FORKLIFT
GUIDE & REGISTER
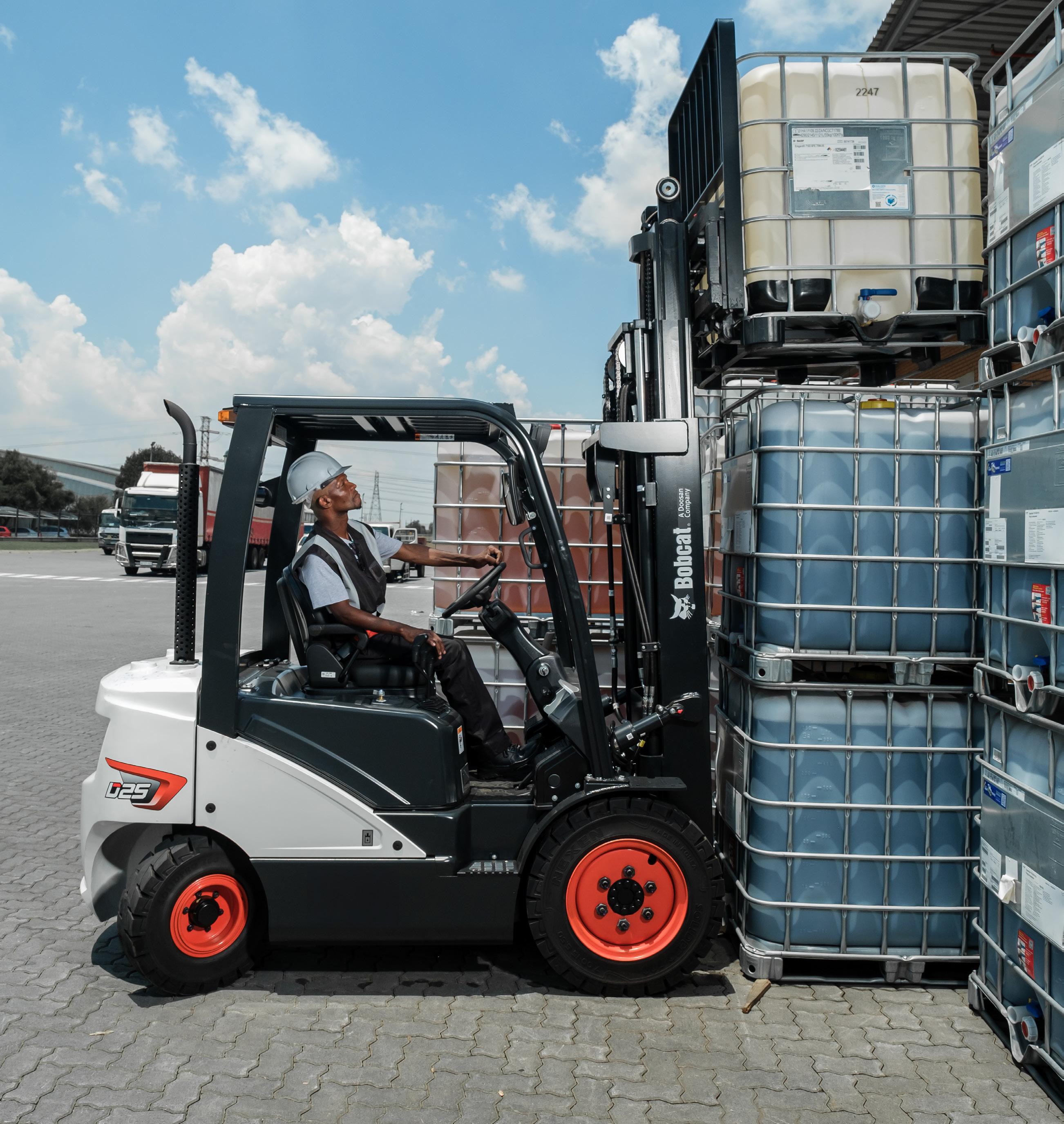
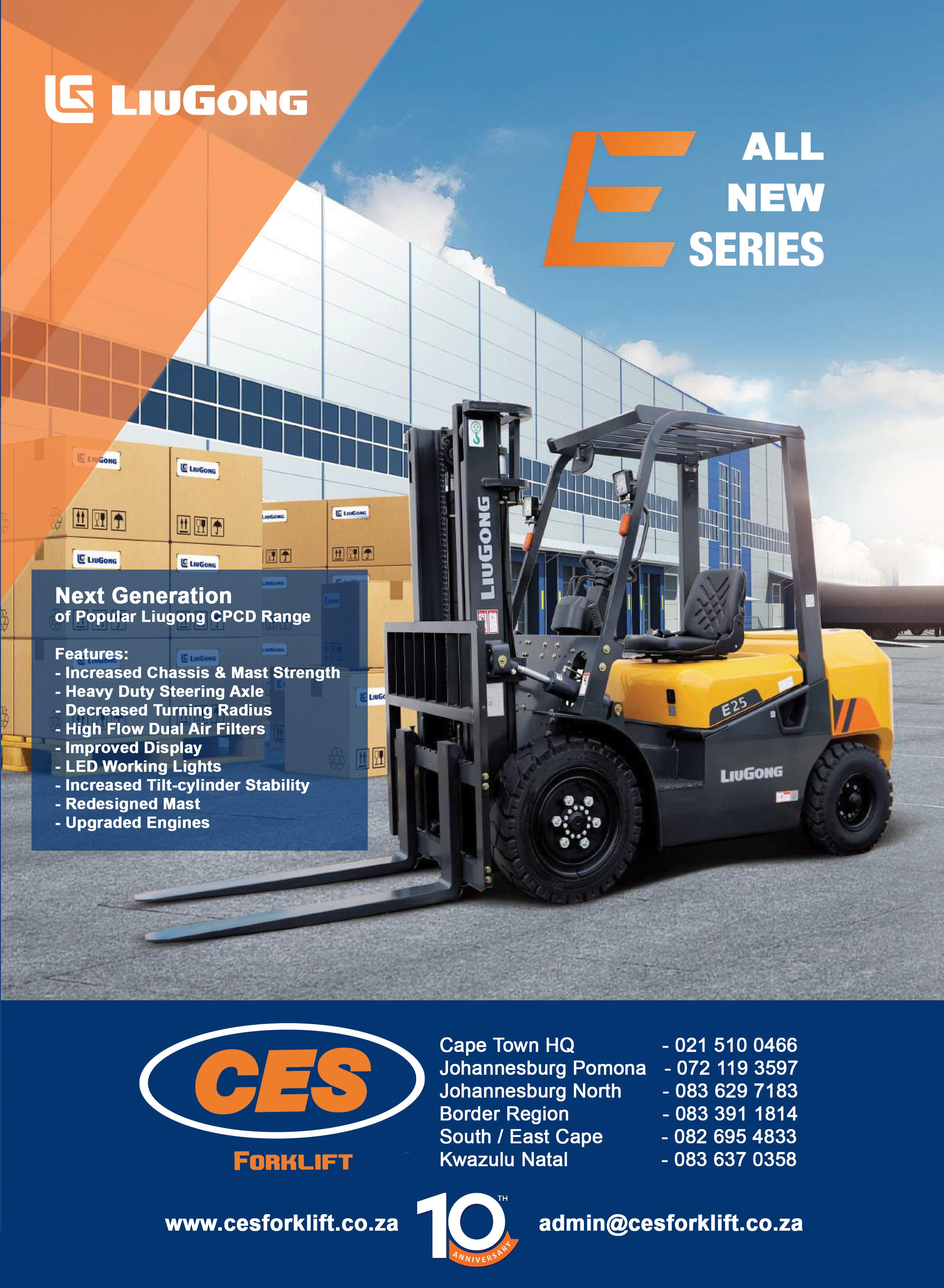
FORKLIFT GUIDE & REGISTER
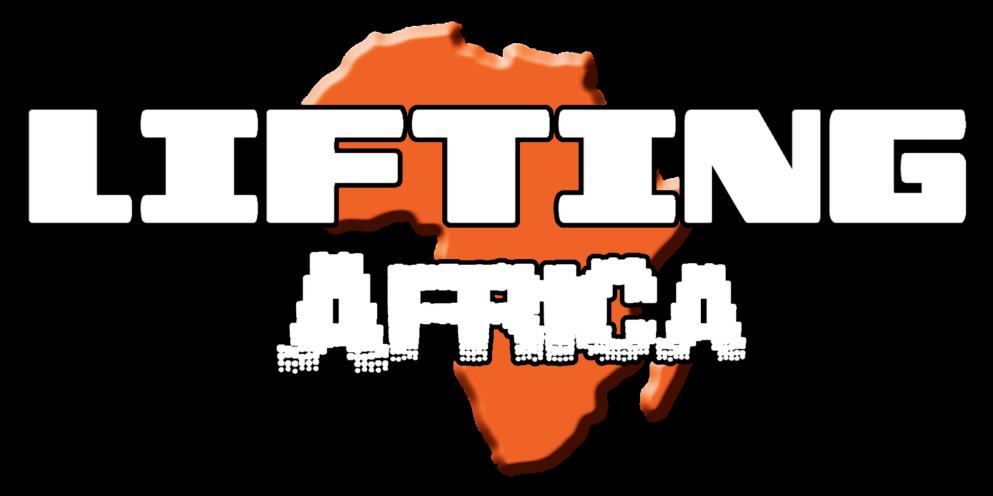
LIFTING AFRICA
Managing Editor: Surita Marx
Tel: +27 (0) 87 700 9834
Cell: +27 83 281 5761
Email: surita@liftingafrica.co.za
Web: www.liftingafrica.co.za
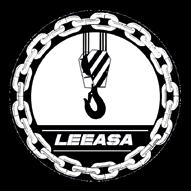
LEEASA
Desirė Davis (LEEASA Administrator)
Tel: +27 (0) 64 507 6857
Email: admin@leeasa.co.za
Website: www.leeasa.co.za
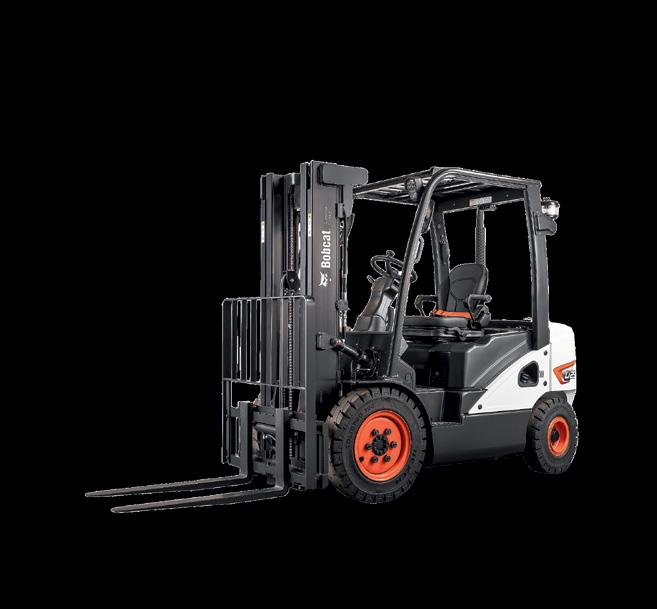
GLT- putting customers at the core
Goscor Lift Trucks (GLT) has supplied the materials handling equipment market with state-of-the-art products and solutions since 1984. Quality defines class and ultimately results in a lower cost of ownership.
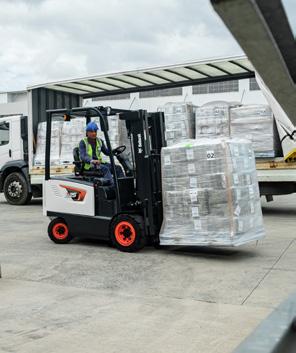
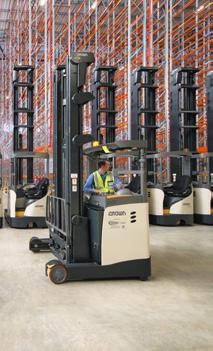
In partnership with its leading global principals, the company continually strives to be at the forefront of technological innovations in the materials handling space, providing local customers with the latest solutions that meet their needs. When it comes to service providers, making the right choice can significantly impact one’s business’s efficiency, productivity, and bottom line. With numerous options available, it’s essential to discern the providers who stand out among the crowd. Goscor has been a stalwart in the industry, weathering various economic climates, technological advancements, and market shifts. With its 40 years of industry experience and commitment to supplying industry-leading brands and bespoke solutions, it is a premier choice for businesses seeking reliability, innovation, and unparalleled service.
resulting in customers ultimately enjoying the lowest total cost of ownership over the lifespan of their equipment BBBEEE level 3, employing more than 1000 staff nationwide, Goscor has offices in all major centres within South Africa while boasting a significant dealer network in surrounding Southern African countries.
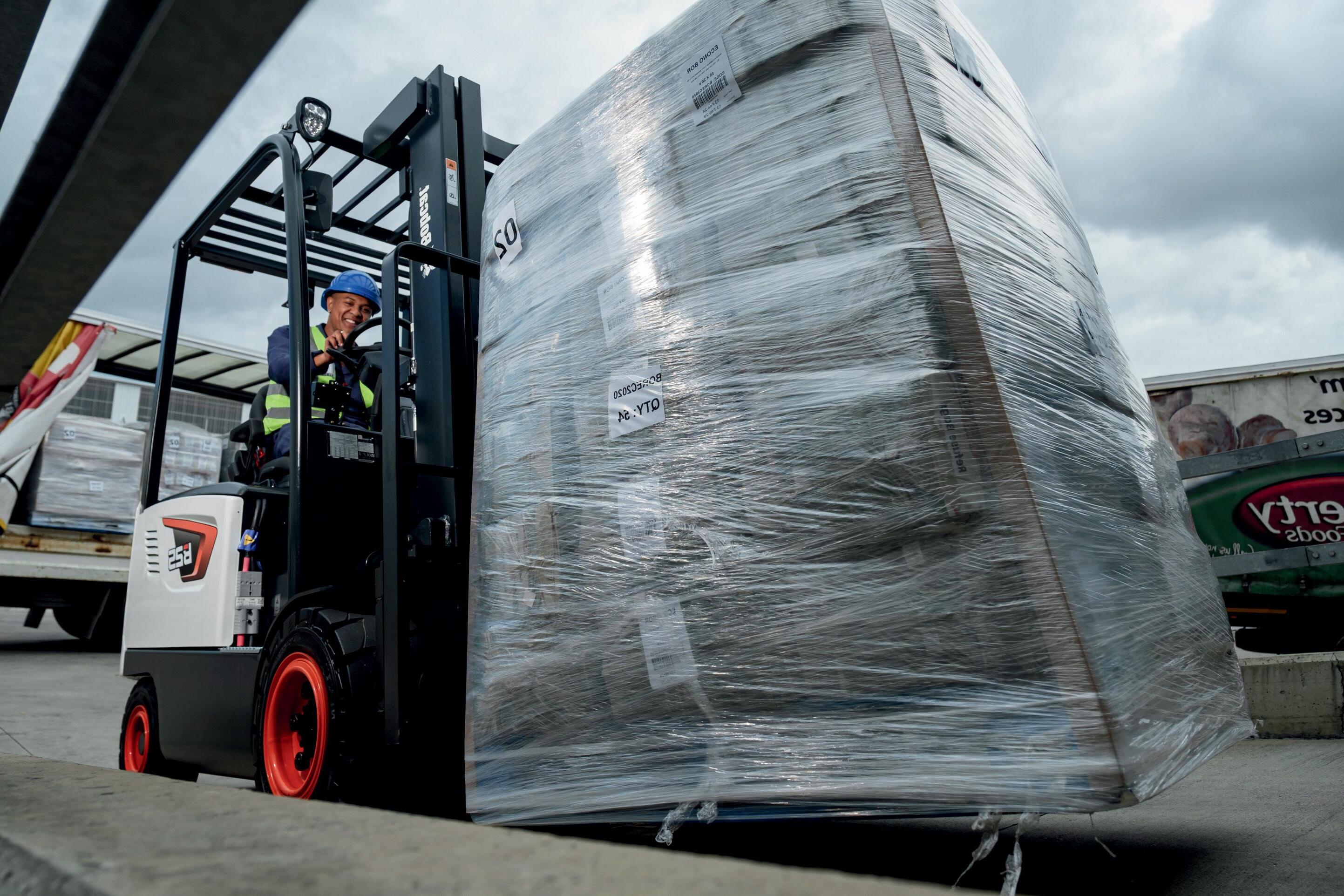
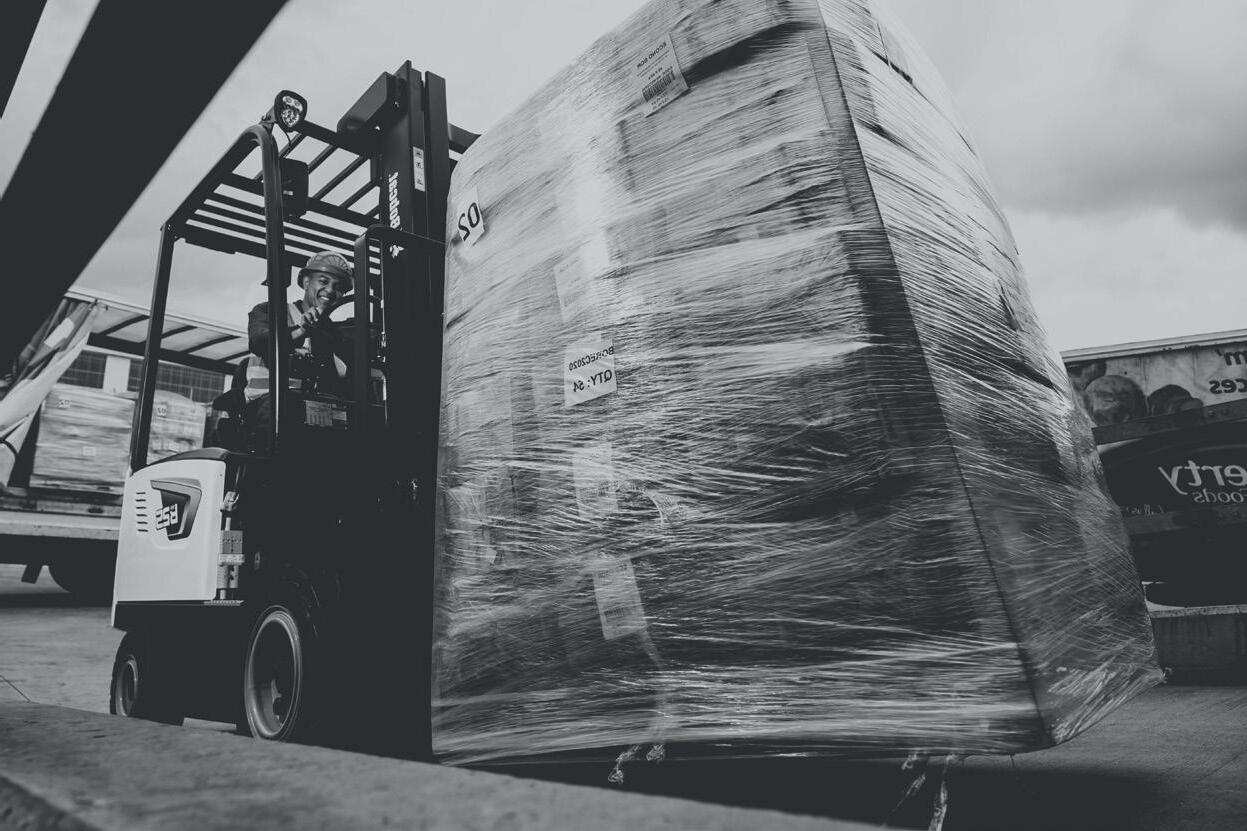
Goscor also stands as a proud member of the Bud Group, a services, manufacturing, and distribution group. Within the integrated framework of the Bud Group, the collective scale, relevance, and diversified business model empower the building of extraordinary businesses across four chosen platforms: manufacturing, industrial services, mineral beneficiation and energy solutions.
Bespoke solutions
Operating with the world’s greatest equipment brands available to the African continent, customers are ensured complete peace of mind. Skilled technicians, comprehensive parts holdings and a national footprint complement the extensive product range. GLT ensures 24/7 support for the equipment it provides,
Amidst diverse customer needs and unique operating conditions, prioritising customer-centricity and tailoring bespoke solutions is paramount for businesses striving to excel in today’s dynamic market. Very few customers are alike, and the ability to offer customers the flexibility they need is critical. Customers are empowered with a spectrum of choices, from outright purchases to flexible short and long-term rental arrangements, complemented by customisable maintenance plans, ensuring their diverse needs are met with precision and flexibility. As a renowned Material Handling Equipment (MHE) supplier, GLT stands out for its ability to tackle any operational challenge with optimal solutions, catering comprehensively to end users’ diverse needs. Recognising that no single piece of equipment can provide a complete warehouse solution, GLT offers a comprehensive array of brands, providing customers with a 360-degree turnkey solution from a single, trusted supplier.
revolutionise horizontal transport for retail operations. These innovative tugs promise safer, faster, and more efficient logistics processes, offering intelligent and sustainable solutions for all horizontal movements. With over fifteen years of experience, Movexx, a Dutch manufacturing company, specialises in providing custom-made solutions by leveraging their expertise in logistics processes. Their compact, manoeuvrable, and highly reliable electric tugs allow for effortless movement of loads weighing up to six tons, enhancing efficiency in retail operations without physical strain.
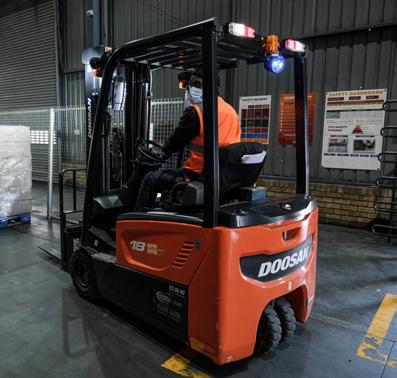
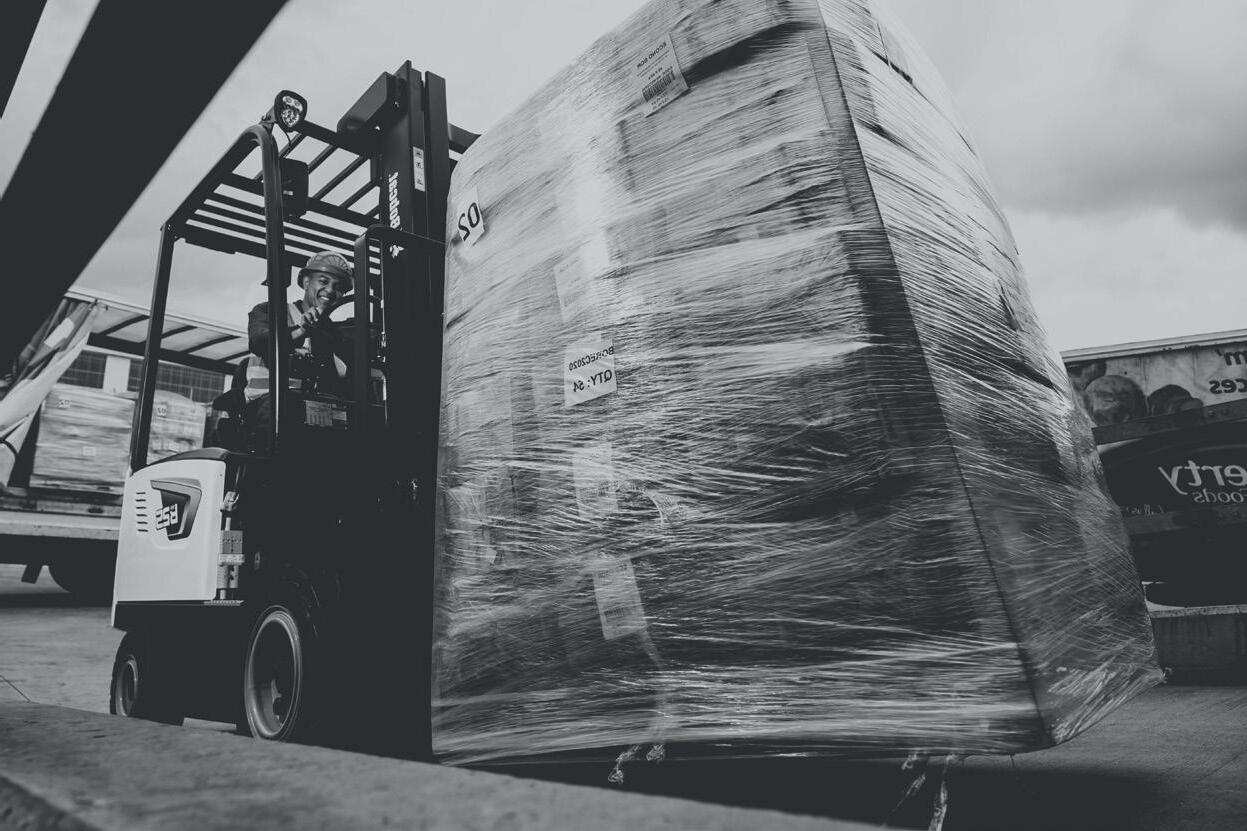
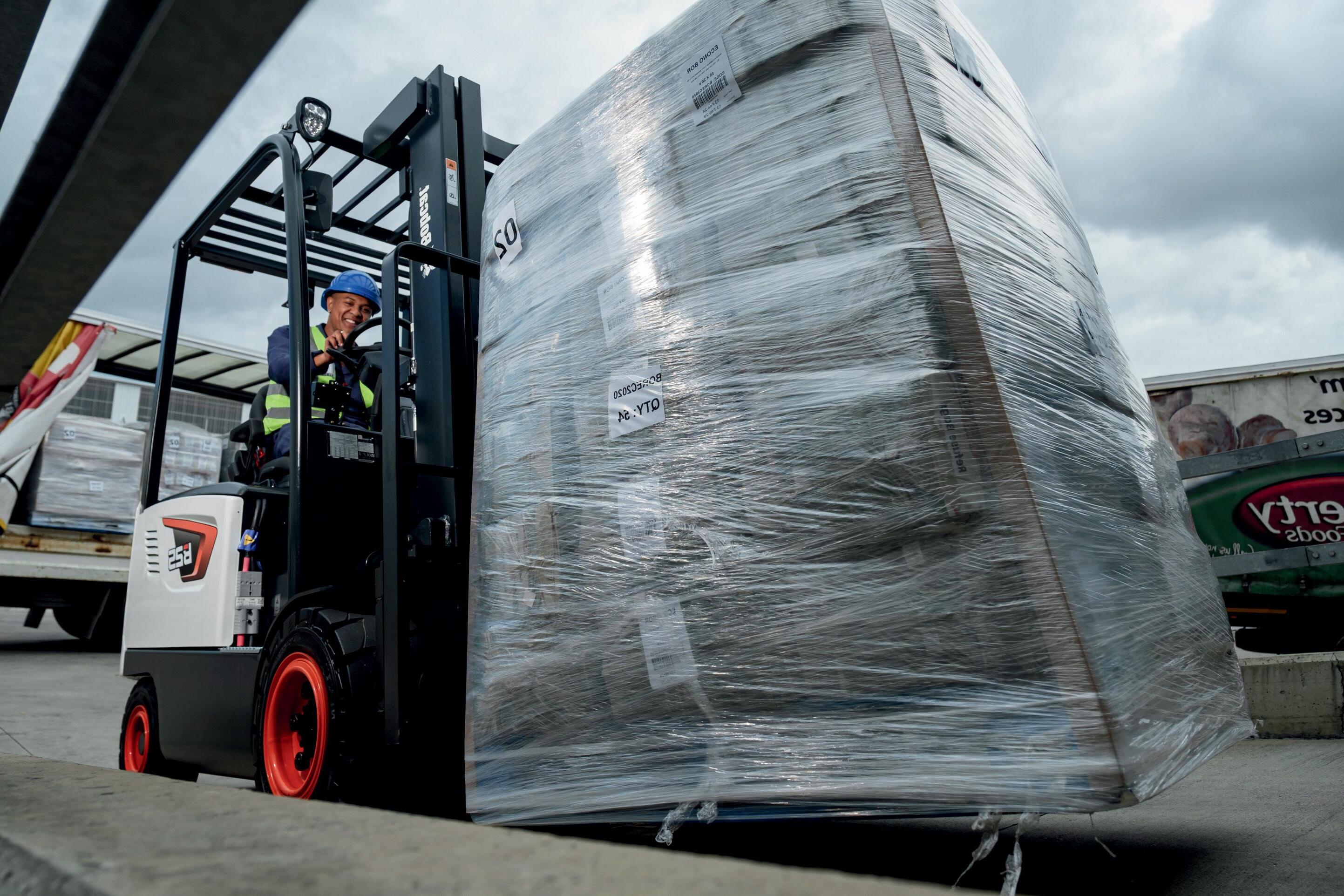
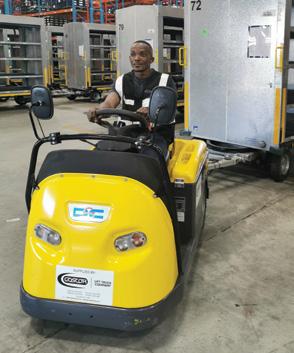
Crown electric warehousing equipment
GLT also offers Crown electric warehousing equipment, including a range of electric-powered lift trucks such as reach trucks, stackers, counterbalance and stand-up forklifts, and order pickers. Crown is recognised as a market leader in South Africa for its award-winning product design, advanced engineering, technology, and commitment to sustainability, ensuring customers benefit from top-notch quality and performance.
Bobcat Forklifts
Another viable option for customers is refurbishment, a service the company offers in recognition of challenging economic conditions. Refurbishing ex-long-term rental units, all refurbishments covering various forklift brands in the company’s portfolio are carried out in-house by experienced technicians. Emphasising quality and long-term utility, each component receives meticulous attention to enhance its lifetime and functionality.
As part of the giant Goscor Group of Companies, GLT is integrated into a diverse ecosystem, offering various solutions for end users. This includes cleaning equipment, earthmoving machinery, power products, and more. Additionally, the Group features its finance division, providing tailor-made financial solutions to cater to customers’ specific needs.
Movexx Electric Tugs
Expanding its product lineup, GLT introduced Movexx smart electric tugs to the South African market, aiming to
As a comprehensive material handling solutions provider, Bobcat offers a diverse lineup of IC, LPG, and electric forklifts, boasting capacities spanning from 1 to 25 tons. With a wide array of models, configurations, and exclusive features unmatched elsewhere, a forklift or lift truck is ideally suited to address your business’s unique material handling demands. Each model comes equipped with advanced safety features, impeccable ergonomic designs, and a commitment to delivering a lower total cost of ownership. When you invest in a Bobcat® forklift, you can trust that your equipment will endure the rigours of your operations, ensuring uninterrupted performance for the long haul. With its steadfast dedication to innovation, quality, and customer satisfaction, GLT stands as a stalwart in the materials handling sector, poised to enhance efficiency, safety, and productivity. Offering a comprehensive suite of products and services meticulously tailored to address the diverse needs of businesses, GLT remains a trusted and reliable partner in advancing logistics operations across Southern Africa.
Goscor Lift Trucks, +27 (0) 10 594 4339, lifttrucks@goscor.co.za, www.goscorlifttrucks.co.za
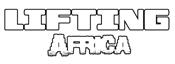

Occupational Health and Safety Act, 1993 Driven Machinery Regulations, 2015
The contractor, employer, user or manager should adhere to the legal requirements regarding the safe use of forklifts as set out in the Occupational Health and Safety Act and Mine Health and Safety Act.

All Forklifts require regular checking and testing at routine intervals. The result must be entered in a register and logbook designed for this purpose.
This Forklift Guide and Register includes detailed task descriptions, maintenance, inspection and load testing of the work and provision for control by the responsible person.
This is a statutory requirement. The Inspections must include all working parts of the forklift to be thoroughly examined and subjected to a performance test, as prescribed by the standard to which the forklift was manufactured and, or the standard incorporated, which is SANS 10388 – “The inspection and testing of lift trucks”, by a person who has knowledge and experience of the erection and maintenance of the type of lifting machine involved or similar machine.
Definitions
“Lifting Machine” means a power driven machine that is designed and constructed for the purpose of raising or lowering a load or moving it in suspension, but does not include an elevator, escalator or hand powered lifting device.
In these Regulations, “the Act” means the Occupational Health and Safety Act, 1993 (Act No. 85 of 1993), and any word or expression to which a meaning has been assigned in the Act shall have the meaning so assigned, and, unless the context otherwise indicates “chief inspector” means the officer designated under Section 27 as chief inspector, and includes any officer as chief inspector; “competent person” means a person who has in respect of the work or task to be performed, the required knowledge, training and experience and, where applicable, qualifications, specific to that work or task.
Provided that where appropriate qualifications and training are registered in terms of the provisions of the National Qualification Framework Act, 2008 (Act No. 67 of 2008), those qualifications and that training must be regarded as the required qualifications and training: and (b) is familiar with the Act and with the applicable regulations made under the Act: “ECSA” Engineering Council of SA “inspector” means a person designated under Section28:
“LMI Certificate” means a certificate issued by ECSA confirming the competency of the LMI
“LMI Scope letter” means a letter issued by ECSA confirming a LMI scope that he is allowed to load test “Lift Truck” means a mobile lifting machine, but does not include – (a) a vehicle designed solely for the purpose of lifting or towing another vehicle; (b) a mobile earth-moving machine; or (c) a vehicle designed solely for the removal of a waste bin.
“Lifting machinery entity” means a legal entity approved and registered by the chief inspector in terms of regulation 19; “lifting machinery inspector” means a person who is employed by a Lifting Machinery Entity and who is registered by the Engineering Council of South Africa in terms of the Engineering Profession Act, 2000 (Act No. 46 of 2000).
“Non-integrated work platform” means a basket or cage attached for use in conjunction with lift trucks to elevate persons so they can work at a height but that does not control the lift height of the platform or move the truck “safe working load” means the mass load applicable to a piece of equipment or system as determined by a competent person taking into account the environment and operating conditions; “training provider” means a training provider for lifting machinery operators approved and registered by
the chief inspector in terms of regulation 20 “SETA” means Sector Education and Training Authority
Mandatory Statutory requirements
The Lift Truck is required to undergo a thorough examination by a COMPETENT person, at intervals not exceeding 6 months, as per the Occupational Health and Safety Act 85 of 1993, Driven Machinery Regulations, 2015, sub-section (6).
The Lift Truck is required to undergo a thorough examination and performance test by an ECSA Registered LMI, at intervals not exceeding 12 months, as per the Occupational Health and Safety Act 85 of 1993, Driven Machinery Regulations, 2015, sub-section (5). This must be carried out in accordance with the manufacturer’s standard and the prescribed incorporated standard, which is SANS 10388, “The inspection and testing of lift trucks”.
Important note
a) DMR 18 sub-section 5 refers to 110% of safe working load being applied. This must only be applied to equipment that does not have a prescribed SANS standard. SANS 10388 is the prescribed standard for lift trucks and 110% overload MUST NOT be applied, as SANS 10388 does not permit the overloading of lift trucks, unless under exceptional circumstances and in the presence of an expert engineer. b) An LMI is not a professionally registered engineer otherwise known as a PR-ENG.
Every user of lift trucks is required to keep on their premises a register in which the user shall record the results and full particulars of any examination and performance test referred to in DMR 18 sub-regulations (5) and (6).
The User is also required to keep records of any modifications or repairs to such lift trucks. The user shall ensure that the registers are available at request for inspection by the inspector. This is as per DMR sub-section (7a) and SANS 10388 (8) “Alterations, modifications and major repairs”.
Every user of lift trucks that are leased is required at all times to keep on their premises a register in which the user is required to keep records of the latest applicable inspection and performance test, as per DMR 18 subsection (5) and (6), and service records not older than 12 months. The owner or lessor of the leased forklifts shall keep and maintain full service history records on their premises for at least 10 years. This is as per DMR 18 subsection (7 b), note (b) and SANS 10388 (9) “Reports and Records”.
Every user of Lift Trucks must ensure all personnel that operate the lift truck are specifically trained for the particular type of lift truck. The operators must have a valid license, as set out by the national code of practice. License codes vary according to the type of lift truck.
This license is referred to as a certificate of competence and must be issued by a training provider
that is accredited by the Transport SETA approved for the purpose, by the chief inspector. The training provider must be in possession of a valid approval certificate signed by the chief inspector. As per DMR 18 subsection (11).
Every user shall ensure that the Lifting Machinery Entity and Lifting Machinery Inspectors, appointed to undertake the inspection and performance test of any lift truck is competent to undertake such work and has the scope of “Lift Trucks” or “Fork Lifts” on their scope of competence issued by the Department of Employment and Labour for the Lifting Machinery Entity and ECSA for the Lifting Machinery Inspector. The Onus falls on the owner/user to ensure this is met at all times. If the entity or inspector does not have the scope of competence, the certification issued will be considered null and void. Should an incident occur the owner/user would be placed with unnecessary liability and will be seen as non-compliant.
Refer to LEEASA LME and LMI Vetting Guide available in soft copy on www.leeasa.co.za.
This will guide you in the vetting of service providers. For lift trucks utilising a lifting cradle (personnel cage) to carry personnel requires all operators to be certified to operate the lift truck with certification for the lifting cradle (personnel cage), as per the national code of practice, prescribed by the Occupational Health and Safety Act 85 of 1993.
Any non-integrated work platforms (personnel cage) should comply with SANS 583. This standard specifies the requirements for non-integrated work platforms (cradles) occasionally used on lift trucks to elevate persons performing specific tasks of short duration and where it is not practicable to use specially designed devices. The platforms are not to be used for production activities. No user shall permit any person to be moved by or supported with a lift truck, unless the lift truck is fitted with a lifting cradle (personnel cage) and is approved an inspector from The Department of Employment and Labour.
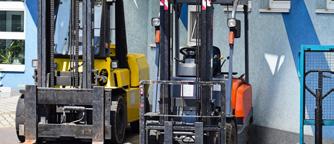
Note:
a) Non-integrated working platforms (personnel cage) must be inspected prior to every use by the responsible person. b) Non-integrated working platforms (personnel cage) shall be inspected by competent person in intervals not exceeding 6 months that will issue documentation confirming the safe use of the non-integrated working platforms. c) Nonintegrated working platforms that do not comply with this standard should be withdrawn from service.
As sumarized by LEEASA.
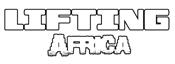

Operating a forklift safely
Operating new forklifts with latest safety features such as a seatbelt interlockers, overload lockout and speed controls can greatly increase operator and nearby pedestrian safety, whilst also reducing stock and capital equipment damage.
Operators must be qualified
• Individuals who have been trained properly and contain a license to operate the equipment should only do operating forklifts.
Appropriate clothing must be worn
• It needs to be ensured that operators wear the appropriate safety work wear; usually consisting of a hard hat, safety shoes and hi-visibility jackets.
• The work wear must be reasonably fitted as any loose clothing can get caught on machinery.
• Don’t operate/hold any of the controls when your hands have grease on them; it may cause them to slide off and cause an accident.
Examine equipment before use
• Operators must do a routine check of the equipment before driving them. Some things you should check for any faults are brakes, steering, controls, warning devices, mast and tyres.
• If there are any noted damages or problems management should be notified and the forklift should not be operated if it needs to be repaired.
• Hydraulic oil needs warm up.
• Always consider the ‘journey’s end’ of a load before picking it up. A convenient position of a load from pick up may not be convenient for stacking.

Starting up the forklift
• For safety purposes, it’s important for the operator to make use of the steps and hand grabs to seat themselves correctly in the forklift.
• Before starting the forklift it’s important to ensure all the equipment’s controls are in reach and the seat position and mirrors are adjusted to the operator’s needs.
• The operator should not start the forklift until they are correctly seated with their safety belt fastened and all parts of their body are safely inside the confines of the operators cabin or the forklift.
• Ensure hydraulic oil has warmed up.
Consider the surrounding environment
• Whilst operating a forklift you must pay attention and follow any work site rules and guidelines.
• The operator must only drive the equipment in the machinery’s designated roadways.
• Observe all signs, especially those on maximum permitted floor loadings and clearance heights.
• Be aware of the height of the load, mast and overhead guard of the forklift when entering or exiting buildings.
• Be careful when operating a forklift near the edge of a loading dock or ramp – the forklift can fall over the edge – keep a safe distance from the edge.
• Do not operate on bridge plates, unless they can support the weight of the forklift and load.

