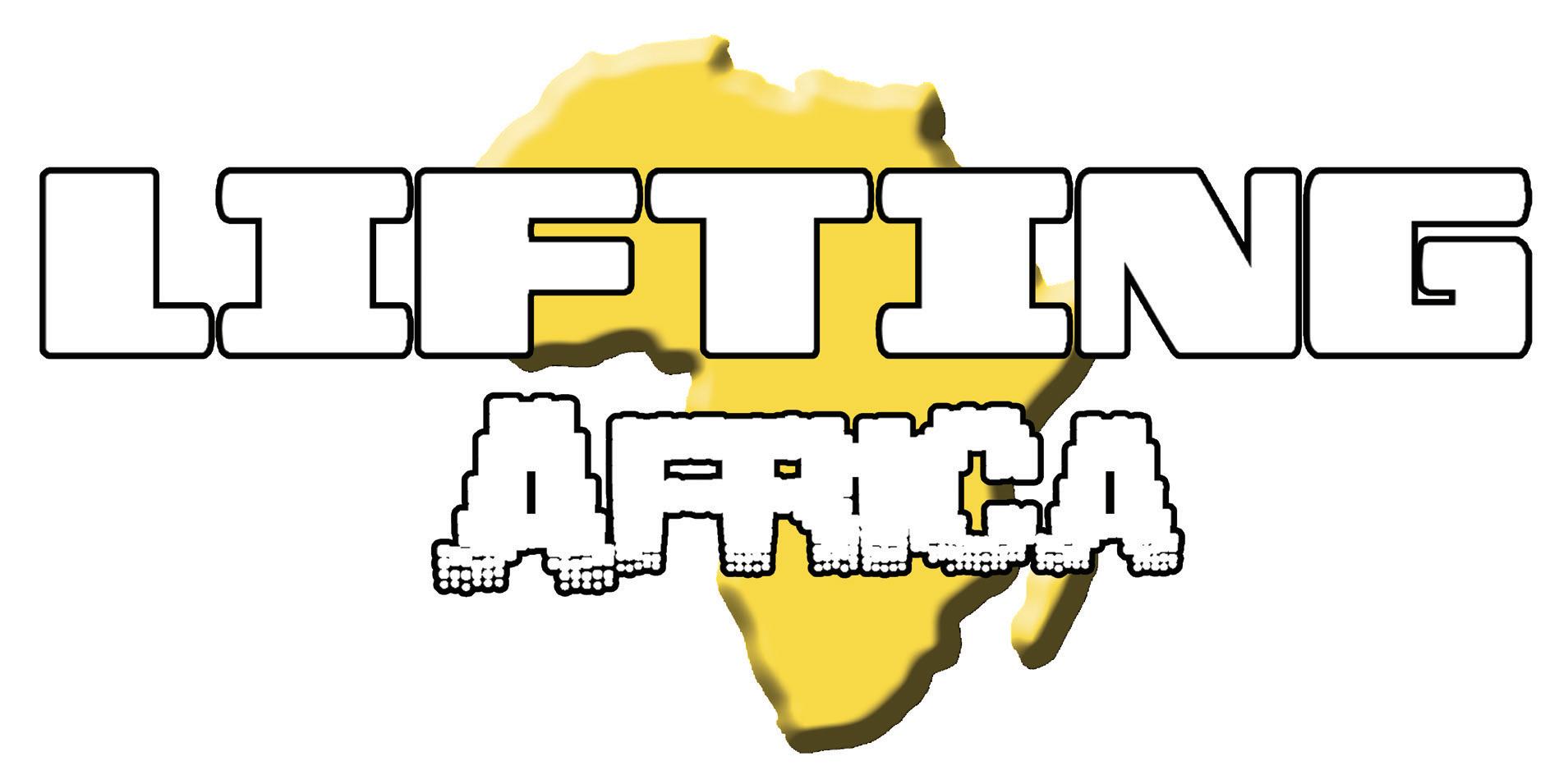
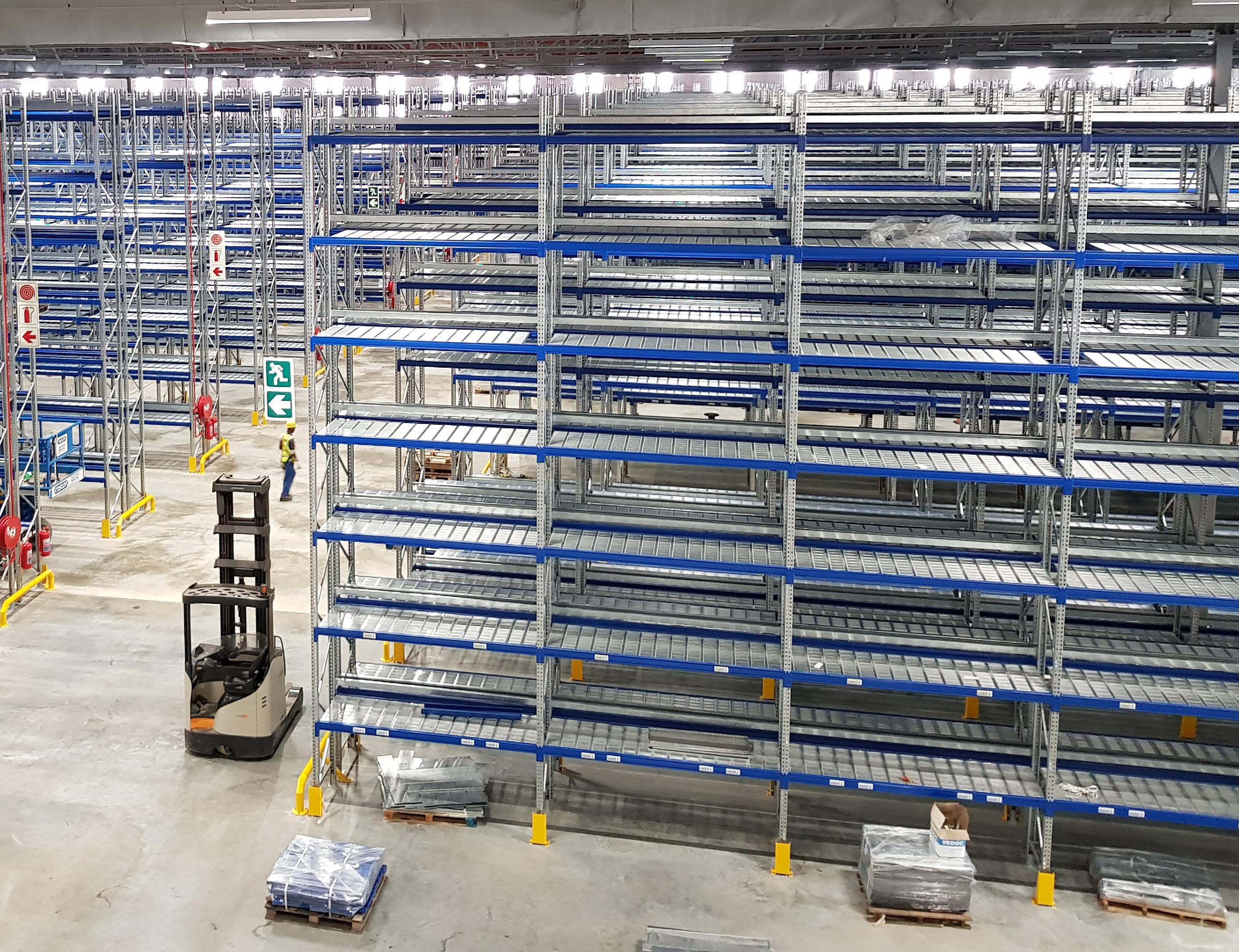
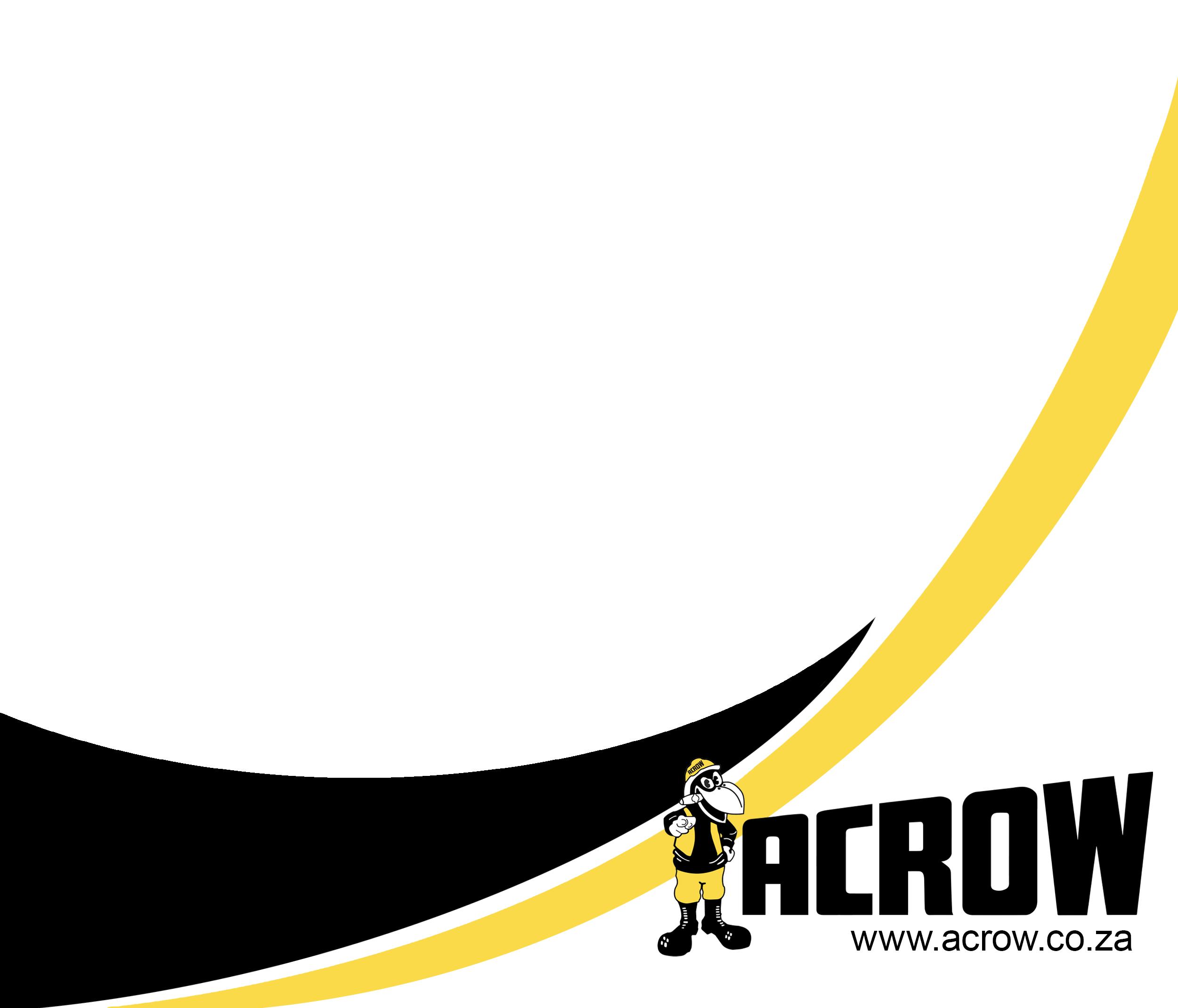


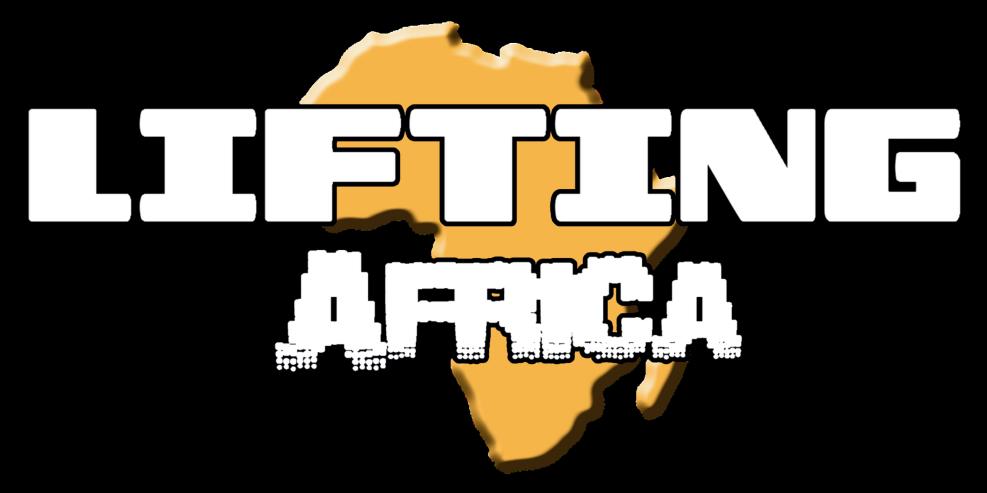
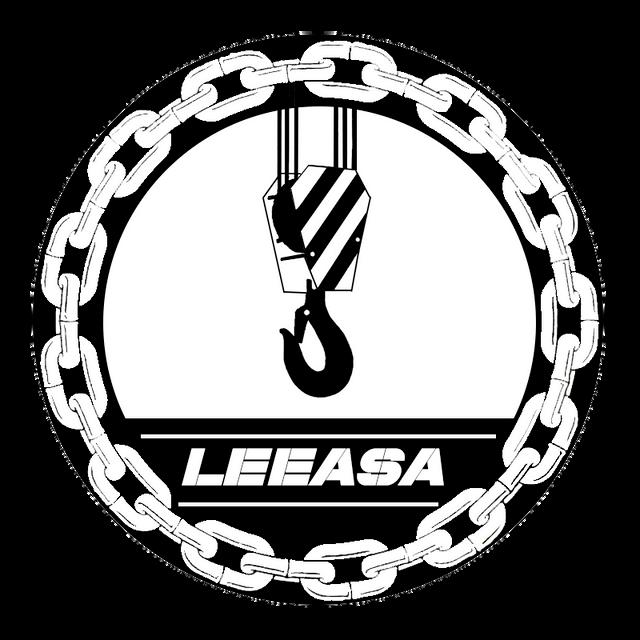

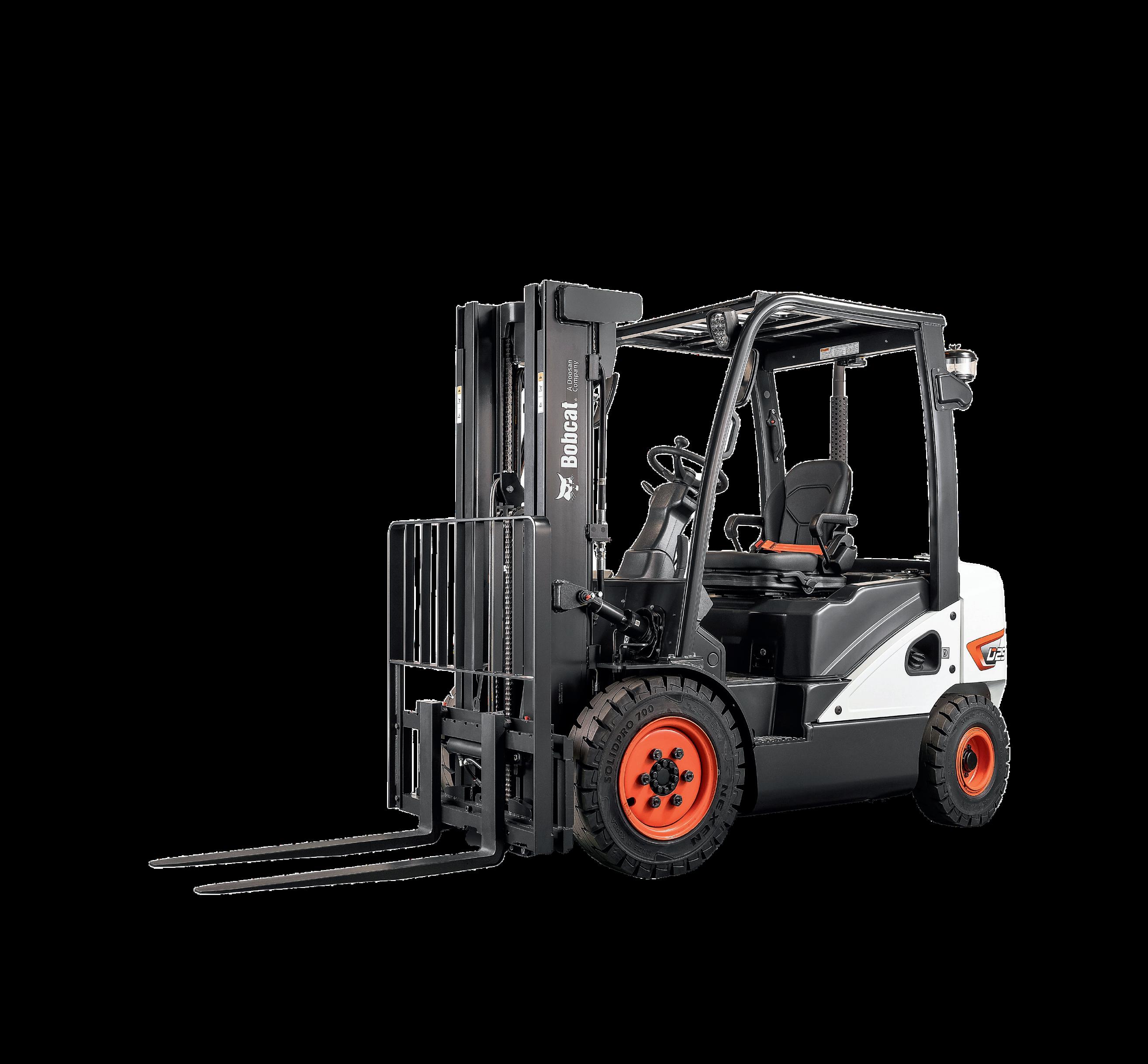
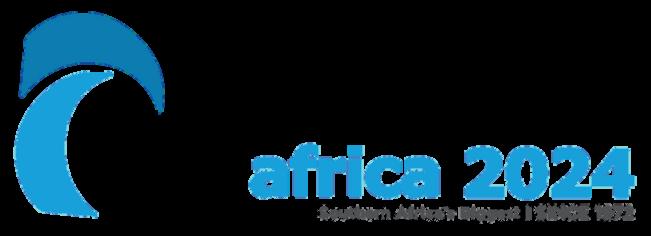
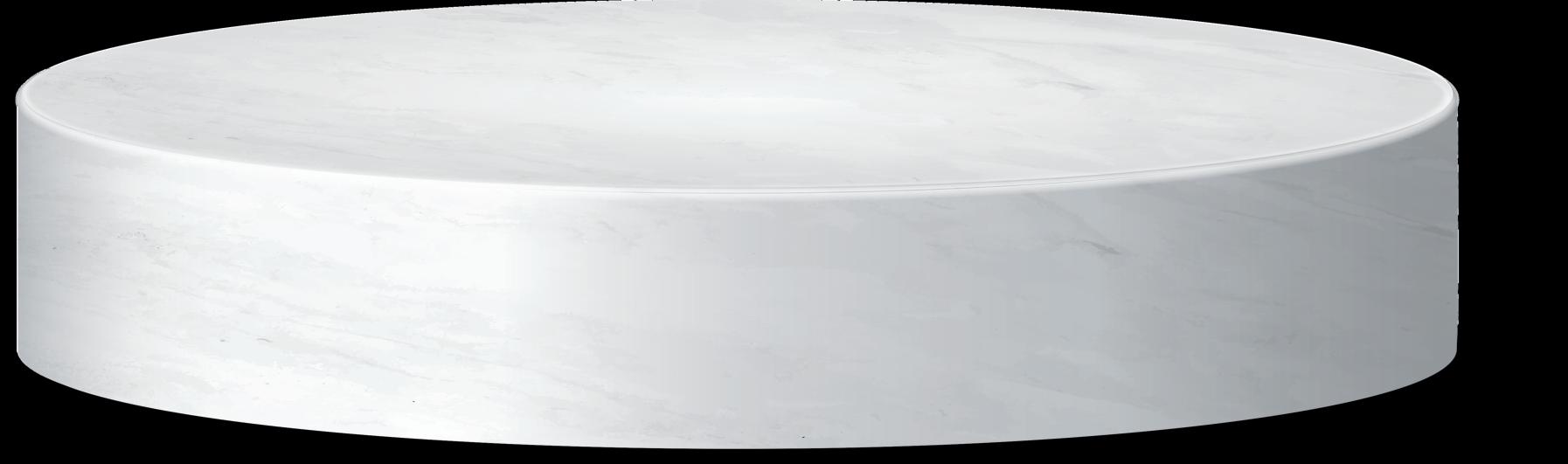


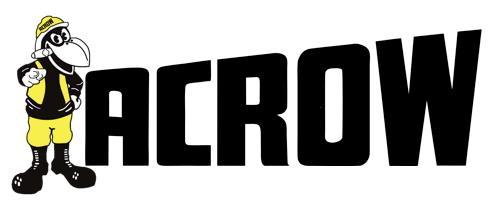



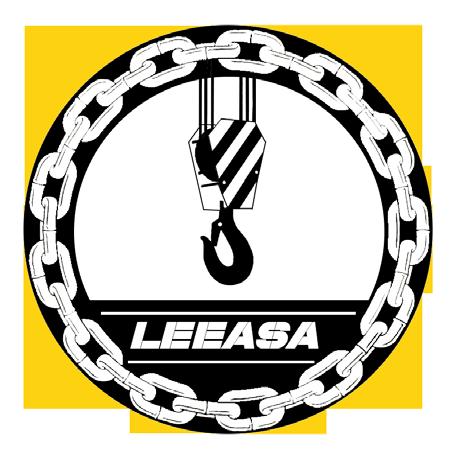

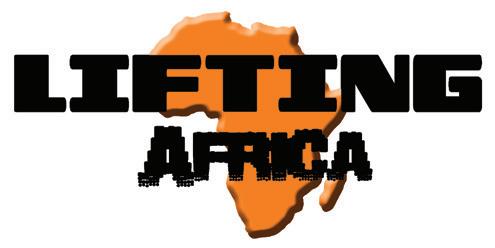
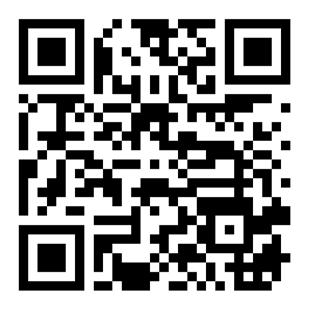
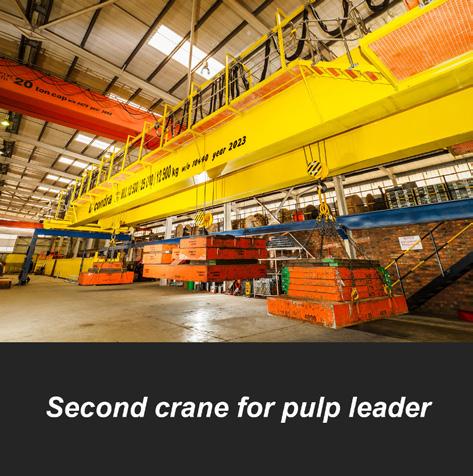
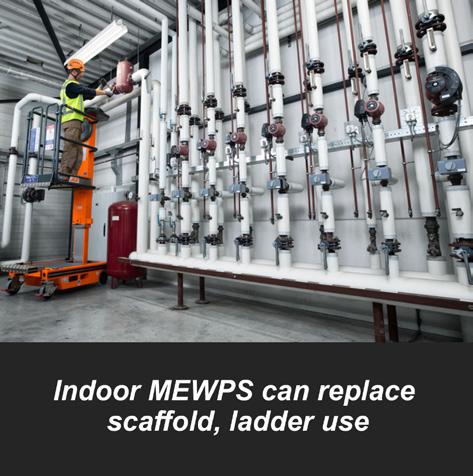

In the wake of the COVID-19 pandemic, businesses worldwide faced unprecedented challenges and disruptions. The economic landscape has been reshaped, and companies must now navigate a terrain marked by uncertainty and rapid change. Lifting Africa spoke to Sandra Moya, CEO of Acrow, on what it takes to remain competitive in this new operating environment.
Adaptability and resilience have become critical traits for companies striving to stand out. From rethinking traditional business models to embracing digital transformation, the ability to pivot and meet evolving consumer demands has never been more crucial. In this new reality, companies must respond to immediate challenges and anticipate future shifts in the market.
“Acrow is a name known worldwide and is one of South Africa’s largest storage and construction equipment manufacturers. Over the years, we have built a solid reputation and are renowned for our quality product range, which consistently meets customers’ needs,” says Moya. “The business environment, however, faced massive disruption over the past few years, and now more than ever, companies need to innovate and differentiate themselves.”
Moya and the team at Acrow also had personal challenges to overcome. She admits that the past three years have been challenging but highlights that the company has emerged more robust than ever following a strategic restructuring process. “Taking a company through such a process is not easy, but the benefits are immense. With this in mind, we set out to deliver a far more sustainable structure capable of taking Acrow into the future,” explains Moya. Part of this restructuring process involved moving away from Acrow’s traditional approach to doing business. “As a family-run business, it has always been very personal, but as we faced unprecedented and unexpected changes, the reality was that we needed to corporatise more and implement solutions that can stand the test of time.”
With Moya at the helm, much thought and effort went into designing the new structure. ‘It was important to me that we create longevity for Acrow. The company needs to be bigger than one person or family,’ she says. It was also an opportunity to recognise the committed and loyal individuals at Acrow, and Moya ensured they were brought on board. “Our people have always been the driving force behind the company’s success, consistently exceeding expectations. Through the restructuring process, we have increased the number of shareholders.”
These shareholders now manage Acrow along with a board of five directors, each overseeing their portfolio, and Moya serving as CEO. “Each person has stepped into the role where they are strongest. We have directors for SHEQ, operations, procurement, sales, and business development. The company now has a far more corporate look and feel, but we have retained the successful qualities of a family business. We have futureproofed this company and are well-positioned to drive growth from where we now are.”
This transformation is already being realised in practice, as new clients have been signed and enquiries are rising.
