the federal government that is interested in financing and supporting purpose-built housing. Cities like Toronto have programs such as the
Rental Housing Supply Program, which provides funding of up to $260,000 for approved rental housing projects. As the building plan coalesces across all levels of government, expect to see even more funding and support options like these.
The key test for these kinds of programs, however, will always be how well every organization and level of government can engage with the people on the ground and build programs that work for them. While criteria must ensure that only bona fide projects are funded, they also need to be flexible enough to allow for widespread use and access.
If the big question about BTR developments is whether they are feasible for the Ontario market, the answer is a resounding yes. If the question is whether traditional builders and developers will embrace this kind of project, the answer is more of a maybe.
There’s no doubt that there are millions of Canadians who can’t afford to do anything but rent. There are hundreds of thousands more who are looking to downsize from larger, family homes into more manageable properties. There are also many families looking for single-family or duplex rentals that offer space for kids, pets and summer cookouts.
So the market is unequivocally there for purpose-built rental housing. But this type of development is also relatively new in Canada, and that means there’s also a little more risk and uncertainty. When companies build rental properties for a REIT or another kind of investor, there’s a clearly defined finish line. They know precisely how much they will make and when they will exit the project. However, when the project is a BTR development, there’s no exit date, and like anything new, that can be daunting for companies that are a little more risk-averse. Of course, with bigger risks comes bigger rewards in the form of long-term, semi-passive income.
There are no crystal balls in construction and real estate. But it certainly seems less risky to build with renting in mind than to bet on enough people being able to afford to buy—at least for the foreseeable future. OHB
WE DIDN’T SEE THAT ONE COMING WELL,
By Tracy Hanes
issing raccoons, infestations of mice and old newspaper clippings are typical surprises renovators come across during the course of a project. But some of the discoveries they’ve come across behind walls, in ceilings or basements are extra weird.
Fifteen years ago, Lindsay Haley, director of construction for Ottawa’s Amsted Design-Build, was in Rockport to check out a house where a homeowner wanted to add a basement. “It was an old home set back off the road, and it was an eerie drive down the driveway and through the woods—the type of job where you don’t know what you’re getting into,” he says. “The property was overrun; there was so much stuff everywhere.”
When Haley knocked on the glass front door, a husky lunged at him from the other side of the glass. The owner soon joined the dog and coaxed it away—by offering it dead mice.
There was no access from the house to the crawl space, so Haley had to shimmy under the house through a tiny basement window.
“When I got in there, it was three feet from the ground to the bottom of the house,” he recalls. “I dug a test
hole and hit something that appeared to be a rock. I discovered it was a large bone, perhaps a human femur. The owner was standing outside, asking what I found. It’s 6:30 at night, it’s getting dark, and I’m lying within inches of the bone I dug up.”
A freaked-out Haley backed out from under the house, told the homeowner about his discovery, and the man called the OPP. A forensic unit was brought in to test the bone. The homeowner called Haley a few days later to share the results: the bone was from a horse, not a human.
Despite Haley’s relief that he had not crawled up on human remains, “that job wasn’t for us,” he says.
On another occasion, Haley was asked to provide a quote for an ensuite bathroom. “I found a goat in the bedroom standing on their bed. It followed me downstairs later and got a drink out of the dog—or should I say goat—bowl.”
You’d think this would have been a once-in-a-lifetime sort of encounter, had it not been for the goat Haley discovered standing on the hood of his car at another job.
Some encounters with creatures haven’t been as whimsical. “We did one job along the St. Lawrence River where we had to move a boat to do the work,” Haley relates. “As we’re moving the boat, gray ratsnakes were slithering out of a back drain hole. The next day, I was working and looked down to see one wrapped around my boot.”
Although Haley wasn’t on this particular job, an Amsted crew had to deal with a nest of camel spiders behind a wall they demolished to create an ensuite bathroom in a second-floor condo in 2023. Usually found in the deserts of the Middle East, in the southwestern U.S. or parts of Asia and Africa, the arachnids aren’t venomous but have a painful bite. Haley says if reptiles, insects or animals are found on a job, they typically don’t try to move or disrupt them but instead call in professional removal services, as they did in this case.
