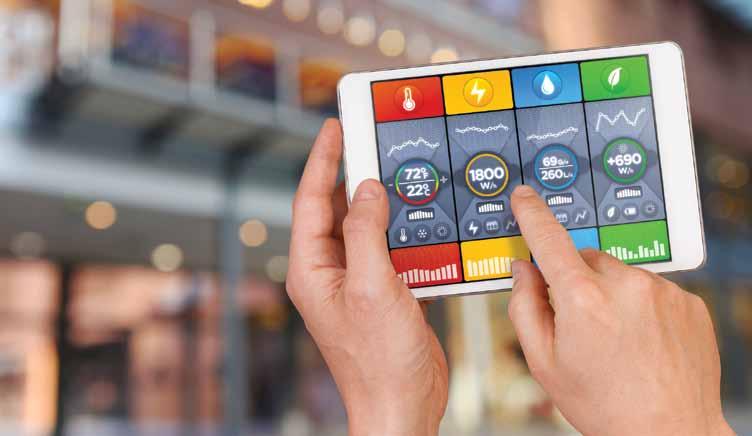
10 minute read
Automating The Process with a Lean Mentality
Engineers have been working on ensuring that manufacturing with Italian machines incorporates the processes of Industry 4.0, including connectivity, remote monitoring and more.
When Ford Motor Company needed a redesigned body shop to make the planet’s first full-size, aluminum-body pickup, the F-150, it partnered with a global leader in automated manufacturing innovation—Comau SpA.
Advertisement
Comau’s (Turin, Italy; www.comau.com) ComauFlex modular modular assembly line, with its separate but interconnected supply and work areas, offered the vehicle manufacturer the flexibility and efficiency it needed to work with advanced processes and materials, like the aluminum alloy in the F-150.
During the development of ComauFlex over the last 15 years, the Italian company threw out traditional plant layouts—where components were typically assembled in different areas requiring complex logistics, and with multiple standards—and adopted a more logical strategy for material flow, with uniform standards.
“Our systems are very flexible and very efficient,” said Brent Kelso, director of business development for Comau LLC (Southfield, MI; www. comau.com), the company’s 32-year-old North American offshoot.
Other automotive companies have incorporated ComauFlex into their operations, including Fiat Chrysler Automobiles (Comau’s parent company), General Motors Company, Volvo and Tesla, among others. That widespread adoption contributed to robust growth for Comau, although the increase was mainly attributable to its body assembly, powertrain and robotics businesses, according to the FCA 2015 annual report. The company’s year-over-year increase in net revenues from 2014 ($1.7 million) to 2015 ($2.2 million) was 26%.
Activity in North America accounts for about 25% of those net revenues, said Kelso.
In the United States, Comau operates in three locations in Michigan, including seven manufacturing plants and one innovation center. The company employs over 1,200 people in America, and an additional 600 in Mexico.
In addition to body joining and assembly, Comau’s capabilities include powertrain machining and assembly, robotics and maintenance, as well as advanced production systems and environmental services. It works with a wide range of industrial sectors, including aerospace, rail, renewable energy, heavy industrial, commercial vehicles and general industry, in addition to automotive. Big in Robotics
The United States is Italy’s most important trading partner outside of the European Union, with 7.5% of Repubblicana Italiana’s total yearly exports shipped across the Atlantic to America.
Among those exports are automated manufacturing machines and systems, with Italy holding fourth place in the world for making machine tools, and third place for their export, according to an article in the digital business publication ItalyEurope24. When it comes to robotics in machine tool systems, Italy is the United States’ third-largest supplier.
Some Italian machine tools and robotics companies are so successful in the United States that, like Comau, they’ve established a presence in America. Over time, Italian companies have made a large investment in America, with at least 65 direct subsidiaries located in the United States. In a majority of cases, production is still in Italy.
From General Motors to Ford, from FCA to Tesla, from Boeing to Lockheed Martin, there is virtually no “giant” of American industry that is not a customer of Italian manufacturers.
Contributing to the success of Italian companies in the United States is the engineering for which Italy is widely known.
Those engineers have been working on ensuring that manufacturing with Italian machines incorporates the processes of Industry 4.0, including connectivity, remote monitoring and more.
“The vast majority of the most complex plants for plastics and rubber processing are usually already sold with remote control systems,” says Alessandro Grassi, president of ASSOCOMAPLAST - The Plastics and Rubber Processing Machinery and Mould Manufacturers’ Association (www.assocomaplast.org). “This way, the manufacturer can check machinery operating parameters and monitor anomalies, providing just in time the technical assistance which in the past would have required the presence on site of a technician.” Other Italian manufacturing companies active in plant automation are members of ASSOFOODTEC - The Italian Association of Machinery and Plant Manufacturers for Food Production, Processing, Preservation (www.assofoodtec.it) and ASSOFLUID - The Italian Association of Manufacturing and Trading Companies in Fluid Power Equipment and Components (www.assofluid.it). Innovation leads to success
Persico Group SpA (Bergamo, Italy; www.persico.com/en), which established Persico USA (Rochester Hills, MI; www.persico. com/en) just three years ago, continues to impress American companies with its fully automated rotational molding machines and other manufacturing equipment.
