Lifting
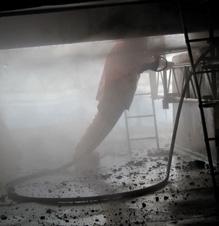
Up
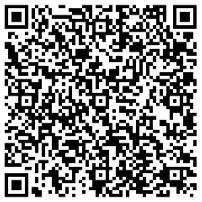

Using drones could mean a welcome goodbye to rope access and scaffolding
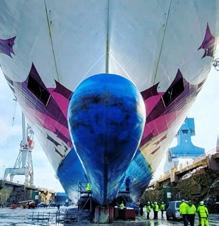
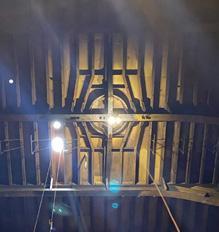
Lifting
Using drones could mean a welcome goodbye to rope access and scaffolding
ECONOMICAL HIGH QUALITY
Experience the full range of Hammelmann ship cleaning systems:
ENVIRONMENTALLY FRIENDLY SAFE
SURFACE PREPARATION WITH AN EDGE SPIDERJET® M Edge
Powerful and versatile with a uniform removal pattern right up to every edge.
This is the newest addition to our unique product line of high-performance ship cleaning systems.
OUR UNIQUE RANGE OF SHIP CLEANING SYSTEMS IS YOUR EDGE ON THE COMPETITION
Working heights: up to 32 m
Working widths: 374 – 1000 mm
Operating pressures: up to 3000 bar
Flow rates: up to 94 l/min
GET IN TOUCH FOR A CUSTOMIZED SOLUTION, PERFECT FOR YOUR DEMANDS
www.hammelmann.com
4 Lifting the Lid A study commissioned by the Water Jetting Association (WJA) into the management of high-pressure fluid injection injuries has become one of the most important research papers on the topic in the world and has been accessed online more than 10,000 times since it was published in 2019
14 Spotlight The Spotlight in this issue is turned on drone inspection, highlighting how using a drone to inspect FPSO tanks not only reduces the time required but also virtually eliminates the safety risk, and how a combined visual and UT (ultrasonic testing) drone platform could mean a welcome goodbye to rope access and scaffolding
8 Up Front Security Jotun’s Clean Shipping Survey takes a deep dive into the shipping industry’s knowledge of biofouling on ships’ hulls, the technologies available to manage it, and whether international regulations play a part in developing a response to the issue
42 Analysis Hydropower Cold-curing polymeric repair and protection materials can provide a novel means of bypassing the challenges arising in maintenance operations in hazardous environments such as the oil & gas and petrochemical industries
The World of MontiPower® is all about the power of innovation for clean and safe surface preparation, and to create reliable cleaning, removal and anchor profiling solutions for various substrates
A study commissioned by the Water Jetting Association (WJA) into the management of high-pressure fluid injection injuries has become one of the most important research papers on the topic in the world.
Jotun’s Clean Shipping Survey takes a deep dive into the shipping industry’s knowledge of biofouling on ships’ hulls, the technologies available to manage it, and whether international regulations play a part in developing a response to the issue.
How PPG’s powder coatings are delivering robust corrosion protection for liquid propane gas tanks, Hempel’s solution for underwater hulls can achieve up to 2.5% in fuel savings, and Silja Serenade has been repainted with Jotun coatings.
Facilities maintenance in hazardous environments such as the oil & gas and petrochemical industries can face particular challenges that coldcuring polymeric repair and protection materials can help solve.
Corrosion protection of pipes in the ship repair environment achieves faster installation, less downtime when temporary coatings are used. Polymeric repair and protection materials are suitable for extending the in-service life of assets in a multitude of industries, including equipment in the petrochemical industry.
Using drones for FPSO tank inspection not only reduces the time required but also virtually eliminates the safety risk. How a combined visual and UT (ultrasonic testing) drone platform could mean a welcome goodbye to rope access and scaffolding.
Editor: Mark Langdon mark@pce-international.com
Contributing Editor: Mike Garside mike@pce-international.com
Advertisement Manager: Nick Carugati nick@pce-international.com
Production Manager: Tatum Le Patourel tatum@satzuma-creative.co.uk
Designer: Fiona Andreanelli
fiona.andreanelli@mpigroup.co.uk
Accounts: Claire Long claire.long@mpigroup.co.uk
Publisher: Andrew Deere andrew.deere@mpigroup.co.uk
There are positive signs for PaintExpo 2024, with registrations for the world’s leading trade fair for industrial coating technology already at an excellent level one year before the event.
The latest products, appointments and industry news.
MPI Group
Peel House, Upper South View
Farnham, Surrey GU9 7JN, England
Tel: +44 (0) 1252 732220
Email: info@mpigroup.co.uk www.mpigroup.co.uk
MPI Group, as a body, is not responsible for any opinions expressed in PCE by contributors. All rights reserved. No part of this publication may be reproduced, stored in a retrieval system, or transmitted, in any form or by any means, electronic, mechanical, photocopying, recording or otherwise, without prior permission of MPI Group.
© Marine Publications International Ltd 2021
One year in the tropical sun.
Just a few weeks in here.
Bring the outside into your lab with Atlas. Configurable to precisely simulate environmental conditions, our weathering instruments set the standard for accuracy and reliability. It’s no wonder that Atlas is the platform of choice for durability testing worldwide.
A study commissioned by the Water Jetting Association (WJA) into the management of high-pressure fluid injection injuries has become one of the most important research papers on the topic in the world.
The study has been accessed online more than 10,000 times since it was published in 2019, and has been cited in five specialist medical papers over the same period. Now, a water jetting injury treatment guide developed from the research has been extensively redesigned to make it easier to use.
Water jetting is essential for a huge range of tasks, including pressure washing, cleaning tubes and chambers in oil and gas, petrochemicals and energy plants, de-fouling ships and marine structures, hydro-demolition of concrete, sewer and tank cleaning, and precision materials cutting.
The WJA water jetting injury treatment algorithm gives step-by-step best practical guidance on the treatment of water jetting injuries from first response through to definitive hospital care.
It has been praised as a game-changer in aiding effective responses to water jetting injuries which, if not treated correctly, can result in life-changing and sometimes fatal consequences.
The WJA-funded research was led by Dr Sancho Rodriguez-Villar, an intensive care consultant at King’s College Hospital, London, and Dr Robert Charles Kennedy (PhD), the WJA’s Clinical Research and Development Advisor.
“The study is clearly one of the most important sources of expert opinion on highpressure fluid injection injuries in the world,” explains Dr Rodriguez-Villar. “It is a complex multidisciplinary piece of research involving knowledge from industry and three medical specialties.
“It is highly likely that doctors and surgeons around the world are searching for advice on such injuries, finding this research, and using it to guide their treatment.
“The study is having the desired and very important effect of educating clinical teams about how to treat these unique and serious injuries. This, in turn, will be greatly improving the treatment outcomes for patients, contributing to their long-term health and wellbeing, and possibly saving lives.”
The WJA is the member organisation for the water jetting industry in the UK. Its codes of practice and City & Guilds-accredited training courses are respected for setting water jetting standards in the UK and internationally.
The study, called the Management of Industrial High Pressure Fluid Injection Injuries (IHPFII): the Water Jetting Association Experience with Water Driven Injuries, is published in the European Journal of Trauma and Emergency Surgery.
It is also available via the medical database Researchgate. The WJA funded a publishing agreement to allow it to be free to download, to ensure it is seen and used as widely as possible.
IHPFII injuries can be caused with water pressures as low as seven bar, or 100 pounds per square inch (PSI) – while water pressures for industrial applications can exceed 1,700 bar, or 24,650 psi.
They are characterised by small entry wounds, caused by fine fluid jets, and no exit wounds. This can mask the extensive internal disruption they can cause. Debris and bacteria
can be also carried far into the body, increasing the risk of serious infection.
These factors can lead to delays in patients receiving the appropriate emergency treatment. This can result in complications that, in worst cases, cause life-changing serious injury or death.
The WJA water jetting injury treatment algorithm is designed to help first aiders, paramedics and clinicians optimise treatment and make correct treatment decisions throughout a patient journey, reducing the risk of death, long-term disability or unnecessarily prolonged periods of recovery.
The WJA has now created an A4 version which is easier to view, both online and offline. Its sections have also been colour-coded so users can easily follow a patient’s journey through a treatment pathway.
“The evidence shows that, without early and correct intervention, the outcome for those injured is often catastrophic,” says Kennedy. “We strongly advise all parties to observe the WJA’s algorithm for the management of highpressure injection injuries.”
The algorithm can be instantly accessed via a red tab on the home page of the WJA website. ■
The study is having the desired and very important effect of educating clinical teams about how to treat these unique and serious injuries.
Jotun’s Clean Shipping Survey takes a deep dive into the shipping industry’s knowledge of biofouling on ships’ hulls, the technologies available to manage it, and whether international regulations play a part in developing a response to the issue.
If the shipping industry took a more proactive approach to hull cleaning, “we as an industry could save as much as 198 million tonnes of CO2, which is more than six times the volume produced by the nation of Norway annually,” explains Morten Sten Johansen, Global Marketing Director, Hull Performance Category. “As we are a global industry, it is imperative that we take a united international approach if we are to succeed in reducing emissions, preserving fuel and protecting the oceans’ biodiversity.”
In 2020, the Global Industry Alliance for Marine Biosafety moved to address head-on what stakeholders called the shipping industry’s ‘poor understanding’ of the relationship between ships’ biofouling and fuel consumption/greenhouse gas (GHG) emissions.
Jotun established Hull Performance Solutions (HPS) in 2011 to make it easy for operators to maximise hull performance and thereby reduce both fuel costs and greenhouse gas emissions. The solution consists of Jotun’s advanced antifouling products, combined with a transparent method for measuring the impact of antifouling on vessel energy efficiency.