According to Moya, scaffolding and formwork have always been a part of the Acrow portfolio, but during the COVID-19 pandemic, this division closed its doors. “It was a difficult decision at the time, but considering the bigger picture, we opted to close this part of our business even though Acrow as a company was born with these products as an integral part of the range.”
Three years on – and with the world facing somewhat more normal circumstances – Moya has opted to re-
open the scaffolding and formwork division. “We have joined forces with Acrow Egypt and are very excited about the prospects for bringing back scaffolding and formwork to our product line.” She says the decision to collaborate with Acrow Egypt was not taken lightly. “It is a major company with some 18 branches and has all the necessary technical expertise and know-how that will allow us to grow this part of the business. It allows us to draw from their technical skills and undoubtedly delivers a competitive edge to what we can offer.
“With construction having been hard-hit during Covid, the sector has seen major recovery around the world, and demand for scaffolding has significantly increased,” says Moya, indicating this is a part of the business that she expects to see improvement on thanks to their ability to now offer a wide range of products and services to the building sector. Demand is also not just local but across Sub-Saharan Africa. “The construction industry is on an upward trend, and with a shortage of scaffolding in Africa, we are positioning ourselves to serve this market extensively.”
Moya remains optimistic about the future despite the changed – and often more challenging – business environment post-COVID. “We continue to see demand for our products. Delivering quality solutions to one’s clients remains critical, and with this in mind, we continue to invest not only in our equipment and infrastructure but also in our people. Skills development and training remain important at Acrow as we ensure we have the expertise and know-how to meet our clients’ needs.”
She says overcoming challenges is par for the course. “At Acrow, we continue to reinvent ourselves, diversifying our product range to ensure we can service as wide a range of customers as possible while introducing agility and flexibility to our operations to meet the challenges headon.”
As the third quarter commences there has been a lot of development and change in the LEEASA camp. May saw us finalise the LEEASA directorship after the members voted on new council members, this saw some new appointments and some old familiar faces. The new Board of Directors then voted on the Chair and Vice Chairperson positions as per the MOI requirements.
The incoming board of directors is as follow – Kyle Graham (Chairperson), Ashley Davis (Vice Chairperson), Surita Marx, Francois Weideman, Roger Day, Katiso Mogaki and Carlos Marques.
The new council will be announced at the AGM once the financial statements have been completed and signed off by LEEASA’s auditors.
With that we say goodbye to our former vice chairperson Andries Agenbag and Kevin Reckas. Both Andries and Kevin contributed immensely to the progress we have made thus far in the association, and we thank them for their contributions and time over the years. While it is sad to see them go it is not goodbye for good. Both Andries and Kevin are valuable members of the association and will continue to contribute when required going-forward. With that we say a big THANK YOU to Andries and Kevin. We look forward to working with both of you gentlemen in the future.