While many unusual finds are discovered at lower levels, one could be described
as ‘high’ for Scott Wootton. The former owner of Kawartha Lakes Construction, who now works in marketing for the company, Wootton remembers being hired to refinish an attic in an older two-and-ahalf-storey house in Peterborough for the home’s new owner. As the crew got busy with the attic reno, which took place before marijuana was legalized in Canada, they found a medium-sized bag hidden deep in a recessed corner of a hipped roof.
“It was about the size of a kitchen-sized garbage bag and was clear plastic,” says Wootton. “It was full of weed. There was a lot. I’d say there was about a pound of it.”
“IT’S 6:30 AT NIGHT, IT’S GETTING DARK, AND I’M LYING WITHIN INCHES OF THE BONE I DUG UP.”
They hung the bag off the collar ties and put it in plain sight to see what would happen. The insulators came in and moved it, and it disappeared somewhere during the drywall stage.
Wootton knew the prior owner of the house and, a few years later, ran into her by chance. Knowing that “she was cool,” he told her about the bag of weed found in the attic of her former house and asked her if one of her kids used to smoke pot. He did.
A renovation job in Milton left no stone unturned, and that yielded a startling discovery for Sedgwick Marshall Heritage Homes Ltd. The Milton-based company restores and rehabilitates century heritage homes that new home builders such as Mattamy, Argo and Branthaven acquire on properties they plan to develop. A find made during a restoration of a house on Robert Street in Milton 20 years ago was strange, but that was just the beginning of an even stranger story.
While the home’s original pathway was being torn up to make way for a new one, a large mid-1800s tombstone was unearthed. It had been turned upside down and used as a stepping stone.
Mirella Marshall and her partner, Mandy Sedgwick, belong to the Milton Historical Society and knew another member, John Duignan, who collected local historical memorabilia. They asked him if he wanted the stone, and he said yes.
Duignan has an insurance office in downtown Milton and rented part of his building to a new-age metaphysical supply firm. The building is old, and Duignan and his staff claim to have experienced multiple other-worldly encounters, such as a playful spirit that once yanked files back from a staff member who was trying to pull them off a shelf. A medium visiting the shop walked up to Duignan’s office to investigate the spirit in the file room. She told Duignan she was receiving messages from Jennifer, Duignan’s late sister, who had died from cancer. In addition to reassuring Duignan that his sister was fine, the medium said Jennifer was trying to introduce him to someone named Jacob.
“I don’t know any Jacob,”
“I THOUGHT I’D BETTER CHECK THAT THE TOMBSTONE WASN’T MISSING FROM A CEMETERY.”
Duignan said. The next day, he went to Marshall’s to pick up the tombstone and was surprised to see the name on it: Jacob Inglehart, who died on April 7, 1852, at age 54.
“I thought I’d better check that the tombstone wasn’t missing from a cemetery,” Duignan relates. “I went online and came across the tombstone, which had been located in the Fifty Cemetery in Winona.”
Duigan learned that it had overlooked Jacob’s grave for 18 years, but when Inglehart’s widow, Jane, died in 1870, the original tombstone was removed and replaced with a larger one with both their names on it. How the original stone ended up in a Milton pathway 50 km away remains a mystery.
Upon researching Inglehart, Duignan “got goosebumps.” Jacob was one of his ancestors. “Now I know why my sister was introducing him. It was incredibly wild.”
Today, the tombstone sits proudly at the front of Duignan’s home.
Recently, Mark Ashton of Ashton Renovations in Toronto was doing a renovation of an older house in the city. As the crew removed an old fireplace mantel, they came across an original artwork, 10 by 10 inches, that had fallen behind the mantel. It was an abstract watercolour but clearly a nude portrait. A nearby resident recognized the subject and explained that the former homeowner had been the artist, and the nude model for the painting had been the homeowner’s next-door neighbour.