Operate at a safe speed
• Never proceed past the speed limit.
• Take corners and any turns slowly to minimise risk of tipping.
• Make any changes in direction or any stops gradually and slowly.
Avoid hazards
• Steer clear of any bumps or uneven ground surfaces along with slippery conditions.
• Steer clear of loose ground objects which could cause loss of control over the equipment or a load to move around.
• Use the horn when closing in on a corner or doorway/entrance and around people to alert pedestrians or other forklift operators of your whereabouts to avoid any unnecessary collision.
• Keep a safe distance from other trucks in case they move in an unpredictable manner.
• Make sure that you always have enough space to stop safely.
Ensure your load is stable and secure
• Check the loads carefully before moving them for stability and damage.
• It is important to ensure that the load is tilted back with the forks sitting low whilst transporting in order to increase truck stability.
• Check for any overhead objects before lifting or stacking loads.
• Do not lift or move loads that are not safe or stable.
• Make sure loads are correctly stacked and positioned across both forks.
• Stack the load on the pallet or skid safely and correctly.
• Use securing measures such as ropes or bindings if required.
Make sure you have clear visibility
• Operate the forklift in reverse when it improves visibility; except when moving up ramps.
• It is important to make sure you can see the racking clearly in which you are positioning your load.
• If visibility is poor do not continue driving; in some circumstances, you may need a lookout helper to assist you.
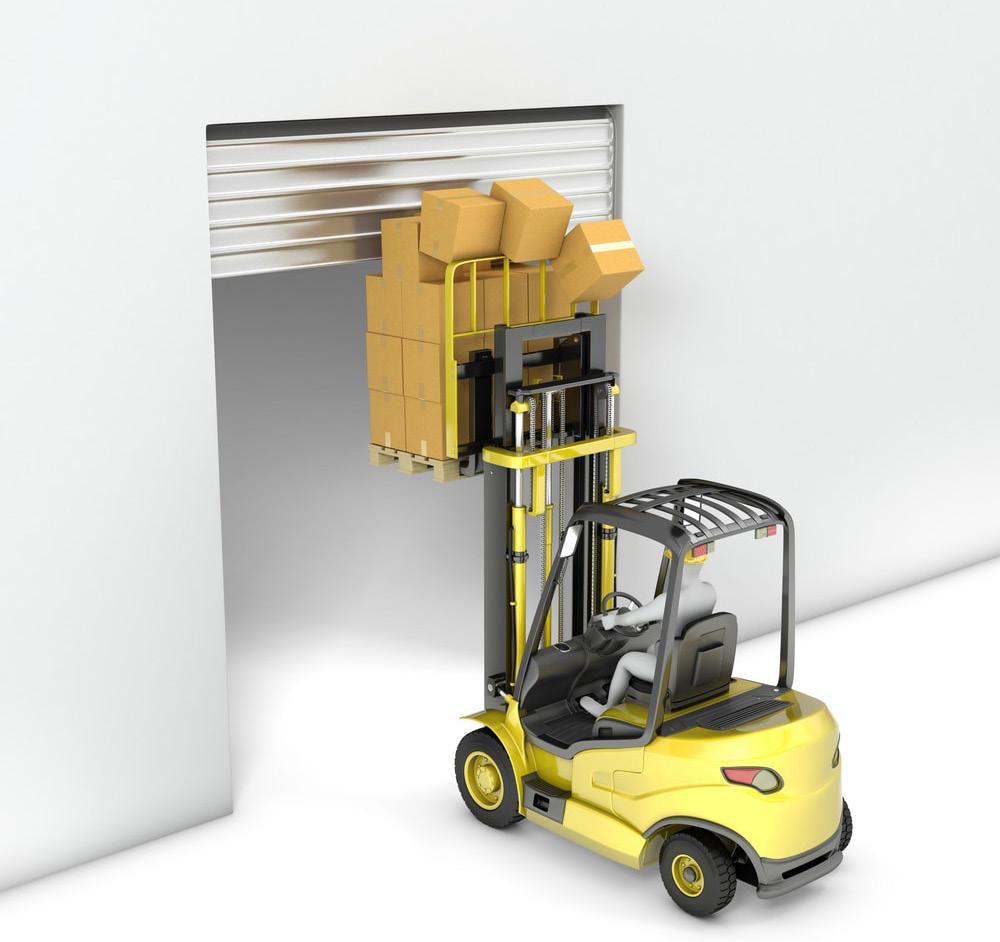
Forklifts are for carrying loads only
• If a person has to be lifted, use only a securely attached work platform and cage and follow the appropriate operating instructions.
Keep clear of the mast
• Do not authorise anyone to stand or walk under the load or forklift machinery – The load can fall causing injury or death.
• Keep hands and feet clear of the cross members of the mast – Serious injury can be caused if the mast is lowered while your hand is on it.
Driving on Ramps
• When driving up ramps’ move in a forward direction and down ramps in reverse, especially while carrying loads.
• Do not load or unload goods or turn whilst on a ramp.
FORKLIFT SAFETY
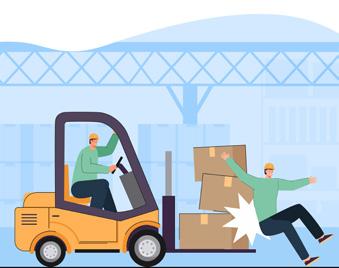
Ensure the forklift is not over-loaded
• Do not use the tip of the forks as a lever to raise a heavy load.
• Do not push a load with the tip of the forks.
• Know the capacity of your forklift and any attachments being used and never exceed this capacity.
• An overload can cause the rear tyres to be raised off the ground and may cause the forklift to tip over.
Ensure the load is evenly distributed
• Do not lift or move a load unless both forks are fully under the load.
• Do not lift a load with one fork. Use pallets and skids that can withstand the weight of the load.
• Do not use damaged, deformed or decayed pallets for holding loads.
Refuelling
• A forklift should only be refuelled or battery is charged at specially designated locations.
• Switch off the forklift.
• For IC engine forklifts, no open flame or sparks are permitted, and refuelling should take place in a wellventilated area.
When the shift ends
• After use ensure the forklift is parked in a designated or authorised area.
• Fully lower the forks to the floor and apply the park brake.
• Turn the forklift “off” and remove the key.
• Do not leave a forklift running whilst unattended
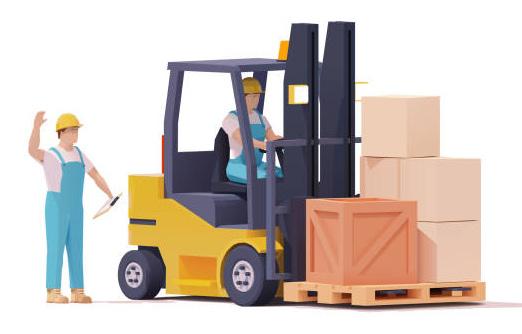
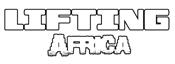

Inspections and load testing
Every company or owner of lifting machinery has a lawful obligation to have their lifting machinery load tested annually and inspected 6 monthly.
The Occupational Health & Safety Act, Act 85 of 1993, Driven Machinery Regulation requires that:
The Lift Truck is required to undergo a thorough examination by a COMPETENT person, in intervals not exceeding 6 months, as per the Occupational Health and Safety Act 85 of 1993, Driven Machinery Regulations, 2015, sub-section (6).
The Lift Truck is required to undergo a thorough examination and performance test by a ECSA Registered LMI, in intervals not exceeding 12 months, as per the Occupational Health and Safety Act 85 of 1993, Driven Machinery Regulations, 2015, subsection (5). This must be carried out in accordance with the manufacturers’ standard and the prescribed incorporated standard, which is SANS 10388, “The inspection and testing of lift trucks”.
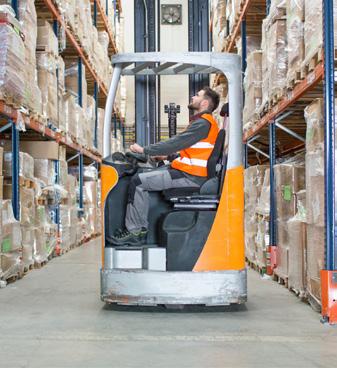
Some of the most common causes for failure during testing:
ITEM NON COMPLIANCE - REFERENCE SANS10388
Carriage Carriage wear, stoppers, cracks & excessive play etc
Chains Stretched, parts missing, side wear etc.
Data Plate No plate, wrong specs, info not legible etc.
Forks Heel wear, cracks, straightness, wrong capacity etc.
Horn Not working
Hoist Cylinders Leaking, uneven lift, bleeding back etc.
Hoses Leaks etc.
Load backrest No load backrest, broken, loose, cracked etc.
Lights Not working, broken etc.
Mast Channels Cracked, worn, bent etc.
Parking Brake Not holding
Safety Devices Not working, bypassed etc.
Tyres Worn, cracked through limit ring, chunking etc.
Every user of lift trucks is required to keep on their premises a register in which the user shall record the results and full particulars of any examination and performance test referred to in DMR 18 subregulations (5) and (6).
The User is also required to keep records of any modifications or repairs to such lift trucks. The user shall ensure that the register are available at request for inspection by the inspector. This is as per DMR sub-section (7 a).
Every user of lift trucks that are leased, are required at all times to keep on their premises a register in which the user is required to keep records of the latest applicable performance test & 6 monthly inspection, as per DMR 18 subsection (6), and service records not older than 12 months.
The owner or lessor of the leased shall keep and maintain full service history records on their premises for at least 10 years. This is as per DMR 18 subsection (7 b) and note (b).
Checklist to ensure the legality of your inspections and load test:
• The service provider, which is appointed, and is accredited with the Department of Employment and Labour as a Lifting Machine Entity (LME) and must have the relevant scopes to undertake the work. You can refer to LEEASA’s LME and LMI Vetting guide, available on soft copy from www.leeasa.co.za.
• The LMI performing the load test must be accredited by ECSA with the correct scope to undertake the work. You can refer to LEEASA’s LME and LMI Vetting guide, available on soft copy from www.leeasa.co.za.
Inspections and annual testing of lift trucks
When appointing a service provider to undertake work to certify lift trucks it is essential that you understand the following, of what is required of an inspector. Here are some points to be cognitive of:
• The inspector is required to undertake a thorough examination of the lift truck, as per SANS 10388, and this shall be performed according SANS 10388, prior to the commencement of testing. The findings of the inspector shall be documented in full English. The inspector shall have the correct measuring equipment such as, but not limited to; forklift chain gauge, fork calliper, laser or tape measure, vernier.
What is being checked during a lift truck inspection?
• Chains • Fork Arms
• Hydraulic System
• Braking systems – wear and functions
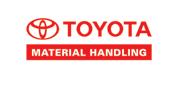
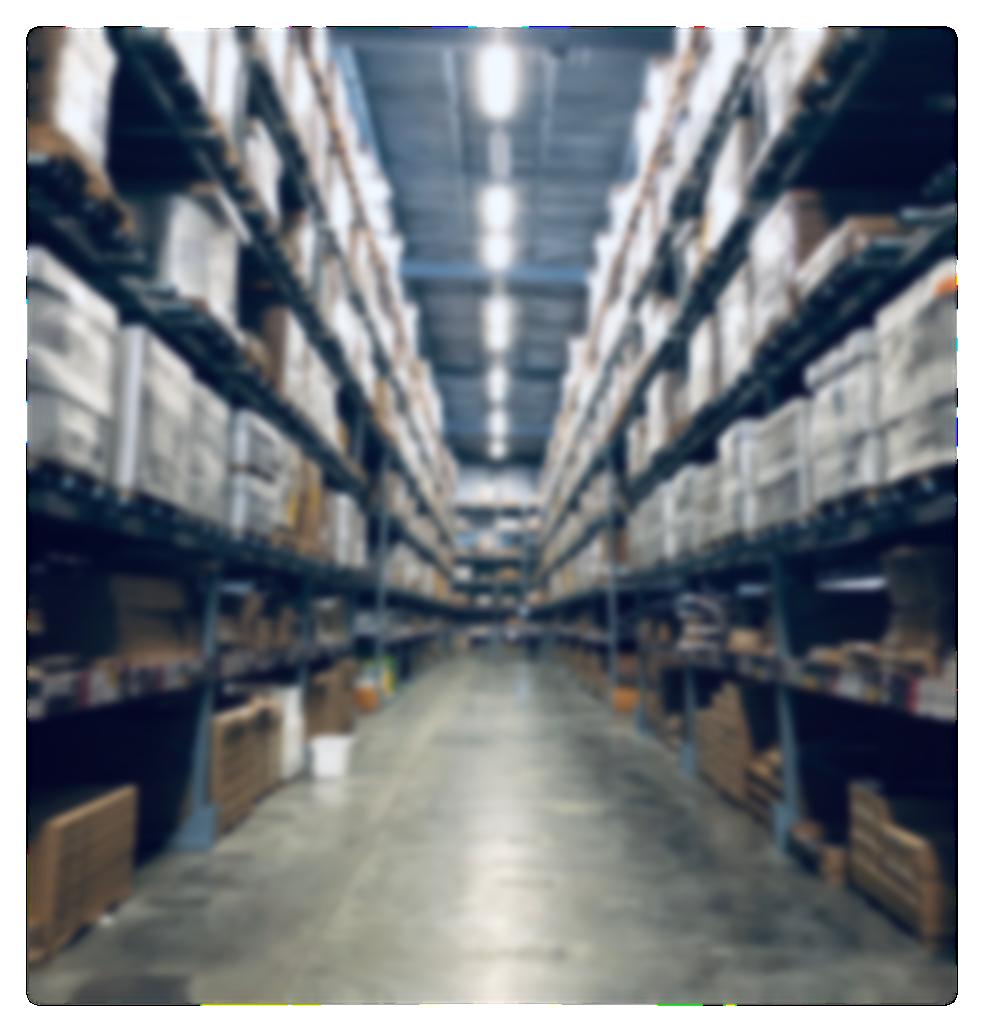
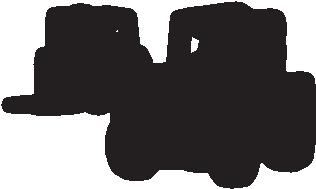
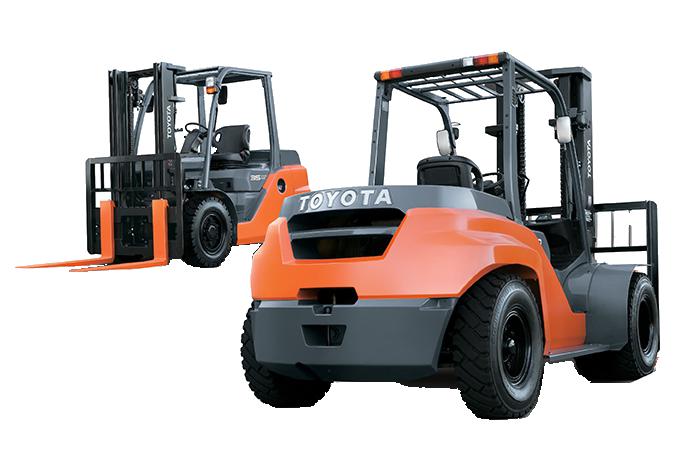

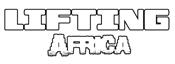

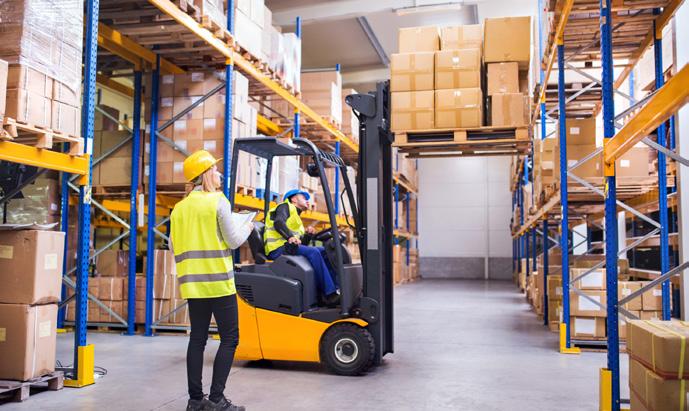
The method is incorrect and applied by utilising slings and a load cell to simulate a “load”.
Why we cannot evaluate this with the static pull method is because of the following:
• Stability can not be assessed when the lift truck is being pulled against itself on the mast or counterweight. When pulling an anchor point in the ground, natural creep will occur and once again the inspector will be unable to assess the stability of the lift truck.
• The load is being simulated by pulling an anchor point, counterweight or off the mast itself. Once the natural creep of the machine occurs, which is allowed and must be measured according to the manufactures specifications, the tension on slings will reduce and
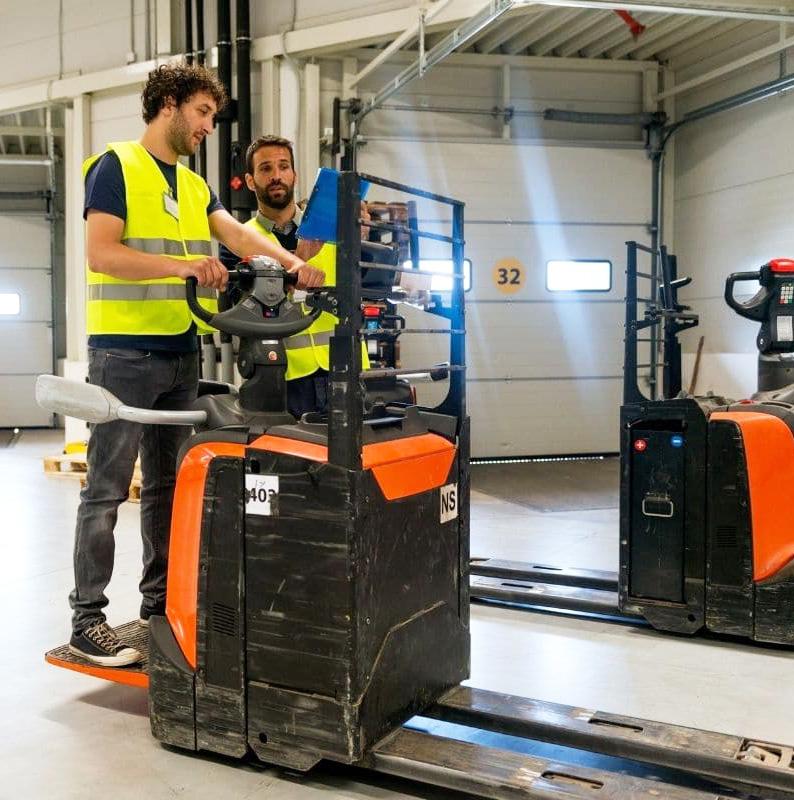
the natural creep will not be able to be measured, as the force will be reduced.
• The inspector is unable to assess the ability of the lift truck to sustain its rated capacity, through the full working range as per the load chart, as the load is simulated with slings that are different lengths, taking into account full working range requires the load to be lifted from the lowest point to the highest point, according to the load chart. While maintaining a standard load centre, which will be according to the manufacturers’ specification and visible on the data plate of the machine. The load must be applied from the bottom to the top of the working range of the lift truck. This is not possible using slings and a load cell. Why is this method found in the industry?
• The reason this method is used which is incorrect is because it is cheaper to transport load cells and slings than test weights.
• The entity undergoing the testing of lift trucks does not have test weights or the correct equipment.
A performance test must be conducted in such a way that every component of the forklift is placed under stress in order to determine the serviceability and safety of the forklift and its components.
In the event of any incidents and accidents occurring within the workplace and the respective forklift being without a valid forklift load test certificate, this could land you as a person or entity into serious trouble for non-compliance with OHSA and the Driven Machinery regulations.
This could mean being held liable, upon conviction, for a financial penalty or imprisonment for up to 12 months, as per DMR 18 sub-section 22.
As sumarized by LEEASA
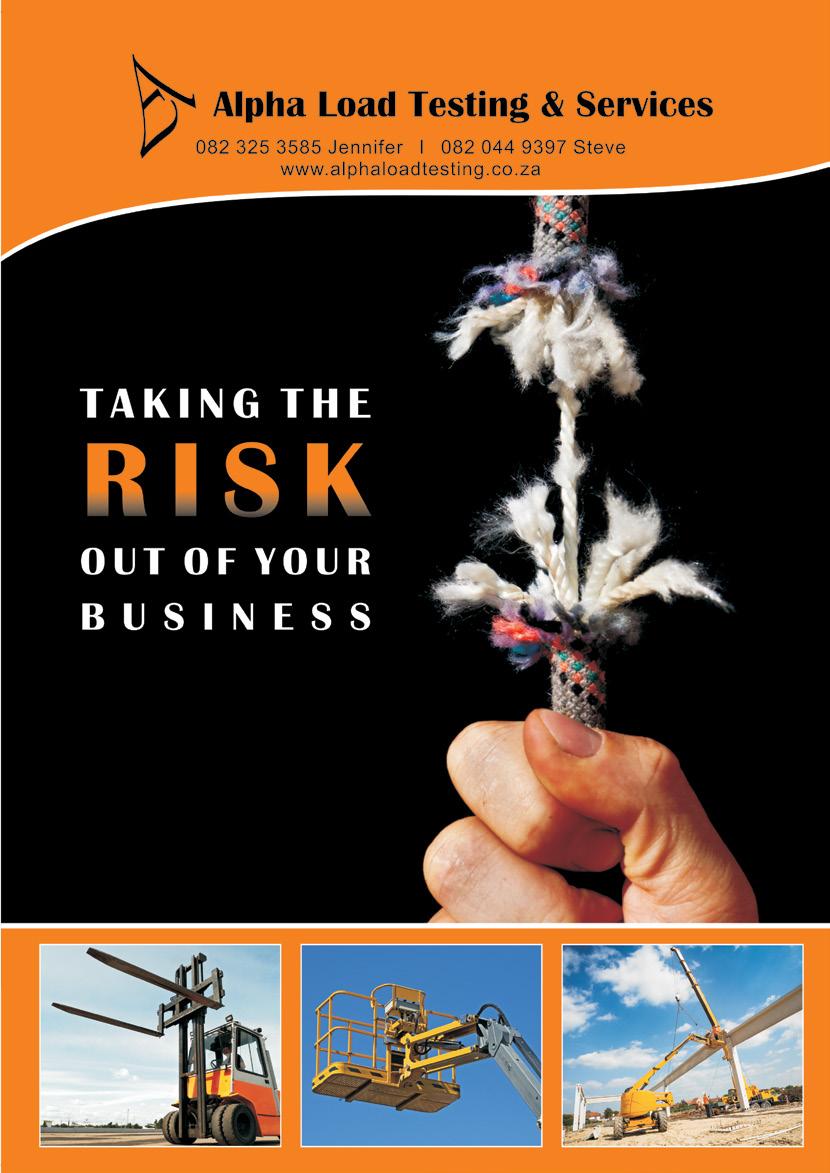
Basic forklift hand signals every operator should know
Forklift signals let operators communicate with spotters while moving heavy loads. In loud, cramped environments, these signals ensure clear communication with anyone behind the wheel of a forklift.
Every year, forklifts will get into a workplace accident. Hand signals for forklift operators play a key role in workplace safety.
According to SANS 10296 the requirements for hand signals are:
1. Only signals illustrated in this standard shall be used;
2. Misunderstanding should be avoided with clear and concise signals
3. Non-specific one-arm signals shall be acceptable using either arm (left or right indication is a specific signal);
4. The signaler shall
1) Have a clear view of the load or equipment;
2) Be clearly visible to the operator, and
3) Be in a safe position,
5. Only one person shall give signals to the operator. The only exception to this shall be the
6. The emergency stop signal;
7. Where applicable a combination of signals may be combined and used;
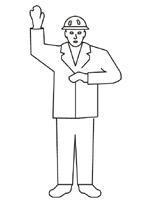
Raise one arm above the head, with the hand open and the palm facing forwards. Hold the other arm horizontally in front of the chest, with the hand open and the palm facing downwards.
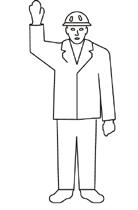
Raise one arm above the head, with the hand open and the palm facing forwards.
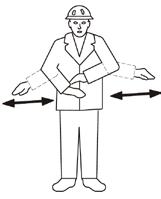
Hold the hands horizontally at waist level, with the hands open and the palms facing downwards. Repeatedly move the arms horizontally towards and away from each other.
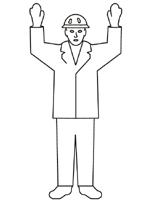
Raise both arms above the head, with the hands open and the palms facing forwards.

Keep both arms at the sides of the body with the forearms held vertically, both hands open, palms facing forwards. Repeatedly move the forearms up and down.
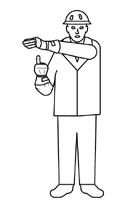
Use raising signal with one hand and other palm motionless on top of the hand that gives the signal.
LOWER THE LOAD AT A STEADY RATE
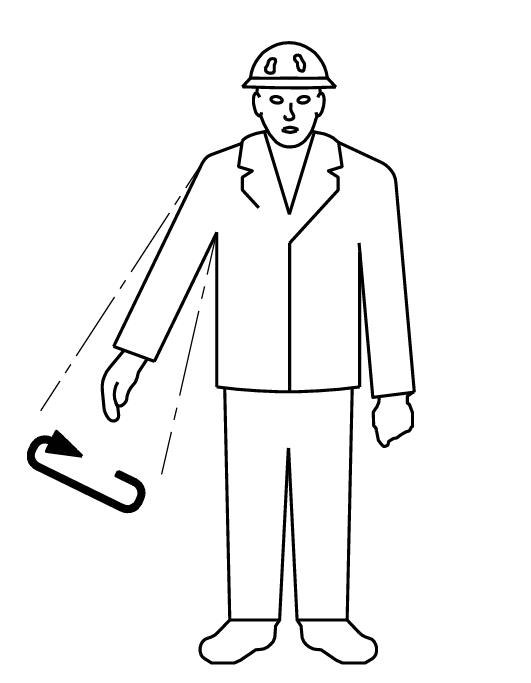
Extend one arm downwards but away from the body, with the hand closed and the index finger pointing downwards. Make small flat circles with the forearm.
LOWER SLOWLY

Use lowering signal with one hand with the other palm motionless below facing the hand that gives the signal.
INDICATING HORIZONTAL DISTANCE
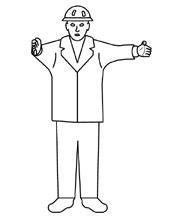
Keep both arms extended horizontally in front of the body with palms facing each other.
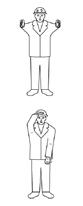
Keep both arms extended forward, parallel and horizontally, and turn 90 in the direction of turn over. TURN
OF FORKS
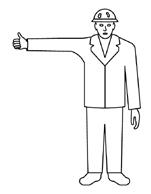
Keep one arm extended horizontally with the thumb up.
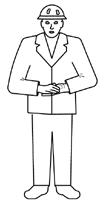
Rub palms in a circular motion against each other. After this signal, any other applicable hand signals shall apply.
TRAVELLING AWAY FROM ME

Keep both arms at the sides of the body with the forearms held horizontally to the front, both hands open, and the palms facing upwards. Repeatedly move the forearms up and down between the horizontal and the vertical positions.
INDICATING VERTICAL DISTANCE
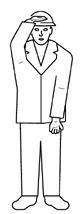
Keep both arms extended in front of the body, one above the other with palms facing each other.
OF FORKS
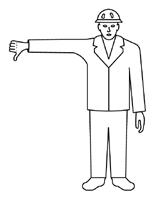
Keep one arm extended horizontally with the thumb down.
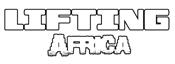

How to get your forklift license
FORKLIFTS LICENSE
If you’re looking to get your forklift license, now is a great time. The number of forklift driver jobs is escalating due to the increasing usage of counterbalance forklift trucks in the manufacturing and warehousing industries.
A forklift is a lifting truck that uses forks or other attachments for transporting goods over short distances. It is used for loading and offloading. You can apply for a course at a forklift training school to acquire an operator’s license and certificate.
Forklift training school
The best forklift schools are accredited and recognized by TETA/CETA to provide forklift safety training.
In order to get your forklift operator’s license, you must receive:
• Formal instruction
• Hands-on training and evaluation
• Certification
Formal instruction
“Formal instruction” simply means classroom teaching. It can consist of a “lecture, discussion, interactive computer learning, video, and/or written material” But the instruction must also cover certain topics to be considered comprehensive.
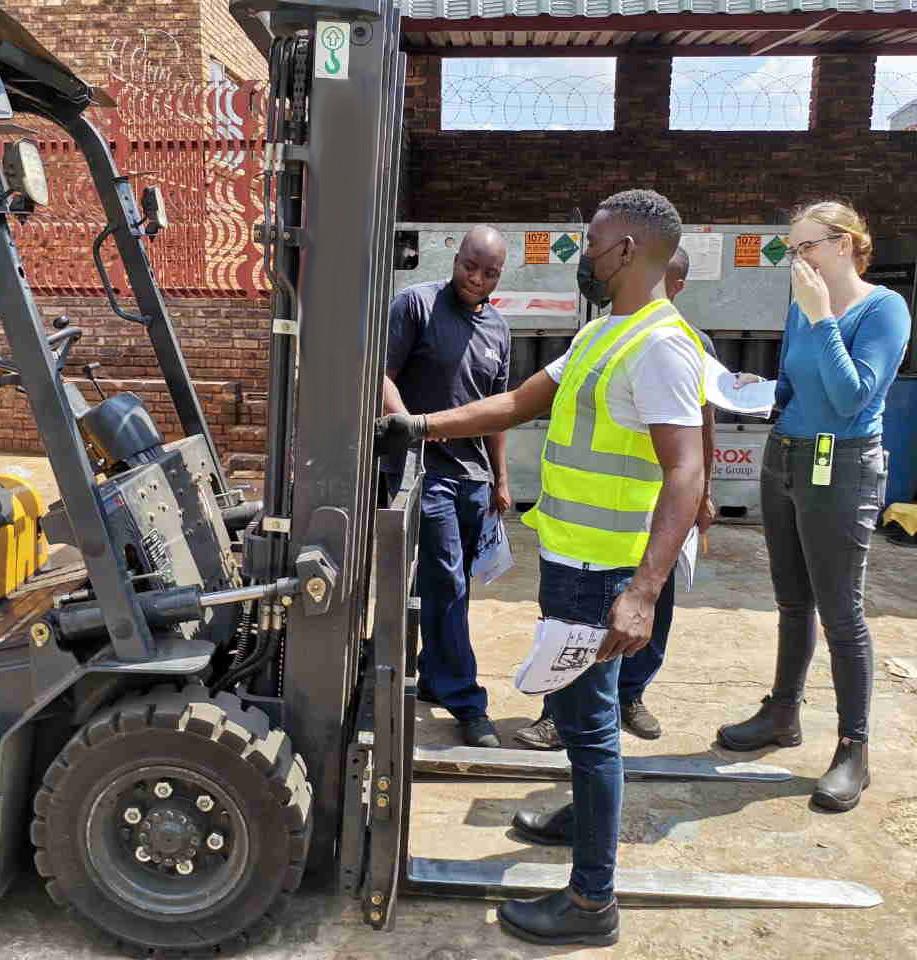
Basically any training program should cover:
• How to operate the different types of truck the operator will be using (instructions, safety precautions, limitations, etc.)
• Forklift capacity, stability, steering, maneuvering, and visibility
• How to construct, transport, stack, and unstack loads
• Pre-shift inspections and any maintenance the operator will be required to perform
• How forklift attachments work
• The dangers of operating in confined/hazardous
spaces and the necessary precautions drivers should take when doing so
• How to refuel (internal combustion trucks) and/or charge batteries (electric trucks)
• How to safely operate a fork truck on different surface conditions, ramps, and slopes
• How to work safely around pedestrians in the workplace
Hands-on training and evaluation
This portion of training must consist of “demonstrations performed by the trainer and practical exercises performed by the trainee” In other words, you must be shown how to actually operate a forklift and also be observed doing so.
Certification
To become a forklift certified driver, you should attend the training in one of the accredited skills development providers. You should apply for the 242974 SAQA Unit Standard titled “Operate counter-balanced lift truck” or the 244365 SAQA Unit Standard titled “Lift and move material and equipment by means of a forklift”. After the training, the school assesses you to determine whether you are competent. By the end of the forklift operator training course, you should be able to operate a counter-balanced lift truck safely, conduct pre and post inspections, and handle the loading and storage of freight. You will get a forklift license after the training that allows you to operate the machine. Forklift training and certification take 1-2 weeks.
Forklift license renewal
A forklift license expires after two years in South Africa and can be renewed in a day. You might be required to drive a forklift during the reassessment.
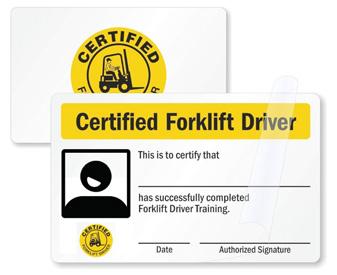
This process is called recertification. Your ID, old forklift license, and certificate are required when renewing your license.
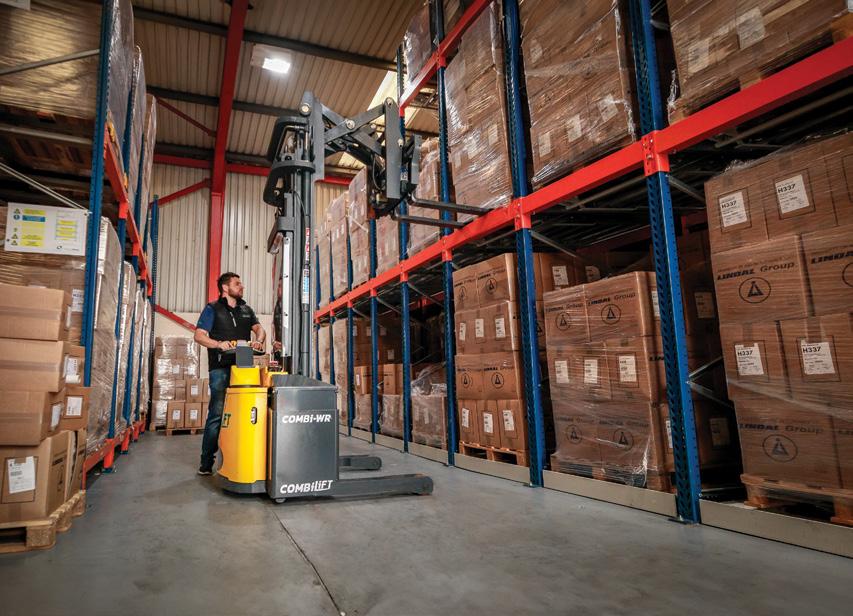
COMBI SAFELIFT
Combilift’s new product, the Combi SafeLift, is an antioverload device that prevents a load from being lifted if the forks are not fully engaged in the pocket or if the load exceeds the forklift-rated capacity, avoiding the pitfalls of potential overloading and its serious consequences.
The lift will cut-out if there is a risk of overloading or the forks are not fully engaged, an audible alarm will warn the operator, and the “traffic light” load moment indicator, which is fitted to the dashboard in the cab, will illuminate in red.
COMBILIFT PEDESTRIAN FORKLIFT TRUCKS: THE COMBILIFT PATENTED TILLER ARM
Combilift’s stackers and pallet trucks are equipped with the award-winning, patented tiller arm, which allows the operator to stand clear of the rear ‘crush zone’ behind the machine.
The side-operated function, made possible by Combilift’s tiller arm, allows you to drive and steer the unit from the side and provides excellent visibility of the product, rack, and aisle enhancing overall safety, and efficiency.
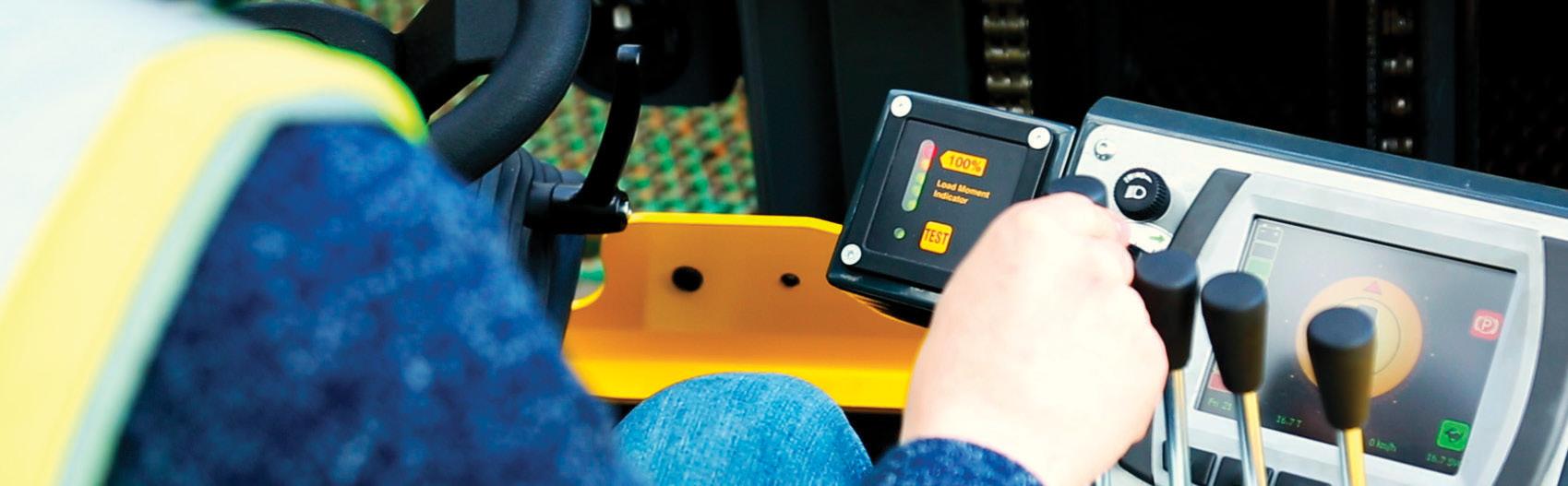
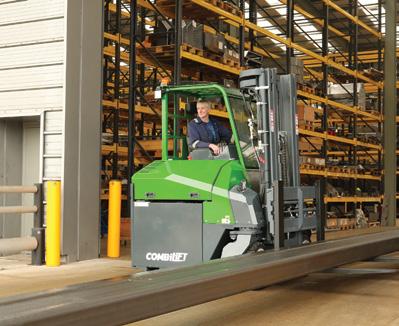
MULTIDIRECTIONAL - COMBI-CB & C-SERIES
The Combilift multidirectional range (Combi-CB & C-Series) has been designed with a very low center of gravity. This feature allows you to travel with your load low to the ground and eliminates the need for traveling with elevated loads, even when negotiating around machinery or any other obstacles that may be on the forklift’s path.
Additionally, they have the ability to quickly change the direction of their wheels and move in any direction. This 4-way movement gives the Combi-CB and C-Series the versatility to transport long loads through narrow doorways and around objects with confidence and utmost safety.
CONTACT US TODAY
To find out how Combilift can help you unlock the safest operations.
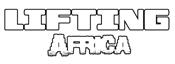

