
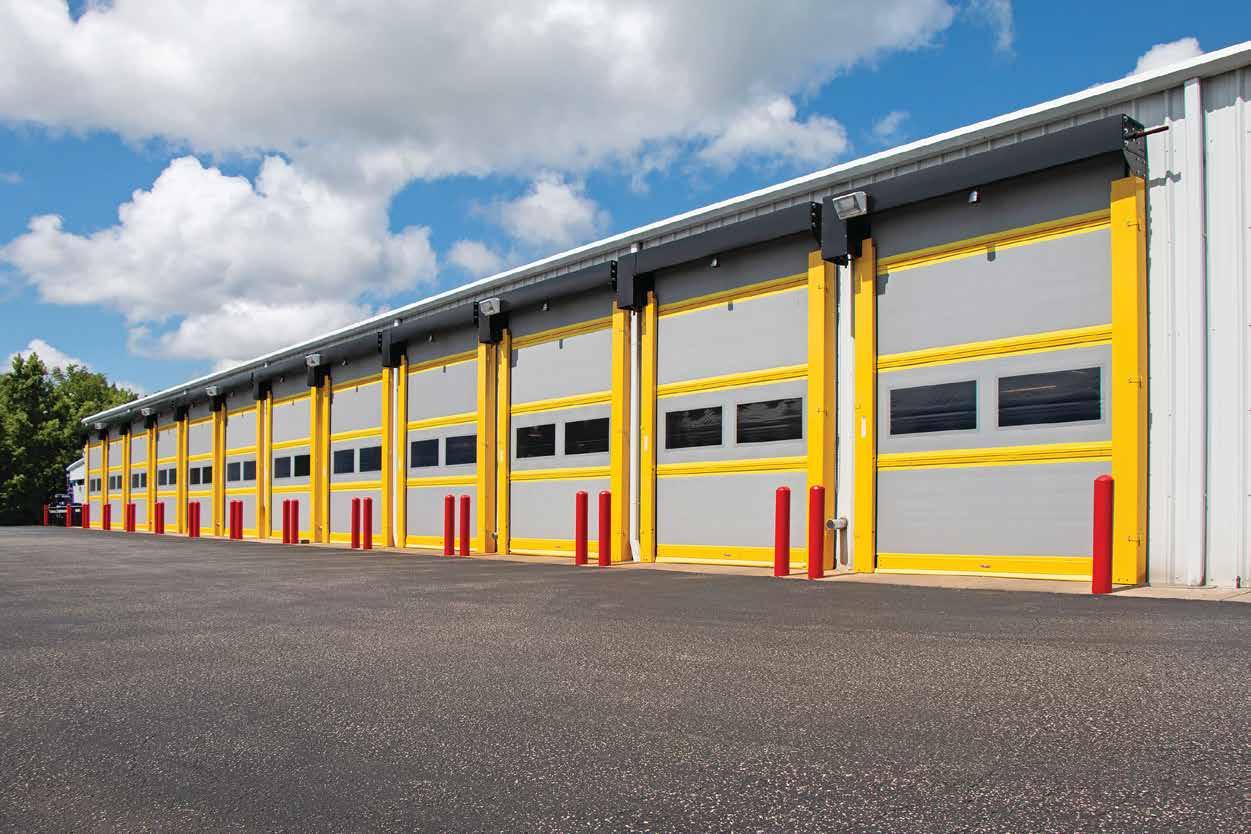
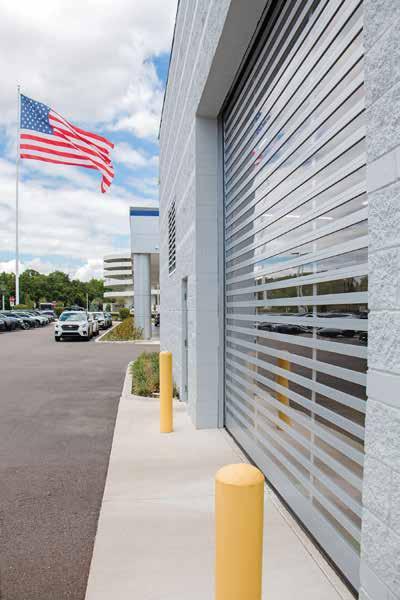
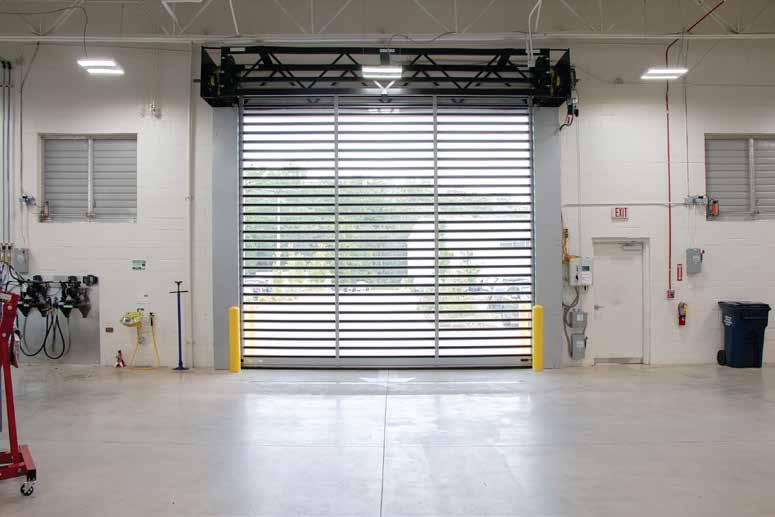
Go beyond. Repeat.
Trust your next construction project to PJ Dick.
PUBLISHER
Master Builders’ Association of Western PA www.mbawpa org
MANAGING EDITOR
Ben Atwood 412-922-3912 ben@mbawpa.com
EDITOR Jeff Burd jburd@talltimbergroup.com
PRODUCTION
Carson Publishing, Inc.
Kevin J. Gordon
ART DIRECTOR
Carson Publishing, Inc.
GRAPHIC DESIGN Blink
CONTRIBUTING PHOTOGRAPHY
CREW Pittsburgh Ferry Electric Company
Gerville Photography
Chad Isaiah Photography Mark J Media
Massery Photography
Master Builders’ Association of Western PA NAIOP Pittsburgh Nala Marketing Andrew Rugge Stellar Image Studios
SPONSORSHIP DIRECTOR Mary Chuderewicz mchuderewicz@mbawpa org
MORE INFORMATION:
BreakingGroundTM is published by the Master Builders’ Association of Western Pennsylvania, 412-922-3912 or www.mbawpa.org
Archive copies of BreakingGroundTM can be viewed at www.mbawpa.org
No part of this magazine may be reproduced without written permission by the Publisher. All rights reserved.
This information is carefully gathered and compiled in such a manner as to ensure maximum accuracy. We cannot, and do not, guarantee either the correctness of all information furnished nor the complete absence of errors and omissions. Hence, responsibility for same neither can be, nor is, assumed.
Built for Speed and Resilience: How Prefabrication Shaped Carnegie Mellon University’s Forbes Beeler Apartments
Building a Future Without Waste: A Case for Greener Construction
Michael Volpatt, Vice President of Marketing and Innovation, Volpatt Construction and Bhavini Patel, Executive Director, Sustainable Pittsburgh
Activity slowed somewhat in Western PA as the second quarter wound down. Following the typical surge in bidding at universities for summer break projects, and end-of-fiscal year bidding at the two major hospital systems, the pace of new opportunities slowed for general contractors and construction managers. Uncertainty about the U.S. economy and certainty about reduced federal funding chilled decision-making for capital projects in the private sector and institutional markets.
There were also the first signs of declining backlogs overall. While there are numerous major projects under construction, the slower winter bidding season meant that contractors’ work in progress is outpacing backlog building. While this will not be true for all contractors, the overall impact of the shift in the market resulted in a 10 percent decline in hours worked for the building trades in the first quarter compared to a year earlier.
The second-quarter slowdown followed a first quarter that had boosted the work in the pipeline, so the comparison to 2024 looks unusually similar. Through the first week in June, projects underway or contracted totaled $1.824 billion. During that same period in 2024, construction starts and new contracts totaled $1.979 billion, excluding the work put in place at the UPMC Presbyterian Heart and Transplant Hospital. Activity after the first five months of 2025 would have been higher but several large projects slated to get underway, notably the $140 million AHN South Hospital in Canonsburg, were deferred until at least later in 2025.
Among the most active non-residential sectors, waste and water treatment plants saw $241 million in starts and contract awards, followed by industrial at $154 million, K-12 education at $142 million, healthcare at $141 million, and retail at $122 million. The sector with the largest investment was multi-family, which saw $467 million in construction since the start of the year.
Multi-family construction has maintained a similar pace of construction as in 2024, which was an above-average year, despite the dual challenges of higher costs and challenging financing environment. Through May 31, developers had pulled permits for nearly 1,360 new apartment units. That is about 14 percent fewer than in 2024, but 27 percent more than the average through five months since
2020. Rents in metropolitan Pittsburgh have declined slightly year-over-year but the fundamental drivers of demand for new construction – increased employment among younger workers, growth in retiree population, and low inventory of single-family homes – are all pushing demand higher. Owners of new apartment buildings continue to report leasing activity that meets pro forma schedules and solid traffic.
Similar challenges, plus an acute shortage of buildable lots, dragged the construction of new single-family homes lower by 15.9 percent, compared with the first five months of 2024.
Conditions were particularly tight for the construction of new single-family detached homes. Permits were issued for 721 new detached homes through May 31, a decline of more than 25 percent. Demand for new construction was suppressed by mortgage rates that have been close to seven percent all year, and costs that have pushed prices higher by double-digits.
Prices for existing homes have increased at a lower rate. Residential real estate services report that the average sales price was higher by 2.5 to 4.8 percent in May 2025 compared with a year earlier. Firms report that more homes were for sale in May versus April or a year earlier; however, sales data for Allegheny County shows that sales declined roughly 30 percent year-over-year in May. There were 693 home sales in Allegheny County in May at an average cost-per-square-foot that was $177.91, or $5 lower than a year ago.
Pittsburgh’s economy continues to be solid, despite the ongoing decline in the civilian workforce. The commonwealth’s
Source: Bureau of Labor Statistics, Federal Reserve Bank of St. Louis
Source: Allegheny County
Department of Labor and Industry’s latest employment data shows unemployment in the eight-county metropolitan area remained at 3.5 percent in April. That is identical to the statewide unemployment rate and 40 basis points lower than the U.S. unemployment rate of 3.9 percent.
Hiring in Pittsburgh improved from March and April 2024. There were 1,215,000 people employed in Pittsburgh in April 2025, an increase of 13,800 from March and 13,700 from a year earlier. April’s employment level lags the 30-year high of December 2019 by less than 6,000 jobs. Only 42,800 were unemployed. Compared to April 2024, employment grew the fastest in healthcare and social services, which added 8,300 jobs. Ambulatory healthcare employment grew by 3,400 jobs. Construction employment was 400 jobs higher. Manufacturing showed the largest decline, shedding 1,800 jobs over the past year.
The most recent Beige Book from the Federal Reserve Bank showed the super-regional economy faring better than most regions and the country overall, although responses did not reflect robust activity. At the U.S. level, responses from business owners about the April-May period showed increased pessimism about the economy and a slowdown in investment decisions. Businesses in the
Federal Reserve Bank of Cleveland’s Fourth District footprint, which includes Western PA, suggested flat business activity and expectations of the same in the coming months.
Businesses reported a pullback in consumer spending and demand for manufactured goods, but that demand for professional and business services increased. Employers reported increased employment levels, although there were more mentions of layoffs. More businesses reported better labor availability and lower wage pressure; however, nonlabor cost inputs were reported as growing at a robust pace because of tariffs, which was pushing selling prices moderately higher.
The feedback on prices reflected the general uncertainty about trade policy and future demand. Contacts from multiple sectors noted that tariffs were now increasing the costs of materials that they import, but also that domestic suppliers were raising prices because of overtime costs needed to meet growing demand for non-imported materials. The share of firms reporting that they increased prices was higher than in the February-March period. Construction-related firms noted more often that they had increased prices because of tariffs on key materials like steel.
Reports from residential construction and real estate contacts suggested moderate growth in demand for homes in recent weeks. On balance, residential construction and real estate contacts anticipated continued growth in demand in the
said that uncertainty around economic policy was causing businesses to be more cautious with their construction investment decisions. Contacts expected flat demand in the coming months, anticipating that economic and policy uncertainty will continue to weigh on activity.
One metric that indicates economic deterioration, the number of business bankruptcy filings, turned more negative in the first quarter of 2025. According to the records of the Administrative Clerk of the U.S. Bankruptcy Court for Western Pennsylvania, 51 businesses filed for bankruptcy in January through March, an increase of 24 percent from a year earlier.
While the increase is a source of concern, the makeup of the businesses seeking protection are mostly limited to industries experiencing macroeconomic stresses. Nearly 20 percent of the bankruptcies were for coal-based companies. The balance was primarily in healthcare-related services and commercial real estate. Several of the bankruptcy filings were for commercial properties in receivership. The one positive trend from the first quarter’s bankruptcy filings was that only 19 were for Chapter 7 liquidations. That level was 26.9 percent lower than the first quarter of 2024.
Going into the second half of the year, the outlook is more uncertain than six months ago. The prospects for capital spending in higher education and healthcare are poor, with the exception of the major capital projects underway. Pending Allegheny Health Network’s reevaluation of the project in
Rooted in Pittsburgh, our client demand expanded the firm’s reach to 19 offices in 10 states. Call us for construction and surety-related questions.
William D. Clifford & W. Alan Torrance, Jr.
Included in The Best Lawyers in America 2023 Commercial Litigation, Construction Law, and Litigation-Construction
Canonsburg, and the $400 million cardiovascular tower at Allegheny General Hospital, that sector could see a boost in activity before year’s end. Those projects aside, hospital systems continue to focus on infrastructure and upgrades to clinical or diagnostic services with certainty about reimbursement.
Public construction is healthier than it has been since before the pandemic, although that market has seen numerous projects dashed by higher construction costs. Despite the higher volume of construction, several school districts have bid major projects that came in higher than expected. The $25 million Mars Area Elementary School and $18 million Carnegie Elementary School are two examples projects that bid in the spring, and attracted good coverage from the market, but were nonetheless over budget.
Infrastructure spending remains higher than normal. The $325 million wet weather pump station at ALCOSAN, part of its massive infrastructure upgrade, bids in late August. No other major waste and water projects are expected to bid until late 2025 or 2026.
