Ng HM and Fadeyi MO (2020). A solution to optimise the process for consolidating asset information into asset information requirements (AIR) template. Built Environment Applied Research Sharing #02, ISSUU Digital Publishing Platform.
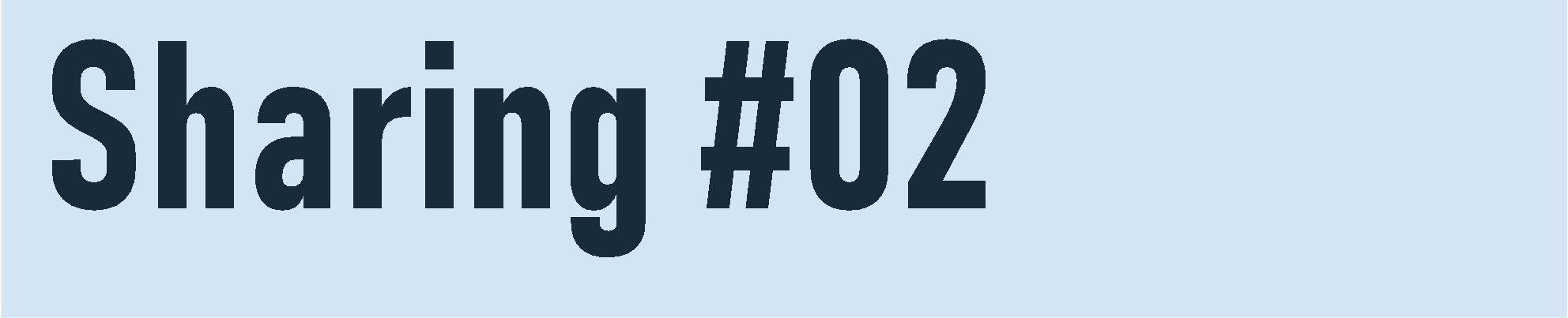
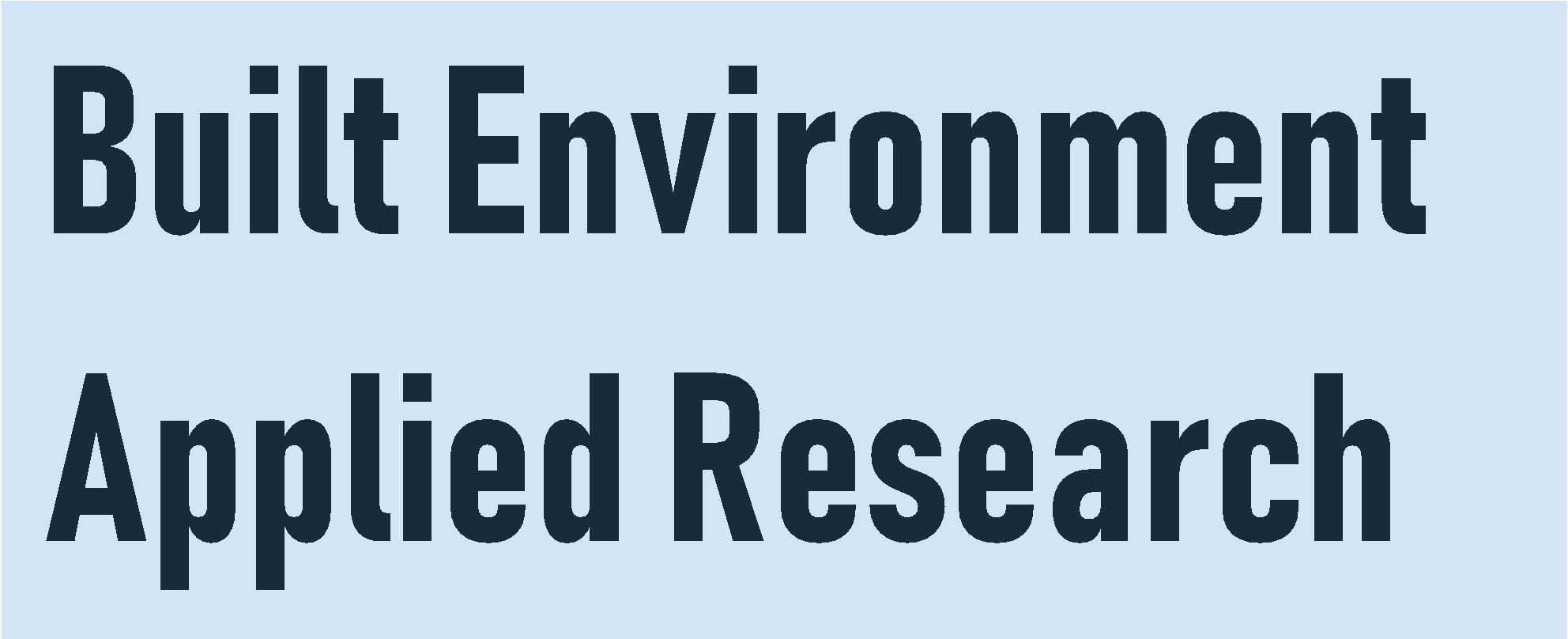
Ng HM and Fadeyi MO (2020). A solution to optimise the process for consolidating asset information into asset information requirements (AIR) template. Built Environment Applied Research Sharing #02, ISSUU Digital Publishing Platform.
