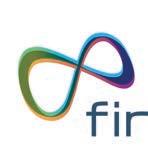
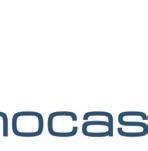
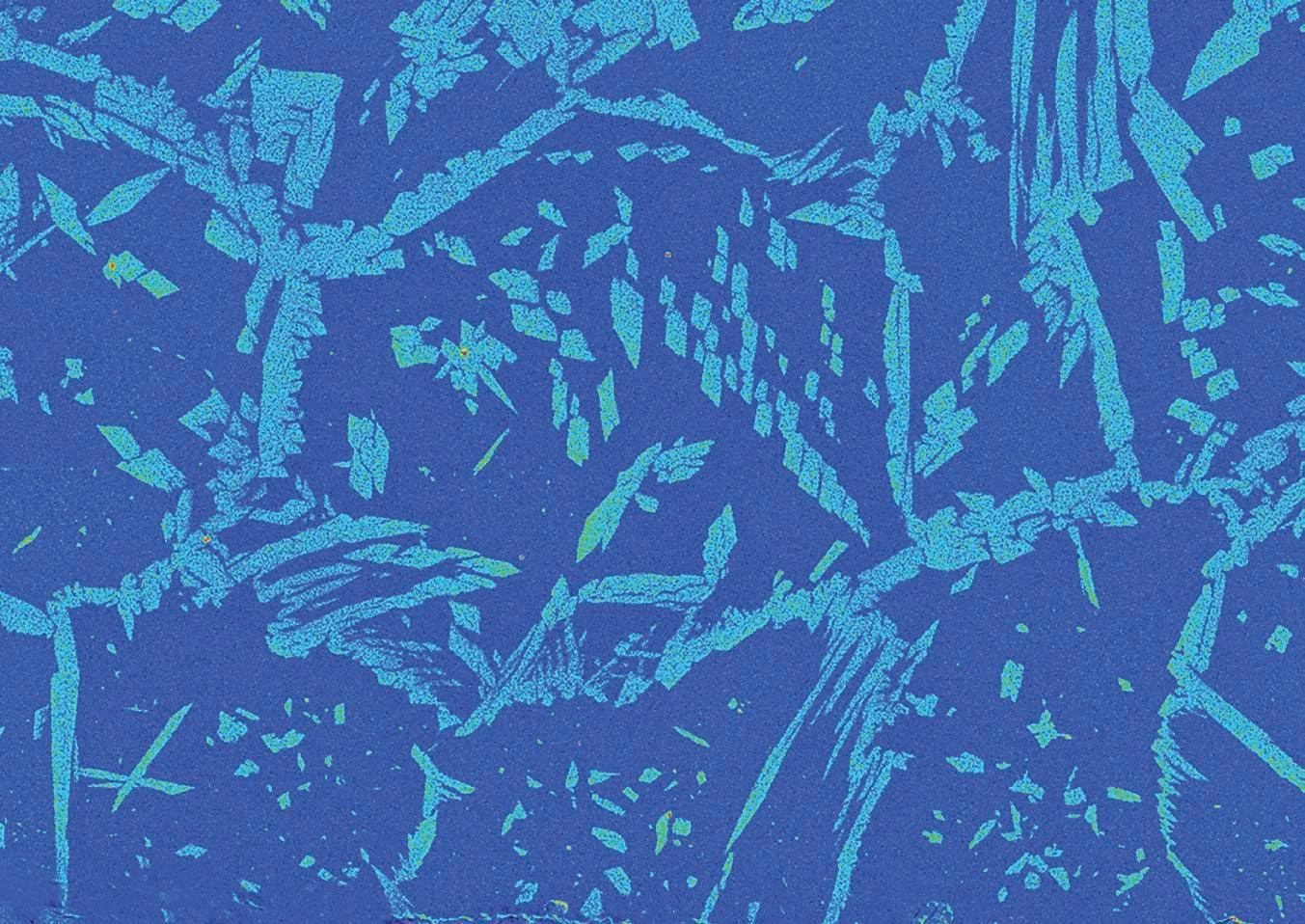
2022-2023
2022-2023
Cover: Chemical element mapping by Field-Emission Electron Probe Micro-Analysis equipped with Soft X-ray spectrometer, visualizing N-concentration in a polished steel sample
TEXT
OCAS team, Wright Communications
EDITOR
Steven Keyzer
GRAPHIC DESIGN
Filip Erkens
PHOTOGRAPHY & ILLUSTRATIONS
Adobe (p. 42), Ahmed Abouelyazied (p. 105), Aniruddha Dutta (p. 163), Annick Willems (p. 153), Athina Puype (p. 160, 176), Dennis Van Hoecke (p. 62), Filip Erkens (p. 7, 73, 74, 194, 197), Jens Conderaerts (p. 32, 36), Jeroen Van Wittenberghe (p. 122, 124, 126, 128), Johan Verlee (p. 144), Kurp Dach (p. 140), Kurt Lejaeghere (p. 185), Marc Vanderschueren (p. 118, 138), Maria Salta (p. 26, 29), Marian Flores Granobles (p. 44), Michal Mroz (p. 170), Michiel Corryn (p. 136), Nanni Noel (p. 24), Nathalie Van den Bossche (p. 100, 102, 103), Nelis Vandermeiren (p. 34), Nigel Mestach (p. 188), Nikolas Mavrikakis (p. 106), Northern lights (p. 54), Okan Yilmaz (p. 109, 131), Philippe verpoort (p. 143, 146), Robin Dedoncker (p. 159, 169), Rolf Berghammer (p. 156), Shutterstock (p. 48, 52, 56, 64, 80, 90, 95, 109, 169, 172), Steven Keyzer (p. 61, 76), Tom Dhaenens (p. 116, 120), with the courtesy of ArcelorMittal (p. 46, 50, 110, 150, 164, 167), with the courtesy of Emotors (p. 96), with the courtesy of ENDURES (p. 82, 84, 149), with the courtesy of Guaranteed (p. 175), with the courtesy of JUUNOO (p. 15), with the courtesy of MagREESource (p. 13), with the courtesy of MAXIMA (p. 99), Xiaolong Zhang (p. 22)
RESPONSIBLE PUBLISHER
Sven Vandeputte, General Manager FINOCAS, Pres. J.F. Kennedylaan 3, 9060 Zelzate - Belgium
DISCLAIMER
Although care has been taken to ensure that the information contained in the activity report 2020-2021 is meticulous, correct and complete, FINOCAS Group cannot give any guarantee, either explicitly or implied, with regard to the accuracy, precision and/or the completeness of the aforementioned information. FINOCAS Group as well as it directors, management, employees and appointees in the broadest sense possible, therefore assume no responsibility, and shall in no event be held liable, for any direct, indirect, special or incidental damage resulting from, arising out of or in connection with the use of this information, nor for any infringement of third party intellectual property rights which may result from its use.
H2 steel for H2 a future for hydrogen (& molecules)
Dedicated steel grades with enhanced resistance to hydrogen embrittlement 63
HyMatch®: a steel that transports hydrogen
International partnerships: a window on the world
No Hydrogen ENTRY: Re-use of existing pipeline systems for H2 transport via surface functionalisations inhibiting hydrogen ingress
OCAS’s hydrogen research in the international community
OCAS advises customers on hydrogen-material compatibility
OCAS fortifies for hydrogen testing
FEATHER: steel For nExt generATion H2 cylindERs
Demand for greater hydrogen storage above-ground pushes design to its limits
New saline resistant weathering steel plate for topside offshore structures .
Promising new spray coating concepts on offshore wind infrastructure
Securing the supply of heavy plates for wind energy
Weld-toe-angle optimisation for fatigue improvement
Elevating infrastructures for solar energy with Innovative High-Strength Steels
New steels for an electrified world
The potential of non-oriented electrical steel in electric power systems
Extending material knowledge to the final product
Modular AXIal flux Motor for Automotive: optimal manufacturing processes for mass production
Adhesive bonding, the next generation fixation for electric motors
Downsizing energy consumption of traction motors
the offer of ultra-high-strength steels
OCAS as pioneer in the lab production of High Entropy Alloys
in the aviation and space sectors
OCAS, ENDURES and GUARANTEED participate in an international doctoral network to create more sustainable metals
First of all, OCAS’s laboratory has experienced substantial growth. An R&D laboratory naturally evolves with a continual refreshment of talent. Still, over the last two years, we have recruited about 25% of our current personnel – which is a sizeable influx of new highly-skilled people with new ideas and competencies.
The last two years have been quite challenging –for the society in which we operate, and for our companies in the FINOCAS Group too. As we review the past two years of activities, we report with pride the successes and clear progress we have made in the midst of these times of change.
With the emphasis on decarbonisation of the steel industry in general, our lab is concentrated on our primary growth fields of electrification and energy transition. Of course, not neglecting our activities and support in commercial success fields like ultra-high-strength steels and protective metallic coatings such as Magnelis®. Market volume is growing in these fields. And so growth has characterised OCAS for these last two years, as we sustain the basis of our core activities while attending to these growth fields.
We have moved forward on the expansion of our structural partnerships, proving once more that the outcome of such collaboration is more than the sum of the individual parts. At the end of 2022, we decided to enter into a joint venture with FINOCAS and the Belgian Welding Institute, which strengthens the local base of metal-related R&D and
metal-related services. We’ve enjoyed a long-standing relationship with the Belgian Welding Institute, but now the formal partnership opens up a lot more opportunities for optimal collaborations. So, 2023 was a year of implementation – and we are very pleased that our vision for the partnership has materialised successfully.
In the field of decarbonisation, ArcelorMittal’s goal is to decrease its CO2 footprint in Europe by 35% by 2030 in order to be carbon-neutral by 2050. This will be achieved through a combination of technologies –including electric arc furnaces to melt more scrap – which means a significant increase in our recycling quantities.
One of the main challenges is to use much more low-quality scrap (in addition to the high-quality scrap we have always used), which contains residuals and impurities like copper and tin. In the future, with our new processes, we will continue to deliver high-added-value products that might contain a certain level of impurities but still satisfy the product performance criteria.
As an R&D centre, OCAS continues its special support of, and cooperation with, the ArcelorMittal Ghent plant, which aims to be a leader in this field. Together we foresee playing a key role in this decarbonisation journey for the next decade, thus having a major impact on the sustainability of the siderurgical industry.
In the future, we will continue to deliver highadded-value products that might contain a certain level of impurities but still satisfy the product performance criteria
Our contribution to energy transition includes decarbonisation and electrical steels for the automotive market, as well as developing harsh environment resistant steel grades and coatings for a variety of industries, including infrastructure for solar panels and wind turbines in diverse environments ranging from offshore to desert regions. We support the wind turbine contractors by enabling them to design their products to be less expensive and longer-lasting through fatigue-resistance. OCAS is also helping in the re-engineering
We support the wind turbine contractors by enabling them to design their products to be less expensive and longerlasting
and conversion of ‘energy carriers’ – another element in the broad field of energy transition. Our work here is to ensure a transition from carbon to hydrogen in support of the infrastructure for storing and transporting energy carriers in a safe and economically-viable way.
Furthermore, we are investing in the infrastructure to deliver on the energy transition components. The foremost investment is in a dedicated cold rolling unit for making electrical steels, which will be operational by the end of 2024. Along with our investments in additional lab space and sophisticated equipment for material testing with different energy carriers – in particular, hydrogen-based ones – we are investing several millions of euros. It is important to note that our CAPEX is a clear signal of our commitment to these future directions.
Manager, FINOCAS
FININDUS is a Belgium based venture capital investment company funded by ArcelorMittal and the Flemish Region and closely linked to OCAS and ENDURES, its sister companies within the FINOCAS Group and BWI Industry, structural partner of FINOCAS through its joint venture with the Belgian Welding Institute. FININDUS currently has 18 companies in portfolio and a total of 180 MEUR in assets under management.
FININDUS provides early stage and growth financing to innovative companies offering smart and green industrial technologies in the fields of materials, sustainable manufacturing and industry 4.0. FININDUS teams up with outstanding entrepreneurial teams and like-minded investors to bring sustainable industrial innovations to full commercial maturity and impact.
FININDUS invests across Europe, with Flanders as its home base and sweet spot. In addition, FININDUS invests globally in technology companies at the very core of its expertise and aligned with the strategic interests of its shareholders.
Passive cooling for power electronics, battery pads and processors, BE www.calyos-tm.com
Passive cooling for power electronics and processors, BE www.calyos-tm.com
Passive cooling for power electronics and processors, BE www.calyos-tm.com
Passive cooling for power electronics and processors, BE www.calyos-tm.com
Innovative using ultra , NO
www.hystar.com
Innovative electrolyzers using ultra-thin membranes, NO www.hystar.com
Innovative electrolyzers using ultra-thin membranes, NO www.hystar.com
Innovative electrolyzers using ultra-thin membranes, NO www.hystar.com
Re-usable interior wall partitioning systems and office pods, BE www.juunoo.com
Re-usable partitioning systems and office pods, BE www.juunoo.com
Re-usable interior wall partitioning systems and office pods, BE www.juunoo.com
Re-usable interior wall partitioning systems and office pods, BE www.juunoo.com
Surface hardening of stainless steel and titanium, DK www.expanite.com
Surface hardening of stainless steel and titanium, DK www.expanite.com
Surface hardening of stainless steel and titanium, DK
www.expanite.com
Surface hardening of stainless steel and titanium, DK
Wire & arc additive manufacturing of large metal parts, BE www.guaranteed.be
Wire & arc additive manufacturing of large metal parts, BE www.guaranteed.be
Wire & arc additive manufacturing of large metal parts, BE www.guaranteed.be
Patented friction drive system www.imsystems.nl
www.expanite.com
Wire & arc additive manufacturing of large metal parts, BE www.guaranteed.be
High performance materials for electrolysers and fuel cells, CA www.ionomr.com
Patented friction drive system for robotics, NL
Patented friction drive system for robotics, NL www.imsystems.nl
www.imsystems.nl
Patented friction drive system for robotics, NL
www.imsystems.nl
Tapered and spiral-welded wind turbine towers, US
www.keystonetowersystems.com
Tapered welded wind turbine towers, US
www.keystonetowersystems.com
Tapered and spiral-welded wind turbine towers, US www.keystonetowersystems.com
Tapered and spiral-welded wind turbine towers, US www.keystonetowersystems.com
High performance materials for electrolysers and fuel cells, CA www.ionomr.com
High performance materials for electrolysers and fuel cells, CA www.ionomr.com
High performance materials for electrolysers and fuel cells, CA www.ionomr.com
High-temperature thermal energy storage, GE
thermal energy storage, GE
www.kraftblock.com
High-temperature thermal energy storage, GE www.kraftblock.com
High-temperature thermal energy storage, GE www.kraftblock.com
Recycling of permanent magnets, FR www.magreesource.org
Recycling of permanent magnets, FR www.magreesource.org
Recycling of permanent magnets, FR www.magreesource.org
Recycling of permanent magnets, FR www.magreesource.org
Platform vision intelligence in smart machines, BE www.robovision.ai
Platform to manage vision intelligence in smart machines, BE www.robovision.ai
Platform to manage vision intelligence in smart machines, BE www.robovision.ai
Platform to manage vision intelligence in smart machines, BE www.robovision.ai
Machine health monitoring based on artificial intelligence, SW www.robovision.ai
Machine health monitoring based on artificial intelligence, SW www.robovision.ai
Machine health monitoring based on artificial intelligence, SW www.vikinganalytics.se
Teaching railway vehicles to drive autonomously, BE www.otiv.ai
Teaching railway vehicles to drive autonomously, BE www.otiv.ai
Teaching railway vehicles to drive autonomously, BE www.otiv.ai
Teaching railway vehicles to drive autonomously, BE www.otiv.ai
Fibre for structural health monitoring, BE www.senteatech.com
Fibre optics interrogators for structural health monitoring, BE www.senteatech.com
Fibre optics interrogators for structural health monitoring, BE www.senteatech.com
Fibre optics interrogators for structural health monitoring, BE www.senteatech.com
AI-powered industrial process optimization software, LU
AI-powered process optimization software, LU www.wizata.com
AI-powered industrial process optimization software, LU www.wizata.com
Machine health monitoring based on artificial intelligence, SW www.robovision.ai AI-powered industrial process optimization software, LU www.wizata.com
Hybrid steel-fibre reinforced composites for tough and lightweight (bicycle) parts, BE www.rein4ced.com
Teaching railway vehicles to drive autonomously, BE www.otiv.ai
Teaching railway vehicles to drive autonomously, BE www.otiv.ai
Teaching railway vehicles to drive autonomously, BE
Solvent- magnet wire mobility, IT www.tau.group
Solvent-free coatings for magnet wire used in e-mobility, IT www.tau.group
Solvent-free coatings for magnet wire used in e-mobility, IT www.tau.group
Solvent-free coatings for magnet wire used in e-mobility, IT www.tau.group
Solid state lidar technology for advanced driver assistance, BE www.xenomatix.com
Solid state technology for advanced driver assistance, BE www.xenomatix.com
Solid state lidar technology for advanced driver assistance, BE www.xenomatix.com
Solid state lidar technology for advanced driver assistance, BE www.xenomatix.com
The global energy transition is enfolding, initiating a shift from primarily fossil fuels towards more renewable energy sources.
Both electrification and green hydrogen production will be important vectors towards a more sustainable future.
With sustainability as one of our investment domains and guiding principles, FININDUS is actively investing in green industrial innovations. With Ionomr and Hystar, we support two portfolio companies that are enabling the hydrogen economy. Through Keystone Tower Systems, the US-based scale-up that is producing tapered and spiral-welded towers for wind turbines, we tap into renewable energy. The solvent-free high-performance magnet wires produced by Tau can become a game-changer for the e-mobility market. And at the start of 2023,
we invested in a promising technology company that can secure the current supply chains for permanent magnet materials used both in wind energy and electric vehicles: MagREESource.
MagREESource is capitalizing on more than 30 years of research and development in recycling of permanent magnets at CNRS.
The French start-up company, with roots in Grenoble, is currently industrializing a ‘short-loop’ recycling process. The company has invented an innovative method to split magnetic materials at the grain boundaries, without affecting the individual grains. The resulting magnetic powder is reused in producing bonded, sintered and 3D printed permanent magnets. The rare earth elements that grant the magnets their unique properties listen to poetic names such as neodymium, dysprosium and samarium.
Permanent magnets are used in e.g. wind turbine generators and the motors of electric vehicles, and hence are a cornerstone in the decarbonization of our society. Currently, China is dominating the market for rare earth elements, and the European Commission is encouraging investments in local capacity to ensure access to these critical raw materials. Our investment in MagREESource at an early stage reflects our belief in the technology, the market potential and the societal relevance of recycling permanent magnets. The smart recipe to recycle rare earth elements is also a metaphor for our approach to venture capital: FININDUS invests, grows, harvests and redeploys with an ambition to maximize its contribution to smart and sustainable industries.
MagREESource is a frontrunner in the recycling of rare earth metals from permanent magnets, essential materials for the further electrification of our society. The company’s technology and vision fit perfectly into the framework defined by the European Green Deal and the Critical Raw Materials Act. They provide a clear response to the call-to-action launched by the European Critical Materials Alliance to ensure local access to the critical raw materials needed to achieve carbon neutrality
Hans Maenhout Investment Director at FININDUS
Embedded in our industrial DNA, we embrace opportunities to reduce the environmental footprint of products, processes and supply chains, leveraging cutting edge technologies. Guaranteed, the joint venture between OCAS, FININDUS and ArcelorMittal Belgium, provides unique metal wire and arc additive manufacturing capabilities. Their 3D printing and repair services enable both lifetime extension and footprint reduction for large metal parts. The fibre optic interrogators of Sentea are a key component of wind turbine monitoring systems, e.g. for ice detection on the blades or condition monitoring of the generator. And the solid-state LIDAR technology of Xenomatix may prove to be a game-changer for the advent of self-driving cars and road condition monitoring.
In recent years, FININDUS also invested in another Flemish company with sustainability at the heart of its business model: JUUNOO. This vibrant start-up is developing novel, modular and reusable wall partitioning solutions. Their system is based on
a patented extendable metal stud frame to which a range of wall finishing can easily be connected. Such systems are straightforward to install and easy to dismantle and reuse. From office pods to demountable walls and glass partitions, the JUUNOO catalogue offers a broad range of sustainable solutions for the office market.
JUUNOO’s cold-rolled profiles are produced from ArcelorMittal XCarb™ steel. The use of high-strength steel with a low carbon footprint is testament to JUUNOO’s green philosophy. By embracing a material which is strong, slender and infinitely recyclable, JUUNOO is shaping sustainable solutions to address today’s challenges whilst leaving a legacy of circularity for the next generations.
Partnering with Finindus provides JUUNOO with invaluable insights and strategies essential for our growth. Their founder-friendly approach fosters better decision-making and aligns seamlessly with our vision of sustainability and circularity. Findindus’s commitment and deep-rooted industry knowledge empower us to scale to new heights, whilst contributing to economic and environmental value creation in Flanders
Chris Van de Voorde Founder and CEO at JUUNOO
Guaranteed was created in 2019 as a spin-off of Finindus, ArcelorMittal Belgium and OCAS. Its focus is on (re) producing, repairing or rebuilding large, slow-moving metal components beyond what is possible using conventional manufacturing technologies – thereby prolonging the life of ageing industrial equipment, reducing long lead times, and eliminating storage costs.
Guaranteed uses a technology called Wire & Arc Additive Manufacturing (WAAM), which combines well-known, mature welding technology and robotics with state-ofthe-art computing and automation in order to (re)create, re-manufacture or refurbish metallic objects in 3D.
Guaranteed’s vision is to keep industrial assets operational by producing spare parts on-demand, reproducing obsolete parts, and refurbishing damaged components or optimizing existing ones. The company’s unique facilities allow it to provide extra-large-scale metal wire and arc additive manufacturing services for customers all over the world. At the same time, Guaranteed aspires to contributing to a more eco-friendly manufacturing future. The company’s WAAM manufacturing facility is capable of producing parts up to 10x6x5 meters, and weighing up to 20 tons, in a broad variety of metals ranging from carbon steels, to stainless steel, Ni-based alloys, titanium, aluminum, and more.
Ageing installations are a common issue in many industries. Because assets are increasingly being used beyond their designed lifespan, they are susceptible to non-productive downtime or failure. Maintaining the integrity of equipment is difficult, since the machine’s original parts are no longer available because the equipment model is obsolescent or engineering standards have changed.
1. Serial supply of class approved parts to the maritime industry: The long-term involvement of Guaranteed in setting-up a guideline for the qualification of 3D printed parts for oil&gas and maritime industry, resulted in 2023 in the achievement of class approval from DNV for a hybrid manufactured maritime component. The printed part was demonstrated to be more cost effective as compared to the original die-forged component but also resulted in reduction of lead time and CO2 footprint for the customer. This ultimately led to the fact that Guaranteed was registered as serial supplier.
2. Industrialisation of a production critical repair application in the steel industry: After a complete year of severe field trials during which prototypes of additively repaired cooled support rolls were tested under the harsh production conditions of a continuous casting line, these pilot rolls were dismounted and thoroughly inspected. This post-mortem analysis revealed that the AM-repaired rolls performed as expected and no damage could be observed which allowed the steel plant to industrially validate the new Guaranteed concept, which from that point onwards has also become the new standard practice for repair of cooled continuous casting support rolls at ArcelorMittal Belgium
3. Performance and cost improvement at an Italian valve producer: At Formnext 2023, Guaranteed demonstrated together with an Italian valve producer that a standard valve, which design was modified to make it “design for AM” proof, could allow to combine at the same time 35% reduction in cost and lead time as well as 35% improvement in performance
Joachim Antonissen, General Manager, GUARANTEED
After a successful trail and evaluation period, Guaranteed’s repair concept is now qualified as the new standard practice for repair at our customer
Michiel Debel
The company’s 11 employees are divided into 2 groups of expertise: Corrosion & Failure analysis and Biofilm (Anti-fouling, Microbiologically Induced Corrosion - MIC). ENDURES helps customers select the right materials and then effectively protect those materials. This unique combination of disciplines – all under one roof – constitutes ENDURES’s unique selling point.
ENDURES, an OCAS sister company, is soon celebrating its 60th anniversary. That means 60 years of experience in materials selection, failure analyses, optimal design, enhanced corrosion protection, and lowering costs. ENDURES is active in a variety of industries, ranging from shipping and maritime infrastructure to renewable energy and fire extinguishing systems. Over the last couple of years, ENDURES and OCAS further integrated their activities.
With the goal of extending the life of materials, ENDURES conducts research under both in-practice and laboratory conditions. The company also conducts damage studies on ships, installations and structures to determine the type of corrosion that is occurring, the particular circumstances that are playing a role, and how such damage can be prevented in the future. ENDURES combines microbiological expertise, electrochemistry and materials science to investigate whether the problem is a material failure or a design issue. The two main questions it seeks to answer are: how can I overcome this corrosion, and how can I design something better?
In brief, the services that ENDURES provides include the following:
Advice on corrosion and corrosion prevention
Root cause failure analysis & advice on material selection
Coating failure analysis and advice on protective coatings
Anti-fouling (various techniques to prevent or reduce fouling)
MIC (Microbiologically Influenced
Corrosion, corrosion caused by micro-organisms)
Soil corrosion: advice on protecting underground metal components
ENDURES has over 500 customers, who benefit from the company’s cost-effective and authoritative assessments and advice in all of these areas.
For example, ENDURES performs analysis of the customer’s underwater movies and makes an overview of the progressing fouling and growth or marine species. This
is advantageous for customers who want to follow up and monitor the impact of fouling on their underwater infrastructure, such as offshore wind foundations. In every case, ENDURES tailors its approach, designing tests that focus on the customer’s unique problem situation. Which allows ENDURES to develop the optimal solution by the most efficient, straightforward route.
During the last two years, ENDURES also changed its focus to more green and sustainable projects. For instance, clean ship hulls reduce the greenhouse gas emission of marine transport. ENDURES will investigate the effects of in-water hull cleaning, as this may have a negative impact on the environment because of paint particles or micro-plastic releases into the ocean. Another example is the impact of alternative fuels (bio-fuels) on materials. Some of them might induce increased risks for MIC. Those are typical topics in which ENDURES participates with its customers and enters into a research project with them.
Last but not least, ENDURES is a highly trusted partner for the Dutch marine defence agency. In the future, ENDURES will continue to work closely with the agency on the new ships that are being built and the new submarines that will arrive within 10 years. ENDURES’s unique knowledge and facilities are essential to the success of this venture.
