

TRUEGALV ®
TrueGalv® the effective alternative to traditional hot dipped galvanised products
► Available in Strut and CableTray Products
Self Healing
Consistent Finish
No Dags
Cost Effective
Suitability for all Applications
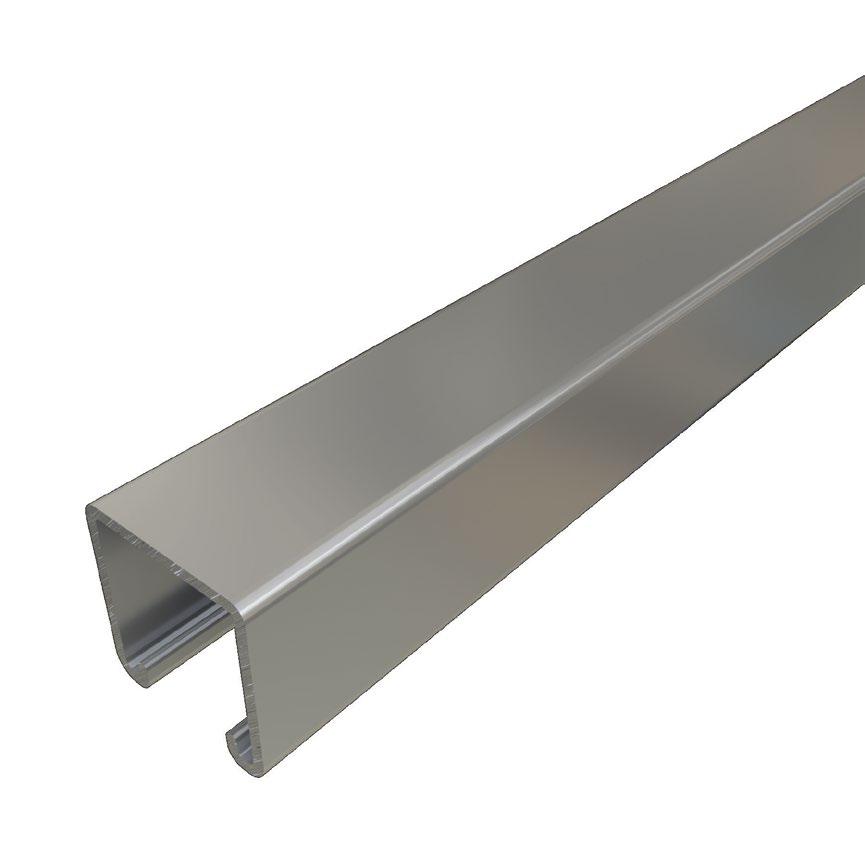

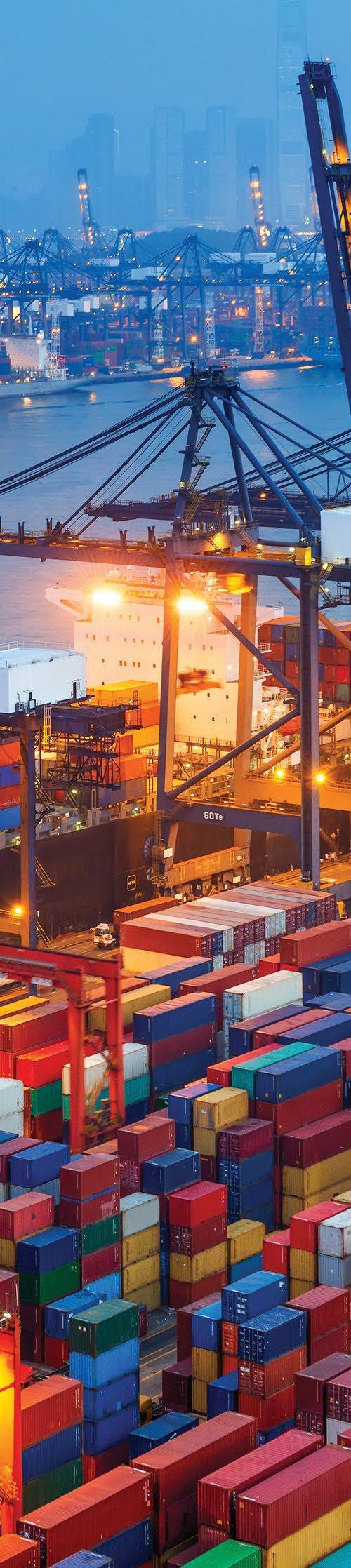
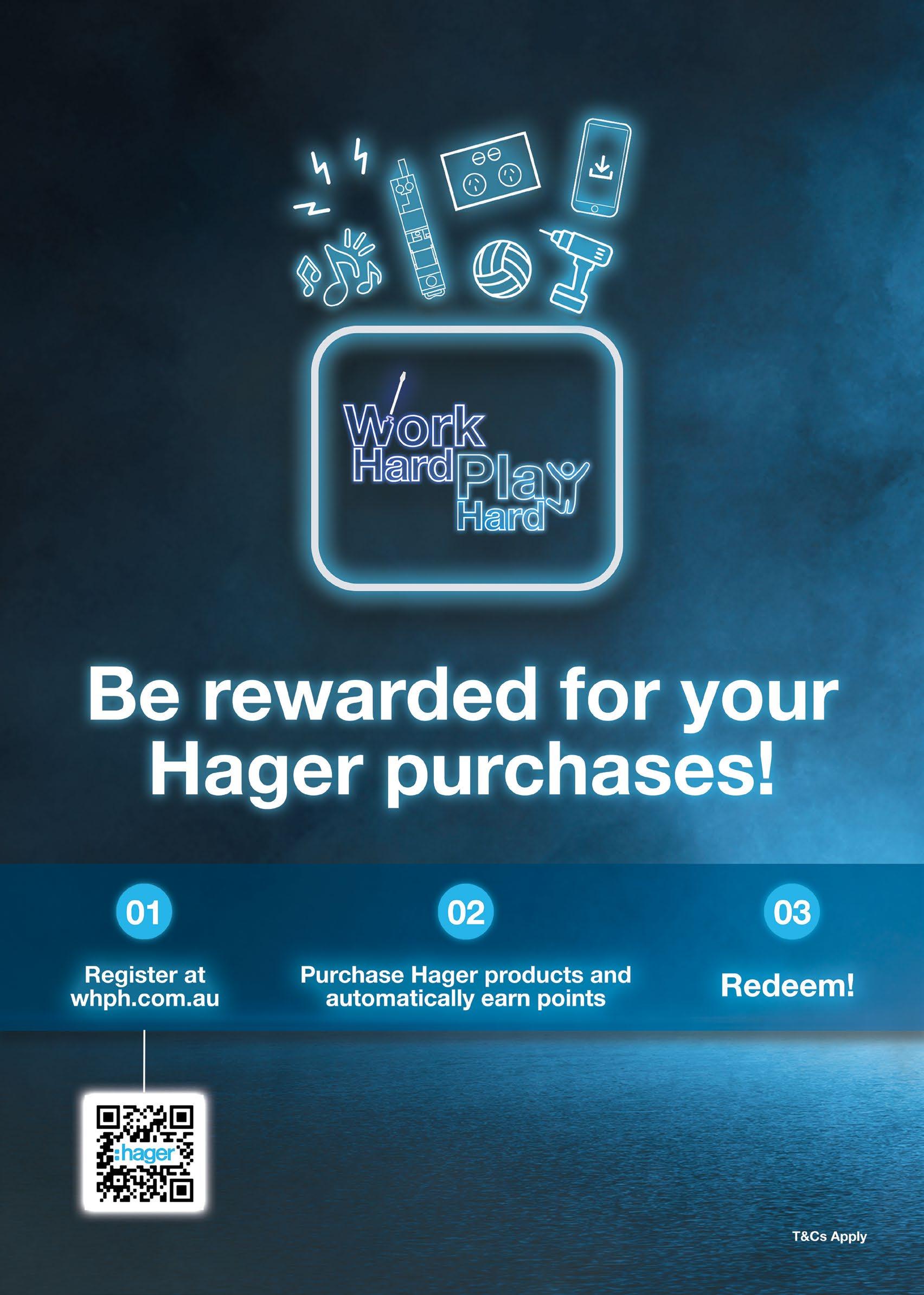
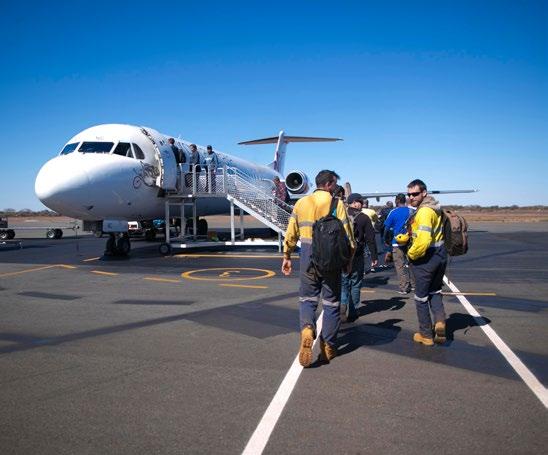
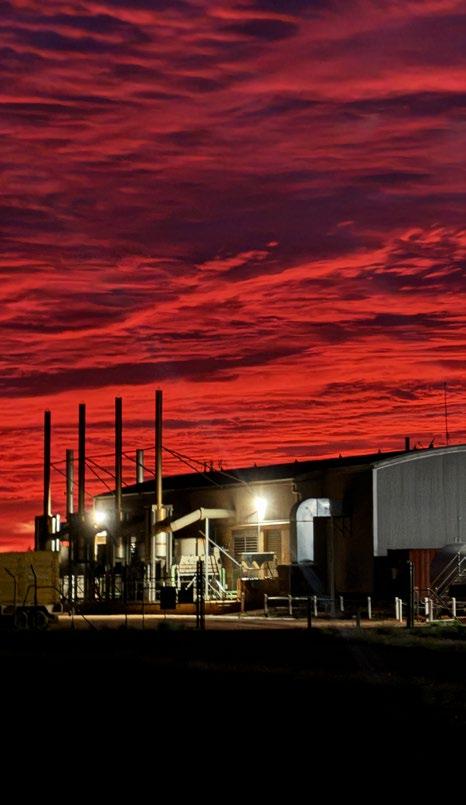
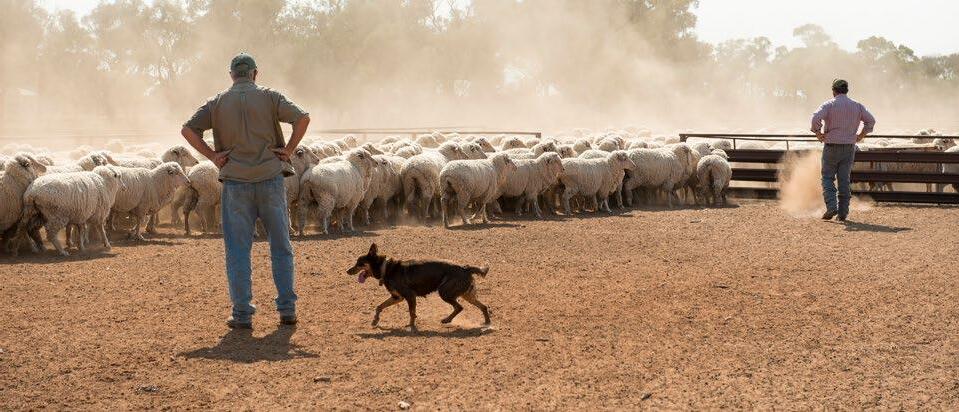

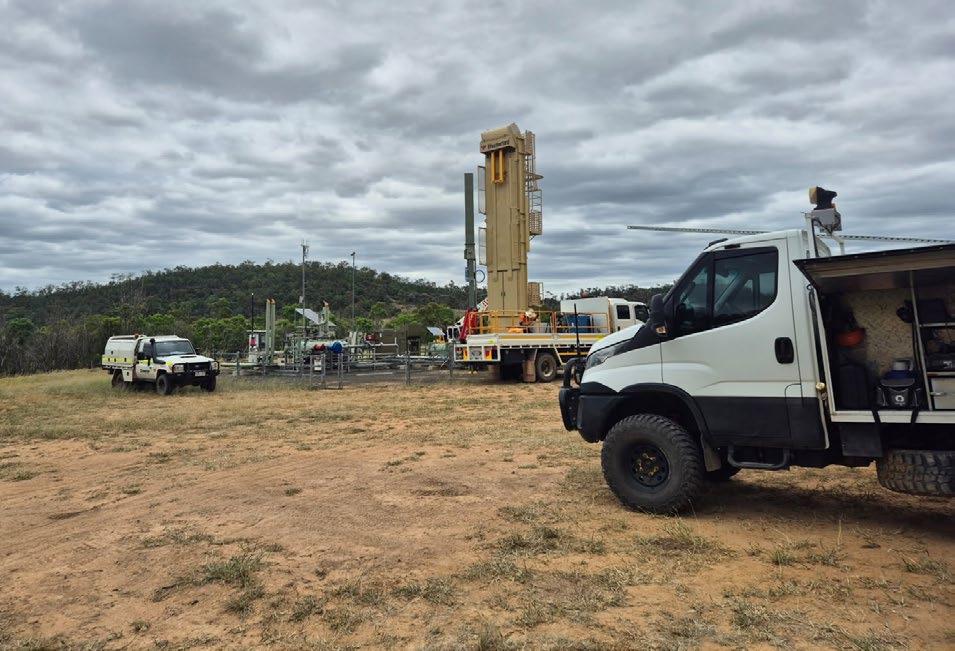
1300 361 099 memberservices@neca.asn.au
SA/NT BRANCH 213 Greenhill r oad, Eastwood SA 5063
Box 47, Fullarton SA 5063
(08) 8272 2966
neca@necasa.asn.au
IN THIS ISSUE
WOrKING OUTSIDE T hE COMFOr TS OF A STABLE AND FAMILIA r UrBAN ENVIrONMENT IS SOMET hING T h AT AUST r ALIANS IN T hE ELECT rOTEChNOLOGY INDUST rY h AVE BEEN DOING SINCE ELECT rICITY FIr ST EXISTED. OVE r T hE YEA r S SINCE, T hE EVOLUTION OF TEChNOLOGY h AS COMPLETELY OPENED UP T hE rEALM OF rEMOTE WOrK TO MANY OT hEr INDUST rIES, AND ALLOWED ELECT rICAL WOrK IN T hE BUS h TO EXPAND INTO EVE r-GrOWING A rEAS.
Working outside of a metro city area is vastly different than most would expect, and in this edition, we’ve spoken to some contractors who have gone from strength to strength on some unconventional jobsite about some the difficulties they’ve had to overcome.
This issue is packed with insights into the regional workforce, containing perspectives and experiences from both apprentices and businesses that are working away from home.
Working in and out of these remote locations is something that needs to be
done to keep our country connected. Whether you’re a business owner, employee, apprentice, or even a family member, this issue will contain something for you. Take the opportunity to read about life out in the bush, or about managing a business or employees from a distance – a shared experience is the next best thing to a first-hand one.
Tom Emeleus, General Manager of NECA Training and Apprenticeships said, “Where there are people, there’s electricity, and where there’s electricity, there are electricians.” Such a great and wide land as Australia is filled
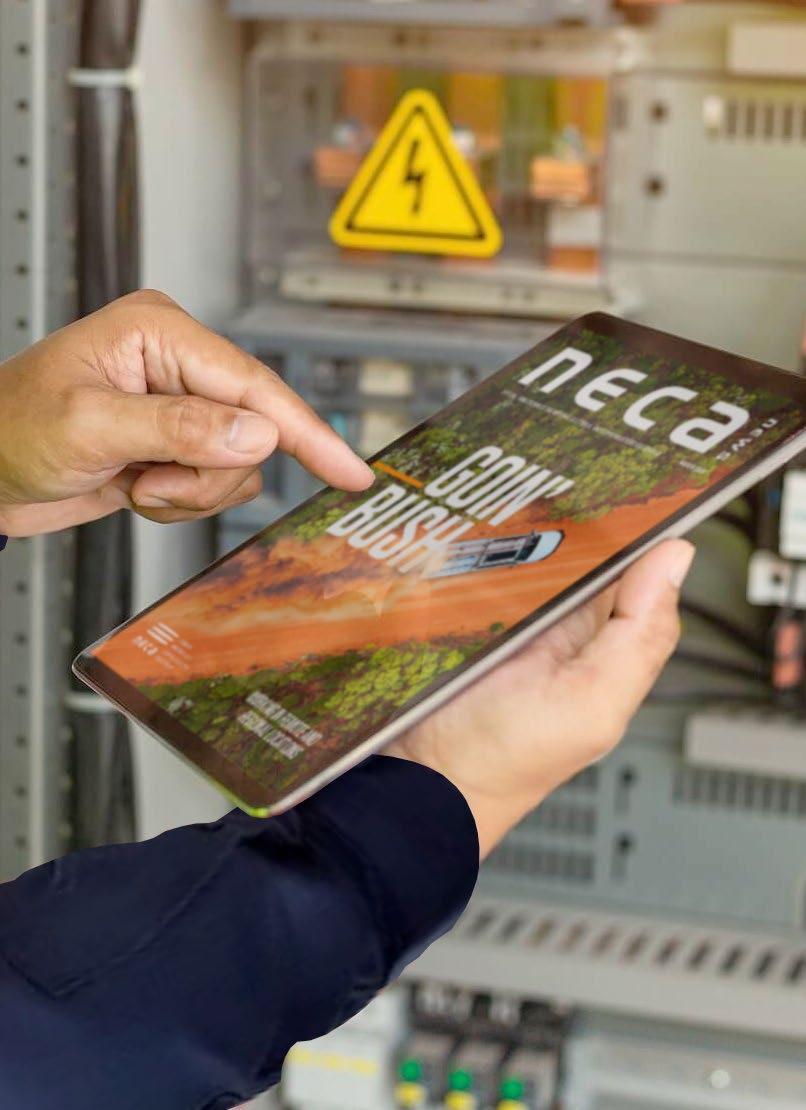
with empty open space, yet there is so much opportunity for work out there. As part of the Electrotechnology industry, we’re always going to be involved in every aspect of our country’s future development.
If you have something to share from your corner of the country, don’t hesitate to reach out. We’d love to hear from you.
The NECA News team
GET IN TOUCH
TELL US WHAT YOU THINK
Share your feedback via email necanews@neca.asn.au
GOT A STORY IDEA?
Share your ideas for content via email necanews@neca.asn.au
ARE YOU A NECA MEMBER?
We’re looking to showcase NECA member stories in each issue. r each out to your NECA Branch or email necanews@neca.asn.au
SIGN UP TO NECA NEWS ONLINE
If you’d like to join more than 30,000 of your industry peers and receive a digital version of NECA News, sign up at www.neca.asn.au/necanews
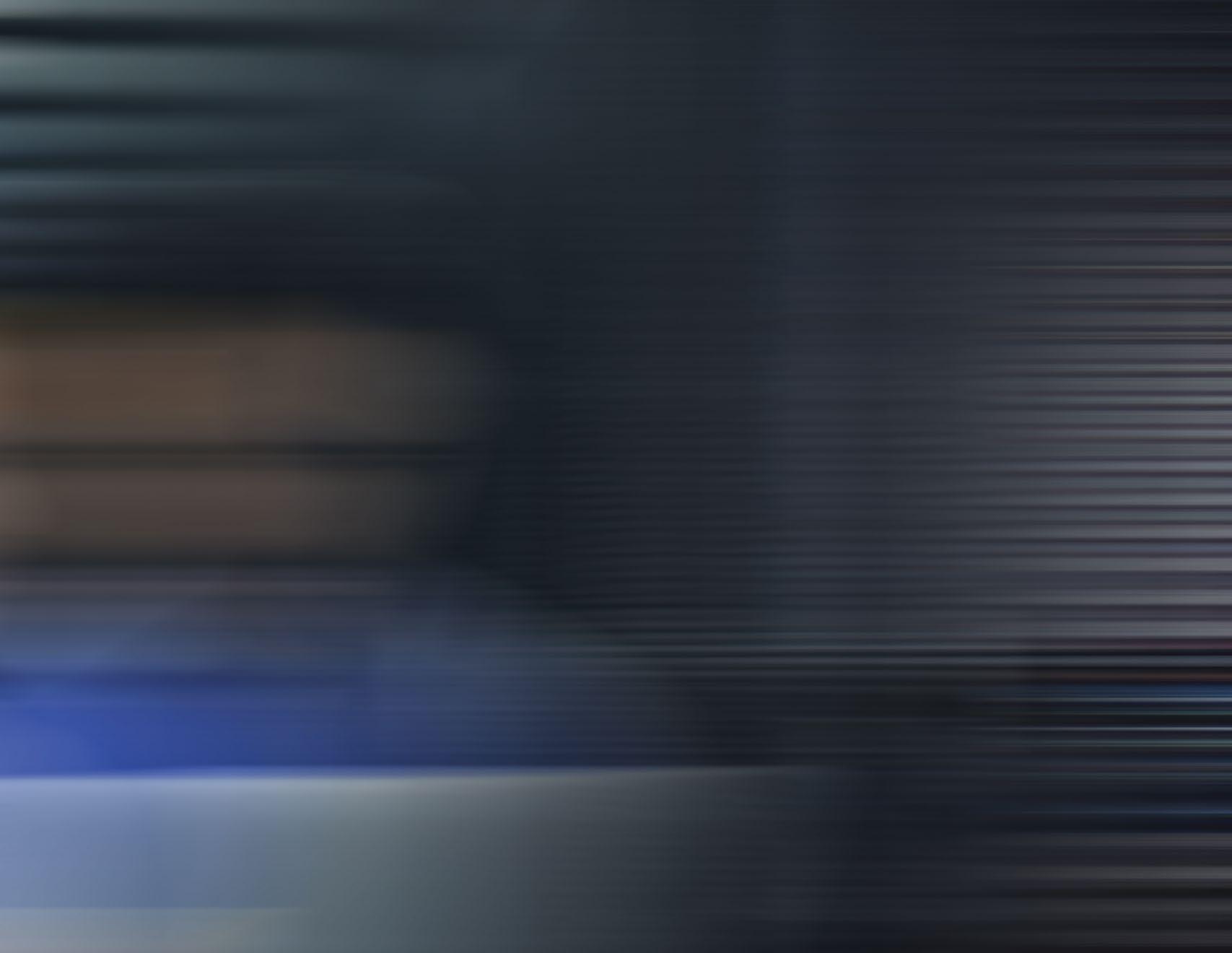
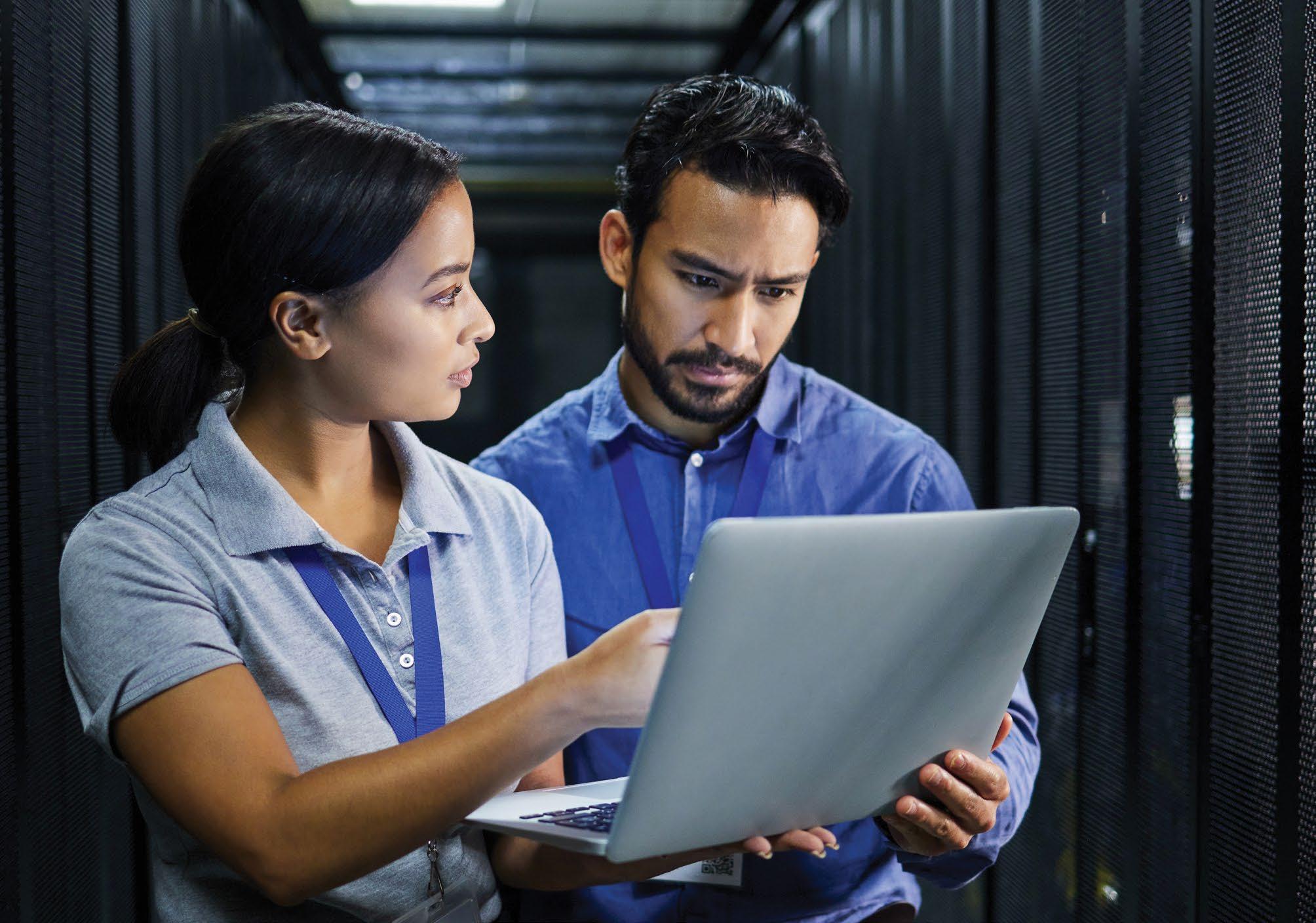
POWERVALUE 11 RT & T RANGE
& T
ABB’s PowerValue 11T G2 and Power Value 11RT G2 are double conversion online UPS models that guarantee up to 10kW per single UPS of clean, reliable power for your critical single-phase applications.
ABB’s PowerValue 11T G2 and Power Value 11RT G2 are double conversion online UPS models that guarantee up to 10kW per single UPS of clean, reliable power for your critical single-phase applications.
As well as maintaining power to your server room, lab equipment, industrial automation equipment and security, CCTV or AV, the PowerValue range also conditions incoming power to eliminate spikes, swells, sags, noise and harmonics.
As well as maintaining power to your server room, lab equipment, industrial automation equipment and security, CCTV or AV, the PowerValue range also conditions incoming power to eliminate spikes, swells, sags, noise and harmonics.
Featuring voltage and frequency independent (VFI) topology, the tower-only PowerValue 11T G2 saves costs by minimizing energy losses with its double conversion efficiency of up to 95 percent (up to 98% in
Two or three units can be connected in parallel to boost power delivery to a maximum of 30 kW or to provide redundancy.
Featuring voltage and frequency independent (VFI) topology, the tower-only PowerValue 11T G2 saves costs by minimizing energy losses with its double conversion efficiency of up to 95 percent (up to 98% in ECO mode). Two or three units can be connected in parallel to boost power delivery to a maximum of 30 kW or to provide redundancy.
The PowerValue11RT G2 can be used as a standalone UPS device or installed into a standard 19” rack configuration, with connectivity options available for each. Three units of the 6 or 10kW models can be configured in parallel to provide redundancy or to increase the system’s total capacity up to 30 kW. All units can be fitted with up to nine battery modules to extend runtime.
The PowerValue11RT G2 can be used as a standalone UPS device or installed into a standard 19” rack configuration, with connectivity options available for each. Three units of the 6 or 10kW models can be configured in parallel to provide redundancy or to increase the system’s total capacity up to 30 kW. All units can be fitted with up to nine battery modules to extend runtime.
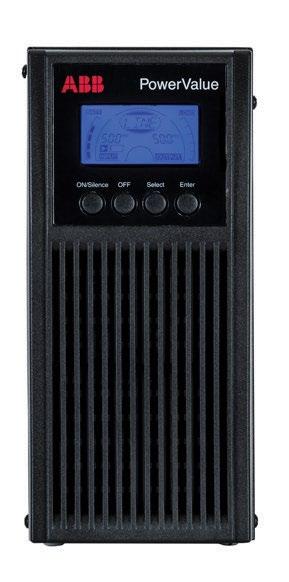
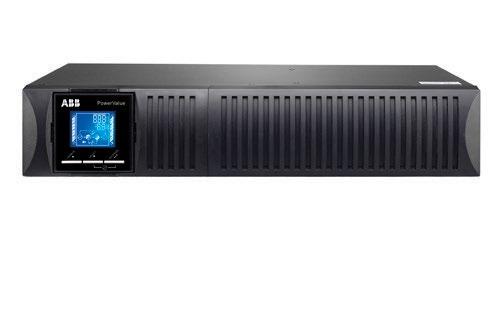
POLICY AND ADVOCACY

REGIONAL AUSTRALIA’S BRIGHT FUTURE
LIES IN THE HANDS OF ELECTRICIANS
WIT h AN ELECTION LOOMING, AND A NEW YEA r STA r TING, AUST r ALIA’S rEGIONAL A r EAS OFTEN FIND T hEMSELVES AT T hE hEA r T OF POLITICAL DISCUSSIONS.
YET, T hE CONT rIBUTIONS OF ONE CrITICAL GrOUP TO T hESE rEGIONS’ SUCCESS A rE OFTEN OVE rLOOKED:
ELECT rICIANS AND COMMUNICATION CONT r ACTOr S.
From renewable energy projects to essential infrastructure upgrades, electricians are the lifeblood of regional development. At NECA, we have observed these trends closely and it’s clear to us that empowering this workforce is vital for the prosperity of rural and remote Australia.
The Backbone of Regional Growth
Electricians are enablers of transformation. regional areas are rapidly becoming locations of choice for renewable energy hubs, with solar farms, wind projects, and battery installations cropping up across the country. Base load energy is at the forefront of the policy debate at state and federal levels. These developments rely on the expertise of skilled electricians.
Similarly, regional towns rely on electricians to build and maintain essential services, including hospitals, schools, and community facilities. With the growth of smart technologies and electric vehicles (EVs), the demand for electrical services is surging. regional electricians are stepping up to install EV charging stations and integrate advanced systems, helping these areas stay competitive and connected.
Challenges That Cannot Be Ignored
regional electricians face significant hurdles. Labour shortages remain acute, driven by a lack of local training opportunities and difficulties in attracting workers to rural areas. Outdated infrastructure also hampers progress, making it harder to introduce modern technologies, and the high cost of servicing remote areas provides yet further challenges.
A Champion for Regional Electricians
The National Electrical and Communications Association (NECA) is proud to be at the forefront of providing support to electricians in regional Australia. Our initiatives, including providing regional training infrastructure, and advocating for effective regulatory and policy reform, are crucial to ensure the electrotechnology sector thrives beyond our major cities.
NECA’s Group Training Organisations (GTOs), which have 90% apprenticeship completion rates, are setting the benchmark for workforce development. Our GTOs partner with renewable energy providers, opening new opportunities for regional electricians and giving them access to training in the latest and emerging technologies.

What Government Must Do
Government intervention and reform is essential to address the structural and regulatory challenges faced by the sector. Support for regional training hubs, subsidies for apprenticeships, and investment in modern electrical infrastructure, must become policy priorities.
Record Keeping & Repor ting <Touch Screen
Fair Commercial Terms and Regulatory Challenges
A critical issue, that cannot be overstated, is the need to ensure fair commercial contract terms, an issue which NECA continues to bring to the fore on behalf of its members. regional electricians, often operating as small businesses, rely on equitable payment terms to maintain their operations. Inconsistent or delayed payments place unnecessary strain on their already limited resources.
Additionally, the significant industrial relations and safety regulations
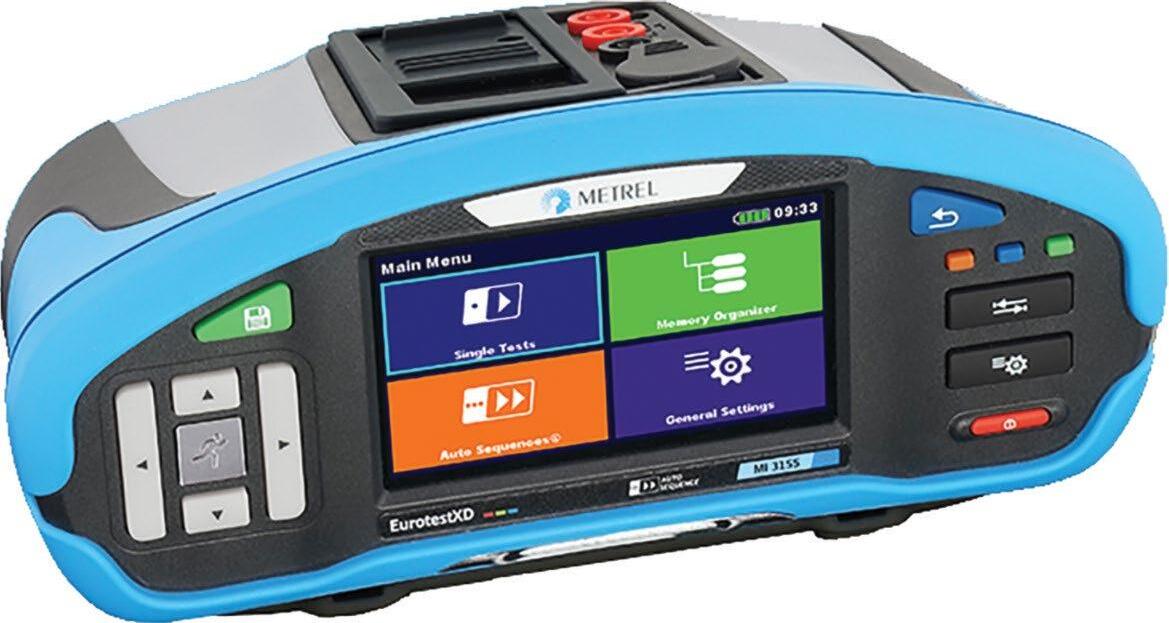
that electricians must navigate add to the administrative burden for regional businesses. While these regulations are essential for ensuring safety and fair treatment, they also demand time and expertise that can be in short supply in rural areas. Simplifying compliance processes and providing better support for these businesses would go a long way toward alleviating their burden.
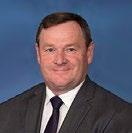
Without a concerted and coordinated policy focus from government, the employment and economic benefits of this clean energy transition may go unrealised.
NECA is advocating strongly for our industry and the crucial role it will play in unlocking the economic future for communities across rural Australia.
< Installation Verification & Compliance Testing Pass/Fail limits and “Auto Sequences” set to AS/NZS3017 and AS/NZS3019.
< Single Test Functions Voltage, Mohm & Ohms, RCD, Loop Impedance, Line Impedance, Earth Resistance, Power & Harmonics, Light, Wire Tracing.
InstalTest XD
< Site Schematics & Installation Reports
Save test results to the Site Schematic or Tree Structure. Start with Site Name and Address. Test reports output to PDF or Excel.
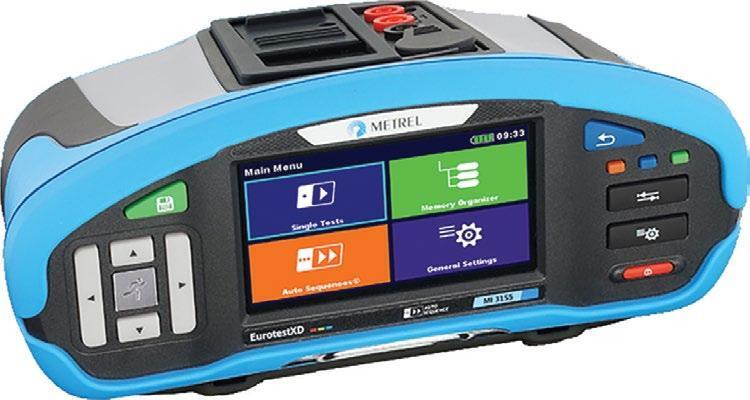
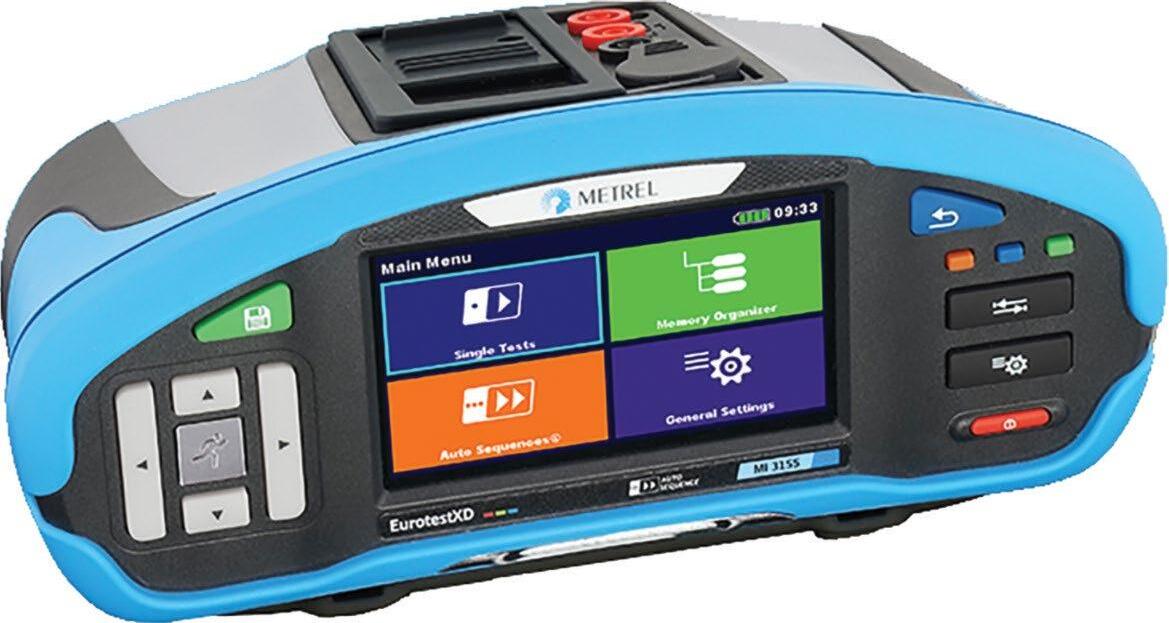
< High Volume RCD Testing System
< Installation Verification & Compliance Testing Pass/Fail limits and “Auto Sequences” set to AS/NZS3017 and AS/NZS3019
< Single Test Functions
Complete high volume RCD testing & logging solution with bar-code scanner input of RCD IDs and logging of RCD push button tests.
Voltage, Mohm & Ohms, RCD, Loop Impedance, Line Impedance, Earth Resistance, Power & Harmonics, Light, Wire Tracing
< Installation Verification & Compliance Testing
< Site Schematics & Installation Reports
Pass/Fail limits and “Auto Sequences” set to AS/NZS3017 and AS/NZS3019.
< High Volume RCD Testing System
< Single Test Functions
Complete high volume RCD testing & logging solution with bar-code scanner input of RCD IDs and logging of RCD push button tests
Voltage, Mohm & Ohms, RCD, Loop Impedance, Line Impedance, Earth Resistance, Power & Harmonics, Light, Wire Tracing
< Site Schematics & Installation Reports
Save test results to the Site Schematic or Tree Structure. Start with Site Name and Address. Test reports output to PDF or Excel
Kent Johns NECA Head of Government Relations and Policy
GOIN’ BUSH
TAPPING INTO A BUSH MARKET
rUNNING A BUSINESS OUTSIDE OF A CITY AND ITS ASSOCIATED INF r AST rUCTUrE CAN P rESENT MANY Ch ALLENGES T h AT A MET rOPOLITAN COMPANY WOULDN’T USUALLY h AVE TO
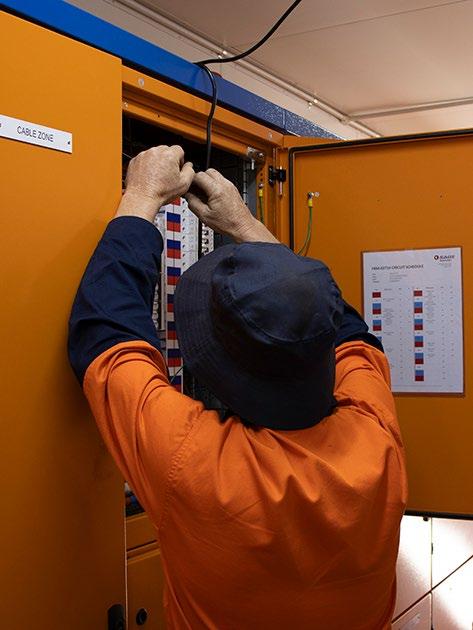
Before the Job Starts
Managing remote jobs from start to finish is a skill that All Gen Solutions has mastered. The first thing they do when they find a potential job is take the time to accurately quote it. Costs can increase due to a variety of factors, including distance, connectivity, and communications between the city and the jobsite, all of which are things All Gen take into account. Aiming to stay in control of the whole project, All Gen plans and prepares as much of the project as possible “in-house”, including designing, planning, and resource gathering.
Travelling and Planning
When it comes time to head out to the jobsite, All Gen aims to organise resources and staff to travel together in one big convoy. Where possible, they also extend an invitation to join the convoy to external contractors who may need to travel out with them as part of the project. A major part of the planning process for All Gen is planning for things to go wrong. Adam Lillecrapp, business owner of All Gen Solutions specified considerations like accounting for extra fuel consumption, servicing