Should you buy or rent a forklift
There are pros and cons for buying and renting. It’s a business individual needs and operations that determine if you should rent or buy.
How many forklifts do you run in a day?
The answer to this question will make it clear if you need to buy or rent a forklift. However, there is a number of other variables that should be considered before you rent/buy forklift. These factors include evaluating your financial capabilities, and cost of renting v/s ownership among other factors. With all these different variables, it’s best to understand the pros and cons to help you decide which is better for your business needs.
Pros of buying a forklift
Ownership
Once the sale is complete, you will own the forklift, so you can make any modifications necessary. Maintenance is your sole responsibility, which means you have to ensure problems are fixed immediately. You do not need to wait for the forklift rental company to address mechanical problems or need permission to make modifications. Since you are the owner, you can sell the forklift once you are done with it, giving you an opportunity to recover some of the initial cost.
Tax incentives
SARS allows you to fully deduct the cost of some of the newly purchased machinery in the first year. If your forklift fails to meet the threshold, you may file for depreciation deduction for it.
No usage limits
Since you own the forklift, you are free to use it at any time without any obligations. With a rental, you are generally billed on the number of hours you us the lift. Your own employees will also have a better opportunity of mastering it since it is at their disposal any time.
Cons of buying a forklift
Higher initial cost
You will be required to meet a higher initial cost that
may be difficult to budget. You may find it also difficult to pay for the forklift all at once. The higher initial cost may make it impossible to buy the model you want and may force you to buy a lower-cost option.
Maintenance cost
You are solely responsible for all maintenance cost, and this can be high depending on the mechanical issues at hand. You could end up burdened with a broken forklift that you cannot sell or return.
Does your forklift warranty cover repairs? Keep an eye to know for how long it is covered.
Getting stuck with an outdated model
Even though ownership is probably the biggest advantage to purchasing a forklift, it can also be the main disadvantage. If you buy a high-tech forklift, you run the risk that the machine may become technologically obsolete down the road.
What happens when a forklift becomes technologically obsolete? You will be forced to buy a new forklift long before you had budgeted for.
Pros of renting a forklift
Flexibility
Renting a forklift gives your business significant flexibility with its operations. If your business is experiencing a decline in business or rapid growth, you can easily remove or add a forklift rental from your fleet.
Predictable monthly spending
Some rental companies include the cost of forklift maintenance as part of the monthly rental fee. This is known as the maintenance package.
What is the benefit of buying a maintenance package? It makes it easy for you to budget since you do not have to deal with any unpleasant surprises from forklift breakdown.
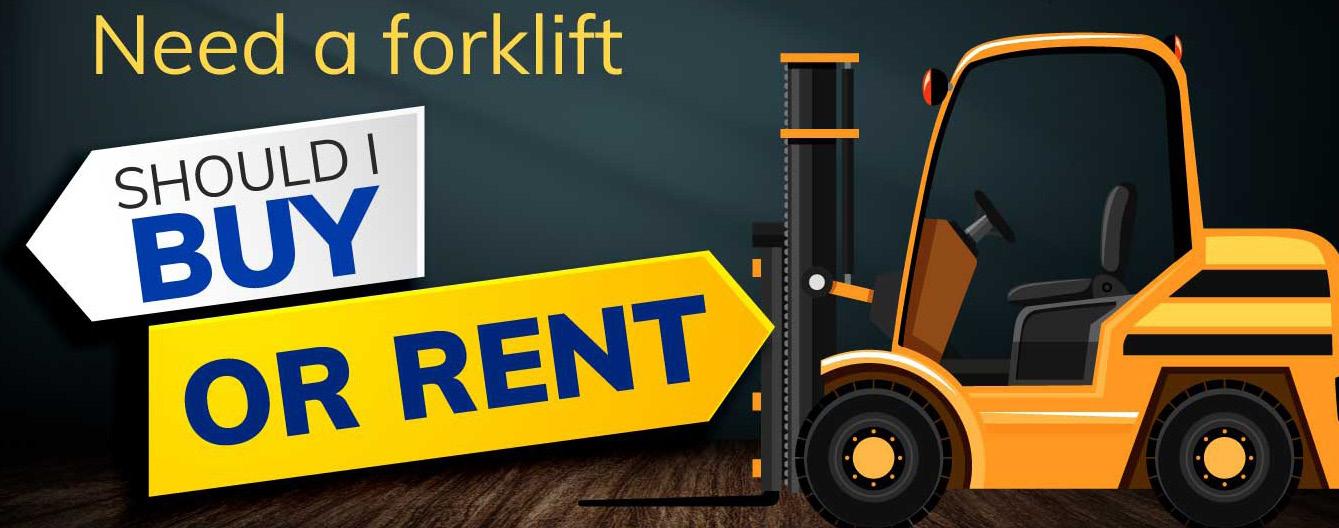
Test new equipment
By utilizing a rental program, you can test new models without having the obligation to buying it. After the rent term, you can decide whether to buy your own or rent it once more.
Improved productivity
Most rental programs have frequent replacement schedules aimed at reducing the average age of their client’s fleet.
This gives you an opportunity to have relatively new fleet, hence reducing downtime and boosting the likelihood of peak efficiency.
Regular equipment replacement
Renting allows for regular equipment replacement. This means you have a chance to use newer models of forklifts. Your employees will enjoy the safety and productivity benefits associated with newer models.
Lower initial costs
Renting helps your business benefit from the high performance of newer technologies without incurring the cost of buying it. If your business is new, you do not have to incur the high cost of buying forklifts.
This flexibility makes it easy to scale your business and offers you room to make adjustments. If your needs change at any given point in time, you can easily request for a different type of forklift.
Cons of Renting a Forklift
High monthly cost
Renting a forklift is likely to have a high monthly cost compared to buying a forklift. The rental company charges for their equipment since they incur the cost
BUY OR RENT FORKLIFTS
all these expenses and that is why the monthly fee of renting forklift is usually higher.
It doesn’t cater to specialised needs
A forklift’s rental company usually supplies the most common types of forklifts. What happens if you have a specialised need? You will have to buy a forklift.
Where is your business located?
Have you considered the location of your company before deciding to rent? If you don’t have a rental provider near you, you may incur huge transportation costs for delivering and picking up the forklift. Therefore, it is advisable to buy your forklift if your business’s location is a challenge.
There are allowable hours of usage
Some rental companies specify the maximum usage hours. What happens if you exceed a maximum number of hours allowed?
Violation is likely to attract penalties. Fully understand every Pro and Con before renting a forklift Considered alone, any of the above pros or cons could be the determinant factor in your decision.
However, you should take each pro and con into consideration and fully understand each before renting a forklift or buying.
That means, for instance, comparing the relative cost to your business needs or your potential maintenance services might outweigh the cost of your location (or vice versa).
Whatever your decision, just ensure you have a committed forklift rental partner who will make your rental experience more beneficial. Are you looking for
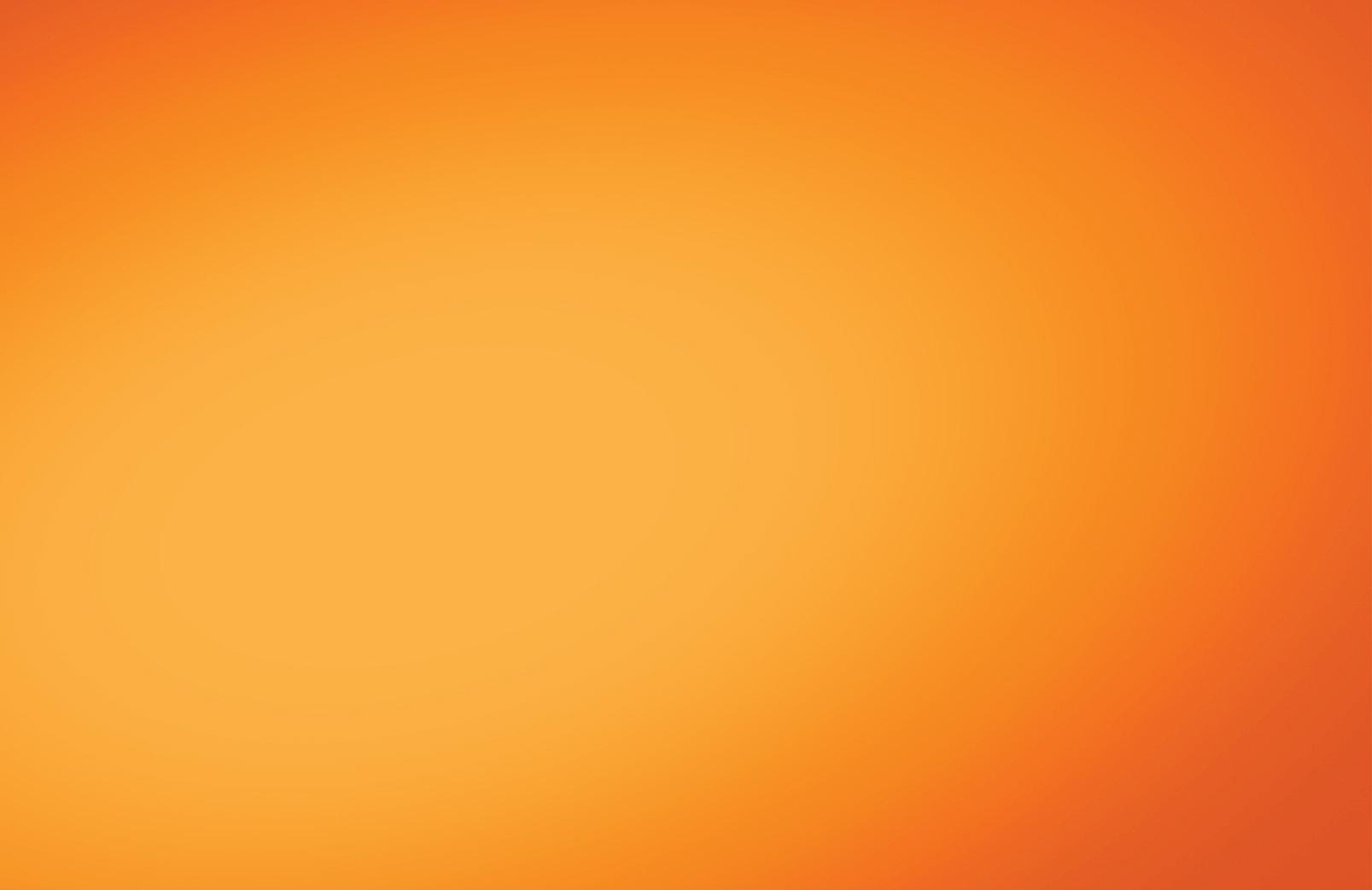


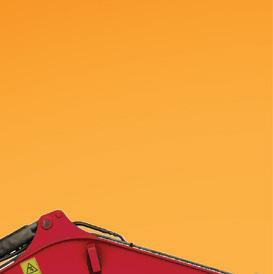
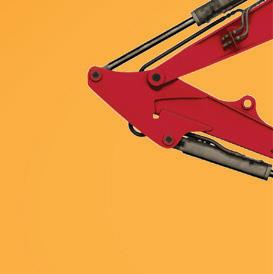
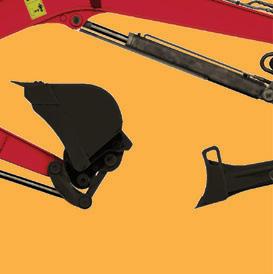
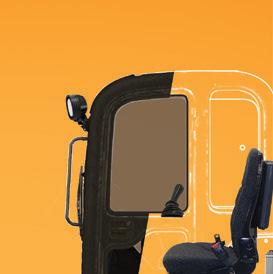

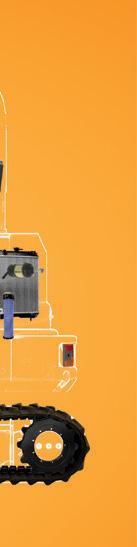
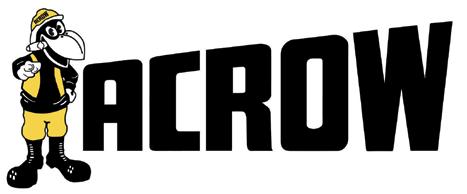


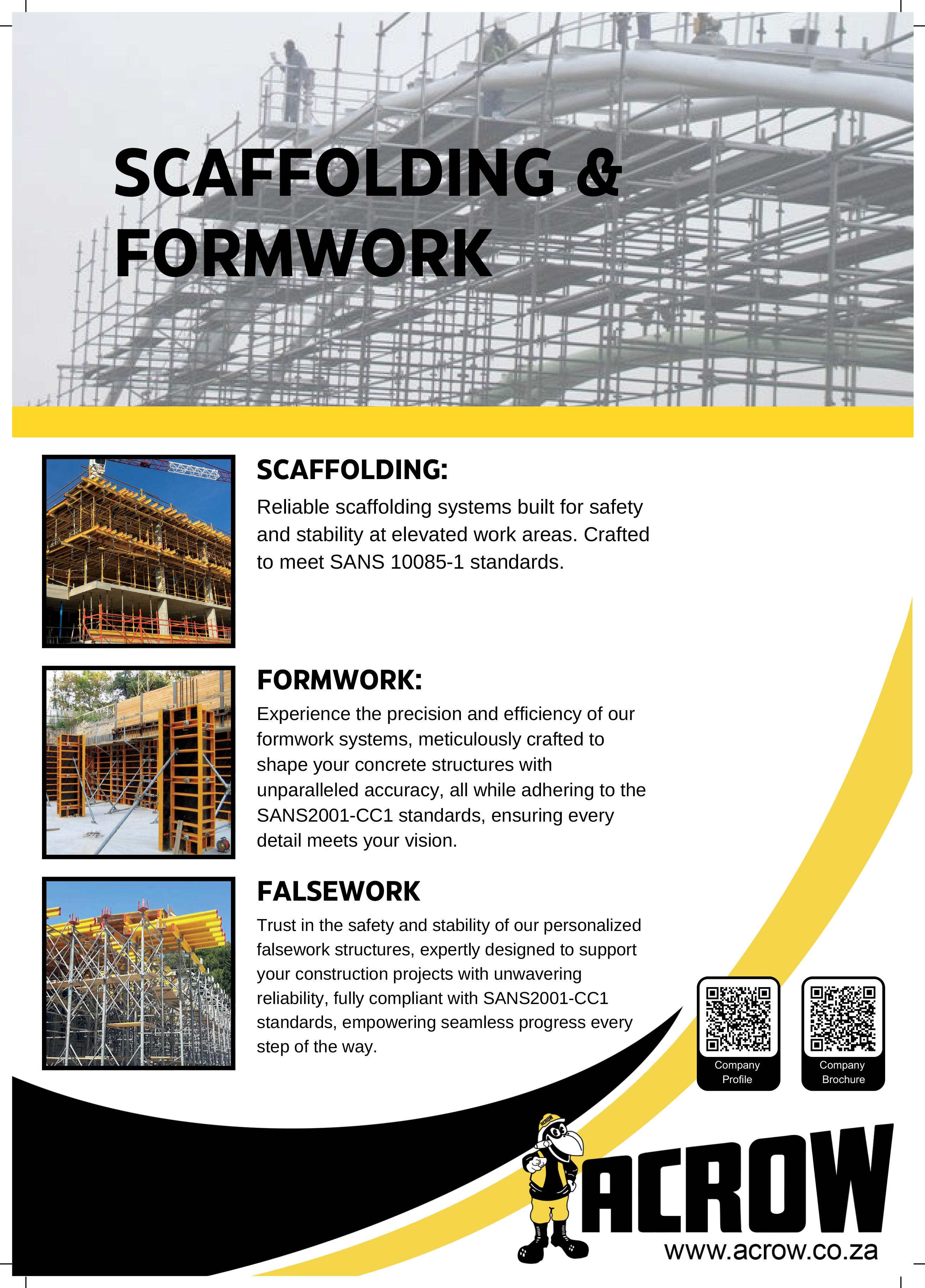
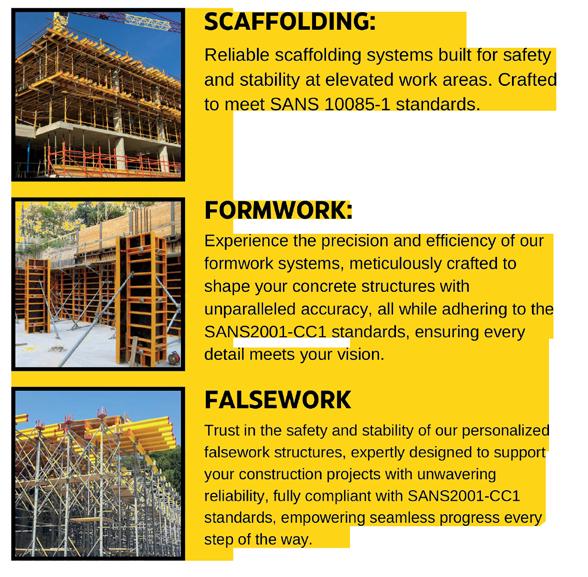
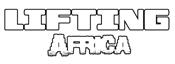

Do’s and Don’ts on a forklift
Workplace safety depends on a combination of factors. Attentive supervision helps. So does comprehensive training, with a keen eye toward DMR 18 rules & regulations. But at the end of the day, safety is ultimately determined by each individual.
And that means forklift drivers should act in the best interests of total job safety. Sure, performance matters, but safety is the most important part of day-to-day forklift driving.
One of the most important parts of safe forklift operation is training. Without proper instruction, operating powered industrial trucks (forklifts, pallet jacks, man lifts, etc.) is a dangerous undertaking. Accidents and injuries are bound to happen without a comprehensive training program in place
What to do and what not to do on a forklift
Safe forklift driving is all about what to keep your eye on – and also, specific things to avoid.
Forklift safety do’s: tips & tricks for drivers
When it comes to forklift safety, there are many things that lift operators should do day after day, such as:
Do ensure forklift load is secure, especially on inclines and other tricky surfaces. If you operate forklift outside, pay attention to the terrain conditions, especially when it’s raining or snowing.
Do travel with a load at axle height. By keeping the load at axle height, a forklift operator can minimise the risk of an accident.
Do carry loads with the lift’s forks tilted back. Forklifts are top-heavy, so you need to ensure that the lift’s forks are approximately 15 – 25cm above the ground to avoid potential ground hazards.
Do use three points of contact when getting on or off a forklift. Use two hands and one foot or one hand and two feet as you climb up or down a lift. In addition, you should always face the lift any time you enter or exit.
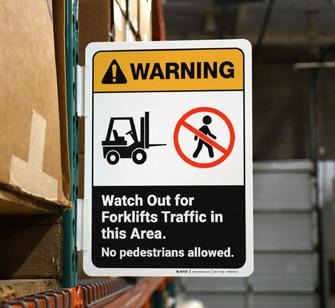

Do wear the correct clothing. If you’re driving outdoors in the winter, hats, gloves & extra layers always help. Don’t think you can brave the cold or harsh elements – a distracted forklift driver is more susceptible to accidents!
Do wear a seatbelt. Buckle up any time you use a lift. Because, if you fail to do so, you risk falling out of a lift, particularly if you are using the lift on bumpy terrain.
Do follow your company’s safety guidelines. Established policies & procedures are in place for a reason. They work.
Do take your scheduled break. Fatigue is another big factor in workplace mishaps. Tired forklift drivers are more dangerous forklift drivers. It’s all about avoiding distractions and keeping focus – see “correct clothing” above.
Do get a feel for your surroundings. If you’re working in a new area, take a quick inventory of blind spots, entries & exits, pedestrian walkways and more. The great unknown is never a good place to operate a forklift.
Forklift safety don’ts: what not to do on a forklift
Now that you have a good idea of forklift do’s, it’s time to learn about some forklift don’ts. Don’t carry or raise loads while the lift is moving. Only raise or lower loads when a forklift is stopped. Also, loads should never be raised or lowered while a forklift is turning.
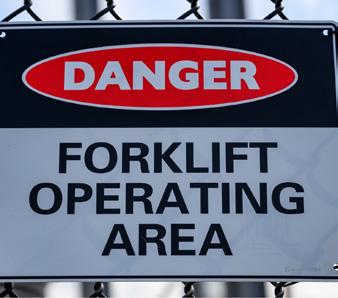
Don’t exceed a lift’s rated capacity. Weigh a load before you use a lift to raise or lower it. Under no circumstances should a load exceed the lift’s rated capacity; otherwise, if the load is too heavy, it may cause a forklift to tip over.
Don’t use a forklift if it does comply with operational standards. Use an inspection checklist to verify the quality of a forklift and ensure that it meets DMR18 standards. If a forklift is not up to code, the lift should be taken out of use until it is repaired.Don’t leave a forklift unattended. Remember, anyone can access an unattended forklift, which can lead to an accident.
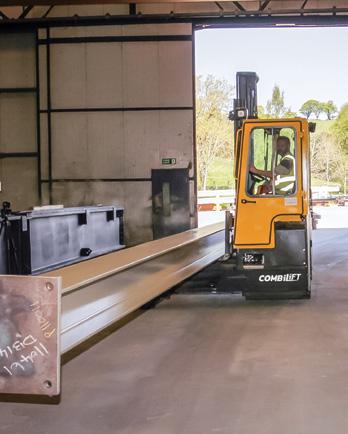
Don’t skip forklift maintenance. Many accidents are the direct cause of poorly maintained lifts. Loose hoses, bald tires, non-working safety signals and more – when talking about forklift do’s and don’ts, maintenance should be at the top of your list. And speaking of lists, keeping a well-documented checklist of forklift maintenance activities is a great way to ensure all safety checks are accounted for!
Don’t forget your forklift certification renewal. If you’re training credentials are about to expire, make sure you go through the correct protocol for the renewal certificate. Don’t ignore spills, poor lighting and other hazards.
Safe drivers always alert their co-workers and supervisors to potential pitfalls.
Don’t think everything’s a one-man job. Sometimes, having a spotter or “eyes in the back of your head” can help avoid accidents.
The buddy system works! Many accidents have been caused by not using a spotter or other driver to help with heavy loads, blind spots, and other dangerous scenarios.
Don’t be a follower. Proper safety requires leadership – the willingness to speak out when you think something’s wrong, and also going the extra mile.
If you’re serious about safety, take charge of the situation. Form a safety committee. Sign up for training. Be proactive!
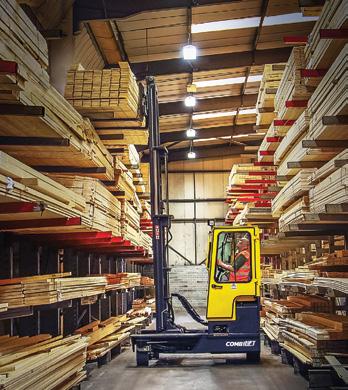
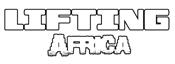

The different types of forklifts
Forklifts are an essential part of many industries and warehouses, making it easier to move heavy items. There are a few different types of forklifts available, so you’ll need to know which one is best for your needs. In this article, we’ll discuss the different types of forklifts available and what they can do for you.
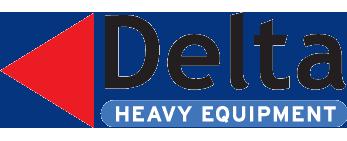

Counterbalance forklifts
Counterbalance forklifts offer the ultimate in stability and manoeuvrability, making them a great choice for any warehouse. They feature a counterweight on the rear of the lift which helps to balance out a load, allowing it to carry heavier items with ease. Counterbalance forklifts are also easy to operate, as they have a simple joystick control system that makes them accessible even for those with no prior experience in operating such machinery. Additionally, these machines come in various sizes and capacities so that warehouses can choose the model that best suits their needs.
Electric counterbalance forklifts are becoming increasingly popular due to their environmental friendliness and cost-efficiency. These lifts are powered by electric motors rather than combustion engines which reduces emissions and operational costs over time. This type of machine is ideal for indoor use as it produces little noise pollution while maintaining impressive power levels comparable to other types of machinery.
Diesel counterbalance forklifts provide superior power compared to other models, making them ideal for outdoor applications where heavy lifting is necessary or where an extended running time is required. Diesel models tend to be more expensive than electric models but require less maintenance over time due to their robust construction and reliable performance capabilities.
When it comes to choosing the right type of forklift for your needs, it’s important to consider your budget as well as the size and capacity requirements of your warehouse before making a decision. Counterbalance forklifts offer excellent stability, manoeuvrability and affordability, making them a great choice for any business looking for an efficient way to move materials around their facility quickly and safely.
Reach Trucks are great for those tight spaces – they’ll help you get the job done quickly and easily! These trucks have a slim design that allows them to move in narrow aisles, making them ideal for warehouses or other settings where space is limited. The reach truck also has an extendable arm with forks that can raise and lower pallets from high shelves. This makes it much easier to access stock at higher levels without having to use ladders or other devices. Plus, these forklifts come with adjustable speed settings, so you can tailor your machine to fit the needs of any task. Not only do rich trucks make it easier to safely move materials in tight spaces, but they’re also incredibly reliable. They have low maintenance requirements and are usually powered by electric batteries, meaning you don’t need to worry about fumes or noise pollution like you would with gas-powered models. They’re also easy to operate and come with safety features like emergency stop buttons as standard equipment. Reach trucks are versatile machines that can be used in many different industries including manufacturing, warehousing, retail stores, and even hospitals.

Whether you’re stocking shelves or moving pallets of goods around a warehouse floor, a reach truck will save you time and energy while keeping everyone safe on the job site.
The cost of purchasing one of these machines is usually quite reasonable compared to other types of forklifts available on the market today. With minimal upkeep costs and plenty of uses across various industries, investing in a reach truck could be just what your business needs for efficient material movement!
Narrow aisle forklifts
For tight spaces, narrow aisle forklifts are the perfect solution – they’re compact and can manœuvre through even the most confined areas! These types of forklifts are ideal for warehouses and other storage environments that do not have a lot of space since they take up much less room than standard models. Narrow aisle forklifts come in electric and combustion varieties, so there is an option to fit almost any need.
Electric narrow aisle forklifts offer advantages like lower maintenance costs and reduced noise levels compared to their combustion counterparts. They also require less energy while running, making them more cost-effective over time. In addition, many electric models feature advanced safety features such as sensors that automatically stop the lift when it comes too close to an object or person.
Combustion narrow aisle forklifts provide higher power output and increased lifting capacity compared to electric lifts. This makes them well-suited for jobs that involve heavier loads or longer distances between locations within the warehouse facility. Additionally, these types of lifts often come with additional attachments such as side-shifters which can help with more precise placement of goods onto shelves or pallets.
Regardless of whether you choose an electric or combustion model, narrow aisle forklifts will provide a great deal of efficiency in your warehouse operations due to their high manoeuvrability and smaller size relative to standard lift trucks. With their excellent performance capabilities and ease of use, narrow aisle forklifts are sure to make your job easier no matter what type of environment you find yourself in!
Order pickers
If you’re looking for a forklift that can easily navigate tight spaces and provide precision picking, then order pickers are the perfect choice! These electric-powered forklifts have narrow frames made up of an operator’s platform, counterweight and mast. They also come with adjustable forks which allow them to reach higher heights than other types of forklifts. With their precise design, order pickers can access hard-to-reach places in warehouses and retail stores – making them ideal for retrieving items from high shelves or racks. Plus, they don’t require any additional equipment like scissor lifts or ladders to get the job done. Order pickers offer operators more control over
their movements compared to larger forklifts since they feature a drive system known as “walkie”, which allows them to move around at slow speeds without having to shift gears. This walkie system also helps operators maintain better posture while operating the machine since it eliminates the need for frequent acceleration or deceleration when turning corners. Furthermore, order pickers come equipped with advanced safety features like anti-rollback protection and automatic speed reduction when cornering –ensuring maximum safety while on the job.
The most popular type of order picker is the reach truck which features adjustable forks that can extend up to 55 feet in height – allowing it to access even higher shelves or racks without needing extra equipment such as ladders or scissor lifts. Another great benefit of using an order picker is its low cost of ownership due to its easy maintenance requirements compared to other types of forklifts – making it an attractive option for businesses looking for a costeffective way to move goods quickly and safely around their warehouse or store.
Finally, when choosing an order picker one must consider all factors such as weight capacity, lift height and battery life before purchasing to ensure they are getting the best machine for their needs. Order pickers provide greater efficiency than other types of forklifts by offering precision picking capabilities along with excellent manoeuvrability in tight spaces – making them ideal for busy warehouses and stores alike!
Pallet stackers
Pallet stackers are the perfect choice for those looking to quickly and efficiently move pallets around their warehouse or store. These forklifts typically feature a large platform that is designed specifically to transport pallets. They come in both electric and internal combustion models, depending on your needs and preferences. Pallet stacker models usually have lift capacities ranging from 1,500−2,000 pounds, but some can be much larger than this depending on the model you choose. In addition to being able to lift and transport pallets, these forklifts also offer features such as adjustable forks so you can accommodate different sizes of pallets with ease.

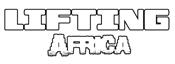

When it comes to performance, pallet stackers provide excellent manoeuvrability. Their low turning radius allows them to make tight turns and navigate narrow aisles of warehouses with ease. This makes them great for getting into tight spaces where other types of forklifts would struggle to fit. Additionally, operators will find that they’re easy to drive due to their intuitive controls and ergonomic design features like adjustable seats and tilt steering wheels.
Safety is always an important factor when considering any type of forklift purchase or rental agreement. Fortunately, most modern models of pallet stackers come with several safety features as standard including backup alarms that alert workers in the area when the vehicle is moving in reverse; emergency brakes; audible warning indicators for all functions; seatbelts; rollover protection systems; illuminate running lights; motion sensors; push buttons for controlling speed selection; automatic shut offs if certain criteria aren’t met; plus more!
Pallet stackers provide a great combination of power, performance, reliability, safety and affordability making them an ideal choice for many businesses today. With their wide range of features and capabilities, they’re sure to give you the productivity boost you need while keeping your workers safe in the process!
Electric forklifts
You’ll be amazed by the power and performance of electric forklifts! Electric forklifts come in a variety of sizes, styles, and capacities, so no matter what your needs are you can find an option that fits. They’re powered by batteries, making them incredibly energyefficient and reliable. With no emissions or loud noises from their engines, they’re also much better for the environment than traditional gas-powered models. Plus, since they don’t require any regular maintenance like fueling up or changing oil, they cost less to operate in the long run.
Electric forklifts provide great manoeuvrability due to their lightweight and high torque motors that allow them to move quickly when needed. This makes them perfect for indoor use where space is limited. If you need something that can handle heavier loads on smoother surfaces outdoors, there are electric models designed for those scenarios too.
Many businesses prefer these types of lifts because they help reduce overall fatigue levels among workers which leads to improved efficiency and safety on the job site.
When shopping for an electric forklift, it’s important to consider a few factors such as your budget, the type of terrain you will be using it on (indoor/outdoor), the size of the load being lifted (small/large), desired speed (fast/slow) and other features such as lift height capacity or battery life options available with different models. You should also think about how often you plan on using it – if you need something more durable and powerful then go with a higher-end model. Still, if only occasional use is expected then a lower-end model may suffice just fine. Overall electric forklifts offer many benefits compared to gas-powered models which makes them well worth considering when looking for workplace solutions that save time and money while reducing environmental impact at the same time!

Internal combustion forklifts
With their powerful engines and increased hauling capacity, internal combustion forklifts are the perfect choice for heavy-duty jobs that require maximum lifting power. These types of forklifts use gasoline or diesel fuel to operate, giving them greater power than electric models, and allowing them to handle larger loads with ease. Internal combustion forklifts come in a variety of sizes and configurations so you can choose the one that best suits your needs. They’re also commonly used outdoors because they don’t require an external power source.
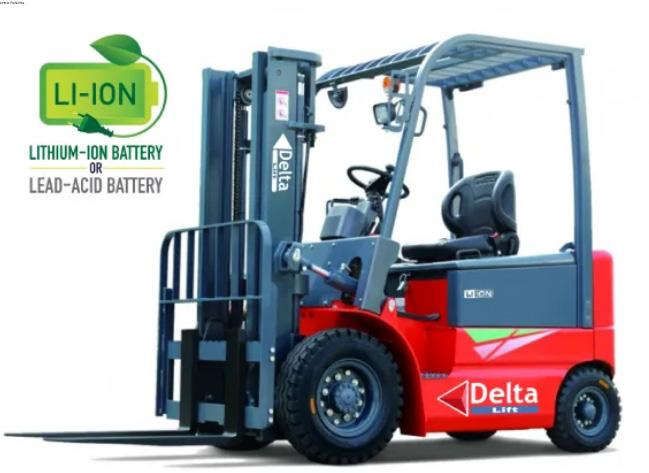
The downside to using internal combustion forklifts is that they produce more emissions than electric models and may not be suitable for indoor environments due to air pollution concerns. They also require regular maintenance such as changing oil and filters to ensure optimal performance. Additionally, these types of forklifts tend to be noisier than electric models, which could be a problem in certain workplaces where noise levels need to be kept low.
Despite their drawbacks, internal combustion forklifts remain popular due to their durability and reliability as well as their ability to handle heavier loads than other types of lift trucks.
They are often used in industrial settings such as warehouses and factories where large amounts of
material need to be moved quickly and efficiently. Furthermore, many manufacturers offer customization options so you can tailor the lift truck’s features according to your specific needs or applications.
Internal combustion forklifts provide great value by offering superior performance at a lower cost when compared with electric models – making them an attractive option for businesses looking for an economical way to move heavy materials safely and efficiently without compromising on quality or performance standards.
Rough terrain forklifts
Moving away from internal combustion-powered forklifts, let’s look at rough terrain forklifts. These are designed for outdoor outdoor areas with unpaved surfaces or uneven terrain. They’re the perfect choice for construction sites, farms, and other outdoor locations where you need a lot of power but don’t want to worry about damaging the ground.
Diesel engines usually power rough terrain forklifts, although electric models are becoming more widely available. They have four-wheel drive so they can handle slippery or hilly surfaces with ease, and their large tyres provide extra traction and stability on difficult ground conditions. The forks on these types of lifts can be lowered below ground level to pick up heavy loads even when there is no flat surface available.
These machines come in several different sizes and configurations, depending on your needs. Some rough terrain lift trucks feature adjustable forks that can be raised to reach higher levels or tilted back to fit through narrower spaces than conventional lifts would allow. There are also telescopic versions which enable operators to access heavy loads from further away than usual – ideal for working in tight areas such as warehouses or narrow streets.
No matter what type of environment you’re working in, a rough terrain forklift provides the power and manoeuvrability necessary to get the job done quickly and safely – without sacrificing productivity or endangering personnel or property. So if you need a reliable machine that can handle tough conditions while still providing plenty of lifting power, consider investing in a rough-terrain forklift today!
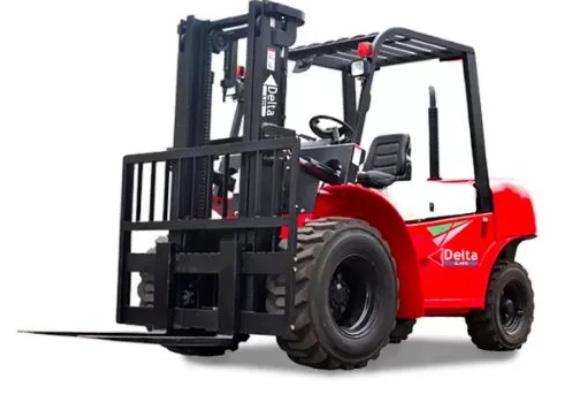
TYPES OF FORKLIFTS
Telehandlers
Telehandlers offer the same power and manoeuvrability of a forklift, but with an added boom to help reach items at greater heights – allowing you to get to those hard-to-reach places with ease.
This type of lift is often used in construction sites or farms, as they can be outfitted with different attachments to handle specific tasks.
Telehandlers also provide excellent stability, thanks to their four-wheel-drive systems and all-wheel steering capabilities. The machine’s frame also helps keep the load even across all four wheels during operation, reducing wear and tear on your equipment.
Telehandlers are designed for more heavy-duty operations than standard forklifts because of their increased lifting capacity; they can lift up to 12 tons depending on the model.
They also have a much higher reach than many other types of lifts, allowing you to move items that may otherwise be too far away from the ground for safe transport.
Additionally, telehandlers come equipped with various safety features such as rollover protection systems and counterweighting mechanisms that ensure safe operation when using these machines.
The versatility of telehandlers makes them ideal for any worksite or project requiring high levels of precision and accuracy when moving materials around. You can use these machines in both indoor and outdoor settings; they are especially useful in areas where space is limited due to their ability to manœuvre into tight spaces easily without compromising on safety or performance.
Additionally, telehandlers require minimal maintenance compared to other types of lifts which makes them cost-effective over time and reduces downtime due to repairs or required servicing needs. Whether you need something basic for quick jobs around the warehouse or something more powerful for large-scale projects outdoors, telehandlers are sure to meet your needs and exceed your expectations! Their strength combined with their flexibility make them essential pieces of equipment on any job site looking for a reliable solution when it comes to material handling needs.
Conclusion
There are a variety of forklifts available to suit your specific needs. From counterbalanced forklifts for heavier loads to reaching trucks for narrow aisles, and even ordering pickers and pallet stackers, you’ve got plenty of options.
Whether you’re looking for an electric forklift, an internal combustion one, or even a rough terrain model, there’s something out there that’ll work perfectly for you. Don’t let yourself be overwhelmed by the choices – take your time and consider all the options carefully before making your decision!
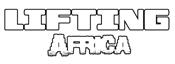

When to repair or replace your forklift
Forklifts are important machines in many work environments. They perform a variety of jobs that can make a warehouse or other job site more efficient and productive. Yet, they also cost a lot to buy and maintain, and most don’t have a very long service life. That’s why the decision to repair or replace a forklift is so important.
Most of the time, it is more cost-effective to repair rather than replace. But sooner or later trucks will wear out. That’s when forklift replacement becomes a safety issue as well as an economic one.
Forklift replacement: the lifespan of the truck
The average lifespan of a forklift is around 10,000 to 12,000 hours. This comes to about seven years of daily use. Some high-end forklifts have a lifespan of 20,000 hours or more. Many factors can affect how long a truck lasts before needing forklift replacement.
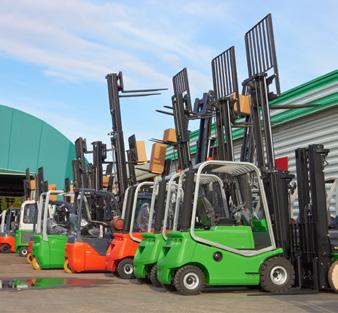
These include:
• Type of forklift. Electric forklifts tend to last longer than those powered by gas, diesel, or propane. They have fewer moving parts to wear out and need fewer repairs.
• Work application. Forklifts used in rough terrain or harsh environments are exposed to more wear and tear. This results in a shorter lifespan. Frequent accidents can also cause excess wear, which can shorten the life of a truck.
• The average use of a forklift is around 2,000 hours per year. More use than that will require more frequent maintenance and repairs. Forklifts that work longer shifts will wear out sooner.
• This is the biggest factor in the lifespan of a forklift. Nothing will extend the life of a truck more than regularly scheduled maintenance.
It would seem the best time to replace a forklift is when it reaches the end of its operational life. But this isn’t always the case.
Planned forklift replacement
Forklifts actually have two types of lifespans –economic and useful. The useful life is the amount of
time the forklift can still do the job. It ends when no amount of repairs can keep it going. The economic life is the time for which it makes economic sense to maintain the forklift.
This ends when it costs more to repair the forklift than to purchase a new one. If an old truck is in good condition and can likely provide two or three more years of use, repairing it may be the better option. After a certain point, older machines will start having performance problems, higher operating costs, and other expenses.
Many companies use planned forklift replacement. This involves replacing a truck when it reaches a certain age, regardless of its condition. This approach takes the guesswork out of repair versus forklift replacement decisions. It makes it easier to budget for the cost of buying or leasing a new truck. It also improves performance and safety by having new and efficient forklifts. The downside to this approach is that you may get rid of trucks that still have several years of service life left in them.
Forklift replacement parts
Timely maintenance will help ensure your forklifts have a long service life. Using forklift replacement parts can also help. Parts most often replaced tend to be engine components. For example, oil and air filters, chains, and spark plugs. Other parts can be replaced as well, ranging from driver seats to tires, forks, batteries, and more.
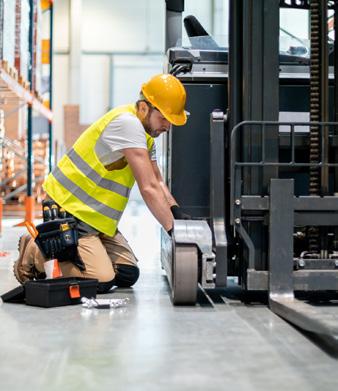
Forklift replacement seats
One common forklift replacement part is the driver’s seat. When seats get worn out they become uncomfortable to the driver. This can cause distractions that lead to accidents.
Forklift seats are hard to repair unless the damage is minor. Forklift replacement seats are often the better choice because they improve productivity and safety. Some forklift replacement seats come with built-in safety switches to make sure drivers put on their seat belts before starting a job.
Forklift wheel replacement
Worn forklift wheels and tires present a real safety hazard. They should always be replaced rather than repaired. It’s time for forklift wheel replacement when you spot any of these signs:
• Less than 2cm from the lettering on the tyres to the top of the tires
• When the tyre is worn down to the safety line
• The tyre has damage in the form of chunking, tearing or cracking
• Flat spots on the tyre
There are different types of forklift tyres. When making a forklift wheel replacement, be sure to get the correct type for your truck. Never have different types of tyres on a forklift.
Forklift repairs
Forklift repairs are easier and less costly when they are performed as soon as the damage is noticed. The best way to do that is with daily inspections. When checking the forks, if you see any of these signs, they need to be repaired or replaced:
• Surface cracks.
• The blade or shank isn’t straight.
• The fork angle from the blade to the shank is not straight.
• There is a difference in height.
• The positioning lock isn’t in working order.
• The fork blade shows signs of wear.
• There is wear on the fork hooks.
• The fork marking is not readable
Look for these signs when inspecting the safety attachments:
• Seat belts and similar restraints are torn.
• Horns and backup alarms do not sound when the forklift moves/reverses.
• The fire extinguisher has expired—the seal on the neck has weakened.
• Warning lights do not flash.
• Directional signals and brake lights do not light up.
• Mirrors are broken.
• Look for these signs when inspecting hoses that need repair:
• Abrasions; blisters; nicks; cracks; cuts; hardness, or color changes.
• Leaks—look for puddles of fluid around the equipment, low fluid levels in the reservoir, or greasy/ dirty hoses.
RENT OR REPLACE FORKLIFTS
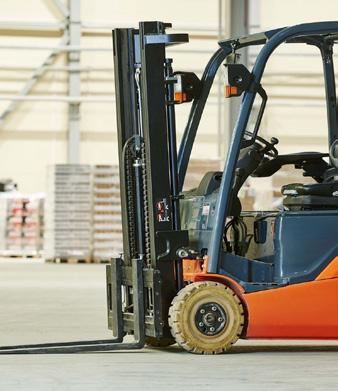
• Contact with other hoses or metal parts.
• Close proximity to a high heat source.
• Twisting or kinking–make sure there is enough slack to allow for length changes under pressure.
Fuel:
• Make sure the fuel tank is not dented in any area.
• Make sure the fuel tank is secure, the valve opens, and check the fuel level.
• Check the hydraulic tank’s oil level for any leaks.
• Additional areas to inspect on a forklift before operating include:
• The air cleaner indicator—clean or change it as needed.
• The radiator’s coolant levels and for leaks.
• Make sure the overhead guard isn’t damaged.
Once you’ve finished performing these maintenance checks, you may wonder if they are truly worth it.
Here are a few of the many benefits you can experience with preventative maintenance:
• Efficient production.
• Improved use of in-shop maintenance personnel with less emergency work.
• Increased control of spare parts inventory and reduced parts usage.
• Less downtime with equipment that is being repaired with scheduled inspections.
• Increased life expectancy of forklifts and other equipment.
• Fewer costs are given to premature purchases of new equipment.
• Reduced repair costs from less frequent equipment breakdowns.
• Reduced number of injuries and fatalities.
Your sound judgment combined with regular checks will ultimately determine when your forklift needs to be repaired and replaced
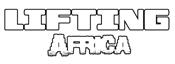

Forklift attachments and their uses
Forklifts are used for lifting and transporting heavy loads. You can fit them with a variety of attachments to increase their functionality. For example, material handlers and movers can use attachments to transport everything from carpet rolls to propane tanks.
Carpet poles
Carpet poles or rug poles extend out from the forklift, allowing the driver to insert them into a rolled carpet’s center core. Once secured, the carpet can be lifted from its current position and moved to a different location.
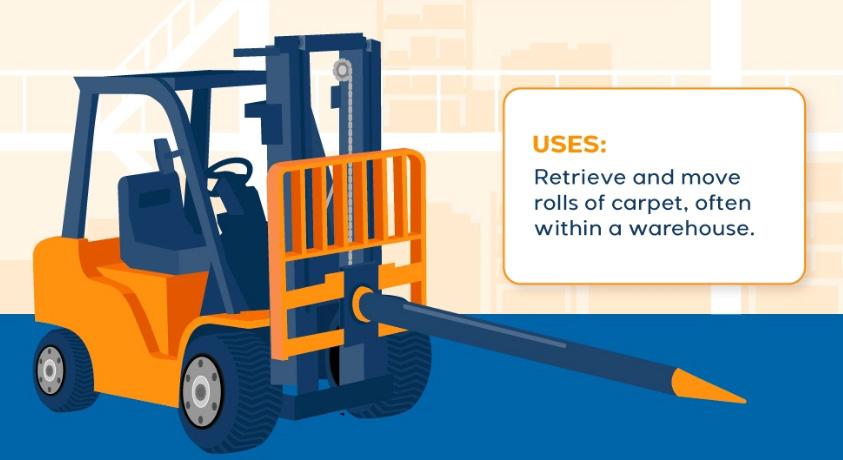
Cylinder caddies
Cylinder caddies are steel attachments with spaces to accommodate several liquid propane tanks for transport. They allow you to move propane cylinders securely from one place to another. Safety chains keep the cylinders upright and in place while they’re being moved.
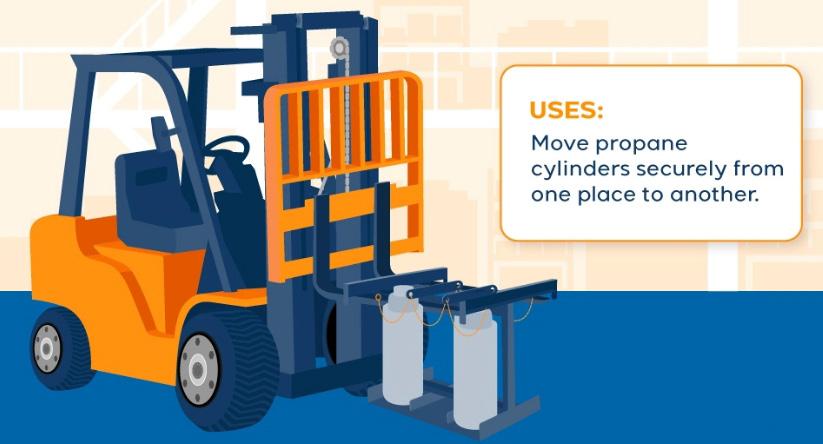
Fork extensions
If you have a larger load than will fit on your standard fork, you can add extensions to increase your carrying ability. They come equipped with restraining straps to keep the load in place and guard against slipping.