“We just left it on site,” says Ashton.
Old newspaper clippings found behind
walls are among what Ashton finds the most interesting. “It’s like going back in time. We once found an article talking about plans to go to the moon. It’s strange looking at it from the perspective of the time.”
If there’s a discovery Ashton despises, it’s raccoons. “When one jumps out from a wall and hisses at you, it’s startling. We call in animal control. We had one that ate through a steel trap. They are savage. Even in a new build, they’ll find their way in.”
Scott Wennick of Ottawa’s ARTium Design
Build has encountered numerous unusual discoveries, particularly in older homes.
“We were doing a renovation on an early ’60s bungalow that had a finished basement that the homeowners wanted to turn into an apartment,” says Wennick. “We were pulling down the ceiling in a closet, and there was a hatch to a hidden
space. We found a big machete and a box of gun shells but threw them out. Fortunately, we didn’t find any blood.”
He also came across an old safe in a basement that a homeowner wanted removed and disposed of. “We couldn’t open it and talked to a moving company about taking it away. Safes are heavy and hard to move, so things like that often get buried or built around. The older the house, the more secrets you find.”
Wennick’s company often works in houses built from 1945 to 1950. The production of World War II equipment, such as tanks and planes, created a significant shortage of steel, making steel beams nearly impossible to source.
“I’ve seen three houses of that era with a piece of railway track as the main beam in the middle of the house,” says Wennick. “They were each situated next to what used to be a railyard or railway line. The Queensway that runs through
WENT OUT AND PICKED UP SOME TRACK.”
Ottawa’s centre core used to be a railway corridor. The houses with the railway track beams aren’t far away from there. Some industrious builder, probably in the dead of night, likely went out and picked up some track. I imagine carrying a railway track would need four or five people. They are 30 feet long—almost the perfect size to build a house.”
Wennick says a project ARTium carried out on an 1880s Ottawa home was also intriguing. While the basement was being renovated, the crew came across what the client had dubbed “the murder room” due to its small, dark and creepy nature—an 8’x15’ ‘apartment’ with one tiny window. It was a difficult-to-access space at the back of the house that had allegedly been rented out in its previous history.
Basements often are where you find the “neat stuff,” Wennick notes. And sometimes the smelliest. Consider a basement reno ARTium executed on an 1850s house near the Parliament Buildings. At the time, cast iron was the material of choice for sewage lines, and it eventually rusts. As the crew broke up concrete to install a new bathroom, they
discovered that there was no plumbing left. It had all rusted away, and when the toilet was flushed, a cesspool was created below. Wennick says they kept breaking up the floor and finally found a piece of pipe intact and called in a specialist company to perform a “pipe within a pipe” injection.
“This homeowner was lucky. As the house was built on a cliff, there was enough rock and gravel that the fluid could gradually drain away,” Wennick says. “If it had been on flat ground, it would’ve had nowhere to go except back into the house.”
As fate would have it, Wennick is helping plant the seeds of future discoveries. As it’s the company’s 25th anniversary, ARTium is supplying time capsules to its clients to fill with whatever they want. Once filled, Wennick’s crew will secure the capsules behind the walls.
“We thought it would be a fun thing to do, and most people took advantage of it,” he says.
Who knows what will be unearthed when these hidden treasures are discovered decades from now. Perhaps a painting of the neighbour. OHB
a multi-year partnership with OCAD University. The collaboration includes mentorship bursaries and a newly launched minor in public art, helping shape the future of urban creativity in Toronto.
Renowned British artist Ryan Gander unveiled his first permanent public artwork in Canada this spring. Installed at Lanterra Developments’ Artists’ Alley master planned community between Simcoe and St. Patrick Streets, a stone’s throw from downtown’s famed art corridor, The Cat, the Clock and the Rock sculpture merges art, science and storytelling. The mirrored, precision-milled stainless-steel clock
rests on a digitally replicated 4.3-billion-year-old rock from the Hudson Bay region, with a stone cat curled peacefully nearby. Together, they create an unexpected and moving meditation on time, permanence and the everyday.
