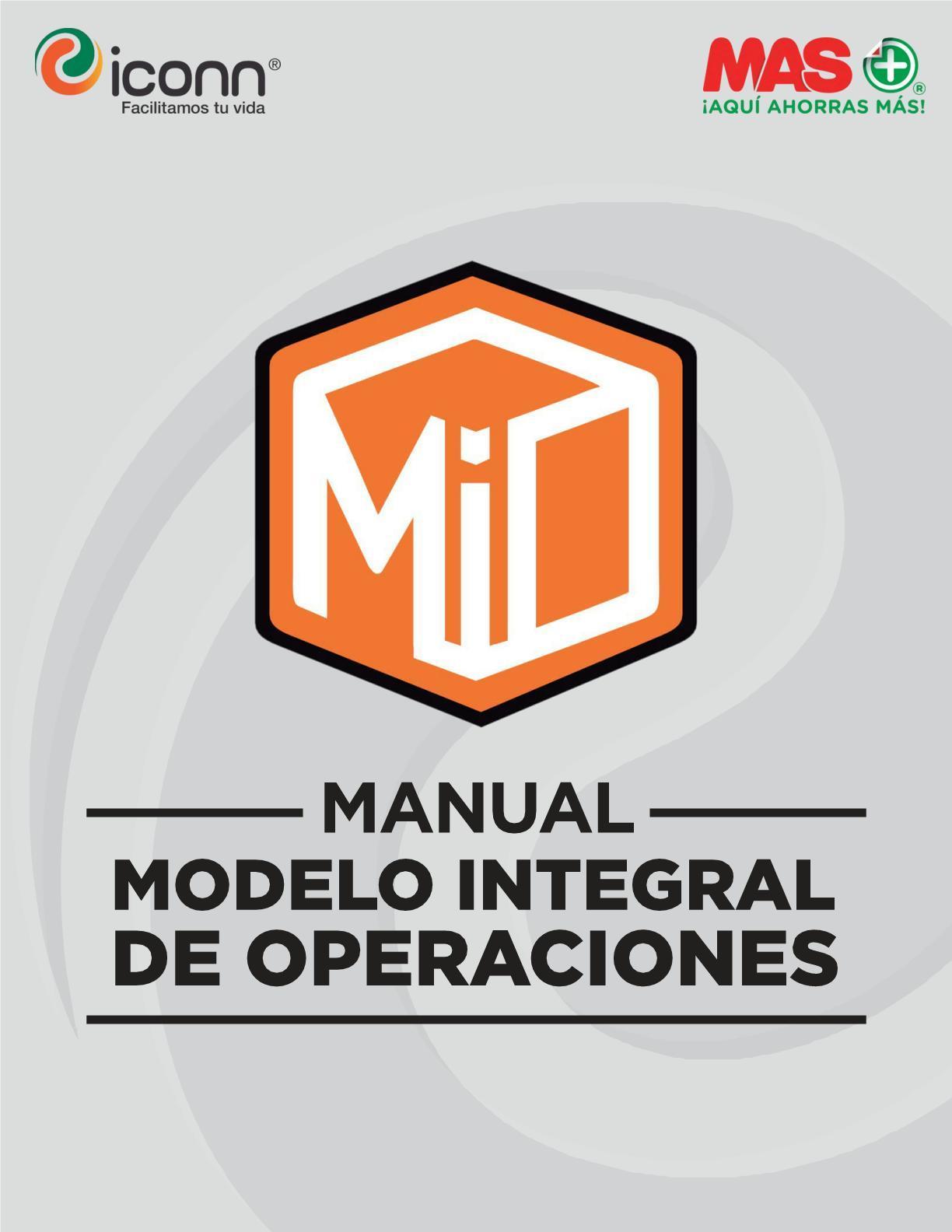
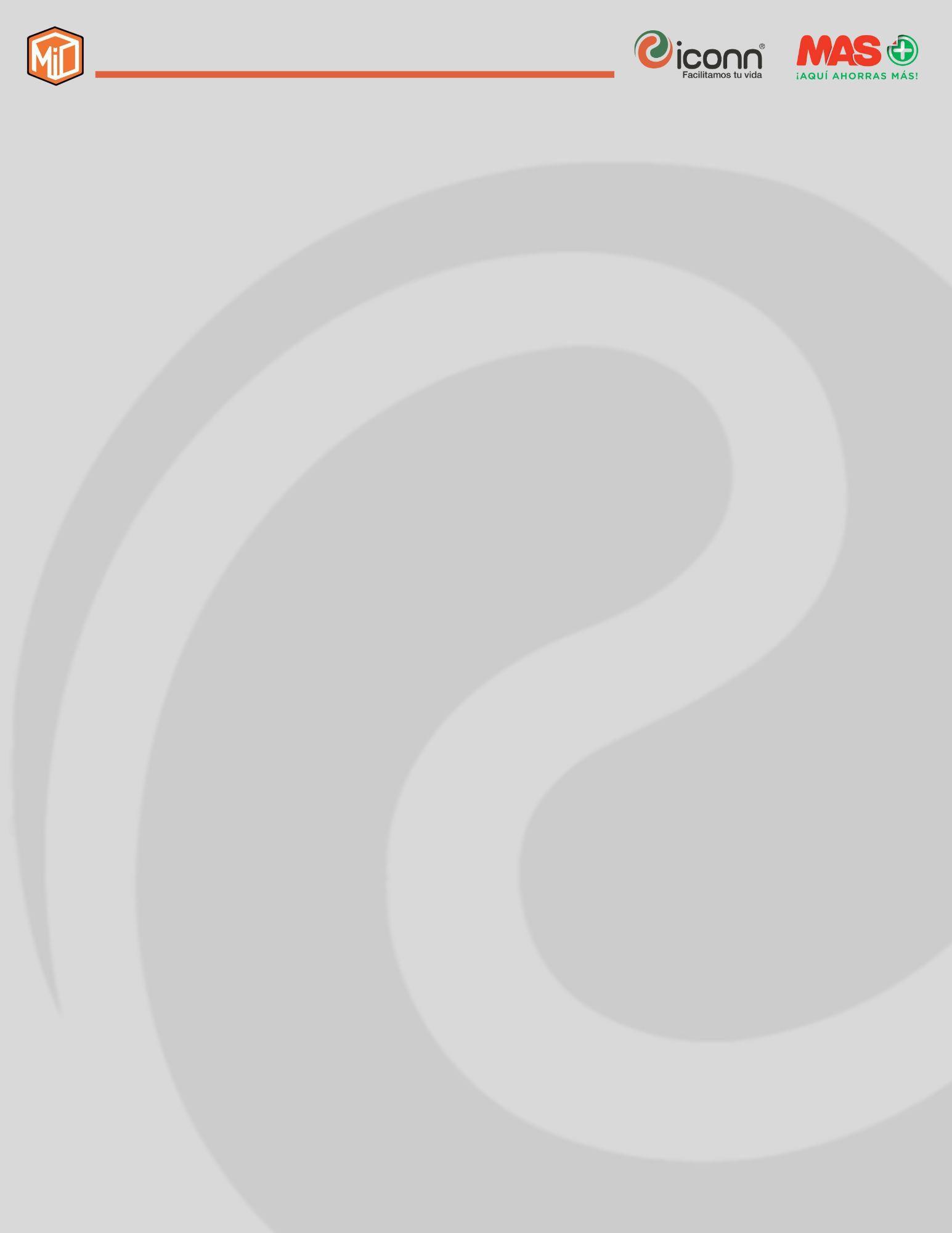
T Acacia
P-T-G
G
ACME [ AlfaCeMSe - Master Label - Ecef ]
Actitudes y Comportamientos
E
Automatización + Inteligencia
Artificial
CeMSe [ Centro de Monitoreo y Servicio ]
Compensación
Variable
Cumplimiento Regulatorio
Documentación, Actualización, Visibilidad de Procesos
/BENEFICIO
Implementación de herramienta tecnológica para mejorar la gestión de inventarios en la cadena de demanda integrada alineados a un pronóstico de ventas.
