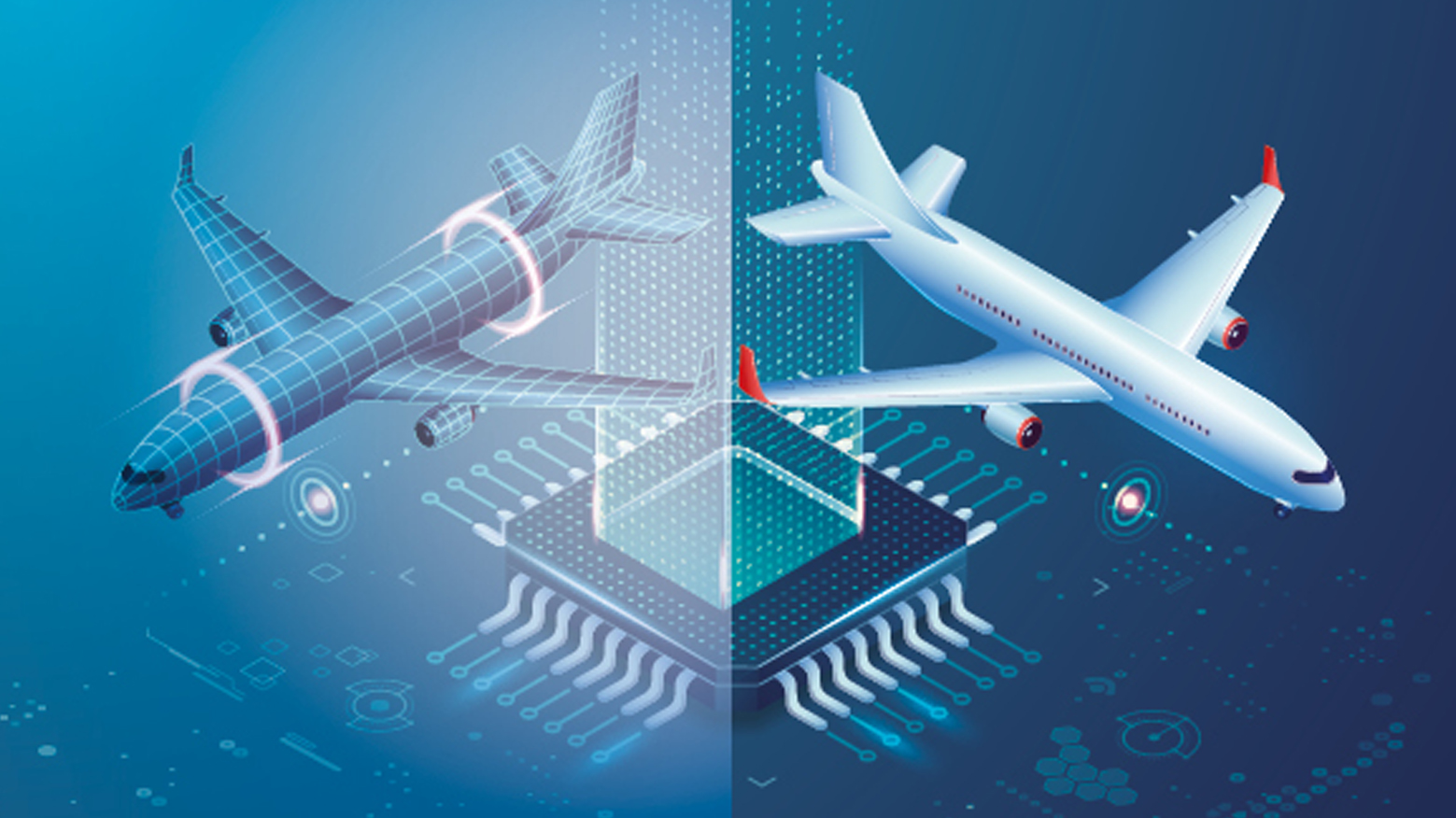
8 minute read
Industrial Metaverse
Auf Tuchfühlung mit dem digitalen Zwilling
Keine Frage, Virtualität hat Vorteile. Man kann Handgriffe an großen Maschinen üben, die nur schwer oder teuer zu beschaffen sind. Oder durchtesten, bevor man Abläufe in der Realität umorganisiert: Das Industrial Metaverse ist ein großes Experimentierfeld – und in manchem M+E-Betrieb doch schon erprobte Praxis.
