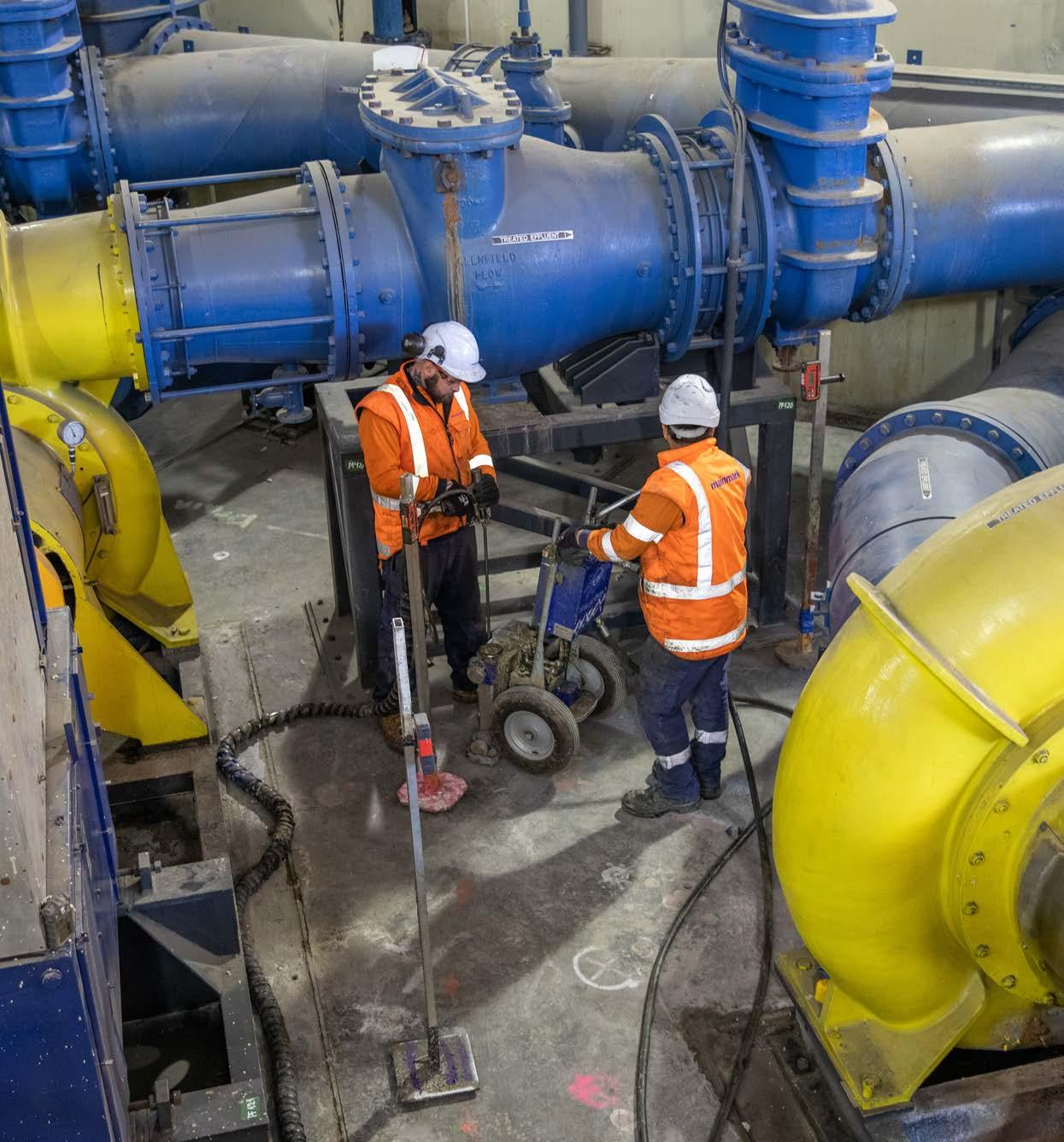
Teretek® Ground Improvement

Resin Injection for Ground Improvement
For more than 35 years, Mainmark have been developing and delivering non-invasive level correction and ground improvement solutions throughout Australasia, having successfully completed thousands of projects from homes, critical infrastructure and civil engineering applications, through to large scale projects such as the re-levelling of the 33,000 tonne Christchurch Art Gallery. Mainmark won the International Project of the Year Award at the 2016 Ground Engineering Awards.
