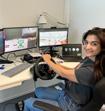
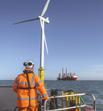

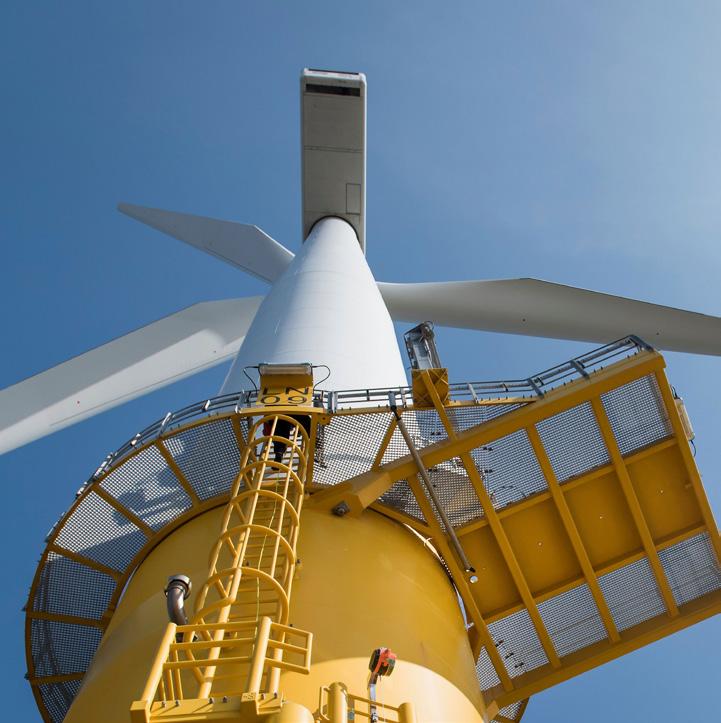
With PPG SIGMAGLIDE 2390 fouling release coating
Tested and proven to deliver:
Up to 35% CO2 savings CO2
Up to 20% power reduction
Up to 150 days’ static protection
Max. 1% speed loss performance
Biocidefree
The suitability of PPG SigmaShield 1200 from PPG Protective & Marine Coatings for wind tower foundation protection is supported by full compliance with Norsok M501- System 7A performance requirements
2 Lifting the Lid
Greek engineer Eleni Boviatsi has a PlayStation setup as her workstation to remotely control Jotun’s greatest innovation.
6 Up Front
PPG reviews the typical protective anticorrosion coating technologies used on fixed and floating offshore wind tower foundations.
14 Analysis
Hempel helps boost the performance of wind turbines.
18 Spotlight
Marine coatings are put under the spotlight with flashes from Nor-Maali, PPG and Subsea Industries and drone innovation from GDI.
44 In Focus
The focus is on nano technology with updates from Hexigone and Graphite Innovation & Technologies.
52 Update
Belzona distributor Rezitech provides a turnkey solution to combat corrosion under insulation on an ammonium sulphate feed tank and Castolin Eutectic provides a new dimension to laser cladding.
62 Review
AkzoNobel protects 18th century windmills in the Netherlands and Ystral provides state-of-the-art mixing and dispersion technology to Steen Hansen.
70 News
The latest products, appointments and industry news.
■ Volume No.16
■ Issue No.1 January – March 2024
■ ISSN No. 2054-1813
Editor: Mark Langdon mark@pce-international.com
Contributing Editor: Mike Garside mike@pce-international.com
Advertisement Manager: Nick Carugati nick@pce-international.com
Production Manager: Tatum Le Patourel tatum@satzuma-creative.co.uk
Designer: Fiona Andreanelli fiona.andreanelli@mpigroup.co.uk
Accounts: Claire Long claire.long@mpigroup.co.uk
Publisher: Andrew Deere andrew.deere@mpigroup.co.uk
Greek engineer Eleni Boviatsi has a PlayStation setup as her workstation. Her current throne is in Norway, where she is on a short-term assignment playing with Jotun’s greatest innovation.
Boviatsi puts on a big smile and says: “When I tell people what I do for a living, they usually go Wow!”
The 30-year-old, who joined Jotun in 2021, grew up in a small Greek village and took her mechanical engineering degree at the University of Patras, two hours’ drive from Athens.
“I am a Skate Operator – meaning I operate the Jotun HullSkater – our first robotic device designed to clean a ship’s underwater hull,” explains Boviatsi.
In the job interview, she was asked about any gaming experience. “I played many FPS (first person shooting) games in my youth, but most of all, I was playing Gran Turismo (car game) on PlayStation. This taught me about screen perspectives and camera directions. Now I have the same kind of steering wheel at work. It has been valuable, because I can operate the robot with the same logic,” she says.
The HullSkater was created through collaboration between the Norwegian companies Kongsberg and Jotun. By cleaning a ship’s hull and thereby preventing fouling, the robot works together with an applied antifouling system and does three things:
• Reduces fuel consumption,
• Reduces CO2 emissions
• Reduces the spread of invasive species.
“We launch the robot, assess the hull and perform a proactive cleaning,” says Boviatsi. “We remove incipient biofilm and thereby prevent biofouling from growing. With minimal friction, the ship glides easily in the water. Afterwards, we share our findings with the shipowner and our colleagues, to make sure we continue the learning process,” she adds.
Right now, Boviatsi is one of eight skater operators in Jotun.
“There are four operators in Korea, two in Singapore, one in Athens and me in Sandefjord,” she continues. “Geographic location doesn’t matter that much, really, as I can operate a robot in Panama or anywhere in the world from my workstation.”
Two years after joining Jotun, Boviatsi had the opportunity to go on a temporary assignment at the group headquarters in Sandefjord, Norway.
“Now, I’m mostly testing and developing new releases of the HullSkater system that the robot is a part of, as well as training new skate operators. We are always looking into the future, in terms of new designs, how to install the robot on the ship, and so on,” she explains.
A few months remain of her short-term assignment in Norway. This is a Jotun concept enabling employees to take on a temporary role. The employee develops new skills and finds new inspiration. For the organisation, the sharing of knowledge and perspectives across departments and borders is the key.
“It was shocking to experience snow in April, but it has been great,” says Boviatsi. “Temporarily living here – enjoying Norwegian culture, meeting new people, learning new things – without having to do big, long-term changes in my life, has been wonderful.
“I have made friends for life, and I would recommend such an assignment to anyone,” she concludes. ■
PPG
SigmaShield 1200 is highly resistant to water, solvents, and corrosive species, making it ideal for use in harsh environments
A review of typical protective anticorrosion coating technologies used on fixed and floating offshore wind tower foundations that are qualified by leading performance standards such as Norsok M-501, by a team from PPG Protective & Marine Coatings.
As a result of measures to fight climate change, there is a growing need for energy generation from natural sources such as wind and solar radiation. For both energy generation routes, solar and wind, increasing investments are made by governments, energy and operating companies owning and running these installations.
In 2021, of the total 830 GW of wind capacity installed, 93% were onshore systems, with the remaining 7% offshore wind farms. Onshore wind is a developed technology, present in 115 countries worldwide, while offshore wind is at the early stage of expansion, with capacity present in just 19 countries.
Although the installation of large-size onshore wind parks leads to economical electricity production, installing large offshore wind parks has gained enhanced interest because of its higher production efficiency. According to a report from the International
Energy Agency, cumulative offshore wind capacity is forecast to more than triple by 2026, reaching almost 120 GW. By then, offshore wind additions are expected to account for one-fifth of the global wind market. Global capacity additions of offshore wind are set to reach 21 GW by 2026, thanks to rapid expansion in new markets beyond Europe.
However, the construction and operation of offshore wind parks bring many technological challenges that need to be overcome to reduce the operational and financial risks of these mega investments. The more difficult installation circumstances, together with the harsh environments to which the wind towers are exposed, are the main challenges to deal with. This requires high-quality construction and protection materials to ensure a prolonged lifetime, together with minimal maintenance, which is difficult and costly.
At present, typical generic coating technologies qualified for fixed offshore wind foundations are either reinforced epoxy- or glassflake unsaturated polyester-based. Both generic coating types have their specific properties and will be further reviewed.
To understand the application and performance properties of the preferred coating categories, deeper insight into the chemistries is needed. Two-pack epoxy coatings – in this case, so-called high build, solvent-free, two-pack epoxy coatings – are composed of a mix of a low viscous epoxy resin and an amine curing agent. This leads to a dense waterimpermeable crosslinked polymer matrix. To further enhance the water impermeability and thus the protective properties of an epoxy coating, so-called novolac phenolic epoxy resins can be used. The resulting coating (for example PPG SigmaShield 1200) has a high crosslink density, which gives it superior mechanical properties such as high stiffness and toughness. The cured coating is also highly resistant to water, solvents and corrosive species, making it ideal for use in harsh environments. Besides the resins used, these coatings are further engineered with mineral or ceramic reinforcement pigments.