Commissioned by Lanterra Developments, the installation is the latest piece in the developer’s growing public art portfolio and celebrates
The Ontario government will soon introduce first-in-Canada changes that will, if passed, create safer workplaces for construction workers by requiring automatic external defibrillators (AEDs) at construction sites. This builds on the lifesaving changes introduced in 2022 that require naloxone kits in at-risk workplaces.
Cardiac events, including sudden cardiac arrest, are a leading cause of workplace fatalities, with data from the Ministry showing that more than 15% of inspection reports associated with “cardiac” or “heart attack” were in the construction sector.
AEDs are electronic devices used to restart a person’s heart if it has stopped beating. When used together with CPR in the first few minutes after a cardiac arrest, AEDs can dramatically improve cardiac arrest survival rates by more than 50%.
“Survival rates decrease by about 10% for every minute without defibrillation,” notes Chuck Resnick president of The Mikey Network. “On construction sites where emergency services
may take time to arrive, an on-site AED can be the difference between life and death. Adding a defibrillator to a construction site isn’t just a lifesaving tool; it’s a proactive investment in workplace safety. It sends a powerful message about prioritizing health and safety from the ground up.”
The proposed amendments would require AEDs on construction projects that are expected to last three months or longer and have 20 or more workers. As of April, the cost to purchase one AED was, on average, $2,300.
To support businesses with these costs, a proposed program through the Workplace Safety and Insurance Board (WSIB) would reimburse constructors for the purchase of an AED through the WSIB insurance fund. The Mikey Network also offers a discounted price ($1,625 including wall cabinet) for the purchase of a Mikey AED. And note that AEDs are a non-taxable purchase.
The AED initiative is part of a larger proposed package that would build upon the groundbreaking actions outlined in six previous Working for Workers Acts since 2021.
Wolseley Canada, a market leader in the wholesale distribution of plumbing, waterworks, HVAC, fire protection and other products, has announced a series of bursaries for post-secondary schools across the country to help offset the cost of skilled trades education programs.
“We see first-hand, the important role that skilled trade workers have across the country,” says Wolseley President Wally Quigg. “We understand the rising costs of pursuing postsecondary education can be a barrier for many, and we’re proud to support students who are pursuing a career in the skilled trades.”
This support includes 21 financial need-based bursaries ranging from $750 to $2,000, from coast to coast. It prioritizes programs related to the plumbing and HVAC industry, with a special focus on the provinces with the greatest skilled trades shortages.
While the cost of land is inching upward, the monetary size of transactions is tumbling. That’s among the highlights of the Q1-2025 GTA High-Rise Land Insights Report , a production of residential market research and advisory firm Bullpen Research Consulting Inc. in partnership with Batory Management, a land-use planning and project management company.
This first-quarter projection and analysis of high-density land sales in the GTA notes that the average high-density land price across the GTA has reached $95 per buildable square foot (pbsf), up modestly from $93 in 2024. However, the average deal size declined significantly to $9.36 million due to smaller average lot sizes (0.76 acres), indicating a continued developer focus on compact and strategic infill sites. By comparison, the average deal size was $14.04 million last year and $115 million as recently as 2021.
The report also cited diverging landto-revenue ratios (LRR) in 416 vs 905. The LRR in the 416 area rose to 9.7%
in Q1-2025, its highest in years, driven by a few high-priced infill sales and declining revenue projections. In contrast, the 905 area saw an LRR of 4.3%, in line with recent years, reflecting more subdued land values and revenue expectations amid continued market softness in the suburbs.
Developers, meanwhile, are increasingly targeting mid-rise projects and adjacent lot additions, particularly in the 416 area. Mid-rise land traded at $142 pbsf in Q1-2025 (unchanged from 2024), above the 3.25-year average of $137 pbsf, while high-rise land traded at $99 pbsf. The smaller site sizes and lower total deal values reflect a cautious approach focused on faster absorption and reduced reliance on investor buyers.