Sibo Buter, Managing Director, ENDURES
1 . Test set-up for steel samples exposed to flowing seawater and for polarization curve measurements
2 . A double chamber reactor for hazardous gas measurements: a steel bar in one chamber and an MMO anode in the other chamber, filled with filtered natural seawater
Thanks to ENDURES’s unique location, experimentation in living seawater is possible and seawater current speeds at different depths in the North Sea could be successfully simulated
Xiaolong Zhang
Steel structures are susceptible to corrosion in seawater. A known method for protecting steel structures from corrosion is the so-called ‘impressed current cathodic protection (ICCP)’. The design of such an ICCP system can be further improved to enhance the protection of wind monopile steel structures. Such improvements reduce maintenance costs, and hence they are very meaningful for the wind industry.
A good corrosion model – characterized by electrochemical parameters such as corrosion potential and corrosion current density (related to corrosion rate) – is the basis of such a system improvement. The corrosion potential and corrosion current density of steel in seawater change with salinity, oxygen concentration, temperature, flow speed, etc. Seawater flow speed plays an important role in steel corrosion, and the flow speed varies with the depth of the seawater.
Thanks to ENDURES’s location close to the sea, experimentation in living seawater is possible. ENDURES enabled access to natural seawater in which the corrosion rate of steel at different water flow speeds
was measured in the lab. By this test set-up, seawater current speeds at different depths in the North Sea could be successfully simulated (Figure 1). The results are very valuable for offshore industry, as they enhance the designing of protective systems in offshore structures.
The application of an ICCP system on wind monopiles is often realized with special anodes made from mixed metal oxides (MMO). The potential levels of such an ICCP provide better protection for the steel structures and do not generate too many hazardous gases.
At ENDURES, two types of MMO anode materials were tested in natural seawater under the application of an ICCP at different potential levels (Figure 2). After the tests, the H2 volume and the Cl2 produced under the
ICCP at different potentials were measured. These insights guide industry in the selection of the most suitable anodic materials for their application. The results have been presented and published in the proceedings of the Annual Congress of the European Federation of Corrosion, EUROCORR 2023.
With our in-house test set-up, we are able to determine whether microbiologically influenced corrosion will accelerate corrosion and which corrosion rate and pitting depth can be expected
Nanni Noel
The use of biodiesel as a renewable alternative fuel is on the rise globally. Biodiesel is composed of fatty acid methyl esters (FAME), which have physical properties like those of conventional diesel. It is also non-toxic and biodegradable. However, methyl esters can absorb considerably more moisture than petroleum-derived diesel and they hold this in suspension in the fuel. Petroleum-derived fuels absorb considerably less moisture by comparison and tend to shed water as a separate layer at the bottom of storage tanks.
When water can contaminate diesel, it provides conditions suitable for microbial growth and can lead to contamination due to fungi and bacteria spreading throughout the fuel. Because FAME is bio-degradable, it is an ideal source of nutrients for microbes. If contamination is left untreated, it can damage the fuel permanently. But microbiologically influenced corrosion (MIC) can also be a reason for concern. If MIC-related microorganisms can establish inside the used mixture, they can accelerate corrosion of storage tanks that are not fully coated. Therefore, ENDURES is investigating which degradation mechanisms can develop close
to the tank bottom of a biodiesel storage tank and whether MIC can be a cause for concern, for such tanks. Founded on our experience, an in-house test set-up was developed (Figure 1). With this test, we are able to determine whether MIC will accelerate corrosion and which corrosion rate and pitting depth can be expected. Representative conditions at the tank bottom are replicated on small coupons exposed to biodiesel at a dedicated time and temperature. After the tests, the samples are carefully investigated and subjected to destructive examination for a full metallurgical characterization. This test set-up was first used to determine the corrosion rates of oils and oil mixtures.
We have adjusted the set-up during the last couple of years, and it can now be used for both microbial testing and failure analysis, including the determination of corrosion rates.
Protection against biofouling is imperative and would contribute to the decarbonisation of the maritime sector.
have extensive knowledge of biofouling, whereby they can provide global mapping of marine growth (across seasons and with depth) and its potential for impacting offshore structures (piles, mooring systems, etc.). ENDURES uses state-of-the-art methodologies to determine drag coefficients exerted on structures such as cables and moorings. The company is internationally working together with academia, research centres, and industry to collectively tackle the challenge of biofouling. As such, ENDURES is playing an essential role in providing guidelines on how to manage biofouling.
Fouling control coatings contribute significantly to reducing biofouling on hulls. However, they often have a finite lifetime, and most often they cannot stop biofilm growth (also known as slime). Reactive in-water hull cleaning is currently the focus of intensive investigation and innovations in such activity could compliment and improve antifouling performance.
ENDURES is currently playing a global pioneering role in evaluating the potential of innovative technologies for in-water
cleaning, such as (but not limited to) cleaning and inspecting robots. ENDURES is assessing which technologies are effective and whether or not there is a consequential impact on the fouling control capacity of commercial and innovative coatings.
ENDURES is addressing these key questions to evaluate emerging technologies that look promising. Our research journey has just begun – but crucial information has already been collected
ENDURES uses state-of-the-art methodologies to determine drag coefficients exerted on structures such as cables and mooring lines
The Belgian Welding Institute Industry started as a joint venture of the Belgian Welding Institute npo (°1942) and FINOCAS in July 2023. Via FINOCAS – in particular, the daughter companies OCAS and ENDURES – BWI Industry receives access to the most performant lab facilities and complementary expertise in the field of metallurgy and materials corrosion. In return, FINOCAS and its daughters benefit from the renowned welding experience of BWI’s highly skilled personnel. During the establishment of BWI Industry, special care was paid to ensure, in a structural way, the independent and neutral position of the new company. This structural partnership ensures that the knowledge and expertise built up by the Belgian Welding Institute in Belgium is anchored for the long-term strategy.
BWI Industry now counts 17 highly experienced people, all engaged in different fields of activities: Failure analysis (welding, corrosion), mechanical testing (fracture mechanics, fatigue), consultancy and R&D projects. Safety, quality and customer focus are of the highest importance for the company and are reflected in its ISO 9001 certification, ISO 17025 accreditation, and VCA* certification.
Each year, on average, the company receives over 600 requests and handles about 500 assignments for about 250 different companies. Failure and corrosion cases arise from diverse industrial sectors: 30% of our customers come from the petrochemical industry, 20% from industrial production, 20% from expertises (court or insurance), and other sectors (e.g., construction).
In addition to failure cases, material testing is also a strong and growing BWI Industry
business. Offshore wind applications, for example, especially value our experience in fracture mechanical testing. In the framework of (funded) research projects, fatigue testing and corrosion-fatigue testing have also been conducted frequently at the BWI Industry test facilities.
Additive Manufacturing and testing of Additively Manufactured parts – mainly Wire and Arc AM (WAAM) produced parts – is another – literally – hot topic at BWI Industry. The knowledge and test methods obtained from the various WAAM-related research projects are now also being further developed and made available to industry. Characterization of the mechanical properties of WAAM printed parts for different industrial partners is now part of our activities, as well as feasibility studies for WAAM printing such as part design and topological optimisation, print strategies and cost-effective manufacturing.
Companies can also call on our welding engineers for short-term assistance or longer-term (temporary) welding coordination assignments – for example, setting up a welding quality system within the framework of the Construction Products Regulation (EN1090) or railway applications (EN15085).
Regarding the future, we look forward to further cooperation with the various partners within the FINOCAS Group. The complementary knowledge, equipment and additional possibilities within the Group enable a more extensive range of services to industry - especially in the area of structural integrity of installations and the associated technical support.
Bart Verstraeten, Managing Director, BWI Industry
BWI Industry is your strong partner for materials testing, R&D projects, consultancy and failure analysis in the field of metals, welding and corrosion
BWI Industry advises on proper material selection taking into account the environmental situation; crucial to prevent the corrosion from re-occurring Jens Conderaerts
Material selection plays a crucial role in preventing corrosion, as choosing corrosion-resistant materials can significantly prolong the lifespan of a product or structure. Factors such as environmental conditions, chemical exposure, and operating temperatures must be carefully considered when selecting materials to mitigate corrosion risks.
A number of leakages were observed in a pipe at a food processing company. The pipe transported soft, hot water at 135°C and was fabricated from stainless steel (AISI 316L). The first leakages were observed after only 1 year in service.
The damage investigation revealed severe pitting and cracking, especially near the weld seams. Metallographic examination revealed transcrystalline and branched cracks, initiating from pits at the inside surface. Corrosion products showed presence of the alloying elements of the stainless steel (iron, chromium, molybdenum), but chlorine (Cl) as well. The cause of failure was attributed to chloride stress corrosion cracking (SCC). This is a particular phenomenon of localised cor-
rosion typical for austenitic stainless steel. For SCC to occur, the stainless steel must be subjected to temperatures above 60°C in the presence of chlorides (Cl-) and tensile stress. In this particular case, residual stresses from welding caused cracking adjacent to the weld seam. Water analysis revealed a chloride content of 50 mg/l, which is sufficient to cause SCC. SCC can even occur at low concentrations of chlorides. Therefore, in the current processing conditions, BWI Industry advised the customer to consider alternative materials for this application – such as duplex stainless steel, titanium or nickel alloys – to prevent the corrosion phenomena from re-occurring.
BWI industry can offer a wide range of fracture mechanical testing, also at elevated temperature
Nelis Vandermeiren
One year before the commissioning of the Hollandse Kust Noord offshore wind park, the Belgian Welding Institute performed destructive- and fracture-mechanic tests on some critical welded joints of the floating offshore substation.
Such substations serve as a hub for collecting the green electricity from multiple wind turbines and then transmitting it efficiently to the shore through underwater power cables. By performing fracture mechanical tests, BWI Industry is ensuring the integrity and reliability of welded offshore constructions and contributing to the realisation of a green and sustainable energy future. Fracture toughness tests are used in engineering applications worldwide in order
to verify the material resistance against the presence of a sharp crack. The Belgian Welding Institute is able to perform multiple fracture toughness tests according to the current ASTM, British Standard (BS) and ISO standard testing methods as input for an engineering critical assessment (Fitness for service, fitness for purpose) or to verify a minimum required fracture toughness property.
In particular, the CTOD (Crack Tip Opening Displacement) test is a fracture mechanical test in which the test piece to be tested, provided with a fatigue pre-crack, is tested under loading conditions that are representative of the operating conditions. So, this test will indicate to what extent a certain material is resistant in the envisaged loading applications when a certain crack is present.
A decent failure analysis to determine the root cause of cracking is essential to defining a procedure for remediation
Faced with cracking during welding, companies rely on the welding engineers of BWI Industry for a cure. When a customer struggles with a new material to weld, or a new welding process, determining the root cause of cracking is essential to defining a procedure for remediation. Two particular weld cracking phenomena are cold cracking and hot cracking.
Cold cracking is a phenomenon in which hydrogen causes a brittle fracture at or near weld seams. Fracture may occur up to 48 hours after welding, when the component has cooled down completely, explaining the name for this type of cracking. Cold cracks originate under the simultaneous presence of the following factors: a temperature below 200°C, the presence of tensile stresses, the presence of hard microstructures (e.g., martensitic microstructure), and the presence of hydrogen. The example figure shows a centreline cold crack in a weld between carbon steel and stainless steel. The weld metal has a hardness of around 400 Vickers. Here, the design of the component should be changed to avoid the dissimilar joint.
Hot cracking is a phenomenon in which cracks originate during solidification of the weld seam. This phenomenon is more common in austenitic stainless steel. While solidifying, low-melting liquid phases with nickel and sulphur may form as a result of sulphur contamination by dirt, grease or oil. This liquid phase is not able to cope with the shrinkage stress that occurs during solidifying. The example figure shows a hot crack in a stainless steel laser weld. The base material itself was susceptible to hot cracking. In this case, by changing the composition of the base material, a weld with some ferritic phase can be obtained, which will reduce the risk for hot cracks.
decarbonisation alternative for the hard-toabate sectors, next to the adoption of renewably produced electricity, the steelmaking process is running through a redesign aiming for net zero and is facing numerous process-related, logistical, and metallurgical challenges. Therefore, OCAS is providing R&D support to face these challenges by fine-tuning and validating metallurgical routes to ensure the product quality of this new product range.
OCAS and its partners, ENDURES, GUARANTEED and BWI INDUSTRY, are also working on solutions to increase durability and product lifetime, efficient refurbishment, and repair methodologies to extend product functionalities prior to circularity principles. OCAS’s industrial asset reliability solutions help asset owners to assess their infrastructure regarding fit-for-purpose. The information and insights such a digital twin can bring are valuable for all kinds of heavy industry asset owners, like ArcelorMittal. In the first place, the monitoring of the
structural health of existing installations safeguards the continuity of operations and contributes to the overall safety of the plant. But also, for new equipment, load monitoring from the very beginning has numerous opportunities for total cost of ownership, such as optimised maintenance schedules and remaining lifetime calculations.
Together with ENDURES and GUARANTEED, we are involved in analysing failures, proposing adequate repair methods and remedy actions to prevent failures from occurring again. So, whilst we develop the steels of tomorrow, we are proving the integrity of today’s steels with new applications as well. OCAS’s expertise is maturing further by adopting digital tools in the world of material science. With the acceleration of AI-assisted modelling and datamining, OCAS is a forerunner and has made impressive progress on plant database analysis, computer vision and digital image analysis in the fields of martensitic steels, electrical steels and high-strength low-alloy steels.
After relocating its microscopy instruments to an open-access service platform, OCAS has welcomed new customers coming from the semiconductor and micro-electronics sector. Our continuous pace of investment in new state-of-the-art equipment that enables nano-characterisation of materials will help OCAS realise its ambition to conduct worldtop research effectively, according to the highest quality standards with maximum scientific profoundness.
We take this opportunity to sincerely thank our customers and partners for their trust and the strong collaborations we have had over the past energising years. We look forward to continuing to provide expertise and services to you all.
Serge Claessens, CTO & COO, OCAS
Sven Vandeputte, Managing Director, OCAS
Europe’s climate ambitions for 2050 are bold and far-reaching. At the heart of these ambitions is the European Green Deal, a comprehensive plan that aims to transform the continent into a climate-neutral economy by 2050. Central to this vision is the goal of reducing net greenhouse gas emissions to zero, effectively ending Europe’s contribution to global warming. In the case of steelmaking, this challenge will require massive transformation of the key processes required to produce steel. The main enablers will be:
– Hydrogen-Based Direct Reduction (DRI), a technology to replace coke with hydrogen as the reducing agent in the steelmaking process. This offers a carbon-neutral production method when combined with ‘green hydrogen’ produced from renewable sources through electrolysis.
– Electric Arc Furnaces (EAFs): Unlike blast furnaces, which rely on coke, electric arc furnaces can use renewable electricity to melt direct reduced iron (above process) and scrap to produce steel.
– Carbon Capture and Utilization (CCU) and Carbon Capture and Storage (CCS) can play a crucial role in mitigating emissions from steelmaking. CCU involves capturing CO2 emissions from steel plants and using them as feedstock for chemicals or building materials, whereas CCS involves capturing CO2 and storing it underground to prevent it from entering the atmosphere.
OCAS’s activities contribute substantially to this journey to zero emission in many ways. Starting with the fact that steel will be a key enabler in rolling out infrastructural needs for CCU/CCS - but several challenges need to be overcome, such as compatibility of steel types with CO2 for pipe transport and storage facilities, specific steel grades needed for storage and shipping of liquified CO2, etc.
Furthermore, we’re working on reducing the footprint of wind energy towers, thanks to the use of low CO2 footprint XCarb™ RRP steels (RRP: Recycled and Renewably Produced).
Last but not least, the steelmaking journey towards net zero calls for numerous process-related, logistical, and metallurgical alternatives as explained above. OCAS’s
R&D activities have grown massively, setting up a program to meet these challenges and prepare ArcelorMittal Europe for high-value product production via the new routes. An important major step in the journey to zero carbon emission lies in the increased use of low-quality ‘recycled’ scrap, which results in a direct reduction of the CO2 emissions per tonne of liquid steel. This perfectly illustrates the potential of the circularity of steelmaking – but, unfortunately, it increases the level of impurities in steel. OCAS is investigating which levels of impurities can be tolerated whilst still ensuring the correct product and application properties. In parallel, we’re also working on completely new metallurgical solutions as needed.
ArcelorMittal is making clear progress with its XCarb™ initiatives, facilitating its customers’ efforts to decarbonise, as well as making investments to foster the development of the technologies needed to further increase the production capacity of these grades. We are proud to see that production of our first low CO2 footprint steel offer, XCarb™ RRP, is ramping up impressively.
We dare to ask the right questions to uncover the technical and economic feasibilities, the challenges, and the risks
Marian Flores Granobles
FINOCAS supports the transition towards a carbon neutral society with its own CO2 competence centre. In this centre, we gather information and build up knowledge independent of any potentially biased source. We make our critical analyses and bundle experience on technologies that aim to lower the footprint of industrial processes. Through its neutral position, the competence centre helps evaluate, assess, and understand technologies that are promoted by universities, research institutions or corporations.
We dare to ask the right questions to uncover the technical and economic feasibilities, the challenges, and the risks. Together with our technological insights, and the non-refutable mass & energy calculations, we can demonstrate the actual capability of promised CO2 reductions that can be realised (by a certain technology of interest), also considering the constraints from an industrial point of view. With the CO2 competence centre, we support our FINOCAS group stakeholders in making smart choices.
The CO2 competence centre touches upon technologies that strive to reduce CO2 emissions by smart gas management in the steelmaking processes. For instance, the residual reducing capacity in the blast furnace gas could be recovered and used to replace part of the pulverised coal in the furnace, which leads to a direct reduction in CO2 emissions. However, a series of gas separation process-
FINOCAS contributes to converting the steel industry’s ambition to reduce its CO2 footprint (following the 2030 and 2050 climate targets set by the EU) into reality. This includes partnerships with technology providers and coupling projects to other industries and relevant players, including identifying and incorporating technically and economically feasible solutions. We shortlist promising technologies that exist at lab scale but have not yet been demonstrated on the industrial level. After upscaling and proven successful, replication in other plants inside and beyond the steelmaking industry can be considered.
es would be needed prior to the re-injection, and that is exactly where the challenge is hidden. For example, if these auxiliary processes have process yields that are too low, insufficient quality, or high energy consumption, the full process technology will not attain cost-competitive advantages and investments could be too risky.
The FINOCAS CO2 competence centre not only interacts with the local ecosystem, such as with the Smart Delta Resources partnership and the Flanders Metals Valley initiative, but it also exchanges with international entities with the intention of exploring opportunities beyond the local area. Through these interactions, the FINOCAS CO2 competence centre can provide autonomous advice to its stakeholders.
The use of low-quality recycled scrap results in direct reduction of CO2 emissions and emphasizes the circularity of steel
ArcelorMittal Ghent is one of the plants in which the ArcelorMittal Group is making massive investments to reach the 35% CO2 footprint reduction target in Europe by 2030. Two important enablers for carbon footprint reduction that are being considered for implementation in Ghent are Direct Reduced Iron (DRI) and Electric Arc Furnaces (EAF).
A Direct Reduction Plant (DRP) is based on a technology to replace coke, used in classic blast furnace processes, with hydrogen as the reducing agent in the steelmaking process. An intermediate step with natural gas (already resulting in a 65% smaller footprint) can also be considered. Operating the DRP with ’green hydrogen’, produced from renewable sources through electrolysis, creates a carbon-neutral production method. Unlike blast furnaces, which rely on coke, Electric Arc Furnaces (EAF) are furnaces that can use renewable electricity to melt direct reduced iron (from the above process) and scrap to produce steel. Both sources of iron can be carbon-footprint-free solutions.
Implementation of these new production processes will have a significant impact on the downstream production processes and the quality of the final product. The impact is caused by small changes in the composition of the final steel, such as increases of impurity residual elements like Cu, Ni or Cr coming from the scrap, and interstitial elements like N, S or P. However, if not well taken into account, these changes can cause multiple deviations in all of the production steps – such as hot rolling defects, changes in the oxide layer’s adherence, under-pickling or residual precipitation in pickling baths, and specific galvanizing defects. Furthermore, the final
mechanical and in-use properties of the steel produced can be impacted.
To monitor these effects, an intense risk mitigation trial plan is running in collaboration between ArcelorMittal Ghent and OCAS to mimick future steel compositions. This will fully prepare the plant to ramp up production with the new equipment quickly, as soon as the tools come online.
The success of XCarb ™ RRP steels can be traced back to the critical role played by OCAS in designing and optimizing the novel EAFbased metallurgical routes and downstream processing parameters
Arunim Ray
OCAS’s metallurgists are gaining the necessary insights to ensure identical steel quality products via alternative metallurgical routes after EAF steelmaking with increased low-quality scrap. This is a new challenge in green steel production
In support of the Paris Agreement and the European Green Deal, ArcelorMittal is playing its part in the fight against climate change by making strong commitments to reduce European CO2 emissions by 35% by 2030 and reaching global carbon neutrality by 2050. In this journey towards net-zero, ArcelorMittal has developed two decarbonised production routes – Smart Carbon and Innovative DRI – both of which hold the potential to deliver carbon-neutral steelmaking.
The Smart Carbon pathway is applicable to the blast furnace (BF) / basic oxygen furnace (BOF) steelmaking by partially replacing coal with alternative sources of circular carbon from waste streams, such as sustainable biomass from agricultural waste or waste plastic. Whereas the Innovative DRI route applies to the direct reduced iron (DRI) / electric arc furnace (EAF) steelmaking, in which iron ore is directly reduced by natural gas and used as metallic input to EAF in addition to scrap. The heart of Innovative DRI involves replacing natural gas with an alternate, clean energy source – hydrogen as the reductant in the DRI process. OCAS R&D is playing a critical role in tackling the numerous challenges introduced by this shift from BF/BOF to DRI/scrap-based EAF steelmaking. Primarily the increased
use of scrap – and, in particular, the use of low-quality scrap – is expected to cause much higher levels of residual elements in the steel, which will require adjustments to – or even a comprehensive redesign of – the metallurgical route to preserve the existing product quality standards as well as meet evolving customer expectations, all while optimizing operational efficiency. A wide range of knowledge-building activities are underway: lab pilot scale studies and industrial trials, numerical simulations, and data-mining efforts to study the effect of residuals on strength, toughness and other in-use performances of the steel, the effect on the galvanising and pickling process, as well as surface quality issues such as hot shortness. This knowledge is expected to generate a clear view on the maximum
levels of tolerable residuals for all product families, with standard guidelines in terms of new processes and metallurgical routes to mitigate the effects in a robust manner. By the way, this metallurgical matter also applies to other sectors like the Aluminium industry.
The complete ArcelorMittal order book needs to have a decarbonized version within a span of about 5 years from now. While the move promises enhanced flexibility and environmental benefits, it also brings complexities that necessitate strategic adaptation. The objective is to achieve these modifications without necessitating significant capital investments in plant capabilities, and therefore extensive R&D support and expertise are required.
Supported by a customer partnership between OCAS and VELUX, improved product design and reduction of the carbon footprint of VELUX roof windows could be attained
Sofie Vanrostenberghe
Co-operations like these will enable decarbonisation of our products, and we look forward to seeing the positive impact on our product and company carbon emissions
Senior Director Procurement at VELUX
The objective of co-development projects is to support our customers in reducing their carbon footprint by using low-carbon-emissions steel supplied by ArcelorMittal. Early involvement is encouraged in each study, as this guarantees the optimal result in terms of value creation, reduction of environmental impact, and process robustness. OCAS has developed innovative approaches over the years to increase our involvement in our customers’ applications.
An example of a co-development partnership is the co-operation with VELUX that started in April 2023. The overall objective is to reduce the carbon footprint of the steel grades used in VELUX roof windows, with the goal of reducing the embedded CO2 by up to 70% compared with conventionally produced steel. VELUX Group is working towards halving scope 3 emissions by 2030, and working with suppliers of materials for its products is essential to achieving this.
An intense collaboration between OCAS and the VELUX design team was launched, specifically focused on further optimising future VELUX product lines through the use of low-carbon-emissions steel.
To ensure optimal performance of the hinges and brackets of the VELUX roof windows, the steel grade needs to be carefully selected. In a first stage, Autoform simulations of the deep drawing process were made to assess the process robustness
during deep drawing. Based on modelling results, design changes were proposed and an optimal thickness-strength combination was selected. Furthermore, topology optimisation is conducted on selected parts to ensure optimal performance under combined loading conditions.
The results of this long-term co-operation will certainly contribute to achieving the goals that have been set and reduce the environmental impact of the steel used in VELUX roof windows.
In line with climate action and goals on sustainability, the wind energy sector is striving towards net-zero CO2 ambitions and clean energy production. From a global point of view as well, the wind energy sector is striving to cut CO2 emissions caused by the construction of wind energy infrastructure. Ørsted and Vestas recently announced that a minimum number of low carbon steel towers will be installed in all of their future joint wind farm projects. The research at OCAS contributed to a cost-competitive decarbonised steel solution that is enabling the wind industry to attain giant savings in CO2 emissions.
As part of the ArcelorMittal XCarb ™ recycled and renewably produced steel initiative (RRP) — a huge technology portfolio to invent smarter steels for people and planet — OCAS has developed an alternative metallurgical processing route for the manufacturing of heavy plates. The use of steel scrap only, and an electric arc furnace (EAF) powered by 100% green energy, realises a reduction of 60% in the CO2 footprint of heavy steel plates for wind towers. After changing the production process, the material properties were thoroughly investigated to check for any differences with respect to the conventional production route. The investigations have demonstrated that the EAF route deliv-
ers mechanical properties equal to those of historical productions by blast furnaces (BF/BOF). For this comparison, a large dataset with +50,000 production records on chemical composition and processing (rolling) parameters was correlated with the material properties obtained via the substitute processing route. Large sets of metallurgical data can be processed efficiently thanks to OCAS’s datamining methodologies.
Future work will evaluate whether this material and greener processing route is suitable for other sectors, such as the construction market and naval applications that decarbonise ship transport.
The new processing route enabled by XCarb ™ allows us to reduce the CO2 footprint of heavy plates for wind industry by 60%
Ulrike Lorenz
The shift towards a carbon neutral society will need the contribution of all available technology, including transitional technologies such as CO2 capture. As part of its energy transition, the capturing, usage and storage (CCUS) of CO2 gas from industrial processes contributes to lower the overall CO2 emissions in the world. At first instance, CCUS is a way to decarbonise existing industrial processes. For heavy industry to meet the climate ambitions, CCUS solutions might be more immediately within reach, since most alternative production processes are still on the drawing table. While new green technologies are being investigated, the CCUS technology is here to support the reduction of CO2 emissions.
CCUS infrastructure involves capturing methodologies, transport and storage. Throughout this CO2 supply chain, important challenges are present for the materials being used. Transporting and storing pure CO2 would be less of an issue – but the captured gasses from industrial processes contain impurities originating from the industrial processes themselves. Inherently, a certain level of impurities will remain in the gas mixture – and those might make it very hard for the material to withstand the operating conditions. Gas purification can be considered to a certain extent, but, due
to the related costs, a convergence will be quickly deployed towards a commercial trade-off between purity and material improvement. OCAS research programmes are designed to close this gap.