Sustainable Infrastructure Engineering (Building Services) Programme, Singapore Institute of Technology, 10, Dover Drive, Singapore 138683, Singapore
*Corresponding author’s email: fadeyi.moshood@singaporetech.edu.sg
The maintenance and operations of the building to ensure suitable building performance requires consolidation of complete and accurate building asset information. The consolidation of building asset information is done in the asset information requirement (AIR) template. The AIR template is designed according to the building owner’s requirements. The risk of consolidating inaccurate asset information into an AIR template increases with an increasing number of building asset information to be consolidated. The current practice in the industry involves manual on-and-forth coping of critical asset information from PDF files and pasting on an excel template cell by cell. This practice causes more time to be spent on consolidation. Companies usually deploy several more staff to do consolidation tasks to reduce the time taken. The risk of errors occurring in the current manual consolidation practice is high due to inherent human error. An automated solution was developed and tested to examine how it could aid the accurate consolidation of building asset information into an AIR template within a short period and with the potential for lesser manpower. The developed solution reduces the time taken to consolidate asset information into an AIR template by 99% with zero error. The developed solution also reduces the need for experienced staff to consolidate. The findings suggest the number of staff required, even with a large building with many critical assets, can be reduced significantly. The solution developed and reported in this paper is essential to improving productivity in the facility management industry.
Facility management, Asset information, Asset Information Requirements (AIR), Digital Facility Management, Productivity
Facility managers and technicians depend heavily on building asset information in the deliveredas-builtdrawings and the operation andmaintenance manualtoperformtheir duties efficiently and effectively (Love et al. 2015). Thus, appropriateness, accuracy, completeness, and creditability of the delivered building asset information at the design, construction, and occupancy stages are essential. As technology advances, appropriateness, accuracy, completeness, and creditability of the building information can be expected to improve.
Buildinginformation modelling (BIM) isidentified intheindustryasameansofusingdigital technology to eliminate wastes and deliver value through the integration of the process of infrastructuredeliveryand people involved intheprocess.Peopleinvolvedintheprocess will benefit from digital technologies, and their productivity will improve if the information generatediswelldocumentedandupdated.Thedocumentationandupdatingof buildingasset informationareofparticularimportancetopeopleinvolvedinthemanagementandoperations ofbuildings.
To increase the efficiency and effectiveness of the current facility management practice, the BIMmodelshouldbeintegratedwithbuildingassetinformationtoenhanceassetmanagement productivity. The integration will facilitate the exchange of building asset information throughout the lifecycle of the asset, especially the critical asset (Patacas, 2016). In facility management terms, critical asset refers to assets which are utilised in the building operation, such as space and building system equipment. When integrating BIM models with asset information, it is important to understand and define asset information requirements (AIR) appropriately and to ensure that all the required critical asset information is accurate and definedaccordingtotheowner’s requirements(Cavka etal., 2017).
Asset information should be accurately integrated into the building architecture and mechanical, electrical, and plumbing (MEP) BIM models to optimise the usability of BIM models forfacility managementand operations. The integration of building asset information with BIM models will also facilitate effective usage of a facility management information system such as a computerised maintenance management systems (CMMS), energy managementsystem(EMS),andbuildingautomationsystem(BAS).However,themainissue with the integration of assetinformationwithBIM models istoensureaccurate consolidation of asset information into an AIR template. The consolidation of asset information usually
requires information to be keyed in manually from several sources. The number of building assets might be inhundreds orthousands, dependingon the building size. By keying building asset information manually, human error is likely, causing the information to be inaccurate. Furthermore,thefragmentedandincompletenessofthebuildingassetinformationwouldlead to more timeneededtoconsolidatecriticalassetsinformationintoanAIRtemplate.
Inaccuratebuildingassetinformationwouldincreasetheriskofmaintenancefailure(Holmgren 2016). There is a need to develop a solution that will ensure the accuracy of consolidating buildingassetinformationintoanAIRtemplateinanefficientmanner.Thispresentstudyaims to provide a solution that can improve the current process of consolidating the building asset information intoan AIR template. The objectivesof the studyare to explore the development of a solution that could (i) reduce the time taken in consolidating building asset information into an AIR template (ii) potentially reduce manpower needed to generate and validate the building asset information consolidated into an AIR template, and (iii) increase the accuracy ofconsolidatingassetinformationintoanAIRtemplate.
