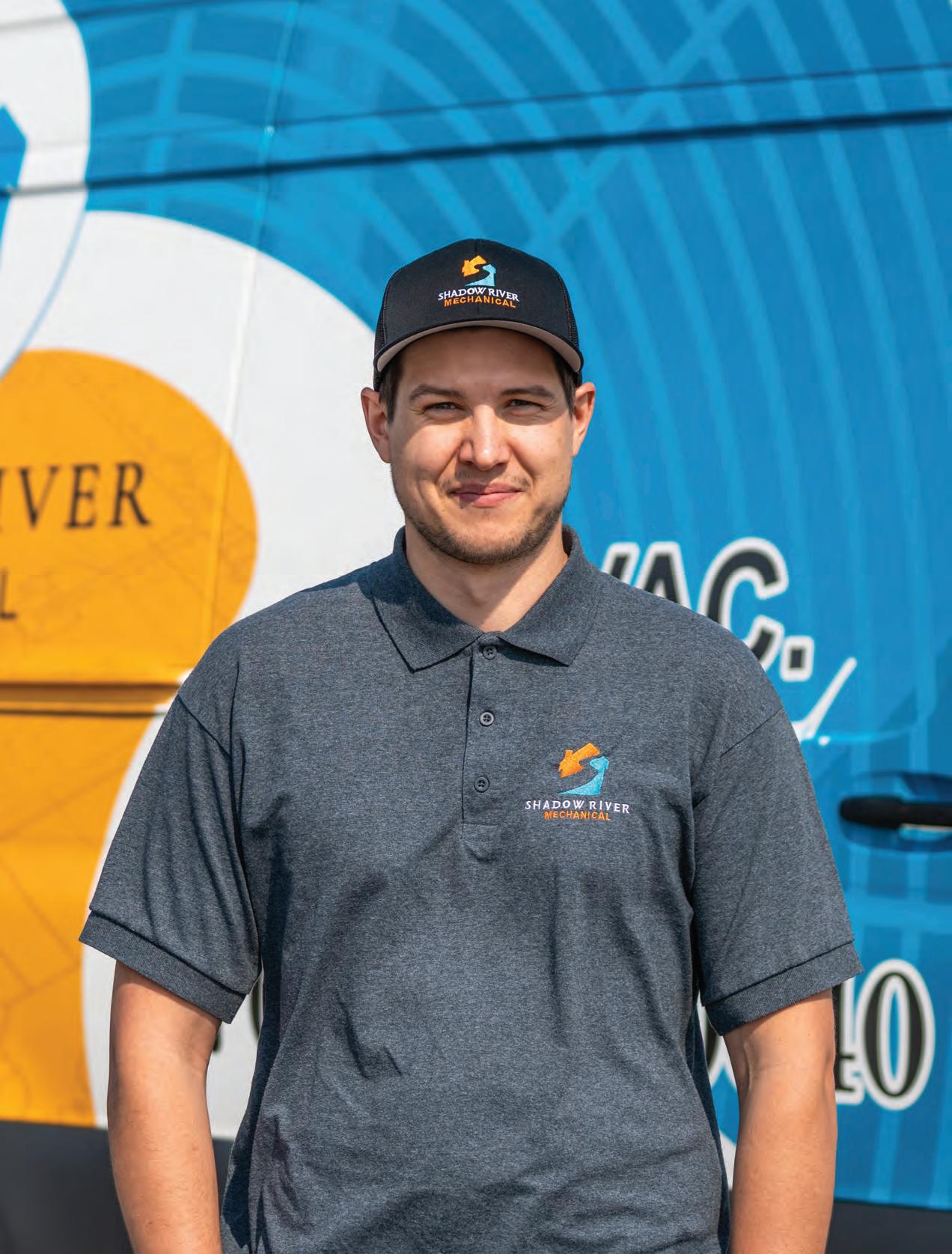
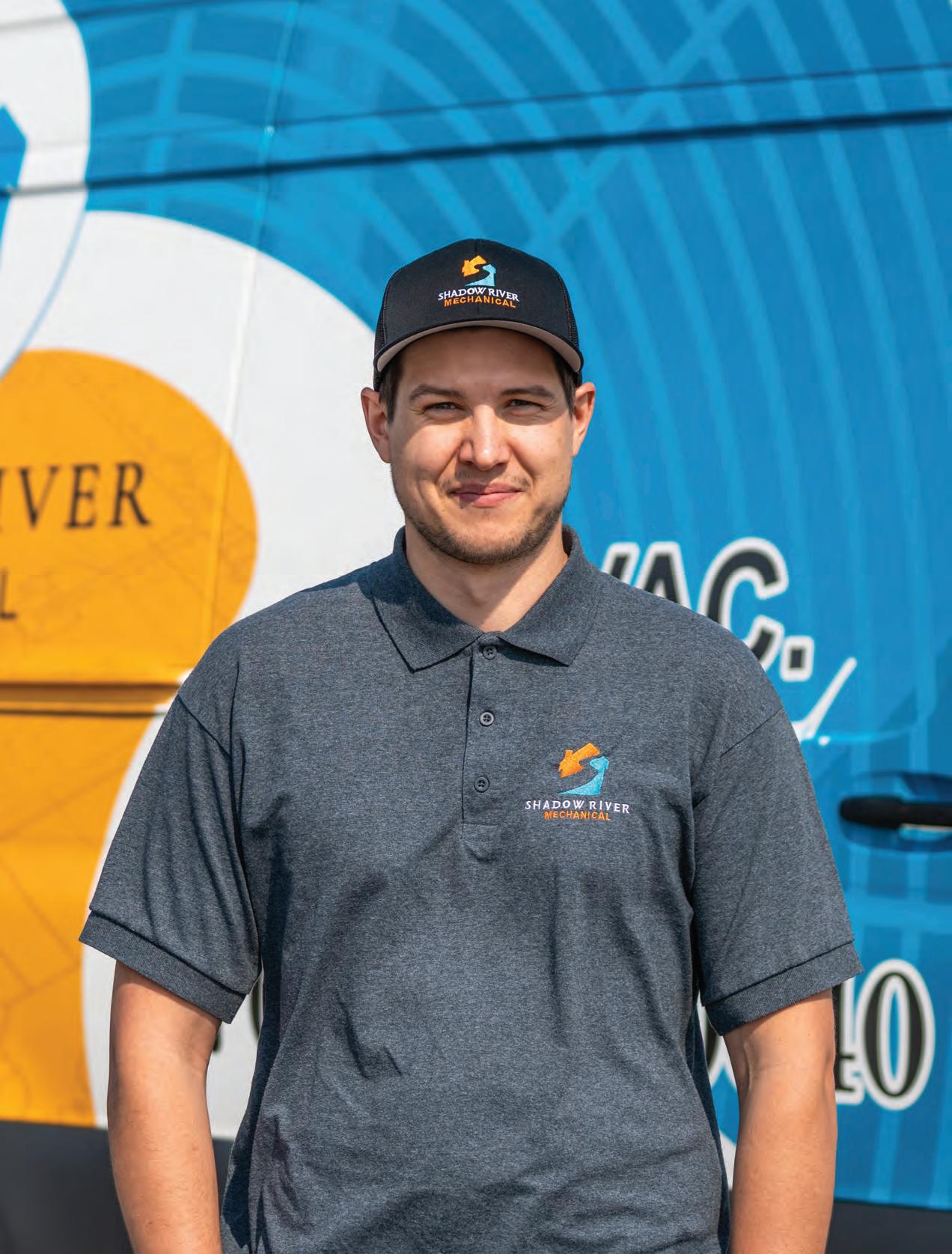
Commercial Condensing Boilers Built to Tackle It All
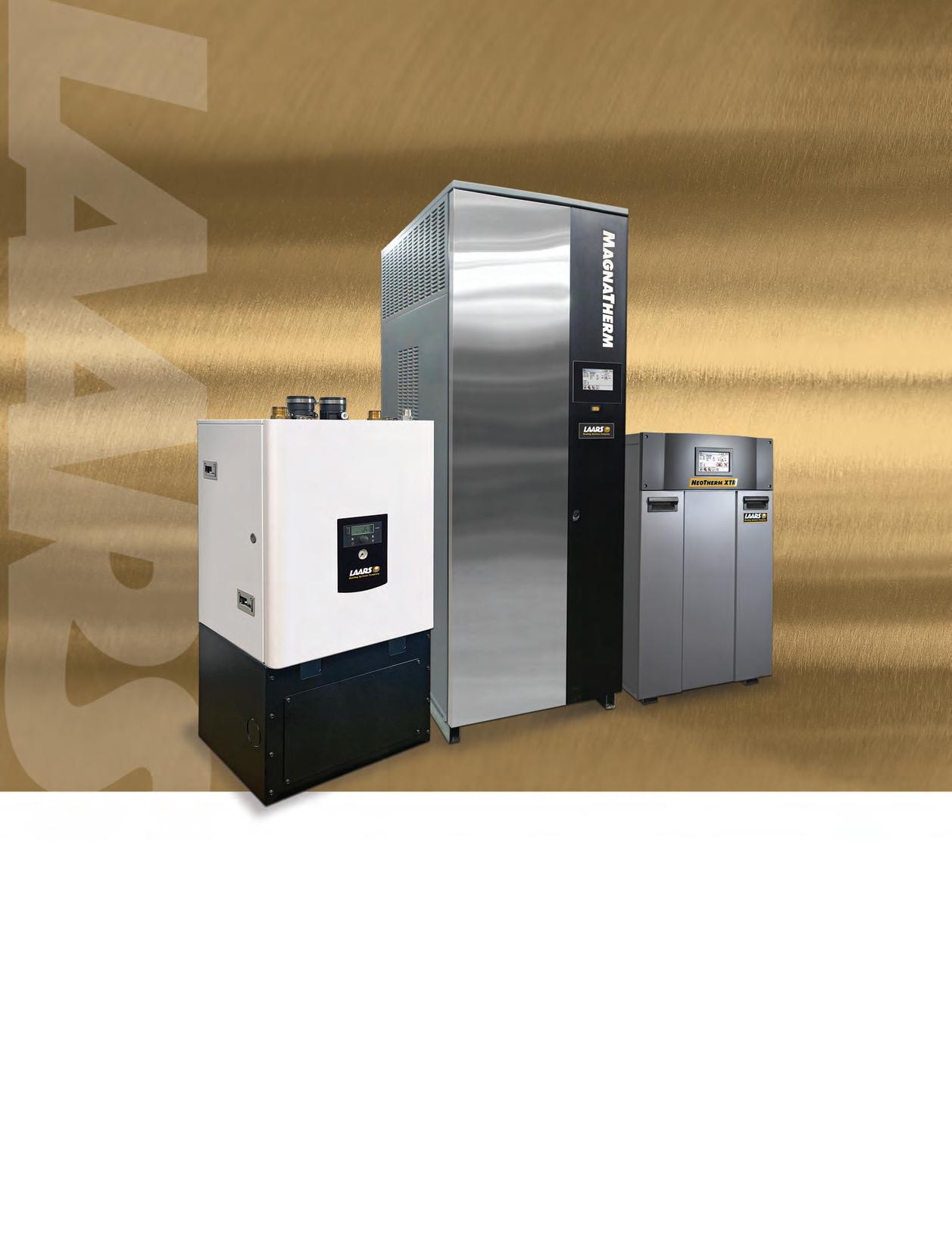
Finding the perfect fit your next commercial project is simpler with LAARS®. Our commercial condensing boilers deliver the high performance you need across a wide range of heating capacities.
• FT Series Commercial Boiler (301 or 399 MBH; 10:1 turndown) our newest commercial boiler converts from wall to floor with optional stand.
• MagnaTherm® (20:1 turndown; 95%+ thermal efficiency) industry-leading fire-tube or water-tube boiler technology including Tru Trac® real-time O2 trim and Laars Linc® intuitive touchscreen control.
• NeoTherm® XTR (399-1500 MBH; 10:1 turndown) our newest boiler and water heater – common vent for up to 8 units.

Discover our full line-up of
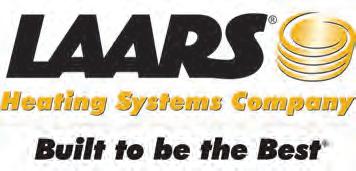
Content Media Group Inc. 2 Campbell Dr., Suite 807 Uxbridge, ON L9P 0A3
Tel: 905.465.2919 www.mechanicalbusiness.com
July/August 2025 Issue
Published 2 times per year.
For All Subscription Inquiries
Shila Naik Circulation Director 905-272-4175 shila.naik@mechanicalbusiness.com
Editor: Kerry Turner, C 416-435-1193 kerry.turner@mechanicalbusiness.com
National Sales Manager: Kyle Badder, C 416-735-1375 kyle.badder@mechanicalbusiness.com
Operations Manager: Caroline Bexfield, C 647-217-2076 caroline.bexfield@mechanicalbusiness.com
Contributing Editor: Carolyn Cooper editorial@mechanicalbusiness.com
Art Direction: Fourteen Orange Graphic Design Inc. davem@fourteenorange.com
Controller: Liz Mills liz.mills@mechanicalbusiness.com
Publisher: Bruce Meacock, C 416-457-9563 bruce.meacock@mechanicalbusiness.com
Get
Diagnosing sudden boiler
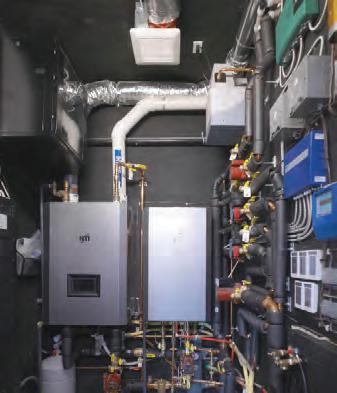
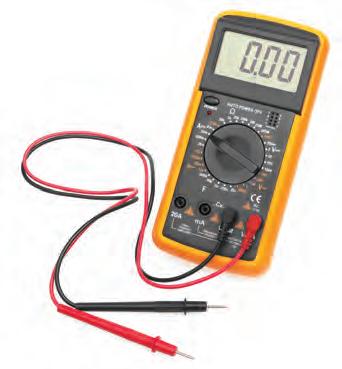
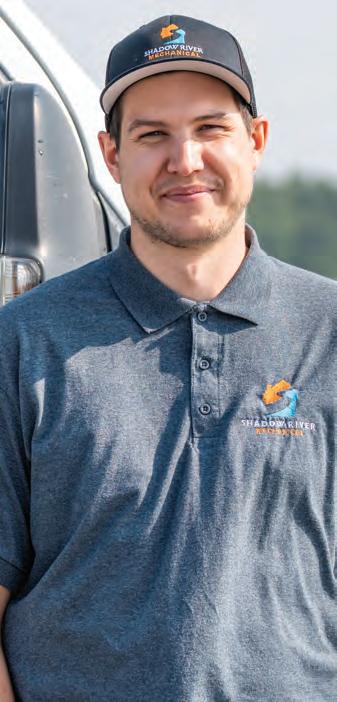
ROAD WARRIOR: SUCCESS ON THE NORTH SHORE
Variety is a way of life for Ben Duncan of Shadow River Mechanical in Ontario’s Muskoka region, where he undertakes everything from servicing isolated island homes, to installing custom systems in multimillion-dollar cottages.
Carolyn Cooper
SYSTEM PERFORMANCE
UNDER PRESSURE: THE HIDDEN FORCES INSIDE HYDRONIC SYSTEMS
To keep your pumps, boilers, and expansion tanks running smoothly, it helps to understand Boyle’s and Henry’s gas laws.
Todd Wiggins
DESIGN RULES TO LIVE
Explore the world of primary variable piping and maximize boiler efficiency.
Matthew Reid
A
Test
Contractor squeezes sophisticated system into tight-fitting mechanical room.
Thomas Renner
Photo: Aiden Rosewell,
CIRCULATORS
Get up to speed on moving fluid
In the hydronic world we move energy around via a fluid, which is mostly inside a pipe or tube. The goal is to move the required amount of fluid around a circuit to accomplish the heating, cooling, or DHW requirement.
Often, we start this process with a load calculation. The load calculation, either heating, cooling or DHW, defines how much energy we need to move through the piping. This basic calculation is important for both new construction projects as well as retrofits. This calculation provides a stable number around which we can design the entire system.
With the load number in hand, we can start the process of sizing pipe, valves and devices, and the heat emitter. In a closed loop system, hydronic or DHW, we also need a method to “move” or circulate the fluid around the circuit.
Pump, circulator or booster?
Many manufacturers create products to do this critical task. This component is called various names. Often it is called a pump; some prefer to call it a circulator. Early on when gravity piping systems were being converted to forced circulation, the device was known as a booster.
First, consider the job this device needs to perform. It needs to move a certain flow of fluid, typically called gallons per minute (GPM). We call this number the design flow rate. Several other pieces of information are needed to select the correct product. The type and temperature of the fluid needs to be identified.
Additionally, we need to know the resistance to flow the piping path presents. We use a term called “head” in the industry, defined as the mechanical energy contained in a fluid. As head is added to the circuit by the pump, circulator, or booster you can observe a change in pressure. Pressure gauges indicate this, like how a thermometer would measure an increase or decrease in temperature.
So, the next step is to select the pump, circulator or booster. Since the term booster has mostly disappeared from the industry, you have the choice of pump or circulator. My suggestion to avoid the naming argument between a pump or a circulator is to call it a circulator pump (CP).
Pump curve charts (just sayin’, that’s what they are called) are what we use to select the correct CP. Locate the flow rate GPM, on one axis, and the head on the other axis.
Manufacturers and their representatives can help you make the best selections of CPs.
By Bob “Hot Rod” Rohr
Bob Rohr is a trainer with Caleffi, and was the recipient of the 2020-2022 CarlsonHolohan Industry Award of Excellence. He has 40+ years of experience as a plumbing, radiant heat and renewable

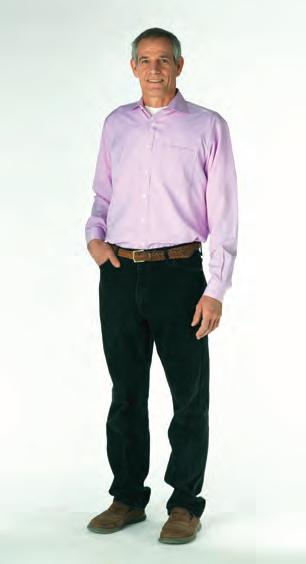
With the ECM’s energy efficient motor design power consumption has dropped by 50 per cent or more in most cases.
Improved technology
Over the years, like most electro-mechanical devices, the circulator pump has seen many changes and improvements. Perhaps one of the biggest changes was the introduction of the wet rotor design. In this type of CP, the motor is contained in the fluid.
Credit goes to Taco for the development of wet rotors around the late 1950s. The wet rotor design is the predominate type for hydronic, solar and DHW applications. Two- and three-piece designs are still common, particularly on the larger sizes. These are based on an air-cooled motor design.
Perhaps the next biggest improvement has been the advance of electronic motors. These are commonly called electronically commutated motors (ECM). This type of CP is sometimes referred to as a “smart pump.” An onboard microprocessor can adjust the operation, record data and provide digital readouts.
Another handy addition is Bluetooth technology. With this option, you can use an app to remotely adjust and monitor the CP operation. I enjoy the ability to “watch” and make fine tuning adjustments from my smart phone to optimize the performance and efficiency. We now have the ability to monitor customers’ systems and be alerted to a fail mode. Summer exercise function is also available right on the CP.
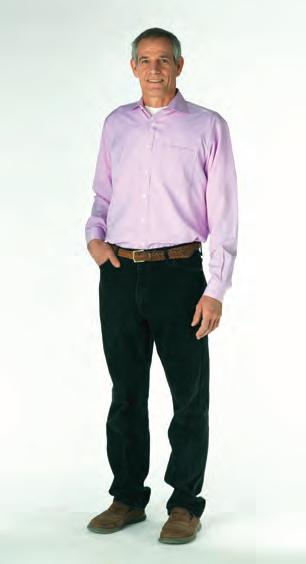
Suggestions, tips and tricks
Consider an isolation valve on both sides of the CP. Service and replacement is so much easier when you do not have to do a complete drain down. There are isolation valves available with swivel flanges and purge ports. The purge port can also be used to attach a pressure gauge for testing and balancing information. Protect the CP from contaminants. A Y-strainer may be adequate. However, with ECM type equipment I highly recommend a dirt separator with a magnetic function.
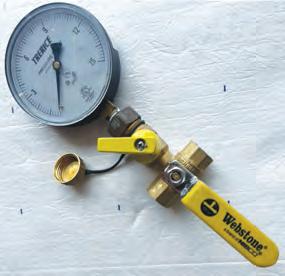
Test pressure gauge added to isolation valve at pump flange.
Avoid flow-restricting valves and devices immediately upstream of the CP.
A check valve should be used on the discharge side of the CP. Most of the current wet rotor designs come with internal checks (IC.) This is a handy feature. I like to see the checks 12 pipe diameters (12D) downstream of the discharge. Keeping the check away from the turbulent conditions at the discharge eliminates the flutter, vibration or rattling of the check valve. I have also witnessed the IC causing an air bubble to be trapped in the CP during an off season shut down. I would also suggest 12D upstream of the CP.