The Nembro, Italy-based company is so successful at its Rochester Hills, MI location because of innovative technology that saves time, money and materials for its users. As a result, the U.S. location has doubled its capacity and sales and added employees in the last year, said Shadi Alshakaa, general manager of Persico USA. The Michigan plant is a Tier 2 supplier to the automotive companies and also sells, installs and services Persico manufacturing equipment.
“We’re basically a turnkey company,” said Alshakaa. “So we can supply the machine or a complete line.”
Persico’s turnkey solutions are similar to many of its fellow Italian companies that are part of the Plastics and Rubber Processing MaComau’s ComauFlex systems, like this body framing station at a Fiat Chrysler Automobiles plant, favors a more logical strategy for material flow, with uniform standards, over traditional plant layouts.
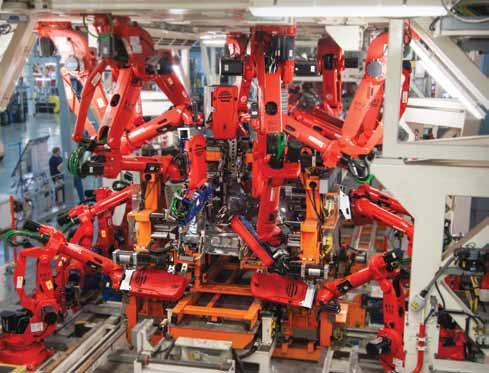
chinery and Mould Manufacturers’ Association, or ASSOCOMAPLAST. “In the last years, a wide change has occurred,” says Alessandro Grassi, president of ASSOCOMAPLAST. “Manufacturers have passed from selling a simple machine to providing a complete service.”
This often includes an automated system, says Grassi. For example, a member company may make an injection-molding machine that produces a product, separates it from excess processing material, and puts the pieces in a box.
Popular with the automotive companies is Persico’s one-step forming and back-injection machine. BMW uses it for door panels and two big OEMs in the United States are incorporating it on their production floors.
The one-step line, which can operate fully automated, takes a 12- 15mm thick sheet of material that’s 50/50 blend of polypropylene and natural plant fiber, and turns out door panels that are 1.8-2.5mm thick and up to 35% lighter than a similar part made of plastic.
Persico also offers glue-less technology that combines the door panel’s substrate with a polymerbased skin, which saves equipment and material costs.
And, of course, Persico USA provides machines and lines for the company’s bread-and-butter technology, rotational molding—but with quality on par with home-baked bread and butter fresh from the farm. Manufacturing large, hollow parts such as oil tanks is much easier and cheaper by rotational molding than any other method. Very little material is wasted using this process, and excess material can often be re-used, making it a very economically and environmentally viable manufacturing process.
The SMART rotational molding machine, which is perfect for lowvolume production, was introduced at the same time Persico established its American operations. It saves time and money via a singlestep operation, direct mold heating and shorter cycle times.
“Most of our customers for rotational molding are agricultural or, for example, the Yeti (Austin, TX) cooler company,” said Alshakaa. “We have multiple companies that we supply in the U.S.”
Those American customers accounted for $8 million in sales for Persico USA in 2015, he said. Refrigerators for the Amish Although environmentally friendly carbon dioxide was widely used as a commercial refrigerant in the United States by the 1920s, its popularity waned soon after in favor of Freon. But now that chlorofluorocarbons like Freon have been shown to have a greenhouse effect in the atmosphere, the use of CO2 is resurging. And companies like refrigeration compressor manufacturer Officine Mario Dorin SpA (Florence, Italy; www.dorin.com) are leaders in commercial CO2 applications worldwide. “I think they make a very good compressor, with very low issues,” said Brian Porter, corporate director of sales for Blissfield Manufacturing (Blissfield, MI; www.blissfield.com), which specializes in heat transfer technology within the automotive, off-highway vehicle, commercial refrigeration and industrial equipment markets. “We don’t have any problems with them.”
Blissfield, located about 70 miles southwest of Detroit, has been the exclusive North American distributor of Dorin compressor products for over 20 years and has rights to distribute its products in 15 international countries.
Take a look at the size of the machines the Milan, Italy-based company makes: You’ll understand their output, and then wonder what giant ordered them. “The majority of what we sell is the open drive (compressor), and our largest customer base is the Amish,” said Porter, explaining that members of the religious sect use them for refrigerators and milk coolers. Those compressors are shipped to Amish communities in California, the Midwest and Pennsylvania, he said.