ThissectiondiscussescurrentAIRadoptionintheindustry.ThefocusisonAIRcurrentmarket strategiesandAIRstandardandtemplate.
AIR template is supposed to be tailored according to the client’s requirements (Cavka et al., 2017). AIR template defines the type of asset information required throughout the assets lifecycle, which will affect the operation and maintenance process. It is crucial for asset informationinanAIRtemplatetobeupdatedregularlytoenhanceknowledgeandinformation management, especially when the following takes place: significant addition and alterations works, changing of assets, a new installation of assets, and change in client’s requirements (Argyres,1999).ThetypicalassetinformationneededtoberecordedinanAIRtemplateisthe description of assets, vendor details, operational asset data, and asset dependencies (Australasian BIM Advisory Board, 2018). However, the required building asset information isfragmentedbetweensystemsandacrossthewhole buildinglifecycle.
Accurate consolidation of building asset information into an AIR template is one of the main tasks required to facilitate effective BIM implementation in facility management practice. However, consolidationof assetinformationintoAIR templatesare usuallydone manuallyin the industry. Building asset information can be retrieved from building information received, equipment list, BIM models, and onsite verification photos. During the onsite verification, photos of assets nameplates are taken for the consolidation of building asset information. Severalsourcesofassetinformationcausedifficultyintheconsolidation.Thecompilerwould need to refer across multiples sources to complete the consolidation of critical asset information.Suchpracticecreatesanavenueforerrorstooccurintheconsolidation.Currently, the Standard of Procedures (SOPs) in place to minimise error is to have different people to verifytheaccuracyofconsolidatedbuildingassetinformationinanAIRtemplate.Thisresults in the consolidation process of asset information to be time-consuming and requires a high numberofworkforce.Currently,inthemarket,nosolutionisabletoquickentheconsolidation process and ensure all asset information in the AIR template is accurate. A solution that can helpbridgethisgapisneeded.
Consolidationofassetinformation,usuallystoredinPDFformat,forallcriticalassets,should atleasthavealltheinformationlistedintheAIRtemplateexampleshowninFigure 1.
Figure1:CriticalassetinformationrequiredinanAIRtemplate(Source:BuildingandConstruction Authority,2018)
Under COBie Standards, the minimum information for all critical assets required to be in an AIR template are Type Name, Category, Type Description, Manufacturer, Model Number, ExpectedLife,ComponentName,StoreyNumber(Level),Location,ComponentDescription, Serial Number, Installation Date, Warranty End Date, and Asset Identifier. However, critical assets information available in practice is usually different from the information listed in COBie Standards. Building owners typically engage BIM professionals and real estate managementteamtorevisetheassetinformationrequiredinanAIRtemplate.
Alocalcompanythatprovidesdigitalfacilitymanagement(DFM) servicesdevelopedan AIR template relevantto the localindustrybasedonthe type of information whichiscriticalwhile conductingmaintenance.Informationinthelocalcompany’sDFMAIRtemplatecanbefound mostly in all equipment’s nameplate. The information includes Equipment Type and Description,EquipmentLabel(AssetCode),Floor(Level),RoomName,LocalMotorControl Panel(LMCP),Manufacturer,Brand,ModelType,Capacity,SerialNumber,InstallationDate, Warranty Expiry Date, and Vendor information. However, consolidation of asset information isstilldonemanually.
ThepracticeofautomatingtheconsolidationofassetinformationintoanAIR templateisnew tothe FMindustry.Thus,thereisverylittleinformationtosupporttheautomationprocesswe intendtoproduce.Togathermoreinformation,severalresearchmethodswereadoptedtoshow the difficulties which the current industry faced in the consolidation of asset information into an AIR templateand why automated process is important. Firstly, interviews were conducted to gather feedbacks on the current manual process of the asset information consolidation into anAIRtemplate.Secondly,experimentwasconductedtoexaminethetimetakenandaccuracy toconsolidateAIRinformationbycomparingthedevelopedautomatedsolutionandthecurrent manualpracticeintheindustry.
Interviewswereconductedwithagroupofpeoplewithexperienceinthemanualconsolidation ofassetinformationintoAIRtemplatestounderstandthedifficultieswhichusersusuallyfaced.
Theunderstandingprovidedinsightintohowthedifficultiescanbesolved.Informationwas gatheredthroughphoneinterviews.TenstafffromalocalcompanyofferingDFMservices wereinterviewed.