The two-pack unsaturated polyester coating is based upon unsaturated polyester resins and cured by minimal amounts of a peroxide catalyst. Adding these catalysts
generates an auto-polymerisation reaction whereby the unsaturated polyester polymer partly crosslinks, partly homopolymerises, and solidifies. To densify and fortify the solidified polyester matrix, typically, large amounts of laminar glass flakes are added. It is claimed that using laminar glass flakes reduces the ingress of water into the coating film, providing better corrosion protection of the steel substrate to which it is applied. However, microscopic pictures of glassflake-containing coating films show a rather disorganised random positioning of the glass flakes within the film, and so the added value to the anticorrosion functioning of the coating can be disputed. High loadings of glass flakes also increase the viscosity of the polyester coating, so considerable amounts of reactive diluents like styrene or vinyl toluene are to be added. These diluents have a strong, pungent smell and make the use of polyester coatings less user-friendly. Recently, styrene-free unsaturated polyester glassflake coatings (styrene-free UPE coatings) have been introduced to reduce the strong smell, making the product more pleasant to use.
This crosslinked resin matrix of high-build epoxy coatings also shows, aside from water resistance, excellent resistance against a variety of chemicals such as alkalis and solvents. Particularly in cases where cathodic protection (CP) systems like galvanic anodes or impressed current are used, the alkali resistance of the polymer matrix is critical. The CP systems will generate an alkaline environment by the electric decomposition of water in case of coating damage or failures. Aside from the alkalinity that develops when CP systems are activated, stationary seawater inside the wind tower foundation gradually increases in pH. The higher the pH of the seawater, the more aggressive it is to
coating systems, mainly when resin systems are susceptible to such an alkaline water environment. Polymerised polyester resin matrices are known to be less tolerant to alkaline exposure environments due to the ester moieties/building blocks within the resin matrix and so are considered to perform less well in these high pH exposure conditions.
Visual, small damages to the coating systems need to be repaired on a regular basis. Generally, annual inspection routines will identify where such damage has occurred. Where possible, power tooling should be used to remove corrosion and poorly adhering coating. Subsequently, rinsing with tap water is required to remove any salt contamination. This is essential to avoid any osmotic blistering of the coating system at a later stage. It is recommended to use a primer coat suitable to be applied to the power tooled and waterrinsed damaged area (St-2 cleanliness). After primer application and curing, the original coating system can be applied. Between each coat, tap water rinsing should be used to ensure that no soluble salts are embedded. The above repair procedures on site at wind tower foundations are quite difficult to execute. User-friendly coating maintenance systems are to be used. Two-pack epoxy coatings and PPG SigmaShield 1200, in combination with the PPG SigmaPrime 200 primer, have such tolerant application properties. Suitable alternative coatings (for example PPG SigmaShield 880), fully qualified for offshore wind tower foundation maintenance procedures, can also be used. Unsaturated polyester coatings are less application-friendly for on-site maintenance procedures. Tuning the mixing ratio with the low amounts of peroxide catalyst
and the resulting short pot life makes manual application under these difficult application conditions hardly possible. Alternative coating repair systems probably need to be used.
The splash/tidal zone is most susceptible to corrosion due to paint system damage or failures. Still, owners and operators would like to rely upon long-term flawless corrosion protection with minimal coating system maintenance.
To provide reliable lifetime projections, the frequent successful use in the shipping and oil and gas industries is a good indication of the excellent protection properties of the PPG SigmaShield 1200 coating system. Track records of multiple vessels and oil and gas installations confirm that after 10 years or more in operation, minimum maintenance is required. Even with ice-going vessels, this coating system shows excellent corrosion protection and outstanding impact damage resistance. The suitability of PPG SigmaShield 1200 for wind tower foundation protection is further supported by full compliance with Norsok M501- System 7A performance requirements.
But how can the industry establish reliable data for longer lifetime expectations, such as 30 years+, as frequently demanded in the offshore wind tower industry? For insight into such lifetime expectations, Electro Impedance Spectroscopy (EIS) testing is most suitable. Accelerated testing and focusing on the eventual degradation of the impermeability function can be monitored. When there is little or no change in impermeability after runs of accelerated testing, extrapolation can be made to the real-life performance of the coating system. Such EIS testing of the PPG SigmaShield 1200 system (2x 500µm) has been performed by the independent test
institute C-Cube International. After 585 days of exposure to 5% NaCl @ 35°C in C-Cube’s tidal cabinet, no signs of any significant coating degradation have been observed (see Table 1).
The EIS measurement data show that the barrier function (BI) after the 585 days of exposure to salt fog, tidal and seawater only dropped about 10% compared to the ideal resistance/insulation behaviour. The permeability of the coating system dropped to minimal or none. The absence of a decline in permeability index (PI) confirms that the coating displays no signs of degradation during the extended test period of 585 days. This allowed C-Cube to conclude a lifetime projection of the PPG SigmaShield 1200 coating system: “Based on extrapolation of the ISO 12944-9 (CX+IM-4) test duration, the system PPG SigmaShield 1200 @ 2x 500 micron is expected to have a technical lifetime of 50 years or beyond.”
Critical for realising a long-term anticorrosion system is secure substrate pretreatment in combination with a correct and high-quality application process of the right heavy-duty coating system.
A grit-blasted surface cleanliness of ISO Sa 2.5 with a minimum surface profile of 50-100µm is required. Soluble salt presence should be avoided and not exceed 20mg/square metre as specified in Norsok M-501 and in wind farm project specifications. Once these substrate requirements are fulfilled, the paint system will show excellent adhesion performance. Moreover, the minimal presence of soluble salts prevents osmotic processes which could lead to blistering and coating detachment, occurring under humid or immersed conditions.
Offshore wind foundation coatings systems are typically specified as two-coat systems. So, easy and fast re-coatability of the cured first coat is essential to minimise hold-ups
in the production process of the wind tower foundations. Here another shortcoming of unsaturated polyesters is being reported. For unknown technical reasons, the inter-coat adhesion of the second applied unsaturated polyester coats can be poor. In order to correct the occurrence of the variable inter-coat adhesion, the surface of the first coat needs to be pretreated; for example, by mechanical disc sanding. It is a time-consuming activity and increases the application costs for the realisation of a full two-coat system. Two-pack epoxies like PPG SigmaShield 1200 show, when applied under the right indoor conditions, no problems in adherence between two coats and without any additional pretreatment of the first coat.
Finally, care should be taken with leftovers of mixed unsaturated polyester coatings. The vigorous reaction speed may develop very high in-can temperatures that may lead to selfignition and therefore risks of fire. The coating suppliers typically recommend adding water to the leftover cans to avoid the fire risk. Clearly, good training and discipline of the application team is required to realise safe coating leftover disposal management.
Offshore wind tower foundations are exposed to extremely harsh environmental and corrosive conditions. For this reason, highquality, very durable coating systems are to be used at the time of the new building. Moreover, any on-site maintenance and repair of the
coating system is difficult and costly. Heavy-duty reinforced epoxy coatings, such as PPG SigmaShield 1200, have longterm and extensive successful track records in a variety of marine exposure conditions, identical to those of offshore wind tower foundations. As such, PPG SigmaShield 1200 will provide excellent corrosion protection over the projected lifetime of these foundations and is therefore preferred over unsaturated polyester or recently-introduced styrene-free UPE coating technologies. Also, the application of unsaturated polyester coatings is less userfriendly compared to epoxy-based coatings. This provides higher risks of coating system imperfections and thus a higher chance of unforeseen costly maintenance and repair procedures. All these aspects should be considered by wind farm stakeholders when selecting anticorrosion coating systems for offshore wind tower foundations.
Authors: C Y Lee, PPG Global Product Support Manager for Protective & Marine Coatings (PMC), Kent Holm, PPG Global Wind Power Segment Manager for PMC; Ronnie Peskens, PPG Global Product Manager for PMC, Eric King, PPG Global Segment Manager, Powder & Mining, for PMC and Gerard Geels, PPG Senior Product Specialist for PMC. ■
The full article can be found on our website https://www.pce-international.com/ research-and-development/
Bring the outside into your lab with Atlas. Configurable to precisely simulate environmental conditions, our weathering instruments set the standard for accuracy and reliability. It’s no wonder that Atlas is the platform of choice for durability testing worldwide.
See the widest range of weathering instruments and laboratory test services at atlas-mts.com.
At Hempel, we aspire to become sustainability leaders within the industries where we operate. While enhancing our products and reducing our environmental footprint are pivotal aspects of this commitment, we strive to take an additional step by reshaping the dominant industry belief that success necessitates more, explains Karima Ajaoud, Hempel Energy and Infrastructure.
Our vision, encapsulated in what we at Hempel call ‘Power of Less’, challenges this notion. “Less maintenance, reduced waste and a smaller environmental footprint not only contribute to heightened efficiency but also bolster sustainability,” says Lars Rindom, Head of Solution Wind Blades. He continues: “Our Leading Edge Protection (LEP) for wind turbines, Hempablade Edge 171, is one of the many Hempel products that actively support the ‘Power of Less’ narrative.”
This product is a cutting-edge solution, specifically crafted for the protection of wind turbine rotor blades. These blades, operating in high-speed airflow conditions exceeding 300 km/h, face a formidable adversary – rain erosion, and other elements.