That assessment came in spite of a coordinated attempt by the International Maritime Organization (IMO), BIMCO, several classification societies and others to promote an understanding of the impact of biofouling on increasing ships’ drag in water.
The poor understanding was also surprising given the overarching search for ways to minimise GHG emissions as the industry transitions to decarbonisation.
Having ascertained respondents’ belief that they had a moderately good knowledge of biofouling, the Jotun survey asked about the impact biofouling had on vessel GHG emissions.
The wide range of answers – from 11% thinking the impact on emissions was minimal (between 0% and 5%) to 27% thinking the impact was very significant (more than
20%) – suggested there is no consensus, even among those well-versed in biofouling.
With one in four respondents thinking the impact lies in the 6-10% range and a similar proportion putting the impact at between 11% and 15%, almost half of respondents appear to accept that biofouling does have an impact on emissions, although that impact is probably underestimated.
Research studies looking at different test surfaces and biofouling conditions have concluded that even a thin layer of slime could trigger an increase in GHG emissions of up to 25%. Medium or heavy calcareous fouling would represent a significantly greater impact.
The conclusion must be that GloFouling Partnership’s observation that the perceived impact of biofouling “is likely to have been historically underestimated” is supported by this survey, which found that the impact is currently underestimated.
The issue of the transfer of invasive aquatic species through ships’ biofouling was first brought formally to IMO’s attention in 2006.
After three years of consultation by IMO member states, the 62nd session of the Marine Environment Protection Committee in July 2011 adopted guidelines for the management of biofouling which, it was hoped, would represent a ‘decisive step’ towards reducing the transfer of invasive species.
Even a thin layer of slime could trigger an increase in GHG emissions of up to 25%
Biofouling guidelines have been updated in the 12 years since MEPC 62, but more attention has been given to the management of ballast water than biofouling on ships’ hulls. This might have contributed to a mixed perception of the impact of hull biofouling among respondents to the Jotun survey.
Responses revealed that the same proportion believed the impact of biofouling on the spread of invasive species was either minimal or very significant. More respondents thought the impact lies between the two extremes; however there is little agreement on its importance.
More research is needed to quantify the significance of biofouling on ships’ hulls in the devastation of native species, and a broader understanding of the spread of invasive species is required across the maritime sector.
Whether the industry believes the issue is significant or not, port states have started to take action by restricting the arrival of ships with fouled hulls. New Zealand introduced antifouling laws in 2018, followed by Australia in 2022. Ships destined for ports in those states will need to clean their hulls ahead of arrival, which could become a problem for shipowners if the practice spreads.
It is likely that hull cleaning technologies that involve not only the removal of microorganisms, algae, plants and animals but also various technologies for proactive and reactive hull cleaning will develop in line with higher awareness of the issue.
The extent of biofouling’s impact on transferring invasive species around the world was highlighted almost 20 years ago. The survey is a snapshot of respondents’ thinking two decades on.
Jotun survey respondents suggest the industry underestimates the impact of biofouling on GHG emissions and on the spread of invasive aquatic species. The first consideration for investment in any emissions reduction technology therefore must be whether such investment is really necessary.
Respondents said they mostly considered the range of emissions technologies through the lens of finance. Ensuring a return on an investment (28%) in a reasonably priced technology (25%) and at an acceptable payback time (18%), were all thought to be important.
Investing in a technology a shipowner
is already familiar with also plays a part, but investing to meet SEEMP (Ship Energy Efficiency Management Plan), CII (Carbon Intensity Indicator) and even ESG (Environmental, Social and corporate Governance) expectations is a weak driver.
Two-thirds of respondents said they had already invested in clean-hull solutions, with optimised antifouling coatings the leading option.
Among the reasons for investing in highergrade coatings (49%) rather than either hull grooming by divers, robotic crawlers (33%) or ultrasonic treatment (13%) is past experience. Premium coatings are not cheap. However, respondents suggest that monitoring performance on other ships in the fleet, staying close to the coatings manufacturer, and recognising the cost savings gained all outweigh the price of a hull coating over time.
In contrast, respondents who had used hull grooming technologies picked out cost savings as the key consideration, while the few who had used ultrasonic treatment said they had had good experience on other ships.
It seems clear from this survey that shipowners’ investment in new technologies needs to overcome two obstacles: the first is
making sure the finance is well spent, but the second is persuading the investor that the decision is justified.
Although regulatory compliance per se should not be the most important consideration in biofouling management, it mustn’t be presumed that regulations do not have an impact on investor thinking. Only 5% of respondents to the Jotun survey said the Carbon Intensity Indicator (CII) regulation would have no influence on their proposals for tackling biofouling.
Some 29% of respondents said CII would ‘definitely’ be a consideration, with a further 20% saying ‘very probably’. One comment described tackling biofouling as ‘part of the whole picture’; another observed that while biofouling is not directly mentioned in the CII regulation, it should still be considered as part of the response.
Among respondents who believed tackling biofouling would ‘probably’ impact decisionmaking in future, the comment was made that global pressure on environmental matters would only increase.
That is certain. The IMO’s updates to regulations and guidelines covering ballast water management and the transfer of invasive aquatic species will get stricter – revised guidelines are subject to approval at MEPC 80 in July 2023 – and coastal state regulations will limit where hull cleaning can take place and how it should be performed.
New coatings technology, along with improved hull grooming and antifouling innovation, are all developing to meet demand. There is a close relationship between regulations and innovation, and it is clear from responses to the Jotun survey that the majority of industry stakeholders are aware of the equally close relationship between ships’ hull biofouling, GHG emissions and the spread of invasive species.
Unfortunately perhaps, regulators move at a slower pace than innovators. For an international industry such as shipping, regulations ought to be applied globally, but because invasive species have a targeted impact, regional or local regulations must be anticipated. ■
*Analysis undertaken by Richard Clayton, Chief Correspondent at Lloyd’s ListA combined visual and UT (ultrasonic testing) drone platform could mean a welcome goodbye to rope access and scaffolding, explains Simon Ruddick, Director at Marine Inspection Services Ltd. Ever since he started out as a trainee in a local UK company in the late 80s, Ruddick has been inspecting and surveying ships for a living. He is now a leading expert in visual surveying and nondestructive testing (NDT) of ships and offshore installations.
All commercial ships are built to the standards of class societies, laws and international conventions, and they are surveyed repeatedly for compliance. A vessel simply cannot operate without being certified by a class society.
Ultimately, the owner is the one responsible for the safety and integrity of the vessel and the staff. But tremendous responsibility rests on the classification societies, and the limit to their liability is a matter of continuous discussion. To maintain a reliable classification process, it is vital that they remain an independent third party and avoid conflicts of interest. For example, they must be able to demand high-quality inspection data of good coverage as a basis for their assessment, without being responsible for producing the data themselves.
Therefore, the vessel owner must arrange for the inspection data to be produced by someone with the necessary expertise, equipment and focus, such as inspection companies.
It’s a job that involves entering enormous, emptied cargo hulls, cargo tanks, ballast tanks and other enclosed spaces to assess their structural integrity. You must know what you’re doing, to gather all information in a safe manner. Got an inspection job that is dark, dirty and dangerous and where tremendous values are at stake? That’s when you call companies like Marine Inspection Services. Drone inspections are an important safety measure as they can replace lots of hours of working at height. Drone inspections also save lots of time and money and allow for much more flexible and efficient inspection schemes.
On an oil tanker, these tanks are typically about 20 metres high, 20 metres wide and, say, 27 metres long. Surveying just a single tank for corrosion or other damage is a comprehensive process, traditionally requiring working at height and a lot of time.
Workers traditionally use ropes and harnesses to climb inside the tanks to access all the surfaces – sometimes even needing to put in place gigantic constructions of scaffolding. Needless to say, operations like these take up a lot of resources and time.
Through advancements in technology, a lot is changing in the industry. Surveyors are now able to automate processes with real-time reporting, doing visual inspections remotely by drone.
In many cases you’re removing the need for the surveyor to be up on scaffolding which takes days to put up and costs a huge amount of money.
However, climbing, scaffolding and manual readings are still required for some tasks, such as ultrasonic thickness measurements (UTM). Years of use in rough conditions wears at the metal plates in a ship’s construction, the degradation being potentially invisible to the naked eye and to most cameras.
Measuring the plate thickness to gauge exactly how much is corroded and how much is left is vital to assess structural integrity. There is also magnetic particle inspection (MPI), which is often used to determine surface cracks, or slight sub-surface defects.
Eddy current techniques are used to assess welds and to find cracks. Such techniques have the advantage over MPI in that they do not require coating removal.
But UTM is the technique for plate thickness and corrosion assessment inside vessels. So in terms of structural integrity assessments, visual and UTM equipment gets you the data you need, when you know how to get it.
The employees of Marine Inspection Services are a small team of sought-after experts that travel the world doing their thing. Sometimes, they will get on a ship in one port, do the survey while it’s sailing and get off at the next port. They normally travel as a team of two or three and may be away for weeks at a time.
Over the last decade or so, using drones has increasingly become a big part of the job.
With the ship’s schedule and cost of cleaning for inspection, it’s critical to work efficiently. You must get it right the first time, because you really don’t get a second chance. When you come out of the tank, that tank is closed and you’re not going back in there. It’s too much effort for everyone to get the tank ready for you to come out and say: I’ll have to go back and get some more footage.
Today, we’ll typically be doing a combination of using the existing structure – walking around on the platforms or stringer levels – as well as doing rope access and using drones. The drones are mainly used for visual surveys. They go up quickly and give us good results across the different structures, to look at the condition, look for cracks, look at the coating and so on.
The drone simply brings your eyes to where you need them. They are a ladder to get to the structure, enabling you to do your job once there – and they record everything!
The Scout 137 Drone captures 4K video and photos and uses a 3D LiDAR sensor to map the entire space in 3D – and the drone’s exact position within that space – in real time. The pilot can fly the drone beyond visual line of sight (BVLOS) and know exactly where it is and where it’s heading all the time.