Trazabilidad de punta a punta de las iniciativas desarrolladas del 2019 al 2023
Capacidad de liderear para asegurar resultados extraordinarios, compromiso de servir para lograr la satisfacción de sus clientes y colaboradores y carácter para hacer lo correcto para generar confianza y un ambiente de respeto.
Surtido cajas vía robots autodirigidosAMRs (Autonomous Mobile Robots)- / Reconocimiento de Objetos (fotografías ECEF), soportados con Ejercicios de Simulación como elementos de apoyo para incremento de productividad, control y trazabilidad.
Brindar soporte para reaccionar de manera inmediata ante alarmas, emergencias o eventos haciendo uso de sistemas de información. Área de apoyo tecnológico central que brinde la trazabilidad en tiempo real, tanto para el usuario como para el cliente final.
Evaluar la compensación variable actual alineando las necesidades operativas y tendencias de mercado para que la oferta de valor que ofrecemos sea un diferenciador para todos los colaboradores.
Conocer y Asegurar que se cumplan las normas gubernamentales y todos los procesos, formas y comportamientos regulados en nuestro Código de Ética y Conducta, así como en el Sistema de Auditoría Interna (SAI).
Realización del mapeo, elaboración de flujos o redacción de procedimientos y su publicación para los diversos departamentos, para tener una estandarización en todos los Centros de Operación.
Proyectos, Operaciones, Administración y Talento
- 2024 Q4-2024 (CeDis)
Estrategia Integral de Mantenimiento
Optimización del modelo de distribución en CDC Mty, asegurando los niveles de servicio objetivo y contribuyendo con el bienestar laboral.
Reevaluación de los Servicios Tercerizados de Mantenimiento a Unidades de Reparto que contribuyan con la disponibilidad para su operación y con una vida útil adecuada.
Transformar la Estructura Organizacional de acuerdo con las necesidades operativas y de expansión, alineando la propuesta de valor integral para nuestros colaboradores.
Análisis y Habilitación de Nuevos CeDis, CDCs, Cross Docks y Plazas Mayoreo permitiendo la continuidad de servicio a nuestros clientes y consumidores.
Contar con un espacio donde compartir aprendizajes, prácticas y cápsulas de sensibilización, que nos ayuden a construir una cultura segura.
Modelo de gestión que permite planear y tener sintonía entre las áreas involucradas en la Cadena de Demanda Integrada para poder gestionar planes y resultados con una perspectiva de 18 meses.
Desarrollo de Algoritmos que nos de sugerencias basada en datos para eficientizar la Cadena de Demanda Integrada.
Optimizar entrega recepción entre MB y 7E (paperless, notificación hora de llegada, notas de crédito, desincentivación de ajustes).
Contar con Espacios dignos y que nos hagan sentir orgullosos de pertenecer a Iconn.
Migración de WMS
Actualización, Renovación de Software SIMAS a nueva Plataforma.
T
MIO [ Modelo Integral de Operaciones ]
Modelo de Abastecimiento Diferenciado
Modelo de Gestión de Proveedores
Modelo de mejora continua que mediante el análisis y uso de herramientas causa raíz se entreguen resultados superiores de manera sostenida.
Gestión de reabasto de productos, en particular para las plazas de Mayoreo para incrementar el nivel de servicio.
Definición de la metodología para evaluar el desempeño de los proveedores, enfocado en el OTIF (entrega a tiempo y completo) y el cumplimiento de citas.
Modelo Dinámico de Capacidad
Modelo Predictivo de Demanda
Establecer con anticipación los planes de acción y necesidades de recursos, para soportar el crecimiento de demanda futura.
Incorporación de las múltiples variables (clima y otras premisas) para tener un pronóstico de demanda más preciso en el corto plazo.
Análisis del costo de distribución de pedidos del Canal de Ventas Detalle y ejecución de propuesta de mejora para incrementar la rentabilidad de las rutas de entrega.
Actualización periódica al Catálogo de Artículos y determinación de Políticas de Días Inventarios, contribuyendo a la Reducción de Merma e Inventario Inhábil.
Agradecer, valorar, celebrar y reconocer que somos seres humanos al servicio de seres humanos.
Realización periódica en todas las operaciones para revisar las condiciones de las instalaciones y de las herramientas de trabajo, que permitan reducir paulatinamente incidentes y accidentes laborales.
Actualización, Renovación de Software Voxware a nueva Plataforma.
Vivir nuestros Valores y aprender que el Liderazgo impacta y deja huella en todos los que nos rodean, enfocándonos en nuestra seguridad.
¿Qué es MIO?
Es un modelo de mejora continua que construye capacidades y comportamientos para entregar resultados superiores de manera sostenida.
El objetivo del modelo es instaurar una cultura de mejora continua, que requiere la integración de capacidades, comportamientos y liderazgo. El modelo de trabajo por sí solo no es suficiente; los líderes deben comprenderlo, adoptarlo y respaldar activamente esta mentalidad para su éxito.
El modelo se inspiró en Sistema Integrado de trabajo (IWS) creado por la empresa P&G el cual es una forma de mejorar la fiabilidad de la fabricación, reducir costos y aumentar la productividad. Se adapto este modelo de trabajo a un modelo ICONN el cual se enfoca en la operación logística utilizando los mismos principios de IWS.
Enfoque
El MIO busca fomentar la construcción de comportamientos, promoviendo ideas y mejoras que surgen de forma ascendente desde el nivel operativo, diseñando planes de acción que involucren a todos los niveles de la organización. Al cumplir con estos planes, se anticipa mejora continua en la operación, reflejando progreso operativo y validando que las personas se sienten escuchadas, respaldando así la efectividad de la metodología.
El implementar una metodología de mejora continua es indispensable para toda empresa que busque mantenerse competitiva haciendo su forma de trabajar más eficiente, reduciendo su costo y aumentando su utilidad. Dentro de los beneficios que brinda esta metodología se encuentran:
MAYOR CALIDAD EN LOS PRODUCTOS Y SERVICIOS
MAYOR SATISFACCIÓNDE LOS
La metodología MIO debe estar alineada con los objetivos de la empresa y para lograrlo se han establecido las prioridades de negocio. Estas prioridades representan los requisitos o necesidades que la empresa busca cumplir en un periodo determinado, con apego a la metodología.