As for many questions related to material susceptibility or compatibility, the solution often lies in the fundamental understanding of molecular and atomic interactions with the material surface at the microstructure level. For these metallurgical phenomena, OCAS’s knowledge is key. OCAS researchers
are conducting metallurgical investigations and extensive experimental work to reveal the mechanisms responsible for the root cause of material degradation. Once this is clear, dedicated material testing can be defined to assess the appropriate material aspects and identify the possible impacts on the mechanical and the corrosion properties. The knowledge and understanding also allows for the design and development of improved material grades that are no longer prone to the degradation mechanisms at play during operation.
Because the capture, utilisation and storage of CO2 is rather new, the industry is still looking for standards and exploitation guidelines
The transport and storage of CO2 waste streams related to carbon capture, utilisation and storage (CCUS) is envisaged in more industrial areas and raises inquiries and concerns from different points of view. Looking at the exposure of materials in new and existing assets, attention is being paid to the mechanical integrity and corrosion aspects. Because CCUS is rather new, the industry is still looking for standards and exploitation guidelines. Exchange of international experience between operators and research institutions is helping us gain insights and identify the risks, as we try to come to a common test methodology and acceptance criteria.
OCAS is part of the international working groups and is closely monitoring the leading research on CO2 in the world. OCAS’s research focus lies on the transport of CO2 via pipeline and shipping. Both applications require materials that have different mechanical properties: whilst CO2 transport via ship is at mild cryogenic conditions and low pressures, the conditions in a pipeline are at higher pressures (x10) and ambient or seabed temperatures. Hence the material challenge exhibits two sides. On the one hand the request for high-
er toughness. The toughness results from the microstructural properties such as grain size and plays a major role to compensate in local brittle behaviour and in arresting crack propagation. On the other hand, an excellent corrosion resistance is needed to avoid any degradation provoked by the impurities in the CO2 gas, such as H2S, SOX, NOX and H2O.
In the coming years, OCAS will further increase knowledge on the mechanical
and corrosion behaviour in CO2 mixed with impurities by conducting exposure tests in autoclaves on existing and new steel grades. New steel concepts can be developed, that meet the most severe requirements imposed by the CCUS applications.
cal instabilities that necessitate EU members becoming independent and securing their own supplies of energy, as stated in the REPowerEU strategy by helping the EU save energy, produce clean energy, and diversify energy supplies, or other aspects such as supply of critical raw materials.
In addition, remarkable efforts are being exerted to improve the lifetime of solar infrastructure and improve soil corrosion performance with optimized coatings.
As reaction to global warming, humankind is facing a big leap to transform the world, our energy production, consumption and industry processes, our way of living, our transport of products and people around the globe. The transformation is being driven by efforts to reduce – and later avoid – the emission of CO2. Ambitious goals have been set by the European Union towards net-zero by 2050. And industry is pulling out all the stops, making tremendous efforts and investments in research and development to mature technologies for attaining these targets. The change is transitional, reducing fossil fuels while new renewable energy sources will emerge — in pilots, in first industrial deployments, and later in new projects. The energy transition is now — amidst geopoliti-
With the generation of renewable energy on the rise, the infrastructure for renewable energy production represents an opportunity for the steel sector.
OCAS’s key competence on materials integrity is contributing to the deployment of the energy transition by optimizing the steel grades for larger production units, which allows higher capacity, optimized design and fabrication of the infrastructure to extend lifetime, or the reduction of maintenance cost by adding functional properties to the steel.
The OCAS team has been working on accelerating the deployment of wind infrastructure by optimizing fabrication and qualification methods to reduce production time and cost, as well as increasing lifetime extension by improving fatigue design, corrosion performance and combined corrosion-fatigue performance.
As part of the energy transition, much is expected of the electrification that must take place in the coming years, along with the exploitation of renewable energy sources.
Electrification is the most dynamic pillar of the energy transition. At the forefront of electrification is the technological revolution of electromotors and Electrical Steel, which is an essential part of the motor. Electrical Steels play a fundamental role in electric generators to convert the renewable energy sources — such as wind and hydro — into clean electrical energy, which supports the establishment of sustainable energy installations. In addition, Electrical Steel is an essential component in optimising traction and propulsion delivered by motors that enable the ongoing trend of vehicle electrification.
Due to the booming global electric vehicle market, and the European Union’s forthcoming ban on the sale of new passenger cars equipped with internal combustion en-
gines starting in 2035, there is a strong need to optimize electric traction motors, which serve as the primary component in electric vehicle (EV) powertrains. Today, traction motors with Rare-Earth Permanent Magnets (REPMs), such as NdDyFeB, dominate the market thanks to the great energy of such magnets. However, in order to achieve the ambitious climate targets, the guidelines from the raw materials act, and for sustainability reasons – linked to the environmental impact of obtaining Nd and Dy, the scarcity of Dy and its geopolitical aspects — there is a need to reduce the use of REPMs. With vehicle electrification, the need for raw materials is shifting and ever-increasing. Electrical Steels (ES) used as core materials in the ‘heart’ of electric motors are definitely a cornerstone in e-mobility. In this context, the choice of Electrical Steel for stator and rotor cores is playing a vital role in meeting all motor requirements that are high energy efficiency combined with high power density, sustainable and low-cost design. Other fuels are emerging to cover the need to balance the energy systems. Green hydrogen production is being proposed in many
models as an energy vector to accumulate the excess of renewable energy production. Additionally, hydrogen offers a unique opportunity to reduce greenhouse emissions of hard-to-abate sectors, such as the steel or cement industries, or mobility for heavy-duty vehicles. A dedicated infrastructure for the hydrogen economy has been designed and tested in numerous demonstration projects around the world. Shipping of liquified hydrogen derivates such as ammonia, hydrogenated organic compounds, or even shipping liquified hydrogen directly, will allow transportation of large amounts of hydrogen at a global level (e.g., between continents). Hydrogen compressed through pipelines is the most cost-effective solution for ranges below 1000 km or land-locked areas. The cost-effective infrastructure deployment able to move large volumes at a low cost will facilitate the up-scaling of the hydrogen economy. The OCAS team has been working on de-constraining the deployment of the infrastructure by optimizing steel for pipelines and tanks with a performance-based design. The team has focused on both aspects — steels qualified for adequate
resistance to fracture in hydrogen gas, and the development of the corresponding qualification methods.
The capture of CO2 produced in industrial processes using fossil fuels has also emerged as a significant player for the energy transition. Part of the captured CO2 is utilized in other industrial processes. The excess is stored geologically on depleted oil and gas fields, saline aquifers, or other suitable geological formations. The CO2 can be transported from the emitter site to the geological storage sites via shipping in liquified form or compressed through pipelines. The OCAS team has been working on the structural integrity of the steels for pipelines and tanks.
OCAS’s advanced and industry-oriented research and development on materials to enable and realise innovative solutions for the renewable energy industry — as well as on revolutionary technologies serving electrification — will be illustrated by some striking examples in this section.
Martin Liebeherr, Nuria Sanchez & Steven Keyzer
Hydrogen is an important fuel for cutting Greenhouse Gas (GHG) emissions, and it will become a part of the future energy mix. Especially for the hard-to-abate industry sectors (e.g., steel industry, cement industry) for which alternative options – such as electrification – to decarbonise its processes and products are not in immediate reach. Hydrogen, as well as other hydrogen-related energy carriers, will play an important role in keeping industries local.
Hydrogen brings us back to one of OCAS’s core competencies: the knowledge and understanding of the interaction between hydrogen and metal substrates. During the steelmaking process, it is of utmost importance for safety and quality to control the hydrogen content in the steel throughout the different metallurgical phases. The experience built up over the years on the modelling, experimentation, and quantification of hydrogen interactions - either on surfaces or in its crystal structure - enables OCAS to perform research at a world-top level.
Given this historical experience, and the fact that there is a future for Hydrogen in the energy mix, OCAS cannot stay on the sidelines. Therefore, our research activities focus mainly on the metal-intensive applications, like infrastructure for transport and storage of hydrogen, including other hydrogen energy carriers like biomethane, methanol and ammonia, under any operational condition (concentration, pressure, temperature, purity, etc. ). OCAS contributes to the research in ArcelorMittal’s big Global Energy Transition portfolio, some of whose activities are illustrated further in this report.
...
Regarding infrastructure for the transport of hydrogen through pipelines, the transmission and distribution system operators look at the possibilities for re-purposing sections from the existing gas grid – as well as construction of new-built pipeline segments. Although hydrogen-related technologies are evolving very fast and are thus difficult to forecast, in its 2023 ‘Energy Technology Perspectives’ study the International Energy Agency (IEA) predicts 13,500 km of new hydrogen pipeline (NZE Scenario). Whether it concerns re-purposing infrastructure or new-built sections, material aspects cannot
be neglected, as the structural integrity and hydrogen-resistance of the network will determine whether safe grid exploitation is feasible. The aspects will be discussed in the following sections.
Solutions must be sought for the purpose of intermediate and temporary storage of hydrogen as well. Hydrogen working pressures are on the rise, which is a challenge but also an opportunity for metallic materials. This report further illustrates how OCAS’s experience with hydrogen enables next-generation pressure vessels for the storage of hydrogen in different applications.
Whether it concerns material challenges in re-purposing infrastructure, new-built sections, structural integrity and hydrogen-resistance, OCAS has a broad history of experience to rely on
Nuria Sanchez Mourino
Today’s steel grades are of great interest in the context of the research programme on the global energy transition. The infrastructure is installed and operational ... but is the steel grade suitable for hydrogen? What is the impact of servicing and repairs throughout the history of the grid? Questions are on the rise about the compatibility between the current state of the steel substrate and hydrogen when considering re-purposing an application. Since one knows that some steel grades interact with hydrogen, one must make sure such steel is not improperly exposed to hydrogen environments. But how can this be demonstrated?
For almost 20 years now, OCAS researchers have been focusing on hydrogen in steels and on steels for hydrogen. Materials that are prone to degradation caused by hydrogen cannot be used. As part of extensive research programmes, existing steel grades for traditional purposes (oil and gas) were screened and compared. Their sensitivity was mapped and correlated to their microstructural parameters. This recently completed investigation gives OCAS a clear understanding of the key microstructural parameters controlling hydrogen pick-up, diffusion, trapping and embrittlement.
With this new level of insight, OCAS has now moved into the design of dedicated grades with enhanced resistance to hydrogen embrittlement. By means of this research approach, OCAS is gaining a full and fundamental understanding of the interaction between hydrogen and metallic materials. The lessons learned from thorough investigation of the existing material define what kinds of micro-structures work best – setting specifications and tolerance levels for next-generation alloys. OCAS knows what is important and what microstructural aspects have to be looked at.
Understanding the key microstructural parameters that control the susceptibility of existing steel grades to hydrogen embrittlement serves as input for the design of a dedicated line pipe grade with improved resistance to hydrogen embrittlement
Marc-Antoine Thual
Hydrogen is considered to be an important fuel for the future in order to cut greenhouse emissions to fight climate change. With the growth of a hydrogen-based economy, a vast pipeline network is needed to transport gaseous H2 from one place to another, because such infrastructure provides a sustainable and cost-effective way for long-distance transport. But the ingress of hydrogen (at parts per million level) into pipeline structures is known to significantly degrade the structural integrity by a phenomenon called Hydrogen Embrittlement, which affects the pipeline’s lifetime.
The problem can get even worse when hydrogen is transported at high pressure –because the pressure causes more hydrogen to diffuse into the structure. Therefore, for the safe transportation of hydrogen to support the economy, we need a hydrogen -embrittlement-resistant steel grade.
OCAS has started an interdisciplinary research initiative to develop a new propri-
etary hydrogen-compatible steel, traded under the name HyMatch®. Researchers are aiming for a dedicated steel grade that demonstrates greater hydrogen resistance than the steel grades used today. Metallurgical features of HyMatch® steels will cover engineered microstructures with optimized internal soundness to increase the hydrogen trapping efficiency, while using functional surfaces capable of limiting hydrogen ingress in the steel.
HyMatch® hydrogenembrittlement-resistant steel ensures the safe transportation of hydrogen; an essential aspect in the hydrogen value chain
Tuhin
Das
Through multiple interactions, we identify new and emerging technologies and keep track of the different players on the market
Dennis Van Hoecke
The hydrogen economy and value chain is an international concern. OCAS is involved in several international projects and partnerships for keeping a window on the world and staying in dialogue with regulations and other industries. This is established via cooperation in joint industry projects as well as funded projects, international workshops, and participation in conferences and exhibitions. Considering the research projects alone, we connect with a group of almost 40 different universities, research centres and industrial companies. Through these interactions, we identify new and emerging technologies and keep track of the different players on the market.
OCAS participates in Joint Industry Projects such as the DNV JIP Transportation of hydrogen gas in offshore pipelines — H2Pipe — which is a joint industry project to develop the world’s first guideline for transporting hydrogen gas in existing and new offshore pipelines.
OCAS participates in funded projects under the Horizon Europe Framework and Research Fund for Coal & Steel Programmes such as:
PilgrHYm, a Clean Hydrogen Partnership project in which researchers focus together with grid operators and various testing labs
on the structural integrity of gas pipe for re-purposing to hydrogen. Experimental data will be generated on serviced materials that are typically used in EU gas grids at operating conditions typical for these grids. This empirical work will generate insights on the behaviour of grid steel material under the conditions of interest. In this project, a methodology will also be investigated for accelerating the experimental characterisation that is needed to scale up the scope of materials and conditions towards the future. It is key to know the appropriate test methodology: which aspects of a test enable the correct and optimal characterisation of a material. OCAS contributes knowledge and
experience on modelling and in-situ hydrogen testing. The experiments are conducted on ex-service pipeline material to validate the numerical simulations. The ultimate goal of the project is to use this pre-normative research to optimise design codes and standards for hydrogen pipelines. More information can be found on the project website and LinkedIn: www.linkedin.com/ pulse/pilgrhym-twelve-european-partners-join-drwuc/
In another project, OCAS’s fundamental understanding of the hydrogen-metal interaction is highly valued. HyWay, digital and emerging technologies for competi-
tiveness and fit for the Green Deal project, will advance experimental capabilities to reveal hydrogen-material interactions by compiling characterisation methodologies across length scales. Furthermore, adaptive multi-scale and multi-physics material modelling tools will be developed to disclose how hydrogen alters material behaviour under various service conditions. The experimental and numerical activities go hand-in-hand and complement each other. The capabilities of the developed models will be demonstrated through different use cases related to hydrogen storage and transport. OCAS is closely involved in the macro-scale model development, which will be capable of simulating hydrogen diffusion and describing the impact of hydrogen on plasticity and ductile damage behaviour. OCAS will also supply coil and pipe material for one of the use cases.
More information can be found on the project website and LinkedIn: https://www.linkedin. com/showcase/hyway-project/
SAFEH2PIPE, a project funded by the Research Fund for Coal & Steel Programme, aims to develop guidelines for the material selection and the qualification process for H2 pipelines, focusing on how the structural integrity of a pipeline can be ensured in
the case of external damage (e.g., dents or corrosion damage).
FEATHER targets developing a steel For nExt generATion H2 cylindERs with outstanding strength – ultimate tensile strength (UTS) of 1.3 GPa, which exceeds the current solution by 30% – in addition to improved performance in high-pressure H2, whilst guaranteeing safe performance.
New metallurgical concepts will be investigated on laboratory scale for flat, billet, as well as tube process routes and tested on their resistance to hydrogen embrittlement, hydrogen-microstructure interactions, fracture toughness and fatigue under high pressure hydrogen. In an upscaling exercise, in-use properties will be tested on first batches of prototype pressure vessels. A coherency check and gap analysis (including Finite Element Modelling) between lab and prototype results will validate FEATHER's approach.
More information can be found on the project website: https://feather.steelyhydrogen.be
Re-use of existing pipeline systems for H2 transport would be the most preferred solution from an economical and climate impact point of view. However, the key aspect here is the structural integrity of the pipeline systems, which could become affected by hydrogen-induced cracks following the pick-up of hydrogen atoms by the pipeline’s surface layer.
The NoHentry project aims to provide strategies for surface conditioning of the interior of existing linepipe systems and compressor components, in order to make them impenetrable for hydrogen gas. This will be realized by mapping the key parameters influencing hydrogen penetration through a metallic or non-metallic surface: the nature of the surface at the atomic scale, with, in particular, the effect of the steel alloying. The fundamental processes of hydrogen dissociation, surface adsorption and diffusion that dictate the material properties are being investigated in this project.
The mapping of the hydrogen processes is approached via atomistic simulations as well as via experimental evaluation, assisted with results from studies on serviced parts that are sampled from the real gas grid.
In the first year of the project, some promising results were obtained:
– Synthesis of a series of unique binary and ternary alloys with a fully ferritic microstructure without any second phases. As the ferrite phase has a different stability region for every alloy, a dedicated choice of chemical composition and annealing
treatment was chosen. This allows us to assess the isolated fundamental effect of added elements in the ferrite matrix on the interactions with hydrogen. This was a unique approach, not done previously in hydrogen-related research. The bar chart indicates the composition of the binary alloys that were cast at OCAS for the project. The targeted composition (in dark green) and the measured composition (in light green) have similar values in all cases. In addition, an illustration of the clean ferritic microstructures that were achieved is shown on the inset of the figure.
The hydrogen economy is a global concern. The related challenges for the value chain, the infrastructure and the materials are being continuously discussed in the international community. Even though countries have their own specific policies and views on the establishment of a future hydrogen economy, the behaviour of materials in contact with hydrogen is of common scientific interest. Therefore, researchers from all over the world are connecting to de-risk technologies and unlock barriers to ensure safe solutions.
International working groups, research communities and exchange of knowledge is of utmost importance. For years now, OCAS has been creating a forum for such knowledge-sharing by organising the SteelyHydrogen conference under the lead of an international scientific jury. The conference brings researchers from academia and industry together in one place and puts research on the stage. In 2022, it was again time to gather the world’s hydrogen community in Belgium to discuss the newest insights amongst hydrogen research experts, particularly for the current material challenges connected to the role of hydrogen in the global energy transition. The SteelyHydrogen conference provides a unique
environment for sharing and exchanging experiences on the link between metals and the various aspects of hydrogen. This fourth edition of the SteelyHydrogen conference was a great success, with more than 240 participants, of which the majority attending physically in Ghent; more than 100 abstracts were given stage - of which about 50 were addressed by an oral presentation. More info on: https://steelyhydrogen.be/
Another source of international collaboration and networking is the role OCAS plays in Hydrogen Europe, a leading organization representing European-based companies and stakeholders that are committed to moving towards a (circular) carbon-neutral
society by accelerating the European hydrogen industry. Their research association, Hydrogen Europe Research, comprises over 150 universities and research & technology organisations from 29 countries across Europe and beyond. This is where research meets industry to re-define the possibilities of hydrogen and jointly enable the development of mature hydrogen technologies. As a member of this association, OCAS enters into public-private partnerships, projects partly funded by the European Commission and the industry, to tackle specific hurdles and develop solutions for materials in future hydrogen applications. With a strong focus on materials for the transport and storage of hydrogen, OCAS researchers are members of the Horizon Europe
By dedicated organisation of events and participation in the scientific hydrogen community, OCAS ensures its active involvement in the latest progress on hydrogen materials’ research
Lode Duprez
CLEANH2 Partnership, technical committees for production, distribution, cross-cutting, supply chain and hydrogen valleys.
OCAS researchers are active members in joint industry projects, such as DNV’s
H2Pipe, and many materials research consortia, such as ARCOR Association for Research on Corrosion and Corrosion Protection Member Research Cluster H2, EMIRI (Energy Materials Industrial Research Initiative) and ESTEP (European Steel Technology Platform).
OCAS experts are active in standardisation bodies, including NACE, ASME, ISO and API, and pipeline research groups, such as EPRG (European Pipeline Research Group).
OCAS’s fundamental understanding of the hydrogenmetal interaction is highly valued; With the help of OCAS, customers can make the right choices Steven Keyzer
For almost 20 years, OCAS’s researchers have been looking at hydrogen in steel and towards solutions for coping with this particular phenomenon. Unlike other gases, hydrogen molecules can dissociate at the metal substrate surface and travel into the metal lattice. Hydrogen atoms are small enough the go inside the material and distort the crystal lattice of some metallic materials. Unsurprisingly, this does not happen without any negative effects. In fact, the impact on some of the materials can give rise to very dangerous situations because of hydrogen-induced degradation. Structural components can lose their mechanical properties to a significant degree, and massive accidents can happen.
Before a material is brought into contact with hydrogen — e.g., exposure to operating conditions with hydrogen, even in very small quantities — one has to make sure that the hydrogen is not causing degradation. When too little is known about the material’s behaviour under such conditions, an extensive metallurgical assessment needs to be conducted in order to exclude all related risks.
As the hydrogen economy has gained momentum in the last few years, we have seen questions arising from a variety of sectors on the suitability of their application in hydrogen environments. Applications that were not initially developed for use in exposure
to hydrogen might suddenly be re-purposed to enter into contact with a hydrogen environment. And for such re-purposing, the materials in contact with hydrogen must be compatible. The metal-hydrogen interaction that might occur in some metallic materials needs to be carefully understood. When it is known that certain risks may exist, the appropriate mitigation actions need to be in place to secure safe operation of the application with hydrogen.
OCAS provides its customers with advice on such questions dealing with possible compatibility issues between hydrogen and metallic materials. Candidate materials are
screened for their susceptibility to hydrogen damage, and the materials are ranked according to their resistance to hydrogen. Then, customers can make the right choices between either material selection or modification of the operating conditions. OCAS’s experience, and our understanding of the metallurgical phenomena in the hydrogen-metal interaction, make us a preferred partner for metallurgical recommendations. In close collaboration with witnessing organisations, notified bodies and regulatory institutions, OCAS has conducted complex research and testing programmes demonstrating the compatibilities and risks of the customer’s innovative ideas.
Soon, the additional mechanical tests that we can run in this new lab will enable deeper insights into the behaviour of materials operating in gaseous hydrogen
Since the establishment of OCAS, research on hydrogen and metals is in the core of our strengths. Throughout the years, fundamental knowledge has been built up and international recognition for our activities has grown. OCAS has a state-of-the-art lab with advanced equipment to support its research activities. For years now, OCAS knows how to charge and test metal samples in hydrogen, and we are certified for the quantitative determination of hydrogen. OCAS is also qualified to conduct experiments with deuterium to accurately determine all aspects of the hydrogen-metal interaction, the root cause of material degradation.
To stay at the forefront of Europe’s leading hydrogen research, and to maintain our ability to answer all customer inquiries related to hydrogen applications, OCAS is making a considerable investment in the construction of a hydrogen lab Fort H2, a dedicated lab that obeys all safety measures for the in-situ testing of materials in a high-pressure gaseous hydrogen environment. With the extensive designing and engineering phase now behind us, we can start the construction of the lab.
Soon, the additional mechanical tests that we can run in this lab will enable deeper insights into the behaviour of materials operating in gaseous hydrogen. Are the materials compatible with specific operating con-
ditions? Is the material resistant enough? What if not only static but also cyclic loads are exerted on the material. What are the associated failure mechanisms? With the acquired data and knowledge, OCAS aims to provide answers beyond today’s material standards. Static and dynamic mechanical tests will allow us to evaluate the fracture toughness and fatigue properties of metallic samples being introduced in a high-pressurized chamber and exposed to hydrogen-containing gasses, under non-standard conditions as well. Such tests will clarify material uncertainties, map the risks, and allow us to mitigate the risks necessary to making the hydrogen economy operate in a safe, economical and reliable way.
OCAS FORT H2 lab will closely collaborate with the VKhyLab, an initiative of the Von Karman Institute for Fluid Dynamics (VKI) and the Belgian federal government, to build an open innovation infrastructure to test hydrogen technologies, products and applications at an industrial scale. The competencies of VKI, as future operator of the VKhyLab, which are focusing on fluid dynamics and related physical sciences, are fully complementary to OCAS’ strengths in metallic materials; therefore VKI and OCAS have agreed that also the testing infrastructures of VKhyLab and FORT H2 will complement each other. It is foreseen that OCAS’ equipment for the mechanical testing of metallic materials in high-pressurised gaseous hydrogen will also be accessible via an associated partnership with the VKhyLab.
The project will define a series of metallurgical concepts with tailored alloy chemistries and processing methodology
Tuhin Das
Hydrogen bottles (or cylinders) for storage and mobility is yet another application that belongs to OCAS’s research programme. The fact that such bottles are pressurised up to (very) high levels with hydrogen entails extra challenges for the materials. Today, high-pressure cylinders use high-strength steels that only allow hydrogen storage at rather low pressure (up to 500 bar). Higher pressure storage cylinders — towards 750 bar and beyond — would require materials with even higher strength and toughness. Both key material properties need to be enhanced without compromising the steel’s resistance to Hydrogen Embrittlement. Because an increase in strength often goes hand-in-hand with increasing susceptibility to hydrogen embrittlement, there are big challenges ahead.
Such challenges can only be addressed by a multi-disciplinary team, involving strategic partners from the entire value chain. Within the framework of the FEATHER project, funded through the EU Research Fund for Coal and Steel programme, a consortium was established together with Faber, a leading manufacturer of high-pressure cylinders, and other key research centres — ABS Centre Métallurgique (France), Atomic Energy and Alternative Energies Commission (CEA France), and Fraunhofer IWM (Germany). OCAS contributes with custom alloy synthesis, alloy processing and characterisation, and testing in an H2
environment. A role for which OCAS is well recognized given its expertise and unique facilities. The project will define a series of metallurgical concepts with tailored alloy chemistries and processing methodology. After casting and rolling of the new materials by means of the semi-industrial equipment at the OCAS lab, an extensive testing campaign will be conducted on the various materials to screen and rank the performance and see whether the final customer requirements have been met.
More information on project website: https://feather.steelyhydrogen.be/
The outcome of a sensitivity analysis indicates the way in which alloy chemistries and processes could be improved to achieve better hydrogen resistance
Tuhin Das
Pressurised tanks for above-ground hydrogen storage are already in use in industry today. Such pressure vessels are made of heavy plates welded into large bullet tanks or spheres, and they are commonly pressurised at relatively low pressure (below 50 bar). However, the need for greater hydrogen storage capacity is pushing the design of such above-ground storage up to its limits.