Like in the first half of 2025, the strongest market segment for the balance of the year might be multi-family, although most of the projects in the apartment pipeline have seen similar struggles with budgets. Higher construction costs and higher borrowing costs have made it tougher to reconcile with the potential rents. Among the multi-family projects in the queue 412-281-7272
Bowles Rice continues to expand its respected construction law practice into Pennsylvania, Ohio, and beyond. Our senior construction attorneys in Pennsylvania have over 90 years of construction experience between them, representing every facet of the construction industry—from general contractors, subcontractors, suppliers, and developers to design professionals and municipal and private owners. We focus on providing responsive, efficient, and cost effective representation for our construction industry clients. We understand the business, and we understand the law that you will be required to navigate and overcome to be successful.
• Contract Negotiation and Formation
• Project Delivery System Analysis
• Project Management Assistance
• Dispute Avoidance and Dispute Resolution
• Payment and Performance Bond Claims
• Mechanics’ Lien Claims
• Delay, Disruption and Acceleration Claims
• Federal and State Prevailing Wage Issues
• OSHA Compliance and Citations
• Bid Disputes
• Prompt Payment Act Claims
• Employment Disputes
• AAA Arbitration/Mediation Panel Members
Brad Mellor bmellor@bowlesrice.com
Damon Thomas dthomas@bowlesrice.com
Tom Weiers tom.weiers@bowlesrice.com
Attorney: Taylor Frankovitch
BY BEN ATWOOD
idway through 2025, U.S. markets and economic indicators present a mixed but stabilizing picture. Ongoing concerns about tariffs are keeping businesses and consumers on edge, but economic data points remain healthy.
On April 2nd, President Trump announced reciprocal tariffs on many countries. On April 9th, the rates went into effect but before the end of that day the administration suspended most of the higher tariffs to allow 90 days for negotiations while maintaining a 10 percent levy on nearly all global goods except for China.
This escalated trade tensions with China considerably, with each country retaliating with increasingly tariffs hitting unprecedented levels in mid-April. On May 8th, the U.S. and Britain reached a deal and on May 12th, the U.S. and China agreed to roll back most of the extreme tariffs declaring a 90-day truce. On May 25th a similar pause occurred with the European Union, delaying their 50 percent tariff hikes until July 9th.
On May 28th, the U.S. Court of International trade halted most of the President’s tariffs, ruling that he overstepped his authority. The next day, The Court of Appeals for the Federal Circuit temporarily paused the effect of the rulings, meaning the tariffs remained in place while the case proceeds. That same day, the President signed executive orders relaxing some of the 25 percent tariffs on automobiles and auto parts to ease import taxes for vehicles made with foreign parts but assembled domestically.
The uncertainty and back and forth has muddied the economic waters, with consumer sentiment and fears not entirely aligning with economic data. The S&P 500 has declined by 2.7 percent over the past six months, with the index experiencing a sharp drop in early April following the announcements of new global tariffs.
But the market has partially recovered as some of those measures were reversed, renegotiated, or halted by courts. From May to June, the S&P has gained 3.39 percent. The Dow Jones Industrial Average followed a similar trajectory, up 1.5 percent from May to June while remaining down 6.3 percent since the start of the year.
The Federal Reserve’s GDPNow model was updated in late May and now forecasts real GDP growth of 3.8 percent for the second quarter, a notable revision from its March projection of a 3 percent contraction. The uptick is largely attributed to improved net export performance. In parallel, the Bureau of Economic Analysis (BEA) released its second estimate for first quarter gross domestic product (GDP). It reported a 0.2 percent decline, an improvement from their initial estimate of 0.3 percent. BEA revised its GDP price index slightly downward to 3.3 percent, while personal consumption expenditures (PCE) price index remained at 3.6 percent.
The Federal Reserve Bank of Cleveland, which covers western Pennsylvania, reported that commercial construction activity experienced a slight decline. This downturn was attributed to the uncertainty regarding the overall economy and the impact of tariffs. Builders and developers expressed concerns that the uncertainty would persist, leading them to anticipate flat demand in the coming quarter. Despite these concerns, residential construction and real estate contacts remained more optimistic.
The Federal Open Market Committee (FOMC) met on May 28th and opted to maintain current interest rates. Officials within the FOMC emphasized continued inflationary concerns and the growing uncertainty in bond markets. As of June 4th, the yield on the U.S. 10-year Treasury stands at 4.46 percent, a modest increase from 4.41 percent a year ago and slightly above the longterm average of 4.25 percent. The recent uptick in yields is attributed to investor concerns over tariffs and the growing federal deficit.
The FOMC also warned that a shift in the U.S. dollar’s safehaven status could have long lasting economic implications. Fed commentary acknowledges potentially difficult
“We partnered with the Local 66 in 2011. Since then, we’ve been able to take on many more clients, more difficult work, due to the contribution of their great staff.”
J.J. Stefanik - President Stefanik’s Next Generation Contracting Co.
policy tradeoffs ahead, especially if inflation persists while growth and employment weaken.
Goldman Sachs President Jason Waldron noted on May 29th that the investment banking outlook remains “quite good,” citing continued activity in large scale mergers and acquisitions that are occurring despite ongoing market volatility. That same month, Goldman also raised its forward outlook for the S&P 500 from 19.5 to 20.4 and increased its 12-month price target for the index from 6,200 to 6,500. The bank also reduced its recession probability from 45 percent to 35 percent.
PNC Chief Economist Gus Faucher, in an early June outlook, also advised that the firm does not forecast a recession. On May 13th, JP Morgan Chase also withdrew its previous recession call for 2025, citing the easing trade restations with China. The bank now expects GFP growth of 0.6 percent for the year, up from its earlier project of 0.2 percent, while Barclay’s updated its 2025 forecast
”Mascaro Construction Company is a regional general contractor that’s been around for 33 years. Proud to say that 30 of those years, we’ve had a relationship with the Operating Engineers providing us with skilled craftspeople that run all the equipment that we have.”
John C. Mascaro Jr. - President Mascaro Construction
years.”
dismissing the possibility of a recession entirely.
The labor market continues to show modest growth. According to the latest Bureau of Labor (BLS) jobs report, non-farm payrolls rose by 139,000 in May. Job gains occurred in health care, transportation, warehousing, and financial activities, while federal employment declined. Health care added 62,000 jobs and leisure and hospitality added 48,000.
Average hourly earnings rose by 0.4 percent in April and are up 3.9 percent year over year. BLS also revised downward previous payroll figures by a combined 95,000 for March and April.
The unemployment rate held firm at 4.2 percent through May.
Long term unemployment (27 weeks or more) increased by 179,000 to 1.7 million, accounting for 23.5 percent of the total unemployed population. Other labor force metrics, including participation rate and involuntary part time employment, showed little change but continued a long-term slow decline.
More ominous was the 546,000 workers who ceased looking for work from April to May.
Data from ADP, a private payroll processer, also indicates modest levels of employment growth. Their early June release shows private sector employers added 37,000 to their
payroll in May. Interestingly, mid-sized firms led growth, while small and larger firms reported net losses in payroll. Financial activities added 20,000 to their payrolls, while leisure and hospitality gained 38,000.
Despite the stable employment gains, consumers remain rattled by all the uncertainty of the ongoing tariff implementation. The University of Michigan’s Consumer Sentiment index held flat at 52.2 in May, down from 69.1 from that same month in 2024. The current conditions sub-index fell 1.5 percent month over month and is down 15 percent year over year. Consumer expectations rose slightly to 47.9 percent but remain 30 percent below last year’s levels.
Retail sales rose in April, according to the latest data from the National Retail Federation (NRC). Excluding automobiles and gasoline, sales increased by 0.72 percent month over month, and 6.75 percent year over year. The NRC attributed its growth to consumers front loading purchases ahead of anticipated tariff-driven price increases.
Construction showed a gain of 6,000 to the payroll, though construction activity shows some signs of cooling. The Census Bureau reported a 0.4 percent decline in total construction spending in April, down 0.5 percent from the prior year. However, year-to-date spending for 2025 is up 1.4 percent versus the same period last year. Public construction fell 0.5 percent month over month and rose 2.2 percent year over year, while private construction fell 0.4 month over month and is up 1.8 percent over the past 12 months.
New residential construction remains mixed. Housing permits fell by 4.0 percent in April to the lowest levels since May of last year. Starts were slightly stronger at 1.5 percent month over month growth. New single-family home sales rose to a
seasonally adjusted annual rate of 743,000 in April, a 10.9 percent increase from March and 3.3 percent higher than April of 2024. The median sales price rose by 0.8 percent from March to April but remained 2.0 percent lower year over year.
On June 2nd, the S&P Global Manufacturing PMI registered at 52.0, marking the fifth consecutive month of expansion but falling short of the forecasted figure of 52.3. S&P Chief Business Economist Chris Williamson noted renewed concern around tariffs, which have led to supplier delays and the highest input price increases since late 2022, with smaller firms experiencing the brunt of the impact.
The commercial real estate market continues to show bifurcated trends. According to CoStar, the national office vacancy rate remains at 14 percent, with net absorption down five million square feet year over year. However, leasing activity in the first quarter hints at early signs of ongoing stabilization. In the multifamily sector, national vacancies dropped to 8.0 percent in the first quarter of 2025, ending a 13-quarter upward trend.
Responses from recent surveys of lenders found that more business owners are eager to obtain a loan, even though fewer might qualify. For the first time since 2022, loan demand grew at the end of 2024, with a net 4 percent of lenders that responded to the Federal Reserve Bank survey reporting stronger loan demand. Still, that increased demand was met with more rejections, and the credit quality of loan applicants also dropped for the 11th quarter in a row.
The improvement in demand did not extend to small businesses. The Federal Reserve Bank of Kansas City in a recent survey found new term loans for small businesses dropped 9 percent in the fourth quarter of 2024 compared to the same time in 2023. Of those new loans, total balances dropped by 5.6 percent. Additionally, lending standards, as judged by the Federal Reserve Bank of Kansas City, tightened for the 13th quarter in a row.
Source: Federal Reserve Bank of Kansas City Small Business Lending Survey
The Federal Reserve’s bimonthly survey of business conditions, better known as the Beige Book, reflects the tentative nature of the economy. The most recent Beige Book covers April and May. All 12 Federal Reserve districts show responses that indicate economic activity has declined slightly since the previous report. Half of the districts reported slight to moderate declines in activity, with the others split evenly between no change and slight growth. All districts reported elevated levels of economic and policy uncertainty, which have led to increased caution in business and household decisions. BG
March of Dimes will present its 15th Annual Pittsburgh Transportation, Building, & Construction Awards Luncheon, honoring outstanding leaders and projects from both public and private sectors of these industries.
Tuesday, September 30, 2025
Construction Champion of the Year
Jim Kephart, Member/Director—
Construction Operations, Rocky Bleier
Construction Group
Industry Leader of the Year
Kimberly Kennedy, Director of Engineering & Construction, ALCOSAN
Local Labor Leader of the Year
Jim Cassidy, Business Manager, Insulators Local #2
The Westin Pittsburgh 1000 Penn Avenue, Pittsburgh, PA 15222
Building Project of the Year
F.N.B. Corporation Headquarters, F.N.B. Corporation
Infrastructure of the Year
ALCOSAN North End Plant Expansion, ALCOSAN
Transportation Project of the Year
Rehabilitation of the Roberto Clemente Bridge, Allegheny County Department of Public Works
To learn more, please contact Becky Clement at rclement@marchofdimes.org or 412-301-7433, or visit marchofdimes.org/events/pittsburghtbc.
March of Dimes leads the fight for the health of all moms and babies. The US is the most dangerous high-income country for childbirth—but with the help of our supporters, we’re working to change that. Through research, education, advocacy, and programs, we’re there for families throughout their pregnancies to ensure they get the best possible start.
# W e A r e V o l p a t t ustrial institutional
BY BEN ATWOOD
n June 12th, The Bureau of Labor Statistics released its monthly pricing index updates for May of 2025, which slightly outperformed expectations. No inflation surge has been experienced from President Trump’s ongoing tariffs and overall inflation were slightly lower than many Wall Street economists forecast.
But this recent data also shows that there is upward pressure on construction pricing. Of the 79 data series most relevant to the construction industry, the overwhelming majority experienced price increases, with 48 series seeing modest month-over-month growth of less than one percent, and seven seeing a price change of over one percent. A total of fifteen indexes declined, eight of which were less than one percent, and seven by over one percent.
Unadjusted consumer price index (CPI) is up 0.2 percent over the past month and 2.4 percent over the past year. The figure remains in line with the average monthly growth since 2020 and is down slightly from a rolling three-year average of measured month over month change.
The producer price index (PPI) jumped 0.1 percent from April to May, missing the expected mark of 0.3 percent. Year-over-year growth for this index is 2.6 percent, which matched the consensus expectation. May’s PPI observation is slightly under the three-year rolling average of 0.2 percent.
New construction projects experienced a modest uptick in prices, save for warehouses, which declined very slightly. New school, office, and industrial construction all rose by around .45 percent. Final demand construction, construction for private capital investment and construction for government all saw modest gains of 0.2, 0.2, and 0.3 percent respectively, each coming in under their rolling three-year average.
Total inputs to construction experienced a modest growth of 0.3 percent month over month and have climbed by 1.9 percent over the past twelve months. This monthly measurement compares unfavorably to the rolling threeyear average, which is -0.1 percent. Inputs to construction goods rose by .22 percent from April to May, while energy rose by 0.9 percent.
Prices for processed goods important to the construction industry also largely rose, with some notable exceptions. Aluminum mill
shapes declined by -3.6 percent month over month, while paving mixtures dropped by -2.3 percent and lumber and plywood dropped by -1.3 percent.
Prices also rose for #2 diesel fuel, which has largely been trending downward for the past three years. Notable month over month growth was experienced by asphalt felts and coatings (3.1 percent), prepared asphalt (3.7 percent), and steel mill products (7.1 percent). BG
Source: Bureau of Labor Statistics. Updated June 12, 2025.
What is “hot” exactly? If you work in the construction industry in metro Pittsburgh, that concept is typically more muted than if that word was used to describe part of the industry in another part of the U.S. It has been a while, probably since the Marcellus shale boom in the early 2010s, that a sector of the construction industry was truly hot in Pittsburgh.
That has not changed. Pittsburgh is still a conservative construction market, with neither methods of construction nor market sectors getting too far ahead of the mainstream. With that caveat, there are a couple of areas where a significant, if not major, impact could be occurring. One, data centers, can be transformational in ways that have been promised before without delivering. The other, prefabrication, has been boosted by major projects and could mitigate the effects of a declining construction workforce.