Fork-mounted drum handling equipment
Drum attachments are equipped with arched clamps that can extend to grab plastic or steel drums. They come in several configurations, such as grabbers, lifters, and carriers. They’re available to fit drums of different capacities.

Fork positioners
Fork positioners allow you to move the forks without leaving your seat. Powered by hydraulics, they’re an efficient and effective alternative to repositioning your forks manually. This is especially useful when you have to handle pallets of different widths on a regular basis. This attachment can reduce pallet and product damage.
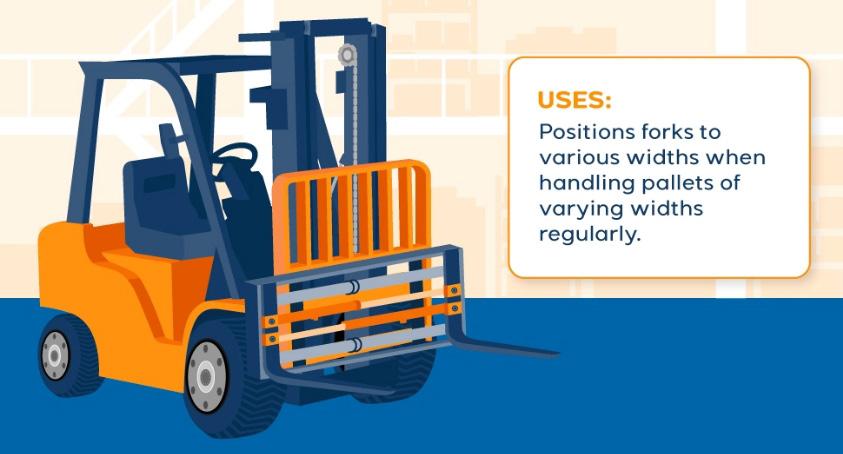
Multiple load handlers
Multiple load handlers add extra forks to your forklift, allowing you to carry more pallets at once. You can expand your capacity to two or even three side-by-side sets of forks.
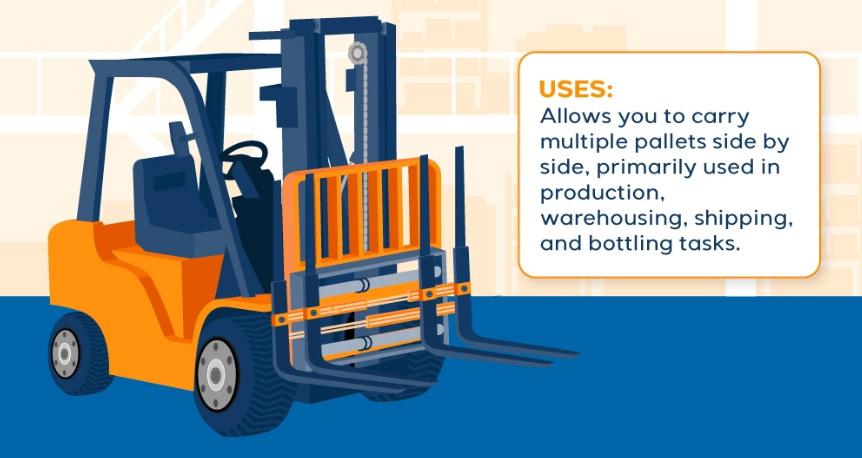
Masts
Forklifts have several types of mast options: singlestage, two-, three-, and four-stage, each allowing you to hoist material to greater heights. Mast extensions are lifting attachments that allow you to raise the materials higher without needing a forklift with a larger mast.

Paper roll clamp
Paper roll clamps are large, sturdy attachments that can secure and move large rolls of paper without damaging it. They can handle one to eight rolls at a time, of various sizes and weights.
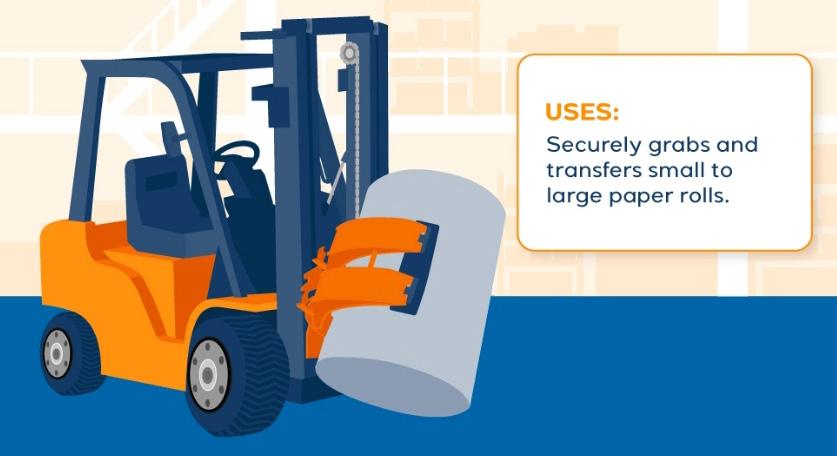
Push-pull clamp
This hydraulic attachment extends forward and clamps around a load, squeezing it between a faceplate and gripper to transport it without the use of pallets. Materials are packed onto slip sheets instead.

Rollerforks
Rollerforks are specialized attachments that eliminate the need for pallets. Two layers of rollers are used. The lower layer moves forward while the upper layer moves backward, helping to secure the load. Rollerforks are often used with slip sheets, but may be used without them for certain load types.
FORKLIFT ATTACHMENTS

Rotators
Rotators allow you to rotate the forklift’s forks to one side in a tipping motion. The advantage of rotators is they can be used to pour out the contents of bins. You can also tip containers to one side so you can reach in and retrieve something.

Side shifters
This attachment allows you to move a load that’s being carried from side to side. A side shifter can help you maneuver a forklift in close quarters, so you can reposition loads to be stored without having to move the forklift itself.

Which attachment do i need?
Take into account weight and height requirements, as well as the nature of the job site and what you’ll be moving. Safety is an important consideration as well. Project type
What you’re moving and the space you’re working with will determine which forklift attachments may be beneficial. Attachments such as carpet poles, paper roll clamps, and cylinder caddies are designed to move specific kinds of materials. If you’re operating in close quarters, you might want to consider a side shifter; if you want additional height or need more capacity, you can choose a mast extender, multiple load handler, or fork extension.
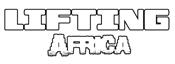

WHY RENT A FORKLIFT
5 Reasons why renting a forklift is the best choice for small businesses
Forklifts are essential for many small businesses that require the efficient movement of heavy materials, such as in warehouses, factories, and construction sites. Forklifts can handle a variety of tasks, from loading and unloading goods to transporting heavy items over long distances. Without a forklift, businesses may struggle to maintain productivity and meet their deadlines.
1. Cost Savings
Comparison of rental costs vs. purchasing costs
One of the biggest advantages of renting a forklift for small businesses is the potential cost savings. Purchasing a forklift can be a significant investment, with prices ranging from several thousand Rands to over R1000,000 for larger models. In contrast, rental costs are typically much lower, with rates varying based on factors such as rental duration and the type of forklift required.
Furthermore, when purchasing a forklift, businesses may need to make a down payment and obtain financing, which can add to the total cost. Renting a forklift, on the other hand, typically requires no down payment, and rental fees can be expensed as a tax deduction.
Explanation of how rentals can save money on maintenance and repairs
Another way that forklift rentals can save small businesses money is through maintenance and repair costs. When purchasing a forklift, businesses are responsible for all maintenance and repair costs, which can add up over time. Forklifts require regular maintenance, including routine inspections, oil changes, and part replacements, all of which can be costly. In contrast, rental companies are responsible for maintaining and repairing their equipment, which can save businesses significant amounts of money.
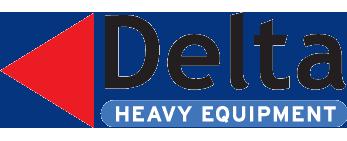
Furthermore, rental companies often use the latest equipment and technology, which can reduce the likelihood of breakdowns and minimise repair costs.
Case studies of businesses that saved money by renting instead of buying
Several case studies demonstrate the cost savings that small businesses can achieve by renting forklifts instead of buying them.
For example, a small warehouse business that needed a forklift for a specific project found that renting was more cost-effective than purchasing.
By renting the forklift for the duration of the project, the business was able to complete the job without incurring the high costs associated with purchasing and maintaining a forklift long-term.
Another case study involves a small manufacturing business that had to replace an old forklift. Rather than purchasing a new one, the business decided to rent a forklift instead. By renting, the business was able to save money on the upfront purchase cost, reduce its maintenance and repair expenses, and gain access to the latest technology.
Overall, for small businesses that need a forklift for a short-term project or that cannot afford the upfront costs of purchasing one, renting a forklift can be an excellent way to save money while still meeting their material handling needs.

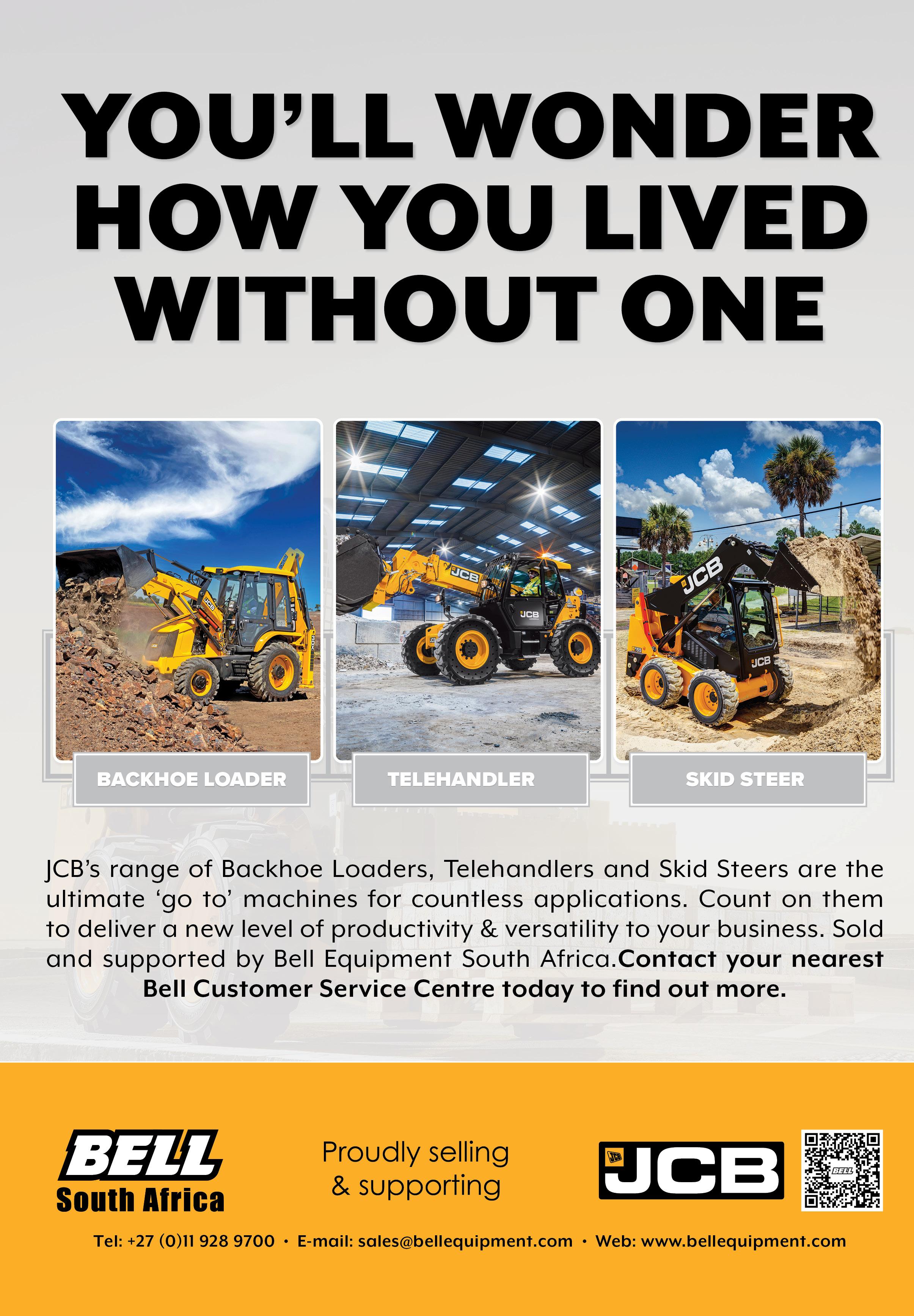
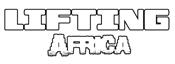

2. Flexibility
Explanation of how rental agreements offer flexibility for changing needs
One of the primary benefits of renting a forklift for small businesses is the flexibility that rental agreements offer. Many small businesses have changing needs, and renting a forklift provides the ability to scale up or down as needed without the longterm commitment of purchasing. Rental agreements can be structured to meet the specific needs of a business, including short-term, long-term, seasonal, or project-based rentals. This flexibility allows businesses to respond quickly to changing market conditions and adjust their forklift fleet accordingly.
Case studies of businesses that benefited from rental flexibility
There are many examples of businesses that have benefited from the flexibility of forklift rentals. For instance, a small construction company that specialises in interior renovation projects may only need a forklift for a few weeks at a time. Renting a forklift for short-term projects provides them with the equipment they need without committing to a longterm purchase. Similarly, a small warehouse that experiences seasonal fluctuations in demand may benefit from a seasonal rental agreement that allows them to scale up or down during peak periods.
Comparison of rental options (short-term, longterm, seasonal, etc.)
Rental companies offer a variety of rental options to meet the needs of different businesses. Short-term rentals are typically for a few days or weeks, and are ideal for businesses that have temporary needs, such as a special event or short-term project.
Long-term rentals are for several months or years and are ideal for businesses that require a forklift for a longer period of time, but still do not want to commit to purchasing.
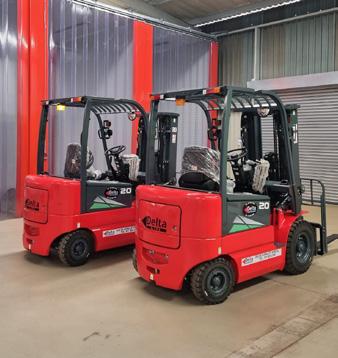
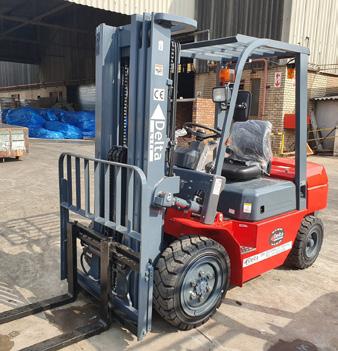
Seasonal rentals are for businesses that have fluctuating demand during certain times of the year, such as the holiday season. Project-based rentals are for businesses that need a forklift for a specific project, such as a construction project. By comparing different rental options, businesses can choose the rental agreement that best meets their needs and budget.
In summary, the flexibility of forklift rentals offers small businesses the ability to adjust their forklift fleet to meet changing needs without the longterm commitment of purchasing. Businesses can choose from a variety of rental options to meet their specific needs, and there are many case studies that demonstrate the benefits of rental flexibility.
3. Maintenance
Explanation of how rental companies maintain their equipment
Rental companies are responsible for maintaining their equipment to ensure it operates safely and efficiently for their clients. They follow a strict maintenance schedule that includes routine inspections, oil changes, filter replacements, and other critical maintenance tasks to keep their forklifts running smoothly.
Moreover, rental companies have a team of expert technicians who are trained to handle all types of repairs, from minor repairs to major overhauls. They use advanced diagnostic tools and techniques to identify and fix any issues that may arise during the rental period.
In addition, rental companies keep their fleets up to date with the latest technology and equipment, which ensures that their clients have access to the most advanced and efficient forklifts available in the market.
Comparison of rental maintenance vs. in-house maintenance
While in-house maintenance might seem like an attractive option, it can be a significant cost and time
burden for small businesses that lack the resources and expertise to maintain their forklifts. In-house maintenance requires businesses to purchase the necessary equipment, hire qualified technicians, and provide training, which can be a significant expense. Furthermore, in-house maintenance can be timeconsuming, causing disruptions in day-to-day operations. It can also result in downtime when forklifts need major repairs or servicing, causing delays in fulfilling orders and other tasks.
In contrast, rental maintenance services are included in the rental agreement and managed by the rental company. This means that businesses do not have to worry about purchasing equipment or hiring staff to handle maintenance and repairs. They can focus on their core business operations and leave the maintenance of their forklifts to the rental company.
Case studies of businesses that benefited from rental maintenance services
For example, ABC Manufacturing, a small manufacturing business, decided to rent a forklift from a local rental company to handle their increasing production demands. The rental agreement included maintenance services, and ABC Manufacturing did not have to worry about the maintenance and repair of the forklift. This allowed the business to focus on their core operations and saved them money on maintenance costs.
Similarly, XYZ Distribution, a small distribution business, rented a forklift from a rental company with maintenance services included in the agreement. When the forklift needed repairs, the rental company dispatched a technician to their location and fixed the issue quickly, minimising downtime and ensuring that their operations were not disrupted. In both cases, renting a forklift with maintenance services included in the agreement allowed the businesses to focus on their core operations and saved them money on maintenance costs. The rental company was responsible for maintaining and repairing the forklift, ensuring that it operated safely and efficiently throughout the rental period.
4. Access to Latest Technology
Explanation of how rental companies offer the latest forklift models and technology
One of the biggest advantages of renting a forklift is the access to the latest technology.
Rental companies are constantly updating their fleet with the latest forklift models and technological advancements. This means that businesses can take advantage of the newest and most advanced forklifts without having to make a large investment in purchasing new equipment. Rental companies also typically offer a range of forklift types, including electric, gas, and diesel-powered models, giving businesses a variety of options to choose from based on their specific needs. In addition to the latest forklift models, rental companies also offer a range of technological advancements that can improve safety and efficiency. For example, many rental forklifts are equipped with advanced safety features, such as sensors and cameras that can detect obstacles and help prevent accidents. They also offer technology that can improve the efficiency and productivity of the forklift, such as GPS tracking and telematics systems that allow for remote monitoring and maintenance.
Comparison of rental technology vs. outdated inhouse equipment
While it can be tempting for businesses to hold onto their older forklift models in an effort to save money, outdated equipment can actually end up costing more in the long run. Older forklift models are often less efficient and less safe than newer models, leading to decreased productivity and potentially costly accidents. In-house equipment also requires regular maintenance and repairs, which can add up over time. On the other hand, rental forklifts offer the latest technology and advancements, which can help improve safety and efficiency while reducing overall costs. By renting, businesses can take advantage of the most up-to-date equipment without having to make a large investment in purchasing new forklifts. Case studies of businesses that benefited from rental technology advancements
There are numerous case studies of businesses that have benefited from renting forklifts with the latest technology. For example, a manufacturing company that switched from older forklift models to newer, rental models equipped with GPS tracking and telematics systems saw a significant increase in productivity and a decrease in maintenance costs. The advanced technology allowed the company to more effectively monitor and maintain their forklift fleet, resulting in less downtime and increased efficiency.
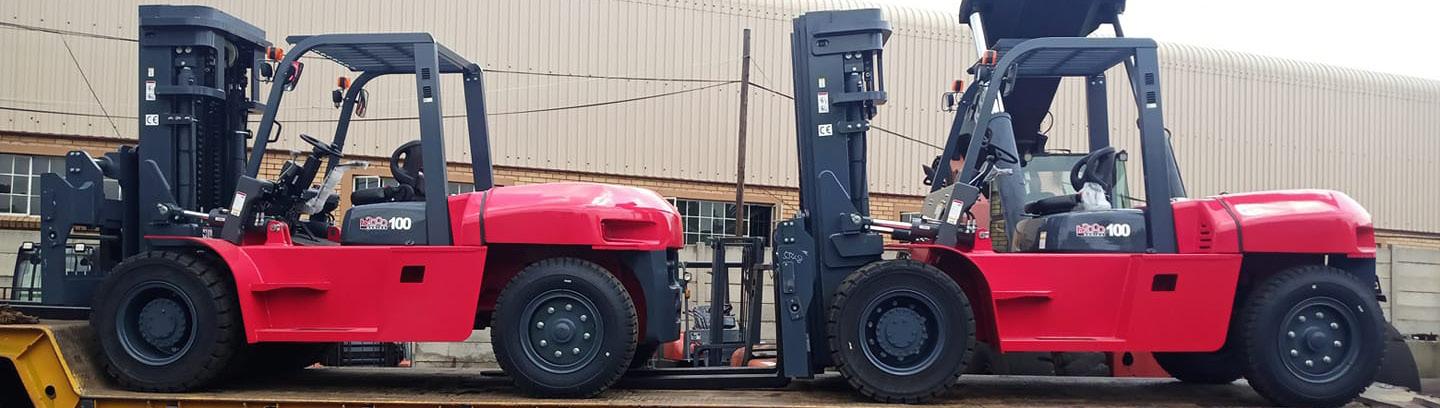
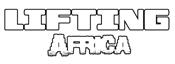

Another example is a construction company that rented forklifts with advanced safety features, such as cameras and sensors. The safety features helped prevent accidents and injuries on the job site, resulting in decreased workers’ compensation costs and improved employee morale.
Overall, by renting forklifts with the latest technology, businesses can improve safety, efficiency, and productivity, while also reducing costs associated with outdated in-house equipment.
5. No Long-term Commitments
Explanation of how rental agreements offer businesses the freedom to scale up or down
One of the biggest benefits of forklift rental is the flexibility it offers businesses. Rental agreements provide businesses with the freedom to scale up or down based on their changing needs.
For example, if a business experiences a seasonal increase in demand, they can rent additional forklifts to meet the demand without having to purchase new equipment.
On the other hand, if a business experiences a slowdown, they can return or reduce the number of rented forklifts without the financial burden of owning the equipment. This flexibility also allows businesses to try out different models or types of forklifts before committing to a purchase, which can save money in the long run.
Comparison of rental agreements vs. long-term financing commitments
Long-term financing commitments, such as leases or loans, can be expensive and lock businesses into lengthy payment plans. These commitments can also require businesses to put up collateral or make significant down payments, which can strain cash flow. Forklift rentals, on the other hand, do not require businesses to make long-term financial commitments or put up collateral. Rental agreements also typically include maintenance and repair services, which can further reduce costs for businesses.
Case studies of businesses that benefited from rental
flexibility
Many businesses have benefited from forklift rental flexibility. For example, a small manufacturing business that experiences seasonal demand spikes may rent additional forklifts during those busy periods and return them when demand slows down.
This can save the business money on equipment costs and prevent them from having to lay off employees during slow periods. Similarly, a construction company that takes on different types of projects may rent different types of forklifts for each project, rather than purchasing a variety of forklifts that may not be used frequently. This can save the business money and allow them to complete projects more efficiently. In conclusion, the flexibility provided by forklift rental agreements can be a major benefit for small businesses.
WHY RENT A FORKLIFT

By allowing businesses to scale up or down based on their needs, rental agreements can save businesses money, prevent financial strain, and provide access to a wider variety of forklift models and technology.
Conclusion
Recap of the top 5 benefits of renting a forklift for small businesses:
Cost Savings: Renting a forklift can be more costeffective than purchasing one, especially for small businesses with limited budgets. Rental companies handle maintenance and repairs, saving businesses money on upkeep costs.
Flexibility: Rental agreements offer flexibility for businesses with changing needs. Rental options can range from short-term to long-term and seasonal, giving businesses the freedom to adjust their equipment as necessary.
Maintenance: Rental companies handle forklift maintenance, ensuring that the equipment is always in good working condition. This can save businesses time and money on in-house maintenance.
Access to Latest Technology: Rental companies offer the latest forklift models and technology, which can improve efficiency and safety in the workplace. This is especially important for businesses that can’t afford to purchase the latest equipment.
No Long-term Commitments: Rental agreements offer businesses the freedom to scale up or down as necessary without long-term financing commitments. This can be especially beneficial for small businesses with unpredictable growth.
Final thoughts on the importance of forklift rentals for small businesses:
Renting a forklift can be a smart decision for small businesses that need the flexibility to adjust their equipment as necessary without making a long-term financial commitment. With rental companies handling maintenance and repairs, businesses can save money on upkeep costs and ensure that their equipment is always in good working condition. Access to the latest forklift technology can also improve efficiency and safety in the workplace. Overall, forklift rentals can provide small businesses with the equipment they need to succeed without breaking the bank.

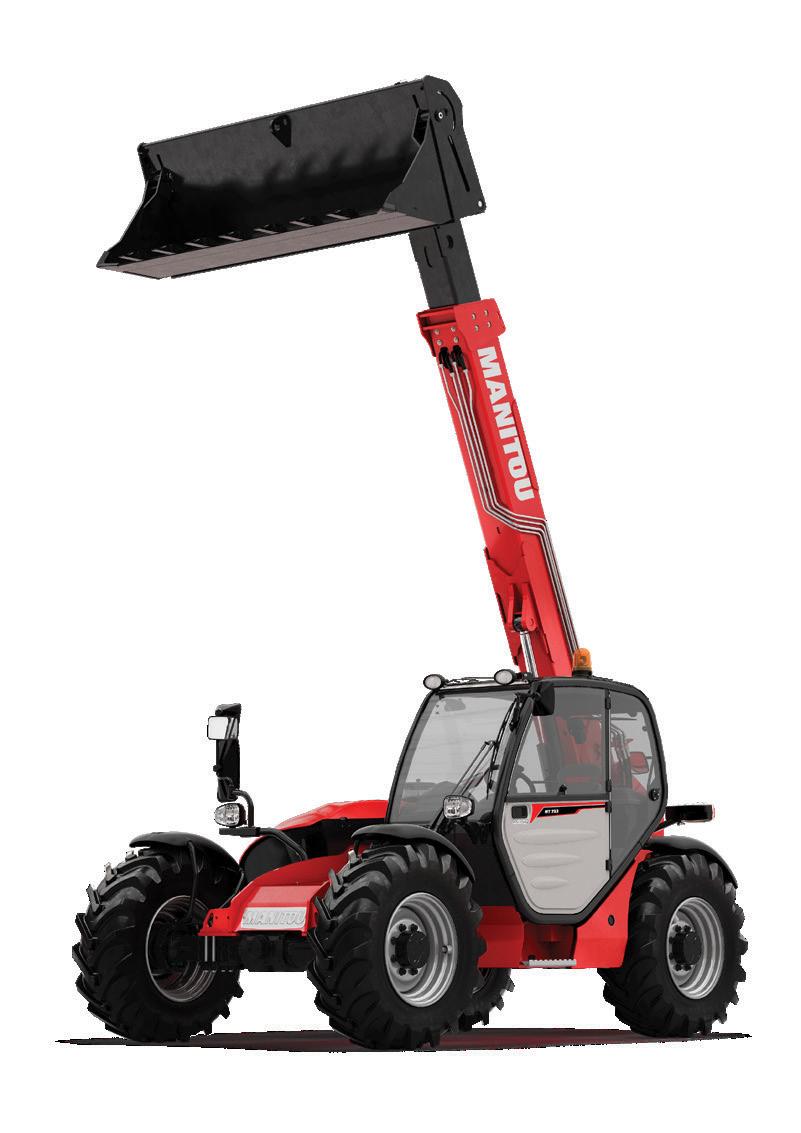

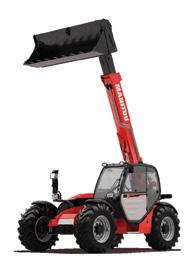

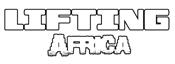

Forklift tyres
When properly maintained, your forklift tyres can reduce fuel consumption, increase safety in the workplace and improve productivity.
Forklift tyres types
Cushion/press-on tyres are made of solid rubber moulded to a steel band. The rubber can either be traction or smooth. These tyres are very durable and are best suited for indoor or light outdoor use on smooth surfaces.
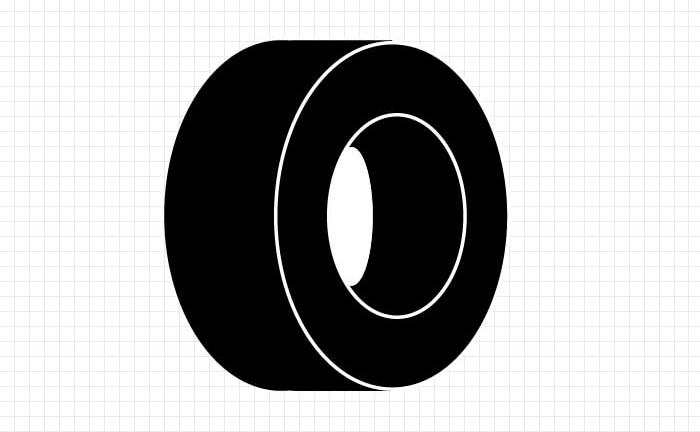
Pneumatic tyres are similar to a car tyre. They are made of traction rubber and filled with compressed air. Some companies fill their pneumatic tyres with foam to avoid the upfront cost of solid pneumatic tyres.
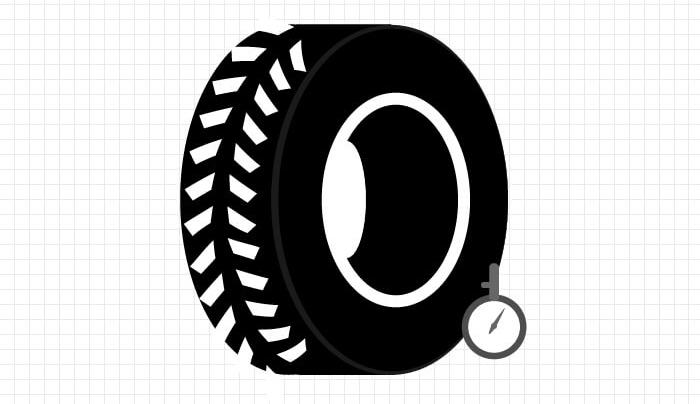
Solid pneumatic forklift tyres are made out of solid rubber. These tyres are very durable and can’t be punctured or deflated, which makes them ideal for industries with sharp debris like recycling centers or lumberyards.
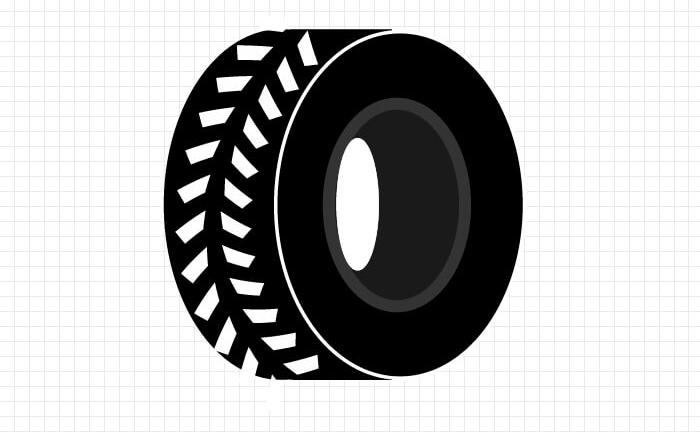
Polyurethane tyres, a type of press-on tyre, are lightweight and more resistant to splitting, tearing or chunking out under a load than rubber tyres. They combine good traction with low-rolling resistance. Polyurethane tyres generally experience about twice the lifespan of rubber tyres and should be used indoors only for light applications like warehousing.
These tyres will wear more easily in a heavy usage indoor environment so consider cushion tyres if your application requires high usage.
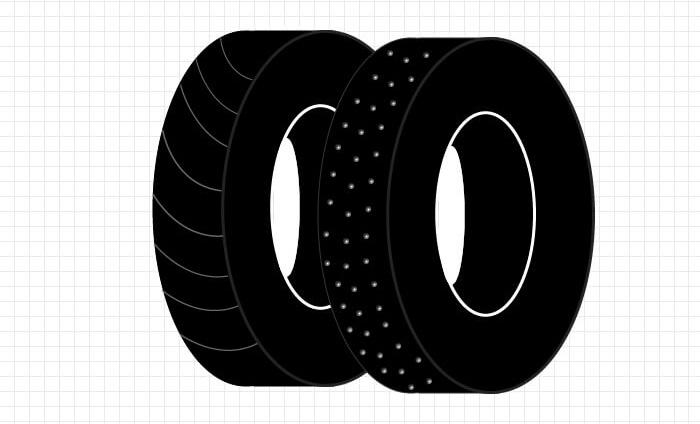
Non-marking forklift tyres are made with hydrated silicas and special additives for eliminating black marks on floors. They are available for pneumatic, solid pneumatic and cushion tyres. These tyres have a short life span and are prone to cause static electricity, which means they require an anti-static strip on the forklift.
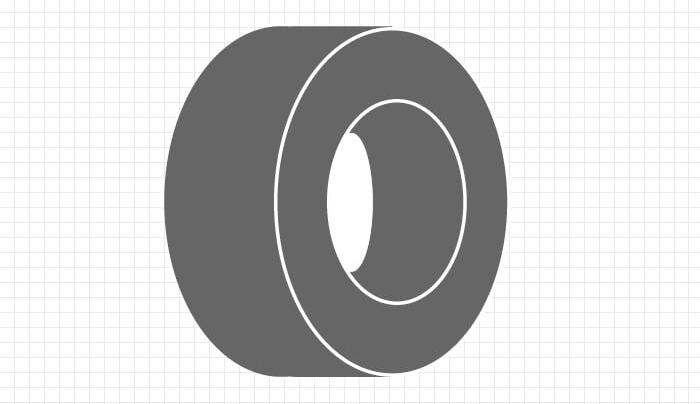
How to read forklift tyres sizes
The basic components of your forklift tyres are:
• Sidewall – shows important tyre information like the tyre brand, size, tyre type, and wear line
• Tread – Raised rubber that comes in contact with the ground
• Rim – Metal portion of the wheel that holds the tyre in place
You can find your forklift tyre size on the sidewall of the tyre. If you don’t see the size there, you can always check the operator’s manual or call your local
forklift dealer with the model. They should be able to tell you the tyre size for your model forklift. Press-on tyre sizes are shown as the Outer Diameter x Width x Rim Diameter.
An example would be: 16 x 6 x 10.5. Pneumatic or solid pneumatic tyres sizes are noted as the Width x Rim Diameter. An example would look like: 6.50 x 10.
How to measure forklift tyres
If you need to measure your forklift tyre size grab your average tape measure.
1. Measure the outer diameter, picture the tyre as a compass with north at the top of the tyre. Make sure you’re placing the tape measure at the center of the tyre and run the tape measure east to west.
2. Measure the rim diameter, stay in the center of the tyre but only extend the tape measure to each edge of the rim.
3. Measure the width of the tyre, simply position the tape measure on the part of the tyre that would make contact with the ground and run the tape measure from edge to edge.
Press-on tyres you need to measure the outer diameter, the width of the tyre, and the rim diameter. For pneumatics or solid pneumatics measure the width and the rim size.
How to choose the right forklift tyres
Take into consideration your application, forklift and work environment when choosing a tyre type. Can you put pneumatic tyres on a cushion tyre forklift? Your forklift’s wheels and frame are generally designed for
FORKLIFT TYERS
a specific tyre type (usually pneumatic or cushion), so it is best to verify with your local dealer and your forklift’s manual if you want to go with a different tyre type than what is recommended.
You’ll often be able to switch from smooth cushion to traction cushion, or pneumatic to solid pneumatic tyres, but it is rare you can go from a cushion tyre to a pneumatic tyre and vice versa. When it comes time to replace the tyres, ensure both sides of the forklift are the same tyre type. The front and back tyres can differ, but both front tyres and both back tyres must be the same type.
Tyre recommendations for your application
Indoor applications
Indoor applications that have no debris on the floor surface are best suited for cushion tyres. In this environment, cushion tyres last longer, provide increased manoeuvrability and improve traction.
Outdoor & rough terrain applications
Outdoor and rough-terrain applications generally use pneumatic or solid pneumatic tyres since they offer better traction and increased stability on uneven, loose terrain.
Warehouse applications
Applications, such as warehousing, that frequently use order pickers will often use polyurethane tyres. In fact, order pickers almost exclusively use polyurethane tyres since they can improve upon the expected battery life of the machine and provide additional stability and traction.
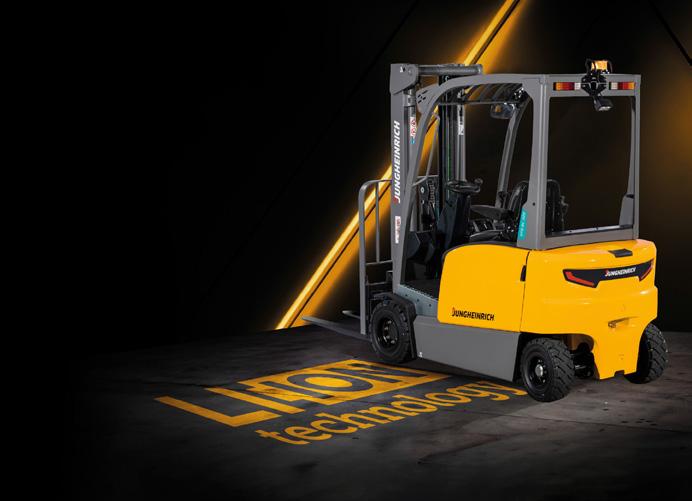
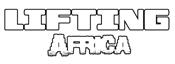

Cold environments
Cold environments or environments with consistently wet floors typically use polyurethane tyres with micro grips (small, raised dots) or razer sipes (narrow, diagonal grooves) since they provide increased traction and braking ability.
Oil spills
If your environment experiences standing oil or consistent oil spills, consider using polyurethane tyres, which will resist the oil and experience less breakdown.
Sensitive applications
Sensitive applications, such as food, paper or printing are often required to use non-marking tyres since standard tyres contain carbon black. This creates a fine dust particle during use that can cause crosscontamination issues.
How long should forklift tyres last?
Usage
The hours you put on your forklift tyres make a huge difference.
Tyre types
Some tyre types are naturally more prone to wear and tear than others. Pneumatic tyres typically wear out more quickly than solid pneumatics. Plus, they can be punctured causing a flat tyre which will then need to be patched. To get the most out of your pneumatic tyres, make sure you monitor the air pressure carefully. Low air pressure equals more contact with the floor surface and that means more wear. In contrast, solid pneumatic tyres have a longer life than pneumatics. They’re extremely durable and resilient to wear.
When it comes to press-on tyres, polyurethane tyres typically see up to two times the life of cushion tyres.
Floor conditions
The abrasiveness of the ground surface can limit your tyres’ life. The best case scenario for a long forklift tyre life is sealed concrete or black top.
Surfaces with lots of debris are going to shorten your tyre life too. Running over debris isn’t a good idea. Not only does it damage your tyres, but it’s not safe for forklift operation and it can be uncomfortable for the operator too.