When installing multiple CPs on a system, consider a method of hydraulic separation. Assure the header piping is sized to supply adequate flow, in GPM, when all circulators are running at full capacity.
Use approved, non-ferrous CPs on open and potable water systems.
Of course, refer to the instruction manual regarding proper orientation. Always locate the expansion tank connection on the inlet side of the CP. The expansion tank establishes the point of no pressure change (PONPC) when you “pump away” from the expansion. Learn more about this in Dan Holohan’s book Pumping Away. Every installer, troubleshooter, and designer should read and understand this concept.
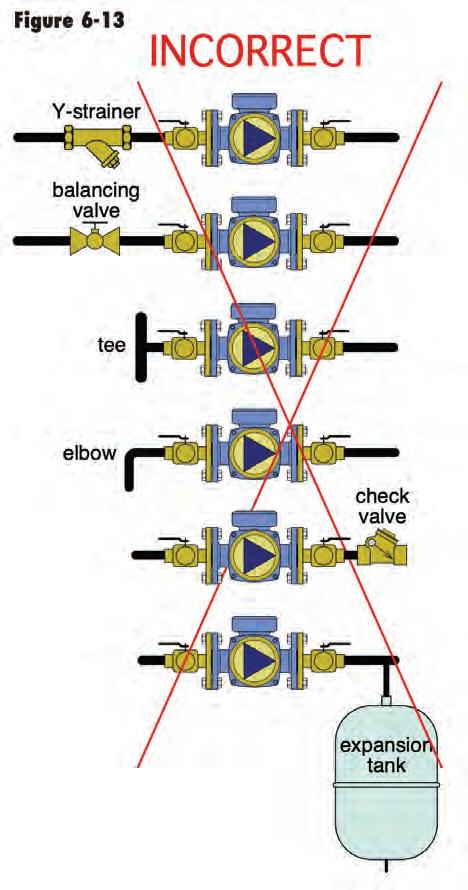
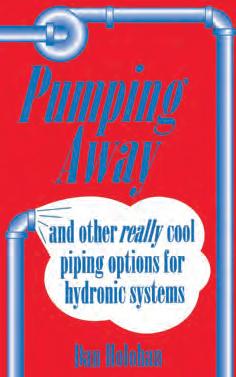
Finally, do yourself a favour and enroll in a CP (or booster or pump) training course, in person or online. So much has changed and improved recently in the circulation world. Make sure you are up to speed (or flow rate!)
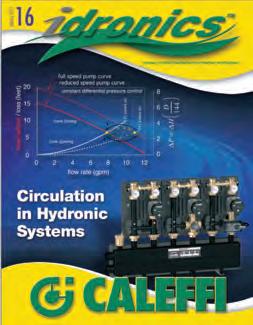
Resource
Check out this document at caleffi.com for all things circulator pump.
Never install Y-strainers near the inlet of circulators. As they accumulate debris, this type of strainer creates increasingly higher pressure drops.
Get your team together for a day of pure Canadian spirit at The Princess Margaret Road Hockey to Conquer Cancer, fuelled by Longo’s - the world’s largest road hockey fundraiser.
Join over 1,500 players and 150+ teams, alongside NHL and PWHL stars like Wendel Clark, Blayre Turnbull, Jeremy Roenick, Darcy Tucker, Erica Howe, and Renata Fast for a day of hockey, music, and community. Draft Night kicks off on September 26, with game day on September 27.
Every dollar raised supports life-saving cancer research at Princess Margaret Cancer Centre, helping drive early detection and breakthrough treatments for patients across Canada.
Lace up. Step up. Let’s face off against cancer together.
Join or donate today: www.roadhockeytoconquercancer.ca
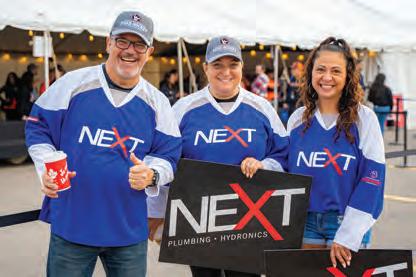
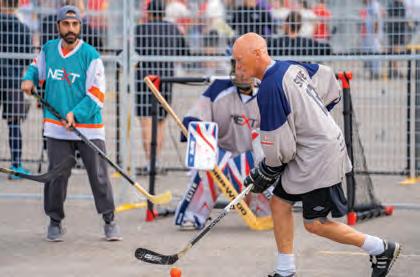
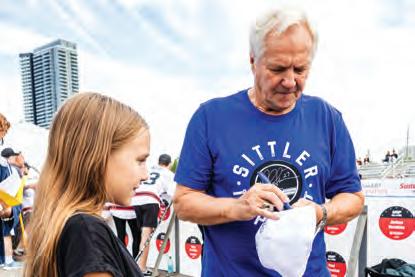
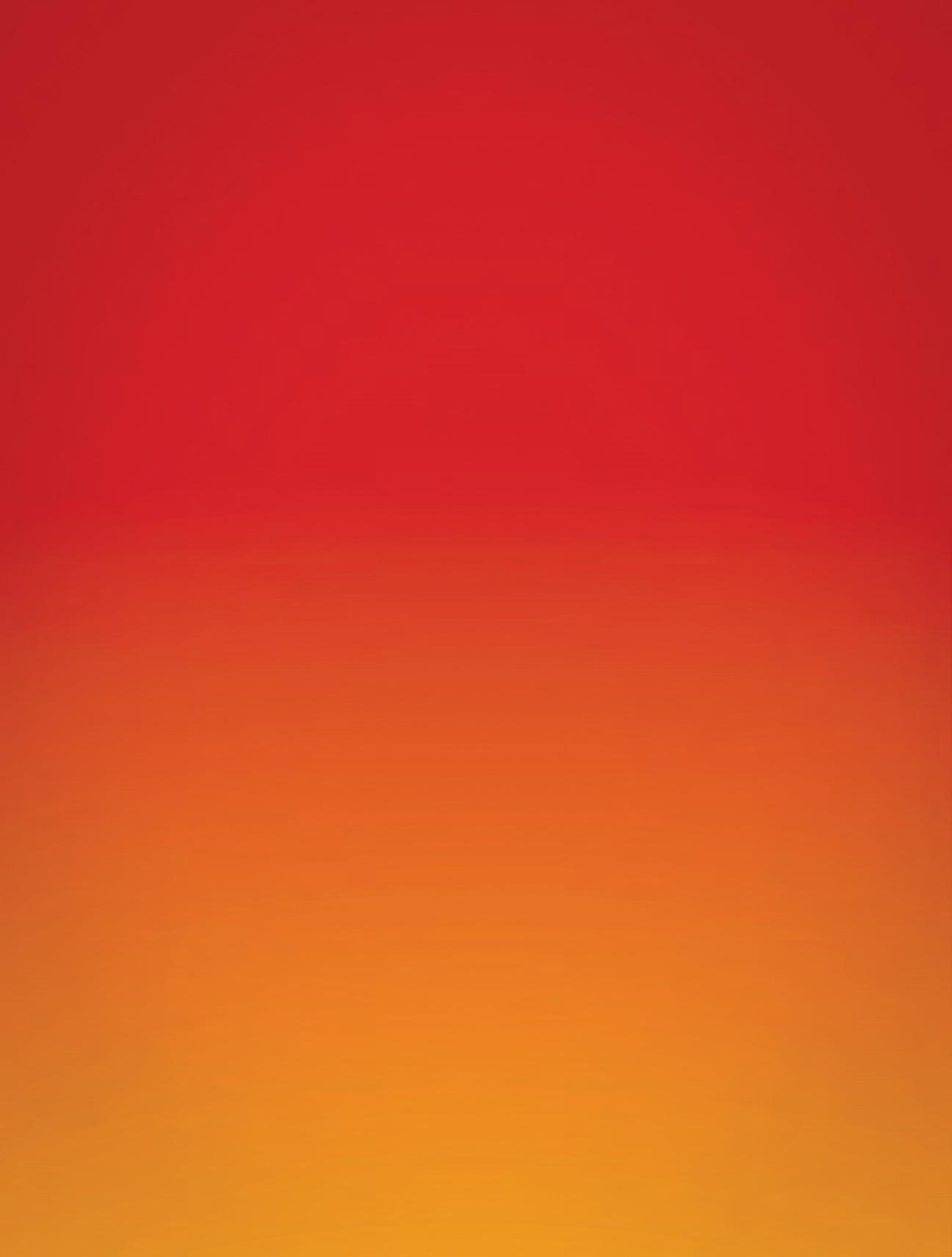
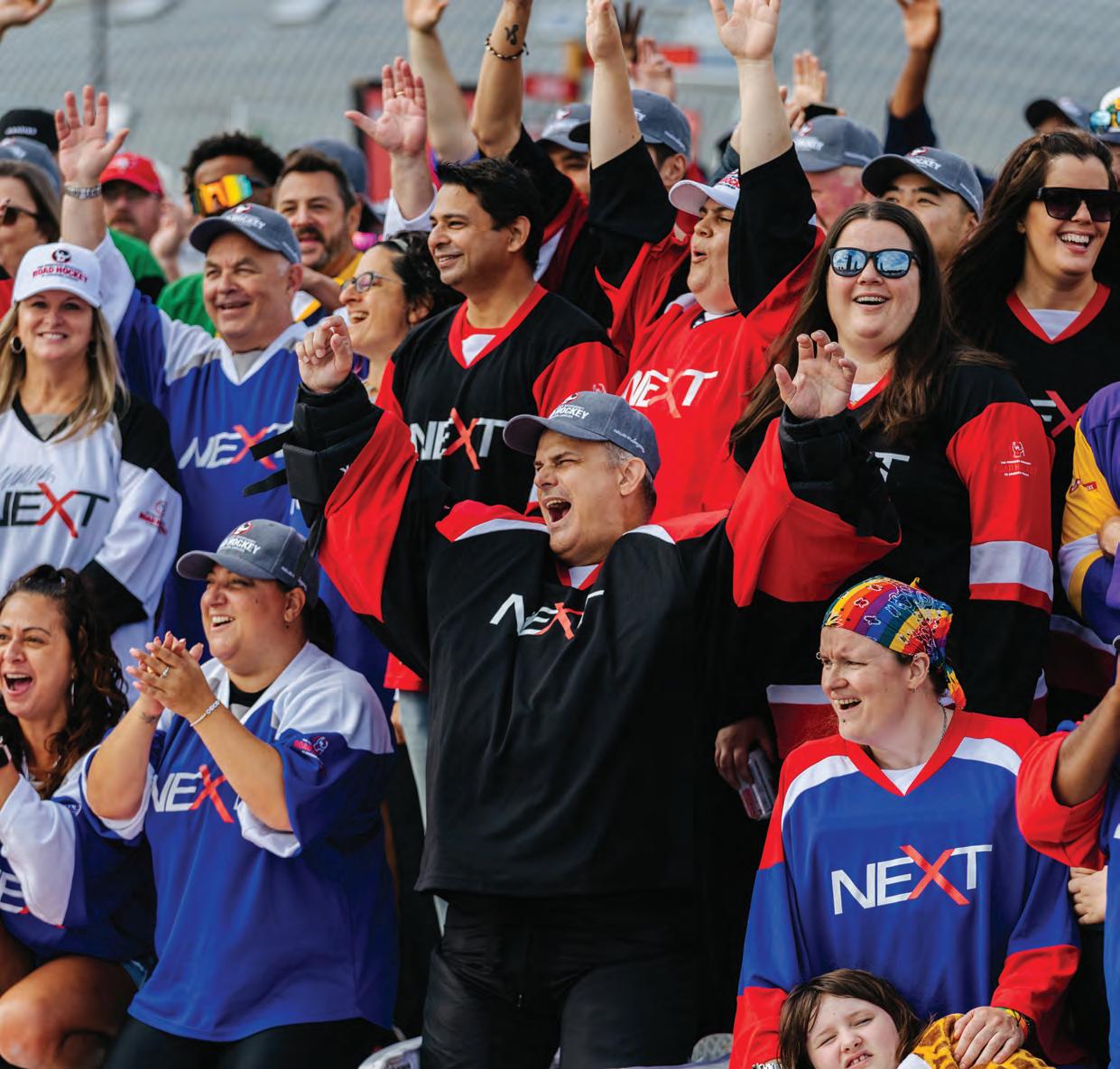
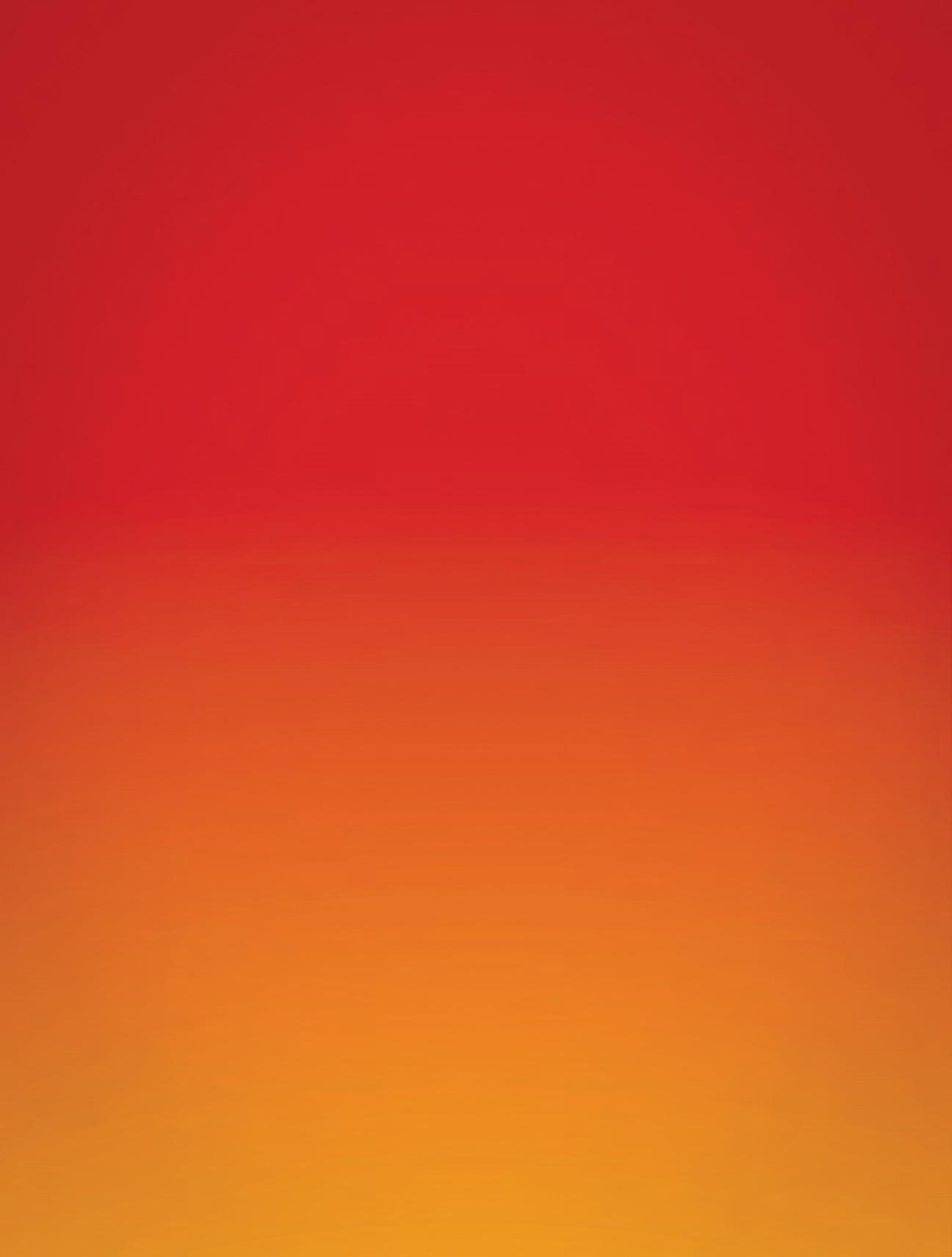
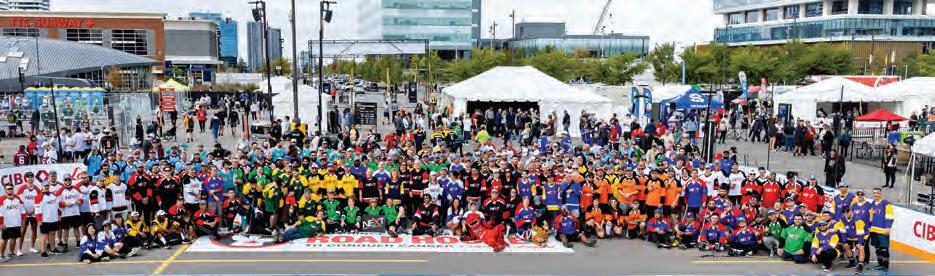

SUPPORT GAME-CHANGING CANCER RESEARCH WITH NEXT
Cancer demands a united front. That’s why we’re rallying every donor, every player, and every company team to join us at Road Hockey to Conquer Cancer, fuelled by Longo’s.
Every winning team needs a captain, and we’re excited to have Michael Storfer, CEO of Next Plumbing & Hydronics Supply, leading the charge as our Honorary Chair this year. And to the entire Next Supply team, your support has been unmatched, raising over $2.25 million since 2018 for Princess Margaret Cancer Centre. With over 25 teams hitting the pavement last year, this is the kind of teamwork that fuels crucial research, groundbreaking discoveries, and treatment at one of the world’s leading cancer centres, helping us change lives.
Now, it’s your turn to make a difference. Assemble your company team, challenge your rivals, and bring your best. Every dollar raised will support early detection, innovative treatments, and comprehensive support so that we can create a world free from the fear of cancer. Together, we’ll show cancer the power of our spirit and passion. Thank you for helping us Carry The Fire.