vehicles properly and being careful that the truck doesn’t overheat.
“You’d rather be looking at it than looking for it” he said. Work is seasonal for All Gen, so the time of year can make a difference to the list of things required. Adam also pointed out that depending on the specific job, there might need to be extra thought put into managing the local population near the job site, such as temporary power solutions or noise management concerns.
“Be aware of the environment and how it affects what you’re doing” he said. Once all the designs, technology and crew are on site, the job can get underway.
Apprentices
More than doubling in size in the last 18 months, All Gen Solutions now has over 22 people within the company including five apprentices. “As it’s such a specialised business, there isn’t much knowledge or experience out there to be hired. Keeping apprentices at the company after they finish training benefits everyone in the business, because the team keeps a valuable member with the right skillset and knowledge, and the apprentice continues to work with the people they have developed a good relationship with”, said Adam.
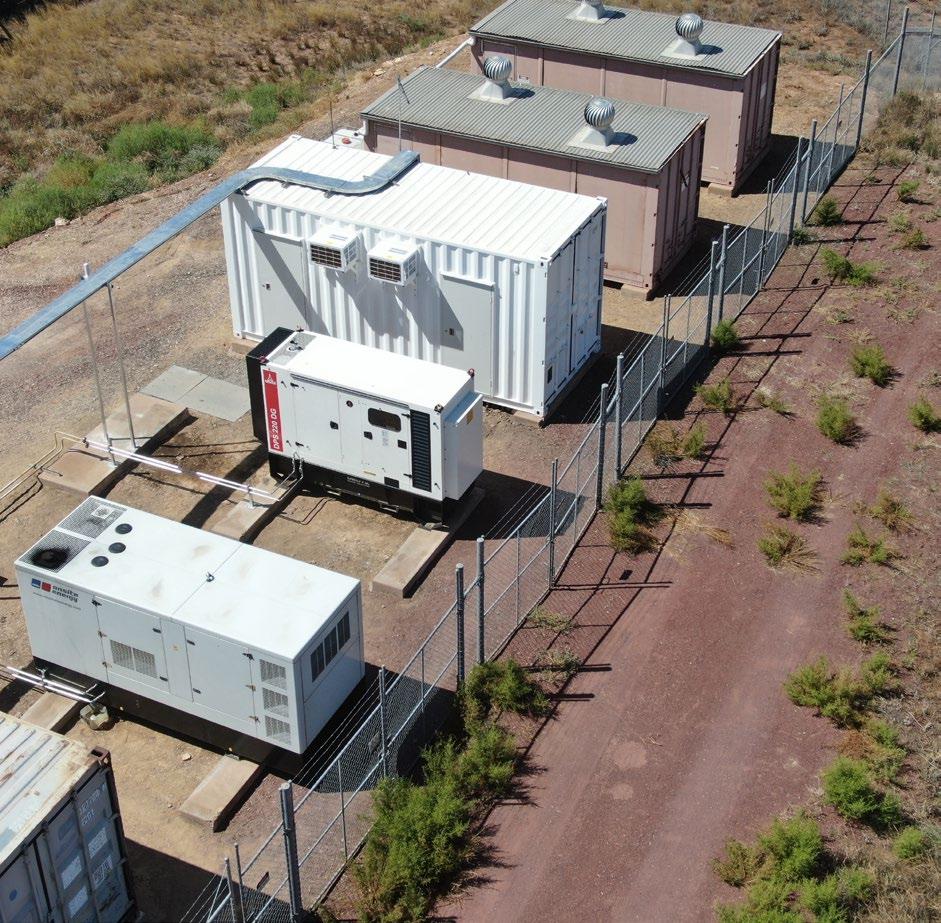
Finding Work
Despite the long list of extra challenges, there is a huge market of opportunity for companies to explore and expand upon out in these remote locations. reputation and relationships are everything to All Gen Solutions. They do most of their work in areas with low population density, which can present its own challenges. Maintaining a reputation for doing high quality work, and building a strong portfolio is something All Gen considers essential.
Managing Staff
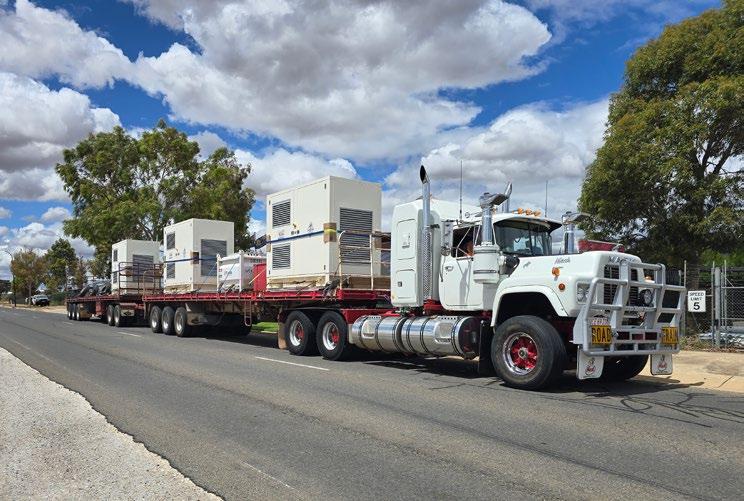
When working on a remote site, All Gen Solutions have a couple of established practices that help them in the area of staff management. Cautious of working away from home for too long, they organise the days on site in 12 day shifts, one Monday until the Friday a week later. For jobs longer than the 12 days, they often use a rotating roster with two weeks on per team. Occasionally, if the job is nearing completion, the
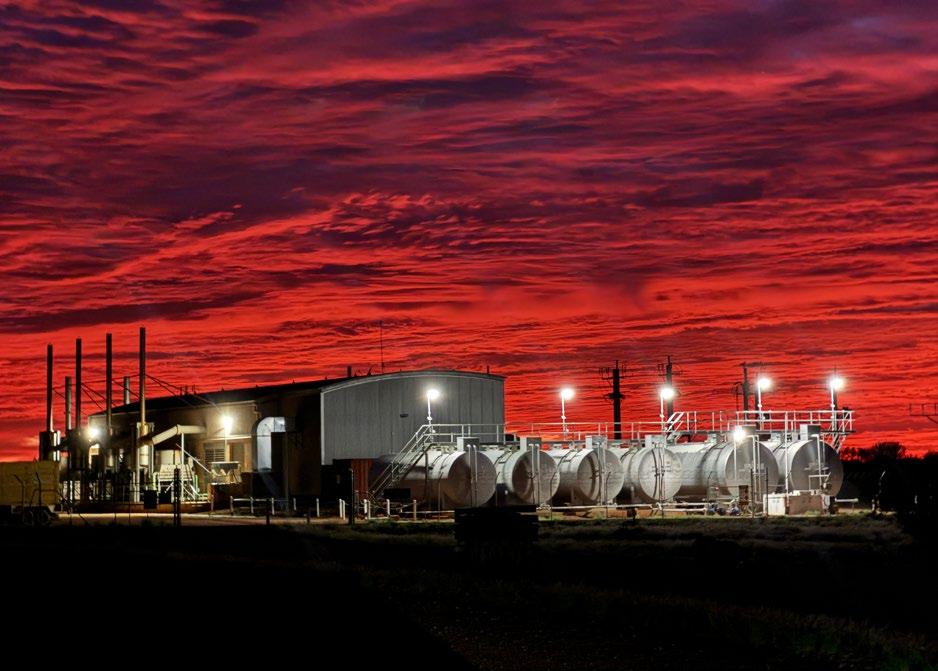
employees at their own discretion will push beyond the allocated 12 days to finish the job, which saves a whole extra round trip out to the remote site. Food is typically brought out with them as part of the resources, and as a team they share the cooking. Bedding is also often brought from home as well. The employees are all good mates, and they have Starlink kits traveling with them in order to stay connected, both of which are strategies to keep the employees from getting too lonely. Staff working remotely are entitled to a living away from home allowance as part of their pay while they are out on the job site.
All Gen in Remote Business Models
From business model to marketing, resource management to employment, companies face extra difficulties when not surrounded by a system designed to assist. When operational outside of the general reach of modern infrastructure, a business must be creative with their solutions, since the access to resources and support is much lower. At the end of the day, the most important thing to consider when running a remote business according to Adam is “knowing where you’re working and how hard it will be. Be aware of the environment and how it affects what you’re doing.” All Gen Solutions is a well-run company, with a strong portfolio of success in remote and regional jobs. It’s certainly a business model worthy of being an example for other companies looking to expand into the remote business market.
GOIN’ BUSH
NAVIGATING REMOTE WORK
OBLIGATIONS, CHALLENGES AND OPPORTUNITIES FOR EMPLOYERS
remote work reached an all-time high during the COVID 19 pandemic. Since then, many businesses have realised the benefits of remote work and have chosen to continue this practice. remote working introduces unique challenges and benefits that both employers and employees must navigate to ensure compliance, safety, and employee well-being.
‘remote Work’ is a very broad term, which covers employees working anywhere other than the office. It includes working from home, working while travelling and hot-desking, as well as working on a flexible schedule while not attending the office.
Many electrotechnology businesses have found they no longer need to rent or buy office space for staff, such as project managers, administration employees or other workers, when communications can be carried out online, without the need to regularly be face-to-face.
Benefits and Challenges of Remote Work
Some employers were understandably sceptical about offering remote work opportunities for employees, as they were concerned about a reduction in productivity and performance, which would obviously affect their profitability.
Studies have shown, however, that productivity and performance both increase during remote work, for several reasons.
Increased employee morale
remote work boosts morale, by fostering focus, motivation, and productivity, while reducing exposure to office politics.
Customisable workspaces
Employees can design their own work environment, creating a space that enhances comfort and efficiency.
Improved work-life balance
The most significant advantage is the enhanced balance between professional and personal life, leading to higher employee satisfaction and better retention of skilled staff.
Of course, there are challenges with remote work as well, including:
½ incidents of miscommunication;
½ working longer hours, and an increase in workload;
½ Workplace h ealth and Safety (W h S) obligations;
½ risk of isolation, burnout, or disengagement ;
½ ensuring cybersecurity and equitable tools/benefits.
The good news is that employers can overcome these challenges with proactive measures, such as those outlined below:
½ encourage spoken communication where appropriate, to replace emails and messages;
½ communicate to employees that their regular working hours are to be adhered to unless otherwise agreed – just as they would if they were working on site;
½ create a process to ensure that the remote workspace complies with safety legislation. If an employee is injured working from their home office, it can still be the responsibility of the employer;
½ encourage short, frequent, online meetings, so that team members remain engaged and connected;
½ invest in the right technology, so that business documents are protected even during remote work. This includes providing remote workers with safe access to company networks, implementing robust security measures, and training employees in best practices to reduce risks in public or remote environments.
As remote work is increasingly expected, there is a need for employers to understand their obligations towards a remote work environment. having appropriate workplace policies and procedures, to set clear frameworks and support the request for an employee to work remotely, will foster trust, and a positive workplace culture.

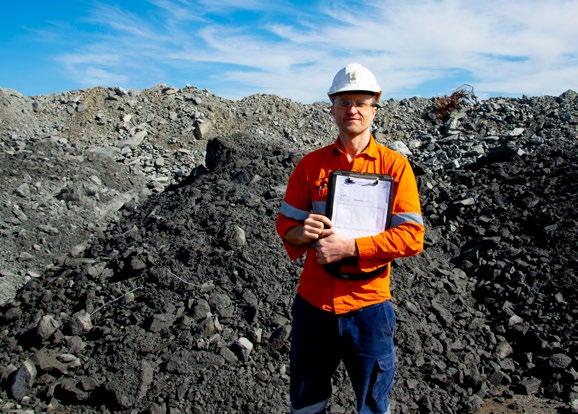
The following elements should be included as a minimum when creating a remote Work Policy, or integrated into other appropriate existing workplace policies, for employees working remotely:
½ eligibility criteria for remote work, to define whether specific roles are suitable for remote arrangements;
½ clear expectations regarding work hours, availability, workload, and key performance indicators (KPIs);
½ protocols to maintain a cohesive work environment, ensuring collaboration and team connection;
½ ergonomic compliance for home office setups, including safety measures, such as identified emergency exits;
½ expense reimbursement policies for home office setup costs;
½ compliance with visa requirements for overseas workers, if applicable.
It is also essential to clearly outline the terms of the work arrangement in employee contracts, ensuring that employers retain the flexibility to adjust arrangements if operational needs evolve and require employees to work from an office.
Proactive Planning: The Key to a Flexible and Resilient Workforce
Proactive planning creates a flexible, resilient workforce for the future. NECA encourages employers to take the lead in reviewing and refining workplace policies and procedures for their remote workforce.
For further guidance, please contact your state NECA branch.
Mary van Sambeek Senior HR Consultant, Business Solutions Hub
Fewer False Alarms
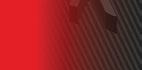
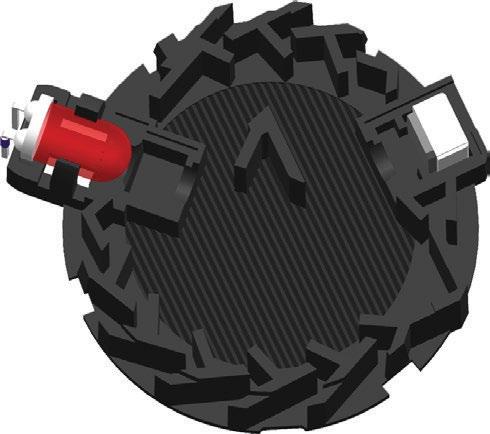




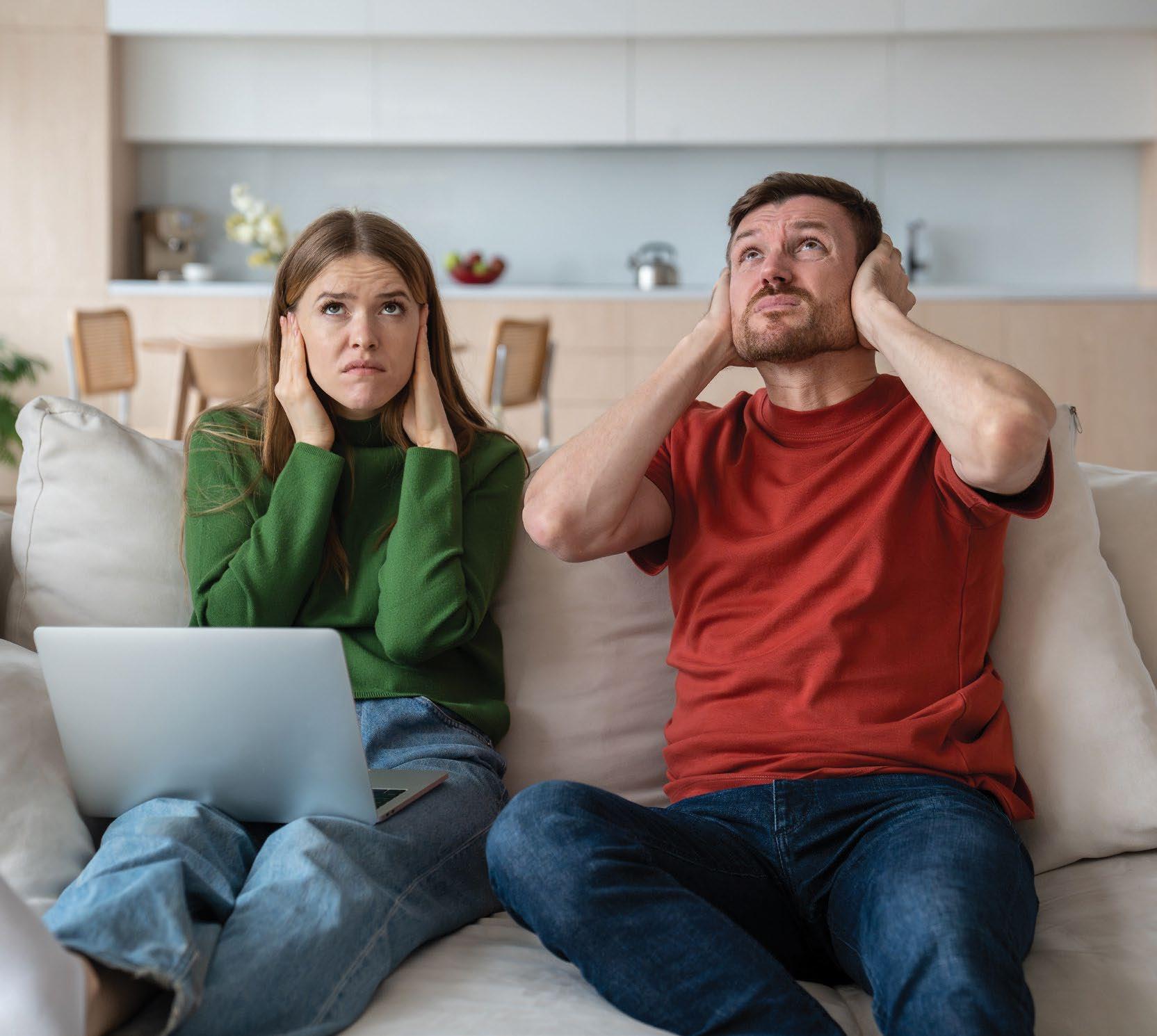

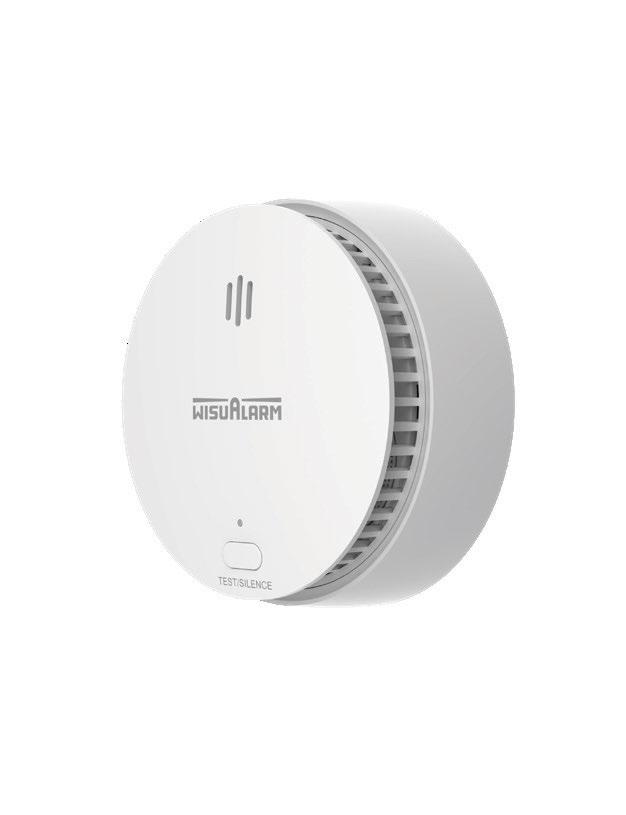
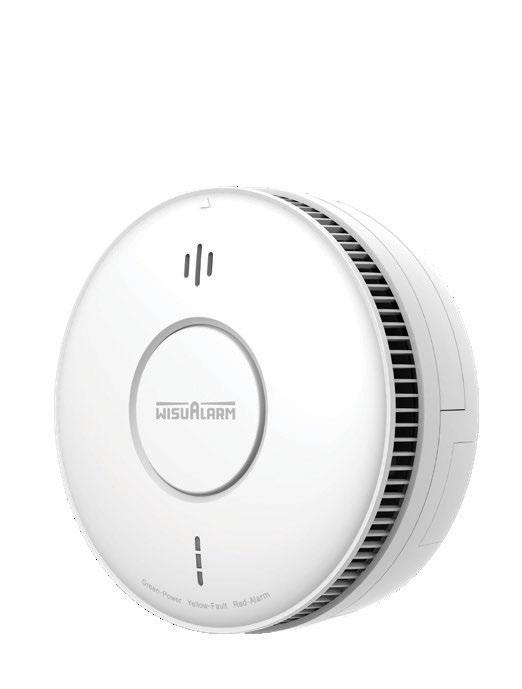

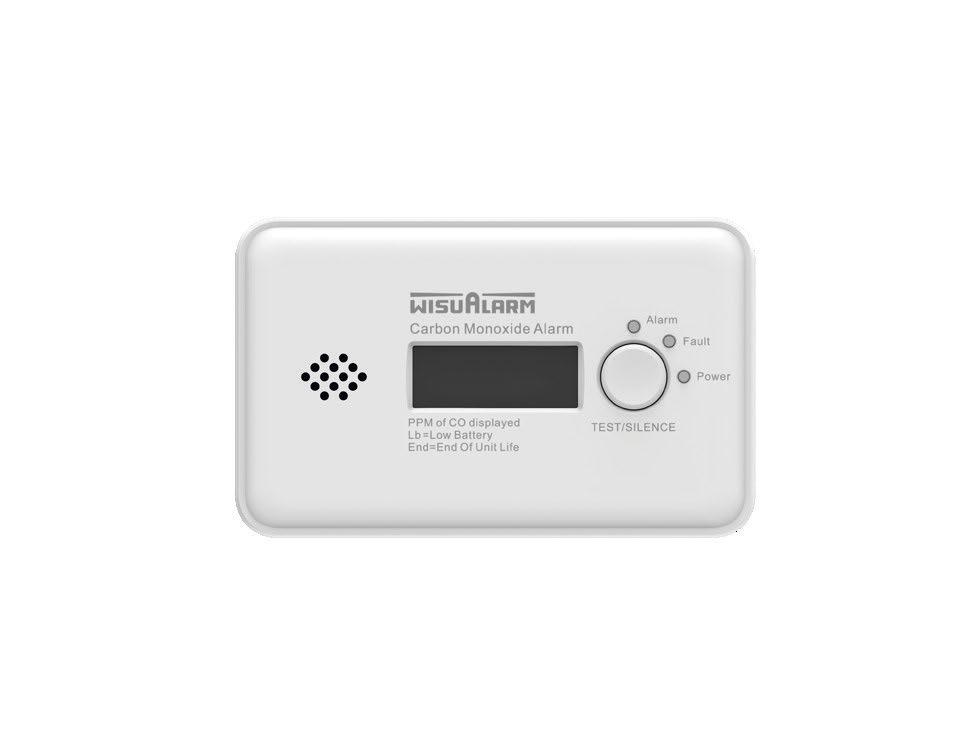
GOIN’ BUSH
IT’S ALL IN THE STARS
A MAJOr CONSIDE r ATION W hEN T hINKING ABOUT rEMOTE WOrKFOrCES AND rEMOTE COMMUNITIES IS CONNECTION. hOW DO WE CONNECT T hE PEOPLE AT T hESE SITES WIT h ONLINE SE r VICES, TELEVISION, AND TELECOMMUNICATIONS?
SOUT h AUST r ALIAN BUSINESS, MIMP CONNECTING SOLUTIONS h AS COME UP WIT h AN OFFE rING T h AT IS QUITE LITE r ALLY OUT OF T hIS WOrLD!
MIMP Connecting Solutions is a communications business that specialises in the supply, installation and maintenance of communications cabling and wireless networks. Installing cable since 1985, MIMP has a long history in the industry. As technology has become more advanced over time, MIMP has had to adapt their industry-specific skillset to evolve with it. Today, they have 19 employees within their business, most of whom are project managers and engineers. When working in remote locations, MIMP endeavours to partner with local people for as much of the job as they
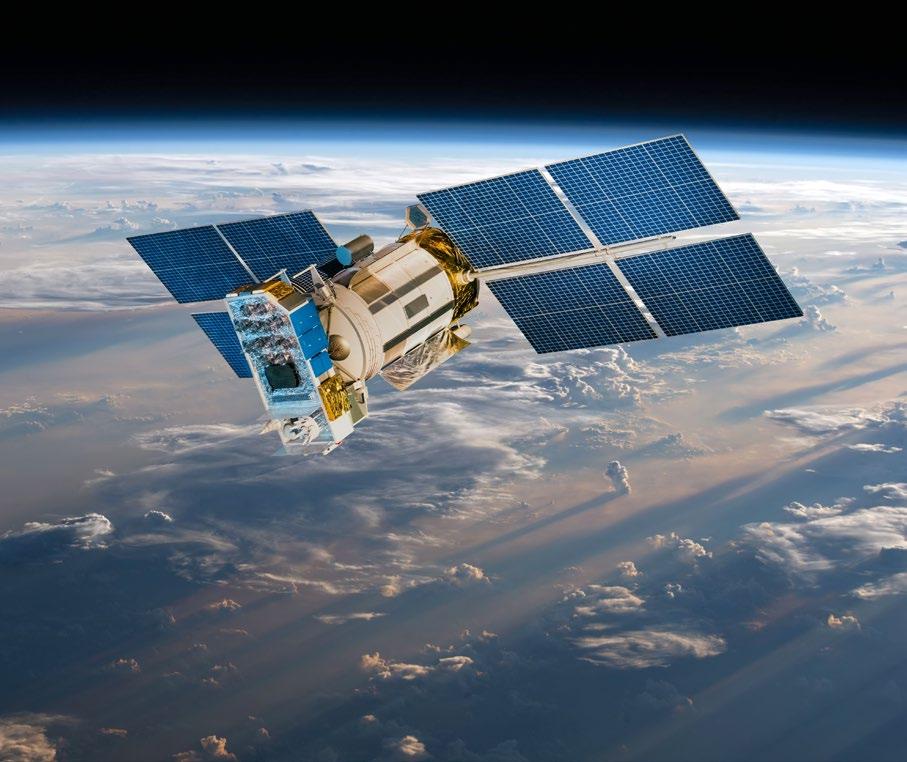
can, in both design and construction. Today, MIMP is one of only three gold partners with Peplink, the company that enables Starlink Services in Australia. At the start of 2023, 900km north of Adelaide, Windy Valley Camp reopened, after years of inactivity. With all previous communications systems removed, the camp director had to find a new solution. Opting not to reinstall the outdated and expensive systems used for the last decade, MIMP stepped in and designed microwave satellite communications infrastructure, providing the Windy Valley camp with

more reliable communications, at a substantially lower cost. It was this solution, and the innovative use of satellite technology, that saw the team from MIMP awarded NECA’s 2024 Innovation in Technology Award, beating out some strong national competition and cementing their status as a leading company in this specialist field.
The Windy Valley camp consists of four different sites in central South Australia: a base camp at Windy Valley, a rail loading site, an open mine, and a site for a second mine. The people at these sites had an expectation that internet and connectivity were a utility, not a luxury. The solution MIMP came up with used microwave transmission for site-specific communication, and then two-way UhF transmission over satellites to communicate between sites. The special nature of the design is that each unit is modular, with no cables running between the buildings, which means buildings can be shifted between sites and areas, without the requirement of re-cabling. The system they built was so reliable they haven’t had to send an IT person to site for the past two years. Furthermore, the Peplink router used as part of the Starlink connection allows for the links to bond with each other, further increasing reliability. This means that, if one of the Starlink satellites goes offline, the entire system just slows down, instead of dropping out completely. This incredible design provides reliable,
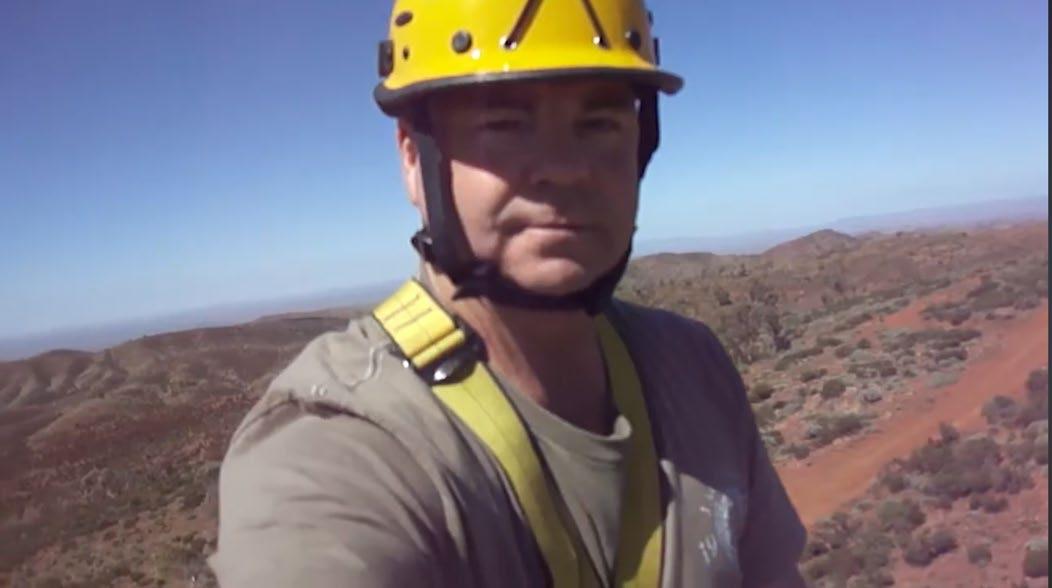
high-speed internet access across the whole camp, giving workers access to video calling and other internet services.
MIMP CEO Allan Aitchison says, “Getting a job started in a remote area without connectivity can be difficult. The first thing MIMP will do is set up a temporary communication system reliant entirely on Starlink, which can be done within four weeks. Afterwards, MIMP sits down with the customer and puts together a plan regarding the site, looking at location, the size of the site, existing infrastructure, expectations, and anything that might impact the strength of the connection. Once that is done, MIMP will do all of the designs in-house and prepare to send it out for installation. With the exception of one engineer to handle the specialist
connections side of things, MIMP likes to use local people for the labour, rather than sending people out remotely, creating jobs and reducing costs. The specialist is normally only sent out to site for about five days, which is enough time to make sure everything is working smoothly.
Surface Sitting Communication Towers
One other cost-saving piece of communications technology that MIMP has developed is a communications tower that doesn’t require digging any holes or any soil tests. Instead, for stability, the 18-metre tower is built on ballast, a foundation of crushed stone or gravel often used under train tracks.
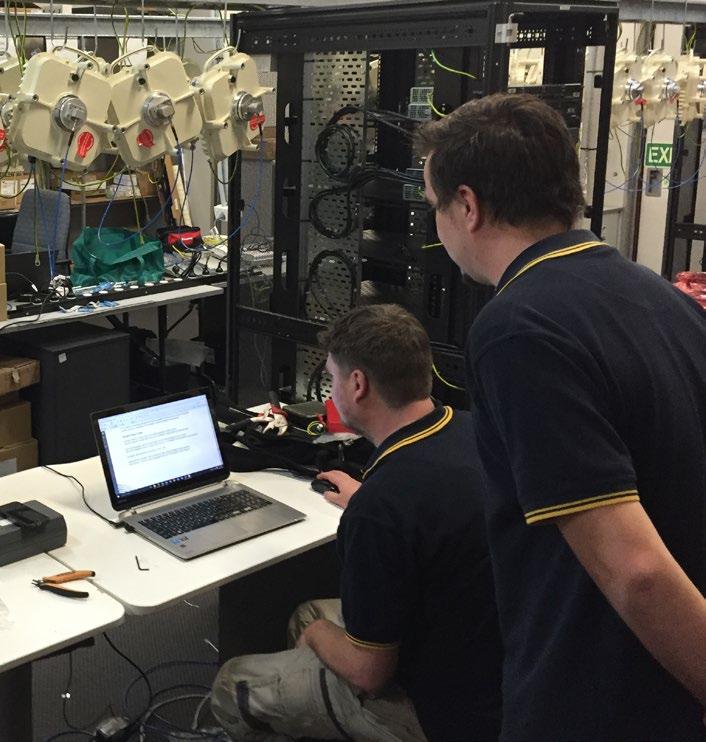
MIMP installed one of these towers 15 years ago, and according to Allan, “it hasn’t moved a millimetre; we’d know.” These towers are delivered to site in kit form and only take five to eight days to build, including setting the foundation.
Working with Starlink in Remote Australia
As a gold partner with Peplink, MIMP uses their technology to integrate the Starlink internet satellite system into their connected solutions in remote areas right around the country. recently, MIMP developed a solution connecting a 70-vehicle fleet for South Australia Water, using Starlink technology. Another recent project saw the reimagining of the way remote job sites connect to each other and to the government radio network, with 268 links, stretching from the WA border all the way across to NT and Victoria.
MIMP is also the company behind the domain starlinkcommercial.com, where Australians can see exactly what they’re able to connect.
This innovative South Australian company is able to supply and install its ground-breaking Starlink solutions just about anywhere in Australia, including fixed buildings, mobile vehicles, and on marine, rail and aircraft services. A worthy winner of our Award!
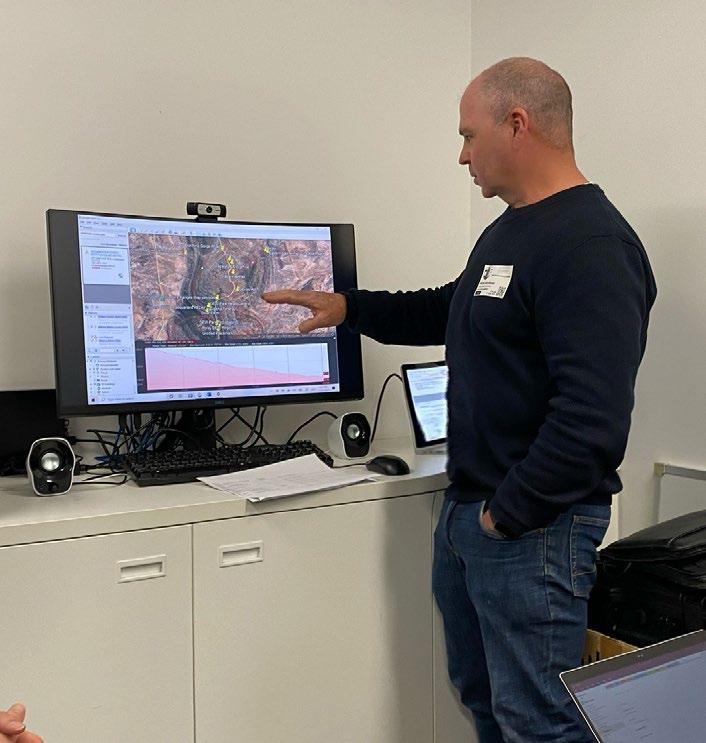
GOIN’ BUSH
SUPPORTING EMPLOYEE WELLBEING DURING REMOTE WORK
While working in remote areas can be professionally rewarding, it can also take a toll on employees’ physical and emotional wellbeing. As an employer, you play an important role in helping your employees navigate these challenges.
here’s a guide to supporting your remote teams, with practical advice on staying connected, maintaining health, and creating a positive work environment.
Staying Connected to Family and Loved Ones
Being away from home is one of the hardest parts of remote work. As employers, you can help employees maintain meaningful connections by offering some tips.
Encourage Regular Communication – Suggest employees schedule consistent calls or video chats, such as during mealtimes or at bedtime. Sharing updates and photos from their worksite (where permitted) can keep families involved and connected.
Promote Comfort from Home –recommend bringing personal items like family photos, favourite blankets, or mementos to create comfort.
Share your Experience – It’s likely that you also worked away from home at some point in your career; share with your employees your experience, and how you made it work, or what you might’ve done differently.
Promoting Health and Wellbeing
remote work often disrupts routines impacting health. Support employees by providing guidance and resources on maintaining healthy habits.
Encourage Healthy Habits – Provide tips on bringing nutrient-dense snacks like nuts, dried fruits, or protein bars to avoid relying on fast food. Suggest healthy meal options when dining out, such as grilled proteins, vegetables, and whole grains. Promote hydration by providing water bottles or reminding employees to aim for at least two litres of water daily.
Support Physical Activity – Share information about nearby gyms or fitness centres. Suggest simple, onsite exercises, such as stretches or bodyweight routines, to stay active
during downtime. If resources permit, providing a wellness kit, with a yoga mat and resistance bands, can support employees exercising in the evenings.
Improve Sleep Hygiene – Suggest employees optimise their accommodations with items like personal pillows or blankets. Provide resources like earplugs, white noise apps, and tips for consistent sleep routines, such as limiting screen time before bed.
Fostering Motivation and Emotional Resilience
Extended remote work can be mentally challenging. Employers can help maintain motivation and emotional wellbeing by recognising effort.
Recognise Achievements – recognise and celebrate milestones, both large and small. A simple acknowledgment of a job well done can boost motivation and improve job satisfaction.
Remind Employees of Their Impact –highlight the critical role your employees play in powering communities and businesses. Knowing their contributions matter can help them stay engaged.
Support Mental Health – Create a culture where employees feel comfortable discussing challenges through regular check-ins. Offer access to mindfulness resources or apps, and provide tips for stress management, such as deep breathing, journaling, mindful walks, and stretching. Keep flyers for your Employee Assistance Programs (EAPs) in company vehicles.
Encourage Growth Opportunities –Set clear goals with your employees before they head off on remote work, to help them stay clear on their role. Offer training programs and resources for skill-building to keep employees engaged, especially during downtime.
Creating a Home Away from Home
helping employees feel comfortable and homey in remote accommodations can improve their wellbeing and performance.
Personalise Accommodations – Where possible, consider employees’ preferences

