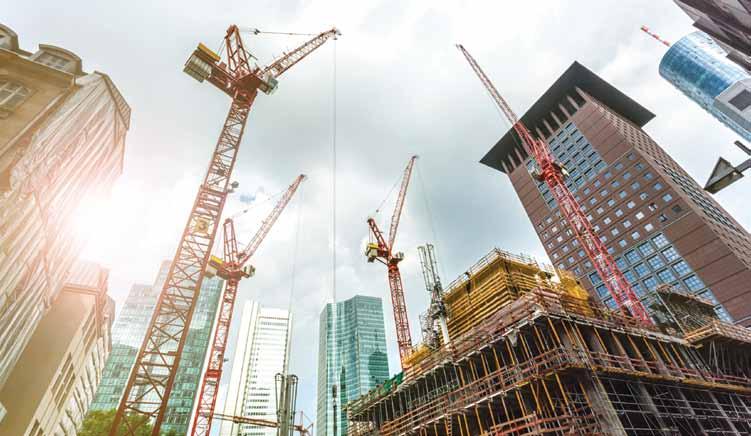
11 minute read
Construction Industry Building the Future
Makers of earthmoving equipment have established a global presence amid tough competition with these companies build high-quality, reliable, heavy, medium and light equipment for worldwide use, valued at over $3 billion a year.
That the Italians have a long and glorious history of working with stone is as obvious as the giant coliseum in Rome. What might be surprising is the fact that Italians dominate the worldwide market for automated machines that quarry and process natural stone. It’s a big market too, CONFINDUSTRIA MARMOMACCHINE - The Italian Association of Manufacturers of Machinery and Other Equipment for Natural Stone Quarrying and Processing (www.assomarmomacchine. com), the 184 member Italian association of these machine manufacturers, says Italy’s exports in this area soared 15% in 2015 to $1.2 Billion Euros, with Italy’s share of the world market at about 60%. The US is their top destination, with Canada and Mexico also contributing to over 40% growth in North America.
Advertisement
Centuries of stone-working tradition wedded to state-of-the-art technology
Key players include member companies GMM SpA (Gravellona Toce, Italy; www.gmm.it), OMAG SpA (Zanica/Bergamo, Italy; www.omagspa.it/en/), and SASSOMECCANICA Srl (San Benedetto del Tronto, Italy; www.sassomeccanica.it/en), all of which make machines that cut, shape, and polish stone after it’s quarried. In that niche, Italian technology accounts for 90% of the machines sold around the world, according to Taf Wharton, GMM’s General Manager in North America. “Construction is our primary focus,” says Wharton, “whether that be interior decorative materials for tiny kitchens in downtown Atlanta or the outsides of massive skyscrapers in New York.” All three companies point to Italy’s strong tradition in the
industry. As Mark Lauzon, SASSOMECCANICA’s West Coast sales manager in the US puts it, “One of the advantages of working with the Italians is that they have a culture and a history of working with stone and they truly understand what it takes.”
Wharton says “the most important difference between these machines is the interface. In other words, how easy is it for an operator to get the most out of the machine. We offer large screen controls and icon driven programs that make it easy to handle all common tasks.” Lauzon also points to automation and touch screen programming. All agree that today’s machines (at least the saws and machining centers) must offer simultaneous 5-axis interpolation. OMAG even offers machines with up to 12 axes to do forming, routing, engraving, milling, sculpting, sawing, polishing and lathe work all on one unit, whether the material is glass, marble, granite, or any other type of stone.
Being competitive also requires high output, and that’s what these Italian machines deliver. Lauzon says SASSOMECCANICA is especially proud their new in-line polishing machine, the Revolution. Like other line machines, it uses polishing heads moving in a toroidal motion to put a finished edge on a countertop, enabling an “array of profiles from demi-bullnose, to bullnose, crescent, bevel and other shapes. Any toroidal profile can be applied by this machine and you can get lots of product through. What used to take hours by hand takes minutes. The Revolution is a fourteen spindle machine that can produce a three centimeter eased edge with a very small radius at 25 inches per minute. That’s a big deal.” home who could cut and polish custom granite countertops. Now there might be 400. They’re all fighting for clients.
“There are more clients of course, in part because the price of the product has come down so much. Years ago granite counter tops elicited a ‘wow.’ Now hard wood floors, stainless steel appliances, and granite counter tops are often standard features. Because the product has lost some if its ‘wow’ factor they need to really hustle to get the job, which means servicing the client more quickly, more precisely, and if they can, knocking the price down a little bit.
“So today someone would come to your kitchen with a digitizing system and take exact laser measurements. This laser file would be translated into a CAD file. They’d put it on an automated piece of equipment and without any operator involvement get exactly the shape of your kitchen, not just straight lines. You’d have the sink exactly where you want it, every hole exactly where you want it... Everything is taken care of bespoke to what the client wants.”
This approach requires a change in mindset for some customers and Lauzon says SASSOMECCANICA is “really good at is helping the customer make the change from the analog world to the digital world. We show them how to work with the data, how to store the data, how to manage the work flow...things that help them be successful beyond just how to run the machine. But it is a challenge. If you get a digital saw, that means digital templating and now you have all this data to manage. We provide the training and support for them to be successful across the whole digital spectrum and not just on that one piece of equipment.”
Marco Cavalleri, OMAG’s Managing Director, says their “large and modern machine shop, with many computer controlled machines, is a striking advantage over <their> competitors. This permits extensive testing of different concepts, tools and materials. Our experi
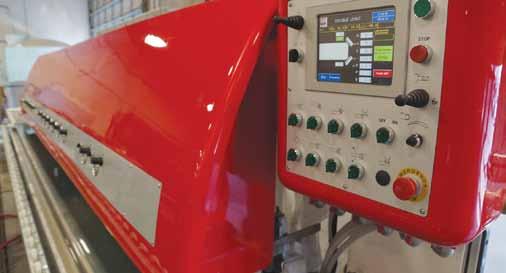
Customize or die
Fast programming and versatility are critical because most of the customers in this highly competitive industry live or die on their ability to customize products. Take granite countertops, perhaps the biggest application for this equipment. Wharton says “twenty-five years ago there might be four companies within a 100 mile radius of your The new Sassomeccanica Revolution can produce a three centimeter eased edge with a very small radius at 25 inches per minute. Like SASSO’s other models, it’s also a beautiful machine, with a red fiberglass cover from an Italian company specializing in speedboats.
ence with computerized manufacturing helps us develop software inhouse, which is then test extensively before release. This approach ensures reliability and professional and punctual service.”
Each company is committed to providing strong support in North America, with US based technicians and parts supplies. Lauzon says SASSOMECCANICA’s “customers would not be able to discern us from a reputable American company when it comes to product support. Our techs also answer calls after hours. And because our Italian techs answer our calls at two o’clock in the morning, it works out really well.”
The OMAG Multicut can cut and contour circles and more.
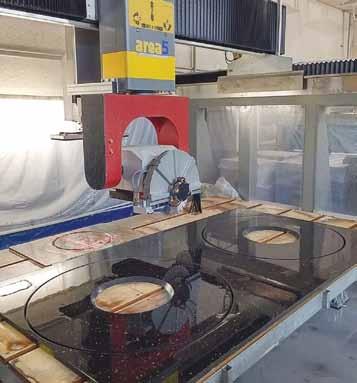
Customization also applies to the machines
Pasqualino Pietropaolo, CONFINDUSTRIA MARMOMACCHINE’s Communications Manager, says the aftermath of the recession and greater foreign competition have made customization and price the primary factors in machine sales. “Demands from customers all over the world are now very precise and you’ll sell only if you offer the customer exactly what he wants, no more and no less, at the lowest price.” So companies like GMM, which builds 350-75 machines per year, keep advancing the technology and offering choices. “What used to be half a dozen items for each machine is now pages of options,” says Wharton. Echoing Pietropaolo he adds, “Naturally customers don’t take something they don’t want because it costs them money, they’re not going to use it, and it doesn’t make them any money. So while the logistics are a challenge, we give our clients a great many options to choose from.” Each company also offers a range of sizes to fit different shops as well. Lauzon says “We have small machines to do back splashing and countertops costing $50,000 and machines as big as a school bus costing $250,000. By the same token, we serve factories with hundreds of people producing 3,000 square feet of material or more per day and shops as small as five guys producing one kitchen a day. In some cases they’re using the same saw. It’s just a question of how that shop deploys that equipment. The more abrasives, the more heads you put on the machine, the faster you can run.”
Reinventing the world of ceramics
Not to be outdone by the wizards with stone discussed above, ACIMAC - The Association of Italian Manufacturers Machinery and Equipment For Ceramics (www.acimac.it) boasts equally remarkable members. Perhaps most notably, SYSTEM SpA (Fiorano Modenese, Italy; www.system-ceramics.com) has introduced technology that can create ceramic surfaces up to 5.2 feet wide by 15.7 feet long (1,600 mm x 4,800 mm) in thicknesses ranging from 0.1 to 1.2 inches (3 to 30 mm). Called “Lamina,” the process can also create unique surfaces, reproducing the finish of rusted metal, or the tactile sensation of wood and its natural vein, and more. And because it’s created in ceramic, the surface will maintain the same qualities over time.
After years of R&D, market observation, process analyses, and overcoming major challenges...
Lamina starts with batching units that ensure uniform spreading of the mix of raw material powder onto a conveyor that transfers the material to a mould-less press that SYSTEM calls GEA, the most powerful press of its kind. Thanks to a specially designed hydraulic circuit, GEA implements a dedicated work cycle where the pressing force can reach peaks of 44,000 tons, guaranteeing large format sheets (5.2 x 15.7 ft.) and a wide range of thicknesses (from 0.1 to 1.2 in.) with no internal stress. The raw materials are processed with an innovative system of specially designed belts that enable the creation of smooth and structured finishes as thin as 0.1 inches, the latter obtained thanks to a laser incision system installed on the belts.
After this compacting phase, the system goes on to high definition digital print decorations, open to the creation of any graphic pattern required. Digital processes then apply protective matt and gloss varnishes. The last phase is firing in the kiln, which reaches a maximum temperature of 2,282 F° (1,250 C°).
The Lamina GEA press is the most powerful of its kind, with forces reaching peaks of 44,000 tons, guaranteeing large format sheets and a wide range of thicknesses with no internal stress.
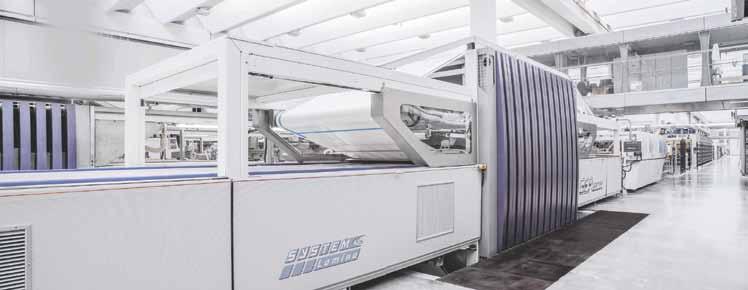
On exit from the kiln, the ceramic surface undergoes a series of phases in preparation for sales worldwide. In another remarkable achievement, the entire production process is completely automated, managed by a simple Man-Machine-Interface developed in-house by SYSTEM.
As SYSTEM puts it “There are infinite applications, where man is free with his imagination to retrace paths of antiquity, in choosing perhaps marble, granite or the more precious stones in nature, or take a more adventurous approach towards avant-garde architecture with cements, resins and metal effects to portray a futuristic vision of the world. Palaces, buildings, public and commercial spaces can be clad internally and externally, like a special tailor-made suit with a highly personalised touch of originality.”
SYSTEM also points out that technical ceramics “stand up to wear, resist absorption, are antibacterial, easy to clean, able to withstand low and high temperatures, and never alter over time, keeping the authentic feel of the original material and the researched and special appearance.
“It also worth noting that ceramics are completely natural materials, present in the life of man since ancient times, with the significant advantage of the possibility of re-use in other production processes, while maintaining the same properties and environmentally sustainable nature.”
Italian glass industry continues to shine
The Italian glass industry has seen growth fueled by exports. GIMAV - The Association of Italian Manufacturers and Suppliers of Machinery, Equipment and Special Products for Glass Processing (www.gimav.it), recently reported that exports to the NAFTA countries rose 58% last year, including growth of 73.27% in sales to Mexico. For machinery, products, and accessories for the processing of flat glass in particular, international sales rose by 5.40%, with the United States being the main market.
Members include the Intermac division of the BIESSE Group SpA (Pesaro, Italy; www.biessegroup.com). The Intermac division (Pesaro, Italy; www.intermac.com) develops and sells machines for float glass processing companies and, more generally, to the furniture, construction and automotive industries. Their product lines include the Genius glass cutting systems, Primus waterjet cutting systems, F-P Series machines and systems for double edge grinding, and Master CNC work centers. They are distributed through a network of branch offices located in strategic markets, including three offices in the US and Canada.
Moving the earth, Italian style
Makers of earthmoving equipment have established a global presence amid tough competition. COMAMOTER - The Italian Manufacturers of Earthmoving Machinery, Attachments and Components (www.comamoter.com), represents roughly 40 of these companies. These companies build high-quality, reliable, heavy, medium and light equipment for worldwide use, valued at over $3 billion a year. Members include the CAST Group SrL (Mirano, Italy; www.castgroup.it), which manufactures multifunctional articulated compact mini loaders, and the FAE Group (Fondo, Italy; www.fae-group. com). FAE designs and manufactures a wide range of professional shredders for both surface and in-depth applications in the forestry and agriculture sectors and for the disposal of all wooden residues. They also have a leading position in the construction of machinery for dirt roads and soil stabilization. FAE’s large US office is near Atlanta. Whether your construction needs call for stone, ceramics, glass, or moving dirt and vegetation, an Italian manufacturer probably has the “intelligente” answer.