Two other looming trends have the potential to be hot later in the decade. Artificial intelligence (AI) is already hot for many industries that are not construction. As applications for AI expand, construction has numerous problems that can be solved through large language models, predictive analytics, and spatial observation. In 2025, however, the intentional application of AI to construction or design is still limited. And, an unexpected trend, the unusual generosity of Baby Boomers, may provide a lifeline to higher education that carries colleges and universities through the demographic desert that currently plagues the sector and unlocks a boom in capital spending.
In the meantime, prefabrication and data centers have moved from trends happening elsewhere to potential opportunities for real change in Western PA.
For decades, the steady growth of Internet-based applications drove almost non-stop expansion of data center construction. The demand for increased security and power also continually grew, meaning that more effective and efficient data centers were needed, as well as more capacity. The shift that made data centers arguably the hottest, and most impactful, segment of the construction market was the emergence of AI applications.
According to JLL’s North America Data Center Report for year-end 2024, leasing of data centers grew by a compound annual growth rate (CAGR) of 28 percent from 2020 to 2024, reaching 4.4 gigawatts last year. During the same period, construction of new data centers grew at a robust 20 percent CAGR, which was insufficient to meet new demand. As a result, the vacancy rate at North American co-located data centers fell from 9.8 percent in 2020 to 2.6 percent at the end of last year.
The model for data center development was like other commercial real estate. Buildings were built with the characteristics data center users needed and were leased to the market. Multiple users co-located in those centers to take advantage of the economies of scale and to reduce the capital costs and balance sheet exposure of the users. Co-locators got the same benefits and took similar risks as other landlords.
With the emergence of hyperscale users, like Amazon, Apple, Google, Microsoft, and others, the development model for data centers changed. The scale of the facilities grew ten- or one hundred-fold, changing the risk profile for the property owner, which was historically a co-locating landlord. New data centers are frequently billion-dollar investments. This new scale of risk meant that developers would be doing build-tosuit construction instead of speculative, or partly speculative, facilities. Today’s data center developers have become a specialized segment of the commercial real estate market, with investors and partners that have extensive experience with the needs of hyperscale AI users.
While the largest data center owners remain Amazon Web Services, Microsoft Azure, Google Cloud Platforms, and Meta Platforms, developers are closing in on top rankings. QTS, Equinix, Digital Reality, and NTT Global Data Centers are the largest co-locator-turned-developers. Equinix and Digital are real estate investment trusts, giving them access to the infusions of capital needed to build new centers. Dallasbased Cyrus One, the fourth largest developer, raised $12 billion for expansion in July 2024, with $9.7 billion of that dedicated to new data centers in the U.S. That figure, though impressive, would not cover the development of more than one hyperscale center.
Data center development may be one of the hottest sectors in construction, but new construction has been challenged over the past year or two because of two main countervailing forces: scarcity of power and slowing supply chain. Those challenges have created potential for opportunities in Western PA.
The epicenter for hyperscale data center development has been northern Virginia, specifically the Ashburn, VA area. Several projects are under construction there now, but Dominion Energy, the region’s primary utility provider, has paused approvals for new connections and is signaling that additional capacity won’t be available until 2026–2028. In Silicon Valley, land is scarce and permitting is difficult. Pacific Gas & Electric has likewise limited to add capacity for new or expanded data centers. And grid capacity is severely limited in the Dallas and Phoenix markets, which were hot spots for data center development in recent years.
“AI, and data centers in particular, are huge energy consumers and need a large amount of power. One of the big advantages Western PA
has is the natural gas assets that are also connected to old industrial sites,” says Matt Smith, chief growth officer at the Allegheny Conference on Community Development. “We are also very much out of the natural disaster zones.”
These restrictive market pressures represent an opportunity for other cities, including Pittsburgh, to become data center hubs. While Pennsylvania’s electric grid also faces severe stress, there are multiple large sites that have access to, or will develop, gas-fired power generation that is off the grid. Indeed, as of mid-June, at least five sites in Western PA were competing for proposed data centers, not including the Homer City Redevelopment Site in Indiana County. However, the prospects for data center development in the region could be greatly improved, a reality that proved fatal to a recent deal.
A $7 billion data center well into preconstruction in Beaver County, reported to be for Open AI’s Stargate Project, was scheduled to be announced in early May. At the eleventh hour, the user shifted the project to a site in Texas, after finding a partner that was already well underway there. The user was concerned about the uncertainty of the regulatory cycle in Pennsylvania, estimating that building the project in Texas would bring the data center online as much as two years earlier.
To combat that concern, on April 22 a bipartisan group of three legislators announced plans to dramatically reduce the permitting time. State Representatives Eric Nelson (R-Westmoreland), Kyle Mullens (D-Lackawanna) and Jamie Barton (R-Berks and Schuylkill) plan to introduce legislation to create accelerated data center permitting. The legislation
CELEBRATING 50 YEARS OF
CHALLENGING OURSELVES TO EXCELLENCE AND BEING THE LEADER IN THE MECHANICAL CONSTRUCTION INDUSTRY
would direct the PA Department of Environmental Protection to generate approved earthwork, stormwater and air permits to developers who commit to improved environmental outcomes by meeting, or exceeding, design standards. The law would enable simultaneous pursuit of additional permits and processes, like Highway Occupancy Permits, Environmental Justice Permits, land use, and other approvals, which can considerably delay project development. The lawmakers also want to include a suspension of the permit deadlines in the event of a lawsuit challenging the project, until the dispute is resolved.
“Our biggest roadblock is the government bureaucracy. It’s the permitting process and the threat of targeted lawsuits that are causing private investors to go elsewhere,” Rep. Nelson explains. “The law doesn’t reduce or bypass standards, and it’s a bipartisan bill. It just allows the developer to be able to commit that they will meet or exceed those design standards in exchange for a more reliable, timely process.”
The accelerated permitting legislation is not expected to move forward until after the 2025-2026 budget is completed, but the three hope that Rep. Mullens’ sponsorship will ensure that the Democratic majority acts upon it.
“The one big thing that is always going to be needed to attract data centers is speed. We are constantly pushing at the local, state, and federal level for improved permitting systems,” says Smith. “I think the state is improving its permitting process with the bipartisan Fast Track program that was instituted by
the legislature and governor. But you can never have enough speed and that area we will be constantly pushing.”
Dan Adamski, executive managing director for JLL in Pittsburgh, explains that the commonwealth’s reputation for slow regulatory approval is more widespread than elected officials believe, and is only one challenge facing those trying to make Western PA a data center hub.
“If you go 150 miles west of us, Columbus has seen 100 new data centers and we’re seeing zero. What is the reason? Regulation is definitely one. There’s the perception that by the time you get through approvals in Pennsylvania, the data center could be up and running somewhere else. With speed to market so important to hyperscalers, when you compare Pennsylvania to Ohio right across the border, Ohio has been winning,” he explains. “There is also a herd mentality among hyperscale users. They want to be clustered with other data centers. Once one of the big five users is located someplace, it validates proof of concept. Other users know that the big boys did the homework for them. They know they will have access to the grid, to fiber and water. We’re working with a user of 100 megawatts that wants to be in Pennsylvania, but we need that first domino to fall.”
Adamski notes that Pittsburgh has a topographical disadvantage to the flatter regions of the country. The current rule of thumb is an acre per megawatt for data center development. Given the topography of Western PA, compared to Texas or central Ohio for example, that requirement limits the potential sites for hyperscale centers.
One of Western PA’s most significant competitive advantages is its potential for energy generation that could keep up with data center growth. With requests for grid connection running an average of four years’ review time – and no assurance of approval – operators are increasingly looking at on-site power
generation. Natural gas turbines have quickly emerged as the leading alternative power source, which favors locations with access to natural gas. Nuclear generation, especially from small modular reactors like those being developed by Westinghouse in Etna, is also quickly gaining favor.
Landing data centers would doubtless be an economic win for the region, but success would mean different benefits than a manufacturing plant or corporate headquarters. Locating data centers in Western PA is critical to the growing AI research and development; indeed, Carnegie Mellon University is one of the customers pushing demand for one, but data centers are not employment drivers. For the construction industry, a string of data center projects would be a double-edged sword. The billions in construction would draw thousands of workers to each project, while a small slice of the local contractor base would be positioned to compete for the work.
What data centers do offer is a significant increase to the tax base with minimal impact on the local infrastructure, including the public education and public safety resources of the local municipality.
Development of hyperscale data centers in Western PA would be a net positive for the region, especially if there are numerous projects over the rest of the decade. If Pittsburgh is indeed to become one of the main centers for AI research and commercialization, that market position will be enhanced by an abundance of data processing in close proximity. CMU’s Ralph Horgan reports that, in addition to needing to find a new home for its supercomputing center, the university will be looking for an enterprise-level data center within a few years. Failing to support one of the potential pillars of the future regional economy could force emerging information technology elsewhere.
Off-site prefabrication has been employed by specialty contractors, particularly the mechanical and electrical contractors, for decades as a way to improve productivity and safety. The impending skilled worker shortage motivated contractors to expand the intentional use of prefabrication more than a decade ago. Now, with that shortage a daily reality, and with construction costs soaring since the pandemic, offsite prefabrication has penetrated the construction market to a degree that is transforming companies.
Gumpher, Inc. was a small electrical contracting business when it signed an agreement with IBEW Local 5 in 2023, employing 27 workers at the time. After attending a National Electrical Contractors Association (NECA) conference in Philadelphia that year, Zach Gumpher, vice president, says the firm’s leadership saw the light on prefabrication.
“We got the idea for setting up a prefab shop at the NECA convention and began selling our capabilities,” Gumpher recalls. “We landed a couple of contracts that lined up perfectly for how we wanted to unroll prefabrication. We now have two or three electricians in our prefabrication shop at any one time. We prefabbed 13,000 end wall assemblies for Presby Tower with just two workers.”
Prefabrication has received front page coverage recently because of the project Gumpher referenced, the UPMC Presbyterian Heart and Transplant Hospital. Gumpher, Inc. handled a relatively small piece of that electrical work, with Clista Electric, Lighthouse Electric, and Ferry Electric each responsible for larger portions of the electrical construction, which accounts for more than 20 percent of the overall project. All three of those firms prefabricated much of the scope of work, often in concert with another specialty.
Those larger electrical contractors invested heavily in space and equipment to expand their prefabrication capabilities 10 or 15 years ago. Most of the larger mechanical contractors have also prefabricated pipe assemblies and/or ductwork for
decades. The difference today is in how much of the scope of work can be prefabricated and how much integration with other trades can be accomplished off site.
UPMC saw off-site prefabrication as a solution to multiple concerns it had about the construction of its new bed tower on Fifth Avenue in Oakland.
“We contemplated prefabrication in the early planning of this project, even when [retired vice president of corporate
real estate] Eric Cartwright was involved back in 2017 and 2018. Much of it was based on the confinement of the site and the fact that we knew Pitt was going to be doing a lot of work concurrently on campus,” says Roger Altmeyer, director of community project development at UPMC. “We tried to get as much work at ground level as we possibly could. That eliminated safety risks, the congestion of boxes, and products, and materials associated with construction.”
To facilitate the high level of prefabrication that is being done on the Presbyterian bed tower, UPMC is renting 100,000 square feet of warehouse space at Gateway View Plaza on the South Side. That space is in addition to the proprietary prefabrication shops for the electrical contractors and McKamish Inc., which is partnered with Ruthrauff Sauer for mechanical construction. What has garnered more attention is the fact that more of what would be typically built on site is being prefabricated, including the patient room demising walls and more than 600 patient bathrooms.
Rich Yohe, president of Easley & Rivers, explains that the predictability of off-site construction allowed Easley & Rivers to estimate the bathroom construction properly, without accounting for the risks associated with that scope of work.
“When we work in hospitals, we know there will be pluses and minuses, and we know the bathrooms are going to be a big minus. They are difficult and time consuming. If we were only doing the bathrooms and building them on site, we would have to add significant costs to our bid,” Yohe says.
“When you prefabricate the way we are at Presby, there is no minus to the bathrooms. We can hit our productivity units. We can hit the labor goals we have set in that environment. And the end user gains in schedule.”
“Typically, we prefabricate exterior walls. We elected to prefabricate the interiors on the UPMC project,” says Fred Episcopo, president of Wyatt Inc. “We prefabricated the metal framing, wrapped and folded the board at the shop, and installed it on the prefab framing to build the walls. These are four- or six-foot wide sections. It’s a typical patient room that we load on an A-frame at the shop and deliver to the site, trading A-frames.”
Episcopo notes that the curved shape of the UPMC Heart and Transplant Hospital
means that the wall sections cannot be laid out as normal, but his staff is able to use the building information model (BIM) to fit the wall panels to the twist of the beams that create the curved wall shape. McKamish also points out that the prefabricated racks of piping, ductwork, electrical conduit, and ceiling assemblies must be engineered to follow the unique shape of the building. Within the perimeter of the hospital’s 12 patient floors, most of the interiors and building systems are being fabricated off site instead of construction in place.
There is universal agreement that the increased level of prefabrication has minimized the number of workers on site and streamlined the logistics, but the question of cost savings seems to be unresolved. There are certainly savings in safety costs, but aside from a significant reduction in the insurance for the project, those are hard to quantify.
“It has worked out wonderfully well, but I am not personally convinced that it is any less expensive because of all the transportation of materials, and we are renting a 100,000 square foot warehouse for a year and a half after all,” says Altmeyer. “We were doing so much repetition that it seemed that this was a good opportunity for prefabrication. There is a marginal return on some level, but I don’t know what that is.”
“There is on-site time savings and safety costs, but the cost to build them off site, from the standpoint of what we paid versus what we estimated, was not less,” notes Jeff Turconi, executive vice president at PJ Dick who is serving as project executive Whiting Turner-PJ Dick joint venture overseeing the new hospital. Turconi feels that the newness of this scale of prefabrication makes it difficult for the specialty contractors to quantify any cost savings.
“I have to believe they’re more efficient because they were in a controlled work environment with the same people doing the same activities every day; but it’s hard to reflect that until there is some history and they are comfortable that the saving can be passed on to the owner,” he says.
It seems that there is more certainty about the value proposition of prefabrication among the specialty contractors.
“Our prefabrication probably saves us in the neighborhood of eight to ten percent of total labor cost by being able to do it in a
controlled environment,” says Marc Mushnok, vice president of operations for McKamish, Inc. “The evaluation about prefab happens when we’re bidding on the project and then post award we look to see if there are other opportunities for prefabrication on the project. When we do modular units like the racks at Presby, we coordinate the electrical, fire protection, and insulation through our shop.”
Mushnok estimates that McKamish’s workforce at the UPMC jobsite would increase by 75 percent if its scope of work was being built on site. Gumpher, whose fabrication shop has only been fully established in 2025 cites similar field labor savings on the end wall assemblies.