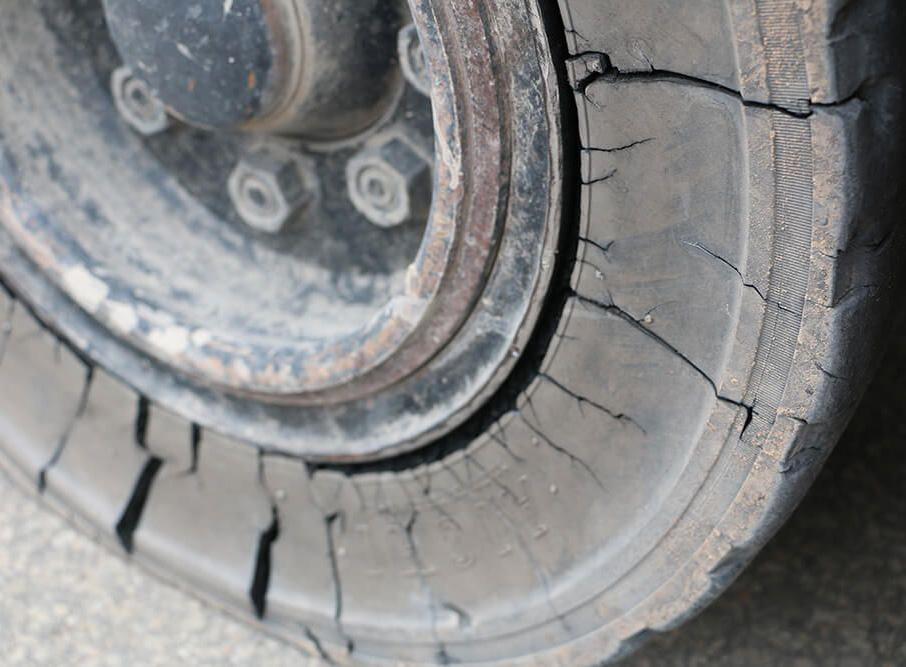
Applications like recycling centers and lumber yards might have a hard time avoiding debris. Solid pneumatic tyres are a durable option for these environments but it’s still best to avoid running over debris whenever possible.
Operating conditions
Your general work environment and operating conditions can shorten the life of your forklift tyres.
Something as simple as humidity can be a major issue. A very humid environment can make the floor sweat which causes the tyres to spin more. And spinning tyres means worn out tyres. It’s not just the environmental conditions.
Your load affects the tyres too. While you don’t want to overload the lift truck, running the forklift without a load also shortens your tyre life. Without a load on the forks, the counterweight presses down on the steer tyres which causes them to wear more quickly.
Operator behavior
Your forklift operator’s driving habits and abilities affect the life of your tyres too.
Spinning the tyres, quick starts and stops, excessive speed and sharp cornering all reduce the life of your forklift tyres. If you’re zipping around the warehouse, taking tight turns and stopping abruptly, it’ll take a toll on your forklift tyres.
Getting the most out of your forklift tyres
A tyre in good condition will increase your forklift’s efficiency, improve productivity and reduce operator fatigue. Plus, getting the most out of your tyre means a better bottom line and a safer workplace.
So how can you keep your tyres in good condition? It starts with operator education, but it also depends on your tyre type and your environment.
Operator education
Poor operator habits are one of the most influential causes of reduced tyre life. These basic reminders for operators can increase safety in the workplace and improve the life of the tyre.
Operators should not:
• Spin the tyres
• Overload the vehicle
• Run over debris
Operators should avoid:
• Quick starts
• Quick stops
• Excessive speed
• Sharp, aggressive cornering
Air pressure
You should check the air pressure on your pneumatic tyres before each use. If that isn’t possible, try to check daily. You can find the recommended PSI on the sidewall of the tyre. Tyre air pressure needs to be checked often because air pressure fluctuates with increasing and decreasing temperatures. Higher temperatures increase air pressure, and lower temperatures decrease air pressure. This is not just a seasonal concern but a year-round responsibility as temperature can change drastically in a very short period of time.
Why does air pressure matter?
Under-inflated tyres lead to poor traction, which can cause accidents. Over-inflated tyres can cause a blowout, which causes downtime and profit loss. Checking tyre air pressure is an easy way to avoid more serious problems that reduce productivity. The best way to get better traction is to increase the surface area connecting with the ground.
Pneumatic tyres have more flex than solid pneumatics which increases the surface area contacting the ground and improves traction.
When to replace your forklift tyres
Not replacing forklift tyres at the appropriate time can lead to reduced fuel efficiency but that isn’t the worst of it. Tyres in poor condition cause operator fatigue, which leads to mistakes and can be dangerous for others in the area. Extensive damage can also be done to your equipment if the tyres aren’t replaced in time.
Checking your tyres for wear & damage
Regularly inspect your forklift tyres to check for wear and damage. Your operators should include this in their pre-operation inspections. They’ll be able to catch issues before they become a serious problem which is good for their safety and your bottom line.
Wear line or safety line – Many tyre manufacturers provide a wear line on the tyre. If the rubber has been worn down to the line, it’s time to replace the tyre.
Usage
Lettering – Another way to check for tyre wear is on the sidewall of the tyre. Once the tyre reaches the top of the numbering or lettering on the sidewall, the tyre needs replacement.
Tread – Similar to a car tyre, visually check the tread height on the tyre to determine if the tyre needs replacing. If the tyre is balding, replace it.
Chunking– Chunking occurs when the tyres are
FORKLIFT TYERS
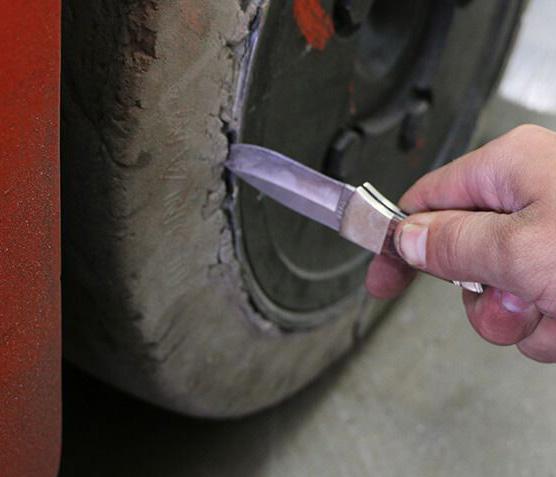
repeatedly running over debris and cause large pieces to fall off the tyre. This can cause a bumpy ride for the operator, increasing fatigue and therefore mistakes. Damage to the load or product may also occur as a result of chunking.
Flat Spots – Sometimes flat spots can appear on the tyre caused by spin or aggressive braking. This creates an uneven and uncomfortable experience for the operator. You can prevent flat spots by training operators on appropriate speeds and braking procedures.
Radial cracking – Radial cracking can occur when heat builds up within the tyre often due to overloading the machine. If you’re consistently seeing radial cracking on your pneumatic or cushion tyres, consider using a larger or wider tyre to spread the weight of the load over more area.
Heat build up is also caused by traveling long distances with no weight on the forks. In these situations the counterweight rests on the steer tyres instead of being evenly distributed.
Check for damage - Bond failures occur when the rubber has separated from the metal band. If you can stick a screwdriver or a knife into the separated area, it is time to replace the tyre.
Visually inspect the tread - For traction cushion tyres, visually check the tread as there is no definitive tool to help determine tread wear. When 25-30% of the available tread is worn, the tyre should be replaced.
Solid pneumatic tyres - If there are no obvious signs of damage, go by the amount of wear. When solid pneumatics have lost 75-80% of the available tread, they should be replaced. Though this rule works for most cases, you’ll want to take your operators and your application into consideration.
Polyurethane tyres - One of the more common signs of wear on poly tyres is radial cracking. This occurs when heat builds up within the tyre material and escapes through the exterior of the tyre. Polyurethane tyres with radial cracking are ready for replacement.
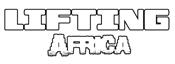

Lithium Ion vs Lead Acid forklift batteries:
Which is better for you?

What are Lead-Acid forklift batteries?
Lead-Acid forklift batteries are rechargeable batteries with a high power-to-weight ratio and are sought after due to their lower cost. They are known as motive batteries, AKA the motor of the vehicle. What most people don’t think of is the sheer size and weight of lead-acid batteries. One of the benefits of the leadacid battery is its weight. Forklifts lift heavy objects hundreds of meters high, so they need something to help balance the weight. In this case, the battery is a counterbalance and keeps the forklift from tipping over when lifting heavy loads.
What are Lithium-Ion forklift batteries?
Lithium-Ion forklift batteries are rechargeable lithium and graphite batteries with a very high energy density, low discharge rate and no memory loss. While lithium is a much lighter material, these batteries still require either a bodybuilder or a machine to move them. This lighter battery means less weight that your forklift is carrying, so sometimes you’ll even see a metal plate
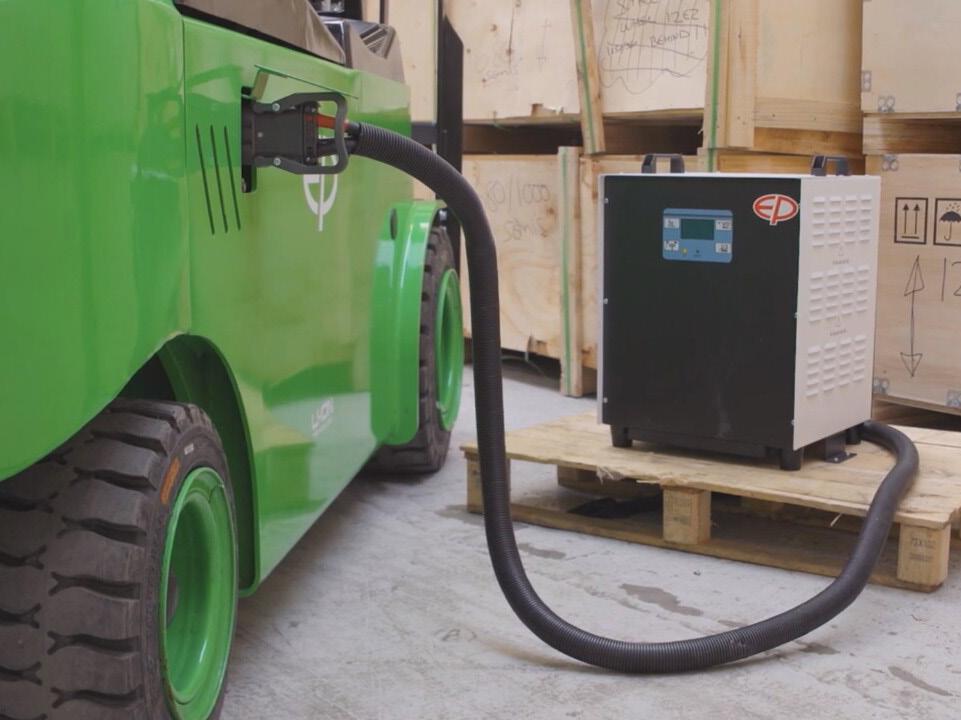
to help provide additional weight to keep the forklift from tilting when carrying heavy loads. There are some pros and cons to each of these battery types.
Maintenance
Lead-Acid Batteries require more maintenance. Now the longer version is that lead-acid batteries require watering. What happens is water fills the individual cells in your battery to provide a functional level of chemicals and electrolytes that will produce power. Even if you run a one-shift application your batteries will probably need to be watered once a week or at the very least bi-weekly. And this requires special equipment and the right level of care because you water too much or too little and you’ll damage your battery.
Other maintenance steps to take are:
• Service semi-annually to control acid and corrosion
• Inspect for any defects
• Keep electrolyte level above separator protectors
• Keep the vent caps on tight
Lithium-Ion batteries
Lithium-ion batteries save you thousands because they do not require the most expensive maintenance piece… watering.
However, there are a few things you should make sure to check on every so often. These are listed below.
• Check wear plugs & cables
• Monitor charger for fault conditions
• Make sure your software is up to date
• Keep your batteries at room temperature
• Allow partial discharges and avoid letting the battery die, it is best to charge when you’re around 15-25% of battery left
• Keep away from moisture
Charging Lead-Acid batteries
If you take great care of your battery you will get about 1,500 charge cycles. This equates to about 5 years if you charge the battery once per day. But, if we are going to be more realistic, you should expect about 3.5 years of life. That isn’t too bad, but the problem arises when you have a 2 or 3-shift application. In these cases, you will need at least two batteries per truck because charge time will take 8 hours and then you will need a cool down time of 8 hours as well.
Lithium-Ion batteries
As you can see above lithium-ion can be 4-16x more effective when it comes to charging production. But, what about degradation? You can put a checkmark next to lithium-ion on this one as well. Lithium-ion batteries generally last about 2,000 – 3,000 cycles. Which is almost double what you can expect with a lead-acid battery.
Energy usage Lead-Acid batteries
The energy density of a lead acid battery is 80-90 Wh/L with a specific energy of 35-40 Wh/kg. All that seems confusing, but all it means is the measure of how much energy is stored in the battery. Lead-acid batteries are not good at keeping their energy. They lose amps while moving, charging, lifting and idling. As a shift carries on the forklift will become weaker and weaker as the battery level goes down. The energy density of a lithium-ion battery is 100-265 Wh/ kg. That is 3-6 times stronger than lead-acid. Lithiumion batteries keep a constant voltage level during their discharge cycle. This can equal 50% savings in energy compared to lead-acid. Charging a lithium-ion battery can be done without removing the battery from the forklift. Unlike lead-acid batteries, lithium-ion gives users the chance to use opportunity charging between shifts or even during break time.
This is a huge advantage because now you do not need a second battery and your charging space will be just that, a charging space. Typically with lead-acid you will need a space dedicated to storing your extra batteries while they charge. This is a major advantage because now you can take that dedicated charging space and restructure it to be additional storage space.
Conclusion
The easy answer is lithium-ion is the better, more reliable, more efficient, and bigger bang for your buck option. However, this is only an obvious choice if you are running a 2-3 shift application with a few forklifts. If you have a warehouse with only a couple of forklifts and pallet jacks that are not used around the clock then you may be better off using lead-acid. Lithium-ion batteries take the W when it comes to maintenance, charge rate, charging capacity, degradation, lifespan, safety and overall ROI. However, lead-acid batteries are much cheaper and if they are only used intermittently, then they are probably the better option for you.
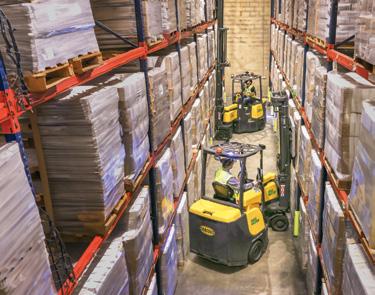
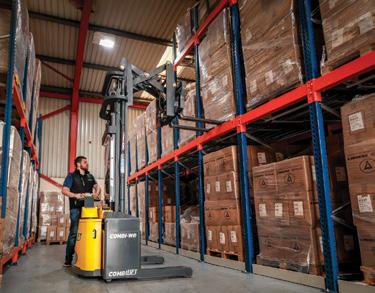
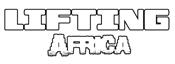

The cost-benefit of a gas forklift
GAS FORKLIFTS
The range of possibilities for using a gas forklift is very wide, as it is stronger. More powerful and faster compared to other types of forklifts.
It can be used in practically all types of terrain and is resistant to climatic variations and adversities. The cost-effectiveness of any type of forklift depends solely on the use you make of it. The gas forklift allows possibilities that other forklifts. Do not, due to its agility and high lifting capacity. Evaluate whether this type of forklift is worth it for you and your company. Keep reading!
What is a gas forklift?
A gas forklift is equipment that has its own driving force, through the operation of its engine. This, in turn, is activated by the chemical reaction that occurs between a substance and a gas (oxygen), that is, by combustion. The combustion forklift can have several applications. As it is a strong machine that remains efficient, even in different terrains and temperatures. It is recommended to use in open places, such as carriers and warehouses, for safety reasons. Despite the recommendation to be used outdoors, it emits much fewer pollutants and risks than a diesel forklift, for example. As long as there is ventilation, it is possible to operate this machine in places where there is less ventilation, in a safe way.
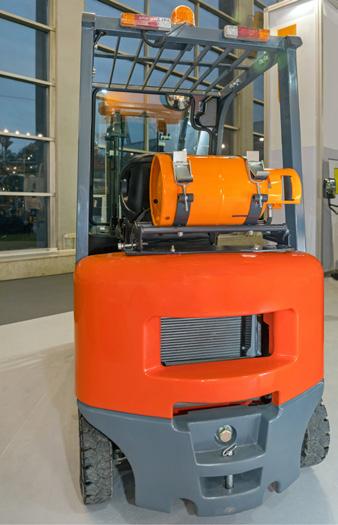
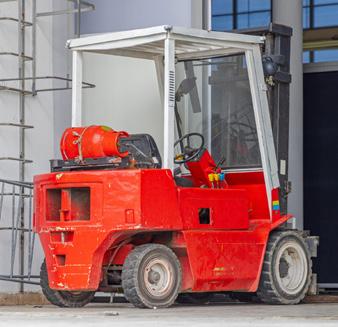
Move heavier loads:
A big advantage of the gas forklift is that it has enough strength to move very heavy loads without losing speed and balance. The strength of the gas forklift is greater than that of other types of forklifts. Some models of combustion forklifts are capable of supporting up to seven tons.
Greater potency:
The gas forklift has more power than other types of forklifts, which makes it possible for them to move easily on any type of terrain.
A combustion forklift can easily use terrain with slopes, very rough, with mud and other changes due to the climate.
Lifting capacity:
Another very interesting feature, which makes people opt for the gas forklift, is the lifting capacity. This forklift potentially lifts loads up to 6 meters high. This makes many companies prefer or specifically need a gas powered forklift.
Speed:
The gas forklift reaches a higher speed than other types of forklifts such as diesel powered or electric. Speed, in this case, can be a great ally, because, as a large amount of displacement can be done per day, the operation saves a lot of time in its entirety.
Resistance:
These forklift models, being strong and quite powerful, are much more resistant to adverse conditions that may arise during use. Setbacks, with rain, mud, cold, humidity and other types of weather possibilities are not a problem for a gas powered forklift.
MAINTENANCE

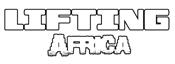
Maintenance contract benefits
Forklifts, like most things, can decline over time with regular use. When it comes to forklifts, the purchase price is not the only cost to consider. The cost of ownership of your forklift can be affected by fuel, maintenance, labour, electricity and incorrect use of the material handling equipment.
Train
your forklift operators
A forklift can do a lot of damage to a building, warehouse racking, the operator and or other people if the forklift driver is not fully competent on how to operate a forklift properly. For this reason, it is important to properly train all warehouse employees that operate forklifts.
This training will not only allow the driver to get familiar with the equipment, it will also teach them what to look for when the truck is not operating in prime condition.
Complete your daily checks
DMR18 requires that every forklift operator perform a pre-operation inspection prior to their shift to make sure everything is working properly. Oils, tires, water and safety items like seatbelt, rating plate, and mirrors should be checked before every shift to ensure top performance of your forklift and safety of your employees.
Pay attention to application of your equipment
Be sure you are using the correct equipment for the task at hand. You can use data to measure this. Turn on your forklift and take a look at the hour meters. If the drive motors have considerably more hours than the lift motor, it could mean your lift truck is not
being used correctly. A more appropriate piece of equipment, like a pallet truck or pallet jack, could be used in its place.
Make sure your batteries and chargers are taken care of if you run electric forklifts
If your material handling warehouse runs on electric forklifts, it is important to take care of your batteries. Damaged batteries, forklifts or injuries can result from improper battery handling. A mistake that often happens is mismatching the voltage size of battery to the charger.
If you are not sure of what voltage the battery is, count the cells and multiply that number by two. Also, be sure your industrial forklift batteries are watered after five to ten charges depending on the age of the battery.
Prevent expensive repairs with a forklift maintenance
For optimal performance, it’s important to take care of the forklifts in your fleet. The easiest way to ensure this is by adding a scheduled preventative maintenance plan to your forklift fleet to make sure your forklifts are in prime working condition. Over time, this preventative maintenance will save you from money lost from downtime and costly major repairs.
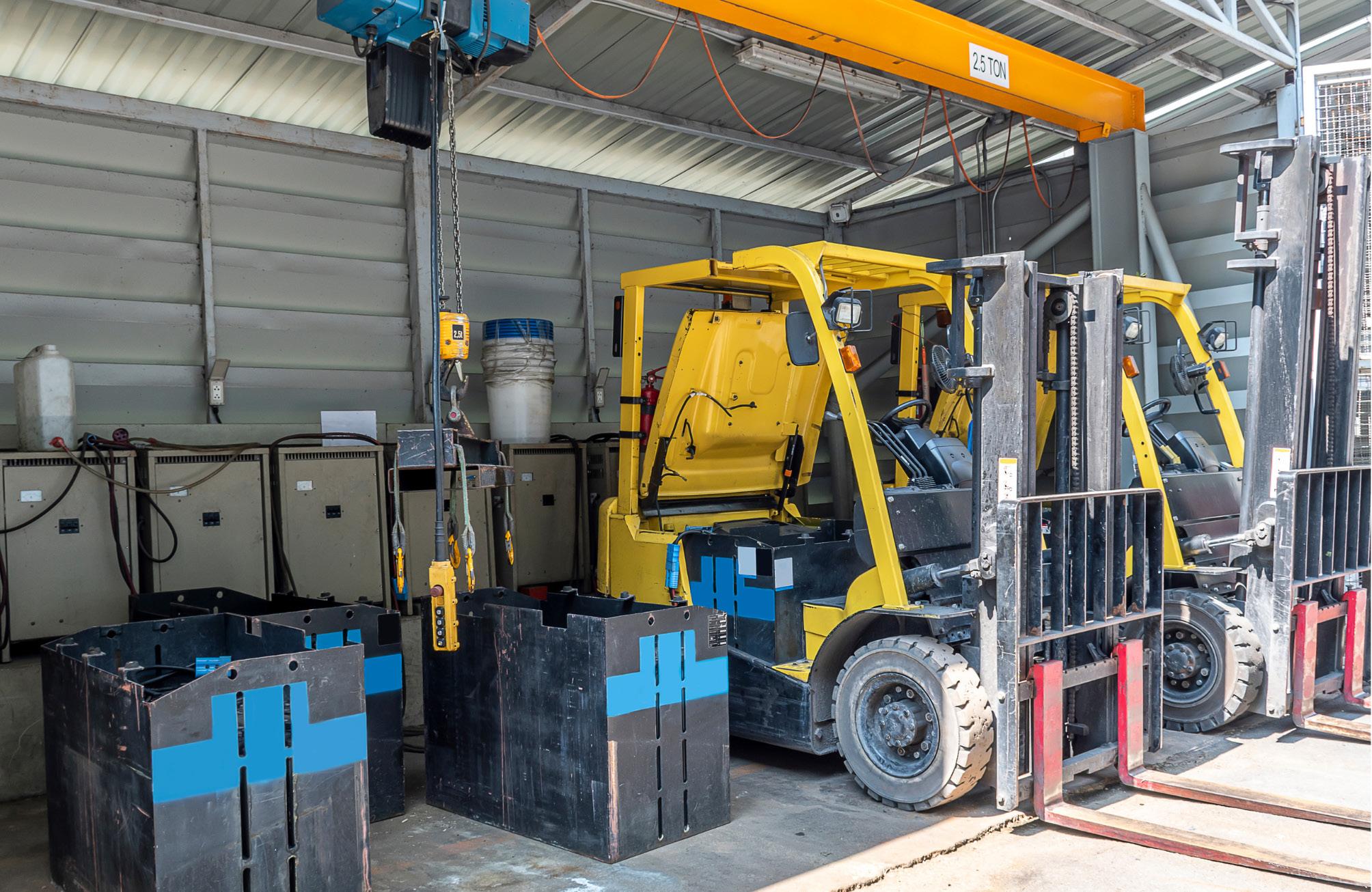
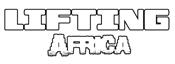

Warehouse safety tips
While proper training is important for fostering a safe place to work, it’s also crucial to adhere to commonsense warehouse safety tips. When used together, forklift training and a comprehensive safety plan is your best bet against preventing workplace calamities.
Learn what the most common forklift accidents are, and what the most important warehouse safety tips are to prevent injuries and fatalities below.
The most common warehouse forklift accidents
When proper warehouse safety practices are ignored, accidents involving forklifts are all too common and can cause serious injuries and deaths. Here are a few of the most common kinds of forklift accidents – and how to prevent them from happening in your warehouse:
Overturning
Tipping over a forklift is probably the single most catastrophic event that can happen to a powered industrial truck. It may occur when travelling on steep slopes, driving over slippery surfaces, being unevenly or heavily loaded, travelling too fast, especially around corners, moving a load at a dangerous height, crossing uneven ground or going over curbs or uneven steps. While these are mostly behavioural issues that can be corrected by proper training, overturning may be prevented by taking measures in the warehouse such as:
• Posting speed limits
• Installing anti-slip flooring
• Minimizing the opportunities for sharp turns
Pedestrian accidents
The best way to avoid forklifts coming into contact with pedestrians is to arrange the work area in such a way that the two populations are isolated from each other. A further protective measure is to insist that all pedestrians, employees, visitors, vendors, contractors, etc., wear a reflective high-visibility vest while on the floor where forklifts are operating.

Forklift falls and crush injuries
Crush forklift injuries often happen when a forklift tips over and the driver tries to leap free of the vehicle.
The Number One rule for reacting to an overturning forklift is to remain inside and keep all parts of the body under the protective canopy. This is against human nature and needs to be reinforced by keeping seat belts fastened, training and constant reinforcement in the form of signs in the workplace.
The top warehouse safety tips
Gear up
Personal protective equipment can make all the difference when it comes to performing a task safely. Safety gloves, hard hats, reflective tape and other attire should be worn at all times..
Define hazard zones
The importance of warehouse organisation is often overlooked when it comes to creating a safe work environment. For certain areas in your warehouse, it’s a good idea to keep non-essential employees from entering. Deploy yellow caution tape, orange cones or even extra personnel to ensure special procedures, heavy loads and other uncommon tasks can be performed without distraction.
Keep it clean
A clean workplace is a safer workplace, and that certainly applies to warehouses. If you notice a spill in the aisle, clean it up immediately. For larger spills, notify your supervisor. For those areas near truck loading docks, weather can pose unique safety challenges. A slick or wet loading surface is the cause of many warehouse accidents. Assigning dedicated cleaning tasks to each employee can help keep everyone invested in maintaining a safe working environment.
Have an exit plan
Does your warehouse have easy-to-read exit signs? This is a frequently overlooked factor, but simply knowing where to exit the warehouse is a matter of life or death during a fire. Should a warehouse evacuation be necessary, you’ll want your team to know where to head well in advance of an emergency.
Take matters into your own hands
When it comes to warehouse safety, personal responsibility is everything. Leave nothing to chance and implement your own safety plan that’s above and beyond normal requirements. Ensure each shift has properly trained emergency response personnel available. Offer CPR training. Put extra first aid kits throughout the warehouse.
Preventative action is great, but what happens when something goes wrong? As the only saying goes, “Hope for the best, prepare for the worst.” Of course, the best way to take safety matters into your own hands is to get forklift certified and maintain your certification every three years.
Follow a maintenance schedule
Keep a rigorous maintenance program for all of your equipment – forklifts, pallet jacks and more. Many workplace accidents are caused by faulty, defective forklifts. With regular maintenance a part of your daily plan, safety will naturally take care of itself. It’s amazing what you can accomplish with just a few minutes of dedicated maintenance tasks each day.
Check your racks & shelves
Remember, warehouse safety isn’t all about forklifts all the time. Your cargo and goods need a stable, safe place for storage. This means that your racks and shelves should meet & exceed load standards. Ensure your forklift operators aren’t overloading the maximum capacity requirements – if they are, big problems could be headed your way.
All clean hands on deck
After the daily grind, make sure your floors are clean for the next shift. Fork-mounted brooms are a great idea in this regard. A clean sweep will help the next group of workers enjoy a clean, safer workspace. All spills and hazardous obstacles should be cleared immediately. This is a good idea for warehouses, dock areas, shipyards and other areas where forklifts and industrial equipment are active.
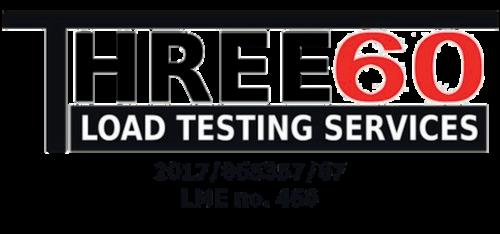
YOUR ONE - STOP LOAD TESTING COMPANY
Looking for a quality Load Testing Company you can depend on? Well, look no further.
Here at 360 Load Testing Services (Pty) Ltd we are available where you need us, when you need us. In Africa we’ve been committed to being the best at what we do, serving clients by not just meeting their expectations, but exceeding them.
All Lifting Machine Inspectors that are utilized by 360 Load Testing Services are registered with the Engineering Council of South Africa (ECSA) and the Department of Labour (D.o.L) to carry out compulsory inspections and load tests of Lifting Machines and Lifting Tackle.
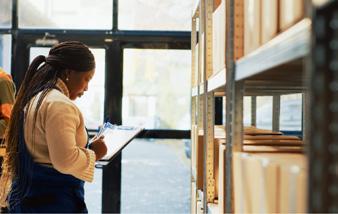
Limit forklift operation to only fully trained personnel
Even if it’s “just a little job,” no forklift action should be undertaken by someone who isn’t properly instructed and trained. The deadly risks vastly outweigh any minor convenience you might gain from having an untrained colleague help you out.
Remember to break
Long shifts, overtime, covering for someone who called off – there are many times when an extra 15 minutes turns into 2 hours out in the warehouse.
Invest in education for your workplace
While there is no foolproof way on how to keep your warehouse safe, all of the common causes of forklift fatalities can be remedied by modifying the conduct of everyone on the shop floor. Even the most carefully laid-out warehouse is no match for the fallibility of the human.
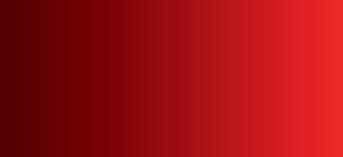
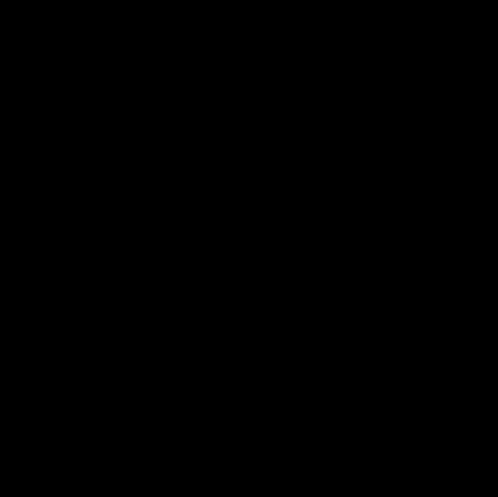
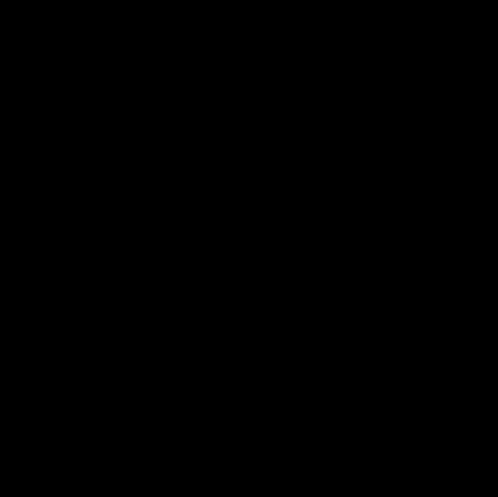

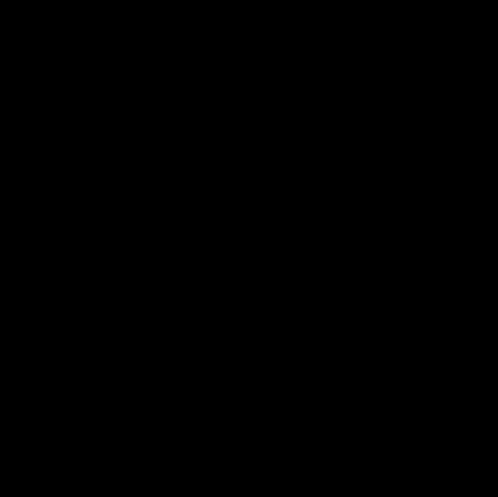
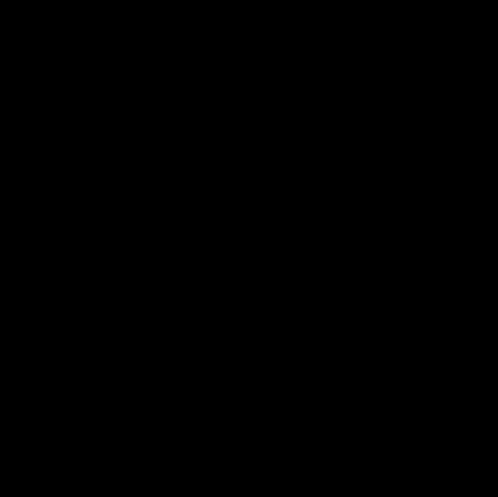


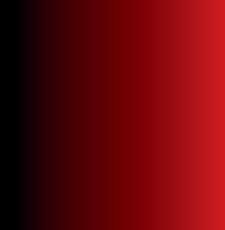
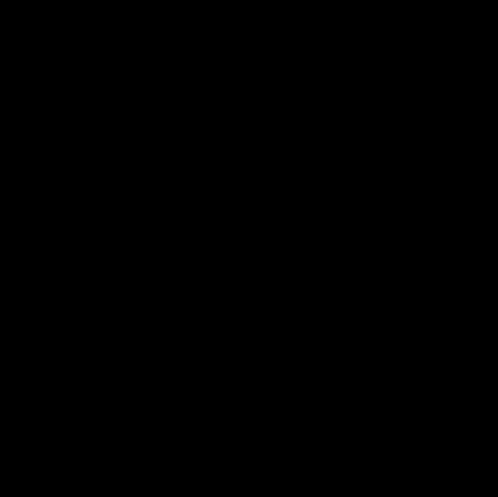
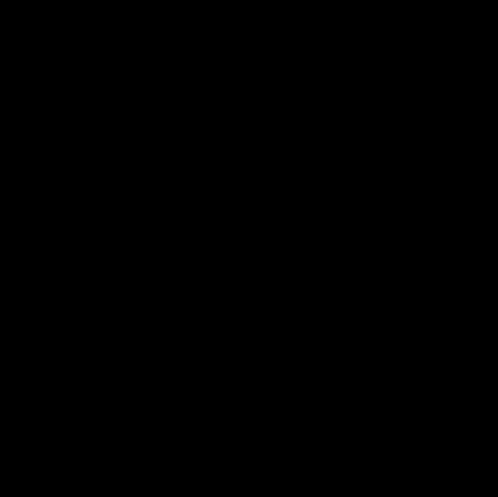
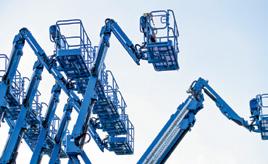