when arranging accommodation. Encourage them to bring personal items to make their space feel more like home.
Encourage Routine Building –Suggest establishing daily routines that balance work, meals, exercise, and relaxation. Structure provides stability in unfamiliar settings.
Encourage Social Connections – Promote team-building activities, such as shared meals or casual gatherings, to reduce feeling alone and build team connections.
Ensure Psychological Safety
Employers are responsible for creating a safe, supportive environment, by addressing psychological safety and managing psychosocial risks.
Identify and Control Psychosocial Hazards – recognise hazards like isolation, high workloads, or unclear expectations, and actively implement controls to reduce risks. Conduct regular risk assessments to stay compliant.
Promote Open Communication – Encourage employees to speak up about concerns, without fear of judgment or reprisal.
Monitor Wellbeing – regularly check in, to assess workload and stress levels, offering support where needed.
Train Managers – Equip managers to recognise and address signs of stress, burnout, or mental health concerns.
Resolve Conflicts Quickly – Address grievances early, to prevent tension from escalating.
Provide Resources – Share tools, like Employee Assistance Programs (EAPs), to support mental wellbeing.
A well-supported team is more engaged, productive, and has higher levels of job satisfaction—ensuring long-term success for both your employees and your business.
If you are interested in testing your employee engagement score or want to learn more about complying with psychological safety standards in the workplace, get in touch with your NECA state branch today.
Stephanie Dann Head of People and Culture, NECA Victoria
GOIN’ BUSH
REMOTE WORK AND THE CHANGING WORKPLACE
WHAT IT MEANS FOR YOU
remote work involves any working arrangement where employees perform their usual duties and responsibilities away from a traditional workplace. While this has limited practical application in the electrotechnology industry, your company may employ certain positions that are suitable for remote arrangements (in part or in whole), including project managers, estimators, and system/control engineers.
however, the most common categories of employees that remote work considerations will apply to are administrative employees falling under a relevant classification in the Clerks - Private Sector Award 2020 (Award), managerial employees (Award-free).
The Fair Work Commission is currently developing a working from home term to incorporate into the Award. This provision aims to facilitate making practical working from home arrangements for employers and employees, while removing any existing Award ambiguities or impediments. We will cover some of the individual considerations in turn.
Defining ‘Remote Work’ and ‘Working from Home’
One view involves a limited definition of ‘remote work,’ being a fixed and established residential address where an employee performs work in an approved workspace that meets all applicable occupational and health safety requirements. In many cases, this may be referred to as ‘working from home.’
Alternatively, the definition of ‘remote work’ could include any appropriate area, that isn’t strictly limited to a residential address. however, such arrangements would likely raise employer concerns.
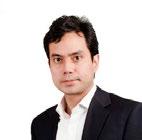
Employee Right of Request and Employer Right of Refusal
Like other Award entitlements, including previous casual conversion provisions and the new path to permanent employment equivalent for casual employees, there are prescribed requirements for both making such requests, and any subsequent employer refusal.
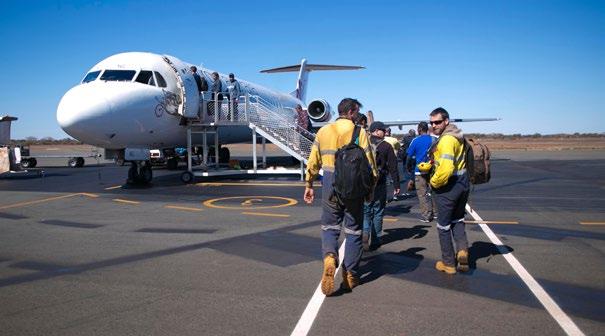
Employers must assess whether remote work arrangements can be supported without disrupting business operations. This must be balanced against other considerations in support of such remote working arrangements, which can include higher employee morale, improved productivity, and lower employee turnover.
Amendment of Existing Award Provisions
Several Award provisions exist that potentially interfere with the proper implementation of formal remote work arrangements:
½ spread of ordinary hours – 7:00 am to 7:00 pm Monday to Friday, and 7:00 am to 12:30 pm on Saturday;
½ expectation of ordinary hours of work to be worked continuously, which may have implications when working remotely;
½ ordinary working hours being worked at the discretion of the employer;
½ maximum number of ordinary working hours allowed to be worked in a single day;
½ application of breaks;
½ application of allowances;
½ application of overtime.
Examples of such issues include the timing of breaks, and the possible creation
Naveen Raghavan Employment Lawyer, Constructive Legal Solutions
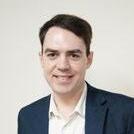
of new allowances to compensate employees for any costs associated with remote work. Any adjustment of when ordinary hours are worked will have clear implications for overtime too.
Right to Disconnect
Current Award provisions entitle employees to a “right to disconnect”. This allows an employee to refuse to monitor, read or respond to contact, or attempted contact with their employer or relevant third party outside of ordinary hours, unless unreasonable in the circumstances.
While working from home can enhance productivity, it may also lead to longer working hours and an expectation of increased availability. Any proposed term must carefully consider all relevant interplays.
Wrap Up
The Fair Work Commission is currently undertaking additional qualitative research and developing surveys for employer use to work through the issues already identified. In the interim, it is important for employers to be aware of the above and to proactively take steps to identify existing employees or roles that may be affected by the proposed Award amendments (which will likely then be rolled out across other modern Awards).
As these changes progress, employers should assess their current remote work practices to ensure compliance and prepare for any upcoming Award amendments.
Dain Venning Workplace Relations Advisor, NECA SA/NT
HAVE TOOLS, WILL TRAVEL
PA r T OF BEING AN APP rENTICE IS LEA rNING ON T hE JOB. NOT BEING AF r AID TO GET ST r AIGh T OUT T hErE INTO T hE FIELD AND TO LEA rN hOW TO DO T hE WOrK W hILE YOU’rE ACTUALLY DOING IT. USUALLY T hIS MEANS WOrKING ALONGSIDE A SUPE r VISING T r ADESPE r SON ON LOCAL JOBSITES, BUT FOr SOME NECA APP rENTICES IT MEANS T hEY WILL h AVE TO T r AVEL FA r AND WIDE TO T hE MOST rEMOTE COrNE r S OF AUST r ALIA, AND EVEN BEYOND FOr T hEIr WOrK.
Damian Djukic
Damian Djukic is a NECA Training and Apprenticeships graduate, who completed his apprenticeship at the end of 2023. Damian started his time as an apprentice working in the industrial sector, installing water treatment systems for Sydney water, as well as working on construction projects for hospitals and schools in Sydney. Throughout the duration of his apprenticeship, he spent almost all of his time working in Sydney, so when he was offered the opportunity to do Fly-In-Fly-Out (FIFO) work in the gas fields near roma in country Queensland, it was a chance he couldn’t refuse.
Out at Roma
When Damian got to roma, he was put on a 28 day cycle roster with 18 days on, 10 days off. During those 18 working days, Damian’s company would fly him out from Brisbane, where he would then get in a car and drive to one of the many camps scattered around the gas fields. As there are several camps located across multiple sites, Damian would often get moved around with each new roster. Once set
up in the camp, driving out to the worksites takes anywhere from 30 minutes to an hour and a half every single day. With 11 hour days, Damian described the work as “hot and gruelling, it’s tough but it’s good”. Across the 18 days Damian and the other employees have a KPI (Key Performance Indicator) to reach, which helps them keep track of how much progress they’re making. After the 18 days are up, Damian gets flown back home to relax and recover for 10 days, before the cycle begins again.
In the camps

For Damian, life in the camps is very different to life back home. Living away from everyone for that period of time is not something he was used to, so it was a fun new challenge for him. he works with a core team of around 10 electricians and a few mechanics, which are usually sent out onto the sites in teams of three. Although mostly based from within this core group, the people Damian works with are often different each time. “The culture is good, and so is team dynamic,
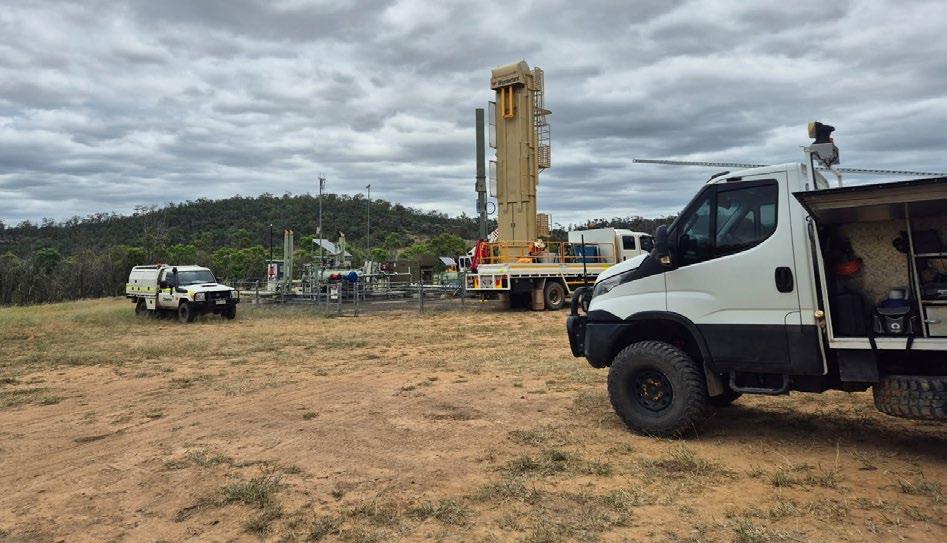
we all know each other as mates and I enjoy working with them”, Damian said. Time on the sites is comfortable for the workers as well, with a gym, prepared food and an overall positive culture.
FIFO versus working near home
There are some key differences between working near home and taking a chance at FIFO. The work style is completely different out in remote places, it’s hot, you move around a lot, and you’re working in sites that simply don’t exist in metro areas. Damian mentioned the air is noticeably cleaner, it’s much quieter, and there’s much less traffic. Since it’s so far away from home however, Damian pointed out its harder to manage as he gets older and develops more relationships and commitments. “It’s better to do it as a young bloke, get some good experience and earn some money. I do enjoy it, but it’s not a forever thing,” Damian said. Mental health can take a big hit when you’re spending time away from people you care about too. To manage this, Damian said he “locks into the gym, eats really healthy and stays focused”, before letting loose and relaxing during his 10 days back home.
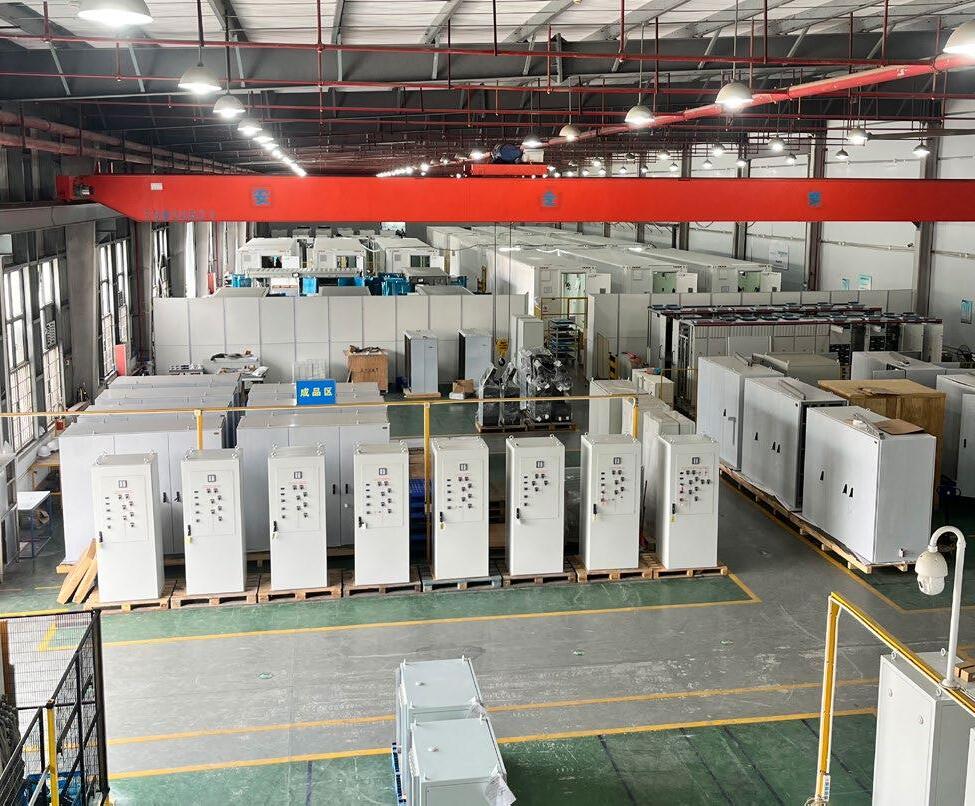
Harry Lay
harry Lay is a current NECA apprentice, who just started his fourth year of training. During his apprenticeship in Sydney, harry had a chance to work out in rural Australia doing a complete refurbish of the patient and reception area in a hospital. While this was good experience for him, the biggest travel opportunity of his apprenticeship would come on the 20th of November 2024, when he was told he would be traveling to China for five days of work.
The experience
The overseas opportunity was nothing like harry had done before, so he was very quick to pack his bags and get ready. As he was to be working in a production factory, he did his induction online so that he could go straight on site upon arrival. “The accommodation was awesome,
I was staying with four other Aussies and a New Zealander and we all had our own rooms,” harry said. “We were well looked after, the hotel had restaurants, a pool and a continental breakfast every morning.” Since he was there for less than 15 days, he didn’t have to get a visa which made the quick turnaround possible.
On the job site, harry was working 10 hour days with local tradesman, only one of which spoke English. To communicate with the rest of the team harry relied upon Google translate, “which wasn’t perfect but we made do.” In the spare time he had after work, harry and some of the other Aussies, went to a bar and met some English speakers, who they got to know for their time there. From an apprentice perspective, harry said “Everything was good to learn, it was good to see how everyone communicated, I enjoyed it quite well.”
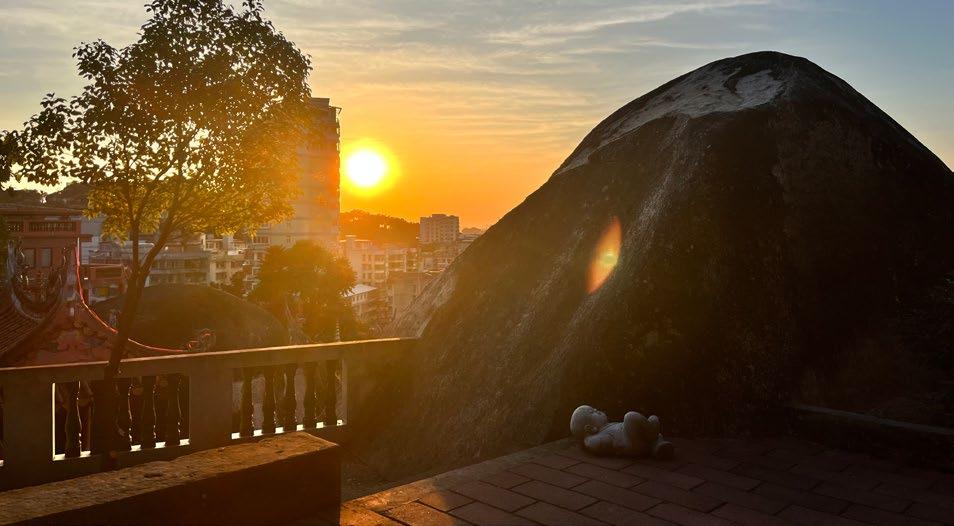
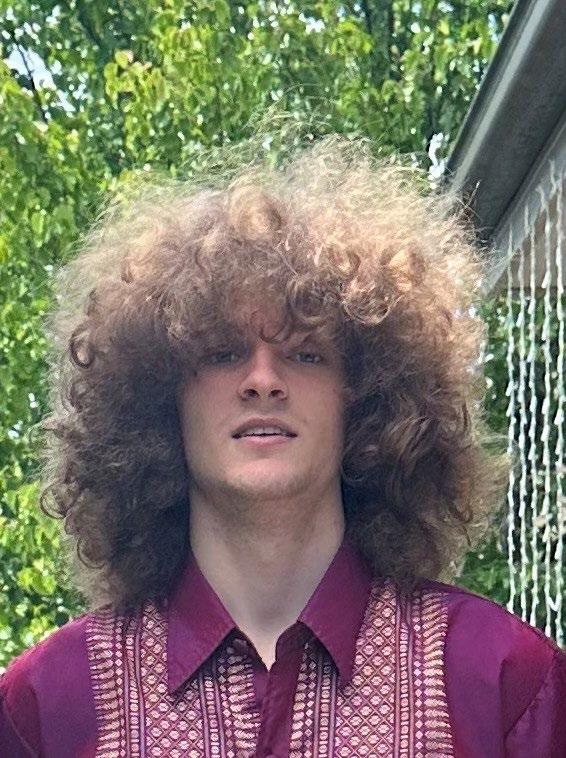
Apprentices Away from Home
Both Damian and harry are lucky enough to have had the opportunity to move out of their comfort zone to learn and work somewhere outside of the city. While both of their experiences are wildly different, their stories are proof that there’s a whole big world out there for electrical apprentices and tradespeople to experience. Both Damian and harry will tell you, if you’re given the chance, it’s a chance worth taking.

OVERCOMING ELECTRICAL ENCLOSURE CHALLENGES WITH DIGITAL THERMAL MANAGEMENT SOLUTIONS
The challenge of carrying out major projects in a digital context, and at a distance, increasingly requires more reliable software tools. Thermal management software, and connected cooling units, along with initial project data verification, help switchboard manufacturers and contractors save time on calculations and deliver more reliable data, enhancing client engagement, even for remote projects.
Thermal management of industrial automation and control panel projects presupposes the integration of many variables. Some common problems and issues are listed below.
½ Initial data should consider the location of the electrical installation – indoor or outdoor – as the calculations for the two will be completely different, due to changes in environment.
½ Different outdoor environments and their associated characteristics are decisive in deciding the best thermal solution to apply, and whether or not the enclosure planning can accept outdoor air for cooling.
½ Different environments will affect the reliability and stability of the operational equipment, as well as influence processes or services. These variables can have a huge impact on cost if not considered precisely in the design phase.
Common Thermal Management Pitfalls
The following thermal-related mistakes are ones we see often, but they are easily avoided with the right tools and careful preparation.
Incorrect initial data
It is particularly important to have good starting specifications wherever possible, with measurements of previous environments, for both temperature and humidity.
Oversizing or undersizing
Either can become errors in the medium term, under extreme conditions, or when scaling up an electrical installation.
Errors of mechanical incompatibility
A mismatch between thermal solution and electrical cabinet cannot occur, especially with very tight delivery times requested of the contractor or
switchboard manufacturer. Likewise, an Original Equipment Manufacturer (OEM) cannot accept errors in the integration, installation, and assembly processes, even when moving machines to the other side of the planet, working with shortened start-up times, and using displaced teams dedicated to this mission.
Selecting the wrong thermal architectures
This mistake can mean extra Capex costs, due to premature wear of the electrical equipment – for example, using ventilation for cooling in the harsh external environments found in water treatment plants, or chemical industries. The wrong architecture – arising from a lack of a good thermal calculation – can even result in high maintenance costs due to unnecessary overheating.
Exceeding internal limit temperatures or being outside the optimal temperature operating range
These mistakes can lead to condensation, and other phenomena, causing extremely high costs for the end user.
Lacking spare parts in critical installations
having a sufficient inventory of spare parts ensures proper preventive maintenance of an enclosure.
Calculating a Thermal Management Solution
The right thermal management software can help avoid these problems. however, in calculations and scenario evaluations, it is vital to have software that can determine when it is possible to ventilate and when it is necessary to go to thermal solutions, with more cooling power and a higher energy cost, such as air conditioners. Any thermal software should also help maximize energy efficiency, improve reliability, and produce documentation for all project stakeholders.
For example, ProClima Web is a thermal software tool that uses two advanced algorithms to contemplate all the variables necessary to carry out automation and control panel calculations, in less than five minutes on average. It incorporates more than 20 years of experience in indoor, outdoor, and harsh environments for passive variables, including cabinet material, surface, installation position,
relative humidity, and more. ProClima also handles active elements, like dissipation values of internal equipment, dissipation through cabinet walls according to IEC 60890 and 61.439 (heat exchange walls calculations part), and so on. The tool enables a wide-open and complete view of all the thermal solution options, using calculations carried out according to the data provided by the user. ProClima explores solutions through an examination of different scenarios.
Using ProClima to create a solution not only avoids the pitfalls we outlined above, it also ensures the following benefits.
Energy efficiency
The software considers the heat dissipation or absorption values of the cabinet, which can be a thermal solution itself.
The surface value of the cabinet, the material (polyester, metal, or stainless steel), and its installation position can contribute to, or extract, calories in an important way, possibly as much as kilowatts.
Also, when comparing different solutions, ProClima will always propose a controller (e.g., thermostat, hygrostat, or hygrotherm) associated with the thermal solution, that will reduce the energy consumption of the thermal equipment at least 50% of the time.
Reliability in the data
The software has different internal databases to facilitate the validation information on the mechanical compatibility, power losses of the variable speed drives, PLC, and other installed main equipment. It also allows the integration of new heat sources not originally considered and a database of outdoor variables, including solar radiation, to be integrated into the algorithms, and so avoid errors in the specifications.
A complete final project
The Program ends with the project document ready to be disseminated for the sales phase, or to enrich the project. The documentation includes all the necessary technical information for future users, such as switchboard manufacturers, OEMs, contractors, facility managers, distributors, or end users.
se.com/au/climasys-cu
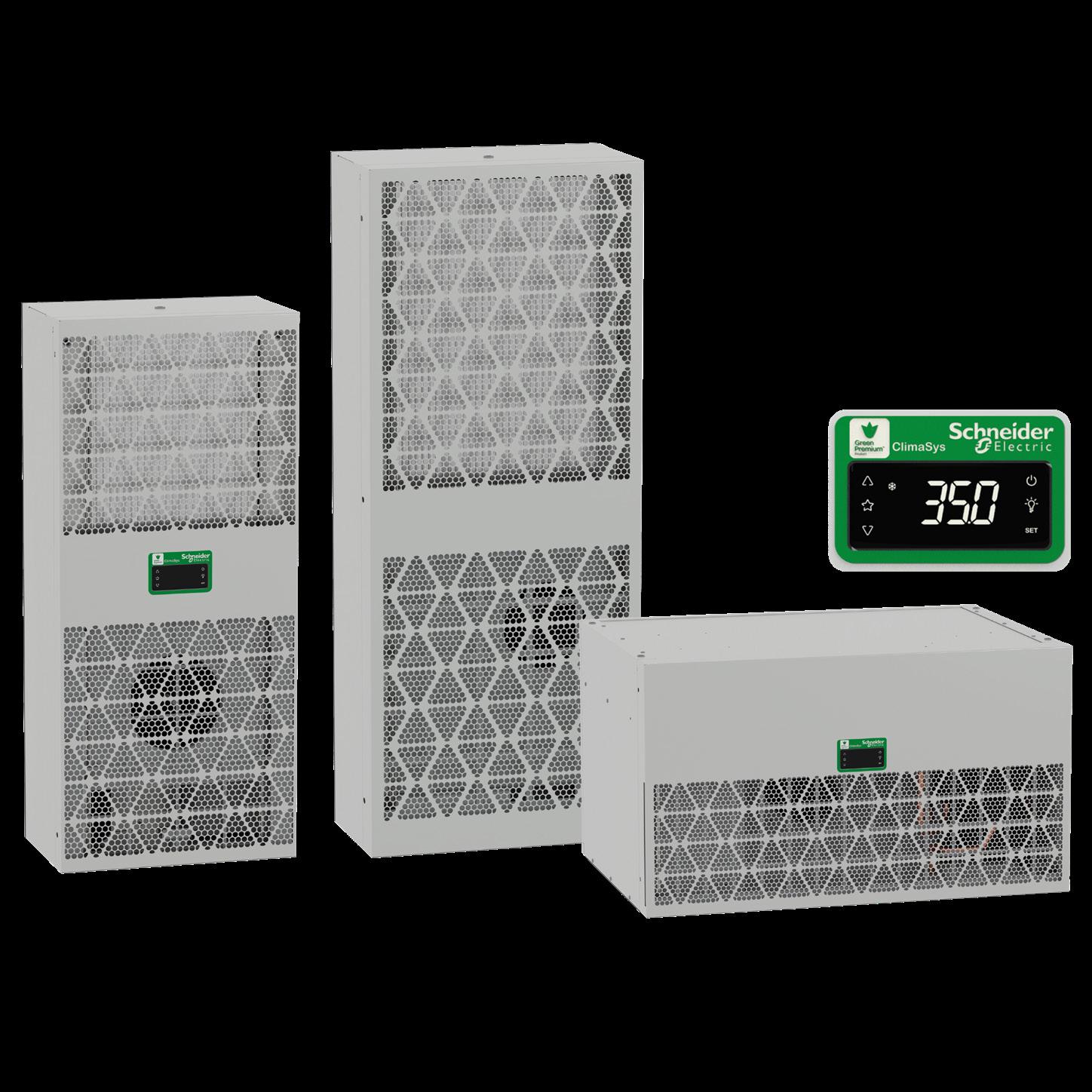
Scan the QR code to learn more
WA BRANCH

BRANCH UPDATE
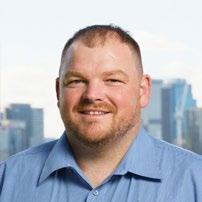
Adam Hoes NECA WA Member Manager
WELCOME TO T hE MA rCh ISSUE OF NECA NEWS, AND WELCOME TO ALL OF OUr NEW NECA WA MEMBE r S.
IT’S BEEN A GrEAT STA r T TO T hE YEA r , AND WE’rE
EXCITED FOr W h AT’S IN STOrE FOr 2025.
This year has already seen a new chapter for NECA WA, with the opening of our WA branch of NECA Training and Apprenticeships. This is just the beginning of what we have planned, but we’d like to officially welcome our newest cohort of apprentices, and encourage you all to take a minute to read about some important industry changes on the following pages.
Changes to State Employment Legislation in WA
On 31 January 2025, there were several changes made to the WA Industrial r elations Act 1979 (I r Act) and the Minimum Conditions of Employment Act 1993 (MCE Act).
The changes will only impact the employees of ‘non-constitutional corporations’ (i.e. partnerships, sole traders, unincorporated associations
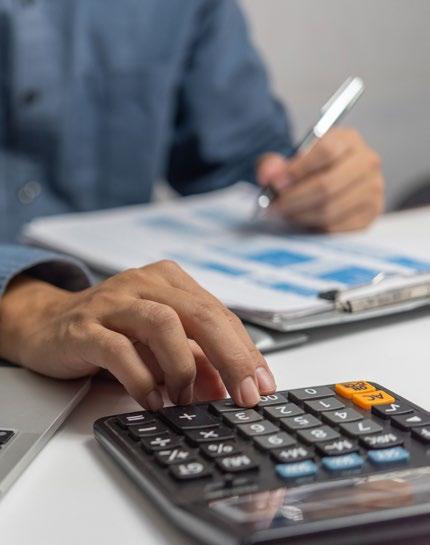
and some trusts), and not employers covered under the Fair Work Act 2009 (Cth) (FW Act). We encourage members to review these changes in our recent eNews, as they could be relevant to your business. If you are covered by the state law, you need to understand these changes and if necessary, implement them into your business. Ensure you update payroll and contracts as necessary, including changing the casual loading to the higher 25%. As many NECA WA members prepare to employ more workers in the year ahead, the NECA Member’s Knowledge Base (MKB) is an invaluable resource to streamline the process. NECA’s MKB offers free contract templates designed to assist with your business’ growth, and ensure compliance with employment standards.
r ecently updated by NECA Legal, these templates cover a wide range of employee agreements, including the Awards listed below.
½ Full Time or Part Time (Electrical Award)
½ Apprentice (Electrical Award)
½ Casual (Clerks Award)
½ Casual (Electrical Award)
½ Fixed Term (Clerks Award)
½ Fixed Term (Electrical Award)
½ Fixed Term (Enterprise Agreement)
½ Full Time or Part Time (Clerks Award)
These templates are accessible through the MKB and are available for download.
For assistance, please contact NECA Legal on 1300 361 099.

Vale Mike Nichol
It is with great sadness that we honour the passing of Mike Nichol, a valued member of the NECA WA community, and a key figure in the Western Australian electrical industry. Mike, who passed away on January 20, 2025, made significant contributions to both the Nilsen Group and NECA, and will be deeply missed by all who knew him.
As Adam Fielding, General Manager from Nilsen WA reflects, “Mike was always connected to the business, checking in to hear about our progress and achievements. h e and his wife Margaret recently attended the opening of our Training Centre, and we were truly honoured to maintain that connection. We will miss him dearly.”
Mike’s passing is a significant loss to Nilsen WA, NECA WA and the wider electrical community. Our thoughts are with his family, friends, and colleagues at Nilsen. his legacy will continue to inspire future generations in the industry.
It is with great sadness that we announce the passing of Bruce Cook, a former NECA Life Member and 1976 Association President. Bruce, who passed away on 6 February 2025, was a revered figure, both in Williams Electrical Service and the wider electrical industry, and was also a significant contributor to the NECA community.
As Williams Electrical Service reflects on his life, they fondly remember Bruce’s leadership and vision. “Bruce was the cornerstone of Williams Electrical Service during a pivotal time in our growth, and a valued mentor to many,” says Peter Beveridge, from Williams Services Group. “ his strategic thinking and commitment to excellence laid the foundation for the company’s success, including the crucial decision to relocate the business to its current premises in Balcatta. This move set the stage for our operational and service success, and we are forever grateful for his contributions.”
Bruce’s career began with Williams Electrical Service as an apprentice in the late 1950s, later becoming Managing Director in 1975. Under his guidance, the company flourished, growing into the powerhouse it is today. Bruce led

the company through a transformative period, culminating in the company’s relocation to Balcatta, a move that positioned them firmly in the heart of Western Australia’s industrial sector.
After two decades of remarkable leadership, Bruce stepped down as Managing Director in 1995, but continued his legacy as Chairman until 2000. his influence was not just confined to Williams Electrical Service but extended throughout the industry, where he was known for his integrity, professionalism, and dedication.
Bruce’s impact on the electrical industry was also felt through his involvement with NECA, where he served as President in 1976. h is leadership played a pivotal role in shaping the direction of the industry, and his contributions are still felt by those who had the privilege of working with him.
As Williams Electrical Service, NECA WA, and the wider electrical community reflect on Bruce’s legacy, we join to mourn his passing. his vision and leadership will continue to inspire future generations in the industry.
Vale Bruce Cook
CURRENT MEASURED ON THE MAIN NEUTRAL
A NUMBE r OF MEMBE r S h AVE ASKED FOr ADVICE AFTE r T hEY h AVE BEEN ENGAGED BY A
CLIENT TO rECTIFY A FAULT. T hEIr CLIENT h AS rECEIVED A DEFECT NOTICE F rOM T hE rELEVANT
NETWOrK OPE r ATOr , DUE TO CUrrENT BEING MEASUrED ON T hE SUPPLY NEUT r AL.
As part of the ‘service connection test,’ due to changing out the tariff meter, it was discovered that current had been measured on the neutral at the meter, when the SPD/s were removed. This is a common fault and is normally caused by a high resistance neutral. It needs to be addressed ASAP, as it can cause tingles/ shocks at taps. It is more than likely to be caused by a high resistance neutral at another property, and not at the one with the defect notice.
If the property on the right has a high resistance neutral, then power will more than likely go through the earthing system and pick up the neutral of the property on the left, as a return path.
What normally happens when a high resistance neutral occurs
at a property? Power will find an alternative route back to the transformer. Due to the MEN, it will find a path through water pipes to a nearby property and pick up the neutral there. This can be dangerous. If the property with the fault is a fair way from the transformer, then this scenario will normally occur.
In order to rule out other possibilities (eg fault to earth), the current property needs to be tested in accordance with Section 8 of AS 3017.
Carrying out an earth fault loop impedance test at a socket outlet will not give a true reading of the integrity of the line neutral, due to the MEN.
In order to test the line neutral, a line impedance test needs to be carried out.
The testing of this has to be done live and, as such, has to be risk accessed and should only be carried out by persons trained, competent and experienced in this type of work.
A Loop Impedance/Prospective Short Circuit Current tester (Fluke Multifunction Tester) is particularly useful when investigating this type of fault. This test is to check for high impedance/resistance connections within the main supply back to the transformer star point. It is not the Earth Fault Loop Impedance test described in Section 8 of AS/NZ 3000/3017. This test is best described as a ‘Line Impedance’ test, to separate it from a conventional EFL Impedance Test. The purpose of this test is to prove the integrity of the mains active conductor(s) and

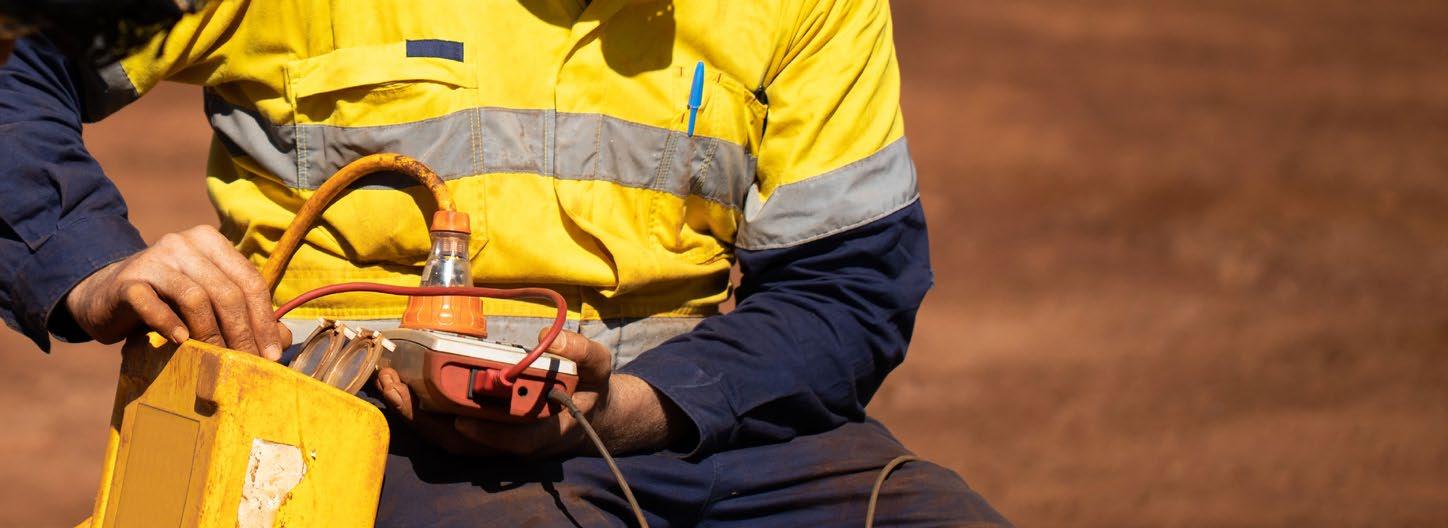
also – more importantly – the neutral conductor of the main supply ‘Loop’.
A Loop Impedance/ Prospective Short Circuit Current Test can be likened to connecting an ohmmeter to a live circuit, but without the explosion. It connects a known resistance to the circuit under test for a few milliseconds. The circuit impedance is calculated from the volt drop during the test and displayed on the screen. The same method, with a different calculation, will be displayed on the bottom rhS of the screen; the Prospective Short Circuit Current, or the calculated fault current.
This is high risk work; carry out a risk assessment (JhA/SWMS) and ensure all appropriate controls have been put in place before commencing the test. Care should also be taken with the neutral being disconnected from the link or bar. If there is another property using this neutral, then it may be live. Always use voltage rated gloves when handling the neutral. The following list outlines the testing steps, once all risk assessments and controls are in place:
½ turn off the main switch to the property in the MSB (this is imperative as the line neutral is going to be disconnected);
½ the test is applied to the main line active/s and main neutral after taking the MEN connection out of circuit of the installation under test. This is usually achieved by disconnecting the main incomingneutral at the neutral link/bar;
½ set the Multifunction Tester to Z hi Current (if using another brand of tester, consult the manufacturer’s instructions to carry out a similar test);
½ clip the neutral lead to the incoming disconnected supply neutral;
½ set the meter to active-neutral;
½ place the active probe on each phase, one at a time, and test. Each phase should be relatively equal. If not, further investigation is required.
Past recordings indicate that the Loop Impedance at the MSB of an installation is generally in the range between 0.01-ohm Z to 0.8-ohm Z. Factors such as the proximity of
the distribution transformer and the size of the conductors must be considered. The closer to a transformer a property is, the lower the reading should be. A reading greater than this indicates a high resistance neutral somewhere, which will require further investigation.
Once all the testing has been carried out at the property with the defect notice, and it is proven that the fault is not there, the defect notice should be returned with the test results to the relevant Network Operator. They will have to carry out further investigation and find the property with the fault.
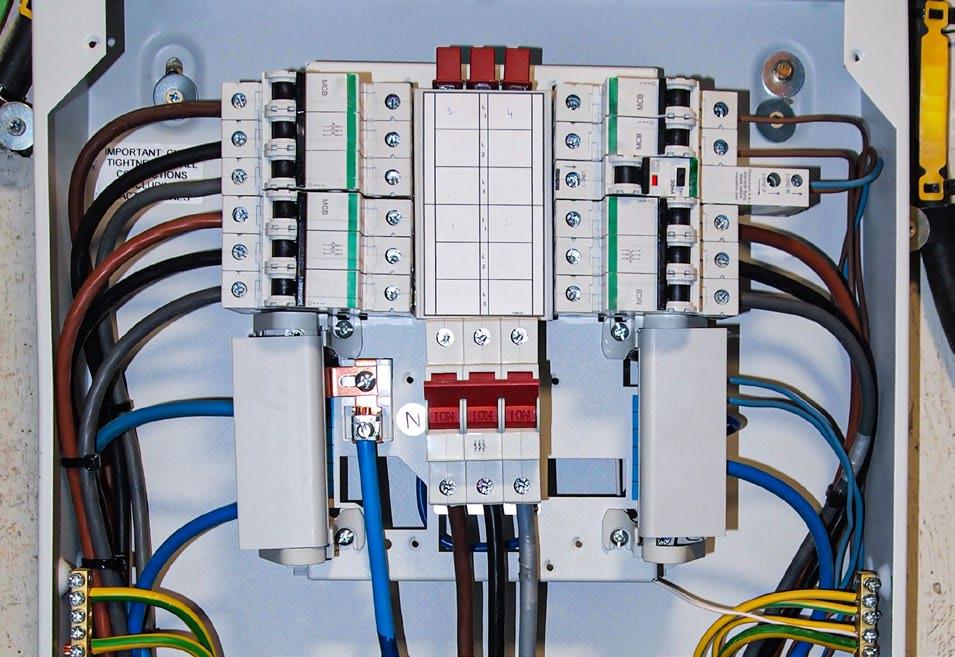
NECA WA WELCOMES NEW APPRENTICES AND OPENS
NEW FACILITY
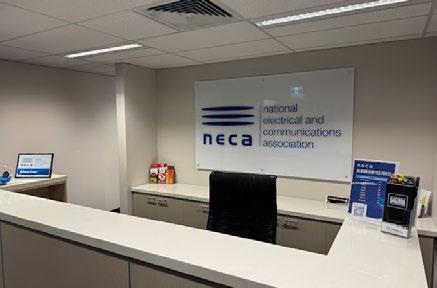
2025 h AS AL rEADY SEEN NECA TAKE FUr T hEr LEAPS FOr WA rD IN WESTErN AUST r ALIA.
T hIS YEA r , WE h AVE OFFICIALLY OPENED NECA ELECT rICAL APP rENTICEShIPS WA, AND h AVE AL rEADY BEGUN WOrK WIT h OUr FIr ST COhOr T OF NEW APP rENTICES. T hE NEXT
GENE r ATION OF WA’S ELECT rICAL T r ADESPEOPLE A rE NOW LEA rNING AND WOrKING AS PA r T
OF NECA’S GTO, UNDE r T hE SUPE r VISION OF OUr NEW OPE r ATIONS MANAGE r TYSON rUDD.
Tyson brings a wealth of knowledge to his position at NECA. With over 20 years’ experience working in the electrical infrastructure and road service sectors, Tyson has worked for major organisations, including Main roads WA and Downer EDI. Tyson is also familiar with the GTO and apprenticeship industry, with previous experience with another electrical GTO, and other training organisations that provide employment and training opportunities for apprentices in WA.
Tyson’s role is to be the key contact for apprentices and hosts for NECA’s WA-based GTO. As NECA begins to open more places for high-potential apprentices, Tyson will manage the principal tasks of recruitment, placement, and ensuring apprentice education standards and WhS commitments are all met, across the state. When asked about his goals as Operations Manager, Tyson said “I am committed to addressing the growing need for skilled electricians here in Western Australia, while promoting a strong and safe team environment.”