To our outgoing Chairperson, who has been appointed as our new Vice Chairperson, Ashley Davis – thank you for your contribution over the last 4 years. We have walked a long road together and the effort that you have put in over the years is seen. Just as reference, I can uniquely say that LEEASA would not be where we are today without Ashley at the helm. When Ashley took over as Chairperson there was no continuity in the association, the association lacked compliance in every aspect and there was no record keeping at all. It took Ashley many late nights over 3 years to get everything into a state whereby LEEASA is 100% up to date and in a state whereby we can undergo an audit at any time with previous records in place. We now have systems in place that ensure the continuity of the association for future generations. Thank you, Ashley, for your tireless work. I have big shoes to fill.
group of available VPM’s. As we progress with this, we shall relay information on how registered persons can get involved. For persons that received VPM training recently – please ensure that you have returned your appointment letter to ECSA. LEEASA shall follow up on appointment letters.
Over the past few months LEEASA has been pushing forward on a number of matters with ECSA and The DEL. We have managed to make great progress and forge ahead to growing a good relationship with ECSA, whereby open lines of communication have been established. ECSA faces some challenges, that LEEASA has agreed to assist with and ensure that ECSA can function effectively with regards to registered persons participation. There seems to be a shortage of available registered persons with Virtual Pannel Members (VPM) with VPM training at ECSA and this is delaying the registration process, as ECSA relies heavily on a small
With that being said I think it would be good to highlight some concerns in the industry. We asked ECSA for a detailed demographic in terms of registered persons in the Specified Category (SC) for LMI’s. To shed some light on the information received. We currently have 954 LMI’s registered at ECSA. Of that 307 LMI’s are in the age group 60 - +70 years old, this means that these registered persons are reaching retirement or have retired.
That leaves our industry with 647 LMI’s between the age groups of 20 – 59 years old. There are 241 LMI’s between the age group of 50-59 years old. This is quite alarming as there are over 616 registered LME’s. This means that there should be 1,05 LMI’s per registered LME’s. Which we know is not the case as many LME’s employ multiple LMI’s. This means there are registered LME’s trading without LMI’s. The DEL and LEEASA shall be on the lookout for this and will begin to investigate this as a matter of urgency.
This means in the next 10-15 years we will see these registered persons retiring. Leaving us with only 406 LM’s that are in the age groups of 20-49 years old. I was also surprised to see that we only have nine register female LMI’s. We would love to see this number grow.
At present ECSA are receiving approximately ten applications per submission period. We know that not all applicants are successful. This means we could be potentially registering 20 LMI’s per year. This will not be enough to ensure sustainability for future generations. Therefore, we find ourselves at a crossroad whereby we need to ensure the sustainability of the profession. To do this – I encourage all companies, big or small, to ensure that when undertaking work with LMI assistants to enable the assistant to learn from what they are doing and upskill these persons to becoming a registered LMI. This is the most sustainable way of doing things and will ensure that persons actively working in the industry are being upskilled and becoming registered persons in the future.
Many companies have assistants employed that are more than competent on the practical side of the inspections and testing, we need to ensure that we educate them on the theoretical side of the profession with the Regulations and Standards. This can be done in house at no expense. Once we do this, we will be able to actively grow the profession and ensure sustainability going-forward, while actively addressing transformation and giving previously disadvantaged individuals a
chance to grow and succeed. LEEASA, The DEL and ECSA shall work together to formulate plans to encourage individuals to get involved in the profession. Starting with trying to get the SAQA qualification content in place. This will take a while; we are in discussion with a few stakeholders to get this off the ground. As we progress on this, we shall relay information to our members.
LEEASA’s website is to undergo a complete overhaul and upgrade in the next few weeks/month. This will see the phasing in of backend login functionality for members that will be able to access a host of information including document libraries that will assist in their daily tasks and work. This functionality will be available for all LEEASA paid up members in the next few months. It is a mammoth task to undertake, please bear with us on the timelines. We will require assistance from all OEM’S, OEM agents or members with libraries of OEM technical specifications to assist us in populating this document library.
LEEASA is also currently working on “The LEEASA Inspection App” that is in the late stages of development currently. This App will be available to all LEEASA Members at a fee. This fee will be a reasonable fee and will enable the industry to standardize reporting in line with legislation and specifications and will in turn reduce paperwork and administration for companies and LMI’s. We are hoping to launch the App once all testing has been completed, at The LEEASA Electra Mining Conference, which will take place from 4-5 September 2024 at NASREC. The last event saw over 59 000 people attend and this year will be bigger.
All members and non-members are encouraged to join The LEEASA Electra Mining Conference, we will have a host of new topics to present, including one or two presentations from a LEEA representative and Yoke Industrial Corp international consultant that has taken the time to fly down to present in person at the conference. This will most certainly add value to our attendees. We encourage all to attend The Electra Mining Show and come to see what exhibitors have to offer.
LEEASA and Lifting Africa Magazine will be hosting our second Forklift Driver Competition at the Electra Mining Show on 2-6 September 2024. After the success of the event in 2022, the organisers have given us an even better position within the outdoor exhibition area, in remarkably close proximity to the main entrance and we hope to drive foot traffic to the competition area. This competition will open to all forklift operators that hold a valid license. The competition will see 1st place walk away with R 15 000.00, 2nd place with R 10 000.00 and 3rd place with R 5 000.00. We encourage all LME’s and LMI’s that have forklift operators or licenses to come and compete and try walk away with the BIG cheques. Please also encourage your clients to come enter as well, as it is a wonderful way to drive staff moral. You can email forkliftcompetition@liftingafrica.co.za for more information or to enter.
Lastly, I want to end off by saying thank you to all members that took the time to vote for the new LEEASA Board of Directors, the contribution is apricated very much. As the new Chairperson, with my team, shall strive to ensure the growth, continuity and the expand the value proposition for our members. We shall ensure we continue to fulfil our function and address all industry related issues to grow the industry and ensure compliance and safety to all stakeholders. We as LEEASA have an open-door policy. Please feel free to contact any of us at any times for assistance or to address any industry, DEL or ECSA related issues. Our contact information is available on our website under the “Meet the team” Tab or below this article.
Looking forward to the next 2 years at the helm. Let us walk the path together and grow our industry. Feel free to reach out to the board members if the need requires.
Chairman: Kyle Graham: kyle@leeasa.co.za
Vice Chair: Ashley Davis: ashley@leeasa.co.za
Ordinary Members: Surita Marx: surita@leeasa.co.za
Francois Weideman: francoisw@leeasa.co.za
Roger Day: roger@leeasa.co.za
Katiso Mogaki: katiso@leeasa.co.za
Carlos Marques: carlos@leeasa.co.za
Administration: Desiré Davis: admin@leeasa.co.za
Marketing and Design: Xane Roestroff: production@leeasa.co.za
Yours in SAFE LIFTING, Kyle Graham and the LEEASA team
Mr. Aaldrik Graham Kiewiet
Mr. Alan Victor Botha
Mr. Albert Anthony Freeme
Mr. Albert Olof Jansen Van Vuuren
Mr. Alfa Janes Grouws
Mr. Amogelang Gilbert Mmusi
Mr. Ananias Zhou
Mr. Andre Coetzee
Mr. Andre van der Merwe
Mr. Andrew John Ferguson
Mr. Andries Aucamp
Mr. Andries Gordon
Mr. Andries Josias Agenbag
Mr. Antoni Frederik Janse van Niewenhuizen
Mr. Armand du Plessis
Mr. Arnoul Spitsbaard
Mr. Arnoux de Bruin
Mr. Ashley Mark Davis
Mr. Barend Andreas Lubbe
Mr. Bartholomeus Jakobus Erasmus
Mr. Bless Msweli
Mr. Brian George Mezieres
Mr. Brian Leonard Meintjies
Mr. Carel Gustavus Potgieter
Mr. Carel Hendrik Ferreira
Mr. Carlos Macuacua
Mr. Challe Andre Bonhamme
Mr. Charl van Heerden Strauss
Mr. Charles Casgoigne
Mr. Chris Lotheringen
Mr. Christiaan Charles Supra
Mr. Christiaan Ernst Gerhard Schutte
Mr. Christiaan Hendrik Van Wyk
Mr. Christo Pieter Barnard
Mr. Christo Van Eyk
Mr. Christo van Huyssteen
Mr. Clifford Mubvuta
Mr. Coenraad Hendrik Heunis
Mr. Cyril Raymond Laredo
Mr. Damien Oscar Stephen
Mr. Daniel Ntatenyane Mangwegape
Mr. Darrin Ian Cass
Mr. David Dos Santos Cruz
Mr. David Henry Cooks
Mr. David-Lee Alan Dewelzim
Mr. Dean Edwin White
Mr. Dean Eppel
Mr. Deon Bonthuyzen
Mr. Desmond Errol Lloyd
Mr. Dewald Schutte
Mr. Diederik Arnoldus Dahms
Mr. Dirk Johannes Christoffel Geldenhuys
Mr. Divan van Zyl
Mr. Drean Johannes Kotze
Mr. Edius Topera Mashamba
Mr. Edward Kruger
Mr. Edward Nachiwe
Mr. Emile de Koning
Mr. Enock Mugwede
Mr. Ernest Khanyile
Mr. Ettiene Pollard
Mr. Eugene Terence Redelinghuys
Mr. Evans Farai Chabata
Mr. Ferdinand Pieterse
Mr. Francois Dewald Blignaut
Mr. Francois Frederikus Le Grange
Mr. Francois Weideman
Mr. Frank Warrick Saayman
Mr. Frederek Gerhardus Opperman
Mr. Frederik Wilhelm Stonehouse
Mr. Freedom Nsele
Mr. Funganayi Makhuza
Mr. Gavin Rayson
Mr. George Cornelius Krafft
Mr. George Khehla Kuhlase
Mr. Gerhardus Jacobus Oosthuizen
Mr. Gert Vos
Mr. Given Nyathi
Mr. Glenton William Rebello
Mr. Happy Tafara Tati
Mr. Harris Naidoo
Mr. Hendrick Rapule Mahuma
Mr. Hendrik de Jong
Mr. Hendrik de Kock
Mr. Henry Oswald Kerr
Mr. Hermanus Barend Dahms
Mr. Ian O’Hara
Mr. Ibrahimo Brento Hassane
Mr. Imraan Moolla
Mr. Irvin Charles Murrish
Mr. Jeen-Pierre Groenewald
Mr. Jetro Mzwandile Ngwenya
Mr. Joannes Lugt
Mr. Joao Carlos de Freitas Marques
Mr. Johan Frederick Herselman
Mr. Johan Smith
Mr. Johann du Plessis
Mr. Johannes (Jaco) van Biljon
Mr. Johannes Gideon Kruger
Mr. Johannes Hendrik Snyder
Mr. Johannes Jurgens Marais
Mr. Johannes Mnyameni
Mr. Johannes Roos
Mr. John Carsten Allers
Mr. Joseph Johannes van Huyssteen
Mr. Joseph Mabaso
Mr. Justin Henry Brown
Mr. Karel Johannes Francois Du Toit
Mr. Kebareng Daniel Molausi
Mr. Keith van Vreden
Mr. Kesekang Segole
Mr. Kevin Clive Reckas
Mr. Kevin Keith Godfrey
Mr. Khathutshelo John Phalandwa
Mr. Kobus Van Tonder
Mr. Kyle Graham
Mr. Kyle Streak
Mr. Lake Johane Ndhlela
Mr. Leon Johan Snyders
Mr. Lesiba Willie Sebothoma
Mr. Linton Moodley
Mr. Lodewickus Robert van de Venter
Mr. Lukas Petrus Beukes
Mr. Makalele Selwyn Makofane
Mr. Malcolm Ivan Claase
Mr. Malose Kenneth Mabela
Mr. Marius Marais
Mr. Marius van der Merwe
Mr. Mark James Totman
Mr. Mark Leonard Munnery
Mr. Mark Leslie O’Connor
Mr. Mark Warren Minott
Mr. Marthinus Swart
Mr. Matthys Daniel Taljaard
Mr. Matthys Michiel Brink
Mr. Mboshoa Simon Skosana
Mr. Michael Fernandes De Souza
Mr. Michael Henry Hassett
Mr. Michael John Hendry
Mr. Michael Lionel Roberts
Mr. Michael Richard Slabbert
Mr. Michael Varty
Mr. Milton Mhlanga
Mr. Mogakolodi Gregory Thamage
Mr. Norman David Graham
Mr. Octovias Lebakang Mabelane
Mr. Pastor Noosi
Mr. Paul Pillay
Mr. Paulo Jorge de Freitas Marques
Mr. Peter Abraham du Toit
Mr. Petr Kluson
Mr. Petrus Abraham Bester
Mr. Phata Simon Mailula
Mr. Philippus Stefanus Kruger
Mr. Phillip Demetrius Kemp
Mr. Pieter Albert Schoeman
Mr. Isidro Ernesto Fernando
Mr. Israel Mooketsi
Mr. Jacobus Rudolph Kruger
Mr. Jacques Jonker
Mr. Jaen Pienaar
Mr. James Nicholas Hamilton Wells
Mr. Jan Frederick van Niekerk
Mr. Jan Louis Venter
Mr. Janus Jacobus Van Biljon
Mr. Jason Brett Mulder
Mr. Mohamed Hoosen Dawood
Mr. Moses Karukwayo
Mr. Mzinhle Leonard Sibenya
Mr. Napo Michael Noosi
Mr. Nathaniel Happy Sambo
Mr. Neil Naude
Mr. Nelson Chaita Moyane
Mr. Nicolaas Benjamin Smit
Mr. Nicolaas Theunissen Wynant
Mr. Nkosinathi Richard Mavimbela
Mr. Nkosini Owen Ngcobo
Mr. Noel Nyamukoho
Mr. Ralph Errol Shamrock
Mr. Raphael Letsema Shobane
Mr. Reino Schutte
Mr. Robert Du Toit
Mr. Robert Wayne Milne
Mr. Rodney Bassingthwaighte
Mr. Roger Ian Day
Mr. Roland Henry Murray
Mr. Ronald John Laing
Mr. Royden Stewart Turner
Mr. Rudzani Collins Masiagwala
Mr. Russel Henning Boshoff
Mr. Rutendo Job Sadomba
Mr. Sarel Petrus Jacobus Dreyer
Mr. Seth Laredo
Mr. Shadrack Mikel Dlamini
Mr. Shimane Martin Diutlwileng
Mr. Siegfried Schrader
Mr. Sifiso Ngwenya
Mr. Sizwesihle Blessing Ntombela
Mr. Stefan Ivanov Babatchev
Mr. Stephen Andrew McGregor
Mr. Steven Duvenage
Mr. Stuart Mark Love
Mr. Stuart Swart
Mr. Thokazani Bright Mkhize
Mr. Thulani Ndlovu
Mr. Timothy Tatenda Zindi
Mr. Trevor Sefoka
Mr. Tshisamphiri Moses Mukoma
Mr. Victor Manuel Batista Ferreira
Mr. Victor Sithole
Mr. Victor Thedor Sargent
Mr. Vishay Ramkaran
Mr. Warren Naude
Mr. Wayne Garnett Shaw
Mr. Weddington Chimbane Moyo
Mr. Werner De Bruyn
Mr. Werner Hermann Schroer
Mr. Werner Snyman
Mr. Wesley Horak
Mr. Willem Abram (Bossie) Prinsloo
Mr. Willem Petrus van den Heever
Mr. William Charles Palvie
Mr. William Henry Pepler
Mr. William Peter Park
Mr. Wynand Byleveldt
Mr. Yogandren (Donny) Soobramoney
Mr. Zaheer Shameer Khan
Mr. Zenzele Siphamandla Ntshakala
Mrs. Ruwaida Mahomed
Mrs. Sandile Wyeth Mzimela
Mrs. Surita Marx
Ms. Lynda Lake
“These records are up to date at the time of going to print”
Casper, Phillips & Associates Inc. (CP&A) has delivered a presentation to port authorities titled, ‘Peer Review of Container Cranes’, to assist in future procurement processes.