Las prioridades de negocio las visualizamos mediante una placa, en relación con el giro de la compañía (logística), en donde vemos los objetivos trazados en el plan hacia el 2026.
95 = 95% de nivel de servicio
98 = 98% de oportunidad de entrega
8 = 0.08% de merma
0 = 0 accidentes
QR = liga de manual MIO
2026 = Año objetivo para alcanzar las metas
La metodología consiste en 5 elementos significativos: Reuniones de Desempeño, Indicadores diarios de Trabajo (IDT), Herramientas Causa Raíz, Tableros MIO y Líderes. Cada uno de estos elementos desempeña una función específica que contribuye de manera significativa a la mejora continua. A continuación, detallaremos la función de cada uno de estos componentes.
Líderes
IDT
(Indicadores diarios de trabajo)
Rol MIO
Región Noreste MTY
Op y G. Dist G. Op G. Dist CDC G. Op. J. Op. J. Dist.
Mas Bak
Op G. Prod CD Rey
Región CentroSur CDMX CeDis
Gerente Operaciones y Distribución
Dist
Dist.
Región Pacífico GDL CeDis Gerente Operaciones y Distribución
Cadena de suministro
Planeación de la demanda
Op J. Op. J. Dist. CDC S. Op J. Dist
Mas Bak J. Proud. J. Proud.
Planta de Demanda
Las reuniones de desempeño son un elemento dentro de la metodología MIO la cual consiste en tener reuniones diarias, fijas y obligatorias. Se busca tener un proceso guiado paso a paso logrando tener una mejora continua.
Las reuniones de desempeño definen hacia donde vamos, dirigiendo planes de acción, midiendo y ejecutando los IDT. Prácticamente son el corazón de esta metodología.
Existen diferentes tipos de reuniones las cuales tienen la finalidad de tener un escalamiento hacia niveles superiores con el fin de apoyar soluciones propuestas por los niveles anteriores que no cuentan con los recursos necesarios a su alcance.
Reuniones de Escalamiento
Reunión de Desempeño Operativo (RDO)
Reunión de Desempeño Staff (RDS)
Reunión de Desempeño Gerencia (RDG)
Reunión de Desempeño Dirección (RDD)
Reuniones de Seguimiento
Reunión de Seguimiento (RS)
Reunión Semanal de Desempeño (RSD)
Reunión Mensual de Desempeño (RMD)
Objetivo: Los equipos dedicarán de 10 a 15 minutos diariamente y se enfocarán en resolver desviaciones recurrentes a través de planes de acción de corto a mediano plazo según aplique y mediante el uso de herramientas de análisis de causa raíz (ACD)
Supervisor
• Conduce la sesión
• Registra y repasa resultados día anterior en tablero IDTs de Operación
• Asegura que cualquier IDT que se encuentre fuera del objetivo (semáforo en rojo) cuente con su análisis causa raíz y plan de acción.
• Promueve el cumplimiento de compromisos y escala a la Reunión de Desempeño Staff (RDS) aquellas iniciativas que requieren de apoyo del Líder de Operación
• Cumplen con los compromisos de calidad, productividad, orden, limpieza, aporta ideas y sugerencias de mejora e innovación.
Identifícate y contribuye al logro de las prioridades de negocio
Objetivo: Los equipos dedicarán de 20 a 30 minutos diariamente y se enfocarán en resolver desviaciones recurrentes a través de planes de acción de corto a mediano plazo según aplique y mediante el uso de herramientas de análisis de causa raíz (ACR).
• Conduce la sesión.
• Asegura que los IDTS sean revisados cada 6 0 12 meses para seguir alineados con las estrategias del negocio.
• Contribuye con Jefatura y Supervisor en facilitar el cumplimiento de los planes de solución e innovación de corto y mediano plazo.
• Escala a la Reunión de Desempeño Gerencial (RDG) las iniciativas que requieren del apoyo de Gerencia.
• Expone resultados del día anterior
• Asegura que cualquier IDT que se encuentre fuera del objetivo (semáforo en rojo) cuente con su análisis causa raíz y plan de acción.
• Contribuye con Supervisor en facilitar el cumplimiento del plan de solución e innovación y determ ina clasificación de plazo de solución.
• Asegura la calidad de la información y reporta/registra resultados en tableros IDTs de Staff
• Analiza Causa Raíz de oportunidades y establece e inicia planes de acción.
• Encargado de realizar y llenar los formatos de salud, es decir asegura que se mantenga el enfoque acorde a la metodología (asistentes, tiempo, temas, fechas compromiso).
• Ayuda a sustentar las oportunidades repetitivas resultado de la evaluación de las soluciones propuestas en los análisis causa raíz.
Identifícate y contribuye al logro de las prioridades de negocio
Objetivo: Los equipos dedicarán de 20 a 30 minutos diariamente y se enfocarán en resolver desviaciones recurrentes a través de planes de acción de mediano a largo plazo según aplique y mediante el uso de herramientas de análisis de causa raíz (ACR).
• Conduce la sesión.
• Contribuye con Líder y Jefatura y áreas de soporte (administración y talento) en facilitar el cumplimiento de los planes de solución e innovación de mediano y largo plazo.
• Asegura que los IDTs sean revisados cada 6 0 12 meses para seguir alineados con las estrategias del negocio.
• Expone resultados del día anterior.
• Asegura que cualquier IDT que se encuentre fuera del objetivo (semáforo en rojo) cuente con su análisis causa raíz y plan de acción.
• Contribuye con Jefatura en facilitar el cumplimiento de los planes de solución e innovación.
• Se compromete a la terminación en tiempos objetivo.
• Apoya decisiones relacionadas a la solución de oportunidades, cuidando políticas y lineamientos de adquisición de insumos y/o servicios
• Apoya decisiones relacionadas con la plantilla cuidando políticas y lineamientos de estructuras.
• Encargado de reportar/registrar el estatus de cobertura de personal, así como de accidentes, incidentes, enfermedades en general.
Identifícate y contribuye al logro de las prioridades de negocio
Objetivo: Los equipos dedicarán de 20 a 30 minutos diariamente y se enfocarán en resolver desviaciones recurrentes a través de planes de acción mediano a largo plazo según aplique y mediante el uso de herramientas de análisis de causa raíz (ACR).
• Conduce la sesión.
• Contribuye con Gerencias y áreas de Soporte (Administración y Talento) en facilitar el cumplimiento de los planes de solución e innovación de mediano y largo plazo.
• Asegura que los IDTs sean revisados cada 6 0 12 meses para seguir alineados con las estrategias del negocio.
• Impulsa y promueve la generación de nuevas ideas y la homologación de las operaciones
• Asegura la calidad de la información y reporta/registra resultados en tableros IDTs de Dirección.