Among the report’s other findings, Toronto and North York remain the priciest municipalities for high-density land, averaging $157 and $97 pbsf, respectively, over the past seven-plus years. Scarborough has a long-run average of $53 pbsf, though its Q1-2025 value was $66 pbsf, with a small sample size of transactions.
Average Price and Average Price per-Buildable-SF for High-Density Land Transactions by Year, GTA, 2018 to 2024 & Q1-2025
In Q1-2025, the average estimated price per-buildable-sf was $95, up slightly from 2024 ($93 pbsf) based on a sample of 20 transactions. Numerous factors influence land value and the prices paid by these buyers. These include location, lot size, potential buildable gross floor area, development scope (e.g., mid-rise vs. high-rise), parking requirements, municipal tax policies and existing holding income.
The Ontario Government has continued its strong investment in the skilled trades through the Skills Development Fund and other steps outlined in the 2025 Ontario budget. The focus includes retraining, health and safety, and supporting Black and Indigenous youth in entering these fields.
“Working together and inspiring the next generation of skilled trade and technology leaders is crucial to our success and future as a province, and we are looking forward to continuing to provide learning opportunities to all Ontarians,” notes Skills Ontario CEO Ian Howcroft, whose association supports several new initiatives including the investment of an additional $1 billion for the Skills Development Fund and an additional $50 million for the Better Jobs Ontario program.
Our most established clay brick product line. The Legacy Series offers a range of colours, subtle textures and is available in a traditional Premier Plus size. Pair these textured bricks with our stone veneer products for endless design options, and to bring a stately aesthetic to your home or building project.
BP Canada, a leading manufacturer of building materials, is looking good on its 120th birthday. The story began in 1905, when the Bird & Sons Corporation built what would eventually become the current fibreboard plant in Pont-Rouge, Quebec.
Notable innovations include the market’s first oversized 42” asphalt roofing shingle and the development of patented Weather-Tite and WeatherTite Plus technologies, which allow the company to offer warranties
against winds up to 220 km/h—equivalent to a Category 4 hurricane.
Over time, the company has changed ownership several times, including being owned by Esso in the 1960s and 1970s. In September 2023, BP Canada joined Saint-Gobain alongside companies such as CertainTeed, Kaycan and Bailey Metal Products.
Today BP has global network of over 161,000 employees in 80 countries.
To mark its 120th anniversary, BP Canada has unveiled an updated logo. From now on, it will no longer be known as Building Products of Canada but simply as BP Canada.
AWARDS & HONOURS
The 2025 edition of CHBA’s Home Building Week in Canada, held in Victoria, B.C., in May, shone the spotlight on OHBA members. Greater Ottawa HBA’s Gary Sharp of Sharp Home Technologies earned Member of the Year honours, while Windsor Essex HBA’s Vince Lapico was named Rooftopper Membership Recruitment Champion. On the association side, CHBA Association Leadership Awards went to (pictured above, left to right) WEHBA’s Mike Collins-Williams (Executive Officer of the Year – Large HBA), Guelph & District HBA’s Melissa Jonker (Executive Officer of the Year – Small HBA) and London HBA’s Jared Zaifman (claiming his local’s Community Service Award).
Salvaged airport artifacts and lush meadows with an innovative water feature have all come together to create the Plaza and Playscape at YZD, a 370-acre redevelopment of the former Downsview Airport lands led by Toronto-based Northcrest Developments. The Plaza was revealed at the Global Placemaking Summit, an annual international event that convenes hundreds of placemakers and urbanists from around the world—held in Toronto for the first time.