CP&A offers a wide variety of services, including specification, design, manufacturing review, modification, and accident investigation; and it is well positioned to remind terminal operators and fellow stakeholders of the risks involved with container crane procurement. Including transport and offloading in the peer review scope is a good way to manage some of these risks — but that’s just the start.
Richard Phillips, mechanical engineer at CP&A, said: “The procurement process for container cranes is somewhat unique and presents many challenges. Unfortunately, some procurement decision makers believe buying container cranes is the same as acquiring any other piece of equipment, such as a forklift or a company van.” As should be unanimously accepted by crane manufacturers, a peer is someone with approximately equal qualifications to the design team. While there is no universal set of criteria as to what makes an engineer a peer, a good starting point is professional licensure
and relevant design experience in the appropriate disciplines. The team should have an expert in the prevailing hazards such as high wind, seismic, or other location dependent hazards.
A peer review is when a neutral third party checks the design for compliance with the performance specification. A performance specification states what the crane needs to do — rated load, hoist and travel speeds, operating wind speed, etc. — but it does not specify how the crane manufacturer needs to meet the specification.
Importantly, a design review is about compliance; it is not about the design reviewer’s preference for how he or she would have designed the crane. There is a level of professionalism expected for design reviews.
While there will always be debate, comments that are not backed up by analysis, specification, or code requirements should be avoided. Phillips said: “It’s a big red flag if a large number of comments are generated without supporting calculations or citations
of specification requirements. It’s not constructive for the designer to have to refute a large volume of comments that may not be contractually required or may be speculation since they are not supported by calculations. The reviewer should be performing enough analysis to back up their comments.”
Container cranes are custom designed to meet the unique requirements of each port. Some of these requirements may include being in a hurricane or earthquake zone; exposure to extreme temperatures; or proximity to other geological hazards. Sometimes a container terminal is located near an airport, or a crane may need to pass under a bridge during delivery, resulting in height restrictions.
A naval architect provides the sea states and predicted voyage motions for the designers to analyze and brace the crane accordingly. The crane manufacturer owns the cranes until handover. Some crane manufacturers own their own fleet; others subcontract this work. It
can be beneficial for the design reviewer to check the voyage bracing prior to shipping.
There are other operational considerations, such as where hatch covers are stored; the use of dual trollies; and how many containers the crane can lift: single 40 ft., twin 20 ft., tandem 40 ft., quad 20 ft., etc. All things considered the planning phase has great variance. Sometimes it starts at the wharf design stage, other times the wharf is already designed, and existing cranes are being replaced. Depending on the level of customization, once a crane is awarded, it can be up to three years before delivery.
Phillips, who himself conducts peer reviews of contractors’ crane designs, including some of the largest container cranes in the world, pointed to CP&A’s crane base anti-seismic isolation system (BASIS), which is built on nonlinear time history analysis (NLTHA) and can protect a crane’s main structure from damage even in contingency level earthquakes.
“We are always improving our software,” said Phillips. “Our crane analysis software can be thought of as a custom workbench specifically made for cranes. There is a much larger market for buildings and bridge design, so the commercial software packages tend to focus on larger markets such as those [see below]. That led CP&A to create our own crane code checking software. One example is that we have incorporated wind tunnel test data into our pre-processor, which develops the wind load forces on
a crane. Obviously, a commercial building will not have integrated wind tunnel data for container cranes.”
Cranes are significant structures
Interestingly, due to the geological and environmental hazards, cranes should be treated more like bridges and skyscrapers instead of mass produced cars and airplanes. However, for cars and airplanes, there are crash tests and full-scale testing, which is impractical with cranes.
ASCE 7-16 1.3.1.3.4 covers minimum design loads and associated criteria for buildings and other structures; this particular clause covers peer reviews for significant structures.
Phillips added: “When you start thinking about how bridges, stadiums, and skyscrapers are designed it starts to become clear. For significant structures the [AISC 7] code requires a peer review. Are cranes significant structures? In our opinion they are; however, it is up to the local jurisdiction to make that decision.” Even at the time of going to press, CP&A was wrapping up peer review and procurement assistant projects related to rubbertired gantry, rail-mounted gantry, and ship-to-shore cranes. Are your procurement processes for these hulking container cranes up to standard?
Casper, Phillips & Associates Inc, richard@casperphillips.com, www.casperphillips.com
Condra is to manufacture a second maintenance crane for Sappi’s Saiccor Mill. Ordered for turbine maintenance duty, the 25-tonner will join a 12,5/25/12,5 ton overhead travelling crane manufactured by Condra last year for one of the mill’s dryer lines
Both cranes are part of Sappi’s 7,7-billion rand expansion and upgrade programme to position Saiccor among the world’s leaders in dissolving pulp production. Dissolving pulp is a key input in the textile industry, in pharmaceuticals and in food processing.
The latest crane will be similar to its predecessor. Both feature identical double girder, 25-metre span frames, and differ only in the number of hoists: one on the new crane and three on the first.
Load lifts on both cranes are failsafe, with secondary emergency
brakes on the hoists’ rope drums backing up standard brakes on the electric motors.
As before, Condra will use corrosion-resistant materials to manufacture specific components, and apply a high-spec coating to girders, end-carriages and the hoist itself. This will protect the crane for operation in a highly corrosive environment. Handrails will be of stainless steel, with platforms and walkways made from fiberglass grating instead of ordinary steel tread plate.
On the electrical side, Condra will
fit armoured power cables and insulate all stainless steel motor and electrical panels to IP65 standard. Commenting on the order, a Condra spokesman said that the design of both cranes will facilitate simple maintenance by authorised agent Natal Cranes.
“Our South Coast partner has spare parts holdings more than sufficient to ensure fastest possible repair and maximum machine uptime. Overall lifetime cost will be the lowest possible,” the spokesman said.
“We have a third crane – a singlegirder machine – that has been working at Saiccor Mill for forty years, so Natal Cranes already has a good working relationship with the staff at Saiccor, and long experience of the operating environment there. We are ready to ensure maximum machine uptime for the new double-girder installations,” the spokesman concluded. Saiccor Mill’s second Condra crane is scheduled for delivery later this year to coincide with a planned shutdown for plant maintenance.
Condra (Pty) Ltd, +27 (0) 11 776 6000, sales@condra.co.za, www.condra.co.za
The two new Liebherr BOS 2600 cranes have been acquired by an integrated energy company located in Canada. The Board Offshore Cranes are destined for an FPSO unit operating off the coast of Newfoundland. The BOS crane series is one of the latest series of Liebherr offshore cranes.
Known for its reliability and versatile deployment possibilities, it is the perfect choice for the FPSO unit in harsh environments.
Rostock (Germany), June 2024 –Out with the old, in with the new. The Compact Board Offshore cranes with their distinctive A-frame design have reached the end of their useful life after almost two decades in continuous operation.
The cranes were commissioned in 2006. Since then, the two cranes from the CBO series have been providing service and are now replaced.
Liebherr was able to offer a convincing solution with the BOS series 2600 models. With a possible maximum reach of up to 60 metres and a lifting capacity of up to 100 tonnes, the BOS 2600 is suitable for dynamic lifting when servicing platforms, jack-up platforms or drilling rigs, for example, as well as for work on board. The BOS series is characterized by a modular design with standardised components for
maximum reliability. These include the overload protection system (MOPS & AOPS) and Liebherr Litronic, the crane management system for highly efficient operation.
“We always strive to meet our customer’s needs. We have been able in developing a customized solution that focuses on ease of maintenance without compromising on other aspects,” expresses Stefan Schneider, Global Application Manager General Purpose Offshore Cranes at Liebherr in Rostock. Robust cranes for harsh offshore environments
The BOS 2600 series features many technical improvements. The crane has maximum stability and reliability thanks to the unique design.
The slewing platform, which is the core element of the crane, contains the A-frame, the machine housing, the cabin, and the luffing winch. The machine housing is composed of durable steel parts and holds the
components that are easy to access, such as the drive unit, the oil tank, and the control cabinets.
The focus of the completed project was on maximizing ease of maintenance. The northern Atlantic Ocean off the coast of Newfoundland is characterized by rough weather conditions, which can make maintenance work a challenge for the crew.
High winds, corrosive seawater, and extreme temperatures make regular maintenance essential to prevent equipment failure, maximise efficiency, and ensure the safety of personnel.
Customised solutions enable greater ease of maintenance
In collaboration with the customer, additional technical innovations have been designed and implemented to make the cranes even easier to maintain in the future. If the main winch in the boom needs to be repaired or replaced, this is usually only possible by laboriously dismantling
it into its individual parts. A drop hatch specially designed for the cranes makes this process much easier.
The main winch is lowered to the deck level using a hatch and a new winch can be easily installed. This eliminates the need for timeconsuming disassembly of the winch into its individual parts. Walk-in facilities have been created that will simplify processes during operation.
A platform has been installed in front of the cabin to make it easier to change the windscreen wipers. In addition, access is made possible by a staircase instead of ladders, which increases both the comfort and safety of the crane operator.
The successful completion of the project once again proved one of Liebherr’s core values – that Liebherr is a reliable partner. Erwin OBrien, Product Support Manager from Liebherr Canada, is satisfied: “The cooperation between Liebherr Canada and our colleagues in Germany to close the deal reflects the excellent collaboration. We can
use our international presence to provide our customer with excellent solutions. Seamless communication, strong relationships within the Liebherr network, coupled with excellent customer service, are the key to providing the customer
with an unforgettable customer experience.”
Liebherr Africa, +27 (0) 11 365 2000, info.laf@liebherr.com, www.liebherr.com
Mechanical lifting in the oil and gas industry is a high-stakes venture, whether it’s about mechanical lifting or any other operations. The risks are inherent and demand our utmost attention.
While the risks of mechanical lifting in the oil and gas industry can’t be completely eradicated, they can be effectively managed and controlled. This is a crucial aspect that we must all be aware of. The perception that mechanical lifting in the oil and gas industry primarily involves large-scale, heavy-lifting tasks is partly accurate but somewhat superficial. While these operations are indeed complex and hazardous, they receive considerable attention, which helps mitigate and control the associated risks.
It is essential to be aware that the mechanical lifting discipline encompasses not only large-scale, heavy-lifting operations but also routine and simple daily crane, rigging and mechanical handling tasks. Despite their perceived lower criticality, even being equally dangerous, routine and simple tasks often lack visibility and recognition compared to their larger counterparts. As a result, these routine and simple operations are now the leading source of incidents and accidents in the oil and gas industry, and sometimes, they have
severe consequences, including injuries, equipment damage, and environmental pollution.
Analysis of the last industry incident/accident reports reveals that human factors, rather than equipment failure or inadequate load planning, are the primary causes of accidents during noncritical tasks.
Additionally, improper preparation for lift execution and equipment failure plays a significant role.
The main objective of mechanical lifting discipline is how to prepare, organise, and execute non-critical routines and simple operations in a balanced, safe, and efficient manner.
To address this objective, a harmonised Lifting Management System has been developed, focusing on four primary areas: procedures, equipment integrity, personnel competence, and site organisation.
Note: This system draws inspiration from the Swiss Cheese model, ensuring all mechanical lifting
operations are executed safely and efficiently.
Swiss Cheese Model (Lifting Management System)
Latent Conditions:
Procedures: Simple, harmonised, and comprehensible procedures tailored to different organisational levels are essential.
These procedures must cover all aspects of mechanical lifting, recognising that onshore and offshore environments require different approaches.
Site Organization: Proper site organisation is crucial, including storing portable lifting equipment, adequate cargo laydown areas, effective communication means, and necessary infrastructure.
Equipment Integrity: Equipment must be fit for purpose and suitable for the specific environment. This includes adequate equipment availability, strict adherence to inspection and maintenance protocols, and ensuring equipment integrity through robust evaluation systems.
Active Failures:
Personnel Competence: Personnel involved in mechanical lifting must be competent and capable of performing their roles in the defined environment. This Lifting Management System model involves strict evaluation and verification of competencies, especially when transitioning between onshore and offshore environments.
Limited Windows of Opportunity: Luck Factor: Luck can influence outcomes, but it should never be relied upon. Ensuring comprehensive risk assessments and preparations can minimise the reliance on luck.
“Mechanical Lifting Operations Everywhere”
*One Side of the Coin*
The oil and gas industry operates in diverse environments, each imposing unique requirements for safe and efficient execution. For example, offshore lifting operations involve dynamic environments with harsh conditions, requiring meticulous preparation and consideration of various additional factors compared to onshore operations.
Note: The offshore environment is harsh and harmful for personnel and equipment.
Example of additional preparation for offshore mechanical lift
Vessel and Environmental Factors: Considerations include vessel size, class, Dynamic Positioning (DP) capabilities, pitching and rolling dynamics, and sea state.
Compliance and Condition of Equipment: Offshore conditions necessitate heavy-duty designs, appropriate material grades, and rigorous equipment integrity evaluation.
Personnel Competence: Operators, slingers, riggers, and supervisors must possess competencies relevant to offshore environments. A robust evaluation and verification system for personnel competence is essential.
This why the relevant and sufficient level of personnel directly involved in mechanical lifting is crucial, and we are implementing robust training, evaluation, and certification systems in an offshore environment to ensure personnel are adequately prepared for modern mechanical lifting operations. This involves not only completing initial training but also gaining practical experience and maintaining a positive attitude. Competence in offshore mechanical lifting operations requires balancing knowledge, experience, attitude, and skills. This holistic approach ensures personnel will be well-prepared for the unique challenges of modern mechanical lifting operations in an offshore environment.