Fisch trifft auf Stahl, genauer frischer Lachs auf rotierende Klingen. Wie die Maschine Tonnen ausgewachsener Lachse aus der Aquakultur so schnell in Reihe und damit auf Filetierlinie bringt, ist nicht genau auszumachen. „Da steckt Physik drin“, sagt Thomas Raths. Der Leiter Automation in der Forschungs- und Entwicklungsabteilung bei BAADER zeigt das Video von der norwegischen Lachsfabrik nicht auf einer Lebensmittelmesse. Vielmehr ist es Teil einer Präsentation zum Thema Industrial Metaverse.
„Ein Buzzword“, konstatiert Raths. Für den Diplom-Ingenieur steht es vor allem für die Arbeit mit digitalen Zwillingen, die helfen, Risiken zu reduzieren und neue Prototypen zu testen, bevor man in die reale Umsetzung geht. „Maschinen vollumfänglich virtuell zu validieren und zu verifizieren“, heißt das in der Fachsprache technischer Prüfverfahren. Je nachdem, was man simulieren will –und mit welchem finanziellen Aufwand –, werden ganze Fabriken, bestimmte Prozesse oder nur einzelne Maschinen in einem „digital twin“ abgebildet. „Man muss das Beste für sich dabei heraussuchen“, betont Raths. Bei großen Playern wie Siemens kann das schon mal eine ganze Fabrik sein, die erst virtuell abgebildet und dann mit realen Produktdaten gespeist wird. Das hat im Erlanger Werk schon Abläufe schneller und kostengünstiger gemacht. Die Modellierung vereinfache aber auch die Planung neuer Fabriken, weiß Raths: „Wo müssen welche Maschinen und Fertigungsschritte sein. Das wird getestet, bevor es gebaut wird.“ Das familiengeführte Unternehmen in Lübeck ist für den Münchner Technologiekonzern eine gern präsentierte Erfolgsgeschichte: BAADER setzt seit 2021 bei der Entwicklung von Spezialmaschinen in der Lebensmittelverarbeitung auf die Simulation durch digitale Zwillinge – mit einer Steuerung aus dem Hause Siemens.
Seitdem wurde am Standort Lübeck die Entwicklungsabteilung um- und Expertise aufgebaut: Mechaniker, Elektriker und IT arbeiten parallel, entwickeln und testen neue Filetiermaschinen zunächst virtuell. Reibung, Masse, Trägheit eines neuen Werkzeug-Prototyps lassen sich so gut erfassen. Schwieriger wird es beim Zusammenwirken zwischen Maschine und Material. Fisch ist nun einmal nicht Stahl, Lachs nicht Hering und nicht einmal Hering gleich Hering: Größenunterschiede, saisonale und regionale Einflüsse sollen im Modell berücksichtigt werden. „Die Interaktion zwischen Werkzeug, Maschine und Fisch zu simulieren, ist unser Zukunftsthema“, sagt Raths.
Das Industrial Metaverse ist Zukunft und in allen Branchen ist dazu etwas unterwegs, auch wenn es nicht immer unter diesem Begriff gehandelt wird. Um sich von der Welt der Spiele und sozialen Netzwerke abzusetzen, sprechen Unternehmen lieber von der digitalen Fabrik oder Fabrik der Zukunft. Das kann den Bohrer meinen, der an einer Stelle, wo kein Loch gebohrt werden muss, gar nicht erst anspringt. Einen Laserpointer, der aufzeigt, welche Schraube als nächstes angezogen werden muss. Und digitales Übungsmaterial, mit dem der Lehrling hinter der VR-Brille erst mal experimentieren kann, bevor er sich an das echte teure Material heranwagt.