• Expone resultados del día anterior, contribuye y se compromete al cumplimiento de los indicadores.
• Asegura que cualquier IDT que se encuentre fuera de objetivo (semáforo en Rojo) cuente con su análisis causa raíz y su plan de acción
• Comparte actividades, datos o eventos relevantes (positivos / negativos).
• Proporcionar soporte administrativo para mitigación de desviaciones y/o riesgos en gastos operativos.
• Apoya decisiones relacionadas con la plantilla cuidando políticas y lineamientos de estructuras.
• Encargado de reportar/registrar el estatus de cobertura de personal, así como de accidentes, incidentes, enfermedades en general.
Identifícate y contribuye al logro de las prioridades de negocio
Objetivo: Los equipos dedicarán de 10 a 15 minutos en una sesión diaria al concluir operaciones y se enfocarán en retroalimentar el cierre del plan de acción establecido en la Reunión de Desempeño Staff (RDS) o Reunión de Desempeño Gerencial (RDG) según aplique
• Conduce la sesión
• Realiza repaso a los pendientes del día, reconoce los avances y compromete cumplimiento.
• Apoya con soporte, analiza la información, registra y monitorea compromisos.
• Exponen los resultados de los planes de acción.
Identifícate y contribuye al logro de las prioridades de negocio
Objetivo: La gerencia con sus equipos de operaciones y de distribución dedicarán de 50 a 60 minutos en una sesión semanal y se enfocarán en revisar los avances a los planes de acción a mediano plazo, la aportación de nuevas iniciativas y la gestión de solicitudes de apoyo
• Conducen la sesión, define la agenda y participantes.
• Dan soporte a solicitudes de presupuesto
• Asegura que la contribución/beneficios propuestos cumplan con la rentabilidad de negocio.
• Guían al equipo para apegarse a la visión estratégica de la organización.
• Exponen los avances a iniciativas de mejora e innovación conforme a la definición y determinación de prioridades a los planes de acción.
• Presentan acciones como resultado del comportamiento de las sesiones diarias de Operación y Staff.
• Asegura el cumplimiento a las buenas prácticas de conducción de modelo/metodología.
• Orienta e impulsa el uso de las herramientas causa raíz y formatos.
• Da orientación a la elaboración de análisis varios
• Contribuye con la organización de necesidades de capacitación.
• Expone resumen del comportamiento de las sesiones diarias de Operaciones y Staff.
• Presenta soporte de análisis de planes de acción basado en el uso de formatos de la metodología.
Identifícate y contribuye al logro de las prioridades de negocio
Alcance: Nacional
Objetivo: Los equipos en sesiones virtuales dedicarán de 60 a 90 minutos mensualmente y se enfocarán en contribuir con Iniciativas de Mejora e Innovación en asuntos asociados con la Eficiencia en Operaciones, en Distribución, en Calidad, en Procesos, en Inventarios y en Seguridad, a través de establecer Planes de Acción mediante el uso de Herramientas de Análisis de Causa Raíz ACR .
MES Ene Feb Mar Abr May Jun Jul Ago Sept Oct Nov Dic
SEMANA 1 2 3 4 5
ÁREAS Inventario & Inhábil Operaciones Distribución Calidad Seguridad
HORARIO
LÍDER DE SESIÓN
ROL DE LÍDER DE SESIÓN
Establecido por cada líder de sesión
Gerencia Administración Jefatura Proyectos Jefatura CeMSe Gerencia CDC Mty Gerencia de Talento
Conduce sesión, define agenda, participantes, asegura una reunión efectiva y registra en minuta acuerdos y compromisos.
• Cumple con acuerdos y compromisos a través del uso de herramientas Análisis Causa Raíz y monitorea y expone resultados.
• Promueve, apoya, impulsa y gestiona con sus equipos de trabajo el uso de herramientas ACR para las iniciativas de mejora e innovación, valida la contribución costo-beneficio.
• Brinda orientación, verifica alineación con las prioridades estratégicas y aprueba o replantea iniciativas
Identifícate y contribuye al logro de las prioridades de negocio
Las reuniones se tienen en horarios y lugares específicos, cada unidad de negocio los establece de acuerdo con sus operaciones. Es importante con base a tu rol y tus funciones conocer en cual te corresponde participar.
OPERACIONES EMBARQUE Y DISTRIBUCIÓN
Tipo de reunión
Reunión
Horarios Participan
RDO Inicio de turno
RDS
Reuniones de escalamiento
RDG
RDD
Establecido el por Líder MIO
Establecido por la Gerencia
Establecido por el Director
RS
Reuniones de seguimiento
RDS
RMD
Final de turno
El establecido por Gerente Regional
Establecido por el líder de la sesión
Colaboradores Supervisores
Supervisores
L. Procesos Jefaturas Líder MIO
Horarios Participan
Inicio de turno
Colaboradores Supervisores
El establecido el por Líder MIO Supervisores
Administración Talento
Administración Talento Proyectos
Gerente Líder MIO
L. Procesos
J. Procesos
Gerente Líder MIO
L. Procesos
J. Procesos
El establecido por Gerente Regional
El establecido por Gerente Regional
Inventarios & inhábil Operaciones
L. Procesos Jefaturas Líder MIO
Líderes MIO Gerente
Gerente Cadena Sum Dir. Op.
Gerente Líder MIO
L. Procesos
J. Procesos
Gerente Líder MIO
L. Procesos
J. Procesos
Distribución Seguridad Calidad
Dentro de la metodología MIO, el indicador diario de trabajo (IDT) es un elemento cuya finalidad es indicar responsabilidad, pertenencia y monitoreo. Con el fin de dar seguimiento a resultados y actuar cuando un proceso tenga desviación.
El indicador diario de trabajo busca concientizar al equipo en que se tienen que enfocar, construyendo comportamientos y capacidades.
Cada IDT es establecido por el responsable de cada área y alcance para el cumplimiento estratégico de la compañía.