Figure2showsthetypicalprocess,asgatheredfromtheinterviewees,ofconsolidatingasset informationintoanAIRtemplate.Theonandforthcopingofcriticalassetinformationfrom PDFfilesandpastingonexceltemplatecellbycellcantakeseveraldaysofworkwhen workingonlargebuildings.Theintervieweesrevealedthatthetediouseffortcanbementally drainingandmakethestafflosefocus,therebyresultinginincompleteandinaccurate consolidationofassetinformationinanAIRtemplateinexcelformat.Alltheinterviewees thoughtautomationoftheentireprocessofconsolidatingtheassetinformationwillhelpreduce thetimeandnumberofmanpowerusedinthisprocess.However,allofthemarestillnotable tofindalternativesolutiontoimprovetheentireconsolidationprocess.
Figure2:Typicalprocessofconsolidatingassetinformationatfacilitymanagement(FM)stage
3.2PrototypingProcess
Fromtheinterviewresults,theimportanceofautomatingtheconsolidationprocesswas recognised.Beforecreatingtheprototype,researchwasconductedonthetypeofsoftwareto beusedbeforecreatinganAutomatedAIRTemplate.
MicrosoftExcelisaninternationalspreadsheetprogrammewhichiscommonlyusedaround theworld.Excelisapplicableinasituationwhentheconsolidationofinformationisneededto beintegratedwiththird-partysoftwaretodevelopadashboard.Excel'sabilitytosupportVisual
Basic for Applications (VBA) – a programming language for accessing data from external sources – makes its usage very popular. In DFM practice, the AIR template is consolidated usingMicrosoftExcel,astheinformationwillneedtobeintegratedintoathird-partyplatform. Thedeveloped Automated AIR Template reportedin thispaperwillbe usingMicrosoftExcel to solve theproblemofconsolidatingassetinformationintotheAIRtemplate.
Programmingsoftware is requiredto automatetheprocessof consolidatingasset information. With the function of VBA, the consolidation of asset information can be done semiautomatically. VBA works similarly to other programming software, such as C++ Programming, that allows code to be written to automate the overall process of consolidating assetinformation.Theembedmentof VBAintoExcelenablesuserstocreatetablesforfilling in informationautomatically.
The user interface of the developed Automated AIR Template should be easy to understand and inaccordance with the AIRStandardsetbyCOBie. The prototype solutionisexpected to be implemented into the DFM services working process of consolidating asset information. Thus,theprototype solution shouldadheretotheAIR templatestandardintheDFMservices.
AsthemainfunctionsofthedevelopedsolutionaretoallowuserstouploadmultiplePDFfiles andextractinformationfromthePDFfilesintothedevelopedAutomatedAIRTemplate,there should be two buttons clearly showing the icon for uploading of the folder (Browse) and extractingofinformationfromPDFfiles.
Asset information should be categorised into different types of building services to provide a more organised and clearer display of information for all critical assets. With more organised structure,clientsortechnicianswillbeabletofindspecificassetinformationefficiently.Figure
3showstheuserinterfaceofthedevelopedAutomatedAIRTemplate,whichisadefaultpage thatuserswillseeoncetheyopenthefile.TheAutomatedAIRTemplateisnotcomplicatedas it is straightforward, which even users with no experience in consolidating asset information into an AIR template will know what they need to do. The information reported in this paper will also serve as guidance for new users to know the critical information needed in the AIR templateandhowtoconsolidatetheinformation.
Figure3:AuserinterfaceofthedevelopedAutomatedAIRTemplate
Thefollowingarethebasicworkingprinciplesofthedevelopedprototype solution.
Step1: UploadfunctionwhichallowsuserstouploadthefoldercontainingdifferentPDF filesofthebuildingequipmentlist,operation,andmaintenanceManual,etc.
Step 2: Users to click on Extract function, which indicates the start of the extracting information process. If a user forgot to upload a PDF folder, a pop-up message wouldprompttheusertoupload.Theuserwillalsobeguidedtowheretoupload.
Step3: IdentificationofthePDFfolderwhereinformationwillneedtogetextractedfrom.
Step4: ConversionofallPDFfilesintoExcelfiles..
Step5:Afterconversion,convertedexcelfileswillbeaddedintotheworkingfileasnew sheetsnamed“Setting”.
Step 6: Information will be copied from the “Setting” sheet into the main working sheet oftheworkingfileunderthefollowingcriteria:
Identification of the matching building services in which the copied informationwillbepastedonbydetectingkeywords.