Mainmark’s ground improvement using engineered resin injection, is suitable for both liquefaction mitigation in seismically active areas and also for general bearing capacity enhancement under static conditions, beneath existing structures and greenfield applications. Resin injection is proven to be effective, fast, clean, non-invasive and able to be applied with minimal business disruption to occupants.
Mainmark’s Teretek® resin injection for ground improvement works primarily as a result of densification of the soil from an aggressively expanding polyurethane resin – although other secondary effects such as improvement in composite stiffness, cementation, and horizontal stress increases are also present.
The Process
Typically, injection tubes are installed into the ground via small 12-20mm penetrations at regular intervals
across the target area of treatment. At each injection point material is injected into the target treatment zone to create the resin soil matrix. The Area Replacement Ratio (ARR), target treatment zone, injection array, injection sequence and other project specific criteria are all designed to site specific conditions. Actual injection methodology can consist of ‘top down’ or ‘bottom up’, static or continuous injection. In a typical ‘bottom up’ installation, the tube is withdrawn either in set stages with set volumes of material injected at each stage, or it is withdrawn slowly on a continuous basis, with set volumes of material being injected per unit length that the tube is withdrawn. All injection parameters are monitored, captured and recorded throughout the operation via automated wireless equipment.
During injection of the treatment zone, the low viscosity resin both permeates the soil and also penetrates under pressure along planes of weakness within the soil profile. The material reacts after injection, rapidly expanding to many times it original volume. The expansion of the injected material results in compaction of the adjacent soils due to new material being introduced into a relatively constant soil volume.
It should be noted that this process does not produce regular columns or ‘bulbs’ of material distributed down the vertical injection line. Instead it typically results in a ‘veining’ of expanded material distributed through the soil mass as dykes, sills or networks of sheets or plates; typically tens of millimetres thick.
Teretek®Liquefaction Mitigation
Liquefaction Mitigation using resin injection
Resin injection has been used by Mainmark globally for the lifting or level correction of buildings for over 30 years. Expanding resin mixes are injected into the ground at relatively shallow depths, resulting in ground heave and building lift.
Mainmark’s resin injection was initially tested within the 2013 Science Trials undertaken by the NZ Government within the Christchurch ‘Red Zone’. These trials showed an increase in liquefaction resistance via a number of measures. The overall density of the soil increased, as measured by Cone Penetration Testing (CPT) tip resistance. The composite stiffness of the improved soil block increased, as measured by shear wave velocity testing. The cyclic strains in the soils during shaking were decreased, as measured during T-Rex testing. Pore pressure response and liquefaction induced settlements were significantly reduced during the shaking and blasting trials.
The release of internationally peer-reviewed research has found that Resin Injection is a proven method for increasing soil density, foundation bearing capacity and mitigating liquefaction. Mainmark initiated a series of trials over a four-year period in Christchurch,
New Zealand’s liquefaction-affected ‘Red Zone’, with partial funding from the Earthquake Commission (EQC) and the Ministry of Business, Innovation and Employment (MBIE).
These field trials revealed that Mainmark’s ground
The Resin Injection Ground Improvement Research Trials peer reviewed report can be viewed on the New Zealand Geotechnical Society website: www.nzgs.org/library/ resin-injection-groundimprovement-research-trials
Settlement analysis pre and post injections
Red Zone trials following the Christchurch Earthquake Sequence demonstrated reduction in vertical settlements of over 70% across a wide range of PGA values, from 145mm to 40mm. These results were verified by CPT testing. With predicted differential settlements of less than 25 mm in an earthquake, the structural rectification of a building can be significantly reduced with Mainmark’s Liquefaction Mitigation solution.