Four Main Pillars of Competence: Knowledge: Accumulated information and understanding gained through education and experience.
Experience: Practical knowledge and familiarity with various situations.
Attitude: An individual’s approach
and mindset towards their role.
Skills: Talents and abilities derived from training and practice.
*The Other Side of the Coin*
In response to industry changes, the emphasis on digitalisation, multitasking, and simplified competence development processes has led to misconceptions about the ease of securing offshore jobs.
Achieving competence requires a prolonged development process, and adherence to stringent quality and compliance standards is crucial for safety and efficiency.
Certification and Compliance:
Ensuring lifting equipment meets internationally recognised standards and addressing discrepancies between different regional standards.
Industry Engagement: Direct engagement with industry suppliers and manufacturers to ensure strict quality control and adherence to rigorous standards.
Mechanical lifting in the oil and gas industry is inherently dangerous but manageable through effective risk mitigation, comprehensive competence assessment, and adherence to stringent standards.
By addressing human factors, ensuring proper preparation, and maintaining robust competence and compliance systems, the industry can achieve safe and efficient mechanical lifting operations across various environments.
It requires careful management and prioritising safety through comprehensive risk assessments, strict adherence to procedures, and robust competence and compliance standards.
Efficient collaboration between human oversight and equipment is also essential.
By dispelling misconceptions, fostering industry engagement, and ensuring compliance with quality standards, we can mitigate risks and ensure the safety and efficiency of mechanical lifting operations.
Victor SARGENT , vicsargent@gmail.com
Vanguard was proud to be announced as the winner of the Rigging Job of the Year award ($150,000 - $750,000 category) at this years Specialized Carriers and Rigging Association (SC&RA) annual conference.
The shortlisted companies presented their entries to the judging panel on Thursday 18th April. The winners were then announced at the recognition dinner on the evening of Friday 19th April, with the gala event attended by more than 800 representatives of some of the most prominent heavy lift and rigging companies within America and across the world.
“These awards attract the very best in our industry and to be recognised as performing the world’s most complex rigging job, within the last 12 months, is testament to Vanguard and the company we are today.” commented Bryan Hodgkinson, Director at Vanguard.
“The extensive planning and engineering work that was involved in the project is evident in the precision of the execution. It was a true team effort that required approximately 1,600 man-hours and was meticulously performed
with zero lost time incidents. It was a privilege to present our entry on behalf of the whole team and to demonstrate the capabilities within our business to the judging panel.”
The winning project involved a complex lifting operation to upright a bark rigged sailing vessel, named the Europa, at the Victoria and Alfred Waterfront Dock Yard in Cape Town. The vessel, which had been undergoing maintenance, slipped from the keel supports and rolled onto its starboard side. Vanguard was subcontracted by Resolve Marine to engineer and perform an up-righting operation to realign the vessel with the center line of the track system.
The vessel, which weighed 650ton and measured 44.5m in length and 7.45m in width was lying at approximately 38° to starboard, it had shifted approximately 1.2m off center of the keel dollies. Vanguard engineered a solution utilising four 186ton hydraulic strand jacks and
four independent hydraulic gantry systems (8 hydraulic legs). Four heavy duty header beams were used to support the stand jacks and were installed between the gantries and positioned over the vessel and between the masts so as to minimise any further impact to the masts and rigging.
The strand jack system, which was rigged to keel brackets that had been custom fabricated for the operation, provided a high degree of accuracy and enabled the Vanguard team to lift and upright the vessel in a controlled and precise manner, using a series of controlled lifts and movements. Once the vertical lift had been completed, Vanguard successfully completed a transverse skidding operation to realign the 650ton vessel with the track system.
Vanguard, +27 (0) 11 616 1800, info@vanguard.co.za, vanguardheavylift.com
Cranes (Pty) Ltd has been appointed as the official authorised dealer for Hoeflon
This partnership marks a significant milestone for us, as we bring to our customers this cutting-edge technology and innovation from Hoeflon, a renowned designer, manufacturer, and supplier of compact cranes, Based in Barneveld, the Netherlands.
Hoeflon Compact Cranes, also known as mini cranes, spider cranes, or compact crawlers, are revolutionising the way heavy lifting is done in confined or hard-to-access spaces.
These compact cranes are ideal for tasks such as placing glass with precision or accurately positioning steel beams and pipes. What sets Hoeflon Cranes apart is their exceptional lifting capacity, being the only compact crane capable of lifting more than its own weight. The possibilities with Hoeflon Compact Cranes are truly endless!
Trusted by professionals worldwide, the Hoeflon series perfectly complements our existing range of used and refurbished mobile cranes. This collaboration allows us to offer our customers in South Africa/Africa access to top-of-the-line compact crane solutions that cater to a diverse range of industry and lifting requirements.
At Fastlift Cranes, we take pride in being a leading supplier of quality used cranes in South Africa/Africa. This new partnership with Hoeflon further solidifies our commitment to providing our customers with the best-in-class lifting equipment and solutions.
We are excited about the opportunities that this partnership brings and look forward to serving our customers with the exceptional performance and reliability of Hoeflon Compact Cranes. Join us as we continue to elevate the standards in the crane industry in South Africa/Africa and beyond.
For more information about our range of Hoeflon Compact Cranes and how they can benefit your operations, contact us at Fastlift Cranes. Experience the power and versatility of compact lifting with Hoeflon!
Assuring you of our best service and attention at all times.
Demand for MEWPs (mobile elevating work platforms) is hitting a new market inflection point as this type of access equipment becomes more widely adopted in applications that traditionally have used ladders or scaffolding.
Indoor construction and maintenance tasks often need to be done in areas that are difficult to navigate with larger, heavier aerial equipment lifts, including traditional slab scissor lifts.
Indoor MEWPs aren’t one-sizefits-all. There are many styles and options from which to choose based on the size of the product and environmental sensitivities. For example, compact scissor lifts, low-level access lifts and vertical scissor lifts are all examples of
indoor MEWPs. And, humanpowered lifts are lighter in weight and quieter than their batterypowered counterparts. While still small, battery-powered units tend to have a slightly larger footprint, are heavier and have a higher platform capacity, allowing renters to bring more tools and materials with them to the work area, reducing the number of times they need to ascend/descend during the workday.
The variety in these types of lifts
means that equipment distributors, like rental centers, need to help their customers to choose the right model based on the job.
Here are some insights into how indoor MEWPs can be matched to meet specific job site needs.
requirements
Indoor MEWPs are being utilized more frequently so contractors can meet core job site requirements, such as:
• Smaller footprint to fit smaller spaces
• Lighter weight for use on different types of sensitive surfaces, like finished flooring
• Short- or zero-turning radius for enhanced maneuverability
• Ability to fit in freight elevators
These types of indoor MEWPs also allow users to access high-reaching or overhead tasks in hard-to-reach places like areas obstructed by infrastructure, tight racking, ducts, pipes, ceiling tiles or joists. Some vertical mast lifts have up-andover capabilities to give operators the ability to maneuver around
fixed obstacles at height to work. And because these machines are lightweight and compact, they can be pushed into place or between work areas while requiring minimal storage space.
As contractors consider using indoor MEWPs as an alternative to more traditional ways of completing work at height, these machines are being used in a wide variety of applications. Their popularity continues to grow thanks to their ability to be used on sensitive flooring and fit into and moved between floors in elevators for ongoing facility maintenance, from airports and data centers to high-rise buildings and just about anything in between.
Additionally, because of their size and weight, they are also wellsuited for fit-out and finish work on construction sites, such as painting, installing fire alarms or sprinkler systems, putting in or replacing lighting and dropping in ceiling tiles. Other common applications for indoor MEWPs include refitting
retail displays and updating seasonal décor, as well as maintaining production equipment in a manufacturing environment.
Indoor MEWPs are also gaining favor among companies focused on eco-friendly solutions and sustainability.
For example, human- and batterypowered lifts run quieter and eliminate or reduce emissions altogether, so they can be used in clean rooms, data centers, hospitals, schools, libraries and office buildings.
Ladders and scaffolding have been around for a long time, but the increasing market demand for indoor MEWP equipment is being driven by safety, productivity and ergonomics.
These factors are becoming increasingly more important with the rapid rise of labor rates, workers’ compensation and an aging workforce.
JLG Industries, communications@jlg.com, www.jlg.com
Are you constantly ordering new lifting slings because your previous ones were damaged? Well, you are not alone. Across the lifting and rigging industry, it’s common to view your lifting slings—primarily synthetic lifting slings— as disposable items.
Every sling on a job site should be considered a special tool needing special protection. Not doing so increases your operations cost and puts your workers at risk. With more awareness on workplace safety (including increased OSHA fines), safeguarding your lifting slings is now a necessity—not a recommendation. But with so many options out on the market, it can be confusing as to what solution you should invest in.
Those researching sling protection are looking for three main outcomes: improve worker safety, protect their loads from damage, and increase the life of their lifting slings. When considering potential solutions, you should pick one that increases safety and is cost-effective. For over 70 years, Mazzella has put state-of-the-art solutions in the hands of lifting and rigging professionals. And to help answer potential questions you may have during your decision-making process, we wrote this article to discuss topics like:
• What’s the difference between
cut protection and abrasion protection?
• What types of cut protection are available?
• When and where do you need cut protection?
• What is the CornerMax® Sleeve?
• What are the best lifting applications for a CornerMax® Sleeve?
• Is a CornerMax® Sleeve right for you?
What Types of Sling Protection Products are Available?
While there are many types of lifting slings, there are even more options for sling protection, including:
Pads
Corner pads, specifically SlingMax®’s CornerMax® Pads, create a “tunnel” of cut protection where the sling doesn’t contact the load’s edge.
Pads
Commonly used with wire rope and chain slings, wear pads act as a buffer between the load and the sling.
Lightweight and easy to use, magnetic corner protectors are placed directly onto the corners and edges of steel loads, instead of placing them on the lifting sling. Additionally, they can be used on synthetic, wire rope, and synthetic rope liftings slings, and they have a maximum loading capacity of 12,500 PSI.
Covers and Sleeves
Covers and sleeves are ideal for protecting synthetic slings when it’s not practical to use a corner pad.
An endless sling with butted edges sewn together to double the sling width.
What’s the Difference Between Abrasion and Cut Protection?
During your research, you will come across two types of protection: Abrasion protection is ideal for lifting any rounded, rough edges. For example, when lifting a large stone or concrete slab, an abrasion protection sleeve will keep it safe
from a rough edge, preventing additional damage to your sleeve.
Cut protection is best when lifting loads at a 90-degree angle. No matter how dull the angle may appear, it can still cut into a sleeve with enough applied pressure. You would want to use cut protection for lifting steel beams and loading and unloading steel coils.
When Would You Use Synthetic Sling Protection?
On a job site, every lift should be seen as critical, meaning every lift performed should have protection. Whether you’re using synthetics, wire ropes, wire mesh, or alloy chains, any lifting sling on a job site should have protection.
While many see synthetic slings as easily disposable items, they’re still an integral part of every lift.
What Is the CornerMax® Sleeve and What are Its Benefits?
Developed by SlingMax Rigging Solutions, the CornerMax® Sleeve is a lab-tested, extremely cut-resistant sleeve designed for protecting synthetic lifting slings.
Unlike lifting pads, which are ideal for loads with 90-degree straight edges, the sleeve can form around most geometric shapes. Whether it’s a steel coil, an I-beam, or a stone slab, the CornerMax® Sleeve’s flexible shape makes it a versatile tool at your job site.
Because it’s made from a High Modulus Polyethylene fiber (HMPE) and features a tight weave, the CornerMax® Sleeve can reach 25,000 pounds per square inch of sling width, exceptional by industry standards.
What are the Biggest Benefits of Using a CornerMax® Sleeve?
Historically, synthetic web slings were viewed as disposable items. While popular for being ergonomic and affordable, their material makes them susceptible to damage in certain applications, especially those involving sharp edges.
With a CornerMax® Sleeve, synthetic lifting slings can now be used in applications dominated by wire rope slings, alloy chains, and mesh.
Not only will you save money by not having to purchase wire ropes and alloy chain slings, but the CornerMax® Sleeve also extends the lifespan of your current slings— eliminating the need to constantly replace damaged ones.
Can a CornerMax Sleeve Only Be Used with Slingmax® Products?
One of the biggest benefits of a CornerMax® Sleeve is its versatility. While it’s made by Slingmax®, the CornerMax® Sleeve is not exclusive to their slings. In addition to Slingmax®’s high–performance Twin-Path® and Single-Path slings, our safety experts encourage anyone needing cut protection to use CornerMax® Sleeve on their flat web slings, polyester roundslings, or any synthetic lifting sling on your job site.
Can You Use CornerMax® Sleeves on Alloy Chains or Wire Rope Slings?
Because of the CornerMax Sleeve’s specific design, our experts recommend not using it with any wire rope or chain lifting slings. Since the sleeve is specifically designed for synthetic material, wire rope or chain lifting slings would put immense pressure on the sleeve, crushing and / or tearing it.
Additionally, you would not get that guaranteed protection of 25,000 pounds per usable inch of sling width.
What Inspection Criteria Comes with a CornerMax® Sleeve?
With the CornerMax Sleeve, you would inspect it just like any other lifting sling. Go through and see if there are any tears, holes, punctures, or fraying at the edges. If any of these are found, immediately remove the sleeve from the job site.
What are the Best Practices for Using a CornerMax® Sleeve?
Before lifting a load, ensure the CornerMax Sleeve is fully connected to the entire surface. You will want to avoid placing just the edge of the sleeve on the surface, as you won’t achieve complete protection.
Is a CornerMax® Sleeve Right for You?
Making your lifting operations safer and more cost-effective doesn’t have to be an ultimatum. With state-of-the-art solutions like the CornerMax® Sleeve, both your equipment and workers are put in a safer position.
With decades of first-hand experience in safeguarding lifting projects, Mazzella has plenty of useful, informative content to help you in your decision-making process.
Mazzella Companies, marketing@mazzellacompanies.com, www.mazzellacompanies.com
Konecranes S-series is not just a hoist it’s a game-changer
The Konecranes S-series hoist redefines industrial lifting, integrating synthetic rope and Smart Features engineered for enhanced safety and productivity. With a lifting capacity of up to 20 tons, the Konecranes S-series rope hoist adapts to diverse girder configurations.
The hoist’s advanced design, durable material selections, stepless hoisting and safety enhancements not only optimize load handling but also mitigate structural twisting and wear, as well as reducing maintenance requirements.
Enhanced versatility with low headroom option
The recent addition of the S-series low headroom option further enhances its versatility.
This compact model offers excellent approach dimensions and smooth, stepless lifting with a loaddependent lifting motor.
Its strong, lightweight and durable synthetic rope enhances safety and ease of handling. Integrated Smart Features, such as Snag Prevention, Hook Centering and Follow Me help boost productivity.