“A typical end wall assembly takes 45 minutes. We built them in about 7.5 minutes in the shop,” he says. “We’re now prefabricating certain elements all the time. We’re doing a lot of underground prefabrication. That seems to have the highest efficiency delta. We’re building it at a shop at working height in 70 degrees, as opposed to being outdoors in a ditch in all kinds of weather.”
The increased use of prefabrication by specialty contractors has been driven by cost savings, worker shortages, and quality control benefits. Contractors can use prefabricated work to train less experienced workers. The reduction in onsite workforce on prefabricated work allows the contractor to pursue other profitable work with those available resources. Many Pittsburgh-based specialty contractors have embraced prefabrication as a strategic matter. Dan White from W. G. Tomko says most of its work is design-assist, which has a significant amount of prefabrication built into the projects. Lighthouse Electric is so committed to prefabrication that it displays a mockup of one of its underground assemblies for the Airport Terminal Modernization Program as if it were a sculpture in its corporate headquarters.
On May 6, Turner Construction Company announced it had launched xPL Offsite as a subsidiary business that intends to expand the application of manufacturing and offsite construction in project delivery. Turner announced that they will use a 200,000 square foot facility in Decatur, AL, for research and prefabrication. According to Turner, roughly $400 million in contracts have been secured by xPL as parts of nine projects around the U.S.
Drew Kerr, general manager of xPL Offsite and formerly general manager of Turner’s office in Pittsburgh, explains that the AI data center is a prototypical example of the kind of project that offsite construction benefits.
“If you’re doing a mega project in Oakland, there’s an available labor force with the skills to build in a traditional way. Our logic is that many of these mega projects are in isolated sites that aren’t served by enough labor to source 5,000 skilled workers,” Kerr says. “How would you build a very complex data center? That is the solution we are trying to provide. We’re trying to save thousands of miles, hours, and workers on these projects.”
Larry Payne, managing principal at WTW Architects, an AE Works Ltd. Company, recalls his firm designed a student residence hall at State University of NY (SUNY) College of Environmental Science and Forestry near Syracuse that had significant modular prefabrication for the same reasons Kerr cites.
“We were creating the housing units the general contractor would pick up off a trailer and stack. A big reason that it went modular was because of the remoteness of the workforce to the actual project site. There weren’t even hotels close where the workers could stay during the week,” Payne recalls. He also sees prefabrication playing a significant role in what he calls “prevention through design” – the concept that designing more manufactured parts of the building will prevent safety and scheduling problems.
Kerr explains that xPL Offsite will take advantage of Turner’s SourceBlue procurement power and focus on design for manufacturing and assembly (DFMA) principals at a centralized prefabrication facility to control much of the design and construction process for clients looking for specific solutions. He concedes that limits the market segments somewhat and works best on mega projects, meaning there will be fewer opportunities in Western PA for now.
“In addition to data centers, we see xPL having application in semiconductor, large industrial, advanced manufacturing, biopharma, life sciences, and healthcare. There are some applications for arenas and convention centers,” Kerr says. “It’s effective where speed to market is the most important consideration.”
There are a few current trends that are likely to become market disruptors or drivers as the decade unfolds. The most
obvious is AI, which is already having an impact on the data center market discussed above. Although it is driving one hot real estate sector, AI is not being adopted rapidly by the construction industry. A recent informal survey of Associated General Contractors’ (AGC) offices across the country returned just a handful of members actively utilizing AI, and many stated their use was limited to the creation of social media posts and proofing documents.
Rene Morkos, CEO of Alice Technologies, says that digitizing construction data was, quite recently, daunting.
“You look at something like finance…that’s very easy to digitize. It’s just numbers. Construction is all this messy information that doesn’t lend itself to bits. But what’s changing,” says Morkos, “is that the industry’s information is digitizing. You are starting to see companies digitizing everything pertaining to construction. Site capture, procurement, all of it.”
Construction applications have also begun making use of “transformer” algorithms, which make it possible to train AI models on large, varied datasets – including photos, drone footage, and BIM models, for example – across multiple machines efficiently. These algorithms allow tech firms to begin looking at how to capture, process, and learn three-dimensional spatial information from construction sites and apply it in meaningful ways. One company working on construction applications is Open Space, which uses cameras with 360-degree
“From revitalizing abandoned steel mills and industrial sites into thriving business and technology parks to transforming underutilized land into locations built for job-creating companies, RIDC has created a unique blend of economic development advocacy, community and regional revitalization, and high-quality job creation that could be a model for other regions that were once powerhouses of America’s industrial economy.”
Pre-order from Amazon, Barnes & Noble and booksellers around the region.
lenses mounted onto hard hats to take a photo every half second, compiling images to create a living breathing digital map of a construction site. Applying AI to those images, however, is not an easy task.
“Capturing the images is the easy part,” said Open Space’s CEO Michael Fleischman, in a 2024 webinar. “Placing those pictures in the context of a specific time and place within a specific project is incredibly hard.”
AI developers express optimism that the pace of development and adoption of AI is growing rapidly in construction, which will help drive more useful applications that will benefit the riskier elements of construction, like estimating and project management in the field.
Another interesting potential trend is related to higher education and demographics, but in a good way for a change. For two decades, colleges and universities have been dreading the demographic cliff that is sapping enrollments across the region; however, an echo of the demographic boom of the 1960s and 1970s may usher in another type of boom: planned giving. A series of large donations have been given by wealthy, grateful Baby Boomer alumni to regional colleges, both with and without restrictions to use.
These gifts are making capital projects possible at Allegheny College, Geneva College, Washington & Jefferson College,
St. Vincent University, and Grove City College. Donations made in just the past two years are facilitating more than $100 million in current construction projects, many of which would not go forward without the gifts. Baby Boomers are the wealthiest generation America has seen and are just reaching the age when major gifts and bequests are made. Were it to become a trend for Baby Boomers to be benefactors for their alma maters, it would mark a dramatic reversal of fortune in higher education.
Larry Payne sees adaptive reuse as a potential hot market for higher education, as colleges and universities struggle to match facilities to smaller enrollments and new technology. An influx of donations could pay for a boom in adaptation of long-term buildings.
“We have projects where an academic tower is being converted into student housing. When we did the Patee Paterno library at Penn State we used demountable walls and low-profile floors because Penn State knew that the library’s programs were going to change over time and they needed flexible infrastructure,” Payne says. “We architects are trying to plan for that flexibility for the future.” BG
Building with INTEGRITY since 1975
•We remain true to our founding values of quality,
•We have worked on many wide-ranging and integrity and hard work. different projects the past 50 year such as
•RAM, as a primary construction company in local schools, colleges, churches, businesses, southwestern PA, has delivered, and will continue banks, restaurants and institutions. to deliver, top-notch quality services to our clients.
•Proud to continue partnering with many
•RAM: delivers the highest standard of craftsmanship. top-notch general contractors and architects.
RAM Acoustical: celebrating the past, anticipating the future with even more success!
Southwestern Pennsylvania is our home. Being supportive and active member of our community is a priority and we are committed to strengthening friendships, serving others and investing in our region.
RAM Acoustical Corporation is proud to play an important role in the region’s economy by employing a Union work force generating millions of dollars in wages, pensions, health benefits, and state/local taxes. RAM also participates in a multitude of community projects
Acoustical
•We believe in staying on the cutting edge of building trends & remain committed to excellence and professional management with all our construction partners,
•From start to finish, we are detailed-oriented on all jobs.
•Successfully completing over 3,500 plus projects.
Orchard Hill Church is a non-denominational Christian church located on a hill overlooking Soergel’s farm in the northwestern corner of Franklin Park. Founded in May 1989, Orchard Hill Church has expanded steadily, both on and off its North Hills campus. The growth of its youth programs created the need for a significant addition after the pandemic ended.
“This was an expansion of what we call the Next Generation or Nextgen wing. We have a first floor and gym that was constructed in 2011 as an expansion of the church. We called that the ‘Kidsburg’ because it was mostly for the kids,” says Mark Lunsford, executive pastor at Orchard Hill. “As we’ve grown, we needed more space, not only for the Nextgen room and for students, but also for small groups and discipleship studies.”
The church commissioned an architect from outside the region to develop a schematic design. Very early in the process, however, Lunsford and the committee overseeing the project decided on a project delivery method that shifted the process. Joe Burchick, founder and president of Burchick Construction, is
an active member of Orchard Hill Church. Lunsford valued the work Burchick’s firm had done on two earlier projects and the advice Joe had given the leadership on facilities issues. It was decided that the Nextgen wing addition would be delivered by design-build with Burchick Construction as the lead.
“My experience has been that it’s helpful to have one key pivot point that I can deal with that is also managing the architect and the construction team. My experience working with an architect and then hiring a contractor has been what I call the ‘triangle of death’,” Lunsford laughs. “The church becomes the pivot point with the others pointing their fingers at each other and we’re powerless to enact change. When we worked with Joe in the past it was a win-win”
With Burchick Construction on board as the design-build lead, it was decided that a local architect would complete the design. RSH Architects was hired because of its experience working with Burchick Construction and religious facilities. Its task was to take the schematic design and make it work.
Photo by Massery Photography
“There were elements of the design that we kept and elements that were changed, but the overall program stayed basically the same. There weren’t any major difficulties or challenges with the program,” recalls David Noss, principal and president at RSH Architects. “One of the challenges is just that it’s a massive building. There were questions about where the systems were and how to get the systems to the addition, or whether the bathrooms should remain as is or rotate. There are a lot of small design issues like that.”
Noss notes that there is always a challenge working on a design-build delivery because the hierarchy of the project differs from how most projects are delivered.
“You have three masters.
The contract is with the general contractor. You have obligations to the owner, and you have obligations to the public, to satisfy code,” he says. “On this project it worked well. I am a big proponent, and I believe Joe is too, that at the end of the day you realize that the project is for the client. The project just goes better.”
Design on the project kicked off in October 2023, with construction commencing in January 2024. The addition totaled 13,650 square feet, with cosmetic renovations to the existing first floor.
“The project was mostly a vertical addition above an existing one-story structure, with a horizontal addition that tied into the high bay where the sanctuary is,” says Joe Wardman, vice president,
by Massery Photography
construction operations at Burchick Construction Co., Inc. “We had to tie the steel into the existing steel structure. We built the monumental stairway and another stairwell that punched through horizontally to tie into the existing intercommunicating stairwell.”
“The church had envisioned adding a second floor on that part of the building so the foundations and structural steel were designed for that. Even the concrete roof slab was poured at a finished floor level, so when we tore the roof off there was a structural slab ready to go,” explains Burchick.
Pastor Lunsford credits the leadership in 2011 for making the decisions necessary to anticipate the growth that came afterwards.
“My experience in building a church is when you get two-thirds through the project, you get to the point where you figure what to cut. You cut the things you may never use, but they didn’t do that in 2011,” he says. “That foresight enabled us to do the square footage on the second floor without any exterior work.”
For Burchick Construction, the main challenges of the project fell into two categories, those that were resolved during design and those that were peculiar to the difficulty of tying a vertical addition into an existing occupied building.
During preconstruction most of the discussions with the owner, RSH, and interior designer LAMA Design Group centered on constructability and reconciling the design choices to the church’s budget and expectations for quality. One significant challenge involved a redesign of the roof structure.
“The roof was designed essentially at a flat elevation. When we were pricing and doing value engineering analysis, we saw the tapered roof insulation went up to about a foot thick at one end to get the slopes required to get to the drains. We suggested that if we raised the outside of the steel and lowered the inside elevation to create the slope with the steel, we could avoid the one-foot insulation. That saved about $50,000, so we got the same outcome at a lower cost,” says Wardman.
As construction got to the vertical stage, an unexpected challenge arose that threw a wrench into the schedule. The steel fabricator had not communicated to Burchick Construction that it was in the process of closing its doors, which led to less than half the anticipated structural steel being delivered to the site when the addition was to commence. After some heated phone calls, Burchick Construction arranged to pay the steel supplier directly and Joe Burchick worked with another church member, Pat Gallagher, owner of PGT Trucking, to deliver the remaining fabricated steel. The issue set the project back almost two months.
“That problem was out of everybody’s control and Burchick Construction did a good job of keeping us informed,” says Lunsford. “I sensed from them an eagerness to complete the project earlier, as we did. We knew they were fighting to get things done.”
Another of the schedule-related challenges was not unique to the Orchard Hill project. Much of the exterior envelope of the addition was composite metal panels (ACM), which require more preparation and adjustment to customize. Wardle explains that
the field measurement for the wall panels occurs even after shop drawings are done, and after all the windows have been set and the building has been wrapped. To ensure that the reveals and seams between the panels are uniform, panels were installed in small sections and new measurements were taken to fabricate each section that followed. This added a level of unreliability that Wardle had to manage when sequencing tasks related to the exterior envelope.
Orchard Hill Church included some scope beyond the new space that added complexity to the project.
“Part of this project was converting the HVAC from electric to gas,” says Burchick. “The church was at one time all electric. I think there were still four or five air handlers serving various parts of the building and the kids’ area on the first floor. We replaced equipment and brought a new, larger gas service line to the building.”
“We had to maintain the electric units while we built the addition to keep the space conditioned that they served,” Wardman adds. “The addition had to be completely weatherproof before we could set the new gas units on the roof behind the addition and eliminate the electric units.”
The replacement of the roof-top units was complicated by the fact that the units were set on what was to become the floor of the addition. That meant that the structure of the addition had to be completed and the building fully weatherproofed, including the finished new roof, before the electric units could be replaced, since the air handlers conditioned space that was being used throughout construction. The ductwork, controls, and appurtenance for the new gas units were fully connected and ran in parallel to the existing system for a few days before the old units were removed from the original roof, which then had to be patched and prepared to become the floor for the upper level of the Nextgen wing.
“The church added replacing the finishes on the lower level, which had to be done while the space was occupied. That meant installing new carpeting, trim, and painting with disrupting activities,” says Wardle. “We started a sequential program of emptying and refinishing a room while the other rooms were occupied and then moved on to another room.”
Conducting the construction activities with little or no disruption was a high priority for the church and Burchick Construction. That meant building the construction schedule and sequencing around Orchard Hill’s activities, which involve daily use of many of the facilities. Once the addition moved horizontally to connect with the existing building, temporary structures were built to isolate the new stairway from the active hallway during construction. Wardman said he felt confident that the area would be too tempting for kids to avoid otherwise. Lunsford praises Burchick Construction’s communication with Orchard Hill’s staff to manage the potential conflicts.