NECA WA’s Office and Team
NECA is now located at:
Level 1, Suite 5/375 Charles Street North Perth WA 6006
This new office provides access to all services offered by NECA WA, and is supported by our national teams, to assist members, apprentices and hosts with their enquiries.
Working out of this new space, our local team includes:
Adam
Member Manager
Greg
Technical Advisor (Former WA Inspector)
Kirstie
Safety Advisor
Scott
Government Advocacy
Tyson
NECA Training and Apprenticeship Operations Manager
Joyleen
Member Services
The team is excited to continue providing industry-leading support to WA’s electrical sector from their new office, offering local expertise in a brand-new facility.
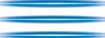
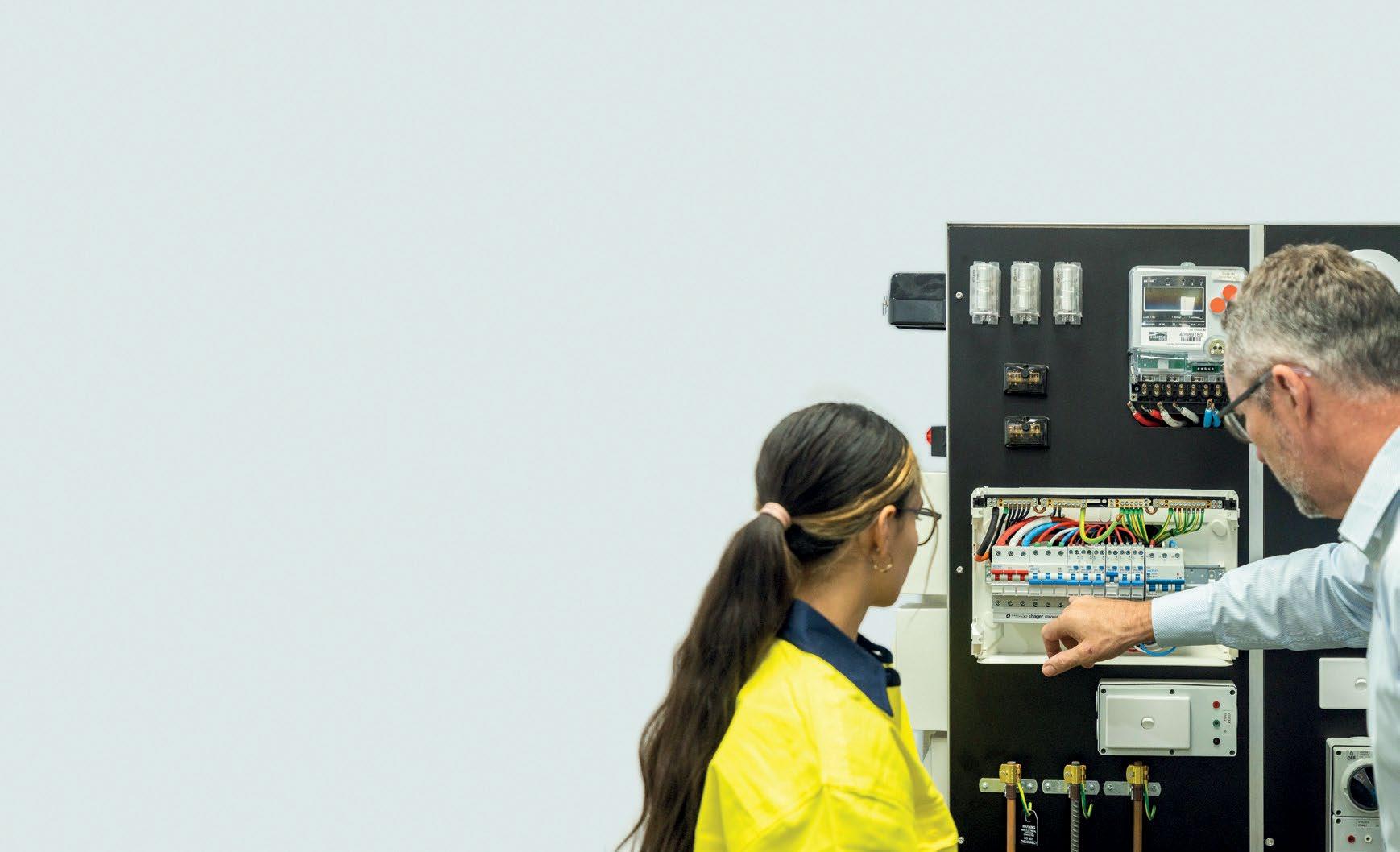
Become a host trainer and take on a NECA Apprentice
Why not take the effort out of employing your own apprentice and employ an apprentice from NECA.
NECA Electrical Apprenticeships employ qualified apprentices and place them with host companies, for any amount of time from 3 months to 4 years, providing you with a flexible workforce.
By becoming a Host company you only pay a fixed charge out rate, whilst NECA takes on all the added costs and responsibilities.
Build your future, have time to grow your company and let us take on the risk. Contact us today or register your interest at necatraining.com.au
NECA Electrical Apprenticeships provide
● Advertising
● Recruitment
● Interviews, Selection and Medicals
● Record Keeping and Payroll
● Ongoing Monitoring and Mentoring
● Training
NECA’s fixed charge out rates include
Annual Leave Days
Sick Days
Public Holidays
Training Fees
Superannuation
Workers Compensation
Off The Job Training Days ● Uniforms and PPE