Identification of the column header of which information in the “Setting” sheetbelongstoandpastetheinformation
Steps1and2areaction-basedcoding,whichrequiresuserstoperformaspecificactionforthe coding to start and proceed to the next step. Steps 3 to 6 are based on backend coding. The userswillnotbeabletoseetheprogrammerunning.Theywillonlybeabletoseetheresultin the developed Automated AIR Template. The coding for the developed solution is separated into three main parts which consist of Uploading Function, Extracting Information Function, andCopyPasteFunction.
Figure 4a shows the coding, which allows users to select the folder which contains the PDF files. Firstly, it identifies a name for picking PDF Folder name as PDFFldr and sets it to the Excel applicationfunction, which isa Folderpicker. Secondly, a pop-up window will prompt theusertoselectthedesiredPDFFolder,asshowninFigure4b.Lastly,thecodingwillidentify the path of thefolderand display it on the AIR template. After completing the overall coding for Uploading Function, it is crucial to assign the set of coding to the “Browse” button, as
shown in Figure 4c. This is to ensure the set of coding will be activated after the user clicked onto the“Browse”button.
A B C
Figure4a:Uploadingfunctioncoding;Figure4b;ExcelPDFfolderselectionpop-upwindow;Figure 4c:AutomatedAIRTemplate“Browse”button.
Extract function coding is the crucial part of the developed Automated AIR Template which will perform PDF file conversion to Excel, and the combination of converted excel files with an active working file. Before the extraction of asset information, there are times when users forgot to upload their PDF folder. Hence, the developed Automated AIR Template should be abletoidentifyifthePDFfolderpathwasleftempty.Figure5ashowsthesetofcoding,which willpromptusersandguidethemto uploadtheirrespectivePDFfolder.Afteridentifyingthat usersdidnotuploadtheirPDFFolder,themessagepop-upboxwillfirstpop-uptonotifyusers abouttheissue,asshowninFigure5b. Thentheywill proceedtouploadtheirfolder.
Figure5a:CodingwhichwillpromptusersandguidethemtouploadtheirrespectivePDFfolder.
Figure5b:Messagepop-upboxtonotifyusers
AfterusersuploadedtheirPDFfolderscontainingallthePDFfilestoextractinformationfrom, thedevelopedAutomated AIRTemplatewillneedtobeabletoidentifywherethe PDFfolder is and which of the files in the folder are in PDFformat. Figure 5c shows the coding that aid theAutomatedAIRtemplateidentificationofPDFfolderandfiles.
CodinginvolvingloopswasdevelopedtoidentifythefilesinPDFformat.‘ForLoopFunction’ isutilisedinthesetofcodingstatedinFigure5dafteridentifyingwhichPDFfoldertoextract thefilesfrom.ThesetofcodingwillrunthroughallfilesinthePDFfolderandidentifyifthere is a PDF formatted file. If PDF formatted file is identified, the programme will open the file with MicrosoftWord, selectallcontentsinthedocumentandcopiedalltheselectedcontents.
A new sheet will be created and named as “Setting” which all the copied contents from MicrosoftWordwillbepastedon.Figure5eshowscodingforextractingPDFinformationinto Setting. However, the template in the “Setting” sheet, See Figure 5f, is not identified as the AIR Standards. Hence, asset information will need to be copied and pasted over to the “AutomatedAIRTemplate”sheetwhichfollowsCOBieandDFMstandards.
Figure5e:CodingforextractingPDFinformationintoSetting
Figure5f:SettingSheetwithPDFinformation
InFunction3,thesetofcodingwillbeabletoperformtheactionofcopyinginformationfrom the “Setting” sheet and paste on the Automated AIR Template sheet based on the criteria identified in Function2. Firstly, thecodingwill needto performthemain criteria, which is to identify the type of asset information from the “Setting” sheet to be pasted in the Automated AIRTemplatesheetbyjustdetectingthekeywords.Figure6ashowsasetofcodingforfinding matching asset information. The selected information will be copied and pasted onto the AutomatedAIRTemplatesheetaccordingtowhichassetitbelongsto.
Figure6a:Codingthataidstheidentificationofmatchingbuildingservicesinformation
As the column header of Setting and Automated AIR Template sheets are named differently, mapping of the column header was listed on a hidden sheet as a backend setting. Figure 6b showscodingforfindingmatchingcolumninformationbyrunningthroughinformationineach column.Ifmatchingheaderwerefound,assetinformationwouldbecopiedandpastedontothe mappedcolumn.
After going through the three functions, the Automated AIR Template will be filled with criticalassetsinformationofdifferentbuildingsystems–seeFigure6c.Thesetsofcodingalso help to remove empty rows betweenthe information, which allows the developed Automated AIRTemplate tobemorecompact.