“The impact of rain erosion is not just a cosmetic concern; it directly influences aerodynamic performance, leading to efficiency loss and a subsequent need for maintenance, which represents the biggest operational cost within the wind industry. Hempablade Edge 171 is strategically formulated to tackle this challenge head-on,” explains Rindom. “This best-in-class LEP protection system also offers the market´s best RET (Rain Erosion Test) to DFT (Dry Film Thickness) and has endured over
600 exhausting test sessions since 2019 in our in-house Rain Erosion Test facility, delivering an impressive level of quality and reliability.”
Designed for application in both onshore and offshore settings, whether for new blades or during maintenance scenarios, Hempablade Edge 171 acts as a top-layer coating. Its primary function is to provide robust protection against rain erosion, minimising blade maintenance costs, reducing service intervals and increasing turbine uptime.
Comprising a two-layer system, Hempablade Edge 171 sets the standard for erosion protection in wind turbine applications. However, for urgent maintenance needs, a single-layer application also proves effective. What sets this solution apart is its ease of application and fast-cure system, making it particularly suitable for situations demanding high productivity.
In essence, Hempablade Edge 171 stands as a practical and efficient ally in the ongoing battle against leading edge erosion, offering not just a protective coating, but a tangible solution to enhance the durability and boost performance of wind turbines. ■
Experience the full range of Hammelmann ship cleaning systems:
SURFACE PREPARATION WITH AN EDGE SPIDERJET® M Edge
Powerful and versatile with a uniform removal pattern right up to every edge.
This is the newest addition to our unique product line of high-performance ship cleaning systems.
OUR UNIQUE RANGE OF SHIP CLEANING SYSTEMS IS YOUR EDGE ON THE COMPETITION
Working heights: up to 32 m
Working widths: 374 – 1000 mm
Operating pressures: up to 3000 bar Flow rates: up to 94 l/min
GET IN TOUCH FOR A CUSTOMIZED SOLUTION, PERFECT FOR YOUR DEMANDS
www.hammelmann.com
Hammelmann GmbH
Carl-Zeiss-Straße 6–8 59302 Oelde / Germany
mail@hammelmann.de
The world’s largest cruiseship, Icon of the Seas, was painted with coatings supplied by Nor-Maali.
Icon of the Seas, a luxurious cruiseship built by Meyer Turku, left the shipyard at the end of November 2023. The ship’s steel surfaces were painted with Jotun’s Jotamastic 90, Hardtop AX and SeaQuantum Classic S high-quality paints supplied by Nor-Maali Oy.
The luxury cruiseship, ordered by Royal Caribbean International, was handed over from the Meyer Turku shipyard at the end of November. Before the ship started operating in the Caribbean at the beginning of 2024, it headed to Spain for finishing touches. This first Icon class ship is currently the largest cruiseship in the world.
The first of three Icon class Royal Caribbean International has ordered three ocean cruiseships from Meyer Turku, of which Icon of the Seas is the first of the series. The shipyard is currently building the second in the series, the Star of the Seas, which will be completed in 2025. The third ship is scheduled to be completed in 2026. All three ships are approximately the same, both in terms of tonnage and passenger capacity.
Icon of the Seas uses advanced propulsion technology, where an environmentally-friendly LNG drive system ensures significant emission reductions. Wärtsilä’s six multi-fuel engines can use both LNG and diesel as fuel. The ship also has other alternative energy features, such as the use of fuel cells to produce electricity and fresh water. Icon of the Seas is the first Royal Caribbean ship to utilise this alternative, more
environmentally-friendly energy technology. The Icon of the Seas attracts attention with its appearance. The outside areas of the ship are really colourful and comfort is increased with a large amount of plants and trees. However, some of the interior areas are calmer and more classic in colour. The ship has 20 decks with many unique areas, such as Thrill Island, the largest water park at sea with seven pools and six water slides, and the much-acclaimed AquaDome.
The bow of the Icon of the Seas is decorated with a large glass dome – the AquaDome. This 25m-high and 50m-wide structure weighs 363 tons and consists of 673 glass panels and 712 aluminium panels, and is the largest glass and steel structure installed on a cruiseship. The planning and preparation of the lifting work took months. The hurricane-class wind-resistant dome offers facilities for numerous bars and restaurants as well as versatile entertainment experiences. The theatre in the AquaDome has, among other things, a nearly 17m high waterfall, which adds to the ship’s uniqueness.
The steel surface paints for the Icon of the Seas were supplied by Nor-Maali Oy together with Jotun. Construction of the vessel started in June 2021 and the construction method was the shipyard’s own block production combined with the block production of partners as subcontracted work. Nor-Maali Oy delivered paint and gave technical support to several countries.
The total amount of paint supplied by Nor-Maal for painting steel surfaces was approximately 750,000 litres. Of this amount, there were more than 370,000 litres of epoxy paint, most of which, around 250,000 litres, was Jotamastic 90 paint. The share of two-component topcoats was about 90,000
litres, with Hardtop AX being the largest individual product with a flow of over 80,000 litres. About 90,000 litres of single-component products were used in the interior of the ship. The Icon of the Seas is the largest single new construction site in terms of litres of paint to date where Nor-Maali Oy has acted as paint supplier.
Jotamastic 90 is the flagship product of Jotun’s successful mastic series for the 2020s. The product is a modern version of the original Jotamastic 87, and special attention has been paid to the product’s usability and drying times, not forgetting top-class corrosion resistance, even on lightly cleaned surfaces. Hardtop AX, on the other hand, is a modern polyurethane topcoat that stands out from the others with excellent gloss retention and colour retention. Hardtop AX is also an easyto-apply product, which is important in such a demanding location.
Fuel costs are one of the biggest expenses in operating ships, including cruiseships. Improving the performance of ships and saving fuel also go hand in hand with the need to reduce emissions. Alternative fuels such as LNG play an essential role in this. As alternative fuels are more expensive, optimising ship efficiency and minimising fuel consumption are key.
According to the GloFouling report published in October 2022, the effect of biofouling on fuel consumption is significant, but greatly underestimated. Underwater hull growth prevention and maintenance solutions could reduce fuel consumption by up to 17.7%, reduce CO2 emissions by 19% and lead to a better CII rating.
Since one of the focuses of the Icon of the Seas design was consideration of the environment and energy efficiency, the best possible antifouling solution was also chosen for painting the underwater sections in the form of Jotun’s SeaQuantum Classic S.
SeaQuantum Classic S is an antifouling based on silyl acrylate binder and hydrolysis reaction, which enables linear and predictable performance. SeaQuantum Classic S reduces fuel consumption and CO2 emissions by up to 10.2% and enables very low friction resistance in the underwater hull, thanks to its excellent biofouling control and smooth self-polishing surface profile. SeaQuantum Classic S keeps the ship’s speed loss at only 2.5%, compared to an average of 5.9% for other products on the market.
Currently, Meyer’s Turku shipyard is building TUI’s Mein Schiff 7, due to be completed this year, and the second Icon-class Star of the Seas, which will be completed in 2025. ■
PPG’s SigmaShield 1200 coating has delivered exceptional protection for two vessels in harsh ice-going operations and needed just a few litres of touch-up paint at drydocking after eight years of service, explains Bert Adema, PPG Key Account Manager, Marine Coatings.
Wagenborg Shipping, based in Delfzijl, the Netherlands, is a multipurpose shipping company operating in Northwest Europe, the Mediterranean, transAtlantic routes and beyond. The company has a fleet of around 160 modern dry cargo vessels with capacities ranging from 2,000 tonnes to 23,000 tonnes making 8,000 port calls a year.
Wagenborg was looking for a reliable, efficient coating system for the B-Class Roll on-Roll off (Ro-Ro) vessels Balticborg and Bothniaborg, which operate between the Netherlands, Germany, Sweden and the UK. The vessels face severe ice conditions in winter, so the hulls needed long-lasting protection to ensure reliable performance.
The key requirements were that the coating chosen would need to minimise damage, reduce subsequent repair costs and improve operational efficiency to ensure maximum return on investment for the owner. It also had to be suitable for application during limited time in drydock at the BLRT Grupp Estonia’s Tallinn Shipyard.
Based on the anticipated ice conditions during service life, PPG proposed its PPG SigmaShield 1200 abrasion- and ice-resistant coating to provide optimal underwater hull protection. PPG Sigmashield 1200 coating is based on a novolac phenolic epoxy with very hard filler composition, which provides excellent anti-abrasion and impact-resistance properties
Project The Balticborg and Bothniaborg B-class vessels
Challenge Provide a reliable, efficient coating system for two vessels operating in heavy ice-going conditions and to a very tight time schedule in the Baltic Sea suitable for application during limited time in drydock
Coatings system
Benefits
PPG SigmaShield 1200 solvent-free phenolic epoxy coating
• Outstanding impact- and abrasion resistance
• Excellent cathodic protection and creep resistance
• Standard- and low-temperature version for enhanced curing performances
• Excellent application properties; also possible in winter conditions
• Single-coat application using standard equipment
• Easy maintenance and repair
• Excellent creep resistance, reducing size (and hence cost) of repair areas
• Recognised by Lloyd’s Register as an abrasion-resistant ice coating
• Recognised by Aker as a low-friction surface coating for ice-breaking ships
and also has great creep resistance.
