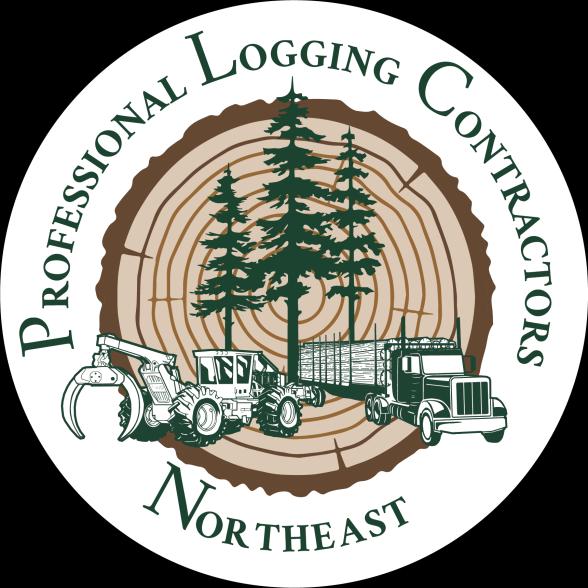
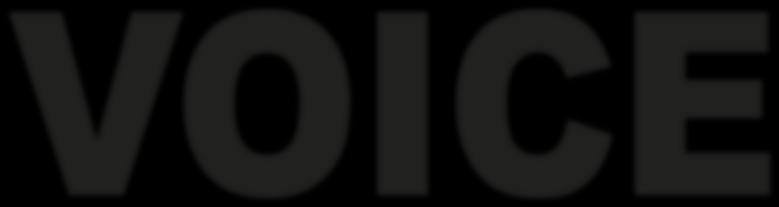
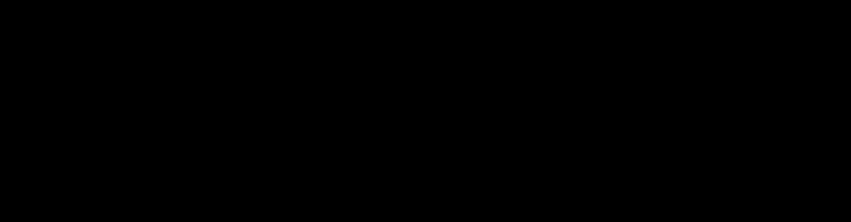
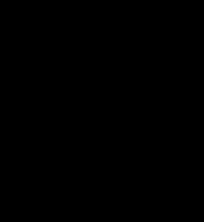

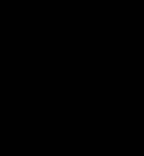

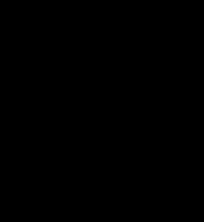
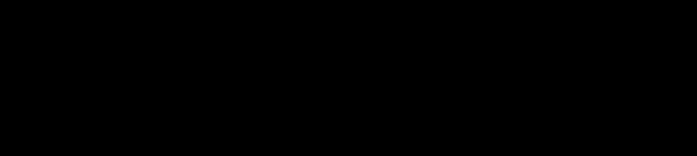
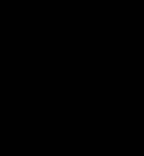

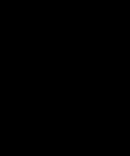
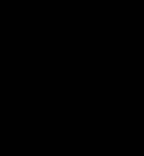

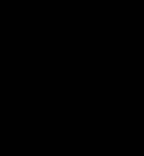
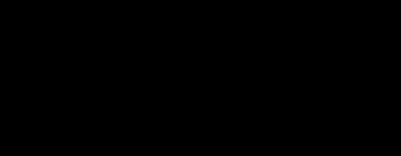
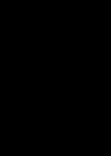
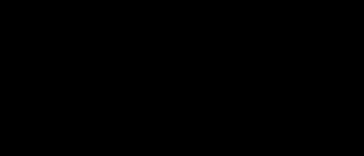
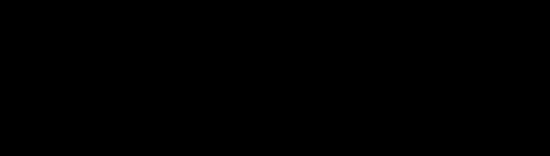
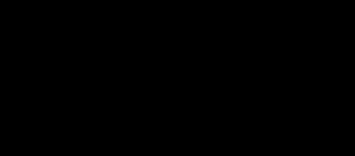
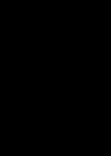

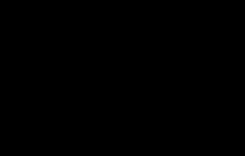
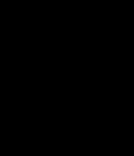
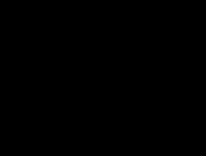
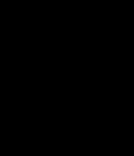

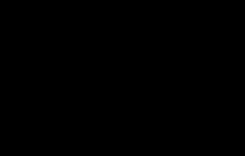
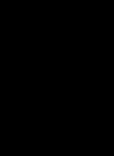
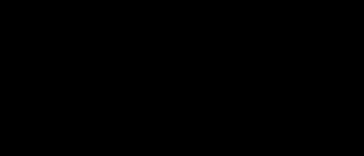
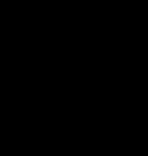
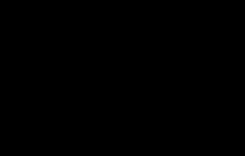
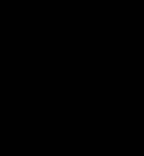
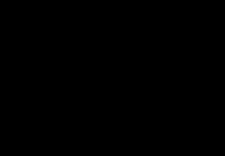
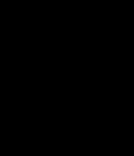
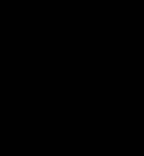
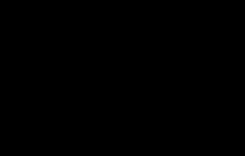
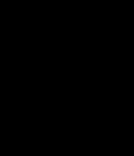
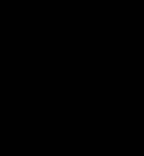
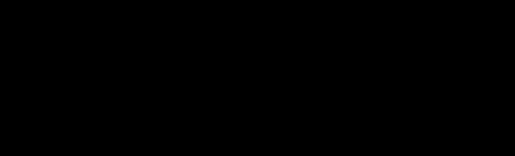
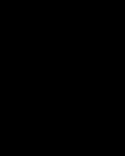
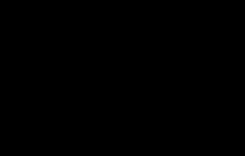
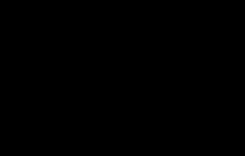
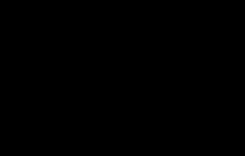
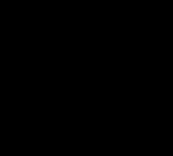
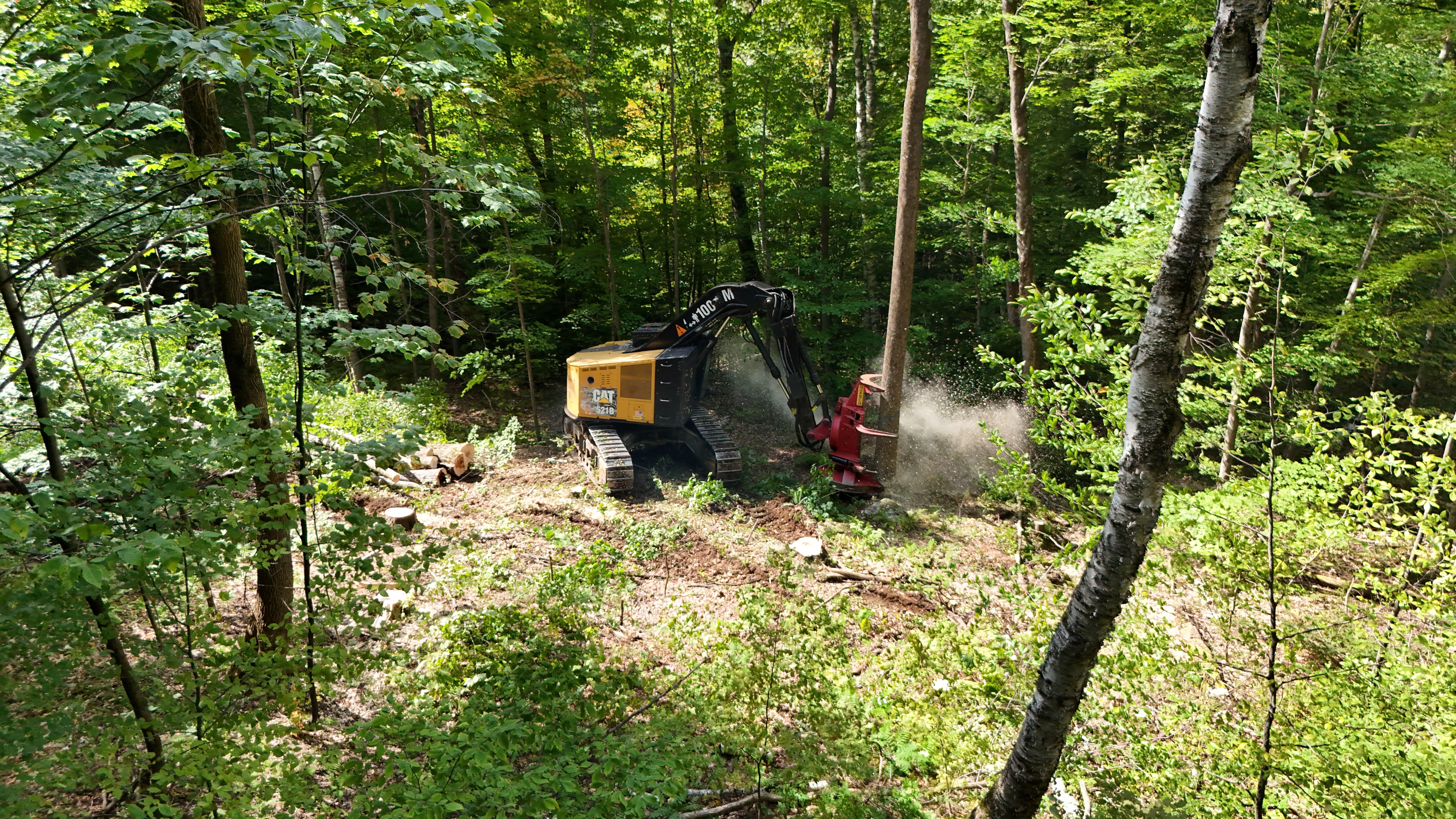

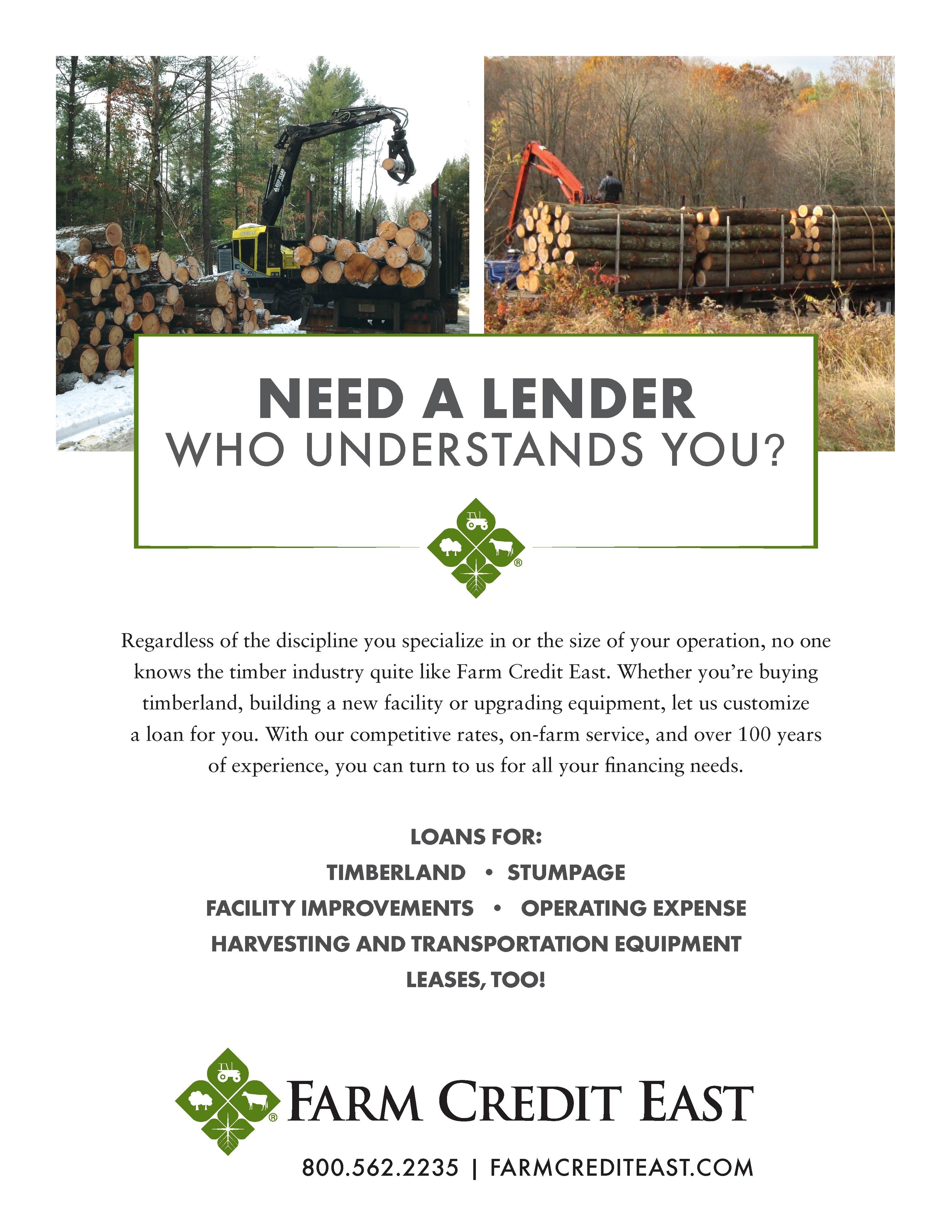
Ben Grant ben@plcloggers.org Deputy
jessica@plcloggers.org Deputy
hannah@plcloggers.org
Donald
Cover photo: Matt McAllister, owner of Matt McAllister Logging, harvesting with a feller buncher in Starksboro, Vermont in September, 2024.

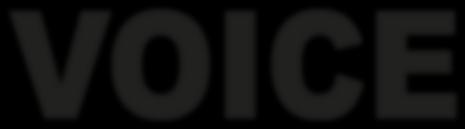
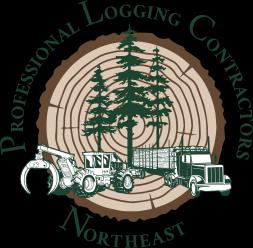
Ben Grant ben@plcloggers.org Deputy
jessica@plcloggers.org Deputy
hannah@plcloggers.org
Donald
Cover photo: Matt McAllister, owner of Matt McAllister Logging, harvesting with a feller buncher in Starksboro, Vermont in September, 2024.
Do you have news to share?
The PLC is always seeking news from our Members that showcases our industry’s professionalism, generosity, and ingenuity. Send ideas to communications@plcloggers.org
Hello Everyone,
the President
By Chuck Ames
My question for everyone is, what would the world look like without trees and the wood products they make to enhance our everyday lives, and the loggers who manage the forests sustainably as a renewable resource in our everyday lives?
Let's start by looking at our everyday lives and how much we rely on wood products. From waking up in the morning when our feet hit the floor made of wood, to using the bathroom where your toilet paper and even your toothpaste are made of or contain wood products. Moving to the kitchen where the floor you're walking on is wood, and you grab your cereal bowl from the kitchen cabinet made of wood along with the box your cereal comes in made of wood fiber. Even our vehicles have wood in them. From the paper
products you use at the office, to the bed you lay your head down in at night, wood impacts our lives every day.
Now take away all products made from wood. No houses, paper, toothpaste, toilet paper and many other things we take for granted in our everyday lives. Almost everything we use today derives from trees, and I think we need to make this a loggers’talking point because I do not think people realize just what would happen without wood products in our everyday lives.
Think of plastic houses which would be non-recyclable, all the way down to toilet paper that I can safely assume would not be as pleasant to use if it were made from plastic or metal. So, when you see a logger, you might want to thank them for making your everyday life a little easier!
DNLLogging LLC of Jackman, ME joined the PLC as a new Contractor Member in September 2024. The company has a professional staff of 1. For more information contact David Lessard at (207) 668-6465 or email David.lessard20@hotmail.com
CPLogging Inc. of Fort Kent, ME joined the PLC as a newAffiliated Contractor Member in September 2024. The company has a professional staff of 1. For more information contact Cody Plourde at (207) 834-6539 or email codyplourde5@gmail.com