Join NEXT in the world’s largest road hockey fundraiser. Email roadhockey@thepmcf.ca
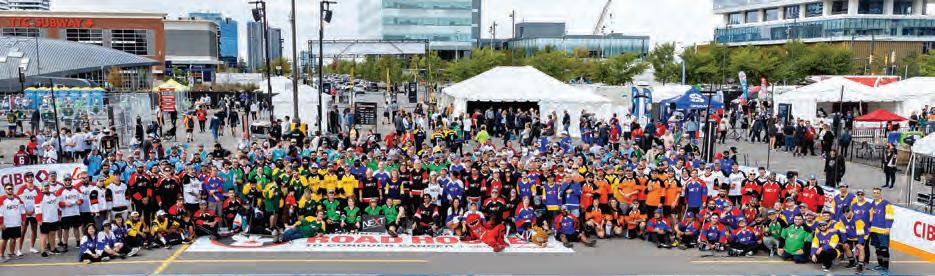
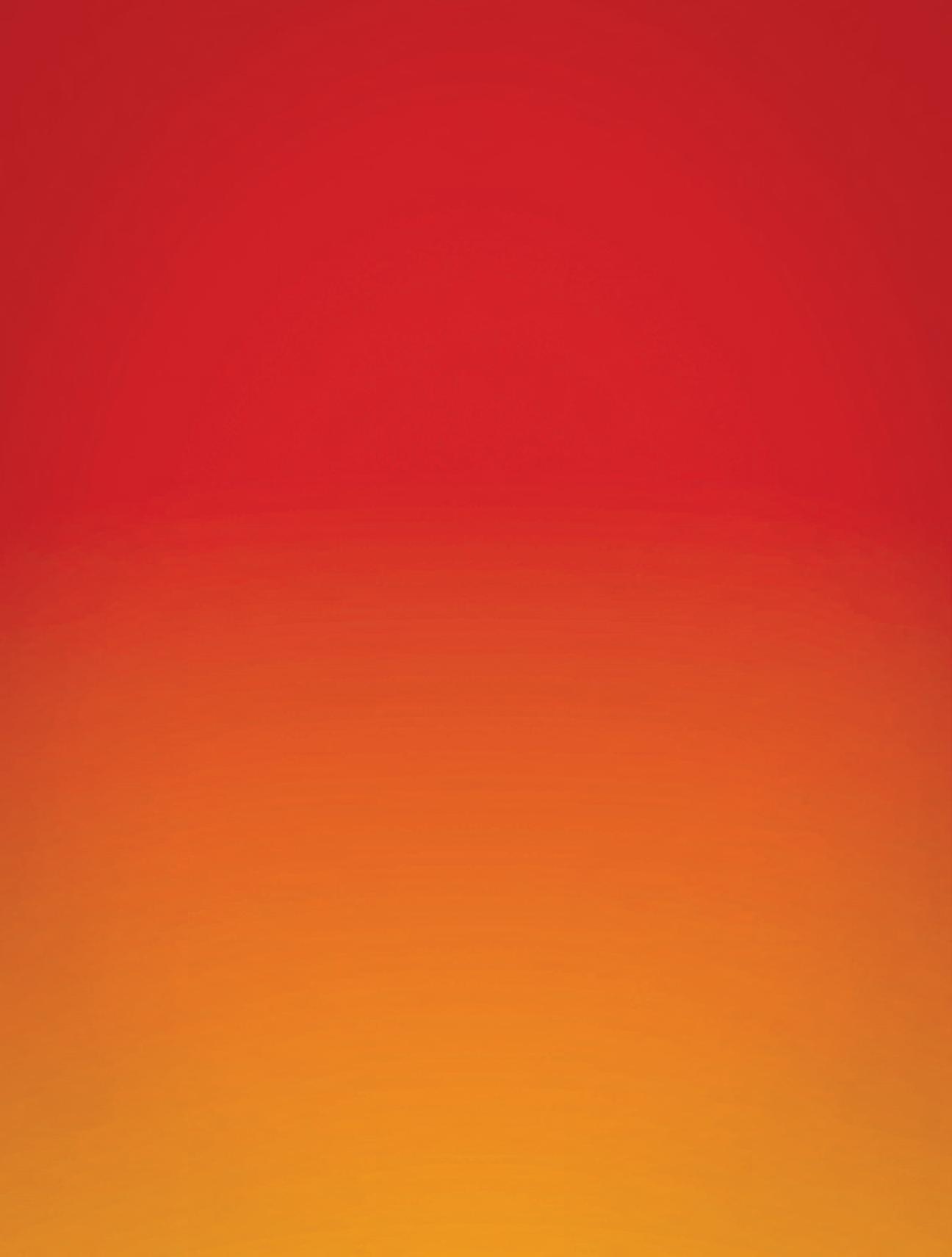
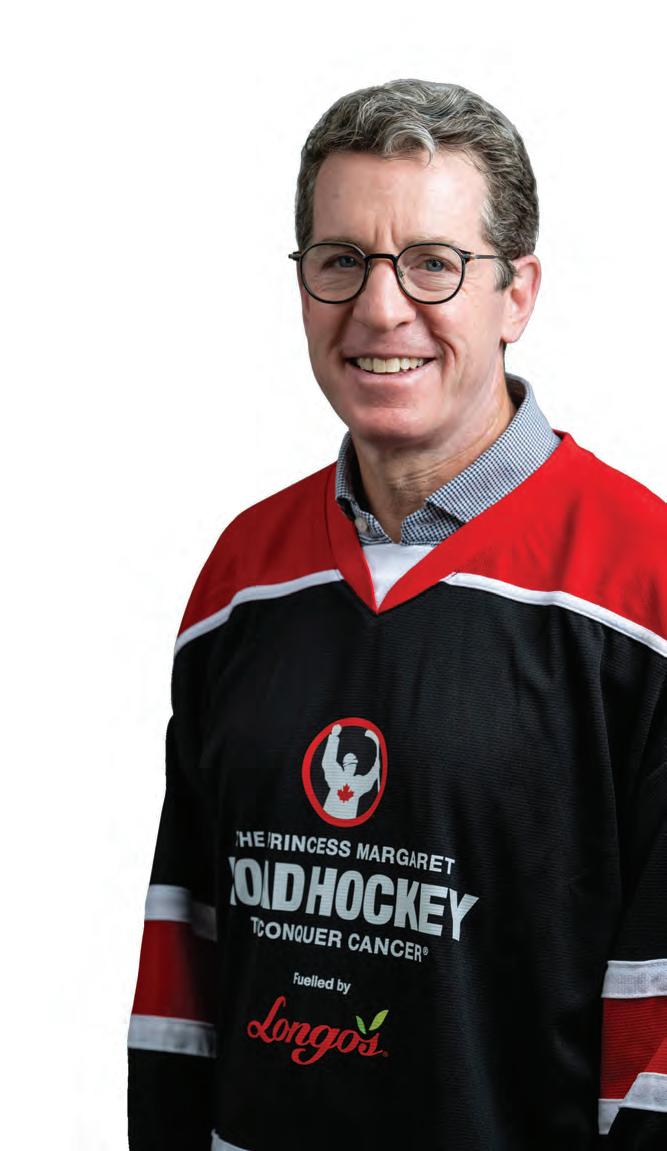
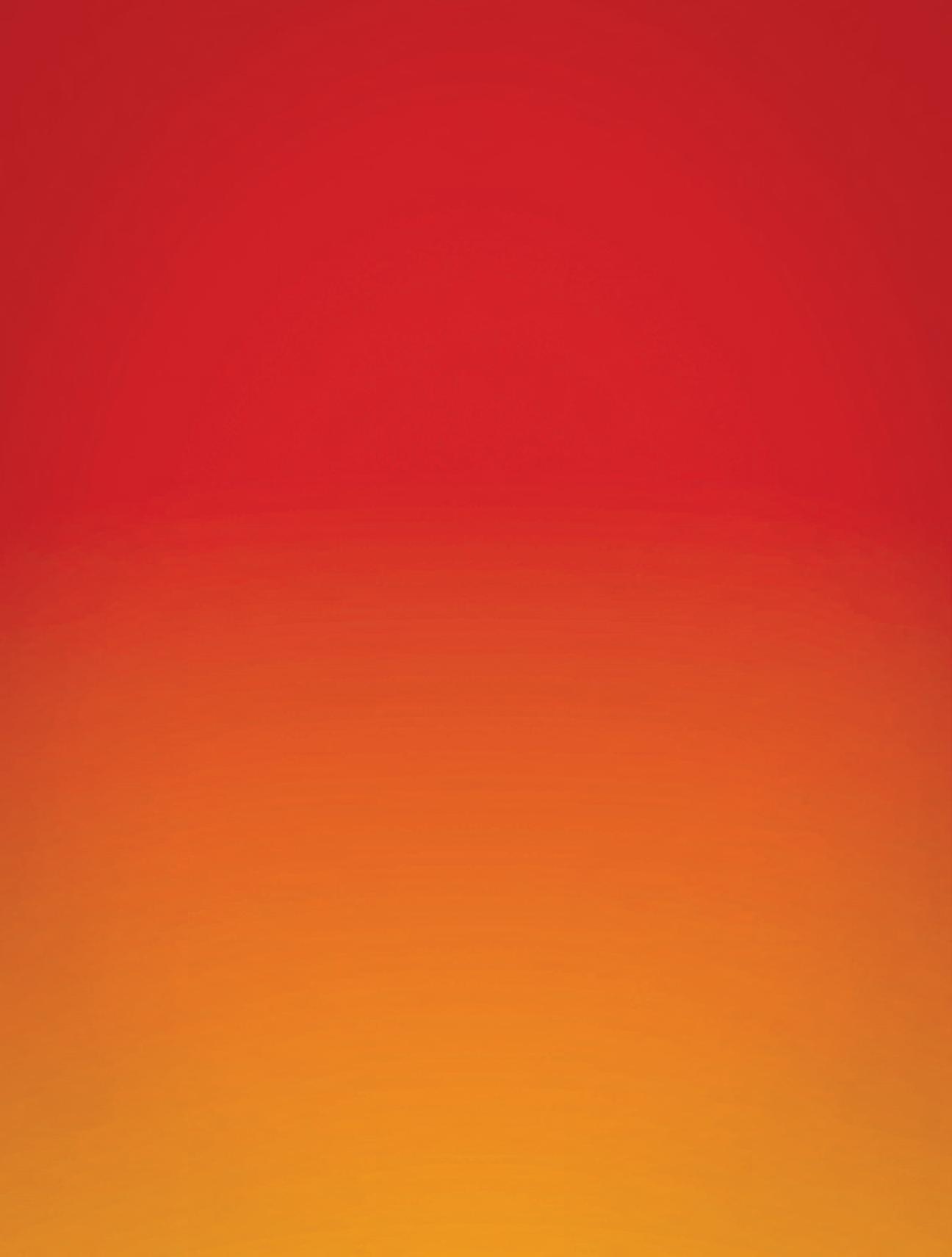
ROAD WARRIOR
Ben Duncan
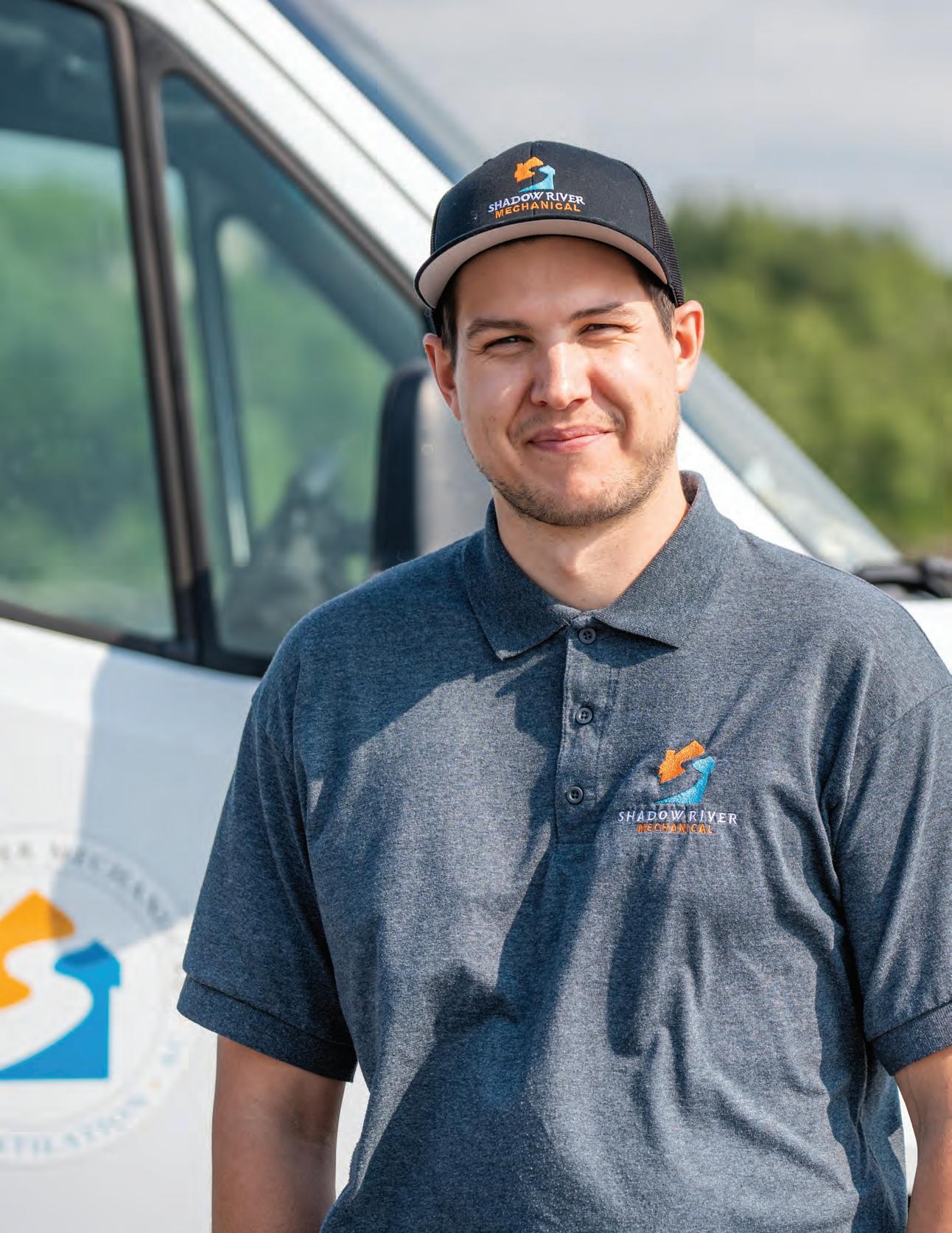
Name: Ben Duncan
Company: Shadow River Mechanical
Job Title: Owner
Born in: Parry Sound, ON
Lives in: Seguin, ON
Age: 30
Spouse: Hartley Duncan Son: Theo Duncan
Pet: An Australian Shepherd named Leia
Ben Duncan: Success on the north shore
“You have to do a little bit of everything to be successful up here,” says Ben Duncan, owner of Shadow River Mechanical in Rosseau, ON. Being situated in Ontario’s exclusive Muskoka region means Duncan does everything from servicing isolated island homes by boat, to installing customized HVAC systems in multi-million dollar cottages.
Homes in the region also have a wide range of heating and cooling technology. “I have lots of customers with century homes and old-school boilers with cast iron rads,” says Duncan. “Most houses have forced air of some sort, and then quite a few cottages have hydronics as well. And once a week I’m up on Georgian Bay going to different cottages. It’s definitely different out there, because there is no power to a lot of these places, so they rely on propane equipment a lot more than your average person does, and you see a lot of natural draft equipment out there. And then there are some pretty major cottages I’ve worked on that have three or four different systems in them.”
Duncan established Shadow River Mechanical in 2022 after working for many years as a marine mechanic during the summer, and an HVAC technician during the winter. Although he has just one other technician working for him, he’s already looking for more help as his business continues to grow thanks to steady cottage renovations and new builds in the popular tourist region. “It’s been pretty consistent growth,” says Duncan. “To be honest, I was shocked, I didn’t think it would grow as fast as it did.”
Hydronic heating is a popular choice in the area, and Duncan says “most cottages that are over a million and a half usually have hydronics of some sort in them,” from single zones in basements to systems throughout the house. “I finished a project at a new build cottage about a year ago that was pretty cool. It had full zoning through the whole house, about 5,000 sq. ft., and was all hydronically heated. We also did a full furnace and a modulating heat pump, and full duct work through it, humidifiers, HRV, pretty much everything you can possibly do.”
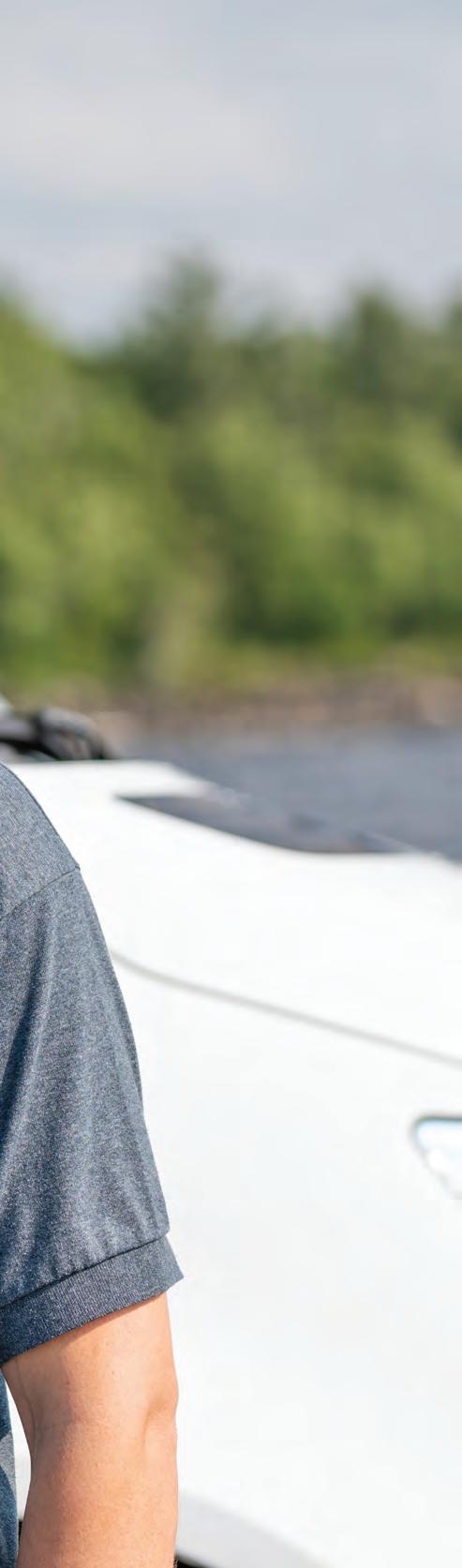
Designing and installing boilers and hydronic systems are Duncan’s favourite parts of the job. “Hydronics is super interesting to me, just from a design perspective,” he says. “I love designing the system, figuring out all the different ways you can do it. It’s a really versatile type of heating system. And then you get to decide on how you want to actually do it. And with heat pump hydronic systems coming around, it opens more avenues for cooling as well.” The challenges come, he says, when he encounters systems that have been improperly installed. “You know, hydronics can seem easy, but there’s a lot of very specific things you’ve got to do to make them work properly. I mean, you can make it work with not a ton of knowledge, but to actually get it to work efficiently and properly is a bit harder.”
In the mechanical industry since: 2013
By Carolyn Cooper
The most useful tool in your toolbox: Multi-bit screwdriver
If you were granted one wish: For my kids to be successful in whatever they want to pursue
Best concert you ever attended: The Arkells
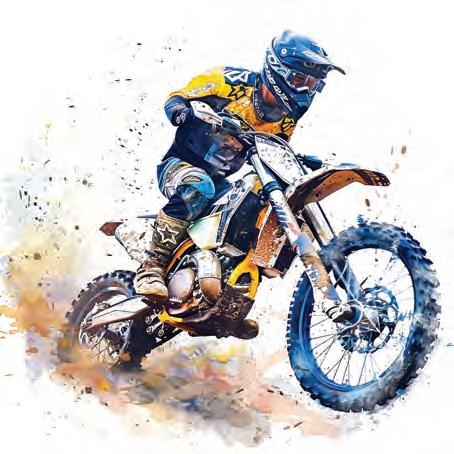
Favourite teacher: Bill Moore
Favourite class: Physics
Best advice you’ve ever received: If you’re going to take the time to do something, take the time to do it right
Advice for young people considering entering the trades: Get all the licences you can while you’re young
The current work ride: 2024 Mercedes Sprinter
Service area: Parry Sound, Muskoka, and parts of Georgian Bay
Any area you like to get dispatched to: Muskoka Lakes or Georgian Bay
Favourite part of the job: Solving problems, whether they be with equipment or with the business
Your favourite tool in your toolbox: Automatic flaring tool
Tool you wish you had: Milwaukee MX threader
Favourite magazine: Mechanical Business
Favourite book: Two-stroke Tuner’s Handbook by Gordon Jennings
Favourite TV show: Two and a Half Men
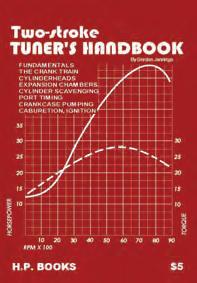
Favourite movie: Happy Gilmore
Favourite outdoor activity: Dirt biking
Favourite sport: Basketball
Favourite vehicle of all time: 2001 Nissan Skyline GT-R V-Spec II
Favourite video game and preferred gaming system: Halo 3, PC
Favourite season: Fall
Favourite restaurant: Crossroads Restaurant
Favourite food: Pizza
Favourite snack: Oranges
Favourite place to be: Wherever my friends and family are
Hobbies: Cars, dirt bikes, boating (anything with an engine really), computers, working out, and various sports
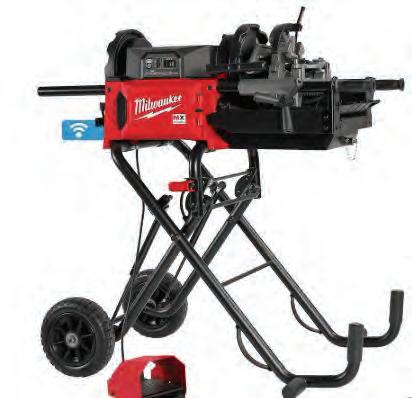
Last book you read: CSA/ANSI/IGSHPA C448
Favourite website: YouTube
Biggest pet peeves: Having no cell phone reception when I’m trying to work
One place in the world you would like to visit: Italy
SYSTEM PERFORMANCE
By Todd Wiggins
Todd Wiggins is technical sales representativeSouthern Alberta with Armstrong Fluid Technology.
Under pressure: The hidden forces inside hydronic systems
Haveyou ever wondered why a hydronic system will act up for no obvious reason? Chances are that air pressure and dissolved gases are playing tricks behind the scenes. To keep your pumps, boilers, and expansion tanks running smoothly, it helps to understand two age-old gas laws: Boyle’s and Henry’s. They’re not just high school science − they’re key to keeping systems efficient and components protected.
Boyle’s Law: Pressure versus volume
More than 300 years ago, Robert Boyle discovered that pressure and volume have an inverse relationship. When one increases, the other decreases, assuming temperature and the amount of gas stay the same. This simple principle is surprisingly relevant to hydronics.
Think of a pop bottle. Turn it upside down and open the cap. As the liquid drains, the air pocket inside expands to fill the space. As the volume of the air increases, the pressure decreases. That’s Boyle’s Law in action. If the internal pressure drops enough, outside air pressure might cause the bottle to collapse.
I first came across this concept in 2013, thanks to the book Pumping Away by Dan Holohan. He used the pop bottle example to explain how pressure and volume interact. That story stuck with me and is a key part of how I explain pressure changes in closed-loop systems.