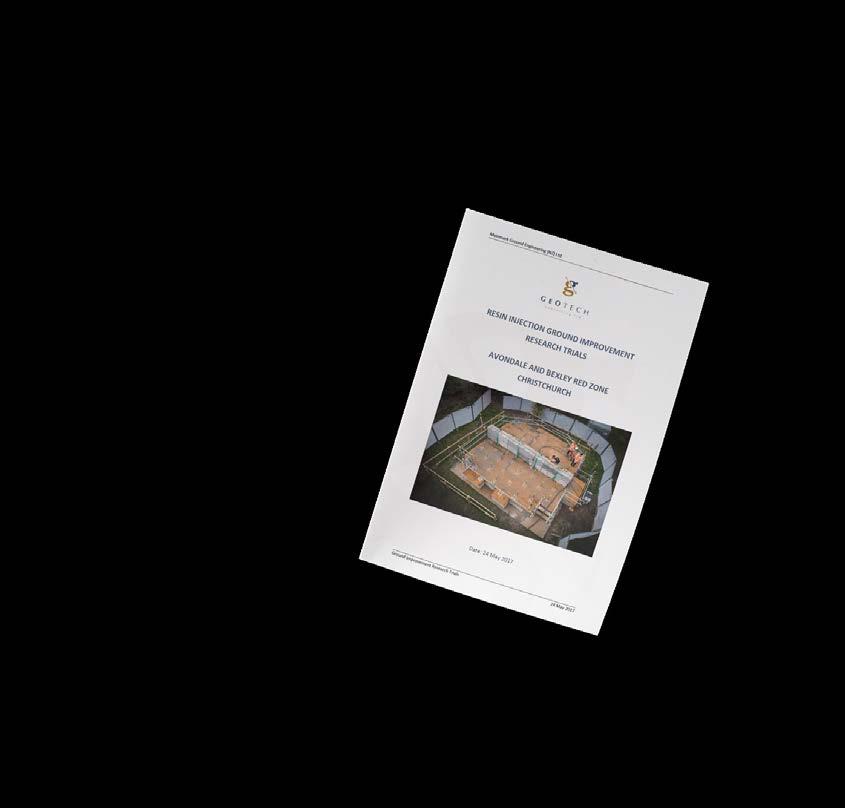
Precentage Reduction
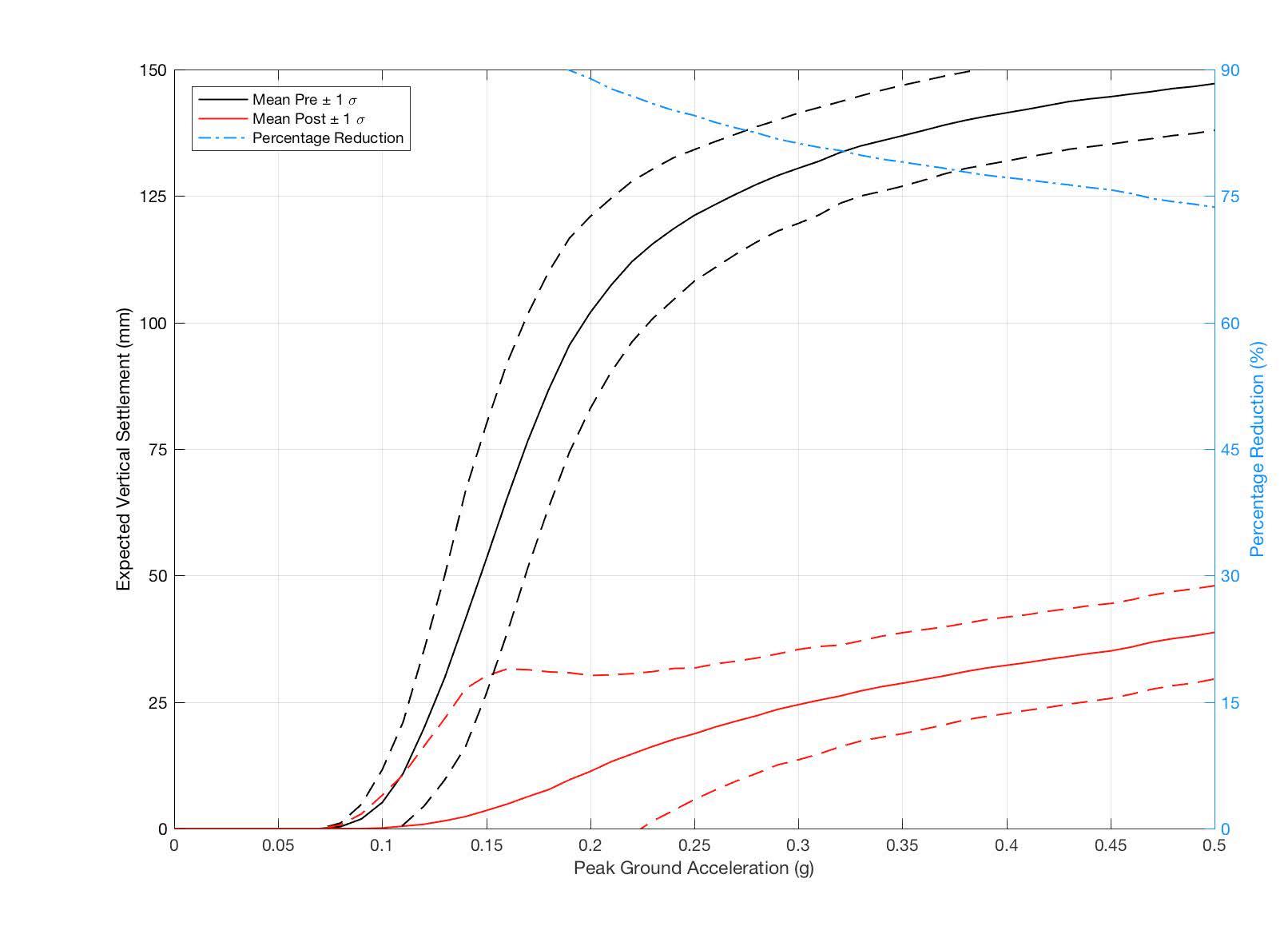
Test Results
As can be seen from the summary graphs, resin injection has demonstrably improved the density and stiffness of the treated ground, as measured by several means.
CPT cone resistance (qc) has increased noticeably - in the order of 80% on average - and therefore it is implied that soil densities have significantly increased. The derived value qc1Ncs, which accounts for soils fines content, has also therefore increased considerably (on average 70%). This variable (qc1Ncs) is used in the calculation of liquefaction triggering and therefore also settlements and LSN values – calculated settlements have reduced by 50 – 80%, and LSN values have decreased by similar amounts. The implied surface damage potential for these sites from seismic liquefaction has therefore reduced dramatically.
Measured cross-hole shear wave velocities (Vs) have increased in the order of 40%, indicating a large increase in stiffness. Shear modulus is related to Vs as follows:

Therefore (even assuming a constant soil density) the shear modulus (i.e. the shear stiffness of the soil) has approximately doubled.
Dilatometer testing (DMT) also indicated increases in KD of about 80%, which implies a further potential 50% increase in the resistance of the soils to liquefaction. Mainmark is further investigating the longevity of the increase in horizontal stress, this effect has not however been taken into account in the previously discussed settlement or LSN results.