Additionally, a new safety light gives a visual indication of the location of the hoist at ground level, further enhancing safety and convenience. Moreover, the Konecranes S-series low headroom hoist radio features an easy-to-read display that indicates the lifted
load, active Smart Features, battery life and other useful information. True stepless buttons help increase safety and accuracy, particularly during slow and demanding lifting operations.
“In the S-series low headroom hoist, we have combined the best features of our previous rope hoist products and introduced new, exciting innovations. As a result, we have created a strong, durable, compact, high-tech and smart rope hoist that prioritizes safety above all. The S-series low headroom hoist will be a market-leading product for years to come,” says Jussi Luokomaa, Product Manager for Europe, the Middle East and Africa at Konecranes.
Innovative design features minimize mechanical wear
Before launching the S-series with a synthetic rope, Konecranes conducted thousands of hours of testing to ensure safety and durability. The synthetic rope is fast to install and reduces wear on reeving components. A totally re-designed hoist structure provides smooth and stable lifting,
minimizing wear and tear to the reeving parts.
Commitment to sustainability
Environmental sustainability is a fundamental focus in Konecranes’ product design. The S-series normal headroom hoist is significantly lighter than previous corresponding hoist models due to an optimized design and material selections, consuming fewer raw materials and therefore reducing climate impact.
Additionally, the use of synthetic rope and guide rollers in the S-series hoist enhances its performance and durability while simultaneously reducing maintenance requirements. Our in-house designed and manufactured gears and motors, along with the adoption of inverter lifting technology, enable precise motor speed control and optimized hoisting energy consumption.
The latest low-headroom hoist also includes features such as a thrust rocker—one example of smart design selections leading to reduced steel consumption for decreased environmental impact.
TRUCONNECT Remote Monitoring provides real-time data for operations and maintenance planning, resulting in enhanced reliability, reduced environmental impact associated with unexpected downtime, and extended equipment lifetime.
Tried and tested Konecranes S-series hoists have already proven their worth in diverse industrial environments.
Hakkers BV, a Dutch company specializing in hydraulic engineering and steel construction, has leveraged the S-series hoist in wall console cranes that act as auxiliaries, for more efficient hook placement and to achieve a higher level of flexibility in their operations.
In the energy sector, Hitachi Energy in the Czech Republic has utilized S-series hoists to help maintain stringent cleanliness standards in the manufacturing of gas-insulated conductors. The synthetic ropes eliminate the need for lubrication, preventing contamination for a clean production environment.
Similarly, the LTC Group in the UAE has also integrated S-series cranes into their new production facility. The integration of Adaptive Speed Range (ASR) technology enables quicker hook movement when unloaded, significantly reducing cycle times. A strong focus on customers and commitment to business growth and continuous improvement make Konecranes a
material handling industry leader. This is underpinned by investments in digitalization and technology, plus our work to make material flows more efficient with solutions that decarbonize the economy and advance circularity and safety.
Konecranes, +27 (0) 11 568 1701, Parts.ZA@konecranes.com, www.konecranes.com
For 25 years, Combilift has been revolutionising the way companies handle and store goods. Our pioneering product range of multidirectional, articulated and pedestrian forklifts, straddle carriers and container loaders allows you to manoeuvre long loads safely, reduce aisle widths and increase the amount of space available for storage. CONTACT US TODAY
To find out how Combilift can help you unlock every inch of your storage space.
JLG uses an all-encompassing four-step approach to teaching accident avoidance on telehandlers. Here are the steps and the important questions to ask for each:
At the center of these four steps is a machine that stands on a triangular footprint and lifts heavy weights to impressive heights. Of course, there are other dangers, but the key objective is to keep the telehandler upright.
Telehandler center of gravity
The two front wheels and the rearaxle pivot point form a telehandler’s triangular base. The rear wheels are not part of the base because the rear axle typically oscillates. As long as the machine’s center of gravity (the point in three dimensions around which the machine’s weight
is balanced) remains oriented inside this stability triangle, the telehandler remains upright.
Shifting the stability triangle forward (right) and shifting the stability triangle up (right)
Adding a load to the forks while the boom is down moves the center of gravity forward and down. Raising the load will move the center of gravity up and to the rear, while at the same time causing the stability triangle to shrink. The higher you lift a load, the less margin for error you have because the stability triangle becomes smaller.
The stability triangle on a telehandler
A small stability triangle leaves less room for the center of gravity to wander left or right if the frame is not perfectly level. Imagine the center of gravity as a plumb bob hanging from the boom. You’ll always find the center of gravity somewhere on a perfectly vertical line between a point on the boom and the center of the Earth. If the frame’s not level, the center of gravity will not be oriented over the machine’s centerline. But the stability triangle is always aligned with the telehandler centerline.
With the boom raised and extended (the stability triangle is very small), the frame only has to be slightly out of level to make the center of gravity drift to either side of the triangle. The laws of physics are as certain as gravity. The moment the machine’s center of gravity moves beyond the boundaries of the stability triangle, the telehandler begins to tip.
Shifting the center of gravity outside the stability triangle
At any job site, there are things
affecting the stability of a telehandler other than where you put the boom. You may be on a 1-degree side slope, in a 5-mile-perhour wind. There may be a little ice under your wheels, and one tire a little low on air pressure. If the machine goes over, there may be no single cause. It was a combination of factors that are all things you can catch and correct or avoid if you do all of the Four Steps.
A safe lift starts well before putting the boom in motion, or even before the operator assesses the site for hazards. Most of today’s telehandlers are designed with a quick-attach coupler at the end of the boom. Before installing an attachment, be sure it’s approved by the telehandler manufacturer and that its specific capacity chart is in the cab of the telehandler.
It’s an OSHA violation to run a machine if the proper load chart for that particular combination of machine and attachment isn’t in the machine.
Make sure forks haven’t been tampered with. Other than block forks, all forks should be used in matched pairs. Block forks are used in matched sets.
The maximum capacity of a telehandler-and-attachment combination will be the lightest of these: capacity stamped on the attachment identification plate, the fork capacities stamped on the side of each fork (fork capacity is multiplied by the number of forks on the attachment, not to exceed the maximum on the attachment ID plate), maximum capacity indicated on the proper load chart, or the load rating of the telehandler.
Whenever you test the limits of the load chart you should do a test pick without a load on the forks — position the telehandler as you plan for the actual lift and run the forks up to where you plan to place the load. By noting the boom extension and boom angle at the extreme point of the lift, this exercise confirms the vertical height from ground level where the load is to be placed, and the horizontal distance from the front tires to where the load will be placed.
On the capacity chart, find the horizontal line for the height of the lift and follow it over to where it intersects the line for the distance. The point where the two lines meet should fall within a load zone marked on the chart. If it doesn’t, the machine and attachment can’t complete this lift. The weight indicated in the zone where the height and distance lines intersect is the maximum capacity for this lift. If the two lines meet on a boundary between zones, use the lighter of the two weights for this lift’s limit. Check the boom-extension and boom-angle limits of this load zone on the capacity chart. When the load is in the air, no matter what happens, do not exceed those boom-extension and angle limits or the machine will tip.
All of the loads shown on capacity charts are assigned with the assumption that the machine is on firm ground with the frame level; forks positioned evenly on the carriage; load centered on the forks; proper size tires properly inflated, and the telehandler in good operating condition. Failing to comply with any of these conditions could tip the machine over.
Once you’ve determined that the lift is within the telehandler’s and attachment’s capabilities, it’s time to set up the machine. Never engage a load or lift a load more than four feet above ground unless the telehandler is level.
Stop the machine on a stable surface in the best place to lift and
place the load, set the parking brake, and shift the transmission into neutral. Before raising the boom, check the level indicator to see if the frame needs to be leveled from side to side. Many telehandlers have hydraulically tilting main frames that allow you to compensate for uneven terrain. Some have outriggers. Set the boom in the “carry” position — forks less than four feet off the ground — and level the machine. The machine should be ready to make the lift.
Never use the leveling system (sometimes called “frame level”) or outriggers to level the telehandler after the load is more than four feet off the ground. After the load is in the air, if you discover that the telehandler is not level, bring the load back down before leveling the frame.
The higher up you go, the closer the sides of the stability triangle are — you don’t have to go very far to move the center of gravity outside the triangle. If you use the frame level with a load high in the air, the boom only has to move a couple of degrees right or left and the machine may tip over.
If the telehandler isn’t level when you reach the limits of the frameleveling system, don’t attempt the lift until the problem is solved. Reposition the telehandler on more-level ground or have the surface where it is standing leveled.
Always lift the load slowly, watching closely for changes in the footing or
other conditions that could cause the frame to shift out of level. Don’t move the machine once the load is more than four feet off the ground.
Placing a load at height requires a careful combination of multiple functions — boom down, boom out, while holding the forks level.
Once the lift is complete, the boom should be retracted and lowered to the carry position before the telehandler is moved.
Telehandlers are designed to handle rough terrain, but that doesn’t mean they can be driven without regard for the terrain. Risk of tipping or load loss is much greater when traveling on slopes. If you must drive on a slope, keep the load low, tilted back, and proceed slowly with care. If the load exceeds the height of the carriage, a backrest extension will be needed. Before you get on the slope, downshift to a lower gear as engine braking
will help control the telehandler’s speed. Avoid turning on a slope.
Never drive across excessively steep slopes under any circumstances. Ascend and descend slopes with the heavy end of the telehandler pointing up the incline.
When there’s no load on the forks, the counterweighted rear of the machine is the heavy end, so you should back up slopes. When the telehandler is loaded, the front of the machine is the heavy end, so you should back down slopes.
The load or the forks cut the widest swath in a tight turn on a four-wheel-steer machine. But on the rear-pivot machine, it’s the counterweight or the outermost rear wheel that’s at the edge of the turning radius. In either case, the operator must look in the direction of travel to be sure the path is clear. But in cases where the operator is using a machine with rear-pivot
steering, it’s especially important to be aware of the counterweight.
It is vital that the operator ensure safe use of a telehandler. Accidents tend to happen when people neglect basic safety requirements in the name of speed.
Industry-leading training programs from the access industry leaders, bringing safety and confidence to your team: JLG Training. Make sure you are compliant with the most up-to-date ANSI and OSHA regulations with expert-designed training plans.
From online supervisor training to telehandler operator and equipment service training, JLG offers comprehensive training to fit your telehandler needs.
JLG Industries, communications@jlg.com, www.jlg.com
Manitou Group, as a world reference in handling, aerial work platforms and earth moving sectors, and Kiloutou, Europe’s third largest equipment rental company, are previewing the first “retrofit” electric telehandler. An opportunity for the groups to test a solution that is both sustainable and circular.
The partnership between Manitou Group and Kiloutou, which first began in early 2023, is really coming into its own with the exclusive presentation of the first electric telehandler based on a used combustion model.
+After studying the technical feasibility of the project for the past year, Manitou Group’s R&D and Services & Solutions teams have come up with an electrification kit in line with the specifications shared by Kiloutou. All the safety criteria are met, and performance is equivalent to the internal combustion version.
The retrofit is a transitional solution that is both sustainable and circular, with a 40% reduction in greenhouse gas emissions compared with an internal combustion machine. Once fitted with its electrification kit, the converted equipment will be integrated into the IMPAKT offer, dedicated to alternative, more environmentally friendly
powertrains and available from Kiloutou branches in France.
Michel Denis, CEO of the Manitou Group, adds: “We are proud to present this first ‘retrofit’ telehandler. I would like to thank all the teams involved in this virtuous project. This close collaboration with rental customers like Kiloutou shows just how important it is to join forces to make quicker progress on sustainable solutions for the users of our machines. This development is fully in line with the objectives of our CSR roadmap, which aims to make the circular economy a priority.”
François Renault, Director of Equipment & Sustainable Development, Kiloutou Group, explains: “At a time when electric is set to become the norm and gradually replace fossil fuels, we see retrofitting as an alternative to mass replacement. It is perfectly aligned with a comprehensive fleet upgrade program, without the
need to buy everything back. This project with Manitou Group pushes back the limits of the possible in terms of the circular economy and decarbonization. I’m delighted with this project, which enables our respective teams to share their know-how, and I’m particularly proud to see the expertise of Kiloutou’s Test Center and Purchasing Department at work.”
The two companies are now in the process of concluding a usage partnership with a major construction company, starting in September 2024. Over a period of one year, it will enable the equipment to be tested on various worksites and indicators such as range, charging methods and customer feedback to be analyzed in real-life conditions.”
Manitou Group, +27 (0) 11 601 3000, info.msa@manitou-group.com, www.manitou.com
4-5 Sept 2024
All registered ECSA members can claim 1 CPD point per day for attending the conference
Quality and reliability, along with the heavy-lifting capabilities of Genie® XC™ boom lifts and FE hybrid technology, prevented unnecessary downtime and helped keep the project on track.
At the end of last year, the Tambrig landfill in Oberfelden, Switzerland, underwent an expansion to include a new processing hall that offers protection from precipitation, as well as space for separating delivered material. Three Genie® boom lifts were on site for several months during the construction, which occurred on the site of the former Tambrig gravel pit, to facilitate the work.
Bau-Trans Ag in Liechtenstein, a part of the Felbermayr Group, provided a Genie SX™-105 XC™ telescopic boom lift, an S®-85 XC telescopic boom lift, and a hybrid Z®-60 FE articulating boom lift between June and November 2023 to perform a variety of work at height, including assembly work.
“The Genie booms were extremely reliable, which helped make sure that work could continue, without interruption, for the tight construction period. The project had to be finalized before the winter set-in, therefore we needed the most reliable machines,” said Roger Beck, Rental Manager for mobile cranes, special and heavy transport, forklifts and aerial work platforms of Bau-Trans
AG. “Downtime can have a very significant negative impact on any project, but particularly one with a tight timeline, which is why it was so important to us to provide highquality and reliable equipment. Our customer was very satisfied with the Genie booms, which we were able to deliver on short time notice for the entire period of the project, which was finished on time thanks, at least in part, to the booms. BauTrans AG and I would like to thank everyone involved for the great order.”
Beck continued: “Our tagline is: ‘We bring Power in Motion. There’s no such thing as impossible!’”
The hybrid Z-60 FE boom was used primarily to help with assembly of external walls up to its maximum working height of 20.16 m. A 1.52 m articulating jib with 135° of vertical rotation helped operators accurately position themselves for work, while full-time active oscillating axles and 4WD helped maintain traction on rough terrain. Like all Genie FE hybrid boom lifts, the Z-60 FE can work an entire, standard work day on a single charge or a full, standard work week on a single tank of
fuel. Genie’s FE technology also eliminates downtime by allowing operators to operate the machine even if the battery is flat, and by charging the battery while the lift is operating in hybrid mode.