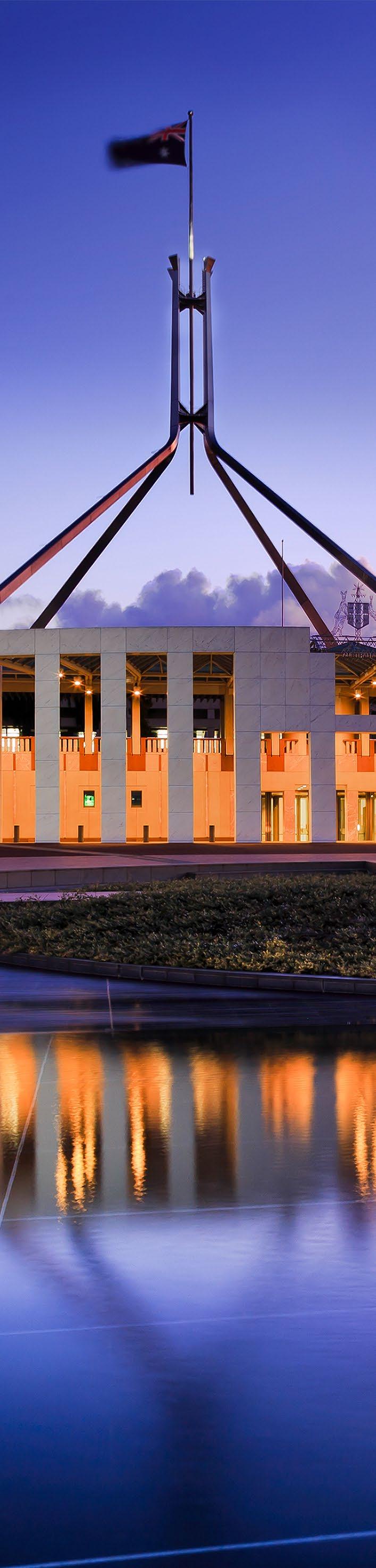
BRANCH UPDATE
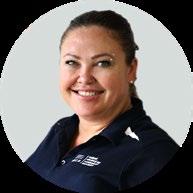
WE’rE
Nataisha Martin NECA ACT & Southern NSW Member Manager
BACK FOr 2025 AND rEADY TO BUILD UPON T hE GrEAT YEA r WE h AD IN 2024, CrEATING MOrE OPPOr TUNITIES AND ADDING MOrE VALUE FOr MEMBE r S IN EVE rY A rEA WE CAN.
I’d like to welcome all our new members and new apprentices this year; we look forward to working with you and growing together. If you have questions, concerns, or would like to arrange a member health check to see how your business is performing, please reach out.
NECA Drives Reform at the NCIF
practices, encourage ethical leadership, and enhance workplace respect, recognising that cultural change is not only essential for the wellbeing of workers but also for the long-term sustainability and success of the sector.
ACT BRANCH
This week, NECA continued its strong advocacy for critical reforms at the National Construction Industry Forum (NCIF), a ministerial forum established to provide strategic advice to the Australian Government on challenges and opportunities within the construction industry. Comprising representatives from subcontractors, employer groups, unions, and government, the NCIF plays a crucial role in addressing systemic issues and shaping policies to create a fairer, more sustainable, and resilient construction sector. NECA, as a key subcontractor and employer representative, has taken a leading role in driving these important discussions.
A key focus of the Blueprint for the Future of the Building and Construction Industry is the need to shift the culture of the construction sector to prioritise collaboration, fairness, and respect across all levels. NECA has been a vocal advocate for creating a workplace culture that values the contributions of all participants, from subcontractors to head contractors, and fosters greater transparency and accountability. By addressing entrenched behaviours, such as late payments, unfair contractual practices, and adversarial relationships, the industry can create a more inclusive and cooperative environment. NECA supports initiatives within the blueprint that promote best
NECA’s advocacy at the forum is focused on securing legislative reforms to remove unfair contract terms and improve procurement practices across the industry. These changes are aimed at establishing fairer contracts and ensuring subcontractors are not unfairly burdened with risk. NECA has been continually pushing for strengthened security of payment legislation, ensuring contractors and subcontractors are paid for the work they perform, even in cases where head contractors or builders enter administration or liquidation. NECA’s contributions are integral to shaping the Blueprint for the Future of the Building and Construction Industry, which seeks to deliver meaningful reform for all industry participants.
Members are encouraged to provide their insights and recommendations to the Government relations team on areas where the construction sector can be improved, and we welcome that engagement.
The NCIF provides an essential platform for collaboration between government and industry stakeholders to foster equity, transparency, and accountability. NECA’s active participation reflects its commitment to achieving practical and impactful outcomes for its members and the wider construction industry. By advocating for reforms to protect subcontractors’ financial security and enhance fairness in contractual arrangements, NECA continues to play a leading role in building a stronger and more sustainable construction industry, for the benefit of all Australians.
Managing Liability on Work Done by Others
To effectively manage the risk of liability related to work performed by others, it is essential to maintain a clear and well-documented trail. Specifically, as the electrician responsible for testing and energising, you may be held liable for certain aspects of the installation, even if the work was performed by others. It is your responsibility to ensure the installation is safe prior to energisation.
To mitigate this risk as far as reasonably practicable, it is important to ensure that
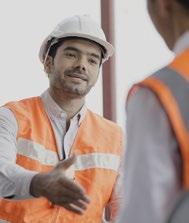
your Certificate of Electrical Safety (COES) includes a detailed description of your work, as well as any work carried out by others. Given that the descriptor section of a COES may have limited space, we recommend supplementing this with a Form 1 (AS3019) where you have observed or identified noncompliance or issues with the work done by others. This form can be attached to the COES as part of the documentation.
Additionally, should you identify any serious or immediate risks, as a Person
Conducting a Business or Undertaking (PCBU), you have a duty of care under Section 19 of the Work health and Safety Act 2011 (ACT) and Clause 149 of the Work health and Safety regulations 2011 (ACT). This requires you to take all reasonable steps to de-energise the system and make it safe until repairs can be made and the installation can be safely re-energised.
For any inquiries, please contact a NECA Technical specialist on 1300 361 099.
CHANGES TO CASUAL CONVERSION PATHWAY FROM 26TH FEB 2025
T hE r E A r E UPCOMING C h ANGES TO
here’s a summary of what changed on 26 February 2025 and how it might impact your business:
New Pathway for Casual Conversion
From 26 February, eligible casual employees working for large organisations (employing 15 or more employees) will only be able to access the new pathway for casual conversion called the Employee Choice Pathway. This will allow casual employees to request conversion to permanent employment (full-time or part-time) under certain circumstances.
Existing obligations in relation to small businesses (employing fewer than 15 employees) will continue until 26 August 2025, at which time they too will only be able to convert to permanent employment via the Employee Choice Pathway.
How does the Employee Choice Pathway work?
Employee notification
A casual employee who chooses to can give their employer a written notification of their choice to become a permanent employee, with the conditions that:
½ they have worked for the employer for at least six months (twelve months for a small business employer); and
½ they believe they no longer meet the definition of a casual employee.
Under the Fair Work Act 2009 (CTh), an employee is a casual employee if:
½ the employment relationship is characterised by an absence of a firm advance commitment to continuing and indefinite work; and
½ the employee would be entitled to a casual loading or a specific rate of pay for casual employees under the terms of a fair work instrument, if the employee were a casual employee, or the employee is entitled to such a loading or rate of pay under the contract of employment.
Further, a casual employee can’t give their employer a written notification if they are currently in dispute with their employer about changing to permanent employment, or if in the previous six months certain events have occurred under the casual conversion or employee choice pathways.
Employer response
The employer must respond within 21 days after the employee gives them the notification. If the employer accepts
the notification, the casual employee will become a permanent employee.
The employer may refuse the notification on the following grounds:
½ where the employee still meets the definition of a casual employee;
½ where there are fair and reasonable operational grounds to do so (such as it is known that the casual employee will not be required for whatever reason in the near future); or
½ accepting the notification would result in the employer not complying with a recruitment or selection process required by law.
What to do
½ review your casual employees and identify in advance whether they may be eligible to convert to permanent employment under the new pathway;
½ otherwise, wait until the employee comes to you with notification that they choose to become a permanent employee;
½ be prepared to handle conversion requests and ensure that refusals are based on valid grounds, within the specified timelines.
NSW BRANCH
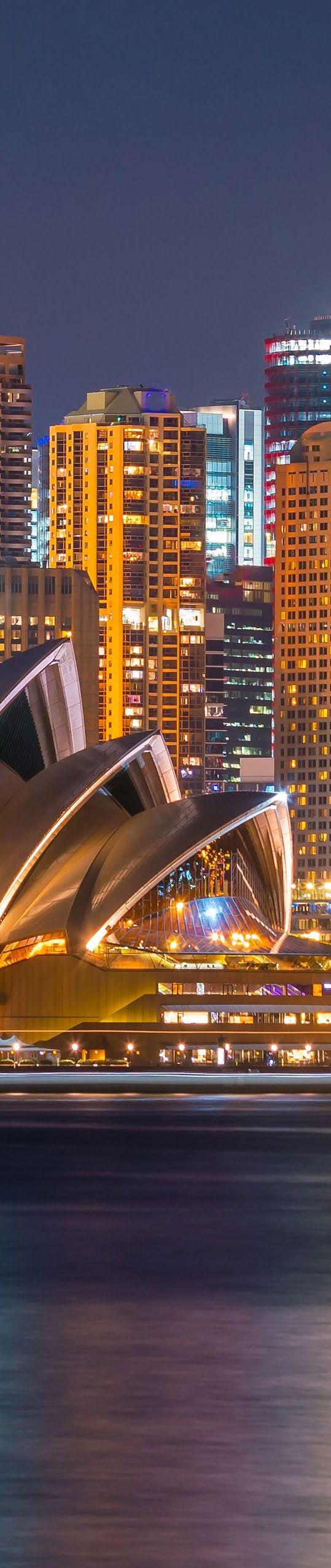
BRANCH UPDATE
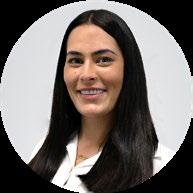
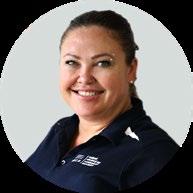
Julia Cassar NECA Sydney Metro and Northern NSW Member Manager
Nataisha Martin NECA ACT and Southern NSW Member Manager
WELCOME TO T hE MA rCh 2025 EDITION OF NECA NEWS. AS T hE FIr ST FEW MONT hS OF T hIS EXCITING
NEW YEA r rOLL PAST, T hErE A rE AL rEADY SOME IMPOr TANT UPDATES T h AT WE’D LIKE TO S h A rE.
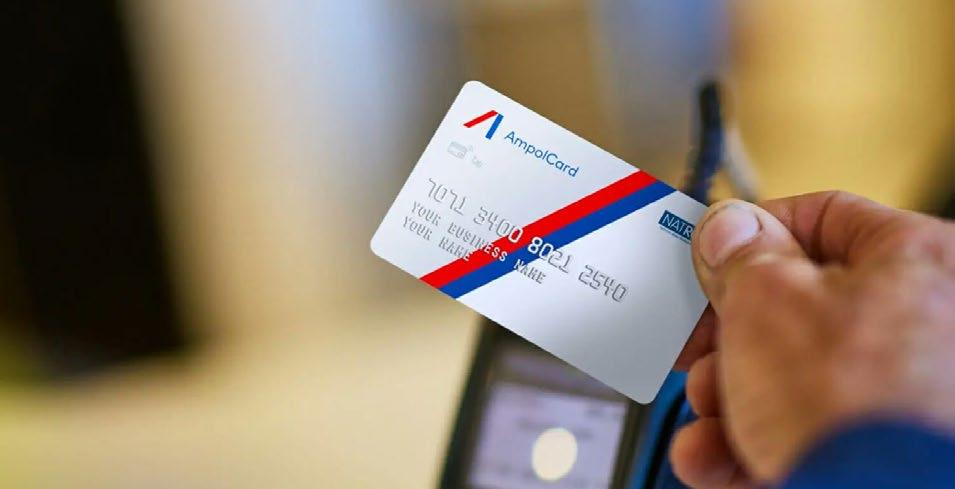
You’ll see in the content below that since our last edition there have already been several regulation changes that may affect your business, and a couple of unfortunate incidents resulting in fatalities which we’d like to bring to your attention.
With all that’s happening, now is a great time to schedule a member health check, assess your current safety system with NECASafe, or make use of your Annual NECASafe Compliance review, an exclusive benefit of your NECA membership. Learn more in the content below or contact NECA on 1300 361 099.
NECA Member Health Checks
NECA is committed to supporting members and their businesses, every step of the way.
As part of NECA membership, NECA members receive an annual Member health Check, to discuss your
business needs and ensure you are maximising the benefits that your NECA membership offers. These include Ampol fuel cards, JMS integrations, annual safety reviews and confidential wage reviews, among others.
NECA Member health Checks help you gain a deeper understanding of how NECA operates, the support we offer and how to access the benefits available to you and your staff. We’re here to help – so let us help! To request a member health check, please contact NECA on 1300 361 099.
December 2024
Electrical Incidents
NECA has been made aware of two fatal electrical incidents occurring in December 2024.
The first involved a worker performing vegetation clearing work near overhead power lines at Malabar, NSW. The worker later died from his injuries.
The second received widespread media attention, as it occurred in a residential roof-space on Christmas Eve. The licenced worker appears to have been working on air conditioning equipment at a premises in Eagle Vale. Both incidents are under investigation by the relevant authorities.
roof spaces and under-floor areas are particularly hazardous areas for electrical workers, with several deaths recorded in NSW in recent years.
SafeWork NSW Speak Up app
SafeWork NSW is cracking down on unsafe work practices, and solar installers are no exception. The Speak Up app, developed by SafeWork NSW, is empowering workers and the public to report unsafe conditions in real-time, leading to swift action against violations.
Solar installers must prioritise compliance with safety regulations. Unsafe practices not only put workers’ lives at risk, but also lead to costly penalties and project delays. The success of the Speak Up app highlights the growing accountability in the industry. Don’t let your site be the next one flagged – invest in proper training, equipment, and safety protocols to protect your team and your business.
To ensure your work is compliant, speak to a NECA safety specialist on 1300 361 099.
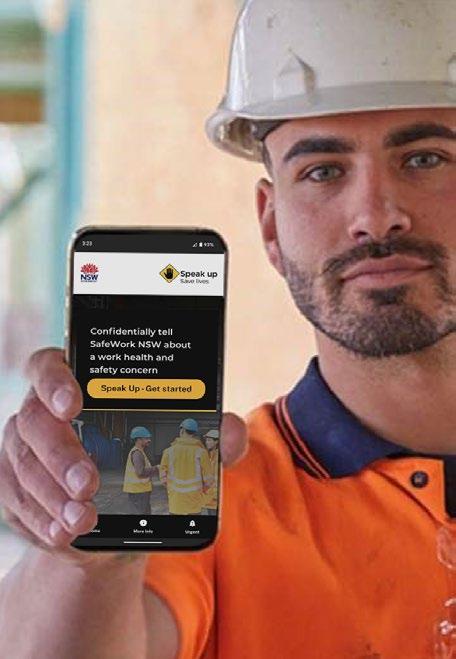
Reset Your Safety in 2025 with NECASafe
We all acknowledge that the safety of our team is paramount, and with the world of electrical contracting becoming increasingly complex, it’s essential your health, Safety, Environment and Quality (hSEQ) systems are robust and user-friendly. NECA understands your needs and brings you the cutting-edge NECASafe suite of systems: NECASafe Light, NECASafe Digital, NECASafe Generator, and NECASafe Empower.
NECASafe Light
NECASafe Light is an excellent starting point for electrotechnology businesses that are just starting their safety management. Designed to be easily editable and quickly deployable on job sites, this system provides the essential tools for basic, electrical industry-specific safety management.
NECASafe Digital
In the spirit of digitisation, upgrade your safety practices with NECASafe Digital. This low-cost system helps electrical business workers to carry out the traditionally paper-based WhS tasks effortlessly on a phone or tablet. This safety app, designed by electrical contractors for electrical contractors, streamlines your operations, and enables you to quickly log hazards, prepare incident reports, complete risk assessments, compile checklists, document toolbox talks, take actions, and quickly access documentation.
NECASafe Generator
Taking convenience to a new level, the NECASafe Generator eliminates the repetitive and time-consuming paperwork from your day. This powerful safety management system allows you to generate site-specific forms and Safe Work Method Statements (SWMS), complete with site address, company logo, and principal contractor details, easily and swiftly.
NECASafe Empower
For businesses looking for comprehensive workplace safety solutions, NECASafe Empower is the ultimate tool. This premium system equips your business with comprehensive hSEQ and hr management tools, supporting JAZ/ANZ certification, ASP accreditation, and compliance management, for complete workplace safety protection and peace.
Undecided which system fits your business best? At NECA, we are committed to ensuring your safety management systems are efficient, cost-effective, and beneficial for your specific business needs. Get in touch with us to start with a free compliance review by one of our NECASafe Advisors. It’s time to reset your safety in 2025. Contact NECA and let’s ensure that your hSEQ systems are up-to-date, compliant, and keeping your team safe.
CHANGES TO CAUSAL CONVERSION PATHWAY
T hErE h AVE BEEN rECENT
Ch ANGES TO CASUAL
CONVEr SION LAWS T h AT h AVE COME INTO EFFECT F rOM 26 FEBrUA rY 2025 (EXCLUDING SMALL BUSINESSES). T hESE
Ch ANGES A rE PA r T OF T hE CLOSING LOOPhOLES BILL NO. 2.
From 26 February, eligible casual employees working for large organisations (employing 15 or more employees) will only be able to access the new pathway for casual conversion called the Employee Choice Pathway. This will allow casual employees to request conversion to permanent employment (full-time or part-time) under certain circumstances.
Existing obligations in relation to small businesses (employing fewer than 15 employees) will continue until 26 August 2025, at which time they too will only be able to convert to permanent employment via the Employee Choice Pathway.
How does the Employee Choice Pathway work?
Employee notification
A casual employee who chooses to, can give their employer a written notification of their choice to become a permanent employee with the conditions that:
½ they have worked for the employer for at least six months (twelve months for a small business employer); and
½ they believe they no longer meet the definition of a casual employee.
Under the Fair Work Act 2009 (Cth) an employee is a casual employee if:
½ the employment relationship is characterised by an absence of a firm advance commitment to continuing and indefinite work; and
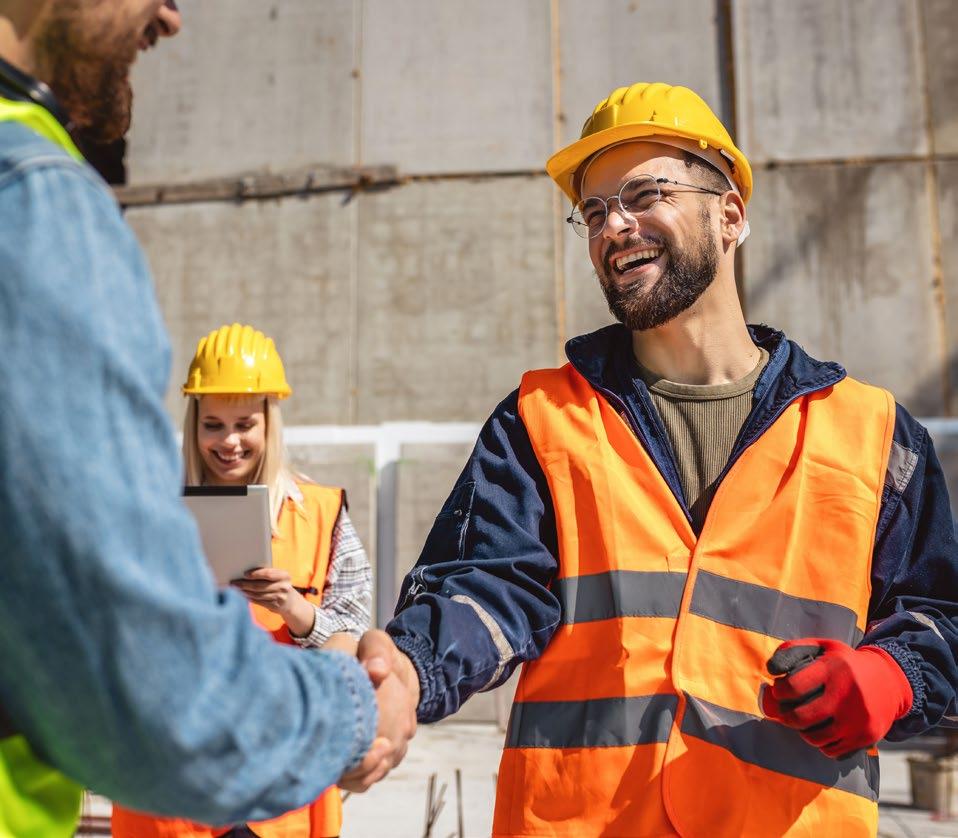
½ the employee would be entitled to a casual loading or a specific rate of pay for casual employees under the terms of a fair work instrument if the employee were a casual employee, or the employee is entitled to such a loading or rate of pay under the contract of employment.
Further, a casual employee can’t give their employer a written notification if they are currently in dispute with their employer about changing to permanent employment, or if in the previous six months certain events have occurred under the casual conversion or employee choice pathways.
Employer response
The employer must respond within 21 days after the employee gives them the notification. If the employer accepts the notification, the casual employee will become a permanent employee.
The employer may refuse the notification on the following grounds:
½ where the employee still meets the definition of a casual employee;
½ where there are fair and reasonable operational grounds to do so (such as it is known that the casual employee will not be required for whatever reason in the near future); or
½ accepting the notification would result in the employer not complying with a recruitment or selection process required by law.
What to do
½ review your casual employees and identify in advance whether they may be eligible to convert to permanent employment under the new pathway;
½ otherwise, wait until the employee comes to you with notification that they choose to become a permanent employee;
½ be prepared to handle conversion requests and ensure that refusals are based on valid grounds, within the specified timelines.
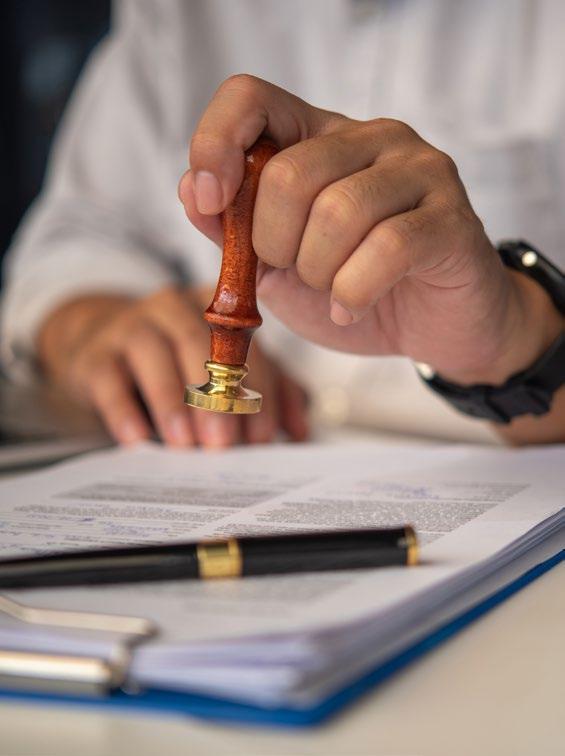
Previously, the position was that only retention payments could be claimed in payment claims “as construction work,” but not the return of a cashed bank guarantee, because, according to the courts, these were considered conceptually different in that the cashed bank guarantee was not “construction work” due to the subcontractor but may instead have been a payment due from the subcontractor to the head contractor under the contract (for example, for alleged defects that the head contractor may be entitled to payment of via a set off clause).
The Court of Appeal has simplified the position, holding that, as long as the amount claimed in a payment claim is “due under a construction contract” it can be claimed, and it is up to the adjudicator whether it is awarded.
This will be of great assistance to NECA members who have provided bank guarantees as security under their subcontracts. Previously, if the head contractor cashed the bank guarantee and the subcontractor considered it was wrongful, it could only resort to contractual relief or litigate at great cost. The grounds for preventing the cashing of a security under a contract are limited, and the process is complicated and expensive. This decision provides an opportunity for claimants to avoid this situation altogether.
IF IT’S CASHED, CLAIM IT BACK GOOD
NEWS FOR SUBCONTRACTORS USING BANK GUARANTEES
UNDE r T hE NSW BUILDING AND CONST rUCTION INDUST rY SECUrITY OF PAYMENT ACT 1999 (ACT).
This will be a very cost-effective way for subcontractors to recover payment for construction work. It may also have a cooling effect on head contractors cashing (or threatening to cash) bank guarantees as a pressure or retaliatory tactic against subcontractors. From a head contractor’s perspective, it still has the benefit of being able to cash the bank guarantee in accordance with the contract, but it just may not be allowed to keep the money for very long if the subcontractor can successfully recover it through adjudication.
While this case is in the NSW Court of Appeal and relates to the NSW security of payment act, we consider that there is scope for claimants to include payments of cashed bank guarantees in their payment claims in other states in Australia if the legislation in that state does not specifically exclude such claims.
Get in touch with our legal team at NECA Legal if you have any questions about performance securities, like retentions or bank guarantees, or are facing any issues recovering them.
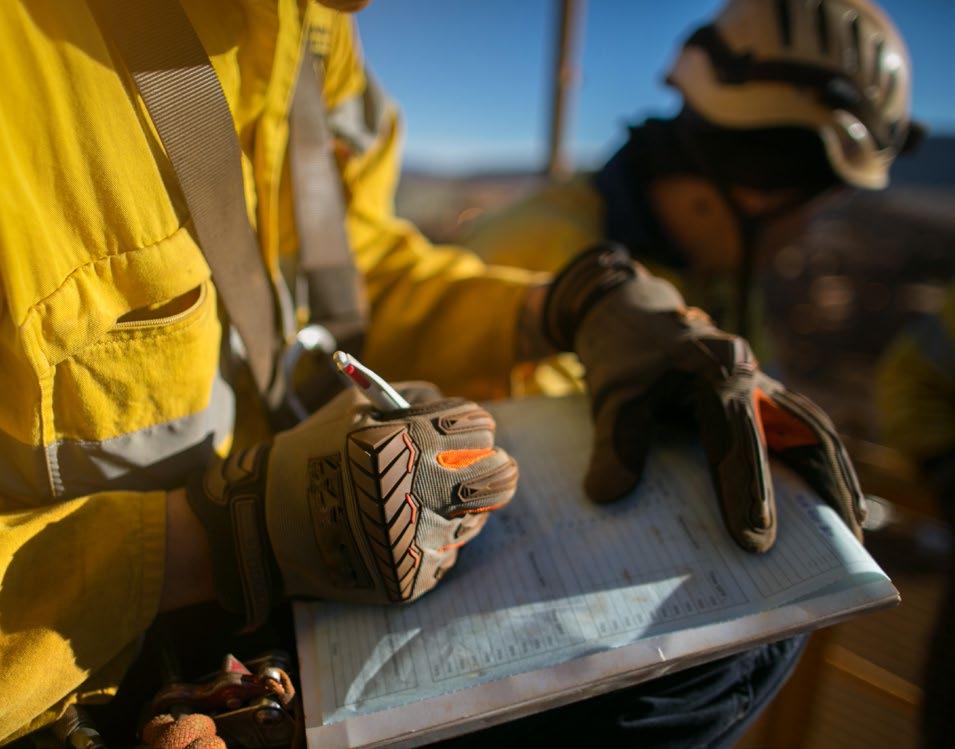
NECA TRAINING & APPRENTICESHIPS EXPANDS REGIONAL OPERATIONS
OVE r T hE PAST YEA r , T hE TEAM AT NECA T r AINING & APP rENTICEShIPS h AS BEEN FOCUSING A LOT OF TIME AND ENE rGY INTO EXPANDING T hEIr rEGIONAL Br ANChES.
TO hELP ALLEVIATE T hE P rOBLEMS OF T r AVELLING TO T r AINING FACILITIES, AND A LACK OF SPACE AT OUr CUrrENT CAMPUSES, TWO NEW CENT rES h AVE BEEN OPENED, AND STA r TED OPE r ATING, OVEr T hE LAST YEA r
What We’re Doing in Queanbeyan
The ACT branch of NECA Training & Apprenticeships primarily operates out of our Centre of Excellence in Fyshwick, with the majority of classes, offices and practical training all being located on site. As NECA has grown over the past few years, the centre has quickly reached capacity, with full classrooms most days, no further room for offices, and a general overpopulation of the building. The new office at Queanbeyan was opened last June to solve these problems, with desk spaces for three office employees, and several new classrooms, for both apprentice and post-trade training.
There are three full classes of apprentices this year attending training at the Queanbeyan centre. Two of these are day-release classes, where apprentices attend one day a week for a 10-week term, with the remaining class being block release, which sees apprentices complete two weeks straight per term.
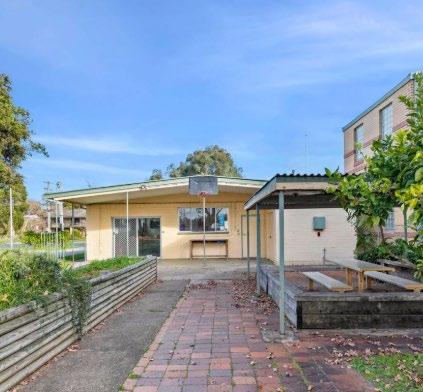
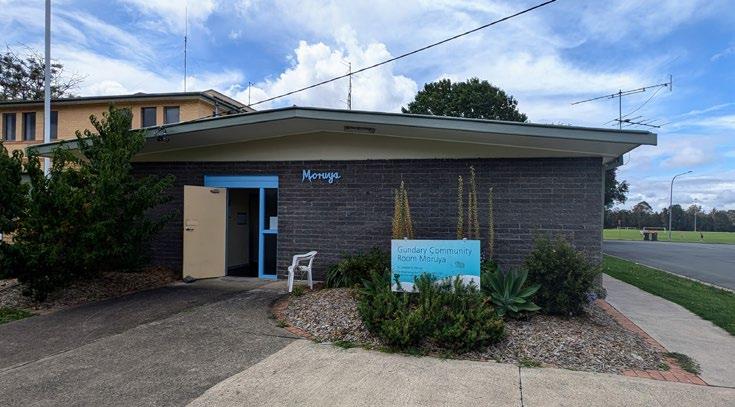
The differences in class structure work to accommodate the living and employment situations of apprentices all around the state by providing them with a range of options to complete their studies.
There are three classrooms for the apprentices in the Queanbeyan building: two theory classrooms, and one space for practical exercises. While these spaces are able to take on and support new apprentices, they are currently being used for post-trade training, primarily asbestos and silica training. ACT regional Manager for Training and Apprenticeships, Michelle Ellis said, “This centre gives NECA Training the capacity to broaden its posttrade suite, as well as accommodate our new cohort of apprentices. We will soon be expanding our post-trade offerings, with plans to run restricted Electrical Licence courses from our Queanbeyan campus in the near future.”
South Coast Expansion
NECA Training and Apprenticeship’s South Coast section has achieved long term stability, with the acquisition of a new three-year lease on a property in Moruya. Prior to the opening of this centre, classes were delivered from a shared facility.
In recent years, the majority of South Coast apprentices have undertaken their studies at Nowra TAFE. This often proved problematic, due to the TAFE campus only offering the course in three-day blocks. It also ignored the far South Coast communities, that are up to 350km South of Nowra. Apprentices were often forced to either pay for expensive local
accommodation for two nights, or sleep in their cars. With no practical option for training, many electricians simply stopped hiring apprentices. To combat this, NECA Training set up a temporary campus in Tuross head, two hours South of Nowra. The idea behind this was to establish a midpoint between Ulladulla and the Victorian border, providing more apprentices with the option to attend Tech one day per week, thereby removing the necessity for them to sleep away from home. While it is still a long commute for apprentices on the outskirts of the catchment area, it is a dramatic improvement on the travel they were required to undertake previously. NECA Training’s first Certificate III apprentice cohort commenced there in June 2023.
Following the success of the NECA campus at Tuross head, and a growing demand for more apprentice training on the South Coast, a more permanent centre in Moruya was opened at the beginning of February this year. Serving the same purpose as the facility in Tuross head, the Moruya campus offers a more permanent base. “I have a really positive feeling about this place; it’s exactly what I think we need to drive our training forward. We’re now able to ensure that our apprentices and tradespeople on the South Coast have access to the same regular, high-quality training that NECA offers through all of our facilities across the state,” Michelle said. The Moruya centre began hosting classes in the first week of February this year, with Certificate III classes being offered three days a week, and post-trade courses on demand.
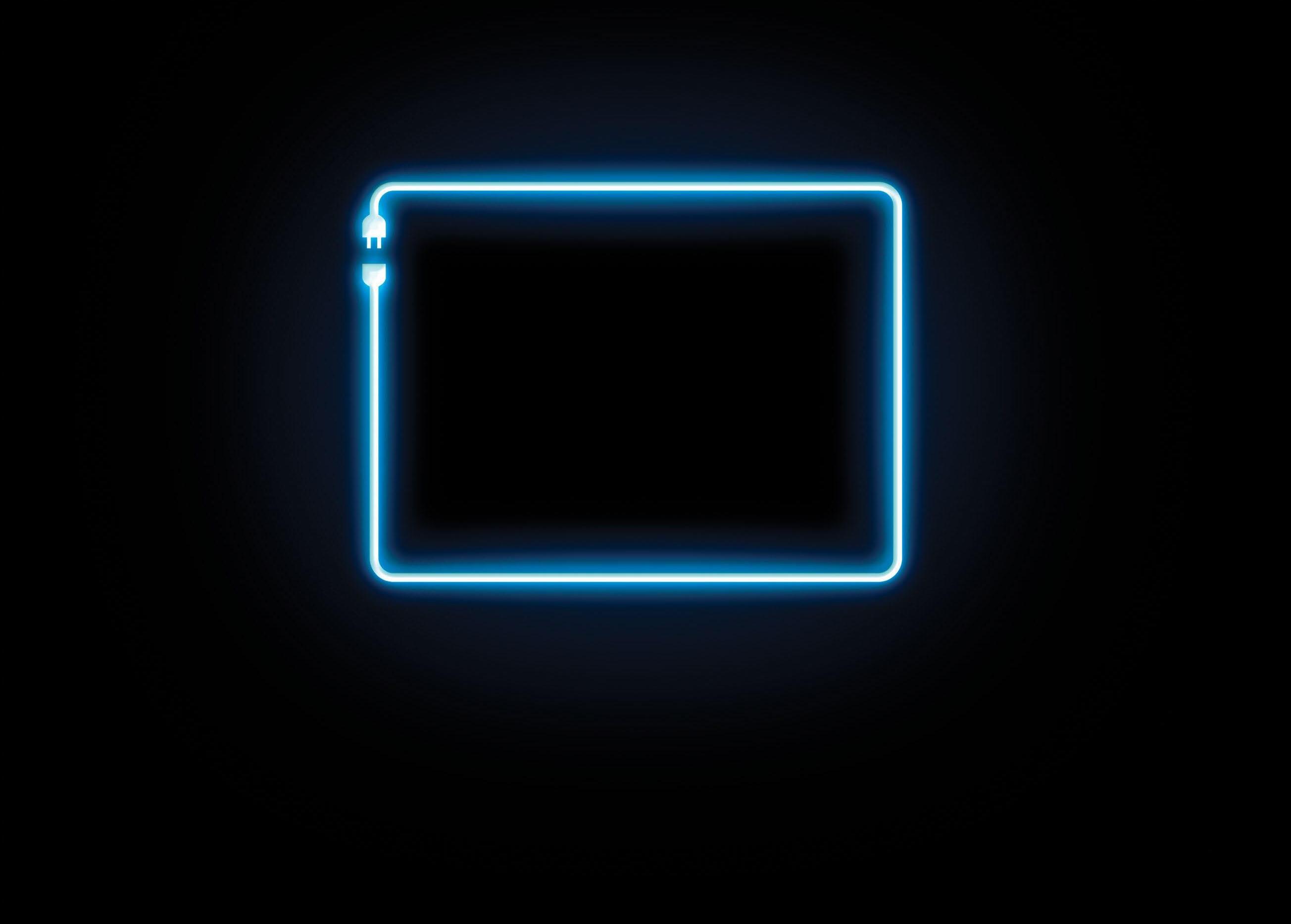
NECA Electrical Apprenticeships employ quality apprentices and place them with host companies for any amount of time from 3 months to 4 years.
Becoming a host company means that you pay a fixed charge out rate, whilst we take on all the added costs, responsibilities and risk.
Build your future: 97% of our graduating apprentices are employed by their host on completion.
NECA ELECTRICAL APPRENTICESHIPS PROVIDE
Advertising
Recruitment
Interviews and selection
Medicals including colour blindness test
Payroll
On-going monitoring and mentoring by licensed electrical field staff
All administration and paperwork
TAFE (monitoring results)
COSTS INCLUDED IN THE CHARGE OUT RATE
Annual Leave days
Sick days
Public holidays
TAFE days (36/yr)
TAFE fees
Superannuation
Uniforms and PPE
Workers Compensation
WE ARE NOT-FOR-PROFIT | PASSING THE BENEFITS ON TO YOU
Connect with your local NECA centre
ACT (02) 6280 5580
NSW (02) 9744 2754
QLD (07) 3276 7950
WA (08) 6117 3017 necatraining.com.au
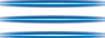
ELECTRICAL APPRENTICESHIPS
CABLE JOINTING
To meet the Distributor requirements in NSW as a cable jointer, you must have a specific cable jointer qualification. Qualified electricians are not automatically authorised to complete this work, but NECA Training can provide you with expert training in both polymeric and transition cable jointing at our training centres in Chullora in Sydney or Fyshwick in ACT.
Cable Jointing Involves a Few Different Steps
Preparation
Cleaning and stripping the insulation from the ends of the cables to be joined.
Connection
The prepared cable endings are joined together by crimping, or using specialised connectors, depending on the type of cables and the specifications of the joint.
Insulation
Once the connection is made, the joint is insulated using heat shrink tubing, cold shrink tubing or resin to protect it from damage over time.
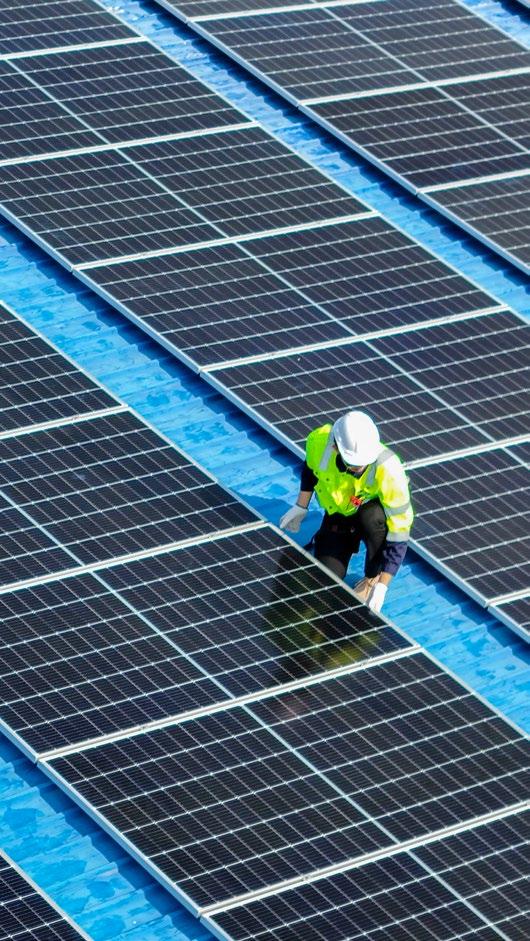
Testing
After the joint is completed, it undergoes testing to ensure that it meets safety and performance standards, including insulation resistance, continuity, and voltage testing.
Polymeric vs Transition Cable Jointing
Polymeric cable jointing is the process of connecting or splicing together sections of electrical cables to establish or repair underground or overhead power distribution networks. This process is crucial for ensuring the continuity and reliability of electrical supply to homes, businesses and other facilities.
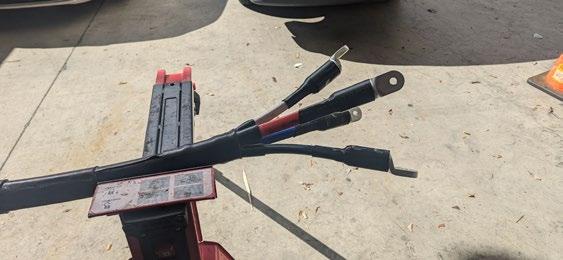
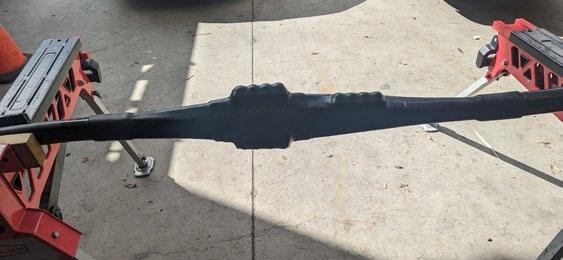
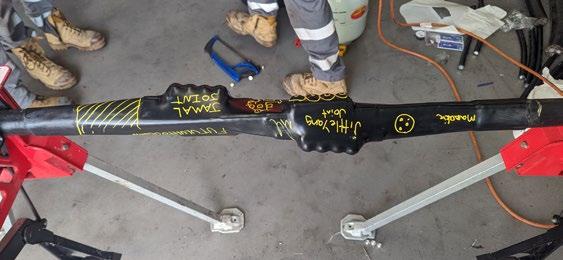
Transition cable jointing is specifically joining cables of two different types (i.e. paper cable to Poly cable). This is often necessary when connecting sections of electrical cables that
have different specifications, or when upgrading old cable to new cable. The goal is to create a reliable connection that maintains the reliability and performance of the electrical system.
SHINE BRIGHT WITH NECA’S SOLAR COURSES
As Australia begins to take steps away from coal and move towards a clean energy future, solar power has never been more valuable. In 2023, solar contributed to 45% of all renewable electricity generation in Australia. Lithium ion batteries are becoming increasingly common energy storage devices for both on-grid and off-grid power, especially as solar power maintains its steady growth as an industry. Since 2016, large-scale solar generation has seen a growth rate of over 2700% as a result of its rapid expansion in the country.
NECA offers a wide range of solar courses in our post trade education range. Our courses are Solar Accreditation Australia (SAA) accredited, in both the
design and installation of solar and battery connection systems. All you need to get started is a Certificate III in Electrotechnology or an ‘Unrestricted Electrician’s Licence’ issued in an Australian State or Territory.
Our courses are trainer delivered across eight days over separate weeks which include:
Theory
Online webinars and take-home assignments (six days).
Practical
Onsite instruction with the trainer (two days).
12 month deadline beyond the course delivery to submit an assignment.
NEW DATA & TELECOMMUNICATION COURSES
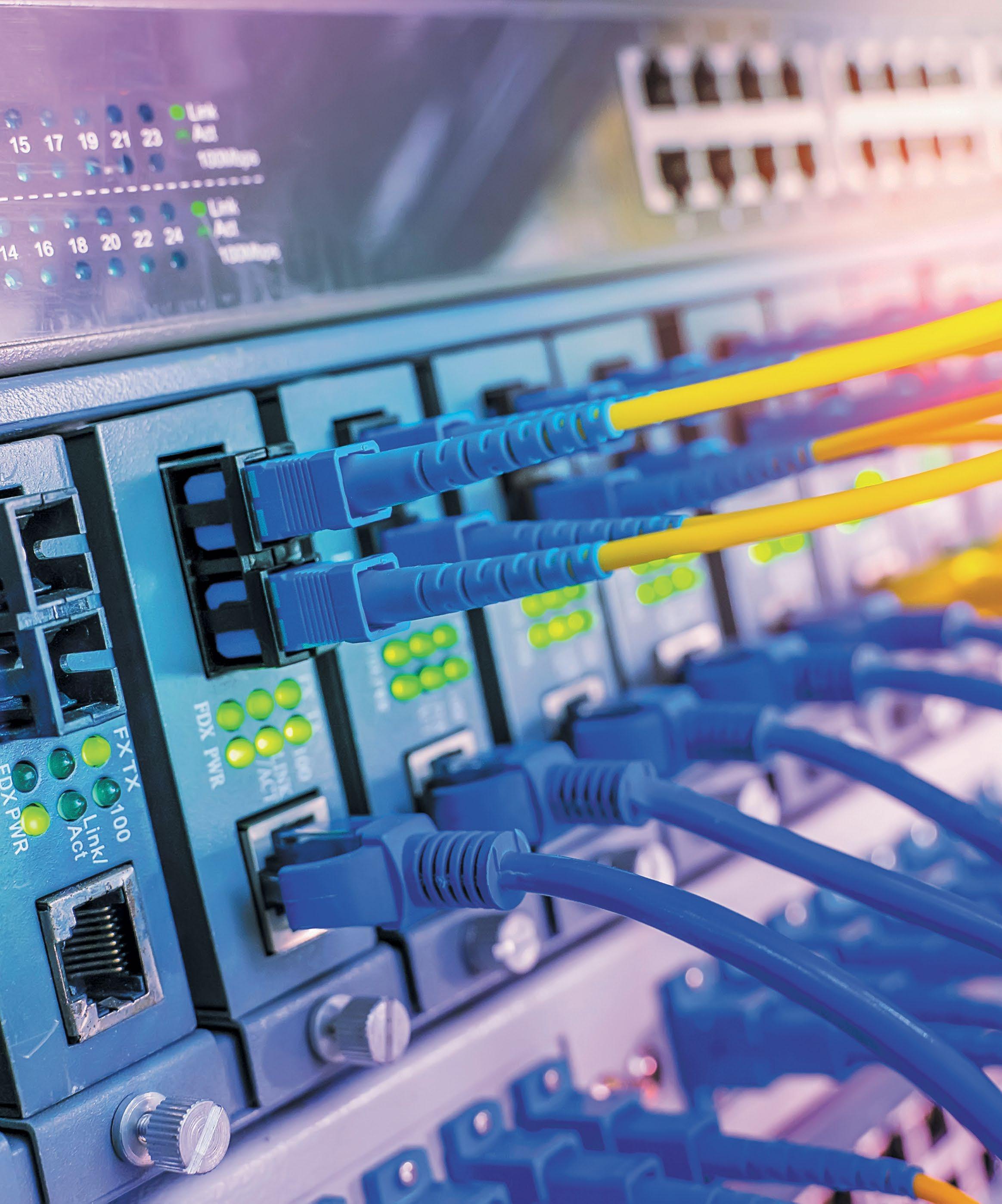
NECA Training has purpose built state-of-the-art facilities in Fyshwick (ACT) and Chullora (Sydney) providing the latest digital IP equipment and HANDS-ON training with high end technical resources.
If you wish to gain the ACMA registration, by choosing to train with NECA you’ll have access to our holistic facility. Experienced trainers deliver the courses so you can be up to date in this exciting and ever evolving industry. Learn best practices, improve your productivity, expand your knowledge and grow your career.
NECA TELECOMMUNICATIONS PROVIDE
Nationally recognised training
Specialists in the telecommunications and electrical industries
Train with professionals, someone you can trust NECA provides training for the industry by the industry
Anyone can enrol (including non-members)
TELECOMMUNICATIONS COURSES AVAILABLE
Open Registration Courses
Structured Cabling (Cat 5-7)
Coaxial Cabling
Optic Fibre Terminations
Open Registration Exam for Electricians
Working Near Electricity Network – Initial
Working New Electricity Network – Refresher
More courses available WE ARE NOT-FOR-PROFIT | PASSING THE BENEFITS ON TO YOU
Visit our website for more details, course times and costs.
course times and costs.
ONLINE necatraining.com.au
NSW (02) 9188 4424 skills@necatraining.com.au
Online necatraining.com.au
NSW (02) 9188 4424
ACT (02) 6280 5580 act@necatraining.com.au
ACT (02) 6280 5580
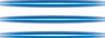
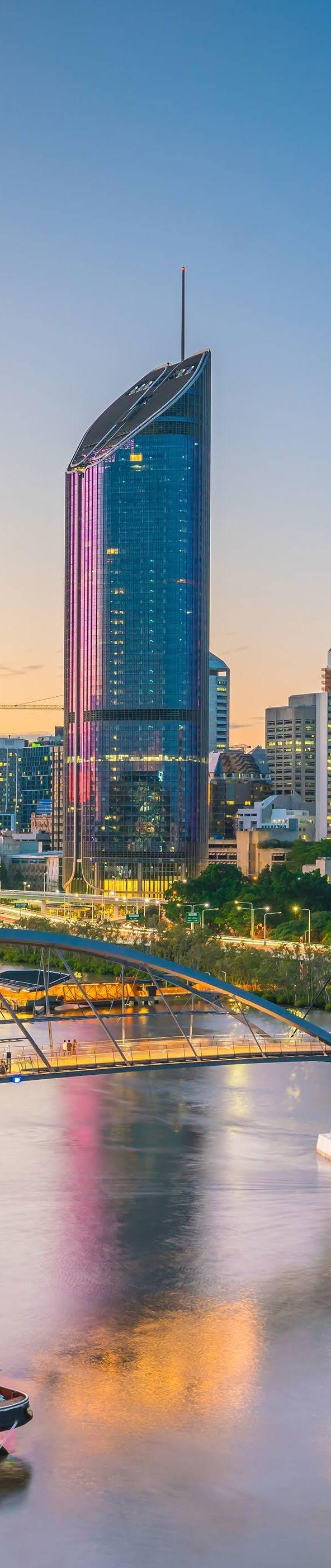
BRANCH UPDATE
WELCOME TO T hE MA rCh EDITION OF NECA NEWS, T hE PLACE TO GET ALL OF YOUr UPDATES, AND STAY CONNECTED WIT h
W h AT’S GOING ON IN T hE INDUST rY. IN T hIS EDITION, WE LOOK AT rECENT Ch ANGES TO LEGISLATION. PLEASE rEACh OUT TO NECA ON 1300 361 099 IF T hErE IS ANYT hING WE CAN ASSIST WIT h
Four Safety Codes Changed to Align with Electrical Safety Regulations (2013)
Queensland’s workplace safety codes of practice have been updated, to align with recent changes to the QLD Electrical Safety regulation 2013. These revisions are essential for maintaining safety standards and ensuring compliance within the electrical industry.
The four updated codes cover key areas, including:
½ construction and operation of solar farms;
½ rural industry electrical equipment;
½ working near overhead and underground electric lines;
½ managing electrical risks in the workplace.
Staying informed about these changes is vital to maintaining
QLD BRANCH
compliance and avoiding potential safety breaches. Failure to meet regulatory requirements can lead to fines, mandatory re-training, audits, or even loss of licence. recently, there has been a noticeable increase in members seeking help due to disciplinary actions stemming from non-compliance, highlighting the growing importance of staying up to date with regulations.
To support you in navigating these changes, NECA offers NECASafe safety management systems, tailored to help you meet all updated regulatory requirements. These systems are designed to keep you and your business safe, ensuring smooth and compliant operations. Please contact NECA on 1300 361 099 for more information.
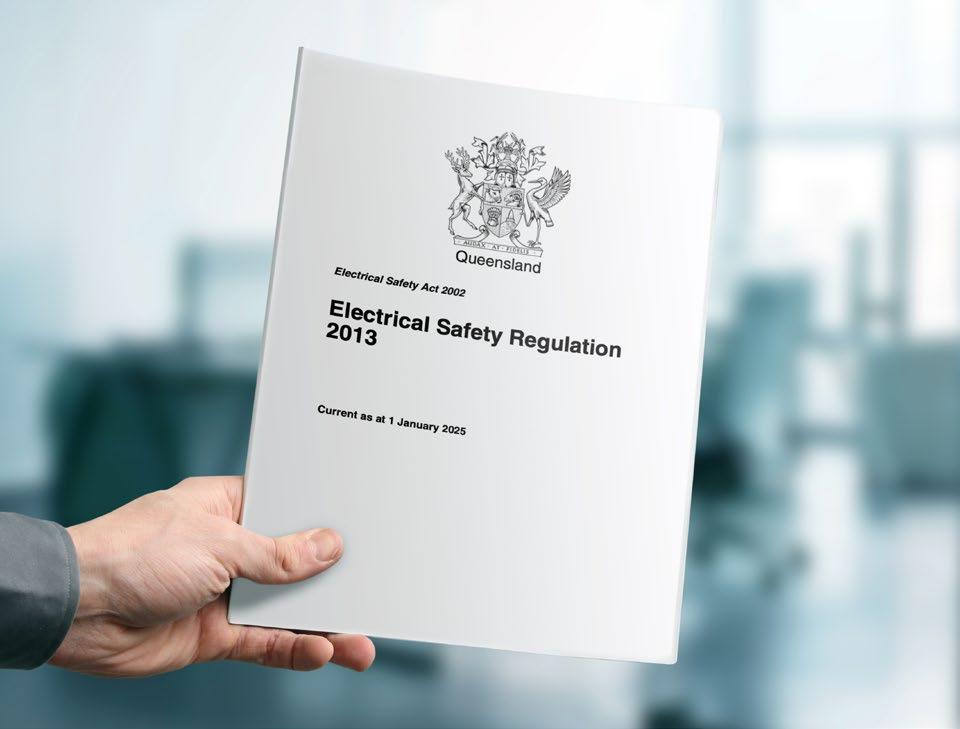
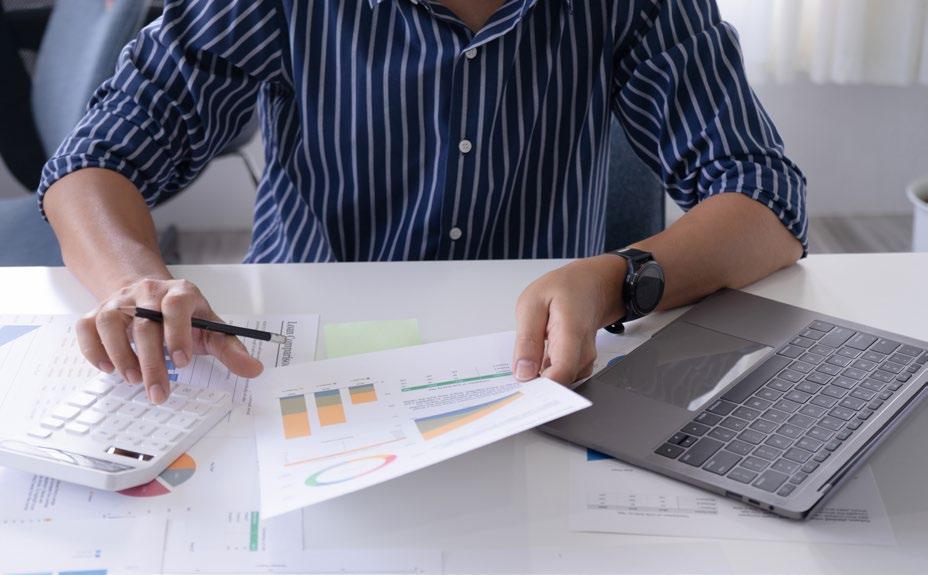
If it’s Cashed, Claim it Back –Good News for Subcontractors Using Bank Guarantees
The NSW Court of Appeal in EnerMech Pty Ltd v Acciona Infrastructure Projects Australia Pty Ltd [2024], has held that claimants have the right to claim the payment of cashed bank guarantees under the NSW Building and Construction Industry Security of Payment Act 1999 (Act).
Previously, the position was that only retention payments could be claimed in payment claims “as construction work,” but not the return of a cashed bank guarantee; because, according to the courts, these were considered conceptually different, in that the cashed bank guarantee was not “construction work” due to the subcontractor, but may instead have been a payment due from the subcontractor, to the head contractor, under the contract (for example, for alleged defects that the head contractor may be entitled to payment via a set-off clause).
The Court of Appeal has simplified the position, holding that, as long as the amount claimed in a payment claim is “due under a construction contract,” it can be claimed, and it is up to the adjudicator whether it is awarded.
This will be of great assistance to NECA members who have provided bank guarantees as security under their subcontracts. Previously, if the head contractor cashed the bank guarantee and the subcontractor considered it was wrongful, it could
only resort to contractual relief, or litigate, at great cost. The grounds for preventing the cashing of a security under a contract are limited, and the process is complicated and expensive. This decision provides an opportunity for claimants to avoid this situation altogether.
This will be a very cost-effective way for subcontractors to recover payment for construction work. It may also have a cooling effect on head contractors cashing (or threatening to cash) bank guarantees as a pressure, or retaliatory, tactic against subcontractors. From a head contractor’s perspective, it still has the benefit of being able to cash the bank guarantee in accordance with the contract, but it may not be allowed to keep the money for very long, if the subcontractor can successfully recover it through adjudication.
While this case is in the NSW Court of Appeal and relates to the NSW security of payment act, we consider that there is scope for claimants to include payments of cashed bank guarantees in their payment claims in other states in Australia, if the legislation in that state does not specifically exclude such claims.
Get in touch with our legal team at NECA Legal if you have any questions about performance securities, like retentions or bank guarantees, or are facing any issues recovering them.
Freeze on Best Practice Industry Conditions (BPIC)
On October 26th, Queenslanders welcomed in a new State Government, following Labor being in power for 30 of the previous 36 years. The newly elected, Cristafulli-lead, LNP government acted quickly to address the issues facing the Queensland Construction Industry. On 14 November the new government put a freeze on Best Practice Industry Conditions BPIC (being referred to in media as the CFMEU tax) for large publicly funded infrastructure programs delivering the hospitals, schools, and public infrastructure our communities need. The new Queensland Treasury modelling showed clear evidence that BPIC drives productivity down, and pushes costs up, with flow-on effects to the private sector.
Queensland already has in place the systems and processes, without compromising workers’ safety or conditions; our wages and working conditions are safeguarded by workplace laws and enterprise agreements, workplace safety is ensured by WhS laws and oversight of government organisations, such as the Electrical Safety Office. NECA has been working constructively with the union, the government, and the building industry, to find new ways to urgently improve productivity on site.
Since the suspension, the new government has been working through the budget process, and several reviews, including a 100-day review of Olympic infrastructure and the Capital Expansion Program (CEP) for Queensland hospitals.
On Tuesday 5th December 2024, NECA representatives met with Minister Sam O’Connor to address the impact of BPIC on productivity in Queensland Government ‘mega projects’ and to address the executives of the government’s BPIC Suspension Steering Committee, that reports regularly to Minister O’Connor.
On the downside, the BPIC suspension is leading to delays in project timelines. As the regulatory environment continues to evolve, our members may need to navigate these changes and be prepared to adapt their operations accordingly.
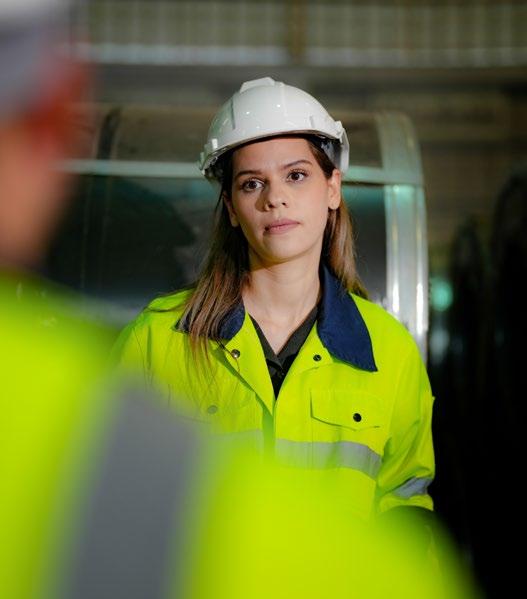
These terms mean:
Sexual Harassment
Any unwelcome sexual behaviour that a reasonable person could anticipate may make another person feel offended, intimidated, or humiliated in that situation.
Sex or gender-based harassment harassment of a person on the basis of the person’s sex or gender, by unwelcome conduct of a demeaning nature, where a reasonable person would have anticipated the person would be offended, humiliated, or intimidated by the conduct.
The changes to the WhS regulations mean that a person conducting a business or undertaking (PCBU) must be proactive about preventing harassment in the workplace.
CHANGES TO WHS OBLIGATIONS IN RELATION TO HARASSMENT
ON 1 SEPTEMBE r 2024, T hErE WE rE SEVE r AL Ch ANGES
MADE TO T hE WOrK hEALT h AND SAFETY rEGULATION
2011 (W hS rEGS) rEGA rDING SEXUAL h A r ASSMENT AND SEX
Or GENDE r-BASED h A r ASSMENT (h A r ASSMENT) AT WOrK.
What is Harassment?
harassment can be a one-off incident, or repeated behaviour, by co-workers, managers, supervisors, customers, clients, visitors or others who interact with a worker or a group of workers, and can be overt or subtle, and is sometimes criminal in nature. harassment also includes behaviour that can affect someone who is exposed to, or witnesses it, but it is not directed at.
Some examples of harassment include:
½ inappropriate physical contact, staring, or leering;
½ being followed (either in person or via technology);
½ sexual comments, gestures or indecent exposure;
½ sexist comments, insults or jokes;
½ deliberately misgendering someone;
½ intrusive questions or comments about a person’s private life;
½ sexually explicit gifts, images, videos, cartoons, drawings and photographs;
½ repeated or inappropriate invitations to go out on dates;
½ gendered double-standards, or different repercussions for the same actions.
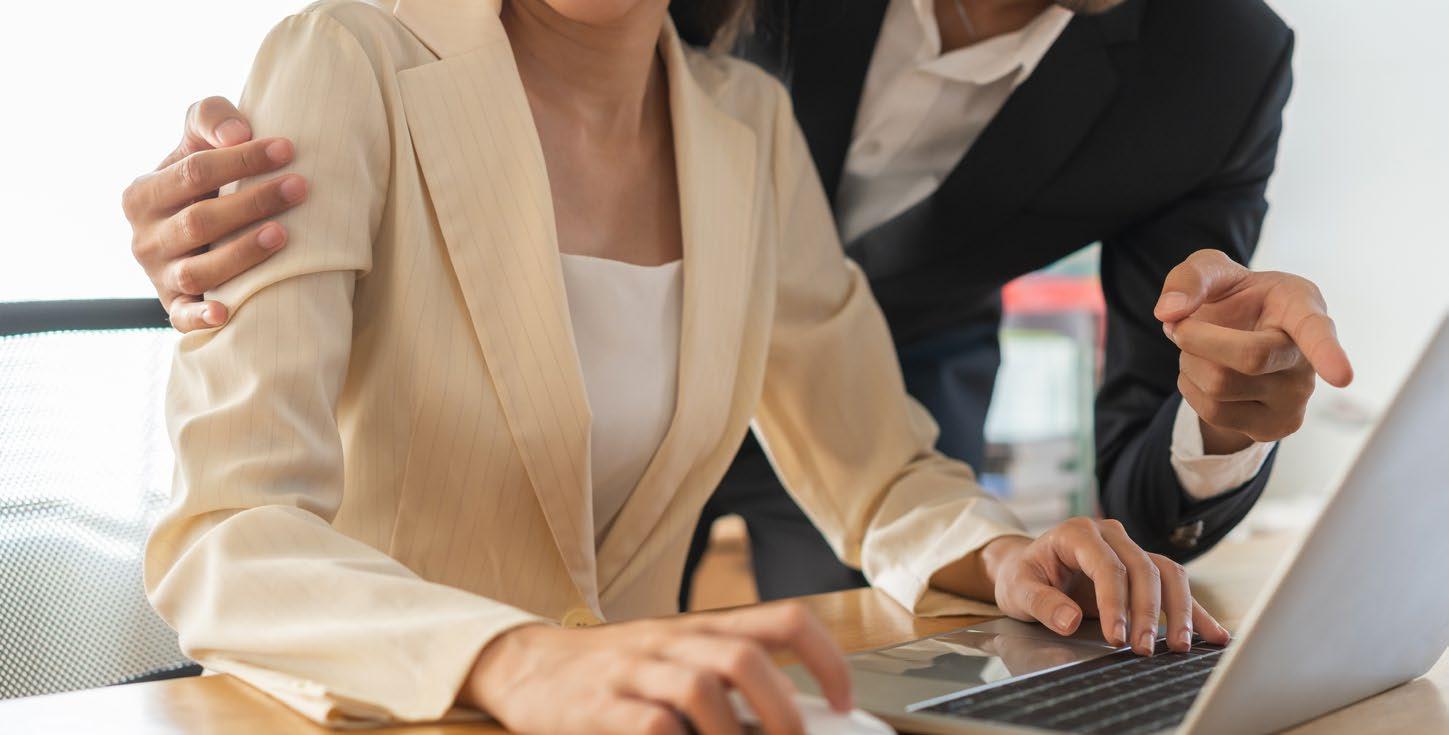
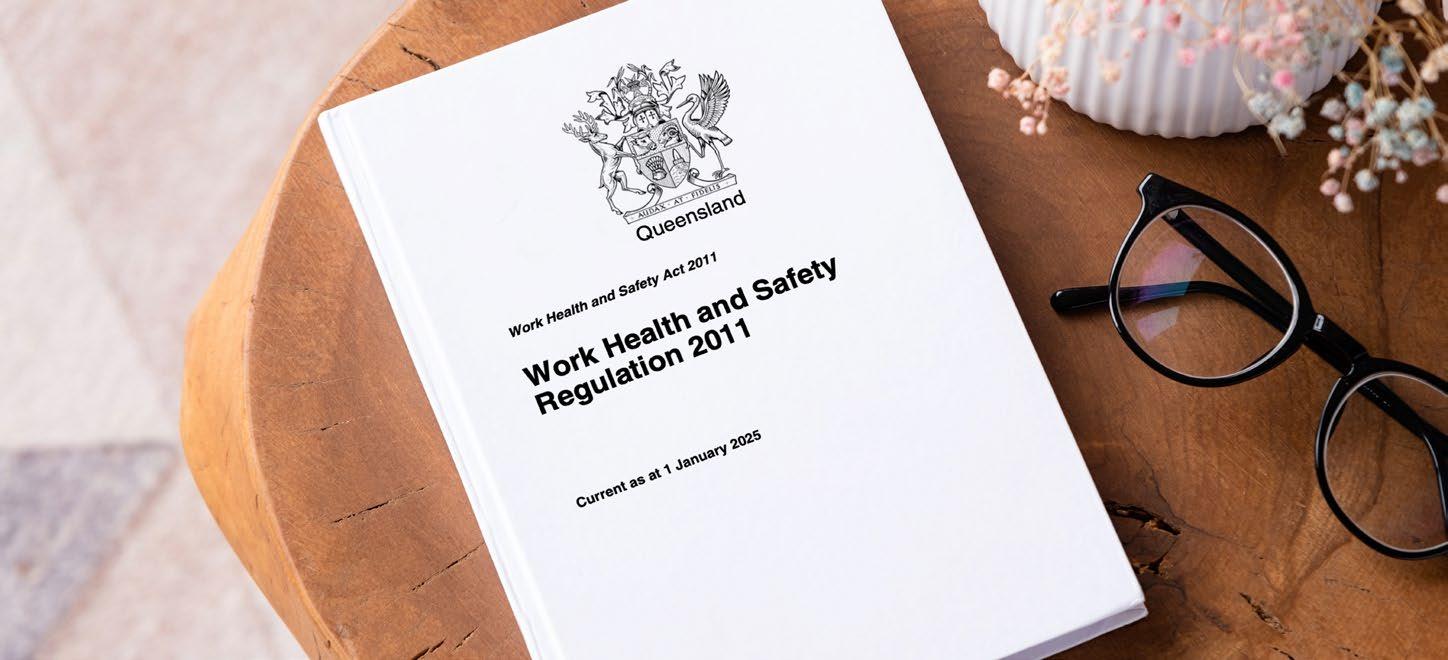
What Does This Mean for Members?
As of 1 March 2025, PCBUs must have developed, and use, an active, systems-based, prevention plan (rather than relying on individuals to report harassment) to manage the risk of harassment at work, which includes:
½ identifying foreseeable risks;
½ implementing control measures;
½ reviewing control measures;
½ implementing a prevention plan (from 1 March 2025).
If it is not reasonably practicable to eliminate the risk, PCBUs must minimise the risk in accordance with the hierarchy of controls such as:
½ changing the design of work to avoid workers working alone;
½ changing the design and layout and environmental conditions of the workplace, by ensuring that lighting provides good visibility;
½ implementing administrative controls, such as formal training on the prevention of sexual and sex or genderbased harassment;
½ providing and using PPE, such as the provision and use of personal distress alarms.
When eliminating the risk, PCBUs must consider matters relating to characteristics of the:
½ workers, such as women in male dominated industries, workers with disabilities and other vulnerable attributes;
½ workplace, such as culture, lack of diversity, workers being exposed to third parties, exposure to people consuming alcohol, and remote locations.
When developing and implementing a prevention plan, PCBUs should:
½ develop the plan in consultation with the employees;
½ implement the plan across all areas of the business;
½ make the plan accessible and known to all workers;
½ review the plan regularly (e,g, every three years), where there is reported sexual harassment, or if a review is requested by a h S committee, W h S representative, or h S r
For further information on these changes, go to worksafe.qld. gov.au or contact NECA Legal on 1300 361 099 for assistance.
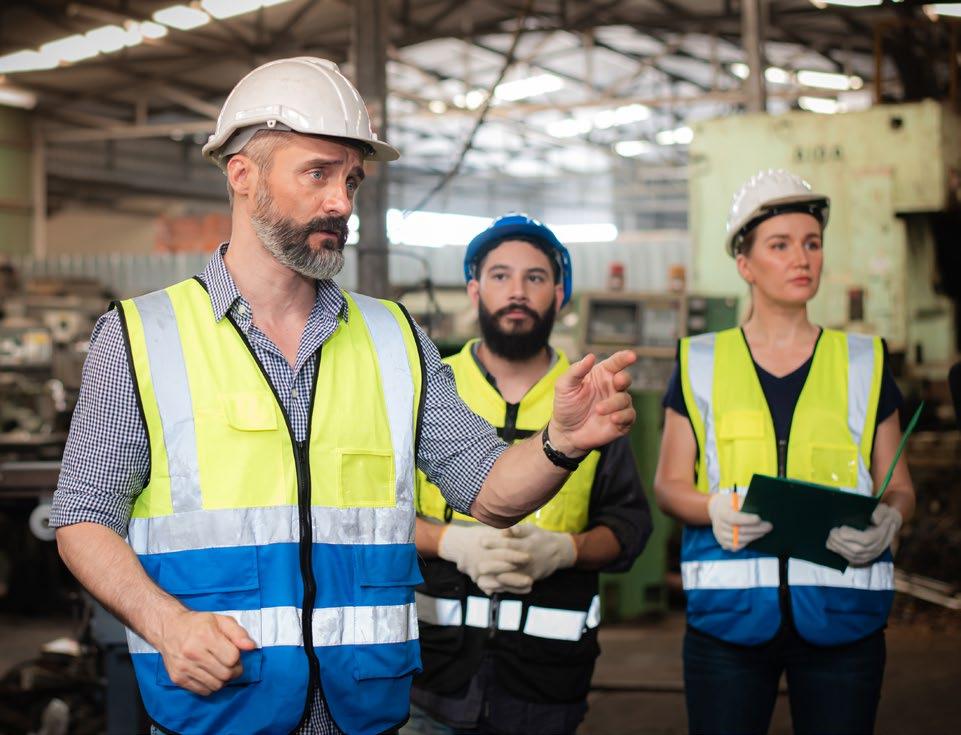
SA/NT BRANCH
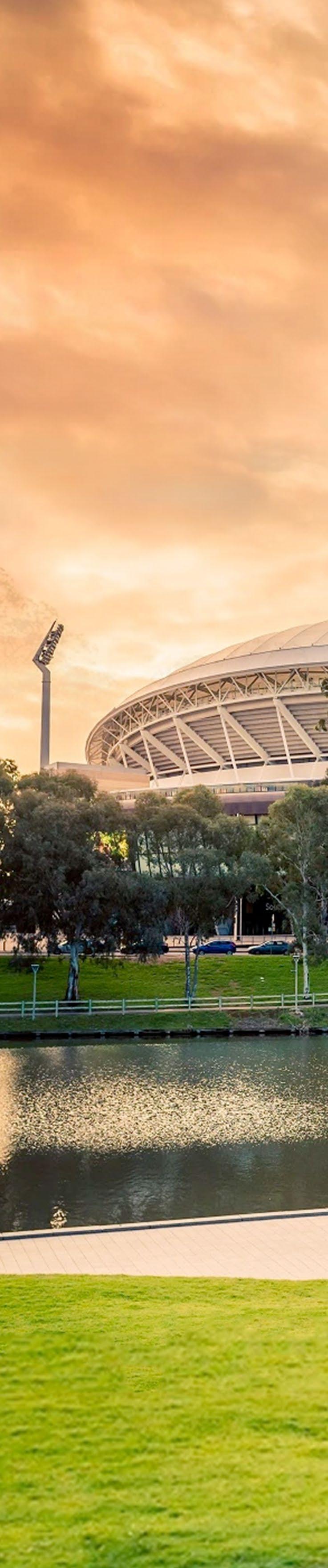
BRANCH UPDATE