The new public Plaza at YZD was designed by a team of creative minds: Danish landscape architecture firm SLA, local firm Gotfryd Group and multidisciplinary arts fabricator Anex Works. At its heart is the Playscape, a deconstructed airplane that has been reinvented into an immense, imaginative playground that spans more than 100 feet. The Skyscape repurposes several airplane elements, including a cockpit, airplane body, rudders and fuselage carts, to create a zip track, a rock-climbing wall, a play structure and elevated seating areas. A mong the other striking features is a collection of five airplane fuselage carts turned into lush, oversized planters. The Plaza also features an interactive water feature built atop a shipping container, repurposing an old Bombardier sink, which irrigates the meadows below. OHB
FOUNDED: 1953 MEMBERS: 119
OHB: You folks were hit rather hard by the March 30 ice storm.
Sandy Tuckey: “The region is still reeling from the damage. Personally, we lost at least 20 trees, and our gazebo, part of our deck, roof and fence were badly damaged. Parts of the region were under a state of emergency for quite a while. A few of our roofers and trades stepped up and offered to look after any local residents who needed help. And I put tons of homeowners in touch with members.”
I see you spent 26 and a half years at the Barrie Examiner before joining SCHBA as the EO. “I worked my way up at the Examiner from age 19 to become director of advertising and publisher. I left the paper in 2016 and Metroland closed it down a year later. In my role there I sold to several builders and had also sat on the SCHBA board from 2011 until I left the Examiner. So when the EO opportunity came up in 2017, I interviewed for the position—actually several interviews. It was a four-month process.”
What makes SCHBA special?
“Our region has around 360,000 residents, but our members are a very close-knit family. Any member can call me and know I’ll immediately address their needs. There’s never a time when a new member comes through the door
at a dinner meeting that I don’t reach out to make sure they feel welcomed. I love getting to know them—their kids, pets’ names. It’s about building relationships. And once you get involved, you’ll probably never leave. Our retention has always been over 90%.”
SCHBA has taken great strides in working with the City of Barrie.
“We’ve been actively working to get a seat at the table when their planning department is looking at new zoning bylaws and other decisions that affect our industry members. Our current president, Heljar Hansen, has been huge in this regard. He helped set up a meeting with the City in May and a second in June, and there will be quarterly meetings after that. That’s a first for us. We’re taking baby steps, but there’s a sense that the City is here to work with us now and not just be a regulator. And we’ve seen new members stepping up to be part of our advocacy committee, which is wonderful.”
As community projects go, you’re in the midst of something very special with Youth Haven.
“Youth Haven is a shelter for at-risk youth aged 16-24 who have left home for multiple reasons, such as fleeing sexually abusive or drug-ridden environments. Executive Director Lucy Gowers reached out in the summer of 2022 and asked if I could get any trades
members to come in and make some cosmetic repairs since their facility was in disrepair—broken tiles, holes in walls, etc. One of our board members at the time, Mark Mulder, toured the building with me. I was in tears over the condition these kids were living in. I shared our experience with our board, and they asked, ‘What more can we do?’ One of our engineer members did a structural walkaround and said it was unsafe. So we unanimously decided to do a community rebuild. It was something our association had often done in the past—builds for the local hospital, Gilda’s Club, etc. And we ran charity ice fishing tournaments for years, always giving back to the community. So we developed a committee.
“It took a while to get everything approved, but we’re taking it from a 16- to 31-bed facility. The footprint is increasing considerably. It will be two beds per room instead of four, so the kids will have more privacy. There will be a physician room, working space for the kids to study, a rec room, and more. It’s a $2 million build. I can’t tell you how much of our community, like the Rotary and Kiwanis Clubs, have provided substantial monetary donations. Many members have supplied extensive materials and labour for free, while others have offered highly discounted rates. Groundbreaking was in October 2024. I can’t wait for the grand opening—likely in September.”
As an HVAC professional, you need systems that deliver performance, reliability, and efficiency— without the hassle. Napoleon’s fully integrated solutions are designed for seamless installation, superior comfort, and long-term energy savings.
Upgrade your installs. Elevate your reputation. Choose Napoleon.
Easy to Install and Service
High-Efficiency Heating and Cooling
Built for North American Homes
Unmatched Innovation and Reliability
Contact a Napoleon Dealer Today!