Productividad
Servicio
Inspección
Programa de Ruteo
Manejo de Defectos
Ausentismo
5S´ s
Conteo De Inventario
Operación CeDis/CDC
IDT
Alcance (ArtPlaza)
Asertividad WMAPE
Ausentismos y retardos (personal)
Distribución CeDis/CDC
Unidad
Producción/Surtido Bakeries
Calculo
# venta real / FCST 122
%
Cadena de suministro
Planeación de la demanda
Tipo de reunión Área
RDS, RDG
desviación absoluta de lo proyectado vs la venta real a nivel bajo RDS, RDG
# # Personal ausente , # Personal con retardo RDO, RDS
Calidad # # Hallazgos de fallas de proceso o producto deficiente RDS, RDG
Caducidad de inventario #
Camiones detenidos #
Center Line #
Cobertura de Plantilla
Consumo Plan IBP
Conteo de inventarios (cajas)
Control de Plaga
#
Monitoreo de fecha de caducidad de productos en inventario
# Camiones descompuestos, # Camiones accidentados, # Camiones en corralón, # Camiones en mantenimiento
RDG
RDS
Revisión de lista de pasos de Center line y reportar desviaciones RDS, RDG
# Vacantes disponibles, # Plantilla activa RDS, RDG
$ venta real / FCST IBP RDS, RDG
#
#
Créditos %
Desabasto de Materias Primas #
# Ubicaciones contadas vs Diferencia de conteo RDO, RDS
# Hallazgos en trampa para animales RDS, RDG
$ Créditos no cargados (7-11) /$ Venta diaria (uds 7-11) RDS, RDG
# De articulos de materia prima en desabasto RDS, RDG
Horas extra # # Horas extra laborales RDS, RDG
Operación CeDis/CDC
Distribución CeDis/CDC
Producción/Surtido Bakeries
IDT Unidad Calculo
Líneas Virtuales %
Manejo de defectos #
Mantenimiento preventivo (Camión/Camio neta) #
Cadena de suministro
$ Créditos no cargados (7-11) / $ Venta diaria ( uds 7-11)
Mantenimiento programado (camiones) vs Mantenimientos realizados (camiones)
Mantenimiento programado (camiones) vs Mantenimientos realizados (camiones)
Merma % $ Traspaso basura / $ Venta total diaria
Merma del producto %
Nivel de servicio consumidor %
Nivel de Servicio (Fill Rate) %
Ocupación de almacén %
Oportunidad de entrega (Pedidos) %
Paros no programados #
Plan Maestro de Limpieza %
Productividad (Bakeries) #
Productividad Cajas/Unidades (CEDIS/CDC) #
Programa de salida de rutas %
Volumen defectuoso (pza) / Volumen producido (pza)
Suma de negados ($) 7E + MD + Venta perdida MB /Suma de lo solicitado ($) 7E + MD + MB
Demanda entregada (pedidos) / Demanda solicitada (pedidos)
Espacios en tarima ocupados en almacén / Espacios en tarima disponibles en el almacén
[No enviados (pedidos) + devueltos (pedidos)] / (entrega total programada (pedidos)]
# De paros de producción no programados
% Cumplimiento de programa de limpieza
# Unidades producidas (día) / Horas laborales (día)
[Producción en Cajas o Unidades (día) / Horas trabajadas (día) / # Operadores (día)
# Rutas que salieron a tiempo / # Total de rutas (día)
Planeación de la demanda
Tipo de reunión Área
RDS
RDO, RDS
RDO, RDS
RDS, RDG, RDD
RDS, RDG
RDG, RDD
RDG, RDD
RDS
RDS, RDG, RDD
RDS, RDG
RDS, RDG
RDS, RDG
RDO,RDS, RDG, RDD
RDS, RDG, RDD
Operación CeDis/CDC
Distribución CeDis/CDC
Producción/Surtido Bakeries
IDT Unidad Calculo
Recibo de viajes #
Recuperación de excepciones Hr
Cadena de suministro
# Pedidos salida a distribución (info CeMSe) / Pedidos devueltos
Tiempo de recuperación de papeles de excepciones
Registro de accidentes # # Accidentes reportados
Rendimiento de combustible (Camión)
Km/L
Rutina de inspección y limpieza #
Rutina de Inspección y lubricación #
Salud de los equipos
Salud de los equipos (Montacargas / Patines)
Seguimiento a camiones
#
#
Kilómetros recorridos/Litros usados
Rutina de inspección y limpieza realizado vs Rutina de inspección y limpieza no realizado
Rutina de inspección y lubricación realizado vs Rutina de inspección y lubricación no realizado
# Camiones fuera de operación vs # Camiones totales en funcionamiento
# Montacargas fuera de operación, # Patines fuera de operación
#
Unidades averiadas en ruta #
Planeación de la demanda
Tipo de reunión Área
RDS, RDG
RDS
RDO, RDS, RDG, RDD
RDS, RDG
RDS
RDS
RDS, RDG
RDS, RDG
# Camiones con procedimiento correctivo, # Camiones con procedimiento preventivo RDS
Unidades averiadas en ruta vs Limite de unidades averiadas
RDS
Venta negada % Venta negada de proveedor / Total venta negada RDS, RDG
Venta perdida $ Producto solicitado – Producto enviado RDS, RDG
Venta Sellout
$ Venta de tienda a consumidor RDS, RDG
En la metodología MIO, los tableros desempeñan un papel crucial al integrar dos herramientas fundamentales: los IDT (Indicadores Diarios Trabajos) y las Herramientas Causa Raíz. Estos tableros constituyen un componente esencial que impulsa la eficacia del proceso al proporcionar un enfoque visual y estructurado para la aplicación de estas herramientas.
Existen dos tipos de tableros en la metodología:
Tablero de Staff/Gerencia (Operación y Distribución)
Tablero de proceso (Operación y Distribución)
Integran IDT y herramientas causa raíz
Incluyen planes de acción a corto y mediano plazo
Ayudan a la visualización de datos
Nos muestran objetivos y resultados
En los tableros de proceso (Operación y Distribución) se ven principalmente los indicadores de productividad, defectos y seguridad. Estos indicadores nos permiten tener una visión de la eficiencia en la parte operativa y de distribución. Además de incluir dentro de los tableros planes de acción a corto y mediano plazo.
Nombre: nombre del colaborador que aporta al proceso
Resultados: Resultado obtenido de IDT (Rojo en fuera de meta, verde dentro de la meta)
Objetivo: es la meta de productividad que se espera por parte del colaborador
Hallazgos: defectos o peligros encontrados en el proceso o área de trabajo
Acciones: las acciones para corregir el defecto
Estatus: Nos indica la situación del defecto, si ya fue solucionado o sigue en proceso de resolver.
Check List: Hace un análisis con información de lo que compone el hallazgo enumerándolo.
En los tableros de Staff/Gerencia, se exhiben todos los IDT del área de operaciones/distribución, ofreciendo una visión más amplia del alcance del área. Los encargados de gestionar estos indicadores son supervisores y jefaturas, mismos que asumen la responsabilidad de implementar acciones pertinentes con el fin de alcanzar las metas y objetivos establecidos por la gerencia regional y la dirección.
IDT: Indicador de trabajo a medir
Área: Área en donde ocurre la metodología MIO
Resultado: Resultado obtenido de IDT (Rojo en fuera de meta, verde dentro de la meta)
Métrica: Especificación de medida de IDT
Resp: Persona responsable de realizar el plan de acción
Plan de acción del día: Acción correctiva para resolver en el mismo día y mantener el IDT dentro de la meta. Utilizando previamente una herramienta Causa Raíz.
Plan de acción mediano plazo: Acción correctiva para resolver a mediano plazo y seguir manteniendo el IDT dentro de la meta. Utilizando previamente una herramienta Causa Raíz.