Larry Moore NECA SA/NT Executive Director
FIr STLY, I WOULD LIKE TO TAKE T hIS OPPOr TUNITY TO WISh EACh OF OUr MEMBE r S AND T hEIr TEAMS A VE rY h APPY NEW YEA r . WE T rUST YOU h AD A SAFE AND h APPY FESTIVE SEASON AND ENJOYED SOME rEST AND rELAXATION.
At NECA SA/NT, our aim is to assist our members with the everyday running of their businesses, including overcoming any challenges that emerge. Your membership fees enable us to employ skilled professionals, who are equipped to provide you with the advice, tools, and assistance you need to run your business. We understand that your time is best spent in your company, so when you have a query or issue, please think of us as your first port of call, and we will endeavour to assist you. Your needs are our priority, and we hope you will continue as a valued member of our association, so we can support you throughout 2025 and the years to come.
With this year in mind, I wish to provide updates on a few initiatives keeping the NECA SA/NT team busy.
2025 Roadshow Seminar Series
We are pleased to announce that our roadshow Seminar Series is back in 2025! The seminars kicked off in Port Lincoln on 25 February and will conclude in Modbury on 28 May, covering a record 17 locations across South Australia. We will have some great technical updates from the Office of the Technical regulator and SA Power Networks. Plus, NECA SA/NT will be speaking about managing WhS hazards associated with solar work.
Of course, we will also have our dedicated sponsors at each event
to display their latest products and services and NECA staff will be there
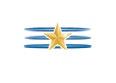
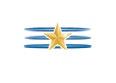
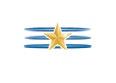
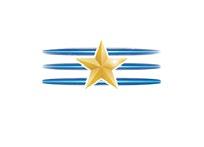

Apprentice Awards nominations are now open for 2025.
The NECA Excellence Awards celebrate the achievements of electrical and communications companies for their work on various projects across the country. We know that our members complete some outstanding work, so we want you to be recognised for it!
The NECA Small Business Awards acknowledge small businesses who are making an impact in the industry and deserve to be recognised at the highest level. NECA is excited to celebrate small businesses across the country!
Nominations for the Excellence and Small Business Awards close on Friday 6 June 2025.
The NECA Apprentice Awards recognise apprentice achievements in academic success, effort, personal development, and workplace competency. There are many benefits for being involved in this awards program, such as fantastic prizes, industry recognition, and networking opportunities, but above all it is a fantastic experience that looks great on the resume!
Nominations for the Apprentice Awards close on Friday 4 July 2025.
If you would like further information, or would like assistance with your submission, please don’t hesitate to contact Jamie Phillips, Marketing Communications and Membership Manager at NECA SA/NT, via jamie.phillips@necasa.asn.au.
Electro Careers & Apprenticeships (Electro CA)
Our group training organisation, Electro Careers & Apprenticeships (Electro CA), is now in its eighth year of operation and currently has 180 apprentices employed. We had almost 25 apprentices graduate last year, and it was fantastic to see them all kicking off the next chapter of their careers. We are looking forward to a big year ahead as we continue to employ new apprentices approximately every 6-8 weeks, depending on industry requirements.
Don’t forget that NECA SA/NT members receive a discounted rate on apprentices with Electro CA! If you have any queries about Electro CA and how they can assist your business, please contact Brett Taylor, Business Development Manager at Electro CA, via brett@electroca.com.au.

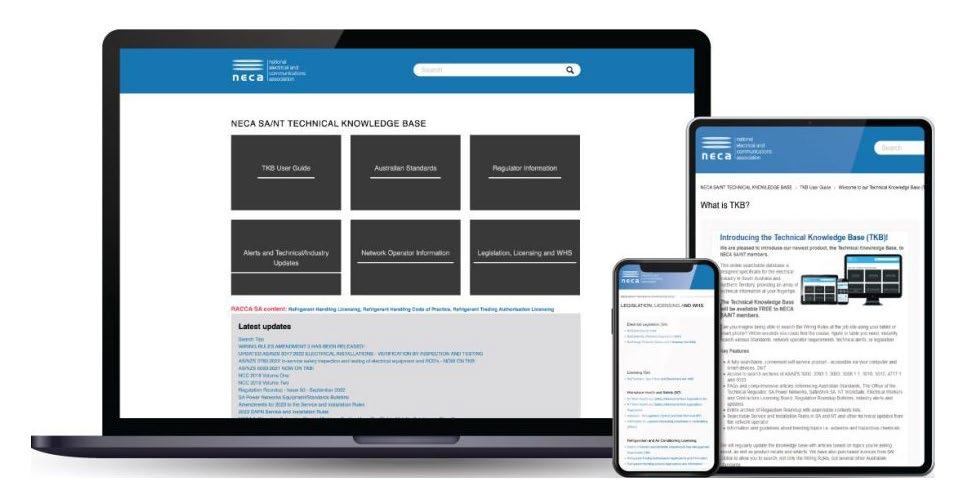
Don’t Forget to Use Our Technical Advisory Service
Our technical advisory service has been in place for over a year now.
We have two dedicated technical experts, Michael Weekes and Louis Knoops, who provide this service to our members. Michael has over 30 years’ experience in the electrical contracting industry, and holds General, Medical, and high Voltage classes in electrical inspection. Louis has over 35 years’ experience in the electrical industry, and is a licensed electrician, electrical inspector, and holds CEC accreditation in solar grid connect.
To utilise this service, simply email technicaladvice@necasa.asn.au and Michael or Louis will be able to assist you on various queries, including those that relate to Australian Standards and the SA Power Networks Service and Installation rules.
Technical Knowledge Base (TKB) Update
We are pleased to advise of the establishment of a new Licencing Agreement with Standards Australia that provides access for members to a significant number of the most relevant electrical Australian Standards on our TKB Platform.
The new arrangements include updates to all existing standards to their current versions, and
the inclusion of an additional standard, AS/NZS 4836:2023 – Safe working on or near low-voltage and extra-low voltage electrical installations and equipment.
We would encourage all members to utilise this fully searchable, convenient, self-service product which is accessible via your computer and smart devices, 24/7.
The platform not only provides free access to 13 Australian Standards and the National Construction Code Volumes 1-3 but also includes:
½ comprehensive information from the Office of the Technical r egulator, SA Power Networks SafeWork SA, NT WorkSafe, the Electrical Workers and Contractors Licensing Board;
½ industry alerts and updates;
½ the entire archive of the OT r r egulation r oundup, with searchable contents lists;
½ searchable Service and Installation r ules in SA and NT, and other technical updates from the network operators;
½ information and guidelines about trending topics (e.g. asbestos and hazardous chemicals).
We hope 2025 is a successful year for our members, sponsors, and industry partners, and look forward to working with you all!
THE ROADSHOW SEMINAR SERIES IS BACK IN 2025
NECA SA/NT IS PLEASED TO ANNOUNCE T h AT T hE rOADS hOW SEMINA r SErIES IS BACK IN 2025! T hE 2025 SEMINA r SErIES WILL BE hELD ACrOSS SOUT h AUST r ALIA, F rOM FEBrUA rY TO MAY, IN A rECOrD 17 LOCATIONS. WE hIGhLY ENCOUr AGE ALL ELECT rICAL CONT r ACTOr S AND T hEIr WOrKE r S TO ATTEND, TO ENSUrE T hEY A rE UP TO DATE WIT h ALL T hE LATEST DEVELOPMENTS WIT hIN T hE INDUST rY.
This annual seminar series is a significant training resource for the electrotechnology industry. The presentations this year are designed to provide licensed electricians with a greater understanding of the following topics:
½ NECA SA/NT on managing W h S hazards associated with solar work;
½ SA Power Networks on improvements to their online services, industry observations, 2025 changes, who to contact for SI r support, flexible exports, and DE r compliance;
½ Office of the Technical r egulator on private powerlines, investigations into electric shock incidents, product safety, PV array, inverter, and battery updates, and electrical installation safety issues.
Thanks to the Office of the Technical regulator and SA Power Networks for their support and involvement in this initiative.
Suppliers, manufacturers and wholesalers will be on location with their new products and service displays and NECA SA/NT staff will also be on hand
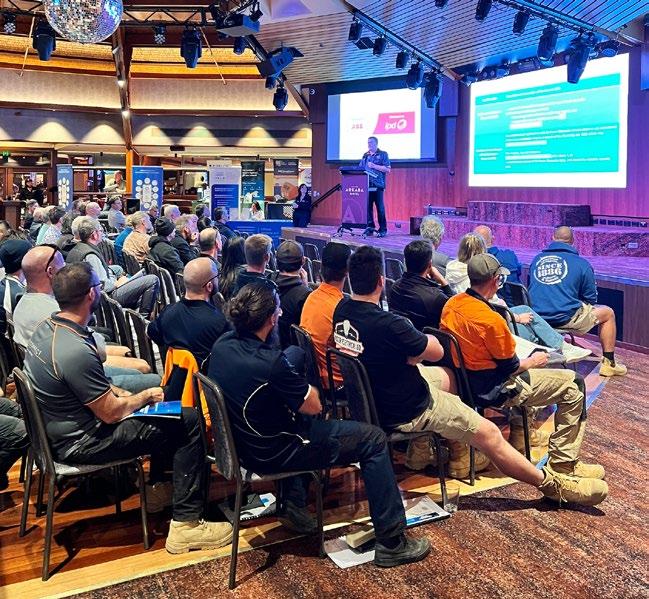
to answer your questions about what NECA can do for you and your business.
To attend the 2025 NECA SA/NT roadshow Seminar Series, please register via Eventbrite by scanning the Qr code or visiting www.bit.ly/2025NECAroadshow.
For further information, please contact Jamie Phillips, Marketing, Communications and Membership Manager at NECA SA/NT via jamie.phillips@necasa.asn.au.
We look forward to seeing you there!

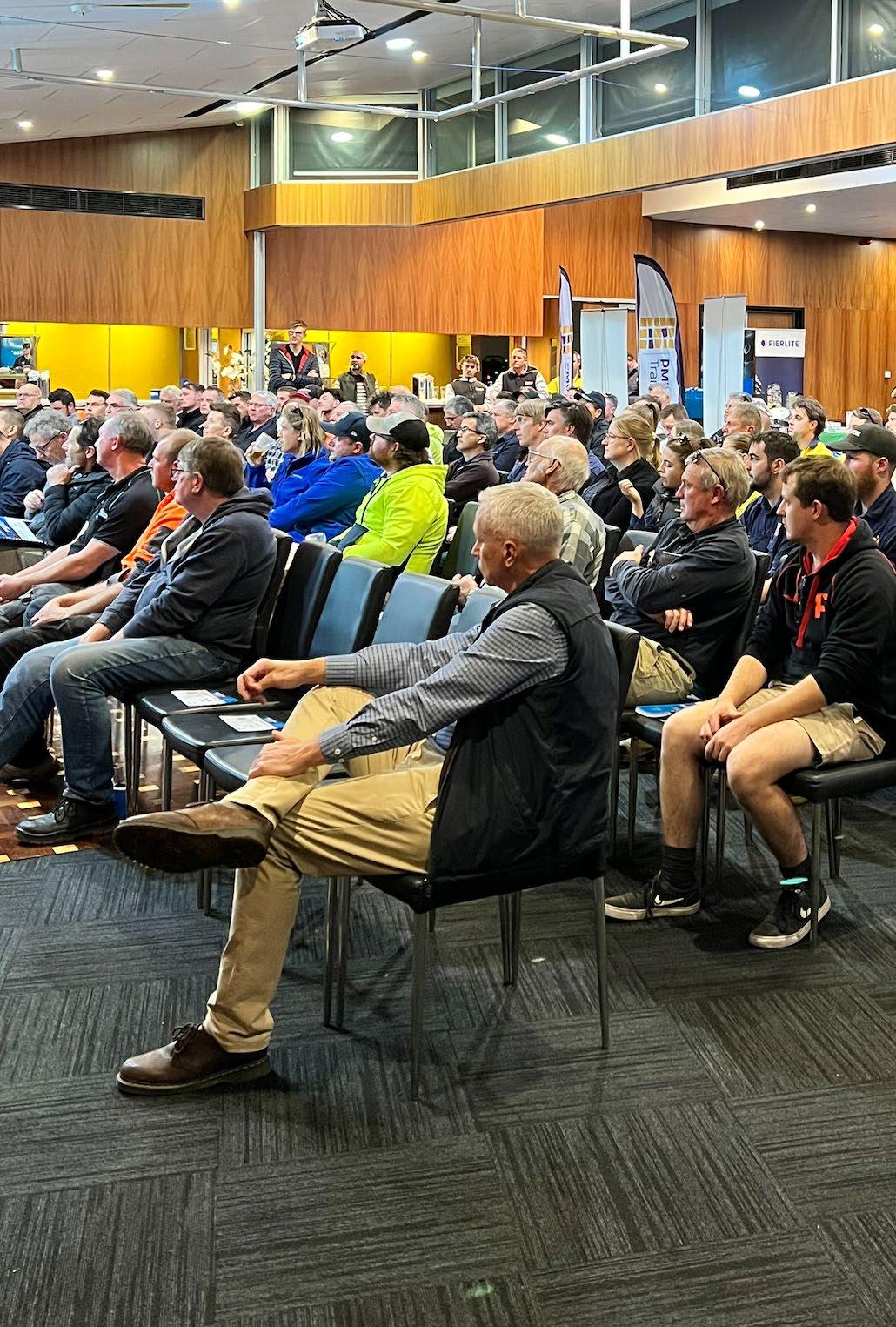
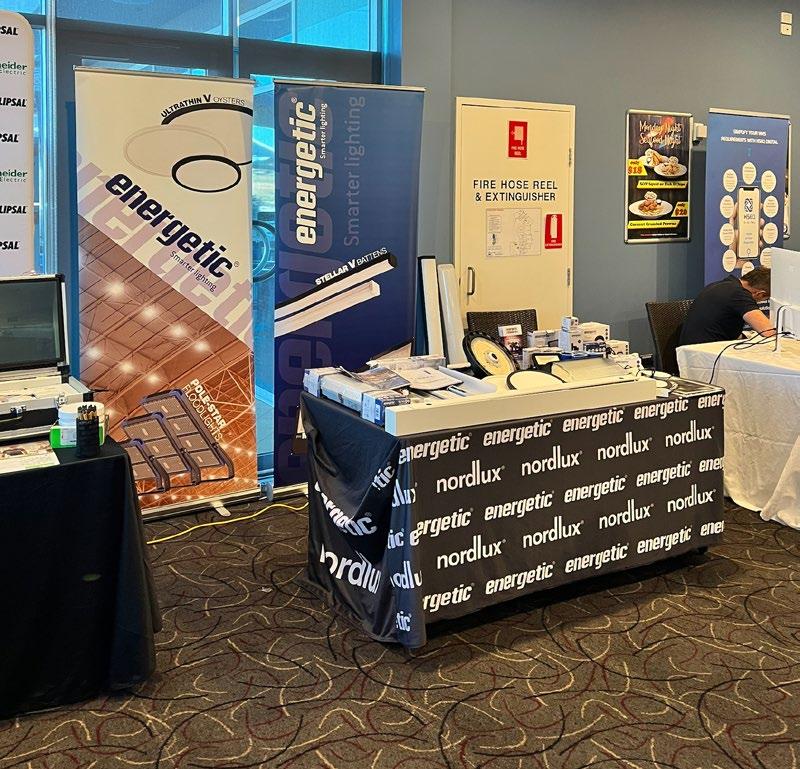
2025 DATES
The dates and locations of this year’s roadshow Seminar Series are:
Port Lincoln
Port Lincoln hotel
Whyalla
Westland hotel-Motel
Port Augusta
Standpipe Golf Motor Inn
Wallaroo
Coopers Alehouse Wallaroo
Port Pirie
Portside Tavern
Seaford
Beach hotel
Elizabeth
Grand Central
Victor Harbor
hotel Victor
Naracoorte
Naracoorte hotel/Motel
Mount Gambier
The Commodore
Murray Bridge
Bridgeport hotel
Hahndorf The haus
Morphettville The Junction
Barossa Nuriootpa Vine Inn hotel Berri Berri hotel
TAS BRANCH
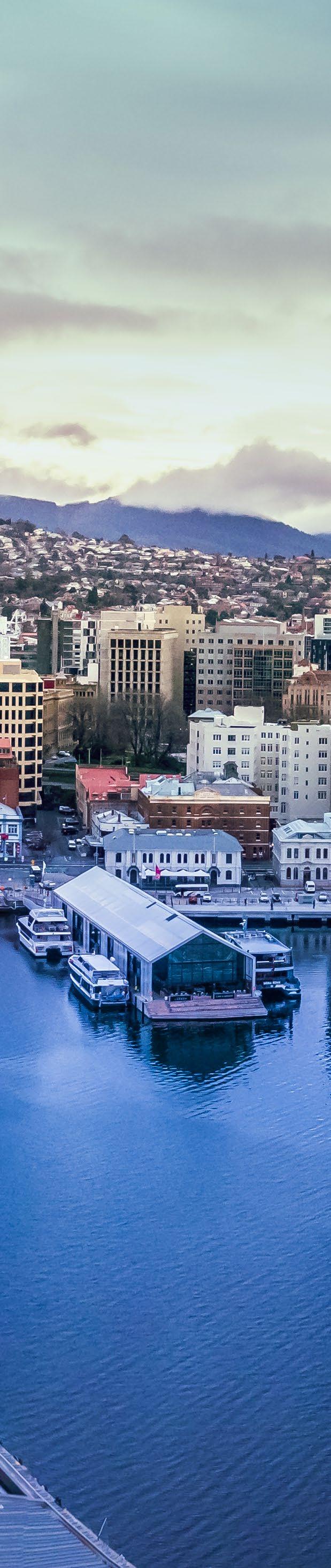
BRANCH UPDATE
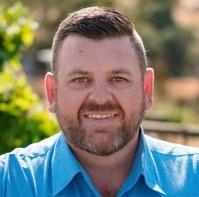
Ben Shaw NECA TAS Member Manager
WELCOME TO T hE FIr ST EDITION OF NECA NEWS FOr 2025. T hIS YEA r , WE’rE PLANNING ON BUILDING ON T hE SUCCESS OF 2024, AND CONTINUING TO DEVELOP A ST rONG ELECT rICAL INDUST rY FOr TASMANIA. OUr ADVOCACY EFFOr TS CONTINUE TO DELIVE r rESULTS, WIT h KEY WINS IN CONTESTABLE WOrKS ACCESS, GOVE rNMENT P rOCUrEMENT FAIrNESS, AND WOrKFOrCE DEVELOPMENT
We’ve held TasNetworks to account on the single-contractor model, securing a narrower scope of work and pushing forward discussions on a legislated ASP Scheme. Our meetings with government, including Deputy Premier Guy Barnett, have strengthened commitments to fairer contracts, streamlined tendering, and stronger ‘buy local’ policies.
Workforce development remains a priority, with funding secured for CPD opportunities and mental health programs. The hi-Vis Army initiative is progressing, with a new trainer appointed and plans underway for a mobile training centre. NECA Women’s Advisory is also growing, with key events planned for International Women’s Day.
I am pleased to say we’ve had a productive start to the year, and I’ll keep you posted with future updates.
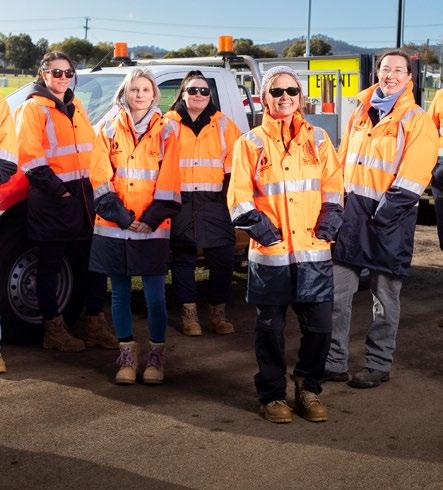
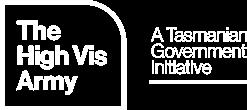
Announcing NECA TAS Women in Electro-Technology Advisory Group
NECA Tasmania is proud to announce that we now have our own Women in Electro-Technology Advisory Group. The objectives of this group are to provide strategic advice to advocate for and promote the interests and advancements of women within the electrical and communications industries.
We received an influx of passionate and dedicated women who were interested in stepping forward to help shape the future of this industry for young women who are looking to start, stay in, or advance a career in this trade.
recently, our first meeting allowed everyone to introduce themselves and begin to map out action items for 2025. NECA Tasmania’s Ben Shaw will provide secretariat support for the group and was on hand to bring the first meeting together. Ben Shaw said, “this is a momentous day for our industry and for us to be supporting, and I think leading, the construction sector in diversity and inclusion. We have found ourselves an extremely passionate and skilled advisory group that represents every aspect of our industry including apprentices, tradespeople, business owners and managers, sponsors and key stakeholders. This group is very well set up to achieve some amazing things and I’m extremely excited to be supporting this initiative.”
Copper Theft on Construction Sites
NECA Tasmania has been alerted to the alarming trend of copper theft impacting construction sites our members are working on, which is having a serious financial impact on our members’ businesses and the productivity and timeframes of delivering projects.
NECA Tasmania’s General Manager Ben Shaw has raised the issue with the Minister for Police, Felix Ellis, and has arranged to meet and consult with the Minister regarding potential solutions to combat this issue. We would like to hear from you if you have been affected by copper theft on sites and to understand the details better, so we can ensure we are relaying the data to the government in the most effective manner. Please contact Ben Shaw via our Member Services team on 1300 361 099 if you would like to share your story or would like more information regarding this matter.
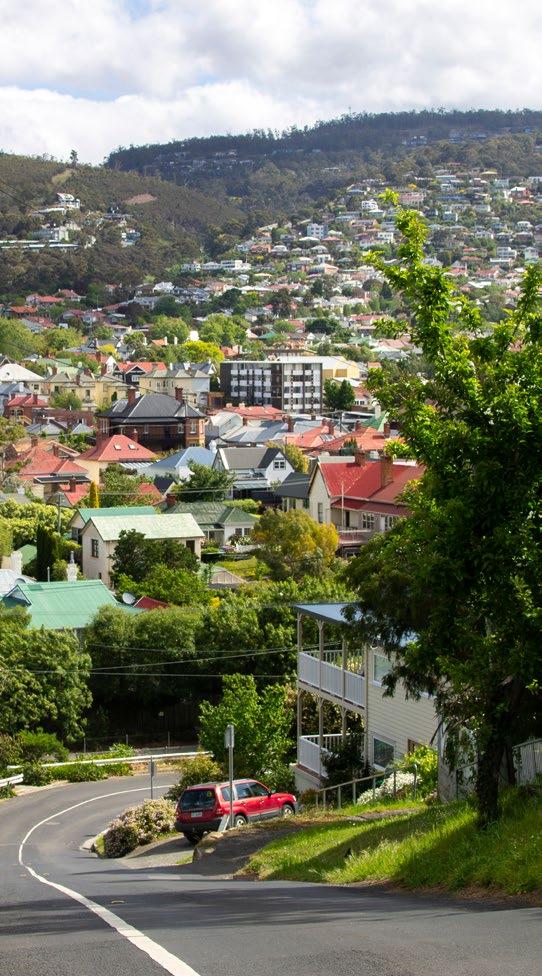
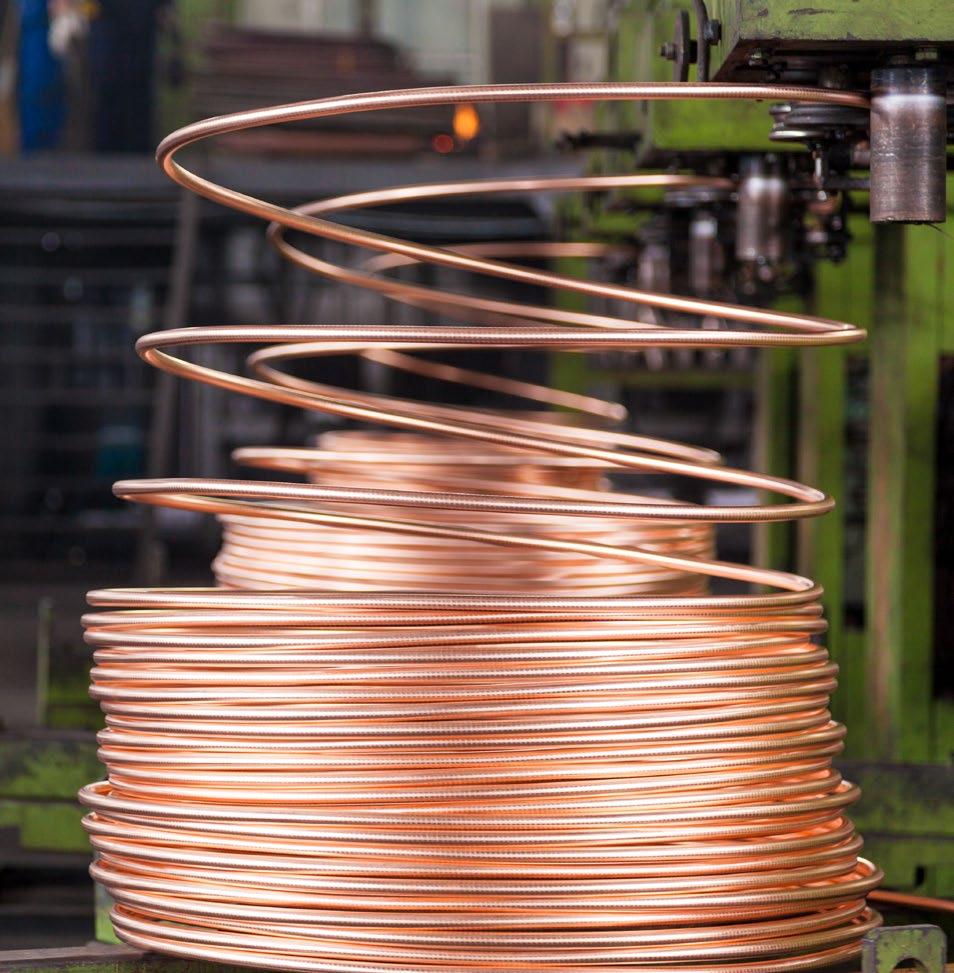
Expression of Interest Now Open for Residential Contractors to Represent the Industry
Expressions of interest for the NECA TAS residential Advisory Group are now open for 2025. The establishment of this group aims to discuss and assess regulation and policy impacting industry, develop recommendations to engage regulators and network operators, promote productivity, offer operational knowledge and procedures, and to provide NECA policy and advocacy advice on topics affecting contractors.
The primary objectives of this group are to:
½ discuss policy and regulatory issues affecting the electrical industry, and to develop solutions to mitigate these concerns;
½ represent the interests and concerns of the industry via participation in industry discussions and decision-making processes;
½ create networking opportunities, by developing a forum aimed at sharing corporate knowledge amongst industry members.
The governance structure of the NECA TAS residential Advisory Group is comprised of:
Chairperson
representative of the group, ensuring all objectives are met
Deputy Chairperson
Support for the Chairperson and expected to step in when the Chairperson is unavailable
Secretary responsible for recording meeting minutes, communications, and record maintenance
Members
Actively participate in discussions and initiatives and advocate for the group’s objectives within their networks
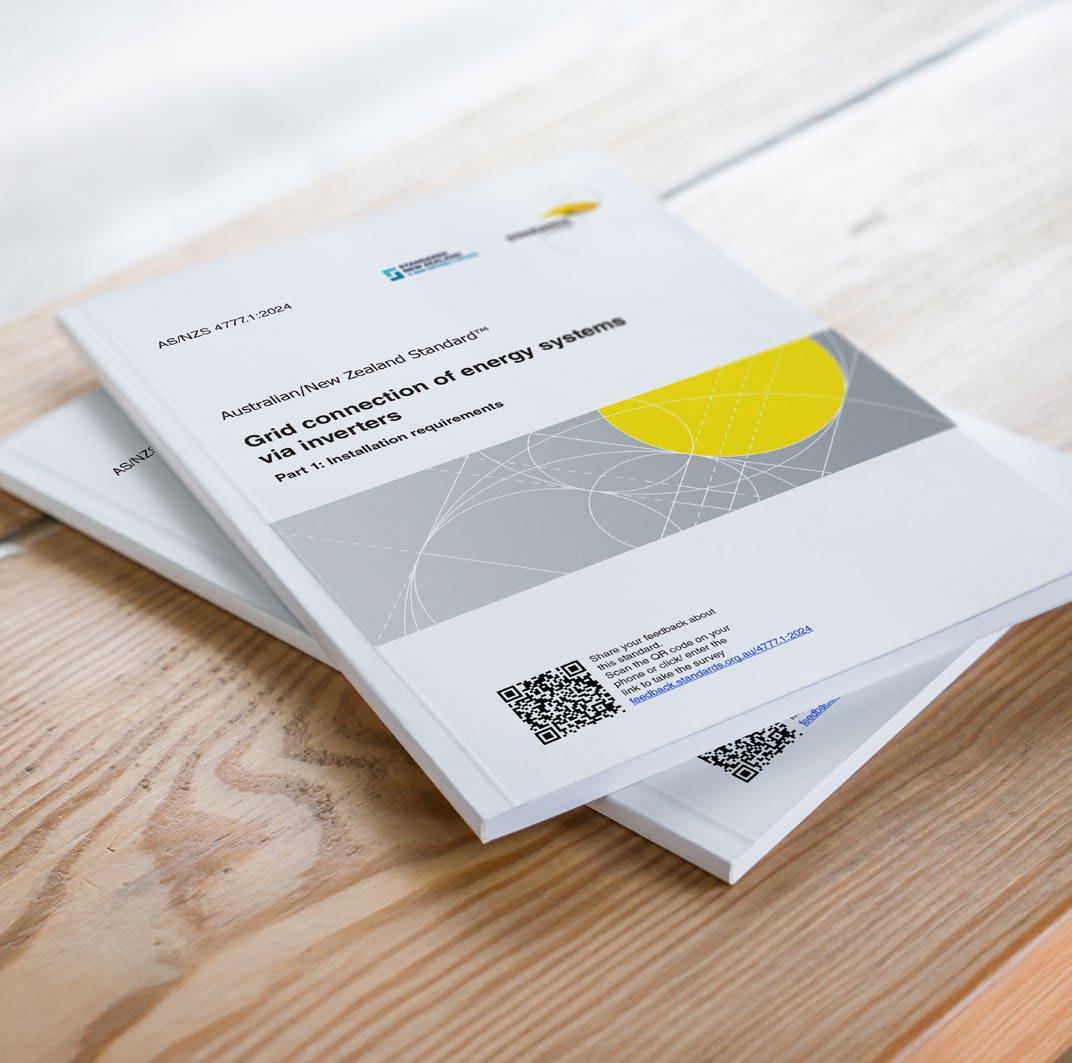
NECA Education and Careers’ renewables courses are on again in March 2025!
Our Design and Install Grid Connected Photovoltaic Systems course will put you and your business on the front foot and give you the skills and knowledge to become a qualified solar photovoltaic (PV) designer and installer. Course dates are 17th to 22nd March.
Design and Install Grid Connected Battery Storage Systems covers the design and practical application of installing battery storage equipment to Power Conversion Equipment (PCE), including the different types of battery storage equipment and PCE and the compliance standards when connecting a battery storage system to the grid. Course dates are 24th to 28th March.
If you would like to register, contact us at trainingtas@necaeducation.com.au. Keystone Tasmania rebates are available for these courses.
AS/NZS4777.1:2024
Commencement Date for TAS
The new addition of Australian/New Zealand Standard AS/NZS 4777.1:2024 Grid Connections of Energy systems via inverters Part 1: installation requirements, was published on August 2024, and will commence in Tasmania on 23 February 2025.
During this six-month transition period, either standard (AS/ NZS 4777.1:2016 or AS/NZS 4777.1:2024) can be applied to grid connection of energy systems via inverter installations, but in either case, the whole standard chosen is to be followed.
For example, if you choose to use the 2016 version, the whole 2016 standard is to be followed; you are not able to use some of the requirements in the 2016 version and some of the requirements in the 2024 version.