In the new design of future above-ground storage tanks, the target storage pressure is now rising from 50 bar to 250 or 300 bar. Using the same materials for these tanks will require increased thickness of the already heavy plate from 30-50 mm to 200-300 mmwith the corresponding fabrication, welding and supply challenges. Therefore, it is clear that, for this application, new steel grades with enhanced performance are needed. For the purpose of this material selection exercise, OCAS started to screen the industrial materials that are already produced today. The potential suitability in terms of hydrogen resistance at elevated pressures is compared in a test campaign, after which the mechanical performance of
the candidate alloys can be ranked relative to each other. As a result, researchers will be able to determine how the existing materials will behave under the circumstances that are envisaged in future pressurised tanks for above-ground storage of hydrogen. This investigation will also provide guidance on how to improve strength levels and eventual embrittlement effect via chemical alloying and microstructural processing. OCAS’s researchers will fit all available data into a model to increase the mechanical performance of the alloy, whilst also preserving the good characteristics for construction like weldability and formability of the plates.
A plate steel product, similar to offshore S355MLO grade, but with enhanced corrosion resistance to atmospheric marine/saline weathering conditions, is being developed
Protection of steel structures against corrosion in offshore environments – in particular, topside offshore structures like sub-stations and towers – is a challenging task compared to rural or industrial environments, mainly due to the harsh conditions caused by the high load of chlorides in the seawater and the atmosphere.
In order to reduce the life-cycle costs of offshore applications, the development of a cost-effective corrosion-resistant steel substrate would be a step forward. The development of the metallurgical concept resulted in steel compositions with a good combination of corrosion-resistance, mechanical properties and weldability. Industrial trials in a heavy-plate mill have proven the concept’s feasibility and robustness. The results of mechanical characterisation showed that an S420 strength level is comfortably achieved for plates of 20 mm thick, and this is within reach for plates of 50 mm thick as well. Research is currently focusing on corrosion testing of the industrially
produced saline-resistant weathering grade, with special attention to real atmospheric exposure testing at marine locations.
Last year, the work focused on the results of corrosion testing of saline weathering steels (SWS) – in conditions that simulate the severe, saline offshore conditions, as well as the real marine exposure itself. The corrosion results after 3 years of exposure in near-shore environment confirm the improved saline corrosion resistance (up to 20%) compared to the conventional S355MLO grade.
Since the enhanced corrosion resistance of weathering steel is attributed to the formation of a patina, an in-depth characterization of the rusts formed after accelerated tests is being performed by advanced surface analytical tools. With the goal of exposing SWS at the customer facilities, efforts are being made to standardise SWS. In 2023, SWS was introduced in the international ISO 630-5:2023 standard for structural steels: Technical delivery conditions for structural steels with improved atmospheric corrosion resistance as “weathering steel with an improved resistance to saline environments (S355WSE)”.
The development of new spray coatings can contribute to extending the lifetime of offshore wind infrastructure, thanks to its improved corrosion and fatigue performance
Beril Corlu
For some applications, the conventional thermal spray coating concepts to protect against corrosion are just not sufficient or compatible with the application goal. Thermal spray coatings are often much thicker and, for some products, it is the preferred coating technique (e.g., for heavy plates). Reducing such coating thickness would mean big savings in material, production and maintenance. A better chemical composition that excels in corrosion protection over the traditional coating systems could realise savings.
Recently, the proof of concept for a novel coating concept was delivered and the resulting outlook is promising. OCAS’s know-how concerning coating development – the fundamental understanding of how coatings work – allows researchers to design new concepts. Developed and proven technologies from hot-dip coating techniques were investigated further and translated into a thermal spray coating concept. Accelerated corrosion tests have demonstrated that the concept works and that the coating
withstands harsher environments for longer exposure times. Now, further strategies for entering the market are being envisaged. Soon, OCAS will initiate the first conversations with offshore energy industries that want to improve the corrosion performance of their coatings and harvest the resulting benefits from reduced maintenance and process costs. Furthermore, this development can also contribute to the lifetime extension of offshore wind infrastructure, thanks to its
improved fatigue performance. The corrosion and fatigue behaviour of new coating concepts will be investigated in the recently approved European project DURALINK –the successful proposal for this project was prepared over the last two years. In this international collaboration, new insights will become available by applying new testing methodologies to thermal spray coatings.
Wind turbine towers, both on- and offshore, are increasing in height and capacity, to reap benefits from better wind conditions higher up and from larger capacity generators. As a result, the market for plates with increasing thickness and/or plate weight is also increasing. However, the number of plate mills that can produce such plates is limited, and a huge investment would be required to set up new facilities.
Therefore, to approach this in a different way, OCAS is investigating the option to weld together same-thickness heavy plates to produce the larger sizes (in particular, length) and weights the market requires. These welded plates would then be used by the tower manufacturers as single plates. The first step in this project was to investigate possible processes for the welding of plates in the 30-80 mm thickness range by studying the literature and discussing with equipment suppliers and research organisations. From the options identified, two were chosen for further investigation, bearing in mind boundary conditions such as productivity and cost, but obviously the weld zone properties as well.
The first process that was selected for further investigation is long stick-out submerged arc welding (SAW) — OCAS is developing this welding procedure, aiming for an optimum in equipment cost, productivity (through high deposition), weld quality, and properties of the weld zone. In addition, a fully single-sided welding procedure, yet with good and consistent weld root quality and profile, is targeted. The second process is reduced pressure electron beam (RPEB) welding for which OCAS is working with a thirdparty company. RPEB can achieve very high penetration and narrow welds, and it would be able to weld through even the largest thickness of interest in a single pass,
leading to very high joint completion rates. Nonetheless, there are other challenges still to be considered in this process, such as weld pool support and/or welding position.
OCAS
is investigating innovative ways to produce heavy plates in order to meet the high market demand for wind energy production
Christoph Gerritsen
Thorough investigation has led to a breakthrough of new production techniques and the adoption of spiral weld tubular sections in new markets
Özlem Esma Ayas Güngör
OCAS’s welding experts have investigated optimised welding conditions for spiral welded pipe (SAWH) manufacturing to improve fatigue performance of seam welds by increasing the weld-toeangle. As a matter of fact, still too little is known about this advanced manufacturing technique with respect to the fatigue performance of tubular sections, which prevents the wide adoption of such spiral welded tubular sections for structural applications (e.g., in the offshore market).
Relying on our welding experience, OCAS researchers have focused on the welding parameters that play a role in fatigue properties. It is known that the resulting weld toe – the weld toe angle – strongly correlates with the fatigue properties of the joint structure. In SAWH, the welding parameters that determine the quality and geometry of such a weld toe include the heat input, the type of flux playing on the viscosity and surface tension, and the arrangement of the multi-wire welding head. By varying these welding process parameters, the key parameters that finally show an influence on the fatigue properties can be identified. More
than 40 different welding conditions have been tried at lab scale. The samples were compared mutually and investigated thoroughly to arrive at a full understanding of all aspects. Together with the corresponding welding parameters, new important insights were attained.
OCAS was able to demonstrate improvement of the weld toe on lab samples, hereby significantly increasing the fatigue lifetime of structural sections over what is typically observed in spiral weld produced pipeline for
onshore. This activity has enabled OCAS to understand and control welding conditions and thus will contribute to a breakthrough of new production techniques and the adoption of spiral weld tubular sections in new markets such as offshore or other structural applications.
Magnelis®-coated ‘HyPer®’ steel grades, engineered to be stronger, more ductile, and lighter, offer superior corrosion protection, meeting the industry's evolving demands
The demand for advanced metallic-coated structural steel in the solar industry is evolving towards materials that are not only stronger but also lighter, thinner, more ductile, and resistant to corrosion. This innovation is key to building more reliable, durable, and affordable solar structures. Rising to meet this challenge, OCAS, in collaboration with several ArcelorMittal plants across Europe, is actively developing an extended range of metallic-coated high-strength steel grades to meet manufacturers’ ever-increasing demand.
MAGNELIS®-COATED HYPER® HIGH-STRENGTH STEEL
Beginning with small lab-scale experiments, OCAS has successfully developed highperformance ‘HyPer®’ steel grades. These grades are manufactured using robust and adaptable metallurgical concepts, employing tightly controlled chemical compositions and micro-alloy strengthened fine-scaled microstructures. Furthermore, Magnelis® emerges as a leading coating solution, renowned for its excellent in-use properties and versatile applicability. It is
also recognized as the most cost-effective option for photovoltaic solar structures. In recent years, the successful industrialization of metallurgical concepts and coating solutions at various ArcelorMittal plants has resulted in the first commercial Magnelis®-coated HyPer® high-strength steel. This steel, with a yield strength exceeding 700 MPa, exhibits excellent ductility and in-use properties. It offers industry-leading corrosion protection, with thicker coatings-up to 430 g/m² and
even more - further enhancing the durability of solar structures.
OCAS is currently fine-tuning metallurgical routes to broaden the ArcelorMittal ‘Magnelis®+HyPer®’ range even further. This includes offering a variety of strength levels at different thicknesses, alongside a range of coating weights across multiple galvanizing lines. This extension will distinguish ‘Magnelis®+HyPer®’ as the preferred choice for solar structures.
Since the launch of ArcelorMittal’s iCARe® brand about ten years ago, OCAS has developed dozens of steel grades for the electromobility, and will continue to do so. But this is only part of the story, since electrical steel requirements are also becoming demanding in the industrial market, especially in the generator segment.
Fully processed non-oriented electrical steel (NOES) is used in electric motors and generators. This is a flat product with specified electromagnetic properties and very low thickness, in the range mainly between 0.2 and 0.5 mm, which is insulated on both sides by a varnish. At the customer, laminates are punched out of the coil product and fabricated into stacks, which then form the rotor and the stator cores of the electric machines. ArcelorMittal is supplying fully processed NOES from SaintChély, a plant that has produced electrical steels since 1917, and soon – starting in 2024 – from a new downstream line in Mardyck. OCAS is the ArcelorMittal Group’s unique research lab for the development and application of NOES. Already involved earlier in the development or support of
fully or semi-processed electrical steels from several plants in Belgium, Spain and Germany, OCAS was put in charge of the Electrical Steels R&D program in 2004. Since then, our lab has supported AM SaintChély in numerous substrate and coating product developments. In parallel, OCAS has constantly improved and extended the capabilities of its electromagnetic lab and investigated the impact of cutting, mechanical stress, etc. on final magnetic properties. A numerical iron loss model was developed over the years and constantly refined by incorporating such effects – and it has been used to support customers during their machine design studies, developments, and production. Until a decade ago, industry was the main market for NOES, requiring coil thicknesses
between 0.5 and 1 mm, occasionally down to 0.35 mm. The industry applications imply an operating frequency of 50 Hz or lower, and sometimes define challenging specifications on core losses (hydro generators) or polarization (wind generators).
The automotive market initially used coil thicknesses in the range of 0.3 to 0.35 mm and then gradually evolved in the direction of 0.25 and even 0.2 mm. NOES for the automotive market is designed for high operating frequencies, generally specified at 400 Hz. Taking into account the typical combinations of specifications for the steels in this market on polarization, losses, and mechanical strength, the iCare® brand was launched in 2012 with three families:
Torque, Save and Speed. In the meantime, the family has grown a bit and now includes a new member, 420 Save, which is a very versatile solution for optimizing motor performance and efficiency.
OCAS is at the heart of these developments and is responsible for the definition of the metallurgical route and the industrialization of the new grades. Without any doubt, continuous renewal of the product offer is the key to ArcelorMittal’s success. Roughly half of the automotive volumes to be delivered in 2024 were industrialized during the last 7 years, and no less than 22% were industrialized in the last two years only. We are confident that we will continue this pace.
Electrical steels development is at the heart of the technological energy transition revolution
Martin Liebeherr
OCAS’s expertise in electromagnetic applications not only facilitates the market introduction of new products and supports motor designers in optimizing their electrical machines. It also assists ArcelorMittal’s commercial marketing team in exploring new market opportunities for non-oriented electrical steels (NOES).
Apart from its intensive use in rotating electromagnetic applications, such as wind generators and traction motors of electrical vehicles, one of the most promising applications for NOES is in stationary inductive components found in electric power systems. A distinguished market, especially with booming smart grids. In principle, stationary inductive components – such as transformers, reactors, and inductors – are widely distributed over electric power systems. They work at a wide range of operating frequencies – i.e., from grid frequency up to radio frequency – with a huge spectrum of component sizes and corresponding power ranges, from miniature electronic components to giant power and distribution transformers.
The market penetration of these components is rapidly increasing with the evolution towards smart – bi-directional – power systems. The quality of these inductive components is very important to minimizing energy losses and meeting the global emission norms. The magnetic core is an essential part of these components, often using low-loss high-polarisation grain-oriented electrical steel (GOES) grades, especially at high power rating operating conditions. However, considering the potential scarcity of GOES and the associated material availability risks, thin gauges of high-quality NOES grades with low losses could serve as a viable substitute. It is crucial to initially understand the market demands and the essential material properties before
determining which segments hold the most promise for NOES grades. Based on an intensive market analysis of this specific segment, coupled with comprehensive modelling of main components such as transformers, we were able to determine the market area of interest for NOES.
For grid-frequency (50-60 Hz) medium/ high power applications, GOES will remain the optimal choice. However, for grid-frequency low power applications, NOES can be beneficial for applications that require simple geometries, such as the so-called EI core. Although from the performance perspective (i.e., size and
efficiency) the use of GOES is better, NOES grades are very promising considering the cost (and eventually material availability) perspectives. At higher frequency levels, GOES undoubtedly outperforms NOES when using the same thickness. However, thin-gauge NOES grades (i.e., ≤ 0.3 mm) can effectively replace thicker-gauge GOES (i.e., ≥ 0.35 mm) especially at high frequency range applications. For small transformers and inductors that currently use relatively high-loss thick-gauge (i.e., ≥ 0.35 mm) industrial NOES grades, automotive NOES grades are often overqualified materials, although they show a noticeable performance improvement. Therefore, replacing GOES with thin-gauge NOES grades would be governed primarily by the cost and material availability trade-off.
Understanding the technical aspects behind the market needs is essential to exploreing the interesting market spots
Ahmed Abouelyazied
Electrical steels are a critical component when you’re trying to build high efficiency engines. ArcelorMittal’s electrical steel grades are a major contributor to our success. They have enabled Emotors to achieve the mechanical and electrical characteristics we required for our EDUs
Our team was able to support the development of a highly advanced product – thanks, in particular, to our R&D expertise
Richard Moore, Head of Materials at Emotors
Vincent Eustache,
Head
of Customer Technical Support Electrical Steels, ArcelorMittal
The support we provide to customers plays a pivotal role in driving innovation, developing robust products, and bridging the gap between development of raw materials and the final product. Our commitment to customer support is not merely a service but a philosophy that drives us to satisfy our customers' needs. We often join together in the R&D journey to boost our strengths by means of true co-development, which results in excellence that neither of us could realise on our own.
In the process of supporting ArcelorMittal’s customers, particularly in the introduction of powertrains for hybrid and battery electric vehicles, our engagement usually begins with selecting the most suitable Electrical Steel grades for their specific requirements. When the off-the-shelf solutions do not meet the customer requirements, we leverage our knowledge to develop customized grades tailored to enhance performance by carefully controlling crucial Electrical Steel properties.
But our support doesn't end with the selection during the pre-development
phase; rather, we stay with our customers throughout the production journey. During the homologation and prototyping phases, we actively contribute by estimating and characterizing Electrical Steel electromagnetic and mechanical properties at each production step (such as punching, welding, etc.). Our goal is to guide our customers to optimal manufacturing steps, maximizing efficiency, minimizing costs, and optimizing processes.
One example of such a commitment is our collaboration with Emotors, which has engaged in a partnership with ArcelorMittal.
Emotors is a joint venture between Stellantis Group and Nidec Leroy-Somer, a leading European entity in electric vehicle powertrain and traction motor production, located in France. This collaboration stands as a proof to the impact of our customer support on final product development and overall success.
This success story is encapsulated in the positive testimonials we receive from our customers. Their words, filled with satisfaction and appreciation, stand as a testament to the tangible impact of our collaborative efforts.
– Unit cost for the complete motor at mass production levels (100,000 units/year) < 6€/kW;
– A recyclability rate >60%.
OCAS’s main contribution is to provide the design team with the most suitable electrical steel grades, given the strict requirements regarding high power density, light weight, and sustainable design. We look forward to exploring the optimal manufacturing processes that enhance the performance of the final product, with a central focus on mass production.
As a dedicated and highly regarded centre in materials science, we serve as a pivotal entity, attracting collaborations from both academia and industry
Ahmed Abouelyazied
Looking forward to driving the next generation electric cars, in which this technology will be implemented. There’s no bigger motivation than seeing the product you have worked on in real life
Stator and rotor cores in a motor are composed of hundreds of stacked soft magnetic electrical steel (ES) lamellas. To obstruct the interlaminar eddy current excited by the alternating magnetic field, there are insulation coatings on both sides of the electrical steel sheet. Conventionally, welding, interlocking and clamping techniques are used to fix the magnetic core. These conventional fixation techniques have a huge impact on the magnetic properties of the electrical steel core.
With interlocking, a mechanical connection is made between adjacent laminations by partially punching a tab through the thickness of the lamination and later press-fitting this tab into a matching depression on the top surface of an adjacent lamination. This approach works well for thicker steels but becomes more challenging for the thinner steels being specified in an electric motor. Interlocking and welding also introduce short circuit paths between the laminations, as they penetrate through, or bridge across, the insulating core plate coating on the steel surface, creating eddy current paths. Al-
though this effect has been known for some time, more recent work has shown that, with the use of thinner steels and higher fundamental core excitation frequencies, the adverse effects of interlocking and welding on unitized core magnetic performance are increased.
To overcome this drawback, over the last 10-15 years, an approach has been developed, whereby the laminations are bonded together using an adhesive. Two different manufacturing approaches exist: (1) the application of a glue on coated lamellas in
the stamping process, and (2) a bondable coating applied already in the steel plant.
The coated electrical steel laminations are joined together by applying an adhesive during the punching process. As the composition of the glue varies with the supplier and comprises organic glue, inorganic glue, or their combinations, it is a challenge to design a coating compatible with different glues.
The bonding varnish is a more universal solution, directly applied on the electrical strip, which has a double functionality: it acts as an insulating material, and it provides the bonding between the ES laminations when it is thermally activated under pressure. In the delivery state, the coating is only partially cured to produce incomplete polymerization without sticking, allowing the sheets to be stacked. The lamination stacks are bonded by heating under pressure. To maintain the high-power density of electric engines, the adhesive layer’s thickness should be uniform and restricted to a minimum, which makes it challenging to reach high strength.
As the demand for bonded assemblies is expected to increase in the near future, OCAS supports ArcelorMittal in extending its coating product range with C5 coatings optimized either for glue adhesion or with double-sided coated bonding varnish. Our contribution is essential: it starts with the identification of suitable varnishes based on lab tests and extensive product characterizations; proceeds with industrial trials in the steel plant with the aim of identifying the most suitable application and curing parameters; and continues in diverse manners during customer tests in the market introduction phase. These efforts have recently enabled ArcelorMittal to provide a number of new products to the automotive market.
The choice of the electrical steel (ES) grade for stator and rotor cores of automotive electric motors plays a vital role in meeting all motor requirements, which are high energy-efficiency combined with high power-density, sustainability and low-cost design. High energy-efficiency in a wide speed range can be obtained by using low-loss electrical steel grades, which maximize the vehicle’s driving range and allows machine designers to downsize the cooling systems. High power-density – in other words, more compact motors for the same power output – can be obtained by using electrical steel grades with higher mechanical yield strength, depending on the motor design strategy. In addition to the performance enhancement requirements, there is a tremendous need to use fewer rare earth (RE) permanent magnets (PM), hence improving the system’s sustainability and overall cost.
One of the achievements in this area is the recently introduced iCARe® 420 Save grades developed by OCAS. The iCARe® 420 Save grades present an elevated mechanical yield strength, reaching 420 MPa, surpassing the standard iCARe® Save grades by 20 MPa without compromising the material’s exceptional magnetic properties. This positions iCARe® 420 Save as an optimal selection for improving the magnetic characteristics required in stators, while maintaining the essential mechanical properties necessary for rotors. Furthermore, the versatility of iCARe® 420 Save extends to both stators and rotors, allowing them to be punched out from the same grade. This not only streamlines the manufacturing process but also contributes to cost reduc-
tion. The iCARe® 420 Save grades prove especially advantageous in traction motor topologies, particularly in applications where the heightened yield strength can be fully utilized, such as in V-shaped rotor interior permanent magnet (IPM) synchronous motors, where the position of PM, and the thickness of the associated iron bridges, are primarily determined by the mechanical strength of the ES grades that are used.
Depending on the designer’s main interest, utilising iCARe® 420 Save grades enables numerous design opportunities, such as designs for more energy-savings, compactness, and fewer RE materials. The following cases illus-
trate these design options, focusing on either maximum energy-savings or the balance between the maximum REPM volume reduction and energy-savings. The quantitative results are obtained using a multidisciplinary electromagnetic-mechanical-thermal finite element model coupled to an optimisation routine, developed at OCAS using JMAG Finite element commercial software.
In this case, the designer’s main interest is energy-savings, without optimising the PM volume. Thanks to lower stator current enabled by shorter iron bridges, the motor can be optimised for energy-savings of up to 7.5%.
On top of the energy-savings, the PM width combined with the PM radial position can be further reduced, which leads to a smaller bridge thickness. This results in more than 5% PM volume reduction in addition to around 3% energy-savings. This implies a significant volume reduction of REPM, leading to a less costly motor design as well as a more sustainable motor design, which enhances the vehicle’s ecological footprint.
Minimizing motor energy consumption is a crucial factor, given its direct influence on the overall energy consumption of the vehicle. To confirm this, OCAS’s methodology involves elevating the analysis from the component level to the system level. In other words, we integrate the detailed motor model (at the component level) into the vehicle dynamic model (at the system level) to calculate the vehicle's energy-savings per 100 km given the standard WLTC driving cycle (the Worldwide harmonized Light vehicles Test Cycle). Based on this analysis, the vehicle’s energy-savings over the standard WLTC driving cycle would reach 10-70 Wh/100 km depending on the design
options, electrical steel grade thickness, and vehicle parameters.
OCAS’s research has enabled the development of iCARe® 420 Save grades with a superior yield strength combined with low losses. This achievement increases the traction motor’s design degrees of freedom by enabling greater energy-savings and sustainable motor design. The benefits derived from these advantages will manifest in the vehicle's energy consumption, potentially resulting in a decreased need for a larger battery size. Consequently, this contributes to a more sustainable and environmentally-friendly footprint.
Modelling is the cornerstone of our approach to valorising innovative electrical steel for future motor designs
Jan Rens
Automotive applications call for Electrical Steels (ES) with excellent magnetic properties and suitable mechanical strength. In terms of magnetic properties, ES must be easily magnetizable thanks to a high permeability, and provide low core losses which is essential for a motor’s energy efficiency. Material properties and performance in application are often dictated by physical phenomena that occur at the atomic scale. Linking such performance-property relationships is a true challenge for metallurgists – but once this is achieved, it can represent a priceless advantage in the effort to create new steel developments.
Consequently, at OCAS, material design does not solely rely on incremental developments but it also dives into scientific knowledge building, in which we aim to obtain a better understanding of the key physical mechanisms at play.
The main focus of our research activities is understanding the small-scale mechanisms that modify the material’s behaviour on greater length scales. An example of this is the evolution of the crystallographic texture during the fabrication of electrical steels. The final crystallographic texture is very important in ES metallurgy, as it can affect the magnetization behaviour and hence modify
the final magnetic permeability of the material. In this context, some alloying strategies were found to modify texture evolutionand we wanted to better comprehend this intriguing observation.
For this purpose, we designed experiments involving some model alloys, which were conducted at the OCAS lab following a methodical experimental plan involving state-of-the-art advanced characterization techniques accessible via the OCAS microscopy centre. First, systematic microstructure and texture analysis by diffraction microscopy was performed at different stages of the material’s thermomechanical processing and microstructure development. Local, near-atomic scale, chemical analysis characterization by means of atom probe
tomography was used to evaluate element segregations at carefully selected sites of interest, such as grain boundaries. These nanoscale observations were essential in understanding how alloying may affect the advancement of the crystallographic texture in ES during static recrystallization of the grain structure. This multi-year project benefited subsequent product developments by optimizing the manufacturing process for improved final magnetic properties.
OCAS, as the ArcelorMittal Group’s unique R&D centre for product development of electrical steels, with years of expertise in electrical steel research and development, aims to continue to excel in the generation of fundamental knowledge that enables smarter materials for the future.
For our customers, electrical traction machines need to have an excellent performance over a wide frequency range to be able to perform optimally in each drive cycle. Moreover, they need to have a high-power density to add as little weight to the vehicle as possible, for a given mechanical output, with reliability coupled with low production costs. To face these challenges, customers are continuously optimizing their designs and are increasingly using electrical steel at its limits.
The need for high-power density for traction machines translates not only into high demands on the electro-magnetic level, but also into a higher level of mechanical constraints. Increased mechanical stresses create fatigue damage risks with complex in-service conditions such as the manufacturing effect of cutting (punching), the thermal effect due to the in-service heating possibly inducing softening of the steel, and a geometry effect around the teeth and permanent magnet cut-outs. Fatigue is a localized damage phenomenon of a component due to repeated cyclic loading, and a cumulative process consisting of crack initiation, propagation, and final fracture. The amount of accumulated fatigue damage depends on the loads introduced during the manufacturing and the in-service life of the component. Small-scale labo-
ratory samples are prepared and tested to supply the necessary material data to our customers’ mechanical design departments so that they can accurately predict the lifetime of a component based on the in-service conditions (loading and temperature), manufacturing aspects, and component geometry. In material testing, we consider the effects known to affect fatigue performance – such as temperature dependency, notch sensitivity, and punched edge effect – along with the inherent statistical variation of fatigue data.
Since fatigue test campaigns are often timeconsuming, customers tend to estimate the expected stress levels for the endurance limit based on accelerated tests in the form of quick-check step-loading fatigue tests. The estimation based on the step-loading scheme is called the Locati method, which is an approach combining the stress-life models with Miner’s cumulative damage law. The method assumes that test data have no scatter, damage law is correct, and the slope of the S-N curve is known in advance. In most cases, this value is not availablehence, a good assumption of the S-N curve slope is required for this method to give good estimates. However, our findings at OCAS have shown that, to improve the degree of confidence in the estimation, an accelerated fatigue test approach based on self-heating or stiffness change would make more sense, as these methods have a physical basis in their assumptions.
We supply the necessary material data to our customers’ mechanical design departments so they can accurately predict the lifetime of a component based on the in-service conditions (loading and temperature), manufacturing aspects, and component geometry
Okan Yilmaz
I am proud of the team translating knowledge into technical specifications
Thanks to equipment available at OCAS, the final annealing cycles to be used in production could be simulated in the lab, saving time and money for starting up a new production line
Martin Liebeherr
Varun Shah
In March 2022, ArcelorMittal had announced an investment of more than €300 million, to create a new production unit for non-oriented electrical steels (NOES) at its Mardyck site in the north of France. The new industrial unit is scheduled to start up in 2024 and will, with a 200,000-tonne production capacity, triple ArcelorMittal’s current deliveries to the NOES market.