“It is always difficult in the middle of construction when you are still using the existing space. It’s important that the contractor work very closely with us as it relates to scheduling and space usage,” he says. “Burchick was always very respectful of our times for services and uses for the building. But that was also a challenge we had to work around weekly.”
Work was completed in October 2024. As a member of the church, Burchick marvels at the effect that the Nextgen addition is having.
“It’s a great youth program and that’s what this was all about,” he says. “The space is comfortable. They’re all kinds of video games there. I mean, the kids actually want to go to church. They’re taking their parents to church.”
Asked what he thinks made the project successful, Wardman says, “It was the collaboration with the church that made things work.”
“Design-build works if the architect and the contractor can align their goals to create a product for the client that meets their needs. It’s not about making the most money or the architect or contractor staying on his high horse. It’s about working the relationship and keeping goals aligned for the owner and I think that was done here,” Noss says. Noss also credited the members of the church who volunteered to oversee the project. “It is not always desirable to work with a committee, but I give kudos to Orchard Hill Church. They were very responsive to anything that was presented to them and made decisions in a timely manner.”
“This is the second project that I’ve worked on with Burchick Construction. They were able to get things done through the subcontractors and the architect. That made it successful for the church,” says Lunsford. “Joe [Burchick] wasn’t involved in the day-to-day but he was involved, and his input was very helpful towards the middle and end of the project to make sure that the quality was high and that design elements that may have been missed stayed intact.
“We’re using that new space every day and it has made a big impact to our student ministry and our kids ministry. It has been so well received by our church.” BG
Burchick Construction Co. Inc. General Contractor
Orchard Hill Church Owner
RSH Architects Architect
McKim & Creed, Inc. Consulting Engineer
LAMA Design Group Interior Designer
Gunning Mechanical Contractors HVAC
J. D. Iovito Contractors Plumbing
Ferry Electric Co. Electrical
Harris Masonry, Inc. Masonry
Easley & Rivers, Inc. Fireproofing
Greer Tile Co.
Fire Fighter Sales & Service
Ceramic Tile
Fire Protection
Hoff Enterprises Casework
Lincoln Fabricating, Inc.
Structural Steel
Over & Under Steel and Rigging Exterior Structural Steel
Keystone Metals Steel Railings
Slippery Rock Commercial Roofing Roofing
Southwest Aluminum & Glass Storefront & Curtain Wall
T. D. Patrinos Painting & Contracting Painting
Wright Commercial Floors Flooring
BY JEREMY K. KNAEBEL
During President Donald Trump’s second term, U.S. trade policy has undergone significant and disruptive changes with the introduction, reintroduction, expansion and retraction of tariffs aimed at protecting domestic industries and manufacturing. The trade policy is continuing to evolve and change daily impacting the greater U.S. economy. For the construction industry—a vital component of the U.S. economy—these policy shifts have created significant commercial risks and business volatility due to increased material costs, supply chain disruption, and project delays necessitating complex contractual considerations. Further, ongoing legal challenges to the tariffs have created an atmosphere of uncertainty, which will undoubtedly directly affect nonresidential construction input prices, which have already seen a 9 percent annualized increase in early 2025 (Hanson Bridgett, 2025). In this regard, the construction industry must stay cognizant of legal challenges to the tariffs and remain vigilant in reviewing and updating contracts to include key contractual provisions to prepare for the commercial and legal challenges that may arrive sooner rather than later.
Steel, Aluminum, Lumber, and Global Material Supply Chains
In March 2025, Section 232 of the Trade Expansion Act of 1962 tariffs were reintroduced and expanded to include a 25 percent duty on all steel and aluminum imports— without exception. Just weeks later, on April 2, 2025, President Trump announced a new tariff strategy, named “Liberation Day, and imposed a new 10 percent baseline tariff on all imports and introduced reciprocal tariffs for countries with significant trade imbalances. These measures have reshaped construction procurement: Canada, Mexico, Japan, and China—all major exporters of building materials—have now been subject to tariffs between 10 percent and 145 percent depending on the various states of trade negotiations or tariff roll out.
hardware, and modular products are also caught in the trade war with China having the highest imposed tariffs.
Ongoing trade negotiations have resulted in temporary suspensions or modifications of tariffs on specific products, yet uncertainty persists. These rapid shifts create challenges for developers trying to manage long-lead procurement cycles. The threat of further escalation remains, especially in light of the administration’s stated goal of realigning global supply chains to prioritize domestic manufacturing.
Tariffs are also hitting downstream products. In addition to raw materials like aluminum and steel, imports of screws, fasteners, curtainwall components, HVAC systems, and electrical panels are subject to reciprocal duties. The construction industry’s reliance on global suppliers leaves it vulnerable to both pricing surges and availability issues. When manufacturers shift production across borders in response to trade policy, it disrupts project schedules and complicates logistics.
For the construction industry—a vital component of the U.S. economy—these policy shifts have created significant commercial risks and business volatility due to increased material costs, supply chain disruption, and project delays necessitating complex contractual considerations.
The volatility introduced by these tariffs has underscored the importance of risk allocation in construction contracts. Contractors and owners alike will be forced to confront how their agreements address (or failed to address) the financial impact of sudden price increases and material shortages. In 2025, construction contracts must be more agile, detailed, and forward-looking than ever before. Five key types of contractual provisions are proving indispensable to mitigate tariff-related risks:
For example, Canada’s tariff affects the supply of lumber—a cornerstone of residential and multifamily development. While the U.S. has domestic timber capacity, it is insufficient in the short term to offset Canadian supply, driving up costs and causing schedule delays. Mexico, which supplies essential goods like rebar and cement-based products, faces similar duties. While Japan’s specialty steel and China’s ceramic tile,
Also known as material cost adjustment provisions, these clauses allow contractors to recover increased costs when material prices rise beyond a defined threshold. The clauses often state that if the cost of certain materials increases more than a certain percentage from the bid date to the date of procurement, the Contractor shall be entitled to an equitable adjustment of the Contract Sum. In other words, the parties may reopen the contract to specifically negotiate material pricing terms. The language should be narrowly tailored to only apply in instances limited by a specific time period or specific condition. Similarly, an Owner can add language capping price escalation and protect itself from skyrocketing
prices. Many contracts lack such clauses or include them only for fuel or concrete. Some contracts have been updated after the supply chain disruptions caused by the 2020 COVID-19 pandemic, but most need a more detailed overhaul. Escalation clauses can become a critical risk-management tool. As tariffs may drive up prices for steel, aluminum, and lumber, owners and contractors without escalation protection may be exposed to calamitous increases to the construction budget. Owners
and contractors can further control and define these clauses by tying them to published indices like the ENR Construction Cost Index or Producer Price Index (PPI).
Traditionally invoked for natural disasters or acts of war, force majeure provisions may be applicable when tariffs disrupt supply chains and extend lead times. However, most force majeure clauses do not expressly include “government trade actions” or “tariff impositions,” making recovery difficult. Forward-thinking contractors and owners may now negotiate broader language that includes governmental acts affecting material availability or cost. These clauses should be tailored to time periods which were unexpected by the parties and for which they had no control.
Revised clause example: “Force majeure shall include government actions, including imposition of tariffs or embargoes, which materially affect the availability or cost of materials, and were unanticipated by either party at the agreement was entered.”
Contracts can also add a specific changein-law clause, which provides more detailed conditions then a general force majeure. These change in law provisions can be specific to include changes to the trade policy or trade law of the United States or the country from which materials are being procured.
When tariffed materials become too expensive or unavailable, substitution clauses may be able to govern whether contractors could propose alternative materials or methods. Some contractors include alternate materials into their contracts as a cost management or cost savings strategy. Such clauses can also be used as a risk mitigation technique for materials which may be subject to volatility in pricing due to trade wars or tariff policy. Owners and design teams have to decide quickly whether to approve substitutions that preserve budget and schedule but deviate from the original specs. Clauses that permit contractor-proposed value engineering or material substitution with owner approval may become a lifeline for maintaining progress in tariff-impacted projects.
Projects awarded on a fixed-price basis (especially lump sum) expose contractors to the greatest tariff risk. Cost-plus or guaranteed
maximum price (GMP) contracts provided more flexibility, particularly when the GMP included shared savings and allowances that could absorb price fluctuations.
Owners and developers can begin scrutinizing contract delivery methods, potential favoring cost plus or GMP or hybrid structures with escalation clauses to balance cost certainty with the economic reality of procurement and cost volatility.
Because the construction industry relies on global suppliers, especially for materials like steel, aluminum, curtainwall systems, mechanical, and electrical components, the terms under which materials are bought and delivered are also crucial in determining who will ultimately absorb the tariff risk. In this context, Incoterms (International Commercial Terms, governed by the International Chamber of Commerce) are essential for defining each party’s obligations for delivery, insurance, and customs clearance. Using the correct terminology in an equipment or material supply agreement may be the best way to protect against increased tariffs that are not directly addressed by other contract terms. There are numerous terms often used in such contracts. For example:
• DDP (Delivered Duty Paid). Under DDP terms, the seller assumes full responsibility for delivering goods to the buyer’s location, including payment of import duties and tariffs. For U.S. contractors during the 2025 tariff uncertainty and trade war, this term may provide clarity and price certainty— tariffs were included in the sale price, reducing risk.
• DAP (Delivered at Place). DAP terms require the seller to deliver the goods to a named place (e.g., a construction site), but the buyer is responsible for duties and tariffs. Construction firms importing DAP shipments during tariff increases often face unbudgeted cost hikes and disputes over who has the ultimate responsibility.
• FOB (Free On Board). Under FOB terms (typically used in maritime shipping), the buyer assumes responsibility once goods are loaded onto the vessel at the port of origin. From that point forward, including shipping, insurance, customs clearance, and tariffs, the buyer is liable. For firms importing structural steel or equipment, FOB purchases during tariff volatility require careful contractual
planning to avoid cost overruns. FOB is less used in the context of international trade and can often lead to confusion if it is not drafted and applied correctly.
Choosing the right Incoterm in supply contracts directly affects a contractor’s exposure to cost fluctuations due to tariffs. In 2025, construction firms that negotiate DDP terms may often be better protected, as the risk of tariff escalation is embedded in the seller’s price.
Conversely, buyers under FOB or DAP terms needed strong escalation clauses or procurement contingencies to recover unexpected tariff costs.
The inclusion of these terms also informs broader project planning and bidding strategy. For example, general contractors can begin requiring disclosure of Incoterms from material vendors and subcontractors, owners can scrutinize whether procurement strategies aligned with project risk profiles, and legal teams can revise standard purchase orders and subcontract templates to clarify tariff responsibility based on Incoterm selection.
In addition to the ongoing changes in US trade policy and tariff imposition, there are also legal challenges, which could bring further uncertainty to tariff application. Two federal courts struck down tariffs imposed under the International Emergency Economic Powers Act (IEEPA). These decisions cover the “Liberation Day” reciprocal tariffs announced on April 2 on the vast majority of US trading partners as well as the earlierimposed tariffs on products of Canada, China, and Mexico related to immigration and fentanyl. The decisions do not cover the tariffs that the Trump Administration imposed under Section 232 of the Trade Expansion Act of 1962 (Section 232) or Section 301 of the Trade Act of 1974 (Section 301).
In V.O.S. Selections Inc. v. Trump, No. 25-00066 (Ct. Int’l Trade May 28, 2025) a three-judge panel at the CIT (Court of International Trade) issued a decision brought by several importers and state governments challenging the IEEPA tariffs. The CIT panel unanimously ruled that the president’s actions to impose tariffs under IEEPA are unlawful, and it granted a nationwide permanent injunction to legally bar the government from collecting the challenged tariffs. However, immediately after the CIT issued its decision, the Federal Circuit granted an administrative stay of the CIT order pending appeal. The effect of the Federal Circuit’s immediate administrative stay is that the government will continue to collect IEEPA tariffs for the time being. Absent any action from the government, the tariffs will continue to apply while the Federal Circuit stay is in place.
On May 29, the US District Court for the District of Columbia (DDC) issued a decision in a case brought by two small businesses selling children’s educational products. In Learning Resources, Inc. v. Trump, No. 25-1248 (D.D.C. May 29, 2025), the DDC found that the IEEPA tariffs are unlawful and granted the plaintiffs’ motion for a preliminary injunction to prevent the government from enforcing the tariffs against the plaintiffs. The government has appealed the DDC decision to the US Court of Appeals for the DC Circuit. On June 3, the DDC stayed its preliminary injunction pending appeal.
Regardless of how the Federal Circuit and the DC Circuit rule on appeal, it is expected that the decisions will ultimately be appealed to the Supreme Court.
Meanwhile, New York Attorney General Letitia James and Governor Kathy Hochul, along with attorney generals from 11 other states, have also filed a lawsuit against the Trump
administration challenging the legality of tariffs imposed under the IEEPA. The lawsuit contends that the tariffs have led to sharply increased costs for critical materials—such as steel, lumber, and construction equipment, thereby harming state economies and violating constitutional limits on executive trade powers.
Several other legal and regulatory developments have emerged and will no doubt continue to emerge in 2025, which directly impacts the construction industry’s exposure to tariffs. Construction stakeholders are responding with a mix of legal adaptation and strategic planning. Some firms are increasing contingency allowances for tariff exposure, particularly on large-scale infrastructure and institutional projects. Others are renegotiating ongoing contracts to include retroactive escalation relief. Design professionals are collaborating with procurement teams earlier in the project lifecycle to identify alternative materials or local suppliers.
Trade associations are lobbying for clearer exemptions for essential infrastructure materials and greater transparency in tariff decision-making. Public owners, including state DOTs and school districts, are adjusting bidding documents to include tariff clauses and requesting updated pricing closer to award dates.
While the intent behind the Trump-era tariffs has been to protect American industry and jobs, the construction sector illustrates the complex and often unintended consequences of protectionist policies.
As the construction industry navigates these 2025 developments, stakeholders must remain vigilant—incorporating robust contractual language, revising procurement terms, and engaging with trade policy developments to manage volatility and protect project viability. BG
Jeremy Knaebel is a partner at Dingess, Foster, Luciana, Davidson & Chleboski LLP. He can be reached at jknaebel@dfllegal.com
BY DREW OLSON AND MATT HANSON
Natural disasters can be devastating for real estate and construction companies. With the potential to cause serious damage to physical locations, operational stability, supply chains, labor markets, and contractor relationships, natural disasters can complicate or extend the insurance recovery process.
Unlike other disruptions, such as structural failures or shifting earth, the root cause of a natural disaster is clear, meaning that the recovery process can begin more quickly. Unfortunately, recovery can still take much longer than other disruptive events because critical resources, including labor and assistance from insurers and adjusters, are often in short supply.