“Ice is indisputably the major source of danger for a hull’s outer shell coating – PPG SigmaShield 1200 coating addresses this potentially destructive situation,” says Adema. “After reviewing PPG’s product specification and guarantee, the customer was confident that the PPG SigmaShield 1200 coating would give the optimal protection for its vessels.”
The coating provides long-lasting durability and outstanding impact and abrasion resistance while its smooth surfaces promote power savings. It is available in standard and low-temperature versions and that, combined with its easy handling and excellent application properties, means that single-coat application is possible in winter conditions using conventional equipment.
The PPG SigmaShield 1200 coating was evaluated on Wagenborg’s offshore vessels Antarticaborg and Articaborg, which operate in the Black Sea during the heaviest ice conditions. The results convinced Wagenborg to apply the coating on two of its Ro-Ro vessels, Balticborg and Bothniaborg.
“Following detailed examination of the Balticborg project, the customer was delighted by the coating’s performance and ease of application,” explains Adema.
“In the wintertime the vessels face severe ice conditions and thus need excellent protection for the hull,” says Izak van Rhijn, Technical Superintendent at Wagenborg Shipping. “After reviewing the specification of the product and the guarantee given by PPG, we were convinced that this product would give the optimal protection to our vessels. Another big benefit of this product is the single-layer application. No undercoat or second layer is required, which saves valuable time (thus saving money) during the drydock period.”
Tallinn Shipyard also reported that few adjustments in working procedures were needed to make the coating application process particularly easy. “Through the good advice by PPG’s technical surveyor and the easy handling of the product, we can decrease our time in applying a heavy ice coating, so we are able to focus on our other maintenance and repair jobs during the drydocking,” explains Maxim Scherbakov, Director Project Management Tallinn BLRT Grupp Estonia.
The coatings received positive feedback from the captain of the Balticborg, Hindrik van der Laan, who said: “The speed is better and the fuel consumption is less.”
During its most recent drydocking, the coating was found to be in good condition, needing just a small amount of touch-up work. ■
The past year has been an especially successful one for Subsea industries. A large number of new applications were completed using different coating systems, and there has been great success with ships drydocking with little damage after sailing with Subsea’s coatings for many years.
The abrasion resistant coating certificate allows owners of vessels of all ice classes to reduce the thickness of the plating of the ice belt if this area is coated with Ecospeed
The Lloyd’s Register certificate that recognises Ecospeed as an abrasionresistant ice coating has been renewed and upgraded in 2024. Based on extended observation of the coating in use, LR changed the classification from Polar Code 6 & 7 to PC1 to PC7. This once again confirms the durability and strength of the coating and shows the lasting trust in Ecospeed given by the classification societies.
The number-one consideration in a hull coating for ice-going vessels and icebreakers is the ability of the coating to protect the hull in the harshest marine environment there is. Only a few types of coatings are capable of providing this protection. Typically they are certified by the classification societies for their ice-abrasion resistance qualities.
The abrasion-resistant coating certificate allows owners of vessels of all ice classes to
reduce the thickness of the plating of the ice belt if this area is coated with Ecospeed. The ice belt is the area on the bow just above the waterline that is most prone to mechanical damage from sailing through ice. This saves money since less steel is required to build the hull and reduces the overall weight of the ship.
Group Ocean has been applying Ecospeed Ice on all its ice-going tugs since January 2012.
“What we were looking for was a 25-year corrosion protection system for our ice-going tugs,” says Patrick Chabot, Director of Fleet Planning and Renewal at Group Ocean in Québec, Canada. “We do not want to do any corrosion/erosion steel work,” he adds.
“I believe we have now found that 25-year solution.”
The Ocean tugs are generally built for service in harsh, icy conditions. The coating used on the hull is very important for a number of reasons. Group Ocean experimented with several options before finding the right one.
The Ecospeed Ice applied in 2012 is still in excellent condition. Olivier Garon, Director of Fleet Maintenance, sees each tug when it comes into drydock. “I am very impressed with the hull condition,” he notes. “When they’re in drydock, I can see right away which vessels were painted with Ecospeed and which were not. The difference is very noticeable. There are maybe just a few little touch-ups to do, probably resulting from mechanical damage rather than from the ice, most likely anchor chain or something like that. The application has been done per instructions, so it lasts. I’m really impressed.”
When they’re in drydock, I can see right away which vessels were painted with Ecospeed and which were not. The difference is very noticeable.
The YE 48 Op Hoop van Zegen is key to the operations of Pols-Bom oyster cultivation company
Ecospeed on the inside of the hold of the YE 48 has remained in excellent condition for over 15 years
Pols-Bom, a certified organic oyster cultivation company operating in Zeeland in the Netherlands, has been using Ecospeed for long-lasting, non-toxic protection of the cargo hold of its cutter YE 48 Op Hoop van Zegen. The coating has held up extremely well for 15 years without needing repainting, requiring only minor touch-ups every few years.
Ecospeed was recommended to Jacques Pols, Director Pols-Bom, in 2007, as the ideal coating for the upper part of the YE 48’s hold. Ecospeed was applied in two coats to a dry film thickness (DFT) of 1,000µm or 40 mils. The boat has been in constant use since then and the original coating has not needed to be replaced. In 2013 and again in 2022, Pols ordered very small quantities of Ecospeed to touch up areas where there was some mechanical damage, but otherwise the coating is protecting the steel as well as it was when first applied. It is
in extraordinarily good condition. “I am a very happy customer,” says Pols.
The 100% non-toxic nature of Ecospeed is an important additional benefit. The oysters are in contact with the coating on the sides of the hold so that if it had any toxicity, it could negate the 100% organic certification.
The energy-efficient sightseeing ferry Brisen was baptised in Oslo, Norway in April 2023. The carbon fibre vessel was built at the Brødrene Aa shipyard in Hyen, for ferry operator Brim Explorer. The ship’s hull is protected with the non-toxic, hard coating system Ecospeed, which is expected to last the ferry’s lifetime. Sister vessel Berg has received the same protection.
“Applying Ecospeed is quite easy if you have some experience applying paint with a spray gun,” says spray paint specialist Torgeir ‘Toggen’ Ulleland, who performed the application on Brisen.
Going forward, Brim Explorer has chosen Ecospeed for its fleet because the company is concerned with all environmental aspects of its operation. “With Ecospeed we eliminate all chemical emissions to the sea, preventing harmful chemicals from disturbing the fragile ecosystems in the areas in which we operate,” says Espen Larsen-Hakkebo, CEO and co-founder of Brim Explorer. “Our business is creating unforgettable experiences: it only
Two layers of Ecospeed were applied on Brisen, offering lasting non-toxic protection
Brisen will operate in Oslo and is the first fully electric ferry owned by Brim Explorer
makes sense to do this causing as little impact to the environment as possible. Ecospeed is therefore our preferred choice over any antifouling system.”
2023 saw the Ecospeed coating system applied on the scrubber pipes, outlets and diffusers of a large number of ships. This demonstrates that Ecospeed is not only the best option for the underwater hull of a ship but can also be used for a wide range of other purposes. The result is a lasting, non-toxic protection against corrosion, cavitation and mechanical damage.
Due to the tight regulations on emissions in the shipping industry, the installation of an exhaust scrubber system has become increasingly widespread. The highly corrosive nature of the effluents from scrubbers has unfortunately led to an increase of corrosion damage on scrubber pipes and outlets, which
can result in water ingress into the engine room, ballast tanks and cargo holds.
Ecospeed however is highly chemically resistant. Using the coating to protect the exterior outlets as well as the interiors of scrubbers prevents corrosion damage and the resulting consequences.
In 2023 Subsea Industries carried out well over 100 Ecoshield applications on rudders and running gear. These were done at yards across the world and on a wide range of ships.
Many of the world’s leading shipping companies rely on Ecoshield to protect the rudders, thruster tunnels and other parts of the underwater ship prone to cavitation erosion and chemical corrosion. Several of these companies have been using Ecoshield successfully for a decade or more. Others are newer to the product but are wasting no time in putting it to use.
Umiak I, one of the world’s most powerful icebreaking cargo ships, had the entire hull from keel to gunnel coated with Ecospeed Ice
All parts of a scrubber can be given the same Ecospeed protection
Ecoshield being applied to a hull vane for a navy ship
The rudder of the Pleiades Evrotas five years after Ecoshield application
To date there have been at least 700 separate Ecoshield applications to rudders, thruster tunnels, Kort nozzles, energy-saving devices such as Becker Twisted Fins, thrusters, stabiliser fins, sea chests, Hull Vanes, bulbous bows and other parts of the underwater ship hull and running gear that need special protection from the effects of cavitation.
An extraordinary fact about Ecoshield is that it need only be applied once. It lasts the life of the vessel without the need for repainting beyond minor touch-ups of mechanical damage. This was discovered when ships were coming into drydock 10 years after the original Ecoshield application and only needing a couple of litres of paint for retouching mechanical damage.
Experience also showed that Ecoshield properly applied makes the use of sacrificial anodes unnecessary. This has been proven time after time.