OCAS became deeply involved in the lay-out of the new production facilities. Mardyck’s engineering team wanted to make sure that the line would be able to produce the steels required by the market over the period of the next, say, 10 years – and therefore, they counted very much on our vision of how to make the steels of the future.
In the steel industry, it is acknowledged that a current product portfolio will become largely obsolete over time: as a rule of thumb, we can assume that 75% of the steel grades that will be requested in about 10 years’ time do not yet exist today. This might be particularly true for the automotive NOES market, because, in view of the electrification of mobility, motor designers are
continuously striving for higher efficiency and performance of their traction motors. Consequently, the requirements on losses, polarization and strength of soft-magnetic steel are expected to constantly increase over the years.
Thanks to its expertise acquired over more than two decades, OCAS was able to provide recommendations for the lay-out of the new production tools beyond the state-of-the-art. This concerned all relevant downstream production steps: hot band annealing, cold rolling, final annealing, and coating. In several cases, experimental proof of the benefit of certain innovative production parameters
for the magnetic properties was required. In this context, we launched a number of lab-scale and – in collaboration with our colleagues from the ArcelorMittal Global R&D Process team – pilot-scale experiments.
Within a few months, we completed a huge amount of experimental work and were able to convince the engineering team (and management as well) to translate our ideas into industrial practice. Now we are sure that we will have all the industrial tools needed to develop the steels required by the market in the near future.
Steel is one of the most common materials used in a variety of applications. It can easily be transformed and joined, it provides excellent value for money, and it is virtually fully recyclable.
But how well does it perform in a critical component or an asset? Durability is a measure of how well a material can maintain its integrity and functionality under different conditions throughout its intended lifespan. So, durability is also considered as an aspect for enhancing product sustainability and reducing ecological footprint. End-users are increasingly aiming to use durable materials, and joints between those materials, that can handle all sorts of challenges without too much degradation. The most common damage mechanisms are corrosion, fatigue, and wear, which all lead to a loss of mechanical properties over the
lifetime of an asset. The understanding of these phenomena – and providing solutions for these issues – is at the core of OCAS’s activities, irrespective of whether it is from a metallurgical, surface, or application point of view.
Problems related to durability of metallic materials or components need to be treated adequately. That’s why the OCAS teams deliver analysis services for critical cases that need rapid intervention. Answers are provided for the cause, the approach we followed, and possible solutions.
Sometimes, a design change needs to be made, or a quality procedure needs to be adapted. Numerical predictions are becoming more and more important as well – but, as the proof of the pudding is in the eating, testing remains a crucial aspect. And OCAS is not alone in this quest within the FINOCAS group. ENDURES assists with its
analysis, testing and inspection expertise in marine and offshore environments, whilst GUARANTEED provides unique solutions to refurbish and repair broken parts, and even upgrade them in their performance.
As we are being confronted in the energy transition with situations that are not always either standard or available, we need to develop adapted, non-standard methodologies to qualify the performance of a material or component. The OCAS experts and testing teams have extensive experience in these matters, both in larger research projects as well as in performance qualification projects with individual customers. Whether it is about determining the fatigue performance on wind foundation joints, construction weld details, new joining methods, or evaluating coating developments for offshore usage, we need to prove what the real behaviour
of the material and its bond are within the operating environment.
But such qualification projects are usually very long, because the individual component testing, sometimes at large scale, takes quite a bit of time. Therefore, OCAS has exerted a lot of effort in developing new methodologies to accelerate the test and obtain lots of data points in a short period of time, thus providing tangible value for the end-customer. In this durability section, you will discover larger R&D projects as well as new projects that we have executed with individual customers - all with one aim: to establish structural integrity and functionality as close to reallife conditions as possible.
Marc Vanderschueren
We aim to separate the effect of surface degradation and fatigue initiation by a combination of simulations and experimental investigations
Offshore wind foundations feature cathodic protection measures against corrosion; alternatively, specific coating systems are applied to (in principle) avoid corrosion. However, in practice, an area expected to be protected from corrosion can become exposed at some point in the life of the component. In that case, unexpected free corrosion conditions come into play. In these situations, the fatigue life according to the design needs to be re-assessed to determine the remaining useful lifetime. These are circumstances for which guidance and current good practice are lacking. If no remedy is applied, the surface would be requalified as a free corrosion surface, with a shorter fatigue life.
In practice, there is a clear need for tools that allow assessment of the remaining useful lifetime of structures that have experienced damage. The industry needs guidelines to adapt models for lifetime, maintenance and inspection intervals when coated structures suddenly become prone to corrosion. Such a model would allow for an accurate digital twin of the operating structure, taking into account the true degradation at the level of the components. In the move towards longer lifetimes of offshore wind turbine monopile structures, there is a need for a better understanding of the FATigue CORrosion mechanisms. Therefore, OCAS has set up a project with Belgian partners in the framework of the Energy Transition Fund. Together with
Ghent University, the Belgian Welding Institute (Belgisch Instituut voor Lastechniek), Rentel, Parkwind and Iemants (Smulders), the FATCOR project was established with the clear objective of developing a qualitative and quantitative understanding of the mechanisms of corrosion fatigue in seawater, with a focus on the consequence of a local surface degradation. To this end, a series of corrosion, fatigue and corrosion-fatigue experiments have been performed and complemented with finite element simulations of local mechanical behaviour around corrosion pits and cracks. At the end of the project, this fundamental understanding will be transformed into guidelines for the estimation of the remaining fatigue life of monopile structures.
Whilst monopiles are the dominant foundation design solution in offshore wind farms, the importance of jackets is increasing due to the move into deeper waters and the ever-increasing turbine size. The Jacket Connection (JACO) project aims to investigate whether we could improve the fatigue performance of full-size tubular jacket nodes by means of robotic welding and have them stress-tested using both conventional (hydraulic) and innovative (resonant) testing techniques. An improvement of a critical joint’s fatigue performance results in a lower cost of the jacket foundation design.
The participating developers — Ørsted, Vattenfall, Iberdrola (Scottish Power Renewables), ENBW, Equinor, Siemens Gamesa Renewables, Shell and SSE Renewables — funded the project alongside the Scottish Government, under the umbrella of the Offshore Wind Accelerator (OWA) of The Carbon Trust. The project could not have materialised without the precious support of the supply chain participants - ArcelorMittal, Dillinger, Salzgitter Mannesmann Renewables, EEW, BIFAB, BLADT, Navantia, Heerema Fabrication Group, Aker Solutions - the certification bodies DNV, Bureau Veritas, German authority BAM, and an independent
technical advisor of TU Hamburg. BAM also performed fatigue tests on a bench with hydraulic actuators to supply comparative data to the resonance tests performed by OCAS. Such a consortium proves that JACO has been a real European project from 2017 to 2023.
At the end of this joint-industry project, the achievements of the JACO project cannot be underestimated:
– Establishment of a unique cooperation of the European supply chain towards optimisation in jacket fabrication and design.
– Identification of at least four node manufacturers capable of robotic welding of full-scale complex 3-D joints of jacket nodes and validation of their individual fatigue performance.
– Generation of an extensive set of new fatigue data representative for current state-of-the-art production, including geometries, plate thicknesses and diameters. The amount of available data points in the literature now has been at least tripled.
– Proof that robotic welding can be better than manual welding. At least two robotic welding node suppliers, who are the most
The JaCo project has been an incredible journey in terms of international cooperation whilst pushing the boundaries of fatigue data, full scale testing and critical component fabrication
Marc Vanderschueren
advanced in their process, can reach the target of 20% fatigue strength improvement, which equals about a 10% cost reduction.
– Acceptance by certification bodies that an improved fatigue curve can be implemented into production of such nodes, provided clear and minimum quality requirements have been put in place that are unique to robotic welding.
– Validation of the equivalence of the OCAS accelerated fatigue testing method to traditional, hydraulic testing equipment. This new method becomes the standard for fatigue testing of tubular connections (in air) at full scale. It is not only 20 to 40 times faster than classical testing methods, but it is also less energy-consuming in use.
A major take-away: the importance of JACO is two-fold: the project has qualified the OCAS testing method, dramatically reducing the time to obtain crucial data on fatigue performance of full-scale offshore foundation specimens, and it has established new ground towards successful implementation of robotic welding in jacket node fabrication. All in all, the JACO project has been an incredible journey in terms of international cooperation, whilst pushing the boundaries of fatigue data, full-scale testing, and critical component fabrication. And Carbon Trust OWA and OCAS have made it happen, along with some of the leading offshore wind industry players!
JACO has been an incredible journey when it comes to the introduction of robotic welding, accelerated testing of full-scale foundation specimens, and the mobilisation of the European offshore wind industry. JACO has also been a very successful example of industry-led collaborative research and development
Dr James Sinfield, Technology Acceleration Manager, The Carbon Trust OWA .
A small change to welding methods used on offshore wind foundations could significantly reduce fabrication and manufacturing times and costs. That’s why the Belgian Research Centre OCAS has been funded by The Carbon Trust and a consortium of wind power companies to investigate the viability of single-sided welds for tubular joints in offshore structures
Reuters Events in their publication “50 offshore wind companies to watch in 2024”
In the Jacket Connection (JACO) project, the tubular jacket nodes for offshore wind farm foundations were welded from both sides, at the outside and inside. This standard practice avoids a failure from the inside of a welded tubular, where it is impossible to inspect. However, such practice complicates the logistics during production and makes the node production more labour intensive with Health & Safety restrictions, which slow down the production rate and increase the foundation cost. Singlesided welds (from the outside only) are accepted, but they come at a severe penalty in the standards when it comes to fatigue performance. So, although no observations of such inside failures are documented, single-sided welding has no cost advantage today.
To overcome this hurdle, OCAS initiated the ASSISI project – Assessment of Single Sided welds – under the umbrella of The Carbon Trust OWA. This joint-industry project is funded by a partnership between EDF Renewables, Parkwind, Scottish Power Renewables, Shell, SSE Renewables, TotalEnergies and Vattenfall, and is being delivered by OCAS in collaboration with foundation manufacturer Iemants (Smulders). The project has also received funding from the NextGenerationEU programme, made available through the Flemish Agency for Innovation and Enterprise (VLAIO).
The problem of single-sided welds is that it is more difficult to guarantee that the root of the weld will be defect-free. For this reason, standards apply a penalty in the fatigue design of structures if they are welded from one side only. The objective of ASSISI is to investigate the effect of a root-defect on the fatigue life of a component. Two configurations are investigated: a stub on a monopile, for example for a boat landing construction, and a tubular joint as in a jacket. The 3-year project will conduct 15 full-scale fatigue tests across different types of single-sided large-
scale structures with intentional defects at the root of the welds, in addition to a number of small-scale fatigue tests to determine detectable flaw size and provide indications about the expected life of the considered components. A successful outcome will instil confidence and see single-sided welding become the industry standard, potentially accelerating and further cutting the costs of fabrication for offshore wind foundations.
Hot-rolled sections have been successfully applied in tied arch bridge designs with spans reaching up to 120 metres. The success is due to the cost-effectiveness of the solution linked with simple, effective, and fatigueresistant steelwork details. The current test program is linked to the tied arch bridge design containing vertical or radial vertical hanger arrangements as used in a specific Polish railway bridge. This bridge is constructed using a steel grade produced by ArcelorMittal — HISTAR®460 — with an optimised design from the colleagues from ArcelorMittal Global R&D Esch. The welded hanger connection had not been qualified before.
To quantify the fatigue resistance of the welded connection between hanger plates and the HISTAR hot-rolled arch profile of tied arch bridges, an experimental test program has been carried out utilising largescale beams in resonant bending fatigue. Such testing could only be conducted thanks to OCAS’s unique fatigue bench CRONOS. A large number of tests have been
carried out on samples in which the cyclic stress was oriented perpendicular to the hanger plate. Fatigue life test results are in accordance with a higher fatigue category in the standards than the weld details. Hence, we have proven that the HISTAR samples show a fatigue behaviour superior to that required. Once more, rapid full-scale fatigue testing has been made possible by OCAS.
In this collaborative research project with ArcelorMittal Global R&D Esch, our unique accelerated CRONOS fatigue testing system proved to be an enabler for efficient fullscale validation testing Jeroen Van Wittenberghe
We are proud to announce that our full-scale test program for wrapped composite joints has been successfully executed at OCAS. In front of a large international audience of interested parties from the Offshore Wind sector, we demonstrated that full-scale wrapped composite joints outperform the static and fatigue resistance of welded joints Tree Composites, in their online publication .
Welding is, of course, the main method for joining tubulars safely and reliably. But it requires specials skills and is labour intensive. Tree Composites, a spin-off from the Delft University of Technology (TUD) in the Netherlands, has developed a fibre reinforced composite wrap that can revolutionise the manufacturing of jacket foundations, which are multi-membered tubular structures. The improvement compared to welding is that the load is transferred through a dedicated composite wrap over a large area and not through the small surface of the weld. The brace members (diagonals) are bonded to the chord members (legs) through a coupling formed by composite wrapping. The wrap creates a sufficiently large internal bonding surface.
To increase confidence in their technology, the WRAPNODE I project was set up, supported by Rijksdienst voor Ondernemend Nederland (RVO), in which the feasibility of the technology was shown at a smaller scale. Together with TUD, OCAS set up a full-scale testing programme and demonstrated that these wrapped composite joints, also at their full-scale, have real superior performance in tensile and fatigue resistance versus traditionally welded joints. This is an important milestone for Tree Compos-
ites and TUD, who have developed this joint as a high-performance alternative to welding of foundations for offshore wind turbines. Whilst steel remains the preferred material for the joints of jacket foundations, this technology has the potential to reduce costs or, alternatively, lead to a longer lifespan.
The project partners organised a successful full-scale demonstration day. During that day, a full-scale test for the wrapped composite joints was executed live at OCAS’s
premises before a large international audience of interested parties from the Offshore Wind sector. OCAS has added real value by accelerating the test program during the upscaling phase of this new joining technology.
The SAFELIFE project has been the start of our journey into the Structural Health Monitoring area
Jeroen Van Wittenberghe
The SAFELIFE project represented our first steps towards lifetime prediction and management of fatigue-loaded welded steel structures based on structural health monitoring. The goal of this project was to develop and validate robust structural health monitoring methods and numerical tools based on load and damage monitoring to enable a more accurate lifetime prediction of fleets of quasi-identical welded steel structures, such as railway bridges, crane-way girders, and jacket offshore platforms.
The lifetime assessment is essential to supporting decisions for quantifying lifetime extension and optimising predictive maintenance by industrial partners. In the end, this will lead to a substantial reduction in operation and maintenance costs for players in different sectors.
In the project, the assets of three industrial partners were analysed: crane runway girders at ArcelorMittal Gent, railway bridges of Infrabel, and offshore wind platforms from C-Power. Other partners of this VLAIO-funded Intercluster project under the joint umbrella of the spearhead clusters SIM and IBN
Offshore Energy were: Sentea, 24Sea, Ghent University and VUB. The work performed involved load and damage monitoring and analysis and the development of a damage prediction and crack inspection strategy, and implementing them on both laboratory specimens and site assets. In addition, numerical tools for structural analysis, fatigue analysis and lifetime assessment at different levels of complexity, including the structural behaviour of industrial cases, were evaluated. This project has provided a solid base for the development of our structural monitoring activities on cranes and runway girders, which OCAS is developing further.
Our HIPNOS test can be a step change in online lifetime prediction of critical components, especially in an offshore environment
Jeroen Van Wittenberghe
In laboratory conditions, it is possible to detect cracks during a fatigue test using strain gauges located near the expected crack location. However, such an approach becomes impractical when an exact crack initiation location is not known. In such a case, optical fibre technology with distributed strain sensing opens a window of opportunities. Such capabilities were demonstrated in the BOPTIC project, a collaboration between Marlinks, IMDC, Engie-Laborelec, Ghent University, VUB University Brussels, Com&Sens, and OCAS in the framework of the Belgian spearhead cluster ’De Blauwe Cluster’ with funding support from the Flemish government, VLAIO.
The project activities were aimed at determining the structural integrity in terms of (remaining) lifetime prediction. The objective was to test the lifetime behaviour of optical cables mounted on real offshore geometries, as the use of actual material properties in a component behaviour towards full structural remaining lifetime determination becomes critical.
Throughout the project, we have demonstrated the application of distributed fibre optic strain sensing for early detection and location of fatigue cracks in welds in steel tubular test specimens. To do so, we have subjected welded tubular specimens
instrumented with optical fibre sensors to resonant bending load on our HIPNOS, an accelerated fatigue testing bench designed by OCAS for medium-scale specimens, operating on the resonance principle. Consequently, we have measured the strain distributions in the test samples in a continuous way, without interrupting the test throughout its entire duration. We showed that the fatigue cracks, which initiate from the inner surface of the wall of the specimens, can be successfully detected and located in real time using the novel measurement method. We conclude that the detection of the crack initiation may provide relevant information
serving the estimation of the remaining lifetime of the component.
Going forward, the ability to locally measure crack initiation online during testing without having to stop the test rig at frequent intervals would enhance the benefit of the resonant bending test acceleration dramatically. This would be a step change in online lifetime prediction of critical components, especially in an offshore environment. These could be components like repaired connections and their remaining life assessment or testing of bolted connections (flanged bolt/nut system) and the degradation mechanisms.
ArcelorMittal’s Amstrong® Ultra MCL series – with a minimum yield strength ranging from 650 to 1100 MPa – is ideal for thinner, lighter, and smarter solutions, leading to weight reduction, fuel and energy savings, higher payloads, and material cost-savings. Target applications include (but are not limited to) yellow and green goods, trucks, tippers, cranes, and heavy mechanical equipment, where stringent fatigue and toughness requirements must be met during design.
Decreasing the thickness of current products for weight reduction results in increased stresses, which make the use of ultra-highstrength steels essential. These materials have higher yield and tensile strengths, and better fatigue resistance, than conventional mild steels. To ensure safety under repeated loading, it must be known that fatigue failure typically originates from stress raisers. These stress raisers can be inherent in the microstructure (non-metallic inclusions), due to surface condition (poor surface quality, high roughness), or they result from joining, cutting, and forming procedures.
OCAS has an in-house fatigue testing setup to consider the complex effect of cold forming in predicting the number of cycles of a formed part. Finite-element analysis is used to predict the number of cycles. Utilizing a hybrid approach that combines experimental and numerical outputs, we can quantify the accuracy of simulations and define a design space to account for forming parameters such as bending ratio (r/t, punch radius over thickness). The accurate quantification of the effect of cold forming on fatigue life is crucial for applications with fatigue-critical formed sections.
Decreasing the thickness of current products for weight reduction results in increased stresses, which make the use of ultra-highstrength steels essential
Okan Yilmaz
A new understanding of the relation
between
microstructure and fatigue performance is the key to developing fatigue-resistant grades in the future
Steven Cooreman
Advanced high-strength steel (AHSS) applications on different structural components are becoming more attractive. The required property profile demanded by the application, along with a lean alloying concept for reasons of weldability, is achieved by microstructural processing: a process controlled through thermomechanical processing and annealing.
On the microscopic level, the mechanical response of multiphase steels to external loads is heterogeneous due to the individual properties of the involved phases. This leads to peaks in stress and strain fields that determine the effective mechanical property profile of the materials. Hence, the fatigue resistance of multiphase steels is strongly governed by the interactions among different microstructure constituents. As the measures to control internal purity have become very effective, inclusions might lose their status as the most important initiation site for fatigue cracks. Therefore, a new understanding of the relation between mi-
crostructure and fatigue performance is the key to developing fatigue-resistant grades in the future.
To take a step forward, OCAS and RWTH Aachen have initiated a collaboration with the overall objective of developing a numerical finite-element simulation framework, which allows investigating the effect of microstructural features – such as phase fraction, grain size distribution, texture, and inclusions – on the fatigue properties of AHSS.
A representative volume element generator was developed and validated to be a reliable tool for constructing microstructural models. In the treatment of statistical microstructural data, a sophisticated machine learning algorithm was used. Crack growth and stress-life (S-N) curve prediction models were validated using experimental data. Future efforts will focus on improving the calibration of crystal plasticity parameters and further automation of the model workflow to widen its applicability.
Abrasion is a commonly occurring wear mechanism observed in multiple industrial applications, such as automotive, transportation, mineral processing and agriculture. This phenomenon consists of the loss of material due to the contact and interaction between several bodies. The associated cost of wear is significant because it leads to equipment failures and loss of functionality. So, the ultimate goal of reducing wear is to extend service life and minimize downtime. Depending on the application, different wear mechanisms may be active, and the correlation with the material hardness is not always obvious as a material’s resistance to abrasion is a very complex response and involves many variables. The selection of appropriate materials for machine components through wear testing methodologies is of great importance in reducing the replacement costs. OCAS has built its rich experience in wear performance evaluation on 3 pillars: experimental work, numerical modelling, and field testing.
To compare the performance of diverse steels in terms of wear resistance, several tests already exist that try to replicate different forms of abrasion - for example, the ASTM G65 for sliding abrasion, or the in-house developed tumbler-impeller for impact abrasion.
New efforts have been made at OCAS to develop additional testing methodologies
for the study of wear for bulk materials, such as the single scratch test. This test replicates the abrasion process by sliding a rigid indenter against a smooth surface with precise control of load, position and speed. Rephrase this last sentence as such: developing a consistent test methodology is necessary because it has been widely used for coating evaluation but less so for wear performance.
In developing the testing methodology, modelling work is fundamental to try different conditions, such as forces, indenters or
scratch lengths, as well as to check trends in experimental and numerical results. In terms of material behaviour, the material models that were considered apply isotropic behaviour. More complex models, including material damage, are sometimes considered to improve the accuracy of the results, but they require intense testing to obtain calibrated parameter information.
In the field, a complex interaction of processes can lead to unexpected problems with material reliability. A range of portable measurement tools (microscopy,
Controlling wear is a way to extend lifetime, contributing to overall product circularity
Michiel Corryn
ultra-sound, hardness measurements, and 3D-scanning/roughness measurements) are available for in-situ assessment. Another approach is placing materials in operating conditions known to be severe. These so-called demonstrator cases help validate material selections based on labwork.
Our ultimate goal is to perfectly predict actual behaviour in industrial applications, where components are worn out continuously at different loads and abrasive particle shapes. This will make the selection of materials for wear applications more efficient.
Date
Demonstrator case with different steel types in coal grinding application as feedback for material selection .
Like all rotary machines and rotating components, lubricants are needed to ensure smooth operation between moving surfaces from sliding contacts. Lube oils, grease, gels and the like are used in components such as gearboxes, shafts, and bearings to reduce friction between moving parts. Proper lubrication of bearings is essential to minimise wear, extend the equipment's lifespan, and improve overall efficiency.
Offshore floating wind turbines, regardless of wind conditions, are constantly moving under the effect of tides. Due to the significant inertia of the rotor blades, the main bearings are in oscillation most of the time — and as long as the turbine gently rotates, the movements continuously distribute the lubricant. However, in a worst-case scenario without rotation, the lubricant is less effective and galling may occur. Galling is the adhesion of two metal surfaces in, for example, a sliding contact, and it depends on the metal crystal structure, which can be prone to forming such a cold weld contact and consequentially becomes stuck. This is to be avoided at all times.
On the request of a lubricant developer and provider, OCAS is reproducing the situations that could lead to galling in offshore wind turbine components. The setup enables qualifying the performance of different lubricants in the lab. OCAS tribology experts designed the required equipment and generated a quick but effective methodology that allowed for ranking of different products. The customer can then benchmark their new and modified lubricant on lab scale. The improved performance can be visualised and compared to its predecessors, so that the best product for preventing galling from happening can be selected. It is a challenging task to reproduce failure phenomena from the field on a small-scale
lab setup. We succeeded by sampling from an actual component, creating a custom sample holder, and carefully scaling the tribological input parameters.
It is a challenging task to reproduce failure phenomena from the field on a small-scale lab setup
Michiel Corryn
The SKYBOX material and component qualification programme is an excellent fit to OCAS’s total research testing and assessment capabilities
Magnelis® has known a record high sales level of more than 1 million tons in 2023 to meet customer orders from all over the world
The development of Magnelis®, a Zn-Al-Mg coating to protect steel substrates against corrosion in different environments, is one of our biggest recent success stories. Since its first market introduction a decade ago, the product has experienced continuous growth. The exponential demand for this coating concept is the irrefutable evidence of its excellent corrosion performance. Production volumes are on the rise, with a record high sales level in 2023 to meet customer orders from all over the world. In Europe and beyond, more and more production lines are being made ready for production.
Driven by market requests, the product range is being expanded. OCAS researchers — together with a team of colleagues from other ArcelorMittal Global R&D laboratories — have investigated how the coating concept could be made available in thinner and thicker coating layers. Thinner coatings are applied to substitute the standard galvanised products for the general construction market; whilst the thicker coatings are of especial interest for applications in harsh environments.
For all Magnelis® lines, OCAS is responsible for the product validation testing. This is the assessment to make sure that the final product meets all required criteria, such as proper adherence of the coating to the substrate, the resistance during product forming like bending, and other in-use functional properties. This product guarantee is of great importance, as guarantees on durability are given to customers.
OCAS also provides dedicated customer assistance. We can analyse which coating
concept is the best choice, given the application and the environmental conditions. The expected lifetime of the coating is often the driver in such assessments. OCAS can perform specific test campaigns in which the conditions during operation can be replicated in the lab environment. Long-term and accelerated exposure tests in different media — such as soil, saline, humid, and acidic environments — and at different temperatures are amongst the possibilities to help customers make the right decision.
ation (such as wind and solar) on floating structures is on the rise, material savings are possible when alternatives are found for expensive stainless grades and aluminium alloys. Field and lab corrosion tests are used to investigate whether cheaper material candidates can withstand the harsh environments. The application of a suitable coating can bring new opportunities when both the structural demands and the surface corrosion properties can be met for offshore infrastructures at affordable costs. Luckily, OCAS engineers are developing suitable coatings for the protection of infrastructure in near sea and offshore conditions.
“OCAS’s level of research expertise is one of the most advanced in the world. Thanks to our international recognition and great network, we have access to soil and corrosion testing sites all over the world
Ansbert de Cleene
The advantages in time-savings and throughput as well as from a health and safety point of view justify the investments in cobots
Advanced tests demand advanced methodologies. Nowadays, cobotisation is being used at more places in the lab to support operators in their work — to lighten the workload, make procedures more accurate and reproducible, allow for parallelised actions, and increase throughput. The cobot system also contributes to general health and safety in the lab, since the manipulations can be confined in closed containment and thus prevent possible toxic exposures.