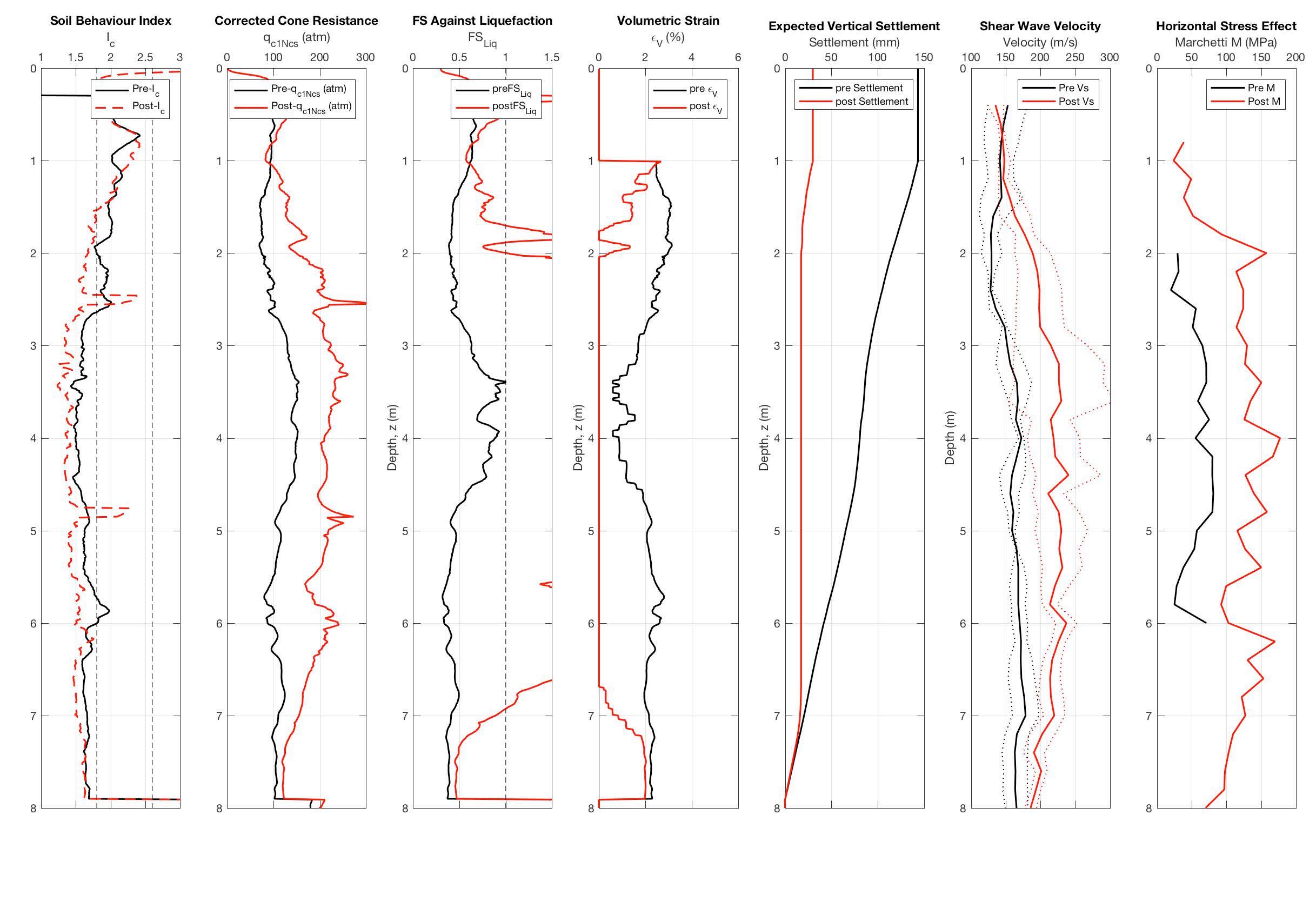
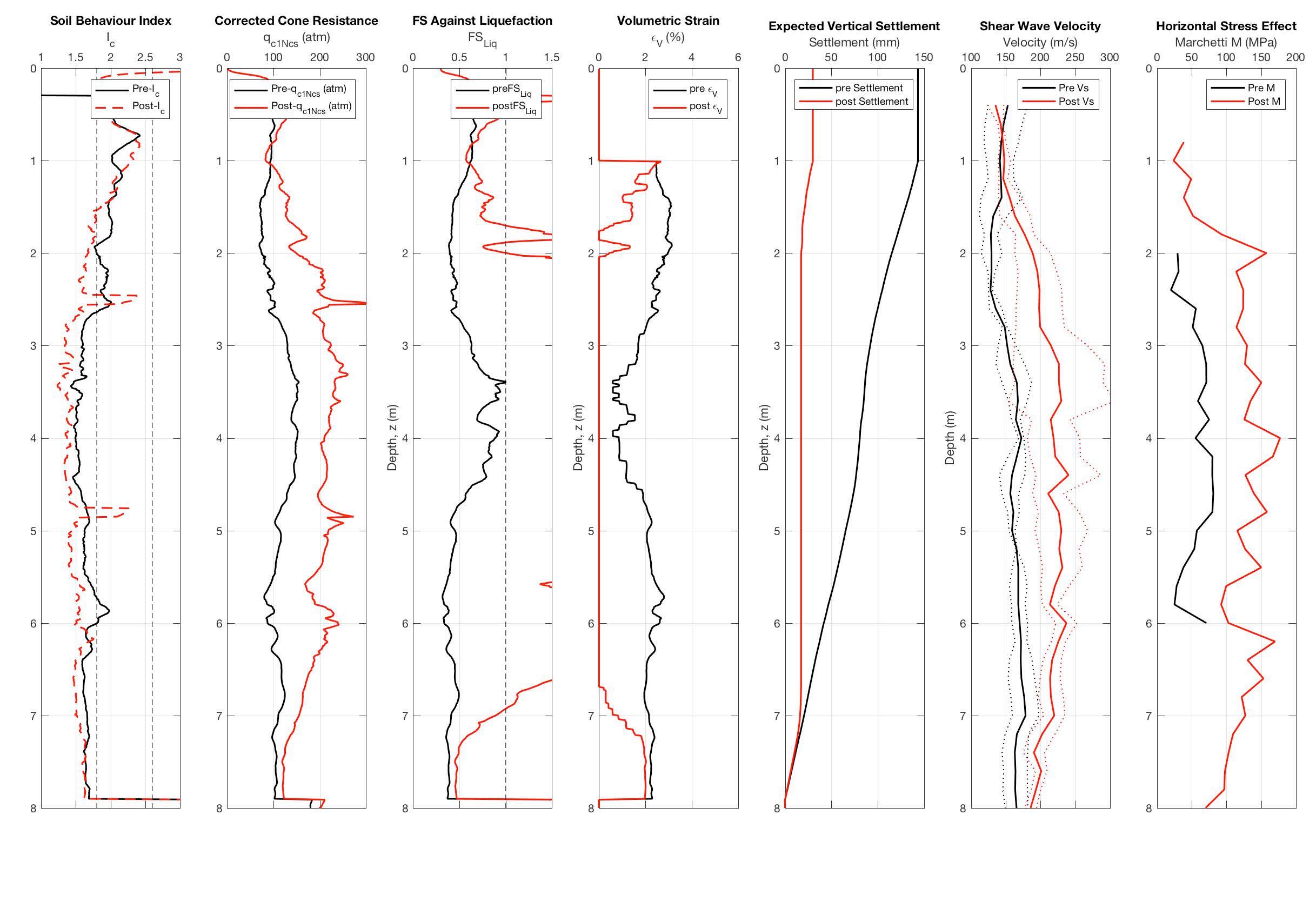
Teretek® Ground Improvement
Material Characteristics
Service life and durability
Underground, Teretek resins are intended to last 100 years. “The service life of Teretek resins can be relied on to exceed 50 years . . . and can confidently be expected to be considerably longer.”1 In addition to low thermal conductivity, it is stable and durable.2 Teretek complies with the New Zealand Building Code clause B1.
Environment and ground water
Teretek resins is inert and will not leach into ground water nor affect the environment.3
Moisture resistance
Unique hydro-insensitive resin is used in wet conditions, including below water table level, to ensure structural quality material.
Fungi and bacterial resistance
Fungi, bacteria and mould do not decay Teretek resins.4
Insect resistance
Teretek resins do not nourish insects or rodents.
Biodegradation
Teretek resins will not be subject to biodegradation, even when buried underground.5
Stability in sunlight and UV
Surfaces exposed to sunlight will discolour and embrittle but are then likely to shield underlying layers. Because Teretek resins is exclusively used underground, UV exposure is generally not relevant.
Stability and chemical resistances
Teretek resins are thermoset polymers. Thermoset polymers are those that change irreversibly during their formation reaction into a material that is infusible and insoluble. The stability of polyurethanes is well documented and in the table of chemical resistances.