Ripley & Fletcher of Maine joined the PLC as a new Enhanced Supporting Member inAugust 2024. The company has three locations in Maine that include Ripley and Fletcher Ford of South Paris, the premier dealership in Oxford County since 1909; Ripley & Fletcher Plus in Farmington which is an authorized Bobcat, Massey Ferguson, Star EV and Evolution dealership that also carries a wide selection of preowned automotive inventory; and Ripley & Fletcher Plus of Saco which is an authorized Segway, Star EV and Evolution dealership that also carries a variety of equipment trailers for all your needs and Fisher and Boss snow plows. For more information contact Bill Osgood bosgood@ripleysplus.com or visit www.ripleyandfletcherford.com or www.ripleysplus.com
From the Executive Director
From October 1-4, I attended the American Loggers Council (ALC) Annual Meeting in Sonora, CA with PLC Members, Andy Irish, Irish Family Logging; Chuck Ames, SDR Logging; and Brian Souers, Treeline, Inc. I/We look forward to these meetings as it’s a great opportunity to speak with loggers from across the country and learn about what is happening in their neck of the woods. Maine also has a leadership role with the ALC as
By Dana Doran
Andy is Immediate Past President and Chuck is an ALC Board Member and was just elected as Secretary/ Treasurer. I would encourage more of our members to get involved with the ALC as it continues to evolve and provides more value on a national scale.
While we were there, it gave us the opportunity to take the temperature and ask questions of our colleagues regarding markets, pricing and the overall morale of
loggers in different areas of the country. Do they have hope and is there a ray of sunshine that is keeping them from diversifying or hanging it up altogether? Usually there is some small nugget of good news or development that I can bring back to Maine to signify change is in the air. Unfortunately, it was not that kind of meeting this year.
Loggers from every corner of the country are just
as challenged as those in the Northeast. Markets are down everywhere, regardless of commodity. Pricing is below what it takes to remain profitable and every contractor in the room was about as glum as I have seen them in the 10 years I have attended this meeting.
More on that in a moment, but I thought I would share an update on the reaction I had to my article from the Summer edition of the Voice that should inform you
that misery not only seeks company, but proves that my empathy for you is real.
If you didn’t have a chance to read it, part of my article from July was an update on how the Legislature and Executive Branch in Maine have been equally dismissive of the loggers’ plight in the recent past. As a result of writing that article, I was called to the principal’s office you could say.
Staff from the Maine Governor’s office asked me to meet with them to challenge what I had said. Evidently, I touched a nerve with what I had written and was told that it was offensive.
As a result of this accusation, I asked those on the other side of the table to prove me wrong and to offer any type of evidence they could find that what I had written was indeed not factual. By the end of the meeting, it was clear that they had no such evidence but were simply frustrated for being called out.
When I asked where we go from here, thinking for a second that there actually might be some remorse or compassion on their part, it was clear that likely there would be even less done as a result. From what I can tell since that infamous meeting in July, my suspicions are 100% accurate. In fact, I might even say that a mild case of black balling might be occurring. That will be hard to prove of course, but I will tell you that simple requests to help the industry made in April of 2023, which had been worked on to a point, have suddenly gone quiet. I guess even the public sector is blind to the plight that you are up against and also holds a grudge for those that speak up.
The beginning of the article describes a middleaged shrimp farmer from Bangkok, Thailand, who operated more than two dozen shrimp ponds, employing seven people and making more than enough to support his family just a few years ago. Since then, the prices he gets from purchasers have fallen by half and he’s had to scale back to four workers and about one third of the ponds, some months not breaking even. His wife has also had to take a second job just to support their two children.
The primary point of the article wasn’t that the plight of the shrimp farmer was due to simple supply and demand, but that big Western supermarkets that make windfall profits are aggressively pursuing ever-lower wholesale prices, which is causing misery for people at the bottom end of the supply chain. Sound familiar?
Loggers from every corner of the country are just as challenged as those in the Northeast. Markets are down everywhere, regardless of commodity.