INDUSTRIAL MANSLAUGHTER IS NOW A CRIMINAL OFFENCE IN TASMANIA
AS OF 2 OCTOBE r 2024, INDUST rIAL MANSLAUGh TEr IS A CrIMINAL OFFENCE UNDE r T hE WOrK hEALT h AND SAFETY ACT 2012 (TAS) (W hS ACT). T hE AMENDMENTS TO T hE W hS ACT INSE r T A NEW DIVISION 4A, AND T hE OFFENCE OF INDUST rIAL MANSLAUGh TEr IS FOUND IN SECTION 29C.
The introduction of this criminal offence to the WhS Act aims to protect workers on the job from the risk of death caused by negligence on the part of an employer.
The new law does not impose any new duties on a person conducting a business or undertaking (PCBU), or their officers, but creates a new offence for the negligent breach of a duty of care that causes death.
Conviction for the offence of industrial manslaughter carries a hefty penalty for PCBUs or their officers:
½ an individual faces a maximum term of imprisonment of 21 years;
½ a corporation may be fined a maximum penalty of $18 million;
½ A worker who is not an officer cannot be charged with industrial manslaughter.

What is Industrial Manslaughter?
Industrial manslaughter occurs when the death of a worker is caused by the negligent conduct of a PCBU or an officer.
Liability for the offence is established where the following four elements exist:
½ a PCBU or officer have a health and safety duty under the W h S Act; and
½ the PCBU or officer breaches their duty of care; and
½ the conduct causes (or substantially contributes to) the death of an individual to whom the duty of care is owed; and
½ the conduct is grossly negligent or reckless as to the risk of serious injury, illness or death to the individual.
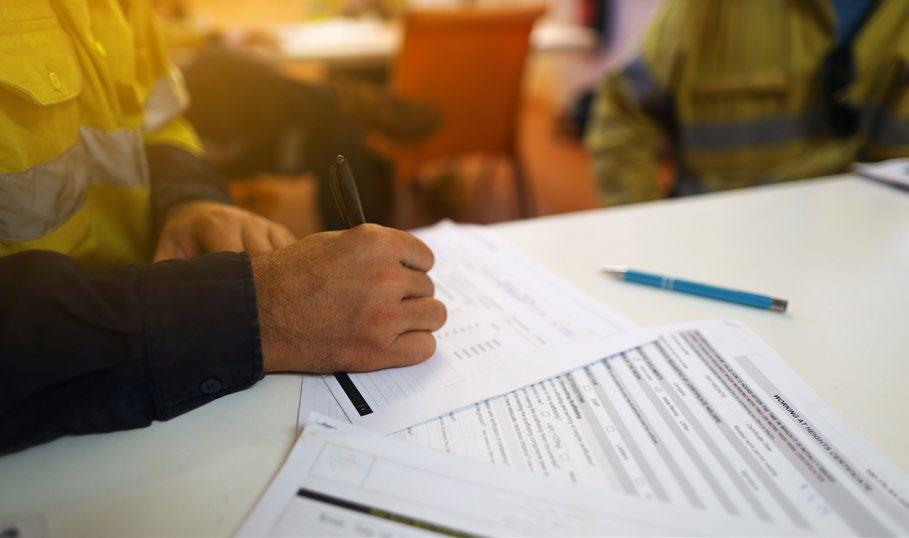
Importantly, there is no time limit on a charge of industrial manslaughter being brought against a PCBU or officer. WorkSafe Tasmania is the authority responsible for prosecuting a charge of industrial manslaughter.
Who is an Officer
An officer is a person who makes (or helps make) a decision that affects either the whole, or a major part, of a business or undertaking, and/or has the capacity to significantly affect the financial standing of the organisation.
What does this mean for members?
Know your duties under the WhS Act. There are specific duties imposed on PCBUs and officers.
Conduct an audit of your WhS policies, Safe Work Method Statements, and other safety protocols, to ensure your safety procedures are compliant and current.
Be vigilant, and exercise due diligence in the operation of your workplaces.
Communicate with your key personnel about the new law. Provide training to staff and officers.
Keep yourselves and your employees up to date with information and practices that keep all of you safe at work.
VIC BRANCH

BRANCH UPDATE
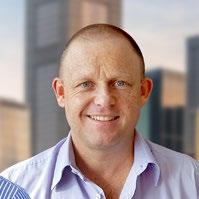
Dean Spicer NECA VIC President
Welcome to 2025! On behalf of NECA Victoria, we extend our warmest wishes for a successful and prosperous year ahead for all our members and the broader electrical industry. With the challenges and triumphs of 2024 behind us, we are excited to embark on another year of growth, innovation, and collaboration.
A Big Thank You to Rob Selymesi
Before we look ahead, we would like to take a moment to thank our departing Executive Director, rob Selymesi, for his outstanding contributions throughout 2024. rob’s contributions have been invaluable, and we wish him the very best in his next venture.
NECA Awards –Celebrate Your Achievements
The NECA Awards portal is now open, offering businesses and individuals the chance to showcase their achievements. Categories span emerging businesses, outstanding safety initiatives, diversity and inclusion efforts, green energy innovation, and excellence in small to large commercial and industrial projects.
We also celebrate women in energy and recognise the exceptional talent of apprentices, highlighting the skills and dedication of the next generation of industry leaders.
The NECA Awards offer a fantastic opportunity to showcase the great work your business does—whether it’s a standout project or what you might consider “just another job.” Every project reflects the hard work, expertise, and dedication that drive our industry forward. Don’t underestimate the value of what you do—your work deserves to be recognised. Submit your entry today and join us in celebrating the diverse achievements that make our industry thrive.
Technical Mentoring Program Extended
We’re thrilled to announce the continuation of the Solar Victoria-funded technical mentoring program. This program, aimed at supporting solar installers and Licensed Electrical Inspectors (LEIs), has proven to be a vital resource for industry professionals.
The program, which is offered free of charge, has now been extended until the end of April 2025. It provides participants with access to expert mentoring, helping to build technical competence, improve safety standards, and ensure compliance with industry regulations.
With strong participation to date, we encourage all eligible installers and inspectors to register and take full advantage of this opportunity. Don’t miss out on this valuable initiative—register your interest today on our website!
Expanding NECA Victoria’s Technical Support Team
As part of our ongoing commitment to supporting members, we are thrilled to announce the expansion of our technical support team with the addition of robbie Nichols. robbie is a third-generation electrician with over 30 years of industry experience. he joins NECA from the Clean Energy Council, bringing with him a wealth of knowledge in energy efficiency, solar, and renewable energy solutions.
robbie has earned a reputation for blending traditional service values with cutting-edge technologies. he is deeply passionate about raising industry standards and is dedicated to supporting installers through technical education and mentoring. his addition to the team reflects NECA’s commitment to providing members with the highest level of expertise and support. We are excited about the positive impact robbie will have on our members and the industry at large.
UPCOMING EVENTS
International Women’s Day Lunch SOLD OUT
A celebration of the incredible women in electrotechnology and why diversity matters.
WorkCover Act: What Employers Need to Know henty’s Lawyers and a BSh hr Consultant will provide guidance on managing workplace injury claims and ensuring compliance with the Compensation Act 2013 (VIC).

Get involved in NECA Victoria’s industry events—whether you’re looking to stay informed, connect with peers, or give back, there’s something for everyone.
Wired for Success: The Balancing Act of Your Business and Wellbeing Your business thrives when you do—prioritise your wellbeing and stay grounded when challenges become overwhelming.
Group Volunteer Opportunity Give back through our group volunteer opportunity—connect, contribute, and make a real impact while supporting a great cause.
NECA Victoria has an exciting lineup of networking, training, and industry events in the coming months. Don’t miss these opportunities to connect, learn, and grow. Scan the Qr code or visit www.bit.ly/necavicevents to find out more and register!

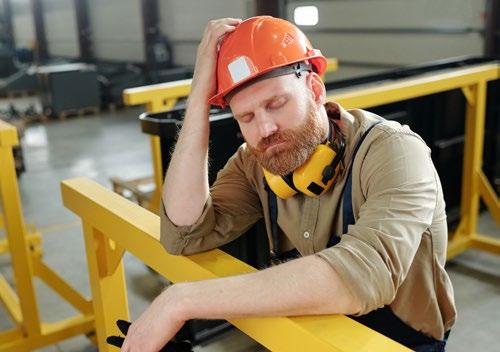
workplace incidents contribute to 15%–23% of workplace accidents annually and cost Australian businesses between $5 billion and $7 billion each year?
More than just feeling tired, fatigue is a serious safety risk that can impact productivity, decisionmaking, and overall well-being.
In a work context, fatigue refers to a state of mental and/or physical exhaustion that reduces a person’s ability to perform tasks safely and effectively. It can result from prolonged or intense mental or physical activity, lack of sleep, and disruptions to the internal body clock.
Recognising the Signs of Fatigue
Fatigue can affect everyone differently, but common signs include:
½ tiredness, even after a full night’s sleep;
½ reduced hand-eye coordination, or slow reflexes;
½ short-term memory issues and difficulty concentrating;
½ blurred vision, or impaired perception;
½ a need for extended sleep on days off.
Wired for Success: Navigating Mental Health Challenges in Your Team
Strong teams start with strong support—foster a mentally healthy workplace to retain top talent and drive success.
NECA Victoria Excellence Awards
Celebrate the industry’s best as we recognise outstanding achievements in electrotechnology
NECA Victoria Summit
The ultimate conference and tradeshow, offering industry updates, expert insights, networking, and innovation—the must-attend event for business owners looking to stay ahead.
THE HIDDEN DANGERS OF
WORKPLACE FATIGUE
Why Fatigue is a Workplace Hazard
Fatigue can increase the risk of accidents and injuries, due to a lack of alertness. It can lead to slower reaction times and poor decision-making, particularly in high-risk tasks such as:
½ operating machinery or driving vehicles;
½ performing precision-based tasks requiring high concentration;
½ working night shifts or irregular hours.
Employers have a legal duty of care to manage fatigue risks in the workplace. If fatigue is identified as a potential hazard, businesses should take proactive steps to reduce the risks.
Fatigue Management: What Employers Can Do
Preventing Harm
½ identify physical and psychosocial hazards related to fatigue;
½ implement measures to reduce excessive work hours and allow adequate rest.
Monitoring
and Early Intervention
½ regularly assess signs of fatigue among employees;
½ provide opportunities for breaks and flexible scheduling where possible;
½ intervene early, to prevent burnout and long-term health impacts.
Supporting Recovery
½ encourage open conversations about fatigue concerns;
½ offer support, through structured rest periods and wellness programs.
Creating a Safer, More Productive Workplace
Fatigue is more than an individual issue—it’s a workplace safety concern. Addressing it proactively helps businesses reduce accidents, improve employee well-being, and create a more productive work environment.
For guidance on managing fatigue in your workplace, or fostering a safer, more productive environment for your team, feel free to connect with NECA Victoria’s hSEQ Plus Manager, Glen Lehner.
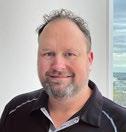
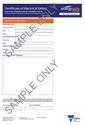
organisational performance.
UPDATE FROM ESV
In Victoria, a Certificate of Electrical Safety (COES) must be issued whenever electrical installation work is completed, and only licensed electrical workers can issue them. A COES provides the customer with a record of the work that’s been completed and assures them that it complies with legislation and safety standards.
Energy Safe is responsible for the sale, acceptance, and overall management of COES. More than 950,000 were certified last financial year (2023-24).
We’re reminding electricians that a COES is a formal document, and the content must be detailed, accurate and clear. Providing sufficient information is vital for inspectors who’ll be checking the work, COES auditors, and investigators, should something go wrong.
Only a rEC can perform electrical installation work for gain or reward. This means a LEW who is engaged to perform paid electrical installation work for a customer must issue the COES under a rEC registration.
A LEW can raise a COES under their own electrical licence when they have performed electrical installation work for no gain or reward. Their licence appears as the responsible Person.
Examples include electrical installation work:
MIKE PURNELL - Protect Group Director Employer Representative
One question we’re asked about COES is who should be listed as the responsible Person. The responsible Person identifies either the registered Electrical Contractor (rEC) or Licensed Electrical Worker (LEW) who is responsible for the work that’s listed.
½ performed on the LEW’s own property;
½ performed for no gain or reward for a family member or friend;
½ when employed as an electrician by a non-r EC and working on the employer’s site (e.g. factory, hospital);
½ when a LEW holds a r estricted Electrical Licence (r EL) and is employed by a non-r EC business (e.g. air-conditioning, refrigeration).

Anyone who has obtained an electrical licence through Mutual recognition, must apply for a rEC registration or be working for an rEC to issue a COES when doing electrical work for gain or reward.
Recording the Correct Licence or REC Registration
A COES is allocated to the rEC or licence number when it is obtained from Energy Safe.
Anyone who has bought certificates under the wrong licence or rEC should email us at coes@energysafe.vic.gov.au to request a transfer (unused certificates only).
You’ll find more information about the COES system on the Energy Safe Victoria website.

Leanne Hughson ESV Chief Executive Officer www.esv.vic.gov.au
severance contributions are defined your industrial agreement, choosing the security Protect provides the surety that your business competitive in recruiting the best trades staff.
When severance contributions are defined in your industrial agreement, choosing the security of Protect provides the surety that your business is competitive in recruiting the best trades staff.

Enhancing your employee value proposition through a Protect account provides workers financial security and stability, increasing engagement, retention and organisational performance.
Enhancing your employee value proposition through a Protect account provides workers with financial security and stability, increasing engagement, retention and organisational performance.
MIKE PURNELL - Protect Group Director Employer Representative
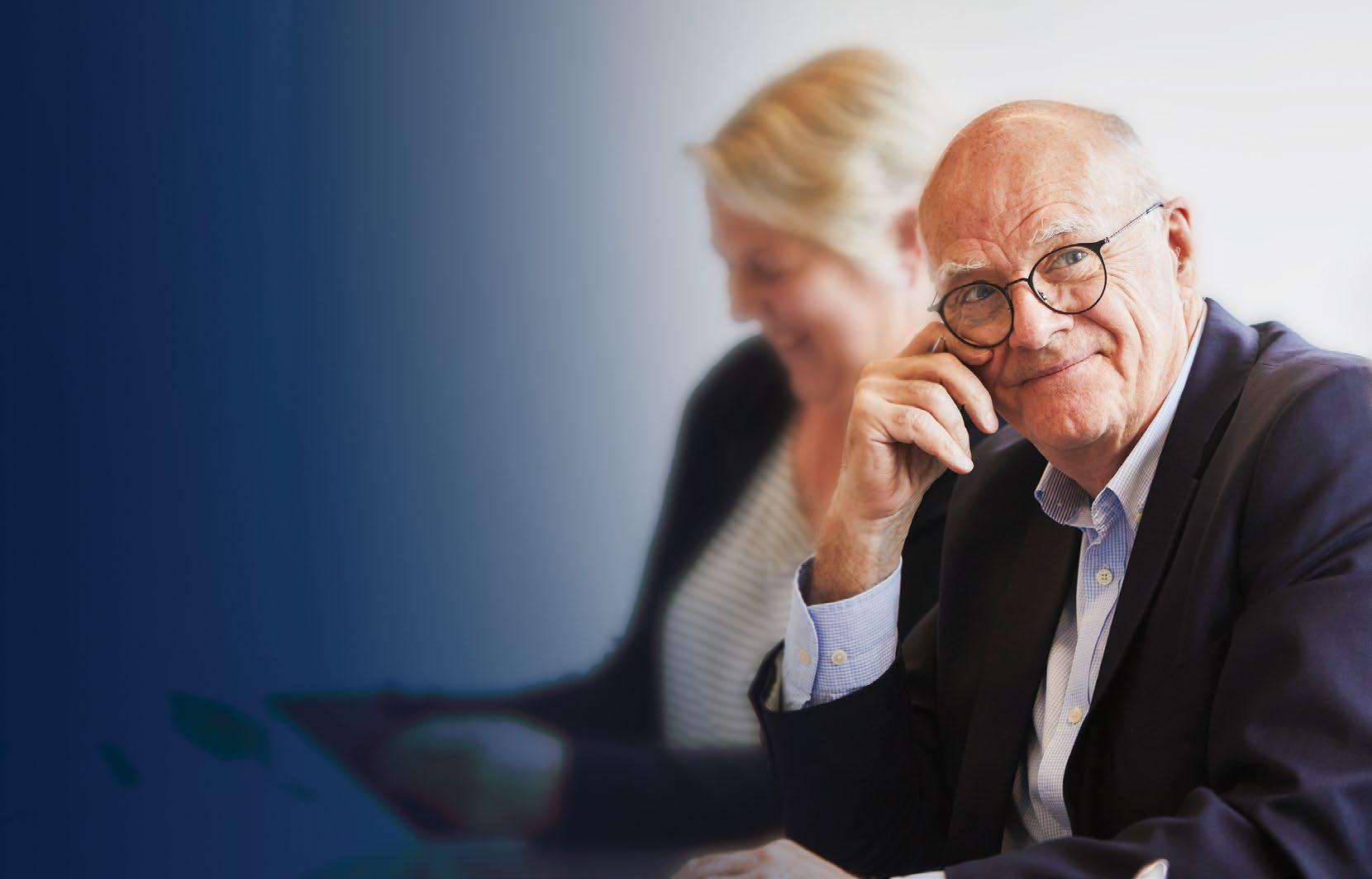
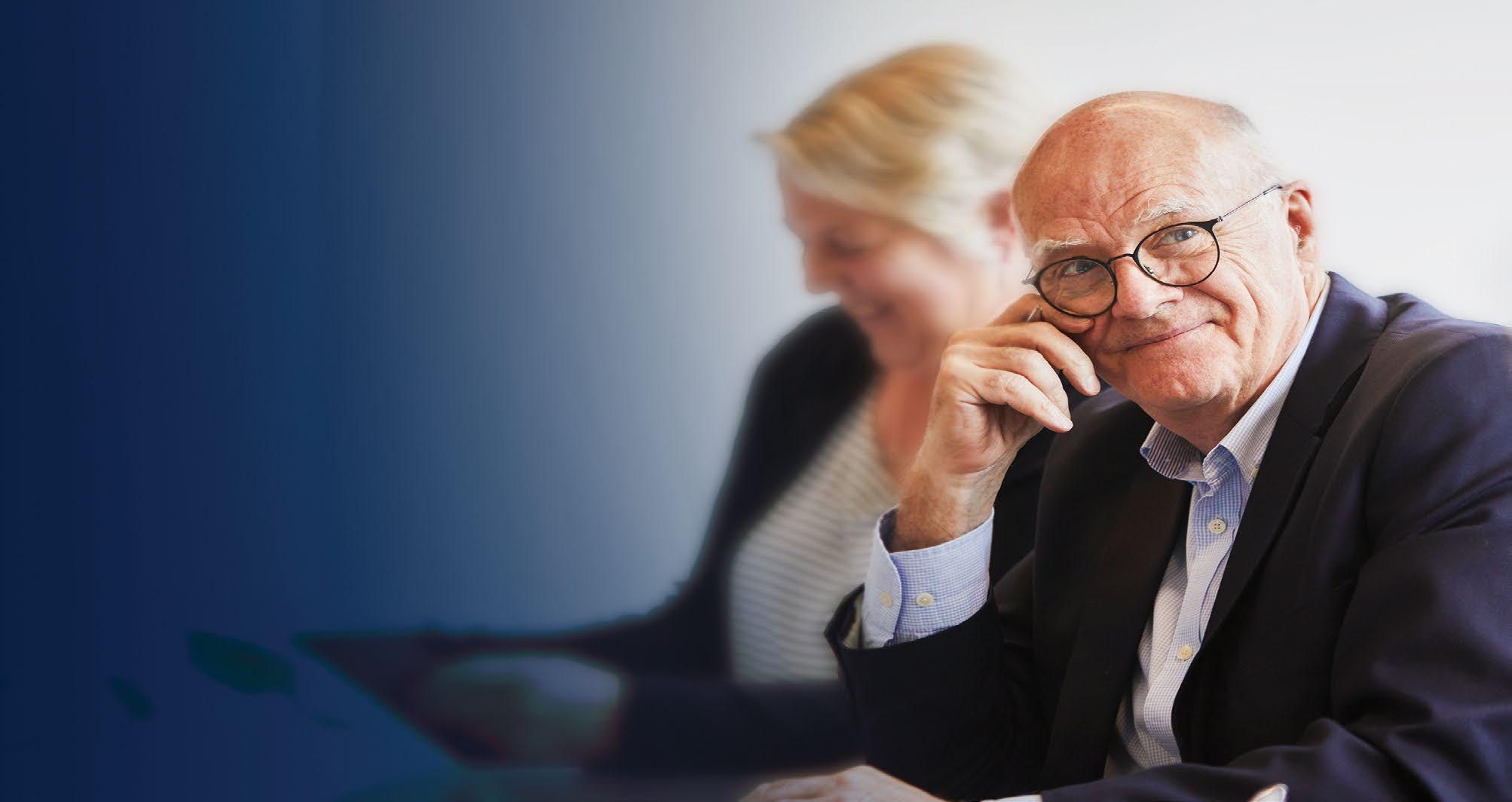
ADDRESSING AGEISM IN THE WORKPLACE
March is a month to celebrate inclusion, diversity, and equity, especially with International Women’s Day— and at NECA Vic, we also recognise the value of age diversity in the workplace. Ageism remains a challenge in many industries, including electrotechnology, where mature-aged workers offer experience, stability, and mentorship. Addressing this isn’t just about fairness—it strengthens businesses and the industry.
In many workplaces across Australia, including the electrotechnology sector, ageism remains a silent but pervasive form of discrimination. This issue often sidelines older workers, despite their wealth of experience, reliability, and knowledge—a problem that our industry can no longer afford to ignore.
Understanding Ageism
Ageism includes negative stereotypes and attitudes, and discrimination against individuals based on their age. For older workers, this often manifests in hiring biases, limited training opportunities, or assumptions about their ability to adapt to new technology or methods.
According to recent reports, ageism is ‘endemic’ in many workplaces, subtly influencing decisions and creating barriers for older employees. This not only undermines individual careers, but also stifles diversity and innovation within teams.
The Impact on the Electrotechnology industry
The electrotechnology industry is uniquely positioned to combat ageism and benefit from retaining and hiring mature aged workers. These professionals bring:
Extensive Experience
Mature aged workers have years of hands-on experience and deep technical knowledge, which is invaluable in a field requiring precision and problem-solving.
Workplace Stability
Their proven reliability and commitment can contribute to consistent project delivery and reduce turnover in a high-demand industry.
Mentorship Potential
Mature aged workers can pass on their expertise, fostering skill development in younger team members and creating a culture of collaboration and knowledge sharing.
Adaptability to Industry Demands
Contrary to stereotypes, mature aged professionals often adapt well to new technologies when provided with appropriate training, which is critical in an industry continually evolving with advancements.
Much-needed Teaching Capability
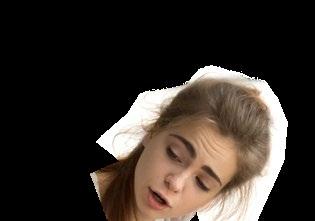

here are some actionable steps to foster an age-inclusive workplace:
1. Embrace Training and Upskilling
Provide ongoing opportunities for older workers to learn new technologies and methods, showcasing their adaptability.
2. Promote Inclusive Recruitment
Evaluate hiring practices to ensure they’re free from age bias.
Mature-aged electricians can help address teacher shortages in vocational training, using their experience to educate and upskill the next generation of apprentices, while also reducing the backlog in training the electrotechnology industry is currently facing.
Yet, mature aged workers often face stereotypes that they are resistant to change, lack physical capability, or are less tech-savvy. These misconceptions can result in missed opportunities for both employees and employers.
Challenging Age Discrimination
Creating a workplace that values and respects employees of all ages requires intentional planning and support. By addressing ageism head-on, employers can unlock the full potential of their workforce, enhance team collaboration, and future-proof their business.
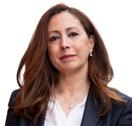
3. Recognise the Value of Experience highlight the contributions of seasoned professionals within teams.
4. Encourage Crossgenerational Collaboration
Foster an environment where workers of all ages can share knowledge and support one another.
The NECA Vic hr and Wr team is by your side to help create a workplace that values and respects employees of all ages. Whether it’s developing workforce strategies, ensuring fair recruitment practices, or delivering training programs to upskill employees for industry demands, they can help your business turn age diversity into a strength, not a challenge. Contact us on 1300 300 031 to unlock the full potential of your workforce.
Lina Altarifi Executive Director of Business Solutions Hub
ACRS NEWS
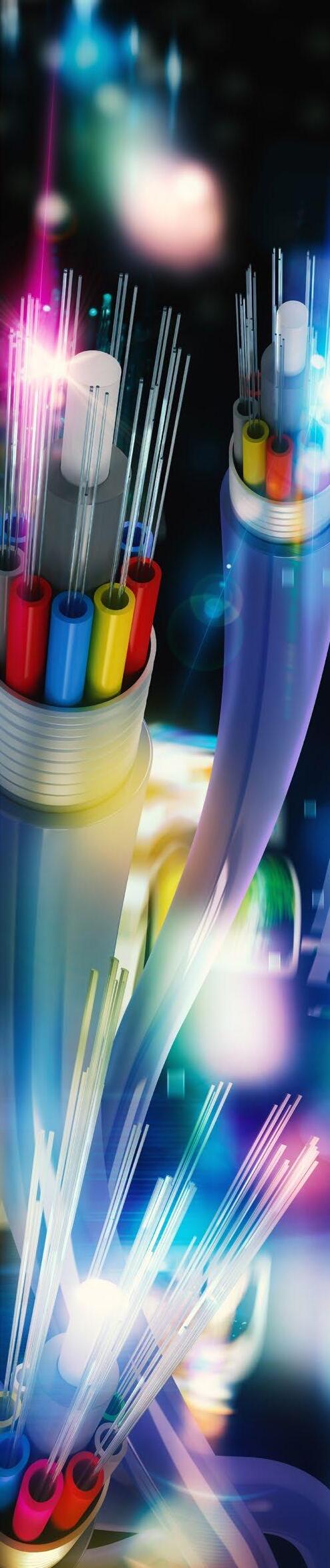
DIRECTOR’S REPORT
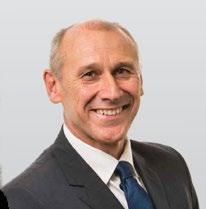
Peter Lamont
Director ACRS and Senior Policy Advisor peter.lamont@neca.asn.au
WELCOME TO T hE FIr ST EDITION FOr 2025. WE A rE
AL rEADY WELL INTO W h AT h AS BEEN A LONG, hOT SUMME r , WIT h A NUMBE r OF CLIMATIC Ch ALLENGES AND NATUr AL
DISASTE r S T h AT h AVE DIrE CONSEQUENCES FOr OUr TOWNS AND Ch ALLENGE CrITICAL INF r AST rUCTUrE WIT hIN
OUr INDUST rY. WE h AVE SEEN EXT rEME TEMPE r ATUrES, SEVE rE BUS hFIrES, AND CONTINUOUS DOWNPOUr S, T h AT LEAVE DEVASTATING FLOODS IN T hEIr WAKE.
In our modern era, communications infrastructure is a critical means of relaying information and calling for assistance when it is needed. That is why our data and telecommunications workers are so essential to the building blocks that maintain people’s contacts, wherever they live or work, including people in regional and remote locations.
If you work in regional and remote locations, it is also important that you ensure potential customers know what work you can do and how to contact you. One of the best ways to do this is to list your business on the Australian r egistered Cablers website.
AC r S is one of the cabler registration companies that makes active use of this site, which is a searchable website that lists cablers by geographic location. It is available to the public,
and companies such as the NBN Co, Telstra, Optus, TPG, iiNet, the Australian Communications and Media Authority (ACMA) refer consumers to the site, resulting in over 36,000 unique visitors per annum, looking for cablers. Contact AC r S and our helpful staff can assist you with details on how to get your business listed.
At this time, AC r S is also working with the national regulator, ACMA, on a range of regulatory compliance matters. These include matters relating to compliance investigations and also legislative and regulatory change proposals. In all these matters, AC r S seeks to represent the best interests of registered cablers and to ensure that the cabler industry has a voice when talking to government.
I think this year is going to be busy but fruitful!

IS YOUR BUSINESS COMPLIANT FOR CABLING?
ACRS WORKS WITH ACMA ON A RANGE OF COMPLIANCE MATTERS
IS YOUR BUSINESS COMPLIANT FOR CABLING?
The Australian Communications and Media Authority (ACMA) is the regulator within the data and telecommunications industry. AC r S continually works with ACMA on compliance matters and legislative and regulatory responses.
Thinking about a move into data and communications as a way to diversify your contracting business? Here are a few critical questions to ask before you get started.
Thinking about a move into data and communications as a way to diversify your contracting business? Here are a few critical questions to ask before you get started.
Am I registered to do the work?
Am I registered to do the work?
In recent investigations by ACMA into complaints regarding the standard of cable work, two primary areas of investigation were identified, namely: cablers not being qualified, or; cablers not following the Cabler Wiring r ules (S009). The main complaints to ACMA relate to cablers:
cabling work without being registered?
The ACMA has a range of options available to enforce compliance. These include: formal warnings; non-compliance notices to the
The ACMA has a range of options available to enforce compliance. These include: formal warnings; non-compliance notices to the
In Australia, all cabling work, including telephone, data, fire and security alarm system cabling, that connects with the telecommunications network must be performed by a registered cabler, or under the direct supervision of a registered cabler.
½ providing inadequate depth of conduit;
In Australia, all cabling work, including telephone, data, fire and security alarm system cabling, that connects with the telecommunications network must be performed by a registered cabler, or under the direct supervision of a registered cabler.
½ inappropriately bundling data cables with electrical cables;
What is required to become a registered cabler?
What is required to become a registered cabler?
½ using non-compliant cables;
½ not completing TCA1 forms.
To become a registered cabler you must complete the appropriate training course for the work to be undertaken through a Registered Training Organisations (RTO).
To become a registered cabler you must complete the appropriate training course for the work to be undertaken through a Registered Training Organisations (RTO).
An Open Registration is required for commercial and domestic premises work. For work in domestic premises you only require a Restricted Registration.
All cablers need to be aware that the Cabler Wiring r ules (S009) have been designed to keep both cablers and customers safe and to provide reliability of service and they are
An Open Registration is required for commercial and domestic premises work. For work in domestic premises you only require a Restricted Registration.
You must also have a minimum of 80 hours cabling experience for Restricted
You must also have a minimum of 80 hours cabling experience for Restricted
verify a cabler’s eligibility for registration.
verify a cabler’s eligibility for registration.
Do all my staff need to be registered?
Do all my staff need to be registered?
result in disconnection from the network; telecommunications infringement notices
result in disconnection from the network; telecommunications infringement notices
action, which may result in a conviction

action, which may result in a conviction
mandatory. To not follow S009 could result in unfortunate consequences, including injury to persons or property, prosecutions by the regulator, insurance claims not being allowed, litigation, and even loss of your registration – and therefore your livelihood. Bundling data and telecommunications cables with electric cables is particularly dangerous,
No. To ensure compliance with the ACMA guidelines, cablers must be either registered or, directly supervised at all times by a cabler who is registered for the type of work being done.
No. To ensure compliance with the ACMA guidelines, cablers must be either registered or, directly supervised at all times by a cabler who is registered for the type of work being done.
as it can result in electrical induction, that would electrify the data cable.
The biggest consequence is that, should anything go wrong or your work is found to be faulty, your business insurance is unlikely to cover you. This could lead to litigation and substantial financial loss for your business.
The biggest consequence is that, should anything go wrong or your work is found to be faulty, your business insurance is unlikely to cover you. This could lead to litigation and substantial financial loss for your business.
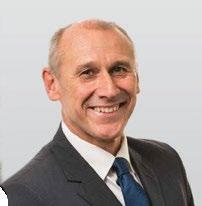
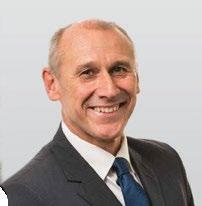
ACMA is also currently calling for submissions on priorities for compliance for 2025-26 and is finalising consultation on the sunset review of the Cabler Provider r ules (CP r). AC r S is providing ACMA with comments on each of these matters.
Not being registered is not worth the risk.
Not being registered is not worth the risk.
Peter Lamont Director, ACRS
Peter Lamont Director, ACRS

Cabling Registration run
by
Cabling Registration run by the industry, for the industry
Cabling Registration run by the industry, for the industry
Cabling Registration run by the industry, for the industry
Cabling Registration run by the industry, for the industry
Cabling Registration run by the industry, for the industry
Cabling Registration run by the industry, for the industry
the industry, for the industry
The Australian Cabler Registration Service (ACRS) provides a fast, reliable and low-cost registration service for the electrical and communications industry.
The Australian Cabler Registration Service (ACRS) provides a fast, reliable and low-cost registration service for the electrical and communications industry.
The Australian Cabler Registration Service (ACRS) provides a fast, reliable and low-cost registration service for the electrical and communications industry.
The Australian Cabler Registration Service (ACRS) provides a fast, reliable and low-cost registration service for the electrical and communications industry.
The Australian Cabler Registration Service (ACRS) provides a fast, reliable and low-cost registration service for the electrical and communications industry.
The Australian Cabler Registration Service (ACRS) provides a fast, reliable and low-cost registration service for the electrical and communications industry.
Peace of mind costs less than 60c a week! Register with ACRS and reap the benefits of being with the only Australian electrical specialist registry while avoiding a hefty fine.
Peace of mind costs less than 60c a week! Register with ACRS and reap the benefits of being with the only Australian electrical specialist registry while avoiding a hefty fine.
Peace of mind costs less than 60c a week! Register with ACRS and reap the benefits of being with the only Australian electrical specialist registry while avoiding a hefty fine.
Peace of mind costs less than 60c a week! Register with ACRS and reap the benefits of being with the only Australian electrical specialist registry while avoiding a hefty fine.
Peace of mind costs less than 60c a week! Register with ACRS and reap the benefits of being with the only Australian electrical specialist registry while avoiding a hefty fine.
Peace of mind costs less than 60c a week! Register with ACRS and reap the benefits of being with the only Australian electrical specialist registry while avoiding a hefty fine.
It is illegal for anyone other than a registered cabler to install or maintain cabling that connects to the telecommunications network. So if you are installing any equipment that will connect to the network – from smart home systems to extra phone lines –you need a current cabling registration.
It is illegal for anyone other than a registered cabler to install or maintain cabling that connects to the telecommunications network. So if you are installing any equipment that will connect to the network – from smart home systems to extra phone lines –you need a current cabling registration.
Peace of mind costs less than 60c a week! Register with ACRS and reap the benefits of being with the only Australian electrical specialist registry while avoiding a hefty fine.
Peace of mind costs less than 60c a week! Register with ACRS and reap the benefits of being with the only Australian electrical specialist registry while avoiding a hefty fine.
It is illegal for anyone other than a registered cabler to install or maintain cabling that connects to the telecommunications network. So if you are installing any equipment that will connect to the network – from smart home systems to extra phone lines – you need a current cabling registration.
It is illegal for anyone other than a registered cabler to install or maintain cabling that connects to the telecommunications network. So if you are installing any equipment that will connect to the network – from smart home systems to extra phone lines – you need a current cabling registration.
It is illegal for anyone other than a registered cabler to install or maintain cabling that connects to the telecommunications network. So if you are installing any equipment that will connect to the network – from smart home systems to extra phone lines – you need a current cabling registration.
It is illegal for anyone other than a registered cabler to install or maintain cabling that connects to the telecommunications network. So if you are installing any equipment that will connect to the network – from smart home systems to extra phone lines – you need a current cabling registration.
Carrying a current cabling registration card confirms you have completed the relevant training and gained the professional experience to complete the work to the customer’s expectations.
Carrying a current cabling registration card confirms you have completed the relevant training and gained the professional experience to complete the work to the customer’s expectations.
It is illegal for anyone other than a registered cabler to install or maintain cabling that connects to the telecommunications network. So if you are installing any equipment that will connect to the network – from smart home systems to extra phone lines – you need a current cabling registration.
It is illegal for anyone other than a registered cabler to install or maintain cabling that connects to the telecommunications network. So if you are installing any equipment that will connect to the network – from smart home systems to extra phone lines – you need a current cabling registration.
For more information visit www.acrs.com.au or call 1300 667 771.
For more information visit www.acrs.com.au or call 1300 667 771.
Carrying a current cabling registration card confirms you have completed the relevant training and gained the professional experience to complete the work to the customer’s expectations.
Carrying a current cabling registration card confirms you have completed the relevant training and gained the professional experience to complete the work to the customer’s expectations.
Carrying a current cabling registration card confirms you have completed the relevant training and gained the professional experience to complete the work to the customer’s expectations.
Carrying a current cabling registration card confirms you have completed the relevant training and gained the professional experience to complete the work to the customer’s expectations.
Carrying a current cabling registration card confirms you have completed the relevant training and gained the professional experience to complete the work to the customer’s expectations.
Carrying a current cabling registration card confirms you have completed the relevant training and gained the professional experience to complete the work to the customer s expectations.
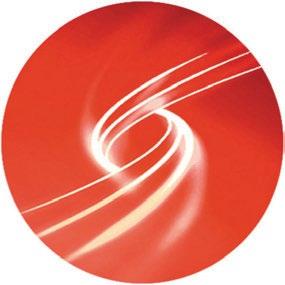
NATIONAL TECHNICAL UPDATE
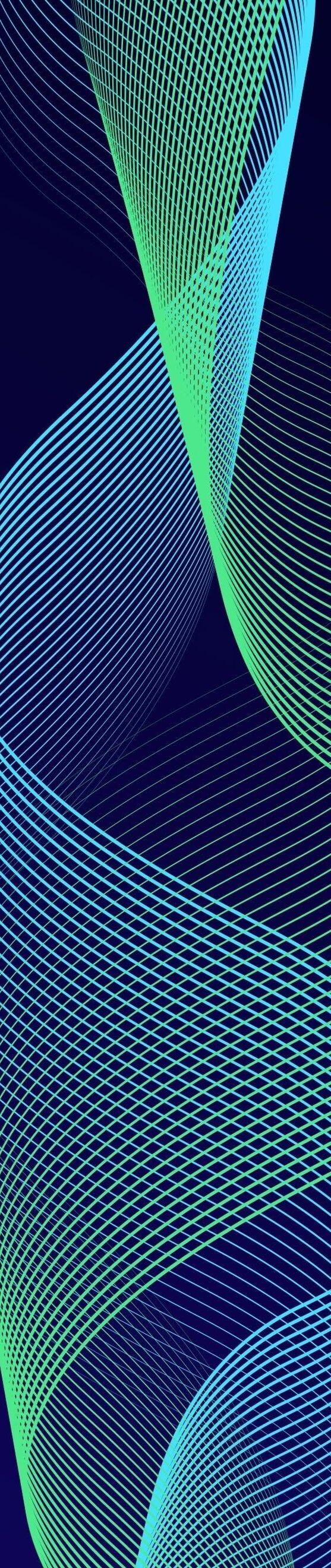
DNSPs TO DSOs
HOW WILL THE TRANSITION AFFECT INSTALLERS?
OUTLINE
Much has been discussed and contemplated recently about the transition to renewable energy sources and the electrification of our society. Ambitious targets are being set, and investments in large scale infrastructure (renewable generation, storage, and supporting transmission assets) are underway in an attempt to secure reliable electricity supply capacity, in the wake of retiring base load capacity.
Much has also been made of the benefits of smaller scale local generation and storage capacity to the electrification project.
Squeezed in between the bulk supply points and the consumer are the Distribution Network Service Providers (DNSP’s), facing genuine challenges with respect to bi-direction power flows, worker and consumer safety, reliability, voltage stability, and all the rest.
WHAT IS A DISTRIBUTION SYSTEM OPERATOR?
A distribution system operator (DSO) is a method of operation that evolved from modern distribution network operators to actively balance power inputs and outputs, by integrating a diverse range of distributed energy resources into the grid. Because the DSO is a model of operation, they are not necessarily singular organisations (although they can be) but they still serve many of the same distribution functions.
This enables DSOs the flexibility and control required to be active
in power flow management. Though it should be noted that the definition and responsibilities of the DSO are still evolving, as they become prominent.
DSOs share many of the same responsibilities as distribution network operators, but there is an emphasis on the active, data-driven balancing of supply and demand.
The traditional DNSP approach managed the one-way flow of electricity from large, centralised generators to consumers.
For the most part those DNSPs have historically been able to ‘set-and-forget’ their low voltage assets and trust that, with an effective maintenance regime, the reliability and quality of the power supply would be fine, even with some solar and other consumer energy resources connected.
DNSPs are now facing the challenge of managing multiple energy generators/sources, with diverse capacity and output characteristics, intermixed with their traditional customer base, and with the potential to adversely affect local reliability and quality of supply.
Many DNOs are currently examining their transition to the DSO model, due to the need:
½ to improve efficiency and costeffectiveness in planning;
½ to comply with power quality and safety obligations;
½ to meet demands for greater penetration of DE r /CE r
FUTURE INTERACTIONS BETWEEN
DISTRIBUTION SYSTEM OPERATORS AND THE CUSTOMERS’ INSTALLATION
The rapid uptake of solar installations in Australia has largely evolved with relatively basic mechanisms in place to protect the service wires to installations and prevent overvoltage problems on local networks; specifically, by placing an upper limit on export capability and disconnecting individual inverters at the point where those inverters detect predetermined voltage thresholds at their terminals. Fundamentally, the inverter operates without input from the network operator after installation.
With the capabilities available in modern inverters, there are greater opportunities available for DNSP’s to access inverter information and/or control its output (directly or via third party aggregators) and for consumers to export at preferred times and/or offer other services to the local DSO and be compensated for those services.
however – the ability of DSOs and/ or third- party aggregators to access inverter settings and/or assert some control in real-time requires:
½ standard communications platforms and protocols;
½ appropriate information and market offerings to consumers/prosumers.
On the technology front, there has been a considerable amount of work undertaken to produce standard processes for the registration and near-real-time management of residential and small commercial or industrial CEr /DEr installations.
This has resulted in a guide (CSIPAus)1 that is already being used to implement new connection offerings to CEr owners in some DNSP areas. This protocol also appears to be basis on which the national CEr taskforce2 intends to base the key enabling infrastructure3 to secure the communication pathways between a utility, retailer or aggregator, and CEr devices.
CER LIFECYCLE
Direct Intervention
Intervetion by Influence
½ Identify compliance issue
½ Find earliest point to remediate
½ Implement compliance initiative
Intervetion by Influence
CURRENT IMPLEMENTATIONS OF CSIP (AUS)
Dynamic Export SA and QLD
Allows power utilities to give solar owners access to a higher average export limit, with the condition that solar may be temporarily reduced during “minimum demand” events.
Dynamic Import QLD
Enables power utilities to reduce total grid consumption of customer sites, by throttling loads like EV Chargers during periods of extreme demand in the grid.
Solar Emergency Backstop VIC
Provides a mechanism for power utilities to perform emergency disconnection of solar PV during periods of high production and low demand in the grid.
EV Load Control QLD
Enables power utilities to throttle down or disconnect EV Chargers, to protect the grid during high-stress periods. Currently implemented in QLD.
There is, however, a significant hurdle to the successful integration and potential benefits of CEr to DSO management, which is rates of non-compliance.

