A robust robotic support system
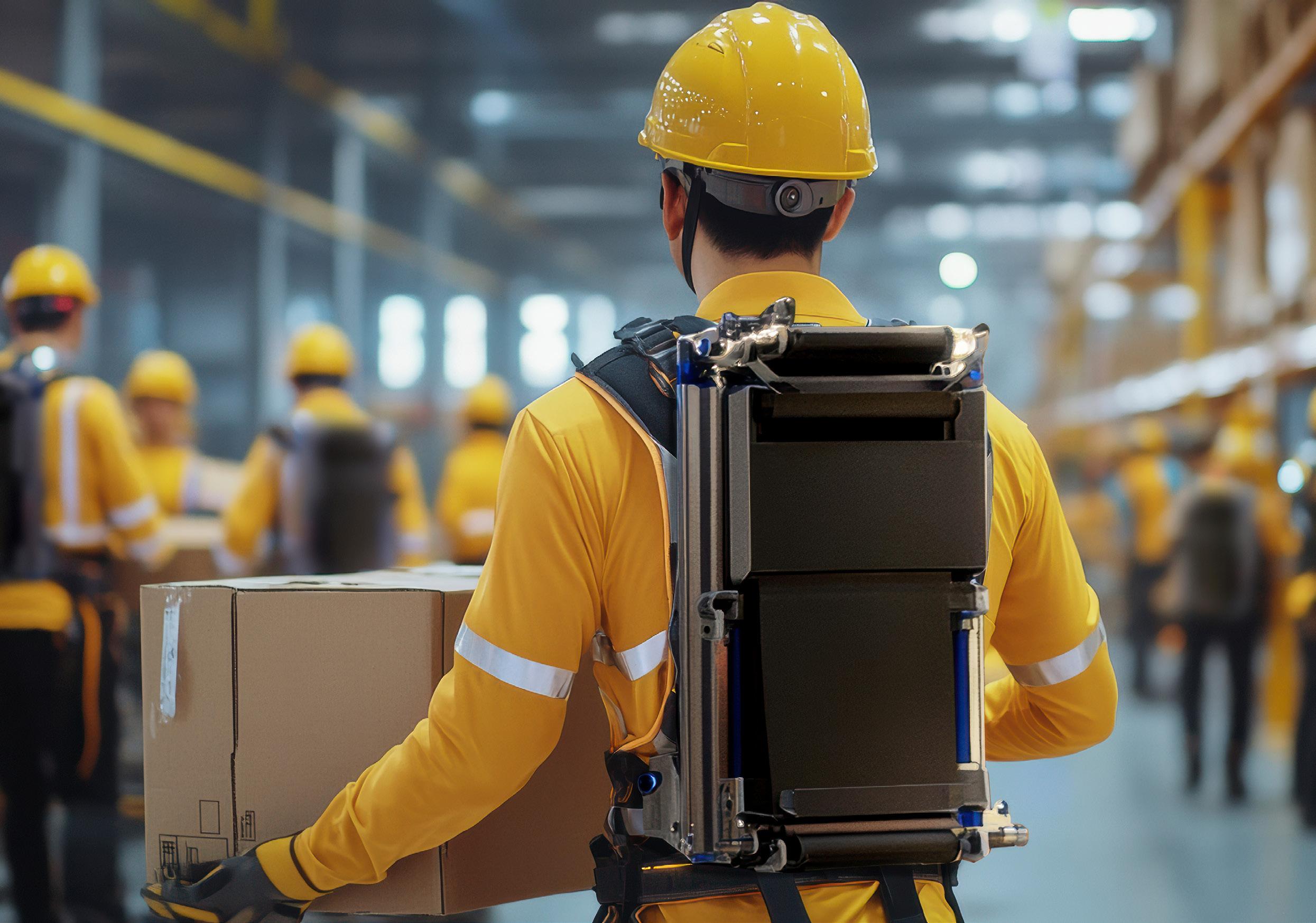
Driven by a differential series elastic actuator, a novel backsupport exoskeleton aids users during lifting tasks, easing strain without adding muscle activation to the back and legs.
f you’ve ever experienced a lower back injury, you know how it can turn everyday tasks into trials. Simple chores become strenuous; workout routines fall by the wayside; even lifting a bag of groceries can feel like a risk. And all too often, a dreaded relapse can deem all recovery efforts null.