To help streamline the insurance recovery process, real estate and construction leaders must understand their insurance policies, what insurance recovery risks they face, and how to avoid them. Doing so will help companies take the right steps in the immediate aftermath of a natural disaster.
Real estate and construction companies face specific insurance risks in the aftermath of a natural disaster. Some of the most prominent risk areas include:
After a natural disaster, companies experience high demand for labor to supervise and execute recovery work. Contractors and subcontractors may impose additional fees for post-disaster work, including work outside the scope of a previously negotiated contract. These extra fees can have multiple layers, with subcontractors marking up their prices by a certain percentage and general contractors adding their own fees on top. In some cases, the final surcharge could total as much as 40% – 50% of the original cost. Builder’s risk policies vary, and some may include provisions that limit coverage for fee increases, potentially leading to disputes with insurers and contractors during fee rate negotiations. Additionally, general contractors are often listed as the beneficiary of insurance policies for ongoing construction projects, even though the policy is held by the owner of the building. This means contractors are typically the ones incurring the costs associated with rebuilding. This dynamic can lead to disputes between owners and contractors when an insurance policy does not cover the full costs of a disaster. Deciding who will ultimately pay the difference can strain an important relationship at a critical time and risk delaying recovery efforts.
Developers will often opt to pay an expediting expense to quickly obtain the resources they need to support their
recovery after a disaster. But in the case of a large natural disaster that affects businesses and organizations across an entire geographic area, expediting prices can skyrocket costs and competition for scarce resources. Companies without coverage for expediting expenses could find themselves in the difficult and costly position of having to pay out-of-pocket or extend their recovery timeline, delaying their return to normal operations.
Other supply chain issues, such as tariffs, can also increase the cost of expediting shipments. As U.S. trade and tariff policies rapidly shift under the new administration, real estate and construction leaders should closely monitor tariff changes to better forecast how much coverage they might need to support future expediting needs.
When a construction project is delayed following a natural disaster, the developer will need to pay an incremental rate on a construction-owned balance during the loss period. That rate will be higher so long as interest rates remain high. While these payments are typically covered by insurance policies, developers should confirm whether they have enough coverage to recover the full interest from a loss period. If their policy does not cover the full amount, the developer will have to pay the difference. This added cost could be difficult to absorb on top of the already expensive disaster recovery process.
Best practices for avoiding insurance recovery pitfalls can be grouped into two categories: navigating policy nuances and maintaining robust documentation.
Insurance policies contain many nuances and limitations, the implications of which may not always be apparent to a policyholder. Disputes between the insured and insurer, or between other parties like the owner and general contractor, often come down to disparate understandings about what costs are covered.
By asking detailed questions about all insurance policies they benefit from, companies can make sure their interpretation matches that of the insurer. For example, builder’s risk policies can have wide variations in coverage level. When damage delays construction, some policies may only cover basic repair costs, while others will examine the project as a whole and consider the ripple effects of delayed construction timelines. Verifying policy limitations like these ahead of time can help avoid disputes or confusion during recovery.
The value of an insurance claim is largely dependent on the policyholder’s ability to demonstrate the true cost of the disruption to the insurer. The burden of proof in a claim always lies with the policyholder — meaning those without robust documentation policies risk forfeiting their chance to tell their own side of the story.
To make sure they have the right documentation available
when needed, companies should implement policies that mandate the preservation of all contemporaneous documents in the wake of a disaster. Organic communications, for example, can be a powerful tool for demonstrating the company’s understanding of the scope of a disruption. Companies should memorialize all verbal communications through detailed notes that can be referred to later, and preserve any external-facing communications with clients, vendors, suppliers, or customers.
For construction projects, documentation around schedules is crucial to the insurance recovery process. Scheduling documentation that lays out the critical path to a construction deadline, and any deviations from it, can help companies illustrate the extent of their additional costs following an event. Without such documentation, companies may have a hard time proving that delays or setbacks were specifically the result of a disaster, and not a different cause. This also means that construction companies need to regularly update and maintain their schedules throughout the course of a project, to better demonstrate the specific impacts of a disaster.
Presenting a claim supported by accurate, robust documentation can help expedite the claims process during a tumultuous time, when insurers may take longer than usual to conduct reviews and resolve disputes. A streamlined process can help companies receive an accurate claim payment and return to normal operations as fast as possible.
This insight was originally published at www. BDO.com. BG
Drew Olson is principal, Risk, Insurance at BDO. Matt Hanson is managing director, Rick, Insurance at BDO. For more information contact Heath Winsheimer, manager, Assurance at hwinsheimer@ bdo.com.
S C A N to learn more
S C A N to learn more
BUILT BY
BY
The Green Building Innovation Expo will highlight t he region’s most notable high-performance building projects and feature a mo rning session led by regional design and construction leaders.
Green Building Innovation Expo
September 2, 2025 | 8:30 a.m. - 3 p.m.
The Highline: 317 East Carson St, Pittsburgh Morning Presentations: 9 a.m.
Expo Open to the Public: 10:30 a.m. to 3 p.m. Email info@gba.org for more information.
Exhibitor space is limited!
Scan the QR code or visit https://www.surveymonkey.com/r/9BVFJYY to apply by August 2.
It may be a reach to label a segment that is less than 10 percent of the total market as “hot,” but when that segment doubles in three years, it is at least worth noting.
Clearly, there are some qualifications to ranking the office market among “what’s hot.” There are no new speculative office buildings under construction in Pittsburgh. As with the rest of the U.S. office market, Pittsburgh’s office buildings continue to see more vacancy. Numerous landlords are facing untenable situations because of the dramatic decline in property values since the pandemic and the 500-basis point hike in interest rates that followed it. The overhyped solution of converting obsolete office buildings to residential is proving to be difficult to execute, as limitations by building floor plates and conversion costs render most projects unfeasible.
So, what makes it hot? It is the tenant improvement (TI) market. The rising vacancy rate is creating more opportunities for movement, even for large users. Not every landlord has been unlucky in timing its financing or investing in its building. In Pittsburgh, the market is ripe for tenants with expiring leases to negotiate favorable deals, unlike in the mid-2010s, including sizable allowances for tenant improvements in exchange for long-term leases.
“I’m working with a group that just received proposal from a landlord for around 24,000 square feet that will provide a $125 per square foot tenant improvement allowance,” says Patrick Sentner, at Colliers Pittsburgh. “That is what’s
needed, unfortunately, to get the newer office environments that stronger clients are looking for.”
“Most tenants in the market are still doing a flight to quality,” reports Amy Broadhurst, president and principal of Lee and Associates’ Western PA office. “Most tenants are going to need to invest $90 or more per square foot in the space to make it appealing to their employees. That is if there isn’t sublease space in the market that makes sense.”
It is a tenant’s market. The pandemic started a sequence of events that drained buildings of daily occupants, while sparking inflation that pushed interest rates 500 basis points higher in an 18-month period. Landlords that financed properties prior to the pandemic are in the position of having to add equity to successfully refinance when loans mature. Competition for tenants is heated, meaning that landlords have to offer free rent and higher tenant improvement allowances to maintain or attract tenants. Costs of construction are at least 40 percent higher than in 2020. And the prevailing trend in leasing is downsizing and consolidation. Landlords are now writing checks instead of cashing them.
“There are certain buildings in the market where landlords and their lenders may not have the capacity to fund their improvements because the building is in a unique position. Lenders are not looking to invest heavily in tenant improvements unless it’s a deal that makes sense,” says Broadhurst. “The good buildings are going to continue to be in a good position. Buildings like Nova Place and One Oxford can afford the TI. Oxford’s ownership basically transferred at a lower cost basis, so they have the capacity to invest, but it was always a flight-toquality building.”
These are bad trends for landlords but good ones for tenants, and for the contractors that service the office construction market.
“If there is any definitive trend it is of shrinking footprints. I don’t see an end in sight in terms of consolidation, which drives modifications to an existing footprint,” says Brad Totten, principal and managing director of the Pittsburgh office of Avison Young. “If you consolidate from 25,000 square feet to 18,000, that involves interior work tied to an extension of a lease term or relocation. It’s unfortunate when you play that out over the entire market, but that is driving a robust tenant improvement market.”
“We are seeing tenants justifying the higher costs because they’re consolidating and bringing their overhead rent down, but want to do something more material to their space to get or keep employees coming back to the office,” Totten continues.
If there is anything that is a drag on the TI market it is the amount of good space available for sublease. While the major real estate firms differ slightly in the total amount of space available for sublease, the consensus puts the total in the market at a minimum of two million square feet. At least two-thirds of that is Class A space, much of which has been improved within the past five years. Broadhurst notes that new tenants at 3 Crossings or Bakery Square can choose high quality space with recent TI, furniture, furnishings, and equipment in place, instead of the raw space available in those developments that would be finished at much higher construction costs.
The amount of space for sublease has fallen a full percentage point over the past 18 months, but there remains enough to be a viable option for most small-to-medium tenants. That proved to be the case for robotics manufacturer ST Engineering Aethon when it opted to lease the 20,000 square foot first floor in the Burns White Building at 3 Crossings.
Even with the alternative of sublease space, the office TI market shows few signs of slowing down, although the market characteristics may be changing.
“We are doing quite a few test fits so that tells you that there are a lot of people looking in the market right now. We’re doing a new test fit every week, which is always a good indicator for us that things are busy,” says Mary Rose Hopkins, associate and director of business development at LGA Partners. “And we are definitely looking at more projects to improve amenities and what they can offer tenants to stay or attract. If anything, that’s ramped up a bit.”
Jeff Young, managing principal of Perkins Eastman’s Pittsburgh studio, notes a decline in the number of opportunities but attributes it to a change in the mix of tenants in the market. In contrast to the employers - like Google, Apple, Dickie McCamey, and others - that were fully engaged in the process of using real estate as an extension of corporate culture, Young sees a certain amount of commodification of space.
“We’re seeing a race for the best financial deal,” he says. “Tenants know that it is a tough market. The question seems to be more often what will the landlord do for us and what is the best deal we can make to get into the space turnkey.”
Dan DeLisio, principal and owner of NEXT Architecture, reports that his firm continues to see a steady flow of tenant improvement opportunities, landing a handful of projects in mid-June. Eric Booth, president of Desmone Architects,
says that design activity and new opportunities slowed after a brisk first quarter. He notes, however, that the office furniture and furnishings companies are reporting continued higher activity, another indicator that sublease space is attracting more tenants.
Workscape’s CEO, Ginny Rothschild, confirms that both the interior construction and furniture systems sides of Workscapes business are busier and she’s cautiously optimistic that will not change soon. Ralph Dallier, principal at Franklin Interiors, confirms that demand is stronger than average. The improved business conditions as a byproduct of the post-pandemic struggle to attract and retain talent.
“Employers that are trying to get or keep the best talent know they can’t do that with outdated or unattractive offices,” she says. “Design matters more today than ever, regardless of the kind of building,” Dallier says. “Good leadership is willing to invest in creating good culture.”
Since rates spiked in 2022, tenant improvement construction spending in metro Pittsburgh rose 60 percent from $165.5 million to $257.8 million in 2024 and is forecasted to increase again in 2025. Tenant reps note that there will be one or two leases over 100,000 square feet expiring annually during the next few years, and several 50,000-to-80,000 square foot users that are new to the market.
Dan Adamski, executive managing director for JLL in Pittsburgh, believes that the current market bias towards tenants should prevail for the next few years, absent any major economic disruption; however, he notes that two milestones later in the decade have potential for more disruption and uncertainty.
“It will be interesting to see what happens after BNY Mellon’s master lease at 500 Grant Street expires in 2028 and UPMC’s lease at 600 Grant Street expires in 2030,” he says. “I don’t see UPMC leaving Downtown, but will they still need a million square feet?”
Before those milestones pass, there is still plenty of disruption in the office market that will drive tenant relocation or refreshment of existing space. For example, BNY Mellon’s move across the street to its Client Service Center at 500 Ross Street is creating upwards of $100 million in renovations to that building. Sentner thinks the current trend will continue until the money runs out and is seeing evidence that lenders are protecting their assets.
“Ultimately the lenders will be the deciding factor. I know that sounds obvious, but they have not shown anything for us to judge any change in the market,” he says. “We recently did an expansion for System One in the K&L Gates Building. We negotiated that lease with the lender. That was a first for me. Even though that building is technically with the lender, they are conducting business in the manner that the landlord typically would because they don’t want the building back.”
2219 Ridge Road South Park, PA 15129
(724) 538 -8227
Erin Joyce, Executive Director erin@asawpa.org
BY STEPHANIE PAYNTER AND CHRISTINE LYONS
In today’s construction market, speed, quality, and cost control are top priorities, and Carnegie Mellon University’s (CMU) Forbes Beeler Apartments project demonstrates that prefabrication can achieve all three. Completed in 2023, the $49 million, 113,500 square foot residence hall provides 266 upperclassmen with a new apartment-style living experience just steps from CMU’s campus. Beyond features like game lounges, a wellness room, and Red List–free materials, Forbes Beeler Apartments stand out as a case study in the strategic use of off-site fabrication to address complex site, scheduling, and labor challenges.
With a tight hillside site stretching horizontally across an urban block, traditional construction methods would have created major sequencing and logistical hurdles. Due to the site’s natural slope, the building rises four stories above Forbes Avenue but only two at the rear, complicating access and requiring strategic coordination of construction activities across varying elevations. The structure’s long, linear footprint added further complexity, demanding a construction method that could maintain pace and precision across its entire length.
Early in the design process, Goody Clancy (architect of record), IKM Architecture (associate architect), and Mosites Construction & Development Company (construction manager) worked together to identify ways to streamline construction without compromising quality. Prefabricated exterior wall panels offered a solution to accelerating the building enclosure and simplifying onsite workflows by fabricating panels off-site, including the framing and air/ vapor barrier. The panels measured 40 feet by 8 feet for the four-story front elevation and 20 feet by 8 feet for the two-story rear. This allowed the segments to be craned into place side by side, significantly accelerating installation and minimizing congestion on the tight site.
“Sequencing the work was critical,” said Christine Lyons, Senior Project Architect at IKM Architecture. “We needed a method that let trades move efficiently around the site without bottlenecks. Prefabrication allowed us to maintain a rhythm, getting the building enclosed faster and setting up interior work ahead of schedule.” Because the enclosure happened rapidly, shared scaffolding was installed early and used by multiple trades, including window installers, glazers, and masons, helping avoid unnecessary duplication of effort and improving overall site coordination.
The results were tangible: prefabrication shaved three months off the construction schedule, allowing CMU to bring the building online earlier and accommodate summer
move-ins instead of waiting for the fall semester. Early enclosure also enabled interior concrete pours during Pittsburgh’s winter, when scheduling pours would typically be difficult and weather sensitive.