Blissfield’s sales volume of Dorin compressors is close to 1,000 units each year, representing sales of about $1 million. Pietro Carnaghi offers flexible manufacturing solutions, a full-turnkey option that includes all aspects of manufacturing, including part processing and programming, tooling and all work-holding systems.
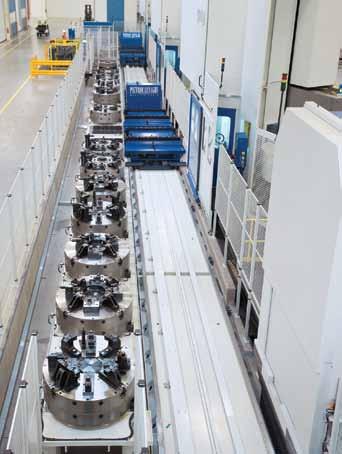
Dorin’s compressors, which range from 1/6 horsepower to keep the beer on ice on a pleasure boat to 60 horsepower for use in a supermarket or ice rink, have very low noise levels and low vibrations. They’re known to virtually eliminate system pipe breaks because of their optimized mass balance and low gas pulsation.
Established in 1918 as a manufacturer of machine tools, broaches and adjustments, air compressors and repairers of motor vehicle engines, Dorin began producing open type compressors for refrigeration systems in 1932. Soon, compressors became the company’s core business, and today the company manufacturers 50,000 piston compressor a year.
Between 1983 and 1998, Dorin expanded its offerings by adding to its range of compressors, to include: machines with 6 cylinders (30 to 50 Hp with displacement from 84 to 138 m3/h) and those with 8 cylinders (60 to 75 Hp with displacement from 184 to 200 m3/h). software coordinates overall operation, ensuring full line integration with the customer’s information system.
Machines for giants
It seems curious to learn that Pietro Carnaghi Machine Tools SpA (Cortese, Italy; www.pietrocarnaghi.com) produces 40 machines annually. But take a look at the size of the machines the Milan, Italy-based company makes: You’ll understand their output, and then wonder what giant ordered them.
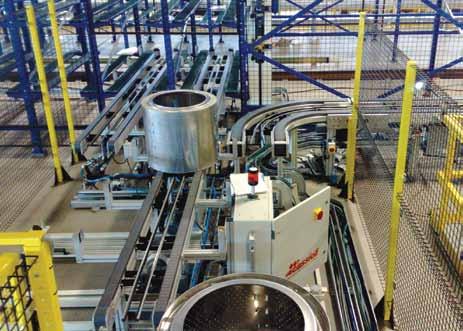
Fully automated lines
The material handling and industrial automation company Cassioli Group Srl (Siena, Italy; www.cassioli.com) started working working with Whirlpool in 2001, with installations at the home appliance maker’s plants in Cassinetta and Siena, both in Italy.
Eight years later, in 2009, the company established Cassioli USA (Southfield, MI; www.cassioli. com), a sales office with four employees in the United States, when it won a major contract with Whirlpool for work in America.
Cassioli, with 315 employees at six plants in three countries, and customers in more than 30 countries, was founded in 1943. Its annual turnover amounts to $49 million, with Cassioli USA accounting for $1.3 million of that amount.
In addition to home appliance manufacturers like Whirlpool, Cassioli also makes automated lines for the automotive, airport, pharmaceutical, food and beverage, wood and furniture, mechanical components, tire and textiles industries.
In an area of more than 35,000 square meters, the company produces automated warehouses, customized handling systems, laser and induction driven carts, assembly and serving lines, testing systems, picking systems and holding devices for anthropomorphic robots. It also offers customized handling systems.
The solutions offered range from a simple pick-and-place system to complex multi-axis systems designed as a single station or as a fully automated assembly line. The most sophisticated solutions include video systems with an elevated processing capacity that allow for greater intelligence in the workplace.
Cassioli offers shop layout design, process simulation, plant deployment and personnel training. The company’s specially designed Manufacturers in the energy/power generation, aeronautics/ aerospace and mining/earthmoving industries use the company’s vertical lathes, gantry milling machines and flexible manufacturing system cells worldwide. Its North American operations accounted for $10 million in sales in 2015.
“We have several machine cell systems which we designed and installed for Caterpillar in Winston-Salem, NC,” said Conor James Knox, North American sales manager. “These cells are a series of machines which communicate among themselves and completely process several axel transmission components with almost no human interference.” For years, Pietro Carnaghi has worked in close partnerships with CNC manufacturers, enhancing CNC machining through a deep study of the controls, with constant development and improvements. This partnership involves continual, integrated solutions to the construction of machine tools as well. The synergies between Pietro Carnaghi and its partners have proven to be mutually beneficial and have marked Pietro Carnaghi as a champion in the era of Industry 4.0. Cassioli Group makes automated lines for home appliance manufacturers like Whirlpool, shown here, but also configures automated lines for many other industries.