Also over the last few months, I have taken notice of what feels like other industries that are treated similarly to logging.
In a recent article written by David Rising of the Associated Press, entitled, “As big supermarkets pursue profits, research shows growing exploitation of shrimp farmers”, Mr. Rising takes a deep dive into what has been happening recently to those who farm shrimp for a living. His research focuses on shrimp farmers not here in Maine, or even in the United States, but in Southeast Asia. However, the supermarkets are actually here in our backyard.
I know, you might be asking yourself why I am talking about shrimp farmers right now, but the similarities to logging are striking.
An investigation of the industry in Vietnam, Indonesia and India, which provide about half of the shrimp in the world’s top four markets, found a 20%-60% drop in earnings from pre-pandemic levels as producers struggle to meet pricing demands by cutting labor costs. In many places, this has meant unpaid and underpaid work through longer hours, wage insecurity and many not even making minimum wage. The primary culprit of this change, supermarket procurement practices.
Most who read this article will mutter to themselves, well, it’s a third world country, so it’s not surprising. However, this same type of practice has been happening for far too long in the forest products industry, in our own backyard.
As I have made mention over the last three years, we have lost about 40% of the logging capacity in the Northeast. This is due to massive market reductions, downward price pressure from the markets that remain and inflation on everything that loggers need and use.
For the last two years, most market issues were relegated specifically to the pulp and paper industry. Global pulp demand decreased significantly and the mills that remain have essentially gone to wintertime purchasing and operations until things change.
While pulp mills suffered, the solid wood markets stayed relatively steady over the last four years, until the end of mud season, when the bottom essentially dropped out on every commodity except white cedar.
We know from experience that markets are cyclical and the normal cycle ebbs and flows about every
ten years. We were actually due for a market reduction in 2020, which we could generally accept. However, that market disruption was artificially delayed by the pandemic but compounded by the loss of the Pixelle mill in Jay, Maine and the constant misery that has been inflicted on the region with the loss of pulp and biomass plants over the last 12 years.
Adding insult to injury for contractors in the last four years is the fact that every segment of the industry profited from the pandemic, except for the loggers. Further, not only did pricing for contractors never rise and stay at a higher level during the pandemic and shortly thereafter, but contractors were hit with a double whammy of staggering price inflation for their consumables, as well as a sharp rise and fall of prices. For the most part, contractors were forced to get smaller and/or reduce operations to sustain the double hit, just like the shrimp farmers.
At this point, with a Presidential election on the horizon, very little movement in interest rates, and employee wages at an all-time high, the future looks dim, and morale is low.
Most economists are predicting that things will not turn around until sometime in 2026 but more likely 2027. This also tracks with new markets that are trying to commence operations (Timber HP), planned operations for startups (Godfrey Forest Products) and stalwarts in pulp and paper and solid wood manufacturing.
For contractors, the question becomes, can they hang on and make it another two to three years until things improve? Based upon what I’m hearing and seeing, I have my doubts. Morale out there seems to be at an all-time low with no end in sight.
I always ask how the crews are doing and how much equipment is running or parked. The majority have gotten smaller, have more equipment parked than running, and surprisingly, have stated that they would like to get out of the industry if they could only find a buyer. Unfortunately, those buyers are not waiting in the wings as the situation is much the same across the country.
For the first time during my tenure in this position, I am nervous about what the next 24-36 months will hold for our membership. I would like to say that this too shall pass, and the future is right around the corner, but I’m not sure I can put the lipstick on at this point.
I also do not want to be perceived as the boy that cried wolf, promoting an abyss when change is constant and could shift with the wind. However, it is different now for sure and that is more true now than ever.
For contractors, the question becomes, can they hang on and make it another two to three years until things improve?
Why do I say this? I have talked to our membership enough over the years to be able to sense optimism, pessimism, or neutrality. This time is different.
Over the last month or so, we have been calling the membership to encourage them to attend our legislative receptions across the state with legislative candidates. From a group that has always been very politically active and come out in force to attend any/all political events we have held in the past, the voices on other end have not been overly happy or even reserved. Many have not only lost faith in their ability to operate, but also feel a politician is not going to change this from their perspective.
As part of my conversations with the membership,
For those who read this article, you might agree with what I have to say, or you may call me a conspiracy theorist. If wood still crosses the scale, it will likely be the latter and not the former.
However, you can’t argue with what has happened with capacity over the last four years and it can’t be brought back overnight or even in a matter of years without sustained change and market consistency. That has not happened in the Northeast in more than a decade and I don’t think contractors are naïve enough to believe it, even if it happens for a few months.
We are at a critical moment for this industry. The majority of environmentalists believe that harvesting should be reduced or stopped even though they don’t realize the impact it will have on their lives. The public sector has put its head in the sand and has no concept of what is teetering on the edge unless they can control it. And markets are suffering all around us and the void is deep and wide. However, without a logger, no forest product can be produced or sold and that will become more apparent the longer this goes on.
If ever there was a time to understand the dilemmas as well as the plight, it is now. Three years from now, there might not be capacity to bring those markets back, so denial is not going to move us forward.
Please stay safe, be well and stay in touch.
The Professional Logging Contractors (PLC) of the Northeast raised a combined $111,262 at its two Maine Log A Load for Kids golf tournaments in 2024. The southern tournament raised $47,843 on Aug. 23 at Kezar Lake Country Club in Lovell and the northern tournament raised an additional $63,419 on Sept. 13 at JaTo Highlands Golf Course in Lincoln.
The PLC tournaments benefit Children’s Miracle Network Hospitals in Maine. Funds support the Barbara Bush Children’s Hospital in Portland and Northern Light Eastern Maine Medical Center in Bangor and go to support research and training, purchase equipment, pay for uncompensated care, and benefit the Neonatal Intensive Care Units in a mission to save and improve the lives of as many children as possible.
“The dedication of the PLC s loggers and truckers and our many friends and supporters in the industry to this cause never wavers no matter how difficult conditions in the industry may be,” Dana Doran, Executive Director of the PLC, said.
Once again this amazing group has stepped up faithfully to make a difference for the kids and their families, and I am very proud of everyone involved.”
The PLC also raises funds for Log A Load at a live auction at its annual membership meeting each year and this year raised a record $186,007 at the
The PLC’s Log A Load efforts have now raised more than $2.4 million since 1995.
Thanks again to Jacob Thiboutot and his lemonade stand helpers at the southern tournament!
The Log A Load for Kids program started in 1988. Originally, the concept was for loggers, wood-supplying businesses, and other industry supporters in various states including Maine to donate the value of a load of logs to their local Children’s Miracle Network Hospitals. Nationally, Log A Load for Kids is a leader in CMN hospitals’ fundraising, raising more than $2 million annually through golf tournaments, fishing events, dinners, truckloads of log donations and other events.
For more information, please visit www.logaload.org
$111,262 Raised for Log A Load for
Clockwise from top left: Grilling at the Lincoln tournament; the family of Daniel Phillips (the northern tournament was dedicated to his memory); on the course in Lincoln; family of Matt Jacobs at the southern tournament, air cannon in action at the southern tournament.
Logger’s Voice ▪ Fall 2024
Vermont loggers join recovery efforts after historic flooding in the Green Mountain State
Matt McAllister, owner of Matt McAllister Logging, surveys the remains of a crossing on the Lamoille River in Greensboro, VT washed out by flooding in July. Opposite page: His son Walker visited the crossing in September, weeks after the McAllisters rebuilt it to restore access for residents stranded by the flood.
GREENSBORO BEND, VT – Matt McAllister Logging did not cut a tree in 2024 from late February until early September, but moved plenty of wood during that time, mostly out of ditches, streams, and washed-out roads.
After unusually warm weather in February started mud season off early, the PLC Member logging company
suspended logging operations for more than six months and instead focused on road, bridge and culvert repairs along with debris removal work during and after the longest and most severe stretch of flooding in Vermont in living memory.
Owner Matt McAllister grew up here and has
never seen flooding like what the area experienced in the last couple of years.
“We’ve never had 6-8 inches of rain in four hours before, it was torrential, it just didn’t stop, when you can see inches of water coming down across a slope, I’ve just never seen that in my life in Greensboro until this
summer,” Matt said. Matt has been logging for decades and clearly recalls the days back before he moved into mechanization when he, his father, and his brother were all cutting wood by hand and yarding it with cable skidders. The weather then was different.
Floods Continued from Page 15
“It used to be so dry and so hot in the summer we’d pray for it to rain that night, but we haven’t done that for 10 years,” Matt said. “We don’t pray for rain anymore; we pray for it to stop.”
Matt McAllister Logging is not alone. Across Vermont, logging contractors with the right equipment have been working on the massive effort to clean up and repair the damage from repeated floods and severe weather in the Green Mountain State over the past two years.
Lincoln Farm Timber Harvesting feller buncher removing debris from the Passumpsic River in Lyndonville, VT.
Vermont is not the only Northeast state that has been affected by extreme weather events over that period, but there is no doubt it has suffered more than its share of flooding damage.
John Goff is a senior service hydrologist at the National Weather Service office in Burlington, VT who oversees hydrological programs including flood programs. To find comparable flooding in Vermont’s history he has to go back to Hurricane Irene in 2011, and before that all the way to 1927.
Vermont’s current run of extreme flooding events kicked off on July 10-11 of 2023 when up to 9 inches of rain fell in a 48-hour period. Many communities in the state set rainfall records, and rivers across the state overflowed their banks. The deadly storm paralyzed much of Vermont.
Almost a year later to the day, the remnants of Hurricane Beryl swept into Vermont in July of 2024 and hammered much of the northern half of the state including
many of the hardest hit areas from 2023.
“Then we had a more isolated event on July 30 that affected part of the Northeast Kingdom of Vermont, specifically the St. Johnsbury Lyndon area and then up through Island Pond and Morgan, those are some of those areas which are large logging areas up in there and there were some historic rainfall amounts,” Goff said.
The rainfall amount in St. Johnsbury in that one event was nearly 8 inches in 6 hours, according to some reports.
Sandwiched in between these major flooding events was a historic Dec. 18-19, 2023 heavy rainfall and rapid snowmelt event that caused severe damage across much of the Northeast, including Vermont.
The combination of factors that appear to have produced Vermont’s persistent heavy rainfalls are complicated, but the reasons they have been a problem are simple. Mainly this comes down to a combination of Vermont’s hilly terrain being cut by many small streams and rivers, and to the state’s history of early development of communities and infrastructure along waterways, Goff said.
“These are primarily smaller rivers that are fed by a lot of smaller streams that are in rugged terrain and that are extremely prone to flash flooding,” Goff said. “The other thing that can compound the problem is that we live in an old part of the country where the development of many of these towns goes back over 200 years. They were centered around these mills and sawmills where they relied on waterpower, so a lot of the commerce and roads were around these small streams and rivers and they’re still there today.”
The scale of the damage the flooding caused along those waterways is hard to grasp for those who did not witness it firsthand.
PLC Member company Blue Hill Land & Timber based in Stowe has worked on recovery efforts for the town, and owner Jed Lipsky said in Stowe and in many other areas the debris swept up by the water included massive tangles of wood that could block culverts and damage or destroy things in their path including bridges, homes and utility poles and lines. Blocked culverts then forced water out of streams and rivers onto roads and property along the waterways.
“I’d say 85 percent of Stowe’s damage to public infrastructure and private came from these massive walls and wads of trees – root balls, giant, in some cases they might be 10-12 feet high.” Jed said.
Sam Lincoln, owner of PLC Member Lincoln Farm Timber Harvesting of Randolph Center coordinated with several other PLC companies during recovery efforts including Eastman Trucking & Excavation LLC of Hartford, VT; Russell Riendeau & Sons Inc. of Lyndonville, VT; and HB Logging LLC of Kirby, VT. The scenes they saw in and around the Great Brook in Plainfield and the east branch of the Passumpsic River in
Lyndonville were unbelievable.
“There were places where not only were the homes gone, but the real estate that was under them doesn’t exist anymore,” Sam said, recalling one site where the only evidence left of a family’s home was a mailbox and a wellhead sticking out of the water. “It was pretty staggering.”
Vermont’s rugged terrain can limit routes in and out of many areas to one or two roads, so the loss of roads and bridges stranded hundreds. The debris left behind by the floods included far more than wood, dirt, and stone.
“There was trash, vehicles, household debris, plastic, fiber optic cables, tires, guardrails, just everything,” Sam said.
If the damage from the storms that pummeled Vermont was unprecedented, the role logging companies have played in the recovery is also unprecedented.
National Weather Service rainfall totals from the July 10-11, 2024 storm. Record rainfall was recorded in some areas of northern Vermont.
Jed is not just a logger, but an Independent state representative for Vermont’s Lamoille -1 District. In the wake of the flooding disasters, he said the state and Governor Phil Scott wisely recognized the need to temporarily suspend some rules governing activity in and around waterways to facilitate recovery efforts. This allowed removal of woody debris from waterways that could threaten roads, bridges, culverts, homes, and businesses.
As contractors including PLC Members were
rivers with cables, and off highway vehicles splashing through the shallows to restore Vermont’s battered infrastructure.
Sam said Lincoln Farm Timber Harvesting could not have done the work it tackled without the help of fellow PLC Member companies Russell Riendeau & Sons Inc. renting a staging area to him and providing low bed, forwarder, and dump truck service, and HB Logging handling the grinding and trucking of thousands of yards of wood debris.
brought into the recovery efforts this led to unusual scenes including feller bunchers, excavators and other heavy equipment in waterways, processors pulling logs from
The offroad haul trucks, staff, and other resources of Eastman Trucking & Excavation were critical to the efforts, Sam said.
“Jim Eastman played a really big role, and I wouldn’t have been able to undertake the Great Brook debris removal job without his experience, his network, his resources. He put a lot on hold to make the project happen,” Sam said. “When AOT asked me to mobilize immediately to clear log jams on four miles of the stream, I asked Jim to help ‘for a few days’ to get it started, and his crew was there for six weeks, from the first load out of the river right until the grass seed was spread the last day of closing the job out.”
Funding for the recovery work has come primarily from federal, state, and local sources. In the case of Lincoln Farm Timber Harvesting, the employer was the Vermont Agency of Transportation.
The agency hired more than one logging contractor
A Vermont Agency of Transportation technician assesses a log jam on the Great Brook in Plainfield, VT. Jams like these were a common result of the widespread flooding that has plagued the state in the past two years.
to remove debris from and around waterways, according to Jeremy Reed, Chief Engineer for the Department’s Highway Division.
“It was critical to remove this debris as it represented a risk to life and property in the event of another highwater episode,” Jeremy said. “These efforts are winding down now, and we expect all the identified work to be completed by November 1.”
As the wet weather of July gave way to drier weather in August and September, Vermont finally began to dry out and recovery projects to wrap up.
Late in September, Matt’s son Walker spent part of a morning visiting some of the jobs the company had worked on in its area. Some of the most noteworthy jobs included a bridge replacement on Shadow Lake Road; two eight foot culverts and 128 loads of gravel on Sparhawk Road; more than 50 loads of gravel and stone and some culverts on Flagg Pond Road; 110 loads of gravel and stone and some culverts on Overlook Road; major work on School House Road with 2700 yards of
The PLC is working to ensure that $1 million included in Vermont's state budget to create a new water quality program for logging contractors that would reimburse them for resilience practices such as culverts, gravel, hay, and silt fencing will be made available soon by the Vermont Department of Forests, Parks and Recreation. Securing this funding was a PLC priority in the last legislative session and it is critical to aiding the industry as it grapples with increasingly wet conditions.
material moved; and work on several smaller washes and culverts across town as well as three private bridges. The McAllister’s run a diversified company with a wide mix of equipment, and are as comfortable doing earthwork as logging, and so they we were wellequipped to handle the work.
On a job on Cemetery Ridge Road, water ran down both sides of the road causing damage, and sediment had to be removed from both ditches, culverts replaced, and then loads of stone brought in to better prepare the road for future heavy rainfall events, Walker said.
On Sparhawk Road, which is close to the McAllister’s home, the situation was more serious, with the crossing destroyed after the flooding swept through.
“There were about 30 people stranded there the day after, they couldn’t get out,” Walker said. “There were 128 loads we put in in two days to get those people out.”
Just south of there, Walker parked on the edge of a farm belonging to his grandfather on a tributary of the
Lamoille River where flooding damaged sections of Stannard Mountain Road, washed out the bridge across to Orton Road, and destroyed a bridge his grandfather used to cross the water just downstream. Only the Lamoille River Rail Trail walking bridge high above the water escaped the flood.
For the McAllister’s the flood recovery work was wrapping up in late September and Matt McAllister was finally back logging at a job in Starksboro. Elsewhere, other PLC Members were also back in the woods or finishing up recovery projects.
While the record-breaking rainfalls and repeated flooding Vermont has experienced in the last two years has undoubtedly hindered the state’s logging industry by making it nearly impossible to cut or move wood for long stretches of time, the recovery work has been a silver lining for some contractors, allowing them to keep workers on the job and money coming in despite the wet conditions.
adaptability of loggers in handling it may also have reminded the state and municipalities how valuable loggers are to Vermont, a resource not just in the woods but there to be called on in emergencies.
“Logging companies are uniquely qualified to perform this work,” Jeremy at the Vermont Agency of Transportation, said. “The specialized equipment that they bring to bear allows them to remove the debris with a smaller footprint than traditional heavy construction equipment.” “I think it’s become very evident that the logging equipment and the allterrain, all-conditions skills we have are providing critical surge capacity to the state, and it’s important to recognize what loggers bring to the table in a statewide response,” Sam agreed.
At the same time, the recovery work and the
Thank you to PLC Member Companies Matt McAllister Logging, Blue Hill Land & Timber, Lincoln Farm Timber Harvesting, and HB Logging LLC for contributing images and/or information for this article.
Trailer Inc. decided they wanted to do more to support the Professional Logging Contractors (PLC) of the Northeast’s annual Log A Load for Maine Kids fund-raising efforts, and so a decision was made to donate a portion of sales from the company’s new online Parts2Go ordering system to the cause.
Parts2Go is one of many improvements and additions the company is making to better serve customers and position itself for the future, and Maine Trailer has pledged to donate $75 for every first qualifying purchase of $500 or more on the system to Log A Load.
The PLC’s Log A Load efforts support Children’s Miracle Network (CMN) Hospitals including Eastern Maine Medical Center (EMMC) in Bangor, making it a very important and personal cause to Maine Trailer’s Chief Executive Officer Rod Hathaway and his family, who credit EMMC’s neonatal intensive care unit (NICU) with saving his grandson’s life more than a decade ago, and which the family also supports through an annual “Hathaway
importance as well as thousands of dollars to support it.
Rod said he would like nothing better than to write a large check in support of Log A Load if the new effort is successful.
“If you’re a customer and you need parts, you buy them from us and a portion of that is going to go back into that fund and we hope that this is going to be accepted by the PLC membership as a way to raise money for it,” Rod said. “Here's something that they use in their everyday business - they need drums, bearings, seals, and parts for their log trailers - and I have them, I'm competitive and I'm going to give back to the PLC, I think it’s a win-win.”
The PLC agrees.
“Maine Trailer Inc. deserves credit for coming up with this new way to partner with the PLC to increase our annual Log A Load fund raising efforts,” PLC Executive Director Dana Doran, said. “This is a great example of a Preferred Supporting Member of the PLC going above and beyond to make a
difference in the lives of the kids and their families.”
Maine Trailer Inc. joined the PLC in 2018, but it’s relationship with Maine loggers goes back decades.
The company was founded 40 years ago by husband and wife Irwin and Susan Singer, who then owned Furniture World on Broadway Street in Bangor, ME.
“They started this business because they needed extra storage for furniture, so they bought some trailers and the rest is kind of history after that, their friends asked where they got them and whether they could get some, and that got them into the storage business.” Rod said, adding the couple are now retired but stay in touch with him regularly.
From that simple beginning Maine Trailer Inc. began expanding, moving into trailer sales and semi-trailer leasing. That created a need for a service department, and the service department needed parts and so that led to adding a parts department.
“Today of course, parts is a huge business between the company and PLC Member contractors, but the relationship between us was not always the same,” Rod said. “Back in the early 2000s we were predominantly paper haulers, we had the rental trailers that the guys rented to haul paper, and every mill you went to there was always a group of Maine Trailer trailers somewhere in that parking lot.”
In those days Maine Trailer Inc. – then known as Maine Trailer Leasing – had locations in Ashland, Scarborough and Auburn in addition to Hampden, but when the economy collapsed in the late 2000s and took with it much of Maine’s paper industry the company lost a lot of business as accounts with hundreds of leased trailers serving the mills dried up. The workforce contracted, and the company’s locations were reduced to Hampden and Auburn.
“We really had to reinvent ourselves after that point, so we diversified tremendously into other areas,” Rod said.
In the years since, the company of today emerged, focusing on five distinct businesses. Those businesses include:
∙Trailer leasing and rental, which is predominantly large dry vans and flatbeds as well as intermodal.
∙Trailers sales including large trailers as well as utility trailers.
∙Trailer registration, with the company acting as a statutory agent for Maine’s Department of Motor Vehicles, and four full-time employees handling registration for Maine tags and titles all across the country including Alaska and Hawaii.
Maine Trailer Inc. today has 27 employees and serves the entire state of Maine. That includes managing about 2,200 rental units, and the company has also become a huge player in the container storage business, importing
Maine Trailer Inc. has a fleet of large and small trucks, full-time drivers, and a sophisticated system to track and manage deliveries. The company also has a an in-person parts counter as well as an active phone and online business and a mobile parts showroom.
∙Trailer service with six bays and six mechanics devoted to the department and options for both in-house and on the road service.
∙Trailer parts with an in-person parts counter as well as an active phone and online business and a Mobile Parts Showroom.
large containers directly from overseas manufacturers to rent or sell. They also customize those containers, and some are turned into small offices and camps.
Providing parts, trailers, and containers statewide also means Maine Trailer Inc. has a fleet of large and small trucks, full-time drivers, and a sophisticated system to track and manage it all.
customers on islands, driving products deep into Maine s north woods to reach remote sites, and in one case being towed by skidders to reach the top of a mountain.
“Some deliveries are more challenging than others for sure, but pretty much if we can get there we'll get there,” Chris said.
Maine Trailer Inc. is still in business today because it has adapted and changed, and Rod intends for that to continue.
“That’s one thing that I recognized early on, there’s going to come a time where there has to be a change, and for the last five years that’s what I’ve been doing and preparing for,” Rod said, “We’ve been here for 40 years and got a plan to be here for another 40 years, I've got a succession plan in place and we just keep changing.”
Change has meant hiring younger employees as well as nontraditional employees including former teachers and a former merchant marine. It has also meant recognizing that the old days of a salesman in a pickup truck are gone and that the future of sales is online.
That realization led to the launch of the Parts2Go program, which functions much like an Amazon account for customers and allows both the company and the customer to benefit from its 24 hour a day availability, quick and easy sales system, and expanded inventory choices.
“So at 9 o’clock at night when a logger gets in and figures he’s got to do a brake job next week on a trailer, he can log online, see my inventory, price me out, but he can also look deeper into what the master warehouse has and maybe there's alternatives he wants to look at, say he likes brand X but he's willing to try brand Y,” Rod said. “He can have the products on his shelf with our statewide delivery that next week so he's ready to go, and if you can go online
Inc. has become a huge player in the storage container business. The company rents, sells and customizes containers.
and do your own shopping, it’s cost savings for us and them.”
An online trailer registration system is also planned for the fall of 2024 as another way to improve options for customers, Rod added.
Since joining the PLC, Maine Trailer Inc. has stepped up for the organization in many ways. The company has been a sponsor for PLC events and supported the PLC’s quarterly Logger’s Voice magazine through extra ad purchases. It has provided discounts to PLC Members and a discounted mobile container office for the PLC’s Mechanized Logging Operations and Forest Trucking Program. In 2022, the company won the PLC’s Community Service Award for its annual Hathaway Holiday Lights effort.
Maine Trailer Inc. and the region’s logging industry have both come through some difficult times together and they depend on each other, and the company
FAIRFIELD, ME – The Mechanized Logging Operations and Forest Trucking (MLOFT) Program, a unique 20-week certificate course providing unmatched training and preparation for careers in logging and forest trucking, is now underway for its eighth straight year.
The program is an expanded version of the original logging operations certificate program created in 2017 by the Professional Logging Contractors (PLC) of the Northeast, the Maine Community College System, and industry partners, that now includes Commercial Driver’s License (CDL) training.
The MLOFT program is being hosted by Kennebec Valley Community College (KVCC) at its Alfond Campus on U.S. Route 201 but is administered by Northern Maine Community College (NMCC) in Presque Isle.
Students began classwork and safety training in late June at the Alfond Campus before progressing to hands-on training with mechanized logging machines at an active timber harvest on the campus in late July. That training continued into the fall with a graduation for the students planned for Nov. 7 at the Alfond Campus.
qualified logging operators and forest truckers in an efficient and affordable way,” PLC Executive Director Dana Doran said. “We could not offer this unique opportunity to students without the support of Maine’s Congressional delegation, which secured Congressional Directed Spending (CDS) support for it, or our industry partners, who ensure we have the equipment to offer a topnotch training experience.”
The opportunity to earn a CDLA permit and receive preparation for the state driving exam was a significant addition to the program in 2023.
Students enrolled in the postsecondary training program harvest timber and operate trucks using sophisticated state-of-the-art machines like those they will encounter in the logging industry. The hands-on experience students gain operating equipment is an opportunity unavailable anywhere else in Maine and neighboring states.
“This remains the only program of its kind in our region, and it is critical to addressing Maine’s shortage of
Students pay no tuition or fees. The project is funded 100% by a $1M grant from the U.S. Department of Labor, Employment and Training Administration. To learn more about the program visit: plcloggers.org/plc-resources/career-training-opportunity/
Members of the PLC's Board of Directors toured the Mechanized Logging Operations and Forest Trucking program in Fairfield Sept. 12, meeting the students and instructors at the site where they are actively harvesting timber. This was a unique opportunity for the students to hear firsthand about the logging industry and get answers to their questions directly from potential employers. A huge thank you to the PLC Board for giving their time today for the future tomorrow.
On Wednesday July 10, PLC Executive Director Dana Doran was a guest panelist forSkowhegan Savings Bank’s Economic Forum. The event held at Bigelow Brewing in Skowhegan featured a panel discussion by state and local experts sharing their insights on Central Maine’s economic outlook. Dana shared the stage with Heather Johnson, the Commissioner of the Department of Economic and Community Development (at left), Aaron Bolster, President and Broker of Allied Realty (at right) , and Kristina Cannon, the President and CEO of Main Street Skowhegan (second from left). They discussed a variety of topics including the state of the economy, significant regional investment projects, the importance of innovation in the forestry sector and real estate market in Central Maine. It was a great opportunity for the PLC to share the struggles and successes of the logging and forest trucking industry.
The PLC provides Members with regular email updates and alerts on important issues. If you are not receiving these emails please reach out to our office at 207-688-8195 or email communications@plcloggers.org so we can correct the issue!
FMCSA Removes Four Devices from List of Registered ELDs...
July 23, 2024,
WASHINGTON - Today, the U.S. Department of Transportation Federal Motor Carrier Safety Administration (FMCSA) removed CTE-LOG ELD, ELD VOLT, POWERTRUCKS ELD, and TFM ELD devices from the list of registered Electronic Logging Devices (ELD). FMCSA placed these ELDs on the Revoked Devices list due to the companies’ failure to meet the minimum requirements established in 49 CFR part 395, subpart B, appendix A. The removals are effective July 23, 2024.
FMCSA will send an industry-wide email to inform motor carriers that all who use these revoked ELDs must take the following steps:
Discontinue using the revoked ELDs and revert to paper logs or logging software to record required hours of service data.
Replace the revoked ELDs with compliant ELDs from the Registered Devices list before September 21, 2024.
Motor carriers have up to 60 days to replace the revoked ELDs with compliant ELDs. If the ELD providers correct all identified deficiencies for their devices, FMCSA will place the ELDs back on the list of registered devices and inform the industry of the update.
During this time, safety officials are encouraged not to cite drivers using these revoked ELDs for 395.8(a) (1) –“No record of duty status” or 395.22(a) –“Failing to use a registered ELD.” Instead, safety officials should request the driver’s paper logs, logging software, or use the ELD display as a back-up method to review the hours of service data.
Beginning September 21, 2024, motor carriers who continue to use the revoked devices listed above will be considered as operating without an ELD. Safety officials who encounter a driver using a revoked device on or after September 21, 2024 should cite 395.8(a)(1), and place the driver out-of-service (OOS) in accordance with the Commercial Vehicle Safety Alliance OOS Criteria FMCSA strongly encourages motor carriers to take the actions listed above now to avoid compliance issues in the event that the deficiencies are not addressed by the ELD providers.
FMCSA Removes Two Devices from List of Registered ELDs...
August 15, 2024,
WASHINGTON – Today, the U.S. Department of Transportation Federal Motor Carrier Safety Administration (FMCSA) removed BLUE STAR ELD and RELIABLE ELD devices from the list of registered Electronic Logging Devices (ELD). FMCSA placed these ELDs on the Revoked Devices list due to the companies’ failure to meet the minimum requirements established in 49 CFR part 395, subpart B, appendix A. The removals are effective August 15, 2024.
FMCSA will send an industry-wide email to inform motor carriers that all who use these revoked ELDs must take the following steps:
Discontinue using the revoked ELDs and revert to paper logs or logging software to record required hours of service data.
Replace the revoked ELDs with compliant ELDs from the Registered Devices list before October 14, 2024. Motor carriers have up to 60 days to replace the revoked ELDs with compliant ELDs. If the ELD providers correct all identified deficiencies for their devices, FMCSA will place the ELDs back on the list of registered devices and inform the industry of the update.
During this time, safety officials are encouraged not to cite drivers using these revoked ELDs for 395.8(a) (1) –“No record of duty status” or 395.22(a) –“Failing to use a registered ELD.” Instead, safety officials should request the driver’s paper logs, logging software, or use the ELD display as a back-up method to review the hours of service data.
Beginning October 14, 2024, motor carriers who continue to use the revoked devices listed above will be considered as operating without an ELD. Safety officials who encounter a driver using a revoked device on or after October 14, 2024 should cite 395.8(a)(1), and place the driver out-of-service (OOS) in accordance with the Commercial Vehicle Safety Alliance OOS Criteria.
FMCSA strongly encourages motor carriers to take the actions listed above now to avoid compliance issues in the event that the deficiencies are not addressed by the ELD providers.
WESTBROOK, Maine (9, 2024) Acadia Insurance, a W. R. Berkley Company, recently announced that it will pay $419,241 in premium dividends to eligible policyholder members of the Professional Logging Contractors of the Northeast (PLC) Safety Group. Since 1999, Acadia has distributed over $14.5 million in premium dividends to eligible participants of this safety group*.
Founded by Acadia Insurance, the PLC Safety Group dividend program rewards logging companies and sole proprietors for having a safe workplace by refunding a portion of their insurance premium if certain measures are met by the entire safety group. In addition, Acadia Insurance, in coordination with the PLC, provides risk management and mitigation expertise to members to help ensure the long-term sustainability of the logging industry.
since 1995 and aims to give independent logging contractors a voice in the ever-changing logging industry. The PLC focuses on advocacy, safety, quality operations and business innovation for loggers. The PLC is a logging organization run by loggers that understands the importance of the logging industry and its impact on the Northeast economy.
For more information about the Professional Logging Contractors of the Northeast Safety Group, please contact Robyn Sukeforth, Territory Marketing Specialist, Acadia Insurance, at robyn.sukeforth@acadia-ins.com
“I am pleased that Acadia is once again able to return premium to the Maine-based members for the PLC,” said Douglas Freeman, Regional Vice President of Acadia Insurance’s Maine Branch. “Our partnership with the PLC, which spans over a quarter-century, continues to grow. Favorable results that qualify for a dividend can only be attained through the diligent effort of our logging contractor policyholders, the agency professionals who work with them, the team at the PLC, and Acadia’s team of dedicated Loss Control, Underwriting, and Claims experts.”
The PLC of the Northeast has been serving loggers
Acadia Insurance is a regional underwriter offering commercial and specialty property casualty insurance coverages through independent insurance agents with local offices in Connecticut, Maine, Massachusetts, New Hampshire, and New York. Rated A+ (Superior) by A.M. Best, Acadia Insurance Company is a member company of W. R. Berkley Corporation, one of the nation’s premier commercial lines property casualty insurance providers. Please visit www.acadiainsurance.com.
*Dividends are not guaranteed. Dividends are based on experience, are subject to Board approval, and the terms and conditions of the program. The amount of dividends paid historically is not indicative of what may be payable in the future.
ByDonaldBurr PLCSafety&TrainingConsultant
Logging can be one of the most hazardous professions, especially when it involves mechanized logging equipment. This equipment, designed to increase efficiency and productivity, comes with inherent risks tied to various forms of energy mechanical, hydraulic, electrical, thermal, and gravity. Understanding and recognizing these dangers and implementing effective safety measures is crucial for protecting ourselves in this demanding environment.
1. Mechanical Energy: The mechanical energy present in logging equipment poses significant dangers. These machines have powerful moving parts that can cause severe injuries through entanglement, crushing, or impacts. For instance, operators and mechanics can be caught in the machine’s cutting heads, belts & pinch points, leading to devastating injuries or fatalities.
2. Hydraulic Energy: Mechanized logging equipment relies on hydraulic systems to operate functions such as lifting, cutting, and maneuvering. Hydraulic systems operate under high pressure, which can lead to catastrophic failures.Asudden hose rupture or disconnection of a hose that is under pressure can release pressurized fluid, potentially causing injury or even propelling debris at high speeds. Workers must be cautious during maintenance and operation. Never look for a hydraulic leak using any part of your body. Hydraulic injection injuries are dangerous and can be deadly.
3. Electrical Energy: Many modern logging machines are equipped with sophisticated electronic systems for monitoring and control. However, this introduces electrical hazards. Faulty wiring or exposed components can result in electric shocks or fires. Most of the newer equipment is 24 volts. I once asked a mechanic
how hot 24 volts are when they are shorted out to the machine, and his answer was simple, “hot enough to weld with.”
4. Thermal Energy: Logging equipment can generate substantial heat during operation, especially in engines and hydraulic systems. Workers are at risk of burns from hot surfaces, hydraulic fluid, or exhaust systems. I know of two equipment operators who opened a hot radiator and received substantial burns. Never open anything that is hot & under pressure. In our climate, we need to watch out for icy or snowy conditions, increasing the likelihood of slips and falls due to hidden hazards. Always look before you step.
To mitigate the dangers associated with mechanized logging equipment, several essential safety measures should be implemented:
1. Training: Proper training is crucial for all personnel operating or working near mechanized logging equipment. This training should cover equipment operation, hazard recognition, emergency procedures, and maintenance protocols. Regular refresher courses help keep safety practices at the forefront of workers’minds.
2. Lockout/Tagout (LOTO): The Lockout/Tagout procedure is critical to prevent accidental energization during maintenance. Before performing any work on equipment, operators should ensure that all energy sources mechanical, hydraulic, thermal, and electrical are properly shut down and released or secured. Tagging and or locking the machinery clearly communicates that this machine should not be started or moved until the person who put the tab/lock on the equipment determines that it is now safe and removes the tag. Alock or a tag should never be removed by anybody other than the person
who put the tag or lock on.
3. Personal Protective Equipment (PPE): Wearing the appropriate PPE is essential for safeguarding against risks. Remember that PPE is the last line of defense in keeping you safe and that it does not make you bulletproof. Only Superman is bulletproof, and Superman is too busy fighting crime to be a logger.
4. Safety Signage and Communication: Clear and visible signage indicating potential hazards can help maintain awareness among workers. Establishing a culture of open communication allows workers to report unsafe conditions or near misses without fear of repercussion. Regular safety meetings can reinforce the importance of vigilance in preventing accidents.
hazards. However, logging operations can significantly reduce these risks through rigorous training, adherence to safety protocols, and a commitment to ongoing maintenance. Operators should always ask where the energy is and how it can hurt them before starting work on their equipment.
The dangers of energy when working on mechanized logging equipment are significant and varied. The potential for serious injury is ever-present, from mechanical and hydraulic risks to electrical and thermal
Ultimately, prioritizing safety protects workers and enhances overall productivity and morale. By fostering a culture that values safety and encourages proactive measures, the logging industry can work towards minimizing accidents and creating a safer working environment for all.
In the insurance industry, we generally track numbers pretty closely to look for any alarming trends that may indicate a larger problem that needs to be addressed. This year the number that seems to be rising significantly over past years is the amount of equipment fires we have been seeing. The fires range from very minor to significant and there does not seem to be one manufacturer, or one type of machine to blame. As with anything, a periodic reminder is a critical step in curbing a concerning trend. I have written this article to share some useful tips to consider when training employees on the effective use of fire suppression in the event of a machine fire.
Fires on logging machinery is something that is always in the back of our minds. With significant amounts of fuel, wood debris, high temperatures and lots of electrical wires, the chance of a fire is significant and often times serious when they occur. Throw in challenging markets where profits are down, the temptation may be to push off machinery maintenance, reduce cleaning frequency, and run machinery harder than what you may do if the markets are good. While understandable, it is critical to make sure the machines are cleaned out frequently and maintained properly in order to reduce the exposure to a fire on the machine which could have a detrimental effect on your business.
When a fire occurs, the operator taking immediate and effective action can make the difference between a machine that suffers zero to minor damage and a machine that suffers a significant fire loss. Because of this fact, an occasional reminder to operators about how to fight an equipment fire can be extremely helpful if a fire occurs. While every situation is different, the following steps can be taken to help reduce the damage caused by a fire:
1. Don’t get hurt. Machines are replaceable but the operator is not. If the fire is too big or you are not comfortable that you can extinguish the fire safely, you should stand back and take precautions to prevent the fire from spreading onto the ground or other equipment in the area. It is not worth risking the operator’s safety to extinguish a fire.
2. Call for help immediately. Tell other operators in the area what is going on and ask them to come help you. Often times the other machines can carry water or additional handheld fire extinguishers to assist in extinguishing the fire.
3. Shut machine down by turning off the key, grounding out hydraulics and, if possible, shut off the master switch. Shutting the machine down completely and grounding out the hydraulics will help you reduce the amount of additional fuel, such as fuel, being introduced to the fire. Shutting the master switch off will help to remove a potential source of re-ignition.
4. Activate your fire suppression system. If the system has not yet activated, you should immediately activate it manually. Activating it manually can prevent the fire from growing by suppressing it enough to allow you to
utilize a handheld extinguisher on remaining flames. It should be noted here that fire suppression systems may differ in how they are activated and you should familiarize yourself with your own system before a fire occurs.
5. Get ready with your portable extinguishers. A portable extinguisher, such as a loaded stream, can be helpful in extinguishing a fire once it has been suppressed. Most manufacturers recommend leaving the engine compartment closed to prevent the fire from getting more oxygen while also allowing the suppression agent to do its job. Because of this, most equipment manufacturers have designated locations around the machine where you can insert a fire extinguisher hose and discharge it.
6. Standby at the machine. Fires have been known to rekindle on machinery up to several hours after the initial fire was presumed to be extinguished. After the fire appears to have been extinguished, you should wait at your machine with additional handheld fire extinguishers until you are comfortable that it has been completely extinguished. While the fire is taking place, there is a lot of information that can be helpful in figuring out what caused the fire to ignite. Below are some observations you can make to help investigators figure out the cause of the fire:
1. What color was the smoke? A surprising amount of information can be gathered by the color of smoke. The color of the smoke can help point towards where the fire ignited as well as what was fueling the fire.
2. What did you hear? You may hear an alarm indicating the fire suppression system discharged. You may hear crackling, potentially pointing to an electrical problem. Simple observations like these can help investigators find the cause of the fire.
3. What did you see? Note areas on the machine where you first see flames. Where was the fire most intense? What happened when the suppression system went off?
4. Take a video or pictures. If you are no longer able to fight the fire, and as long as it is safe to do so, standing back and taking a video and/or photos can be helpful to investigators.
Fires on machinery are hazardous and can cause significant downtime for a logging contractor. While manufacturers of equipment and fire suppression systems continue to work diligently to prevent fires from ever occurring, it remains true that as long as you are cutting wood with machinery, fire is always going to be a possibility. Simple steps like those listed above can go a long way in preventing the severity of a fire and getting your machinery back to work quickly.
Acadia is pleased to share this material for the benefit of its customers. Please note, however, that nothing herein should be construed as either legal advice or the provision of professional consulting services. This material is for informational purposes only, and while reasonable care has been utilized in compiling this information, no warranty or representation is made as to accuracy or completeness.
By Brie Weisman, OTR/L with Maine AgrAbility
Is sitting for hours on end the “new smoking?” Some people may laugh off the question, but the health profession is taking this notion very seriously.
Researchers at the Mayo Clinic analyzed 13 studies of sitting time and activity levels and found that those who sat for more than eight hours a day without participating in an exercise routine to counter it had a risk of dying similar to that posed by obesity and smoking. That should not be particularly shocking as a sedentary lifestyle is, after all, quite literally unnatural. Our bodies are made for regular, vigorous motion: for gathering and chasing down food; for fleeing to avoid becoming someone else's food; for exploring and learning about our environment whenever our more immediate needs are met. Sitting, historically and evolutionarily, is what we are supposed to do in the few moments when all our work is done at last–the exception, not the rule. A sedentary lifestyle is a very new phenomenon. Retirement, the combustion engine, and the first screens all arrived in the last, razor-thin sliver of humanity’s existence. Chairs have been around slightly longer–about the last 1.5% of our time on the planet.
And they’ve caught on in a big way. According to the CDC, for adults ages 19-64, sitting four to eight hours is considered a moderately sedentary lifestyle. Eight or more hours is a high risk lifestyle. Loggers and fleet truck drivers should take note. It’s hard to find a logger today who does not sit in their equipment for less than eight hours. Most don’t take hourly breaks, and many remain in their cab for more than two hours between breaks. This falls within the high risk lifestyle already–without accounting for the hours spent on the road driving to and from the work site, or time at home at the kitchen table or in front of some sort of screen at the end of the day.
Interestingly, loggers now engage in less physical activity than most office workers. The office affords the opportunity for increasingly popular sit-to-stand desks, and employees are encouraged to take regular, scheduled breaks. In addition to that, they take additional walks to the water cooler or coffee machine or copier, to associates’ desks and offices, to meetings, and perhaps to lunch down the street. The daily lunchtime exercise walk is steadily growing in popularity. At a bare minimum, loggers should adopt a similar workday habit, with regular time outside of
equipment, standing up, stretching out, and walking about for a minute or two.
What are the specific dangers of a sedentary lifestyle?
Perhaps counterintuitively, sitting increases rather than decreases the compressive forces on the spine–by as much as 40%. The natural curve of the spine supports the body evenly while standing, and motion creates a constant redistribution and sharing of the body’s weight across
muscle groups. Sitting in more or less the same position all the work day increases the risk of musculoskeletal injuries: lower back trouble, tight shoulders, sore neck, even aching hands and circulatory problems can be a consequence of sitting too much. Have you ever felt that your shoes are tight at the end of the day, or noticed swelling in your legs? That’s a symptom of too much sitting. Other chronic diseases highly correlated with long term sedentary lifestyles include obesity, diabetes, depression, dementia, muscle loss, osteoporosis, multiple types of cancers, stroke and heart disease.
So, what’s a logger to do? In general, a regular exercise program is important for everyone. While on the job, short microbreaks should be considered an essential part of every logger’s day. Getting out of the cab and walking around your machine for just one minute every half hour will go a long way to countering the problems of a sedentary job. A single minute! That adds up to a mere 3% of your day. Not only does science say it’s good for the body–a wealth of research says it’s also good for the bottom line. Short mental breaks from a task undertaken for long periods of time makes any worker more efficient and less prone to costly errors in the long run. A walk around inspection of your machine in that single minute may also identify an issue to address that will prevent the need for a costly larger repair and time down. Micro breaks that increased worker health and productivity, combined with quick, regular preventative inspections of expensive equipment should be a no-brainer not only allowed, but insisted upon by every logging company.
Now, this article is of course for loggers, but we’re also parents, role models, citizens. And the issue of sedentary lifestyles reaches well beyond logging. It has grown to become a national concern. A January 2024 CDC article noted that 110,000 deaths could be prevented annually if US adults would increase their moderate-tovigorous physical activity level by just 10 minutes a day. Ten minutes! Sadly, a mere one in four adults currently meet even this minimal effort.
Sedentary-related issues also cost us $117 billion a
year. That’s a lot of money. So much that it could pay for every student leaving high school in America this year to attend a state university or trade school. Twice over. With more than a few billion to spare. What about joining the military as another option? Unfortunately, an astonishing 77% of today’s young adults are physically unfit for US military service.
We need to do better. Fitness affects happiness, longevity, productivity, and as a society we have neglected it for so long that it’s become a national security concern. Be good to yourself, and be an example to your family, friends, and coworkers. Get off your butt! Start now.
For More Information, visit Maine LogAbility, part of the Maine AgrAbility program: https://extension.umaine.edu/agrability/
The Maine Forest Service (MFS) has announced results of its 2022-2023 study on the implementation and effectiveness of Best Management Practices (BMPs) in timber harvesting across the state. According to MFS, the 2022-2023 results are consistent with previous years, showing a solid commitment to BMPs within Maine's forestry and logging community.
Notably, there was a 5% decrease in sedimentation associated with crossing structures since the 2020-2021 report, with the report stating, "Sediment entry to the waterbody was observed at 29% of all crossings, a decrease from an average of 34% reported between 2020 and 2021." Historically, sedimentation is most often linked to crossing structures.
This positive result coincides with a dramatic increase in recent years in BMP workshops conducted by the Northeast Master Logger Certification Program® in Maine and neighboring states. Master Logger is the only organization providing true hands-on BMP training to contractors and their employees in the region.
Key findings of the Maine Report included:
• 70% BMP Application on Crossings: Seventy percent of sites had BMPs correctly applied on crossings and approaches, or crossings were completely avoided. BMPs emphasize planning harvests to minimize stream crossings whenever feasible.
• 84% Effectiveness in Preventing Sedimentation: Eighty-four percent of BMP observations indicated that no sediment entered a waterbody, achieving the primary goal of BMPs to keep sediment out of water sources.
A Master Logger Best Practices Workshop underway in Jay, Maine in 2023.
BMP use or avoidance strategies.
• 97% Wetland Protection: Ninety-seven percent of sites had no wetland crossings, demonstrating effective
The Professional Logging Contractors of the Northeast (PLC) encourages all loggers who are not Master Logger certified to consider certification as a way to improve and market their business and access quality training opportunities. PLC members also receive a discount on Master Logger renewal fees.
Learn more about certification by visting masterloggercertification.com or by ontacting Master Logger Program Manager Sydney Andersen at (207) 688-8195 Opt. 2 or sydney@tcnef.org
Are you a Master Logger® in Maine who is buying new equipment? Take advantage of the Direct Link Loan Program and get an interest rate reduction of up to 2% on qualifying equipment. Details of the program and how you can take advantage of it may be found on the Master Logger® website at masterloggercertification.com/programs/
PLC had a great two days with Acadia Insurance at Timber Talks in Lincoln, ME and St. Agatha, ME in July, with presentations on changes to forms, rechargeable battery safety, fire suppression systems and an update about logger health from NEC Logger Health & Safety. A big thank you to Acadia for their commitment to the safety and financial well-being of PLC members.
The Maine Forest Service (MFS) has conducted statewide monitoring of Best Management Practices (BMPs) on timber harvesting operations since 2000 to assess the use and effectiveness of BMPs in Maine. The Maine BMP monitoring effort helps to track progress through the years, measure outcomes and identify priorities for future MFS educational programs. Data from the BMP monitoring effort are also used to produce a biennial report to summarize and analyze findings. The newest report, from 2022-2023 monitoring seasons, was released this month.
Data for this report were collected and analyzed using a standardized method detailed in the “Best Management Practices Implementation Monitoring Protocol.” This protocol assesses the overall rate of appropriate BMP application, as well as the effectiveness of the suite of BMPs used in preventing erosion and sedimentation on a given site. The following are key findings of this year’s report:
Seventy percent (70%) of sites had BMPs applied appropriately on crossings and approaches, or crossings were avoided.
∙Eighty-four percent (84%) of observations of BMP use and effectiveness found no sediment entered a waterbody.
∙Ninety-seven percent (97%) of sites showed no evidence of chemical spills.
∙When applied appropriately, BMPs are effective at preventing sedimentation from entering waterbodies.
Ninety-seven percent (97%) of sample sites had no wetland crossing.
The 2022-23 BMP monitoring results are generally consistent with the past few years and continue to show a general acceptance of the use of effective BMPs by the state’s forestry and logging communities. As has been well documented by previous monitoring reports and numerous studies from around the country, when BMPs are properly applied, they work to achieve the objective of protecting water resources. Conversely, when not applied or applied inadequately the risk of detrimental impacts greatly increases. This reinforces the conclusion that continued
ByTomGilbert
monitoring, education, and training are key to sustaining the progress that has been made with forestry BMPs and will allow Maine’s forestry community to continually improve in the future.
The full report is available online in the water resources section of the MFS website: https:// www.maine.gov/dacf/mfs/policy_management/ water_resources/bmps.html
President MikeAlbrecht
On May 16, 2024, I had the distinct pleasure and honor to cosign, along with Forest Service Chief, Randy Moore, a “Memorandum of Understanding” between the American Loggers Council (ALC) and the USDA Forest Service.
Initiated by the Forest Service, this MOU was fully endorsed by the American Loggers Council Board of Directors at our April 19th Spring Meeting. Our ALC Executive Director, Scott Dane, deserves tremendous credit for steering this MOU effort, working with key Forest Service staff through sessions of editing and compromise.
The final result is a document titled, “American Loggers Council and USDA Forest Service Collaborative Efforts for Healthy Forests, Markets, and Logging Industry.”
At this point, I suggest you let that rather lengthy title “sink in” for a moment. No, it is not a misprint. This title now represents what every American logger and every Forest Service employee should understand. We are now encouraged and expected to work collaboratively (read: together) to produce healthy forests, healthy timber markets, and a healthy logging industry.
To further underscore what we should all now understand, the MOU has a “Statement of Mutual Benefits and Interests.” I will quote a portion of these mutual interests as follows:
“The Forest Service utilizes professional logging contractors and timber haulers through various contracts and agreements to accomplish forest restoration and hazardous fuels treatment projects on National Forest System (NFS) lands. The ALC works to support, as part of its mission, an economically viable, healthy, and sustainable logging workforce with a ready supply of timber and restoration byproducts and robust markets to deliver raw materials to. The Forest Service depends on an adequate professional logging/hauling contract workforce
National Wildfire Crisis Strategy and the goal of accelerating the pace and scale of forest restoration can be accomplished and sustained into the future.”
The press release that followed the MOU signing quotes Forest Service Chief Moore saying, “Loggers are on the front line every day, contributing directly to the health of the nation’s forests . . . while also creating jobs and strengthening local economies.” And I added to that: “America’s loggers are the “boots on the ground” providing essential wood products while helping to protect and restore our forests to their fullest potential. We cannot do our job without a strong working relationship with the United States Forest Service.”
In the discussions that followed the signing of this MOU, one of the Forest Service officials was inspired to say, “We are a team; we can’t exist without each other.” Well, if we are truly a team, and our goal is “working together for healthy forests, markets, and logging industry” . . . then who are we competing with? My answer: up until recently, there hasn’t been any other team – we’ve been faced off against each other.
Many, if not most, of you are better historians than me, although I find history fascinating and insightful. In my opinion, the best book chronicling the history of American forestry was published back in 1971. Written by Henry Clepper, it is titled, Professional Forestry in the United States. No, it doesn’t include the past 50 years, but it does provide a detailed and accurate accounting of the storied events that shaped America’s current forest management policies.
Chapter 1 is aptly titled, “The Plunder of the Pineries,” recalling when loggers and lumbermen operating in the 1800’s were described as, “villains, scoundrels, and thieves.” Chapter 10, titled, “Timber Famine Warnings: Prelude to Regulation,” ushers in the notion that America’s forests would soon be depleted. This concern gave birth to the US Forest Service and two teams. The American timber industry and the Forest Service began to battle in an
undeclared war, perpetuated by misunderstanding.
There were cease fires along the way that allowed for progress. America’s wildfire events gave birth to Smokey the Bear, who became the Forest Service symbol for an effective wildfire prevention program, and despite a litany of government regulations, America built a vibrant timber industry.
But misunderstandings continued to polarize the two sides, prompting Henry Clepper to note that, “to more than one contemporary observer, it appeared strange that, as industrial forestry became better, the attitude of the regulators became more critical.” As the design of logging equipment became more environmentally friendly, more public land was designated as wilderness, near natural, wild and scenic, and roadless. Timber operators are now licensed and take continuing education courses but remain untrustworthy in the eyes of many within an agency I still hear referred to as the “Forest Circus.”
Bottom line, in 2024, even though America’s forests now cover almost 800 million acres, we have become the world’s leading IMPORTER of softwood lumber. We are losing sawmills at the rate of about two per month. Over the past ten years, the Forest Service has lost 40% of its non-firefighting workforce.
It’s time for a reset.
Enter the 2024 ALC/USFS Memorandum of Understanding. This historic and very positive document outlines a path forward to promote the three priorities listed in its title: Healthy Forests, Healthy Markets, and a Healthy Logging Industry. It underscores the following statement made recently by Chief Moore as he addressed the Department of the Interior Appropriations Subcommittee: “I can tell you with certainty that if we do not have a vibrant timber industry, we are not going to be able to manage our forests and keep them healthy and resilient.”
Let me say with certainty that the American Loggers Council completely agrees with Chief Moore’s statement, but a final step is required to make the MOU more than 3 holes punched into a binder. It needs to be
circulated, read, and understood. Every Regional Forester should brief his/her staff. Every Forest Supervisor and District Ranger should brief their staff and employees. To have teeth, the concepts in this MOU need to be integrated into forest plans and there needs to be accountability showing progress in achieving the stated goals.
Every state logging association needs to share this MOU with their Board of Directors, passing it on to all their membership. The only way this MOU will result in additional acres treated, fires prevented, and more wood products for America, is to have it communicated through the Forest Service and the timber industry, thoroughly understood, and transformed from a “Memorandum” into an “Action Plan.”
My request to you is that you read the Memorandum of Understanding for yourself. All the main points are discussed in the first 3 ½ pages. It takes ten minutes to read and understand it. If and when we agree with it, the doors of “understanding” and “action” open wider. You can find the MOU at www.amloggers.com: on the menu, go to News & Issues, Latest News, May 2024.
Mike Albrecht has a master’s degree in forestry from Duke University, is a Registered Professional Forester in California, and has worked for over 45 years in forest management and the forest products industry.
Mike currently serves as president of the American Loggers Council and is a past president of Associated California Loggers and the Sierra Cascade Logging Conference.
Q: What do Proctor & Gamble, Poland Springs, and Backyard Farms have in common? A: They all ship their products – from personal care items to refreshing drinking water to delicious tomatoes – to market in packaging made right here in Maine at International Paper’s Auburn Box Plant.
I recently had the pleasure of joining in a celebration of the 50th anniversary of the Auburn plant. From its opening in 1974 to today, this manufacturing operation has been a tremendous asset to our State, providing $13 million in payroll and benefits and $9 million to small and medium-sized business suppliers.
This success is the result of energetic leadership and a dedicated workforce joining together to meet the demands of an evolving e-commerce global economy. With skill and ingenuity, the 130 members of the Auburn team transform renewable resources into a wide range of packaging, strengthening Maine’s forest-products industry.
International Paper was founded in 1898 and now employs more than 39,000 with operations around the world. Maine has been an important part of this success story from the very start. Although co-founder Hugh Chisholm was born in Canada, he built his career here in our State with lasting accomplishments in the pulp and paper industry and sustainable forest management. In addition to his success as an entrepreneur, Mr. Chisholm is
remembered for his philanthropy and commitment to the welfare of his employees.
The naming this spring of Bucksport native Andrew Silvernail as CEO continues IP’s Maine connection and its founding ethic of providing opportunity, protecting natural resources, and being a force for good in communities around the world. That force is strong at the Auburn Plant, such as with its donation of 10,000 boxes each year to Wreaths Across America to honor fallen service members. The generous support of Toys for Tots, Operation Reboot, the Shriners Hospital for Children, the Trinity Jubilee Center, and United Way demonstrate an ongoing commitment to service.
Coming from a six-generation forest-products family, I know the challenges the industry faces. In the Senate, I continue to support legislation that strengthens an essential sector of our State’s economy. This includes trade agreements that are free and fair, providing certainty that biomass is a carbon-neutral energy source, and tax policies that encourage business investment and job creation. In addition, I am committed to supporting workforce development initiatives and improvements to our transportation and energy infrastructure.
This year, I have again led a bipartisan resolution designating October 12 as National Loggers Day to honor the skilled and resilient loggers in Maine and across the country and recognize the critical role they play in supplying Americans with the products needed to live safe and healthy lives. From the woods to factories like the IP Auburn Box Plant, Maine’s forest products industry is a vital part of our history. Working together, we can help ensure it is a vital part of our future.
There will be no column from Senator Angus King in this edition due to Senate Ethics Committee rules stipulating that no sitting member of the Senate can participate in mass communications in the 60 days leading up to an election in which the member is a candidate.
As a representative of Maine’s First District, I’ve seen firsthand how invasive species are threatening our forests and the livelihoods that depend on them. In Maine, our forests are not only an economic powerhouse, supporting industries like timber, paper, and recreation, but they also play a critical role in sustaining our environment. However, invasive species are wreaking havoc on our forests, and we must act decisively to protect them.
The emerald ash borer, which was first detected in Maine in 2018, has caused widespread damage to ash trees, which are vital to our ecosystems and the economy.
Similarly, the hemlock woolly adelgid threatens our hemlock trees, which help maintain stream health and support biodiversity. These pests, along with many others, are putting our forests and the industries that depend on them at serious risk.
That’s why I’m proud to cosponsor the Invasive Species Prevention and Forest Restoration Act, introduced by my colleague Congresswoman Becca Balint of Vermont. This bill aims to strengthen the biosecurity measures needed to keep invasive species from entering the U.S. in the first place. It’s far less costly to prevent invasive species from taking root than to try and control them once they’ve arrived. This legislation would ensure the U.S. Department of Agriculture (USDA) also has the funding and tools necessary to prevent and respond to invasions, protect our ecosystems, and support research into sustainable solutions.
Through its Invasive Species Program, the U.S.
Forest Service has funded projects that help manage and mitigate the impact of invasive species on forested land. In Maine, the Forest Service has supported efforts to control pests like the emerald ash borer and balsam woolly adelgid. This work is essential for protecting not just the trees, but the biodiversity and economic value that our forests provide. I was proud to vote in support of the Bipartisan Infrastructure Law, which provided funding for these projects. As Ranking Member of the House Appropriations Interior, Environment, and Related Agencies Subcommittee, which oversees the Forest Service, I’m committed to ensuring that the Forest Service has the resources it needs to continue this important work.
As Congress continues its work on the fiscal year (FY) 2025 appropriations process, the House Appropriations Interior Subcommittee proposed report highlights the increasing pressures on our forests due to invasive species. The language stresses that invasive
I hope you’ve all had a great summer and have been able to spend lots of quality time with the people you care most about. It’s the perfect season to enjoy everything Maine has to offer, and I’ve been lucky to experience it with Mainers in every corner of the state the past several weeks. With the August recess behind us, I’m back in D.C. working on the federal budget and the issues that matter most to Mainers. That includes addressing challenges in the forest products industry and laying strong foundations for its future success.
One of those challenges is the upcoming implementation of the European Union’s (E.U.) point-oforigin regulations. While addressing global deforestation is certainly a meaningful goal, it’s obvious that the U.S. and Maine in particular lead the world in modern sustainable forest management. Our forest products industry shouldn’t be subjected to onerous or even impossible new standards because of bad actors in other parts of the world.
It’s why I’ve joined a letter pushing the president to negotiate a pause to the E.U.’s new system and am staying diligent as its estimated launch date creeps closer. Thankfully, we’re not the only ones concerned even stakeholders in the E.U. are worried about what a rushed implementation would look like. Ultimately, I believe the United States should be exempted from the standards altogether, in recognition of our sustainable practices. I’ll keep you posted as more updates are available to report.
I also think this issue is a good reminder about why the work you do is so important. For centuries you have set the bar for what a responsible industry looks like. But it’s
species are already having profound effects on our natural resources, and are contributing to tree mortality, ecosystem degradation, and loss of economic opportunities in forestdependent communities. These findings underline the urgency of passing legislation like the Invasive Species Prevention and Forest Restoration Act to bolster prevention efforts and restore affected areas.
Our fight against invasive species is also a fight for our future, and the future of our wood products industry. As climate change accelerates, it creates new challenges for forest management, allowing pests to spread more easily and further destabilizing already fragile ecosystems. We must be proactive in addressing these intersecting crises, not only to safeguard our forests but also to ensure that our rural communities continue to thrive. With bipartisan action in Congress, we can ensure that our forests remain resilient and sustainable for generations to come.
also been a model for how to create good-paying jobs in rural communities and a critical link in the supply chain for everything from paper products to home insulation to energy. Plus, it’s pride in the distinctive way of living that generations of Mainers have enjoyed.
We sometimes call our working forests a “heritage industry,” but it’s so much more than that. The Maine woods connect our past and our present. And they hold the keys to a promising future.
Today, the folks at TimberHP have the Madison mill roaring again because they found new uses for wood. Imagine if lawmakers captured that same innovative spirit: For example, what if Maine passed a law to ensure that taxpayer-funded construction in Maine uses wood from Maine? Or that taxpayer dollars advance energy independence by prioritizing wood-based biomass, not just heat pumps and solar panels?
I believe we can achieve great things through the grit and ingenuity of our forest products industry. So thank you for all you do, and I’m looking forward to speaking with you all soon.
As always, if you have questions about resources for the industry or need any support, please send our team an email at ME02JG@mail.house.gov. We will get back to you quickly.
Even if it is not related to your job, my team and I are always here to help. Please let us know if we can help you solve problems you or your family is having with Medicare, Social Security, the VA, or other federal programs or agencies.
You can reach my staff at:
Lewiston: (207) 241-6767
Caribou: (207) 492-6009
Bangor: (207) 249-7400
You can also send us an email at: golden.house.gov/contact/email-me
Vermont Senator Bernie Sanders, Vermont Congresswoman Becca Balint and Vermont Congressman Peter Welch declined to include articles in this edition of The Logger’s Voice.
The PLC held several legislative events this summer and fall including “Meet the Reps” events for legislators and PLC Members in Poland September 24 (top right), Skowhegan September 26 (top left), Fort Kent October 10, and Lincoln October 11.
The PLC also held legislative tours of the Mechanized Logging Operations and Forest Trucking Program (MLOFT) in Fairfield (at left) on August 27 and September 4.
We would like to thank all legislators who attended these events and to thank the many PLC contractors who took time away from their busy schedules to attend as well.