© WindWhisper Racing Team
The drone simply brings your eyes to where you need them. They are a ladder to get to the structure, enabling you to do your job once there – and they record everything! .
This is very handy even if you go inside the tank. For example, you may remain on the lowest stringer level and even inspect that from the underside, without climbing down to the floor just for visual line-of-sight to that final part.
You put the drone in and you do a full visual inspection across the top of the tank, something that otherwise would require scaffolding or rope access. For an oil tanker, this would take days to do without the drone, if not weeks, and cost thousands of dollars. With the drone, it’s a matter of hours.
Unlike other battery-powered drones, the ScoutDI drone is tethered. That means the operator doesn’t have to worry about losing signal or power or having to fly back and forth changing batteries.
With a battery-powered drone, remaining battery life is constantly in the back of your mind. If you’re surveying a whole tank, then you need to constantly remember, let’s get this frame done with this battery, and then we’ll come down and then we’ll do the next bulkhead with that battery.
With a tethered drone like the ScoutDI, you don’t need to think about that – it’s not even in your mind, so you concentrate more on the inspection side of things.
Using the drone saves a lot of time and effort, and allowing this level of focus on the job is an important safety factor. One caveat though, is that you still sometimes have to go climbing anyway – but this too is about to change.
As mentioned before, you often have to do both visual inspection and non-destructive testing (NDT) to survey a ship according to class requirements. The latter is done with Ultrasonic Thickness Measurements (UTM). Even if you use a drone for the visual part of the inspection, until now someone has still needed to carry out measurements with a hand-held measuring probe using ropes or other access methods.
You may save lots of time on visual inspection with a drone. But if you still need to put on that harness and climb around for the UTM part after the drone is back in its case, then there is still room for time-saving improvement, not to mention data coverage.
If you’re doing manual UTM, then normally
you’re only doing sample locations. The thickness measurements with rope access might only take one day, but that is only in sample locations. You’re covering a tiny percentage of the tank and it’s taking you half or even multiple days.
Manual UTM is vital but time-consuming and only sampled, fractional coverage is practically achievable. Wouldn’t it be nice if a drone could do both the visual inspection and the UTM part? This could enable a small team to complete a job in half a week – something that used to take a dozen workers 45 days or more.
NDT using ultrasound (UT) is the most requested addition to indoor inspection drone systems.
ScoutDI is working to enable visual inspection and UTM in the same drone platform. This happens with a UT option that can be mounted on the Scout 137 without requiring a separate drone.
As a world first, both the resulting visual and UT data is location-tagged. So when you replay the inspection in the Scout Portal, you can see precisely where any specific piece of footage or UT measurement was taken.
With the possibility to add a UT add-on to the drone, the thickness measurements can be done remotely. Not only saving you time, but the measurements can be done more quickly and thoroughly as well. This is a potential gamechanger for inspection of many types of assets.
We inspect lots of chemical tankers as well, and for such cases UT on a drone is brilliant because chemical carriers are much cleaner than oil tankers. You don’t have to scrape off the thick residue from the crude oil, so you can in fact do the entire job just using the drone.
If you can eliminate climbing from structural assessment jobs, great benefits in terms of safety, time and cost are unlocked. Offering visual inspection with a camera, and UT measurements in the same drone platform, this is exactly what we’ll be doing.
The drone reaching all the same locations as a climber, and much faster than a climber can, you no longer have to be content with only sample locations. Much greater coverage is within reach and consequently a much more comprehensive and reliable dataset.
It is a long-awaited change and a major step on the way to digitalisation of heavy industries. ■
Floating production, storage, and offloading (FPSO) vessels offer effective and flexible infrastructures for offshore oil production operations. These huge ships can process and store oil until it can be transported by tanker or pipeline. They are easy to install and can be relocated as required to optimise a production portfolio.
FPSOs have a high development cost, but a long lifespan because they can be relocated as required and used well beyond the life of a single production facility if maintained. Typically, the processing equipment is located above the vessel’s deck, while oil storage is located below the deck in the double hull. These vessels hold a crew of between 50-70 people. For safety and environmental reasons, the vessels must be inspected and certified every few years.
Inspection experts TEXO were asked to perform an inspection on the oil tanks in an FPSO.
A vessel in drydock can be inspected relatively easily by setting up scaffolding and utilising a large team of inspectors, but inspecting an FPSO on station is much more difficult and time consuming. Oil tanks cannot be emptied all at the same time for efficient inspection, both because the vessel must be balanced for safety and for continuity of operations. Generally, operators make two tanks available at a time – simply preparing the tanks for inspection can take weeks. Tank inspections traditionally require four to five rope access technicians, who may be left waiting for several weeks to be deployed while the tanks are prepared. When the tanks are available for inspection, rope access work is dangerous and time consuming, with the inspection of two tanks taking significantly longer than drone inspection. In some cases, scaffolding may be required, which introduces new risks. In addition to the danger to the staff working at height, scaffolding can cause damage to tank coatings and
dropped objects can contribute additional risk to the tank and the personnel.
While the labour is expensive, TEXO points out that the production slowdown while the tanks are unavailable is even more costly. Inspection is a certification requirement and promotes preventative maintenance: workers look for distortion, defects, buckling, and cracks, especially in toe wells and other high stress areas. Any problems found must be addressed during the process, adding more downtime if the defect is found late in the inspection process.
TEXO utilised the Elios 3 drone to perform the oil tank inspection in one week after the emptying and cleaning process, with a team of only two people. With the pilot located safely outside the tank, TEXO says that there is virtually no risk to the personnel, with the team performing four flights to map the tank, then creating a 3D point cloud of the asset.
The Elios solution represents a very significant savings in cost – but also offers better, more reliable data for repair and maintenance.
“Elios is such a good tool that it really just requires two people, versus five people for many days,” says TEXO’s Xiang Wong. “But also, it gives the surveyors on shore a lot of confidence that the entire tank has been inspected. Utilising the flight trajectory ensures teams have not missed any of the highly repetitive structure.”
Using rope access teams, says Wong, “You have to put your entire faith in the team that is working for you, because all of the pictures look the same. With the Elios 3 you can track where you have been – you have the video continuity. That’s a major benefit. A single set of data can be reinvestigated by multiple inspectors all with their own experience adding layer upon layer of expertise to it.”
The Elios 3 solution also allows the TEXO team to become more efficient in maintenance, to minimise downtime and the related costs. “With drones, you can inspect critical points, hot spots, or stress concentration areas first, and identify any problems right away,” explains Wong. “When you have identified a defect early on, you can work with the naval architects and surveyors to develop a solution while the tanks are still empty.”
The steam heating coils found on the bottom or sides of the tank offer a particularly
good case in point. Heating elements form a dangerous environment and are fragile and easily breakable. Human inspectors are not always able to identify the exact source of a problem: flying a complex pattern with the collision-proof Elios solution and creating a point cloud representation of the system allows engineers to identify a problem more easily. Point cloud data can be merged with topside data to form a complete picture of the tank, helping engineers to identify the correct placing of any cut into the tank for repair.
TEXO was able to provide its client with an accurate inspection, including point cloud data that was previously unavailable. The inspection
was performed in only four days, compared to a usual timeframe of up to two weeks, and the client feedback was positive. The client is now interested in pursuing further use of the Elios solution for FPSO inspections.
The Elios inspection provided the inspection with no risk to personnel, and was able to offer onshore surveyors complete confidence that the entire area had been reviewed.
TEXO sees significant value in using the collision-proof Elios solution for a variety of oil and gas inspection projects. The TEXO team has used both Elios 2 and Elios 3. While Elios 2 offers many benefits over traditional rope access inspection, TEXO cites the
advantages of location referencing and point clouds using Elios 3. “If there are no problems in an inspection, the Elios 2 is great,” says Wong. “But for fixing issues, the Elios 3 is needed.” In future, TEXO is looking forward to exploring further use cases, like semisubmersible vessels. “Semi-submersibles are almost like a maze to navigate,” explains Wong. “The Elios 3 is the perfect tool for that. Elios really negates the need to put men in confined spaces.”
TEXO Group is certified by DNV (Det Norske Veritas) as a service supplier approved for surveying using remote inspection techniques (UAV) as an alternative means for a close-up survey of the structure of ships and mobile offshore units. ■
Over 50 years ago, Antonio Merloni
Pressure Vessels started manufacturing liquid propane gas cylinders, eventually adding the production of small and large capacity tanks in the 1970s.
Today, with production sites in Matelica and Sassoferrato, Italy, the company serves more than 1,200 customers in 48 countries and is one of the largest European manufacturers of cylinders and tanks for LPG storage. All its products require adherence to stringent construction standards and compliance with UNI EN 1442 European Directive 2010/35/EU for cylinders or UNI EN 12542 European Pressure Equipment Directive (PED) 2014/68/EU for tanks.
In 2020, under the new leadership of Paolo Sparvoli and the support of a PPG team based in Verbania, Antonio Merloni began to implement a plant renewal and modernisation programme to increase productivity and product quality, upgrade facilities and reduce its environmental impact.
Phase one of the process started with transitioning the painting lines of the above and underground tanks — with capacities of 290 to 3,000 litres, diameters of 800mm to 1.2m and heights of up to three metres — from liquid to powder coatings.
“Sustainability is one of our corporate values, requiring respect of the environment and enhancement of the workplace,” says Valeria Tassotti, Merloni Technical Manager. “Because powder coatings are generally made without solvents that release harmful volatile organic compounds, it is a more sustainable technology and eliminates the need to manage hazardous wastewater that is inherent in the liquid coating process.”
But the transition also had benefits that extended beyond good environmental stewardship. According to Tassotti, the change also improved the overall wellbeing and productivity of plant workers who were now able to operate in a cleaner setting.
Powder coating is a multi-step surface finishing process, and Antonio Merloni invested in a fully automated chain painting system to measure all machine operating parameters and, consequently, improve finish quality.