Las herramientas causa raíz son una parte muy importante de la metodología MIO, estas nos permiten encontrar el problema principal que afecta la operación. Al descubrir la causa raíz, podemos desarrollar un plan de acción pertinente para abordar la problemática y adoptar mejores prácticas. Entre las herramientas empleadas en esta metodología, se incluyen:
Gemba Walk SIPOC ES/NO ES Diagrama causa y efecto 5 ¿por qué? 5W+2H DMAIC
Definir
Medir
Analizar
Gemba Walk SIPOC ES / NO ES
SIPOC Diagrama de Flujo
Diagrama Causa-Efecto
5 Por qués ES / NO ES
Implementar la mejora 5W + 2H
Controlar
IDT´s
Se identifica y define la oportunidad de mejora
Se establece el estado inicial del proceso
Se determina la causa raíz
Se establecen actividades que permitan mantener los resultados
Se establecen actividades que permitan mantener los resultados
El Gemba Walk es una herramienta que consiste en realizar un recorrido por el lugar de trabajo cuyo fin es observar e identificar tareas con oportunidad de mejorar productividad.
7 pasos para preparar el recorrido Gemba
1
Escoge un tema
2
Compartir experiencias
2
Recopilar información
2
Guarda las observaciones
2
Prepara un equipo
3
Observar el proceso, no la persona
2
Identificar el flujo de valor
Realiza un Gemba Walk por el almacén para encontrar áreas de oportunidad para mejorar productividad.
7 pasos:
1. Elección del tema: Encontrar Defectos en almacén.
2. Equipo: Líder de proceso, Supervisor, jefe de almacén.
3. Área por observar: Proceso de unidades 7 eleven.
4. Identificación del Flujo de valor: Proceso de surtido de pedido.
5. Documentar Observaciones: Audio fallaba al momento de operación.
6. Preparar reporte para realizar plan de acción resolver el defecto encontrado.
7. Compartir resultados en RMD.
La herramienta SIPOC se utiliza para identificar y visualizar los elementos y actividades de un proceso, así como conocer la forma en la que están interconectadas en las áreas.
El acrónimo SIPOC refiere a Suppliers (proveedores), Inputs (entradas), Process (proceso), Outputs (salidas) y Customers (clientes). S I P O C
¿Qué insumos necesitamos?
¿Quién suministra lo que se necesita para ejecutar el proceso?
¿Qué hace el proceso?
1
¿Cuál es el resultado esperado del proceso?
¿Qué clientes necesitan la salida del proceso?
Realiza un diagrama SIPOC de la empresa (MAS Bodega) para identificar las entradas de materiales de proveedores.
S I P O C
PROVEEDORES ENTRADAS PROCESOS SALIDAS CLIENTES
Pepsico
Papitas, refrescos, galletas
Pallets con producto solicitado 7 eleven
BAT Cigarros Mercadia
Essity
Papel de baño, servilletas
Mayoreo
P&G Shampoo, jabón Detalle
Servidespensa
Recibo y almacenaje de producto
Alerta de pedido solicitado
Recolecció de producto solicitado
Verificación de productos del pedido
Esta herramienta consiste en hacerse preguntas como "¿Qué es?" y "¿Qué no es?", de modo que se logre delimitar el problema o aclare la situación, lo que facilita el proceso de identificación de las causas.
En otras palabras, la matriz “Es / No Es” nos sirve para determinar con precisión que es un problema y que no lo es.
Esta matriz consiste en descubrir en todas sus dimensiones respondiendo a las preguntas:
¿QUÉ?
¿DÓNDE?
• Qué objeto presenta el problema
• Qué problema exhibe el objeto
¿CUÁNDO?
• Dónde geográficamente se presenta el problema
• Dónde en el objeto se presenta el problema
¿CUÁNTO?
• Cuándo se observó el inicio del problema
• Con qué frecuencia se observa el problema
• Cuándo en el ciclo de vida (del producto) se observa el problema
• En qué momento de la actividad se observa el problema
• Cuántos ítems tiene el problema
• Qué tan grande en extensión es el problema
• Qué proporción de los ítems presentan el problema
• Cuál es la tendencia del problema
En una empresa hace 3 días se detectó fuga de aceite en la válvula de limpieza del filtro 1 ubicado en la esquina noreste de planta de filtrado.
¿QUÉ?
¿DÓNDE?
¿CUÁNDO?
Objeto Filtro 1
Filtro 2-5
Defecto Fuga de aceite -
Geográficamente Esquina noreste Resto de la planta En el objeto Válvula de limpieza Otras válvulas, tuberías y cerrojos
Inicio Hace 3 días Antes de 3 días
Frecuencia Continuamente Esporádicamente
un idades/Objetos
¿CUÁNTO?
Sólo filtro 1 Otros filtros
Extensión 20—40 litros/turno
Tendencia
Estable
Diferente de 20 40 lt/turno
Aumenta / Disminuye
El diagrama de causa y efecto, también conocido como diagrama de Ishikawa o de espina de pescado, es una herramienta visual que ayuda a identificar y entender las posibles causas de un problema específico. Representa el problema (efecto) en el extremo derecho y las categorías de posibles causas se ramifican desde él, básicamente representan la relación entre un efecto (problema) y todas las posibles causas que lo ocasionan.
Para la elaboración del diagrama se consideran 6 factores críticos que nos ayudan a encontrar la causa raíz del problema, estos son:
• Maquinaria
• Método
Medición • Mano de obra
Materiales
Medio ambiente
Aspectos vinculados con personas, personal y organizaciones Ejemplo:
• ¿Las personas están capacitadas?
• ¿Tienen conocimientos adecuados?
• ¿Hay variación de persona a persona?
• ¿Las personas tienen exceso de trabajo?
Causas relacionadas a como se realiza el trabajo o actividad Ejemplo:
• ¿Los procedimientos son correctos?
• ¿Cómo se realiza la operación?
• ¿Qué podría ser inusual?
Aspectos vinculados con la medición de proceso o resultado
Ejemplo:
• ¿Las basculas están calibradas?
• ¿La información es buena?
• ¿Los datos están disponibles?
• ¿El sistema de medición es válido?
Medio Ambiente
Aspectos vinculados al ambiente de trabajo, condiciones del mercado y cuestiones reglamentarias
Ejemplo:
• ¿El lugar de trabajo es seguro y cómodo?
• ¿Existe control de plagas?
• ¿Las regulaciones tienen impacto en el negocio?
Causas relacionadas a partes, suministros , formularios e información para ejecutar un proceso Ejemplo:
• ¿Las partes o suministros son obsoletos?
• ¿El producto venia en buen estado?
Aspectos vinculados con herramientas utilizadas en el proceso Ejemplo:
• ¿Las máquinas han sido reparadas eficientemente?
• ¿Cuál es el tiempo de actividad?
• ¿las herramientas han recibido mantenimiento adecuado?
El primer paso es identificar el problema, especificando el estándar o parámetro que se desvió. Por ejemplo, si hay una disminución en la producción debido a fallas en los equipos, se debe describir la magnitud de la desviación. Además, es esencial determinar cuándo y dónde ocurrió el problema.
Luego es importante, a través de un equipo multidisciplinario proponer posibles causas al problema.
Una técnica utilizada es que con ayuda de post-it o una pizarra, cada integrante del equipo identifique 3 causas.