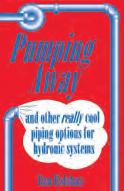
Where Boyle’s Law applies: Expansion tanks
Expansion tanks are a great example of Boyle’s Law at work. When water heats up, it expands. That extra volume needs somewhere to go. In a closed-loop system, it pushes into an expansion tank, which has a flexible bladder separating water from a cushion of air.
As the water enters the tank, it compresses the air. When volume decreases, pressure increases. This pressure rise balances the system and helps prevent over-pressurization. It also protects the system from airlocks and poor circulation.
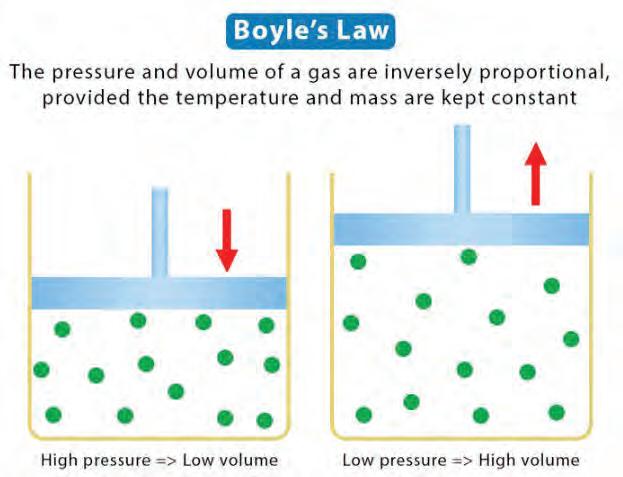
Boyle’s Law
The pressure and volume of a gas are inversely proportional, provided the temperature and mass are kept constant
High pressure => Low volumeLow pressure => High volume
Boyle’s Law relies on three simple conditions:
• Constant temperature – gas molecules move at the same speed
• Fixed amount of gas – nothing added or removed
• Changing volume – pressure shifts as the gas expands or contracts
Since the temperature stays the same, it’s known as an isothermal process, which is important to remember when considering how it impacts real-world systems.
Henry’s Law: Dissolved gas and pressure
Now let’s look at Henry’s Law. William Henry discovered that the amount of gas dissolved in a liquid is directly related to the gas’s pressure above the liquid, as long as the temperature stays constant. More pressure means more gas dissolves in the fluid.
Open a bottle of soda, and you’ll see this in action. While the bottle is sealed, carbon dioxide stays dissolved in the liquid. Once opened, the pressure above the liquid drops and the gas escapes as bubbles.
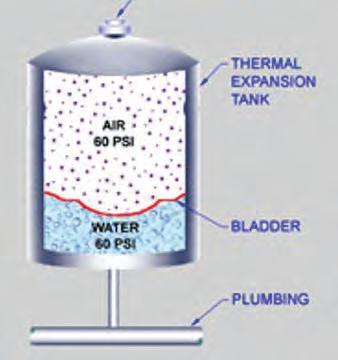
Bladder compression during thermal expansion.
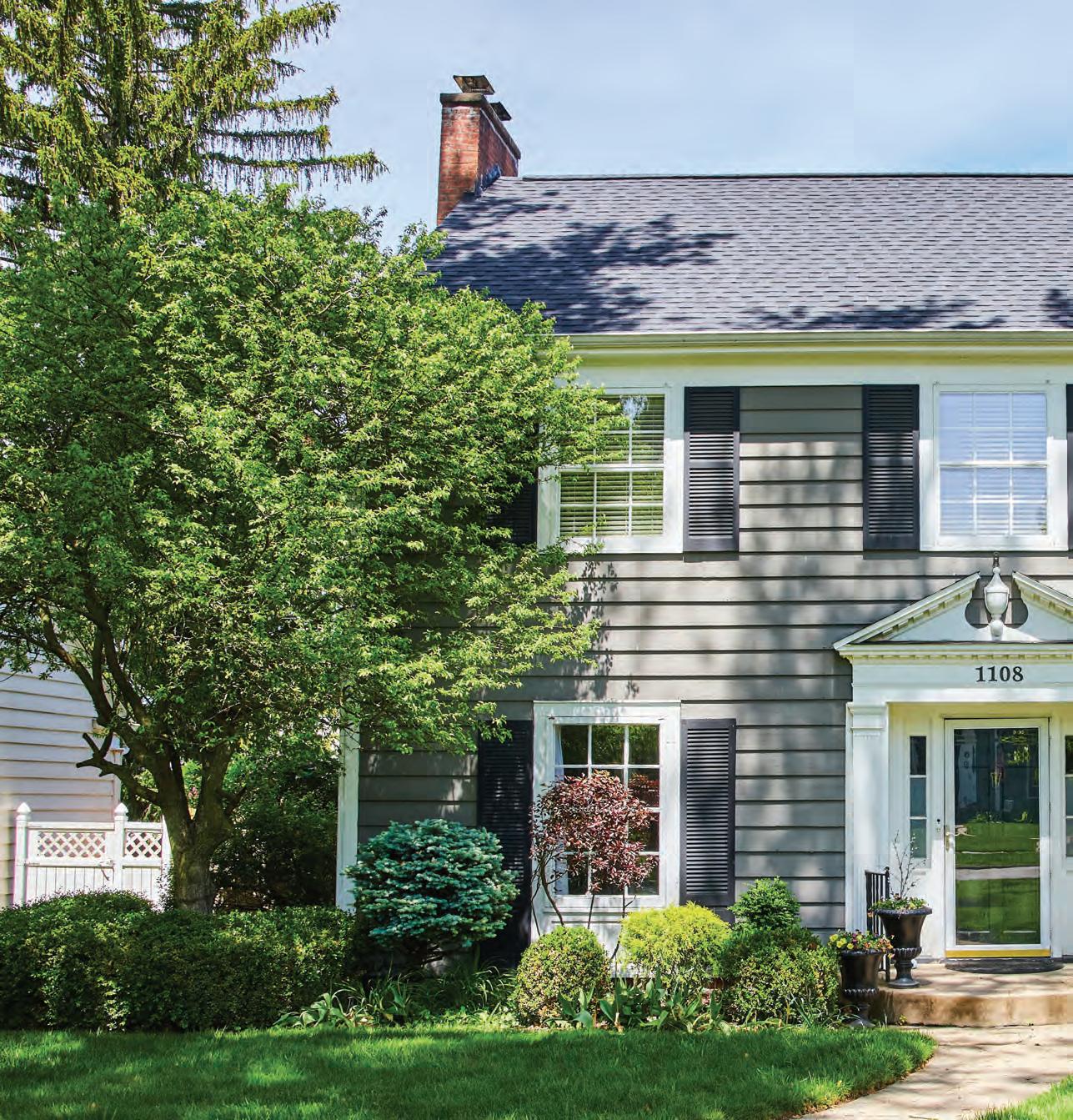
Offering market leading efficiency and a 20 year average life span, the Smart 316 Indirect Fired Water Heater provides a solution for every home.
Exclusive Tank-in-Tank Technology
Stainless Steel 316L Tank
Built-in Aquastat
Lowest Pressure Drop in the Industry
Available in 7 Sizes: 30, 40, 50, 60, 80, 100, 120 Gallons
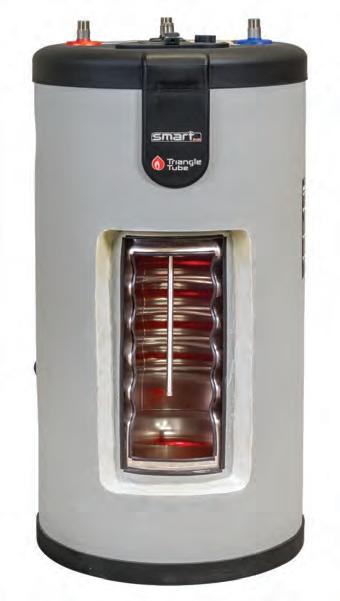
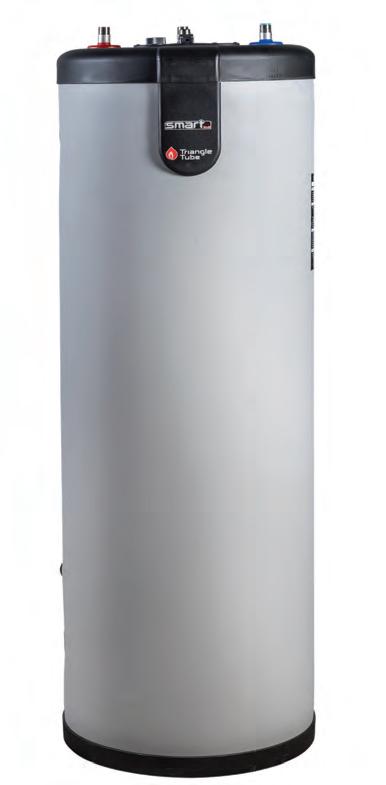
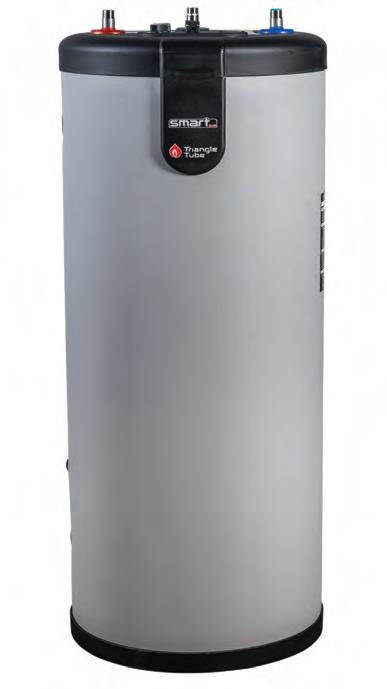
Triangle Tube
Why this matters
Air is the number one enemy of closed-loop hydronic systems. It causes corrosion, especially in cast iron components. It also leads to cavitation near pump suctions, where vapour bubbles collapse and damage internal components. Proper air management prevents these issues and improves overall efficiency.
Air separators and Henry’s Law
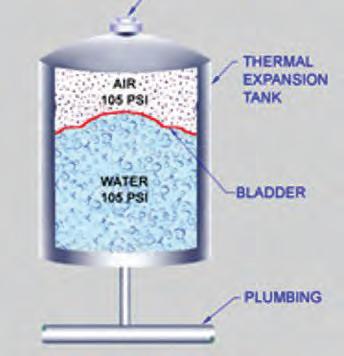
This same process happens inside hydronic systems.
It’s how gases enter and exit the fluid, which is critical to managing system performance.
When air collects at the high points of a system, pressure drops created by the circulator allow water to absorb the air. These microbubbles then move through the system and into an air separator. Inside, the fluid slows down, and a mesh collects the air, which vents out through an air vent.
The pump’s pressure differential and the separator work together. Henry’s Law explains how the gas enters the
fluid, and the separator makes sure it gets removed. The result is quieter operation, better heat transfer, and fewer maintenance calls.
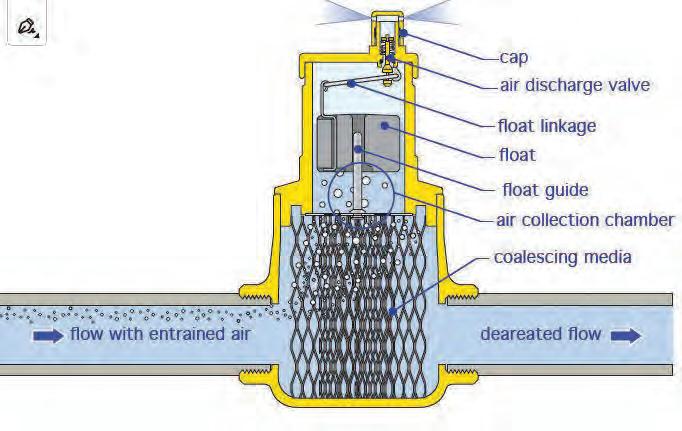
Microbubble separation and release.
CARING FOR WATER. WITH PASSION.
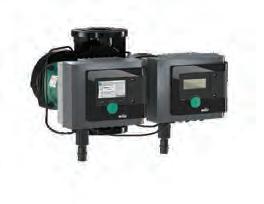
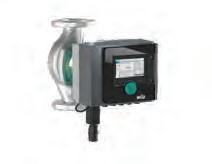
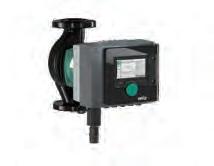
Final thoughts
Boyle’s and Henry’s Laws are more than just theory. They explain the invisible forces that affect pressure and air management in hydronic systems. Knowing how they work helps you make better decisions, solve problems faster, and design systems that perform more reliably.
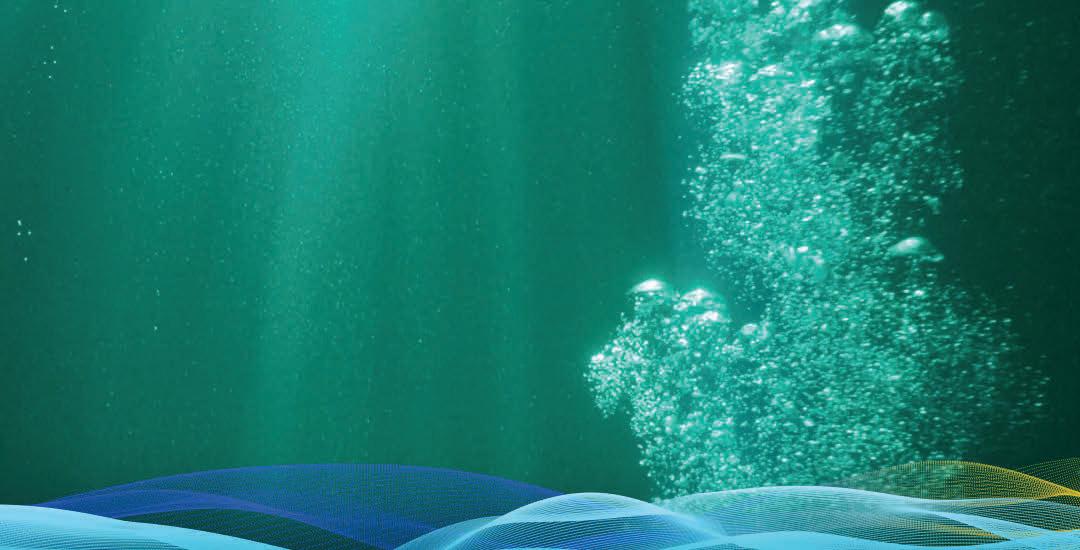
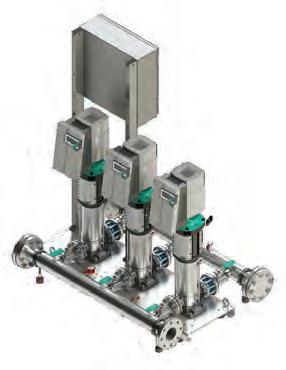
From big to small, we’ve got it all! With optimized and innovative energy-saving features, we deliver the future of pump technology to your doorstep.

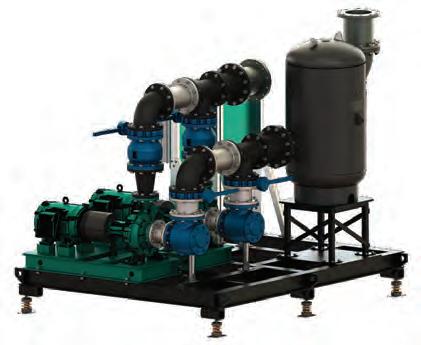
Graphic courtesy Caleffi
THE BEST KNIGHT EVER ®
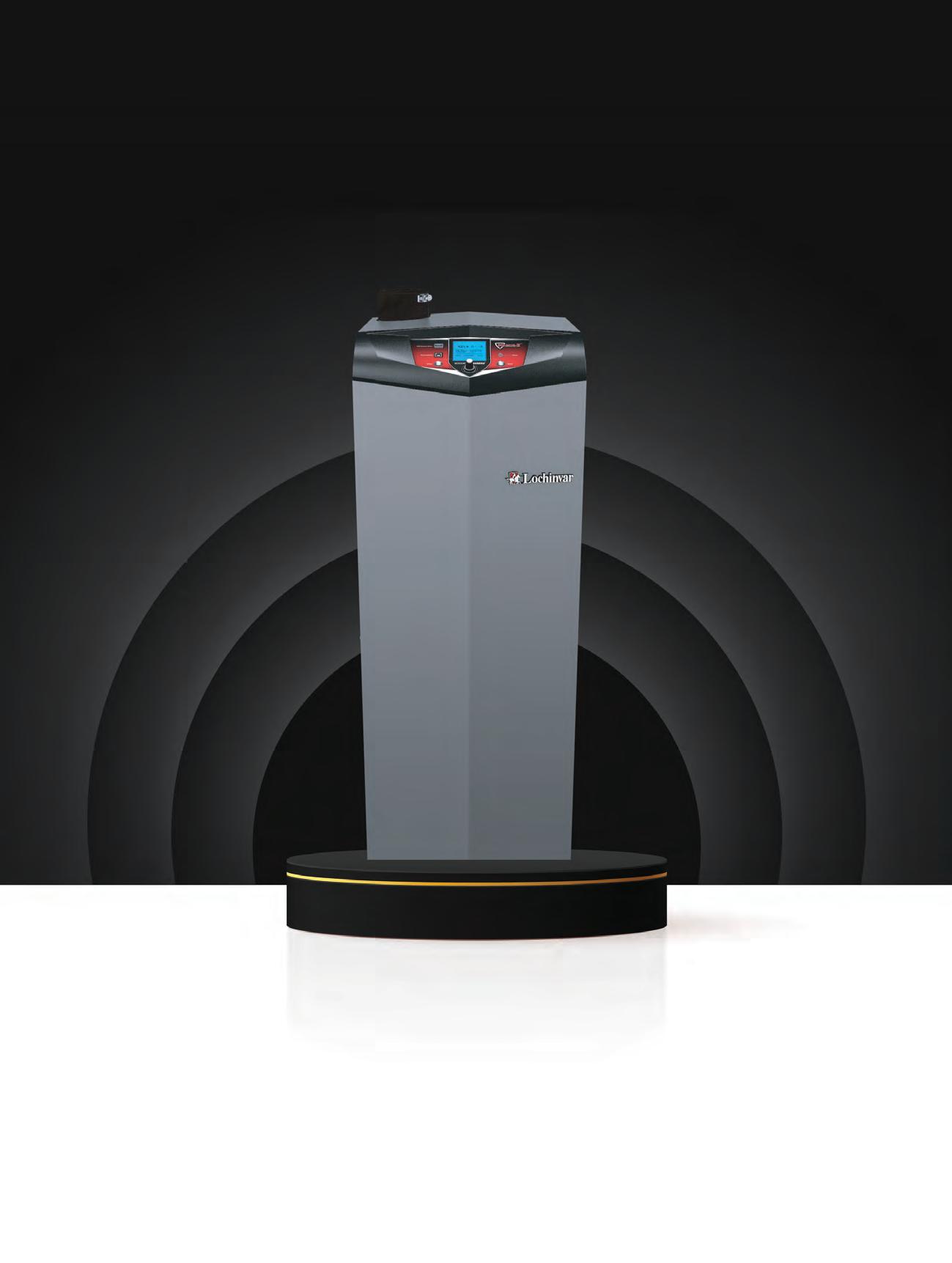
The industry-leading, high-efficiency KNIGHT® residential boiler is at the head of the class with 13 models available in either floor-standing or wall-mount configurations. The KNIGHT heating boiler has a multitude of adjustable parameters to suit your unique application making it one of the most flexible residential boilers you can install. Learn more about Knight Residential Gas Boiler at lochinvar.com.

Lochinvar
Design rules to live by
Over the last few decades I have seen my fair share of the good, bad and the ugly when it comes to piping. I have been in beautiful mechanical rooms with shiny new equipment and impeccable attention to detail but the systems were completely inoperable due to bad piping choices.
I have also been in rooms where you feel as if you need a tetanus shot just from looking at the old school pipes; pipes that actually work impeccably because they followed some very simple rules when it comes to near boiler piping. I will share three easy rules to follow when it comes to the boiler pipe. These rules may or may not be controversial, but they always work.
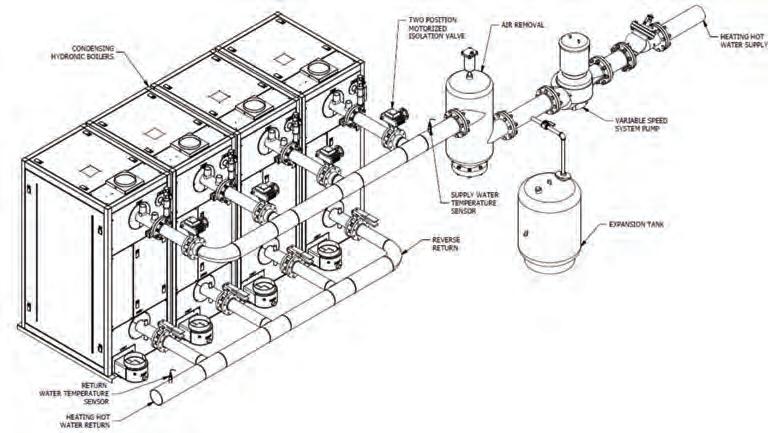
Rule #1: When in doubt, pipe primary secondary. There isn’t a boiler manufacturer I can think of that would be upset with this set up. Primary secondary is very common and it’s also easy to work with.