The two higher-reaching, heavylifting Xtra Capacity™ boom lifts provided the capacity needed to take multiple operators and their materials to height. Both the SX105 XC and the S-85 XC boast an unrestricted capacity of 300 kg and a restricted capacity of 454 kg.
With a max working height of 34 m and a 1.52 m articulating jib, the SX-105 XC is frequently used for work like bridge inspections and maintenance, in stadiums and sports arenas, and in oil and gas, industrial and utility applications. The S-85 XC, which has a max working height of 27.91 m and a 1.52 m articulating jib, is popular with general construction and industrial jobs thanks to its reach and lifting capacity.
Goscor Access Solutions, +27 (0 11 393 6437, accesssolutions@goscor.co.za, www.goscoraccesssolutions.co.za
Intermat is one of the top construction machinery events. Magni TH has chosen this international stage for the unveil of two new telescopic handlers and two innovative attachments.
Excellent performance and compact size from the TH 3.6 fixed telescopic handler
With capacity of 3 tonnes (6613 lbs) and lifting height of 5.8 metres (19 ft), the new TH 3.6 combines small size with impressive performance. In fact, the most compact fixed telescopic handler in the TH range,
intended for the construction and logistics sectors and soon also for agriculture, is able to lift its maximum load to a height of 5.4 metres (17.7 ft), 2,500 kg (5511 lbs) to the maximum height and 1,100 kg (2425 lbs) to a horizontal reach of more than 3 metres (10 feet). Its low-level design makes it ideal for tight spaces, while retaining optimal ground clearance for uneven terrains.
These characteristics, together with a Deutz Stage V engine of 55 kW (75 hp) give it a top speed of 35 km/h (21 mph). The four-wheel drive and steering, with hydrostatic transmission, provide superlative stability and manoeuvrability with 3 steering modes: front, concentric and crab.
With the launch of the TH 3.6 Magni also presents the new compact cab, which maintains the same development approach as its predecessor in the TH range together with a new dashboard that optimises the user experience through the ergonomic placing of the main controls. It also features USB ports (3.0 and c-type) for
charging electronic devices and a handy cup holder. The new cab’s standard outfit is completed by the air-suspended seat, adjustable steering column, heating and radio. Consulted via the 7 inch touch screen, the MCTS (Magni Combi Touch System) on-board software provides complete control of the machine with icon-based navigation. From the main menu, the operator can access the themed screens with the various functions, including load charts.
Unlike competitor models on the market, which have the usual load cell systems, the TH 3.6 is the only machine equipped with a more sophisticated, precise tipping protection mechanism to maximise performance and safety, in line with the entire TH range. This is the LMI (Load Moment Indicator), which enables constant monitoring of the machine’s movements to prevent any kind of overload.
The new RHT 6.31 EC: concentrated efficiency and comfort
Magni launches three models derived from the market’s bestselling rotating telescopic handlers,
the RTH 6.22, 6.26 and 6.31, all equipped with elevating cab. This feature is designed to optimise work in conditions that demand greater visibility and to guarantee the very best comfort level by providing the operator with an ergonomic position, especially when handling delicate loads or using specialist attachments. In these situations, greater visibility means safe, effective movements in even the most complex procedures, such as use of the tree cutting and log handling attachment.
The hydraulic mobile support is able to raise the cab to a height of 1.5 metres (5 ft) and tilt it between 0° and +16° for optimal control in conditions where movements must be exceptionally precise.
Two new attachments: the 3D-Film handler and the tilting rotating forks
At the Paris show, Magni also reveals two new attachments for the RTH and TH ranges: the 3D-Film handler and the 5T tilting rotating forks.
Intended for the movie industry, the 3D-Film handler has a surface fitted to support equipment such as LED light panels or floodlights used during filming in the studio or on location. With a capacity of 2.5 tonnes (5511 lbs) and continuous
rotation through 360°, it provides unbeatable manoeuvrability and versatility to offer the optimal response to this specific sector’s needs.
The tilting rotating forks, on the other hand, are designed for handling bulky materials in tight spaces. Unlike standard forks, they rotate and swivel to optimise movement of the weight during loading and unloading. They deliver frontal lifting capacity of up to 5
tonnes (11,000 lbs), rotated load capacity of up to 2.5 tonnes (5511 lbs), continuous rotation through 360° and positive tilting up to 70°. With targeted solutions for the demands of a constantly growing sector, Magni TH further extends its range of products to continue its expansion at the global level.
Magni SA, +27 (0) 11 383 2227, info@magnisa.co.za, www.magnisa.co.za
As extremely active importers and exporters of goods to boost and grow the economy, South African businesses require high-calibre inspection and expediting services. Dekra Industrial SA has recently launched a division dedicated to meet this growing requirement.
With decades of experience in non-destructive testing (NDT) and inspection services, the company brings a wealth of inspection-related expertise to a broad range of clients in industry sectors such as power generation, petrochemicals, steel, fabrication and mining. JP Muller, the Business Line Manager spearheading Dekra Industrial’s vendor inspection and expediting services locally
explains:
“In addition to meeting the requirements of the country’s import and export sectors, we saw an opportunity to expand the services provided by DEKRA Industrial in South Africa. The fact that as a country, we export and import creates a multi-billion rand industry, and a great need for supply chain inspection. Companies want to know the correct quantities of their goods coming in and going
out of the country - and that they are also receiving the correct product as per their original order.”
Seamless collaboration and support
Globally, Dekra already provides inspection and expediting services in more than 60 countries, with over 2000 inspectors worldwide.
“It therefore made sense that we would also launch this muchneeded service locally, as we can leverage our extensive global network, collaborating seamlessly on a daily basis - particularly in key markets such as India and China, with which we work closely,” says Johan Gerber, DEKRA Industrial SA Managing Director.
“The decision to provide vendor inspection and expediting services to our South African and panAfrican clients also aligns with our commitment to delivering quality inspection and testing services worldwide,” Gerber says.
“We also recognise the importance of agility and adaptability in today’s fast-paced business environment, and our goal is to empower South African businesses with the tools and resources they need to thrive in
an increasingly competitive global market.”
Internationally, Dekra’s inspectors are highly trained, and adept at providing accurate and dependable product verification. Collaborations with global transport and logistics stalwarts such as DHL further enhance the vendor inspection and expediting service offering. To this end, Dekra Industrial South Africa will engage only the best inspectors locally with sector-relevant experience, providing quality, dependability and consistency, as well as fast inspection report turnaround times.
These inspectors - from such diverse backgrounds as engineering and agriculture – will undergo rigorous selection processes to meet the company’s high standards. “For complex contracts requiring specialised vendor inspections expertise, we will tap into our global network of experienced inspectors, underscoring our commitment to excellence,” highlights Gerber. In addition to its core vendor inspection services, Dekra Industrial will also provide value-added services such assisting clients with supply chain optimisation and regulatory compliance. By offering a holistic approach to inspection and expediting, the company aims to position itself as a trusted partner for businesses across a wide range of sectors.
Although each project has its own dynamics, Muller points out that the company’s standard turn-around time on vendor inspections is 24 hours. “Time is money as the saying goes in business. If we perform an inspection for the client quickly and efficiently, we know they will come back. The quicker we can perform their inspection and reporting, the quicker our clients can export – or sell - their products,” he enthuses.
“Our commitment to excellence extends beyond the confines of traditional inspection services,” notes Muller. “We aim to be a strategic asset – and ally – to our clients, providing them with the insights and support they require to achieve their import and export-related business objectives. This service will enable us to offer more value to our clients: not only by saving them money, but by safeguarding their integrity, credibility and reputation which – in the business of import and export – is very dependent on the verification of quality and of accurate product quantities. “What sets us apart is our expertise, global footprint and comprehensive vendor inspection and expediting solutions, which can also be tailored as required.”
The honesty and integrity with which we operate is also appreciated by our clients. This service is very dependent on the trust which clients have in inspections service provider, and its perceived credibility and integrity. Performing competent and reliable product verifications has built Dekra’s credibility globally as an experienced vendor inspection company with high professional standards – and we aim to offer our local clients the same dependable service, Muller concludes.
DEKRA Institute of Learning, +27 (0) 87 095 2725, info@dekrainstitute.co.za, www.dekraiol.co.za
From drones to the Cloud to AI, the world is progressing at the speed of light. It’s not always easy staying on top of the latest innovations in your field. But at Electra Mining Africa 2024, you’ll find all the latest cuttingedge technology on display, hear talks from trailblazers in the industry and meet hundreds of exhibitors across the areas of mining, electrical, automation, manufacturing, power and transport all in one place.
Taking place at the Expo Centre in Nasrec, Johannesburg from 2-6 September, this year’s event will be one of the biggest Electra Mining Africa exhibitions to date. The show will extend across 35,000+ m² of exhibition space and accommodate over 850 exhibitors, demonstrating the popularity of the show. It’s focus is largely on local industry suppliers and manufacturers with top brands participating, together with an international contingent from countries including the UK,
USA, Canada, Australia, Italy, Germany, Switzerland, Taiwan, India and China.
As the largest trade show of its kind in Southern Africa and with its over five decades of experience, Electra Mining Africa offers an outstanding opportunity for both exhibitors and visitors, buyers and sellers, to connect face-to-face and develop long-lasting business relationships. Hundreds of live demonstrations will bring machinery and equipment
to life, with thousands of new products and innovations displayed throughout the five exhibition halls and extensive outside exhibit areas.
“We’re looking forward to this year’s show,” says Gary Corin, Managing Director of Specialised Exhibitions, a division of Montgomery Group. “The industry gave its full support to Electra Mining Africa 2022, which had just over 30,000 visitors through the gates. We’re expecting to exceed those numbers this year. Large organisations and SMMEs will be represented across the areas of mining, electrical, automation, manufacturing, power and transport. Some have exhibited with us for over 50 years, with their businesses growing alongside the growth of Electra Mining Africa. What better way to bring a brand to life: on the floor of an exhibition where you’re engaging with your target market face-to-face. It’s a unique value-proposition to participate in an exhibition like this.”
The Electra Mining Africa Innovation and New Products Awards will be taking place again this year, following its success in
2022. Organised in partnership with the South African Capital Equipment Export Council (SACEEC),the awards recognise the outstanding levels of innovation at the show. Many entries are anticipated again this year.
Charlene Hefer, Portfolio Director at Specialised Exhibitions, spoke about the various attractions, citing the Forklift Driver competition and the focused automation hall as two of the exciting elements at this year’s show.
“The Forklift Driver competition organised in conjunction with Lifting Africa and LEEASA is back this year on a much bigger scale. It’s where exceptional forklift driver skills will be put to the test with Forklift operators competing for the coveted title of Forklift Driver Champion,” explains Hefer. “We’re also thrilled that the automation hall, a huge attraction in 2022, has received overwhelming support from industry again this year and will be filled with ground-breaking innovations. In addition, for the first time this year, Electra Mining Africa is incorporating the Local
Southern African Manufacturing Expo.” Education and learning is important to Electra Mining Africa. Industry experts will be delivering free-to-attend talks on latest trends and developments at the Seminar Theatre in Hall 9, hosted by the South African Institute of Mechanical Engineering (SAIMechE). Topics will be aligned with the show’s theme days of sustainability, women and skills development, , safety and lifting, innovation and South Africa day. The Lifting Equipment Engineering Association of SA (LEEASA) and
the Southern African Institute of Mining and Metallurgy (SAIMM) will be hosting conferences alongside the show. Women in Mining South Africa (WiMSA) will be hosting a half-day women in mining workshop. “Electra Mining Africa is going to be a great show and the innovation on display will be mindblowing,” concludes Hefer.
Montgomery Group, +27 (0)11 835 1565, natasha.heiberg@ montgomerygroup.com, www.electramining.co.za
When cranes suffer from premature wheel wear, rail wear, structural component failures, crane noise, bad positioning or drive faults it is normally the result of incorrect crane geometry.
Konecranes’ CraneQ Geometric Survey and RailQ 3D Runway Survey assist in finding the cause of these symptoms to so that major problems and costly downtime can be avoided. They work together to create a complete view of the crane and rail geometry to be inspected and assessed.
Ian Grobler, Sales Manager for Konecranes and Demag South Africa explains “The CraneQ Crane Geometric Survey and RailQ 3D Runway Survey are used to verify the alignment and square of a crane and to deliver accurate information on the alignment of the rail. Both surveys help locate where the problem lies when an operator experiences a performance that is problematic. The surveys provide recommendations for any needed corrective actions with a highly detailed and accurate analysis”.
CraneQ
Cranes that are straight, square, and aligned, experience less repair costs and have a higher level of reliability. The CraneQ Crane Geometric Survey provides the information that is required for detailing the alignment and the square of a crane. It measures dimensional tolerances of wheels, guide rollers, end trucks, girders, and other components of the crane.
The CraneQ Survey provides more accurate information than traditional surveying techniques because it is based on advanced
surveying methods developed specifically for crane geometry. Konecranes’ specialised software and their skilled survey technicians will provide a geometric analysis of your crane as well as present feedback on what corrective actions need to be taken.
The survey also minimises downtime due to component wear by assuring correct component alignment.
RailQ 3D Runway Survey uses highdefinition surveying techniques combined with point cloud data analysis to provide information on runway condition. The 3D visual inspection will provide information on runway span, straightness, elevation and rail-to-rail elevation.
Symptoms that may indicate the need for a runway survey:
• Crane tracking and skewing issues
• Excessive wear on wheels and rails
• Loose rail fasteners
• Abnormal noises during bridge travel
• Frequently replacing bridge
couplings, rail splices, rail sections and crane wheel axles
• Broken wheel flanges, etc.
Two major benefits resulting from the RailQ 3D Runway Survey, are that it is safer to perform than a traditional runway survey because it uses a remotely operated data collection instrument, and that the survey gathers more data in less time than a traditional survey delivering the same information.
“Performing RailQ 3D as part of a periodic inspection program
on your critical production crane runways helps identify chronic issues. This approach allows you to plan maintenance far in advance and implement corrective actions during planned outages and production stoppages to limit the effects of lost production.” said Grobler. “It’s not rocket science to see the benefits of the CraneQ and RailQ 3D assessment interventions. The cost savings that can result from the analysis of highly accurate data is immense, especially when preventive
maintenance is scheduled. Couple that with decreased downtime in the production cycle makes it a win-win situation for all industries that require continuous cycles of production” concluded Grobler. All CraneQ and RailQ 3D Survey reports are loaded onto the yourKonecranes customer portal for quick and easy access by the customer.
Konecranes and Demag, +27 (0) 11 898 3500, info.za@konecranes.com, www.konecranes.com
Jekko is pleased to announce its partnership with SkyJacks, a premier supplier of powered access and material handling solutions based in Johannesburg, South Africa.