Testing of Ecoshield on the Dutra trailing suction hopper dredger Stuyvesant shows that the coating promises to be a viable solution for protecting the hopper of a dredger.
Dredgers generally experience high wear as a result of their normal activities. In the case of the Stuyvesant, this occurs mainly on the flat bottom and inside the hopper. To try to mitigate some of the wear and reduce the need for steel replacement and repair, in August 2022 Dutra Fleet Manager Iain Searle decided to run tests of Ecoshield on parts of
the Stuyvesant that were particularly prone to abrasion damage.
Inspection of the hopper was carried out in mid-June 2023, 10 months after application. The dredger had been in normal use during that period.
Searle was very pleased with the results. “To be honest,” he said, “I was expecting it to be gone in a few weeks, so I am surprised it is holding up at all.”
Overall, the coating is all in place and looking surprisingly good, considering the constant barrage of dredged material to which it is subjected. Clearly since the coating is intact, no damage to the steel has occurred and there has been no erosion or corrosion. ■
GDI, an award-winning provider of applied technology solutions, has now added the use of the Skygauge drone to its range of marine sector capabilities.
By adding airborne robotics, GDI can now take ultrasonic thickness measurements of large uncoated and painted surfaces, such as corrugated bulkheads and web frames. The technology has been proven, with certain limitations on the areas that can be reached, in demonstrations with four major classification societies.
“GDI has the equipment and the skills needed to take valuable measurements efficiently and safely in conjunction with approved Thickness Measurement (TM) suppliers,” commented David Knukkel, GDI’s CEO. “Although GDI is not an approved TM-supplier, certain classification societies are open to innovative technology and partnerships between approved RIT (Remote Inspection Technology) and TM-suppliers.”
During discussions with various class societies, GDI was provided with information regarding the working relationship between companies certified by TM and RIT.
. ABS approves the cooperation between RIT and TM-certified companies, provided both have procedures in place and the TM-certified companies are mentioned on the RIT certificate.
. ClassNK also allows cooperation between RIT and TM-certified suppliers, but they expect some form of agreement between both approved suppliers. While specific suppliers are not mentioned on the certificate, some form of agreement is expected.
. Bureau Veritas allows cooperation between RIT and TM-certified suppliers, but they do not mention this on the certificate. They encourage both suppliers to agree on the details of the cooperation.
. Lloyd’s Register only certifies the TM company for the use of drones, regardless of whether the drone company is RIT-certified.
. DNV has yet to indicate whether it has a drone programme for TM-certified companies.
. RINA has not provided any official feedback on this matter.
Working in conjunction with approved TM suppliers does not change the process of liability, validation of measurements, and reporting. GDI considers the drone to be a new additional tool which wirelessly supports
the work of the TM engineer. The TM engineer remains responsible for validating measurements by executing a proper calibration and judging the accuracy by looking at the full A-scan. The TM engineer will report the values as usual within the different formats of each individual classification society. “We will continue to work closely with the classification societies to ensure that eventually the procedures and certification will be fully aligned,” said Knukkel.
Among the salient characteristics of the Skygauge drone is the fact that 100% alignment with the contact surface is not required. The drone aligns itself by arranging an equal cup pressure of 20 Nm to the surface. Furthermore, artificial aids based on LIDAR assist the operator in estimating the alignment and movement to the next measurement position. The system’s software provides continuous measurements and delivers an indication of the accuracy of the readings as well as a final reading.
GDI points out that there are certain limitations, with some environments posing a challenge to the onboard sensors. According to Knukkel, “It is a matter of time and effort to increase the operating areas of the drone. This technology is like a river; you need to control and steer the flow by learning how to live with and use the possibilities rather than trying to fight nature.” ■
In the coatings industry, achieving optimal anticorrosion protection while being resource-efficient can be a challenge. Traditional approaches often rely on high loadings of corrosion inhibitors, which can lead to increased costs and environmental impact. However, with Hexigone’s revolutionary Intelli-ion technology, a paradigm shift is underway.
Hexigone’s Intelli-ion technology operates on a smart-release mechanism, wherein corrosion inhibitors are released precisely when and where they are needed most
The term ‘loadings’ refers to the amount of a particular ingredient, such as a corrosion inhibitor, added to a coating formulation. In the case of zinc phosphate, loadings of about 3-20% are often necessary to achieve desired levels of corrosion protection. However, this approach comes with drawbacks such as increased material costs, reduced formulation flexibility, and environmental drawbacks due to the presence of heavy metals.
The Intelli-ion difference
Hexigone’s Intelli-ion technology represents a game-changer in the realm of anticorrosion coatings. Unlike traditional inhibitors, it operates on a smart-release mechanism, wherein corrosion inhibitors are released precisely when and where they are needed most.
However, what truly sets Intelli-ion apart is its lower specific gravity (1.35) compared with conventional inhibitors. This unique characteristic allows it to occupy more volume within the coating matrix, reducing the overall amount of inhibitor required for optimal performance. For example, the 1% in weight of Intelli-ion will take-up 3% volume in the dry film thickness. As a result, coatings formulated with Intelli-ion require a third of the loading versus zinc phosphate (ZnP), leading to environmental benefits while maintaining anticorrosion performance.
If you have previously formulated for 3% of anticorrosive pigment as part of your pigment volume concentration (PVC) in the dry film thickness, incorporating 1% of AX1 into your formulation will seamlessly integrate without compromising the critical CPVC (critical
pigment volume concentration) of the system. This allows for the effective enhancement of corrosion protection while maintaining the integrity and performance of your coating.
The testing imagery shown showcases panel results following 1,000 hours salt-spray testing (ASTM-B117). A leading primer coating containing 5% ZnP was compared with formulations containing 0.5% and 1% of Intelli-ion’s quickrelease ion-exchange inhibitor – yielding excellent results. Significantly reducing the inhibitor loadings can offer coatings manufacturers lower costs (although this depends on current inhibitor loadings) and currently inhibitor costs, improved adhesion and differentiation in the coatings market.
Intelli-ion also works alongside ZnP to allow manufacturers to make a step-change
in their coatings formulation rather than completely replacing their current inhibitor – as demonstrated by the 1,000 salt spray results shown (ASTM-B117). Manufacturers are optimising their formulations to at least half the amount of ZnP to add 0.5-2% of Intelli-ion to take advantage of synergistic protection mechanisms and reduced raw material costs.
In summary, Hexigone’s Intelli-ion technology offers a compelling solution for achieving the highest anticorrosion protection while minimising material usage. By requiring lower loadings than competitor products like zinc phosphate, it can deliver cost savings, enhanced efficiency, and reduced environmental impact. With Intelli-ion, coatings manufacturers can truly do more for less, ushering in a new era of sustainable corrosion protection. ■
The XGIT-FUEL graphene technology, developed by Graphite Innovation & Technologies (GIT) Coatings, has the potential to reduce fuel consumption and resulting greenhouse gas emissions.
XGIT-FUEL is a hard foul release hull coating that creates an ultra-low friction surface to increase vessel performance, without the use of biocides, silicon oils or toxic components. The coating is expected to provide fuel savings of 5-7% by decreasing the friction between the hull and the water and removing marine growth as the ship travels.
This latest application follows Stolt Tankers’ work with GIT Coatings last year to apply the graphene coating to the propellers of more than 40 ships – another world first.
Adopting this technology supports Stolt Tankers’ commitment to explore solutions that have the potential to enhance the efficiency of its fleet and reduce the impact of its operations on the environment. It also supports Stolt Tankers’ ambition to reduce its carbon intensity by 50% (relative to the 2008 baseline) by 2030, and helps customers in reducing their Scope 3 emissions.
“The collaboration with GIT Coatings is a great example of how innovation is helping the maritime industry on its journey to a carbonfree future,” says Lucas Vos, President of Stolt Tankers. “Cutting-edge technology like this isn’t just about preventing wear and tear to our ships. The coating is a simple way we can help protect marine ecosystems, while maintaining operational efficiency.”
Mo AlGermozi, CEO of GIT Coatings, added:
“This is a fantastic collaboration that speaks for itself. Stolt Tankers has so far coated the propellers on more than 40 ships and has now begun the process on its ship hulls. This helps both companies continue to deliver on their commitment to protecting the climate and the ocean. Thanks to forward-looking partners like Stolt Tankers.”
In early November 2023, the 30,000dwt Stolt Lotus was drydocked in China for five days where the sustainable hull coating was applied. It is expected to last for approximately 10 years, with an evaluation at five years to confirm if any maintenance is required. ■
At a major global blue-chip nickel mine in Australia, authorised Belzona distributor Rezitech provided a full turnkey solution to combat corrosion under insulation on an ammonium sulphate feed tank. Within the space of 24 hours, the 9.5m (31.2ft) diameter tank, with a height of two metres (6.6ft) from ground level, was repaired and protected against future corrosion with the industrial composite wrap system Belzona SuperWrap II, explains Belzona’s Chloe Hirst.
The mine refines granulated nickel matte from its smelter into premium-grade nickel powder and briquettes containing 99.8% nickel. Nickel powder is further processed into nickel sulphate at a refinery in Australia. Nickel sulphate is an essential ingredient in the lithium-ion batteries that drive electric vehicles (EVs).