Geolokalisiertes Handwerkzeug
Bei Premium AEROTEC in Varel, Zulieferer von Flugzeugstrukturen, hat die Fabrik der Zukunft schon vor zwei Jahren begonnen. „2022 haben wir den Piloten gemacht, ein Jahr später lief er störungsfrei und dann kamen schon weitere Kollegen und wollten das auch haben“, so Senior Manager Dr. Thomas Bielefeld über die Einführung geolokalisierter Handwerkzeuge, „Smart Tools“ genannt. Erprobt wurden sie in der Tür- und Torrahmenmontage. Das sind Ausschnitte in der Flugzeugschale, die versteift und dann mit Türen versehen werden. Es handele sich um komplexe Bauteile aus Aluminium, Titan, CFK, also kohlefaserverstärkte Kunststoffe, bei Sonderanfertigungen bis zu sieben Meter hoch, erklärt der Ingenieur. Bis zu hundert Bauteile müssen in Varel dafür angebohrt oder geschraubt werden – mit den Smart Tools geht das fehlerfrei: „Das Werkzeug weiß, ob es an der richtigen Stelle ist.“
Die Flugzeugindustrie gilt nicht gerade als Vorreiter bei der Automatisierung. Das hat mit strengen Qualitätsvorschriften und Produkten mit einer Lebensdauer von gut 40 Jahren zu tun. Dennoch sei es gelungen, Datendurchgängigkeit für jeden einzelnen Produktionsschritt von der Zerspanung bis zur Lackierung herzustellen. „Wenn ich Digitalisierung zu Ende denke, muss ich die notwendigen Daten ohne Umbrüche für die folgenden Produktionsschritte zur Verfügung stellen können“, sagt Manager Bielefeld. Genau darum ging es auch bei einem Forschungsprojekt mit dem langen Titel „Vertikal integrierte, nachhaltige End-To-End-Fabrik“, kurz „VE2E“, das in der Coronazeit den Luftfahrtstandort Niedersachsen fördern wollte. Außer vier Forschungsinstituten waren vier industrielle Partner unter Leitung der Premium AEROTEC beteiligt. Das Forschungsprojekt ist inzwischen abgeschlossen. In einer Pressemitteilung ist die Rede von einer Produktivitätssteigerung von mehr als 300 Prozent in der additiven Fertigung bei gleichzeitiger Reduzierung der Ressourcenverbräuche um 70 Prozent, etwa beim Titan.
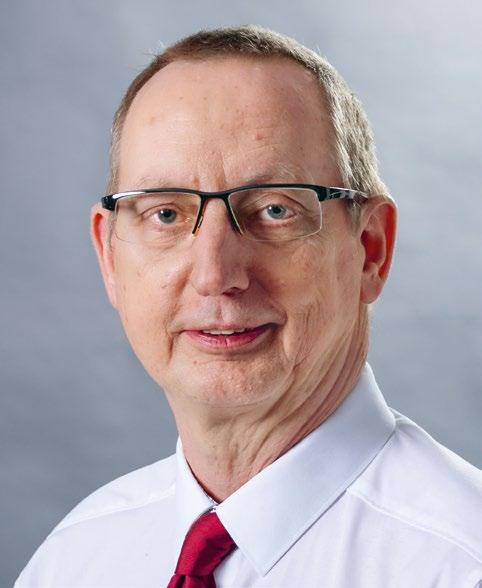
Dem gegenüber stehen hohe Investitionen: Ein Smart Tool kostet rund achtmal so viel wie ein herkömmliches Druckluftwerkzeug. Das rechne sich, so Projektleiter Bielefeld, weil es die Qualitätskontrolle datenbasiert beschleunige, Fehlerkosten minimiere und dem Fachkräftemangel entgegenwirke. „Man kann Mitarbeiter viel schneller anlernen.“
Die Beschäftigten bekommen über ein Display Fertigungsinformationen bereitgestellt, sie können den Arbeitsfortschritt sehen, etwa wo sie vor der Pause genau aufgehört haben, zu bohren oder zu schrauben. Dafür brauchen sie keine VR-Brille zu tragen, zumindest nicht dauerhaft, keine liebgewordene Gewohnheit bei der Reihenfolge der Arbeitsschritte aufzugeben und auch nicht den angestammten Werkplatz. „Wir versuchen, das so flexibel wie möglich zu gestalten“, sagt Bielefeld. Das bedeute zwar mehr Aufwand in der Programmierung, habe aber auch die Skeptiker überzeugt. „Das Smart Tool stört nicht und man kann nichts mehr falsch machen“, laute das Fazit der Beschäftigten.
Vom Fisch zum Fleisch, vom Stahl zum Titan: Die Beispiele zeigen die Chancen, die mit einer durchgängigen 3-D-Datenkette einhergehen können. Diese gilt als Rückgrat digitaler Zwillinge und erzeugt selbst wiederum Daten, etwa für die Entwicklung neuer Maschinen, Wartung und Instandhaltung, Aus- und Weiterbildung. „Große Maschinen kann man supergut im Metaverse darstellen. Das Potenzial für die Metall- und Elektroindustrie ist riesig“, sagt Dr. Sirkka Freigang. Die Bildungsberaterin hat über „Smart Learning Environments“ promoviert und ist beim Corporate Learning Camp 2024 aufgetreten, das NORDMETALL mitveranstaltet hat.