Primary secondary does a great job of hydraulically separating the boiler loop from the system loop. This strategy can eliminate a lot of common flow issues and it also eliminates the boiler from system troubleshooting issues because it is on its own loop.
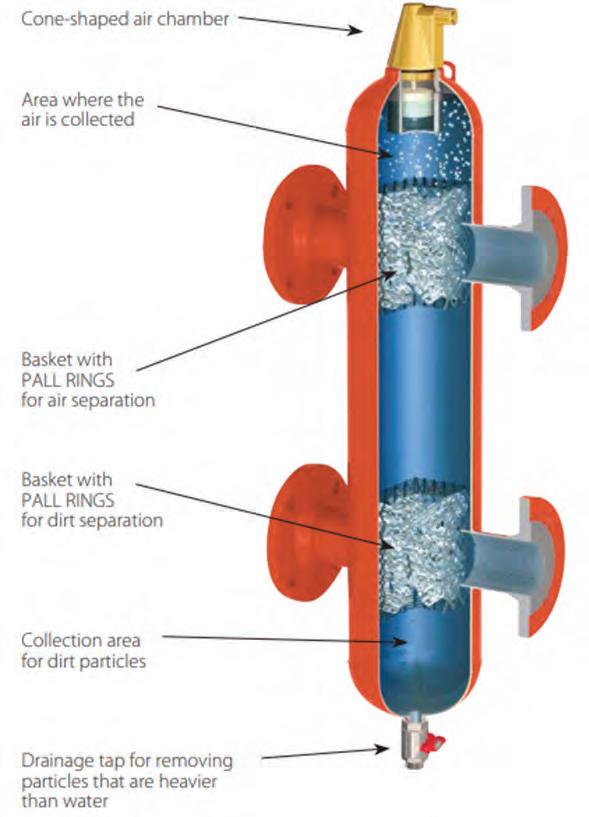
Multiple boilers piped primary variable.
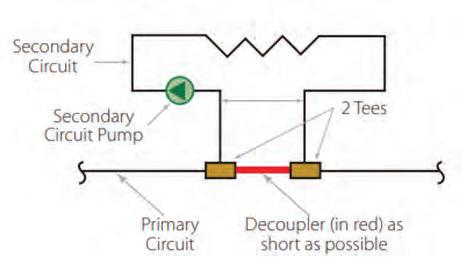
Runs of tees should be as close together as possible.
Primary secondary employs the rule of closely spaced tees. The “rule” is to keep the runs of the tees as close together as possible, ideally within four times the pipe diameter apart, and ensure a minimum of eight pipe diameters of straight pipe run on either side of the tees.
It should be mentioned that the tees do need to be on the same pipe. I was at one project where, although the tees were literally right beside each other, they were on two separate pipes. Yes friends, I have seen it all.
Rule #2: When piping primary secondary use a low loss header (LLH) This may be controversial but those who do utilize LLH know the savings in pipe and labour are what really drives this product to the forefront when it comes to the install.
There are many advantages to using a LLH, such as built-in coalescing media that makes the LLH operate as both a high efficiency air separator and a dirt separator. It’s also becoming common to add magnets directly into the LLH adding another level of protection against magnetite and other malicious ferrous metals in the system.
Also known as hydraulic separators, LLHs are a magnificent piece of trim that take all of the guess work out of the spacing of the tees.
Decoupler
This is not to say that the LLH is without compromise. The drawback you can get with a LLH is something called low delta T syndrome. This occurs when the flow between the boiler side and the system side isn’t equal. This is often a result of having just a standard single speed circulator on the oiler and variable speed circulator on the system.
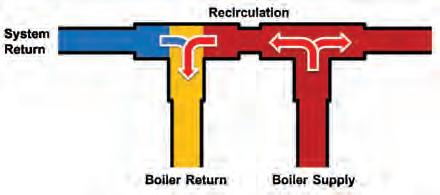
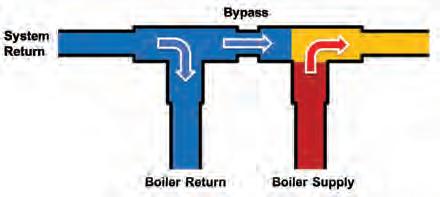
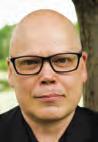
By Matthew Reid
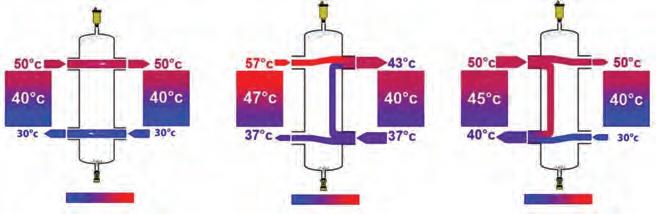
Multiple boilers piped primary secondary.
Image left shows a perfectly balanced system where flow for boiler matches flow in the system. This rarely happens as it only occurs under design conditions.
Image centre will occur when the system flow is higher than boiler flow. This is resulting in a cooler blended temperature going to the system so the boiler has to overfire to compensate to hit desired temperature. The higher boiler temp means higher return temperature that lowers the condensate produced leading to lower efficiency of the boiler.
Image right will occur when the boiler flow is higher than system flow. This occurs in warmer days where the temperature outside is higher than design and results in a warmer return temperature to the boiler, lowering the condensate produced from the boiler and lowering the efficiency.
If the boiler has more flow than the system you aren’t able to give off all of the heat that the boiler has provided. The additional boiler flow goes directly back to the boiler at output temperature along with a smaller amount of system return water leading to a higher return temperature than designed for. The warmer the boiler return the less condensate the boiler will produce; the less condensate the less latent heat we are able to transfer into the boiler and the lower the efficiency.
There are ways to combat this with variable speed circulators on both sides but this can lead to higher costs and create some controls struggles. Still, this is an excellent way to ensure flow for both the boiler and the system. In retrofit projects this is a great way to protect the boiler from low flow situations, which are much worse than higher return temps.
Rule #3: Whenever possible avoid primary secondary. I am aware that I just spent the first two thirds of this article talking you into primary secondary but it is advantageous to explore the world of primary variable (PV) piping. Although this type of system must meet certain criteria and require a degree of engineering input, it is by far the best way to pipe a boiler system to maximize boiler efficiency. PV cannot be
used everywhere and it cannot be used with every boiler type so that’s why the rule is written as “whenever possible.”
PV ensures boiler return temperature is always the lowest it can be so we can condense as much as possible. It is also the lowest cost for boiler piping accessories. In primary secondary there will be multiple pumps both for the boiler side and the system side. Depending on how many boilers there are you may have a very large number of pumps in a system. PV incorporates just one pump (or N+1) that can handle the flow of both the boiler and the system. This means the boiler should have a very low head loss through the HX and should also have very low or no minimum flow requirements. PV also requires you to use isolation valves for multiple boilers to ensure you only get flow through the boiler that is firing.
Design considerations are paramount for PV type systems and you can’t just pipe up and walk away. Engineering is required. The system is similar to how we piped those big mid-efficiency cast iron boilers from years ago. It worked then, albeit not very efficiently, but it absolutely works today because we have the controls and strategies to make this design the most efficient way to pipe.
Matthew Reid is technical director – heating division at E.H. Price Solutions’ Richmond Hill, ON office. He can be reached at mreid@enviroair.ca
System flow > boiler flow
Boiler flow > system flow
HYDRONIC PRODUCTS
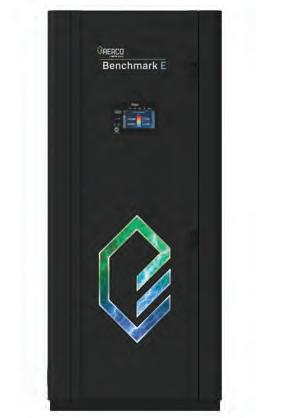
Electric boiler
The AERCO Benchmark E is a zero-emissions electric boiler featuring peak load management and hybrid plant capability. It can sequence up to 16 boilers, including hybrid configurations with gas-fired units. Pair it with AERCO’s SmartPlate EV for a fully electric, vent-free heating and hot water plant. Available in five sizes (216-684 kW), Benchmark E supports up to 350 GPM.
www.
aerco.com
Monoblock heat pump
The Anesi gas absorption heat pump operates on natural gas, propane, or blends. Using 100 per cent natural R717 refrigerant and combustion heat, it achieves up to 140 per cent AFUE or a 1.43 COP. It delivers steady-state water temperatures up to 62.7°C. It has a 4:1 turndown ratio and ambient reset, and retains 65 per cent capacity at -28.8°C. The heat pump operates down to -41.6°C with a steady 51,000 BTU/hr output.
www.
anesicomfort.com
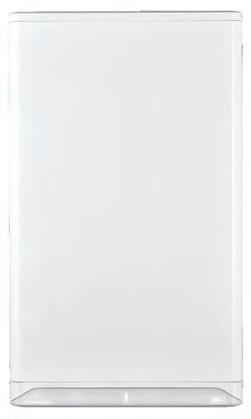
Buffer tanks
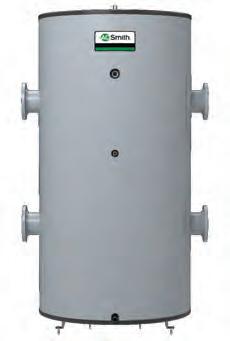
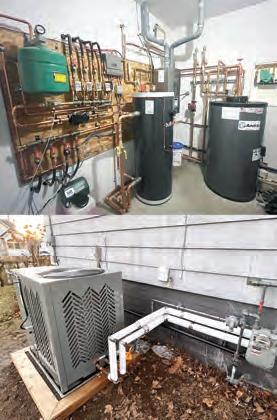
Wireless cascade capability
The IBC Superflow SFB is a high-efficiency condensing boiler offering up to 96 per cent AFUE. It features only four moving parts and an aluminum heat exchanger with copper waterways. Wireless cascade capability allows up to eight units to operate together without communication cables. Compact and contractor-friendly, it includes a touchscreen control panel, ECM pump, and outdoor reset technology. It is designed for residential or light commercial use, the SFB delivers efficient, low-maintenance heating with a strong sustainability profile and ENERGY STAR certification. www. ibcboiler.com
A. O. Smith’s hydraulic separator buffer tanks (ABV) and chilled water buffer tanks (ACV) are engineered for commercial HVAC systems requiring thermal storage and flow separation. The ABV models (120 to 1,000 USG) act as hydraulic separators, isolating boiler flow from system flow to reduce short cycling. The ACV models (120 to 1,000 USG) create volume in chilled water systems. Both feature ASME Sec VIII, U-stamped vessels, flange or NPT connections, and options for 125 to 160 psi working pressure.
www. hotwatercanada.ca
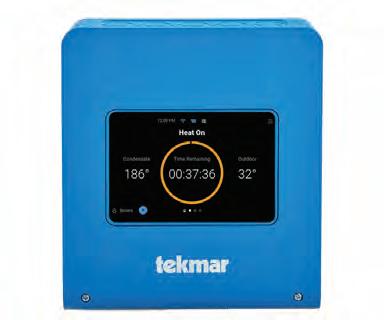
Steam control
The tekmar Smart Steam Control 289 simplifies steam boiler management with real-time remote access across multiple properties via Nexa by Watts, enabling adjustments from a phone or desktop. It can be retrofitted to any boiler, regardless of age and offers energy savings of up to 20 per cent through outdoor reset, indoor temperature feedback, and warm weather shut down technology. Key features include system alerts, a 5-in. colour touchscreen, and compatibility with all boiler brands.
www. watts.ca
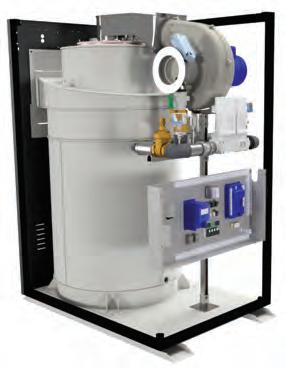
Higher Turndown Hydronics
Avenger® Series II
Heating & Domestic Hot Water Boiler
5000 & 6000 MBH
The Avenger® Series II is an advanced two-pass, counter-flow firetube commercial boiler, providing efficient hot water for demanding commercial needs.
» Industry-leading 40:1 turndown
» Thermal efficiencies of up to 96%
» Designed for today’s higher turndown variable primary and low pressure systems
» 3 to 4 week lead-time with stock units available for quick ship
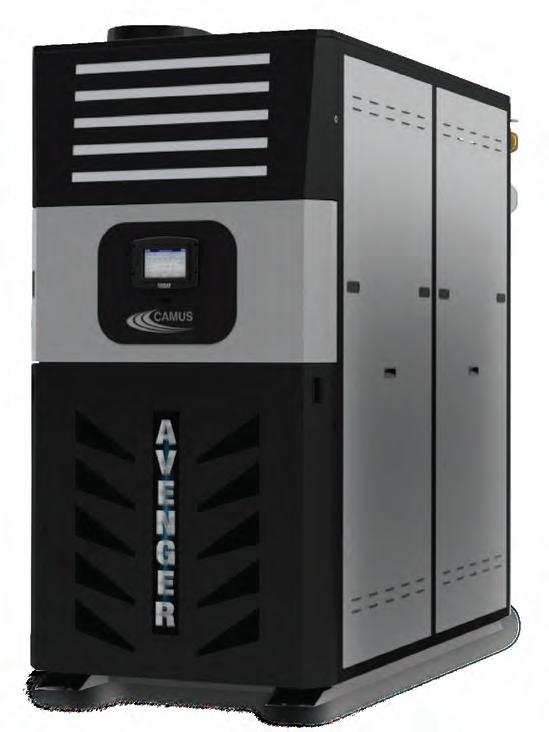
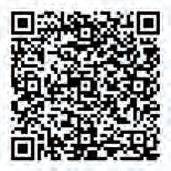
www.camus-hydronics.com/HigherTurndownHydronics
CAMUS
HYDRONIC PRODUCTS
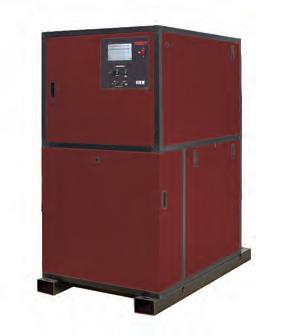
Fire tube boiler
Watertube boilers
RBI Torus condensing commercial watertube boilers and water heaters have a compact footprint and HeatNet 3.0 touchscreen cascade control. The Tru-Flow fuel/air coupling system has 10:1 turndown and capacities to 4000 MBH. Torus uses a pressure driven mixing system with no moving parts to provide a 10:1 turndown, without lowering the CO2 per cent while avoiding ignition lockouts. The heat exchangers are made from 316 L stainless steel.
www.
rbiwaterheaters.com
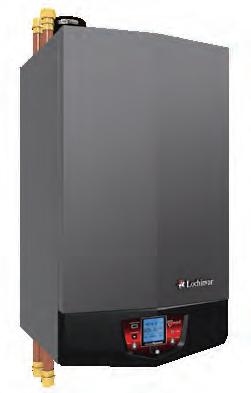
HIGH
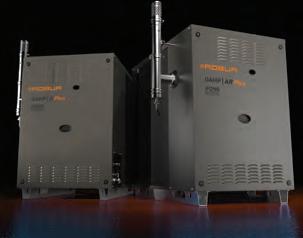
Gas absorption heat pumps
The KNIGHT fire tube boiler line is available from Aqua-Tech in six models from 55,000 to 285,000 BTU/hr, with 95 per cent AFUE and up to 10:1 turndown ratio. Models come with ECM variable speed boiler pumps, with features such as Smart System operating control and CON·X·US Remote Connect Capable. The boilers qualify for the POV Program. www.
aquatech-canada.com
info@aquatech-canada.com
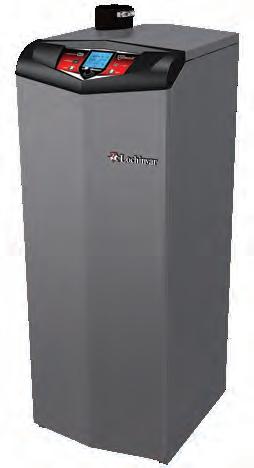
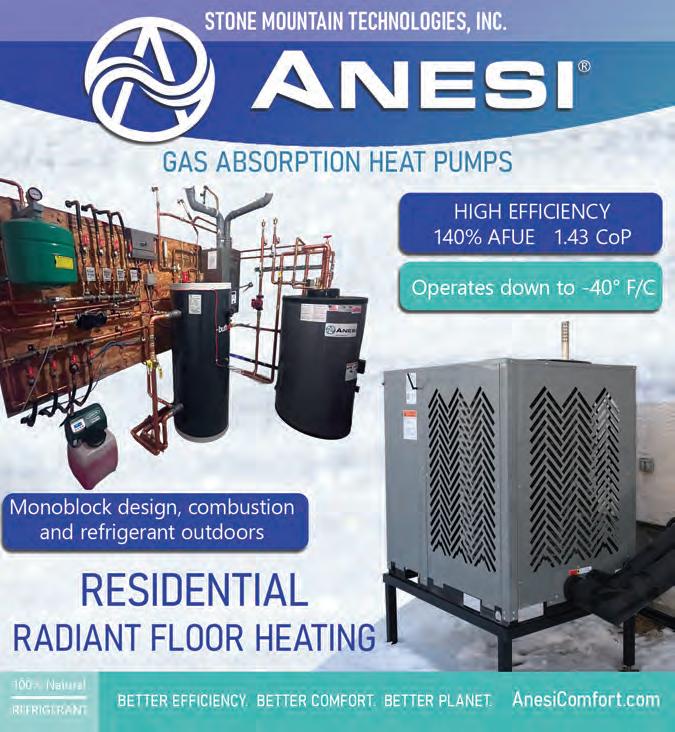
The Robur GAHP Plus Range gas absorption heat pumps deliver high-efficiency domestic hot water heating, space heating, and cooling from 48.8°C to -40°C without backup. They produce up to 65°C hot water with ultra-low NOx emissions. With 120,000 BTU/hr capacity and AFUE over 110 per cent, they are 20 per cent hydrogen ready and use R717 natural refrigerant, F-Gas and are PFAS free. Remote monitoring is available. www.
roburcorp.com
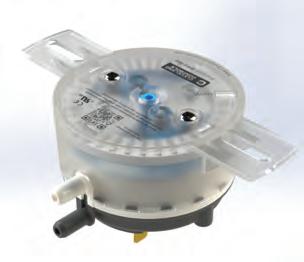
Air pressure sensing switch
The ANS2 Series air pressure switch from Cleveland Controls is a universal, field-adjustable switch for residential and commercial HVAC systems, outdoor radiant heating products, pool and spa heating equipment, and more. Calibration is achieved by turning the key on the adjustment cover with an Allen wrench using the scale to select the set point. The ANS2 is available in three set point ranges: ANS2-1000: 0.08 in. wc to 1.0 in. wc, ANS2-2000: 0.15 in. wc to 2.0 in. wc, and ANS23000: 2.0 in. wc to 10.0 in. wc. www. clevelandcontrols.com
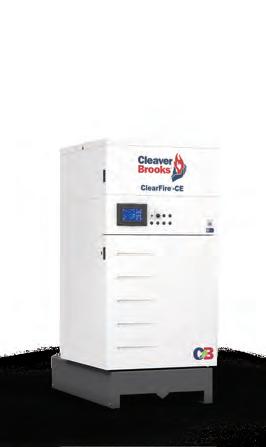
Scalable boiler
HYDRONIC PRODUCTS
The Cleaver-Brooks Clear Fire-CE (CFC-E) is a high-efficiency, condensing hydronic boiler designed for commercial and industrial applications. With up to 99 per cent efficiency, it features the TurboFer heat exchanger, 10:1 turndown, and advanced controls. It has less than 20 ppm NOx (sub-7 ppm optional) emissions. The CFC-E supports flexible system integration and is scalable from 500 to 6,000 MBH to meet a variety of hydronic heating needs. www. cleaverbrooks.com
Fast-filling kit
The Caleffi AutoFill Automatic fast-filling combo is a kit designed to fast fill a hydronic system to set pressure then automatically shut off the water feed. There are no levers to flip or buttons to push. A builtin shut-off valve and check valve allow isolation of system from supply to stop makeup water if desired. It is precalibrated for hydronic systems. Before charging the system, turn the dial to desired system pressure with a screwdriver (factory preset to 15 psi). The kit includes a FlowShield DuC-AV backflow preventer, which complies with
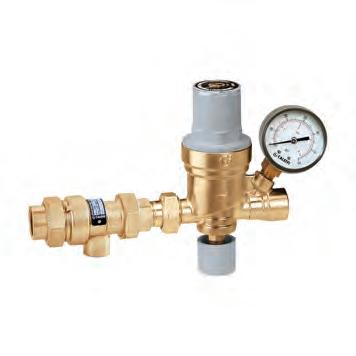
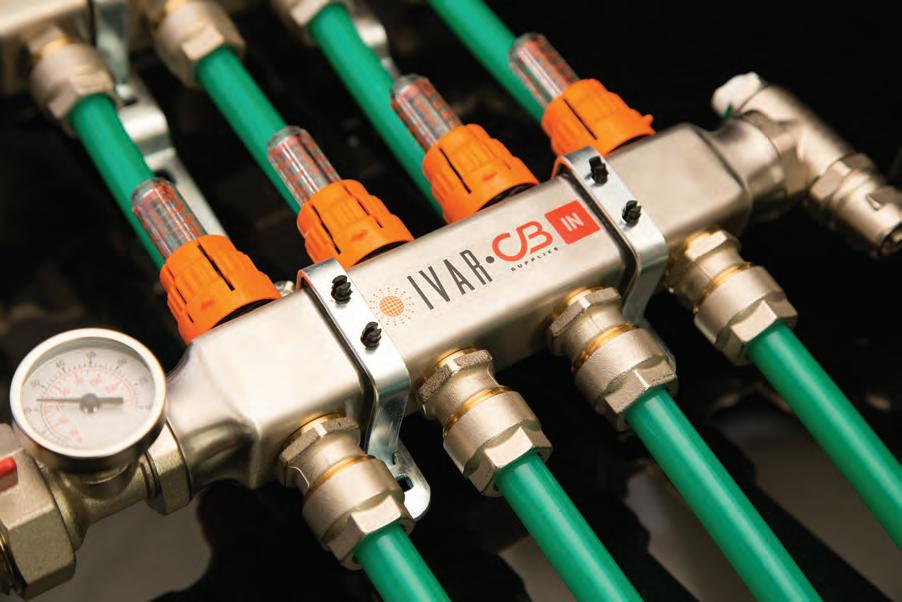

Gas adaptive technology
Eco-friendly and ENERGY STAR certified Conforto high-efficiency condensing gas boilers offer up to 95 per cent AFUE. Designed for wall-mounted or floorstanding installations, they feature gas adaptive technology, integrated advanced intelligence for optimal efficiency, and a compact design for space saving. Combi models provide both space heating and domestic hot water, eliminating the need for a separate water heater, with flow rates of up to five gallons per minute. www.
confortohvac.com
The Perfect BALANCE
The ideal manifold and tubing for the distribution of heating fluid in radiant systems
Thanks to our ideal set-up for installers using our unique flow meters on each manifold loop, IVAR stainless-steel manifolds guarantee perfect system balancing, optimizing energy use, while providing premium thermal comfort.