“With powder coatings, we can automate each phase of the application and rely on the machine parameterisation for more accurate data control of the production flow compared to liquid coating,” explains Tassotti. “We can monitor data about temperatures and times of all application steps, for instance, but also the translation and rotation speed of the piece that helps us to quickly detect the causes of any quality defects.”
For Antonio Merloni, the success of the project depended, above all, on the reliability of the company that installed the new coating plant and the powder supplier, as well as on their ability to collaborate.
Every year, Antonio Merloni Pressure Vessels produces one million small cylinders for domestic use with a capacity of 5-25kg at their plant in Sassoferrato, Italy. Aside from their size differences, these powder-coated cylinders also have different coating cycles, colours and protection requirements compared to the tanks.
A powder production facility in Verbania, Italy, once part of Arsonsisi’s powder coating business before PPG acquired it last year, had been providing the plant with polyester powder coatings for domestic use small cylinders since 2015.
With the decision to replace liquid with powder coatings on the small tanks produced at their Matelica plant, Antonio Merloni needed a new powder coating system and new customised powders for the small tanks produced there. PPG immediately proved to be the right partner for the project.
Antonio Merloni Pressure Vessels inaugurated its new, fully automated powder coating facility at the plant in Matelica in the spring of 2022.
“In such a large, new coatings plant, it takes a while before reaching a constant production flow, as you must troubleshoot any initial problems arising from the plant itself or from the conditions of the powder before you set the optimal plant parameters,” explains Fabrizio Delgrande, PPG Sales Engineer for powder coatings. “PPG’s R&D powder coatings lab carried out several tests before finalising the product formulas.”
Sustainability is one of our corporate values, requiring respect of the environment and enhancement of the workplace.
Standards in the pressure vessel manufacturing sector require that a tank’s final finish be resistant to both soil and atmospheric corrosion. The coating process plays a key role in the efforts, along with the sandblasting pretreatment, to prevent corrosion and ensure the safety of the tank.
Both the sheet metal and the vessel structure’s welding provide resistance to pressure. But the tank must also resist
corrosion from the soil or the atmosphere, and this is where the finishing makes a difference.
“The corrosion rate makes the sheet metal thinner and no longer resistant to pressure. If the tank is well protected, then it will operate safely the way it was designed,” explains Tassotti.
For the underground tanks, PPG developed and customised the epoxy powders according to the customer’s coating system and tank colours.
“Antonio Merloni employs the single-layer fusion-bonded epoxy technology for the corrosion protection of the underground steel pipelines used for the transport of gas, oil and water,” explains Delgrande. “These pipes, like the tanks, are first sandblasted and then coated with epoxy powders with excellent resistance to corrosion in tough soils and mechanical shock.”
Temperature is a key element in the underground tank painting cycle, where the coating film must have a greater thickness
The corrosion rate makes the sheet metal thinner and no longer resistant to pressure. If the tank is well protected, then it will operate safely the way it was designed.
Underground Envirocron P551E2202R anti-corrosive epoxy coating (PCM - P5 Series), Green
Above ground Envirocron P853P2109R zinc-free epoxypolyester primer (PCF - P8 Series), Avorio Envirocron P451W2010R polyester architectural topcoat (PCS - P4 Series), RAL 9010 Pure White
to ensure anticorrosive and mechanical performance. In order to obtain a 500μm thickness and reach paint crosslinking with a single coat of green epoxy powder coating, the tanks must be preheated at a temperature ranging between 130-140°C.
The above-ground tanks are protected from corrosion by a double coat of an epoxy polyester primer, followed by a Qualicoat Class 1-certified white polyester topcoat.
The epoxy polyester primer is formulated to be very versatile both for heat retention during curing and for overpainting, while the polyester topcoat helps to maintain gloss and colour, even in adverse weather conditions.
The above-ground tanks are optimally protected from the elements by a two-coat system comprised of a PPG epoxy polyester primer, followed by a white polyester topcoat that is Qualicoat Class 1 certified.
To protect the underground tanks, a single coat of PPG green epoxy powder coating with a 500μm thickness is applied to elevate anti-corrosion performance.
Today, Antonio Merloni Pressure Vessels produces more than 40,000 tanks every year; 30,000 of them are now coated with PPG powder coatings. ■
w i t h r e d e s i g n e d k e y p a d f o r q u i c k m e n u n a v i g a t i o n
n N E W We a t h e r p r o o f , d u s t p r o o f , a n d w a t e r- r e s i s t a n t I P 6 5 - r a t e d e n cl o s u r e
n Fa s t r e s p o n s e p r e c i s i o n s e n s o r s p r o v i d e a c c u r a t e , r e p e a t a b l e r e a d i n g s n A u t o L o g m o d e a u t o m a t i c a l l y r e c o r d s e n v i r o n m e n t a l p a r a m e t e r s a t u s e r- s e l e c t e d i n t e r v a l s
N E W M a g n e t i c p r o b e a t t a c h e s t o s t e e l s t r u c t u r e s f o r m o n i t o r i n g cl i m a t i c c o n d i t i o n s
B a c k w a rd s C o m p a t i b i l i t y ! T h e r e d e s i g n e d Po s i Te c t o r g a g e b o d y a c c e p t s A L L c o a t i n g t h i c k n e s s , s u r f a c e p r o f i l e , e n v i r o n m e n t a l , s o l u b l e s a l t , h a r d n e s s , a n d u l t r a s o n i c w a l l t h i c k n e s s p r o b e s m a n u f a c t u r e d s i n c e 2 0 1 2 .
Hempel’s solution for underwater hulls can achieve up to 2.5% in fuel savings and can be applied during routine drydockings.
Key messages
. The SeamFlow weld fairing system for ship hulls can reduce vessel fuel consumption by up to 2.5% and help owners and operators meet emission reduction targets
. In one five-year drydock cycle SeamFlow can reduce carbon emissions by 12,000 tonnes and bring fuel savings of up to $1.8 million
. The patented SeamFlow system is a simple way to reduce costs and meet environmental targets without extending drydocking time
. After drydocking, Hempel can use out-of-dock data to calculate fuel savings impact, helping to quantify savings delivered to customers
Hempel showcased its unique new solution SeamFlow for the first time in Asia at Sea Asia in Singapore. The world’s first seam fairing solution for ship hulls is designed to reduce friction on the underwater area of vessel hulls and can reduce fuel consumption by up to 2.5%. Over one five-year drydocking cycle it can also save up to 12,000 tonnes of carbon emissions and $1.8 million in fuel costs.
SeamFlow is a complete system of coating, application tools and dedicated service, designed to reduce the friction created as a ship’s hull sails through water. By smoothing the welding seams created when the steel
sheets of a ship’s hull meet, friction can be significantly reduced.
A ship’s hull has around 5km of weld seams, and although the welds protrude by only three to nine millimetres, their dragging effect on a vessel’s operation adds up to a significant amount.
“SeamFlow has been available for application on vessels since last year and, with the positive results seen on all applications until now, Hempel is delighted to share the possible positive impact of SeamFlow,” said Mads Raun Bertelsen, Marine Data and Technology Director at Hempel, speaking at Sea Asia. “By reducing the drag created by the welds on a ship’s hull,
After the SeamFlow weld fairing system has been applied to the seam reducing drag and obtaining up to 2.5% fuel savings
we are able to deliver considerable fuel savings to industry and also support owners’ and operators’ emission-reduction pathways.”
SeamFlow is applied during routine drydocking after the hull has been coated with one coat of anti-corrosive primer. Two SeamFlow applicator teams then apply the modified epoxy to the welding seams using specially developed equipment. Hempel-approved experts are onsite to guide the application and carry out quality checks. After 10-12 hours the specialised epoxy coating will be dry and ready for the final tie-coat and top-coat as usual. Hempel
also offers in-service performance monitoring to help quantify the customer’s return on investment.
“SeamFlow is a smart and simple solution for shipowners to reduce costs and meet environmental targets without the need for any significant additional downtime,” explains Nikhil Lakhiani, SeamFlow Solution Owner at Hempel. “The application can be easily accommodated in the drydocking schedule, and if planned well, becomes a smooth and integral part of drydock operation.”
SeamFlow is compatible with all Hempel products, which offer further efficiencies and cost-saving opportunities. ■
The Silja Serenade was repainted with Jotun coatings in January, with the prevailing weather conditions imposing their own restrictions. The drydocking lasted 16 days, during which the ship’s underwater hull, topside and part of the tanks were painted.
The Silja Serenade is a Ro-Ro cruise ferry owned by the Estonian Tallink Grupp, which operates under the Silja Line brand on the Helsinki-Mariehamn-Stockholm route. The ship was built in 1990 at the Masa-Yards Turku shipyard and can accommodate 2,852 passengers and 450 cars.
Silja Serenade underwent maintenance and painting at the Turku Repair Yard, during which the ship’s underwater hull, topside and part of the tanks were pre-treated and painted. Painting was performed with Jotun products supplied by Nor-Maali.
Outdoor drydockings differ significantly from new construction, where during the block phase a large part of the painting is done indoors. In the outfitting phase, the newbuilding is mostly covered and heated.
In outdoor dockings, the weather forecast needs to be followed very closely and one must react quickly to changes in temperature and humidity. Environmental conditions determine the schedule and scope of the repair, and in the worst case, the planned work has to be cancelled.
During the drydocking of Silja Serenade, the environmental conditions were quite challenging. The temperature varied between -2°C and +3°C and there was no cover over the vessel during maintenance. Heavy rain was avoided, but the cold temperature and the wind blowing in from the sea created challenging conditions for painting.
Interior painting was easier to carry out. However, in some interior spaces, the temperature of the steel was very low (+7 to +8 °C) because the spaces adjoined the ship’s outside shell, which faced cold air on the other side of the plate. Heaters were used during painting of the bio-tanks, but the ballast tanks, for example, could not be heated during surface treatment. This resulted in the conditions inside them being practically the same as outside the ship.