Una vez listadas todas las Causas, se deberán agrupar causas repetidas (si las hubiese) y clasificarlas en la categoría de las 6M que corresponda: (máquinas, personas, métodos, materiales etc..) dentro del diagrama; se deben mantener las causas detallando claramente con datos y/o.
En esta etapa se priorizarán y resaltarán las causas probables. Después de clasificarlas, el equipo debe analizar cuáles descartar y cuáles mantener, enfocándose en destacar las causas más probables. Para una toma de decisiones basada en datos, se debe anotar información específica como: #registros de fallas, periodos de mantenimiento, registros de capacitaciones, etc.
Una vez identificadas las causas posibles a través del diagrama de causa efecto, se procede a abordarlas de manera más específica mediante la aplicación de la técnica de los "5 por qué".
Supongamos que trabajamos en un centro de distribución de Mas Bodega que arman tarimas con producto solicitado por tiendas 7 eleven. Existe un turno que desde hace un tiempo está teniendo menos producción. En concreto se puede establecer como problema “El turno A, durante el mes de agosto tuvo 9% menos producción que el Plan Operativo”.
Para lo cual se cita al equipo de lideres de proceso, operadores y las personas de recursos humanos para discutir posibles causas, a partir de lo
Causa Posible
Los "5 por qué" es una herramienta que consiste en preguntar sucesivamente "por qué" cinco veces para identificar y profundizar en las causas de un problema, con el objetivo de llegar a la causa raíz. Esta metodología se apoya en el diagrama causa-efecto para obtener las causas, las cuales pueden ramificar. El analista debe recopilar evidencia para determinar la dirección de la causa raíz.
Una vez identificadas las causas posibles a través del diagrama de causa efecto, se procede a abordarlas de manera más específica mediante la aplicación de la técnica de los "5 por qué".
A partir del problema identificado en el diagrama de causa y efecto, se inicia el proceso formulando la primera pregunta: "¿Por qué ocurrió el problema?" Luego, se registra la respuesta. Posteriormente, se continúa el proceso con la siguiente pregunta: "¿Por qué ocurrió esa respuesta?" y se anota la respuesta asociada. Este proceso se repite de hasta completar cinco iteraciones.
En cada nivel de "por qué", se deben reunir evidencia (registros históricos, registros de mantenimiento, bitácoras, etc.,) que respalden o refuten las posibles ideas, de manera que se hace un análisis con ideas que parecen ir en la dirección correcta.
La efectividad de los 5 porqués se comprueba cuando la solución aborda cada nivel de causas identificado en el proceso. Si resuelve las razones detrás de cada "por qué", es probable que se haya identificado la causa raíz del problema. Además, es crucial atender las causas que no llegaron al quinto por qué, ya que su resolución es esencial para mejorar la eficiencia operativa.
Enfocándonos en la causa raíz obtenida de los 5 porques procedemos a utilizar la herramienta 5w+2H para la creación de un plan de acción que nos ayude a solucionar la causa raíz del problema.
En base al ejemplo de la anterior herramienta causa raíz “diagrama causa efecto”, acerca del problema de baja producción en el turno A, realiza un 5 ¿por qué? sobre las posibles causas seleccionadas.
Nivel del problema
Problema
1er Porqué
2do Porqué
3er Porqué
4to Porqué
5to Porqué
Causa Potencial
Descripción
Turno A durante el mes de Agosto tuvo 9% menos producción que Plan Operativo
Nivel correspondiente de la solución
Falta de 15 Equipos Handheld en el área de surtido Comprar Handheld Faltantes
Porque las Handheld presentaron daños lo que no permitía su funcionamiento correcto
Porque los operadores no operan con el cuidado adecuado para la operación.
No se les ha dado una capacitación ni instrucciones de trabajo para el uso de Handheld
Por el desconocimiento del supervisor sobre el manejo adecuado de la herramienta
Reparación y mantenimiento a los equipos.
Comprar equipo de protección en las Handheld para evitar daños
Elaborar un manual para el uso correcto de la herramienta
Capacitación al supervisor por parte del proveedor para el uso y cuidado de la herramienta.
Nivel del problema
Descripción
Problema Turno A durante el mes de Agosto tuvo 9% menos producción que Plan Operativo
1er Porqué
2do Porqué
3er Porqué
50 % del personal tiene poca experiencia en turno A
Porque hubo mala administración del personal por parte del supervisor
Porque el personal en ese periodo de tiempo tuvo una alta rotación
Causa Posible
Nivel correspondiente de la solución
Asignar personal con más experiencia en el área
Equilibrio de experiencia a trabajar en las distintas áreas de la bodega
Incentivos para lograr permanencia del personal en temporada de alta demanda
Nivel del problema
Descripción
Problema Turno A durante el mes de Agosto tuvo 9% menos producción que Plan Operativo
1er Porqué
2do Porqué
3er Porqué
Faltante de estándares en operación
Por la falta de mapeo de procesos por parte de los lideres de procesos
Por la falta de IDT para medir los procesos correctos de cada área de la operación
Nivel correspondiente de la solución
Asignar a un supervisor a documentar las actividades de sus procesos
Realización de un manual sobre cómo se debe realizar cada actividad y que proceso seguir
Asignar en Reuniones de Desempeño un indicador de realización de revisión de procesos y documentación
El modelo 5W2H se basa en responder siete preguntas clave para la propuesta de solucion realizada en los 5 porques. Las 5W, que corresponden a 'What' (qué), 'Why' (por qué), 'Where' (dónde), 'When' (cuándo) y 'Who' (quién), junto con las 2H, que representan 'How' (cómo) y 'How much' (cuánto), forman el acrónimo. Al realizar estas preguntas, se busca resolver la causa raíz del problema y encontrar soluciones efectivas.
What - Qué
Why — Por qué
Where — Dónde
When - Cuándo
Who - Quién
How - Cómo
How many /How much - Cuántos / Cuánto
¿Qué se debe de hacer? ¿Cuál es la accion de mejora a implementar?
¿Por qué se implementan dichas acciones? Razones que lo justifican
Tema
Razón
¿En dónde se va a implementar dicha mejora? Ubicación
¿En qué momento del día o del proceso se implementará? ¿Qué fecha se hara?
¿Quién es el responsable o los responsables de realizar esta mejora?
¿Cómo se va a implementar? ¿Cuáles son las actividades necesarias para realizarse?
¿Cuánto va a costar (Dinero, Tiempo, Recursos) la implementación ?
¿Desde cuándo se va a ejecutar y cuánto va a durar dicha propuesta?
Secuencia
Personas
Método
Cantidad
Tomando en cuenta el mismo problema utilizado en el diagrama Causa Efecto y 5 porque ´ s , se desarrolló un plan de acción con la herramienta 5W+2H.
What - Qué
Why — Por qué
Where — Dónde
When - Cuándo
Who - Quién
How - Cómo
How many /How much -
Cuántos / Cuánto
Capacitación al supervisor por parte del proveedor para el uso y cuidado de la herramienta Handheld
Por la baja de 9% de producción en el Turno A, lo que puede ocasionar faltantes en tiendas
Los cursos de capacitación se realizarán en la sala polivante a todos los supervisores que utilicen Handheld
Se realizarán el lunes de la próxima semana. (Fecha detonada por el proveedor)
El proveedor, mandara personal de capacitación y un manual para el uso de la herramienta.