Every manifold set is supplied with all components included in the box, ensuring a smooth commissioning process for radiant system installers.
Pair the IVAR Manifolds with our premium VIPERT™ (PE-RT) Oxygen Barrier Tubing, manufactured specifically for radiant systems, and you have a winning solution every time.
Take advantage of our in-house hydronic expertise, including LoopCAD design and layouts customized for each of your residential and commercial projects.
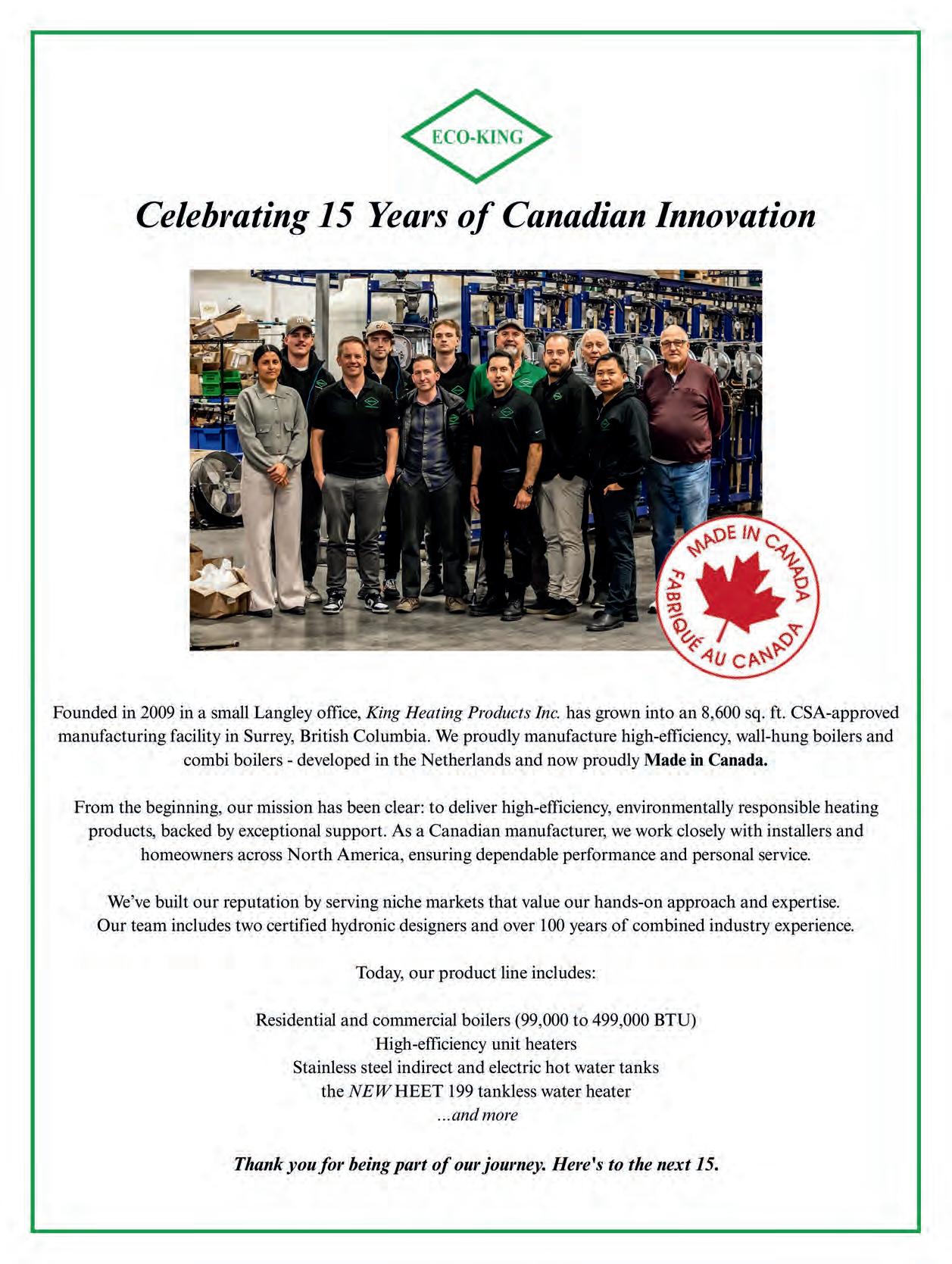
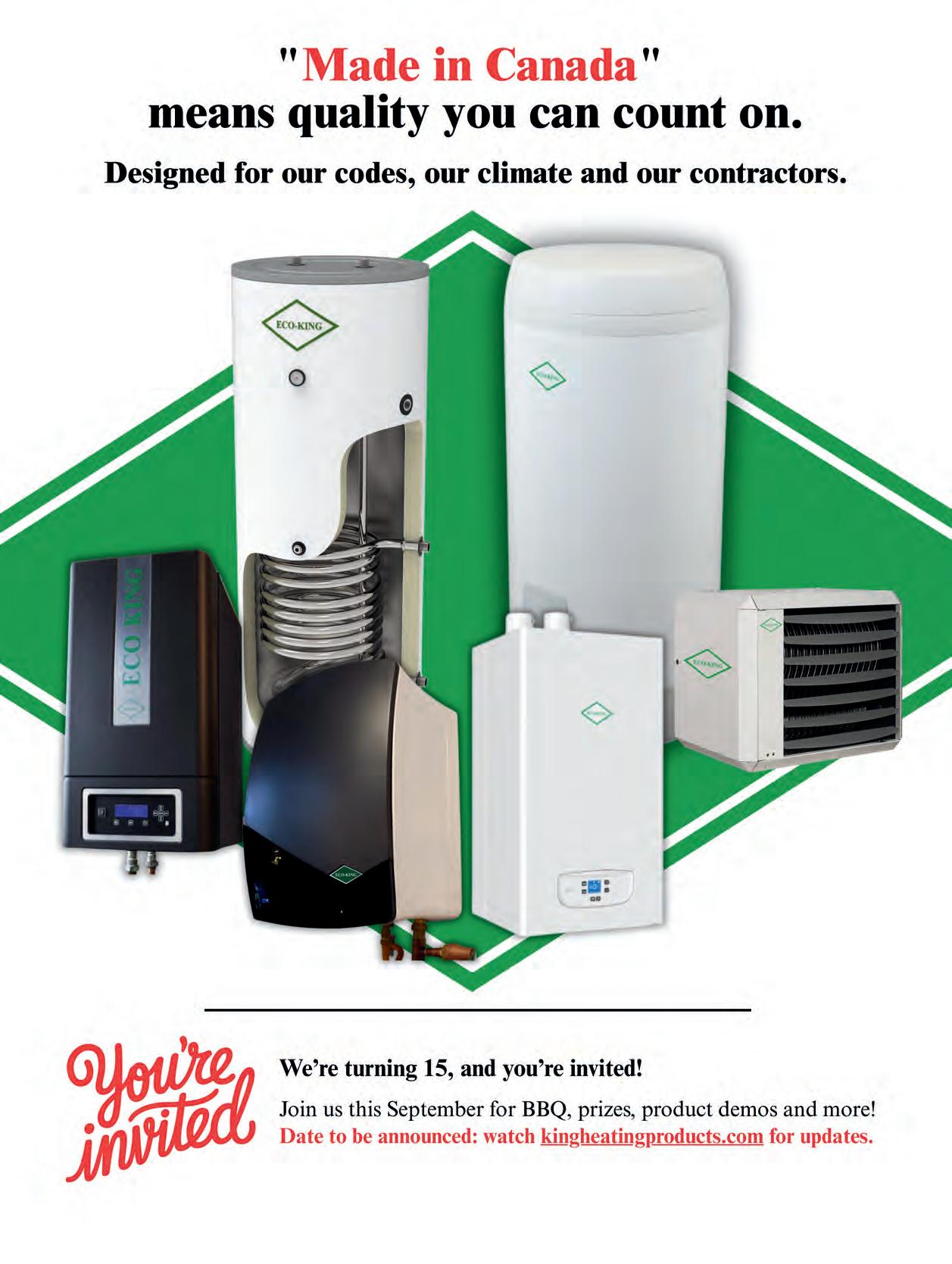
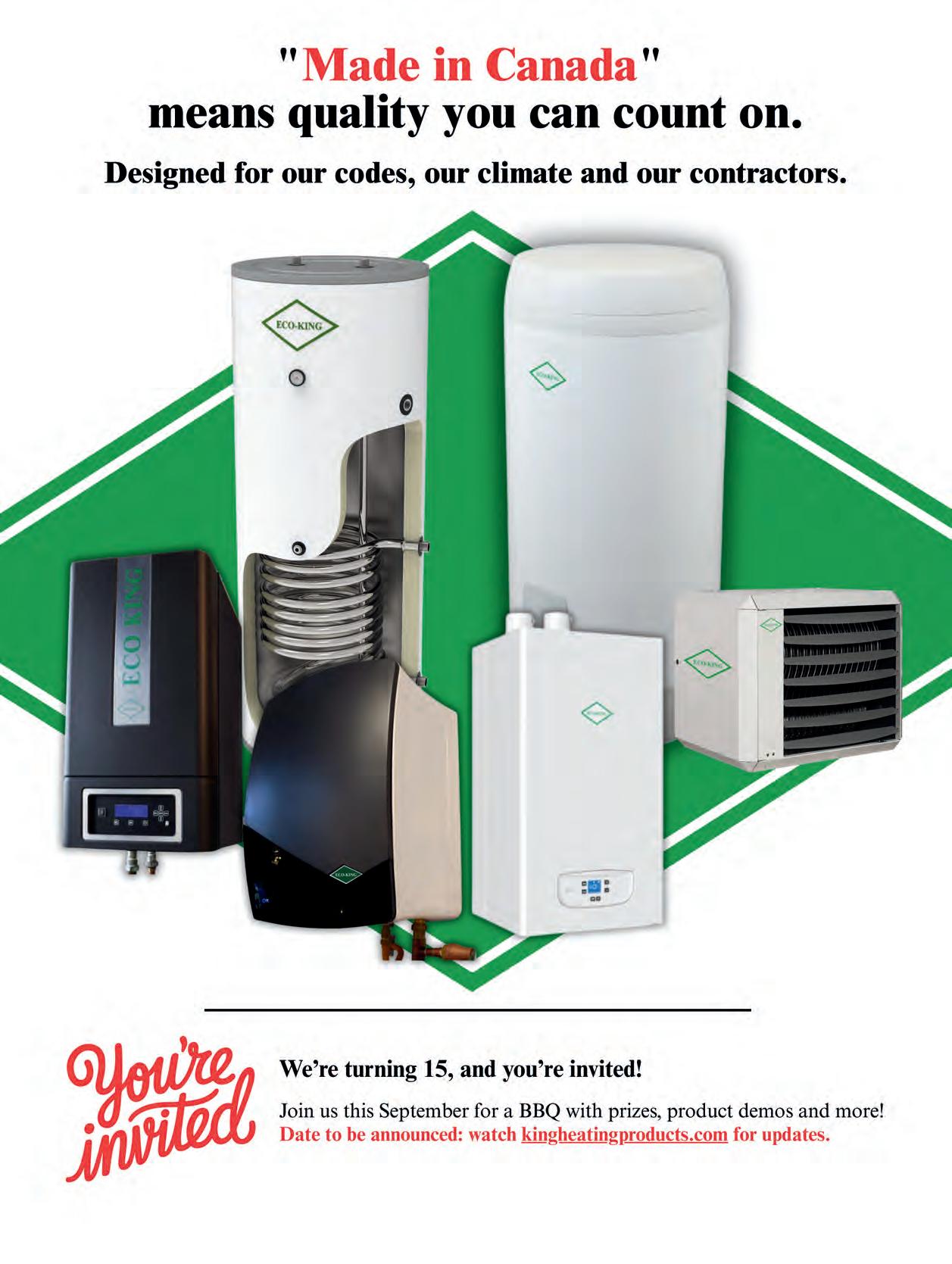
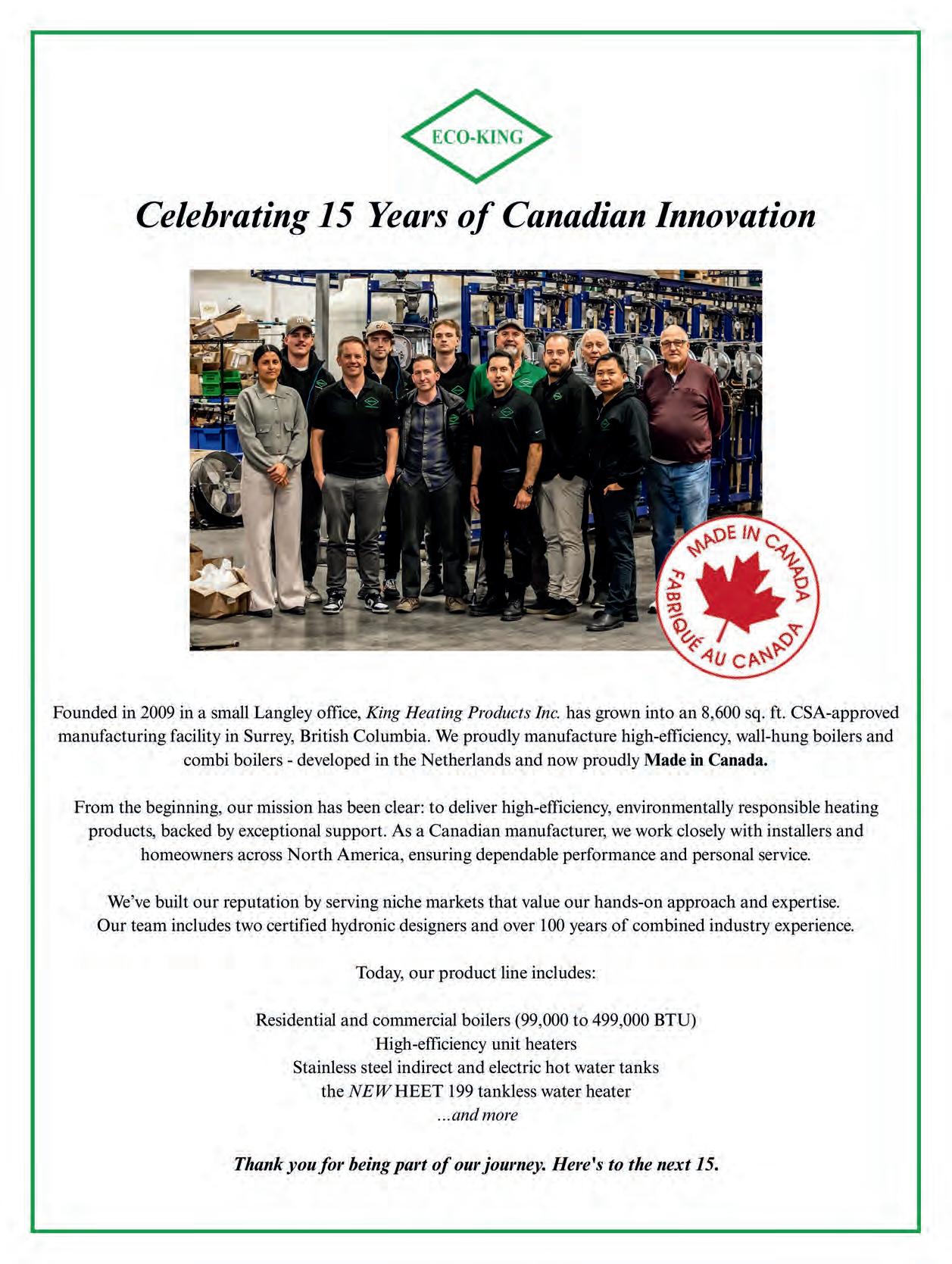
HYDRONIC PRODUCTS
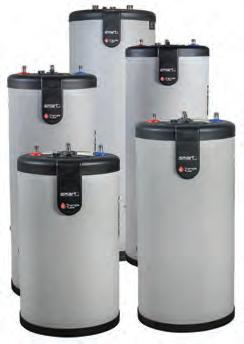
Tank-in-tank technology
The Smart 316 indirect water heater from Triangle Tube offers stainless steel inner 316 L tank-in-tank technology – a hot water tank immersed within an outer tank which contains the system water to quickly heat domestic water. The outer tank is covered with highquality insulation, and is protected by a shock-resistant plastic jacket. Features include a built-in aquastat, acid pickling for increased corrosion resistance, and low pressure drop. The units have a heating water capacity of 5 to 43 gallons, and boiler output of 87,000 to 420,000 BTU/hr.
www.
triangletube.com
Pump relay controls
Salus pump relay controls are available in both wired and wireless configurations, enabling users to control circulator pumps in a variety of hydronic applications. They include essential features like priority for domestic hot water, boiler delay input, and several dry contacts for boiler and accessory control, and can be expanded with controller/worker configuration. The wireless models can also be internet connected for remote control via smartphone, tablet or PC.
www.
braeburnonline.com
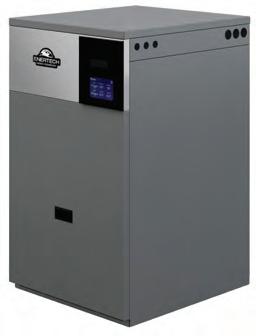
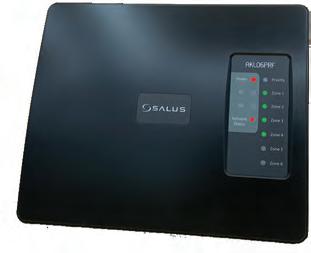
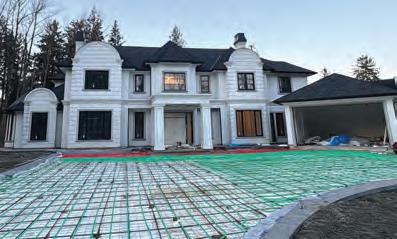
Potable & radiant tubing
CB Supplies’ VIPERT PE-RT tubing delivers flexibility, hydrostatic strength, and is recyclable and suited to hydronic systems, including radiant heating, cooling, and snow melt. The tubing is compatible with crimp, push-fit, and cold expansion fittings. Available in coils from 100 to 1,200 ft. and diameters from 3/8 to 2 in. Radiant tubing comes in green. Pair with the IVAR radiant manifold, complete in one box with manual shutoff valves and optional actuators for precise control. www.
cbsupplies.ca
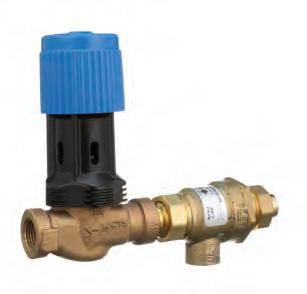
Backflow preventer
Geothermal heat pump
Enertech introduces the WV, a variablespeed water to water geothermal heat pump which delivers radiant in-floor heating, forced air heating and cooling, and 100 per cent of residential domestic hot water. The compact unit offers a capacity range of 0.5 to 5 tons, and dual-fuel compatibility with seamless modulating boiler integration, without requiring a buffer tank. Other features include real time data logging, EPIC Connected Controls, 4.3-in. colour screen, and 9 kW electric heating or modulating boiler control www.
enertechusa.com
The Series BD911 from Watts is a high-capacity combination fill valve and backflow preventer designed for boiler feed lines. It automatically supplies makeup water to the boiler while preventing backflow when supply pressure drops below system pressure. Featuring a Model 9D backflow preventer and BD1156F feed water pressure regulator, this pre-assembled unit simplifies installation. Its push-button fast fill function with auto-stop prevents over-pressurization, while a built-in dial indicator eliminates the need for a separate pressure gauge.
www.
watts.ca
HYDRONIC PRODUCTS
A2W heat pump
The monobloc Solstice R32 Series cold climate air to water heat pump utilizes low GWP R32 refrigerant. The compact and quiet unit is available in three sizes for applications in low load passive homes to largescale commercial with 20 units. Full inverter-driven operation combined with EVI compressor technology produces high-performance heating in outdoor temperatures as low as -30°C and delivers reliable water temperatures as high as 60°C. www. spacepak.com
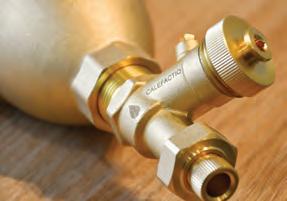
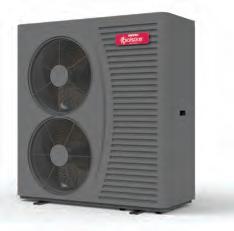
Hydro-furnace
Navien’s Ultra-Low NOx NPF hydrofurnace is available in upflow and horizontal configurations in 60,000, 80,000 and 100,000 BTU/hr sizes that boast 97 per cent AFUE. NPF has a stainless steel heat exchanger to heat water in an isolated compartment out of the airstream. Heated water is circulated through a hydronic coil which transfers heat into the airstream to improve operational control and energy efficiency, and reduce operating sounds. The hydro-furnace also features variable capacity modulating down to 15 per cent.