It could be argued that the increase in sales of EVs is one of the biggest climate wins of 2023. Indeed, according to the 2023 report
from Climate Action Tracker, of the 42 sectors that need to achieve net zero status by 2050, the only sector which is on track is the share of EVs in light-duty vehicle sales. Considering how road transport currently accounts for 11% of global greenhouse gas emissions, EVs play a vital role in reducing these emissions. As such, the polymeric technology required to repair and improve assets within the EV industry equally plays a vital role in supporting the transition to net zero. Repairing damaged assets instead of
decommissioning and sending them to landfill significantly reduces the climate impact that would otherwise be incurred in this process.
The customer’s stainless steel feed tank was suffering from corrosion under insulation (CUI) and chloride-induced stress corrosion cracking (SCC). They required a solution that would not only restore the integrity of the substrate, but also protect the asset against
future corrosion damage. Not only this, but as the tank operates at elevated temperatures of approximately 70°C (158°F) and processes highly corrosive medium, the repair solution would need to be able to withstand these harsh conditions.
This composite wrap system is comprised of a fluid-grade resin system, a bespoke hybrid reinforcement sheet, based on fibreglass and carbon fibre, as well as a release film to compact and consolidate the application.
Composite wrap solution specified
Having worked with Rezitech over the course of five years, the customer had complete confidence in the range of Belzona metal epoxy repair composites and industrial repair coatings the distributorship offers. As such, they decided to contact Rezitech again for their advice and system recommendation. Following an inspection by Heath Westell, Sales Engineer at Rezitech, the composite wrap system Belzona SuperWrap II was specified. “This composite wrap system is comprised of a fluid-grade resin system, a bespoke hybrid reinforcement sheet, based on fibreglass and carbon fibre, as well as a release film to compact and consolidate the application,” explains Westell. “The system is specially formulated to restore the strength of holed, weakened and corroded pipe and tank walls, making it the ideal solution for protecting the asset against corrosion under insulation for the long term. In addition, thanks to the cold-curing properties of the composite wrap system, this mitigates the need for hot work, making it a reliable alternative to welding.”
Firstly, all traces of oil and grease contamination were removed using a suitable Rezitech degreaser. Following this, the surfaces were grit-blasted to provide a surface cleanliness compliant with ISO 8501-1 SA 2½ (ASNZ 1627.4 class 2.5) with a minimum 75µm (3mil) rough angular profile. Once the surface was prepared, the Belzona 9381 reinforcement sheet was measured out and then wetted out with the Belzona resin system. The resin was then systematically applied to the areas to be repaired. Following this, the Belzona reinforcement sheets were applied to the tank in three layers. The compression film was then added to the top of the application area. Next, using a roller, the Belzona SuperWrap II composite wrap system was spread, rolled and compressed to the surface of the tank. The system was then left to cure for approximately eight hours.
Investing in the Belzona composite wrap solution enabled the customer to successfully bypass the need to replace the corroded asset, and instead prolong the lifespan of the asset for years to come. This offered significant savings in both time and money. In addition, given the important role EVs play in reducing global carbon emissions, it could be argued that polymeric technology also plays a fundamental role in supporting this transition by safeguarding the integrity of key assets within this industry. ■
Elevate your coatings expertise with
When you purchase both Fitz’s Atlas of coating surveys and Fitz’s Atlas of coating defects. Only £300 for both (usually £189 each)
Streamline your coating surveys with Fitz’s Atlas of coating surveys - a handy guide containing comprehensive detail and visual assessment for coatings evaluation.
Understand coating defects with Fitz’s Atlas 2, providing a detailed visual guide with a a description of the defect, probable causes, how to prevent it and how to repair it.
To order visit Fitzsatlas.com +44(0)1252 732220 keely.moss@mpigroup.co.uk
Thomas
Coating
Castolin Eutectic, explains how a new generation of iron (Fe)-based metal powders can eliminate the high costs and potential health risks of using nickel alloys in plasma transferred arc (PTA) and laser cladding processes.
Eichhorn, Global Product Line Manager atThe new family of Fe-based powders has been developed in our R&D lab in Dublin specifically for use with the latest state-of-the-art processes that apply coatings to components to provide resistance against abrasive wear and pressure. These coatings are used typically for repair of cast-iron forming tools and press moulds; rebuilding and protecting machine parts and edge wearfacing of steel tools for injection moulding. Applications for these Fe-based powders can be found in various industries such as automotive, plastic extrusion and general machine building.
The PTA process uses a high-energy plasma arc and metal powder to create a molten weld pool on the surface of the component. This results in a metallurgically-bonded surface layer with improved mechanical strength, as well as corrosion and wear resistance, compared with wearfacing layers applied using traditional welding techniques.
Laser cladding is complementary to thermal spray coating and PTA. It uses a laser beam to create a molten pool at the workpiece surface, to which the coating powder is added simultaneously. The exposure time is short and cooling is quick. This makes it more reliable than coatings created by thermal spraying, and compared to hard chrome plating, an ecofriendly alternative.
The laser cladding powder may be similar to the substrate material in the case of repairs and rapid prototyping. Or the cladding may
have a higher performance to offer enhanced corrosion resistance or wear resistance. Because it happens so quickly, a particular benefit of laser cladding is that it ensures reduced mixing between the substrate and coating, with dilution limited to just 2-5% for maximum purity.
Excellent process stability and the need for reduced post-application processes such as heat treatment or machining means that laser cladding is suitable for many industrial fields. It is especially useful where modern production lines require reliable, automated and flexible systems with little maintenance that achieve optimum profitability. With the latest highspeed laser cladding systems, it is now possible to clad large areas at speeds of over 300 square metres per hour.
PTA and laser cladding techniques have facilitated the introduction of Fe-based metal powders. This is mainly due to their higher process temperatures, which has reduced the need for the self-fluxing properties of alloy powders with a significant nickel (Ni) content.
Nickel is a particularly costly alloying element, so using metal powder that does not include it offers an immediate cost-benefit.
The pricing of nickel on metal markets has also tended to increase in recent years – up by 40% between 2021 and 2022. Furthermore, nickel pricing is also very volatile – in one day in 2022
it surged by 90%. Elimination of nickel allows greater price stability for Fe-based powders.
There are a number of human health issues associated with nickel. Contact with the metal is known to have side effects such as allergies, cardiovascular, lung and kidney diseases.
In addition to human contact, nickel should be prevented from entering the atmosphere or water cycle. According to the German Water Hazard Class (WGK), nickel is ranked between 2: hazard to waters and 3: severe hazard to water. In contrast, iron is ranked 1: low or even zero hazard to waters.
For these reasons, using Fe-based powder rather than alloys containing nickel can promote a healthier working atmosphere.
Fe-based metal powders are generally manufactured from carbon steel alloyed with chromium (Cr) and molybdenum (Mo). The structure of the applied layer is martensitic/ ferritic. Using these powders results in a surface layer ranging in hardness from 40, 45, 50 through to 55 HRC. They provide average to high resistance against abrasive wear and good toughness at temperatures up to 450°C.
Coatings deposited using Fe-based powders are easy to machine at lower hardness. For the higher hardness range, specially selected tools suitable for use at greater than 60 HRC should be specified.
Fe-based coatings have a high toughness that gives them good resistance to cracking. There is no limit to the number of passes that can be applied. The recommendation to ensure optimum coating properties is to use a minimum of three layers. This ensures that the dilution of the substrate material is controlled.
Operators of PTA and laser cladding who are already experienced in applying coatings using higher-alloyed materials will experience little difficulty in making a change to Fe-based powders. If they have any concerns, they can call on the assistance of Castolin Eutectic’s Research and Development centre. Our team of engineers is well equipped to resolve most complex wear phenomena affecting industrial productivity to create a total coating solutions concept.
We have made the benefits of Fe-based metal powders available in our new EuTroLoy ranges 16039D, 16045D, 16050D and 16056D. They are available in particle sizes from 45-125 and 53-150µm, while other sizes can be supplied on request.
These new ranges are an important extension to our existing ranges of metal powders for PTA and laser cladding that cover a wide variety of different formulations, including nickel, cobalt-based alloys and carbide blends for specific applications. ■
The iconic 18th century windmills at Kinderdijk in the Netherlands are being preserved with help from AkzoNobel’s Sikkens brand.
AkzoNobel has signed a six-year agreement to protect the 19 windmills, which were built around 1740 and declared a UNESCO World Heritage Site in 1997.
The partnership – with the Kinderdijk World Heritage Foundation – will involve using AkzoNobel’s technical expertise and innovative coatings to preserve the windmills and restore them to their original colours.
“Kinderdijk is unique and irreplaceable,” explains Peter-Jan van Steenbergen, Director of the Kinderdijk World Heritage Foundation. “Our UNESCO site sets an example to the world and only the best maintenance plans and products are good enough. We’re therefore extremely pleased to have agreed this partnership with AkzoNobel.”
Regarded by many as a national treasure, the Kinderdijk windmills have come to symbolise how the Dutch have mastered the art of smart and sustainable water management over hundreds of years. They are also a longestablished tourist attraction, with more than 350,000 people visiting every year.