Issue 04 | January 2025 Forging New Frontiers
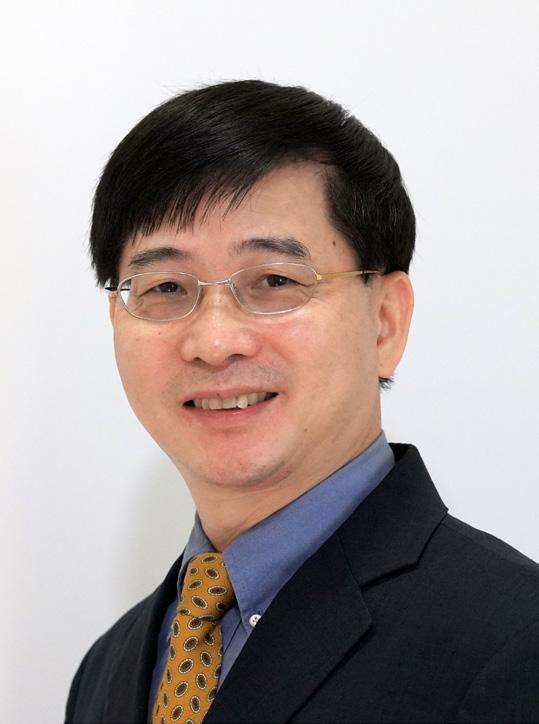
For industries heavy on physical labour, back injuries carry a hefty price tag — costing more than USD$200 billion annually in lost productivity, medical expenses and absenteeism. Against a backdrop of an ageing population, coupled with declining fertility rates, protecting those who handle heavy loads — from warehouse workers to construction crews to hospital orderlies — has come to the fore.
Associate Professor Yu Haoyong wants to give lowerback protection a shot in the arm. At the Department of Biomedical Engineering, College of Design and Engineering, National University of Singapore, he has led a team to develop an exoskeleton designed to reduce strain on the lower back during heavy lifting. This suit offers a new line of defence against chronic injuries in physically demanding workplaces.
The team’s work was published in IEEE Transactions on Robotics on 9 November 2023.
Taking the strain out of heavy lifting
Back-support exoskeletons (BSEs), worn directly by the user, help reduce lower back strain by providing supportive torque at the hip joints, connecting the trunk to the thighs. Conventional passive BSEs rely on elastic materials, such as springs or carbon fibre, to provide support. This design lacks adaptability — as the support strength of the components is fixed, making them less effective for tasks requiring varied levels of exertion.
Active BSEs, driven by motors and sensors, were developed to bridge this gap. But this configuration, too, has its limitations. Active BSEs generally require two motors, one for each hip joint, to deliver adjustable torque as needed — but the added weight and complexity can lead to discomfort and balancing issues for the user.
“We thought that using only one motor could offer a better solution — but three requirements had to be met,” says Assoc Prof Yu. “First, the device should allow for natural differences in hip angles during movement. Second, precise force control is essential to deliver the right level of support to the user. Third,
04 | January 2025
the exoskeleton should automatically recognise when a user is lifting versus walking, so that it doesn’t make natural movement awkward.”
With these goals in mind, Assoc Prof Yu’s team set out to design a single-motor BSE with a differential series elastic actuator (D-SEA) as its centrepiece. “This actuator allows the exoskeleton to provide balanced torque to both hips, even when hip movements differ — such as when walking with one leg in front of the other,” explains Assoc Prof Yu. Using a custom-built cable-roller system, the D-SEA can transfer force smoothly to each hip joint, while a high-precision feedback controller keeps support consistent and responsive to the user’s movements.
“The D-SEA enables ‘backdrivability’, meaning that when users aren’t lifting, they can move naturally without resistance.”