Con 2 Sesiones de capacitación y un manual para todos lo supervisores y operadores que tengan uso con la herramienta.
La capacitación de la herramienta tiene costo 0 al estar incluido dentro el producto(Handheld) que compramos y se realizara una vez cada 3 meses para el personal de nuevo ingreso
DMAIC es una herramienta para la mejora continua en donde se tienen conceptos como definir, medir, analizar, mejorar y controlar. Realizando DMAIC obtienes como resultado recolección de información y veracidad de los datos como base de una mejora.
(Se requieren herramientas previamente vistas)
Define el problema (Gemba Walk, SIPOC)
Mantener controlado la mejora (IDT)
Implementación de mejora y verificación
Cuantifica el problema (SIPOC, 5S)
Analiza el problema (Diagrama CausaEfecto)
La salud MIO desempeña un papel crucial en nuestra metodología, ya que poseer una buena salud implica reuniones de alta calidad, un uso adecuado de tableros, una evaluación constante de los IDT (Indicadores Diarios de Trabajo) y la correcta aplicación de herramientas de análisis de causas raíz. Esta condición nos conduce a una mejora continua constante y nos permite adoptar mejores prácticas laborales.
Para medir la salud se diseñó un formato en el cual se evalúan los elementos importantes de la metodología. Este formato se utiliza dentro de la reunión de desempeño y es evaluado por los lideres de proceso (Operación y Distribución).
Salud de Reuniones de Desempeño
Fecha: Reunión: Evaluador:
1 Las reuniones comienzan a la hora programada
2 Todas las áreas tienen a su representante asistiendo diariamente
3 La pizarra está llena antes de comenzar la MIO
4 Se tienen causas probables antes de la MIO
5 Se diferencia con colores la pizarra
6 Cada IDT de la pizarra tiene un responsable asignado
7 Se le da seguimiento a los pendientes del día anterior
8 Los pendientes cierran en la fecha compromiso
9 La MIO fluye de manera adecuada
10 Se generan planes de acción cuando un IDT está en rojo
11 Prestan los participantes la atención requerida
12 Las reuniones terminan a la hora programada
0 La MIO se lleva de manera puntual, todos los asistentes atienden a la hora especificada.
Se presentan todos los involucrados correspondientes a la junta MIO.
Verifica que toda la información esté actualizada al momento de comenzar la MIO.
No esperar que se genera lluvia de ideas durante la MIO, se hizo un análisis previo.
IDT fuera de meta, así como las actividades que NO se terminan en tiempo y forma deben estar en color rojo, los IDT dentro de meta en color Verde y los pendientes nuevos en negro o azul.
Debe estar asignado a un Supervisor, Líder de Línea, Líder de Procesos, Jefatura o Gerencia.
Se toca el tema rápidamente para que exista retroalimentación de parte del responsable de la actividad.
Asegurar que todas las actividades de concreten en la fecha asignada por el responsable, Si hay actividades vencidas de más de un día NO se cumple con este punto.
No se escalan cosas que no agregan valor a la MIO. Todos los participantes prestan atención. No se utiliza celular/laptop durante la reunión (en cosas que no tienen que ver con la MIO).
Monitorear que durante la reunión se agreguen actividades a la pizarra (con responsable asignado) y que NO sean ajenas al IDT que se está revisando
Los participantes no se enfocan en otras actividades que no tengan relación con la reunión MIO
La MIO se lleva de manera puntual, dura el tiempo indicado en la agenda.
Ausentismos y Retardos (Personal)
Medición de personal que no se presentó a laborar y personal con asistencia después de la hora establecida
Calidad
Medición del producto dentro de los estándares establecidos.
Camiones en detención
Es una Medición de unidades fuera de servicio (mantenimiento, corralón, etc).
Center Line
Medición para permanecer a un nivel estándar y avisar en cuanto aparezcan anomalías.
Cobertura de Plantilla
Medición de la cantidad de personal necesaria para el área de trabajo.
Conteo Inventario (Cajas)
Medición de inventario mediante el conteo de cajas y comparando diferencias con respecto al sistema.
Control de Plaga
Medición para mantener el lugar de trabajo limpio fuera de bacterias que pudiera llegar a tener algún animal.
Desabasto de Materias Primas
Medición de material para producir para evitar incumplir con el pedido.
Horas extra
Medición de trabajo extra por parte del personal
Inspección Inventario (Cajas)
Medición de numero de inspecciones realizadas en el día
Líneas Virtuales
Es un centro de costos de los canales en donde se cargan los créditos de rutas.
Créditos
Es el costo de un producto faltante de los pedidos ya enviados.
Manejo de defectos (Área)
Medición de características indeseables de un objeto, proceso o persona que suelen traer consecuencias negativas
Mantenimiento preventivo
Es el conjunto de actividades que tienen como propósito conservar o reactivar un equipo para que cumplan sus funciones
Merma
Es una pérdida o reducción de un cierto número de mercancías o la diferencia entre el contenido de los libros de inventario y la cantidad real de productos.
Nivel de Servicio (fill rate)
Medición para entender cuántos pedidos estamos entregados del total de todos
Oportunidad de entrega (Pedidos)
Medición para evaluar los pedidos que no se entregaron y realizar acciones para evitarlo
Paros no programados
Medición de veces que para la producción sin estar programado
Plan Maestro de Limpieza
Medición para evaluar el seguimiento del plan de limpieza del lugar de producción
Productividad (Cajas/Uds)
Es un indicador que define cuántos productos o servicios se han llegado a producir por cada uno de los recursos utilizados en su elaboración (mano de obra, tiempo y capital, etc) dentro de un lazo determinado
Programa de salidas de rutas
Medición para evaluar cuantas rutas están saliendo en tiempo
Recibo de Viajes
Es una Medición para evaluar los pedidos devueltos en comparación de los pedidos enviados.
Recuperación de excepciones
Tiempo en el que devuelven los papeles de excepciones.
Registro de accidentes
Es un suceso no planeado y no deseado que provoca un daño, lesión u otra incidencia negativa sobre un objeto o sujeto.
Rendimiento de Combustible (Camiones)
Medición de rendimiento de camión con el fin de ahorrar combustible.
Rutina de Inspección y Lubricación
Medición del número de veces que se realiza inspección y lubricación en las áreas de trabajo.
Salud de los equipos
Es un estado de bienestar o de equilibrio aplicado a procesos, estado físico entre otros
Seguimiento a camiones
Medición para evitar la falla y deterioro de unidades de transporte.
Unidades Averiadas en Ruta
Medición de unidades fuera de servicio durante una entrega de pedido.
Con el Modelo Integral de Operaciones como pilar fundamental hacia la mejora continua, y contando con tu entusiasta participación y contribución mediante propuestas innovadoras, alcanzaremos: