
8 minute read
Smart Manufacturing Spreads Its Wings and Begins to Soar
Defining “smart manufacturing” can be a challenge in itself, but it’s newer approach that calls for the integration of machines, tools, automation, sensors and equipment that is, in and of itself, more advanced than before.
By Dean Bartles Contributing Editor
Advertisement
Somaschini SpA (Trescore Balneario, Italy; www.somaschini. com/en) has been making gears in Northern Italy outside Bergamo since 1922 through four generations of entrepreneurs.
In 2012, that mission finally brought Somaschini to the United States, at the request of a customer, Daimler AG, which needed the company known for its high quality ground gears to supply its heavy-duty truck production in North America.
Since then, Somaschini has invested $22 million in South Bend, Indiana, where it built a 50,000-square-foot smart manufacturing facility. It now has the capacity to churn out 70,000 gears per month with just 30 employees who rely on sophisticated machine tools, automation, metrology and software for high volume production.
“Everybody can buy a good machine—we know how to use it consistently,” said Chief Executive Officer Dr. Andrea Scanavini. The company’s smart manufacturing approach helps it deliver what Scanavini called “constant quality,” which is measured in a defect rate consistently under 50 PPM annually. He noted that the company’s metrology and technical office also plays a big role in the family-owned company.
In South Bend, the company largely supplies gears for heavy duty vehicles, but it recently secured business for a light vehicle line, too. Globally, the company produces cylindrical ground gears, ground beveloid gears, ground scissor gears, among other products. It is a member of ASSIOT - The Italian Transmission Elements and Gear Manufacturers Association (www.assiot.it), and in addition to automotive customers, which make up 80% of its business, the company also supplies gears globally to the power transmission, robotics, agricultural and industrial sectors.
Scanavini, who is also a board member of AGMA, the American Gear Manufacturing Association, said the processes used for manufacturing in South Bend are “copy and paste” replicas of the smart, high-tech methods at Somaschini’s two production facilities in Italy.
For example, in South Bend, the company invested in an extremely automated production line where the ratio of robots to people is 5:1 for each shift. Robots are outfitted with vision systems for correct positioning and other high-tech features. In addition to enabling throughput, the robots help with consistency for quality.
“Fundamentally our gears are high quality,” Scanavini said.
Global Perspective
The Somaschini story highlights the ongoing changes in manufacturing—especially in the US where skilled labor is difficult to find. Across all sectors, manufacturers are turning to so-called “smart manufacturing technologies” for a variety of benefits. Among them: faster throughput, improved quality and, many times, products that are simply converted from raw material to finished good in fewer steps—sometimes—even one step.
Defining “smart manufacturing” can be a challenge in itself, but it’s newer approach that calls for the integration of machines, tools, automation, sensors and equipment that is, in and of itself, more advanced than before. Increasingly, these devices communicate with one another through wired or wireless connections, in an Internet of Things (IoT) network, and provide skilled workers more data to optimize processes, predict needed maintenance and troubleshoot.
This newer approach to manufacturing is enabled by more plug-and-play machine tools, automation and software that comes ready to go, simplifying integration. Emmeci SpA (Tuscany, Italy; www.emmecifucecchio.com), has its North American office in Rhode Island, is a world leader in automation equipment for luxury packaging and rigid boxes. Its equipment produce high quality premium boxes and paperboard products in a highly automated manner. It is a member of the ACIMGA - The Italian Manufacturers Association of Machinery for the Graphic, Converting and Paper Industry (www.acimga.it),
If you’ve ever bought a smartphone, perhaps you took a moment to admire how it came in a beautiful high-quality box with perfect edges and flat surfaces, and, perhaps, you’ve admired the work of an Emmeci Luxury Packaging Machine.
Rigid boxes such as this are also made for showcasing luxury cosmetics, chocolates, and increasingly, jewelry, electronics and spirits. In addition to the beautiful boxes Emmeci machines make, their equipment is also used to manufacture turned-edge products, such as traditional board games and puzzles that make for a night of family fun.
The Emmeci MC 2016 APP is an advanced luxury packaging rigid box machine that “includes all of the “mechatronic” developments of the last few years,” the company said, including a camera vision systems for spotting and other features, including a onetouch setup.
“The MC 2016 APP has been an evolutionary development that used the foundation of the Emmeci MC 2004 Platform,” said Dominick Archino, President of Emmeci USA, LLC. He noted that in some cases, sensor systems have been upgraded to camera

High Technology Manufacturing
Examples of this newer approach to manufacturing technology are plentiful, and Italian companies have been leaders of developments in this area. One industry that has benefited from new technology is packaging.
Take the MC 2016 APP from Emmeci SpA, which was launched at Drupa in Düsseldorf, Germany, this May and June. Emmeci SpA is leader for design, production, installation and servicing of automatic lines and machines for rigid set-up boxes and technical paper manufacturing.
Casting Technology by Gauss Automazione Srl
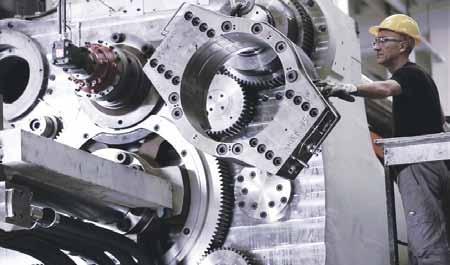
systems and hydraulics have been replaced with servomotors. The result is improved accuracy, productivity and best-in-class finished product quality.
Emmeci USA LLC came to the US in 1998, where it has North American headquarters in East Providence, RI, and it has long held the No. 1 market share position in rigid box making automation. Similar Italian packaging companies are represented by UCIMA - The Italian Packaging Manufacturers Association (www.ucima.it) Because of the sophistication of today’s converting machines, rigid cardboard boxes, often wrapped in high-quality papers, are also replacing plastic and other types of rigid containers for a wide variety of luxury goods.
Smart Technology for Oversight, Control and Service At Gauss Automazione Srl (Brescia, Italy; www. gaussautomazione.com), located outside of Milan, smart technologies are changing the way customers monitor, control and service their custom casting machining cells. Gauss, which is a member of AMAFOND - The Italian Association of Companies Which Produce Machinery, Plants, Furnaces Products and Services for the Foundry Industry (www.amafond.com), has been doing business in the United States for a little over 15 years.
Its North American headquarters in Toledo, Ohio, sells two Gauss brands that cover the molten metal market: Aside from the Gauss brand, which offers gravity and low pressure die casting machines, it also sells Italpresse Srl (Capriano Del Colle, Italy; www.italpresse.it) high-pressure die casting machines. Most customers buy custom machine cells from Gauss. “We provide all the automation, a turnkey solution,” explained Scott Burkett, Vice President of North American operations.
Gauss does a robust business in the US, mostly due to the automotive sector. For example, the company recently sold eight $5.5 million casting cells to a major automaker. About 90% of the Italpresse business is automotive, while it’s about 75% of the Gauss brand business, where appliances and the aerospace sector also represent a healthy amount of sales.
A little over a year ago, Gauss teamed up with Schneider Electric to build out its smart manufacturing offerings for digital oversight and control of machine systems.
Today, Burkett said, “You can watch your machines run and you can change parameters on the machines.”
Top Quality is Smart Manufacturing
Smart manufacturing and technology sometimes means continuing to deliver a high-quality, robust product that customers already love. Take Sitrex, USA, part of Sitrex SpA (Trestina, Italy; www.sitrex. com). Sitrex is a member of FederUnacoma - The Italian Agricultural Machinery Manufacturers Federation (www.federunacoma.it).
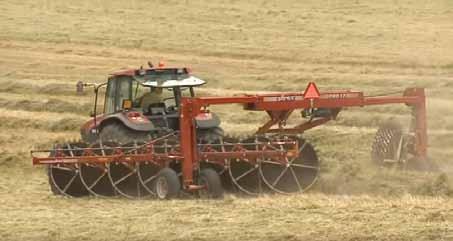
SITREX PRO/17 Heavy-Duty Wheel Rake
Emmeci MC 2016 APP is an advanced luxury packaging rigid box machine.
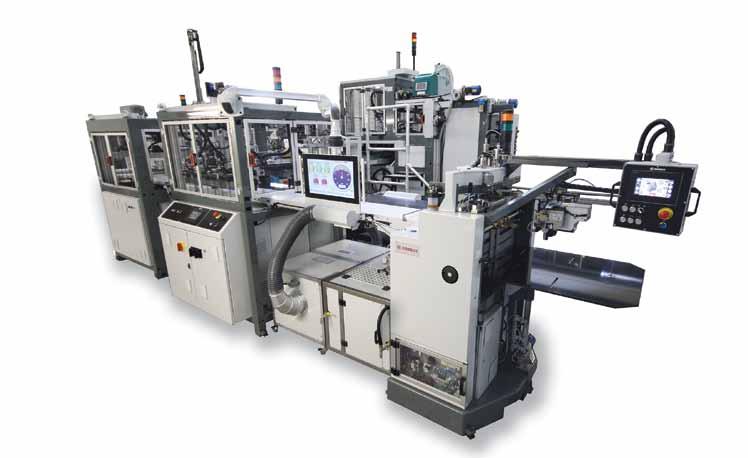
Kent Zimmerman, agriculture sales manager for the John Day Co., a leading supplier in the ag and industrial markets, has been distributing Sitrex hay equipment for 18 years out of Omaha, Nebraska; Milan, Illinois; and Redwood Falls, Minnesota. Sitrex manufactures popular hay equipment in Italy for the US, such as the PRO 17 and MKE16, which are known for high quality by faithful customers.
“There’s not a lot of electronics, just a good, dependable piece of equipment,” often using robust hydraulic systems, as in the PRO17 rake, Zimmerman said.
“Quality control has been very good,” he said, of the company’s high-capacity rake lines, which ranges in size from 2- to 20-wheel rakes. Innovative new approaches to the machines mean that new models such as the MKE16, part of the Magnum Evolution “V” Rakes, can now use 55” or 60” diameter rake wheels on the base frame. The hay rakes of the Magnum Evolution line are designed in such a way that adjustments are simple to accomplish.
Sitrex is a major player in the space, and also makes private label equipment for other US brands.
And one that is important to agriculture customers. “They tend to stick with it,” he said of the Sitrex brand. John Day also represents Ferri Srl (Tamara, Italy; www.ferrisrl.it), which makes 3-point mounted boom and offset mowers in Northern Italy. With service technicians in short supply, Burkett said, the technology also allows customers to work directly with Italy through a digital connection to troubleshoot machines—a popular feature. Given how vast the United States is, it’s also been difficult to find technicians willing to cover large service areas, which require substantial travel.
Now, he said: “You can simply troubleshoot your machine directly in Italy.”
Dean Bartles is the Founding Executive Director of the Digital Manufacturing and Design Innovation Institute and has had a distinguished 35-year career in manufacturing, implementing multi-million dollar programs domestically and internationally with responsibilities in research and development, technology transfer, program management, and manufacturing operations. Prior to joining DMDII, he held several positions at General Dynamics and its predecessor companies, most recently serving as Vice President and General Manager of a key Strategic Business Unit in the Ordnance and Tactical Systems division within General Dynamics.