Recently, OCAS has automated the conduction of the corrosion product removal procedure by means of cobots. The methodology involves the repetitive removal of corrosion products to determine the corrosion rate by means of chemical etching. The cobot system reproduces exactly the steps operators perform. In between the etching steps, samples are properly cleaned, rinsed and dried by the cobot. We’ve been able to realise significant time savings, allowing operators to multi-task while supervising the cobot in process. The design of experiments can eventually be enlarged to cope with more environmental conditions, with shorter
review intervals. What-if scenarios can be applied (e.g., a specific environmental parameter goes above the expected limit) to gain insights into the sensitivity of the system. Increasing the available data generally allows for better training of the statistical models.
The installation of automated systems, as well as the programming of the cobots and the development of user interfaces, come at a considerable cost and require the right experience. However, the advantages in time-savings and throughput described here
— in the organisation of the work as well as from a health and safety point of view — are obvious and justify the investments. The OCAS electromechanical engineering team is identifying opportunities for automation within the lab facilities. When the benefits are clear, our engineers take care of the full process automation and integration, with the support of the operators.
The availability of models for the prediction of corrosion in different contact areas and conditions is highly valued by our customers, who rely upon OCAS for their designs and material choices
Ansbert De Cleene
The availability of models for the prediction of corrosion in different contact areas and conditions is highly valued by our customers, who rely upon OCAS’s simulation and testing capabilities for their designs and material choices. For bigger projects, customers use OCAS’s assistance to generate data for the engineering of their constructions. Increased material knowledge can result in huge differences — especially for specific applications, operating in environments where too little is known, harsh conditions typically with higher acidity, salinity, a certain presence of impurities, and so on. OCAS conducts lab and field tests taking the local conditions into account to bring clarity on the coating system’s behaviour and allow proper predictions.
An improved coating concept, with potentially improved protection in offshore conditions, was installed on a floating demonstrator, called SeaVolt, a realisation by Tractebel, DEME and Jan De Nul.
In a co-development track with Zimmermann, OCAS looks together with its customer to the onset and progress of corrosion in and above water surfaces. Depending the geographical location, water compositions and the environment just above the surface can be very different – and yet they determine the performance of the coating system. So, water, climate and weather conditions are closely monitored. Advanced datamining allows for the correlation of all parameters involved. The numerical models can be trained with this field data so
that predictions on corrosion become possible even in such specific environments.
And environments can become even more complex. When agriculture and solar power production are combined, agrivoltaics – new principles for the exploitation of solar energy over growing crops or next to livestock –have new challenges ahead that need to be unlocked before installations can be realised. An interplay of soil, water and organisms, chemicals from fertilizers, increased amount of nitrogen, acids, etc. requires an advanced protection shield to prevent steel structures from corrosion. OCAS’s lab and field-testing approach can cope with the most severe conditions and yield the operational window in which coating concepts applied on sub-structures perform well.
Sensitivity analyses, on customer request, are not limited to alternative environments. Changes in product design or production process can also lead to inquiries for de-risking. For instance, together with Zimmermann, OCAS investigated the impact on the structure’s lifetime by changing the bending radius of coated steel profiles. Customer benchmarking tests were performed to enable customers to produce optimised profiles with less material, without compromising strength while keeping the same anti-corrosion properties. A customer-oriented testing campaign can then demonstrate and ensure that the promised lifetime of a dedicated coating system is met in the envisaged circumstances.
With the North Sea as the central hub of the 2 Seas region, both geographically and economically, corrosion is a highly underestimated problem for the whole region. The range of environmental conditions and industrial applications that are available within the cross-border area have allowed the SOCORRO methodology and application to be tested thoroughly to demonstrate its usefulness. There is also the need for a large consortium — with a range of expert knowledge — from different economic sectors from all over the region, and for demonstrations and subsequent dissemination to be organised per region to allow for national differences, regulations and traditions.
OCAS and ENDURES are using their competencies and infrastructure to support the development of a tool for corrosion risk management: the SOCORRO system. This is a simple, rapid, in-situ sensor system, which is able to monitor a range of environmental markers over time that are specific for the corrosion of steel submerged in (sea)water. The data from these markers have been statistically treated to an overall corrosion risk estimate. Via this tool, companies have an independent measurement to assess the corrosion risks in their installations. This way, customers are more aware of their assets and can take appropriate actions for preventive maintenance.
OCAS, together with ENDURES, has contributed with accelerated corrosion tests, real
outdoor exposure corrosion testing, and a corrosion demonstrator in the harbour of Den Helder. This is one of the 11 different industrial demonstration cases — including wind turbines at sea, water desalination/ sanitation, ship’s hulls and ballast tanks, harbour sheet piles, process water, etc. — to assess and optimise the industrial applicability of the SOCORRO system.
The raft exposure facility in the harbour of Den Helder is accessible only by boat. The raft is a floating metal platform, used for corrosion and anti-fouling testing. For the installation of the environmental sensor, the sensor’s hardware (battery and Wifi module) was deployed with connections to
the railing of the raft and the sensor itself was positioned about 1 meter under the water line, the same depth as the samples to be tested. The corrosion sensor was also mounted at the same depth under the water line, and the solar panel and data loggers of the corrosion sensor were secured to the raft side railing.
Every month, the metal samples and sensors are evaluated. The metal samples are corroded and covered by bio-fouling organic matter. The visual inspection and the corrosion data of the metal samples are analysed. The corrosion of the metal samples is evaluated by the new corrosion sensor (ER-probe) and the mass loss of the metal coupons which were weighed before and after the exposure.
The adaptations that are made on the sensors show that the they are able to function in the North Sea’s very severe conditions. The corrosion prediction of the corrosion sensor shows a trend similar to the results obtained by mass loss determination, but the absolute values of the corrosion current show a factor of 3-4 difference. This needs to be further investigated in order to improve the corrosion prediction.
SOCORRO is a project realised with funding by INTERREG 2 Seas Mers Zeeën.
For more information: https://www.socorro.eu/
Thanks to SOCORRO customers are more aware of their assets and can take appropriate actions for preventive maintenance
To ensure healthy working conditions, OCAS conducts a chemical risk assessment to identify the presence of potentially hazardous chemical components in paints on old components before starting maintenance
Philippe Legros
OCAS has a wide range of customers from different application industries that count on OCAS for technical support and advice. In the last two years as well, customers have relied on our experience and dedication to assist them in tackling difficult issues, like corrosion, forming problems, welding troubles, health and safety risk analyses, and environmental issues.
As an example, OCAS helped the ArcelorMittal steel plant in Ghent make a risk analysis on overhead crane components in the context of electrical conversion. In a preparatory phase, and prior to the works that could involve grinding of the paint and welding, OCAS focused on the disassembled crane components. In fact, during such maintenance activities, hazardous compounds – such as hexavalent chromium Cr(VI), lead Pb, and other heavy metals can be released, and end up in the human body. To avoid this in all circumstances, OCAS carried out a health risk analysis by sampling paint flakes on the cranes and then analysing the possible presence of hazardous compounds that could be
released during the maintenance operations on the cranes. Paint coatings also comprise substances that could form hazardous organic compounds, such as benzene, when welding.
In the lab, the hazardous Cr(VI) compound was extracted from the paint flakes and its concentration was measured carefully following a specific methodology based on Ion Chromatography coupled with inductively coupled plasma mass spectrometry (IC-ICP-MS). Lead (Pb) and other heavy metals were also dissolved and measured by ICP-MS.
Such risk analysis serves as an important guideline to indicate whether there is a real danger associated with the activity. It is not used to determine the effective exposure of people in the workplace, since this would depend on the working conditions. Such chemical analysis is very helpful in identifying risks; and in addition to overhead crane components, such analyses have also been conducted on bridges and in old buildings to ensure an appropriate health and safety mapping of the work environment prior to maintenance activities.
Next to being a leading product development lab, OCAS also serves as technical support lab to both neighbouring ArcelorMittal steelmaking plants and companies outside the ArcelorMittal Group. A dedicated research and service division at OCAS stays stand-by for all plant-related issues. As such, the production plant can call upon fast intervention and benefits from the lab’s competencies and specialised test equipment in order to ensure full operability of the production plant in addition to safety. That is, dedicated root cause analysis of failures or potentially dangerous situations will prevent re-occurrence and ensure that proper mitigation actions are taken.
OCAS offers industrial asset reliability tools to its customers. The offer comprises:
– Incoming inspections for materials arriving at the plant. This involves, for instance, a local inspection of newly purchased equipment or refurbished equipment to check for non-conformities at part-critical locations.
– Fitness for purpose evaluation – which gives advice on material selection and design optimisation. During such studies, we think together with the customer concerning remediation of a critical situation to avoid failures.
– Root cause analysis after failure of broken components.
The lessons learned from such failure cases are used to sensitise monitoring tools to increase the overall level of safety in steelmaking production plants and also in our training programmes on material failure mechanisms. Sharing return of field experience with colleagues inside and outside the company increases awareness and reduces potential incidents.
Skip cars are used to charge the steelmaking plant’s blast furnaces. They bring iron ore sinter and cokes to the top of the blast furnace. This is understandably a crucial component in the steel production plant. In the last two years, two failures occurred on the axles of two different skip cars, whose shafts had been in place for 1 and 5 years, respectively. This premature failure is highly unusual, and the root cause was investigated in the OCAS labs. The analysis revealed the presence of fatigue cracks that, in the first case, initiated at a large casting defect, and in the other case, in the heat-affected zone near the root of the weld. Based on the findings, the steel plant was advised to non-destructively inspect similar areas of the skip cars currently in service.
When a leak was discovered in a water tube that transports cooling water to the cokes plant, OCAS experts visited the site. The leakage appeared after only 6 months of service, which is highly unusual. The damaged section was cut out and subjected to failure investigation in the lab. The examination revealed evidence of corrosion, bacterial cellulose, which refers to microbiologically induced corrosion. When this combines with insufficient post-weld heat treatment of the tube joints, the corrosion mechanism leads extremely rapidly to material damage.
Our
direct support to production plants ensures operability and safety by investigating root causes and mitigating risks
Annick Willems & Veerle Van Lierde
In the past few decades, steel has been a driver in reducing energy consumption and CO2 emissions by enabling weight reduction (increased strength), extending lifetime (improved corrosion resistance and wearability), optimising operating conditions (higher creep resistance, allowing higher operating temperatures in electricity generation), and so on.
As one of the leading product development labs, OCAS has been involved in the conception and industrial upscaling of the various steel grades and coatings that enable those environmental improvements. Of course, we continue to develop steel grades with further improved performance, while the steel industry is unfolding plans to move to net zero CO2 emission steelmaking, which is discussed in Chapter 1 about “Decarbonisation”.
A first important driver is the further development of new generations of high-strength steels, with a focus on both pushing known metallurgies such as highstrength low-alloy steels or martensites to the ultimate limit of their performance, as well as enabling the industrialisation of exciting new metallurgical concepts such as medium Mn austenite-containing steels, high Mn austenitic steels, and intermetallic precipitation strengthened steels.
It’s important to note that, in addition to the lab exploration and conception work, several of these concepts are now entering the industrialization phase.
Another enabler to further pushing the lifetime of a steel component is to optimise its protective coating. Driven by the enormous success of the Magnelis® new high-performing zinc-aluminiummagnesium alloyed corrosion coating,
which is substituting pure Zn in record time, OCAS is already preparing the next upgrade for which extensive lab screening and pilot scale production have led to first industrialization efforts as well.
Simultaneously, OCAS is expanding its lab synthesis product offer and combinatorial capabilities, which should allow us to expand our customer base and move into new market segments. In order to further align our capabilities with customers’ requests, we continually work to improve our quality and to enlarge our competence in the production of specialised alloys such as high-N steels, Oxide DispersionStrengthened steels, high entropy alloys, etc.
Next to our steelmaking capabilities, it is important to highlight our unique rolling
mill capabilities, such as fully instrumented and automated hot rolling of thin and heavy gauge plates, direct connection to flexible cooling equipment, and planned extensions for cold rolling of ultra-thin and fragile materials.
And last but not least, we have state-ofthe-art welding equipment that can be combined with specialized computational modelling capabilities in order to guide customers how to join the new steel grades.
Tom Waterschoot & Steven Keyzer
By excellent teamwork and metallurgical expertise, we successfully extended the Amstrong® Ultra S700 production to a new plant
Rolf Berghammer
The Amstrong® Ultra family offers steel grades for yellow goods (heavy-duty machinery for groundworks and construction equipment like cranes, excavators, lifting trucks, …), green goods (equipment for agriculture like tractors, etc.), and the heavy transport sector, where they are used for trailers, truck chassis and crane booms. These steel grades combine ultra-high-strength with excellent formability, good toughness, fatigue resistance and weldability. On top of that, these hot strip products are a cost-effective alternative to the quench and tempered plate products that are frequently used in this market.
The use of higher-strength grades allows for longer crane booms – and, thanks to reducing the machinery’s weight, its loading capacity increases. Driven by customer requirements and the general trend towards reducing weight, Amstrong® grades (minimum yield strength of 240-620 MPa) are being replaced more and more by higher-strength products of the Amstrong® Ultra (minimum yield strength of 650-1100 MPa) range. This ongoing shift to higher-strength grades requires continual product improvement and extension of the dimensional feasibility.
To better serve the European market, OCAS has worked to extend the production of Amstrong® Ultra 700MC(T) to other ArcelorMittal sites. Due to different feasibilities at the plants, changes to the processing route had to be made. In a current project, the OCAS metallurgy team successfully adapted a concept used at other sites to a new mill. Within a relatively short development time, Amstrong® Ultra 700MC(T) can now be delivered to the Eastern European
market with a short supply chain, reduced transportation costs and CO2 footprint, short lead times, and improved service levels. To supply a larger portion of the market, products with a higher strength than 700MPa are necessary. Thanks to several years of development, ArcelorMittal is already offering Amstrong® Ultra S900 and S960 grades. To reach these strength levels, another metallurgy is required. Quenching and possibly heat treatments, together with the right chemistry, allow us to obtain a martensitic product that offers good strength-ductility-toughness balance
By starting up the production of Durabor® boron steels in a new steel plant close to its customers, ArcelorMittal is reducing its supply chain, CO2 footprint, and lead times all at the same time
Marc-Antoine Thual
while keeping the cost-effective advantage of the hot strip products over the common plate products. OCAS is currently fine-tuning next-level products of these grades to guarantee improved properties (especially elongation) compared to the existing solutions. These developments are at a rather advanced stage, as several homologations at different customers are on-going. Amstrong® Ultra S700 is offered with different toughness guarantees for a wide range of thicknesses, which has led to numerous chemical composition variants. By statistical analysis and processing improvements, R&D was able to redefine the dimensional split up and significantly reduce the number of concepts used. This will lead to cost-savings, more flexibility in production planning, and a better service level.
By changing the processing route significantly, the OCAS metallurgy team was able to expand the Amstrong® Ultra product range up to very heavy gauges with high widths – and thus achieve optimal differentiation of the product portfolio amongst the applications in the market. With a shift to larger, state-of-the-art laser cutting tables at customer sites, wider sheets will help improve nesting and thereby reduce scrapping as well.
Furthermore, progress was made on surface quality and galvanisability; and, in addition, excellent flatness, as well as improved low cycle fatigue, are being taken into account.
Like its work on Amstrong® Ultra, OCAS is working towards extending the production of Durabor® boron steels to another ArcelorMittal site to better supply the Eastern European market. Here as well, due to different feasibilities at the plant, some changes to the processing routes have had to be made. The plant quality team and the OCAS metallurgy team successfully adapted the existing concept to the specificities of the new mill – and first orders have been successfully supplied. Production ramp-up is underway to finalize the development. The mill is already passing to the next strength level. With these developments, we are bringing production closer to the customer – reducing its supply chain, and, hence, reducing its transportation costs, CO2 footprint and lead times, whilst also improving the level of customer service.
OCAS’s planned extensions for cold rolling of ultra-thin metal sheets will enable breakthrough research and development in next gen steel metallurgies
Tom Waterschoot
OCAS has made significant progress in understanding how to process lightweight steels, completely based on thermodynamic data
Wahib Saikaly
New steel metallurgies based on Al and Mn concepts have been further explored to breaking through the limits and the common material property trade-offs (known in conventional metallurgical solutions).
Being able to do this requires a profound understanding of the steel metallurgy and the microstructural phenomena. In its recent research activities, OCAS has screened the opportunities of chemical compositions and possible microstructural processing methodologies that could be given to the alloy during and after hot rolling also known as thermo-mechanical controlled processing. This processing route results in fine-tuned material properties, the well-known structure-property relationship of materials.
At the Metals Processing Centre, OCAS is equipped with sophisticated semiindustrial rolling mills and cooling possibilities to investigate the impact of different processing parameters (starting temperature, rolling forces, reduction, strain rate, cooling rate, time, etc.) on the resulting material properties. The condition of the material is closely followed by insitu monitoring of a series of parameters. Moreover, novel processing techniques –such as a high-speed camera – have been
used on the rolling stand to capture the material’s behaviour during deformation. Interpretation of such images yields insights that have never before been possible. The high-speed camera enabled the precise demonstration of when crack initiation began and how crack propagation occurred. The hot rolling process could then be tuned to avoid edge cracking. This experience was implemented for the first time during an international collaboration in the framework of the DELIGHTED project. Thanks to this partnership, OCAS has made significant progress in understanding how
to process lightweight steels, completely based on thermodynamic data.
Introducing significant amounts of aluminium into the chemical composition of Mn steels can achieve important weight reductions. Such low-density steels consume less energy when used in transport applications – resulting in either fewer CO2 emissions or higher autonomy of a limited power source. The excellent lightweighting, high strength, and high strain rates showing high work hardenability are amongst the important parameters of materials for defence applications, such as ballistic steels for tanks and other armoured vehicles.
High and Medium Mn steel concepts are being thoroughly investigated for transport and storage applications at mild-cryogenic temperatures. A variety of applications are envisaged that experience exposure to liquified forms of transportation fuels such as components in tankers and vessels.
Driven by the energy transition, the switch will be made from LNG to green energy carriers like liquid ammonia, (bio-)methane, liquid hydrogen, or even a multi-fuel compatible solution.
The medium Mn-based steel alloy solution serves as a good low-cost substitution for conventional metallurgies and excels in terms of toughness at low temperature conditions because of the very stable
austenitic dual-phase microstructure, resulting in very low ductile to brittle transition temperature. In recent years, OCAS has gained an in-depth understanding of the process control needed to obtain good properties, as well as extensive alloying knowledge for structural and mild-cryogenic applications. OCAS has used very high-end microscopy techniques – like HR TEM and APT – to understand the chemical composition variations at the micro- and nano-level scales. Segregation in metals directly correlates to the macroscopic properties that we see both in strength and toughness. This knowledge has enabled the good understanding of the structureproperty relationship, a quite complex interplay in multi-phased ultra-fine-grain material structures.
The way we look at the data is completely new – the use of high-speed cameras unlocks information that has never been monitored before during the rolling process
Aniruddha Dutta
Developing hot-rolled steel materials with an improved surface quality has been a topic of interest for many years. The surface aspect is important, since it guarantees ease of processing and lower maintenance costs. However, the challenges of achieving a thin oxide scale layer with excellent adhesion to the steel substrate – a Micro Adherent Scale (MASC) – became even bigger with the development of new steel grades and with heavier gauges.
The surface quality of hot-rolled steel is impacted by the adherence of the thin oxide scale layer. Multiple process and logistic conditions contribute to physical phenomena that alter the final properties of the scale layer and could improve or deteriorate the final aspect of the material dramatically: the main ones are the transformation of wustite-rich oxide conditions, the final scale morphology and properties.
OCAS is investigating the properties of the scale layer, including its adherence, morphology, chemical composition, and so on. Mutual comparison of the results with respect to steel process parameters allows us to establish guidelines for the production in order to reach high-quality MASC
properties. Experience from thin sheets and low carbon steel grades is now being extended to heavy gauges and new steel grades. Thanks to OCAS’s understanding of the scale formation, appropriate process recommendations can be made to assure MASC quality, taking into account the limits like production line speed and the process cooling rate.
Moreover, OCAS is carefully investigating the possible influences following the use of more scrap – which is contributing to the global decarbonisation actions in the steelmaking process. The introduction of more secondary alloying elements is believed to have beneficial effects on the
scale adherence, leading to a superior surface aspect of hot-rolled materials. This is due to the role that some chemical elements can play in the scale growth, which alters its final quality.
The green move will enhance the adherence of the thin oxide scale that grows on hot-rolled materials during processing
Joost De Strycker
The continuous improvement of our concepts concerning enhanced corrosion protection should keep us in the leading position in the field of metallic coatings. The next generation coatings are being developed within the ArcelorMittal IMPACT programme, and new concepts have come out in a very short time. After screening promising coating concepts in the lab, the work, in close collaboration with colleagues from other Global R&D laboratories, has brought us forward to first industrial trials.
After the scaling up of the concepts on a semi-industrial hot dip galvanising pilot coating line, a series of chemical compositions and associated processing parameters were shortlisted. Such intermediate testing in an upscale pilot is very important in order to translate lab concepts into an industrial environment. Because the test runs at conditions closer to industrial circumstances, new information is brought to light that was not previously accessible. This step provides us with a better understanding of the entire process.
We then performed an industrial trial considering two different chemical baths, a
selection of key processing parameters, and dedicated surface passivation treatments. Two full days were taken from the operating line to produce real-size steel coils with the new coating concepts, including inline defect monitoring and passivation weight. Samples are being taken back to the lab for thorough characterisation of the production trials. The results will show which of the experimental parameters produces the most preferred coating properties, which will indicate the next steps. The realisation of industrial trials in such a short time is a real milestone achievement.
The time frame in which the developments and scale-ups have been realised is unprecedented. Thanks to the multi-competence global R&D team’s experience and readiness, the challenge to achieve rapid development could be met, and the advancements are a great success on the level of product development. At a certain moment, it even became challenging for the accelerated corrosion test to provoke degradation in such a short period of time. Therefore, even more aggressive tests were adopted to push the limits, evolving to faster tests at harsher environments. OCAS, together with colleagues from other Global R&D laboratories,
now have unique experience of accelerated corrosion testing, which enables us to rank materials in a very short time.
Going forward, OCAS’s R&D teams specialized in metallic coatings have an ambitious plan and are preparing for the next iterations. At least two industrial trials are scheduled at the galvanising line, which allows us to take a step closer towards further ramping up and implementation. Temporary results already indicate that the new concepts have the potential to fill in the gaps where current coating systems lack.
With two industrial trials on the schedule, our plans are ambitious and will be able to down-select the best and most confident coating system for the future.
Beril Corlu
As part of a consortium funded by RFCS, OCAS has investigated the corrosion resistance of novel high-strength maraging steels for next-generation aerospace and corrosion applications. The strengthening effect in this type of alloy is achieved by the nucleation and growth of NiAl and Ni3Ti precipitates during an annealing treatment.
The impact of these nano-precipitates was thoroughly examined via PSP correlation studies – the relationship between Process, Structure and Properties. Both the choice of chemical composition and the fine-tuning of annealing parameters are of crucial importance for realising strength levels of over 1900 MPa, generated by atomic scale interactions between the precipitates. Furthermore, the study demonstrated how these alloys also perform excellently in corrosive environments and exhibit great resistance against hydrogen embrittlement.
The use of high-strength maraging alloys in landing gears, for example, could realise
lighter structures and contribute to overall CO2 reduction in the aerospace sector.
In particular, OCAS has developed physical lab route methodologies for accelerated screening, processing and characterization of metal alloys. Such a screening tool allows for a fast and efficient screening of a large number of generic alloys. In this way, it was possible to select the most promising alloy combinations in a first step, and further optimize the properties by investigating different annealing parameters in a following step. The empirical results enabled a better understanding of the strengthening mechanism by Ni-Al-Ti-based intermetallic
nano-precipitation. The optimized laboratory alloy was then replicated on an industrial scale for evaluating in-use properties. OCAS has now finished the project together with industry-leading companies Aubert & Duval and Liebherr Aerospace, as well as partner research centres RWTH Aachen and Montanuniversität Leoben.
More info at: www.initial.ocas.be
OCAS’s accelerated screening tool, which is based on a physical lab route, has enabled the fast and efficient selection of the most promising candidate alloy combinations
Robin Dedoncker
Competence building via funded projects and internal developments have put OCAS on the map for High-Entropy Alloy synthesis
For some years now, OCAS has been pioneering in the lab production of High Entropy Alloys (HEA) for R&D purposes. The casting and metal processing equipment at OCAS is a unique advantage and opportunity for OCAS to enlarge its competencies in liquid phase metallurgy to ever more complex and higher-melting-temperature alloys. HEA are being looked at by academia and research institutes, since they exhibit excellent mechanical and corrosion properties. Because of the huge number of chemical formulations possible, OCAS’s methodology for fast screening and ranking of alloy properties accelerates the identification of promising candidate compositions.
OCAS’s recent engagement in the Horizon Europe project FORGE leveraged the development of a set of cost-effective, highly protective coatings, based on novel compositionally complex materials – both metal alloys and ceramics. By casting and screening about 30 different chemical compositions, OCAS joined a research consortium in its search to develop new coatings to protect against CO2 corrosion, H2 embrittlement, wear/mechanical damage, and thermal stability.
The knowledge obtained from this project is enabling OCAS to better predict the feasibility of new HEA chemical compositions. Together with computational thermodynamics, more information is available beforehand about the alloy’s castability and formability. In addition, the valorisation of the existing combinatorial synthesis flow for more complex materials than steel could be demonstrated. Additional competence and knowledgebuilding on up-scaling HEA castings have
put OCAS on the map. OCAS demonstrated the casting of 100 kg Cantor alloy, and this did not go unnoticed. The demo casting helped OCAS drive business for HEA castings in small (1 kg) and larger (up to 100 kg) volumes for R&D purposes. OCAS investigated the alloying and solidification route to obtain homogeneous casts well within the envisaged compositional tolerance levels. The material is being adopted for several research purposes, from rolling trials in plate/sheet, to powder manufacturing, to cladding.
By contributing to research and development in aviation and space, FINOCAS Group companies are increasing awareness of their capabilities and competencies in new sectors and boosting collaboration with new customers
FINOCAS Group companies also engage in material product development for the aviation and space sector. Our recent collaborations with leading space industries and the European Space Agency provide the best examples for companies to choose to join forces with OCAS and thus complement competencies to progress their research and development programmes.