Located around 15km east of Rotterdam, most of the 19 windmills are still inhabited, with one family having been resident for 10 generations. In many ways, they embody the country’s centuries-old struggle with water and how the Netherlands has managed to survive below sea level for so long.
“We believe our paint expertise and focus on sustainability can make a genuine difference at Kinderdijk,” adds Kees-Jan Starrenburg, Country Director for AkzoNobel Netherlands. “I’m proud to see our products being used at this beautiful UNESCO site, which highlights the importance we attach to safeguarding cultural heritage for future generations.”
The six-year agreement builds on a relationship which AkzoNobel first established with the Kinderdijk World Heritage Foundation in 2016.
Kinderdijk is one of several UNESCO World Heritage Sites that feature the company’s coatings. They include La Sagrada Familia in Barcelona, Spain, Westminster Abbey in London, UK, Göbekli Tepe in Turkey, Melaka and George Town in Malaysia and the historic town of Ouro Preto in Brazil. ■
Steen-Hansen, a Norwegian manufacturer of fouling prevention and net protecting solutions for aquaculture use as well as of specialised industrial paint systems, has not only successfully overcome quality problems with its newly developed antifouling coatings, but also significantly shortened process times. This has been achieved by simply switching its production facilities to state-of-the-art mixing and dispersion technology from Ystral.
Ystral Jetstream Mixers perform mixing processes with a turbulent micro-mixing zone in the mixing head and almost turbulence-free macro-mixing of the entire vessel contents
Steen-Hansen has been a leading provider of antifouling coatings for nets in industrial fish farming for more than 30 years. Antifouling coatings reduce the growth of algae and other organisms on the nets, meaning they can be used for longer periods of time.
In addition to conventional copper-based antifouling coatings, copper-reduced – not to mention completely copper-free and biocidefree – coatings are becoming increasingly important in the fish farming industry. SteenHansen is a pioneer in the development and manufacture of coating solutions like these with a reduced environmental footprint.
Manufacturer Steen-Hansen initially used dissolvers, which it also used for its copperbased coatings, to make these innovative antifouling coatings. However, the company found that using conventional production techniques for copper-reduced or copper-free coatings resulted in quality deficiencies, since the long process times in the dissolver caused strong, undesirable foaming in the product.
Several factors were responsible for this foaming. On the one hand, powders contain a great deal of air. Even heavy powders such as titanium dioxide contain more than 75% air by volume. If this air is not fully substituted by liquid and separated, but rather dispersed together with the powder particles, this creates micro foam, which is exactly what happens in a dissolver process. Additionally, the fact that – in a dissolver – the powder is added to the open vessel from above leads to the creation of vortexes, which introduce large amounts of additional air. Since SteenHansen‘s products are water-based, another factor is the process water foaming, regardless of the technology used.
Steen-Hansen managed to counteract this undesirable foaming by using defoamers, but only to a certain extent. This is why the company was looking for a way to disperse the powdered raw materials in a gentler, more product-friendly way, ultimately opting for the technology offered by German-based mixing and dispersion technology specialist Ystral.
“Ystral’s process engineering solution allowed us to overcome the quality problems and, at the same time, significantly shorten our
production times,” explains Stig Bjarte Fagerlid, Plant Manager at Steen-Hansen.
In the Ystral process system installed in 2019, the intense process steps of powder wetting and dispersion take place outside the vessel with the Ystral Conti-TDS inline powder wetting and dispersing machine, while the contents of the vessel are simultaneously mixed in a continuously homogeneous manner with a Ystral Jetstream Mixer.
Using the vacuum expansion method, the inline disperser achieves complete deagglomeration and wetting of the powder particles in a matter of microseconds. Due to an induction vacuum built up directly in the wetting and dispersing zone, the air contained in the powder is expanded many times over, enormously increasing the distances between the particles and allowing the particles to be completely wetted immediately, one by one, on contact with the liquid. The air contained in the powder is separated from the significantly heavier dispersion through the centrifugal effect of the fast-running rotor, and coalesces to large air bubbles. These are then pumped to the process vessel with the liquid flow, where they can easily escape. There are no vortexes and there is no additional air intake during the entire process. This can help to significantly reduce the use of defoamers.
Based on this experience, Steen-Hansen decided to install two more Ystral process systems while modernising and expanding its production capacities. “We completely reorganised our production facilities as part of a relocation, and aligned our entire production infrastructure with Ystral technologies,” says Fagerlid. “Ystral technologies allow us to fully automate our production processes. But at our old site, we were unable to exploit this potential. So we used the move as an opportunity to comprehensively automate the peripheral devices of the Ystral systems with powder and liquid handling.”
Whereas at the old production site the operators still opened bags manually and poured their contents into the system’s powder hopper, now all the powder materials are fed from the silo to the Ystral systems by means of a fully automatic chain conveyor.
At its new site, Steen-Hansen uses one system each for producing antifouling coatings containing copper, for making copper-free
coatings, and for manufacturing industrial paints. A system consists of two process vessels with Ystral Jetstream Mixers, a powder vessel and the Ystral Conti-TDS inline disperser, which is operated alternately on one of the two process vessels. While powder and liquid handling at Steen-Hansen is performed using a central control system, each system is fed from separate silos and tanks. This eliminates the possibility of the copper-free coating products being contaminated with copper particles, for example.
The Ystral control system (YCS) professional +, with the highest degree of automation, is used as the control software for the three systems. The operator starts and monitors the process using a graphical user interface, and dosing and feeding of the liquid components and solids is fully automatic. Every single process step is exactly reproducible, and creating new recipes is child’s play with the recipe handler.
By using modern mixing and dispersing technology and centrally controlled peripheral devices with automated feeding and dosing of powder and liquid components, Steen-Hansen successfully tripled its production capacity at its new site, all the while keeping its staff levels the same. The three Ystral systems
can be operated by just one employee. With the dissolvers previously used, the process often lasted one to two hours, but this was shortened to between 10 and 15 minutes with the Ystral technology. While Steen-Hansen was barely able to meet the rapidly growing demand for its products with the production infrastructure it used previously, even in twoshift operation, it has now switched to oneshift operation in the new factory.
The significantly shorter process time also goes hand in hand with a considerable reduction in energy consumption – which is particularly important to Norwegian producer Steen-Hansen, since electricity prices are high in Norway. Measured in terms of electricity demand per litre of finished product, SteenHansen cut its electricity demand at the new site by about 75% – simply by using more efficient mixing and dispersing technology and energy-saving building technology. ■
A SteenHansen employee operating the YCS Professional + control software
Biofouling after 140 days in an uncoated aquaculture net (right), and an aquaculture net with SteenHansen’s copperfree coating (left)
Extreme conditions call for extreme testing. Not that there is too much building activity going on at the South Pole, but if Jotun’s coatings can get the job done there, they can do it anywhere.
Earlier this year one of Jotun’s dedicated partners from Telenor jumped out of an airplane in Antarctica, close to the South Pole. Not only did he take in the beautiful scenery. He was carrying a highly advanced sensor kit supplied by Jotun R&D in his backpack.
It’s been four years since Jotun established a test station with coated metal
panels close to the Norwegian Antarctic Research station ‘Troll’ (which was built in 1994 and still stands fully protected with Jotun coatings). This enabled Jotun to directly monitor the environmental conditions and link them to how the company’s paints and coatings perform in this extreme environment. The site made up a great supplement to Jotun’s existing test stations in Dubai, Malaysia, Svalbard and so on.
The beauty of digitalising this entire process – by connecting the test panels with a highly advanced sensor – is that scientists can
extract live and precise data whenever they want, without having to book a flight, travel down there and register the findings manually.
Telenor made this possible by expanding its 5G network to enable fast and reliable data transfers – even from this remote part of the world.
It would be fascinating to consider what Jotun’s founder Odd Gleditsch Sr would have said – almost 100 years after he sailed these waters and observed ships and steel structures corroding away – had he known the opportunities modern technology gives us today.
Normathane 50 FD guarantees a fast production turnaround time
Normathane 50 FD is NorMaali’s new solvent-based polyurethane topcoat, which guarantees a fast production turnaround time. Together with a fast-drying epoxy primer, this semi-gloss polyurethane topcoat makes the production process more efficient.
The new Normathane 50 FD polyurethane topcoat is designed for anticorrosion painting of steel surfaces together with an epoxy primer. The product represents modern polyurethane paint technology, but still offers the reliability of traditional polyurethane paint.
The main advantage of Normathane 50 FD topcoat is its fast drying time. This feature not only speeds up the drying process in the paint shop, but also allows for quick packing and assembly of the painted pieces. Normathane 50 FD is ready to use after 1.5 hours (+23°C) after painting.
Although drying is really fast, it is still easy to paint with the product. The usage time of Normathane 50 FD is one hour and the open time of the paint film is relatively long compared with the drying time. Even a complex piece can be painted before the paint film dries too much.
Nor-Maali’s recommends that primers to be used are NorECOat FD
Primer and NorECOat HS
Primer with a higher dry matter content. The twolayer painting system can be painted during one work shift thanks to the fast drying time.
In two-layer painting systems, corrosion protection is achieved with an epoxy primer and weather resistance and surface hardness with a polyurethane topcoat. By increasing the film thickness of the epoxy paint, the desired corrosion class is reached.
Graco recently marked a significant milestone with the inauguration of its Middle East Application Centre in Dubai, underscoring the company’s commitment to the region. This new facility, strategically located in the city of Dubai, will serve as a pivotal hub, supporting local contractors, distributors and material manufacturers offering comprehensive training programmes and facilitating material validations.
The inauguration of the centre signifies a robust expansion for Graco within the EMEA region, complementing its EMEA headquarters in Maasmechelen, Belgium. The centre in Dubai is purposebuilt, featuring state-ofthe-art amenities including a dedicated spray booth, workbenches, a demonstrative area for texture applications and well-equipped meeting rooms.
Designed to be a focal point for immersive learning experiences, the application centre will deliver a spectrum of training encompassing both theoretical insights and hands-on practical sessions. It will function as a nucleus for material testing
and validations across diverse applications such as fireproofing, architectural painting, interior and exterior textures, insulation, protective coatings, pavement marking and process and sanitary applications.
Highlighting the significance of the new centre, Caroline Chambers, EMEA President at Graco, said: “This new facility reinforces our commitment to the region and our esteemed network of distributors and material manufacturers. It serves as an avenue for our partners to showcase our comprehensive equipment range, organise training sessions, and collaborate on material testing and validation.”
Graco will curate a spectrum of training modules and courses aimed at optimising the utilisation of its equipment. A team of seasoned training experts and product specialists will be on hand to impart their knowledge and assist distributors, material manufacturers and clients in demonstrations, material validations and in elevating their proficiency levels.
Belzona UK recently opened its independent
UK distributorship. This investment into the UK market with state-of-the-art training, distribution, and in-house application service marks a new milestone in Belzona’s industry leading enterprise.
The £3m facility in Hawarden, Deeside has been carefully selected and designed to provide the UK market with a new training and application area, featuring a fully equipped presentation suite and newly built practical workshop space, measuring an immense 585 square metres, continuing Belzona’s focus on training raising nationwide application standards. A fully stocked and operational warehouse measuring 900 square metres accompanies the floor space.
“Today, as we open this new Office, we are reinforcing
our dedication to the UK market,” says Philip Robinson, Applications and Training Director. “Although the Belzona brand has branched out to the furthest reaches of the globe over the years, the UK remains one of the most important markets Belzona has.”
Hitachi High-Tech Analytical Science has expanded its coatings and materials analysis range with the launch of the new FT210 XRF analyser.
The FT210 includes a proportional counter detector for routine measurements of common platings, and incorporates advanced userfriendly features designed to enhance high-volume testing needs.
The launch of the FT210 also includes an updated version of FT Connect software for all FT200 Series models, with enhanced usability features for reporting, creating calibrations and data handling. This new version of FT Connect expands the RoHS screening capabilities of the FT230. FT Connect V1.2 software is compatible with both new and existing instruments.
The FT210, much like the
FT230, includes features to improve productivity by reducing the time needed to set up a measurement and act on data. To accelerate analysis set up, the FT200 Series comes with the largestin-industry sample view, wide view camera, auto-focus and auto approach, and a smart recognition feature called Find My Part, which automatically recognises features to be measured and chooses the correct analytical method.
New FT Connect software updates mean that the FT230 can now be used to check more materials for conformity to the latest hazardous substance directives. The RoHS screening capabilities are built into the FT Connect’s market-leading interface, ensuring analysis is simple and seamless.
The British Coatings Federation (BCF) secured a win in the Publication of the Year category at the 2024 Trade Association Forum (TAF) Awards ceremony in London, in front of over 350 delegates.
The Publication of the Year Award was presented to BCF for the in-house production and design of the UK coatings industry’s first-ever edition of its Road to Net Zero document, a substantial and comprehensive report that outlines the industry’s progress so far in reducing carbon emissions, the baseline and targets, and practical information for members on how they can measure and reduce their carbon footprint. The roadmap concludes with recommendations for government to support the industry on this journey, and what is needed from the wider
n NEW Larger 2 8” impact resistant color touchscreen and redesigned keypad for quick menu navigation
n NEW Weatherproof, dustproof, and water-resistant IP65-rated enclosure
n NEW Updated user interface retains the same layout and menus
n NEW Up to 30% longer batter y life
n NEW On-gage help explains menu items at the touch of a button
n NEW Ergonomic design with durable rubberized grip
supply chain to ensure that the industry is successful.
BCF was also Highly Commended for TAF’s Diversity and Inclusion Award for its work with its members promoting a more diverse workforce in the UK coatings industry. BCF has historically recognised talent within the industry and existing initiatives through its diversity
and inclusion, Young Leader of the Year, and Apprentice of the Year Awards at its annual BCF Awards ceremony.
HMG Paints’ range of coatings will once again be taking to the track on race circuits across the world. But this year it’ll be on the spectacular new Aston Martin Vantage GT3. As technical partner with Prodrive, one of the world’s largest and most successful motorsport and technology businesses, HMG will provide its paints for a number of cars throughout the upcoming season.
The Vantage GT3 is a comprehensive evolution of the ultra-successful and
recently retired Vantage GTE and GT3 cars, which made their debuts in 2018. Sharing their mechanical architecture – and that of the new Vantage road car – the Vantage GT3 is built around Aston Martin’s proven bonded aluminium chassis structure and powered by its fearsome twin-turbo 4.0-litre V8 engine. Boasting a dramatic, all-new nose-to-
tail aerodynamic package, comprehensively revised suspension and state-of-theart electronics, together they endow this latest-generation Aston Martin GT racer with world-beating potential. Built to comply with all FIA GT3 class regulations, including the new-for-2024 LMGT3 category, the new Vantage GT3 is a truly global
competitor. The Vantage GT3 will be fighting for victory at the Nürburgring 24 Hours, Spa-Francorchamps 24 Hours and – most iconic of all – the 24 Hours of Le Mans later this year. The Vantage GT3 will also see action in a host of national GT championships around the globe – including the Japanese Super GT Championship and British GT
AkzoNobel’s newly expanded Powder Coatings site in Como, Italy
Championship – underlining Aston Martin’s leading role in world motorsport.
HMG’s partnership with Prodrive dates back to 2013, and has seen HMG’s range of paints and coatings appear on a number of iconic cars built and run by Prodrive in several global racing series.
A major capacity expansion has been completed at AkzoNobel’s Powder Coatings site in Como, Italy, which will help secure supply to customers across Europe, the Middle East and Africa (EMEA). Four new manufacturing lines are now operational following the €21m project – two of them dedicated to automotive primers and two to architectural coatings. New bonding equipment lines have also been added, ensuring that the products meet and exceed industry standards.
“Increasing our capabilities in Como is a significant milestone which supports our ambition to create safety of supply for our customers,” explains Sanal Limoncuoglu, Commercial Director of AkzoNobel’s Powder Coatings business in South and East Europe (S&EE) and Middle
East Africa (MEA). “We’re now well equipped to serve all our customers in the EMEA region with highly efficient lines that are state-of-the-art in terms of consistency and quality.” The extra capacity in Como has been installed in a renovated building where powder coatings were originally made – a sustainable reuse of an existing part of the site, which was established in 1992. The new lines also use recycled energy and are focused on meeting the highest standards in sustainable production, supporting the company’s ambition to reduce its carbon emissions by 50% by 2030.
ProXL, the leading provider of refinishing and painting products for the automotive and industrial sectors, has launched a revolutionary water-based rust remover capable of effortlessly and safely eliminating corrosion while also caring for the environment.
Following extensive research and development over a period of three years, ProXL Rust Remover benefits from an innovative formula, allowing it to remove rust
easily without the need for dismantling and isolating panels, scrubbing or sanding, making it a versatile solution for a wide range of applications – perfect for use in body shops and by amateur restorers.
Adhering to the highest of environmental standards, ProXL’s non-toxic rust remover has been specifically created to eradicate deep-seated rust from a range of mild steel and iron surfaces, giving it the power to restore rusted metal while also being gentle on materials including copper, brass, aluminium, plastic, rubber, vinyl, lead and solder points. Adding to its versatility, the remover’s intelligent selective action enables it to preserve non-oxide coatings like paint or chrome that remain firmly bonded to metal surfaces.
Further adding to its appeal, ProXL Rust Remover delivers a user-friendly experience thanks to its non-toxic, non-corrosive, and non-flammable makeup. No fumes or unpleasant odours are produced during use. Meanwhile, its water-soluble, biodegradable ingredients mean it is safe on working hands, adding to its ecofriendly ‘green’ credentials. ■
Surfex is the UK’s event for the paints, inks, coatings and surface technology industry featuring a large exhibition running alongside a comprehensive programme of scientific, technical and topical industry content.
With extensive access to a whole spectrum of suppliers, scientists and industry experts, Surfex delivers the ideal meeting place to develop new ideas, source solutions to technical challenges, find inspiration, enhance knowledge and address key issues.
Visit www.surfex.co.uk to find out more and investigate exactly what you can achieve at Surfex.
Supported by:
Organised by: