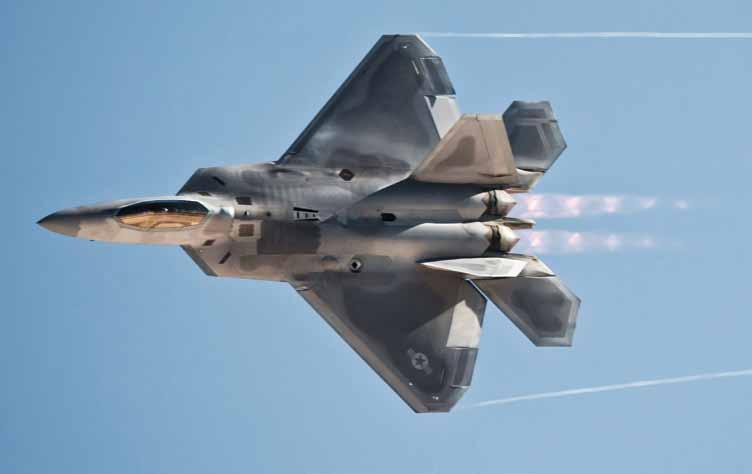
11 minute read
Aerospace Manufacturers Race to Meet Demand
Not only on the ground but in the air as well, Italian solution providers are helping to keep the skies safer.
How do you satisfy the insatiable demands of the North American aerospace market? Vladi Parpajo, President & CEO of the Parpas Group SpA (Padova, Italy; www. gruppoparpas.com) wryly answers: “That’s easy: Faster, better, cheaper.” It’s a theme you’ll hear from all the Italian machine tool builders. But you’ll also hear a lot of interesting details that go into actually delivering on those three promises. For example, Parapajo points to increased automation and the “evolution of intelligent monitoring <that> allow the development of autonomous decision-making processes, faster and more efficient.”
Advertisement
Automating and integrating to maximize productivity Alfredo Mariotti, General Manager of UCIMU-SISTEMI PER PRODURRE - the Italian Machine Tool, Robotics, Automation Systems and Ancillary Products Manufacturers’ Association (www.ucimu.it/en/home), also thinks “cyber physical systems able to take ‘decentralized decisions’ on their own and to perform their tasks as autonomously as possible” are a key factor in competitiveness. He adds that member companies (which include Parpas) are implementing other Industry 4.0 concepts, like “information transparency, in order to create a virtual copy of the physical world through information systems, by enriching digital plant models with data sensors and by aggregating information for solving urgent problems and the ability of cyber physical systems to physically support humans by conducting a range of tasks that are too exhausting, or unsafe for the employees.”
He adds that the vast field of ergonomics now embraces solutions from “automation and ICT (information and communications
technology)...to support and help operators in performing their working tasks, interfacing with the machines, reducing stress, risks and mistakes. Here we can find a number of technologies ranging from human interfaces to wearable devices—supporting and driving operators with task-related information—to cooperative robotics solutions helping operators perform heavy, complex or high precision operations that are almost impossible for human beings, especially if repeated for long periods.”
He sees manufacturers in this sector building “flexible manufacturing systems...with machine tools and ancillary equipment all integrated together, going to create a ‘working zone’ where each operation is connected with the next in an automated manner with the aim to minimize energy waste and to maximize productivity.”
At IMTS 2016, to be held Sept. 12–17 at Chicago’s McCormick Place, UCIMU will be present to provide information on the organization’s role and the roles of its member companies in the global aerospace industry. Representatives of the association can be found in Booth WB-916. cut titanium, aluminum and composite materials with precision to a hundredth of a millimeter.”
Blending machine tools and robots Another UCIMU member, Jobs SpA (Piacenza, Italy; www.jobs. it) also points to automation as a key ingredient to success in machining aircraft components. “In particular,” says Vice President of Sales, Marketing, & Service Antonio Dordoni, “we have focused our efforts on all matters related to piece variability in machining composite parts and subassemblies.”

Taking off with the F35 “with precision to a hundredth of a millimeter”
Parpas produces a variety of 3-5 axis highspeed machining centers in moving column and gantry styles, as well as boring mills and rotary and traversing tables. They hold a number of patents for manufacturing solutions requiring consistently high long-term accuracy, particularly in areas with big daily and seasonal temperature variations. That’s critical for machining large aerospace structures.