Prefabrication demands intense early coordination because every panel needs to fit precisely, with minimal field modification. To ensure successful installation, shop drawings, mockups, and clash detection modeling were critical. IKM, Goody Clancy, and Mosites worked closely with Wyatt Inc., a Pittsburgh-based fabricator, to optimize panel sizes for transportation and erection.
Prefabrication also significantly reduced the number of contractors needed on-site for enclosure. Instead of coordinating framing, sheathing, and air barrier application separately with multiple crews, the team consolidated those scopes into a single product, assembled off-site, and ready for efficient installation. This reduction in onsite labor and minimized coordination complexity was a clear advantage in Pittsburgh’s tightening skilled labor market.
Mosites played a key role in sequencing and construction phasing. Their leadership in orchestrating the delivery, staging, and installation of the panels ensured the team could maintain momentum throughout the build. “Prefabrication requires you to front-load a lot of the work,” Lyons explained. “It’s not just about making the panels; it’s about planning crane access, truck routes, and even the sequence in which the panels arrive. But if you do that leg work early, construction will become much smoother, faster, and more predictable.”
The team’s rigorous quality control processes also helped prevent problems. IKM and Goody Clancy conducted off-site observations at the fabrication facility to inspect the application of air/vapor barriers, ensure consistent treatment of panel joints and window openings, and identify any sealant or attachment concerns. That early investment paid off as the building envelope achieved an air infiltration rate of 0.06 CFM/square foot @ 75 Pa, exceeding Passive House standards. This level of performance delivers longterm energy efficiency benefits without compromising aesthetics or constructability.
The Forbes Beeler Apartments offers a compelling case study for developers and contractors navigating a tightening labor market and increasing pressure on project schedules. The project demonstrates that prefabrication isn’t a shortcut; it’s a shift in how projects are coordinated and executed. Design-assist collaboration with contractors
during preconstruction and hands-on client and design team engagement helped ensure seamless transitions from fabrication to site assembly.
By using prefabrication, the team recognized tangible labor benefits using a smaller, more efficient installation crew.
By fabricating the enclosure off-site, the team reduced the need for multiple sequential trades on-site and minimized the impact of local labor shortages. At a time when Pittsburgh’s construction industry was experiencing skilled labor constraints, the ability to consolidate scopes and manage work in a controlled warehouse setting provided both scheduling and staffing advantages.
Lyons emphasized that client buy-in was essential. “You have to show owners how prefabrication will directly benefit them, not just make construction easier for the team. For CMU, the ability to open the building sooner and welcome summer residents was a powerful motivator.”
Prefabrication supported CMU’s commitment to quality by helping meet the university’s requirement that all new buildings be designed for a 100-year life expectancy. With a high-performance envelope, durable materials, and careful attention to building tightness and thermal performance, Forbes Beeler meets those standards while delivering a modern, apartment-style student experience. This long-term perspective is a key advantage of prefabrication, as it ensures the building’s quality and performance for future generations.
In addition to construction innovation, student wellness, accessibility, and comfort were prioritized. The building includes amenities like game lounges, a wellness room with ondemand hot water taps, and Red List-free materials to support healthier indoor environments. Feedback from residents has been overwhelmingly positive. The residence hall is now CMU’s most requested housing option, with waiting lists reflecting its popularity.
“Students really feel the difference,” Lyons said. “It’s not just the aesthetics; it’s the thoughtfulness behind the comfort, durability, and livability of the space.”
As prefabrication continues to gain momentum in Western Pennsylvania, the Forbes Beeler Apartments stand as a model of how strategic innovation can simultaneously achieve multiple project goals: faster schedules, greater quality control, operational savings, and better user experiences. For Pittsburgh’s construction market and higher education institutions everywhere, Forbes Beeler Apartments proves that building smarter starts long before the first panel arrives. BG
Stephanie Paynter is marketing coordinator at IKM Architecture. She can be reached at spaynter@ikminc.com. Christine Lyons, AIA, is a senior associate and senior project manager at IKM. She can be reached at clyons@ikminc.com The article was written in collaboration with Goody Clancy.
Size: 113,500 square feet
Budget: $49 million
Client: Carnegie Mellon University
Architect of Record: Goody Clancy
Associate Architect: IKM Architecture
Prefabrication Partner: Wyatt Inc.
Construction Manager: Mosites Construction
Completion: 2023
Sustainability: LEED Gold Certified
International Brotherhood of Electrical Workers
L ocal Union No. 5
5 Hot Metal Street • Southside • Pittsburgh, PA
For more than 125 years , I.B.E.W. Local 5 has been lighting up Pittsburgh’s sports arenas, its hospitals and its skyscrapers.
Acrisure Stadium, PNC Park, Pittsburgh International Airport, PPG Place, UPMC Children’s Hospital of Pittsburgh and the new FNB Tower. Behind Pitts burgh’s major buildings is I.B.E.W. Local 5.
The
for the Massaro Family Fund for Alzheimer’s Research.
MICA members are interior contractors who share a common mission: to provide their customers with the highest quality craftsmanship. We partner with the union trades that supply the best trained, safest and most productive craftsmen in the industry.
Alliance Drywall Interiors, Inc.
Easley & Rivers, Inc.
Giffin Interior & Fixture, Inc.
JLJI Enterprises
J. J. Morris & Sons, Inc.
T. D. Patrinos Painting & Contracting Company
Precision Builders Inc.
RAM Acoustical Corporation
Schlaegle Design Build Associates
TRE Construction
Wyatt Inc.
Carnegie Mellon University Margaret Morrison Commons
Interior contractor: TRE Construction
Another high quality MICA project
Avison Young creates real economic, social and environmental value as a global real estate advisor, powered by people. Our integrated talent realizes the full potential of real estate by using global intelligence platforms that provide clients with insights and advantage. Together, we can create healthy, productive workplaces for employees, cities that are centers for prosperity for their citizens, and built spaces and places that create a net benefit to the economy, the environment and the community.
Governor Josh Shapiro visited the Arts Landing jobsite to observe the progress of the revitalization project envisioned by the Pittsburgh Cultural Trust. Pictured, from left to right, are Mascaro Construction’s Steve
Governor Shapiro, and Mascaro’s Chris
from VVA, and Mascaro’s Roman
Mascaro won the award for Talent Recruitment & Retention at the 2025 Engaging Pittsburgh: Innovative People Practices Awards hosted by the Pittsburgh Human Resources Association. The award recognizes workforce development efforts. Accepting the award are Brian Solkovy, Jakob Seman, Kara Seebacher, Jamie Gildersleeve, and Bill Greb.
(From Left) TEDCO’s Kyra Sarver, Miranda Anderson from Atlantic Engineering, the MBA’s Ben Atwood, and Kim Harkobusic from Henderson Brothers at the CREW Pittsburgh Golf Outing at South Hills Country Club on May 19.
and
On Earth Day, May 2, 35 members of the MBA Young Constructors joined forces with Allegheny County Executive Sara Innamorato and the Allegheny County Park Rangers to plant 125 native trees, from sugar maples to flowering dogwoods, as part of a trail renovation in a major county park.
Allegheny County park ranger instructs volunteers from the Young Constructors and Tree Pittsburgh.
Four industrial parks & RIDC Westmoreland Innovation Center. The PennSTART test track site. Excellent connectivity. Westmoreland Technology Drive Industrial Complex is ready for your site-selection needs.
For more than a decade, DFL Legal has provided companies with the most effective solutions in resolving unique construction and engineering disputes.
Our success has been achieved by offering our clients proven, big case experience, along with the efficiencies and flexibility of a boutique firm.
Find out how our experience can be put to work for you.
These are the hallmarks the region’s union construction trades and contractors bring to the jobsite everyday. Our professional tradespeople and contractors bring the dreams and visions of our fast-growing region to life with a dedication that only those who live here, work here, and raise their families here can commit to. It is, after all, our home, our legacy.
We are also committed to providing opportunity for all who share these values and want to pursue a lifelong, lucrative and satisfying career. For more information on building with our union trades and contractors, or to explore career opportunities, please visit www.buildersguild.org where you will find direct links to our Trade Unions, Joint Apprenticeship Training Centers and Contractor Associations.
G.M. McCrossin was awarded a $7.5 million general construction contract for the Towanda Municipal Authority’s $10.2 million wastewater treatment plant improvements in Bradford County. Stiffler McGraw & Associates is the engineer.
Massaro Corporation is the general contractor for the Starbucks at the Smith Student Center at Slippery Rock University. Stantec is the architect.
Slippery Rock University awarded Massaro Corporation the general construction contract for its $2.1 million Rhoads Hall Dormitory First Wing Renovations. The architect is WTW Architects, an AE Works company.
Massaro Corporation was the successful contractor on the $1,653,000 renovations to the lower level of Cooper-Siegel Community Library for the Borough of Fox Chapel. Axis Architecture is the architect.
Carl Walker Construction was the successful contractor on the $14 million renovations to UPMC Shadyside Hospital Centre Avenue Garage. The architect is Desman.
Winthrop Management awarded Shannon Construction the contract for the tenant improvements for Meyer Unkovic & Scott’s office at 600 Grant Street. The architect for the $2 million buildout is Stantec.
Uhl Construction was awarded a contract for the Brand Image Renovation and Addition to Century III Kia in West Mifflin. The project involves renovation of the existing showroom to update Kia branding and 19,183 square feet of new construction. The architect is Avon Design Group.
Tri-County Landfill, Inc. selected Uhl Construction as general contractor for its new leachate tank facility outside Grove City, PA. The project includes major site work and utility construction, a new leachate tank enclosure, tank installation, and related piping. BAI Group is the engineer.
Facility Support Services was awarded the UPMC Presbyterian AHU 3-G-1 Replacement. The Design Group is the architect. Osborn Engineering is the mechanical engineer.
The University of Pittsburgh awarded TEDCO Construction the contract for the $7 million Scaife Hall Winter Institute for Simulation, Education, and Research (WISER) Renovations Phases 2 and 3. The architect is Moshier Studio.
108 Properties Inc. selected GEM Building Contractors, an E&G Development Inc. company, as general contractor for the buildout of tenant space at 108 Commerce Boulevard in Cecil Township.
Mascaro’s Heavy/Industrial Group was awarded the contract for Pittsburgh Water’s ABC System Enhancement project. This project consists of the renovation of the existing Aspinwall Pump Station building, construction of a new Bruecken Pump Station building, and the installation of a new large-diameter Clearwell bypass pipe.
Rycon is renovating a 10,400 square foot office space for Excelitas Technologies within Riverfront East, part of the 3 Crossings campus in Pittsburgh’s Strip District.
Armstrong County Memorial Hospital selected Landau Building Company to serve as construction manager on the Electrical Infrastructure Upgrade Project. Working alongside levelHEADS Architects, Allen + Shariff, and Clista Electric, the scope involves the removal and replacement of the main electrical infrastructural system while keeping the hospital fully operational. Work involves main distribution switchgear, emergency power switchgear, automatic transfer switches, utility transformer, new and temporary generators, as well as structural steel, concrete, and restoration work.
UPMC selected Landau Building Company to complete a roof replacement project at Magee-Women’s Hospital, with HDG Architects serving as the design professional.
PJ Dick is the CM at risk for the Sewickley Academy Senior School renovations. The renovations include new interior cosmetic finishes, an updated HVAC system, new LED lighting throughout, new modern lockers, a new roofing system, and the removal of a CMU load bearing wall to open the student lounge space.
PJ Dick continues its relationship with Manchester Craftsmen’s Guild with two renovation projects to the second-floor youth and jazz spaces and the first-floor box office / archives center. The project consists of alterations to five rooms totaling 5,080 square feet at the existing and currently occupied jazz venue and training center. The alternations include finishes, electrical, and mechanical upgrades.
PJ Dick is the CM at risk for renovations to the 20,000 square foot, 21-unit Franklin Court Apartment Building on University of Pittsburgh’s Oakland campus. The renovations include life safety and mechanical/electrical upgrades, including all new electrical service and surface mounted distribution, new electrical devices and fixtures, new plumbing fixtures, new carpet and LVT flooring, new unit entry doors, and paint.
PJ Dick is managing construction for a new Cleveland Brothers facility in Pleasant Valley, WV. The project consists of two buildings that total approximately 75,000 square feet of floor space, including a second-floor mezzanine.
PJ Dick is managing the final phase of the four-phase renovation to the Lemington School.
PJ Dick is the CM at risk for a partial renovation to the sixth floor of Duquesne University’s Fisher Hall for the School of Nursing simulation center. The project consists of the demolition and renovation to 8,600 square feet of classroom space.
PJ Dick is managing the renovation to existing hockey operations at the UPMC Lemieux Sports Complex in Cranberry Township.
Search MBA's directory to find top general contractors, construction managers, subcontractors, suppliers and service providers for your next project. MBA membership accounts for more than 80% of commercial construction in our region. mbawpa.org/ member-directory
mbawpa.org
To assure that the industry maintains its commitment to safety, MBA offers essential training and services. These services include information, interpretation, and consultation on OSHA regulations for member contractors.
mbawpa.org/safety
Get connected to the largest commercial construction trade association in the region. Learn more about the benefits of MBA Membership at mbawpa.org/join-mba
Facility Support Services moved its office to 4200 Walnut Street, Suite 9, McKeesport, PA 15132..
Independence Excavating Inc. announced that Hunter Survey has joined as the traveling Field safety specialist.
Independence Excavating Inc. welcomed Joe Rozzi as a traveling project manager.
Turner Pittsburgh welcomed eight interns for the summer. Returning interns include Justin Bass, Jobi Cook, Anthony DeCostello, and Sage Smith. Joining Turner for their first summer are Kam Chan, Jevontae Jones, Alexandra Romanchik, and Bailey Serevicz
Rycon Pittsburgh is pleased to welcome Clemson University alumnus, Vincent Romano, as an assistant project manager.
Alex Tyson, a Liberty University alumnus, has joined Rycon Pittsburgh as an assistant project manager.
Rycon Pittsburgh welcomed Makayla Walk back as a project
engineer. After interning with Rycon last summer, she returns full time post-graduation from Pennsylvania State University.
Craftworks USA welcomed La Roche University alumna, Carley Denner, as a drafter.
Brandon Irish, with over 22 years’ experience, has joined Craftworks USA as a senior estimator.
Dominike Rangel joined Craftworks USA as a drafter.
Bill Taylor joined PJ Dick as an MEP estimator.
PJ Dick’s West Chester office welcomed Kaci Gregory to its business development team.
Josh Beightley joined PJ Dick as superintendent.