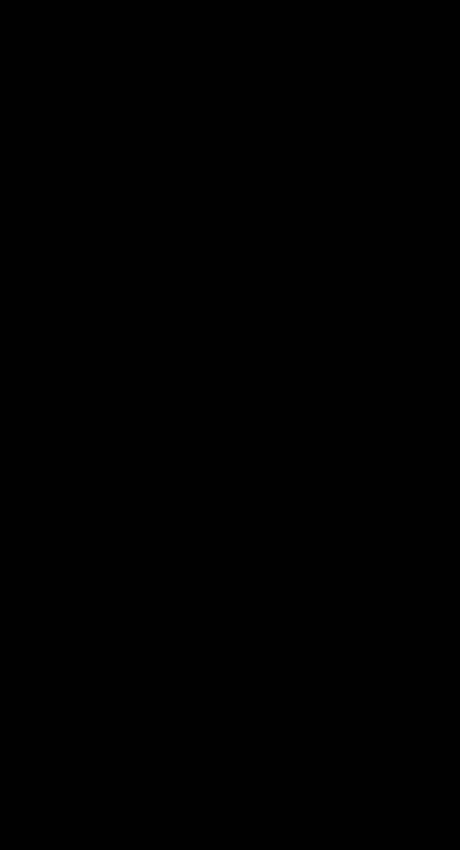
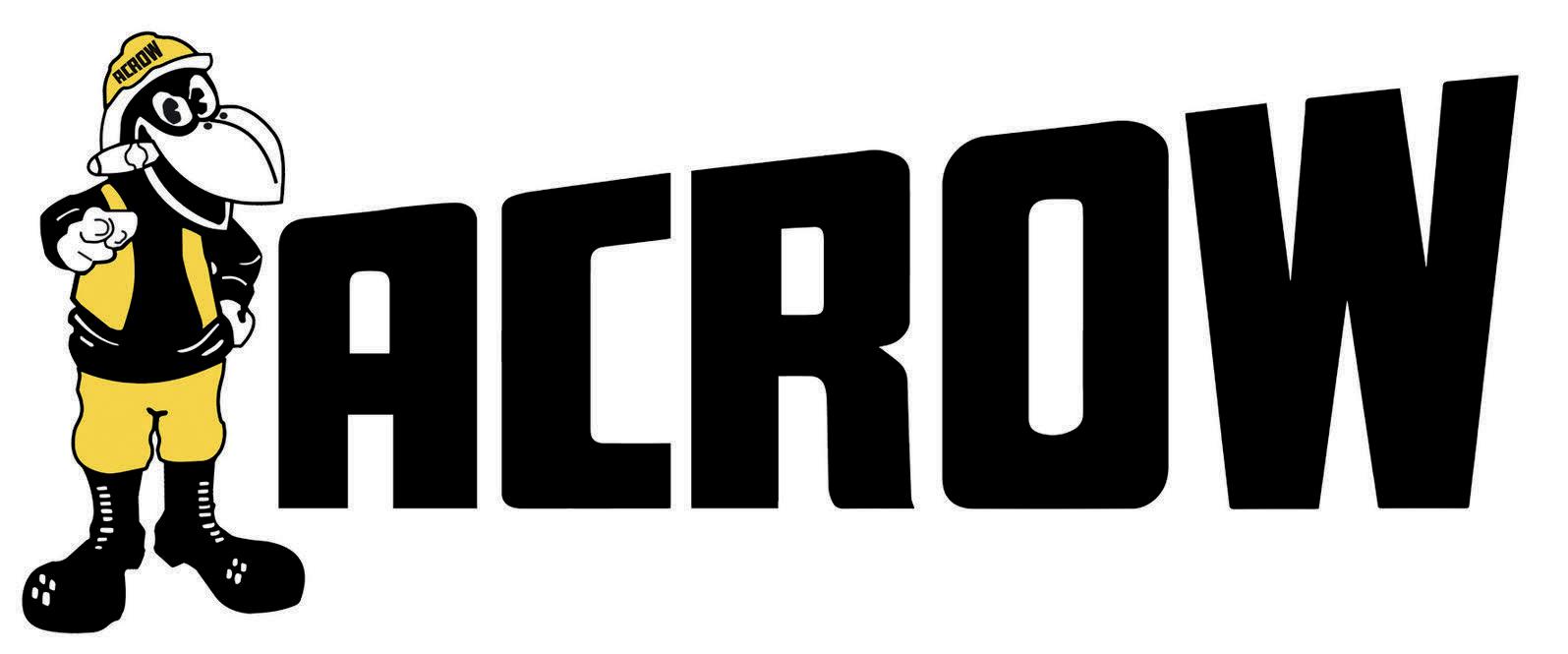
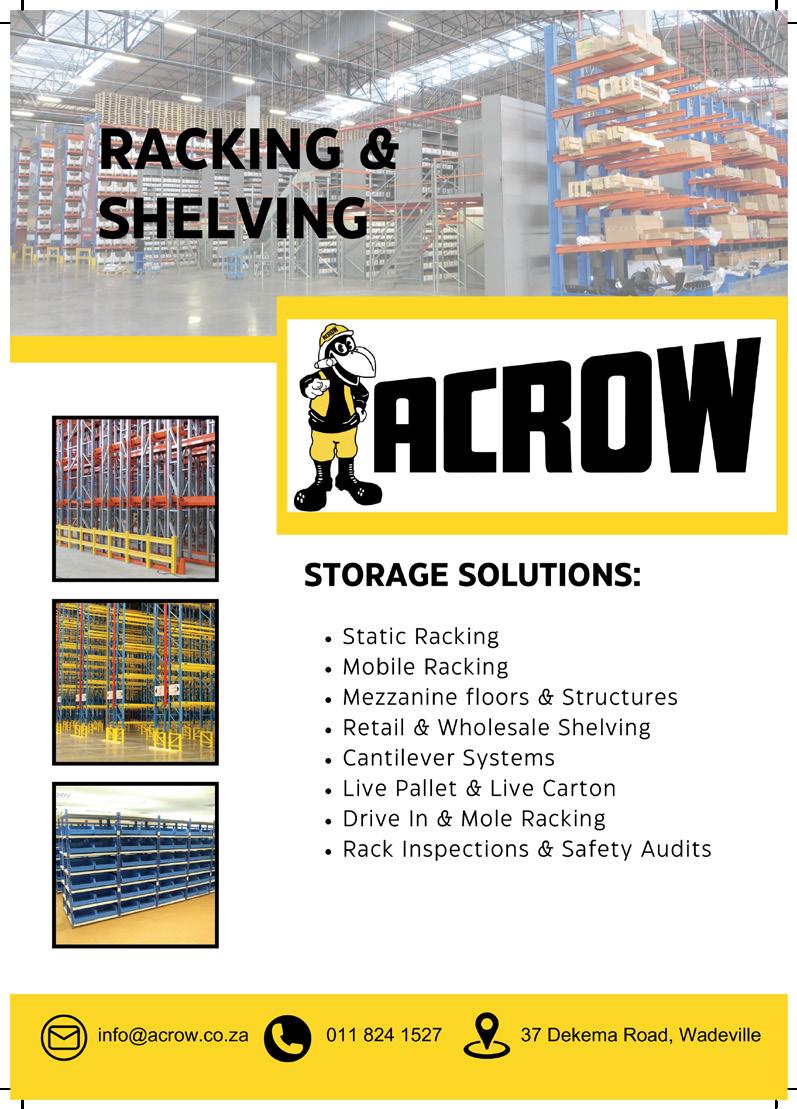


Avoid moving beam levels:
Keep beam levels in their original positions. Adjusting beam levels to accommodate larger pallets or increase space can significantly reduce the racking’s loading capacity. Consult with a racking manufacturer if you need to change beam levels.
Train staff on forklift safety:
Train your staff on forklift safety, inspecting pallets for damage, and correctly placing pallets on beams. Operating a forklift in confined areas is challenging, and minor bumps can happen. Install protective products on racking to minimize damage and ensure drivers report any incidents.
Regular inspections:
Conduct weekly in-house inspections and annual inspections by a qualified racking inspector.
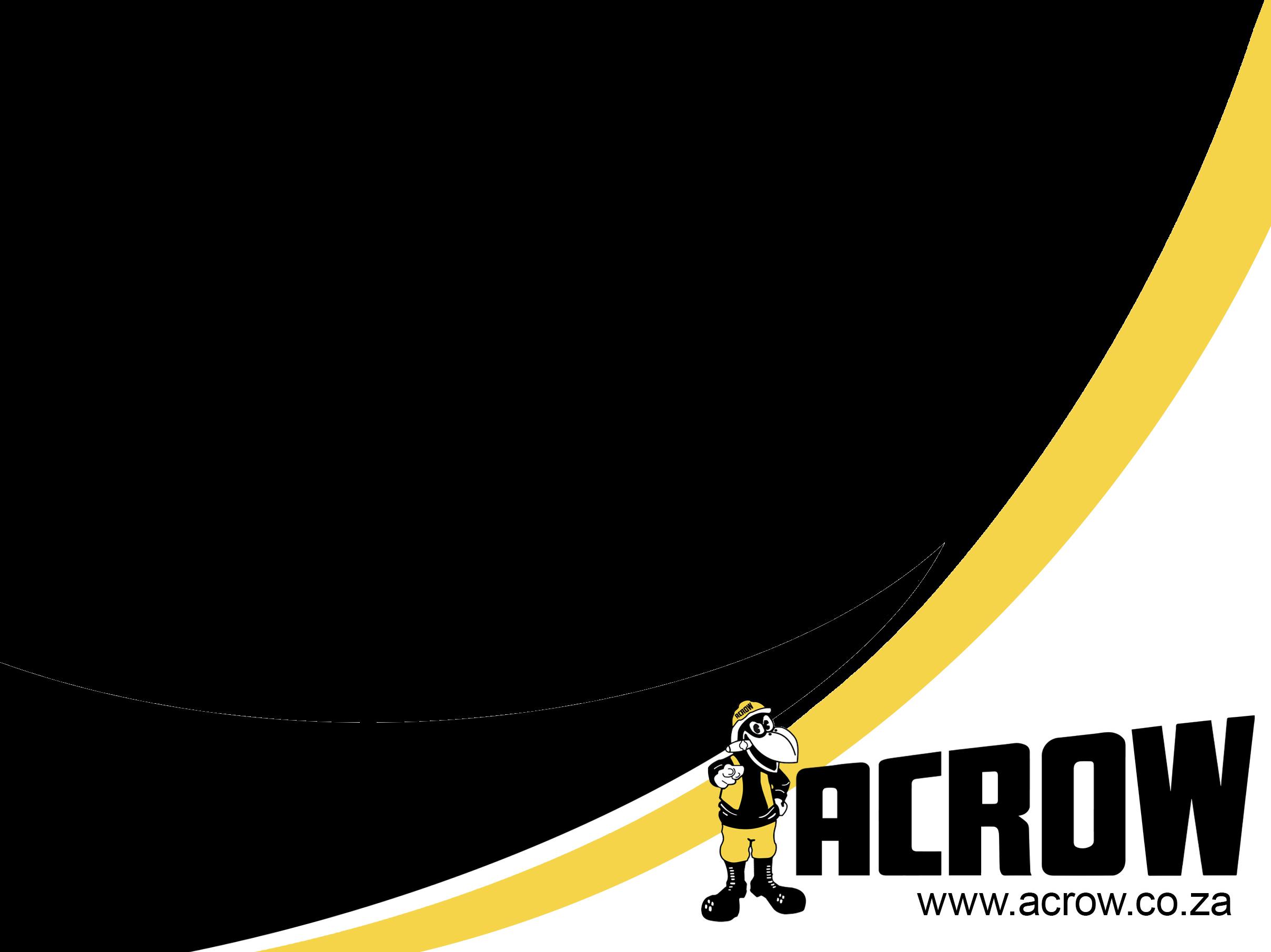
Many racking manufacturers offer yearly inspections and can replace any damaged components. Utilize these services to identify problem areas and quickly replace dangerous equipment.
Unsafe racking poses a significant danger. More businesses are recognizing the importance of health and safety requirements and are taking steps to mitigate these risks.
Regular maintenance and adherence to safety protocols are essential to preventing racking collapses and ensuring a safe working environment.
Acrow can assist in incorporating racking safety procedures into your ISO policies. We provide comprehensive training to your teams, ensuring they remain safety conscious at all times.
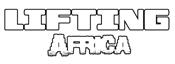

The Do’s and Don’ts of racking
When it comes to installing and maintaining a pallet racking system in a warehouse, there are a host of critical factors to understand to ensure safety and promote efficiency. An adequate understanding of what a pallet racking can and cannot do will not only eliminate accidents but can also save a business time and money.
Pallet racking systems may seem simple, but the variety of material they hold and space they occupy raises important concerns. Warehouse size, load types, and the type of racking system itself should all be thoroughly considered. As well, failing to understand the cost of maintenance or what to do if the system is damaged could result in money loss or unsafe working conditions.
Here are several do’s and don’ts to consider when it comes to pallet racking systems:
Pallet racking systems: what to do
• The number one consideration for choosing a pallet racking system is size. Not the size of the system, but the total floor space and vertical space the warehouse has to accommodate a pallet racking system. There are several pallet racking systems available:
• Selective pallet racks are the most common type of warehouse pallet racking. These racks have beams that slide into place using a teardrop-shaped opening in the uprights. Fast and easy to install, and accessible from both sides of the aisle, this racking type is versatile.
• Structural pallet racks use bolts to lock beams into place onto the uprights. Structural racking is for heavier loads, or if the chance of damage is to the racks is higher.
• Drive in racking is also for smaller spaces and/or delicate or perishable loads. These pallet racks are a

last in, first out design, so space optimization is key as they can be placed against walls.
• Develop a procedure for identifying, reporting, and fixing damaged systems. Pallet Racks can deal with hundreds of thousands of pounds, so any dent, missing bolt or unsecured rack must be repaired immediately.
As with any business, the safety of employees is paramount. Having a clear, concise procedure for reporting rack damage is imperative. All employees should be clear on those procedures, and they should be continually emphasized.
• Install guard rails. Guard rails can save a company money and keep employees safe by protecting the most vulnerable, high traffic areas around pallet racking. Corner uprights are particularly in danger of collision with lifts; having guard rails eliminates that risk. Whether a company chooses removable guard rails, or the permanent, double barred type depends on their environment.
Pallet racking systems: what not to do
• Do not write off used pallet racking for the warehouse. Used pallet racking can be an excellent choice for a new business with limited capital looking for an effective racking system. On the other hand, if you want to upgrade your existing pallet racking, you can sell your old racking. Whether or not you buy or sell used pallet racking, it is a viable option for keeping costs down without sacrificing safety or efficiency
• Do not buy just what you need. Flexibility for a growing business is critical, and only buying just enough racking for current need is a mistake. Buying enough racking to suit only current needs could pose problems in the future. For instance, there could be compatibility issues between the racking systems if there is a significant period between the purchases.
• Do not “cheap out” with a pallet racking system. Pallet racking is a significant safety concern in a warehouse as there can be cumbersome items sitting high above the heads of workers. If racking becomes overloaded because poor quality racking cannot handle the load given, it will break.
Also, if a business bought drive-in racking to save on costs, then had to switch to a FIFO (first in, first out) model instead, it would cost them unnecessary time and money to replace.
Conclusion
Safety is the most crucial aspect to consider when purchasing and maintaining a pallet racking system. Regardless of the type of system a business chooses to invest in, regular maintenance and understanding the capabilities of each type of system are important.

FORKLIFT REGISTER
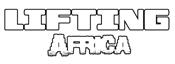
COMPANY:
LOCATION:
FROM DATE: TO DATE:
FORKLIFT ID:
OPERATOR:
SHIFT:

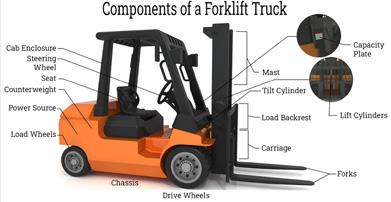
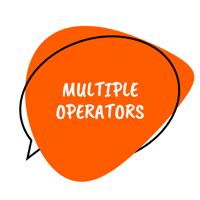
INSPECTION CHECK LIST
Write “YES”, “NO” or “N/A” for each finding in this register under the relevant date. In the event of a “NO”, the details of the following:
DEVIATION DETECTED AND CORRECTIVE ACTION
Must be recorded on the form designed for this purpose on the last page of the register.
PRE-OPERATIONAL CHECKLIST
A certified operator/driver must complete the pre-operational checklist before their shift starts. They must report any defects to their supervisor. In case of a “NO”, the forklift MAY NOT leave the premises until the problem is corrected, and before the checklist is signed off by their supervisor.
6 MONTHLY INSPECTION CHECKLIST SHOULD BE USED IN CONJUNCTION WITH THE PRE-OPERATIONAL CHECKLIST
A competent person must inspect equipment every 6 months. All findings should be recorded and available on site. If the equipment is defective, it must be tagged as DEFECTED and reported to the person responsible for its repairs.

BOBCAT FORKLIFTS ARE HERE
DOOSAN FORKLIFTS NOW A PART OF THE BOBCAT FAMILY
The innovation and durability synonymous with Bobcat equipment merge seamlessly with decades of experience in designing reliable material handling equipment from Doosan. The incorporation of the built-to-last and easy to maintain Bobcat DNA into solutions for intralogistics and distribution facilities aims to enhance their profitability. Bobcat forklifts are here to empower you and your business to accomplish even more.
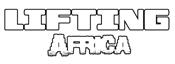

ITEM TO BE CHECKED
All oil level correct / any oil leaks
All pipes and hoses in good condition
Battery terminals, cables mounting secure
Beacon or strobe warning light
Brake in good working condition / fluid levels correct
Caps secure (fuel, oil, radiator etc secure)
Control levers in good working order
Driver's compartment / seat good condition
Electrolyte levels
Enter and adjust seat and mirrors
Fan belt & blades good condition & tension
Fork condition
Fork position and fork locks
Fuel leaks / levels adequete
Gas shut-off valve operational
Gas tank mounting secure
Gauges before switching on and after
General bodywork
Hoisting mechanism in good working order
Horn in good working order
Hydraulic cylinders
Ignition key operative
Indicators
Load backrest and carriage
Lights in good working order
Lubrication adequate
Mast and chain
Pedal rubbers
Overhead guard/cab
Park brake engaged
Reverse siren
Battery Mounting
Radiator water level & oil levels (leaks)
Raise & lower - cylinder & chain
Safety belt in good condition
Steering lock to lock
Steering play
Switches in good working order
Tilt- cylinder condition
Transmission oil
Tyre pressure, wheels & rims good condition
Water leaks
Wheel nuts & bolts secure
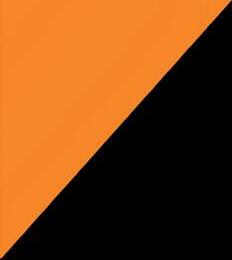
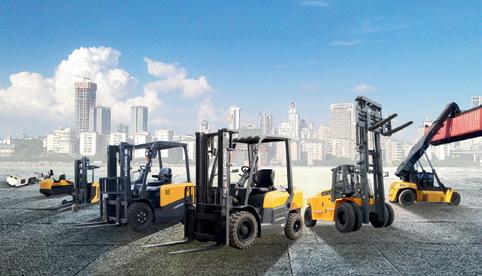
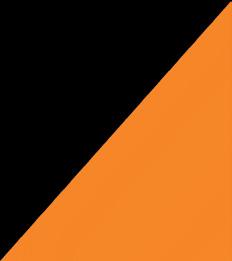
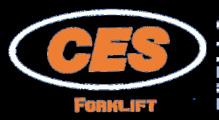
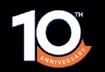
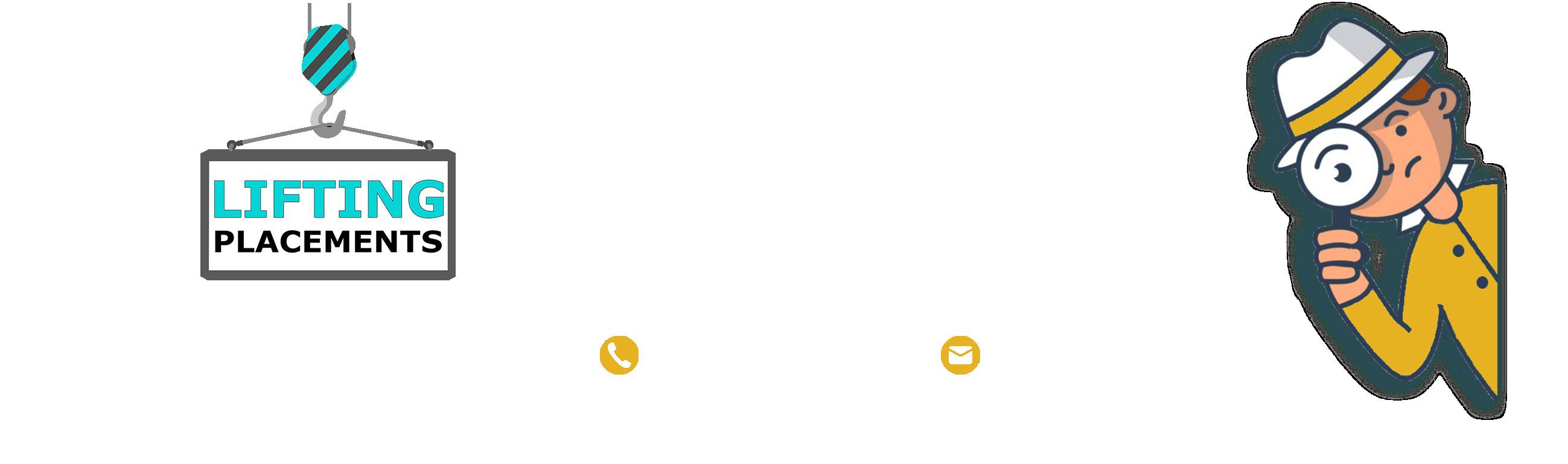
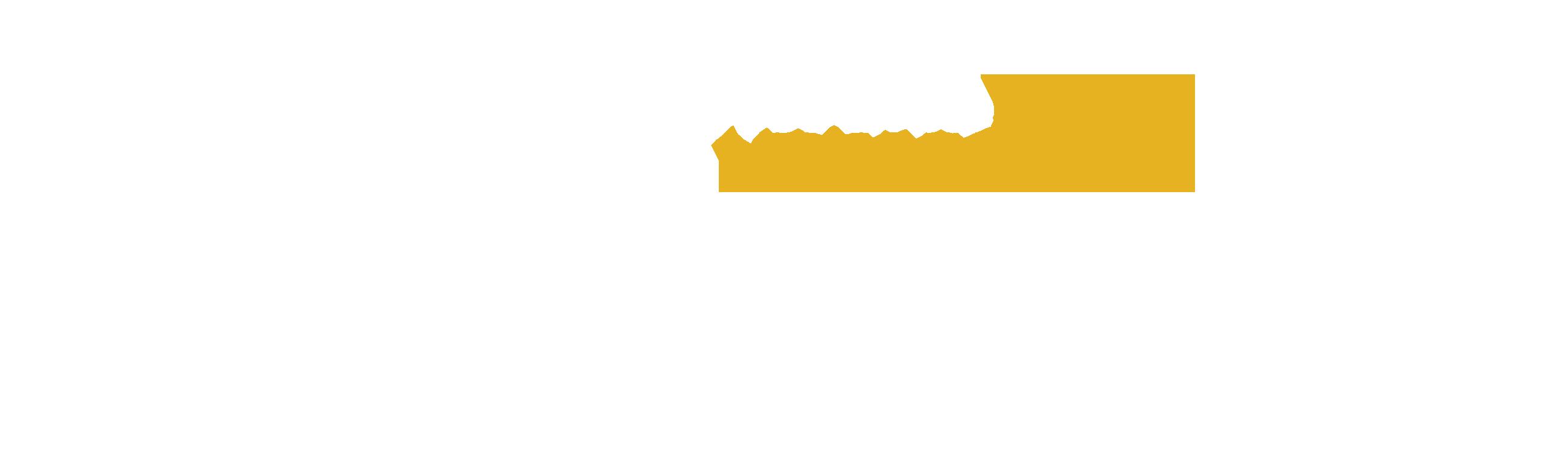
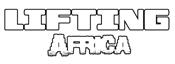

ITEM TO BE CHECKED
All oil level correct / any oil leaks
All pipes and hoses in good condition
Battery terminals, cables mounting secure
Beacon or strobe warning light
Brake in good working condition / fluid levels correct
Caps secure (fuel, oil, radiator etc secure)
Control levers in good working order
Driver's compartment / seat good condition
Electrolyte levels
Enter and adjust seat and mirrors
Fan belt & blades good condition & tension
Fork condition
Fork position and fork locks
Fuel leaks / levels adequete
Gas shut-off valve operational
Gas tank mounting secure
Gauges before switching on and after
General bodywork
Hoisting mechanism in good working order
Horn in good working order
Hydraulic cylinders
Ignition key operative
Indicators
Load backrest and carriage
Lights in good working order
Lubrication adequate
Mast and chain
Pedal rubbers
Overhead guard/cab
Park brake engaged
Reverse siren
Battery Mounting
Radiator water level & oil levels (leaks)
Raise & lower - cylinder & chain
Safety belt in good condition
Steering lock to lock
Steering play
Switches in good working order
Tilt- cylinder condition
Transmission oil
Tyre pressure, wheels & rims good condition
Water leaks
Wheel nuts & bolts secure

WE
HAVE A LOT OF

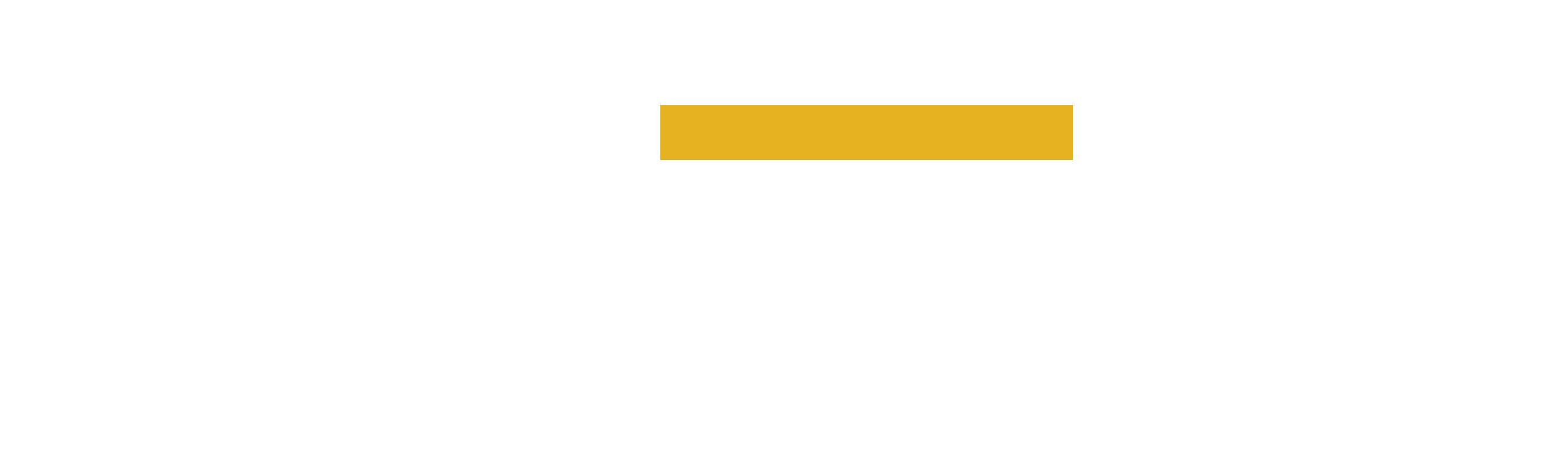
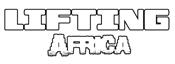

ITEM TO BE CHECKED
All oil level correct / any oil leaks
All pipes and hoses in good condition
Battery terminals, cables mounting secure
Beacon or strobe warning light
Brake in good working condition / fluid levels correct
Caps secure (fuel, oil, radiator etc secure)
Control levers in good working order
Driver's compartment / seat good condition
Electrolyte levels
Enter and adjust seat and mirrors
Fan belt & blades good condition & tension
Fork condition
Fork position and fork locks
Fuel leaks / levels adequete
Gas shut-off valve operational
Gas tank mounting secure
Gauges before switching on and after
General bodywork
Hoisting mechanism in good working order
Horn in good working order
Hydraulic cylinders
Ignition key operative
Indicators
Load backrest and carriage
Lights in good working order
Lubrication adequate
Mast and chain
Pedal rubbers
Overhead guard/cab
Park brake engaged
Reverse siren
Battery Mounting
Radiator water level & oil levels (leaks)
Raise & lower - cylinder & chain
Safety belt in good condition
Steering lock to lock
Steering play
Switches in good working order
Tilt- cylinder condition
Transmission oil
Tyre pressure, wheels & rims good condition
Water leaks
Wheel nuts & bolts secure
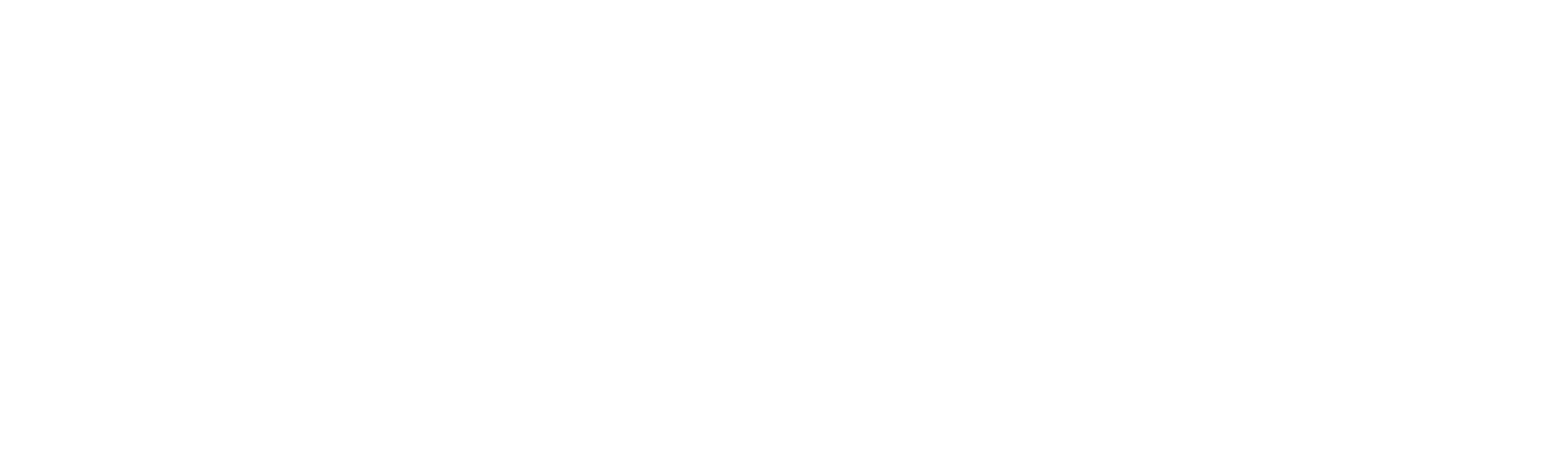
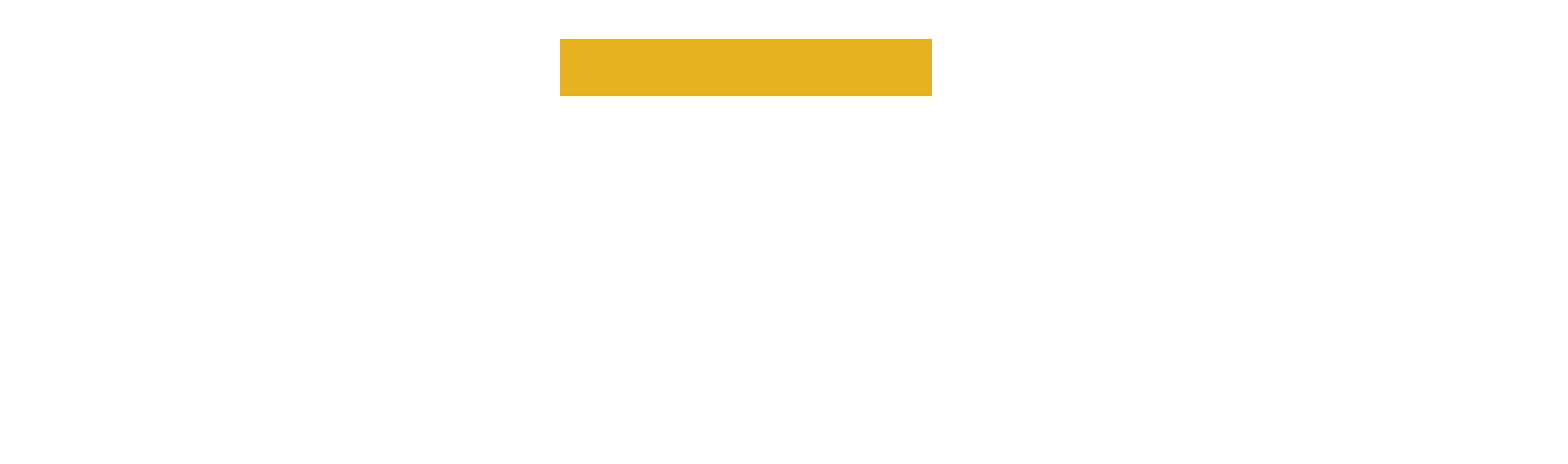
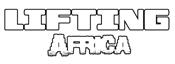

ITEM TO BE CHECKED
All oil level correct / any oil leaks
All pipes and hoses in good condition
Battery terminals, cables mounting secure
Beacon or strobe warning light
Brake in good working condition / fluid levels correct
Caps secure (fuel, oil, radiator etc secure)
Control levers in good working order
Driver's compartment / seat good condition
Electrolyte levels
Enter and adjust seat and mirrors
Fan belt & blades good condition & tension
Fork condition
Fork position and fork locks
Fuel leaks / levels adequete
Gas shut-off valve operational
Gas tank mounting secure
Gauges before switching on and after
General bodywork
Hoisting mechanism in good working order
Horn in good working order
Hydraulic cylinders
Ignition key operative
Indicators
Load backrest and carriage
Lights in good working order
Lubrication adequate
Mast and chain
Pedal rubbers
Overhead guard/cab
Park brake engaged
Reverse siren
Battery Mounting
Radiator water level & oil levels (leaks)
Raise & lower - cylinder & chain
Safety belt in good condition
Steering lock to lock
Steering play
Switches in good working order
Tilt- cylinder condition
Transmission oil
Tyre pressure, wheels & rims good condition
Water leaks
Wheel nuts & bolts secure

REACH NEW HEIGHTS
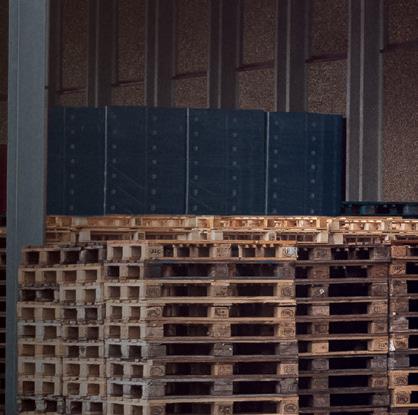
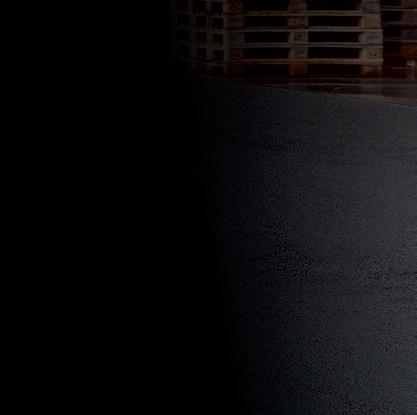
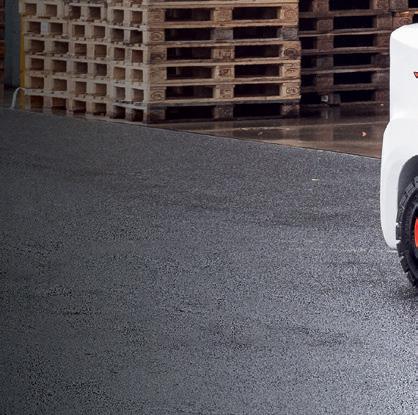

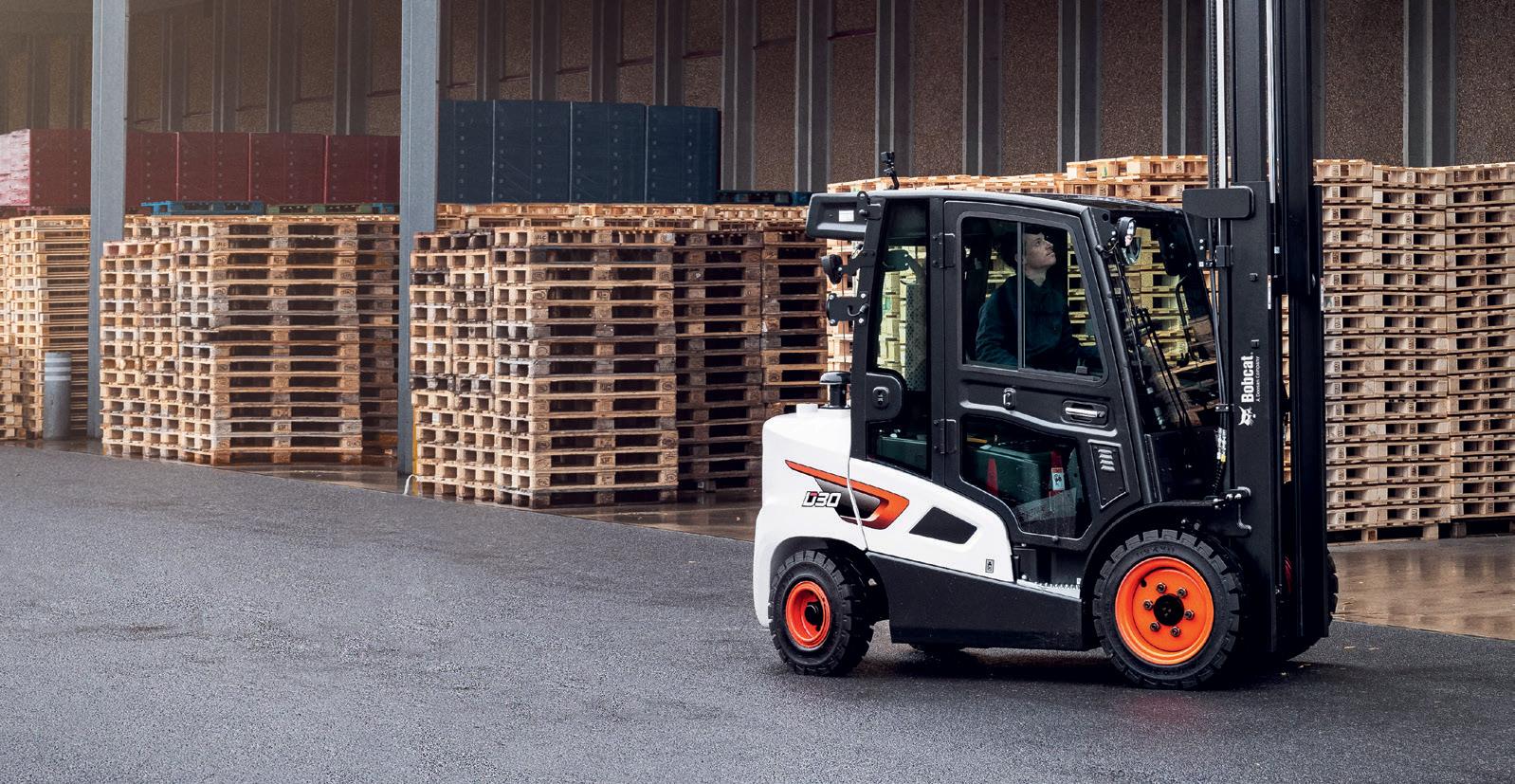


BOBCAT FORKLIFTS ARE HERE
DOOSAN FORKLIFTS NOW A PART OF THE BOBCAT FAMILY
The innovation and durability synonymous with Bobcat equipment merge seamlessly with decades of experience in designing reliable material handling equipment from Doosan. The incorporation of the built-to-last and easy to maintain Bobcat DNA into solutions for intralogistics and distribution facilities aims to enhance their profitability. Bobcat forklifts are here to empower you and your business to accomplish even more.
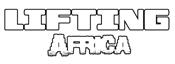

ITEM TO BE CHECKED
All oil level correct / any oil leaks
All pipes and hoses in good condition
Battery terminals, cables mounting secure
Beacon or strobe warning light
Brake in good working condition / fluid levels correct
Caps secure (fuel, oil, radiator etc secure)
Control levers in good working order
Driver's compartment / seat good condition
Electrolyte levels
Enter and adjust seat and mirrors
Fan belt & blades good condition & tension
Fork condition
Fork position and fork locks
Fuel leaks / levels adequete
Gas shut-off valve operational
Gas tank mounting secure
Gauges before switching on and after
General bodywork
Hoisting mechanism in good working order
Horn in good working order
Hydraulic cylinders
Ignition key operative
Indicators
Load backrest and carriage
Lights in good working order
Lubrication adequate
Mast and chain
Pedal rubbers
Overhead guard/cab
Park brake engaged
Reverse siren
Battery Mounting
Radiator water level & oil levels (leaks)
Raise & lower - cylinder & chain
Safety belt in good condition
Steering lock to lock
Steering play
Switches in good working order
Tilt- cylinder condition
Transmission oil
Tyre pressure, wheels & rims good condition
Water leaks
Wheel nuts & bolts secure
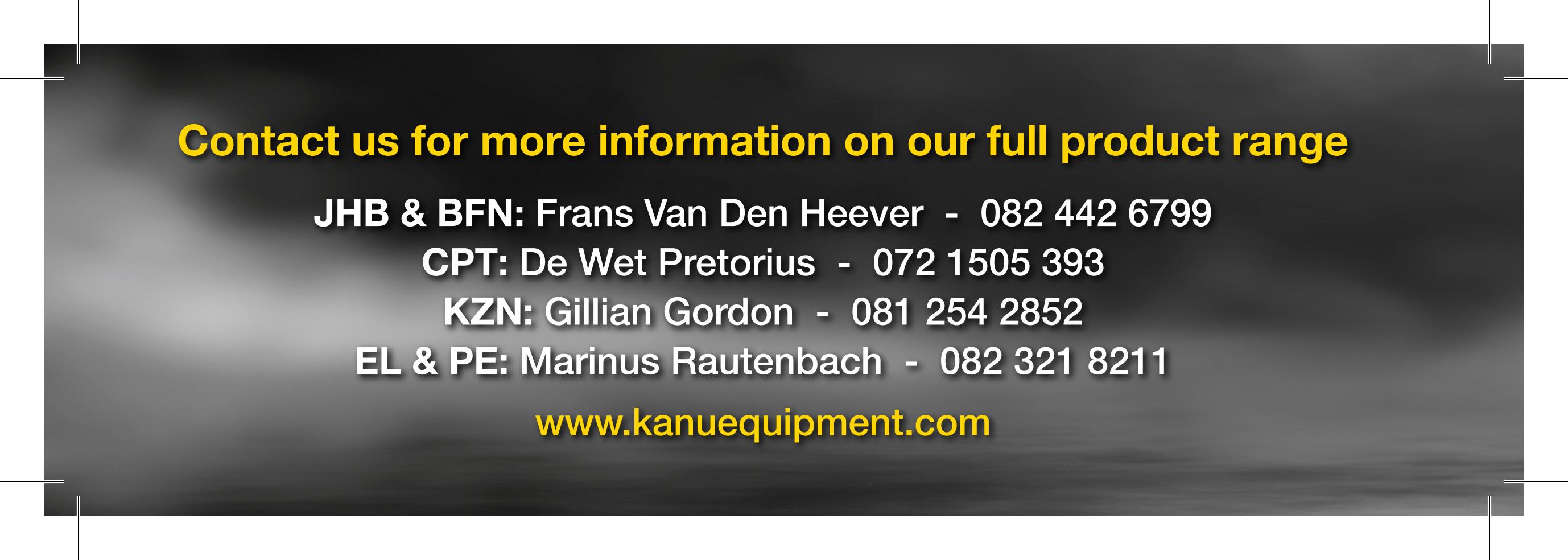