Over the last two years, a first activity for ESA with Von Karman Institute – an internationally recognised research institute for fluid dynamics – was successfully completed. OCAS contributed its knowledge and advanced equipment to conduct material surface characterisation at the highest precision. Surface aspects are key to understanding and improving space vehicles' aerodynamics, as they re-enter the atmosphere at extreme speeds and temperatures. Thanks to our joint research and unlocking technological barriers, ESA is considering a continuation of the project. Furthermore, OCAS’s expertise in corrosion testing is being valorised in a collaboration with SONACA and UCLouvain for the purpose of developing next generation aluminium alloy products. The project
focuses on the long-term corrosion behaviour of Aluminium-Lithium alloys, and, in particular, their friction stir welded joints, in different environments. Via accelerated corrosion testing, the behaviour of welded samples with and without passivation coating will be fully characterised. The availability of more data on cryogenic and corrosion properties, as well as stress corrosion cracking of thin sheets, enables the wider adoption of this promising material in space applications for future ESA space missions. By contributing to research and development in aviation and space, FINOCAS Group companies are increasing awareness of their capabilities and competencies in new sectors and boosting collaboration with new customers. The projects allow us to valorise and further
develop methodologies in the lab for the experimental testing of material samples in different load cases and different conditions. Given the industry-oriented focus, together with the broad range of disciplines represented by the companies in the FINOCAS Group, the Group’s members and synergies offer partners a unique chance to complete R&D consortia.
FINOCAS companies are associated partners in the VUB-EUTOPIA project
DurAMat, which receives one of five prestigious Marie Sklodowska-Curie Doctoral Network Grants and aims to create more sustainable metals via 3D printing.
FINOCAS Group research companies
OCAS, ENDURES and GUARANTEED are participating in an international doctoral network. 10 highly-skilled PhD students are funded via the prestigious Marie Sklodowska-Curie Doctoral Network Grants, in the framework of Horizon Europe, to work on the sustainable production, processing and modelling of durable additive manufactured materials for enhanced performance and long-term service in complex environments.
The aim of the Marie Sklodowska-Curie Doctoral Network Grant is to create world
citizens who can enhance the European economy. Europe has a solid position in additive manufacturing, but it’s tough going up against competitors such as China.
That’s why it’s important that we train excellent and innovative researchers.
The project called DurAMat has been approved by the European Commission and received an extraordinary score of 98.6%. The doctoral network runs over a period of three years and is granted a total of 2.7 million EUR. FINOCAS looks forward to the continuation of these international collaborations.
The students will work at five of the universities in the EUTOPIA alliance: VUB in Brussels (Belgium), NOVA University in Lisbon (Portugal), the University of Gothenburg (Sweden), the Technische Universität Dresden (Germany) and the University of Warwick (UK).
Additive manufacturing – or 3D printing of metals – is a sustainable answer to our product-intensive society. It contributes to the creation of safer metals with longer lifespans in an ecologically and
economically responsible way. The objective is to investigate various properties of the 3D-printed metals, such as strength and corrosion, and then to improve them.
FINOCAS Group companies will be working in close connection with the Vrije Universiteit Brussel and other universities, research centers and industry partners in Europe. The network facilitates secondments taking place at the different partners and organizes top-level lectures and student teaching sessions.
One of the doctorates is dedicated to the understanding and improvement of
corrosion properties of parts produced and/or repaired via Wire and Arc Additive Manufacturing (WAAM), primarily facilitated at GUARANTEED. The investigations at OCAS’s lab will focus on hydrogen embrittlement in additive manufactured stainless steels and hydrogen fatigue corrosion testing. The performance testing of additively manufactured coatings in marine environment is made possible via the collaboration with ENDURES, which has unique access to outdoor exposure testing equipment in living seawater.
The objective is to investigate various properties of the 3D-printed metals, such as strength and corrosion, and then to improve them
Krista Van den Bergh
In the ever-evolving landscape of materials science, OCAS keeps pushing the boundaries of alloy development. OCAS is involved in the creation of RAFM (Reduced Activation Ferritic/Martensitic) castings doped with specific elemental isotopes, strategically engineered to be less susceptible to irradiation – a groundbreaking feat capable to revolutionise nuclear applications.
RAFM alloys, vital for structural components in nuclear reactors, face challenges related to irradiation-induced embrittlement. To address this, OCAS, together with EUROFusion, embarked on a mission to enhance the resilience of these alloys by incorporating isotopes renowned for their stability under intense irradiation conditions. This innovative approach not only fortifies the structural integrity of the castings but also extends the lifespan of critical components in nuclear environments.
As OCAS continues to chart new territories in alloy development, the RAFM castings with enhanced isotopes stand as a testament to the centre's ability to tailor materials for specific, demanding niches. In an era in which the quest for safer and more efficient nuclear technologies is intensifying, OCAS's advancements in nuclear alloys are paving the way for a future in which materials are not just functional but truly transformative. In addition to its groundbreaking work in alloy development, OCAS is playing
a pivotal role in facilitating R&D studies on RAFM grades with isotopes, enabling researchers and organizations to delve deeper into the potential applications and performance characteristics of these advanced materials. Through collaborative initiatives and partnerships, OCAS provides access to its state-of-the-art facilities, expertise, and resources – empowering stakeholders to conduct comprehensive investigations and experiments tailored to their specific needs in nuclear alloy technology.
New steel metallurgies are under development in various research portfolios, and they often require guarantees in terms of weldability. Since these compositions are new and not yet commercially available for full-scale weldability testing, OCAS has developed a model that allows us to predict hardness evolutions in the heat-affected zones (HAZ) of multi-pass welded joints.
When a single weld pass is applied, the base material near the fusion line is heat-affected. The zone closest to the fusion line has seen temperatures above 1150°C and is called the Coarse-Grained Heat-Affected Zone (CGHAZ). Other zones, which were subjected to lower temperatures, are the Fine-Grained HAZ (FGHAZ), the InterCritical HAZ (ICHAZ), and the SubCritical HAZ (SCHAZ). The base material properties are conserved outside of the HAZ. When a subsequent welding pass is applied, each of these zones is thermally affected.
It is known that the chemical composition, as well as the welding parameters that
are used, have a pronounced effect on the material properties in the HAZ. Therefore, in order to study the effect of a second pass on the hardness of the heat-affected zone, OCAS conducted a series of dilatometer experiments that simulate welding conditions.
The design factors of the experimental setup were the chemical composition, and, for each pass, the peak temperature and cooling time between 800°C and 500°C, as well as the interpass temperature applied during multi-pass arc welding. The experimental results were used to make a model that
predicts the hardness. This cross-validated model – including interactions between the predictors – yielded a very good fit (R2 = 0.98).
The final model allows us to predict hardness in different areas of HAZ for single- and multi-pass arc welding, using a wide range of welding parameters, including heat inputs and cooling times. This tool will be useful in future projects for screening the weldability of varying alloying compositions during the development of new line pipe steel grades.
Already in the early stages of metallurgical development, this model has proven to be very useful, as it can give a first indication of a material’s behaviour during a welding operation
Patrick Goes
As a hub of interdisciplinary collaboration, OCAS thrives on the synergies between metallurgy, materials science, and engineering
Pieter Vanduynslager
OCAS represents innovation and multidisciplinary excellence in alloy production and processing. Boosting recent upgrades and continuous enhancements, OCAS delivers customized material synthesis, dedicated rolling, tailored heat treatments, and beyond.
At the core of OCAS's capabilities lies its proficiency in lab synthesis of customised alloys. Leveraging cutting-edge techniques and a wealth of expertise, the centre pioneers the development of alloys tailored to the precise R&D needs of diverse industries. Whether it's enhancing the strength-toweight ratio for aerospace applications or processing newly developed material for nuclear applications, OCAS's bespoke solutions are redefining the boundaries of material performance.
OCAS’s commitment to excellence extends beyond synthesis, with dedicated rolling facilities capable to transform raw ingots into plates, sheets or strips. Through stateof-the-art machinery and process control, the centre ensures the production of alloy components with precise compositional accuracy, thermo-mechanical controlled processing, and mechanical properties.
Furthermore, OCAS's repertoire encompasses tailored heat treatments that unlock the
full potential of alloy compositions. From quenching and tempering to annealing in different atmospheres, the centre's metallurgists employ a myriad of techniques to refine microstructures and fine-tune material properties. This bespoke approach can focus on enhancing mechanical strength and durability, but it can also develop alloys tailored towards resilience to thermal stresses or corrosion.
OCAS’s ambition has always been and remains to carry out our research effectively, according to the highest quality standards and with maximum scientific profundity. That’s why, several years ago, ‘digitalisation’ and ’nano-characterisation’ were defined as key enablers for the research centre. Each pillar is handled by a transversal pool of people (a ‘cell’) - for example, the digital cell ’DICE’ and the nano-investigation cell ’NICE’ - that constitutes the motor to keep our performances in these domains at the highest level in a quickly evolving research landscape.
Initially having a focus on nano-scale characterization, the scope of NICE has recently expanded to all our high-tech analytical microscopy equipment. A major recent achievement is the maturing of our microscopy service programme, which has experienced steady growth in the last few years and is now serving clients in a variety
of fields. Various case studies have been realized with pleasing results, in particular:
– Our Field-Emission Electron Probe MicroAnalysis (in short FE-EPMA) allowed us to repeatedly reveal compositional details in metals and metallic coatings at the micro-scale - with, in particular, a better sensitivity to light elements (B, C, N, O, F).
– Atom Probe Tomography (APT) and Transmission Electron Microscope (TEM) have evidenced structural details and compositional variations on the nanoscale in the most advanced complex alloy systems.
– Focussed Ion Beam (FIB) & Scanning Electron Microscopy (SEM), combined with advanced post analysis, allows us to make 3D-reconstructions of microstructural features, revealing in high detail the 3D-morphology of microstructural constituents and allowing us to correlate these with the material’s performance.
In terms of equipment capabilities, two highlights are: the new nano-indentor that has been commissioned recently, and the realization of a high-throughput automated metallographic workflow that will enable us to capture over 1 million microstructural images each year.
In terms of digitalisation, the last two years have brought huge advancements in our AI/ML augmented materials research with multiple achievements:
– Data-mining studies have brought significant progress to our clients in various aspects. This has allowed us to provide them with in-depth rootcause analysis, AI/ML-supported trial definitions and process improvements, AI-based product qualification, and more.
– Tremendous progress has been made on our computer vision activities - in particular, for each of the 3 strategic pillars we defined a few years ago: microstructural analysis, damage
and fracture investigation, and corrosion research. In particular, our funded ‘HSLAi’ project and in-house ‘microShazam’ development will propel a leap in microstructure research.
Several of the above-mentioned digital activities have resulted in initial web tools that are now in the beta-testing phase before final roll-out to our clients. Benchmarking our AI/ML strategic choices confirmed our alignment with the state-of-the-art internationally and demonstrated that we are very well advanced in several of our key domains today. In conclusion, we are on track to keep the lab in the forefront of the accelerating digital transformation in materials science and engineering.
Lode Duprez
OCAS’s Digital Cell, DICE, has developed a tool to compare microscopic images of steel samples to allow technicians and researchers to assess microstructural similarity and identify trends, quickly gaining insight into new materials.
Ask metallurgists why a given steel behaves the way it does, and chances are they will inquire about its microstructure. A material’s properties are linked to the particular combination of different phases, their shapes, morphologies and orientations. That’s why microscopy constitutes an important part of steel research. A close-up look at a steel’s surface or cross-section often yields information that no other tool can provide. To bring out the microstructural features of interest, the skills of OCAS’s microscopy lab in selecting the most suitable sample preparation, etching agent and microscopic technique are vital. Moreover, our experts can rely on their years of experience to translate this information into insights essential to the research question at hand.
To assist them in this task, OCAS’s Digital Cell (DICE) has developed an application based on artificial neural networks, internally referred to as ‘MicroShazam’.
MicroShazam starts from a conceptually simple premise: if we can translate microstructural images into mathematical vectors, we can map out all possible microstructures as a multi-dimensional landscape. DICE’s tool allows researchers to chart a course through that landscape. The software locates new images relative to landmark microstructures that were investigated previously. It allows our researchers to home in on similar materials from the past and dig through the expertise acquired at that time. Moreover, if the image you upload has been seen before, the tool spots that and gives you an exact match. Search results are
linked to the associated information in JobManager, OCAS’s in-house developed Lab Information Management System, which gives researchers unprecedented opportunity to not only identify microstructures, but also trace back how the materials were produced and what their properties were.
MicroShazam exposes broader trends too, positioning steel grades with respect to each other. It uses unsupervised Machine Learning to identify clusters of related micrographs without relying on user input. Even when steels of unknown grades are considered, the software makes sure the user never sails blindly. Instead, it assesses the probability of assigning an image to various grades, providing quantified uncertainty estimates. This powerful feature also makes the application an important support
3D representation of some microstructural images, inherently clustered by steel grade (colour) . For some grades, smaller clusters can be distinguished, indicating different sub-types per grade .
tool to OCAS’s high-throughput metallography efforts. To store and analyse large numbers of microscopic images, labelling each of them correctly, is of utmost importance. However, labelling images by hand is typically a very labour-intensive task. The unsupervised option allows large numbers of images to be processed in batch without human intervention.
Based on its inherent clustering capabilities, MicroShazam has one last card up its sleeve.
Its unsupervised image processing may also serve as a foundation for more sophisticated models. Rather than building tailor-made computer vision models for dedicated tasks, the application’s translation of images into vectors gives access to a wide range of vector-based methods that can be built on top of MicroShazam’s output. This puts OCAS in pole position for further digital exploitation of microstructural images in the years to come.
OCAS’s work on imagebased Machine Learning allows it to harvest and exploit microstructural information at an unprecedented level Kurt Lejaeghere
OCAS’s unique bulk combinatorial experimentation and high-throughput sample processing provide a multitude of microstructure images to generate an extensive and novel metallurgical dataset
Thanks to combinatorial methodology to generate thousands of mechanical properties in combination with thousands of microstructures on both lab and industrial material, AI type of analysis was made possible at OCAS
John Vande Voorde
Simon Vander Vennet
Within the context of digitalization of metallurgical research, a project is running with significant regional funding from Vlaio. The goal of this project is the development of AI methods to investigate Process-microStructure-Property correlations for future high-strength low-alloy (HSLA) metallurgies.
Models directly linking process parameters and material properties exist, and some can even be quite advanced. However, these models do not take into account information available in microstructure images, although such images are becoming more and more plentiful. The objective of the project is to take the additional information from these microstructure images into the bath to uncover hitherto unknown effects and correlations. Our unique bulk combinatorial experimentation and high-throughput sample processing provides the multitude of microstructure images, with numbers
ranging in the thousands of HSLA materials and tens of thousands of images. This way, an extensive and novel metallurgical dataset is being generated.
Modern image processing techniques, utilising machine learning and deep learning, were developed to extract as much information as possible from the microstructure images. Similarly, advanced time series characterization is used to process processing and material properties. This data has already unearthed promising correlations between processing, properties and microstructures - and a first tool has been developed to
estimate the recrystallization fraction from a microstructure image.
However, this is but barely scratching the surface. Next, the multitudes of features will be fed into deep learning algorithms, such as artificial neural networks, to hone more advanced models. The developments in this project can be used to develop the next generation of HSLA steel grades. This project very much represents a leap into the future, in terms of both knowledge-building and streamlining experimentation.
High throughput corrosion inspector allows for the mutual comparison of different coatings in a variety of circumstances in an objective methodology. The tool visualises the degradation over time to show customers the difference in coating performance
Nigel Mestach
We’ve entered the next level in corrosion research with the use of AI-assisted models. We are making a tremendous step forward in data mining and correlation, using huge sets of data, clouds of datapoints that suddenly go far beyond the limits. High throughput data processing, massive amounts of data able to be processed in a very short time by means of neural network algorithms – this is material science in the current era.
OCAS conducts a lot of corrosion characterisation, coming from a broad range of corrosion tests on different alloys. In one year, we handle several hundred different samples, taking different images at different times to monitor the corrosion degradation over time. The need for high-throughput characterisation tools is higher than ever before. Time savings made in the analysis can immediately boost the lab’s capacity or else can be adopted to increase the inspection area, the number of iterations or test conditions. And most importantly - the evaluation of the data is becoming even more objective.
OCAS has developed a tool – called the corrosion inspector – to accelerate the evaluation of hundreds of corrosion images at the same time. In a few clicks, a set of images is aligned, cropped, analysed and segmenteddelivering unvarying images from laboratory images over time and segmentation-based data nicely presented in graphs or tables. A trained model lies at the base of this magical tool. Extensive training of a model is indispensable. OCAS researchers at the OCAS DIGITAL CELL – DICE – have pulled out all the stops to get the model in shape. The tool is now able to recognise corrosion phenomena and
measure (among other things) corroded surface areas, volume fractions based on colour appearance (white versus red rust), and defects, and plot these parameters versus the progressing time. A supplementary application has been developed to facilitate rapid and precise labelling of extensive datasets by domain experts. This approach fosters interdisciplinary collaboration, thereby enhancing the efficacy of the AI-model training process. In future, it will be possible to make corrosion predictions and indicate preventive actions in a timely manner.
.
Based on metallurgical know-how, data science, statistics, and high-throughput laboratory equipment, OCAS can enable a data-driven high-quality program for decarbonised steel production!
Filip Geenen
A successful automation of sampling, labelling, preparing, and imaging has proven the capability to capture thousands of microstructural images on a daily basis
Ann De Vyt
Metallographic images, produced by an optical microscope, show us the structure of steel at the micrometer scale. They visualise the different phases (such as ferrite and martensite) and show the size and shape of each structural component. This information gives us a better understanding of the behaviour and various properties of the steel grades in question.
Image recognition and digital microstructural analysis enhance the possibilities of extracting useful information from images. However, using the power of Artificial Intelligence and Machine Learning to explore the correlations between microstructural data, properties and process parameters requires a large set of data – in this case, a large set of images!
The Metallo 4.0 project was launched to increase the capacity of the metallography lab by one-to-two orders of magnitude: i.e., the ability to capture 106 images per year. Standardization and automation are keys to gaining speed and reaching this goal.
The project is based on 4 pillars:
– Sample management is the very start of it. Samples need a unique labelling that enables tracing back to the material’s origin. Our LIMS system Jobmanager was adapted to create samples in large numbers in such a way that they are continuously linked to materials they originate from, and to images they generate.
– The second pillar is experimental cobotisation.
• Rapid and uniform sample preparation by setting up a cobotised chain for sampling and labelling, again linked to Jobmanager.
• Efficient metallographic sample preparation by automation.
• Automated image acquisition at high speed without loss of quality.
– Pillars 3 and 4 are handled by the OCAS Digital Cell (DICE). They include the digital microstructure analysis to extract correct data from the images, and datamining to correlate the image data with properties and process data.
First pilot tests have run across this entire chain. A successful automation of sampling, labelling, preparing, and imaging has proven the capability to capture thousands of microstructural images on a daily basis! Even without further optimization, this is a tremendous increase of capacity and a definite proof of concept.
As from the start of the microscopy service programme we serve customers in a variety of fields, from metallurgy to semi-conductor to micro-electronic industries
Steven Keyzer
Two years ago, OCAS launched its initiative on microscopy services, an infrastructure-based platform open to third-party customers.
OCAS provides microscopy as a service to companies active in various sectors, in which the tiny details of materials do matter and an in-depth understanding of structures is necessary. At this point, the microscopy program can be called a great success. We have now assisted customers in Belgium and neighbouring countries with advanced analysis using our electron microscopy tools.
OCAS provides access to its brand-new microscopy lab for customers to investigate their samples. This enables nanocharacterisation for customers without the need for them to invest in equipment and infrastructure. The infrastructure is offered as a service, and, next to this, OCAS’s highly
skilled operators can conduct the analysis or assist the customers who want to run their analysis by themselves in our lab. Thanks to this initiative, OCAS helps customers reduce costs and risks.
Thanks to this initiative and OCAS’s knowhow, customers can reduce their risk and benefit from a time- and cost-effective approach for their investigations. The OCAS microscopy platform offers a one-stop-shop as different microscopy techniques can be combined depending on the needs of the investigation.
As from the start, the microscopy service programme has realized steady growth, serving customers in a variety of fields,
from metallurgy to semi-conductor to micro-electronic industries. We offer a microscopy lab that is close at hand and can react quickly to urgent demands – two requirements that seem to be of utmost importance in today’s industry. The easy communication between OCAS and the customer, and the mutual understanding of experts in their fields, each from their side, have contributed to the successful launch of this initiative.
Customers who have specific requirements in terms of confidentiality or procedures can also be helped at OCAS. As you read further in this report, you will discover how we coped with a specific customer demand for cleaning samples before TEM-analysis.
Over the last two years, we have seen interest growing for the microscopy platform and the wide range of tools we have been making available to customers in the service offer. Once customers make the step to discuss their technical inquiries with our experts, we see that they can become inspired by our techniques and methodologies to attain results efficiently. That is one of the advantages of the microscopy platform – customers can count on running equipment, next to appropriate advice by experts working with these tools day after day. Their insights into how to come to conclusive results is invaluable, because that can accelerate the R&D process.
In order to offer this service level, we are continuously investing in the lab. Next to the regular maintenance of our equipment that we also guarantee in our service agreements, new equipment has been purchased and integrated into the service platform to enlarge the service offer. To stay at the forefront of nano characterisation, OCAS continuously looks for strategic investments in innovative and outperforming analysis equipment.
A new nano indentor has been commissioned recently. The equipment enables ultra-fine hardness and elastic modulus measurements and 3D topography mappings. Furthermore, its nano-level
characterisation enables visualisation of mechanical properties in the microstructure. The tool has a diamond tip that scans along a 2D area of interest, delivering the hardness and elastic modulus of the substrate at each location. The varying properties can be shown in heat maps, which facilitates the interpretation of the results.
One of the advantages of having different microscopy tools available in one and the same lab is the possibility of correlative investigations. During such analysis, the same sample surface is subjected to different techniques, each yielding a specific piece of information. The results – graphs, heatmaps, images, etc. – can be brought together, even literally by overlaying images and mappings, to reveal information that
can only be unlocked as a marriage of two techniques. Each microscopy tool renders a part of the puzzle. One of OCAS’s strengths is the selection of the appropriate techniques to come to reliable results quickly and efficiently.
We also facilitate the introduction of new equipment to comply with customer analysis procedures once we enter into a structural collaboration, often backed by a service level agreement. In such framework agreements, reservation of equipment time is estimated on an annual basis, and customers enjoy priority access to our lab equipment. OCAS’s fast response times
What drives our customers’ enthusiasm is our state-of-the-art equipment with high accessibility at democratic prices
Nico De Wispelaere
enable customers to meet deadlines in challenging circumstances.
In the past, OCAS purchased a PLASMACLEANER in order to help a customer perform cleaning operations on their samples prior to analysis. The availability of such a tool enabled the customer to follow its proper methodology for sample analysis. By facilitating such
an environment and quality standards, there is no difference in samples being analysed at the customer’s site or OCAS’s lab. This has fortified our collaboration with these customers, who now regard OCAS’s microscopy lab as a 100% backup solution in case of a sudden capacity shortage or unforeseen outage.
OCAS’s FE-EPMA tool is complemented by a Soft X-ray spectrometer (SXES), which enables the quantification of light elements in trace concentration, levels smaller than 0.1wt% Mélanie Gauvin
to reveal compositional details on metals and metallic coatings at the micro-scale
The chemical variations among different micro-phases within a material are key to evaluating the product’s properties and fine-tune processes. At OCAS, we use FieldEmission Electron Probe Micro-Analysis (FE-EPMA) to reveal compositional details on metals and metallic coatings at the micro-scale. FE-EPMA features a better sensitivity to light elements (B, C, N, O, F), lower detection limit, and better energy resolution for a broad range of elements (B to U) than Energy-Dispersive Spectroscopy (EDS), another well-known chemical characterization tool used in scanning electron microscopy. Our FE-EPMA is complemented by a Soft X-ray spectrometer (SXES) which enables the quantification of
light elements in trace concentration (levels smaller than 0.1 wt%) and the distinction of chemical state based on the element’s peak shape.
In this example, FE-EPMA was used to visualize details of nitrogen-distribution within several grains in a dual-phase microstructure. The colour-scale indicates the signal intensity in relation to N-concentration. When comparing the grain structure as shown in the electron image and the corresponding N-mapping, light blue N-rich grains and dark-blue N-poor grains are well identified. Furthermore, the N-content in each phase was quantified using SXES analysis.
Electron image of a microstructure of a polished steel sample .
The strengths of TEM in revealing the elemental composition of nanostructures are essential to understanding the materials’ behaviour during processing – and, hence, how ultimate properties can be attained in manufacturing
Vahid Samaee
Transmission electron microscopy (TEM) is an analytical technique used to visualize structures in a material down to the atomic scale. When combined with energy dispersive spectroscopy (EDS), TEM can reveal the elemental composition of nanostructures. At OCAS, we use TEM to image fine grains or precipitates in order to determine their local chemical composition and crystallographic structure.
The investigation requires the fabrication of a micro-lamellae with a 100-nm thickness using a focus ion beam (FIB) milling machine, which is also available in our lab. Medium-Mn steels show a beneficial balance of strength and ductility. Their mechanical properties are greatly affected by retained austenite (RA), which is stabilized during an intercritical annealing process. The typical nano-scale size of the RA grains provides a challenging situation to characterize the microstructure and quantify locally the chem-
ical composition. Thus, TEM was used to image RA grains within their ferritic matrix and resolve the Mn distribution throughout the different phases. Finally, TEM could evidence variations in the Mn composition of RA, which could be linked to the processing history of the bulk samples.
The ultimate resolution of TEM, in combination with its analytical capabilities, make it an essential tool for the detailed charac-
terization of nanoscale structures, where chemistry and morphological differences provide crucial understanding of the microstructure-property-processing relationship of such materials.
OCAS’s state-of-art microscopy lab enables the use of different techniques on the same sample to reveal more information than each technique is capable of alone. In this example, the combination of EBSD and EDS analysis on metallic coatings provides direct evidence of their microstructure and composition.
Galvanising is the most common method for protecting steel products from corrosion. The metal surface is dipped in a molten zinc bath, and a thin layer forms on top of the surface. The elemental and crystallographic properties of the coating layer are a result of the process and determine the quality of the coating. In this example, two different coating samples are mutually compared.
Sample 1: Coupling EDS and EBSD over a relatively small field of view, 32 x 74 μm (Figure 1) reveals how the first coating crystallizes over the substrate. In the EBSD phase map, Zn is clearly distributed over the sample surface. The Inverse Pole Figure (IPF) Z map reveals multiple grains with different crystallographic orientations. The EDS maps of Al and Mg confirm the
product description and depict that Al and Mg are indeed present on the surface of the substrate.
Sample 2: A large area map, 800 x 450 μm of a second coating (Figure 2) reveals a different elemental distribution than that found in the first coating. This image is composed of many maps stitched together and, at this magnification, reveals the size of grains and their particular shape. Here, zinc is the primary phase present in the EBSD map. EDS maps of Al and Mg show that these elements are found primarily in between Zn grains. These two metallic coatings cannot be distinguished from the independent EDS and EBSD data, but coupling them together reveals clear differences: in particular, the grain morphology and the distribution of Al and Mg. The correlative investigation is
a still more powerful tool. Combining both strengths, the investigation can differentiate between the two coatings and fully characterise all particularities.