Figure6b:Codingforfindingmatchingcolumninformation
The experiment was conducted to test the effectiveness of the developed Automated AIR Templateandhaveinsightintoimprovementneededanditspossibleapplicationinthemarket. The Automated AIR Template solution is developed to ensure the users will need to upload their asset information, and the solution will be able to extract and tabulate the information accordingtotheAIRstandardtemplateautomatically.Eveniftheprocesshadbeenshortened, the accuracy of the information should not be compromised, and it should be 100% accurate. Additionally,userswithnoexperienceinconsolidatingAIRinformationshouldstillbeableto usethesolution.
Six participants were recruited to fulfill the objectives of the study. Three of the participants have experience in consolidation of asset information into an AIR template while the other three participants have no such experience. Only six people were recruited for the study because the main goal isto get an indication of the effectiveness of the developedAutomated AIR Template. We believe that preliminary adoption or a field study of the developed AutomatedAIRTemplateinactualpracticeintheindustrywillbemoreappropriatetoconfirm its effectiveness. The three participants with experience were from a company in Singapore, providingDFMservices.Theotherthreeparticipantswithoutanyexperienceassetinformation consolidation in the AIR template have a building services engineering background. Asset informationconsolidation training was providedto participants with noexperience before the startoftheexperiment.
Eachparticipantwasinvolvedintwosetsofexperiments.Thefirstsetofexperimentsinvolved the manual entry of data from PDF file to conventional AIR template. The second set of experiments involved the use of the developed Automated AIR Template to consolidate asset information. A total of 42 critical assets were used for the study. The time taken to complete each experiment was recorded. The participants did not participate in the experiment at the sametime.Theexperimentswereconductedattheagreedtimebytheparticipants.Eachofthe participants did their experimental sessions in an air-conditioned room. Efforts were made to ensure the participants were comfortable with the indoor environmental conditions and were feeling well throughout their experimental sessions. Time taken by each participant to consolidate asset information into an AIR template was recorded. The time recorded was the actual time spentbythe participantsincompleting the consolidation of AIR information. The
timetakenforbreaksorquestionsontheconsolidationofassetinformationwasexcluded.The authors anticipated that the possible stress caused by the manual entry of AIR information couldleadtoemployeestotakemanybreaks,includingbreakstorelaxorgototoiletandother needsthatmayeasetheirstress.Breaktimecouldalsobeasourceoferrorsintheconsolidation ofassetinformation.
The developed solution was tested several times to ensure that the information extracted will beaccurate andavoidanyproblemsthatmightbeleftundiscoveredin thedevelopmentof the solution.ThemeasurewastakentoensuretheAutomatedAIR Templatesolutioniserror-free for users to use. Any unforeseen problem with the developed Automated AIR Template may be a source of error in experimental data. All AIR template submitted, after the manual and automated solution, by each participant were checked three times for possible errors. The principle behind the error check is described below. A full (100%) check of all asset information in the AIR template was conducted. When no error was found, the second round ofcheckingwasconductedbecause itwaspossible tohavemissedonedueto humanerror.In the second round of checking, 50% of the asset information across all building systems was randomly checked. When no error was found, the final round of checking was conducted on 25% of the asset information randomly checked across all building systems in the AIR template.Whenevererrorswerefoundinanyroundofchecking,thetypeandquantityoferror found were documented. Checking of information did not proceed to the next stage when an errorwasfound.Thenextstageofcheckingwillonlyproceedaftercorrectingalltheerrors.
TheprimarypurposeoftheAutomatedAIRTemplateistohaveasinglebuttonthatwillallow theaccuratetransferringofassetinformationinseveralPDFfilesintotheAIRtemplatewitha single click. The time taken when asset information was consolidated manually and automaticallyconsolidationprocessisnotthesameasexpected.Table1showsthecomparison between the time taken by all the participants, irrespective of their experience status when required to use the manual and automated method of consolidating asset information. It was observedthatparticipantstookbetweenmorethan25minutesandabout1hour15minutesfor the manual method. However, when the participants used the developed automated solution,
the time takenbythe participantswasfrom 22 seconds and upto 39seconds. Onaverage, the time recorded for using the developed Automated AIR Template is 28 seconds while the manuallyconsolidatedassetinformation,onaverage,2588seconds.Thereisa99%timesaving when automated method – the developed Automated AIR Template is adopted. The finding shows that the developed automated solution could significantly reduce the time taken to consolidate assetinformationintoanAIRtemplate.
Table1:Timetakenbyallthe participantswhenmanualandautomatedmethodsareadopted toconsolidateassetinformationintoanAIRtemplate.