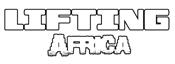

ITEM TO BE CHECKED
All oil level correct / any oil leaks
All pipes and hoses in good condition
Battery terminals, cables mounting secure
Beacon or strobe warning light
Brake in good working condition / fluid levels correct
Caps secure (fuel, oil, radiator etc secure)
Control levers in good working order
Driver's compartment / seat good condition
Electrolyte levels
Enter and adjust seat and mirrors
Fan belt & blades good condition & tension
Fork condition
Fork position and fork locks
Fuel leaks / levels adequete
Gas shut-off valve operational
Gas tank mounting secure
Gauges before switching on and after
General bodywork
Hoisting mechanism in good working order
Horn in good working order
Hydraulic cylinders
Ignition key operative
Indicators
Load backrest and carriage
Lights in good working order
Lubrication adequate
Mast and chain
Pedal rubbers
Overhead guard/cab
Park brake engaged
Reverse siren
Battery Mounting
Radiator water level & oil levels (leaks)
Raise & lower - cylinder & chain
Safety belt in good condition
Steering lock to lock
Steering play
Switches in good working order
Tilt- cylinder condition
Transmission oil
Tyre pressure, wheels & rims good condition
Water leaks
Wheel nuts & bolts secure
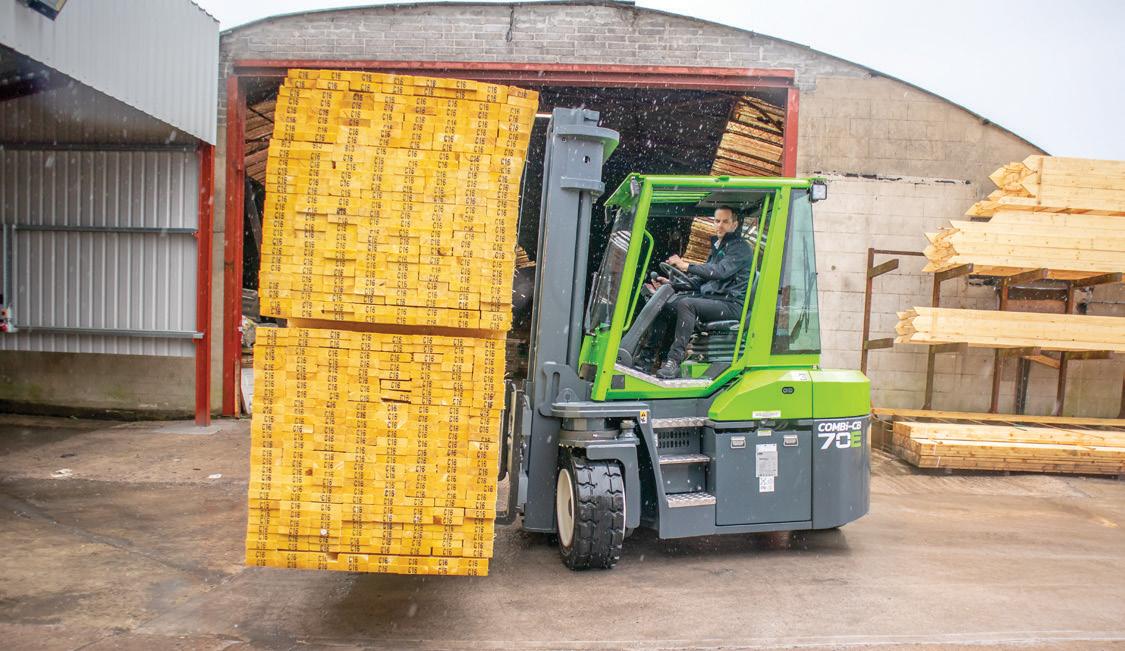
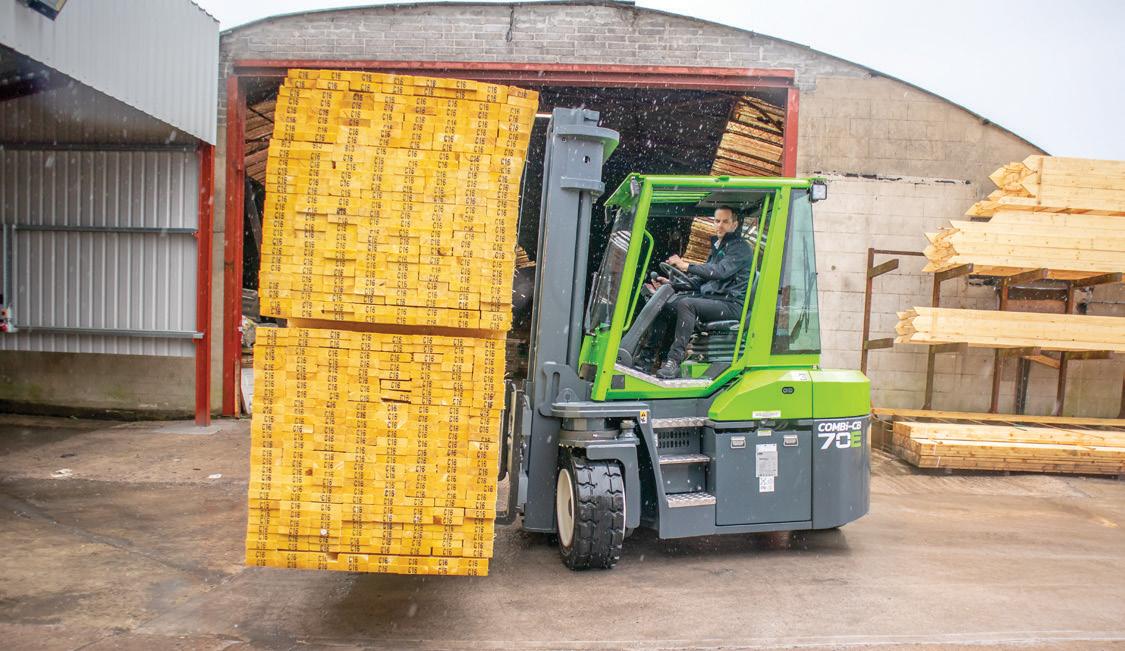
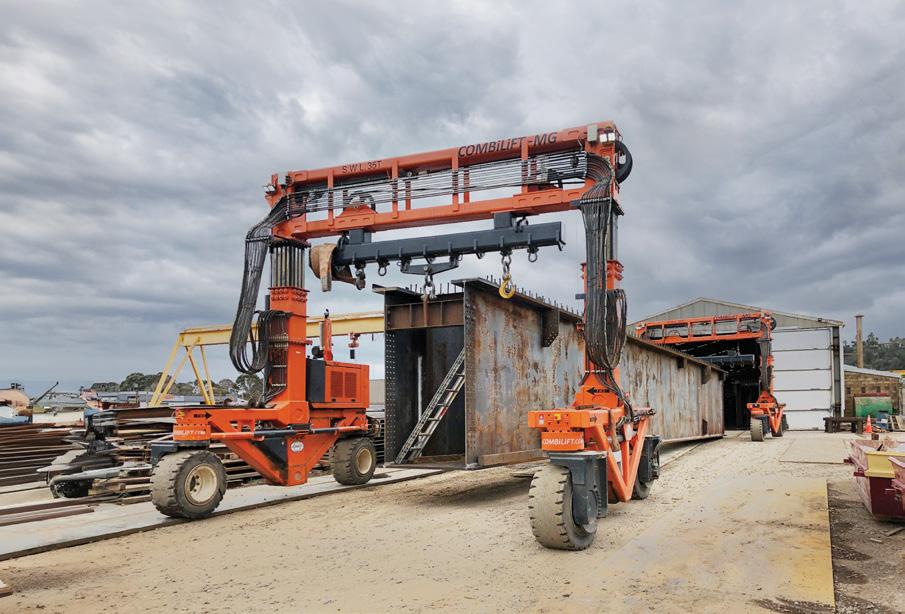
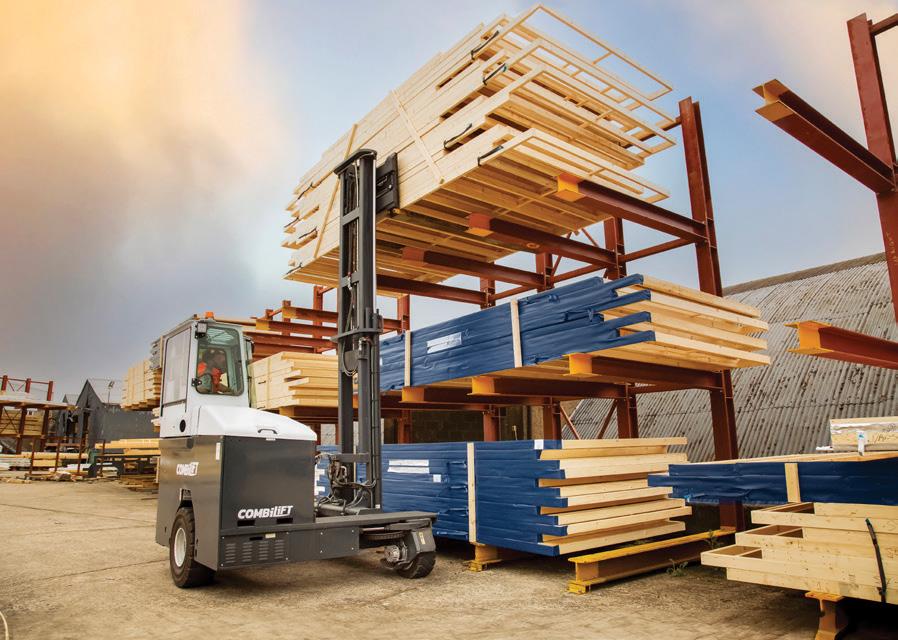
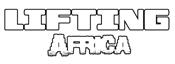

ITEM TO BE CHECKED
All oil level correct / any oil leaks
All pipes and hoses in good condition
Battery terminals, cables mounting secure
Beacon or strobe warning light
Brake in good working condition / fluid levels correct
Caps secure (fuel, oil, radiator etc secure)
Control levers in good working order
Driver's compartment / seat good condition
Electrolyte levels
Enter and adjust seat and mirrors
Fan belt & blades good condition & tension
Fork condition
Fork position and fork locks
Fuel leaks / levels adequete
Gas shut-off valve operational
Gas tank mounting secure
Gauges before switching on and after
General bodywork
Hoisting mechanism in good working order
Horn in good working order
Hydraulic cylinders
Ignition key operative
Indicators
Load backrest and carriage
Lights in good working order
Lubrication adequate
Mast and chain
Pedal rubbers
Overhead guard/cab
Park brake engaged
Reverse siren
Battery Mounting
Radiator water level & oil levels (leaks)
Raise & lower - cylinder & chain
Safety belt in good condition
Steering lock to lock
Steering play
Switches in good working order
Tilt- cylinder condition
Transmission oil
Tyre pressure, wheels & rims good condition
Water leaks
Wheel nuts & bolts secure

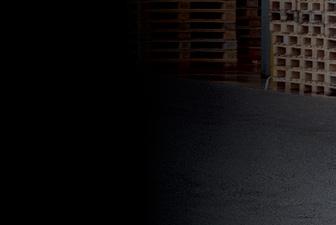

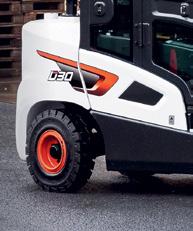
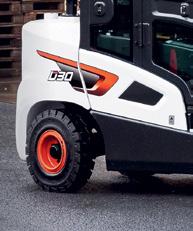

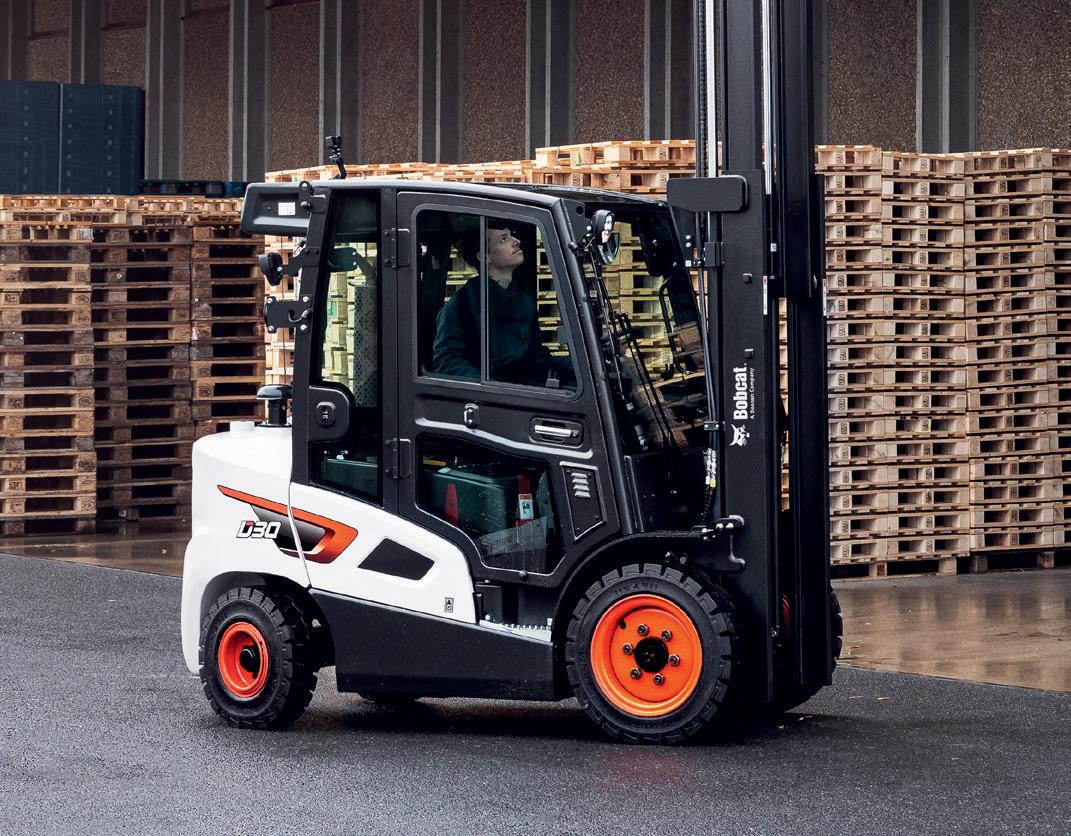
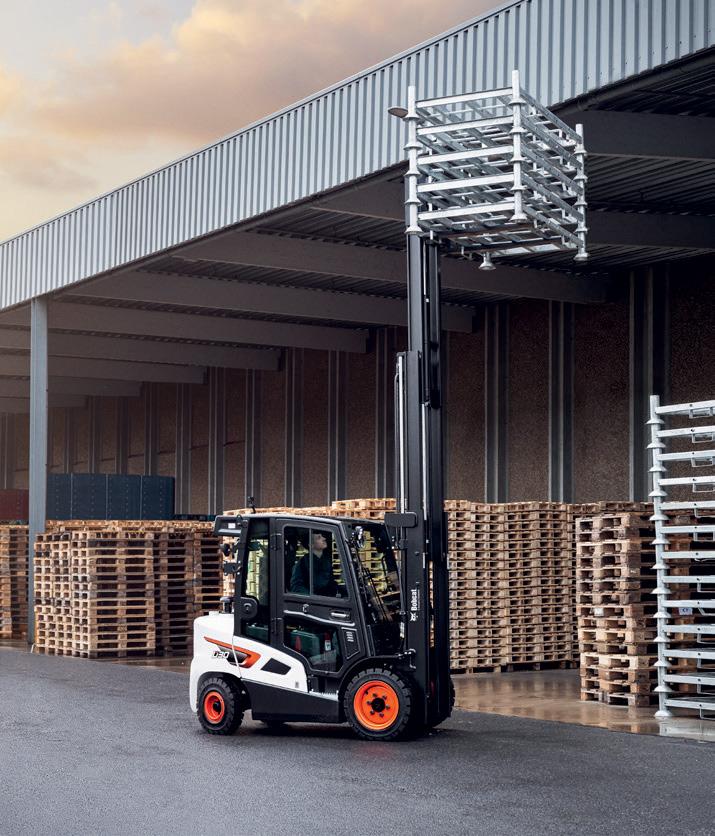
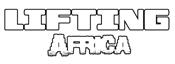

ITEM TO BE CHECKED
All oil level correct / any oil leaks
All pipes and hoses in good condition
Battery terminals, cables mounting secure
Beacon or strobe warning light
Brake in good working condition / fluid levels correct
Caps secure (fuel, oil, radiator etc secure)
Control levers in good working order
Driver's compartment / seat good condition
Electrolyte levels
Enter and adjust seat and mirrors
Fan belt & blades good condition & tension
Fork condition
Fork position and fork locks
Fuel leaks / levels adequete
Gas shut-off valve operational
Gas tank mounting secure
Gauges before switching on and after
General bodywork
Hoisting mechanism in good working order
Horn in good working order
Hydraulic cylinders
Ignition key operative
Indicators
Load backrest and carriage
Lights in good working order
Lubrication adequate
Mast and chain
Pedal rubbers
Overhead guard/cab
Park brake engaged
Reverse siren
Battery Mounting
Radiator water level & oil levels (leaks)
Raise & lower - cylinder & chain
Safety belt in good condition
Steering lock to lock
Steering play
Switches in good working order
Tilt- cylinder condition
Transmission oil
Tyre pressure, wheels & rims good condition
Water leaks
Wheel nuts & bolts secure


BOBCAT FORKLIFTS ARE HERE
DOOSAN FORKLIFTS NOW A PART OF THE BOBCAT FAMILY
The innovation and durability synonymous with Bobcat equipment merge seamlessly with decades of experience in designing reliable material handling equipment from Doosan. The incorporation of the built-to-last and easy to maintain Bobcat DNA into solutions for intralogistics and distribution facilities aims to enhance their profitability. Bobcat forklifts are here to empower you and your business to accomplish even more.
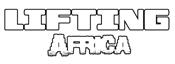

ITEM TO BE CHECKED
All oil level correct / any oil leaks
All pipes and hoses in good condition
Battery terminals, cables mounting secure
Beacon or strobe warning light
Brake in good working condition / fluid levels correct
Caps secure (fuel, oil, radiator etc secure)
Control levers in good working order
Driver's compartment / seat good condition
Electrolyte levels
Enter and adjust seat and mirrors
Fan belt & blades good condition & tension
Fork condition
Fork position and fork locks
Fuel leaks / levels adequete
Gas shut-off valve operational
Gas tank mounting secure
Gauges before switching on and after
General bodywork
Hoisting mechanism in good working order
Horn in good working order
Hydraulic cylinders
Ignition key operative
Indicators
Load backrest and carriage
Lights in good working order
Lubrication adequate
Mast and chain
Pedal rubbers
Overhead guard/cab
Park brake engaged
Reverse siren
Battery Mounting
Radiator water level & oil levels (leaks)
Raise & lower - cylinder & chain
Safety belt in good condition
Steering lock to lock
Steering play
Switches in good working order
Tilt- cylinder condition
Transmission oil
Tyre pressure, wheels & rims good condition
Water leaks
Wheel nuts & bolts secure
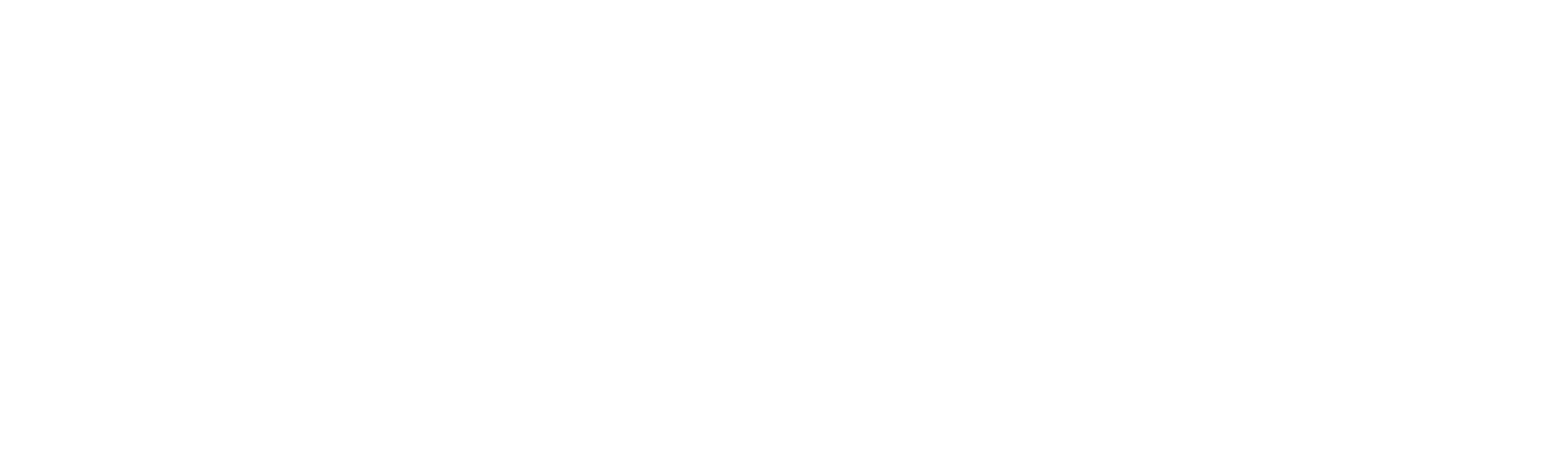
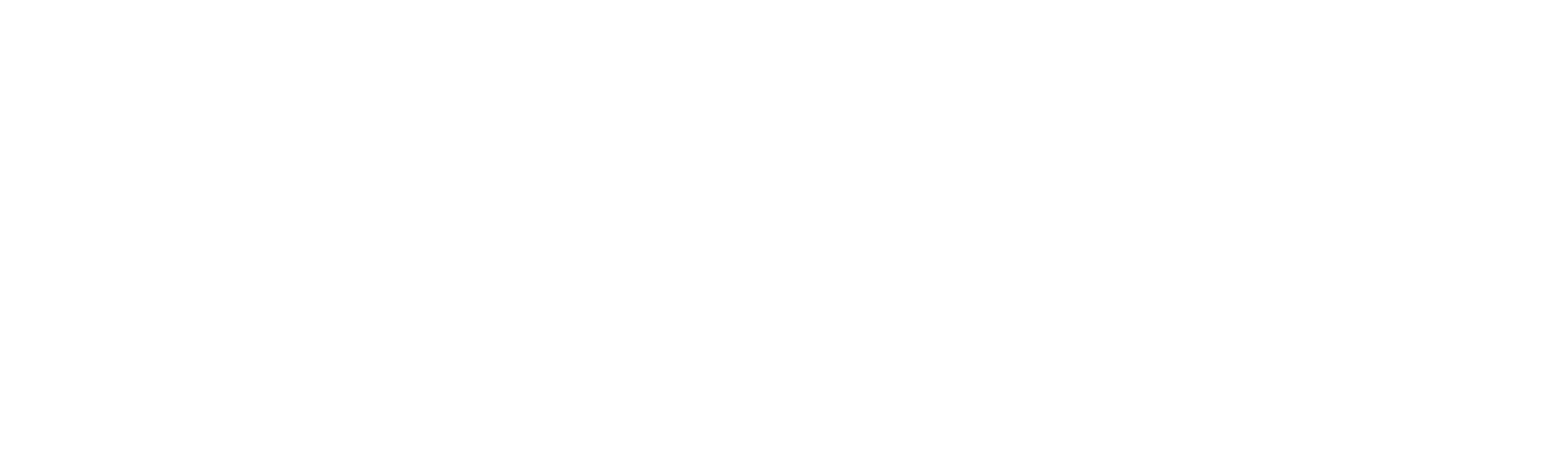
Alpha Load Testing and Services provides on-site service ensuring your lifting equipment and machines comply with legal requirements and are safe to use.
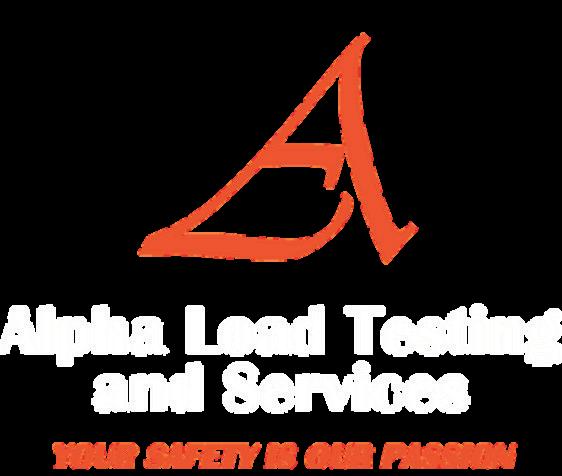

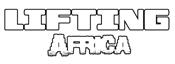

ITEM TO BE CHECKED
All oil level correct / any oil leaks
All pipes and hoses in good condition
Battery terminals, cables mounting secure
Beacon or strobe warning light
Brake in good working condition / fluid levels correct
Caps secure (fuel, oil, radiator etc secure)
Control levers in good working order
Driver's compartment / seat good condition
Electrolyte levels
Enter and adjust seat and mirrors
Fan belt & blades good condition & tension
Fork condition
Fork position and fork locks
Fuel leaks / levels adequete
Gas shut-off valve operational
Gas tank mounting secure
Gauges before switching on and after
General bodywork
Hoisting mechanism in good working order
Horn in good working order
Hydraulic cylinders
Ignition key operative
Indicators
Load backrest and carriage
Lights in good working order
Lubrication adequate
Mast and chain
Pedal rubbers
Overhead guard/cab
Park brake engaged
Reverse siren
Battery Mounting
Radiator water level & oil levels (leaks)
Raise & lower - cylinder & chain
Safety belt in good condition
Steering lock to lock
Steering play
Switches in good working order
Tilt- cylinder condition
Transmission oil
Tyre pressure, wheels & rims good condition
Water leaks
Wheel nuts & bolts secure
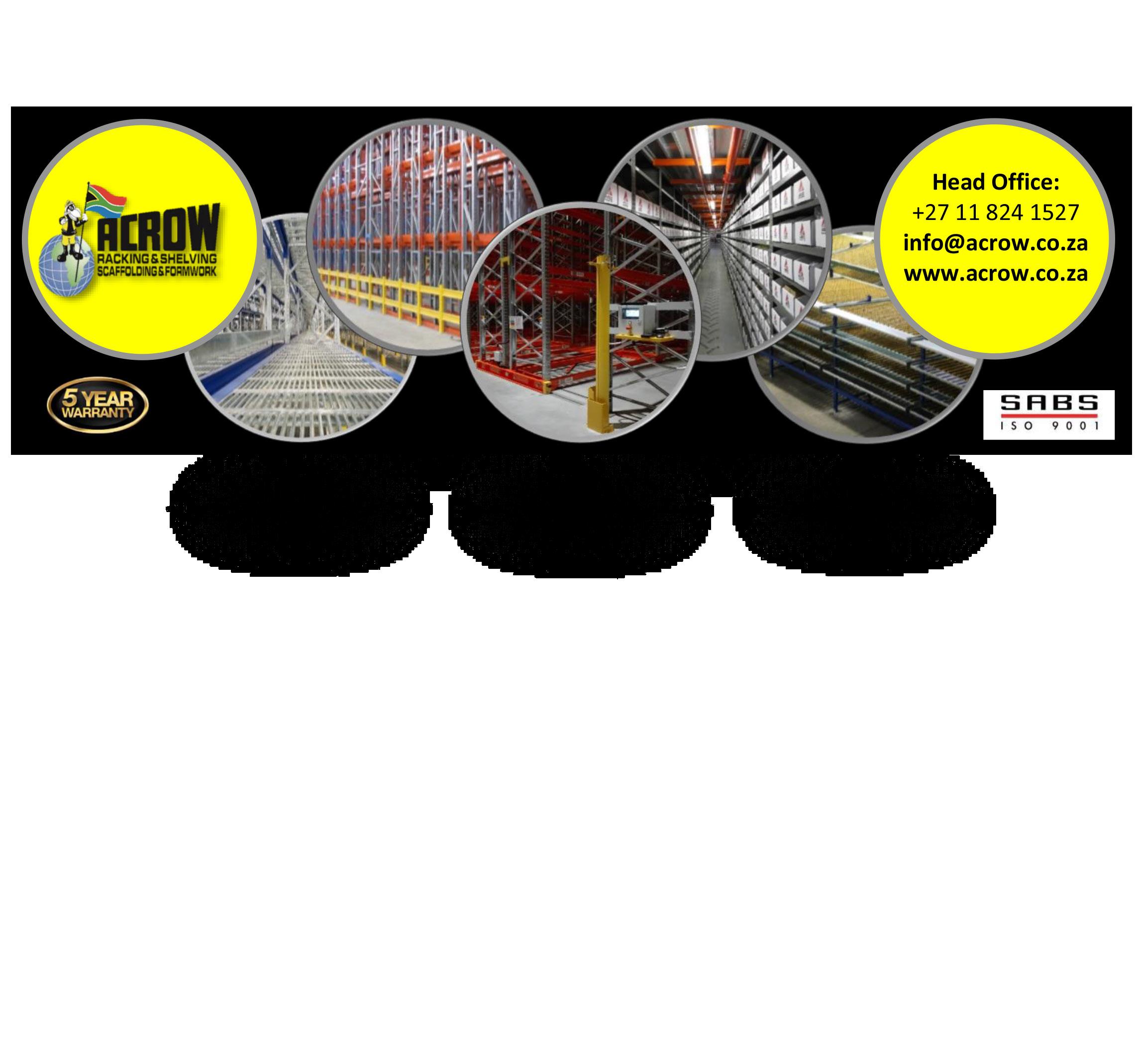
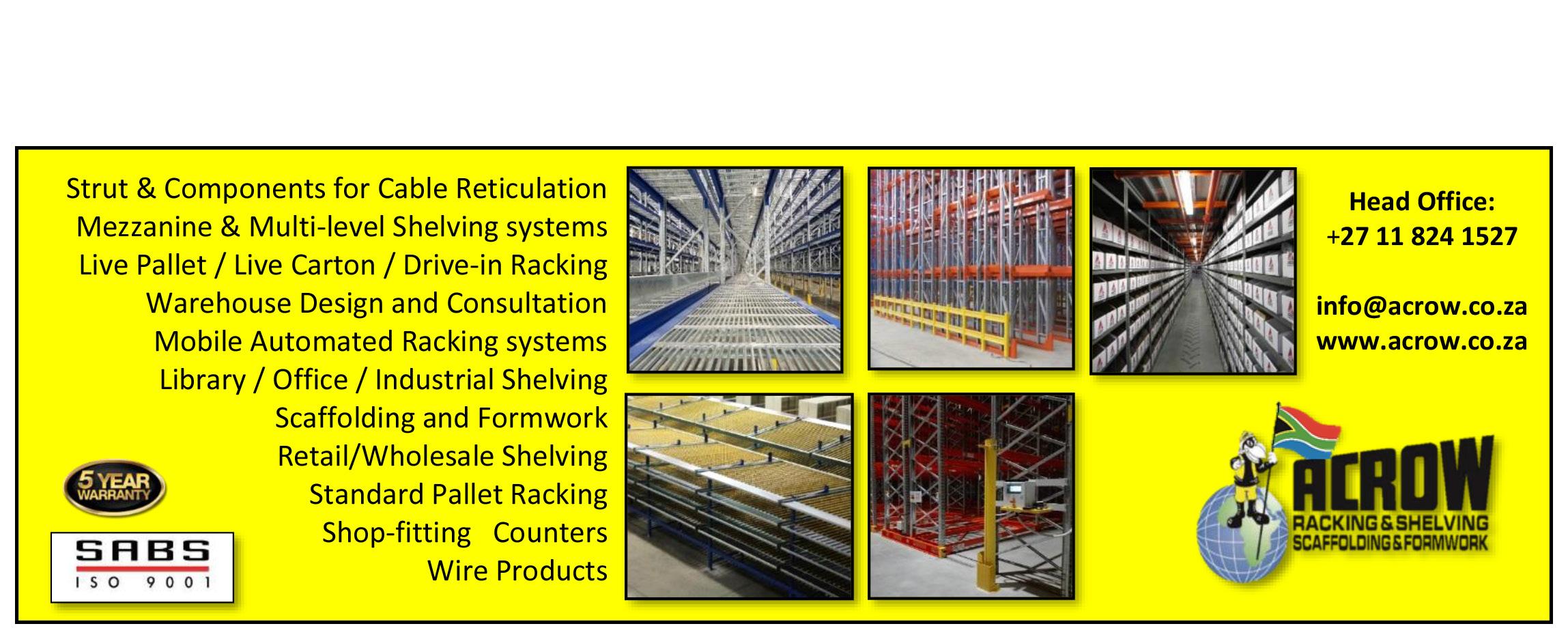
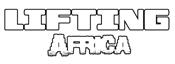

ITEM TO BE CHECKED
All oil level correct / any oil leaks
All pipes and hoses in good condition
Battery terminals, cables mounting secure
Beacon or strobe warning light
Brake in good working condition / fluid levels correct
Caps secure (fuel, oil, radiator etc secure)
Control levers in good working order
Driver's compartment / seat good condition
Electrolyte levels
Enter and adjust seat and mirrors
Fan belt & blades good condition & tension
Fork condition
Fork position and fork locks
Fuel leaks / levels adequete
Gas shut-off valve operational
Gas tank mounting secure
Gauges before switching on and after
General bodywork
Hoisting mechanism in good working order
Horn in good working order
Hydraulic cylinders
Ignition key operative
Indicators
Load backrest and carriage
Lights in good working order
Lubrication adequate
Mast and chain
Pedal rubbers
Overhead guard/cab
Park brake engaged
Reverse siren
Battery Mounting
Radiator water level & oil levels (leaks)
Raise & lower - cylinder & chain
Safety belt in good condition
Steering lock to lock
Steering play
Switches in good working order
Tilt- cylinder condition
Transmission oil
Tyre pressure, wheels & rims good condition
Water leaks
Wheel nuts & bolts secure
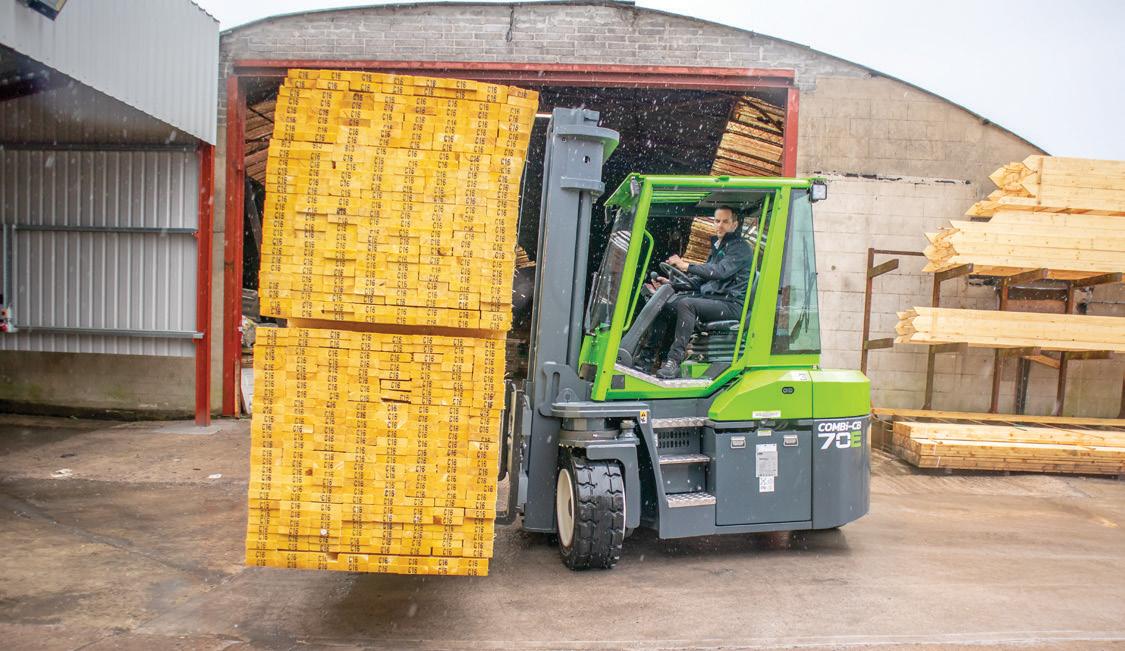
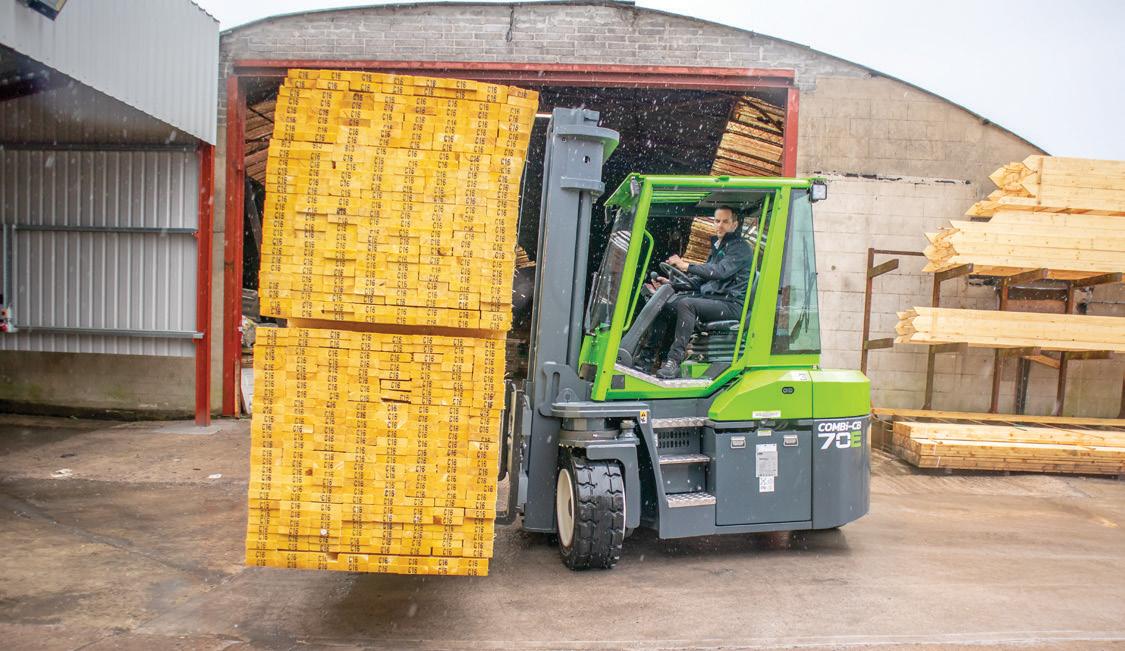
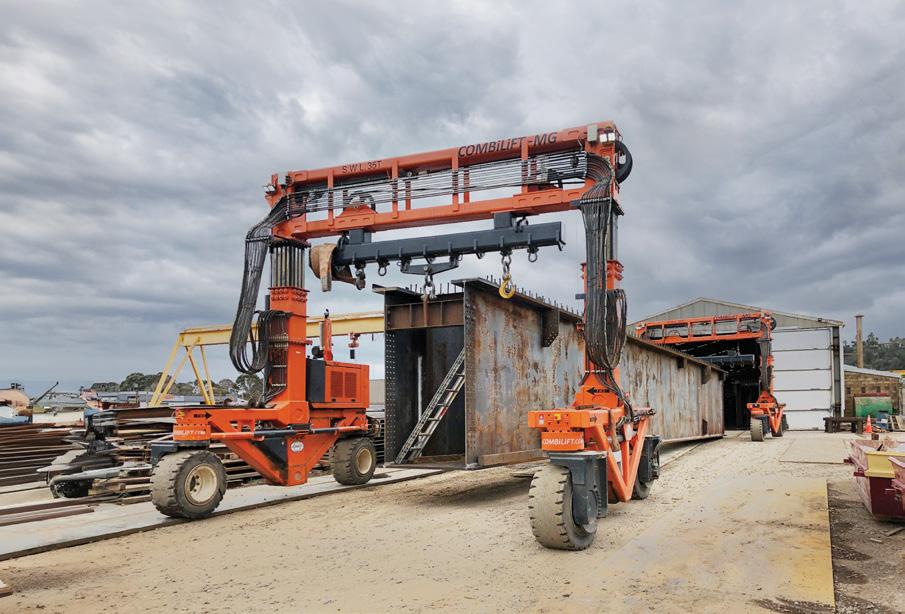
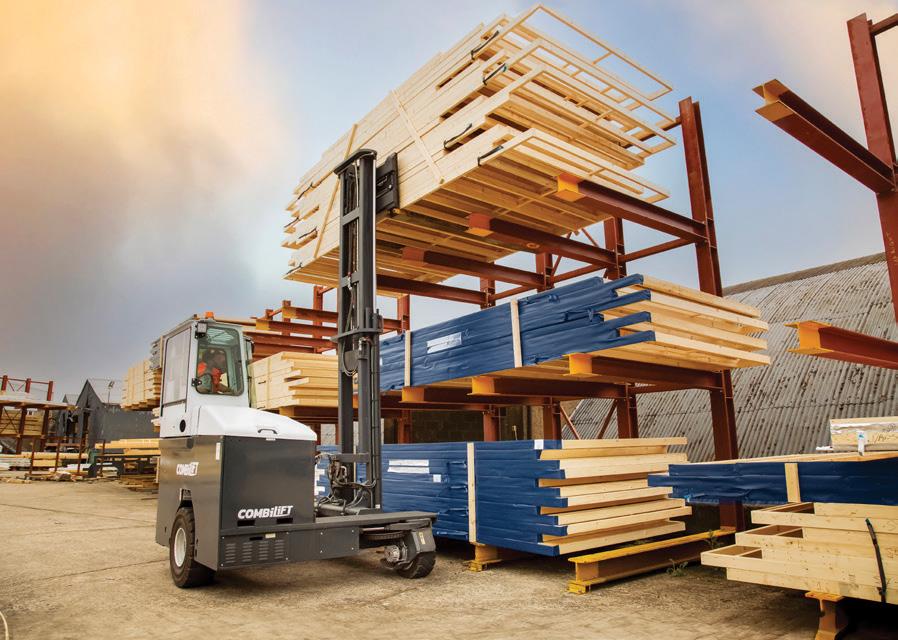
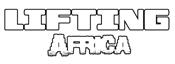