OCAS’s state-of-art microscopy lab enables the use of different techniques on the same sample to reveal more information than each technique is capable of alone
Mélanie Gauvin
Figure 1 . A mixed ForeScatter Diode (FSD) image reveals topography and the orientation of different grains on the sample surface EDS maps of Al and Mg convey elemental distribution The phase map of Zn shows that Zn is the primary phase present in the material, while the IPF Z map shows the size of grains in this field of view .
Figure 2 . An IPF Z map shows the size of grains, their orientation and distribution . EDS maps of Al and Mg depict elemental distribution over a large field of view .
The observation of the path of the propagation of cracks in 3D can provide insights into the damage mechanisms
Houssem Chaieb
Analysis of microstructure in 3D gives access to valuable information, especially when dealing with defectology. OCAS has developed a methodology for 3D reconstruction and quantification of volume fractions.
3D reconstruction of volumes relies on the acquisition of a stack of images using microscopes, like FIB (Focused Ion Beam), for example. After the definition and preparation of a region of interest, the Slice&View tool is used to get successive portions of the area by milling, and images are captured progressively. Finally, a stack of SEM images is obtained and reconstructed.
The challenge for 3D reconstruction is in the post-processing of the image stack. The images need to be segmented to classify the
different phases/defects. The reconstruction can then be performed. This offers multiple options for visualizations and quantification of volume fractions. Appropriate software toolkits support the classification of images by interactive learning and segmentation. This methodology was demonstrated on a sample coated with Magnelis®. 3D data were processed to visualise the volume fractions of the segmented phases. The resulting stack of images can be observed in multiple directions. The slices reveal insights into metallurgical phenomena, such as the solidification process throughout the thickness of
the coating. The technique can be even more interesting if the region of interest includes some defects like cracks. The observation of the path of the propagation of cracks in 3D can provide insights into the damage mechanisms. Furthermore, the technique can be extended to other types of analyses, like elemental composition (3D EDX analysis).
FINOCAS Group consolidated turnover 2023: 25,8 M EUR The FINOCAS Group staff members comprise the staff of FINOCAS N.V. and of its daughter companies OCAS N.V. and ENDURES B.V.*
Status 31/12/2023
* No separate payroll FININDUS
Belgium excels in Research and Development and harbours a strong materials ecosystem of companies acting together, which leads to world-class technology innovation. The existing network of companies, universities, research institutions and industry, is well-positioned to contribute to a world of change. Energy transition, materials circularity and recycling, climate neutrality, sustainability, and so on, are ambitions that can only be met when people work together. Here is a brief overview of FINOCAS Group memberships to illuminate FINOCAS’s involvement in regional and national networking groups.
Flanders Metals Valley (FMV) is a bottomup initiative launched by companies and institutions active in the metallurgical sector in Flanders. The organisation consists of a vast mix of people practicing in the metals industry, combined with universities and knowledge centres that, while being at the core of ground-breaking research for the future, also want to be relevant to the industry’s challenges of today. The main focus of Flanders Metals Valley is to create a climate-neutral circular metals industry in Flanders that is innovative and futureoriented and recognised as an essential, competitive pillar of Flemish industry. A lot of attention is also being paid to training and education in this respect.
Agoria Energy Technology Club is a unique community of 130 top players from the Belgian technology sector. The club members have services, products or bespoke solutions in-house for oil and gas, nuclear and renewable energy. The business club brings energy players, contractors and project developers into contact with groundbreaking, innovative technologies that have often already proven their value in other energy forms or industries. The mission of the Energy Technology Club is to develop and maintain an ecosystem of energy technology and energy services companies with a strong international focus.
The Hydrogen Industry Cluster (WICWaterstof Industrie Cluster) is an industrial collaborative partnership, uniting companies, knowledge institutions, governments and authorities that want to collaborate on projects involving hydrogen as a storage medium for renewable energy and its use for zero-emission mobility, heat or industrial applications. The cluster encourages collaboration, but also initiates and facilitates possible hydrogen projects. It aims to establish itself as a representative spokesperson and point of contact for policies relating to hydrogen.
Smart Delta Resources (SDR) is a transnational partnership of large energy and resource-intensive companies in the Schelde-Delta region. As a joint effort of the SDR region, SDR companies, and the respective governments, SDR strives to play a pioneering role in the industrial energy transition.
This cross-border collaboration takes place between major industries from the chemical, steel, energy and food sectors, and ports and governments in this Schelde-Delta region (Zeeland/West-Brabant/East Flanders). The Dutch and Belgian organizations work together for a future-proof, sustainable industry in the region.
The Flemish Airspace Group (FLAG) unites companies active in the aerospace market. FLAG aims to support the development of aerospace and related technologies and to improve the visibility of the Flemish aerospace industry globally to achieve a growing market share.
The Flemish aerospace industry boasts a broad range of technologies and services well suited to address the upcoming challenges of the new era driven by sustainability and (European Green Deal) urban air mobility. The SMEs and multinationals engaged in FLAG have, or can develop, the innovative know-how in key areas – like structures, systems, propulsion, and airport and ground support – to establish and strengthen their place in supply chains. Already today, FLAG members supply OEMs worldwide.
Vlaamse Ruimtevaart Industry (VRI) and Flanders Space are the Belgian and Flemish cluster of the space sector. Flanders Space aims to further shape the space economy in Flanders and put it on the international map. Flanders Space’s activities focus on 4 areas: attracting young talent, supporting competitiveness and entrepreneurship, providing R&D funding, and science communication. Flanders Space wants to offer all opportunities to the Flemish socio-economic actors and to graduating young people to work with space data and infrastructure. The ambitious program puts space firmly on the map in Flanders for the first time.
The Belgian Association for Surface Techniques of Materials (VOM - Vereniging voor Oppervlaktechnieken van Materialen) provides general and technical information related to all disciplines in surface treatment and represents the sector to industry and government. The association provides a network of about 260 companies specialised in surface treatments, including: integrated companies, contracting firms, suppliers, control-and expert bodies, and scientific institutions.
Belgian Industrial R&D (BiR&D) is the association of international industrial companies having major R&D operations in Belgium. Its mission is to stimulate and improve both the attractiveness and effectiveness of R&D execution in Belgium.
The BiR&D network explores, develops and shares best practices among its members for delivering excellent R&D, modes of cooperation with universities and research centers, ways to improve the image of industrial R&D, and attracting, recruiting and keeping talent in an R&D environment.
STEM – Science, Technology, Engineering and Mathematics – and STEM-related activities are crucial for fostering critical thinking, problem-solving skills and innovation. FINOCAS actively contributes to STEM-related events. We want to empower students to explore the wonders of the universe, tackle real-world challenges, and contribute to advancements that shape our future. Through hands-on experiences, collaboration, and creativity, STEM activities inspire curiosity and prepare the next generation of leaders, innovators, and problem-solvers to make meaningful contributions to society.
This year as well, FINOCAS supported a number of initiatives to promote STEM in higher education. Within the VLAJOinitiative – ‘Ondernemer voor de STEM-klas’ – FINOCAS contributed with thematic guest lectures on ’Energetic Entrepreneurship’ adapted to the level of 3rd grade secondary classes (student ages 17 - 18 years).
Furthermore, several visits were organised for groups of students in the framework of their technical courses, such as welding, construction, and electromechanics. The visits took place at OCAS’s laboratories and/ or at the ArcelorMittal Ghent steelmaking plant.
FINOCAS also participates and contributes to Learning & Training programmes for professionals – such as the workshop organised by Smart Delta Resources, North-C Innovation, about climate-related
topics, as well as the workshop organised by EduXL for the further professionalisation of teachers in STEM courses. Such lifelong and continuous learning initiatives ensure a good fit between academy and industry and a common focus in a socially-relevant context.
OCAS also participated in the Beroepenrally metaal en technologie – a Flemish initiative and annually recurring event to familiarise students in the fourth year of secondary education (approx. age of 16) with technical professions in an experience-oriented way. Students are given the opportunity to participate in practical activities at companies active in the Metals and Technology sector in the Ghent area. During this workshop, OCAS introduced the students to steel for electric motors.
OCAS is a member of the steering committee of ‘Expo ferro non ferro’, an initiative of the Ghent Industry Museum. The steering committee helped the researchers from the museum in the visualisation of the historical evolution of metal, and metal production and processing, in a way that is interactive and didactic for a broad audience. As part of the exposition, demonstrations and workshops about metal are also organised. Visitors are enthusiastic about the hands-on activities in the metal workshop. Especially the “feel steel” interaction in which visitors literally feel the difference between a strip of mild steel and one with identical geometry made of high-strength steel.
When sharing knowledge about the fascinating properties of metals I’m always impressed by the spontaneous enthusiasm displayed by young students
Katrien Meseure
Publication Title
Buckling resistance of star-battened angle members made of high-strength steel
The effect of nano-sized κ-carbides on the mechanical properties of an Fe-Mn-Al-C alloy
Fatigue weld crack detection using distributed fiber optic strain sensing
Kinetics of static recrystallization in Sn-added Fe-Si alloys
Vibration-induced crack tip flipping: A closer look at an unfamiliar phenomenon in pipeline failure analysis
FEM modelling to predict spatiotemporally resolved water uptake in organic coatings: Experimental validation by odd random phase electrochemical impedance spectroscopy measurements
Sediment-driven plastisphere community assembly on plastic debris in tropical coastal and marine environments
TEM investigation of reduced activation ferritic martensitic alloys developed by thermodynamic modeling
Author(s)
Bezas M.-Z., Antonodimitraki S., Beyer A., Anwaar M.-O., Maesschalck J., Jaspart J.-P., Demonceau J.-F., Van Wittenberghe J.
Banis A., Gomez A., Dutta A., Sabirov I., Petrov R.
Mikhailov S., van Wittenberghe J., Luyckx G., Thibaux P., Geernaert T., Berghmans F.
Dumont M., Mavrikakis N., Saikaly W., Mangelinck D.
Paermentier B., Cooreman S., Coppieters S., Talemi R.
Meeusen M., van Dam J.P.B., Madelat N., Jalilian E., Wouters B., Hauffman T., …, Terryn H.
Koh J., Bairoliya S., Salta M., Cho Z.T., Fong J., Neo M.L., …, Cao B.
Kachko O., Puype A., Terentyev D., Duerrschnabel M., Klimenkov M., Petrov R.H.
Journal/Reference
Structures Vol. 58 (2023) n° 105274
Materials Characterization Vol. 205 (2023) n° 113364
International Journal of Fatigue Vol. 176 (2023) p. 9
Metallurgical Research and Technology Vol. 120, 5, (2023) p. 9
Theoretical and Applied Fracture Mechanics Vol. 127 (2023) n° 104031
Progress in Organic Coatings Vol. 182 (2023) n° 107710
Environment International Vol. 179 (2023) n° 108153
Journal Of Nuclear Materials Vol. 582 (2023) p. 11
Quantitative analysis of CO2 emissions reduction potential of alternative light olefins production processes
Microstructure evolution and mechanical behavior of Fe–Mn–Al–C low-density steel upon aging
Micro- to Nanoscale Microstructural Differences
Induced by Intercritical Annealing in a Hot-Rolled Medium Manganese Steel
On the suitability of premium OCTG tubing connections for CCS CO2 injection wells – a full scale physical evaluation
Identification of carbon-containing phases in electrodeposited hard Fe–C coatings with intentionally codeposited carbon
The role of alloying elements in NiAl and Ni3Ti strengthened Co-free maraging steels
Priorities to inform research on marine plastic pollution in Southeast Asia
Flores-Granobles M., Saeys M.
Prediction of properties on large diameter welded pipe: case study on 32” x 16mm X65 HSAW pipe
A dynamic tensile Tear test methodology to characterise dynamic fracture behaviour of modern High-Grade pipeline steels
Development of RAFM steels for high temperature applications guided by thermodynamic modelling
Banis A., Gomez A., Bliznuk V., Dutta A., Sabirov I., Petrov R.H.
Gauvin M., Dutta A., Lorenz U., Duprez L., Waterschoot T.
van Riet E., Van Wittenberghe J., Van Hoecke D., Roijmans R., Vanderschueren M., Thibaux P.
Marcoen K., Gauvin M., De Cleene A., Nielsen J.O., Baert K., Terryn H., De Strycker J., Hauffman T., Pantleon K.
Zeisl S., Landefeld A., Van Steenberge N., Chang Y., Schnitzer R.
Omeyer L.C., Duncan E.M., Aiemsomboon K., Beaumont N., Bureekul S., Cao B., Salta M., …, Godley B.J.
Cooreman S., Van Hoecke D., Abotula S., Luccioni H., Voudouris N., Tazedakis A.
Paermentier B., Cooreman S., Verleysen P., Chandran S., Coppieters S., Talemi R.
Kachko O., Puype A., Terentyev D., Bonny G., Van Renterghem W., Petrov R.
Green Chemistry Vol. 25 (2023) pp. 6459-6471
Materials Science And Engineering - A - Structural Materials Vol. 875 (2023) n° 145109
Steel Research International Vol. 94, 11 (2023) pp. 9
International Journal of Greenhouse Gas Control Vol. 123 (2023) n° 103834
Surface And Interface Analysis Vol. 55, 5 (2022) pp. 336-346
Materials Science And Engineering - A - Structural Materials Vol. 861 (2022) n° 144313
Science of The Total Environment Vol. 841 (2022) n° 156704
Journal of Pipeline Science and Engineering Vol. 2, 3 (2022) n° 100071
Engineering Fracture Mechanics Vol. 272 (2022) n° 108687
Nuclear Materials and Energy, Vol. 32 (2022), n° 101211
Early biofilm and streamer formation is mediated by wall shear stress and surface wettability: A multifactorial microfluidic study
How Sn addition influences texture development in single-phase Fe alloys: Correlation between local chemical information, microstructure and recrystallisation
4D microstructural evolution in a heavily deformed ferritic alloy: A new perspective in recrystallisation studies
High-throughput method development for in-situ quantification of aquatic phototrophic biofilms
Towards accurate processing-structure-property links using deep learning
Chun A.L., Mosayyebi A., Butt A., Carugo D., Salta M.
Mavrikakis N., Saikaly W., RodriguezCalvillo P., P.C.Campos A., Jacomet S., Bozzolo N., Mangelinck D., Dumont M.
Yildirim C., Mavrikakis N., Cook P.K., Rodriguez-Lamas R., Kutsal M., Poulsen H.F., Detlefs C.
Microbiology Open Vol. 11, 4 (2022) e1310
Materials Characterization Vol. 190 (2022) n° 112072
Scripta Materialia Vol. 214 (2022) n° 114689
Papadatou M., Knight M., Salta M. Biofouling Vol. 38, 5 (2022) pp. 521-535
Larmuseau M., Theuwissen K., Lejaeghere K., Duprez L., Dhaene T., Cottenier S.
Localized Corrosion of Mooring Chain Steel in Seawater Zhang X., Noël-Hermes N., Ferrari G., Hoogeland M.
Contribution of the microtexture evolution induced by plastic deformation on the resistance of a hot-rolled pipeline steel to flat cleavage fracture and to brittle delamination cracking
Tankoua F., Crépin J., Thibaux P., Cooreman S., Gourgues-Lorenzon A.-F.
Scripta Materialia Vol. 211 (2022) n° 114478
Corrosion and Materials Degradation Vol. 3, 1 (2022) pp. 53-74
International Journal of Fracture Vol. 233 (2022) pp. 211–237
Publication Title
Numerical modelling of the dynamic plasticity and fracture behaviour of X70 pipeline steel
Effect of Ti/N ratio on heat-affected zone properties of girth welds
Prediction of Properties on Large Diameter Welded Pipe: case study on 32” x 16mm X65 HSAW Pipe
Effect of microalloying on weldability of seamless Q&T steels for offshore sour pipelines
Effects of surface roughness on anaerobic marine biofilm formation and microbiologically influenced corrosion of UNS G10180 carbon steel
Higher-strength low-loss electrical steels impact on rareearth permanent magnet volume reduction in electric traction motors
The role of nano-segregation in the evolution of {411}< 148> recrystallization texture in ferritic alloys
Next generation electrical traction machines: material investigation for optimal machine performance
Author(s)
Chandran S., Cooreman S., Liu W., Lian J., Münstermann S., Verleysen P.
Güngör Ö.E., Sanchez N., Liebeherr M., Luccioni H.
Cooreman S., Van Hoecke D., Abotula S., Luccioni H., Voudouris N., Tazedakis A.
Güngör Ö.E., Sanchez N., Liebeherr M., Jansto S.
Jones L., Salta M., Skovhus T.L., Thomas K., Illson T., Wharton J., Webb J.
Abdallh A., Vandenbossche L., Lastra L.
Conference
2022/03/29 - Gent, Belgium - Technology for future and aging pipelines TFAP 2022
2022/03/29 - Gent, Belgium - Technology for future and aging pipelines TFAP 2022
2022/03/29 - Gent, Belgium - Technology for future and aging pipelines TFAP 2022
2022/03/29 - Gent, Belgium - Technology for future and aging pipelines TFAP 2022
2022/04/04 - London, UK - Microbiology Society Conference
2022/04/26 - Aachen, GermanyInternational Electric Steel Sheet Summit 2022
Mavrikakis N., Saikaly W., Bozzolo N., Mangelinck D., Dumont M.
Jacobs S., Rens J.
Design and analysis of electromagnetic suspension for hyperloop Rens J., Jacobs S.
2022/05/01 - Ghent, Belgium - Texture & Anisotropy workshop 2022
2022/05/02 - Grenoble, France - 25th conference Soft Magnetic Materials (SMM)
2022/05/02 - Grenoble, France - 25th conference Soft Magnetic Materials (SMM)
Impact of stray fields due to the structural integration of a linear synchronous machine for hyperloop technology
Rens J., Jacobs S., Di Silvestro E., Sellitto G.
Upscale Capabilities for High Entropy Alloy Casting and Processing at OCAS
Processability of Nb-alloys
On the Feasibility of Large-Scale Resonant Fatigue Testing to study Bolt Force Relaxation
Next generation ferromagnetic materials for reduced critical rare earth electrical traction machine topologies
Boosting the power density of highly efficient traction motors in electric drive trains with higher strength, lower loss electrical steels
Recommendations on the application of high-strength steel bolted connections from the perspective of fatigue performance
On the effect of bolted joint parameters on the fatigue performance of bolted assemblies in high strength steel
Microbiologically influenced corrosion of steel sheet pilings in a Dutch harbor- fast corrosion and unexpected mass loss.
2022/05/03 - Stuttgart, Germanyt12th International Conference Energy Efficiency in Motor Driven Systems (EEMODS)
De Wispelaere N., Keyzer S., Duprez L. 2022/05/12 - Dresden, Germany - High Entropy Alloy symposium
Van Steenberghe N., Keyzer S., Duprez L., De Wispelaere N.
Van Wittenberghe J., Vanden Haute C., Shirzadeh R., Thibaux P.
Jacobs S., Rens J.
2022/05/30 - Reutte, Austria - Plansee Seminar
2022/06/06 - Hamburg, GermanyOMAE2022 Offshore Mechanics and Arctic Engineering
2022/06/13 - Milan, Italy - 10th International Conference on Magnetism and Metallurgy
Abdallh A., Vandenbossche L., Lastra L. 2022/06/19 - Milan, Italy - Steels for Cars and Trucks (SCT2022)
Yılmaz O., Jiménez-Peña C., Debruyne D. 2022/06/20 - Milan, Italy - Steels for Cars and Trucks (SCT2022)
Yılmaz O., Jiménez-Peña C., Coppieters S., Debruyne D.
Noel-Hermes N., Salta M.
Saline resistant weathering steel for saline applications Van den Bergh K., De Strycker J., Liebeherr M.
2022/06/20 - Milan, Italy - Steels for Cars and Trucks (SCT2022)
2022/08/19 - Berlin, Germany - Eurocorr 2022
2022/08/19 - Berlin, Germany - Eurocorr 2022
Microbiologically influenced corrosion of mooring chains- a state of the art review combined with a field study example
Effects of surface roughness on anaerobic marine biofilm formation and microbiologically-influenced corrosion of UNS G10180 carbon steel
Multiscale Exploration of Texture and Microstructure
Development in Recrystallization Annealing of Heavily Deformed Ferritic Alloys
Effects of Repetitive Underwater Cleaning Operations on Two Fouling Release Coatings
Optimalisatie en pre-kwalificatie van plaat uit lasbaar constructiestaal voor vaste, buitengaatse constructies
Microbiologically-influenced corrosion (MIC):
Development of a model system to investigate the role of biofilm communities within MIC and their control using industrial biocides
Effect of higher-strength low-loss electrical steel on the electric energy saving of traction motors considering thermal analysis
Identification of the large strain flow curve of high strength steel via the torsion test and FEMU
Exploring 4D microstructural evolution in a heavily deformed ferritic alloy
Salta M., Noel-Hermes N.
CO2 Emissions Reduction Potential of Alternative Light Olefins Production Processes
Jones L., Skovhus T.L., Webb J., Wharton J., Salta M., Illison T., Thomas K.
Yildirim C., Mavrikakis N., Cook P.K., Rodriguez-Lamas R., Poulsen H.F., Detlefs C., Kutsal M.
Di Fino A., Salta M., Coppoolse K.
Gerritsen C., Veys X., Liebeherr M., Vigil J.
Jones L., Skovhus T.L., Webb J., Wharton J., Salta M., Illson T., Thomas K.
2022/08/19 - Berlin, Germany - Eurocorr 2022
2022/08/19 - Berlin, Germany - Eurocorr 2022
2022/09/05 - Roskilde, Denmark - 42nd Risø International Symposium on Materials Science
2022/09/05 - Hamburg, GermanyPortPIC 2022
2022/10/04 - Gorinchem, The Netherlands - BIL Lassympopsium WELDINGWEEK
2022/11/16 - London, UK - Reservoir Microbiology Forum
Abouelyazied A., Vandenbossche L., Lastra L.
Vancraeynest N., Cooreman S., Coppieters S.
Yildirim C., Detlefs C., Zelenika A., Poulsen H.F., Rodriguez-Lamas R., Cook P.K., Kutsal M., Mavrikakis N.
Flores-Granobles M., Saeys M.
2022/11/29 - Regensburg , Germany - 12th International Electric Drives Production Conference (EDPC)
2023/04/19 - Krakow, Poland - ESAFORM 2023
2022/05/15 - Chongqing, China8th International Conference on Recrystallization and Grain Growth
2023/05/28 - Les Diablerets, Switzerland
- Carbon Capture, Utilisation and Storage Gordon Research Conference
Thermo-mechanical Characterization of High-strength Steel through Inverse Methods
Microbiologically influenced corrosion (MIC) of mooring chains a field study example
Biodiesel storage tanks can be impacted by MIC: what we know, where can we go next?
Rossi M., Morichelli L., Cooreman S.
Noel-Hermes N., Salta M.
Salta M., Noel-Hermes N.
Investigation of Detrimental Gases Generated from ICCP Zhang X.
Novel Metal Bionanohybrids against MIC Consortia
Development of a model system to investigate the effects of surface roughness and media on marine biofilm formation and microbiologically influenced corrosion
Fatigue capacity of tubular joints by robotic welding
Salta M., Noel-Hermes N., Ortega Nieto C., Palomo J.M.
Jones L., Salta M., Skovhus T.L., Thomas K., Illson T., Wharton J., Webb J.
2023/06/05 - Orlando, USA - SEM Annual Conference
2023/06/20 - Paris, France - Seanergy
2023/06/27 - Edinburgh, UK - 9th int. symposium on applied microbiology and molecular biology in oil systems (ISMOS)
2023/08/27 - Brussels, Belgium - Eurocorr 2023
2023/08/27 - Brussels, Belgium - Eurocorr 2023
2023/08/27 - Brussels, Belgium - Eurocorr 2023
Thibaux P., Vanderschueren M. 2023/08/28 - Bremen, Germany - 11th Annual Offshore Wind Foundations & Substations conference IQPC
Multi-scratch test: comparison of subsurface hardened layer evolution across different materials
Effectiveness of Compositionally Complex Alloys as Hydrogen Barriers
Electrical steel and motor design synergy: Unveiling the benefits through a coupled analysis with JMAG
Ship hull cleaning and ROVs: what we know and where do we go next?
Corryn M., Ben Hamouda H. 2023/09/04 - Leeds, UK - Leeds-Lyon Symposium on Tribology 2023
Navarro-Lopez A., De Wispelaere N., Duprez L., Keyzer S., Bianchin A.
2023/09/05 - Frankfurt, Germany - FEMS EuroMat conference 2023
Abouelyazied A., Vandenbossche L. 2023/09/09 - Frankfurt, GermanyPowersys E-motor Design Conference
Salta M., Di Fino A. 2023/09/12 - Gothenburg, SwedenInternational Antifouling Conference
Inverse identification of a 3D anisotropic yield function through an information-rich tensile test and multi-sDIC
Phase-field Modelling of Dendritic Growth in ZnAlMg Coatings
In-situe Characterization of the Mechanical Behaviour of Hot-Dip Zn-5Al Coating: An overview of the deformation and damage mechanisms.
ZnAl3.5Mg3.0 Supporting the Renewable Energy Transition
Background and Practice of offshore pre-qualifications, explained using thick plates as example
Coppieters S., Zhang Y., Vancraeynest N., Lambrughi A, Cooreman S.
Aristondo M.B., Ammar K., Forest S., Maurel V., Chaieb H.E., Mataigne J.-M.
Chaieb H.E., Maurel V., Forest S., Ammar K., Nozahic F., De Strycker J., Mataigne J.-M., Tanguy A., Héripré E.
De Cleene A., Verpoort P., Corlu B., De Strycker J., Gonzalez E.D.
Gerritsen C., Veys X., Liebeherr M., Vigil J.
2023/09/24 - Cannes, France - 14th International Conference on the Technology of Plasticity (ICTP)
2023/10/15 - Seoul, South KoreaGalvatech 2023
2023/10/15 - Seoul, South KoreaGalvatech 2023
2023/10/15 - Seoul, South KoreaGalvatech 2023
2023/11/21 - Rostock, Germany - 13th Rostock Welding days (Rostocker Schweisttage)
FINOCAS is a joint venture between the Flemish Region and ArcelorMittal Belgium. OCAS and ENDURES are the research centres of FINOCAS, while Finindus is its investment company. Guaranteed is a spin-off company from OCAS, Finindus and ArcelorMittal Belgium and is active in repairing or rebuilding metal parts. FINOCAS has a structural partnership with the Belgian Welding Institute through their joint venture BWI Industry.
www.finindus.be | www.guaranteed.be | www.endures.nl | www.ocas.be