Consolidationofassetinformationusing manual method–TimeTaken(h:m:s)
Consolidationofassetinformationusing theautomatedmethod–TimeTaken(h:m:s)
0:25:45 0:00:23 0:35:50 0:00:22 0:30:35 0:00:25 0:40:50 0:00:39 1:15:20 0:00:32 0:50:30 0:00:28
On average, the experienced participants spent 1843 seconds, while non-experienced participants spent 3333 seconds. Thus, the difference between experienced and nonexperienced participants was 1490 seconds. However, when an automated method –Automated AIR Template – was adopted, the need for the experience was reduced. The difference in the average time spent between experienced participants and nob-experienced participants was only 10 seconds. Onaverage, the experienced participants spent 23 seconds, whilenon-experiencedparticipantsspent33seconds.Whatthefindingsmeanisthatnewstaff with no experience can complete the consolidation of asset information into an AIR template inashortpossibletimeif theautomatedmethodisadopted.
Table2:Comparisonbetweenthetime takenbyexperiencedandnon-experienced participantstoconsolidateassetinformationwhenmanualmethisadopted
Consolidationofassetinformationusingmanualmethod
Experiencedparticipants–TimeTaken(h:m:s)
Non-experiencedparticipants–TimeTaken(h:m:s)
0:40:50 0:35:50 1:15:20 0:30:35 0:50:30
0:25:45
Table3:Comparisonbetweenthetimetakenbyexperiencedandnon-experienced participantstoconsolidate assetinformationwhenautomatedprocessisadopted
Automatedconsolidationmethodusing AutomatedAIRTemplate
Experiencedparticipants –Time Taken(h:m:s)
Non-experiencedparticipants–Time Taken(h:m:s)
0:00:23 0:00:39 0:00:22 0:00:32 0:00:25 0:00:28
Allgeneratedinformationbyparticipantsduringtheexperimentwereconsolidatedandverified againstthe original equipment list. After conducting the 100% checkof all information, there were errorsfoundinthesubmissionof the non-experiencedgroup. Onecommonmistake was thattheycopidthe wrongEquipmentTypeandDescriptionfromtheequipmentlist,asshown in Figure7.
Figure7:ErrorfoundinconsolidatedAIR(left)comparedtocorrectinformation(Right)
After conducting a 100%check on the manuallyconsolidated information, errors were found intheAIRtemplatesubmittedby3ofthe6participants.Outofthe3participants,2participants werefromthenon-experiencedgroup.Afterthat,50%checkwasconductedafterrectification
wasmadetotheidentifiederrors.Errorspreviouslynotidentifiederrorsbyadoptingthe100% check. After conducting a 50% check, errors were found in the AIR template submitted by 4 participants – 2 participants each from the experienced and non-experienced group. This observation means committingerrors when manually consolidating assetinformation into the AIR template does not depend on users having experience or not. Even with the experienced staff, errors can still be committed mostly due to human errors. As errors were found during the 50% check, the authors did not proceed to conduct a 25% check on the manually consolidatedAIRinformation.
Instead, checks were made to consolidate asset information into the AIR template automatically. No error was found after conducting the 100% check. Thereafter 50% check was conducted, and no error was found in the consolidated asset information. The authors proceeded to conduct a 25% check on the automatically consolidatedassetinformation in the AIR template. No error was found after conducting the 25% check. Being through the three stagesofverificationcheckwithnoerrorsuggeststhatthedevelopedAutomatedAIRTemplate has the capability of ensuring the accuracy of information when extracting the information withina shortperiodoftime.
The shortage of qualified and skilled manpower is a major problem in many companies providing DFM services. Additionally, staff may have to handle several projects at the same timewithlimiteddeadlines. The shortage of manpower and pressure posed by one staff handling several projects at the sametimewithinlimiteddeadlineswillincreasethevulnerabilityofstafftocommittingerrors.
OurexperienceoftheDFMservicesindustrysuggeststhataslittleastwostaffmayberequired toconsolidatemorethan1000criticalassetswithintwodays. Afterconsolidatinginformation, different stages of verifying and checking of information will need to be done by different people.Theverificationprocessistime-consuming,andmoremanpowerisrequiredtoperform the verifications. With our developed Automated AIR Template, consolidation of asset information can be done within a few minutes or even a few seconds for large buildings with accuracy. Whereas, the manual process can take hours or days dependingon the extentof the
critical asset information to be consolidated. Even though the developed Automated AIR Informationisabletoresolvetheissueswhichthecurrentmarketisfacing,therearestillsome advancedfeaturewhichcanbeintegratedintothesystem toimprove itseffectivenessfurther.
After the first stage of automatic consolidating asset information into the AIR template, there will always be some information that is missing. Usually, when there is missing information, thepersonwhoconsolidatestheassetinformationwillneedtocheckacrossmultiplePDFfiles andimagessuchasoperatingandmaintenancemanual,equipmentcatalogue,as-builtbuilding model,equipmentnameplate,andonsitephotos.AutomatedAIRTemplatewillneedtoinclude afunctionwhichcancheckacrossmultiplePDFfiles,detectmissinginformation,copyingand pastingof missinginformationintotheAIRtemplate.