Hydraulic separator
navieninc.ca
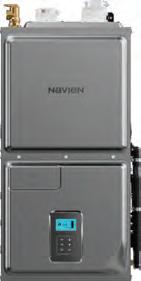
Calefactio expands its 4-In-1 hydraulic separator line with a brass model. The compact unit isolates the primary and secondary circuits while removing air, micro-bubbles, dirt and ferrous debris from fluid. Dirt settles at the bottom for drainage, and air is automatically released through the Calvent float air vent. A built-in magnet captures ferrous debris and helps remove cross-contaminants from the system. Compatible with water and glycol mixtures up to 50 per cent, the separator is available with NPT or PRESS connections of 1 and 1 1/4 in. and is rated for pressures up to 125 PSI and temperatures up to 110°C. www. calefactio.com
PRECISION DIELECTRIC WATERWAY® FITTINGS
THREAD X THREAD
The Precision Dielectric Waterway® fittings are Precision Plumbing Products new offering, it has a thermoplastic liner with pre-formed end shields. Our Precision Dielectric Waterway® fittingsare available in thread x thread sizes 1/2” NPT, 3/4” NPT, 1” NPT and 2” NPT. More options will soon be available.
Assembled at our ISO 9001 and ISO 14001 certified-green factory.
Meets BABAA Build American Buy America Act and American Iron and Steel.
Precision Dielectric Waterway® fittings are designed to meet the requirements of ASTM standard F1545 for continuous use at temperatures of up to +225 oF (+-5 oF) and for pressures up to 300 psi.
Precision Dielectric Waterway® is listed by IAPMO/UPC.
Precision Plumbing/PPP

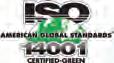

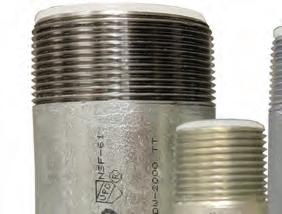
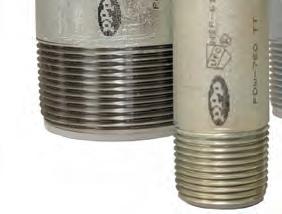
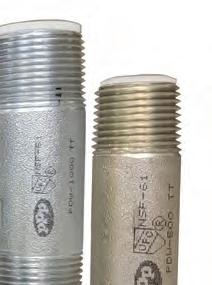
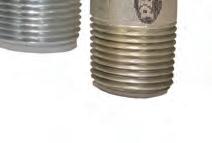
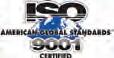
HYDRONIC PRODUCTS
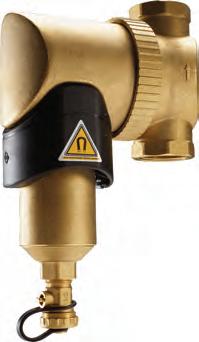
Dirt eliminator
The Spirotrap Magnet eliminates dirt from hydronic systems. Magnets properly located around the flow path ensure removal of ferrous particulate. Non-ferrous particulate can often be removed in less than 100 system circulations. This technology, which can be installed horizontally or vertically, helps provide improved heat transfer efficiency. Available in 3/4-, 1-, 1 1/4-, 1 1/2, and two-in. sizes with NPT, sweat and pressfit.
ontor.com
Circulating pump
UPSe is a high-efficiency heating circulator from Grundfos. Built with an ECM motor, it has an energy rating of 193 (based on the Hydraulic Institute Energy Rating). The pump has a range of controls, including constant pressure (zone valve), proportional pressure (TRV), and constant curve (zone pump), each with three settings, making it suitable for many hydronic applications. Features include intelligent dry-run protection, self-venting ability, and unblocking capability.
grundfos.com
Residential mixing panels
HeatLink’s TMP 3-way prefabricated residential threeway mixing panel’s primary application is as a single zone mixing device where there are no flow requirements in the primary loop. Intended to be used with DHW tanks as a heat source, the PLC is programmed with a 24-hour timer for potable applications. When not used with a DHW tank as a heat source, secondary zoning downstream of the panel is possible. Panels can also be used as subpanels to provide additional mixed temperature loops on larger systems. Multiple panels can be used for each unit in a multi-residential complex. www.
heatlink.com
app
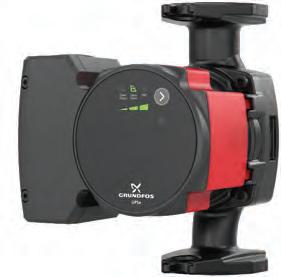
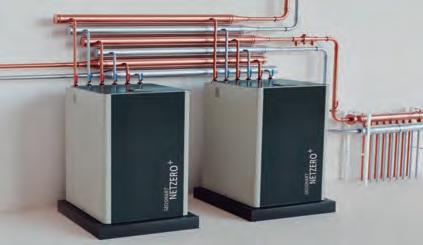
W2W heat pump
GeoSmart NetZero variable capacity water to water inverter heat pumps use low GWP R454B refrigerant. With a COP of over 5.0 the units reduce the climate-related energy consumption of a building using a variety of renewable energy sources. Ground source, air source or hybrid, these inverter-driven heat pumps are available in power ranges from 1 kW to 22 kW. www.
geosmartnetzero.com
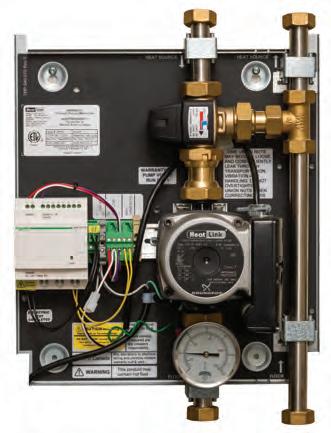
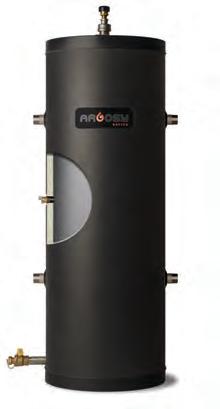
Pressurized buffer tank
The Flexcon Argosy is a pressurized composite buffer tank that won’t rust. The lightweight unit works for hot or chilled potable and non-potable water, and improves system efficiency by reducing heat pump short cycling during low load periods. It has a reinforced durable continuous strand fibreglass inner tank, threaded stainless steel water connections, stainless steel reinforced thermal well port, injected High-R value closed cell foam to minimize temperature loss, lower drain, and black plastic outer jacket. Models available from 22 to 110 volume gallons. www. flexconind.com
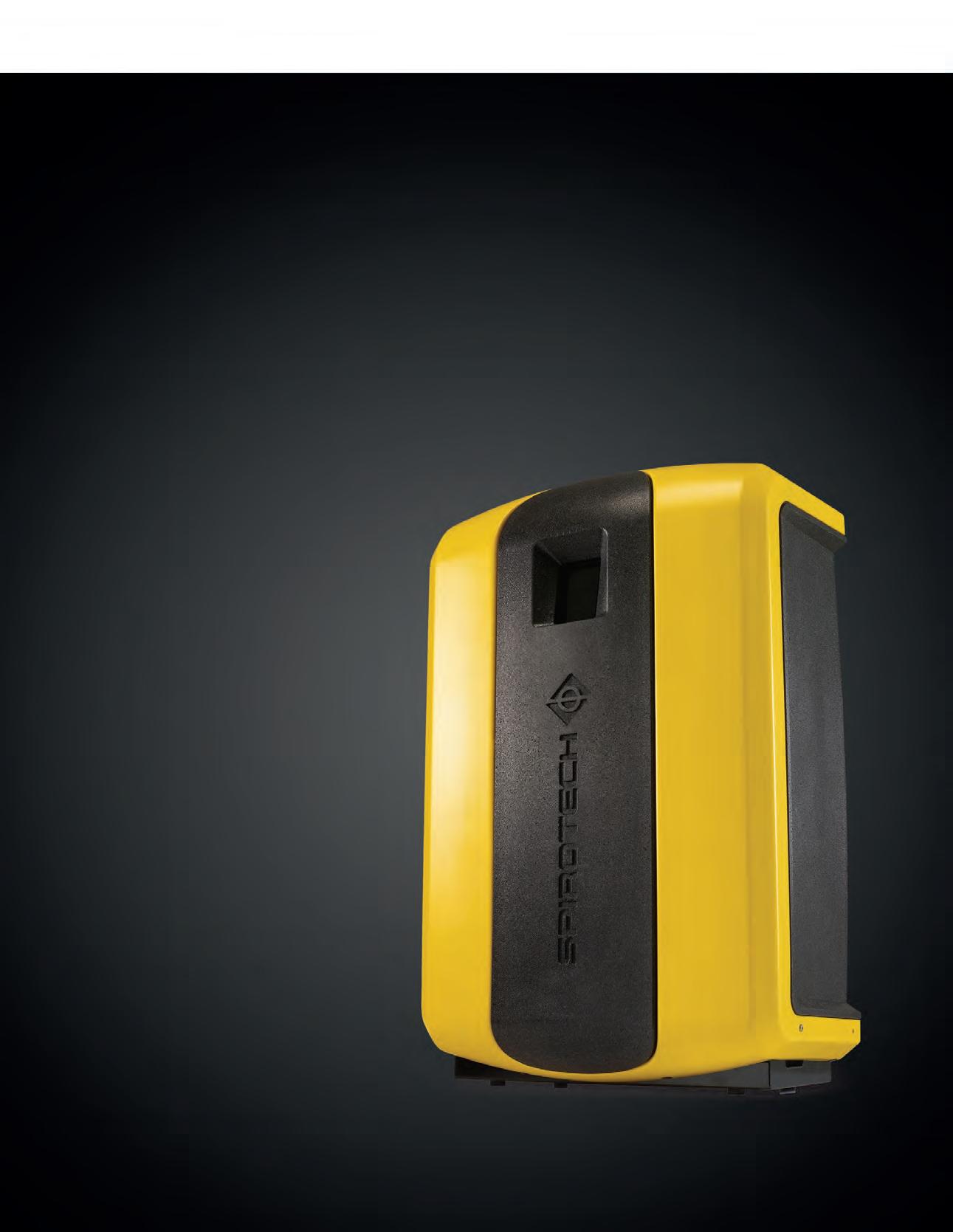
Regardless of installation location, pressure or temperature, the Spirovent Superior removes all dissolved gases from heating and cooling water systems. Once degassed, air problems can no longer occur, at any point, in the system. The Spirovent Superior can be installed at almost any point in a system and optionally replenish system water deficits.
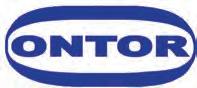
12 Leswyn Road, Toronto, Ontario M6A 1K3
Tel: (416) 781-5286 Fax: (416) 781-7680
E-mail: info@ontor.com Orders: orderdesk@ontor.com
Covering Canada Coast-to-Coast www.ontor.com
By Ray Wohlfarth
Diagnosing sudden boiler faults
You are dispatched to a no heat call on a Friday afternoon and the weather forecast calls for the temperature to drop significantly. The dispatcher said it was a Weil-McLain furnace. That’s not a furnace brand I know, you think. Arriving on site, you see a cast iron sectional boiler in the basement and start feeling the hairs on the back of your neck rise. You’ve never worked on a boiler before and to make matters worse, it’s steam. Relax, we’ve got this.
The owner said the boiler stopped working today. Remember, most sudden boiler faults are due to something electrical. Mechanical failures usually give a warning before failing. For example, the inducer fan or circulator may start squealing or vibrating before failing.
Let’s start by looking at the wiring diagram. I like to use the ladder diagram as its easier for me to troubleshoot. On the ladder diagram, the power is on the left, marked with an H, and the neutral side is on the right, marked with an N.
Remember each circuit requires a minimum of three things: power, a load, and a neutral. Without any one of these, we will have no circuit or heat. The circuit between the power and the load may have switches in the circuit, such as a thermostat or a low water cutoff.
The first thing I do is to identify the loads. The load is anything in the wiring diagram that consumes electricity. This could be a motor, valve, relay coil, circulator, light bulb, damper, transformer, or fan. I’ve identified four loads in this diagram, which means we have four different circuits: 1- transformer, 2low water cutoff, 3- vent damper, and 4- spark ignitor. I didn’t include the gas valve as that is an article by itself.
The next thing I do is determine the starting and end point for the boiler to fire. In this case, the starting point is where the 120 volts feeds the boiler (red star). The ending point is the universal spark ignition control (green star). Now we just have to figure out how to get voltage from the red star to the green star.
Ray Wohlfarth of Fire & Ice Heating & Cooling is an international author, columnist, and consultant specializing in commercial boilers. He has 40 years’ experience in air conditioning, boilers, burners, controls, steam and hydronics. Wohlfarth can be reached at ray@fireiceheat.com.
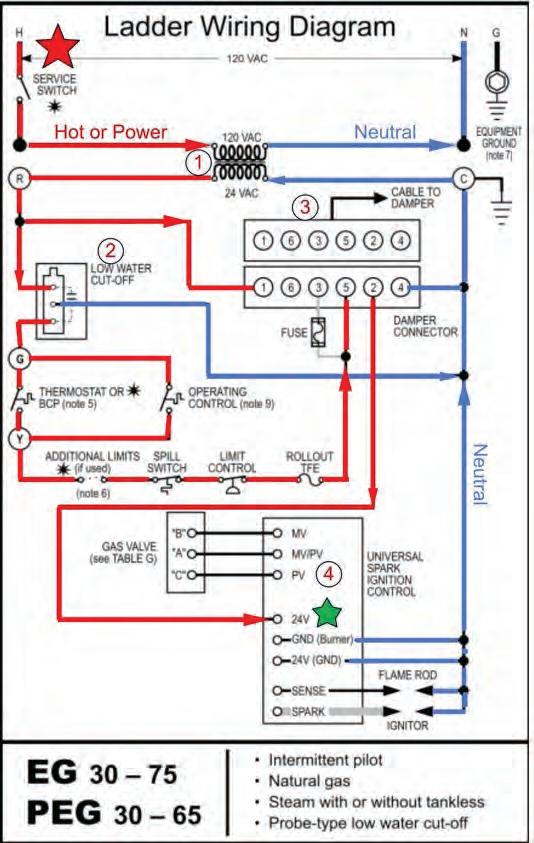
Ladder Wiring Diagram
On the ladder diagram above, the power is on the left, marked with an H, and the neutral side is on the right, marked with an N. Remember each circuit requires a minimum of three things: power, a load, and a neutral. Without any one of these, we will have no circuit or heat. The circuit between the power and the load may have switches in the circuit, such as a thermostat or a low water cutoff.
START WITH WHAT YOU KNOW
We know the vertical line on the far right is a neutral wire and any wire touching it is also a neutral wire. If a power wire touched the neutral wire, it would cause a short circuit and blow a fuse or trip a circuit breaker. I highlight or mark the wiring diagram neutral wires. In this case, they are marked blue. Once I mark all the neutrals, the remaining wires are going to be hot or power wires and I highlight them in red. It makes it easier to follow. Yes, I have been known to colour-code wiring diagrams on site using highlighters. The technician after you will thank you.
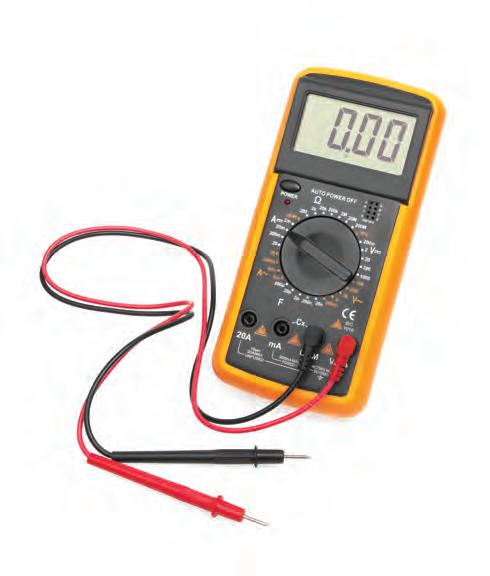
We now have a choice. You can either start at the 120-volt side (red star) and trace the path to the ignition control or work your way backward from the ignition control (green star).
If I were on this job, I would verify there was 120-volt power to the boiler. If there is no power, check for a tripped breaker, switch turned off, or a blown fuse feeding the boiler. Once I have 120 volts to the boiler, I will check for 24 volts on the ignition control. If there is power to the ignition control, it tells me two things. The first is the switches in the safety circuit are made and the second is the problem is on the fireside of the boiler. It could be the ignition control, igniter, flame sensor, or gas valve.
If there is no power on the ignition control, I know one of the safety controls are open. All the safety controls in the safety control circuit are wired in series. This means that if any control senses something out of the ordinary, it will shut off the boiler. I like to think of the switches in the safety circuit like steps to the gas valve or ignition control.
Let’s start at the red arrow and work our way down. We know there are 120 volts, so we move to the transformer outlet. (Load 1). We should have 24 volts there. If not, the transformer may be defective or tripped. When you see a circle with a letter or number inside, this usually ndicates terminal connection. You can test for 24 volts at the R terminal.
In the safety control wiring, we see this boiler has multiple switches; 24 volts leaves the transformer and flows to the first switch, the low water cutoff. If the boiler water is above the setpoint, the power should pass through the low water cutoff. If you have 24 volts on the G terminal, it means the low water cutoff is satisfied. The voltage then
goes to the second switch, the thermostat, BCP, or operating control. The BCP is a boiler control panel. This is the call for heat for the system. You can verify the boiler has a call for heat by testing terminal Y. If we have 24 volts on terminal Y, there is a call for heat.
The power leaves terminal Y and goes through any additional limits. If there are no additional limit controls, this may be jumped. Once that circuit is made, the power goes to the spill switch. The spill switch would be under the draft diverter and will shut off the boiler if it senses heat, meaning the boiler is having rollout or spillage.
If the temperature is below the spill switch temperature setpoint, the 24 volts flows to the limit control. The limit control on a steam boiler is a pressure control. A hydronic boiler will cycle on temperature. If the pressure on the boiler is less than the pressure control setpoint, 24 volts goes to the rollout TFE or thermal fuse element. The rollout TFE will melt the sensor and interrupt 24 volts if the temperature is excessive. It is usually mounted above where the gas enters the boiler. This is usually a one and done control and has to be replaced if it melts.
The last safety control is the end switch inside the flue damper. On a call for heat, the flue damper drives the damper open. Once open, the damper makes an end switch and allows voltage to pass. It will then travel to the spark ignition control (green star).