Before the painting, the areas to be painted were high-pressure washed (approx. 300 bar) in order to remove water-soluble salts and other impurities. Washing was possible in this project because the temperature was above 0°C. If the temperature had been below zero, water washing would not have been done.
After washing with water, the damaged areas were blast cleaned to SA 2.5. In addition, the edges of existing paint were feathered in order to have the best possible corrosion protection at the overlap of old and new paint.
Silja Serenade’s underwater hull and topside were painted with Jotacote Universal N10 and Hardtop AX. The underwater hull was touched up, i.e. only the damaged areas were treated. After pre-treatment, the bottom was painted with two layers of Jotacote Universal N10 epoxy coating and the boottop got a full coat. In addition to the repairs made with epoxy, the topside was painted with Hardtop AX polyurethane topcoat. The topside was washed to remove impurities prior to the application of the topcoat.
The painting had to be carried out quickly, so a product that works in the cold and can be quickly overcoated was chosen as the touch-up paint. The first choice for such conditions was Jotacote Universal N10, which can be used down to -10°C. Under the prevailing conditions, the product could be overcoated after just 15 hours. This fitted into the schedule, where the overcoating had to be done the next day. Jotacote Universal N10
cures quickly, with the curing able to continue in water, which enabled early launching of the ship. This is especially useful in cold weather.
The short overcoating interval and the cold weather brought their own challenges to measuring the paint film thickness. In some cases, film thicknesses could not be measured, but had to be estimated using the wet film comb technique and the paint consumption.
Jotacote Universal N10 is a polyamine-cured pure epoxy coating. It is a fast drying, high solids and high build, abrasionresistant product. It is specially designed as a universal, allround, all-year, newbuilding and maintenance coating where a fast dry-to-handle time is required. It can also be applied at sub-zero surface temperatures.
Typical uses in the marine industry for Jotacote Universal N10 are exterior and interior areas, including the outside of the hull, superstructure, deck, cargo holds and water ballast tanks. This product has very high flexibility, making it especially suitable for the temperature variation experienced in crude oil, chemical and shuttle tankers. It is approved for IMO PSPC (Performance Standard for Protective Coatings) crossover testing with a wide range of shop primers.
Hardtop AX is aliphatic acrylic polyurethane coating with a high gloss finish and very good gloss retention, so it is well suited for topsides, decks and superstructures. It has good chemical resistance and is also an easy-to-apply product, which is important in such a demanding location.
Drydocking was carried out in Naantali at Turku Repair Yard. This is the largest drydock in Northern Europe, established in 1989. The shipyard employs
around 100 employees and in addition 250300 subcontractors. The shipyard mainly repairs car ferries and tankers, but also smaller fishing vessels and warships. Every year, 80-100 vessels are repaired at the shipyard. In addition to repairs, the shipyard carries out ship modifications, extensions and painting.
Turku Repair Yard is a part of Estonian BLRT Grupp. ■
Facilities maintenance operations can face challenges in hazardous environments such as the oil & gas and petrochemical industries
Facilities maintenance operations can face different circumstantial challenges that require modern solutions. Particularly for hazardous environments such as the oil & gas and petrochemical industries, cold-curing polymeric repair and protection materials can provide a novel means of bypassing these challenges.
This application demonstrates the use of Belzona’s cold-curing epoxy two-part structural adhesive, Belzona 7311, to navigate these challenges in the petrochemical industry to fulfil maintenance needs. A metal storage tank in a chemical plant containing concentrated sulfuric acid required attention to both the base and roof. The customer needed to bond
pipe supports to the top of the tank to reinforce the pipes directly above. However, the tank was installed with a rubber lining, ruling out any hot work such as welding as a means of attaching the pipe supports. Meanwhile, the existing tank base coating had been exposed to chemical attack and needed to be replaced with a suitable chemical-resistant coating to protect the tank from future chemical spills.
Belzona’s first-ever structural adhesive, Belzona 7311, proved to be the optimal cold bonding solution to fulfil the requirements due to its high mechanical strength, cleavage and shear resistance. By using this technology, the supports could be cold bonded to the top of the metal tank without the associated risks of welding, such as damage to the rubber lining and metal distortion due to HAZ. Heat Affected Zones (HAZ) can be the result of the intense process of heating and cooling the substrate, leading to weaknesses in the metal and compromising the integrity of the weld joint.
The contractor specified that the best way of attaching pipe supports was to cold bond six 254mm by 254mm metal plates to the top of the tank, which could then be cold bonded to the pipe supports. The chosen areas were marked with tape, before being prepared using hand-held surface preparation tools. The application areas were prepared to SSPC-SP11 standard, producing a bare metal surface and a minimum 25μm (1 mil) profile for a high level of adhesion. The two-part epoxy adhesive Belzona 7311 was then mixed and applied to both the substrate and the underside of the metal plates, before being held in place with no additional weight or pressure while the product was allowed to cure. Once the plates had been cold bonded to the metal tank, the pipe
This metal tank needed maintenance to both the base and the roof The tank base had been exposed to chemical attackBackwards Compatibility! The redesigned PosiTector gage body accepts ALL coating thickness (6000/200), environmental (DPM), surface profile (SPG/RTR), salt contamination (SST), hardness (SHD/BHI), and ultrasonic wall thickness (UTG) probes manufactured since 2012
supports were subsequently attached to reinforce the pipes in operation above the tank.
Belzona 4311 (Magma CR1) was specified to protect the tank base due to its chemical resistance qualities, having encountered no significant deterioration after a year of immersion in up to 98% sulfuric acid at 40°C (104°F), when tested in accordance with ISO 2812-1.
The previous tank base coating was removed and the concrete surface was prepared with an ATEX-rated power tool and conditioned using Belzona 4911 (cleaner/degreaser) to ensure maximum adhesion for the new coating.
Two coats of Belzona 4311 (Magma CR1) were applied to provide long-term protection to the tank base, avoiding the harmful financial, safety and environmental consequences of a future leak.
The sulfuric acid tank base will be protected against chemical attack for the long term by the chemical resistant properties of Belzona 4311 (Magma CR1). Meanwhile, the customer was impressed by the ability of Belzona 7311 to solve the challenges caused by the tank’s rubber lining, cold bonding the metal pipe supports securely without the need for welding. The customer was also very satisfied by the high mechanical strength, cleavage and shear resistance demonstrated by the cold bonding solution during the application.
This application presented an example of the opportunities provided by the epoxy two-part structural adhesive Belzona 7311 as a cold bonding solution, offering an effective and safe alternative to welding. The solution can be used for structural bonding applications requiring high mechanical strength, cleavage and shear resistance, including ladders, handrails and plate bonding, and is suitable for harsh service environments. ■
Far left: Belzona 4311 (Magma CR1) was applied to the tank base.
Left: The chemical resistant coating will provide protection in the case of chemical spills
The strength of the cold bonding solution allowed the pipe supports to be seamlessly attached to the top of the tank
Pipes for the marine environment are built specially, with several types of pipe used. They are used in different mechanical operations on ships as well as in offshore systems. Harsh atmospheric conditions in marine environments expose pipes to high corrosion levels. Removable coatings are an excellent way to ensure faster installation and less downtime by keeping corrosion at bay.
Corrosion is the gradual deterioration of a material or its properties through a chemical reaction with its environment, and can be described as the destructive attack of a material by reaction with its environment. Oceangoing ships travel globally, and as such they experience the extreme conditions of marine environments which greatly accelerate the decline in their material state. Corrosion resistance is extremely important in marine operations and aboard ships. In these highly corrosive environments, turning to smart corrosion protection methods is the best approach engineers can take. Corrosion protection conducted properly can enable significant savings in time and money, and even more importantly prevent hazards and accidents that can jeopardise human lives.
Corrosion affects both the pipe’s interior and exterior until a pipe failure occurs and can result in a pipe rapidly losing fluid. Pipes penetrate almost every confined space above and below the waterline. Pipe failure can result in total loss in the case of engine cooling or fire suppression. It is very important therefore that engineers inspect and maintain the pipe interior and offer corrosion protection solutions to seal leaks, prevent corrosion and extend the life of pipes on vessels.
Damage from corrosion in shipbuilding or corrosion that occurs in the operation of vessels is especially harsh. Corrosion protection of such structures is a big part of the cost of the manufacturing process. Quality corrosion protection in the construction phase of a ship is of crucial importance for its functionality due to the ship’s demanding and complex structure and its exposure to extremely aggressive environments. Optimal and smart corrosion protection is one of the key factors in the quality and price of the ship. Structures in shipbuilding, offshore and marine industries contain parts that are difficult to access or can even be completely inaccessible for quality and long-lasting protection. Parts of the ship structure are derived from a number of
brackets, frames, stiffeners and reinforcements which makes their proper preparation and coatings protection difficult.
In all these cases, the most efficient and economical technical solution is the use of Cortec’s patented VpCI corrosion inhibitors. This special group of inhibitors protects the
metals from atmospheric corrosion and is able to stop corrosion at a molecular level. The organic substances vaporise and travel to all parts of the metal surfaces, reaching even inaccessible areas.
VpCIs have a very high range of application and their utilisation is the result of technological as well as economic progress, when it comes to corrosion protection in
shipbuilding. They are increasingly used in shipbuilding and marine industries due to their excellent properties, including a unique ability to protect hard-to-reach areas.
VpCI inhibitors are highly recommended for protection of inaccessible areas of marine structures. They are also highly efficient in the protection of pipelines and marine and naval equipment, as well as electrical contacts. After
contact with the metal surface, the vapour condenses and forms a thin monomolecular film that protects the metal. The protective layer re-heals and self-replenishes itself through further condensation of the vapour. VpCI reaches every area of the metal part, protecting its exterior as well as hard-to-reach interior surfaces. It provides complete product protection during storage as well as during domestic and overseas shipment.
VpCI inhibitors are recommended for corrosion protection of heating and cooling systems, main and auxiliary engines, heating systems for crew and passengers, amongst many others. The economical properties of VpCI inhibitors are especially evident in recirculation systems where the VpCI is slowly consumed. The application of VpCI inhibitors in hydrostatic testing systems is of great importance as the testing water can be aggressive to pipeline materials. VpCI inhibitors could eliminate the possibility of corrosion before use.
In the application of VpCI 645 for hydrostatic testing of ship storage tanks using seawater it is very important to use products which are environmentally friendly and have a water safety permit certificate because this allows the water to be drained into the sea after testing.
Flange faces on the end of pipes form a critical connection for pressure containment. If any of these surfaces are damaged it can jeopardise the integrity of that connection, making preservation imperative for safety and performance. Cortec recommends two removable coatings for flange face protection. VpCI-391 is a water-based temporary coating with low VOC (0.4 lbs/gal [48 g/L]). It leaves a clear non-tacky film that is virtually unnoticeable and can be easily removed with alkaline cleaners such as Cortec’s VpCI-41x Series (which offers flash rust protection) before the pipe is installed. VpCI-391 provides protection in harsh, outdoor, unsheltered applications and has excellent UV resistance. Since the coating leaves a dry film, it is ideal
for transit applications where pipes and flanges may be repeatedly handled. For the most extreme conditions, VpCI-368 offers even heavier-duty protection. This fast-drying solvent-based coating leaves a slightly brown waxy finish and should be removed prior to flange installation using an alkaline cleaner from the VpCI-41x Series.
As previously suggested, the main benefit of removable flange coatings is to avoid the ramifications of corrosion. Eric Uutala, Cortec’s Technical Sales and Product Manager, explains
the alternative: “If a raised face is damaged, either from corrosion or mechanical impact, it can cause significant delays in construction. In the case of gramophone raised faces, the re-surfacing process can be very time consuming, which could lead to further downtime and financial loss.”
By taking the removable coating route, the protective mechanism conforms directly to the surface of the metal, not requiring an additional covering (a plastic film for example) except what is needed for standard mechanical protection. In the case of VpCI-391, there is minimal change to appearance – a plus for manufacturers concerned about aesthetics – and the coating is especially easy to remove. Uutala reminds workers that flange preservation can be done at any point in the pipe’s lifecycle – at the manufacturing plant, in the storage yard, or at the final site. He outlines the flange coating process as follows:
. Make sure the flange face is clean and free of rust, dirt, coatings, and any other contaminants.
. Apply either VpCI-368 (for brown, waxy film) or VpCI-391 (for clear, dry film) by brush.
. Allow to dry for one to two (or more) hours before covering with rigid flange cover or other approved mechanical protection (avoid wood covers because they absorb moisture).
Ultimately, the condition of the flange face directly affects the condition of the system and is at risk at any point up to installation. Taking preventative measures to protect vulnerable flange faces from corrosion and mechanical damage in marine environments can go a long way toward preserving flange faces in their original state. A little time spent cleaning the flange and applying a coating now could translate into many hours and dollars saved later by avoiding resurfacing delays and minimising system downtime. ■
Belzona’s polymeric repair and protection materials are suitable for extending the in-service life of assets in a multitude of industries, including equipment in the petrochemical industry which often functions in harsh environments.
Belzona’s products are suitable for both small-scale assets and extremely large projects, such as the recent restoration of a mammoth pipeline in a Thai petroleum production facility.
The facility, based in the north of Thailand, found that a huge pipeline carrying highpressure water for injection into oil wells was suffering from thin wall defects. The pipeline in question was made of 12m pipe lengths that had been welded together. However, upon inspection it was found that the 2,000 psi water contents and the weld filler material used had resulted in internal corrosion defects at every circumferential weld joint. This caused the deterioration of pipe wall thickness, risking high pressure leaks.
The customer had used Belzona previously and had a good relationship with the local distributor, Pan Mechanic Engineering Co, Ltd. They were very impressed by Belzona’s cold bonding capabilities when they were demonstrated by the distributor on a defective joint, leading to their agreement to undertake the repair of the entire pipeline, requiring an estimated 5,0007,000kg of Belzona 1111 (Super Metal).
Due to the massive scale of the project, it was decided to complete the repair in three stages. More than 1,000 joints were repaired in 2020 and the remaining defects were addressed in November and December 2022. The joints repaired in stage one were demonstrating excellent performance in service and the distributor also invited two technical services engineers from the Belzona Asia Pacific office to observe the second stage of the project.
Belzona repaired a pipeline made out of 12 metre pipe lengths in the petrochemical industry using cold bondingThe use of welding had been problematic in the past, leading to the customer’s preference for a cold bonding solution. The distributor initially proposed the use of Belzona SuperWrap II to restore pipe wall strength, but testing found that attaching carbon steel reinforcing plates using Belzona 1111 (Super Metal) as a bonding agent would be more appropriate. The simpler cold bonding repair would be more cost effective and ensure a faster return to service in line with the customer’s requirements.
The surface was prepared using garnet blasting and Belzona 9111 (cleaner/degreaser) to achieve an average minimum ≥75μm (3mils) profile and SA2.5 surface cleanliness for maximum adhesion. The atmospheric conditions were then tested to ensure that the relative humidity was below the maximum permitted 85% needed for the application to take place.
Welding rods were used to create a shim between the steel plates and the repair area to control the thickness of the application. The welding rods were bonded to the steel reinforcing plates with a small quantity of
Belzona 1111 (Super Metal) and the repair area was identified using masking tape. Belzona 1111 (Super Metal) was first applied to two of the four plates and the damaged pipeline joint, and held in place using a fixed hoist while the product cured. Once the first two plates had bonded, the final two plates were applied and allowed to cure, fully encompassing the circumferential joint.
The customer was delighted that the Belzona repair restored the integrity of the joints and protected the pipeline from future thin wall defects. The success of such a large-scale project led the customer to indicate an interest in applying Belzona solutions to other pipelines at their facility. This could include similar cold bonding applications or the specification of Belzona SuperWrap II for more complex pipe geometries. Polymeric repair and protection materials are ideal for facilities in the oil and gas and petrochemical industries due to their easy application and quick return to service with no hot work required. ■
Belzona’s cold bonding solutions had previously repaired other areas of the pipeline
(centre) The pipeline was exposed to corrosion at the joints where sections had previously been welded together
Belzona 1111 (Super Metal) was applied as a bonding agent
Registrations for the world’s leading trade fair for industrial coating technology are already at an excellent level one year before the next edition of the event opens its doors. From 9 to 12 April 2024, PaintExpo will once again be providing a global showcase for the latest trends in industrial coating. The who’s who of the coating technology industry exhibits at PaintExpo 2024 in Karlsruhe.
With around 430 exhibitors from 27 countries and more than 9,000 trade visitors from 57 countries, PaintExpo was successfully restarted in 2022 following the pandemic break. More than one in three exhibitors travelled from abroad. Visitors included a large number of key decision-makers, specialists and managers, with around 90% of visitors to the previous PaintExpo able to influence investment decisions in their companies.
Preparations for PaintExpo 2024 are in full swing. With one year still to go before the trade fair opens its doors, around 250 companies have registered and more than 70% of the exhibition space of the previous event is already sold. “The response from the industry has been great,” says Markus Geisenberger, Chief Executive Officer of Leipziger Messe. “This clearly confirms that PaintExpo is a well-positioned, must-attend event for everyone in the industry. In April of next year, PaintExpo will once again serve as a worldwide showcase for innovations and future technologies as well as providing a platform for practical solutions in industrial coating technology.” Registration information is available on the PaintExpo website.
Global market and technology leaders will join innovative medium-sized companies in three exhibition halls at this world-leading trade fair to present their latest products and applications in industrial coating technology. Exhibitors will include important industry players from Germany and abroad such as Axalta, DeFelsko, Dürr, Eisenmann, FreiLacke, Gema Switzerland, J Wagner, Krautzberger, Louis Schierholz, Nordson, PPG and Venjakob. In addition, interesting new exhibitors were also convinced by the trade fair concept: Among those in Karlsruhe presenting their range of products and services for the first time at PaintExpo will be Mitsuda, a Turkish supplier of cleaning and pretreatment technology, and Neybo, a specialist in heating up industrial containers.
The coming edition of PaintExpo also has a lot to offer internationally: Most exhibitors will be from Western European countries. Alongside Germany, they will primarily be from Italy, Switzerland, Austria, the Netherlands and Spain. However, companies from countries such as Turkey and Greece have also already booked their stands. The proportion of international exhibitors is, as of today – around 40%.
The products and services on display at PaintExpo cover the full spectrum of industrial coatings. Next year, the range of exhibits will again include surface treatment solutions, quality assurance, paints and paint finishing lines, as well as powders and powder coating systems. The industry platform offers a comprehensive package of coating solutions for all industries, applications and materials, from wet coating and powder coating to coil coating. ■
Global market and technology leaders will join innovative medium-sized companies in three exhibition halls at this world-leading trade fair to present their latest products and applications in industrial coating technology.
Airlines and operators now have the opportunity to optimize the paint maintenance schedules for their entire fleets thanks to a digital management system developed by AkzoNobel’s Aerospace Coatings business.
Known as Aerofleet Coatings Management, the system uses data that’s gathered over several years to help ensure that aircraft are only repainted when needed, not according to a fixed time schedule alone. “Planes are often repainted while the coating still has life left in it,” explains Patrick Bourguignon, Director of AkzoNobel’s Automotive and Specialty Coatings business. “Using our service will help to reduce costs, while increasing aircraft availability by anything up to a year.”
Currently, aircraft tend to be taken out of service for maintenance every six or seven years, without really knowing for certain if a repaint is needed. Aerofleet addresses this issue by capturing data from both manual and droneoperated inspections and creating a database of every aircraft in a fleet. The individual histories include details of the coatings used (such as singlestage or basecoat/clearcoat coatings), as well as flight path data – such as weather conditions – which can affect the longevity of the coating applied. “By analysing this information and mapping it over several years, it becomes easier and more accurate to determine when an aircraft needs to be repainted, rather than simply using time or flight hours,” adds Tami Swearingin,
of AkzoNobel’s Aerospace and Film Coatings business. “Over time, the frequency with which aircraft need to be repainted will fall, which is significantly better for an airline’s bottom line. It also means less waste, so it will be better for the planet as well.”
Ideally suited for fleets in excess of 100 aircraft, the inspection service is provided by experts from AkzoNobel Aerospace Coatings, using a digital application. The app stores all the information collected, such as dry film thickness, colour variation, gloss and general appearance. The data is then fed back to a database which tracks the fleet’s performance over time.
In an update to Hempel A/S’ Executive Group Management, Ana Henriques has been appointed as Executive Vice President, Head of Decorative as of 1 August 2023.
Henriques joins Hempel A/S from the position of Global Vice President, Head of Global NonAlcoholic Business at AB InBev. She is a Brazilian national and will be relocating to Denmark from the US. She succeeds Joe Devitt, who has decided to retire after more than 30 years with Crown and Hempel.
An experienced international executive with
close to 20 years’ experience in fast-moving consumer goods, Henriques led a crossfunctional team in AB InBev’s non-alcoholic portfolio, a multi-billion dollar business that spans more than 60 global brands. Prior to her time with AB InBev, she has worked for PepsiCo in the United States and China.
“We are really pleased to be able to attract an experienced executive like Ana to the Hempel Group,” says Michael Hansen, Group President and CEO of Hempel A/S. “With her extensive experience in leading and growing brands globally, I am confident that Ana will add new perspectives to our decorative business and I am excited to welcome her to Hempel and the Executive Group Management.”
Henriques will head up Hempel’s largest customer segment, its €775 million decorative business, representing 36% of Hempel’s revenue. Hempel counts Farrow & Ball, Crown Paints, Wattyl, Renaulac and J.W. Ostendorf, among others, in its decorative brand portfolio.
“I am thrilled to join Hempel and embark on a journey of working with exceptional decorative brands, esteemed customers across trade and retail, as well as discerning consumers who in many cases
are truly devoted to those brands,” says Henriques. “What truly sets Hempel apart is not just its remarkable market presence, but also its ownership by the Hempel Foundation that is dedicated to giving back to society. This unique aspect aligns closely with my personal values and provides a deep sense of purpose in our collective mission. Together, we will build upon Hempel’s legacy, driving innovation and sustainable solutions while making a positive impact on the communities we serve.”
Joe Devitt decided to retire after more than 30 years with Crown Paints and Hempel. “Joe has been a phenomenal colleague and he will be greatly missed in the Executive Group Management and throughout Hempel,” says Hansen. “As head of our decorative business, Joe has been instrumental to the segment’s growth over the years and the prosperous development of our strong decorative brands. We will make sure to celebrate his many achievements as we bid him a fond farewell by the end of August.”
FIRST Chromium trioxide derivatives are classified as CMR substances and the unrestricted use of these substances in the European Union expired in 2017. Although the European Commission issued authorisation for further use, the ultimate deadline will be September 2024. This extensive ban on the use of chromium trioxide derivatives affects many industrial sectors and consequently also the transformers production.
Paint & Coatings focuses on the formulation, supply, manufacture and distribution of paints, coatings, adhesives and sealants, recognizing the importance of keeping up with developments in paint and coating creation, a complex and demanding process that leads to from concept to consumer.
For more information contact paintcoatings@step-exhibitions.com or by calling +34 689 063 340
Therefore, a change to chromium-free solutions is crucial.
Since chromates are hardly replaceable due to their excellent hydrolysis and corrosion resistance as well as their good electro-insulating properties, the aim was to develop equivalent solutions. After working intensively on the innovation, the R&D specialists at Rembrandtin, a member of Kansai Helios, developed a chromium-free coating system, REMISOL EB 5320 - the first chromium-free coating on the market.
The hydrolysis and corrosion resistance of this new eco-friendly product is also equivalent to chromium (VI)-based coatings. It’s an inorganic coating of class C5-G according to ASTM 976 and serves as electrical insulation for grain-oriented steel. This one-component system is available as a clear or pigmented version. With this type of pigmentation, it is possible to achieve the homogeneous appearance of the coated electrical steel desired by many steel manufacturers. This innovative solution is long-lasting without any loss of quality over the months and it is suitable as a more environmentally friendly alternative.
The aim is to contribute to a greener planet, and with the development of this advanced and eco-friendly coating system, Kansai Helios
AkzoNobel has launched My Interpon Portal, an extended digital e-commerce platform with enhanced features and functionalities to give customers fast, easy access to the information and products they need to keep their powder coating lines rolling and stay one step ahead of the competition. My Interpon Portal is much more than an online shop for customers to buy Interpon products. Instead, it is a central online resources platform to help coaters not only discover the world’s leading range of Interpon powder coatings, but also see and experience how a multitude of colours and textures will perform through a 3D lightbox colour visualisation tool. Intelligent features and functionality enable customers to easily navigate the site and search for, find and compare hundreds of Interpon products, all at the touch of the button.
Administration has also been made easy, to manage new, ongoing and repeat orders. A Track and Trace feature enables customers to see how their order is progressing, while past and present invoices can also
be accessed, reviewed, printed, and filed.
Ordering has also been made simple: users can instantly see what’s in stock and how quickly they can get the powder coatings they need, with the corresponding technical specification data which can be downloaded to help them make the right decision.
Jeff Jirak, Director of AkzoNobel’s Powder Coatings business, says the launch is further evidence of AkzoNobel’s commitment to customers: “We strive to make things easier for our customers with practical tools and support that makes us collectively more efficient. A significant development of our existing e-commerce site, we will continue to enrich and enhance the functionality of My Interpon Portal with new features to help customers access the powder coatings they need for the most urgent of urgent jobs.”
My Interpon Portal is being rolled out globally starting with UK, US, Spain, Australia, Germany, Belgium, The Netherlands, and Canada in the upcoming months.
PPG has launched PPG Phenguard 985 phenolic epoxy tank lining, which represents a significant breakthrough for the marine and tank storage sectors. The premium tank lining is designed to deliver
is making an invaluable contribution that many generations will be able to benefit from.
extremely high chemical resistance to a wide range of aggressive chemicals and higher temperature resistance for chemicals that contain fatty acids.
“The latest addition to our PPG Phenguard range, PPG Phenguard 985 tank lining, features a patent-pending formulation that can be applied in two or three coats instead of the traditional three coats without compromising chemical resistance,” explains Bart Martens, PPG Global Product Manager, Chemical Protection, Protective and Marine Coatings. “This gives asset owners and contractors flexibility to apply their preferred coating system build-up while having full confidence in the end result.”
PPG Phenguard 985 tank coating has outstanding chemical resistance to thousands of chemicals. Its key value is in the protection it offers to over 300 different cargoes that are composed of, or contain, fatty acids. These highly aggressive chemicals can cause problems for operators, as the temperature window required for their storage can be narrow and difficult to manage. As a result, temperature overshoots are a regular risk and can jeopardise the efficacy of the tank lining, leading to additional expense. To combat this, PPG Phenguard 985 tank lining has been specifically designed to accommodate an extended temperature window.
“In an increasingly competitive operating environment for asset owners, PPG Phenguard 985 creates the opportunity to reduce tank lining application and servicing costs while also maximising
cargo opportunities,” says Martens. “As well as the initial application cost savings from moving from three to two coats, the liner’s higher thickness tolerance reduces the need for costly rework in case of over-application.”
Castolin Eutectic, a leading innovator in the protective
coatings industry, has launched XupersoniClad, a new thermal spraying service that leverages supersonic spraying technology. This new development promises significant advantages in the protection of components, vessels, and structures from abrasion, erosion, and wear, offering a unique service in the European market.
PPG Phenguard 985 phenolic epoxy tank lining is designed to deliver extremely high chemical resistance
Developed from the high-velocity air-fuel (HVAF) process, XupersoniClad applies abrasion-resistant wear coatings in forms like metal, carbide, and metal alloy powders. It also provides an effective solution for newgeneration high entropy alloy (HEA) coatings, combining five or more elements to outperform traditional materials in both room and high-temperature scenarios.
XupersoniClad comes as a breakthrough for industries requiring enhanced abrasion, wear, and erosion resistance, notably recycling, concrete, brick, and tile production industries, as well as vessel and boiler interiors. One significant new application is in mitigating the damaging effects of cavitation on liquid
pumps, propellers, impellers, and control valves.
XupersoniClad is a warm spray process, more efficient than the previous highvelocity oxy-fuel (HVOF) process, operating at lower temperatures and higher particle velocity, making it suitable for almost all common thermal spray materials, except ceramics.
The advantages of XupersoniClad are numerous, from a range of coating thicknesses with minimal heat input into the substrate, low deformation, and a smooth, ductile finish, to the creation of a dense, consistent microstructure ideal for corrosion resistance. This process also offers the capacity to apply thin, precisely layered coatings
while maintaining high bond strength and resistance to stress-induced delamination.
With the ability to apply coatings to the internal diameter of pipes down to 80mm, XupersoniClad expands its usability even further. An additional feature that accelerates the process is the capability for ‘hot grit’ blasting, which is faster, more focused, and energy-efficient than traditional surface preparation methods.
To deliver XupersoniClad’s benefits widely, Castolin Eutectic has upgraded its facility in Belgium with a mobile container for on-site services, ensuring accuracy and repeatability with the help of a cobot (collaborative robot) to manage large projects.
XupersoniClad allows the application of various coatings, such as nickel alloys, carbide coatings, and low melting point metal spraying, across numerous industries. These include chemical, waste-to-energy, and biomass plants, and sectors requiring increased resistance to surface abrasion, corrosion protection, and friction coefficient improvement.
This innovative approach also extends to protection against cavitation, offering a well-bonded, dense, and ductile protective coating that can withstand the shock waves that typically damage traditional hard coatings.