As the current matching header setting in the developed solution is done according to the simulatedequipmentlist.Inafutureimplementation,thedevelopedAutomatedAIRTemplate shouldbeabletoreadthe equipmentlistwithBIMauthoringsoftwaredetails,e.g.,Revit,asa header. As buildings are required to have Revit models, it will become an international languageastheheaderof thegeneratedequipmentlist.
TheAutomatedAIRTemplatemusthavethecapabilityofgeneratingasummaryorstatisticof the overall critical asset information. For example, a dashboard showcasing the type of assets within the building, the total number of assets, and the number of assets at each level. This information is crucial at the initial stage of project management, which is to perform the budgetaryestimation.Withallthequantitiesdisplayedonadashboard, ithelpstosimplifythe processofcountingthenumberofassetsmanually,whichistime-consuming.
In the current DFM work process, information of all critical assets is being keyed into each asset Revit model individually. This process is time-consuming and tedious, which errors are
oftenfoundduetohumanerror.ErrorsfoundinbuildingRevitModelsarecriticalastheywill affect the implementation of BIM into facility management and operations processes. As the process of consolidating asset information had become automated, data entry for each asset should also be automated with the use of Dynamo. Critical assets in BIM models should be abletodetectwhichassetinformationinAIRtemplatebelongstothemandcopiedinformation intotheassetpropertiesintheBIMmodels.
AssetInformationRequirement(AIR)isoneofthecrucialpiecesofinformationtobedelivered acrossdifferentbuildinglifestages.Intraditionalfacilitiesmanagementpractice,consolidation of AIR information had always been done manually, which is an inefficient and ineffective method. Having errors in the AIR template with manually consolidated asset information is inevitable due tohumanerror. However, there isno alternative solution whichable to resolve thisissuecurrentlyintheindustry.Themainpurposeofthispaperistostudytheissuecurrently facedintheindustrywhen consolidatingassetinformationinto the AIR template anddevelop an appropriate solution. Our findings reveal that the developed Automated AIR Template has the potential to significantly shorten the time taken to consolidate asset information into the AIRtemplate.Thedevelopedautomaticsolutioncouldsavetimeby99%with100%accuracy. This study only focuses on the automatic consolidation of asset information into the AIR template.Thereisstillroomforimprovement.Identifiedareasforfuturestudyincludeacrossreference to multiple PDF files, reading of asset information directly from BIM authouring software, creation of AIR template dashboard, and integration of asset information into BIM models.
ThesupportoftheSingaporeInstituteofTechnologyincarryingoutthisappliedresearchstudy isgratefullyacknowledged.Ms.NgHuiMindidtheworkandcontentsofthispaperaspartof her BEng final year design project in the Sustainable Infrastructure Engineering (Building Services) programme. Dr. Moshood Olawale Fadeyiguidedthedevelopment of theprototype solutionandexperimentaldesigntotesttheeffectivenessofthedevelopedsolution. Dr.Fadeyi alsocontributedtothedevelopmentofthisarticle.
Argyres, N. S. (1999). The impactof informationtechnologyon coordination: Evidence from theB-2“Stealth” bomber. OrganizationScience,10(2), 162-180.
AustralasianBIMAdvisoryBoard(2018).Assetinformationrequirementsguide:Information required for the operation and maintenance of an asset. Australasian BIM Advisory Board (ABAB).
Cavka, H. B., Staub-French, S., and Poirier, E. A. (2017). Developing owner information requirements for BIM-enabled project delivery and asset management. Automation in construction,83,169-183.
Holmgren, M. (2006). Maintenance-related incidents and accidents: aspects of hazard identification (Doctoraldissertation,Luleåtekniskauniversitet).
Love,P.E., Matthews,J.,Lockley,S., Kassem,M.,Kelly, G., Dawood,N.,andSerginson, M.(2015).BIMinfacilitiesmanagementapplications:acasestudyofalarge university complex. Built EnvironmentProjectandAssetManagement.5(3),261-277
Patacas, J. (2016). Supporting Building owners and Facility Managers in the Validation and Visualisation of Asset Information Models (AIM) through open standards and open technologies. JournalofInformationTechnology in Construction,1874-4753.
Clickthelinkbelow toview additional information. Download the PowerPoint slides toview the videos of the proposed solution in the slides. The authors reserved the right to the informationprovidedintheslides.
https://www.dropbox.com/s/45zl8rd2f8jn5lw/Supplementary%20Information_Proposed%20 Solution_Ng%20and%20Fadeyi%202020.pptx?dl=0