I hope this helps you effectively use a wiring diagram to troubleshoot a boiler on a Friday afternoon.
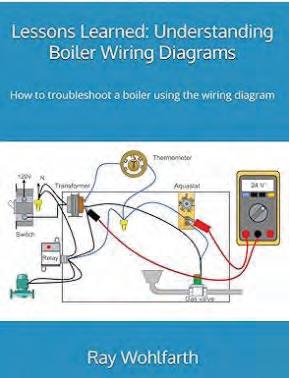
Wohlfarth recently released his wiring troubleshooting book.
PROJECT PROFILE
By Thomas Renner
SLIM SUITE
Contractor squeezes sophisticated system into tight-fitting mechanical room
Good
things often come in small packages. A complex installation by Stott HVAC Systems at a custom-built Toronto, ON home delivers outsized performance from a compressed mechanical room.
Working within a 36-sq. ft., space, Tyler Stott’s team installed heating and hot water components for a two-storey, 12-car garage that covers 2,500 sq. ft. and an 800- sq. ft. cabana room. The heating elements also deliver nearly 1,000 sq. ft. of heat for a snow and ice melt (SIM) system. The garage and cabana room − an enclosed space adjacent to a pool − were additions to a 20-year-old, 10,000-sq. ft. home.
“It was more like a closet than a mechanical room,” Stott said. “We had to use every square inch and had to share the room with the electrician and the plumber. We were all fighting for our space.”
In the mechanical room for the cabana and garage, Stott selected a high efficiency condensing gas boiler. He also replaced four boilers in the home with the same model boiler. The cabana room mechanicals include a wall-mounted indirect water heater. Stott mentioned that installing and squeezing the equipment into the tightfitting mechanical room was one of the most challenging aspects of the project.
TIGHT FIT
Mechanical rooms are sometimes referred to as the “brains of the house.” They include critical components for comfortable living, such as HVAC equipment, plumbing systems, electrical panels and wiring and security control panels. A well-designed “brain” provides easy access for maintenance and repairs, ensuring the long-term functionality of critical systems. Whenever an issue arises, your first stop to diagnose the problem will likely be the mechanical room.

Stott HVAC Systems installed elements for heating and hot water for a two-storey, 12-car garage and a cabana room in a 36-sq. ft. mechanical room. The system also directs a snow melt system.
Thomas Renner writes on building, construction and other trade industry topics.
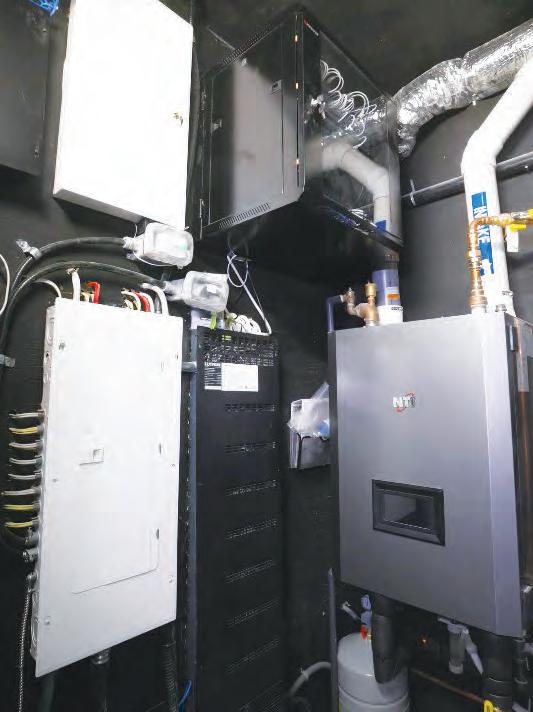
The mechanical room includes a boiler, indirect tank for domestic hot water and thermostats. Equipment for electrical and other mechanical services is also included in the tight-fitting space.
Sometimes, however, builders, architects or even homeowners pinch the mechanical room footprint in order to increase square footage in other areas of the home where they can add living functionality.
“A lot of times we get jammed up in closets where it’s not going to look the most pretty,’’ Stott said. “In this case, there wasn’t a ton of space to begin with. My suggestion was to create a mechanical room in the garage, but the client didn’t want to give up any of that space. He is a car collector, so that was not going to be an option. Instead, he agreed to sacrifice some cabana room space. We were trying to accomplish a lot in a limited space.” Stott explained that the mechanical room was six feet by six feet. “It would have been optimal to have double that size,” Stott said.
SOPHISTICATED SETUP
The heating components alone are quite extensive. A boiler delivers in-floor heating for the cabana and to a SIM system around the garage and cabana room. The mechanical room also includes an indirect tank for domestic hot water.
Photos by Stott HVAC
“I wanted to have all the same boilers throughout the house,’’ Stott said. “I also put together parts packages, so I have every single replacement part for the boilers on site. If there’s ever a failure, our team will show up and all the parts are already there. There won’t be any downtime for the client.”
“We also installed thermostats in the mechanical room, and each zone is run off of slab and sensors,’’ Stott states. “People won’t even realize that they are there. We removed that wall acne from the interior space, and it’s all controlled from the mechanical room and is Wi-Fi compatible.”
Despite the space crunch, Stott said the subcontractors who installed components in the mechanical room worked together to accommodate all parties.
“The installation was staggered,’’ Stott explained. “There’s barely enough space in that room for one person. We coordinated the space and got on the same page about what was going where. We worked with the builder to make it happen, and the client was very accommodating.”
MULTIPLE BOILERS
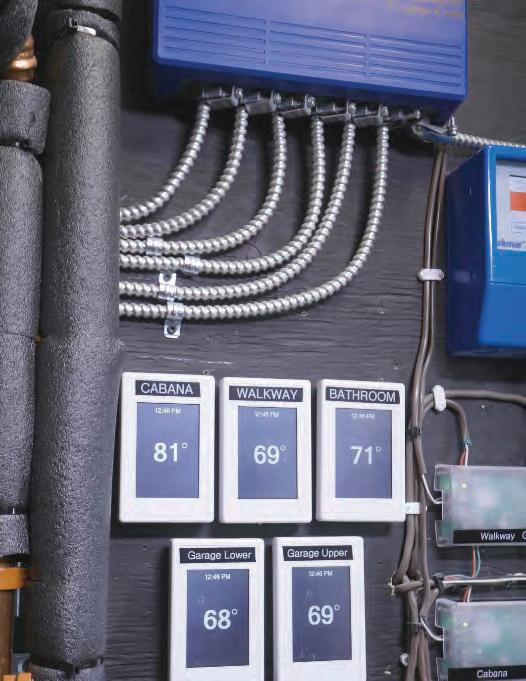
“A lot of times we get jammed up in closets where it’s not going to look the most pretty,’’ Stott said. “In this case, there wasn’t a ton of space to begin with.”
Stott, lead team member Jay Singh and the crew also replaced four other boilers in the home with 324 MBH units. The boilers have onboard Wi-Fi and a touchscreen that is easy and intuitive, but also powerful. The boilers deliver 95.4 per cent thermal efficiency.
“I wanted to have all the same boilers throughout the house,’’ Stott said. “I also put together parts packages, so I have every single replacement part for the boilers on site. If there’s ever a failure, our team will show up and all the parts are already there. There won’t be any downtime for the client.”
The mechanical room indirect unit features CFC-free 2 in. ultra-high density EPS insulation to ensure low standby losses and each unit came complete with a thermostatic mixing valve, tank sensor and T&P valve. Recovery rates exceed most industry standards. The space-saving design was also an important consideration for the small space.
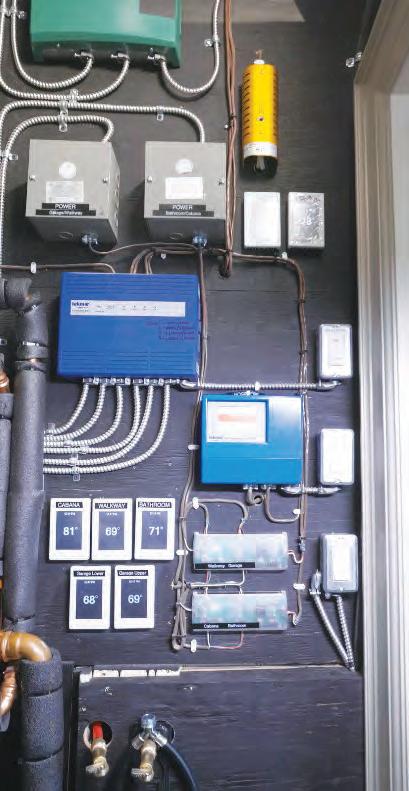
SIGNATURE PROJECT
The elaborate project is one of the highlights of Stott’s extensive career experience. Opportunities are rare to install equipment for mansions of such opulence.
“It’s definitely on our Top 10 list,’’ Stott said. “I’ve never worked on a project that included a two-floor garage. It was an amazing opportunity to be part of it, and we got to take care of one of our best clients.”
Zones are all controlled from the mechanical room.
JOBSITE JARGON
WIN!
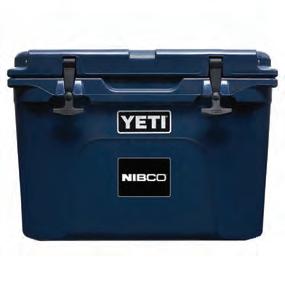
Match the terminology you hear in the field to the correct definition or function by September 9, 2025 and enter for your chance to win a Yeti cooler from NIBCO. This contest is open to Mechanical Business subscribers in Canada. Send your answers to kerry.turner@mechanicalbusiness. com or enter online at mechanicalbusiness.com.
JOBSITE JARGON
4) Air-cooled chiller B) Fans pull ambient air through the condensing coil to eliminate heat
Answer 4,B
Thank you for participating!
A) Transfers air to small (2 in. ID) round outlets in each room through flexible tubing that weaves in between spaces in the walls, ceilings or floors
B) Fans pull ambient air through the condensing coil to eliminate heat
C) Describes the use of water as a heat-transfer medium in heating systems, and a cooling-transfer medium in cooling systems
D) Indicate a system’s capacity to store energy
E) Relies on a single phase alternating current (AC) in the stator winding to create a rotating magnetic field
F) Comprised of a HP and thermal storage tanks (ideally one for DHW and another one for space heating and cooling)
G) A small device installed in a closed system of fluid in residential and light commercial applications
H) Sets out the minimum provisions for the installation, extension, alteration, and renewal of hydronic heating systems
I) Heating loads, other than those for space heating and domestic hot-water heating
J) Designed to reduce incoming water or steam pressure to a safer constant predetermined downstream level
K) Condensing system is connected to a cooling tower for heat rejection
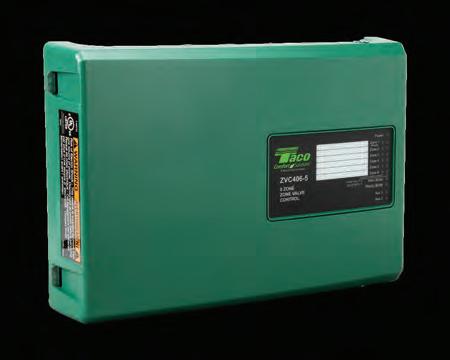
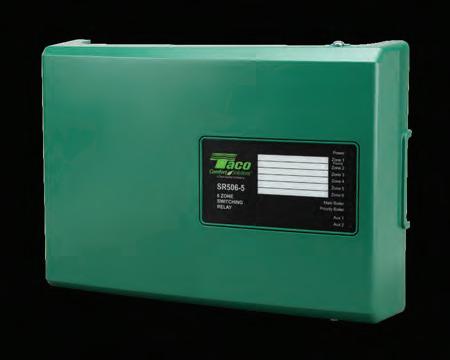
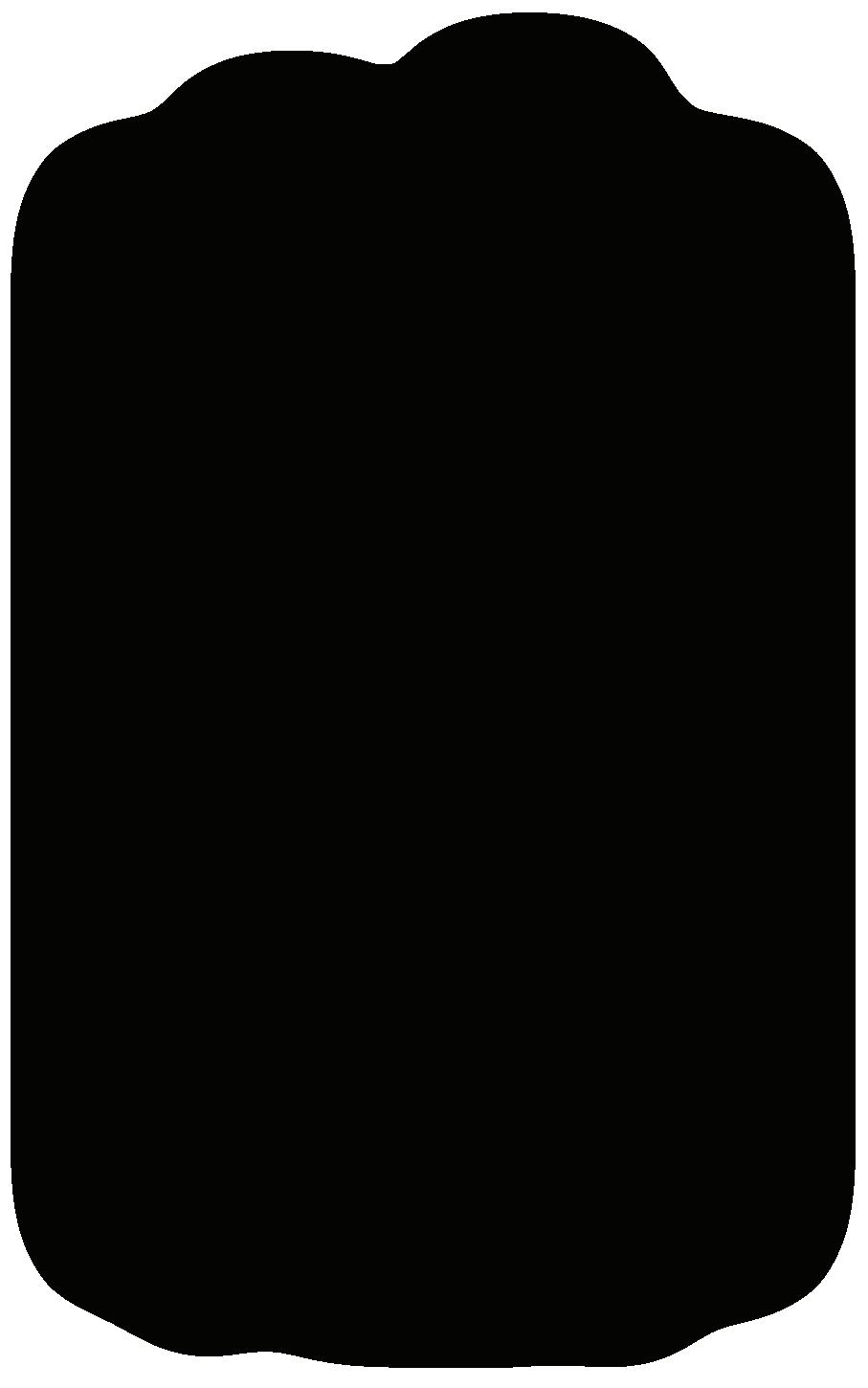
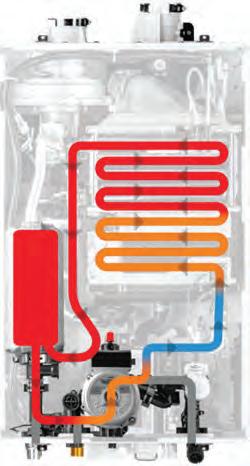
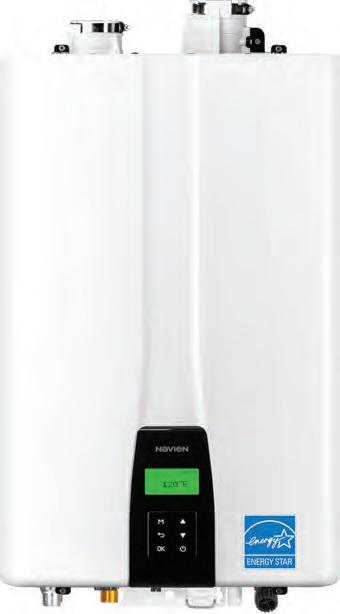
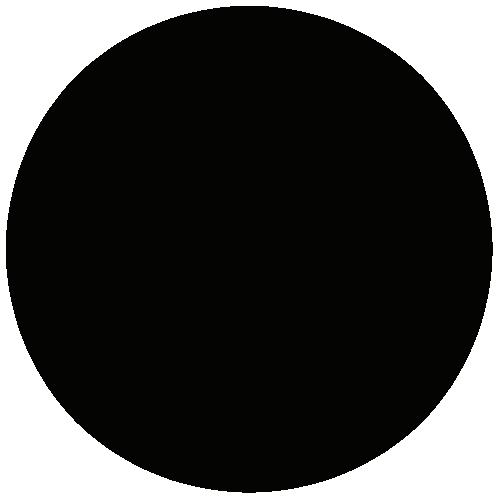
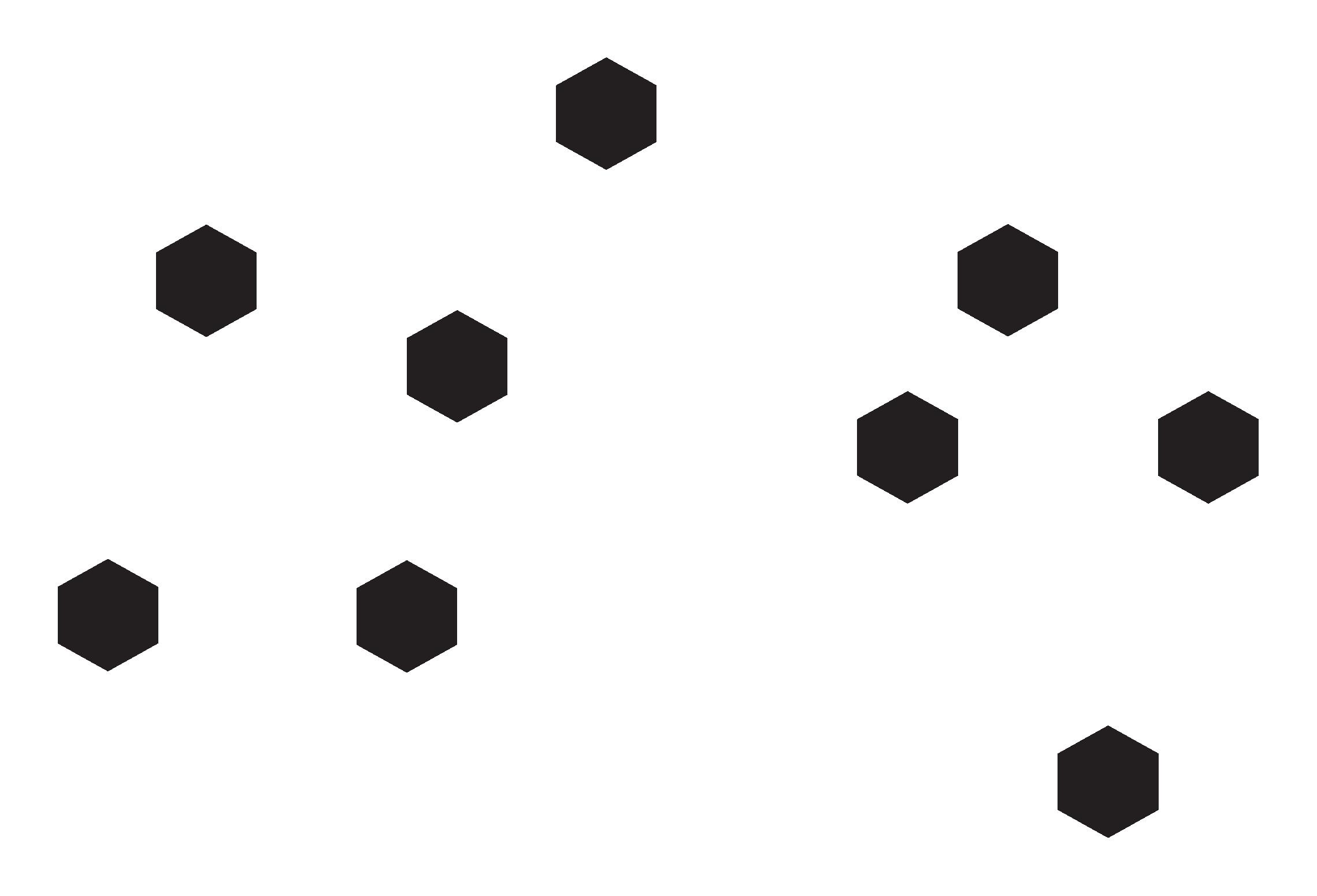

Wolseley