Parpas’ ability to maintain a constant temperature in their machines in any environment contributed to their winning a $40 Million project to provide a turnkey solution for machining the forward fuselage of the F35, the most advanced multi-role fighter in the world. Lockheed Martin set a target of increasing machining precision and quality, increasing safety, and reducing production, all within a fully automated machining process. Parpas delivered with a machine tool robotic transfer line that performs automatic fuselage load/unload, full machining, and automatic load/unload in the wash station; all running 24/7. The turnkey solution reduced manual moves from 18 to 2 (with increased safety and shorter cycle times), cut the cycle time for each part by 26% (saving money), and increased machining precision and quality (which also had advantages for the next stages in the aircraft’s construction).
Parpajo rightly boasts that in winning this order Parpas “overcame the principal world firms of the sector: German, Japanese, French and obviously American.” He credits their “technological capacity to respond to customer needs,” with “machines that can Jobs makes high-speed, high-power machining systems and custom turnkey solutions. Their latest product is the RoboDrim 200. Dordoni says it “blends features and capabilities from both machine tools and robots, in order to offer to the customer a new and innovative set of functionalities never integrated before on a single system.
“More specifically, RoboDrim is conceived to address the challenges related to the geometrical variability caused by the use of composite parts and subassemblies that are becoming the norm in civil and military aircraft design. As a result of all the R&D coming from this project, we can offer to our customers unique and customizable best-fitting systems specifically conceived for high-speed 5-axis machining operation, spindle sensing systems, adaptive roto-translation routines for partial or complete part machining and much more to meet this new wave of technical requirements.” The Jobs RoboDrim 200 5-axis machining center working on a composite panel. Accurate hole location and depth are critical for many aerospace assemblies and Italian machining technology delivers.
Going from the Flintstones to the Jetsons Breton SpA (Castello di Godego, Italy; www.breton.it) is another UCIMU member company that produces high performance multipurpose machining centers. Daniel Rochowiak, national sales manager for their Machine Tool Division in the US, likens the challenge some companies face in changing their machining mindset to “going from the Flintstones to the Jetsons.” Breton itself started building machines for cutting and polishing stone in 1963. But during the last 20 years its machine tool division has created five and six axis machines specializing in large aerospace components and very tight tolerances.
Rochowiak says “Breton can produce equipment for very large applications with travels >65 meters in length and four meters in the Z axis. Our largest machine for composite machining has a Y axis of five meters across the bridge. But these are all highly accurate machines, not routers.” He’s serious about the accuracy. Some models offer X-Y positioning uncertainty (P) on the order of 0.0003” over 4 meters and positional scatter (Ps) as low as 0.0002”. No wonder they “are competing with the best 5-axis solutions in the world.”
Breton offers machines to cut anything from resin, composites, and foam to super-alloys like titanium, Hastelloy, and Inconel. Breton machine tool applications extend to all manufacturing sectors, including power generation, die-mold, and requirements demanding very accurate results. Rochowiak says “Ironically, in many cases we quote our most accurate machines for composites cutting applications, as the required accuracies mandate this. Breton uses ball screws for Z axis movement on all machines. X and Y axis are either ball screw, or double rack and pinion, depending on the machine classification. “Anytime you’re molding something you must allow for a release angle to be able to remove the part from the mold. So in some cases you can’t mold the entire shape you need in one piece. As we use more composites and carbon fibers in aircraft structures, we create lots of these situations, so the ability to make components that mate up perfectly so they can be fastened together is critical. This drives the need for machines that can create the necessary holes with a high degree of accuracy, and also machines that can create the molds for similar precision. We satisfy both requirements.” How do they hold tenths over 4 meters?
To some extent it’s ancient history, but Rochowiak says Breton has taken lessons learned in cutting stone and applied it to their metalworking and composites machines. “For example, all bellows on the machines are air pressurized, keeping any contaminants off the ball screws, rails, and so forth. This enhances both the machine’s uptime and its accuracy. In fact, we advertise 95% uptime for all our equipment. We also have completely enclosed systems that safely evacuate all the dust produced in dry machining of composites, including carbon fiber, which is highly flammable. “The shoulders, rams, and bridges of our machines are electro-welded and normalized. The components on our higher-end machines are also filled with a polymeric compound patented by Breton called METALQUARTZ. It [helps] dampen vibration and provides a better surface finish on the part. Other builders will fill their bridges or other components with material to add weight, possibly a type of concrete, but this material will have a different growth coefficient than the steel. So it basically becomes like a rock shaking inside the casting. Whereas ours is a rubbersteel mixture with a growth coefficient comparable to steel’s. So it gives a true dampening effect. This makes our equipment unique.”