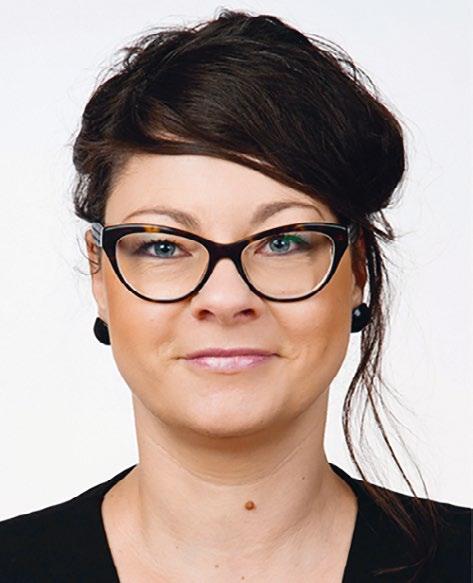
Ideales Lernumfeld
Das Metaverse ist für Freigang ein ideales Lernumfeld. „Es ist kein passives Lernen mehr an Powerpoints oder Videos, sondern eine interaktive Erfahrung“, betont sie. Azubis könnten am digitalen Zwilling trainiert werden – ohne Transferprobleme und Verletzungsrisiken. „Die Produktion muss dafür nicht angehalten werden.“ Die Beraterin kennt die Vorbehalte der Unternehmen, riesige Echtzeitdatenpakete vorzuhalten und für die automatische Produktionssteuerung zu nutzen, weil das als Einfallstor für Hacker gesehen werde. Unkritisch sei es dagegen, dreidimensionale Welten für Training, Coaching und Ausbildung zu nutzen, so Freigang. Der Aufwand sei nur beim ersten Mal hoch, ein digitaler Zwilling ist skalierbar. „Einmal virtuell nachgebaut, kann die Maschine überall auf der Welt genutzt werden.“
Der immersive Ansatz, bei dem Azubis mittels digitaler Technologien wie Virtual Reality (VR) oder Augmented Reality (AR) in ein Lernumfeld eintauchen, gilt als besonders wirksam: „Die Lernenden verknüpfen den Inhalt mit dem Raum, das bleibt in Erinnerung“, so die Lernberaterin. Als störend könne aber das Tragen der VR-Brille empfunden werden. „Ich kann mir nicht vorstellen, dass ein Werksleiter acht Stunden mit der Brille das Werk managt.“ Sirkka Freigang macht sich daher stark für webbasierte Plattformen, die man auch über Smartphones und Tablets abrufen kann und für die man lediglich einen Browser sowie ein stabiles Netz benötigt.
Simulationen locken Fachkräfte
Premium AEROTEC nutzt die Smart Tools in der Tür und Torrahmenmontage operativ. Künftig sollen die Daten Mitarbeiterinnen und Mitarbeitern in nachgelagerten Prozessen zur Verfügung stehen, um so zu ermitteln, wo eine Qualitätsprüfung oder Nacharbeit erforderlich ist. Das sei aber erst der Anfang, sagt Thomas Bielefeld: „Wir wollen eine komplett durchgängige digitale Prozesskette schaffen. Von der ersten Bohrung bis zur Auslieferung an unseren Kunden.“
Bei BAADER ist die Digitalisierung Geschäftsmodell und soll die Fischverarbeitung automatisieren. „Dort wo der Fisch verarbeitet wird, gibt es eigentlich gar nicht mehr genügend Leute, die das machen wollen“, sagt Thomas Raths. In der Entwicklung wiederum kann das Schlagwort vom Industrial Metaverse ein Pluspunkt sein, um junge IT-Fachkräfte für den Lübecker Standort und Simulationsaufgaben zu gewinnen. „Das sind komplexe Tools, die fundierte naturwissenschaftliche Expertise erfordern“, sagt der Diplomingenieur.

Mit Hard- und Software allein ist es eben nicht getan. „Wir haben zwei Experten, die alles können und den digitalen Zwilling bauen“, so Raths. Nicht ganz so fundiert muss das Simulations-Know-how in der „Adaption“ sein. In der „Anwendung“ wird der digitale Zwilling für die Programmierung genutzt und auf die Probe gestellt. Damit ist BAADER nicht nur Technologieführer, sondern auch Vorbild: „Wir sind gut dabei, viele Mittelständler überlegen das noch“, lautet das Raths-Fazit aus Vorträgen und Messebesuchen. Er rät, sich mit dem Industrial Metaverse intensiv zu beschäftigen und das Potenzial abzuklopfen. „Es ist nie zu spät, einzusteigen.“ Die Reise in die Zukunft hat erst begonnen.
Deike Uhtenwoldt