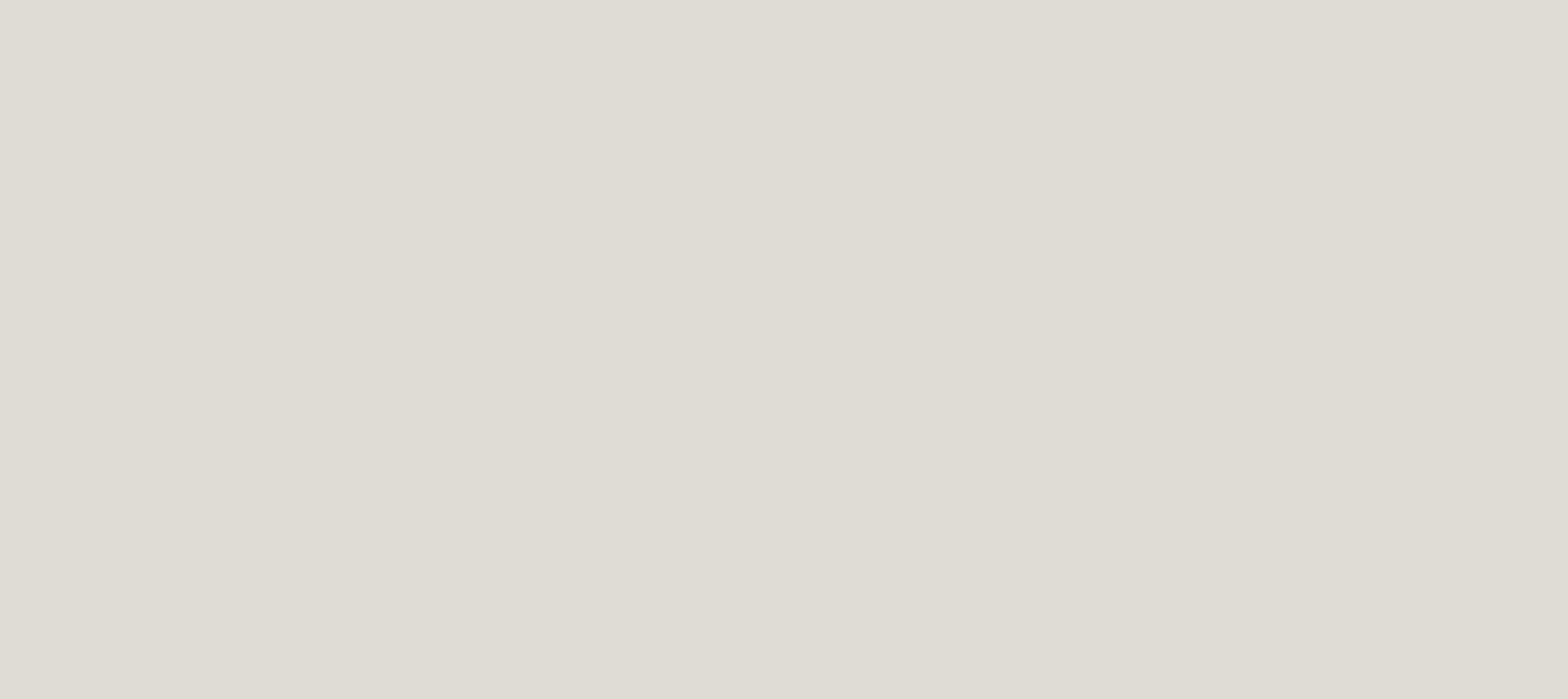
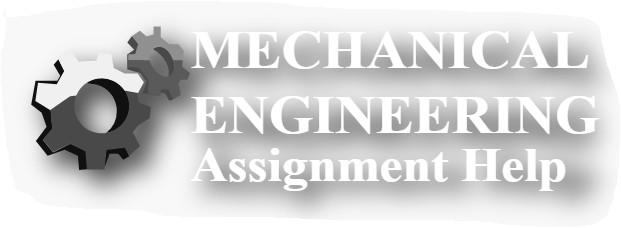
2.Question: A cantilever beam with a length of 4 meters is subjected to a point load of 10 kN at its free end. The beam has a rectangular crosssection with a width of 50 mm and a height of 100 mm. Determine the maximum deflection of the beam.
Solution: To determine the maximum deflection, we can use the formula for deflection of a cantilever beam under a point load: δ = (P * L^3) / (3 * E * I)
Where: P = Point load (10 kN) L = Length of the beam (4 m) E = Young's modulus of the material I = Moment of inertia of the beam cross-section For a rectangular cross-section, the moment of inertia (I) can be calculated as: I = (b * h^3) / 12
Given: b = 50 mm = 0.05 m (beam width) h = 100 mm = 0.1 m (beam height) E = Young's modulus of the material (depends on the material)
Substituting the values: I = (0.05 * 0.1^3) / 12 I = 0.00004167 m^4
Now, we need to convert the point load to Newtons: P = 10 kN = 10,000 N
Substituting the values into the deflection formula: δ = (10,000 * 4^3) / (3 * E * 0.00004167) δ = (10,000 * 64) / (3 * E * 0.00004167) δ ≈ 384,000 / (E * 0.00004167)
Therefore, the maximum deflection of the cantilever beam depends on the Young's modulus of the material used. You would need to know the specific material properties to calculate the exact value of the deflection.