Breton has also introduced a special probe for carbon fiber machining. Rochowiak explains: “The material tends to flex and you need to know the exact position in order to drill the holes accurately. So we probe the surface mechanically and identify the flex point. The head automatically takes the point data and positions the tool exactly perpendicular to the surface. This makes our positioning and accuracy of hole depths perfect.” Ultra-fast cutting technologies
All Breton’s machines are built for high-speed machining, generally running HSK63 spindles at 28,000 RPM up to 40,000, with Breton offers ultrasonic machining solutions for cutting carbon fiber and honeycomb rapidly, accurately, and without noise or dust.

broad torque bands for use in different materials. They also offer 100 Nm 18,000 RPM HSK63 spindles and HSK100 spindles with 300 Nm at 14,000 RPM. Rochowiak adds “we also implement trochoidal machining, which optimizes the edge of the tool for the greatest possible material removal. The axes are also very fast, 3,500 inches per minute for some of the movement, though of course those speeds are used only for tool change and positioning, not for machining.
Italians are realistic, so we are good at quickly finding practical solutions “Breton also offers engineered solutions with ultrasonic machining. We’re able to tool change the ultrasonic head into our standard spindle. It’s a great approach to cutting through sandwiched honeycomb structure platforms. It cuts with amazing speed and accuracy, without any noise or dust.” What’s next for aerospace machining?
Dordoni says the major changes are technological, as “the way we conceive, design and build airplanes is changing. Consequently, tasks that were previously easily managed with more traditional technologies are today more difficult to handle with the advent of technologies related, for example, to carbon or titanium. If it is relatively easy to find a Tier 1 or Tier 2 to carry out structural parts or aluminum skins machining, a different situation occurs for composite components or structural parts in titanium.”
Parpajo sees “a constant need to increase productivity and quality of the products.” He also says the “financial and political stability of the markets is what is missing and it is a big concern.” Dordoni echoes this, saying “In this moment the biggest concerns originate from factors other than technology. They depend on other factors such as the stability of the market, the recovery of investment volume, the stabilization of exchange rates, and above all, the stabilization of the power relations existing today among the four important market entities, i.e. Europe, the United States, Russia and China.”
UCIMU’s Mariotti says a number of factors are contributing to short term but widespread uncertainty throughout all manufacturing, such as the fall in energy prices. Committed to delivering what you need
At the same time, it’s clear the Italian providers have made a strong commitment to North America, providing highly productive, customized solutions with excellent support. All three of the companies discussed here have offices in Michigan and either additional service locations or independent distributors with service capabilities. As Dordoni puts it, users are “willing to do worldwide research to find the best production terms for each product. In this case it is not necessarily a winning point having the production plant adjacent to the point of sale. However, it is essential to have top quality services for the product near the installation site, which are expected from our clients, particularly in the United States. It is for this reason that we have a subsidiary in the United States and service centers throughout the territory because we are convinced of its importance.”
As far as customization, it appears most aerospace projects require it and the Italians deliver. As Parpajo expresses it “our customers need to achieve higher productivity and better quality with sustainable investment levels, so the challenge is driving us towards the development of customized solutions.” “Custom” doesn’t mean it’s fanciful or takes forever, though Dordoni cautions that “the best in the shortest time do not get along.” If you want an innovative solution you have to allow some time. As Parpas’ Export Manager, Gianluca Battisti concludes: “We Italians are realistic, so we are good at quickly finding practical solutions.” Lockheed invested in a machine tool robotic transfer line from Parpas SpA to build the forward fuselage for the F35 Joint Strike Fighter. Parpas’ turnkey system performs automatic fuselage load/unload, full machining, and automatic load/unload in the wash station; all running 24/7. It reduced manual moves from 18 to 2, cut the cycle time for each part by 26%, and increased machining precision and quality.
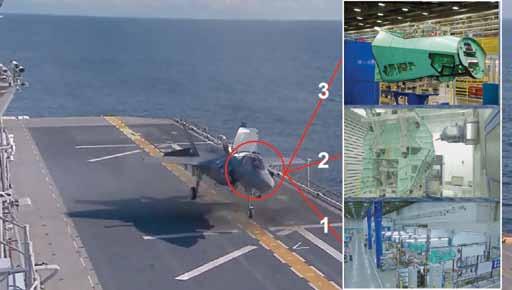