Chemical resistance
Brine (saturated)
Diesel
Ethyl Alcohol
Jet A1
Kerosene
Hand‐exhumed resin veins and hydro‐exhumed resin veins in an approximate 5m by 5m by 1m deep
Excellent
Excellent
Poor
Excellent
Excellent
Methanol Poor
Mineral oil Excellent
Petrol/Benzene
Toluene
Turpentine
Excellent
Excellent
Good
Water Excellent
Acids and bases
Ammonium Hydroxide Good
Ammonium Nitrate Excellent
Hydrochloric acid (10%) Excellent
Nitric Acid (10%) Poor
Sodium Hydroxide Excellent
Sulphuric Acid (10%) Excellent

Strength
The compressive strength of the Teretek resin as installed for ground improvement is 1.5 MPa to 5 MPa; dependent upon initial ground strength. Compressive strength testing was carried out at the University of Padua geotechical laboratory to UNI Standard 6350-68.
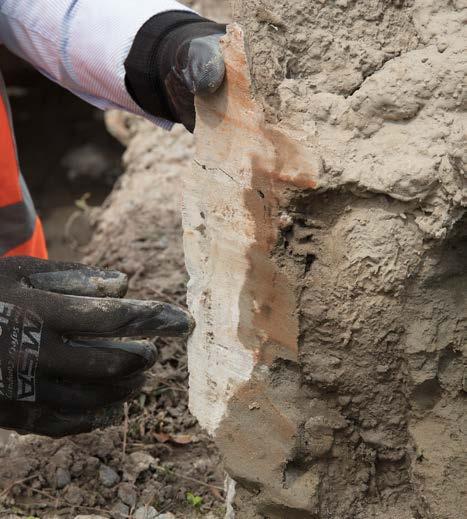
Creep under dynamic stress
Long term performance is mandatory. According to research, “Resin layers should not exhibit any creep deformation under normal traffic loads”.6
Teretek has a high rate of expansion
In non-cohesive soils, the Teretek reisn expands between three and seven times its initial volume. The extent of expansion is dependent upon the confinement provided by the soil. The pressure exerted by Teretek as it expands is a key element of the technology. This pressure, which can exceed 10 MPa facilitates the penetration of the Teretek resin into fine soils through a process of hydraulic fracturing.
Stability over time
Teretek materials have been specifically engineered to resist shrinkage or deterioration and are warranted by Mainmark in accordance with the product durability requirements of the applicable Local, State or National Building Code.
Permeability coefficient
Teretek resin has a permeability coefficient of 10-8 m/s. This value, if compared with the soil permeability, is similar to that of clay and is far less than those of sand and gravel.
REFERENCES
1 Dossier No. FX2639 BaySystems - R&D manager, Dr. Sir. Allard van der Wal. 07-02-09 2 Thermal insulation materials made of PUR/PIR, BING, October 2006 3 Chemical/ toxicological tests on the dual-component polyurethane system designated Geoplus A/Geoplus B, Hygiene Institut des Ruhrgebiets, 30-01-2004 4 Determining the resistance of a synthetic polymeric material to fungal and bacterial growth, March 2009, University of Wageningen. 5 What happens to polyurethane foam in a Landfill: study by Carnegie-Mellon University’s Department of Biological Sciences, (William E. Brown). 6 Institut DR.-Ing Gauer Ingenieur-GmbH. Test report No. 7037-B1-A dated 23.04.2007.
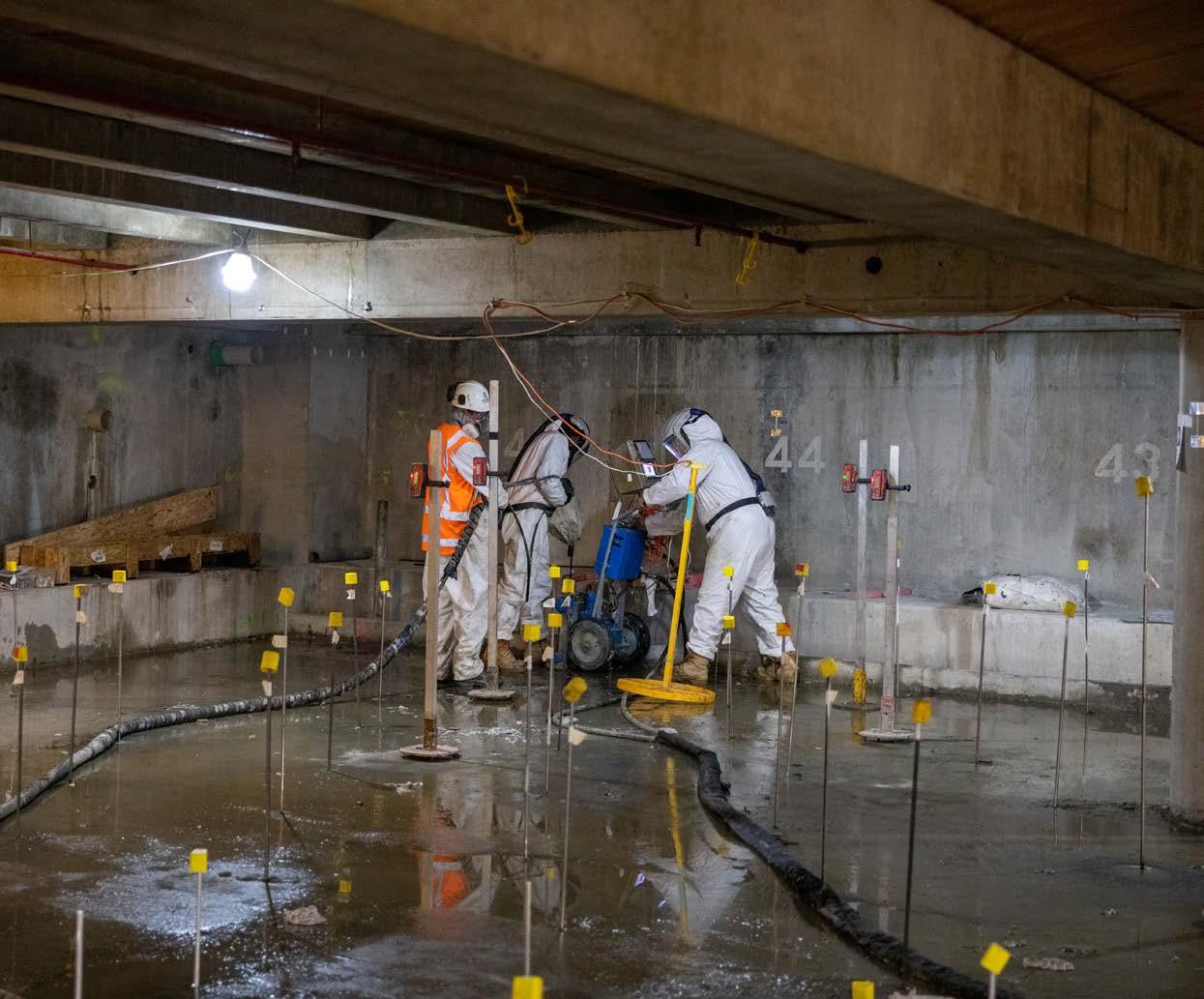
The Mainmark group of companies are leaders in advanced ground engineering and asset preservation technologies. For more than 35 years, Mainmark has led the world in offering unique, innovative solutions for foundation repair, and rectifying problems in residential, industrial, commercial, civil engineering, and mining situations.
In Australasia, the Mainmark group of companies has been in operation since 1995, with seven offices throughout Australia and New Zealand. Since 2001, we have also operated wholly-owned subsidiaries in Thailand and Japan.
We are a privately-owned company with highly-trained technicians and state-of-the-art equipment. Our solutions are all non-toxic, inert, and environmentally neutral. All of our works are planned, supervised, and executed by our own experienced personnel. We guarantee our products.
Companies of the Mainmark group present creative, effective solutions to many types of ground engineering problems in a wide range of sectors: industrial; commercial; residential; civil; and mining. Some of the companies offer related solutions in the building and construction areas. Many of these solutions are unique to Mainmark and its associates.
New Zealand
Mainmark Ground Engineering (NZ) LTD mge.nz@mainmark.com
0800 873 835
www.mainmark.co.nz