Project Engineer Simon Lingle joined PJ Dick. Simon is a 2025 civil engineering graduate from the University of Pittsburgh.
Andrew Upvall joined PJ Dick as a project manager.
President
Michael R. Mascaro
Mascaro Construction Company, LP
Vice President and Treasurer
Alexander G. Dick
Dick Building Company
Secretary/Executive Director
David D. Daquelente
2025 MBA BOARD OF DIRECTORS
John P. Busse
F.J. Busse Company, Inc.
James T. Frantz
TEDCO Construction Corporation
Michael Kuhn
Jendoco Construction Corporation
Jennifer P. Landau
Landau Building Company
Anthony F. Martini
A. Martini & Co.
Steven M. Massaro
Massaro Corporation
David P. Meuschke, P.E.
Burchick Construction Company, Inc.
M. Dean Mosites
Mosites Construction Company
Jake Ploeger
PJ Dick Incorporated
Jodi L. Rennie
Turner Construction Company
John Sabatos
Rycon Construction, Inc.
Raymond A. Volpatt, Jr., P.E., Past President
Volpatt Construction Corporation
Neal Rivers (MICA President)
Easley & Rivers, Inc.
A. Martini & Co.
AIMS Construction
Allegheny Construction Group, Inc.
Burchick Construction Company, Inc.
Caliber Contracting Services, Inc.
Carl Walker Construction, Inc.
CH&D Enterprises, Inc.
CPS Construction Group, Inc.
Dick Building Company, LLC
DiMarco Construction Co., Inc.
E&G Development, Inc.
Elwood Construction Corporation
F.J. Busse Company, Inc.
Facility Support Services, LLC
FMS Construction Company
Fred L. Burns, Inc.
Gilbane Building Company
Higley Construction
Independence Excavating, Inc.
Jendoco Construction Corporation
Kokosing Industrial Incorporated
Landau Building Company
Mascaro Construction Company, LP
Massaro Corporation
McCrossin
Menard USA
Mosites Construction Company
Nicholson Construction Company
PJ Dick Incorporated
Rocky Bleier Construction Group
Rycon Construction, Inc.
Shannon Construction Company
Stevens Engineers & Constructors, Inc.
TEDCO Construction Corporation
Turner Construction Company
Uhl Construction Company, Inc.
Volpatt Construction Corporation
2bn contracting
A Crane Rental, LLC
A. Folino Construction, Inc.
A.J. Vater & Company, Inc.
Abate Irwin, Inc.
ABMECH Acquisitions, LLC
ACE Lightning Protection, Inc.
Advantage Steel & Construction, LLC
All Crane Rental of Pennsylvania, LLC
Alliance Drywall Interiors, Inc.
Amelie Construction & Supply, LLC
Amthor Steel, Inc.
BrandSafway Industries LLC
Brayman Construction Corporation
Bristol Environmental, Inc.
Bruce & Merrilees Electric Company
Bryan Construction, Inc.
Build with MD
Burke & Company, LLC dba S.P. McCarl & Company
Burnham Industrial Contractors, Inc.
Buzzelli Group LLC
Casework Installation Company, LLC
CaseWorks Inc.
Centerpoint Painting Systems
Century Steel Erectors Co., LP
Clista Electric, Inc.
Cost Company
Costa Contracting, Inc.
Cuddy Roofing Company, Inc.
Dagostino Electronic Services
D-M Products, Inc.
Dom DeMarco Construction, Inc.
Donley’s Concrete Group
Douglass Pile Company, Inc.
E2 Landscape & Construction
Easley & Rivers, Inc.
EMCOR Services Scalise Industries
Fay, S&B USA Construction
Ferry Electric Company
First American Industries, Inc.
Flooring Contractors of Pittsburgh
Franco Associates
G. Kidd Inc.
Gaven Industries, Inc.
Geo V Hamilton, Inc.
Giffin Interior & Fixture, Inc.
Gregori Construction Inc.
Gumpher, Inc.
Gunning, Inc.
Hanlon Electric Company
Harris Masonry, Inc.
Hatzel & Buehler, Inc.
HOFF Enterprises, Inc.
Howard Concrete Pumping, Inc.
Hunt Valley Environmental, LLC
J.J. Morris & Sons, Inc.
JLJI Enterprises, Inc.
K & I Sheet Metal, Inc.
Kalkreuth Roofing & Sheet Metal, Inc.
KELLER North America
Keystone Electrical Systems, Inc.
Kirby Electric, Inc.
Kusler Masonry, Inc.
L & E Concrete Pumping Inc.
Lanco Electric, Inc.
Lighthouse Electric Company, Inc.
Lisanti Painting Company
Manheim Dellovade LLC
Marsa, Inc.
Massaro Industries, Inc.
Master Woodcraft Corporation
Matcon Diamond, Inc.
Maxim Crane Works, LP
McCrossin Foundations, LLC
McKamish, Inc.
Mele & Mele & Sons, Inc.
Mohawk Construction & Supply Co., Inc
Next 150 Construction LLC
Noralco Corporation
O. Z. Enterprises, LLC
Paramount Flooring Associates, Inc.
Phoenix Roofing, Inc.
Pittsburgh Interior Systems, Inc.
Precision Environmental Company
Pullman SST
RAM Acoustical Corporation
Redstone Flooring, LLC
Renick Brothers Construction Co.
Richard Goettle, Inc.
Right Electric, Inc.
Ruthrauff | Sauer, LLC
Saint’s Painting Company, Inc.
Sargent Electric Company
Schindler Elevator
Schlaegle Design Build Associates, Inc.
Schnabel Foundation Company
Solid Platforms, Inc.
Specified Systems, Inc.
Spectrum Environmental, Inc.
SSM Industries, Inc.
Steel City Scaffolding of Pittsburgh, LLC
Swank Construction Company, LLC
T.D. Patrinos Painting & Contracting Company
Tarax Service Systems, Inc.
TRE Construction
Triple 3 Construction, LLC
Tri-State Flooring, Inc.
W.G. Tomko, Inc.
W.O. Grubb Steel Erection, Inc.
Wayne Crouse, Inc.
Wright Commercial Floors
Wyatt Incorporated
4CTechnologies
84 Lumber Company
A. L. Harding & Company
A.R. Chambers and Son, Inc.
ADMAR Construction Equipment and Supply
AEC Online Store
African American Chamber of Commerce of Western PA
Allegheny County Airport AuthorityPittsburgh International Airport
Alliant
American Contractors Insurance Group
American Producers Supply Company, Inc.
AmeriServ Wealth & Capital Management
Aon
Atlantic Engineering Services
Atlas Wholesale Co., Inc.
AUROS Group
Babst Calland
Baker Tilly Virchow Krause, LLP
BDO USA, P.A.
Beth-Hanover Supply Co., Inc.
Black Diamond Equipment Rental
Bowles Rice
Bronder & Company, P.C.
Building Point Ohio Valley
Burns & Scalo Real Estate Services, Inc.
Burns White, LLC
CAD Construct LLC
Cadnetics, Inc.
Case | Sabatini
Chartwell Investment Partners
Chubb Group of Insurance Companies
Civil & Environmental Consultants, Inc.
Clark Hill PLC
Cleveland Brothers Equipment Co., Inc.
CliftonLarsonAllen LLP
Cohen and Company
Cohen Seglias Pallas Greenhall & Furman PC
Computer Fellows Inc.
Cozen O’Connor
CTR Payroll & HR
DesignGroup
Desmone Architects
Dickie, McCamey & Chilcote, P.C.
Dingess, Foster, Luciana, Davidson & Chleboski LLP
Dollar Bank
DRAW Collective Architecture
Eckert Seamans Cherin & Mellott
ECS Mid Atlantic, LLC
EPIC Insurance Brokers & Consultants
EquipmentShare
Fahringer, McCarty, Grey, Inc.
Falk-PLI Engineering and Surveying
FASTSIGNS of Pittsburgh
FDR Safety, LLC
FieldForce Equipment Sales & Rentals, LLC
First National Insurance Agency
Fisher Phillips
GM Equipment Corp.
Graystone Consulting Pittsburgh
H2R CPA
Henderson Brothers, Inc.
Henry Rossi & Co., LLP
HHSDR Architects/Engineers
Highstreet Insurance Partners
Hillis Carnes Engineering Associates, Inc.
HUB International
Huth Technologies LLC
IMA Corp
Interior Supply, Inc.
Intertek - PSI
J.S. Held
JLL
K&L Gates LLP
Karpinski Engineering
Kehm Oil Company
L & W Supply
LaFace & McGovern Associates, Inc.
Langan Engineering & Environmental Services
Liberty Insurance Agency
Liberty Mutual Surety
Lytle EAP Partners/Lytle Testing Services, Inc.
Maiello, Brungo & Maiello
MarinoWare
Marsh
Marthinsen & Salvitti Insurance Group
McKim & Creed, Inc.
McNees Wallace & Nurick LLC
Meyer, Unkovic & Scott LLP
Meyers Company
Michael Baker International
Michael Brothers Companies
Milwaukee Tool
Mobile Air, Inc.
Mobile Medical Corporation
Monster Smash, LLC
Morgan, Lewis & Bockius LLP
MSA Safety
MSW Supply
Multivista
NCI - Nursing Corps
Ohio Valley Drywall Supply
OnPoint Industrial Services
OVD Insurance
PenTrust Real Estate Advisory Services, Inc.
PGH Networks
Philadelphia Insurance Companies
Pietragallo Gordon Alfano Bosick & Raspanti, LLP
Pittsburgh Mobile Concrete, Inc.
ProShare Services LLC
R.J. Bridges Corporation
Reed Building Supply
Repco II
Republic Services, Inc.
RETTEW Associates
RJR Safety Inc.
Roofing & Exterior Products Services
Saxton & Stump
Schneider Downs & Company, Inc.
Scotti Law Group
Security 101 Pittsburgh
Seubert & Associates, Inc.
Solutions 21
Sprague Energy
Stanley Black & Decker
Stephany Associates, Inc.
Steptoe & Johnson, PLLC
STI, Inc.
Suburban Propane
Sunbelt Rentals, Inc.
Susanin, Widman & Brennan, PC
The Gateway Engineers, Inc.
The Reschini Group / Evergreen Insurance
The Sherwin-Williams Co.
T-Mobile
Tom Brown, Inc.
Travelers Bond & Financial Products
Triangle Fastener Corporation
Triumph Modular
Tucker Arensberg, P.C.
UBS Financial Services, Inc.
Unified Door & Hardware
United Rentals
UPMC Work Partners
USI Insurance Services
W. R. Meadows of Pennsylvania
White Cap
WNA Engineering, Inc.
WTW - Willis Towers Watson
Zurich NA Construction
BY BHAVINI PATEL AND MICHAEL VOLPATT
While so many people now recognize the importance of keeping trash out of landfills, in the construction industry, this remains a challenge. Beyond LEED© requirements, which mandate diverting at least 75 percent of waste for certification, our industry is one of the largest contributors to landfill waste. Demolition alone accounts for 90 percent of the materials we haul away and discard.
As professionals from two different sectors, one leading a sustainability nonprofit and the other running a construction company, we see both the challenges and opportunities in reducing construction waste. Addressing this issue requires a nuanced understanding of how businesses operate and how to align environmental goals with economic realities. Construction waste is not only an environmental issue; it’s a structural challenge deeply tied to costs, logistics, and policy.
Although I, Michael, grew up in commercial construction, my early career took me elsewhere. For years, I consulted with technology companies across the globe, helping them tell their stories and build awareness. Living in the Bay Area, I saw firsthand how recycling, composting, and source separation were second nature—woven into daily life.
Returning home to work in my family’s construction business, I was struck by the staggering amount of waste our industry generates, while navigating the pressures of tight margins, aggressive timelines, and the practical barriers to waste diversion. Looking at the economics of construction, it’s clear why contractors often default to what we call “smash and trash.” Demolition done quickly and cheaply saves money. In a competitive market where the lowest bid often wins, time is a significant cost driver. Deconstructing carefully, sorting materials, and salvaging reusable components all take time and money.
But if we are among the biggest contributors to landfill waste, shouldn’t we also lead efforts to reduce it?
Construction operates on thin margins. Profitability in a cost-driven market makes waste diversion an afterthought unless mandated by an owner or required for LEED certification. Too often, the construction industry takes the path of least resistance, discarding everything and ignoring what vanishes into the dumpster.
This is where policy can help. What if tax incentives rewarded companies for reducing landfill waste? What if diverting materials became an environmental decision and an economic one?
In 2019, Allegheny County updated its waste management plan to address the region’s evolving environmental and economic challenges. A key focus of the revision was extending landfill capacity while supporting policies that promote sustainable waste diversion. The plan set forth objectives such as working toward Pennsylvania’s statewide 35 percent recycling goal, identifying innovative strategies to enhance recycling infrastructure, and exploring funding mechanisms to support waste reduction programs. These
efforts highlight the need for practical incentives that make sustainability a viable choice for businesses, particularly in construction, where waste diversion remains an uphill battle.
Beyond incentives, contractors can take proactive steps. Before mobilizing, collaborating with owners and architects to conduct a salvage assessment can identify materials for reuse, resale, or donation. Organizations like Construction Junction, Doors Unhinged, Global Links, and Michael Brothers offer pathways to keep valuable materials out of landfills. We call this Phase Zero demolition planning, and it works. Defining waste streams before breaking ground, streamlines the process and can even provide a competitive edge.
As the leader of a sustainability nonprofit, I believe this approach goes beyond waste diversion. It’s about identifying tangible opportunities within business operations that can drive long-term carbon emissions reductions while also fostering equitable job creation. Leadership in sustainability means recognizing that every industry, including construction, has a role to play in advancing regional climate goals. By working directly with business owners to uncover efficiencies in their systems and structures, we not only reduce waste but also build stronger, long-lasting coalitions that drive systemic change. This moment calls for bold action, innovation, and collaboration—setting a new standard for how industries can lead in environmental responsibility. Waste diversion is not just an environmental checkbox; it is a gateway to a resilient and thriving region, where sustainability, economic success, and equitable workforce development go hand in hand.
Yes, cost remains a challenge, but there is a viable business case. Making waste diversion financially feasible through incentives can establish it as a standard practice—one that strengthens both the industry and the environment. This is not just about sustainability; it’s about innovation, job creation, and a more resilient economy. By working together across industries, we can drive meaningful, longterm change.
Patel is the executive director of Sustainable Pittsburgh. She can be reached at Bpatel@sustainablepittsburgh.org. Michael Volpatt is vice president of marketing and innovation at Volpatt Construction. He can be reached at michael@volpatt.com.
THURSDAY, FEBRUARY 26, 2026