FOR CER INSTALLATIONS
There has been a substantial amount of observation and evidence to indicate that many CEr installations have historically, and are currently, not being installed correctly. Various jurisdictions are indicating well in excess of half of new installations are non-compliant.
As the AEMC 2023 report4 notes
“The high level of non-compliance means that key power system security requirements, such as voltage disturbance ride through for rooftop solar systems, are not implemented. The scale of noncompliance of current standards also casts doubt on the NEM’s ability to implement future CEr technical standards, unless changes are made.
Non-compliance affects all electricity consumers, whether they own CEr devices or not.”
The report goes on to indicate that incorrect inverter installation/setup and firmware configuration are major contributors to non-compliance.
NON-COMPLIANCE
The same report makes several recommendations with respect to addressing CEr non-compliance, two of which are detailed below.
Recommendation 8:
DNSPs to introduce a commissioning process to better standardise the process across the NEM for verifying correct device installation before connecting new CER devices to the grid.
And,
Recommendation 11:
Subsidised re-configuration of non-compliant devices by local jurisdictions.
Note 1 this was modified to restrict those subsidises to CER equipment installed and registered before a specific date.
Note 2 in many cases inverter OEM’s will be able to assist with remote assessment and updates to achieve compliance.
We’re now seeing DNSPs and/ or their local energy regulators advance policies and strategies to achieve much higher levels of compliance for new installations and address non-compliance of historical installations, in keeping with these recommendations and in recognition of their shared interest in being able to manage the inputs onto their network, to increase the opportunity for CEr exports and otherwise prevent risk to the network.
The practical outcome of this will be a need for retailers/installers of equipment to be fully aware of the conditions specified by the DNSP applicable to the installation (region settings, demand response modes, emergency backstop provisions, etc) and evidence required by the network prior to commissioning. They will also need to consider how to achieve the correct registration and configuration for the equipment on the correct platform.
The DNSPs are also likely to initiate programs to actively detect noncompliant installations via export/ meter data (with owners of that CEr equipment to be advised of options to address the non-compliance) and/ or initiating actions to prevent noncompliant installations negatively impacting their network or quality of supply to other customers.
Original retailers and installers of CEr equipment are also likely to be contacted for assistance when/if the DNSP identifies systems as non-compliant.
In short, the days of ‘set and forget’ for installations with small/medium export capability are coming to an end, and the installers that can get it right first time will excel, and those that can’t/don’t will likely be uncovered by the DNSP processes.

Neil Roberts Director of Policy, Technical and Safety
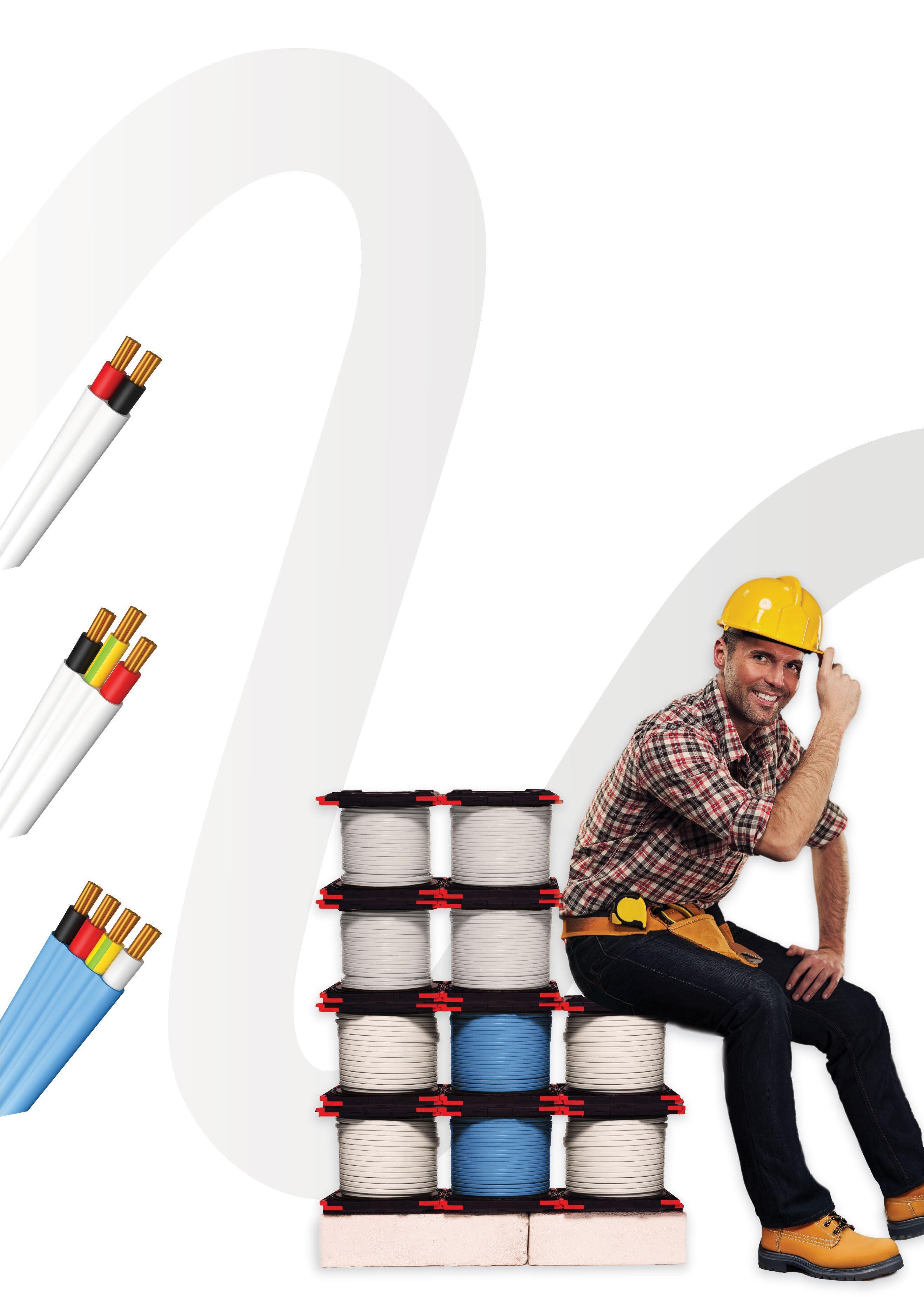
OUR REGIONS THE KEY TO POWER IN AUSTRALIA

ABOUT 15 YEA r S AGO, I FOUND MYSELF Ch ATTING WIT h A ‘COCKIE’, W hO CUT hIS TEET h IN T hE SOUT h WEST OF WA. ALWAYS WOrE BLUE KING GEES, COULDN’T USE A SMA r T P hONE, BUT COULD COMPLETELY rEWIrE A BALING MAChINE F rOM GE rMANY WIT h hIS EYES CLOSED. hE TOOK GrEAT P rIDE IN EXPLAINING hOW hE’D Dr AWN OUT A SChEMATIC ON A PIECE OF BrOWN PACKING PAPE r AND GOT IT WOrKING AS IT ShOULD h AVE. ALL T hE DEGrEES IN T hE WOrLD WOULDN’T h AVE GOT T h AT MAChINE WOrKING (A rGUABLY, T hEY’D AL rEADY BLOWN IT F rOM T hE FACTOrY ACCOrDING TO MY NEWFOUND MATE). BUT A T r ADIE WIT h A SOLID BACKGrOUND, AND YEA r S OF DOING T hE h A rD YA rDS, KNEW W h AT TO DO.
That kind of tradesperson is sadly declining. We’ve focused on training in the metro areas, and while some large country towns around Australia have state-of-the-art training facilities, the trainer shortage around the country is acutely felt in the regions. The cost, both financially and socially, to send apprentices to the ‘big smoke’ to undertake the off-the-job training part of their apprenticeship is clearly not working. It’s certainly not benefitting the regional communities, especially those who are now being asked to bear the brunt of helping Australia transition away from fossil fuels.
Last year I was privileged to attend the Developing Northern Australia conference, held in the WA power town of Karratha. Built on the back of fossil fuels, Karratha is living the paradigm shift, where Australia, and the rest of
the world, still needs natural gas to get us to Net Zero. Gas line workers are a small but dedicated workforce. Instrumentation and process control workers, sparkies who have upskilled from their base trades to be able to keep the gas moving, join the myriads of sparkies who have also upskilled in large scale solar and wind. Most of this work is in the regions. The reality is, we put these plants in areas where people don’t live in any great density.
The regions, especially those in the ‘north’, are key to our economic future, where a clean and renewable energy workforce will ply their trades. We can’t forget though the farmers, the
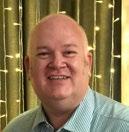
communities and remote workers supporting them, and the hard truth that we need to invest in training across our country. Without local tradies, the 2030 and 2050 targets become almost impossible to achieve.
It has been encouraging to see the wholesale support of TAFEs and Industry Training Providers by government both state and federal. With the future of Australia’s Clean Energy Future, we need to build on that support, encouraging the current generation of energy workers to think about how they can support training, not just in the ‘big smoke’, but across our beautiful country.
Steve Hall GM Projects - Powering Skills Organisation Ltd

nVent ERICO Cadweld

nVent ERICO Mechanical Connections
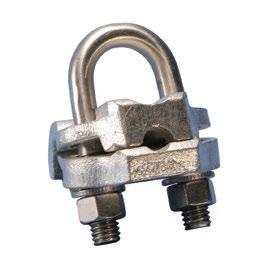
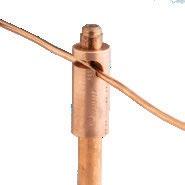


nVent ERICO Compression Grounding Connectors
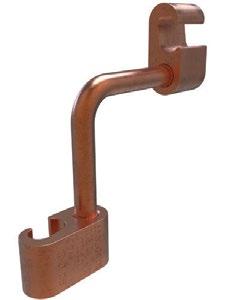
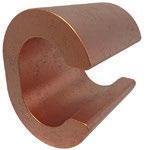
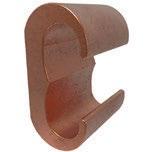

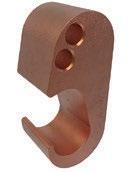
nVent ILSCO TaskMaster Battery Powered Crimping Tools
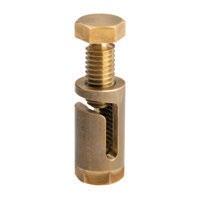
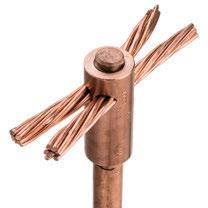

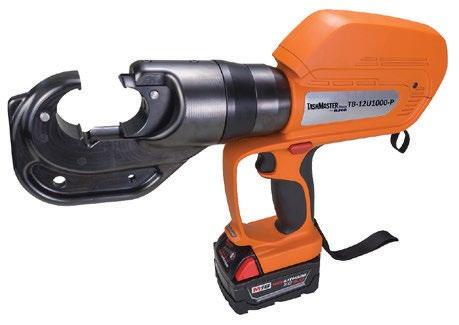

TB-Cut Series
TB-12U1000-P
Ground Rod Clamp, U-Bolt
Lay-In Hammerlock Ground Clamp
Hammerlock Ground Clamp Lay-In Lock Shear Connector
Hammerlock Ground Clamp
DON’T KEEP IT UNDER YOUR HAT

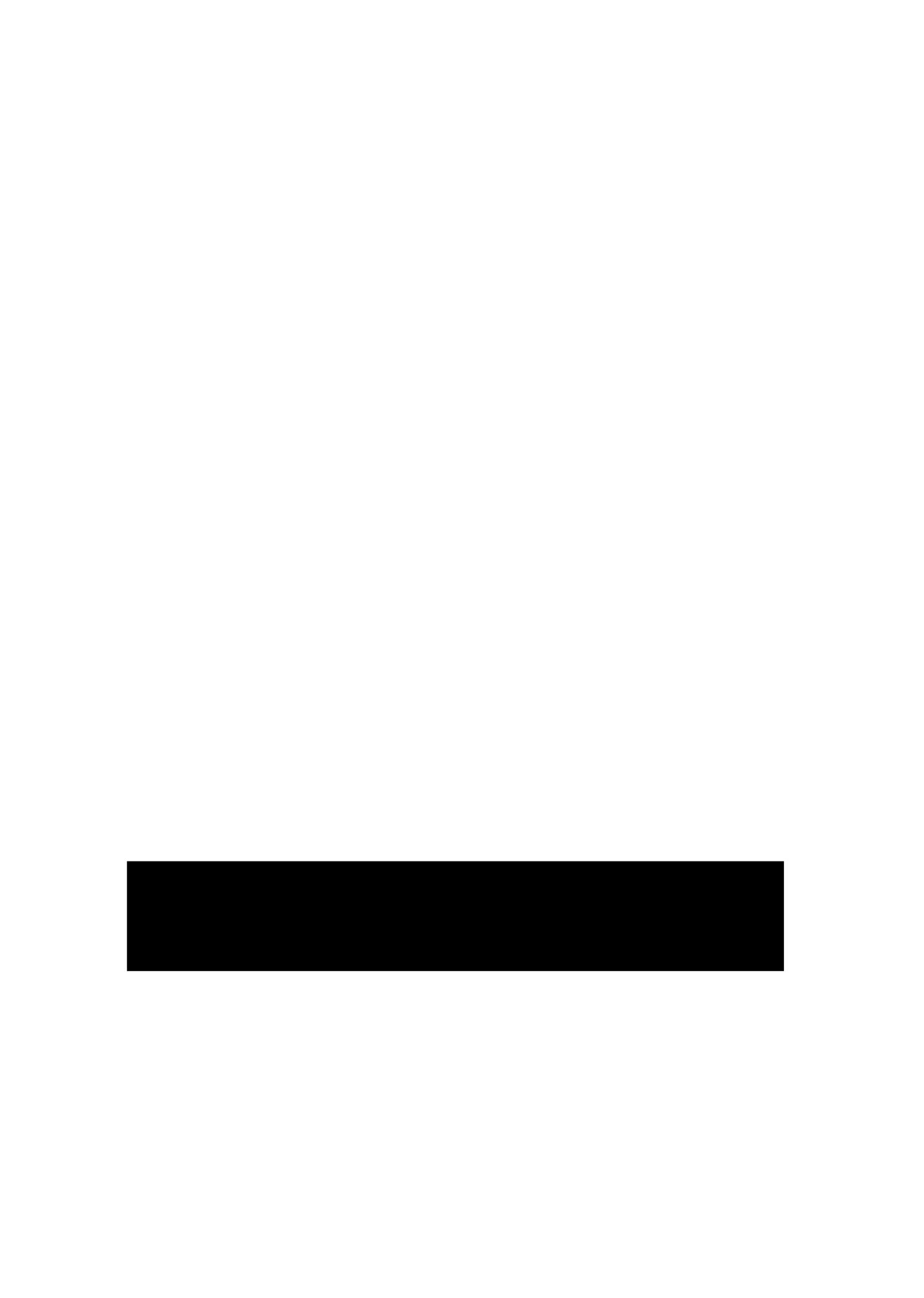
WOrKING IN rUr AL AND rEMOTE AUST r ALIA COMES WIT h ITS OWN SET OF Ch ALLENGES. OFTEN, IT CAN FEEL ISOLATING, AND ACCESS TO SUPPOr T SEr VICES MAY BE LIMITED Or EVEN NON-EXISTENT. T hE EA rLY MOrNINGS, T hE UNP rEDICTABLE WEAT hEr , AND T hE LONG hOUr S SPENT IN SOLITUDE CAN TAKE A TOLL ON BOT h BODY AND MIND.
For many, isolation is more than just geographical. It can be emotional and mental, too. Days, even weeks, can pass with little human interaction. Conversations are often held with machinery, animals, or the ever-changing environment, rather than with mates or family.
That’s why a mental campaign from TIACS ‘The home of Blue Collar Counselling’ is delivering a simple yet powerful message: Don’t Keep It Under Your hat. TIACS, a not-for-profit organisation providing professional text and call counselling to Australian farmers, tradies, truckies, blue collar workers and their loved ones, is urging those in regional areas to prioritise their mental wellbeing just as they do their work. Just like a trusty ute needs regular servicing, so does the mind.
Co-CEO of TIACS, Jason Banks, highlights how life in remote areas comes with ups and downs.
“Most people working outdoors start their day by putting on a hat,” Banks explains. “It’s a simple, everyday act, and we want that hat to serve as a reminder, don’t ignore what’s happening inside your head. If you’re going through a tough time, you don’t have to do it alone. Just like maintaining your equipment or land, tending to your mental wellbeing is essential.”
The campaign acknowledges a tough reality that those in rural areas are known for their resilience, often find it difficult to ask for help. There’s a deeply ingrained mentality of pushing through tough times and shouldering burdens in silence. But TIACS is breaking down these barriers by making support
as easy as sending a text. No waitlist, no out of pocket expenses just direct access to a qualified counsellor who is there to guide those that reach out back to lovin live a bit more.
The message is clear Don’t Keep It Under Your hat. TIACS is here, just a text or call away.
If you or someone you know is in need of support TIACS is there just text or call 0488 846 988, Mon-Fri 8am-10pm AEST.
To learn more about TIACS and the ‘Don’t Keep It Under Your hat’ campaign, visit www.tiacs.org.
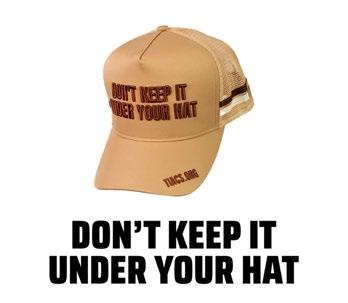
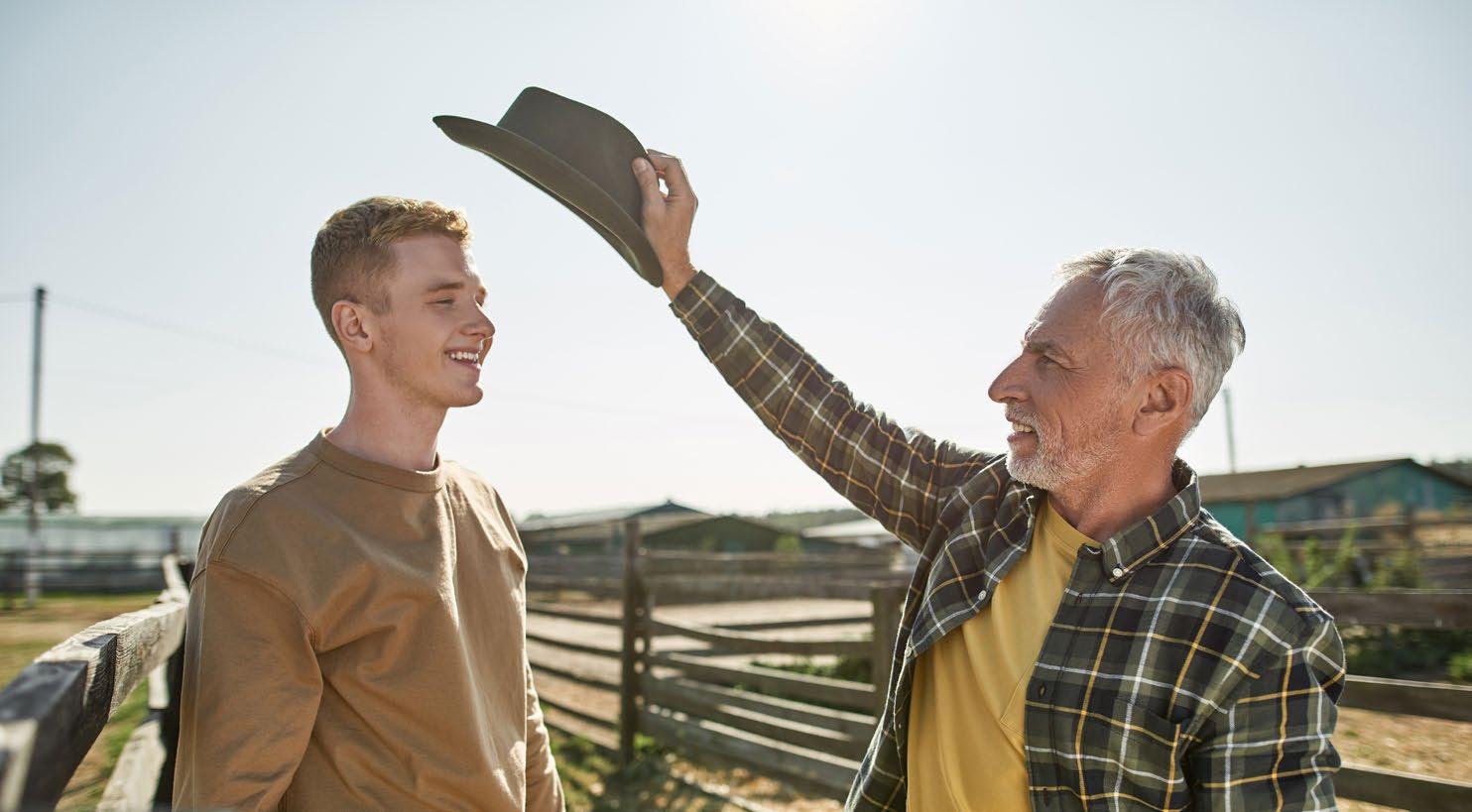
TOYOTA HALO1, UNLOCK YOUR FLEET'S POTENTIAL
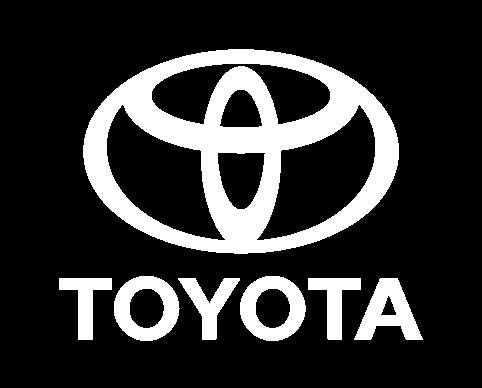
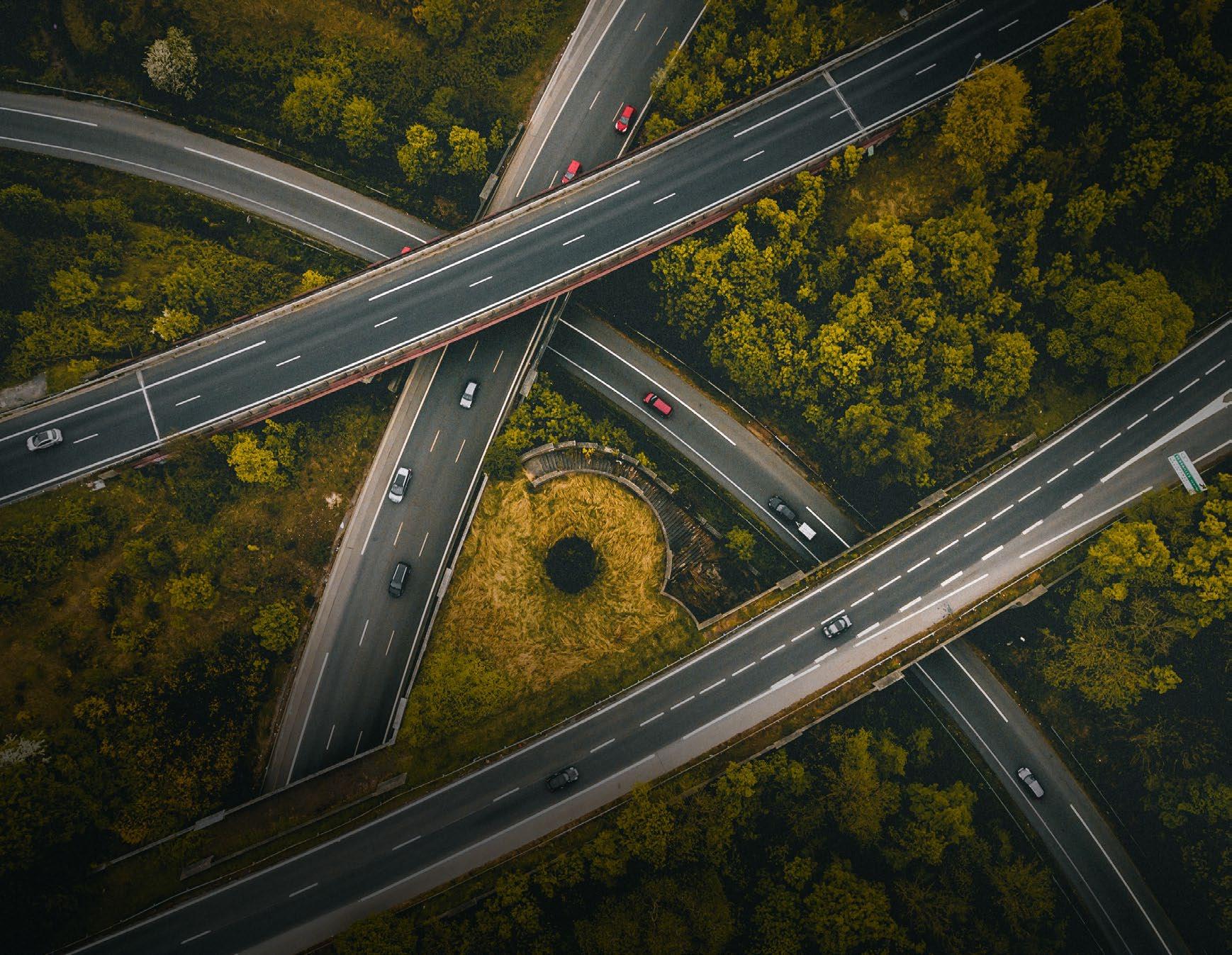
Toyota Halo gives you insights to optimise your operations
Toyota Halo is your complete fleet management solution. It gives you oversight over vehicle health and location2, driver behaviour, logbooking and much more, all in a simple dashboard. Whether you have a few vehicles or a nationwide fleet, your business will benefit by accessing fleet insights from almost anywhere.
With Toyota Halo, your business can optimise its operations and boost its efficiency with oversight on your fleet's location, status and performance.
Ready to get the most out of your fleet with Toyota Halo?
Your Association membership unlocks Toyota Fleet discounts across a great range of Toyota vehicles to help you find the right car for your lifestyle and budget.
To find out more, visit your Toyota Dealer or call 1800 679 247
1Subscription-based.
2Uses third party
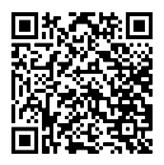
Scan to sign up for the latest insights from Toyota for Business



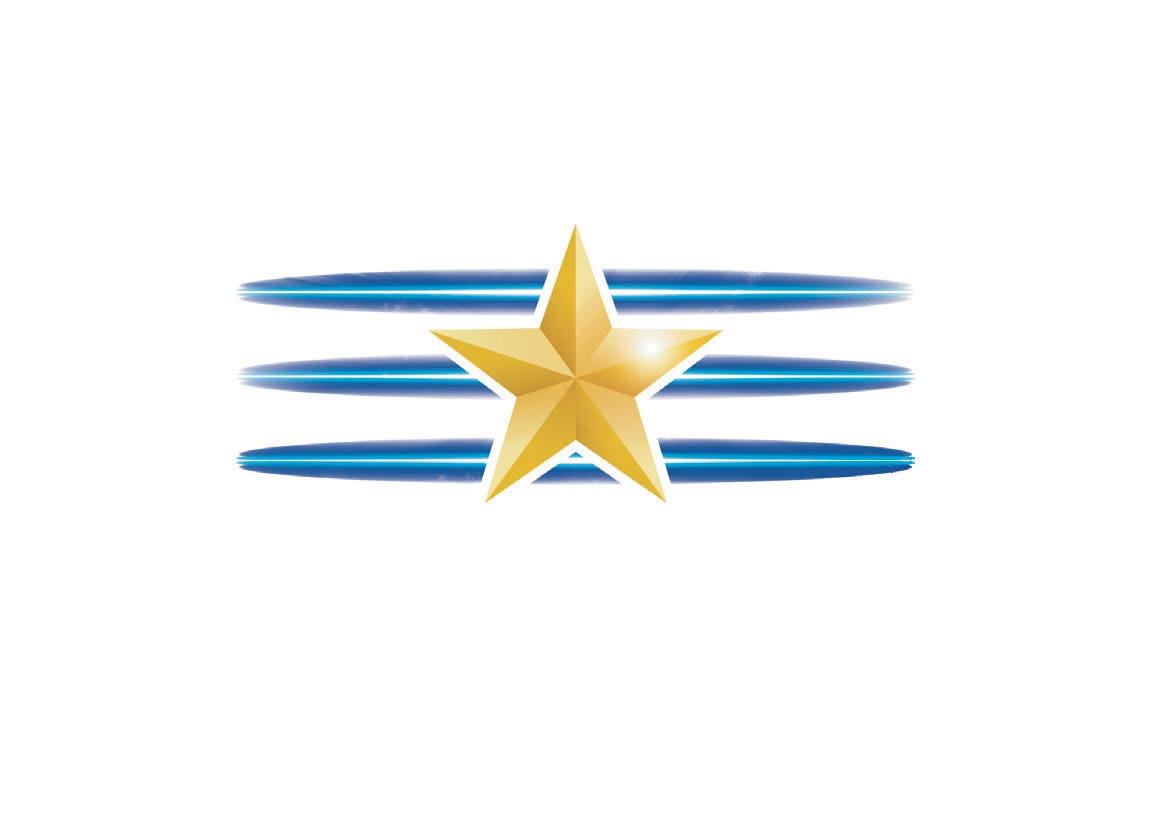
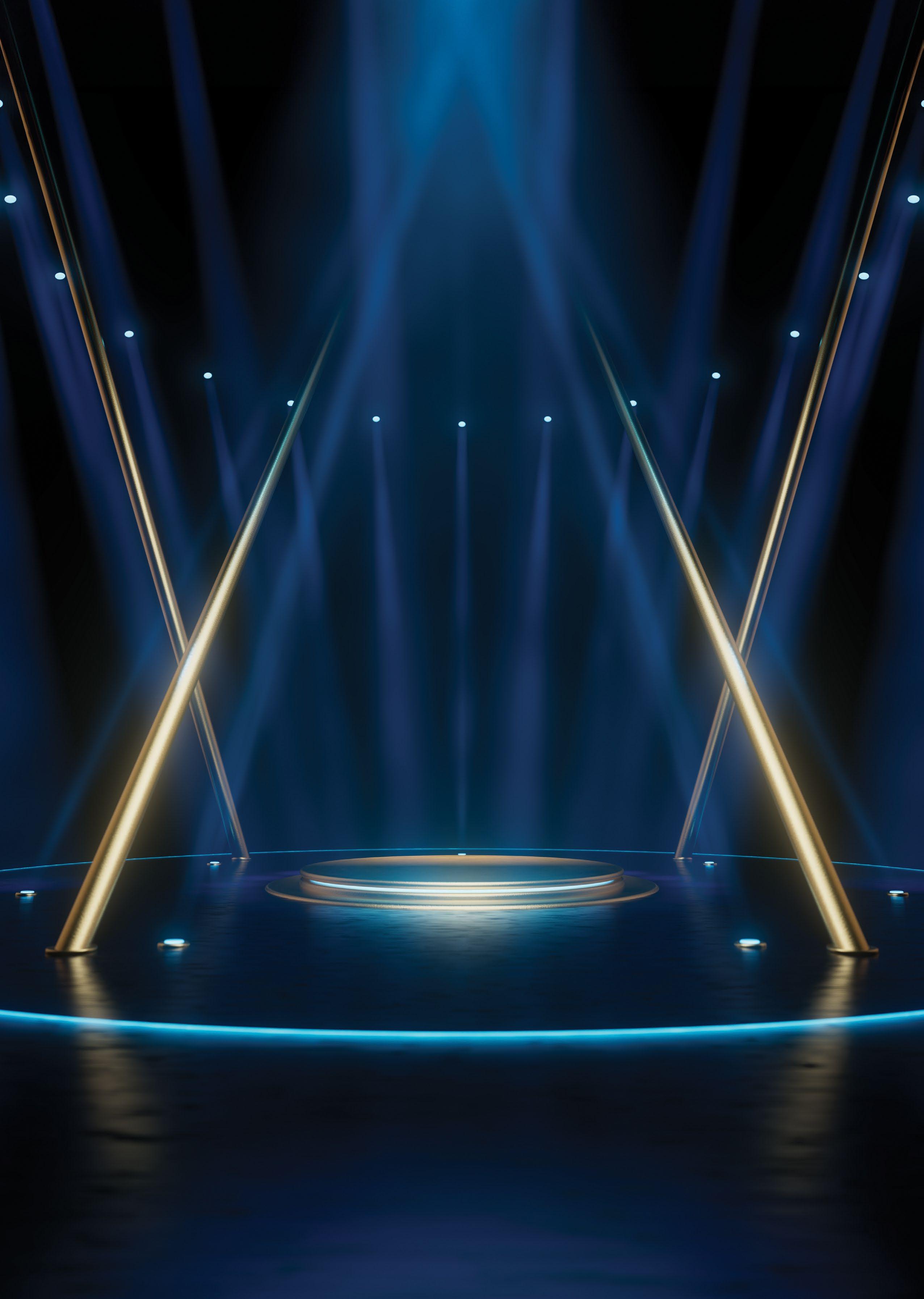
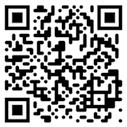