“All this allows users to walk as if the suit isn’t there at all. The D-SEA enables ‘backdrivability’, meaning that when users aren’t lifting, they can move naturally without resistance. Secondly, an intelligent assistive technology automatically shifts support modes based on movement, delivering force when lifting and yielding during walking. This means users can carry loads to their destination without obstruction — a key feature in workplaces that require frequent cargo handling.” adds Assoc Prof Yu.
At just 5.3 kilograms, the team’s design is the lightest active BSE available, prioritising portability while ensuring balanced, comfortable support during strenuous tasks. In experiments, it reduced back muscle activation by up to 40% during lifting, without adding strain to the back or legs during walking — a prevalent drawback with many other active BSEs.
Backing workers, boosting productivity
The team’s exoskeleton suits made waves behind the scenes of the 2024 National Day Parade (NDP). Worn by Singapore Armed Forces personnel working on the packing and shipping of over 300,000 NDP packs, the suits provided support as they lifted boxes ranging from 10 to 45 kilograms. One soldier noted that with the suit, he felt as though he was carrying only half the box’s weight.
Issue 04 | January 2025


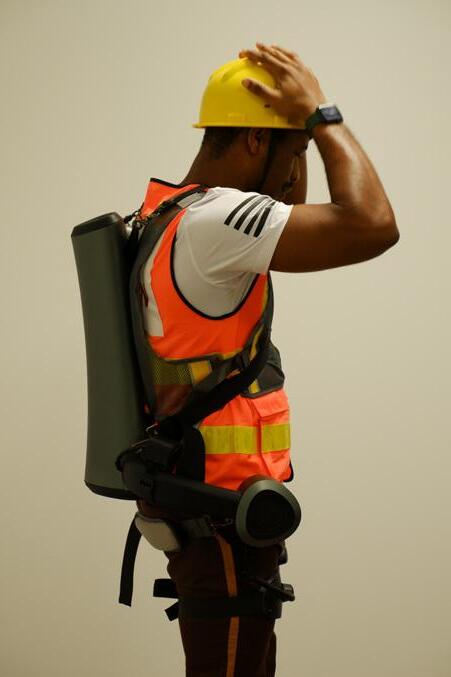
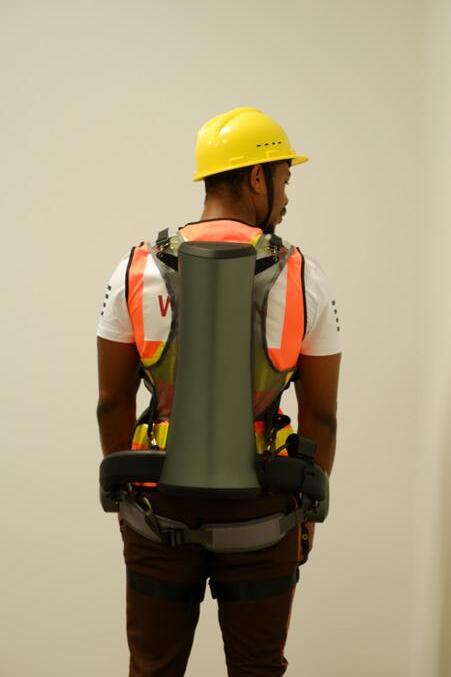
Feedback from the deployment further underscored the exoskeleton’s potential. According to a survey, 80% of participants felt their performance improved while using the device, 70% expressed confidence operating it and 90% found it useful enough to use again in the future.
“The suit could lower injury risks while boosting both productivity and wellbeing in the workforce,” says Assoc Prof Yu. “The idea is to protect workers from when they are young so that they can maintain quality performance for much longer.”
The prototype suits have also been trialled by, among others, baggage handlers at Singapore Changi Airport and workers at a chemical plant. Data collected from these trials, including the NDP deployment, will be an important step in optimising the suit’s design and advancing its commercialisation. In addition, the researchers are exploring how regular use of the exoskeleton might impact the long-term incidence of back-related musculoskeletal disorders.
With this exoskeleton, heavy lifting might just get a little lighter on the back.