Case studies with concrete moulds, cooler plates in cement factories, cyclones, and steel industry fume ducts have showcased XupersoniClad’s potential to revolutionise protection in these key areas.
Kansai Helios Coatings GmbH, a European consolidated subsidiary of Kansai Paint Co, Ltd has completed its acquisition of CWS Lackfabrik GmbH. Kansai Helios has acquired all CWS shares and has become its new owner.
CWS is a well-established paint manufacturer founded in 1864 with over 150 years of business experience and a solid position in the
manufacture and sale of industrial powder coatings and synthetic resins in Germany and other European countries as well as the US. The powder coatings market is expected to grow significantly worldwide in the future from the perspectives of the environment and quality of life. This acquisition is a perfect complement and extension of company competences in powder coatings and synthetic resins business, and will further strengthen the Kansai Paint Group’s competitiveness.
Kansai Paint Group has set ‘aggressive investment in growing market’ as one of the key principles in its 17th Medium-term Management Plan. The company says it will expand overseas businesses
by reinforcing its strengths, mainly in Europe and India, and promoting small- and medium-sized M&A within the ¥20 billion (€1.27 billion) framework with the aim of having them mutually complementing each other.
A bespoke sculpture made by a budding metalworker has been protected against the elements, thanks to a local galvanising company. East Anglian Galvanizing Ltd was called upon to galvanise a life-sized sculpture of a stag for 20-year-old, Cambridgeshire-based sculptor Harry Jackson. Standing at two metres tall (from hoof to antlers),
For more information, call +44(0)1252 732220
the stag sculpture was first designed digitally before being cut out of 2mm hot rolled mild steel sheets using Jackson’s homemade CNC plasma cutter. All parts were then cleaned through a wire wheel, bent on a homemade press brake, and finally tacked together and dressed down in preparation for galvanising.
“After creation, I enlisted the help of East Anglian Galvanizing to finish the piece off,” explains Jackson. “I’ve worked with them before when I galvanised two other animal sculptures, and they were incredibly helpful.”
The galvanising process saw the stag entirely dipped in a large bath of molten zinc at 450°C, ensuring it’s protected from corrosion for more than 70 years.
“Harry is exceptionally talented, and it’s been a real pleasure supporting him in galvanising his sculptures,” says Jake Pinner, Sales Manager at East Anglian Galvanizing. “It’s so very
refreshing to see someone of his age take such an interest in this sector, and be so proactive and dynamic in approaching us.”
East Anglian Galvanizing is part of Wedge Group Galvanizing Ltd, the largest hot-dip galvanising organisation in the UK with 14 plants strategically placed across the country and a history dating back over 150 years.
BlastOne has acquired VertiDrive BV, located in Rotterdam, The Netherlands. BlastOne is a leading global provider of blasting and painting equipment and supplies, and has been acting as a sales partner for VertiDrive for more than five years. The acquisition of VertiDrive will enable BlastOne to improve support for customers and provide innovative solutions for automating their blasting and painting processes.
The addition of VertiDrive’s robotics technology will enhance BlastOne’s ability to serve a wide range of industries, including shipbuilding, ship refurbishment, chemical industries, heavy fabrication and infrastructure. BlastOne’s industry leading experience and VertiDrive’s superior technology are a natural fit, and complement the superior performance customers have come to expect from BlastOne solutions.
“We are excited to welcome VertiDrive to the BlastOne family,” said Matthew Rowland, CEO of BlastOne. “Their cutting-edge robotics technology is a perfect complement to our existing product line, and we believe it will be a valuable asset as we continue to grow and serve our customers.”
“We are thrilled to join forces with BlastOne and bring our robotics technology to a larger audience,” said Stefan van Diessen, Managing Director of VertiDrive. “We believe this partnership will allow us to accelerate the development and deployment of our robots, and we are looking forward to working with the talented team at BlastOne.”
HMG Paints, a leading manufacturer of paints and coatings, has been named the Manufacturing Family Business of the Year at the prestigious Family Business of the Year Awards 2023. The awards, hosted by Family Business United, took place in the serene Medicine Garden located within the grounds of the Royal College
of Physicians, London. The event aimed to recognise and celebrate the invaluable contributions made by family firms to the national economy.
“Family businesses are the engine room of the UK economy and with 6 million family firms employing around 14 million people in all corners of the country they make a massive impact each and every day,” commented Paul
Andrews, Managing Director of Family Business United.
“Incomes are generated, jobs provided and wealth created but as one of the family members said to me, ‘That is just the tip of the iceberg. Family businesses care and want to be seen as doing the right thing, doing business the right way’.”
The accolade of Manufacturing Family Business
of the Year is a testament to HMG Paints’ commitment to excellence, innovation, and the preservation of its family legacy, with the judges also recognising the company’s support for the wider family business community. As a multi-generation family-owned business, HMG Paints has consistently demonstrated its dedication to producing high-quality paint products
and industry-leading solutions for over nine decades.
John Falder, Chairman of HMG Paints, expressed his gratitude for the recognition received by the company, stating, “Being named the Manufacturing Family Business of the Year is an incredible honour for HMG Paints. We are immensely proud of our heritage and the values that have guided our family business since its inception. This award is a testament to the hard work and dedication
of our team, who consistently strive for excellence in everything we do.”
HMG Paints Ltd has been at the forefront of the manufacturing industry, continuously delivering innovative products and solutions to a diverse range of customers. The company’s commitment to sustainability, customer satisfaction, and community engagement has further strengthened its reputation as an industry leader.
Can makers and coil coaters ramping up their bisphenolfree transition have a ready alternative in a new BPA-NI internal coating for beverage can ends, from AkzoNobel Packaging Coatings.
As a BPA-NI coating, Accelshield 700 does not use BPA or bisphenol-based epoxies as part of its manufacturing process. It complies with both Food and Drug Administration (FDA) and EU regulations.
The product will help meet the surge in demand for alternative coatings that’s expected after the European Food Safety Authority (EFSA)’s recent opinion of BPA restrictions in metal packaging of food and beverage products. Bisphenols are currently ubiquitous throughout the manufacturing industry, a situation with growing urgency for change following EFSA’s opinion.
“With today’s technological advancements, bisphenols are
no longer required to create safe coatings for state-ofthe-art metal can packaging,” says Chris Bradford, Industrial Coatings Marketing Director, AkzoNobel Packaging Coatings. “BPA-NI coatings are a significant innovation, marking a critical turning point for the industry. Accelshield 700 will help can makers future-proof their selection.”
The new coating has been designed for challenging foods and liquids – including those that are very acidic or require
high-temperature sterilisation processes, such as yogurt drinks, milk and coffee – in addition to soft drinks and beer.
Integrating easily into customers’ existing manufacturing processes, Accelshield 700 also respects the need for can makers to mitigate disruption to their production lines.
AkzoNobel’s approach to the BPA and bisphenol transition prioritizes consumer safety and sustainability with responsible material substitutions, while taking care to limit disruption to the value chain. The company is working closely with customers to help accelerate the adoption of bisphenol alternatives.
An openly accessible online energy savings calculator for all users of powder coatings has been launched by AkzoNobel. For the first time, all powder coatings customers can instantly calculate the energy and carbon reduction they could achieve with the company’s Interpon products and related services. It’s the latest example of how the company is continuing to work towards its ambition of reducing carbon emissions across the full value chain by 50% by 2030. “Sustainability is critical for all of us and helping customers to reduce energy is one of the many ways we can work with –and for – them in order to meet our shared ambitions,” says Jeff Jirak, Director of AkzoNobel’s Powder Coatings business. “We’re proud to be the first in the industry to introduce this kind of openly
available online resource,” he continues. “It will enable us to create better awareness and enable customers to really get to grips with the potential energy and carbon reductions that can be achieved with low cure powder coatings.”
Jirak adds that in order to understand the full range of possible benefits for individual users, further details of customer-specific situations would be required. To make using the tool as easy as possible, the calculator –currently only available in Europe – is supported by a detailed guide, which helps customers better understand how even making small changes in the powder coating process can have a big impact in terms of becoming more energy efficient. These include checking for leakages in compressed air systems, improving insulation and ensuring all process equipment is regularly serviced and maintained.
Customers also receive expert support from Interpon’s technical service team.
Songwon Industrial, the second largest manufacturer of polymer stabilisers in the world and global specialty chemicals player, is pleased to announce that it has entered a distribution partnership with Krahn Italia for its Business Unit (BU) coatings.
Under the partnership agreement, Krahn Italia becomes the exclusive distributor for Songwon’s BU Coatings range of Songnox CS antioxidants, Songsorb CS UV absorbers and Songsorb CS HALS products in Italy as of July 1, 2023 in the liquid coatings market. By selecting Krahn Italia as its exclusive distributor, Songwon seeks to further enhance its position in Italy, which is one of the key regions in Europe for the coatings industry.
“Italy is an important market for us and we are very pleased to have such an experienced partner join Songwon’s extensive global distributor network,” says Simona De Gradi, Sales Manager EMEAI at Songwon. “We are confident that Krahn Italia’s expertise, strong market relationships and excellent customer service, combined with Songwon’s products, will help us build and cement our position as the supplier of choice for additives for liquid coatings in Italy.”
Based in Milan, Krahn Italia specialises in the marketing and distribution of specialty chemicals.
A sales and distribution partner to leading international chemical manufacturers for more than 100 years, Krahn Italia offers its partners an extensive, high-quality product range, comprehensive technical services as well as in-house laboratory support. ■
PCE July - September 2023 Issue
The Leading Protective Coatings Magazine
• Epoxy Coatings
• Offshore
• Concrete
• Transport
Event Distribution: Paint Expo, Istanbul
PCE will continue to showcase its regular features; Lifting the Lid, Upfront and Spotlight, as well as featuring the latest news and developments in marine and offshore coatings
contact Nick Carugati: nick@pce-international.com