SkyJacks has been appointed as the exclusive dealer for Jekko products in South Africa, further expanding Jekko’s global presence and providing customers in the region with access to cutting-edge lifting technology.
With over 45 years of experience, SkyJacks has established itself as a trusted provider of innovative solutions for working at height and material handling challenges in Southern Africa. The company’s extensive portfolio includes suspended access platforms, aerial work platforms, telehandlers, and construction hoists, backed by a commitment to excellence in product quality and customer service.
The partnership between Jekko and SkyJacks signifies a shared dedication to delivering reliable and efficient lifting solutions to customers across various industries, including construction, mining, and industrial maintenance. By joining forces, Jekko and SkyJacks aim to meet the evolving needs
of the South African market and enhance productivity and safety in challenging working environments.
“With Alistair and his team, we have known each other for many years.” said Alberto Franceschini, Sales & Marketing Director at Jekko. “They visited us already 7 years ago, but at that time Jekko’s size, organization, machinery, and quality were not up to the level of a major player like SkyJacks in South Africa. It is personally satisfying to see that, after all this time, SkyJacks has witnessed the incredible growth of Jekko on the international markets, in its organization, in products, and in quality, which is why it was finally easy to choose to distribute for us. Furthermore, it’s impressive to witness that more and more dealers are combining in their catalogs a brand of telehandlers and a brand of mini cranes. The two products are remarkably complementary, not in competition, providing the dealer with an extremely versatile, innovative, and comprehensive product package. I am greatly
satisfied with this trend.” SkyJacks Managing Director Alistair Bennett commented, “Over the last 45 years, SkyJacks has been trusted to provide working at height and material handling solutions in some of Southern Africa’s most challenging working environments. Initially, our focus was on suspended access platforms and aerial work platforms.”
“As the company evolved, our offerings grew to include telehandlers and construction hoists. Continuing to innovate, we believe that adding Jekko mini cranes to our offering is a natural progression that will allow us to meet the changing demands of the construction, mining, and industrial maintenance sectors in Southern Africa. We are proud to be a Jekko dealer and look forward to our shared success.”
SkyJacks, +27 (0 11 397 2730, keithf@skyjacks.co.za, www.skyjacks.co.za
Devoted to supplying scalable heavylifting solutions for a global market, Raimondi delivers international experience and technical versatility following the Italian tradition of excellence.
Raimondi’s high-performance cranes are easy-to-install and operate, and offer a radius of 76m with lifting capacities ranging between 3 and 24 tonnes.
Customer-centric, on-demand services include overnight spare parts delivery, field support for commissioning, and onsite application engineering with remote diagnostics. www.raimondi.co export@raimondicranes.com
LEEASA
T: +27 (0) 64 507 6857
E: admin@leeasa.co.za
W: www.leeasa.co.za
Kempston Controls
T: +27 (0) 140 776 2888
E: holyhead@kempstoncontrols.co.uk
W: www.kempstoncontrols.co.uk
Condra Cranes
T: +27 (0) 11 776 6000
E: sales@condra.co.za
W: www.condra.co.za
Cooper & Cooper Group
T: +27 (0) 11 493 4355
E: info@coopergroup.co.za
W: www.coopergroup.co.za
Palfinger Africa
T: +27 (0) 11 608 3670/1/2/3/4
E: sales@palfingerafrica.co.za
W: www.palfinger.co.za
Johnson Crane Hire
T: +27 (0) 11 455 9222
E: PeterY@jch.co.za
W: www.jch.co.za
Liebherr Africa
T: +27 (0) 11 365 2000
E: info.laf@liebherr.com
W: www.liebherr.com
True Lift services
T: +27 (0) 83 710 5390
E: Trueliftservices@gmail.com
W: www.trueliftservices.za.live
Bell Equipment Southern Africa
T: +27 (0) 11 928 9846
E: susanmy@bell.co.za
W: www.bellequipment.com
Jungheinrich
T: +27 (0) 10 596 8460
E: info@jungheinrich.co.za
W: www.jungheinrich.co.za
Kempston Controls
T: +27 (0) 140 776 2888
E: holyhead@kempstoncontrols.co.uk
W: www.kempstoncontrols.co.uk
Yale Lifting Solutions
T: +27 (0) 11 794 2910
F: +27 (0) 11 794 3560
E: crm@yalelift.co.za
W: www.cmco.com
DEMAC SRL
T: +39 (0)2 9784488
F: +39 (0)2 97003509
E: info@demac.it
W: www.demac.it
Econo Flex
T: +27 (0) 16 933 5705
E: econoflex@econoflex.co.za
W: www.econoflex.co.za
Econo Flex
T: +27 (0) 16 933 5705
E: econoflex@econoflex.co.za
W: www.econoflex.co.za
IY Safety & Inspections
T: +27 (0) 82 773 7019
C: +27 (0) 82 956 3176
E: bianca@iysafetyinspection.co.za
Morris Material Handling SA
T: +27 (0) 11 748 1000
F: +27 (0) 11 748 1093
E: sales@morris.co.za
W: www.morris.co.za
W: www.iysafetyinspection.com LOAD
3 60 5 Services
T: +27 (0) 72 207 7443
T: +27 (0) 64 687 7270
E: sales@3605services.co.za
W: www.3605services.co.za
Morris Material Handling SA
T: +27 (0) 11 748 1000
F: +27 (0) 11 748 1093
E: sales@morris.co.za
W: www.morris.co.za
Rhino Lifting Maintenance
T: +27 (0) 16 971 2348/49
E: sales@rhinolm.co.za
W: www.rhinolm.co.za
Yale Lifting Solutions
T: +27 (0) 11 794 2910
F: +27 (0) 11 794 3560
E: crm@yalelift.co.za
W: www.yale.co.za
GregBev Enterprise
C: +27 (0) 82 854 5143
C: +27 (0) 72 395 4342
T: +27 (0) 53 285 0842
E: admin@gregbev.co.za
W: www.gregbev.co.za
GregBev Enterprise
C: +27 (0) 82 854 5143
C: +27 (0) 72 395 4342
T: +27 (0) 53 285 0842
E: admin@gregbev.co.za
W: www.gregbev.co.za
Yale Lifting Solutions
T: +27 (0) 11 794 2910
F: +27 (0) 11 794 3560
E: crm@yalelift.co.za
W: www.cmco.com
Econo Flex
T: +27 (0) 16 933 5705
E: econoflex@econoflex.co.za
W: www.econoflex.co.za
GregBev Enterprise
C: +27 (0) 82 854 5143
C: +27 (0) 72 395 4342
T: +27 (0) 53 285 0842
E: admin@gregbev.co.za
W: www.gregbev.co.za
Integrate Lifting Specialist Africa
T: +27 (0) 12 141 3615
T: +27 (0) 86 571 4387
E: info@integrateliftingsa.com
W: www.integrateliftingsa.com
IY Safety & Inspections
T: +27 (0) 82 773 7019
C: +27 (0) 82 956 3176
E: bianca@iysafetyinspection.co.za
W: www.iysafetyinspection.com
Margisia Lifting Solutions
T: +27 (0) 14 763 1849
C: +27 (0) 83 992 2222
E: info@margisia.co.za
W: www.margisia.co.za
Rhino Lifting Maintenance
T: +27 (0) 16 971 2348/49
E: sales@rhinolm.co.za
W: www.rhinolm.co.za
Kempston Controls
T: +27 (0) 140 776 2888
E: holyhead@kempstoncontrols.co.uk W: www.kempstoncontrols.co.uk
Levi’s Trio Engineering
T: +27 (0) 11 907 9258
F: +27 (0) 86 742 9410
E: admin@levistrio.co.za
W: www.levistrio.co.za
Morris Material Handling SA
T: +27 (0) 11 748 1000
F: +27 (0) 11 748 1093
E: sales@morris.co.za
W: www.morris.co.za
Econo Flex
T: +27 (0) 16 933 5705
E: econoflex@econoflex.co.za
W: www.econoflex.co.za
FB Cranes
T: +27 (0) 11 902 3271
E: info@fbcranes.co.za
W: www.fbcranes.co.za
HP Cranes Consulting
T: +27 (0) 11 740-9725/28/33
F: +27 (0) 11 740 8416
E: admin1@hpcranes.co.za
W: www.hpcranes.co.za
IY Safety & Inspections
T: +27 (0) 82 773 7019
C: +27 (0) 82 956 3176
Shosholoza Consulting
T: +27 (0) 14 495 1994
C: +27 (0) 79 391 2990
E: info@shosholoza.africa
W: www.shosholoza.africa
Yale Lifting Solutions
T: +27 (0) 11 794 2910
F: +27 (0) 11 794 3560
E: crm@yalelift.co.za
W: www.cmco.com
Cooper & Cooper Group
T: +27 (0) 11 493 4355
E: info@coopergroup.co.za
W: www.coopergroup.co.za
J Express Crane Services
T: +27 (0) 11 864 8402
M: +27 (0) 83 425 5535
F: +27 (0) 11 864 8408
E: jexpress@telkomsa.net
Liebherr Africa
T: +27 (0) 11 365 2000
E: info.laf@liebherr.com W: www.liebherr.com
Chimaera
T: +27 (0) 84 506 1209
E: ndt@chimaera.co.za
W: www.chimaera.co.za
By Carpel SRL - Italy
T: + 39 (0) 39 532 0952
F: + 39 (0) 39 532 0825
E: info@bycarpel.it
W: www.bycarpel.it
Condra Cranes
T: +27 (0) 11 776 6000
E: sales@condra.co.za
W: www.condra.co.za
E: bianca@iysafetyinspection.co.za W: www.iysafetyinspection.com
J Express Crane Services
T: +27 (0) 11 864 8402
M: +27 (0) 83 425 5535
F: +27 (0) 11 864 8408
E: jexpress@telkomsa.net
Kempston Controls
T: +27 (0) 140 776 2888
E: holyhead@kempstoncontrols.co.uk
W: www.kempstoncontrols.co.uk
KL Cranes and Lifting Equipment
T: +267 397 4853
C: +267 71344438
E: annelieze@klcranesbot.com W: www.klcranesbot.com
Morris Material Handling SA
T: +27 (0) 11 748 1000
F: +27 (0) 11 748 1093
E: sales@morris.co.za W: www.morris.co.za
V & S Automation/Cranes
T: +27 (0) 10 442 7478
C: +27 (0) 82 787 2343
E: victor@vsautomation.co.za
W: www.vandsautomation-cranes. co.za
ACROW
T: +27 (0) 11 824 1527
E: info@acrow.co.za
W: www.acrow.co.za
Lifting Placements
C: +27 (0) 61 063 1687
E: info@liftingplacements.co.za
W: www.liftingplacements.co.za
Kempston Controls
T: +27 (0) 140 776 2888
E: holyhead@kempstoncontrols.co.uk
W: www.kempstoncontrols.co.uk
T: +39 (0)39 5951 1277 E: giovenzana@giovenzana.com W: www.giovenzana.com
Express Crane Services
T: +27 (0) 11 864 8402
C: +27 (0) 83 425 5535
F: +27 (0) 11 864 8408
E: jexpress@telkomsa.net
C:
F:
E: jexpress@telkomsa.net
Haggie
T: +27 (0) 11 601 8400
E: distribution@haggie.co.za
W: www.scaw.co.za
STEEL WIRE ROPES
CB Lifting
T: +27 (0) 22 719 1437
E: info@cblifting.co.za
W: www.cblifting.co.za
Haggie
T: +27 (0) 11 601 8400
E: distribution@haggie.co.za
W: www.scaw.co.za
Umholi
T: +27 (0) 11 914 2210/11
F: +27 (0) 11 914 2209
E: umholi@umholi.co.za
W: www.umholi.co.za
Combi Lift
T: +27 (0) 11 900 8010
E: victor@solutions-4u.co.za
W: www.combilift.co.za
Kemach Forklifts
T: +27 (0) 11 826 6710
E: info@kemachjcb.co.za
W: www.kemachjcb.co.za
Manitou
T: +27 (0) 10 601 3000
E: info.msa@manitou-group.com
W: www.manitou.com
Liebherr Africa
T: +27 (0) 11 365 2000
E: info.laf@liebherr.com
W: www.liebherr.com
MH Dawood Plant Services
T: +27 (0) 11 496 1007
F: +27 (0) 11 496 1198
E: info@mhdawood.co.za
W: www.mhdawood.co.za
LMI Academy
T: +27 (0) 11 475 5876
E: info@lmi-academy.co.za
W: www.lmi-academy.co.za
MCLS Training
T: +27 (0) 82 506 5899
T: +27 (0) 73 089 0624
E: sinky@mclstraining.co.za
W: www.mclstraining.co.za
Phakamisa Safety Consultants
T: +27 (0) 11 462 9620/1
F: +27 (0) 11 462 9620
E: potto@icon.co.za
W: www.phakamisasafety.co.za
Crane Clinic
T: +27 (0) 11 902 7379
E: reception@craneclinic.co.za
W: www.craneclinic.co.za
Palfinger Africa
T: +27 (0) 11 608 3670/1/2/3/4
E: sales@palfingerafrica.co.za
W: www.palfinger.co.za
Smith Capital Equipment
T: +27 (0) 11 873 9830
E: mail@smithcapital.co.za
W: www.smithcapital.co.za
Dymot Engineering
T: +27 (0) 11 970 1920
F: +27 (0) 11 970 1979
E: pa@dymot.co.za
W: www.dymot.co.za
16th – 17th October 2024 Olympia West, London REGISTER YOUR VISITOR TICKET NOW
Includes the LEEA Accredited Training Scheme Seminar
2 days of training sessions
FREE TO ATTEND
LiftEx is the premier networking exhibition for the lifting equipment and height safety industries, now in its 19th year. Attended by professionals involved in operating, inspecting, and testing lifting equipment in multiple sectors.
Unrivaled Reliability
Boom Length
Best in-class reach
Smart Chart
Expands the customary circular work area to take advantage of the maximum available lifting capacity
AML-E
Advanced control system with enhanced features
Unique Quality
Reduced Fuel Consumption
• Fuel Monitoring
• Eco Mode System
• Automatic Pump Disconnect
Take a closer look
Discover how Tadano RT cranes deliver maximum lifting performance with unrivaled reliability.
Tadano RT cranes give your business the next-generation features you need to work safer, faster and more effectively than ever. Tadano View gives your operators a birds-eye view of the crane’s surroundings on a large, multi-function display inside the cab. Reduce fuel consumption with Fuel Monitoring, Eco Mode and Automatic Pump Disconnect. And expand the working area to get the best crane performance in any outrigger extension setup with Smart Chart.
Take a closer look at what Tadano can do for your business. Learn which models are available in your region at tadano.com.