ITEM TO BE CHECKED
All oil level correct / any oil leaks
All pipes and hoses in good condition
Battery terminals, cables mounting secure
Beacon or strobe warning light
Brake in good working condition / fluid levels correct
Caps secure (fuel, oil, radiator etc secure)
Control levers in good working order
Driver's compartment / seat good condition
Electrolyte levels
Enter and adjust seat and mirrors
Fan belt & blades good condition & tension
Fork condition
Fork position and fork locks
Fuel leaks / levels adequete
Gas shut-off valve operational
Gas tank mounting secure
Gauges before switching on and after
General bodywork
Hoisting mechanism in good working order
Horn in good working order
Hydraulic cylinders
Ignition key operative
Indicators
Load backrest and carriage
Lights in good working order
Lubrication adequate
Mast and chain
Pedal rubbers
Overhead guard/cab
Park brake engaged
Reverse siren
Battery Mounting
Radiator water level & oil levels (leaks)
Raise & lower - cylinder & chain
Safety belt in good condition
Steering lock to lock
Steering play
Switches in good working order
Tilt- cylinder condition
Transmission oil
Tyre pressure, wheels & rims good condition
Water leaks
Wheel nuts & bolts secure

REACH NEW HEIGHTS
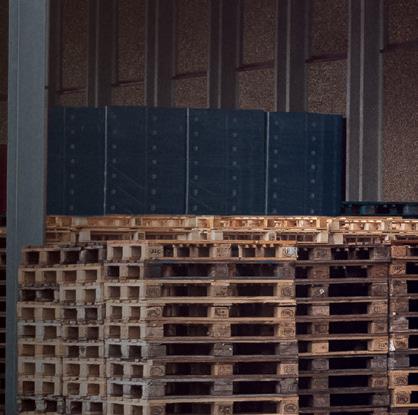
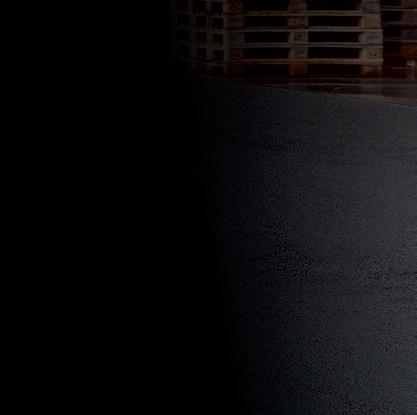
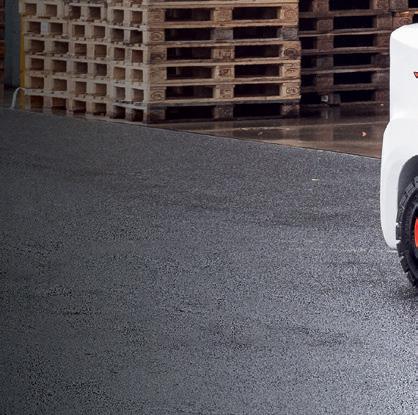

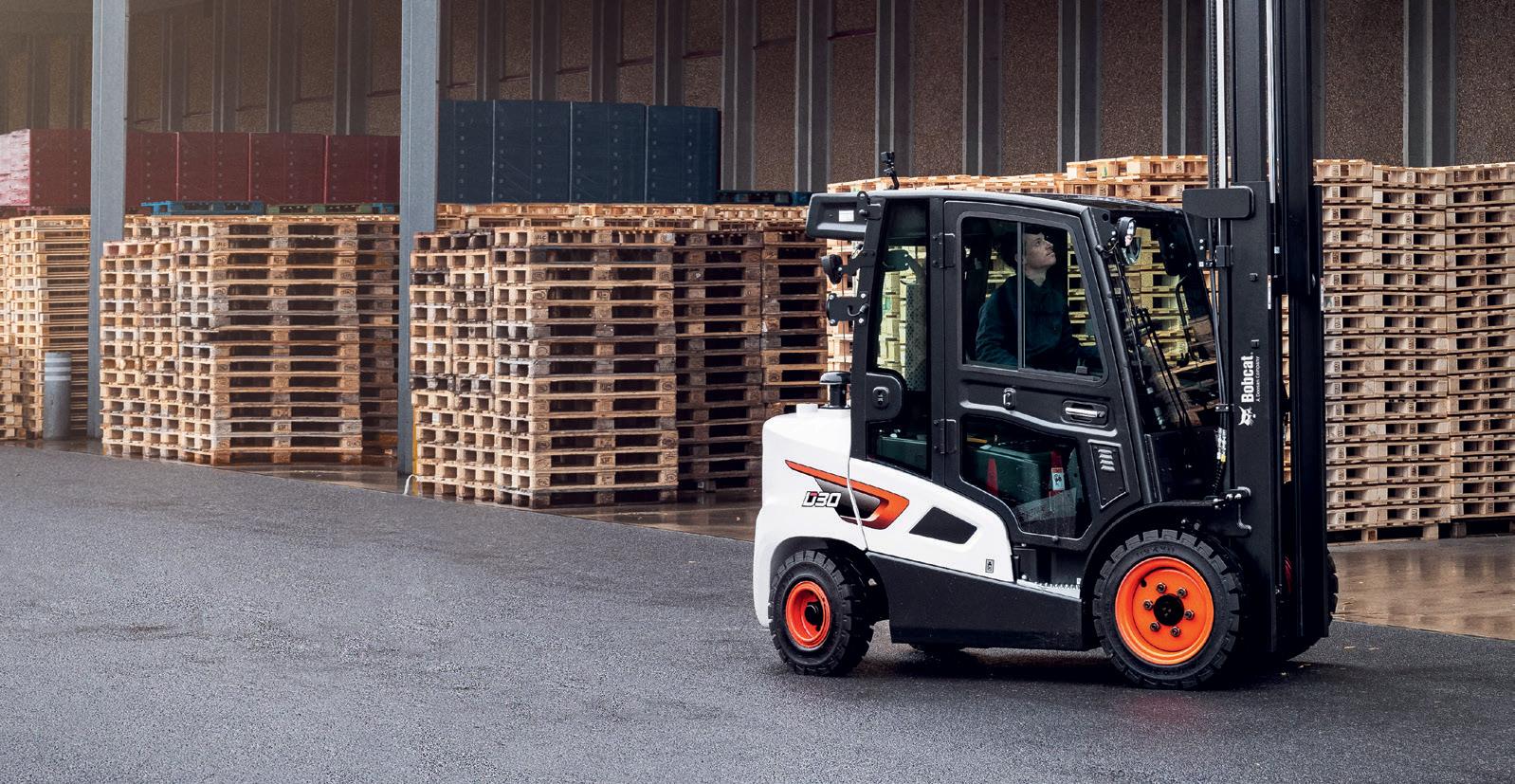


BOBCAT FORKLIFTS ARE HERE
DOOSAN FORKLIFTS NOW A PART OF THE BOBCAT FAMILY
The innovation and durability synonymous with Bobcat equipment merge seamlessly with decades of experience in designing reliable material handling equipment from Doosan. The incorporation of the built-to-last and easy to maintain Bobcat DNA into solutions for intralogistics and distribution facilities aims to enhance their profitability. Bobcat forklifts are here to empower you and your business to accomplish even more.
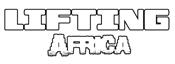

ITEM TO BE CHECKED
All oil level correct / any oil leaks
All pipes and hoses in good condition
Battery terminals, cables mounting secure
Beacon or strobe warning light
Brake in good working condition / fluid levels correct
Caps secure (fuel, oil, radiator etc secure)
Control levers in good working order
Driver's compartment / seat good condition
Electrolyte levels
Enter and adjust seat and mirrors
Fan belt & blades good condition & tension
Fork condition
Fork position and fork locks
Fuel leaks / levels adequete
Gas shut-off valve operational
Gas tank mounting secure
Gauges before switching on and after
General bodywork
Hoisting mechanism in good working order
Horn in good working order
Hydraulic cylinders
Ignition key operative
Indicators
Load backrest and carriage
Lights in good working order
Lubrication adequate
Mast and chain
Pedal rubbers
Overhead guard/cab
Park brake engaged
Reverse siren
Battery Mounting
Radiator water level & oil levels (leaks)
Raise & lower - cylinder & chain
Safety belt in good condition
Steering lock to lock
Steering play
Switches in good working order
Tilt- cylinder condition
Transmission oil
Tyre pressure, wheels & rims good condition
Water leaks
Wheel nuts & bolts secure
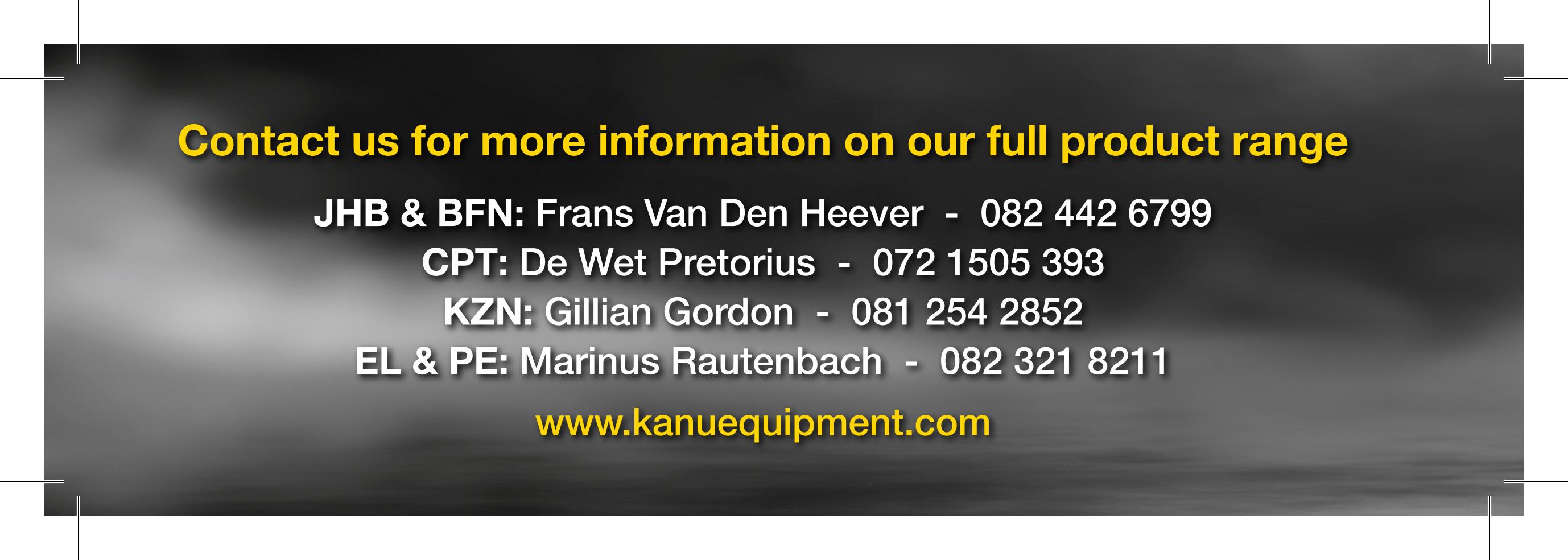
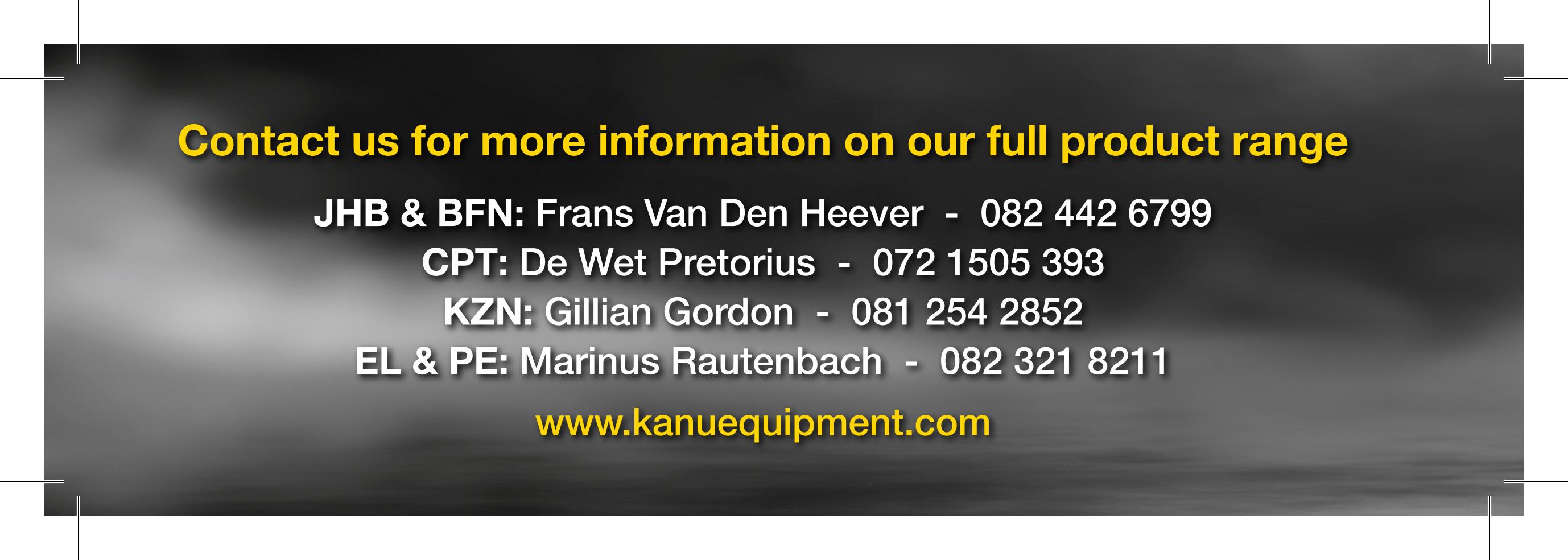

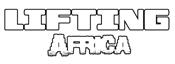

ITEM TO BE CHECKED
All oil level correct / any oil leaks
All pipes and hoses in good condition
Battery terminals, cables mounting secure
Beacon or strobe warning light
Brake in good working condition / fluid levels correct
Caps secure (fuel, oil, radiator etc secure)
Control levers in good working order
Driver's compartment / seat good condition
Electrolyte levels
Enter and adjust seat and mirrors
Fan belt & blades good condition & tension
Fork condition
Fork position and fork locks
Fuel leaks / levels adequete
Gas shut-off valve operational
Gas tank mounting secure
Gauges before switching on and after
General bodywork
Hoisting mechanism in good working order
Horn in good working order
Hydraulic cylinders
Ignition key operative
Indicators
Load backrest and carriage
Lights in good working order
Lubrication adequate
Mast and chain
Pedal rubbers
Overhead guard/cab
Park brake engaged
Reverse siren
Battery Mounting
Radiator water level & oil levels (leaks)
Raise & lower - cylinder & chain
Safety belt in good condition
Steering lock to lock
Steering play
Switches in good working order
Tilt- cylinder condition
Transmission oil
Tyre pressure, wheels & rims good condition
Water leaks
Wheel nuts & bolts secure

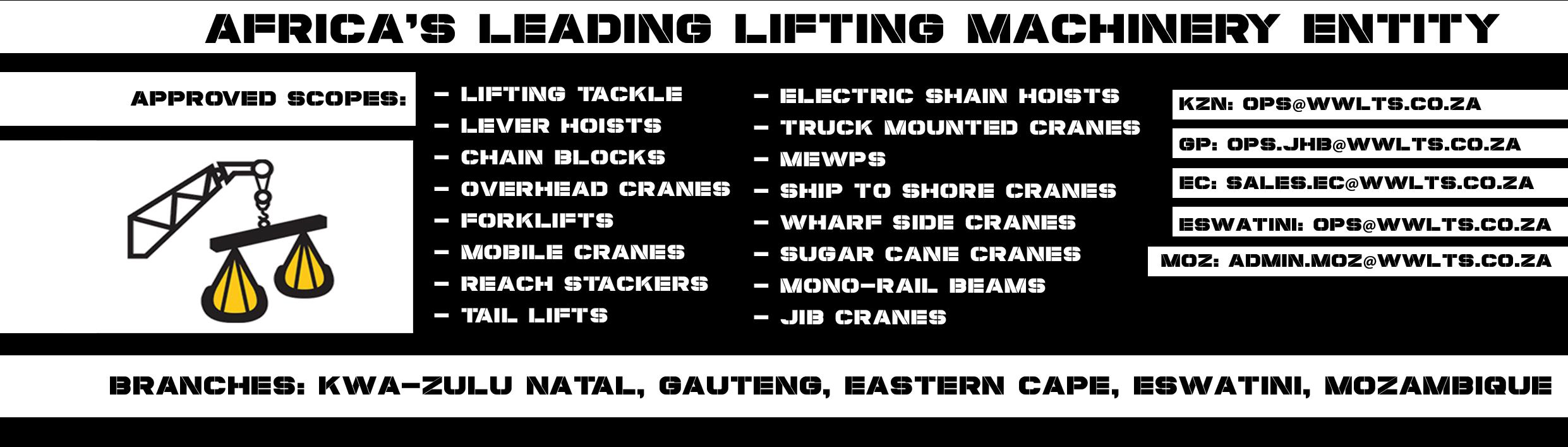
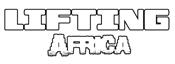

ITEM TO BE CHECKED
All oil level correct / any oil leaks
All pipes and hoses in good condition
Battery terminals, cables mounting secure
Beacon or strobe warning light
Brake in good working condition / fluid levels correct
Caps secure (fuel, oil, radiator etc secure)
Control levers in good working order
Driver's compartment / seat good condition
Electrolyte levels
Enter and adjust seat and mirrors
Fan belt & blades good condition & tension
Fork condition
Fork position and fork locks
Fuel leaks / levels adequete
Gas shut-off valve operational
Gas tank mounting secure
Gauges before switching on and after
General bodywork
Hoisting mechanism in good working order
Horn in good working order
Hydraulic cylinders
Ignition key operative
Indicators
Load backrest and carriage
Lights in good working order
Lubrication adequate
Mast and chain
Pedal rubbers
Overhead guard/cab
Park brake engaged
Reverse siren
Battery Mounting
Radiator water level & oil levels (leaks)
Raise & lower - cylinder & chain
Safety belt in good condition
Steering lock to lock
Steering play
Switches in good working order
Tilt- cylinder condition
Transmission oil
Tyre pressure, wheels & rims good condition
Water leaks
Wheel nuts & bolts secure
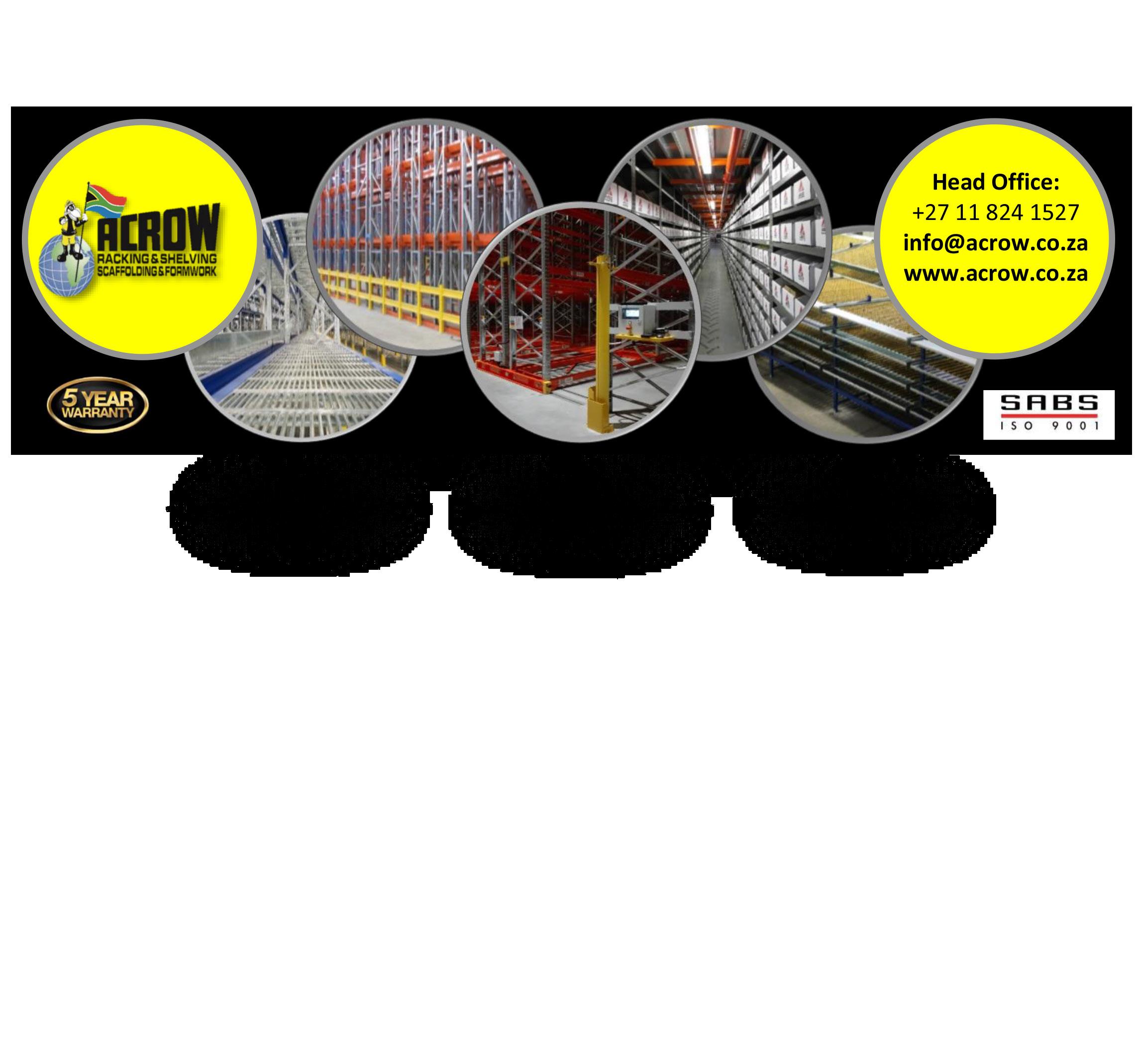

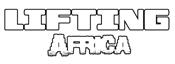
Date of inspection
Initials and surname of person conducting test
Employer or person conducting inspection/test
Inspection/test conducted
Remarks
Forklift safe to use? (yes/no)
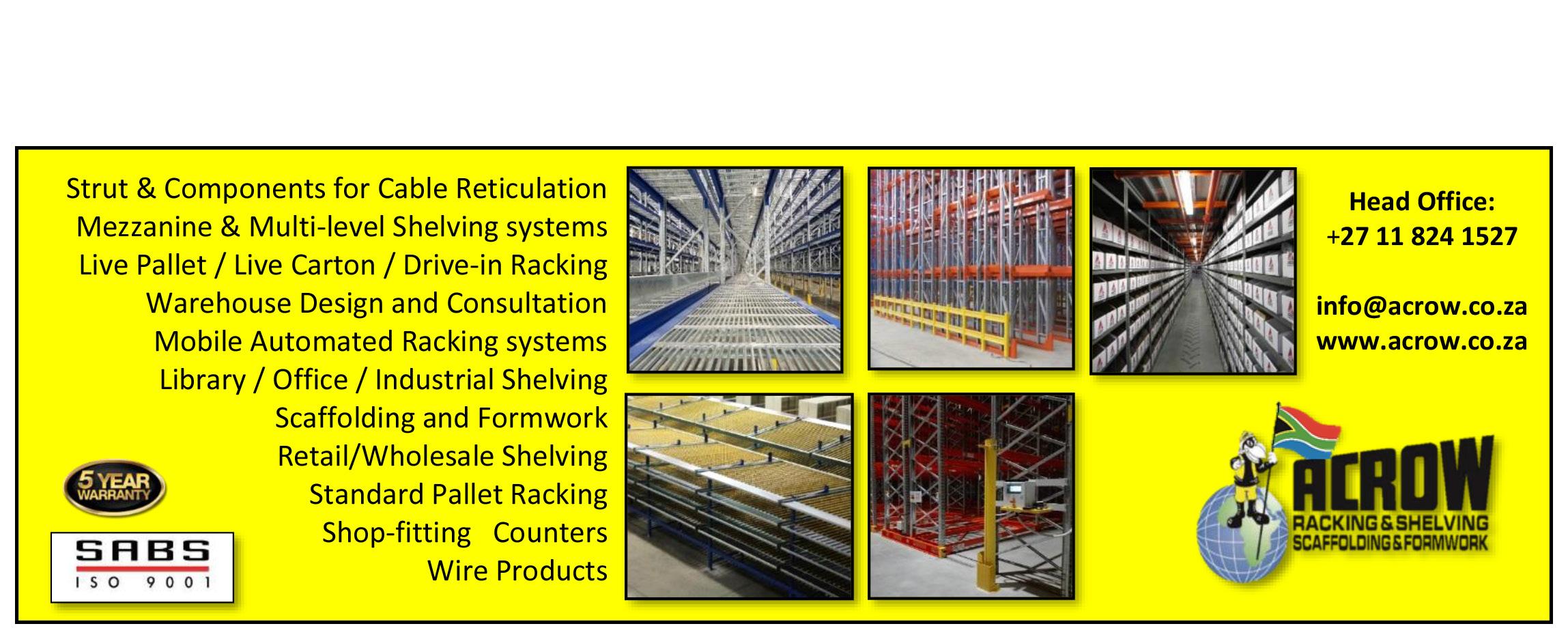
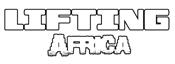

OPERATOR TRAINING
Name of operator: _____________________________________________
Certificate of training date: ______________________________________
Expiry date:
Issued by:
OPERATOR TRAINING
Name of operator: _____________________________________________
Certificate of training date:
Expiry date:
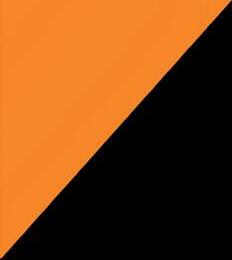
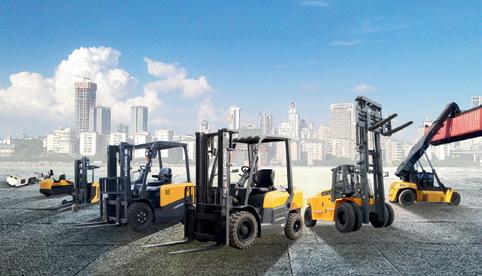
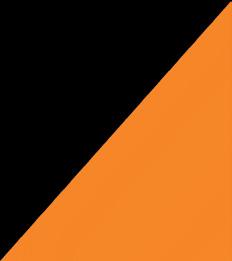
OPERATOR TRAINING
Name of operator: _____________________________________________
Certificate of training date:
Expiry date:
Issued by: ____________________________________________________
OPERATOR TRAINING
Name of operator: _____________________________________________
Certificate of training date: ______________________________________
Expiry date:
Issued by:
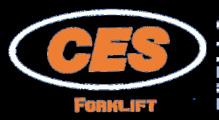
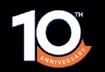
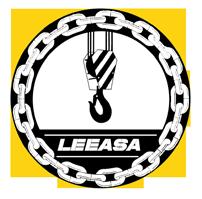
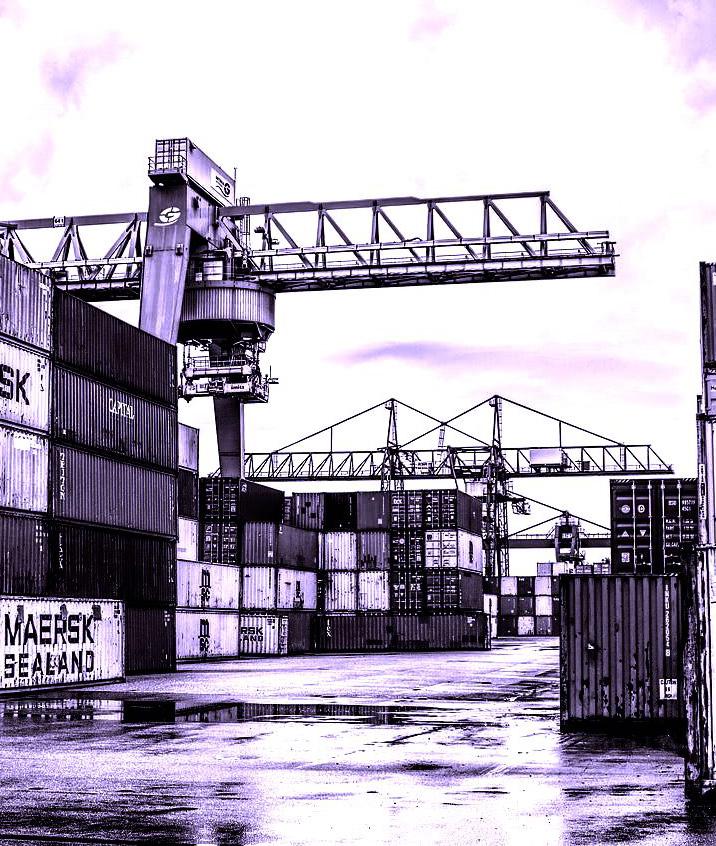
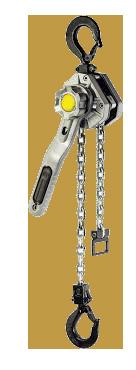

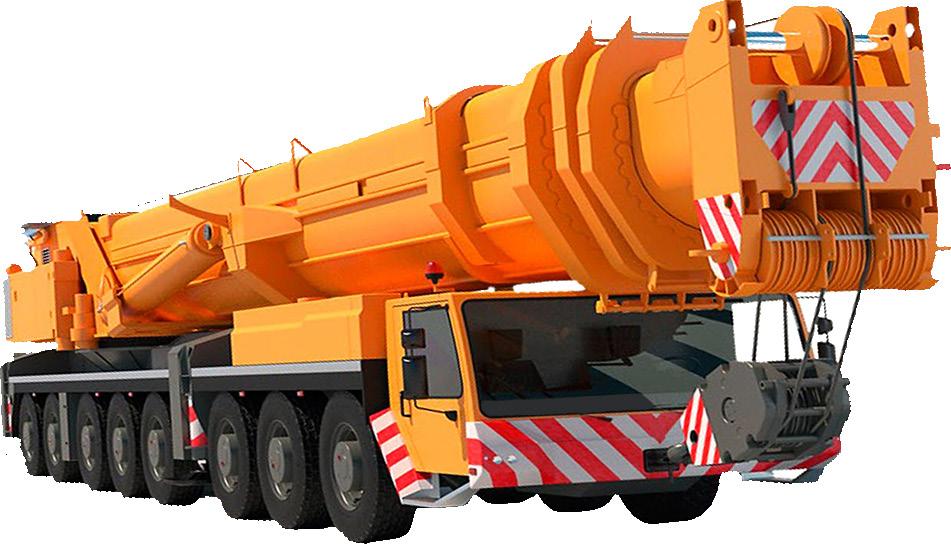
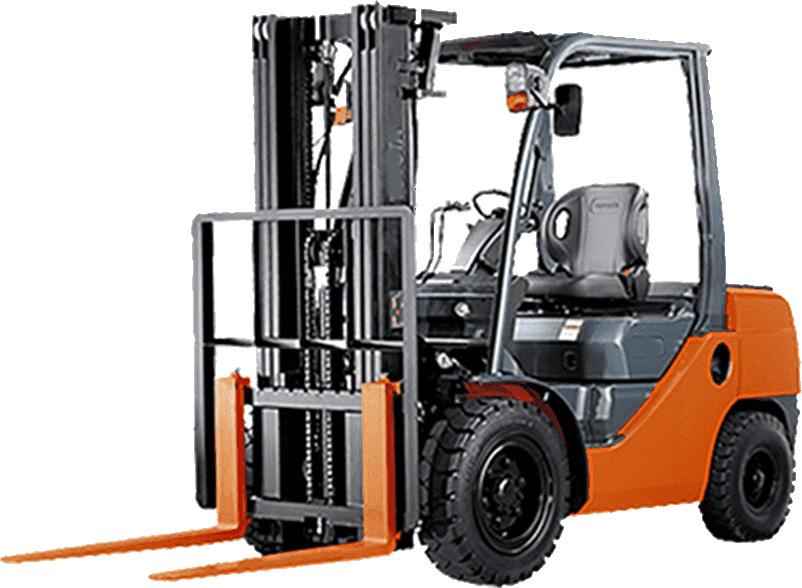
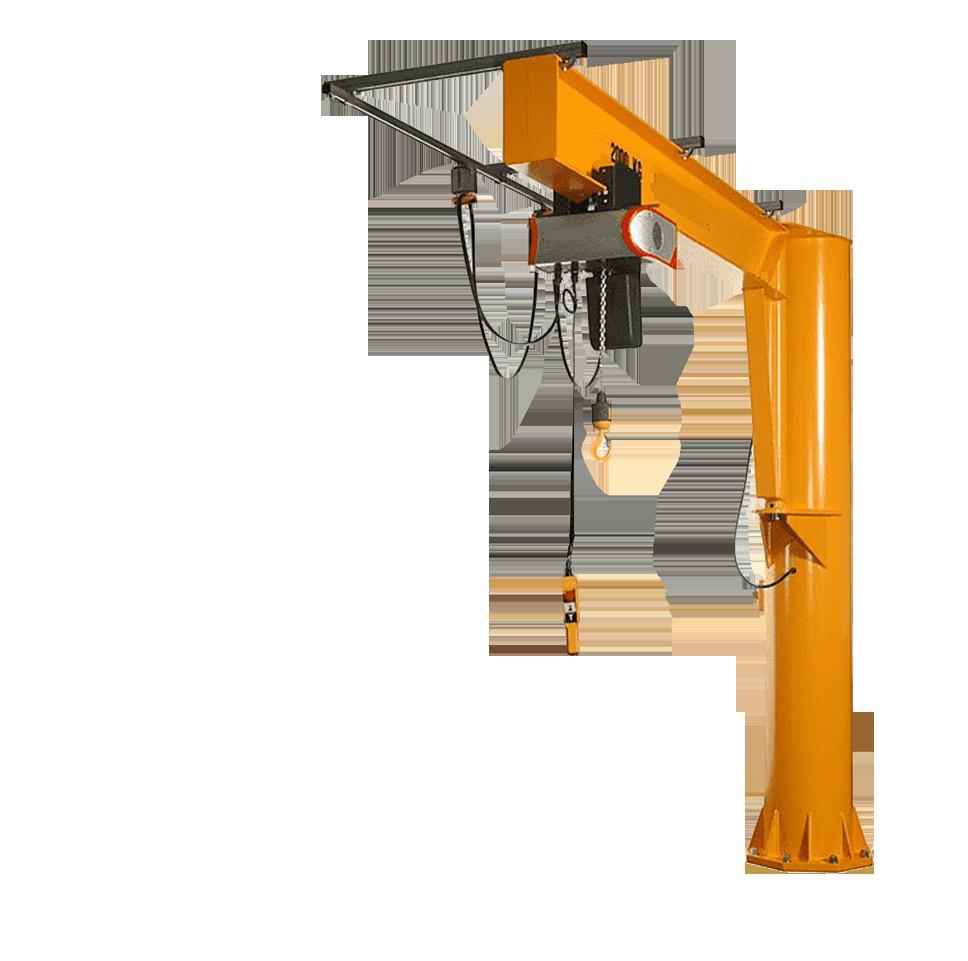
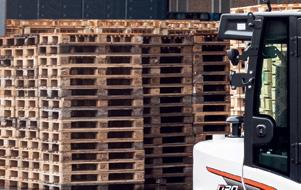

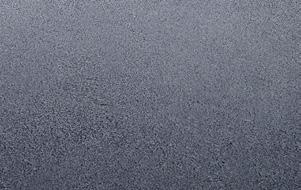
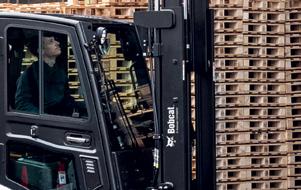
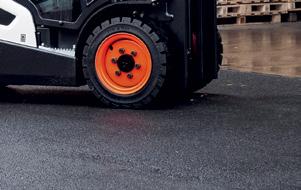
REACH NEW HEIGHTS



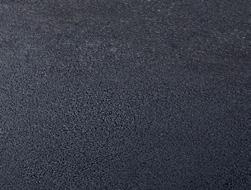
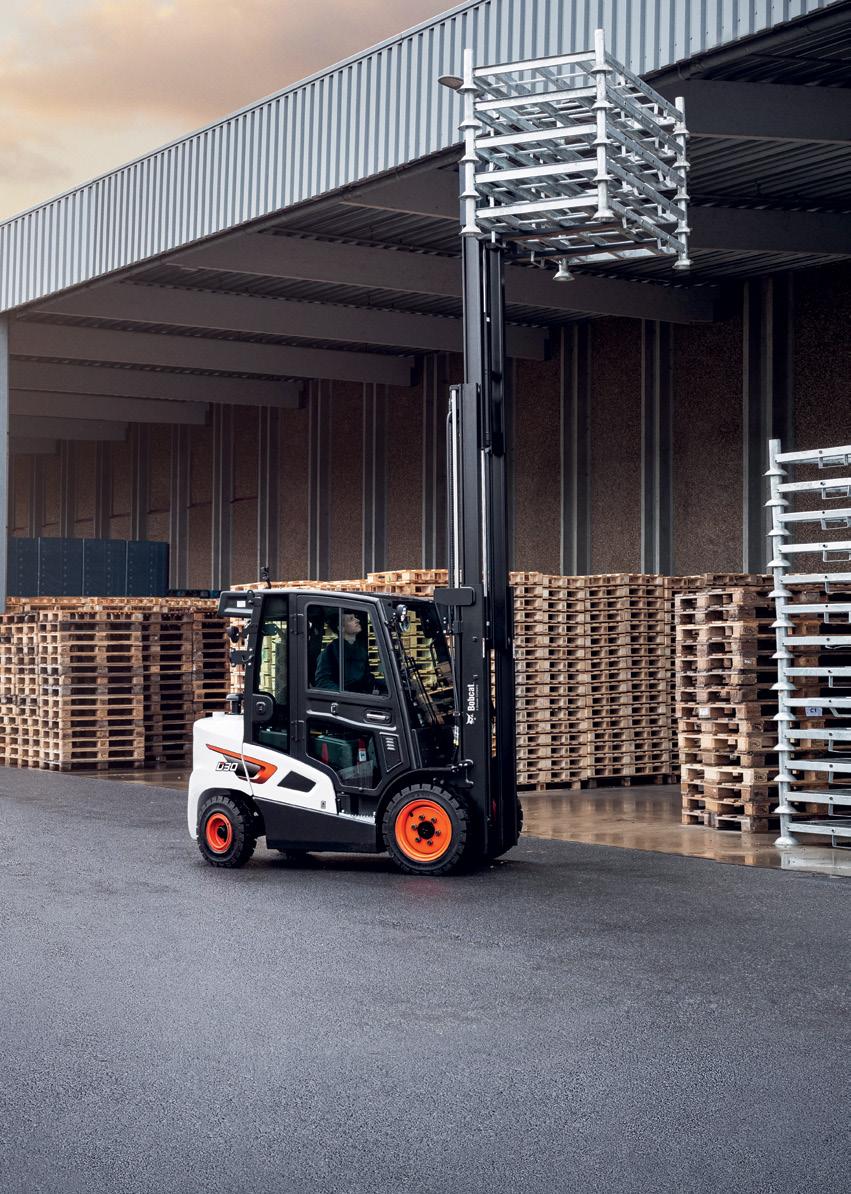