For Any Help Regarding Mechanical Engineering Assignment Help Visit:- https://www.mechanicalengineeringassignmenthelp.com/
1.Question: A heat exchanger consists of a shell-and-tube design with two fluids. The hot fluid enters at 300°C and leaves at 150°C, while the cold fluid enters at 20°C and leaves at 100°C. The heat transfer coefficient on the hot fluid side is 200 W/m²·K, and on the cold fluid side is 500 W/m²·K. Calculate the overall heat transfer coefficient and the heat transfer area required to achieve a heat transfer rate of 500 kW.
Solution: To calculate the overall heat transfer coefficient (U), we can use the following equation: 1/U = 1/hi + R + 1/ho
Given: hi = 200 W/m²·K (hot fluid heat transfer coefficient) ho = 500 W/m²·K (cold fluid heat transfer coefficient) R = Thermal resistance of the wall separating the two fluids (depends on the material and thickness)
Assuming R to be negligible, the equation simplifies to: U = (hi^(-1) + ho^(-1))^(1)
Substituting the given values: U = (200^(-1) + 500^(-1))^(-1) U = (0.005 + 0.002)^(-1) U = (0.007)^(-1) U = 142.86 W/m²·K
Now, to calculate the heat transfer area (A), we can use the following equation: Q = U * A * ΔTlm
Given: Q = 500 kW (heat transfer rate) ΔTlm = (ΔT1 - ΔT2) / ln(ΔT1/ΔT2)
ΔT1 = 300°C - 20°C = 280°C ΔT2 = 150°C - 100°C = 50°C
Substituting the values: ΔTlm = (280 - 50) / ln(280/50) ΔTlm = 230 / ln(5.6) ΔTlm ≈ 88.85°C
500,000 = 142.86 * A * 88.85 A = 500,000 / (142.86 * 88.85) A ≈ 39.09 m²
Therefore, the overall heat transfer coefficient is 142.86 W/m²·K, and the heat transfer area required to achieve a heat transfer rate of 500 kW is approximately 39.09 m².
3.Question: A gas turbine power plant operates on an ideal Brayton cycle. The compression ratio is 10, and the maximum cycle temperature is 1400°C. Determine the thermal efficiency of the cycle.
Solution: The thermal efficiency (η) of the Brayton cycle can be calculated using the following formula:
η = 1 - (1 / r^(γ-1))
Where: r = Compression ratio γ = Specific heat ratio of the working fluid
Given: r = 10 (compression ratio)
The specific heat ratio (γ) depends on the working fluid. For air, γ is typically 1.4.
Substituting the values: η = 1 - (1 / 10^(1.4-1)) η = 1 - (1 / 10^0.4) η = 1 - (1 / 2.5119) η ≈ 0.6006
Therefore, the thermal efficiency of the ideal Brayton cycle in this gas turbine power plant is approximately 60.06%.
4.Question: A rotating shaft made of steel with a diameter of 80 mm is subjected to a torque of 500 Nm. Determine the maximum shear stress and the maximum angle of twist along the length of the shaft.
Solution: To determine the maximum shear stress (τ) in the shaft, we can use the formula:
τ = (T * r) / (J * τ_max)
Where: T = Applied torque (500 Nm) r = Radius of the shaft (diameter/2 = 80 mm/2 = 40 mm = 0.04 m) J = Polar moment of inertia of the shaft cross-section
τ_max = Maximum shear stress (depends on the material)
For a solid circular shaft, the polar moment of inertia (J) can be calculated as: J = π * (d^4) / 32
Given: d = 80 mm = 0.08 m (shaft diameter)
Substituting the values: J = π * (0.08^4) / 32 J = π * 0.000004096 / 32 J ≈ 1.2825e7 m^4
Now, we need to convert the torque to Nm: T = 500 Nm
Substituting the values into the shear stress formula: τ = (500 * 0.04) / (1.2825e-7
* τ_max) τ = 20,000 / (1.2825e-7 * τ_max) τ ≈ 1.557e+14 / τ_max
To determine the maximum angle of twist (θ) along the length of the shaft, we can use the formula:
θ = (T * L) / (G * J)
Where: L = Length of the shaft G = Shear modulus of the material
Given: L = Length of the shaft (depends on the specific problem) G = Shear modulus of steel (depends on the steel grade, typically around 79 GPa)
Substituting the values: θ = (500 * L) / (79e9 * 1.2825e-7) θ ≈ 3.911e+18 * L
Therefore, the maximum shear stress in the shaft is approximately 1.557e+14 / τ_max (depends on the material), and the maximum angle of twist along the length of the shaft is approximately 3.911e+18 times the length of the shaft (L).